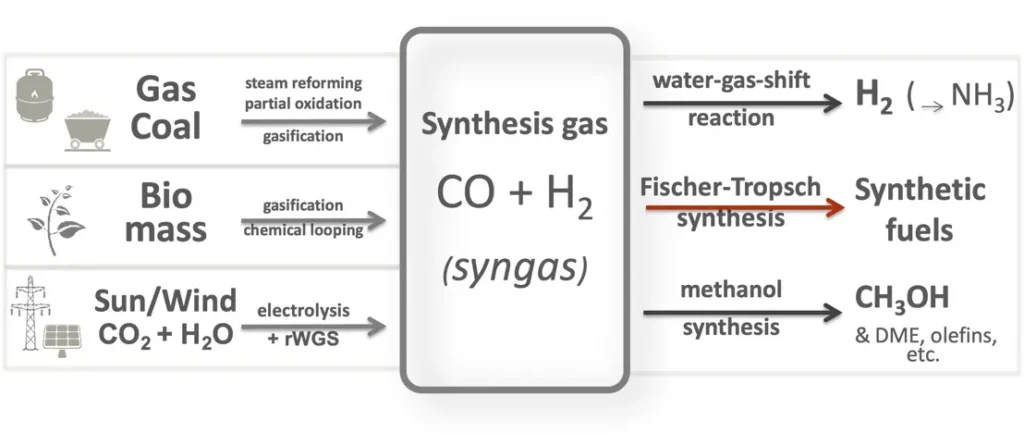
Wood gas, also known as producer gas, is a renewable and alternative energy source derived from the thermal conversion of wood or other biomass materials. This process, known as gasification, involves heating organic materials in a low-oxygen environment to produce a combustible gas composed mainly of carbon monoxide, hydrogen, and methane. Wood gas has been utilized for various applications throughout history, ranging from fuel for vehicles to providing heat for residential and industrial purposes.
Wood Gas
The gasification of wood involves subjecting it to high temperatures in a controlled environment, typically in a gasifier. The absence of oxygen or the controlled supply of oxygen during this process prevents complete combustion, leading to the production of wood gas. The primary reactions during gasification include the thermal decomposition of wood into volatile gases, followed by reactions that form the desired fuel gases.
Composition of Wood Gas:
The composition of wood gas can vary depending on factors such as the type of biomass, gasification conditions, and the design of the gasifier. Generally, wood gas consists of carbon monoxide (CO), hydrogen (H2), methane (CH4), carbon dioxide (CO2), nitrogen (N2), and traces of other gases. The energy content of wood gas is substantial, making it a viable energy source.
Applications:
- Power Generation: Wood gas can be used to generate electricity through internal combustion engines or gas turbines. This application is particularly relevant in off-grid or remote areas where traditional power sources may be unavailable.
- Transportation: During World War II, wood gasifiers were used to power vehicles in response to fuel shortages. While the technology has evolved, wood gas still holds potential as a sustainable fuel for transportation, particularly in areas with abundant biomass resources.
- Heating: Wood gas can be utilized for heating applications in residential, commercial, or industrial settings. This can include space heating, water heating, and even industrial processes requiring high-temperature heat.
- Cogeneration: Combined heat and power (CHP) systems can utilize wood gas to simultaneously generate electricity and provide heat for various applications, enhancing overall energy efficiency.
Challenges and Considerations:
- Tar and Impurities: One challenge in wood gasification is the presence of tar and other impurities in the gas, which can lead to engine or equipment fouling. Proper filtration and cleaning systems are necessary to address this issue.
- Efficiency: The efficiency of wood gasification systems can be influenced by factors such as the choice of gasifier design, biomass feedstock, and operating conditions. Ongoing research focuses on optimizing these parameters to improve overall efficiency.
- Infrastructure and Integration: Implementing wood gas technology requires specific infrastructure and integration with existing energy systems. Adapting engines, generators, or appliances to run on wood gas may pose challenges but is essential for successful deployment.
Conclusion:
Wood gas represents a versatile and renewable energy source with the potential to contribute to a more sustainable energy future. While challenges exist, ongoing research and technological advancements continue to enhance the efficiency and applicability of wood gasification systems, making them a promising component of the renewable energy landscape.
Gasification:
Gasification is a thermochemical process that transforms organic materials, such as wood or biomass, into a gaseous fuel known as producer gas. This intricate process occurs in a controlled environment, typically a gasifier, where the feedstock undergoes a sequence of chemical reactions in the absence or limited supply of oxygen. The primary objective of gasification is to extract combustible gases, including carbon monoxide, hydrogen, and methane, while preventing complete combustion.
The gasification process involves heating the biomass to high temperatures, causing it to release volatile compounds. These volatile gases then undergo further reactions to produce a mixture of gases that can be used as a fuel source. Gasification is a versatile technology with applications ranging from power generation and heating to producing fuels for vehicles.
One key advantage of gasification is its ability to utilize a variety of feedstocks, including wood, agricultural residues, and municipal solid waste. This flexibility makes gasification an attractive option for sustainable energy production. Researchers and engineers continue to explore and refine gasification processes to enhance efficiency, reduce emissions, and expand its role in the transition to a more sustainable and diversified energy landscape. The ongoing development of gasification technology holds promise for addressing energy challenges and promoting a cleaner, more sustainable future.
Biomass Energy:
Biomass energy encompasses the use of organic materials, such as wood, agricultural residues, and other biological matter, as a renewable source of energy. The conversion of biomass into usable energy can occur through various processes, with one prominent method being gasification. Biomass gasification involves subjecting organic materials to high temperatures in a controlled environment to produce a gaseous fuel known as producer gas.
Wood, a common biomass feedstock, can be sustainably harvested and used for energy production without contributing to a net increase in carbon dioxide levels, making it a carbon-neutral energy source. Biomass energy has been harnessed for centuries, from traditional wood-burning stoves to modern, advanced technologies like gasifiers.
The utilization of biomass energy has several environmental benefits, including reducing dependence on fossil fuels, mitigating greenhouse gas emissions, and promoting sustainable land use practices. Additionally, biomass energy systems can contribute to waste reduction by utilizing agricultural residues and forestry by-products.
As the world seeks cleaner and more sustainable alternatives to traditional energy sources, biomass energy, including gasification processes, continues to play a crucial role in the development of environmentally friendly and renewable energy solutions. Advances in biomass energy technology, coupled with responsible resource management, position biomass as a key player in the global effort to transition towards a more sustainable and resilient energy future.
Producer Gas:
Producer gas, also known as wood gas, is a combustible mixture of gases produced through the gasification of organic materials, such as wood, biomass, or other carbonaceous substances. This gasification process takes place in a controlled environment, typically within a device called a gasifier, where the feedstock is heated in a low-oxygen or oxygen-starved atmosphere.
The composition of producer gas can vary, but it generally consists of carbon monoxide (CO), hydrogen (H2), methane (CH4), carbon dioxide (CO2), nitrogen (N2), and traces of other gases. The ratio of these components depends on factors such as the type of biomass used, gasification conditions, and the design of the gasifier.
Producer gas has been historically used for various applications, with its heyday during times of fuel shortages, such as in World War II. It has found applications in power generation, transportation, and heating. Despite the advent of more conventional fuels, interest in producer gas has seen a resurgence due to its potential as a renewable and sustainable energy source.
As technology continues to evolve, producer gas is gaining attention as an alternative to traditional fossil fuels. Researchers and engineers are exploring ways to optimize gasification processes, improve gas cleaning techniques, and integrate producer gas into modern energy systems. This renewed focus on producer gas highlights its potential role in addressing energy challenges and reducing the environmental impact of energy production.
Wood Gas Generator:
A wood gas generator is a device designed to convert wood or biomass into a usable gaseous fuel through the process of gasification. This technology has a rich history, dating back to the early 19th century, and gained prominence during periods of fuel scarcity, such as World War II. Wood gas generators have since evolved, becoming a subject of renewed interest as the world explores sustainable and renewable energy alternatives.
The generator typically consists of a gasification chamber, where wood or biomass is subjected to high temperatures in a controlled environment with limited oxygen. This leads to the release of volatile gases, which are then collected and cleaned to form wood gas. The wood gas can be utilized for various applications, including power generation, heating, and even as a fuel for internal combustion engines.
Wood gas generators have proven to be versatile and adaptable to different scales, from small, decentralized systems for residential heating to larger units for industrial applications. The simplicity of the technology, coupled with the abundance of biomass resources, makes wood gas generators an attractive option for regions seeking energy self-sufficiency and reduced reliance on conventional fuels.
Ongoing research and development in wood gas generator technology focus on improving efficiency, reducing emissions, and exploring novel applications. As the world continues to seek sustainable energy solutions, wood gas generators offer a bridge between historical practices and modern innovations, providing a glimpse into the potential of decentralized, biomass-based energy systems.
Renewable Fuel:
Renewable fuel refers to a type of energy derived from sources that are replenished naturally and sustainably over time. Unlike fossil fuels, which are finite and contribute to environmental degradation, renewable fuels harness the power of natural processes such as sunlight, wind, and organic matter. Wood gas, produced through the gasification of wood or biomass, stands out as a renewable fuel with significant potential in the transition to a more sustainable energy landscape.
Wood gas is considered renewable because the carbon released during combustion is part of the natural carbon cycle. As trees and plants grow, they absorb carbon dioxide from the atmosphere. When used for wood gas production, the carbon stored in the biomass is released, but as long as new trees are planted to replace those harvested, the process remains carbon-neutral.
Renewable fuels, including wood gas, play a crucial role in mitigating climate change by reducing reliance on non-renewable and carbon-intensive energy sources. They contribute to the diversification of the energy mix, promoting resilience and reducing dependence on finite resources. Governments, industries, and individuals are increasingly recognizing the importance of renewable fuels in achieving energy security and environmental sustainability.
As technology continues to advance, the efficiency and cost-effectiveness of renewable fuel production, including wood gas, are improving. The integration of renewable fuels into existing energy infrastructure is a key step towards a greener future, offering a sustainable alternative that aligns with global efforts to address climate change and build a more resilient and environmentally friendly energy system.
Carbon Monoxide:
Carbon monoxide (CO) is a colorless, odorless, and tasteless gas composed of one carbon atom and one oxygen atom. It is a byproduct of incomplete combustion processes and is a key component of wood gas produced through biomass gasification. While carbon monoxide is known for its toxicity and potential health hazards in certain concentrations, when managed properly, it becomes a valuable component of wood gas with various industrial applications.
In the context of wood gas production, carbon monoxide is a primary combustible gas generated during the gasification of organic materials like wood or biomass. It contributes to the energy content of the gas and can be used as a fuel for internal combustion engines, gas turbines, and other applications. The controlled production and utilization of carbon monoxide in wood gas highlight its role as an energy carrier in renewable energy systems.
However, it is crucial to emphasize the importance of safety measures and efficient gas cleaning processes to minimize the release of carbon monoxide into the environment. Properly designed gasification systems include measures to control and monitor CO levels, ensuring that the gas can be utilized safely without posing risks to human health or the environment.
As industries and researchers explore the potential of wood gas and other biomass-based energy sources, understanding and managing carbon monoxide become essential components of developing sustainable and safe energy solutions. Advances in gasification technology and safety protocols aim to harness the energy potential of carbon monoxide while minimizing associated risks, contributing to the ongoing evolution of cleaner and more efficient energy systems.
Hydrogen Production:
Hydrogen (H2) production is a critical aspect of wood gasification, as hydrogen is one of the key components of the gas generated during the thermochemical conversion of biomass. In the context of renewable energy, hydrogen is recognized for its versatility as a clean fuel and its potential to play a crucial role in the transition to a low-carbon economy.
Wood gas produced through gasification typically contains a significant proportion of hydrogen, making it an attractive source for hydrogen production. Hydrogen can be separated from the wood gas through various processes, such as gas cleaning and purification techniques. Once isolated, hydrogen can be utilized as a fuel for fuel cells, an energy carrier for various applications, or as a feedstock for industrial processes.
The production of hydrogen from wood gas has environmental advantages, particularly when the biomass feedstock is sourced sustainably. When hydrogen is used as a fuel, it produces only water vapor as a byproduct, making it a clean and environmentally friendly energy carrier. The integration of hydrogen into the energy landscape is part of global efforts to reduce greenhouse gas emissions and achieve a more sustainable energy future.
Ongoing research focuses on improving the efficiency of hydrogen production from wood gas, exploring advanced separation technologies, and developing integrated systems that maximize the overall energy yield. As the world seeks cleaner and more sustainable alternatives to conventional fuels, the role of wood gas in hydrogen production becomes increasingly significant, contributing to a greener and more diversified energy mix.
Gasification Technology:
Gasification technology is a process that converts organic materials, such as wood, biomass, or municipal solid waste, into a gaseous fuel through controlled chemical reactions. The heart of this technology is the gasifier, a device that operates in a low-oxygen or oxygen-starved environment to prevent complete combustion and instead generate producer gas.
Gasification involves a series of complex thermochemical reactions, typically categorized into drying, pyrolysis, combustion, and reduction stages. In the drying stage, moisture is removed from the biomass. Pyrolysis then occurs, where the biomass breaks down into volatile gases, tars, and char. In the combustion stage, a controlled amount of oxygen is introduced to partially oxidize the char, and finally, in the reduction stage, the remaining char reacts with carbon dioxide and water vapor to produce the desired combustible gases.
The choice of gasification technology depends on various factors, including the type of feedstock, desired end products, and application. Common gasifier designs include updraft, downdraft, and fluidized bed configurations. Each design has its advantages and disadvantages, impacting factors such as efficiency, tar content, and ease of operation.
Gasification technology is versatile, with applications ranging from decentralized power generation and heating to the production of syngas for industrial processes. Continuous research and development aim to optimize gasification processes, enhance efficiency, and explore innovative applications, positioning this technology as a key player in the transition to a more sustainable and diversified energy future.
As gasification technology advances, its integration into various sectors holds the potential to contribute significantly to reducing dependence on conventional fossil fuels and mitigating environmental impact, marking a crucial step towards a cleaner and more sustainable energy landscape.
Alternative Energy:
Alternative energy refers to non-traditional sources of energy that differ from conventional fossil fuels like coal, oil, and natural gas. Wood gas, produced through the gasification of wood or biomass, stands as a notable alternative energy source, offering a renewable and sustainable option for meeting energy needs. The quest for alternative energy sources has gained momentum in response to environmental concerns, climate change, and the finite nature of fossil fuel resources.
Wood gas as an alternative energy source aligns with the broader goal of reducing reliance on fossil fuels and mitigating the environmental impact associated with their extraction, processing, and combustion. Gasification of wood provides an eco-friendly alternative by utilizing biomass, a resource that can be replenished through responsible forestry and agricultural practices.
The use of alternative energy sources like wood gas has implications for both decentralized and centralized energy systems. Decentralized applications include small-scale power generation, heating in remote areas, and off-grid solutions. On a larger scale, wood gas can be integrated into existing energy infrastructure, contributing to a diversified energy mix that incorporates cleaner and more sustainable options.
Governments, industries, and individuals worldwide are increasingly recognizing the importance of alternative energy sources in addressing energy security, reducing carbon emissions, and fostering a more sustainable future. As technological advancements continue to make alternative energy options more economically viable, the integration of wood gas into the energy landscape represents a significant step towards a cleaner, more resilient, and environmentally conscious energy sector.
Syngas:
Syngas, short for synthesis gas, is a versatile mixture of gases produced through the gasification of organic materials, such as wood, biomass, or coal. The term “syngas” encompasses a range of compositions, but it typically consists of carbon monoxide (CO), hydrogen (H2), carbon dioxide (CO2), methane (CH4), and other trace gases. The production of syngas is a key outcome of gasification processes and holds significant importance in various industrial applications.
One of the primary uses of syngas is as a feedstock for the production of chemicals and fuels through processes like Fischer-Tropsch synthesis. Syngas can be further processed to yield liquid fuels, such as synthetic gasoline or diesel, providing a bridge between renewable biomass resources and conventional transportation fuels. Additionally, syngas is employed in the production of methanol, ammonia, and other valuable chemicals.
The flexibility of syngas extends to power generation, where it can be utilized in internal combustion engines, gas turbines, or fuel cells. Its ability to be employed in different energy conversion technologies makes syngas a versatile energy carrier, facilitating its integration into various sectors of the energy landscape.
Research efforts continue to focus on optimizing syngas production, enhancing its composition, and exploring innovative applications. The utilization of syngas contributes to the development of sustainable and environmentally friendly energy solutions, fostering a more diversified and resilient energy mix. As the world transitions towards cleaner energy sources, syngas produced from wood gasification emerges as a valuable component in the journey towards a more sustainable and low-carbon future.
Cogeneration:
Cogeneration, also known as combined heat and power (CHP), is a highly efficient energy utilization strategy that involves the simultaneous production of electricity and useful heat from a single energy source. Wood gas, derived through the gasification of wood or biomass, plays a significant role in cogeneration systems, contributing to energy efficiency and sustainability.
In a cogeneration system powered by wood gas, the gas is used to fuel an internal combustion engine or a gas turbine, generating electricity. Simultaneously, the heat produced during the combustion process is captured and utilized for heating purposes, such as space heating, water heating, or for industrial processes that require thermal energy.
The synergy between electricity and heat production in cogeneration systems enhances overall energy efficiency compared to separate generation processes. Traditional power plants often release excess heat into the environment, resulting in lower overall efficiency. Cogeneration addresses this inefficiency by making productive use of the heat that would otherwise be wasted.
Wood gas-based cogeneration systems find applications in various settings, including industrial facilities, commercial buildings, and residential areas. These systems contribute to energy independence, reduce greenhouse gas emissions, and provide a sustainable alternative to conventional energy production methods.
As the world seeks more sustainable and resilient energy solutions, the integration of wood gas in cogeneration systems represents a promising avenue for optimizing resource use and minimizing environmental impact. Ongoing research and technological advancements aim to further enhance the efficiency and applicability of wood gas-based cogeneration, making it a valuable component in the transition towards a more sustainable and integrated energy future.
Gasifier Design:
Gasifier design is a crucial aspect of wood gasification, influencing the efficiency, performance, and environmental impact of the overall gasification process. Gasifiers are devices designed to convert solid biomass, such as wood, into a gaseous fuel through controlled thermochemical reactions. Different gasifier designs have emerged, each with its unique characteristics and advantages.
- Updraft Gasifiers: In updraft gasifiers, biomass is loaded from the top, and the gasification process progresses downward through the fuel bed. The combustion zone is located at the bottom, with the produced gases passing through the hot bed of char and ash. Updraft gasifiers are known for their simplicity, ease of operation, and suitability for a wide range of biomass feedstocks.
- Downdraft Gasifiers: Downdraft gasifiers, on the other hand, introduce biomass from the top, and the gasification reactions progress downward, opposite to updraft gasifiers. Downdraft designs typically achieve higher gas quality and reduced tar content compared to updraft configurations. They are commonly used in applications requiring cleaner gas for engines or fuel cells.
- Fluidized Bed Gasifiers: Fluidized bed gasifiers suspend the biomass particles in an upward-flowing air or gas stream, creating a fluidized bed. This design enhances mixing and allows for efficient gasification at lower temperatures. Fluidized bed gasifiers are known for their ability to handle a variety of feedstocks and offer good tar reduction.
The choice of gasifier design depends on factors such as the desired gas quality, the specific application, and the characteristics of the biomass feedstock. Ongoing research focuses on optimizing gasifier designs to improve efficiency, reduce tar content, and enhance the overall performance of wood gasification systems. As technology advances, innovative gasifier designs continue to contribute to the evolution of gasification technology, making it a key player in sustainable and decentralized energy solutions.
EMS Power Machines
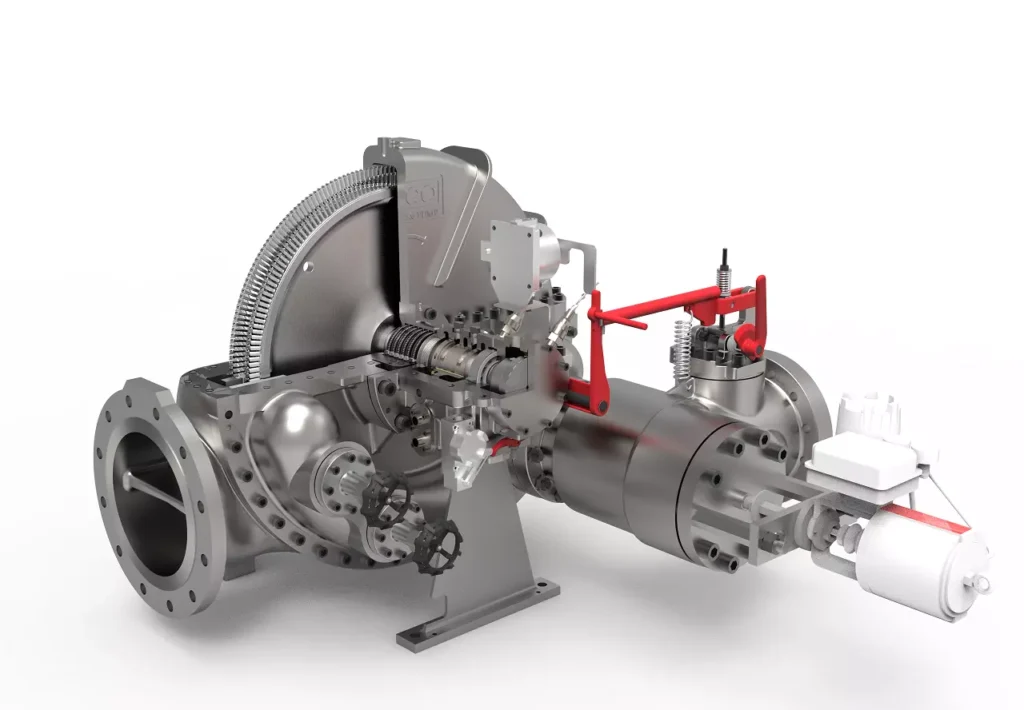
We design, manufacture and assembly Power Machines such as – diesel generators, electric motors, vibration motors, pumps, steam engines and steam turbines
EMS Power Machines is a global power engineering company, one of the five world leaders in the industry in terms of installed equipment. The companies included in the company have been operating in the energy market for more than 60 years.
EMS Power Machines manufactures steam turbines, gas turbines, hydroelectric turbines, generators, and other power equipment for thermal, nuclear, and hydroelectric power plants, as well as for various industries, transport, and marine energy.
EMS Power Machines is a major player in the global power industry, and its equipment is used in power plants all over the world. The company has a strong track record of innovation, and it is constantly developing new and improved technologies.
Here are some examples of Power Machines’ products and services:
- Steam turbines for thermal and nuclear power plants
- Gas turbines for combined cycle power plants and industrial applications
- Hydroelectric turbines for hydroelectric power plants
- Generators for all types of power plants
- Boilers for thermal power plants
- Condensers for thermal power plants
- Reheaters for thermal power plants
- Air preheaters for thermal power plants
- Feedwater pumps for thermal power plants
- Control systems for power plants
- Maintenance and repair services for power plants
EMS Power Machines is committed to providing its customers with high-quality products and services. The company has a strong reputation for reliability and innovation. Power Machines is a leading provider of power equipment and services, and it plays a vital role in the global power industry.
EMS Power Machines, which began in 1961 as a small factory of electric motors, has become a leading global supplier of electronic products for different segments. The search for excellence has resulted in the diversification of the business, adding to the electric motors products which provide from power generation to more efficient means of use.