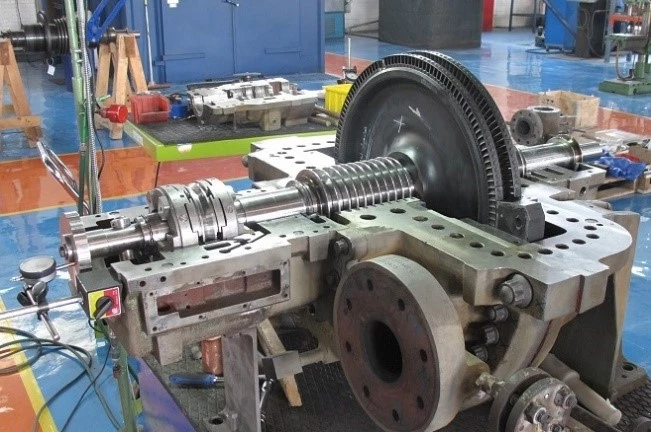
Steam Turbine Generators for Sale: Steam turbines are critical components in modern power generation systems, converting thermal energy from steam into mechanical energy and, ultimately, into electrical power. Their role is central in various energy production methods, including fossil fuel plants, nuclear power stations, and renewable energy facilities. The basic operation of a steam turbine involves the high-pressure steam generated in a boiler or reactor being directed onto turbine blades, causing the rotor to spin. This rotary motion is then transferred to a generator, where it is converted into electricity.
The development and utilization of steam turbines have significantly contributed to the industrialization and modernization of energy systems worldwide. They are integral to both large-scale power plants and smaller, specialized industrial setups. Steam turbines are known for their high efficiency, reliability, and ability to operate under a wide range of conditions, making them indispensable in the global energy landscape.
The versatility of steam turbines extends beyond electricity generation. They are also used in marine propulsion, where their robust design and ability to generate large amounts of power efficiently make them suitable for naval ships and commercial vessels. Additionally, steam turbines are employed in various industrial processes, where they drive machinery, compressors, and other equipment, contributing to overall operational efficiency.
Historical Development of Steam Turbines
The history of steam turbines can be traced back to the early 19th century, although the principles behind them were understood much earlier. The steam engine, which predates the steam turbine, was a pivotal invention that powered the Industrial Revolution. However, the steam engine’s reciprocating motion had limitations in efficiency and speed, leading to the development of the steam turbine.
The first practical steam turbine was developed by Sir Charles Parsons in 1884. Parsons’ design was revolutionary, using high-speed rotary motion to generate electricity more efficiently than steam engines. His turbine was initially used to power electrical generators, and the success of this application quickly led to widespread adoption in power plants.
The development of steam turbines continued throughout the 20th century, with significant advancements in materials, aerodynamics, and thermodynamics. These improvements allowed steam turbines to operate at higher pressures and temperatures, significantly increasing their efficiency and power output. The introduction of multi-stage turbines, where steam expands through several stages of blades, further enhanced their performance.
In the mid-20th century, steam turbines became the dominant technology for electricity generation, especially as demand for power increased globally. Their ability to efficiently convert thermal energy into electrical energy made them the preferred choice for large power plants, particularly those using fossil fuels or nuclear reactors.
The evolution of steam turbines also paralleled the development of new materials and manufacturing techniques. Advances in metallurgy allowed for the creation of turbine blades and rotors that could withstand higher temperatures and stresses, enabling turbines to operate at greater efficiencies. The introduction of computer-aided design (CAD) and computational fluid dynamics (CFD) further optimized turbine designs, reducing energy losses and improving overall performance.
Today, steam turbines are a mature technology, yet they continue to evolve. Innovations in digital controls, materials science, and integration with renewable energy systems are pushing the boundaries of what steam turbines can achieve. As the world transitions to cleaner energy sources, steam turbines are expected to play a critical role in hybrid systems, combining traditional and renewable energy sources to create more sustainable and reliable power generation solutions.
Importance in Modern Energy Systems
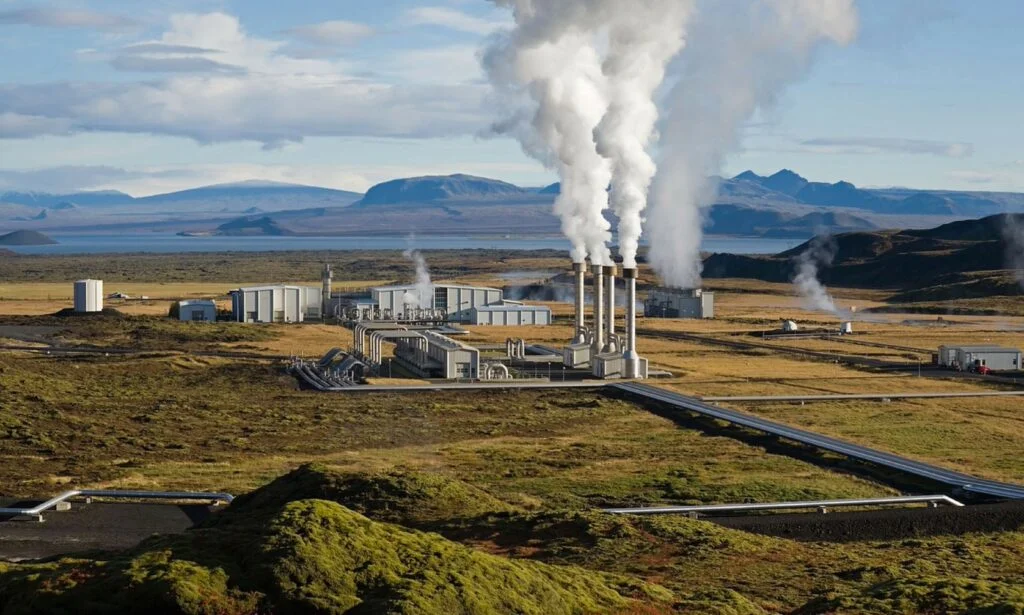
In the contemporary energy landscape, steam turbines are essential due to their efficiency, reliability, and adaptability to various power generation scenarios. They are crucial in baseload power generation, where they operate continuously to meet the constant demand for electricity. Steam turbines are particularly important in countries that rely heavily on coal, nuclear, and natural gas power plants, as these plants use steam turbines to convert thermal energy into electrical power.
Steam turbines are also integral to the operation of cogeneration systems, where they provide both electricity and process heat. This dual-function capability enhances the overall energy efficiency of power plants, making steam turbines a valuable asset in industries where both power and heat are required, such as in chemical manufacturing, oil refining, and paper production.
The role of steam turbines in renewable energy systems is growing as well. In biomass power plants, for example, steam turbines convert the energy released from burning organic materials into electricity. Similarly, in concentrated solar power (CSP) plants, steam turbines are used to convert heat captured from the sun into electrical energy. These applications demonstrate the versatility of steam turbines and their ability to contribute to reducing carbon emissions and enhancing energy security.
Moreover, steam turbines are vital in the marine industry, where they are used in propulsion systems for both naval and commercial vessels. The high power output and reliability of steam turbines make them suitable for driving large ships over long distances. In the naval sector, steam turbines are preferred for their ability to operate efficiently under demanding conditions, providing the necessary power for various shipboard systems.
The importance of steam turbines extends to their economic impact as well. They are a key component in the global energy infrastructure, supporting industries, economies, and communities worldwide. The efficiency improvements and operational reliability of steam turbines translate into lower energy costs and reduced environmental impacts, making them a critical technology for achieving global energy goals.
Looking ahead, steam turbines are expected to remain a cornerstone of power generation. As the energy industry continues to evolve, steam turbines will adapt to new challenges and opportunities, including the integration of more renewable energy sources and the development of more efficient and flexible turbine designs. Their ability to generate large amounts of power reliably and efficiently ensures that steam turbines will continue to play a vital role in meeting the world’s energy needs.
Working Principle of Steam Turbines
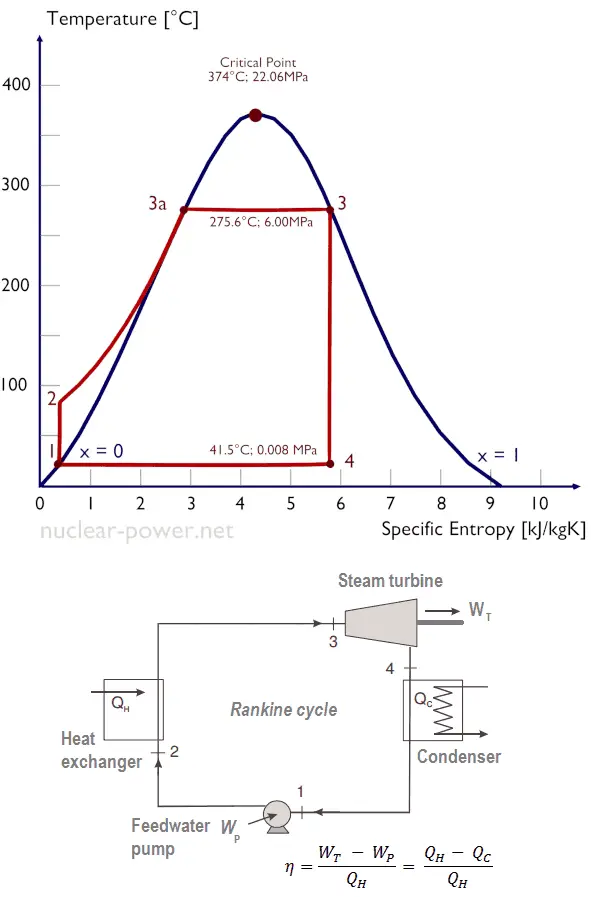
How Steam Turbines Work
Steam turbines operate on the principle of converting the thermal energy contained in high-pressure steam into mechanical energy through a rotary motion, which is then typically converted into electrical energy by a generator. The process begins with the generation of steam in a boiler, where water is heated to its boiling point and converted into steam at high pressure and temperature. This high-energy steam is then directed into the steam turbine.
Inside the turbine, the steam passes through a series of stationary and rotating blades. The stationary blades, also known as nozzles, direct the steam flow onto the rotating blades. The design of the rotating blades is crucial, as they capture the kinetic energy of the steam, causing the rotor to spin. This rotational motion is the core of the turbine’s functionality, as it drives the generator that produces electricity.
There are two primary types of turbines based on the method of energy extraction from the steam: impulse turbines and reaction turbines.
- Impulse Turbines: In an impulse turbine, the steam is expanded in nozzles before it hits the turbine blades. This expansion converts the steam’s pressure energy into kinetic energy, producing high-velocity jets of steam that strike the turbine blades, causing the rotor to turn. Impulse turbines typically have several stages, with each stage consisting of a set of nozzles and blades, allowing for efficient energy extraction at each stage.
- Reaction Turbines: In a reaction turbine, the steam expands both as it passes through the stationary nozzles and as it moves over the rotating blades. The steam’s pressure decreases continuously across both the stationary and rotating blades, causing a reactive force that turns the rotor. Reaction turbines tend to operate more smoothly and are often used in situations where gradual energy extraction is required over multiple stages.
Both types of turbines are often combined in a single unit to maximize efficiency. The high-pressure steam first enters the impulse section, where a significant portion of its energy is extracted. The partially expanded steam then moves into the reaction section, where further energy is extracted before the steam is exhausted from the turbine.
Key Components of a Steam Turbine
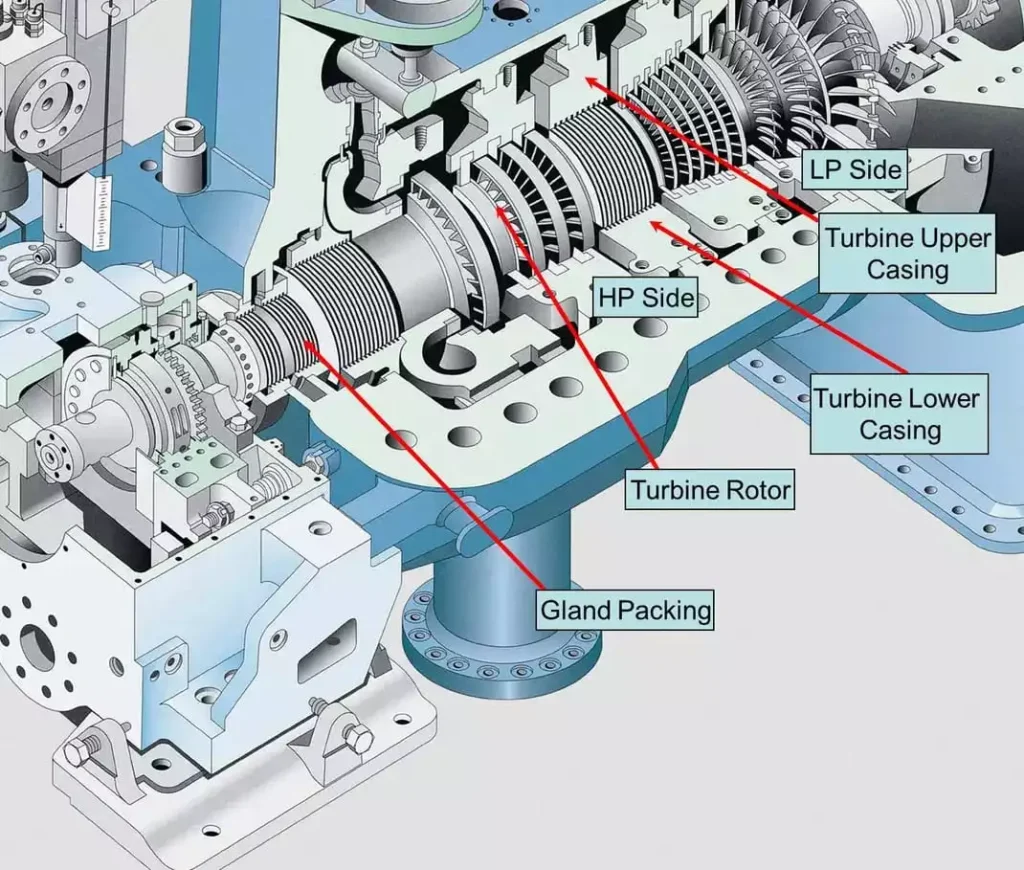
Understanding the key components of a steam turbine is essential to grasp how these machines convert steam energy into mechanical energy. Below are the primary components and their functions:
- Rotor: The rotor is the central shaft that carries the turbine blades and rotates as the blades interact with the steam. The rotor’s rotation is the fundamental mechanical action that drives the generator.
- Blades: The blades are the components that interact directly with the steam. They are attached to the rotor and are designed to efficiently capture the kinetic and pressure energy of the steam. Blades must be carefully engineered to handle the extreme temperatures and pressures of the steam while maintaining their structural integrity.
- Casing: The casing is the outer shell that contains the steam within the turbine and supports the stationary components. It is designed to withstand high pressures and temperatures and to ensure the safe and efficient operation of the turbine.
- Nozzles: Nozzles are stationary blades that convert the steam’s pressure energy into kinetic energy by accelerating it into high-speed jets. These nozzles direct the steam onto the rotating blades, ensuring that the energy transfer is as efficient as possible.
- Bearings: Bearings support the rotor and allow it to spin freely while minimizing friction. They are crucial for maintaining the stability and smooth operation of the turbine.
- Governor Valve: The governor valve controls the flow of steam into the turbine. By regulating the steam flow, the governor valve helps maintain the turbine’s speed and power output, ensuring stable operation.
- Condensers: Condensers are used to cool the exhaust steam from the turbine, converting it back into water so it can be reused in the boiler. This process is essential for maintaining the efficiency of the steam cycle.
- Control Systems: Modern steam turbines are equipped with sophisticated control systems that monitor and adjust the turbine’s operating parameters in real time. These systems help optimize performance, prevent failures, and ensure safe operation.
Steam Turbine Cycle Diagram
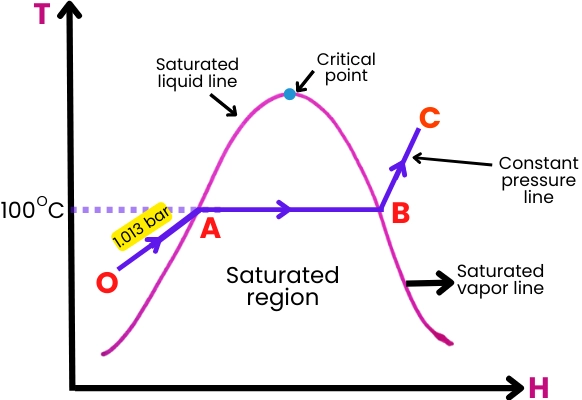
The operation of a steam turbine within a power generation system can be represented by the Rankine cycle, which is the thermodynamic cycle that describes the conversion of heat into work.
- Boiler (Steam Generator): The cycle begins in the boiler, where water is heated to produce high-pressure, high-temperature steam. This steam is the working fluid that drives the turbine.
- Turbine: The high-pressure steam is introduced into the turbine, where it expands and loses pressure and temperature while doing work on the turbine blades, causing the rotor to spin. The mechanical energy generated by the rotor is then converted into electrical energy by the generator.
- Condenser: After leaving the turbine, the steam enters the condenser, where it is cooled and condensed back into water. The condenser is typically cooled by water from a nearby natural source or a cooling tower.
- Pump: The condensed water is then pumped back into the boiler, where it is reheated to produce steam, completing the cycle.
- Superheating and Reheating: To improve the efficiency of the Rankine cycle, the steam can be superheated (heated beyond its boiling point at constant pressure) before entering the turbine. This reduces the moisture content of the steam as it expands, minimizing erosion on the turbine blades. Additionally, reheat cycles can be employed, where steam is partially expanded in the turbine, reheated in the boiler, and then returned to the turbine for further expansion.
- Efficiency Considerations: The efficiency of a steam turbine cycle depends on several factors, including the temperature and pressure of the steam entering the turbine, the effectiveness of the condenser, and the design of the turbine itself. Enhancements such as regenerative feedwater heating, where steam is used to preheat the feedwater before it enters the boiler, can further increase cycle efficiency by reducing the amount of energy required to heat the water.
Thermodynamics and Steam Turbines
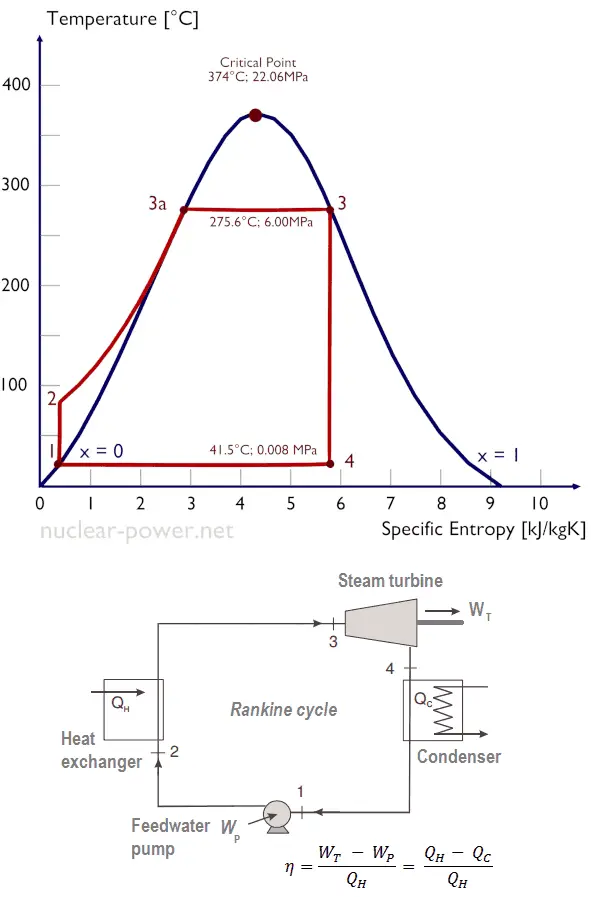
The operation of steam turbines is governed by the principles of thermodynamics, particularly the laws of energy conservation and entropy.
- First Law of Thermodynamics (Energy Conservation): This law states that energy cannot be created or destroyed, only converted from one form to another. In the context of a steam turbine, the thermal energy of the steam is converted into mechanical energy (rotational motion of the rotor) and then into electrical energy by the generator.
- Second Law of Thermodynamics (Entropy): The second law introduces the concept of entropy, which is a measure of the disorder or randomness in a system. In practical terms, it means that not all the thermal energy in the steam can be converted into useful work; some of it is inevitably lost as waste heat. This is why no heat engine, including a steam turbine, can be 100% efficient.
- Isentropic Process: Ideally, the expansion of steam in a turbine would be an isentropic process, meaning it would occur without any increase in entropy. In reality, however, factors such as friction and turbulence cause the process to be less efficient, leading to some energy losses.
- Enthalpy-Entropy (h-s) Diagram: The performance of steam turbines is often analyzed using an h-s diagram, which plots the enthalpy of the steam against its entropy. The diagram helps engineers visualize the energy conversion process and identify areas where efficiency improvements can be made.
Real-World Applications of Steam Turbines
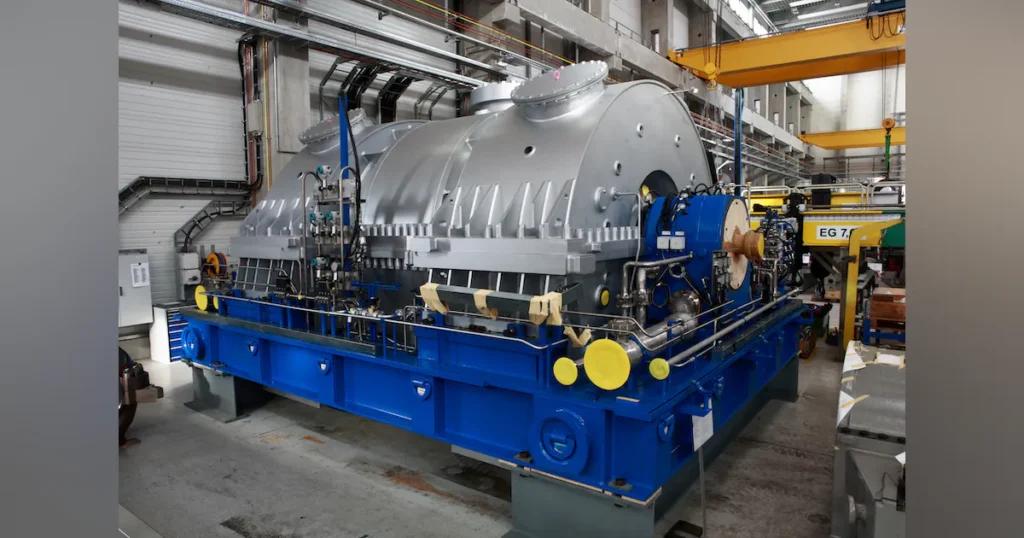
Steam turbines are used in a wide range of applications beyond electricity generation in power plants. Some of these include:
- Marine Propulsion: Steam turbines are commonly used in naval ships and some commercial vessels due to their ability to generate large amounts of power efficiently. They provide propulsion as well as power for onboard systems.
- Industrial Processes: Many industries use steam turbines to drive mechanical equipment, such as pumps and compressors, as part of their manufacturing processes. These turbines are often part of cogeneration systems that produce both electricity and process heat.
- District Heating: In some urban areas, steam turbines are used as part of district heating systems, where they generate electricity and provide heat to residential and commercial buildings.
- Renewable Energy: Steam turbines are increasingly being integrated into renewable energy systems, such as biomass power plants and concentrated solar power (CSP) plants, where they convert the thermal energy generated from these renewable sources into electricity.
Types of Steam Turbines and Their Applications
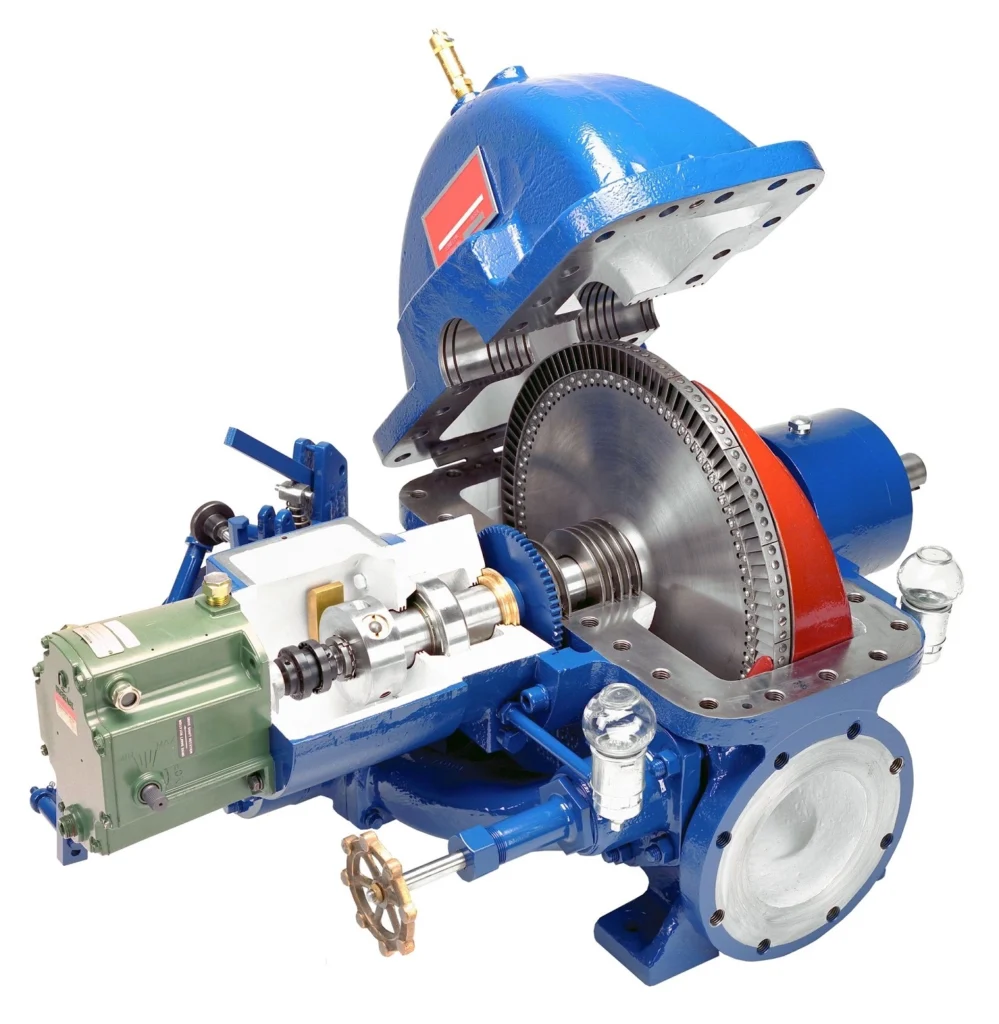
High-Pressure (HP) Steam Turbines
High-Pressure (HP) steam turbines are designed to operate with steam at very high pressures and temperatures. These turbines are typically the first stage in a multi-stage turbine setup, where they handle the most intense thermal and mechanical loads.
- Design and Operation
HP steam turbines are constructed with materials that can withstand extreme conditions. The blades are often made of special alloys to endure thermal stress and mechanical strain. The energy extracted in this stage is substantial, making HP turbines crucial to the overall efficiency of the power plant. - Applications
HP turbines are used in:- Large Thermal Power Plants: Coal-fired, gas-fired, and nuclear power stations, where they form the first stage of electricity generation.
- Combined Cycle Power Plants: HP turbines work alongside gas turbines to enhance efficiency.
- Industrial Cogeneration Plants: Where high-pressure steam is utilized for industrial processes before being sent to lower-pressure turbines.
3.2 Low-Pressure (LP) Steam Turbines
Low-Pressure (LP) steam turbines operate at lower pressures, typically as the final stage in the power generation process.
- Design and Operation
LP turbines are designed to extract as much remaining energy as possible from the steam before it is condensed. They typically have larger blades and operate at lower rotational speeds compared to HP turbines. - Applications
LP turbines are used in:- Thermal Power Plants: Following HP and intermediate-pressure (IP) turbines.
- Nuclear Power Plants: Handling steam after it has passed through HP turbines.
- Marine Propulsion: In naval ships, as part of the propulsion system.
Impulse Turbines
An impulse turbine operates by directing high-velocity steam jets onto the turbine blades. The steam is expanded in nozzles before striking the blades, imparting kinetic energy to the rotor.
- Design and Operation
Impulse turbines have a simple design with multiple stages. The energy transfer occurs primarily through changes in the steam’s velocity. - Applications
Impulse turbines are used in:- Small to Medium Power Generation: Due to their simplicity and ease of maintenance.
- High-Pressure Stages: In large steam turbines, where they handle initial high-energy steam expansion.
- Industrial Applications: Where precise control over power output is required.
Reaction Turbines
Reaction turbines rely on the steam undergoing expansion as it flows over both stationary and moving blades. This type of turbine uses both pressure drop and velocity changes of the steam to generate power.
- Design and Operation
In a reaction turbine, the steam expands in both stationary and moving blades, creating a reactive force that causes the rotor to spin. This design allows for more stages, making them suitable for applications requiring gradual energy extraction. - Applications
Reaction turbines are used in:- Large Power Generation: Particularly where continuous operation is required, such as in nuclear power plants.
- Marine Propulsion: Due to their smooth operation and ability to handle fluctuating loads.
- Industrial Processes: Where they drive compressors and pumps.
Turbine Stages
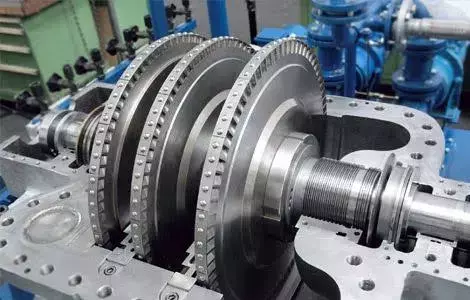
Steam turbines consist of multiple stages, each designed to extract energy from the steam progressively. These stages are arranged in series to maximize energy conversion from the high-pressure steam at the inlet to the low-pressure steam at the outlet.
- Single-Stage vs. Multi-Stage Turbines
- Single-Stage Turbines: Found in small applications, simpler and cheaper but less efficient for large-scale power generation.
- Multi-Stage Turbines: More complex, used in large power plants. Multi-stage turbines ensure maximum efficiency and power output by allowing gradual steam expansion across several stages.
- Applications
Multi-stage turbines are used in:- Large Power Plants: To ensure maximum efficiency and power output.
- Industrial Cogeneration: Where both electricity and process steam are required.
- Marine Propulsion: In large ships, where efficient and reliable power generation is critical.
Specialized Steam Turbines
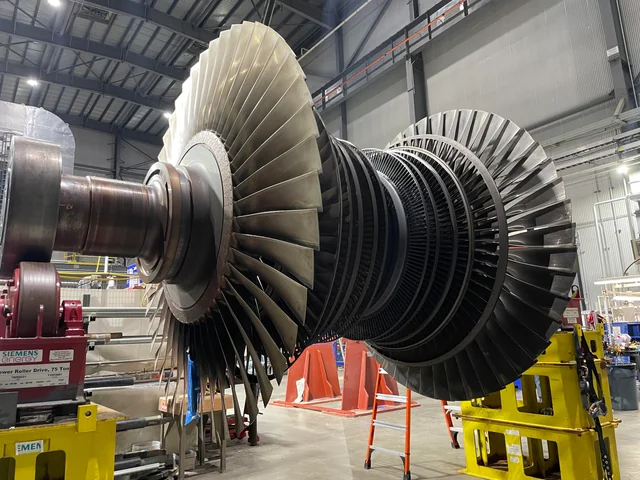
There are specialized turbines designed for specific applications, often tailored to meet unique demands.
- Marine Steam Engines
Marine steam engines, including steam turbines, have been historically and currently used in naval and commercial vessels for reliable propulsion over long distances and challenging conditions.- Applications
- Naval Ships: Providing reliability and high power output for military vessels.
- Commercial Ships: Used in older vessels where steam propulsion was standard.
- Marine Auxiliary Systems: Smaller turbines used in shipboard power generation systems.
- Applications
- Biomass-Fueled Steam Turbines
Biomass power plants use steam turbines that operate on steam generated from burning organic materials.- Applications
- Biomass Power Plants: Converting energy from burning organic materials into electricity.
- Cogeneration Plants: Using biomass to provide both heat and power for industrial and residential use.
- Applications
- Mini and Micro Steam Turbines
These small-scale turbines are designed for applications where compact size and lower power output are required.- Applications
- Decentralized Power Generation: In remote or off-grid locations.
- Industrial Applications: Where small amounts of steam power are needed for specific processes.
- Renewable Energy Systems: Such as solar thermal plants or small-scale biomass plants.
- Applications
Steam Turbine Components and Accessories
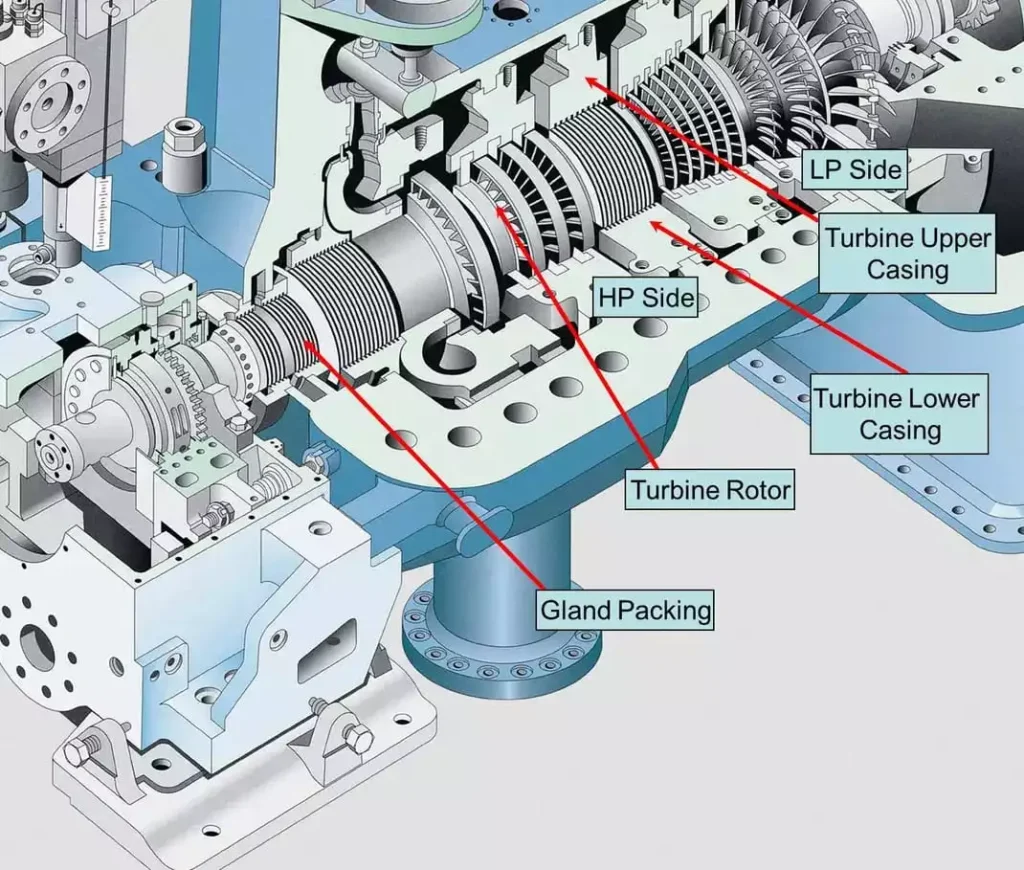
Parts of a Steam Turbine
A steam turbine is a complex machine composed of several critical components that work together to efficiently convert thermal energy into mechanical energy. Understanding these parts is essential for grasping how steam turbines function and how they can be optimized for different applications.
- Rotor
The rotor is the central rotating component of the steam turbine. It consists of a shaft to which turbine blades are attached. The rotor spins at high speeds as the steam passes over the blades, converting the steam’s kinetic energy into rotational energy. - Blades
The blades are crucial for capturing the energy of the steam. They are attached to the rotor and come in two main types:- Moving Blades: These rotate with the rotor and are responsible for the actual energy conversion.
- Stationary Blades (Nozzles): These direct the flow of steam onto the moving blades, ensuring that the energy transfer is as efficient as possible.
- Casing
The casing encloses the rotor and blades, containing the high-pressure steam and directing it through the turbine. It also supports the stationary blades and is designed to withstand the extreme pressures and temperatures within the turbine. - Bearings
Bearings support the rotor and allow it to spin with minimal friction. They are critical for maintaining the alignment and stability of the turbine during operation. - Governor Valve
The governor valve controls the flow of steam into the turbine. It adjusts the steam flow to maintain the desired turbine speed and power output, playing a key role in the turbine’s efficiency and stability. - Shaft Seal
The shaft seal prevents steam from leaking out of the turbine casing where the rotor shaft exits the casing. Effective sealing is crucial for maintaining the turbine’s efficiency and safety. - Exhaust System
The exhaust system channels the spent steam out of the turbine, often directing it to a condenser where it is cooled and condensed back into water. This water can then be recycled back into the boiler for reuse.
Governor Valve Operation
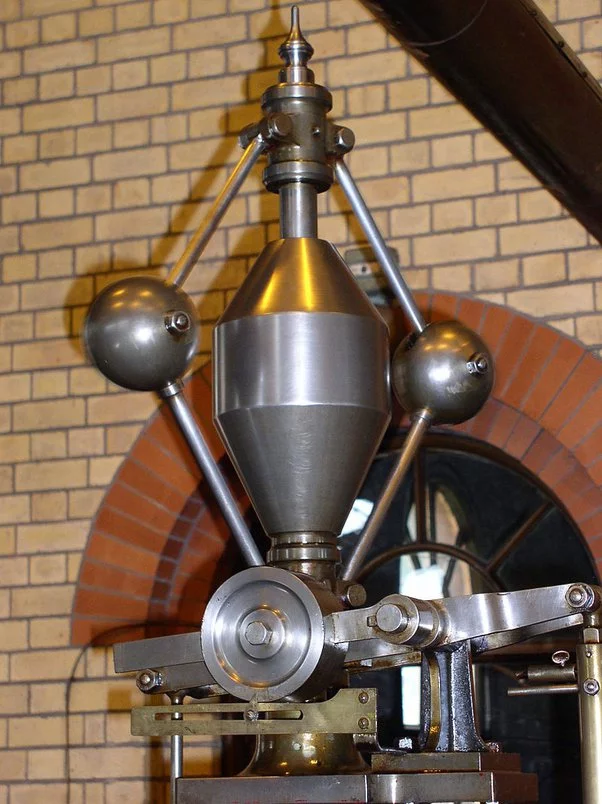
The governor valve is a vital component of steam turbines, responsible for regulating the flow of steam into the turbine and thus controlling its speed and power output.
- Design and Function
The governor valve is typically located at the steam inlet of the turbine. It operates based on signals from the turbine’s control system, which monitors parameters such as load demand, turbine speed, and steam pressure. By adjusting the valve opening, the governor can increase or decrease steam flow, directly influencing the turbine’s performance.Different types of governor valves include:- Throttle Valves: These control steam flow by varying the valve opening.
- Control Valves: Provide precise control over steam flow, often used in combination with throttle valves.
- Stop Valves: Act as safety devices that can shut off steam flow entirely in emergencies.
- Operation Mechanism
The governor valve responds to changes in the turbine’s speed. If the turbine begins to overspeed, the valve partially closes to reduce the steam flow, slowing down the turbine. Conversely, if the turbine’s speed drops, the valve opens wider to increase the steam flow and bring the speed back up.The valve’s movement is typically controlled by a hydraulic actuator, which receives signals from the turbine’s electronic governor. This system ensures rapid and precise adjustments to the steam flow, maintaining optimal turbine performance under varying conditions. - Importance in Power Generation
The governor valve is crucial for maintaining the stability of the power grid, especially in large power plants where fluctuations in turbine speed can lead to frequency deviations. By ensuring the turbine operates at the correct speed, the governor valve helps prevent mechanical damage and contributes to the overall efficiency of the power generation process.
Electronic Governors
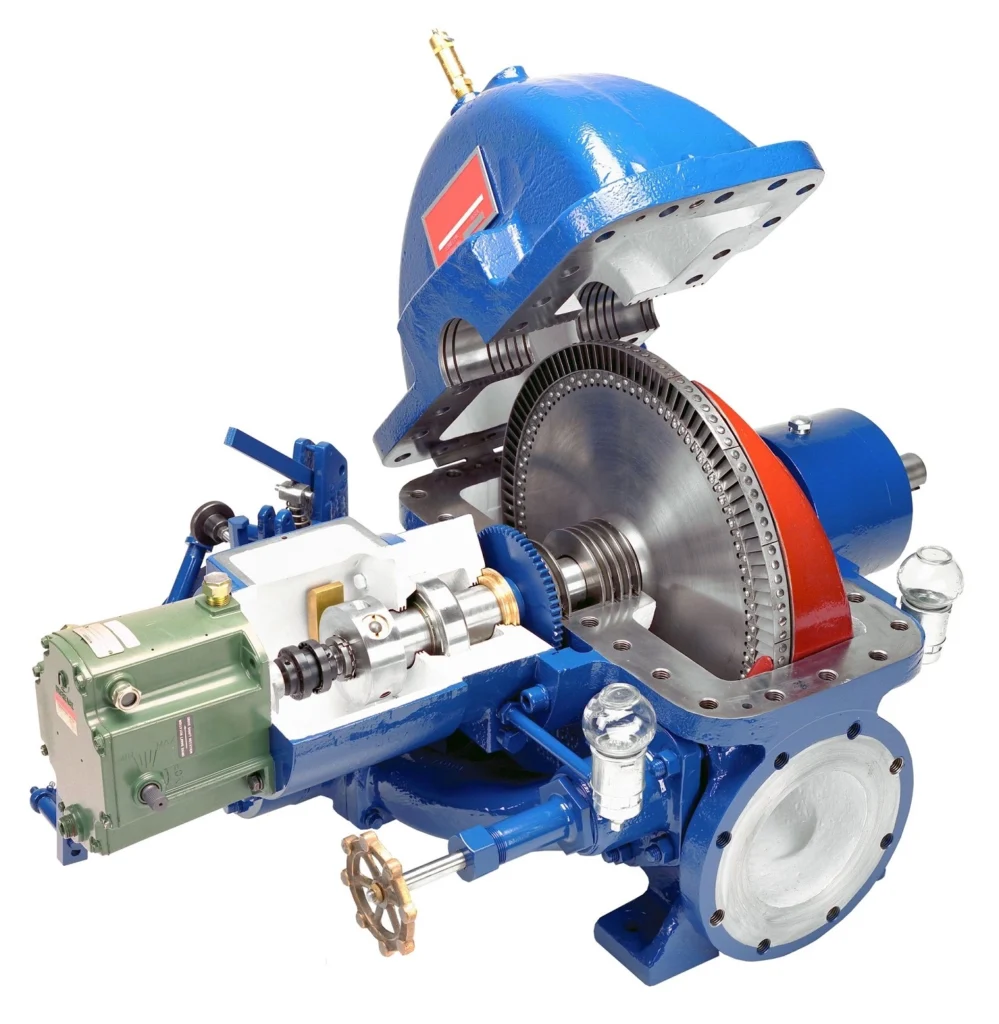
Electronic governors are a modern advancement in steam turbine control, offering more precise and responsive regulation of turbine speed and power output compared to traditional mechanical governors.
- Function and Advantages
Electronic governors use digital technology to monitor and control the turbine’s operation. They receive input from various sensors that measure parameters like speed, temperature, and pressure. The data is processed by a central control unit, which then sends commands to the hydraulic actuators controlling the governor valve.The key advantages of electronic governors include:- Precision: They provide more accurate control of turbine speed and output.
- Flexibility: Easier integration with modern control systems and automation technologies.
- Responsiveness: Faster adjustments to changes in load demand and operating conditions.
- Safety: Enhanced protection features, such as automatic shutdown in case of system faults.
- Integration with Modern Control Systems
Electronic governors are often integrated with advanced control systems that manage the entire power plant. This integration allows for better coordination between the turbine and other plant components, leading to improved efficiency and reliability. - Applications in Modern Steam Turbines
Electronic governors are standard in most new steam turbines, particularly in large power plants and industrial cogeneration systems. They are also used in retrofitting older turbines to improve performance and extend operational life.
Turbine Rotors and Materials
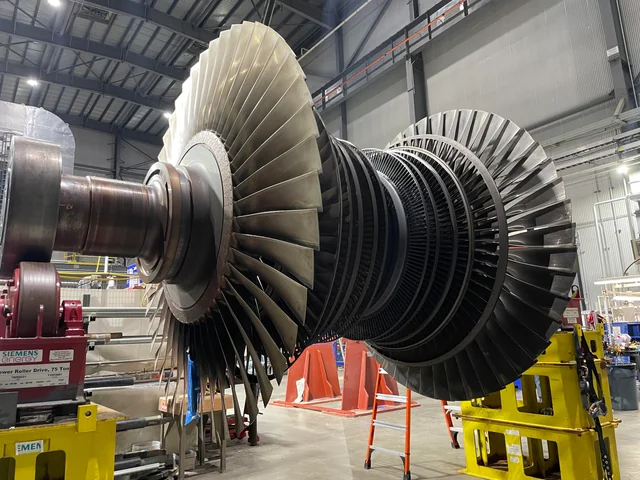
The turbine rotor is the central component of the steam turbine, responsible for converting the thermal energy of the steam into mechanical energy. The rotor consists of a shaft to which turbine blades are attached, and it rotates at high speeds during operation.
- Design and Construction
Turbine rotors must withstand the extreme forces generated by high-speed rotation and the thermal stresses caused by the steam. The material used for the rotor must be capable of withstanding high temperatures, pressures, and centrifugal forces without deforming or failing. Common materials include high-strength alloys, such as chromium-nickel steels, which offer a good balance of strength, ductility, and resistance to thermal fatigue.The construction of the rotor involves precision engineering to ensure perfect balance and alignment. Any imbalance in the rotor can lead to excessive vibration, which can cause damage to the turbine and reduce its efficiency. - Blades and Blade Assembly
The blades attached to the rotor are crucial for capturing the energy from the steam. They are typically made from materials like titanium alloys or nickel-based superalloys, which offer high strength and resistance to corrosion and thermal fatigue. The blades are carefully shaped and positioned on the rotor to maximize the energy transfer from the steam.Blade assembly on the rotor must be done with extreme precision to ensure that the turbine operates smoothly. Blades are often assembled in stages, with each stage designed to handle a specific range of steam pressures and velocities. The correct assembly of blades is critical to the turbine’s performance and longevity. - Maintenance and Lifespan
The rotor and its blades are subject to wear and tear over time, especially in high-demand environments. Regular maintenance, including inspection for cracks, erosion, and other signs of wear, is essential to ensure the continued safe and efficient operation of the turbine. The lifespan of a turbine rotor can vary depending on the operating conditions, but with proper maintenance, it can last for decades.
Steam Turbine Condensers
Condensers play a vital role in the steam turbine cycle by converting the exhaust steam from the turbine back into water, which is then recycled into the boiler. This process increases the efficiency of the steam cycle and reduces the need for fresh water input.
- Function and Importance
Condensers operate by cooling the exhaust steam, typically using cooling water from a nearby source, such as a river, lake, or cooling tower. The condensed water, now in liquid form, is pumped back into the boiler to be reheated and converted into steam, thus completing the cycle. By lowering the temperature and pressure of the exhaust steam, condensers also help maintain the vacuum in the turbine, which is crucial for maximizing efficiency. - Types of Condensers
There are two main types of condensers used in steam turbines:- Surface Condensers: These are the most common type, where the steam passes over tubes containing cooling water. The steam condenses on the outside of the tubes, while the cooling water remains isolated within the tubes.
- Direct-Contact Condensers: In these condensers, the steam directly contacts the cooling water, mixing with it and condensing immediately. This type is less common and is typically used in specific applications where water quality and availability are less of a concern.
- Maintenance and Optimization
Regular maintenance of condensers and associated accessories is crucial for maintaining the efficiency and reliability of the steam turbine system. This includes inspecting for leaks, cleaning tubes, and ensuring that cooling water quality is maintained. Optimizing the operation of condensers and other accessories can significantly improve the overall efficiency of the power generation process.
Steam Turbine Accessories
In addition to the primary components, several accessories are essential for the operation of steam turbines. These accessories enhance the performance, efficiency, and safety of the turbine system.
- Deaerators
Deaerators are used to remove dissolved gases, particularly oxygen, from the feedwater before it enters the boiler. Removing these gases is crucial for preventing corrosion in the boiler and turbine components. - Feedwater Heaters
Feedwater heaters preheat the water before it enters the boiler, improving overall efficiency by reducing the energy needed to convert water into steam. This process helps to reduce fuel consumption and increase the thermal efficiency of the power plant. - Steam Traps
Steam traps remove condensate and non-condensable gases from the steam lines, ensuring that only dry steam reaches the turbine. This is important for maintaining the efficiency and preventing damage to the turbine blades. - Pumps
Pumps are used to circulate the feedwater and condensate within the steam cycle, maintaining the necessary pressure and flow rates. They are critical for ensuring that the steam cycle operates smoothly and efficiently. - Valves and Safety Devices
Various valves and safety devices are installed throughout the steam turbine system to control steam flow, pressure, and temperature. These devices are essential for maintaining safe and efficient operation, protecting the turbine from damage due to overpressure or other abnormal conditions. - Instrumentation and Control Systems
Modern steam turbines are equipped with sophisticated instrumentation and control systems that monitor and adjust various operational parameters in real-time. These systems help to optimize performance, prevent failures, and ensure safe operation.
Steam Turbine Performance and Efficiency
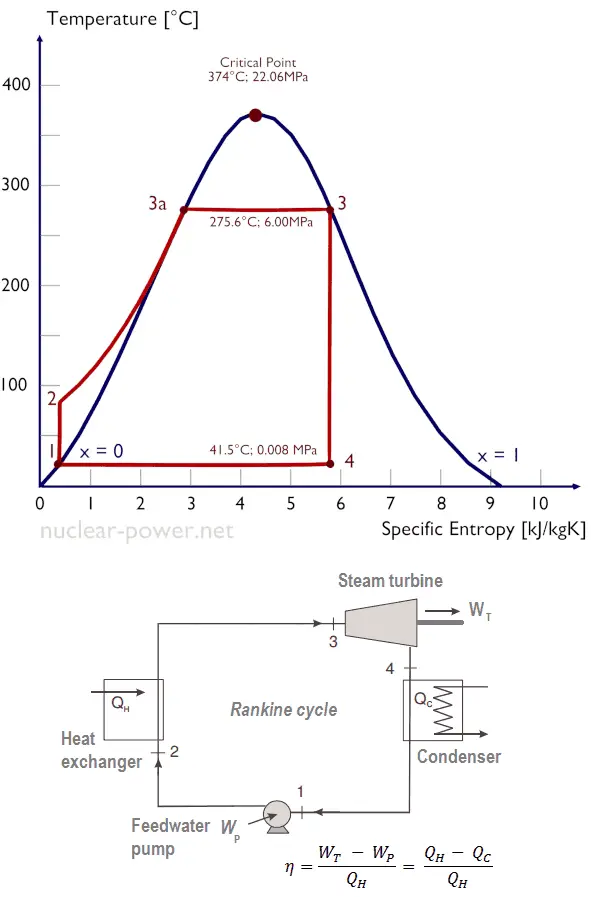
Key Performance Metrics for Steam Turbines
Understanding and measuring the performance of a steam turbine is crucial for optimizing its operation and ensuring that it meets desired power output and efficiency levels. Several key performance metrics are used to evaluate the effectiveness of steam turbines in power generation:
- Thermal Efficiency
Thermal efficiency represents the ratio of useful energy output to the energy input in the form of steam. Steam turbines’ thermal efficiency is influenced by factors like steam pressure, temperature, and the efficiency of individual turbine stages. Higher steam temperatures and pressures generally lead to better thermal efficiency, as they allow more energy to be extracted from the steam. - Power Output
The power output of a steam turbine is measured in megawatts (MW) and indicates the amount of electrical energy the turbine can generate. This metric is directly related to the turbine’s design, size, and the amount of steam it can process. Power output is a key factor in determining the turbine’s suitability for specific applications, such as large power plants or smaller industrial settings. - Heat Rate
The heat rate measures the energy input required to produce one kilowatt-hour (kWh) of electricity, typically expressed in British Thermal Units per kWh (BTU/kWh). A lower heat rate indicates a more efficient turbine, as it requires less fuel to generate the same amount of electricity. The heat rate is influenced by factors such as the efficiency of the boiler, steam conditions, and the overall design of the turbine. - Load Factor
The load factor measures the ratio of the actual energy produced by the turbine over a given period to the maximum possible energy it could have produced if it operated at full capacity. A high load factor indicates that the turbine is being used effectively, while a low load factor may suggest inefficiencies or underutilization. - Availability and Reliability
Availability refers to the percentage of time the turbine is operational and capable of generating power, while reliability indicates the turbine’s ability to operate without failure. Both metrics are essential for power plants that require consistent and dependable energy production. High availability and reliability are often achieved through regular maintenance, monitoring, and the use of advanced control systems.
Turbine Generator Efficiency
Turbine generator efficiency is a critical aspect of overall plant performance. It represents how effectively the turbine converts steam energy into mechanical energy and then into electrical energy. Improving turbine generator efficiency involves optimizing several factors:
- Blade Design and Aerodynamics
The design of the turbine blades plays a significant role in efficiency. Modern turbines use blades with advanced aerodynamic shapes that minimize energy losses due to friction and turbulence. The precision with which the blades are manufactured and assembled also affects efficiency, as even small imperfections can lead to significant energy losses. - Steam Conditions
The pressure, temperature, and quality of the steam entering the turbine are crucial for efficiency. Superheated steam, which has a higher temperature and lower moisture content, is generally more efficient than saturated steam. Optimizing the steam conditions to match the turbine design can lead to significant gains in efficiency. - Turbine Stages and Reheat Cycles
Multi-stage turbines with reheat cycles can improve efficiency by allowing steam to expand in stages, extracting energy more gradually and effectively. In a reheat cycle, steam is partially expanded in the turbine, then reheated in the boiler before returning to the turbine for further expansion. This process increases the thermal efficiency of the cycle. - Minimizing Mechanical Losses
Mechanical losses in the turbine, such as friction in bearings and seals, can reduce overall efficiency. Using high-quality materials and advanced engineering techniques can minimize these losses. Regular maintenance is also essential to prevent wear and tear that can lead to increased mechanical losses over time. - Generator Efficiency
The efficiency of the electrical generator connected to the turbine is also a critical factor. Modern generators are designed to convert mechanical energy into electrical energy with minimal losses. This involves using high-efficiency materials in the generator’s windings and optimizing the magnetic field generation.
Managing Vibration and Ensuring Stability
Vibration is a common issue in steam turbines that can affect both performance and longevity. Excessive vibration can lead to mechanical failures, reduced efficiency, and increased maintenance costs. Understanding the causes of vibration and implementing strategies to mitigate it is essential for maintaining turbine stability:
- Causes of Vibration
Vibration in steam turbines can be caused by several factors, including:- Imbalance in the Rotor: Even minor imbalances in the rotor can cause significant vibration, particularly at high rotational speeds.
- Misalignment of Components: Misalignment of the rotor, bearings, or other components can lead to uneven forces within the turbine, resulting in vibration.
- Blade Deformation or Damage: Blades that are worn, deformed, or damaged can disrupt the smooth flow of steam, leading to vibration.
- Bearing Wear: Worn or damaged bearings can introduce additional friction and instability, causing vibration.
- Steam Flow Instabilities: Variations in steam pressure, temperature, or flow rate can create uneven forces on the turbine blades, leading to vibration.
- Vibration Monitoring and Diagnostics
Modern steam turbines are equipped with advanced vibration monitoring systems that detect and analyze vibration levels in real time. These systems use sensors placed at key points on the turbine, such as the bearings, rotor, and casing. The data collected is analyzed to identify the source of the vibration and determine whether it is within acceptable limits.Vibration diagnostics involves examining the frequency, amplitude, and phase of the vibrations to pinpoint the exact cause. For example, an imbalance in the rotor typically produces a vibration at the same frequency as the rotor’s rotational speed, while misalignment may result in vibrations at harmonics of the rotational frequency. - Mitigation Strategies
To mitigate vibration, several strategies can be employed:- Balancing the Rotor: Ensuring that the rotor is perfectly balanced during manufacturing and after maintenance is critical. Dynamic balancing techniques can be used to correct imbalances that develop over time.
- Proper Alignment: Regular checks and adjustments to the alignment of the rotor, bearings, and other components help maintain stability and reduce vibration.
- Blade Maintenance: Regular inspection and maintenance of the turbine blades are necessary to prevent wear and damage that can lead to vibration. Damaged blades should be repaired or replaced promptly.
- Upgrading Bearings: Using high-quality, low-friction bearings can reduce vibration. In some cases, upgrading to more advanced bearing designs can improve stability.
- Steam Flow Control: Ensuring consistent and stable steam flow through the turbine helps minimize the forces that can cause vibration. This may involve optimizing the steam control system and addressing issues such as steam pressure fluctuations.
Enhancing Thermal Efficiency
Thermal efficiency is a measure of how effectively a steam turbine converts the thermal energy of steam into mechanical energy. Maximizing thermal efficiency is crucial for reducing fuel consumption, lowering emissions, and improving the overall economic performance of a power plant:
- Superheated vs. Saturated Steam
Using superheated steam, which has been heated beyond its boiling point without becoming a liquid, can significantly improve thermal efficiency. Superheated steam contains more energy and is less likely to condense during expansion, which helps maintain the turbine’s performance and reduce moisture-related damage.- Temperature and Pressure Optimization
Increasing the temperature and pressure of the steam entering the turbine can also enhance thermal efficiency. However, this requires careful design and material selection, as higher temperatures and pressures can increase the risk of mechanical failure and require more robust construction materials. - Reheat and Regeneration
Reheating steam after it has partially expanded in the turbine and returning it for further expansion is a proven method to improve thermal efficiency. Reheat cycles reduce the moisture content of the steam, preventing damage to the turbine blades and allowing for more energy extraction.Regeneration involves using extracted steam to preheat the feedwater before it enters the boiler. This process reduces the amount of fuel required to heat the water to steam, thereby increasing the overall efficiency of the cycle.
- Temperature and Pressure Optimization
- Cogeneration Systems
Cogeneration, or combined heat and power (CHP) systems improve thermal efficiency by using the waste heat from the steam turbine for other processes, such as heating or industrial applications. This dual use of energy maximizes the output from the fuel used and reduces the overall environmental impact. - Steam Turbine Upgrades
Upgrading older steam turbines with modern technologies can lead to significant improvements in thermal efficiency. This might include retrofitting with advanced blade designs, installing more efficient control systems, or converting from saturated to superheated steam operation. - Operational Optimization
Continuous monitoring and optimization of turbine operation are essential for maintaining high thermal efficiency. This involves adjusting operating parameters, such as steam flow, pressure, and temperature, in real time to match the current load and demand. Advanced control systems and predictive maintenance strategies can also help identify potential issues before they lead to efficiency losses.
Improving Efficiency with Cogeneration and Combined Cycle Systems
Cogeneration and combined cycle systems are advanced techniques that enhance the efficiency of steam turbines by making use of waste heat and integrating multiple energy conversion processes:
- Cogeneration (Combined Heat and Power – CHP)
In a cogeneration system, the steam turbine generates electricity while the waste heat from the turbine’s exhaust is captured and used for heating, industrial processes, or further power generation. This process significantly increases the overall efficiency of the system, as it utilizes energy that would otherwise be wasted.- Applications of Cogeneration
- Industrial Plants: Where both electricity and process heat are needed, cogeneration can reduce energy costs and improve overall plant efficiency.
- District Heating: Cogeneration systems can supply heat to nearby residential or commercial buildings, providing a sustainable and cost-effective heating solution.
- Waste-to-Energy Plants: In these plants, cogeneration is used to maximize the energy output from waste materials, providing both electricity and heat.
- Applications of Cogeneration
- Combined Cycle Power Plants
Combined cycle power plants integrate gas turbines with steam turbines to achieve higher efficiency. The gas turbine generates electricity and produces exhaust gases, which are then used to produce steam in a heat recovery steam generator (HRSG). The steam is then used to power a steam turbine, generating additional electricity.- Advantages of Combined Cycle Systems
- Increased Efficiency: Combined cycle systems can achieve efficiencies of up to 60% or more, significantly higher than standalone gas or steam turbines.
- Flexibility: These systems can respond quickly to changes in demand, making them ideal for modern power grids that require flexible and reliable energy sources.
- Lower Emissions: By utilizing waste heat and improving fuel efficiency, combined cycle systems produce fewer emissions per unit of electricity generated.
- Advantages of Combined Cycle Systems
- Challenges and Considerations
Implementing cogeneration and combined cycle systems requires careful planning and design to ensure compatibility between the various components and to optimize overall performance. These systems are more complex than single-cycle plants, requiring advanced control systems and regular maintenance to maintain efficiency and reliability.
Steam Power Plant Applications
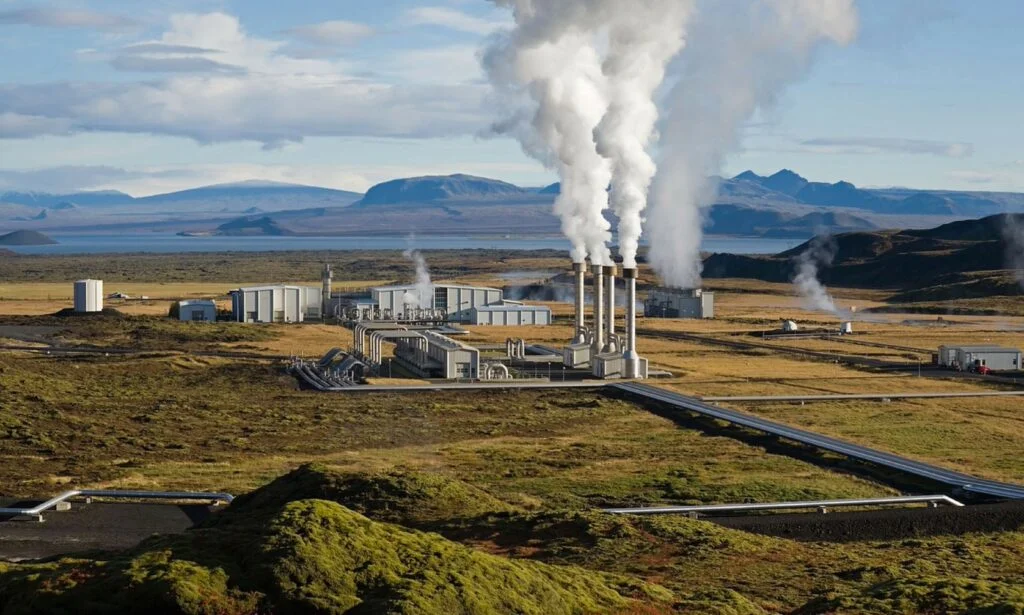
Applications in Power Generation
Steam turbines are a cornerstone of modern power generation, particularly in thermal power plants where their ability to efficiently convert steam energy into electrical energy is unmatched. The versatility of steam turbines allows them to be used in various types of power plants, each with unique characteristics and requirements.
- Fossil Fuel Power Plants
In fossil fuel power plants, steam turbines generate electricity by converting the thermal energy produced from burning coal, natural gas, or oil. These plants are typically designed for baseload power generation, meaning they operate continuously to meet the steady demand for electricity.- Coal-Fired Power Plants: Coal remains one of the most widely used fuels for steam power generation, particularly in developing countries. In these plants, coal is burned in a boiler to produce high-pressure steam, which drives a steam turbine connected to a generator.
- Natural Gas-Fired Power Plants: Natural gas plants often use combined cycle technology, where a gas turbine generates electricity, and the exhaust gases are used to produce steam for a steam turbine, increasing overall efficiency.
- Oil-Fired Power Plants: Although less common today due to environmental concerns and high fuel costs, oil-fired plants still use steam turbines to generate electricity, particularly in regions where oil is more readily available.
- Nuclear Power Plants
Nuclear power plants rely on steam turbines to convert the heat generated by nuclear fission into electricity. In these plants, the heat produced in a nuclear reactor is used to generate steam, which drives a turbine in much the same way as in fossil fuel plants. The key difference lies in the fuel source and the specific safety and operational requirements of nuclear power.- Pressurized Water Reactors (PWRs): In PWRs, water under high pressure is heated by the reactor core and circulated through a steam generator. The generated steam then drives the steam turbine.
- Boiling Water Reactors (BWRs): In BWRs, water is boiled directly in the reactor core to produce steam, which is then used to power the steam turbine. Both types of reactors rely on the steam turbine for the final conversion of thermal energy into electricity.
- Renewable Energy Power Plants
Steam turbines are also used in renewable energy applications, where they convert thermal energy from renewable sources into electricity.- Biomass Power Plants: Biomass power plants use organic materials like wood, agricultural residues, and waste to generate steam. This steam is then used to drive a steam turbine, generating electricity. Biomass power plants are particularly valuable for their ability to utilize waste materials and reduce carbon emissions compared to fossil fuels.
- Geothermal Power Plants: In geothermal power plants, steam or hot water from underground reservoirs is used to drive a steam turbine. These plants are highly efficient and provide a continuous, stable source of renewable energy.
- Solar Thermal Power Plants: Solar thermal plants use mirrors or lenses to concentrate sunlight and generate heat, which is then used to produce steam. The steam drives a turbine, converting solar energy into electricity. Solar thermal plants are an important part of the transition to clean, renewable energy sources.
Biomass Renewable Energy
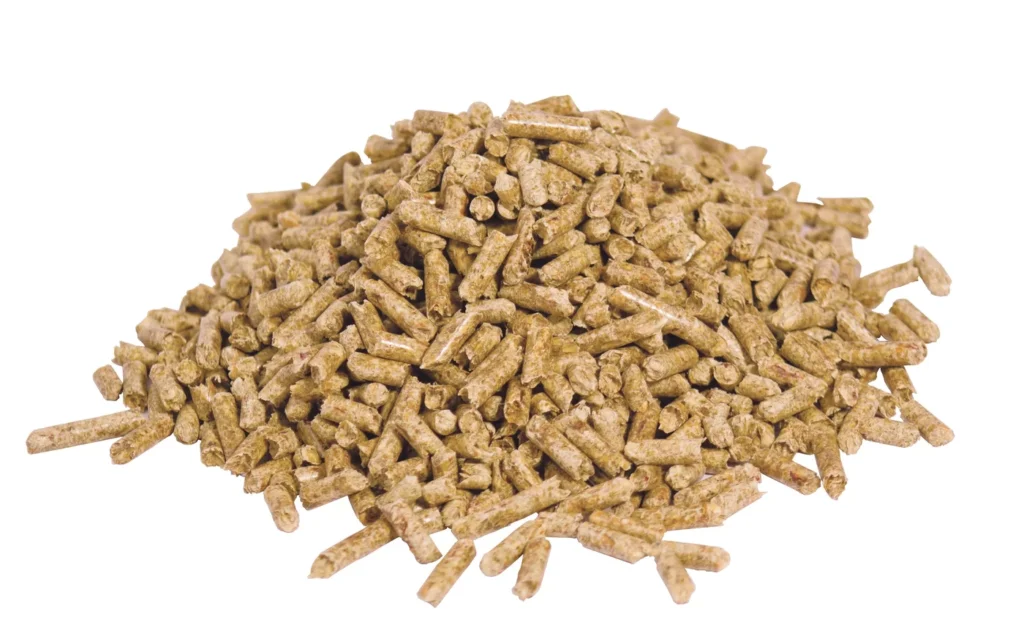
Biomass renewable energy involves using organic materials to produce electricity, often through the combustion of biomass to generate steam. Steam turbines are a key component of biomass power plants, where they convert the thermal energy from burning biomass into mechanical and then electrical energy.
- Types of Biomass
Biomass power plants can use a variety of organic materials as fuel, including:- Wood and Wood Residues: Such as sawdust, wood chips, and forestry residues.
- Agricultural Residues: Including straw, corn stover, and sugarcane bagasse.
- Energy Crops: Specially grown crops like switchgrass and miscanthus, cultivated specifically for energy production.
- Waste Materials: Including municipal solid waste (MSW), food waste, and animal manure.
- Steam Generation from Biomass
In a biomass power plant, the biomass fuel is burned in a boiler to produce high-pressure steam. This steam is then used to drive a steam turbine, which generates electricity. The process is similar to that of a traditional coal-fired power plant, but with biomass as the fuel source.- Advantages of Biomass Power
- Carbon Neutrality: Biomass is considered carbon-neutral because the CO2 released during combustion is offset by the CO2 absorbed during the growth of the biomass.
- Waste Reduction: Using waste materials for biomass energy helps reduce landfill use and mitigates environmental pollution.
- Energy Security: Biomass can be sourced locally, reducing dependence on imported fossil fuels.
- Challenges in Biomass Power
- Fuel Quality and Consistency: Biomass fuels can vary widely in quality and energy content, affecting the efficiency and operation of the steam turbine.
- Ash and Emissions Management: Burning biomass produces ash and other emissions that need to be managed and treated to minimize environmental impact.
- Infrastructure Requirements: Biomass plants require significant infrastructure for fuel storage, handling, and processing.
- Advantages of Biomass Power
- Applications of Biomass Power
Biomass power plants are particularly suitable for rural and agricultural areas where biomass is readily available. They can be used for both grid-connected power generation and off-grid applications, providing a sustainable energy solution for remote communities.
Onsite Power Generation
Onsite power generation refers to the production of electricity at or near the point of use, rather than relying on centralized power plants and long-distance transmission lines. Steam turbines are often used in onsite power generation systems, particularly in industrial and commercial settings where there is a need for both electricity and process heat.
- Advantages of Onsite Power Generation
- Increased Energy Efficiency: Onsite power generation can reduce energy losses associated with long-distance transmission, leading to higher overall efficiency.
- Reliability and Independence: Facilities with onsite power generation are less dependent on the grid, reducing the risk of power outages and improving energy security.
- Cost Savings: By generating electricity onsite, businesses can reduce their energy costs and avoid peak demand charges.
- Flexibility: Onsite power generation systems can be tailored to meet specific energy needs, including the use of renewable energy sources.
- Applications of Steam Turbines in Onsite Power Generation
Steam turbines are particularly well-suited for onsite power generation in industries with significant heat and power requirements.- Industrial Cogeneration: Many industrial facilities use cogeneration systems, where steam turbines generate electricity and provide process heat for manufacturing processes. Examples include chemical plants, paper mills, and food processing facilities.
- Commercial Buildings: Large commercial buildings, such as hospitals, universities, and office complexes, may use steam turbines in combined heat and power (CHP) systems to generate electricity and provide heating and cooling.
- District Energy Systems: In urban areas, steam turbines can be used in district energy systems to provide electricity, heating, and cooling to multiple buildings within a district.
Industrial and Marine Applications
Steam turbines are widely used in industrial and marine applications, where their reliability, efficiency, and adaptability make them ideal for various processes and systems.
- Industrial Applications
In industrial settings, steam turbines are used to drive machinery, compress gases, and generate electricity.- Process Industry: Steam turbines are commonly used in industries such as chemicals, petrochemicals, and pharmaceuticals, where they provide mechanical power for pumps, compressors, and other equipment.
- Paper and Pulp Industry: Steam turbines are used to drive paper machines and other equipment in the paper and pulp industry, where steam is a byproduct of the manufacturing process.
- Oil and Gas Industry: Steam turbines are used in the oil and gas industry to drive compressors and pumps, particularly in refineries and petrochemical plants.
- Marine Applications
Steam turbines have been used in marine propulsion systems for over a century, powering ships and submarines with their reliable and efficient operation.- Naval Vessels: Steam turbines are used in various naval vessels, including aircraft carriers, destroyers, and submarines. They provide the necessary power for propulsion and onboard systems, offering a combination of high power output and durability.
- Commercial Ships: Some older commercial ships still use steam turbines for propulsion, particularly in the case of large tankers and bulk carriers. Although modern ships often use diesel engines, steam turbines remain relevant in certain niche applications.
- Marine Auxiliary Systems: In addition to propulsion, steam turbines are used in auxiliary systems onboard ships, such as for generating electricity and powering pumps and compressors.
Challenges and Future Directions
While steam turbines continue to play a critical role in power generation and industrial applications, they face several challenges that must be addressed to ensure their continued relevance and efficiency.
- Environmental Concerns
As the world shifts towards cleaner energy sources, steam turbines in fossil fuel power plants face increasing scrutiny due to their carbon emissions. The future of steam turbines may involve greater integration with renewable energy sources and the development of carbon capture and storage (CCS) technologies to mitigate environmental impacts. - Fuel Diversification
The diversification of fuel sources, including the use of biomass, waste, and hydrogen, presents both opportunities and challenges for steam turbines. Adapting steam turbine technology to handle a broader range of fuels while maintaining efficiency and reliability will be essential. - Technological Advancements
Advances in materials science, digital control systems, and turbine design are expected to improve the performance and efficiency of steam turbines. Innovations such as additive manufacturing (3D printing) and the use of advanced composites could lead to lighter, stronger, and more efficient turbine components. - Integration with Smart Grids and Renewable Energy
Steam turbines will need to integrate more effectively with smart grids and renewable energy systems. This may involve developing more flexible and adaptable turbine designs that can respond quickly to fluctuations in renewable energy supply and demand. - Market and Economic Pressures
The global energy market is evolving, with increasing competition from alternative energy technologies such as wind, solar, and energy storage systems. Steam turbine manufacturers and operators will need to adapt to changing market conditions and economic pressures, including the need for cost-effective and scalable solutions.
Comparative Analysis of Steam Turbine Technologies
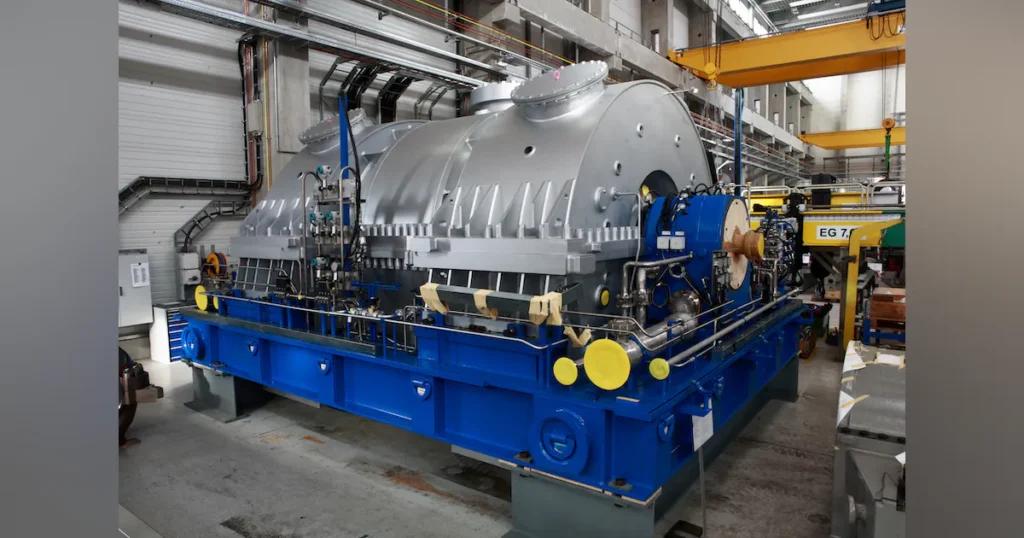
Saturated Steam vs. Superheated Steam
Saturated steam and superheated steam are two key types of steam used in steam turbines, each with distinct characteristics that influence turbine performance, efficiency, and application suitability.
- Saturated Steam
Saturated steam is steam that is in equilibrium with water at a given pressure and temperature, meaning it contains moisture and is at the boiling point for that pressure. Saturated steam is commonly used in low-pressure applications where the presence of moisture is not a significant concern.- Advantages
- Simpler Equipment: Turbines designed for saturated steam are generally simpler and less expensive, as they do not require specialized materials or cooling systems to handle high temperatures.
- Lower Energy Input: Generating saturated steam typically requires less energy compared to superheated steam, making it suitable for applications where efficiency is less critical.
- Wider Availability: Saturated steam is easier to produce and manage, making it accessible for a range of industrial and power generation applications.
- Disadvantages
- Lower Efficiency: Saturated steam turbines are generally less efficient because the moisture content can cause erosion of turbine blades and reduce overall energy conversion efficiency.
- Limited Power Output: Saturated steam is typically used in low to medium power applications, as its lower energy content limits the power output of the turbine.
- Applications
- Industrial Processes: Saturated steam is often used in industries such as food processing, paper manufacturing, and chemical production, where precise control over temperature and pressure is required.
- District Heating: In district heating systems, saturated steam is commonly used to transfer heat over short distances to residential and commercial buildings.
- Advantages
- Superheated Steam
Superheated steam is steam that has been heated beyond its boiling point, without any water content, at a given pressure. This type of steam is commonly used in high-efficiency power generation applications, where maximizing energy output is critical.- Advantages
- Higher Efficiency: Superheated steam allows for higher thermal efficiency, as it can expand more within the turbine, producing more work for the same amount of energy input.
- Reduced Moisture-Related Issues: The absence of moisture in superheated steam reduces the risk of blade erosion and other damage, leading to longer turbine life and lower maintenance costs.
- Greater Power Output: Turbines designed for superheated steam can operate at higher temperatures and pressures, leading to greater power output and efficiency.
- Disadvantages
- Complex Equipment: Superheated steam turbines require more sophisticated materials and cooling systems to handle the higher temperatures and pressures, increasing the initial capital costs.
- Higher Energy Input: Producing superheated steam requires more energy, making it less suitable for applications where energy input needs to be minimized.
- Applications
- Power Plants: Superheated steam is the standard in large-scale power plants, including coal-fired, nuclear, and concentrated solar power (CSP) plants, where maximizing efficiency is paramount.
- Industrial Cogeneration: In industries where both high-temperature process heat and electricity are needed, superheated steam is used to drive turbines and supply process heat.
- Advantages
Impulse Turbine vs. Reaction Turbine
The design and operation of impulse turbines and reaction turbines differ significantly, each offering unique advantages and disadvantages depending on the application.
- Impulse Turbines
Impulse turbines operate by converting the kinetic energy of a high-velocity steam jet into mechanical energy. The steam is expanded in nozzles before striking the turbine blades, causing the rotor to spin.- Advantages
- Simple Design: Impulse turbines have a simpler design with fewer moving parts, making them easier to manufacture and maintain.
- High Efficiency at High Speeds: Impulse turbines are particularly efficient at high rotational speeds, making them ideal for applications where speed and power output are critical.
- Less Susceptible to Steam Quality: The performance of impulse turbines is less affected by changes in steam quality, as the steam expands before it contacts the blades.
- Disadvantages
- Limited Efficiency in Low-Pressure Applications: Impulse turbines are less efficient at low steam pressures, limiting their use in certain applications.
- Higher Noise Levels: The high-velocity steam jets can create significant noise, which may be a concern in certain environments.
- Applications
- High-Pressure Stages in Power Plants: Impulse turbines are often used in the high-pressure stages of steam turbines, where they efficiently handle the initial expansion of high-pressure steam.
- Small-Scale Power Generation: Due to their simplicity and efficiency at high speeds, impulse turbines are used in small-scale power generation applications, such as in microturbines and portable power systems.
- Advantages
- Reaction Turbines
Reaction turbines rely on both the pressure drop and velocity change of steam as it passes through the turbine. The steam expands in the moving blades, creating a reaction force that causes the rotor to spin.- Advantages
- High Efficiency in Multi-Stage Configurations: Reaction turbines are highly efficient in multi-stage configurations, where the steam gradually expands through multiple stages, extracting energy more effectively.
- Smooth Operation: Reaction turbines operate smoothly with less vibration, making them ideal for applications where stability and continuous operation are essential.
- Better at Low-Pressure Stages: Reaction turbines are more efficient than impulse turbines at lower steam pressures, making them suitable for the latter stages of a multi-stage turbine system.
- Disadvantages
- Complex Design: The design of reaction turbines is more complex, with a greater number of moving parts and a higher initial cost.
- Susceptibility to Steam Quality: Reaction turbines are more sensitive to changes in steam quality, particularly moisture content, which can reduce efficiency and cause blade erosion.
- Applications
- Multi-Stage Power Plants: Reaction turbines are commonly used in the low- and intermediate-pressure stages of multi-stage steam turbines, where they efficiently extract energy from lower-pressure steam.
- Marine Propulsion: Due to their smooth operation and ability to handle varying loads, reaction turbines are often used in marine propulsion systems.
- Advantages
Material Considerations for Turbine Components
The materials used in the construction of steam turbine components are critical to their performance, durability, and efficiency. Different materials are selected based on the specific requirements of each component, including factors such as temperature, pressure, and environmental conditions.
- Turbine Blades
Turbine blades are exposed to extreme conditions, including high temperatures, pressures, and corrosive environments. The material used for turbine blades must have high strength, resistance to thermal fatigue, and good corrosion resistance.- Materials Used
- Nickel-Based Superalloys: These materials are commonly used in high-temperature applications due to their excellent strength and resistance to thermal creep and oxidation.
- Titanium Alloys: Used in situations where weight reduction is critical, titanium alloys offer a good balance of strength, corrosion resistance, and fatigue resistance.
- Stainless Steel: In some cases, stainless steel is used for turbine blades due to its good corrosion resistance and relatively lower cost compared to superalloys.
- Challenges
- Material Fatigue: Over time, the extreme operating conditions can cause fatigue in turbine blades, leading to cracks and eventual failure. Regular inspection and maintenance are required to prevent these issues.
- Erosion and Corrosion: The presence of moisture in the steam can cause erosion and corrosion of turbine blades, particularly in the later stages of the turbine where the steam is at a lower pressure and temperature.
- Materials Used
- Turbine Rotors
The rotor is the central shaft to which the turbine blades are attached. It must withstand high rotational speeds and the associated centrifugal forces while maintaining structural integrity under high temperatures and pressures.- Materials Used
- Chromium-Nickel Steels: These high-strength steels are commonly used for turbine rotors due to their excellent mechanical properties and resistance to thermal fatigue.
- Alloy Steels: In some cases, alloy steels with specific heat treatments are used to enhance the rotor’s strength and durability.
- Challenges
- Thermal Stress: The rotor experiences significant thermal stress due to the temperature gradients between the steam and the rotor material. This stress can lead to deformation or cracking over time if not properly managed.
- Balancing and Alignment: Ensuring that the rotor is perfectly balanced and aligned is crucial for minimizing vibration and extending the lifespan of the turbine.
- Materials Used
- Casing and Nozzles
The casing and nozzles of the steam turbine are responsible for containing the steam and directing it onto the turbine blades. These components must be designed to withstand high pressures and temperatures while minimizing energy losses due to friction and turbulence.- Materials Used
- Carbon Steel: Carbon steel is often used for the turbine casing due to its strength and ability to withstand high pressures.
- Stainless Steel: In cases where corrosion resistance is critical, stainless steel is used for nozzles and other components that come into direct contact with steam.
- Challenges
- Thermal Expansion: The casing and nozzles must be designed to accommodate thermal expansion and contraction without compromising the integrity of the turbine.
- Sealing: Effective sealing is required to prevent steam leaks, which can reduce efficiency and lead to performance issues.
- Materials Used
Comparative Analysis of Efficiency and Applications
When choosing between different steam turbine technologies, several factors must be considered, including efficiency, cost, and suitability for the intended application. The following comparisons highlight the key differences between saturated vs. superheated steam, impulse vs. reaction turbines, and the material choices for turbine components.
- Efficiency
- Superheated Steam vs. Saturated Steam: Superheated steam turbines are generally more efficient, particularly in large-scale power generation, where maximizing energy output is critical. However, saturated steam turbines are more cost-effective for smaller, low-pressure applications.
- Impulse vs. Reaction Turbines: Impulse turbines excel in high-pressure, high-speed applications, while reaction turbines offer better efficiency in multi-stage configurations and at lower pressures.
- Cost
- Material Considerations: The choice of materials significantly impacts the cost of the turbine. High-performance materials like nickel-based superalloys and titanium alloys increase the initial cost but offer longer lifespans and better performance in harsh conditions.
- Technology Selection: Choosing between impulse and reaction turbines, as well as between saturated and superheated steam systems, involves balancing upfront costs with long-term efficiency and maintenance considerations.
- Applications
- Power Generation: Superheated steam turbines and reaction turbines are typically used in large-scale power plants, including fossil fuel, nuclear, and renewable energy applications. Impulse turbines and saturated steam systems are more common in smaller power generation setups and industrial applications.
- Industrial and Marine: The choice of turbine technology in industrial and marine applications depends on the specific operational requirements, including load conditions, environmental factors, and the need for flexibility in power output.
Emerging Trends and Innovations in Steam Turbines
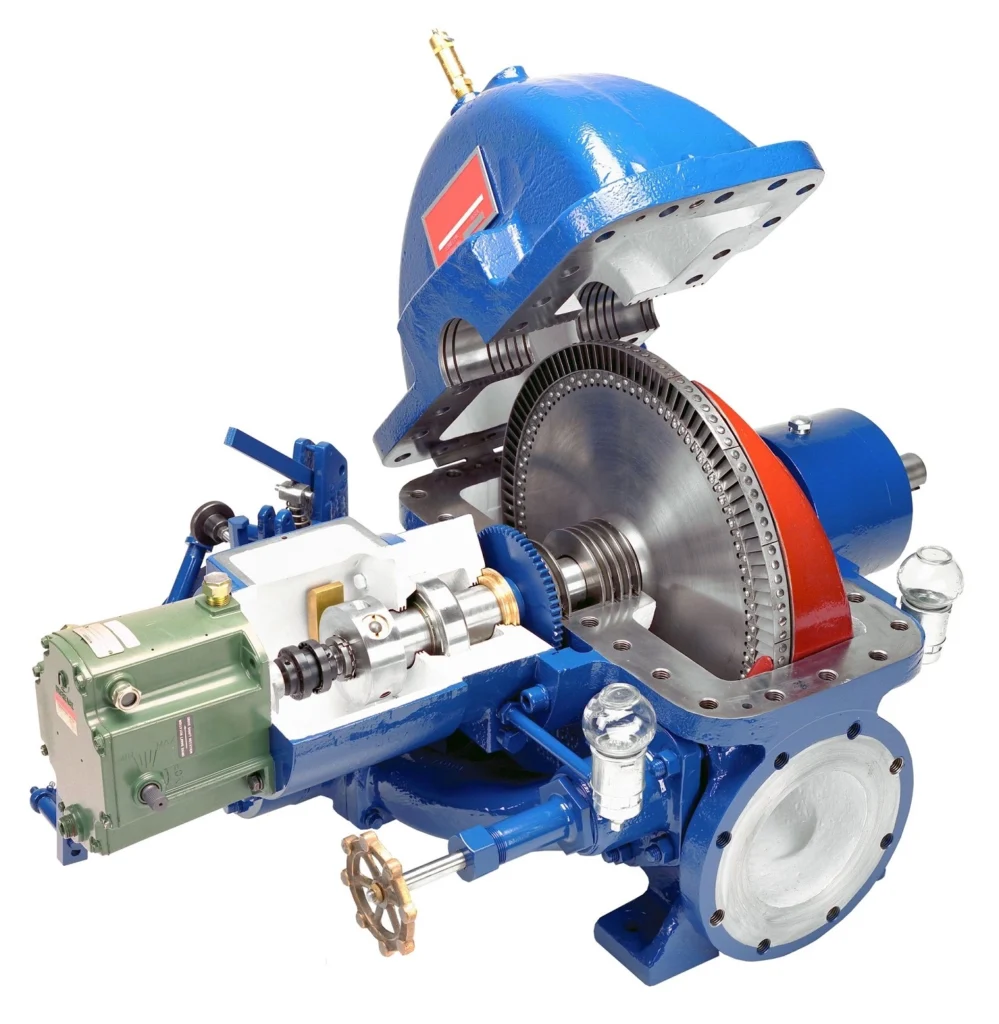
Advanced Manufacturing Techniques
One of the most significant trends in steam turbine technology is the adoption of advanced manufacturing techniques. These methods have the potential to enhance turbine performance, reduce costs, and improve the reliability and longevity of steam turbine components.
- Additive Manufacturing (3D Printing)
Additive manufacturing, commonly known as 3D printing, is revolutionizing the production of steam turbine components. This technology allows for the creation of complex geometries that are difficult or impossible to achieve with traditional manufacturing methods.- Benefits
- Customization and Complexity: 3D printing enables the production of customized turbine blades and components with optimized shapes for specific operating conditions. The ability to create intricate internal cooling channels within turbine blades, for example, can significantly improve thermal efficiency.
- Reduced Lead Times: 3D printing can shorten production lead times, allowing for faster prototyping and quicker implementation of design improvements.
- Cost Reduction: By reducing the need for multiple machining steps and material waste, 3D printing can lower the overall cost of manufacturing turbine components.
- Material Innovation: 3D printing facilitates the use of advanced materials, including composite materials and high-performance alloys, which can enhance the strength, durability, and thermal resistance of turbine components.
- Benefits
- Advanced Materials
The development and application of advanced materials are crucial for improving the efficiency, durability, and environmental performance of steam turbines. Innovations in materials science are leading to the creation of stronger, lighter, and more heat-resistant materials that can withstand the extreme conditions inside a steam turbine.- Ceramic Matrix Composites (CMCs): CMCs are increasingly being used in high-temperature applications within steam turbines due to their superior heat resistance and lower weight compared to traditional metal alloys. These materials help improve turbine efficiency by allowing for higher operating temperatures without compromising the structural integrity of the components.
- High-Entropy Alloys (HEAs): HEAs are a new class of materials that combine multiple elements in near-equal proportions, resulting in alloys with exceptional mechanical properties, including high strength, corrosion resistance, and thermal stability. These materials are being explored for use in turbine blades and other critical components.
- Superalloys: While already widely used in steam turbines, ongoing research into superalloys is focused on further enhancing their properties, particularly their resistance to creep, fatigue, and oxidation at high temperatures.
Digitalization and Smart Control Systems
The integration of digitalization and smart control systems into steam turbine operations is another major trend shaping the future of the industry. These technologies offer new ways to monitor, optimize, and maintain steam turbines, leading to increased efficiency, reduced downtime, and enhanced reliability.
- Predictive Maintenance
Predictive maintenance uses data analytics, machine learning, and advanced sensors to predict when turbine components are likely to fail or require maintenance. By identifying potential issues before they cause significant problems, predictive maintenance can reduce unplanned downtime and extend the life of turbine components.- Real-Time Monitoring: Sensors embedded in turbine components continuously monitor parameters such as temperature, pressure, vibration, and stress. This data is analyzed in real time to detect anomalies that could indicate impending failures.
- Data Analytics and Machine Learning: Advanced algorithms analyze the vast amounts of data generated by turbine sensors to identify patterns and predict maintenance needs. These systems can also optimize maintenance schedules based on the actual condition of the components, rather than relying solely on fixed intervals.
- Smart Control Systems
Smart control systems leverage digital technologies to optimize the performance of steam turbines under varying operating conditions. These systems can dynamically adjust turbine parameters such as steam flow, temperature, and pressure to maintain optimal efficiency and stability.- Adaptive Control: Adaptive control systems use real-time data to adjust turbine operation in response to changes in load demand, steam conditions, and other variables. This ensures that the turbine operates at peak efficiency across a wide range of operating conditions.
- Integration with Smart Grids: Smart control systems enable steam turbines to better integrate with smart grids, which require flexible and responsive power generation to accommodate fluctuations in renewable energy sources like wind and solar. This integration helps maintain grid stability and ensures a reliable power supply.
- Digital Twins
The concept of a digital twin involves creating a virtual model of a steam turbine that replicates its physical counterpart in real time. This digital twin can be used for simulations, performance analysis, and predictive maintenance.- Benefits of Digital Twins: Digital twins allow operators to simulate various operating scenarios, test different configurations, and predict the impact of changes without risking damage to the actual turbine. They also enable continuous monitoring and optimization of turbine performance.
Integration with Renewable Energy Systems
As the world shifts towards cleaner energy sources, steam turbines are increasingly being integrated into renewable energy systems. This trend is driven by the need to enhance the efficiency and reliability of renewable energy generation while reducing carbon emissions.
- Biomass and Waste-to-Energy Plants
Steam turbines are a key component in biomass and waste-to-energy plants, where they convert the heat generated from burning organic materials or waste into electricity. These plants help reduce reliance on fossil fuels and contribute to a circular economy by turning waste into valuable energy.- Hybrid Systems: In some cases, biomass or waste-to-energy plants are combined with other renewable energy sources, such as solar thermal or geothermal energy, to create hybrid systems. Steam turbines in these hybrid systems can operate more efficiently by leveraging multiple energy sources.
- Concentrated Solar Power (CSP) Plants
CSP plants use mirrors or lenses to concentrate sunlight and generate heat, which is then used to produce steam. The steam drives a turbine, generating electricity. Steam turbines in CSP plants must be able to operate efficiently at varying loads, depending on the availability of sunlight.- Thermal Storage: To improve the reliability and efficiency of CSP plants, thermal energy storage systems are often used. These systems store excess heat generated during peak sunlight hours, which can then be used to produce steam and generate electricity when sunlight is not available, such as during the night.
- Geothermal Power Plants
Geothermal power plants use steam or hot water from underground reservoirs to drive steam turbines. These plants provide a continuous, stable source of renewable energy, making them an essential part of the renewable energy mix.- Enhanced Geothermal Systems (EGS): EGS technology involves enhancing or creating geothermal reservoirs by injecting water into hot rock formations. Steam turbines used in EGS plants must be designed to handle the specific challenges of these environments, including high levels of dissolved minerals and gases.
Sustainability and Environmental Impact
As environmental concerns become increasingly important, the sustainability and environmental impact of steam turbines are under greater scrutiny. Innovations in turbine technology are helping to address these challenges by reducing emissions, improving efficiency, and enabling the use of cleaner fuels.
- Carbon Capture and Storage (CCS)
CCS technology involves capturing CO2 emissions produced during the combustion of fossil fuels and storing them underground to prevent them from entering the atmosphere. Steam turbines in power plants equipped with CCS must be designed to operate efficiently with the additional processes involved in capturing and compressing CO2.- Retrofitting Existing Plants: Many existing fossil fuel power plants are being retrofitted with CCS technology to reduce their carbon emissions. Steam turbines in these plants may need to be upgraded or modified to maintain efficiency with the added CCS processes.
- Hydrogen as a Fuel
Hydrogen is being explored as a clean alternative fuel for power generation. In steam turbines, hydrogen can be used as a fuel to produce steam, either through direct combustion or in combination with natural gas.- Hydrogen-Compatible Turbines: Developing steam turbines that can efficiently and safely operate with hydrogen as a fuel is a key area of research. These turbines must be able to handle the unique properties of hydrogen, such as its lower energy density and higher combustion speed.
- Efficiency Improvements
Increasing the efficiency of steam turbines directly contributes to reducing their environmental impact. Higher efficiency means that less fuel is required to generate the same amount of electricity, leading to lower emissions and reduced resource consumption.- Material Innovation: The use of advanced materials, such as those mentioned earlier, allows steam turbines to operate at higher temperatures and pressures, which increases efficiency and reduces emissions.
- Waste Heat Recovery: Techniques such as waste heat recovery and cogeneration further improve the efficiency of steam turbines by making use of energy that would otherwise be wasted.
- Regulatory Compliance and Standards
As environmental regulations become stricter, steam turbine manufacturers and operators must ensure that their technologies and practices comply with current and future standards.- Emissions Standards: Steam turbines in power plants must meet stringent emissions standards, particularly regarding CO2, NOx, and SOx emissions. Innovations in combustion technology, fuel processing, and emissions control are essential for meeting these requirements.
- Lifecycle Assessment: A lifecycle assessment approach to turbine design and operation considers the environmental impact of a turbine over its entire lifespan, from manufacturing to decommissioning. This approach helps identify areas for improvement and ensures that sustainability is prioritized throughout the turbine’s lifecycle.
Practical Considerations and Cost Analysis
Cost of Steam Turbines
The cost of steam turbines is influenced by several factors, including the size and capacity of the turbine, the materials used in its construction, and the complexity of its design. Understanding these cost factors is crucial for making informed decisions in power generation projects.
- Initial Capital Costs
The initial capital cost of a steam turbine includes the cost of manufacturing, shipping, installation, and commissioning. This cost varies widely depending on the turbine’s capacity, with larger turbines typically being more expensive due to the increased amount of materials and more complex engineering required.- Turbine Size and Capacity: Larger turbines, such as those used in utility-scale power plants, can cost significantly more than smaller turbines used in industrial or onsite power generation. For example, a 1 MW steam turbine generator might cost between $1 million and $3 million, while a 100 MW turbine could cost upwards of $50 million.
- Materials and Manufacturing: High-performance materials, such as superalloys and advanced composites, increase the cost of steam turbines. These materials are necessary for turbines operating at high temperatures and pressures but add to the overall expense.
- Design Complexity: Turbines with advanced features, such as reheat cycles, multi-stage configurations, or custom designs, are more expensive to produce. The complexity of the control systems and the integration with other power plant components also contributes to the cost.
- Operating Costs
Operating costs include the expenses associated with running and maintaining the steam turbine over its lifetime. These costs are ongoing and can vary depending on the turbine’s efficiency, the quality of the steam, and the operating conditions.- Fuel Costs: The fuel used to generate steam, whether it’s coal, natural gas, biomass, or another source, is a significant operating cost. The efficiency of the turbine directly impacts fuel consumption, with more efficient turbines requiring less fuel to generate the same amount of electricity.
- Maintenance and Repair: Regular maintenance is essential to keep the turbine operating efficiently and to prevent costly breakdowns. Maintenance costs include routine inspections, parts replacement, lubrication, and more significant overhauls, such as blade replacement or rotor balancing.
- Energy Losses: Inefficiencies in the turbine, such as energy losses due to friction, steam leaks, or suboptimal operating conditions, can increase operating costs. These losses can be minimized through careful design, regular maintenance, and the use of advanced control systems.
- Lifecycle Costs
The total lifecycle cost of a steam turbine includes both the initial capital costs and the ongoing operating costs over the turbine’s expected lifespan. This holistic view helps in understanding the true cost of ownership and operation.- Depreciation: Steam turbines have a long operational life, often exceeding 30 years. Depreciation of the turbine’s value over time is a factor in the overall lifecycle cost.
- Efficiency Improvements: Investing in more efficient turbines or upgrading existing turbines can reduce lifecycle costs by lowering fuel consumption and maintenance requirements.
- Decommissioning: At the end of its life, a steam turbine must be safely decommissioned and disposed of. Decommissioning costs include dismantling the turbine, disposing of hazardous materials, and potentially recycling certain components.
Maintenance and Lifespan of Steam Turbines
The lifespan of a steam turbine depends on several factors, including the quality of the materials used, the operating conditions, and the effectiveness of the maintenance program. Proper maintenance is critical to extending the life of a steam turbine and ensuring its reliable operation.
- Routine Maintenance
Routine maintenance involves regular inspections and minor repairs to keep the turbine operating efficiently. This includes checking and replacing lubrication, inspecting bearings and seals, and monitoring vibration and other performance indicators.- Scheduled Inspections: Regular inspections are scheduled based on the turbine’s operating hours or other performance criteria. These inspections are designed to detect early signs of wear, corrosion, or other issues that could lead to more significant problems if left unaddressed.
- Lubrication and Cooling: Proper lubrication of bearings and cooling of key components are essential to prevent overheating and reduce friction, which can cause wear and tear on the turbine’s moving parts.
- Preventive Maintenance
Preventive maintenance involves more in-depth inspections and repairs to address potential issues before they lead to equipment failure. This may include non-destructive testing (NDT) techniques to detect cracks, erosion, or other forms of damage that are not visible during routine inspections.- Nondestructive Testing (NDT): Techniques such as ultrasonic testing, radiography, and thermography are used to inspect turbine components without causing damage. These tests help identify areas of stress, fatigue, or other issues that could compromise the turbine’s integrity.
- Component Replacement: Certain turbine components, such as blades and seals, may need to be replaced periodically as part of preventive maintenance. Replacing these components before they fail can prevent more extensive damage to the turbine.
- Major Overhauls
Major overhauls are comprehensive maintenance procedures that involve disassembling the turbine, inspecting all components, and repairing or replacing parts as necessary. These overhauls are typically conducted every 5 to 10 years, depending on the turbine’s operating conditions.- Rotor Balancing: Balancing the rotor is crucial to reducing vibration and ensuring smooth operation. An unbalanced rotor can cause excessive wear on bearings and seals, leading to premature failure.
- Blade Replacement and Refurbishment: Over time, turbine blades can become worn, eroded, or cracked due to exposure to high temperatures, pressures, and corrosive steam. Replacing or refurbishing these blades during a major overhaul helps maintain turbine efficiency and extends its lifespan.
- Extending Lifespan Through Upgrades
Upgrading a steam turbine with modern components and control systems can significantly extend its lifespan. These upgrades can include installing more efficient blades, improving the steam path design, and integrating advanced control systems for better performance monitoring.- Retrofitting with Advanced Materials: Replacing older components with new materials, such as advanced alloys or composites, can improve the turbine’s resistance to wear and corrosion, thereby extending its operational life.
- Digital Upgrades: Integrating digital control systems, such as predictive maintenance tools and smart sensors, allows for more precise monitoring and management of the turbine’s performance, helping to identify and address potential issues before they lead to failure.
Market for Used and Mini Steam Turbines
The market for used and mini steam turbines is growing, driven by demand from smaller-scale power generation projects and cost-conscious buyers looking for more affordable options.
- Used Steam Turbines
Purchasing a used steam turbine can be a cost-effective option for power generation projects with limited budgets. The market for used turbines includes equipment from decommissioned power plants, as well as turbines that have been refurbished and resold.- Benefits
- Lower Initial Costs: Used steam turbines are significantly less expensive than new turbines, making them an attractive option for smaller projects or startups.
- Availability: Used turbines are often available for immediate delivery, whereas new turbines may have long lead times due to manufacturing and customization processes.
- Refurbishment Opportunities: Many used turbines are refurbished before resale, with worn components replaced or upgraded, which can extend the life and improve the performance of the turbine.
- Considerations
- Condition and Performance: The condition of a used turbine can vary significantly depending on its previous use and maintenance history. It is essential to conduct a thorough inspection and performance assessment before purchasing.
- Compatibility: Ensuring that a used turbine is compatible with the existing power plant infrastructure and meets the specific requirements of the project is crucial.
- Warranty and Support: Used turbines may not come with the same warranty or support as new turbines, which can increase the risk of unforeseen maintenance and repair costs.
- Benefits
- Mini and Micro Steam Turbines
Mini and micro steam turbines are designed for smaller-scale power generation applications, such as onsite power generation, industrial cogeneration, and renewable energy projects.- Applications
- Decentralized Power Generation: Mini turbines are ideal for decentralized power generation in remote or off-grid locations, providing a reliable and efficient source of electricity.
- Industrial Applications: Small steam turbines can be used to generate power for industrial processes, such as in manufacturing facilities, refineries, and chemical plants.
- Renewable Energy: Mini turbines are increasingly used in renewable energy projects, such as biomass or waste-to-energy plants, where they can convert steam generated from renewable sources into electricity.
- Cost and Efficiency
- Lower Capital Costs: Mini and micro turbines have lower capital costs compared to larger turbines, making them accessible for smaller projects with limited budgets.
- Efficiency: While smaller turbines may not achieve the same efficiency as larger turbines, advances in design and materials are improving the performance of mini and micro turbines.
- Customization: Mini turbines can be customized to meet specific operational requirements, such as variable steam conditions or fluctuating power demands, making them a versatile option for a wide range of applications.
- Applications
- Market Trends
The market for used and mini steam turbines is expanding as more industries and regions seek cost-effective and sustainable power generation solutions. The availability of refurbished turbines and the growing interest in smaller, decentralized power systems are driving demand in this segment.- Growth in Developing Regions: In developing regions, where access to reliable electricity can be limited, mini and micro turbines are becoming increasingly popular as they offer a scalable solution for local power generation.
- Environmental Regulations: Stricter environmental regulations are encouraging the adoption of smaller, more efficient turbines that can be integrated with renewable energy sources, reducing the overall carbon footprint of power generation.
Case Studies and Real-World Examples
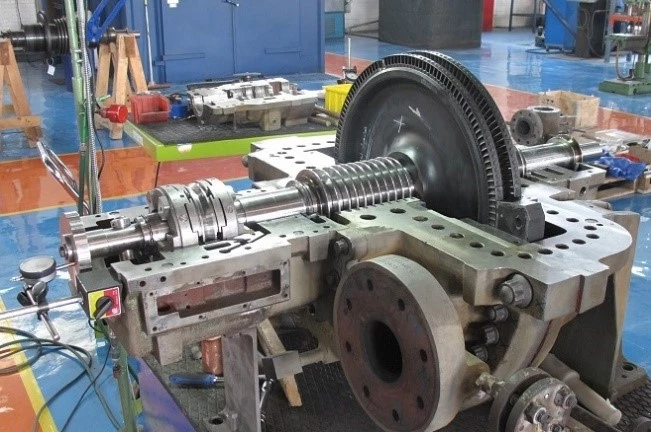
Case Study 1: 1 MW Steam Turbine Generator in Industrial Use
Overview:
This case study examines the deployment of a 1 MW steam turbine generator in an industrial setting, focusing on its role in cogeneration and its impact on overall plant efficiency.
Background:
A medium-sized manufacturing facility required both electricity and process heat for its operations. The facility opted for a 1 MW steam turbine generator as part of a cogeneration system. The turbine was chosen for its ability to efficiently convert steam from the plant’s existing boiler into electrical power while simultaneously providing process steam for manufacturing.
Implementation:
The steam turbine generator was integrated into the plant’s existing infrastructure, with modifications to the steam distribution system to optimize performance. The turbine operated on superheated steam at 400°C and 40 bar, which was supplied by a natural gas-fired boiler. The electrical power generated was used to meet the plant’s energy needs, reducing its reliance on the external power grid.
Results:
The installation of the 1 MW steam turbine generator resulted in significant improvements in energy efficiency. The cogeneration system allowed the facility to achieve an overall energy efficiency of 75%, compared to the 40-50% efficiency typically seen in separate power and heat production. The reduction in energy costs and improved reliability of power supply provided a strong return on investment, with the system paying for itself within five years.
Conclusion:
This case study highlights the benefits of using a 1 MW steam turbine generator in industrial applications, particularly in cogeneration systems where both electricity and process heat are required. The system’s high efficiency and cost-effectiveness make it a valuable asset for industrial facilities looking to reduce energy costs and improve sustainability.
Marine Steam Engine for Sale and Its Applications
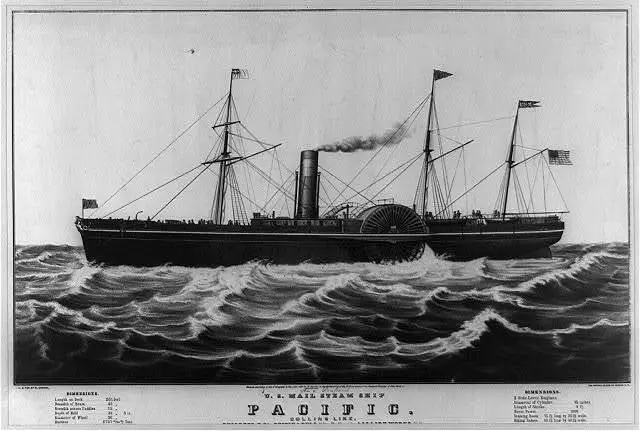
Overview:
This case study explores the application of a marine steam engine, examining its operation, efficiency, and suitability for various maritime vessels.
Background:
A maritime company sought to purchase a used marine steam engine to power a vintage steamship that was being restored for heritage cruises. The steam engine was selected for its historical authenticity and ability to provide reliable propulsion under the conditions expected during the cruises.
Implementation:
The selected marine steam engine was a refurbished triple-expansion engine originally built in the early 20th century. The engine was overhauled to meet modern safety and performance standards while retaining its historical design. The engine operated on saturated steam at 150 psi and was connected to a propeller shaft via reduction gearing to optimize torque and efficiency.
Results:
The restored steamship, powered by the marine steam engine, successfully completed its initial sea trials and began regular operations. The engine provided reliable propulsion and was capable of maintaining a steady cruising speed of 10 knots. The efficiency of the engine, combined with the use of modern materials and seals, ensured that fuel consumption remained within acceptable limits.
Conclusion:
The use of a refurbished marine steam engine in this application demonstrates the continued relevance of steam technology in niche maritime markets. For heritage vessels and other specialized maritime applications, steam engines offer a unique combination of reliability, authenticity, and operational efficiency.
15 MW Biomass Power Plant
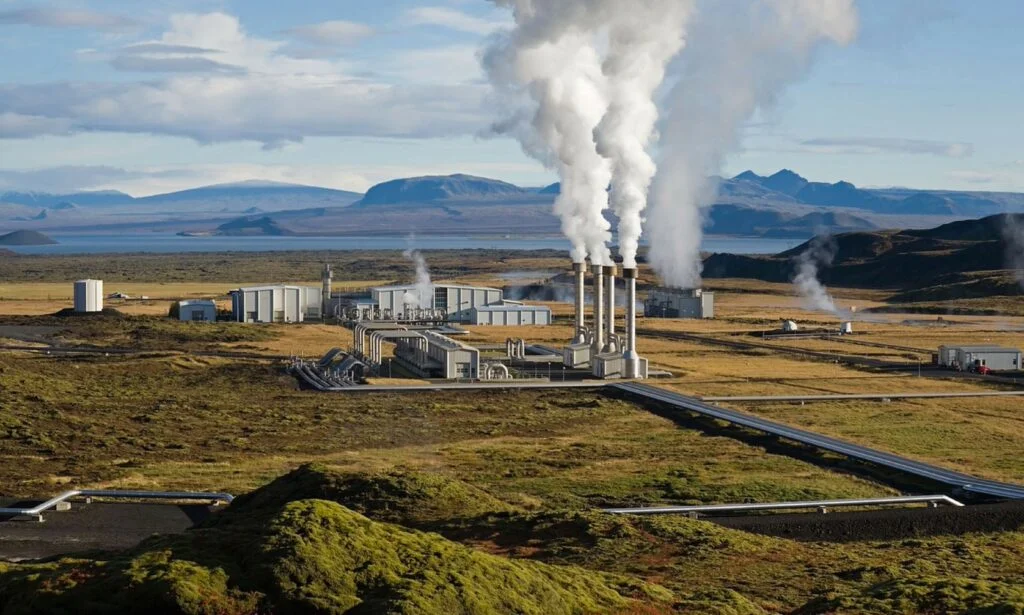
Overview:
This case study examines the operation of a 15 MW biomass power plant that utilizes a steam turbine to convert the energy from burning organic materials into electricity.
Background:
Located in a rural area, the 15 MW biomass power plant was developed to provide renewable energy to the local grid while supporting local agricultural activities. The plant was designed to use a variety of biomass fuels, including wood chips, agricultural residues, and energy crops, to generate steam for power production.
Implementation:
The biomass power plant featured a high-pressure steam boiler that produced steam at 500°C and 60 bar. The steam was directed into a multi-stage steam turbine, which was specifically designed to handle the variability in steam quality associated with biomass fuels. The electricity generated by the turbine was fed into the local grid, providing a reliable source of renewable energy to the surrounding communities.
Results:
The biomass power plant successfully achieved its target output of 15 MW, with an overall efficiency of 30%, which is typical for biomass-fired plants. The plant’s operation also contributed to local economic development by providing a market for agricultural residues and creating jobs in biomass collection, processing, and plant operation. The environmental benefits included a significant reduction in greenhouse gas emissions compared to fossil fuel-based power generation.
Conclusion:
The 15 MW biomass power plant case study illustrates the potential of steam turbines in renewable energy projects. By effectively utilizing locally sourced biomass, the plant provides a sustainable and environmentally friendly energy solution while supporting the local economy.
Ship Steam Engine in Modern Naval Applications
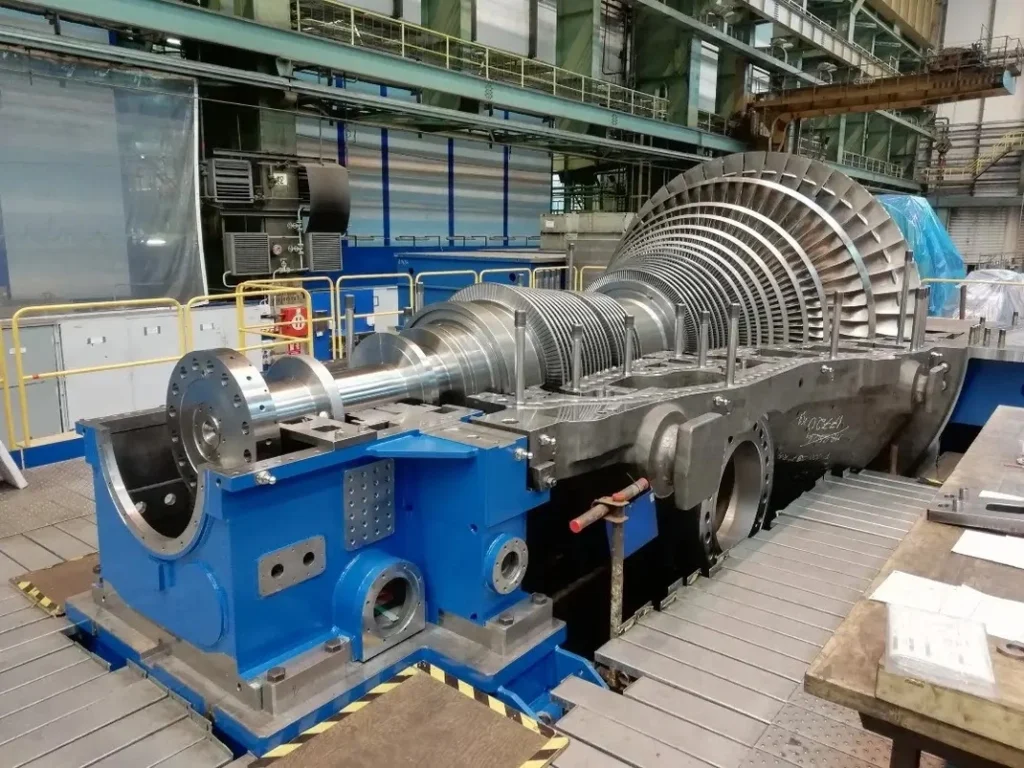
Overview:
This case study investigates the use of a steam turbine engine in a modern naval vessel, focusing on performance, efficiency, and operational advantages.
Background:
A modern naval destroyer was equipped with a steam turbine propulsion system as part of a hybrid power configuration. The steam turbine was chosen for its ability to provide high-speed propulsion and power for onboard systems during extended missions.
Implementation:
The steam turbine used in the destroyer was a high-performance, high-pressure unit designed to operate on superheated steam at 600°C and 100 bar. The turbine was coupled to a gearbox that drove the ship’s propeller shaft, providing efficient propulsion at both high and cruising speeds. The turbine was integrated with an auxiliary gas turbine system, allowing the vessel to switch between power sources as needed.
Results:
The steam turbine provided reliable and efficient propulsion, enabling the destroyer to achieve speeds of over 30 knots. The hybrid power configuration allowed the ship to optimize fuel consumption and maintain operational flexibility, particularly during long deployments. The steam turbine also contributed to the vessel’s overall power generation, supplying electricity to various onboard systems.
Conclusion:
This case study demonstrates the continued viability of steam turbine propulsion systems in modern naval applications. The combination of high-speed capability, efficiency, and operational flexibility makes steam turbines a valuable asset for naval vessels designed for extended missions and complex operational environments.
Steam Microturbine in a Small-Scale Renewable Energy Project
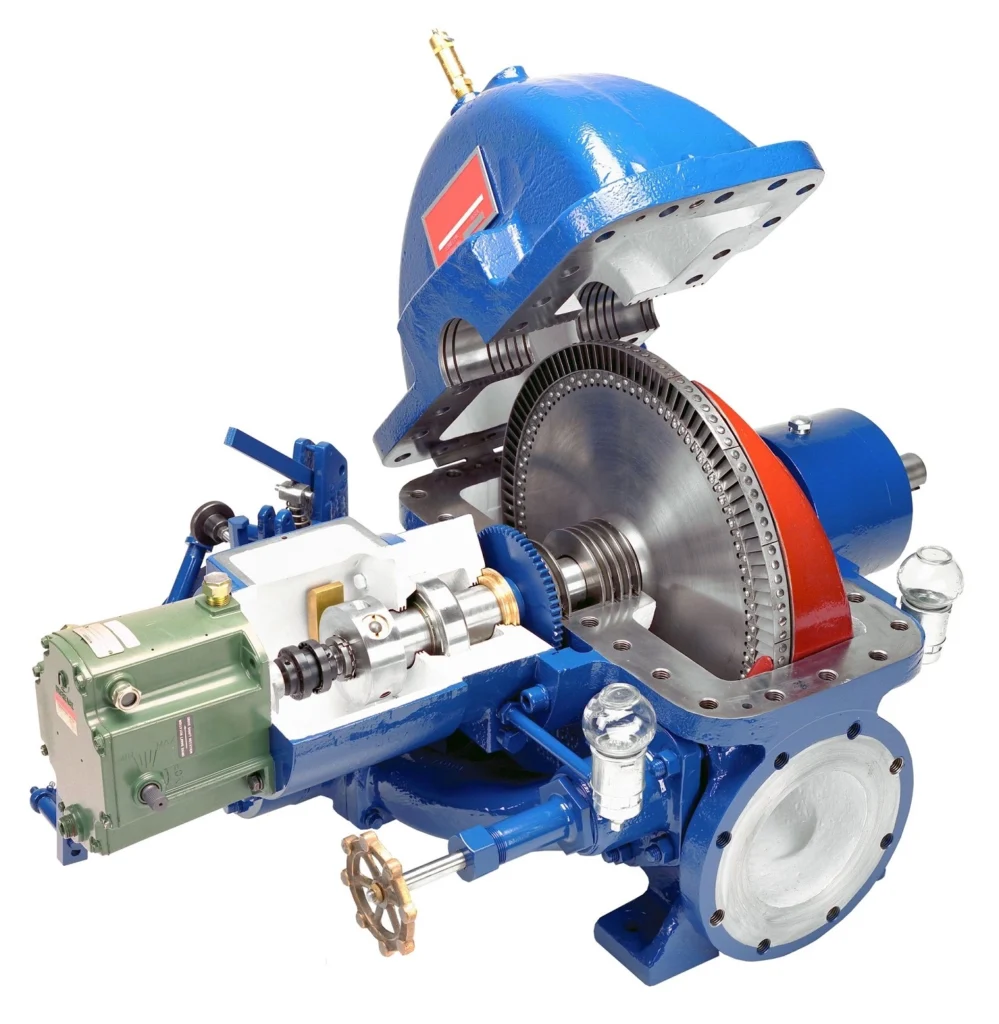
Overview:
This case study explores the use of a steam microturbine in a small-scale renewable energy project, highlighting its role in decentralized power generation.
Background:
A small community in a remote area sought to establish a decentralized power generation system using locally available resources. A steam microturbine was selected as the primary power generation technology, with biomass from local agricultural waste serving as the fuel source.
Implementation:
The project installed a 100 kW steam microturbine, which was connected to a biomass boiler. The boiler produced steam at 250°C and 20 bar, which was sufficient to drive the microturbine and generate electricity for the community. The microturbine’s compact size and relatively simple installation process made it ideal for the remote location.
Results:
The steam microturbine successfully provided a reliable source of electricity to the community, reducing reliance on diesel generators and improving energy security. The system operated with an overall efficiency of 25%, which was considered satisfactory given the scale of the project and the variability of the biomass fuel. The project also had a positive environmental impact by utilizing waste materials that would otherwise be burned or left to decompose.
Conclusion:
The use of a steam microturbine in this small-scale renewable energy project demonstrates the technology’s potential for decentralized power generation in remote areas. The ability to utilize local resources and the relatively low cost of installation and operation make steam microturbines a viable solution for communities seeking sustainable energy independence.
Conclusion and Future Outlook
Summary of Key Points
Throughout this document, we have explored the vast and intricate world of steam turbines, covering their working principles, types, components, performance metrics, and applications. Steam turbines have proven to be a cornerstone of power generation and industrial processes, offering a reliable and efficient means of converting thermal energy into mechanical and electrical energy.
Future of Steam Turbines
As the global energy landscape continues to evolve, steam turbines will remain a critical technology. Innovations in materials, manufacturing techniques, and digital control systems are poised to enhance the efficiency and sustainability of steam turbines, ensuring their relevance in a future where renewable energy sources and environmental considerations are increasingly important.
Final Thoughts
The steam turbine’s ability to adapt to new challenges and integrate with emerging technologies will be key to its continued success. Whether in large-scale power plants, industrial cogeneration, or decentralized renewable energy projects, steam turbines will continue to play a vital role in meeting the world’s energy needs.
Steam turbines are mechanical devices that convert the thermal energy in steam into mechanical energy through rotary motion. This process is fundamental in power generation, making steam turbines a cornerstone of both traditional and modern energy systems. The principle behind steam turbines involves steam under high pressure and temperature striking the turbine blades, causing them to spin. This rotary motion is then transferred to a generator, producing electricity.
Steam turbines are highly versatile and can be found in various applications, from large-scale power plants to smaller, specialized industrial setups. Their ability to efficiently convert heat energy into mechanical work has made them a preferred choice in many energy generation scenarios. The versatility of steam turbines extends beyond electricity production; they are also integral in marine propulsion systems, industrial processing, and cogeneration systems where they contribute to heating and electricity generation simultaneously.
The design and operation of steam turbines have evolved significantly since their inception, with advancements in materials, efficiency, and control systems. Modern steam turbines are equipped with sophisticated electronics that enhance their performance and adaptability to different operating conditions. These improvements have made steam turbines more efficient, reliable, and crucial to the global energy infrastructure.
1.2 History and Evolution
The history of steam turbines dates back to the early 19th century, with the development of steam engines serving as a precursor to turbine technology. The transition from reciprocating steam engines to steam turbines marked a significant advancement in energy conversion efficiency. The first practical steam turbine was invented by Sir Charles Parsons in 1884, a breakthrough that revolutionized the power generation industry. Parsons’ design utilized high-speed rotary motion to generate electricity, a concept that remains at the core of steam turbine technology today.
Initially, steam turbines were used primarily in large power plants where their efficiency and scalability could be fully utilized. Over time, technological advancements have enabled the development of smaller and more efficient turbines, broadening their application across various industries. The introduction of materials capable of withstanding higher temperatures and pressures, along with the refinement of blade design and aerodynamics, has further enhanced the performance of steam turbines.
During the 20th century, steam turbines became the dominant technology in power generation, especially as demand for electricity soared worldwide. The integration of steam turbines with nuclear power plants and the development of cogeneration systems further solidified their role in the energy sector. As renewable energy sources have gained prominence in recent decades, steam turbines have also been adapted to work with biomass, geothermal, and solar thermal power plants, demonstrating their flexibility and enduring relevance.
1.3 Importance in Modern Energy Systems
In today’s energy landscape, steam turbines are vital due to their high efficiency, reliability, and adaptability. They play a key role in baseload power generation, where they operate continuously to meet the constant demand for electricity. Steam turbines are particularly crucial in countries where coal, nuclear, and natural gas power plants dominate the energy mix, as these plants rely on steam turbines to convert thermal energy into electrical power.
The ability of steam turbines to integrate with various types of power plants makes them indispensable in the transition to a more sustainable energy future. For example, in biomass power plants, steam turbines convert the energy released from burning organic materials into electricity. Similarly, in solar thermal power plants, steam turbines are used to convert heat captured from the sun into electrical energy. These applications highlight the versatility of steam turbines and their potential to contribute to reducing carbon emissions and enhancing energy security.
Moreover, steam turbines are essential in industrial applications where they provide mechanical power for various processes. In industries such as chemical manufacturing, oil refining, and paper production, steam turbines are used to drive compressors, pumps, and other machinery, often in cogeneration setups where both electricity and heat are required. This dual-purpose capability enhances overall energy efficiency and reduces operational costs.
The future of steam turbines in the energy sector looks promising as innovations continue to improve their performance and reduce their environmental impact. Developments in materials science, advanced manufacturing techniques, and digital control systems are expected to further enhance the efficiency and reliability of steam turbines, making them an integral part of the global energy infrastructure for years to come.
I’ll proceed with the next section, Basic Working Principles of Steam Turbines. This section will cover how steam turbines work, the key components involved, and the steam turbine cycle diagram.
Basic Working Principles of Steam Turbines
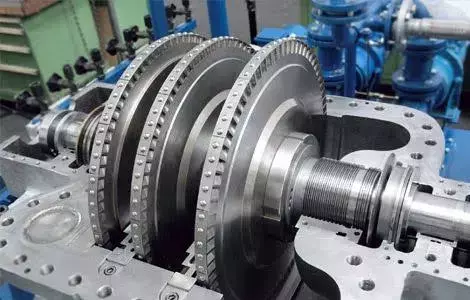
2.1 How Steam Turbines Work
The operation of a steam turbine is based on the principles of thermodynamics, where heat energy from steam is converted into mechanical energy, which in turn can be used to generate electricity. The basic working principle of a steam turbine involves the expansion of steam, which is at high temperature and pressure, through a series of stationary and rotating blades. This expansion results in the steam losing its thermal energy, which is converted into kinetic energy, causing the turbine blades to rotate.
The steam enters the turbine through nozzles, where its pressure is reduced, and its velocity is increased. This high-velocity steam then strikes the turbine blades, transferring its energy to the blades and causing them to rotate. The rotating blades are connected to a shaft, which spins as the blades turn. This shaft is typically connected to an electrical generator, where the mechanical energy is converted into electrical energy.
There are two primary types of steam turbines based on the way they extract energy from the steam: impulse turbines and reaction turbines.
- Impulse Turbines: In an impulse turbine, the steam is expanded in nozzles before it hits the turbine blades. The steam’s pressure drops across the nozzle, and the high-velocity steam jets then strike the blades, imparting kinetic energy to the rotor. The energy transfer occurs primarily through a change in the velocity of the steam. Impulse turbines are characterized by a series of stages where the steam is directed through multiple sets of blades and nozzles to extract energy efficiently.
- Reaction Turbines: In a reaction turbine, the steam undergoes expansion both in the nozzles and as it passes over the blades. This type of turbine relies on both the pressure drop across the nozzles and the reaction forces as steam moves through the blade passages. As the steam expands through the moving blades, it accelerates, creating a reaction force that causes the rotor to spin. Reaction turbines are typically used in applications where a continuous and smooth operation is required, such as in large power plants.
Both types of turbines are often used in conjunction in multi-stage configurations to maximize energy extraction from the steam. This multi-stage approach helps increase the overall efficiency of the turbine by allowing for gradual steam expansion and energy transfer across several stages.
2.2 Key Components and Their Functions
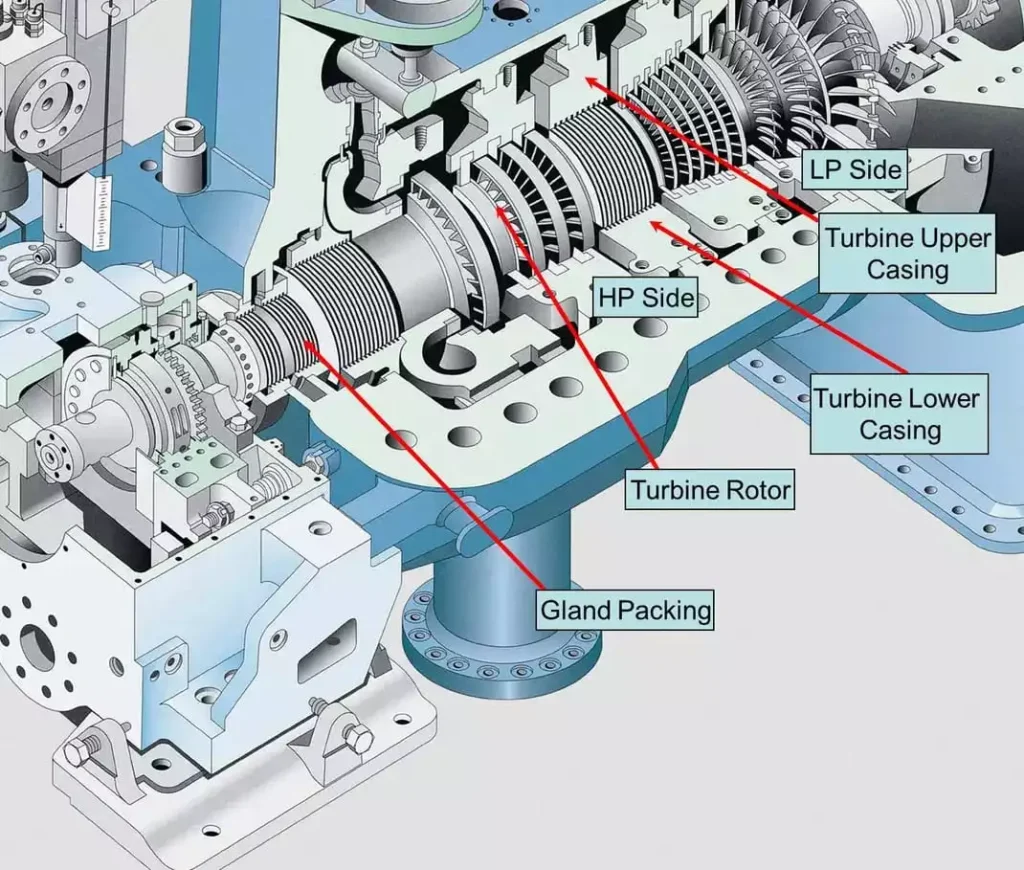
Understanding the components of a steam turbine is crucial to grasping how they function and contribute to the overall operation of the turbine. Below are the key components and their roles in the working of a steam turbine:
- Rotor: The rotor is the rotating part of the turbine that is connected to the generator. It consists of a shaft and the turbine blades, which are mounted on the shaft. The rotor is responsible for converting the energy from the steam into mechanical energy.
- Blades: Turbine blades are designed to efficiently capture the energy from the steam. There are two types of blades in a turbine: moving blades and stationary blades. The moving blades are attached to the rotor and spin as steam passes over them, while the stationary blades, also known as nozzles or guide vanes, direct the steam flow onto the moving blades.
- Casing: The casing is the outer shell that encloses the rotor and blades. It is designed to withstand high pressures and temperatures and to contain the steam within the turbine. The casing also supports the stationary blades and nozzles.
- Nozzles: Nozzles are crucial in impulse turbines, where they convert the pressure energy of the steam into kinetic energy. The nozzles direct the high-velocity steam onto the turbine blades, ensuring efficient energy transfer.
- Bearings: Bearings support the rotating shaft of the rotor, allowing it to spin smoothly with minimal friction. They play a critical role in maintaining the alignment and stability of the turbine during operation.
- Governor Valve: The governor valve controls the flow of steam into the turbine. By regulating the steam flow, the governor valve helps maintain the desired speed and power output of the turbine, ensuring efficient and stable operation.
- Condensers: Condensers are used in steam turbines to condense the exhaust steam from the turbine back into water. This water is then recirculated back into the boiler to produce more steam, enhancing the efficiency of the power generation cycle.
- Control Systems: Modern steam turbines are equipped with advanced control systems that monitor and regulate various operational parameters, such as temperature, pressure, speed, and load. These systems ensure optimal performance, safety, and reliability of the turbine.
- Seals: Seals are used to prevent steam from leaking out of the turbine casing. They ensure that the steam remains within the turbine to maximize energy transfer and maintain efficiency.
Each of these components plays a specific role in the overall operation of the steam turbine, working together to convert the thermal energy of the steam into mechanical and, ultimately, electrical energy.
2.3 Steam Turbine Cycle Diagram
The steam turbine cycle, also known as the Rankine cycle, is the thermodynamic cycle that describes the operation of steam turbines in power generation. The cycle consists of four main stages: the boiler (or steam generator), the turbine, the condenser, and the pump.
- Boiler (Steam Generator): In the boiler, water is heated to produce high-pressure, high-temperature steam. The heat source can be fossil fuels, nuclear reactions, or renewable energy sources such as biomass. The steam generated in the boiler is then directed to the turbine.
- Turbine: The high-pressure steam enters the turbine, where it expands and loses its thermal energy. This energy is transferred to the turbine blades, causing the rotor to spin and generate mechanical energy. The steam pressure and temperature drop as it moves through the turbine stages.
- Condenser: After passing through the turbine, the steam enters the condenser, where it is cooled and condensed back into water. This process is essential for maintaining the efficiency of the cycle, as it allows the water to be reused in the boiler.
- Pump: The condensed water is then pumped back into the boiler to repeat the cycle. The pump increases the pressure of the water to match the conditions in the boiler, ensuring a continuous flow of steam for the turbine.
The efficiency of the steam turbine cycle depends on various factors, including the pressure and temperature of the steam entering the turbine, the effectiveness of the condenser, and the overall design of the system. Enhancements such as reheating and regeneration can be incorporated into the cycle to improve efficiency and performance.
Types of Steam Turbines and Their Applications
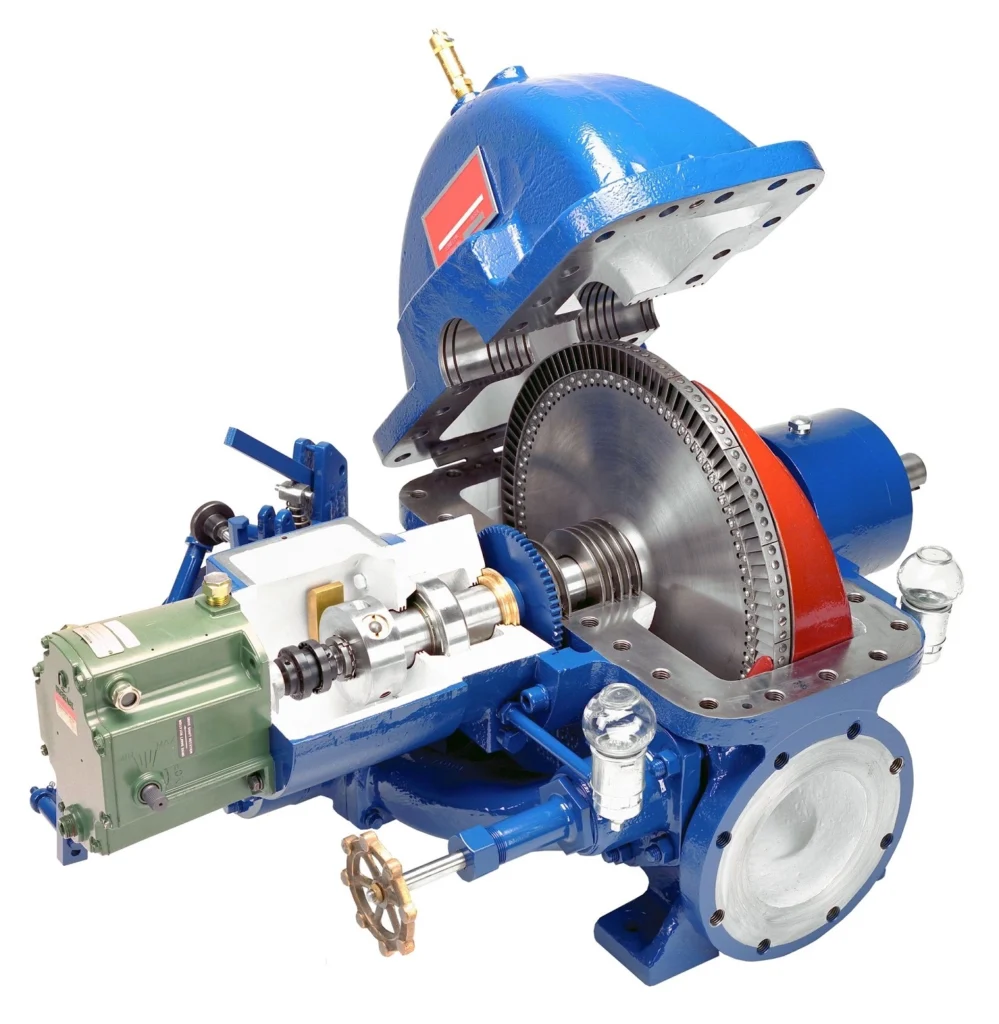
3.1 High-Pressure (HP) Steam Turbines
High-Pressure (HP) steam turbines are designed to operate with steam at very high pressures and temperatures. These turbines are typically the first stage in a multi-stage turbine setup, where they handle the most intense thermal and mechanical loads. HP turbines are used in large power plants, including fossil fuel, nuclear, and advanced renewable energy facilities, where efficiency and power output are critical.
- Design and Operation
HP steam turbines are constructed with materials that can withstand the extreme conditions of high-pressure steam. The blades are often made of special alloys to endure the thermal stress and mechanical strain. These turbines are usually connected directly to the main steam supply, and they extract energy from the steam as it undergoes a significant drop in pressure and temperature. The energy extracted in this stage is substantial, making HP turbines a crucial component in the overall efficiency of the power plant. - Applications
HP turbines are commonly used in:- Large Thermal Power Plants: Including coal-fired, gas-fired, and nuclear power stations where they form the first stage of electricity generation.
- Combined Cycle Power Plants: Where HP turbines work alongside gas turbines to enhance overall efficiency.
- Industrial Cogeneration Plants: Where high-pressure steam is also utilized for industrial processes before being sent to lower-pressure turbines.
Low-Pressure (LP) Steam Turbines
Low-Pressure (LP) steam turbines operate at the opposite end of the pressure spectrum compared to HP turbines. They handle steam that has already passed through one or more stages of energy extraction, making them the final stage in the power generation process.
- Design and Operation
LP turbines are designed to extract as much remaining energy as possible from the steam before it is condensed. These turbines typically have larger blades and operate at lower rotational speeds compared to HP turbines. The design of LP turbines must account for the lower steam pressure and higher volume, which requires efficient steam flow management to avoid losses and ensure effective energy conversion. - Applications
LP turbines are typically used in:- Thermal Power Plants: As part of a multi-stage turbine system, following the HP and intermediate-pressure (IP) turbines.
- Nuclear Power Plants: Where they handle the steam after it has passed through HP turbines.
- Marine Propulsion: In some naval ships, LP turbines are used as part of the propulsion system after high-energy steam has been utilized elsewhere.
3.3 Impulse Turbines
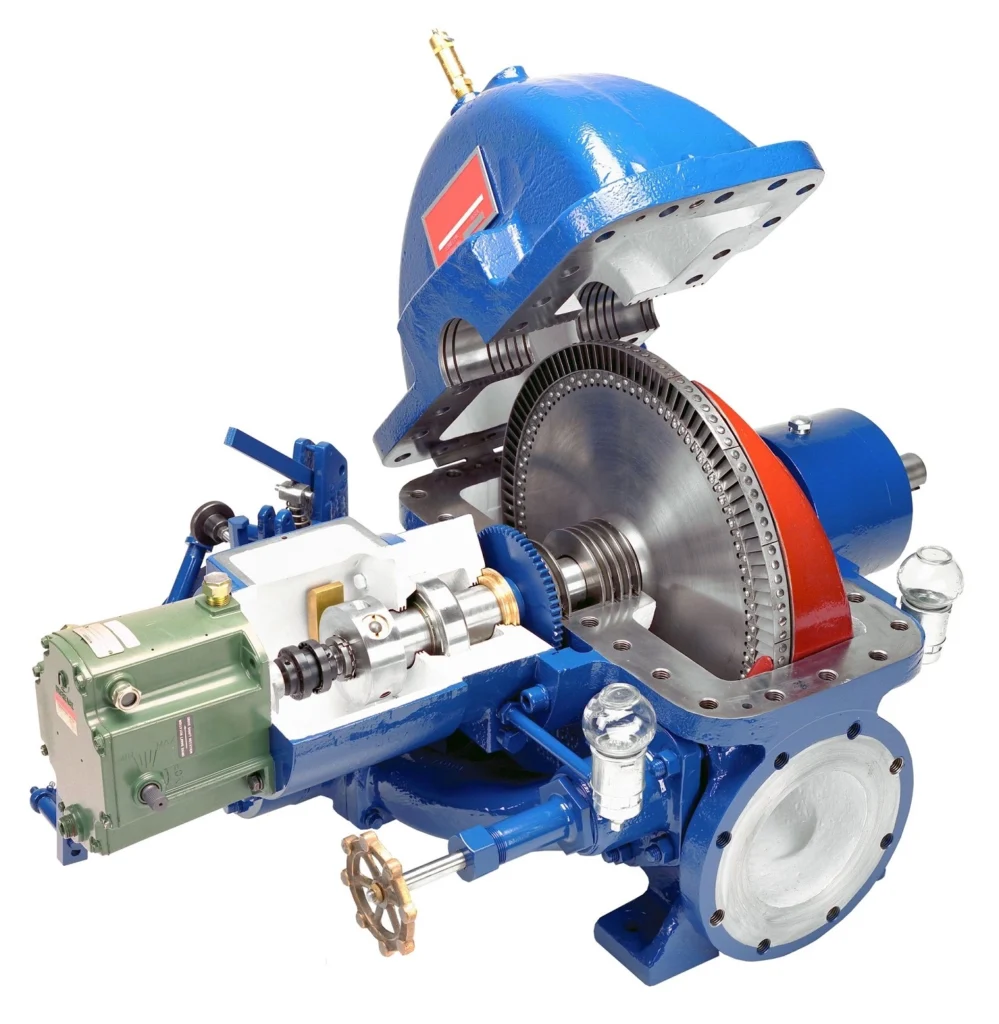
An impulse turbine operates based on the principle of directing high-velocity steam jets onto the turbine blades, which are shaped to efficiently convert the kinetic energy of the steam into mechanical energy. The steam is expanded in stationary nozzles, resulting in a high-speed jet that strikes the blades, causing the rotor to spin.
- Design and Operation
Impulse turbines have relatively simple designs with multiple stages, each consisting of a set of stationary nozzles and a corresponding set of moving blades. The energy transfer in an impulse turbine occurs primarily through changes in the steam’s velocity, rather than pressure, as it passes over the blades. Each stage reduces the steam’s velocity while maintaining the same pressure until it exits the turbine. - Applications
Impulse turbines are often used in:- Small to Medium Power Generation: Due to their simplicity and ease of maintenance.
- High-Pressure Stages: In large steam turbines where impulse stages are preferred for initial high-energy steam expansion.
- Industrial Applications: Where precise control over power output is required.
3.4 Reaction Turbines
Reaction turbines operate on the principle that steam undergoes expansion as it flows over both stationary and moving blades. This type of turbine relies on both the pressure drop and velocity changes of the steam as it moves through the turbine, resulting in a more continuous and smoother operation.
- Design and Operation
In a reaction turbine, the steam expands in the stationary blades and again in the moving blades, generating a reactive force that causes the rotor to spin. This design allows for more stages to be used, making reaction turbines suitable for applications requiring gradual energy extraction. The rotor and stator blades are designed to create a continuous expansion of the steam, which increases the efficiency of energy conversion. - Applications
Reaction turbines are widely used in:- Large Power Generation: Particularly in situations where continuous operation is required, such as in nuclear power plants.
- Marine Propulsion: Due to their smooth operation and ability to handle fluctuating loads.
- Industrial Processes: Where they are used in steam turbines for driving compressors and pumps.
3.5 Turbine Stages
Steam turbines typically consist of multiple stages, each designed to extract energy from the steam progressively. These stages are arranged in series to maximize the energy conversion from the high-pressure steam at the inlet to the low-pressure steam at the outlet.
- Single-Stage vs. Multi-Stage Turbines
- Single-Stage Turbines: Usually found in small applications where only a modest amount of energy needs to be extracted. They are simpler and cheaper but less efficient for large-scale power generation.
- Multi-Stage Turbines: These turbines are more complex and used in large power plants. They consist of multiple stages, including HP, IP (intermediate-pressure), and LP turbines, each designed to extract a specific range of energy from the steam. Multi-stage turbines are essential for optimizing the efficiency of power generation, as they allow for a gradual reduction in steam pressure and temperature across the turbine.
- Applications
- Large Power Plants: Utilize multi-stage turbines to ensure maximum efficiency and power output.
- Industrial Cogeneration: Where both electricity and process steam are required, multi-stage turbines can provide an optimized solution.
- Marine Propulsion: Multi-stage turbines are also used in large ships, where efficient and reliable power generation is critical.
3.6 Specialized Steam Turbines
In addition to the common types of steam turbines, there are specialized turbines designed for specific applications. These turbines are often tailored to meet the unique demands of their respective environments.
- Marine Steam Engines
Marine steam engines, including steam turbines, have been used historically and continue to be relevant in certain naval and commercial vessels. These turbines are designed to provide reliable propulsion over long distances and under challenging conditions. The turbines used in marine applications are often built for durability and efficiency, considering the high loads and continuous operation required at sea.- Applications
- Naval Ships: Turbines in military vessels where reliability and high power output are crucial.
- Commercial Ships: Particularly in older vessels where steam propulsion was standard.
- Marine Auxiliary Systems: Smaller turbines used in shipboard power generation systems.
- Applications
- Biomass-Fueled Steam Turbines
Biomass power plants utilize steam turbines designed to operate on steam generated from the combustion of organic materials. These turbines must be adaptable to the varying quality of steam produced by biomass fuels, which can differ significantly from the steam generated by fossil fuels or nuclear reactors.- Applications
- Biomass Power Plants: Where turbines convert the energy from burning organic materials into electricity.
- Cogeneration Plants: Using biomass to provide both heat and power for industrial and residential use.
- Applications
- Mini and Micro Steam Turbines
These small-scale turbines are designed for specialized applications where compact size and lower power output are required. Mini and micro turbines are used in decentralized energy systems, such as in small industrial plants, remote areas, or as part of renewable energy systems.- Applications
- Decentralized Power Generation: In remote or off-grid locations.
- Industrial Applications: Where small amounts of steam power are needed for specific processes.
- Renewable Energy Systems: Such as solar thermal plants or small-scale biomass plants.
- Applications
Steam Turbine Components and Accessories
4.1 Governor Valve Operation
The governor valve is one of the most critical components in a steam turbine system. It controls the flow of steam into the turbine, thereby regulating the turbine’s speed and power output. The precise operation of the governor valve is essential for maintaining the stability, efficiency, and safety of the steam turbine.
- Design and Function
The governor valve is typically located at the turbine inlet, where it regulates the quantity of steam entering the turbine. It operates based on signals from the turbine’s control system, which continuously monitors various parameters such as load demand, turbine speed, and steam pressure. By adjusting the valve opening, the governor can either increase or decrease the steam flow, directly influencing the turbine’s power output.Governor valves can be of different types, including:- Throttle Valves: Control the steam flow by varying the valve opening.
- Control Valves: Adjust the steam flow more precisely, often used in combination with throttle valves.
- Stop Valves: Serve as safety devices that can shut off steam flow entirely in case of emergency.
- Operation Mechanism
In operation, the governor valve responds to changes in the turbine’s speed. If the turbine begins to overspeed, the governor valve partially closes to reduce the steam flow, slowing down the turbine. Conversely, if the turbine’s speed drops below the desired level, the governor valve opens wider to increase the steam flow and bring the speed back up.The valve’s movement is typically controlled by a hydraulic actuator, which receives signals from the turbine’s electronic governor. This system ensures rapid and precise adjustments to the steam flow, maintaining optimal turbine performance under varying load conditions. - Importance in Power Generation
The governor valve plays a crucial role in maintaining the stability of the power grid, especially in large power plants where fluctuations in turbine speed can lead to frequency deviations. By ensuring that the turbine operates at the correct speed, the governor valve helps prevent mechanical damage to the turbine and associated equipment, and it also contributes to the overall efficiency of the power generation process.
4.2 Electronic Governors
Electronic governors represent a significant advancement in the control of steam turbines. Unlike mechanical governors, which rely on physical components like flyweights and springs, electronic governors use digital technology to precisely control the turbine’s speed and power output.
- Function and Advantages
Electronic governors receive input signals from various sensors that monitor the turbine’s operational parameters, such as speed, temperature, and pressure. These signals are processed by a central control unit, which then sends commands to the hydraulic actuators controlling the governor valve. The use of electronic governors allows for much finer control over the turbine’s operation compared to mechanical systems.The advantages of electronic governors include:- Precision: More accurate control of turbine speed and output.
- Flexibility: Easier integration with modern control systems and automation technologies.
- Responsiveness: Faster adjustments to changes in load demand and operating conditions.
- Safety: Enhanced protection features, such as automatic shutdown in case of system faults.
- Integration with Modern Control Systems
Electronic governors are often integrated with advanced control systems that manage the entire power plant. This integration allows for better coordination between the turbine and other plant components, leading to improved efficiency and reliability. For example, electronic governors can work in conjunction with load-sharing systems in multi-turbine setups to optimize the distribution of power generation across different units. - Applications in Modern Steam Turbines
Electronic governors are now standard in most new steam turbines, particularly in large power plants and industrial cogeneration systems. They are also used in retrofitting older turbines to improve performance and extend their operational life. The ability to fine-tune turbine operation through electronic governors makes them essential for meeting the demands of modern, flexible power generation systems.
4.3 Turbine Rotors and Materials
The turbine rotor is the central component of the steam turbine, responsible for converting the thermal energy of the steam into mechanical energy. The rotor consists of a central shaft, to which the turbine blades are attached, and it rotates at high speeds during operation.
- Design and Construction
Turbine rotors are designed to withstand the extreme forces generated by the high-speed rotation and the thermal stresses caused by the steam. The material used for the rotor must be capable of withstanding high temperatures, pressures, and centrifugal forces without deforming or failing. Common materials include high-strength alloys, such as chromium-nickel steels, which offer a good balance of strength, ductility, and resistance to thermal fatigue.The construction of the rotor involves precision engineering to ensure perfect balance and alignment. Any imbalance in the rotor can lead to excessive vibration, which can cause damage to the turbine and reduce its efficiency. - Blades and Blade Assembly
The blades attached to the rotor are crucial for capturing the energy from the steam. They are typically made from materials like titanium alloys or nickel-based superalloys, which offer high strength and resistance to corrosion and thermal fatigue. The blades are carefully shaped and positioned on the rotor to maximize the energy transfer from the steam.Blade assembly on the rotor must be done with extreme precision to ensure that the turbine operates smoothly. Blades are often assembled in stages, with each stage designed to handle a specific range of steam pressures and velocities. The correct assembly of blades is critical to the turbine’s performance and longevity. - Maintenance and Lifespan
The rotor and its blades are subject to wear and tear over time, especially in high-demand environments. Regular maintenance, including inspection for cracks, erosion, and other signs of wear, is essential to ensure the continued safe and efficient operation of the turbine. The lifespan of a turbine rotor can vary depending on the operating conditions, but with proper maintenance, it can last for decades.
4.4 Condensers and Other Accessories
Condensers play a vital role in the steam turbine cycle by converting the exhaust steam from the turbine back into water, which is then recycled into the boiler. This process increases the efficiency of the steam cycle and reduces the need for fresh water input.
- Function and Importance
Condensers operate by cooling the exhaust steam, typically using cooling water from a nearby source, such as a river, lake, or cooling tower. The condensed water, now in liquid form, is pumped back into the boiler to be reheated and converted into steam, thus completing the cycle. By lowering the temperature and pressure of the exhaust steam, condensers also help maintain the vacuum in the turbine, which is crucial for maximizing efficiency. - Types of Condensers
There are two main types of condensers used in steam turbines:- Surface Condensers: These are the most common type, where the steam passes over tubes containing cooling water. The steam condenses on the outside of the tubes, while the cooling water remains isolated within the tubes.
- Direct-Contact Condensers: In these condensers, the steam directly contacts the cooling water, mixing with it and condensing immediately. This type is less common and is typically used in specific applications where water quality and availability are less of a concern.
- Other Accessories
In addition to condensers, several other accessories are essential for the operation of steam turbines:- Deaerators: Remove dissolved gases from the feedwater to prevent corrosion in the boiler and turbine components.
- Feedwater Heaters: Preheat the water before it enters the boiler, improving overall efficiency by reducing the energy needed to convert water into steam.
- Steam Traps: Remove condensate and non-condensable gases from the steam lines, ensuring that only dry steam reaches the turbine.
- Pumps: Circulate the feedwater and condensate within the steam cycle, maintaining the necessary pressure and flow rates.
- Maintenance and Optimization
Regular maintenance of condensers and associated accessories is crucial for maintaining the efficiency and reliability of the steam turbine system. This includes inspecting for leaks, cleaning tubes, and ensuring that cooling water quality is maintained. Optimizing the operation of condensers and other accessories can significantly improve the overall efficiency of the power generation process.
Performance, Efficiency, and Optimization
5.1 Steam Turbine Performance Metrics
Understanding and measuring the performance of a steam turbine is crucial for optimizing its operation and ensuring that it meets the desired power output and efficiency levels. Several key performance metrics are used to evaluate the effectiveness of steam turbines in power generation.
- Thermal Efficiency
Thermal efficiency is one of the most critical metrics, representing the ratio of useful energy output to the energy input in the form of steam. In steam turbines, thermal efficiency is affected by factors such as steam pressure, temperature, and the efficiency of individual turbine stages. Higher steam temperatures and pressures generally lead to better thermal efficiency, as they allow for more energy to be extracted from the steam. - Power Output
The power output of a steam turbine is measured in megawatts (MW) and indicates the amount of electrical energy the turbine can generate. This metric is directly related to the turbine’s design, size, and the amount of steam it can process. Power output is a key factor in determining the turbine’s suitability for specific applications, such as large power plants or smaller industrial settings. - Heat Rate
The heat rate is a measure of the energy input required to produce one kilowatt-hour (kWh) of electricity. It is typically expressed in British Thermal Units per kWh (BTU/kWh). A lower heat rate indicates a more efficient turbine, as it requires less fuel to generate the same amount of electricity. The heat rate is influenced by factors such as the efficiency of the boiler, steam conditions, and the overall design of the turbine. - Load Factor
The load factor measures the ratio of the actual energy produced by the turbine over a given period to the maximum possible energy it could have produced if it operated at full capacity. A high load factor indicates that the turbine is being used effectively, while a low load factor may suggest inefficiencies or underutilization. - Availability and Reliability
Availability refers to the percentage of time the turbine is operational and capable of generating power, while reliability indicates the turbine’s ability to operate without failure. Both metrics are essential for power plants that require consistent and dependable energy production. High availability and reliability are often achieved through regular maintenance, monitoring, and the use of advanced control systems.
5.2 Turbine Generator Efficiency
Turbine generator efficiency is a critical aspect of overall plant performance. It represents the effectiveness with which the turbine converts steam energy into mechanical energy and then into electrical energy. Improving turbine generator efficiency involves optimizing several factors.
- Blade Design and Aerodynamics
The design of the turbine blades plays a significant role in efficiency. Modern turbines use blades with advanced aerodynamic shapes that minimize energy losses due to friction and turbulence. The precision with which the blades are manufactured and assembled also affects efficiency, as even small imperfections can lead to significant energy losses. - Steam Conditions
The pressure, temperature, and quality of the steam entering the turbine are crucial for efficiency. Superheated steam, which has a higher temperature and lower moisture content, is generally more efficient than saturated steam. Optimizing the steam conditions to match the turbine design can lead to significant gains in efficiency. - Turbine Stages and Reheat Cycles
Multi-stage turbines with reheat cycles can improve efficiency by allowing steam to expand in stages, extracting energy more gradually and effectively. In a reheat cycle, steam is partially expanded in the turbine, then reheated in the boiler before returning to the turbine for further expansion. This process increases the thermal efficiency of the cycle. - Minimizing Mechanical Losses
Mechanical losses in the turbine, such as friction in bearings and seals, can reduce overall efficiency. Using high-quality materials and advanced engineering techniques can minimize these losses. Regular maintenance is also essential to prevent wear and tear that can lead to increased mechanical losses over time. - Generator Efficiency
The efficiency of the electrical generator connected to the turbine is also a critical factor. Modern generators are designed to convert mechanical energy into electrical energy with minimal losses. This involves using high-efficiency materials in the generator’s windings and optimizing the magnetic field generation.
5.3 Vibration and Stability
Vibration is a common issue in steam turbines that can affect both performance and longevity. Excessive vibration can lead to mechanical failures, reduced efficiency, and increased maintenance costs. Understanding the causes of vibration and implementing strategies to mitigate it is essential for maintaining turbine stability.
- Causes of Vibration
Vibration in steam turbines can be caused by several factors, including:- Imbalance in the Rotor: Even minor imbalances in the rotor can cause significant vibration, particularly at high rotational speeds.
- Misalignment of Components: Misalignment of the rotor, bearings, or other components can lead to uneven forces within the turbine, resulting in vibration.
- Blade Deformation or Damage: Blades that are worn, deformed, or damaged can disrupt the smooth flow of steam, leading to vibration.
- Bearing Wear: Worn or damaged bearings can introduce additional friction and instability, causing vibration.
- Steam Flow Instabilities: Variations in steam pressure, temperature, or flow rate can create uneven forces on the turbine blades, leading to vibration.
- Vibration Monitoring and Diagnostics
Modern steam turbines are equipped with advanced vibration monitoring systems that detect and analyze vibration levels in real time. These systems use sensors placed at key points on the turbine, such as the bearings, rotor, and casing. The data collected is analyzed to identify the source of the vibration and determine whether it is within acceptable limits.Vibration diagnostics involves examining the frequency, amplitude, and phase of the vibrations to pinpoint the exact cause. For example, an imbalance in the rotor typically produces a vibration at the same frequency as the rotor’s rotational speed, while misalignment may result in vibrations at harmonics of the rotational frequency. - Mitigation Strategies
To mitigate vibration, several strategies can be employed:- Balancing the Rotor: Ensuring that the rotor is perfectly balanced during manufacturing and after maintenance is critical. Dynamic balancing techniques can be used to correct imbalances that develop over time.
- Proper Alignment: Regular checks and adjustments to the alignment of the rotor, bearings, and other components help maintain stability and reduce vibration.
- Blade Maintenance: Regular inspection and maintenance of the turbine blades are necessary to prevent wear and damage that can lead to vibration. Damaged blades should be repaired or replaced promptly.
- Upgrading Bearings: Using high-quality, low-friction bearings can reduce vibration. In some cases, upgrading to more advanced bearing designs can improve stability.
- Steam Flow Control: Ensuring consistent and stable steam flow through the turbine helps minimize the forces that can cause vibration. This may involve optimizing the steam control system and addressing issues such as steam pressure fluctuations.
5.4 Thermal Efficiency and Optimization Techniques
Thermal efficiency is a measure of how effectively a steam turbine converts the thermal energy of steam into mechanical energy. Maximizing thermal efficiency is crucial for reducing fuel consumption, lowering emissions, and improving the overall economic performance of a power plant.
- Superheated vs. Saturated Steam
Using superheated steam, which has been heated beyond its boiling point without becoming a liquid, can significantly improve thermal efficiency. Superheated steam contains more energy and is less likely to condense during expansion, which helps maintain the turbine’s performance and reduce moisture-related damage.- Temperature and Pressure Optimization
Increasing the temperature and pressure of the steam entering the turbine can also enhance thermal efficiency. However, this requires careful design and material selection, as higher temperatures and pressures can increase the risk of mechanical failure and require more robust construction materials. - Reheat and Regeneration
Reheating steam after it has partially expanded in the turbine and returning it for further expansion is a proven method to improve thermal efficiency. Reheat cycles reduce the moisture content of the steam, preventing damage to the turbine blades and allowing for more energy extraction.Regeneration involves using extracted steam to preheat the feedwater before it enters the boiler. This process reduces the amount of fuel required to heat the water to steam, thereby increasing the overall efficiency of the cycle.
- Temperature and Pressure Optimization
- Cogeneration Systems
Cogeneration, or combined heat and power (CHP), systems improve thermal efficiency by using the waste heat from the steam turbine for other processes, such as heating or industrial applications. This dual-use of energy maximizes the output from the fuel used and reduces the overall environmental impact. - Steam Turbine Upgrades
Upgrading older steam turbines with modern technologies can lead to significant improvements in thermal efficiency. This might include retrofitting with advanced blade designs, installing more efficient control systems, or converting from saturated to superheated steam operation. - Operational Optimization
Continuous monitoring and optimization of turbine operation are essential for maintaining high thermal efficiency. This involves adjusting operating parameters, such as steam flow, pressure, and temperature, in real time to match the current load and demand. Advanced control systems and predictive maintenance strategies can also help identify potential issues before they lead to efficiency losses.
5.5 Cogeneration and Combined Cycle Systems
Cogeneration and combined cycle systems are advanced techniques that enhance the efficiency of steam turbines by making use of waste heat and integrating multiple energy conversion processes.
- Cogeneration (Combined Heat and Power – CHP)
In a cogeneration system, the steam turbine generates electricity while the waste heat from the turbine’s exhaust is captured and used for heating, industrial processes, or further power generation. This process significantly increases the overall efficiency of the system, as it utilizes energy that would otherwise be wasted.- Applications of Cogeneration
- Industrial Plants: Where both electricity and process heat are needed, cogeneration can reduce energy costs and improve overall plant efficiency.
- District Heating: Cogeneration systems can supply heat to nearby residential or commercial buildings, providing a sustainable and cost-effective heating solution.
- Waste-to-Energy Plants: In these plants, cogeneration is used to maximize the energy output from waste materials, providing both electricity and heat.
- Applications of Cogeneration
- Combined Cycle Power Plants
Combined cycle power plants integrate gas turbines with steam turbines to achieve higher efficiency. The gas turbine generates electricity and produces exhaust gases, which are then used to produce steam in a heat recovery steam generator (HRSG). The steam is then used to power a steam turbine, generating additional electricity.- Advantages of Combined Cycle Systems
- Increased Efficiency: Combined cycle systems can achieve efficiencies of up to 60% or more, significantly higher than standalone gas or steam turbines.
- Flexibility: These systems can respond quickly to changes in demand, making them ideal for modern power grids that require flexible and reliable energy sources.
- Lower Emissions: By utilizing waste heat and improving fuel efficiency, combined cycle systems produce fewer emissions per unit of electricity generated.
- Advantages of Combined Cycle Systems
- Challenges and Considerations
Implementing cogeneration and combined cycle systems requires careful planning and design to ensure compatibility between the various components and to optimize overall performance. These systems are more complex than single-cycle plants, requiring advanced control systems and regular maintenance to maintain efficiency and reliability.
Steam Power Plant Applications
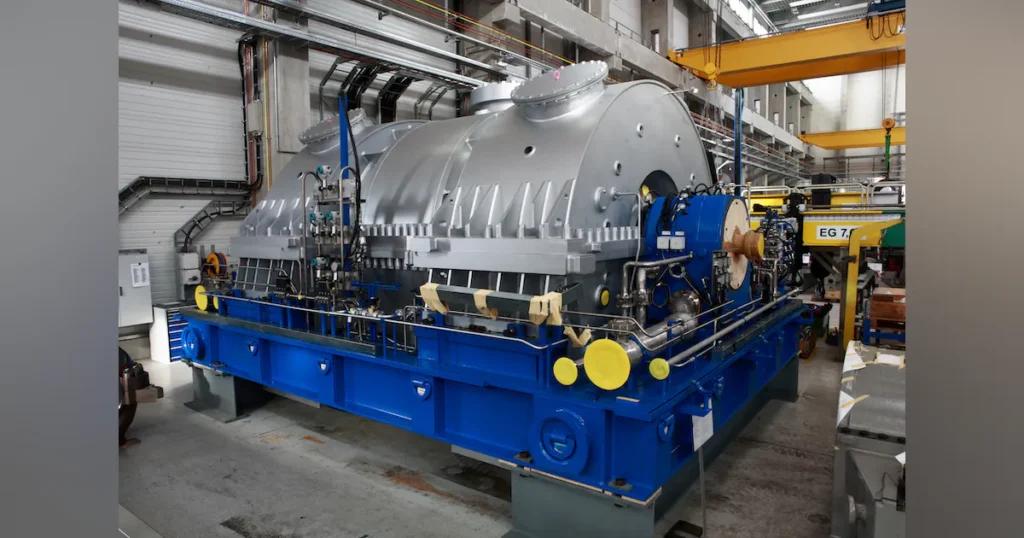
6.1 Applications in Power Generation
Steam turbines are a cornerstone of modern power generation, particularly in thermal power plants where their ability to efficiently convert steam energy into electrical energy is unmatched. The versatility of steam turbines allows them to be used in various types of power plants, each with unique characteristics and requirements.
- Fossil Fuel Power Plants
In fossil fuel power plants, steam turbines are used to generate electricity by converting the thermal energy produced from burning coal, natural gas, or oil. These plants are typically designed for baseload power generation, meaning they operate continuously to meet the steady demand for electricity.- Coal-Fired Power Plants: Coal remains one of the most widely used fuels for steam power generation, particularly in developing countries. In these plants, coal is burned in a boiler to produce high-pressure steam, which drives a steam turbine connected to a generator.
- Natural Gas-Fired Power Plants: Natural gas plants often use combined cycle technology, where a gas turbine generates electricity, and the exhaust gases are used to produce steam for a steam turbine, increasing overall efficiency.
- Oil-Fired Power Plants: Although less common today due to environmental concerns and high fuel costs, oil-fired plants still use steam turbines to generate electricity, particularly in regions where oil is more readily available.
- Nuclear Power Plants
Nuclear power plants rely on steam turbines to convert the heat generated by nuclear fission into electricity. In these plants, the heat produced in a nuclear reactor is used to generate steam, which drives a turbine in much the same way as in fossil fuel plants. The key difference lies in the fuel source and the specific safety and operational requirements of nuclear power.- Pressurized Water Reactors (PWRs): In PWRs, water under high pressure is heated by the reactor core and circulated through a steam generator. The generated steam then drives the steam turbine.
- Boiling Water Reactors (BWRs): In BWRs, water is boiled directly in the reactor core to produce steam, which is then used to power the steam turbine. Both types of reactors rely on the steam turbine for the final conversion of thermal energy into electricity.
- Renewable Energy Power Plants
Steam turbines are also used in renewable energy applications, where they convert thermal energy from renewable sources into electricity.- Biomass Power Plants: Biomass power plants use organic materials like wood, agricultural residues, and waste to generate steam. This steam is then used to drive a steam turbine, generating electricity. Biomass power plants are particularly valuable for their ability to utilize waste materials and reduce carbon emissions compared to fossil fuels.
- Geothermal Power Plants: In geothermal power plants, steam or hot water from underground reservoirs is used to drive a steam turbine. These plants are highly efficient and provide a continuous, stable source of renewable energy.
- Solar Thermal Power Plants: Solar thermal plants use mirrors or lenses to concentrate sunlight and generate heat, which is then used to produce steam. The steam drives a turbine, converting solar energy into electricity. Solar thermal plants are an important part of the transition to clean, renewable energy sources.
6.2 Biomass Renewable Energy
Biomass renewable energy involves the use of organic materials to produce electricity, often through the combustion of biomass to generate steam. Steam turbines are a key component of biomass power plants, where they convert the thermal energy from burning biomass into mechanical and then electrical energy.
- Types of Biomass
Biomass power plants can use a variety of organic materials as fuel, including:- Wood and Wood Residues: Such as sawdust, wood chips, and forestry residues.
- Agricultural Residues: Including straw, corn stover, and sugarcane bagasse.
- Energy Crops: Specially grown crops like switchgrass and miscanthus, cultivated specifically for energy production.
- Waste Materials: Including municipal solid waste (MSW), food waste, and animal manure.
- Steam Generation from Biomass
In a biomass power plant, the biomass fuel is burned in a boiler to produce high-pressure steam. This steam is then used to drive a steam turbine, which generates electricity. The process is similar to that of a traditional coal-fired power plant, but with biomass as the fuel source.- Advantages of Biomass Power
- Carbon Neutrality: Biomass is considered carbon-neutral because the CO2 released during combustion is offset by the CO2 absorbed during the growth of the biomass.
- Waste Reduction: Using waste materials for biomass energy helps reduce landfill use and mitigates environmental pollution.
- Energy Security: Biomass can be sourced locally, reducing dependence on imported fossil fuels.
- Challenges in Biomass Power
- Fuel Quality and Consistency: Biomass fuels can vary widely in quality and energy content, affecting the efficiency and operation of the steam turbine.
- Ash and Emissions Management: Burning biomass produces ash and other emissions that need to be managed and treated to minimize environmental impact.
- Infrastructure Requirements: Biomass plants require significant infrastructure for fuel storage, handling, and processing.
- Advantages of Biomass Power
- Applications of Biomass Power
Biomass power plants are particularly suitable for rural and agricultural areas where biomass is readily available. They can be used for both grid-connected power generation and off-grid applications, providing a sustainable energy solution for remote communities.
6.3 Onsite Power Generation
Onsite power generation refers to the production of electricity at or near the point of use, rather than relying on centralized power plants and long-distance transmission lines. Steam turbines are often used in onsite power generation systems, particularly in industrial and commercial settings where there is a need for both electricity and process heat.
- Advantages of Onsite Power Generation
- Increased Energy Efficiency: Onsite power generation can reduce energy losses associated with long-distance transmission, leading to higher overall efficiency.
- Reliability and Independence: Facilities with onsite power generation are less dependent on the grid, reducing the risk of power outages and improving energy security.
- Cost Savings: By generating electricity onsite, businesses can reduce their energy costs and avoid peak demand charges.
- Flexibility: Onsite power generation systems can be tailored to meet specific energy needs, including the use of renewable energy sources.
- Applications of Steam Turbines in Onsite Power Generation
Steam turbines are particularly well-suited for onsite power generation in industries with significant heat and power requirements.- Industrial Cogeneration: Many industrial facilities use cogeneration systems, where steam turbines generate electricity and provide process heat for manufacturing processes. Examples include chemical plants, paper mills, and food processing facilities.
- Commercial Buildings: Large commercial buildings, such as hospitals, universities, and office complexes, may use steam turbines in combined heat and power (CHP) systems to generate electricity and provide heating and cooling.
- District Energy Systems: In urban areas, steam turbines can be used in district energy systems to provide electricity, heating, and cooling to multiple buildings within a district.
6.4 Industrial and Marine Applications
Steam turbines are widely used in industrial and marine applications, where their reliability, efficiency, and adaptability make them ideal for various processes and systems.
- Industrial Applications
In industrial settings, steam turbines are used to drive machinery, compress gases, and generate electricity.- Process Industry: Steam turbines are commonly used in industries such as chemicals, petrochemicals, and pharmaceuticals, where they provide mechanical power for pumps, compressors, and other equipment.
- Paper and Pulp Industry: Steam turbines are used to drive paper machines and other equipment in the paper and pulp industry, where steam is a byproduct of the manufacturing process.
- Oil and Gas Industry: Steam turbines are used in the oil and gas industry to drive compressors and pumps, particularly in refineries and petrochemical plants.
- Marine Applications
Steam turbines have been used in marine propulsion systems for over a century, powering ships and submarines with their reliable and efficient operation.- Naval Vessels: Steam turbines are used in various naval vessels, including aircraft carriers, destroyers, and submarines. They provide the necessary power for propulsion and onboard systems, offering a combination of high power output and durability.
- Commercial Ships: Some older commercial ships still use steam turbines for propulsion, particularly in the case of large tankers and bulk carriers. Although modern ships often use diesel engines, steam turbines remain relevant in certain niche applications.
- Marine Auxiliary Systems: In addition to propulsion, steam turbines are used in auxiliary systems onboard ships, such as for generating electricity and powering pumps and compressors.
6.5 Challenges and Future Directions
While steam turbines continue to play a critical role in power generation and industrial applications, they face several challenges that must be addressed to ensure their continued relevance and efficiency.
- Environmental Concerns
As the world shifts towards cleaner energy sources, steam turbines in fossil fuel power plants face increasing scrutiny due to their carbon emissions. The future of steam turbines may involve greater integration with renewable energy sources and the development of carbon capture and storage (CCS) technologies to mitigate environmental impacts. - Fuel Diversification
The diversification of fuel sources, including the use of biomass, waste, and hydrogen, presents both opportunities and challenges for steam turbines. Adapting steam turbine technology to handle a broader range of fuels while maintaining efficiency and reliability will be essential. - Technological Advancements
Advances in materials science, digital control systems, and turbine design are expected to improve the performance and efficiency of steam turbines. Innovations such as additive manufacturing (3D printing) and the use of advanced composites could lead to lighter, stronger, and more efficient turbine components. - Integration with Smart Grids and Renewable Energy
Steam turbines will need to integrate more effectively with smart grids and renewable energy systems. This may involve developing more flexible and adaptable turbine designs that can respond quickly to fluctuations in renewable energy supply and demand. - Market and Economic Pressures
The global energy market is evolving, with increasing competition from alternative energy technologies such as wind, solar, and energy storage systems. Steam turbine manufacturers and operators will need to adapt to changing market conditions and economic pressures, including the need for cost-effective and scalable solutions.
Comparative Analysis of Steam Turbine Technologies
7.1 Saturated Steam vs. Superheated Steam
Saturated steam and superheated steam are two key types of steam used in steam turbines, each with distinct characteristics that influence turbine performance, efficiency, and application suitability.
- Saturated Steam
Saturated steam is steam that is in equilibrium with water at a given pressure and temperature, meaning it contains moisture and is at the boiling point for that pressure. Saturated steam is commonly used in low-pressure applications where the presence of moisture is not a significant concern.- Advantages
- Simpler Equipment: Turbines designed for saturated steam are generally simpler and less expensive, as they do not require specialized materials or cooling systems to handle high temperatures.
- Lower Energy Input: Generating saturated steam typically requires less energy compared to superheated steam, making it suitable for applications where efficiency is less critical.
- Wider Availability: Saturated steam is easier to produce and manage, making it accessible for a range of industrial and power generation applications.
- Disadvantages
- Lower Efficiency: Saturated steam turbines are generally less efficient because the moisture content can cause erosion of turbine blades and reduce overall energy conversion efficiency.
- Limited Power Output: Saturated steam is typically used in low to medium power applications, as its lower energy content limits the power output of the turbine.
- Applications
- Industrial Processes: Saturated steam is often used in industries such as food processing, paper manufacturing, and chemical production, where precise control over temperature and pressure is required.
- District Heating: In district heating systems, saturated steam is commonly used to transfer heat over short distances to residential and commercial buildings.
- Advantages
- Superheated Steam
Superheated steam is steam that has been heated beyond its boiling point, without any water content, at a given pressure. This type of steam is commonly used in high-efficiency power generation applications, where maximizing energy output is critical.- Advantages
- Higher Efficiency: Superheated steam allows for higher thermal efficiency, as it can expand more within the turbine, producing more work for the same amount of energy input.
- Reduced Moisture-Related Issues: The absence of moisture in superheated steam reduces the risk of blade erosion and other damage, leading to longer turbine life and lower maintenance costs.
- Greater Power Output: Turbines designed for superheated steam can operate at higher temperatures and pressures, leading to greater power output and efficiency.
- Disadvantages
- Complex Equipment: Superheated steam turbines require more sophisticated materials and cooling systems to handle the higher temperatures and pressures, increasing the initial capital costs.
- Higher Energy Input: Producing superheated steam requires more energy, making it less suitable for applications where energy input needs to be minimized.
- Applications
- Power Plants: Superheated steam is the standard in large-scale power plants, including coal-fired, nuclear, and concentrated solar power (CSP) plants, where maximizing efficiency is paramount.
- Industrial Cogeneration: In industries where both high-temperature process heat and electricity are needed, superheated steam is used to drive turbines and supply process heat.
- Advantages
7.2 Impulse Turbine vs. Reaction Turbine
The design and operation of impulse turbines and reaction turbines differ significantly, each offering unique advantages and disadvantages depending on the application.
- Impulse Turbines
Impulse turbines operate by converting the kinetic energy of a high-velocity steam jet into mechanical energy. The steam is expanded in nozzles before striking the turbine blades, causing the rotor to spin.- Advantages
- Simple Design: Impulse turbines have a simpler design with fewer moving parts, making them easier to manufacture and maintain.
- High Efficiency at High Speeds: Impulse turbines are particularly efficient at high rotational speeds, making them ideal for applications where speed and power output are critical.
- Less Susceptible to Steam Quality: The performance of impulse turbines is less affected by changes in steam quality, as the steam expands before it contacts the blades.
- Disadvantages
- Limited Efficiency in Low-Pressure Applications: Impulse turbines are less efficient at low steam pressures, limiting their use in certain applications.
- Higher Noise Levels: The high-velocity steam jets can create significant noise, which may be a concern in certain environments.
- Applications
- High-Pressure Stages in Power Plants: Impulse turbines are often used in the high-pressure stages of steam turbines, where they efficiently handle the initial expansion of high-pressure steam.
- Small-Scale Power Generation: Due to their simplicity and efficiency at high speeds, impulse turbines are used in small-scale power generation applications, such as in microturbines and portable power systems.
- Advantages
- Reaction Turbines
Reaction turbines rely on both the pressure drop and velocity change of steam as it passes through the turbine. The steam expands in the moving blades, creating a reaction force that causes the rotor to spin.- Advantages
- High Efficiency in Multi-Stage Configurations: Reaction turbines are highly efficient in multi-stage configurations, where the steam gradually expands through multiple stages, extracting energy more effectively.
- Smooth Operation: Reaction turbines operate smoothly with less vibration, making them ideal for applications where stability and continuous operation are essential.
- Better at Low-Pressure Stages: Reaction turbines are more efficient than impulse turbines at lower steam pressures, making them suitable for the latter stages of a multi-stage turbine system.
- Disadvantages
- Complex Design: The design of reaction turbines is more complex, with a greater number of moving parts and a higher initial cost.
- Susceptibility to Steam Quality: Reaction turbines are more sensitive to changes in steam quality, particularly moisture content, which can reduce efficiency and cause blade erosion.
- Applications
- Multi-Stage Power Plants: Reaction turbines are commonly used in the low- and intermediate-pressure stages of multi-stage steam turbines, where they efficiently extract energy from lower-pressure steam.
- Marine Propulsion: Due to their smooth operation and ability to handle varying loads, reaction turbines are often used in marine propulsion systems.
- Advantages
7.3 Material Considerations for Turbine Components
The materials used in the construction of steam turbine components are critical to their performance, durability, and efficiency. Different materials are selected based on the specific requirements of each component, including factors such as temperature, pressure, and environmental conditions.
- Turbine Blades
Turbine blades are exposed to extreme conditions, including high temperatures, pressures, and corrosive environments. The material used for turbine blades must have high strength, resistance to thermal fatigue, and good corrosion resistance.- Materials Used
- Nickel-Based Superalloys: These materials are commonly used in high-temperature applications due to their excellent strength and resistance to thermal creep and oxidation.
- Titanium Alloys: Used in situations where weight reduction is critical, titanium alloys offer a good balance of strength, corrosion resistance, and fatigue resistance.
- Stainless Steel: In some cases, stainless steel is used for turbine blades due to its good corrosion resistance and relatively lower cost compared to superalloys.
- Challenges
- Material Fatigue: Over time, the extreme operating conditions can cause fatigue in turbine blades, leading to cracks and eventual failure. Regular inspection and maintenance are required to prevent these issues.
- Erosion and Corrosion: The presence of moisture in the steam can cause erosion and corrosion of turbine blades, particularly in the later stages of the turbine where the steam is at a lower pressure and temperature.
- Materials Used
- Turbine Rotors
The rotor is the central shaft to which the turbine blades are attached. It must withstand high rotational speeds and the associated centrifugal forces while maintaining structural integrity under high temperatures and pressures.- Materials Used
- Chromium-Nickel Steels: These high-strength steels are commonly used for turbine rotors due to their excellent mechanical properties and resistance to thermal fatigue.
- Alloy Steels: In some cases, alloy steels with specific heat treatments are used to enhance the rotor’s strength and durability.
- Challenges
- Thermal Stress: The rotor experiences significant thermal stress due to the temperature gradients between the steam and the rotor material. This stress can lead to deformation or cracking over time if not properly managed.
- Balancing and Alignment: Ensuring that the rotor is perfectly balanced and aligned is crucial for minimizing vibration and extending the lifespan of the turbine.
- Materials Used
- Casing and Nozzles
The casing and nozzles of the steam turbine are responsible for containing the steam and directing it onto the turbine blades. These components must be designed to withstand high pressures and temperatures while minimizing energy losses due to friction and turbulence.- Materials Used
- Carbon Steel: Carbon steel is often used for the turbine casing due to its strength and ability to withstand high pressures.
- Stainless Steel: In cases where corrosion resistance is critical, stainless steel is used for nozzles and other components that come into direct contact with steam.
- Challenges
- Thermal Expansion: The casing and nozzles must be designed to accommodate thermal expansion and contraction without compromising the integrity of the turbine.
- Sealing: Effective sealing is required to prevent steam leaks, which can reduce efficiency and lead to performance issues.
- Materials Used
7.4 Comparative Analysis of Efficiency and Applications
When choosing between different steam turbine technologies, several factors must be considered, including efficiency, cost, and suitability for the intended application. The following comparisons highlight the key differences between saturated vs. superheated steam, impulse vs. reaction turbines, and the material choices for turbine components.
- Efficiency
- Superheated Steam vs. Saturated Steam: Superheated steam turbines are generally more efficient, particularly in large-scale power generation, where maximizing energy output is critical. However, saturated steam turbines are more cost-effective for smaller, low-pressure applications.
- Impulse vs. Reaction Turbines: Impulse turbines excel in high-pressure, high-speed applications, while reaction turbines offer better efficiency in multi-stage configurations and at lower pressures.
- Cost
- Material Considerations: The choice of materials significantly impacts the cost of the turbine. High-performance materials like nickel-based superalloys and titanium alloys increase the initial cost but offer longer lifespans and better performance in harsh conditions.
- Technology Selection: Choosing between impulse and reaction turbines, as well as between saturated and superheated steam systems, involves balancing upfront costs with long-term efficiency and maintenance considerations.
- Applications
- Power Generation: Superheated steam turbines and reaction turbines are typically used in large-scale power plants, including fossil fuel, nuclear, and renewable energy applications. Impulse turbines and saturated steam systems are more common in smaller power generation setups and industrial applications.
- Industrial and Marine: The choice of turbine technology in industrial and marine applications depends on the specific operational requirements, including load conditions, environmental factors, and the need for flexibility in power output.
EMS Power Machines
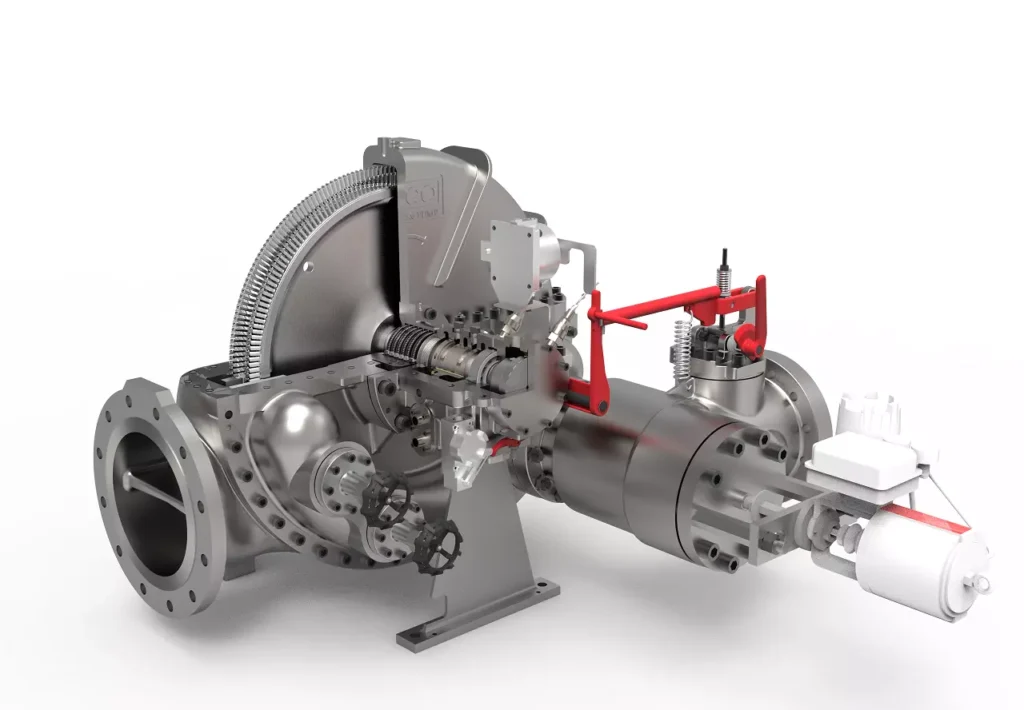
We design, manufacture and assembly Power Machines such as – diesel generators, electric motors, vibration motors, pumps, steam engines and steam turbines
EMS Power Machines is a global power engineering company, one of the five world leaders in the industry in terms of installed equipment. The companies included in the company have been operating in the energy market for more than 60 years.
EMS Power Machines manufactures steam turbines, gas turbines, hydroelectric turbines, generators, and other power equipment for thermal, nuclear, and hydroelectric power plants, as well as for various industries, transport, and marine energy.
EMS Power Machines is a major player in the global power industry, and its equipment is used in power plants all over the world. The company has a strong track record of innovation, and it is constantly developing new and improved technologies.
Here are some examples of Power Machines’ products and services:
- Steam turbines for thermal and nuclear power plants
- Gas turbines for combined cycle power plants and industrial applications
- Hydroelectric turbines for hydroelectric power plants
- Generators for all types of power plants
- Boilers for thermal power plants
- Condensers for thermal power plants
- Reheaters for thermal power plants
- Air preheaters for thermal power plants
- Feedwater pumps for thermal power plants
- Control systems for power plants
- Maintenance and repair services for power plants
EMS Power Machines is committed to providing its customers with high-quality products and services. The company has a strong reputation for reliability and innovation. Power Machines is a leading provider of power equipment and services, and it plays a vital role in the global power industry.
EMS Power Machines, which began in 1961 as a small factory of electric motors, has become a leading global supplier of electronic products for different segments. The search for excellence has resulted in the diversification of the business, adding to the electric motors products which provide from power generation to more efficient means of use.