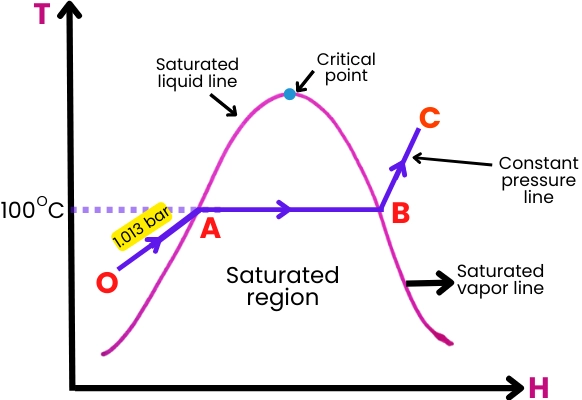
Steam pressure is a critical parameter in the realm of thermal systems, particularly in the context of boilers and steam generators. It is a measure of the force exerted by steam within a confined space, and understanding its characteristics is fundamental to ensuring the efficient and safe operation of steam-based systems.
Boilers play a central role in steam generation, where water is heated to produce steam under controlled pressure conditions. Saturation pressure is a key concept in this process, representing the pressure at which water and steam coexist in equilibrium. The transition from liquid water to saturated steam occurs at this specific pressure, a crucial point in the steam generation cycle.
Differentiating between saturated steam and superheated steam is essential. Saturated steam is at its saturation point and contains the maximum amount of energy, ready for use in processes such as power generation or heating. Superheated steam, on the other hand, has been further heated beyond the saturation point, providing specific advantages in certain applications.
The design of boilers, whether water tube or fire tube, takes into account factors like steam pressure, steam temperature, and the overall efficiency of the system. The steam drum serves as a central component, facilitating the separation of water and steam, ensuring the production of high-quality steam for various industrial processes.
Steam pressure is a fundamental concept in the realm of thermodynamics and industrial processes. It is intricately tied to the operation of boilers, where water undergoes transformation, reaching its saturation point to become steam under a specific pressure. This pressure, a key determinant in the efficiency of steam-based systems, is closely monitored through pressure gauges and controlled with precision to optimize performance.
Boilers, the heart of steam generation, are pressure vessels designed to withstand the high internal pressures generated during the steam production process. The steam pressure within these vessels plays a critical role in ensuring the effective transfer of heat energy from the burning fuel to the water, creating the conditions for steam to be harnessed as a potent source of power.
Understanding the saturation point is crucial in comprehending steam pressure dynamics. This point represents the conditions at which water transitions into steam, defining the boundary between liquid and vapor phases. Engineers carefully manipulate these conditions to achieve the desired steam pressure for specific applications.
The introduction of superheated steam goes beyond the saturation point, elevating the steam temperature and pressure. This enhancement contributes to the efficiency of the Rankine cycle, a thermodynamic process commonly employed in power plants where steam turbines convert the energy of high-pressure, high-temperature steam into mechanical work.
Steam generators are integral to maintaining the desired steam pressure in various industrial settings. These devices efficiently produce steam by applying heat to water, contributing to the continuous operation of power plants, HVAC systems, and other processes that rely on controlled steam pressure.
Pressure control mechanisms, often regulated by sophisticated systems, ensure that steam pressure remains within optimal ranges. Safety valves act as a fail-safe, releasing excess pressure to prevent potentially hazardous situations, safeguarding both equipment and personnel from the consequences of overpressure.
The steam engine, a classic application of steam power, relies on the force generated by steam pressure to drive pistons or turbines. Whether in steam locomotives or industrial machinery, the controlled release of steam at the right pressure is paramount for achieving efficient and reliable mechanical work.
Pressure gauges provide real-time feedback on steam pressure levels, allowing operators to monitor and adjust the system for optimal performance. These instruments are indispensable in maintaining the delicate balance required for efficient heat transfer, expansion, and power generation in steam-based systems.
Heat transfer, intricately linked to steam pressure, is the process by which thermal energy is exchanged between the steam and surrounding surfaces. Efficient heat transfer is essential for maintaining the desired steam pressure and, consequently, maximizing the overall efficiency of steam-driven processes.
Power plants, the epitome of steam utilization, showcase the comprehensive integration of steam pressure in electricity generation. Steam turbines, driven by high-pressure steam, convert the energy into mechanical work, ultimately generating electrical power for diverse applications.
Steam Pressure
In the broader context, steam turbines are devices that harness the energy of high-pressure steam to produce mechanical work. Steam pressure directly influences the performance and efficiency of these turbines, making it a critical parameter in their design and operation.
Controlling steam pressure is a dynamic process, involving mechanisms such as pressure regulators and safety valves. Pressure vessels, where steam is contained under pressure, adhere to specific codes and regulations to ensure their integrity and safe operation. Steam pressure gauges and transmitters provide real-time monitoring, contributing to the safe and efficient functioning of steam systems.
Understanding steam quality is crucial in optimizing processes. It refers to the proportion of saturated steam in a steam-water mixture and directly impacts the efficiency of heat transfer and other thermodynamic processes. Achieving and maintaining the desired steam pressure is not only about performance but also about safety, ensuring that systems operate within specified limits to prevent accidents and equipment failures.
Pressure vessels, crucial components in industrial settings, are designed to withstand the forces exerted by steam and other substances under high pressure. These vessels play a pivotal role in diverse applications, ranging from steam boilers to chemical processing units, ensuring the containment of materials at specified pressures to maintain operational safety.
The study of thermodynamics delves into the principles governing the behavior of steam pressure within systems. Thermodynamic analyses aid engineers in optimizing processes, ensuring that steam pressure is harnessed effectively for various applications, including power generation and industrial heating.
Saturation point, a key concept in thermodynamics, defines the equilibrium conditions at which water transforms into steam at a specific pressure. Engineers meticulously manipulate this point to control the phase transition, enabling the precise generation of steam at desired pressures for specific industrial processes.
Superheated steam, a state where steam exceeds its saturation point, holds elevated temperature and pressure levels. This modification enhances the efficiency of power generation processes, allowing steam turbines to extract more energy and convert it into useful work.
The Rankine cycle, a thermodynamic cycle underpinning many power plants, meticulously incorporates variations in steam pressure to maximize efficiency. The cycle involves the expansion and compression of steam, strategically manipulating pressure to optimize the conversion of thermal energy into mechanical work.
Steam chambers, where steam pressure is harnessed for mechanical work, serve as the focal points in steam-based systems. These chambers facilitate the controlled expansion of steam, driving pistons or turbines to generate the mechanical energy required for various industrial applications.
Steam temperature, intricately linked with pressure, dictates the energy content of steam. Engineers carefully tailor the temperature-pressure relationship to achieve the desired balance for efficient heat transfer and power generation in systems relying on steam as a working fluid.
Steam traps, essential components in steam systems, regulate steam pressure by removing condensate and non-condensable gases. These devices ensure that the steam pressure remains within optimal ranges, contributing to the efficient operation and longevity of steam-based equipment.
Steam distribution systems, a network of pipes and conduits, intricately manage the flow of steam from boilers to various points of use. The design and maintenance of these systems are critical in maintaining consistent steam pressure levels and optimizing energy transfer across industrial processes.
Steam pressure regulation, achieved through sophisticated control systems, is a dynamic process that adapts to changing demands. Precise regulation ensures that steam pressure remains within prescribed limits, aligning with the requirements of diverse applications such as manufacturing, heating, and power generation.
Boiler Systems
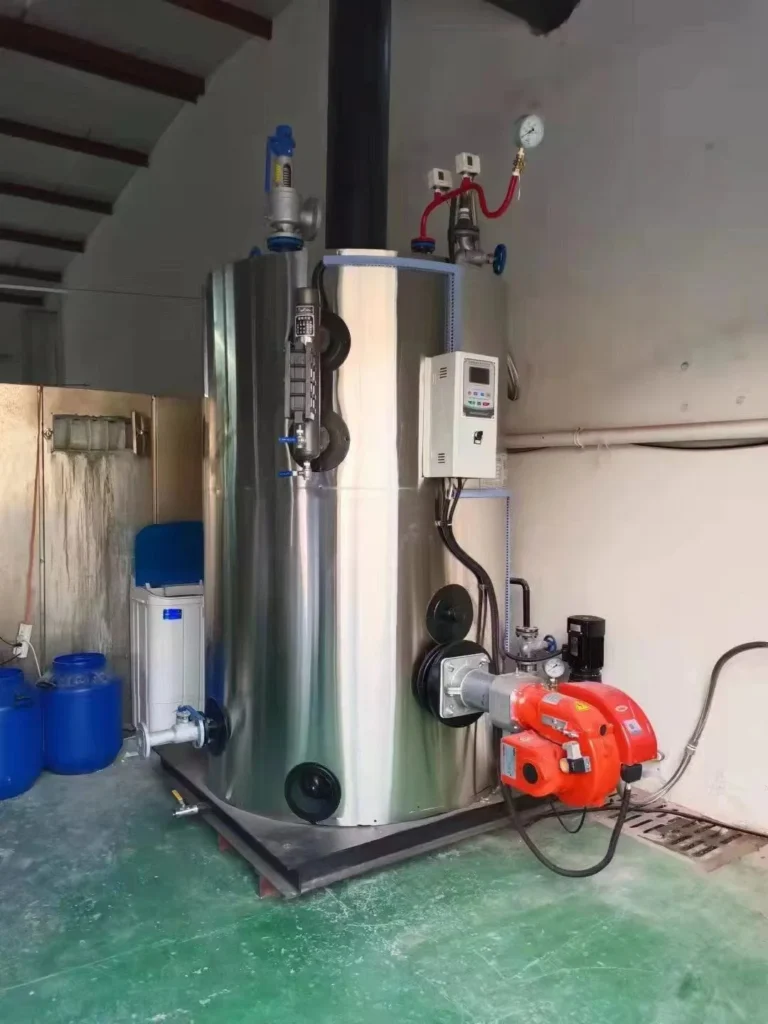
Boiler systems are integral to various industries, relying on the precise control of steam pressure for efficient and safe operation. In the intricate design of these systems, water tube boilers and fire tube boilers are prominent. Water tube boilers circulate water through tubes, absorbing heat and producing high-pressure steam. In contrast, fire tube boilers pass hot gases through tubes, heating water and generating steam. The careful consideration of design elements ensures optimal steam pressure conditions within these boilers.
Steam drums are essential components in boiler systems, serving as reservoirs for water and steam separation. This separation process is critical for producing high-quality steam while maintaining the desired steam pressure. The steam pressure control mechanisms, including pressure regulators and safety valves, are central to preventing overpressure situations, ensuring the safety of both the boiler and the entire system.
Steam pressure gauges are indispensable tools in monitoring and regulating steam pressure. These instruments provide real-time feedback, allowing operators to adjust parameters to maintain optimal conditions. Steam pressure transmitters enhance this monitoring process, transmitting data for remote observation and control.
High-pressure steam and low-pressure steam find application in different industrial processes. High-pressure steam is suitable for power generation and other energy-intensive applications, while low-pressure steam is utilized in processes requiring controlled and moderate temperatures.
Steam headers are distribution systems that transport steam from the boiler to various parts of a facility. Ensuring uniform steam pressure across different points in the system is crucial for consistent performance and process efficiency. Steam traps play a vital role in removing condensate and maintaining the desired steam pressure levels.
Steam pressure reducing valves are key components in managing steam pressure variations. These valves reduce the pressure of incoming steam to a set level, contributing to the safe and efficient operation of downstream equipment. Proper sizing and maintenance of these valves are essential for reliable performance.
The understanding of steam pressure extends beyond boiler systems to various industrial applications, including steam turbines. Steam turbines are driven by the expansion of high-pressure steam, converting thermal energy into mechanical work. The design and operation of steam turbines involve meticulous consideration of steam pressure conditions to optimize efficiency.
In essence, steam pressure is a linchpin in the intricate web of thermal systems, influencing the design, safety, and performance of boilers, steam distribution networks, and other applications. Its control and regulation are paramount in achieving the desired outcomes in diverse industrial processes.
Safety valves are indispensable guardians in systems where steam pressure is a critical factor. These valves act as fail-safes, releasing excess pressure to prevent catastrophic failures or potential hazards. Their role is paramount in maintaining the integrity of pressure vessels, boilers, and other equipment, ensuring the safety of both personnel and the industrial infrastructure.
Steam engines, whether driving locomotives or powering industrial machinery, rely on the controlled release of steam at specific pressures to perform mechanical work. The rhythmic expansion and contraction of steam under pressure drive pistons or turbines, exemplifying the transformative power of steam in the conversion of thermal energy into kinetic energy.
Pressure gauges, essential instruments in steam systems, provide real-time monitoring of steam pressure levels. Operators depend on these gauges to make informed decisions, adjusting control mechanisms to maintain optimal pressure conditions. The data gleaned from pressure gauges is crucial for ensuring the efficiency and reliability of steam-based processes.
Pressure control mechanisms, often governed by advanced automation, play a pivotal role in regulating steam pressure within industrial systems. These mechanisms ensure that steam pressure remains within prescribed limits, contributing to the stable and efficient operation of processes ranging from power generation to chemical manufacturing.
Steam pressure sensors, integral components in control systems, provide continuous feedback on pressure levels. These sensors contribute to the automation of pressure control, allowing for real-time adjustments to maintain optimal operating conditions and prevent deviations that could impact system performance.
Pressure relief valves serve as vital components in steam systems, designed to automatically release excess pressure when it exceeds predetermined levels. These valves safeguard equipment and personnel by preventing overpressure situations, emphasizing the importance of pressure management in industrial environments.
Steam systems, designed for various applications, rely on precise pressure maintenance. Engineers carefully calibrate pressure control mechanisms to ensure that steam pressure aligns with the requirements of specific processes, guaranteeing efficiency while mitigating the risk of equipment damage.
Pressure drop, a phenomenon occurring as steam moves through pipes and components, is a consideration in the design of steam systems. Engineers meticulously calculate and manage pressure drop to optimize energy transfer, ensuring that steam pressure remains at desired levels throughout the system.
Steam quality, a metric encompassing the dryness and purity of steam, is critical in maintaining effective pressure conditions. Quality steam, free from liquid water and impurities, contributes to efficient heat transfer and the prevention of issues such as erosion and corrosion in steam-based equipment.
Pressure fluctuation, variations in steam pressure over time, can impact the stability and performance of industrial processes. Engineers employ sophisticated control systems to minimize fluctuations, ensuring that steam pressure remains within narrow bands to uphold the reliability of the entire system.
Steam Pressure in Thermal Systems
Steam pressure, a cornerstone in thermal systems, is intricately connected to the dynamic world of control mechanisms and safety measures. Among these mechanisms, the steam pressure relief valve stands out as a critical component. This valve is designed to release excess pressure in a controlled manner, preventing catastrophic failures due to overpressure conditions. The careful calibration and regular maintenance of these relief valves are imperative for the safety and reliability of steam systems.
Transmitting information about steam pressure is the role of steam pressure transmitters. These devices convert the pressure data into electrical signals, facilitating remote monitoring and control. The integration of modern technology, such as electronic sensors and communication protocols, enhances the precision and efficiency of these transmitters in capturing and transmitting real-time steam pressure data.
As steam pressure is a dynamic parameter, it necessitates precise control. Steam pressure regulators play a pivotal role in this regard. These devices modulate the flow of steam to maintain consistent pressure levels. The accurate and responsive operation of pressure regulators is crucial for the stable performance of various steam-dependent processes.
Within the realm of steam pressure applications, the concept of steam pressure cycles becomes relevant. Understanding the variations in steam pressure throughout different operational cycles is essential for optimizing energy efficiency and ensuring the longevity of components within the system. Engineers meticulously analyze and fine-tune these cycles to strike a balance between energy conservation and operational requirements.
Steam pressure calculation is a fundamental aspect of designing and operating steam systems. Engineers utilize mathematical models and equations to predict and optimize steam pressure levels under different conditions. This calculation process involves considerations such as heat transfer, fluid dynamics, and thermodynamics to ensure accurate predictions of steam pressure behavior.
Monitoring and adjusting steam pressure is an ongoing endeavor, particularly in scenarios where steam pressure variations may impact system performance. Steam pressure control systems, equipped with sensors, actuators, and controllers, provide a comprehensive approach to maintaining desired pressure levels. These systems are crucial for stable and efficient operation in industries ranging from power generation to manufacturing.
Units of measurement are vital in expressing and comprehending steam pressure values. Understanding steam pressure units, such as pounds per square inch (psi) or pascals (Pa), is essential for effective communication and collaboration within the engineering and industrial sectors. Consistent use of standardized units ensures clarity and precision in conveying steam pressure information.
The steam pressure curve, a graphical representation of how steam pressure changes over time or under different conditions, aids engineers in visualizing system behavior. Analyzing the curve provides insights into the dynamics of the steam pressure variations and assists in optimizing control strategies for enhanced system performance.
In summary, the world of steam pressure extends beyond its numeric value, delving into intricate control systems, safety measures, and dynamic cycles. A nuanced understanding of steam pressure dynamics empowers engineers to design robust and efficient systems, ensuring the safe and reliable operation of diverse industrial processes.
In the complex landscape of steam pressure, the concept of steam pressure drop emerges as a crucial consideration. Steam pressure drop refers to the reduction in pressure as steam travels through pipes and components within a system. Understanding and managing this drop are essential for maintaining optimal pressure levels at different points in the system and ensuring efficient heat transfer and power generation.
The effects of steam pressure drop extend to various components, including valves, pipes, and fittings. Engineers carefully select and size these components to minimize pressure losses and enhance the overall performance of the steam system. Proper design considerations help mitigate energy losses and maintain the desired steam pressure for effective operation.
Steam pressure losses can result from factors such as friction, turbulence, and changes in elevation. These losses, quantified through calculations and measurements, guide engineers in optimizing system layouts and configurations. The goal is to achieve a balance between minimizing pressure losses and meeting the specific requirements of the intended industrial processes.
Steam pressure fluctuations, another facet of the dynamic steam environment, can impact the stability and efficiency of a system. Uncontrolled fluctuations may lead to operational challenges and compromise the integrity of equipment. Engineers implement strategies such as pressure control valves and surge tanks to manage and stabilize steam pressure under varying conditions.
Flash steam, a phenomenon arising from rapid pressure reductions, is a noteworthy consideration in steam systems. When high-pressure condensate encounters lower pressure conditions, it can instantly transform into flash steam. Proper management of flash steam is crucial for preventing pressure disturbances, ensuring safety, and recovering energy within the system.
The critical pressure of steam is a defining point that influences its behavior during expansion or compression. Understanding this critical point is essential for predicting phase changes and determining the appropriate thermodynamic models for different operational scenarios. Engineers leverage this knowledge to optimize processes and maintain stable steam pressure conditions.
Exploring steam pressure standards reveals a set of guidelines and specifications that govern the design, construction, and operation of steam systems. Adherence to these standards ensures uniformity, safety, and interoperability across diverse industrial applications. Steam pressure standards contribute to the reliability and longevity of steam-based equipment.
The intricacies of steam pressure effects on materials and components underscore the importance of material selection in system design. Steam pressure, temperature, and corrosion considerations guide engineers in choosing materials that can withstand the harsh conditions prevalent in steam systems. This proactive approach ensures the durability and safety of the entire system.
The realm of steam pressure technology continually evolves, driven by advancements in materials, sensors, and control systems. Innovative technologies, such as advanced sensors and predictive analytics, empower engineers to monitor and manage steam pressure in real time. These technological interventions enhance system efficiency, reduce downtime, and contribute to sustainable and reliable steam operations.
In summary, the journey through steam pressure intricacies delves into pressure drops, fluctuations, material considerations, and evolving technologies. Engineers navigate this landscape to design resilient systems that harness the power of steam while ensuring safety, efficiency, and longevity in diverse industrial applications.
The interplay of steam pressure in practical applications extends to the realm of steam pressure safety regulations. Adhering to established safety standards is paramount in industries where steam plays a pivotal role. These regulations outline specific guidelines for the design, installation, and operation of steam systems to safeguard personnel, equipment, and the environment.
Steam pressure safety valves are critical components in upholding these regulations. These valves act as a last line of defense, releasing excess pressure to prevent overpressurization and potential catastrophic failures. Regular testing, maintenance, and compliance with safety valve standards are essential for ensuring their effectiveness in safeguarding steam systems.
Steam pressure fluctuations, a common occurrence in dynamic industrial processes, necessitate the implementation of comprehensive steam pressure control systems. These systems, equipped with feedback mechanisms and automated controls, continuously monitor and adjust steam pressure to maintain stability and prevent sudden pressure spikes that could compromise safety.
The steam pressure relief system encompasses a broader set of safety measures beyond safety valves. It includes redundant safety features, emergency shutdown procedures, and alarms to address potential hazards. A well-designed relief system is a cornerstone of safe and reliable steam operations, providing layers of protection against unforeseen events.
Safety considerations also extend to the selection and installation of pressure vessels within steam systems. Pressure vessels, designed to contain steam under pressure, must adhere to codes and standards to ensure their structural integrity. Rigorous inspections, testing, and compliance with pressure vessel codes are essential for preventing failures and ensuring operational safety.
Steam pressure safety technology has evolved with the integration of advanced sensors, monitoring systems, and predictive analytics. These technologies enable real-time assessment of steam pressure conditions, allowing for proactive interventions and predictive maintenance. The adoption of such innovations enhances overall safety, minimizes downtime, and optimizes the performance of steam systems.
Beyond technological advancements, ongoing training and awareness programs are crucial components of a robust steam pressure safety strategy. Personnel involved in the operation and maintenance of steam systems must be well-versed in safety protocols, emergency response procedures, and the importance of adherence to safety regulations.
In the broader context, steam pressure safety aligns with a commitment to sustainability and environmental responsibility. Efficient steam systems that operate within safe pressure limits contribute to reduced energy consumption, lower emissions, and overall environmental stewardship.
The integration of safety into the fabric of steam pressure management reflects a comprehensive approach that goes beyond mere compliance. It encompasses a culture of safety consciousness, continuous improvement, and a shared responsibility among all stakeholders involved in the design, operation, and maintenance of steam systems.
In conclusion, the narrative of steam pressure safety unfolds within a framework of regulations, valves, relief systems, advanced technologies, and a steadfast commitment to personnel safety and environmental sustainability. This holistic approach ensures that steam, a powerful force in industrial processes, is harnessed with due consideration for safety and reliability.
Steam pressure plays a pivotal role in the dynamic cycle of steam power plants, specifically within the context of the Rankine cycle. This thermodynamic cycle is a cornerstone in power generation, relying on the careful manipulation of pressure to maximize efficiency. As steam undergoes expansion and compression, its pressure variations are meticulously orchestrated to extract the maximum amount of energy for mechanical work in steam turbines.
Steam chambers, where the magic of steam pressure unfolds, are central to the operation of steam engines and turbines. In these chambers, steam undergoes controlled expansion, propelling pistons or turning turbine blades to convert the potential energy stored in pressure into kinetic energy that can be harnessed for a myriad of industrial applications.
Steam temperature, intimately linked with pressure, shapes the energy content of steam. Engineers deftly navigate the temperature-pressure relationship to achieve the optimal balance for efficient heat transfer and power generation. The delicate interplay of temperature and pressure is a key factor in the design and operation of steam-based systems.
Steam traps, the unsung heroes of steam systems, contribute to pressure regulation by efficiently removing condensate and non-condensable gases. These devices prevent the unwanted buildup of pressure, ensuring that steam pressure remains within prescribed limits and that the system operates with maximum efficiency.
Steam pressure is intricately tied to the pressure relief system, which includes safety valves and relief valves. These components act as a last line of defense, automatically releasing excess pressure to prevent catastrophic failures. The pressure relief system is a crucial element in maintaining the safety and integrity of pressure vessels and steam systems.
Pressure relief valves, within the broader pressure relief system, are meticulously calibrated to open at specific pressures, venting excess steam to prevent overpressure situations. These valves are instrumental in protecting equipment from potential damage and ensuring the safety of personnel working with steam systems.
Steam pressure is a fundamental consideration in the calculation and design of industrial steam systems. Engineers must meticulously calculate and manage pressure drop to optimize energy transfer within the system, ensuring that steam pressure remains consistent and meets the specific requirements of various processes.
High-pressure steam, characterized by elevated pressure levels, is a hallmark of certain industrial applications. The controlled release and utilization of high-pressure steam contribute to the efficient performance of steam turbines, enhancing the overall efficiency of power generation in steam-based systems.
Low-pressure steam, in contrast, is employed in applications where lower pressure levels suffice. This versatility allows for the adaptation of steam systems to meet the specific needs of various processes, ranging from industrial heating to certain types of manufacturing.
Saturated steam, existing at its saturation point where liquid and vapor phases coexist, embodies a critical state in the steam pressure cycle. The careful control of saturation conditions ensures that steam is produced at the desired pressure and temperature, aligning with the requirements of specific industrial operations.
Pressure measurement in steam systems is a fundamental aspect of maintaining operational precision. Engineers deploy various instruments, including pressure gauges and transmitters, to obtain accurate readings of steam pressure. This real-time data is essential for monitoring and adjusting the system, ensuring that steam pressure aligns with the specific requirements of diverse industrial applications.
Steam pressure units are critical in expressing the magnitude of pressure within steam systems. Common units include pounds per square inch (psi), bars, and kilopascals. Engineers and operators rely on these units to communicate and interpret pressure values accurately, facilitating effective collaboration in the management of steam systems.
Boiler efficiency, a key performance metric in steam systems, is intricately linked to the combustion process and steam pressure. Engineers strive to optimize boiler efficiency by fine-tuning factors such as fuel combustion, heat transfer, and pressure levels to ensure the effective conversion of thermal energy into steam.
Pressure maintenance is an ongoing consideration in steam systems to uphold optimal performance. Engineers implement measures to sustain consistent pressure levels, preventing fluctuations that could compromise system efficiency. This involves meticulous attention to pressure control mechanisms and the overall design of the steam system.
Pressure drop, encountered as steam flows through pipes and components, is a phenomenon that engineers carefully manage in steam systems. Minimizing pressure drop is essential for maintaining the desired pressure conditions throughout the system, ensuring efficient energy transfer and performance.
Steam quality, a measure of the dryness and purity of steam, is closely associated with pressure conditions. Quality steam, free from liquid water and impurities, is crucial for preventing issues such as erosion and corrosion in steam-based equipment, contributing to the overall reliability of the system.
Pressure fluctuation, the variation in steam pressure over time, requires vigilant control in steam systems. Engineers deploy sophisticated control systems to minimize fluctuations, ensuring that pressure remains within narrow bands to guarantee the stability and reliability of the entire steam system.
Steam pressure regulation involves the deployment of advanced control systems that dynamically adapt to changing demands. These systems maintain steam pressure within prescribed limits, aligning with the specific requirements of diverse applications, including manufacturing, heating, and power generation.
Steam pressure sensors, embedded in control systems, continuously monitor pressure levels within steam systems. These sensors provide essential feedback for automated pressure regulation, contributing to real-time adjustments that maintain optimal operating conditions and prevent deviations that could impact system performance.
Steam pressure transmitter, an integral component of pressure measurement, converts pressure readings into electrical signals for interpretation and control. This transmitter is a key element in the automation of pressure regulation, facilitating seamless integration with control systems for efficient steam system operation.
What is a Steam Turbine?
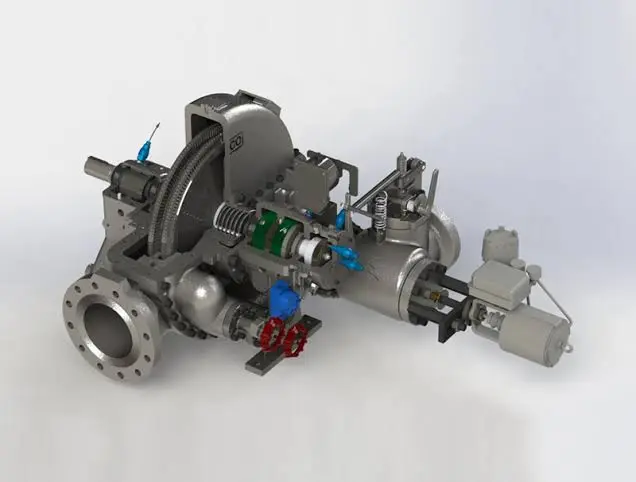
Steam turbines have been a cornerstone of industrial power generation for over a century, providing a reliable and efficient means of converting thermal energy into mechanical energy. As a critical component in electricity generation and various industrial processes, steam turbines play a pivotal role in the global energy landscape. Their ability to operate at high efficiencies and adapt to a wide range of applications has made them indispensable in sectors ranging from power plants to petrochemical industries.
The purpose of this article is to provide an in-depth exploration of steam turbines, focusing on their design, operation, and applications, as well as the latest technological advancements shaping their development. Targeted towards professionals in the field, this comprehensive guide aims to enhance understanding and facilitate informed decision-making in the deployment and management of steam turbine technology.
This article will delve into the historical evolution of steam turbines, examining the key milestones that have defined their progress. It will discuss the fundamental principles underlying their operation, including the thermodynamic processes and mechanical components that drive their performance. The article will also categorize different types of steam turbines, highlighting their specific applications and advantages.
Furthermore, this guide will address the benefits and drawbacks of steam turbines, providing a balanced perspective on their environmental and economic impacts. Recent innovations and future trends in steam turbine technology will be explored, offering insights into the direction of ongoing research and development.
In addition to technical aspects, the article will discuss the operational challenges and maintenance requirements associated with steam turbines, underscoring the importance of proper upkeep in ensuring their longevity and efficiency. By examining case studies of turbine failures and recoveries, readers will gain valuable insights into best practices and strategies for overcoming common obstacles.
Overall, this article aims to serve as a valuable resource for professionals seeking to deepen their knowledge of steam turbines and their role in modern power generation and industrial processes.
History of Steam Turbines
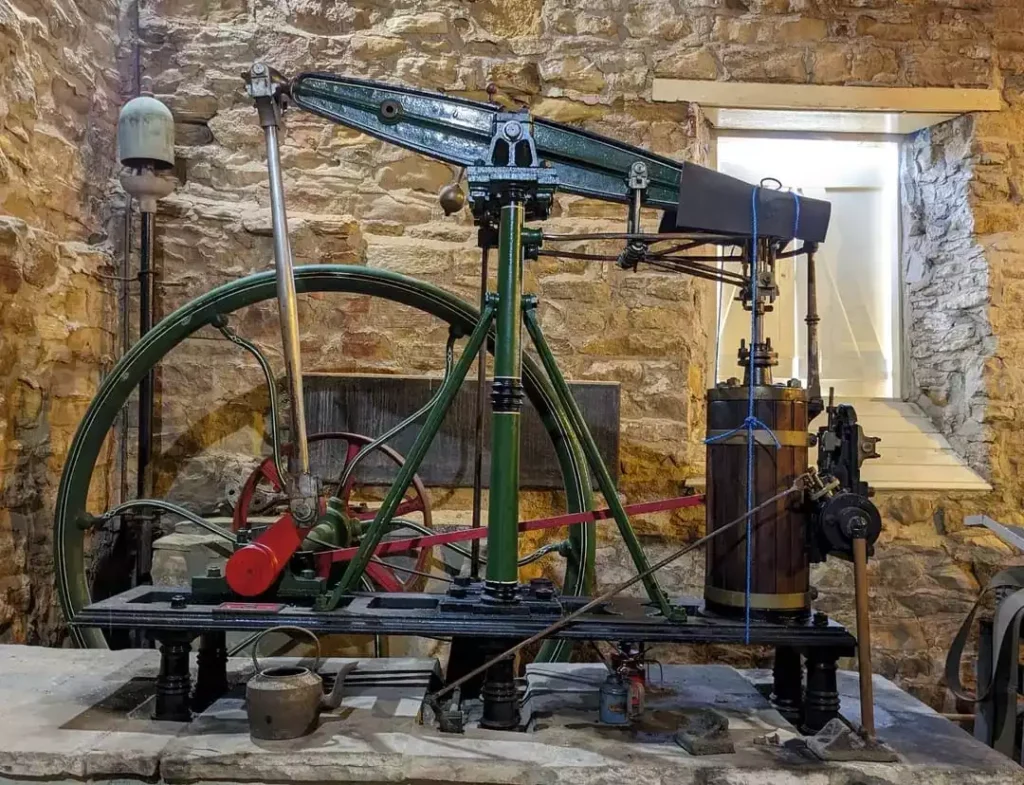
The history of steam turbines dates back to the late 19th century, a period marked by significant innovation and industrial growth. The development of steam turbines was driven by the need for more efficient power generation methods, as traditional steam engines were limited in their efficiency and capacity. This section will explore the historical milestones and key figures that have shaped the evolution of steam turbines over the years.
Early Development and Pioneers
The concept of using steam to perform mechanical work has ancient roots, with early devices such as the Aeolipile, invented by Hero of Alexandria in the 1st century AD, demonstrating the potential of steam power. However, it wasn’t until the 19th century that steam technology began to advance rapidly, leading to the development of the steam turbine.
Sir Charles Parsons is credited with the invention of the modern steam turbine in 1884. Parsons’ design utilized a series of rotating blades to convert steam energy into rotational motion, a significant improvement over the reciprocating steam engines of the time. His invention revolutionized power generation, offering greater efficiency and higher power output. Parsons’ steam turbine was first demonstrated in 1897 aboard the Turbinia, a steam-powered ship that showcased the potential of this new technology.
In parallel, Swedish engineer Gustaf de Laval developed an impulse steam turbine in 1883, which used a high-velocity steam jet to strike blades attached to a rotor. De Laval’s design was particularly suited for applications requiring high rotational speeds, such as in centrifugal pumps and small-scale power generation.
Evolution Over the 20th Century
The early 20th century saw rapid advancements in steam turbine technology, driven by the increasing demand for electricity and the expansion of industrial activities. Steam turbines quickly became the preferred choice for power generation due to their superior efficiency and ability to operate continuously under high loads.
One of the key developments during this period was the introduction of the reaction turbine by Sir Charles Parsons. Unlike impulse turbines, which rely on steam jets to impart momentum to the blades, reaction turbines utilize the pressure difference across the blades to produce rotational motion. This design allowed for more efficient energy conversion and became widely adopted in large power plants.
The expansion of the electricity grid and the growth of industries such as steel production, chemical manufacturing, and transportation further fueled the demand for steam turbines. Advances in materials science, such as the development of high-strength alloys, enabled turbines to operate at higher temperatures and pressures, enhancing their performance and reliability.
Key Technological Milestones
Several key technological milestones have marked the evolution of steam turbines over the decades:
- Supercritical Steam Conditions: The introduction of supercritical steam conditions in the mid-20th century represented a significant leap in turbine efficiency. By operating at pressures and temperatures above the critical point of water, supercritical turbines achieved higher thermal efficiencies and reduced fuel consumption.
- Combined Cycle Power Plants: The integration of steam turbines into combined cycle power plants, where waste heat from gas turbines is used to produce steam, further improved overall plant efficiency. This approach maximized energy extraction from fuel and minimized environmental impact.
- Nuclear Power Generation: The advent of nuclear power in the mid-20th century presented new opportunities for steam turbine technology. Nuclear reactors produce large quantities of steam, making steam turbines an ideal choice for electricity generation in nuclear power plants.
- Digital Control Systems: The incorporation of digital control systems in the late 20th century enhanced the operational efficiency and reliability of steam turbines. Advanced monitoring and control technologies allowed for precise regulation of turbine parameters, optimizing performance and reducing downtime.
Basic Principles of Operation
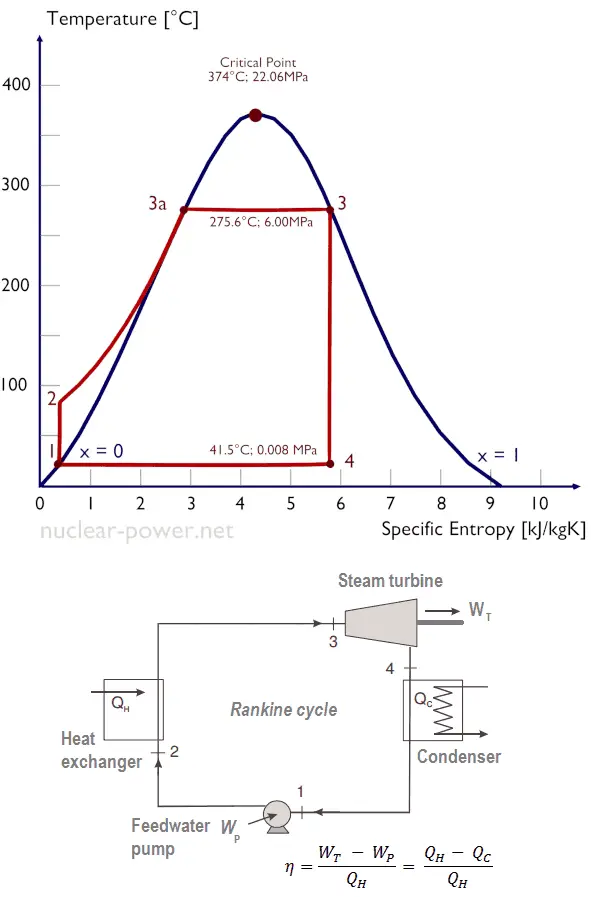
Steam turbines operate on the principles of thermodynamics, converting thermal energy from steam into mechanical energy through a series of carefully designed processes. This section will explore the fundamental principles underlying steam turbine operation, including the thermodynamic cycles and the types of turbines commonly used in various applications.
Thermodynamics of Steam Turbines
At the core of steam turbine operation lies the conversion of thermal energy into mechanical work. This process is governed by the laws of thermodynamics, which describe the relationships between heat, work, and energy. Steam turbines primarily operate based on the Rankine cycle, a thermodynamic cycle that involves the following key processes:
- Boiler (Heat Addition): In the boiler, water is heated to produce high-pressure steam. This steam is the primary energy source for the turbine and is typically superheated to increase efficiency.
- Turbine (Expansion and Work Extraction): The high-pressure steam is directed into the turbine, where it expands and imparts its energy to the turbine blades. As the steam expands, it undergoes a decrease in pressure and temperature, causing the turbine rotor to spin and produce mechanical work.
- Condenser (Heat Rejection): After passing through the turbine, the low-pressure steam is condensed back into water in the condenser. This process removes excess heat from the system and allows the water to be reused in the cycle.
- Pump (Pressurization): The condensed water is pumped back to high pressure and returned to the boiler, completing the cycle.
The efficiency of a steam turbine is influenced by factors such as steam pressure, temperature, and the effectiveness of the condensation process. By optimizing these parameters, engineers can maximize the energy conversion efficiency and minimize losses.
Types of Steam Turbines
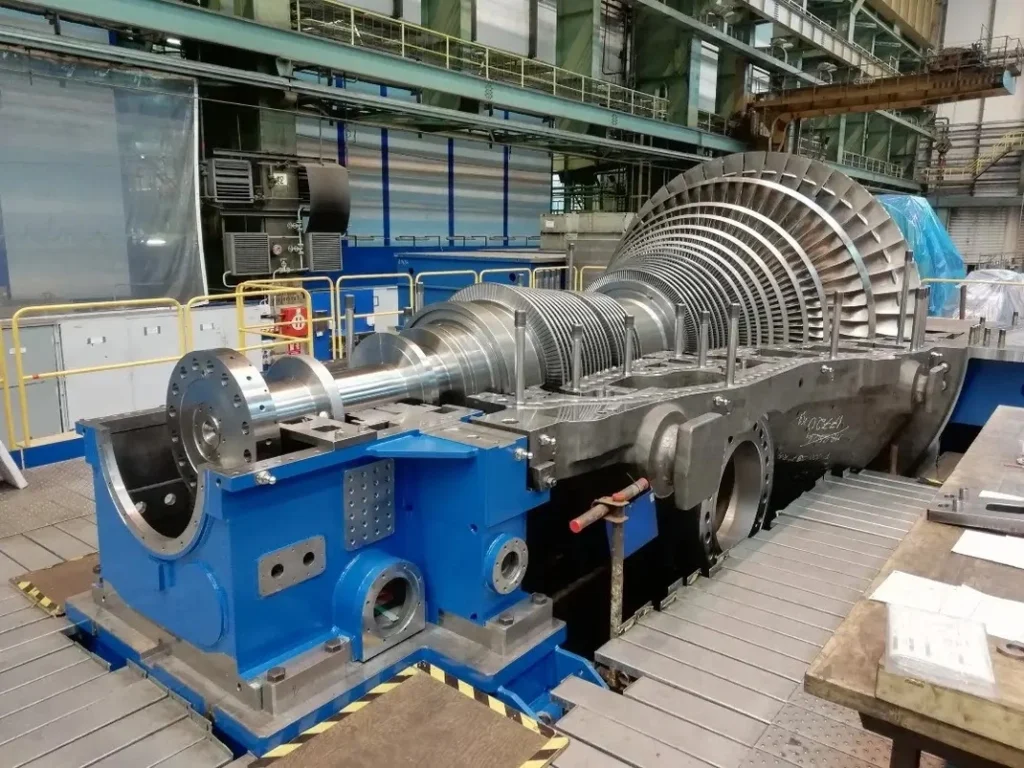
Steam turbines are broadly categorized into two main types: impulse turbines and reaction turbines. Each type operates on distinct principles and is suited to specific applications.
- Impulse Turbines: In an impulse turbine, high-velocity steam jets are directed onto the turbine blades, causing them to rotate. The steam pressure remains constant across the blades, and energy is transferred primarily through the change in steam velocity. Impulse turbines are often used in applications requiring high rotational speeds, such as small-scale power generation and marine propulsion.
- Reaction Turbines: Reaction turbines, on the other hand, utilize the pressure drop across the blades to produce rotational motion. As steam flows through the blades, it experiences a change in both pressure and velocity, resulting in a more continuous energy transfer. Reaction turbines are commonly used in large power plants and industrial applications due to their higher efficiency and ability to handle large steam volumes.
The Rankine Cycle
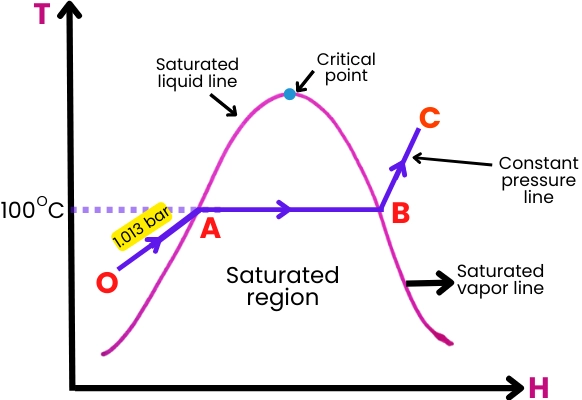
The Rankine cycle is the thermodynamic cycle that underpins the operation of steam turbines. It consists of a series of processes that convert thermal energy into mechanical work, and its efficiency is a key determinant of overall turbine performance. The Rankine cycle is characterized by four main stages:
- Isentropic Expansion: In the turbine, high-pressure steam undergoes isentropic expansion, where its energy is converted into mechanical work. This process is adiabatic, meaning no heat is transferred to or from the system.
- Isobaric Heat Rejection: After expansion, the low-pressure steam enters the condenser, where it undergoes isobaric heat rejection. The steam is cooled and condensed into liquid water, releasing heat to the surroundings.
- Isentropic Compression: The condensed water is then pumped back to high pressure in the feed pump, undergoing isentropic compression. This process is also adiabatic and increases the pressure of the water without adding heat.
- Isobaric Heat Addition: Finally, the high-pressure water is returned to the boiler, where it undergoes isobaric heat addition. The water is heated and converted into high-pressure steam, completing the cycle.
The efficiency of the Rankine cycle is influenced by factors such as the temperature and pressure of the steam, the effectiveness of the condenser, and the degree of superheating. Engineers strive to optimize these parameters to maximize the efficiency of steam turbines and minimize fuel consumption.
Design and Components
The design of steam turbines is a complex engineering endeavor that involves the integration of various components and materials to achieve optimal performance and reliability. This section will explore the key design elements and components of steam turbines, highlighting the challenges and considerations involved in their construction.
Major Components
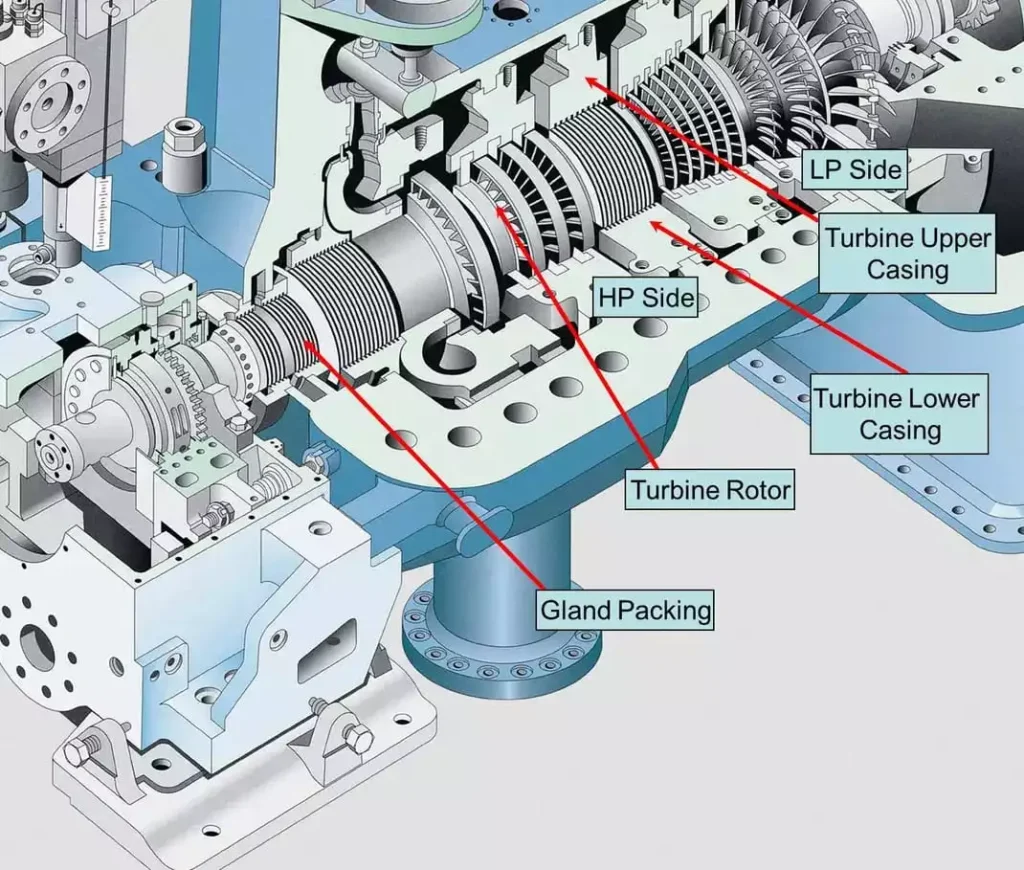
Steam turbines are comprised of several critical components, each playing a vital role in the conversion of thermal energy into mechanical work. The major components of a steam turbine include:
- Rotor: The rotor is the central shaft that supports the turbine blades and transmits the mechanical energy generated by the steam. It is typically made of high-strength materials, such as forged steel, to withstand the stresses and temperatures encountered during operation.
- Blades: The blades, also known as buckets or vanes, are the airfoil-shaped components that interact with the steam flow to produce rotational motion. Blades are carefully designed to maximize energy extraction while minimizing losses due to friction and turbulence.
- Casing: The casing, or housing, encloses the turbine and directs the flow of steam through the blades. It provides structural support and helps maintain the desired pressure and temperature conditions within the turbine.
- Nozzles: In impulse turbines, nozzles are used to direct high-velocity steam jets onto the turbine blades. The design of nozzles is critical to achieving the desired steam velocity and flow characteristics.
- Bearings: Bearings support the rotor and allow it to rotate smoothly with minimal friction. They are typically designed to handle both radial and axial loads and are lubricated to reduce wear and heat generation.
- Governor: The governor is a control mechanism that regulates the turbine’s speed and output by adjusting the steam flow. It ensures that the turbine operates within safe and efficient parameters, responding to changes in load demand and system conditions.
Materials Used in Construction
The materials used in the construction of steam turbines are chosen based on their ability to withstand high temperatures, pressures, and mechanical stresses. Key material considerations include:
- High-Temperature Alloys: Turbine components exposed to high temperatures, such as blades and rotors, are often made from nickel-based or cobalt-based superalloys. These materials exhibit excellent strength and resistance to creep, oxidation, and corrosion at elevated temperatures.
- Stainless Steel: Stainless steel is commonly used for turbine casings and other structural components due to its corrosion resistance and durability.
- Titanium: Titanium alloys are sometimes used in turbine blades for their high strength-to-weight ratio and resistance to fatigue and corrosion.
- Ceramics and Composites: Advanced ceramics and composite materials are being explored for use in steam turbines to improve efficiency and reduce weight. These materials offer potential benefits in terms of thermal insulation and resistance to wear.
Design Considerations and Challenges
The design of steam turbines involves several complex considerations and challenges that must be addressed to achieve optimal performance and reliability. Key design factors include:
- Thermal Efficiency: Maximizing thermal efficiency is a primary goal in turbine design. This involves optimizing the thermodynamic cycle, minimizing losses due to friction and turbulence, and maximizing energy extraction from the steam.
- Mechanical Stress and Fatigue: Turbine components are subjected to high mechanical stresses and cyclic loading during operation. Engineers must carefully analyze stress distributions and fatigue life to ensure the durability and reliability of the turbine.
- Vibration and Noise: Vibration and noise can impact the performance and lifespan of steam turbines. Design strategies such as balancing, damping, and noise reduction measures are employed to mitigate these effects.
- Cooling and Heat Management: Effective cooling and heat management are essential to prevent overheating and ensure the safe operation of the turbine. This involves the design of cooling systems, such as steam or air cooling, and the selection of materials with appropriate thermal properties.
- Environmental Impact: Minimizing the environmental impact of steam turbines is an important consideration. This includes reducing emissions, improving efficiency, and designing for recyclability and sustainability.
Types of Steam Turbines
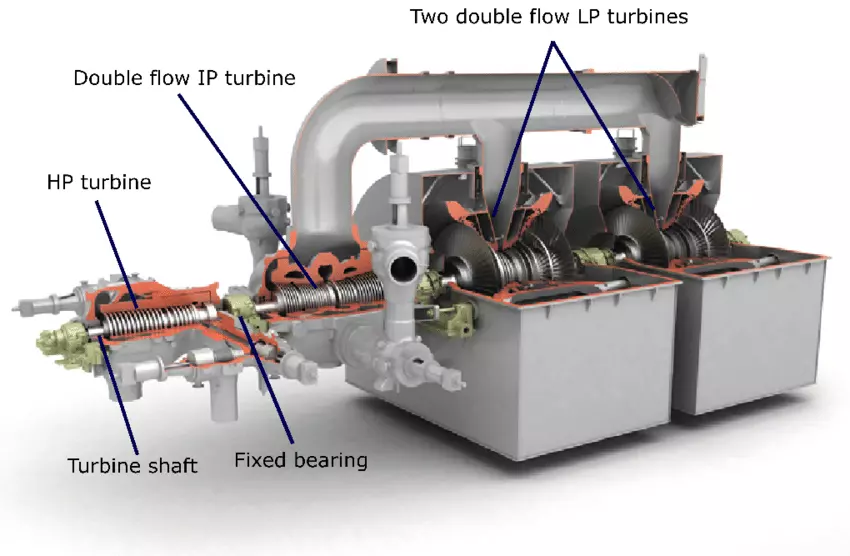
Steam turbines are classified into various types based on factors such as size, application, and design characteristics. This section will explore the different types of steam turbines, highlighting their specific features and applications.
Classification by Size and Application
Steam turbines are broadly categorized into three main types based on their size and application:
- Industrial Steam Turbines: Industrial steam turbines are typically used in manufacturing and process industries for power generation and mechanical drive applications. They range in size from small units producing a few kilowatts to large turbines generating several megawatts. Industrial turbines are often designed for flexibility, allowing them to operate efficiently under varying load conditions.
- Utility Steam Turbines: Utility steam turbines are large-scale turbines used in power plants to generate electricity for the grid. They are designed for high efficiency and reliability, with capacities ranging from hundreds of megawatts to over a gigawatt. Utility turbines are often part of combined cycle power plants, where they work in conjunction with gas turbines to maximize energy output.
- Specialized Steam Turbines: Specialized steam turbines are designed for specific applications, such as geothermal, nuclear, and marine propulsion. These turbines are tailored to the unique conditions and requirements of their respective industries, such as handling corrosive steam in geothermal plants or operating in a compact space on a ship.
Industrial Steam Turbines
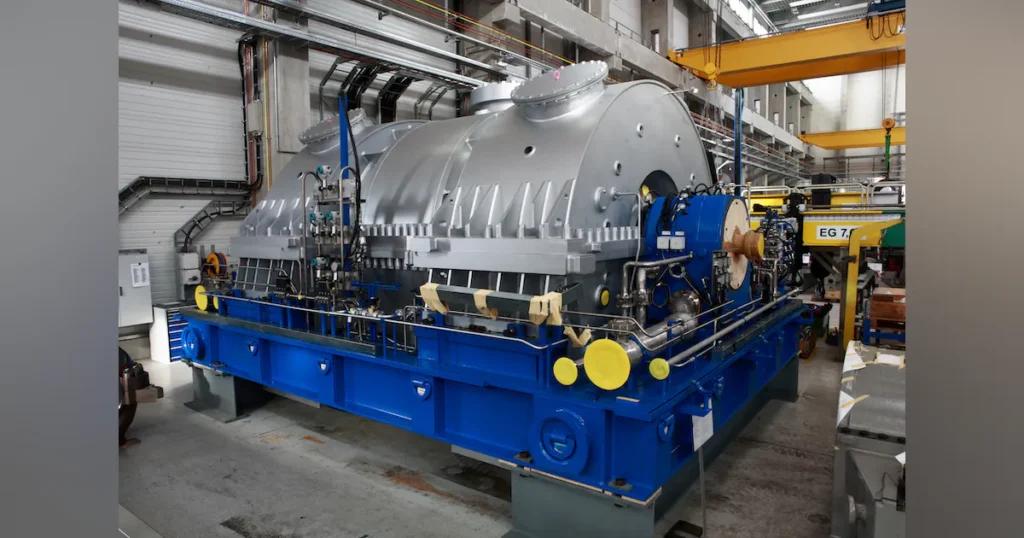
Industrial steam turbines are versatile machines used in a wide range of applications, including:
- Cogeneration and Combined Heat and Power (CHP) Systems: Industrial turbines are often used in cogeneration and CHP systems, where they generate electricity and provide process heat for industrial facilities. This approach improves energy efficiency and reduces waste.
- Mechanical Drives: Steam turbines are used as mechanical drives for equipment such as compressors, pumps, and fans in industries such as oil and gas, petrochemicals, and pulp and paper.
- District Heating: In district heating systems, industrial turbines generate electricity and provide steam for heating residential and commercial buildings. This integrated approach enhances energy utilization and reduces emissions.
Utility Steam Turbines
Utility steam turbines are the backbone of power generation in many countries, providing reliable and efficient electricity to the grid. Key features of utility turbines include:
- High Efficiency: Utility turbines are designed for maximum efficiency, with advanced blade designs and optimized thermodynamic cycles. This allows them to extract the maximum amount of energy from the steam and reduce fuel consumption.
- Load Flexibility: Utility turbines are capable of operating under varying load conditions, allowing them to respond to fluctuations in electricity demand. This flexibility is essential for maintaining grid stability and reliability.
- Combined Cycle Operation: Many utility turbines are part of combined cycle power plants, where they work in tandem with gas turbines to maximize energy output and minimize emissions. In this configuration, waste heat from the gas turbine is used to produce steam for the steam turbine, enhancing overall plant efficiency.
Specialized Steam Turbines
Specialized steam turbines are designed to meet the unique requirements of specific industries and applications. Examples include:
- Geothermal Steam Turbines: Geothermal turbines are designed to operate with steam extracted from geothermal reservoirs, which often contains corrosive impurities. These turbines are built with materials and coatings that resist corrosion and scaling.
- Nuclear Steam Turbines: Nuclear turbines are used in nuclear power plants to convert steam produced by nuclear reactors into electricity. They are designed to handle the high pressures and temperatures associated with nuclear steam and are subject to stringent safety and regulatory requirements.
- Marine Steam Turbines: Marine turbines are used for propulsion in ships and submarines. They are designed for compactness and reliability, with features such as gear reduction systems to optimize performance in marine environments.
Applications of Steam Turbines
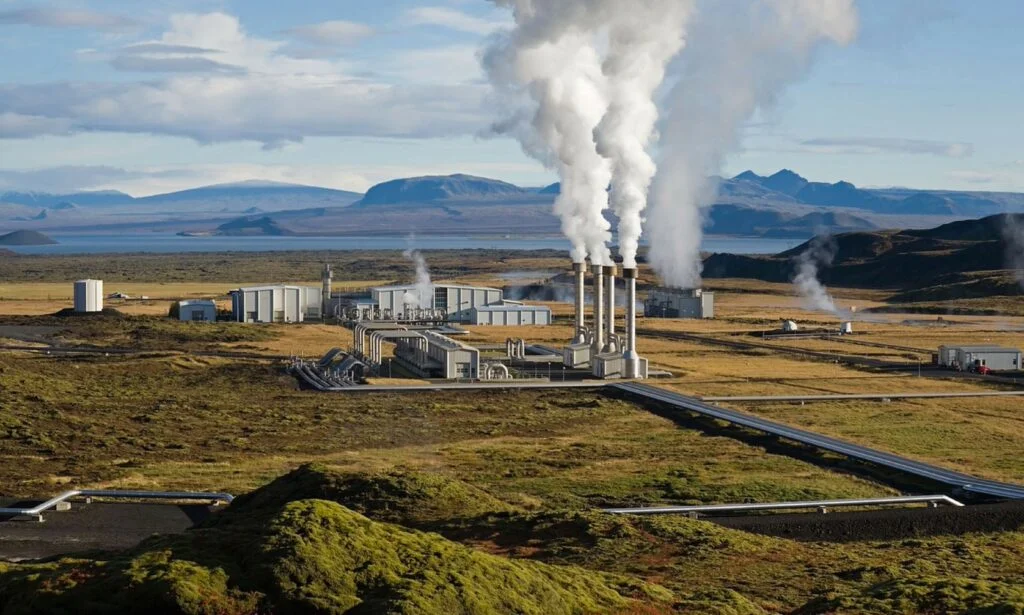
Steam turbines are employed in a wide range of applications across various industries, owing to their versatility and efficiency. This section will explore the diverse applications of steam turbines, highlighting their role in power generation, industrial processes, and other sectors.
Power Generation in Different Sectors
Steam turbines are a cornerstone of power generation, providing reliable and efficient electricity for residential, commercial, and industrial use. Key applications in power generation include:
- Fossil Fuel Power Plants: Steam turbines are widely used in fossil fuel power plants, where they convert heat energy from burning coal, oil, or natural gas into electricity. These plants are a major source of electricity in many countries and are equipped with advanced turbines designed for high efficiency and low emissions.
- Nuclear Power Plants: In nuclear power plants, steam turbines convert heat generated by nuclear fission into electricity. The turbines used in these plants are designed to withstand the high temperatures and pressures associated with nuclear steam and are subject to rigorous safety and regulatory standards.
- Renewable Energy Sources: Steam turbines are also used in renewable energy applications, such as geothermal and biomass power plants. In geothermal plants, steam extracted from underground reservoirs is used to drive turbines and generate electricity. In biomass plants, steam produced from burning organic materials powers turbines for electricity generation.
Use in Combined Heat and Power (CHP) Systems
Combined Heat and Power (CHP) systems, also known as cogeneration, are an efficient method of generating electricity and useful heat simultaneously. Steam turbines play a crucial role in CHP systems by providing the mechanical energy needed for electricity generation while also supplying steam for heating and industrial processes. Applications of CHP systems include:
- Industrial Facilities: CHP systems are commonly used in industrial facilities, where they provide electricity and process steam for manufacturing operations. This integrated approach enhances energy efficiency and reduces waste, leading to cost savings and environmental benefits.
- District Heating: In district heating systems, steam turbines generate electricity and provide steam for heating residential and commercial buildings. This approach improves energy utilization and reduces emissions, contributing to sustainable urban development.
- Hospitals and Universities: CHP systems are used in hospitals and universities to provide reliable electricity and heating. The ability to generate both power and heat from a single fuel source enhances energy security and reduces operational costs.
Role in Industrial Processes
Steam turbines are integral to a variety of industrial processes, where they provide mechanical power and heat for manufacturing and processing operations. Key applications in industrial processes include:
- Petrochemical Industry: In the petrochemical industry, steam turbines drive compressors, pumps, and other equipment used in the production and refining of chemicals and fuels. The high efficiency and reliability of steam turbines make them well-suited for demanding industrial applications.
- Pulp and Paper Industry: Steam turbines are used in the pulp and paper industry to generate electricity and provide steam for the pulping and drying processes. The use of steam turbines in these operations enhances energy efficiency and reduces environmental impact.
- Food and Beverage Industry: Steam turbines are employed in the food and beverage industry to provide power and steam for cooking, sterilization, and other processes. The ability to integrate steam turbines into cogeneration systems allows for efficient energy utilization and cost savings.
Advantages and Disadvantages
Steam turbines offer numerous advantages in terms of efficiency, reliability, and versatility, but they also have certain disadvantages and limitations. This section will provide a balanced perspective on the advantages and disadvantages of steam turbines, comparing them with other power generation technologies.
Advantages of Steam Turbines
- High Efficiency: Steam turbines are known for their high efficiency in converting thermal energy into mechanical work. Advanced designs and materials have enabled turbines to achieve thermal efficiencies exceeding 40% in modern power plants.
- Reliability and Durability: Steam turbines are highly reliable and durable, with the ability to operate continuously under high loads for extended periods. Their robust construction and materials ensure long service life and minimal maintenance requirements.
- Versatility: Steam turbines are versatile machines that can be used in a wide range of applications, from power generation to industrial processes. Their ability to operate with various fuel sources, including fossil fuels, nuclear, and renewable energy, makes them adaptable to different energy landscapes.
- Low Emissions: Steam turbines can achieve low emissions when used in combination with advanced combustion and emission control technologies. Combined cycle power plants, for example, utilize steam turbines to reduce greenhouse gas emissions and improve overall plant efficiency.
- Scalability: Steam turbines are available in a wide range of sizes and capacities, making them suitable for both small-scale and large-scale applications. This scalability allows for flexible deployment in diverse industries and settings.
Disadvantages of Steam Turbines
- Complexity and Cost: The design and construction of steam turbines involve complex engineering and high costs. The need for specialized materials, precision manufacturing, and advanced control systems contributes to the overall expense of turbine installation and maintenance.
- Start-up Time: Steam turbines require a relatively long start-up time compared to other power generation technologies, such as gas turbines. The need to heat up the boiler and reach operational temperatures can delay the response to changes in electricity demand.
- Water Consumption: Steam turbines rely on water for steam generation and cooling, making them dependent on water availability. This can pose challenges in regions with limited water resources or during periods of drought.
- Environmental Impact: While steam turbines can achieve low emissions, their environmental impact is influenced by the type of fuel used and the efficiency of the overall system. Fossil fuel-based steam turbines contribute to greenhouse gas emissions and air pollution.
- Maintenance Requirements: Steam turbines require regular maintenance to ensure optimal performance and prevent issues such as corrosion, fouling, and wear. The complexity of turbine systems necessitates skilled personnel and specialized equipment for maintenance and repair.
Comparison with Other Power Generation Technologies
Steam turbines are often compared with other power generation technologies, such as gas turbines, internal combustion engines, and renewable energy systems. Key comparisons include:
- Gas Turbines: Gas turbines offer faster start-up times and greater flexibility compared to steam turbines, making them well-suited for peaking power plants and rapid response to changes in electricity demand. However, steam turbines typically achieve higher thermal efficiencies and are more suitable for base-load power generation.
- Internal Combustion Engines: Internal combustion engines are compact and suitable for small-scale power generation, but they are less efficient and have higher emissions compared to steam turbines. Steam turbines are preferred for large-scale applications where efficiency and reliability are paramount.
- Renewable Energy Systems: Renewable energy systems, such as wind and solar, offer the advantage of zero emissions and sustainability. However, steam turbines remain a critical component of the energy mix due to their ability to provide reliable base-load power and support the integration of intermittent renewable sources.
Recent Technological Advancements
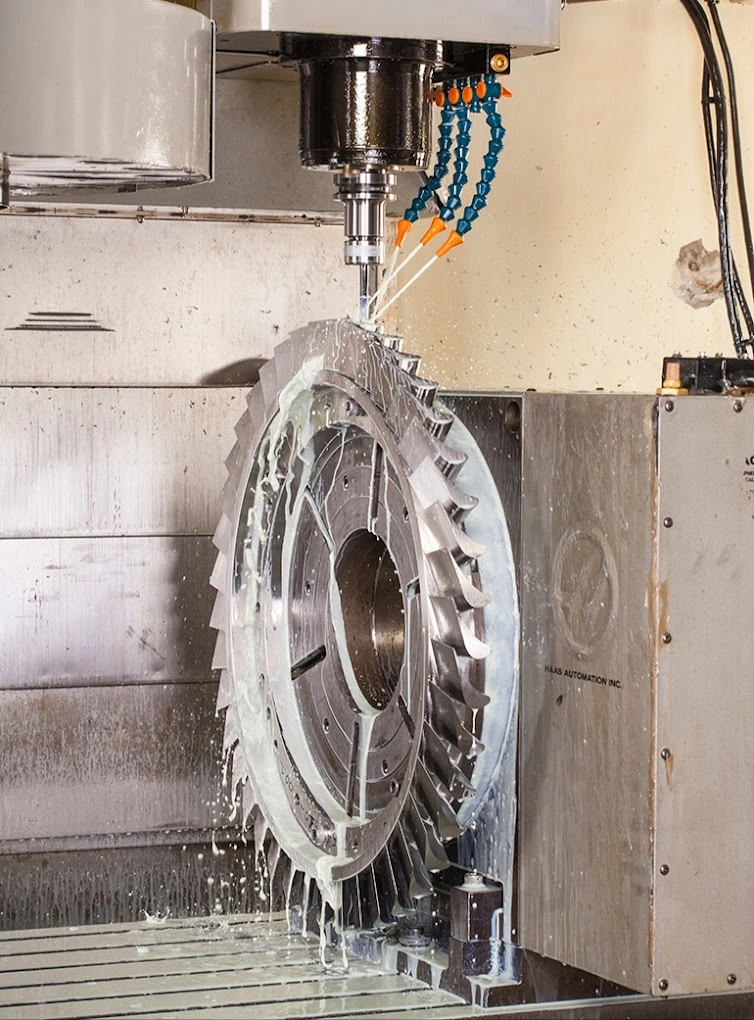
The field of steam turbine technology has witnessed significant advancements in recent years, driven by the need for improved efficiency, reliability, and environmental performance. This section will explore recent technological advancements in steam turbine design, materials, and control systems, highlighting the trends shaping the future of steam turbine technology.
Innovations in Design and Materials
Advancements in steam turbine design and materials have focused on enhancing efficiency and performance while reducing environmental impact. Key innovations include:
- Advanced Blade Designs: Modern steam turbines feature advanced blade designs optimized for aerodynamic performance and reduced losses. Computational fluid dynamics (CFD) and computer-aided design (CAD) tools are used to model and refine blade geometries, improving energy extraction and reducing turbulence.
- High-Temperature Materials: The development of high-temperature materials, such as nickel-based superalloys and ceramics, has enabled turbines to operate at higher temperatures and pressures, improving thermal efficiency and reducing fuel consumption. These materials exhibit excellent resistance to creep, oxidation, and corrosion, ensuring long-term durability.
- 3D Printing and Additive Manufacturing: Additive manufacturing techniques, such as 3D printing, are being used to produce complex turbine components with high precision and reduced lead times. This technology enables the production of lightweight and intricate designs that enhance performance and reduce manufacturing costs.
- Cooling Technologies: Advanced cooling technologies, such as steam-cooled and air-cooled designs, have been developed to manage heat and improve efficiency. These cooling systems optimize temperature distribution and reduce the risk of overheating, enhancing turbine reliability.
Digitalization and Control Systems
Digitalization and advanced control systems are transforming the operation and maintenance of steam turbines, offering new opportunities for optimization and efficiency. Key developments in this area include:
- Digital Twins: Digital twin technology involves creating a virtual replica of a physical turbine, allowing for real-time monitoring, simulation, and analysis. Digital twins enable predictive maintenance, performance optimization, and troubleshooting, reducing downtime and operational costs.
- Advanced Monitoring and Diagnostics: Modern steam turbines are equipped with advanced sensors and monitoring systems that provide real-time data on key parameters such as temperature, pressure, and vibration. These systems enable early detection of issues and facilitate proactive maintenance and decision-making.
- Automated Control Systems: Automated control systems, powered by artificial intelligence and machine learning algorithms, optimize turbine operation by adjusting parameters in response to changing conditions. These systems enhance efficiency, reduce emissions, and improve overall performance.
- Remote Monitoring and Control: Remote monitoring and control capabilities allow operators to oversee turbine performance from centralized locations, enabling quick responses to issues and enhancing operational efficiency. This technology is particularly valuable for managing large fleets of turbines across multiple sites.
Future Trends in Steam Turbine Technology
The future of steam turbine technology is shaped by ongoing research and development efforts aimed at improving efficiency, sustainability, and integration with emerging energy systems. Key trends include:
- Integration with Renewable Energy: Steam turbines are increasingly being integrated with renewable energy systems, such as solar thermal and geothermal, to enhance efficiency and provide reliable base-load power. Hybrid systems that combine renewable sources with steam turbines are expected to play a significant role in the future energy landscape.
- Decarbonization and Emissions Reduction: Efforts to reduce carbon emissions and environmental impact are driving innovations in steam turbine technology. Carbon capture and storage (CCS) systems, advanced combustion technologies, and improved efficiency are key areas of focus in reducing the carbon footprint of steam turbines.
- Energy Storage and Grid Integration: The integration of steam turbines with energy storage systems, such as batteries and thermal storage, is being explored to enhance grid stability and support the integration of intermittent renewable sources. These systems enable flexible and reliable power generation, contributing to a more resilient energy grid.
- Micro and Small-Scale Turbines: The development of micro and small-scale steam turbines is gaining attention for decentralized power generation and off-grid applications. These turbines offer the potential for localized energy solutions and enhanced energy security, particularly in remote and underserved areas.
Maintenance and Operational Challenges
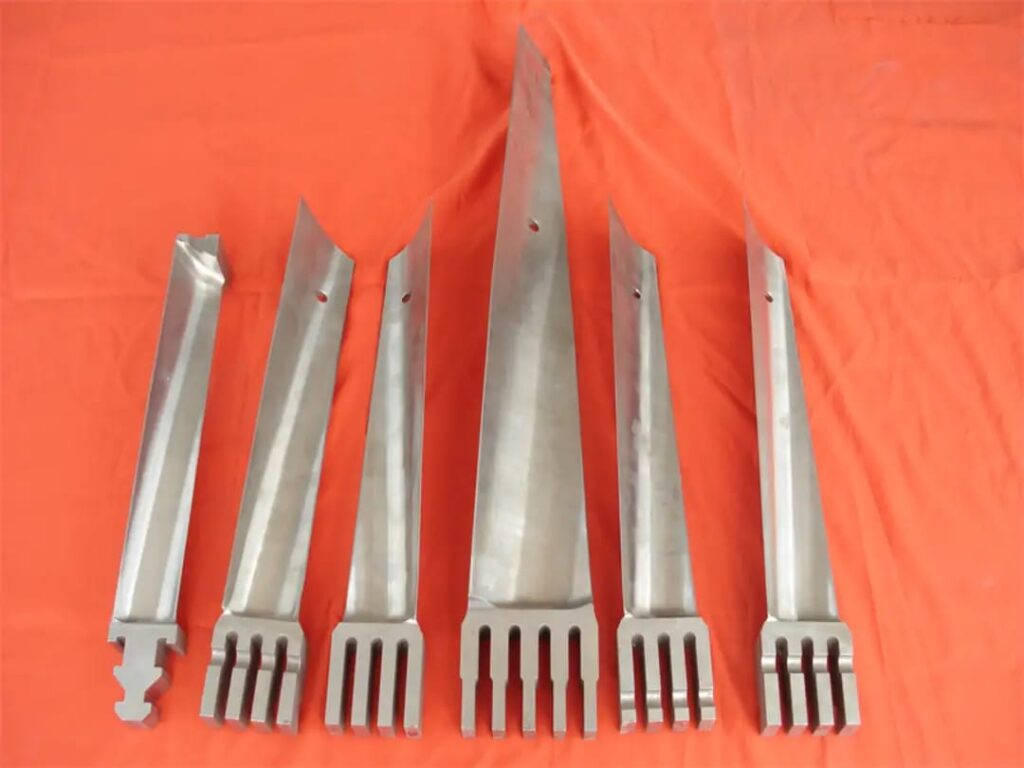
The operation and maintenance of steam turbines present various challenges that must be addressed to ensure optimal performance, reliability, and longevity. This section will explore common maintenance and operational challenges associated with steam turbines, highlighting best practices and strategies for overcoming these issues.
Common Issues and Solutions
Steam turbines are complex machines subject to a range of operational challenges that can impact performance and efficiency. Common issues include:
- Corrosion and Erosion: Corrosion and erosion are significant challenges in steam turbines, particularly in components exposed to high temperatures and aggressive environments. These issues can lead to reduced efficiency, increased maintenance costs, and shortened component lifespans. Solutions include using corrosion-resistant materials, implementing protective coatings, and optimizing steam chemistry to minimize corrosive agents.
- Fouling and Deposits: Fouling and deposits can accumulate on turbine components, reducing heat transfer efficiency and impairing performance. Regular cleaning and maintenance, as well as the use of advanced filtration and water treatment systems, can help mitigate fouling and deposits.
- Vibration and Noise: Vibration and noise can affect the performance and lifespan of steam turbines, potentially leading to mechanical failures and operational disruptions. Engineers use techniques such as balancing, damping, and vibration analysis to identify and address the sources of vibration and noise.
- Thermal Stress and Fatigue: Steam turbines are subjected to thermal stress and fatigue due to cyclic loading and temperature fluctuations. These conditions can lead to cracking, deformation, and other structural issues. Engineers use advanced materials, design optimization, and thermal management strategies to mitigate thermal stress and fatigue.
- Seal and Gasket Failures: Seals and gaskets are critical components that prevent leaks and maintain pressure differentials within the turbine. Failures can lead to reduced efficiency and increased maintenance requirements. Proper selection, installation, and maintenance of seals and gaskets are essential to ensure reliable operation.
Importance of Regular Maintenance
Regular maintenance is crucial to the reliable and efficient operation of steam turbines. Key maintenance practices include:
- Scheduled Inspections: Regular inspections are essential to identify potential issues and ensure that turbine components are in good condition. Inspections may involve visual examinations, non-destructive testing, and performance evaluations.
- Predictive Maintenance: Predictive maintenance techniques, such as vibration analysis and thermal imaging, are used to monitor turbine performance and identify potential issues before they become critical. This proactive approach minimizes downtime and reduces maintenance costs.
- Lubrication Management: Proper lubrication is essential to minimize friction and wear in turbine components. Regular monitoring and maintenance of lubrication systems ensure optimal performance and extend component lifespans.
- Cleaning and Servicing: Cleaning and servicing of turbine components are necessary to remove fouling, deposits, and other contaminants that can impair performance. Regular cleaning improves heat transfer efficiency and reduces the risk of mechanical failures.
- Calibration and Adjustment: Calibration and adjustment of control systems, sensors, and actuators are necessary to maintain accurate and reliable operation. Regular calibration ensures that turbines operate within safe and efficient parameters.
Case Studies of Failure and Recovery
Case studies of steam turbine failures and recoveries provide valuable insights into best practices and strategies for overcoming operational challenges. Examples include:
- Turbine Blade Failure: A power plant experienced a sudden loss of power due to a turbine blade failure caused by fatigue cracking. An investigation revealed that inadequate maintenance and inspection had contributed to the failure. The plant implemented a comprehensive maintenance program, including regular inspections and predictive maintenance techniques, to prevent future issues.
- Corrosion-Induced Shutdown: A chemical processing facility faced a prolonged shutdown due to corrosion in the turbine’s steam path. The facility adopted advanced materials and coatings to enhance corrosion resistance and implemented a steam chemistry optimization program to reduce corrosive agents.
- Vibration-Related Performance Issues: A paper mill experienced reduced efficiency and increased maintenance costs due to excessive vibration in its steam turbines. Engineers conducted a detailed vibration analysis and implemented balancing and damping solutions to address the issue, resulting in improved performance and reliability.
Conclusion
Steam turbines remain a vital component of the global energy landscape, offering reliable and efficient power generation across various industries and applications. This article has provided a comprehensive overview of steam turbines, exploring their history, design, operation, and applications, as well as recent technological advancements and maintenance challenges.
Summary of Key Points
- Historical Evolution: Steam turbines have evolved significantly since their invention in the late 19th century, with advancements in design, materials, and technology driving improvements in efficiency and performance.
- Principles of Operation: Steam turbines operate based on the principles of thermodynamics, converting thermal energy from steam into mechanical work through the Rankine cycle. The efficiency and performance of steam turbines are influenced by factors such as steam pressure, temperature, and the effectiveness of the condensation process.
- Design and Components: The design of steam turbines involves the integration of various components, including rotors, blades, casings, and nozzles. Advances in materials and manufacturing techniques have enhanced turbine performance and reliability.
- Applications: Steam turbines are employed in a wide range of applications, including power generation, industrial processes, and combined heat and power (CHP) systems. Their versatility and efficiency make them a preferred choice for many industries.
- Advantages and Disadvantages: Steam turbines offer numerous advantages, such as high efficiency, reliability, and scalability, but they also have certain disadvantages, including complexity, cost, and environmental impact.
- Technological Advancements: Recent advancements in steam turbine technology, including innovations in design, materials, and digitalization, are shaping the future of the industry and enhancing efficiency and sustainability.
- Maintenance and Operational Challenges: The operation and maintenance of steam turbines present various challenges, including corrosion, fouling, vibration, and thermal stress. Regular maintenance and best practices are essential to ensure optimal performance and reliability.
Future Outlook for Steam Turbines
The future of steam turbines is shaped by ongoing research and development efforts aimed at improving efficiency, sustainability, and integration with emerging energy systems. As the energy landscape continues to evolve, steam turbines are expected to play a key role in supporting the transition to a more sustainable and resilient energy future. Key areas of focus include:
- Decarbonization: Efforts to reduce carbon emissions and environmental impact will drive innovations in steam turbine technology, including carbon capture and storage (CCS) systems and advanced combustion technologies.
- Integration with Renewables: The integration of steam turbines with renewable energy systems, such as solar thermal and geothermal, will enhance efficiency and provide reliable base-load power, contributing to a more sustainable energy mix.
- Digitalization and Automation: Advances in digitalization and automation will enable more efficient and reliable operation of steam turbines, reducing maintenance costs and enhancing performance.
- Energy Storage and Grid Integration: The integration of steam turbines with energy storage systems and advanced grid technologies will support the transition to a more flexible and resilient energy grid.
In conclusion, steam turbines continue to be a cornerstone of the global energy industry, offering reliable and efficient power generation solutions for a wide range of applications. As technology advances and the energy landscape evolves, steam turbines will remain an essential component of the energy mix, contributing to a more sustainable and resilient energy future.
New Materials in Steam Turbine Construction
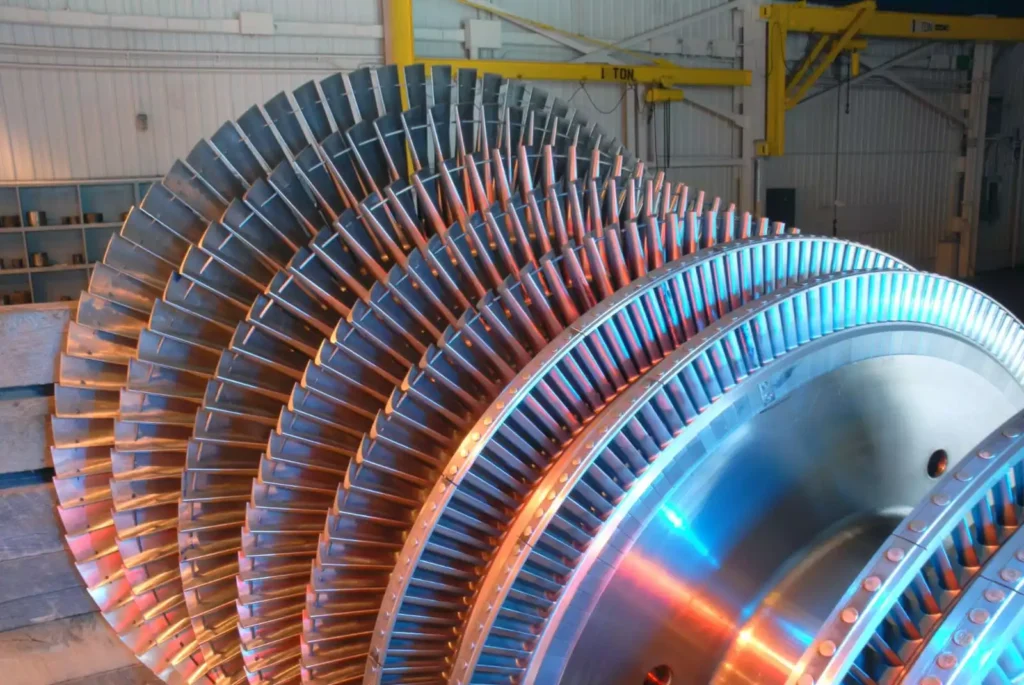
The development of new materials for steam turbines is crucial for improving their efficiency, reliability, and durability. These advancements in materials science have enabled steam turbines to operate at higher temperatures and pressures, enhancing their overall performance and reducing maintenance requirements. This section explores the latest innovations in turbine materials, their benefits, and the challenges associated with their implementation.
High-Temperature Alloys
High-temperature alloys are essential for steam turbine components exposed to extreme conditions. These materials must withstand high temperatures, pressures, and corrosive environments while maintaining mechanical strength and resistance to degradation.
- Nickel-Based Superalloys: Nickel-based superalloys are widely used in steam turbine blades and rotors due to their exceptional high-temperature strength and resistance to creep, oxidation, and corrosion. These alloys can operate at temperatures exceeding 700°C (1292°F), allowing for more efficient energy conversion. Recent advancements have focused on optimizing the microstructure and composition of these alloys to further enhance their performance. Examples of nickel-based superalloys include Inconel 718, René 80, and Nimonic 263.
- Cobalt-Based Superalloys: Cobalt-based superalloys are known for their excellent thermal fatigue resistance and are used in components where thermal cycling is a concern. They also offer good corrosion resistance and are often used in environments with high sulfur content. Cobalt-based alloys such as Haynes 188 and FSX-414 are common in specific turbine applications.
- Titanium Alloys: Titanium alloys are valued for their high strength-to-weight ratio, making them suitable for low-pressure turbine blades and components where weight reduction is essential. Titanium alloys such as Ti-6Al-4V are used in applications where both corrosion resistance and mechanical strength are required. Advances in processing techniques, such as powder metallurgy, have improved the properties of titanium alloys, making them more competitive with traditional materials.
Ceramic and Composite Materials
Ceramic and composite materials are being explored for use in steam turbines due to their unique properties, such as high-temperature resistance, low density, and excellent thermal insulation. These materials offer potential benefits in terms of efficiency and environmental impact.
- Ceramic Matrix Composites (CMCs): CMCs are lightweight materials that can withstand extremely high temperatures, making them suitable for turbine blades and other hot-section components. They offer superior thermal stability, corrosion resistance, and reduced weight compared to traditional metal alloys. CMCs, such as silicon carbide (SiC) and alumina-based composites, are being used to improve the efficiency of steam turbines by allowing for higher operating temperatures.
- Silicon Carbide (SiC) Ceramics: SiC ceramics are known for their high thermal conductivity, low thermal expansion, and excellent wear resistance. They are used in turbine components such as nozzles and seals, where durability and thermal stability are critical. Advances in manufacturing techniques, such as chemical vapor infiltration, have enabled the production of complex SiC ceramic components with improved properties.
- Glass and Carbon Fiber Composites: Glass and carbon fiber composites are used in non-load-bearing components, such as casings and covers, to reduce weight and improve thermal insulation. These materials offer high strength-to-weight ratios and can be tailored to specific applications through variations in fiber orientation and resin matrices.
Coatings and Surface Treatments
Coatings and surface treatments play a vital role in enhancing the performance and lifespan of steam turbine components. They provide protection against corrosion, erosion, and thermal degradation, improving overall reliability and efficiency.
- Thermal Barrier Coatings (TBCs): TBCs are applied to turbine blades and vanes to insulate the underlying metal from high temperatures, allowing for higher operating temperatures and improved efficiency. These coatings typically consist of a ceramic layer, such as yttria-stabilized zirconia (YSZ), which provides thermal insulation, and a metallic bond coat that enhances adhesion and protects against oxidation. Recent developments in TBC technology have focused on increasing the thermal stability and durability of these coatings, enabling turbines to operate at even higher temperatures.
- Erosion and Corrosion-Resistant Coatings: Erosion and corrosion-resistant coatings protect turbine components from wear and chemical attack, extending their service life and reducing maintenance requirements. These coatings are typically applied using techniques such as thermal spraying, physical vapor deposition (PVD), or chemical vapor deposition (CVD). Advances in nanostructured coatings have improved their effectiveness, offering enhanced protection against aggressive environments.
- Oxidation-Resistant Coatings: Oxidation-resistant coatings are used to protect metal components from high-temperature oxidation, which can lead to material degradation and failure. These coatings are often composed of aluminide or platinum-aluminide layers, which form a protective oxide scale on the surface. Researchers are exploring new coating compositions and application methods to further improve oxidation resistance and extend component lifespans.
Challenges and Considerations
While new materials offer significant advantages for steam turbines, their implementation also presents several challenges and considerations:
- Cost and Availability: Advanced materials, such as superalloys and CMCs, can be expensive and may require specialized manufacturing processes. Balancing material performance with cost-effectiveness is a critical consideration in turbine design and production.
- Manufacturing and Fabrication: The fabrication of complex turbine components using new materials requires advanced manufacturing techniques, such as additive manufacturing and precision casting. Ensuring consistency and quality in material properties and component dimensions is essential for reliable turbine operation.
- Compatibility and Integration: Integrating new materials into existing turbine designs may require modifications to component geometries and assembly methods. Compatibility with other materials and systems, such as cooling and lubrication, must be carefully evaluated to avoid issues such as thermal expansion mismatch and galvanic corrosion.
- Testing and Validation: Extensive testing and validation are necessary to ensure that new materials meet the performance and reliability requirements of steam turbines. This includes evaluating material properties under simulated operating conditions, such as high temperatures, pressures, and cyclic loading.
Conclusion
The development of new materials for steam turbines is driving significant advancements in their performance, efficiency, and reliability. High-temperature alloys, ceramics, composites, and advanced coatings are enabling turbines to operate at higher temperatures and pressures, improving energy conversion efficiency and reducing environmental impact. As research and development continue, these materials will play a crucial role in shaping the future of steam turbine technology, contributing to a more sustainable and efficient energy landscape.
Improvements in Steam Turbine Lifespan
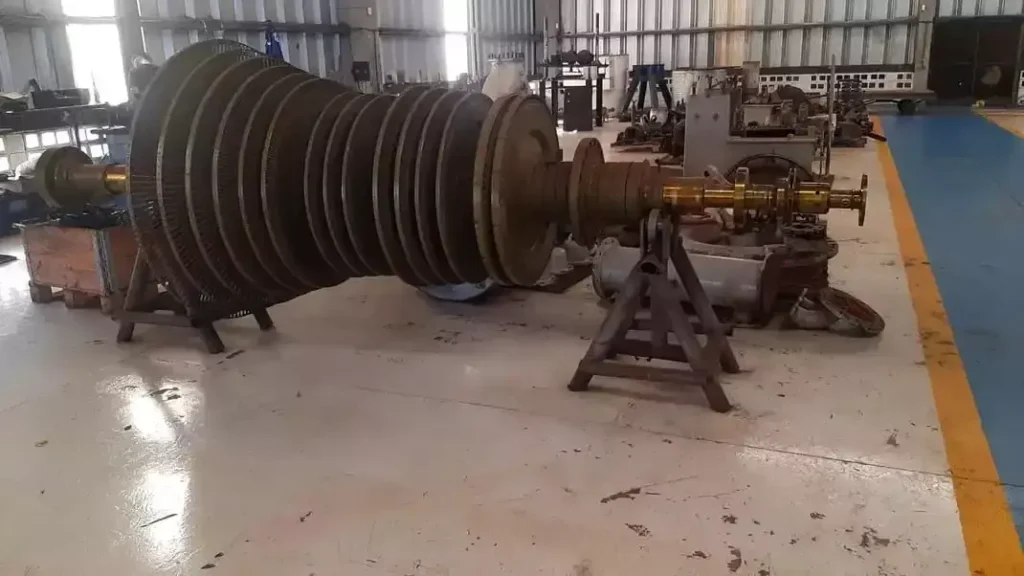
Improving the lifespan of steam turbines is a critical aspect of modern engineering, as it directly impacts the reliability, efficiency, and overall cost-effectiveness of power generation systems. Enhancements in materials, design, maintenance practices, and technological innovations have all contributed to extending the operational life of steam turbines. This section explores these improvements in detail, focusing on key factors that contribute to longer turbine lifespans.
Extending the lifespan of steam turbines is essential for optimizing the economic and operational performance of power generation systems. Advances in materials, design, maintenance practices, and technology have all contributed to enhancing the longevity and reliability of steam turbines. This section explores key strategies and innovations that improve turbine lifespan.
Advanced Materials and Coatings
The use of advanced materials and coatings plays a vital role in increasing the lifespan of steam turbines by enhancing their resistance to high temperatures, corrosion, erosion, and mechanical stresses.
- High-Temperature Alloys: The development of high-temperature alloys, such as nickel-based superalloys and titanium alloys, has significantly improved the durability of turbine components. These materials offer excellent mechanical strength, creep resistance, and corrosion resistance at elevated temperatures, allowing turbines to operate more efficiently and reliably over extended periods.
- Ceramic Matrix Composites (CMCs): CMCs are increasingly used in turbine blades and hot-section components due to their superior thermal stability and resistance to wear and corrosion. By reducing the thermal stresses experienced by metal components, CMCs help extend the life of critical turbine parts.
- Advanced Coatings: Protective coatings, such as thermal barrier coatings (TBCs), erosion-resistant coatings, and anti-corrosion coatings, are applied to turbine components to protect them from environmental damage and mechanical wear. These coatings reduce material degradation and extend component lifespans, leading to longer turbine operation and reduced maintenance costs.
Design Optimization
Innovations in turbine design have focused on reducing mechanical stresses, improving thermal efficiency, and enhancing the overall reliability of turbines, contributing to longer lifespans.
- Optimized Blade Design: Advances in computational fluid dynamics (CFD) and computer-aided design (CAD) have enabled engineers to optimize blade geometries for improved aerodynamic performance and reduced mechanical stresses. Optimized blades experience less fatigue and wear, resulting in extended service life.
- Cooling Technologies: Effective cooling systems, such as steam-cooled and air-cooled designs, help manage the heat load on turbine components, reducing thermal stress and extending the lifespan of critical parts. These cooling technologies ensure that components operate within safe temperature limits, preventing overheating and material degradation.
- Vibration Control: Vibration and resonance can lead to mechanical fatigue and failure in turbine components. Design strategies that minimize vibration, such as improved balancing and damping systems, contribute to the longevity and reliability of steam turbines.
- Stress-Relief Techniques: Design modifications that reduce stress concentrations, such as smooth transitions and rounded corners in component geometries, help prevent crack initiation and propagation. These stress-relief techniques improve the durability of turbine components and extend their operational life.
Enhanced Maintenance Practices
Regular maintenance and monitoring are critical to ensuring the long-term performance and reliability of steam turbines. Advances in maintenance practices have contributed to improved turbine lifespans.
- Predictive Maintenance: Predictive maintenance techniques, such as condition monitoring, vibration analysis, and thermal imaging, allow operators to detect potential issues before they become critical. By identifying signs of wear, corrosion, or mechanical stress early, predictive maintenance enables timely interventions and prevents costly failures.
- Regular Inspections and Servicing: Scheduled inspections and servicing ensure that turbine components are in good condition and operating within specified parameters. Routine maintenance tasks, such as cleaning, lubrication, and calibration, help maintain optimal performance and extend the life of turbine components.
- Component Refurbishment and Replacement: Refurbishment and replacement of worn or damaged components are essential to extending turbine lifespan. By renewing key parts, such as blades, rotors, and bearings, operators can restore turbine performance and prevent further degradation.
- Operator Training and Expertise: Well-trained operators and maintenance personnel are critical to the effective management of steam turbines. Comprehensive training programs and access to technical expertise ensure that turbines are operated and maintained correctly, reducing the risk of failures and extending lifespan.
Technological Innovations
Recent technological innovations have contributed to the improved lifespan of steam turbines by enhancing performance, efficiency, and reliability.
- Digital Twin Technology: Digital twins are virtual models of physical turbines that enable real-time monitoring, simulation, and analysis. By providing detailed insights into turbine performance and health, digital twins facilitate predictive maintenance and optimization strategies, extending turbine lifespan.
- Advanced Control Systems: Automated control systems, powered by artificial intelligence and machine learning algorithms, optimize turbine operation by adjusting parameters in response to changing conditions. These systems enhance efficiency, reduce emissions, and improve overall performance, contributing to longer turbine lifespans.
- Remote Monitoring and Diagnostics: Remote monitoring and diagnostics capabilities allow operators to oversee turbine performance from centralized locations, enabling quick responses to issues and enhancing operational efficiency. This technology is particularly valuable for managing large fleets of turbines across multiple sites.
- Energy Management Systems: Advanced energy management systems optimize the operation of steam turbines in conjunction with other power generation assets, such as gas turbines and renewable energy sources. By coordinating energy production and consumption, these systems improve overall efficiency and reduce wear on turbine components, extending their lifespan.
Case Studies and Success Stories
Examining real-world examples of turbine lifespan improvements can provide valuable insights into best practices and strategies for extending the life of steam turbines.
- Combined Cycle Power Plant Optimization: A combined cycle power plant implemented a comprehensive maintenance and optimization program, including predictive maintenance techniques, advanced coatings, and digital twin technology. As a result, the plant extended the lifespan of its steam turbines by 30%, reducing maintenance costs and improving overall efficiency.
- Geothermal Plant Erosion Mitigation: A geothermal power plant faced challenges with erosion and corrosion due to the presence of abrasive particles and corrosive impurities in the steam. By implementing erosion-resistant coatings and optimizing steam chemistry, the plant significantly extended the life of its turbine components, enhancing reliability and performance.
- Nuclear Power Plant Component Refurbishment: A nuclear power plant conducted a detailed analysis of its steam turbine components and identified key areas for refurbishment and replacement. By renewing critical parts and implementing advanced materials and coatings, the plant extended the lifespan of its turbines and improved safety and efficiency.
Conclusion
Enhancing the lifespan of steam turbines is a multifaceted challenge that requires advancements in materials, design, maintenance practices, and technology. By leveraging high-temperature alloys, ceramic composites, advanced coatings, and digital technologies, engineers can significantly extend the operational life of steam turbines, improving reliability, efficiency, and cost-effectiveness. As research and development continue, further innovations in turbine materials and technology will play a crucial role in achieving a more sustainable and efficient energy future.
Turbine Efficiency Gains
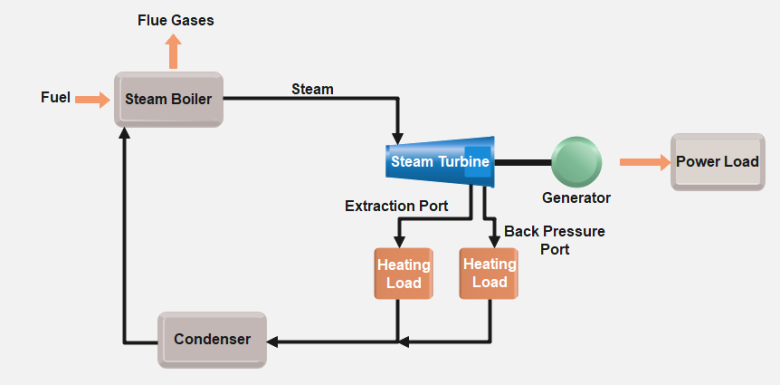
Improving the efficiency of steam turbines is a major focus in power generation, as even small gains can lead to significant reductions in fuel consumption and greenhouse gas emissions. Over the years, advancements in materials, design, and technology have contributed to notable improvements in steam turbine efficiency. This section explores the various factors and innovations that have driven efficiency gains in steam turbines.
The efficiency of steam turbines is crucial for optimizing power generation and reducing environmental impact. Advances in design, materials, technology, and operational practices have all contributed to significant efficiency gains in steam turbines. This section examines the key factors and innovations driving these improvements.
Thermodynamic Principles and Efficiency
The efficiency of steam turbines is governed by thermodynamic principles, primarily focusing on the conversion of thermal energy into mechanical work. The Rankine cycle, which is the basis for steam turbine operation, involves several stages: heat addition, expansion, heat rejection, and compression. The efficiency of a steam turbine can be enhanced by optimizing these stages.
- Higher Steam Temperatures and Pressures: One of the most effective ways to increase turbine efficiency is to operate at higher steam temperatures and pressures. By increasing the thermal energy available for conversion, higher steam conditions enable greater energy extraction. Modern supercritical and ultra-supercritical turbines operate at pressures above the critical point of water (22.1 MPa) and temperatures above 600°C, achieving efficiencies of over 45%.
- Reheat and Regenerative Cycles: The use of reheat and regenerative cycles can improve turbine efficiency by minimizing energy losses. In a reheat cycle, steam is partially expanded in the turbine, reheated in a boiler, and then expanded further in another turbine stage. This process increases the average temperature at which heat is added, improving efficiency. Regenerative cycles use feedwater heaters to preheat the water entering the boiler, recovering waste heat and reducing fuel consumption.
- Advanced Thermodynamic Cycles: Innovations in thermodynamic cycles, such as the combined cycle and organic Rankine cycle (ORC), have also contributed to efficiency gains. Combined cycle power plants integrate gas turbines with steam turbines, using waste heat from the gas turbine to generate steam and improve overall efficiency. ORC systems utilize organic fluids with lower boiling points than water, enabling efficient energy conversion from low-temperature heat sources.
Advanced Materials and Blade Design
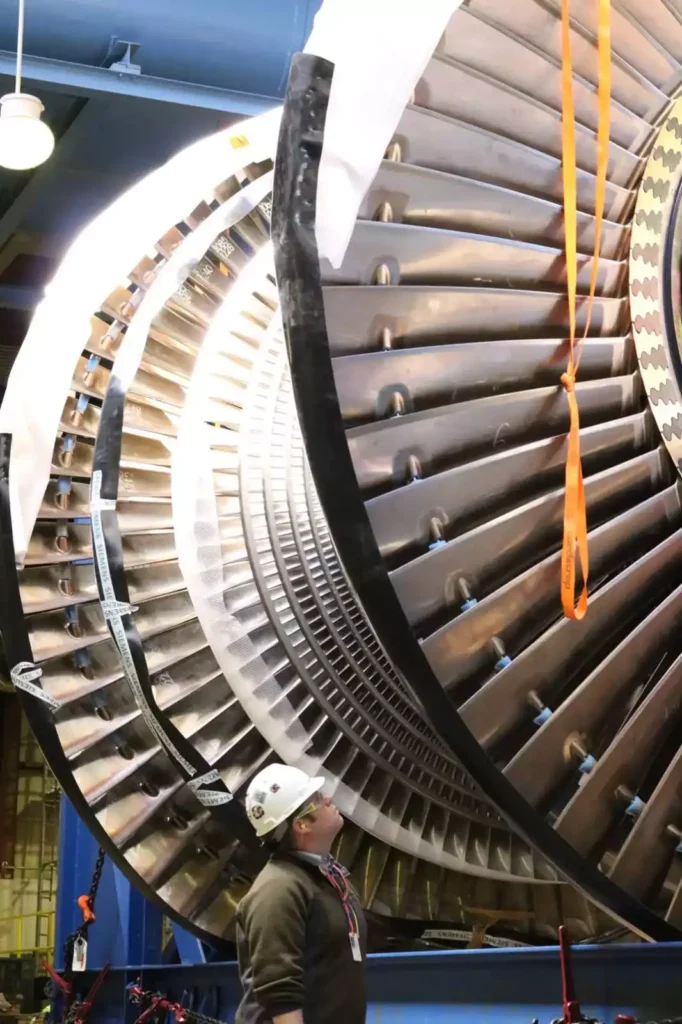
The development of advanced materials and optimized blade designs has played a significant role in enhancing steam turbine efficiency.
- High-Temperature Materials: The use of high-temperature materials, such as nickel-based superalloys and ceramic matrix composites (CMCs), allows turbines to operate at higher temperatures and pressures, improving thermal efficiency. These materials offer excellent strength, corrosion resistance, and thermal stability, enabling more efficient energy conversion.
- Aerodynamic Blade Design: Advances in computational fluid dynamics (CFD) and computer-aided design (CAD) have enabled the optimization of blade geometries for improved aerodynamic performance. Modern turbine blades are designed to minimize aerodynamic losses and maximize energy extraction, reducing turbulence and increasing efficiency. Techniques such as 3D blading and contoured endwalls further enhance aerodynamic performance.
- Tip Clearance Control: Minimizing tip clearance between turbine blades and the casing reduces aerodynamic losses and improves efficiency. Advanced tip clearance control systems, such as active clearance control and abradable coatings, help maintain optimal clearances and reduce leakage losses.
- Blade Coatings and Surface Treatments: The application of advanced coatings and surface treatments to turbine blades enhances their resistance to erosion, corrosion, and thermal degradation, improving efficiency and extending lifespan. Thermal barrier coatings (TBCs) and erosion-resistant coatings help maintain blade integrity and performance.
Digitalization and Control Systems
Digitalization and advanced control systems have transformed the operation and efficiency of steam turbines.
- Real-Time Monitoring and Diagnostics: Advanced sensors and monitoring systems provide real-time data on key turbine parameters, such as temperature, pressure, and vibration. This data enables operators to optimize turbine performance and efficiency, detect potential issues early, and implement corrective actions.
- Automated Control Systems: Automated control systems, powered by artificial intelligence and machine learning algorithms, optimize turbine operation by adjusting parameters in response to changing conditions. These systems enhance efficiency, reduce emissions, and improve overall performance.
- Digital Twins: Digital twin technology creates virtual models of physical turbines, allowing for real-time simulation and analysis. Digital twins enable predictive maintenance and optimization strategies, improving efficiency and reliability.
- Predictive Maintenance: Predictive maintenance techniques, such as condition monitoring and vibration analysis, help identify potential issues before they become critical. By enabling timely interventions and optimizing maintenance schedules, predictive maintenance contributes to improved turbine efficiency and reduced downtime.
Operational Strategies and Best Practices
Operational strategies and best practices play a crucial role in maximizing steam turbine efficiency.
- Load Optimization: Operating turbines at optimal load levels ensures maximum efficiency and minimizes energy losses. Advanced control systems and real-time monitoring enable operators to adjust turbine output based on demand, optimizing efficiency.
- Startup and Shutdown Procedures: Efficient startup and shutdown procedures minimize energy losses and thermal stress, reducing wear on turbine components and improving efficiency. Advanced control systems automate these procedures, ensuring consistent and optimal performance.
- Fuel Quality and Steam Purity: Maintaining high fuel quality and steam purity is essential for efficient turbine operation. Impurities in fuel and steam can cause fouling, corrosion, and erosion, reducing efficiency and increasing maintenance requirements. Regular monitoring and treatment of fuel and steam ensure optimal performance.
- Waste Heat Recovery: Implementing waste heat recovery systems, such as heat exchangers and economizers, recovers energy from exhaust gases and other heat sources, improving overall plant efficiency. Combined cycle power plants and cogeneration systems are examples of effective waste heat recovery.
Case Studies and Success Stories
Real-world examples of efficiency improvements provide valuable insights into best practices and strategies for enhancing steam turbine efficiency.
- Ultra-Supercritical Power Plant Efficiency Gains: An ultra-supercritical power plant implemented advanced materials, optimized blade designs, and digital control systems to achieve efficiencies of over 47%. By operating at high temperatures and pressures, the plant reduced fuel consumption and emissions while maximizing energy output.
- Combined Cycle Plant Optimization: A combined cycle power plant integrated advanced monitoring and control systems, along with waste heat recovery techniques, to improve efficiency. The plant achieved overall efficiencies of over 60%, demonstrating the potential of combined cycle technology for efficient power generation.
- Geothermal Plant Efficiency Enhancement: A geothermal power plant implemented organic Rankine cycle (ORC) technology and advanced blade coatings to improve efficiency. By utilizing low-temperature heat sources and minimizing energy losses, the plant increased energy output and reduced operational costs.
Conclusion
Enhancing the efficiency of steam turbines is a multifaceted challenge that requires advancements in materials, design, technology, and operational practices. By leveraging high-temperature materials, optimized blade designs, digitalization, and advanced control systems, engineers have achieved significant efficiency gains in steam turbines, reducing fuel consumption and environmental impact. As research and development continue, further innovations in turbine technology will play a crucial role in achieving a more sustainable and efficient energy future.
Components of a Steam Turbine and Their Manufacturing
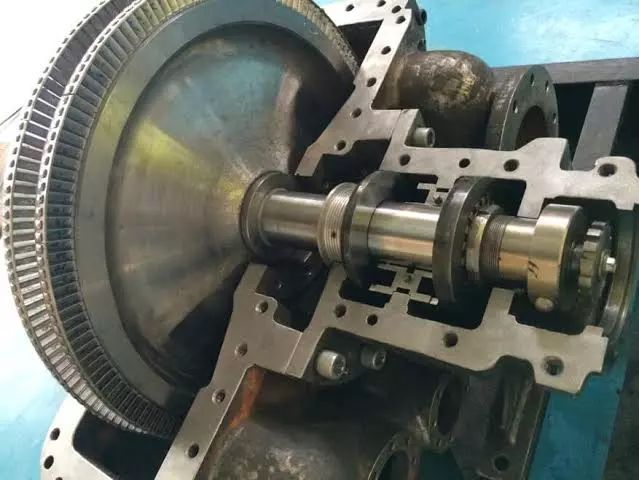
Steam turbines are complex machines comprised of various components, each playing a crucial role in the conversion of steam energy into mechanical work. Understanding the components and their manufacturing processes provides insights into the engineering and technology involved in steam turbine construction.
1. Rotor
Description
The rotor is the central shaft of the steam turbine to which the turbine blades are attached. It is a critical component that converts steam energy into mechanical energy and transmits the rotational motion to the generator or mechanical load.
Manufacturing Process
- Material Selection: Rotors are typically made from high-strength, low-alloy steels, such as chromium-molybdenum-vanadium (CrMoV) alloys, which offer excellent mechanical properties and resistance to thermal stresses.
- Forging: The rotor is usually manufactured through a hot forging process, where a large billet of steel is heated to high temperatures and shaped into a rough form using a hydraulic press or hammer. This process aligns the grain structure and enhances the strength and toughness of the material.
- Machining: After forging, the rotor undergoes precision machining to achieve the desired dimensions and surface finish. Computer numerical control (CNC) machines are used to mill, turn, and grind the rotor to exact specifications. Machining operations ensure tight tolerances and balance, which are crucial for minimizing vibration and maximizing efficiency.
- Heat Treatment: The rotor is subjected to heat treatment processes, such as quenching and tempering, to enhance its mechanical properties. Heat treatment improves the rotor’s strength, toughness, and resistance to creep and fatigue.
- Balancing: Dynamic balancing is performed to ensure that the rotor operates smoothly at high speeds without causing excessive vibration. Balancing involves adding or removing material from the rotor to achieve even weight distribution.
- Inspection and Testing: The rotor undergoes rigorous inspection and testing, including non-destructive testing (NDT) techniques such as ultrasonic testing and magnetic particle inspection, to detect any defects or inconsistencies.
2. Blades
Description
Turbine blades are airfoil-shaped components that extract energy from the steam and convert it into rotational motion. They are critical for the efficiency and performance of the steam turbine.
Manufacturing Process
- Material Selection: Blades are typically made from high-performance materials such as nickel-based superalloys or titanium alloys. These materials offer excellent resistance to high temperatures, corrosion, and mechanical stresses.
- Precision Casting: Investment casting, also known as lost-wax casting, is commonly used to manufacture turbine blades. This process involves creating a wax model of the blade, coating it with ceramic material to form a mold, and then melting away the wax. Molten metal is poured into the mold to form the blade.
- Directional Solidification: Advanced casting techniques, such as directional solidification and single-crystal growth, are used to enhance the mechanical properties of turbine blades. These techniques control the grain structure of the material, improving resistance to creep and fatigue.
- Machining and Finishing: After casting, blades undergo precision machining and finishing processes to achieve the desired shape and surface quality. CNC machines are used to mill and grind the blades to exact specifications.
- Coating Application: Blades are coated with protective coatings, such as thermal barrier coatings (TBCs) and erosion-resistant coatings, to enhance their durability and performance. Coatings are applied using techniques such as thermal spraying or chemical vapor deposition (CVD).
- Inspection and Testing: Blades undergo rigorous inspection and testing, including non-destructive testing methods, to ensure they meet quality and performance standards. High-resolution imaging and ultrasonic testing are commonly used to detect defects.
3. Casing
Description
The casing, or housing, encloses the steam turbine and provides structural support. It directs the flow of steam through the turbine stages and helps maintain pressure and temperature conditions.
Manufacturing Process
- Material Selection: Casings are typically made from cast steel or ductile iron, offering a good balance of strength, toughness, and thermal resistance.
- Casting: The casing is usually manufactured through sand casting, where a pattern of the casing is made from wood or metal, and sand is packed around it to form a mold. Molten metal is poured into the mold to create the casing.
- Machining: After casting, the casing undergoes machining to achieve the required dimensions and tolerances. CNC machines are used to machine flanges, openings, and mounting surfaces.
- Heat Treatment: Heat treatment processes, such as annealing, are used to relieve internal stresses and improve the mechanical properties of the casing.
- Assembly and Welding: Large casings may consist of multiple sections that are assembled and welded together. Welds are inspected using non-destructive testing methods to ensure quality and integrity.
- Inspection and Testing: Casings undergo inspection and testing, including pressure testing and dimensional checks, to ensure they meet performance and safety standards.
4. Bearings
Description
Bearings support the rotor and allow it to rotate smoothly with minimal friction. They are critical for maintaining the alignment and stability of the turbine shaft.
Manufacturing Process
- Material Selection: Bearings are typically made from materials such as high-strength steel, babbitt (a soft metal alloy), or ceramics. Material selection depends on the specific application and operating conditions.
- Precision Machining: Bearings are manufactured using precision machining techniques to achieve tight tolerances and smooth surfaces. CNC machines are used to machine the bearing races and rolling elements.
- Heat Treatment: Heat treatment processes, such as case hardening, are used to enhance the wear resistance and fatigue strength of bearing components.
- Assembly and Inspection: Bearings are assembled with rolling elements, such as balls or rollers, and subjected to inspection and testing to ensure proper fit and function.
- Lubrication System Integration: Bearings are integrated with lubrication systems to reduce friction and wear. Lubrication systems are designed to deliver a consistent supply of lubricant to the bearing surfaces.
5. Governor
Description
The governor is a control mechanism that regulates the speed and output of the steam turbine by adjusting the steam flow. It ensures that the turbine operates within safe and efficient parameters.
Manufacturing Process
- Component Fabrication: The governor consists of various components, such as valves, linkages, and actuators, which are manufactured using precision machining and fabrication techniques.
- Assembly: The components are assembled to create the governor mechanism, which is designed to respond to changes in turbine speed and load.
- Calibration and Testing: The governor is calibrated to ensure accurate and reliable control of the turbine speed and output. Testing involves simulating operating conditions to verify the governor’s performance.
- Integration with Control Systems: The governor is integrated with the turbine’s control systems, which may include digital controllers and sensors, to optimize performance and efficiency.
6. Nozzles
Description
Nozzles are used in impulse turbines to direct high-velocity steam jets onto the turbine blades, imparting momentum and causing rotation.
Manufacturing Process
- Material Selection: Nozzles are typically made from high-strength alloys that can withstand high temperatures and pressures, such as stainless steel or nickel-based superalloys.
- Precision Machining: Nozzles are manufactured using precision machining techniques to achieve the desired shape and flow characteristics. CNC machines are used to drill, mill, and shape the nozzle passages.
- Heat Treatment: Heat treatment processes, such as annealing or quenching, are used to enhance the mechanical properties of the nozzles.
- Coating Application: Nozzles may be coated with protective coatings to enhance their resistance to erosion and corrosion.
- Inspection and Testing: Nozzles undergo inspection and testing, including flow testing and dimensional checks, to ensure they meet performance standards.
7. Seals and Gaskets
Description
Seals and gaskets prevent steam leaks and maintain pressure differentials within the turbine. They are critical for efficient operation and preventing losses.
Manufacturing Process
- Material Selection: Seals and gaskets are made from materials that offer good sealing properties and resistance to high temperatures and pressures. Common materials include elastomers, graphite, and metal alloys.
- Molding and Cutting: Seals and gaskets are manufactured using molding or cutting processes, depending on the material and design. Rubber and elastomeric seals are typically molded, while metal gaskets are cut from sheets.
- Coating and Treatment: Seals and gaskets may undergo surface treatments, such as coatings or impregnations, to enhance their sealing properties and durability.
- Inspection and Testing: Seals and gaskets are inspected and tested for dimensional accuracy and sealing performance to ensure they meet quality standards.
Conclusion
The manufacturing of steam turbine components involves advanced materials, precision engineering, and rigorous quality control to ensure optimal performance, efficiency, and reliability. Each component plays a critical role in the overall operation of the turbine, and advancements in materials and manufacturing processes continue to drive improvements in turbine technology. As research and development progress, further innovations in turbine component manufacturing will contribute to a more sustainable and efficient energy future.
Steam Turbines
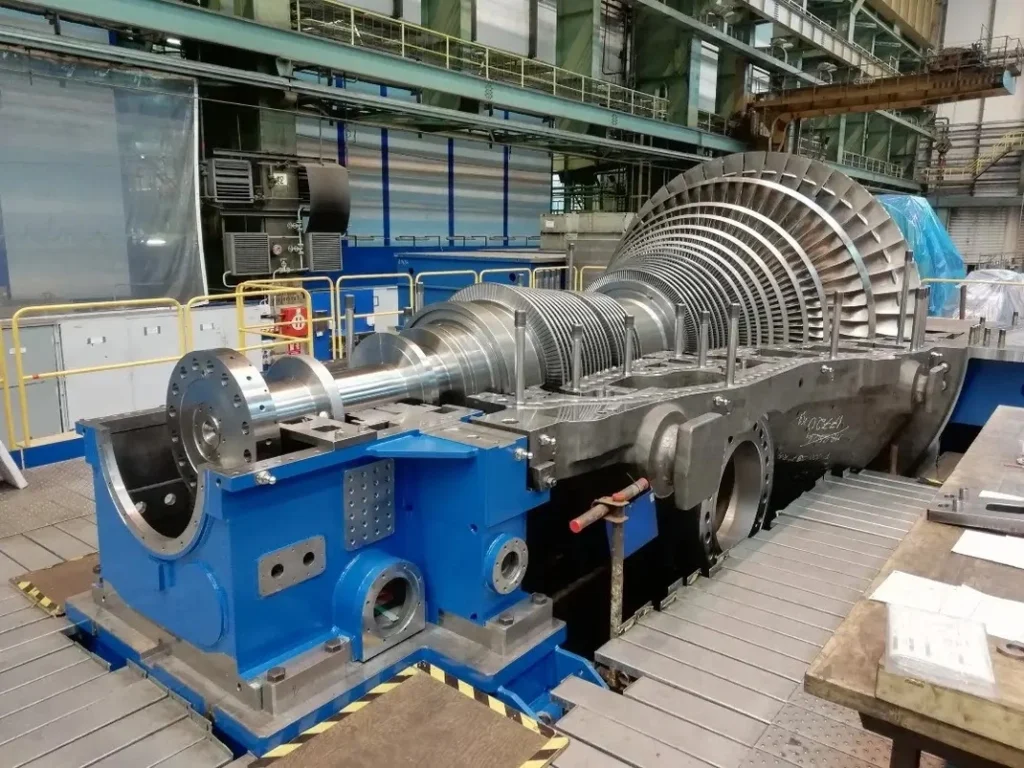
Steam turbines are a fundamental component of modern power generation and various industrial processes. They convert thermal energy from steam into mechanical energy, which can then be used to generate electricity or drive machinery. The concept of harnessing steam power dates back to ancient times, with early attempts to use steam for mechanical purposes seen in the aeolipile, a simple steam-powered device invented by Hero of Alexandria in the 1st century AD. However, it wasn’t until the 19th century that steam turbines, as we know them today, began to take shape.
The breakthrough in steam turbine technology came in the late 19th century with the work of Sir Charles Parsons and Gustaf de Laval. Sir Charles Parsons is often credited with inventing the modern steam turbine in 1884, when he developed a prototype capable of driving an electrical generator. This invention marked a significant leap in efficiency compared to earlier steam engines. Parsons’ steam turbine quickly became the preferred method for generating electricity, and its design principles are still used in modern turbines.
Gustaf de Laval, a Swedish engineer, made significant contributions to the development of steam turbines, particularly in high-speed turbines. His work in the 1880s and 1890s led to the creation of impulse turbines, which use the kinetic energy of steam to drive the turbine blades. These developments laid the foundation for the widespread adoption of steam turbines in various industries.
Importance in Modern Industry
Today, steam turbines play a crucial role in the global energy landscape. They are used in thermal power plants to generate a significant portion of the world’s electricity. In a typical thermal power plant, steam is produced by burning fossil fuels such as coal, natural gas, or oil, or by utilizing nuclear energy. The steam is then directed into the turbine, where it expands and drives the turbine blades, converting thermal energy into mechanical energy. This mechanical energy is then used to rotate an electrical generator, producing electricity.
Steam turbines are also integral to various industrial processes. They are used in the petrochemical industry to drive compressors and pumps, in the steel industry for mechanical drives, and in the paper industry to generate electricity and drive machinery. Additionally, steam turbines are employed in marine propulsion systems, particularly in large vessels like aircraft carriers and submarines, where their reliability and efficiency are highly valued.
The versatility and efficiency of steam turbines make them indispensable in both traditional and modern energy systems. They are compatible with a wide range of energy sources, including fossil fuels, nuclear power, and renewable sources such as biomass, geothermal, and concentrated solar power. This adaptability ensures that steam turbines will continue to play a vital role in the global energy mix as the world transitions towards more sustainable energy solutions.
Fundamentals of Steam Turbines
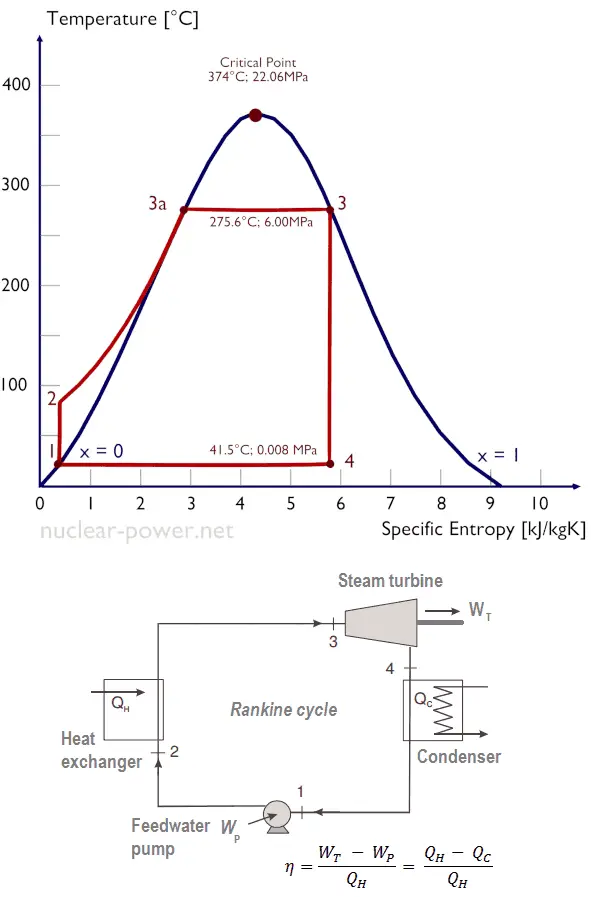
Basic Principles
At the core of a steam turbine’s operation is the conversion of thermal energy from steam into mechanical energy. This process is grounded in the principles of thermodynamics, specifically the Rankine cycle, which is the fundamental thermodynamic cycle used in steam turbine operations.
In simple terms, the Rankine cycle involves four main processes:
- Heat Addition: In a boiler, water is heated at constant pressure, transforming it into steam. This high-pressure steam contains a significant amount of thermal energy.
- Expansion: The high-energy steam is directed into the turbine, where it expands. As the steam expands, its pressure and temperature drop, and it imparts kinetic energy to the turbine blades, causing them to rotate. This rotational energy is then transferred to a shaft connected to an electrical generator or mechanical equipment.
- Condensation: After passing through the turbine, the steam is exhausted into a condenser, where it is cooled and condensed back into water.
- Pumping: The condensed water is then pumped back to the boiler to begin the cycle again.
The efficiency of a steam turbine is determined by how effectively it converts the thermal energy in the steam into mechanical energy. Factors such as steam pressure, temperature, and the design of the turbine blades play crucial roles in determining this efficiency.
Key Components
Steam turbines consist of several critical components, each playing a specific role in the turbine’s operation:
- Rotor: The rotor is the rotating part of the turbine and consists of a shaft and attached blades. As steam passes through the turbine, it causes the rotor to spin, converting thermal energy into mechanical energy.
- Stator: The stator is the stationary part of the turbine that surrounds the rotor. It contains fixed blades that direct the flow of steam onto the rotor blades in an efficient manner.
- Casing: The casing encases the entire turbine, providing structural support and containing the steam within the turbine. It also protects the internal components from external elements.
- Blades: The turbine blades are crucial for the conversion of energy. There are two main types of blades: fixed blades (attached to the stator) and moving blades (attached to the rotor). The design and arrangement of these blades are critical for the efficient operation of the turbine.
- Steam Supply System: This system includes the pipes, valves, and other components that deliver steam to the turbine at the required pressure and temperature. It also controls the flow of steam into the turbine.
- Condenser: The condenser cools the exhaust steam from the turbine, converting it back into water to be reused in the cycle. It is typically a heat exchanger that removes the latent heat of vaporization from the steam.
- Governor: The governor is a control mechanism that regulates the turbine’s speed by adjusting the steam flow. It ensures that the turbine operates at the desired speed and can respond to changes in load demand.
Types of Steam Turbines
Steam turbines are classified based on their design, method of steam expansion, and application. The main types include:
- Impulse Turbines: In impulse turbines, high-pressure steam is directed onto the turbine blades through nozzles. The steam jets strike the blades, causing them to move, but the steam pressure remains constant as it passes over the blades. The rotor’s motion is purely due to the impulse force from the steam. Impulse turbines are often used in high-speed applications and are suitable for driving generators in power plants.
- Reaction Turbines: Unlike impulse turbines, reaction turbines utilize both the impulse of steam and the reaction force generated as steam expands and accelerates through the moving blades. The steam pressure drops as it passes through the blades, and this pressure drop is what drives the rotor. Reaction turbines are commonly used in lower-speed applications and are often found in industrial settings.
- Condensing Turbines: These turbines are designed to exhaust steam at a lower pressure, usually into a condenser, where the steam is condensed into water. Condensing turbines are widely used in power generation, where maximum efficiency is required.
- Non-Condensing Turbines: Also known as back-pressure turbines, these turbines exhaust steam at a pressure higher than atmospheric pressure. The exhaust steam can be used for heating or other industrial processes. Non-condensing turbines are commonly used in cogeneration systems where both electricity and process steam are needed.
- Extraction Turbines: Extraction turbines are designed to extract steam at one or more points along the turbine for industrial processes or heating. The remaining steam continues through the turbine for power generation. These turbines provide flexibility in applications where steam at different pressures is required.
- Reheat Turbines: In reheat turbines, steam is expanded through a high-pressure stage of the turbine, reheated in the boiler, and then expanded further in a lower-pressure stage. Reheating improves the efficiency of the cycle and reduces the moisture content of the steam, which can help to reduce blade erosion.
- Industrial Turbines: These are designed for specific industrial applications, such as driving compressors, pumps, or fans. Industrial turbines can be either impulse or reaction types, depending on the specific application requirements.
- Marine Turbines: Used in naval vessels and large commercial ships, marine turbines are designed to be highly reliable and capable of operating under the challenging conditions at sea. They are typically reaction turbines and are designed to drive propellers or generators for propulsion.
Thermodynamics and Fluid Mechanics
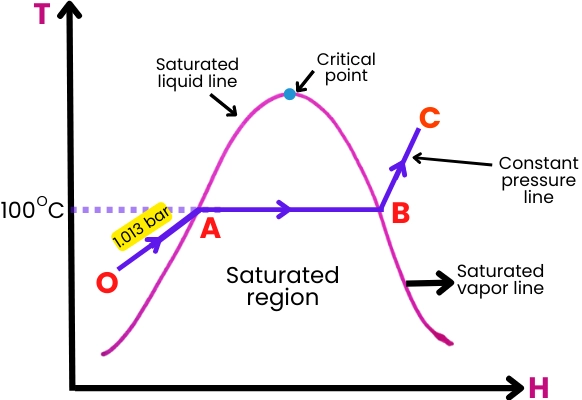
Thermodynamic Cycles
The operation of steam turbines is fundamentally based on thermodynamic cycles, with the Rankine cycle being the most important for understanding how these machines work. The Rankine cycle, named after William John Macquorn Rankine, is a closed-loop cycle that converts heat into work, making it the backbone of steam turbine operations in power plants and industrial settings.
- The Rankine Cycle: The Rankine cycle consists of four main processes:
- Isentropic Compression: The working fluid (water) is pumped from a low pressure to a high pressure. This process requires work input, typically provided by a pump.
- Isobaric Heat Addition: The high-pressure water is heated in a boiler at constant pressure, turning it into high-pressure steam.
- Isentropic Expansion: The high-pressure steam is expanded in the turbine, doing work by turning the turbine’s rotor. As the steam expands, its pressure and temperature drop.
- Isobaric Heat Rejection: The expanded steam is condensed at constant pressure back into water, completing the cycle.
- Reheat Cycle: In a reheat cycle, steam is expanded in a high-pressure turbine, reheated in the boiler, and then expanded again in a low-pressure turbine. This process increases the thermal efficiency of the cycle by allowing the steam to expand through a greater pressure range, reducing the moisture content at the turbine’s exhaust, which in turn minimizes turbine blade erosion.
- Regenerative Cycle: The regenerative cycle improves efficiency by preheating the feedwater entering the boiler using steam extracted from various stages of the turbine. This reduces the amount of fuel needed to heat the water to the desired temperature, thereby improving overall efficiency.
- Combined Cycle: The combined cycle is a modern approach that combines a gas turbine cycle with a steam turbine cycle. The exhaust gases from the gas turbine are used to generate steam in a heat recovery steam generator (HRSG), which then powers a steam turbine. This setup allows for very high overall efficiency, often exceeding 60%.
Fluid Dynamics in Steam Turbines
Fluid dynamics plays a crucial role in the operation of steam turbines, as the efficient conversion of steam energy into mechanical work depends on the controlled flow of steam through the turbine.
- Steam Flow and Velocity Triangles: The flow of steam through a turbine is characterized by velocity triangles, which are geometric representations of the velocity of steam relative to the blades of the turbine. These triangles help in analyzing the energy conversion process as the steam flows through both the stationary (stator) and moving (rotor) blades.
- Absolute Velocity: This is the velocity of the steam relative to the stationary components of the turbine.
- Relative Velocity: This is the velocity of the steam relative to the moving blades of the rotor.
- Blade Velocity: The velocity at which the turbine blades move.
- Impulse and Reaction Principles: Steam turbines operate on either impulse or reaction principles, or a combination of both.
- Impulse Turbines: In impulse turbines, steam is expanded through nozzles, converting its pressure energy into kinetic energy before it hits the rotor blades. The rotor blades are designed to absorb this kinetic energy, causing the rotor to spin.
- Reaction Turbines: In reaction turbines, the steam undergoes a pressure drop as it passes through the rotor blades, which are shaped to act as nozzles. The pressure drop results in a reactive force that turns the rotor. This principle is similar to how a jet engine works.
- Expansion and Losses: As steam expands through the turbine, it loses energy due to several factors, including friction, heat losses, and mechanical losses. These losses reduce the overall efficiency of the turbine. Understanding and minimizing these losses is crucial for optimizing turbine performance.
- Frictional Losses: Occur due to the friction between steam and the turbine blades and internal surfaces.
- Heat Losses: Result from the heat exchange between steam and the turbine casing or the environment.
- Mechanical Losses: Include losses in bearings, seals, and other mechanical components of the turbine.
Heat Transfer Mechanisms
Heat transfer is a critical aspect of steam turbine operation, influencing both efficiency and performance. The primary heat transfer mechanisms involved are conduction, convection, and radiation.
- Conduction: Conduction is the transfer of heat through a solid material, such as the turbine casing or blades. In steam turbines, conduction occurs when heat flows through the metal components from the high-temperature steam to cooler regions. The thermal conductivity of the materials used in turbine construction is an important factor, as it affects the rate of heat transfer and the temperature distribution within the turbine.
- Convection: Convection is the transfer of heat between a solid surface and a fluid, in this case, steam. It occurs when steam flows over the turbine blades and heat is transferred from the steam to the blade material. The efficiency of this process is influenced by factors such as steam velocity, turbulence, and the surface roughness of the blades.
- Forced Convection: In steam turbines, forced convection occurs as steam is forced through the turbine at high velocities. The design of the turbine blades and the flow paths are optimized to enhance heat transfer through forced convection.
- Natural Convection: Natural convection plays a lesser role in steam turbines but can occur in areas where steam or air is stagnant. Managing natural convection is important in turbine cooling and in maintaining structural integrity.
- Radiation: Radiation is the transfer of heat through electromagnetic waves. In steam turbines, radiation heat transfer is typically less significant than conduction and convection but can become important at very high temperatures, such as those found in the superheater sections of a boiler or in high-temperature turbines.
- Thermal Radiation: The turbine components emit thermal radiation based on their temperature. This radiation can contribute to heat losses if not properly managed through insulation and other thermal management techniques.
Design and Manufacturing of Steam Turbines
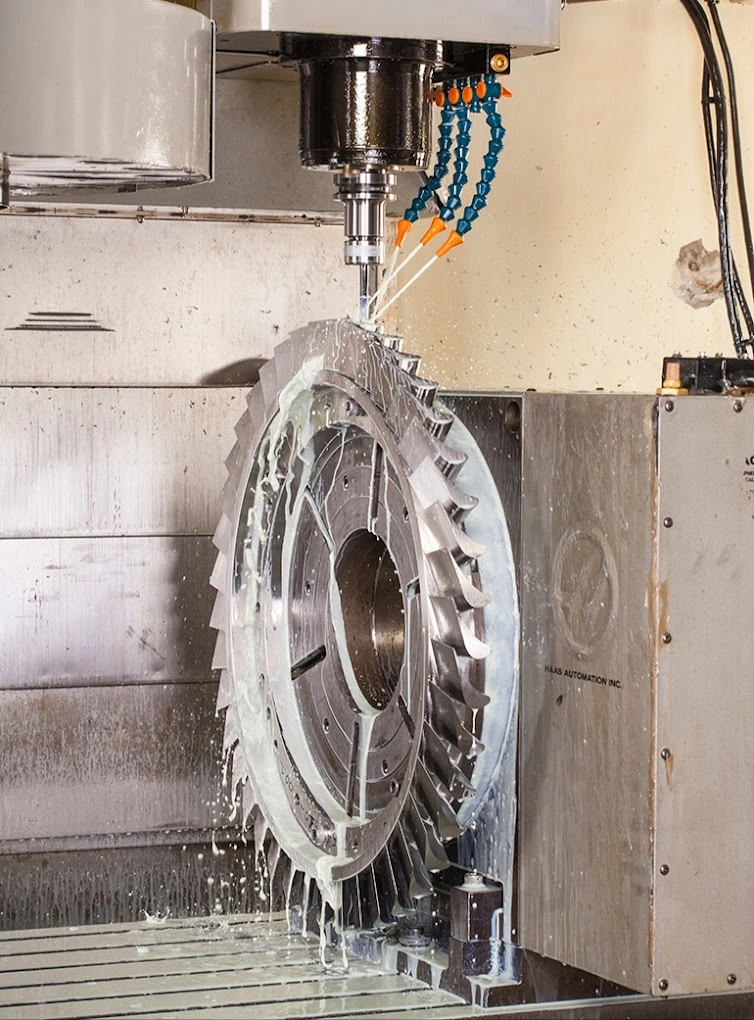
Design Process
Designing a steam turbine is a complex process that requires a deep understanding of thermodynamics, fluid mechanics, materials science, and mechanical engineering. The primary goals in designing a steam turbine are to maximize efficiency, ensure reliability, and meet the specific operational requirements of the application.
- Thermodynamic Efficiency: The design begins with thermodynamic calculations to determine the optimal operating conditions, such as steam pressure, temperature, and flow rate. Engineers use these calculations to design the turbine stages, ensuring that each stage extracts the maximum possible energy from the steam.
- Blade Design: The design of the turbine blades is crucial for efficiency and reliability. Blades must be aerodynamically optimized to maximize energy extraction while minimizing losses due to friction, turbulence, and separation. The shape, angle, and length of the blades are carefully calculated, often using computational fluid dynamics (CFD) simulations to model the flow of steam through the turbine.
- Material Selection: The materials used in turbine construction must withstand high temperatures, pressures, and mechanical stresses. Material selection is driven by the need for strength, durability, resistance to corrosion and erosion, and the ability to maintain performance under thermal cycling. Common materials include high-strength alloys, stainless steel, and nickel-based superalloys.
- Cooling and Heat Management: In high-temperature turbines, especially those used in power generation, cooling is a critical design consideration. Blades and other components are often internally cooled using air or steam to prevent overheating and maintain structural integrity. Advanced cooling designs, such as film cooling or transpiration cooling, may be used in particularly demanding applications.
- Rotor Dynamics and Balancing: The rotor is a critical component that must be carefully designed to ensure smooth and reliable operation. Engineers must account for rotor dynamics, including the natural frequencies of the rotor, to avoid resonance that could lead to mechanical failure. Additionally, the rotor must be precisely balanced to prevent excessive vibrations, which can cause wear and tear on bearings and other components.
- Sealing and Clearance Control: Minimizing steam leakage between different stages of the turbine is essential for maintaining efficiency. Engineers design precise seals and control clearances between rotating and stationary parts to reduce losses. Advanced sealing techniques, such as labyrinth seals and brush seals, are often used.
- Mechanical Integrity and Safety: The design must ensure that the turbine can operate safely under all expected conditions, including start-up, shutdown, and emergency situations. This involves designing for mechanical integrity, with components capable of withstanding high mechanical loads, thermal stresses, and the effects of transient conditions such as pressure surges or steam hammer.
- Modularity and Scalability: Modern steam turbines are often designed with modularity in mind, allowing for scalability and customization to meet different power outputs or industrial requirements. This modular approach also facilitates maintenance and component replacement.
Materials Used
The materials used in the construction of steam turbines are chosen for their ability to withstand the extreme conditions present during operation, such as high temperatures, pressures, and mechanical stresses. The selection of materials is crucial for ensuring the turbine’s performance, longevity, and safety.
- High-Strength Alloys: High-strength alloys, such as chromium-molybdenum steel, are commonly used for turbine rotors, casings, and other critical components. These alloys offer a good balance of strength, toughness, and resistance to thermal fatigue.
- Nickel-Based Superalloys: Nickel-based superalloys are frequently used in high-temperature sections of the turbine, such as the blades and vanes in the high-pressure stages. These superalloys are specifically designed to maintain their mechanical properties at elevated temperatures, making them ideal for use in environments where temperatures can exceed 1000°C.
- Stainless Steel: Stainless steel is used for components that require excellent corrosion resistance, such as parts exposed to wet steam or aggressive industrial environments. Austenitic stainless steels, in particular, are favored for their high-temperature performance and resistance to oxidation.
- Ceramic Coatings: To further enhance the high-temperature performance of turbine blades, ceramic coatings are often applied. These coatings provide a thermal barrier, reducing the amount of heat transferred to the underlying metal, which helps to protect against thermal degradation and extends the life of the blades.
- Titanium Alloys: Titanium alloys are sometimes used in low-pressure turbine blades due to their high strength-to-weight ratio and resistance to corrosion. Their lower density compared to steel or nickel-based alloys makes them advantageous in applications where weight savings are critical.
- Creep-Resistant Materials: Creep, the tendency of materials to deform permanently under constant stress at high temperatures, is a significant concern in steam turbines. Creep-resistant materials, such as advanced ferritic steels, are used
Manufacturing Techniques
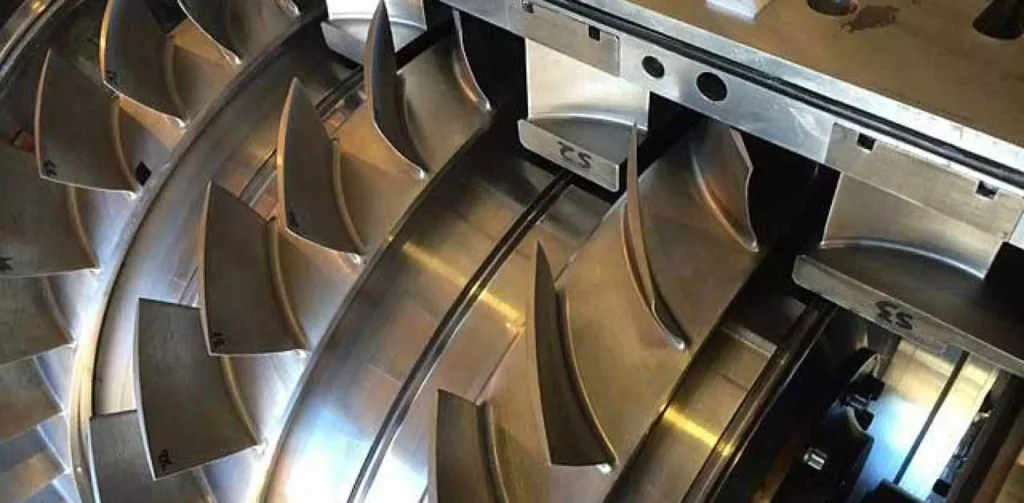
The manufacturing of steam turbines involves a series of highly specialized processes that ensure the precise fabrication and assembly of components capable of withstanding extreme operational conditions. The techniques used vary depending on the size, complexity, and specific requirements of the turbine.
- Casting: Many components of steam turbines, particularly the rotor and casing, are produced using casting techniques. Casting involves pouring molten metal into a mold shaped like the final part. Once the metal solidifies, the mold is removed, leaving behind a rough component that is further refined. Investment casting and sand casting are common methods used for creating intricate parts like blades, where precision and material integrity are crucial.
- Forging: Forging is another critical manufacturing process used to create strong, high-integrity components such as rotors and discs. In forging, a metal workpiece is heated and then shaped under high pressure, which aligns the metal’s grain structure, resulting in enhanced mechanical properties. Forged components are typically stronger and more resistant to fatigue and creep than cast parts, making them ideal for high-stress areas of the turbine.
- Machining: After casting or forging, most turbine components undergo machining to achieve the necessary dimensions, surface finishes, and tolerances. Machining processes include milling, turning, drilling, and grinding. Computer numerical control (CNC) machines are often used to ensure high precision and repeatability, especially for components like blades, where aerodynamic properties are critical.
- Heat Treatment: Heat treatment processes, such as annealing, quenching, and tempering, are used to enhance the mechanical properties of turbine components. These processes alter the microstructure of the metal, improving its strength, toughness, and resistance to wear and thermal fatigue. For instance, heat treatment is crucial for blades that must maintain their integrity at high operating temperatures.
- Surface Treatments and Coatings: To protect against corrosion, erosion, and high-temperature oxidation, turbine components often undergo surface treatments and coatings. Techniques such as thermal spraying, chemical vapor deposition (CVD), and physical vapor deposition (PVD) are used to apply protective coatings. Ceramic coatings, as mentioned earlier, are commonly applied to blades to provide thermal insulation and reduce heat transfer.
- Welding and Joining: Welding is a critical process in the assembly of steam turbines, particularly for joining large sections of the casing or connecting blades to the rotor. Advanced welding techniques, such as electron beam welding and laser welding, are used to create high-strength joints with minimal defects. These techniques are especially important for maintaining the structural integrity of the turbine under high-pressure and high-temperature conditions.
- Balancing and Assembly: Once all the components are manufactured, they are carefully assembled. The rotor, which is one of the most critical components, must be precisely balanced to ensure smooth operation at high speeds. Balancing involves adjusting the distribution of mass around the rotor’s axis to minimize vibrations. This is typically done using specialized balancing machines that measure and correct any imbalance.
- Quality Control and Testing: Quality control is paramount in steam turbine manufacturing. Each component undergoes rigorous inspection and testing to ensure it meets the required specifications. Non-destructive testing (NDT) methods, such as ultrasonic testing, radiography, and dye penetrant inspection, are used to detect any internal or surface defects. The assembled turbine is also subjected to performance testing, where it is run under controlled conditions to verify its efficiency, output, and operational stability.
- Final Assembly and Installation: After passing all tests, the turbine is finally assembled and prepared for shipment to its installation site. Installation requires precise alignment and calibration to ensure that the turbine operates correctly within its intended system, whether it’s a power plant, industrial facility, or marine vessel. The installation process includes integrating the turbine with the steam supply, electrical systems, and other necessary infrastructure.
Operation and Maintenance
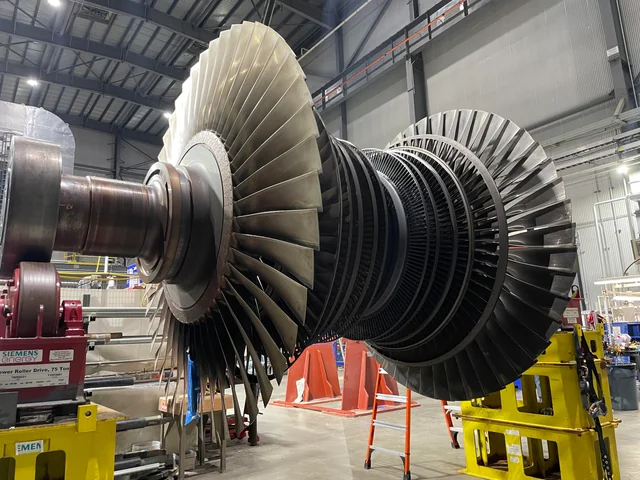
Operating Conditions
Steam turbines operate under demanding conditions, where factors such as temperature, pressure, steam quality, and load variations can significantly impact their performance and longevity. Understanding these conditions is essential for optimizing turbine operation and ensuring reliable performance.
- Temperature and Pressure: Steam turbines are designed to operate at high temperatures and pressures. In typical power generation applications, steam enters the turbine at temperatures ranging from 500°C to 600°C and pressures up to 30 MPa (megapascals). These extreme conditions enable the turbine to extract maximum energy from the steam, but they also impose significant thermal and mechanical stresses on the components.
- Steam Quality: The quality of the steam entering the turbine is critical for efficient operation. Ideally, the steam should be dry and superheated to prevent condensation inside the turbine, which can lead to erosion of the blades and reduced efficiency. However, in some applications, such as nuclear power plants, saturated steam may be used, requiring careful design and operation to manage the associated risks.
- Load Variations: Steam turbines often operate under varying loads, depending on the demand for electricity or the specific requirements of the industrial process they are powering. The ability to quickly and efficiently respond to load changes is crucial for maintaining stable operation. Turbines must be capable of ramping up or down without excessive wear or risk of damage.
- Startup and Shutdown Procedures: The processes of starting up and shutting down a steam turbine are critical periods that require careful control. During startup, the turbine components must be gradually brought up to operating temperature to avoid thermal shocks, which can cause cracking or deformation. Similarly, shutdown procedures involve slowly cooling the turbine to prevent damage.
- Control Systems: Modern steam turbines are equipped with sophisticated control systems that manage various operational parameters, such as steam flow, temperature, pressure, and rotational speed. These systems ensure that the turbine operates within its design limits and responds appropriately to changes in load or other operating conditions.
Maintenance Practices
Regular maintenance is essential to ensure the long-term reliability and efficiency of steam turbines. Maintenance practices are typically divided into preventive, predictive, and corrective maintenance.
- Preventive Maintenance: Preventive maintenance involves routine inspections and servicing of the turbine to prevent potential issues from arising. This includes tasks such as:
- Lubrication: Regular lubrication of bearings and other moving parts to reduce friction and wear.
- Inspection of Blades and Seals: Checking for signs of wear, erosion, or corrosion on turbine blades and seals.
- Cleaning: Removing deposits or scale from turbine components to maintain optimal performance.
- Calibration: Ensuring that control systems and sensors are accurately calibrated to prevent operational errors.
- Predictive Maintenance: Predictive maintenance uses condition monitoring techniques to predict when maintenance is needed before a failure occurs. This approach allows for maintenance to be scheduled based on the actual condition of the turbine rather than on a fixed schedule. Key techniques include:
- Vibration Analysis: Monitoring the vibrations of the turbine to detect imbalances, misalignment, or bearing issues.
- Thermography: Using infrared cameras to detect hotspots or uneven temperature distributions that may indicate a problem.
- Oil Analysis: Analyzing the lubrication oil for signs of contamination, wear particles, or chemical degradation.
- Corrective Maintenance: When a component fails or a problem is detected, corrective maintenance is performed to repair or replace the affected parts. This type of maintenance can involve:
- Blade Replacement: Replacing damaged or worn blades to restore turbine efficiency and prevent further damage.
- Seal Repair or Replacement: Addressing issues with seals that may cause steam leakage or reduced efficiency.
- Bearing Replacement: Replacing worn or damaged bearings to prevent rotor imbalance and excessive vibrations.
- Outage Planning: Steam turbines typically undergo scheduled outages for extensive inspections, repairs, and overhauls. These outages are carefully planned to minimize downtime and ensure that the turbine is returned to service in optimal condition. During an outage, the turbine may be disassembled, with major components like the rotor, blades, and casing inspected and refurbished as necessary.
Common Issues and Solutions
Steam turbines, despite their robust design, can encounter various issues during operation. Identifying and addressing these issues promptly is key to maintaining reliable performance.
- Blade Fouling and Erosion: Fouling occurs when deposits form on the turbine blades, often as a result of impurities in the steam. Erosion, on the other hand, is caused by high-velocity steam or water droplets impinging on the blades, gradually wearing away the material. These issues can lead to reduced efficiency and, if left unchecked, can cause serious damage.
- Solution: Regular cleaning and maintenance can prevent fouling, while erosion-resistant coatings can extend blade life. Additionally, improving the quality of the steam entering the turbine can reduce the risk of these problems.
- Vibration and Rotor Imbalance: Excessive vibration is a common issue in steam turbines and can be caused by rotor imbalance, misalignment, bearing wear, or other mechanical problems. Vibration can lead to accelerated wear of components and, in severe cases, catastrophic failure.
- Solution: Vibration analysis and regular balancing of the rotor can help detect and correct these issues before they cause significant damage. Proper alignment during installation and routine bearing inspections are also critical.
- Steam Leakage: Steam leakage can occur due to worn seals, poor sealing surfaces, or cracks in the casing. This leads to a loss of efficiency and can also cause damage to surrounding components.
- Solution: Regular inspection of seals and replacement when necessary can mitigate steam leakage. In some cases, upgrading to more advanced sealing technologies, such as brush seals, can provide a better seal and longer service life.
- Thermal Fatigue and Creep: Thermal fatigue occurs when turbine components are subjected to repeated cycles of heating and cooling, leading to the formation of cracks. Creep is a gradual deformation of materials under constant high temperature and stress. Both issues can significantly impact the structural integrity of the turbine.
- Solution: Using materials specifically designed to resist thermal fatigue and creep, along with careful control of operating conditions, can minimize these risks. Regular inspection and monitoring for signs of fatigue or creep are also essential.
- Control System Failures: The control systems of steam turbines are vital for safe and efficient operation. Failures in these systems can lead to incorrect steam flow, pressure surges, or even turbine trips.
- Solution: Regular testing and calibration of control systems, along with the use of redundant systems, can help prevent control system failures. Upgrading older systems to modern, digital control systems can also enhance reliability.
Applications of Steam Turbines
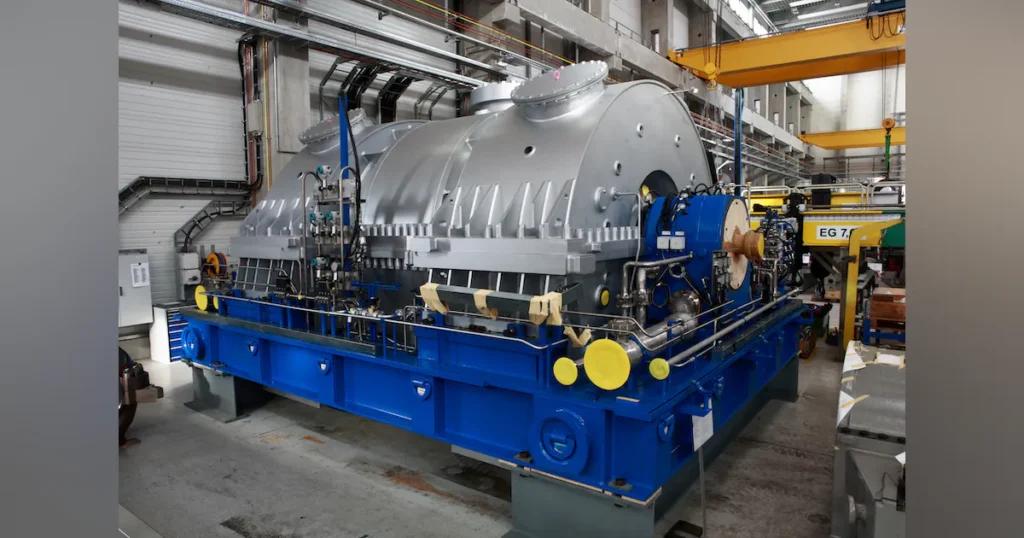
Power Generation
Steam turbines are central to power generation and are used in a variety of settings, from large-scale thermal power plants to smaller, decentralized energy systems. The following subsections outline the main applications of steam turbines in power generation:
- Coal-Fired Power Plants:
- Overview: Coal-fired power plants have historically been one of the most common applications of steam turbines. In these plants, coal is burned in a boiler to produce high-pressure steam, which is then directed into a steam turbine to generate electricity.
- Role of Steam Turbines: Steam turbines in coal-fired plants are designed to handle the high temperatures and pressures associated with coal combustion. They convert the thermal energy from the steam into mechanical energy, which drives an electrical generator.
- Environmental Considerations: While coal-fired power plants are efficient, they are also a significant source of greenhouse gas emissions. Many modern plants incorporate emission control technologies and are transitioning to cleaner coal technologies, such as supercritical and ultra-supercritical steam cycles, to improve efficiency and reduce emissions.
- Nuclear Power Plants:
- Overview: In nuclear power plants, steam turbines are used to convert the thermal energy generated by nuclear fission into electricity. These plants use nuclear reactors to heat water and produce steam.
- Role of Steam Turbines: The steam produced in a nuclear reactor is typically at a lower temperature and pressure compared to that in fossil-fuel plants. However, the turbines must be extremely reliable and durable due to the safety-critical nature of nuclear power generation. The turbines in nuclear plants are often large, with high power outputs to match the continuous energy production of the reactor.
- Special Considerations: The design of steam turbines for nuclear power includes considerations for safety, such as the ability to operate reliably under potential emergency conditions and withstand the corrosive effects of certain types of steam.
- Gas-Fired Power Plants (Combined Cycle):
- Overview: Combined cycle power plants use both gas and steam turbines to generate electricity. In these plants, a gas turbine generates electricity and its exhaust heat is used to produce steam, which then powers a steam turbine.
- Role of Steam Turbines: The steam turbine in a combined cycle plant enhances the overall efficiency of the plant by utilizing the waste heat from the gas turbine. This process significantly increases the plant’s thermal efficiency, often reaching levels above 60%.
- Advantages: Combined cycle plants are known for their high efficiency, flexibility, and lower carbon emissions compared to traditional coal-fired plants. Steam turbines in these plants are integral to achieving these benefits.
- Geothermal Power Plants:
- Overview: Geothermal power plants use steam turbines to generate electricity from geothermal energy, which is the heat stored within the Earth.
- Role of Steam Turbines: In geothermal plants, steam is extracted from underground reservoirs and used to drive turbines. These turbines must be designed to handle steam with varying temperatures and pressures, as well as the potential presence of corrosive gases and minerals.
- Challenges and Solutions: The main challenges in geothermal power generation include scaling, corrosion, and the management of non-condensable gases. Turbine designs that include corrosion-resistant materials and advanced sealing technologies are essential for long-term operation in these environments.
- Solar Thermal Power Plants:
- Overview: Solar thermal power plants, also known as concentrating solar power (CSP) plants, use steam turbines to generate electricity from solar energy.
- Role of Steam Turbines: In CSP plants, mirrors or lenses concentrate sunlight to heat a fluid, which is then used to produce steam. The steam drives a turbine, converting thermal energy into mechanical energy for electricity generation.
- Innovations: Some CSP plants incorporate thermal storage systems, allowing them to generate electricity even when the sun is not shining. The steam turbines in these plants must be adaptable to varying steam inputs and capable of operating efficiently with the thermal storage systems.
Industrial Applications
Beyond power generation, steam turbines are widely used in various industrial processes where they provide mechanical power for a range of applications.
- Petrochemical Industry:
- Overview: Steam turbines are essential in the petrochemical industry, where they are used to drive compressors, pumps, and other machinery involved in the processing of chemicals and petroleum products.
- Role of Steam Turbines: The turbines in this industry are often designed for continuous operation, high efficiency, and reliability under harsh conditions, including high temperatures and corrosive environments.
- Advantages: Using steam turbines in petrochemical plants helps improve overall energy efficiency by recovering waste heat and converting it into useful mechanical or electrical energy.
- Pulp and Paper Industry:
- Overview: The pulp and paper industry relies on steam turbines for both electricity generation and mechanical drives in processes such as pulping, drying, and paper making.
- Role of Steam Turbines: Steam turbines in this industry often operate in cogeneration setups, where they simultaneously produce electricity and steam for the manufacturing process. This combined heat and power (CHP) approach enhances energy efficiency.
- Challenges: The main challenges include handling fluctuating loads and ensuring reliable operation in environments with high moisture content and potential corrosive chemicals.
- Steel Manufacturing:
- Overview: In steel manufacturing, steam turbines are used to drive blowers, compressors, and rolling mills. The steam used often comes from waste heat recovery systems, making the process more energy-efficient.
- Role of Steam Turbines: Steam turbines help reduce the overall energy consumption of steel mills by utilizing waste heat to generate power for various processes.
- Benefits: Integrating steam turbines into steel manufacturing processes not only reduces energy costs but also helps in meeting environmental regulations by lowering emissions.
- Sugar Industry:
- Overview: The sugar industry uses steam turbines extensively in the production of sugar and ethanol. The turbines are part of the cogeneration systems that use bagasse (the fibrous residue left after extracting sugar juice) as fuel.
- Role of Steam Turbines: In this industry, steam turbines generate electricity and provide mechanical power for the crushing and refining processes. The use of biomass like bagasse makes the process more sustainable and reduces dependence on fossil fuels.
- Sustainability: The integration of steam turbines into sugar production highlights the potential for renewable energy sources in industrial applications.
Marine Propulsion
Steam turbines have a long history of use in marine propulsion, particularly in naval vessels and large commercial ships. Their reliability, efficiency, and power output make them ideal for this demanding application.
- Naval Vessels:
- Overview: Steam turbines have been a mainstay in naval propulsion, especially in large vessels such as aircraft carriers, destroyers, and submarines.
- Role of Steam Turbines: Naval turbines are designed for high power output, reliability, and efficiency. They must operate under extreme conditions, including rapid speed changes and prolonged high-speed operation.
- Advancements: Modern naval steam turbines often incorporate advanced materials and cooling technologies to withstand the harsh marine environment and to operate quietly, which is crucial for stealth in military operations.
- Commercial Shipping:
- Overview: In commercial shipping, steam turbines are used in large vessels such as tankers and bulk carriers. Although diesel engines have become more common, steam turbines are still used in certain applications, particularly where high power and long-range operation are required.
- Advantages: Steam turbines offer smooth operation, reduced vibration, and lower maintenance requirements compared to other propulsion systems, making them suitable for large ships.
- Trends: The use of steam turbines in commercial shipping has declined with the rise of more fuel-efficient diesel engines. However, they remain in use in specific scenarios where their benefits outweigh those of alternative technologies.
Renewable Energy Integration
Steam turbines are also finding applications in renewable energy systems, contributing to the generation of clean and sustainable energy.
- Biomass Power Plants:
- Overview: Biomass power plants use organic materials, such as wood, agricultural residues, and waste, to produce steam, which then drives turbines to generate electricity.
- Role of Steam Turbines: In biomass plants, steam turbines must handle steam generated from a variety of biomass sources, which can vary in quality and consistency. The turbines are designed to be flexible and efficient, maximizing the energy extracted from biomass.
- Environmental Benefits: Biomass power generation is considered carbon-neutral, as the CO2 released during combustion is offset by the CO2 absorbed during the growth of the biomass. Steam turbines play a key role in making this a viable and sustainable energy source.
- Concentrated Solar Power (CSP):
- Overview: In CSP plants, steam turbines are used to convert solar energy into electricity. The plants use mirrors or lenses to concentrate sunlight onto a receiver, where it heats a fluid to produce steam.
- Role of Steam Turbines: The turbines in CSP plants must be designed to operate efficiently with steam generated from fluctuating solar input, as well as to integrate with thermal storage systems that allow for power generation even when the sun is not shining.
- Innovation and Future Potential: As CSP technology advances, steam turbines are expected to play an increasingly important role in providing renewable, dispatchable power, helping to stabilize grids with high penetration of intermittent renewable sources like wind and solar PV.
Efficiency and Performance Optimization
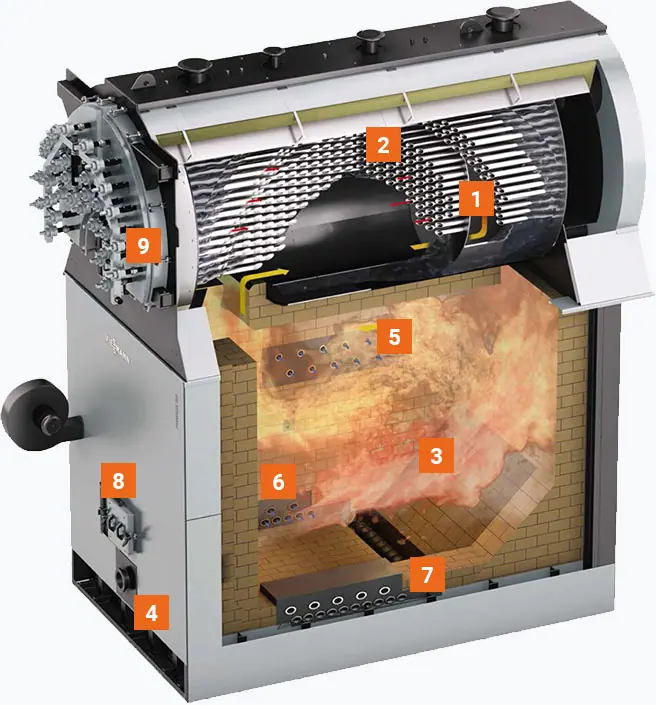
Factors Affecting Efficiency
The efficiency of a steam turbine is a critical aspect of its performance, influencing the overall energy conversion process and the economic viability of power plants and industrial applications. Several factors can impact the efficiency of a steam turbine:
- Steam Conditions:
- Temperature and Pressure: The higher the steam temperature and pressure at the turbine inlet, the greater the potential for energy extraction. Superheated steam, with higher energy content, allows the turbine to produce more work, thereby increasing efficiency. However, materials and design must be capable of withstanding these extreme conditions.
- Steam Quality: The quality of steam, particularly its dryness fraction, affects turbine performance. Wet steam can cause erosion of turbine blades and reduce efficiency due to the presence of water droplets. Maintaining a high dryness fraction or superheating the steam minimizes these losses.
- Design and Aerodynamics:
- Blade Design: The design of turbine blades, including their shape, angle, and surface finish, plays a significant role in efficiency. Aerodynamically optimized blades reduce losses due to friction and turbulence, allowing for more effective energy conversion from steam to mechanical work.
- Stage Efficiency: Steam turbines are often divided into multiple stages, each designed to extract energy from steam at progressively lower pressures. The efficiency of each stage contributes to the overall turbine efficiency. Proper staging, with carefully calculated blade profiles and angles, is essential for maximizing efficiency.
- Mechanical Losses:
- Friction and Wear: Mechanical losses due to friction in bearings, seals, and other moving parts can reduce overall turbine efficiency. Regular maintenance, proper lubrication, and the use of advanced materials can help minimize these losses.
- Vibration and Imbalance: Imbalances in the rotor or excessive vibrations can lead to mechanical inefficiencies, as energy is lost in the form of unwanted movements. Ensuring that the turbine is properly balanced and that vibrations are controlled through effective damping mechanisms is crucial.
- Thermodynamic Losses:
- Heat Losses: Heat losses occur when steam or other components transfer heat to the surrounding environment. Proper insulation of the turbine casing and piping, as well as minimizing the temperature gradient within the turbine, can help reduce these losses.
- Entropy Generation: Inefficiencies in the expansion process within the turbine stages can lead to increased entropy, reducing the available work output. Reducing these losses involves optimizing the expansion process and minimizing irreversible losses within the turbine.
Optimization Techniques
Improving the efficiency of steam turbines involves a combination of design optimization, operational strategies, and technological innovations. The following techniques are commonly used to enhance turbine performance:
- Advanced Blade Design:
- Computational Fluid Dynamics (CFD): CFD is widely used in the design and optimization of turbine blades. By simulating the flow of steam through the turbine, engineers can identify areas where losses occur and adjust blade shapes and angles to improve efficiency. CFD allows for the testing of multiple design iterations in a virtual environment, reducing the need for physical prototypes.
- 3D Blade Profiling: Advanced manufacturing techniques, such as 3D printing and precision machining, enable the production of complex blade profiles that are tailored to specific operating conditions. 3D blade profiling can result in blades that offer better aerodynamic performance and reduced losses.
- Steam Temperature and Pressure Control:
- Superheating and Reheating: Increasing the temperature of steam before it enters the turbine (superheating) or reheating steam between turbine stages can significantly improve efficiency. Reheating, in particular, allows for more energy extraction by reducing the moisture content in the later stages of the turbine.
- Pressure Optimization: Operating the turbine at the optimal steam pressure for each stage can maximize efficiency. This involves careful control of steam pressure throughout the turbine, ensuring that each stage operates at its most efficient point on the pressure-enthalpy curve.
- Energy Recovery Systems:
- Regenerative Feedwater Heating: Regenerative feedwater heating is a technique where steam is extracted from intermediate stages of the turbine and used to preheat the feedwater before it enters the boiler. This reduces the amount of fuel needed to reach the desired steam temperature, thereby improving the overall efficiency of the Rankine cycle.
- Condensate Recovery: Efficient recovery and reuse of condensate (water) from the turbine exhaust can reduce the energy required to heat and pressurize water for subsequent cycles. This also minimizes the need for additional water treatment, contributing to overall efficiency improvements.
- Load Optimization:
- Variable Load Operation: Modern steam turbines are designed to operate efficiently across a range of loads, not just at full capacity. By optimizing turbine performance under partial loads, power plants can improve overall efficiency, especially in applications where demand fluctuates throughout the day.
- Load Matching: Load matching involves adjusting the turbine’s operation to match the specific energy demand at any given time. This can involve varying the steam flow rate, adjusting the number of active turbine stages, or modulating the turbine’s output to match real-time load requirements.
- Monitoring and Control Systems:
- Real-Time Performance Monitoring: Advanced sensors and control systems allow for real-time monitoring of turbine performance, including temperature, pressure, vibration, and efficiency metrics. By continuously monitoring these parameters, operators can make adjustments to optimize performance and prevent issues before they lead to inefficiencies or failures.
- Predictive Maintenance: Using data analytics and machine learning, predictive maintenance systems can forecast potential issues based on historical performance data. This allows for maintenance to be performed proactively, reducing downtime and improving overall turbine efficiency.
Monitoring and Performance Analysis
Maintaining optimal efficiency in steam turbines requires ongoing monitoring and analysis of performance data. The following approaches are commonly used to assess and enhance turbine efficiency:
- Key Performance Indicators (KPIs):
- Heat Rate: The heat rate is a measure of the amount of energy used by the turbine to generate electricity. It is typically expressed as the amount of fuel energy required per unit of electrical output (e.g., BTU/kWh). Monitoring the heat rate helps identify inefficiencies in fuel use and overall turbine performance.
- Thermal Efficiency: Thermal efficiency measures the ratio of useful work output to the total heat input. It is a key indicator of how effectively the turbine converts thermal energy into mechanical energy. Higher thermal efficiency indicates better performance.
- Capacity Factor: The capacity factor is the ratio of the actual output of the turbine over a period of time to its maximum possible output. It reflects how well the turbine is being utilized relative to its full capacity.
- Performance Testing:
- Acceptance Testing: Acceptance testing is conducted when a turbine is first installed or after a major overhaul to ensure it meets the specified performance criteria. These tests typically measure parameters such as output power, efficiency, and steam consumption under controlled conditions.
- Routine Testing: Periodic performance testing is conducted to monitor the ongoing efficiency of the turbine. Routine tests help detect gradual declines in performance, allowing for timely interventions to restore efficiency.
- Data Analytics and Optimization:
- Data Logging and Trend Analysis: Continuous data logging allows for the collection of vast amounts of performance data, which can be analyzed to identify trends, detect anomalies, and assess the impact of operational changes on efficiency.
- Digital Twins: A digital twin is a virtual model of the steam turbine that simulates its real-world counterpart in real time. By comparing the digital twin’s performance with actual operational data, operators can identify inefficiencies and test potential optimizations without risking the physical turbine.
- Diagnostic Tools:
- Vibration Monitoring: Vibration analysis is a critical diagnostic tool for detecting mechanical issues such as rotor imbalance, misalignment, or bearing wear. By identifying and correcting these issues early, operators can prevent efficiency losses and extend the life of the turbine.
- Thermal Imaging: Thermal imaging is used to detect hotspots and assess the distribution of temperature across the turbine components. This helps identify areas where heat losses are occurring and where insulation or cooling might be needed.
Environmental Impact and Sustainability
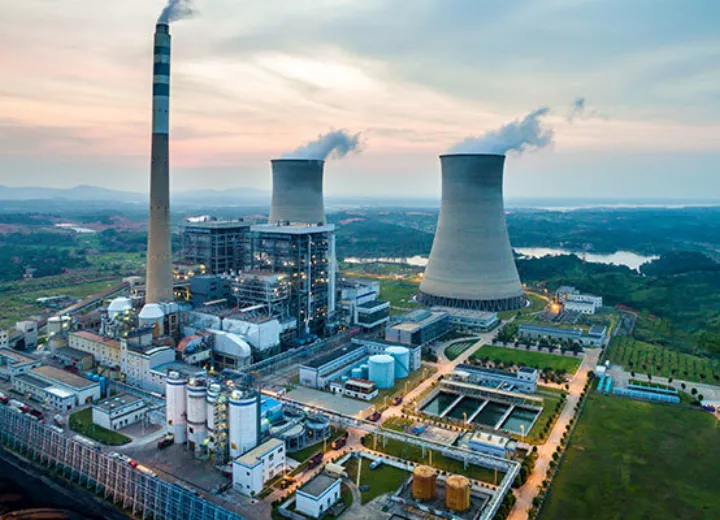
Environmental Concerns
Steam turbines, while crucial to power generation and industrial processes, are associated with several environmental concerns. These issues stem primarily from the energy sources used to produce steam and the byproducts of turbine operation.
- Greenhouse Gas Emissions:
- Fossil Fuel Combustion: Steam turbines used in coal, oil, and natural gas-fired power plants contribute significantly to greenhouse gas emissions, particularly carbon dioxide (CO2). The combustion of fossil fuels releases CO2, which is a major contributor to global warming and climate change.
- Mitigation Strategies: Efforts to reduce greenhouse gas emissions include improving the efficiency of steam turbines, transitioning to cleaner fuels, and integrating carbon capture and storage (CCS) technologies. Higher efficiency means that less fuel is required to produce the same amount of electricity, thereby reducing emissions per unit of energy generated.
- Air Pollutants:
- Sulfur Dioxide (SO2) and Nitrogen Oxides (NOx): Fossil fuel combustion in power plants can release harmful air pollutants, including SO2 and NOx, which contribute to acid rain and respiratory problems in humans. These pollutants are particularly prevalent in coal-fired power plants, where sulfur content in the fuel is higher.
- Control Technologies: Technologies such as flue gas desulfurization (FGD) and selective catalytic reduction (SCR) are used to reduce SO2 and NOx emissions from power plants. Additionally, low-NOx burners and other combustion optimization techniques help minimize the formation of these pollutants at the source.
- Water Usage and Thermal Pollution:
- Cooling Water Requirements: Steam turbines, particularly in large power plants, require substantial amounts of water for cooling. The withdrawal of water from natural sources can impact local ecosystems, especially if not managed sustainably. Furthermore, the discharge of heated water back into the environment can cause thermal pollution, which negatively affects aquatic life.
- Mitigation Strategies: To mitigate these impacts, power plants can adopt closed-loop cooling systems that minimize water withdrawal and reduce thermal discharge. Additionally, dry cooling systems, which use air instead of water, are increasingly being implemented, particularly in water-scarce regions.
- Solid Waste and Byproducts:
- Coal Ash and Slag: The combustion of coal in power plants produces solid byproducts such as ash and slag, which can contain heavy metals and other toxic substances. These byproducts must be managed carefully to prevent soil and water contamination.
- Disposal and Reuse: Modern waste management practices include the safe disposal of ash in lined landfills and the beneficial reuse of ash in construction materials, such as cement and concrete. By converting waste into valuable products, the environmental impact of coal ash can be minimized.
Sustainability Initiatives
In response to environmental concerns, the steam turbine industry is increasingly adopting sustainability initiatives aimed at reducing its environmental footprint and supporting the transition to a low-carbon economy.
- Integration with Renewable Energy:
- Biomass and Waste-to-Energy: Steam turbines are being integrated with renewable energy sources such as biomass and waste-to-energy plants. These systems use organic waste materials to produce steam, which is then converted into electricity by steam turbines. Biomass is considered carbon-neutral, as the CO2 released during combustion is offset by the CO2 absorbed during the growth of the biomass.
- Geothermal and Solar Thermal: Geothermal and concentrated solar power (CSP) plants also utilize steam turbines to generate electricity. These renewable energy sources produce little to no greenhouse gas emissions, making them attractive options for sustainable power generation. The use of steam turbines in these settings supports the broader adoption of renewable energy technologies.
- Efficiency Improvements:
- Supercritical and Ultra-Supercritical Steam Cycles: Advancements in turbine technology have led to the development of supercritical and ultra-supercritical steam cycles, which operate at higher temperatures and pressures than conventional steam cycles. These cycles achieve higher efficiencies, meaning that less fuel is needed to produce the same amount of electricity, resulting in lower emissions.
- Cogeneration and Combined Heat and Power (CHP): Cogeneration, or CHP, systems simultaneously produce electricity and useful heat from the same energy source. By capturing and utilizing the waste heat from steam turbines, CHP systems significantly improve overall energy efficiency, reducing fuel consumption and emissions.
- Carbon Capture and Storage (CCS):
- CCS Technology: Carbon capture and storage is a technology designed to capture CO2 emissions from power plants and industrial processes, preventing them from entering the atmosphere. The captured CO2 is then transported and stored underground in geological formations. When integrated with steam turbines, CCS can greatly reduce the carbon footprint of fossil fuel-based power generation.
- Challenges and Opportunities: While CCS has the potential to mitigate climate change, it faces challenges such as high costs, energy requirements, and the need for suitable storage sites. However, ongoing research and development efforts aim to overcome these barriers, making CCS a viable option for large-scale emission reductions.
- Material and Resource Efficiency:
- Recycling and Waste Minimization: The steam turbine industry is adopting practices to minimize waste and improve resource efficiency. This includes the recycling of metals and other materials used in turbine manufacturing, as well as the reduction of material waste through precision manufacturing techniques.
- Life Cycle Assessment (LCA): Life cycle assessment is a tool used to evaluate the environmental impacts of a product throughout its entire life cycle, from raw material extraction to disposal. By conducting LCAs, manufacturers can identify areas where environmental impacts can be reduced, leading to more sustainable turbine production and operation.
Regulatory Framework
The operation of steam turbines, particularly in power generation, is subject to a range of environmental regulations aimed at minimizing their impact on the environment. These regulations vary by region but generally focus on emissions control, water usage, and waste management.
- Emissions Regulations:
- Clean Air Act (U.S.): In the United States, the Clean Air Act (CAA) regulates air emissions from power plants and industrial sources, including those using steam turbines. The CAA establishes limits for pollutants such as SO2, NOx, and particulate matter, and mandates the use of best available control technologies (BACT) to reduce emissions.
- European Union Emissions Trading System (EU ETS): The EU ETS is a cap-and-trade system that sets a limit on the total amount of greenhouse gases that can be emitted by certain industries, including power generation. Steam turbine operators in the EU must comply with emission allowances or purchase additional allowances if they exceed their limits.
- Water Usage and Discharge Regulations:
- Clean Water Act (U.S.): The Clean Water Act (CWA) regulates the discharge of pollutants into U.S. waters and sets standards for water quality. Power plants using steam turbines must obtain permits for water withdrawal and discharge, ensuring that their operations do not harm aquatic ecosystems.
- EU Water Framework Directive: In the European Union, the Water Framework Directive establishes a framework for protecting water resources, including the regulation of water usage and thermal discharges from power plants. Compliance with these regulations is essential for the sustainable operation of steam turbines.
- Waste Management and Disposal:
- Resource Conservation and Recovery Act (RCRA): In the U.S., the RCRA governs the management of hazardous and non-hazardous waste, including coal ash from power plants. The act requires safe disposal practices and encourages the recycling and reuse of industrial byproducts.
- EU Waste Framework Directive: The EU Waste Framework Directive sets guidelines for waste management across member states, promoting recycling and the reduction of waste generation. Steam turbine operators must comply with these regulations to minimize their environmental impact.
- International Standards and Guidelines:
- ISO 14001 Environmental Management Systems: The ISO 14001 standard provides a framework for organizations to manage their environmental responsibilities in a systematic manner. Compliance with ISO 14001 helps steam turbine operators reduce their environmental footprint and improve sustainability.
- World Bank Environmental and Social Standards: The World Bank’s Environmental and Social Standards (ESS) provide guidelines for managing environmental and social risks in projects financed by the World Bank. These standards are often used in the development of power plants and other large-scale projects involving steam turbines.
Future Trends and Innovations
Technological Advances
The steam turbine industry is continuously evolving, driven by the need for greater efficiency, reliability, and environmental performance. Several technological advances are shaping the future of steam turbines:
- Advanced Materials:
- Superalloys: The development of advanced nickel-based superalloys is enabling steam turbines to operate at higher temperatures and pressures, which improves efficiency. These materials are designed to resist creep, corrosion, and thermal fatigue, making them ideal for use in the most demanding sections of the turbine.
- Ceramic Matrix Composites (CMCs): CMCs are gaining attention for their potential to replace traditional metal alloys in high-temperature turbine components. These materials offer excellent thermal stability, low density, and resistance to oxidation, allowing turbines to operate at even higher temperatures without compromising structural integrity.
- Additive Manufacturing: Also known as 3D printing, additive manufacturing is revolutionizing the production of turbine components. This technology allows for the creation of complex, optimized geometries that are difficult or impossible to achieve with traditional manufacturing methods. Additive manufacturing also reduces material waste and shortens production times.
- Advanced Blade Design:
- 3D-Aerodynamic Blades: Innovations in blade design, particularly through the use of 3D aerodynamic modeling, are improving the efficiency and performance of steam turbines. These blades are designed to optimize the flow of steam, reducing losses due to turbulence and friction. The use of computational fluid dynamics (CFD) simulations allows engineers to refine blade shapes for maximum efficiency.
- Shrouded and Shroudless Blades: Shrouded blades, which include a cover on the blade tips to reduce leakage, are being optimized to further improve efficiency. At the same time, advancements in shroudless blade designs are being explored to reduce weight and mechanical complexity while maintaining aerodynamic performance.
- Digitalization and Smart Turbines:
- Digital Twins: The concept of a digital twin, a virtual model of the steam turbine that runs in parallel with the physical machine, is becoming a critical tool in the industry. Digital twins allow operators to monitor turbine performance in real-time, predict maintenance needs, and optimize operations. By simulating different scenarios, digital twins can help identify potential issues before they occur and suggest the best course of action for maintenance or operational adjustments.
- Artificial Intelligence (AI) and Machine Learning: AI and machine learning are being increasingly used to enhance turbine control systems. These technologies enable more precise control of operating parameters, such as steam flow, pressure, and temperature, optimizing turbine efficiency under varying load conditions. AI-driven analytics can also predict equipment failures, reducing downtime and extending the life of turbine components.
- Modular and Scalable Designs:
- Modularity: The development of modular steam turbines is a trend aimed at improving flexibility and reducing costs. Modular turbines can be easily scaled up or down depending on the power generation requirements, making them suitable for both large-scale power plants and smaller, decentralized energy systems. Modularity also facilitates easier maintenance and component replacement, reducing downtime.
- Scalability for Microgrids: Steam turbines are being adapted for use in microgrids and distributed energy systems. These scalable turbines are designed to provide reliable power in remote locations or as part of a hybrid energy system that integrates renewable energy sources with traditional power generation.
Integration with Smart Grids
As the energy landscape evolves, steam turbines are being integrated into smart grid systems, which offer enhanced flexibility, reliability, and efficiency in power generation and distribution.
- Role of Steam Turbines in Smart Grids:
- Load Balancing: Steam turbines are essential in smart grids for load balancing, especially during peak demand periods. They can be ramped up or down to match the demand, helping to maintain grid stability and prevent blackouts. The ability to quickly respond to changes in demand makes steam turbines a valuable component of smart grids.
- Integration with Renewable Energy: Smart grids are increasingly incorporating renewable energy sources such as solar and wind. Steam turbines, particularly those in combined heat and power (CHP) plants, can provide backup power when renewable sources are intermittent, ensuring a continuous and reliable energy supply. By integrating with smart grid technologies, steam turbines can optimize their operation based on real-time data from the grid.
- Advanced Control Systems:
- Real-Time Monitoring and Control: Advanced control systems are being developed to allow steam turbines to operate more efficiently within a smart grid. These systems use real-time data to adjust operating parameters, such as steam pressure and temperature, to optimize performance. Real-time monitoring also helps detect potential issues before they lead to failures, reducing downtime and maintenance costs.
- Grid Synchronization: Steam turbines are being equipped with advanced synchronization technologies that allow them to seamlessly integrate with smart grids. These technologies ensure that the turbines can synchronize their output with the grid’s frequency and voltage, maintaining power quality and reliability.
- Demand Response and Energy Storage:
- Demand Response Programs: Steam turbines are playing a role in demand response programs, where power generation is adjusted based on real-time demand. In these programs, steam turbines can reduce their output during periods of low demand or increase it during peak times, helping to balance the grid and reduce the need for additional peaking power plants.
- Integration with Energy Storage: Steam turbines are being integrated with energy storage systems, such as batteries and thermal storage, to enhance their flexibility and efficiency. Energy storage allows turbines to store excess energy produced during periods of low demand and release it when needed, improving overall grid stability and efficiency.
Research and Development
Ongoing research and development (R&D) efforts are focused on advancing steam turbine technology to meet the evolving demands of the energy industry and address environmental challenges.
- High-Efficiency Steam Cycles:
- Supercritical and Ultra-Supercritical Cycles: R&D is driving the development of supercritical and ultra-supercritical steam cycles, which operate at higher temperatures and pressures than conventional cycles. These advanced cycles offer higher thermal efficiencies, reducing fuel consumption and emissions. Researchers are exploring new materials and designs that can withstand the extreme conditions of these cycles.
- Thermodynamic Cycle Innovations: Innovative thermodynamic cycles, such as the Kalina cycle and the Organic Rankine Cycle (ORC), are being explored for their potential to improve efficiency in specific applications. These cycles use different working fluids or configurations to optimize energy conversion, particularly in low-temperature or waste heat recovery applications.
- Low-Carbon and Carbon-Neutral Technologies:
- Hydrogen-Fueled Steam Turbines: Research is underway to develop steam turbines that can operate on hydrogen, a carbon-free fuel that can be produced using renewable energy. Hydrogen-fueled turbines have the potential to provide reliable, low-carbon power generation, particularly in conjunction with renewable energy sources.
- Carbon Capture Integration: Integrating carbon capture and storage (CCS) technologies with steam turbines is a key area of research aimed at reducing CO2 emissions from fossil fuel-based power generation. Ongoing R&D efforts are focused on improving the efficiency and cost-effectiveness of CCS, making it a viable option for large-scale deployment.
- Enhanced Durability and Reliability:
- Advanced Coatings and Surface Treatments: R&D is focused on developing advanced coatings and surface treatments that can extend the life of turbine components by protecting them from corrosion, erosion, and high-temperature oxidation. These coatings are essential for improving the durability and reliability of turbines operating under harsh conditions.
- Predictive Maintenance and AI: Research into predictive maintenance technologies, powered by AI and machine learning, is helping to improve the reliability of steam turbines. By analyzing historical performance data and identifying patterns that precede failures, these technologies enable more accurate predictions of maintenance needs, reducing unexpected downtime and extending the lifespan of turbine components.
Challenges and Opportunities
As the steam turbine industry evolves, it faces a range of challenges and opportunities that will shape its future.
- Challenges:
- Environmental Regulations: Increasingly stringent environmental regulations, particularly those related to greenhouse gas emissions and water usage, pose a challenge for the steam turbine industry. Meeting these regulations requires ongoing innovation in turbine design, materials, and operational strategies.
- Competition from Alternative Technologies: The rise of alternative power generation technologies, such as wind, solar, and energy storage, presents a challenge to the steam turbine industry. These technologies are becoming more cost-competitive and are often favored in policies aimed at reducing carbon emissions.
- Aging Infrastructure: Many existing steam turbines, particularly those in older power plants, are reaching the end of their operational life. Upgrading or replacing these turbines with more efficient, modern designs presents a significant challenge, particularly in terms of cost and downtime.
- Opportunities:
- Decarbonization Initiatives: The global push for decarbonization presents an opportunity for the steam turbine industry to develop low-carbon and carbon-neutral technologies. This includes the integration of steam turbines with renewable energy sources, hydrogen, and CCS technologies.
- Energy Transition: As the energy industry transitions towards more sustainable sources, steam turbines have the opportunity to play a key role in hybrid systems that combine renewable energy with traditional power generation. These hybrid systems can provide reliable, continuous power while reducing overall carbon emissions.
- Emerging Markets: Emerging markets, particularly in Asia and Africa, present significant growth opportunities for the steam turbine industry. As these regions continue to industrialize and expand their energy infrastructure, the demand for reliable and efficient power generation technologies, including steam turbines, is expected to increase.
Case Studies and Industry Examples
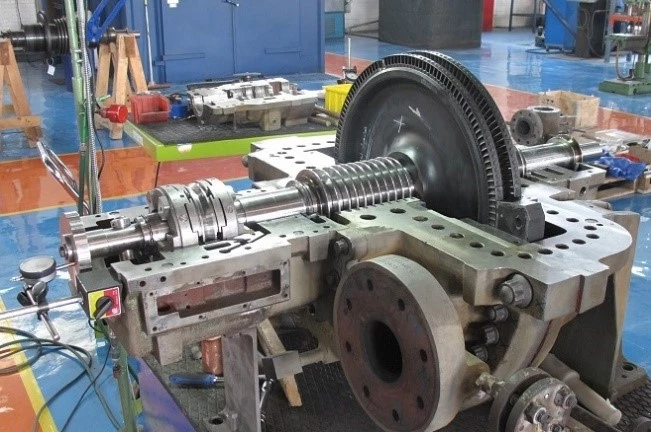
Notable Projects
Real-world applications of steam turbines showcase their versatility and efficiency across various industries. The following case studies highlight significant installations and the impact of steam turbines in different settings:
- The Taichung Power Plant, Taiwan:
- Overview: The Taichung Power Plant is one of the largest coal-fired power plants in the world, located in Taiwan. With an installed capacity of 5,500 MW, it plays a critical role in meeting the energy demands of Taiwan’s population and industry.
- Role of Steam Turbines: The plant uses a series of large-scale steam turbines to convert the thermal energy from coal combustion into electricity. These turbines are designed to operate at high efficiency, utilizing supercritical steam conditions to maximize energy extraction.
- Environmental Impact: Despite being a coal-fired plant, Taichung has implemented advanced emission control technologies, including flue gas desulfurization and selective catalytic reduction, to minimize its environmental footprint. The plant also serves as a benchmark for efficiency improvements in large-scale fossil fuel power generation.
- The Olkaria Geothermal Plant, Kenya:
- Overview: The Olkaria Geothermal Plant is the largest geothermal power plant in Africa, located in Kenya’s Great Rift Valley. It has a capacity of over 800 MW and contributes significantly to Kenya’s renewable energy mix.
- Role of Steam Turbines: The plant utilizes steam turbines specifically designed to handle the unique challenges of geothermal steam, such as the presence of corrosive gases and minerals. The turbines efficiently convert geothermal energy into electricity, providing a reliable source of power with low carbon emissions.
- Sustainability: The success of the Olkaria Geothermal Plant demonstrates the potential of geothermal energy in providing sustainable, baseload power in regions with geothermal resources. The plant’s expansion over the years highlights the scalability of geothermal projects and the crucial role of steam turbines in this renewable energy sector.
- The Ivanpah Solar Electric Generating System, United States:
- Overview: Ivanpah is one of the largest concentrated solar power (CSP) plants in the world, located in California’s Mojave Desert. It has a capacity of 392 MW and uses mirrors to concentrate sunlight onto boilers, generating steam to drive turbines.
- Role of Steam Turbines: The steam turbines at Ivanpah are designed to operate with the variable steam input characteristic of CSP plants. They play a crucial role in converting solar energy into electricity, with the ability to start and stop quickly in response to solar conditions.
- Innovation: Ivanpah is an example of how steam turbines can be effectively integrated into renewable energy systems. The project demonstrates the potential for CSP technology to provide utility-scale renewable energy, supported by advanced steam turbine technology.
Industry Leaders
Several companies and institutions have made significant contributions to the development and deployment of steam turbines. These industry leaders have pioneered technological advancements and set benchmarks for efficiency and reliability.
- Siemens Energy:
- Overview: Siemens Energy is a global leader in the design and manufacture of steam turbines, with a portfolio that includes turbines for power generation, industrial applications, and marine propulsion. The company is known for its focus on innovation and efficiency.
- Key Contributions: Siemens has been at the forefront of developing high-efficiency steam turbines, including those for supercritical and ultra-supercritical applications. Their turbines are widely used in power plants around the world, contributing to both fossil fuel and renewable energy projects. Siemens is also a leader in digitalization, offering advanced monitoring and control systems that enhance turbine performance and reliability.
- General Electric (GE):
- Overview: General Electric is another major player in the steam turbine industry, with a long history of innovation and engineering excellence. GE’s steam turbines are used in a variety of applications, including power generation, industrial processes, and marine propulsion.
- Key Contributions: GE has been instrumental in advancing turbine efficiency through the development of high-performance blades, advanced materials, and integrated control systems. The company has also been a pioneer in the use of digital twins and predictive maintenance technologies, helping operators optimize turbine performance and reduce operational costs.
- Mitsubishi Power:
- Overview: Mitsubishi Power, a subsidiary of Mitsubishi Heavy Industries, is a leading manufacturer of steam turbines, particularly in Asia. The company offers a wide range of turbines for power generation, including those for coal, nuclear, and gas-fired plants, as well as renewable energy projects.
- Key Contributions: Mitsubishi Power is known for its advanced steam turbine designs, which prioritize efficiency and reliability. The company has made significant strides in the development of ultra-supercritical turbines and has played a key role in the deployment of large-scale geothermal and biomass projects. Mitsubishi Power is also actively involved in R&D efforts focused on hydrogen-powered turbines and carbon capture integration.
Lessons Learned
The deployment of steam turbines across various industries provides valuable insights into the challenges and best practices associated with these technologies. Key lessons learned from these projects include:
- The Importance of Customization:
- Project-Specific Design: One of the most important lessons from successful steam turbine projects is the need for customization. Each project has unique requirements based on the type of fuel, operating conditions, and environmental regulations. Tailoring the design of the steam turbine to these specific conditions is crucial for achieving optimal performance and reliability.
- Adaptation to Local Conditions: In projects like the Olkaria Geothermal Plant, adapting the turbine design to handle the specific characteristics of geothermal steam, such as high moisture content and corrosive gases, was essential for long-term success. This highlights the importance of understanding local conditions and incorporating them into the turbine design process.
- Efficiency as a Key Driver:
- Focus on Efficiency: Efficiency improvements have been a central focus in the development of steam turbines, driven by the need to reduce fuel consumption and emissions. Projects like the Taichung Power Plant demonstrate how supercritical and ultra-supercritical steam conditions can significantly enhance efficiency, leading to lower operational costs and reduced environmental impact.
- Innovation in Blade Design: Advances in blade design, such as 3D-aerodynamic blades and the use of advanced materials, have been critical in improving turbine efficiency. Lessons from industry leaders like Siemens and GE show that continuous innovation in turbine components is necessary to maintain competitiveness in the market.
- The Role of Digitalization:
- Embracing Digital Technologies: The integration of digital technologies, such as digital twins, AI, and real-time monitoring systems, has emerged as a best practice in the steam turbine industry. These technologies enable operators to optimize performance, predict maintenance needs, and reduce downtime, leading to improved overall efficiency and reliability.
- Data-Driven Decision Making: The use of data analytics to monitor turbine performance and predict potential issues is becoming increasingly important. Industry leaders have demonstrated that data-driven decision-making can significantly enhance the operational efficiency and lifespan of steam turbines.
- Sustainability and Environmental Compliance:
- Sustainability Initiatives: The growing emphasis on sustainability has led to the adoption of cleaner energy sources, such as biomass, geothermal, and solar thermal, in steam turbine projects. Lessons from projects like Ivanpah show that steam turbines can play a key role in the transition to renewable energy, provided they are integrated with the appropriate technologies.
- Regulatory Compliance: Ensuring compliance with environmental regulations is a critical aspect of steam turbine projects. The successful implementation of emission control technologies, as seen in the Taichung Power Plant, highlights the importance of adhering to regulatory standards to minimize environmental impact and ensure project viability.
Conclusion
Summary of Key Points
Steam turbines have been a cornerstone of power generation and industrial applications for over a century, demonstrating remarkable adaptability and efficiency across various settings. This comprehensive exploration of steam turbines has covered their historical development, fundamental principles, design and manufacturing processes, and the wide range of applications in which they are employed.
- Fundamentals: At their core, steam turbines operate by converting thermal energy from steam into mechanical energy, which can then be used to generate electricity or drive machinery. The efficiency of this process depends on factors such as steam conditions, blade design, and the thermodynamic cycles employed, with the Rankine cycle being the most common.
- Design and Manufacturing: The design of steam turbines is a complex process that requires careful consideration of thermodynamics, materials science, and mechanical engineering. Advances in materials, such as superalloys and ceramic matrix composites, along with innovations in blade design and digitalization, are driving improvements in turbine efficiency and reliability. The manufacturing process, which includes casting, forging, machining, and heat treatment, ensures that turbines can withstand the extreme conditions under which they operate.
- Operation and Maintenance: Steam turbines require careful operation and regular maintenance to ensure their longevity and performance. Maintenance practices such as preventive and predictive maintenance, along with the use of advanced diagnostic tools, help prevent issues like blade erosion, rotor imbalance, and steam leakage. Proper operation, including control of steam quality and adherence to startup and shutdown procedures, is essential for maximizing efficiency and minimizing wear.
- Applications: Steam turbines are used in a wide variety of applications, from power generation in coal, nuclear, and geothermal plants to industrial processes in the petrochemical, pulp and paper, and steel industries. They also play a critical role in marine propulsion and are increasingly being integrated into renewable energy systems, such as concentrated solar power and biomass plants.
- Efficiency and Optimization: The efficiency of steam turbines is a key driver of their performance, with advancements in blade design, steam conditions, and energy recovery systems contributing to ongoing improvements. The use of digital twins, AI, and real-time monitoring systems is enhancing the ability to optimize turbine performance, reduce downtime, and extend the lifespan of turbine components.
- Environmental Impact and Sustainability: The environmental impact of steam turbines, particularly those powered by fossil fuels, is a significant concern. However, sustainability initiatives, such as the integration of renewable energy sources, the development of supercritical and ultra-supercritical steam cycles, and the adoption of carbon capture technologies, are helping to mitigate these impacts and support the transition to a low-carbon future.
- Future Trends and Innovations: The steam turbine industry is poised for continued innovation, with advances in materials, digitalization, and integration with smart grids driving the future of the technology. Research into low-carbon and carbon-neutral technologies, such as hydrogen-fueled turbines and enhanced carbon capture systems, will play a critical role in the industry’s evolution. The challenges posed by environmental regulations, competition from alternative technologies, and aging infrastructure present both obstacles and opportunities for the industry.
The Future of Steam Turbines
As the global energy landscape continues to evolve, steam turbines will remain a vital component of power generation and industrial processes. Their ability to adapt to changing technologies, integrate with renewable energy systems, and improve efficiency will ensure their continued relevance in the coming decades.
The push for decarbonization and the need for more sustainable energy solutions will drive further innovation in steam turbine technology. The development of ultra-efficient steam cycles, the integration of digital technologies, and the exploration of new materials and designs will be essential for meeting the growing demand for clean, reliable, and efficient power.
Moreover, the role of steam turbines in emerging markets and in hybrid energy systems that combine traditional power generation with renewable sources presents significant growth opportunities. As these regions continue to industrialize and expand their energy infrastructure, the demand for steam turbines that can deliver high efficiency, reliability, and sustainability will increase.
In conclusion, steam turbines have a rich history of innovation and adaptation, and their future looks promising as they continue to evolve in response to the challenges and opportunities of the 21st century. The ongoing commitment to improving efficiency, reducing environmental impact, and integrating with advanced energy systems will ensure that steam turbines remain a cornerstone of global energy production for years to come.
Introduction to Power Generation with Steam Turbines
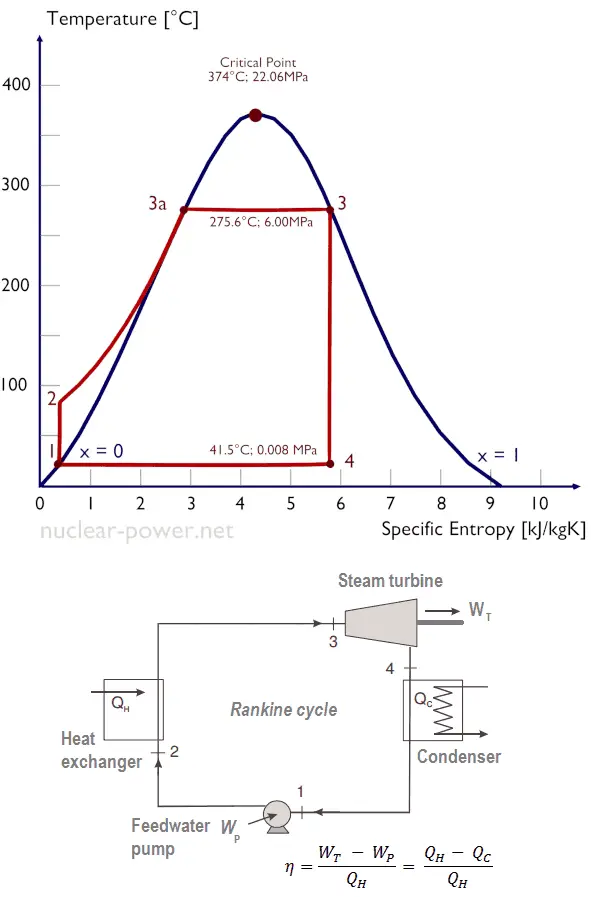
Steam turbines have been at the heart of power generation for over a century. Invented by Sir Charles Parsons in 1884, steam turbines quickly became the dominant technology for converting thermal energy into mechanical energy and, subsequently, into electrical energy. Their versatility and efficiency have made them the backbone of electricity generation worldwide.
In modern power generation, steam turbines are used in a variety of settings, from large-scale fossil fuel plants to renewable energy installations. They operate on the principle of converting the energy from high-pressure steam into mechanical energy by driving a rotor connected to a generator. The flexibility of steam turbines allows them to be integrated into diverse energy systems, including coal, nuclear, natural gas, geothermal, and solar thermal power plants.
The importance of steam turbines lies in their ability to efficiently produce large amounts of electricity. With advancements in technology, steam turbines have evolved to operate at higher temperatures and pressures, increasing their efficiency and reducing fuel consumption. These improvements have also led to a reduction in greenhouse gas emissions per unit of electricity generated, making steam turbines a critical component in the transition to more sustainable energy systems.
Types of Power Plants Using Steam Turbines
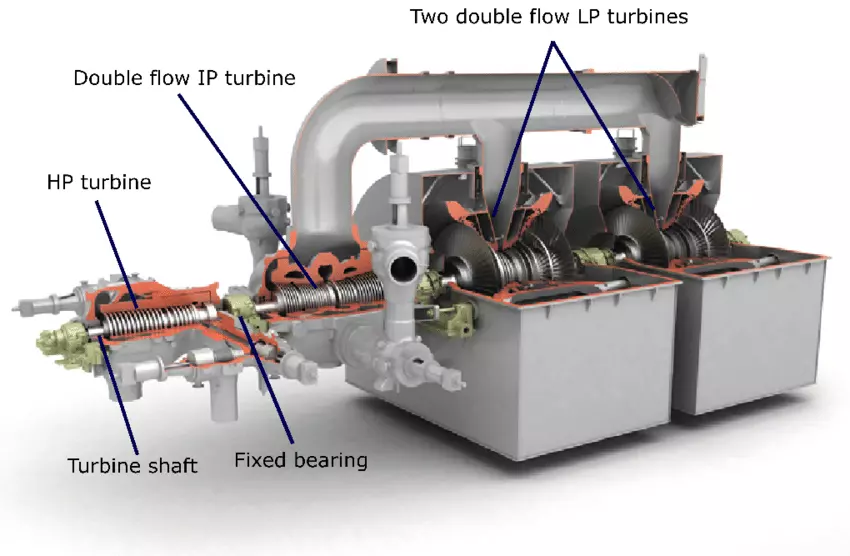
Coal-Fired Power Plants
Coal-fired power plants are among the most common applications of steam turbines. In these plants, coal is burned in a boiler to produce high-pressure steam, which is then directed into a steam turbine to generate electricity. Despite the environmental challenges associated with coal, such as CO2 emissions and air pollution, it remains a significant energy source, particularly in developing countries.
The efficiency of coal-fired power plants has improved over the years, thanks to advancements in steam turbine technology. Supercritical and ultra-supercritical steam conditions, where steam is generated at temperatures and pressures above the critical point, allow for higher thermal efficiency. This means that more electricity can be generated from the same amount of coal, reducing the overall environmental impact.
Emission control technologies, such as flue gas desulfurization (FGD) and selective catalytic reduction (SCR), are employed to reduce the emission of pollutants like SO2 and NOx. Additionally, carbon capture and storage (CCS) technologies are being developed to capture CO2 emissions from coal plants, although these are still in the early stages of adoption.
Nuclear Power Plants
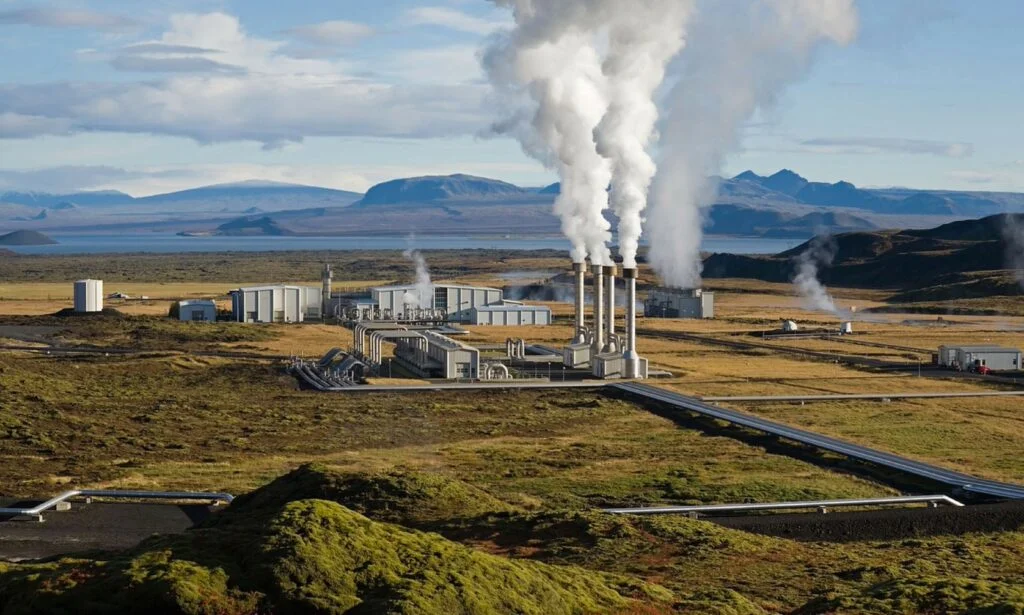
In nuclear power plants, steam turbines play a crucial role in converting the heat generated by nuclear fission into electricity. Nuclear reactors heat water to produce steam, which then drives a steam turbine connected to a generator. The steam turbines used in nuclear power plants are typically large and must be highly reliable, given the safety-critical nature of nuclear energy.
One of the key challenges in nuclear power generation is managing the steam conditions, which differ from those in fossil fuel plants. The steam produced in nuclear reactors is often at a lower temperature and pressure, which requires specific turbine designs to operate efficiently under these conditions. Additionally, the turbines must be capable of withstanding radiation and operating in a highly controlled environment.
The efficiency of nuclear power plants is influenced by the design of the steam cycle, with some plants employing reheat cycles to improve thermal efficiency. Advances in materials and turbine design continue to enhance the performance of steam turbines in nuclear applications, contributing to the overall reliability and safety of nuclear power generation.
Gas-Fired Power Plants (Combined Cycle)
Combined cycle power plants represent a significant advancement in the use of steam turbines. These plants combine a gas turbine with a steam turbine to maximize efficiency. In a combined cycle setup, a gas turbine generates electricity, and the waste heat from the gas turbine’s exhaust is used to produce steam, which then drives a steam turbine to generate additional electricity.
The efficiency of combined cycle power plants is among the highest of any power generation technology, often exceeding 60%. This is because the steam turbine effectively captures and utilizes energy that would otherwise be lost as waste heat. Combined cycle plants are also more flexible than traditional power plants, as they can be ramped up or down quickly in response to changes in electricity demand.
The integration of steam turbines in combined cycle plants has made natural gas a more attractive option for power generation, particularly in countries looking to reduce their reliance on coal and lower their carbon emissions. The ability to combine gas and steam turbines in a single plant allows for greater efficiency and lower environmental impact, making combined cycle plants a key component of the modern energy mix.
Geothermal Power Plants
Geothermal power plants harness the Earth’s natural heat to generate electricity, and steam turbines are central to this process. In these plants, steam is extracted from underground reservoirs and used to drive turbines. Geothermal steam often contains corrosive gases and minerals, which presents unique challenges for turbine design and operation.
The efficiency of geothermal power plants depends on the temperature and pressure of the geothermal steam. Higher temperature resources allow for the use of more efficient steam cycles, similar to those used in fossil fuel plants. However, geothermal plants typically operate at lower pressures, requiring turbines that can handle a wider range of steam qualities.
One of the key advantages of geothermal energy is its ability to provide baseload power, as geothermal resources are available 24/7. Steam turbines in geothermal plants must be robust and reliable, capable of operating continuously with minimal downtime. Innovations in turbine materials and designs are helping to improve the longevity and efficiency of geothermal turbines, making geothermal energy an increasingly important part of the renewable energy landscape.
Concentrated Solar Power (CSP) Plants
Concentrated Solar Power (CSP) plants use mirrors or lenses to concentrate sunlight onto a receiver, where it heats a fluid to produce steam. This steam then drives a turbine to generate electricity. CSP is unique among renewable energy technologies in that it can produce electricity even when the sun is not shining, thanks to thermal storage systems that store heat for later use.
Steam turbines used in CSP plants are designed to operate with variable steam inputs, as the intensity of sunlight can fluctuate throughout the day. The turbines must be capable of starting and stopping quickly and efficiently to match the availability of solar energy. CSP plants often use steam turbines with advanced blade designs and materials that can withstand the thermal cycling associated with intermittent solar input.
One of the key innovations in CSP is the integration of molten salt thermal storage, which allows the plant to store heat during the day and use it to generate steam at night or during cloudy periods. This ability to provide dispatchable power makes CSP with steam turbines a valuable addition to the renewable energy mix, particularly in regions with high solar irradiance.
Efficiency Considerations in Steam Turbine Power Generation
Efficiency is a critical factor in steam turbine power generation, as it determines how effectively fuel or energy resources are converted into electricity. Several factors influence the efficiency of steam turbines, including thermodynamic principles, technological advancements, and operational strategies.
Thermodynamic Efficiency
The efficiency of a steam turbine is largely governed by the principles of thermodynamics, particularly the Rankine cycle, which is the basic cycle used in steam power plants. The Rankine cycle involves four main processes: isentropic compression, isobaric heat addition, isentropic expansion, and isobaric heat rejection. The efficiency of this cycle can be improved through several methods:
- Superheating and Reheating: Increasing the temperature of steam (superheating) before it enters the turbine, or reheating the steam between turbine stages, can significantly improve efficiency by reducing the moisture content in the steam and allowing more energy to be extracted.
- Higher Pressure Ratios: Operating the turbine at higher pressures increases the amount of energy that can be extracted from the steam, improving overall cycle efficiency. Supercritical and ultra-supercritical steam conditions, where steam is generated at pressures above the critical point, represent the highest efficiency levels in modern power plants.
- Regenerative Feedwater Heating: Extracting steam from intermediate stages of the turbine to preheat the feedwater before it enters the boiler reduces the amount of fuel needed to produce steam, thereby improving the overall efficiency of the power plant.
Technological Advances
Advances in steam turbine technology have played a significant role in improving efficiency. Innovations in blade design, materials, and manufacturing techniques have allowed turbines to operate at higher temperatures and pressures, leading to greater energy conversion efficiency.
- Advanced Blade Designs: The design of turbine blades has a significant impact on efficiency. Modern blades are aerodynamically optimized to reduce losses due to turbulence and friction. The use of computational fluid dynamics (CFD) allows engineers to design blades that maximize the energy extracted from steam.
- High-Performance Materials: The development of advanced materials, such as nickel-based superalloys and ceramic matrix composites, has enabled steam turbines to operate at higher temperatures without compromising structural integrity. These materials resist creep, corrosion, and thermal fatigue, allowing for more efficient and durable turbine operation.
- 3D Printing and Precision Manufacturing: Additive manufacturing technologies, such as 3D printing, have enabled the production of turbine components with complex geometries that are optimized for efficiency. Precision manufacturing techniques also reduce material waste and improve the consistency and reliability of turbine components.
Operational Strategies
Operational strategies also play a crucial role in optimizing the efficiency of steam turbines. By carefully managing the operating conditions and load profiles, power plant operators can maximize the performance of steam turbines.
- Load Optimization: Steam turbines are most efficient when operating at or near their design capacity. However, power plants often experience varying demand throughout the day. By optimizing the load on the turbine, operators can maintain high efficiency even during periods of lower demand. Techniques such as load matching and peak shaving help ensure that turbines operate within their optimal range.
- Real-Time Monitoring and Control: Modern steam turbines are equipped with advanced monitoring and control systems that allow operators to adjust operating parameters in real-time. These systems use sensors and data analytics to monitor performance metrics such as steam temperature, pressure, and flow rate. By continuously optimizing these parameters, operators can improve efficiency and prevent issues before they lead to performance losses.
- Maintenance and Reliability: Regular maintenance is essential for maintaining the efficiency of steam turbines. Predictive maintenance, which uses data analytics to predict when components are likely to fail, helps minimize downtime and ensures that turbines continue to operate at peak efficiency. Proper lubrication, vibration analysis, and blade inspection are all critical components of an effective maintenance strategy.
Environmental Impact and Mitigation Strategies
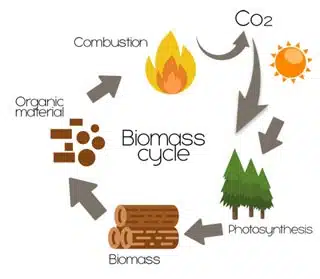
Steam turbines play a central role in power generation, but they also contribute to environmental challenges, particularly when powered by fossil fuels. Understanding and mitigating these impacts is crucial for the sustainable operation of steam turbines.
Greenhouse Gas Emissions
The combustion of fossil fuels in steam turbines, particularly in coal and gas-fired power plants, is a significant source of CO2 emissions. These greenhouse gas emissions contribute to global warming and climate change, making it imperative to reduce the carbon footprint of steam turbine power generation.
- Carbon Capture and Storage (CCS): CCS is a technology that captures CO2 emissions from power plants and stores them underground in geological formations. When integrated with steam turbines, CCS can significantly reduce the carbon emissions of fossil fuel-based power generation. While CCS is still in the early stages of adoption, ongoing research and development are focused on making it more cost-effective and scalable.
- Transition to Low-Carbon Fuels: Another strategy for reducing greenhouse gas emissions is transitioning from coal to lower-carbon fuels, such as natural gas, or even carbon-neutral fuels like biomass. Combined cycle power plants, which use both gas and steam turbines, offer higher efficiency and lower emissions compared to traditional coal-fired plants.
Air and Water Pollution
In addition to CO2, fossil fuel combustion in steam turbines also produces other air pollutants, such as sulfur dioxide (SO2), nitrogen oxides (NOx), and particulate matter. These pollutants contribute to acid rain, smog, and respiratory problems in humans.
- Emission Control Technologies: Technologies such as flue gas desulfurization (FGD) and selective catalytic reduction (SCR) are used to reduce SO2 and NOx emissions from power plants. Particulate matter can be controlled using electrostatic precipitators and baghouse filters. These technologies help mitigate the environmental impact of air pollution from steam turbines.
- Water Usage and Thermal Pollution: Steam turbines require significant amounts of water for cooling, which can impact local water resources. Additionally, the discharge of heated water back into the environment can cause thermal pollution, affecting aquatic ecosystems. To address these issues, power plants are increasingly adopting closed-loop cooling systems that minimize water withdrawal and reduce thermal discharge. Dry cooling systems, which use air instead of water, are also being implemented, particularly in water-scarce regions.
Renewable Energy Integration
The integration of steam turbines with renewable energy sources presents an opportunity to reduce the environmental impact of power generation. By leveraging steam turbines in conjunction with renewable energy technologies, such as biomass, geothermal, and concentrated solar power (CSP), it is possible to produce electricity with a lower carbon footprint.
- Biomass Power Generation: Biomass power plants use organic materials, such as wood, agricultural residues, and waste, to produce steam that drives turbines. Biomass is considered carbon-neutral, as the CO2 released during combustion is offset by the CO2 absorbed during the growth of the biomass. Steam turbines play a critical role in converting biomass energy into electricity, providing a sustainable alternative to fossil fuels.
- Geothermal and Solar Thermal: Geothermal power plants harness the Earth’s natural heat to produce steam, while CSP plants use concentrated sunlight to generate steam. Both technologies rely on steam turbines to convert thermal energy into electricity. These renewable energy sources produce little to no greenhouse gas emissions, making them attractive options for sustainable power generation.
Future Trends and Innovations in Steam Turbine Power Generation
The steam turbine industry is continuously evolving, with new technologies and trends shaping the future of power generation. These innovations are focused on improving efficiency, reducing environmental impact, and enhancing the flexibility of steam turbines in a changing energy landscape.
Decarbonization Initiatives
As the world moves toward decarbonization, steam turbines are being adapted to operate with low-carbon and carbon-neutral fuels. Hydrogen, in particular, is emerging as a promising fuel for steam turbines.
- Hydrogen-Fueled Steam Turbines: Hydrogen can be produced using renewable energy through electrolysis, resulting in a carbon-free fuel. Research is underway to develop steam turbines that can operate on hydrogen, either alone or in combination with other fuels. Hydrogen-fueled turbines have the potential to provide reliable, low-carbon power generation, especially in conjunction with renewable energy sources.
- Hybrid Energy Systems: Steam turbines are increasingly being integrated into hybrid energy systems that combine traditional power generation with renewable energy. These systems can provide continuous power while reducing carbon emissions. For example, a hybrid system might use a natural gas-fired steam turbine in combination with solar or wind power, with the turbine providing backup power when renewable sources are intermittent.
Digitalization and Smart Grids
Digital technologies are transforming the operation of steam turbines, making them more efficient, reliable, and responsive to grid demands.
- Artificial Intelligence and Machine Learning: AI and machine learning are being used to optimize turbine operations by analyzing data from sensors and control systems. These technologies can predict maintenance needs, optimize load distribution, and improve efficiency by adjusting operating parameters in real-time. AI-driven analytics are also helping to identify patterns and trends that can lead to better decision-making and improved turbine performance.
- Digital Twins: The concept of a digital twin, a virtual model of the steam turbine that runs in parallel with the physical machine, is becoming increasingly important in the industry. Digital twins allow operators to monitor turbine performance in real-time, simulate different scenarios, and optimize operations without risking the physical turbine. This technology is particularly valuable for predicting and preventing issues before they occur, reducing downtime and maintenance costs.
- Smart Grid Integration: Steam turbines are being integrated into smart grid systems, which offer enhanced flexibility and efficiency in power generation and distribution. Advanced control systems and real-time monitoring enable steam turbines to respond quickly to changes in electricity demand, helping to balance the grid and prevent blackouts. The integration of steam turbines with energy storage systems, such as batteries, also enhances grid stability and allows for more efficient use of renewable energy.
Research and Development
Ongoing research and development (R&D) efforts are focused on advancing steam turbine technology to meet the evolving demands of the energy industry and address environmental challenges.
- High-Efficiency Steam Cycles: R&D is driving the development of supercritical and ultra-supercritical steam cycles, which operate at higher temperatures and pressures than conventional cycles. These advanced cycles offer higher thermal efficiencies, reducing fuel consumption and emissions. Researchers are exploring new materials and designs that can withstand the extreme conditions of these cycles, making them more viable for widespread adoption.
- Carbon Capture Integration: Integrating carbon capture and storage (CCS) technologies with steam turbines is a key area of research aimed at reducing CO2 emissions from fossil fuel-based power generation. Ongoing R&D efforts are focused on improving the efficiency and cost-effectiveness of CCS, making it a viable option for large-scale deployment.
- Advanced Materials and Coatings: The development of new materials and coatings that can withstand high temperatures and corrosive environments is essential for improving the durability and efficiency of steam turbines. Research into advanced coatings, such as thermal barrier coatings and anti-corrosion treatments, is helping to extend the life of turbine components and reduce maintenance costs.
Conclusion
Steam turbines have been a cornerstone of power generation for over a century, and their role continues to evolve in response to changing energy needs and environmental challenges. This comprehensive overview of steam turbine power generation has highlighted the versatility, efficiency, and sustainability of steam turbines across a range of applications.
From coal-fired and nuclear power plants to renewable energy systems like geothermal and concentrated solar power, steam turbines are critical to producing reliable and efficient electricity. Technological advancements, including supercritical steam cycles, advanced blade designs, and digitalization, have significantly improved the performance of steam turbines, making them more efficient and environmentally friendly.
As the world transitions to a low-carbon economy, steam turbines will play an essential role in decarbonization efforts. The integration of hydrogen as a fuel, the adoption of carbon capture technologies, and the development of hybrid energy systems are just a few of the ways steam turbines are being adapted to meet the demands of a more sustainable energy future.
The future of steam turbines is bright, with ongoing research and innovation driving continued improvements in efficiency, reliability, and environmental performance. As digital technologies like AI and digital twins become more prevalent, steam turbines will become even more integrated with smart grid systems, enhancing their flexibility and responsiveness to changing energy demands.
In conclusion, steam turbines will remain a vital component of global power generation for years to come. Their ability to adapt to new technologies and integrate with renewable energy sources ensures that they will continue to play a key role in the transition to a more sustainable and resilient energy system.
EMS Power Machines
We design, manufacture and assembly Power Machines such as – diesel generators, electric motors, vibration motors, pumps, steam engines and steam turbines
EMS Power Machines is a global power engineering company, one of the five world leaders in the industry in terms of installed equipment. The companies included in the company have been operating in the energy market for more than 60 years.
EMS Power Machines manufactures steam turbines, gas turbines, hydroelectric turbines, generators, and other power equipment for thermal, nuclear, and hydroelectric power plants, as well as for various industries, transport, and marine energy.
EMS Power Machines is a major player in the global power industry, and its equipment is used in power plants all over the world. The company has a strong track record of innovation, and it is constantly developing new and improved technologies.
Here are some examples of Power Machines’ products and services:
- Steam turbines for thermal and nuclear power plants
- Gas turbines for combined cycle power plants and industrial applications
- Hydroelectric turbines for hydroelectric power plants
- Generators for all types of power plants
- Boilers for thermal power plants
- Condensers for thermal power plants
- Reheaters for thermal power plants
- Air preheaters for thermal power plants
- Feedwater pumps for thermal power plants
- Control systems for power plants
- Maintenance and repair services for power plants
EMS Power Machines is committed to providing its customers with high-quality products and services. The company has a strong reputation for reliability and innovation. Power Machines is a leading provider of power equipment and services, and it plays a vital role in the global power industry.
EMS Power Machines, which began in 1961 as a small factory of electric motors, has become a leading global supplier of electronic products for different segments. The search for excellence has resulted in the diversification of the business, adding to the electric motors products which provide from power generation to more efficient means of use.