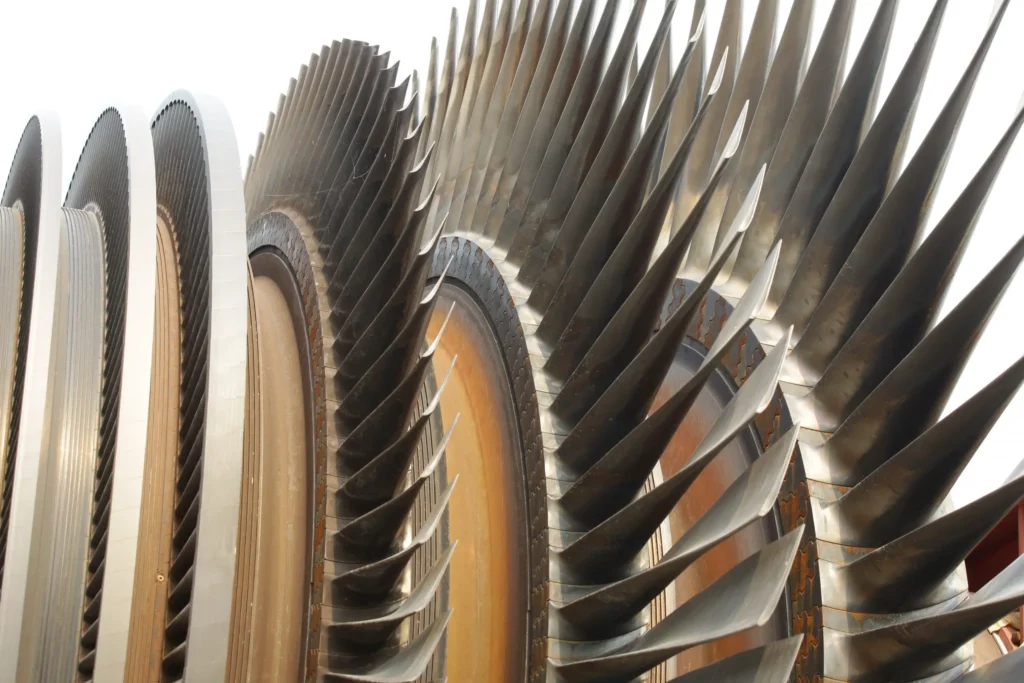
Single stage and multistage turbine types are two distinct types of turbines used in various applications to convert fluid energy (usually steam or gas) into mechanical work, such as rotating a shaft or generating electricity. They differ in design and operation, each offering specific advantages and disadvantages. Here’s a detailed comparison between single-stage and multistage turbines:
Single-Stage Turbine:
- Design: Single-stage turbines have only one set of rotating blades (rotor) and stationary blades (stator) for expanding the working fluid. The expansion occurs in a single stage.
- Expansion: In a single-stage turbine, the fluid enters the nozzle or guide vanes, gains velocity and kinetic energy, and then passes over the rotor blades, causing the rotor to rotate and generate mechanical work. All of the expansion occurs in this single stage.
- Simplicity: Single-stage turbines are relatively simple in design and construction. They are less complex and often less expensive than multistage turbines.
- Applications: Single-stage turbines are suitable for applications where efficiency is not the primary concern. They are commonly used in smaller-scale power generation, mechanical drive systems, and specific industrial processes.
- Efficiency: Single-stage turbines may have lower efficiency compared to multistage turbines because all the expansion occurs in one stage, which can result in less efficient utilization of the energy in the working fluid.
Multistage Turbine:
- Design: Multistage turbines have multiple sets of rotating blades (rotors) and stationary blades (stators) arranged in sequential stages. Each stage performs a portion of the expansion process, with the fluid passing through multiple stages in series.
- Expansion: In a multistage turbine, the fluid enters the first stage, undergoes partial expansion, and then proceeds to subsequent stages. Each stage extracts additional energy from the fluid, achieving a more gradual and efficient expansion.
- Efficiency: Multistage turbines are known for their high efficiency because they can extract energy more effectively from the working fluid by spreading the expansion over multiple stages. This results in better utilization of the fluid’s energy.
- Applications: Multistage turbines are commonly used in large-scale power generation, aviation (jet engines), and other applications where efficiency, performance, and power output are crucial.
- Complexity: Multistage turbines are more complex in design and construction due to the presence of multiple stages, which can increase manufacturing and maintenance costs.
Summary:
- Single-stage turbines are simpler and cost-effective, suitable for smaller-scale applications where efficiency is less critical.
- Multistage turbines are more complex but offer higher efficiency and performance, making them ideal for larger-scale power generation and applications where energy conversion is crucial.
The choice between a single-stage and a multistage turbine depends on the specific application, power requirements, efficiency considerations, and budget constraints. Each type of turbine has its own set of advantages and limitations, and the selection should align with the desired performance and operational goals.
Single-stage and multistage turbines are two types of turbines that differ in their design and application.
Single-stage turbines
A single-stage turbine is a turbine that has only one stage of blades. This means that the steam or gas is expanded only once as it passes through the turbine. Single-stage turbines are typically used for applications where the pressure difference is small, such as in small power plants or in turbochargers.
Multistage turbines
A multistage turbine is a turbine that has multiple stages of blades. This means that the steam or gas is expanded multiple times as it passes through the turbine. Multistage turbines are typically used for applications where the pressure difference is large, such as in large power plants or in aircraft engines.
Comparison of single-stage and multistage turbines
Here is a table comparing single-stage and multistage turbines:
Feature | Single-stage turbine | Multistage turbine |
---|---|---|
Number of stages | 1 | Multiple |
Applications | Low-pressure difference applications | High-pressure difference applications |
Efficiency | Lower | Higher |
Power output | Lower | Higher |
Complexity | Simpler | More complex |
Cost | Lower | Higher |
Conclusion
In general, single-stage turbines are simpler and less expensive than multistage turbines. However, multistage turbines are more efficient and can produce more power. The best type of turbine for a particular application will depend on the specific requirements of that application.
Here are some additional points to consider when choosing between a single-stage and multistage turbine:
- The pressure difference across the turbine. If the pressure difference is low, a single-stage turbine may be sufficient. If the pressure difference is high, a multistage turbine will be more efficient.
- The desired power output. If a low power output is required, a single-stage turbine may be sufficient. If a high power output is required, a multistage turbine will be necessary.
- The available space. Single-stage turbines are typically smaller than multistage turbines. If space is limited, a single-stage turbine may be a better choice.
- The cost. Single-stage turbines are typically less expensive than multistage turbines. If cost is a major concern, a single-stage turbine may be a better choice.
Single Stage Turbine
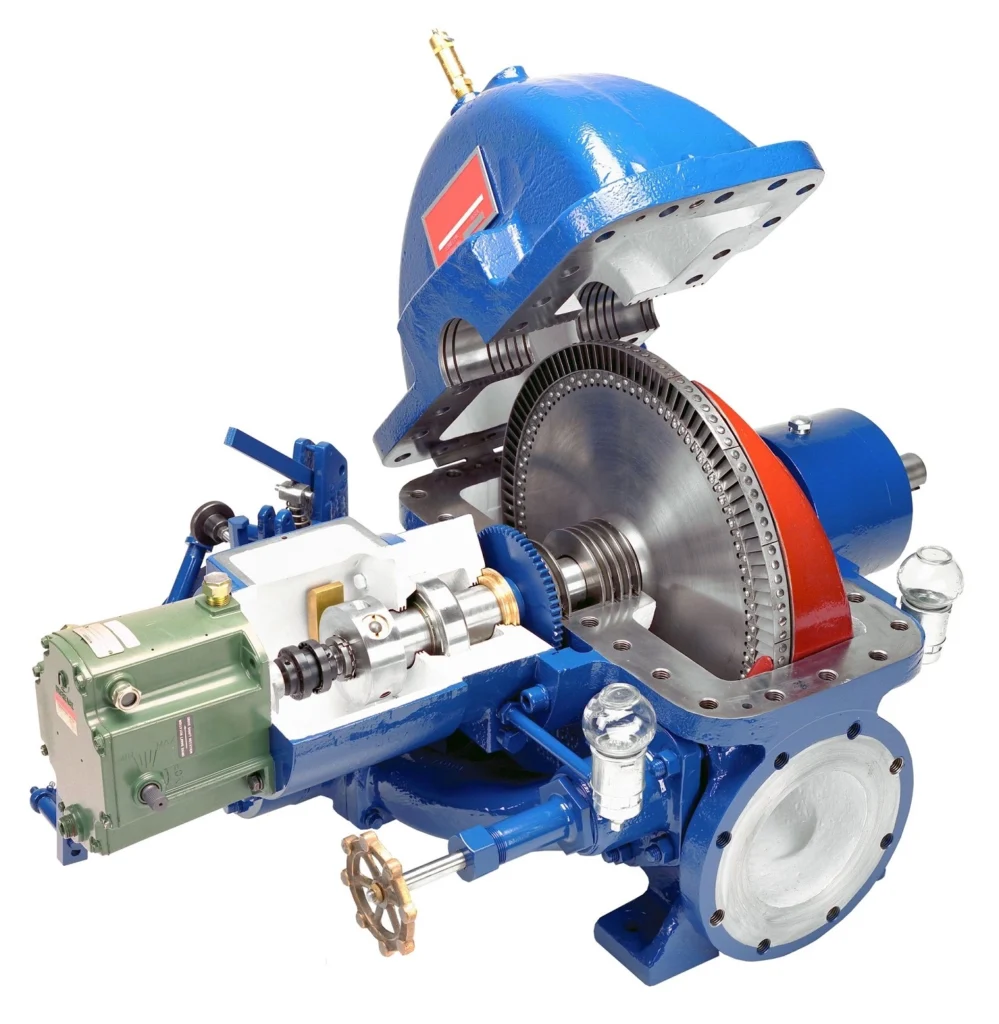
A single-stage steam turbine, also known as a single-cylinder steam turbine, is a type of steam turbine that has only one set of rotating blades or a single stage for expanding high-pressure steam. Unlike multi-stage steam turbines that have multiple stages for gradual steam expansion, a single-stage turbine is relatively simple in design and operation. Here’s an overview of the key characteristics and applications of single-stage steam turbines:
Key Characteristics of Single-Stage Steam Turbines:
- Single Stage: As the name suggests, single-stage steam turbines have only one set of rotating blades or a single stage for steam expansion. This means that the high-pressure steam enters the turbine and expands through a single set of blades, directly producing mechanical work.
- Steam Inlet: High-pressure and high-temperature steam is supplied to the inlet of the single-stage turbine. The steam is typically obtained from a steam generator, such as a boiler.
- Steam Expansion: The high-pressure steam flows into the single stage of the turbine, where it undergoes controlled expansion as it passes over the turbine blades. This expansion causes the blades to rotate, generating mechanical work in the form of shaft power.
- Mechanical Work Generation: The mechanical work generated by the rotating shaft of the single-stage turbine can be harnessed to drive various types of machinery, such as pumps, compressors, or electrical generators, depending on the specific application.
- Exhaust Steam: After passing through the single stage of expansion, the steam exits the turbine as exhaust steam. The pressure and temperature of the exhaust steam depend on the design and operational parameters of the turbine.
Applications of Single-Stage Steam Turbines:
Single-stage steam turbines are used in a variety of applications, including:
- Small Power Generation: They are often used in smaller-scale power generation systems, such as decentralized power plants, small industrial facilities, or for specific localized power needs.
- Mechanical Drive: Single-stage turbines can be employed for mechanical drive applications, where the generated mechanical work is used directly to drive machinery such as pumps or compressors.
- Process Industries: They are used in certain process industries where the primary goal is to generate mechanical work for specific processes.
- Experimental and Educational Purposes: Single-stage turbines are sometimes used in educational institutions and research facilities for experimental purposes and to teach the principles of steam turbine operation.
- Backup Power: In some cases, single-stage steam turbines may serve as backup power sources in industries where continuity of operations is critical.
It’s important to note that single-stage steam turbines are simpler and less efficient than multi-stage turbines for high-pressure steam expansion. Multi-stage turbines are typically preferred for large-scale power generation applications where maximizing efficiency is essential. However, single-stage turbines can be cost-effective and suitable for smaller-scale or specialized applications where their simplicity and lower initial cost are advantageous.
Single-stage Steam Turbine Characteristics
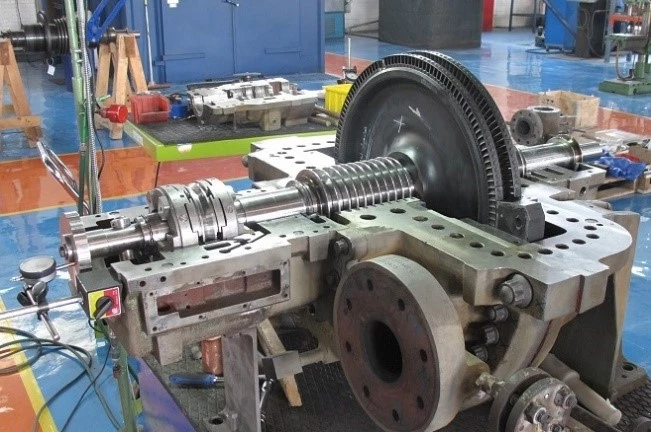
Single-stage steam turbines are a type of steam turbine that consists of only one set of rotating blades, or a single stage, through which steam flows to produce mechanical work. These turbines are commonly used in various applications, including power generation, industrial processes, and marine propulsion. Here are some key characteristics and features of single-stage steam turbines:
- Simplicity: Single-stage steam turbines are relatively simple in design compared to multi-stage turbines. They have fewer components, making them easier to manufacture, operate, and maintain.
- Limited Pressure Drop: Since single-stage turbines have only one set of blades, they are typically used in applications where the available steam pressure drop is relatively small. They are not as efficient as multi-stage turbines in extracting energy from high-pressure steam.
- Lower Efficiency: Single-stage turbines tend to have lower overall efficiency compared to multi-stage turbines, especially when operating with high-pressure steam. This is because they cannot effectively extract all of the available energy in the steam.
- Compact Size: These turbines are compact and have a smaller footprint compared to multi-stage turbines, which makes them suitable for installations with space constraints.
- High Speed: Single-stage steam turbines often operate at high rotational speeds due to the limited expansion of steam across a single set of blades. This may require additional speed reduction equipment when connected to other machinery or generators.
- Limited Power Output: Single-stage turbines are typically used for applications with lower power requirements. They are not as suitable for large-scale power generation as multi-stage turbines.
- Cost-Effective: Due to their simplicity, single-stage steam turbines are often more cost-effective to manufacture and maintain compared to multi-stage turbines. This can make them a practical choice for certain applications.
- Versatility: Single-stage turbines can be used in a variety of applications, including driving pumps, compressors, and small generators. They are also found in some industrial processes where moderate power output is needed.
- Start-Up Time: Single-stage turbines can start up relatively quickly, which is advantageous in applications where rapid response to changing load conditions is required.
- Maintenance: Maintenance requirements for single-stage turbines are generally lower than for multi-stage turbines. However, regular inspections and servicing are still essential to ensure proper operation and longevity.
It’s important to note that the choice between a single-stage and multi-stage steam turbine depends on the specific requirements of the application, including the available steam pressure, desired power output, efficiency goals, and budget considerations. Single-stage turbines are best suited for applications where simplicity and cost-effectiveness are prioritized over maximum efficiency and power output.
Single Stage
A single-stage refers to a system or process that consists of only one distinct step or phase, as opposed to multiple stages or steps. In various contexts, “single stage” implies simplicity and a lack of complexity. Here are a few common examples where the term “single stage” is used:
- Single-Stage Manufacturing: In manufacturing and production processes, a single-stage manufacturing process involves a single step or operation to produce a final product. This contrasts with multi-stage manufacturing, where multiple steps are involved in transforming raw materials into finished goods. For example, a lathe operation that shapes a metal part from a single piece of material is a single-stage manufacturing process.
- Single-Stage Rocket: In aerospace engineering, a single-stage rocket is a type of rocket that does not have separate stages that detach during flight. It consists of a single propulsion stage that burns fuel throughout the entire flight, from launch to reaching its desired altitude or velocity. Single-stage rockets are simpler but often have limitations in terms of payload capacity and range compared to multi-stage rockets.
- Single-Stage Amplifier: In electronics and electrical engineering, a single-stage amplifier is an amplifier circuit that consists of only one amplifying element, such as a transistor or vacuum tube. It amplifies the input signal in a single step without additional intermediate amplification stages.
- Single-Stage Paint: In the automotive and painting industry, single-stage paint refers to a type of paint system where the color and protective clear coat are combined into a single layer. This contrasts with two-stage paint systems, where the color coat and clear coat are applied separately. Single-stage paint can simplify the painting process but may not provide the same level of gloss and durability as two-stage systems.
- Single-Stage Snow Blower: In the context of snow removal equipment, a single-stage snow blower is a compact snow blower with a single auger (rotating blade) that both scoops up and propels snow out of the chute. It’s typically used for lighter snowfalls and is simpler in design compared to two-stage snow blowers, which have an additional impeller to assist in snow removal.
In each of these contexts, the “single stage” designation highlights the simplicity and efficiency of a process or system that can achieve its intended goal with just one step or phase. However, it’s essential to consider the trade-offs and limitations associated with single-stage systems, as they may not always be suitable for complex or demanding applications.
Steam Inlet
A steam inlet is a port or opening in a device, machine, or system through which high-pressure steam is introduced. Steam inlets are essential components in various industrial processes, power generation, and heating systems where steam is used as a source of energy or for heating purposes. Here are some key aspects and applications of steam inlets:
- Industrial Boilers: Steam inlets are commonly found in industrial boilers, which are used to generate steam by heating water. High-pressure steam is produced within the boiler and then directed through the steam inlet to be used for various purposes, such as driving turbines, providing process heat, or heating buildings.
- Steam Turbines: In power generation facilities, steam inlets play a critical role in steam turbines. High-pressure steam enters the turbine through the steam inlet, causing the turbine blades to rotate and generate mechanical work that is ultimately converted into electricity.
- Steam Engines: Steam engines, which are used in some industrial applications and historical transportation systems, also have steam inlets. The high-pressure steam is introduced into the engine through the steam inlet, driving a piston or other mechanical components.
- Industrial Processes: Many manufacturing and industrial processes require high-pressure steam for various applications, such as sterilization, drying, or chemical reactions. Steam inlets are used to introduce steam into these processes, where it can transfer heat or energy.
- Heating Systems: Steam is often used as a heat source in heating systems for buildings, including large commercial and industrial facilities. Steam inlets introduce steam into heating coils or radiators, where it releases thermal energy to heat the surrounding air or space.
- Steam Distribution Networks: In large-scale industrial facilities or district heating systems, steam inlets are part of a network that distributes steam to various users through pipes. These inlets are strategically located to ensure efficient steam delivery.
- Safety Features: Steam inlets may be equipped with safety features such as pressure relief valves or control valves to regulate the flow and pressure of steam, preventing overpressure and ensuring safe operation.
- Material and Design: Steam inlets are typically made from materials that can withstand high temperatures and pressures, such as stainless steel or alloy steel. Their design and size depend on the specific requirements of the system.
- Maintenance: Proper maintenance of steam inlets is essential to ensure their reliability and safe operation. This includes regular inspections, cleaning, and testing of safety devices.
Steam inlets are fundamental components in systems that rely on steam as a source of energy or heat. The design and operation of steam inlets must adhere to industry standards and safety regulations to prevent accidents and maintain system efficiency.
Steam Expansion
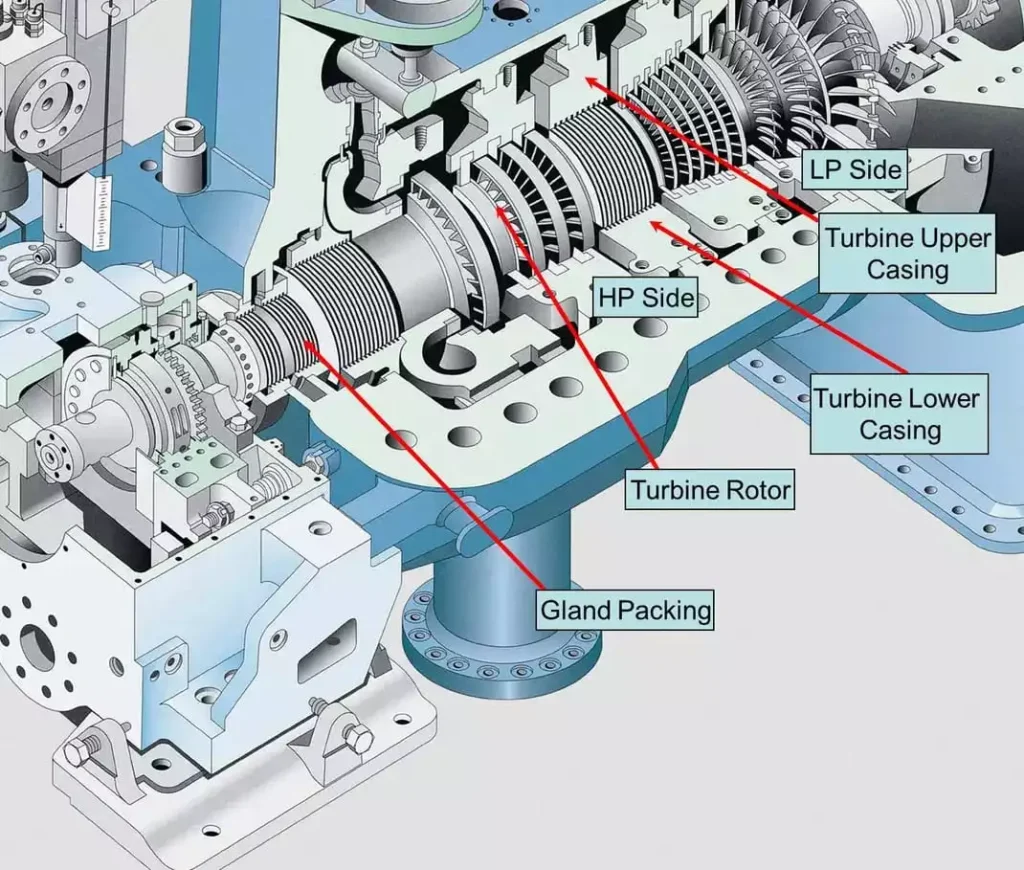
Steam expansion refers to the process by which steam undergoes a change in volume and pressure as it flows from a region of higher pressure to a region of lower pressure. This expansion of steam is a fundamental principle in thermodynamics and is crucial in various industrial and engineering applications. Steam expansion can occur in several scenarios, and its behavior is governed by the laws of thermodynamics. Here are some key aspects of steam expansion:
- Adiabatic Expansion: Steam expansion is often considered an adiabatic process, meaning there is no heat transfer into or out of the system during the expansion. In practical terms, this means that the total energy within the steam remains constant.
- Pressure and Temperature Drop: As steam expands from a higher-pressure region to a lower-pressure region, both its pressure and temperature decrease. The decrease in pressure is a direct consequence of the expansion process and follows Boyle’s law, which relates pressure and volume inversely.
- Volume Increase: The most noticeable effect of steam expansion is the significant increase in volume. Steam occupies a much larger volume at lower pressures than at higher pressures. This increase in volume can be harnessed for various purposes in power generation and industrial processes.
- Work Output: Steam expansion can be used to perform mechanical work. In steam turbines, for example, the expansion of high-pressure steam against turbine blades causes them to rotate, generating mechanical energy that can be converted into electricity or used for other purposes.
- Energy Conversion: Steam expansion is a crucial step in converting thermal energy (heat) into mechanical work. This energy conversion is the basis for the operation of steam engines, turbines, and many industrial processes.
- Phase Change: Depending on the initial pressure and temperature of the steam and the extent of expansion, steam may undergo phase changes during expansion. For example, superheated steam may partially condense as it expands and cools.
- Efficiency: The efficiency of a steam expansion process depends on several factors, including the initial pressure and temperature of the steam, the expansion ratio, and the design of the equipment used to harness the work output. Higher initial pressures and larger expansion ratios can yield more efficient energy conversion.
- Applications: Steam expansion is utilized in a wide range of applications, including power generation in steam turbines, refrigeration and air conditioning systems, industrial processes like steam engines and chemical reactors, and geothermal power plants.
- Control: In many applications, the rate and extent of steam expansion must be carefully controlled to achieve desired results. Control valves, turbines, and other equipment are used to regulate the expansion process.
Steam expansion is a fundamental concept in thermodynamics and is at the heart of many energy conversion processes. Understanding how steam behaves during expansion is crucial for optimizing the efficiency and performance of steam-based systems and machinery.
Single-stage Back Pressure Steam Turbine
A single-stage back-pressure steam turbine is the simplest type of steam turbine, typically employed for small-scale applications where electricity generation is not the primary objective. These turbines utilize a single set of turbine blades to expand the steam and convert its thermal energy into mechanical energy.
Key Features of Single-Stage Back-Pressure Steam Turbines:
- Simplicity: Single-stage turbines are relatively simple and compact, making them cost-effective and easy to maintain.
- Low Cost: The single-stage design minimizes manufacturing complexity and material requirements, resulting in a lower overall cost compared to multi-stage turbines.
- Suitability for Small-Scale Applications: Single-stage turbines are well-suited for small and medium-sized power plants, industrial processes, and district heating systems.
- Low Steam Pressure and Flow Requirements: Single-stage turbines operate efficiently at lower steam pressures and flow rates, making them ideal for applications with limited steam resources.
- Simplified Control Systems: Single-stage turbines typically have simpler control systems, reducing complexity and maintenance requirements.
Applications of Single-Stage Back-Pressure Steam Turbines:
- Heating Systems: Single-stage turbines are often used in industrial heating systems to provide steam for drying, sterilization, and other process heating applications.
- Process Steam Production: In smaller industrial settings, single-stage turbines can be employed to generate process steam for specific manufacturing processes.
- District Heating: Single-stage turbines can be integrated into district heating systems to provide steam or hot water for heating residential and commercial buildings.
- Cogeneration Systems: Single-stage turbines can be used in small-scale cogeneration systems to produce electricity and process steam simultaneously.
- Remote Power Generation: Single-stage turbines are well-suited for providing electricity to remote locations or microgrids where large-scale power generation is impractical or cost-prohibitive.
In summary, single-stage back-pressure steam turbines offer a simple, cost-effective, and versatile solution for generating steam and providing low-power applications. Their compact size and ease of maintenance make them attractive for a wide range of industrial and heating requirements.
A back pressure steam turbine, also known as a non-condensing or extraction steam turbine, is a type of steam turbine used in various industrial and power generation applications. Its primary characteristic is that it releases the exhaust steam at a pressure higher than atmospheric pressure, and this steam is often used for specific industrial processes or heating applications. Here are the key features and applications of back-pressure steam turbines:
Key Features:
- Exhaust Steam Pressure: Unlike condensing steam turbines that exhaust steam at or near atmospheric pressure, back-pressure turbines release the exhaust steam at a pressure greater than atmospheric. The specific pressure depends on the design and application but is typically chosen to meet the requirements of industrial processes or district heating.
- Extraction Points: Back-pressure turbines often have multiple extraction points along the length of the turbine. At these extraction points, a portion of the steam is tapped off for specific industrial processes. These extraction points allow for the flexibility to provide steam at different pressures and temperatures for various applications.
- Process Steam Generation: One of the primary applications of back-pressure steam turbines is the generation of process steam for industrial purposes. The high-pressure exhaust steam is used for tasks such as heating, drying, or chemical processes in industrial facilities.
- Combined Heat and Power (CHP): Back-pressure turbines are commonly used in combined heat and power (CHP) systems, where they generate electricity while simultaneously providing thermal energy (steam) for industrial or heating applications. This co-generation approach increases overall energy efficiency.
- District Heating: In district heating systems, back-pressure steam turbines play a crucial role in supplying high-pressure steam for space heating and domestic hot water production in urban areas.
Working Principle:
The working principle of a back-pressure steam turbine is similar to other steam turbines:
- High-pressure and high-temperature steam is supplied to the inlet of the turbine.
- The steam expands as it flows through the turbine blades, causing the blades to rotate and generate mechanical work. This mechanical work can be used to drive equipment or electrical generators.
- After passing through the turbine blades, the steam exits the turbine at the desired back pressure, which is higher than atmospheric pressure.
- The high-pressure exhaust steam is then directed to industrial processes, district heating networks, or other applications that require steam at specific pressures and temperatures.
Advantages:
- Energy Efficiency: Back-pressure turbines maximize energy efficiency by utilizing the exhaust steam for process heating, thus avoiding the energy losses associated with steam condensation in condensing turbines.
- CHP Benefits: They are well-suited for combined heat and power (CHP) systems, where they contribute to both electricity generation and heat supply, reducing overall energy costs.
- Flexibility: Multiple extraction points allow for the customization of steam supply to meet the needs of various industrial processes.
Challenges:
- Limited Electricity Generation: Back-pressure turbines are less efficient for pure electricity generation compared to condensing turbines because they do not fully utilize the thermal potential of the steam.
- Steam Quality: The exhaust steam may have a higher moisture content, making it less suitable for applications that require high-quality steam.
In summary, back-pressure steam turbines are designed to release high-pressure exhaust steam for industrial processes, heating, and co-generation applications. Their ability to provide both electricity and process steam makes them valuable in industries and district heating systems where energy efficiency and flexibility are essential.
Back Pressure Steam Turbine
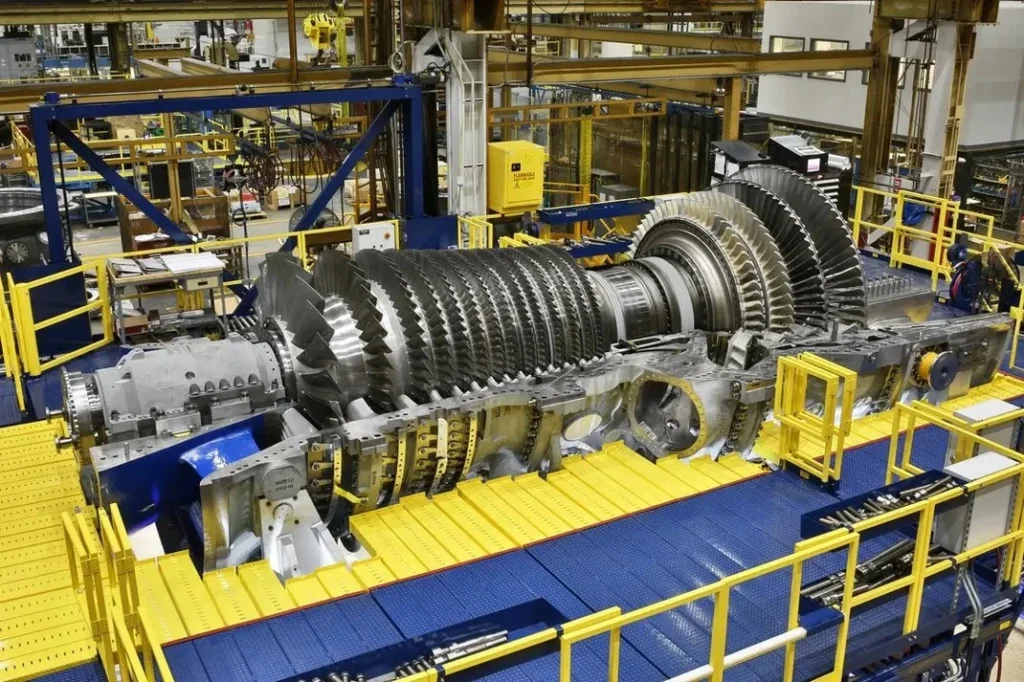
A back-pressure steam turbine is a type of steam turbine that is specifically designed to produce steam at a lower pressure for downstream applications, unlike condensing turbines which exhaust steam at very low pressures. Back-pressure turbines exhaust steam at higher pressure, typically between 5 and 20 psig (pounds per square inch gauge). This exhaust steam can then be used for various purposes, such as heating, process steam, or district heating.
Working Principle of a Back-Pressure Steam Turbine:
- High-pressure steam from the boiler enters the steam turbine.
- As the steam passes through the turbine’s stages, it expands, and its pressure decreases.
- This expansion converts the steam’s thermal energy into mechanical energy.
- The mechanical energy generated by the turbine is used to rotate a generator, producing electricity.
- The exhaust steam, still containing significant thermal energy, exits the turbine at a lower pressure.
- The back-pressure steam is then directed to downstream applications, such as heating systems, process steam requirements, or district heating networks.
Advantages of Back-Pressure Steam Turbines:
- Efficient Energy Utilization: Back-pressure steam turbines extract additional useful energy from the steam before it is discharged, improving overall energy efficiency.
- Reduced Fuel Consumption: By utilizing back-pressure steam for downstream needs, the demand for direct fuel combustion in boilers is reduced, leading to lower fuel consumption and cost savings.
- Environmental Benefits: Minimizing fuel consumption and utilizing waste heat from steam turbines contribute to reducing greenhouse gas emissions and minimizing the environmental impact of industrial processes.
- Versatility: Back-pressure steam turbines can be tailored to meet specific industrial or district heating requirements, offering flexibility in steam pressure and capacity.
Applications of Back-Pressure Steam Turbines:
- Industrial Process Steam Generation: Back-pressure steam is commonly used to provide steam for various industrial processes, such as papermaking, textile processing, and food production.
- District Heating Systems: Back-pressure steam can be used to heat buildings and provide hot water in district heating systems, replacing direct combustion of fossil fuels for heating purposes.
- Cogeneration Systems: Back-pressure steam turbines are often employed in cogeneration systems, where they simultaneously produce electricity and process steam, maximizing energy utilization.
- Steam Recompression: In some cases, back-pressure steam can be recompressed using a booster compressor to elevate its pressure, enabling its reuse in higher-pressure processes or for power generation.
In summary, back-pressure steam turbines play a crucial role in optimizing energy efficiency, reducing environmental impact, and providing valuable steam for various industrial processes and heating applications. By effectively utilizing back-pressure steam, industries and communities can conserve fuel, reduce emissions, and enhance the overall sustainability of their energy systems.
Back Pressure in a Steam Turbine Calculation
Calculating the back pressure in a steam turbine involves considering the properties of the exhaust steam and the specific conditions at the turbine outlet. The back pressure is typically expressed in pressure units such as pounds per square inch (psi), pascals (Pa), or bar. Here are the steps to calculate the turbine back pressure:
- Determine the Steam Properties:
- Gather information about the properties of the steam entering the turbine, including its pressure (P_in) and temperature (T_in). These values can be obtained from the steam source or the steam cycle.
- Understand the Turbine Characteristics:
- Familiarize yourself with the design and specifications of the steam turbine, including any extraction points (if applicable) and the desired back pressure level. Extraction points allow for the extraction of steam at various pressures for specific processes.
- Calculate the Isentropic Expansion:
- Determine the isentropic efficiency (η_isentropic) of the turbine, which represents how efficiently the turbine converts the enthalpy of the incoming steam into mechanical work. This efficiency is usually provided by the turbine manufacturer or can be estimated based on the type and design of the turbine.
- Calculate the enthalpy (h_out_isentropic) at the turbine outlet if the expansion were isentropic (adiabatic and reversible). This can be calculated using the steam tables or software tools specific to steam properties.
- Calculate the Actual Outlet Enthalpy:
- Use the isentropic efficiency to calculate the actual outlet enthalpy (h_out_actual) of the steam from the turbine:h_out_actual = h_in – η_isentropic * (h_in – h_out_isentropic)
- h_in is the enthalpy of the incoming steam.
- h_out_isentropic is the enthalpy at the outlet if the expansion were isentropic.
- Determine the Back Pressure:
- Based on the desired outlet pressure or back pressure (P_back_pressure) for your specific application, you can calculate the corresponding enthalpy at that pressure. This can be done using the steam tables or thermodynamic software.
- Ensure that the desired back pressure is within the operational capabilities of the turbine.
- Verify the Actual Back Pressure:
- Compare the calculated enthalpy at the desired back pressure to the actual outlet enthalpy (h_out_actual) from the turbine. The actual outlet pressure (P_out_actual) should match the desired back pressure as closely as possible.
- Calculate the actual back pressure (P_back_actual) using the enthalpy obtained at the desired back pressure.
Keep in mind that this calculation assumes ideal conditions and does not account for factors like mechanical losses or other losses in the turbine. It provides an approximate back pressure value based on the properties of the incoming steam and the turbine’s isentropic efficiency. Additionally, it’s important to consult the manufacturer’s specifications and guidelines for accurate calculations and operational limits specific to your turbine.
Turbine back pressure is the pressure of the steam exiting the turbine’s outlet. It is a crucial parameter that determines the efficiency and utilization of the steam turbine system.
Factors Affecting Turbine Back Pressure:
- Steam Supply Pressure: The pressure of the steam entering the turbine directly influences the backpressure level. Higher steam supply pressure generally results in higher backpressure.
- Steam Flow Rate: The amount of steam flowing through the turbine affects the backpressure. Increased steam flow can lead to a rise in backpressure.
- Turbine Design: The design of the turbine, including blade geometry, stage configuration, and exhaust piping, influences the backpressure level.
- Downstream Steam Utilization: If the exhaust steam from the turbine is utilized for other purposes, such as heating or process applications, the backpressure level is typically maintained at a specific value to provide the required steam pressure for those downstream applications.
Calculating Turbine Back Pressure:
The backpressure of a turbine can be calculated using various methods, including:
- Steam Cycle Analysis: By analyzing the steam cycle of the turbine system, including the properties of steam at different stages, the backpressure can be determined using mathematical equations and thermodynamic principles.
- Empirical Correlations: Empirical correlations based on experimental data and turbine design parameters can be used to estimate the backpressure level.
- Manufacturer’s Data: Turbine manufacturers often provide backpressure curves or tables for their specific turbine models, which can be used to determine the backpressure for different operating conditions.
- Turbine Instrumentation: In some cases, direct measurements of backpressure may be available from instrumentation installed on the turbine’s exhaust piping.
Optimizing Turbine Back Pressure:
The optimal backpressure level for a steam turbine system depends on the specific application and the balance between electricity generation and exhaust steam utilization. In cogeneration systems, the backpressure level is carefully selected to maximize both electricity production and steam availability for industrial processes.
Conclusion:
Turbine back pressure plays a critical role in steam turbine systems, influencing both energy extraction and exhaust steam utilization. By carefully calculating and optimizing the backpressure level, steam turbine systems can achieve optimal efficiency, provide valuable steam for various industrial applications, and contribute to energy conservation efforts.
Back Pressure Steam
Back pressure steam is steam that is exhausted from a steam turbine at a lower pressure than the boiler’s operating pressure. This steam is still available for use in various applications, such as industrial processes, heating, and district heating systems.
Characteristics of Back Pressure Steam:
- Lower Pressure: Back pressure steam exits the turbine at a lower pressure than the boiler’s operating pressure. This lower pressure is a result of the expansion of the steam as it passes through the turbine’s stages.
- Still Contains Thermal Energy: Despite the lower pressure, back pressure steam still contains significant thermal energy that can be utilized for various purposes.
- Suitability for Downstream Applications: Back pressure steam can be used in a variety of downstream applications, such as process steam, heating, and district heating systems.
Factors Affecting Back Pressure:
- Turbine Design: The design of the steam turbine, particularly the blade configuration and stage spacing, influences the back pressure generated.
- Boiler Pressure: The operating pressure of the boiler dictates the maximum pressure of the steam entering the turbine.
- Turbine Load: The load on the turbine affects the back pressure, as higher loads result in lower back pressures due to increased steam flow.
- Condensate Return: Effective condensate return helps maintain the boiler’s water level and prevents overpressurization, which can affect back pressure.
Optimization of Back Pressure:
- Matching Demand and Supply: Balancing the supply of back pressure steam with the demand for downstream applications is crucial for efficient utilization.
- Pressure Control: Controlling the back pressure can be achieved through adjusting the turbine’s control valves or adjusting the boiler’s operating pressure.
- Stream Conditioning: In some cases, back pressure steam may require conditioning to remove impurities or adjust its temperature for specific downstream applications.
- Waste Heat Recovery: Back pressure steam can be used as an input for waste heat recovery systems, further extracting useful energy from the steam.
Benefits of Back Pressure Steam Utilization:
- Energy Efficiency: Utilizing back pressure steam for downstream applications enhances overall energy efficiency by extracting additional useful energy from the steam before it is discharged.
- Reduced Fuel Consumption: Redirecting back pressure steam to downstream uses can reduce the need for direct fuel combustion in boilers, leading to lower fuel consumption and cost savings.
- Environmental Benefits: Minimizing fuel consumption and utilizing waste heat from steam turbines contribute to reducing greenhouse gas emissions and minimizing the environmental impact of industrial processes.
- Water Savings: In some cases, back pressure steam can be used for process steam production, reducing the demand for fresh water, conserving water resources.
- Versatility: Back pressure steam can be used in a wide range of industrial processes and heating applications, making it a versatile and valuable energy source.
Conclusion:
Back pressure steam plays a significant role in optimizing energy efficiency and reducing environmental impact in steam turbine systems. By effectively utilizing back pressure steam for various downstream applications, industries can conserve fuel, reduce emissions, and extract additional value from their steam-generating processes.
Steam Supply Pressure
Steam supply pressure refers to the pressure of steam entering the turbine. It is a crucial parameter that affects the efficiency, performance, and overall operation of the steam turbine system.
Factors Affecting Steam Supply Pressure:
- Boiler Design and Capacity: The design and capacity of the boiler directly influence the maximum steam supply pressure that can be achieved. Larger boilers with more powerful pumps can generate steam at higher pressures.
- Fuel Type and Quality: The type and quality of fuel used in the boiler can affect the steam supply pressure. Higher-quality fuels, such as natural gas or oil, can produce steam at higher pressures compared to lower-quality fuels, such as coal.
- Boiler Efficiency: Boiler efficiency plays a role in determining the steam supply pressure. A more efficient boiler can generate steam at a higher pressure without excessive energy consumption.
- Condensate Return System: The effectiveness of the condensate return system, which collects and recycles condensed steam, can influence the steam supply pressure. Proper condensate return reduces the load on the boiler and allows for higher steam pressure generation.
Impact of Steam Supply Pressure:
- Turbine Efficiency: Higher steam supply pressure generally leads to higher turbine efficiency, as the steam molecules have more kinetic energy and can expand more effectively in the turbine stages.
- Power Generation: Higher steam supply pressure can increase the power output of the turbine, allowing for greater electricity generation.
- Heat Transfer Efficiency: Higher steam pressure can enhance heat transfer efficiency in steam-driven heat exchangers, improving their ability to transfer heat to various processes.
- Process Steam Production: In cogeneration systems, higher steam supply pressure can lead to increased production of high-pressure steam for industrial processes.
Optimizing Steam Supply Pressure:
The optimal steam supply pressure for a specific application depends on the desired balance between power generation, heat transfer, and exhaust steam utilization. In cogeneration systems, the steam supply pressure is adjusted to maximize both electricity production and steam availability for industrial processes.
Conclusion:
Steam supply pressure is a critical parameter that significantly impacts the performance and efficiency of steam turbine systems. By optimizing the steam supply pressure, steam turbine systems can achieve higher power generation, improve heat transfer efficiency, and maximize the utilization of exhaust steam for various industrial applications.
Boiler Design and Capacity
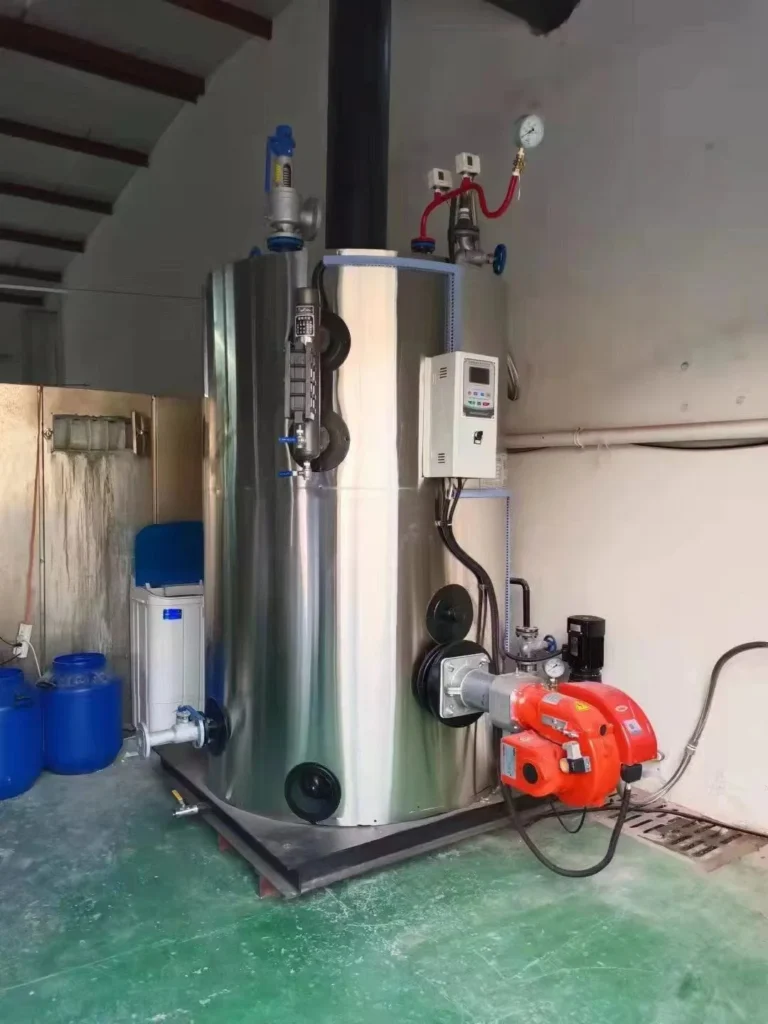
Boiler design and capacity play a crucial role in determining the efficiency, performance, and overall operation of steam turbine systems. The type and size of boiler selected must be carefully matched to the specific requirements of the steam turbine and the application it serves.
Factors Affecting Boiler Design:
- Steam Turbine Power Output: The steam turbine’s power output is a primary determinant of the boiler’s required capacity. Larger turbines with higher power ratings demand larger boilers capable of generating sufficient steam.
- Steam Pressure and Temperature: The desired steam pressure and temperature levels influence the boiler’s design parameters, such as the combustion chamber size and heat transfer surface area. Higher steam pressure and temperature requirements generally necessitate larger and more sophisticated boilers.
- Fuel Type and Efficiency: The type of fuel used in the boiler influences its design and operating characteristics. Boilers designed for certain fuel types, such as natural gas or oil, may have different combustion chambers, heat exchangers, and pollution control systems compared to boilers for coal or biomass.
- Condensate Return System: The effectiveness of the condensate return system, which collects and recycles condensed steam, can impact boiler design. Efficient condensate handling reduces the load on the boiler and allows for a smaller boiler size.
Impact of Boiler Design:
- Steam Production Efficiency: Boiler design significantly affects steam production efficiency. A well-designed boiler can minimize heat losses and maximize steam generation for a given amount of fuel input.
- Turbine Efficiency: Efficient steam production can directly impact turbine efficiency. Adequate steam pressure and temperature levels, along with minimizing impurities and contaminants in the steam, contribute to higher turbine efficiency.
- Reliability and Durability: Boiler design plays a crucial role in ensuring the reliability and durability of the boiler. Proper materials selection, corrosion protection measures, and effective maintenance practices can extend boiler lifespan and reduce downtime.
- Emissions Control: Boiler design can incorporate emissions control technologies to minimize harmful pollutants emitted during combustion. These technologies, such as flue gas desulfurization and Selective Catalytic Reduction, help protect the environment and meet environmental regulations.
Optimizing Boiler Design:
The optimal boiler design for a specific application depends on the desired steam pressure, temperature, and power output, as well as the fuel type and emission control requirements. By carefully considering these factors, boiler designers can select the most appropriate boiler type and size to meet the application’s needs and operate efficiently and sustainably.
Conclusion:
Boiler design and capacity are critical aspects of steam turbine systems, influencing their performance, efficiency, emissions control, and overall operation. By optimizing boiler design, steam turbine systems can maximize energy production, minimize environmental impact, and operate reliably for extended periods.
Fuel Type and Quality
Fuel type and quality play a significant role in the performance and efficiency of steam turbine systems. The appropriate selection and utilization of fuel can directly impact the steam production process, turbine operation, and overall energy generation.
Factors Affecting Fuel Selection:
- Steam Supply Requirements: The steam supply pressure, temperature, and flow rate requirements of the steam turbine determine the type of fuel that can be utilized effectively. Higher steam pressure and temperature demands may necessitate specific fuel types or blends.
- Fuel Availability and Cost: The availability and cost of different fuel sources in the region or locality influence the fuel selection process. Economic viability and supply chain considerations play a role in fuel choice.
- Environmental Regulations: Environmental regulations and emission standards can restrict the use of certain fuels or impose limits on pollutant emissions. Adherence to environmental norms is essential in fuel selection.
- Fuel Handling and Storage: The type of fuel also influences handling, storage, and transportation requirements. Some fuels, such as natural gas, require specialized infrastructure for transport and storage, while others, such as coal, can be handled using conventional methods.
Impact of Fuel Quality:
- Steam Production Efficiency: Fuel quality directly impacts steam production efficiency. High-quality fuels, such as natural gas or low-sulfur coal, produce cleaner and more efficient combustion, leading to higher steam generation rates for a given amount of fuel.
- Turbine Performance: Fuel quality can affect turbine performance by influencing steam purity and the presence of contaminants. Impurities in the steam, such as ash or sulfur compounds, can erode turbine blades and reduce efficiency.
- Emissions Control: Fuel quality plays a role in emissions control. Low-sulfur fuels produce fewer sulfur oxides (SOx), while low-nitrogen fuels reduce nitrogen oxide (NOx) emissions. Fuel choice can contribute to environmental compliance.
- Maintenance Requirements: Fuel quality can impact maintenance requirements. High-quality fuels generally lead to less fouling and corrosion in boilers and turbines, reducing maintenance frequency and costs.
Optimizing Fuel Selection and Quality:
- Fuel Analysis and Evaluation: Conducting regular fuel analysis and evaluation helps identify fuel quality variations and potential issues. This information can inform fuel selection decisions and optimize fuel blending strategies.
- Fuel Pre-Treatment: Pre-treatment processes, such as coal washing or fuel oil purification, can improve fuel quality and reduce impurities, leading to more efficient steam generation and cleaner emissions.
- Advanced Combustion Technologies: Utilizing advanced combustion technologies, such as fluidized bed combustion or staged combustion, can enhance fuel utilization and minimize pollutant formation.
- Fuel Management Systems: Implementing fuel management systems can optimize fuel usage, monitor fuel quality, and provide real-time data for fuel selection and blending decisions.
Conclusion:
Fuel type and quality are crucial aspects of steam turbine systems, influencing their efficiency, environmental performance, and overall operation. By selecting appropriate fuels, ensuring fuel quality, and implementing fuel management strategies, steam turbine systems can operate more effectively, reduce environmental impact, and contribute to sustainable energy production.
Boiler Efficiency
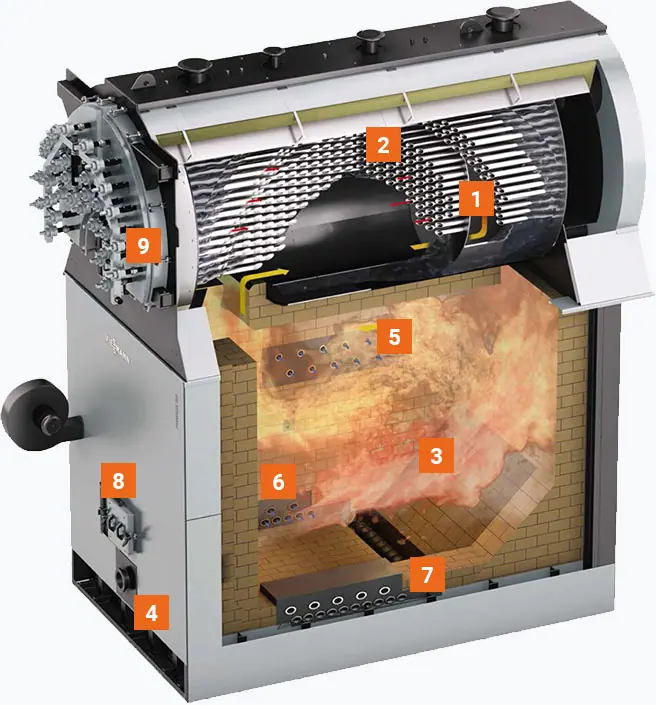
Boiler efficiency is a measure of how effectively a boiler converts the chemical energy in fuel into heat energy in steam. It is calculated by dividing the useful heat output by the total energy input. Boiler efficiency is typically expressed as a percentage, and can range from as low as 50% to as high as 98%.
Factors Affecting Boiler Efficiency:
- Boiler Design: The design of the boiler, including its combustion chamber, heat exchangers, and insulation, plays a significant role in determining its efficiency. Well-designed boilers minimize heat losses and maximize heat transfer to the water or steam being heated.
- Fuel Type and Quality: The type of fuel used in the boiler can affect its efficiency. Higher-quality fuels, such as natural gas or low-sulfur coal, produce cleaner and more efficient combustion, leading to lower heat losses and higher steam generation rates for a given amount of fuel.
- Combustion Control: Efficient combustion is crucial for maximizing boiler efficiency. Proper combustion control ensures that the correct amount of fuel and air is mixed, resulting in complete combustion and minimal heat losses.
- Boiler Maintenance: Regular maintenance and cleaning of the boiler, including its heat exchangers, burners, and tubes, are essential for maintaining efficiency. Fouling and corrosion can reduce heat transfer and lower efficiency.
- Water Treatment: The quality of the water used to generate steam can also impact boiler efficiency. Impurities in the water can lead to scale formation, which reduces heat transfer and increases energy consumption.
Improving Boiler Efficiency:
- Upgrade to High-Efficiency Boilers: Replacing old boilers with newer, more efficient models can significantly improve efficiency. Modern boilers incorporate advanced technologies and design features that minimize heat losses and enhance steam generation.
- Conduct Regular Boiler Maintenance: Implement a regular boiler maintenance schedule to ensure optimal performance and prevent efficiency losses. Maintenance should include cleaning, inspection, and replacement of worn or damaged components.
- Optimize Combustion Control: Employ advanced combustion control systems to ensure the precise mixing of fuel and air, leading to complete combustion and reduced heat losses.
- Utilize Efficient Fuel Blending: Blending different fuel types can optimize combustion and improve boiler efficiency. For instance, blending low-sulfur coal with higher-sulfur coal can reduce sulfur oxide emissions while maintaining efficiency.
- Implement Water Treatment Systems: Install appropriate water treatment systems to remove impurities from the boiler feedwater, preventing scale formation and maintaining heat transfer efficiency.
- Utilize Waste Heat Recovery Systems: Implement waste heat recovery systems to capture and utilize the heat lost in flue gases or other exhaust streams, increasing overall energy efficiency.
Conclusion:
Boiler efficiency is a critical parameter that directly influences the performance and cost-effectiveness of steam turbine systems. By optimizing boiler design, fuel selection, combustion control, and maintenance practices, steam turbine systems can achieve higher efficiency, reduce fuel consumption, and contribute to sustainable energy production.
Condensate Return System
A condensate return system is an integral part of a steam turbine system, responsible for collecting and returning condensed steam back to the boiler feedwater tank. This process plays a crucial role in improving steam turbine efficiency and reducing energy consumption.
Purpose of Condensate Return System:
The primary purpose of a condensate return system is to recover the thermal energy contained in the condensed steam and reuse it in the steam generation process. By recycling condensed steam, the boiler requires less energy to produce the same amount of steam, leading to significant fuel savings.
Working Principle of Condensate Return System:
- Condensate Collection: Condensate is collected from various points in the steam system, such as steam traps, heat exchangers, and process equipment. These collection points are typically located at low-pressure areas of the system.
- Condensate Transfer: The collected condensate is transported back to the boiler feedwater tank using pumps and piping. Condensate pumps provide the pressure differential required to overcome frictional losses and elevate the condensate to the desired pressure level.
- Condensate Treatment: Before being fed back to the boiler, the condensate may undergo treatment to remove impurities and contaminants that could cause corrosion or scale buildup in the boiler. This treatment may involve filtration, demineralization, or chemical conditioning.
- Condensate Storage: The treated condensate is stored in the boiler feedwater tank, where it is preheated by steam extraction or other means before being fed to the boiler. Preheating the condensate further reduces the boiler’s energy consumption.
Benefits of Condensate Return System:
- Improved Steam Turbine Efficiency: Reusing condensed steam reduces the energy required to generate steam, leading to higher steam turbine efficiency. This, in turn, improves overall power generation efficiency and reduces fuel consumption.
- Reduced Water Consumption: By recycling condensate, the need for fresh water for boiler feed is minimized. This conserves water resources and reduces the environmental impact of water extraction and treatment.
- Lower Operating Costs: The combination of improved efficiency and reduced water consumption leads to lower operating costs for the steam turbine system.
- Extended Boiler Life: By minimizing the introduction of impurities into the boiler, condensate return systems help protect the boiler from corrosion and scale buildup, extending its lifespan and reducing maintenance costs.
- Environmental Sustainability: Recycling condensate contributes to a more sustainable approach to steam turbine operation, reducing energy consumption, water usage, and environmental impact.
Conclusion:
A condensate return system is an essential component of a steam turbine system, playing a critical role in improving efficiency, reducing energy costs, and promoting environmental sustainability. By effectively collecting, treating, and reusing condensed steam, steam turbine systems can minimize their environmental footprint and contribute to a more sustainable energy future.
Turbine Efficiency
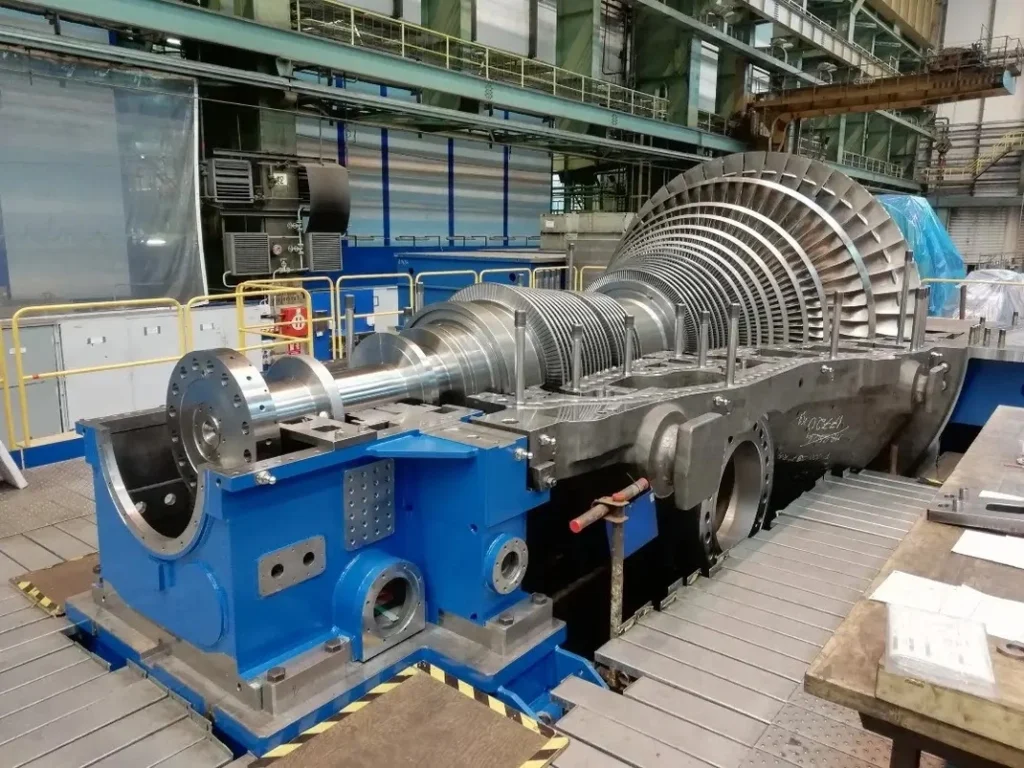
Turbine efficiency is a measure of how effectively a turbine converts the kinetic energy of a fluid, such as steam, water, or gas, into mechanical energy. It is typically expressed as a percentage, with higher values indicating better performance.
Factors Affecting Turbine Efficiency:
- Turbine Design: The design of the turbine, including the shape and size of the blades, the number of stages, and the overall geometry, plays a significant role in determining its efficiency. Well-designed turbines minimize energy losses and maximize energy conversion.
- Fluid Properties: The properties of the fluid flowing through the turbine, such as its density, pressure, and temperature, can affect efficiency. Higher density, pressure, and temperature generally lead to higher efficiency.
- Turbine Speed: The rotational speed of the turbine can also influence efficiency. Too slow a speed can reduce energy conversion, while too high a speed can lead to increased friction and energy losses.
- Fluid Entrance Conditions: The conditions at the turbine inlet, such as the uniformity and turbulence of the fluid flow, can affect efficiency. Smooth and uniform flow contributes to higher efficiency.
- Blade Erosion and Corrosion: Over time, turbine blades can experience erosion and corrosion due to the continuous exposure to high-velocity fluids. These degradations can reduce blade efficiency and overall turbine performance.
Improving Turbine Efficiency:
- Advanced Blade Design: Utilizing advanced blade designs, such as twisted or tapered blades, can improve fluid flow and reduce energy losses, leading to higher efficiency.
- Material Selection: Selecting materials with superior strength, erosion resistance, and corrosion resistance for turbine blades can extend their lifespan and maintain efficiency over time.
- Optimized Turbine Geometry: Optimizing the overall geometry of the turbine, including the blade angles, stage spacing, and flow path, can enhance energy conversion and reduce losses.
- Advanced Flow Control Systems: Implementing advanced flow control systems, such as variable inlet guide vanes or nozzle control mechanisms, can regulate the fluid flow and optimize turbine performance for different operating conditions.
- Regular Maintenance and Inspection: Regular maintenance and inspection of the turbine, including blade cleaning, surface repair, and component replacement, can prevent efficiency losses due to wear, erosion, or corrosion.
Conclusion:
Turbine efficiency is a crucial parameter that directly impacts the performance and cost-effectiveness of various power generation and industrial applications. By employing advanced design techniques, selecting appropriate materials, optimizing turbine geometry, implementing control systems, and conducting regular maintenance, turbine efficiency can be improved, leading to increased power output, reduced fuel consumption, and lower operating costs.
Back Pressure Steam Flow Rate
Steam flow rate, also known as steam mass flow rate, is a critical parameter that determines the power output and efficiency of steam turbine systems. It refers to the mass of steam passing through a specific point or section of the steam system per unit time. Steam flow rate is typically measured in kilograms per second (kg/s) or pounds per second (lb/s).
Importance of Steam Flow Rate:
- Power Output Determination: Steam flow rate is a primary input in calculating the power output of a steam turbine. The amount of steam passing through the turbine directly influences the kinetic energy available for conversion into mechanical energy.
- Efficiency Assessment: Steam flow rate is also used to assess the efficiency of steam turbine systems. By comparing the actual power output to the theoretical power output for a given steam flow rate, the efficiency of the turbine can be determined.
- Steam System Control: Steam flow rate is a crucial parameter for controlling and optimizing the performance of steam systems. By regulating the steam flow rate, various aspects of the system, such as turbine power output, steam pressure, and temperature, can be controlled.
- Process Steam Utilization: In cogeneration systems, where steam is used for both power generation and industrial processes, steam flow rate is important for ensuring adequate steam supply for both power generation and process needs.
- Boiler Operation: Steam flow rate is also relevant for boiler operation, as it impacts the boiler’s ability to generate steam at the desired pressure and temperature. Monitoring steam flow rate helps maintain proper boiler operation and prevent overproduction or underproduction of steam.
Methods of Measuring Steam Flow Rate:
- Venturi Meter: A Venturi meter is a device that measures the differential pressure between two tapered sections of a pipe. By knowing the pressure difference and the pipe diameter, the steam flow rate can be calculated.
- Orifice Plate: An orifice plate is a device that creates a localized constriction in a pipe, causing a pressure drop. By measuring the pressure drop and the pipe diameter, the steam flow rate can be determined.
- Turbine Inlet Nozzle Pressure: In some cases, the steam flow rate can be estimated based on the pressure at the turbine inlet nozzle. This method is less accurate than direct flow measurement but can be used for monitoring and control purposes.
- Ultrasonic Flowmeters: Ultrasonic flowmeters utilize the principle of Doppler shift to measure the velocity of steam flowing through a pipe. By knowing the velocity and the pipe diameter, the steam flow rate can be calculated.
- Coriolis Mass Flowmeters: Coriolis mass flowmeters measure the mass flow rate of a fluid based on the principle of Coriolis force. These meters are highly accurate and can be used for measuring steam flow rate in various applications.
Conclusion:
Steam flow rate is a fundamental parameter in steam turbine systems, influencing power output, efficiency, process steam utilization, and boiler operation. By accurately measuring and controlling steam flow rate, steam turbine systems can operate efficiently, produce the desired power output, and provide adequate steam for various industrial processes.
Turbine Design
Turbine design is a critical aspect of steam turbine systems, influencing their performance, efficiency, and overall operation. The design of a steam turbine encompasses various aspects, including blade geometry, stage configuration, flow path optimization, and material selection.
Key Elements of Turbine Design:
- Blade Design: The shape and size of turbine blades play a crucial role in efficiently converting the kinetic energy of steam into mechanical energy. Different blade designs, such as twisted or tapered blades, can be employed to optimize fluid flow and maximize energy extraction.
- Stage Configuration: The number of stages in a turbine determines the pressure drop and efficiency. Multi-stage turbines typically exhibit higher efficiency compared to single-stage turbines.
- Flow Path Optimization: The flow path through the turbine should be designed to minimize losses and maximize energy transfer. This includes optimizing blade angles, stage spacing, and the overall geometry of the turbine passages.
- Material Selection: Turbine materials must be carefully chosen to withstand the high temperatures, pressures, and corrosive effects of steam. Stainless steels, nickel alloys, and other high-performance materials are commonly used for turbine components.
Factors Influencing Turbine Design:
- Steam Parameters: The properties of the steam, such as its pressure, temperature, and flow rate, significantly impact turbine design. Higher steam pressure and temperature generally allow for higher efficiency and power output.
- Power Requirements: The desired power output of the turbine is a primary factor in determining its design. Larger turbines with more stages can produce higher power outputs.
- Application: The specific application of the steam turbine, such as power generation, process steam production, or marine propulsion, influences design considerations.
- Operational Conditions: The expected operating conditions, such as continuous or intermittent operation, load variations, and environmental factors, also influence turbine design.
Advanced Turbine Design Techniques:
- Computational Fluid Dynamics (CFD): CFD software allows for the simulation of fluid flow through the turbine, providing insights into aerodynamic performance and optimizing blade design.
- Additive Manufacturing (3D Printing): Additive manufacturing enables the fabrication of complex turbine components with intricate geometries, enhancing performance and material utilization.
- Smart Materials and Sensors: Embedded sensors and smart materials can provide real-time data on turbine performance and operating conditions, enabling predictive maintenance and optimized operation.
- Numerical Control (NC) Machining: Highly precise NC machining techniques allow for the production of turbine components with tight tolerances, ensuring efficient energy conversion and reducing losses.
Conclusion:
Turbine design is an intricate and evolving field, with advancements in materials, computational techniques, and manufacturing processes leading to more efficient, durable, and optimized steam turbine systems. By carefully considering the operating conditions, application requirements, and material properties, turbine designers can create turbines that meet the demands of various industries and contribute to sustainable energy production.
Back Pressure Downstream Steam Utilization
Downstream steam utilization refers to the use of steam that has already passed through a steam turbine and exited the turbine at a lower pressure. This exhaust steam, while no longer suitable for direct power generation, still contains significant thermal energy that can be utilized for various purposes in industrial processes and heating applications.
Applications of Downstream Steam Utilization:
- Process Steam: Exhaust steam can be used as process steam in various industrial applications, such as papermaking, textile processing, food production, and chemical manufacturing. Process steam provides heat for drying, sterilization, and other process steps.
- Heating and Space Conditioning: Exhaust steam can be employed for heating buildings, providing hot water, and maintaining comfortable temperatures in industrial facilities. This reduces the reliance on direct combustion of fossil fuels for heating purposes.
- Steam Recompression: In cogeneration systems, low-pressure exhaust steam can be recompressed using a booster compressor to elevate its pressure, enabling its reuse in higher-pressure processes or for power generation.
- Steam Jet Refrigeration: Exhaust steam can be used to drive steam jet ejectors, which create a vacuum and can be used for refrigeration or other vacuum applications.
- Steam Desalination: In desalination plants, exhaust steam can be used to heat seawater and facilitate the evaporation process, producing freshwater from seawater.
Benefits of Downstream Steam Utilization:
- Improved Energy Efficiency: Utilizing exhaust steam for downstream applications enhances overall energy efficiency by extracting additional useful energy from the steam before it is discharged.
- Reduced Fuel Consumption: By utilizing exhaust steam for process heating or other purposes, the need for direct fuel combustion is reduced, leading to lower fuel consumption and cost savings.
- Environmental Benefits: Minimizing fuel consumption and utilizing waste heat from steam turbines contribute to reducing greenhouse gas emissions and minimizing the environmental impact of industrial processes.
- Water Conservation: In cogeneration systems, utilizing exhaust steam for process steam production can reduce the demand for fresh water, conserving water resources.
- Diverse Applications: Exhaust steam can be used in a wide range of industrial processes and heating applications, making it a versatile and valuable energy source.
Challenges of Downstream Steam Utilization:
- Steam Quality: Exhaust steam may contain impurities, such as moisture or dissolved solids, that need to be removed before it can be utilized in certain applications.
- Steam Pressure Requirements: The pressure of the exhaust steam may not always be suitable for all downstream applications, requiring additional pressure boosting or steam conditioning.
- Piping and Distribution: Efficient distribution of exhaust steam to various downstream locations may require extensive piping networks and proper insulation to minimize energy losses.
- Condensation Management: Condensate generated from downstream steam utilization needs to be properly collected and returned to the boiler feedwater system to maintain water balance and optimize cycle efficiency.
- Matching Supply and Demand: Balancing the availability of exhaust steam with the demand from downstream applications requires careful planning and coordination.
Conclusion:
Downstream steam utilization plays a crucial role in maximizing energy efficiency and reducing the environmental impact of steam turbine systems. By effectively utilizing exhaust steam for various industrial processes and heating applications, industries can conserve fuel, reduce emissions, and extract additional value from their steam-generating processes.
Multi Stage Turbine
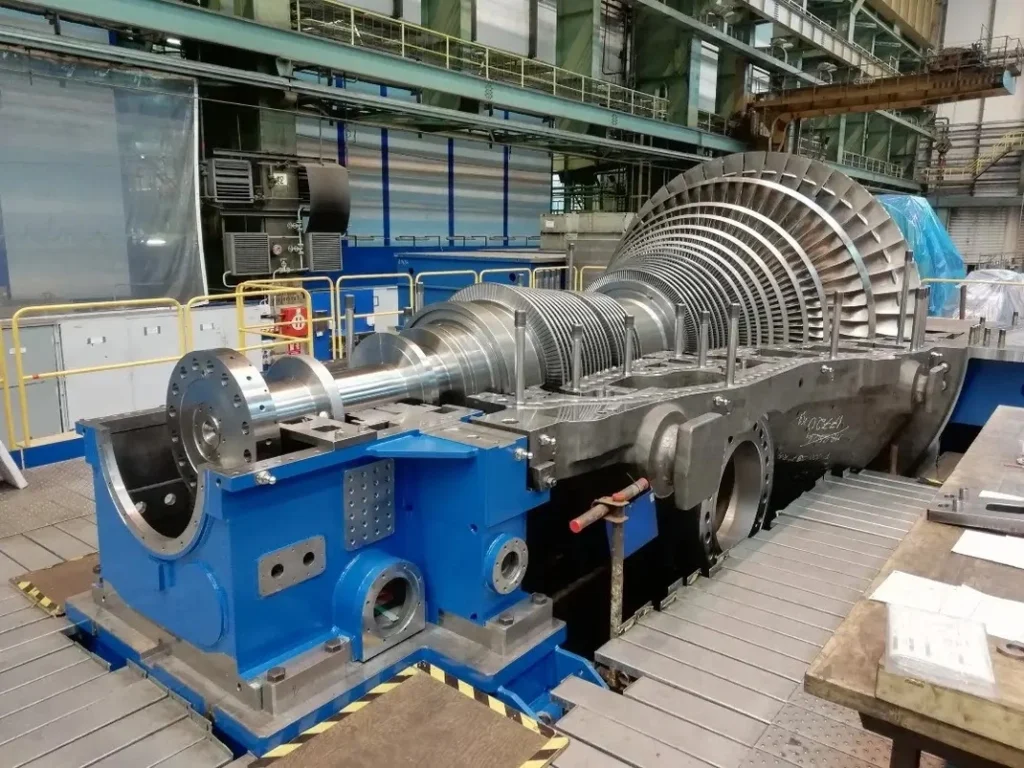
A multistage turbine is a turbine that utilizes multiple stages of blades to extract energy from a fluid, typically steam or gas, more efficiently than a single-stage turbine. This multistage design allows for more gradual expansion of the fluid, maximizing energy conversion and enhancing overall efficiency.
Working Principle of a Multistage Turbine:
- Fluid Entry and Expansion: High-pressure fluid enters the first stage of the turbine through a nozzle or inlet valve, gaining velocity and decreasing pressure.
- Blade Interaction: The fluid strikes the rotor blades of the first stage, transferring its kinetic energy to the blades. This interaction causes the blades to rotate, generating rotational motion.
- Stage Transition: The partially expanded fluid exits the first stage and enters the second stage through intermediate passages or ducts.
- Repeated Expansion: The fluid undergoes further expansion and energy extraction as it passes through subsequent stages, each with its own set of rotor blades.
- Exhaust Stage and Exit: The fully expanded and low-pressure fluid exits the final stage through an exhaust port or nozzle.
Advantages of Multistage Turbines:
- Higher Efficiency: Multistage turbines achieve higher thermal efficiencies compared to single-stage turbines due to the gradual expansion of the fluid across multiple stages.
- Reduced Blade Loading: The multistage design distributes the energy extraction over multiple stages, reducing the load on individual blades and minimizing blade stress.
- Enhanced Power Output: Multistage turbines can generate more power for the same amount of fluid input compared to single-stage turbines due to the more efficient energy extraction process.
- Wider Range of Applications: Multistage turbines can handle a wider range of fluid pressures and flow rates, making them suitable for various applications.
- Adaptability to Variable Conditions: Multistage turbines can be designed to operate efficiently under variable fluid conditions, such as fluctuating inlet pressure or temperature.
Applications of Multistage Turbines:
- Power Generation: Multistage steam turbines are the primary technology for generating electricity in large-scale power plants. They efficiently convert steam energy into mechanical energy, driving generators to produce electricity.
- Marine Propulsion: Multistage steam turbines were traditionally used in marine propulsion, particularly in large ships and submarines. However, their use in this sector has declined in favor of more efficient and environmentally friendly propulsion systems.
- Aircraft Engines: Multistage gas turbines are the primary propulsion systems for modern aircraft. They efficiently convert the energy of hot, pressurized gas into thrust, enabling airplanes to fly.
- Turbochargers: Multistage turbines are used in turbochargers to increase the air intake and boost the power output of internal combustion engines.
- Industrial Applications: Multistage turbines are employed in various industrial applications, such as driving pumps, compressors, and expanders in process industries.
Conclusion:
Multistage turbines play a crucial role in various power generation, propulsion, and industrial applications. Their ability to extract energy efficiently from fluids, coupled with their adaptability and versatility, makes them a preferred choice for a wide range of technological applications.
Steam Turbines
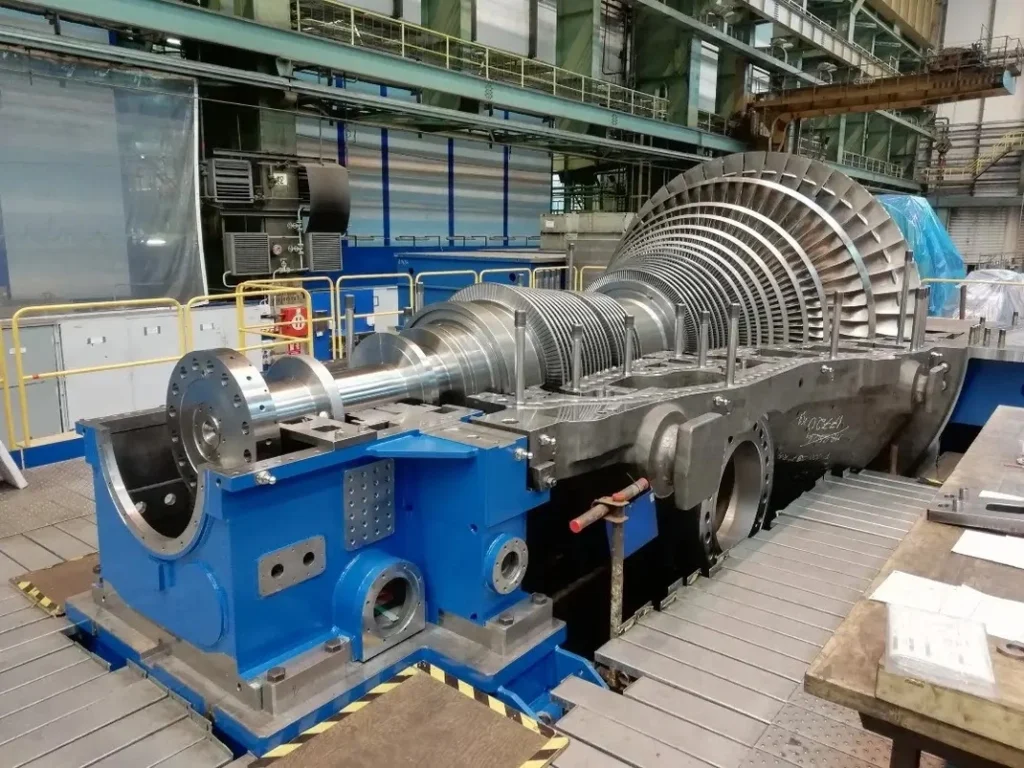
Steam turbines are a fundamental component of modern power generation and various industrial processes. They convert thermal energy from steam into mechanical energy, which can then be used to generate electricity or drive machinery. The concept of harnessing steam power dates back to ancient times, with early attempts to use steam for mechanical purposes seen in the aeolipile, a simple steam-powered device invented by Hero of Alexandria in the 1st century AD. However, it wasn’t until the 19th century that steam turbines, as we know them today, began to take shape.
The breakthrough in steam turbine technology came in the late 19th century with the work of Sir Charles Parsons and Gustaf de Laval. Sir Charles Parsons is often credited with inventing the modern steam turbine in 1884, when he developed a prototype capable of driving an electrical generator. This invention marked a significant leap in efficiency compared to earlier steam engines. Parsons’ steam turbine quickly became the preferred method for generating electricity, and its design principles are still used in modern turbines.
Gustaf de Laval, a Swedish engineer, made significant contributions to the development of steam turbines, particularly in high-speed turbines. His work in the 1880s and 1890s led to the creation of impulse turbines, which use the kinetic energy of steam to drive the turbine blades. These developments laid the foundation for the widespread adoption of steam turbines in various industries.
Importance in Modern Industry
Today, steam turbines play a crucial role in the global energy landscape. They are used in thermal power plants to generate a significant portion of the world’s electricity. In a typical thermal power plant, steam is produced by burning fossil fuels such as coal, natural gas, or oil, or by utilizing nuclear energy. The steam is then directed into the turbine, where it expands and drives the turbine blades, converting thermal energy into mechanical energy. This mechanical energy is then used to rotate an electrical generator, producing electricity.
Steam turbines are also integral to various industrial processes. They are used in the petrochemical industry to drive compressors and pumps, in the steel industry for mechanical drives, and in the paper industry to generate electricity and drive machinery. Additionally, steam turbines are employed in marine propulsion systems, particularly in large vessels like aircraft carriers and submarines, where their reliability and efficiency are highly valued.
The versatility and efficiency of steam turbines make them indispensable in both traditional and modern energy systems. They are compatible with a wide range of energy sources, including fossil fuels, nuclear power, and renewable sources such as biomass, geothermal, and concentrated solar power. This adaptability ensures that steam turbines will continue to play a vital role in the global energy mix as the world transitions towards more sustainable energy solutions.
Fundamentals of Steam Turbines
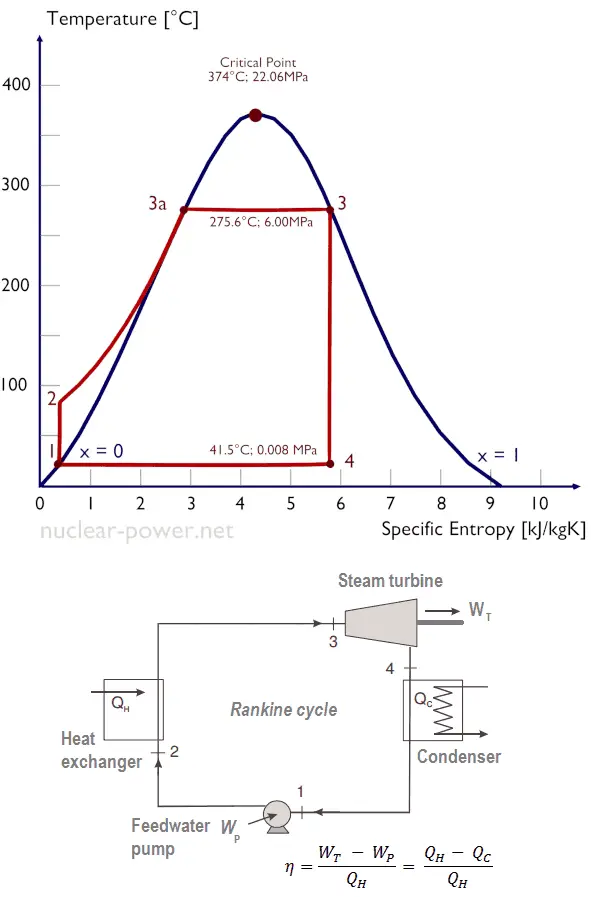
Basic Principles
At the core of a steam turbine’s operation is the conversion of thermal energy from steam into mechanical energy. This process is grounded in the principles of thermodynamics, specifically the Rankine cycle, which is the fundamental thermodynamic cycle used in steam turbine operations.
In simple terms, the Rankine cycle involves four main processes:
- Heat Addition: In a boiler, water is heated at constant pressure, transforming it into steam. This high-pressure steam contains a significant amount of thermal energy.
- Expansion: The high-energy steam is directed into the turbine, where it expands. As the steam expands, its pressure and temperature drop, and it imparts kinetic energy to the turbine blades, causing them to rotate. This rotational energy is then transferred to a shaft connected to an electrical generator or mechanical equipment.
- Condensation: After passing through the turbine, the steam is exhausted into a condenser, where it is cooled and condensed back into water.
- Pumping: The condensed water is then pumped back to the boiler to begin the cycle again.
The efficiency of a steam turbine is determined by how effectively it converts the thermal energy in the steam into mechanical energy. Factors such as steam pressure, temperature, and the design of the turbine blades play crucial roles in determining this efficiency.
Key Components
Steam turbines consist of several critical components, each playing a specific role in the turbine’s operation:
- Rotor: The rotor is the rotating part of the turbine and consists of a shaft and attached blades. As steam passes through the turbine, it causes the rotor to spin, converting thermal energy into mechanical energy.
- Stator: The stator is the stationary part of the turbine that surrounds the rotor. It contains fixed blades that direct the flow of steam onto the rotor blades in an efficient manner.
- Casing: The casing encases the entire turbine, providing structural support and containing the steam within the turbine. It also protects the internal components from external elements.
- Blades: The turbine blades are crucial for the conversion of energy. There are two main types of blades: fixed blades (attached to the stator) and moving blades (attached to the rotor). The design and arrangement of these blades are critical for the efficient operation of the turbine.
- Steam Supply System: This system includes the pipes, valves, and other components that deliver steam to the turbine at the required pressure and temperature. It also controls the flow of steam into the turbine.
- Condenser: The condenser cools the exhaust steam from the turbine, converting it back into water to be reused in the cycle. It is typically a heat exchanger that removes the latent heat of vaporization from the steam.
- Governor: The governor is a control mechanism that regulates the turbine’s speed by adjusting the steam flow. It ensures that the turbine operates at the desired speed and can respond to changes in load demand.
Types of Steam Turbines
Steam turbines are classified based on their design, method of steam expansion, and application. The main types include:
- Impulse Turbines: In impulse turbines, high-pressure steam is directed onto the turbine blades through nozzles. The steam jets strike the blades, causing them to move, but the steam pressure remains constant as it passes over the blades. The rotor’s motion is purely due to the impulse force from the steam. Impulse turbines are often used in high-speed applications and are suitable for driving generators in power plants.
- Reaction Turbines: Unlike impulse turbines, reaction turbines utilize both the impulse of steam and the reaction force generated as steam expands and accelerates through the moving blades. The steam pressure drops as it passes through the blades, and this pressure drop is what drives the rotor. Reaction turbines are commonly used in lower-speed applications and are often found in industrial settings.
- Condensing Turbines: These turbines are designed to exhaust steam at a lower pressure, usually into a condenser, where the steam is condensed into water. Condensing turbines are widely used in power generation, where maximum efficiency is required.
- Non-Condensing Turbines: Also known as back-pressure turbines, these turbines exhaust steam at a pressure higher than atmospheric pressure. The exhaust steam can be used for heating or other industrial processes. Non-condensing turbines are commonly used in cogeneration systems where both electricity and process steam are needed.
- Extraction Turbines: Extraction turbines are designed to extract steam at one or more points along the turbine for industrial processes or heating. The remaining steam continues through the turbine for power generation. These turbines provide flexibility in applications where steam at different pressures is required.
- Reheat Turbines: In reheat turbines, steam is expanded through a high-pressure stage of the turbine, reheated in the boiler, and then expanded further in a lower-pressure stage. Reheating improves the efficiency of the cycle and reduces the moisture content of the steam, which can help to reduce blade erosion.
- Industrial Turbines: These are designed for specific industrial applications, such as driving compressors, pumps, or fans. Industrial turbines can be either impulse or reaction types, depending on the specific application requirements.
- Marine Turbines: Used in naval vessels and large commercial ships, marine turbines are designed to be highly reliable and capable of operating under the challenging conditions at sea. They are typically reaction turbines and are designed to drive propellers or generators for propulsion.
Thermodynamics and Fluid Mechanics
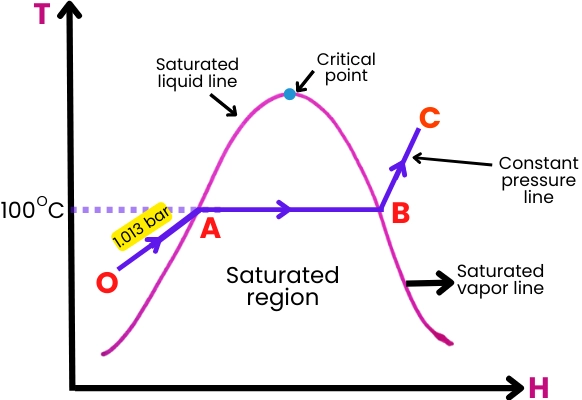
Thermodynamic Cycles
The operation of steam turbines is fundamentally based on thermodynamic cycles, with the Rankine cycle being the most important for understanding how these machines work. The Rankine cycle, named after William John Macquorn Rankine, is a closed-loop cycle that converts heat into work, making it the backbone of steam turbine operations in power plants and industrial settings.
- The Rankine Cycle: The Rankine cycle consists of four main processes:
- Isentropic Compression: The working fluid (water) is pumped from a low pressure to a high pressure. This process requires work input, typically provided by a pump.
- Isobaric Heat Addition: The high-pressure water is heated in a boiler at constant pressure, turning it into high-pressure steam.
- Isentropic Expansion: The high-pressure steam is expanded in the turbine, doing work by turning the turbine’s rotor. As the steam expands, its pressure and temperature drop.
- Isobaric Heat Rejection: The expanded steam is condensed at constant pressure back into water, completing the cycle.
- Reheat Cycle: In a reheat cycle, steam is expanded in a high-pressure turbine, reheated in the boiler, and then expanded again in a low-pressure turbine. This process increases the thermal efficiency of the cycle by allowing the steam to expand through a greater pressure range, reducing the moisture content at the turbine’s exhaust, which in turn minimizes turbine blade erosion.
- Regenerative Cycle: The regenerative cycle improves efficiency by preheating the feedwater entering the boiler using steam extracted from various stages of the turbine. This reduces the amount of fuel needed to heat the water to the desired temperature, thereby improving overall efficiency.
- Combined Cycle: The combined cycle is a modern approach that combines a gas turbine cycle with a steam turbine cycle. The exhaust gases from the gas turbine are used to generate steam in a heat recovery steam generator (HRSG), which then powers a steam turbine. This setup allows for very high overall efficiency, often exceeding 60%.
Fluid Dynamics in Steam Turbines
Fluid dynamics plays a crucial role in the operation of steam turbines, as the efficient conversion of steam energy into mechanical work depends on the controlled flow of steam through the turbine.
- Steam Flow and Velocity Triangles: The flow of steam through a turbine is characterized by velocity triangles, which are geometric representations of the velocity of steam relative to the blades of the turbine. These triangles help in analyzing the energy conversion process as the steam flows through both the stationary (stator) and moving (rotor) blades.
- Absolute Velocity: This is the velocity of the steam relative to the stationary components of the turbine.
- Relative Velocity: This is the velocity of the steam relative to the moving blades of the rotor.
- Blade Velocity: The velocity at which the turbine blades move.
- Impulse and Reaction Principles: Steam turbines operate on either impulse or reaction principles, or a combination of both.
- Impulse Turbines: In impulse turbines, steam is expanded through nozzles, converting its pressure energy into kinetic energy before it hits the rotor blades. The rotor blades are designed to absorb this kinetic energy, causing the rotor to spin.
- Reaction Turbines: In reaction turbines, the steam undergoes a pressure drop as it passes through the rotor blades, which are shaped to act as nozzles. The pressure drop results in a reactive force that turns the rotor. This principle is similar to how a jet engine works.
- Expansion and Losses: As steam expands through the turbine, it loses energy due to several factors, including friction, heat losses, and mechanical losses. These losses reduce the overall efficiency of the turbine. Understanding and minimizing these losses is crucial for optimizing turbine performance.
- Frictional Losses: Occur due to the friction between steam and the turbine blades and internal surfaces.
- Heat Losses: Result from the heat exchange between steam and the turbine casing or the environment.
- Mechanical Losses: Include losses in bearings, seals, and other mechanical components of the turbine.
Heat Transfer Mechanisms
Heat transfer is a critical aspect of steam turbine operation, influencing both efficiency and performance. The primary heat transfer mechanisms involved are conduction, convection, and radiation.
- Conduction: Conduction is the transfer of heat through a solid material, such as the turbine casing or blades. In steam turbines, conduction occurs when heat flows through the metal components from the high-temperature steam to cooler regions. The thermal conductivity of the materials used in turbine construction is an important factor, as it affects the rate of heat transfer and the temperature distribution within the turbine.
- Convection: Convection is the transfer of heat between a solid surface and a fluid, in this case, steam. It occurs when steam flows over the turbine blades and heat is transferred from the steam to the blade material. The efficiency of this process is influenced by factors such as steam velocity, turbulence, and the surface roughness of the blades.
- Forced Convection: In steam turbines, forced convection occurs as steam is forced through the turbine at high velocities. The design of the turbine blades and the flow paths are optimized to enhance heat transfer through forced convection.
- Natural Convection: Natural convection plays a lesser role in steam turbines but can occur in areas where steam or air is stagnant. Managing natural convection is important in turbine cooling and in maintaining structural integrity.
- Radiation: Radiation is the transfer of heat through electromagnetic waves. In steam turbines, radiation heat transfer is typically less significant than conduction and convection but can become important at very high temperatures, such as those found in the superheater sections of a boiler or in high-temperature turbines.
- Thermal Radiation: The turbine components emit thermal radiation based on their temperature. This radiation can contribute to heat losses if not properly managed through insulation and other thermal management techniques.
Design and Manufacturing of Steam Turbines
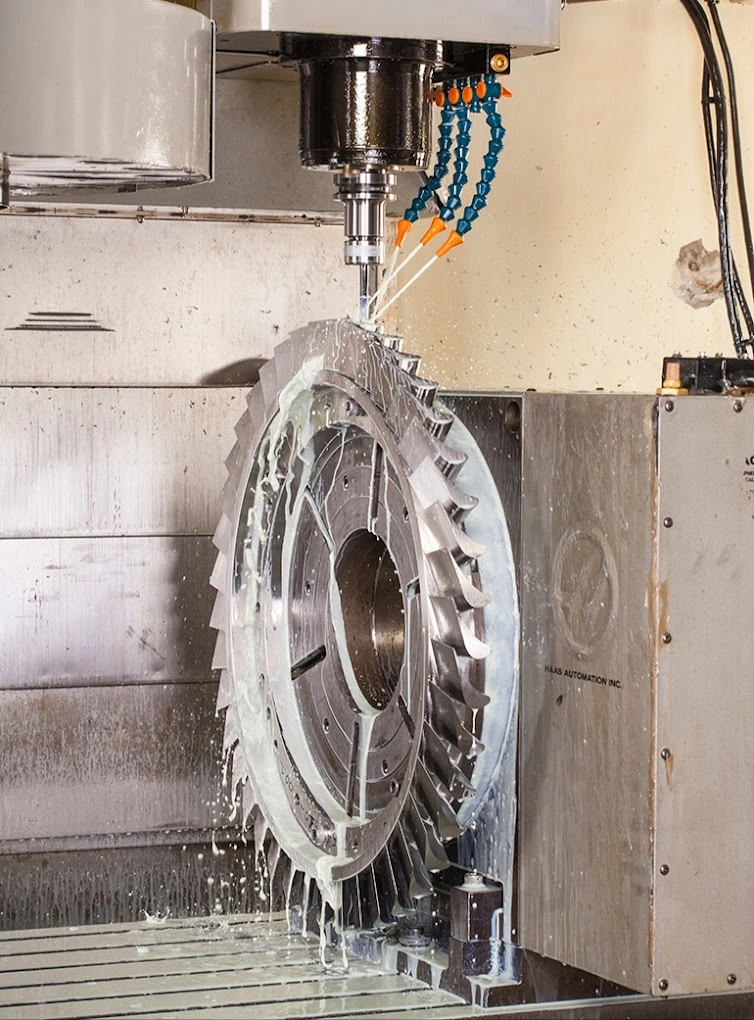
Design Process
Designing a steam turbine is a complex process that requires a deep understanding of thermodynamics, fluid mechanics, materials science, and mechanical engineering. The primary goals in designing a steam turbine are to maximize efficiency, ensure reliability, and meet the specific operational requirements of the application.
- Thermodynamic Efficiency: The design begins with thermodynamic calculations to determine the optimal operating conditions, such as steam pressure, temperature, and flow rate. Engineers use these calculations to design the turbine stages, ensuring that each stage extracts the maximum possible energy from the steam.
- Blade Design: The design of the turbine blades is crucial for efficiency and reliability. Blades must be aerodynamically optimized to maximize energy extraction while minimizing losses due to friction, turbulence, and separation. The shape, angle, and length of the blades are carefully calculated, often using computational fluid dynamics (CFD) simulations to model the flow of steam through the turbine.
- Material Selection: The materials used in turbine construction must withstand high temperatures, pressures, and mechanical stresses. Material selection is driven by the need for strength, durability, resistance to corrosion and erosion, and the ability to maintain performance under thermal cycling. Common materials include high-strength alloys, stainless steel, and nickel-based superalloys.
- Cooling and Heat Management: In high-temperature turbines, especially those used in power generation, cooling is a critical design consideration. Blades and other components are often internally cooled using air or steam to prevent overheating and maintain structural integrity. Advanced cooling designs, such as film cooling or transpiration cooling, may be used in particularly demanding applications.
- Rotor Dynamics and Balancing: The rotor is a critical component that must be carefully designed to ensure smooth and reliable operation. Engineers must account for rotor dynamics, including the natural frequencies of the rotor, to avoid resonance that could lead to mechanical failure. Additionally, the rotor must be precisely balanced to prevent excessive vibrations, which can cause wear and tear on bearings and other components.
- Sealing and Clearance Control: Minimizing steam leakage between different stages of the turbine is essential for maintaining efficiency. Engineers design precise seals and control clearances between rotating and stationary parts to reduce losses. Advanced sealing techniques, such as labyrinth seals and brush seals, are often used.
- Mechanical Integrity and Safety: The design must ensure that the turbine can operate safely under all expected conditions, including start-up, shutdown, and emergency situations. This involves designing for mechanical integrity, with components capable of withstanding high mechanical loads, thermal stresses, and the effects of transient conditions such as pressure surges or steam hammer.
- Modularity and Scalability: Modern steam turbines are often designed with modularity in mind, allowing for scalability and customization to meet different power outputs or industrial requirements. This modular approach also facilitates maintenance and component replacement.
Materials Used
The materials used in the construction of steam turbines are chosen for their ability to withstand the extreme conditions present during operation, such as high temperatures, pressures, and mechanical stresses. The selection of materials is crucial for ensuring the turbine’s performance, longevity, and safety.
- High-Strength Alloys: High-strength alloys, such as chromium-molybdenum steel, are commonly used for turbine rotors, casings, and other critical components. These alloys offer a good balance of strength, toughness, and resistance to thermal fatigue.
- Nickel-Based Superalloys: Nickel-based superalloys are frequently used in high-temperature sections of the turbine, such as the blades and vanes in the high-pressure stages. These superalloys are specifically designed to maintain their mechanical properties at elevated temperatures, making them ideal for use in environments where temperatures can exceed 1000°C.
- Stainless Steel: Stainless steel is used for components that require excellent corrosion resistance, such as parts exposed to wet steam or aggressive industrial environments. Austenitic stainless steels, in particular, are favored for their high-temperature performance and resistance to oxidation.
- Ceramic Coatings: To further enhance the high-temperature performance of turbine blades, ceramic coatings are often applied. These coatings provide a thermal barrier, reducing the amount of heat transferred to the underlying metal, which helps to protect against thermal degradation and extends the life of the blades.
- Titanium Alloys: Titanium alloys are sometimes used in low-pressure turbine blades due to their high strength-to-weight ratio and resistance to corrosion. Their lower density compared to steel or nickel-based alloys makes them advantageous in applications where weight savings are critical.
- Creep-Resistant Materials: Creep, the tendency of materials to deform permanently under constant stress at high temperatures, is a significant concern in steam turbines. Creep-resistant materials, such as advanced ferritic steels, are used
Manufacturing Techniques
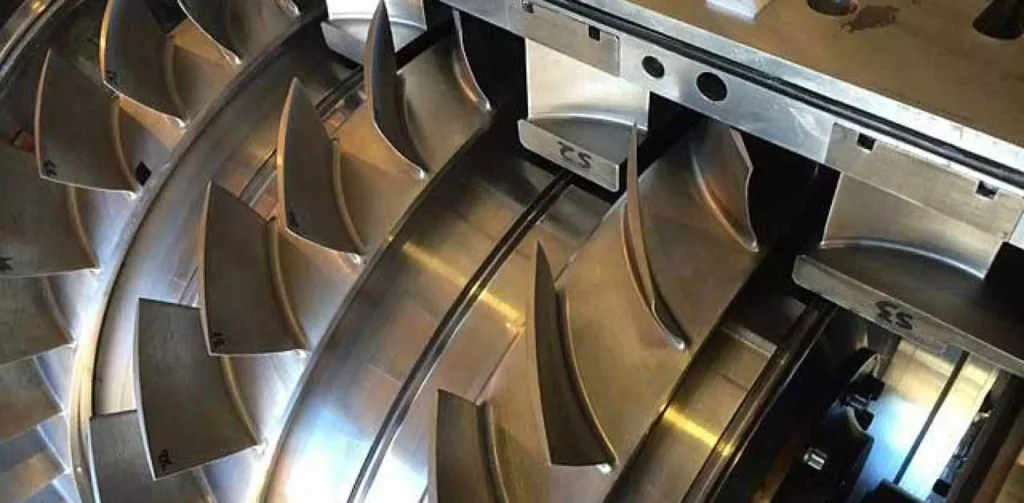
The manufacturing of steam turbines involves a series of highly specialized processes that ensure the precise fabrication and assembly of components capable of withstanding extreme operational conditions. The techniques used vary depending on the size, complexity, and specific requirements of the turbine.
- Casting: Many components of steam turbines, particularly the rotor and casing, are produced using casting techniques. Casting involves pouring molten metal into a mold shaped like the final part. Once the metal solidifies, the mold is removed, leaving behind a rough component that is further refined. Investment casting and sand casting are common methods used for creating intricate parts like blades, where precision and material integrity are crucial.
- Forging: Forging is another critical manufacturing process used to create strong, high-integrity components such as rotors and discs. In forging, a metal workpiece is heated and then shaped under high pressure, which aligns the metal’s grain structure, resulting in enhanced mechanical properties. Forged components are typically stronger and more resistant to fatigue and creep than cast parts, making them ideal for high-stress areas of the turbine.
- Machining: After casting or forging, most turbine components undergo machining to achieve the necessary dimensions, surface finishes, and tolerances. Machining processes include milling, turning, drilling, and grinding. Computer numerical control (CNC) machines are often used to ensure high precision and repeatability, especially for components like blades, where aerodynamic properties are critical.
- Heat Treatment: Heat treatment processes, such as annealing, quenching, and tempering, are used to enhance the mechanical properties of turbine components. These processes alter the microstructure of the metal, improving its strength, toughness, and resistance to wear and thermal fatigue. For instance, heat treatment is crucial for blades that must maintain their integrity at high operating temperatures.
- Surface Treatments and Coatings: To protect against corrosion, erosion, and high-temperature oxidation, turbine components often undergo surface treatments and coatings. Techniques such as thermal spraying, chemical vapor deposition (CVD), and physical vapor deposition (PVD) are used to apply protective coatings. Ceramic coatings, as mentioned earlier, are commonly applied to blades to provide thermal insulation and reduce heat transfer.
- Welding and Joining: Welding is a critical process in the assembly of steam turbines, particularly for joining large sections of the casing or connecting blades to the rotor. Advanced welding techniques, such as electron beam welding and laser welding, are used to create high-strength joints with minimal defects. These techniques are especially important for maintaining the structural integrity of the turbine under high-pressure and high-temperature conditions.
- Balancing and Assembly: Once all the components are manufactured, they are carefully assembled. The rotor, which is one of the most critical components, must be precisely balanced to ensure smooth operation at high speeds. Balancing involves adjusting the distribution of mass around the rotor’s axis to minimize vibrations. This is typically done using specialized balancing machines that measure and correct any imbalance.
- Quality Control and Testing: Quality control is paramount in steam turbine manufacturing. Each component undergoes rigorous inspection and testing to ensure it meets the required specifications. Non-destructive testing (NDT) methods, such as ultrasonic testing, radiography, and dye penetrant inspection, are used to detect any internal or surface defects. The assembled turbine is also subjected to performance testing, where it is run under controlled conditions to verify its efficiency, output, and operational stability.
- Final Assembly and Installation: After passing all tests, the turbine is finally assembled and prepared for shipment to its installation site. Installation requires precise alignment and calibration to ensure that the turbine operates correctly within its intended system, whether it’s a power plant, industrial facility, or marine vessel. The installation process includes integrating the turbine with the steam supply, electrical systems, and other necessary infrastructure.
Operation and Maintenance
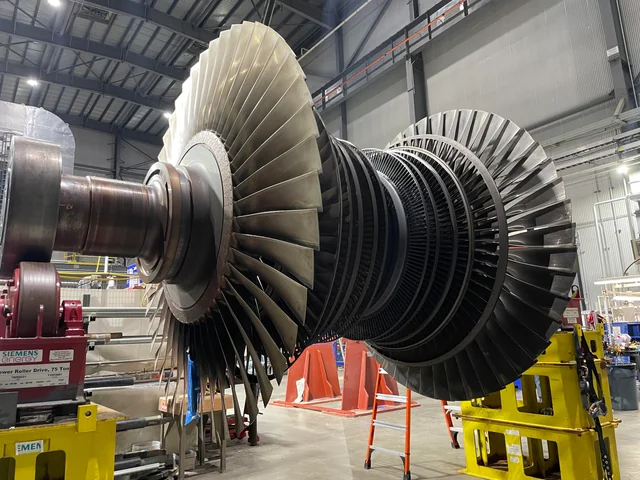
Operating Conditions
Steam turbines operate under demanding conditions, where factors such as temperature, pressure, steam quality, and load variations can significantly impact their performance and longevity. Understanding these conditions is essential for optimizing turbine operation and ensuring reliable performance.
- Temperature and Pressure: Steam turbines are designed to operate at high temperatures and pressures. In typical power generation applications, steam enters the turbine at temperatures ranging from 500°C to 600°C and pressures up to 30 MPa (megapascals). These extreme conditions enable the turbine to extract maximum energy from the steam, but they also impose significant thermal and mechanical stresses on the components.
- Steam Quality: The quality of the steam entering the turbine is critical for efficient operation. Ideally, the steam should be dry and superheated to prevent condensation inside the turbine, which can lead to erosion of the blades and reduced efficiency. However, in some applications, such as nuclear power plants, saturated steam may be used, requiring careful design and operation to manage the associated risks.
- Load Variations: Steam turbines often operate under varying loads, depending on the demand for electricity or the specific requirements of the industrial process they are powering. The ability to quickly and efficiently respond to load changes is crucial for maintaining stable operation. Turbines must be capable of ramping up or down without excessive wear or risk of damage.
- Startup and Shutdown Procedures: The processes of starting up and shutting down a steam turbine are critical periods that require careful control. During startup, the turbine components must be gradually brought up to operating temperature to avoid thermal shocks, which can cause cracking or deformation. Similarly, shutdown procedures involve slowly cooling the turbine to prevent damage.
- Control Systems: Modern steam turbines are equipped with sophisticated control systems that manage various operational parameters, such as steam flow, temperature, pressure, and rotational speed. These systems ensure that the turbine operates within its design limits and responds appropriately to changes in load or other operating conditions.
Maintenance Practices
Regular maintenance is essential to ensure the long-term reliability and efficiency of steam turbines. Maintenance practices are typically divided into preventive, predictive, and corrective maintenance.
- Preventive Maintenance: Preventive maintenance involves routine inspections and servicing of the turbine to prevent potential issues from arising. This includes tasks such as:
- Lubrication: Regular lubrication of bearings and other moving parts to reduce friction and wear.
- Inspection of Blades and Seals: Checking for signs of wear, erosion, or corrosion on turbine blades and seals.
- Cleaning: Removing deposits or scale from turbine components to maintain optimal performance.
- Calibration: Ensuring that control systems and sensors are accurately calibrated to prevent operational errors.
- Predictive Maintenance: Predictive maintenance uses condition monitoring techniques to predict when maintenance is needed before a failure occurs. This approach allows for maintenance to be scheduled based on the actual condition of the turbine rather than on a fixed schedule. Key techniques include:
- Vibration Analysis: Monitoring the vibrations of the turbine to detect imbalances, misalignment, or bearing issues.
- Thermography: Using infrared cameras to detect hotspots or uneven temperature distributions that may indicate a problem.
- Oil Analysis: Analyzing the lubrication oil for signs of contamination, wear particles, or chemical degradation.
- Corrective Maintenance: When a component fails or a problem is detected, corrective maintenance is performed to repair or replace the affected parts. This type of maintenance can involve:
- Blade Replacement: Replacing damaged or worn blades to restore turbine efficiency and prevent further damage.
- Seal Repair or Replacement: Addressing issues with seals that may cause steam leakage or reduced efficiency.
- Bearing Replacement: Replacing worn or damaged bearings to prevent rotor imbalance and excessive vibrations.
- Outage Planning: Steam turbines typically undergo scheduled outages for extensive inspections, repairs, and overhauls. These outages are carefully planned to minimize downtime and ensure that the turbine is returned to service in optimal condition. During an outage, the turbine may be disassembled, with major components like the rotor, blades, and casing inspected and refurbished as necessary.
Common Issues and Solutions
Steam turbines, despite their robust design, can encounter various issues during operation. Identifying and addressing these issues promptly is key to maintaining reliable performance.
- Blade Fouling and Erosion: Fouling occurs when deposits form on the turbine blades, often as a result of impurities in the steam. Erosion, on the other hand, is caused by high-velocity steam or water droplets impinging on the blades, gradually wearing away the material. These issues can lead to reduced efficiency and, if left unchecked, can cause serious damage.
- Solution: Regular cleaning and maintenance can prevent fouling, while erosion-resistant coatings can extend blade life. Additionally, improving the quality of the steam entering the turbine can reduce the risk of these problems.
- Vibration and Rotor Imbalance: Excessive vibration is a common issue in steam turbines and can be caused by rotor imbalance, misalignment, bearing wear, or other mechanical problems. Vibration can lead to accelerated wear of components and, in severe cases, catastrophic failure.
- Solution: Vibration analysis and regular balancing of the rotor can help detect and correct these issues before they cause significant damage. Proper alignment during installation and routine bearing inspections are also critical.
- Steam Leakage: Steam leakage can occur due to worn seals, poor sealing surfaces, or cracks in the casing. This leads to a loss of efficiency and can also cause damage to surrounding components.
- Solution: Regular inspection of seals and replacement when necessary can mitigate steam leakage. In some cases, upgrading to more advanced sealing technologies, such as brush seals, can provide a better seal and longer service life.
- Thermal Fatigue and Creep: Thermal fatigue occurs when turbine components are subjected to repeated cycles of heating and cooling, leading to the formation of cracks. Creep is a gradual deformation of materials under constant high temperature and stress. Both issues can significantly impact the structural integrity of the turbine.
- Solution: Using materials specifically designed to resist thermal fatigue and creep, along with careful control of operating conditions, can minimize these risks. Regular inspection and monitoring for signs of fatigue or creep are also essential.
- Control System Failures: The control systems of steam turbines are vital for safe and efficient operation. Failures in these systems can lead to incorrect steam flow, pressure surges, or even turbine trips.
- Solution: Regular testing and calibration of control systems, along with the use of redundant systems, can help prevent control system failures. Upgrading older systems to modern, digital control systems can also enhance reliability.
Applications of Steam Turbines
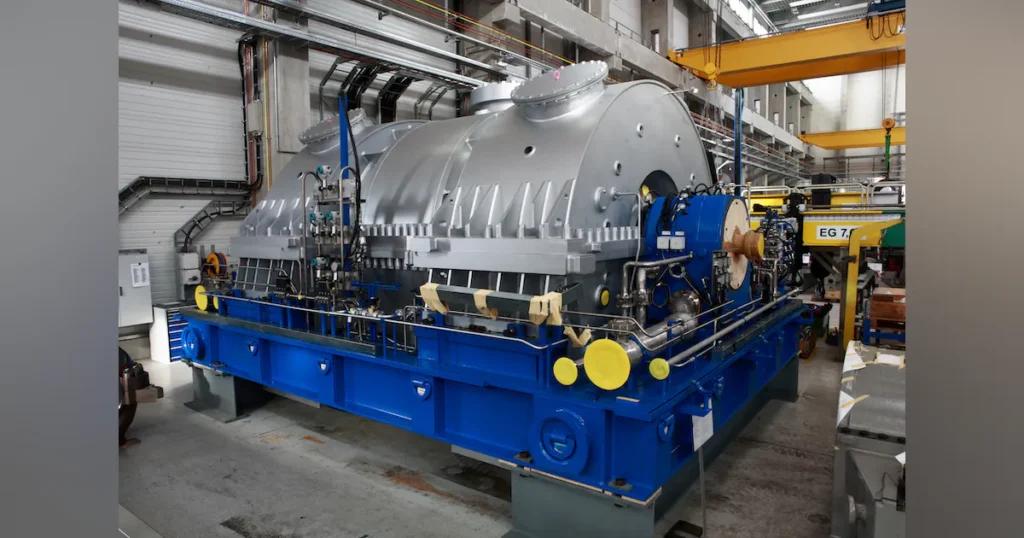
Power Generation
Steam turbines are central to power generation and are used in a variety of settings, from large-scale thermal power plants to smaller, decentralized energy systems. The following subsections outline the main applications of steam turbines in power generation:
- Coal-Fired Power Plants:
- Overview: Coal-fired power plants have historically been one of the most common applications of steam turbines. In these plants, coal is burned in a boiler to produce high-pressure steam, which is then directed into a steam turbine to generate electricity.
- Role of Steam Turbines: Steam turbines in coal-fired plants are designed to handle the high temperatures and pressures associated with coal combustion. They convert the thermal energy from the steam into mechanical energy, which drives an electrical generator.
- Environmental Considerations: While coal-fired power plants are efficient, they are also a significant source of greenhouse gas emissions. Many modern plants incorporate emission control technologies and are transitioning to cleaner coal technologies, such as supercritical and ultra-supercritical steam cycles, to improve efficiency and reduce emissions.
- Nuclear Power Plants:
- Overview: In nuclear power plants, steam turbines are used to convert the thermal energy generated by nuclear fission into electricity. These plants use nuclear reactors to heat water and produce steam.
- Role of Steam Turbines: The steam produced in a nuclear reactor is typically at a lower temperature and pressure compared to that in fossil-fuel plants. However, the turbines must be extremely reliable and durable due to the safety-critical nature of nuclear power generation. The turbines in nuclear plants are often large, with high power outputs to match the continuous energy production of the reactor.
- Special Considerations: The design of steam turbines for nuclear power includes considerations for safety, such as the ability to operate reliably under potential emergency conditions and withstand the corrosive effects of certain types of steam.
- Gas-Fired Power Plants (Combined Cycle):
- Overview: Combined cycle power plants use both gas and steam turbines to generate electricity. In these plants, a gas turbine generates electricity and its exhaust heat is used to produce steam, which then powers a steam turbine.
- Role of Steam Turbines: The steam turbine in a combined cycle plant enhances the overall efficiency of the plant by utilizing the waste heat from the gas turbine. This process significantly increases the plant’s thermal efficiency, often reaching levels above 60%.
- Advantages: Combined cycle plants are known for their high efficiency, flexibility, and lower carbon emissions compared to traditional coal-fired plants. Steam turbines in these plants are integral to achieving these benefits.
- Geothermal Power Plants:
- Overview: Geothermal power plants use steam turbines to generate electricity from geothermal energy, which is the heat stored within the Earth.
- Role of Steam Turbines: In geothermal plants, steam is extracted from underground reservoirs and used to drive turbines. These turbines must be designed to handle steam with varying temperatures and pressures, as well as the potential presence of corrosive gases and minerals.
- Challenges and Solutions: The main challenges in geothermal power generation include scaling, corrosion, and the management of non-condensable gases. Turbine designs that include corrosion-resistant materials and advanced sealing technologies are essential for long-term operation in these environments.
- Solar Thermal Power Plants:
- Overview: Solar thermal power plants, also known as concentrating solar power (CSP) plants, use steam turbines to generate electricity from solar energy.
- Role of Steam Turbines: In CSP plants, mirrors or lenses concentrate sunlight to heat a fluid, which is then used to produce steam. The steam drives a turbine, converting thermal energy into mechanical energy for electricity generation.
- Innovations: Some CSP plants incorporate thermal storage systems, allowing them to generate electricity even when the sun is not shining. The steam turbines in these plants must be adaptable to varying steam inputs and capable of operating efficiently with the thermal storage systems.
Industrial Applications
Beyond power generation, steam turbines are widely used in various industrial processes where they provide mechanical power for a range of applications.
- Petrochemical Industry:
- Overview: Steam turbines are essential in the petrochemical industry, where they are used to drive compressors, pumps, and other machinery involved in the processing of chemicals and petroleum products.
- Role of Steam Turbines: The turbines in this industry are often designed for continuous operation, high efficiency, and reliability under harsh conditions, including high temperatures and corrosive environments.
- Advantages: Using steam turbines in petrochemical plants helps improve overall energy efficiency by recovering waste heat and converting it into useful mechanical or electrical energy.
- Pulp and Paper Industry:
- Overview: The pulp and paper industry relies on steam turbines for both electricity generation and mechanical drives in processes such as pulping, drying, and paper making.
- Role of Steam Turbines: Steam turbines in this industry often operate in cogeneration setups, where they simultaneously produce electricity and steam for the manufacturing process. This combined heat and power (CHP) approach enhances energy efficiency.
- Challenges: The main challenges include handling fluctuating loads and ensuring reliable operation in environments with high moisture content and potential corrosive chemicals.
- Steel Manufacturing:
- Overview: In steel manufacturing, steam turbines are used to drive blowers, compressors, and rolling mills. The steam used often comes from waste heat recovery systems, making the process more energy-efficient.
- Role of Steam Turbines: Steam turbines help reduce the overall energy consumption of steel mills by utilizing waste heat to generate power for various processes.
- Benefits: Integrating steam turbines into steel manufacturing processes not only reduces energy costs but also helps in meeting environmental regulations by lowering emissions.
- Sugar Industry:
- Overview: The sugar industry uses steam turbines extensively in the production of sugar and ethanol. The turbines are part of the cogeneration systems that use bagasse (the fibrous residue left after extracting sugar juice) as fuel.
- Role of Steam Turbines: In this industry, steam turbines generate electricity and provide mechanical power for the crushing and refining processes. The use of biomass like bagasse makes the process more sustainable and reduces dependence on fossil fuels.
- Sustainability: The integration of steam turbines into sugar production highlights the potential for renewable energy sources in industrial applications.
Marine Propulsion
Steam turbines have a long history of use in marine propulsion, particularly in naval vessels and large commercial ships. Their reliability, efficiency, and power output make them ideal for this demanding application.
- Naval Vessels:
- Overview: Steam turbines have been a mainstay in naval propulsion, especially in large vessels such as aircraft carriers, destroyers, and submarines.
- Role of Steam Turbines: Naval turbines are designed for high power output, reliability, and efficiency. They must operate under extreme conditions, including rapid speed changes and prolonged high-speed operation.
- Advancements: Modern naval steam turbines often incorporate advanced materials and cooling technologies to withstand the harsh marine environment and to operate quietly, which is crucial for stealth in military operations.
- Commercial Shipping:
- Overview: In commercial shipping, steam turbines are used in large vessels such as tankers and bulk carriers. Although diesel engines have become more common, steam turbines are still used in certain applications, particularly where high power and long-range operation are required.
- Advantages: Steam turbines offer smooth operation, reduced vibration, and lower maintenance requirements compared to other propulsion systems, making them suitable for large ships.
- Trends: The use of steam turbines in commercial shipping has declined with the rise of more fuel-efficient diesel engines. However, they remain in use in specific scenarios where their benefits outweigh those of alternative technologies.
Renewable Energy Integration
Steam turbines are also finding applications in renewable energy systems, contributing to the generation of clean and sustainable energy.
- Biomass Power Plants:
- Overview: Biomass power plants use organic materials, such as wood, agricultural residues, and waste, to produce steam, which then drives turbines to generate electricity.
- Role of Steam Turbines: In biomass plants, steam turbines must handle steam generated from a variety of biomass sources, which can vary in quality and consistency. The turbines are designed to be flexible and efficient, maximizing the energy extracted from biomass.
- Environmental Benefits: Biomass power generation is considered carbon-neutral, as the CO2 released during combustion is offset by the CO2 absorbed during the growth of the biomass. Steam turbines play a key role in making this a viable and sustainable energy source.
- Concentrated Solar Power (CSP):
- Overview: In CSP plants, steam turbines are used to convert solar energy into electricity. The plants use mirrors or lenses to concentrate sunlight onto a receiver, where it heats a fluid to produce steam.
- Role of Steam Turbines: The turbines in CSP plants must be designed to operate efficiently with steam generated from fluctuating solar input, as well as to integrate with thermal storage systems that allow for power generation even when the sun is not shining.
- Innovation and Future Potential: As CSP technology advances, steam turbines are expected to play an increasingly important role in providing renewable, dispatchable power, helping to stabilize grids with high penetration of intermittent renewable sources like wind and solar PV.
Efficiency and Performance Optimization
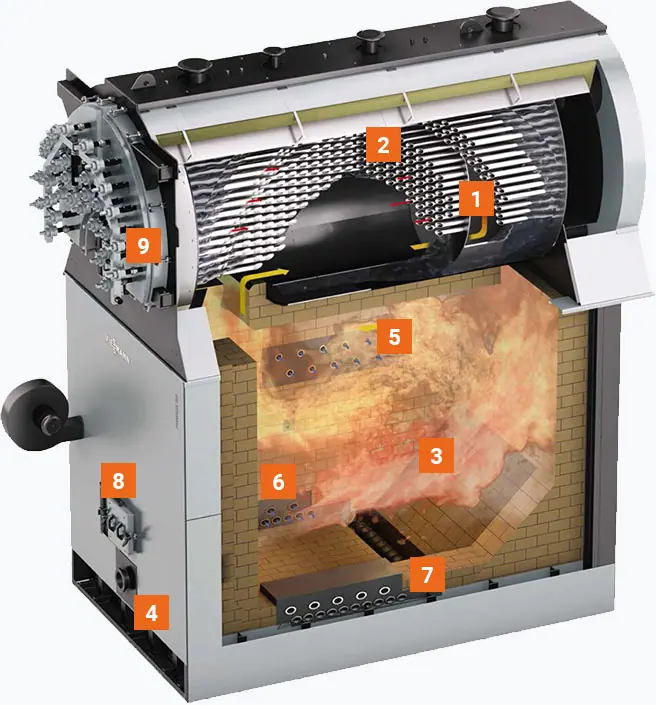
Factors Affecting Efficiency
The efficiency of a steam turbine is a critical aspect of its performance, influencing the overall energy conversion process and the economic viability of power plants and industrial applications. Several factors can impact the efficiency of a steam turbine:
- Steam Conditions:
- Temperature and Pressure: The higher the steam temperature and pressure at the turbine inlet, the greater the potential for energy extraction. Superheated steam, with higher energy content, allows the turbine to produce more work, thereby increasing efficiency. However, materials and design must be capable of withstanding these extreme conditions.
- Steam Quality: The quality of steam, particularly its dryness fraction, affects turbine performance. Wet steam can cause erosion of turbine blades and reduce efficiency due to the presence of water droplets. Maintaining a high dryness fraction or superheating the steam minimizes these losses.
- Design and Aerodynamics:
- Blade Design: The design of turbine blades, including their shape, angle, and surface finish, plays a significant role in efficiency. Aerodynamically optimized blades reduce losses due to friction and turbulence, allowing for more effective energy conversion from steam to mechanical work.
- Stage Efficiency: Steam turbines are often divided into multiple stages, each designed to extract energy from steam at progressively lower pressures. The efficiency of each stage contributes to the overall turbine efficiency. Proper staging, with carefully calculated blade profiles and angles, is essential for maximizing efficiency.
- Mechanical Losses:
- Friction and Wear: Mechanical losses due to friction in bearings, seals, and other moving parts can reduce overall turbine efficiency. Regular maintenance, proper lubrication, and the use of advanced materials can help minimize these losses.
- Vibration and Imbalance: Imbalances in the rotor or excessive vibrations can lead to mechanical inefficiencies, as energy is lost in the form of unwanted movements. Ensuring that the turbine is properly balanced and that vibrations are controlled through effective damping mechanisms is crucial.
- Thermodynamic Losses:
- Heat Losses: Heat losses occur when steam or other components transfer heat to the surrounding environment. Proper insulation of the turbine casing and piping, as well as minimizing the temperature gradient within the turbine, can help reduce these losses.
- Entropy Generation: Inefficiencies in the expansion process within the turbine stages can lead to increased entropy, reducing the available work output. Reducing these losses involves optimizing the expansion process and minimizing irreversible losses within the turbine.
Optimization Techniques
Improving the efficiency of steam turbines involves a combination of design optimization, operational strategies, and technological innovations. The following techniques are commonly used to enhance turbine performance:
- Advanced Blade Design:
- Computational Fluid Dynamics (CFD): CFD is widely used in the design and optimization of turbine blades. By simulating the flow of steam through the turbine, engineers can identify areas where losses occur and adjust blade shapes and angles to improve efficiency. CFD allows for the testing of multiple design iterations in a virtual environment, reducing the need for physical prototypes.
- 3D Blade Profiling: Advanced manufacturing techniques, such as 3D printing and precision machining, enable the production of complex blade profiles that are tailored to specific operating conditions. 3D blade profiling can result in blades that offer better aerodynamic performance and reduced losses.
- Steam Temperature and Pressure Control:
- Superheating and Reheating: Increasing the temperature of steam before it enters the turbine (superheating) or reheating steam between turbine stages can significantly improve efficiency. Reheating, in particular, allows for more energy extraction by reducing the moisture content in the later stages of the turbine.
- Pressure Optimization: Operating the turbine at the optimal steam pressure for each stage can maximize efficiency. This involves careful control of steam pressure throughout the turbine, ensuring that each stage operates at its most efficient point on the pressure-enthalpy curve.
- Energy Recovery Systems:
- Regenerative Feedwater Heating: Regenerative feedwater heating is a technique where steam is extracted from intermediate stages of the turbine and used to preheat the feedwater before it enters the boiler. This reduces the amount of fuel needed to reach the desired steam temperature, thereby improving the overall efficiency of the Rankine cycle.
- Condensate Recovery: Efficient recovery and reuse of condensate (water) from the turbine exhaust can reduce the energy required to heat and pressurize water for subsequent cycles. This also minimizes the need for additional water treatment, contributing to overall efficiency improvements.
- Load Optimization:
- Variable Load Operation: Modern steam turbines are designed to operate efficiently across a range of loads, not just at full capacity. By optimizing turbine performance under partial loads, power plants can improve overall efficiency, especially in applications where demand fluctuates throughout the day.
- Load Matching: Load matching involves adjusting the turbine’s operation to match the specific energy demand at any given time. This can involve varying the steam flow rate, adjusting the number of active turbine stages, or modulating the turbine’s output to match real-time load requirements.
- Monitoring and Control Systems:
- Real-Time Performance Monitoring: Advanced sensors and control systems allow for real-time monitoring of turbine performance, including temperature, pressure, vibration, and efficiency metrics. By continuously monitoring these parameters, operators can make adjustments to optimize performance and prevent issues before they lead to inefficiencies or failures.
- Predictive Maintenance: Using data analytics and machine learning, predictive maintenance systems can forecast potential issues based on historical performance data. This allows for maintenance to be performed proactively, reducing downtime and improving overall turbine efficiency.
Monitoring and Performance Analysis
Maintaining optimal efficiency in steam turbines requires ongoing monitoring and analysis of performance data. The following approaches are commonly used to assess and enhance turbine efficiency:
- Key Performance Indicators (KPIs):
- Heat Rate: The heat rate is a measure of the amount of energy used by the turbine to generate electricity. It is typically expressed as the amount of fuel energy required per unit of electrical output (e.g., BTU/kWh). Monitoring the heat rate helps identify inefficiencies in fuel use and overall turbine performance.
- Thermal Efficiency: Thermal efficiency measures the ratio of useful work output to the total heat input. It is a key indicator of how effectively the turbine converts thermal energy into mechanical energy. Higher thermal efficiency indicates better performance.
- Capacity Factor: The capacity factor is the ratio of the actual output of the turbine over a period of time to its maximum possible output. It reflects how well the turbine is being utilized relative to its full capacity.
- Performance Testing:
- Acceptance Testing: Acceptance testing is conducted when a turbine is first installed or after a major overhaul to ensure it meets the specified performance criteria. These tests typically measure parameters such as output power, efficiency, and steam consumption under controlled conditions.
- Routine Testing: Periodic performance testing is conducted to monitor the ongoing efficiency of the turbine. Routine tests help detect gradual declines in performance, allowing for timely interventions to restore efficiency.
- Data Analytics and Optimization:
- Data Logging and Trend Analysis: Continuous data logging allows for the collection of vast amounts of performance data, which can be analyzed to identify trends, detect anomalies, and assess the impact of operational changes on efficiency.
- Digital Twins: A digital twin is a virtual model of the steam turbine that simulates its real-world counterpart in real time. By comparing the digital twin’s performance with actual operational data, operators can identify inefficiencies and test potential optimizations without risking the physical turbine.
- Diagnostic Tools:
- Vibration Monitoring: Vibration analysis is a critical diagnostic tool for detecting mechanical issues such as rotor imbalance, misalignment, or bearing wear. By identifying and correcting these issues early, operators can prevent efficiency losses and extend the life of the turbine.
- Thermal Imaging: Thermal imaging is used to detect hotspots and assess the distribution of temperature across the turbine components. This helps identify areas where heat losses are occurring and where insulation or cooling might be needed.
Environmental Impact and Sustainability
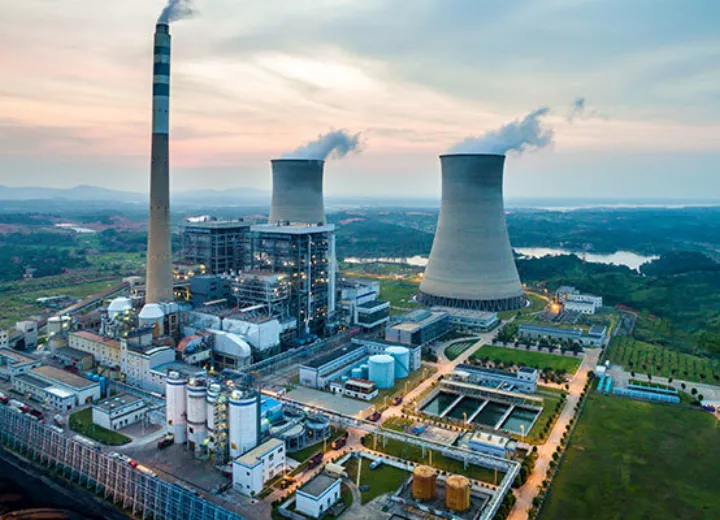
Environmental Concerns
Steam turbines, while crucial to power generation and industrial processes, are associated with several environmental concerns. These issues stem primarily from the energy sources used to produce steam and the byproducts of turbine operation.
- Greenhouse Gas Emissions:
- Fossil Fuel Combustion: Steam turbines used in coal, oil, and natural gas-fired power plants contribute significantly to greenhouse gas emissions, particularly carbon dioxide (CO2). The combustion of fossil fuels releases CO2, which is a major contributor to global warming and climate change.
- Mitigation Strategies: Efforts to reduce greenhouse gas emissions include improving the efficiency of steam turbines, transitioning to cleaner fuels, and integrating carbon capture and storage (CCS) technologies. Higher efficiency means that less fuel is required to produce the same amount of electricity, thereby reducing emissions per unit of energy generated.
- Air Pollutants:
- Sulfur Dioxide (SO2) and Nitrogen Oxides (NOx): Fossil fuel combustion in power plants can release harmful air pollutants, including SO2 and NOx, which contribute to acid rain and respiratory problems in humans. These pollutants are particularly prevalent in coal-fired power plants, where sulfur content in the fuel is higher.
- Control Technologies: Technologies such as flue gas desulfurization (FGD) and selective catalytic reduction (SCR) are used to reduce SO2 and NOx emissions from power plants. Additionally, low-NOx burners and other combustion optimization techniques help minimize the formation of these pollutants at the source.
- Water Usage and Thermal Pollution:
- Cooling Water Requirements: Steam turbines, particularly in large power plants, require substantial amounts of water for cooling. The withdrawal of water from natural sources can impact local ecosystems, especially if not managed sustainably. Furthermore, the discharge of heated water back into the environment can cause thermal pollution, which negatively affects aquatic life.
- Mitigation Strategies: To mitigate these impacts, power plants can adopt closed-loop cooling systems that minimize water withdrawal and reduce thermal discharge. Additionally, dry cooling systems, which use air instead of water, are increasingly being implemented, particularly in water-scarce regions.
- Solid Waste and Byproducts:
- Coal Ash and Slag: The combustion of coal in power plants produces solid byproducts such as ash and slag, which can contain heavy metals and other toxic substances. These byproducts must be managed carefully to prevent soil and water contamination.
- Disposal and Reuse: Modern waste management practices include the safe disposal of ash in lined landfills and the beneficial reuse of ash in construction materials, such as cement and concrete. By converting waste into valuable products, the environmental impact of coal ash can be minimized.
Sustainability Initiatives
In response to environmental concerns, the steam turbine industry is increasingly adopting sustainability initiatives aimed at reducing its environmental footprint and supporting the transition to a low-carbon economy.
- Integration with Renewable Energy:
- Biomass and Waste-to-Energy: Steam turbines are being integrated with renewable energy sources such as biomass and waste-to-energy plants. These systems use organic waste materials to produce steam, which is then converted into electricity by steam turbines. Biomass is considered carbon-neutral, as the CO2 released during combustion is offset by the CO2 absorbed during the growth of the biomass.
- Geothermal and Solar Thermal: Geothermal and concentrated solar power (CSP) plants also utilize steam turbines to generate electricity. These renewable energy sources produce little to no greenhouse gas emissions, making them attractive options for sustainable power generation. The use of steam turbines in these settings supports the broader adoption of renewable energy technologies.
- Efficiency Improvements:
- Supercritical and Ultra-Supercritical Steam Cycles: Advancements in turbine technology have led to the development of supercritical and ultra-supercritical steam cycles, which operate at higher temperatures and pressures than conventional steam cycles. These cycles achieve higher efficiencies, meaning that less fuel is needed to produce the same amount of electricity, resulting in lower emissions.
- Cogeneration and Combined Heat and Power (CHP): Cogeneration, or CHP, systems simultaneously produce electricity and useful heat from the same energy source. By capturing and utilizing the waste heat from steam turbines, CHP systems significantly improve overall energy efficiency, reducing fuel consumption and emissions.
- Carbon Capture and Storage (CCS):
- CCS Technology: Carbon capture and storage is a technology designed to capture CO2 emissions from power plants and industrial processes, preventing them from entering the atmosphere. The captured CO2 is then transported and stored underground in geological formations. When integrated with steam turbines, CCS can greatly reduce the carbon footprint of fossil fuel-based power generation.
- Challenges and Opportunities: While CCS has the potential to mitigate climate change, it faces challenges such as high costs, energy requirements, and the need for suitable storage sites. However, ongoing research and development efforts aim to overcome these barriers, making CCS a viable option for large-scale emission reductions.
- Material and Resource Efficiency:
- Recycling and Waste Minimization: The steam turbine industry is adopting practices to minimize waste and improve resource efficiency. This includes the recycling of metals and other materials used in turbine manufacturing, as well as the reduction of material waste through precision manufacturing techniques.
- Life Cycle Assessment (LCA): Life cycle assessment is a tool used to evaluate the environmental impacts of a product throughout its entire life cycle, from raw material extraction to disposal. By conducting LCAs, manufacturers can identify areas where environmental impacts can be reduced, leading to more sustainable turbine production and operation.
Regulatory Framework
The operation of steam turbines, particularly in power generation, is subject to a range of environmental regulations aimed at minimizing their impact on the environment. These regulations vary by region but generally focus on emissions control, water usage, and waste management.
- Emissions Regulations:
- Clean Air Act (U.S.): In the United States, the Clean Air Act (CAA) regulates air emissions from power plants and industrial sources, including those using steam turbines. The CAA establishes limits for pollutants such as SO2, NOx, and particulate matter, and mandates the use of best available control technologies (BACT) to reduce emissions.
- European Union Emissions Trading System (EU ETS): The EU ETS is a cap-and-trade system that sets a limit on the total amount of greenhouse gases that can be emitted by certain industries, including power generation. Steam turbine operators in the EU must comply with emission allowances or purchase additional allowances if they exceed their limits.
- Water Usage and Discharge Regulations:
- Clean Water Act (U.S.): The Clean Water Act (CWA) regulates the discharge of pollutants into U.S. waters and sets standards for water quality. Power plants using steam turbines must obtain permits for water withdrawal and discharge, ensuring that their operations do not harm aquatic ecosystems.
- EU Water Framework Directive: In the European Union, the Water Framework Directive establishes a framework for protecting water resources, including the regulation of water usage and thermal discharges from power plants. Compliance with these regulations is essential for the sustainable operation of steam turbines.
- Waste Management and Disposal:
- Resource Conservation and Recovery Act (RCRA): In the U.S., the RCRA governs the management of hazardous and non-hazardous waste, including coal ash from power plants. The act requires safe disposal practices and encourages the recycling and reuse of industrial byproducts.
- EU Waste Framework Directive: The EU Waste Framework Directive sets guidelines for waste management across member states, promoting recycling and the reduction of waste generation. Steam turbine operators must comply with these regulations to minimize their environmental impact.
- International Standards and Guidelines:
- ISO 14001 Environmental Management Systems: The ISO 14001 standard provides a framework for organizations to manage their environmental responsibilities in a systematic manner. Compliance with ISO 14001 helps steam turbine operators reduce their environmental footprint and improve sustainability.
- World Bank Environmental and Social Standards: The World Bank’s Environmental and Social Standards (ESS) provide guidelines for managing environmental and social risks in projects financed by the World Bank. These standards are often used in the development of power plants and other large-scale projects involving steam turbines.
Future Trends and Innovations
Technological Advances
The steam turbine industry is continuously evolving, driven by the need for greater efficiency, reliability, and environmental performance. Several technological advances are shaping the future of steam turbines:
- Advanced Materials:
- Superalloys: The development of advanced nickel-based superalloys is enabling steam turbines to operate at higher temperatures and pressures, which improves efficiency. These materials are designed to resist creep, corrosion, and thermal fatigue, making them ideal for use in the most demanding sections of the turbine.
- Ceramic Matrix Composites (CMCs): CMCs are gaining attention for their potential to replace traditional metal alloys in high-temperature turbine components. These materials offer excellent thermal stability, low density, and resistance to oxidation, allowing turbines to operate at even higher temperatures without compromising structural integrity.
- Additive Manufacturing: Also known as 3D printing, additive manufacturing is revolutionizing the production of turbine components. This technology allows for the creation of complex, optimized geometries that are difficult or impossible to achieve with traditional manufacturing methods. Additive manufacturing also reduces material waste and shortens production times.
- Advanced Blade Design:
- 3D-Aerodynamic Blades: Innovations in blade design, particularly through the use of 3D aerodynamic modeling, are improving the efficiency and performance of steam turbines. These blades are designed to optimize the flow of steam, reducing losses due to turbulence and friction. The use of computational fluid dynamics (CFD) simulations allows engineers to refine blade shapes for maximum efficiency.
- Shrouded and Shroudless Blades: Shrouded blades, which include a cover on the blade tips to reduce leakage, are being optimized to further improve efficiency. At the same time, advancements in shroudless blade designs are being explored to reduce weight and mechanical complexity while maintaining aerodynamic performance.
- Digitalization and Smart Turbines:
- Digital Twins: The concept of a digital twin, a virtual model of the steam turbine that runs in parallel with the physical machine, is becoming a critical tool in the industry. Digital twins allow operators to monitor turbine performance in real-time, predict maintenance needs, and optimize operations. By simulating different scenarios, digital twins can help identify potential issues before they occur and suggest the best course of action for maintenance or operational adjustments.
- Artificial Intelligence (AI) and Machine Learning: AI and machine learning are being increasingly used to enhance turbine control systems. These technologies enable more precise control of operating parameters, such as steam flow, pressure, and temperature, optimizing turbine efficiency under varying load conditions. AI-driven analytics can also predict equipment failures, reducing downtime and extending the life of turbine components.
- Modular and Scalable Designs:
- Modularity: The development of modular steam turbines is a trend aimed at improving flexibility and reducing costs. Modular turbines can be easily scaled up or down depending on the power generation requirements, making them suitable for both large-scale power plants and smaller, decentralized energy systems. Modularity also facilitates easier maintenance and component replacement, reducing downtime.
- Scalability for Microgrids: Steam turbines are being adapted for use in microgrids and distributed energy systems. These scalable turbines are designed to provide reliable power in remote locations or as part of a hybrid energy system that integrates renewable energy sources with traditional power generation.
Integration with Smart Grids
As the energy landscape evolves, steam turbines are being integrated into smart grid systems, which offer enhanced flexibility, reliability, and efficiency in power generation and distribution.
- Role of Steam Turbines in Smart Grids:
- Load Balancing: Steam turbines are essential in smart grids for load balancing, especially during peak demand periods. They can be ramped up or down to match the demand, helping to maintain grid stability and prevent blackouts. The ability to quickly respond to changes in demand makes steam turbines a valuable component of smart grids.
- Integration with Renewable Energy: Smart grids are increasingly incorporating renewable energy sources such as solar and wind. Steam turbines, particularly those in combined heat and power (CHP) plants, can provide backup power when renewable sources are intermittent, ensuring a continuous and reliable energy supply. By integrating with smart grid technologies, steam turbines can optimize their operation based on real-time data from the grid.
- Advanced Control Systems:
- Real-Time Monitoring and Control: Advanced control systems are being developed to allow steam turbines to operate more efficiently within a smart grid. These systems use real-time data to adjust operating parameters, such as steam pressure and temperature, to optimize performance. Real-time monitoring also helps detect potential issues before they lead to failures, reducing downtime and maintenance costs.
- Grid Synchronization: Steam turbines are being equipped with advanced synchronization technologies that allow them to seamlessly integrate with smart grids. These technologies ensure that the turbines can synchronize their output with the grid’s frequency and voltage, maintaining power quality and reliability.
- Demand Response and Energy Storage:
- Demand Response Programs: Steam turbines are playing a role in demand response programs, where power generation is adjusted based on real-time demand. In these programs, steam turbines can reduce their output during periods of low demand or increase it during peak times, helping to balance the grid and reduce the need for additional peaking power plants.
- Integration with Energy Storage: Steam turbines are being integrated with energy storage systems, such as batteries and thermal storage, to enhance their flexibility and efficiency. Energy storage allows turbines to store excess energy produced during periods of low demand and release it when needed, improving overall grid stability and efficiency.
Research and Development
Ongoing research and development (R&D) efforts are focused on advancing steam turbine technology to meet the evolving demands of the energy industry and address environmental challenges.
- High-Efficiency Steam Cycles:
- Supercritical and Ultra-Supercritical Cycles: R&D is driving the development of supercritical and ultra-supercritical steam cycles, which operate at higher temperatures and pressures than conventional cycles. These advanced cycles offer higher thermal efficiencies, reducing fuel consumption and emissions. Researchers are exploring new materials and designs that can withstand the extreme conditions of these cycles.
- Thermodynamic Cycle Innovations: Innovative thermodynamic cycles, such as the Kalina cycle and the Organic Rankine Cycle (ORC), are being explored for their potential to improve efficiency in specific applications. These cycles use different working fluids or configurations to optimize energy conversion, particularly in low-temperature or waste heat recovery applications.
- Low-Carbon and Carbon-Neutral Technologies:
- Hydrogen-Fueled Steam Turbines: Research is underway to develop steam turbines that can operate on hydrogen, a carbon-free fuel that can be produced using renewable energy. Hydrogen-fueled turbines have the potential to provide reliable, low-carbon power generation, particularly in conjunction with renewable energy sources.
- Carbon Capture Integration: Integrating carbon capture and storage (CCS) technologies with steam turbines is a key area of research aimed at reducing CO2 emissions from fossil fuel-based power generation. Ongoing R&D efforts are focused on improving the efficiency and cost-effectiveness of CCS, making it a viable option for large-scale deployment.
- Enhanced Durability and Reliability:
- Advanced Coatings and Surface Treatments: R&D is focused on developing advanced coatings and surface treatments that can extend the life of turbine components by protecting them from corrosion, erosion, and high-temperature oxidation. These coatings are essential for improving the durability and reliability of turbines operating under harsh conditions.
- Predictive Maintenance and AI: Research into predictive maintenance technologies, powered by AI and machine learning, is helping to improve the reliability of steam turbines. By analyzing historical performance data and identifying patterns that precede failures, these technologies enable more accurate predictions of maintenance needs, reducing unexpected downtime and extending the lifespan of turbine components.
Challenges and Opportunities
As the steam turbine industry evolves, it faces a range of challenges and opportunities that will shape its future.
- Challenges:
- Environmental Regulations: Increasingly stringent environmental regulations, particularly those related to greenhouse gas emissions and water usage, pose a challenge for the steam turbine industry. Meeting these regulations requires ongoing innovation in turbine design, materials, and operational strategies.
- Competition from Alternative Technologies: The rise of alternative power generation technologies, such as wind, solar, and energy storage, presents a challenge to the steam turbine industry. These technologies are becoming more cost-competitive and are often favored in policies aimed at reducing carbon emissions.
- Aging Infrastructure: Many existing steam turbines, particularly those in older power plants, are reaching the end of their operational life. Upgrading or replacing these turbines with more efficient, modern designs presents a significant challenge, particularly in terms of cost and downtime.
- Opportunities:
- Decarbonization Initiatives: The global push for decarbonization presents an opportunity for the steam turbine industry to develop low-carbon and carbon-neutral technologies. This includes the integration of steam turbines with renewable energy sources, hydrogen, and CCS technologies.
- Energy Transition: As the energy industry transitions towards more sustainable sources, steam turbines have the opportunity to play a key role in hybrid systems that combine renewable energy with traditional power generation. These hybrid systems can provide reliable, continuous power while reducing overall carbon emissions.
- Emerging Markets: Emerging markets, particularly in Asia and Africa, present significant growth opportunities for the steam turbine industry. As these regions continue to industrialize and expand their energy infrastructure, the demand for reliable and efficient power generation technologies, including steam turbines, is expected to increase.
Case Studies and Industry Examples
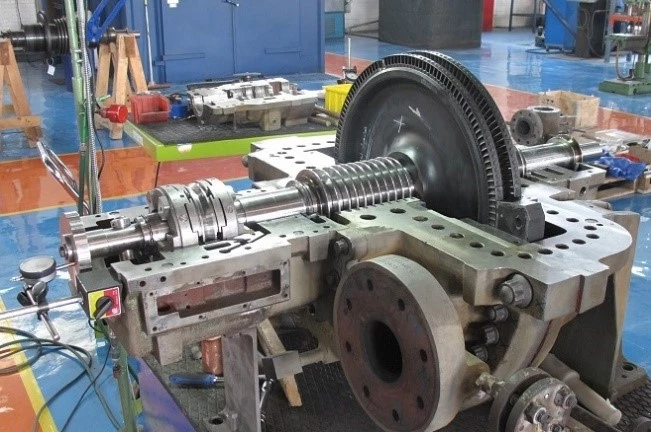
Notable Projects
Real-world applications of steam turbines showcase their versatility and efficiency across various industries. The following case studies highlight significant installations and the impact of steam turbines in different settings:
- The Taichung Power Plant, Taiwan:
- Overview: The Taichung Power Plant is one of the largest coal-fired power plants in the world, located in Taiwan. With an installed capacity of 5,500 MW, it plays a critical role in meeting the energy demands of Taiwan’s population and industry.
- Role of Steam Turbines: The plant uses a series of large-scale steam turbines to convert the thermal energy from coal combustion into electricity. These turbines are designed to operate at high efficiency, utilizing supercritical steam conditions to maximize energy extraction.
- Environmental Impact: Despite being a coal-fired plant, Taichung has implemented advanced emission control technologies, including flue gas desulfurization and selective catalytic reduction, to minimize its environmental footprint. The plant also serves as a benchmark for efficiency improvements in large-scale fossil fuel power generation.
- The Olkaria Geothermal Plant, Kenya:
- Overview: The Olkaria Geothermal Plant is the largest geothermal power plant in Africa, located in Kenya’s Great Rift Valley. It has a capacity of over 800 MW and contributes significantly to Kenya’s renewable energy mix.
- Role of Steam Turbines: The plant utilizes steam turbines specifically designed to handle the unique challenges of geothermal steam, such as the presence of corrosive gases and minerals. The turbines efficiently convert geothermal energy into electricity, providing a reliable source of power with low carbon emissions.
- Sustainability: The success of the Olkaria Geothermal Plant demonstrates the potential of geothermal energy in providing sustainable, baseload power in regions with geothermal resources. The plant’s expansion over the years highlights the scalability of geothermal projects and the crucial role of steam turbines in this renewable energy sector.
- The Ivanpah Solar Electric Generating System, United States:
- Overview: Ivanpah is one of the largest concentrated solar power (CSP) plants in the world, located in California’s Mojave Desert. It has a capacity of 392 MW and uses mirrors to concentrate sunlight onto boilers, generating steam to drive turbines.
- Role of Steam Turbines: The steam turbines at Ivanpah are designed to operate with the variable steam input characteristic of CSP plants. They play a crucial role in converting solar energy into electricity, with the ability to start and stop quickly in response to solar conditions.
- Innovation: Ivanpah is an example of how steam turbines can be effectively integrated into renewable energy systems. The project demonstrates the potential for CSP technology to provide utility-scale renewable energy, supported by advanced steam turbine technology.
Industry Leaders
Several companies and institutions have made significant contributions to the development and deployment of steam turbines. These industry leaders have pioneered technological advancements and set benchmarks for efficiency and reliability.
- Siemens Energy:
- Overview: Siemens Energy is a global leader in the design and manufacture of steam turbines, with a portfolio that includes turbines for power generation, industrial applications, and marine propulsion. The company is known for its focus on innovation and efficiency.
- Key Contributions: Siemens has been at the forefront of developing high-efficiency steam turbines, including those for supercritical and ultra-supercritical applications. Their turbines are widely used in power plants around the world, contributing to both fossil fuel and renewable energy projects. Siemens is also a leader in digitalization, offering advanced monitoring and control systems that enhance turbine performance and reliability.
- General Electric (GE):
- Overview: General Electric is another major player in the steam turbine industry, with a long history of innovation and engineering excellence. GE’s steam turbines are used in a variety of applications, including power generation, industrial processes, and marine propulsion.
- Key Contributions: GE has been instrumental in advancing turbine efficiency through the development of high-performance blades, advanced materials, and integrated control systems. The company has also been a pioneer in the use of digital twins and predictive maintenance technologies, helping operators optimize turbine performance and reduce operational costs.
- Mitsubishi Power:
- Overview: Mitsubishi Power, a subsidiary of Mitsubishi Heavy Industries, is a leading manufacturer of steam turbines, particularly in Asia. The company offers a wide range of turbines for power generation, including those for coal, nuclear, and gas-fired plants, as well as renewable energy projects.
- Key Contributions: Mitsubishi Power is known for its advanced steam turbine designs, which prioritize efficiency and reliability. The company has made significant strides in the development of ultra-supercritical turbines and has played a key role in the deployment of large-scale geothermal and biomass projects. Mitsubishi Power is also actively involved in R&D efforts focused on hydrogen-powered turbines and carbon capture integration.
Lessons Learned
The deployment of steam turbines across various industries provides valuable insights into the challenges and best practices associated with these technologies. Key lessons learned from these projects include:
- The Importance of Customization:
- Project-Specific Design: One of the most important lessons from successful steam turbine projects is the need for customization. Each project has unique requirements based on the type of fuel, operating conditions, and environmental regulations. Tailoring the design of the steam turbine to these specific conditions is crucial for achieving optimal performance and reliability.
- Adaptation to Local Conditions: In projects like the Olkaria Geothermal Plant, adapting the turbine design to handle the specific characteristics of geothermal steam, such as high moisture content and corrosive gases, was essential for long-term success. This highlights the importance of understanding local conditions and incorporating them into the turbine design process.
- Efficiency as a Key Driver:
- Focus on Efficiency: Efficiency improvements have been a central focus in the development of steam turbines, driven by the need to reduce fuel consumption and emissions. Projects like the Taichung Power Plant demonstrate how supercritical and ultra-supercritical steam conditions can significantly enhance efficiency, leading to lower operational costs and reduced environmental impact.
- Innovation in Blade Design: Advances in blade design, such as 3D-aerodynamic blades and the use of advanced materials, have been critical in improving turbine efficiency. Lessons from industry leaders like Siemens and GE show that continuous innovation in turbine components is necessary to maintain competitiveness in the market.
- The Role of Digitalization:
- Embracing Digital Technologies: The integration of digital technologies, such as digital twins, AI, and real-time monitoring systems, has emerged as a best practice in the steam turbine industry. These technologies enable operators to optimize performance, predict maintenance needs, and reduce downtime, leading to improved overall efficiency and reliability.
- Data-Driven Decision Making: The use of data analytics to monitor turbine performance and predict potential issues is becoming increasingly important. Industry leaders have demonstrated that data-driven decision-making can significantly enhance the operational efficiency and lifespan of steam turbines.
- Sustainability and Environmental Compliance:
- Sustainability Initiatives: The growing emphasis on sustainability has led to the adoption of cleaner energy sources, such as biomass, geothermal, and solar thermal, in steam turbine projects. Lessons from projects like Ivanpah show that steam turbines can play a key role in the transition to renewable energy, provided they are integrated with the appropriate technologies.
- Regulatory Compliance: Ensuring compliance with environmental regulations is a critical aspect of steam turbine projects. The successful implementation of emission control technologies, as seen in the Taichung Power Plant, highlights the importance of adhering to regulatory standards to minimize environmental impact and ensure project viability.
Conclusion
Summary of Key Points
Steam turbines have been a cornerstone of power generation and industrial applications for over a century, demonstrating remarkable adaptability and efficiency across various settings. This comprehensive exploration of steam turbines has covered their historical development, fundamental principles, design and manufacturing processes, and the wide range of applications in which they are employed.
- Fundamentals: At their core, steam turbines operate by converting thermal energy from steam into mechanical energy, which can then be used to generate electricity or drive machinery. The efficiency of this process depends on factors such as steam conditions, blade design, and the thermodynamic cycles employed, with the Rankine cycle being the most common.
- Design and Manufacturing: The design of steam turbines is a complex process that requires careful consideration of thermodynamics, materials science, and mechanical engineering. Advances in materials, such as superalloys and ceramic matrix composites, along with innovations in blade design and digitalization, are driving improvements in turbine efficiency and reliability. The manufacturing process, which includes casting, forging, machining, and heat treatment, ensures that turbines can withstand the extreme conditions under which they operate.
- Operation and Maintenance: Steam turbines require careful operation and regular maintenance to ensure their longevity and performance. Maintenance practices such as preventive and predictive maintenance, along with the use of advanced diagnostic tools, help prevent issues like blade erosion, rotor imbalance, and steam leakage. Proper operation, including control of steam quality and adherence to startup and shutdown procedures, is essential for maximizing efficiency and minimizing wear.
- Applications: Steam turbines are used in a wide variety of applications, from power generation in coal, nuclear, and geothermal plants to industrial processes in the petrochemical, pulp and paper, and steel industries. They also play a critical role in marine propulsion and are increasingly being integrated into renewable energy systems, such as concentrated solar power and biomass plants.
- Efficiency and Optimization: The efficiency of steam turbines is a key driver of their performance, with advancements in blade design, steam conditions, and energy recovery systems contributing to ongoing improvements. The use of digital twins, AI, and real-time monitoring systems is enhancing the ability to optimize turbine performance, reduce downtime, and extend the lifespan of turbine components.
- Environmental Impact and Sustainability: The environmental impact of steam turbines, particularly those powered by fossil fuels, is a significant concern. However, sustainability initiatives, such as the integration of renewable energy sources, the development of supercritical and ultra-supercritical steam cycles, and the adoption of carbon capture technologies, are helping to mitigate these impacts and support the transition to a low-carbon future.
- Future Trends and Innovations: The steam turbine industry is poised for continued innovation, with advances in materials, digitalization, and integration with smart grids driving the future of the technology. Research into low-carbon and carbon-neutral technologies, such as hydrogen-fueled turbines and enhanced carbon capture systems, will play a critical role in the industry’s evolution. The challenges posed by environmental regulations, competition from alternative technologies, and aging infrastructure present both obstacles and opportunities for the industry.
The Future of Steam Turbines
As the global energy landscape continues to evolve, steam turbines will remain a vital component of power generation and industrial processes. Their ability to adapt to changing technologies, integrate with renewable energy systems, and improve efficiency will ensure their continued relevance in the coming decades.
The push for decarbonization and the need for more sustainable energy solutions will drive further innovation in steam turbine technology. The development of ultra-efficient steam cycles, the integration of digital technologies, and the exploration of new materials and designs will be essential for meeting the growing demand for clean, reliable, and efficient power.
Moreover, the role of steam turbines in emerging markets and in hybrid energy systems that combine traditional power generation with renewable sources presents significant growth opportunities. As these regions continue to industrialize and expand their energy infrastructure, the demand for steam turbines that can deliver high efficiency, reliability, and sustainability will increase.
In conclusion, steam turbines have a rich history of innovation and adaptation, and their future looks promising as they continue to evolve in response to the challenges and opportunities of the 21st century. The ongoing commitment to improving efficiency, reducing environmental impact, and integrating with advanced energy systems will ensure that steam turbines remain a cornerstone of global energy production for years to come.
Introduction to Power Generation with Steam Turbines
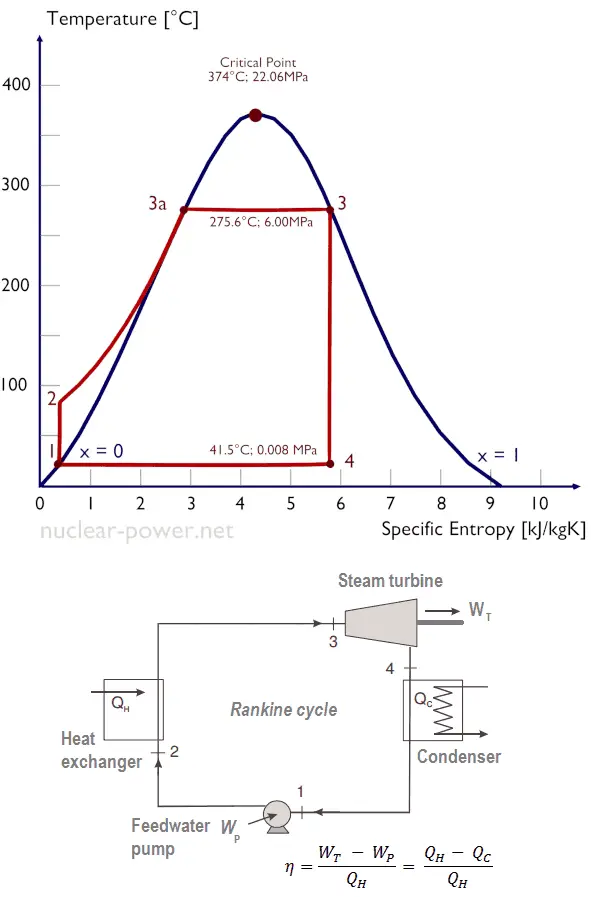
Steam turbines have been at the heart of power generation for over a century. Invented by Sir Charles Parsons in 1884, steam turbines quickly became the dominant technology for converting thermal energy into mechanical energy and, subsequently, into electrical energy. Their versatility and efficiency have made them the backbone of electricity generation worldwide.
In modern power generation, steam turbines are used in a variety of settings, from large-scale fossil fuel plants to renewable energy installations. They operate on the principle of converting the energy from high-pressure steam into mechanical energy by driving a rotor connected to a generator. The flexibility of steam turbines allows them to be integrated into diverse energy systems, including coal, nuclear, natural gas, geothermal, and solar thermal power plants.
The importance of steam turbines lies in their ability to efficiently produce large amounts of electricity. With advancements in technology, steam turbines have evolved to operate at higher temperatures and pressures, increasing their efficiency and reducing fuel consumption. These improvements have also led to a reduction in greenhouse gas emissions per unit of electricity generated, making steam turbines a critical component in the transition to more sustainable energy systems.
Types of Power Plants Using Steam Turbines
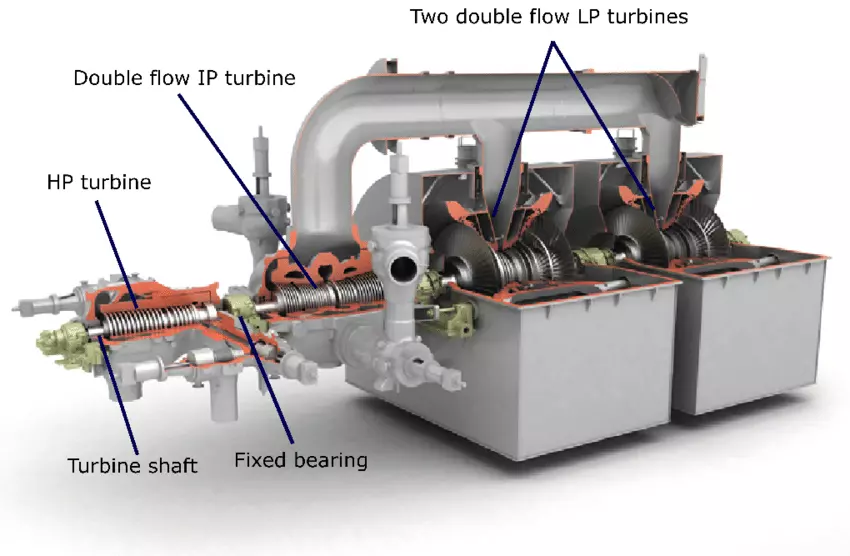
Coal-Fired Power Plants
Coal-fired power plants are among the most common applications of steam turbines. In these plants, coal is burned in a boiler to produce high-pressure steam, which is then directed into a steam turbine to generate electricity. Despite the environmental challenges associated with coal, such as CO2 emissions and air pollution, it remains a significant energy source, particularly in developing countries.
The efficiency of coal-fired power plants has improved over the years, thanks to advancements in steam turbine technology. Supercritical and ultra-supercritical steam conditions, where steam is generated at temperatures and pressures above the critical point, allow for higher thermal efficiency. This means that more electricity can be generated from the same amount of coal, reducing the overall environmental impact.
Emission control technologies, such as flue gas desulfurization (FGD) and selective catalytic reduction (SCR), are employed to reduce the emission of pollutants like SO2 and NOx. Additionally, carbon capture and storage (CCS) technologies are being developed to capture CO2 emissions from coal plants, although these are still in the early stages of adoption.
Nuclear Power Plants
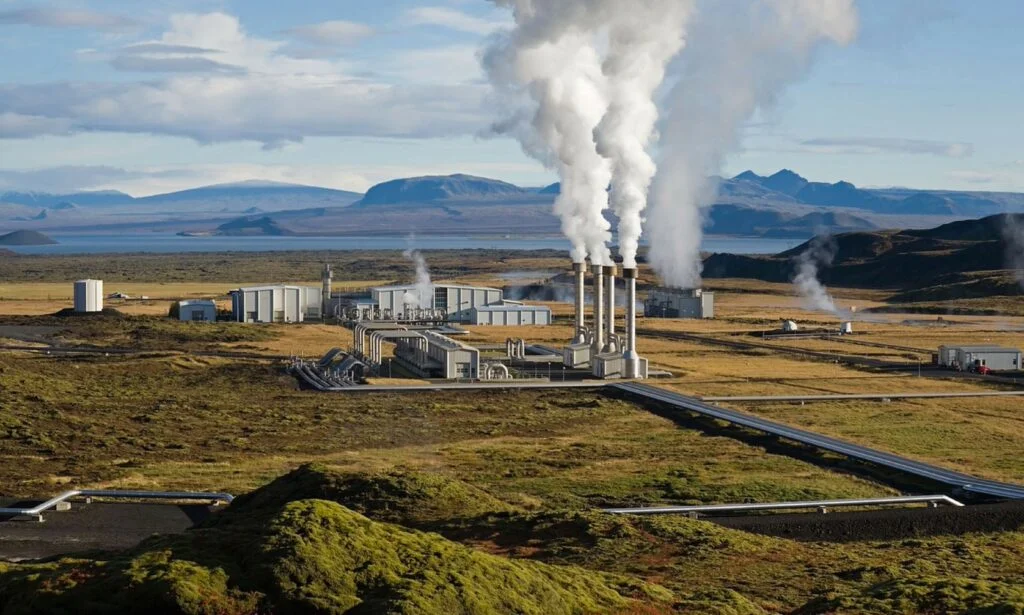
In nuclear power plants, steam turbines play a crucial role in converting the heat generated by nuclear fission into electricity. Nuclear reactors heat water to produce steam, which then drives a steam turbine connected to a generator. The steam turbines used in nuclear power plants are typically large and must be highly reliable, given the safety-critical nature of nuclear energy.
One of the key challenges in nuclear power generation is managing the steam conditions, which differ from those in fossil fuel plants. The steam produced in nuclear reactors is often at a lower temperature and pressure, which requires specific turbine designs to operate efficiently under these conditions. Additionally, the turbines must be capable of withstanding radiation and operating in a highly controlled environment.
The efficiency of nuclear power plants is influenced by the design of the steam cycle, with some plants employing reheat cycles to improve thermal efficiency. Advances in materials and turbine design continue to enhance the performance of steam turbines in nuclear applications, contributing to the overall reliability and safety of nuclear power generation.
Gas-Fired Power Plants (Combined Cycle)
Combined cycle power plants represent a significant advancement in the use of steam turbines. These plants combine a gas turbine with a steam turbine to maximize efficiency. In a combined cycle setup, a gas turbine generates electricity, and the waste heat from the gas turbine’s exhaust is used to produce steam, which then drives a steam turbine to generate additional electricity.
The efficiency of combined cycle power plants is among the highest of any power generation technology, often exceeding 60%. This is because the steam turbine effectively captures and utilizes energy that would otherwise be lost as waste heat. Combined cycle plants are also more flexible than traditional power plants, as they can be ramped up or down quickly in response to changes in electricity demand.
The integration of steam turbines in combined cycle plants has made natural gas a more attractive option for power generation, particularly in countries looking to reduce their reliance on coal and lower their carbon emissions. The ability to combine gas and steam turbines in a single plant allows for greater efficiency and lower environmental impact, making combined cycle plants a key component of the modern energy mix.
Geothermal Power Plants
Geothermal power plants harness the Earth’s natural heat to generate electricity, and steam turbines are central to this process. In these plants, steam is extracted from underground reservoirs and used to drive turbines. Geothermal steam often contains corrosive gases and minerals, which presents unique challenges for turbine design and operation.
The efficiency of geothermal power plants depends on the temperature and pressure of the geothermal steam. Higher temperature resources allow for the use of more efficient steam cycles, similar to those used in fossil fuel plants. However, geothermal plants typically operate at lower pressures, requiring turbines that can handle a wider range of steam qualities.
One of the key advantages of geothermal energy is its ability to provide baseload power, as geothermal resources are available 24/7. Steam turbines in geothermal plants must be robust and reliable, capable of operating continuously with minimal downtime. Innovations in turbine materials and designs are helping to improve the longevity and efficiency of geothermal turbines, making geothermal energy an increasingly important part of the renewable energy landscape.
Concentrated Solar Power (CSP) Plants
Concentrated Solar Power (CSP) plants use mirrors or lenses to concentrate sunlight onto a receiver, where it heats a fluid to produce steam. This steam then drives a turbine to generate electricity. CSP is unique among renewable energy technologies in that it can produce electricity even when the sun is not shining, thanks to thermal storage systems that store heat for later use.
Steam turbines used in CSP plants are designed to operate with variable steam inputs, as the intensity of sunlight can fluctuate throughout the day. The turbines must be capable of starting and stopping quickly and efficiently to match the availability of solar energy. CSP plants often use steam turbines with advanced blade designs and materials that can withstand the thermal cycling associated with intermittent solar input.
One of the key innovations in CSP is the integration of molten salt thermal storage, which allows the plant to store heat during the day and use it to generate steam at night or during cloudy periods. This ability to provide dispatchable power makes CSP with steam turbines a valuable addition to the renewable energy mix, particularly in regions with high solar irradiance.
Efficiency Considerations in Steam Turbine Power Generation
Efficiency is a critical factor in steam turbine power generation, as it determines how effectively fuel or energy resources are converted into electricity. Several factors influence the efficiency of steam turbines, including thermodynamic principles, technological advancements, and operational strategies.
Thermodynamic Efficiency
The efficiency of a steam turbine is largely governed by the principles of thermodynamics, particularly the Rankine cycle, which is the basic cycle used in steam power plants. The Rankine cycle involves four main processes: isentropic compression, isobaric heat addition, isentropic expansion, and isobaric heat rejection. The efficiency of this cycle can be improved through several methods:
- Superheating and Reheating: Increasing the temperature of steam (superheating) before it enters the turbine, or reheating the steam between turbine stages, can significantly improve efficiency by reducing the moisture content in the steam and allowing more energy to be extracted.
- Higher Pressure Ratios: Operating the turbine at higher pressures increases the amount of energy that can be extracted from the steam, improving overall cycle efficiency. Supercritical and ultra-supercritical steam conditions, where steam is generated at pressures above the critical point, represent the highest efficiency levels in modern power plants.
- Regenerative Feedwater Heating: Extracting steam from intermediate stages of the turbine to preheat the feedwater before it enters the boiler reduces the amount of fuel needed to produce steam, thereby improving the overall efficiency of the power plant.
Technological Advances
Advances in steam turbine technology have played a significant role in improving efficiency. Innovations in blade design, materials, and manufacturing techniques have allowed turbines to operate at higher temperatures and pressures, leading to greater energy conversion efficiency.
- Advanced Blade Designs: The design of turbine blades has a significant impact on efficiency. Modern blades are aerodynamically optimized to reduce losses due to turbulence and friction. The use of computational fluid dynamics (CFD) allows engineers to design blades that maximize the energy extracted from steam.
- High-Performance Materials: The development of advanced materials, such as nickel-based superalloys and ceramic matrix composites, has enabled steam turbines to operate at higher temperatures without compromising structural integrity. These materials resist creep, corrosion, and thermal fatigue, allowing for more efficient and durable turbine operation.
- 3D Printing and Precision Manufacturing: Additive manufacturing technologies, such as 3D printing, have enabled the production of turbine components with complex geometries that are optimized for efficiency. Precision manufacturing techniques also reduce material waste and improve the consistency and reliability of turbine components.
Operational Strategies
Operational strategies also play a crucial role in optimizing the efficiency of steam turbines. By carefully managing the operating conditions and load profiles, power plant operators can maximize the performance of steam turbines.
- Load Optimization: Steam turbines are most efficient when operating at or near their design capacity. However, power plants often experience varying demand throughout the day. By optimizing the load on the turbine, operators can maintain high efficiency even during periods of lower demand. Techniques such as load matching and peak shaving help ensure that turbines operate within their optimal range.
- Real-Time Monitoring and Control: Modern steam turbines are equipped with advanced monitoring and control systems that allow operators to adjust operating parameters in real-time. These systems use sensors and data analytics to monitor performance metrics such as steam temperature, pressure, and flow rate. By continuously optimizing these parameters, operators can improve efficiency and prevent issues before they lead to performance losses.
- Maintenance and Reliability: Regular maintenance is essential for maintaining the efficiency of steam turbines. Predictive maintenance, which uses data analytics to predict when components are likely to fail, helps minimize downtime and ensures that turbines continue to operate at peak efficiency. Proper lubrication, vibration analysis, and blade inspection are all critical components of an effective maintenance strategy.
Environmental Impact and Mitigation Strategies
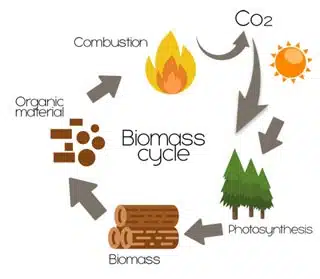
Steam turbines play a central role in power generation, but they also contribute to environmental challenges, particularly when powered by fossil fuels. Understanding and mitigating these impacts is crucial for the sustainable operation of steam turbines.
Greenhouse Gas Emissions
The combustion of fossil fuels in steam turbines, particularly in coal and gas-fired power plants, is a significant source of CO2 emissions. These greenhouse gas emissions contribute to global warming and climate change, making it imperative to reduce the carbon footprint of steam turbine power generation.
- Carbon Capture and Storage (CCS): CCS is a technology that captures CO2 emissions from power plants and stores them underground in geological formations. When integrated with steam turbines, CCS can significantly reduce the carbon emissions of fossil fuel-based power generation. While CCS is still in the early stages of adoption, ongoing research and development are focused on making it more cost-effective and scalable.
- Transition to Low-Carbon Fuels: Another strategy for reducing greenhouse gas emissions is transitioning from coal to lower-carbon fuels, such as natural gas, or even carbon-neutral fuels like biomass. Combined cycle power plants, which use both gas and steam turbines, offer higher efficiency and lower emissions compared to traditional coal-fired plants.
Air and Water Pollution
In addition to CO2, fossil fuel combustion in steam turbines also produces other air pollutants, such as sulfur dioxide (SO2), nitrogen oxides (NOx), and particulate matter. These pollutants contribute to acid rain, smog, and respiratory problems in humans.
- Emission Control Technologies: Technologies such as flue gas desulfurization (FGD) and selective catalytic reduction (SCR) are used to reduce SO2 and NOx emissions from power plants. Particulate matter can be controlled using electrostatic precipitators and baghouse filters. These technologies help mitigate the environmental impact of air pollution from steam turbines.
- Water Usage and Thermal Pollution: Steam turbines require significant amounts of water for cooling, which can impact local water resources. Additionally, the discharge of heated water back into the environment can cause thermal pollution, affecting aquatic ecosystems. To address these issues, power plants are increasingly adopting closed-loop cooling systems that minimize water withdrawal and reduce thermal discharge. Dry cooling systems, which use air instead of water, are also being implemented, particularly in water-scarce regions.
Renewable Energy Integration
The integration of steam turbines with renewable energy sources presents an opportunity to reduce the environmental impact of power generation. By leveraging steam turbines in conjunction with renewable energy technologies, such as biomass, geothermal, and concentrated solar power (CSP), it is possible to produce electricity with a lower carbon footprint.
- Biomass Power Generation: Biomass power plants use organic materials, such as wood, agricultural residues, and waste, to produce steam that drives turbines. Biomass is considered carbon-neutral, as the CO2 released during combustion is offset by the CO2 absorbed during the growth of the biomass. Steam turbines play a critical role in converting biomass energy into electricity, providing a sustainable alternative to fossil fuels.
- Geothermal and Solar Thermal: Geothermal power plants harness the Earth’s natural heat to produce steam, while CSP plants use concentrated sunlight to generate steam. Both technologies rely on steam turbines to convert thermal energy into electricity. These renewable energy sources produce little to no greenhouse gas emissions, making them attractive options for sustainable power generation.
Future Trends and Innovations in Steam Turbine Power Generation
The steam turbine industry is continuously evolving, with new technologies and trends shaping the future of power generation. These innovations are focused on improving efficiency, reducing environmental impact, and enhancing the flexibility of steam turbines in a changing energy landscape.
Decarbonization Initiatives
As the world moves toward decarbonization, steam turbines are being adapted to operate with low-carbon and carbon-neutral fuels. Hydrogen, in particular, is emerging as a promising fuel for steam turbines.
- Hydrogen-Fueled Steam Turbines: Hydrogen can be produced using renewable energy through electrolysis, resulting in a carbon-free fuel. Research is underway to develop steam turbines that can operate on hydrogen, either alone or in combination with other fuels. Hydrogen-fueled turbines have the potential to provide reliable, low-carbon power generation, especially in conjunction with renewable energy sources.
- Hybrid Energy Systems: Steam turbines are increasingly being integrated into hybrid energy systems that combine traditional power generation with renewable energy. These systems can provide continuous power while reducing carbon emissions. For example, a hybrid system might use a natural gas-fired steam turbine in combination with solar or wind power, with the turbine providing backup power when renewable sources are intermittent.
Digitalization and Smart Grids
Digital technologies are transforming the operation of steam turbines, making them more efficient, reliable, and responsive to grid demands.
- Artificial Intelligence and Machine Learning: AI and machine learning are being used to optimize turbine operations by analyzing data from sensors and control systems. These technologies can predict maintenance needs, optimize load distribution, and improve efficiency by adjusting operating parameters in real-time. AI-driven analytics are also helping to identify patterns and trends that can lead to better decision-making and improved turbine performance.
- Digital Twins: The concept of a digital twin, a virtual model of the steam turbine that runs in parallel with the physical machine, is becoming increasingly important in the industry. Digital twins allow operators to monitor turbine performance in real-time, simulate different scenarios, and optimize operations without risking the physical turbine. This technology is particularly valuable for predicting and preventing issues before they occur, reducing downtime and maintenance costs.
- Smart Grid Integration: Steam turbines are being integrated into smart grid systems, which offer enhanced flexibility and efficiency in power generation and distribution. Advanced control systems and real-time monitoring enable steam turbines to respond quickly to changes in electricity demand, helping to balance the grid and prevent blackouts. The integration of steam turbines with energy storage systems, such as batteries, also enhances grid stability and allows for more efficient use of renewable energy.
Research and Development
Ongoing research and development (R&D) efforts are focused on advancing steam turbine technology to meet the evolving demands of the energy industry and address environmental challenges.
- High-Efficiency Steam Cycles: R&D is driving the development of supercritical and ultra-supercritical steam cycles, which operate at higher temperatures and pressures than conventional cycles. These advanced cycles offer higher thermal efficiencies, reducing fuel consumption and emissions. Researchers are exploring new materials and designs that can withstand the extreme conditions of these cycles, making them more viable for widespread adoption.
- Carbon Capture Integration: Integrating carbon capture and storage (CCS) technologies with steam turbines is a key area of research aimed at reducing CO2 emissions from fossil fuel-based power generation. Ongoing R&D efforts are focused on improving the efficiency and cost-effectiveness of CCS, making it a viable option for large-scale deployment.
- Advanced Materials and Coatings: The development of new materials and coatings that can withstand high temperatures and corrosive environments is essential for improving the durability and efficiency of steam turbines. Research into advanced coatings, such as thermal barrier coatings and anti-corrosion treatments, is helping to extend the life of turbine components and reduce maintenance costs.
Conclusion
Steam turbines have been a cornerstone of power generation for over a century, and their role continues to evolve in response to changing energy needs and environmental challenges. This comprehensive overview of steam turbine power generation has highlighted the versatility, efficiency, and sustainability of steam turbines across a range of applications.
From coal-fired and nuclear power plants to renewable energy systems like geothermal and concentrated solar power, steam turbines are critical to producing reliable and efficient electricity. Technological advancements, including supercritical steam cycles, advanced blade designs, and digitalization, have significantly improved the performance of steam turbines, making them more efficient and environmentally friendly.
As the world transitions to a low-carbon economy, steam turbines will play an essential role in decarbonization efforts. The integration of hydrogen as a fuel, the adoption of carbon capture technologies, and the development of hybrid energy systems are just a few of the ways steam turbines are being adapted to meet the demands of a more sustainable energy future.
The future of steam turbines is bright, with ongoing research and innovation driving continued improvements in efficiency, reliability, and environmental performance. As digital technologies like AI and digital twins become more prevalent, steam turbines will become even more integrated with smart grid systems, enhancing their flexibility and responsiveness to changing energy demands.
In conclusion, steam turbines will remain a vital component of global power generation for years to come. Their ability to adapt to new technologies and integrate with renewable energy sources ensures that they will continue to play a key role in the transition to a more sustainable and resilient energy system.
EMS Power Machines
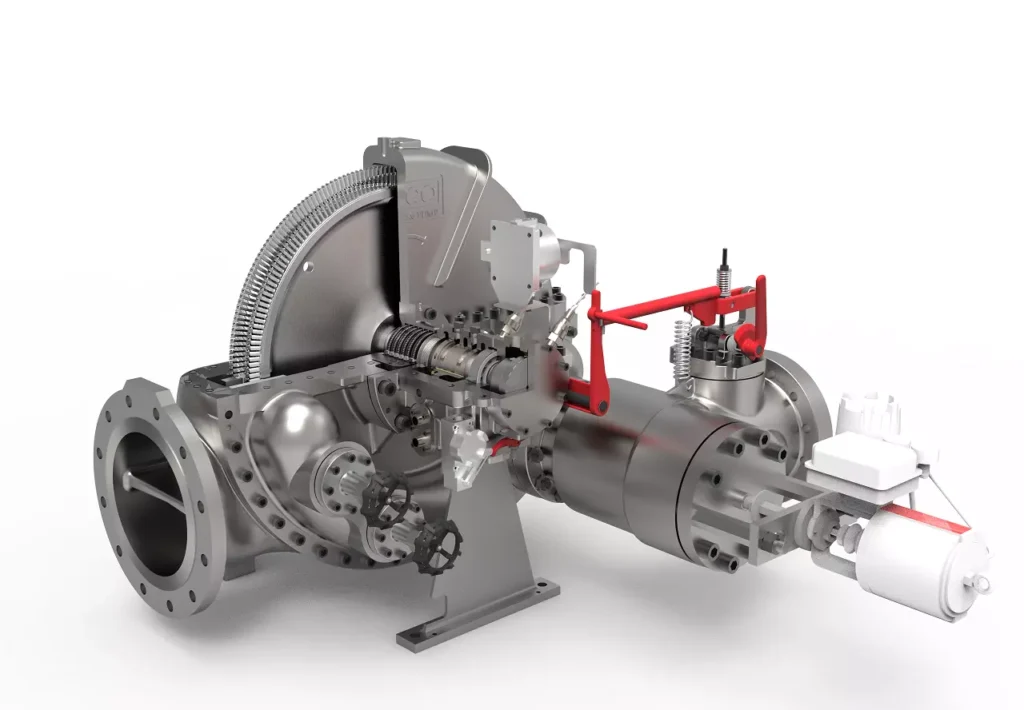
We design, manufacture and assembly Power Machines such as – diesel generators, electric motors, vibration motors, pumps, steam engines and steam turbines
EMS Power Machines is a global power engineering company, one of the five world leaders in the industry in terms of installed equipment. The companies included in the company have been operating in the energy market for more than 60 years.
EMS Power Machines manufactures steam turbines, gas turbines, hydroelectric turbines, generators, and other power equipment for thermal, nuclear, and hydroelectric power plants, as well as for various industries, transport, and marine energy.
EMS Power Machines is a major player in the global power industry, and its equipment is used in power plants all over the world. The company has a strong track record of innovation, and it is constantly developing new and improved technologies.
Here are some examples of Power Machines’ products and services:
- Steam turbines for thermal and nuclear power plants
- Gas turbines for combined cycle power plants and industrial applications
- Hydroelectric turbines for hydroelectric power plants
- Generators for all types of power plants
- Boilers for thermal power plants
- Condensers for thermal power plants
- Reheaters for thermal power plants
- Air preheaters for thermal power plants
- Feedwater pumps for thermal power plants
- Control systems for power plants
- Maintenance and repair services for power plants
EMS Power Machines is committed to providing its customers with high-quality products and services. The company has a strong reputation for reliability and innovation. Power Machines is a leading provider of power equipment and services, and it plays a vital role in the global power industry.
EMS Power Machines, which began in 1961 as a small factory of electric motors, has become a leading global supplier of electronic products for different segments. The search for excellence has resulted in the diversification of the business, adding to the electric motors products which provide from power generation to more efficient means of use.