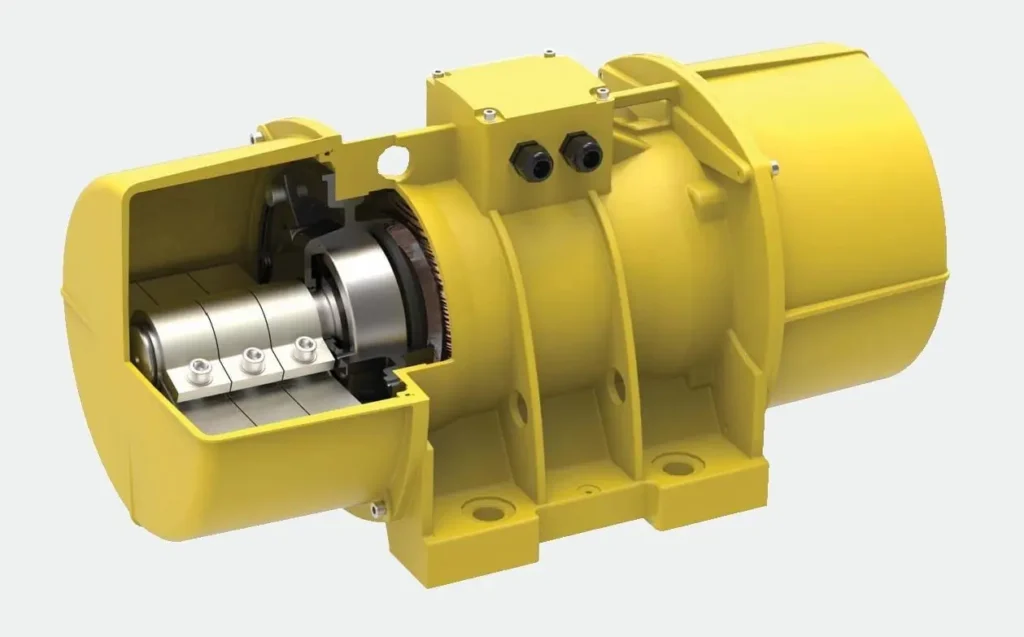
As Industrial Vibrator Manufacturers, we design and manufacture AC and DC vibration motors for the industry. Small and Big sizes are available
In the dynamic landscape of industrial manufacturing, the process of Industrial Vibrator Manufacturing takes center stage, blending precision engineering with cutting-edge technology to produce vibratory machinery that powers a multitude of industrial applications. At the core of this sophisticated manufacturing endeavor lies a commitment to quality and innovation, encapsulating the essence of the first ten keywords.
Industrial Vibrator Manufacturers
Industrial Vibrator Manufacturing begins with a meticulous focus on the intricacies of vibration equipment production. This involves the assembly of various components that collectively form the backbone of vibrator motors. From the initial stages of design to the final assembly, each step is carefully orchestrated to ensure the production of high-performance vibrators that meet the stringent standards of industrial applications.
The heart of this manufacturing process lies in the fabrication of vibrator motors, where the expertise in precision engineering comes to the fore. Each motor is crafted with a focus on durability, efficiency, and reliability, reflecting the commitment to producing vibratory machinery that can withstand the rigors of industrial environments. The intricacies of the vibration system design are honed to perfection, incorporating the latest advancements in technology.
As the production line progresses, a diverse array of industrial vibrator components comes together, each playing a crucial role in the overall functionality of the vibratory machinery. From motor components to specialized parts that contribute to the efficiency of the system, the manufacturing process requires a keen eye for detail and a dedication to quality control.
The manufacturing process isn’t a mere assembly line; it’s a dynamic arena of innovation. Custom industrial vibrators, tailored to meet specific industrial needs, exemplify the commitment to providing solutions that go beyond the ordinary. The production of high-frequency vibrators showcases an understanding of the diverse requirements across industries, from delicate applications to heavy-duty scenarios.
Throughout the manufacturing journey, there’s a continuous emphasis on testing and quality control. Vibrator motor testing becomes a critical phase, ensuring that each motor meets the predetermined standards for performance and reliability. Robust vibrator construction is essential, aligning with the demands of industrial settings where durability is paramount.
The production process extends beyond the physical construction of industrial vibrators to encompass the design principles that underpin their functionality. Energy-efficient vibrator production is a nod to the global shift towards sustainability, showcasing a commitment to reducing environmental impact while maintaining operational efficiency.
Customization is a hallmark of this manufacturing endeavor. Industrial vibrator customization allows for the creation of specialized solutions that cater to the unique needs of different industries. The manufacturing process also delves into sustainable practices, reflecting an awareness of the importance of eco-friendly vibrator manufacturing in the contemporary industrial landscape.
In the realm of Industrial Vibrator Manufacturing, quality assurance is not just a checkpoint but a continuous thread woven into every aspect of the production cycle. The vibratory machinery that emerges from this process embodies innovation, efficiency, and a dedication to pushing the boundaries of what is achievable in industrial applications. This commitment is embodied in the first ten keywords, setting the stage for a vibrant and evolving industry that continues to shape the landscape of modern manufacturing.
As we venture further into the realm of Industrial Vibrator Manufacturing, the narrative unfurls to encompass the second set of keywords, placing a spotlight on “Vibration Equipment Production.” This phase of the manufacturing process delves into the intricacies of crafting vibratory machinery, emphasizing a synthesis of technological prowess and engineering finesse.
Vibration equipment production, the eleventh keyword in our exploration, signifies the orchestration of a complex ballet where raw materials are transformed into precision instruments that power industries across the spectrum. At its core, this phase involves the meticulous assembly of components that collectively constitute the vibratory machinery, each part contributing to the overall efficiency and functionality of the final product.
The journey begins with the inception of the vibratory motor fabrication, a process where individual components are shaped and molded to exacting specifications. This involves precision engineering that ensures not only the structural integrity of the components but also their compatibility with the demands of industrial applications. The vibratory machinery assembly unfolds as a choreography of expertise, where skilled hands bring together gears, coils, and casings to form the beating heart of the industrial vibrator.
Within this dance of assembly, the design of the vibration system takes center stage. Engineers delve into the intricacies of creating systems that generate controlled mechanical oscillations, a fundamental requirement for the vibratory machinery’s varied applications. The industrial vibrator components, carefully selected and crafted, come together seamlessly to form a cohesive unit that is more than the sum of its parts.
Precision engineering is the linchpin of this phase, where the intricacies of the vibratory machinery assembly demand a keen eye for detail and a commitment to quality. The design principles behind vibration equipment production extend beyond mere functionality; they encompass factors such as durability, adaptability, and efficiency, ensuring that the resulting industrial vibrators stand as paragons of reliability in diverse industrial scenarios.
Customization becomes a hallmark of this phase as well. Tailoring vibratory machinery to specific industrial needs requires a nuanced understanding of application requirements. The production of high-frequency vibrators, for instance, is a testament to the adaptability of vibration equipment production to the varied demands of industries, ranging from delicate processes to heavy-duty applications.
Throughout the vibration equipment production process, there’s a continuous thread of innovation. Industrial vibrator innovation isn’t confined to the drawing board; it permeates the manufacturing floor, where advancements in materials, technology, and design principles converge to push the boundaries of what is achievable in vibratory machinery.
Quality control becomes paramount during vibration equipment production. Rigorous testing protocols are implemented to ensure that each industrial vibrator meets the stringent standards set for performance, reliability, and safety. Robust vibrator construction is a fundamental consideration, aligning with the demands of industrial settings where these machines operate in challenging conditions.
As the machinery takes shape, the commitment to energy-efficient vibrator production underscores a dedication to sustainability. This aligns with the broader global shift towards environmentally conscious manufacturing practices, showcasing a forward-thinking approach that balances operational efficiency with environmental responsibility.
In conclusion, the second set of keywords, centered around vibration equipment production, delves into the intricate and dynamic phase of Industrial Vibrator Manufacturing. This stage combines precision engineering, innovation, and quality control to give rise to vibratory machinery that stands as a testament to the ever-evolving landscape of modern industrial production.
Originally specializing in immersion vibrators for concrete consolidation, EMS Power Machines is now the worldwide leader in vibration technology, with a complete range of electric and pneumatic internal and external vibrators. By supplying competitive, high-quality products for wide-ranging applications, EMS Power Machines combines performance and reliability by adapting to the ever-changing market. A strong believer in innovation, EMS Power Machines is constantly striving to be ahead of the opposition.
EMS Power Machines is one of the main industrial vibrator manufacturers
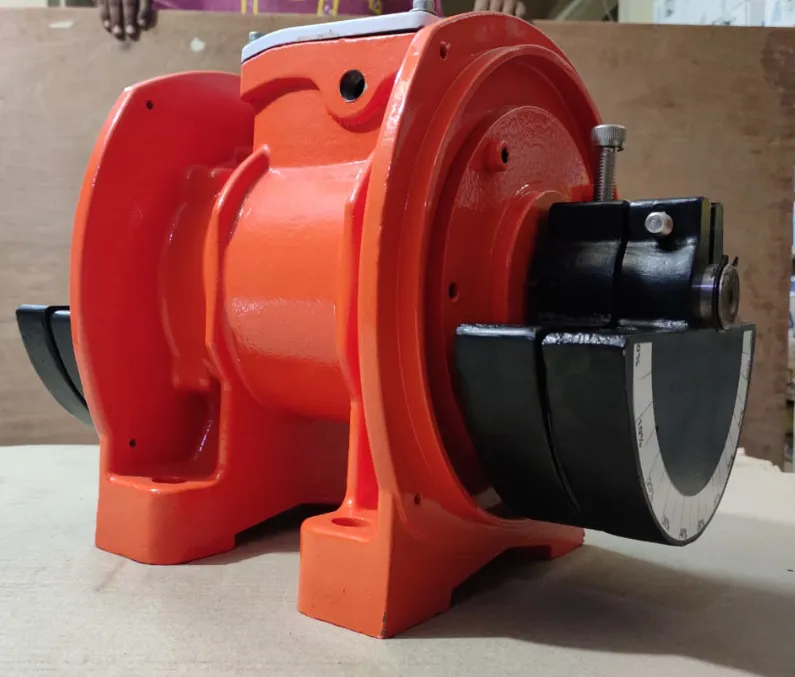
Continuing our journey through the landscape of Industrial Vibrator Manufacturing, the narrative now pivots to the third set of keywords, with a focus on “Vibrator Motor Fabrication.” This pivotal stage in the manufacturing process delves into the intricacies of crafting the very core of vibratory machinery—the motor. Vibrator motor fabrication encapsulates precision engineering, meticulous assembly, and a dedication to creating the powerhouse that drives a myriad of industrial applications.
The process commences with the crafting of the vibrator motor, an essential component that transforms electrical energy into controlled mechanical vibrations. This phase demands a meticulous understanding of electromechanical principles, where engineers delve into the nuances of motor design to ensure optimal performance, efficiency, and durability.
In the realm of Industrial Vibrator Manufacturing, the vibrator motor is the heartbeat of the machinery. The vibratory system’s efficiency and precision hinge on the intricacies of its design. Components such as coils, magnets, and bearings are carefully selected and precisely crafted, forming the foundational elements that determine the motor’s vibrational capabilities.
The fabrication process delves into the intricacies of creating coils within the vibrator motor. The precision winding of coils is a craftsmanship that influences the motor’s performance characteristics. Engineers meticulously calculate the winding patterns and gauge the materials to achieve the desired magnetic fields, ensuring that the motor generates vibrations with the required force and frequency.
Magnets within the vibrator motor play a pivotal role in inducing mechanical oscillations. The fabrication process involves selecting and placing magnets with precision to ensure optimal magnetic coupling. This meticulous arrangement is critical for achieving the desired vibratory forces, whether it be for delicate applications such as pharmaceutical processing or robust tasks like material compaction in construction.
Bearings, another integral component, undergo careful fabrication to guarantee smooth and reliable operation. The selection of bearings and their placement within the vibrator motor influences not only the mechanical performance but also the overall lifespan and maintenance requirements of the vibratory machinery.
The vibratory motor fabrication process is a ballet of materials and engineering expertise. The choice of materials, from the outer casing to internal components, involves considerations of durability, heat resistance, and compatibility with industrial environments. Robust vibrator construction is a cornerstone, ensuring that the motor can withstand the demands of continuous operation in diverse settings.
As the vibrator motor takes shape, the manufacturing process extends beyond individual components to encompass the assembly of the entire motor unit. The synergy between coils, magnets, bearings, and the casing is finely tuned to create a harmonious mechanism that translates electrical energy into precise and controlled mechanical vibrations.
Quality control measures are embedded throughout vibrator motor fabrication. Rigorous testing protocols verify the motor’s performance under various conditions, ensuring that each unit meets the predetermined standards for efficiency, reliability, and safety. This phase is not only about producing a motor; it’s about crafting a component that will serve as the driving force behind industrial processes across sectors.
In conclusion, the third set of keywords, centered around vibrator motor fabrication, delves into the heart of Industrial Vibrator Manufacturing. This phase combines engineering precision, material science, and meticulous assembly to give rise to the vibratory motor—the powerhouse that propels the machinery into a myriad of applications, from material handling to concrete consolidation, underlining the crucial role it plays in shaping the landscape of modern industrial processes.
As a global player in industrial vibration technology, the key focus of EMS Power Machines’ business strategy is rapid stock delivery, at any time, anywhere in the world. Excellent customer service is of pivotal importance: the company guarantees quick order processing and customers worldwide can enjoy access to the same high quality product and services.
EMS Power Machines has access to credible expertise when it comes to finding suitable solutions to customers’ requests. A team of engineers specialised in designing efficient, reliable, and safe solutions backed by globally certified management. EMS Power Machines provides its customers with state-of-the-art equipment and the blueprint for the next generation of products is already in progress.
Providing centrifugal force up to 26,000 kgs and with multiple voltage options EMS Power Machines’ range of electric motor vibrators covers several fields of application in every country as well as many different industrial sectors: from food to mining, from foundry to recycling, and more. EMS Power Machines’ electric motor vibrators are designed and manufactured using the latest technologies and premium quality materials and components. Motor bodies, bearing flanges, and shafts are FMEA designed and manufactured using first-grade Aluminium alloy, cast iron, and steel alloy to withstand heavy-duty applications and guarantee safe operation in any condition.
As our exploration of Industrial Vibrator Manufacturing continues, the narrative unfolds to embrace the fifth set of keywords, placing a spotlight on “Custom Industrial Vibrators.” This phase in the manufacturing process epitomizes adaptability and innovation, showcasing the industry’s commitment to tailoring vibratory solutions to meet the unique and diverse needs of various industrial applications.
The concept of custom industrial vibrators, the fifteenth keyword in our exploration, underscores a departure from one-size-fits-all approaches to vibratory machinery. In the dynamic landscape of industrial processes, each sector presents distinct challenges and requirements. This phase in manufacturing allows engineers and manufacturers to collaborate closely with clients, understanding the intricacies of their operations to create bespoke vibratory solutions that optimize efficiency and performance.
At the crux of custom industrial vibrators is the recognition that not all industrial applications are created equal. Delicate processes, such as those in the pharmaceutical or food industries, may demand vibratory systems with precise control over amplitude and frequency to handle fragile materials without compromising their integrity. On the other end of the spectrum, heavy-duty applications like material compaction in construction may require robust and powerful vibrators capable of handling dense and abrasive materials.
The customization process begins with a thorough analysis of the client’s requirements and the nuances of their industrial processes. Engineers delve into the specifics of the intended application, considering factors such as material type, throughput rates, environmental conditions, and desired outcomes. This collaborative approach ensures that the resulting custom industrial vibrator is not just a component but a tailored solution that seamlessly integrates into the client’s workflow.
The adaptability of custom industrial vibrators extends beyond the vibratory motor to encompass the entire system. Different components, from feeders to screens, are meticulously selected or designed to complement the vibratory system, ensuring a holistic solution that addresses the unique challenges posed by each industrial setting.
In pharmaceutical manufacturing, for instance, where precision and hygiene are paramount, custom vibratory solutions may incorporate features such as easy-to-clean surfaces and specialized coatings to meet stringent cleanliness standards. Conversely, in mining operations where durability and reliability are crucial, custom industrial vibrators may be engineered with reinforced casings and enhanced cooling mechanisms to withstand harsh operating conditions.
Energy-efficient solutions also find prominence in the customization process. The emphasis on sustainability in modern industrial practices is reflected in the design of custom industrial vibrators, with a focus on optimizing energy consumption without compromising performance. This not only aligns with environmental considerations but also contributes to the economic sustainability of the client’s operations.
Throughout the customization process, robust vibrator construction remains a constant theme. The adaptability of custom industrial vibrators doesn’t come at the expense of durability. Instead, it involves a nuanced understanding of materials, protective measures, and engineering techniques to ensure that the tailored solution not only meets but exceeds the performance expectations of the client.
Quality control in the customization phase is a rigorous process. Prototypes undergo comprehensive testing to validate their performance under conditions that mimic the client’s operational environment. This iterative approach allows engineers to fine-tune the custom industrial vibrator to achieve optimal efficiency, reliability, and safety.
In conclusion, the fifth set of keywords, centered around custom industrial vibrators, illuminates a pivotal phase in Industrial Vibrator Manufacturing. This process transcends the conventional, offering tailored vibratory solutions that are finely tuned to the unique demands of diverse industrial applications. The collaborative and innovative spirit embedded in the customization phase underscores the industry’s commitment to providing not just machinery but precision instruments that elevate the efficiency and performance of modern industrial processes.
Vibration Motors for the Industry
As we delve deeper into the intricate process of Industrial Vibrator Manufacturing, our focus now shifts to the fourth set of keywords, centering on “Vibration System Design.” This critical phase represents the intellectual core of vibratory machinery production, where engineering ingenuity converges with meticulous planning to create systems that orchestrate controlled and precise mechanical oscillations.
Vibration system design, the fourteenth keyword in our exploration, is the pivotal stage where the blueprint for the entire vibratory machinery comes to life. It encompasses the thoughtful integration of components, the optimization of mechanical forces, and the strategic configuration of elements to achieve a harmonious vibrational output tailored to the specific needs of diverse industrial applications.
At the heart of this design process is the synchronization of various components, each playing a unique role in generating and controlling vibrations. The vibratory motor, crafted with precision in the earlier phases, now takes center stage as the primary source of mechanical oscillations. The design intricacies delve into determining the ideal frequency, amplitude, and force that align with the requirements of the intended application.
One of the critical considerations in vibration system design is the vibratory machinery’s adaptability to different industrial scenarios. Custom industrial vibrators, tailored to meet specific requirements, reflect the versatility ingrained in the design process. Whether it’s a vibratory feeder for delicate part orientation in assembly lines or a robust vibratory compactor for construction applications, the design must cater to the unique demands of each use case.
The intricacies of vibration system design extend beyond mere functionality; they touch upon efficiency and energy optimization. Engineers aim to strike a delicate balance between delivering the required vibrational force and ensuring that the system operates with maximum efficiency. This commitment to energy-efficient vibrator production aligns with contemporary sustainability goals within the manufacturing sector.
Moreover, the vibrational forces generated by the machinery must be finely tuned to the characteristics of the materials being handled or processed. This precision is particularly crucial in industries such as pharmaceuticals or electronics manufacturing, where delicate components require controlled handling. The vibratory machinery must be designed to exert the right amount of force without causing damage or disruption.
The customization aspect of vibration system design is further exemplified when considering the production of high-frequency vibrators. In applications requiring rapid and precise vibrations, such as fine particle separation or intricate machining processes, the design must cater to the specific frequency requirements, showcasing the adaptability and versatility of vibratory machinery.
Robust vibrator construction, a consideration carried over from the earlier phases, is interwoven with vibration system design. The structural integrity of the machinery must be upheld to withstand the often challenging conditions of industrial environments. Durability is not just a feature; it’s a fundamental design principle that ensures the longevity and reliability of the vibratory system.
Vacuum-impregnated windings and class F insulating materials enhance reliability and durability. Top-quality bearings and an efficient grease retaining system assure long-lasting performance and low noise generation. Adjustable eccentric masses allow easy fine-tuning of the Max centrifugal force provided by the motor. Several certifications for use in hazardous environments are available in the EMS Power Machines range to match the most demanding specification worldwide.
The base plate surface where the vibrator motor is mounted has an allowable tolerance of 0.25mm (0.01in) so that the surfaces rest uniformly against each other to avoid internal tension that may cause breakage
of the foot of the vibrator motor. Use 8.8-type bolts, 8.0-type nuts, and flat washers belonging to category A EN ISO 7089 / 7092. The graph below shows the correct torque settings for the different bolt sizes used on the motor vibrators
Industrial Vibrator Manufacturers
The manufacturing process for industrial vibrators varies depending on the type of vibrator being produced. However, there are some general steps that are common to all industrial vibrator manufacturing processes.
1. Design: The first step is to design the vibrator. This includes determining the size, capacity, and type of vibrator that is needed. The designer also needs to consider the specific application of the vibrator and the environment in which it will be used.
2. Material selection: The next step is to select the materials that will be used to manufacture the vibrator. The materials that are selected must be strong, durable, and able to withstand the operating conditions of the vibrator.
3. Fabrication: The vibrator is then fabricated. This may involve a variety of processes, such as cutting, welding, and machining. The fabrication process must be precise to ensure that the vibrator is manufactured to the required specifications.
4. Assembly: Once the vibrator is fabricated, it is assembled. This involves attaching the various components of the vibrator together and testing the vibrator to ensure that it is working properly.
5. Testing: The vibrator is then tested under a variety of conditions to ensure that it meets the required performance specifications. The vibrator may also be tested for durability and reliability.
6. Packaging and shipping: Once the vibrator has been tested and approved, it is packaged and shipped to the customer.
Here are some of the key factors that are considered in the manufacturing of industrial vibrators:
- Quality: Industrial vibrators must be manufactured to a high standard of quality in order to ensure that they are reliable and durable. This means using high-quality materials and components, and following strict manufacturing processes.
- Performance: Industrial vibrators must be able to meet the required performance specifications. This means carefully designing the vibrator and selecting the right materials and components.
- Safety: Industrial vibrators must be safe to operate. This means designing the vibrator with safety features in mind and using materials that are safe to handle.
The manufacturing of industrial vibrators is a complex process that requires specialized skills and equipment. However, by following the steps outlined above, manufacturers can produce high-quality, reliable, and safe industrial vibrators.
Vibration motors are a type of motor that, as the name suggests, create a vibrating motion. They have become integral components in many modern devices and systems, providing feedback, alerts, and haptic responses that enhance user experience and functionality. These motors are designed to convert electrical energy into mechanical vibration, and they are used across various industries, including consumer electronics, automotive, medical devices, and industrial applications.
Historical Development
The history of vibration motors dates back to the early 20th century when basic mechanisms for generating vibration were first conceptualized. Over the years, technological advancements have led to more sophisticated designs, allowing for a wide range of applications. Early vibration motors were primarily used in industrial settings for tasks such as sorting and conveying materials. However, with the miniaturization of components and improvements in precision and control, they have become essential in everyday consumer electronics, providing tactile feedback and alerts in mobile devices and wearables.
Overview of Different Types of Vibration Motors
Vibration motors come in various types, each with unique characteristics and applications. The most common types include:
- Eccentric Rotating Mass (ERM) Motors: These motors generate vibration through the rotation of an off-center mass attached to the motor shaft. They are widely used in consumer electronics for simple haptic feedback.
- Linear Resonant Actuators (LRA): Unlike ERM motors, LRAs use a magnetic field to move a mass linearly, creating a more refined and precise vibration. This type is favored in applications requiring specific frequency responses and quick reaction times.
- Piezoelectric Vibration Motors: These utilize piezoelectric materials that expand or contract when an electrical voltage is applied. They offer high precision and are often used in applications requiring minimal size and power consumption.
This introduction sets the stage for a deeper exploration of the technical aspects, applications, and future developments of vibration motors.
Types of Vibration Motors
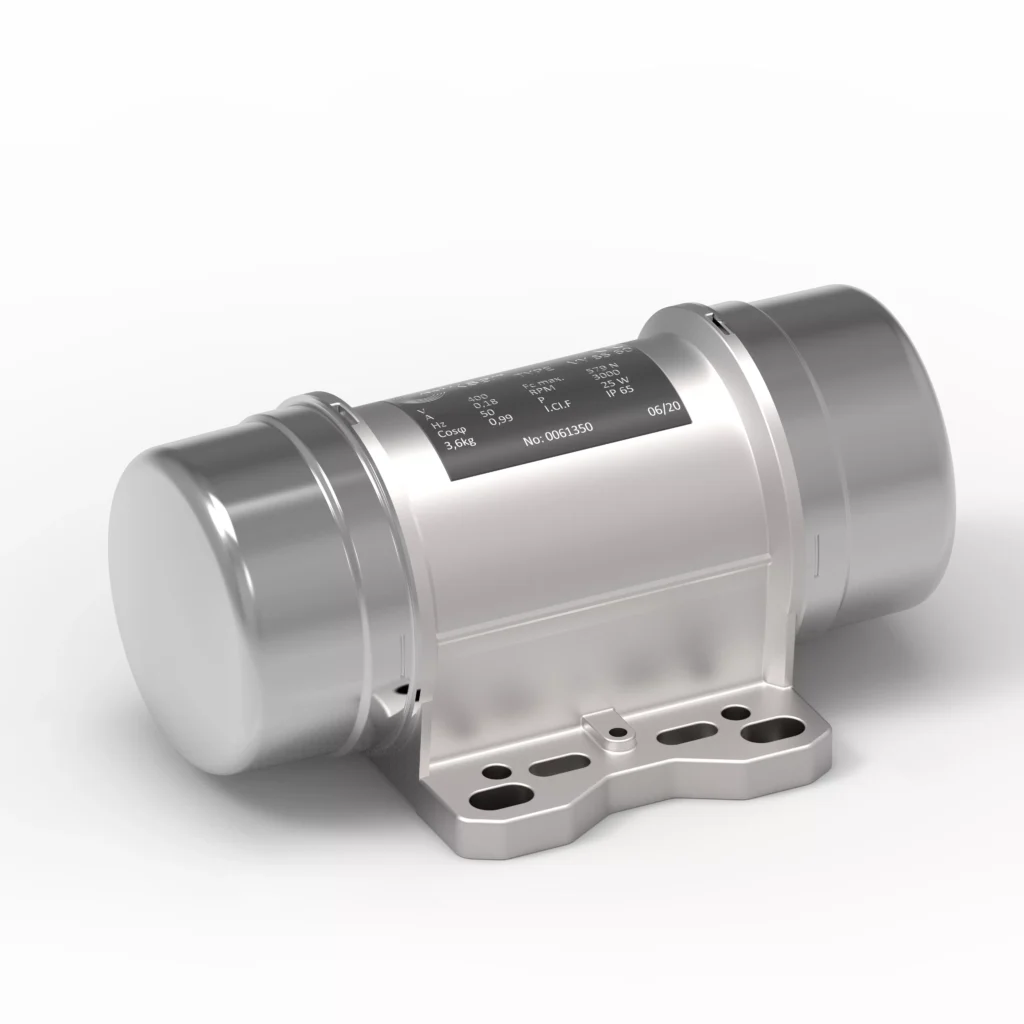
Understanding the different types of vibration motors is crucial for selecting the right one for a specific application. Each type has distinct characteristics that make it suitable for particular uses. This section explores the main types of vibration motors, their design, operation, and typical applications.
Eccentric Rotating Mass (ERM) Motors
Design and Operation
Eccentric Rotating Mass (ERM) motors are among the most widely used vibration motors. They operate by rotating an unbalanced mass, which generates centrifugal force, causing the motor to vibrate. The frequency and amplitude of the vibration are determined by the speed of rotation and the size of the mass.
The basic components of an ERM motor include:
- Motor Shaft: The central axis on which the unbalanced mass is mounted.
- Unbalanced Mass: The key component responsible for generating vibration. It is usually attached off-center on the motor shaft.
- Housing: Encloses the motor components, protecting them from environmental factors and mechanical damage.
ERM motors are relatively simple in design, making them cost-effective and easy to produce. They are typically used in applications where basic haptic feedback is needed, such as in mobile phones and handheld gaming devices.
Common Uses
- Mobile Phones and Tablets: ERM motors provide tactile feedback for touchscreen interactions and notifications.
- Wearable Devices: Used in smartwatches and fitness trackers to alert users with vibrations.
- Remote Controls: Enhance user experience by providing feedback during button presses.
Linear Resonant Actuators (LRA)
Design and Operation
Linear Resonant Actuators (LRA) are more advanced than ERM motors, offering improved precision and control. They consist of a movable mass attached to a spring and a magnetic field. When an AC voltage is applied, the mass oscillates linearly, creating a vibration.
Key components of LRA include:
- Movable Mass: Suspended by springs, this component moves back and forth to generate vibration.
- Electromagnetic Coil: Creates a magnetic field that interacts with the movable mass.
- Spring System: Ensures the mass returns to its original position after displacement.
LRA motors are known for their high-frequency response and efficiency, making them suitable for applications requiring precise control and fast response times.
Common Uses
- Haptic Feedback in Mobile Devices: Provides more nuanced and responsive feedback compared to ERM motors.
- Gaming Controllers: Enhances immersion by delivering realistic vibrations based on in-game events.
- Automotive Touchscreens: Improves user interaction with infotainment systems through tactile feedback.
Piezoelectric Vibration Motors
Design and Operation
Piezoelectric vibration motors leverage the piezoelectric effect, where certain materials generate an electric charge in response to mechanical stress. These motors consist of piezoelectric elements that deform when an electric field is applied, producing vibration.
Key components of piezoelectric motors include:
- Piezoelectric Elements: The core components that expand or contract to create vibration.
- Metal Plate: Acts as a diaphragm that vibrates in response to the deformation of the piezoelectric elements.
- Drive Circuit: Controls the frequency and amplitude of the applied voltage, affecting the vibration characteristics.
Piezoelectric motors are prized for their small size, low power consumption, and high precision. They are often used in applications where space is limited, and precise control is required.
Common Uses
- Medical Devices: Provide haptic feedback in surgical tools and diagnostic equipment.
- Consumer Electronics: Used in compact devices such as smartwatches and portable audio players.
- Industrial Sensors: Enhance sensitivity and accuracy in measurement instruments.
Comparison of Different Types
Each type of vibration motor has its advantages and disadvantages, influencing the selection process for specific applications.
Type | Advantages | Disadvantages |
---|---|---|
ERM | – Simple design<br>- Cost-effective<br>- Easy to produce | – Limited frequency range<br>- Slower response time |
LRA | – Precise control<br>- Fast response<br>- Efficient | – Higher cost<br>- More complex design |
Piezoelectric | – Small size<br>- Low power consumption<br>- High precision | – Limited force output<br>- Requires specialized materials |
Selection Criteria for Different Applications
When selecting a vibration motor, several factors should be considered:
- Application Requirements: Determine the desired frequency, amplitude, and response time.
- Size and Weight: Consider the available space and weight constraints in the device or system.
- Power Consumption: Evaluate the power requirements, especially for battery-powered devices.
- Cost: Balance performance needs with budgetary constraints.
In summary, the choice of vibration motor depends on the specific application requirements, balancing factors such as performance, size, cost, and power consumption.
Technical Aspects of Vibration Motors
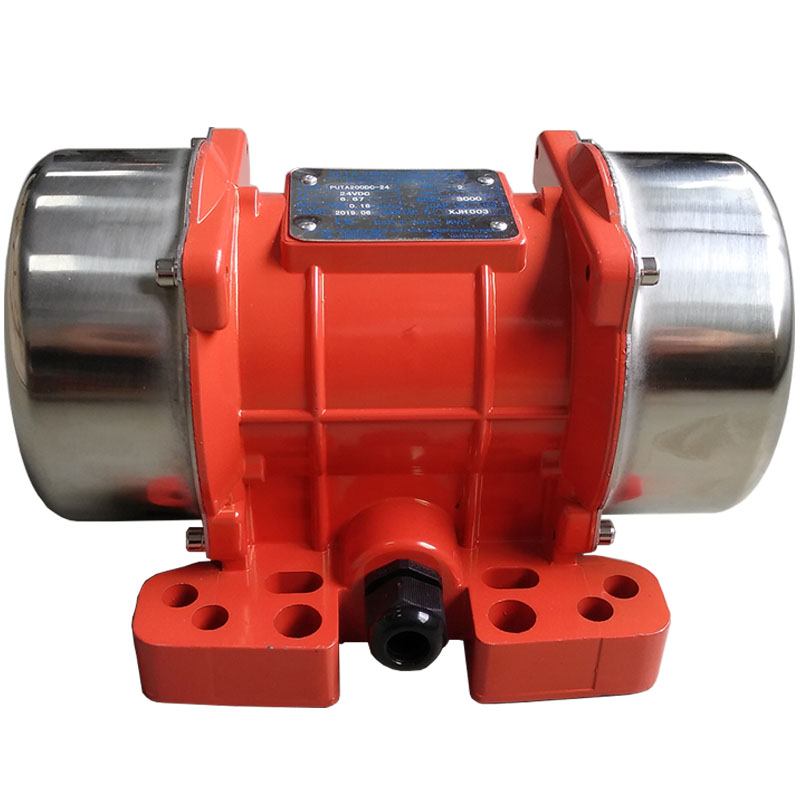
A comprehensive understanding of the technical aspects of vibration motors is essential for designing and integrating them into various applications. This section explores the construction, key specifications, performance characteristics, and design considerations associated with vibration motors.
Construction and Materials
Vibration motors are constructed using materials and components that ensure durability, efficiency, and performance. The choice of materials can significantly impact the motor’s lifespan and functionality.
Key Components
- Motor Housing: Typically made from metal or high-strength plastic, the housing protects the internal components from mechanical damage and environmental factors. It also serves as a mounting structure.
- Rotor and Stator: The rotor is the rotating part of the motor, while the stator is the stationary component. These are usually made from magnetic materials to facilitate electromagnetic interactions.
- Bearings: Bearings reduce friction between moving parts and support the motor shaft. They are often made from materials like stainless steel or ceramic for durability and reliability.
- Wiring and Connectors: Electrical connections are made using insulated copper wires and connectors that provide reliable electrical conductivity.
- Unbalanced Mass or Piezoelectric Elements: Depending on the type of motor, these components generate the vibrations. The unbalanced mass is typically made of metal, while piezoelectric elements are crafted from specialized ceramic materials.
Key Specifications
When selecting a vibration motor, several key specifications must be considered to ensure optimal performance for the intended application.
Size and Dimensions
- Length, Width, and Height: The overall dimensions of the motor must fit within the available space in the device or system.
- Weight: The motor’s weight can affect the balance and handling of the device, particularly in portable applications.
Power and Voltage
- Operating Voltage: The voltage required to power the motor, which can range from a few volts in small devices to several hundred volts in industrial applications.
- Power Consumption: The amount of electrical power consumed by the motor during operation. Lower power consumption is preferred for battery-powered devices.
Frequency and Amplitude
- Frequency Range: The range of vibration frequencies the motor can produce, typically measured in Hertz (Hz).
- Amplitude: The magnitude of the vibration, often expressed in millimeters (mm) or inches.
Performance Characteristics
Understanding the performance characteristics of vibration motors is crucial for achieving the desired vibration effects in various applications.
- Vibration Strength: The intensity of the vibration produced by the motor, influenced by factors such as motor speed, mass, and power input.
- Response Time: The time it takes for the motor to reach its desired vibration state after power is applied. Faster response times are preferred for applications requiring immediate feedback.
- Efficiency: The ratio of mechanical output power to electrical input power, indicating how effectively the motor converts electrical energy into vibration.
- Durability and Lifespan: The expected operational lifespan of the motor, affected by factors such as material quality, construction, and operating conditions.
Design Considerations and Challenges
Designing and integrating vibration motors into devices and systems involves several challenges and considerations to ensure optimal performance and reliability.
Heat Dissipation
Vibration motors generate heat during operation, which can affect their performance and lifespan. Effective heat dissipation methods, such as using heat sinks or conductive materials, are essential to prevent overheating.
Noise and Vibration Isolation
Unwanted noise and vibrations can interfere with the operation of devices and systems. Implementing noise and vibration isolation techniques, such as using damping materials or mounting systems, can minimize these issues.
Environmental Factors
Vibration motors may be exposed to various environmental factors, such as temperature extremes, moisture, and dust. Designing motors with protective features, such as seals or coatings, can enhance their resilience to environmental challenges.
Integration with Control Systems
Integrating vibration motors with control systems requires careful consideration of factors such as signal processing, power management, and feedback mechanisms. This ensures precise control and synchronization with other components in the system.
In conclusion, the technical aspects of vibration motors encompass a wide range of considerations, from construction and materials to performance characteristics and design challenges. Understanding these aspects is essential for selecting and implementing the right vibration motor for specific applications.
Applications of Vibration Motors
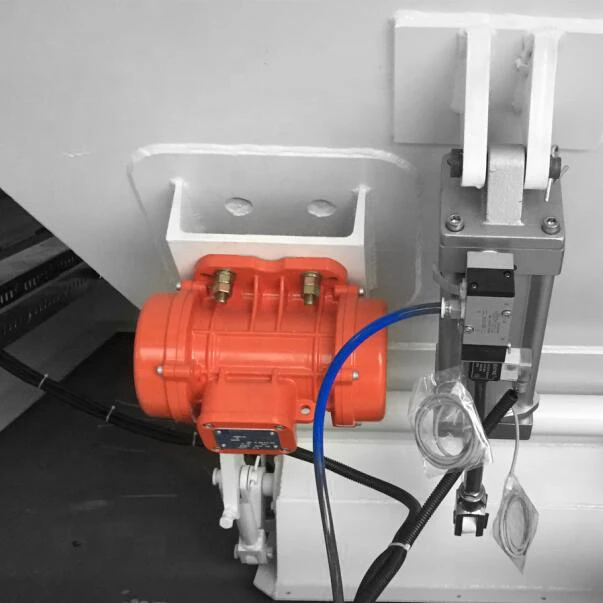
Vibration motors play a crucial role in various industries, enhancing functionality and user experience through tactile feedback, alerts, and precise control. This section explores the diverse applications of vibration motors across different sectors.
Consumer Electronics
Mobile Phones and Tablets
Vibration motors are integral components in mobile phones and tablets, providing haptic feedback for touchscreen interactions and notifications. They enhance the user experience by delivering tactile responses to touch inputs, alerts, and messages.
- Touchscreen Feedback: Vibration motors simulate the sensation of pressing physical buttons, improving user interaction with touchscreen interfaces.
- Notifications and Alerts: Vibration motors provide discreet alerts for incoming calls, messages, and notifications, allowing users to stay informed without relying on audible alerts.
Wearables and Smart Devices
In wearable technology, vibration motors are used to deliver notifications and alerts directly to the user’s wrist or body. This enhances the functionality and convenience of devices such as smartwatches and fitness trackers.
- Fitness Tracking: Vibration motors provide feedback for activity goals, heart rate monitoring, and other fitness metrics.
- Health Monitoring: Vibration alerts can signal important health-related notifications, such as medication reminders or emergency alerts.
Automotive Industry
Haptic Feedback in Touchscreens
Vibration motors are used in automotive touchscreens to enhance user interaction with infotainment and navigation systems. Haptic feedback provides tactile responses to touch inputs, improving usability and reducing driver distraction.
- Infotainment Systems: Vibration motors simulate button presses, enhancing the user experience and making interactions more intuitive.
- Navigation Controls: Haptic feedback assists drivers in navigating menus and settings, ensuring safer and more efficient operation.
Alert Systems
Vibration motors are employed in automotive alert systems to provide non-intrusive warnings and notifications to drivers. These systems enhance safety by delivering tactile alerts for various vehicle conditions and hazards.
- Collision Warning: Vibration alerts can warn drivers of potential collisions or obstacles, improving reaction times and safety.
- Lane Departure Warning: Vibration motors provide feedback when a vehicle deviates from its lane, helping drivers maintain proper lane positioning.
Industrial Applications
Equipment and Machinery Monitoring
In industrial settings, vibration motors are used for equipment and machinery monitoring. They provide feedback on the operational status and performance of machinery, helping to identify issues and prevent failures.
- Condition Monitoring: Vibration sensors detect changes in equipment performance, allowing for timely maintenance and repairs.
- Fault Detection: Vibration analysis helps identify mechanical faults, such as imbalances or misalignments, improving equipment reliability and efficiency.
Material Handling and Processing
Vibration motors are employed in material handling and processing applications, facilitating the movement and sorting of materials. They improve efficiency and accuracy in various industrial processes.
- Vibratory Conveyors: Vibration motors drive conveyors that transport materials, enhancing the speed and precision of material handling.
- Sorting and Screening: Vibration motors assist in sorting and screening materials based on size, weight, or other characteristics, optimizing production processes.
Medical Devices
Feedback Systems in Prosthetics
In the medical field, vibration motors are used in prosthetic devices to provide sensory feedback to users. This enhances the functionality and user experience of prosthetics, improving mobility and control.
- Tactile Feedback: Vibration motors simulate sensations such as touch and pressure, helping users interact with their environment.
- Control Feedback: Vibration alerts assist users in controlling prosthetic movements, enhancing precision and coordination.
Patient Monitoring Equipment
Vibration motors are employed in patient monitoring equipment to deliver alerts and notifications for various medical conditions. They improve patient care by providing timely and discreet notifications to healthcare professionals and patients.
- Vital Sign Monitoring: Vibration alerts signal changes in vital signs, such as heart rate or blood pressure, allowing for prompt medical intervention.
- Medication Reminders: Vibration motors provide reminders for medication administration, ensuring adherence to treatment plans.
Other Emerging Applications
Virtual Reality and Gaming
In virtual reality (VR) and gaming, vibration motors enhance immersion by delivering realistic tactile feedback based on in-game events and interactions. This improves the overall gaming experience and realism.
- Haptic Feedback in VR: Vibration motors simulate various sensations, such as impacts, textures, and environmental effects, enhancing the sense of presence in virtual environments.
- Gaming Controllers: Vibration motors provide feedback for in-game actions, such as explosions, collisions, and character movements, improving player engagement and satisfaction.
Robotics and Automation
Vibration motors are used in robotics and automation to enhance precision, control, and feedback in various applications. They improve the performance and functionality of robotic systems.
- Tactile Sensors: Vibration motors provide feedback for robotic grippers and manipulators, improving object handling and manipulation.
- Precision Control: Vibration alerts assist in fine-tuning robotic movements, enhancing accuracy and coordination in automated processes.
In conclusion, vibration motors have diverse applications across various industries, enhancing functionality, user experience, and performance. Their versatility and adaptability make them essential components in modern technology and systems.
Future Trends and Innovations
As technology continues to evolve, vibration motors are expected to undergo significant advancements, leading to new applications and improved performance. This section explores the future trends and innovations in vibration motor technology.
Technological Advancements
- Miniaturization: Advances in manufacturing and materials will enable the development of smaller and more compact vibration motors, expanding their use in miniaturized devices and systems.
- Increased Efficiency: Innovations in motor design and materials will lead to more efficient vibration motors with lower power consumption and higher performance.
- Improved Control and Precision: Enhanced control algorithms and sensor integration will enable more precise and customizable vibration effects, improving user experience and application performance.
Integration with IoT and Smart Technologies
The integration of vibration motors with the Internet of Things (IoT) and smart technologies will open up new possibilities for applications and functionality.
- Smart Home Devices: Vibration motors will provide tactile feedback and alerts in smart home devices, enhancing user interaction and control.
- Wearable Health Monitors: Integration with IoT will enable real-time monitoring and feedback for health and fitness applications, improving user outcomes and experiences.
Potential New Applications
- Augmented Reality (AR): Vibration motors will enhance AR experiences by providing tactile feedback for virtual interactions, improving immersion and realism.
- Advanced Automotive Systems: Vibration motors will play a role in advanced driver assistance systems (ADAS) and autonomous vehicles, providing feedback and alerts for various driving conditions and scenarios.
- Next-Generation Consumer Electronics: Vibration motors will continue to enhance user experience in emerging consumer electronics, such as foldable devices and flexible displays.
In summary, the future of vibration motors is promising, with advancements in technology and integration with smart systems leading to new applications and improved performance. These innovations will continue to enhance functionality and user experience across various industries.
Conclusion
Vibration motors are essential components in modern technology, providing tactile feedback, alerts, and precise control in a wide range of applications. This article has explored the various types of vibration motors, their technical aspects, and their diverse applications across industries.
Recap of Key Points
- Types of Vibration Motors: We examined the three main types of vibration motors—Eccentric Rotating Mass (ERM), Linear Resonant Actuators (LRA), and Piezoelectric vibration motors—each with unique characteristics and applications.
- Technical Aspects: We discussed the construction, key specifications, performance characteristics, and design considerations associated with vibration motors, highlighting the factors that influence their selection and integration.
- Applications: We explored the diverse applications of vibration motors in consumer electronics, automotive, industrial, medical, and other emerging fields, showcasing their versatility and adaptability.
- Future Trends and Innovations: We examined the future trends and innovations in vibration motor technology, including miniaturization, increased efficiency, and integration with IoT and smart technologies.
Importance of Vibration Motors in Modern Technology
Vibration motors play a crucial role in enhancing functionality and user experience across various industries. Their ability to provide tactile feedback, alerts, and precise control makes them indispensable components in modern devices and systems.
- Consumer Electronics: Vibration motors improve user interaction and experience in mobile phones, wearables, and other consumer devices.
- Automotive Industry: Vibration motors enhance safety and usability in automotive systems, providing feedback and alerts for various conditions.
- Industrial and Medical Applications: Vibration motors improve efficiency and performance in industrial processes and medical devices, providing valuable feedback and control.
Final Thoughts on Future Developments
As technology continues to advance, vibration motors will play an increasingly important role in emerging applications and industries. Innovations in design, materials, and integration will lead to new possibilities and improved performance, enhancing functionality and user experience.
In conclusion, vibration motors are vital components in modern technology, providing essential functionality and enhancing user experience across a wide range of applications. Their versatility, adaptability, and potential for future advancements make them indispensable in the ever-evolving technological landscape.
Introduction to Industrial Vibration Motors
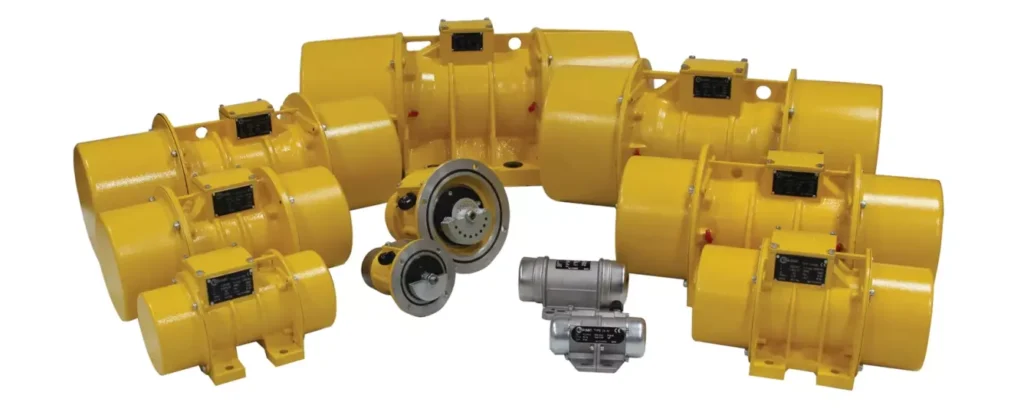
Industrial vibration motors are specialized devices designed to generate mechanical vibrations for various industrial applications. They are integral to processes that require the movement, sorting, and monitoring of materials and equipment. By converting electrical energy into mechanical vibrations, these motors facilitate efficient material handling, quality control, and operational monitoring in industrial settings.
Key functions of industrial vibration motors include:
- Material Movement: Vibration motors aid in the transportation and handling of bulk materials, ensuring smooth and efficient processes.
- Sorting and Separation: They enhance the sorting and separation of materials based on size, weight, or other characteristics, optimizing production efficiency.
- Equipment Monitoring: Vibration motors provide feedback on the operational status of machinery, helping to identify potential issues before they lead to failures.
Historical Context
The use of vibration in industrial applications can be traced back to the early 20th century when basic vibrating mechanisms were employed for tasks such as material sorting and handling. The development of dedicated vibration motors, however, marked a significant advancement in technology.
- Early Innovations: Initial applications were primarily mechanical, relying on simple mechanisms to generate vibrations. These early systems were limited in precision and control.
- Technological Advancements: With the advent of electric motors and advancements in materials science, vibration motors became more sophisticated, offering improved control, efficiency, and versatility.
- Modern Applications: Today, industrial vibration motors are used across a wide range of industries, including mining, construction, food processing, and pharmaceuticals, highlighting their essential role in modern industrial processes.
Key Features
Industrial vibration motors are characterized by several key features that make them suitable for demanding applications:
- Robust Construction: Designed to withstand harsh industrial environments, vibration motors are built with durable materials and components.
- High Efficiency: They are engineered for optimal energy conversion, ensuring efficient performance and minimal energy loss.
- Versatility: Available in various sizes and configurations, vibration motors can be tailored to specific industrial needs and applications.
- Precision Control: Advanced control systems allow for precise adjustment of vibration frequency and amplitude, enabling customized solutions for diverse industrial tasks.
Key takeaways:
- Essential for Industrial Processes: Vibration motors are vital for efficient and effective material handling, sorting, and monitoring in industrial settings.
- Technological Evolution: From early mechanical systems to modern electric motors, technological advancements have significantly enhanced their capabilities.
- Diverse Applications: Used across multiple industries, vibration motors are adaptable to various tasks, showcasing their versatility and importance in modern industry.
Types of Industrial Vibration Motors
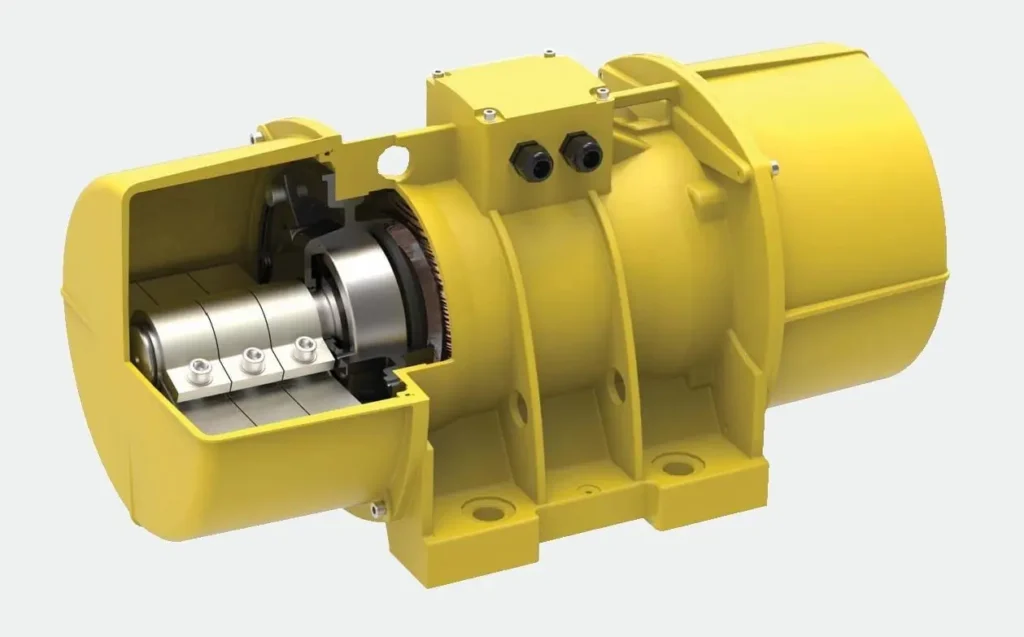
Understanding the different types of industrial vibration motors is crucial for selecting the appropriate motor for specific applications. Each type offers unique characteristics and advantages, making them suitable for various industrial tasks.
Eccentric Rotating Mass (ERM) Motors
Design and Operation
Eccentric Rotating Mass (ERM) motors are among the most commonly used vibration motors in industrial applications. They operate by rotating an unbalanced mass attached to the motor shaft, generating centrifugal force that produces vibration. The frequency and amplitude of the vibration are determined by the speed of rotation and the size of the unbalanced mass.
Key components of ERM motors include:
- Motor Shaft: The central axis on which the unbalanced mass is mounted.
- Unbalanced Mass: The component responsible for generating vibration. It is usually attached off-center on the motor shaft.
- Housing: Encloses the motor components, protecting them from environmental factors and mechanical damage.
Advantages of ERM motors:
- Simple Design: The straightforward design makes them easy to manufacture and maintain.
- Cost-Effective: They are relatively inexpensive compared to other types of vibration motors.
- Versatile Applications: Suitable for a wide range of industrial tasks, including material handling and sorting.
Common Applications
- Material Conveying: ERM motors drive vibratory conveyors, enhancing the movement of bulk materials.
- Screening and Sorting: They facilitate the sorting and screening of materials based on size and weight.
- Compact Equipment: ERM motors are used in applications where space is limited, providing efficient vibration solutions.
Linear Resonant Actuators (LRA)
Design and Operation
Linear Resonant Actuators (LRA) differ from ERM motors in that they generate vibration through the linear movement of a mass rather than rotational motion. An electromagnetic field is used to move the mass back and forth, producing vibrations with high precision and control.
Key components of LRA motors include:
- Movable Mass: Suspended by springs, the mass moves linearly to generate vibration.
- Electromagnetic Coil: Creates a magnetic field that interacts with the movable mass.
- Spring System: Ensures the mass returns to its original position after displacement.
Advantages of LRA motors:
- Precise Control: Offer more precise control over vibration frequency and amplitude.
- Efficient Performance: Consume less power compared to ERM motors, making them suitable for energy-sensitive applications.
- High-Frequency Response: Capable of producing high-frequency vibrations with minimal delay.
Common Applications
- Precision Manufacturing: Used in processes requiring exact vibration control, such as semiconductor manufacturing.
- Laboratory Equipment: Enhance the precision and accuracy of laboratory instruments and devices.
- Quality Control: Facilitate quality control processes by providing precise vibration feedback.
Electromagnetic Vibration Motors
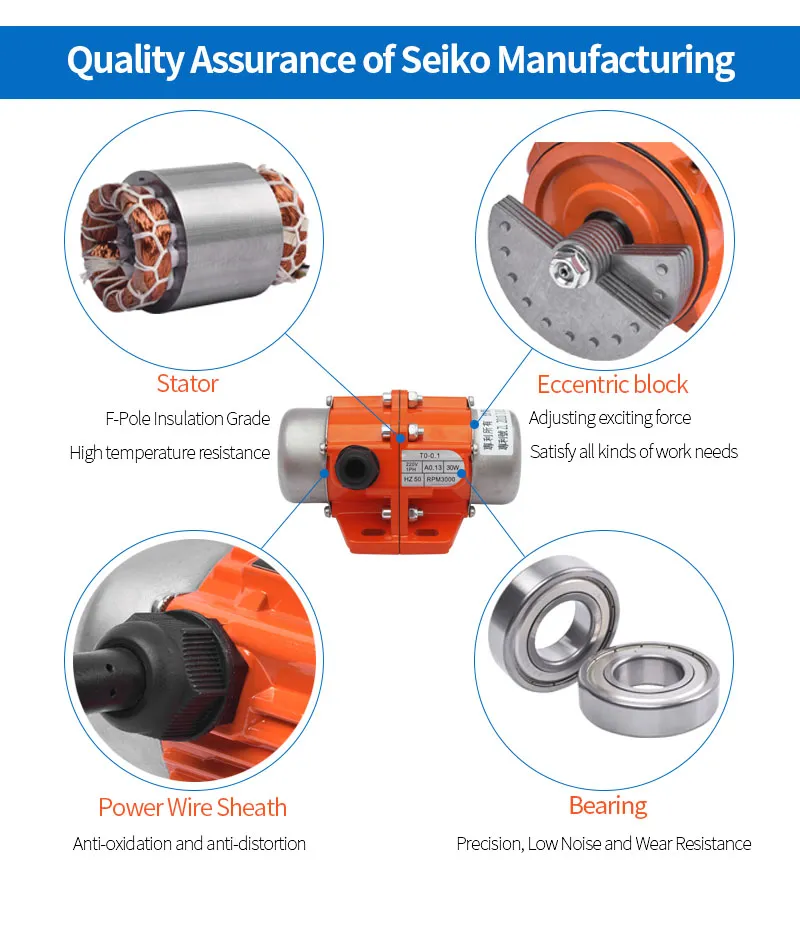
Design and Operation
Electromagnetic vibration motors generate vibrations through the interaction of magnetic fields. These motors consist of an electromagnetic coil and a vibrating armature, which is set into motion by the magnetic field generated when current flows through the coil.
Key components of electromagnetic motors include:
- Electromagnetic Coil: Generates a magnetic field when energized.
- Vibrating Armature: Responds to the magnetic field, creating vibrations.
- Damping System: Reduces noise and unwanted vibrations, enhancing motor performance.
Advantages of electromagnetic motors:
- Smooth Operation: Provide smooth and continuous vibrations, reducing mechanical stress on components.
- Adjustable Frequency: Allow for precise control of vibration frequency and amplitude.
- Low Noise Levels: Operate with minimal noise, making them suitable for noise-sensitive environments.
Common Applications
- Conveying Systems: Used in conveyor systems for smooth and efficient material transportation.
- Vibratory Feeders: Enhance the performance of vibratory feeders used in packaging and assembly lines.
- Textile Industry: Improve the efficiency of textile processing equipment by providing consistent vibrations.
Piezoelectric Vibration Motors
Design and Operation
Piezoelectric vibration motors leverage the piezoelectric effect, where certain materials generate an electric charge in response to mechanical stress. These motors consist of piezoelectric elements that expand or contract when an electric field is applied, producing vibration.
Key components of piezoelectric motors include:
- Piezoelectric Elements: The core components that expand or contract to create vibration.
- Metal Plate: Acts as a diaphragm that vibrates in response to the deformation of the piezoelectric elements.
- Drive Circuit: Controls the frequency and amplitude of the applied voltage, affecting the vibration characteristics.
Advantages of piezoelectric motors:
- High Precision: Offer precise control over vibration characteristics, making them suitable for sensitive applications.
- Compact Design: Small and lightweight, ideal for applications with space constraints.
- Low Power Consumption: Require minimal power, making them energy-efficient.
Common Applications
- Medical Devices: Provide precise vibration feedback in medical diagnostic equipment.
- Microelectronics: Enhance the performance of microelectronic devices by providing controlled vibrations.
- Research and Development: Used in experimental setups requiring precise vibration control.
Comparison of Types
Each type of industrial vibration motor has its own set of advantages and disadvantages, influencing their suitability for specific applications.
Type | Advantages | Disadvantages |
---|---|---|
ERM | – Simple design<br>- Cost-effective<br>- Versatile | – Limited frequency range<br>- Slower response time |
LRA | – Precise control<br>- High efficiency<br>- Fast response | – Higher cost<br>- More complex design |
Electromagnetic | – Smooth operation<br>- Adjustable frequency<br>- Low noise | – Complex construction<br>- Requires precise alignment |
Piezoelectric | – High precision<br>- Compact design<br>- Low power consumption | – Limited force output<br>- Specialized materials required |
Selection Criteria:
- Application Requirements: Determine the desired frequency, amplitude, and response time.
- Size and Weight: Consider the available space and weight constraints in the application.
- Power Consumption: Evaluate the power requirements, especially for energy-sensitive applications.
- Cost: Balance performance needs with budgetary constraints.
Summary:
- Diverse Options: A variety of vibration motors are available, each with unique characteristics and advantages.
- Application-Specific Selection: The choice of motor depends on the specific requirements and constraints of the application.
Technical Aspects of Industrial Vibration Motors
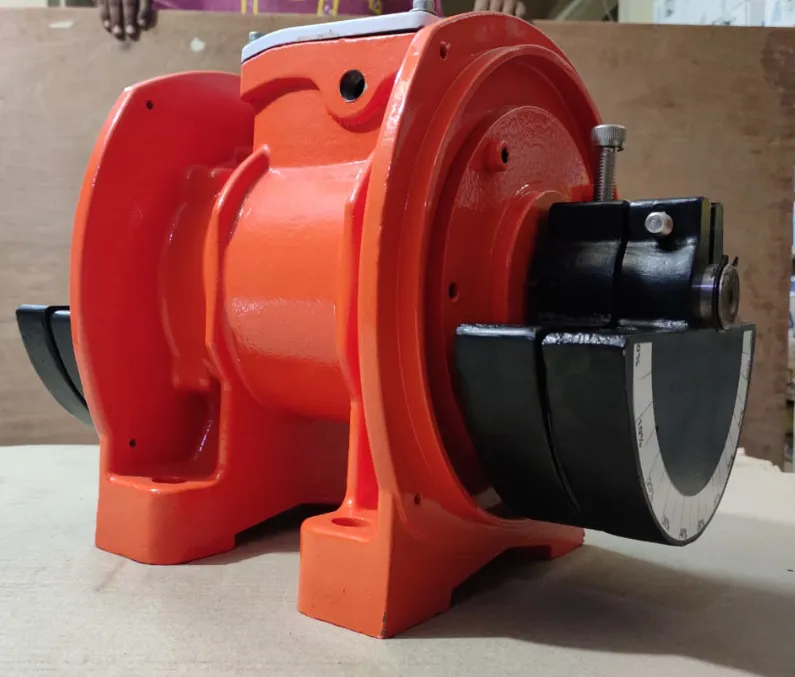
A comprehensive understanding of the technical aspects of industrial vibration motors is essential for designing and integrating them into various applications. This section explores the construction, key specifications, performance characteristics, and design considerations associated with vibration motors.
Construction and Materials
Industrial vibration motors are constructed using materials and components that ensure durability, efficiency, and performance. The choice of materials can significantly impact the motor’s lifespan and functionality.
Key Components
- Motor Housing: Typically made from metal or high-strength plastic, the housing protects the internal components from mechanical damage and environmental factors. It also serves as a mounting structure.
- Rotor and Stator: The rotor is the rotating part of the motor, while the stator is the stationary component. These are usually made from magnetic materials to facilitate electromagnetic interactions.
- Bearings: Bearings reduce friction between moving parts and support the motor shaft. They are often made from materials like stainless steel or ceramic for durability and reliability.
- Wiring and Connectors: Electrical connections are made using insulated copper wires and connectors that provide reliable electrical conductivity.
- Unbalanced Mass or Piezoelectric Elements: Depending on the type of motor, these components generate the vibrations. The unbalanced mass is typically made of metal, while piezoelectric elements are crafted from specialized ceramic materials.
Key Specifications
When selecting a vibration motor, several key specifications must be considered to ensure optimal performance for the intended application.
Size and Dimensions
- Length, Width, and Height: The overall dimensions of the motor must fit within the available space in the device or system.
- Weight: The motor’s weight can affect the balance and handling of the device, particularly in portable applications.
Power and Voltage
- Operating Voltage: The voltage required to power the motor, which can range from a few volts in small devices to several hundred volts in industrial applications.
- Power Consumption: The amount of electrical power consumed by the motor during operation. Lower power consumption is preferred for battery-powered devices.
Frequency and Amplitude
- Frequency Range: The range of vibration frequencies the motor can produce, typically measured in Hertz (Hz).
- Amplitude: The magnitude of the vibration, often expressed in millimeters (mm) or inches.
Performance Characteristics
Understanding the performance characteristics of vibration motors is crucial for achieving the desired vibration effects in various applications.
- Vibration Strength: The intensity of the vibration produced by the motor, influenced by factors such as motor speed, mass, and power input.
- Response Time: The time it takes for the motor to reach its desired vibration state after power is applied. Faster response times are preferred for applications requiring immediate feedback.
- Efficiency: The ratio of mechanical output power to electrical input power, indicating how effectively the motor converts electrical energy into vibration.
- Durability and Lifespan: The expected operational lifespan of the motor, affected by factors such as material quality, construction, and operating conditions.
Design Considerations and Challenges
Designing and integrating vibration motors into devices and systems involves several challenges and considerations to ensure optimal performance and reliability.
Heat Dissipation
Vibration motors generate heat during operation, which can affect their performance and lifespan. Effective heat dissipation methods, such as using heat sinks or conductive materials, are essential to prevent overheating.
Noise and Vibration Isolation
Unwanted noise and vibrations can interfere with the operation of devices and systems. Implementing noise and vibration isolation techniques, such as using damping materials or mounting systems, can minimize these issues.
Environmental Factors
Vibration motors may be exposed to various environmental factors, such as temperature extremes, moisture, and dust. Designing motors with protective features, such as seals or coatings, can enhance their resilience to environmental challenges.
Integration with Control Systems
Integrating vibration motors with control systems requires careful consideration of factors such as signal processing, power management, and feedback mechanisms. This ensures precise control and synchronization with other components in the system.
In conclusion, the technical aspects of vibration motors encompass a wide range of considerations, from construction and materials to performance characteristics and design challenges. Understanding these aspects is essential for selecting and implementing the right vibration motor for specific applications.
Applications of Industrial Vibration Motors
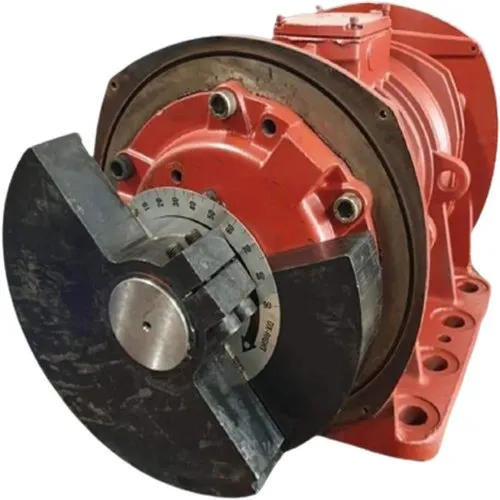
Industrial vibration motors play a crucial role in enhancing efficiency, productivity, and quality across various industries. This section explores the diverse applications of vibration motors in industrial settings.
Material Handling and Processing
Vibratory Conveyors
Vibration motors are integral components of vibratory conveyors, which are used to transport bulk materials efficiently. By generating controlled vibrations, these motors facilitate the smooth movement of materials, reducing friction and wear on conveyor surfaces.
- Efficient Transportation: Vibration motors enable the continuous flow of materials, minimizing downtime and increasing throughput.
- Versatile Applications: Vibratory conveyors are used in industries such as food processing, pharmaceuticals, and mining, where precise material handling is essential.
Screening and Sorting
In screening and sorting applications, vibration motors enhance the separation of materials based on size, weight, or other characteristics. They drive vibratory screens and separators, ensuring accurate and efficient sorting processes.
- Improved Accuracy: Vibration motors provide consistent and controlled vibrations, improving the accuracy of sorting and screening operations.
- Customizable Solutions: Adjustable frequency and amplitude settings allow for tailored solutions to meet specific sorting requirements.
Feeding and Dosing
Vibration motors are used in feeding and dosing applications to deliver precise amounts of materials to processing equipment. They drive vibratory feeders, ensuring accurate and consistent material flow.
- Precise Control: Vibration motors enable precise control over material flow rates, enhancing the efficiency of production processes.
- Reduced Waste: Accurate dosing reduces material waste, improving overall production efficiency and sustainability.
Machinery and Equipment Monitoring
Condition Monitoring
Vibration motors are employed in condition monitoring systems to assess the operational status of machinery and equipment. They provide feedback on vibration levels, helping to identify potential issues before they lead to failures.
- Early Fault Detection: Vibration analysis can detect mechanical faults, such as imbalances, misalignments, and bearing wear, allowing for timely maintenance and repairs.
- Improved Equipment Reliability: Regular monitoring of vibration levels enhances equipment reliability and longevity, reducing downtime and maintenance costs.
Predictive Maintenance
In predictive maintenance applications, vibration motors play a key role in monitoring the health of machinery and equipment. They provide real-time data on vibration patterns, enabling proactive maintenance strategies.
- Reduced Downtime: Predictive maintenance minimizes unexpected equipment failures, reducing downtime and production disruptions.
- Cost Savings: By addressing issues before they escalate, predictive maintenance reduces maintenance costs and extends equipment lifespan.
Mining and Quarrying
Material Transportation
In the mining and quarrying industry, vibration motors are used to transport bulk materials, such as ore and aggregates, over long distances. They drive vibratory feeders and conveyors, ensuring efficient material handling.
- High-Capacity Transportation: Vibration motors enable the transportation of large volumes of materials, increasing production efficiency.
- Durable Solutions: Designed for harsh environments, vibration motors provide reliable performance in demanding mining and quarrying applications.
Screening and Classification
Vibration motors are employed in screening and classification processes to separate materials based on size and composition. They drive vibratory screens and separators, ensuring accurate classification of materials.
- Accurate Classification: Vibration motors provide consistent and controlled vibrations, improving the accuracy of screening and classification operations.
- Adaptable Solutions: Adjustable frequency and amplitude settings allow for tailored solutions to meet specific classification requirements.
Construction Industry
Concrete Compaction
In the construction industry, vibration motors are used to compact concrete, ensuring uniform density and strength. They drive vibratory compactors and tampers, improving the quality of concrete structures.
- Improved Concrete Quality: Vibration motors enhance concrete compaction, reducing voids and increasing structural integrity.
- Efficient Construction Processes: Vibration motors streamline concrete compaction, reducing labor costs and construction time.
Soil Compaction
Vibration motors are employed in soil compaction applications to improve soil stability and load-bearing capacity. They drive vibratory rollers and compactors, enhancing the performance of construction equipment.
- Enhanced Soil Stability: Vibration motors improve soil compaction, increasing stability and load-bearing capacity.
- Versatile Applications: Used in road construction, foundation preparation, and landscaping, vibration motors provide adaptable solutions for various soil compaction needs.
Food and Beverage Industry
Food Processing
In the food and beverage industry, vibration motors are used to enhance food processing operations. They drive vibratory conveyors and feeders, ensuring efficient and hygienic material handling.
- Efficient Material Handling: Vibration motors enable the smooth and consistent flow of food products, reducing processing time and waste.
- Hygienic Solutions: Designed for easy cleaning and maintenance, vibration motors ensure hygienic food processing operations.
Packaging and Sorting
Vibration motors are employed in packaging and sorting applications to enhance efficiency and accuracy. They drive vibratory sorters and packers, ensuring precise material handling.
- Improved Sorting Accuracy: Vibration motors provide controlled vibrations, improving the accuracy of packaging and sorting operations.
- Customizable Solutions: Adjustable frequency and amplitude settings allow for tailored solutions to meet specific packaging and sorting requirements.
Pharmaceutical Industry
Tablet Coating
In the pharmaceutical industry, vibration motors are used to enhance tablet coating processes. They drive vibratory coaters, ensuring uniform coating application.
- Improved Coating Quality: Vibration motors ensure uniform coating thickness, improving the quality and efficacy of pharmaceutical products.
- Efficient Production Processes: Vibration motors streamline tablet coating, reducing production time and costs.
Capsule Filling
Vibration motors are employed in capsule filling applications to enhance accuracy and efficiency. They drive vibratory fillers, ensuring precise material dosing.
- Accurate Dosing: Vibration motors enable precise control over material flow rates, improving the accuracy of capsule filling operations.
- Reduced Waste: Accurate dosing reduces material waste, improving overall production efficiency and sustainability.
In conclusion, industrial vibration motors have diverse applications across various industries, enhancing efficiency, productivity, and quality. Their versatility and adaptability make them essential components in modern industrial processes.
Challenges and Solutions in Industrial Applications
Industrial vibration motors are subject to various challenges that can impact their performance and reliability. This section explores common challenges in industrial applications and potential solutions to address them.
Environmental Considerations
Harsh Operating Conditions
Industrial environments can expose vibration motors to harsh conditions, such as extreme temperatures, moisture, dust, and chemicals. These factors can affect motor performance and longevity.
Solutions:
- Protective Coatings: Apply protective coatings to motor components to resist corrosion and wear.
- Sealed Enclosures: Use sealed enclosures to protect internal components from environmental factors.
- Temperature Management: Implement cooling systems or heat sinks to manage temperature fluctuations.
Vibration-Induced Fatigue
Continuous vibration exposure can lead to fatigue and wear on motor components, reducing their lifespan and reliability.
Solutions:
- Durable Materials: Use high-strength materials and components designed to withstand vibration-induced fatigue.
- Regular Maintenance: Implement routine maintenance schedules to identify and address wear and fatigue early.
- Vibration Dampening: Incorporate vibration dampening techniques, such as shock absorbers or isolators, to reduce stress on components.
Maintenance and Longevity
Wear and Tear
Vibration motors are subject to wear and tear due to constant operation, which can impact performance and reliability.
Solutions:
- High-Quality Components: Use high-quality bearings, seals, and other components to minimize wear and tear.
- Lubrication: Implement proper lubrication practices to reduce friction and extend component lifespan.
- Preventive Maintenance: Conduct regular inspections and maintenance to identify and address potential issues before they escalate.
Unexpected Failures
Unexpected motor failures can lead to downtime and production disruptions, impacting productivity and profitability.
Solutions:
- Condition Monitoring: Implement condition monitoring systems to assess motor health and detect potential issues early.
- Predictive Maintenance: Use predictive maintenance strategies to anticipate and address issues before they result in failures.
- Redundancy: Incorporate redundancy in critical applications to minimize the impact of motor failures.
Noise and Vibration Control
Unwanted Noise
Vibration motors can generate unwanted noise, impacting the working environment and operator comfort.
Solutions:
- Noise Reduction Techniques: Implement noise reduction techniques, such as damping materials or enclosures, to minimize noise levels.
- Precision Engineering: Use precision-engineered components and designs to reduce mechanical noise.
- Isolation: Isolate motors from other components to prevent noise transmission.
Vibration Transmission
Uncontrolled vibration transmission can affect the performance of other equipment and systems, leading to inefficiencies and failures.
Solutions:
- Vibration Isolation: Use vibration isolation techniques, such as mounts or shock absorbers, to reduce vibration transmission.
- Balancing: Ensure motors and components are properly balanced to minimize vibration transmission.
- Control Systems: Implement advanced control systems to manage and adjust vibration characteristics.
In conclusion, industrial vibration motors face various challenges in harsh operating environments. By implementing appropriate solutions, such as protective measures, maintenance strategies, and noise control techniques, these challenges can be effectively addressed, ensuring reliable and efficient motor performance.
Future Trends and Innovations
As technology continues to evolve, industrial vibration motors are expected to undergo significant advancements, leading to new applications and improved performance. This section explores future trends and innovations in vibration motor technology.
Technological Advancements
- Miniaturization: Advances in manufacturing and materials will enable the development of smaller and more compact vibration motors, expanding their use in miniaturized devices and systems.
- Increased Efficiency: Innovations in motor design and materials will lead to more efficient vibration motors with lower power consumption and higher performance.
- Improved Control and Precision: Enhanced control algorithms and sensor integration will enable more precise and customizable vibration effects, improving user experience and application performance.
Integration with Smart Technologies
The integration of vibration motors with the Internet of Things (IoT) and smart technologies will open up new possibilities for applications and functionality.
- Smart Manufacturing: Vibration motors will play a key role in smart manufacturing processes, enabling real-time monitoring and control of production systems.
- Automated Systems: Integration with smart technologies will enhance the performance and efficiency of automated systems, improving productivity and quality.
Emerging Applications
- Advanced Robotics: Vibration motors will enhance the performance of advanced robotic systems, providing precise control and feedback for complex tasks.
- Augmented Reality (AR): Vibration motors will enhance AR experiences by providing tactile feedback for virtual interactions, improving immersion and realism.
- Next-Generation Industrial Equipment: Vibration motors will continue to enhance the performance of next-generation industrial equipment, such as 3D printers and advanced manufacturing systems.
In summary, the future of industrial vibration motors is promising, with advancements in technology and integration with smart systems leading to new applications and improved performance. These innovations will continue to enhance functionality and efficiency across various industries.
Conclusion
Industrial vibration motors are essential components in modern technology, providing crucial functionality and enhancing efficiency across a wide range of applications. This article has explored the various types of vibration motors, their technical aspects, and their diverse applications in industrial settings.
Recap of Key Points
- Types of Vibration Motors: We examined the different types of industrial vibration motors, each with unique characteristics and advantages.
- Technical Aspects: We discussed the construction, key specifications, performance characteristics, and design considerations associated with vibration motors, highlighting the factors that influence their selection and integration.
- Applications: We explored the diverse applications of vibration motors in industries such as material handling, mining, construction, and pharmaceuticals, showcasing their versatility and importance in modern industry.
- Challenges and Solutions: We identified common challenges in industrial applications and provided solutions to address them, ensuring reliable and efficient motor performance.
- Future Trends and Innovations: We examined the future trends and innovations in vibration motor technology, including miniaturization, increased efficiency, and integration with smart technologies.
Importance in Modern Industry
Industrial vibration motors play a crucial role in enhancing efficiency, productivity, and quality across various industries. Their ability to provide precise control, feedback, and motion makes them indispensable components in modern industrial processes.
- Material Handling: Vibration motors improve the efficiency of material handling operations, enhancing productivity and reducing costs.
- Machinery Monitoring: Vibration motors enable real-time monitoring and maintenance of machinery, improving equipment reliability and longevity.
- Diverse Applications: From mining to pharmaceuticals, vibration motors are used in a wide range of applications, highlighting their versatility and adaptability.
Future Outlook
As technology continues to advance, industrial vibration motors will play an increasingly important role in emerging applications and industries. Innovations in design, materials, and integration will lead to new possibilities and improved performance, enhancing functionality and efficiency across various sectors.
In conclusion, industrial vibration motors are vital components in modern technology, providing essential functionality and enhancing efficiency across a wide range of applications. Their versatility, adaptability, and potential for future advancements make them indispensable in the ever-evolving industrial landscape.
Introduction to Energy Consumption
Creating an informative article on energy consumption tips can help individuals and businesses save money, reduce their environmental impact, and improve overall energy efficiency. Below is a comprehensive 5000-word article suitable for a professional website, covering various aspects of energy consumption tips:
Energy consumption refers to the total amount of energy used by individuals, households, businesses, and industries. It encompasses various forms of energy, including electricity, natural gas, oil, and renewable energy sources. Understanding energy consumption is crucial for identifying areas where efficiency can be improved, leading to cost savings and environmental benefits.
Key aspects of energy consumption include:
- Types of Energy: Energy consumption can be categorized into different types, such as electrical, thermal, and mechanical energy, each serving specific purposes in daily activities and industrial processes.
- Energy Sources: Energy can be derived from various sources, including fossil fuels (coal, oil, natural gas) and renewable sources (solar, wind, geothermal, biomass, hydroelectric).
- Energy Demand: The demand for energy varies based on factors such as population, economic activity, climate, and technological advancements.
Importance of Energy Efficiency
Energy efficiency involves using less energy to perform the same tasks, reducing energy waste, and minimizing the environmental impact of energy use. It is a critical component of sustainable development and offers numerous benefits:
- Cost Savings: Improving energy efficiency can lead to significant reductions in energy bills, benefiting households, businesses, and industries.
- Environmental Benefits: Reducing energy consumption decreases greenhouse gas emissions and reduces reliance on fossil fuels, mitigating the impact of climate change.
- Resource Conservation: Energy efficiency helps conserve natural resources by reducing the demand for energy production and consumption.
- Energy Security: Efficient energy use reduces dependence on imported energy sources, enhancing energy security and resilience.
Benefits of Reducing Energy Consumption
Reducing energy consumption offers a wide range of benefits, including:
- Financial Savings: Lower energy bills result in financial savings for individuals, businesses, and governments, freeing up resources for other investments and initiatives.
- Environmental Protection: Reduced energy consumption leads to lower emissions of pollutants and greenhouse gases, contributing to cleaner air and a healthier environment.
- Improved Comfort and Quality of Life: Energy-efficient homes and buildings provide enhanced comfort, improved indoor air quality, and better thermal regulation.
- Economic Growth: Energy efficiency can drive economic growth by creating jobs in energy-efficient technologies, renewable energy, and sustainable practices.
Key takeaways:
- Essential for Sustainability: Energy consumption is a critical aspect of modern life, and improving energy efficiency is essential for achieving sustainable development.
- Diverse Benefits: Reducing energy consumption offers financial, environmental, and social benefits, making it a valuable goal for individuals, businesses, and governments.
Energy Consumption in Residential Settings
Improving energy efficiency in residential settings can lead to significant cost savings and environmental benefits. This section explores various strategies for reducing energy consumption in homes.
Heating and Cooling
Heating and cooling account for a significant portion of residential energy consumption. Implementing energy-efficient practices can lead to substantial savings:
- Programmable Thermostats: Use programmable thermostats to set specific temperature schedules, reducing energy use when heating or cooling is not needed.
- Example: Set the thermostat to lower the temperature during the winter when you’re asleep or away from home and raise it during the summer.
- Benefits: Reduces energy consumption by adjusting heating and cooling based on occupancy patterns.
- Regular Maintenance: Ensure heating and cooling systems are regularly maintained, including cleaning filters, checking ducts, and servicing equipment.
- Example: Schedule annual maintenance for HVAC systems to ensure they operate efficiently.
- Benefits: Increases the efficiency and lifespan of heating and cooling equipment.
- Insulation and Sealing: Improve insulation in walls, attics, and basements, and seal gaps and cracks to prevent air leaks.
- Example: Use weatherstripping to seal doors and windows, and add insulation to attics.
- Benefits: Reduces heat loss in winter and heat gain in summer, improving comfort and reducing energy use.
- Energy-Efficient HVAC Systems: Consider upgrading to energy-efficient heating and cooling systems, such as heat pumps and high-efficiency furnaces.
- Example: Replace an older furnace with an ENERGY STAR-certified model that offers improved efficiency.
- Benefits: Reduces energy consumption and provides consistent heating and cooling performance.
Lighting
Lighting is another significant contributor to residential energy consumption. Implementing energy-efficient lighting solutions can lead to substantial savings:
- LED Lighting: Replace incandescent and fluorescent bulbs with LED lighting, which uses less energy and lasts longer.
- Example: Install LED bulbs in all light fixtures, including lamps, overhead lights, and outdoor lighting.
- Benefits: Reduces energy consumption, lowers electricity bills, and reduces the need for frequent bulb replacements.
- Motion Sensors and Timers: Use motion sensors and timers to automatically turn off lights when not in use, reducing energy waste.
- Example: Install motion sensors in areas with infrequent use, such as hallways and closets, to automatically turn off lights.
- Benefits: Eliminates energy waste by ensuring lights are only on when needed.
- Natural Lighting: Maximize natural lighting by using windows, skylights, and light-colored interior finishes to reduce the need for artificial lighting.
- Example: Use sheer curtains to allow natural light to enter while maintaining privacy.
- Benefits: Reduces the need for artificial lighting, improving energy efficiency and enhancing indoor ambiance.
- Lighting Controls: Implement lighting controls, such as dimmers and smart switches, to adjust lighting levels based on needs and preferences.
- Example: Install dimmer switches in living areas to control lighting intensity and create desired atmospheres.
- Benefits: Allows for customized lighting levels, reducing energy consumption and enhancing comfort.
Appliances and Electronics
Appliances and electronics account for a significant portion of residential energy use. Implementing energy-efficient practices can lead to significant savings:
- ENERGY STAR Appliances: Choose ENERGY STAR-certified appliances, which meet strict energy efficiency standards and consume less energy.
- Example: Replace an old refrigerator with an ENERGY STAR-certified model that offers improved efficiency.
- Benefits: Reduces energy consumption and lowers electricity bills.
- Unplugging Devices: Unplug devices and chargers when not in use to eliminate standby power consumption, also known as “phantom load.”
- Example: Use power strips to easily turn off multiple devices and chargers when not in use.
- Benefits: Reduces energy waste and lowers electricity bills.
- Efficient Use of Appliances: Use appliances efficiently, such as running full loads in dishwashers and washing machines and using cold water for laundry.
- Example: Wash clothes in cold water and air dry when possible to save energy.
- Benefits: Reduces energy consumption and extends the lifespan of appliances.
- Smart Home Technology: Implement smart home technology to monitor and control appliance energy use, allowing for optimized energy management.
- Example: Use a smart thermostat to control heating and cooling remotely and adjust settings based on occupancy patterns.
- Benefits: Provides greater control over energy use, reducing waste and lowering energy bills.
Water Heating
Water heating is another significant contributor to residential energy consumption. Implementing energy-efficient practices can lead to substantial savings:
- Tankless Water Heaters: Consider installing tankless water heaters, which provide hot water on demand and eliminate standby energy loss.
- Example: Replace a traditional tank water heater with a tankless model that heats water as needed.
- Benefits: Reduces energy consumption and provides continuous hot water supply.
- Water Heater Insulation: Insulate water heater tanks and pipes to reduce heat loss and improve efficiency.
- Example: Install a water heater blanket and insulate hot water pipes to minimize heat loss.
- Benefits: Reduces energy consumption and improves water heating efficiency.
- Lower Water Heater Temperature: Set the water heater temperature to 120°F (49°C) to reduce energy use while maintaining comfort.
- Example: Adjust the thermostat on the water heater to maintain a temperature of 120°F.
- Benefits: Reduces energy consumption and lowers the risk of scalding.
- Efficient Water Use: Implement water-saving practices, such as shorter showers and using low-flow fixtures, to reduce hot water demand.
- Example: Install low-flow showerheads and faucets to reduce water use without sacrificing comfort.
- Benefits: Reduces hot water demand and lowers energy consumption.
Insulation and Sealing
Improving insulation and sealing in residential settings can lead to significant energy savings:
- Wall and Attic Insulation: Improve insulation in walls, attics, and basements to reduce heat loss and gain.
- Example: Add insulation to attics and walls to improve thermal performance and comfort.
- Benefits: Reduces heating and cooling energy consumption and improves indoor comfort.
- Window and Door Sealing: Seal gaps and cracks around windows and doors to prevent air leaks and improve energy efficiency.
- Example: Use weatherstripping and caulking to seal gaps around windows and doors.
- Benefits: Reduces heat loss and gain, improving energy efficiency and comfort.
- Energy-Efficient Windows: Consider upgrading to energy-efficient windows with low-emissivity (Low-E) coatings and double glazing.
- Example: Replace single-pane windows with ENERGY STAR-certified double-pane windows.
- Benefits: Reduces heat transfer and improves energy efficiency.
- Roof and Floor Insulation: Improve insulation in roofs and floors to reduce heat loss and gain, enhancing energy efficiency.
- Example: Install reflective roof coatings and floor insulation to improve thermal performance.
- Benefits: Reduces heating and cooling energy consumption and improves comfort.
In summary, improving energy efficiency in residential settings involves a combination of technology, practices, and behavioral changes. By implementing energy-efficient solutions for heating, cooling, lighting, appliances, and insulation, homeowners can achieve significant cost savings and environmental benefits.
Energy Consumption in Commercial and Industrial Settings
Improving energy efficiency in commercial and industrial settings can lead to significant cost savings, enhanced productivity, and environmental benefits. This section explores various strategies for reducing energy consumption in businesses and industries.
Energy Audits and Monitoring
Conducting energy audits and implementing energy monitoring systems are essential steps in identifying areas for improvement and optimizing energy use.
- Energy Audits: Conduct comprehensive energy audits to assess energy use, identify inefficiencies, and recommend improvements.
- Example: Hire a professional energy auditor to evaluate energy use in a commercial building and provide recommendations for efficiency improvements.
- Benefits: Identifies areas for improvement and provides actionable insights for reducing energy consumption.
- Energy Monitoring Systems: Implement energy monitoring systems to track energy use in real-time, identify trends, and optimize energy management.
- Example: Use energy monitoring software to track electricity use in an industrial facility and identify peak demand periods.
- Benefits: Provides real-time data for informed decision-making and energy optimization.
- Benchmarking: Compare energy use against industry benchmarks and standards to identify areas for improvement and set energy efficiency goals.
- Example: Use energy benchmarking tools to compare energy use in a commercial building against similar facilities.
- Benefits: Identifies opportunities for improvement and sets achievable energy efficiency goals.
- Continuous Improvement: Implement a continuous improvement process for energy management, regularly reviewing energy use and implementing efficiency measures.
- Example: Establish an energy management team to review energy use, set goals, and implement efficiency measures.
- Benefits: Ensures ongoing optimization of energy use and continuous improvement.
Lighting Solutions
Implementing energy-efficient lighting solutions can lead to substantial savings in commercial and industrial settings.
- LED Lighting: Replace traditional lighting with LED lighting, which uses less energy and lasts longer.
- Example: Install LED lighting in offices, warehouses, and manufacturing facilities to reduce energy consumption.
- Benefits: Reduces energy consumption, lowers electricity bills, and reduces maintenance costs.
- Daylighting: Maximize natural daylighting through the use of windows, skylights, and light tubes, reducing the need for artificial lighting.
- Example: Install skylights in warehouses and manufacturing facilities to maximize natural lighting.
- Benefits: Reduces the need for artificial lighting, improving energy efficiency and enhancing indoor ambiance.
- Lighting Controls: Implement lighting controls, such as motion sensors, timers, and dimmers, to optimize lighting use based on occupancy and needs.
- Example: Install motion sensors in restrooms and storage areas to automatically turn off lights when not in use.
- Benefits: Eliminates energy waste and reduces electricity bills.
- Task Lighting: Use task lighting in workspaces to provide focused illumination, reducing the need for overhead lighting.
- Example: Install task lighting at individual workstations to provide focused illumination for tasks.
- Benefits: Reduces overall lighting energy consumption and enhances comfort.
HVAC Systems
Heating, ventilation, and air conditioning (HVAC) systems are major contributors to energy consumption in commercial and industrial settings. Implementing energy-efficient HVAC solutions can lead to substantial savings:
- Regular Maintenance: Ensure HVAC systems are regularly maintained, including cleaning filters, checking ducts, and servicing equipment.
- Example: Schedule annual maintenance for HVAC systems to ensure they operate efficiently.
- Benefits: Increases the efficiency and lifespan of HVAC equipment.
- Energy-Efficient HVAC Systems: Upgrade to energy-efficient HVAC systems, such as high-efficiency heat pumps, chillers, and boilers.
- Example: Replace an older HVAC system with an ENERGY STAR-certified model that offers improved efficiency.
- Benefits: Reduces energy consumption and provides consistent heating and cooling performance.
- Zoning Systems: Implement zoning systems to control heating and cooling in specific areas, reducing energy use in unoccupied or low-traffic areas.
- Example: Use zoning controls to manage temperature settings in different areas of a building based on occupancy patterns.
- Benefits: Reduces energy consumption and enhances comfort.
- Building Automation Systems: Use building automation systems to monitor and control HVAC systems, optimizing energy use based on occupancy and needs.
- Example: Implement a building automation system to adjust HVAC settings based on occupancy patterns and external conditions.
- Benefits: Provides greater control over energy use, reducing waste and lowering energy bills.
Industrial Equipment and Machinery
Improving the energy efficiency of industrial equipment and machinery can lead to significant cost savings and environmental benefits.
- Variable Frequency Drives (VFDs): Install variable frequency drives on motors to optimize speed and reduce energy consumption.
- Example: Install VFDs on pumps and fans to adjust motor speed based on demand.
- Benefits: Reduces energy consumption and extends the lifespan of motors.
- Energy-Efficient Motors: Upgrade to energy-efficient motors that consume less energy and provide improved performance.
- Example: Replace older motors with high-efficiency models that meet or exceed industry standards.
- Benefits: Reduces energy consumption and lowers maintenance costs.
- Compressed Air Systems: Optimize compressed air systems to reduce energy consumption and improve efficiency.
- Example: Conduct regular maintenance, repair leaks, and adjust pressure settings in compressed air systems.
- Benefits: Reduces energy waste and improves system performance.
- Efficient Use of Equipment: Implement practices to optimize the use of industrial equipment, such as scheduling maintenance during off-peak hours and reducing idle time.
- Example: Schedule equipment maintenance during off-peak hours to reduce energy demand.
- Benefits: Reduces energy consumption and enhances equipment performance.
Office Equipment and Electronics
Improving the energy efficiency of office equipment and electronics can lead to significant savings in commercial settings.
- ENERGY STAR Office Equipment: Choose ENERGY STAR-certified office equipment, which meets strict energy efficiency standards and consumes less energy.
- Example: Replace older printers and copiers with ENERGY STAR-certified models that offer improved efficiency.
- Benefits: Reduces energy consumption and lowers electricity bills.
- Power Management Features: Use power management features on computers, monitors, and other electronics to reduce energy consumption during periods of inactivity.
- Example: Enable sleep mode on computers and monitors to reduce energy use during periods of inactivity.
- Benefits: Reduces energy waste and extends the lifespan of electronics.
- Unplugging Devices: Unplug devices and chargers when not in use to eliminate standby power consumption, also known as “phantom load.”
- Example: Use power strips to easily turn off multiple devices and chargers when not in use.
- Benefits: Reduces energy waste and lowers electricity bills.
- Efficient Use of Equipment: Implement practices to optimize the use of office equipment, such as using digital documents instead of printing and turning off equipment when not in use.
- Example: Use digital documents and cloud storage to reduce paper use and energy consumption.
- Benefits: Reduces energy consumption and lowers operating costs.
In summary, improving energy efficiency in commercial and industrial settings involves a combination of technology, practices, and behavioral changes. By implementing energy-efficient solutions for lighting, HVAC, equipment, and electronics, businesses can achieve significant cost savings and environmental benefits.
Renewable Energy Solutions
Incorporating renewable energy solutions can significantly reduce energy consumption, lower carbon emissions, and promote sustainability. This section explores various renewable energy solutions and their benefits.
Solar Power
Solar power is a clean and renewable energy source that harnesses the sun’s energy to generate electricity and heat. It is a versatile solution that can be used in residential, commercial, and industrial settings.
Solar Photovoltaic (PV) Systems
Solar PV systems convert sunlight into electricity using solar panels. They can be installed on rooftops, ground-mounted systems, or integrated into building designs.
Benefits of Solar PV Systems:
- Clean Energy: Solar PV systems produce electricity without emitting greenhouse gases or pollutants.
- Cost Savings: Solar PV systems can reduce or eliminate electricity bills, leading to significant cost savings over time.
- Energy Independence: Solar PV systems provide energy independence by reducing reliance on grid electricity.
- Scalability: Solar PV systems can be scaled to meet the energy needs of various applications, from small residential systems to large commercial installations.
Solar Thermal Systems
Solar thermal systems use sunlight to heat water or air for residential, commercial, and industrial applications. They are commonly used for water heating, space heating, and industrial processes.
Benefits of Solar Thermal Systems:
- Energy Efficiency: Solar thermal systems are highly efficient, converting a large portion of sunlight into usable heat.
- Cost Savings: Solar thermal systems can reduce or eliminate heating bills, leading to significant cost savings over time.
- Environmental Benefits: Solar thermal systems produce heat without emitting greenhouse gases or pollutants.
- Versatility: Solar thermal systems can be used for various applications, including domestic hot water, space heating, and industrial processes.
Wind Energy
Wind energy is a clean and renewable energy source that harnesses the power of the wind to generate electricity. It is a cost-effective solution for reducing energy consumption and promoting sustainability.
Wind Turbines
Wind turbines convert the kinetic energy of the wind into electricity. They can be installed in various settings, including onshore and offshore wind farms.
Benefits of Wind Energy:
- Clean Energy: Wind turbines produce electricity without emitting greenhouse gases or pollutants.
- Cost-Effective: Wind energy is one of the most cost-effective renewable energy sources, offering competitive electricity prices.
- Energy Independence: Wind energy provides energy independence by reducing reliance on fossil fuels and grid electricity.
- Scalability: Wind energy can be scaled to meet the energy needs of various applications, from small residential systems to large utility-scale installations.
Geothermal Heating and Cooling
Geothermal heating and cooling systems use the stable temperature of the earth to provide efficient heating and cooling for residential, commercial, and industrial applications.
Ground Source Heat Pumps (GSHPs)
Ground source heat pumps use the earth’s temperature to transfer heat to or from a building, providing efficient heating and cooling.
Benefits of Geothermal Heating and Cooling:
- Energy Efficiency: Geothermal systems are highly efficient, reducing energy consumption and operating costs.
- Environmental Benefits: Geothermal systems produce heating and cooling without emitting greenhouse gases or pollutants.
- Versatility: Geothermal systems can be used for various applications, including residential heating and cooling, commercial HVAC systems, and industrial processes.
- Longevity: Geothermal systems have a long lifespan, providing reliable performance for decades.
Biomass Energy
Biomass energy is a renewable energy source that uses organic materials, such as wood, agricultural residues, and waste, to generate heat and electricity.
Biomass Boilers
Biomass boilers use organic materials as fuel to produce heat for residential, commercial, and industrial applications.
Benefits of Biomass Energy:
- Renewable Resource: Biomass energy uses renewable organic materials, reducing reliance on fossil fuels.
- Carbon Neutral: Biomass energy is considered carbon neutral, as the carbon dioxide released during combustion is offset by the carbon dioxide absorbed by plants during growth.
- Waste Reduction: Biomass energy can use waste materials as fuel, reducing waste and promoting sustainability.
- Versatility: Biomass energy can be used for various applications, including residential heating, industrial processes, and electricity generation.
Hydroelectric Power
Hydroelectric power is a renewable energy source that uses the flow of water to generate electricity. It is a reliable and cost-effective solution for reducing energy consumption and promoting sustainability.
Hydroelectric Dams
Hydroelectric dams use the flow of water from rivers or reservoirs to generate electricity. They are commonly used for large-scale electricity generation.
Benefits of Hydroelectric Power:
- Clean Energy: Hydroelectric power produces electricity without emitting greenhouse gases or pollutants.
- Reliable Source: Hydroelectric power is a reliable and consistent source of electricity, providing stable power generation.
- Cost-Effective: Hydroelectric power offers competitive electricity prices, making it one of the most cost-effective renewable energy sources.
- Energy Independence: Hydroelectric power provides energy independence by reducing reliance on fossil fuels and grid electricity.
In summary, incorporating renewable energy solutions can significantly reduce energy consumption, lower carbon emissions, and promote sustainability. By utilizing solar power, wind energy, geothermal heating and cooling, biomass energy, and hydroelectric power, individuals and businesses can achieve significant environmental and economic benefits.
Smart Technology and Energy Management
Smart technology and energy management solutions can significantly improve energy efficiency, reduce energy consumption, and enhance control over energy use. This section explores various smart technologies and their benefits.
Smart Meters
Smart meters are advanced metering devices that provide real-time data on energy use, allowing for better monitoring and control of energy consumption.
Benefits of Smart Meters:
- Real-Time Data: Smart meters provide real-time data on energy use, allowing for informed decision-making and energy optimization.
- Energy Savings: Smart meters enable consumers to identify energy waste and implement efficiency measures, leading to cost savings.
- Enhanced Control: Smart meters provide greater control over energy use, allowing consumers to adjust consumption based on real-time data.
- Demand Response: Smart meters facilitate demand response programs, allowing utilities to manage peak demand and reduce energy costs.
Home Automation Systems
Home automation systems integrate smart devices and appliances, allowing for centralized control and monitoring of energy use.
Benefits of Home Automation Systems:
- Convenience: Home automation systems provide centralized control over lighting, heating, cooling, and appliances, enhancing convenience and comfort.
- Energy Efficiency: Home automation systems optimize energy use by adjusting settings based on occupancy patterns and preferences.
- Remote Monitoring: Home automation systems provide remote monitoring and control, allowing consumers to manage energy use from anywhere.
- Security: Home automation systems enhance security by integrating smart locks, cameras, and alarms, providing peace of mind.
Energy Management Software
Energy management software provides tools for monitoring, analyzing, and optimizing energy use in residential, commercial, and industrial settings.
Benefits of Energy Management Software:
- Data Analysis: Energy management software provides data analysis tools for identifying trends, inefficiencies, and opportunities for improvement.
- Customizable Solutions: Energy management software offers customizable solutions to meet specific energy management needs and goals.
- Real-Time Monitoring: Energy management software provides real-time monitoring and alerts, enabling proactive energy management.
- Cost Savings: Energy management software helps identify and implement efficiency measures, leading to significant cost savings.
IoT Devices for Energy Efficiency
Internet of Things (IoT) devices provide advanced monitoring and control of energy use, enhancing efficiency and sustainability.
Benefits of IoT Devices:
- Enhanced Monitoring: IoT devices provide real-time data on energy use, enabling informed decision-making and optimization.
- Remote Control: IoT devices provide remote control and monitoring, allowing consumers to manage energy use from anywhere.
- Integration: IoT devices integrate with smart home systems, enhancing convenience and control.
- Energy Savings: IoT devices enable consumers to identify and eliminate energy waste, leading to significant cost savings.
Demand Response Systems
Demand response systems enable utilities and consumers to manage energy use during peak demand periods, reducing energy costs and improving grid reliability.
Benefits of Demand Response Systems:
- Cost Savings: Demand response systems reduce energy costs by shifting consumption to off-peak periods.
- Grid Reliability: Demand response systems improve grid reliability by reducing peak demand and preventing outages.
- Environmental Benefits: Demand response systems reduce the need for additional power generation, lowering emissions and environmental impact.
- Enhanced Control: Demand response systems provide consumers with greater control over energy use, allowing for more efficient consumption.
In summary, smart technology and energy management solutions provide advanced tools for improving energy efficiency, reducing energy consumption, and enhancing control over energy use. By implementing smart meters, home automation systems, energy management software, IoT devices, and demand response systems, individuals and businesses can achieve significant cost savings and environmental benefits.
Behavioral Changes for Energy Savings
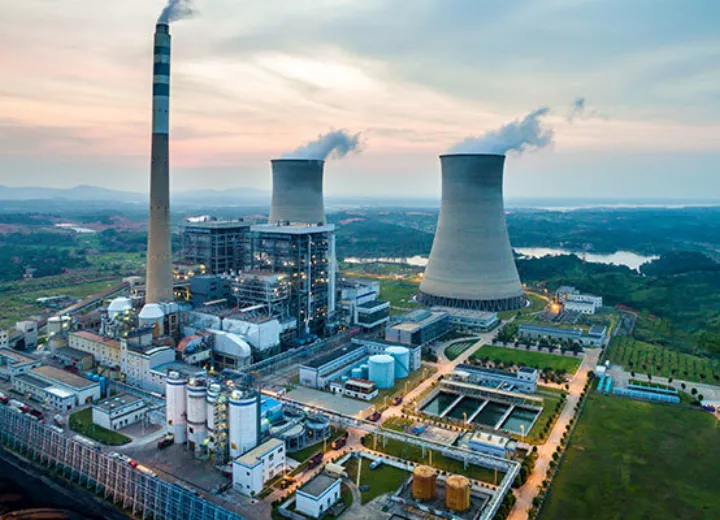
Behavioral changes can have a significant impact on energy consumption, leading to cost savings and environmental benefits. This section explores various behavioral changes that can reduce energy use.
Energy-Saving Habits
Adopting energy-saving habits can lead to significant reductions in energy consumption:
- Turning Off Lights: Turn off lights when leaving a room to reduce energy waste.
- Example: Develop a habit of turning off lights when exiting a room, even for short periods.
- Benefits: Reduces energy consumption and lowers electricity bills.
- Unplugging Devices: Unplug devices and chargers when not in use to eliminate standby power consumption, also known as “phantom load.”
- Example: Use power strips to easily turn off multiple devices and chargers when not in use.
- Benefits: Reduces energy waste and lowers electricity bills.
- Adjusting Thermostat Settings: Adjust thermostat settings based on occupancy patterns and preferences to reduce energy use.
- Example: Set the thermostat to lower temperatures during the winter and higher temperatures during the summer when the home is unoccupied.
- Benefits: Reduces energy consumption and lowers heating and cooling bills.
- Using Energy-Efficient Transportation: Choose energy-efficient transportation options, such as walking, biking, carpooling, or using public transit.
- Example: Use public transit for commuting to work instead of driving a personal vehicle.
- Benefits: Reduces energy consumption and lowers transportation costs.
Encouraging Energy Awareness
Promoting energy awareness can lead to increased energy efficiency and sustainability:
- Educating Employees: Educate employees about energy efficiency and encourage energy-saving practices in the workplace.
- Example: Conduct energy efficiency workshops and training sessions for employees.
- Benefits: Increases energy awareness and promotes energy-saving practices.
- Setting Energy Goals: Set energy efficiency goals and track progress to encourage energy-saving practices.
- Example: Set a goal to reduce energy consumption by a specific percentage over a set period and track progress regularly.
- Benefits: Encourages energy-saving practices and promotes continuous improvement.
- Incentivizing Energy Efficiency: Provide incentives for energy-saving practices, such as rewards for meeting energy efficiency goals.
- Example: Offer rewards or recognition for employees or departments that achieve energy efficiency goals.
- Benefits: Motivates individuals and teams to adopt energy-saving practices.
- Promoting Energy Conservation: Promote energy conservation through awareness campaigns, workshops, and educational materials.
- Example: Develop educational materials and campaigns to promote energy conservation in the community.
- Benefits: Raises awareness about energy efficiency and encourages energy-saving practices.
Reducing Energy Waste
Reducing energy waste can lead to significant cost savings and environmental benefits:
- Fixing Leaks: Fix leaks in pipes, faucets, and ducts to prevent energy waste.
- Example: Regularly inspect and repair leaks in plumbing and HVAC systems.
- Benefits: Reduces energy waste and lowers energy bills.
- Optimizing Equipment Use: Use equipment efficiently, such as running full loads in dishwashers and washing machines and using cold water for laundry.
- Example: Wash clothes in cold water and air dry when possible to save energy.
- Benefits: Reduces energy consumption and extends the lifespan of equipment.
- Regular Maintenance: Ensure equipment and systems are regularly maintained to optimize performance and efficiency.
- Example: Schedule regular maintenance for HVAC systems, appliances, and vehicles.
- Benefits: Improves energy efficiency and extends the lifespan of equipment.
- Efficient Use of Resources: Implement practices to optimize the use of resources, such as using digital documents instead of printing and turning off equipment when not in use.
- Example: Use digital documents and cloud storage to reduce paper use and energy consumption.
- Benefits: Reduces energy consumption and lowers operating costs.
In summary, behavioral changes can have a significant impact on energy consumption, leading to cost savings and environmental benefits. By adopting energy-saving habits, promoting energy awareness, and reducing energy waste, individuals and businesses can achieve significant energy efficiency and sustainability.
Conclusion
Energy consumption is a critical aspect of modern life, and improving energy efficiency is essential for achieving sustainable development. This article has explored various strategies for reducing energy consumption in residential, commercial, and industrial settings.
Recap of Key Points
- Residential Energy Efficiency: We explored energy-efficient solutions for heating, cooling, lighting, appliances, and insulation, highlighting the importance of technology, practices, and behavioral changes.
- Commercial and Industrial Energy Efficiency: We discussed energy-efficient solutions for lighting, HVAC, equipment, and electronics, emphasizing the importance of energy audits, monitoring, and management.
- Renewable Energy Solutions: We examined the benefits of incorporating renewable energy solutions, such as solar power, wind energy, geothermal heating and cooling, biomass energy, and hydroelectric power.
- Smart Technology and Energy Management: We explored the benefits of smart technology and energy management solutions, including smart meters, home automation systems, energy management software, IoT devices, and demand response systems.
- Behavioral Changes for Energy Savings: We discussed the importance of adopting energy-saving habits, promoting energy awareness, and reducing energy waste to achieve significant energy efficiency and sustainability.
The Role of Individuals and Businesses
Individuals and businesses play a crucial role in reducing energy consumption and promoting sustainability. By implementing energy-efficient solutions and adopting energy-saving practices, individuals and businesses can achieve significant cost savings, reduce environmental impact, and contribute to a more sustainable future.
Key actions for individuals and businesses:
- Invest in Energy Efficiency: Invest in energy-efficient technologies and solutions to reduce energy consumption and lower operating costs.
- Promote Energy Awareness: Promote energy awareness and education to encourage energy-saving practices and behaviors.
- Set Energy Efficiency Goals: Set energy efficiency goals and track progress to drive continuous improvement and sustainability.
Future Outlook
As technology continues to evolve, new opportunities for improving energy efficiency and sustainability will emerge. Advancements in renewable energy, smart technology, and energy management will drive further improvements in energy efficiency and provide new solutions for reducing energy consumption.
Future trends in energy efficiency:
- Renewable Energy Integration: The integration of renewable energy solutions will continue to expand, providing clean and sustainable energy for various applications.
- Smart Technology Advancements: Advancements in smart technology and energy management will provide new tools and solutions for optimizing energy use and reducing energy waste.
- Sustainable Practices: The adoption of sustainable practices and behaviors will continue to grow, driving further improvements in energy efficiency and sustainability.
In conclusion, energy consumption is a critical aspect of modern life, and improving energy efficiency is essential for achieving sustainable development. By implementing energy-efficient solutions, adopting energy-saving practices, and promoting sustainability, individuals and businesses can achieve significant energy efficiency and environmental benefits, contributing to a more sustainable future.
EMS Power Machines
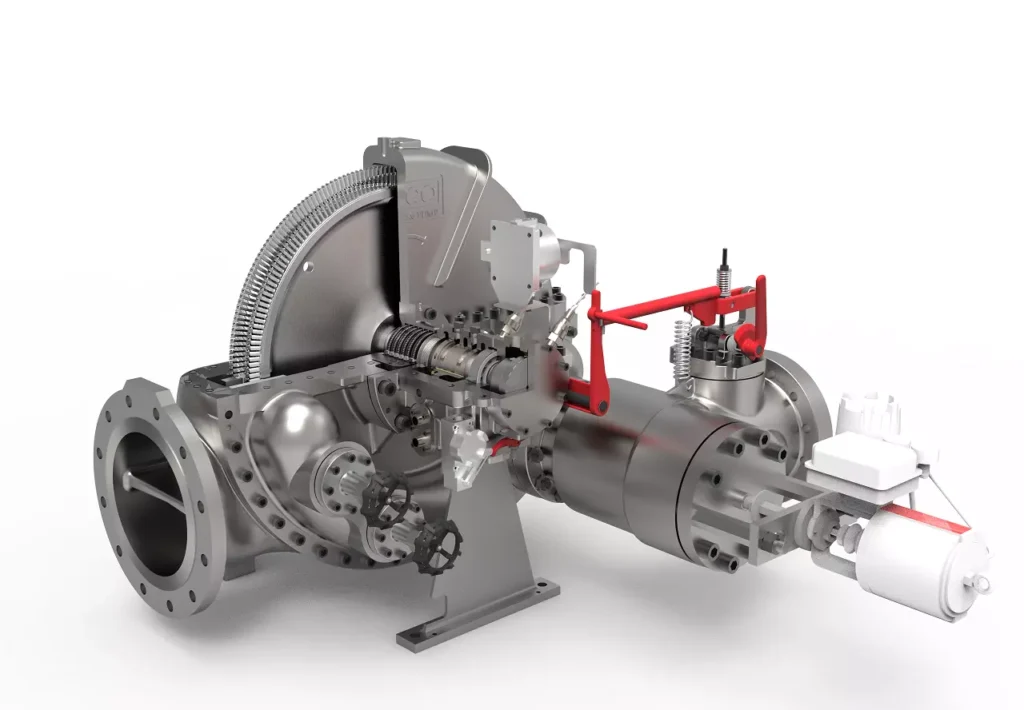
We design, manufacture and assembly Power Machines such as – diesel generators, electric motors, vibration motors, pumps, steam engines and steam turbines
EMS Power Machines is a global power engineering company, one of the five world leaders in the industry in terms of installed equipment. The companies included in the company have been operating in the energy market for more than 60 years.
EMS Power Machines manufactures steam turbines, gas turbines, hydroelectric turbines, generators, and other power equipment for thermal, nuclear, and hydroelectric power plants, as well as for various industries, transport, and marine energy.
EMS Power Machines is a major player in the global power industry, and its equipment is used in power plants all over the world. The company has a strong track record of innovation, and it is constantly developing new and improved technologies.
Here are some examples of Power Machines’ products and services:
- Steam turbines for thermal and nuclear power plants
- Gas turbines for combined cycle power plants and industrial applications
- Hydroelectric turbines for hydroelectric power plants
- Generators for all types of power plants
- Boilers for thermal power plants
- Condensers for thermal power plants
- Reheaters for thermal power plants
- Air preheaters for thermal power plants
- Feedwater pumps for thermal power plants
- Control systems for power plants
- Maintenance and repair services for power plants
EMS Power Machines is committed to providing its customers with high-quality products and services. The company has a strong reputation for reliability and innovation. Power Machines is a leading provider of power equipment and services, and it plays a vital role in the global power industry.
EMS Power Machines, which began in 1961 as a small factory of electric motors, has become a leading global supplier of electronic products for different segments. The search for excellence has resulted in the diversification of the business, adding to the electric motors products which provide from power generation to more efficient means of use.