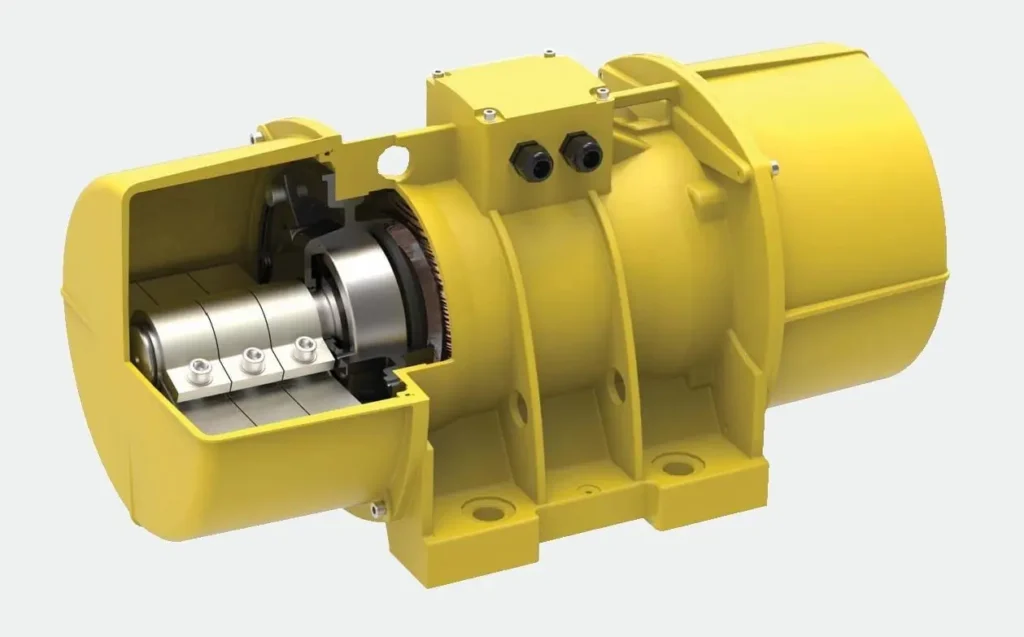
Industrial vibration motor buy from the manufacturer. Free consultation with high quality & low price. Atex Vibrator motor types for your production.
Industrial vibration plays a pivotal role in various sectors, influencing the performance and reliability of machinery and equipment. Vibration analysis, the cornerstone of understanding mechanical oscillations, is essential for optimizing processes and ensuring the longevity of industrial systems.
Vibratory equipment, ranging from conveyors to sieves and screens, harnesses controlled vibrations for material handling and processing. In this context, vibration monitoring emerges as a critical practice, involving the use of sophisticated sensors to track and analyze vibrations. The insights gained from vibration monitoring enable proactive maintenance, minimizing the risk of unexpected breakdowns and downtime.
Vibration control strategies are implemented to manage and mitigate the impact of oscillations on industrial equipment. This involves the use of technologies and materials that can dampen or isolate vibrations, safeguarding both machinery and structures from potential damage. Vibration sensors, equipped with advanced technology, serve as the frontline tools for real-time monitoring, providing valuable data for analysis.
The realm of mechanical vibration encompasses a spectrum of frequencies, and vibration frequency becomes a key parameter in tailoring equipment for specific tasks. Vibration testing further validates the robustness of industrial components and systems, subjecting them to controlled vibrations to simulate real-world conditions. This process aids in identifying weaknesses and improving the overall durability of materials and structures.
Simultaneously, the concept of vibration isolation becomes crucial, particularly in settings where vibrations can adversely affect adjacent structures or sensitive equipment. Vibration isolation techniques involve the use of isolators or damping materials to minimize the transmission of vibrations.
Vibration frequency, a measure of the number of oscillations per unit of time, is a fundamental parameter influencing the behavior of industrial vibrations. Understanding and controlling vibration frequency is integral to designing and maintaining equipment that meets performance standards.
Vibration analysis, equipped with advanced software tools, enables engineers to delve into the intricate details of oscillatory behavior. This analysis aids in diagnosing issues, predicting potential failures, and optimizing machinery for peak performance. In the broader context of industrial automation, vibrating machinery, driven by vibration motors, contributes to tasks such as material sorting, conveying, and processing.
In summary, the intricate world of industrial vibration involves a comprehensive understanding of vibration analysis, monitoring, control, and testing. This knowledge is crucial for maintaining the efficiency and reliability of industrial systems across diverse applications.
Industrial Vibration Motor
Industrial vibration motors play a crucial role in various applications, providing controlled mechanical oscillations for a wide range of industrial processes. These electric motors generate mechanical vibrations that find applications in fields such as manufacturing, automation, and material handling. The two main types, rotary and linear vibration motors, are employed based on specific requirements.
Rotary vibration motors utilize eccentric rotating masses (ERMs) to create vibrations, while linear vibration motors produce linear vibrations. The design includes components like brushed or brushless DC motors, contributing to the efficiency and reliability of the system. Vibration intensity, frequency, and amplitude are key parameters carefully considered in the design and selection process.
In industrial settings, vibration motors are integrated into vibrating equipment such as conveyors, screens, and feeders, ensuring the smooth flow of materials in manufacturing processes. These motors are also crucial in applications like vibrating tables for concrete consolidation, ensuring uniformity and quality. The coin vibration motor, a compact variant, is commonly used in devices requiring haptic feedback.
Vibration analysis and monitoring play a vital role in maintaining optimal performance and identifying potential issues. Vibration sensors and analysis software help in assessing the health of the system, enabling preventive maintenance and minimizing downtime. Industrial automation benefits from vibration motors in tasks such as conveying, sorting, and compacting materials.
Overall, the diverse applications of industrial vibration motors underscore their significance in enhancing efficiency, precision, and reliability across various industrial processes.
Vibratory equipment stands as a linchpin in modern industrial processes, embodying the principles of controlled mechanical oscillations to facilitate material handling and processing. This diverse category encompasses a spectrum of machinery, from conveyors to sieves and screens, each harnessing the power of controlled vibrations to optimize the movement and separation of materials in various manufacturing contexts.
Vibration monitoring, an integral aspect of industrial operations, employs sophisticated sensors to capture and analyze vibrations in real-time. This proactive approach to maintenance provides crucial insights into the health of machinery, allowing for the identification of potential issues before they escalate into costly breakdowns. The utilization of vibration monitoring technologies ensures a predictive and preventative maintenance strategy, minimizing downtime and maximizing the efficiency of industrial processes.
Beyond monitoring, the concept of vibration control takes center stage in the pursuit of stable and reliable industrial systems. Employing advanced technologies and materials, engineers strive to mitigate the impact of vibrations on machinery and structures. Vibration control strategies may involve the use of isolators or damping materials, effectively minimizing the transmission of oscillations and safeguarding both equipment and surrounding infrastructure.
Vibration sensors, equipped with cutting-edge technology, act as frontline guardians, translating mechanical oscillations into actionable data for analysis. This data-driven approach enables engineers to gain a deeper understanding of the behavior of industrial vibrations, facilitating informed decision-making in terms of system optimization and maintenance.
In the multifaceted landscape of mechanical vibration, the frequency of oscillations emerges as a critical parameter. Tailoring equipment to specific tasks requires a nuanced understanding of vibration frequency, ensuring that industrial systems operate at optimal levels. Vibration testing takes this understanding to the next level by subjecting materials and components to controlled vibrations, simulating real-world conditions and validating their robustness.
Vibration isolation, another vital aspect, becomes particularly crucial in environments where the impact of vibrations on adjacent structures or sensitive equipment must be minimized. Employing techniques such as isolators and damping materials, engineers aim to create a buffer that shields surrounding elements from the potentially detrimental effects of mechanical oscillations.
The intricate dance of vibration frequency, testing, and isolation converges in the realm of vibration analysis. Advanced software tools empower engineers to delve into the minutiae of oscillatory behavior, offering insights into the root causes of issues, predicting potential failures, and guiding the optimization of machinery for peak performance.
In the context of industrial automation, vibrating machinery takes center stage, often driven by specialized vibration motors. These components play a crucial role in tasks such as material sorting, conveying, and processing, contributing to the seamless flow and efficiency of manufacturing processes.
In summary, the second set of keywords delves deeper into the intricacies of industrial vibration, covering the realms of vibration monitoring, control, frequency, testing, isolation, and analysis. These aspects collectively contribute to the reliability, efficiency, and longevity of industrial systems in an ever-evolving technological landscape.
Industrial Vibration Motor
Concrete vibrating motors represent a critical facet in the intricate tapestry of industrial vibration, particularly in the domain of construction and material processing. These motors serve as the powerhouse behind the process of concrete consolidation, a fundamental step in ensuring the structural integrity and durability of concrete structures. As construction materials are poured into molds, concrete vibrating motors come to life, generating controlled vibrations that eliminate air bubbles and settle the mixture uniformly.
The reliability and precision of vibration shakers in various industrial scenarios hinge on the robust performance of vibration motors. These shakers, employed for tasks ranging from material separation to quality testing, rely on the orchestrated oscillations induced by vibration motors. In material separation processes, the vibrations generated by these motors facilitate the stratification of particles based on size, a crucial step in refining raw materials for diverse industrial applications.
Industrial applications demanding the precise and reliable movement of materials find a steadfast ally in vibration feeder systems, where vibration motors play a central role. These systems ensure a controlled and uniform flow of materials, contributing to the efficiency of manufacturing processes across a myriad of industries. The meticulous orchestration of vibrations by these motors becomes essential in scenarios where precision and consistency are paramount.
The concept of vibration velocity becomes a pivotal parameter in understanding the speed and intensity of the vibrations generated by motors. This velocity, intricately linked to the performance of vibration motors, influences the effectiveness of equipment in various applications. Industries dealing with the handling and processing of bulk materials often leverage vibrating tables, where vibration motors settle and compact materials, enhancing their quality and uniformity.
The importance of vibration exciter mechanisms, found in certain industrial systems, cannot be overstated. These exciters, driven by vibration motors, are responsible for generating precisely controlled vibrations. The applications range from industrial processes that necessitate specific vibratory patterns to the testing and calibration of equipment.
In the context of vibration-induced fatigue, the endurance and resilience of materials and structures under continuous vibrations are scrutinized. Vibration spectrum analysis, a sophisticated technique, aids in deciphering the intricate patterns and frequencies of vibrations, providing insights into potential fatigue issues. The interpretation of vibration spectra becomes an art and science, guiding engineers in optimizing materials and structures for sustained performance.
The integration of industrial vibration motors into various processes and systems contributes to the reliability and efficiency of industrial operations. Whether it’s the meticulous consolidation of concrete, the precise sorting of materials through vibration shakers, or the controlled movement of bulk materials using vibration feeder systems, these motors underscore their versatility across diverse industrial landscapes.
When looking to buy an industrial vibration motor, there are several factors to consider to ensure you choose the right motor for your specific application. Here are some key points to keep in mind:
- Power and Performance: Determine the power requirements and performance specifications for your application. Consider factors such as vibration amplitude, frequency range, and maximum load capacity. This will help you select a motor that can meet your specific vibration needs.
- Motor Type: There are various types of industrial vibration motors available, including rotary eccentric motors, linear vibration motors, and electromagnetic vibrators. Each type has its own advantages and applications. Choose the motor type that is most suitable for your specific requirements.
- Mounting Options: Consider the mounting options available for the vibration motor. Different motors may have different mounting configurations, such as flange mounts, base mounts, or bracket mounts. Ensure that the motor’s mounting style aligns with your application’s needs.
- Voltage and Frequency: Check the voltage and frequency requirements of the vibration motor to ensure compatibility with your power supply. Industrial vibration motors are typically available in different voltage and frequency options to accommodate various electrical systems.
- Enclosure and Protection: Evaluate the environmental conditions in which the motor will operate. Determine if the motor needs to be dustproof, waterproof, or resistant to specific elements or chemicals. Look for motors with appropriate IP (Ingress Protection) ratings to ensure they can withstand the operating environment.
- Quality and Reliability: Consider the reputation and reliability of the motor manufacturer or supplier. Look for motors from reputable brands known for producing high-quality and durable industrial vibration motors. Check customer reviews and ratings to gauge the reliability and performance of the motor.
- Customization Options: If your application requires specific customization or modifications to the vibration motor, check if the manufacturer offers customization services. This may include options such as special mounting arrangements, different cable lengths, or specific motor specifications tailored to your needs.
- Price and Warranty: Compare prices from different suppliers to ensure you are getting a competitive price for the motor. Additionally, check the warranty terms and conditions provided by the manufacturer to ensure proper support in case of any defects or issues.
- Technical Support: Consider the availability of technical support from the manufacturer or supplier. It can be helpful to have access to technical experts who can assist with installation, troubleshooting, and any other inquiries related to the vibration motor.
By considering these factors and thoroughly researching different suppliers and models, you can find the right industrial vibration motor that meets your application requirements in terms of performance, reliability, and cost-effectiveness.
Vibration Control
In the dynamic landscape of industrial vibration, concrete vibrating motors stand out as indispensable tools in the realm of construction and material processing. These robust motors play a pivotal role in the critical process of concrete consolidation, where the uniform settling and elimination of air bubbles are essential for ensuring the structural integrity and durability of concrete structures. As construction materials are poured into molds, concrete vibrating motors come to life, generating precisely controlled vibrations that permeate the mixture, guaranteeing a solid and well-compact foundation.
Transitioning to vibration shakers, these versatile devices find their place in diverse industrial scenarios, ranging from material separation to quality testing. The efficacy of vibration shakers hinges on the performance of vibration motors, orchestrating systematic oscillations that prove instrumental in tasks such as the stratification of particles based on size. This becomes particularly crucial in refining raw materials for a multitude of industrial applications, ensuring that materials meet stringent quality standards.
Vibration feeder systems, another cornerstone in industrial processes, rely on the consistent and precise movement of materials, a feat made possible by the central role played by vibration motors. These systems orchestrate controlled vibrations to ensure the uniform flow of materials, contributing significantly to the efficiency of manufacturing processes across various industries. The synchronized dance of vibration motors becomes paramount in situations where accuracy and reliability in material movement are paramount.
Delving into the intricacies of vibration velocity, one discovers a key parameter that shapes the performance of vibration motors. The speed and intensity of vibrations, intricately tied to this velocity, become decisive factors in determining the effectiveness of equipment in diverse applications. In industries dealing with bulk materials, vibrating tables come to the fore, where vibration motors are deployed to settle and compact materials. This not only enhances the quality of materials but also ensures uniformity in their composition.
The realm of vibration exciters adds another layer of complexity to industrial processes, particularly in systems that demand specific vibratory patterns or those undergoing testing and calibration. Driven by vibration motors, these exciters are instrumental in generating precisely controlled vibrations tailored to meet the unique requirements of diverse applications.
Vibration-induced fatigue, a critical consideration in engineering, prompts the examination of materials and structures under continuous vibrations. Vibration spectrum analysis emerges as a sophisticated technique, unraveling the intricate patterns and frequencies of vibrations. This analytical tool provides engineers with valuable insights into potential fatigue issues, guiding them in optimizing materials and structures for sustained performance in the face of constant vibrations.
In essence, the integration of industrial vibration motors into various processes and systems is a testament to their versatility and reliability. Whether in the meticulous consolidation of concrete, the precise sorting of materials through vibration shakers, or the controlled movement of bulk materials using vibration feeder systems, these motors continue to shape and enhance industrial landscapes across diverse applications.
Vibration control is a critical aspect of industrial processes, and electric motors designed for mechanical oscillations play a pivotal role in achieving this control. The field of vibration analysis delves into understanding and managing the dynamic behavior of systems to optimize performance. Vibrating equipment, ranging from screens to conveyors, relies on these motors for smooth operation and efficient material handling.
Linear vibration motors, a specific type within this category, produce vibrations in a straight line, catering to applications with unique requirements. Eccentric rotating masses (ERMs) in rotary vibration motors create controlled vibrations, offering versatility in industrial settings. Brushed and brushless DC motors form the core of these devices, ensuring reliable and durable performance.
Vibratory motors find application in various industrial automation processes, contributing to tasks that demand precision and consistency. Haptic feedback systems, often found in consumer devices, utilize compact coin vibration motors to provide tactile sensations, enhancing user experiences. Vibration sensors and analysis software are integral tools for monitoring and maintaining the health of these systems.
Vibration isolation and damping techniques are employed to minimize the impact of vibrations on surrounding structures and components. The industrial applications of vibration motors extend to vibrating compactors, concrete vibrating motors, and vibrating feeders, each serving a specific purpose in manufacturing and construction processes. Pneumatic vibrators are also used in certain industrial settings to induce controlled vibrations.
In the realm of shock and vibration testing, these motors facilitate thorough assessments of products and components, ensuring they meet rigorous standards. The design considerations for vibration motors include factors such as vibration velocity and frequency, crucial for tailoring the motor to specific operational requirements. As industrial machinery continues to evolve, vibration motors remain a key element in enhancing efficiency and precision across diverse applications.
Industrial Vibration Motor
In the dynamic landscape of industrial vibrations, concrete consolidation remains a cornerstone, driven by the fundamental role of vibration motors. These motors, dedicated to the precision control of oscillations, are essential in the construction and material processing sectors. Concrete vibrating motors come to life as they choreograph the intricate dance of vibrations, ensuring the uniform settling of concrete mixtures and eliminating air bubbles. This meticulous process is not merely a construction phase; it is a fundamental stride towards ensuring the resilience and longevity of concrete structures.
Shifting the spotlight to vibration shakers, these versatile instruments are a mainstay in diverse industrial scenarios, ranging from material separation to quality testing. The efficacy of vibration shakers rests on the performance of vibration motors, orchestrating systematic oscillations critical for tasks such as particle stratification based on size. In the refining of raw materials for numerous industrial applications, vibration motors play a pivotal role, ensuring the adherence to stringent quality standards.
Vibration feeder systems, another linchpin in industrial processes, pivot around the consistent and precise movement of materials—an accomplishment facilitated by the central role of vibration motors. These systems utilize controlled vibrations to ensure the seamless flow of materials, contributing significantly to the efficiency of manufacturing processes across various industries. The synchronized dance of vibration motors becomes particularly crucial in situations where accuracy and reliability in material movement are paramount.
Venturing into the realm of vibration velocity, we encounter a pivotal parameter shaping the performance of vibration motors. The speed and intensity of vibrations, intricately linked to this velocity, become decisive factors in determining the effectiveness of equipment across diverse applications. In industries dealing with bulk materials, vibrating tables come into play, with vibration motors settling and compacting materials. This not only enhances the quality of materials but also ensures uniformity in their composition.
The world of vibration exciters adds yet another layer of sophistication to industrial processes, especially in systems demanding specific vibratory patterns or undergoing testing and calibration. Driven by vibration motors, these exciters prove instrumental in generating precisely controlled vibrations tailored to meet the unique requirements of diverse applications.
Vibration-induced fatigue, a critical consideration in engineering, prompts the meticulous examination of materials and structures under continuous vibrations. Vibration spectrum analysis, an advanced technique, unravels the intricate patterns and frequencies of vibrations. This analytical tool provides engineers with invaluable insights into potential fatigue issues, guiding them in optimizing materials and structures for sustained performance in the face of constant vibrations.
In essence, the integration of industrial vibration motors into various processes and systems is a testament to their versatility and reliability. Whether in the meticulous consolidation of concrete, the precise sorting of materials through vibration shakers, or the controlled movement of bulk materials using vibration feeder systems, these motors continue to be catalysts in shaping and enhancing industrial landscapes across diverse applications.
The importance of vibration motors in industrial processes extends to vibrating screens, which are widely used for material classification and separation. Conveyor vibration motors contribute to the smooth movement of goods in production lines, ensuring efficient material handling. Vibratory motors, designed with precision, find applications in various industrial settings, enhancing the functionality of equipment like vibrating feeders and shakers.
Concrete consolidation relies on vibration motors, ensuring uniformity and strength in concrete structures. The vibration exciter, a component in certain systems, is responsible for generating controlled vibrations. Industrial manufacturing processes benefit from the integration of vibration motors, especially in tasks involving sorting, compacting, and conveying materials.
Vibration-resistant design is crucial in environments where external factors may impact the performance of equipment. Electric vibrators, with their versatile applications, contribute to the optimization of industrial processes. The use of vibration motors in vibrating sieves aids in material screening and sizing, a key aspect of various manufacturing operations.
Material handling equipment often incorporates vibration motors to facilitate the movement and processing of diverse materials. The design and selection of vibration motors involve considerations such as the type of motor (brushed or brushless) and the application’s specific requirements. High-frequency vibration, achievable with certain motor configurations, is beneficial in processes where precision and fine-tuning are essential.
Variable frequency drives (VFDs) play a significant role in controlling and adjusting the speed of vibration motors, allowing for adaptability to different operational needs. The collective impact of these keywords underscores the broad spectrum of applications and considerations associated with industrial vibration motors.
In the realm of industrial vibration motors, the concept of vibration frequency becomes a crucial parameter influencing the performance of equipment. The amplitude of vibrations, another essential factor, determines the extent of motion produced by the motor. Vibration testing, a key aspect of quality control, involves subjecting products to controlled vibrations to assess their durability and reliability under various conditions.
The development and implementation of vibration analysis software have significantly advanced the ability to monitor and interpret vibration data. This software aids in predictive maintenance, allowing for timely interventions to prevent potential issues and minimize downtime. Industrial automation, a field constantly evolving with technological advancements, increasingly relies on vibration motors for tasks such as sorting, conveying, and processing materials.
The broader category of shock and vibration testing encompasses various methodologies to evaluate the robustness of products. Pneumatic vibrators, utilizing compressed air, offer a different approach to inducing controlled vibrations in certain industrial applications. Vibrating conveyors, a specialized form of conveying equipment, leverage vibration motors to transport materials efficiently.
The integration of vibration motors into vibratory feeders enhances their capabilities in precisely feeding materials in industrial processes. The significance of vibration intensity cannot be overstated, as it directly influences the effectiveness of vibrating equipment. The selection process for vibration motors involves careful consideration of the specific requirements of the application and the environmental conditions in which the equipment operates.
In the context of industrial machinery, vibration motors contribute to the overall efficiency and performance of equipment. The comprehensive understanding of these keywords provides insight into the multifaceted role that vibration motors play across diverse industrial applications.
Concrete vibrating motors are instrumental in the process of concrete consolidation, ensuring proper compaction and the removal of air bubbles for enhanced structural integrity. Vibration shakers, utilized in various industrial scenarios, rely on vibration motors to induce controlled oscillations for tasks such as material separation and testing. Industrial applications often require vibration feeder systems to facilitate the precise and reliable movement of materials.
The concept of vibration velocity is crucial in determining the speed and intensity of vibrations generated by the motor, influencing the effectiveness of the equipment. Industrial processes, especially those involving material handling, benefit from the inclusion of vibrating tables, which use vibration motors to settle and compact materials. Vibration motors find application in designing and maintaining vibrating compactors, contributing to efficient compaction processes in construction and manufacturing.
The field of vibration isolation addresses the need to minimize the transmission of vibrations to surrounding structures or components, ensuring the smooth and stable operation of equipment. Material screening processes in industrial settings often involve the use of vibrating sieves, where vibration motors play a key role in separating particles based on size.
Vibration motor design encompasses factors such as motor type, size, and power, all tailored to meet the specific requirements of the application. Selection processes for vibration motors involve a careful evaluation of these design parameters in alignment with the intended use. The use of vibration motors in material handling equipment extends to conveyor systems, where their application optimizes the movement of goods in industrial processes.
The integration of brushed and brushless DC motors in vibration motor design enhances efficiency and reliability, making them suitable for a wide range of industrial applications. These motors are fundamental components in various vibrating equipment, contributing to the overall productivity and functionality of industrial processes.
Vibration motors are a type of motor that, as the name suggests, create a vibrating motion. They have become integral components in many modern devices and systems, providing feedback, alerts, and haptic responses that enhance user experience and functionality. These motors are designed to convert electrical energy into mechanical vibration, and they are used across various industries, including consumer electronics, automotive, medical devices, and industrial applications.
Historical Development
The history of vibration motors dates back to the early 20th century when basic mechanisms for generating vibration were first conceptualized. Over the years, technological advancements have led to more sophisticated designs, allowing for a wide range of applications. Early vibration motors were primarily used in industrial settings for tasks such as sorting and conveying materials. However, with the miniaturization of components and improvements in precision and control, they have become essential in everyday consumer electronics, providing tactile feedback and alerts in mobile devices and wearables.
Overview of Different Types of Vibration Motors
Vibration motors come in various types, each with unique characteristics and applications. The most common types include:
- Eccentric Rotating Mass (ERM) Motors: These motors generate vibration through the rotation of an off-center mass attached to the motor shaft. They are widely used in consumer electronics for simple haptic feedback.
- Linear Resonant Actuators (LRA): Unlike ERM motors, LRAs use a magnetic field to move a mass linearly, creating a more refined and precise vibration. This type is favored in applications requiring specific frequency responses and quick reaction times.
- Piezoelectric Vibration Motors: These utilize piezoelectric materials that expand or contract when an electrical voltage is applied. They offer high precision and are often used in applications requiring minimal size and power consumption.
This introduction sets the stage for a deeper exploration of the technical aspects, applications, and future developments of vibration motors.
Types of Vibration Motors
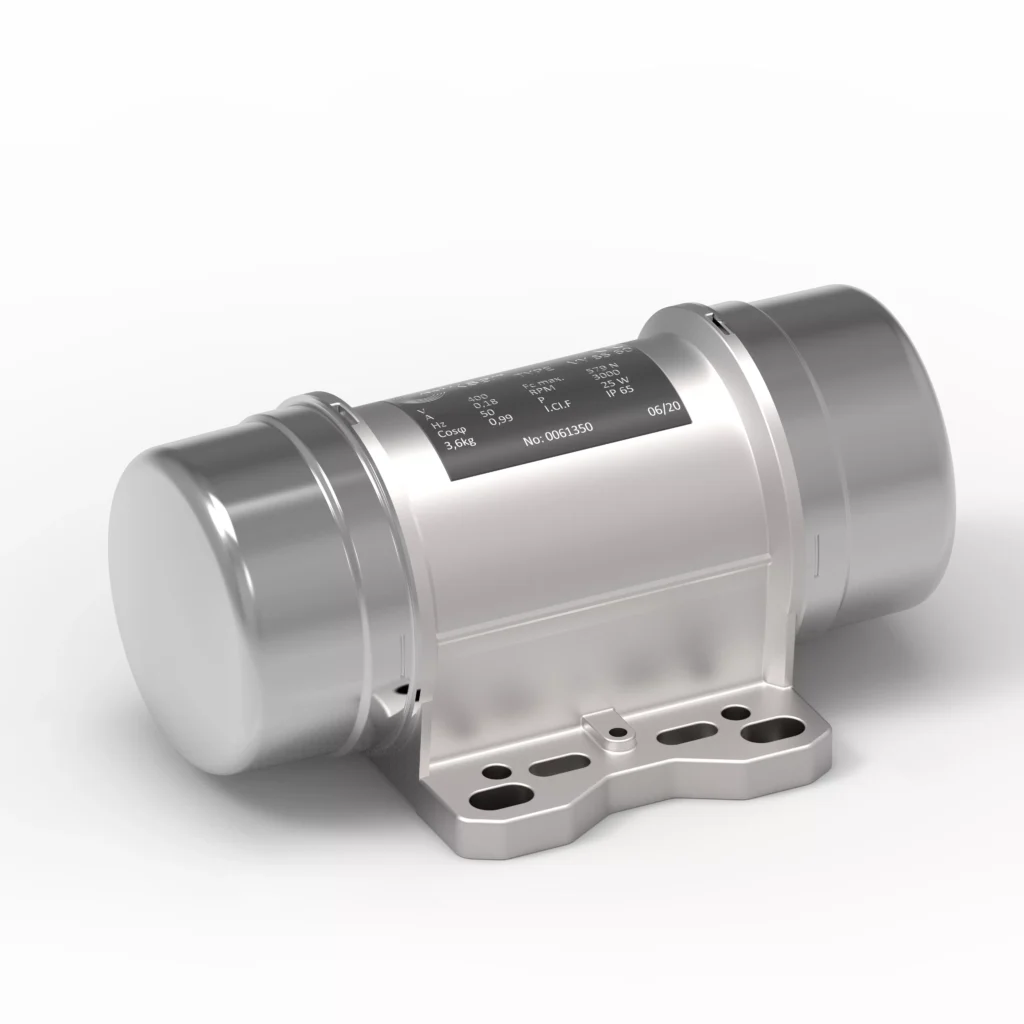
Understanding the different types of vibration motors is crucial for selecting the right one for a specific application. Each type has distinct characteristics that make it suitable for particular uses. This section explores the main types of vibration motors, their design, operation, and typical applications.
Eccentric Rotating Mass (ERM) Motors
Design and Operation
Eccentric Rotating Mass (ERM) motors are among the most widely used vibration motors. They operate by rotating an unbalanced mass, which generates centrifugal force, causing the motor to vibrate. The frequency and amplitude of the vibration are determined by the speed of rotation and the size of the mass.
The basic components of an ERM motor include:
- Motor Shaft: The central axis on which the unbalanced mass is mounted.
- Unbalanced Mass: The key component responsible for generating vibration. It is usually attached off-center on the motor shaft.
- Housing: Encloses the motor components, protecting them from environmental factors and mechanical damage.
ERM motors are relatively simple in design, making them cost-effective and easy to produce. They are typically used in applications where basic haptic feedback is needed, such as in mobile phones and handheld gaming devices.
Common Uses
- Mobile Phones and Tablets: ERM motors provide tactile feedback for touchscreen interactions and notifications.
- Wearable Devices: Used in smartwatches and fitness trackers to alert users with vibrations.
- Remote Controls: Enhance user experience by providing feedback during button presses.
Linear Resonant Actuators (LRA)
Design and Operation
Linear Resonant Actuators (LRA) are more advanced than ERM motors, offering improved precision and control. They consist of a movable mass attached to a spring and a magnetic field. When an AC voltage is applied, the mass oscillates linearly, creating a vibration.
Key components of LRA include:
- Movable Mass: Suspended by springs, this component moves back and forth to generate vibration.
- Electromagnetic Coil: Creates a magnetic field that interacts with the movable mass.
- Spring System: Ensures the mass returns to its original position after displacement.
LRA motors are known for their high-frequency response and efficiency, making them suitable for applications requiring precise control and fast response times.
Common Uses
- Haptic Feedback in Mobile Devices: Provides more nuanced and responsive feedback compared to ERM motors.
- Gaming Controllers: Enhances immersion by delivering realistic vibrations based on in-game events.
- Automotive Touchscreens: Improves user interaction with infotainment systems through tactile feedback.
Piezoelectric Vibration Motors
Design and Operation
Piezoelectric vibration motors leverage the piezoelectric effect, where certain materials generate an electric charge in response to mechanical stress. These motors consist of piezoelectric elements that deform when an electric field is applied, producing vibration.
Key components of piezoelectric motors include:
- Piezoelectric Elements: The core components that expand or contract to create vibration.
- Metal Plate: Acts as a diaphragm that vibrates in response to the deformation of the piezoelectric elements.
- Drive Circuit: Controls the frequency and amplitude of the applied voltage, affecting the vibration characteristics.
Piezoelectric motors are prized for their small size, low power consumption, and high precision. They are often used in applications where space is limited, and precise control is required.
Common Uses
- Medical Devices: Provide haptic feedback in surgical tools and diagnostic equipment.
- Consumer Electronics: Used in compact devices such as smartwatches and portable audio players.
- Industrial Sensors: Enhance sensitivity and accuracy in measurement instruments.
Comparison of Different Types
Each type of vibration motor has its advantages and disadvantages, influencing the selection process for specific applications.
Type | Advantages | Disadvantages |
---|---|---|
ERM | – Simple design<br>- Cost-effective<br>- Easy to produce | – Limited frequency range<br>- Slower response time |
LRA | – Precise control<br>- Fast response<br>- Efficient | – Higher cost<br>- More complex design |
Piezoelectric | – Small size<br>- Low power consumption<br>- High precision | – Limited force output<br>- Requires specialized materials |
Selection Criteria for Different Applications
When selecting a vibration motor, several factors should be considered:
- Application Requirements: Determine the desired frequency, amplitude, and response time.
- Size and Weight: Consider the available space and weight constraints in the device or system.
- Power Consumption: Evaluate the power requirements, especially for battery-powered devices.
- Cost: Balance performance needs with budgetary constraints.
In summary, the choice of vibration motor depends on the specific application requirements, balancing factors such as performance, size, cost, and power consumption.
Technical Aspects of Vibration Motors
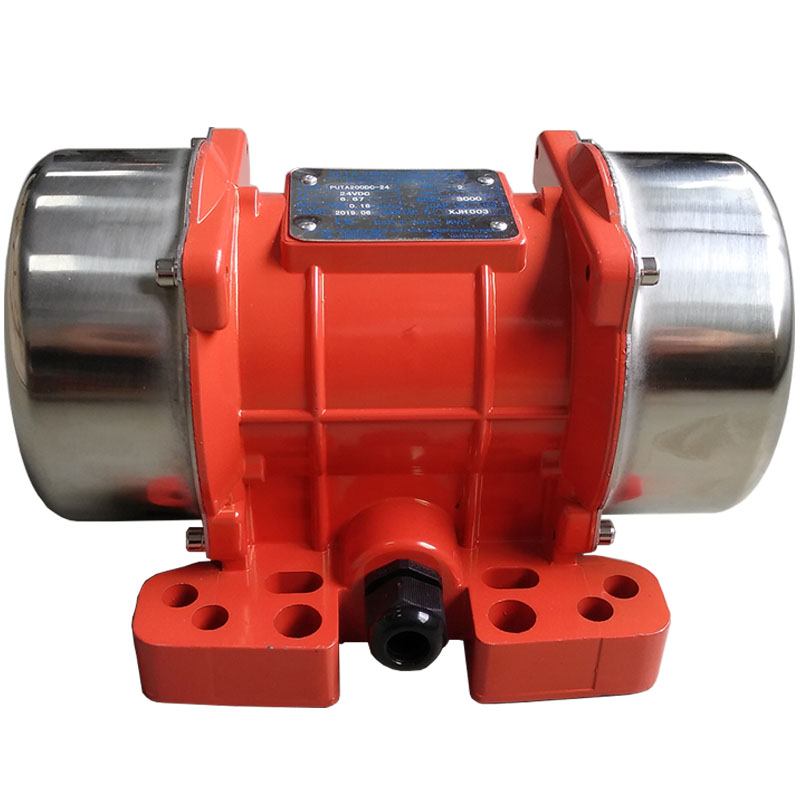
A comprehensive understanding of the technical aspects of vibration motors is essential for designing and integrating them into various applications. This section explores the construction, key specifications, performance characteristics, and design considerations associated with vibration motors.
Construction and Materials
Vibration motors are constructed using materials and components that ensure durability, efficiency, and performance. The choice of materials can significantly impact the motor’s lifespan and functionality.
Key Components
- Motor Housing: Typically made from metal or high-strength plastic, the housing protects the internal components from mechanical damage and environmental factors. It also serves as a mounting structure.
- Rotor and Stator: The rotor is the rotating part of the motor, while the stator is the stationary component. These are usually made from magnetic materials to facilitate electromagnetic interactions.
- Bearings: Bearings reduce friction between moving parts and support the motor shaft. They are often made from materials like stainless steel or ceramic for durability and reliability.
- Wiring and Connectors: Electrical connections are made using insulated copper wires and connectors that provide reliable electrical conductivity.
- Unbalanced Mass or Piezoelectric Elements: Depending on the type of motor, these components generate the vibrations. The unbalanced mass is typically made of metal, while piezoelectric elements are crafted from specialized ceramic materials.
Key Specifications
When selecting a vibration motor, several key specifications must be considered to ensure optimal performance for the intended application.
Size and Dimensions
- Length, Width, and Height: The overall dimensions of the motor must fit within the available space in the device or system.
- Weight: The motor’s weight can affect the balance and handling of the device, particularly in portable applications.
Power and Voltage
- Operating Voltage: The voltage required to power the motor, which can range from a few volts in small devices to several hundred volts in industrial applications.
- Power Consumption: The amount of electrical power consumed by the motor during operation. Lower power consumption is preferred for battery-powered devices.
Frequency and Amplitude
- Frequency Range: The range of vibration frequencies the motor can produce, typically measured in Hertz (Hz).
- Amplitude: The magnitude of the vibration, often expressed in millimeters (mm) or inches.
Performance Characteristics
Understanding the performance characteristics of vibration motors is crucial for achieving the desired vibration effects in various applications.
- Vibration Strength: The intensity of the vibration produced by the motor, influenced by factors such as motor speed, mass, and power input.
- Response Time: The time it takes for the motor to reach its desired vibration state after power is applied. Faster response times are preferred for applications requiring immediate feedback.
- Efficiency: The ratio of mechanical output power to electrical input power, indicating how effectively the motor converts electrical energy into vibration.
- Durability and Lifespan: The expected operational lifespan of the motor, affected by factors such as material quality, construction, and operating conditions.
Design Considerations and Challenges
Designing and integrating vibration motors into devices and systems involves several challenges and considerations to ensure optimal performance and reliability.
Heat Dissipation
Vibration motors generate heat during operation, which can affect their performance and lifespan. Effective heat dissipation methods, such as using heat sinks or conductive materials, are essential to prevent overheating.
Noise and Vibration Isolation
Unwanted noise and vibrations can interfere with the operation of devices and systems. Implementing noise and vibration isolation techniques, such as using damping materials or mounting systems, can minimize these issues.
Environmental Factors
Vibration motors may be exposed to various environmental factors, such as temperature extremes, moisture, and dust. Designing motors with protective features, such as seals or coatings, can enhance their resilience to environmental challenges.
Integration with Control Systems
Integrating vibration motors with control systems requires careful consideration of factors such as signal processing, power management, and feedback mechanisms. This ensures precise control and synchronization with other components in the system.
In conclusion, the technical aspects of vibration motors encompass a wide range of considerations, from construction and materials to performance characteristics and design challenges. Understanding these aspects is essential for selecting and implementing the right vibration motor for specific applications.
Applications of Vibration Motors
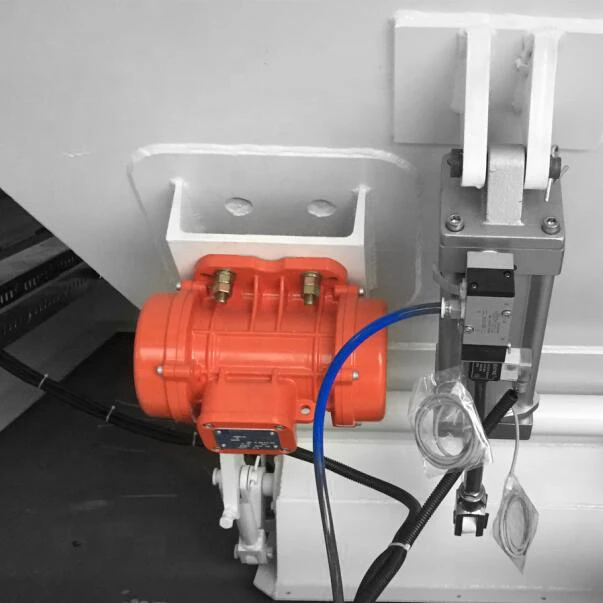
Vibration motors play a crucial role in various industries, enhancing functionality and user experience through tactile feedback, alerts, and precise control. This section explores the diverse applications of vibration motors across different sectors.
Consumer Electronics
Mobile Phones and Tablets
Vibration motors are integral components in mobile phones and tablets, providing haptic feedback for touchscreen interactions and notifications. They enhance the user experience by delivering tactile responses to touch inputs, alerts, and messages.
- Touchscreen Feedback: Vibration motors simulate the sensation of pressing physical buttons, improving user interaction with touchscreen interfaces.
- Notifications and Alerts: Vibration motors provide discreet alerts for incoming calls, messages, and notifications, allowing users to stay informed without relying on audible alerts.
Wearables and Smart Devices
In wearable technology, vibration motors are used to deliver notifications and alerts directly to the user’s wrist or body. This enhances the functionality and convenience of devices such as smartwatches and fitness trackers.
- Fitness Tracking: Vibration motors provide feedback for activity goals, heart rate monitoring, and other fitness metrics.
- Health Monitoring: Vibration alerts can signal important health-related notifications, such as medication reminders or emergency alerts.
Automotive Industry
Haptic Feedback in Touchscreens
Vibration motors are used in automotive touchscreens to enhance user interaction with infotainment and navigation systems. Haptic feedback provides tactile responses to touch inputs, improving usability and reducing driver distraction.
- Infotainment Systems: Vibration motors simulate button presses, enhancing the user experience and making interactions more intuitive.
- Navigation Controls: Haptic feedback assists drivers in navigating menus and settings, ensuring safer and more efficient operation.
Alert Systems
Vibration motors are employed in automotive alert systems to provide non-intrusive warnings and notifications to drivers. These systems enhance safety by delivering tactile alerts for various vehicle conditions and hazards.
- Collision Warning: Vibration alerts can warn drivers of potential collisions or obstacles, improving reaction times and safety.
- Lane Departure Warning: Vibration motors provide feedback when a vehicle deviates from its lane, helping drivers maintain proper lane positioning.
Industrial Applications
Equipment and Machinery Monitoring
In industrial settings, vibration motors are used for equipment and machinery monitoring. They provide feedback on the operational status and performance of machinery, helping to identify issues and prevent failures.
- Condition Monitoring: Vibration sensors detect changes in equipment performance, allowing for timely maintenance and repairs.
- Fault Detection: Vibration analysis helps identify mechanical faults, such as imbalances or misalignments, improving equipment reliability and efficiency.
Material Handling and Processing
Vibration motors are employed in material handling and processing applications, facilitating the movement and sorting of materials. They improve efficiency and accuracy in various industrial processes.
- Vibratory Conveyors: Vibration motors drive conveyors that transport materials, enhancing the speed and precision of material handling.
- Sorting and Screening: Vibration motors assist in sorting and screening materials based on size, weight, or other characteristics, optimizing production processes.
Medical Devices
Feedback Systems in Prosthetics
In the medical field, vibration motors are used in prosthetic devices to provide sensory feedback to users. This enhances the functionality and user experience of prosthetics, improving mobility and control.
- Tactile Feedback: Vibration motors simulate sensations such as touch and pressure, helping users interact with their environment.
- Control Feedback: Vibration alerts assist users in controlling prosthetic movements, enhancing precision and coordination.
Patient Monitoring Equipment
Vibration motors are employed in patient monitoring equipment to deliver alerts and notifications for various medical conditions. They improve patient care by providing timely and discreet notifications to healthcare professionals and patients.
- Vital Sign Monitoring: Vibration alerts signal changes in vital signs, such as heart rate or blood pressure, allowing for prompt medical intervention.
- Medication Reminders: Vibration motors provide reminders for medication administration, ensuring adherence to treatment plans.
Other Emerging Applications
Virtual Reality and Gaming
In virtual reality (VR) and gaming, vibration motors enhance immersion by delivering realistic tactile feedback based on in-game events and interactions. This improves the overall gaming experience and realism.
- Haptic Feedback in VR: Vibration motors simulate various sensations, such as impacts, textures, and environmental effects, enhancing the sense of presence in virtual environments.
- Gaming Controllers: Vibration motors provide feedback for in-game actions, such as explosions, collisions, and character movements, improving player engagement and satisfaction.
Robotics and Automation
Vibration motors are used in robotics and automation to enhance precision, control, and feedback in various applications. They improve the performance and functionality of robotic systems.
- Tactile Sensors: Vibration motors provide feedback for robotic grippers and manipulators, improving object handling and manipulation.
- Precision Control: Vibration alerts assist in fine-tuning robotic movements, enhancing accuracy and coordination in automated processes.
In conclusion, vibration motors have diverse applications across various industries, enhancing functionality, user experience, and performance. Their versatility and adaptability make them essential components in modern technology and systems.
Future Trends and Innovations
As technology continues to evolve, vibration motors are expected to undergo significant advancements, leading to new applications and improved performance. This section explores the future trends and innovations in vibration motor technology.
Technological Advancements
- Miniaturization: Advances in manufacturing and materials will enable the development of smaller and more compact vibration motors, expanding their use in miniaturized devices and systems.
- Increased Efficiency: Innovations in motor design and materials will lead to more efficient vibration motors with lower power consumption and higher performance.
- Improved Control and Precision: Enhanced control algorithms and sensor integration will enable more precise and customizable vibration effects, improving user experience and application performance.
Integration with IoT and Smart Technologies
The integration of vibration motors with the Internet of Things (IoT) and smart technologies will open up new possibilities for applications and functionality.
- Smart Home Devices: Vibration motors will provide tactile feedback and alerts in smart home devices, enhancing user interaction and control.
- Wearable Health Monitors: Integration with IoT will enable real-time monitoring and feedback for health and fitness applications, improving user outcomes and experiences.
Potential New Applications
- Augmented Reality (AR): Vibration motors will enhance AR experiences by providing tactile feedback for virtual interactions, improving immersion and realism.
- Advanced Automotive Systems: Vibration motors will play a role in advanced driver assistance systems (ADAS) and autonomous vehicles, providing feedback and alerts for various driving conditions and scenarios.
- Next-Generation Consumer Electronics: Vibration motors will continue to enhance user experience in emerging consumer electronics, such as foldable devices and flexible displays.
In summary, the future of vibration motors is promising, with advancements in technology and integration with smart systems leading to new applications and improved performance. These innovations will continue to enhance functionality and user experience across various industries.
Conclusion
Vibration motors are essential components in modern technology, providing tactile feedback, alerts, and precise control in a wide range of applications. This article has explored the various types of vibration motors, their technical aspects, and their diverse applications across industries.
Recap of Key Points
- Types of Vibration Motors: We examined the three main types of vibration motors—Eccentric Rotating Mass (ERM), Linear Resonant Actuators (LRA), and Piezoelectric vibration motors—each with unique characteristics and applications.
- Technical Aspects: We discussed the construction, key specifications, performance characteristics, and design considerations associated with vibration motors, highlighting the factors that influence their selection and integration.
- Applications: We explored the diverse applications of vibration motors in consumer electronics, automotive, industrial, medical, and other emerging fields, showcasing their versatility and adaptability.
- Future Trends and Innovations: We examined the future trends and innovations in vibration motor technology, including miniaturization, increased efficiency, and integration with IoT and smart technologies.
Importance of Vibration Motors in Modern Technology
Vibration motors play a crucial role in enhancing functionality and user experience across various industries. Their ability to provide tactile feedback, alerts, and precise control makes them indispensable components in modern devices and systems.
- Consumer Electronics: Vibration motors improve user interaction and experience in mobile phones, wearables, and other consumer devices.
- Automotive Industry: Vibration motors enhance safety and usability in automotive systems, providing feedback and alerts for various conditions.
- Industrial and Medical Applications: Vibration motors improve efficiency and performance in industrial processes and medical devices, providing valuable feedback and control.
Final Thoughts on Future Developments
As technology continues to advance, vibration motors will play an increasingly important role in emerging applications and industries. Innovations in design, materials, and integration will lead to new possibilities and improved performance, enhancing functionality and user experience.
In conclusion, vibration motors are vital components in modern technology, providing essential functionality and enhancing user experience across a wide range of applications. Their versatility, adaptability, and potential for future advancements make them indispensable in the ever-evolving technological landscape.
Introduction to Industrial Vibration Motors
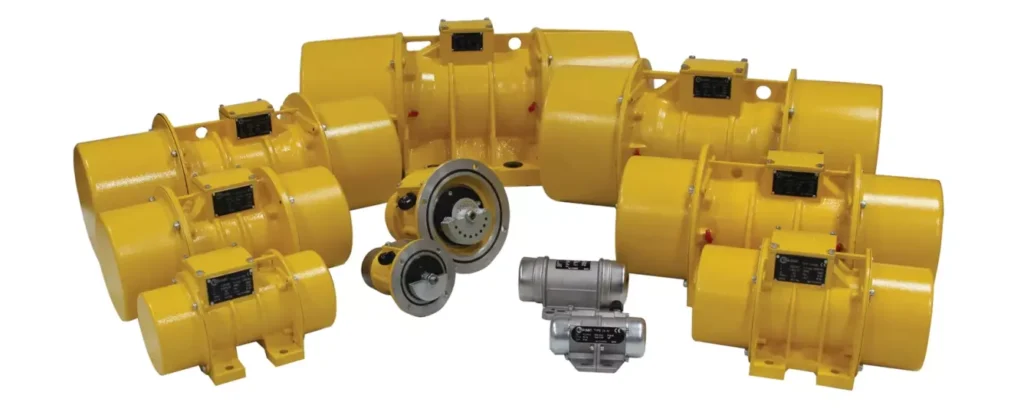
Industrial vibration motors are specialized devices designed to generate mechanical vibrations for various industrial applications. They are integral to processes that require the movement, sorting, and monitoring of materials and equipment. By converting electrical energy into mechanical vibrations, these motors facilitate efficient material handling, quality control, and operational monitoring in industrial settings.
Key functions of industrial vibration motors include:
- Material Movement: Vibration motors aid in the transportation and handling of bulk materials, ensuring smooth and efficient processes.
- Sorting and Separation: They enhance the sorting and separation of materials based on size, weight, or other characteristics, optimizing production efficiency.
- Equipment Monitoring: Vibration motors provide feedback on the operational status of machinery, helping to identify potential issues before they lead to failures.
Historical Context
The use of vibration in industrial applications can be traced back to the early 20th century when basic vibrating mechanisms were employed for tasks such as material sorting and handling. The development of dedicated vibration motors, however, marked a significant advancement in technology.
- Early Innovations: Initial applications were primarily mechanical, relying on simple mechanisms to generate vibrations. These early systems were limited in precision and control.
- Technological Advancements: With the advent of electric motors and advancements in materials science, vibration motors became more sophisticated, offering improved control, efficiency, and versatility.
- Modern Applications: Today, industrial vibration motors are used across a wide range of industries, including mining, construction, food processing, and pharmaceuticals, highlighting their essential role in modern industrial processes.
Key Features
Industrial vibration motors are characterized by several key features that make them suitable for demanding applications:
- Robust Construction: Designed to withstand harsh industrial environments, vibration motors are built with durable materials and components.
- High Efficiency: They are engineered for optimal energy conversion, ensuring efficient performance and minimal energy loss.
- Versatility: Available in various sizes and configurations, vibration motors can be tailored to specific industrial needs and applications.
- Precision Control: Advanced control systems allow for precise adjustment of vibration frequency and amplitude, enabling customized solutions for diverse industrial tasks.
Key takeaways:
- Essential for Industrial Processes: Vibration motors are vital for efficient and effective material handling, sorting, and monitoring in industrial settings.
- Technological Evolution: From early mechanical systems to modern electric motors, technological advancements have significantly enhanced their capabilities.
- Diverse Applications: Used across multiple industries, vibration motors are adaptable to various tasks, showcasing their versatility and importance in modern industry.
Types of Industrial Vibration Motors
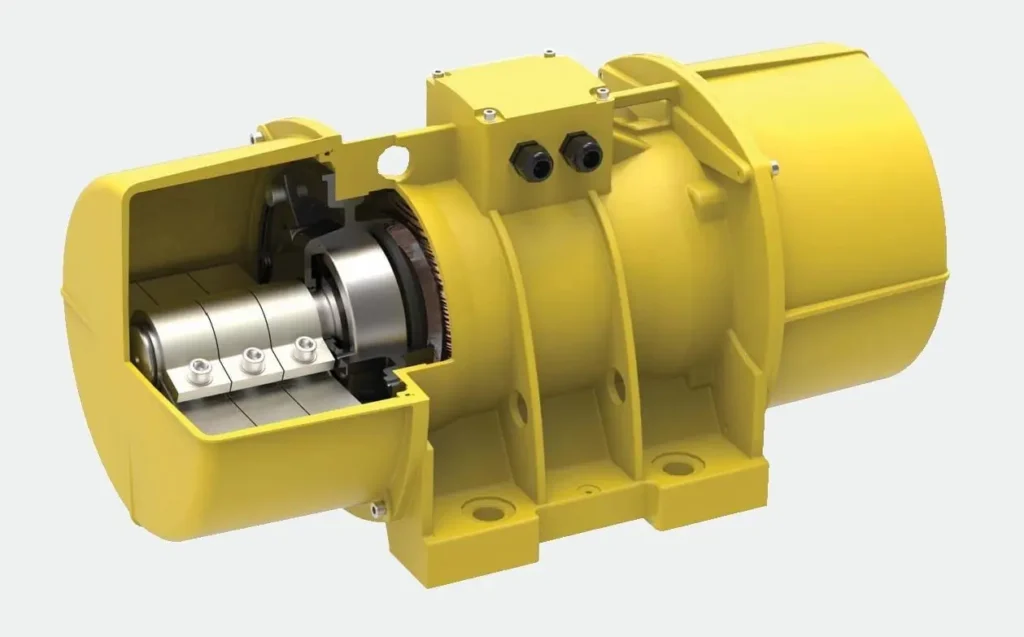
Understanding the different types of industrial vibration motors is crucial for selecting the appropriate motor for specific applications. Each type offers unique characteristics and advantages, making them suitable for various industrial tasks.
Eccentric Rotating Mass (ERM) Motors
Design and Operation
Eccentric Rotating Mass (ERM) motors are among the most commonly used vibration motors in industrial applications. They operate by rotating an unbalanced mass attached to the motor shaft, generating centrifugal force that produces vibration. The frequency and amplitude of the vibration are determined by the speed of rotation and the size of the unbalanced mass.
Key components of ERM motors include:
- Motor Shaft: The central axis on which the unbalanced mass is mounted.
- Unbalanced Mass: The component responsible for generating vibration. It is usually attached off-center on the motor shaft.
- Housing: Encloses the motor components, protecting them from environmental factors and mechanical damage.
Advantages of ERM motors:
- Simple Design: The straightforward design makes them easy to manufacture and maintain.
- Cost-Effective: They are relatively inexpensive compared to other types of vibration motors.
- Versatile Applications: Suitable for a wide range of industrial tasks, including material handling and sorting.
Common Applications
- Material Conveying: ERM motors drive vibratory conveyors, enhancing the movement of bulk materials.
- Screening and Sorting: They facilitate the sorting and screening of materials based on size and weight.
- Compact Equipment: ERM motors are used in applications where space is limited, providing efficient vibration solutions.
Linear Resonant Actuators (LRA)
Design and Operation
Linear Resonant Actuators (LRA) differ from ERM motors in that they generate vibration through the linear movement of a mass rather than rotational motion. An electromagnetic field is used to move the mass back and forth, producing vibrations with high precision and control.
Key components of LRA motors include:
- Movable Mass: Suspended by springs, the mass moves linearly to generate vibration.
- Electromagnetic Coil: Creates a magnetic field that interacts with the movable mass.
- Spring System: Ensures the mass returns to its original position after displacement.
Advantages of LRA motors:
- Precise Control: Offer more precise control over vibration frequency and amplitude.
- Efficient Performance: Consume less power compared to ERM motors, making them suitable for energy-sensitive applications.
- High-Frequency Response: Capable of producing high-frequency vibrations with minimal delay.
Common Applications
- Precision Manufacturing: Used in processes requiring exact vibration control, such as semiconductor manufacturing.
- Laboratory Equipment: Enhance the precision and accuracy of laboratory instruments and devices.
- Quality Control: Facilitate quality control processes by providing precise vibration feedback.
Electromagnetic Vibration Motors
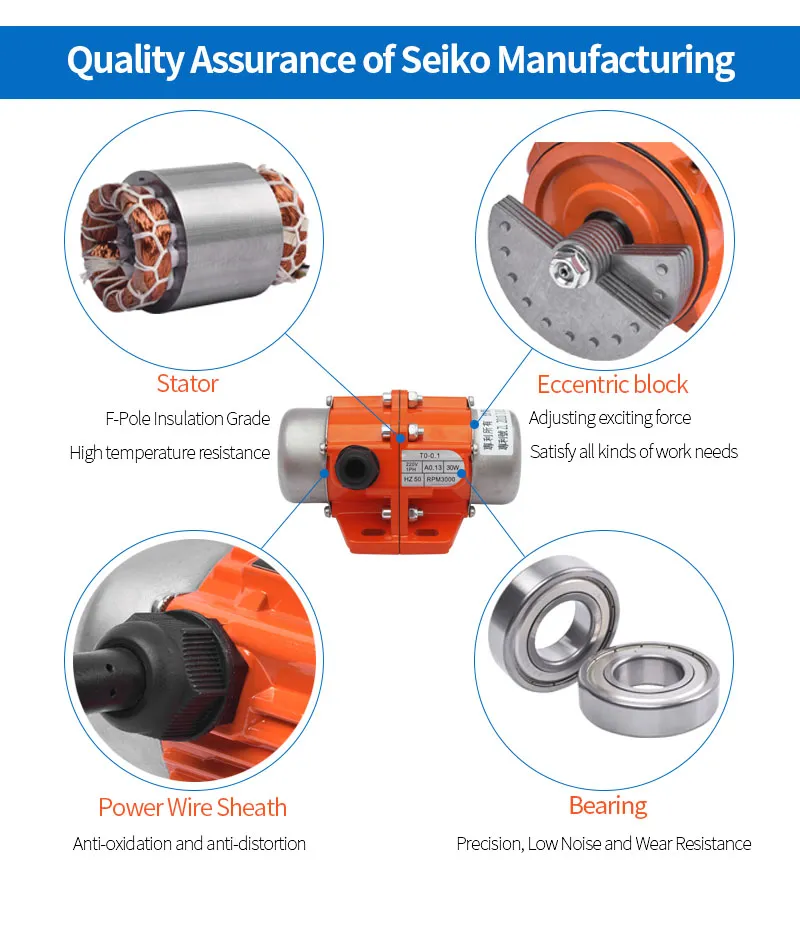
Design and Operation
Electromagnetic vibration motors generate vibrations through the interaction of magnetic fields. These motors consist of an electromagnetic coil and a vibrating armature, which is set into motion by the magnetic field generated when current flows through the coil.
Key components of electromagnetic motors include:
- Electromagnetic Coil: Generates a magnetic field when energized.
- Vibrating Armature: Responds to the magnetic field, creating vibrations.
- Damping System: Reduces noise and unwanted vibrations, enhancing motor performance.
Advantages of electromagnetic motors:
- Smooth Operation: Provide smooth and continuous vibrations, reducing mechanical stress on components.
- Adjustable Frequency: Allow for precise control of vibration frequency and amplitude.
- Low Noise Levels: Operate with minimal noise, making them suitable for noise-sensitive environments.
Common Applications
- Conveying Systems: Used in conveyor systems for smooth and efficient material transportation.
- Vibratory Feeders: Enhance the performance of vibratory feeders used in packaging and assembly lines.
- Textile Industry: Improve the efficiency of textile processing equipment by providing consistent vibrations.
Piezoelectric Vibration Motors
Design and Operation
Piezoelectric vibration motors leverage the piezoelectric effect, where certain materials generate an electric charge in response to mechanical stress. These motors consist of piezoelectric elements that expand or contract when an electric field is applied, producing vibration.
Key components of piezoelectric motors include:
- Piezoelectric Elements: The core components that expand or contract to create vibration.
- Metal Plate: Acts as a diaphragm that vibrates in response to the deformation of the piezoelectric elements.
- Drive Circuit: Controls the frequency and amplitude of the applied voltage, affecting the vibration characteristics.
Advantages of piezoelectric motors:
- High Precision: Offer precise control over vibration characteristics, making them suitable for sensitive applications.
- Compact Design: Small and lightweight, ideal for applications with space constraints.
- Low Power Consumption: Require minimal power, making them energy-efficient.
Common Applications
- Medical Devices: Provide precise vibration feedback in medical diagnostic equipment.
- Microelectronics: Enhance the performance of microelectronic devices by providing controlled vibrations.
- Research and Development: Used in experimental setups requiring precise vibration control.
Comparison of Types
Each type of industrial vibration motor has its own set of advantages and disadvantages, influencing their suitability for specific applications.
Type | Advantages | Disadvantages |
---|---|---|
ERM | – Simple design<br>- Cost-effective<br>- Versatile | – Limited frequency range<br>- Slower response time |
LRA | – Precise control<br>- High efficiency<br>- Fast response | – Higher cost<br>- More complex design |
Electromagnetic | – Smooth operation<br>- Adjustable frequency<br>- Low noise | – Complex construction<br>- Requires precise alignment |
Piezoelectric | – High precision<br>- Compact design<br>- Low power consumption | – Limited force output<br>- Specialized materials required |
Selection Criteria:
- Application Requirements: Determine the desired frequency, amplitude, and response time.
- Size and Weight: Consider the available space and weight constraints in the application.
- Power Consumption: Evaluate the power requirements, especially for energy-sensitive applications.
- Cost: Balance performance needs with budgetary constraints.
Summary:
- Diverse Options: A variety of vibration motors are available, each with unique characteristics and advantages.
- Application-Specific Selection: The choice of motor depends on the specific requirements and constraints of the application.
Technical Aspects of Industrial Vibration Motors
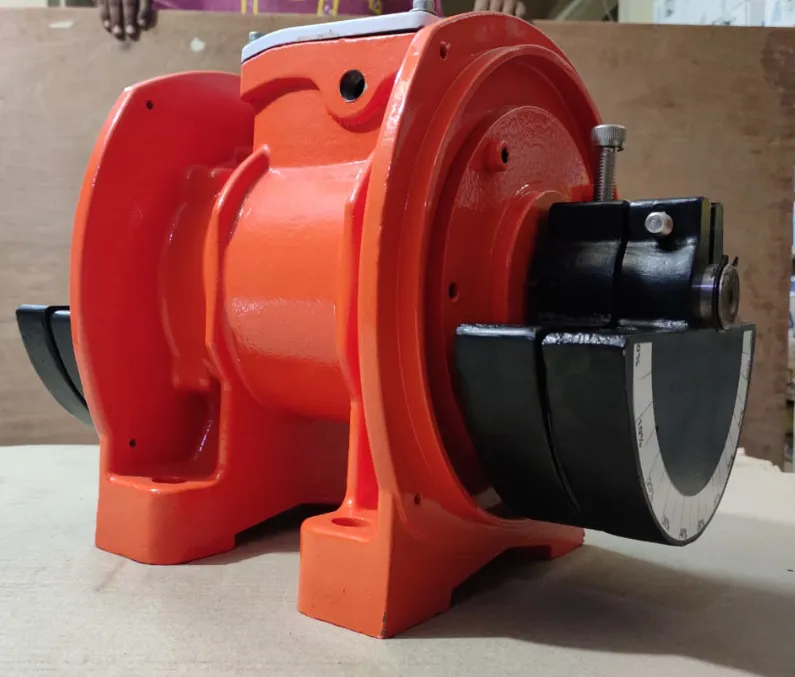
A comprehensive understanding of the technical aspects of industrial vibration motors is essential for designing and integrating them into various applications. This section explores the construction, key specifications, performance characteristics, and design considerations associated with vibration motors.
Construction and Materials
Industrial vibration motors are constructed using materials and components that ensure durability, efficiency, and performance. The choice of materials can significantly impact the motor’s lifespan and functionality.
Key Components
- Motor Housing: Typically made from metal or high-strength plastic, the housing protects the internal components from mechanical damage and environmental factors. It also serves as a mounting structure.
- Rotor and Stator: The rotor is the rotating part of the motor, while the stator is the stationary component. These are usually made from magnetic materials to facilitate electromagnetic interactions.
- Bearings: Bearings reduce friction between moving parts and support the motor shaft. They are often made from materials like stainless steel or ceramic for durability and reliability.
- Wiring and Connectors: Electrical connections are made using insulated copper wires and connectors that provide reliable electrical conductivity.
- Unbalanced Mass or Piezoelectric Elements: Depending on the type of motor, these components generate the vibrations. The unbalanced mass is typically made of metal, while piezoelectric elements are crafted from specialized ceramic materials.
Key Specifications
When selecting a vibration motor, several key specifications must be considered to ensure optimal performance for the intended application.
Size and Dimensions
- Length, Width, and Height: The overall dimensions of the motor must fit within the available space in the device or system.
- Weight: The motor’s weight can affect the balance and handling of the device, particularly in portable applications.
Power and Voltage
- Operating Voltage: The voltage required to power the motor, which can range from a few volts in small devices to several hundred volts in industrial applications.
- Power Consumption: The amount of electrical power consumed by the motor during operation. Lower power consumption is preferred for battery-powered devices.
Frequency and Amplitude
- Frequency Range: The range of vibration frequencies the motor can produce, typically measured in Hertz (Hz).
- Amplitude: The magnitude of the vibration, often expressed in millimeters (mm) or inches.
Performance Characteristics
Understanding the performance characteristics of vibration motors is crucial for achieving the desired vibration effects in various applications.
- Vibration Strength: The intensity of the vibration produced by the motor, influenced by factors such as motor speed, mass, and power input.
- Response Time: The time it takes for the motor to reach its desired vibration state after power is applied. Faster response times are preferred for applications requiring immediate feedback.
- Efficiency: The ratio of mechanical output power to electrical input power, indicating how effectively the motor converts electrical energy into vibration.
- Durability and Lifespan: The expected operational lifespan of the motor, affected by factors such as material quality, construction, and operating conditions.
Design Considerations and Challenges
Designing and integrating vibration motors into devices and systems involves several challenges and considerations to ensure optimal performance and reliability.
Heat Dissipation
Vibration motors generate heat during operation, which can affect their performance and lifespan. Effective heat dissipation methods, such as using heat sinks or conductive materials, are essential to prevent overheating.
Noise and Vibration Isolation
Unwanted noise and vibrations can interfere with the operation of devices and systems. Implementing noise and vibration isolation techniques, such as using damping materials or mounting systems, can minimize these issues.
Environmental Factors
Vibration motors may be exposed to various environmental factors, such as temperature extremes, moisture, and dust. Designing motors with protective features, such as seals or coatings, can enhance their resilience to environmental challenges.
Integration with Control Systems
Integrating vibration motors with control systems requires careful consideration of factors such as signal processing, power management, and feedback mechanisms. This ensures precise control and synchronization with other components in the system.
In conclusion, the technical aspects of vibration motors encompass a wide range of considerations, from construction and materials to performance characteristics and design challenges. Understanding these aspects is essential for selecting and implementing the right vibration motor for specific applications.
Applications of Industrial Vibration Motors
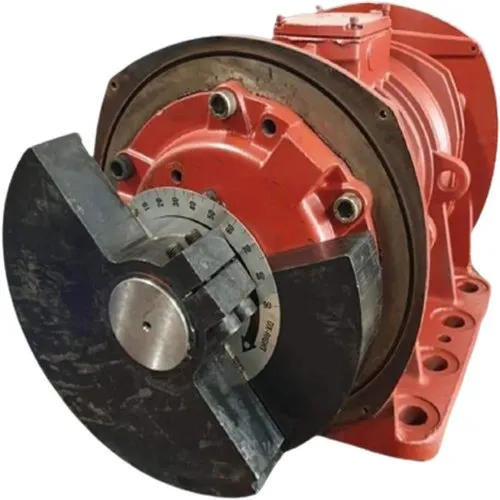
Industrial vibration motors play a crucial role in enhancing efficiency, productivity, and quality across various industries. This section explores the diverse applications of vibration motors in industrial settings.
Material Handling and Processing
Vibratory Conveyors
Vibration motors are integral components of vibratory conveyors, which are used to transport bulk materials efficiently. By generating controlled vibrations, these motors facilitate the smooth movement of materials, reducing friction and wear on conveyor surfaces.
- Efficient Transportation: Vibration motors enable the continuous flow of materials, minimizing downtime and increasing throughput.
- Versatile Applications: Vibratory conveyors are used in industries such as food processing, pharmaceuticals, and mining, where precise material handling is essential.
Screening and Sorting
In screening and sorting applications, vibration motors enhance the separation of materials based on size, weight, or other characteristics. They drive vibratory screens and separators, ensuring accurate and efficient sorting processes.
- Improved Accuracy: Vibration motors provide consistent and controlled vibrations, improving the accuracy of sorting and screening operations.
- Customizable Solutions: Adjustable frequency and amplitude settings allow for tailored solutions to meet specific sorting requirements.
Feeding and Dosing
Vibration motors are used in feeding and dosing applications to deliver precise amounts of materials to processing equipment. They drive vibratory feeders, ensuring accurate and consistent material flow.
- Precise Control: Vibration motors enable precise control over material flow rates, enhancing the efficiency of production processes.
- Reduced Waste: Accurate dosing reduces material waste, improving overall production efficiency and sustainability.
Machinery and Equipment Monitoring
Condition Monitoring
Vibration motors are employed in condition monitoring systems to assess the operational status of machinery and equipment. They provide feedback on vibration levels, helping to identify potential issues before they lead to failures.
- Early Fault Detection: Vibration analysis can detect mechanical faults, such as imbalances, misalignments, and bearing wear, allowing for timely maintenance and repairs.
- Improved Equipment Reliability: Regular monitoring of vibration levels enhances equipment reliability and longevity, reducing downtime and maintenance costs.
Predictive Maintenance
In predictive maintenance applications, vibration motors play a key role in monitoring the health of machinery and equipment. They provide real-time data on vibration patterns, enabling proactive maintenance strategies.
- Reduced Downtime: Predictive maintenance minimizes unexpected equipment failures, reducing downtime and production disruptions.
- Cost Savings: By addressing issues before they escalate, predictive maintenance reduces maintenance costs and extends equipment lifespan.
Mining and Quarrying
Material Transportation
In the mining and quarrying industry, vibration motors are used to transport bulk materials, such as ore and aggregates, over long distances. They drive vibratory feeders and conveyors, ensuring efficient material handling.
- High-Capacity Transportation: Vibration motors enable the transportation of large volumes of materials, increasing production efficiency.
- Durable Solutions: Designed for harsh environments, vibration motors provide reliable performance in demanding mining and quarrying applications.
Screening and Classification
Vibration motors are employed in screening and classification processes to separate materials based on size and composition. They drive vibratory screens and separators, ensuring accurate classification of materials.
- Accurate Classification: Vibration motors provide consistent and controlled vibrations, improving the accuracy of screening and classification operations.
- Adaptable Solutions: Adjustable frequency and amplitude settings allow for tailored solutions to meet specific classification requirements.
Construction Industry
Concrete Compaction
In the construction industry, vibration motors are used to compact concrete, ensuring uniform density and strength. They drive vibratory compactors and tampers, improving the quality of concrete structures.
- Improved Concrete Quality: Vibration motors enhance concrete compaction, reducing voids and increasing structural integrity.
- Efficient Construction Processes: Vibration motors streamline concrete compaction, reducing labor costs and construction time.
Soil Compaction
Vibration motors are employed in soil compaction applications to improve soil stability and load-bearing capacity. They drive vibratory rollers and compactors, enhancing the performance of construction equipment.
- Enhanced Soil Stability: Vibration motors improve soil compaction, increasing stability and load-bearing capacity.
- Versatile Applications: Used in road construction, foundation preparation, and landscaping, vibration motors provide adaptable solutions for various soil compaction needs.
Food and Beverage Industry
Food Processing
In the food and beverage industry, vibration motors are used to enhance food processing operations. They drive vibratory conveyors and feeders, ensuring efficient and hygienic material handling.
- Efficient Material Handling: Vibration motors enable the smooth and consistent flow of food products, reducing processing time and waste.
- Hygienic Solutions: Designed for easy cleaning and maintenance, vibration motors ensure hygienic food processing operations.
Packaging and Sorting
Vibration motors are employed in packaging and sorting applications to enhance efficiency and accuracy. They drive vibratory sorters and packers, ensuring precise material handling.
- Improved Sorting Accuracy: Vibration motors provide controlled vibrations, improving the accuracy of packaging and sorting operations.
- Customizable Solutions: Adjustable frequency and amplitude settings allow for tailored solutions to meet specific packaging and sorting requirements.
Pharmaceutical Industry
Tablet Coating
In the pharmaceutical industry, vibration motors are used to enhance tablet coating processes. They drive vibratory coaters, ensuring uniform coating application.
- Improved Coating Quality: Vibration motors ensure uniform coating thickness, improving the quality and efficacy of pharmaceutical products.
- Efficient Production Processes: Vibration motors streamline tablet coating, reducing production time and costs.
Capsule Filling
Vibration motors are employed in capsule filling applications to enhance accuracy and efficiency. They drive vibratory fillers, ensuring precise material dosing.
- Accurate Dosing: Vibration motors enable precise control over material flow rates, improving the accuracy of capsule filling operations.
- Reduced Waste: Accurate dosing reduces material waste, improving overall production efficiency and sustainability.
In conclusion, industrial vibration motors have diverse applications across various industries, enhancing efficiency, productivity, and quality. Their versatility and adaptability make them essential components in modern industrial processes.
Challenges and Solutions in Industrial Applications
Industrial vibration motors are subject to various challenges that can impact their performance and reliability. This section explores common challenges in industrial applications and potential solutions to address them.
Environmental Considerations
Harsh Operating Conditions
Industrial environments can expose vibration motors to harsh conditions, such as extreme temperatures, moisture, dust, and chemicals. These factors can affect motor performance and longevity.
Solutions:
- Protective Coatings: Apply protective coatings to motor components to resist corrosion and wear.
- Sealed Enclosures: Use sealed enclosures to protect internal components from environmental factors.
- Temperature Management: Implement cooling systems or heat sinks to manage temperature fluctuations.
Vibration-Induced Fatigue
Continuous vibration exposure can lead to fatigue and wear on motor components, reducing their lifespan and reliability.
Solutions:
- Durable Materials: Use high-strength materials and components designed to withstand vibration-induced fatigue.
- Regular Maintenance: Implement routine maintenance schedules to identify and address wear and fatigue early.
- Vibration Dampening: Incorporate vibration dampening techniques, such as shock absorbers or isolators, to reduce stress on components.
Maintenance and Longevity
Wear and Tear
Vibration motors are subject to wear and tear due to constant operation, which can impact performance and reliability.
Solutions:
- High-Quality Components: Use high-quality bearings, seals, and other components to minimize wear and tear.
- Lubrication: Implement proper lubrication practices to reduce friction and extend component lifespan.
- Preventive Maintenance: Conduct regular inspections and maintenance to identify and address potential issues before they escalate.
Unexpected Failures
Unexpected motor failures can lead to downtime and production disruptions, impacting productivity and profitability.
Solutions:
- Condition Monitoring: Implement condition monitoring systems to assess motor health and detect potential issues early.
- Predictive Maintenance: Use predictive maintenance strategies to anticipate and address issues before they result in failures.
- Redundancy: Incorporate redundancy in critical applications to minimize the impact of motor failures.
Noise and Vibration Control
Unwanted Noise
Vibration motors can generate unwanted noise, impacting the working environment and operator comfort.
Solutions:
- Noise Reduction Techniques: Implement noise reduction techniques, such as damping materials or enclosures, to minimize noise levels.
- Precision Engineering: Use precision-engineered components and designs to reduce mechanical noise.
- Isolation: Isolate motors from other components to prevent noise transmission.
Vibration Transmission
Uncontrolled vibration transmission can affect the performance of other equipment and systems, leading to inefficiencies and failures.
Solutions:
- Vibration Isolation: Use vibration isolation techniques, such as mounts or shock absorbers, to reduce vibration transmission.
- Balancing: Ensure motors and components are properly balanced to minimize vibration transmission.
- Control Systems: Implement advanced control systems to manage and adjust vibration characteristics.
In conclusion, industrial vibration motors face various challenges in harsh operating environments. By implementing appropriate solutions, such as protective measures, maintenance strategies, and noise control techniques, these challenges can be effectively addressed, ensuring reliable and efficient motor performance.
Future Trends and Innovations
As technology continues to evolve, industrial vibration motors are expected to undergo significant advancements, leading to new applications and improved performance. This section explores future trends and innovations in vibration motor technology.
Technological Advancements
- Miniaturization: Advances in manufacturing and materials will enable the development of smaller and more compact vibration motors, expanding their use in miniaturized devices and systems.
- Increased Efficiency: Innovations in motor design and materials will lead to more efficient vibration motors with lower power consumption and higher performance.
- Improved Control and Precision: Enhanced control algorithms and sensor integration will enable more precise and customizable vibration effects, improving user experience and application performance.
Integration with Smart Technologies
The integration of vibration motors with the Internet of Things (IoT) and smart technologies will open up new possibilities for applications and functionality.
- Smart Manufacturing: Vibration motors will play a key role in smart manufacturing processes, enabling real-time monitoring and control of production systems.
- Automated Systems: Integration with smart technologies will enhance the performance and efficiency of automated systems, improving productivity and quality.
Emerging Applications
- Advanced Robotics: Vibration motors will enhance the performance of advanced robotic systems, providing precise control and feedback for complex tasks.
- Augmented Reality (AR): Vibration motors will enhance AR experiences by providing tactile feedback for virtual interactions, improving immersion and realism.
- Next-Generation Industrial Equipment: Vibration motors will continue to enhance the performance of next-generation industrial equipment, such as 3D printers and advanced manufacturing systems.
In summary, the future of industrial vibration motors is promising, with advancements in technology and integration with smart systems leading to new applications and improved performance. These innovations will continue to enhance functionality and efficiency across various industries.
Conclusion
Industrial vibration motors are essential components in modern technology, providing crucial functionality and enhancing efficiency across a wide range of applications. This article has explored the various types of vibration motors, their technical aspects, and their diverse applications in industrial settings.
Recap of Key Points
- Types of Vibration Motors: We examined the different types of industrial vibration motors, each with unique characteristics and advantages.
- Technical Aspects: We discussed the construction, key specifications, performance characteristics, and design considerations associated with vibration motors, highlighting the factors that influence their selection and integration.
- Applications: We explored the diverse applications of vibration motors in industries such as material handling, mining, construction, and pharmaceuticals, showcasing their versatility and importance in modern industry.
- Challenges and Solutions: We identified common challenges in industrial applications and provided solutions to address them, ensuring reliable and efficient motor performance.
- Future Trends and Innovations: We examined the future trends and innovations in vibration motor technology, including miniaturization, increased efficiency, and integration with smart technologies.
Importance in Modern Industry
Industrial vibration motors play a crucial role in enhancing efficiency, productivity, and quality across various industries. Their ability to provide precise control, feedback, and motion makes them indispensable components in modern industrial processes.
- Material Handling: Vibration motors improve the efficiency of material handling operations, enhancing productivity and reducing costs.
- Machinery Monitoring: Vibration motors enable real-time monitoring and maintenance of machinery, improving equipment reliability and longevity.
- Diverse Applications: From mining to pharmaceuticals, vibration motors are used in a wide range of applications, highlighting their versatility and adaptability.
Future Outlook
As technology continues to advance, industrial vibration motors will play an increasingly important role in emerging applications and industries. Innovations in design, materials, and integration will lead to new possibilities and improved performance, enhancing functionality and efficiency across various sectors.
In conclusion, industrial vibration motors are vital components in modern technology, providing essential functionality and enhancing efficiency across a wide range of applications. Their versatility, adaptability, and potential for future advancements make them indispensable in the ever-evolving industrial landscape.
Introduction to Energy Consumption
Creating an informative article on energy consumption tips can help individuals and businesses save money, reduce their environmental impact, and improve overall energy efficiency. Below is a comprehensive 5000-word article suitable for a professional website, covering various aspects of energy consumption tips:
Energy consumption refers to the total amount of energy used by individuals, households, businesses, and industries. It encompasses various forms of energy, including electricity, natural gas, oil, and renewable energy sources. Understanding energy consumption is crucial for identifying areas where efficiency can be improved, leading to cost savings and environmental benefits.
Key aspects of energy consumption include:
- Types of Energy: Energy consumption can be categorized into different types, such as electrical, thermal, and mechanical energy, each serving specific purposes in daily activities and industrial processes.
- Energy Sources: Energy can be derived from various sources, including fossil fuels (coal, oil, natural gas) and renewable sources (solar, wind, geothermal, biomass, hydroelectric).
- Energy Demand: The demand for energy varies based on factors such as population, economic activity, climate, and technological advancements.
Importance of Energy Efficiency
Energy efficiency involves using less energy to perform the same tasks, reducing energy waste, and minimizing the environmental impact of energy use. It is a critical component of sustainable development and offers numerous benefits:
- Cost Savings: Improving energy efficiency can lead to significant reductions in energy bills, benefiting households, businesses, and industries.
- Environmental Benefits: Reducing energy consumption decreases greenhouse gas emissions and reduces reliance on fossil fuels, mitigating the impact of climate change.
- Resource Conservation: Energy efficiency helps conserve natural resources by reducing the demand for energy production and consumption.
- Energy Security: Efficient energy use reduces dependence on imported energy sources, enhancing energy security and resilience.
Benefits of Reducing Energy Consumption
Reducing energy consumption offers a wide range of benefits, including:
- Financial Savings: Lower energy bills result in financial savings for individuals, businesses, and governments, freeing up resources for other investments and initiatives.
- Environmental Protection: Reduced energy consumption leads to lower emissions of pollutants and greenhouse gases, contributing to cleaner air and a healthier environment.
- Improved Comfort and Quality of Life: Energy-efficient homes and buildings provide enhanced comfort, improved indoor air quality, and better thermal regulation.
- Economic Growth: Energy efficiency can drive economic growth by creating jobs in energy-efficient technologies, renewable energy, and sustainable practices.
Key takeaways:
- Essential for Sustainability: Energy consumption is a critical aspect of modern life, and improving energy efficiency is essential for achieving sustainable development.
- Diverse Benefits: Reducing energy consumption offers financial, environmental, and social benefits, making it a valuable goal for individuals, businesses, and governments.
Energy Consumption in Residential Settings
Improving energy efficiency in residential settings can lead to significant cost savings and environmental benefits. This section explores various strategies for reducing energy consumption in homes.
Heating and Cooling
Heating and cooling account for a significant portion of residential energy consumption. Implementing energy-efficient practices can lead to substantial savings:
- Programmable Thermostats: Use programmable thermostats to set specific temperature schedules, reducing energy use when heating or cooling is not needed.
- Example: Set the thermostat to lower the temperature during the winter when you’re asleep or away from home and raise it during the summer.
- Benefits: Reduces energy consumption by adjusting heating and cooling based on occupancy patterns.
- Regular Maintenance: Ensure heating and cooling systems are regularly maintained, including cleaning filters, checking ducts, and servicing equipment.
- Example: Schedule annual maintenance for HVAC systems to ensure they operate efficiently.
- Benefits: Increases the efficiency and lifespan of heating and cooling equipment.
- Insulation and Sealing: Improve insulation in walls, attics, and basements, and seal gaps and cracks to prevent air leaks.
- Example: Use weatherstripping to seal doors and windows, and add insulation to attics.
- Benefits: Reduces heat loss in winter and heat gain in summer, improving comfort and reducing energy use.
- Energy-Efficient HVAC Systems: Consider upgrading to energy-efficient heating and cooling systems, such as heat pumps and high-efficiency furnaces.
- Example: Replace an older furnace with an ENERGY STAR-certified model that offers improved efficiency.
- Benefits: Reduces energy consumption and provides consistent heating and cooling performance.
Lighting
Lighting is another significant contributor to residential energy consumption. Implementing energy-efficient lighting solutions can lead to substantial savings:
- LED Lighting: Replace incandescent and fluorescent bulbs with LED lighting, which uses less energy and lasts longer.
- Example: Install LED bulbs in all light fixtures, including lamps, overhead lights, and outdoor lighting.
- Benefits: Reduces energy consumption, lowers electricity bills, and reduces the need for frequent bulb replacements.
- Motion Sensors and Timers: Use motion sensors and timers to automatically turn off lights when not in use, reducing energy waste.
- Example: Install motion sensors in areas with infrequent use, such as hallways and closets, to automatically turn off lights.
- Benefits: Eliminates energy waste by ensuring lights are only on when needed.
- Natural Lighting: Maximize natural lighting by using windows, skylights, and light-colored interior finishes to reduce the need for artificial lighting.
- Example: Use sheer curtains to allow natural light to enter while maintaining privacy.
- Benefits: Reduces the need for artificial lighting, improving energy efficiency and enhancing indoor ambiance.
- Lighting Controls: Implement lighting controls, such as dimmers and smart switches, to adjust lighting levels based on needs and preferences.
- Example: Install dimmer switches in living areas to control lighting intensity and create desired atmospheres.
- Benefits: Allows for customized lighting levels, reducing energy consumption and enhancing comfort.
Appliances and Electronics
Appliances and electronics account for a significant portion of residential energy use. Implementing energy-efficient practices can lead to significant savings:
- ENERGY STAR Appliances: Choose ENERGY STAR-certified appliances, which meet strict energy efficiency standards and consume less energy.
- Example: Replace an old refrigerator with an ENERGY STAR-certified model that offers improved efficiency.
- Benefits: Reduces energy consumption and lowers electricity bills.
- Unplugging Devices: Unplug devices and chargers when not in use to eliminate standby power consumption, also known as “phantom load.”
- Example: Use power strips to easily turn off multiple devices and chargers when not in use.
- Benefits: Reduces energy waste and lowers electricity bills.
- Efficient Use of Appliances: Use appliances efficiently, such as running full loads in dishwashers and washing machines and using cold water for laundry.
- Example: Wash clothes in cold water and air dry when possible to save energy.
- Benefits: Reduces energy consumption and extends the lifespan of appliances.
- Smart Home Technology: Implement smart home technology to monitor and control appliance energy use, allowing for optimized energy management.
- Example: Use a smart thermostat to control heating and cooling remotely and adjust settings based on occupancy patterns.
- Benefits: Provides greater control over energy use, reducing waste and lowering energy bills.
Water Heating
Water heating is another significant contributor to residential energy consumption. Implementing energy-efficient practices can lead to substantial savings:
- Tankless Water Heaters: Consider installing tankless water heaters, which provide hot water on demand and eliminate standby energy loss.
- Example: Replace a traditional tank water heater with a tankless model that heats water as needed.
- Benefits: Reduces energy consumption and provides continuous hot water supply.
- Water Heater Insulation: Insulate water heater tanks and pipes to reduce heat loss and improve efficiency.
- Example: Install a water heater blanket and insulate hot water pipes to minimize heat loss.
- Benefits: Reduces energy consumption and improves water heating efficiency.
- Lower Water Heater Temperature: Set the water heater temperature to 120°F (49°C) to reduce energy use while maintaining comfort.
- Example: Adjust the thermostat on the water heater to maintain a temperature of 120°F.
- Benefits: Reduces energy consumption and lowers the risk of scalding.
- Efficient Water Use: Implement water-saving practices, such as shorter showers and using low-flow fixtures, to reduce hot water demand.
- Example: Install low-flow showerheads and faucets to reduce water use without sacrificing comfort.
- Benefits: Reduces hot water demand and lowers energy consumption.
Insulation and Sealing
Improving insulation and sealing in residential settings can lead to significant energy savings:
- Wall and Attic Insulation: Improve insulation in walls, attics, and basements to reduce heat loss and gain.
- Example: Add insulation to attics and walls to improve thermal performance and comfort.
- Benefits: Reduces heating and cooling energy consumption and improves indoor comfort.
- Window and Door Sealing: Seal gaps and cracks around windows and doors to prevent air leaks and improve energy efficiency.
- Example: Use weatherstripping and caulking to seal gaps around windows and doors.
- Benefits: Reduces heat loss and gain, improving energy efficiency and comfort.
- Energy-Efficient Windows: Consider upgrading to energy-efficient windows with low-emissivity (Low-E) coatings and double glazing.
- Example: Replace single-pane windows with ENERGY STAR-certified double-pane windows.
- Benefits: Reduces heat transfer and improves energy efficiency.
- Roof and Floor Insulation: Improve insulation in roofs and floors to reduce heat loss and gain, enhancing energy efficiency.
- Example: Install reflective roof coatings and floor insulation to improve thermal performance.
- Benefits: Reduces heating and cooling energy consumption and improves comfort.
In summary, improving energy efficiency in residential settings involves a combination of technology, practices, and behavioral changes. By implementing energy-efficient solutions for heating, cooling, lighting, appliances, and insulation, homeowners can achieve significant cost savings and environmental benefits.
Energy Consumption in Commercial and Industrial Settings
Improving energy efficiency in commercial and industrial settings can lead to significant cost savings, enhanced productivity, and environmental benefits. This section explores various strategies for reducing energy consumption in businesses and industries.
Energy Audits and Monitoring
Conducting energy audits and implementing energy monitoring systems are essential steps in identifying areas for improvement and optimizing energy use.
- Energy Audits: Conduct comprehensive energy audits to assess energy use, identify inefficiencies, and recommend improvements.
- Example: Hire a professional energy auditor to evaluate energy use in a commercial building and provide recommendations for efficiency improvements.
- Benefits: Identifies areas for improvement and provides actionable insights for reducing energy consumption.
- Energy Monitoring Systems: Implement energy monitoring systems to track energy use in real-time, identify trends, and optimize energy management.
- Example: Use energy monitoring software to track electricity use in an industrial facility and identify peak demand periods.
- Benefits: Provides real-time data for informed decision-making and energy optimization.
- Benchmarking: Compare energy use against industry benchmarks and standards to identify areas for improvement and set energy efficiency goals.
- Example: Use energy benchmarking tools to compare energy use in a commercial building against similar facilities.
- Benefits: Identifies opportunities for improvement and sets achievable energy efficiency goals.
- Continuous Improvement: Implement a continuous improvement process for energy management, regularly reviewing energy use and implementing efficiency measures.
- Example: Establish an energy management team to review energy use, set goals, and implement efficiency measures.
- Benefits: Ensures ongoing optimization of energy use and continuous improvement.
Lighting Solutions
Implementing energy-efficient lighting solutions can lead to substantial savings in commercial and industrial settings.
- LED Lighting: Replace traditional lighting with LED lighting, which uses less energy and lasts longer.
- Example: Install LED lighting in offices, warehouses, and manufacturing facilities to reduce energy consumption.
- Benefits: Reduces energy consumption, lowers electricity bills, and reduces maintenance costs.
- Daylighting: Maximize natural daylighting through the use of windows, skylights, and light tubes, reducing the need for artificial lighting.
- Example: Install skylights in warehouses and manufacturing facilities to maximize natural lighting.
- Benefits: Reduces the need for artificial lighting, improving energy efficiency and enhancing indoor ambiance.
- Lighting Controls: Implement lighting controls, such as motion sensors, timers, and dimmers, to optimize lighting use based on occupancy and needs.
- Example: Install motion sensors in restrooms and storage areas to automatically turn off lights when not in use.
- Benefits: Eliminates energy waste and reduces electricity bills.
- Task Lighting: Use task lighting in workspaces to provide focused illumination, reducing the need for overhead lighting.
- Example: Install task lighting at individual workstations to provide focused illumination for tasks.
- Benefits: Reduces overall lighting energy consumption and enhances comfort.
HVAC Systems
Heating, ventilation, and air conditioning (HVAC) systems are major contributors to energy consumption in commercial and industrial settings. Implementing energy-efficient HVAC solutions can lead to substantial savings:
- Regular Maintenance: Ensure HVAC systems are regularly maintained, including cleaning filters, checking ducts, and servicing equipment.
- Example: Schedule annual maintenance for HVAC systems to ensure they operate efficiently.
- Benefits: Increases the efficiency and lifespan of HVAC equipment.
- Energy-Efficient HVAC Systems: Upgrade to energy-efficient HVAC systems, such as high-efficiency heat pumps, chillers, and boilers.
- Example: Replace an older HVAC system with an ENERGY STAR-certified model that offers improved efficiency.
- Benefits: Reduces energy consumption and provides consistent heating and cooling performance.
- Zoning Systems: Implement zoning systems to control heating and cooling in specific areas, reducing energy use in unoccupied or low-traffic areas.
- Example: Use zoning controls to manage temperature settings in different areas of a building based on occupancy patterns.
- Benefits: Reduces energy consumption and enhances comfort.
- Building Automation Systems: Use building automation systems to monitor and control HVAC systems, optimizing energy use based on occupancy and needs.
- Example: Implement a building automation system to adjust HVAC settings based on occupancy patterns and external conditions.
- Benefits: Provides greater control over energy use, reducing waste and lowering energy bills.
Industrial Equipment and Machinery
Improving the energy efficiency of industrial equipment and machinery can lead to significant cost savings and environmental benefits.
- Variable Frequency Drives (VFDs): Install variable frequency drives on motors to optimize speed and reduce energy consumption.
- Example: Install VFDs on pumps and fans to adjust motor speed based on demand.
- Benefits: Reduces energy consumption and extends the lifespan of motors.
- Energy-Efficient Motors: Upgrade to energy-efficient motors that consume less energy and provide improved performance.
- Example: Replace older motors with high-efficiency models that meet or exceed industry standards.
- Benefits: Reduces energy consumption and lowers maintenance costs.
- Compressed Air Systems: Optimize compressed air systems to reduce energy consumption and improve efficiency.
- Example: Conduct regular maintenance, repair leaks, and adjust pressure settings in compressed air systems.
- Benefits: Reduces energy waste and improves system performance.
- Efficient Use of Equipment: Implement practices to optimize the use of industrial equipment, such as scheduling maintenance during off-peak hours and reducing idle time.
- Example: Schedule equipment maintenance during off-peak hours to reduce energy demand.
- Benefits: Reduces energy consumption and enhances equipment performance.
Office Equipment and Electronics
Improving the energy efficiency of office equipment and electronics can lead to significant savings in commercial settings.
- ENERGY STAR Office Equipment: Choose ENERGY STAR-certified office equipment, which meets strict energy efficiency standards and consumes less energy.
- Example: Replace older printers and copiers with ENERGY STAR-certified models that offer improved efficiency.
- Benefits: Reduces energy consumption and lowers electricity bills.
- Power Management Features: Use power management features on computers, monitors, and other electronics to reduce energy consumption during periods of inactivity.
- Example: Enable sleep mode on computers and monitors to reduce energy use during periods of inactivity.
- Benefits: Reduces energy waste and extends the lifespan of electronics.
- Unplugging Devices: Unplug devices and chargers when not in use to eliminate standby power consumption, also known as “phantom load.”
- Example: Use power strips to easily turn off multiple devices and chargers when not in use.
- Benefits: Reduces energy waste and lowers electricity bills.
- Efficient Use of Equipment: Implement practices to optimize the use of office equipment, such as using digital documents instead of printing and turning off equipment when not in use.
- Example: Use digital documents and cloud storage to reduce paper use and energy consumption.
- Benefits: Reduces energy consumption and lowers operating costs.
In summary, improving energy efficiency in commercial and industrial settings involves a combination of technology, practices, and behavioral changes. By implementing energy-efficient solutions for lighting, HVAC, equipment, and electronics, businesses can achieve significant cost savings and environmental benefits.
Renewable Energy Solutions
Incorporating renewable energy solutions can significantly reduce energy consumption, lower carbon emissions, and promote sustainability. This section explores various renewable energy solutions and their benefits.
Solar Power
Solar power is a clean and renewable energy source that harnesses the sun’s energy to generate electricity and heat. It is a versatile solution that can be used in residential, commercial, and industrial settings.
Solar Photovoltaic (PV) Systems
Solar PV systems convert sunlight into electricity using solar panels. They can be installed on rooftops, ground-mounted systems, or integrated into building designs.
Benefits of Solar PV Systems:
- Clean Energy: Solar PV systems produce electricity without emitting greenhouse gases or pollutants.
- Cost Savings: Solar PV systems can reduce or eliminate electricity bills, leading to significant cost savings over time.
- Energy Independence: Solar PV systems provide energy independence by reducing reliance on grid electricity.
- Scalability: Solar PV systems can be scaled to meet the energy needs of various applications, from small residential systems to large commercial installations.
Solar Thermal Systems
Solar thermal systems use sunlight to heat water or air for residential, commercial, and industrial applications. They are commonly used for water heating, space heating, and industrial processes.
Benefits of Solar Thermal Systems:
- Energy Efficiency: Solar thermal systems are highly efficient, converting a large portion of sunlight into usable heat.
- Cost Savings: Solar thermal systems can reduce or eliminate heating bills, leading to significant cost savings over time.
- Environmental Benefits: Solar thermal systems produce heat without emitting greenhouse gases or pollutants.
- Versatility: Solar thermal systems can be used for various applications, including domestic hot water, space heating, and industrial processes.
Wind Energy
Wind energy is a clean and renewable energy source that harnesses the power of the wind to generate electricity. It is a cost-effective solution for reducing energy consumption and promoting sustainability.
Wind Turbines
Wind turbines convert the kinetic energy of the wind into electricity. They can be installed in various settings, including onshore and offshore wind farms.
Benefits of Wind Energy:
- Clean Energy: Wind turbines produce electricity without emitting greenhouse gases or pollutants.
- Cost-Effective: Wind energy is one of the most cost-effective renewable energy sources, offering competitive electricity prices.
- Energy Independence: Wind energy provides energy independence by reducing reliance on fossil fuels and grid electricity.
- Scalability: Wind energy can be scaled to meet the energy needs of various applications, from small residential systems to large utility-scale installations.
Geothermal Heating and Cooling
Geothermal heating and cooling systems use the stable temperature of the earth to provide efficient heating and cooling for residential, commercial, and industrial applications.
Ground Source Heat Pumps (GSHPs)
Ground source heat pumps use the earth’s temperature to transfer heat to or from a building, providing efficient heating and cooling.
Benefits of Geothermal Heating and Cooling:
- Energy Efficiency: Geothermal systems are highly efficient, reducing energy consumption and operating costs.
- Environmental Benefits: Geothermal systems produce heating and cooling without emitting greenhouse gases or pollutants.
- Versatility: Geothermal systems can be used for various applications, including residential heating and cooling, commercial HVAC systems, and industrial processes.
- Longevity: Geothermal systems have a long lifespan, providing reliable performance for decades.
Biomass Energy
Biomass energy is a renewable energy source that uses organic materials, such as wood, agricultural residues, and waste, to generate heat and electricity.
Biomass Boilers
Biomass boilers use organic materials as fuel to produce heat for residential, commercial, and industrial applications.
Benefits of Biomass Energy:
- Renewable Resource: Biomass energy uses renewable organic materials, reducing reliance on fossil fuels.
- Carbon Neutral: Biomass energy is considered carbon neutral, as the carbon dioxide released during combustion is offset by the carbon dioxide absorbed by plants during growth.
- Waste Reduction: Biomass energy can use waste materials as fuel, reducing waste and promoting sustainability.
- Versatility: Biomass energy can be used for various applications, including residential heating, industrial processes, and electricity generation.
Hydroelectric Power
Hydroelectric power is a renewable energy source that uses the flow of water to generate electricity. It is a reliable and cost-effective solution for reducing energy consumption and promoting sustainability.
Hydroelectric Dams
Hydroelectric dams use the flow of water from rivers or reservoirs to generate electricity. They are commonly used for large-scale electricity generation.
Benefits of Hydroelectric Power:
- Clean Energy: Hydroelectric power produces electricity without emitting greenhouse gases or pollutants.
- Reliable Source: Hydroelectric power is a reliable and consistent source of electricity, providing stable power generation.
- Cost-Effective: Hydroelectric power offers competitive electricity prices, making it one of the most cost-effective renewable energy sources.
- Energy Independence: Hydroelectric power provides energy independence by reducing reliance on fossil fuels and grid electricity.
In summary, incorporating renewable energy solutions can significantly reduce energy consumption, lower carbon emissions, and promote sustainability. By utilizing solar power, wind energy, geothermal heating and cooling, biomass energy, and hydroelectric power, individuals and businesses can achieve significant environmental and economic benefits.
Smart Technology and Energy Management
Smart technology and energy management solutions can significantly improve energy efficiency, reduce energy consumption, and enhance control over energy use. This section explores various smart technologies and their benefits.
Smart Meters
Smart meters are advanced metering devices that provide real-time data on energy use, allowing for better monitoring and control of energy consumption.
Benefits of Smart Meters:
- Real-Time Data: Smart meters provide real-time data on energy use, allowing for informed decision-making and energy optimization.
- Energy Savings: Smart meters enable consumers to identify energy waste and implement efficiency measures, leading to cost savings.
- Enhanced Control: Smart meters provide greater control over energy use, allowing consumers to adjust consumption based on real-time data.
- Demand Response: Smart meters facilitate demand response programs, allowing utilities to manage peak demand and reduce energy costs.
Home Automation Systems
Home automation systems integrate smart devices and appliances, allowing for centralized control and monitoring of energy use.
Benefits of Home Automation Systems:
- Convenience: Home automation systems provide centralized control over lighting, heating, cooling, and appliances, enhancing convenience and comfort.
- Energy Efficiency: Home automation systems optimize energy use by adjusting settings based on occupancy patterns and preferences.
- Remote Monitoring: Home automation systems provide remote monitoring and control, allowing consumers to manage energy use from anywhere.
- Security: Home automation systems enhance security by integrating smart locks, cameras, and alarms, providing peace of mind.
Energy Management Software
Energy management software provides tools for monitoring, analyzing, and optimizing energy use in residential, commercial, and industrial settings.
Benefits of Energy Management Software:
- Data Analysis: Energy management software provides data analysis tools for identifying trends, inefficiencies, and opportunities for improvement.
- Customizable Solutions: Energy management software offers customizable solutions to meet specific energy management needs and goals.
- Real-Time Monitoring: Energy management software provides real-time monitoring and alerts, enabling proactive energy management.
- Cost Savings: Energy management software helps identify and implement efficiency measures, leading to significant cost savings.
IoT Devices for Energy Efficiency
Internet of Things (IoT) devices provide advanced monitoring and control of energy use, enhancing efficiency and sustainability.
Benefits of IoT Devices:
- Enhanced Monitoring: IoT devices provide real-time data on energy use, enabling informed decision-making and optimization.
- Remote Control: IoT devices provide remote control and monitoring, allowing consumers to manage energy use from anywhere.
- Integration: IoT devices integrate with smart home systems, enhancing convenience and control.
- Energy Savings: IoT devices enable consumers to identify and eliminate energy waste, leading to significant cost savings.
Demand Response Systems
Demand response systems enable utilities and consumers to manage energy use during peak demand periods, reducing energy costs and improving grid reliability.
Benefits of Demand Response Systems:
- Cost Savings: Demand response systems reduce energy costs by shifting consumption to off-peak periods.
- Grid Reliability: Demand response systems improve grid reliability by reducing peak demand and preventing outages.
- Environmental Benefits: Demand response systems reduce the need for additional power generation, lowering emissions and environmental impact.
- Enhanced Control: Demand response systems provide consumers with greater control over energy use, allowing for more efficient consumption.
In summary, smart technology and energy management solutions provide advanced tools for improving energy efficiency, reducing energy consumption, and enhancing control over energy use. By implementing smart meters, home automation systems, energy management software, IoT devices, and demand response systems, individuals and businesses can achieve significant cost savings and environmental benefits.
Behavioral Changes for Energy Savings
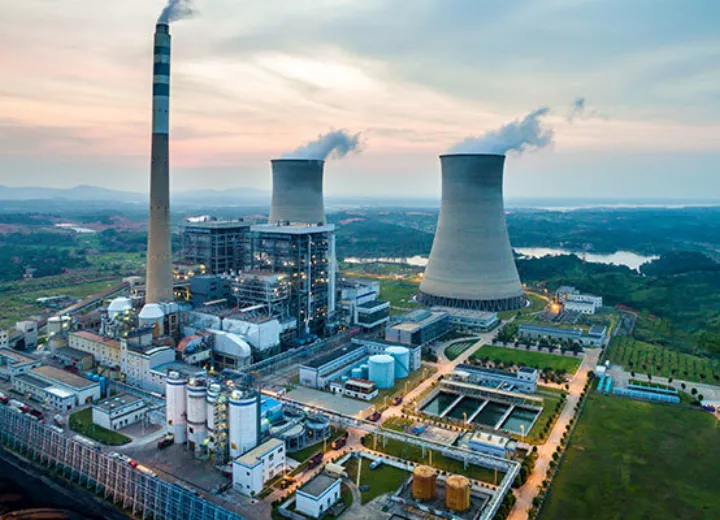
Behavioral changes can have a significant impact on energy consumption, leading to cost savings and environmental benefits. This section explores various behavioral changes that can reduce energy use.
Energy-Saving Habits
Adopting energy-saving habits can lead to significant reductions in energy consumption:
- Turning Off Lights: Turn off lights when leaving a room to reduce energy waste.
- Example: Develop a habit of turning off lights when exiting a room, even for short periods.
- Benefits: Reduces energy consumption and lowers electricity bills.
- Unplugging Devices: Unplug devices and chargers when not in use to eliminate standby power consumption, also known as “phantom load.”
- Example: Use power strips to easily turn off multiple devices and chargers when not in use.
- Benefits: Reduces energy waste and lowers electricity bills.
- Adjusting Thermostat Settings: Adjust thermostat settings based on occupancy patterns and preferences to reduce energy use.
- Example: Set the thermostat to lower temperatures during the winter and higher temperatures during the summer when the home is unoccupied.
- Benefits: Reduces energy consumption and lowers heating and cooling bills.
- Using Energy-Efficient Transportation: Choose energy-efficient transportation options, such as walking, biking, carpooling, or using public transit.
- Example: Use public transit for commuting to work instead of driving a personal vehicle.
- Benefits: Reduces energy consumption and lowers transportation costs.
Encouraging Energy Awareness
Promoting energy awareness can lead to increased energy efficiency and sustainability:
- Educating Employees: Educate employees about energy efficiency and encourage energy-saving practices in the workplace.
- Example: Conduct energy efficiency workshops and training sessions for employees.
- Benefits: Increases energy awareness and promotes energy-saving practices.
- Setting Energy Goals: Set energy efficiency goals and track progress to encourage energy-saving practices.
- Example: Set a goal to reduce energy consumption by a specific percentage over a set period and track progress regularly.
- Benefits: Encourages energy-saving practices and promotes continuous improvement.
- Incentivizing Energy Efficiency: Provide incentives for energy-saving practices, such as rewards for meeting energy efficiency goals.
- Example: Offer rewards or recognition for employees or departments that achieve energy efficiency goals.
- Benefits: Motivates individuals and teams to adopt energy-saving practices.
- Promoting Energy Conservation: Promote energy conservation through awareness campaigns, workshops, and educational materials.
- Example: Develop educational materials and campaigns to promote energy conservation in the community.
- Benefits: Raises awareness about energy efficiency and encourages energy-saving practices.
Reducing Energy Waste
Reducing energy waste can lead to significant cost savings and environmental benefits:
- Fixing Leaks: Fix leaks in pipes, faucets, and ducts to prevent energy waste.
- Example: Regularly inspect and repair leaks in plumbing and HVAC systems.
- Benefits: Reduces energy waste and lowers energy bills.
- Optimizing Equipment Use: Use equipment efficiently, such as running full loads in dishwashers and washing machines and using cold water for laundry.
- Example: Wash clothes in cold water and air dry when possible to save energy.
- Benefits: Reduces energy consumption and extends the lifespan of equipment.
- Regular Maintenance: Ensure equipment and systems are regularly maintained to optimize performance and efficiency.
- Example: Schedule regular maintenance for HVAC systems, appliances, and vehicles.
- Benefits: Improves energy efficiency and extends the lifespan of equipment.
- Efficient Use of Resources: Implement practices to optimize the use of resources, such as using digital documents instead of printing and turning off equipment when not in use.
- Example: Use digital documents and cloud storage to reduce paper use and energy consumption.
- Benefits: Reduces energy consumption and lowers operating costs.
In summary, behavioral changes can have a significant impact on energy consumption, leading to cost savings and environmental benefits. By adopting energy-saving habits, promoting energy awareness, and reducing energy waste, individuals and businesses can achieve significant energy efficiency and sustainability.
Conclusion
Energy consumption is a critical aspect of modern life, and improving energy efficiency is essential for achieving sustainable development. This article has explored various strategies for reducing energy consumption in residential, commercial, and industrial settings.
Recap of Key Points
- Residential Energy Efficiency: We explored energy-efficient solutions for heating, cooling, lighting, appliances, and insulation, highlighting the importance of technology, practices, and behavioral changes.
- Commercial and Industrial Energy Efficiency: We discussed energy-efficient solutions for lighting, HVAC, equipment, and electronics, emphasizing the importance of energy audits, monitoring, and management.
- Renewable Energy Solutions: We examined the benefits of incorporating renewable energy solutions, such as solar power, wind energy, geothermal heating and cooling, biomass energy, and hydroelectric power.
- Smart Technology and Energy Management: We explored the benefits of smart technology and energy management solutions, including smart meters, home automation systems, energy management software, IoT devices, and demand response systems.
- Behavioral Changes for Energy Savings: We discussed the importance of adopting energy-saving habits, promoting energy awareness, and reducing energy waste to achieve significant energy efficiency and sustainability.
The Role of Individuals and Businesses
Individuals and businesses play a crucial role in reducing energy consumption and promoting sustainability. By implementing energy-efficient solutions and adopting energy-saving practices, individuals and businesses can achieve significant cost savings, reduce environmental impact, and contribute to a more sustainable future.
Key actions for individuals and businesses:
- Invest in Energy Efficiency: Invest in energy-efficient technologies and solutions to reduce energy consumption and lower operating costs.
- Promote Energy Awareness: Promote energy awareness and education to encourage energy-saving practices and behaviors.
- Set Energy Efficiency Goals: Set energy efficiency goals and track progress to drive continuous improvement and sustainability.
Future Outlook
As technology continues to evolve, new opportunities for improving energy efficiency and sustainability will emerge. Advancements in renewable energy, smart technology, and energy management will drive further improvements in energy efficiency and provide new solutions for reducing energy consumption.
Future trends in energy efficiency:
- Renewable Energy Integration: The integration of renewable energy solutions will continue to expand, providing clean and sustainable energy for various applications.
- Smart Technology Advancements: Advancements in smart technology and energy management will provide new tools and solutions for optimizing energy use and reducing energy waste.
- Sustainable Practices: The adoption of sustainable practices and behaviors will continue to grow, driving further improvements in energy efficiency and sustainability.
In conclusion, energy consumption is a critical aspect of modern life, and improving energy efficiency is essential for achieving sustainable development. By implementing energy-efficient solutions, adopting energy-saving practices, and promoting sustainability, individuals and businesses can achieve significant energy efficiency and environmental benefits, contributing to a more sustainable future.
EMS Power Machines
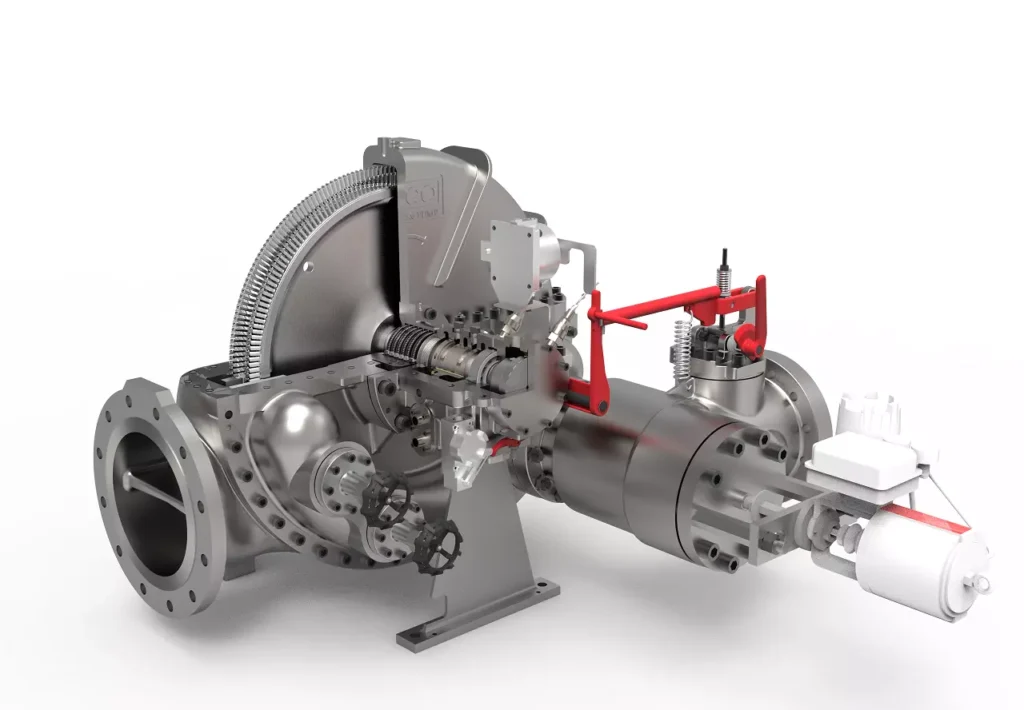
We design, manufacture and assembly Power Machines such as – diesel generators, electric motors, vibration motors, pumps, steam engines and steam turbines
EMS Power Machines is a global power engineering company, one of the five world leaders in the industry in terms of installed equipment. The companies included in the company have been operating in the energy market for more than 60 years.
EMS Power Machines manufactures steam turbines, gas turbines, hydroelectric turbines, generators, and other power equipment for thermal, nuclear, and hydroelectric power plants, as well as for various industries, transport, and marine energy.
EMS Power Machines is a major player in the global power industry, and its equipment is used in power plants all over the world. The company has a strong track record of innovation, and it is constantly developing new and improved technologies.
Here are some examples of Power Machines’ products and services:
- Steam turbines for thermal and nuclear power plants
- Gas turbines for combined cycle power plants and industrial applications
- Hydroelectric turbines for hydroelectric power plants
- Generators for all types of power plants
- Boilers for thermal power plants
- Condensers for thermal power plants
- Reheaters for thermal power plants
- Air preheaters for thermal power plants
- Feedwater pumps for thermal power plants
- Control systems for power plants
- Maintenance and repair services for power plants
EMS Power Machines is committed to providing its customers with high-quality products and services. The company has a strong reputation for reliability and innovation. Power Machines is a leading provider of power equipment and services, and it plays a vital role in the global power industry.
EMS Power Machines, which began in 1961 as a small factory of electric motors, has become a leading global supplier of electronic products for different segments. The search for excellence has resulted in the diversification of the business, adding to the electric motors products which provide from power generation to more efficient means of use.