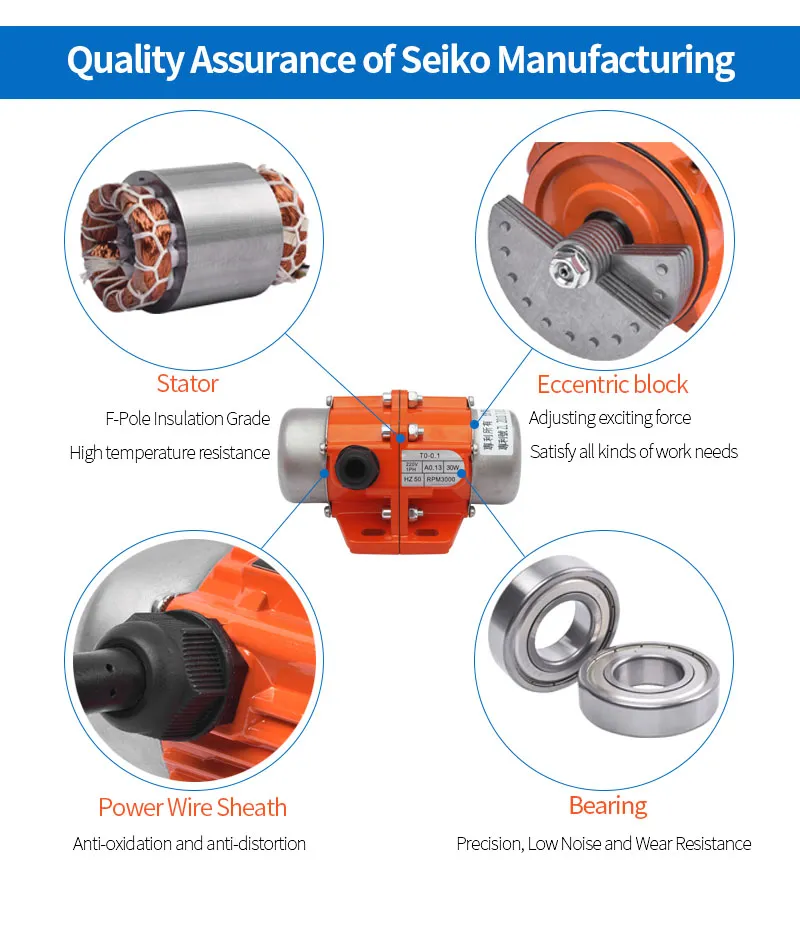
How do vibration motors work? Here you will get some brief information about vibration motors and their applications in the industry. Vibrator motors are here.
How Do Vibration Motors Work?
Vibration motors, also known as shakers or vibrators, are electromechanical devices that convert electrical energy into mechanical vibration. They are commonly used in a wide range of applications, including mobile phones, gaming controllers, and medical equipment.
Working Principle of Vibration Motors:
- Electromagnetism: A vibration motor consists of an electromagnet and a movable mass, such as a weight or armature.
- Electrical Current: When an electrical current is applied to the coil of the electromagnet, it creates a magnetic field.
- Attraction and Repelling: The moving mass is attracted to and repelled by the magnetic field, causing it to oscillate back and forth.
- Vibration Generation: The oscillations of the moving mass translate into mechanical vibrations, which can be felt or heard.
Types of Vibration Motors:
- Eccentric Rotating Mass Motors: These motors have an eccentric mass attached to the rotating shaft, which creates a centrifugal force that causes vibration.
- Voice Coil Motors (VCMs): These motors use a voice coil, which is a conductor suspended in a magnetic field, to create vibration.
- Ultresonic Motors: These motors generate ultrasonic vibrations by using a piezoelectric crystal.
Applications of Vibration Motors:
- Feedback Mechanisms: Vibration motors are used in mobile phones and gaming controllers to provide haptic feedback, simulating the feeling of buttons being pressed.
- Shakers and Massagers: Vibration motors are used in personal care devices to provide a massaging or shaking effect.
- Medical Equipment: Vibration motors are used in medical equipment, such as endoscopes and ultrasound machines, to help with tissue manipulation and cleaning.
- Manufacturing Processes: Vibration motors are used in manufacturing processes to help with mixing, sorting, and deburring.
- Alarms and Warning Signals: Vibration motors can be used to generate alarms or warning signals in emergency situations.
Advantages of Vibration Motors:
- Compact Size: Vibration motors are relatively small and lightweight, making them suitable for portable devices.
- Low Cost: Vibration motors are relatively inexpensive, making them a cost-effective solution for many applications.
- Versatility: Vibration motors can be used in a wide range of applications.
Challenges of Vibration Motors:
- Noise: Vibration motors can generate noise, which may be a concern in some applications.
- Power Requirements: Vibration motors can require a significant amount of power to operate, which may be a limiting factor in some devices.
- Durability: Vibration motors can be susceptible to wear and tear, especially in high-usage applications.
Future Trends in Vibration Motor Technology:
- Miniaturization: Efforts are focused on miniaturizing vibration motors to make them even smaller and more integrated into devices.
- Improved Efficiency: Research is being conducted to improve the efficiency of vibration motors to reduce power consumption.
- Smart Vibration Control: Smart control systems are being developed to optimize the vibration of motors to improve performance and reduce noise.
CAN ALL SIZES OF ROTARY ELECTRIC VIBRATORS BE PURCHASED IN 120V SINGLE-PHASE?
No. 120V Industrial Vibrators are only available in a limited line of smaller-sized Vibrators. The reason for the size limitation is the torque requirement during start-up. Electrically, a stator can only provide a fixed amount of torque.
The amount of torque required to rotate a specifically sized set of eccentric weights (used to generate force output), increases dramatically as the size of the weights increases. 120V single-phase Vibrators are limited in the amount of torque the Motor can effectively produce based on the size and efficiency of the electrical characteristics of the Motor.
CAN A 120V SINGLE-PHASE ROTARY ELECTRIC VIBRATOR BE DIRECTLY PLUGGED INTO A 120V OUTLET?
No. Typically you cannot simply plug a 120V single-phase Vibrator into an outlet and operate the Motor. Most 120V Vibrators require a start and/or run capacitor in order to operate correctly. The capacitor requirements vary according to the size of the Vibrator Motor.
CAN A RHEOSTAT BE USED ON A SINGLE-PHASE ROTARY ELECTRIC VIBRATORY MOTOR TO ADJUST THE RPM?
Yes. Depending on the design of the Vibrator, a rheostat can be used to adjust RPM. Some single-phase Motor manufacturers allow the use of a rheostat on their Motors and some do not. Initially, it must be determined if the Vibrator being used is suited to have the RPM adjusted via a rheostat. If the answer is “yes”, the user must be aware that because a rheostat drops the voltage, there will also be a drop in starting torque.
With this in mind, it is recommended to always start the Vibrator with the rheostat set at maximum RPM, and to then slow the Vibrator down to the required speed. It is also important to note that most single-phase Vibratory Motors require capacitors for start-up and/or running. This capacitor requirement means that if a rheostat to be used, it must be compatible with capacitor operation.
ARE SINGLE-PHASE ROTARY ELECTRIC VIBRATORS SUITABLE FOR OUTDOOR, COLD-WEATHER USE?
Yes. Single-phase Vibrators (both 120V & 240V) can be used in outdoor, cold-weather applications, but they are not ideal because of the low torque single-phase motors generate. Combine this inherent torque limitation with cold temperatures (<32°F) and resultant “stiff” grease, and the Vibrator may not generate enough torque to overcome the load imposed by the swinging mass of the eccentric weights during initial start-up.
Typically, once a single-phase Vibrator is running and warmed up, it will start/stop and run without issue on a cold day. Therefore, we’re not saying you can’t use single-phase Vibrators outdoors, many people do, what we are saying is that start-up issues can occur, and the colder the temperature and longer the “OFF” interval, the greater the likelihood of problems. What we suggest is that wherever possible, you use a 3-phase Vibrator for outdoor, cold weather use because 3-phase Vibrators develop enough torque that start-up and run issues rarely occur.
ARE THREE-PHASE ROTARY ELECTRIC VIBRATORY MOTORS PREFERRED OVER SINGLE-PHASE VIBRATORY MOTORS?
Yes. There are a number of reasons why three-phase Vibratory Motors are preferred over single-phase Industrial Vibrators. The primary reason is the size limitation of single-phase versus three-phase Vibratory Motors. Single-phase Motors are limited to smaller force output Motors. This size limitation can be attributed to two major factors. First, the amount of torque required to rotate a Vibrator’s set of eccentric weights.
A Vibrator’s starting torque increases as the weight sizes increase which means the current required also increases. Single-phase power will quickly and dramatically increase the amperage required to overcome the starting torque requirements, it simply becomes inefficient to use single-phase power as the Vibratory Motor size increases. Further, single-phase Motors don’t react well to cold temperatures.
The lower the temperature, the higher the starting torque – a problem in cold temperature applications. Second, the nature of electricity when used in single-phase applications. This type of electricity is not suited for higher amperage usage. Typically, capacitors are needed to increase the amperage required to power the start-up.
In order to use single-phase electricity in a high amp situation, both the capacitors and conductor wire-gauge required become large quickly. Again, it becomes very inefficient to use larger capacitors as the power consumption increases, and, of course, single-phase power is more expensive to use than three-phase power. In summary, single-phase Vibratory Motors do have value in some specific
applications, but they are limited by size and application.
CAN A 50HZ ROTARY ELECTRIC VIBRATOR BE RUN AT 60HZ, OR A 60HZ VIBRATOR AT 50 HZ?
Yes and No. Using 3000/3600 RPM Motors as an example, 50Hz (3000 RPM) and 60 Hz (3600 RPM) Vibrators of the same size typically use the same stator. As long as the Motors share the same stator design, and the stator is designed to run at variable frequencies, you can run the Motors safely at the other frequency. Where problems will be encountered is mechanical with the eccentric weight sets.
For example, assume a 50 Hz Motor running at 3000 RPM, producing 1107 lbs of centrifugal force (CF) output, and using a weight with a static moment rated at 4.3 in-lbs. Taking the same 50 Hz/3000 RPM Motor and running it at 60 Hz/3600 RPM, the 4.3 in-lbs weight set will produce 1583 lbs of CF. At 60 Hz/3600 RPM, the 1583 pounds of CF is too much for the bearings and they will fail. In the alternative, running the 60 Hz/3600 version of the Motor at 50Hz/3000 RPM will produce much less CF than anticipated.
For example, assume a 60 Hz motor running at 3600 RPM, producing 1036 lbs of CF output, and using a weight with a static moment rated at 2.8 in-lbs. Taking the same 60 Hz/3600 RPM Motor and running it at 50 Hz/3000 RPM, the 2.8 in-lbs weight set will produce only 716 lbs of CF. At 50 Hz/3000 RPM, the 716 lbs of CF is far less than this Motor can safely produce with properly sized weights. The same type of relationships
exist with Vibratory Motors at other operating speeds, ie, 1500/1800 RPM, 1000/1200RPM and 750/900RPM.
To summarize the results, we can safely operate a higher frequency/speed Vibrator Motor at a lower frequency/speed and not damage the Motor, albeit with much lower CF results. We cannot operate a lower frequency/speed Motor at a higher frequency/speed without subjecting the bearings to excessive stress due to the weight sizes associated with the specific speed requirements.
CAN A ROTARY ELECTRIC VIBRATOR BE RUN ON AN INVERTER?
Yes. It is generally ok to run Vibratory Motors on an Inverter. Most three-phase 60Hz Vibrators are designed to run safely between 20 Hz to 60 Hz with no issue. Also, most three-phase 50Hz Vibrators can be run safely between 20 Hz to 50 Hz with no issue. Typically, it is stated on the Vibrator’s nameplate if it is safe to operate on an Inverter. It is important to note, the nameplate amp draw should never be exceeded
throughout the entire frequency range.
CAN THE CENTRIFUGAL FORCE OUTPUT OF A ROTARY ELECTRIC VIBRATORY MOTOR BE INCREASED OR DECREASED BY ONLY CHANGING THE ECCENTRIC WEIGHTS ON ONE SIDE OF THE MOTOR?
No. Weights on an individual Vibratory Motor must be set equal to each other. The eccentric weights or both ends of the Vibrator must be adjusted to exactly the same setting. Failure to adhere to this rule will result in premature failure of the Vibrator.
DO TWO INDIVIDUAL ROTARY ELECTRIC VIBRATORS ON A SINGLE PIECE OF VIBRATORY
DOES EQUIPMENT NEED TO BE ELECTRICALLY INTERLOCKED?
Yes. When operating two electric Vibrators on a single piece of Vibratory Equipment, the Vibrators should be controlled with a single motor starter that has overload protection dedicated to each individual Vibrator. The overloads must be electrically interlocked such that a fault with one Vibrator will de-energize both Vibrators. This is required to avoid damage to the Vibratory Equipment and/or the individual Vibrators.
HOW FLAT AND THICK DOES A MOUNTING SURFACE NEED TO BE TO CORRECTLY MOUNT A ROTARY ELECTRIC VIBRATOR?
The Vibrator mounting surface must be ridged and strong enough for the vibration energy transfer to take place without damaging the structure or the Vibrator. The mounting surface must be clean and flat within 0.010 inches across mounting feet, and free of paint, rust, and foreign debris. The minimum thickness of the plate should be equal to or greater than the major diameter of the mounting bolts, eg, ½” mount bolts means a ≥ ½ ” thick plate is needed. It is also important that the feet of the Vibrator are clean and free of debris prior to installation.
WHAT TYPE OF MOUNTING HARDWARE SHOULD BE USED TO MOUNT A ROTARY ELECTRIC VIBRATOR?
Always use new bolts, nuts, and compression washers for each installation or reinstallation. Never reuse hardware that has been previously torqued. The bolts should be a Grade-5 or Grade-8 (Internationally 8.8 and 12.9 respectively). Grade-5 bolts are suitable for the majority of applications. Use only compression washers – do not use split lock washers or any other kind of washer or nut with a locking feature.
All bolts must be torqued to the manufacturer’s recommended torque values. After initial installation, the bolts should be torque-checked after the first 15 minutes of run-time, and then again after 8 hours of Vibrator run-time. Thereafter, the bolt torque should be checked at every 6-month interval.
WILL LOW-VOLTAGE AFFECT MY VIBRATORY MOTOR?
Yes. Operating a Vibratory Motor with a voltage that is lower than the nameplate voltage (≤ 10%) will alter the Motor’s performance. Some performance characteristics will change slightly, while others, such as amp draw, will change dramatically. A Vibratory Motor is classified as a “heavily loaded motor” (power factor is high), especially at start-up.
The amount of power a Motor draws is a direct correlation between voltage and amperage (V = IR). If Voltage (V) is low, then Current (I) must increase to provide the same amount of power because the Resistance (R) is fixed. As the Current increases, heat builds in the Motor. Without corrective action, the heat will damage the Motor’s windings and bearings.
The extent of Motor damage is based on the frequency and duration of the low-voltage abuse. Notable facts about Low-Voltage supply to Vibratory Motors: • Single-phase Vibratory Motors are less adversely affected by Low-Voltage than are Three-phase Vibratory Motors.
- Vibratory Motor efficiency drops significantly with Low-Voltage resulting in more cost to operate and a shorter motor life
- Ironically, the power factor improves with Low-Voltage.
- As Voltage decreases, the Current will increase in the same proportion. This will cause the Motor’s nameplate Full-Load Amp (FLA) Draw to be exceeded.
- Low-Voltage reduces starting torque, which in turn increases stress on the windings due to heat build-up.
- The low-Voltage operation will shorten the life of a Vibratory Motor. The downtime of this critical equipment can be avoided by ensuring that the proper voltage is supplied to all Vibratory Motors.
WILL HIGH VOLTAGE AFFECT MY VIBRATORY MOTOR?
Yes. Operating a Vibratory Motor with a voltage that is higher than the nameplate Voltage (> 10%) will alter the Motor’s performance. Many users mistakenly believe that because Low-Voltage increases the amp draw, that High-Voltage will lower the amp draw. In reality, High-Voltage will put the magnetic portion of the winding into saturation. (Motor Saturation, simply stated, means the Motor needs a larger magnetic circuit to operate.) Saturation causes the magnetic-iron portion of the winding to be pushed beyond its limits which in turn increases Current.
As the Current increases, heat builds in the Motor. Without corrective action, the heat will damage the Motor’s windings and bearings. The extent of the Motor damage is based on the frequency and duration of the high-voltage abuse. Notable facts about High-Voltage supply to Vibratory Motors:
- High-Voltage causes in-rush Current (at Startup) to exceed “safe” limits
- High-Voltage causes Vibratory Motor efficiency to drop resulting in more cost to operate and a shorter motor life
- 1200 and 900-RPM Vibrators are more sensitive to High-Voltage supplies when compared to 3600 and 1800-RPM Vibrators. The lower speed Motors are damaged more rapidly when being supplied High-Voltage.
- Single-phase Motors are more adversely affected by High-Voltage than are Three-phase Vibratory Motors
- The power factor of a Vibratory Motor quickly drops with High-Voltage
- High-Voltage drives up amperage and heat damage of even lightly loaded Motors because a Vibratory Motor is a heavily loaded Motor, it suffers even greater heat damage as the voltage supply rises. The high-Voltage operation will shorten the life of a Vibratory Motor. The downtime of this critical equipment can be avoided by ensuring that the proper voltage is supplied to all Vibratory Motors.
WHAT OPERATIONAL PARAMETERS NEED TO BE INSPECTED DURING THE INITIAL START-UP OF A ROTARY ELECTRIC VIBRATOR?
Make sure the power supplied matches the nameplate requirements. Assure the mounting hardware is properly sized, is minimum Grade-5, and is torqued to the manufacturer’s specifications. Verify the motor starter is
properly sized and set to protect the Vibrator during operation.
While a slight bearing noise is normal and should be expected, excessive noise during operation could indicate a problem. Upon start-up, the amp-draw line current could exceed the nameplate value, but this should drop quickly after the motor is broken-in. If, after a few hours, the amp draw still exceeds the nameplate value, there could be problems with the mounting or the Vibrator, and the Vibrator must be shut off until the issue(s) is resolved.
Never permanently operate the Vibrator above the amp value shown on the nameplate. After 15 minutes, and then again after 8 hours of operation, re-torque the mounting hardware. After 8 hours, verify the amp draw is at or below the nameplate value.
HOW OFTEN SHOULD A ROTARY ELECTRIC VIBRATOR BE LUBRICATED?
Typically every 2000 hours. It is important to use only the specified type and amount of the manufacturer-recommended grease. Use of non-recommended grease and/or over- or under-lubricating the Vibrator will
result in short Vibrator life. Vibrators in some specific applications and Vibrators exposed to excessive heat and/or high wear applications will require more frequent lubrication.
CAN ROTARY ELECTRIC VIBRATORY MOTORS BE REBUILT MECHANICALLY AND ELECTRICALLY?
Yes, But It depends on the size of the Vibrator. All Vibrators, no matter the size, can have the bearings replaced in the event of a mechanical failure, as long as it is cost-effective. Only factory-supplied bearings
should be installed and the manufacturer’s recommended type and quantity of grease must be used. In the event of a stator failure, some stators are replaceable.
The ability to replace a failed stator depends on the OEM’s method of installation. If the stator has been installed in the housing with epoxy, it is probably not cost-effective to replace or rewind the stator. If the stator has been press fitted into the housing, it is usually cost-effective to replace or rewind the stator. Rewinding of a stator should only be performed by qualified electrical rewind shops that are both aware of and follow the special requirements of a stator used in Vibratory Motors.
CAN A ROTARY ELECTRIC VIBRATOR BE TEST RUN WITH THE WEIGHTS SET AT ZERO PERCENT OR WITH THE WEIGHTS REMOVED?
No. Do not test run a Vibrator with no centrifugal load on the bearings. Vibratory Motor bearings are oversized to handle the extreme loads they encounter during operation. Operation of the Vibrator without a centrifugal weight load will cause the bearings to skid (rather than rotate) and build up excessive heat which deprives the bearings of lubrication. This bearing damage occurs rapidly when no bearing load is used during testing.
CAN I GET ADDITIONAL INFORMATION ON TROUBLESHOOTING ROTARY ELECTRIC VIBRATORS?
Yes. Contact us at info@ems-powermachines.com for a complimentary copy of How to Select, Locate, Mount, Repair, and Troubleshoot Rotary Electric Vibrators.
EMS Power Machines
We design, manufacture and assembly Power Machines such as – diesel generators, electric motors, vibration motors, pumps, steam engines and steam turbines
EMS Power Machines is a global power engineering company, one of the five world leaders in the industry in terms of installed equipment. The companies included in the company have been operating in the energy market for more than 60 years.
EMS Power Machines manufactures steam turbines, gas turbines, hydroelectric turbines, generators, and other power equipment for thermal, nuclear, and hydroelectric power plants, as well as for various industries, transport, and marine energy.
EMS Power Machines is a major player in the global power industry, and its equipment is used in power plants all over the world. The company has a strong track record of innovation, and it is constantly developing new and improved technologies.
Here are some examples of Power Machines’ products and services:
- Steam turbines for thermal and nuclear power plants
- Gas turbines for combined cycle power plants and industrial applications
- Hydroelectric turbines for hydroelectric power plants
- Generators for all types of power plants
- Boilers for thermal power plants
- Condensers for thermal power plants
- Reheaters for thermal power plants
- Air preheaters for thermal power plants
- Feedwater pumps for thermal power plants
- Control systems for power plants
- Maintenance and repair services for power plants
EMS Power Machines is committed to providing its customers with high-quality products and services. The company has a strong reputation for reliability and innovation. Power Machines is a leading provider of power equipment and services, and it plays a vital role in the global power industry.
EMS Power Machines, which began in 1961 as a small factory of electric motors, has become a leading global supplier of electronic products for different segments. The search for excellence has resulted in the diversification of the business, adding to the electric motors products which provide from power generation to more efficient means of use.