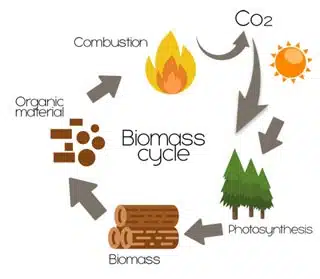
Gasification is a thermochemical process that converts carbonaceous feedstocks such as biomass, coal, or waste materials into a synthesis gas, or syngas, consisting primarily of carbon monoxide (CO), hydrogen (H2), and carbon dioxide (CO2). Unlike combustion, which involves the complete oxidation of fuel in the presence of excess oxygen, gasification occurs in an oxygen-starved environment, leading to partial oxidation and the production of a fuel-rich gas mixture.
The gasification process typically involves several interconnected steps:
- Feedstock Preparation: Carbonaceous feedstocks are first prepared and sized to facilitate handling, feeding, and uniform conversion in the gasification reactor. Biomass feedstocks may undergo drying, grinding, or densification to improve their physical properties and increase energy density.
- Pyrolysis: Upon entering the gasifier, the feedstock undergoes pyrolysis, a thermal decomposition process in which organic materials are heated in the absence of oxygen, leading to the release of volatile compounds such as tar, methane, and other hydrocarbons. Pyrolysis temperatures typically range from 500°C to 800°C, depending on the feedstock composition and gasification conditions.
- Gasification Reactions: In the presence of heat and a controlled amount of oxygen, the volatile compounds produced during pyrolysis undergo further reactions to form syngas. The gasification reactions include:
- Partial Oxidation: The partial oxidation of carbonaceous materials by oxygen or steam generates carbon monoxide and hydrogen, according to the following reactions: C + O2 → CO + CO2 C + H2O → CO + H2
- Water-Gas Shift Reaction: The water-gas shift reaction converts carbon monoxide and steam into additional hydrogen and carbon dioxide: CO + H2O → CO2 + H2 These reactions occur at elevated temperatures (typically between 700°C and 1200°C) and are facilitated by the presence of a gasification agent such as air, oxygen, or steam.
- Syngas Composition: The composition of the syngas produced during gasification depends on various factors, including feedstock composition, gasification conditions (temperature, pressure, residence time), and gasification agent. Typically, syngas consists of approximately 20-30% carbon monoxide, 10-20% hydrogen, 10-20% carbon dioxide, with traces of methane, nitrogen, and other impurities.
- Gas Cleanup: The raw syngas produced from the gasification process contains impurities such as tar, particulates, sulfur compounds, ammonia, and alkali metals, which must be removed or converted to meet product specifications for downstream applications. Gas cleanup technologies such as tar cracking, particulate filtration, sulfur removal, and ammonia scrubbing are employed to purify the syngas and enhance its quality and usability.
- Energy Conversion: The syngas can be utilized for various energy conversion processes, including power generation, heat production, or synthesis of fuels and chemicals. Depending on the application, the syngas may undergo further processing, such as catalytic conversion, Fischer-Tropsch synthesis, or methanation, to produce desired end products.
Gasification
Gasification offers several advantages over conventional combustion and other thermochemical processes:
- Fuel Flexibility: Gasification can utilize a wide range of carbonaceous feedstocks, including biomass, coal, municipal solid waste, or industrial residues, providing flexibility in feedstock selection and resource utilization.
- Energy Efficiency: Gasification can achieve high energy conversion efficiencies compared to traditional combustion processes, especially when combined with advanced gas cleanup and energy recovery technologies.
- Emissions Reduction: Gasification can result in lower emissions of pollutants such as sulfur dioxide, nitrogen oxides, and particulate matter compared to conventional combustion, especially when integrated with gas cleanup technologies and carbon capture and storage (CCS) systems.
Gasification has applications in various sectors, including power generation, industrial processes, transportation fuels, and chemical production. As renewable energy and sustainability efforts continue to gain momentum, gasification technologies are expected to play an increasingly important role in enabling the transition towards a low-carbon, circular economy.
Biomass
Biomass refers to organic matter derived from plants, animals, and microorganisms, which can be utilized as a renewable and sustainable feedstock for various energy and industrial applications. Biomass encompasses a wide range of materials, including agricultural residues, forest residues, energy crops, organic waste, and algae, which can be converted into bioenergy, biofuels, bioproducts, and biochemicals through biochemical, thermochemical, or physicochemical processes.
The use of biomass as a renewable energy source offers several advantages:
- Renewable and Sustainable: Biomass is derived from organic materials that can be replenished through natural processes, making it a renewable and sustainable energy source that can contribute to reducing dependence on finite fossil fuels and mitigating greenhouse gas emissions.
- Carbon Neutral: Biomass absorbs carbon dioxide (CO2) from the atmosphere during photosynthesis, and when used for energy production, the CO2 released during combustion or conversion is offset by the CO2 sequestered during biomass growth, resulting in net-zero carbon emissions and contributing to climate change mitigation.
- Resource Availability: Biomass resources are widely available in diverse forms and locations, including agricultural lands, forests, urban areas, and industrial facilities, providing opportunities for decentralized energy production, rural development, and waste valorization.
- Waste Utilization: Biomass can utilize organic waste materials such as crop residues, forest residues, agricultural byproducts, food waste, and municipal solid waste, diverting these materials from landfills or incineration and converting them into useful energy products, fuels, or chemicals.
- Energy Security: Biomass resources are domestically available and can reduce reliance on imported fossil fuels, enhancing energy security, resilience, and independence, particularly in regions with abundant biomass feedstocks and limited access to conventional energy sources.
- Economic Development: Biomass utilization can stimulate economic growth, create employment opportunities, and support rural economies through biomass production, harvesting, processing, and utilization activities, fostering local value chains and entrepreneurship.
Biomass can be converted into various forms of energy and products through different conversion pathways:
- Biochemical Conversion: Biomass can undergo biochemical conversion processes such as anaerobic digestion, fermentation, or enzymatic hydrolysis to produce biofuels such as biogas, bioethanol, or biodiesel, as well as biochemicals such as organic acids, enzymes, or bioplastics.
- Thermochemical Conversion: Biomass can undergo thermochemical conversion processes such as combustion, gasification, or pyrolysis to produce heat, electricity, biochar, or syngas, which can be utilized for power generation, heating, or synthesis of fuels and chemicals.
- Physicochemical Conversion: Biomass can undergo physicochemical conversion processes such as torrefaction, hydrothermal liquefaction, or solvent extraction to modify its physical or chemical properties and enhance its suitability for energy or industrial applications.
Biomass utilization faces several challenges and considerations, including:
- Feedstock Availability: Biomass availability, quality, seasonality, and logistics vary depending on feedstock type, location, and harvesting practices, requiring sustainable sourcing strategies, feedstock management, and supply chain optimization to ensure reliable and cost-effective biomass supply.
- Conversion Efficiency: Biomass conversion technologies may exhibit varying degrees of efficiency, scalability, and reliability depending on feedstock characteristics, process conditions, and equipment design, requiring continuous research, development, and optimization to improve performance and reduce costs.
- Environmental Impacts: Biomass utilization may have environmental impacts such as land use change, biodiversity loss, water consumption, and air emissions, particularly when biomass production, harvesting, or processing practices are not sustainable or environmentally responsible, requiring comprehensive life cycle assessments and environmental management practices.
- Technological Innovation: Biomass utilization relies on technological innovation and research in biomass conversion, process integration, product development, and market deployment, requiring collaboration between industry, academia, government, and other stakeholders to advance clean energy technologies and solutions.
Overall, biomass represents a valuable and versatile renewable resource with significant potential to contribute to sustainable development, energy transition, and climate change mitigation. As renewable energy and sustainability efforts continue to evolve, biomass utilization will play an increasingly important role in diversifying energy sources, promoting circular economy principles, and fostering resilience in energy systems for future generations.
Feedstock
In the context of biomass utilization and renewable energy production, feedstock refers to the raw material or resource that is used as input for bioenergy conversion processes. Feedstocks can encompass a wide range of organic materials, including agricultural residues, forestry biomass, energy crops, organic waste, algae, and animal manure. The choice of feedstock depends on factors such as availability, accessibility, cost, energy content, and suitability for specific conversion technologies and end-use applications.
- Agricultural Residues: Agricultural residues are leftover biomass materials from crop production processes, including crop stalks, straw, husks, shells, stems, leaves, and other plant parts. Common agricultural residues include corn stover, wheat straw, rice husks, sugarcane bagasse, and cotton gin trash. Agricultural residues are abundant and widely available, especially in agricultural regions, making them attractive feedstocks for bioenergy production.
- Forestry Biomass: Forestry biomass refers to woody biomass materials derived from forest management activities, including logging residues, sawmill residues, tree trimmings, branches, tops, and bark. Forestry biomass can also include non-timber forest products such as leaves, needles, and understory vegetation. Forestry biomass is generated from sustainable forest management practices and can serve as a valuable feedstock for bioenergy production, forest restoration, and wildfire mitigation efforts.
- Energy Crops: Energy crops are specifically grown or cultivated for biomass production and bioenergy purposes, including dedicated bioenergy crops, perennial grasses, short-rotation woody crops, and agroforestry systems. Common energy crops include switchgrass, miscanthus, willow, poplar, eucalyptus, and hybrid poplar. Energy crops offer opportunities for sustainable biomass production on marginal lands, degraded lands, or underutilized agricultural areas, providing additional revenue streams for farmers and landowners.
- Organic Waste: Organic waste materials from various sources, including municipal solid waste (MSW), food waste, agricultural residues, forestry residues, and industrial byproducts, can serve as feedstocks for bioenergy production through anaerobic digestion, composting, or thermochemical conversion processes. Organic waste diversion and valorization can reduce landfilling, methane emissions, and environmental pollution while producing renewable energy, biogas, biofertilizers, or biochemicals.
- Algae: Algae biomass refers to photosynthetic microorganisms that can grow in diverse aquatic environments, including freshwater, seawater, wastewater, and industrial effluents. Algae biomass can be cultivated in open ponds, closed photobioreactors, or raceway systems and harvested for biofuel production, bioremediation, wastewater treatment, or high-value biochemicals. Algae offer high growth rates, high biomass productivity, and potential for carbon capture and utilization (CCU) in bioenergy applications.
Feedstock selection and management are critical factors in biomass utilization and bioenergy production, influencing process efficiency, product quality, environmental sustainability, and economic viability. Considerations for feedstock utilization include:
- Availability and Accessibility: Feedstock availability, proximity, seasonality, and logistics affect the feasibility and cost-effectiveness of biomass supply chains, requiring reliable sourcing strategies, transportation networks, and storage facilities to ensure continuous feedstock supply to bioenergy conversion facilities.
- Energy Content and Composition: Feedstock characteristics such as moisture content, ash content, volatile matter, and elemental composition influence energy density, combustion properties, gasification performance, and biochemical conversion yields, requiring feedstock characterization and testing to optimize process efficiency and product quality.
- Sustainability and Environmental Impact: Feedstock production, harvesting, and conversion practices should be environmentally sustainable, socially responsible, and economically viable, minimizing negative impacts on land, water, air, biodiversity, and local communities while maximizing ecosystem services, carbon sequestration, and resource efficiency.
- Economic Viability and Market Dynamics: Feedstock costs, prices, availability, and market dynamics vary depending on regional, national, and global factors such as energy policies, subsidies, incentives, regulations, market demand, and competition from other sectors, requiring market analysis, risk assessment, and business planning to ensure profitability and competitiveness in bioenergy markets.
Overall, feedstock management plays a crucial role in biomass utilization and bioenergy production, requiring integrated approaches, interdisciplinary collaboration, and stakeholder engagement to address technical, economic, environmental, and social challenges and maximize the potential of biomass resources for sustainable development and renewable energy transition.
Syngas
Syngas, short for synthesis gas, is a versatile mixture of carbon monoxide (CO) and hydrogen (H2), along with varying amounts of carbon dioxide (CO2), methane (CH4), water vapor (H2O), and trace contaminants such as nitrogen (N2), sulfur compounds (e.g., H2S), and particulates. Syngas is produced through the gasification of carbonaceous feedstocks such as biomass, coal, natural gas, or waste materials in the presence of heat, steam, and a controlled amount of oxygen or air.
- Composition: Syngas composition varies depending on feedstock type, gasification process, operating conditions, and gasification agent. Typically, syngas contains approximately 15-30% carbon monoxide (CO), 20-50% hydrogen (H2), 10-30% carbon dioxide (CO2), and traces of methane (CH4), water vapor (H2O), nitrogen (N2), and other impurities. The ratio of CO to H2, known as the syngas ratio, influences the suitability of syngas for different applications, such as fuel synthesis, chemical production, or power generation.
- Production: Syngas is produced through thermochemical processes such as gasification, pyrolysis, or reforming, where carbonaceous feedstocks are heated in the presence of a gasification agent (e.g., air, oxygen, steam) to initiate chemical reactions that convert solid or liquid feedstock into gaseous products. Gasification is the most common method for syngas production and involves partial oxidation of carbonaceous materials in an oxygen-starved environment to produce a fuel-rich gas mixture.
- Applications: Syngas is utilized as a feedstock for various industrial processes, chemical synthesis reactions, and energy conversion technologies, including:
- Fuel Synthesis: Syngas can be converted into liquid fuels such as synthetic gasoline, diesel, methanol, or dimethyl ether (DME) through catalytic processes such as Fischer-Tropsch synthesis or methanol synthesis. These synthetic fuels can be used as drop-in replacements for conventional petroleum-based fuels in transportation, heating, or industrial applications.
- Chemical Production: Syngas serves as a precursor for the synthesis of a wide range of chemicals and intermediates, including ammonia, methanol, hydrogen, synthetic natural gas (SNG), olefins, alcohols, and organic acids. These chemicals are used in various industries such as agriculture, petrochemicals, plastics, pharmaceuticals, and fertilizers.
- Power Generation: Syngas can be utilized as a fuel in gas turbines, internal combustion engines, or combined cycle power plants for electricity generation and cogeneration of heat and power (CHP) in industrial, commercial, or residential applications. Syngas-based power generation offers high efficiency, low emissions, and fuel flexibility compared to conventional combustion technologies.
- Hydrogen Production: Syngas can be reformed, purified, or electrolyzed to produce high-purity hydrogen gas (H2) for fuel cell vehicles, hydrogen fueling stations, industrial processes, or energy storage applications. Syngas-derived hydrogen offers a clean and versatile energy carrier for decarbonizing transportation, industry, and power sectors.
- Gas Cleanup: Raw syngas produced from gasification contains impurities such as tar, particulates, sulfur compounds, ammonia, and alkali metals, which must be removed or converted to meet product specifications for downstream applications. Gas cleanup technologies such as tar cracking, particulate filtration, sulfur removal, and ammonia scrubbing are employed to purify the syngas and enhance its quality and usability.
- Environmental Impact: Syngas utilization offers several environmental benefits compared to conventional fossil fuel combustion, including lower greenhouse gas emissions, reduced air pollutants (e.g., sulfur dioxide, nitrogen oxides, particulate matter), and decreased reliance on finite fossil fuel resources. However, syngas production and utilization may also have environmental impacts such as land use change, water consumption, and waste generation, depending on feedstock selection, process efficiency, and emissions control measures.
Overall, syngas is a valuable intermediate energy carrier and chemical feedstock with diverse applications in renewable fuels production, chemical synthesis, and power generation. As renewable energy and sustainability efforts continue to advance, syngas technologies will play an increasingly important role in enabling the transition towards a low-carbon, circular economy and addressing global energy and environmental challenges for future generations.
Thermal Decomposition
Thermal decomposition, also known as pyrolysis, is a chemical process in which organic materials are heated in the absence of oxygen or in an oxygen-starved environment, leading to the breakdown of complex molecules into simpler compounds, gases, liquids, and solids. Thermal decomposition occurs at elevated temperatures, typically between 300°C and 800°C, depending on the type of feedstock and the desired products.
- Process Overview: During thermal decomposition, the organic material undergoes rapid heating, causing the breakdown of chemical bonds and the release of volatile compounds such as water vapor, hydrocarbons, and other organic gases. As the temperature increases, thermal cracking and rearrangement reactions occur, leading to the formation of smaller molecular fragments, char, and tar-like substances.
- Reaction Mechanisms: Thermal decomposition involves various chemical reactions, including:
- Dehydration: Removal of water molecules from organic materials, resulting in the release of water vapor and the formation of unsaturated hydrocarbons.
- Depolymerization: Breakdown of long-chain polymers into smaller molecules, such as aromatics, olefins, and aliphatic compounds.
- Cracking: Cleavage of carbon-carbon bonds within organic molecules, leading to the formation of hydrocarbon fragments, radicals, and free radicals.
- Carbonization: Conversion of organic materials into carbonaceous residues, char, or carbon black, through thermal stabilization and carbonization processes.
- Tar Formation: Condensation of volatiles and intermediates into tar-like substances, which can accumulate as liquid or solid residues and require further treatment or processing.
- Product Formation: The products of thermal decomposition depend on factors such as feedstock composition, heating rate, residence time, and process conditions. Common products include:
- Gases: Hydrogen (H2), methane (CH4), carbon monoxide (CO), carbon dioxide (CO2), ethylene (C2H4), propylene (C3H6), and other hydrocarbons, depending on the type of feedstock and the temperature range.
- Liquids: Pyrolysis oil, bio-oil, or bio-crude, consisting of a complex mixture of oxygenated hydrocarbons, phenolics, aldehydes, ketones, and organic acids, which can be further processed into biofuels, biochemicals, or platform chemicals.
- Solids: Char, biochar, or carbonaceous residues, containing carbonaceous materials, minerals, and ash, which can be used as soil amendments, adsorbents, or precursors for carbon materials.
- Applications: Thermal decomposition has applications in various sectors, including:
- Biomass Conversion: Thermal decomposition is used to convert biomass feedstocks such as wood, agricultural residues, or waste materials into bioenergy, biofuels, biochar, or biochemicals through pyrolysis, gasification, or combustion processes.
- Waste Valorization: Thermal decomposition processes such as pyrolysis or gasification can convert organic waste materials such as plastics, tires, or municipal solid waste into syngas, bio-oil, or recovered carbon products, reducing waste disposal and environmental pollution.
- Material Synthesis: Thermal decomposition is used to synthesize carbon materials such as carbon nanotubes, graphene, activated carbon, or carbon fibers, through controlled pyrolysis of carbonaceous precursors at high temperatures.
- Challenges and Considerations: Despite its benefits, thermal decomposition processes face challenges such as:
- Energy Efficiency: Achieving high energy efficiency and product yields while minimizing energy consumption, heat loss, and process complexity.
- Product Quality: Ensuring the quality, purity, and consistency of products such as bio-oil, biochar, or syngas for specific applications and end-users.
- Emissions Control: Managing emissions of greenhouse gases, volatile organic compounds (VOCs), particulate matter, and other air pollutants generated during thermal decomposition processes.
- Scale-Up and Commercialization: Scaling up thermal decomposition technologies from laboratory or pilot-scale demonstrations to commercial-scale deployment, addressing technical, economic, and regulatory challenges.
In conclusion, thermal decomposition is a versatile and widely used process for converting organic materials into valuable products such as bioenergy, biofuels, biochemicals, and carbon materials. As renewable energy and circular economy initiatives continue to grow, thermal decomposition technologies will play an increasingly important role in valorizing biomass resources, reducing waste, and advancing sustainable development goals for a greener and cleaner future.
Combustion
Combustion is a chemical process in which a fuel reacts rapidly with oxygen in the air, releasing heat, light, and various combustion products, such as carbon dioxide (CO2), water vapor (H2O), nitrogen oxides (NOx), sulfur oxides (SOx), and particulate matter. Combustion is a common method for converting the chemical energy stored in fuels into thermal energy, which can be used for heating, power generation, propulsion, or industrial processes.
- Process Overview: Combustion occurs when a fuel, such as biomass, coal, natural gas, or petroleum, is oxidized in the presence of a sufficient amount of oxygen (O2) from the air. The combustion process typically involves three main stages: ignition, flame propagation, and combustion completion. During ignition, the fuel is heated to its ignition temperature, initiating the combustion reactions. Flame propagation occurs as the burning fuel releases heat, which sustains the combustion reactions and propagates the flame front through the fuel-air mixture. Combustion completion occurs when the fuel is fully oxidized, and combustion products are formed.
- Chemical Reactions: Combustion reactions involve the oxidation of fuel molecules, which release energy in the form of heat and light. The general combustion reaction for hydrocarbon fuels can be represented as follows: Fuel + Oxygen (O2) → Carbon Dioxide (CO2) + Water Vapor (H2O) + Heat For example, the combustion of methane (CH4) can be represented by the following equation: CH4 + 2O2 → CO2 + 2H2O + Heat In addition to carbon dioxide and water vapor, combustion reactions may also produce nitrogen oxides (NOx) from nitrogen in the air and sulfur oxides (SOx) from sulfur impurities in the fuel.
- Heat Release: Combustion releases heat energy through exothermic chemical reactions, which raises the temperature of the combustion products and surrounding environment. The amount of heat released during combustion depends on factors such as the type of fuel, the stoichiometry of the combustion reaction, and the combustion efficiency. Heat release is typically measured in units such as British thermal units (BTU) or joules per unit of fuel mass or volume.
- Products of Combustion: The primary products of combustion are carbon dioxide (CO2) and water vapor (H2O), which are formed from the oxidation of carbon and hydrogen in the fuel, respectively. However, combustion may also produce other combustion products such as carbon monoxide (CO), nitrogen oxides (NOx), sulfur oxides (SOx), volatile organic compounds (VOCs), and particulate matter (PM), depending on fuel composition, combustion conditions, and emission control measures.
- Applications: Combustion has numerous applications in various sectors, including:
- Heating: Combustion is used for space heating, water heating, and industrial heating applications, utilizing fuels such as natural gas, propane, heating oil, or biomass pellets in furnaces, boilers, heaters, and stoves.
- Power Generation: Combustion is used to generate electricity in power plants, where fossil fuels such as coal, natural gas, or oil are burned to produce steam, which drives turbines connected to generators.
- Transportation: Combustion engines, such as internal combustion engines and gas turbines, are used in vehicles, airplanes, ships, and locomotives to convert fuel into mechanical energy for propulsion.
- Industrial Processes: Combustion is used in various industrial processes, including cement production, metal smelting, glass manufacturing, and chemical synthesis, providing heat, steam, or process heat for production processes.
- Environmental Impact: Combustion of fossil fuels and biomass can have environmental impacts such as air pollution, greenhouse gas emissions, and climate change. Emissions from combustion processes, including carbon dioxide (CO2), nitrogen oxides (NOx), sulfur oxides (SOx), volatile organic compounds (VOCs), and particulate matter (PM), can contribute to air quality degradation, acid rain, smog formation, and respiratory health problems. To mitigate environmental impacts, combustion technologies often incorporate emission control measures such as fuel combustion optimization, flue gas desulfurization, selective catalytic reduction (SCR), and particulate filtration.
In conclusion, combustion is a fundamental process for energy conversion and heat generation, with widespread applications in heating, power generation, transportation, and industrial processes. While combustion provides essential energy services, it also presents environmental challenges related to air pollution and climate change, highlighting the importance of cleaner combustion technologies, energy efficiency improvements, and renewable energy alternatives for a sustainable future.
Oxygen-starved environment
An oxygen-starved environment refers to a condition in which the concentration of oxygen (O2) is significantly reduced or limited, relative to the stoichiometric requirements for complete combustion or oxidation reactions. In such environments, the availability of oxygen is insufficient to support complete combustion of fuel molecules, leading to partial oxidation, pyrolysis, or gasification processes that produce different chemical products and energy carriers.
- Characteristics: An oxygen-starved environment is characterized by a reduced or controlled supply of oxygen relative to the amount required for complete combustion. This can be achieved through various means, including oxygen deprivation, oxygen dilution, or oxygen exclusion, depending on the specific application and process requirements.
- Partial Oxidation: In an oxygen-starved environment, fuel molecules undergo partial oxidation reactions, where only a portion of the fuel is oxidized to produce combustion products such as carbon monoxide (CO), hydrogen (H2), and volatile organic compounds (VOCs), along with carbonaceous residues such as char, biochar, or soot. Partial oxidation occurs when the supply of oxygen is limited, preventing complete combustion and resulting in the formation of intermediate combustion products and byproducts.
- Pyrolysis: In addition to partial oxidation, an oxygen-starved environment can facilitate pyrolysis reactions, where organic materials are thermally decomposed in the absence of oxygen to produce volatile gases, liquids, and solids. Pyrolysis occurs at elevated temperatures, typically between 300°C and 800°C, and leads to the release of hydrocarbons, aromatics, and other volatile compounds, along with char, bio-oil, or biochar residues.
- Gasification: An oxygen-starved environment is also conducive to gasification processes, where carbonaceous feedstocks such as biomass, coal, or waste materials are heated in the presence of a gasification agent (e.g., steam, carbon dioxide) to produce synthesis gas (syngas), consisting primarily of carbon monoxide (CO) and hydrogen (H2). Gasification occurs at high temperatures (typically above 700°C) and in oxygen-deficient conditions, allowing for the partial oxidation of fuel molecules and the generation of syngas for energy conversion or chemical synthesis applications.
- Applications: Oxygen-starved environments are utilized in various industrial processes and technologies, including:
- Biomass Gasification: Oxygen-starved conditions are employed in biomass gasification processes to produce syngas for power generation, heat production, or synthesis of fuels and chemicals. Biomass feedstocks are heated in a gasifier reactor with limited oxygen supply, leading to partial oxidation and gasification reactions that produce syngas as the primary product.
- Pyrolysis: Oxygen-starved environments are utilized in pyrolysis processes to convert biomass, plastics, or waste materials into biochar, bio-oil, or syngas. By controlling the oxygen supply and heating conditions, pyrolysis reactors can optimize the production of desired products while minimizing combustion and emission of pollutants.
- Waste Treatment: Oxygen-starved conditions are employed in waste treatment technologies such as anaerobic digestion, composting, or thermal conversion, where organic waste materials are decomposed or converted into biogas, compost, or biochar under controlled environmental conditions that limit oxygen availability and promote microbial activity or thermal degradation.
- Advantages and Challenges: Oxygen-starved environments offer several advantages, including higher energy efficiency, lower emissions of greenhouse gases and air pollutants, and greater flexibility in feedstock utilization. However, oxygen-starved processes also pose challenges such as reactor design complexity, heat management, and control of reaction kinetics, requiring careful optimization of operating parameters and integration of process controls to ensure efficient and reliable operation.
In conclusion, an oxygen-starved environment plays a crucial role in various thermochemical processes such as gasification, pyrolysis, and waste treatment, enabling the conversion of organic materials into valuable energy products, fuels, and chemicals. By controlling oxygen availability and reaction conditions, oxygen-starved processes offer opportunities for sustainable resource utilization, waste valorization, and renewable energy production, contributing to environmental stewardship and climate change mitigation efforts.
Gasification Reactor
A gasification reactor is a specialized vessel or chamber where the thermochemical conversion process known as gasification occurs. Gasification reactors are designed to convert carbonaceous feedstocks, such as biomass, coal, or waste materials, into a synthesis gas (syngas) consisting primarily of carbon monoxide (CO) and hydrogen (H2), along with other gases such as carbon dioxide (CO2), methane (CH4), and trace contaminants.
- Principle of Operation: Gasification reactors operate on the principle of partial oxidation, where carbonaceous feedstocks are heated in a controlled environment with a limited supply of oxygen (or other gasification agent) to induce chemical reactions that convert solid or liquid fuels into gaseous products. The gasification process typically occurs at high temperatures (above 700°C) and in an oxygen-starved or oxygen-limited environment to prevent complete combustion and promote gasification reactions.
- Types of Gasification Reactors: Gasification reactors come in various designs and configurations, each with its own advantages, limitations, and applications. Common types of gasification reactors include:
- Fixed-Bed Gasifiers: Fixed-bed gasifiers consist of a stationary bed of solid fuel particles (e.g., coal, biomass) through which a gasification agent (e.g., air, oxygen, steam) is passed from below or above the bed. Examples include updraft gasifiers, downdraft gasifiers, and fluidized bed gasifiers, which differ in the direction of gas flow and fluidization characteristics.
- Fluidized Bed Gasifiers: Fluidized bed gasifiers suspend solid fuel particles in a stream of gasification agent (usually air or steam) to create a fluidized bed of particles with high heat and mass transfer rates. Fluidized bed gasifiers offer excellent fuel flexibility, uniform temperature distribution, and efficient gas-solid mixing, making them suitable for a wide range of feedstocks and operating conditions.
- Entrained Flow Gasifiers: Entrained flow gasifiers entrain pulverized or finely ground feedstock particles in a high-velocity stream of gasification agent (usually oxygen or steam) to promote rapid heating, devolatilization, and gasification reactions. Entrained flow gasifiers operate at high temperatures and pressures, enabling complete conversion of feedstock into syngas with high heating value and low tar content.
- Biomass Gasifiers: Biomass gasifiers are specialized gasification reactors designed specifically for converting biomass feedstocks (e.g., wood chips, agricultural residues) into syngas for bioenergy, biofuels, or biochemicals production. Biomass gasifiers may utilize fixed-bed, fluidized bed, or entrained flow configurations, depending on feedstock characteristics, process requirements, and scale of operation.
- Process Steps: Gasification reactors typically involve several process steps, including:
- Feedstock Preparation: Solid or liquid feedstocks are prepared and conditioned to meet size, moisture, and composition requirements for efficient gasification.
- Fuel Feeding: Feedstocks are fed into the gasification reactor continuously or intermittently, depending on reactor design and operating mode.
- Gasification: Feedstocks undergo thermochemical conversion reactions, including pyrolysis, oxidation, and reduction, to produce syngas consisting primarily of carbon monoxide (CO) and hydrogen (H2).
- Gas Cleaning: Syngas is cooled, cleaned, and conditioned to remove impurities such as tar, particulates, sulfur compounds, and moisture before further processing or utilization.
- Heat Recovery: Waste heat from the gasification process is recovered and utilized for preheating feedstocks, generating steam, or supplying process heat for downstream applications.
- Applications: Gasification reactors have diverse applications in renewable energy production, waste valorization, and industrial processes, including:
- Bioenergy Production: Biomass gasification reactors produce syngas for power generation, heating, or synthesis of biofuels such as synthetic gasoline, diesel, or methanol.
- Waste-to-Energy: Waste gasification reactors convert municipal solid waste (MSW), industrial waste, or agricultural residues into syngas for energy recovery and waste reduction.
- Chemical Synthesis: Gasification reactors supply syngas for chemical synthesis reactions, such as Fischer-Tropsch synthesis, methanol synthesis, ammonia production, and hydrogen production.
- Hydrogen Production: Gasification reactors produce hydrogen gas (H2) from carbonaceous feedstocks for fuel cell vehicles, industrial processes, or energy storage applications.
- Challenges and Considerations: Gasification reactors face challenges such as feedstock variability, reactor fouling, tar formation, corrosion, and gas cleanup requirements, which necessitate robust reactor design, process control, and emission management strategies. Additionally, economic viability, scale-up considerations, and regulatory compliance play key roles in the deployment and commercialization of gasification technologies.
In conclusion, gasification reactors play a critical role in converting carbonaceous feedstocks into valuable synthesis gas (syngas) for renewable energy production, waste management, and industrial applications. Continued research, development, and innovation in gasification technology are essential for overcoming technical challenges, improving process efficiency, and realizing the full potential of gasification for sustainable development and energy transition.
Syngas Cleaning
Syngas cleaning, also known as gas cleanup or gas conditioning, is a crucial step in the gasification process that involves the removal of impurities, contaminants, and byproducts from the raw syngas produced during thermochemical conversion. Syngas cleaning is essential to meet product specifications, ensure the efficient operation of downstream processes, and minimize environmental emissions and equipment fouling.
- Purpose: Syngas cleaning serves several important purposes, including:
- Product Quality: Removing impurities such as tar, particulates, sulfur compounds, ammonia, and alkali metals improves the quality and purity of the syngas, making it suitable for various end-use applications such as power generation, fuel synthesis, or chemical production.
- Equipment Protection: Preventing the deposition of tar, particulates, and contaminants in downstream equipment such as gas turbines, heat exchangers, and catalysts helps maintain operational efficiency, reliability, and longevity of process equipment.
- Environmental Compliance: Reducing emissions of harmful pollutants such as sulfur dioxide (SO2), nitrogen oxides (NOx), volatile organic compounds (VOCs), and particulate matter (PM) ensures compliance with environmental regulations and standards for air quality and emission control.
- Syngas Impurities: Raw syngas produced from gasification processes contains various impurities and contaminants that must be removed or reduced to acceptable levels, including:
- Tar and Hydrocarbons: Condensable hydrocarbons and tar-like substances can condense and solidify at lower temperatures, leading to fouling, corrosion, and reduced efficiency in downstream equipment. Tar removal is essential to prevent equipment fouling and maintain syngas quality.
- Particulate Matter: Solid particles, ash, and char residues suspended in the syngas stream can cause abrasion, erosion, and fouling in process equipment, affecting performance and reliability. Particulate removal is necessary to protect downstream equipment and ensure product purity.
- Sulfur Compounds: Hydrogen sulfide (H2S), carbonyl sulfide (COS), and sulfur dioxide (SO2) are common sulfur compounds present in syngas, which can contribute to corrosion, catalyst poisoning, and environmental emissions. Sulfur removal is critical for meeting product specifications and emission limits.
- Ammonia and Amines: Ammonia (NH3) and amine compounds may be present in syngas as contaminants from feedstock decomposition or gasification reactions, leading to corrosion, fouling, and emission of nitrogen oxides (NOx). Ammonia removal helps mitigate environmental impact and protect downstream equipment.
- Alkali Metals: Potassium (K), sodium (Na), and other alkali metals present in biomass feedstocks can catalyze tar formation, promote ash agglomeration, and deactivate catalysts in downstream processes. Alkali metal removal is essential for preventing equipment fouling and ensuring process efficiency.
- Syngas Cleaning Technologies: Various technologies are available for syngas cleaning and purification, including:
- Catalytic Tar Cracking: Tar cracking reactors utilize catalysts to thermally decompose condensable hydrocarbons and tar-like substances into lighter gases such as methane, hydrogen, and carbon monoxide, which are easier to remove or utilize.
- Particulate Filtration: Particulate filters, such as ceramic filters, bag filters, or electrostatic precipitators, are used to capture solid particles, ash, and char residues from the syngas stream, improving product purity and protecting downstream equipment.
- Desulfurization: Desulfurization processes, including adsorption, absorption, chemical reaction, and membrane separation, remove sulfur compounds from syngas through physical or chemical means, reducing environmental emissions and corrosion risks.
- Ammonia Removal: Ammonia removal technologies, such as selective catalytic reduction (SCR), wet scrubbing, or adsorption, capture ammonia and amine compounds from syngas streams, reducing nitrogen oxide emissions and protecting downstream equipment.
- Alkali Metal Removal: Alkali metal removal techniques, including acid washing, chemical treatment, or adsorption onto solid sorbents, remove potassium, sodium, and other alkali metals from syngas to prevent equipment fouling and catalyst deactivation.
- Process Integration: Syngas cleaning technologies are often integrated into gasification plants as part of a comprehensive gas cleanup system, which may include multiple cleaning steps and units to achieve desired product specifications and performance targets. Process integration involves optimizing operating conditions, flow rates, temperatures, pressures, and residence times to maximize efficiency, minimize energy consumption, and ensure reliable operation of the gasification process.
- Economic and Environmental Considerations: Syngas cleaning represents a significant portion of the overall capital and operating costs in gasification plants, impacting the economic viability and competitiveness of syngas-based processes. Therefore, selecting cost-effective and efficient cleaning technologies while considering energy efficiency, waste management, and environmental compliance is essential for successful project development and operation.
In conclusion, syngas cleaning is a critical step in gasification processes to remove impurities, contaminants, and byproducts from raw syngas streams, ensuring product quality, equipment reliability, and environmental compliance. By employing advanced cleaning technologies and process integration strategies, gasification plants can achieve higher efficiency, lower emissions, and greater sustainability in syngas production for renewable energy, biofuels, and chemical synthesis applications.
Syngas Utilization
Syngas utilization involves the conversion of synthesis gas (syngas), a mixture primarily composed of carbon monoxide (CO) and hydrogen (H2), into valuable end products such as fuels, chemicals, and energy carriers. Syngas, produced through thermochemical processes such as gasification or reforming, offers versatility and flexibility for various industrial, commercial, and residential applications, contributing to renewable energy production, waste valorization, and sustainable development.
- Fuel Synthesis: Syngas serves as a feedstock for the synthesis of liquid fuels such as synthetic gasoline, diesel, methanol, dimethyl ether (DME), and synthetic natural gas (SNG) through catalytic processes such as Fischer-Tropsch synthesis, methanol synthesis, or hydrocarbon reforming. These synthetic fuels can be used as drop-in replacements for conventional petroleum-based fuels in transportation, heating, and industrial applications, offering renewable and low-carbon alternatives to fossil fuels.
- Chemical Production: Syngas is utilized as a precursor for the synthesis of a wide range of chemicals, intermediates, and specialty products, including ammonia, methanol, hydrogen, olefins, alcohols, organic acids, and polymers. These chemicals are essential for various industries such as agriculture, petrochemicals, plastics, pharmaceuticals, and specialty chemicals, serving as building blocks for manufacturing processes, consumer products, and industrial applications.
- Power Generation: Syngas can be utilized as a fuel in gas turbines, internal combustion engines, or combined cycle power plants for electricity generation and cogeneration of heat and power (CHP) in industrial, commercial, or residential applications. Syngas-based power generation offers high efficiency, low emissions, and fuel flexibility compared to conventional combustion technologies, making it suitable for distributed energy systems, microgrids, and renewable energy integration.
- Hydrogen Production: Syngas can be reformed, purified, or electrolyzed to produce high-purity hydrogen gas (H2) for fuel cell vehicles, hydrogen fueling stations, industrial processes, or energy storage applications. Syngas-derived hydrogen offers a clean and versatile energy carrier for decarbonizing transportation, industry, and power sectors, enabling zero-emission mobility and renewable energy integration.
- Bioenergy and Biofuels: Syngas produced from biomass gasification or biomass-to-liquids (BTL) processes can be used to generate renewable bioenergy and biofuels, including bioelectricity, biogas, bioethanol, biodiesel, and renewable natural gas (RNG). Biomass-derived syngas offers carbon-neutral or carbon-negative energy solutions, utilizing organic waste materials, agricultural residues, or dedicated energy crops to produce sustainable bioenergy and mitigate greenhouse gas emissions.
- Waste Valorization: Syngas can be utilized for waste valorization and resource recovery from organic waste streams such as municipal solid waste (MSW), agricultural residues, forestry residues, or industrial waste materials. Waste-to-energy technologies such as gasification, pyrolysis, or anaerobic digestion convert organic waste into syngas, biochar, bio-oil, or biogas for energy production, waste reduction, and environmental sustainability.
- Carbon Capture and Utilization (CCU): Syngas can serve as a platform for carbon capture and utilization (CCU) technologies, where carbon dioxide (CO2) from syngas production or other industrial processes is captured, purified, and utilized for chemical synthesis, enhanced oil recovery (EOR), carbon mineralization, or other value-added applications. CCU technologies enable the conversion of CO2 emissions into valuable products, contributing to climate change mitigation and circular carbon economy objectives.
- Renewable Energy Integration: Syngas utilization supports the integration of renewable energy sources such as biomass, biogas, or waste-derived feedstocks into the energy system, providing dispatchable, baseload, or backup power generation capabilities. Syngas-based energy systems complement intermittent renewable energy sources such as solar and wind power, enhancing grid stability, reliability, and resilience while reducing reliance on fossil fuels and mitigating environmental impacts.
In conclusion, syngas utilization offers diverse opportunities for renewable energy production, waste valorization, chemical synthesis, and carbon management, contributing to sustainable development goals, energy security, and environmental stewardship. By leveraging advanced technologies and innovative solutions, syngas can play a significant role in transitioning towards a low-carbon, circular economy and addressing global energy and climate challenges for a cleaner and greener future.
Fischer-Tropsch Synthesis
Fischer-Tropsch synthesis (FTS) is a catalytic chemical process used to convert syngas (a mixture of carbon monoxide and hydrogen) into liquid hydrocarbons and other valuable products. Named after the German chemists Franz Fischer and Hans Tropsch who developed the process in the 1920s, FTS has been widely employed for producing synthetic fuels, lubricants, waxes, and chemicals from coal, natural gas, biomass, or waste-derived syngas.
- Principle: Fischer-Tropsch synthesis involves a series of chemical reactions in which carbon monoxide (CO) and hydrogen (H2) molecules, derived from syngas, are catalytically converted into hydrocarbons through chain-growth polymerization and hydrogenation reactions. The process occurs over heterogeneous catalysts, typically based on transition metals such as iron (Fe), cobalt (Co), or ruthenium (Ru), under elevated temperature and pressure conditions.
- Reaction Mechanism: The Fischer-Tropsch synthesis comprises several elementary steps, including:
- Adsorption: CO and H2 molecules adsorb onto the catalytic surface, forming chemisorbed species that are activated for subsequent reactions.
- Chemisorption: CO molecules dissociate into surface-bound carbon (C) atoms, while H2 molecules dissociate into surface-bound hydrogen (H) atoms.
- Chain Growth: Surface-bound carbon atoms undergo chain-growth polymerization reactions, where successive carbon atoms are added to growing hydrocarbon chains through carbon-carbon (C-C) bond formation.
- Hydrogenation: Unsaturated hydrocarbon chains are hydrogenated to saturate double bonds, producing saturated hydrocarbons (paraffins) and removing oxygen functionalities.
- Desorption: Saturated hydrocarbons desorb from the catalyst surface as liquid products, while residual hydrogen and carbon monoxide are recycled for further conversion.
- Product Distribution: Fischer-Tropsch synthesis produces a range of hydrocarbon products with varying molecular weights, structures, and properties, including:
- Paraffins: Saturated hydrocarbons with straight-chain or branched structures, resembling conventional diesel, gasoline, or jet fuels.
- Olefins: Unsaturated hydrocarbons with double bonds, which can be further processed into specialty chemicals, plastics, or polymers.
- Oxygenates: Oxygen-containing compounds such as alcohols, aldehydes, or esters, which may be formed as intermediate or byproducts during FTS reactions.
- Aromatics: Aromatic hydrocarbons such as benzene, toluene, and xylene, which are valuable precursors for petrochemicals, solvents, or additives.
- Catalysts: Fischer-Tropsch synthesis catalysts play a crucial role in controlling reaction kinetics, product selectivity, and catalyst stability. Supported metal catalysts, such as iron-based (Fe), cobalt-based (Co), or ruthenium-based (Ru) catalysts, are commonly used due to their activity, selectivity, and resistance to deactivation. Catalyst properties such as particle size, morphology, composition, and promoter additives influence catalytic performance and product distribution.
- Process Conditions: Fischer-Tropsch synthesis operates under specific temperature, pressure, and syngas composition conditions to optimize reaction kinetics, product yields, and catalyst performance. Typical operating conditions include temperatures ranging from 150°C to 350°C, pressures ranging from 10 to 50 bar, and syngas molar ratios (H2/CO) ranging from 1 to 2, depending on the desired product slate and reactor configuration.
- Applications: Fischer-Tropsch synthesis has diverse applications in energy, transportation, and chemical industries, including:
- Synthetic Fuels: Fischer-Tropsch synthesis produces synthetic fuels such as diesel, gasoline, and jet fuel from coal, natural gas, or biomass-derived syngas, offering alternatives to conventional petroleum-based fuels for transportation and heating.
- Lubricants and Waxes: Fischer-Tropsch synthesis generates high-quality lubricants, waxes, and specialty oils with excellent thermal stability, low pour points, and tailored molecular structures for automotive, industrial, and cosmetic applications.
- Chemical Feedstocks: Fischer-Tropsch synthesis provides chemical feedstocks and intermediates for manufacturing a wide range of chemicals, polymers, plastics, and pharmaceuticals, contributing to the production of value-added products and materials.
- Environmental and Economic Considerations: Fischer-Tropsch synthesis offers several environmental and economic benefits, including:
- Reduced Emissions: Synthetic fuels produced via Fischer-Tropsch synthesis exhibit lower sulfur, nitrogen, and aromatic content compared to conventional petroleum fuels, resulting in reduced emissions of pollutants such as sulfur oxides (SOx), nitrogen oxides (NOx), and particulate matter (PM).
- Resource Diversification: Fischer-Tropsch synthesis enables the utilization of diverse feedstocks such as coal, natural gas, biomass, or waste-derived syngas, reducing dependence on petroleum resources and enhancing energy security and supply resilience.
Syngas to Methanol
The conversion of synthesis gas (syngas) to methanol is a catalytic chemical process known as methanol synthesis. Methanol, also known as wood alcohol, is a versatile chemical compound used as a fuel, solvent, antifreeze, feedstock for chemical synthesis, and as a renewable energy carrier. The synthesis of methanol from syngas is a key industrial process with significant applications in energy production, transportation, and chemical manufacturing.
- Reaction Mechanism: Methanol synthesis from syngas primarily involves the catalytic hydrogenation of carbon monoxide (CO) and carbon dioxide (CO2) with hydrogen (H2) over a heterogeneous catalyst. The primary reaction steps include:
- CO Hydrogenation: CO molecules react with hydrogen to form methanol (CH3OH) via intermediate species such as formate (HCOO) and methyl (CH3) radicals. This step is catalyzed by metal-based catalysts, typically copper (Cu), zinc (Zn), or a combination of metals supported on alumina or silica supports.
- CO2 Hydrogenation: Carbon dioxide can also undergo hydrogenation to produce methanol, although the reaction kinetics are slower compared to CO hydrogenation. CO2 activation and hydrogenation occur through similar mechanisms involving metal catalysis and surface reactions.
- Catalysts: Methanol synthesis catalysts play a crucial role in determining reaction rates, selectivity, and catalyst stability. Copper-based catalysts are widely used due to their high activity and selectivity for methanol production. Promoters such as zinc (Zn), aluminum (Al), or alkali metals (e.g., potassium, potassium) are often added to enhance catalyst performance and stability. Catalyst properties such as surface area, particle size, morphology, and metal dispersion influence catalytic activity and product distribution.
- Process Conditions: Methanol synthesis operates under specific temperature, pressure, and syngas composition conditions to optimize reaction kinetics and product yields. Typical operating conditions include temperatures ranging from 200°C to 300°C, pressures ranging from 50 to 100 bar, and syngas molar ratios (H2/CO) ranging from 2 to 3, depending on catalyst formulation and reactor design.
- Syngas Composition: The composition of syngas significantly influences methanol synthesis performance and product selectivity. Syngas with a stoichiometric ratio of hydrogen to carbon monoxide (H2/CO) close to 2 is optimal for methanol synthesis, although variations in syngas composition can affect reaction equilibrium, catalyst activity, and methanol yield. Syngas impurities such as sulfur compounds, ammonia, and trace contaminants may also impact catalyst performance and require removal or mitigation.
- Product Purification: Methanol synthesis produces a crude methanol product containing methanol, water, unreacted syngas components, and trace impurities. Crude methanol undergoes purification steps such as distillation, pressure swing adsorption (PSA), or membrane separation to remove water, volatile impurities, and byproducts, yielding high-purity methanol suitable for commercial use.
- Applications: Methanol is a versatile chemical intermediate with diverse applications in various industries, including:
- Fuel: Methanol can be used as a direct fuel or fuel additive for internal combustion engines, fuel cells, and alternative fuel blends (e.g., M85, M100). Methanol’s high octane rating, clean combustion characteristics, and low emissions make it a viable alternative to gasoline or diesel fuels for transportation and power generation.
- Chemical Feedstock: Methanol serves as a feedstock for producing a wide range of chemicals, including formaldehyde, acetic acid, methyl methacrylate, dimethyl ether (DME), olefins, and polymers. Methanol-derived chemicals are used in plastics, resins, coatings, adhesives, solvents, and pharmaceuticals, among other applications.
- Energy Storage: Methanol can be utilized as an energy carrier for storing and transporting renewable energy from intermittent sources such as wind, solar, or biomass. Methanol can be synthesized from renewable hydrogen and captured carbon dioxide, offering a carbon-neutral energy storage solution with potential applications in grid-scale energy storage, fuel cells, and remote power systems.
- Environmental and Economic Considerations: Methanol synthesis offers several environmental and economic benefits, including:
- Carbon Utilization: Methanol synthesis from syngas enables the utilization of carbonaceous feedstocks such as coal, natural gas, biomass, or captured carbon dioxide, reducing greenhouse gas emissions and contributing to carbon capture and utilization (CCU) initiatives.
- Renewable Methanol: Methanol can be produced from renewable feedstocks such as biomass-derived syngas or electrolytic hydrogen, offering a renewable and sustainable alternative to fossil-based methanol. Renewable methanol can help decarbonize transportation, industry, and chemical sectors while promoting circular economy principles and resource efficiency.
- Energy Security: Methanol synthesis diversifies energy sources and reduces reliance on conventional petroleum fuels, enhancing energy security, supply resilience, and geopolitical stability. Methanol’s versatility as a liquid fuel, chemical feedstock, and energy carrier contributes to energy transition efforts and sustainable development goals.
Syngas to Synthetic Natural Gas (SNG)
Synthetic natural gas (SNG), also known as substitute natural gas, is a gaseous fuel produced from the conversion of synthesis gas (syngas) derived from coal, biomass, or waste feedstocks. SNG closely resembles natural gas in composition and properties, making it compatible with existing natural gas infrastructure and suitable for various energy applications, including heating, power generation, and transportation.
- Conversion Process: The conversion of syngas to synthetic natural gas (SNG) involves several steps, including:
- Syngas Production: Syngas is produced through thermochemical processes such as gasification, steam reforming, or biomass pyrolysis, where carbonaceous feedstocks undergo partial oxidation or reforming reactions to produce a mixture of carbon monoxide (CO) and hydrogen (H2).
- Methanation: Syngas undergoes catalytic methanation reactions, where CO and H2 molecules react over a methanation catalyst to form methane (CH4) and water (H2O). Methanation catalysts are typically based on nickel (Ni) or cobalt (Co) supported on high-surface-area substrates such as alumina or silica.
- Gas Conditioning: The methane-rich gas stream produced from methanation undergoes conditioning steps such as purification, compression, and drying to remove impurities, moisture, and trace contaminants. Gas conditioning ensures the quality, purity, and stability of the synthetic natural gas product.
- Compression and Storage: Synthetic natural gas is compressed to pipeline pressures and stored in storage tanks or underground reservoirs for distribution and utilization. Compression increases the energy density and transportability of SNG, facilitating storage, transportation, and delivery to end-users.
- Composition: Synthetic natural gas (SNG) closely resembles natural gas in composition, with methane (CH4) as the primary component along with minor quantities of other hydrocarbons, inert gases, and trace contaminants. The composition of SNG may vary depending on feedstock composition, conversion technology, and process conditions but typically contains high methane content (>90%) with low levels of impurities such as carbon monoxide (CO), hydrogen (H2), nitrogen (N2), carbon dioxide (CO2), sulfur compounds, and trace contaminants.
- Applications: Synthetic natural gas (SNG) has diverse applications in energy, heating, and industrial sectors, including:
- Natural Gas Replacement: SNG can be blended with or substituted for conventional natural gas in residential, commercial, and industrial applications such as space heating, water heating, cooking, and process heating. SNG’s compatibility with existing natural gas infrastructure, appliances, and combustion equipment makes it a viable alternative for energy users seeking cleaner, renewable fuel options.
- Power Generation: Synthetic natural gas can be utilized as a fuel for combined-cycle gas turbines (CCGT), gas engines, or fuel cells to generate electricity and cogenerate heat and power (CHP) in distributed energy systems, microgrids, or utility-scale power plants. SNG-based power generation offers high efficiency, low emissions, and dispatchable energy supply, complementing intermittent renewable energy sources such as wind and solar power.
- Transportation Fuels: SNG can be compressed or liquefied for use as a transportation fuel in natural gas vehicles (NGVs), buses, trucks, and ships. SNG-powered vehicles offer lower emissions of greenhouse gases (GHGs), nitrogen oxides (NOx), particulate matter (PM), and sulfur oxides (SOx) compared to conventional diesel or gasoline vehicles, contributing to air quality improvement and climate change mitigation.
- Industrial Applications: Synthetic natural gas finds applications in industrial processes such as steam generation, kiln firing, thermal drying, and chemical synthesis as a clean, efficient, and versatile fuel or feedstock. SNG can replace conventional fossil fuels such as coal, oil, or propane in industrial boilers, furnaces, and kilns, reducing emissions, energy costs, and environmental footprint.
- Environmental Benefits: Synthetic natural gas (SNG) offers several environmental benefits compared to conventional fossil fuels, including:
- Reduced Greenhouse Gas Emissions: SNG produced from renewable or low-carbon feedstocks such as biomass or waste offers carbon-neutral or carbon-negative emissions profiles, mitigating greenhouse gas emissions and climate change impacts. SNG production from carbon capture and utilization (CCU) technologies also reduces carbon dioxide (CO2) emissions by recycling captured CO2 as a feedstock for methanation.
- Air Quality Improvement: SNG combustion produces lower emissions of criteria pollutants such as sulfur dioxide (SO2), nitrogen oxides (NOx), particulate matter (PM), and volatile organic compounds (VOCs) compared to conventional fossil fuels, contributing to improved air quality, public health, and environmental sustainability.
- Resource Conservation: SNG production from biomass, waste, or stranded natural gas resources enhances resource conservation, energy security, and supply resilience by utilizing renewable or underutilized feedstocks and reducing dependence on finite fossil fuel reserves.
In conclusion, synthetic natural gas (SNG) offers a promising pathway for decarbonizing energy systems, reducing emissions, and advancing sustainable development goals. By leveraging syngas conversion technologies, such as methanation and gas conditioning, SNG enables the utilization of diverse feedstocks for renewable energy production, waste valorization, and carbon management, contributing to a cleaner, greener, and more resilient energy future.
Syngas to Fischer-Tropsch Liquids (FTL)
Syngas to Fischer-Tropsch liquids (FTL) conversion involves the catalytic synthesis of liquid hydrocarbons and other valuable products from synthesis gas (syngas) through the Fischer-Tropsch (FT) process. FTL synthesis offers a versatile and flexible route for producing synthetic fuels, lubricants, waxes, and chemicals from a variety of carbonaceous feedstocks, including coal, natural gas, biomass, or waste-derived syngas.
- Fischer-Tropsch Synthesis: The Fischer-Tropsch process comprises a series of catalytic reactions in which carbon monoxide (CO) and hydrogen (H2) molecules derived from syngas are polymerized and hydrogenated to form liquid hydrocarbons. The key steps in Fischer-Tropsch synthesis include:
- Adsorption: CO and H2 molecules adsorb onto the surface of a heterogeneous catalyst, typically based on metals such as iron (Fe), cobalt (Co), or ruthenium (Ru) supported on high-surface-area substrates like alumina or silica.
- Chain Growth: Surface-bound CO molecules undergo chain-growth polymerization reactions, where successive carbon atoms are added to growing hydrocarbon chains through carbon-carbon (C-C) bond formation.
- Hydrogenation: Unsaturated hydrocarbon chains are hydrogenated by surface-bound hydrogen atoms, forming saturated hydrocarbons (paraffins) and removing oxygen functionalities.
- Product Formation: Saturated hydrocarbons desorb from the catalyst surface as liquid products, ranging from light gases (e.g., methane, ethane) to heavier hydrocarbons (e.g., diesel, waxes).
- Catalysts: Fischer-Tropsch catalysts play a critical role in determining reaction kinetics, product selectivity, and catalyst stability. Cobalt-based catalysts are widely used for FTL synthesis due to their high activity and selectivity for long-chain hydrocarbon formation. Iron-based catalysts are also employed for specific applications, offering advantages in terms of catalyst cost and stability. Catalyst properties such as particle size, composition, morphology, and promoter additives influence catalytic performance and product distribution.
- Product Slate: Fischer-Tropsch liquids (FTL) encompass a range of hydrocarbon products with varying molecular weights, structures, and properties. The product slate typically includes:
- Paraffins: Saturated hydrocarbons with straight-chain or branched structures, resembling conventional petroleum-derived fuels such as diesel, gasoline, and jet fuel.
- Olefins: Unsaturated hydrocarbons with double bonds, which can be further processed into specialty chemicals, plastics, or polymers.
- Waxes: High-molecular-weight hydrocarbons with long-chain structures, used in applications such as lubricants, coatings, candles, and personal care products.
- Lubricants: Synthetic lubricants with tailored properties such as viscosity, thermal stability, and oxidative resistance, suitable for automotive, industrial, and aerospace applications.
- Process Integration: Fischer-Tropsch synthesis is often integrated into larger gas-to-liquids (GTL) or biomass-to-liquids (BTL) plants, which may include syngas production, gas cleanup, product upgrading, and downstream processing units. Process integration involves optimizing operating conditions, reactor design, catalyst performance, and product recovery to maximize overall process efficiency, product yields, and economic viability.
- Applications: Fischer-Tropsch liquids (FTL) have diverse applications in energy, transportation, and chemical industries, including:
- Transportation Fuels: FTL serve as drop-in replacements for conventional petroleum-based fuels such as diesel, gasoline, and jet fuel in transportation applications, offering renewable and low-carbon alternatives for reducing greenhouse gas emissions and fossil fuel dependence.
- Chemical Feedstocks: FTL provide chemical feedstocks and intermediates for manufacturing a wide range of chemicals, polymers, plastics, and specialty products in petrochemical, pharmaceutical, and materials industries, contributing to value-added product synthesis and industrial processes.
- Lubricants and Waxes: FTL-derived lubricants, waxes, and specialty oils offer tailored properties and performance characteristics for automotive, industrial, and consumer applications, providing high-quality, sustainable alternatives to petroleum-derived counterparts.
- Power Generation: FTL can be used as fuel in stationary engines, gas turbines, or combined-cycle power plants for electricity generation and cogeneration of heat and power (CHP), offering high efficiency, reliability, and flexibility in distributed energy systems and grid integration.
- Environmental Considerations: Fischer-Tropsch liquids (FTL) offer several environmental benefits compared to conventional petroleum-based fuels, including:
- Reduced Emissions: FTL exhibit lower sulfur, nitrogen, and aromatic content compared to conventional fuels, resulting in reduced emissions of criteria pollutants such as sulfur dioxide (SO2), nitrogen oxides (NOx), particulate matter (PM), and volatile organic compounds (VOCs), contributing to air quality improvement and public health protection.
- Carbon Utilization: FTL production from renewable or low-carbon feedstocks such as biomass or waste offers carbon-neutral or carbon-negative emissions profiles, mitigating greenhouse gas emissions and climate change impacts. FTL synthesis from carbon capture and utilization (CCU) technologies also reduces carbon dioxide (CO2) emissions by recycling captured CO2 as a feedstock for hydrocarbon synthesis.
In conclusion, syngas to Fischer-Tropsch liquids (FTL) conversion offers a sustainable pathway for producing renewable fuels, chemicals, and value-added products from diverse feedstocks while reducing environmental impacts and enhancing energy security. By leveraging advanced catalytic technologies, process integration strategies, and renewable feedstock utilization, FTL synthesis contributes to the transition towards a low-carbon, circular economy and sustainable energy future.
Syngas to Hydrogen
Syngas, a mixture primarily composed of carbon monoxide (CO) and hydrogen (H2), can be converted into pure hydrogen gas (H2) through various thermochemical processes. Hydrogen production from syngas offers a clean, versatile, and renewable energy carrier for a wide range of industrial, commercial, and transportation applications.
- Steam Reforming: Steam reforming, also known as steam methane reforming (SMR) when applied to natural gas, is the most widely used method for producing hydrogen from syngas. In steam reforming, syngas reacts with steam over a catalyst, typically nickel (Ni) or platinum (Pt) supported on alumina or other substrates, at high temperatures (700-1000°C) and moderate pressures (1-30 bar) to produce hydrogen and carbon dioxide according to the following reaction:CH4 + H2O → CO + 3H2CO + H2O → CO2 + H2The water-gas shift reaction (WGSR) further converts CO to CO2, releasing additional hydrogen:CO + H2O → CO2 + H2Steam reforming is highly efficient and scalable, making it the dominant method for large-scale hydrogen production from natural gas, biogas, or refinery off-gas streams.
- Partial Oxidation: Partial oxidation (POX) is another thermochemical process for producing hydrogen from syngas, involving the partial combustion of hydrocarbons with oxygen or air at high temperatures (>1000°C) and pressures (5-50 bar) to generate hydrogen and carbon monoxide. Partial oxidation reactions typically proceed exothermically and are favored by the presence of oxygen-rich environments and fast-reacting catalysts such as supported noble metals (e.g., platinum, palladium). Partial oxidation can be applied to various feedstocks, including natural gas, refinery gases, or liquid hydrocarbons, offering flexibility in hydrogen production.
- Autothermal Reforming: Autothermal reforming (ATR) combines elements of steam reforming and partial oxidation, utilizing both steam and oxygen or air to generate syngas from hydrocarbon feedstocks. In autothermal reforming, a controlled amount of oxygen is introduced along with steam to the reforming reactor, allowing for simultaneous steam reforming and partial oxidation reactions to occur. Autothermal reforming offers advantages in terms of process efficiency, heat integration, and syngas composition control, making it suitable for integrated hydrogen production systems and fuel cell applications.
- Water-Gas Shift Reaction: The water-gas shift reaction (WGSR) plays a critical role in hydrogen production from syngas, converting carbon monoxide (CO) to carbon dioxide (CO2) while generating additional hydrogen. The WGSR is typically catalyzed by high-temperature shift (HTS) catalysts such as iron oxide (Fe3O4) or copper-zinc oxide (CuO/ZnO) supported on alumina or other substrates. The reaction proceeds according to the following equation:CO + H2O → CO2 + H2The water-gas shift reaction is essential for reducing CO concentrations in syngas to levels acceptable for downstream processes such as hydrogen purification and fuel cell operation, ensuring product purity and performance.
- Hydrogen Purification: Following syngas conversion, hydrogen purification is required to remove impurities such as carbon monoxide (CO), carbon dioxide (CO2), water vapor, sulfur compounds, and trace contaminants from the hydrogen stream. Purification techniques include pressure swing adsorption (PSA), membrane separation, cryogenic distillation, and selective catalytic conversion, depending on the desired purity, flow rate, and operating conditions. Hydrogen purification ensures the quality, safety, and reliability of hydrogen for various applications, including fuel cells, ammonia production, chemical synthesis, and metallurgical processes.
- Applications: Hydrogen produced from syngas has diverse applications in energy, transportation, industry, and residential sectors, including:
- Fuel Cells: Hydrogen fuel cells convert hydrogen and oxygen into electricity and water through electrochemical reactions, offering high efficiency, zero emissions, and quiet operation for powering vehicles, stationary power systems, and portable electronics.
- Ammonia Production: Hydrogen is a key feedstock for ammonia synthesis, where it reacts with nitrogen to produce ammonia (NH3) for fertilizer production, chemical synthesis, and industrial applications.
- Refinery Upgrading: Hydrogen is used in petroleum refining processes such as hydrocracking, hydrotreating, and catalytic reforming to upgrade crude oil fractions, remove impurities, and produce cleaner fuels with lower sulfur and aromatic content.
- Methanol Synthesis: Hydrogen is utilized in methanol synthesis from syngas, where it reacts with carbon monoxide (CO) over a catalyst to produce methanol (CH3OH), a versatile chemical feedstock for plastics, solvents, and fuels.
- Environmental Considerations: Hydrogen production from syngas offers several environmental benefits compared to conventional fossil fuel-based processes, including:
- Reduced Emissions: Hydrogen produced from renewable or low-carbon sources such as biomass, biogas, or electrolysis offers carbon-neutral or carbon-negative emissions profiles, mitigating greenhouse gas emissions and climate change impacts.
- Air Quality Improvement: Hydrogen combustion produces no greenhouse gases (GHGs) or criteria pollutants such as sulfur dioxide (SO2), nitrogen oxides (NOx), particulate matter (PM), or volatile organic compounds (VOCs), contributing to improved air quality, public health, and environmental sustainability.
- Resource Conservation: Hydrogen production from renewable feedstocks promotes resource conservation, energy security, and supply resilience by utilizing abundant, sustainable resources such as biomass, water, or renewable electricity for hydrogen generation, reducing dependence on finite fossil fuel reserves.
In conclusion, hydrogen production from syngas offers a clean, versatile, and sustainable pathway for meeting growing energy demands, reducing environmental impacts, and advancing the transition towards a low-carbon, hydrogen-based economy. By leveraging advanced conversion technologies, renewable feedstock utilization, and hydrogen infrastructure development, syngas-to-hydrogen processes contribute to global energy transition efforts and sustainable development goals for a cleaner, greener future.
Syngas to Synthetic Natural Gas (SNG)
Synthetic natural gas (SNG) production involves the conversion of synthesis gas (syngas) derived from various feedstocks such as coal, biomass, or natural gas into a gas mixture that closely resembles natural gas. SNG serves as a versatile and clean energy carrier with applications in heating, power generation, and transportation.
- Gasification: The first step in SNG production is gasification, where carbonaceous feedstocks such as coal, biomass, or waste materials are converted into syngas through thermochemical processes. Gasification typically involves partial oxidation or pyrolysis of feedstocks at high temperatures (>700°C) and controlled oxygen or steam conditions to produce a mixture of carbon monoxide (CO), hydrogen (H2), carbon dioxide (CO2), and other gases.
- Syngas Cleanup: The raw syngas produced from gasification contains impurities such as tar, sulfur compounds, particulates, and trace contaminants, which need to be removed to ensure the quality and stability of the final SNG product. Syngas cleanup processes include tar removal, sulfur removal (desulfurization), particulate filtration, and trace contaminant removal through scrubbing, adsorption, or catalytic conversion.
- Methanation: After syngas cleanup, the resulting clean syngas undergoes catalytic methanation reactions to convert carbon monoxide (CO) and carbon dioxide (CO2) into methane (CH4), the primary component of natural gas. Methanation reactions are typically catalyzed by nickel-based or cobalt-based catalysts at elevated temperatures (>300°C) and pressures (5-30 bar), with hydrogen (H2) acting as a reducing agent. Methanation enhances the energy content and stability of SNG while reducing CO and CO2 emissions.
- Hydrogenation: In addition to methanation, hydrogenation reactions may occur to further saturate unsaturated hydrocarbons and oxygenated compounds present in syngas, producing higher concentrations of methane and enhancing the energy density of SNG. Hydrogenation reactions are promoted by metal-based catalysts under suitable process conditions, such as temperature, pressure, and hydrogen-to-carbon ratio (H2/CO), to maximize methane yield and minimize byproduct formation.
- Product Conditioning: The methane-rich gas stream produced from methanation undergoes conditioning steps such as cooling, compression, and drying to adjust temperature, pressure, and moisture content for pipeline transport or storage. Product conditioning ensures the stability, safety, and compatibility of SNG with existing natural gas infrastructure and end-use applications.
- Quality Control: SNG quality control measures involve monitoring and adjusting key parameters such as methane content, heating value, impurity levels, and odorant addition to meet regulatory standards, customer specifications, and safety requirements. Quality control ensures the reliability, performance, and compliance of SNG for distribution, combustion, and utilization in residential, commercial, and industrial sectors.
- Applications: Synthetic natural gas (SNG) has diverse applications in energy, heating, power generation, and transportation sectors, including:
- Heating: SNG can be used as a direct substitute for natural gas in residential, commercial, and industrial heating applications such as space heating, water heating, cooking, and process heating, offering clean, efficient, and reliable energy supply with minimal environmental impact.
- Power Generation: SNG can be utilized as a fuel for combined-cycle gas turbines (CCGT), gas engines, or fuel cells to generate electricity and cogenerate heat and power (CHP) in distributed energy systems, microgrids, or utility-scale power plants. SNG-based power generation offers high efficiency, low emissions, and dispatchable energy supply, complementing intermittent renewable energy sources such as wind and solar power.
- Transportation Fuels: SNG can be compressed or liquefied for use as a transportation fuel in natural gas vehicles (NGVs), buses, trucks, and ships. SNG-powered vehicles offer lower emissions of greenhouse gases (GHGs), nitrogen oxides (NOx), particulate matter (PM), and sulfur oxides (SOx) compared to conventional diesel or gasoline vehicles, contributing to air quality improvement and climate change mitigation.
- Industrial Applications: Synthetic natural gas finds applications in industrial processes such as steam generation, kiln firing, thermal drying, and chemical synthesis as a clean, efficient, and versatile fuel or feedstock. SNG can replace conventional fossil fuels such as coal, oil, or propane in industrial boilers, furnaces, and kilns, reducing emissions, energy costs, and environmental footprint.
- Environmental Considerations: Synthetic natural gas (SNG) offers several environmental benefits compared to conventional fossil fuels, including:
- Reduced Emissions: SNG combustion produces lower emissions of criteria pollutants such as sulfur dioxide (SO2), nitrogen oxides (NOx), particulate matter (PM), and volatile organic compounds (VOCs) compared to conventional fossil fuels, contributing to improved air quality, public health, and environmental sustainability.
- Carbon Utilization: SNG production from renewable or low-carbon feedstocks such as biomass, biogas, or captured carbon dioxide offers carbon-neutral or carbon-negative emissions profiles, mitigating greenhouse gas emissions and climate change impacts.
- Resource Conservation: SNG production enhances resource conservation, energy security, and supply resilience by utilizing diverse feedstocks such as coal, biomass, or waste materials, reducing dependence on finite
Syngas to Power (Electricity Generation)
The conversion of synthesis gas (syngas) into electricity involves several steps and technologies aimed at harnessing the energy content of syngas for power generation. Syngas, a mixture primarily composed of carbon monoxide (CO) and hydrogen (H2), can be produced from various feedstocks such as coal, biomass, or natural gas through gasification or reforming processes.
- Gasification: Gasification is the thermochemical process of converting solid or liquid carbonaceous feedstocks into syngas by reacting them with oxygen or steam at high temperatures (>700°C) in the presence of a gasification agent such as air, oxygen, or steam. Gasification technologies include entrained-flow, fixed-bed, fluidized-bed, and integrated gasification combined cycle (IGCC) systems, each offering unique advantages in terms of feedstock flexibility, syngas quality, and process efficiency.
- Syngas Cleanup: The raw syngas produced from gasification contains impurities such as tar, sulfur compounds, particulates, and trace contaminants, which need to be removed to ensure the reliability and efficiency of downstream power generation equipment. Syngas cleanup processes include tar removal, sulfur removal (desulfurization), particulate filtration, and trace contaminant removal through scrubbing, adsorption, or catalytic conversion.
- Power Generation Technologies: Several power generation technologies can utilize syngas as a fuel to produce electricity, including:
- Gas Turbines: Syngas can be combusted directly in gas turbines to drive electrical generators and produce electricity. Gas turbines offer high efficiency, fast start-up times, and low emissions, making them suitable for base-load, peaking, or grid-balancing applications in power generation systems.
- Combined Cycle Power Plants: Integrated gasification combined cycle (IGCC) power plants combine gasification and gas turbine technologies with heat recovery steam generators (HRSGs) and steam turbines to maximize overall efficiency and power output. In IGCC plants, syngas is used as fuel for gas turbines, and the waste heat from turbine exhaust is recovered to produce steam for driving steam turbines, resulting in higher overall efficiency and lower emissions compared to conventional coal-fired power plants.
- Fuel Cells: Syngas can be used as a feedstock for fuel cells, electrochemical devices that convert chemical energy directly into electrical energy through redox reactions between hydrogen and oxygen. Syngas-fed fuel cells such as solid oxide fuel cells (SOFCs) or molten carbonate fuel cells (MCFCs) offer high efficiency, low emissions, and quiet operation for distributed power generation, backup power, or combined heat and power (CHP) applications.
- Internal Combustion Engines: Syngas can be utilized as fuel in internal combustion engines (ICEs) such as reciprocating engines or gas turbines for distributed power generation, remote off-grid applications, or transportation electrification. Syngas-powered engines offer flexibility, scalability, and compatibility with existing infrastructure, making them suitable for decentralized energy systems and microgrid integration.
- Performance and Efficiency: The performance and efficiency of syngas-based power generation systems depend on various factors, including syngas composition, calorific value, energy content, fuel flexibility, combustion characteristics, turbine design, heat recovery efficiency, and plant configuration. Optimizing process parameters, controlling emissions, and integrating advanced control systems can enhance overall system performance and efficiency, reduce operational costs, and maximize power output.
- Environmental Considerations: Syngas-based power generation offers several environmental benefits compared to conventional fossil fuel-based power plants, including:
- Reduced Emissions: Syngas combustion produces lower emissions of greenhouse gases (GHGs) such as carbon dioxide (CO2), sulfur dioxide (SO2), nitrogen oxides (NOx), particulate matter (PM), and volatile organic compounds (VOCs) compared to coal-fired power plants, contributing to air quality improvement and climate change mitigation.
- Carbon Utilization: Syngas production from renewable or low-carbon feedstocks such as biomass, biogas, or captured carbon dioxide offers carbon-neutral or carbon-negative emissions profiles, mitigating greenhouse gas emissions and supporting carbon capture and utilization (CCU) initiatives.
- Resource Efficiency: Syngas-based power generation enhances resource efficiency, energy security, and supply resilience by utilizing diverse feedstocks such as coal, biomass, or waste materials, reducing dependence on finite fossil fuel reserves and promoting sustainable energy development.
In conclusion, syngas-based power generation technologies offer a flexible, efficient, and environmentally sustainable pathway for producing electricity from diverse feedstocks while reducing emissions, enhancing energy security, and supporting the transition towards a low-carbon, renewable energy future. By leveraging gasification, cleanup, and power generation technologies, syngas-to-power systems contribute to global energy transition efforts and sustainable development goals for a cleaner, greener world.
Syngas to Synthetic Natural Gas (SNG) Storage
Synthetic natural gas (SNG) storage is a crucial component of the overall SNG production and distribution system, enabling the efficient, safe, and reliable storage of SNG for future use in various energy applications. SNG, produced from synthesis gas (syngas) through methanation and conditioning processes, is typically stored in storage tanks, underground reservoirs, or existing natural gas infrastructure for later distribution and utilization.
- Storage Technologies: Several storage technologies are employed for storing synthetic natural gas (SNG), including:
- Above-Ground Storage Tanks: SNG can be stored in above-ground storage tanks made of steel, concrete, or composite materials. These tanks are commonly used for short-term storage or buffer storage at production facilities, distribution terminals, or end-user sites. Above-ground tanks offer flexibility, accessibility, and relatively low installation costs but may require additional safety measures and environmental controls.
- Underground Storage Tanks: Underground storage tanks or caverns are used for long-term storage of SNG in geological formations such as depleted natural gas reservoirs, salt caverns, or aquifers. Underground storage provides greater capacity, security, and stability for storing large volumes of SNG over extended periods. Geological storage sites offer natural containment, insulation, and pressure management, minimizing environmental impacts and land use requirements.
- Pipeline Storage: SNG can be stored temporarily in natural gas transmission pipelines or distribution networks during periods of low demand or excess production. Pipeline storage relies on compressors, valves, and pressure regulation systems to maintain gas flow, pressure, and volume within pipeline networks. Pipeline storage offers rapid response, continuous operation, and seamless integration with existing gas infrastructure but may require additional compression and control infrastructure.
- Storage Capacity: The storage capacity of SNG storage facilities depends on various factors, including storage technology, facility design, operating conditions, safety regulations, and market demand. Storage capacity is typically expressed in terms of volume (cubic meters or cubic feet) or energy content (megajoules or gigawatt-hours) and can range from small-scale distributed storage tanks to large-scale underground reservoirs or caverns capable of storing millions of cubic meters of SNG.
- Safety and Environmental Considerations: SNG storage facilities must comply with strict safety, environmental, and regulatory standards to ensure the integrity, reliability, and compliance of storage operations. Key safety considerations include:
- Pressure Management: SNG storage facilities must maintain safe operating pressures within design limits to prevent over-pressurization, leakage, or rupture of storage vessels. Pressure relief systems, safety valves, and emergency shutdown procedures are employed to mitigate risks and protect personnel, equipment, and the environment.
- Leak Detection and Monitoring: Continuous monitoring and surveillance systems are used to detect and localize leaks, spills, or emissions from storage facilities. Leak detection technologies such as gas sensors, infrared cameras, acoustic detectors, and remote sensing systems provide early warning of potential hazards and enable rapid response and containment measures.
- Environmental Protection: SNG storage facilities implement environmental management practices to minimize air emissions, water contamination, soil degradation, and ecosystem impacts associated with storage operations. Environmental monitoring, remediation, and mitigation measures are employed to prevent, mitigate, or remediate potential environmental hazards and ensure compliance with regulatory requirements.
- Operational Flexibility: SNG storage facilities offer operational flexibility and system resilience to accommodate fluctuations in supply, demand, and market conditions. Storage operators utilize inventory management, scheduling, and dispatching strategies to optimize storage utilization, minimize inventory costs, and meet customer requirements. Operational flexibility enables SNG storage facilities to serve as strategic assets for balancing energy supply and demand, optimizing grid stability, and supporting renewable energy integration.
- Integration with Distribution Networks: SNG storage facilities are integrated with natural gas distribution networks, pipelines, and infrastructure to facilitate seamless transport, distribution, and utilization of SNG across various end-use sectors. Storage operators collaborate with gas utilities, transmission companies, and regulatory authorities to ensure interoperability, reliability, and safety of SNG storage and distribution systems.
In conclusion, synthetic natural gas (SNG) storage plays a critical role in the SNG value chain, enabling the efficient, safe, and reliable storage of SNG for future use in energy, heating, power generation, and transportation applications. By leveraging diverse storage technologies, safety protocols, and operational practices, SNG storage facilities support the transition towards cleaner, more resilient energy systems and contribute to sustainable development goals for a low-carbon, renewable energy future.
Syngas to Synthetic Natural Gas (SNG) Transmission
Synthetic natural gas (SNG) transmission involves the transportation of SNG from production facilities to distribution networks, end-users, and consumption points through pipelines, compression stations, and storage facilities. SNG, produced from synthesis gas (syngas) through methanation and conditioning processes, is transported over long distances using existing natural gas infrastructure or dedicated SNG pipelines.
- Pipeline Infrastructure: SNG transmission relies on a network of pipelines, compressors, valves, meters, and control systems to transport gas from production sites to distribution hubs, industrial facilities, or residential areas. Pipeline infrastructure includes transmission pipelines, distribution mains, gathering lines, and interconnection points interconnected through a grid-like network spanning vast geographic regions.
- Pipeline Design and Construction: SNG pipelines are designed and constructed to meet stringent engineering, safety, and regulatory standards for pressure containment, corrosion resistance, material integrity, and environmental protection. Pipeline materials such as steel, polyethylene, or composite materials are selected based on factors such as operating pressure, temperature, soil conditions, and terrain characteristics. Pipeline construction involves site preparation, trenching, welding, coating, installation, testing, and commissioning to ensure structural integrity, leak tightness, and compliance with design specifications.
- Pipeline Operation and Maintenance: SNG pipelines are operated and maintained according to strict protocols, procedures, and best practices to ensure safe, reliable, and efficient transportation of gas. Pipeline operators monitor pipeline integrity, pressure, flow rates, and temperature using remote monitoring systems, supervisory control and data acquisition (SCADA) systems, and advanced analytics tools. Routine inspection, maintenance, and repair activities such as pigging, corrosion control, cathodic protection, and valve maintenance are conducted to prevent leaks, spills, or accidents and maintain pipeline integrity.
- Compression and Boosting: SNG transmission pipelines may require compression or boosting stations along the route to maintain gas flow, pressure, and volume over long distances or elevation changes. Compressor stations utilize centrifugal or reciprocating compressors driven by electric motors or gas turbines to increase gas pressure and overcome frictional losses, elevation differentials, or flow restrictions. Booster stations are deployed strategically to enhance pipeline capacity, reliability, and throughput in high-demand areas or remote locations.
- Interconnection and Integration: SNG transmission pipelines are interconnected with existing natural gas infrastructure, distribution networks, and storage facilities to facilitate seamless transport, distribution, and utilization of gas across different regions and sectors. Interconnection points, metering stations, and valve stations enable gas flow control, measurement, and diversion to ensure system reliability, flexibility, and interoperability. Integration with renewable energy sources, power generation plants, and industrial facilities supports energy transition efforts and enhances system resilience.
- Safety and Regulatory Compliance: SNG transmission pipelines adhere to rigorous safety, environmental, and regulatory standards set forth by government agencies, industry organizations, and international bodies. Pipeline operators implement risk management, emergency response, and safety protocols to prevent, detect, and mitigate potential hazards such as leaks, ruptures, or third-party damage. Regulatory compliance includes adherence to pipeline codes, standards, permits, inspections, and reporting requirements to ensure public safety, environmental protection, and stakeholder engagement.
- Capacity Expansion and Optimization: SNG transmission infrastructure is continuously expanded, upgraded, and optimized to meet growing demand, accommodate new supply sources, and improve system efficiency. Capacity expansion projects involve pipeline looping, parallel routing, diameter upgrades, or new pipeline construction to increase throughput, reduce bottlenecks, and enhance system reliability. Optimization measures such as flow modeling, pressure management, and asset management improve pipeline performance, energy efficiency, and cost-effectiveness over the lifecycle.
- Environmental Impact and Mitigation: SNG transmission pipelines undergo environmental impact assessments, mitigation measures, and monitoring programs to minimize ecological disturbance, habitat fragmentation, and land use conflicts associated with pipeline construction and operation. Environmental considerations include soil erosion control, wetland protection, wildlife conservation, and stakeholder consultation to mitigate adverse impacts and promote sustainable development.
In conclusion, synthetic natural gas (SNG) transmission plays a vital role in the energy value chain, enabling the efficient, reliable, and sustainable transport of gas from production sites to end-users across diverse geographic regions. By leveraging advanced pipeline technologies, operational practices, and regulatory frameworks, SNG transmission systems support energy security, economic development, and environmental stewardship in the transition towards a low-carbon, renewable energy future.
Syngas to Synthetic Natural Gas (SNG) Distribution
Synthetic natural gas (SNG) distribution involves the delivery of SNG from transmission pipelines or storage facilities to end-users, including residential, commercial, industrial, and transportation sectors, through local distribution networks, meters, regulators, and service lines. SNG, produced from synthesis gas (syngas) through methanation and conditioning processes, is distributed via existing natural gas infrastructure or dedicated SNG distribution systems.
- Distribution Networks: SNG distribution networks consist of a network of pipelines, valves, regulators, meters, and service lines interconnected to deliver gas to individual customers or consumption points within a geographic area. Distribution networks include high-pressure transmission mains, medium-pressure distribution mains, low-pressure service lines, and customer meters, designed to maintain safe, reliable, and efficient gas delivery to end-users.
- Pipeline Infrastructure: SNG distribution pipelines are typically made of steel, polyethylene, or composite materials and are designed and installed according to local building codes, safety standards, and regulatory requirements. Distribution pipelines are buried underground to minimize environmental impact, prevent corrosion, and protect against external damage, with valves, regulators, and access points installed at strategic locations for system control and maintenance.
- Regulation and Measurement: SNG distribution networks incorporate pressure regulators, flow meters, and control valves to regulate gas pressure, flow rates, and distribution to individual customers. Pressure regulation ensures safe operation and consistent gas delivery within acceptable pressure ranges, while flow measurement enables accurate billing, monitoring, and control of gas consumption at customer sites.
- Metering and Billing: SNG distribution systems utilize gas meters installed at customer premises to measure gas consumption for billing purposes. Gas meters can be mechanical, electronic, or smart meters capable of remote reading, data logging, and communication with utility systems. Billing practices may include volumetric pricing, peak demand charges, or time-of-use rates to incentivize energy efficiency and demand management.
- Service Lines and Connections: SNG distribution networks connect individual customers to the gas grid through service lines, risers, and meters installed at building entry points. Service lines convey gas from distribution mains to customer premises, where meters measure consumption, regulators maintain pressure, and safety valves ensure system integrity. Service connections comply with building codes, safety standards, and utility specifications to ensure safe, reliable, and compliant gas supply.
- Safety and Reliability: SNG distribution systems prioritize safety, reliability, and system integrity through rigorous design, construction, operation, and maintenance practices. Safety measures include leak detection, odorization, corrosion control, emergency response, and public awareness programs to mitigate risks, protect public health, and prevent accidents. Reliability measures such as redundancy, system monitoring, and contingency planning ensure continuous gas supply and service reliability for customers.
- Emergency Response and Contingency Planning: SNG distribution operators implement emergency response plans, procedures, and protocols to address gas leaks, fires, explosions, or other incidents that may pose risks to public safety or system integrity. Emergency response teams, communication channels, and coordination with local authorities facilitate rapid deployment of resources, evacuation, and mitigation measures to minimize impacts and restore service.
- Infrastructure Expansion and Modernization: SNG distribution infrastructure undergoes continuous expansion, modernization, and upgrades to accommodate population growth, urban development, technological advancements, and regulatory requirements. Infrastructure investments may include pipeline replacement, system reinforcement, asset management, and automation to improve system performance, efficiency, and resilience over time.
- Customer Engagement and Education: SNG distribution utilities engage with customers through outreach, education, and communication programs to promote energy efficiency, safety awareness, and environmental stewardship. Customer education initiatives cover topics such as gas safety, appliance maintenance, energy conservation, and emergency preparedness to empower customers to make informed decisions and contribute to sustainable energy use.
- Environmental Impact Mitigation: SNG distribution activities incorporate environmental impact assessments, mitigation measures, and sustainability practices to minimize ecological disturbance, habitat fragmentation, and carbon emissions associated with gas distribution operations. Environmental initiatives include pipeline integrity management, leak detection, greenhouse gas reduction, and community engagement to enhance environmental stewardship and social responsibility.
In conclusion, synthetic natural gas (SNG) distribution plays a critical role in delivering clean, reliable, and affordable energy to end-users across diverse sectors and geographic regions. By leveraging advanced infrastructure, safety protocols, and customer services, SNG distribution systems support energy transition efforts and sustainable development goals for a cleaner, greener future.
EMS Power Machines
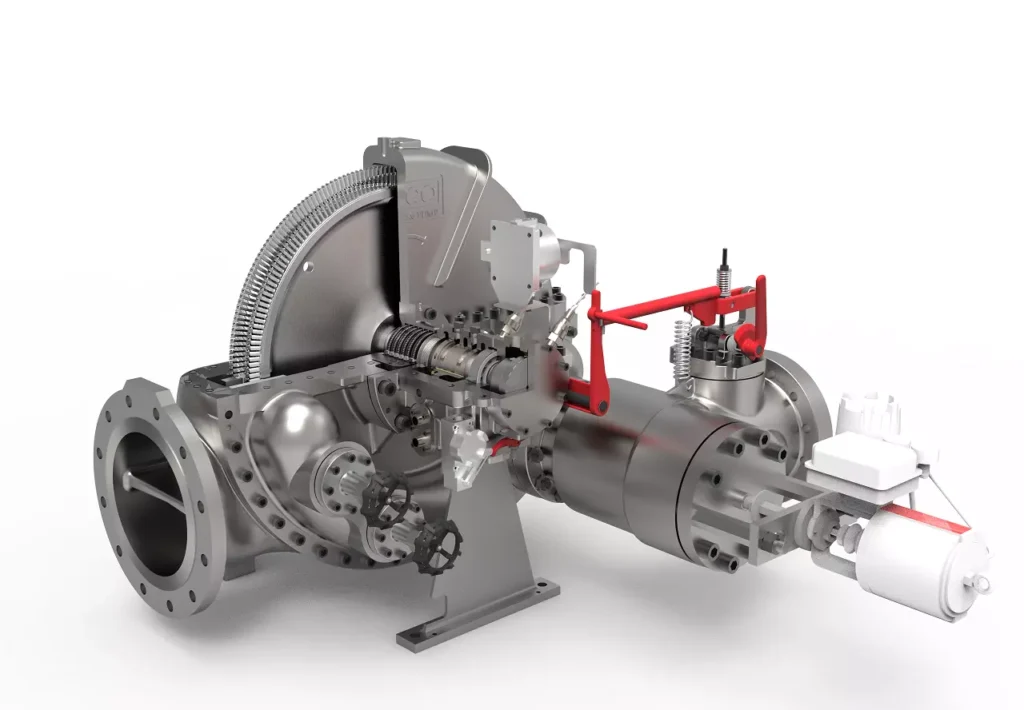
We design, manufacture and assembly Power Machines such as – diesel generators, electric motors, vibration motors, pumps, steam engines and steam turbines
EMS Power Machines is a global power engineering company, one of the five world leaders in the industry in terms of installed equipment. The companies included in the company have been operating in the energy market for more than 60 years.
EMS Power Machines manufactures steam turbines, gas turbines, hydroelectric turbines, generators, and other power equipment for thermal, nuclear, and hydroelectric power plants, as well as for various industries, transport, and marine energy.
EMS Power Machines is a major player in the global power industry, and its equipment is used in power plants all over the world. The company has a strong track record of innovation, and it is constantly developing new and improved technologies.
Here are some examples of Power Machines’ products and services:
- Steam turbines for thermal and nuclear power plants
- Gas turbines for combined cycle power plants and industrial applications
- Hydroelectric turbines for hydroelectric power plants
- Generators for all types of power plants
- Boilers for thermal power plants
- Condensers for thermal power plants
- Reheaters for thermal power plants
- Air preheaters for thermal power plants
- Feedwater pumps for thermal power plants
- Control systems for power plants
- Maintenance and repair services for power plants
EMS Power Machines is committed to providing its customers with high-quality products and services. The company has a strong reputation for reliability and innovation. Power Machines is a leading provider of power equipment and services, and it plays a vital role in the global power industry.
EMS Power Machines, which began in 1961 as a small factory of electric motors, has become a leading global supplier of electronic products for different segments. The search for excellence has resulted in the diversification of the business, adding to the electric motors products which provide from power generation to more efficient means of use.