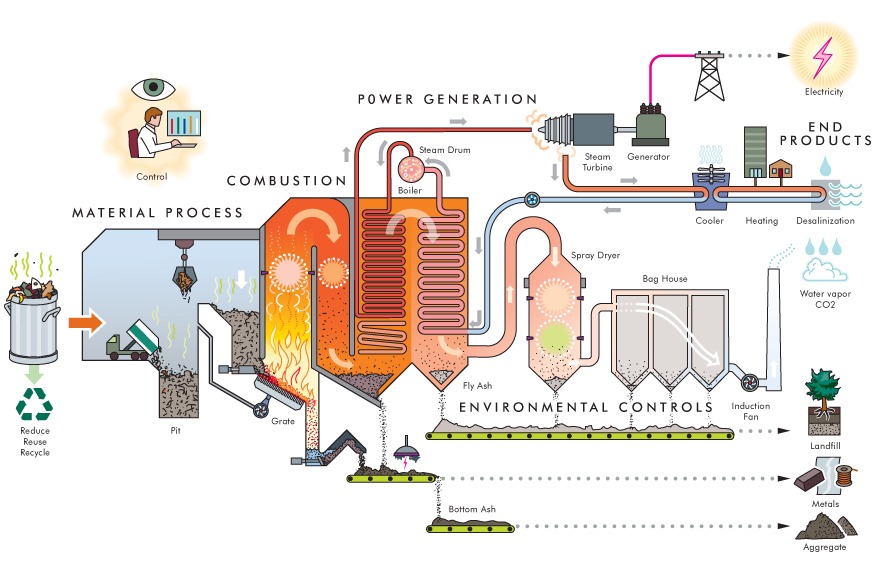
Factories Turn Waste Heat into Electricity: A steam turbine generator is a critical component in power generation, converting thermal energy from steam into mechanical energy and then into electrical energy. The process begins with high-pressure steam produced in a boiler, where water is heated using a fuel source such as coal, natural gas, nuclear energy, or renewable biomass. The high-pressure steam is directed onto the blades of a steam turbine, causing the rotor to spin. This rotation is transferred to an electrical generator, where electromagnetic induction generates electricity. The efficiency of a steam turbine generator depends on several factors, including steam pressure, temperature, turbine blade design, and the effectiveness of the condenser system that recycles steam into water for reuse.
Steam turbine generators are widely used in various types of power plants, including fossil fuel, nuclear, geothermal, and solar thermal plants. In coal-fired and natural gas power plants, steam turbines operate using high-temperature steam produced by burning fuel. In nuclear power plants, the heat from nuclear reactions generates steam to drive the turbine. Geothermal power plants use naturally occurring steam or high-temperature water from beneath the Earth’s surface, while solar thermal power plants concentrate sunlight to produce steam. The versatility and efficiency of steam turbines make them a preferred choice for large-scale electricity generation, as they can operate continuously with minimal downtime.
There are two main types of steam turbines based on their exhaust conditions: condensing and back-pressure turbines. Condensing turbines are used primarily for electricity generation in power plants. They exhaust steam at very low pressure, often close to a vacuum, to maximize energy extraction before the steam is condensed back into water in a condenser. This process ensures maximum efficiency and energy output. In contrast, back-pressure turbines exhaust steam at a higher pressure, which can be used for industrial applications such as heating, drying, or mechanical drive systems. These turbines are often used in cogeneration, where both electricity and thermal energy are utilized, improving overall energy efficiency.
A key factor in the performance of a steam turbine generator is its design and the materials used in its construction. The turbine consists of multiple stages of blades, each designed to extract energy from the expanding steam efficiently. High-pressure turbines handle steam at extreme conditions, while intermediate- and low-pressure turbines extract additional energy as the steam expands. The materials used in turbine blades and casings must withstand high temperatures, pressures, and corrosive environments. Advanced alloys and coatings are employed to improve durability and efficiency.
Steam Turbine Generator
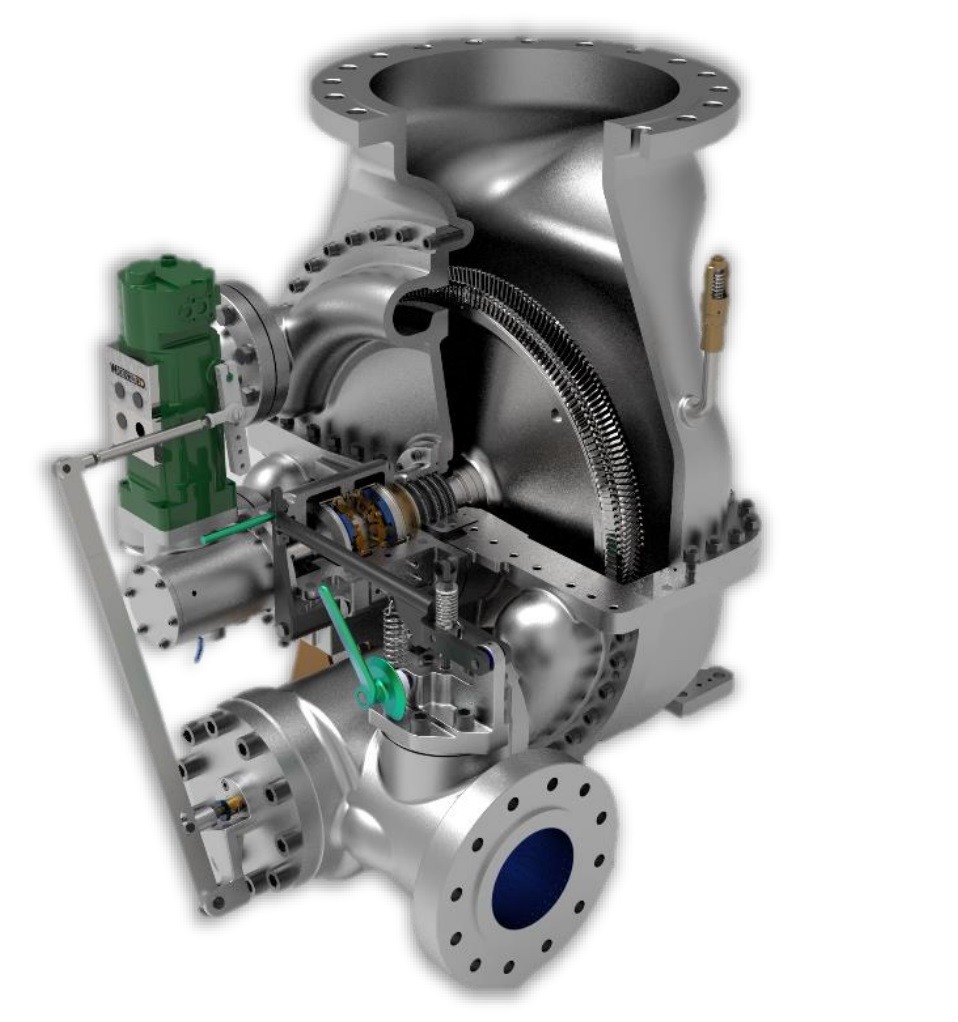
The generator connected to the steam turbine operates on the principle of electromagnetic induction. It consists of a rotor and a stator. The rotor is attached to the turbine shaft and spins within the stator, a stationary set of coils that generate electricity when the rotor’s magnetic field induces an electrical current. The generated electricity is then transmitted to the power grid for distribution. The efficiency of this conversion process is critical to optimizing energy output and minimizing losses.
Cooling and condensate systems play a vital role in the operation of steam turbine generators. Once the steam has passed through the turbine, it must be condensed back into water to maintain a continuous cycle. This is typically done in a condenser, where cooling water absorbs heat from the exhaust steam. The condensed water, known as condensate, is then pumped back to the boiler for reuse. Various cooling methods, such as once-through cooling, cooling towers, and air-cooled condensers, are used depending on the availability of water and environmental considerations.
Advanced control systems and monitoring technologies enhance the performance and reliability of steam turbine generators. Digital control systems allow operators to monitor parameters such as temperature, pressure, rotational speed, and power output in real-time. Predictive maintenance techniques, utilizing sensors and data analytics, help identify potential issues before they lead to failures. The implementation of automation and artificial intelligence further optimizes turbine efficiency, reduces emissions, and extends the lifespan of components.
The integration of steam turbine generators with renewable energy sources is gaining attention in modern power generation. Hybrid systems combining solar thermal energy with steam turbines can enhance efficiency and provide stable power output. Similarly, biomass-fueled steam turbines offer a sustainable alternative to fossil fuels by utilizing organic materials such as wood, agricultural waste, and municipal solid waste. These advancements contribute to reducing greenhouse gas emissions and promoting cleaner energy solutions.
As energy demand continues to grow, steam turbine technology is evolving to improve efficiency, reliability, and environmental sustainability. Research and development efforts focus on higher steam temperatures and pressures, advanced materials, and improved blade designs to increase power output while minimizing energy losses. The adoption of supercritical and ultra-supercritical steam cycles, which operate at higher temperatures and pressures, significantly enhances efficiency and reduces fuel consumption.
Steam turbine generators remain an essential part of global power generation, providing reliable and efficient electricity production. Their widespread use across various industries and energy sectors highlights their importance in meeting energy demands. With continued advancements in turbine design, materials, and control systems, steam turbine technology will play a crucial role in shaping the future of sustainable and efficient power generation.
Another critical aspect of steam turbine generator operation is the efficiency of the thermodynamic cycle it follows. Most modern steam turbines operate on the Rankine cycle, which consists of four key processes: heat addition in the boiler, expansion in the turbine, heat rejection in the condenser, and compression in the feedwater pump. The efficiency of this cycle depends on factors such as steam temperature and pressure, as well as the effectiveness of heat recovery systems.
Supercritical and ultra-supercritical steam turbines represent a significant advancement in efficiency. Unlike conventional subcritical steam cycles, supercritical steam turbines operate at pressures above the critical point of water (approximately 22.1 MPa), where there is no distinction between liquid and gas phases. This allows for greater thermal efficiency, reducing fuel consumption and emissions. Ultra-supercritical turbines push these limits further by operating at even higher temperatures and pressures, often exceeding 600°C. These technologies have been widely adopted in modern power plants to improve performance and sustainability.
Another area of development in steam turbine technology is the use of reheating and regenerative cycles. Reheating involves passing partially expanded steam through a secondary heat exchanger before reintroducing it into the turbine for further expansion. This reduces moisture content in the low-pressure stages and improves overall efficiency. Regenerative feedwater heating, on the other hand, uses extracted steam from intermediate turbine stages to preheat the feedwater before it enters the boiler. This process reduces the amount of fuel required to reach operating temperatures, further improving efficiency and reducing emissions.
The maintenance and reliability of steam turbine generators are crucial for their long-term performance. Regular inspections, lubrication, and monitoring of critical components such as bearings, blades, and seals help prevent failures and ensure smooth operation. Condition-based monitoring (CBM) and predictive maintenance strategies use real-time data and machine learning algorithms to detect anomalies and predict potential failures before they occur. This reduces unplanned downtime and extends the lifespan of the equipment.
Steam turbines also play an essential role in industrial applications beyond electricity generation. Many industries, including chemical processing, paper manufacturing, food production, and district heating, utilize steam turbines for mechanical drive applications or cogeneration. In cogeneration systems, also known as combined heat and power (CHP) plants, steam turbines generate both electricity and useful thermal energy from the same fuel source. This improves overall energy efficiency, often reaching levels above 80%, compared to conventional power plants that typically operate at efficiencies of 30-40%.
The environmental impact of steam turbine generators depends on the fuel source used for steam production. Fossil-fuel-powered steam turbines contribute to greenhouse gas emissions, but advancements in carbon capture and storage (CCS) technology aim to mitigate their environmental impact. By capturing carbon dioxide emissions before they reach the atmosphere, CCS systems help reduce the carbon footprint of traditional power plants. Additionally, the integration of steam turbines with renewable energy sources such as biomass, geothermal, and solar thermal energy further enhances sustainability.
Another emerging technology is the use of hydrogen as a clean fuel for steam generation. Hydrogen-fired boilers can produce steam without carbon emissions, offering a potential pathway for decarbonizing steam turbine power plants. Research and development efforts are focused on improving hydrogen production methods, such as electrolysis powered by renewable energy, to make hydrogen-based steam generation more viable on a large scale.
With ongoing advancements in digitalization, automation, and energy storage, the future of steam turbine generators looks promising. Smart grids and demand-response systems are enabling more flexible operation, allowing steam turbines to complement variable renewable energy sources like wind and solar. By integrating with energy storage technologies such as molten salt thermal storage and battery systems, steam turbines can provide stable and reliable power even when renewable energy generation fluctuates.
As global energy demand continues to grow, steam turbines will remain a cornerstone of power generation. Their ability to operate efficiently at large scales, adapt to various fuel sources, and integrate with modern energy management technologies ensures their relevance in the evolving energy landscape. Ongoing research in materials science, thermodynamics, and digital optimization will further enhance the efficiency, reliability, and sustainability of steam turbine generators, securing their role in the future of power generation.
Another important aspect of steam turbine generators is their adaptability to different operational needs and load conditions. In modern power grids, demand for electricity fluctuates throughout the day, requiring power plants to adjust their output accordingly. Steam turbine generators can operate in base-load, intermediate-load, and peaking-load conditions, depending on the plant’s design and the requirements of the grid. Base-load power plants, such as nuclear and large coal-fired plants, run continuously at a steady output to provide a stable electricity supply. Intermediate-load plants adjust their output based on demand variations, while peaking plants operate during high-demand periods.
To improve flexibility, advanced steam turbines incorporate fast-start and load-following capabilities. These features allow the turbine to ramp up or down more quickly, reducing startup times and improving responsiveness to grid fluctuations. Combined cycle power plants (CCPPs), which integrate steam turbines with gas turbines, enhance efficiency and operational flexibility. In a CCPP, a gas turbine generates electricity while its exhaust heat is used to produce steam, which drives a steam turbine. This combined system increases efficiency, reduces fuel consumption, and allows for quicker adjustments to power demand.
Steam turbine performance is also influenced by steam quality, particularly in the low-pressure stages. As steam expands through the turbine, it can become wet, leading to moisture-related erosion and efficiency losses. To mitigate this, moisture separators and reheaters are used to improve steam conditions before it enters the later turbine stages. Blade coatings and advanced materials also help protect components from erosion, corrosion, and thermal stress.
The choice of turbine configuration depends on the specific application. Impulse turbines and reaction turbines are the two primary types used in steam power generation. Impulse turbines rely on high-velocity steam jets to strike the turbine blades, causing them to rotate. The steam expands in nozzles before impacting the blades, leading to efficient energy conversion in high-pressure stages. Reaction turbines, on the other hand, extract energy through a combination of steam pressure drop and reactive force, providing a more gradual expansion and energy transfer. Many modern steam turbines use a combination of both impulse and reaction stages to optimize efficiency across different operating conditions.
In addition to power generation, steam turbines play a critical role in industrial processes that require mechanical power. Industries such as petrochemical refining, pulp and paper production, and desalination use steam turbines to drive pumps, compressors, and other machinery. These applications benefit from the efficiency and reliability of steam turbines, especially when integrated with cogeneration systems. By using extracted steam for heating or other industrial purposes, facilities can significantly improve their overall energy efficiency and reduce waste heat losses.
The future of steam turbine generators is closely tied to advancements in energy efficiency, emissions reduction, and digitalization. Digital twins—virtual models of physical turbines—are increasingly used for real-time monitoring, performance optimization, and predictive maintenance. By simulating different operating conditions and analyzing historical data, digital twin technology helps operators maximize efficiency and minimize downtime. The integration of artificial intelligence and machine learning further enhances turbine performance by identifying patterns and optimizing control strategies.
Another area of innovation is supercritical CO₂ (sCO₂) power cycles, which use supercritical carbon dioxide as a working fluid instead of steam. These systems operate at higher efficiencies and require smaller, more compact turbines. sCO₂ power cycles have the potential to revolutionize power generation by reducing plant size, increasing operational flexibility, and improving efficiency beyond conventional steam Rankine cycles. Research and pilot projects are underway to develop commercial-scale sCO₂ power plants, which could complement or even replace traditional steam turbines in the future.
With global efforts to transition to cleaner energy sources, steam turbines will continue to play a role in bridging the gap between conventional and renewable power generation. The adaptation of steam turbine technology to biomass, hydrogen, and waste-to-energy applications will ensure their continued relevance in a decarbonizing energy landscape. Additionally, the integration of energy storage solutions and hybrid systems will enhance the efficiency and reliability of steam-based power plants, making them more competitive in the evolving energy market.
As technological advancements continue, steam turbine generators will remain a cornerstone of industrial and power generation infrastructure. With improvements in materials, thermodynamics, and digital control systems, they will achieve even greater levels of efficiency, reliability, and sustainability. The ongoing evolution of steam turbines will contribute to a more resilient and adaptable global energy system, ensuring their role in power generation for decades to come.
The ongoing advancements in steam turbine generator technology are driven by the need for increased efficiency, reduced environmental impact, and enhanced operational flexibility. One of the primary research areas is improving turbine blade design. Modern steam turbines use aerodynamically optimized blades with advanced materials such as nickel-based superalloys and ceramic coatings. These materials can withstand extreme temperatures and pressures, reducing wear and improving longevity. Additionally, 3D printing and additive manufacturing are being explored to create complex blade geometries that enhance efficiency and reduce turbulence losses.
Another key area of development is the use of advanced steam cycles to extract more energy from the steam before it is condensed back into water. The ultra-supercritical (USC) steam cycle operates at temperatures above 600°C and pressures exceeding 30 MPa, significantly improving thermal efficiency compared to conventional subcritical systems. These high-efficiency cycles reduce fuel consumption and lower carbon dioxide emissions per unit of electricity generated. Many modern coal-fired power plants are being upgraded to ultra-supercritical status to meet stricter environmental regulations while maintaining economic viability.
Cogeneration, also known as combined heat and power (CHP), continues to gain importance in industrial applications where both electricity and heat are needed. In a cogeneration system, steam turbines generate electricity while capturing waste heat for industrial processes, district heating, or desalination. This dual-purpose use of energy improves overall system efficiency and reduces fuel costs. Many industries, including chemical processing, food production, and pharmaceuticals, are adopting cogeneration to enhance their energy efficiency and sustainability.
The integration of steam turbine generators with renewable energy sources is another promising trend. Concentrated solar power (CSP) plants use mirrors or lenses to focus sunlight onto a receiver, generating high-temperature steam to drive a steam turbine. Unlike photovoltaic solar panels, CSP plants can incorporate thermal energy storage, such as molten salt storage, to provide electricity even when the sun is not shining. Geothermal power plants also use steam turbines, harnessing naturally occurring steam from underground reservoirs to generate electricity with minimal environmental impact.
To further reduce emissions from conventional power plants, carbon capture and storage (CCS) technologies are being integrated with steam turbine generators. In a CCS-equipped power plant, carbon dioxide emissions are captured before being released into the atmosphere and then stored underground or utilized in industrial applications. This technology enables steam turbine power plants to operate with significantly lower greenhouse gas emissions, making them a viable option in a low-carbon energy future. Ongoing research focuses on improving the efficiency and cost-effectiveness of carbon capture systems to facilitate wider adoption.
Digitalization is also transforming steam turbine operations. The use of Internet of Things (IoT) sensors, big data analytics, and machine learning algorithms allows for real-time performance monitoring and predictive maintenance. By continuously analyzing operational data, power plant operators can detect early signs of wear, optimize performance, and extend the lifespan of critical components. Digital twin technology, which creates a virtual replica of a steam turbine generator, enables simulations and testing without disrupting actual plant operations. These innovations contribute to higher reliability, reduced downtime, and lower maintenance costs.
Energy storage solutions are also being explored to complement steam turbine generators. While steam turbines provide steady baseload power, energy storage can help balance supply and demand fluctuations. Technologies such as molten salt thermal storage, compressed air energy storage (CAES), and advanced battery systems allow excess energy generated during low-demand periods to be stored and released when needed. Hybrid power plants that combine steam turbines with energy storage can improve grid stability and increase the flexibility of thermal power generation.
Looking ahead, the role of steam turbine generators in a rapidly evolving energy landscape remains crucial. As global energy demand continues to grow, steam turbine technology will adapt to meet the challenges of efficiency, sustainability, and integration with renewable energy sources. Innovations in materials, digital control systems, and advanced steam cycles will drive further improvements in performance and environmental impact. Whether in large-scale power generation, industrial applications, or hybrid energy systems, steam turbines will continue to play a fundamental role in delivering reliable and efficient energy for decades to come.
An Economic Steam Turbine Generator (ESTG) is designed to provide efficient and cost-effective power generation while minimizing operational and maintenance costs. These turbines are optimized for industries and power plants that require reliable energy production with a strong emphasis on affordability, fuel efficiency, and long-term sustainability. Economic steam turbine generators are used in various applications, including industrial power generation, cogeneration (combined heat and power), and renewable energy integration.
Key Features of an Economic Steam Turbine Generator
- High Efficiency with Lower Fuel Consumption
Economic steam turbines are engineered to maximize energy conversion from steam while minimizing fuel consumption. This is achieved through optimized turbine blade design, advanced materials, and improved thermodynamic cycles such as superheated and reheated steam processes. These enhancements reduce waste energy and improve overall plant efficiency. - Cost-Effective Construction and Operation
The design of economic steam turbine generators prioritizes cost-effective materials and streamlined manufacturing processes to reduce initial capital investment. Modern manufacturing techniques, such as 3D printing and precision machining, contribute to lower production costs while maintaining high performance and durability. - Flexibility in Fuel and Steam Sources
Economic steam turbines can operate using various heat sources, including fossil fuels (coal, natural gas, oil), biomass, geothermal energy, and solar thermal power. This adaptability allows industries and power plants to choose the most cost-effective and locally available fuel sources, reducing dependence on expensive imports. - Compact and Modular Design
Many economic steam turbine generators are designed with modular components that enable easy installation, expansion, and maintenance. This modular approach allows power plants to scale their operations based on demand, reducing initial capital costs and improving long-term economic viability. - Low Maintenance and Extended Lifespan
Economic steam turbines are designed for durability and minimal maintenance requirements. By using high-quality materials, advanced coatings, and self-lubricating components, manufacturers can reduce wear and tear, extending the lifespan of the turbine. Condition-based monitoring systems also help operators detect potential issues early, preventing costly breakdowns. - Integration with Waste Heat Recovery Systems
Many economic steam turbine generators are integrated into waste heat recovery systems (WHRS), allowing them to utilize excess heat from industrial processes. This approach significantly improves efficiency and reduces fuel costs, making them ideal for industries such as cement manufacturing, steel production, and chemical processing. - Suitability for Cogeneration (CHP) Systems
In combined heat and power (CHP) applications, economic steam turbines maximize energy use by simultaneously generating electricity and useful heat. This significantly increases overall system efficiency (often above 80%) and reduces operational costs for industries that require both power and steam for processes. - Environmental and Regulatory Compliance
Economic steam turbines are designed to meet stringent environmental regulations by reducing emissions and optimizing fuel usage. Modern designs incorporate low-emission combustion technologies, carbon capture integration, and improved steam cycle efficiency to comply with global sustainability goals.
Applications of Economic Steam Turbine Generators
- Industrial Power Generation: Factories and manufacturing plants use economic steam turbines to power their operations, reducing dependence on expensive grid electricity.
- Cogeneration Plants: Economic turbines are widely used in CHP plants to provide both power and heat for district heating, food processing, and chemical industries.
- Renewable Energy Projects: Geothermal and solar thermal power plants utilize economic steam turbines to convert heat into electricity efficiently.
- Waste-to-Energy Systems: Economic turbines play a crucial role in converting industrial waste heat into usable electricity, promoting sustainable energy practices.
Future Trends in Economic Steam Turbine Generators
With ongoing advancements in materials science, automation, and digital monitoring, economic steam turbines continue to evolve. Innovations such as artificial intelligence (AI)-driven predictive maintenance, supercritical CO₂ cycles, and hydrogen-based steam generation are shaping the future of economic power generation. These improvements aim to make steam turbine technology even more affordable, efficient, and environmentally friendly.
As global energy markets shift toward sustainability and cost-effectiveness, Economic Steam Turbine Generators will remain a vital component of industrial and power generation systems, ensuring reliable and economical electricity production for years to come.
The increasing demand for cost-effective and sustainable energy solutions continues to drive innovations in Economic Steam Turbine Generators (ESTGs). These turbines are not only essential for industrial power generation but also play a significant role in supporting decentralized energy systems, improving grid stability, and integrating renewable energy sources. Their ability to operate efficiently under varying loads and fuel conditions makes them an attractive choice for both large-scale and small-scale power generation.
Optimization of Economic Steam Turbine Generators
- Enhanced Thermodynamic Cycles for Better Efficiency
Advancements in steam turbine cycles have significantly improved the efficiency of ESTGs. The use of superheated and reheated steam cycles ensures that steam expands through the turbine stages at optimal conditions, reducing moisture content and enhancing energy conversion. Additionally, regenerative feedwater heating is employed to preheat the boiler feedwater using extracted steam, which reduces the energy required for steam generation and improves overall thermal efficiency. - Innovations in Blade Design and Materials
Economic steam turbines utilize aerodynamically optimized blade profiles to minimize energy losses due to turbulence and steam leakage. High-performance alloys, such as nickel-based superalloys and titanium composites, enhance the durability of turbine blades, allowing them to withstand high temperatures and pressures while maintaining efficiency. The use of coatings and erosion-resistant materials further extends turbine lifespan and reduces maintenance costs. - Compact and Lightweight Configurations
To make ESTGs more adaptable for industrial and decentralized power applications, manufacturers are designing compact, modular, and lightweight turbines. These designs reduce installation and transportation costs, making them ideal for industries with limited space or remote locations where logistics are a challenge. - Advanced Control and Monitoring Systems
The integration of digital control systems, IoT-based sensors, and AI-driven analytics has transformed steam turbine operations. These technologies enable real-time monitoring of turbine performance, detecting potential failures before they occur and optimizing operation for maximum efficiency. Predictive maintenance systems reduce downtime and operational costs by ensuring that maintenance is performed only when necessary, rather than on fixed schedules. - Waste Heat Recovery and Combined Cycle Integration
One of the most significant economic advantages of steam turbine generators is their ability to utilize waste heat from industrial processes. Many industries, such as steel production, cement manufacturing, and chemical processing, generate large amounts of waste heat that can be harnessed to produce steam. This steam can then be used to drive turbines, generating electricity at minimal additional cost. Furthermore, ESTGs are increasingly being integrated into combined cycle power plants (CCPPs), where they work in conjunction with gas turbines to maximize fuel efficiency and minimize emissions. - Hybrid Energy Systems and Renewable Energy Integration
Economic steam turbines are becoming a key component of hybrid energy systems, where they operate alongside solar thermal, geothermal, and biomass energy sources. In concentrated solar power (CSP) plants, steam turbines convert solar heat into electricity, providing a stable power output even when solar radiation fluctuates. In geothermal plants, steam turbines use naturally occurring steam from underground reservoirs, offering a low-carbon and cost-effective energy solution. These integrations help reduce reliance on fossil fuels and support the transition to cleaner energy sources.
Cost-Effectiveness and Financial Viability of ESTGs
- Lower Capital and Operational Costs
Economic steam turbines are designed with cost optimization in mind, ensuring that initial investment and long-term operational costs remain low. The use of standardized components, automated manufacturing, and modular construction reduces production expenses. Additionally, longer service intervals and low-maintenance designs further contribute to cost savings over the turbine’s lifespan. - Fuel Flexibility for Economic Operation
The ability of ESTGs to operate on a wide range of fuels, including coal, natural gas, biomass, and waste heat, provides industries with the flexibility to choose the most affordable and locally available energy source. This reduces dependency on expensive imported fuels and stabilizes long-term energy costs. - Government Incentives and Regulatory Support
Many governments are encouraging the adoption of efficient and sustainable energy solutions by offering financial incentives, tax credits, and grants for industries that invest in energy-efficient steam turbines. Policies supporting combined heat and power (CHP) systems, waste heat recovery, and carbon reduction strategies make ESTGs an even more attractive investment for businesses seeking to improve their energy efficiency while complying with environmental regulations.
Future Prospects of Economic Steam Turbine Generators
- Advancements in Supercritical and Ultra-Supercritical Technology
Future developments in supercritical and ultra-supercritical steam cycles will enable steam turbines to operate at even higher temperatures and pressures, further increasing efficiency and reducing fuel consumption. These improvements will be particularly beneficial for large-scale power plants aiming to enhance economic and environmental performance. - Hydrogen-Powered Steam Turbines
With the growing focus on decarbonization, research is underway to develop hydrogen-fueled steam turbines. Hydrogen-fired boilers can generate steam without producing carbon emissions, making steam turbine generators an integral part of future clean energy systems. As hydrogen production technologies become more cost-effective, green hydrogen-based steam power generation will become a viable and sustainable option. - AI and Machine Learning for Smart Operations
The application of AI and machine learning in steam turbine operations is set to revolutionize the industry. Advanced algorithms will continuously analyze operational data, adjusting turbine parameters for optimal performance under varying loads and environmental conditions. Autonomous and self-optimizing turbines will further reduce human intervention and improve overall economic efficiency. - Decentralized Power Generation and Microgrids
The rise of microgrids and decentralized energy systems is creating new opportunities for economic steam turbine generators. Small-scale industries, commercial buildings, and rural communities can deploy compact steam turbines in CHP or waste-to-energy applications, reducing reliance on traditional power grids and enhancing energy security.
Conclusion
Economic Steam Turbine Generators are a cornerstone of cost-effective and efficient power generation. Their adaptability to various fuels, ability to integrate with renewable energy sources, and continuous advancements in efficiency and digitalization make them an essential component of modern energy systems. As industries seek affordable, sustainable, and resilient energy solutions, ESTGs will continue to play a pivotal role in driving global energy efficiency and reducing carbon footprints.
By embracing emerging technologies such as supercritical steam cycles, AI-driven maintenance, hydrogen integration, and hybrid renewable systems, economic steam turbine generators will remain a key player in the evolving energy landscape, ensuring low-cost, reliable, and sustainable power generation for decades to come.
The Role of Economic Steam Turbine Generators in Global Energy Transition
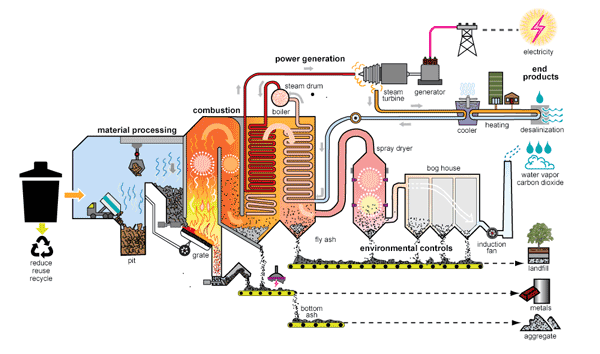
As the world transitions toward cleaner and more sustainable energy sources, Economic Steam Turbine Generators (ESTGs) remain a key component of the power sector. Despite the rise of renewable energy technologies such as wind and solar, steam turbines continue to provide baseload power, ensuring grid stability and reliability. The integration of advanced steam cycles, fuel flexibility, and hybrid energy solutions has further enhanced their economic and environmental viability.
Integration with Modern Energy Systems
- Hybrid Power Plants with Renewable Energy
ESTGs are increasingly being integrated into hybrid power plants, where they complement solar thermal, geothermal, and biomass energy sources. These hybrid configurations improve overall efficiency and ensure continuous power generation, even when renewable sources experience fluctuations. For example:- Concentrated Solar Power (CSP) Plants use steam turbines to generate electricity from stored solar heat, ensuring a steady power supply even after sunset.
- Geothermal Power Plants utilize naturally occurring underground steam to drive turbines, offering a low-cost, sustainable energy solution.
- Biomass and Waste-to-Energy Systems convert agricultural, municipal, and industrial waste into steam, reducing landfill waste while generating electricity.
- Decentralized Energy and Microgrid Applications
As energy distribution models evolve, ESTGs are becoming crucial in microgrids and decentralized energy systems. In remote locations or industrial zones, small-scale steam turbines provide a reliable and cost-effective alternative to grid dependence. These systems:- Reduce transmission and distribution losses.
- Enhance energy security by ensuring on-site power generation for critical industries.
- Support industrial self-sufficiency, lowering electricity costs for manufacturing plants, food processing units, and district heating systems.
- Grid Stability and Load Balancing
With the increasing penetration of intermittent renewable sources such as wind and solar, economic steam turbines play a stabilizing role in power grids. Their ability to rapidly adjust power output makes them an ideal partner for renewable energy by:- Compensating for fluctuations in solar and wind generation.
- Providing inertia and frequency regulation, maintaining grid reliability.
- Operating in flexible load conditions, making them compatible with modern smart grids.
Economic and Environmental Considerations
- Cost-Effective Power Generation
The affordability of ESTGs is a major reason for their widespread adoption in industrial and power generation applications. Compared to gas turbines and diesel generators, steam turbines:- Have lower operating costs due to fuel efficiency and minimal moving parts.
- Offer a longer lifespan, often exceeding 30 years of operation with proper maintenance.
- Utilize a variety of fuels, ensuring adaptability to fluctuating fuel prices and availability.
- Environmental Sustainability and Emission Reduction
Modern ESTGs are designed to meet strict environmental regulations by incorporating low-emission combustion technologies and carbon capture solutions. Some of the key environmental benefits include:- High efficiency, reducing fuel consumption and lowering CO₂ emissions.
- Integration with carbon capture and storage (CCS) technology, making fossil-fuel-based power plants more sustainable.
- Utilization of waste heat recovery, maximizing energy output and reducing overall emissions.
- Government Policies and Incentives
Many governments are supporting the adoption of efficient and clean energy technologies, providing:- Subsidies and tax credits for industries implementing steam turbines in CHP and waste-to-energy applications.
- Carbon pricing mechanisms that encourage the use of high-efficiency turbines with lower emissions.
- Regulatory frameworks promoting renewable-based steam power, such as solar thermal and geothermal projects.
Future Technological Innovations
- Supercritical and Ultra-Supercritical Steam Cycles
The next generation of economic steam turbines will feature supercritical (SC) and ultra-supercritical (USC) technologies, operating at higher temperatures and pressures to increase efficiency. These advancements:- Improve thermal efficiency, reducing fuel consumption by up to 45%.
- Enable lower carbon emissions per megawatt-hour of electricity generated.
- Reduce operational costs over the long term by improving fuel economy.
- AI-Driven Optimization and Digital Twin Technology
Artificial intelligence and machine learning are transforming steam turbine operations through:- Predictive maintenance, using real-time sensor data to detect wear and optimize maintenance schedules.
- Digital twin technology, creating a virtual replica of the turbine to simulate performance and test improvements.
- Automated control systems, dynamically adjusting steam flow, temperature, and load to enhance efficiency.
- Hydrogen-Based Steam Power Generation
As hydrogen production technologies improve, hydrogen-fired steam turbines will become a zero-emission power solution. Hydrogen-based systems:- Reduce reliance on fossil fuels by using green hydrogen from renewable sources.
- Provide long-term energy storage, ensuring reliability in hybrid renewable grids.
- Align with global carbon-neutrality targets, supporting cleaner industrial power generation.
Conclusion
Economic Steam Turbine Generators will continue to evolve and adapt in response to shifting energy demands and sustainability goals. By embracing technological innovations, digitalization, and hybrid energy integration, these turbines will remain a cost-effective, efficient, and environmentally friendly solution for industrial and utility-scale power generation.
As energy markets move toward decarbonization and resilience, ESTGs will play a critical role in ensuring reliable and affordable electricity while supporting the transition to a cleaner energy future. Whether in conventional power plants, industrial cogeneration, or renewable hybrid systems, economic steam turbines will remain a cornerstone of global power infrastructure for decades to come.
Advanced Engineering and Future Developments in Economic Steam Turbine Generators
The continuous evolution of Economic Steam Turbine Generators (ESTGs) is driven by the need for higher efficiency, lower costs, and improved sustainability. Innovations in materials, thermodynamic cycles, digitalization, and integration with renewable energy systems are shaping the next generation of steam turbines. These advancements ensure that steam turbines remain a competitive and essential part of the global energy mix.
Innovations in Steam Turbine Design and Manufacturing
- Next-Generation High-Performance Materials
- The development of high-temperature alloys, such as nickel-based superalloys and ceramic matrix composites, allows steam turbines to operate at higher temperatures and pressures without degradation.
- Coatings and surface treatments improve corrosion resistance, reducing the impact of steam impurities and extending turbine lifespan.
- Advanced 3D printing techniques enable the precise manufacturing of complex turbine components, reducing production costs and material waste.
- Improved Aerodynamics and Blade Efficiency
- Computational fluid dynamics (CFD) simulations are used to optimize turbine blade design, reducing aerodynamic losses and improving efficiency.
- Active clearance control (ACC) systems adjust blade-tip clearances dynamically, minimizing steam leakage and enhancing power output.
- Last-stage blade extensions allow turbines to capture more energy from low-pressure steam, increasing total energy conversion.
- Compact, Modular, and Scalable Designs
- Small and mid-sized steam turbines are being designed with modular components, making them ideal for distributed power generation and microgrid applications.
- Factory-assembled turbine modules reduce installation time and costs, making ESTGs more accessible to industries with limited infrastructure.
- Scalable turbine systems allow businesses to expand their power generation capacity in stages, optimizing capital investment.
Digitalization and Smart Monitoring in ESTGs
- AI-Powered Predictive Maintenance
- Machine learning algorithms analyze sensor data to predict potential failures before they occur, reducing unplanned downtime.
- Automated diagnostics improve turbine reliability by continuously assessing component wear and efficiency.
- Remote monitoring and cloud-based analytics allow operators to manage multiple turbines from a centralized location.
- Digital Twin Technology for Performance Optimization
- Virtual models (digital twins) simulate real-world operating conditions to test new configurations and improve turbine performance.
- Real-time adjustments based on digital twin analysis enhance efficiency, reduce maintenance costs, and extend turbine lifespan.
- Adaptive control systems automatically adjust turbine settings to optimize steam flow and thermal performance.
- Integration with Smart Grids and IoT Networks
- Internet of Things (IoT)-enabled turbines communicate with energy management systems, improving grid stability and demand response.
- Dynamic load balancing allows steam turbines to adjust power output in real-time, supporting fluctuating renewable energy inputs.
- Cybersecurity advancements ensure the protection of digital control systems against cyber threats and operational disruptions.
Sustainability and Environmental Impact
- Carbon Capture and Utilization (CCU) Technologies
- Integrated carbon capture systems allow steam power plants to reduce CO₂ emissions by capturing exhaust gases for storage or reuse.
- CO₂ utilization processes convert captured emissions into industrial products such as synthetic fuels, chemicals, and building materials.
- Enhanced efficiency designs reduce greenhouse gas emissions per megawatt-hour of electricity generated.
- Hydrogen-Ready Steam Turbines
- Hydrogen-fueled steam boilers provide a carbon-neutral alternative to conventional fossil fuel combustion.
- Dual-fuel capability enables steam turbines to operate on a mix of natural gas, biomass, and hydrogen, offering flexibility during the transition to cleaner energy sources.
- Hydrogen-based combined cycle plants integrate gas and steam turbines for near-zero emissions power generation.
- Waste Heat Recovery and Industrial Symbiosis
- Heat recovery steam generators (HRSGs) capture waste heat from industrial processes, converting it into useful power.
- Industrial symbiosis allows multiple industries to share excess heat and steam resources, improving overall energy efficiency.
- Low-temperature steam cycles optimize power production from previously untapped waste heat sources, such as data centers and chemical plants.
Economic and Market Trends for ESTGs
- Cost Reduction Strategies
- Economies of scale in turbine manufacturing lower costs, making ESTGs more accessible to small and mid-sized industries.
- Longer service intervals reduce maintenance expenses, improving the overall return on investment.
- Government incentives for efficient power generation encourage the adoption of high-efficiency steam turbines.
- Rise of Distributed Energy Systems
- More businesses are investing in on-site power generation, reducing dependence on external electricity providers.
- Industrial CHP systems continue to gain traction, offering combined power and heat solutions for manufacturing and processing industries.
- Microgrid applications allow communities and commercial complexes to maintain energy independence with steam turbine-based power generation.
- Growth in Renewable and Hybrid Energy Markets
- Solar-thermal and biomass power plants are expanding their use of steam turbines for sustainable and dispatchable power generation.
- Hybrid energy projects combining wind, solar, and steam turbines provide reliable power with reduced carbon footprints.
- Geothermal energy expansion continues to drive demand for specialized low- and medium-pressure steam turbines.
The Future of Economic Steam Turbine Generators
As global energy demands shift toward efficiency, sustainability, and resilience, ESTGs will remain a vital part of the energy infrastructure. The next generation of steam turbines will integrate advanced materials, digital intelligence, and low-carbon technologies to offer cleaner and more economical power generation. With continuous improvements in automation, fuel flexibility, and hybridization, economic steam turbines will continue to provide reliable, cost-effective, and environmentally responsible power for industries worldwide.
In the coming decades, Economic Steam Turbine Generators will play a key role in supporting industrial growth, enhancing grid stability, and accelerating the transition toward a carbon-neutral energy future.
Self-Sustaining Industrial Power Solutions: A Path to Energy Independence and Efficiency
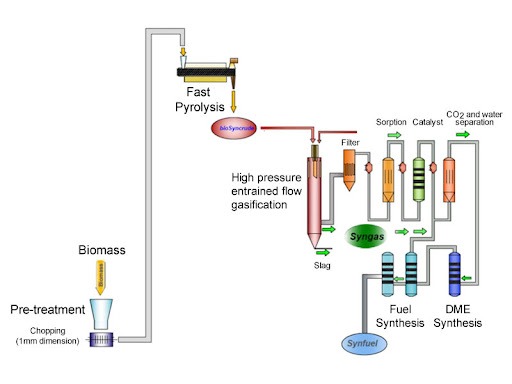
As industries worldwide seek cost-effective, reliable, and sustainable energy solutions, the concept of self-sustaining industrial power has gained significant traction. By integrating on-site power generation, waste heat recovery, renewable energy sources, and advanced energy storage, industries can achieve energy independence, reduced operational costs, and lower environmental impact.
Key Components of Self-Sustaining Industrial Power Solutions
- On-Site Power Generation: The Foundation of Energy Independence
- Cogeneration (CHP – Combined Heat and Power): Utilizing steam turbines or gas turbines to simultaneously produce electricity and useful heat, improving fuel efficiency by up to 80%.
- Industrial Steam Turbines: Powering factories with steam from biomass, waste-to-energy, or geothermal sources, ensuring continuous and reliable energy.
- Microgrids and Distributed Energy Systems: Independent energy networks that allow industries to function off-grid, reducing dependence on unstable external power supplies.
- Waste Heat Recovery: Maximizing Efficiency
- Heat Recovery Steam Generators (HRSGs): Capturing excess heat from industrial processes (e.g., cement, steel, and chemical manufacturing) to produce additional power.
- Organic Rankine Cycle (ORC) Systems: Converting low-temperature waste heat into electricity, improving overall energy efficiency.
- Thermal Energy Storage (TES): Storing surplus heat for later use, ensuring optimal energy utilization.
- Renewable and Alternative Energy Integration
- Biomass and Waste-to-Energy Plants: Converting industrial byproducts, agricultural residues, and municipal waste into sustainable energy.
- Solar Industrial Heating and Power: Using concentrated solar power (CSP) to generate steam for turbine-based electricity production.
- Geothermal Energy: Harnessing underground heat sources for continuous power and process heating in industrial operations.
- Energy Storage and Smart Grid Integration
- Battery Energy Storage Systems (BESS): Storing excess electricity for peak demand periods, reducing reliance on external power grids.
- Hydrogen Storage: Producing and storing green hydrogen for later use in hydrogen-fired steam turbines or fuel cells.
- AI-Powered Energy Management Systems: Using real-time analytics and automation to optimize energy production, consumption, and storage.
Benefits of Self-Sustaining Industrial Power Solutions
- Energy Cost Reduction: By generating electricity on-site, industries avoid transmission costs and peak grid pricing.
- Operational Resilience: Protection against grid failures, blackouts, and fluctuating fuel prices.
- Carbon Emission Reduction: Lower dependence on fossil fuels through renewables, CHP, and waste heat utilization.
- Regulatory Compliance: Meeting sustainability goals and avoiding carbon taxes through cleaner energy practices.
Industries Leading the Shift to Self-Sustaining Power
- Manufacturing and Heavy Industry: Using CHP and waste heat recovery to power operations.
- Chemical and Refining Plants: Deploying steam turbines and hydrogen-based power solutions.
- Food Processing and Agriculture: Utilizing biogas and biomass-fired power plants for energy self-sufficiency.
- Data Centers and Tech Infrastructure: Implementing microgrids and backup storage solutions for uninterrupted operations.
Conclusion
Self-sustaining industrial power solutions are transforming the way industries approach energy security, cost-efficiency, and sustainability. By leveraging a combination of on-site power generation, waste heat recovery, renewables, and energy storage, businesses can achieve true energy independence while reducing their environmental footprint. With advancements in digitalization, hydrogen power, and hybrid energy systems, the future of industrial energy is increasingly resilient, sustainable, and self-sufficient.
Advanced Technologies Driving Self-Sustaining Industrial Power Solutions
Industries are increasingly adopting self-sustaining power solutions to ensure operational continuity, reduce dependence on external energy suppliers, and enhance efficiency. The integration of next-generation energy technologies, automation, and digitalization is transforming industrial power systems into highly efficient, resilient, and cost-effective solutions.
1. Next-Generation Cogeneration and Combined Heat & Power (CHP) Systems
Cogeneration, or Combined Heat and Power (CHP), remains a cornerstone of self-sustaining industrial power solutions by maximizing energy efficiency and minimizing waste. The latest advancements in CHP technology include:
- High-Efficiency Steam Turbines: Modern steam turbines operate at higher temperatures and pressures, increasing fuel utilization efficiency to over 80%.
- Supercritical and Ultra-Supercritical Steam Systems: These technologies allow for greater energy conversion efficiency and lower emissions.
- Hybrid CHP Systems: Integrating renewable sources such as solar thermal and biomass into cogeneration plants to reduce reliance on fossil fuels.
- District Heating and Cooling (DHC) Networks: Utilizing industrial waste heat for heating and cooling urban areas, increasing overall system efficiency.
2. Decentralized Microgrid Solutions for Industrial Independence
Microgrids are revolutionizing industrial power by allowing facilities to operate autonomously from national grids. These self-contained energy systems enhance energy security, optimize load management, and improve resilience against power outages. Key advancements include:
- Smart Microgrid Controllers: AI-driven systems optimize energy flow, balancing power generation, storage, and consumption.
- Peer-to-Peer (P2P) Energy Trading: Blockchain technology enables industries to trade excess power with neighboring facilities, improving economic viability.
- Multi-Source Integration: Advanced microgrids seamlessly integrate power from steam turbines, solar PV, wind, and battery storage, ensuring uninterrupted operation.
3. Digitalization and AI-Driven Power Optimization
Artificial intelligence and machine learning are transforming industrial power systems by providing real-time analytics, predictive maintenance, and automated control mechanisms. Digital technologies improving self-sustaining industrial power include:
- Digital Twin Technology: Virtual models of power systems simulate operations, predict failures, and optimize performance.
- AI-Based Load Forecasting: Predicts energy demand patterns, allowing industries to optimize power production and reduce waste.
- Automated Energy Efficiency Systems: Smart sensors and IoT-enabled controls dynamically adjust energy consumption based on real-time requirements.
4. Waste Heat Recovery and Industrial Symbiosis
Industries generate vast amounts of waste heat, which, if captured and reused, can significantly improve energy efficiency. Innovations in waste heat recovery include:
- Thermoelectric Generators (TEGs): Convert low-grade industrial waste heat into electricity using advanced thermoelectric materials.
- Supercritical CO₂ Cycles: More efficient than traditional steam cycles, enabling better heat recovery from industrial processes.
- Cross-Industry Energy Exchange: Industrial symbiosis systems enable multiple facilities to share excess heat and steam, improving collective efficiency.
5. Hydrogen as a Game-Changer for Industrial Power
As industries move toward decarbonization, hydrogen is emerging as a key component of self-sustaining energy systems. The development of hydrogen-fired steam turbines and fuel cells allows industries to achieve zero-carbon power generation. Key advancements include:
- Hydrogen-Ready Steam Turbines: Designed to operate on a blend of natural gas and hydrogen, reducing carbon emissions.
- Green Hydrogen Production: Electrolyzers powered by renewable energy sources produce hydrogen for on-site energy use.
- Hydrogen Fuel Cells for Backup Power: Providing a clean, long-duration energy storage solution for industrial applications.
Conclusion
With the adoption of advanced cogeneration systems, intelligent microgrids, digital optimization tools, waste heat recovery solutions, and hydrogen-based technologies, industries are transforming into self-sustaining power hubs. These innovations ensure operational efficiency, cost savings, and environmental sustainability, making energy independence a reality for industrial facilities worldwide.
6. Energy Storage Solutions for Industrial Self-Sufficiency
Energy storage is a critical component of self-sustaining industrial power solutions, ensuring continuous power availability, grid stability, and peak demand management. Industries are increasingly integrating advanced storage technologies to optimize power usage and enhance resilience. Key energy storage solutions include:
Battery Energy Storage Systems (BESS)
- Lithium-Ion Batteries: Widely used for short-term energy storage, allowing industries to store excess power and discharge it during peak demand.
- Solid-State Batteries: An emerging technology that offers higher energy density, longer lifespan, and improved safety compared to conventional lithium-ion batteries.
- Flow Batteries (Vanadium Redox and Zinc-Bromine): Suitable for long-duration energy storage, these batteries store energy in liquid electrolytes and can discharge power for extended periods.
Thermal Energy Storage (TES)
- Molten Salt Storage: Used in concentrated solar power (CSP) plants, molten salt can retain heat for hours or even days, enabling continuous steam turbine operation even when sunlight is unavailable.
- Phase Change Materials (PCMs): Advanced PCMs absorb and release thermal energy efficiently, optimizing heat utilization in industrial processes.
- Cryogenic Energy Storage (CES): Utilizes liquefied air or nitrogen to store excess energy, which is then released as power when needed.
Hydrogen Energy Storage
- Green Hydrogen Production: Excess electricity from industrial power systems is used to produce hydrogen through electrolysis, which can be stored and converted back to power when required.
- Hydrogen Fuel Cells: Provide clean backup power for industrial operations, reducing reliance on diesel generators.
- Underground Hydrogen Storage: Large-scale hydrogen storage in salt caverns or depleted gas fields enables long-term energy security for industrial sites.
7. Hybrid and Multi-Source Power Generation
To achieve complete self-sufficiency, industries are adopting hybrid power generation systems that combine multiple energy sources. These systems offer improved reliability, efficiency, and cost savings.
Hybrid Steam Turbine Systems
- Solar-Steam Hybrid Plants: Integrating solar thermal energy with steam turbines enhances efficiency and reduces fuel consumption.
- Biomass-Steam CHP Systems: Utilizing agricultural waste, wood pellets, or municipal waste to generate steam for industrial power and heat applications.
- Geothermal-Steam Power Plants: Industries located near geothermal resources can use low-enthalpy steam cycles to generate clean, continuous power.
Wind and Solar Hybrid Integration
- Wind-Steam Hybrid Systems: Utilizing excess wind energy to preheat boiler feedwater, improving the efficiency of steam turbines.
- Solar PV and Steam Turbine Integration: Solar photovoltaic (PV) panels supply electricity for auxiliary equipment, reducing overall grid dependency.
- Hydro-Steam Power Generation: Utilizing hydropower alongside steam turbines to balance load fluctuations and ensure stable power supply.
8. Smart Grid and Demand-Side Management for Industrial Optimization
Digitalization and AI-driven demand-side management (DSM) are transforming industrial power systems, allowing real-time optimization of energy consumption, storage, and distribution. These smart technologies include:
- AI-Based Predictive Load Management: AI algorithms forecast energy demand, ensuring optimized power generation and reduced energy waste.
- Industrial Demand Response Programs: Industries adjust power consumption in response to grid fluctuations, earning financial incentives while improving overall grid stability.
- Blockchain-Enabled Energy Transactions: Smart contracts enable secure peer-to-peer (P2P) energy trading, allowing industries to buy and sell excess power in real-time.
- Automated Power Dispatch Systems: Intelligent software directs power flow between storage units, turbines, and industrial loads based on real-time needs.
9. Circular Economy and Industrial Sustainability Initiatives
To enhance long-term sustainability, industries are increasingly adopting circular economy principles in power generation and energy use. These initiatives promote waste reduction, resource efficiency, and environmental responsibility.
- Carbon Capture, Utilization, and Storage (CCUS): Capturing CO₂ emissions from industrial power plants and repurposing them for fuel production, chemical processes, or underground storage.
- Industrial Waste-to-Energy Plants: Converting plastic waste, sludge, and agricultural residues into power and heat through advanced gasification and pyrolysis.
- Closed-Loop Water Recycling: Steam power plants implement advanced water treatment and recycling systems, minimizing water usage and environmental impact.
- Green Industrial Parks: Facilities cluster together to share power, heat, and resources, forming a self-sustaining industrial ecosystem.
Conclusion
By integrating energy storage, hybrid power generation, smart grid solutions, and circular economy principles, industries can achieve true energy self-sufficiency while minimizing environmental impact. These innovative, scalable, and cost-effective solutions provide industries with resilience against power disruptions, long-term economic savings, and a path toward carbon neutrality.
With continuous advancements in hydrogen storage, AI-driven energy management, and sustainable waste-to-energy technologies, self-sustaining industrial power solutions will continue to redefine the future of energy independence.
10. Future Trends in Self-Sustaining Industrial Power Solutions
As technology evolves, self-sustaining industrial power systems are set to become even more efficient, reliable, and environmentally friendly. Several emerging trends and innovations are shaping the future of industrial energy independence.
Advanced AI and Machine Learning for Energy Optimization
- AI-Powered Predictive Maintenance: Machine learning models analyze data from turbines, boilers, and storage units to detect anomalies and predict equipment failures before they occur.
- Energy Forecasting and Automated Control: AI-driven systems dynamically adjust power generation, storage, and consumption based on real-time data and weather forecasts.
- Autonomous Power Plants: Future industrial power systems will leverage AI for self-regulation, load balancing, and seamless integration of multiple energy sources.
Decentralized Energy Networks and Industrial Energy Sharing
- Blockchain-Based Energy Trading: Secure, decentralized platforms will allow industries to trade surplus energy with nearby facilities, creating a more flexible and resilient power infrastructure.
- Virtual Power Plants (VPPs): Aggregated industrial power systems will act as a single controllable entity, optimizing power distribution between factories, microgrids, and storage units.
- Collaborative Industrial Energy Hubs: Large-scale industrial zones will integrate shared CHP plants, hydrogen hubs, and waste-to-energy facilities, minimizing energy waste and improving sustainability.
Next-Generation Hydrogen and Ammonia Energy Systems
- Hydrogen-Based Gas Turbines: Industries will transition from natural gas-powered turbines to hydrogen-ready turbines, reducing carbon emissions while maintaining high efficiency.
- Ammonia as an Energy Carrier: Green ammonia (NH₃) will be used for long-term hydrogen storage and direct fuel combustion in industrial turbines.
- On-Site Hydrogen Production: Industries will deploy modular electrolyzers powered by renewables to produce hydrogen for internal energy needs.
Supercritical CO₂ Power Cycles for Higher Efficiency
- Next-Gen Power Conversion: Supercritical CO₂ (sCO₂) turbines will replace traditional steam turbines in high-temperature industrial applications, offering higher efficiency and compact design.
- Low-Carbon Industrial Heat: sCO₂ cycles will enable industries to recover more waste heat, improving overall energy efficiency.
Nuclear Microreactors for Industrial Applications
- Compact, Modular Nuclear Reactors (SMRs): These small, self-contained reactors provide industries with continuous, carbon-free power for decades without refueling.
- Molten Salt and High-Temperature Gas Reactors: Advanced reactor designs will support industrial heat applications, such as hydrogen production and chemical processing.
11. Policy, Investment, and Global Adoption
Governments and industries are investing heavily in self-sustaining power technologies, driven by energy security concerns, economic incentives, and environmental regulations.
Government Policies and Incentives
- Carbon Pricing and Emission Reduction Targets: Industries are being incentivized to transition to low-carbon and energy-efficient technologies.
- Tax Credits and Subsidies: Governments worldwide are offering grants, tax breaks, and subsidies for industries investing in CHP, hydrogen, and renewable energy systems.
- Mandates for Industrial Microgrids: Some regions are requiring critical industries to deploy microgrid solutions to enhance resilience against grid failures.
Corporate Investments and Industrial Adoption
- Major Industrial Companies Going Off-Grid: Large manufacturing and tech companies are investing in self-sustaining energy projects to reduce costs and improve reliability.
- Green Industry Certification Programs: International organizations are launching standards for industries implementing sustainable and self-sufficient energy practices.
- Collaborative Research and Innovation: Joint ventures between governments, research institutions, and private companies are accelerating the development of next-gen power solutions.
Conclusion: The Future of Self-Sustaining Industrial Power
The shift toward self-sustaining industrial power solutions is revolutionizing global energy systems. With advancements in AI-driven optimization, hydrogen storage, decentralized microgrids, and next-generation power cycles, industries are moving closer to achieving energy independence, cost efficiency, and environmental sustainability.
As policies, technologies, and investments align, self-sustaining industrial power is poised to become the new standard for reliable, resilient, and sustainable energy systems. The industries that embrace these innovations will not only gain a competitive edge but also contribute to a cleaner, smarter, and more sustainable future.
Industrial Steam Turbines: Driving Production and Efficiency
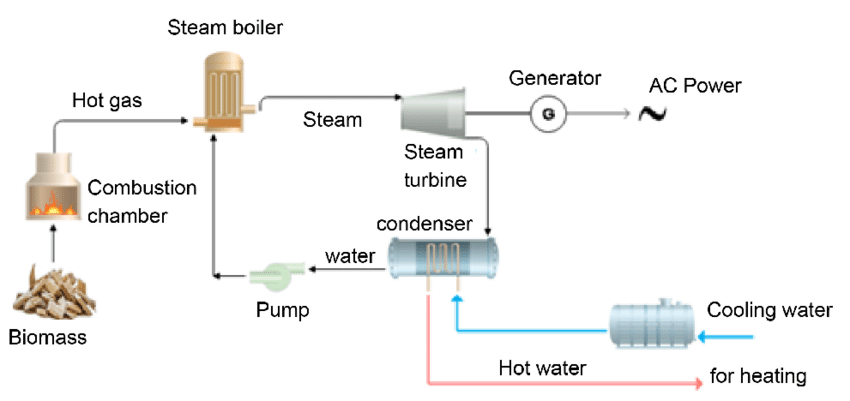
Industrial steam turbines play a crucial role in power generation and mechanical drive applications, enabling industries to achieve high efficiency, reliability, and cost-effective energy utilization. These turbines convert thermal energy from steam into mechanical power, which can be used to generate electricity or directly drive industrial machinery. Their versatility makes them essential across industries such as manufacturing, refining, petrochemicals, pulp & paper, and food processing.
How Industrial Steam Turbines Drive Production
- Power Generation for Industrial Facilities
- Industrial steam turbines are widely used in cogeneration (CHP) and combined cycle power plants to provide electricity and process heat simultaneously.
- Industries with access to biomass, waste heat, or geothermal energy use steam turbines to generate low-cost, on-site power, reducing reliance on external grids.
- Back-pressure turbines supply direct steam for industrial heating and production processes, improving overall efficiency.
- Mechanical Drive Applications
- Many industries use steam turbines to drive pumps, compressors, blowers, and fans, ensuring continuous and stable production.
- Oil refineries and chemical plants use steam turbines to power high-pressure compressors, which are essential for process operations.
- Steam-driven mechanical systems are more robust, long-lasting, and efficient compared to electric motors in high-power applications.
- Waste Heat Recovery for Sustainable Production
- Industries with high-temperature processes, such as cement, steel, and glass manufacturing, recover waste heat to generate steam for turbine operation.
- Steam turbines integrated with Heat Recovery Steam Generators (HRSGs) improve overall energy efficiency by capturing excess heat from industrial processes.
- Organic Rankine Cycle (ORC) systems enable turbines to operate using low-grade waste heat, enhancing sustainability.
- Flexible Operation for Various Industries
- Pulp & paper mills use steam turbines to generate power from biomass or black liquor recovery boilers.
- Food processing plants rely on steam turbines for sterilization, drying, and mechanical drive applications.
- Pharmaceutical and chemical industries use steam turbines for precision heat and power generation, ensuring production consistency.
Advantages of Industrial Steam Turbines in Production
- High Efficiency: Steam turbines convert a high percentage of thermal energy into mechanical work, optimizing fuel usage.
- Long-Term Reliability: With fewer moving parts compared to internal combustion engines, steam turbines offer extended operational life with lower maintenance.
- Fuel Flexibility: They can run on steam produced from coal, natural gas, biomass, geothermal energy, and waste heat, making them adaptable to various industries.
- Reduced Carbon Footprint: When integrated with renewables and waste heat recovery, steam turbines contribute to lower CO₂ emissions and improved sustainability.
Conclusion
Industrial steam turbines are at the heart of modern production facilities, providing efficient, reliable, and sustainable power and mechanical drive solutions. As industries continue to seek cost-effective and environmentally friendly energy sources, steam turbines will remain a cornerstone of industrial efficiency and productivity, driving manufacturing, refining, and processing operations worldwide.
Industrial steam turbines are essential to modern production, providing efficient and reliable power generation and mechanical drive capabilities across various industries. These turbines convert thermal energy from steam into mechanical work, which can then be used to generate electricity or directly drive equipment such as pumps, compressors, and fans. Their ability to operate on various steam sources, including high-pressure boilers, waste heat recovery systems, and renewable biomass, makes them an indispensable solution for industries seeking energy efficiency and sustainability.
Steam turbines are widely used in cogeneration and combined heat and power (CHP) plants, where they simultaneously produce electricity and process steam, optimizing fuel utilization and reducing energy costs. Their applications extend to refineries, petrochemical plants, pulp and paper mills, food processing facilities, and manufacturing plants, where they ensure continuous and stable production. Unlike internal combustion engines, steam turbines have fewer moving parts and experience less wear, resulting in longer operational life and lower maintenance costs. Many industries leverage steam turbines for their flexibility in handling varying loads, making them ideal for fluctuating energy demands. Additionally, their integration with waste heat recovery systems allows facilities to utilize excess thermal energy that would otherwise be lost, further improving efficiency and sustainability.
With advancements in materials, digital monitoring, and automation, modern steam turbines offer even greater performance, reliability, and adaptability to different industrial needs. As industries continue to focus on reducing carbon emissions and improving energy security, steam turbines remain a key technology in the transition toward cleaner and more efficient power generation. Their ability to integrate with renewable energy sources such as biomass and geothermal power further enhances their role in sustainable industrial operations. By driving production with high efficiency and reliability, industrial steam turbines continue to be a cornerstone of global manufacturing, processing, and energy generation, ensuring optimized performance and economic benefits for industries worldwide.
As industries evolve, steam turbines are increasingly integrated with advanced energy management systems and digital technologies to enhance efficiency and operational control. The introduction of smart sensors and real-time monitoring systems allows operators to track turbine performance, optimize steam flow, and predict maintenance needs before failures occur, minimizing downtime and reducing operational costs. AI-driven analytics and machine learning models are being applied to turbine operations, enabling dynamic adjustments to load demand and steam conditions, which improve overall efficiency and extend equipment lifespan.
Hybrid power solutions combining steam turbines with renewable energy sources such as solar thermal, biomass, and geothermal systems are becoming more prevalent, allowing industries to diversify their energy mix and reduce dependence on fossil fuels. In addition to power generation, steam turbines continue to play a vital role in mechanical drive applications where high power output and long-term reliability are required, such as in large-scale chemical processing and oil refining. The ability of steam turbines to operate in harsh environments and under extreme conditions makes them an ideal choice for heavy industrial applications where durability and efficiency are paramount. Furthermore, advancements in turbine blade design and steam path optimization have led to increased thermal efficiency, allowing industries to extract more energy from each unit of steam.
The shift toward sustainable industrial practices has also driven innovations in carbon capture and waste heat recovery systems, enabling steam turbines to contribute to lower emissions and improved energy conservation. Governments and industries are investing in research and development to further enhance steam turbine efficiency, with a focus on supercritical and ultra-supercritical steam cycles that offer even higher energy conversion rates. As regulatory frameworks tighten around energy consumption and carbon footprints, industries are increasingly turning to steam turbines as a proven solution to meet sustainability goals while maintaining high productivity and cost-effectiveness. The continued evolution of steam turbine technology ensures that these systems will remain at the core of industrial power generation and mechanical drive applications, reinforcing their role as a critical component in the global energy landscape.
With the growing emphasis on energy efficiency and decarbonization, steam turbine technology is undergoing continuous improvements to meet the evolving demands of industrial power generation. Advanced materials, including high-temperature alloys and ceramic coatings, are being developed to enhance turbine durability and performance in extreme operating conditions, allowing for greater thermal efficiency and prolonged operational life. Innovations in steam cycle configurations, such as reheat and regenerative cycles, further optimize energy extraction from steam, reducing fuel consumption and lowering greenhouse gas emissions. The integration of steam turbines into industrial microgrids and distributed energy systems is also gaining traction, providing localized, self-sufficient power generation that enhances grid stability and resilience.
Industries with high thermal energy requirements, such as steel production, cement manufacturing, and chemical processing, are increasingly adopting combined heat and power (CHP) systems with steam turbines to maximize energy utilization and improve overall sustainability. Waste heat recovery steam generators (HRSGs) are playing a crucial role in utilizing excess heat from industrial processes to produce additional steam for power generation, further increasing efficiency and reducing environmental impact. The transition toward hydrogen-based energy solutions is also influencing steam turbine applications, with ongoing research exploring hydrogen combustion in boilers and hybrid hydrogen-steam cycles to support low-carbon industrial power generation.
Digital twin technology, which creates virtual models of steam turbines, is revolutionizing maintenance and performance optimization by allowing engineers to simulate different operating conditions, predict potential failures, and implement preventive measures without disrupting real-world operations. The combination of automation, artificial intelligence, and predictive analytics is transforming how steam turbines are monitored and controlled, leading to smarter, more responsive energy systems that adjust dynamically to fluctuating industrial demands. As industries continue to navigate the challenges of energy security, cost efficiency, and environmental responsibility, steam turbines remain a cornerstone technology that provides scalable, flexible, and highly efficient power solutions. Their ability to adapt to emerging energy trends, integrate with renewable sources, and support industrial decarbonization ensures that steam turbines will continue to drive global production for decades to come.
Factories harness waste heat for power
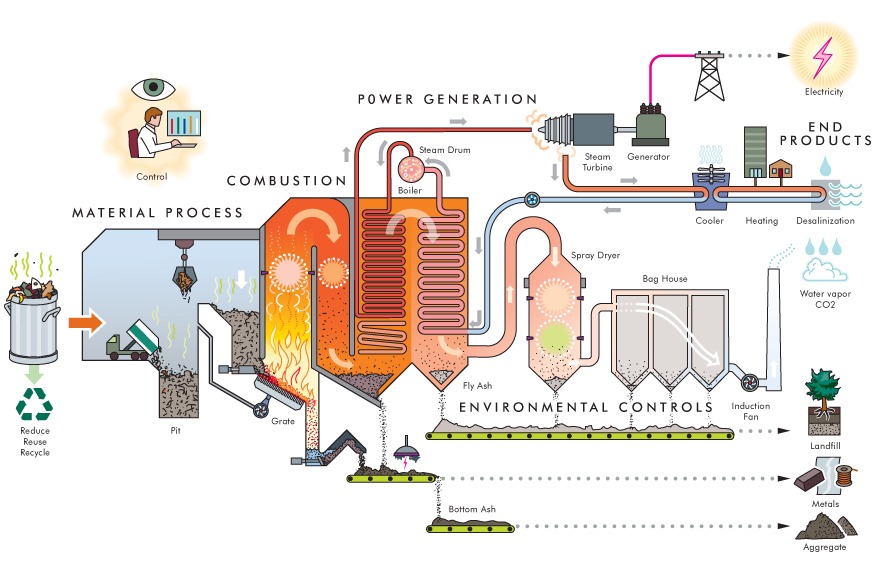
Factories are increasingly turning to waste heat recovery systems to improve energy efficiency, reduce operating costs, and lower environmental impact. In industrial processes, a significant amount of energy is lost as heat, often vented into the atmosphere. By capturing and repurposing this waste heat, factories can generate additional power, improving overall energy utilization and reducing reliance on external electricity sources. One of the most effective ways to harness waste heat is through Heat Recovery Steam Generators (HRSGs), which capture high-temperature exhaust gases from industrial furnaces, kilns, or gas turbines and use them to produce steam. This steam can then drive a steam turbine to generate electricity or be used for direct heating applications in manufacturing processes.
Combined Heat and Power (CHP) systems, also known as cogeneration, are another widely adopted solution, simultaneously producing electricity and useful thermal energy from a single fuel source, significantly increasing efficiency compared to conventional power generation. Many industries, including cement, steel, glass, and petrochemicals, have adopted waste heat recovery technologies to optimize their energy consumption and improve sustainability. Organic Rankine Cycle (ORC) systems offer a viable option for lower-temperature waste heat applications, using organic working fluids with lower boiling points to drive turbines and generate power even from moderate heat sources.
With advances in materials, heat exchangers, and thermodynamic cycle optimization, waste heat recovery solutions are becoming more efficient and cost-effective, making them an attractive investment for factories aiming to enhance profitability and environmental performance. The integration of digital monitoring and predictive maintenance technologies further enhances waste heat recovery efficiency by ensuring optimal performance and minimizing equipment downtime. As industries face increasing pressure to reduce carbon emissions and improve energy security, waste heat recovery is emerging as a critical strategy for sustainable industrial growth. By converting wasted energy into usable power, factories can achieve greater energy independence, lower fuel consumption, and contribute to a more sustainable industrial ecosystem.
As factories continue to seek innovative ways to improve energy efficiency, waste heat recovery technologies are evolving to accommodate a wider range of industrial applications. The development of advanced thermoelectric materials, which can directly convert heat into electricity through the Seebeck effect, offers new possibilities for harnessing low-grade waste heat that was previously considered unusable. These solid-state generators, requiring no moving parts, are gaining interest in industries with continuous waste heat streams, such as metal processing, refineries, and chemical plants. Meanwhile, supercritical CO₂ power cycles are emerging as a more efficient alternative to traditional steam-based systems, enabling factories to extract more energy from high-temperature exhaust gases with a smaller footprint and improved thermodynamic performance.
Industries are also exploring energy storage solutions to maximize the benefits of waste heat recovery, using phase-change materials and thermal batteries to store excess heat for later use during periods of high energy demand. The combination of waste heat recovery with renewable energy sources, such as solar thermal or biomass, is creating hybrid energy systems that provide greater reliability and flexibility for industrial power generation. Government incentives and environmental regulations are further driving the adoption of these technologies, as industries seek to comply with stricter emissions standards while improving their competitiveness. By integrating waste heat recovery into their operations, factories not only reduce greenhouse gas emissions but also lower operational costs, enhance energy security, and contribute to a circular economy where every possible energy resource is efficiently utilized. With ongoing advancements in heat exchanger design, materials science, and process integration, waste heat recovery is becoming a standard feature in modern industrial facilities, shaping the future of sustainable manufacturing and power generation.
The growing adoption of industrial waste heat recovery is also driving innovations in system integration and automation, allowing factories to optimize energy flows in real-time. Smart control systems, powered by artificial intelligence and machine learning, are being implemented to monitor heat sources, predict energy demand, and adjust recovery processes accordingly. These intelligent platforms enable industries to maximize heat utilization, reduce losses, and dynamically respond to operational changes, ensuring that excess thermal energy is directed where it is most needed. Additionally, advances in modular and scalable waste heat recovery systems are making it easier for factories of all sizes to implement energy-efficient solutions without extensive infrastructure overhauls.
Industries that previously found waste heat recovery to be impractical due to high upfront costs or space constraints are now able to adopt compact, high-efficiency heat exchangers and ORC systems that fit within existing plant layouts. Another promising development is the integration of waste heat recovery with district heating networks, where excess thermal energy from industrial facilities is repurposed to supply heat to nearby residential and commercial buildings. This not only improves overall energy efficiency but also strengthens collaborations between industries and local communities, creating a more sustainable and interconnected energy ecosystem.
As regulatory frameworks continue to evolve, industries are finding that investing in waste heat recovery not only helps them comply with environmental policies but also provides a competitive edge through lower energy costs and improved sustainability credentials. The shift toward electrification and hydrogen-based processes is further influencing waste heat recovery strategies, as industries explore innovative ways to capture and reuse heat in emerging clean energy systems. With the convergence of digitalization, advanced thermodynamics, and sustainable energy practices, factories are transforming waste heat from an overlooked byproduct into a valuable asset that enhances efficiency, reduces emissions, and supports the global transition toward a more resilient and low-carbon industrial sector.
As industries continue refining waste heat recovery strategies, emerging technologies are pushing the boundaries of what is possible in energy efficiency and resource utilization. One of the most promising advancements is the application of high-performance nanomaterials in heat exchangers, which enhance thermal conductivity and improve heat transfer efficiency, allowing for more effective energy capture even from low-temperature sources. Additionally, innovations in additive manufacturing, such as 3D-printed heat exchangers with optimized geometries, are enabling more compact and efficient waste heat recovery units that can be customized for specific industrial processes. These breakthroughs are making it increasingly feasible for factories to recover and utilize heat that was once considered too difficult or uneconomical to capture.
Another key development is the integration of waste heat recovery with hydrogen production, where excess heat is used to power electrolysis or steam methane reforming processes, improving the overall efficiency of hydrogen generation. This is particularly relevant as industries transition toward green hydrogen as a clean fuel for industrial applications. Moreover, advancements in absorption and adsorption cooling technologies allow factories to use waste heat to drive cooling systems, reducing the need for traditional electricity-powered refrigeration and air conditioning in large industrial complexes.
The growing adoption of waste heat-to-power solutions is also contributing to the decentralization of energy systems, with more industries generating their own electricity and becoming less dependent on external power grids. As energy markets shift toward decentralized generation and self-sustaining industrial ecosystems, factories are leveraging waste heat recovery not just as a cost-saving measure but as a strategic asset in their long-term sustainability planning. With continued investment in research and development, waste heat recovery is expected to play an even greater role in shaping the future of industrial energy efficiency. By turning previously wasted thermal energy into a valuable resource, factories are positioning themselves at the forefront of sustainable manufacturing, reducing operational costs, lowering carbon footprints, and enhancing overall energy security in an increasingly competitive and environmentally conscious global economy.
Industrial turbines generate large-scale power
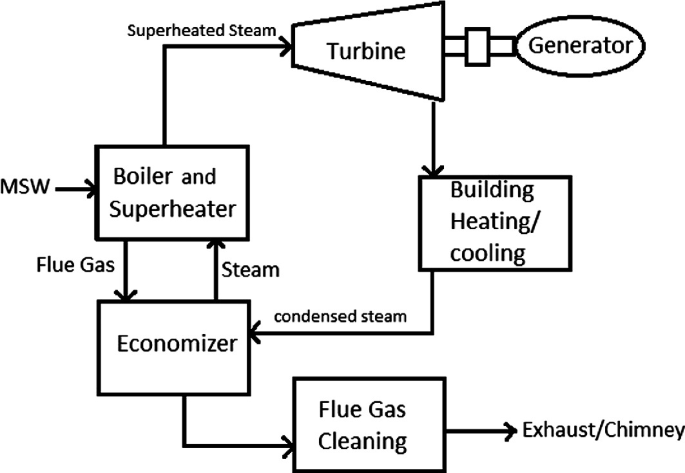
Industrial turbines play a critical role in generating large-scale power for a wide range of applications, from manufacturing and chemical processing to large-scale power plants and district energy systems. These turbines efficiently convert thermal energy from steam, gas, or combustion into mechanical power, which is then used to generate electricity or drive heavy industrial equipment. Steam turbines, in particular, are widely used in power plants, refineries, and cogeneration systems, where they maximize energy utilization by producing both electricity and process heat. Gas turbines, on the other hand, provide high-efficiency power generation with fast startup times, making them ideal for peaking power plants and industrial facilities requiring reliable energy output.
The integration of industrial turbines with combined-cycle power plants has further enhanced their efficiency, allowing facilities to extract more energy from fuel by using waste heat to produce additional steam for secondary turbine stages. This process significantly improves fuel efficiency and reduces emissions, making it a preferred method for large-scale power generation. Advancements in turbine materials, aerodynamics, and cooling technologies have also contributed to higher efficiency, enabling industrial turbines to operate at higher temperatures and pressures while maintaining durability and reliability.
In industries such as steel production, pulp and paper manufacturing, and petrochemicals, industrial turbines provide essential mechanical drive functions, powering compressors, blowers, and pumps that support continuous production processes. Many large-scale industrial operations also incorporate cogeneration (CHP) systems, where turbines generate electricity while utilizing excess heat for on-site heating, drying, or other thermal applications, significantly improving overall energy efficiency.
With the ongoing shift toward sustainability and carbon reduction, industrial turbines are increasingly being adapted to work with alternative fuels, including hydrogen, biofuels, and synthetic gases. Research into supercritical CO₂ turbines and advanced steam cycles is further pushing the boundaries of efficiency, offering new possibilities for clean and sustainable industrial power generation. As industries continue to modernize and optimize their energy usage, industrial turbines will remain a cornerstone of large-scale power production, delivering high-efficiency, reliable, and cost-effective energy solutions for the world’s most demanding applications.
The evolution of industrial turbines continues to be driven by the demand for greater efficiency, lower emissions, and improved operational flexibility. Advances in turbine blade design, including the use of high-performance alloys and ceramic coatings, have enabled turbines to withstand higher temperatures and pressures, increasing their power output while reducing fuel consumption. Computational fluid dynamics (CFD) simulations and digital twin technology are also being applied to optimize turbine aerodynamics, allowing for real-time performance monitoring and predictive maintenance. These innovations help industrial turbines operate with greater efficiency and reliability, minimizing downtime and reducing maintenance costs for large-scale power generation facilities.
One of the most significant developments in industrial turbine technology is the integration of carbon capture and storage (CCS) systems, which enable turbines to generate power with minimal CO₂ emissions. By capturing carbon from exhaust gases and either utilizing it for industrial applications or storing it underground, power plants and factories can significantly reduce their environmental impact while continuing to produce large amounts of electricity. Additionally, the push toward hydrogen-fueled turbines is gaining momentum, with major manufacturers developing turbines capable of operating on 100% hydrogen or hydrogen-natural gas blends. This transition aligns with global decarbonization efforts and the move toward cleaner energy sources.
Another emerging trend is the use of hybrid power systems that combine industrial turbines with renewable energy sources such as solar thermal or wind power. In these setups, turbines provide baseload power, ensuring stability and reliability when renewable generation fluctuates. Some industrial plants are also exploring waste heat recovery solutions, where turbines capture excess heat from other processes to generate additional power, maximizing energy efficiency.
With digitalization playing an increasing role in industrial energy systems, turbine operators are leveraging artificial intelligence and machine learning to fine-tune performance, anticipate equipment failures, and optimize fuel consumption. These intelligent control systems enhance efficiency and enable turbines to adapt to varying load demands, making them even more indispensable for large-scale power generation. As industrial energy needs grow and sustainability becomes a top priority, industrial turbines will continue to evolve, providing high-efficiency solutions that drive global industries while supporting the transition to a cleaner energy future.
As industrial turbines continue to evolve, their role in global energy infrastructure is becoming even more crucial. The increasing integration of renewable energy sources into the grid has highlighted the need for flexible and efficient power generation, and industrial turbines are stepping up to meet this challenge. Advanced load-following capabilities now allow turbines to ramp up or down quickly in response to fluctuations in electricity demand, ensuring grid stability even when intermittent renewable sources such as wind and solar experience variability. These flexible operation modes are particularly valuable for industrial cogeneration and combined-cycle power plants, where efficiency and reliability are paramount.
In addition to operational flexibility, the shift toward lower-carbon fuels is transforming turbine applications. Hydrogen, ammonia, and synthetic fuels are being explored as viable alternatives to traditional fossil fuels, with major turbine manufacturers actively developing systems that can run on these cleaner energy sources. Hydrogen-fired turbines, in particular, offer a promising pathway to achieving near-zero emissions in large-scale power generation. As the hydrogen economy expands, turbines capable of utilizing hydrogen blends are expected to become increasingly common in industrial settings.
Beyond fuel innovation, new developments in supercritical CO₂ (sCO₂) turbine technology are set to revolutionize the efficiency of power generation. Unlike traditional steam turbines, sCO₂ turbines operate at much higher temperatures and pressures, resulting in significantly greater energy conversion efficiency. Their compact size and ability to function in closed-loop cycles make them an attractive solution for industrial power plants seeking to maximize energy output while reducing emissions and footprint.
Waste heat utilization is another area where industrial turbines are driving advancements. More industries are implementing Organic Rankine Cycle (ORC) systems, which allow lower-temperature waste heat to be converted into electricity using organic working fluids with lower boiling points than water. This technology is particularly useful in cement, steel, and chemical manufacturing, where significant amounts of residual heat are available.
The digitalization of turbine operations is also accelerating, with cloud-based monitoring and AI-driven predictive analytics improving efficiency, maintenance scheduling, and operational decision-making. Turbine operators can now remotely monitor equipment health, optimize performance based on real-time data, and implement preventive maintenance strategies to reduce costly downtime. These technological advancements are making industrial turbines not only more efficient but also more intelligent, ensuring that they remain a cornerstone of large-scale power generation for decades to come.
As industrial turbines continue to advance, their integration with emerging energy technologies is reshaping the landscape of large-scale power generation. One of the most transformative developments is the convergence of industrial turbines with energy storage solutions, such as battery storage and thermal energy storage systems. By pairing turbines with high-capacity batteries or molten salt storage, power plants can store excess energy during periods of low demand and release it when demand spikes, improving grid stability and efficiency. This hybrid approach is particularly valuable in industrial settings where energy demand fluctuates throughout the day, allowing for more consistent and reliable power supply.
The role of industrial turbines in decarbonization efforts is also expanding, with increasing adoption of carbon capture, utilization, and storage (CCUS) technologies. In large-scale power plants and industrial facilities, CCUS systems capture CO₂ emissions from turbine exhaust and either repurpose them for industrial use or store them underground. This innovation enables industries to continue using high-efficiency turbines while significantly reducing their carbon footprint. Research into direct air capture (DAC) is further pushing the boundaries, exploring ways to remove CO₂ from the atmosphere and use turbines to support a circular carbon economy.
In addition to reducing emissions, industrial turbines are playing a key role in the hydrogen economy. The development of turbines that can operate on 100% hydrogen or ammonia is accelerating, with several demonstration projects underway to prove their viability for large-scale deployment. Hydrogen-ready turbines offer a direct pathway to achieving carbon-neutral power generation, and as global hydrogen production scales up, these turbines will become integral to the clean energy transition.
Advancements in turbine maintenance and longevity are also driving industry innovation. Predictive maintenance powered by AI and digital twins is revolutionizing how turbines are monitored and serviced. Operators can now simulate performance scenarios, detect potential faults before they occur, and schedule maintenance proactively to avoid unexpected shutdowns. This data-driven approach not only extends turbine lifespan but also improves overall efficiency and cost-effectiveness.
As industries worldwide continue to seek sustainable and resilient power solutions, industrial turbines are evolving to meet the demands of a rapidly changing energy landscape. With continued investment in efficiency improvements, alternative fuel compatibility, and smart grid integration, industrial turbines will remain a cornerstone of large-scale power generation, ensuring that industries have access to reliable, high-performance energy while advancing global sustainability goals.
Heavy industries require stable electricity
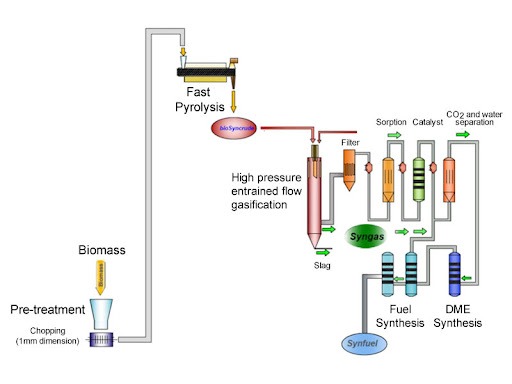
Heavy industries depend on a stable and reliable electricity supply to maintain continuous operations, power large-scale machinery, and support critical production processes. Unlike residential or commercial sectors, where power fluctuations may cause inconvenience, even minor disruptions in electricity supply can lead to substantial losses in manufacturing, metals processing, petrochemicals, and other energy-intensive industries. As a result, industrial facilities prioritize energy security by integrating advanced power generation systems, backup solutions, and grid stabilization technologies to ensure uninterrupted operation.
One of the most common solutions for ensuring stable electricity in heavy industries is on-site power generation, often achieved through steam turbines, gas turbines, or combined heat and power (CHP) systems. These systems provide not only electricity but also valuable process heat, improving overall efficiency and reducing reliance on external power grids. Many large factories also invest in microgrids, which allow them to operate independently or in conjunction with the main power grid, offering greater resilience against power outages and voltage fluctuations.
Energy storage solutions, such as large-scale battery systems and thermal energy storage, are becoming increasingly important in stabilizing industrial power supply. These systems store excess energy during low-demand periods and release it when demand surges, ensuring a consistent and balanced power flow. In industries such as aluminum smelting, steel production, and chemical manufacturing, where energy demand is extremely high and cannot tolerate fluctuations, these technologies help prevent costly downtime and equipment damage.
Another approach to enhancing power stability is through demand-side management and smart grid integration. Advanced energy management systems equipped with AI and real-time monitoring enable industries to optimize energy use, reduce peak loads, and respond dynamically to changes in grid conditions. These technologies not only enhance stability but also improve efficiency and reduce operational costs.
With the global push toward cleaner energy sources, heavy industries are also exploring alternative power solutions such as hydrogen-based power generation and hybrid renewable energy systems. While these technologies are still evolving, they hold great promise for ensuring stable and sustainable electricity for industrial operations. As industries continue to modernize, investments in resilient energy infrastructure will remain a top priority, ensuring that heavy industries can operate efficiently, minimize production risks, and contribute to economic growth while transitioning toward a more sustainable energy future.
As heavy industries continue to evolve, the need for stable and resilient electricity supply is becoming even more critical. With increasing automation, digitization, and the rise of energy-intensive processes such as electric arc furnaces, electrolysis-based hydrogen production, and high-temperature industrial heating, power demand is expected to grow significantly. To meet these demands, industries are adopting more sophisticated energy management strategies, leveraging a combination of on-site generation, storage, and grid support technologies to ensure uninterrupted power supply.
One of the most significant trends in industrial power stability is the integration of renewable energy with conventional power generation. While renewable sources such as wind and solar offer sustainability benefits, they are inherently intermittent. To counter this, industries are investing in hybrid energy systems that combine renewables with gas turbines, steam turbines, and energy storage solutions to create a stable and reliable electricity supply. Advanced power electronics, such as inverters and frequency stabilizers, are also playing a crucial role in managing fluctuations and maintaining grid stability in industrial plants.
Industrial facilities are increasingly deploying digital twin technology and predictive analytics to monitor power consumption, anticipate potential failures, and optimize energy efficiency. These AI-driven systems analyze real-time data from power generation units, transformers, and industrial equipment, allowing operators to adjust loads dynamically, reduce energy waste, and prevent unexpected downtime. By leveraging big data and machine learning, industries can achieve a more precise and responsive approach to energy management.
Microgrid adoption is another growing trend, particularly in remote locations where grid reliability is a challenge. Heavy industries such as mining, oil and gas, and large-scale manufacturing are turning to microgrids powered by a mix of diesel generators, gas turbines, solar panels, and battery storage to maintain stable power supply without relying solely on external utilities. These decentralized systems enhance energy security, reduce transmission losses, and provide backup power in case of grid failures.
As industries transition to a low-carbon future, the stability of electricity supply will remain a top priority. Advances in high-capacity battery storage, hydrogen-based energy storage, and next-generation power management technologies will enable industries to operate with greater flexibility and resilience. By investing in these innovations, heavy industries can ensure not only the reliability of their operations but also improved energy efficiency, cost savings, and alignment with global sustainability goals.
As industries face increasing energy demands and stricter sustainability regulations, the focus on reliable, stable electricity supply is intensifying. The electrification of industrial processes—such as electric steelmaking, high-temperature heat pumps, and hydrogen production—is placing even greater pressure on power infrastructure. To address these challenges, industries are adopting diversified energy strategies that combine traditional baseload generation with advanced energy storage and intelligent grid management systems.
One major development is the adoption of long-duration energy storage (LDES) solutions, which help stabilize industrial power supply by storing excess electricity and discharging it when needed. Technologies such as flow batteries, compressed air energy storage (CAES), and liquid air energy storage (LAES) are gaining traction as they offer longer discharge durations compared to conventional lithium-ion batteries. These systems allow industries to mitigate fluctuations from renewable sources while ensuring a continuous power supply for energy-intensive operations.
At the same time, demand response programs are becoming a crucial tool for maintaining stability in industrial energy systems. These programs enable factories and large facilities to adjust their power consumption based on grid conditions, reducing load during peak demand periods and increasing usage when surplus electricity is available. AI-driven energy management platforms are enhancing demand response strategies by providing real-time analytics and automation, allowing industries to dynamically optimize energy consumption without compromising productivity.
Another key trend is the rise of industrial-scale hydrogen production, which is set to reshape the energy landscape. Many industries are investing in electrolyzers that produce hydrogen using renewable electricity, effectively converting excess power into a storable and transportable energy source. Hydrogen turbines and fuel cells are also emerging as viable options for providing stable backup power, particularly in industries aiming for carbon neutrality. The integration of hydrogen into industrial energy systems will enable greater flexibility, resilience, and sustainability in power supply management.
Looking ahead, advancements in superconducting power cables and solid-state transformers will further enhance electricity stability by reducing transmission losses and improving power quality. Smart substations equipped with real-time monitoring and self-healing capabilities are also being deployed to detect faults and automatically reroute power, minimizing the risk of outages.
By leveraging these innovations, heavy industries are strengthening their energy resilience while accelerating the transition toward cleaner and more efficient power systems. As technology continues to evolve, the combination of on-site generation, storage, and intelligent grid integration will ensure that industries remain powered reliably, efficiently, and sustainably in the face of growing energy challenges.
As industrial power demands grow and energy markets evolve, the ability to maintain a stable electricity supply is becoming a key factor in operational efficiency and competitiveness. The convergence of energy generation, storage, and digital control technologies is leading to the development of highly resilient industrial power systems that can adapt to fluctuations in demand and supply while ensuring continuous production.
One of the most impactful advancements in industrial energy stability is the expansion of hybrid power plants that integrate multiple energy sources into a single, coordinated system. These plants combine gas or steam turbines with renewables such as solar PV or wind, alongside energy storage and smart grid technology. By intelligently managing energy flows between these different sources, industries can ensure that power remains stable even during fluctuations in renewable output. Hybrid power plants also offer the flexibility to shift between fuels, allowing industries to optimize costs and emissions based on market conditions.
Digitalization is playing a crucial role in enhancing power reliability, with industrial facilities increasingly deploying advanced grid monitoring and automation systems. Artificial intelligence and machine learning algorithms are being used to analyze real-time power quality data, detect anomalies, and predict potential failures before they occur. This predictive approach to grid management reduces the risk of power interruptions and allows industries to implement preventative maintenance strategies, minimizing downtime and improving overall efficiency.
Additionally, the rise of decentralized power generation is transforming how industries secure their electricity supply. Instead of relying solely on centralized power plants, many heavy industries are developing localized microgrids that can operate independently or in coordination with the main grid. These microgrids incorporate a mix of power generation assets, such as gas turbines, CHP systems, and renewables, to create a self-sustaining energy ecosystem. Advanced control systems ensure seamless switching between grid-connected and islanded modes, providing industrial facilities with greater autonomy and protection against external grid failures.
The growing role of alternative fuels is also influencing industrial power strategies. In addition to hydrogen and synthetic fuels, ammonia is emerging as a potential energy carrier for industrial power generation. Gas turbines are being adapted to run on ammonia, offering a carbon-free alternative that can be transported and stored more easily than hydrogen. As fuel diversification continues, industries will have more options to enhance power stability while aligning with long-term decarbonization goals.
Looking forward, innovations in superconducting energy storage and direct current (DC) microgrids could further improve industrial electricity stability. Superconducting magnetic energy storage (SMES) systems provide near-instantaneous power delivery, making them ideal for stabilizing voltage and frequency fluctuations in critical industrial applications. Meanwhile, DC microgrids offer more efficient power distribution by reducing conversion losses, particularly in facilities with high-voltage direct current (HVDC) infrastructure.
By integrating these advanced technologies, heavy industries are securing their energy future with a mix of reliability, efficiency, and sustainability. As the industrial sector continues to modernize, the combination of intelligent energy management, diversified power sources, and cutting-edge storage solutions will ensure that factories, refineries, and large-scale manufacturing plants remain resilient in an increasingly complex energy landscape.
Heavy Industries Require Stable Electricity
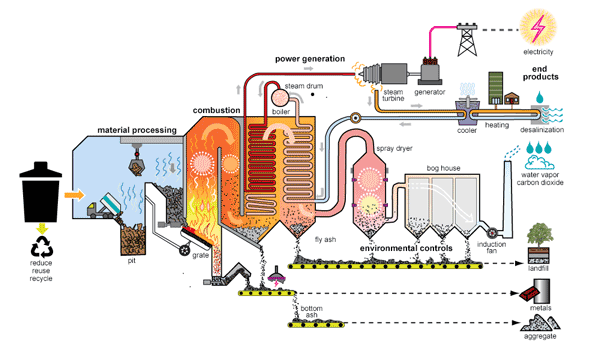
Heavy industries rely on a stable and uninterrupted electricity supply to sustain large-scale production processes, power advanced machinery, and maintain operational efficiency. Unlike residential or commercial sectors, where power fluctuations may cause inconvenience, even brief interruptions in industrial settings can lead to significant financial losses, equipment damage, and reduced productivity. Industries such as steel, aluminum, cement, petrochemicals, and manufacturing require a continuous flow of high-quality power to operate energy-intensive machinery, maintain precise temperature controls, and ensure smooth automation processes.
To achieve this level of stability, industries often invest in dedicated power generation systems, such as gas turbines, steam turbines, and combined heat and power (CHP) units, to reduce their dependence on external grids. Many heavy industries also deploy microgrids—localized networks that can operate independently or in conjunction with the main power grid—to provide an additional layer of reliability. These microgrids integrate multiple energy sources, such as natural gas, renewables, and battery storage, to ensure stable power supply even during grid disturbances or outages.
The integration of energy storage technologies plays a crucial role in stabilizing industrial electricity supply. Large-scale battery systems, pumped hydro storage, and compressed air energy storage help balance fluctuations by storing excess energy during low-demand periods and releasing it when needed. These storage solutions are particularly valuable for industries adopting renewable energy sources, which can be intermittent. By combining renewables with storage and traditional baseload power, industries can enhance energy security while lowering their carbon footprint.
Advanced energy management systems, powered by artificial intelligence and machine learning, further optimize electricity usage and grid interaction. These systems continuously monitor energy consumption patterns, predict demand fluctuations, and adjust power distribution in real time to prevent overloads or voltage instability. AI-driven predictive maintenance also reduces the risk of unexpected power failures by identifying potential equipment issues before they lead to costly downtime.
As industrial energy needs continue to grow, the shift toward alternative fuels such as hydrogen and ammonia is reshaping power stability strategies. Hydrogen-powered turbines and fuel cells are being explored as viable solutions for decarbonized industrial power, while ammonia is emerging as a potential fuel for large-scale power generation. These alternative energy sources offer the potential for cleaner and more resilient electricity supply in the long term.
The future of industrial power stability lies in the integration of smart grids, energy-efficient technologies, and diversified power sources. Heavy industries must continue investing in resilient energy infrastructure to ensure stable operations, minimize financial risks, and align with global sustainability goals. By leveraging cutting-edge innovations in power generation, storage, and digitalization, industries can safeguard their electricity supply while enhancing overall efficiency and competitiveness in an increasingly electrified and decarbonized world.
As global industrial operations become more complex and energy-intensive, ensuring a stable electricity supply remains a top priority for heavy industries. The rise of automation, digital manufacturing, and electrified processes has amplified the need for uninterrupted power, as even minor fluctuations can disrupt production lines, damage sensitive equipment, and lead to costly downtime. To mitigate these risks, industries are increasingly turning to diversified energy strategies that integrate traditional and advanced power generation solutions.
One of the key approaches to achieving power stability is the deployment of highly efficient combined-cycle power plants. These plants utilize both gas and steam turbines to maximize energy output from a single fuel source, significantly improving efficiency and reliability. Many industries are also adopting cogeneration (CHP) systems, which simultaneously produce electricity and useful heat, optimizing fuel utilization and reducing energy costs. These self-sustaining power solutions allow industrial facilities to maintain operational continuity even during external grid disturbances.
The integration of smart grid technology is further strengthening industrial power stability. Smart grids use digital sensors, advanced analytics, and automated control systems to optimize energy distribution and quickly respond to voltage fluctuations or faults. By enabling real-time monitoring and load balancing, smart grids help industries avoid power surges, reduce peak demand stress, and improve overall efficiency. Additionally, demand response programs allow industries to adjust power consumption dynamically based on grid conditions, ensuring stability while reducing energy costs.
Energy storage solutions are also playing a crucial role in industrial power reliability. Lithium-ion and flow batteries provide rapid-response backup power during grid instability, while pumped hydro and compressed air energy storage systems offer long-duration energy reserves. These storage technologies help industries smooth out fluctuations in power supply, particularly when integrating renewable energy sources such as solar and wind. In regions where grid reliability is a concern, large-scale energy storage systems serve as a critical buffer against blackouts and voltage drops.
To further enhance resilience, industries are exploring decentralized energy solutions, such as microgrids and distributed generation. Microgrids enable industrial facilities to operate autonomously by generating power on-site through a mix of turbines, fuel cells, and renewables. These self-contained systems provide an additional layer of energy security, ensuring continued operations even if the main grid experiences disruptions. Advanced microgrid controllers can seamlessly switch between power sources, optimizing efficiency and minimizing reliance on external utilities.
Looking ahead, the development of next-generation power technologies, such as hydrogen turbines, high-efficiency superconductors, and direct current (DC) microgrids, will further enhance industrial electricity stability. By investing in these innovations, heavy industries can not only ensure a continuous and reliable power supply but also improve efficiency, reduce costs, and support global sustainability initiatives. In a world where energy security is increasingly linked to industrial competitiveness, the ability to maintain stable electricity will be a defining factor in long-term success.
As industries continue to expand and modernize, maintaining a stable and resilient electricity supply is becoming even more critical. The increasing electrification of industrial processes—such as electric arc furnaces in steelmaking, large-scale hydrogen electrolysis, and high-temperature industrial heating—places growing demands on power infrastructure. To address these challenges, industrial facilities are investing in advanced energy management solutions, integrating diversified power sources, and leveraging cutting-edge technologies to enhance reliability.
One of the emerging trends in industrial power stability is the use of artificial intelligence (AI) and machine learning for predictive energy management. AI-driven systems analyze vast amounts of real-time data from turbines, transformers, and industrial equipment to detect anomalies, predict maintenance needs, and optimize energy consumption. This proactive approach reduces unexpected failures, prevents costly downtime, and ensures that industrial power systems operate at peak efficiency. Additionally, AI-powered grid stabilization tools can automatically adjust power distribution to maintain voltage and frequency stability, even in complex industrial environments.
Another key innovation in industrial energy stability is the adoption of solid-state transformers (SSTs). Unlike traditional transformers, SSTs offer faster response times, improved voltage regulation, and the ability to integrate with smart grids seamlessly. By improving power quality and reducing losses, these transformers enhance the overall resilience of industrial power networks, ensuring stable electricity for critical processes.
As industries seek cleaner and more sustainable power sources, hydrogen is gaining traction as a reliable alternative for industrial energy security. Hydrogen-powered turbines and fuel cells provide a stable and dispatchable source of electricity, offering an alternative to fossil fuels while reducing carbon emissions. Some industries are developing integrated hydrogen ecosystems, where excess electricity from renewables is used to produce hydrogen via electrolysis, which can then be stored and used to generate power on demand. This approach not only ensures energy stability but also supports long-term decarbonization goals.
Decentralized energy solutions are also reshaping how industries manage power supply. Microgrids, which combine multiple generation sources such as gas turbines, renewables, and battery storage, are becoming a preferred solution for industrial facilities looking to enhance energy resilience. By allowing industries to operate independently from the main grid when needed, microgrids provide a safeguard against power outages, fluctuations, and supply chain disruptions. Advanced microgrid controllers further optimize energy distribution, balancing load demand with available generation capacity in real time.
With the rapid evolution of industrial power technologies, the future of electricity stability will depend on the seamless integration of smart grids, diversified energy sources, and intelligent automation. Heavy industries that proactively invest in resilient energy infrastructure will not only safeguard their operations but also gain a competitive advantage in a global economy where energy efficiency and sustainability are becoming paramount. By adopting innovative solutions and strengthening power security, industrial facilities can achieve long-term stability, reduce costs, and contribute to a cleaner, more reliable energy future.
As industrial energy demands continue to rise, ensuring a stable electricity supply is no longer just about reliability—it is a strategic necessity for operational efficiency, cost control, and long-term sustainability. Heavy industries are moving beyond conventional power solutions and embracing innovative technologies that enhance grid stability, improve energy management, and support the transition to a low-carbon future.
One of the most transformative developments in industrial power stability is the increasing role of digital twin technology. Digital twins create real-time virtual replicas of industrial power systems, allowing operators to simulate different scenarios, predict potential failures, and optimize energy usage. By integrating AI-driven analytics with real-time sensor data, industries can proactively identify weak points in their power networks, optimize load balancing, and implement preventive maintenance strategies that minimize disruptions.
High-voltage direct current (HVDC) technology is also emerging as a game-changer in industrial power distribution. Unlike traditional alternating current (AC) systems, HVDC offers lower transmission losses, higher efficiency over long distances, and improved grid stability. Industrial facilities with large energy needs, such as aluminum smelters, chemical plants, and data centers, are increasingly adopting HVDC-based microgrids to ensure consistent power quality while reducing dependency on external grid fluctuations.
Another key innovation shaping industrial power stability is the advancement of superconducting power cables. These next-generation transmission lines offer near-zero electrical resistance, reducing energy losses and allowing for more efficient electricity distribution within industrial complexes. Superconducting cables also support higher power densities, making them ideal for industries with extreme energy demands, such as steel production and semiconductor manufacturing. As these technologies become more commercially viable, they will play a significant role in enhancing industrial energy resilience.
In addition to technological advancements, regulatory and market-based strategies are also driving improvements in industrial power stability. Demand-side management programs are allowing industries to participate in grid stabilization efforts by adjusting energy consumption during peak demand periods. Some industrial facilities are now engaging in virtual power plant (VPP) networks, where distributed energy resources—such as battery storage, CHP systems, and renewables—are aggregated and controlled as a single entity. This approach not only ensures power reliability for individual industries but also contributes to overall grid resilience.
As industries navigate an increasingly complex energy landscape, the integration of diversified power sources, smart automation, and cutting-edge infrastructure will be essential for maintaining stable electricity supply. Heavy industries that invest in next-generation energy technologies will not only future-proof their operations but also position themselves as leaders in efficiency, sustainability, and resilience. The shift toward a smarter, more adaptive industrial power ecosystem will redefine how factories, processing plants, and large-scale manufacturing facilities operate in the decades to come.
Industrial energy from combined heat and power
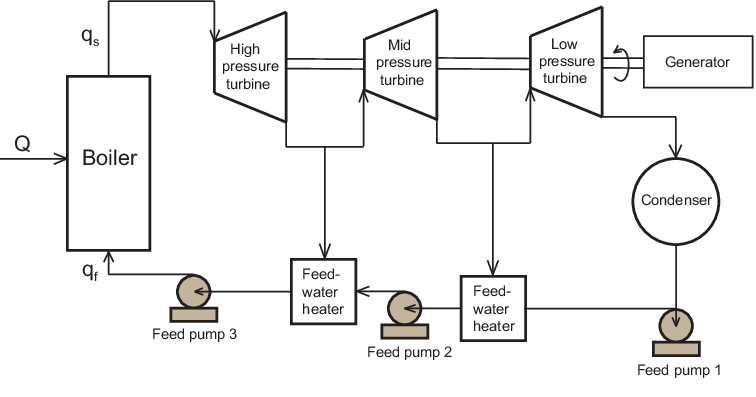
Industrial energy systems are evolving to maximize efficiency, reduce waste, and improve sustainability, with Combined Heat and Power (CHP) emerging as a key solution for reliable and cost-effective energy generation. CHP, also known as cogeneration, simultaneously produces electricity and useful thermal energy from a single fuel source, significantly increasing overall energy efficiency compared to conventional power generation methods. This approach enables industrial facilities to harness more energy from their fuel input while reducing emissions and operational costs.
One of the primary advantages of CHP is its ability to provide continuous, on-site power, reducing reliance on external grids and improving energy security. Heavy industries such as chemical processing, oil refining, paper manufacturing, and food production require large amounts of both electricity and heat for their operations. CHP systems capture and repurpose the heat that would otherwise be wasted in traditional power generation, using it for processes such as steam production, district heating, or cooling through absorption chillers. This efficient utilization of energy allows industries to operate with fuel efficiencies of 70-90%, far exceeding the 30-50% efficiency of conventional power plants.
Industries are integrating various CHP configurations to meet their specific energy needs. Gas turbines and steam turbines are commonly used in CHP systems, depending on the availability of fuel and heat demand. Gas turbine-based CHP systems are widely employed in industries with high electricity and moderate heat requirements, while steam turbine-based systems are preferred in applications where large amounts of process steam are needed. Internal combustion engines and fuel cells are also being adopted for smaller-scale CHP applications, offering flexibility and decentralized power generation capabilities.
As industries transition toward cleaner energy sources, CHP systems are increasingly being adapted to run on alternative and low-carbon fuels. Natural gas has traditionally been the dominant fuel for CHP, but industries are now exploring the use of biogas, hydrogen, and synthetic fuels to further reduce carbon footprints. Hydrogen-fired turbines and fuel-cell-based CHP systems are being developed as part of long-term decarbonization strategies, ensuring that industries can maintain high efficiency while aligning with environmental regulations.
Beyond energy efficiency, CHP contributes to grid stability by providing a decentralized and resilient power source. During periods of grid instability or outages, CHP-equipped industrial facilities can continue operating independently, preventing production losses and safeguarding critical processes. In some cases, excess electricity from CHP systems can be fed back into the grid, supporting local energy infrastructure and improving overall grid reliability.
Advancements in digitalization and automation are further enhancing CHP performance. Smart energy management systems, powered by artificial intelligence and real-time analytics, optimize CHP operation by adjusting fuel input, load balancing, and heat recovery efficiency based on demand fluctuations. Predictive maintenance algorithms are also helping industries reduce downtime and extend the lifespan of CHP equipment, ensuring long-term cost savings and reliability.
As industrial energy needs continue to grow, CHP stands out as a strategic solution for balancing efficiency, sustainability, and energy security. By integrating high-efficiency cogeneration technologies with modern automation and renewable fuel options, industries can achieve greater energy independence while reducing environmental impact. The future of industrial energy will likely see even more innovation in CHP applications, further solidifying its role as a cornerstone of sustainable and resilient industrial power generation.
As industries seek to optimize their energy consumption and reduce emissions, the role of Combined Heat and Power (CHP) in industrial energy systems is expanding. The demand for more resilient and self-sustaining power solutions is driving increased adoption of CHP across sectors that require both electricity and thermal energy for production processes. By capturing and utilizing waste heat that would otherwise be lost, CHP maximizes fuel efficiency and significantly lowers operational costs.
One of the major factors contributing to the rise of CHP in industrial settings is its ability to enhance energy security. With rising energy costs and concerns over grid stability, many industries are prioritizing decentralized power generation. CHP systems enable facilities to produce their own electricity and heat on-site, reducing dependence on external power suppliers and minimizing exposure to fluctuating energy prices. This energy independence ensures uninterrupted production, even during grid failures or energy shortages.
In addition to improving reliability, CHP offers substantial environmental benefits. Since these systems operate at higher efficiencies than separate power and heat generation, they consume less fuel and produce fewer greenhouse gas emissions. Many industries are integrating CHP with cleaner fuel sources such as biomass, biogas, and hydrogen to further reduce their carbon footprint. Hydrogen-powered CHP systems, in particular, are gaining interest as industries transition toward low-carbon energy solutions. By utilizing green hydrogen produced through electrolysis, industrial CHP systems can become an integral part of a sustainable energy ecosystem.
Advancements in CHP technology are also contributing to its growing adoption. Modern systems are increasingly equipped with digital monitoring and control features, allowing operators to optimize energy generation in real time. Smart automation technologies enable predictive maintenance, load balancing, and heat recovery optimization, ensuring that CHP units operate at peak performance with minimal downtime. These innovations help industries maximize their return on investment while enhancing long-term operational efficiency.
The flexibility of CHP systems makes them suitable for a wide range of industrial applications. In chemical and petrochemical plants, CHP provides high-temperature steam for refining processes, while in food and beverage industries, it supplies the thermal energy needed for pasteurization, drying, and refrigeration. Paper mills and textile factories also benefit from CHP, using waste heat to support manufacturing processes. In district energy systems, CHP plays a crucial role in providing combined heating and cooling solutions to industrial parks and large-scale facilities.
As regulatory frameworks increasingly focus on energy efficiency and emissions reduction, government incentives and policy support are further driving CHP adoption. Many countries offer tax benefits, subsidies, and feed-in tariffs for industries that implement high-efficiency cogeneration systems. This financial support is encouraging more businesses to invest in CHP as a long-term energy solution.
Looking ahead, the integration of CHP with renewable energy sources and advanced storage solutions will continue to shape industrial power strategies. Hybrid systems that combine CHP with solar, wind, or energy storage technologies can provide even greater efficiency and sustainability. As industries move toward more decentralized, resilient, and environmentally friendly power generation models, CHP will remain a key enabler of industrial energy transformation, helping businesses achieve both economic and environmental goals.
The continued expansion of Combined Heat and Power (CHP) in industrial energy systems reflects a broader shift toward efficiency-driven and resilient power generation strategies. With global energy demands increasing and sustainability targets becoming more stringent, CHP is proving to be an essential component in industrial energy planning. Its ability to generate both electricity and thermal energy from a single fuel source significantly enhances energy efficiency, reduces emissions, and strengthens operational reliability.
One of the key drivers of CHP adoption is the need for industries to optimize fuel use while maintaining high levels of productivity. Traditional power generation methods result in significant energy losses, particularly in the form of waste heat. CHP systems recover this otherwise wasted thermal energy and repurpose it for industrial processes such as steam generation, drying, and space heating or cooling. This maximization of energy utilization allows industrial facilities to achieve efficiencies exceeding 80%, compared to the 30-50% efficiencies of conventional power plants.
Beyond efficiency gains, CHP is playing a crucial role in decarbonization efforts. Many industrial sectors are integrating CHP with cleaner energy sources such as biogas, synthetic methane, and hydrogen. The development of hydrogen-powered CHP systems is particularly promising, as they offer the potential for near-zero emissions while maintaining the high efficiency of conventional CHP. Industries with access to renewable hydrogen from electrolysis can further improve sustainability while reducing dependence on fossil fuels.
In industrial parks and large-scale manufacturing complexes, CHP is increasingly being deployed as part of microgrid solutions. These localized energy networks enable industries to operate independently of the main grid, ensuring a stable and uninterrupted power supply. By combining CHP with battery storage and renewable energy sources like solar or wind, microgrids provide a diversified energy mix that enhances grid resilience while reducing exposure to energy price volatility. This approach is particularly beneficial in regions where grid reliability is a concern or where industries require stringent power quality standards.
The digitalization of CHP systems is also transforming industrial energy management. Advanced analytics, artificial intelligence, and Internet of Things (IoT) sensors are being integrated into CHP units to enable real-time performance monitoring, automated adjustments, and predictive maintenance. AI-driven energy management platforms optimize fuel consumption, heat recovery, and load balancing, ensuring that CHP systems operate at peak efficiency while minimizing wear and tear. These digital enhancements not only improve reliability but also extend the lifespan of CHP equipment, delivering long-term cost savings.
Industrial sectors that require continuous and high-quality power, such as petrochemicals, steel, cement, and pharmaceuticals, are increasingly adopting CHP to enhance operational stability. The ability of CHP to provide both baseload and backup power makes it an ideal solution for industries that cannot afford power interruptions. In some cases, CHP systems are even designed to operate in “island mode,” allowing facilities to disconnect from the grid and continue running independently during external power disruptions.
Looking forward, the evolution of CHP technology will focus on greater fuel flexibility, deeper integration with renewable energy, and enhanced automation. Hybrid CHP systems that incorporate carbon capture and storage (CCS) technologies could further reduce emissions while maintaining energy efficiency. Additionally, regulatory support for high-efficiency cogeneration is expected to drive further investments in CHP infrastructure, particularly as industries seek to align with global energy transition goals.
By leveraging the advantages of CHP, industries can achieve a more sustainable and cost-effective energy future. As energy efficiency regulations tighten and companies prioritize carbon reduction, the role of CHP in industrial energy strategies will only continue to grow, ensuring long-term resilience, reliability, and economic viability.
The continued advancement of Combined Heat and Power (CHP) technology is revolutionizing industrial energy strategies by offering highly efficient, low-emission power generation solutions. As industries face increasing pressure to optimize energy use and reduce their carbon footprint, CHP provides a practical and cost-effective approach to meeting these demands while ensuring energy security and operational resilience.
One of the most significant advantages of CHP is its adaptability to various industrial applications. Whether in large-scale manufacturing, chemical processing, food production, or district heating networks, CHP systems can be customized to meet specific energy and heat demands. This versatility allows industries to maximize efficiency by tailoring CHP configurations to match their operational requirements. Some facilities require high-temperature steam for processes like refining and metal processing, while others benefit from lower-temperature heat for drying, space heating, or refrigeration through absorption cooling systems. By optimizing heat recovery, industries can significantly cut fuel costs and improve overall energy performance.
The transition toward cleaner energy sources is further enhancing the role of CHP in industrial energy planning. Traditionally reliant on natural gas, CHP systems are now being adapted to run on alternative fuels such as biomass, biogas, synthetic methane, and hydrogen. Hydrogen-fired CHP systems, in particular, are attracting significant interest as industries work toward achieving carbon neutrality. Green hydrogen, produced from renewable energy sources via electrolysis, can serve as a zero-emission fuel for CHP units, creating a pathway toward decarbonized industrial power generation. Moreover, the integration of carbon capture and storage (CCS) technologies with CHP is emerging as a promising solution for industries looking to further reduce emissions while maintaining high energy efficiency.
The resilience of CHP systems is another critical factor driving their adoption. Many industrial operations cannot afford unexpected power outages, as they can lead to substantial financial losses and production delays. CHP systems provide a decentralized and reliable power source, reducing dependence on external grids and mitigating risks associated with grid instability. In industries such as petrochemicals, pharmaceuticals, and semiconductor manufacturing, where strict power quality and continuity are essential, CHP serves as an indispensable tool for maintaining seamless operations. In regions prone to grid failures or unstable power supply, CHP systems operating in island mode offer a viable solution for uninterrupted energy production.
Advancements in automation and digital control systems are further improving the efficiency and reliability of CHP operations. Smart monitoring platforms equipped with AI-driven analytics and IoT sensors enable real-time optimization of power generation and heat recovery. Predictive maintenance algorithms analyze system performance, detect potential issues before they lead to failures, and recommend proactive maintenance measures, reducing downtime and extending equipment lifespan. Additionally, AI-assisted load balancing ensures that CHP systems adjust output in real time based on fluctuations in demand, enhancing overall energy efficiency.
Industrial facilities are also exploring the integration of CHP within hybrid energy systems. By combining CHP with renewable sources such as wind and solar, industries can create hybrid microgrids that provide greater energy resilience while reducing dependence on fossil fuels. Battery storage solutions further complement CHP by storing excess electricity and releasing it when demand peaks, ensuring a more stable and reliable energy supply. These integrated solutions help industries achieve their sustainability goals while maintaining operational efficiency.
Government policies and incentives continue to play a crucial role in the expansion of CHP adoption. Many countries are introducing financial incentives, tax credits, and favorable tariffs for high-efficiency cogeneration projects. Regulatory frameworks supporting CHP deployment are encouraging industries to invest in these systems as a means of reducing energy costs and contributing to national energy efficiency and emissions reduction targets. As policymakers emphasize the need for decarbonization and sustainable industrial practices, the role of CHP in achieving these objectives will only strengthen.
Looking ahead, the future of CHP in industrial energy systems will be shaped by ongoing technological advancements, increased fuel flexibility, and deeper integration with digital energy management solutions. The shift toward hydrogen-based CHP, the expansion of hybrid microgrids, and the adoption of AI-driven optimization tools will further enhance the efficiency, sustainability, and resilience of industrial power generation. As industries prioritize long-term energy security and cost savings, CHP will remain a cornerstone of smart and sustainable energy strategies, driving innovation in industrial power solutions.
Industries rely on self-generated power

Industries worldwide are increasingly turning to self-generated power solutions to ensure reliability, control costs, and improve sustainability. With energy demands rising and grid instability posing risks to continuous operations, many businesses are adopting decentralized power generation strategies that provide greater energy security and independence. Self-generated power enables industries to optimize their energy consumption, reduce reliance on external utilities, and integrate cleaner energy sources into their operations.
One of the primary drivers behind the shift to self-generated power is the need for uninterrupted electricity supply. Many industries, such as petrochemicals, data centers, steel manufacturing, and pharmaceuticals, require stable and high-quality power to maintain precision processes. Any fluctuation or outage can result in costly downtime, product losses, and safety risks. By generating their own electricity on-site, industries can mitigate the risks associated with grid failures, ensuring continuous production and reducing operational disruptions.
Self-generated power solutions come in various forms, depending on an industry’s specific needs and available resources. Combined Heat and Power (CHP) systems, for example, allow industries to produce both electricity and thermal energy from a single fuel source, significantly improving efficiency. Steam turbines, gas turbines, and reciprocating engines are commonly used in industrial CHP applications, providing facilities with stable power while utilizing waste heat for industrial processes. This dual-use approach maximizes fuel efficiency and lowers overall energy costs.
The transition to cleaner energy sources is also shaping the self-generation strategies of many industries. Renewable energy integration, including on-site solar, wind, and biomass power, is becoming more prevalent as industries seek to reduce their carbon footprint and comply with environmental regulations. Hybrid power systems that combine renewables with backup generators or battery storage enhance reliability while reducing dependence on fossil fuels. In regions with high renewable potential, industries are leveraging wind and solar power in combination with energy storage to ensure stable power supply throughout fluctuations in generation.
Microgrids are another key component of self-generated power, allowing industries to create localized energy networks that operate independently or in coordination with the main grid. Industrial microgrids integrate multiple energy sources, including CHP, renewables, and battery storage, to provide a resilient and flexible power supply. These systems can automatically switch between grid-connected and islanded modes, ensuring that industries remain operational even in the event of grid failures. Advanced energy management systems enable real-time monitoring and optimization of energy usage, further enhancing efficiency and cost savings.
Digitalization is playing a crucial role in improving the performance of self-generated power systems. AI-driven predictive maintenance, real-time monitoring, and automated load balancing are helping industries optimize their energy generation and consumption. Smart sensors and IoT-based analytics enable facilities to detect inefficiencies, adjust power output dynamically, and prevent equipment failures before they occur. These digital tools are ensuring that self-generated power systems operate at peak efficiency, reducing maintenance costs and extending equipment lifespans.
As governments and regulatory bodies push for greater energy efficiency and emissions reductions, industries that invest in self-generated power are better positioned to meet compliance requirements and take advantage of financial incentives. Many countries offer tax credits, subsidies, and preferential tariffs for businesses that implement high-efficiency power generation and renewable energy projects. These incentives are accelerating the adoption of self-generation technologies, making them more accessible and financially viable for a broader range of industries.
Looking ahead, the future of industrial self-generated power will be driven by technological innovation, increased fuel flexibility, and greater integration with sustainable energy sources. The expansion of hydrogen-based power systems, advanced battery storage solutions, and AI-driven energy optimization will further enhance the efficiency and reliability of self-generation strategies. As industries continue to prioritize energy security, cost savings, and sustainability, self-generated power will remain a critical pillar of modern industrial energy management.
The increasing adoption of self-generated power among industries reflects a fundamental shift toward energy independence, efficiency, and sustainability. As global energy markets fluctuate and power grids face growing strain, industries are recognizing the advantages of producing their own electricity to mitigate risks, reduce costs, and maintain operational stability. Self-generation not only enhances resilience against power disruptions but also allows companies to tailor their energy solutions to their specific production needs, optimizing both efficiency and environmental impact.
One of the most significant benefits of self-generated power is the ability to maintain consistent and high-quality electricity supply, especially for industries with energy-intensive processes. Manufacturing plants, chemical refineries, and data centers require uninterrupted power to prevent costly downtime and equipment damage. Even a brief outage can lead to production losses, compromised product quality, and safety hazards. By generating power on-site, industries ensure greater control over their energy supply, reducing dependency on centralized grids and minimizing the risk of operational disruptions.
The use of cogeneration and trigeneration systems has been instrumental in improving the efficiency of self-generated power. Combined Heat and Power (CHP) systems capture waste heat from electricity generation and repurpose it for industrial processes, space heating, or cooling applications. Trigeneration systems go a step further by producing electricity, heating, and cooling simultaneously, further optimizing fuel use. These systems can achieve fuel efficiencies of 70-90%, compared to traditional power plants that typically operate at 30-50% efficiency. By utilizing every unit of energy more effectively, industries reduce their overall fuel consumption and operational costs.
The drive toward sustainability is also influencing industrial self-generation strategies. Many companies are investing in renewable energy sources such as solar, wind, and biomass to power their facilities. Hybrid energy systems that combine renewable sources with battery storage and conventional generators offer a balanced approach to self-generation, ensuring reliability even when renewable output fluctuates. In industries with high thermal energy demand, biomass and waste-to-energy solutions are becoming increasingly popular, providing both power and heat while reducing waste disposal costs.
Microgrids are playing a crucial role in the expansion of industrial self-generation. These localized power networks integrate various generation sources, including CHP, renewables, and battery storage, allowing industries to operate independently or in coordination with the main grid. Microgrids provide enhanced flexibility, allowing facilities to switch between grid-connected and islanded modes depending on energy market conditions and grid stability. This capability is particularly beneficial in regions prone to power shortages, where industrial operations rely on self-sufficient energy systems to maintain continuous production.
Digital transformation is further revolutionizing the way industries manage self-generated power. Advanced energy management systems, powered by artificial intelligence and real-time analytics, enable companies to optimize generation, storage, and consumption dynamically. Predictive maintenance tools use machine learning to identify potential issues before they cause failures, minimizing downtime and reducing maintenance costs. Automated load balancing ensures that energy is distributed efficiently across industrial operations, preventing overconsumption and enhancing overall system reliability.
Economic factors are also accelerating the adoption of self-generated power. Rising electricity prices, carbon taxes, and fuel supply uncertainties have prompted industries to seek cost-effective alternatives to traditional grid power. Self-generation allows businesses to hedge against energy price volatility, stabilize long-term costs, and take advantage of government incentives for clean energy investments. Many countries are offering subsidies, tax benefits, and preferential tariffs to encourage industries to adopt high-efficiency cogeneration, renewables, and energy storage solutions.
Looking ahead, the evolution of industrial self-generated power will be shaped by innovations in energy storage, alternative fuels, and grid integration technologies. Hydrogen-powered generation systems are emerging as a viable option for industries aiming to achieve carbon neutrality, while advancements in battery technology are making energy storage more efficient and cost-effective. Smart grid connectivity will further enhance the role of self-generation, enabling industries to participate in demand response programs, trade surplus energy, and contribute to grid stability.
As industries continue to prioritize energy resilience, cost savings, and environmental responsibility, self-generated power will remain a critical component of their long-term energy strategies. The ability to generate, manage, and optimize power on-site not only enhances competitiveness but also aligns with global efforts toward a more sustainable and decentralized energy future.
The expansion of self-generated power in industrial sectors continues to evolve with technological advancements, shifting energy policies, and the growing need for sustainable, cost-effective energy solutions. As industries increasingly recognize the value of generating their own electricity, they are integrating more sophisticated systems that enhance efficiency, improve reliability, and reduce environmental impact.
One of the most significant trends in industrial self-generation is the diversification of energy sources. While natural gas remains a dominant fuel for on-site power generation due to its efficiency and availability, industries are progressively incorporating alternative and renewable sources. Biomass and waste-to-energy systems are gaining traction, especially in sectors with substantial organic waste, such as food processing, agriculture, and paper manufacturing. These systems convert waste materials into valuable energy, simultaneously reducing disposal costs and lowering emissions.
Hydrogen is emerging as a key fuel in the self-generation landscape. Hydrogen-powered turbines and fuel cells offer a clean, high-efficiency alternative to traditional fossil fuel-based generators. Industries investing in green hydrogen, produced through electrolysis using renewable electricity, are positioning themselves at the forefront of the energy transition. As hydrogen infrastructure develops and costs decline, self-generated hydrogen power will play an increasing role in industrial energy strategies, helping companies achieve carbon neutrality.
Energy storage technologies are also transforming industrial self-generation. Battery storage systems enable industries to manage power more effectively by storing excess electricity generated during periods of low demand and deploying it when demand peaks. This capability enhances energy efficiency, reduces strain on generation equipment, and provides an added layer of resilience against power disruptions. Advances in lithium-ion and solid-state battery technology are making energy storage more viable and cost-effective, increasing its adoption in industrial settings.
The digitalization of industrial power systems is further optimizing self-generation strategies. Smart energy management systems equipped with artificial intelligence and predictive analytics allow companies to fine-tune energy production and consumption dynamically. IoT sensors provide real-time data on fuel usage, heat recovery, and system performance, enabling continuous optimization. Predictive maintenance reduces downtime by identifying potential failures before they occur, improving overall system reliability and longevity. AI-driven energy dispatch systems ensure that power generation is aligned with real-time industrial demand, avoiding unnecessary fuel consumption and maximizing efficiency.
Microgrid integration is another crucial development in industrial self-generation. Many industries are moving toward microgrid solutions that combine multiple energy sources—including CHP, renewables, and storage—into a flexible, self-sufficient power network. These microgrids operate independently or in coordination with the main grid, providing greater control over energy resources. In industrial parks, where multiple facilities operate in close proximity, shared microgrids allow for efficient energy distribution and cost savings. Advanced microgrid control systems use AI and blockchain technology to facilitate peer-to-peer energy trading, enabling companies to buy and sell excess electricity within industrial ecosystems.
Regulatory support and financial incentives are accelerating the adoption of self-generated power. Governments worldwide are offering grants, subsidies, and tax credits for industries that invest in high-efficiency cogeneration, renewable energy, and energy storage. Policies promoting grid decentralization and demand-side management are further encouraging industries to adopt self-generation as part of their long-term energy strategy. In some regions, carbon pricing and emissions regulations are making self-generated power even more attractive by helping companies reduce their reliance on grid electricity, which may come from high-carbon sources.
The economic benefits of self-generated power are becoming increasingly clear. By reducing dependence on external energy suppliers, industries gain greater control over costs and hedge against fluctuating energy prices. Additionally, self-generation improves operational efficiency, lowers fuel expenses through optimized heat recovery, and reduces downtime due to power outages. As energy markets continue to evolve, companies that invest in self-generation will be better positioned to navigate volatility and maintain long-term financial stability.
Looking to the future, industrial self-generation will be shaped by continued innovation in decentralized power systems, alternative fuels, and smart energy management. Hydrogen, carbon capture, and next-generation battery technologies will further enhance the sustainability and efficiency of self-generated power solutions. AI-driven automation and digital twins—virtual models that simulate and optimize power systems in real time—will refine industrial energy strategies. As industries strive for energy independence and sustainability, self-generated power will remain a critical pillar of their long-term resilience and competitive advantage.
The future of industrial self-generated power is being shaped by a combination of technological innovation, regulatory shifts, and the increasing demand for energy efficiency and sustainability. As industries continue to move away from complete reliance on traditional power grids, they are developing more advanced, resilient, and flexible energy systems tailored to their operational needs. This shift is not only improving power security but also enabling industries to reduce costs, lower emissions, and enhance overall energy efficiency.
One of the key developments in self-generation is the rapid adoption of hybrid energy systems. Industries are integrating multiple power sources—including combined heat and power (CHP), renewables, hydrogen, and energy storage—to create balanced, optimized energy solutions. Hybrid systems provide the flexibility to switch between different generation methods based on availability, cost, and demand, ensuring uninterrupted power supply even in fluctuating market conditions. By strategically combining renewables with dispatchable sources like gas turbines or biomass generators, industries can maintain stable operations while minimizing their environmental footprint.
Hydrogen continues to emerge as a transformative fuel for self-generated power. Green hydrogen, produced from electrolysis using renewable energy, is becoming increasingly viable as costs decline and production capacity expands. Many industrial facilities are investing in hydrogen-ready gas turbines and fuel cells to future-proof their energy systems. In addition to providing clean electricity, hydrogen can be used for industrial heating, reducing reliance on fossil fuels in energy-intensive sectors such as steelmaking, chemicals, and cement production. As infrastructure for hydrogen production, storage, and distribution develops, it is expected to play a larger role in industrial energy strategies.
Advanced energy storage is further enhancing the efficiency and reliability of self-generated power. Lithium-ion and solid-state batteries are becoming more widely adopted as industries seek to optimize their energy usage and reduce waste. Beyond conventional battery storage, emerging technologies such as flow batteries and thermal energy storage are gaining traction, offering long-duration energy solutions that complement renewable generation. Industrial-scale storage enables facilities to store excess electricity generated during low-demand periods and deploy it when needed, ensuring a consistent and cost-effective power supply.
The integration of artificial intelligence (AI) and automation is revolutionizing industrial self-generation. AI-driven energy management systems continuously analyze real-time data, optimizing power generation, load balancing, and demand forecasting. These systems enable industries to dynamically adjust energy production based on consumption patterns, market prices, and grid conditions, maximizing efficiency and minimizing waste. Predictive maintenance algorithms further enhance reliability by identifying potential equipment failures before they occur, reducing downtime and maintenance costs.
Microgrid development is another major trend shaping the future of self-generated power. Industrial microgrids are evolving into highly intelligent, autonomous networks that can operate independently or interact with the main grid as needed. AI-powered microgrid controllers optimize energy distribution across multiple sources, ensuring seamless transitions between grid-connected and islanded modes. In industrial zones and manufacturing hubs, interconnected microgrids are creating collaborative energy ecosystems where multiple facilities share resources and improve overall efficiency.
Regulatory frameworks and financial incentives are accelerating the adoption of self-generation technologies. Governments worldwide are introducing policies that promote decentralized energy solutions, including tax credits, grants, and carbon pricing mechanisms that reward efficient and sustainable energy use. Industries that adopt self-generation are also benefiting from participation in demand response programs, where they can sell excess power back to the grid during peak periods, generating additional revenue while supporting grid stability.
The economic case for industrial self-generated power continues to strengthen. Rising energy costs, supply chain disruptions, and geopolitical uncertainties are making energy independence a priority for businesses. By generating power on-site, industries gain greater control over their energy expenses, hedge against price volatility, and reduce exposure to potential grid failures. Self-generation also supports long-term cost savings through improved energy efficiency, optimized fuel use, and lower emissions-related compliance costs.
Looking ahead, self-generated power will remain a cornerstone of industrial energy strategies, evolving alongside advancements in renewable integration, hydrogen infrastructure, and digital energy management. The convergence of AI, automation, and decentralized power solutions will enable industries to build even more resilient, cost-effective, and sustainable energy systems. As industries continue to pursue energy security, economic efficiency, and environmental responsibility, self-generation will not only provide a competitive edge but also play a crucial role in the transition toward a cleaner, more decentralized energy future.
Steam turbines supply industrial electricity
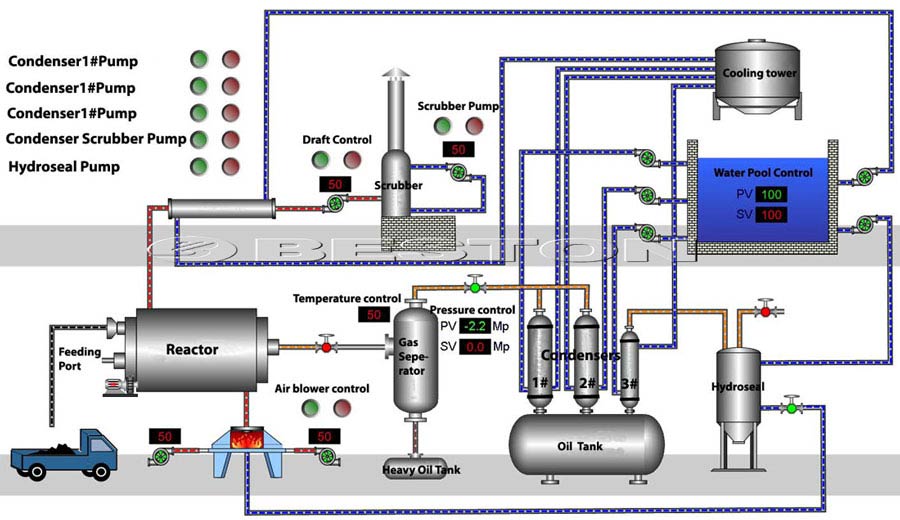
Steam turbines play a critical role in supplying industrial electricity by converting thermal energy into mechanical power, which is then transformed into electrical energy through a generator. These turbines are widely used in power plants and industrial facilities due to their efficiency, reliability, and ability to operate on a variety of fuel sources, including coal, natural gas, biomass, and even waste heat from industrial processes. Their adaptability makes them an essential component in industries where continuous and stable power supply is crucial for operations.
The working principle of a steam turbine involves superheated steam being directed onto a series of blades mounted on a rotating shaft. As the steam expands and loses energy, it imparts rotational motion to the shaft, which is connected to an electrical generator. This conversion process is highly efficient, with modern steam turbines achieving thermal efficiencies of up to 45-50%, particularly when integrated with combined heat and power (CHP) or combined cycle power plants.
Industries with high energy demands, such as petrochemical plants, steel mills, pulp and paper factories, and food processing facilities, rely on steam turbines for both electricity generation and mechanical drive applications. Many of these facilities operate cogeneration systems, where the waste heat from the turbine is captured and used for additional industrial processes, further increasing overall energy efficiency. This ability to utilize heat that would otherwise be lost makes steam turbines an attractive option for industries looking to improve sustainability and reduce fuel consumption.
In addition to large-scale industrial applications, smaller steam turbine generator systems are also used for localized power generation. These units are particularly beneficial for industries with access to process steam or waste heat, allowing them to generate their own electricity while reducing dependence on the grid. This self-generation capability enhances energy security and provides cost savings, especially in regions where grid electricity is expensive or unreliable.
Modern advancements in steam turbine technology have further improved their efficiency and performance. Innovations such as high-efficiency blade designs, advanced materials, and digital monitoring systems have optimized turbine operations, reducing maintenance costs and improving reliability. Digitalization and predictive maintenance technologies help industries detect performance issues before they lead to failures, ensuring uninterrupted electricity supply and extending the lifespan of the equipment.
As industries strive to reduce their carbon footprint and increase energy efficiency, steam turbines remain a vital part of industrial power solutions. Their ability to integrate with renewable and low-carbon energy sources, such as biomass and hydrogen, positions them as a key technology in the transition toward cleaner energy. Moving forward, advancements in turbine efficiency, hybrid energy systems, and carbon capture technologies will further enhance the role of steam turbines in industrial electricity generation, ensuring sustainable and cost-effective power solutions for a wide range of applications.
The continued reliance on steam turbines for industrial electricity generation is driven by their ability to provide stable, efficient, and large-scale power. As industries grow and modernize, the demand for high-efficiency power generation has led to innovations in steam turbine design, materials, and operation, making them more adaptable to various industrial needs. Steam turbines are a preferred choice for industries requiring high power output, as they offer long operational life, high efficiency, and compatibility with multiple energy sources.
One of the major advantages of steam turbines in industrial settings is their ability to operate as part of combined heat and power (CHP) systems. In such configurations, a single fuel source is used to produce both electricity and useful thermal energy, significantly improving overall energy efficiency. CHP systems utilizing steam turbines can achieve efficiencies of up to 80%, compared to the 30-50% efficiency of conventional power plants. This efficiency gain translates into substantial fuel cost savings and lower greenhouse gas emissions, making steam turbines an environmentally and economically viable choice for industries.
Industrial facilities that require continuous and reliable power—such as oil refineries, chemical plants, cement factories, and food processing plants—benefit from steam turbines’ ability to provide consistent output. Unlike other power generation technologies that may be affected by fuel supply fluctuations or weather conditions, steam turbines operate efficiently under a wide range of conditions. Their capability to run on multiple fuel types, including natural gas, coal, biomass, and even waste heat, makes them an essential part of energy resilience strategies for industrial plants.
Recent advancements in steam turbine technology have further enhanced their performance and efficiency. The development of ultra-supercritical steam turbines, which operate at higher temperatures and pressures, has significantly improved the efficiency of power generation. These modern turbines require advanced materials and precision engineering to withstand extreme operating conditions, but they offer considerable benefits in terms of fuel savings and emission reductions.
Digital transformation is also revolutionizing the operation of steam turbines in industrial power generation. The integration of smart sensors, IoT (Internet of Things) technology, and AI-driven analytics allows for real-time monitoring of turbine performance. Predictive maintenance systems use data analytics to detect potential failures before they occur, minimizing downtime and maintenance costs. This level of automation and digital control enhances the reliability and efficiency of steam turbines, ensuring uninterrupted electricity supply for industrial processes.
Steam turbines also play a crucial role in supporting renewable and sustainable energy initiatives. Biomass-fired steam turbines are increasingly being used in industries with access to organic waste, such as sugar mills and wood processing plants. These turbines utilize agricultural and forestry residues as fuel, converting them into clean energy while reducing waste disposal issues. In the future, the use of hydrogen as a fuel for steam turbines is expected to grow, further reducing the carbon footprint of industrial power generation.
As industries face increasing pressure to reduce their environmental impact, the role of steam turbines in achieving energy efficiency and sustainability goals is becoming more prominent. Governments and regulatory bodies worldwide are encouraging industries to adopt cleaner and more efficient energy solutions, including high-efficiency steam turbine technology. Many companies are investing in carbon capture and storage (CCS) systems to further reduce emissions from their steam turbine operations, aligning with global climate initiatives.
The future of industrial electricity generation will likely see continued innovation in steam turbine technology, with improvements in materials, efficiency, and integration with emerging energy sources. Whether in large-scale industrial plants or smaller self-generation facilities, steam turbines will remain a cornerstone of industrial power supply, providing reliable, cost-effective, and sustainable energy solutions for years to come.
The role of steam turbines in industrial electricity generation continues to expand as industries seek more efficient, reliable, and sustainable energy solutions. Their ability to operate on a diverse range of fuel sources, from fossil fuels to renewables, makes them a highly adaptable choice for a variety of industrial applications. As technological advancements improve turbine efficiency and environmental performance, steam turbines remain a cornerstone of industrial power generation, supporting both large-scale facilities and decentralized energy systems.
One of the key benefits of steam turbines is their scalability. They are available in a wide range of capacities, from small turbines generating a few megawatts to massive units producing hundreds of megawatts. This flexibility allows industries to choose a turbine size that aligns with their specific power and thermal energy needs. In many cases, industrial plants integrate multiple steam turbines within a facility to create a reliable, redundant power generation system that ensures continuous operation even in the event of equipment maintenance or unexpected failures.
Efficiency improvements in modern steam turbines are helping industries optimize their energy consumption. Supercritical and ultra-supercritical steam turbines operate at extremely high temperatures and pressures, significantly increasing the efficiency of electricity generation. These advancements lead to reduced fuel consumption and lower emissions, which are critical for industries facing stringent environmental regulations. By upgrading to high-efficiency turbines, industrial facilities can achieve significant cost savings while minimizing their environmental impact.
The integration of steam turbines with combined cycle power plants further enhances their efficiency. In these systems, a gas turbine generates electricity, and the waste heat from the gas turbine is used to produce steam for a steam turbine, resulting in a highly efficient two-stage power generation process. This approach is widely used in industries with high energy demands, such as chemical manufacturing, petroleum refining, and large-scale metal processing, where maximizing energy efficiency is essential for reducing operational costs.
Steam turbines are also playing a vital role in the global transition toward cleaner energy sources. Many industries are replacing coal-fired steam turbines with biomass and waste-to-energy solutions, which utilize organic materials such as agricultural waste, wood chips, and municipal waste to generate electricity. Biomass-fired steam turbines provide a renewable energy alternative that not only reduces reliance on fossil fuels but also helps industries manage waste in an environmentally responsible manner.
The push for decarbonization is driving interest in hydrogen as a fuel for steam turbines. Hydrogen-fired turbines produce electricity with zero carbon emissions when using green hydrogen produced from renewable energy sources. While hydrogen infrastructure is still in the early stages of development, ongoing research and pilot projects are paving the way for its integration into industrial steam turbine systems. As hydrogen production scales up and costs decrease, steam turbines capable of running on hydrogen will become a key component of sustainable industrial power generation.
In addition to fuel diversification, advancements in turbine monitoring and automation are further enhancing performance and reliability. Digital twins—virtual models of steam turbines—allow operators to simulate different operating conditions and optimize efficiency before making adjustments in real-world operations. AI-driven predictive maintenance systems analyze turbine performance data in real time, identifying potential issues before they lead to costly failures or downtime. These innovations are transforming how industries manage and maintain their steam turbine power plants, improving both reliability and cost-effectiveness.
Industrial facilities are also leveraging steam turbines in microgrid and islanded power generation setups. In remote or off-grid locations where access to traditional power infrastructure is limited, steam turbines provide a dependable energy solution. By utilizing locally available fuel sources, such as biomass or geothermal energy, these systems enable industries to achieve energy independence and reduce reliance on external electricity providers. Industrial parks and manufacturing hubs are increasingly adopting microgrid solutions that incorporate steam turbines alongside renewable energy and battery storage, creating highly resilient energy systems.
As industries strive to balance energy efficiency, cost savings, and sustainability, steam turbines will continue to evolve to meet these demands. Future developments in materials science, turbine aerodynamics, and hybrid energy integration will further improve turbine performance and operational flexibility. Whether in large-scale industrial power plants or self-generation applications, steam turbines remain a foundational technology for delivering stable, high-efficiency electricity that supports industrial growth while advancing environmental goals.
The future of steam turbines in industrial electricity generation is being shaped by ongoing advancements in technology, the increasing adoption of sustainable energy sources, and the growing demand for efficient and reliable power systems. As industries continue to evolve, steam turbines remain an essential component of large-scale power generation, offering a balance of efficiency, durability, and flexibility that supports both economic and environmental goals.
One of the most significant trends in steam turbine development is the pursuit of higher efficiency through advanced thermodynamic cycles. Supercritical and ultra-supercritical steam turbines operate at temperatures and pressures far beyond conventional designs, enabling more efficient energy conversion and reducing fuel consumption. These technologies are being adopted by industries with high power demands, such as petrochemical plants, steel mills, and paper manufacturing facilities, where even small efficiency improvements translate into substantial cost savings and emissions reductions.
Another major advancement is the integration of steam turbines into hybrid energy systems. Many industries are combining steam turbines with renewable energy sources, such as biomass, geothermal, and solar thermal power, to create sustainable and self-sufficient energy solutions. In biomass-fired power plants, for example, organic waste materials are converted into steam to drive turbines, providing a renewable and carbon-neutral electricity source. Similarly, geothermal steam turbines utilize heat from beneath the Earth’s surface to generate electricity, offering a reliable and continuous renewable energy option.
The push for decarbonization has also sparked interest in hydrogen-fired steam turbines. Hydrogen, when used as a fuel, produces no carbon emissions, making it an attractive option for industries looking to reduce their environmental impact. While large-scale hydrogen infrastructure is still in development, companies are investing in research to adapt existing steam turbine designs for hydrogen combustion. As hydrogen production technologies improve and become more cost-effective, the integration of hydrogen-fired steam turbines will become a viable solution for industries transitioning to cleaner energy sources.
Digitalization is playing an increasingly important role in the operation and maintenance of steam turbines. Advanced sensors, IoT connectivity, and AI-driven analytics are enabling real-time monitoring of turbine performance, allowing operators to detect inefficiencies, predict maintenance needs, and optimize energy output. Predictive maintenance algorithms analyze data from turbine components, identifying potential issues before they cause failures. This proactive approach minimizes downtime, extends the lifespan of equipment, and reduces maintenance costs, making steam turbines even more reliable and cost-effective for industrial applications.
In addition to efficiency and sustainability improvements, steam turbines are becoming more adaptable to decentralized energy systems. Industrial microgrids, which allow facilities to generate and manage their own power independently from the main grid, are increasingly incorporating steam turbines as a stable baseload power source. In combination with battery storage and renewable energy, these microgrids offer enhanced energy security and resilience, protecting industries from power outages and fluctuating electricity prices.
The role of steam turbines in waste heat recovery is also gaining attention as industries seek to maximize energy efficiency. By capturing and repurposing heat that would otherwise be lost during manufacturing processes, steam turbines can generate additional electricity without increasing fuel consumption. Waste heat recovery systems are particularly valuable in industries with high-temperature processes, such as cement production, glass manufacturing, and oil refining, where excess heat can be harnessed to improve overall energy efficiency.
Looking ahead, continued advancements in materials science, aerodynamics, and digital controls will further enhance the performance and longevity of steam turbines. The development of high-performance turbine blades made from advanced alloys and ceramics will allow for operation at even higher temperatures, improving efficiency and reducing wear and tear. Additionally, AI-powered optimization systems will enable real-time adjustments to turbine operation, maximizing energy output while minimizing fuel usage.
As industries face increasing pressure to balance economic growth with environmental responsibility, steam turbines will continue to play a critical role in meeting energy demands while supporting sustainability initiatives. Their ability to integrate with a wide range of energy sources, from conventional fuels to renewables and hydrogen, ensures their continued relevance in the evolving industrial energy landscape. With ongoing technological advancements and a commitment to efficiency and sustainability, steam turbines will remain a cornerstone of industrial power generation for decades to come.
Industrial Power Plants Fuel Economic Growth
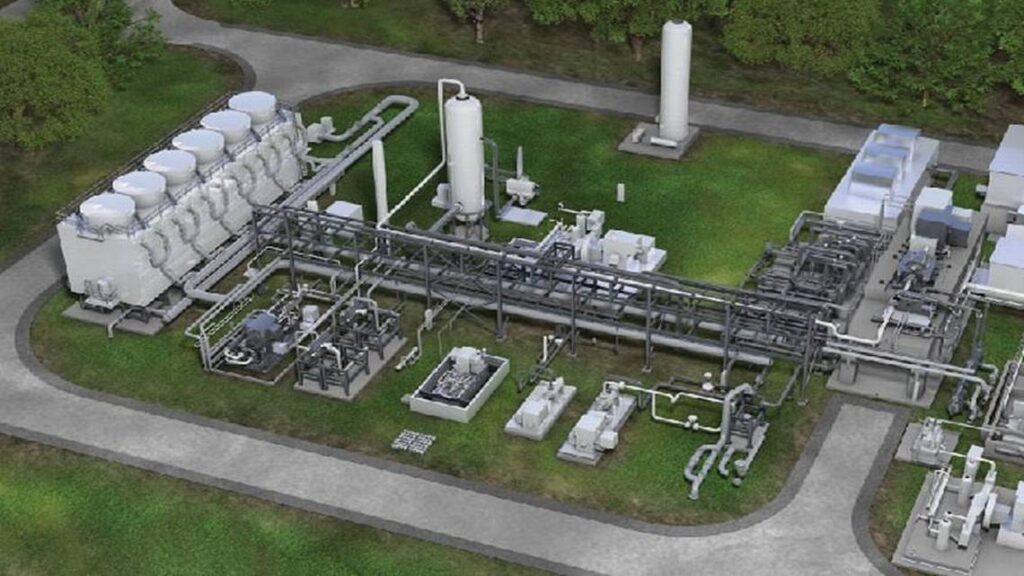
Industrial power plants play a crucial role in fueling economic growth by providing the stable and efficient energy supply necessary for large-scale manufacturing, resource processing, and commercial activities. As industries expand, the demand for reliable electricity increases, making power plants essential to economic development. Steam turbines, as a core technology in industrial power plants, contribute significantly to meeting this demand by generating electricity efficiently and sustainably.
The energy produced by industrial power plants supports various sectors, including steel production, chemical manufacturing, cement production, and food processing. These industries rely on continuous and stable power to maintain operations, optimize production, and minimize downtime. Any disruption in power supply can lead to significant financial losses and impact economic output. Steam turbine-driven power plants ensure uninterrupted energy generation, helping industries maintain productivity and competitiveness in global markets.
One of the key advantages of steam turbines in industrial power plants is their ability to utilize diverse fuel sources. These power plants can operate on coal, natural gas, biomass, waste heat, and even renewable fuels such as hydrogen. This fuel flexibility allows industries to adapt to changing energy prices and availability, ensuring cost-effective power generation. The integration of renewable energy sources into steam turbine systems further enhances sustainability while reducing dependence on fossil fuels.
Economic growth is also driven by energy efficiency improvements, and modern steam turbine power plants are designed to maximize efficiency while minimizing waste. Combined heat and power (CHP) systems, which use waste heat from power generation for industrial processes, increase overall energy efficiency and reduce operating costs. By implementing CHP solutions, industries can optimize their energy usage, lower greenhouse gas emissions, and enhance economic sustainability.
Additionally, industrial power plants create employment opportunities, both directly and indirectly. The construction, operation, and maintenance of power plants require skilled labor, contributing to job creation in engineering, manufacturing, and technical support fields. Furthermore, the availability of stable and affordable energy attracts new industries and investments, stimulating local and national economies.
Advancements in digitalization and automation are further transforming industrial power plants, improving performance and reducing maintenance costs. Smart sensors, AI-driven analytics, and real-time monitoring systems enable predictive maintenance, reducing downtime and enhancing the reliability of steam turbines. These innovations not only improve energy efficiency but also contribute to long-term economic stability by ensuring consistent industrial output.
As countries strive for economic growth while addressing environmental concerns, industrial power plants are evolving to incorporate cleaner technologies. The transition toward low-carbon energy solutions, such as hydrogen-fired steam turbines and carbon capture technologies, supports sustainable industrial growth. Governments and businesses are investing in these technologies to reduce emissions while maintaining the high levels of energy output required for economic expansion.
In conclusion, industrial power plants, powered by steam turbines, are a foundation of economic development. They provide the energy needed to drive industries, support job creation, and enable technological progress. As energy demand continues to grow, the modernization and diversification of industrial power plants will be essential to sustaining economic growth while meeting global sustainability goals. The continued investment in efficient and innovative power generation technologies will ensure that industries remain competitive and economies continue to thrive in an evolving energy landscape.
The continued expansion and modernization of industrial power plants are vital to sustaining economic growth, particularly as industries become more energy-intensive and technologically advanced. The integration of next-generation steam turbines, improved fuel flexibility, and innovative energy management strategies ensures that industrial facilities can meet increasing power demands while optimizing efficiency and reducing costs.
One of the most significant economic benefits of industrial power plants is their role in stabilizing energy costs. By generating electricity on-site or through dedicated industrial power stations, manufacturers can mitigate the impact of fluctuating electricity prices from external grids. This energy independence allows businesses to maintain consistent production schedules and invest in long-term growth strategies without being constrained by unpredictable power supply disruptions. In energy-intensive industries such as aluminum smelting, petrochemical refining, and large-scale manufacturing, self-generated electricity from steam turbines provides a competitive edge by lowering operational expenses.
The reliability of industrial power plants is another key factor in economic development. Unplanned power outages can lead to significant financial losses, especially in industries where continuous operations are critical. For example, in the steel industry, sudden power losses can damage equipment and halt production lines, resulting in costly downtime and material waste. Steam turbine power plants provide stable and dependable electricity, ensuring that industrial processes remain uninterrupted and production targets are met.
In addition to direct economic benefits, industrial power plants support broader infrastructure development. Many large-scale industrial complexes require dedicated energy infrastructure, including transmission networks, substations, and smart grid technologies. The investments in such infrastructure contribute to regional economic development, supporting industries beyond the immediate power plant operations. Furthermore, advancements in microgrid technology are enabling industrial power plants to supply excess energy to nearby communities, fostering local economic resilience and reducing reliance on national grids.
Another crucial factor in economic growth is the role of industrial power plants in driving innovation and technological progress. The adoption of advanced steam turbine designs, high-efficiency heat recovery systems, and digital automation solutions enhances overall productivity while reducing emissions. These technological advancements not only improve industrial energy efficiency but also create opportunities for research, development, and the commercialization of cutting-edge power generation solutions.
As global economies transition toward more sustainable energy models, industrial power plants are adapting to incorporate cleaner technologies without compromising productivity. The development of hybrid power generation systems, which integrate steam turbines with solar thermal, wind, and battery storage, enables industries to diversify their energy sources and reduce carbon footprints. Many companies are also investing in carbon capture and storage (CCS) technologies to offset emissions from fossil-fuel-based power generation, ensuring compliance with environmental regulations while maintaining energy security.
Moreover, industrial power plants are increasingly seen as catalysts for regional economic growth. Large-scale energy projects attract foreign direct investment, drive industrial expansion, and create long-term employment opportunities. Countries that prioritize industrial power generation infrastructure can attract manufacturing, logistics, and technology firms looking for stable and cost-effective energy solutions. In emerging economies, the development of industrial power plants has been a key driver of industrialization, providing the necessary energy backbone for economic diversification and job creation.
As industrial power plants continue to evolve, their economic impact will extend beyond traditional manufacturing sectors. The rise of energy-intensive digital industries, such as data centers, electric vehicle production, and advanced material manufacturing, is increasing the demand for highly efficient and stable power generation solutions. Steam turbine-based power plants are uniquely positioned to support these industries by providing scalable and reliable energy that aligns with their growth objectives.
In conclusion, industrial power plants remain a fundamental driver of economic progress, enabling industries to scale operations, maintain competitive advantages, and contribute to long-term economic stability. By embracing technological advancements and sustainable energy practices, these power plants will continue to play a central role in shaping the industrial landscapes of the future. Their ability to provide affordable, reliable, and clean energy solutions will be instrumental in supporting economic growth, job creation, and industrial innovation on a global scale.
The future of industrial power plants is closely tied to advancements in energy efficiency, sustainability, and digitalization. As industries grow and global energy demand rises, steam turbines and industrial power plants will continue to play a crucial role in ensuring stable and cost-effective electricity generation. Companies are increasingly focusing on optimizing power plant performance through innovative designs, integrated renewable energy solutions, and smart grid technology, all of which contribute to economic growth and industrial expansion.
One of the key trends shaping the future of industrial power plants is the push for higher efficiency in energy conversion. Modern steam turbines are being designed to operate at higher temperatures and pressures, improving thermal efficiency and reducing fuel consumption. Ultra-supercritical steam turbines, for example, achieve significantly higher efficiency rates compared to conventional designs, leading to lower operating costs and reduced environmental impact. These advancements enable industries to generate more power from the same amount of fuel, enhancing profitability and long-term economic sustainability.
Fuel diversification is another critical factor driving the evolution of industrial power plants. While coal and natural gas have traditionally been the dominant fuels for steam turbines, industries are shifting toward alternative energy sources such as biomass, waste heat recovery, and hydrogen. Biomass-fired steam turbines provide an environmentally friendly option for industries looking to reduce their carbon footprint while maintaining reliable power generation. Similarly, waste heat recovery systems allow industrial plants to capture excess heat from production processes and convert it into electricity, improving overall energy efficiency without increasing fuel consumption.
The integration of hydrogen as a fuel source is particularly promising for the future of industrial power plants. Hydrogen-fired steam turbines produce zero carbon emissions, making them a viable solution for industries seeking to decarbonize their energy production. Although large-scale hydrogen infrastructure is still in development, companies are investing in research to adapt existing turbine technology for hydrogen combustion. As hydrogen production becomes more affordable and widely available, industrial power plants will be able to transition toward cleaner energy solutions while maintaining high power output.
Digitalization is also playing a transformative role in industrial power plant operations. The adoption of real-time monitoring systems, artificial intelligence (AI), and predictive maintenance tools allows industries to optimize turbine performance, detect potential issues before they lead to failures, and reduce maintenance costs. Digital twins—virtual models of steam turbines—enable operators to simulate different operating conditions and make adjustments to improve efficiency. These innovations enhance the reliability of industrial power plants, ensuring continuous power generation and minimizing costly downtime.
The shift toward decentralized and self-sufficient energy generation is further driving the adoption of industrial power plants. Many large manufacturing facilities, industrial parks, and processing plants are investing in on-site power generation to reduce dependence on external electricity grids. Industrial microgrids, which combine steam turbines with renewable energy sources and battery storage, provide companies with greater energy security and flexibility. By generating their own electricity, industries can stabilize energy costs, improve resilience against grid failures, and reduce transmission losses associated with long-distance power distribution.
Sustainability remains a major priority for industrial power plants as industries face increasing pressure to meet environmental regulations and reduce greenhouse gas emissions. The implementation of carbon capture and storage (CCS) technology in steam turbine power plants allows industries to capture CO₂ emissions before they enter the atmosphere, significantly lowering their environmental impact. Additionally, advancements in turbine materials and aerodynamics are improving efficiency while reducing wear and tear, ensuring that industrial power plants operate more sustainably over longer lifespans.
Another area of growth is the expansion of industrial power plants in developing economies. As emerging markets continue to industrialize, the demand for stable and scalable energy solutions is rising. Steam turbines provide a proven and cost-effective solution for large-scale industrial power generation, supporting the growth of manufacturing, mining, and resource processing industries. Investments in modern power plants help developing nations improve energy access, create jobs, and drive economic progress.
Looking ahead, the continued evolution of industrial power plants will be shaped by a combination of technological innovation, sustainability goals, and the need for cost-effective energy solutions. Steam turbines will remain at the core of industrial electricity generation, with advancements in fuel flexibility, digital controls, and hybrid energy integration ensuring their continued relevance. As industries adapt to changing energy landscapes, industrial power plants will play a pivotal role in supporting economic growth while meeting the global demand for reliable and sustainable power generation.
As industrial power plants continue to evolve, their role in supporting economic expansion and sustainability becomes increasingly significant. Steam turbines, as a core technology in large-scale power generation, are at the forefront of innovations aimed at improving energy efficiency, reducing environmental impact, and ensuring energy security for industries worldwide. The convergence of advanced materials, digitalization, and renewable energy integration is shaping the next generation of industrial power plants, enabling them to meet the growing demands of modern economies while maintaining long-term viability.
One of the most promising developments in industrial power generation is the growing adoption of hybrid energy systems. By integrating steam turbines with renewable energy sources such as wind, solar, and geothermal power, industries can achieve greater energy diversification and resilience. For instance, solar thermal power plants use concentrated sunlight to generate steam, which then drives a turbine to produce electricity. When combined with traditional fossil-fuel-based power generation, this approach reduces fuel consumption and minimizes carbon emissions, making industrial energy production more sustainable.
Furthermore, advancements in steam turbine materials and design are leading to greater efficiency and operational longevity. The use of high-performance alloys, ceramic coatings, and additive manufacturing techniques enables turbines to withstand higher temperatures and pressures, increasing efficiency and reducing maintenance requirements. Improved blade aerodynamics and steam path optimization also contribute to enhanced performance, allowing power plants to generate more electricity with lower energy losses. These innovations help industries maintain stable power output while lowering operational costs.
The impact of industrial power plants extends beyond energy generation, contributing to local and national economic growth. Large-scale energy projects attract investment, create jobs, and stimulate infrastructure development. In regions where industrialization is accelerating, the establishment of power plants supports the expansion of manufacturing, mining, and resource processing industries, fostering long-term economic progress. Additionally, access to reliable electricity encourages technological innovation and industrial automation, further enhancing productivity and competitiveness.
Energy storage technologies are also becoming an essential component of modern industrial power plants. The integration of large-scale battery storage systems allows industries to manage fluctuations in electricity demand and supply, ensuring consistent energy availability even during peak usage periods. Combined with steam turbines, these storage solutions create more flexible and responsive power systems, helping industries optimize energy usage and reduce dependency on grid-based electricity.
Government policies and environmental regulations are playing a crucial role in shaping the future of industrial power plants. Many countries are implementing stricter emissions standards and incentivizing the adoption of cleaner energy technologies. This has led to increased investment in carbon capture and storage (CCS) solutions, which enable steam turbine power plants to capture and store CO₂ emissions, significantly reducing their environmental footprint. By integrating these technologies, industrial power plants can align with global sustainability goals while maintaining high power output.
Another key development is the rise of industrial power plant automation and AI-driven optimization. Digital monitoring systems equipped with artificial intelligence analyze turbine performance in real time, detecting inefficiencies and predicting maintenance needs before failures occur. These predictive maintenance capabilities help industries avoid unexpected downtime, reduce repair costs, and extend the lifespan of power generation equipment. AI-driven optimization also allows power plants to dynamically adjust their output based on demand, improving overall energy management and reducing waste.
The global transition toward a low-carbon economy is further influencing the direction of industrial power plants. Companies are increasingly exploring alternative fuels such as ammonia and biofuels for steam turbines, reducing their reliance on fossil fuels while maintaining energy efficiency. As hydrogen infrastructure develops, hydrogen-fired turbines will become a viable solution for industries seeking to decarbonize their power generation without compromising reliability. These advancements position industrial power plants as key players in the shift toward cleaner and more sustainable energy solutions.
Looking ahead, the continued advancement of industrial power plants will be driven by the need for efficiency, reliability, and environmental responsibility. As industries embrace digitalization, hybrid energy integration, and next-generation turbine technology, power plants will become more adaptable and resilient to the changing energy landscape. Their ability to provide stable and cost-effective electricity will remain a cornerstone of economic growth, industrial development, and global sustainability efforts. By continuously evolving to meet the challenges of modern energy demands, industrial power plants will continue to fuel economic progress for decades to come.
Factories Turn Waste Heat into Electricity
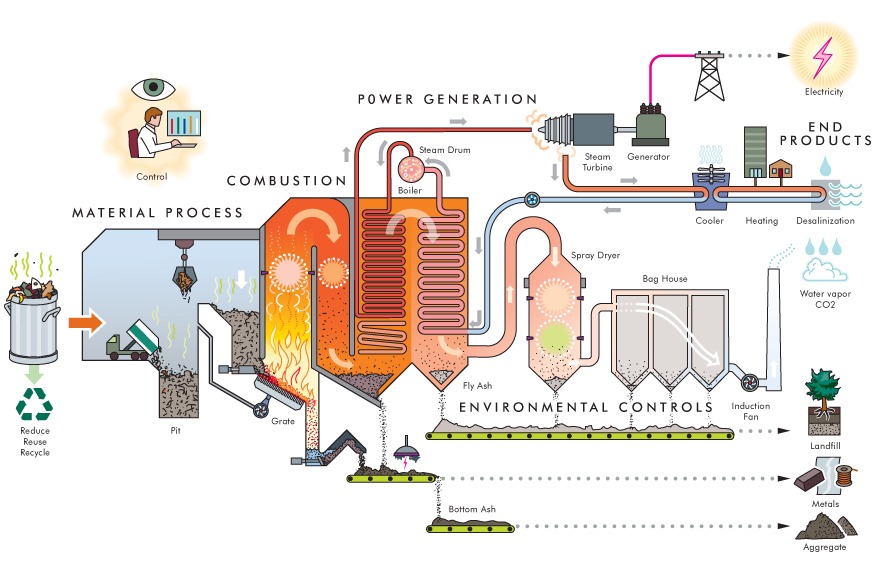
Factories are increasingly turning waste heat into electricity as industries seek to improve energy efficiency, reduce costs, and lower environmental impact. Waste heat recovery systems, combined with steam turbines, are playing a critical role in transforming excess thermal energy from industrial processes into useful power. This approach not only enhances sustainability but also helps industries reduce their dependence on external electricity sources, leading to greater energy security and economic savings.
Industrial processes, such as steel production, cement manufacturing, glassmaking, and chemical processing, generate significant amounts of heat that often go unused. Traditionally, this heat is released into the atmosphere, representing a lost opportunity for energy utilization. However, with the advancement of waste heat recovery technologies, factories can now capture this excess heat and convert it into electricity through steam turbines or organic Rankine cycle (ORC) systems.
The process of turning waste heat into electricity begins with heat exchangers that capture high-temperature exhaust gases, steam, or process heat from industrial equipment such as furnaces, kilns, and boilers. This captured heat is then used to produce steam, which drives a steam turbine connected to an electrical generator. The resulting electricity can either be used on-site to power factory operations or fed into the grid to reduce overall energy costs.
One of the most significant advantages of waste heat recovery is its ability to improve overall energy efficiency. By reusing heat that would otherwise be wasted, factories can reduce fuel consumption, lowering both operational expenses and carbon emissions. This is particularly beneficial in energy-intensive industries, where even small efficiency improvements can lead to substantial cost savings. Additionally, many governments offer incentives and tax benefits for industries implementing waste heat recovery systems, further promoting the adoption of these technologies.
The implementation of combined heat and power (CHP) systems takes waste heat recovery a step further. CHP, also known as cogeneration, allows factories to simultaneously produce electricity and useful thermal energy for heating or cooling purposes. This maximizes energy utilization and provides a more sustainable approach to industrial power generation. CHP systems can achieve efficiency levels of up to 80%, far exceeding the efficiency of conventional power plants, which typically operate at around 35–50%.
Industries that integrate waste heat recovery into their operations benefit from increased energy resilience. By generating their own electricity from waste heat, factories can reduce their reliance on external power grids, protecting themselves from fluctuating energy prices and supply disruptions. This is particularly valuable in regions with unstable electricity supplies, where self-sufficient power generation enhances industrial productivity and reliability.
In addition to economic benefits, waste heat recovery plays a crucial role in reducing greenhouse gas emissions. By making better use of available energy resources, factories can cut down on fossil fuel consumption and decrease their carbon footprint. This supports global efforts to combat climate change and helps industries comply with increasingly strict environmental regulations. Many companies are adopting waste heat recovery as part of their sustainability initiatives, demonstrating their commitment to reducing energy waste and improving corporate environmental responsibility.
Technological advancements continue to improve the feasibility and efficiency of waste heat-to-electricity conversion. Innovations in high-temperature materials, advanced heat exchangers, and energy storage systems are making it easier for factories to capture and utilize waste heat effectively. Furthermore, developments in artificial intelligence and digital monitoring allow industries to optimize waste heat recovery systems in real time, ensuring maximum efficiency and cost-effectiveness.
Looking ahead, waste heat recovery is expected to become an integral part of industrial energy strategies worldwide. As energy costs continue to rise and environmental concerns intensify, more factories will invest in technologies that enable them to harness waste heat for electricity production. Governments and industry leaders are recognizing the potential of waste heat recovery to contribute to a more sustainable and energy-efficient future, driving further research and adoption of these systems.
In conclusion, turning waste heat into electricity represents a powerful opportunity for factories to enhance efficiency, reduce costs, and minimize environmental impact. By integrating waste heat recovery systems with steam turbines and CHP solutions, industries can make the most of their energy resources while improving energy security and sustainability. As the demand for cleaner and more efficient energy solutions grows, waste heat recovery will play an increasingly vital role in shaping the future of industrial power generation.
The growing adoption of waste heat recovery systems is transforming industrial power generation, enabling factories to optimize energy use and reduce operational costs. As energy demands increase and sustainability becomes a priority, industries are investing in advanced waste heat-to-electricity solutions to enhance efficiency and achieve long-term competitiveness.
One of the major advantages of waste heat recovery is its ability to reduce primary fuel consumption. By capturing and repurposing excess heat, industries can generate additional electricity without burning more fossil fuels. This leads to lower energy bills and decreased reliance on external power sources, allowing manufacturers to reinvest savings into process improvements, technology upgrades, and workforce expansion. In industries such as cement, steel, and oil refining, where production requires significant thermal energy, waste heat recovery can cut energy costs by up to 30%, providing substantial financial benefits.
Waste heat recovery is particularly effective in industrial settings where processes generate high-temperature exhaust gases. For example, steel mills release large amounts of heat during the smelting and rolling processes, while cement plants emit hot gases from kilns. By using waste heat boilers and steam turbines, these industries can convert thermal energy into electricity, reducing overall energy waste. Similarly, in chemical and petrochemical plants, where heat-intensive reactions are common, integrating waste heat recovery systems ensures that excess heat is efficiently utilized rather than lost to the environment.
Another important aspect of waste heat-to-electricity conversion is its role in energy resilience. With global energy markets experiencing volatility and power grid instability in many regions, industries are increasingly looking for ways to secure their electricity supply. By generating power from waste heat, factories can reduce their exposure to external energy price fluctuations and mitigate risks associated with grid outages. This is especially valuable for industries operating in remote locations, where reliable access to electricity is a challenge.
As technology advances, more industries are exploring innovative methods for utilizing lower-temperature waste heat. Traditional steam turbines require relatively high temperatures to generate electricity efficiently, but newer technologies, such as organic Rankine cycle (ORC) systems, enable power generation from medium- and low-temperature waste heat. ORC systems use organic fluids with lower boiling points than water, allowing them to operate effectively at lower temperatures. This makes waste heat recovery feasible for industries that produce moderate-temperature exhaust gases, such as food processing, pulp and paper, and textile manufacturing.
Government policies and incentives are also driving the adoption of waste heat recovery in industrial settings. Many countries are introducing tax credits, subsidies, and emissions reduction targets that encourage factories to invest in energy efficiency measures. Regulatory frameworks promoting industrial decarbonization further motivate companies to implement waste heat recovery systems as part of their sustainability strategies. Additionally, carbon pricing mechanisms make waste heat utilization more economically attractive, as companies can reduce emissions-related costs by improving their energy efficiency.
The environmental benefits of waste heat recovery are substantial. By reducing the need for additional fuel combustion, factories can significantly lower their greenhouse gas emissions. This contributes to global efforts to combat climate change and helps industries meet stricter environmental standards. Furthermore, industries that adopt waste heat recovery technologies often enhance their corporate sustainability profiles, improving their reputation among consumers, investors, and regulatory bodies.
Looking to the future, advancements in heat exchanger technology, thermal storage solutions, and AI-driven energy management systems will further improve the efficiency and viability of waste heat recovery. Smart control systems can optimize the operation of waste heat boilers and turbines in real time, ensuring maximum energy savings. Additionally, the integration of waste heat recovery with renewable energy sources, such as solar or biomass, can create highly efficient hybrid power systems, further reducing dependence on fossil fuels.
In summary, waste heat recovery is rapidly becoming a cornerstone of industrial energy strategies. Factories that harness waste heat for electricity generation benefit from lower energy costs, improved efficiency, enhanced energy security, and reduced environmental impact. As industries continue to innovate and adopt sustainable practices, waste heat recovery will play an increasingly vital role in the transition toward cleaner and more efficient industrial power generation.
The continued expansion of waste heat recovery in industrial power generation is being driven by both technological advancements and economic incentives. As factories seek to maximize efficiency and minimize waste, new innovations in heat capture, conversion, and storage are making waste heat-to-electricity systems more viable and effective than ever before. These improvements not only reduce costs but also contribute to global efforts to lower carbon emissions and create more sustainable industrial processes.
One of the most significant advancements in waste heat recovery is the development of highly efficient heat exchangers. These components are crucial in transferring heat from exhaust gases, steam, or other high-temperature industrial byproducts into usable energy. Modern heat exchangers feature improved materials, coatings, and designs that allow for greater thermal conductivity, reducing energy losses and increasing the overall efficiency of the recovery process. Some advanced models incorporate self-cleaning mechanisms that minimize maintenance downtime and prolong equipment life, further improving system performance.
In addition to traditional steam turbines, emerging power generation technologies are expanding the range of waste heat that can be effectively utilized. Organic Rankine cycle (ORC) systems are gaining popularity in industries that generate medium- and low-temperature waste heat, such as food processing, textiles, and wastewater treatment. ORC systems use specialized working fluids with lower boiling points than water, allowing them to operate efficiently at lower temperatures. This technology makes it possible to recover heat that would otherwise be considered too low-grade for conventional steam turbines.
Another key innovation is the integration of thermal energy storage with waste heat recovery systems. Thermal storage solutions enable factories to store excess heat during periods of low demand and use it later when energy needs are higher. This approach enhances the flexibility and reliability of waste heat recovery, ensuring that captured energy is utilized efficiently without requiring immediate electricity generation. Phase-change materials (PCMs) and high-capacity molten salt storage systems are being explored as potential solutions to optimize heat storage and improve system stability.
Industrial automation and artificial intelligence (AI) are also transforming waste heat recovery by improving system monitoring, predictive maintenance, and process optimization. AI-powered analytics can assess real-time data from waste heat recovery units, identifying inefficiencies and optimizing energy flows for maximum performance. Predictive maintenance algorithms help prevent unexpected breakdowns by detecting early signs of wear and tear in turbines, heat exchangers, and piping systems. These digital tools reduce operational costs while ensuring uninterrupted power generation from waste heat sources.
Economic incentives and regulatory policies are further accelerating the adoption of waste heat recovery in industrial applications. Governments around the world are offering tax credits, grants, and low-interest financing options to encourage companies to invest in energy efficiency projects. In some regions, industries that implement waste heat recovery can sell excess electricity back to the grid, generating additional revenue while reducing strain on public energy infrastructure. Carbon pricing mechanisms and stricter emissions regulations also make waste heat recovery more financially attractive by helping companies avoid penalties and compliance costs.
Industries that have successfully adopted waste heat recovery technologies report significant benefits, including reduced operating expenses, improved energy security, and enhanced sustainability. Large manufacturing facilities that integrate waste heat recovery into their production processes can achieve energy savings of 10% to 30%, depending on the industry and system design. In sectors like steel, cement, and petrochemicals, where high-temperature processes are essential, these savings can translate into millions of dollars in annual cost reductions.
Beyond financial savings, waste heat recovery also strengthens corporate sustainability efforts. Companies that reduce their energy waste and carbon footprint gain a competitive advantage in environmentally conscious markets. Many businesses are incorporating waste heat recovery into their broader sustainability strategies, positioning themselves as leaders in industrial energy efficiency and responsible environmental stewardship. By demonstrating a commitment to cleaner and more sustainable operations, these companies improve their reputation among consumers, investors, and regulatory agencies.
Looking ahead, the future of waste heat recovery will likely involve greater integration with renewable energy sources, such as solar thermal and biomass. Hybrid energy systems that combine waste heat recovery with renewables can further improve industrial energy efficiency and reduce dependence on fossil fuels. Additionally, advancements in supercritical CO₂ power cycles—a next-generation energy conversion technology—could offer even greater efficiency in waste heat-to-electricity applications, making industrial power generation more sustainable than ever before.
In conclusion, waste heat recovery is an increasingly vital component of modern industrial power strategies. With continuous technological innovation, supportive policies, and growing economic benefits, factories are finding new ways to harness waste heat for electricity generation. As industries strive to reduce energy costs, improve efficiency, and meet sustainability goals, waste heat recovery will continue to play a crucial role in shaping the future of industrial power generation.
The future of waste heat recovery in industrial power generation is poised for further expansion, driven by ongoing advancements in efficiency, technology integration, and sustainability initiatives. As industries increasingly prioritize energy efficiency and carbon reduction, waste heat recovery systems are evolving to meet these demands with innovative solutions that maximize power generation while minimizing environmental impact.
One of the most promising developments in waste heat recovery is the increasing use of supercritical CO₂ (sCO₂) power cycles. Unlike traditional steam-based systems, sCO₂ turbines operate at higher efficiencies, requiring less space and offering superior energy conversion rates. These systems can extract more electricity from waste heat at lower temperatures, making them highly attractive for industrial applications. The compact nature of sCO₂ turbines also allows for easier integration into existing factory infrastructure, reducing implementation costs and improving feasibility for industries looking to optimize power generation from excess heat.
The rise of decentralized energy systems is further accelerating the adoption of waste heat recovery. Many industries are shifting away from reliance on centralized power grids and instead investing in on-site power generation to improve energy security and reduce transmission losses. Waste heat recovery systems play a crucial role in these self-sustaining power solutions, allowing factories to generate their own electricity efficiently and reliably. By reducing dependence on external energy sources, industrial facilities can protect themselves from fluctuating electricity prices, grid instability, and supply disruptions.
Another important trend in waste heat recovery is the growing role of energy storage and grid integration. As industries capture more waste heat and convert it into electricity, energy storage solutions such as advanced batteries, flywheels, and thermal storage systems enable factories to store excess power for later use. This allows for greater flexibility in energy management, ensuring that generated electricity is available when demand is highest. In some cases, industries are also feeding surplus electricity into local power grids, creating additional revenue streams while contributing to overall grid stability.
In addition to technological advancements, policy frameworks and financial incentives are playing a crucial role in expanding waste heat recovery adoption. Many governments are setting stricter emissions reduction targets and implementing regulations that encourage industries to optimize their energy efficiency. Carbon pricing mechanisms, emissions trading systems, and energy efficiency mandates are pushing industries to invest in waste heat recovery as a cost-effective means of meeting regulatory requirements. Furthermore, financial incentives such as tax credits, grants, and subsidized loans are making it easier for companies to implement these technologies without facing prohibitive upfront costs.
As industries continue to evolve, waste heat recovery is expected to play an integral role in achieving net-zero energy goals. Many industrial sectors are working toward decarbonization by reducing reliance on fossil fuels and increasing the efficiency of their energy use. Waste heat recovery aligns with these goals by making better use of existing energy resources, reducing fuel consumption, and cutting down on greenhouse gas emissions. By integrating waste heat recovery with renewable energy sources such as solar and biomass, industries can create highly efficient hybrid power systems that further reduce their environmental footprint.
The push toward smart manufacturing and Industry 4.0 is also influencing the future of waste heat recovery. Digitalization, artificial intelligence (AI), and the Internet of Things (IoT) are enabling real-time monitoring and optimization of energy flows within industrial facilities. AI-driven predictive analytics can identify patterns in waste heat generation and optimize recovery processes for maximum efficiency. IoT-connected sensors allow for automated adjustments, ensuring that waste heat is captured and converted into electricity with minimal losses. These digital solutions not only improve energy management but also enhance equipment lifespan and reduce maintenance costs.
Beyond economic and environmental benefits, waste heat recovery also contributes to corporate social responsibility (CSR) initiatives. As consumers and investors increasingly favor companies that prioritize sustainability, businesses that implement waste heat recovery can enhance their reputation as leaders in energy efficiency and environmental stewardship. Companies that demonstrate a commitment to reducing energy waste and emissions are more likely to attract environmentally conscious customers and secure partnerships with organizations that prioritize sustainability.
Looking forward, the next generation of waste heat recovery systems will focus on increased adaptability, modular designs, and integration with emerging energy technologies. Researchers are exploring new materials and coatings that improve heat exchanger performance, making waste heat recovery more efficient and cost-effective across a wider range of industrial applications. Advances in low-temperature energy conversion technologies, such as thermoelectric generators and advanced heat pumps, will also expand the potential for utilizing previously untapped waste heat sources.
In conclusion, waste heat recovery is set to play a transformative role in the future of industrial power generation. As industries continue to seek ways to improve efficiency, reduce costs, and meet sustainability goals, waste heat recovery technologies will become increasingly essential. With continued innovation, policy support, and financial incentives, the widespread adoption of waste heat recovery will help industries transition toward more energy-efficient and environmentally responsible operations. By harnessing waste heat for electricity generation, industries can create a more sustainable and resilient energy future while maintaining economic competitiveness in a rapidly evolving global market.
Reliable Power for Large-scale Industries
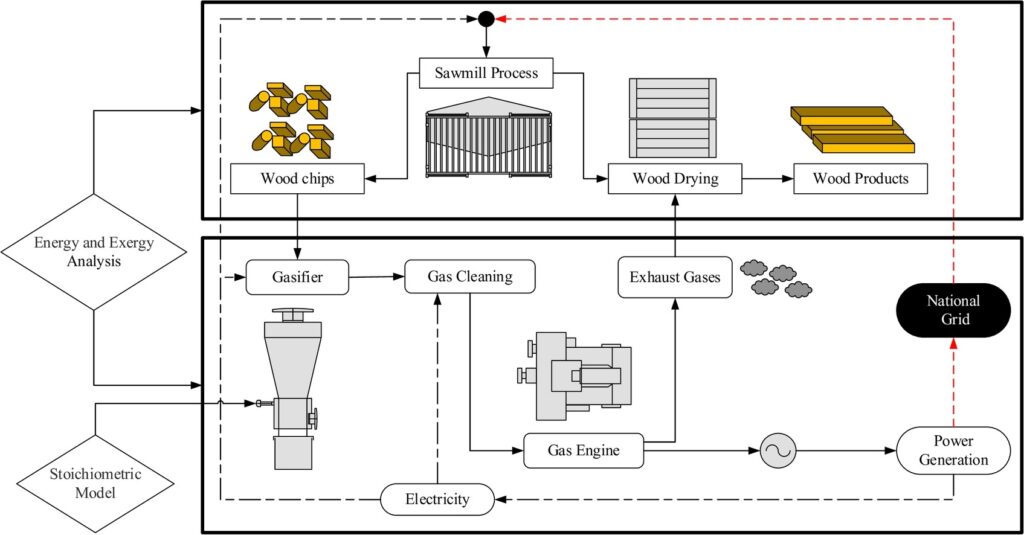
Reliable power is a critical requirement for large-scale industries, where continuous operations and high energy demands make power stability essential. Manufacturing plants, refineries, steel mills, and chemical processing facilities all depend on a steady and efficient power supply to maintain productivity, prevent downtime, and ensure safety. Any interruption in power can lead to significant financial losses, operational inefficiencies, and even equipment damage. As industries expand and modernize, securing a reliable power source has become a top priority, driving the adoption of advanced energy solutions such as steam turbines, waste heat recovery systems, and on-site power generation.
One of the most effective ways for large-scale industries to achieve reliable power is through the use of steam turbine generators. Steam turbines have long been a cornerstone of industrial power generation, providing a stable and efficient means of converting thermal energy into electricity. These systems are highly adaptable and can run on various fuel sources, including natural gas, coal, biomass, and waste heat. Their ability to operate continuously for extended periods with minimal maintenance makes them an ideal choice for industries that require uninterrupted power supply. Furthermore, modern steam turbines are designed with advanced control systems that allow for precise load adjustments, ensuring that power output matches demand while optimizing efficiency.
In addition to steam turbine generators, many industries are turning to combined heat and power (CHP) systems, also known as cogeneration, to enhance reliability and efficiency. CHP systems generate electricity while simultaneously capturing and utilizing excess heat for industrial processes. This dual-use approach significantly improves overall energy efficiency, often reaching efficiency levels of 70-90%, compared to the 30-40% efficiency of conventional power plants. By reducing reliance on external electricity providers and making better use of fuel inputs, CHP systems help industries maintain energy independence and reduce vulnerability to grid failures and price fluctuations.
Waste heat recovery is another key strategy for ensuring reliable power in large-scale industries. Many industrial processes generate significant amounts of waste heat that would otherwise be lost. By capturing this heat and converting it into electricity through waste heat boilers and steam turbines, industries can create an additional power source without increasing fuel consumption. This approach not only enhances power reliability but also reduces operating costs and environmental impact. Industries such as cement production, steel manufacturing, and petrochemical processing have successfully implemented waste heat recovery systems to supplement their energy needs while improving overall efficiency.
On-site power generation is gaining traction as industries seek greater energy security. Large manufacturing plants and industrial complexes are increasingly investing in captive power plants that allow them to generate electricity independently of the public grid. These on-site power systems often include a mix of steam turbines, gas turbines, and renewable energy sources, providing a diversified and resilient power supply. By reducing dependence on external utilities, industries can avoid the risks associated with grid instability, blackouts, and fluctuating energy prices. Additionally, on-site power generation ensures that critical processes remain operational even in the event of power outages, safeguarding productivity and minimizing losses.
Energy storage solutions are also playing an important role in enhancing power reliability for large-scale industries. Advances in battery storage technology allow industrial facilities to store excess energy generated during off-peak hours and use it when demand is high. This capability is especially valuable for industries that experience variable energy consumption patterns or operate in regions with unreliable grid infrastructure. Large-scale energy storage systems can provide backup power during outages, stabilize voltage fluctuations, and support load balancing, further improving the resilience of industrial power networks.
The integration of digitalization and smart grid technologies is further revolutionizing power reliability in industrial settings. Real-time monitoring systems equipped with sensors and artificial intelligence (AI) enable industries to track energy consumption, detect inefficiencies, and predict potential equipment failures before they occur. AI-driven predictive maintenance minimizes downtime by identifying issues early, allowing industries to address problems proactively rather than reactively. Smart grid solutions also enhance coordination between on-site power generation and grid power, ensuring optimal energy distribution and reducing the risk of disruptions.
Government policies and incentives are also supporting the shift toward more reliable and self-sufficient industrial power solutions. Many countries are offering financial incentives, tax credits, and regulatory support for industries that invest in energy-efficient technologies, waste heat recovery, and renewable energy integration. In regions where grid reliability is a concern, policymakers are encouraging industrial sectors to adopt decentralized power generation models to enhance overall energy security. These initiatives help industries transition toward more sustainable and resilient energy systems while reducing their environmental footprint.
Looking ahead, the future of reliable power for large-scale industries will be shaped by continued advancements in energy efficiency, fuel diversification, and smart technology integration. Hybrid energy systems that combine steam turbines, renewable sources, and energy storage will become more prevalent, offering industries greater flexibility and resilience. The adoption of hydrogen as an alternative fuel for power generation may also play a role in reducing emissions while ensuring stable energy supply. Additionally, AI-driven automation and real-time energy management will further optimize industrial power systems, allowing companies to maximize efficiency and minimize risks associated with power disruptions.
In conclusion, reliable power is essential for the success of large-scale industries, and achieving it requires a combination of advanced technologies, strategic energy management, and investment in self-sufficient power solutions. Steam turbine generators, CHP systems, waste heat recovery, and on-site power generation all contribute to enhanced energy security and efficiency. With the integration of smart grid technologies and energy storage solutions, industries can further strengthen their power reliability while reducing costs and environmental impact. As the industrial sector continues to evolve, the focus on sustainable and resilient power generation will remain a key driver of competitiveness and long-term growth.
The growing need for reliable power in large-scale industries continues to drive innovation in energy generation and management. As industrial operations become more complex and energy-intensive, ensuring a stable and uninterrupted power supply is critical to maintaining productivity and competitiveness. Power disruptions, whether due to grid instability, extreme weather, or equipment failures, can result in significant financial losses and operational setbacks. To mitigate these risks, industries are increasingly adopting advanced power solutions that combine efficiency, resilience, and sustainability.
One of the primary methods industries use to secure reliable power is through diversification of energy sources. By integrating multiple power generation technologies, companies can reduce dependence on a single source and improve overall system stability. Steam turbines remain a cornerstone of industrial power generation due to their efficiency and adaptability, but they are now often combined with alternative sources such as gas turbines, solar photovoltaic systems, and biomass power plants. This hybrid approach ensures that industries have a continuous energy supply, even if one source experiences fluctuations or temporary failures.
Cogeneration, or combined heat and power (CHP), continues to gain traction as an effective solution for enhancing power reliability. Large industrial plants that require both electricity and process heat benefit greatly from CHP systems, which generate power while simultaneously recovering and utilizing excess heat. This process not only improves energy efficiency but also ensures a self-sustaining power supply, reducing reliance on external grids. Industries such as chemical manufacturing, food processing, and paper production are increasingly adopting CHP technology to enhance operational stability while lowering energy costs.
To further bolster reliability, industries are turning to microgrids—localized power networks that operate independently or in conjunction with the main grid. Microgrids allow factories to generate, store, and distribute power on-site, providing a safeguard against grid failures. These systems often integrate renewable energy sources and battery storage, ensuring continuous power availability. In the event of a blackout, microgrids can seamlessly switch to stored energy or backup generators, preventing costly downtime and production losses.
Energy storage plays a critical role in industrial power reliability. As factories implement renewable energy sources such as solar and wind, battery storage systems provide a buffer against intermittency. Advanced lithium-ion batteries, flow batteries, and emerging solid-state technologies enable industries to store excess energy and deploy it during peak demand periods or grid disturbances. In addition to batteries, thermal energy storage—using materials such as molten salts or phase-change substances—allows industries to capture and reuse excess heat for power generation, further enhancing efficiency and stability.
Digitalization and automation are transforming how industries manage their energy systems. Smart monitoring solutions equipped with artificial intelligence (AI) and Internet of Things (IoT) sensors enable real-time tracking of energy consumption, system performance, and potential failures. Predictive analytics can anticipate equipment malfunctions before they cause disruptions, allowing for timely maintenance and minimizing unexpected downtime. AI-driven optimization ensures that power generation and consumption are balanced efficiently, reducing waste and improving overall system resilience.
Government policies and regulatory frameworks continue to influence industrial energy strategies. Many countries are implementing stricter emissions targets and energy efficiency standards, encouraging industries to adopt cleaner and more reliable power generation methods. Financial incentives, tax credits, and funding programs for energy-efficient technologies are helping industries transition toward more resilient power systems. Additionally, regulations that support demand-side management, energy storage deployment, and decentralized generation are providing industries with more tools to enhance power reliability.
As industries prepare for the future, the focus on reliable power solutions will only intensify. The development of next-generation energy technologies, including hydrogen-based power systems and advanced nuclear small modular reactors (SMRs), presents new opportunities for large-scale industries to achieve both sustainability and stability. Hydrogen fuel cells, in particular, offer the potential for long-duration energy storage and backup power, while SMRs provide a steady and emission-free source of industrial electricity.
In summary, ensuring reliable power for large-scale industries requires a multifaceted approach that includes energy diversification, advanced generation technologies, smart grid solutions, and digital automation. By investing in resilient power systems, industries can protect themselves against disruptions, reduce operational risks, and maintain high levels of productivity. As global energy trends continue to evolve, industries that prioritize reliability and efficiency will remain competitive and well-positioned for sustainable growth in the years ahead.
As industries continue to expand and modernize, the demand for stable and resilient power infrastructure grows more urgent. The increasing reliance on automation, high-powered machinery, and continuous production cycles necessitates a power supply that is both dependable and efficient. The cost of power disruptions in industrial settings can be substantial, ranging from production losses to equipment damage and safety risks. To address these challenges, industrial facilities are investing in technologies and strategies that enhance power reliability while optimizing energy efficiency.
One key strategy for ensuring reliable industrial power is upgrading and modernizing existing steam turbine systems. Many industrial plants rely on aging power infrastructure, which can be prone to inefficiencies and failures. Retrofitting older turbines with advanced control systems, high-efficiency blades, and upgraded heat recovery units significantly improves performance and reliability. Modern steam turbines are designed with better materials and precision engineering, allowing them to operate continuously with minimal maintenance while delivering higher energy output.
Beyond steam turbines, the integration of renewable energy sources is playing an increasingly important role in industrial power systems. Large-scale industries are incorporating solar, wind, and biomass energy into their power generation mix to reduce dependence on fossil fuels and stabilize electricity costs. Hybrid energy systems that combine traditional steam turbines with renewables and battery storage ensure a steady power supply, even in fluctuating grid conditions. These systems enhance energy security while supporting sustainability goals, helping industries comply with environmental regulations and carbon reduction initiatives.
Another major development in industrial power reliability is the expansion of demand response programs and load management strategies. Industrial facilities with flexible power consumption patterns can participate in demand-side management programs that allow them to adjust electricity usage based on grid conditions. Smart energy management systems analyze real-time power demand and automatically optimize usage to prevent overloading and inefficiencies. By leveraging these capabilities, industries can not only reduce energy costs but also contribute to overall grid stability.
In addition to on-site power generation and efficiency improvements, industries are strengthening their energy resilience through redundancy planning and backup systems. Redundant power systems, such as auxiliary steam turbines, standby generators, and uninterruptible power supply (UPS) units, provide an extra layer of protection against outages. Critical industrial processes, such as those in pharmaceutical manufacturing and semiconductor production, require uninterrupted power supply, making backup power solutions essential. Advances in gas turbine backup generators and rapid-response battery storage systems ensure seamless transitions during power disturbances, preventing costly production halts.
The role of predictive maintenance and AI-driven diagnostics is also transforming how industries maintain power reliability. By utilizing machine learning algorithms and real-time sensor data, predictive maintenance systems can detect anomalies in power generation equipment before failures occur. This proactive approach reduces unplanned downtime, extends the lifespan of industrial power assets, and minimizes repair costs. AI-driven control systems also enable adaptive power management, allowing factories to dynamically adjust generation and distribution based on demand fluctuations.
Industrial power grids are also becoming more decentralized, reducing vulnerability to centralized grid failures. Many large manufacturing hubs and industrial zones are developing their own localized power networks, often incorporating microgrid technology. These self-sufficient grids enhance energy security by balancing power loads across multiple generation sources and enabling industries to operate independently of the main grid when necessary. The increasing deployment of blockchain-based energy trading platforms also allows industries to exchange excess electricity with nearby facilities, further improving reliability and cost-effectiveness.
Government policies and incentives continue to shape industrial power strategies, promoting investments in grid modernization, renewable integration, and energy efficiency. Many governments are offering grants, tax credits, and low-interest loans for industries that implement advanced power solutions, helping offset the initial capital investment. Additionally, stricter reliability standards and performance benchmarks are encouraging industries to adopt cutting-edge technologies that enhance power stability.
Looking ahead, the industrial power landscape will continue to evolve with advancements in energy storage, automation, and alternative fuels. The development of long-duration energy storage systems, such as liquid air energy storage (LAES) and compressed air energy storage (CAES), will further enhance power resilience. Meanwhile, the growing adoption of hydrogen as a clean fuel for industrial power generation could provide an additional layer of reliability and sustainability.
Ultimately, the future of reliable power for large-scale industries lies in the integration of diverse energy solutions, digital intelligence, and proactive management strategies. Companies that invest in these innovations will be better positioned to navigate the challenges of industrial energy demands while ensuring continuous, cost-effective, and sustainable operations.
As industries continue to navigate an evolving energy landscape, the emphasis on securing reliable, cost-effective, and sustainable power is stronger than ever. Industrial power demands are only expected to grow, driven by increased automation, digitalization, and the expansion of energy-intensive sectors such as manufacturing, mining, and chemical processing. Ensuring an uninterrupted power supply requires not just investment in traditional energy sources but also the adoption of innovative technologies and strategies that improve resilience, efficiency, and adaptability.
One of the most significant advancements in industrial power generation is the shift toward hybrid energy systems. These systems integrate conventional steam turbine power with renewable energy sources such as solar, wind, and biomass to create a more resilient and flexible energy mix. By combining multiple energy inputs, industries can ensure greater power stability, reducing the risk of disruptions caused by fuel supply fluctuations or grid failures. Hybrid systems, particularly those incorporating energy storage solutions, allow industries to balance peak demand periods, lower operational costs, and improve overall energy efficiency.
The expansion of energy storage technologies continues to revolutionize industrial power security. Lithium-ion and flow batteries are already proving essential in stabilizing industrial energy networks by providing backup power and enabling peak shaving to optimize electricity usage. As research progresses, new forms of energy storage—including hydrogen storage, solid-state batteries, and molten salt thermal storage—are being explored to further enhance industrial energy resilience. These technologies allow facilities to store excess energy generated during low-demand periods and deploy it when needed, reducing reliance on external grids and minimizing exposure to power price volatility.
The rise of decentralized power generation is also changing how industries manage electricity needs. Large manufacturing plants and industrial complexes are increasingly investing in microgrids—self-sustaining energy networks capable of operating independently from the main grid. Microgrids integrate various power sources, including steam turbines, solar panels, and backup generators, ensuring consistent power availability even in the event of a regional grid failure. With the addition of smart controls and automated switching systems, microgrids optimize energy distribution while improving reliability, making them an attractive solution for industries operating in remote locations or areas with unstable power grids.
Artificial intelligence (AI) and real-time data analytics are playing an increasing role in enhancing industrial power reliability. AI-driven energy management systems analyze operational data, predict equipment failures, and optimize power generation and consumption. Machine learning algorithms can anticipate shifts in energy demand, allowing industrial facilities to adjust generation strategies in real time. Predictive maintenance powered by AI is helping industries reduce downtime by identifying potential failures in steam turbines, generators, and other critical equipment before they lead to costly shutdowns. By adopting these digital solutions, industries can enhance efficiency, reduce maintenance costs, and ensure a continuous power supply.
Government incentives and regulatory frameworks are also shaping industrial power strategies. In many regions, policymakers are introducing stricter energy reliability standards, carbon reduction targets, and financial incentives to encourage investment in modernized power systems. Industries adopting energy-efficient technologies, such as high-efficiency steam turbines, waste heat recovery systems, and low-carbon power generation, are benefiting from tax breaks, grants, and favorable electricity pricing schemes. These policy-driven initiatives are not only improving industrial power security but also accelerating the transition toward cleaner and more sustainable energy sources.
The transition to hydrogen as an industrial energy source is another development gaining momentum. Hydrogen fuel cells and hydrogen-powered gas turbines are emerging as viable solutions for industries looking to diversify their energy sources while reducing carbon emissions. Hydrogen’s ability to provide long-duration energy storage and act as a clean-burning fuel makes it a promising option for large-scale industrial applications. Many industries are already investing in pilot projects to integrate hydrogen into their power mix, with long-term plans to establish hydrogen-based power networks that complement existing steam and gas turbine infrastructure.
Looking forward, the industrial power sector will continue to evolve as technological advancements and energy market dynamics drive new innovations. The integration of blockchain technology in energy trading, the development of next-generation steam turbine designs with even higher efficiency rates, and the expansion of smart grid networks will further enhance industrial power reliability. Industries that proactively invest in these solutions will gain a competitive advantage, ensuring stable operations while reducing long-term energy costs.
Ultimately, the future of industrial power generation is one of diversification, intelligence, and resilience. By embracing advanced energy technologies, adopting digital optimization tools, and leveraging policy-driven incentives, industries can achieve a more reliable, efficient, and sustainable power supply. As the demand for industrial energy grows, the ability to secure uninterrupted, high-quality power will remain a key factor in determining long-term operational success and economic growth.
Cogeneration Boosts Industrial Efficiency
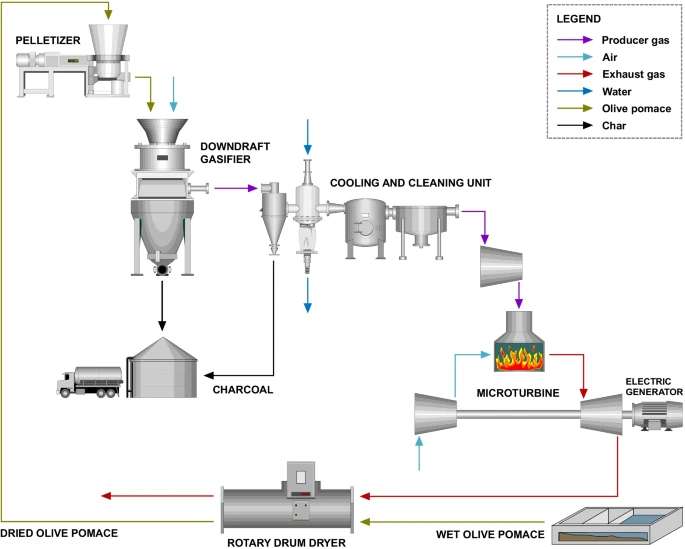
Cogeneration, or combined heat and power (CHP), is transforming industrial energy use by significantly enhancing efficiency and reducing waste. This process involves the simultaneous generation of electricity and useful thermal energy from a single fuel source, allowing industries to maximize energy utilization while lowering overall costs. Unlike traditional power generation, which often wastes excess heat as a byproduct, cogeneration captures and repurposes this heat for industrial processes, space heating, or even cooling. This dual-use approach not only improves fuel efficiency but also reduces greenhouse gas emissions, making it a sustainable and economically viable energy solution.
Industries that require both electricity and thermal energy, such as manufacturing, chemical processing, and food production, benefit the most from cogeneration. Conventional power plants typically operate at an efficiency of 35–45%, losing much of the fuel’s energy potential as waste heat. In contrast, cogeneration systems can achieve efficiency levels of 70–90% by utilizing the heat that would otherwise be discarded. This higher efficiency translates into lower fuel consumption and reduced energy costs, providing industries with a competitive advantage in terms of operational expenses and sustainability.
Steam turbines play a crucial role in industrial cogeneration systems. High-pressure steam produced in boilers or heat recovery steam generators (HRSG) drives steam turbines to generate electricity. The steam exiting the turbine retains significant thermal energy, which can be repurposed for industrial applications such as process heating, drying, or steam-driven equipment. This approach is particularly valuable in industries where thermal processes are integral to production, such as paper mills, refineries, and textile manufacturing.
Gas turbines and reciprocating engines are also commonly used in cogeneration plants. In these systems, the high-temperature exhaust gases from fuel combustion are used to generate steam or hot water, which is then utilized for industrial heating or additional power generation. This flexibility allows industries to select cogeneration technologies that best match their energy needs, ensuring optimal efficiency and cost-effectiveness.
The environmental benefits of cogeneration are substantial. By maximizing fuel efficiency and reducing waste, cogeneration lowers carbon dioxide (CO₂) and nitrogen oxide (NOₓ) emissions compared to separate power and heat generation. Many industrial plants are now integrating renewable fuels, such as biomass or biogas, into their cogeneration systems to further enhance sustainability. Additionally, some cogeneration plants are exploring hydrogen as a clean fuel alternative, paving the way for even lower emissions and a more sustainable industrial energy future.
Regulatory support and government incentives are driving the adoption of cogeneration in industries worldwide. Many countries offer tax incentives, grants, and preferential electricity tariffs for facilities that implement cogeneration systems. Moreover, industries with cogeneration capabilities can participate in demand response programs, selling excess electricity back to the grid during peak demand periods. This not only improves grid stability but also creates additional revenue streams for industrial operators.
The integration of digital technologies is further optimizing cogeneration systems. Advanced monitoring and control systems powered by artificial intelligence (AI) and the Internet of Things (IoT) enable real-time performance tracking, predictive maintenance, and dynamic energy management. These digital tools help industries maximize the efficiency of their cogeneration units, minimize downtime, and ensure seamless operation under varying load conditions.
Looking ahead, the expansion of district heating and industrial microgrids is expected to further drive the adoption of cogeneration. Industrial parks and urban centers are increasingly utilizing cogeneration plants to provide both electricity and heating to multiple facilities, creating interconnected energy networks that improve overall efficiency. As energy costs fluctuate and sustainability targets become more stringent, industries will continue to seek out cogeneration as a reliable and cost-effective solution for meeting their power and thermal energy needs.
In conclusion, cogeneration is a game-changer for industrial energy efficiency, offering a highly effective way to reduce costs, enhance sustainability, and improve overall energy security. By leveraging the simultaneous production of electricity and heat, industries can significantly cut fuel consumption, lower emissions, and increase resilience against energy price volatility. As technology advances and regulatory support grows, cogeneration will remain a key pillar of industrial energy strategy, ensuring a more efficient and sustainable future.
The growing adoption of cogeneration is reshaping the industrial energy landscape, offering unparalleled efficiency and reliability for power-intensive sectors. As industries strive to optimize operations and reduce costs, the ability to generate both electricity and heat from a single fuel source has become an essential strategy for achieving long-term energy sustainability. The flexibility of cogeneration systems allows industries to tailor their energy production to specific needs, ensuring stable and cost-effective power while simultaneously reducing dependence on external electricity grids.
One of the primary drivers behind the increasing use of cogeneration is its role in enhancing energy security. Industrial facilities that generate their own power through cogeneration are less vulnerable to grid disruptions, voltage fluctuations, and rising electricity costs. This energy independence is particularly valuable in industries with continuous operations, such as petrochemical processing, steel manufacturing, and food production, where any power interruption can lead to significant financial losses. By implementing cogeneration, industries can mitigate risks associated with unreliable grid supply, ensuring uninterrupted production.
Another advantage of cogeneration lies in its ability to support energy transition goals while reducing environmental impact. Traditional power generation methods, especially those relying on coal or inefficient gas turbines, contribute to high emissions and fuel wastage. In contrast, cogeneration maximizes fuel utilization, leading to substantial reductions in carbon emissions and other pollutants. Many industrial facilities are now incorporating low-carbon fuels, such as biomass, syngas, and hydrogen, into their cogeneration systems, further improving sustainability. These alternative fuels not only enhance environmental performance but also provide a hedge against fossil fuel price volatility.
Cogeneration is also playing a crucial role in the advancement of industrial microgrids and distributed energy systems. Rather than relying on centralized power plants, industrial facilities are increasingly deploying localized cogeneration units that supply power directly to production processes. When integrated with renewable energy sources like solar or wind, these systems create a balanced energy mix that ensures stability while reducing dependency on fossil fuels. Industrial microgrids equipped with cogeneration are particularly advantageous in remote locations, where grid connectivity is limited or unreliable.
Furthermore, technological advancements are making cogeneration even more efficient and easier to integrate into industrial operations. Innovations in turbine design, heat recovery systems, and digital monitoring tools are enabling industries to optimize performance in real time. Predictive maintenance powered by AI and machine learning ensures that cogeneration units operate at peak efficiency, preventing unexpected failures and reducing maintenance costs. These smart energy management systems help industries fine-tune energy generation based on demand fluctuations, improving overall efficiency and lowering operational expenses.
The economic benefits of cogeneration extend beyond fuel savings and operational efficiency. Many industrial facilities that implement cogeneration are able to sell excess electricity back to the grid, creating an additional revenue stream. In deregulated energy markets, this capability allows industries to participate in energy trading, further enhancing profitability. Additionally, some governments offer incentives for cogeneration adoption, including tax credits, subsidies, and favorable electricity pricing structures. These financial benefits make cogeneration a compelling investment for industries looking to improve their bottom line while enhancing energy resilience.
As industries continue to prioritize sustainability and efficiency, the role of cogeneration will only expand. Emerging technologies such as fuel cell-based cogeneration, advanced thermal storage, and carbon capture integration are expected to further enhance the efficiency and environmental benefits of these systems. By combining cogeneration with next-generation energy solutions, industries can achieve near-zero emissions while maintaining reliable and cost-effective power generation.
In the long term, cogeneration will remain a key pillar of industrial energy strategy, providing a bridge between conventional energy sources and the future of cleaner, more efficient power generation. As more industries recognize its advantages, the widespread adoption of cogeneration will contribute to a more resilient, sustainable, and economically viable energy infrastructure.
The continued evolution of cogeneration technology is driving industries toward a more sustainable and economically efficient energy model. As global energy demand rises and regulatory frameworks emphasize lower carbon footprints, industries are increasingly turning to cogeneration as a solution to balance cost savings, environmental responsibility, and operational stability. The ability to harness both electricity and thermal energy from a single fuel source ensures that industrial facilities maximize their energy efficiency while reducing waste, making cogeneration an essential component of modern industrial energy strategies.
One of the most significant advancements in cogeneration is the integration of waste heat recovery systems. Traditional power generation discards large amounts of heat, but cogeneration systems repurpose this thermal energy to drive additional processes, such as steam production, drying, or even cooling when paired with absorption chillers. This approach not only reduces the need for additional energy inputs but also enhances overall system efficiency, often exceeding 80–90%. As a result, industries benefit from lower fuel consumption, reduced greenhouse gas emissions, and improved energy independence.
Industries with high energy demands, such as chemical production, paper mills, and refining, are particularly well-suited for cogeneration. These sectors require both reliable electricity and substantial amounts of process heat, making cogeneration a cost-effective and environmentally friendly solution. In addition to lowering energy costs, cogeneration helps stabilize energy prices for these industries by reducing dependence on external power suppliers, shielding them from fluctuations in electricity market prices.
Another emerging trend in industrial cogeneration is the integration of renewable and alternative fuels. While traditional cogeneration systems often rely on natural gas or coal, newer installations are incorporating biomass, biogas, and hydrogen to further reduce emissions. Biomass-based cogeneration plants, for example, utilize organic waste materials to generate both heat and electricity, creating a closed-loop system that minimizes waste while providing a sustainable energy source. Similarly, hydrogen-fired cogeneration systems are gaining attention for their potential to deliver zero-emission energy while maintaining the high efficiencies characteristic of cogeneration.
The digitalization of industrial energy systems is also enhancing the performance and reliability of cogeneration plants. Advanced energy management platforms, powered by artificial intelligence (AI) and the Internet of Things (IoT), allow for real-time monitoring and predictive maintenance of cogeneration units. These systems analyze operating conditions, fuel efficiency, and equipment health to optimize performance and prevent unexpected failures. Predictive analytics can detect early signs of wear or inefficiency, enabling proactive maintenance that minimizes downtime and extends the lifespan of cogeneration assets.
Government policies and incentives are further encouraging the adoption of cogeneration. Many countries have introduced regulatory measures that support high-efficiency energy systems, including feed-in tariffs, tax credits, and grants for cogeneration projects. Additionally, industries implementing cogeneration may qualify for carbon offset programs, further improving their financial returns while contributing to sustainability goals. Some regions are even mandating the use of cogeneration in new industrial developments, recognizing its role in reducing overall energy consumption and emissions.
The expansion of district energy networks and industrial microgrids is also driving the adoption of cogeneration. These decentralized energy systems distribute power and thermal energy across multiple facilities, maximizing efficiency while ensuring reliability. Industrial parks, commercial buildings, and even residential areas are increasingly benefiting from cogeneration-powered microgrids, which provide localized, resilient energy supply while reducing strain on centralized power grids. This trend is particularly important in urban areas where energy demand is high, and grid reliability is a concern.
Looking ahead, the next generation of cogeneration systems will likely incorporate even more advanced energy storage solutions. Technologies such as thermal storage, battery integration, and hydrogen-based energy storage will enable cogeneration plants to operate with greater flexibility, storing excess energy for use during peak demand periods. This development will make cogeneration even more attractive to industries seeking to enhance their energy resilience while optimizing cost savings.
As industrial energy requirements continue to grow, the role of cogeneration in meeting these needs efficiently and sustainably cannot be overstated. By maximizing fuel utilization, reducing emissions, and improving energy security, cogeneration is not only a key component of today’s industrial energy landscape but also a critical technology for the future. Industries that embrace cogeneration will position themselves at the forefront of energy efficiency, cost savings, and environmental responsibility, ensuring long-term competitiveness in an increasingly energy-conscious world.
The increasing adoption of cogeneration across industrial sectors highlights its critical role in shaping a more resilient and sustainable energy landscape. As industries continue to prioritize efficiency and cost reduction, the ability to generate electricity and thermal energy from a single fuel source has become a fundamental component of modern energy strategies. With ongoing advancements in technology, policy support, and integration with renewable energy sources, cogeneration is poised to play an even greater role in industrial energy systems in the years ahead.
One of the most compelling reasons for the continued growth of cogeneration is its ability to enhance energy security. Many industries operate in regions where electricity grid reliability is a concern due to aging infrastructure, peak demand constraints, or geopolitical factors. By investing in on-site cogeneration, industrial facilities can achieve greater energy independence, ensuring continuous power supply even in the face of external disruptions. This is particularly valuable for energy-intensive sectors such as steel production, chemical processing, and data centers, where even brief power outages can lead to substantial financial losses and operational downtime.
The economic advantages of cogeneration extend beyond energy security and efficiency. Industrial facilities that implement cogeneration often experience significant cost savings through reduced fuel consumption and lower electricity bills. Additionally, excess electricity generated by cogeneration systems can be sold back to the grid, providing an additional revenue stream for industries operating in deregulated energy markets. Governments and regulatory bodies in many countries are also incentivizing cogeneration adoption through subsidies, tax breaks, and preferential energy tariffs, further improving its financial appeal.
As the global push for decarbonization intensifies, industries are increasingly seeking low-carbon and renewable fuel alternatives for cogeneration. Biomass and biogas have already proven to be viable options for many industrial facilities, offering a sustainable and cost-effective means of generating power while reducing dependence on fossil fuels. Meanwhile, the development of hydrogen-powered cogeneration presents an exciting opportunity for industries to achieve near-zero emissions while maintaining the high efficiency of traditional cogeneration systems. Many countries are investing heavily in hydrogen infrastructure, paving the way for widespread adoption of hydrogen-fueled cogeneration in industrial applications.
The integration of digital technologies is further revolutionizing cogeneration by optimizing performance, minimizing maintenance costs, and enhancing overall efficiency. AI-driven energy management systems provide real-time monitoring, predictive maintenance, and automated adjustments to maximize fuel efficiency and output. The incorporation of IoT sensors enables remote diagnostics and performance tracking, allowing industrial operators to fine-tune cogeneration units for optimal operation. These advancements help prevent unexpected failures, extend equipment lifespan, and improve overall energy reliability.
The expansion of industrial microgrids and district energy systems is also driving increased investment in cogeneration. By decentralizing energy production and distribution, these systems allow multiple facilities to share power and thermal energy, maximizing efficiency and resilience. Industrial parks, large manufacturing complexes, and urban districts are leveraging cogeneration-powered microgrids to reduce energy costs, lower emissions, and enhance reliability. This trend is particularly important in densely populated areas, where demand for sustainable and stable energy supply is growing rapidly.
Looking ahead, continued innovation in energy storage solutions will further enhance the value of cogeneration. The integration of advanced thermal storage, battery storage, and hydrogen-based storage solutions will allow industries to capture excess energy and deploy it during peak demand periods, improving overall system flexibility. As energy markets evolve and regulatory frameworks encourage cleaner and more efficient energy solutions, cogeneration will remain a key pillar of industrial power generation strategies.
Ultimately, industries that embrace cogeneration will be better positioned to navigate the challenges of rising energy costs, regulatory pressures, and sustainability targets. By maximizing fuel efficiency, reducing emissions, and enhancing energy resilience, cogeneration not only provides immediate economic and environmental benefits but also secures a long-term competitive advantage. As the world transitions toward a more sustainable energy future, cogeneration will continue to play a crucial role in ensuring reliable, cost-effective, and efficient industrial power generation.
Industrial Power from Waste Heat Recovery
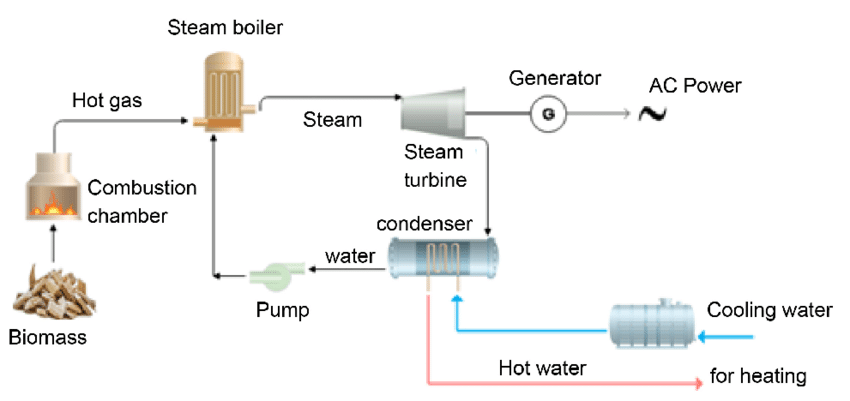
The utilization of waste heat recovery for industrial power generation is revolutionizing energy efficiency in manufacturing and heavy industries. In traditional energy systems, a significant portion of heat produced during combustion or industrial processes is lost to the environment. However, with advanced waste heat recovery technologies, industries can capture this otherwise wasted thermal energy and convert it into useful power, reducing fuel consumption, lowering operational costs, and improving overall energy sustainability.
Waste heat recovery systems work by extracting excess heat from exhaust gases, steam systems, or hot process fluids and repurposing it for electricity generation or secondary industrial applications. This recovered heat can be used to drive steam turbines, organic Rankine cycle (ORC) generators, or combined heat and power (CHP) systems, maximizing the efficiency of industrial operations. Industries such as cement production, steel manufacturing, petrochemicals, and glassmaking, which produce large amounts of high-temperature waste heat, are particularly well-suited for these systems.
One of the key benefits of waste heat recovery is its potential to reduce energy costs. By utilizing waste heat for on-site electricity generation, industries can decrease their reliance on external power sources, mitigating the impact of rising energy prices and improving energy security. Additionally, waste heat recovery enhances fuel efficiency, allowing industrial plants to extract more value from the same energy input while reducing the need for additional fuel purchases.
Beyond cost savings, waste heat recovery plays a crucial role in reducing greenhouse gas emissions and improving environmental sustainability. Since the recovered heat is used to generate electricity or thermal energy without burning additional fuel, carbon dioxide (CO₂) and other pollutant emissions are significantly reduced. Many industries are integrating waste heat recovery as part of their decarbonization strategies, aligning with global climate goals and regulatory requirements for lower emissions. Some companies are also monetizing carbon savings through emissions trading programs, further incentivizing the adoption of these technologies.
Recent advancements in waste heat recovery technologies have expanded their applicability across a wider range of industries. Innovations in heat exchanger design, high-efficiency turbines, and thermal storage solutions allow for more effective energy capture and conversion. Additionally, the development of ORC systems has made it possible to recover low- and medium-temperature waste heat that was previously considered unusable. These improvements are driving greater adoption of waste heat recovery solutions in sectors where implementation was once considered technically challenging or economically unviable.
Government policies and incentives are also playing a major role in accelerating the adoption of waste heat recovery. Many countries offer tax credits, grants, and subsidies to industries that invest in energy efficiency technologies, including waste heat recovery systems. In some regions, regulations mandate the use of waste heat recovery in new industrial facilities, particularly in energy-intensive sectors. These policy measures help offset the initial investment costs and encourage industries to prioritize energy efficiency in their long-term strategies.
The integration of waste heat recovery with industrial microgrids and distributed energy systems is another emerging trend. By combining waste heat recovery with cogeneration, renewable energy sources, and smart grid technologies, industries can create self-sustaining energy ecosystems that maximize efficiency and resilience. Waste heat recovery-based microgrids offer significant advantages, particularly in remote locations where grid electricity is unreliable or expensive.
Looking ahead, the future of industrial power generation will increasingly depend on innovative waste heat recovery solutions. The combination of waste heat recovery with cutting-edge energy storage systems, hydrogen production, and carbon capture technologies will further enhance energy efficiency and sustainability. As industries strive to meet stricter environmental regulations and reduce their carbon footprint, waste heat recovery will remain a cornerstone of industrial energy optimization.
In the long run, businesses that invest in waste heat recovery will gain a competitive edge by lowering energy costs, improving operational efficiency, and achieving sustainability targets. As technology continues to evolve, waste heat recovery will play an even greater role in the transition toward cleaner, more efficient industrial power generation, ensuring that industries can meet growing energy demands while minimizing environmental impact.
The continued advancement of waste heat recovery technologies is driving a fundamental shift in industrial energy management, enabling factories and large-scale manufacturing plants to optimize their operations while reducing their carbon footprint. With growing pressure to enhance energy efficiency and comply with stricter environmental regulations, industries are increasingly turning to waste heat recovery systems as a key solution to improve sustainability without compromising productivity.
One of the most significant advantages of waste heat recovery is its ability to transform previously discarded thermal energy into a valuable power source. In many industrial processes, such as metal smelting, refining, and cement production, a substantial portion of input energy is lost as heat through exhaust gases, cooling systems, and production lines. By capturing and repurposing this waste heat, industries can significantly improve overall energy efficiency, often achieving efficiency levels exceeding 80%.
Waste heat can be recovered through various methods, depending on temperature levels and industrial applications. High-temperature waste heat, typically above 500°C, can be used to generate steam for turbines or drive mechanical systems. Medium- and low-temperature waste heat, often found in exhaust air or cooling water, can be utilized through organic Rankine cycle (ORC) systems, thermoelectric generators, or absorption chillers to produce additional electricity or provide heating and cooling for industrial facilities.
The financial benefits of waste heat recovery are also a major driver of its adoption. Industries that implement these systems can lower their overall energy expenses by reducing the need for purchased electricity and fossil fuels. Additionally, in locations with deregulated energy markets, companies can sell excess electricity generated from waste heat recovery back to the grid, creating a new revenue stream. This not only offsets initial investment costs but also improves the long-term profitability of industrial operations.
As industries work toward decarbonization, waste heat recovery is playing an increasingly critical role in helping businesses meet sustainability goals. By reducing energy waste, these systems contribute to lower greenhouse gas emissions and improved overall energy efficiency. In many cases, industrial facilities that adopt waste heat recovery systems become eligible for carbon credits, government incentives, or tax breaks, further enhancing their financial viability.
Emerging innovations in waste heat recovery are also expanding its potential applications. New developments in advanced heat exchangers, phase-change materials for thermal storage, and AI-driven energy management systems are making waste heat recovery more efficient and accessible across a wider range of industries. Additionally, the combination of waste heat recovery with renewable energy sources, such as solar and biomass, is enabling industries to create hybrid energy systems that maximize reliability and sustainability.
Industrial sectors with high energy consumption, such as steel manufacturing, chemical processing, and power generation, stand to benefit the most from integrating waste heat recovery into their operations. By adopting these technologies, companies can not only improve operational efficiency and reduce costs but also enhance their corporate reputation as leaders in energy sustainability. In an increasingly competitive global market, the ability to operate efficiently while minimizing environmental impact provides a significant strategic advantage.
As regulatory frameworks continue to evolve, waste heat recovery is expected to become a standard component of industrial energy systems. Governments worldwide are recognizing the economic and environmental benefits of these systems, leading to increased policy support and financial incentives for companies that invest in energy-efficient technologies. The future of industrial power generation will increasingly rely on waste heat recovery as a core strategy for reducing energy consumption and enhancing industrial sustainability.
Looking forward, waste heat recovery will remain a crucial enabler of industrial energy transition. With continued technological improvements and greater adoption across industries, these systems will play a vital role in shaping a cleaner, more efficient industrial sector. Businesses that invest in waste heat recovery today will be better positioned to navigate future energy challenges, ensuring long-term cost savings, regulatory compliance, and environmental responsibility.
The future of industrial energy management is becoming increasingly dependent on waste heat recovery as industries strive for greater efficiency, cost savings, and environmental responsibility. With rising energy costs and stricter emissions regulations, companies are recognizing the importance of maximizing every unit of energy consumed in their operations. Waste heat recovery systems not only improve energy efficiency but also contribute to sustainability efforts by reducing fuel consumption and lowering greenhouse gas emissions.
One of the key factors driving the expansion of waste heat recovery is its ability to provide a reliable and continuous source of energy. Unlike intermittent renewable sources such as wind or solar, waste heat recovery utilizes excess thermal energy already produced during industrial processes, ensuring a steady supply of power and heat. This makes it a particularly attractive option for industries that require stable and predictable energy output, such as steel manufacturing, chemical processing, and oil refining.
Recent innovations in waste heat recovery technologies are further enhancing its viability across different sectors. Advanced heat exchangers, for example, allow for more efficient transfer of thermal energy, enabling industries to capture and utilize even low-grade waste heat that was previously difficult to recover. Additionally, developments in organic Rankine cycle (ORC) systems have made it possible to generate electricity from lower-temperature heat sources, expanding the range of industries that can benefit from waste heat recovery.
Energy storage solutions are also playing an increasingly important role in optimizing waste heat recovery systems. By integrating thermal energy storage, companies can store excess recovered heat and use it during peak demand periods, improving overall system efficiency and reducing reliance on external energy sources. This is particularly valuable for facilities that experience fluctuating energy demands throughout the day or operate in regions with time-of-use electricity pricing.
The economic benefits of waste heat recovery continue to be a major incentive for industrial adoption. By reducing energy costs and improving overall efficiency, these systems offer a strong return on investment, often with payback periods of just a few years. Many companies are also leveraging financial incentives, including government grants, tax credits, and carbon offset programs, to further improve the financial feasibility of implementing waste heat recovery. In some cases, industries are even able to sell excess electricity generated through waste heat recovery back to the grid, creating an additional revenue stream.
Beyond individual industrial facilities, waste heat recovery is also gaining traction in district energy systems and industrial clusters. By sharing recovered heat among multiple users, such as factories, commercial buildings, and residential developments, these systems maximize efficiency and reduce overall energy consumption. In urban areas, district heating networks powered by waste heat recovery are helping cities transition toward more sustainable and low-carbon energy solutions.
As industries look to the future, the role of waste heat recovery in meeting sustainability targets will only become more critical. Many companies have set ambitious goals for reducing their carbon footprint, and waste heat recovery provides a practical and cost-effective way to achieve these objectives. By incorporating waste heat recovery into their energy strategies, industries can position themselves as leaders in environmental responsibility while simultaneously improving operational efficiency.
Ultimately, waste heat recovery is not just a technological advancement—it is a fundamental shift in how industries approach energy consumption. As more companies recognize the long-term benefits of maximizing energy efficiency, waste heat recovery will continue to play a pivotal role in shaping the industrial energy landscape. By embracing these solutions today, industries can secure a more sustainable, cost-effective, and resilient energy future.
As industries continue to innovate and optimize their energy strategies, waste heat recovery is becoming an integral part of a more sustainable and cost-effective approach to power generation. The growing emphasis on circular economy principles—where resources are reused, repurposed, and optimized—has placed waste heat recovery at the forefront of industrial energy management. Companies that embrace this technology are not only reducing costs but also strengthening their long-term energy security and competitiveness in an increasingly carbon-conscious market.
One of the most transformative aspects of waste heat recovery is its ability to integrate with other energy solutions, creating highly efficient and resilient industrial power systems. By combining waste heat recovery with cogeneration, industries can maximize their energy output from a single fuel source, reducing waste and increasing overall efficiency. This synergy is particularly valuable in sectors that require both electricity and process heat, such as food processing, pulp and paper manufacturing, and petrochemical industries.
Advancements in digital technology are further improving the efficiency and reliability of waste heat recovery systems. Smart sensors, predictive analytics, and AI-driven optimization tools enable industries to monitor and fine-tune their waste heat recovery processes in real time. By detecting inefficiencies, predicting maintenance needs, and adjusting energy flows dynamically, these digital tools help companies extract maximum value from their recovered heat while minimizing downtime and operational disruptions.
The role of waste heat recovery in decarbonization is also expanding beyond traditional industrial applications. Emerging innovations, such as thermoelectric generators and solid-state heat recovery systems, are opening up new possibilities for capturing and converting waste heat in previously untapped areas. Industries that were once unable to benefit from conventional heat recovery technologies due to process constraints or lower temperature waste heat are now finding new ways to harness energy that would otherwise be lost.
At a broader level, waste heat recovery is contributing to national and global energy transition goals. Governments and regulatory bodies are increasingly supporting waste heat recovery projects through policy incentives, funding programs, and carbon pricing mechanisms. Many countries have incorporated industrial waste heat recovery into their energy efficiency roadmaps, recognizing its potential to reduce overall energy demand and support the transition to cleaner power generation.
Collaboration between industries, technology providers, and policymakers is playing a critical role in accelerating the adoption of waste heat recovery solutions. As more companies share best practices, pilot new technologies, and invest in large-scale waste heat utilization projects, the knowledge base surrounding effective implementation continues to grow. Industry-wide efforts to standardize and improve waste heat recovery solutions are also helping to drive down costs, making the technology more accessible to businesses of all sizes.
Looking ahead, the integration of waste heat recovery with next-generation energy storage, hydrogen production, and carbon capture technologies will further enhance its value in industrial decarbonization efforts. By leveraging these complementary technologies, industries can create flexible, low-carbon energy systems that support both their operational needs and broader sustainability commitments.
Ultimately, the industries that prioritize waste heat recovery today will be the ones best positioned for success in the evolving energy landscape. As global energy markets shift toward greater efficiency, sustainability, and resilience, waste heat recovery will continue to be a critical enabler of industrial innovation. By turning waste into a valuable energy resource, businesses can not only reduce costs and emissions but also build a more secure and sustainable energy future for the long term.
Steam Turbines Drive Industrial Power Plants
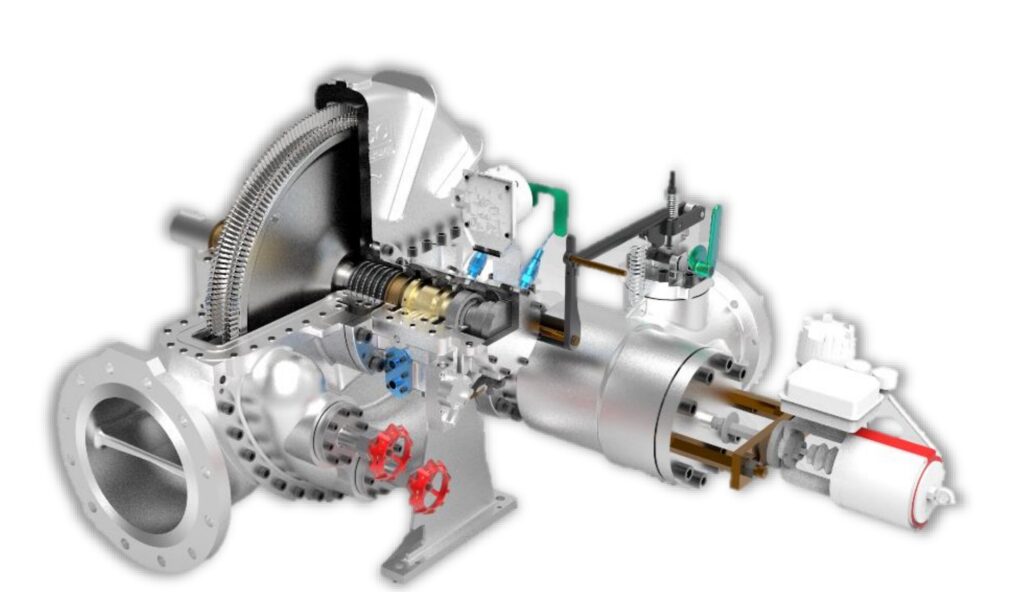
Steam turbines play a crucial role in powering industrial plants, providing reliable and efficient energy for a wide range of manufacturing and production processes. As one of the most established and effective methods of power generation, steam turbines convert thermal energy from high-pressure steam into mechanical power, which is then used to drive generators that produce electricity. This process is fundamental to industries that require continuous, large-scale energy output, such as steel manufacturing, petrochemical processing, paper mills, and power generation facilities.
The efficiency and reliability of steam turbines make them a preferred choice for industrial power plants. Unlike intermittent renewable sources, steam turbines provide consistent power output, ensuring stable operations even in high-demand industrial settings. By utilizing high-pressure steam from boilers or waste heat recovery systems, steam turbines maximize energy efficiency and reduce dependency on fossil fuel-based electricity grids.
One of the key advantages of steam turbines is their ability to integrate with combined heat and power (CHP) systems, also known as cogeneration. In these setups, steam turbines not only generate electricity but also provide thermal energy for industrial processes, space heating, or even district heating. This dual-purpose energy utilization significantly enhances efficiency, allowing industries to achieve overall system efficiencies of 80% or higher. Cogeneration with steam turbines reduces fuel consumption, lowers operational costs, and minimizes environmental impact by optimizing energy use.
Waste heat recovery is another critical application of steam turbines in industrial power plants. Many manufacturing processes release high-temperature waste heat, which can be captured and repurposed to produce steam for turbine-driven power generation. By implementing waste heat recovery steam turbines, industries can reduce energy waste, improve overall plant efficiency, and decrease greenhouse gas emissions. This is particularly beneficial in energy-intensive sectors such as cement production, refineries, and chemical plants, where significant amounts of heat are generated as a byproduct.
Steam turbines also offer flexibility in fuel sources, making them a versatile solution for industrial power generation. They can operate using a variety of fuels, including natural gas, coal, biomass, and even geothermal or solar thermal energy. This adaptability allows industries to optimize their energy strategies based on fuel availability, cost considerations, and sustainability goals. Many companies are increasingly incorporating biomass and renewable fuels into their steam turbine systems to reduce their carbon footprint and comply with stringent environmental regulations.
The durability and long operational lifespan of steam turbines further contribute to their widespread use in industrial power plants. With proper maintenance, steam turbines can operate efficiently for decades, providing industries with a stable and cost-effective power generation solution. Modern advancements in turbine design, materials, and digital monitoring technologies have further improved their reliability, allowing for predictive maintenance, real-time performance optimization, and reduced downtime.
As industrial facilities seek to enhance energy efficiency and reduce environmental impact, steam turbines remain at the forefront of industrial power solutions. With ongoing innovations in turbine technology, waste heat recovery, and fuel flexibility, these systems will continue to play a vital role in powering industries worldwide. By investing in high-efficiency steam turbines, industrial plants can achieve long-term energy savings, operational stability, and environmental sustainability, ensuring a competitive advantage in an increasingly energy-conscious global market.
As industries continue to expand and modernize, steam turbines remain a cornerstone of industrial power generation, offering an unparalleled combination of efficiency, reliability, and adaptability. Their ability to operate at high efficiencies while maintaining stable power output makes them a crucial asset for industries that require uninterrupted energy supply. With the rising demand for sustainable and cost-effective energy solutions, steam turbines are evolving to meet new challenges, incorporating advanced materials, digital monitoring, and integration with renewable energy sources to further enhance their performance.
One of the major benefits of steam turbines in industrial power plants is their scalability. These turbines can be customized to match the specific energy requirements of different industrial applications, ranging from small cogeneration plants to large utility-scale installations. This flexibility allows industries to optimize their power generation systems according to their operational needs, ensuring maximum energy efficiency and cost-effectiveness.
Moreover, the ability of steam turbines to operate in both back-pressure and condensing configurations provides industries with greater control over their energy utilization. Back-pressure steam turbines are commonly used in cogeneration applications where the exhaust steam is utilized for heating or other industrial processes, improving overall energy efficiency. In contrast, condensing steam turbines are designed to maximize electricity generation by condensing the exhaust steam into water, achieving higher power output. Depending on the specific requirements of a facility, industries can choose the most suitable steam turbine configuration to optimize their energy usage.
Recent advancements in steam turbine technology have also contributed to improved efficiency and reduced emissions. The development of high-performance turbine blades, advanced sealing mechanisms, and optimized steam path designs have significantly enhanced the efficiency of modern steam turbines. Additionally, the integration of digital control systems and real-time monitoring has enabled industries to detect potential performance issues early, reducing maintenance costs and improving overall reliability. Predictive maintenance, powered by artificial intelligence and machine learning, is now being widely adopted to ensure optimal turbine operation while minimizing downtime.
The growing emphasis on sustainable energy solutions has further increased the adoption of steam turbines in industrial power plants. Many facilities are transitioning toward renewable and low-carbon energy sources, such as biomass, geothermal, and solar thermal energy, to power their steam turbines. By utilizing these sustainable energy sources, industries can reduce their carbon footprint while maintaining reliable power generation. In biomass power plants, for example, steam turbines convert heat from burning organic waste materials into electricity, offering an environmentally friendly alternative to fossil fuels.
Industries are also exploring hybrid energy systems that combine steam turbines with other forms of power generation, such as gas turbines and energy storage technologies. By integrating multiple energy sources, industrial plants can enhance grid stability, improve energy security, and reduce reliance on traditional fossil fuel-based power generation. The ability of steam turbines to seamlessly operate in conjunction with other energy systems makes them a valuable component of modern industrial power solutions.
As global energy demand continues to rise, the role of steam turbines in industrial power generation is expected to grow even further. Governments and regulatory bodies are increasingly promoting energy-efficient technologies and incentivizing industries to adopt cleaner and more sustainable power solutions. With continued advancements in turbine efficiency, digitalization, and fuel flexibility, steam turbines will remain a key driver of industrial power plants, ensuring long-term energy stability, economic growth, and environmental sustainability.
The evolution of steam turbines in industrial power plants is driven by the need for greater efficiency, lower emissions, and enhanced reliability. As industries strive to optimize their energy consumption, steam turbines are being integrated with advanced technologies that improve performance and reduce operational costs. These improvements make steam turbines an indispensable component of modern industrial energy systems, supporting everything from heavy manufacturing and petrochemical processing to large-scale district heating and combined-cycle power plants.
One of the most significant developments in steam turbine technology is the advancement of high-efficiency materials and coatings. Modern steam turbines utilize high-performance alloys and thermal barrier coatings to withstand extreme temperatures and pressures, reducing wear and extending operational lifespans. These innovations allow turbines to operate at higher efficiencies, converting more steam energy into mechanical work while minimizing energy losses.
Additionally, the implementation of supercritical and ultra-supercritical steam turbines is further improving efficiency in industrial power generation. These turbines operate at extremely high temperatures and pressures, enabling them to achieve greater thermodynamic efficiency compared to conventional steam turbines. By reducing fuel consumption per unit of electricity generated, these advanced turbines help industries lower their operating costs and carbon emissions.
Digitalization and automation are also playing a crucial role in enhancing the performance of steam turbines. The integration of smart sensors, cloud-based monitoring, and predictive analytics enables real-time performance tracking, allowing operators to detect inefficiencies and potential failures before they lead to costly downtime. With AI-driven optimization tools, steam turbines can dynamically adjust operating parameters to maximize output and efficiency under varying load conditions.
Waste heat recovery systems are increasingly being paired with steam turbines to maximize energy utilization in industrial settings. Many industries, such as steel mills, cement plants, and refineries, generate substantial amounts of excess heat that would otherwise be wasted. By capturing this heat and using it to produce steam, steam turbines can convert it into additional electricity, significantly improving overall plant efficiency. This approach not only reduces the need for external energy sources but also lowers greenhouse gas emissions, aligning with global sustainability goals.
Another key trend in industrial power generation is the growing use of renewable energy sources to drive steam turbines. Biomass-fired steam turbines, for example, utilize agricultural residues, wood chips, and other organic waste as fuel, offering a carbon-neutral alternative to fossil fuels. Geothermal steam turbines harness underground heat sources, providing continuous and renewable energy for industrial applications. Additionally, solar thermal power plants use concentrated solar energy to produce steam, which can then be used in steam turbines for electricity generation.
Hybrid power systems that combine steam turbines with other generation technologies, such as gas turbines or energy storage, are also becoming more common. These integrated systems offer greater flexibility, enabling industrial plants to balance fluctuating energy demands and improve grid stability. In combined-cycle power plants, steam turbines work alongside gas turbines to maximize energy extraction from fuel, significantly increasing overall plant efficiency.
With the rising emphasis on sustainability and energy efficiency, steam turbines are being designed to meet stricter environmental regulations. Advanced emission control technologies, such as carbon capture and storage (CCS) systems, are being implemented in steam turbine power plants to reduce CO₂ emissions. These technologies help industries comply with international climate policies while maintaining high levels of power generation efficiency.
As the industrial sector continues to evolve, steam turbines will remain a key driver of energy production, adapting to new challenges and technological advancements. Their ability to deliver stable, high-efficiency power across a range of fuel sources and operational configurations ensures their continued relevance in the future of industrial energy. By investing in modern steam turbine technologies and integrating them with sustainable energy solutions, industries can achieve long-term economic and environmental benefits, securing a more resilient and efficient power infrastructure.
Looking ahead, the role of steam turbines in industrial power generation will continue to expand as industries seek reliable and efficient energy solutions in an increasingly sustainability-focused world. With ongoing advancements in turbine technology, digitalization, and fuel diversification, steam turbines will remain a vital component of industrial power plants, ensuring energy security while reducing environmental impact.
The integration of smart grid technology and energy management systems is further enhancing the capabilities of steam turbines in industrial settings. By connecting turbines to intelligent monitoring platforms, industries can optimize power distribution, balance energy loads, and improve grid stability. These digital tools allow for more precise control over power generation and consumption, leading to reduced energy waste and lower operational costs.
Industries are also exploring the potential of hydrogen as a future fuel source for steam turbines. As hydrogen production technologies advance, steam turbines could be adapted to utilize hydrogen as a clean and sustainable energy source, further reducing their carbon footprint. Hydrogen-based power generation offers a promising alternative to conventional fossil fuels, providing industries with a path toward carbon-neutral energy production.
Moreover, modular and decentralized steam turbine systems are emerging as a viable solution for industries looking to enhance energy independence. Small and medium-sized industrial facilities can benefit from compact steam turbine systems designed for on-site power generation, reducing reliance on external power grids and mitigating the risks associated with grid instability. These decentralized energy solutions are particularly valuable in remote or off-grid industrial operations, where access to reliable electricity is essential for continuous production.
In addition to fuel flexibility and digital integration, future advancements in steam turbine efficiency will be driven by material innovations. Researchers are developing next-generation materials with enhanced thermal resistance and lower maintenance requirements, allowing turbines to operate at even higher temperatures and pressures without compromising durability. These improvements will further increase turbine efficiency, making them even more cost-effective for industrial applications.
As global energy policies continue to prioritize carbon reduction and energy efficiency, steam turbines will play a crucial role in helping industries meet regulatory requirements while maintaining operational efficiency. Governments and energy agencies are incentivizing the adoption of high-efficiency steam turbines and waste heat recovery systems through tax credits, grants, and subsidies, making it easier for industries to invest in sustainable energy infrastructure.
In the coming decades, the industrial power sector will likely see an even greater emphasis on hybrid energy systems, where steam turbines work in synergy with renewable energy sources and advanced storage technologies. By combining steam turbines with solar thermal, wind, and battery storage solutions, industries can create highly resilient and adaptable power systems capable of meeting fluctuating energy demands while reducing overall emissions.
Ultimately, steam turbines will continue to be a cornerstone of industrial power generation, evolving to meet the changing energy landscape. Their ability to provide stable, high-efficiency power, integrate with new technologies, and adapt to cleaner fuel sources ensures their ongoing relevance. As industries transition toward a more sustainable and efficient energy future, steam turbines will remain at the forefront of innovation, driving industrial growth while contributing to global decarbonization efforts.
Factories Generate Electricity On-site
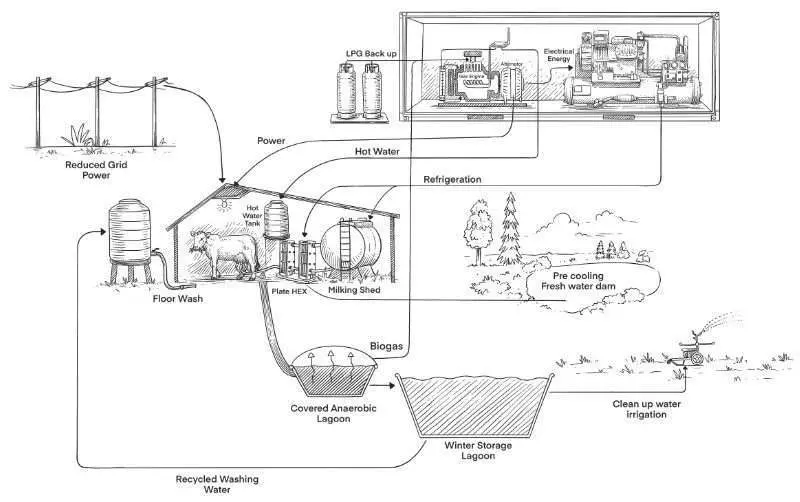
Factories are increasingly turning to on-site power generation to meet their energy demands efficiently and cost-effectively. By producing electricity on-site, industrial facilities can reduce reliance on external power grids, lower operational costs, and improve energy security. Steam turbines play a central role in this shift, enabling factories to generate their own power while optimizing energy utilization through combined heat and power (CHP) systems.
One of the key advantages of on-site power generation is improved energy efficiency. Traditional power plants often experience energy losses during electricity transmission, but generating power within the facility eliminates these inefficiencies. Steam turbines, when integrated with industrial boilers or waste heat recovery systems, allow factories to convert thermal energy into electricity with minimal waste. This setup is particularly beneficial for industries with high energy demands, such as chemical processing, steel production, cement manufacturing, and food processing.
Many industrial facilities use cogeneration, or CHP, to maximize the value of their fuel input. In a CHP system, steam turbines generate electricity while capturing and repurposing the excess heat for industrial processes, space heating, or cooling. This dual-purpose approach can achieve efficiency levels of 80% or higher, significantly reducing energy waste and lowering carbon emissions. By harnessing both electricity and useful heat from a single energy source, factories can optimize their overall energy performance.
Another driving force behind on-site power generation is the ability to utilize diverse fuel sources. Steam turbines can run on various fuels, including natural gas, biomass, waste heat, and even renewable sources like geothermal energy. Many industries are now investing in biomass-fueled steam turbines, using wood chips, agricultural waste, and other organic materials to generate electricity in a sustainable manner. This approach not only reduces dependence on fossil fuels but also helps industries comply with environmental regulations and sustainability goals.
Factories with on-site power generation also benefit from increased operational reliability. Power outages and grid failures can be costly for industrial operations, leading to production downtime and financial losses. By producing electricity on-site, factories can maintain a steady power supply, ensuring uninterrupted production even in the event of external grid disruptions. Additionally, modern steam turbine systems are designed with redundancy and backup power capabilities, further enhancing reliability.
The financial benefits of on-site power generation are also significant. By reducing electricity purchases from the grid, factories can lower their energy expenses and protect themselves from fluctuating electricity prices. In many cases, government incentives and tax credits are available to support industries in adopting energy-efficient power generation technologies, making on-site power solutions even more attractive.
Moreover, advancements in digital monitoring and predictive maintenance have made steam turbines more efficient and easier to manage. Smart sensors and AI-driven analytics allow factory operators to track turbine performance in real-time, optimize energy output, and detect potential maintenance issues before they lead to costly breakdowns. This proactive approach to maintenance extends the lifespan of steam turbines and ensures consistent power generation.
As industries continue to prioritize sustainability and cost savings, on-site power generation with steam turbines will play an increasingly important role. The ability to generate reliable, efficient, and low-emission electricity directly within industrial facilities makes steam turbines a key solution for the future of industrial energy. By investing in modern turbine technology and integrating it with waste heat recovery and renewable energy sources, factories can achieve long-term energy independence, cost stability, and environmental responsibility.
The trend toward on-site power generation is accelerating as industries recognize the advantages of energy independence, efficiency, and sustainability. Steam turbines are at the forefront of this transformation, enabling factories to optimize energy usage while reducing their environmental footprint. By leveraging advanced turbine technology and integrating with modern energy management systems, factories can ensure a continuous and cost-effective power supply.
One of the most compelling reasons for on-site power generation is its ability to enhance overall energy efficiency. When electricity is generated at a remote power plant, significant energy losses occur during transmission and distribution. However, by producing power on-site, factories eliminate these losses and make full use of the energy produced. When combined with waste heat recovery or cogeneration systems, steam turbines can boost efficiency levels far beyond what traditional grid-based power sources can achieve.
Industries with high thermal energy demands particularly benefit from steam turbines, as they allow for seamless integration with industrial processes. Refineries, petrochemical plants, and pulp and paper mills, for example, generate large amounts of heat during production. Rather than letting this heat dissipate as waste, these facilities can channel it into steam turbines to generate electricity. This closed-loop system improves overall plant efficiency and reduces reliance on external energy sources.
Fuel flexibility is another critical advantage of steam turbines in on-site power generation. Factories can choose from a wide range of fuels, including natural gas, coal, biomass, and even waste-derived fuels. Many industries are shifting toward cleaner energy sources, such as biomass and renewable natural gas, to power their steam turbines while minimizing their carbon footprint. By adopting low-emission or carbon-neutral fuel sources, factories can align their power generation strategies with sustainability initiatives and regulatory requirements.
The financial incentives for on-site power generation are also significant. Factories that generate their own electricity can reduce or eliminate their dependence on expensive grid-supplied power, leading to substantial cost savings. Additionally, industries that produce excess power may have the opportunity to sell surplus electricity back to the grid, creating an additional revenue stream. Government policies and incentives further support the transition to on-site power generation, offering grants, tax benefits, and funding programs for energy-efficient technologies.
Reliability is another major factor driving the adoption of on-site power generation. In industries where power interruptions can result in costly downtime, maintaining a stable and uninterrupted electricity supply is crucial. Steam turbines provide a dependable power source that can operate independently of external grids, ensuring that critical industrial processes continue without disruption. Modern turbines are also designed with redundancy features, allowing for continuous operation even in the event of maintenance or system failures.
Technological advancements are making steam turbines even more effective and easier to manage. Digitalization and automation are transforming the way turbines are operated and maintained. Smart sensors, real-time monitoring, and predictive maintenance software enable factory operators to track performance, optimize output, and identify maintenance needs before issues arise. These tools help minimize downtime, extend equipment lifespan, and improve overall plant efficiency.
As industries continue to prioritize sustainability, cost efficiency, and energy security, on-site power generation with steam turbines will play an increasingly vital role. By investing in advanced steam turbine systems, integrating them with waste heat recovery, and adopting renewable fuel sources, factories can create self-sufficient energy solutions that reduce costs and improve environmental performance. The future of industrial power generation lies in decentralized, efficient, and adaptable energy systems, with steam turbines leading the way in providing reliable and sustainable electricity for factories worldwide.
As industries embrace on-site power generation, steam turbines are becoming an integral part of their energy strategies, ensuring efficiency, cost savings, and sustainability. The shift toward self-sufficient energy systems is driven by the need to reduce dependence on external power grids, lower operational expenses, and meet increasingly stringent environmental regulations. With continuous technological advancements, steam turbines are enabling factories to optimize energy usage while enhancing overall productivity and competitiveness.
One of the key benefits of steam turbines in industrial power generation is their adaptability to different energy sources. Unlike many other power generation technologies, steam turbines can operate on a diverse range of fuels, including natural gas, biomass, hydrogen, and even waste-derived fuels. This flexibility allows industries to select the most cost-effective and sustainable energy sources based on availability and economic feasibility. For example, facilities with access to biomass resources can use agricultural residues or wood waste to fuel their turbines, significantly reducing their carbon footprint while generating reliable power.
The ability to integrate with waste heat recovery systems further enhances the efficiency of steam turbines in industrial settings. Many factories generate excess heat as a byproduct of their manufacturing processes. Instead of allowing this heat to dissipate, it can be captured and converted into steam, which then drives a turbine to produce electricity. This combined heat and power (CHP) approach maximizes the use of available energy, reducing overall fuel consumption and improving cost efficiency. CHP systems can achieve efficiency levels of 80% or higher, far exceeding those of conventional power generation methods.
Economic incentives are also playing a crucial role in the adoption of steam turbines for on-site power generation. Many governments and energy regulatory bodies offer financial support, including tax credits, grants, and subsidies, to encourage industries to invest in energy-efficient and low-emission technologies. Factories that implement steam turbine-based power generation not only benefit from lower electricity costs but may also qualify for incentives that improve the return on investment.
Additionally, industries with steam turbine systems often experience increased energy security and reliability. Grid outages and supply disruptions can pose significant risks to industrial operations, leading to production downtime and financial losses. By generating power on-site, factories can mitigate these risks and maintain uninterrupted operations. Advanced steam turbine designs include redundancy features and automated controls, further enhancing reliability and ensuring stable power output even under fluctuating demand conditions.
The digitalization of steam turbine operations is another major advancement improving their effectiveness in industrial applications. Smart sensors, real-time data analytics, and AI-driven maintenance systems allow factory operators to monitor turbine performance with precision. Predictive maintenance technology helps identify potential issues before they result in breakdowns, reducing downtime and maintenance costs. Automated control systems enable dynamic adjustments based on energy demand, optimizing efficiency while reducing waste.
As the push for sustainable energy solutions intensifies, industries are also exploring the potential of hybrid power systems that combine steam turbines with renewable energy sources. For example, solar thermal plants can generate steam from concentrated solar energy, which can then be used to drive turbines. Similarly, hydrogen-powered steam turbines are being researched as a future carbon-neutral alternative. By integrating these technologies, industries can create a diversified and resilient power infrastructure that meets both economic and environmental goals.
Looking ahead, steam turbines will remain a cornerstone of industrial power generation, evolving alongside emerging energy technologies. With their proven efficiency, fuel flexibility, and ability to integrate with sustainable energy solutions, steam turbines will continue to support industrial growth while contributing to global efforts to reduce greenhouse gas emissions. As industries invest in cleaner, smarter, and more efficient energy systems, steam turbines will play a central role in shaping the future of industrial power generation.
The continued evolution of steam turbine technology is shaping the future of industrial power generation, allowing factories to achieve greater energy independence, efficiency, and sustainability. As industries seek to optimize their power consumption, reduce costs, and lower emissions, steam turbines remain a reliable and adaptable solution. Their ability to integrate with waste heat recovery systems, utilize a wide range of fuels, and operate at high efficiency levels makes them a key component of modern industrial energy strategies.
One of the most promising developments in steam turbine applications is their increasing role in decarbonization efforts. With industries under pressure to reduce greenhouse gas emissions, many factories are turning to cleaner fuel sources such as biomass, hydrogen, and synthetic fuels. Biomass-fired steam turbines, for instance, offer a renewable energy solution that allows industries to generate power while utilizing agricultural and forestry waste. Additionally, as hydrogen production technologies advance, hydrogen-powered steam turbines could become a viable alternative to fossil-fuel-based power generation, providing a carbon-neutral energy option.
The rise of hybrid power generation systems is another trend reshaping the industrial energy landscape. Many factories are now combining steam turbines with renewable energy sources like solar thermal and geothermal energy. In solar thermal applications, concentrated solar power (CSP) plants generate steam using sunlight, which then drives a steam turbine to produce electricity. Geothermal steam turbines, on the other hand, harness heat from the Earth’s core, offering a consistent and renewable power source that operates independently of weather conditions. By integrating steam turbines with these renewable technologies, industries can create resilient, low-carbon power systems that enhance long-term sustainability.
Additionally, the digital transformation of industrial power generation is making steam turbines more efficient and easier to manage. Advanced control systems and predictive maintenance technologies are allowing industries to maximize uptime and optimize turbine performance. AI-driven analytics can process vast amounts of operational data in real time, identifying potential inefficiencies or maintenance needs before they lead to costly downtime. This level of automation and intelligence is improving turbine reliability, reducing maintenance costs, and increasing overall energy efficiency.
Industries are also benefiting from innovations in turbine materials and design. The development of high-performance alloys and coatings is enabling steam turbines to operate at higher temperatures and pressures, improving their efficiency while extending their operational lifespan. Advanced manufacturing techniques, such as 3D printing, are allowing for the production of more precise and durable turbine components, further enhancing performance and reliability. These technological advancements are making steam turbines an even more attractive option for industrial power generation.
Energy policies and regulatory frameworks are also playing a critical role in the widespread adoption of steam turbine technology for on-site power generation. Many governments are implementing stricter emissions regulations and offering financial incentives for industries that invest in energy-efficient and low-carbon technologies. By upgrading to high-efficiency steam turbines and integrating them with renewable and waste heat recovery systems, industries can not only comply with regulations but also take advantage of tax credits, subsidies, and other incentives that improve the return on investment.
Looking to the future, steam turbines will continue to be a crucial component of industrial power generation. Their ability to provide stable, high-efficiency power, integrate with new energy technologies, and adapt to cleaner fuel sources ensures their ongoing relevance. As industries transition toward more sustainable and resilient energy solutions, steam turbines will remain at the forefront of innovation, helping factories achieve energy security, cost savings, and environmental responsibility. With advancements in digitalization, materials, and hybrid energy systems, the role of steam turbines in industrial power generation will only continue to grow, driving efficiency and sustainability for decades to come.
Industrial Plants Produce Their Own Power
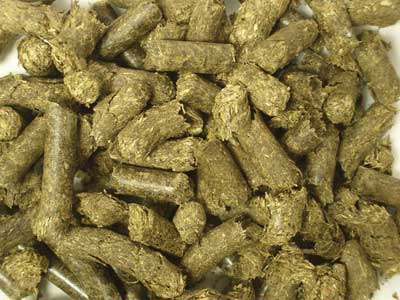
Industrial plants are increasingly producing their own power to reduce costs, improve energy security, and enhance efficiency. On-site power generation allows factories to minimize reliance on external grids, protect against power outages, and optimize energy usage through advanced technologies such as steam turbines and combined heat and power (CHP) systems.
Steam turbines are a key component of industrial power generation, enabling factories to convert thermal energy into electricity with high efficiency. Many industrial processes generate large amounts of waste heat, which can be captured and repurposed to produce steam. This steam drives turbines that generate electricity, allowing plants to make full use of their available energy resources. CHP systems take this a step further by utilizing both electricity and heat from a single energy source, achieving efficiency levels of up to 80% and significantly reducing overall energy waste.
Fuel flexibility is another major advantage of on-site power generation. Industrial plants can utilize a variety of fuels, including natural gas, coal, biomass, and even waste-derived fuels, depending on availability and cost considerations. Many facilities are transitioning to cleaner energy sources such as biomass and hydrogen to align with sustainability goals and reduce carbon emissions. Biomass-fueled steam turbines, for example, enable industries to generate power using wood chips, agricultural waste, or other organic materials, providing a renewable and cost-effective alternative to fossil fuels.
Energy independence is a crucial factor driving the shift toward self-generated power. Industrial operations require a stable and reliable electricity supply, and grid failures can result in costly production downtime. By generating power on-site, plants ensure continuous operations and avoid disruptions caused by external grid instability. Advanced steam turbine designs now include automation and redundancy features, allowing for uninterrupted power generation even in fluctuating demand conditions.
Economic benefits further support the move to on-site power generation. By reducing or eliminating reliance on purchased electricity, industrial plants can lower energy costs and gain protection from fluctuating utility prices. Additionally, some facilities generate excess electricity that can be sold back to the grid, creating an additional revenue stream. Governments and energy regulatory bodies also offer financial incentives, such as tax credits and grants, for industries that invest in energy-efficient power generation technologies, improving the return on investment.
Technological advancements are making steam turbine systems even more efficient and user-friendly. Digital monitoring, real-time analytics, and predictive maintenance systems allow plant operators to track turbine performance, optimize energy output, and identify potential maintenance needs before issues arise. AI-driven analytics and automation improve turbine efficiency while reducing downtime and operational costs.
The future of industrial power generation is increasingly focused on integrating steam turbines with renewable and hybrid energy systems. Solar thermal and geothermal power, for instance, can be used to generate steam, which in turn drives turbines to produce electricity. Hydrogen-powered steam turbines are also being explored as a carbon-neutral alternative for industrial power production. By combining these technologies, industrial plants can create resilient and sustainable power systems that align with long-term environmental and economic goals.
As industries continue to prioritize energy efficiency, sustainability, and cost reduction, on-site power generation with steam turbines will remain a vital solution. By investing in advanced turbine technologies, integrating waste heat recovery, and adopting renewable energy sources, industrial plants can ensure stable, efficient, and environmentally responsible power generation well into the future.
The adoption of on-site power generation in industrial plants is transforming the way factories manage their energy needs. Steam turbines, as a core component of this shift, provide a highly efficient means of generating electricity while utilizing available thermal energy. By implementing self-sufficient power systems, industries can significantly reduce their reliance on external electricity providers and increase overall operational stability.
One of the primary advantages of self-generated power is improved energy efficiency. Traditional electricity generation often involves significant energy losses during transmission from distant power plants to industrial sites. By producing electricity on-site, factories eliminate these transmission losses and can use energy more effectively. When combined with waste heat recovery or cogeneration systems, steam turbines can reach efficiency levels far greater than conventional power generation methods, maximizing the energy potential of fuels and industrial processes.
The ability to utilize diverse fuel sources further enhances the viability of on-site power generation. Industrial plants can choose from a variety of energy inputs, including natural gas, biomass, coal, and even hydrogen. This fuel flexibility allows plants to adapt to changing fuel costs and availability, ensuring long-term energy security. Many industries are also making a conscious shift toward low-carbon or carbon-neutral fuel sources to meet regulatory requirements and sustainability goals. Biomass-powered steam turbines, for example, enable industries to use organic waste materials to generate electricity while reducing greenhouse gas emissions.
Financial benefits are another driving force behind the growing use of on-site power generation. By producing electricity in-house, factories can reduce their energy expenses, especially in regions where grid power is expensive or unreliable. Additionally, companies that generate surplus power may have the opportunity to sell excess electricity back to the grid, turning their energy infrastructure into a potential revenue-generating asset. Government incentives and policy support for energy-efficient technologies further enhance the economic case for investing in steam turbine systems.
Reliability and resilience are critical considerations for industries that require continuous power supply. In sectors such as manufacturing, petrochemicals, and metal processing, even brief power disruptions can lead to production losses, equipment damage, and significant financial consequences. On-site power generation using steam turbines ensures a stable electricity supply, protecting businesses from grid failures, voltage fluctuations, and unforeseen power outages. Modern turbine systems incorporate redundancy features and automated controls, further improving their reliability and operational flexibility.
Technological advancements are also revolutionizing the way steam turbines are managed and operated. Digital monitoring systems equipped with smart sensors allow real-time tracking of turbine performance, optimizing energy efficiency and detecting potential maintenance needs before they become costly issues. Predictive maintenance tools, powered by artificial intelligence and machine learning, help factories extend the lifespan of their turbines while minimizing unplanned downtime. These innovations ensure that industrial plants can operate their on-site power systems with maximum efficiency and minimal maintenance costs.
Looking ahead, the role of steam turbines in industrial power generation will continue to expand. As factories seek to increase sustainability, reduce costs, and enhance energy security, steam turbines will remain a preferred solution for self-sufficient electricity production. The integration of steam turbines with renewable energy sources, such as solar thermal and geothermal systems, will further drive their adoption. Hydrogen-fueled steam turbines are also emerging as a promising future technology, offering a carbon-free alternative to traditional fossil fuels.
By embracing advanced steam turbine technology and on-site power generation, industrial plants can create a more sustainable, cost-effective, and resilient energy infrastructure. This shift not only benefits individual businesses but also contributes to broader energy efficiency and environmental sustainability goals, making industrial self-generated power a key component of the global transition toward cleaner and smarter energy solutions.
The shift toward on-site power generation is becoming a defining trend for industrial plants seeking greater energy efficiency, cost savings, and operational reliability. Steam turbines play a crucial role in this transition by converting thermal energy into electricity with high efficiency. As industries continue to embrace self-sufficient power solutions, steam turbines are being integrated with advanced technologies that optimize performance and sustainability.
One of the major advantages of steam turbines in industrial power generation is their ability to operate with various heat sources. Industrial plants generate significant amounts of waste heat from processes such as metal refining, chemical production, and manufacturing. Instead of allowing this thermal energy to dissipate, steam turbines can harness it to produce electricity, effectively turning waste into a valuable energy resource. This process, known as waste heat recovery, significantly improves overall energy efficiency while reducing fuel consumption and operating costs.
In addition to waste heat utilization, industrial plants are increasingly adopting cogeneration, or combined heat and power (CHP) systems, which maximize energy use by simultaneously generating electricity and useful thermal energy. CHP systems achieve efficiencies of up to 80%, far exceeding the efficiency of traditional grid-based power. This makes them an ideal solution for industries with high heat and power demands, such as food processing, pharmaceuticals, and paper production. By implementing steam turbine-based CHP systems, factories can reduce their dependence on external power suppliers while lowering emissions and overall energy expenses.
Fuel flexibility is another key benefit driving the adoption of steam turbines for industrial power generation. Unlike some energy systems that rely on a single fuel source, steam turbines can operate on a wide range of fuels, including natural gas, coal, biomass, and hydrogen. This adaptability allows industrial plants to choose the most cost-effective and sustainable fuel options based on availability and regulatory requirements. The transition to cleaner fuels, such as biomass and hydrogen, is further strengthening the case for steam turbines as industries aim to reduce their carbon footprint and comply with global emissions targets.
The financial benefits of on-site power generation extend beyond fuel savings. Industrial plants that generate their own electricity can protect themselves from fluctuating energy prices, reducing their exposure to market volatility. Additionally, in some regions, factories can sell excess power back to the grid, creating an additional revenue stream. Many governments also provide tax incentives, grants, and other financial support for industries that invest in energy-efficient and low-carbon technologies, further enhancing the return on investment for steam turbine-based power systems.
Ensuring a reliable and uninterrupted power supply is a top priority for industrial operations, where downtime can result in significant production losses. On-site power generation using steam turbines provides industries with greater control over their energy supply, reducing the risks associated with grid failures or unstable electricity sources. Advanced steam turbine designs now include automation and redundancy features that enhance reliability, ensuring continuous operations even under fluctuating demand conditions.
The integration of digital technology is further improving the efficiency and manageability of steam turbine systems. Real-time monitoring, AI-driven analytics, and predictive maintenance tools enable industrial plants to optimize turbine performance while minimizing unplanned outages. Smart sensors collect operational data, allowing maintenance teams to detect potential issues before they lead to breakdowns. This proactive approach to turbine management extends equipment lifespan and reduces maintenance costs, ensuring long-term reliability and efficiency.
Looking to the future, steam turbines will continue to play a central role in industrial power generation. Innovations in materials and turbine design are increasing efficiency and durability, while the development of hybrid energy systems is opening new opportunities for integrating steam turbines with renewable energy sources. Hydrogen-powered steam turbines, for example, are being explored as a zero-emission alternative to conventional fossil-fuel turbines. By leveraging these advancements, industries can create resilient, low-carbon power systems that align with sustainability goals and regulatory requirements.
As industries worldwide seek more reliable, cost-effective, and environmentally friendly energy solutions, on-site power generation with steam turbines will remain a preferred choice. With their efficiency, adaptability, and ability to integrate with cutting-edge energy technologies, steam turbines will continue to drive industrial power production, ensuring stable and sustainable energy supplies for the future.
Industrial Plants Produce Their Own Power
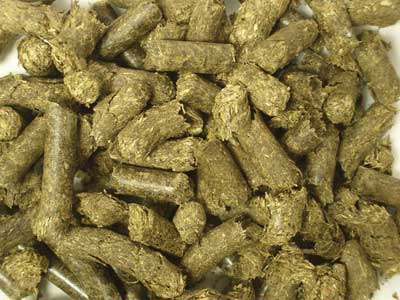
The continued adoption of on-site power generation with steam turbines is reshaping industrial energy strategies, allowing plants to achieve greater self-sufficiency while optimizing efficiency and sustainability. As industries move toward reducing operational costs and minimizing environmental impact, steam turbines offer a proven solution that balances reliability, performance, and flexibility.
One of the most compelling advantages of steam turbines is their ability to leverage multiple energy sources, including waste heat, fossil fuels, and renewable alternatives. In many industrial facilities, high-temperature processes release excess thermal energy that, if not captured, would be lost as waste. By integrating steam turbines with waste heat recovery systems, industries can reclaim this energy to generate electricity, effectively turning a byproduct of production into a valuable resource. This approach not only reduces fuel consumption but also enhances overall plant efficiency, making operations more sustainable and cost-effective.
The role of combined heat and power (CHP) systems in industrial power generation is also expanding. Steam turbines are a key component in CHP applications, where they efficiently generate both electricity and useful thermal energy. This dual-purpose functionality allows industries to achieve energy efficiency levels of up to 80%, compared to the 30–40% efficiency rates of conventional grid power. CHP systems are particularly beneficial in energy-intensive sectors such as chemicals, paper manufacturing, and food processing, where both heat and power are critical for production processes. By adopting steam turbine-driven CHP systems, these industries can enhance their energy resilience while significantly lowering greenhouse gas emissions.
Fuel flexibility remains an important consideration for industrial plants seeking long-term energy security. Steam turbines provide a versatile solution, capable of operating on a diverse range of fuels, from natural gas and coal to biomass and hydrogen. The increasing shift toward low-carbon and renewable fuels is further strengthening the role of steam turbines in industrial energy generation. Biomass-powered turbines, for example, enable plants to use organic materials such as agricultural waste and wood pellets, offering a renewable alternative to fossil fuels. Meanwhile, advancements in hydrogen combustion technology are paving the way for hydrogen-powered steam turbines, which promise a carbon-neutral energy source for the future.
Financial incentives and regulatory support are also contributing to the expansion of on-site power generation. Many governments are implementing policies that encourage industrial facilities to invest in high-efficiency, low-emission technologies. Tax incentives, grants, and subsidies are available for businesses that install CHP systems, waste heat recovery units, and renewable-energy-powered steam turbines. These financial benefits help offset initial capital costs and improve the overall return on investment for industrial power projects. Additionally, in some regions, surplus electricity generated by industrial plants can be sold back to the grid, creating an additional revenue stream and further improving economic viability.
Reliability is another crucial factor driving the adoption of steam turbines for on-site power generation. Industrial operations require a stable and uninterrupted power supply to maintain production efficiency and avoid costly downtime. Power disruptions, voltage fluctuations, or grid failures can have serious financial consequences for manufacturers. By generating electricity on-site, industries gain greater control over their energy supply, ensuring continuous operation even in the event of external power disturbances. Modern steam turbine systems incorporate automation, real-time monitoring, and redundant safety features that enhance their reliability and adaptability to fluctuating energy demands.
Advancements in digital technology are further optimizing the performance of steam turbine systems. Smart sensors, real-time analytics, and artificial intelligence (AI) are being integrated into turbine operations, allowing industries to monitor performance with greater accuracy and precision. Predictive maintenance systems use AI-driven diagnostics to detect potential issues before they result in failures, reducing downtime and extending turbine lifespan. By leveraging digitalization, industrial plants can maximize energy efficiency while minimizing maintenance costs and operational risks.
The future of steam turbines in industrial power generation will be shaped by continued innovation in materials, design, and integration with renewable energy sources. High-performance alloys and advanced coatings are improving turbine durability, enabling them to operate at higher temperatures and pressures with greater efficiency. The integration of steam turbines with hybrid energy systems—such as solar thermal, geothermal, and hydrogen energy—is also expanding their role in the global transition toward sustainable industrial power.
As industries seek to strengthen energy security, reduce costs, and achieve sustainability goals, steam turbines will remain a critical component of industrial power generation. Their efficiency, adaptability, and ability to integrate with advanced energy technologies ensure their continued relevance in the evolving energy landscape. By investing in self-sufficient power solutions, industrial plants can enhance their competitiveness, reduce environmental impact, and contribute to a more sustainable future for global energy production.
Efficient Electricity for Industrial Needs
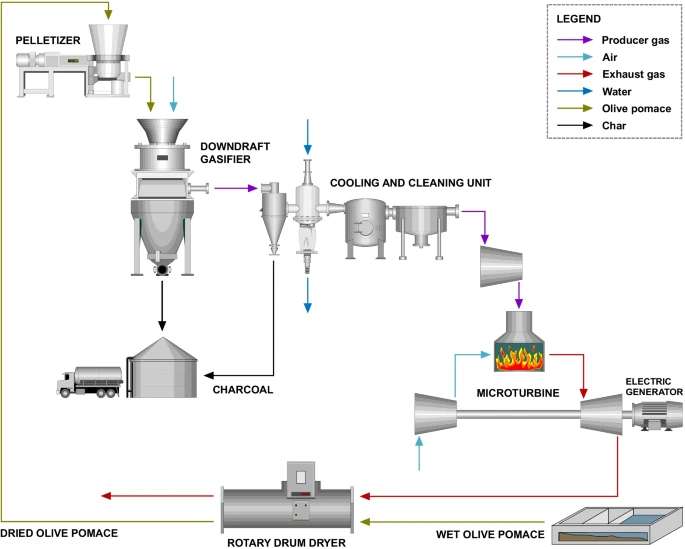
Industrial operations demand a reliable and efficient power supply to sustain continuous production, minimize operational costs, and meet sustainability goals. Steam turbines play a crucial role in addressing these needs by providing efficient and cost-effective electricity generation for a wide range of industrial applications. By leveraging advanced energy conversion technologies, industries can optimize their power consumption, reduce waste, and enhance overall productivity.
Steam turbines offer one of the highest efficiency rates among power generation technologies, especially when integrated with combined heat and power (CHP) or waste heat recovery systems. Traditional power generation often involves significant energy losses during transmission from centralized power plants to industrial sites. By generating electricity on-site, factories eliminate these transmission losses and maximize the use of available energy resources. This not only improves operational efficiency but also contributes to lower energy costs and reduced environmental impact.
Industries that implement steam turbine systems benefit from their versatility in fuel usage. Steam turbines can operate using a variety of fuels, including natural gas, biomass, coal, and hydrogen, providing businesses with flexibility to adapt to changing energy markets and regulatory requirements. The transition to cleaner energy sources is further accelerating the adoption of steam turbines, as they can be integrated with renewable energy systems such as solar thermal and geothermal power. Biomass-fueled turbines, in particular, offer a sustainable solution for industries looking to reduce their carbon footprint while utilizing locally available resources.
The economic advantages of steam turbine-powered electricity generation are significant. Factories that produce their own power can stabilize energy costs, reducing exposure to fluctuations in electricity prices. In many cases, industrial plants can generate surplus electricity that can be fed back into the grid, creating an additional revenue stream. Governments and regulatory bodies also offer incentives, such as tax credits and subsidies, for industries that invest in energy-efficient technologies, further improving the financial viability of steam turbine systems.
One of the key factors driving the adoption of steam turbines in industrial power generation is their reliability. Large-scale manufacturing facilities, refineries, and chemical plants require a consistent power supply to avoid disruptions that can lead to costly downtime and equipment damage. On-site power generation with steam turbines provides industries with greater control over their energy supply, ensuring uninterrupted operations and reducing dependency on external power providers. Advanced control systems, real-time monitoring, and predictive maintenance technologies further enhance turbine reliability, allowing businesses to optimize performance and minimize unexpected failures.
Technological advancements are continually improving the efficiency and functionality of steam turbines. Digital automation and artificial intelligence (AI)-driven analytics are revolutionizing power plant management, enabling industries to track energy consumption, predict maintenance needs, and optimize turbine performance in real-time. Smart sensors and Internet of Things (IoT) solutions allow for seamless integration with industrial processes, ensuring that electricity generation is precisely aligned with production requirements. These innovations not only enhance efficiency but also contribute to cost savings and extended equipment lifespan.
The future of industrial power generation lies in the continued development and integration of high-efficiency steam turbines with sustainable energy sources. As industries move toward carbon neutrality, hydrogen-powered steam turbines are emerging as a promising alternative to traditional fossil fuel-based systems. The potential for hybrid power plants—combining steam turbines with renewable energy solutions—further strengthens their role in the transition to cleaner and more efficient industrial power generation.
By adopting steam turbine technology, industries can achieve a balance between cost-effective electricity production, operational reliability, and environmental responsibility. As global energy demands increase and sustainability becomes a priority, steam turbines will remain a cornerstone of industrial power solutions, ensuring efficient, stable, and scalable electricity generation for years to come.
The continued integration of steam turbines into industrial power generation is driven by their ability to provide efficient, reliable, and cost-effective electricity while meeting the growing demand for sustainable energy solutions. Industries worldwide are prioritizing energy efficiency as a key factor in improving profitability and reducing environmental impact, making steam turbines an indispensable component of modern power infrastructure.
One of the major advantages of steam turbines is their ability to operate in a variety of industrial environments, from large-scale manufacturing plants to petrochemical refineries and pulp and paper mills. These industries require a steady and high-capacity power supply to maintain production efficiency, and steam turbines offer a proven solution for meeting these demands. Their ability to generate electricity on-site eliminates the risks associated with grid dependency, ensuring uninterrupted operations and preventing costly production losses due to power outages or voltage fluctuations.
The economic benefits of using steam turbines for industrial electricity generation are substantial. Rising energy costs and fluctuating electricity prices make it increasingly important for industries to gain control over their energy expenses. By producing their own power, companies can stabilize long-term electricity costs, improve budget predictability, and reduce reliance on external suppliers. Additionally, many governments provide financial incentives, such as tax breaks and grants, to encourage industries to adopt energy-efficient technologies, further enhancing the economic viability of steam turbine installations.
Energy efficiency is a critical consideration for industries looking to reduce waste and optimize resource utilization. Steam turbines are well-suited for cogeneration applications, where they generate both electricity and useful thermal energy from a single fuel source. This combined heat and power (CHP) approach can achieve efficiencies of up to 80%, significantly higher than conventional power plants that waste a large portion of energy as heat. By capturing and repurposing this heat for industrial processes, businesses can maximize their energy efficiency while reducing their carbon footprint and fuel consumption.
Another key factor driving the adoption of steam turbines is their ability to operate with a wide range of fuel sources. Traditional fossil fuels such as coal and natural gas remain widely used, but industries are increasingly turning to renewable alternatives such as biomass and hydrogen. Biomass-powered steam turbines, for example, allow factories to generate electricity using organic waste materials, reducing their reliance on non-renewable energy sources while lowering emissions. Meanwhile, hydrogen-powered steam turbines are emerging as a promising zero-emission technology that could revolutionize industrial power generation in the coming years.
The reliability and longevity of steam turbines make them an attractive investment for industrial facilities. With proper maintenance, steam turbines can operate for decades, providing a stable and cost-effective power source over their lifespan. Advanced monitoring systems and predictive maintenance technologies are further improving their reliability, allowing industries to detect potential issues before they lead to failures. Real-time data analysis and automated diagnostics help optimize turbine performance, reduce downtime, and extend the lifespan of critical components.
As industries continue to embrace digitalization, the integration of smart technologies with steam turbine systems is enhancing operational efficiency. Internet of Things (IoT) sensors, AI-powered analytics, and automated control systems enable precise monitoring and adjustment of turbine operations, ensuring optimal performance under varying load conditions. These innovations help industries maximize energy output, reduce operational costs, and improve overall system efficiency.
Looking ahead, the role of steam turbines in industrial power generation will continue to evolve with advancements in energy storage, hybrid power systems, and low-carbon technologies. The growing emphasis on sustainability and emissions reduction is driving research into high-efficiency turbine designs, improved materials, and new fuel options. As industries strive to meet stringent environmental regulations and global climate goals, steam turbines will remain a key solution for achieving both economic and environmental objectives.
By leveraging the efficiency, flexibility, and reliability of steam turbines, industries can ensure a stable and self-sufficient power supply while reducing energy costs and emissions. As technological advancements continue to enhance their performance and sustainability, steam turbines will play an increasingly vital role in the future of industrial electricity generation.
The ongoing advancements in steam turbine technology are further solidifying their position as a cornerstone of industrial power generation. As global industries strive for energy efficiency, cost control, and sustainability, steam turbines continue to evolve to meet these challenges. Their ability to provide stable and scalable power generation makes them essential for industries that demand high energy output, such as steel manufacturing, cement production, and petrochemicals.
One of the key benefits of steam turbines is their adaptability to various industrial power needs. Whether used in large-scale independent power plants or smaller, factory-specific installations, steam turbines offer a flexible and efficient solution. Industries with high thermal energy requirements benefit from steam turbines integrated with cogeneration systems, where excess steam is used for additional heating or manufacturing processes, improving overall plant efficiency. This dual-purpose capability reduces fuel consumption and maximizes energy utilization, lowering overall operational costs.
Waste heat recovery is another area where steam turbines contribute to industrial efficiency. Many manufacturing processes generate large amounts of heat, which, if not captured, would be wasted. By implementing steam turbines in conjunction with waste heat recovery systems, industries can harness this excess energy to produce electricity, reducing reliance on external power sources. This not only enhances sustainability efforts but also improves overall energy security, especially in regions where electricity prices are volatile or grid reliability is a concern.
The fuel flexibility of steam turbines also plays a crucial role in their widespread adoption. Traditional steam turbines are commonly powered by fossil fuels, such as coal or natural gas, but modern advancements have enabled the use of alternative energy sources. Biomass and biogas-fired steam turbines are gaining popularity in industries looking for carbon-neutral energy solutions. Additionally, hydrogen is emerging as a key fuel option, with research and development efforts focused on hydrogen-compatible steam turbines that could enable zero-emission industrial power generation in the future.
Beyond their fuel efficiency, steam turbines provide long-term economic benefits due to their durability and extended operational lifespan. Unlike internal combustion engines, steam turbines experience lower mechanical wear and require less maintenance over time. With proper care and periodic upgrades, steam turbines can remain in service for decades, making them a cost-effective investment for industrial power generation. This long lifespan, combined with their high efficiency, makes them a preferred choice for industries aiming to reduce lifecycle costs while ensuring consistent power availability.
Another factor driving the increased reliance on steam turbines is their ability to integrate with digital automation and smart monitoring systems. Advances in artificial intelligence (AI), machine learning, and the Internet of Things (IoT) are transforming industrial power generation by enabling real-time performance tracking and predictive maintenance. Modern steam turbine systems are equipped with advanced sensors that continuously monitor parameters such as temperature, pressure, and vibration, allowing operators to optimize performance and prevent potential failures. AI-driven diagnostics can predict maintenance needs before problems arise, reducing downtime and improving operational reliability.
Governments and regulatory bodies are also playing a crucial role in the expansion of steam turbine-based power generation. Many regions are introducing policies that encourage the adoption of high-efficiency energy systems, including combined heat and power (CHP) plants and waste heat recovery technologies. Industries investing in these advanced energy solutions can benefit from financial incentives such as tax credits, grants, and subsidies, which help offset initial capital expenditures. Additionally, some countries allow industries to sell surplus electricity back to the grid, creating an additional revenue stream and further improving the economic case for on-site power generation with steam turbines.
As industries continue to seek ways to minimize their environmental footprint while maintaining reliable energy supplies, steam turbines will remain a key component of the industrial power landscape. With ongoing research into advanced materials, hybrid energy integration, and emissions reduction technologies, the future of steam turbines is set to be even more efficient and sustainable. By embracing these innovations, industrial facilities can achieve greater energy independence, reduce costs, and contribute to a cleaner and more resilient global energy system.
The evolution of steam turbine technology continues to shape the industrial power sector, providing efficient and reliable electricity generation for large-scale manufacturing, processing, and refining industries. As industries increasingly focus on reducing operational costs and improving sustainability, steam turbines offer a proven solution for meeting high energy demands while optimizing fuel use and reducing environmental impact.
One of the most significant advantages of steam turbines is their efficiency in large-scale power generation. Unlike reciprocating engines or other power generation methods that rely on intermittent combustion cycles, steam turbines operate continuously, providing a steady and reliable source of electricity. This is particularly critical for industries that require uninterrupted power supply, such as petrochemical plants, steel mills, and paper production facilities. With the ability to generate power in the megawatt range, steam turbines serve as the backbone of industrial energy infrastructure.
Furthermore, steam turbines are well-suited for integration into combined cycle power plants, where they work alongside gas turbines to maximize energy output. In a combined cycle system, the exhaust heat from a gas turbine is used to produce steam, which then drives a steam turbine to generate additional electricity. This approach significantly improves overall efficiency, often exceeding 60%, compared to conventional single-cycle power plants. Many industrial facilities are adopting this technology to increase their energy output while reducing fuel consumption and emissions.
In addition to combined cycle applications, steam turbines play a vital role in district heating and cogeneration (combined heat and power, CHP) systems. By capturing and utilizing the thermal energy produced during electricity generation, industries can repurpose waste heat for heating, cooling, or other industrial processes. This approach not only boosts overall efficiency but also reduces the need for additional energy sources, lowering operational costs and carbon emissions. In industries such as food processing, chemical manufacturing, and textile production, steam turbines help optimize resource utilization and improve energy self-sufficiency.
The increasing adoption of renewable energy sources is also influencing the future of steam turbine technology. As industries transition away from fossil fuels, steam turbines are being adapted to operate with sustainable energy sources such as biomass, geothermal energy, and solar thermal power. Biomass-fired steam turbines allow industries to use organic waste as a fuel source, creating a closed-loop energy system that minimizes environmental impact. Geothermal power plants rely on steam turbines to convert underground heat into electricity, providing a renewable and consistent energy supply. Solar thermal power plants use concentrated solar energy to generate steam, which then drives a turbine to produce electricity. These emerging applications highlight the versatility of steam turbines in supporting the global shift toward cleaner energy solutions.
Digitalization and automation are further enhancing the performance and efficiency of steam turbine systems. The integration of artificial intelligence (AI), predictive analytics, and remote monitoring technologies allows industries to optimize turbine operations in real time. Advanced control systems enable operators to adjust turbine parameters based on energy demand, fuel availability, and environmental conditions, maximizing efficiency and reducing waste. Predictive maintenance systems use AI-driven insights to detect potential issues before they lead to failures, minimizing downtime and maintenance costs. These digital innovations are transforming industrial power generation, making steam turbines more intelligent, responsive, and cost-effective.
Looking ahead, ongoing research and development efforts are focused on improving steam turbine efficiency through advanced materials and design enhancements. High-performance alloys and ceramic coatings are being developed to withstand higher temperatures and pressures, increasing turbine durability and efficiency. Supercritical and ultra-supercritical steam turbine technologies are pushing efficiency boundaries by operating at extreme conditions, reducing fuel consumption and emissions. Hydrogen-compatible steam turbines are also being explored as part of the transition to carbon-free power generation, offering a long-term solution for industries seeking to decarbonize their energy supply.
As industries continue to prioritize energy efficiency, cost reduction, and sustainability, steam turbines will remain a fundamental component of industrial power generation. Their ability to integrate with diverse energy sources, support cogeneration applications, and leverage digital innovations ensures their relevance in an evolving energy landscape. By investing in steam turbine technology, industries can achieve greater energy security, lower operating costs, and contribute to a more sustainable future for global power generation.
Industries Generate Power with Steam Turbines
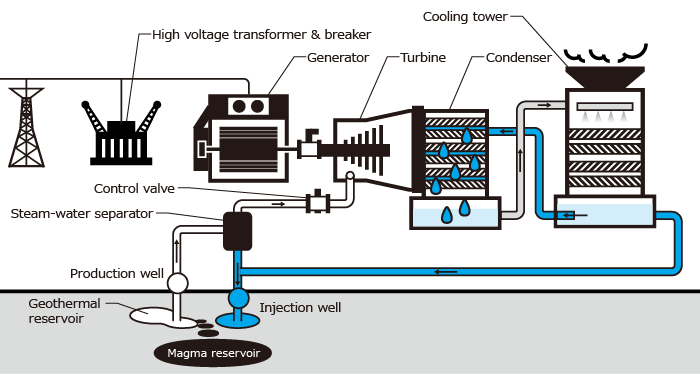
Industries worldwide continue to rely on steam turbines as a primary source of power generation, leveraging their efficiency, reliability, and adaptability to meet growing energy demands. As industries expand and modernize, the need for stable and cost-effective electricity becomes increasingly critical. Steam turbines provide a well-established solution for generating power at scale, making them an essential component of industrial operations across sectors such as manufacturing, petrochemicals, steel production, and paper mills.
One of the key advantages of steam turbines is their ability to convert thermal energy into mechanical work with high efficiency. Unlike internal combustion engines, steam turbines operate through continuous expansion, resulting in smooth and efficient power generation with fewer mechanical losses. This makes them particularly suitable for industrial facilities that require large amounts of electricity and heat to maintain uninterrupted production processes.
Many industries integrate steam turbines into their existing infrastructure to enhance efficiency through cogeneration, also known as combined heat and power (CHP). In these systems, steam turbines generate both electricity and usable thermal energy from a single fuel source. The excess steam produced in the process is repurposed for industrial heating, drying, or chemical reactions, maximizing fuel utilization and minimizing waste. This approach significantly reduces energy costs and lowers greenhouse gas emissions, making it an environmentally friendly option for industrial power generation.
Waste heat recovery is another major application of steam turbines in industrial settings. Many industrial processes generate high-temperature waste gases that, if left unused, would be lost as heat. By capturing this waste heat and using it to produce steam, industries can drive steam turbines to generate additional electricity without consuming extra fuel. This process improves overall energy efficiency and reduces dependence on external power sources, enhancing energy security and cost savings for businesses.
Fuel flexibility is a significant factor contributing to the widespread adoption of steam turbines in industrial power plants. While conventional steam turbines often run on fossil fuels such as coal and natural gas, modern advancements have made it possible to use alternative energy sources, including biomass, geothermal energy, and even hydrogen. Biomass-powered steam turbines enable industries to use organic waste materials as fuel, reducing carbon emissions and promoting sustainable energy practices. Hydrogen-powered turbines, currently in development, have the potential to offer a zero-emission power generation solution, supporting global decarbonization efforts.
In addition to their efficiency and sustainability benefits, steam turbines offer industries long-term economic advantages. Their robust design and low maintenance requirements allow them to operate for decades with minimal interruptions. Unlike reciprocating engines, which experience significant wear and tear due to repeated combustion cycles, steam turbines have fewer moving parts and operate more smoothly, resulting in lower maintenance costs and longer service life.
The integration of digital technology is further revolutionizing industrial power generation with steam turbines. Modern steam turbines are equipped with advanced monitoring systems, predictive maintenance capabilities, and real-time performance optimization tools. Industrial plants can leverage artificial intelligence (AI) and Internet of Things (IoT) technologies to analyze operational data, detect early signs of wear, and optimize efficiency based on changing energy demands. These digital advancements help industries reduce unplanned downtime, improve asset management, and maximize power output with minimal energy waste.
As global industries strive to achieve energy independence and sustainability, steam turbines continue to play a vital role in industrial power generation. Their ability to integrate with renewable energy sources, support waste heat recovery, and enable cogeneration makes them a versatile and efficient solution for meeting industrial electricity needs. With ongoing advancements in turbine design, fuel adaptability, and smart automation, steam turbines will remain a key driver of industrial energy efficiency and economic growth well into the future.
The continued reliance on steam turbines for industrial power generation highlights their unmatched efficiency, adaptability, and long-term cost benefits. As industries scale up operations and modernize their infrastructure, the demand for stable, self-sufficient power solutions grows. Steam turbines meet this need by delivering consistent and large-scale electricity generation while optimizing fuel use and reducing environmental impact. Their versatility allows them to be integrated into various industrial energy systems, from standalone power plants to combined heat and power (CHP) applications.
One of the primary reasons industries generate power with steam turbines is their ability to provide baseload electricity, ensuring uninterrupted operations even in regions with an unreliable grid. Industrial sectors such as steel production, chemical manufacturing, and refining require constant energy to maintain continuous processes. Steam turbines, with their ability to run on various fuel sources—including coal, natural gas, biomass, and even geothermal energy—offer a flexible and secure power generation solution. Their efficiency in converting thermal energy into mechanical work enables industries to achieve lower energy costs while maintaining high productivity levels.
Cogeneration remains a key driver of steam turbine adoption, as industries increasingly seek to maximize energy efficiency. Instead of solely producing electricity, steam turbines in CHP systems simultaneously generate thermal energy for industrial processes, district heating, or even cooling applications. This dual-use approach significantly reduces fuel consumption, as the same energy input is used to produce both electricity and useful heat. The result is higher overall efficiency, lower operating costs, and a reduced carbon footprint. Industrial plants that implement CHP solutions with steam turbines often benefit from government incentives and regulatory support, further enhancing the economic case for adoption.
Waste heat recovery has also become a critical component of industrial power generation, with steam turbines playing a crucial role in utilizing previously lost energy. In many industrial processes, high-temperature exhaust gases are generated as a byproduct. Rather than allowing this heat to dissipate, waste heat recovery systems capture it and convert it into steam, which then powers a steam turbine to generate electricity. This process improves overall energy utilization, reduces the need for additional fuel, and contributes to sustainability efforts. Industries that adopt waste heat recovery not only lower their energy expenses but also minimize greenhouse gas emissions, aligning with global environmental targets.
The durability and longevity of steam turbines provide significant economic advantages for industrial applications. Unlike reciprocating engines or gas turbines, steam turbines have fewer moving parts, reducing mechanical wear and lowering maintenance requirements. Many steam turbines in industrial power plants operate reliably for decades with periodic upgrades and proper maintenance, making them a cost-effective long-term investment. Their ability to operate at high efficiencies over extended periods makes them ideal for industries that prioritize both performance and cost savings.
Advancements in digitalization and automation are further enhancing the efficiency and reliability of steam turbine systems. Modern industrial power plants are increasingly integrating smart monitoring solutions, predictive maintenance algorithms, and real-time performance optimization tools. By leveraging artificial intelligence (AI) and Internet of Things (IoT) technologies, industries can track turbine parameters, detect anomalies before failures occur, and optimize energy output based on demand fluctuations. This level of automation reduces downtime, lowers maintenance costs, and improves overall energy management.
As global industries transition toward more sustainable energy solutions, steam turbines are evolving to accommodate cleaner and more renewable fuel sources. Biomass-fired steam turbines allow factories to utilize agricultural waste, wood pellets, and other organic materials as a fuel source, reducing dependency on fossil fuels. Additionally, research into hydrogen-powered steam turbines presents a promising avenue for zero-emission industrial power generation. With advancements in high-temperature materials and efficiency improvements, future steam turbines will be even more adaptable to low-carbon and renewable energy systems.
Steam turbines remain at the forefront of industrial power generation, supporting energy-intensive industries with reliable, efficient, and scalable electricity solutions. Their ability to integrate with CHP systems, waste heat recovery, and renewable energy sources ensures their continued relevance in an evolving energy landscape. As industrial facilities seek greater energy independence, cost efficiency, and sustainability, steam turbines will play a critical role in meeting these objectives while driving industrial growth and technological innovation.
The role of steam turbines in industrial power generation continues to expand as industries seek efficient, reliable, and sustainable energy solutions. Their ability to provide large-scale, continuous power makes them indispensable for energy-intensive sectors such as petrochemicals, cement production, food processing, and metal refining. As industries modernize and embrace new technologies, steam turbines remain a core component of their energy strategies, offering a balance of efficiency, cost-effectiveness, and environmental responsibility.
One of the most significant advantages of steam turbines is their adaptability to various fuel sources, which allows industries to optimize power generation based on available resources. Traditional coal-fired steam turbines, once the dominant source of industrial power, are gradually being replaced or upgraded to run on cleaner fuels such as natural gas, biomass, and hydrogen. Many industrial facilities are investing in dual-fuel or multi-fuel steam turbines, enabling them to switch between fuel sources depending on market conditions and sustainability goals. This flexibility ensures continuous operation and reduces exposure to fluctuating fuel prices.
Industries are also leveraging steam turbines to improve energy efficiency through combined cycle power generation. By pairing steam turbines with gas turbines in a combined cycle system, industrial power plants can achieve efficiencies exceeding 60%, significantly higher than traditional power generation methods. In this setup, the gas turbine generates electricity while its exhaust heat is used to produce steam, which then drives a steam turbine to generate additional power. This approach maximizes energy output from the same fuel input, reducing waste and lowering overall emissions. Many industrial facilities are adopting combined cycle systems to meet stringent environmental regulations while maintaining cost competitiveness.
The expansion of waste heat recovery systems further highlights the importance of steam turbines in industrial settings. Many industrial processes, such as metal smelting, glass manufacturing, and chemical production, release substantial amounts of waste heat. Rather than letting this energy dissipate, industries are implementing heat recovery steam generators (HRSGs) to capture the heat and produce steam. This steam is then used to drive a steam turbine, generating additional electricity without consuming extra fuel. Waste heat recovery not only improves energy efficiency but also reduces greenhouse gas emissions, helping industries achieve sustainability targets.
Steam turbines also play a critical role in industrial cogeneration (CHP) systems, where both electricity and thermal energy are produced from the same energy source. Many industrial processes require large amounts of heat for operations such as drying, distillation, and chemical reactions. By utilizing steam turbines in CHP configurations, industries can generate electricity while simultaneously supplying process heat, optimizing fuel utilization. This approach significantly reduces energy costs and carbon footprints, making it a preferred choice for industries looking to enhance operational efficiency.
With the increasing push for decarbonization, steam turbines are evolving to accommodate cleaner energy sources. Biomass-powered steam turbines are gaining popularity in industries that generate organic waste as a byproduct. Agricultural processing plants, paper mills, and wood product manufacturers are using biomass fuels such as wood chips, straw, and agricultural residues to produce steam for power generation. By converting waste into energy, these industries not only reduce reliance on fossil fuels but also minimize waste disposal costs.
Hydrogen-based steam turbines are another emerging technology that promises to revolutionize industrial power generation. Hydrogen combustion produces steam without carbon emissions, making it a viable alternative to natural gas in steam turbine applications. While large-scale hydrogen infrastructure is still in development, industries are exploring hybrid solutions that blend hydrogen with natural gas to reduce emissions. Research into high-temperature materials and advanced turbine designs is making hydrogen-powered steam turbines a feasible option for the future.
The integration of digitalization and automation is further transforming industrial steam turbine operations. Advanced monitoring systems equipped with sensors and artificial intelligence (AI) algorithms allow industries to track turbine performance in real-time. Predictive maintenance technologies analyze operational data to detect early signs of wear, enabling industries to address potential issues before they lead to costly failures. Automated control systems optimize steam turbine efficiency by adjusting parameters based on energy demand and fuel conditions. These innovations reduce maintenance costs, improve operational reliability, and maximize energy output.
As industries continue to seek cost-effective, reliable, and sustainable power solutions, steam turbines remain a cornerstone of industrial energy generation. Their ability to integrate with combined cycle systems, support cogeneration, and leverage renewable fuels makes them an adaptable and future-proof technology. With ongoing advancements in materials, digitalization, and fuel flexibility, steam turbines will continue to play a crucial role in industrial power generation, supporting global efforts toward energy efficiency and environmental sustainability.
The continued advancements in steam turbine technology underscore their enduring role in industrial power generation. As industries strive to enhance efficiency, reduce operational costs, and minimize environmental impact, steam turbines provide a scalable and adaptable solution. Their ability to operate in a variety of configurations, from standalone power plants to integrated combined heat and power (CHP) systems, makes them a preferred choice for industries requiring stable and cost-effective electricity.
One of the most critical aspects of steam turbines in industrial power generation is their ability to support decentralized energy production. Many industries are moving toward on-site power generation to reduce reliance on external grids, increase energy security, and lower transmission losses. Steam turbines are at the heart of these industrial power plants, converting steam into electricity with high efficiency. By generating power at the point of use, industries can achieve greater control over their energy costs and improve overall system reliability.
Moreover, steam turbines play a crucial role in industrial sustainability initiatives. As regulations become stricter and industries aim to lower their carbon footprints, steam turbines are being adapted to run on alternative fuels. Biomass and waste-to-energy systems are increasingly being integrated into industrial operations, allowing facilities to use organic byproducts for power generation. This not only reduces fuel costs but also supports circular economy principles by turning industrial waste into a valuable energy source.
In addition to biomass, geothermal energy is another renewable source that is being utilized in conjunction with steam turbines. Many industries located near geothermal resources are leveraging steam turbines to harness underground heat for power generation. Geothermal steam turbines operate on naturally occurring steam or superheated water, providing a continuous and renewable source of electricity. These systems require minimal fuel input, making them a sustainable alternative for industries seeking long-term energy stability.
The push for hydrogen-powered industrial steam turbines is also gaining momentum. Hydrogen combustion produces steam without carbon emissions, making it an attractive fuel for industries looking to transition to cleaner energy sources. While challenges related to hydrogen storage and distribution remain, ongoing research and infrastructure developments are bringing hydrogen-based power generation closer to large-scale implementation. Steam turbines that can efficiently run on hydrogen or hydrogen blends will play a key role in the future of carbon-neutral industrial power.
Another significant innovation in industrial steam turbine technology is the implementation of advanced materials and coatings. High-temperature-resistant alloys and ceramic coatings are being developed to improve turbine efficiency and longevity. These materials allow steam turbines to operate at higher temperatures and pressures, increasing their efficiency and reducing fuel consumption. The use of additive manufacturing (3D printing) is also enabling the production of complex turbine components with enhanced durability and performance characteristics.
Furthermore, digitalization is revolutionizing the way steam turbines are monitored and maintained. Many industries are integrating Internet of Things (IoT) sensors into their steam turbine systems to continuously track performance metrics such as temperature, pressure, and vibration levels. Artificial intelligence (AI)-driven analytics enable predictive maintenance, identifying potential issues before they result in costly downtime. This proactive approach helps industries optimize their operations, extend equipment lifespan, and reduce maintenance expenses.
The integration of steam turbines with energy storage systems is also being explored as industries look for ways to balance power supply and demand more effectively. By pairing steam turbines with battery storage or thermal energy storage systems, industries can store excess electricity generated during off-peak hours and utilize it when demand rises. This hybrid approach improves grid stability and maximizes energy efficiency, making industrial power generation more flexible and resilient.
Steam turbines remain an indispensable technology for industrial power generation, evolving to meet the changing needs of modern industries. Their ability to integrate with renewable energy sources, optimize fuel use through cogeneration, and leverage cutting-edge materials and digital solutions ensures their continued relevance. As industries prioritize energy efficiency, cost savings, and sustainability, steam turbines will play a central role in driving industrial innovation and supporting the global transition toward cleaner and more efficient power generation systems.
Thermal Recycling: Heat into Electricity
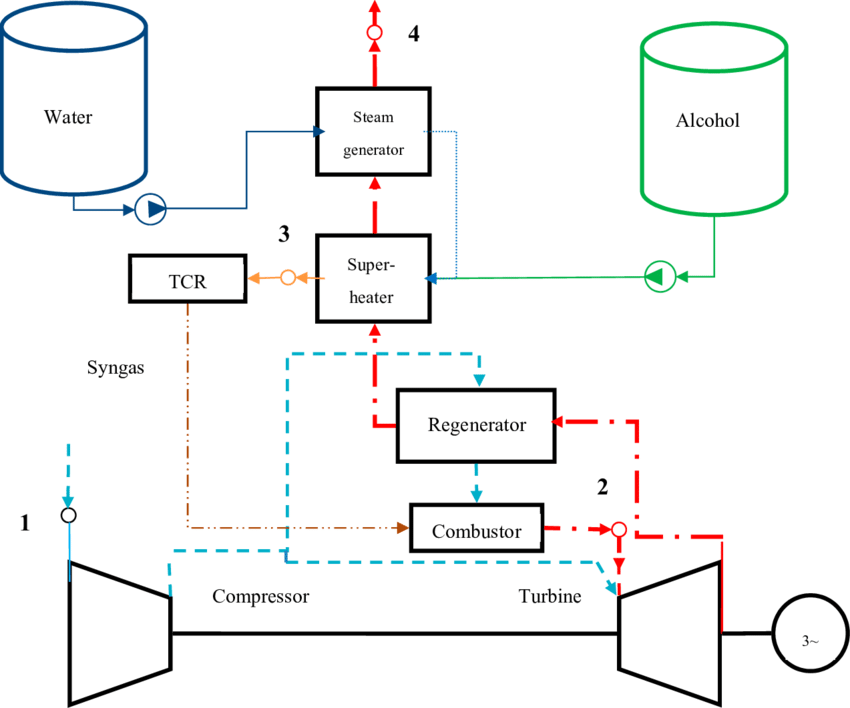
Thermal recycling, the process of converting excess heat into electricity, has emerged as a key strategy for improving energy efficiency in industrial operations. Many industrial processes generate significant amounts of waste heat, which, if left unutilized, represents a lost opportunity for energy savings and cost reduction. By capturing and repurposing this heat through advanced technologies such as waste heat recovery systems and steam turbines, industries can significantly improve overall energy efficiency while reducing their environmental impact.
One of the most effective ways to implement thermal recycling is through waste heat recovery steam generators (HRSGs). These systems capture high-temperature exhaust gases from industrial furnaces, kilns, or gas turbines and use them to produce steam. The generated steam is then directed to a steam turbine, where it is converted into mechanical energy to drive a generator and produce electricity. This process allows industries to maximize the use of energy already consumed in production processes, reducing the need for additional fuel input and lowering operating costs.
In energy-intensive industries such as steel production, cement manufacturing, and petrochemical processing, massive amounts of thermal energy are released as byproducts of production. By integrating thermal recycling solutions, these industries can convert excess heat into a valuable energy source, offsetting a portion of their electricity needs. This not only improves cost efficiency but also reduces dependence on external power sources, increasing energy security and operational stability.
Combined heat and power (CHP) systems represent another highly effective method of thermal recycling. Also known as cogeneration, CHP systems generate both electricity and useful thermal energy from a single fuel source. Instead of allowing waste heat to dissipate, it is captured and repurposed for heating, cooling, or additional power generation. This dual-use approach increases the overall efficiency of energy conversion, sometimes reaching efficiencies of 80% or higher, compared to the 35-40% efficiency of traditional power generation methods. Many industries are investing in CHP systems to lower energy costs while meeting sustainability targets.
Advancements in organic Rankine cycle (ORC) technology have further expanded the scope of thermal recycling. ORC systems work similarly to conventional steam turbines but use organic working fluids with lower boiling points. This enables them to operate efficiently at lower temperatures, making them ideal for recovering waste heat from lower-temperature sources such as exhaust gas streams, geothermal energy, and industrial cooling systems. The adoption of ORC technology has opened new opportunities for industries to extract value from previously untapped heat sources.
Thermal recycling is also playing a crucial role in reducing industrial carbon footprints. By improving energy efficiency and reducing the reliance on fossil fuels, waste heat recovery and cogeneration systems contribute to lower greenhouse gas emissions. Many governments and regulatory bodies are incentivizing industries to implement energy-efficient solutions through tax credits, grants, and carbon reduction programs. As industries face increasing pressure to comply with environmental regulations, the adoption of thermal recycling technologies is becoming a strategic necessity.
Digitalization is further enhancing the effectiveness of thermal recycling systems. Smart sensors, data analytics, and AI-driven predictive maintenance are being used to monitor waste heat recovery systems in real time. By analyzing performance data, industries can optimize heat capture, identify efficiency losses, and proactively address maintenance needs. This ensures maximum energy recovery while minimizing downtime and operational disruptions.
As industries move toward greater sustainability and efficiency, thermal recycling solutions will continue to play a vital role in modern energy strategies. By leveraging waste heat to generate electricity, industrial facilities can enhance profitability, reduce emissions, and contribute to a more sustainable energy future. With ongoing advancements in technology and increasing regulatory support, the adoption of thermal recycling is expected to grow, making it an essential component of industrial energy management worldwide.
The increasing adoption of thermal recycling technologies is reshaping industrial power management, enabling businesses to achieve greater energy efficiency while reducing operational costs. As industries continue to modernize, integrating waste heat recovery systems into existing infrastructure is becoming a priority, driven by both economic and environmental incentives.
One of the key advantages of thermal recycling is its ability to improve overall process efficiency. In traditional power generation and industrial operations, a significant portion of energy is lost as heat. By capturing and converting this excess heat into usable electricity, facilities can optimize energy usage, reducing the need for additional fuel consumption. This not only cuts costs but also lowers emissions, helping industries meet sustainability goals and regulatory requirements.
Industries such as oil refining, chemical processing, and manufacturing are particularly well-suited for thermal recycling due to their high-temperature processes. In oil refineries, for example, vast amounts of heat are produced during crude oil distillation and catalytic cracking. By integrating waste heat recovery boilers, refineries can use this excess thermal energy to generate steam, which then powers steam turbines to produce electricity. This self-sustaining energy cycle reduces dependence on external power sources and enhances energy security.
Similarly, in the cement industry, the kilns used to produce clinker generate enormous amounts of waste heat. Modern cement plants are adopting waste heat recovery power generation (WHRPG) systems, which capture and utilize this heat to produce electricity. This not only lowers operating costs but also reduces the overall carbon footprint of cement production, an industry known for its high energy intensity.
Another promising area of thermal recycling is its application in district heating systems. Many industrial facilities produce surplus heat that can be repurposed to provide heating for nearby residential and commercial buildings. By channeling waste heat into district heating networks, industries contribute to urban energy efficiency while monetizing excess thermal energy. This approach is gaining traction in cities focused on reducing reliance on fossil fuels and promoting sustainable energy solutions.
Beyond large-scale industrial applications, smaller facilities are also beginning to explore thermal recycling options. Advances in modular and scalable waste heat recovery systems are making it easier for small and medium-sized enterprises (SMEs) to implement energy-efficient solutions. Compact ORC systems, for instance, allow businesses with lower-grade waste heat to generate electricity without major infrastructure changes. These innovations are expanding the accessibility of thermal recycling to a broader range of industries.
Government policies and incentives are playing a crucial role in driving the adoption of thermal recycling. Many countries offer tax credits, subsidies, and grants to encourage industries to invest in energy-efficient technologies. Carbon pricing mechanisms and emissions reduction targets further motivate businesses to optimize their energy use and implement waste heat recovery solutions. As regulatory frameworks continue to evolve, industries that proactively adopt thermal recycling will gain a competitive edge in an increasingly sustainability-focused market.
Looking ahead, continued advancements in materials science, heat exchanger design, and digital monitoring technologies will further improve the efficiency and viability of thermal recycling systems. The integration of artificial intelligence (AI) and machine learning in energy management will allow industries to optimize heat recovery processes dynamically, maximizing electricity generation while minimizing waste.
As global energy demand continues to rise, industries must seek innovative ways to reduce consumption, lower costs, and enhance sustainability. Thermal recycling offers a proven, effective strategy for transforming industrial waste heat into a valuable resource. By embracing this technology, businesses can drive long-term economic and environmental benefits, contributing to a more efficient and sustainable industrial landscape.
The future of thermal recycling is increasingly intertwined with advancements in renewable energy integration and smart energy management systems. As industries strive for greater energy independence and carbon neutrality, waste heat recovery is becoming a critical component of hybrid energy solutions that combine multiple power generation methods for optimized efficiency.
One of the most promising developments in this space is the integration of thermal recycling with renewable energy sources such as solar and geothermal power. Hybrid power systems that combine solar thermal energy with waste heat recovery can significantly enhance overall efficiency. For instance, in industrial facilities equipped with concentrated solar power (CSP) systems, the excess heat generated during peak sunlight hours can be stored and later utilized through steam turbines, ensuring continuous power supply even when solar radiation decreases. This approach helps industries stabilize their energy output while maximizing the use of clean energy.
Similarly, industries located near geothermal hotspots are leveraging thermal recycling to enhance geothermal energy utilization. By combining waste heat recovery with geothermal steam cycles, industrial plants can achieve higher efficiency levels while reducing fuel consumption. This synergy enables facilities to generate electricity with minimal environmental impact while ensuring a stable and reliable energy source.
Another emerging trend is the use of supercritical CO₂ (sCO₂) power cycles in thermal recycling applications. Unlike traditional steam-based Rankine cycles, sCO₂ cycles operate at higher efficiencies and can extract more energy from lower-temperature heat sources. This technology is particularly beneficial for waste heat recovery from gas turbines, industrial furnaces, and other medium-temperature processes. As research into sCO₂ systems progresses, their adoption is expected to further improve the viability of thermal recycling across a wide range of industries.
Energy storage is also playing a crucial role in enhancing the effectiveness of thermal recycling. By incorporating thermal energy storage (TES) systems, industries can store excess waste heat for later use, allowing for more consistent power generation. Phase change materials (PCMs) and molten salt storage are among the most promising solutions for retaining heat and discharging it when needed. This capability is particularly valuable in manufacturing and processing industries with fluctuating energy demands, as it ensures a stable power supply while reducing reliance on external electricity sources.
In addition to technological advancements, policy frameworks and market mechanisms are driving the widespread adoption of thermal recycling solutions. Carbon trading schemes, energy efficiency standards, and government-backed incentives are encouraging industries to invest in waste heat recovery technologies. Many countries are implementing stricter regulations on industrial emissions, making energy-efficient practices such as thermal recycling an essential strategy for compliance and cost savings.
Moreover, the role of digitalization in optimizing thermal recycling systems cannot be overlooked. The implementation of artificial intelligence (AI) and machine learning algorithms in industrial energy management is allowing businesses to predict energy consumption patterns, optimize heat recovery processes, and enhance overall system performance. Smart monitoring systems equipped with IoT sensors can continuously track temperature variations, identify inefficiencies, and enable real-time adjustments to maximize waste heat utilization.
As industries transition towards greener and more efficient power solutions, the role of thermal recycling will continue to expand. Innovations in waste heat recovery, energy storage, and hybrid renewable energy systems will make industrial operations more sustainable and cost-effective. With continued investment in research and development, thermal recycling is set to become a cornerstone of future industrial energy strategies, driving efficiency gains, reducing carbon emissions, and contributing to a cleaner global energy landscape.
The widespread adoption of thermal recycling and waste heat recovery will play a crucial role in shaping the future of industrial power generation, improving sustainability, and ensuring long-term energy security. As energy demands continue to rise across various industrial sectors, optimizing existing energy resources through waste heat utilization is becoming a strategic priority for businesses aiming to reduce costs and enhance operational resilience.
One of the key drivers behind the continued expansion of thermal recycling is the rising cost of energy. With fuel prices fluctuating and electricity costs increasing, industries are looking for reliable ways to stabilize energy expenses while reducing reliance on external power grids. Waste heat recovery provides a cost-effective solution by turning otherwise lost energy into a valuable resource. By implementing heat-to-power conversion systems, industries can reduce their overall energy expenditure and improve profit margins.
The environmental impact of industrial energy consumption is another major factor propelling the growth of thermal recycling. Governments worldwide are tightening regulations on carbon emissions and encouraging industries to adopt energy-efficient solutions. By integrating waste heat recovery technologies into their operations, businesses can significantly lower their carbon footprints, helping them meet emissions targets and avoid potential penalties associated with excessive energy consumption. Additionally, companies that prioritize sustainability are gaining a competitive advantage, as customers and investors increasingly prefer environmentally responsible businesses.
The role of decentralized energy generation is also gaining importance in the industrial sector. Instead of depending solely on centralized power plants, many businesses are adopting on-site power generation solutions that include waste heat recovery. This approach not only reduces transmission losses but also ensures a more reliable and resilient energy supply, protecting industries from power grid disruptions. Combined heat and power (CHP) plants, for example, allow factories and industrial facilities to generate electricity while simultaneously utilizing waste heat for heating, cooling, or other processes, improving overall energy efficiency.
Advancements in materials science and engineering are further enhancing the capabilities of waste heat recovery systems. New high-temperature-resistant materials are being developed to withstand extreme conditions, allowing for more efficient heat transfer and improved performance in high-temperature industrial environments. These innovations are enabling industries such as metallurgy, glass manufacturing, and petrochemicals to recover waste heat more effectively and convert it into usable electricity.
The integration of hydrogen production with thermal recycling is another promising development. Many industrial processes produce excess heat that can be used to power electrolysis systems, generating green hydrogen as a byproduct. This hydrogen can then be used as a clean fuel source for industrial applications, transportation, or energy storage. The combination of waste heat recovery and hydrogen production represents a step toward a more sustainable and decarbonized industrial sector.
As industries continue to seek innovative ways to optimize energy use, thermal recycling will remain at the forefront of industrial energy strategies. Companies that invest in waste heat recovery solutions today will be better positioned to navigate future energy challenges, maintain cost efficiency, and meet environmental regulations. By leveraging advanced technologies and integrating smart energy management practices, industries can unlock the full potential of waste heat recovery, paving the way for a more sustainable and energy-efficient future.
EMS Power Machines
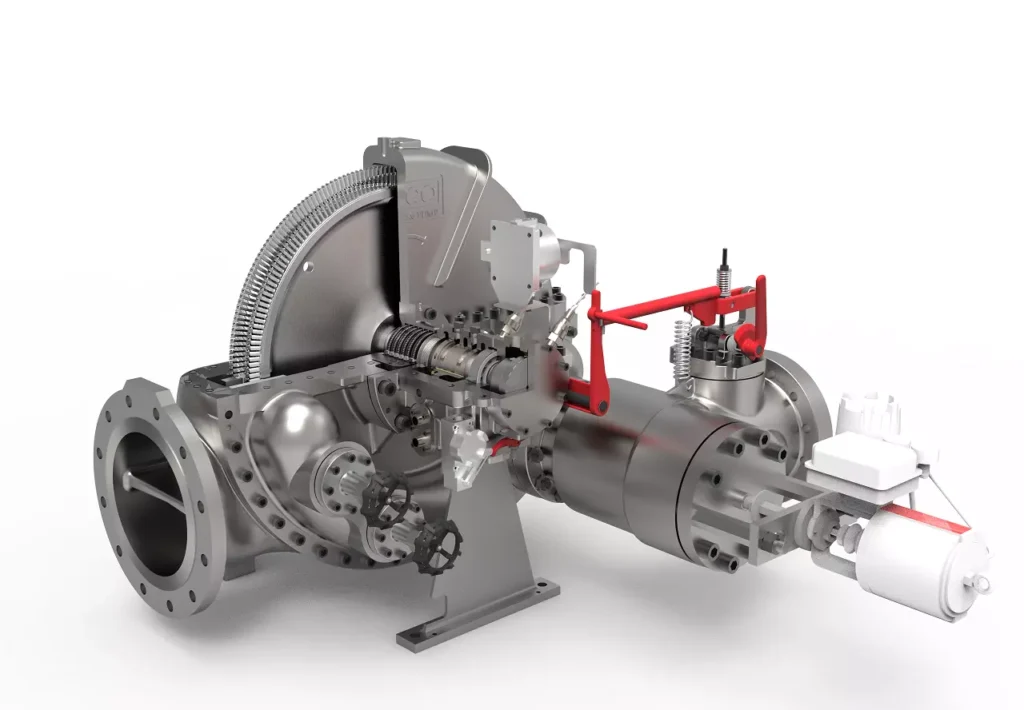
We design, manufacture and assembly Power Machines such as – diesel generators, electric motors, vibration motors, pumps, steam engines and steam turbines
EMS Power Machines is a global power engineering company, one of the five world leaders in the industry in terms of installed equipment. The companies included in the company have been operating in the energy market for more than 60 years.
EMS Power Machines manufactures steam turbines, gas turbines, hydroelectric turbines, generators, and other power equipment for thermal, nuclear, and hydroelectric power plants, as well as for various industries, transport, and marine energy.
EMS Power Machines is a major player in the global power industry, and its equipment is used in power plants all over the world. The company has a strong track record of innovation, and it is constantly developing new and improved technologies.
Here are some examples of Power Machines’ products and services:
- Steam turbines for thermal and nuclear power plants
- Gas turbines for combined cycle power plants and industrial applications
- Hydroelectric turbines for hydroelectric power plants
- Generators for all types of power plants
- Boilers for thermal power plants
- Condensers for thermal power plants
- Reheaters for thermal power plants
- Air preheaters for thermal power plants
- Feedwater pumps for thermal power plants
- Control systems for power plants
- Maintenance and repair services for power plants
EMS Power Machines is committed to providing its customers with high-quality products and services. The company has a strong reputation for reliability and innovation. Power Machines is a leading provider of power equipment and services, and it plays a vital role in the global power industry.
EMS Power Machines, which began in 1961 as a small factory of electric motors, has become a leading global supplier of electronic products for different segments. The search for excellence has resulted in the diversification of the business, adding to the electric motors products which provide from power generation to more efficient means of use.