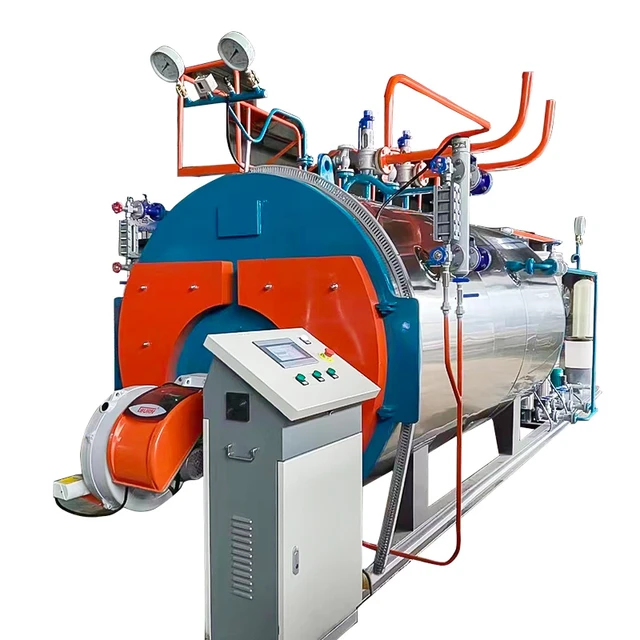
A wood gas generator is a device that converts wood or other biomass materials into combustible gas, known as wood gas or syngas. This gas can be used as a renewable and sustainable fuel source for various applications, including powering internal combustion engines, heating, and electricity generation. Wood gasification has been employed for decades, especially during times when conventional fuels were scarce or expensive.
Wood Gas Generator
Principle of Operation: The basic principle of a wood gas generator involves the thermal conversion of wood through a process called gasification. Gasification occurs when organic materials, such as wood, are heated in a controlled environment with a restricted air supply. In this oxygen-limited environment, the biomass undergoes pyrolysis, where it is broken down into volatile compounds, such as tar and charcoal. The volatile gases are then further reacted with a controlled amount of oxygen or steam, resulting in the production of a combustible gas composed mainly of carbon monoxide, hydrogen, and methane. This wood gas can be utilized as a fuel for various applications.
Components of a Wood Gas Generator:
- Fuel Hopper: This is where the wood or biomass material is loaded into the gasifier. The size and design of the hopper depend on the specific generator model and its intended use.
- Reactor or Gasification Chamber: The heart of the wood gas generator is the reactor, where the actual gasification process takes place. It is designed to provide the necessary conditions for pyrolysis and subsequent gasification of the biomass.
- Filter System: The gas produced in the gasification chamber contains impurities, such as tar and particulate matter. A filtration system is essential to clean the gas before it is used in an engine or other applications.
- Cooling System: The hot wood gas needs to be cooled before it can be utilized effectively. A cooling system, often consisting of a heat exchanger or a series of cooling pipes, helps in condensing the tar and cooling the gas to a suitable temperature.
- Gas Storage: The generated wood gas is typically stored in a gas bag or other storage system before being fed into the engine or other end-use applications.
Applications:
- Internal Combustion Engines: Wood gas generators can be connected to internal combustion engines to power vehicles, machinery, and generators. During World War II, wood gasifiers were used to fuel vehicles when gasoline was scarce.
- Heating Systems: Wood gas can be burned directly for heating purposes in boilers or furnaces.
- Electricity Generation: Wood gas generators can be integrated into power generation systems, producing electricity for off-grid or remote areas.
- Cooking: In some setups, wood gas can be utilized for cooking in stoves designed for gasification.
Advantages and Challenges: Advantages:
- Renewable Energy Source: Wood is a renewable resource, making wood gas a sustainable energy option.
- Waste Utilization: Wood gas generators can utilize wood waste, forestry residues, or other biomass materials, reducing the need for landfill disposal.
- Reduced Carbon Footprint: Wood gasification produces fewer greenhouse gas emissions compared to burning fossil fuels.
Challenges:
- Complexity: Wood gasification systems can be complex to design and operate effectively.
- Tar Formation: Tar produced during gasification can be a challenge, requiring proper filtration and maintenance.
- Energy Density: Wood gas has a lower energy density compared to some conventional fuels, affecting its efficiency in certain applications.
In conclusion, wood gas generators offer a versatile and sustainable solution for energy needs, particularly in situations where conventional fuels may be scarce or expensive. Advances in technology continue to improve the efficiency and reliability of wood gasification systems, making them a viable option in the quest for cleaner and more sustainable energy sources.
Gasification:
Gasification is a thermochemical process that involves converting solid or liquid carbonaceous materials, such as wood or biomass, into a gaseous fuel known as syngas or wood gas. This process occurs in a controlled environment with limited oxygen, preventing complete combustion. Gasification involves several stages, starting with pyrolysis, where the biomass breaks down into volatile components, and then these volatiles undergo further reactions to produce a combustible gas. The resulting syngas can be utilized as a clean and renewable fuel source for various applications, including powering internal combustion engines, generating electricity, and providing heat. Gasification technology plays a crucial role in sustainable energy solutions, offering a way to harness the energy content of biomass while minimizing environmental impact. The gasification process can be customized based on the feedstock used, making it a versatile and adaptable technology for addressing energy challenges in different contexts.
Syngas:
Syngas, short for synthesis gas, is a mixture of hydrogen, carbon monoxide, and other trace gases produced through the gasification of carbonaceous materials like wood, biomass, or coal. The term “syngas” is derived from its versatility, as it serves as a precursor for synthesizing various fuels and chemicals. In the context of a wood gas generator, syngas is the end product of the gasification process, where organic materials undergo pyrolysis and subsequent reactions to form this gaseous mixture. The composition of syngas can vary depending on the feedstock and gasification conditions. The hydrogen and carbon monoxide content makes syngas a valuable fuel for internal combustion engines, power generation, and industrial processes. Syngas can be cleaned and conditioned before use to remove impurities like tar and particulate matter, enhancing its suitability for different applications. Its versatility and renewable nature make syngas a promising component in the quest for sustainable and cleaner energy solutions.
Biomass:
Biomass refers to organic materials derived from living or recently living organisms, such as plants, animals, and microorganisms. In the context of wood gas generators, biomass primarily consists of woody materials, agricultural residues, forestry by-products, and other organic matter that can be used as a feedstock for gasification. Biomass is a renewable and sustainable energy source, as it harnesses the energy stored in organic materials through photosynthesis. In the gasification process, biomass undergoes thermal conversion, releasing volatile components that can be transformed into syngas, a versatile fuel. The use of biomass for energy production is attractive due to its potential to reduce dependence on fossil fuels, mitigate greenhouse gas emissions, and provide a means of utilizing waste materials. The wide variety of biomass sources, including wood, agricultural residues, and energy crops, adds to the flexibility and adaptability of biomass-based energy systems, contributing to a more diverse and sustainable energy portfolio.
Pyrolysis:
Pyrolysis is a key stage in the gasification process, occurring during the thermal conversion of biomass in the absence of sufficient oxygen. This thermochemical decomposition involves subjecting organic materials, such as wood or biomass, to high temperatures, typically in the range of 300 to 800 degrees Celsius. In the context of wood gas generators, pyrolysis initiates the breakdown of complex organic compounds in the biomass into simpler volatile components. As the biomass heats up, it releases gases, liquids, and solid char. The volatile gases produced during pyrolysis include carbon monoxide, hydrogen, methane, and various hydrocarbons. These gases become the building blocks for syngas in subsequent stages of the gasification process. Pyrolysis is a crucial step as it sets the stage for the controlled conversion of biomass into a usable and combustible gas. The conditions during pyrolysis, such as temperature and residence time, influence the composition and characteristics of the resulting syngas, making it an essential aspect of optimizing gasification systems for efficiency and performance.
Renewable Energy:
Renewable energy refers to energy derived from naturally occurring, replenishable sources that are not depleted when used. In the context of wood gas generators, the renewable aspect is associated with the use of biomass, particularly wood, as the primary feedstock for gasification. Unlike finite fossil fuels such as coal, oil, and natural gas, biomass is considered renewable because it can be replenished through sustainable forestry practices, crop cultivation, and waste utilization. Wood gas generators harness the energy stored in biomass to produce syngas, providing a clean and sustainable alternative to traditional fossil fuels. Renewable energy sources contribute to environmental sustainability by reducing greenhouse gas emissions, mitigating climate change, and minimizing dependence on non-renewable resources. Wood gas generators exemplify the utilization of renewable energy for power generation, emphasizing the importance of transitioning towards cleaner and more sustainable energy solutions to meet the growing global demand for power.
Internal Combustion:
Internal combustion refers to the process of burning a fuel inside an engine, where the combustion of fuel and oxidizer (usually air) takes place internally. In the context of wood gas generators, internal combustion engines play a pivotal role in converting the syngas produced through gasification into mechanical energy. Wood gas, composed mainly of carbon monoxide, hydrogen, and methane, serves as a viable fuel for internal combustion engines, such as those found in vehicles, generators, and other machinery. The internal combustion engine’s fundamental operation involves the controlled ignition and combustion of the fuel-air mixture, generating high-pressure gases that act on the engine’s moving parts, ultimately producing mechanical work. Wood gas as a fuel for internal combustion engines has historical significance, especially during periods of fuel scarcity, such as in World War II when vehicles were adapted to run on wood gas. Today, the integration of wood gas generators with internal combustion engines represents a sustainable and efficient way to utilize renewable resources for various applications.
Sustainability:
Sustainability refers to the ability to meet the needs of the present without compromising the ability of future generations to meet their own needs. In the context of wood gas generators, sustainability is a key consideration due to their reliance on biomass, a renewable resource. The use of wood as a feedstock for gasification aligns with sustainable practices, as forests can be managed responsibly to ensure a continuous and renewable supply of wood. Wood gas generators contribute to sustainability by providing an alternative to conventional fossil fuels, reducing dependence on finite resources and minimizing environmental impact. The process of gasification itself can be designed and operated with sustainability in mind, incorporating efficient technologies, minimizing waste, and utilizing by-products for additional purposes. As the world seeks cleaner and more environmentally friendly energy solutions, wood gas generators exemplify a sustainable approach to energy production, addressing both current energy needs and long-term environmental considerations.
Fuelwood:
Fuelwood refers to wood that is specifically harvested and utilized as a source of fuel for various energy applications. In the context of wood gas generators, fuelwood serves as the primary feedstock for the gasification process. Different types of wood, including hardwoods and softwoods, can be used as fuelwood, each with its own combustion characteristics. Fuelwood is chosen based on factors such as availability, energy content, and the specific requirements of the gasification system. Sustainable harvesting practices are crucial to ensure the long-term availability of fuelwood, emphasizing the importance of responsible forestry management. The use of fuelwood in wood gas generators is an example of harnessing the energy stored in biomass for renewable and clean energy production. This practice aligns with the concept of utilizing local resources efficiently, reducing dependence on non-renewable fuels, and contributing to a more sustainable and environmentally friendly energy landscape.
Gasification Chamber:
The gasification chamber is a critical component of a wood gas generator, where the actual process of converting solid biomass into syngas takes place. This chamber is designed to create an oxygen-limited environment to facilitate the controlled thermal breakdown of the biomass through a series of chemical reactions. The key phases within the gasification chamber include pyrolysis and subsequent gasification.
During pyrolysis, the biomass is heated in the absence of sufficient oxygen, leading to the release of volatile compounds. These volatile compounds, including gases like carbon monoxide, hydrogen, and methane, are then subjected to further reactions in the gasification zone, resulting in the formation of syngas.
The design and efficiency of the gasification chamber are crucial for optimizing the wood gas generation process. Factors such as temperature control, residence time, and the distribution of heat play a significant role in determining the composition and quality of the syngas produced. Advances in gasification technology continually strive to enhance the performance of the gasification chamber, aiming for improved efficiency, reduced tar production, and overall reliability in wood gas generators. The gasification chamber’s design is tailored to specific applications, ensuring versatility in utilizing various biomass feedstocks and adapting to different energy needs.
Tar Filtration:
Tar filtration is a crucial aspect of wood gas generator systems, focusing on the removal of tar and other impurities from the syngas produced during the gasification process. Tar is a complex mixture of organic compounds that can condense from the hot gases, potentially causing issues such as clogging, corrosion, and reduced efficiency in downstream equipment, including engines and heat exchangers.
The tar filtration system typically involves a series of filters or scrubbers designed to capture and separate tar from the syngas before it is directed to the end-use application. Various filtration techniques, such as cyclone separators, ceramic filters, and wet scrubbers, are employed to remove tar and particulate matter effectively.
Efficient tar filtration is essential for ensuring the smooth and reliable operation of wood gas generators. It not only helps protect downstream equipment but also contributes to the production of cleaner and more refined syngas. Advances in filtration technology continue to improve the effectiveness and longevity of tar filtration systems, enhancing the overall performance and sustainability of wood gas generators in diverse applications.
Energy Generation:
Energy generation, in the context of wood gas generators, refers to the process of converting the produced syngas into usable energy for various applications. Wood gas can be utilized to generate power through different mechanisms, including internal combustion engines, generators, and combined heat and power (CHP) systems.
Internal combustion engines, adapted to run on wood gas, combust the syngas within the engine cylinders, converting the chemical energy of the gas into mechanical energy. This mechanical energy is then harnessed to perform useful work, such as propelling vehicles, driving machinery, or generating electricity.
Generators connected to wood gas systems also play a crucial role in energy generation. As the wood gas combusts, it drives a generator’s turbine or alternator, converting the rotational energy into electrical power. This electricity can be used for on-site consumption or fed into the grid.
Combined heat and power (CHP) systems further optimize energy generation by capturing and utilizing the heat produced during the wood gas combustion process. This heat can be employed for space heating, water heating, or other industrial processes, enhancing the overall efficiency of the energy conversion.
Wood gas generators provide a sustainable and versatile solution for energy generation, contributing to a more diversified and environmentally friendly energy portfolio.
Wood Gasification System:
A wood gasification system is a complex and integrated set of components designed to convert solid biomass, typically wood, into syngas for energy generation. This system encompasses various stages, each serving a specific purpose in the overall gasification process.
- Fuel Hopper: The system begins with a fuel hopper where wood or biomass material is loaded. This is the starting point for the gasification process, ensuring a continuous supply of feedstock.
- Gasification Chamber or Reactor: The heart of the system, the gasification chamber or reactor, is where biomass undergoes thermal conversion. This controlled environment facilitates pyrolysis and subsequent gasification, resulting in the production of syngas.
- Filter System: To ensure the quality of the syngas, a filter system is employed to capture and remove impurities, such as tar and particulate matter. This step is crucial for protecting downstream equipment and optimizing syngas performance.
- Cooling System: The hot syngas produced needs to be cooled before it is utilized. A cooling system, which may include heat exchangers or cooling pipes, helps condense tar and lower the temperature of the syngas to a suitable level for downstream applications.
- Gas Storage: Once cleaned and cooled, the syngas is stored in a gas bag or other storage system. This provides a reservoir of gas that can be drawn upon as needed for energy generation.
- End-Use Applications: The final stage involves directing the syngas to various end-use applications. This could include powering internal combustion engines, generating electricity through generators, or providing heat for industrial processes.
Wood gasification systems are designed with efficiency, reliability, and adaptability in mind. Ongoing research and technological advancements continue to refine these systems, making them increasingly viable for a wide range of energy needs in a sustainable and environmentally conscious manner.
Carbon Monoxide:
Carbon monoxide (CO) is a colorless, odorless gas and a key component of the syngas produced in wood gas generators. In the context of wood gasification, carbon monoxide is one of the primary combustible gases formed during the gasification process, alongside hydrogen and methane.
The presence of carbon monoxide in syngas is significant for its role as a fuel. When used in internal combustion engines, carbon monoxide undergoes controlled combustion, producing carbon dioxide (CO2) and releasing energy. This energy conversion is fundamental to the operation of wood gas generators, where the chemical energy stored in biomass is transformed into mechanical work or electricity.
Despite its combustible nature, carbon monoxide is also a toxic gas. Proper handling and utilization of syngas are essential to minimize the release of unburned carbon monoxide into the environment. Gasification systems are designed with safety features and emissions control measures to ensure the efficient and clean use of carbon monoxide as a renewable fuel source.
Understanding the behavior and characteristics of carbon monoxide is crucial for optimizing wood gas generators, ensuring both energy efficiency and environmental responsibility in the utilization of this important component of syngas.
Gas Storage:
Gas storage is a critical component within a wood gas generator system, serving as a reservoir for the produced syngas before it is directed to its end-use applications. This component plays a crucial role in ensuring a continuous and reliable supply of gas, particularly in situations where demand may fluctuate or where a steady flow of syngas is necessary for optimal performance.
There are various methods of gas storage in wood gas generator systems:
- Gas Bags: Flexible gas bags or storage balloons are commonly used to store syngas. These bags expand as gas is produced and contract as it is consumed, providing a dynamic storage solution.
- Gas Holders: These are rigid containers that can store a certain volume of syngas. The gas holder’s position can be adjusted to control the pressure and flow of gas, ensuring a consistent supply.
- Gas Tanks or Cylinders: In some applications, syngas may be stored in compressed gas tanks or cylinders. This method is suitable for smaller-scale or portable wood gas generator systems.
Gas storage is crucial for balancing the intermittent nature of gas production in a wood gas generator with the often continuous demand for energy. It allows for smoother operation and ensures that energy needs can be met consistently, making wood gas systems more adaptable to various applications and settings.
Alternative Fuel:
Wood gas, produced through the gasification of wood or biomass, is considered an alternative fuel with significant potential for addressing energy challenges in a sustainable and environmentally friendly manner. As a renewable resource, wood serves as a carbon-neutral fuel source, as the carbon dioxide released during combustion is offset by the carbon absorbed during the growth of the biomass.
Wood gas as an alternative fuel offers several advantages:
- Renewability: Wood is a replenishable resource that can be harvested sustainably, making wood gas a renewable energy option.
- Reduced Greenhouse Gas Emissions: Compared to fossil fuels, the combustion of wood gas produces lower levels of greenhouse gases, contributing to climate change mitigation.
- Waste Utilization: Wood gas generators can utilize wood waste, forestry residues, and other biomass materials, reducing the environmental impact of waste disposal.
- Energy Security: Wood gas provides a decentralized and locally available energy source, contributing to energy security by reducing dependence on centralized fossil fuel infrastructure.
- Versatility: Wood gas can be used in various applications, including internal combustion engines, electricity generation, and heating, offering a versatile alternative to traditional fuels.
The exploration of alternative fuels like wood gas aligns with the global effort to transition towards more sustainable and cleaner energy sources, diversifying the energy mix and reducing reliance on finite fossil fuels. Wood gas generators play a role in promoting energy independence, environmental stewardship, and a resilient energy future.
EMS Power Machines
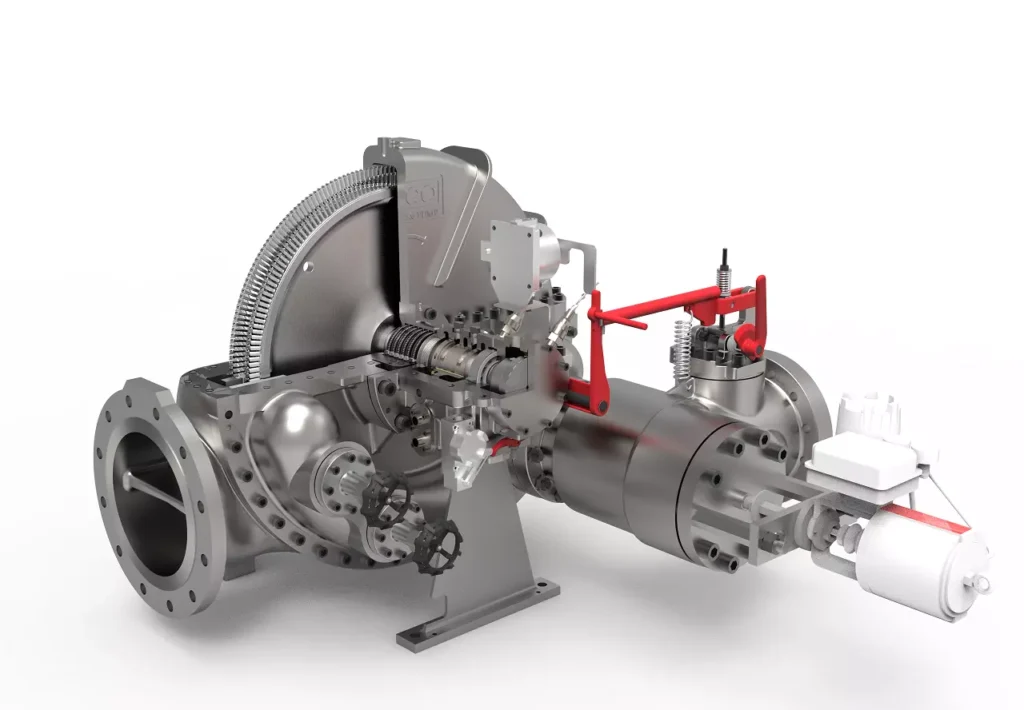
We design, manufacture and assembly Power Machines such as – diesel generators, electric motors, vibration motors, pumps, steam engines and steam turbines
EMS Power Machines is a global power engineering company, one of the five world leaders in the industry in terms of installed equipment. The companies included in the company have been operating in the energy market for more than 60 years.
EMS Power Machines manufactures steam turbines, gas turbines, hydroelectric turbines, generators, and other power equipment for thermal, nuclear, and hydroelectric power plants, as well as for various industries, transport, and marine energy.
EMS Power Machines is a major player in the global power industry, and its equipment is used in power plants all over the world. The company has a strong track record of innovation, and it is constantly developing new and improved technologies.
Here are some examples of Power Machines’ products and services:
- Steam turbines for thermal and nuclear power plants
- Gas turbines for combined cycle power plants and industrial applications
- Hydroelectric turbines for hydroelectric power plants
- Generators for all types of power plants
- Boilers for thermal power plants
- Condensers for thermal power plants
- Reheaters for thermal power plants
- Air preheaters for thermal power plants
- Feedwater pumps for thermal power plants
- Control systems for power plants
- Maintenance and repair services for power plants
EMS Power Machines is committed to providing its customers with high-quality products and services. The company has a strong reputation for reliability and innovation. Power Machines is a leading provider of power equipment and services, and it plays a vital role in the global power industry.
EMS Power Machines, which began in 1961 as a small factory of electric motors, has become a leading global supplier of electronic products for different segments. The search for excellence has resulted in the diversification of the business, adding to the electric motors products which provide from power generation to more efficient means of use.