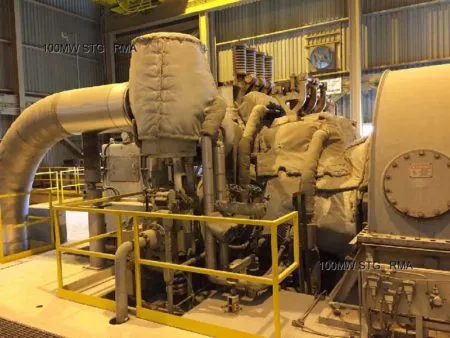
Steam Turbines in Power Generation: Steam turbines are mechanical devices that convert thermal energy from pressurized steam into mechanical energy through the principles of thermodynamics and fluid mechanics. This mechanical energy is typically used to drive electrical generators, pumps, compressors, or other machinery. Steam turbines are a vital component in industries such as power generation, manufacturing, and marine propulsion due to their efficiency and reliability. The operation of a steam turbine is based on the expansion of steam, which undergoes a controlled pressure and temperature drop as it passes through a series of stationary and rotating blades. The stationary blades, often referred to as nozzles, direct and accelerate the steam flow, while the rotating blades, mounted on a rotor, convert the kinetic energy of the steam into rotational energy. This rotation is then transmitted to a shaft, which can perform various tasks, most commonly the generation of electricity.
Steam turbines come in various types, depending on their design and intended application. The two primary classifications are impulse turbines and reaction turbines. In an impulse turbine, steam is expanded entirely in the nozzles, converting the thermal energy into kinetic energy before it strikes the moving blades. The blades are shaped to absorb this kinetic energy and convert it into rotational motion without any significant pressure drop across them. Reaction turbines, on the other hand, involve a continuous pressure drop across both the stationary and moving blades. In these turbines, the moving blades act as nozzles themselves, and the reaction force generated by the expanding steam provides additional torque to the rotor. This fundamental difference in operation influences the design and performance characteristics of each type.
The efficiency of a steam turbine is a critical consideration in its design and operation. It is influenced by factors such as the thermodynamic properties of the steam, the quality of the blades and their aerodynamics, the degree of condensation in the exhaust steam, and the overall system configuration. To maximize efficiency, modern steam turbines are often designed with multiple stages, allowing for the gradual extraction of energy from the steam as it expands. These stages can be arranged in high-pressure, intermediate-pressure, and low-pressure sections, each optimized for specific conditions. In some cases, reheat cycles are incorporated, where partially expanded steam is returned to the boiler for reheating before being sent back to the turbine. This reduces the moisture content of the steam in the later stages, improving efficiency and reducing blade erosion.
Steam turbines are also categorized based on their exhaust conditions, such as condensing turbines, back-pressure turbines, and extraction turbines. Condensing turbines are used when maximum energy extraction is desired, as they operate with the exhaust steam being condensed into liquid form in a condenser, creating a vacuum that enhances efficiency. Back-pressure turbines, by contrast, exhaust steam at a higher pressure for use in industrial processes or district heating, sacrificing some efficiency for the benefit of cogeneration. Extraction turbines combine features of both, allowing a portion of the steam to be extracted at an intermediate pressure for industrial or heating purposes while the remainder continues to the condensing section.
The development of steam turbines has played a significant role in the advancement of power generation technologies. Their ability to handle large capacities, operate at high efficiencies, and integrate seamlessly with various energy sources, such as fossil fuels, nuclear reactors, and renewable systems like concentrated solar power, makes them indispensable in modern energy systems. Additionally, advances in materials science, blade design, and computational fluid dynamics have allowed for the creation of turbines capable of withstanding extreme temperatures and pressures, further enhancing their performance and durability. Overall, steam turbines remain a cornerstone of industrial and energy systems, exemplifying the efficient utilization of thermal energy to meet the demands of modern society.
The historical development of steam turbines traces back to the late 19th century when they were first introduced as a more efficient alternative to reciprocating steam engines. Sir Charles Parsons is often credited with pioneering the modern steam turbine, having invented the first practical design in 1884. His turbine was initially used for generating electricity and demonstrated superior efficiency, smoother operation, and higher reliability compared to steam engines, which were characterized by their bulky design, limited speed, and maintenance challenges. Parsons’ invention laid the foundation for the rapid expansion of electricity generation, enabling the large-scale deployment of centralized power plants that continue to dominate global energy infrastructure.
Over time, steam turbines evolved to meet increasingly complex demands across diverse applications. In power generation, they became central to both thermal and nuclear power plants, operating as the primary mechanism for converting heat into mechanical energy and subsequently into electricity. Fossil-fueled plants rely on burning coal, natural gas, or oil to produce steam at high pressure and temperature, which is then expanded in turbines. In nuclear plants, the steam is generated by transferring heat from the reactor core, where nuclear fission occurs, to a secondary loop. In both cases, steam turbines operate with high efficiency, particularly when combined with modern enhancements like supercritical and ultra-supercritical steam cycles, which push operational parameters to unprecedented levels of temperature and pressure.
Steam turbines are also essential in cogeneration systems, where they are used to optimize the utilization of energy by producing both electricity and thermal energy for heating or industrial processes. In these systems, back-pressure or extraction turbines play a vital role in balancing energy production with thermal demand, making them highly effective for industries such as chemical processing, food production, and pulp and paper manufacturing. Furthermore, steam turbines are widely used in marine propulsion, especially in large ships such as naval vessels and commercial liners, where their ability to deliver high power with low vibration and noise is highly advantageous. In this context, steam turbines are often combined with reduction gear systems to provide the precise control needed for propulsion.
The operational principles of steam turbines rely heavily on the thermodynamic cycle known as the Rankine cycle. In this cycle, water is heated in a boiler to produce high-pressure steam, which is then expanded in the turbine to produce work. After expansion, the steam is either condensed back into water in a condenser or utilized for secondary purposes, such as industrial heating, before being pumped back to the boiler to complete the cycle. The performance of this cycle is influenced by factors like the steam temperature and pressure, the efficiency of the turbine, and the effectiveness of the condenser. Advances in engineering have led to the development of combined cycles, where steam turbines are paired with gas turbines to enhance overall efficiency. In such systems, the exhaust gases from a gas turbine are used to produce steam, which then powers a steam turbine, achieving efficiencies that can exceed 60%.
The materials used in the construction of steam turbines are carefully selected to withstand the harsh conditions of high temperatures, pressures, and the erosive effects of steam. Blades, rotors, and casings are typically made from high-strength alloys, often containing chromium, nickel, and molybdenum to provide resistance against corrosion, creep, and fatigue. Precision engineering and advanced manufacturing techniques, such as 3D printing and laser welding, have further enhanced the durability and performance of turbine components. Additionally, the integration of advanced control systems allows for precise monitoring and optimization of turbine operation, ensuring maximum efficiency and reliability.
Environmental considerations have also driven significant innovations in steam turbine technology. As concerns about carbon emissions and climate change grow, steam turbines are increasingly integrated into renewable energy systems. For instance, concentrated solar power plants use steam turbines to convert thermal energy from solar collectors into electricity, while geothermal plants rely on steam extracted from underground reservoirs. In addition, the development of carbon capture and storage (CCS) systems aims to reduce emissions from fossil-fueled plants by capturing CO2 from the exhaust gases before it is released into the atmosphere. These advancements demonstrate the adaptability of steam turbines to changing energy landscapes and their continued relevance in a sustainable future.
The adaptability of steam turbines to various energy applications underscores their role as one of the most versatile and enduring technologies in modern industry. In addition to their use in power generation, industrial processes, and marine propulsion, steam turbines have also become integral to technological advancements in energy efficiency and grid stability. For instance, steam turbines are often deployed in combined heat and power (CHP) systems, which maximize resource efficiency by simultaneously generating electricity and capturing usable heat for industrial or residential applications. This dual-purpose functionality ensures that the energy potential of the fuel or steam source is utilized to the fullest extent, minimizing waste and improving overall sustainability.
The flexibility of steam turbines is also evident in their ability to operate under varying conditions and integrate with a wide range of fuel sources. From traditional fossil fuels like coal and natural gas to more modern and renewable sources such as biomass, geothermal energy, and solar thermal power, steam turbines can be adapted to efficiently harness the energy produced. In biomass plants, for example, organic materials such as wood, agricultural waste, or municipal solid waste are combusted to generate steam, which drives a turbine to produce electricity. Similarly, in geothermal power plants, steam or hot water extracted from the Earth’s subsurface is used to generate power, with steam turbines functioning as the core energy conversion device. This adaptability makes them a critical component in the global transition to cleaner and more sustainable energy systems.
In addition to their widespread applications, steam turbines are also notable for their scalability. They can be designed to handle power outputs ranging from a few kilowatts in small industrial applications to hundreds of megawatts in large utility-scale power plants. This scalability enables them to meet the demands of diverse operational requirements, from powering a single industrial facility to providing electricity for entire cities. Furthermore, advancements in modular design have allowed for the rapid deployment and customization of steam turbine systems, making them particularly attractive for remote locations, temporary installations, or regions with fluctuating energy demands.
One of the most remarkable advancements in steam turbine technology is the development of supercritical and ultra-supercritical turbines, which operate at conditions exceeding the critical point of water. At these extreme conditions, water transitions into a supercritical fluid, which does not have distinct liquid and gas phases. This enables higher thermal efficiencies by allowing the turbine to extract more energy from the steam. Supercritical and ultra-supercritical turbines are particularly advantageous in reducing fuel consumption and emissions in coal-fired power plants, making them a cornerstone of efforts to improve the environmental performance of fossil-fueled energy systems. These turbines often operate at temperatures exceeding 600°C and pressures of over 30 MPa, requiring advanced materials and engineering techniques to ensure their reliability and longevity.
Maintenance and reliability are critical aspects of steam turbine operation, given the demanding conditions under which they function. Regular maintenance is essential to ensure the efficient and safe operation of turbines, as even minor issues can lead to significant losses in performance or, in extreme cases, catastrophic failure. Predictive maintenance techniques, powered by digital monitoring systems and advanced analytics, have revolutionized how steam turbines are maintained. By collecting and analyzing data on temperature, vibration, pressure, and other parameters, operators can identify potential issues before they become critical, minimizing downtime and repair costs. Digital twin technology, which creates a virtual replica of a turbine, further enhances predictive maintenance by enabling real-time simulations and performance optimization.
The integration of steam turbines with modern control and automation systems has also significantly improved their operational efficiency and responsiveness. Advanced control algorithms can dynamically adjust turbine settings to match changing load conditions, optimize fuel usage, and maintain system stability. This is particularly important in power grids that incorporate a high share of renewable energy sources, such as wind and solar, where output can be intermittent and unpredictable. By acting as a flexible and reliable energy source, steam turbines help balance the grid and ensure a stable electricity supply.
Looking to the future, ongoing research and development efforts aim to further enhance the efficiency, durability, and sustainability of steam turbine technology. Innovations such as advanced blade designs, coatings to reduce erosion and corrosion, and the use of artificial intelligence for operational optimization hold significant promise. Additionally, the exploration of alternative working fluids, such as supercritical CO2, has the potential to further improve the thermodynamic efficiency of turbine systems while reducing environmental impacts. As the energy landscape continues to evolve, steam turbines are likely to remain a cornerstone of energy conversion technologies, adapting to new challenges and opportunities while maintaining their position as a proven and reliable solution.
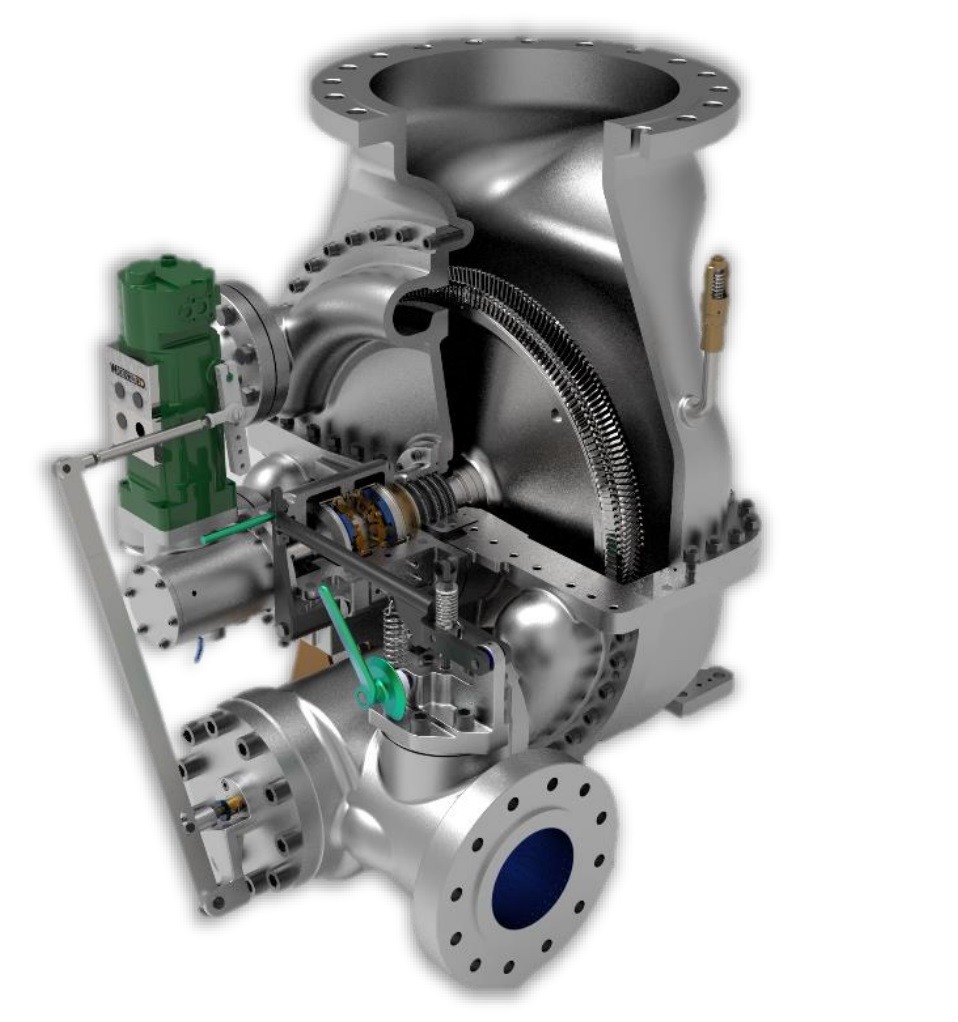
The role of steam turbines in shaping the global energy landscape cannot be overstated. Their contribution spans over a century of technological advancements and remains crucial as industries strive for higher efficiencies, reduced emissions, and sustainable energy solutions. One of the key factors that ensure the continued relevance of steam turbines is their ability to integrate with hybrid and emerging energy systems. In hybrid configurations, steam turbines are paired with other energy conversion technologies, such as gas turbines or renewable energy systems, to create combined cycle or multi-input power plants. These hybrid systems maximize efficiency by utilizing waste heat or renewable energy sources, reducing dependency on fossil fuels, and ensuring stable power generation.
In combined cycle power plants, steam turbines operate in conjunction with gas turbines to achieve exceptionally high efficiencies. The process begins with the combustion of natural gas in a gas turbine, generating electricity while producing hot exhaust gases. These exhaust gases are then routed through a heat recovery steam generator (HRSG), which uses the waste heat to produce steam. The steam is subsequently expanded in a steam turbine to generate additional electricity. This two-stage energy conversion process significantly increases the overall efficiency of the power plant, with some combined cycle systems achieving thermal efficiencies exceeding 60%. The scalability and adaptability of such systems make them an attractive solution for both large-scale utility plants and smaller industrial facilities.
Renewable energy integration is another area where steam turbines demonstrate their versatility. Concentrated solar power (CSP) plants, for instance, use arrays of mirrors or lenses to focus sunlight onto a receiver, which heats a working fluid to generate steam. This steam is then expanded in a turbine to produce electricity. Unlike photovoltaic systems, CSP plants can incorporate thermal energy storage, allowing them to continue generating electricity even when sunlight is unavailable. This capability aligns with the growing demand for renewable energy systems that can provide reliable and consistent power output. Similarly, steam turbines are integral to geothermal energy systems, where steam or hot water is extracted from geothermal reservoirs and used to drive turbines, providing a clean and sustainable energy source with minimal environmental impact.
The adoption of steam turbines in the emerging hydrogen economy also presents exciting opportunities. Hydrogen can be used as a clean fuel to produce high-temperature steam for turbines, either through direct combustion or in combination with fuel cells. In addition, hydrogen can play a role in decarbonizing existing steam turbine applications by blending it with natural gas or other fuels. This transition to hydrogen-based systems is expected to accelerate as industries and governments invest in green hydrogen production, infrastructure, and utilization.
In the context of industrial processes, steam turbines continue to serve as essential components in sectors such as oil and gas, chemicals, pulp and paper, and steel manufacturing. These industries rely on turbines not only for power generation but also for driving mechanical equipment such as compressors, pumps, and blowers. By utilizing waste heat from industrial processes to produce steam, these facilities can improve energy efficiency, reduce operational costs, and minimize environmental impact. The ability to tailor steam turbines to specific process requirements further enhances their utility and effectiveness in diverse industrial applications.
The environmental benefits of steam turbines extend beyond their role in energy efficiency. Modern turbine systems are designed to minimize emissions, reduce water consumption, and operate with lower noise levels. Innovations such as dry cooling systems and advanced condensers have significantly reduced the water requirements of steam turbines, addressing concerns about water scarcity in arid regions. Additionally, turbine designs have been optimized to operate with minimal vibration and noise, making them suitable for installations in urban or noise-sensitive environments.
Digitalization is reshaping the operation and management of steam turbines, bringing them into the era of Industry 4.0. The integration of sensors, data analytics, and cloud-based monitoring systems has enabled real-time performance tracking and predictive maintenance. Operators can now detect anomalies, optimize energy output, and extend the lifespan of turbine components through data-driven insights. Artificial intelligence and machine learning algorithms further enhance these capabilities, offering predictive models that can simulate complex operational scenarios and provide actionable recommendations for improving efficiency and reliability.
Looking forward, the evolution of steam turbine technology will likely focus on achieving even greater efficiency and sustainability. Research into advanced thermodynamic cycles, such as the Kalina cycle and the organic Rankine cycle, holds promise for improving energy recovery and enabling turbines to operate with alternative working fluids. Advances in material science, including the development of ceramics and high-temperature alloys, will allow turbines to withstand increasingly extreme operating conditions, further enhancing performance and durability. These innovations will ensure that steam turbines remain a cornerstone of energy conversion technologies, capable of meeting the challenges of a rapidly changing energy landscape.
As global efforts to combat climate change intensify, steam turbines are poised to play a pivotal role in the transition to a low-carbon future. Their ability to integrate seamlessly with renewable energy systems, hybrid configurations, and advanced technologies makes them a key enabler of sustainable and efficient energy solutions. Whether in large-scale power plants, industrial processes, or emerging energy systems, steam turbines will continue to drive progress, demonstrating their enduring value as a reliable, adaptable, and forward-looking technology.
Steam turbine overview
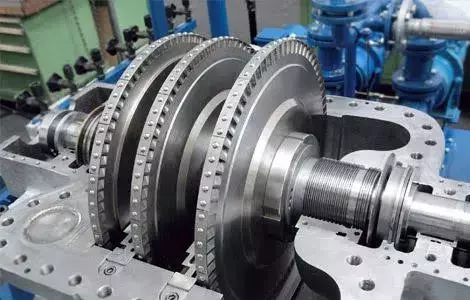
Steam turbines are complex mechanical devices designed to convert the thermal energy of steam into mechanical energy, typically in the form of rotational motion. This mechanical energy is then harnessed for a variety of applications, with electricity generation being the most common. The operation of a steam turbine is grounded in fundamental principles of thermodynamics, where high-pressure, high-temperature steam is expanded through a series of stationary and rotating blades. The stationary blades direct and accelerate the flow of steam, while the rotating blades capture the kinetic energy of the steam, converting it into torque that drives the turbine’s shaft. This seamless conversion process is what makes steam turbines a critical component in energy systems, industrial processes, and transportation applications.
The design and functionality of steam turbines have evolved over more than a century, leading to a wide range of configurations optimized for specific tasks. Broadly speaking, steam turbines are classified into two primary categories based on the way they extract energy from steam: impulse turbines and reaction turbines. Impulse turbines rely on the principle of kinetic energy transfer, where high-velocity steam jets strike the rotating blades, causing them to spin. In this design, the entire pressure drop of the steam occurs in the stationary nozzles, and the moving blades primarily capture the velocity of the steam. Reaction turbines, by contrast, operate on the principle of both pressure and velocity change. The blades in these turbines are shaped like small nozzles, allowing the steam to expand and accelerate as it passes through them, generating a reaction force that contributes to the rotor’s rotation. Each type has its unique advantages and is selected based on efficiency requirements, operational conditions, and application needs.
Steam turbines are further categorized based on their exhaust conditions and intended applications. Condensing turbines, for instance, are widely used in power plants where maximum energy extraction from steam is the priority. These turbines operate with exhaust steam directed into a condenser, where it is cooled and condensed back into water, creating a vacuum that enhances energy efficiency. Back-pressure turbines, on the other hand, exhaust steam at a higher pressure, which is then utilized in industrial processes, district heating, or other thermal applications. These turbines are often favored in cogeneration systems, where both electricity and heat are required. Extraction turbines represent a hybrid configuration, where steam is tapped off at one or more intermediate stages for industrial or heating purposes, while the remaining steam continues through the turbine to produce additional power.
The efficiency of a steam turbine is a critical parameter and depends on several factors, including the inlet steam conditions, the turbine design, and the overall system configuration. High-pressure and high-temperature steam typically results in higher efficiency, as it allows for greater energy extraction during expansion. To further enhance efficiency, modern steam turbines often incorporate advanced design features such as multi-stage expansion, reheating, and regenerative feedwater heating. Multi-stage turbines gradually reduce the pressure and temperature of steam across multiple stages, extracting more energy in the process. Reheating involves sending partially expanded steam back to the boiler to be reheated before continuing through the turbine, reducing moisture content and minimizing erosion in the later stages. Regenerative feedwater heating utilizes steam extracted from intermediate stages to preheat the boiler feedwater, improving the overall thermodynamic cycle efficiency.
Applications of steam turbines extend far beyond electricity generation. In industrial settings, they are used to drive mechanical equipment such as compressors, pumps, and fans, leveraging waste heat from processes to generate steam. They are also crucial in industries like oil refining, chemical manufacturing, and pulp and paper production, where combined heat and power systems improve energy efficiency and reduce costs. In marine propulsion, steam turbines have been employed in large vessels, particularly during the early to mid-20th century, offering reliable and powerful propulsion systems. While their use in this area has declined with the advent of diesel engines, steam turbines remain relevant in naval vessels and specialized ships.
In terms of operational principles, steam turbines are most commonly associated with the Rankine cycle, a thermodynamic cycle that describes the process of heat-to-work conversion. The cycle begins with water being heated in a boiler to produce high-pressure steam. The steam is then expanded in the turbine, where its thermal and kinetic energy are converted into mechanical energy. After leaving the turbine, the steam is either condensed into water or utilized in downstream applications before being returned to the boiler. Enhancements such as the use of supercritical steam—steam at conditions above its critical point where it behaves as a single-phase fluid—have enabled higher efficiencies in modern power plants by allowing turbines to operate at extreme temperatures and pressures.
The materials and construction of steam turbines are carefully engineered to withstand the demanding conditions under which they operate. High-strength alloys are used to ensure resistance to thermal stress, creep, and corrosion. Advances in material science, including the development of coatings and treatments, have further extended the lifespan and reliability of turbine components. Modern manufacturing techniques such as precision casting, 3D printing, and advanced welding have also contributed to the production of highly efficient and durable turbines.
Environmental considerations have increasingly influenced the development and application of steam turbines. As industries and governments prioritize reducing carbon emissions and improving energy sustainability, steam turbines have adapted to integrate with renewable energy systems and cleaner fuel sources. For example, in geothermal power plants, steam turbines use steam generated from natural geothermal reservoirs to produce electricity with minimal greenhouse gas emissions. Similarly, concentrated solar power plants employ steam turbines to convert solar heat into electricity, often with integrated thermal energy storage systems to ensure consistent output. The use of biomass as a fuel source for generating steam has further enhanced the role of turbines in renewable energy applications.
Digitalization and automation have transformed the operation and maintenance of steam turbines, enabling greater efficiency and reliability. Advanced monitoring systems equipped with sensors collect real-time data on parameters such as temperature, pressure, and vibration. This data is analyzed using predictive analytics and artificial intelligence to identify potential issues before they result in failures. Digital twin technology, which creates virtual models of turbines, allows operators to simulate and optimize performance under various operating conditions. These innovations reduce downtime, extend equipment life, and improve overall system performance.
Looking ahead, the future of steam turbines lies in continued innovation and integration with evolving energy systems. Research into alternative working fluids, such as supercritical carbon dioxide, promises to unlock new levels of efficiency and reduce environmental impacts. Advances in blade design, including aerodynamic optimization and the use of advanced materials, will further enhance turbine performance and reliability. As the global energy landscape shifts toward decarbonization and renewable integration, steam turbines will remain a cornerstone technology, demonstrating their enduring versatility and importance in achieving sustainable energy solutions.
The evolution of steam turbines is closely intertwined with the ongoing transition to cleaner and more sustainable energy systems. As the world moves away from traditional fossil fuels and embraces renewable energy sources, steam turbines have demonstrated their ability to adapt and thrive in this changing landscape. One of the most significant trends in this context is the increasing deployment of hybrid systems that combine steam turbines with other technologies to achieve higher efficiencies and lower emissions. For instance, integrated gasification combined cycle (IGCC) plants use gas turbines and steam turbines in tandem, with syngas derived from coal or biomass serving as the fuel source. The waste heat from the gas turbine is utilized to generate steam, which powers a steam turbine, resulting in a highly efficient process with reduced environmental impact.
Another area of innovation is the use of steam turbines in energy storage and grid stabilization. As renewable energy sources like wind and solar become more prevalent, managing their intermittent output has become a critical challenge. Steam turbines can play a role in thermal energy storage systems, where excess electricity is used to generate heat that is stored in insulated reservoirs. When electricity demand rises, the stored heat is used to produce steam, which drives a turbine to generate electricity. This approach not only enhances grid flexibility but also allows for more efficient utilization of renewable energy resources. Similarly, steam turbines are used in load-following applications, where they adjust their output to match fluctuating grid demands, providing a reliable and stable energy supply.
In the industrial sector, steam turbines are increasingly integrated into waste heat recovery systems, where they harness heat from exhaust gases or other high-temperature processes to produce steam. This approach improves overall energy efficiency and reduces the carbon footprint of industrial operations. For example, in steel manufacturing, the heat generated during the production process can be captured and used to produce steam for a turbine, generating electricity or providing mechanical power for auxiliary systems. This not only reduces reliance on external energy sources but also lowers operational costs, making it an attractive option for energy-intensive industries.
The development of advanced control systems has further enhanced the performance and efficiency of steam turbines. Modern turbines are equipped with sophisticated control algorithms that monitor and optimize various parameters, such as steam flow, temperature, and pressure. These systems ensure that the turbine operates at its peak efficiency under varying conditions, minimizing fuel consumption and maximizing energy output. Additionally, automated startup and shutdown procedures have improved the operational flexibility of steam turbines, enabling them to respond more quickly to changes in demand or system requirements. This is particularly important in power grids with a high share of renewable energy, where rapid adjustments are often necessary to maintain stability.
The integration of artificial intelligence (AI) and machine learning (ML) technologies is also transforming how steam turbines are monitored and maintained. AI-powered diagnostic tools analyze operational data in real-time to identify potential issues, predict maintenance needs, and optimize performance. For example, vibration analysis and thermal imaging can detect early signs of wear or damage in turbine components, allowing operators to address problems before they escalate. ML algorithms can also simulate different operating scenarios, helping engineers to design more efficient turbines and refine their control strategies. These advancements not only improve reliability and reduce downtime but also lower maintenance costs and extend the lifespan of turbine systems.
Looking toward the future, research into alternative thermodynamic cycles and working fluids is expected to drive further improvements in steam turbine technology. The organic Rankine cycle (ORC), for instance, uses organic fluids with lower boiling points than water, making it suitable for low-temperature heat sources such as geothermal energy, waste heat, or biomass. ORC systems are particularly advantageous in small-scale applications, where conventional steam turbines may not be cost-effective or efficient. Another promising development is the use of supercritical carbon dioxide (sCO₂) as a working fluid, which offers higher thermal efficiency and a smaller physical footprint compared to traditional steam systems. sCO₂ turbines operate at supercritical conditions, where carbon dioxide exists as a dense fluid, enabling more efficient energy conversion and reduced environmental impact.
The role of steam turbines in nuclear power is also evolving, with advancements in reactor designs and steam cycle efficiency. In particular, small modular reactors (SMRs) are emerging as a promising technology for providing flexible and scalable nuclear power. These reactors are designed to produce lower amounts of steam compared to traditional nuclear plants, making them well-suited for integration with advanced steam turbine systems. Furthermore, research into next-generation nuclear technologies, such as molten salt reactors and high-temperature gas reactors, is expected to open new possibilities for steam turbine applications, leveraging their proven reliability and efficiency in novel energy systems.
Sustainability remains a central focus for the future of steam turbines. Efforts to decarbonize power generation are driving innovations in fuel sources, such as the use of hydrogen or ammonia to produce steam with zero carbon emissions. Additionally, carbon capture and storage (CCS) technologies are being integrated into steam turbine systems to reduce emissions from fossil-fueled power plants. By capturing CO₂ from exhaust gases and storing it underground, these systems mitigate the environmental impact of energy production while allowing existing infrastructure to continue operating during the transition to renewable energy.
In summary, steam turbines represent a cornerstone of energy conversion technology, offering unmatched versatility, efficiency, and adaptability. Their ability to integrate with renewable energy systems, hybrid configurations, and advanced technologies ensures their continued relevance in a rapidly changing energy landscape. As the world faces growing challenges related to climate change, energy security, and resource efficiency, steam turbines will remain a key enabler of sustainable and innovative energy solutions. Through ongoing research, development, and digitalization, steam turbines are poised to meet the demands of the future, driving progress across power generation, industrial processes, and beyond.
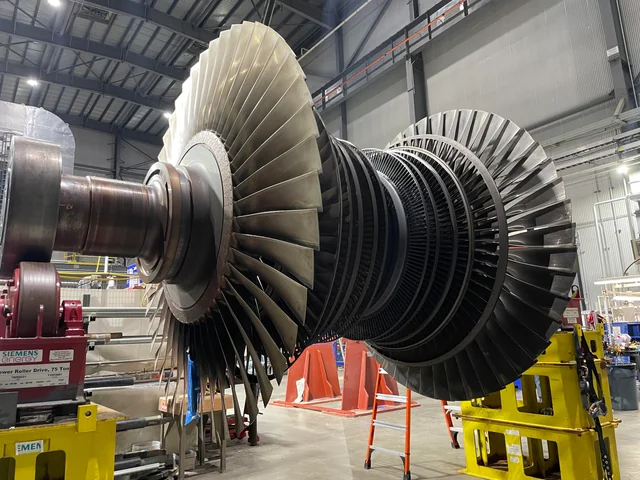
The future of steam turbines is not just about maintaining their current relevance but actively pushing the boundaries of what they can achieve in a decarbonizing, efficiency-driven, and innovation-focused world. Among the many exciting possibilities is the increasing synergy between steam turbines and emerging energy technologies, including hydrogen, ammonia, and advanced renewables.
Hydrogen, often described as the fuel of the future, is set to transform the energy landscape, and steam turbines are positioned to play a vital role in this transformation. Hydrogen can be combusted in a boiler to produce steam for traditional steam turbines, offering a zero-carbon energy source if the hydrogen is produced through electrolysis powered by renewable energy. Additionally, hydrogen could be integrated into existing fossil-fuel-based systems as a blending fuel, enabling a gradual transition to greener energy production. Research into optimizing steam turbines for hydrogen applications is focusing on materials that can handle the unique thermal and chemical properties of hydrogen combustion, as well as on improving the overall efficiency of the steam cycle in such setups.
Ammonia, another promising energy carrier, is also gaining attention as a potential fuel for steam generation. Unlike hydrogen, ammonia can be transported and stored more easily, making it an attractive option for long-term energy storage and international energy trade. Steam turbines operating on ammonia-based systems will require tailored designs to accommodate the combustion characteristics and emissions profile of ammonia, but the potential for a sustainable, carbon-neutral energy system is substantial.
In the realm of renewable energy, the role of steam turbines continues to expand. Concentrated solar power (CSP) plants, which rely on mirrors or lenses to focus sunlight and generate high-temperature steam, are becoming more efficient and scalable with innovations in thermal energy storage. The integration of molten salt storage systems allows CSP plants to produce steam for turbines even during periods of low sunlight, providing a stable and dispatchable source of renewable electricity. This ability to deliver consistent power complements intermittent renewable sources like wind and solar photovoltaic, enhancing the resilience and reliability of the grid.
Geothermal energy, another area where steam turbines are crucial, is being reimagined with advanced drilling technologies and enhanced geothermal systems (EGS). These innovations allow access to geothermal reservoirs in regions where traditional geothermal methods are not viable. Steam turbines adapted for these systems are designed to operate efficiently at lower temperatures and pressures, making geothermal energy a more versatile and widely applicable solution. Moreover, binary cycle geothermal plants, which use secondary working fluids to generate steam in closed-loop systems, are expanding the scope of geothermal energy production to lower-temperature resources.
One of the most transformative aspects of the steam turbine industry is its increasing reliance on digital tools and data-driven solutions. The rise of digital twins—virtual replicas of physical assets—has revolutionized the way steam turbines are monitored, maintained, and optimized. These digital models allow operators to simulate various operating conditions, predict wear and tear, and test potential upgrades or modifications without risking downtime or damage to the actual turbine. The integration of real-time data from sensors enhances the accuracy and utility of digital twins, enabling proactive maintenance strategies that minimize unplanned outages and extend the operational life of turbines.
Artificial intelligence (AI) and machine learning (ML) are further enhancing the capabilities of steam turbine systems. Predictive analytics driven by AI can identify patterns and anomalies in performance data, allowing for early detection of potential issues and enabling more effective decision-making. For example, AI can optimize the scheduling of maintenance activities, reducing costs and improving availability. Additionally, machine learning algorithms can be used to fine-tune turbine operation, dynamically adjusting parameters such as blade angles or steam flow rates to maximize efficiency under changing load conditions.
The materials used in steam turbines are also undergoing significant advancements. Next-generation alloys and composites are being developed to withstand the extreme temperatures and pressures of modern high-efficiency systems. These materials not only improve the durability and performance of turbines but also enable them to operate under more demanding conditions, such as those required by supercritical and ultra-supercritical steam cycles. Coating technologies and surface treatments are enhancing resistance to corrosion and erosion, further extending the lifespan of turbine components.
Environmental considerations are driving the adoption of closed-loop systems and water-saving technologies in steam turbines. Dry cooling systems, which use air instead of water to condense steam, are becoming more prevalent in regions where water scarcity is a concern. These systems reduce the environmental impact of steam turbines and make them viable in arid climates. Furthermore, advancements in condenser design and heat exchanger technology are improving the overall thermal efficiency of steam cycles while minimizing water usage.
As the energy sector continues to prioritize decarbonization, carbon capture and storage (CCS) technologies are being integrated into steam turbine systems. By capturing CO₂ emissions from power plants and industrial facilities and storing them underground or using them in industrial processes, CCS enables the continued use of fossil fuels with a significantly reduced carbon footprint. Steam turbines play a critical role in CCS systems by driving the compression and transport of captured CO₂, as well as by providing power and heat for the capture process itself.
In the context of global energy transitions, steam turbines are evolving to meet the demands of a more distributed and decentralized energy system. Small and modular turbine designs are being developed for applications such as microgrids, remote power generation, and off-grid renewable systems. These smaller turbines are designed to be highly efficient and adaptable, making them ideal for integration with local renewable resources or as backup power sources in critical infrastructure.
In conclusion, the steam turbine, a technology rooted in over a century of innovation, continues to adapt and thrive in a rapidly changing energy landscape. Its versatility, efficiency, and ability to integrate with emerging technologies make it an indispensable tool in the global effort to achieve sustainable, reliable, and low-carbon energy systems. Whether in large-scale power plants, industrial applications, or cutting-edge renewable energy projects, steam turbines remain at the forefront of energy conversion, demonstrating their enduring importance in powering progress and shaping the future of energy.
The enduring relevance of steam turbines is a testament to their unmatched adaptability and efficiency across an ever-expanding array of applications. As the global energy landscape undergoes transformative changes, driven by decarbonization goals, technological advancements, and evolving energy demands, steam turbines continue to evolve, cementing their role as a cornerstone technology in the transition to a sustainable and resilient energy future.
One area where steam turbines are poised for further growth is in the hybridization of energy systems. By integrating with other forms of power generation—such as gas turbines in combined-cycle configurations or renewable energy sources like solar and geothermal—steam turbines help to create highly efficient and flexible energy solutions. Combined-cycle power plants, for instance, achieve some of the highest efficiencies in electricity generation by coupling a gas turbine with a steam turbine. The gas turbine generates power from the combustion of natural gas, while the waste heat from this process is captured to produce steam, which drives the steam turbine. This dual approach maximizes energy output from the same fuel source and significantly reduces emissions per unit of electricity generated.
In addition to efficiency gains, hybrid systems with steam turbines offer enhanced grid stability, especially in regions with high penetrations of variable renewable energy sources like wind and solar photovoltaics. Steam turbines in thermal storage systems or hybrid plants can act as a stabilizing force, providing dispatchable power during periods of fluctuating renewable generation. This flexibility ensures that energy systems can meet demand reliably while supporting the broader integration of clean energy resources.
As energy markets evolve, there is also a growing focus on distributed energy systems, and steam turbines are playing a role here as well. In localized power generation setups, such as industrial cogeneration plants or district heating systems, smaller-scale steam turbines are being developed to optimize energy efficiency and reduce environmental impact. These distributed systems are particularly valuable in regions with energy access challenges or where resilience against centralized grid disruptions is critical. For example, a small industrial facility might use a back-pressure steam turbine to generate electricity from its waste heat while using the exhaust steam for its heating or drying processes. Such setups not only reduce energy waste but also improve the economic viability of industrial operations.
Advances in materials science and manufacturing techniques are further propelling the capabilities of steam turbines. The development of superalloys and composite materials that can withstand extreme operating conditions is enabling the next generation of ultra-supercritical steam turbines. These turbines operate at temperatures and pressures beyond the critical point of water, where efficiency gains are most significant. Precision manufacturing processes, including additive manufacturing (3D printing), are allowing for the creation of highly complex and optimized turbine components, such as blades and vanes, with enhanced performance characteristics. These advancements are reducing production costs, improving efficiency, and extending the operational life of turbines.
Environmental sustainability is another area where steam turbines are making significant contributions. Beyond their traditional role in fossil-fueled power plants, steam turbines are increasingly being utilized in renewable and low-carbon applications. In biomass power plants, for example, steam turbines convert the thermal energy from burning organic materials—such as agricultural waste or wood pellets—into electricity. These plants often operate as part of a circular economy, where waste products are repurposed into valuable energy resources, minimizing environmental impact. Similarly, in waste-to-energy facilities, steam turbines play a critical role in converting the heat from incinerated municipal waste into usable electricity and heat, reducing landfill usage and contributing to energy generation.
Geothermal energy, long recognized as a reliable and sustainable resource, has seen a surge in interest due to technological advancements that expand its accessibility. Steam turbines are central to both traditional and enhanced geothermal systems (EGS), where they convert the heat from Earth’s subsurface into electricity. These turbines are specially designed to handle the unique conditions of geothermal steam, which often contains non-condensable gases and corrosive elements. Innovations in turbine materials and designs are enabling longer lifespans and greater efficiency in these challenging environments.
The role of steam turbines in the emerging hydrogen economy cannot be overstated. As hydrogen production scales up—whether through electrolysis using renewable energy or via other methods like steam methane reforming with carbon capture—there will be a need for efficient systems to convert the energy stored in hydrogen into usable forms. Steam turbines can be employed in hydrogen-fueled power plants or integrated with processes that utilize hydrogen as an industrial feedstock, making them an essential component of a hydrogen-powered future.
Digital transformation is reshaping the operation and maintenance of steam turbines, unlocking new levels of efficiency and reliability. The integration of real-time monitoring systems with advanced analytics platforms is enabling predictive maintenance and performance optimization. Sensors embedded throughout the turbine collect data on critical parameters such as temperature, pressure, vibration, and flow rates. This data is analyzed using artificial intelligence and machine learning algorithms to detect anomalies, predict equipment failures, and optimize performance. For example, a steam turbine operating under varying load conditions can automatically adjust its blade angles or steam flow to maintain optimal efficiency. These digital tools not only reduce operational costs but also enhance the overall safety and reliability of steam turbine systems.
Carbon capture, utilization, and storage (CCUS) technologies are becoming increasingly important as the world seeks to achieve net-zero emissions. Steam turbines are integral to these systems, providing the power and heat required for CO₂ capture processes while also compressing the captured carbon for transport and storage. In some applications, the captured CO₂ is even utilized as a working fluid in enhanced oil recovery or in industrial processes, creating new opportunities for value creation while mitigating emissions.
Looking forward, the future of steam turbines is deeply intertwined with the global pursuit of sustainability, innovation, and resilience. As energy systems become more complex and interconnected, steam turbines will continue to adapt, incorporating new materials, digital technologies, and advanced thermodynamic principles to meet evolving demands. From large-scale power plants and industrial applications to localized energy systems and cutting-edge renewable projects, steam turbines are set to remain a cornerstone of energy conversion technology, powering progress and enabling a sustainable future for generations to come. Their journey of continuous improvement and innovation underscores their indispensable role in shaping the modern energy landscape and meeting the challenges of tomorrow.
Steam Turbine Fundamentals
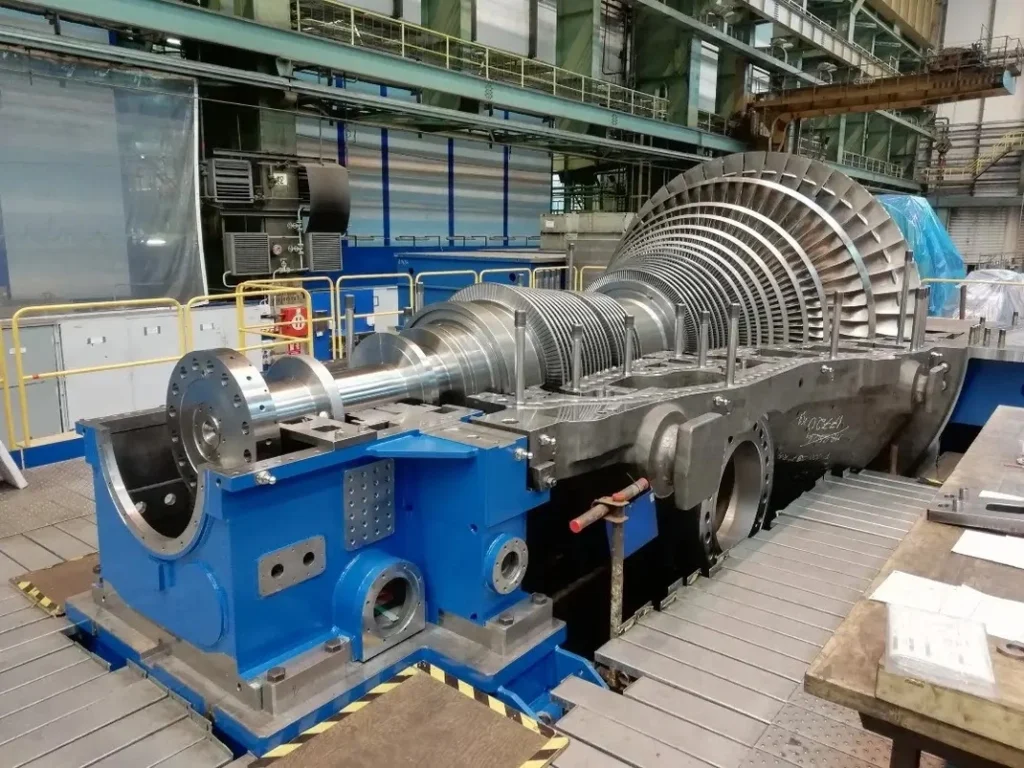
Steam turbine fundamentals revolve around the core principles, design features, and operational mechanics that make these machines a vital part of energy conversion systems. At its essence, a steam turbine is a mechanical device that converts thermal energy from steam into mechanical energy, which is then used to generate electricity or provide mechanical power for various industrial applications. Understanding these fundamentals requires delving into thermodynamics, fluid mechanics, and the engineering design of turbine components.
The working principle of a steam turbine is based on the Rankine cycle, a thermodynamic cycle that describes the conversion of heat into work. In a typical steam turbine system, water is heated in a boiler to produce high-pressure, high-temperature steam. This steam is then directed into the turbine, where it expands and loses pressure as it flows through a series of blades mounted on a rotor. The expansion process causes the blades to rotate, converting the thermal energy of the steam into mechanical work. The rotating shaft of the turbine is connected to a generator, which converts the mechanical energy into electrical energy.
The efficiency of a steam turbine depends on several factors, including the design of its components, the operating conditions, and the quality of the steam. Turbines are classified into two main types based on the flow of steam and the way energy is extracted: impulse turbines and reaction turbines.
Impulse turbines operate by directing high-velocity steam jets onto fixed blades or nozzles, which then impact the rotating blades. The kinetic energy of the steam is converted into mechanical energy as it strikes the blades, causing the rotor to spin. Impulse turbines are typically used for high-pressure, high-velocity steam applications and are characterized by their robust design and simplicity. A classic example is the De Laval turbine, which uses a single-stage impulse design.
Reaction turbines, on the other hand, rely on the pressure drop and expansion of steam as it flows through both the stationary and moving blades. In this type of turbine, the steam expands continuously, creating a reaction force that drives the rotor. Reaction turbines are more commonly used in multi-stage configurations, where the steam undergoes multiple expansions across several stages of blades, allowing for greater energy extraction and higher efficiency. The Parsons turbine is a well-known example of a reaction turbine.
Most modern steam turbines are a combination of impulse and reaction designs, with different stages optimized for specific operating conditions. These hybrid designs allow for improved performance and adaptability across a wide range of applications.
The key components of a steam turbine include:
- Rotors and Blades: The rotor is the central shaft to which the blades are attached. The blades are critical for converting steam energy into mechanical work. They are typically made from high-strength materials such as stainless steel or nickel-based alloys to withstand high temperatures, pressures, and rotational stresses.
- Casings: The casing encloses the rotor and blades, providing a pathway for the steam to flow through the turbine. It also serves as a structural component, maintaining the integrity of the turbine under high-pressure conditions.
- Nozzles and Diaphragms: In impulse turbines, nozzles direct the steam flow onto the blades at high velocity, maximizing energy transfer. In reaction turbines, diaphragms guide the steam as it flows from one stage to the next.
- Bearings and Seals: Bearings support the rotor and allow it to rotate smoothly, while seals prevent steam leakage and maintain the efficiency of the turbine. Advanced sealing systems, such as labyrinth seals or brush seals, are often used to minimize losses.
- Control Systems: Modern steam turbines are equipped with sophisticated control systems that regulate steam flow, pressure, and temperature to optimize performance and ensure safe operation. These systems also monitor parameters like vibration and thermal expansion to detect potential issues early.
Steam turbines can be further classified based on their application and operating conditions:
- Condensing turbines are designed to extract as much energy as possible from the steam, condensing it into water in a condenser at the turbine’s exhaust. These turbines are commonly used in power plants, where maximizing energy efficiency is critical.
- Back-pressure turbines exhaust steam at a higher pressure, which is then used for industrial processes or heating. These turbines are commonly found in cogeneration systems, where they provide both electricity and useful thermal energy.
- Reheat turbines feature an additional stage where partially expanded steam is reheated before being sent back into the turbine for further expansion. This process improves overall efficiency and reduces moisture content in the later stages, which can damage turbine blades.
- Extraction turbines allow some steam to be extracted at intermediate stages for industrial processes or heating, while the remaining steam continues to expand for power generation. This flexibility makes them ideal for combined heat and power (CHP) applications.
The performance of a steam turbine is often measured in terms of efficiency, power output, and reliability. Key performance metrics include:
- Isentropic efficiency, which compares the actual work output of the turbine to the ideal work output if the process were perfectly isentropic (i.e., no energy losses).
- Heat rate, which represents the amount of heat energy required to produce a unit of electrical energy. A lower heat rate indicates higher efficiency.
- Capacity factor, which measures the actual energy output of the turbine over a given period relative to its maximum potential output.
In terms of operation, steam turbines require careful management to avoid issues such as blade erosion, fouling, and thermal stresses. Regular maintenance and monitoring are essential to ensure long-term performance and reliability. Advanced diagnostic tools, such as vibration analysis and thermal imaging, are commonly used to detect potential problems early.
In summary, steam turbine fundamentals encompass the principles of thermodynamics, the design and function of key components, and the various configurations and applications of these versatile machines. By converting the energy of steam into mechanical work with high efficiency, steam turbines have become a cornerstone of modern energy systems, powering everything from large-scale power plants to industrial facilities and renewable energy projects.
The fundamentals of steam turbines extend beyond their basic operation and components, encompassing the principles of thermodynamics, fluid dynamics, material science, and the technological advancements that have continuously improved their efficiency and reliability. Steam turbines operate at the intersection of these scientific and engineering disciplines, making them one of the most sophisticated and efficient energy conversion technologies.
Thermodynamic Principles and the Rankine Cycle
At the heart of steam turbine operation lies the Rankine cycle, which is a closed-loop thermodynamic cycle consisting of four main processes:
- Heat Addition (Boiler): Water is heated in a boiler to produce high-pressure, high-temperature steam. This phase involves adding thermal energy to the working fluid (water) at constant pressure.
- Expansion (Steam Turbine): The high-energy steam expands through the turbine blades, performing work and converting thermal energy into mechanical energy. This is the phase where the turbine operates, governed by the principles of fluid mechanics and thermodynamics.
- Heat Rejection (Condenser): After expansion, the low-energy steam enters a condenser, where it is cooled and condensed back into water, releasing heat into the environment or a cooling medium.
- Compression (Pump): The condensed water is pumped back to the boiler at high pressure, completing the cycle.
The efficiency of the Rankine cycle, and consequently the steam turbine, depends on maximizing the pressure and temperature of the steam entering the turbine while minimizing the temperature at which heat is rejected. Modern advancements in materials and design allow turbines to operate at ultra-supercritical conditions, with steam temperatures exceeding 600°C and pressures above 25 MPa, significantly increasing cycle efficiency.
Fluid Dynamics in Steam Turbines
The flow of steam through the turbine blades is governed by fluid dynamics, particularly the principles of compressible flow. As steam expands in the turbine, its velocity, pressure, and temperature change, driving the rotation of the rotor. Understanding the behavior of steam as a compressible fluid is crucial for optimizing blade design and maximizing energy transfer.
Steam turbines are designed with multiple stages to handle the gradual expansion of steam. Each stage consists of a set of stationary blades (nozzles or guide vanes) and moving blades (rotor blades). The stationary blades direct and accelerate the steam onto the moving blades, where the energy transfer occurs. The design of these blades is critical, as their shape, angle, and material properties directly influence turbine efficiency and performance.
- Velocity Compounding: In velocity-compounded turbines, multiple rows of moving blades are used to gradually extract the kinetic energy of the steam. This design reduces energy losses due to steam velocity and is often employed in impulse turbines.
- Pressure Compounding: Pressure-compounded turbines use multiple stages where the steam undergoes successive expansions at each stage, gradually reducing its pressure. This approach is common in reaction turbines and improves efficiency by minimizing energy losses during expansion.
Material Science and Engineering
The materials used in steam turbines must withstand extreme operating conditions, including high temperatures, pressures, and rotational stresses. Turbine components, especially blades, rotors, and casings, are made from advanced alloys and composites designed for durability and performance. Common materials include:
- Nickel-based superalloys: These are used for high-temperature components due to their excellent thermal and mechanical properties.
- Stainless steel: This material offers good corrosion resistance and is commonly used for components exposed to wet steam.
- Titanium alloys: Lightweight and strong, these alloys are occasionally used for low-pressure turbine blades.
The development of advanced manufacturing techniques, such as 3D printing and precision casting, has enabled the production of complex turbine components with improved efficiency and reliability. Coatings and surface treatments, such as thermal barrier coatings (TBCs) and erosion-resistant layers, further enhance the durability of turbine components.
Efficiency Enhancements and Loss Reduction
Several factors influence the efficiency of steam turbines, and reducing losses is a primary focus in their design and operation. The main types of losses include:
- Thermal losses: These occur due to heat transfer to the environment. Minimizing these losses requires advanced insulation and efficient thermal management.
- Leakage losses: Steam leakage through seals and clearances can reduce efficiency. Modern sealing technologies, such as labyrinth seals and brush seals, help mitigate this issue.
- Moisture losses: As steam expands and cools, it can condense into water droplets, causing erosion and reducing efficiency. Reheating steam between stages and using moisture separators can address this issue.
- Friction and aerodynamic losses: These occur due to the interaction between steam and turbine components. Optimized blade design and surface treatments reduce these losses.
To further enhance efficiency, many turbines incorporate reheating and regenerative feedwater heating. Reheating involves passing partially expanded steam back to the boiler for reheating before further expansion. This reduces moisture content in the later stages and increases overall efficiency. Regenerative feedwater heating uses extracted steam to preheat the feedwater, reducing the heat required in the boiler and improving cycle efficiency.
Control Systems and Automation
Modern steam turbines are equipped with sophisticated control systems that optimize performance, ensure safety, and enable flexible operation. These systems include:
- Governor systems: These regulate the speed and power output of the turbine by controlling steam flow.
- Temperature and pressure monitoring: Sensors provide real-time data on operating conditions, enabling precise control of turbine parameters.
- Condition monitoring systems: Advanced diagnostic tools, such as vibration analysis and thermography, detect potential issues early and support predictive maintenance.
Digitalization and automation are playing an increasingly significant role in steam turbine operation. Digital twins, virtual replicas of physical turbines, allow operators to simulate performance, predict maintenance needs, and test design modifications without affecting the actual equipment.
Applications of Steam Turbines
The versatility of steam turbines makes them suitable for a wide range of applications, including:
- Power generation: Steam turbines are the backbone of fossil fuel, nuclear, and renewable energy power plants, producing a significant portion of the world’s electricity.
- Industrial processes: In industries such as chemical manufacturing, paper production, and oil refining, steam turbines provide mechanical power and drive equipment like compressors and pumps.
- Combined heat and power (CHP): Steam turbines in CHP systems generate electricity and provide thermal energy for heating or industrial processes, improving overall energy efficiency.
- Renewable energy: Steam turbines are integral to geothermal and concentrated solar power (CSP) plants, converting heat from Earth’s subsurface or focused sunlight into electricity.
Conclusion
The fundamentals of steam turbines encompass a blend of physics, engineering, and innovation. From their operation within the Rankine cycle to the intricate design of their components, steam turbines exemplify the pinnacle of energy conversion technology. Their ability to adapt to diverse applications, coupled with continuous advancements in materials, control systems, and efficiency optimization, ensures that steam turbines remain a cornerstone of modern energy systems, powering progress and shaping the future of sustainable energy.
Steam turbines are integral to the efficient conversion of thermal energy into mechanical energy, a process that has evolved significantly since their inception. The core principle remains the same: steam, generated from boiling water, drives blades within a turbine rotor to produce mechanical power. However, the way in which turbines are designed, operated, and optimized has advanced in tandem with scientific discoveries, engineering innovations, and the ever-growing demand for energy efficiency. The design of steam turbines allows for the conversion of heat energy from high-pressure steam into mechanical energy via a process that involves expansion, which reduces steam pressure and temperature while extracting work from the steam. As the steam expands through the turbine’s blades, it pushes the blades, rotating the shaft and ultimately producing mechanical power. This mechanical power is typically used to drive generators that produce electricity or to power industrial equipment in various sectors, including chemical, paper, and steel manufacturing.
The expansion of steam through the turbine happens in multiple stages, with each stage designed to extract a portion of the steam’s energy. As the steam flows from one stage to another, the pressure and temperature gradually decrease, leading to the progressive conversion of thermal energy into mechanical energy. This staged expansion allows steam turbines to operate at a variety of pressures and temperatures, maximizing their efficiency under different conditions. The more stages a turbine has, the better it can extract energy, although it also adds complexity to the design and operation of the turbine.
Modern steam turbines are designed to operate in a range of environments, from high-pressure fossil fuel plants to renewable energy systems like geothermal and concentrated solar power (CSP). Each application has unique requirements in terms of operating conditions, efficiency, and material selection. To meet these demands, engineers have developed turbines capable of handling ultra-supercritical steam conditions, where temperatures exceed 600°C and pressures exceed 25 MPa. These conditions allow for significant increases in thermal efficiency compared to older, subcritical steam turbines. Advances in material science, including the use of high-strength alloys and coatings, have made it possible to design turbines that can withstand these extreme conditions while maintaining high levels of efficiency and reliability.
Turbine blades are one of the most critical components, as they must endure extreme temperatures, pressures, and rotational forces. The materials used in the construction of turbine blades must be durable, heat-resistant, and capable of withstanding corrosion from steam. Superalloys, which retain their strength and resist deformation at high temperatures, are commonly used in blade construction. These materials are also resistant to oxidation, which is crucial in maintaining the turbine’s efficiency and preventing damage that could lead to costly repairs and downtime.
Efforts to optimize steam turbine efficiency have led to the development of technologies such as reheating and regenerative feedwater heating. Reheating involves returning partially expanded steam to the boiler for additional heating, which reduces moisture content in the turbine and helps maintain the structural integrity of the blades. By preventing moisture from accumulating on the blades, reheating reduces erosion and enhances overall turbine efficiency. Regenerative feedwater heating utilizes extracted steam to preheat the water entering the boiler, reducing the energy needed to heat the water and improving the overall thermal efficiency of the cycle.
The efficiency of a steam turbine also depends on minimizing losses at every stage of the process. These losses can arise from factors such as steam leakage, friction, and aerodynamic drag. To address leakage losses, advanced sealing technologies, including labyrinth seals and brush seals, are used to ensure that steam does not escape from the turbine, which would reduce efficiency. Furthermore, friction losses are minimized by optimizing the design of turbine blades and minimizing surface roughness. The design of turbine blades is continually refined to improve aerodynamic performance, reducing drag and allowing steam to flow more smoothly through the turbine, which also helps to reduce energy losses.
Modern steam turbines are equipped with digital control systems that provide real-time monitoring of turbine performance. These systems continuously collect data on parameters such as pressure, temperature, speed, and vibration, enabling operators to optimize performance and identify potential issues before they result in turbine failure. The integration of sensors, artificial intelligence, and machine learning into turbine control systems allows for predictive maintenance, which helps operators detect and resolve issues before they lead to costly repairs. For example, vibration analysis can detect imbalances or wear on turbine components, while temperature sensors can help detect overheating, allowing operators to take corrective action before a failure occurs.
In addition to these technological advancements, steam turbines are increasingly being integrated into combined heat and power (CHP) systems. These systems simultaneously produce electricity and useful heat for industrial processes or district heating. By using the waste heat from electricity generation to provide thermal energy, CHP systems achieve much higher overall efficiency than conventional power plants. Steam turbines in these systems typically operate at lower pressures and temperatures than in traditional power plants, but they still offer significant efficiency gains compared to separate generation of electricity and heat.
Another area of growth for steam turbines is in the hybridization of energy systems. In combined-cycle power plants, steam turbines are used alongside gas turbines to achieve higher overall efficiency. In these systems, gas turbines generate electricity by burning fossil fuels, and the waste heat from the gas turbine is used to produce steam that drives the steam turbine. This configuration maximizes energy output from the same fuel source, improving efficiency and reducing emissions compared to conventional fossil fuel power plants.
Steam turbines are also playing a crucial role in the transition to renewable energy. In geothermal power plants, steam turbines convert the heat from Earth’s subsurface into electricity. These turbines are designed to handle the unique conditions of geothermal steam, which often contains non-condensable gases and minerals that can be corrosive to turbine components. Advances in materials and turbine design have made it possible to build reliable, efficient turbines for geothermal applications. Similarly, concentrated solar power (CSP) plants use steam turbines to generate electricity from sunlight by focusing solar energy onto a heat transfer medium that is used to produce steam. These plants can provide a reliable, dispatchable source of renewable energy, which is particularly valuable in regions where sunlight is abundant.
Despite the many advancements, steam turbines face challenges related to environmental impact. The need for sustainable energy solutions has led to increased focus on reducing emissions from steam turbine-based power plants. Technologies such as carbon capture and storage (CCS) are being integrated into some power plants to capture and store CO₂ emissions. In these systems, steam turbines continue to generate electricity while the CO₂ produced by burning fossil fuels is captured, compressed, and stored underground to prevent it from entering the atmosphere.
In conclusion, steam turbines have evolved significantly over the years, with advancements in material science, thermodynamics, and digital technology driving improvements in efficiency, reliability, and performance. Their ability to convert thermal energy into mechanical power with high efficiency has made them an essential component in a wide range of applications, from power generation to industrial processes. As energy systems continue to evolve and the demand for sustainable energy grows, steam turbines will remain at the forefront of energy conversion technology, adapting to new challenges and contributing to a cleaner, more efficient energy future.
As steam turbines continue to evolve, their role in energy systems becomes even more critical, particularly in the context of global efforts to decarbonize the energy sector. A major driver of innovation in steam turbine technology is the increasing demand for clean and sustainable energy sources. As fossil fuel-based power generation faces growing regulatory and environmental challenges, steam turbines are being adapted to work with lower-carbon and renewable energy sources, enhancing their flexibility and reducing their environmental footprint.
In addition to geothermal and concentrated solar power (CSP), steam turbines are also being integrated into waste-to-energy systems. In these plants, steam turbines are used to generate electricity from the combustion of municipal solid waste or industrial by-products. By converting waste materials into usable energy, these systems reduce landfill waste while simultaneously providing renewable energy. The development of specialized turbines that can handle the unique properties of waste-derived fuels, such as varying moisture content and the presence of contaminants, is an important area of focus.
Another emerging application for steam turbines is in nuclear power generation. In nuclear power plants, steam turbines are driven by the steam produced from the heat generated by nuclear fission in the reactor core. Unlike fossil fuel plants, nuclear plants do not burn fuel to generate heat, making them a low-emission energy source. As nuclear energy becomes an increasingly important part of the global energy mix, the need for efficient and reliable steam turbines in these plants is crucial. Advances in materials and reactor technology are leading to higher operating temperatures and pressures in nuclear plants, and turbines must be designed to withstand these harsher conditions while maintaining efficiency and safety.
In the context of renewable energy, there is also a growing focus on the integration of steam turbines with energy storage systems. As renewable energy sources like wind and solar power are intermittent, energy storage plays a crucial role in ensuring a stable and reliable energy supply. Steam turbines can be coupled with thermal energy storage systems, where heat is stored in materials like molten salts and used to generate steam when needed. This coupling provides a way to dispatch renewable energy on demand, effectively addressing the challenge of variability in renewable generation.
In addition to the technological innovations that enhance turbine performance, there is a greater emphasis on improving the efficiency of the overall steam cycle. One promising avenue of development is the use of combined Rankine cycles, which involve the use of multiple fluids with different boiling points. By using different fluids in different stages of the cycle, these systems can achieve higher efficiencies than traditional steam turbines. Research into organic Rankine cycles (ORC), which use organic fluids with lower boiling points than water, is gaining traction, particularly for small-scale applications or in regions with low-temperature heat sources.
Furthermore, digital technologies are enabling significant advances in the monitoring, control, and maintenance of steam turbines. The use of sensors, advanced data analytics, and artificial intelligence (AI) is transforming the way steam turbines are operated and maintained. Real-time data collection allows for continuous performance optimization, while predictive maintenance techniques help to avoid unplanned downtime and reduce the costs associated with turbine maintenance. For example, vibration analysis can detect early signs of wear and tear, while thermal imaging can identify overheating components before they fail. These technologies not only extend the lifespan of the turbines but also improve their efficiency over time by allowing for more precise control of operational parameters.
The digitalization of steam turbines is also facilitating the transition to more flexible power systems. As the energy grid becomes more dynamic with the growing integration of renewable energy sources, power plants need to be more adaptable to fluctuating demand. Steam turbines can now respond more rapidly to changes in load, providing backup power when renewable generation is low or when electricity demand spikes. This increased flexibility makes steam turbines an important part of modern, low-carbon energy systems that rely on a mix of generation technologies, including both renewables and traditional energy sources.
As global energy markets continue to evolve, the economic pressures on power generation systems are also influencing steam turbine design and operation. Cost-effectiveness is a major consideration in the development of new turbines, and manufacturers are focused on producing turbines that deliver maximum performance at a competitive cost. This is especially important as more countries invest in energy infrastructure to meet growing energy demands. To remain competitive, turbine manufacturers are developing more efficient and cost-effective solutions, incorporating advanced manufacturing techniques and focusing on minimizing both initial investment costs and ongoing operating costs.
Another area of focus is the reduction of the environmental impact of steam turbines. While steam turbines themselves are relatively clean in terms of emissions, the overall environmental footprint of the energy system in which they operate depends on the source of the steam. Power plants using coal or natural gas as fuel produce carbon dioxide (CO₂), a greenhouse gas that contributes to climate change. As the world moves toward decarbonization, steam turbines will increasingly be paired with carbon capture, utilization, and storage (CCUS) technologies. CCUS systems capture CO₂ emissions from power plants before they can enter the atmosphere and store them underground or use them in industrial applications. This integration will allow steam turbines to continue operating in fossil-fuel-based plants while helping to reduce the carbon footprint of these facilities.
With the growing emphasis on sustainability and carbon neutrality, the design and operation of steam turbines will continue to be influenced by environmental and regulatory pressures. Governments around the world are introducing stricter emissions standards and encouraging the development of cleaner energy sources. In response, steam turbine technology is being designed to adapt to new fuels, such as hydrogen, which burns cleanly and produces no CO₂ emissions when used in combustion-based power generation systems. Hydrogen-fueled turbines are emerging as a promising solution for decarbonizing industries and power generation systems that rely on traditional fossil fuels. The ability to operate steam turbines using hydrogen or other low-carbon fuels will play a key role in achieving global climate goals.
As these various technologies and applications evolve, steam turbines will continue to be an essential component of the global energy landscape. Their ability to provide reliable, efficient, and scalable power generation makes them indispensable in the energy mix. With advances in materials science, digital technology, and integration with renewable energy and storage systems, steam turbines will remain at the forefront of energy innovation, helping to meet the world’s growing energy needs while addressing the challenges of climate change and sustainability.
Steam Turbines in Power Generation
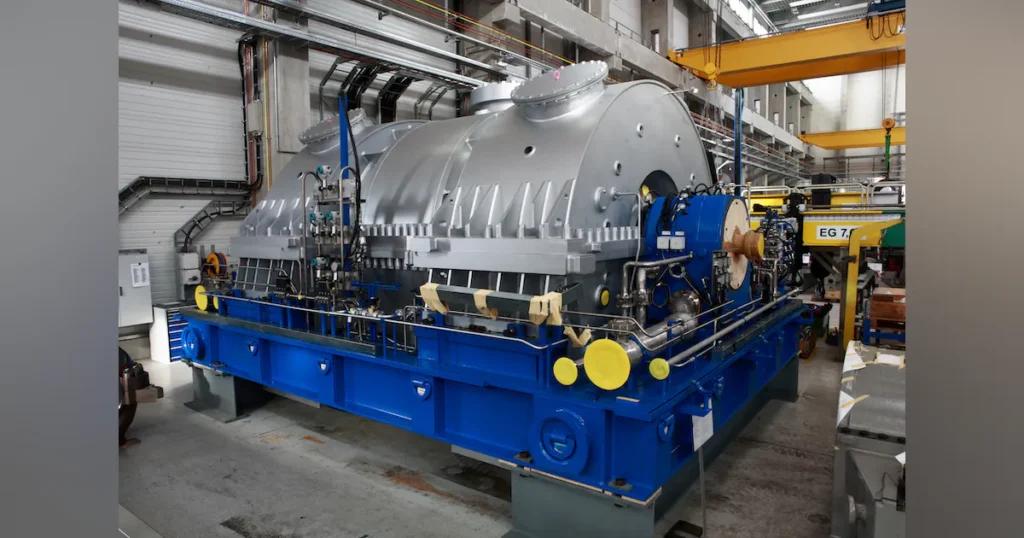
Steam turbines play a pivotal role in power generation, contributing to the majority of electricity produced worldwide. They are an essential component in both conventional and renewable power plants, where their primary function is to convert thermal energy, usually derived from burning fossil fuels or nuclear reactions, into mechanical energy, which is then used to generate electricity.
In fossil fuel power plants, steam turbines work in conjunction with boilers that burn coal, natural gas, or oil to produce steam. The steam generated in the boiler is directed through a series of turbine stages, each designed to extract a portion of the steam’s energy and convert it into mechanical energy. The mechanical energy is transferred to a generator, which then produces electricity. These plants operate on the Rankine cycle, where water is heated, turned into steam, and passed through the turbine. After passing through the turbine, the steam is condensed back into water in a condenser, where heat is released to the environment, and the cycle repeats.
In nuclear power plants, steam turbines serve the same basic function, but the heat to generate steam comes from nuclear fission. The core of the nuclear reactor generates enormous heat through the splitting of atoms, which heats water to produce steam. The steam is then directed to the turbine, where it drives the blades and generates mechanical energy to turn a generator and produce electricity. Nuclear plants have the added complexity of managing radiation and ensuring the safety of turbine components that are exposed to radiation over time. These plants use sophisticated shielding and material selection to prevent damage to critical components.
Beyond fossil fuel and nuclear plants, steam turbines are also used in renewable energy systems, most notably in geothermal and concentrated solar power (CSP) plants. In geothermal power plants, steam turbines convert the heat from the Earth’s core into electricity. Geothermal plants typically involve drilling deep into the Earth’s crust to access hot water or steam reservoirs. This steam is brought to the surface and passed through a turbine to generate electricity. Because geothermal energy is a renewable resource, these systems are a cleaner alternative to traditional fossil fuel plants, providing a constant, baseload power supply.
Similarly, in CSP plants, solar energy is concentrated using mirrors or lenses to heat a working fluid, which produces steam to drive a steam turbine. The advantage of CSP over traditional solar photovoltaic systems is its ability to store heat, allowing CSP plants to generate electricity even when the sun isn’t shining. This makes CSP an attractive option for utility-scale solar power generation, especially in regions with high levels of direct sunlight.
In terms of efficiency, steam turbines in power generation have seen significant advancements in recent years, particularly with the use of supercritical and ultra-supercritical steam conditions. Supercritical steam refers to steam that is heated above its critical point, where it no longer behaves like a liquid or gas. Ultra-supercritical plants take this a step further, achieving even higher steam temperatures and pressures to maximize energy extraction from the steam. These plants can achieve efficiencies upwards of 45%, compared to around 35% for conventional subcritical plants. The higher the efficiency of the steam cycle, the less fuel is required to produce the same amount of electricity, which reduces fuel consumption and lowers emissions.
The move towards higher efficiencies in steam turbines is also closely tied to advancements in materials science. To withstand the higher temperatures and pressures associated with supercritical and ultra-supercritical steam, steam turbine components must be made from advanced alloys that can resist corrosion, erosion, and thermal fatigue. For example, turbine blades are made from high-strength nickel-based superalloys, which offer excellent resistance to both high temperatures and oxidation. Coatings are also used to further enhance the performance of turbine blades, protecting them from wear and improving their longevity.
The increasing focus on reducing emissions has also led to the integration of steam turbines with carbon capture, utilization, and storage (CCUS) technologies. In a CCUS-equipped power plant, CO₂ produced during the combustion of fossil fuels is captured, compressed, and stored underground rather than being released into the atmosphere. By combining CCUS with steam turbines, power plants can continue to generate electricity from fossil fuels while significantly reducing their greenhouse gas emissions. Although the integration of CCUS adds complexity and costs to power plant operations, it is seen as a key technology for meeting global climate targets, especially in regions where fossil fuel use remains dominant.
In addition to CCUS, many power plants are adopting combined-cycle gas turbine (CCGT) systems, which integrate both steam turbines and gas turbines. In a CCGT system, a gas turbine generates electricity using natural gas, and the waste heat from the gas turbine is used to produce steam, which drives a steam turbine and generates additional electricity. This combined cycle results in much higher overall efficiency, often exceeding 60%, compared to a conventional steam-only cycle. The combined-cycle approach is becoming increasingly popular for new power plants due to its efficiency and lower environmental impact.
Steam turbines are also integral to combined heat and power (CHP) systems, also known as cogeneration systems. In these systems, both electricity and useful heat are generated simultaneously. CHP systems are particularly beneficial for industrial applications where both electricity and heat are required. The heat produced in the steam turbine can be used for industrial processes, district heating, or even for driving additional turbines for mechanical power. By utilizing both electricity and heat, CHP systems are much more efficient than conventional separate generation of heat and power. These systems are being used more widely in industrial settings, district heating networks, and even in residential applications.
The continued development of steam turbines in power generation is also closely tied to the broader energy transition. As the global energy mix shifts toward more sustainable and renewable sources, steam turbines will increasingly be used in hybrid power plants that combine traditional and renewable energy technologies. For example, steam turbines can be paired with biomass power generation, where organic materials such as wood, agricultural waste, or municipal solid waste are burned to produce steam for a turbine. Biomass energy is considered carbon-neutral, as the CO₂ released during combustion is offset by the CO₂ absorbed by the plants during their growth cycle.
The role of steam turbines in power generation will continue to evolve as new technologies, materials, and energy sources emerge. As the energy landscape changes, steam turbines will remain a key technology, providing a flexible, reliable, and efficient means of generating electricity across a wide range of applications. Their ability to operate in diverse energy environments, from fossil fuel to renewable energy systems, and their ongoing development in efficiency and emissions reduction, ensures that steam turbines will remain a cornerstone of the global power generation sector for years to come.
As the demand for clean and reliable energy continues to grow, steam turbines will remain a central component in the transition to a more sustainable energy future. In addition to their application in traditional power plants, steam turbines are increasingly being deployed in novel and innovative configurations to meet the evolving needs of the energy sector.
One of the emerging trends is the integration of steam turbines with renewable energy systems in hybrid power plants. Hybrid systems combine multiple power generation technologies to optimize energy output and improve reliability. For example, solar-thermal power plants, which use mirrors or lenses to concentrate sunlight and generate heat, can be paired with steam turbines to produce electricity. By incorporating thermal energy storage systems, such as molten salts, these hybrid plants can continue generating electricity even after the sun sets, providing a stable source of power around the clock. Similarly, wind energy systems can be integrated with steam turbines in some regions, where excess wind energy is used to generate steam that drives the turbine. These hybrid systems offer the potential for higher overall efficiency and lower emissions compared to traditional power generation methods.
Another promising application for steam turbines in the renewable energy sector is in ocean energy systems. Wave, tidal, and ocean thermal energy conversion (OTEC) technologies are being explored to harness the power of the ocean to generate electricity. In some cases, steam turbines can be used in combination with these systems to convert thermal or mechanical energy from ocean water into electrical power. For example, in OTEC systems, temperature differences between warm surface water and cold deep ocean water can be used to produce steam, which is then passed through a turbine to generate electricity. As these technologies develop, steam turbines will play a critical role in helping to unlock the vast potential of ocean energy.
Steam turbines are also being explored for their potential in district heating systems. District heating is a method of providing heat to multiple buildings or communities through a centralized system that generates heat and distributes it through pipes. In this context, steam turbines can help provide both heat and electricity in a combined heat and power (CHP) system. By using waste heat from industrial processes, incineration, or other sources, these systems can reduce the need for additional fuel consumption while providing a reliable and sustainable heat source. District heating systems with steam turbines are already in operation in several European countries and are gaining traction in other parts of the world.
The development of hydrogen as a clean fuel is another area where steam turbines are expected to play a key role. Hydrogen can be burned directly in steam turbines or used to produce steam through fuel cells or other processes. When burned, hydrogen produces only water vapor as a byproduct, making it an attractive option for decarbonizing power generation. Hydrogen-fired steam turbines are being explored as a potential solution for the transition away from fossil fuels, especially in industries and regions where carbon-free power generation is essential. In fact, some gas turbine manufacturers are already working on developing hydrogen-compatible turbines that can seamlessly switch between natural gas and hydrogen. As hydrogen infrastructure continues to develop and the cost of production decreases, the use of hydrogen in steam turbines could become more widespread, further reducing emissions in the power sector.
The ongoing drive for efficiency and sustainability in steam turbine technology is also leading to improvements in turbine design and operation. Advances in computational fluid dynamics (CFD) and turbine blade aerodynamics are enabling the development of more efficient turbines with optimized flow paths. By using advanced simulation techniques, turbine designers can improve the shape of blades and vanes, reduce drag, and increase the energy extracted from the steam. These improvements not only enhance performance but also reduce the wear and tear on turbine components, extending the lifespan of the turbine and lowering maintenance costs.
Furthermore, steam turbine manufacturers are focusing on modular design and manufacturing processes to reduce costs and improve the scalability of turbine systems. Modular turbines can be quickly assembled and integrated into various power generation systems, allowing for more flexible and cost-effective solutions for power producers. These modular designs also make it easier to upgrade or replace individual turbine components, reducing downtime and maintenance costs.
The integration of digital technologies is also a key area of development for steam turbines in power generation. Digital twin technology, which creates a virtual replica of a turbine and simulates its performance in real-time, is being used to optimize operations and enhance decision-making. By continuously monitoring the condition of the turbine and analyzing data from sensors, operators can make more informed decisions about maintenance, performance optimization, and even design improvements. Predictive maintenance systems, powered by artificial intelligence (AI) and machine learning algorithms, are also helping to identify potential issues before they lead to failures. These systems analyze data from turbine sensors, such as temperature, pressure, and vibration, to predict when components will need maintenance or replacement, minimizing unplanned downtime and reducing repair costs.
The increased use of steam turbines in smaller, distributed power generation systems is another trend in the industry. As decentralized energy production becomes more common, especially in remote or off-grid areas, small-scale steam turbines are being used to generate electricity from local heat sources. These systems are often powered by biomass, waste heat, or geothermal energy, offering a sustainable and reliable energy solution for communities that are not connected to the central grid. In such applications, steam turbines provide a cost-effective and efficient way to harness local resources for power generation.
As the world continues to shift towards a low-carbon future, the role of steam turbines in power generation will remain crucial. Whether in large-scale fossil-fuel plants with carbon capture technology, nuclear facilities, renewable energy plants, or hybrid systems, steam turbines will continue to play a central role in ensuring the reliable and efficient generation of electricity. Their versatility, scalability, and ongoing advancements in technology will enable steam turbines to adapt to the changing energy landscape, supporting the global transition to cleaner, more sustainable energy systems. Through continued research, development, and innovation, steam turbines will remain a key enabler of a low-carbon, energy-efficient future.
As the energy landscape continues to evolve, steam turbines will play an increasingly critical role in the global effort to decarbonize the power sector. Their long history of reliability, efficiency, and scalability makes them indispensable in current and future energy systems. However, this role is expanding as new technologies, materials, and operational strategies emerge to meet the pressing needs for clean energy, flexible power generation, and integration with renewable sources.
A key aspect of this transformation is the push toward decarbonizing industrial sectors, where steam turbines are commonly used for combined heat and power (CHP) in facilities such as refineries, chemical plants, and manufacturing plants. By harnessing waste heat from industrial processes and converting it into electricity, CHP systems using steam turbines can significantly reduce the carbon footprint of these industries. In some cases, these industrial turbines can even use low-carbon fuels like biogas or hydrogen to further reduce emissions. Industrial decarbonization is expected to be one of the key drivers for future steam turbine development, as companies seek to comply with stricter regulations and meet sustainability targets.
Along with the adoption of cleaner fuels, hybrid energy systems are emerging as an important trend in the power generation industry. Hybrid systems combine steam turbines with other power generation technologies to improve overall efficiency, reduce emissions, and enhance reliability. For example, some power plants are integrating solar photovoltaics with steam turbines, using solar power during the day to offset demand and steam turbines to provide consistent baseload power during cloudy periods or at night. Additionally, battery storage systems are being used to store excess electricity generated during periods of high renewable output, which can then be released to supplement steam turbine generation when renewable output is low.
The concept of electrification of transportation is also influencing the role of steam turbines in energy systems. As electric vehicles (EVs) become more widespread, demand for electricity is expected to rise significantly. Steam turbines, especially those in combined-cycle and CHP configurations, will be pivotal in meeting this increased demand, especially in areas that rely on fossil fuels for power generation. However, as the world transitions to a cleaner electricity grid, steam turbines will increasingly be paired with renewable energy sources such as wind, solar, and hydroelectricity, reducing the need for fossil-fueled generation.
As governments, industries, and utilities work to reduce emissions in line with international climate agreements, steam turbines are being integrated into carbon capture and storage (CCS) technologies. These systems work by capturing CO₂ produced during the combustion of fossil fuels and storing it underground, preventing it from entering the atmosphere and contributing to climate change. When used in combination with steam turbines in power plants, CCS can significantly reduce the carbon intensity of electricity generation. The development of cost-effective, efficient CCS systems, along with the ongoing evolution of steam turbine technology, is expected to be a key strategy in achieving net-zero emissions targets for the energy sector.
The trend toward decentralized energy generation is also having a significant impact on the role of steam turbines. With more distributed power systems being deployed to meet localized energy needs, smaller-scale steam turbines are being used in community-level and industrial power generation. These turbines, often fueled by biomass, waste heat, or renewable energy sources like geothermal, can be deployed in areas that are not connected to the grid. Decentralized generation using steam turbines offers the benefits of increased energy security, reliability, and resilience, particularly in regions vulnerable to grid outages or energy shortages.
At the same time, digital technologies continue to transform the operation and maintenance of steam turbines. The use of smart sensors and data analytics is improving the efficiency and reliability of turbine operations. By continuously monitoring factors such as vibration, temperature, pressure, and efficiency, operators can detect issues before they lead to catastrophic failures. This predictive maintenance approach, powered by artificial intelligence (AI) and machine learning (ML), enables more efficient use of turbine components, reducing both downtime and operating costs. Additionally, digital twins—virtual replicas of steam turbines—are becoming more prevalent in design and operational optimization, allowing engineers to simulate various operating conditions and predict the performance of turbines under different scenarios. This innovation is helping to optimize energy output and extend the life of turbine components.
Advanced materials are also playing a critical role in improving the performance of steam turbines. As turbines are increasingly exposed to higher temperatures and pressures, the demand for materials that can withstand these harsher conditions is growing. Nickel-based superalloys and ceramic matrix composites are being used to create turbine blades that can endure extreme environments, maintaining strength and resistance to corrosion, erosion, and oxidation. Additionally, thermal barrier coatings are being developed to further protect critical turbine components from heat damage. These materials enable steam turbines to operate at higher efficiencies, pushing the boundaries of what is possible in terms of energy extraction from steam and reducing fuel consumption and emissions.
In power plant design, there is a strong push toward flexible and adaptive operations. With the increasing share of intermittent renewable energy sources in the grid, power plants must be capable of quickly adjusting their output to match fluctuations in renewable generation. Steam turbines, traditionally used for steady, baseload generation, are being adapted to operate in more dynamic environments, providing load-following capabilities. This flexibility is especially important in grids that rely on renewable sources like wind and solar, where generation can vary rapidly. To meet this demand, turbine designs are being refined to respond more quickly to changes in steam conditions and load demand without sacrificing efficiency.
Furthermore, small modular reactors (SMRs), which are compact nuclear reactors, are expected to incorporate steam turbines for power generation. SMRs are designed to provide a flexible and scalable solution to nuclear power, with the potential to be deployed in remote or off-grid locations. These reactors offer a more flexible and cost-effective option compared to traditional large-scale nuclear power plants. By coupling SMRs with steam turbines, these systems can deliver reliable, low-carbon electricity on a smaller scale, making nuclear power more accessible and adaptable to different energy markets.
Looking forward, hydrogen as a fuel is expected to play a significant role in the future of steam turbines. As hydrogen production technologies become more cost-effective and widespread, hydrogen-fired steam turbines could become a viable alternative to conventional fossil-fuel-based turbines. Hydrogen burns cleanly, producing only water vapor as a byproduct, making it an attractive option for reducing carbon emissions in power generation. Steam turbines running on hydrogen could be used in a wide range of applications, from large-scale power plants to industrial processes that require high-temperature heat. Research is already underway to develop turbines capable of burning pure hydrogen or blends of hydrogen with natural gas, providing flexibility as hydrogen infrastructure develops.
Finally, global energy policy and regulatory frameworks are shaping the future of steam turbines in power generation. Governments are increasingly setting ambitious targets for reducing greenhouse gas emissions and transitioning to renewable energy sources. As part of these efforts, there are growing incentives and investments in cleaner technologies, including steam turbines that operate with low-carbon fuels or in hybrid systems. Additionally, regulatory bodies are working to establish new standards for efficiency and emissions reduction, pushing manufacturers to innovate and improve the performance of their turbines.
In conclusion, the role of steam turbines in power generation will continue to expand and evolve in the coming decades. Their ability to integrate with a variety of energy sources, from fossil fuels to renewables and hydrogen, combined with ongoing technological advancements in efficiency, materials, and digital capabilities, positions them as a critical technology for a sustainable and reliable energy future. By supporting cleaner, more flexible, and adaptable power generation systems, steam turbines will remain central to global efforts to reduce carbon emissions, improve energy security, and ensure access to affordable electricity.
As we look toward the future of steam turbines in power generation, several additional factors will continue to shape their role in the global energy transition. The increasing complexity of modern energy systems, coupled with the need to address climate change, demands that steam turbine technology evolve further to meet new challenges and opportunities.
Energy storage integration is one such opportunity. As the penetration of renewable energy sources like wind and solar continues to grow, the ability to store excess energy when generation exceeds demand and release it when needed is crucial. Steam turbines are playing a significant role in enabling this integration by being paired with energy storage systems. One such system is thermal energy storage (TES), where excess renewable electricity is used to generate heat, which is then stored in thermal reservoirs (such as molten salts or other high-capacity materials). When demand for power exceeds renewable output, the stored heat can be used to generate steam and power the turbines. This integration offers a high-efficiency method of balancing supply and demand, and helps smooth the intermittency of renewable energy generation.
Moreover, district cooling systems are beginning to emerge alongside district heating systems, which use steam turbines in cogeneration. By utilizing steam to produce cooling—typically via absorption chillers—these systems allow for both heating and cooling to be provided from a single energy source. This flexibility is particularly beneficial in urban environments where energy demands fluctuate seasonally and in regions with high cooling requirements. Steam turbines can be integrated into district cooling infrastructure to further optimize energy efficiency and reduce costs.
Carbon-neutral fuel adoption will also have a major influence on the future of steam turbines. As governments set ambitious decarbonization targets, there is a growing interest in fuels that offer the potential to eliminate or offset carbon emissions. Synthetic fuels (synfuels), produced from captured carbon dioxide or biomass, can be used in steam turbines with similar characteristics to natural gas or coal. In addition, ammonia—a hydrogen carrier—has emerged as a promising alternative fuel for combustion-based power generation, including use in steam turbines. As these alternative fuels gain traction, turbines must be adapted to handle their unique characteristics, such as different combustion properties, fuel handling, and emissions profiles.
Another important area for future development is the decommissioning and repowering of older steam turbine-based power plants. Many older plants that rely on fossil fuels are reaching the end of their operational life. Rather than shutting down these plants entirely, repowering is being considered as an option for extending their life and improving efficiency. Repowering involves upgrading existing turbines, often by replacing outdated components or integrating cleaner technologies. For example, an old coal-fired power plant could be converted to run on natural gas or biomass, with modern steam turbines that improve thermal efficiency and reduce emissions. Such upgrades allow for continued operation of existing plants while aligning with evolving regulatory requirements.
Distributed power generation is likely to continue its rise, as more communities and industrial clusters seek to produce their own electricity with lower environmental impact. Small-scale steam turbines, often powered by local resources such as biomass, geothermal energy, or waste heat, are already being deployed in remote or off-grid regions. These systems are particularly attractive for industries that produce large amounts of waste heat, like steel, cement, and paper manufacturing, as well as for remote communities with limited access to the grid. Steam turbines in such applications allow for local, sustainable energy generation, reducing reliance on imported electricity and offering increased energy resilience. Distributed generation also helps reduce transmission losses, making it an energy-efficient option.
As climate resilience becomes more of a focus, steam turbines will play a role in enhancing the reliability and adaptability of power systems. In the face of climate change-induced extreme weather events, energy systems need to become more resilient. Steam turbines, particularly those in hybrid or combined-cycle configurations, provide a reliable, dispatchable source of power that can ramp up quickly in response to changes in demand or supply. For example, in regions prone to extreme weather events such as hurricanes, storms, or droughts, steam turbines can help ensure power generation remains stable and that backup power is available when needed. This adaptability will be vital as the world faces growing uncertainty in terms of climate patterns and weather-related challenges.
The drive for circular economy principles will also influence the design and operation of steam turbines. In a circular economy, materials and energy are kept in use for as long as possible, and waste is minimized. This can impact steam turbine applications in several ways. For instance, waste heat recovery technologies will continue to advance, allowing steam turbines to capture more waste heat from industrial processes and convert it into additional power. Additionally, more efficient recycling of turbine components and materials, such as metals and alloys used in turbine construction, will reduce the environmental impact of turbine production. Steam turbines may also play a role in the repurposing of carbon-rich waste materials, converting them into energy through processes like gasification or pyrolysis.
Finally, the global energy landscape is shifting as countries look to enhance energy security, diversify energy sources, and meet their commitments under international climate agreements, such as the Paris Agreement. In this context, steam turbines will play a critical role not only in existing power systems but also in supporting energy access in developing regions. Countries with abundant renewable energy resources (such as geothermal energy or biomass) but limited access to modern energy infrastructure may rely on small-scale steam turbine systems to generate electricity for local communities. These distributed systems offer a way to meet energy demand sustainably, without relying on imported fossil fuels. Additionally, steam turbines will be important in regions that are integrating new renewable technologies into the grid, ensuring reliable backup power generation and a stable electricity supply.
In conclusion, steam turbines will continue to play a central role in power generation, evolving to meet the demands of a low-carbon future. They are adaptable, scalable, and integral to a diverse array of energy systems, from traditional fossil-fuel plants to renewable hybrid systems, and their ongoing development will ensure they remain at the forefront of the energy sector. With advancements in technology, efficiency, and flexibility, steam turbines will support the transition to cleaner, more resilient, and decentralized energy systems. Their contributions to the decarbonization of industrial sectors, energy storage integration, and circular economy principles will further solidify their importance in shaping the future of global energy generation.
Uses of steam turbines
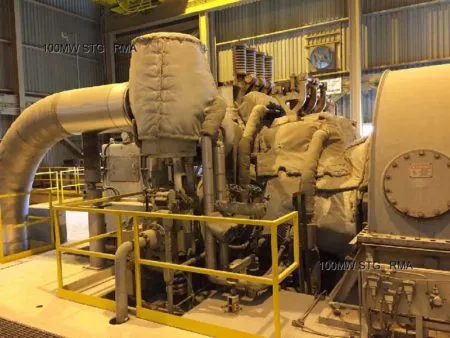
Steam turbines have a wide array of applications across various industries and sectors due to their versatility, efficiency, and reliability. They are primarily used in power generation, but their reach extends to a variety of industrial processes, marine propulsion, and even energy recovery systems. Here’s a look at some of the key uses of steam turbines:
1. Power Generation
The most common use of steam turbines is in power plants, where they are used to convert thermal energy into electrical energy. In traditional fossil-fuel power plants (coal, oil, or natural gas), steam turbines are used to drive generators, producing electricity by using heat from the combustion of fuel to generate steam. Nuclear power plants also use steam turbines, but the heat comes from nuclear reactions rather than combustion. In both cases, steam is produced by heating water with the heat source, and this steam is used to spin turbine blades, which drive a generator to produce electricity.
Combined-Cycle Power Plants: Steam turbines are often integrated into combined-cycle plants, where they are paired with gas turbines. The gas turbine generates power by burning fuel, while the waste heat from the gas turbine is used to produce steam that drives a steam turbine. This configuration increases the overall efficiency of the plant, as it allows for the recovery of waste heat.
2. Marine Propulsion
Steam turbines are widely used in naval and commercial vessels for propulsion. The large-scale ships, such as aircraft carriers, destroyers, and cruise ships, often use steam turbines because they are capable of producing the high power necessary for large vessels. Steam is generated in a boiler and used to drive turbines connected to the ship’s propellers. These turbines are efficient at converting thermal energy into mechanical power, allowing ships to travel at high speeds.
Naval Vessels: Many naval ships, including those used by militaries around the world, have steam turbines for propulsion. Aircraft carriers, for example, use steam turbines that can produce tens of thousands of horsepower to propel the massive vessels.
3. Industrial Applications
In industrial settings, steam turbines are used for a variety of energy-intensive processes, from manufacturing to chemical production. They are often used in combined heat and power (CHP) systems, where steam is used to generate both electricity and heat for industrial operations. This process improves efficiency by utilizing the same source of energy for multiple purposes.
Refineries and Petrochemical Plants: Steam turbines are essential in refineries, where they are used to generate power and provide the steam needed for refining processes like distillation. In petrochemical plants, turbines often play a role in providing energy for the production of chemicals, fuels, and other products.
Paper and Pulp Mills: Steam turbines are commonly used in paper mills to generate the steam required in the paper manufacturing process. The steam is used to dry paper and provide heat for various other steps in the production cycle.
Sugar Mills and Food Processing: Steam turbines are used in the sugar industry for the extraction of juice from sugarcane or sugar beets, as well as in food processing, where steam is necessary for cooking, sterilizing, and drying products.
4. Cogeneration and Combined Heat and Power (CHP) Systems
In cogeneration or CHP systems, steam turbines play a critical role by providing both electricity and useful thermal energy (heat) simultaneously. These systems are particularly popular in industrial and district heating applications where both power and thermal energy are needed.
District Heating Systems: In urban areas or large complexes, steam turbines can be part of a district heating system, where the steam is used to provide heat to residential, commercial, or industrial buildings. The efficiency of such systems is high because they make use of the waste heat from electricity generation.
Biomass Power Plants: Steam turbines can also be used in biomass power plants, where organic materials such as wood, agricultural waste, or other biomass are burned to produce steam. This steam drives turbines to generate electricity while also supplying heat for local use. Biomass plants are considered a renewable energy source because the fuel is carbon-neutral.
5. Geothermal Power Generation
Geothermal energy, which comes from the heat stored beneath the Earth’s surface, is another application where steam turbines are used. In geothermal power plants, steam is extracted from deep underground reservoirs and used to drive a steam turbine. This type of power generation is sustainable and produces little to no emissions, making it an attractive renewable energy option.
Binary Cycle Geothermal Plants: In these plants, steam extracted from the geothermal reservoir is passed through a heat exchanger, where it transfers heat to a secondary fluid with a lower boiling point. The secondary fluid is vaporized and used to drive a turbine. While the steam is not directly used in the turbine, the overall process relies on steam turbine technology for power generation.
6. Nuclear Power Generation
In nuclear power plants, steam turbines are used in a similar manner to fossil-fuel plants, but instead of burning fuel to create heat, the heat is generated by nuclear fission reactions. The heat generated by splitting atoms in a nuclear reactor is transferred to water to create steam, which is then used to drive turbines that generate electricity. Nuclear power plants typically operate at very high temperatures and require turbines that can withstand intense heat and radiation.
7. Waste-to-Energy Plants
Steam turbines are also employed in waste-to-energy plants where municipal solid waste (MSW) is burned to generate steam. This steam is then used to drive turbines, generating electricity. Waste-to-energy technology helps reduce landfill waste while producing clean energy, making it an increasingly popular method for managing urban waste. The energy produced can be used for local consumption or sent to the grid to support the energy needs of surrounding communities.
8. Hydrogen Production
Although steam turbines are typically associated with electricity generation, they are also used in processes that produce hydrogen. For example, in steam methane reforming (SMR)—a process that is commonly used to produce hydrogen from natural gas—steam is combined with methane to produce hydrogen and carbon dioxide. While the SMR process is more about chemical reactions than turbine operation, the energy required for producing the steam can be provided by a steam turbine-based system.
9. Solar Thermal Power Plants
In solar thermal power plants, steam turbines are used to convert solar energy into electricity. Solar thermal plants use mirrors or lenses to concentrate sunlight and generate heat. This heat is transferred to a working fluid, usually water, which produces steam. The steam is then used to drive a turbine, generating electricity. This technology is highly efficient in sunny regions and can be combined with thermal energy storage systems, allowing for power generation even when the sun is not shining.
10. Space Applications (Future)
There has been exploration into using steam turbines in space applications, specifically for power generation aboard spacecraft and space stations. Steam could potentially be generated through nuclear reactors in space, and the resulting heat would be used to create steam to power turbines. Although this technology is still in its nascent stages, steam turbines could offer a reliable and efficient source of energy for long-term space missions.
Conclusion
Steam turbines are highly versatile machines that have applications in many industries beyond traditional power generation. From large-scale energy production in fossil-fuel, nuclear, and renewable power plants to industrial applications in manufacturing, district heating, and waste-to-energy systems, steam turbines are integral to efficient and sustainable energy use. As industries evolve and new technologies emerge, steam turbines will continue to be adapted and optimized to meet the changing needs of energy generation and industrial processes. Their flexibility, reliability, and efficiency make them indispensable in the modern energy landscape, supporting both conventional and emerging energy sources.
Steam turbines are primarily used in power generation, where they convert thermal energy into electrical energy. This is achieved by using heat from various sources, such as fossil fuels, nuclear reactions, or renewable energy, to produce steam that drives turbine blades connected to a generator. In fossil-fuel power plants, steam is generated by burning coal, oil, or natural gas. Nuclear power plants use the heat generated from nuclear fission to produce steam, which powers the turbine. This method of generating electricity is widely adopted due to the reliability and scalability of steam turbines, making them ideal for large-scale power plants. In addition to traditional coal-fired and nuclear power plants, steam turbines are integrated into combined-cycle plants, where they work alongside gas turbines. The gas turbine generates power by burning fuel, while the exhaust heat is used to create steam, further increasing the plant’s overall efficiency.
In marine propulsion, steam turbines have been widely used in naval and commercial vessels. Large ships, including aircraft carriers, cruise ships, and naval warships, use steam turbines to generate the power needed to propel these massive vessels. Steam generated from onboard boilers is used to drive turbines, which are then connected to the ship’s propellers. This technology has been favored for its high power output and efficiency, especially for large ships that require substantial propulsion power. The use of steam turbines in naval vessels is particularly important in military applications, where speed and reliability are crucial, allowing for efficient travel and operation in various maritime conditions.
Steam turbines are also commonly used in industrial applications, especially in processes that require large amounts of heat and electricity. In industries such as oil refining, petrochemicals, and paper manufacturing, steam turbines provide the energy needed for production processes. These industries often use combined heat and power (CHP) systems, where steam turbines generate both electricity and thermal energy. By capturing the waste heat from industrial processes and converting it into steam, the system improves efficiency and reduces fuel consumption. For example, in a refinery, steam is used in distillation and other processing steps, and steam turbines can recover energy from waste heat to generate electricity for use in the plant.
Another significant application is in geothermal power plants, where steam turbines are used to convert the heat from beneath the Earth’s surface into electricity. In geothermal power generation, steam is extracted from geothermal reservoirs, and this steam drives turbines to generate electricity. This method of power generation is environmentally friendly, as it relies on natural heat sources rather than fossil fuels. Geothermal energy offers a sustainable and reliable source of power, especially in regions with abundant geothermal activity, and steam turbines are key to harnessing this energy.
In waste-to-energy plants, steam turbines are employed to generate electricity from the combustion of municipal solid waste (MSW). By burning waste, the heat produced is used to convert water into steam, which then drives turbines connected to generators. This process not only helps reduce the volume of waste in landfills but also provides a renewable source of energy. Steam turbines in waste-to-energy plants help produce power while managing waste effectively, making it a dual-benefit solution for waste management and energy production.
In solar thermal power plants, steam turbines are used to convert concentrated solar energy into electricity. Mirrors or lenses are used to focus sunlight onto a heat exchanger, which transfers the heat to a fluid that is then used to produce steam. This steam is used to drive a turbine, generating electricity. Solar thermal power plants are increasingly being developed in sunny regions, and their integration with thermal energy storage systems allows them to generate electricity even during non-sunny periods. Steam turbines are crucial to the operation of solar thermal power plants, as they efficiently convert thermal energy into usable electrical energy.
The applications of steam turbines are not limited to large-scale power generation. They also play an important role in industrial sectors that require smaller-scale or more specialized energy production. For instance, in industries like food processing, steam turbines provide the necessary heat for cooking, sterilizing, and drying products. In these contexts, turbines can be powered by a variety of fuels, including natural gas, biomass, or waste heat from other industrial processes. In smaller-scale operations, steam turbines offer a flexible and efficient solution for meeting the energy demands of these industries.
Steam turbines are also utilized in combined cycle and cogeneration systems, where they help maximize the efficiency of energy production. In these systems, both electricity and useful thermal energy are produced simultaneously, which helps reduce waste and increase overall efficiency. This approach is increasingly used in industries with high thermal energy needs, such as chemical plants and district heating systems. In district heating systems, steam turbines generate heat that is distributed to homes, offices, and other buildings, providing an efficient means of supplying both electricity and heat to urban areas. These systems are particularly valuable in cold climates, where heating demand is high and can be met through steam turbine-based cogeneration.
Additionally, steam turbines are used in hydrogen production, especially in processes like steam methane reforming (SMR), where natural gas is combined with steam to produce hydrogen and carbon dioxide. Steam turbines can be used to power the processes that produce steam or to convert the generated energy into electricity. With the growing interest in hydrogen as a clean energy carrier, steam turbines could play a crucial role in enabling hydrogen production as part of a broader transition to a low-carbon economy.
In the future, steam turbines may also be integrated into systems that utilize alternative fuels such as ammonia or synthetic fuels, which could be used to generate steam in a manner similar to natural gas. These technologies are still under development, but they hold the potential to further expand the use of steam turbines in clean energy applications. The development of these technologies could help reduce emissions from power generation and industrial processes, making steam turbines a key part of the transition to a sustainable energy future.
In conclusion, steam turbines are indispensable in a variety of applications, from large-scale power generation to industrial processes and renewable energy systems. Their ability to efficiently convert thermal energy into electricity and mechanical power makes them a versatile and reliable technology. Whether used in traditional fossil-fuel plants, nuclear power stations, or renewable energy systems, steam turbines are critical in providing reliable, efficient, and flexible energy solutions for a wide range of industries. As the world moves toward cleaner and more sustainable energy sources, the role of steam turbines will likely continue to expand, with innovations in fuel use, efficiency, and integration with renewable technologies driving their continued importance in the global energy mix.
In addition to their traditional uses, steam turbines are also increasingly employed in more specialized applications, as industries continue to innovate and seek more sustainable solutions. For example, in carbon capture and storage (CCS) facilities, steam turbines are used in processes that capture carbon dioxide from power plants and industrial emissions. The captured carbon is compressed and transported for storage underground or for use in other applications, such as enhanced oil recovery. The energy needed for these compression and storage processes is often provided by steam turbines, ensuring that the carbon capture process is both energy-efficient and scalable.
Steam turbines also find use in hydropower plants, particularly in small and micro-hydropower systems. While large hydroelectric dams often use water turbines to generate power, steam turbines are sometimes used in conjunction with geothermal or biomass-powered systems in remote or off-grid areas. These systems provide local communities with reliable power, especially in regions where access to centralized power grids is limited. Steam turbines, in this case, can help improve the reliability and efficiency of hybrid power plants, which combine different renewable sources to provide consistent energy output.
In the aerospace industry, steam turbines are being investigated for use in aircraft and spacecraft propulsion systems. While this technology is still in its early stages, the concept involves using steam as a working fluid to generate thrust in engines. Given the high energy density and power output of steam turbines, they could provide a lightweight and efficient power solution for future aviation technologies, particularly for high-performance aircraft or space missions where weight and energy efficiency are critical factors.
Steam turbines are also becoming an important part of the emerging energy storage systems. One example is the integration of steam turbines with concentrated solar power (CSP) plants, where steam is generated by focusing sunlight on a receiver. The steam produced is used to drive a turbine connected to a generator, which produces electricity. In some CSP systems, thermal energy storage is also incorporated, allowing excess energy to be stored in materials such as molten salt. The stored energy can be used later to generate steam and produce electricity when sunlight is unavailable, enhancing the plant’s ability to provide reliable, dispatchable power.
Furthermore, steam turbines are being adapted for use in advanced energy systems that combine multiple sources of energy, such as hydrogen or ammonia-based power plants. These systems are particularly important in the transition to a low-carbon economy, as they offer a means to store and use renewable energy in the form of hydrogen or ammonia, which can be converted back into electricity through steam turbines. These advanced systems may be a key part of decarbonizing the energy sector, as they offer the potential for cleaner, more efficient energy production without relying on fossil fuels.
The use of steam turbines is also expanding into remote and off-grid applications, where small-scale, portable steam turbines are employed to generate electricity in isolated communities or during disaster recovery efforts. In these applications, steam can be produced from a variety of local energy sources, including biomass, waste heat, or even solar energy. These small-scale systems are especially valuable in regions where infrastructure is limited or where energy access is unreliable. Steam turbines offer a flexible and sustainable energy solution that can support community development, medical facilities, and other critical services in remote locations.
District heating systems, where heat is distributed to multiple buildings or facilities through a network of pipes, also rely heavily on steam turbines. In these systems, steam is produced centrally and then distributed for heating purposes. This is particularly useful in urban areas or large industrial complexes where there is a need for both heat and electricity. Steam turbines can improve the efficiency of these systems by ensuring that both energy forms are produced simultaneously through combined heat and power (CHP) systems. These systems reduce the overall environmental footprint of energy production, as they use the same energy source for multiple purposes.
Finally, steam turbines are also being integrated into advanced manufacturing processes. In industries such as steel production, glass manufacturing, and cement production, steam turbines are used to harness waste heat from industrial processes. This heat, which would otherwise be wasted, is converted into steam and used to drive turbines, generating electricity or providing additional heat for production. By capturing and reusing waste heat, these industries can increase energy efficiency, reduce their dependence on external energy sources, and lower their overall environmental impact.
In conclusion, the applications of steam turbines are continually expanding as industries adopt more energy-efficient, sustainable, and flexible energy solutions. From traditional power plants to cutting-edge renewable energy systems, steam turbines are a central component in the global transition toward cleaner, more reliable energy. As the demand for low-carbon technologies grows, steam turbines will continue to play a key role in improving energy efficiency, reducing emissions, and enabling new forms of clean energy production. Their versatility and adaptability ensure they will remain an essential technology in the energy mix for the foreseeable future.
Steam turbines continue to evolve with advancements in technology, expanding their role in the energy sector and beyond. The ongoing development of high-efficiency steam turbines plays a significant part in improving the performance and reducing the environmental footprint of power plants, industrial processes, and other applications. These advancements focus on maximizing energy conversion, reducing heat losses, and improving the durability and operational life of turbines.
Next-generation steam turbines are designed to operate at higher temperatures and pressures, which allows them to extract more energy from the steam. One of the key innovations in this area is the development of supercritical steam turbines. In supercritical steam plants, steam is heated above its critical point, which allows it to reach much higher temperatures and pressures than traditional steam plants. These systems are significantly more efficient because they can operate at conditions that are optimal for energy extraction. Supercritical steam turbines are being increasingly adopted in both fossil-fuel and renewable power plants to achieve greater efficiency and reduce fuel consumption.
Another area of significant progress is materials science. The materials used in the construction of steam turbines are critical for their efficiency and longevity. Modern turbines use advanced alloys and coatings that can withstand higher temperatures, pressures, and the erosive effects of steam over long periods of operation. The development of materials such as nickel-based superalloys and ceramic coatings helps to reduce wear and tear, thereby increasing the lifespan of turbines and reducing maintenance costs. These innovations are essential for extending the operational life of steam turbines, especially in high-stress applications like those in nuclear and combined-cycle plants.
In parallel, digitalization and smart monitoring technologies are transforming the way steam turbines are operated and maintained. Through the integration of advanced sensors, predictive maintenance software, and real-time data analytics, turbine operators can monitor the condition of turbines more accurately and effectively. Condition-based monitoring allows for the early detection of issues such as vibration, temperature fluctuations, and blade erosion. By identifying problems before they lead to system failure, operators can schedule maintenance more efficiently, reduce downtime, and extend the service life of the turbine. The use of artificial intelligence (AI) and machine learning algorithms to analyze operational data is also helping to optimize turbine performance and energy efficiency.
Furthermore, steam turbines are increasingly being integrated into hybrid energy systems that combine multiple forms of renewable energy. For example, solar-thermal power plants, which concentrate sunlight to generate heat, often pair steam turbines with photovoltaic solar systems to create a hybrid model. This combination allows the plant to produce electricity both during sunny periods and at night, increasing its reliability and efficiency. Similarly, steam turbines are being paired with wind power in hybrid systems, where steam turbines provide backup power during periods when wind generation is low. These hybrid systems offer the advantage of flexibility and reliability, as they can balance the intermittent nature of renewable energy sources with the steady power generation provided by steam turbines.
The rise of decentralized energy generation is also influencing the role of steam turbines. In contrast to traditional centralized power plants, decentralized systems are designed to generate electricity and heat at the point of use, often on a smaller scale. Steam turbines are being adapted for use in these decentralized systems, particularly in combined heat and power (CHP) applications. This approach is increasingly popular in urban environments, industrial complexes, and even remote areas, where local energy generation is preferred due to cost, reliability, or environmental concerns. Small-scale steam turbines that operate efficiently on biomass or waste-to-energy systems are becoming more common in such settings, providing localized power solutions.
Moreover, steam turbines are contributing to the development of low-carbon technologies. As the world strives to meet climate goals and reduce carbon emissions, steam turbines are integral to carbon capture, utilization, and storage (CCUS) technologies. In power plants and industrial facilities, steam turbines are used in combination with carbon capture systems to provide the necessary energy for capturing CO2 from flue gases. The captured carbon can then be stored underground or used in other applications, such as in the production of synthetic fuels or chemicals. Steam turbines thus play a role in reducing the carbon footprint of energy-intensive industries, particularly in sectors like cement, steel, and petrochemicals.
In green hydrogen production, steam turbines are used in some of the advanced processes designed to produce hydrogen from renewable sources. One such method is water electrolysis, where water is split into hydrogen and oxygen using electricity. Steam turbines can play a role in providing the thermal energy necessary for electrolysis, especially in high-temperature electrolysis systems. The ability to generate hydrogen from renewable sources, such as solar or wind energy, and use steam turbines to improve the efficiency of the process, is seen as a key step in decarbonizing industries that are hard to electrify, such as steelmaking and transportation.
The advent of modular steam turbines also opens up new possibilities for steam turbine use. These smaller, modular systems are designed for flexibility, making them ideal for distributed energy systems, remote locations, and applications with fluctuating power demands. Modular turbines can be quickly deployed and integrated into existing systems, making them valuable for applications where fast and scalable power generation is required. They are particularly suitable for industries that need both power and heat but do not have access to large-scale grid infrastructure.
Another key trend is the development of zero-emission steam turbines. This includes turbines that run on renewable fuels such as hydrogen or ammonia, which produce no carbon emissions when burned. These systems are seen as essential for achieving net-zero emissions goals in the energy sector. By using clean fuels in the steam cycle, these turbines provide a low-carbon alternative to traditional fossil-fuel-based power generation. The development of such technologies aligns with the global push toward reducing emissions and transitioning to a more sustainable energy future.
In the context of sustainable development, steam turbines are being increasingly integrated into circular economy models, where waste is minimized, and resources are used more efficiently. For example, in biogas plants, steam turbines are used to convert organic waste into energy. The methane gas produced from organic matter is used to generate electricity, and the steam turbine is an efficient means of converting that energy into usable power. Such systems contribute to reducing waste and improving the overall environmental performance of industrial processes.
Lastly, steam turbines are at the heart of developing energy recovery technologies in a variety of sectors. In industries such as steel, glass manufacturing, and chemical processing, steam turbines are employed to recover waste heat and convert it into usable power. By capturing the waste heat from furnaces, kilns, or chemical reactors, these industries can reduce their overall energy consumption and decrease greenhouse gas emissions. This energy recovery process not only helps businesses reduce costs but also contributes to meeting sustainability goals by improving energy efficiency.
In conclusion, steam turbines remain a cornerstone of energy generation, and their applications continue to evolve in response to the growing demand for cleaner, more efficient, and sustainable energy solutions. Advances in materials, efficiency, and integration with renewable energy systems, as well as their role in decarbonizing hard-to-electrify sectors, ensure that steam turbines will remain an essential part of the energy landscape. Their ability to adapt to emerging technologies and contribute to a low-carbon economy positions them as a key player in the global transition to sustainable energy.
Steam Turbines in Energy Systems
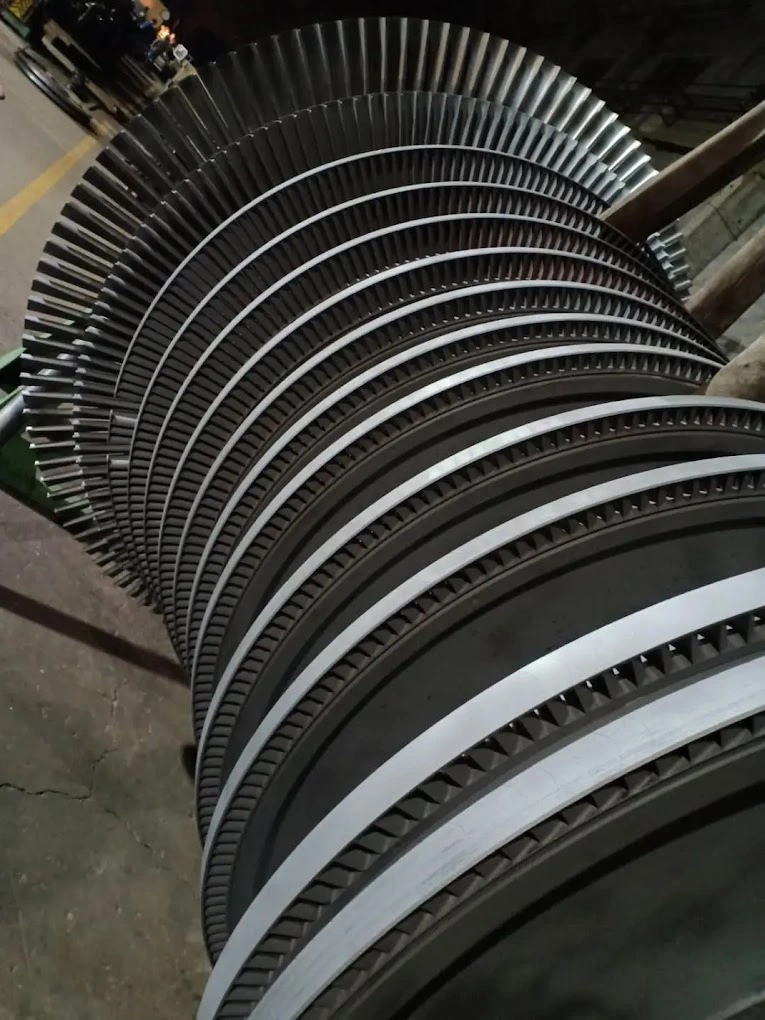
Steam turbines play a critical role in the energy systems that power the modern world. They are employed across a wide range of applications in both conventional and emerging energy technologies. The versatility and efficiency of steam turbines make them integral to many forms of power generation, from traditional fossil-fuel plants to cutting-edge renewable energy solutions. As the world transitions to cleaner and more sustainable energy sources, steam turbines are also evolving to meet new challenges and support advanced energy systems.
In fossil-fuel-based power generation, steam turbines have been the backbone of electricity production for more than a century. In coal, natural gas, and oil-fired power plants, steam is produced by burning these fuels in boilers, and the resulting high-pressure steam drives turbines connected to electrical generators. These systems have evolved over time to become more efficient, with improvements in turbine design, heat recovery, and overall energy conversion. Modern steam turbines used in these plants are capable of operating at supercritical or ultra-supercritical pressures and temperatures, further increasing their efficiency by extracting more energy from the fuel. However, as part of the ongoing transition to a low-carbon future, many of these plants are being integrated with carbon capture and storage (CCS) technologies to reduce their environmental impact.
In combined-cycle power plants, steam turbines are integrated with gas turbines to maximize efficiency. In this configuration, a gas turbine generates electricity by burning natural gas, and the exhaust heat is used to generate steam for a steam turbine, which then produces additional electricity. This process significantly increases the overall efficiency of the power plant, as it takes advantage of the waste heat produced by the gas turbine. Combined-cycle plants are one of the most efficient forms of power generation currently available, and steam turbines are essential to achieving this high level of efficiency.
In nuclear power plants, steam turbines have a critical role in converting the heat generated by nuclear fission into electrical energy. The process begins with nuclear reactors producing heat through controlled fission reactions. This heat is used to create steam, which drives a turbine connected to a generator. Nuclear power plants are capable of providing large-scale, baseload power generation, and steam turbines are vital to ensuring their reliable operation. While nuclear power does not produce the carbon emissions associated with fossil fuels, concerns about waste management, safety, and public perception continue to influence the role of nuclear energy in the global energy mix.
Renewable energy systems are also increasingly utilizing steam turbines, although the source of heat for the steam differs from traditional fossil fuel or nuclear plants. Solar thermal power plants use concentrated solar energy to heat a fluid, often oil or molten salt, which in turn generates steam that drives a steam turbine. This process allows solar power to be generated even when the sun is not shining, as thermal energy can be stored in materials like molten salt and used to generate steam during periods of low sunlight or at night. Steam turbines in solar thermal plants are essential for providing dispatchable, on-demand power, making solar thermal a valuable complement to intermittent renewable sources like solar photovoltaic (PV) and wind power.
In geothermal power plants, steam turbines are employed to generate electricity from the heat stored beneath the Earth’s surface. In these systems, steam or hot water from geothermal reservoirs is brought to the surface, and the steam is used to drive turbines that generate power. Geothermal energy is one of the most reliable and sustainable forms of energy, as it is available 24/7, regardless of weather or time of day. Steam turbines are key to harnessing this energy source efficiently, providing clean, renewable power with minimal environmental impact.
Biomass power plants also utilize steam turbines to generate electricity. Biomass refers to organic materials like wood, agricultural waste, or dedicated energy crops that are burned or converted into biogas to produce heat. This heat is used to generate steam, which drives a turbine connected to a generator. Biomass plants can provide renewable energy, and steam turbines are integral to making these systems efficient. Additionally, in some cases, biomass plants are integrated with carbon capture technologies to reduce the carbon emissions associated with burning biomass, further enhancing their environmental benefits.
One of the most promising applications for steam turbines in modern energy systems is their integration into energy storage systems. Concentrated solar power (CSP) plants, for instance, not only generate electricity using steam turbines but also use thermal energy storage systems, such as molten salt, to store excess energy generated during the day. This stored thermal energy can then be used to generate steam and produce electricity during periods when sunlight is not available, such as at night or during cloudy weather. This ability to store and dispatch solar energy when needed makes CSP systems with steam turbines an important technology for balancing supply and demand in the electricity grid.
In waste-to-energy (WTE) plants, steam turbines are used to generate electricity from the combustion of municipal solid waste (MSW). The waste is burned at high temperatures, producing heat that is used to convert water into steam, which then drives a turbine connected to a generator. WTE plants help reduce the amount of waste sent to landfills while simultaneously providing a renewable source of energy. These plants are particularly useful in urban areas where waste management is a challenge, and steam turbines play a vital role in making these plants efficient and reliable.
In district heating systems, steam turbines are used to generate heat and electricity for communities, particularly in colder climates. In district heating systems, steam is generated at a central location and distributed through a network of pipes to homes, businesses, and other buildings for heating. Steam turbines in these systems help improve the efficiency of the process by generating both heat and power simultaneously through combined heat and power (CHP) systems. This approach reduces energy losses and maximizes the overall efficiency of the system, providing affordable, reliable energy to urban and industrial areas.
As the world increasingly looks to decarbonize its energy systems, hydrogen production is gaining attention as a clean energy source. Hydrogen can be produced through various methods, including water electrolysis, where electricity is used to split water molecules into hydrogen and oxygen. Steam turbines are sometimes employed in hydrogen production facilities to generate the necessary heat or to help power the electrolysis process. Additionally, hydrogen can be used as a fuel in hydrogen-fueled power plants, where it is burned in turbines to generate electricity. In these systems, steam turbines can be used to convert the heat generated from burning hydrogen into usable energy, contributing to a cleaner, more sustainable energy future.
Finally, steam turbines are playing an increasing role in the development of smart grids and decentralized energy systems. These grids, which allow for the integration of various distributed energy resources, such as solar, wind, and biomass, rely on steam turbines to provide backup power when renewable generation is low or when demand spikes. Steam turbines can also be used in microgrids, which are small-scale energy systems that can operate independently or in conjunction with the main grid. By providing flexible and reliable power generation, steam turbines support the integration of renewable energy into the grid and help ensure the stability and resilience of modern energy systems.
In conclusion, steam turbines are integral to a wide range of energy systems, from traditional fossil-fuel power plants to cutting-edge renewable energy technologies. Their ability to efficiently convert heat into mechanical energy makes them indispensable for large-scale electricity generation, and their adaptability allows them to be integrated into emerging energy solutions, such as energy storage systems, hybrid power plants, and decentralized grids. As the world transitions to a cleaner and more sustainable energy future, steam turbines will continue to play a pivotal role in ensuring reliable, efficient, and flexible energy production.
As the energy landscape continues to evolve, steam turbines are becoming even more integral to the success of advanced energy systems, particularly in the context of the global push for sustainability and decarbonization. Innovations in turbine technology are enabling better integration with diverse energy sources, improving efficiency, and reducing emissions. Several key trends and developments illustrate the expanding role of steam turbines in the energy sector.
Hybrid energy systems, combining different renewable and conventional energy sources, are increasingly relying on steam turbines to maintain energy security and reliability. For example, in solar-wind hybrid plants, the intermittent nature of solar and wind energy can create fluctuations in power generation. By integrating steam turbines into such hybrid systems, excess energy can be stored and used to generate steam, which then powers turbines and stabilizes the grid. This flexibility ensures that power plants can provide a consistent supply of electricity, even during periods of low renewable energy output.
Another important development is the incorporation of energy storage systems into steam turbine-based plants. Advanced thermal storage technologies, such as molten salt storage, allow steam turbines to produce electricity on demand, even when renewable generation is not active. In a concentrated solar power (CSP) plant, for instance, steam turbines can be powered by stored heat during the night or on cloudy days, extending the operation hours of the plant and allowing it to act as a reliable, dispatchable power source. Thermal energy storage paired with steam turbines also contributes to grid stability by allowing excess renewable energy to be stored during peak generation periods and released later to meet demand.
Waste heat recovery is another growing application of steam turbines. In industrial settings, steam turbines are increasingly used to recover waste heat from manufacturing processes, chemical production, and other energy-intensive operations. Instead of allowing this heat to be wasted, it is captured and used to generate steam, which drives turbines to produce electricity. This process, often referred to as cogeneration or combined heat and power (CHP), not only improves the energy efficiency of industrial processes but also helps reduce greenhouse gas emissions. Many industries are retrofitting existing systems with steam turbines to recover waste heat and reduce their overall energy consumption and environmental impact.
In the context of distributed energy systems, steam turbines are playing a vital role in smaller, modular power plants that serve localized energy needs. These decentralized systems often use renewable fuels, such as biomass, to generate steam and power turbines. Biomass power plants can be built in remote or off-grid locations, providing reliable electricity where grid infrastructure is unavailable. As these distributed systems become more common, steam turbines offer a scalable, flexible solution that meets the energy demands of both urban and rural areas.
The integration of hydrogen production with steam turbines is also gaining traction as part of the transition to cleaner energy. Green hydrogen, produced through electrolysis powered by renewable electricity, holds promise as a clean fuel for both power generation and industrial processes. Steam turbines can be used in hydrogen-fueled power plants, where hydrogen is combusted to produce heat, which then drives the turbine to generate electricity. Additionally, steam turbines can be employed in hydrogen-based cogeneration systems that produce both power and heat, making them highly efficient and suitable for a variety of applications, including district heating and industrial processes.
Moreover, carbon capture technologies are increasingly being integrated into power plants that use steam turbines. Steam turbines can provide the necessary power for carbon capture, utilization, and storage (CCUS) systems, where CO2 emissions from fossil-fuel or industrial plants are captured and either stored underground or utilized in other processes. This combination helps mitigate the environmental impact of traditional power generation while maintaining the reliable and continuous output that steam turbines are known for. In addition, research into bioenergy with carbon capture and storage (BECCS) systems, where biomass is used as a fuel source and CO2 is captured, shows great potential for reducing net greenhouse gas emissions.
With a growing focus on sustainability, steam turbines are being adapted for use in low-emission technologies. For instance, hydrogen combustion turbines are being developed to burn hydrogen as a clean fuel source, with steam turbines playing a role in generating electricity from the combustion process. By utilizing hydrogen, which produces no carbon emissions when burned, steam turbines can help decarbonize power generation, particularly in sectors where electrification is difficult, such as heavy industry and transportation.
The role of steam turbines in smart grids and advanced grid systems is also expanding. Smart grids rely on advanced communication and control technologies to manage the distribution of electricity from various sources. Steam turbines, particularly in combination with energy storage and demand response systems, can play a crucial role in stabilizing the grid during peak demand periods. By providing backup power or balancing intermittent renewable energy, steam turbines help ensure a reliable and resilient electricity supply. These systems can also incorporate real-time data and predictive analytics to optimize turbine performance and prevent downtime, further enhancing the efficiency and reliability of energy systems.
In the context of decarbonization strategies, steam turbines are positioned to play an increasingly important role in facilitating the transition away from fossil fuels. As countries commit to net-zero emissions goals, the demand for low-carbon energy technologies is growing. Steam turbines, as part of combined-cycle plants, renewable energy systems, and energy recovery systems, are essential for producing clean electricity while maintaining grid stability. They also provide a crucial backup power source, ensuring that renewable energy can be fully integrated into the grid without sacrificing reliability.
In conclusion, steam turbines are becoming even more essential in the context of modern energy systems, as they are integrated into innovative technologies that drive efficiency, sustainability, and decarbonization. From hybrid energy systems and energy storage solutions to advanced grid systems and waste heat recovery, steam turbines continue to support the transition to cleaner, more resilient energy networks. Their ability to provide flexible, reliable power makes them a key component of a sustainable energy future, ensuring that both current and emerging energy sources can work together to meet the world’s growing energy demands while reducing the environmental impact of power generation.
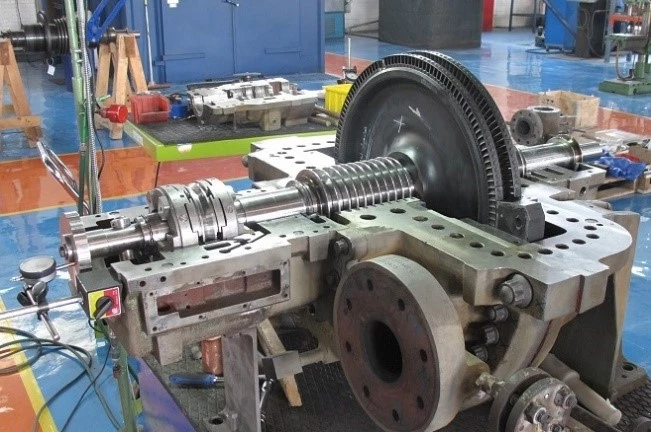
As we move further into the 21st century, the role of steam turbines in energy systems will continue to evolve, driven by technological advancements, shifting energy priorities, and the ongoing need to decarbonize the global economy. The future of steam turbines in energy systems is tied to several critical factors, including their ability to integrate with emerging technologies, support sustainable energy transitions, and contribute to more flexible and resilient grids.
One of the most exciting areas of development is the continued integration of steam turbines with renewable energy systems. While steam turbines have traditionally been associated with fossil-fuel and nuclear power plants, their role in renewable energy applications is expanding significantly. For example, geothermal power plants, which utilize the heat from the Earth’s core to generate steam and drive turbines, are becoming a key component of the renewable energy mix. Geothermal energy is considered one of the most reliable and sustainable forms of power, as it provides a consistent and nearly infinite energy supply. Steam turbines are essential for converting this thermal energy into usable electricity, and ongoing advancements in geothermal technology are expected to enhance the efficiency and scalability of these systems.
The role of steam turbines in concentrated solar power (CSP) systems is also likely to increase as the demand for solar energy grows. CSP plants use mirrors or lenses to concentrate sunlight onto a receiver, which then generates heat to produce steam. This steam drives a turbine to generate electricity. Unlike traditional photovoltaic (PV) solar panels, which can only generate electricity during daylight hours, CSP systems with steam turbines can provide dispatchable power, which is especially valuable for balancing the intermittent nature of solar energy. With advancements in thermal storage technologies, such as molten salt, CSP systems can store excess heat for use during periods of low sunlight, enabling the steam turbines to continue generating electricity during cloudy days or at night.
In the context of wind power, steam turbines could also play a role in hybrid systems that combine wind and thermal energy. While wind energy generation itself does not directly involve steam turbines, integrating steam turbines into hybrid wind-thermal systems could help mitigate the variability of wind power. In such a system, wind power could be used to generate electricity, while excess energy could be converted into thermal energy and stored for later use, where steam turbines would be responsible for generating power when wind generation is insufficient.
Hydrogen production is another area where steam turbines are likely to become increasingly important. Green hydrogen, produced via electrolysis powered by renewable electricity, is seen as a potential game-changer for decarbonizing industries like steel, cement, and chemicals, as well as transportation. Steam turbines can be used in hydrogen plants for applications such as providing the thermal energy needed for high-temperature electrolysis or assisting in hydrogen-fired power plants. As hydrogen infrastructure expands, steam turbines will play a vital role in making hydrogen production and utilization more efficient, helping to establish hydrogen as a significant clean energy source.
Furthermore, small modular reactors (SMRs), a new generation of nuclear power plants, could offer a promising opportunity for steam turbines in future energy systems. SMRs are designed to be more compact, flexible, and safer than traditional nuclear reactors, and they can be deployed in regions where larger reactors may not be viable. These reactors generate heat through nuclear fission, and steam turbines convert this heat into electricity. As SMRs gain traction, steam turbines will continue to be crucial components of this emerging technology, ensuring that these smaller, more flexible nuclear plants can provide reliable, low-carbon electricity to power grids.
Steam turbines will also be central to carbon capture, utilization, and storage (CCUS) systems in the future. Carbon capture involves capturing CO2 emissions from fossil fuel power plants or industrial processes before they are released into the atmosphere, and then either storing them underground or utilizing them in other applications. Steam turbines are often required to power the processes that capture CO2, such as solvent regeneration and compression. Additionally, steam turbines can help in bioenergy with carbon capture and storage (BECCS), where biomass is used as a fuel source, and CO2 is captured and stored, leading to net-negative emissions. The continued development of CCUS technologies will enhance the role of steam turbines in reducing the carbon footprint of traditional and bioenergy plants.
The growing demand for decentralized energy systems is also likely to drive innovation in steam turbine applications. As more businesses, communities, and even households seek to produce their own energy, steam turbines can be used in microgrids and combined heat and power (CHP) systems, where they provide reliable electricity and heat. In microgrids, steam turbines are particularly valuable because they can function independently of the main power grid, ensuring that energy is available even in remote or off-grid locations. These small-scale systems can utilize renewable resources, such as biomass or waste heat, to generate steam and power turbines, offering a more sustainable alternative to traditional centralized power plants.
The potential for steam turbines to play a role in energy recovery systems is also expanding. In industries with high energy consumption, such as cement production, steel manufacturing, and chemical processing, steam turbines are used to recover waste heat and convert it into electricity. By tapping into otherwise wasted energy, these systems improve overall efficiency and reduce energy costs. Furthermore, by recovering waste heat from processes like industrial combustion or chemical reactions, steam turbines help reduce the carbon footprint of industrial operations.
The shift toward smart grids and digitalization will also enhance the role of steam turbines in energy systems. By integrating advanced sensors, artificial intelligence (AI), and machine learning technologies, steam turbines can be optimized for efficiency, performance, and predictive maintenance. Real-time monitoring of turbine conditions allows operators to anticipate potential failures and minimize downtime, ensuring that turbines run at optimal performance levels. This will be particularly important as the world shifts to distributed energy resources (DERs), where power generation is more localized and requires increased coordination to maintain grid stability.
Finally, advanced materials and additive manufacturing are likely to shape the future of steam turbines. The development of high-performance alloys, ceramic coatings, and other materials designed to withstand extreme temperatures and pressures will allow steam turbines to operate more efficiently and last longer. Additionally, 3D printing and additive manufacturing can enable the creation of more complex turbine components, reducing manufacturing costs and increasing customization for specific applications. These technological innovations will enable steam turbines to operate in increasingly challenging environments, such as high-temperature industrial processes, supercritical steam plants, and advanced nuclear reactors.
In conclusion, the future of steam turbines in energy systems is bright, with opportunities in both traditional and emerging technologies. As the world moves toward a cleaner, more sustainable energy future, steam turbines will remain at the heart of many key energy systems. Their ability to generate reliable power from a variety of heat sources, including renewable fuels, nuclear, and waste heat, positions them as essential components in the transition to a low-carbon, decentralized, and resilient energy grid. With ongoing advancements in efficiency, materials, and integration with smart technologies, steam turbines will continue to play a critical role in shaping the global energy landscape.
As the demand for sustainable, reliable, and efficient energy systems continues to rise, the role of steam turbines in shaping the future of global energy production will grow even more pivotal. The convergence of advanced technologies, evolving energy sources, and climate goals is driving steam turbines into new and increasingly sophisticated applications. These turbines will continue to serve as a cornerstone for decarbonizing the power sector, enhancing grid resilience, and facilitating the integration of renewable and low-carbon energy sources.
One of the most notable directions for the future of steam turbines is their increasing role in hybrid power systems. The growing integration of renewable energy with conventional power generation sources requires technologies that can handle variability, maintain stability, and ensure reliable electricity supply. Steam turbines will continue to play a critical role in such hybrid systems by acting as a balancing force between intermittent renewable generation (like solar and wind) and traditional, more stable power plants.
Wind-solar-hybrid power plants are emerging as a solution to address the intermittency issues associated with solar and wind energy. In these plants, renewable power generation from wind or solar farms is often supplemented by thermal generation technologies, which might include steam turbines powered by biomass, waste heat, or concentrated solar thermal energy. In these hybrid systems, the steam turbines provide a continuous power output when renewable generation dips, ensuring a consistent electricity supply. This model helps stabilize the grid, reducing reliance on fossil fuels and supporting the integration of variable renewable energy sources.
Thermal storage systems will also have a growing influence on the future of steam turbines. Systems like molten salt storage can absorb excess heat produced by concentrated solar power (CSP) systems during periods of high solar irradiance and release that heat when needed. In these cases, steam turbines are used to convert stored thermal energy into electrical power during off-peak times, such as at night or during cloudy weather. This ability to store and dispatch renewable energy allows for more efficient and stable integration of solar power into the grid, and steam turbines are a key component of ensuring that this stored energy is converted to electricity when demand is high.
Another emerging trend is the integration of hydrogen as a fuel source. Hydrogen-powered turbines are a promising solution for reducing carbon emissions from power plants. Hydrogen, when burned in a turbine, produces water vapor as the primary byproduct, making it one of the cleanest fuels for power generation. Steam turbines, in combination with hydrogen, could help lower the carbon footprint of fossil fuel-dependent sectors by displacing coal, oil, and natural gas combustion. Hydrogen combustion turbines are being developed to operate on pure hydrogen or blends of hydrogen and natural gas, with steam turbines providing the efficiency needed for power generation in these systems. The technology also aligns with the global push to develop a hydrogen economy, where hydrogen is used not only as a fuel for power generation but also for industrial processes, transportation, and energy storage.
Small modular reactors (SMRs) are another emerging field in which steam turbines will continue to play an important role. SMRs are compact nuclear reactors that are scalable, flexible, and safer compared to traditional large nuclear power plants. These reactors generate heat through nuclear fission, which is used to create steam that drives a turbine to produce electricity. The future development of SMRs will rely on steam turbines to ensure that these plants operate efficiently and safely, providing low-carbon electricity with a significantly smaller environmental footprint than conventional nuclear plants. The development of SMRs is likely to drive innovation in turbine technology, particularly in terms of reliability, safety, and adaptability to smaller, modular designs.
The future also points toward a stronger focus on efficiency and the reduction of operational costs in steam turbines. As global energy demands rise, maximizing the efficiency of power generation systems will be a priority for reducing energy costs and lowering emissions. Advanced materials science will continue to improve the performance of steam turbines. High-temperature alloys, ceramic coatings, and other innovations will allow turbines to operate in increasingly extreme conditions, such as higher steam temperatures and pressures. These materials will contribute to reducing fuel consumption, increasing the power output of turbines, and enhancing their lifespan.
To further improve turbine efficiency, the adoption of digital technologies like artificial intelligence (AI), machine learning, and big data analytics is expected to become more widespread in the operation and maintenance of steam turbines. AI-powered monitoring systems will enable predictive maintenance, allowing operators to anticipate wear and tear before it leads to failures or costly downtime. Real-time data analysis will optimize turbine performance, ensuring that turbines are operating at peak efficiency at all times. These systems can also provide insights into the health of turbines, help identify potential energy savings, and improve their integration with the rest of the power generation system.
Moreover, advancements in additive manufacturing or 3D printing will allow for the production of more complex turbine parts with greater precision. This technology will make it easier to design and manufacture turbine components with optimized shapes, reducing material costs and improving efficiency. In the future, steam turbine components could be manufactured on demand and with more intricate geometries that were previously impossible with traditional manufacturing techniques. This will not only lead to cost savings but also allow for custom solutions to meet the needs of specific applications, such as power generation in remote locations or highly specialized industries.
The ongoing global push for net-zero emissions will also drive steam turbine technology to adapt and help industries decarbonize. Bioenergy with carbon capture and storage (BECCS) systems, which use biomass to generate power and capture the carbon emissions, are expected to become more widespread. Steam turbines play a critical role in converting the thermal energy from biomass combustion into electricity, while carbon capture technologies help remove CO2 from the atmosphere. BECCS offers a way to achieve negative emissions, and steam turbines will be integral to this process.
Additionally, steam turbines will continue to contribute to district heating systems, particularly in areas where urbanization is expanding. District heating involves the generation of heat at a central plant and the distribution of that heat through insulated pipes to residential, commercial, and industrial buildings. In many cases, steam turbines are used to generate both heat and electricity in combined heat and power (CHP) systems, which maximize the efficiency of the plant by utilizing waste heat to meet heating demands. As cities continue to grow and the demand for efficient energy increases, steam turbines will be a key technology for sustainable urban infrastructure.
Steam turbines will also contribute to waste-to-energy (WTE) systems in the future. In these systems, municipal solid waste (MSW) is burned to produce heat, which generates steam that drives a turbine to produce electricity. This process not only reduces the amount of waste sent to landfills but also provides a renewable energy source. As cities continue to grapple with waste management and energy demands, WTE systems with steam turbines will help divert waste from landfills, reduce greenhouse gas emissions, and provide valuable energy.
Finally, as the energy sector becomes more decentralized and more industries and regions seek energy independence, steam turbines will be central to the development of microgrids and off-grid systems. These smaller, localized energy systems rely on renewable energy sources like solar, wind, and biomass, with steam turbines providing backup power or enabling cogeneration systems that produce both electricity and heat. In remote areas or islands, steam turbines can help power communities with limited access to traditional energy infrastructure, ensuring that these populations have reliable, sustainable energy sources.
In conclusion, the future of steam turbines is shaped by their ability to integrate with emerging technologies and new energy sources, while maintaining their core strengths of efficiency, flexibility, and scalability. As the global energy landscape evolves toward greater sustainability, steam turbines will remain an essential technology in the transition to a low-carbon, resilient energy future. Through advancements in materials, efficiency, and digital technologies, steam turbines will continue to play a central role in the diverse and interconnected energy systems of the future, ensuring that we meet growing energy demands while minimizing environmental impacts.
Components of Steam Turbines
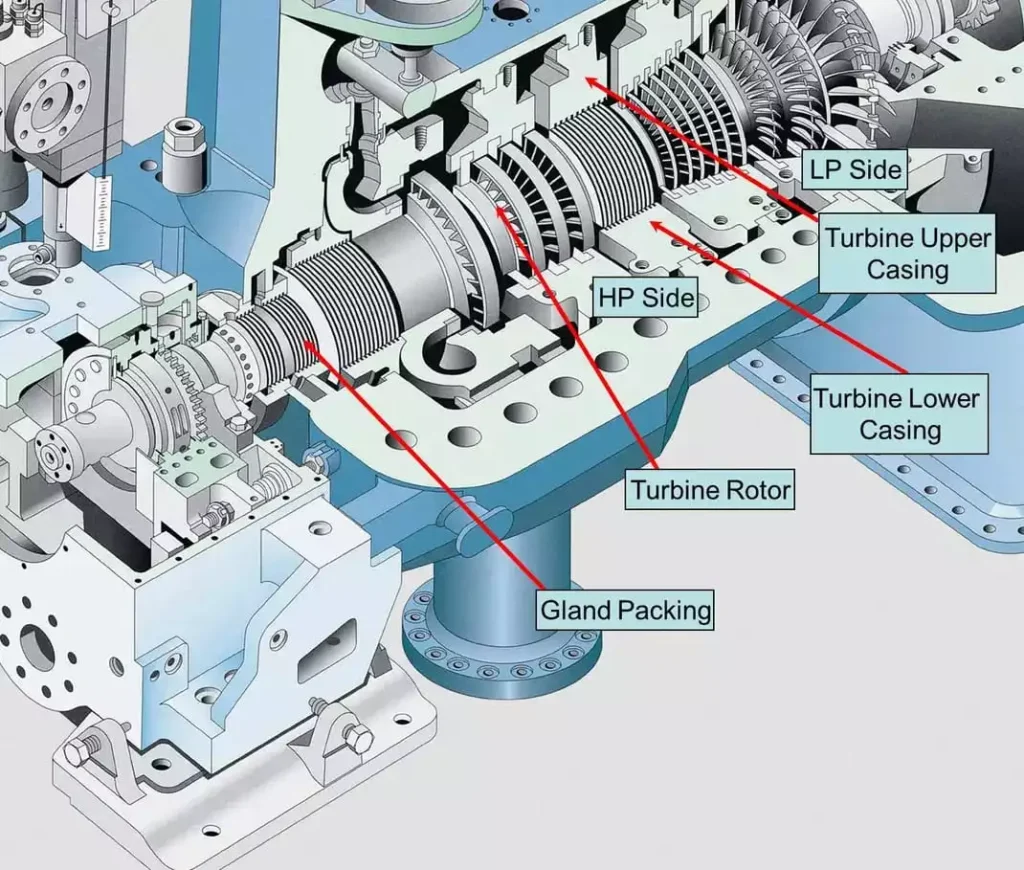
The components of steam turbines are integral to their operation, performance, and efficiency in converting steam energy into mechanical work. Each component plays a specific role in guiding, controlling, and utilizing steam to drive the turbine’s rotor. The design and configuration of these components vary depending on the turbine’s size, purpose, and application (e.g., power generation, industrial processes, or marine propulsion). However, the general structure of a steam turbine includes several key elements that work in harmony to ensure smooth and efficient operation. These components include the rotor, stator, nozzles, blades, bearings, and various control systems.
1. Rotor
The rotor is the central rotating component of the steam turbine. It is connected to the shaft, which transmits the mechanical energy produced by the steam turbine to the generator or other equipment, such as a pump or compressor. The rotor is typically composed of a series of discs mounted on a shaft, with blades attached to the discs. These blades are designed to interact with the high-pressure steam to convert its thermal energy into mechanical energy. The rotor is supported by bearings and is subjected to high mechanical stresses, so it is made from high-strength, durable materials that can withstand extreme temperatures and forces.
2. Stator
The stator is the stationary part of the steam turbine, surrounding the rotor. It consists of several key elements, including casing, nozzle chambers, and diffuser sections, that help direct the steam flow efficiently to the turbine blades. The stator does not rotate but plays a crucial role in guiding the steam towards the rotor blades in an organized and controlled manner. It helps manage the steam’s pressure and velocity, ensuring that the steam is directed at the right angles and with the correct speed to maximize the turbine’s performance.
3. Nozzles
The nozzles are specialized openings in the turbine casing that control the flow of steam into the turbine. Steam enters the turbine at high pressure and is directed through the nozzles, which convert the thermal energy of the steam into kinetic energy by accelerating the steam. The nozzles increase the velocity of the steam, ensuring that it strikes the blades with maximum force. The nozzles are designed to have an optimal shape and size to allow for efficient steam flow, and their design can vary depending on the type of steam turbine and its operating conditions. Impulse turbines, for instance, use nozzles to accelerate steam and then direct it onto the blades, while reaction turbines use a combination of nozzles and blades to manage both steam pressure and velocity.
4. Blades
The blades are the key components of the turbine that interact with the steam to produce rotational motion. There are typically two types of blades in a steam turbine:
- Impulse blades: These blades are struck by high-velocity steam coming from the nozzles. The steam imparts its kinetic energy to the blades, causing them to rotate. The steam’s pressure drops as it passes through the blades, and the energy is transferred into mechanical work.
- Reaction blades: In contrast, reaction blades work in conjunction with the steam’s pressure and velocity. The blades themselves have a special design that causes a drop in pressure as steam flows over them, converting both the kinetic and pressure energy into mechanical energy. In a reaction turbine, steam is directed through a series of moving blades and fixed blades that work together to extract energy.
Blades are carefully engineered for strength, durability, and efficiency, as they must withstand the extreme temperatures and forces of high-pressure steam. Over time, erosion and corrosion can affect the performance of blades, so they are often coated with heat-resistant materials, such as ceramic coatings, to enhance longevity.
5. Bearings
Bearings support the rotor and allow it to rotate smoothly. Bearings are critical components that reduce friction and wear as the rotor spins at high speeds. They also help maintain the rotor’s alignment and prevent it from excessive movement during operation. The bearings used in steam turbines are typically journal bearings, which support the rotor shaft, and thrust bearings, which prevent axial movement of the shaft. In some cases, hydrodynamic bearings may also be used, which operate by creating a layer of lubricant between the bearing and the shaft to reduce friction. The selection and maintenance of bearings are vital to ensuring the efficient and reliable operation of a steam turbine.
6. Casing
The casing encloses the entire steam turbine and holds all the internal components, such as the rotor, stator, and nozzles, in place. The casing is designed to withstand the high pressures and temperatures of the steam as it passes through the turbine. The casing also helps control the flow of steam and contains the exhaust section, where the steam exits the turbine. In addition to its protective role, the casing also acts as an essential structural component, ensuring that all the turbine parts are securely assembled.
In large turbines, multi-stage casings are used to manage the pressure drop across the turbine. Each stage contains a set of nozzles and blades that work together to extract energy from the steam in incremental steps. This multi-stage design helps ensure that the turbine operates efficiently across a range of steam pressures and temperatures.
7. Governor System
The governor system is responsible for regulating the speed of the steam turbine. It monitors the rotational speed of the turbine and adjusts the steam flow to maintain a constant speed or load, depending on the requirements of the system. Governors use mechanisms such as throttling valves to control the amount of steam entering the turbine. In modern turbines, digital governors and automated control systems are used to enhance precision and efficiency in speed regulation.
8. Condensing and Exhaust Sections
In many steam turbines, particularly those used in power generation, the exhaust steam is condensed back into water in a condenser. The condensing section of the turbine operates under vacuum conditions, where steam is cooled and condensed into liquid water, which can be pumped back into the boiler for reuse. This process improves the efficiency of the steam cycle and reduces the energy lost in the form of exhaust steam.
The exhaust section is where the steam leaves the turbine after it has passed through the stages of energy extraction. In a back-pressure turbine, the exhaust steam is used for other purposes, such as heating or industrial processes, while in a condensing turbine, the steam is released to the condenser.
9. Seals
Seals are essential components that prevent steam leakage between rotating and stationary parts of the turbine. As steam passes through the turbine, it is under high pressure, and without effective sealing, steam would escape, reducing efficiency and causing damage. Seals are placed at various locations, including around the rotor shaft and at the interface between rotating and fixed blades. Labyrinth seals are commonly used in steam turbines, as they create a tortuous path that minimizes steam leakage while maintaining low friction.
10. Control and Instrumentation Systems
Modern steam turbines are equipped with sophisticated control and instrumentation systems to monitor performance and optimize operation. These systems include sensors that track key variables, such as steam temperature, pressure, flow rate, and turbine speed. The data from these sensors is used to adjust turbine parameters, perform predictive maintenance, and enhance operational efficiency. Automated control systems, such as programmable logic controllers (PLCs), help regulate steam flow, turbine speed, and other critical aspects of turbine operation.
11. Cooling System
In larger steam turbines, especially those used in industrial and power generation applications, cooling systems are used to manage the temperature of various components. The steam turbine’s internal components, including the bearings, rotor, and casing, generate significant heat during operation. A cooling system, such as forced-air cooling or liquid cooling, is used to dissipate this heat and prevent overheating, which could lead to damage or reduced efficiency. Effective cooling is particularly crucial for high-performance turbines operating at high temperatures.
In summary, the components of a steam turbine are carefully designed and engineered to work together in an efficient and reliable manner. Each part, from the rotor and stator to the bearings, nozzles, and blades, plays a vital role in ensuring that steam energy is effectively converted into mechanical work. The integration of advanced control systems, cooling mechanisms, and materials science continues to enhance the performance and longevity of steam turbines, making them indispensable in modern energy systems.
The rotor in a steam turbine is a crucial component that serves as the heart of the turbine’s ability to convert steam energy into mechanical work. It rotates as the steam passes through it, driving the attached shaft to produce power. The rotor consists of discs or wheels mounted along a shaft, with blades attached to each disc. The materials used to construct the rotor are critical because they must withstand high temperatures, pressures, and stresses. For optimal performance, the rotor is designed with minimal friction, ensuring smooth rotation even at high speeds. Efficient turbine operation relies on the rotor’s ability to interact with steam in a way that maximizes energy conversion without excessive wear or heat-related damage.
Surrounding the rotor, the stator is a stationary structure that serves to guide and direct the steam flow as it enters and interacts with the rotor. The stator contains nozzles and diffusers that control steam velocity and pressure before the steam hits the rotor blades. The stator also houses critical components like the casing, which provides structural integrity and houses the rotor and other key elements. The steam enters the turbine through the nozzles, where its thermal energy is converted into kinetic energy, increasing its velocity. The nozzle design is a delicate balance, as it needs to accelerate steam to high speeds while maintaining efficiency in the conversion process.
As the steam exits the nozzles, it strikes the turbine blades. These blades are designed to capture the kinetic energy of the high-speed steam and convert it into rotational motion. The blade material is crucial because it must resist the erosive effects of steam and high-temperature environments. The steam turbine blades are engineered to withstand the forces acting upon them while also being lightweight to improve efficiency. In a typical turbine, the steam’s kinetic energy causes the blades to move, driving the rotor. Depending on the turbine’s design, the blades might be categorized as impulse or reaction blades. Impulse blades rely solely on the steam’s kinetic energy, whereas reaction blades also interact with steam pressure, creating a more gradual and continuous energy transfer.
Bearings are critical to maintaining the smooth operation of the rotor. The rotor needs to be supported in such a way that it can rotate freely without excessive wobbling or friction. Bearings, typically journal bearings and thrust bearings, are used to support the rotor’s weight and ensure its stability. Thrust bearings prevent the rotor from moving axially, which could result in damage or misalignment. Additionally, journal bearings allow the rotor to spin at high speeds with minimal friction, reducing wear and increasing the turbine’s lifespan. Proper lubrication of bearings is essential to their effectiveness, often provided by high-quality oils or lubricants that reduce friction and dissipate heat.
The casing, or outer shell of the steam turbine, contains all the internal components, including the rotor, stator, and nozzles. It provides structural support and contains high-pressure steam, ensuring that the steam is directed correctly through the system. The casing also serves to protect the turbine’s inner parts from external factors such as dust, dirt, or debris, which could otherwise damage sensitive components. In addition to the casing, seals are used to prevent steam from leaking out of the system at critical points, such as around the shaft or at the interfaces between rotating and stationary parts. The seals help to maintain efficiency and reduce energy loss.
Once steam has passed through the turbine’s blades, it moves toward the exhaust section. In turbines used for power generation, the exhaust steam is typically directed to a condenser, where it is cooled and condensed back into water, completing the thermodynamic cycle. The process of condensation is crucial because it allows the cycle to continue by enabling the reuse of water in the boiler. The condenser typically works under a vacuum, which reduces the pressure on the exhaust steam, improving the overall efficiency of the system. If the steam is used for other applications, such as district heating or industrial processes, it may exit the turbine without being condensed and redirected for reuse.
Cooling systems play a significant role in ensuring that the turbine operates within safe temperature limits. These systems, which can include forced air or liquid cooling, prevent overheating by dissipating the heat generated by the friction and energy conversion inside the turbine. Cooling is especially important for the rotor, bearings, and other components that are subject to intense heat. Effective cooling can help extend the life of the turbine and maintain its performance over time.
The governor system is another important component of modern steam turbines. It is responsible for regulating the turbine’s speed by controlling the amount of steam entering the system. By monitoring the rotational speed and adjusting steam flow accordingly, the governor helps maintain consistent turbine performance. If the turbine speed deviates from the desired setpoint, the governor adjusts the steam supply by opening or closing the valves to maintain equilibrium. In digitalized turbines, automated systems and advanced control mechanisms further optimize the turbine’s response to fluctuating load demands, improving both performance and efficiency.
Moreover, in more advanced turbine designs, sensors and instrumentation systems are integrated to monitor the condition of various turbine components. These systems can detect vibrations, temperature changes, pressure variations, and other operational parameters. The data collected by these sensors is used to optimize turbine performance, detect potential failures, and schedule maintenance before significant damage occurs. The incorporation of digital technologies helps to improve the overall reliability and efficiency of steam turbines, reducing downtime and extending operational lifespans.
In the future, as turbines evolve and incorporate advanced materials and technologies, they will become even more efficient and capable of handling diverse and dynamic power generation needs. Developments in turbine design will continue to emphasize materials that can withstand higher temperatures and pressures, increasing the thermodynamic efficiency of the system. The integration of new control technologies and digital monitoring systems will also contribute to more intelligent and responsive operations, enhancing overall system performance and contributing to more sustainable energy production.
As steam turbine technology continues to advance, several emerging trends and innovations are shaping the future of turbine components and performance. The ongoing focus on efficiency improvements, sustainability, and reliability has prompted the development of new materials, design concepts, and maintenance strategies. One of the significant areas of innovation involves the use of advanced materials that can withstand even higher temperatures and pressures, pushing the boundaries of thermodynamic efficiency. These materials, including superalloys and ceramic coatings, are increasingly being employed to enhance the durability and performance of turbine blades and other critical components, enabling turbines to operate at higher temperatures without suffering from thermal degradation or corrosion.
In addition to materials advancements, turbine blade design has evolved to optimize performance further. Blades are now being designed with more complex geometries, including advanced cooling techniques, to manage the intense heat generated during steam flow. The use of cooled blades allows the turbine to operate at higher temperatures, thus improving efficiency by extracting more energy from the steam. Additive manufacturing (3D printing) is also being explored as a method for producing turbine components with intricate internal cooling channels, which would be impossible to achieve using traditional manufacturing methods. These innovations offer significant gains in turbine efficiency and reliability while also reducing the weight of turbine components.
Another area of focus is the integration of digital technologies and advanced sensors into turbine systems. Modern steam turbines are being equipped with an increasing array of smart sensors and condition monitoring systems that provide real-time data on the turbine’s performance and health. These sensors measure variables such as vibration, temperature, pressure, and rotational speed, allowing operators to closely monitor the turbine’s condition and detect any irregularities before they lead to catastrophic failures. Predictive maintenance, based on data analytics and machine learning, is becoming more prevalent. It allows for more efficient scheduling of maintenance, reducing downtime and optimizing turbine performance. These systems can predict when certain components, such as bearings or blades, are nearing the end of their service life, enabling operators to replace parts proactively rather than reactively.
As the demand for cleaner energy grows, steam turbines are also evolving to work efficiently in renewable energy applications. Many modern turbines are being integrated into combined-cycle plants, where steam turbines are paired with gas turbines to create a more efficient energy generation process. The combination of a gas turbine and steam turbine enables the recovery of waste heat from the gas turbine to produce steam for the steam turbine, improving overall plant efficiency. This process, known as combined heat and power (CHP) or cogeneration, is increasingly being implemented in both industrial settings and power plants to reduce carbon emissions and improve energy efficiency.
Additionally, steam turbines are being optimized for integration with geothermal and solar thermal power plants, where they serve as the prime mover to generate electricity from the heat generated by the Earth’s natural processes or concentrated solar power. Geothermal plants utilize steam extracted from the Earth’s crust, while solar thermal plants use mirrors or lenses to concentrate sunlight to generate steam. These applications offer a renewable source of energy that reduces reliance on fossil fuels, contributing to the global shift toward sustainable power generation.
Another innovation in steam turbine design is the move toward more flexible and adaptable systems. Modern turbines are being engineered to handle variable loads more efficiently, particularly in response to the fluctuating demands of renewable energy sources, such as wind and solar. Since these renewable sources are intermittent, the ability to quickly ramp up or down the output of a steam turbine allows for better integration into grids that rely on both conventional and renewable energy sources. Steam turbines are being designed with greater flexibility in mind, allowing them to operate across a wide range of load conditions without sacrificing performance or efficiency.
In some cases, steam turbines are being adapted to work in smaller, modular applications. The development of small modular reactors (SMRs), which are compact nuclear reactors designed for distributed power generation, incorporates steam turbines to convert nuclear heat into electricity. These smaller, more flexible power plants can be deployed in remote areas or integrated into local grids, offering a more decentralized approach to energy production. Similarly, steam turbines are being used in industrial cogeneration plants, where they help generate both electricity and process heat for industrial applications. These systems can improve energy efficiency and reduce overall carbon emissions, making them a key part of efforts to decarbonize industrial sectors.
The continued refinement of steam turbine technology is also enhancing their sustainability. Innovations aimed at reducing emissions, improving fuel efficiency, and decreasing water usage are making steam turbines more environmentally friendly. For example, air-cooled condensers are being developed to reduce water consumption in power plants, an essential step for reducing the environmental impact of large-scale steam turbine operations, particularly in water-scarce regions. Additionally, turbines that can operate with lower quality fuels or with higher levels of efficiency are helping to reduce the carbon footprint of steam turbine-based power generation.
The increasing digitalization and automation of steam turbine systems also enhance operator safety and ease of maintenance. Remote monitoring and diagnostic systems allow for real-time oversight of turbine operations from anywhere, providing operators with continuous access to performance data. In some cases, these systems can automatically adjust turbine settings to optimize performance, reducing the need for manual intervention and ensuring that turbines operate within optimal parameters. Furthermore, advanced control systems allow for more precise regulation of steam flow, rotor speed, and pressure, enabling turbines to operate with minimal wear and tear while maximizing energy output.
As steam turbine technology continues to evolve, the industry is also focusing on improving turbine life cycle management. Turbines are expensive to build and maintain, so extending their service life and reducing maintenance costs are crucial considerations. Regular monitoring, efficient maintenance practices, and the use of advanced materials and coatings are all contributing to longer turbine lifespans and improved overall reliability. Manufacturers are developing new testing methods and diagnostic tools to detect early signs of fatigue or wear, allowing for more proactive maintenance strategies that help avoid costly repairs or unscheduled downtime.
Overall, steam turbines remain a cornerstone of modern power generation, with ongoing innovations enhancing their efficiency, sustainability, and adaptability. As global energy demands continue to rise, steam turbines will play a central role in meeting those demands, particularly in the context of combined-cycle plants, renewable energy systems, and flexible, distributed power generation. Through ongoing advancements in turbine design, materials science, digital technologies, and maintenance practices, the steam turbine industry is poised to continue evolving and contributing to a more sustainable energy future.
As steam turbine technology progresses, several more key trends and innovations are emerging that will likely shape the future of energy generation and industrial applications. One of the significant areas of development is the integration of advanced combustion technologies with steam turbines. With the push towards decarbonization, the industry is increasingly focusing on turbines that can run on low-carbon and renewable fuels, such as biomass, synthetic fuels, and hydrogen. These alternative fuels can be used in steam turbine-based systems to reduce the overall carbon footprint of power plants while maintaining the high efficiency of traditional steam turbines.
The use of hydrogen in steam turbines, in particular, holds promise for a zero-emissions future. Hydrogen combustion produces only water vapor as a byproduct, making it an ideal fuel for reducing greenhouse gas emissions in power generation. Several companies are actively developing steam turbines that can burn hydrogen or hydrogen-rich fuels, aiming to transition existing infrastructure towards a cleaner energy source. In this context, hydrogen turbines are being optimized to operate at high efficiency and reliability while dealing with the challenges posed by hydrogen’s low energy density and high combustion temperatures.
In parallel with alternative fuels, the integration of carbon capture and storage (CCS) technologies with steam turbines is also gaining momentum. CCS involves capturing carbon dioxide (CO2) emissions from power plants and industrial processes, then transporting and storing the CO2 underground or using it for other purposes. For steam turbines, integrating CCS technologies can allow fossil-fuel-fired plants to continue operating while significantly reducing their environmental impact. While this technology is still in the early stages of widespread adoption, combining steam turbines with CCS could be a critical solution in the transition to a net-zero emissions world.
Furthermore, heat recovery continues to be a focal point in steam turbine innovation. In many power plants, particularly combined-cycle systems, a significant amount of heat is still wasted. Advances in heat recovery systems, such as organic Rankine cycles (ORC) and supercritical steam cycles, aim to capture and reuse this excess heat, improving overall plant efficiency. ORC systems, which use organic fluids with lower boiling points than water, are being applied in conjunction with steam turbines to enhance the overall energy recovery process, especially in low- to medium-temperature waste heat applications. These technologies could enable industries to harness waste heat that would otherwise be lost, driving down costs and enhancing sustainability.
As steam turbines continue to evolve, system integration and optimization have become increasingly important. Many power plants and industrial facilities operate with a combination of different generation technologies, such as gas turbines, wind turbines, and solar. The integration of steam turbines into these hybrid systems is key to balancing supply and demand efficiently. For example, steam turbines used in combined heat and power (CHP) systems can help manage both electricity generation and heating needs, offering a flexible and cost-effective solution for industrial and residential applications.
One innovative solution to enhance flexibility and reliability in steam turbines is the development of fast-starting turbines. Traditionally, steam turbines have required long start-up times, making them less flexible than gas turbines or renewable sources. However, with growing demands for flexibility in power generation, particularly with the rise of renewable energy sources, steam turbines are being redesigned for faster start-up times and improved operational flexibility. These turbines can ramp up and down more quickly in response to changes in demand, improving grid stability while integrating intermittent energy sources like wind and solar. The use of advanced control algorithms and predictive modeling is playing a significant role in enabling faster start-ups by optimizing turbine parameters and operational sequences.
Moreover, digital twins and advanced simulation models are becoming essential tools in the design, operation, and maintenance of steam turbines. A digital twin is a virtual representation of a physical system, such as a steam turbine, that can be used for real-time monitoring and performance analysis. By simulating turbine behavior under different conditions, operators can optimize performance, predict failures, and plan maintenance activities more effectively. The integration of artificial intelligence (AI) and machine learning into digital twin technology allows for more accurate predictions of turbine health and performance, enabling predictive maintenance and reducing the risk of unplanned outages.
In the realm of maintenance and operational reliability, remote diagnostics and predictive maintenance technologies are transforming how steam turbines are managed. By employing sensors and data analytics, operators can monitor key parameters like vibration, temperature, and pressure, providing early warnings of potential issues before they escalate. Machine learning algorithms analyze this data to detect anomalies or patterns that may indicate impending failures, allowing for maintenance activities to be scheduled in advance, reducing downtime, and improving turbine lifespan. This approach also helps in cost optimization by preventing unnecessary maintenance and extending the intervals between overhauls.
As the world continues to prioritize sustainability, steam turbines are also being designed with recyclability in mind. The materials used in turbine construction, such as high-strength alloys and composites, are being developed with a focus on reducing their environmental impact at the end of the turbine’s life. Efforts to recycle turbine components, such as blades and casings, are gaining traction. At the same time, manufacturers are exploring ways to reduce the material intensity of turbine designs, making them more resource-efficient. This trend is contributing to the circular economy, where the focus is on extending the life of equipment and minimizing waste.
The future of steam turbines will also be shaped by decentralized power generation. With the growing adoption of distributed energy resources (DERs) and microgrids, steam turbines are being adapted for smaller, more flexible power generation systems. These decentralized systems, which can operate independently or in tandem with the main grid, are ideal for areas where centralized power infrastructure is not feasible or economically viable. By integrating smaller-scale steam turbines into these systems, it becomes possible to generate reliable power while reducing transmission losses and enhancing energy security. The development of small modular turbines (SMTs), which can be deployed in remote locations or urban areas, offers the flexibility needed for decentralized power generation.
Lastly, the integration of steam turbines in hybrid renewable systems represents a growing trend in the energy industry. These systems combine renewable energy sources, such as solar, wind, or geothermal, with steam turbines to create more efficient and stable power generation. For example, geothermal power plants often use steam turbines to convert the heat from the Earth’s crust into electricity, and when combined with solar thermal energy, they can achieve higher efficiency rates due to the continuous availability of heat. These hybrid systems also allow for better grid integration, providing base-load generation while accommodating intermittent renewable sources.
In conclusion, steam turbines remain a cornerstone of modern energy systems, and the technology continues to evolve to meet the growing demands for efficiency, sustainability, and flexibility. With advancements in materials, combustion technology, and integration into hybrid and decentralized systems, steam turbines will play a critical role in the transition to a cleaner, more resilient energy future. From fast-starting turbines to digital twins, predictive maintenance, and hybrid renewable systems, the ongoing innovation in steam turbine design promises to enhance their performance and contribution to the global energy mix.
Steam Turbine Technology Advancements
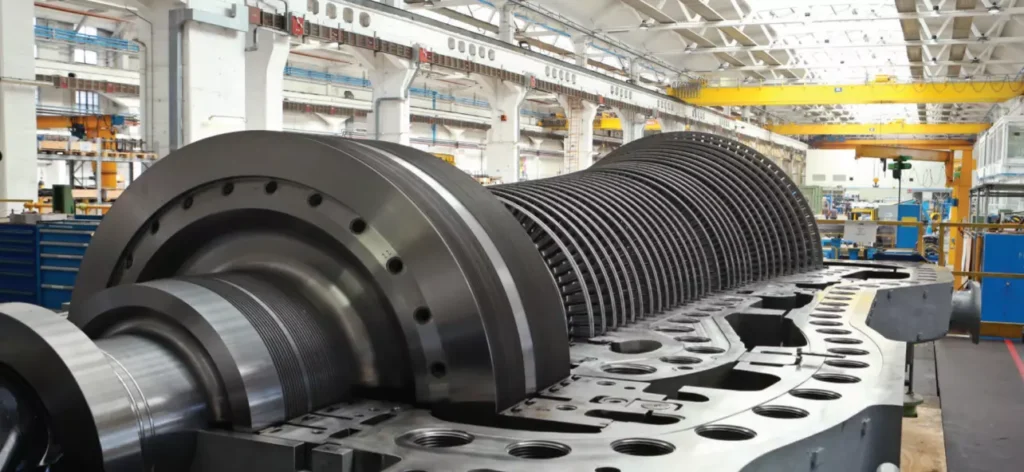
Steam turbine technology has seen numerous advancements in recent years, driven by the need for higher efficiency, sustainability, and reliability. These advancements span various aspects of turbine design, materials science, control systems, and integration with new energy sources. As the global energy landscape continues to evolve, steam turbines are adapting to meet the demands of a more sustainable, flexible, and digitally optimized future.
Advanced Materials and Coatings
One of the most significant advancements in steam turbine technology has been the development of advanced materials and coatings to improve the performance and durability of critical turbine components, such as blades, rotors, and casings. These materials are designed to withstand the extreme temperatures, pressures, and corrosive conditions inside a steam turbine. High-performance superalloys and ceramic coatings are being used to enhance the heat resistance of turbine blades, allowing them to operate at higher temperatures without degrading. These innovations enable steam turbines to achieve higher efficiency by extracting more energy from the steam, thus improving overall system performance.
For example, single-crystal superalloys are used for turbine blades, offering greater resistance to thermal creep and fatigue compared to conventional polycrystalline materials. The addition of thermal barrier coatings (TBCs) helps to protect the blades from extreme heat and corrosion. These materials allow steam turbines to operate at higher temperatures, which directly translates into better efficiency, as the higher thermal gradients between the hot and cold sides of the turbine result in more efficient energy conversion.
Advanced Blade Design and Cooling Techniques
The design of turbine blades has also evolved significantly in recent years. Advanced aerodynamic blade designs, such as airfoils with more complex geometries, are being used to optimize steam flow and increase energy extraction. Blades are being designed to handle higher steam velocities and pressures, which further contributes to increased efficiency. Additionally, modern blades incorporate advanced cooling technologies to deal with the intense heat generated during steam flow.
For instance, internal cooling channels have become a standard feature in many high-efficiency turbine blades. These channels circulate coolant gases or fluids through the blades, absorbing excess heat and maintaining the material’s integrity. Additive manufacturing (3D printing) is being explored to create blades with highly intricate internal structures that would be impossible to achieve using traditional manufacturing methods. These complex cooling systems allow the turbine blades to operate at even higher temperatures, thereby improving turbine performance and extending their lifespan.
Improved Efficiency with Supercritical and Ultra-Supercritical Cycles
Supercritical and ultra-supercritical steam cycles have emerged as key advancements in steam turbine technology. These cycles operate at higher pressures and temperatures than conventional subcritical steam cycles, enabling turbines to extract more energy from the steam and achieve higher efficiency levels. In supercritical cycles, the steam is heated beyond its critical point, where it no longer behaves as a liquid or gas but as a supercritical fluid. This supercritical steam has higher energy content and can be used more efficiently in turbines, leading to improved thermal efficiency.
Ultra-supercritical cycles take this a step further by operating at even higher pressures and temperatures, allowing for even greater efficiency gains. These advancements are particularly important in power plants, where increasing the efficiency of steam turbines can significantly reduce fuel consumption and carbon emissions. The development of materials that can withstand the extreme conditions of supercritical and ultra-supercritical cycles is essential for their widespread adoption in modern power plants.
Digitalization and Advanced Control Systems
The integration of digital technologies has transformed the operation and maintenance of steam turbines. One of the most notable advancements in this area is the use of digital twins, which create virtual replicas of turbine systems that can be monitored and analyzed in real-time. By simulating turbine performance under various operating conditions, digital twins allow operators to optimize performance, predict failures, and identify areas for improvement before issues arise.
Predictive maintenance is another key advancement enabled by digitalization. By leveraging data from sensors embedded within the turbine, operators can monitor critical parameters such as vibration, temperature, and pressure. Machine learning algorithms analyze this data to detect anomalies and predict when components are likely to fail. This approach allows for condition-based maintenance, where maintenance activities are scheduled based on the actual condition of the turbine rather than a fixed timeline. This reduces downtime, lowers maintenance costs, and extends the lifespan of the turbine.
Additionally, modern steam turbines are equipped with advanced control systems that use real-time data to automatically adjust steam flow, turbine speed, and other parameters. These systems ensure that turbines operate within optimal performance ranges, improving efficiency and reducing wear and tear. The use of artificial intelligence (AI) in control systems can further enhance the turbine’s ability to respond dynamically to changing load demands and optimize fuel use.
Flexible and Rapid Response Turbines
As renewable energy sources such as solar and wind become a larger part of the energy mix, there is increasing demand for power generation systems that can quickly respond to fluctuations in supply and demand. Steam turbines have traditionally been less flexible than other types of turbines, such as gas turbines, due to their longer start-up times and fixed operational parameters. However, recent advancements have focused on improving the flexibility and fast-starting capabilities of steam turbines.
New steam turbines are being designed with faster start-up times and the ability to ramp up and down more quickly, making them more compatible with renewable energy sources. Hybrid systems that combine steam turbines with gas turbines or battery storage are also being developed to provide a more flexible response to grid demand. These hybrid systems allow steam turbines to operate more efficiently while supporting the integration of intermittent renewable energy sources, thereby ensuring grid stability and reliability.
Integration with Carbon Capture and Storage (CCS)
As the world continues to focus on reducing greenhouse gas emissions, the integration of carbon capture and storage (CCS) technologies with steam turbines is gaining momentum. CCS involves capturing carbon dioxide (CO2) emissions from power plants and industrial processes and storing them underground or utilizing them for other purposes, such as enhanced oil recovery or industrial processes.
Steam turbines can be integrated into CCS systems to reduce the carbon footprint of fossil fuel-based power plants. By capturing and storing CO2 emissions, power plants can continue to operate while minimizing their environmental impact. This combination of steam turbines and CCS can help make existing power plants more environmentally sustainable, particularly in regions where renewable energy sources are not yet able to meet all of the electricity demands.
Hybrid and Modular Systems
The development of hybrid and modular systems is another area where steam turbine technology is advancing. Hybrid systems combine multiple power generation technologies, such as gas turbines, solar thermal, and geothermal, to provide more efficient and flexible energy production. For instance, combined-cycle plants that integrate steam turbines with gas turbines can recover waste heat from the gas turbine exhaust to produce additional power with minimal fuel consumption.
Small modular reactors (SMRs), which are compact nuclear reactors, also use steam turbines to convert nuclear heat into electricity. These small, flexible systems can be deployed in remote or industrial areas, providing reliable, low-carbon power. The use of modular steam turbines allows for scalable, customizable systems that can be adapted to different energy needs, further enhancing the flexibility and sustainability of steam turbine technology.
Integration with Renewable Energy
Steam turbines are increasingly being used in conjunction with renewable energy sources, such as solar thermal and geothermal power plants. In solar thermal plants, mirrors or lenses concentrate sunlight to generate steam, which is then used to power a steam turbine. Similarly, geothermal power plants harness heat from the Earth’s crust to generate steam for turbine operation. The integration of steam turbines with these renewable sources helps to diversify the energy mix, reduce reliance on fossil fuels, and improve the overall sustainability of power generation.
In conclusion, steam turbine technology is advancing rapidly, with significant improvements in efficiency, flexibility, materials, and control systems. These advancements are driving the evolution of steam turbines in power plants, industrial settings, and hybrid renewable energy systems. As the demand for cleaner, more efficient energy generation continues to rise, steam turbines will remain a critical component of the global energy mix, helping to meet the world’s growing energy needs while minimizing environmental impact.
The ongoing advancements in steam turbine technology are not only improving their efficiency but also addressing the evolving energy demands driven by the global push for decarbonization and sustainability. In addition to the innovations in materials, cooling systems, and digital technologies, the role of steam turbines in hybrid and renewable energy systems is becoming increasingly important. The integration of steam turbines with renewable energy sources is enabling more sustainable and flexible power generation.
The shift towards low-carbon and zero-emission technologies has led to the increased use of hydrogen as a fuel for steam turbines. Hydrogen combustion offers the potential for steam turbines to generate electricity without producing harmful carbon emissions. Efforts are underway to develop steam turbines that can efficiently burn hydrogen, which has a lower energy density than conventional fossil fuels. Research is focused on overcoming the challenges associated with hydrogen’s high combustion temperatures and ensuring that turbine components can withstand these extreme conditions. Once fully developed, hydrogen-powered steam turbines could significantly contribute to the transition to a carbon-neutral energy grid.
In the context of energy storage and grid balancing, steam turbines are being integrated into systems designed to smooth out the variability of renewable sources like wind and solar. One example is the use of thermal energy storage systems, which store excess energy as heat and convert it back into electricity when demand is high. These systems, often coupled with steam turbines, offer the advantage of providing reliable power when renewable generation is low, thereby improving grid stability and supporting the integration of intermittent renewable sources. Molten salt storage, which absorbs heat and stores it for later use, is commonly used in conjunction with solar thermal power plants that employ steam turbines for electricity generation. These energy storage solutions are part of a broader trend toward integrating energy storage technologies into the power generation mix to ensure reliable, continuous energy supply.
Additionally, the importance of flexible operation in steam turbines has grown as the energy grid becomes more complex and demand patterns become more unpredictable due to the rise of renewable energy. Steam turbines, traditionally seen as stable, base-load generation sources, are now being designed with rapid-response capabilities. The ability to start quickly and adjust to varying loads is crucial for providing backup power when renewable generation fluctuates. Fast-starting steam turbines, paired with gas turbines or battery storage systems, can help provide flexible, on-demand electricity without compromising efficiency or reliability. These systems are becoming increasingly valuable in managing the transition to a low-carbon grid while maintaining the stability of electricity supply.
At the same time, the application of digitalization is playing a critical role in improving the operational efficiency and safety of steam turbines. Smart sensors, condition monitoring systems, and real-time data analytics are helping operators to optimize performance, predict maintenance needs, and reduce unplanned downtime. By using advanced algorithms and machine learning, digital tools can analyze turbine performance data and predict potential failures before they occur, allowing for proactive maintenance and repairs. This shift from reactive to predictive maintenance is helping reduce the costs associated with turbine operation and extend the lifespan of turbine components, making steam turbines even more cost-effective over the long term.
The continuous development of smart grids is also influencing the evolution of steam turbines. These grids leverage digital communication technology to optimize the distribution and management of electricity. Steam turbines are being integrated into microgrids, which are smaller, decentralized energy systems that can operate independently or in conjunction with the main grid. By providing localized generation capacity, steam turbines can help ensure energy reliability in remote or off-grid locations, where traditional infrastructure might be limited or unavailable. These microgrids often combine various energy sources, such as solar, wind, and natural gas, with steam turbines to create resilient, flexible power systems that are more responsive to local energy needs.
As part of these advancements, steam turbines are also being utilized in industrial cogeneration systems, where they not only generate electricity but also provide thermal energy for industrial processes. These systems, often called combined heat and power (CHP) systems, are highly efficient because they capture and use the heat that would otherwise be wasted during electricity generation. This is particularly valuable in industries such as manufacturing, chemical production, and paper mills, where both electricity and heat are required. The adoption of CHP systems is increasing as industries look for ways to reduce their energy consumption, lower costs, and meet sustainability targets.
Furthermore, the development of modular steam turbines is enabling more flexible and scalable power generation systems. These smaller, more adaptable turbines can be used in distributed generation applications, where smaller, localized power plants can meet the energy needs of specific areas or industries. The growing trend of distributed energy generation is reducing the reliance on large, centralized power plants, offering the benefits of lower transmission losses, greater energy security, and increased grid resilience. Modular turbines can also be integrated into small modular reactors (SMRs), providing a compact, reliable source of electricity for applications such as remote communities or industrial facilities that are off the main grid.
Moreover, the ongoing effort to enhance the environmental sustainability of steam turbines includes research into reducing the amount of water used in cooling processes. Air-cooled condensers, which eliminate the need for large quantities of water, are becoming increasingly common, especially in regions where water resources are scarce. By reducing the environmental impact of cooling systems, air-cooled condensers contribute to making steam turbine-based power plants more sustainable and suitable for areas with limited access to water.
Hybrid power systems that combine gas turbines with steam turbines in combined-cycle power plants continue to be an important area of innovation. These systems are more efficient than standalone gas or steam plants because they use the waste heat from the gas turbine to produce additional electricity via the steam turbine. The integration of gas and steam turbines can result in an efficiency improvement of 50% to 60%, compared to conventional power generation systems. Combined-cycle plants are often deployed in areas with high energy demand, where both peak-load and base-load generation capacity are needed. The flexibility and high efficiency of these systems make them an attractive option for reducing the carbon footprint of conventional power generation.
Looking ahead, the development of fusion energy and next-generation nuclear power plants could further transform the role of steam turbines in energy production. Fusion reactors and advanced nuclear reactors, such as molten salt reactors and high-temperature gas reactors, will likely use steam turbines to convert heat generated from nuclear fusion or fission reactions into electricity. As these technologies mature, they could offer new, safe, and clean sources of energy, with steam turbines playing a key role in their energy conversion processes.
Overall, the advancements in steam turbine technology are positioning them as a cornerstone of the future energy landscape. With innovations in materials, digital technologies, fuel flexibility, and efficiency improvements, steam turbines will continue to play a vital role in meeting the world’s growing energy needs while contributing to the global transition to a more sustainable and low-carbon energy system. Through ongoing technological development, steam turbines will remain adaptable to changing energy landscapes and continue to provide reliable, efficient, and environmentally friendly power for years to come.
As the energy landscape continues to evolve, steam turbines will need to adapt to emerging challenges and opportunities. One key aspect of this is the increasing emphasis on decarbonization across all sectors of energy production. Steam turbines are poised to play a significant role in this transition, particularly in industries that rely heavily on fossil fuel-based power generation. By integrating carbon capture and storage (CCS) technologies with steam turbines, power plants can significantly reduce their CO2 emissions, making it possible to continue using conventional fuels while limiting their environmental impact. The effectiveness of CCS systems, combined with the high efficiency of steam turbines, can help industries meet stringent emissions standards and contribute to the global goal of net-zero emissions.
Moreover, as the world’s energy mix becomes more diversified, steam turbines are likely to be a key part of a broader, multifuel energy strategy. The growing importance of bioenergy and synthetic fuels—including biomass, biofuels, and synthetic natural gas (SNG)—will open new opportunities for steam turbines to operate in power plants and industrial facilities that use alternative fuels. These fuels, which can be derived from organic or waste materials, often produce lower emissions than traditional fossil fuels, and steam turbines will need to be designed to efficiently convert the energy from these fuels into electricity while maintaining operational reliability.
Additionally, as smart grid technologies continue to advance, steam turbines will be integrated into distributed generation systems. These decentralized systems allow for power generation closer to the point of use, reducing transmission losses and providing greater energy security. Distributed energy resources (DERs), including small-scale steam turbines, can be paired with renewable energy sources such as solar and wind to create hybrid systems that provide reliable, on-demand power even when renewable generation fluctuates. This concept of distributed generation, which is made possible by digitalization and advancements in energy storage, will allow steam turbines to play an important role in the transition to a more decentralized, resilient energy grid.
Microgrids, which are localized power systems that can operate independently or in conjunction with the main grid, are also becoming increasingly relevant. Steam turbines, when paired with renewable energy and energy storage systems, can provide the flexible, reliable power needed to meet the energy demands of remote communities, industrial facilities, and critical infrastructure. The integration of steam turbines into microgrids will enhance the resilience and flexibility of the power supply, especially in areas prone to power outages or with limited access to centralized grid infrastructure. By combining distributed generation with advanced control and communication technologies, steam turbines can support the reliable operation of microgrids while contributing to the reduction of energy costs.
Another critical advancement is the growing interest in energy storage solutions. Thermal energy storage systems, which store heat generated during periods of low demand, can be integrated with steam turbines to provide electricity when demand is high or when renewable energy generation is low. This concept of storing thermal energy and converting it back into electricity using steam turbines has the potential to enhance grid stability and improve the efficiency of renewable energy systems. The integration of thermal storage with steam turbines is expected to become more common as energy storage technologies continue to mature, offering a sustainable and cost-effective means of balancing supply and demand in modern energy grids.
Steam turbines are also adapting to meet the diverse needs of industrial applications. Beyond power generation, steam turbines are widely used in cogeneration (also known as combined heat and power, or CHP) systems, where they simultaneously produce electricity and useful heat for industrial processes. This dual-purpose operation increases the overall efficiency of energy systems and reduces fuel consumption. In industries such as chemical manufacturing, steel production, and food processing, steam turbines are integral in providing the necessary heat and power for various processes. As energy efficiency and sustainability become more important to industrial operations, steam turbines will continue to play a vital role in optimizing energy use and minimizing environmental impact.
The development of hybrid power plants, which combine steam turbines with other generation technologies, such as gas turbines or solar thermal systems, is another promising direction. Hybrid systems offer greater flexibility, enabling power plants to produce electricity more efficiently and respond quickly to fluctuations in demand. For example, combined-cycle plants, which integrate gas and steam turbines, have become a popular solution for providing highly efficient, reliable power. These plants use the waste heat from the gas turbine to generate additional electricity through the steam turbine, resulting in an overall efficiency improvement of up to 60%. Hybrid plants also offer the advantage of being able to switch between different fuel sources, providing greater fuel flexibility and reducing the reliance on any one energy source.
As nuclear power undergoes a renaissance with the development of next-generation nuclear reactors, steam turbines will continue to play a critical role in converting nuclear heat into electricity. Small modular reactors (SMRs), which are compact nuclear reactors that can be deployed in a modular fashion, are expected to use steam turbines to generate electricity in the coming decades. These reactors offer significant advantages over traditional large-scale nuclear power plants, including lower construction costs, improved safety, and scalability. Steam turbines will be essential in enabling these next-generation nuclear reactors to operate efficiently and reliably.
In addition to traditional industrial applications, steam turbines are expected to become more integral in district heating systems, which provide centralized heating and cooling to urban areas or industrial parks. By harnessing waste heat from industrial processes or power plants, steam turbines can produce additional electricity, improving overall system efficiency and reducing environmental impact. The adoption of district energy systems that incorporate steam turbines is expected to grow, particularly in urban centers, as part of broader efforts to decarbonize heating and cooling.
As the demand for energy continues to increase globally, particularly in emerging economies, steam turbines will play a critical role in ensuring that energy is produced efficiently and reliably. By continuing to develop innovative turbine designs, materials, and control systems, steam turbines can meet the challenges of a rapidly changing energy landscape. From powering industrial facilities to supporting renewable energy integration, steam turbines will remain a crucial technology for the sustainable generation and use of energy in the 21st century.
Overall, the future of steam turbines lies in their ability to adapt to new energy sources, integrate with advanced grid technologies, and improve their performance through innovative design and materials. With the ongoing emphasis on efficiency, flexibility, and sustainability, steam turbines are expected to remain a cornerstone of global energy systems for decades to come. Whether in large-scale power plants, renewable energy systems, or distributed generation applications, steam turbines will continue to play an essential role in meeting the world’s energy needs while minimizing environmental impact.
Looking to the future, steam turbines are poised to be at the forefront of the ongoing evolution of energy systems, playing a critical role in meeting the diverse challenges of global energy needs. As the world moves toward more sustainable, low-carbon energy solutions, steam turbines will be integrated into a range of next-generation power systems that will rely on cleaner, more efficient technologies. Key factors that will shape the development of steam turbine technology in the coming years include decarbonization efforts, innovation in turbine design, fuel diversification, and advancements in digital and predictive technologies.
One of the most pressing goals for steam turbine technology is further decarbonization. The energy sector’s focus on reducing carbon emissions is driving research into steam turbines that can operate efficiently with low-carbon fuels and renewable energy sources. The successful integration of green hydrogen as a fuel in steam turbines is one of the most promising areas of development. Hydrogen, when combusted in a turbine, produces only water vapor as a byproduct, making it an ideal candidate for decarbonizing hard-to-abate industries, including power generation. Steam turbines capable of burning hydrogen are currently under development, with progress being made to ensure they are as efficient and durable as those powered by traditional fossil fuels. This development represents a pivotal shift in power generation, as it would allow for a carbon-free energy cycle.
The hybridization of power plants is also an important area of focus. As renewable energy sources such as solar and wind become more widespread, the need for reliable backup power is intensifying. Steam turbines are well-suited for integration into hybrid systems that combine gas turbines, battery storage, or solar thermal energy. These systems offer an efficient way to balance intermittent renewable generation with the consistent demand for electricity. By using steam turbines as part of a combined-cycle power system or integrating them with energy storage technologies, plants can reduce reliance on fossil fuels and increase the utilization of renewable resources. As power systems evolve, hybrid plants will become an increasingly common feature, offering greater flexibility and reliability.
Furthermore, advanced turbine designs will continue to evolve, pushing the boundaries of efficiency and performance. Supercritical steam turbines, which operate at higher temperatures and pressures than conventional turbines, will become more prevalent as they offer significant improvements in efficiency. These turbines are already in use in modern power plants and are part of the effort to reduce fuel consumption and emissions. Research into ultra-supercritical and advanced ultra-supercritical steam cycles is expected to further enhance the thermal efficiency of steam turbines, ensuring that less fuel is needed to generate electricity. These advancements not only improve efficiency but also reduce the environmental impact of steam turbine-based power generation.
Another trend is the increasing focus on digitalization and smart technologies in steam turbine operations. The integration of IoT sensors, big data analytics, and machine learning into turbine control systems is enabling more intelligent and optimized operations. By collecting real-time data on turbine performance, these technologies can provide insights into areas such as efficiency, wear and tear, and potential points of failure. Predictive maintenance and condition-based monitoring are becoming more common, allowing operators to anticipate problems before they occur and perform repairs at the most opportune time. This shift towards proactive, data-driven maintenance reduces unplanned downtime and extends the lifespan of turbines. Furthermore, predictive algorithms help improve overall turbine efficiency by optimizing operational parameters based on current conditions, leading to better fuel utilization and fewer emissions.
The trend towards modular and flexible systems is also likely to gain momentum in the coming years. As the need for distributed and decentralized power generation grows, small-scale, modular steam turbines will become more popular in both industrial and residential applications. These turbines can be combined with microgrids to create localized power solutions that are more resilient to disruptions in the broader grid. Modular turbines offer the advantage of scalability and customization, making them ideal for use in remote areas or off-grid communities where traditional infrastructure is unavailable. Additionally, modular systems can be deployed rapidly, providing flexible, on-demand power when and where it is needed most.
The role of steam turbines in industrial applications will also evolve significantly. In industries that require both electricity and thermal energy, such as petrochemicals, refining, and cement production, steam turbines used in cogeneration systems will continue to be vital for improving energy efficiency and reducing operational costs. Industrial cogeneration plants can operate with much higher overall efficiencies by utilizing waste heat from manufacturing processes to generate electricity through steam turbines. This dual-purpose use of energy significantly reduces fuel consumption and carbon emissions, making it an attractive option for companies looking to enhance sustainability while minimizing energy costs. Additionally, industries are increasingly adopting digital twin technologies to simulate turbine performance under different operational conditions, allowing for the optimization of processes and reducing downtime.
The integration of renewable energy sources with steam turbines will become increasingly important as global demand for clean energy grows. Steam turbines are already employed in concentrated solar power (CSP) systems, where mirrors or lenses concentrate sunlight to generate high-temperature steam, which is then used to drive a turbine. CSP plants with steam turbines provide a significant advantage over traditional solar photovoltaic (PV) systems because they can store energy as heat and dispatch it when the sun isn’t shining. This dispatchability gives steam turbines an important role in stabilizing the energy grid as more variable renewable energy sources come online.
In the field of carbon capture and storage (CCS), steam turbines will continue to be integrated into power plants that aim to capture and store CO2 emissions. In CCS systems, steam turbines are used to power the compressors and pumps that are involved in the CO2 capture process. As regulations around carbon emissions tighten, the need for CCS technologies will grow, and steam turbines will be integral to their efficient operation. As steam turbines become more versatile and adaptable to new applications, their role in reducing greenhouse gas emissions will be crucial in meeting global climate targets.
Finally, as global energy systems evolve toward greater interconnectivity and resilience, steam turbines will play a vital part in ensuring that power generation remains reliable and efficient in an increasingly complex and decentralized energy grid. The combination of digitalization, renewable energy integration, fuel flexibility, and advanced materials will continue to drive the development of steam turbines, allowing them to meet the growing energy demands of the future while contributing to sustainability goals.
In conclusion, the ongoing advancements in steam turbine technology will ensure that these systems remain a cornerstone of power generation for the foreseeable future. As the world transitions to a cleaner, more sustainable energy grid, steam turbines will continue to be adapted and optimized for new fuels, new operational conditions, and new energy applications. Whether in large-scale power plants, hybrid energy systems, industrial facilities, or microgrids, steam turbines will play a key role in driving efficiency, reducing emissions, and ensuring the resilience of global energy systems. Through innovation, collaboration, and the adoption of emerging technologies, steam turbines will remain indispensable to the global pursuit of a sustainable energy future.
Purpose of Steam Turbines
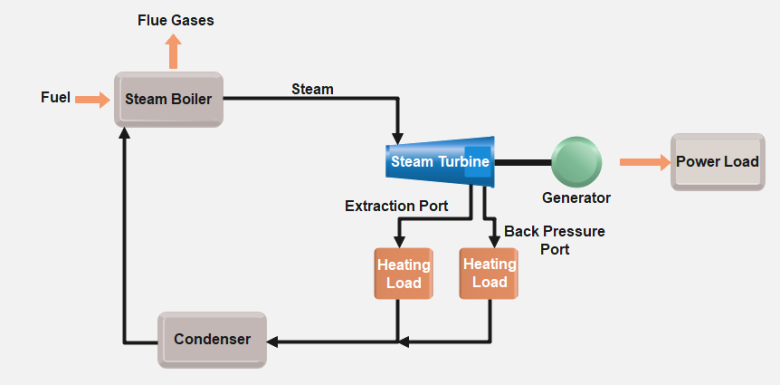
The primary purpose of steam turbines is to convert thermal energy from steam into mechanical energy, which can then be used to generate electricity or perform mechanical work. This fundamental function makes steam turbines an essential component in various energy generation systems, ranging from large power plants to industrial applications. Their efficiency in converting heat into mechanical energy is key to their widespread use in power generation and other industries. The versatility of steam turbines also allows them to operate on a variety of fuels, including fossil fuels, biomass, and nuclear energy, as well as to be integrated with renewable energy systems such as concentrated solar power (CSP) and geothermal power.
One of the key purposes of steam turbines in power generation is to provide a reliable and efficient method of electricity production. Steam turbines are used in thermal power plants to drive generators, which produce electricity by converting the mechanical energy of the turbine’s rotation into electrical energy through electromagnetic induction. In these plants, steam is generated by heating water using the heat produced from burning fossil fuels (such as coal, natural gas, or oil) or from nuclear reactions. The resulting steam is directed onto the turbine blades, which causes the turbine to spin, generating power that is transmitted to the electrical grid.
In addition to their use in large-scale power plants, steam turbines also serve important functions in cogeneration or combined heat and power (CHP) systems. These systems simultaneously generate both electricity and useful heat from a single energy source. In industrial settings, steam turbines are used to produce both electrical power for operational needs and steam for industrial processes, such as heating, drying, or powering mechanical systems. By capturing and utilizing waste heat that would otherwise be lost, CHP systems increase overall energy efficiency, reduce fuel consumption, and lower emissions. This makes steam turbines a key technology in industrial energy efficiency.
Steam turbines are also widely used in marine propulsion systems, particularly in large ships and naval vessels. In these applications, steam turbines are driven by steam produced by boilers fueled by oil, coal, or nuclear energy. The mechanical energy generated by the turbine is used to turn propellers, propelling the ship through the water. Steam turbines in marine applications offer high efficiency and the ability to generate large amounts of power in compact spaces, making them ideal for large vessels with high energy demands.
In industrial sectors, steam turbines have a crucial role in various energy-intensive processes. Many industries, including chemical processing, refining, and paper production, require both mechanical power and heat. Steam turbines can provide a reliable and efficient way to generate electricity while also supplying the necessary steam for manufacturing processes. For example, in a chemical plant, steam turbines may be used to provide power to machinery while also supplying steam for heating reactors or distillation columns. By incorporating steam turbines into their energy systems, industries can optimize their energy use, reduce costs, and lower their carbon footprint.
Furthermore, steam turbines play a critical role in district energy systems, which deliver centralized heating and cooling to multiple buildings or entire neighborhoods. These systems can use steam turbines to generate both electricity and thermal energy from a single source, such as a biomass plant, waste-to-energy facility, or natural gas plant. District heating systems powered by steam turbines are highly efficient and can be an effective solution for reducing urban energy consumption, particularly in densely populated areas where centralized heating is more cost-effective than individual heating systems.
Steam turbines also have an important purpose in nuclear power plants, where they convert heat from nuclear fission reactions into electricity. In these plants, steam turbines are typically coupled with pressurized water reactors (PWR) or boiling water reactors (BWR), which generate heat by splitting atoms of uranium. This heat is used to produce steam that drives a turbine connected to an electrical generator. The use of steam turbines in nuclear power plants is crucial to their operation, enabling them to generate large amounts of electricity with low carbon emissions.
In terms of renewable energy applications, steam turbines are integral to concentrated solar power (CSP) plants, which use mirrors or lenses to focus sunlight onto a receiver, creating high-temperature steam. The steam is then used to drive steam turbines to generate electricity. CSP plants can store the generated heat for later use, allowing for electricity production even when the sun isn’t shining. This makes steam turbines a valuable component in solar energy systems, contributing to a more reliable and dispatchable renewable energy supply.
Another important purpose of steam turbines is their role in grid stabilization and peak-load power generation. In many regions, power grids rely on steam turbines to help meet peak electricity demand, which occurs during periods of high consumption, such as hot summer days when air conditioning use surges. Steam turbines, especially those in combined-cycle or gas-steam hybrid plants, offer a fast-response solution to meet these high-demand periods. They can also be employed in load-following operations, adjusting their output to match fluctuating demand throughout the day.
In conclusion, the primary purpose of steam turbines lies in their ability to convert thermal energy into mechanical work for electricity generation, industrial applications, and more. Their role is central to modern energy systems, providing reliable, efficient, and flexible power generation across various sectors. Steam turbines contribute significantly to the decarbonization of the energy sector, particularly as they are integrated into renewable energy systems, hybrid power plants, and carbon capture technologies. With the ongoing advancements in technology, steam turbines will continue to serve a vital function in providing sustainable energy solutions for a growing world population while supporting the global transition to cleaner and more efficient energy sources.
The versatility of steam turbines extends beyond traditional power generation and industrial applications, with several emerging uses that reflect the growing need for clean, efficient, and reliable energy sources. One of the most exciting developments in the purpose of steam turbines is their potential to contribute significantly to the decarbonization of the energy sector. As the global push for net-zero emissions intensifies, steam turbines will continue to evolve to handle low-carbon fuels, including green hydrogen, ammonia, and biomass, which are seen as vital components in achieving sustainable energy goals. The ability of steam turbines to run on these cleaner fuels ensures that they remain relevant in a future energy system that prioritizes reducing greenhouse gas emissions.
In addition to their role in renewable energy integration, steam turbines are also essential in energy storage applications, particularly in systems that store thermal energy. By utilizing thermal energy storage (TES), steam turbines can help balance supply and demand in electricity grids, making it possible to store energy generated during off-peak hours and release it when demand spikes. This technology is especially beneficial in regions that rely on solar thermal power plants or combined heat and power (CHP) systems. By storing the heat in a medium such as molten salt, steam turbines can continue to generate electricity during periods when solar power production is not feasible, offering a form of energy storage that complements other technologies like batteries and pumped hydro storage.
Steam turbines also play a crucial role in supporting grid stability by providing frequency regulation and voltage control. As modern power grids increasingly rely on variable renewable energy sources, such as wind and solar, there is a need for flexible, reliable technologies that can adjust to fluctuations in generation and demand. Steam turbines, especially when used in combined-cycle power plants, offer the capability to quickly adjust their output in response to changes in grid conditions. This makes them an important tool for ensuring that electricity supply remains stable, even when renewable generation is inconsistent.
The use of steam turbines is also expanding in industrial processes, where their ability to generate both power and heat simultaneously is a significant advantage. In sectors such as petrochemicals, food processing, and paper production, steam turbines are integrated into cogeneration systems to produce both electricity and thermal energy that can be used for manufacturing processes. This combined use of energy maximizes efficiency, reduces energy costs, and lowers environmental impact. As industrial plants seek to improve their energy performance and reduce emissions, steam turbines are playing a central role in achieving these goals by enabling greater resource efficiency.
Marine propulsion is another important area where steam turbines have a longstanding purpose. In large ships, including naval vessels, steam turbines provide the power necessary for propulsion. The ability of steam turbines to generate high amounts of mechanical energy in relatively compact systems makes them ideal for applications where space and weight are crucial considerations. In the future, with growing interest in zero-emission ships, steam turbines may be adapted to run on clean fuels like hydrogen or ammonia, making them a viable option for decarbonizing maritime transportation.
Waste-to-energy technologies also benefit from the use of steam turbines. In these plants, municipal waste is converted into electricity by burning it to produce steam, which drives a steam turbine. This process helps reduce the volume of waste in landfills while simultaneously producing electricity in an environmentally friendly manner. Steam turbines are especially well-suited to this application because they can efficiently convert the heat from burning waste into electricity. As waste-to-energy plants continue to expand, the demand for efficient steam turbines will grow, providing a sustainable way to manage waste while generating power.
In the context of district heating, steam turbines are used in centralized systems that deliver heat and hot water to multiple buildings from a single plant. By producing both electricity and thermal energy, these systems provide an efficient solution for cities and towns, reducing the need for individual heating systems and improving overall energy efficiency. As cities strive to reduce their carbon footprint and transition to more sustainable energy systems, steam turbines in district heating applications will continue to be an essential tool for providing reliable and cost-effective energy.
The nuclear power sector also relies on steam turbines to generate electricity. In nuclear reactors, steam turbines are used to convert the heat produced by nuclear fission into electricity. This process is similar to that in conventional thermal power plants but involves the use of nuclear energy instead of fossil fuels. As the demand for clean energy grows, nuclear power, with steam turbines at its core, is expected to play a larger role in providing baseload power without emitting carbon dioxide. Advances in small modular reactors (SMRs) and other next-generation nuclear technologies will likely lead to new applications of steam turbines in the nuclear energy sector.
Finally, the transportation sector has seen an increasing interest in the use of steam turbines for electric vehicles (EVs) and hybrid vehicles. Although this application is still in its early stages, the potential for steam turbines to contribute to transportation energy systems is significant. By using waste heat recovery systems and small-scale steam turbines, vehicles could become more energy-efficient, further contributing to the goal of reducing emissions in the transportation sector.
In conclusion, the purpose of steam turbines is expanding as energy systems continue to evolve. They are no longer just a central component in power generation plants; they are becoming integral to a wide variety of applications, including renewable energy integration, energy storage, industrial processes, waste management, and even transportation. The ability of steam turbines to provide flexible, reliable, and efficient power solutions across different sectors ensures that they will continue to play a critical role in meeting the world’s energy needs while contributing to sustainability and decarbonization efforts. With technological advancements and increasing global demand for clean energy, steam turbines will remain a cornerstone of modern energy systems, adapting to new fuels, new processes, and new operational challenges.
As we look ahead, the role of steam turbines in global energy systems will continue to evolve and expand, driven by technological innovations, the growing demand for sustainable energy solutions, and the shift towards a cleaner, more efficient energy mix. One of the key aspects of this evolution is the increasing flexibility and adaptability of steam turbines, which will enable them to operate across a broader range of energy sources and applications.
A major driver of this transformation is the integration of renewable energy technologies with steam turbines. With the global emphasis on reducing greenhouse gas emissions and transitioning to a low-carbon future, steam turbines will be further optimized for use in hybrid power systems that combine renewable energy sources, such as solar, wind, and biomass, with traditional steam turbine-based power generation. For example, concentrated solar power (CSP) systems use steam turbines to generate electricity by concentrating sunlight to heat a fluid that produces steam. This technology is especially valuable because it can store thermal energy for later use, providing a dispatchable and reliable source of power when the sun isn’t shining. In these systems, steam turbines are essential for converting solar energy into electricity, and ongoing improvements in thermal storage systems will further enhance the ability of CSP plants to contribute to grid stability.
In addition, the development of green hydrogen as a fuel source is one of the most promising innovations for steam turbine technology. Hydrogen, particularly green hydrogen produced from renewable electricity, has the potential to decarbonize industries and power generation systems that rely heavily on fossil fuels. Steam turbines capable of running on hydrogen are already being tested, and as hydrogen infrastructure expands, it is expected that more power plants will use hydrogen as a fuel for steam turbines. This move toward hydrogen-powered turbines represents a significant opportunity to achieve carbon-neutral electricity generation, aligning with global efforts to combat climate change and meet international climate targets.
Moreover, steam turbines will continue to be central to combined-cycle power plants, which integrate steam turbines with gas turbines to achieve higher efficiencies. In a combined-cycle system, gas turbines generate electricity by burning natural gas, and the waste heat from the gas turbines is used to produce steam that powers a steam turbine. This combination maximizes the efficiency of the power plant, making it an effective solution for both peak-load and base-load power generation. As the energy landscape evolves, combined-cycle plants are expected to play an even greater role in reducing fuel consumption and minimizing emissions while meeting the growing demand for electricity.
In addition to their role in power generation, steam turbines are playing an increasingly important role in industrial applications and process optimization. Many industrial processes require both mechanical power and heat for various manufacturing operations, and steam turbines are an ideal solution for providing both in a single, integrated system. For instance, in the chemical, petrochemical, and paper industries, steam turbines are used to generate both electricity and steam that can be used for heating, drying, and processing. This cogeneration or combined heat and power (CHP) approach allows industries to optimize their energy consumption, reduce fuel usage, and decrease operational costs while simultaneously lowering their carbon emissions.
With the global push towards more sustainable industrial practices, steam turbines are likely to become even more integral to achieving greater energy efficiency in industries that traditionally consume large amounts of energy. In these industries, the adoption of energy recovery technologies, including waste heat recovery systems powered by steam turbines, will help recover and reuse energy that would otherwise be wasted, further enhancing the environmental benefits of industrial operations.
The trend towards digitization and smart technologies in the energy sector is also influencing the role of steam turbines. Through the integration of Internet of Things (IoT) devices, real-time data analytics, and artificial intelligence (AI), steam turbines are becoming smarter and more efficient. The ability to monitor turbine performance in real time, predict maintenance needs, and optimize operations based on data analytics is revolutionizing turbine management. This approach not only increases the reliability and lifespan of turbines but also enhances their overall efficiency by ensuring that they operate at optimal performance levels, minimizing downtime and reducing operational costs.
In the realm of energy storage, steam turbines will increasingly be used in thermal energy storage (TES) systems. These systems can store energy in the form of heat, which can then be converted into electricity using steam turbines when demand is high. This technology is particularly useful in areas where renewable energy sources, such as solar or wind, are abundant but intermittently available. By storing excess energy as thermal energy during periods of high renewable generation and converting it into electricity later, steam turbines help ensure a stable, reliable energy supply. As energy storage technologies continue to develop, steam turbines will play a key role in supporting a more flexible and resilient energy grid.
In the context of carbon capture and storage (CCS), steam turbines will also be crucial to the success of clean coal and natural gas power plants that aim to reduce their carbon emissions. CCS technologies capture carbon dioxide (CO2) emissions from the combustion of fossil fuels and store them underground or use them for other purposes, such as enhanced oil recovery. Steam turbines are used in these systems to provide the mechanical power necessary to compress and transport the captured CO2. As the pressure to reduce emissions grows, the demand for CCS systems will increase, making steam turbines an essential component of these efforts.
Additionally, small modular reactors (SMRs) and other advanced nuclear technologies are emerging as key players in the energy transition. In these systems, steam turbines will continue to be central to converting the heat generated by nuclear fission into electricity. As nuclear power expands to meet growing global energy demand, particularly in regions seeking to reduce reliance on fossil fuels, steam turbines will remain an important part of the nuclear power generation process. The ability of steam turbines to operate efficiently in high-temperature, high-pressure environments makes them ideal for use in next-generation nuclear power plants.
Finally, as global demand for decentralized and distributed energy systems grows, microgrids powered by steam turbines are becoming more common. Microgrids are small, localized energy networks that can operate independently of the main power grid. In areas where traditional grid infrastructure is unreliable or unavailable, microgrids powered by steam turbines can provide reliable, on-demand electricity. These systems are particularly beneficial in remote or off-grid areas, where access to centralized power plants is limited. The scalability and flexibility of steam turbines make them well-suited for these types of applications, offering a sustainable solution for communities in need of reliable power.
In conclusion, the future of steam turbines is bright, with their purpose continuing to evolve to meet the needs of a rapidly changing energy landscape. Their ability to adapt to new fuels, new energy systems, and new technologies ensures that steam turbines will remain a key component in a variety of applications. As the world transitions to a more sustainable, low-carbon energy future, steam turbines will continue to play a critical role in power generation, industrial processes, and renewable energy integration, driving efficiency, reducing emissions, and enhancing energy security. Through ongoing innovation and technological advancement, steam turbines will remain at the forefront of efforts to create a more sustainable, resilient, and decarbonized energy future.
As we move further into the future, the role of steam turbines will continue to expand and evolve, embracing new technological advancements and helping to address the global demand for clean, efficient, and sustainable energy solutions. These turbines will not only remain central to traditional energy generation systems but also contribute significantly to the development of next-generation energy infrastructure. This continued evolution will bring with it numerous innovations, including advances in turbine efficiency, emissions reduction, and system flexibility.
One of the key trends in the future of steam turbines is their integration with advanced control systems. The growing availability of digitalization technologies, such as advanced sensors, cloud computing, and machine learning algorithms, will enable steam turbines to be operated more efficiently and with higher precision than ever before. Predictive maintenance, driven by real-time data and AI-powered analytics, will allow for more proactive management of turbines, minimizing downtime and reducing repair costs. By integrating digital technologies into steam turbine systems, operators can anticipate potential failures, schedule maintenance based on actual turbine condition, and optimize operational performance across the turbine’s lifecycle. This will lead to extended turbine lifespan, lower operational costs, and improved overall system reliability.
The drive for greater energy efficiency is another significant force shaping the future of steam turbine technology. New materials and manufacturing techniques are being developed to enhance the efficiency and durability of steam turbines. For example, advanced alloys and ceramic coatings that can withstand higher temperatures and pressures will enable turbines to operate at even higher thermodynamic efficiencies, resulting in less fuel consumption, reduced emissions, and improved overall performance. These innovations in materials science will play a key role in optimizing steam turbines for use in high-efficiency power plants, combined-cycle systems, and renewable energy integration.
Moreover, the reliability and flexibility of steam turbines will become increasingly important as the energy grid transitions to a more decentralized and distributed structure. Microgrids, district heating systems, and off-grid solutions will rely on steam turbines as a flexible, efficient, and reliable power source. In these applications, steam turbines must be able to operate in dynamic environments where energy demand can fluctuate, and the integration of multiple energy sources, including solar, wind, and battery storage, requires turbines that can adjust their output quickly and efficiently. Advanced control systems, integrated with digital technologies, will be essential for managing steam turbine performance in these dynamic energy systems, ensuring reliable and stable operation despite variations in energy supply.
Carbon capture and storage (CCS) will also play an increasingly vital role in the future of steam turbines. As more industries and power plants seek to reduce their carbon emissions and contribute to global climate goals, steam turbines will be central to CCS technologies that capture CO2 emissions from combustion processes. By using steam turbines to drive compressors and other critical equipment in CCS systems, these turbines will help reduce the environmental impact of fossil-fuel-based power generation while supporting the transition to cleaner energy systems. The continued development of low-carbon technologies and carbon-neutral fuels, such as hydrogen and biofuels, will ensure that steam turbines remain compatible with both existing and emerging carbon-reduction strategies.
The growth of nuclear energy and the increasing focus on small modular reactors (SMRs) will further enhance the role of steam turbines in the energy sector. As next-generation nuclear reactors come online, steam turbines will continue to be used to convert heat from nuclear fission reactions into electricity. These advanced nuclear technologies, which are designed to be more compact, safer, and cost-effective than traditional nuclear reactors, will require steam turbines that are both efficient and adaptable to new reactor designs. The ability of steam turbines to provide power in a variety of operating conditions and to integrate with advanced nuclear plants will solidify their place in the future energy mix, as nuclear power remains an important source of low-carbon baseload electricity.
In the renewable energy space, hydropower and geothermal energy systems will continue to benefit from steam turbines. Geothermal plants, which rely on the heat from the Earth’s core to produce steam, have long utilized steam turbines to generate electricity. As the demand for renewable energy grows, geothermal energy will likely see expanded use, particularly in regions with significant geothermal potential. Steam turbines’ ability to efficiently convert geothermal heat into electricity ensures their continued relevance in this field. Similarly, pumped hydro storage systems, which store energy by moving water between two reservoirs at different elevations, often use steam turbines to generate electricity during peak demand periods. With the growing importance of energy storage in stabilizing grids powered by intermittent renewable energy sources, steam turbines will continue to play a crucial role in these systems.
Another area in which steam turbines are poised to make an impact is sustainable transportation, particularly in the maritime sector. As shipping companies seek to decarbonize their fleets and reduce reliance on fossil fuels, steam turbines could be adapted to run on alternative fuels such as green hydrogen or ammonia. These turbines would drive the propulsion systems of large vessels, offering an energy-efficient, low-emission alternative to conventional marine engines. The maritime industry, which is responsible for a significant portion of global greenhouse gas emissions, has a strong incentive to explore new technologies that can reduce its environmental impact. Steam turbines, with their efficiency and adaptability to different fuels, may be a key solution in this transition.
The development of fusion energy is also an exciting possibility for the future of steam turbines. Fusion power, which seeks to replicate the process that powers the sun by fusing hydrogen atoms to produce energy, has long been considered a potentially revolutionary energy source. While fusion energy remains in the experimental stage, steam turbines may play a role in future fusion reactors by converting the heat generated from the fusion process into electricity. The ability of steam turbines to operate in high-temperature, high-pressure environments makes them well-suited to the challenges posed by fusion energy, and their involvement in this emerging energy source could open up new frontiers in clean power generation.
In conclusion, the future of steam turbines is characterized by a continuous drive for efficiency, flexibility, and sustainability. These turbines will remain a central technology in the energy sector, contributing to carbon reduction efforts, supporting the integration of renewable energy, and enabling new clean energy technologies. As global energy systems evolve to meet the challenges of climate change, energy security, and growing demand, steam turbines will continue to play a crucial role in ensuring that energy is produced in an efficient, reliable, and environmentally responsible manner. With technological advancements and increasing innovation, steam turbines are poised to remain a cornerstone of the modern energy landscape for many years to come.
EMS Power Machines
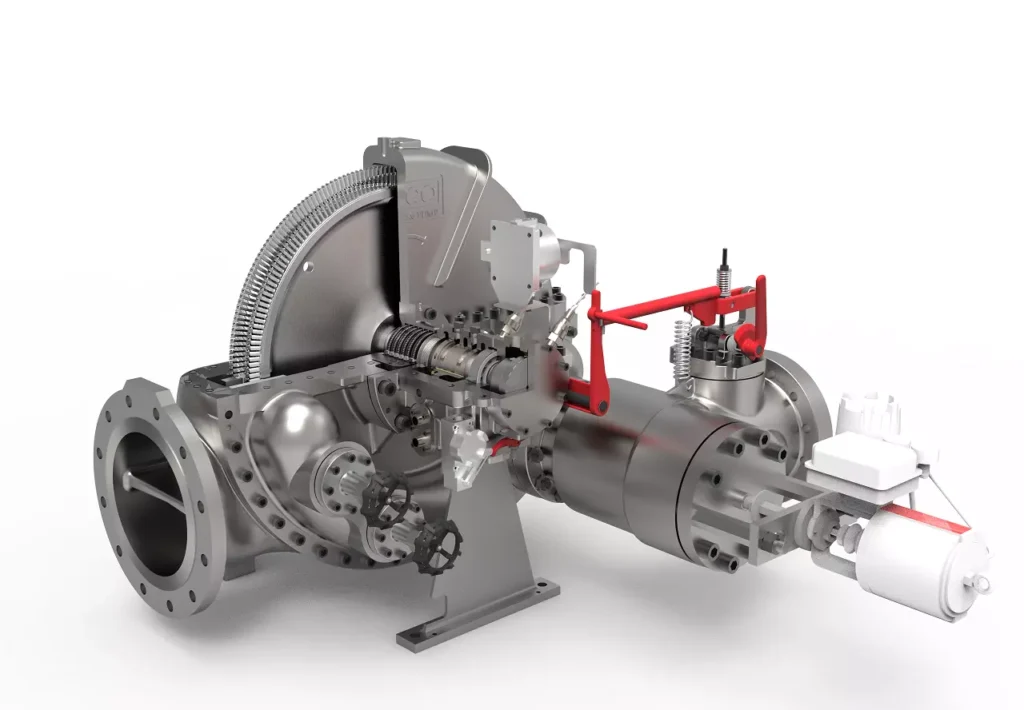
We design, manufacture and assembly Power Machines such as – diesel generators, electric motors, vibration motors, pumps, steam engines and steam turbines
EMS Power Machines is a global power engineering company, one of the five world leaders in the industry in terms of installed equipment. The companies included in the company have been operating in the energy market for more than 60 years.
EMS Power Machines manufactures steam turbines, gas turbines, hydroelectric turbines, generators, and other power equipment for thermal, nuclear, and hydroelectric power plants, as well as for various industries, transport, and marine energy.
EMS Power Machines is a major player in the global power industry, and its equipment is used in power plants all over the world. The company has a strong track record of innovation, and it is constantly developing new and improved technologies.
Here are some examples of Power Machines’ products and services:
- Steam turbines for thermal and nuclear power plants
- Gas turbines for combined cycle power plants and industrial applications
- Hydroelectric turbines for hydroelectric power plants
- Generators for all types of power plants
- Boilers for thermal power plants
- Condensers for thermal power plants
- Reheaters for thermal power plants
- Air preheaters for thermal power plants
- Feedwater pumps for thermal power plants
- Control systems for power plants
- Maintenance and repair services for power plants
EMS Power Machines is committed to providing its customers with high-quality products and services. The company has a strong reputation for reliability and innovation. Power Machines is a leading provider of power equipment and services, and it plays a vital role in the global power industry.
EMS Power Machines, which began in 1961 as a small factory of electric motors, has become a leading global supplier of electronic products for different segments. The search for excellence has resulted in the diversification of the business, adding to the electric motors products which provide from power generation to more efficient means of use.