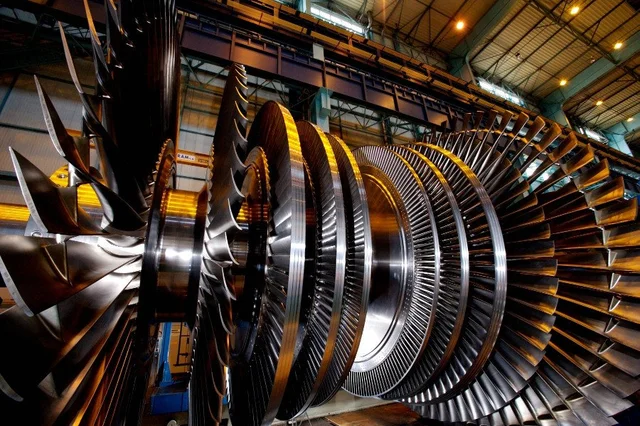
Steam Turbines in Metallurgical Plants: Steam turbines for process steam applications are widely used in various industries due to their ability to efficiently convert thermal energy into mechanical power while also supplying steam for heating, drying, and other industrial processes. These turbines operate based on the thermodynamic principle of expanding high-pressure steam through a series of blades, generating rotational energy that can be used to drive pumps, compressors, or electrical generators. Unlike purely power-generating steam turbines, which maximize efficiency for electricity production, process steam turbines are specifically designed to extract steam at one or more intermediate pressures to meet the needs of industrial operations.
The two main types of steam turbines used in process steam applications are back-pressure turbines and extraction turbines. Back-pressure turbines exhaust steam at a pressure higher than atmospheric, making it available for downstream processes such as chemical reactions, paper drying, food processing, or district heating. These turbines are ideal for cogeneration systems, where both mechanical power and steam are needed. The efficiency of a back-pressure turbine is inherently high since almost all the available energy in the steam is utilized either in power generation or in process applications. The exhaust pressure is typically controlled to match the process requirements, ensuring a steady supply of steam.
Extraction turbines, on the other hand, allow steam to be extracted at one or more points along the expansion path, providing steam at different pressures for multiple process needs. These turbines can operate in either a controlled or uncontrolled extraction mode. Controlled extraction allows precise regulation of steam flow for process needs, while uncontrolled extraction depends on load variations and turbine operation conditions. Extraction turbines are often used in refineries, petrochemical plants, and pulp and paper mills, where different processes require steam at varying pressures and temperatures. In cases where process steam demand fluctuates, extraction turbines offer better flexibility compared to back-pressure turbines.
The selection of a suitable steam turbine for process steam applications depends on factors such as steam supply conditions, process steam pressure and flow requirements, energy efficiency targets, and operational flexibility. Steam conditions, including pressure and temperature, influence the efficiency and power output of the turbine. High inlet pressures and superheated steam improve efficiency but may require additional investment in boiler and turbine components. The design must also consider the quality of the steam, as excessive moisture can cause erosion of turbine blades and reduce performance. To mitigate this, steam separators or reheaters may be incorporated into the system.
Industries that benefit from steam turbines for process steam include chemical plants, sugar mills, food processing facilities, textile industries, and district heating networks. In these industries, steam is not only used for power generation but also for critical processes such as distillation, drying, sterilization, and heating. Cogeneration, or combined heat and power (CHP) systems, are particularly advantageous in such applications because they maximize fuel utilization by simultaneously producing electricity and useful steam. This reduces energy costs and environmental impact by lowering greenhouse gas emissions compared to separate power and heat generation systems.
Maintenance and reliability are crucial for ensuring the long-term performance of process steam turbines. Regular inspections, proper lubrication, and monitoring of vibration levels help prevent unexpected failures. Blade fouling, steam path erosion, and seal leakage are common issues that need to be addressed through routine maintenance. Advanced condition monitoring systems, such as vibration analysis and thermal imaging, can help detect early signs of wear and tear, allowing for predictive maintenance strategies that reduce downtime and operational costs.
Overall, steam turbines for process steam play a vital role in industrial energy systems, providing a reliable and efficient means of utilizing steam energy for both mechanical power and thermal processes. Their integration into cogeneration systems enhances overall energy efficiency, reduces fuel consumption, and supports sustainable industrial operations. The ongoing development of advanced turbine materials, improved steam cycle configurations, and digital monitoring solutions continues to enhance the efficiency, reliability, and operational flexibility of these turbines, making them a key component in modern industrial energy management strategies.
Another important aspect of steam turbines for process steam applications is their integration with various heat recovery and steam distribution systems. In many industrial plants, steam is generated in high-pressure boilers and then expanded through turbines to produce both mechanical power and useful process steam. The configuration of these systems depends on process requirements, plant layout, and economic considerations. Proper design ensures that energy is utilized optimally, minimizing waste and reducing overall fuel consumption.
One of the key benefits of using steam turbines for process steam is their ability to enhance overall plant efficiency through cogeneration. In a typical cogeneration setup, high-pressure steam is expanded in a turbine to generate electricity, while the lower-pressure exhaust steam is used for industrial processes. This simultaneous production of power and thermal energy significantly improves energy utilization, often reaching efficiencies of 70% or higher, compared to conventional power plants, which may have efficiencies below 40%. The economic advantage of cogeneration lies in reduced fuel costs and lower greenhouse gas emissions, making it an attractive option for industries seeking to optimize energy use and comply with environmental regulations.
Process steam turbines must be carefully designed to ensure that steam supply remains stable and reliable. The process load can vary due to changes in production demand, seasonal variations, or operational shifts, requiring the turbine to be flexible enough to adjust to these fluctuations. In some cases, steam accumulator systems or bypass arrangements are used to balance supply and demand, preventing disruptions to process operations. Additionally, modern control systems equipped with advanced sensors and automation technology help regulate steam flow and turbine speed, improving efficiency and reliability.
In terms of turbine construction, materials and component design play a crucial role in ensuring durability and performance. High-temperature steam conditions demand robust materials that can withstand thermal expansion, corrosion, and erosion. Turbine blades are often made from high-strength alloys with protective coatings to resist wear. Bearings and seals must also be designed to handle high-speed rotation and prevent steam leakage, which can reduce efficiency. Advances in metallurgy and manufacturing techniques, such as additive manufacturing and precision casting, have contributed to improved turbine lifespan and reduced maintenance requirements.
Another consideration in process steam turbine applications is steam quality and water treatment. The presence of impurities in steam, such as dissolved salts and silica, can lead to deposits on turbine blades, reducing efficiency and causing potential damage. Proper water treatment systems, including demineralization and filtration, help maintain steam purity, ensuring smooth turbine operation. Additionally, the use of reheating and steam superheating can further improve efficiency by reducing moisture content in the steam, which helps minimize blade erosion.
Industries that utilize process steam turbines continue to explore ways to improve energy efficiency through waste heat recovery and integration with renewable energy sources. For example, some facilities implement biomass-fired boilers or waste heat recovery boilers to generate steam, reducing dependence on fossil fuels. In regions with abundant geothermal energy, steam turbines can be integrated into geothermal power plants, providing a sustainable source of both electricity and process steam. Similarly, solar thermal power plants can use steam turbines to generate power while supplying excess steam for industrial processes.
Digitalization and smart monitoring systems are also transforming the way process steam turbines operate. By incorporating real-time data analytics, predictive maintenance, and artificial intelligence-based control systems, industries can optimize turbine performance, detect potential failures early, and improve overall efficiency. Remote monitoring capabilities allow plant operators to track performance metrics such as steam pressure, temperature, vibration levels, and energy output, enabling data-driven decision-making and proactive maintenance strategies.
In the future, the role of steam turbines in industrial energy systems will likely continue to evolve with advancements in efficiency improvements, automation, and sustainability initiatives. The integration of carbon capture technologies, hydrogen-based steam generation, and hybrid energy systems will further enhance the viability of steam turbines in industrial applications. As industries strive to reduce their carbon footprint and transition to more sustainable energy sources, steam turbines will remain a critical component in achieving energy efficiency, operational reliability, and economic viability in process steam applications.
Another crucial factor in the application of steam turbines for process steam is the optimization of steam cycle configurations to achieve maximum efficiency and cost-effectiveness. Various cycle designs are employed depending on process requirements and energy balance considerations. The Rankine cycle remains the foundation of steam turbine operation, but modifications such as regenerative feedwater heating, reheat cycles, and combined heat and power (CHP) configurations enhance its performance. In CHP plants, steam turbines are integrated with waste heat recovery systems to maximize thermal energy utilization. For instance, in industries where excess heat is available from furnaces, kilns, or chemical reactions, heat recovery steam generators (HRSGs) can produce steam without additional fuel consumption, making the process highly efficient.
Back-pressure turbines, which are widely used in process industries, provide an effective means of supplying steam at a controlled pressure while simultaneously generating mechanical power. These turbines are commonly employed in paper mills, sugar refineries, chemical plants, and food processing units, where steam is required for drying, evaporation, cooking, or sterilization. The turbine exhaust pressure is carefully regulated to ensure a consistent supply of steam at the required conditions for downstream applications. Unlike condensing turbines, which prioritize electricity generation by exhausting steam to a condenser at low pressure, back-pressure turbines ensure that virtually all the available energy in the steam is either converted into mechanical power or utilized as process steam. This results in a high overall efficiency for industrial plants.
Extraction turbines provide an additional layer of flexibility by allowing steam to be withdrawn at different pressures for various process needs. These turbines are particularly beneficial in multi-stage industrial processes where different units operate at different steam pressures. For example, in petroleum refining and petrochemical industries, certain processes require high-pressure steam for chemical reactions, while others need lower-pressure steam for heating or distillation. Controlled extraction allows precise steam delivery at intermediate stages, ensuring optimal energy usage. Uncontrolled extraction, on the other hand, depends on the natural flow of steam within the turbine and can vary based on load conditions.
From an operational perspective, steam turbine performance depends on factors such as steam inlet conditions, turbine design, and system integration. Higher inlet pressures and temperatures generally improve turbine efficiency, but they also require robust materials and advanced manufacturing techniques to withstand the extreme operating conditions. Blade design is a critical aspect of turbine efficiency, with aerodynamic shaping, precision machining, and advanced coatings contributing to reduced losses and improved durability. Additionally, the use of steam reheating between turbine stages helps maintain high efficiency by reducing the moisture content in the steam, thereby preventing blade erosion and improving the overall energy conversion process.
Maintenance and reliability are essential for ensuring the continuous operation of steam turbines in process steam applications. Regular maintenance schedules typically include inspections of blades, bearings, seals, and control systems. Over time, issues such as steam path contamination, erosion, and deposition of impurities can affect turbine efficiency and performance. Implementing a proactive maintenance strategy with real-time condition monitoring and predictive analytics can help prevent unexpected failures, reducing downtime and operational costs. Techniques such as non-destructive testing (NDT), vibration analysis, and thermographic inspections play a crucial role in detecting potential issues before they escalate into significant problems.
The environmental benefits of steam turbines in process steam applications are also significant, especially in cogeneration and waste heat recovery systems. By utilizing steam more efficiently, industries can reduce fuel consumption, lower greenhouse gas emissions, and minimize waste heat losses. Many industries are shifting toward cleaner energy sources, integrating biomass, biogas, or waste-derived fuels into their steam generation systems to further enhance sustainability. Additionally, the use of advanced emission control technologies, such as carbon capture and storage (CCS), flue gas desulfurization (FGD), and selective catalytic reduction (SCR), helps mitigate environmental impact while maintaining high efficiency.
Looking ahead, advancements in turbine technology, materials science, and digitalization will continue to shape the future of steam turbines for process steam. The integration of smart sensors, artificial intelligence (AI)-driven diagnostics, and cloud-based monitoring platforms is revolutionizing turbine operation and maintenance. Digital twins—virtual replicas of physical turbines—allow engineers to simulate performance, predict failures, and optimize operational parameters in real time. These innovations enhance reliability, improve efficiency, and extend the service life of turbines, making them even more valuable assets in industrial energy systems.
Furthermore, the role of steam turbines in decarbonization efforts is gaining attention as industries explore ways to transition to cleaner energy sources. The potential use of hydrogen as a fuel for steam generation, hybrid systems combining renewable energy with steam turbines, and innovations in supercritical and ultra-supercritical steam cycles are paving the way for a more sustainable future. As industries face increasing pressure to improve energy efficiency and reduce emissions, steam turbines will remain at the core of process steam applications, evolving with new technologies and sustainable energy solutions.
Here are five key reasons to use steam turbines:
- High Efficiency in Cogeneration – Steam turbines are ideal for combined heat and power (CHP) systems, where they generate electricity while also providing process steam for industrial applications. This maximizes energy utilization, often achieving efficiencies of 70% or higher, compared to conventional power generation.
- Fuel Flexibility – Steam turbines can operate on various heat sources, including fossil fuels (coal, natural gas, oil), biomass, waste heat, and even renewable energy sources like geothermal or solar thermal power. This flexibility allows industries to optimize fuel use based on availability and cost.
- Reliable and Durable Operation – Steam turbines have a long operational life, often exceeding 30 years with proper maintenance. Their robust design and fewer moving parts compared to gas turbines or reciprocating engines result in high reliability and lower maintenance costs.
- Process Steam Integration – Many industries, such as refineries, chemical plants, paper mills, and food processing facilities, require steam for heating, drying, and other processes. Steam turbines efficiently provide both mechanical power and process steam at required pressures, improving overall plant efficiency.
- Environmental and Cost Benefits – By using waste heat recovery and cogeneration, steam turbines reduce fuel consumption and greenhouse gas emissions. Industries can lower operational costs while complying with environmental regulations, making steam turbines a sustainable and economically viable energy solution.
Steam Turbine
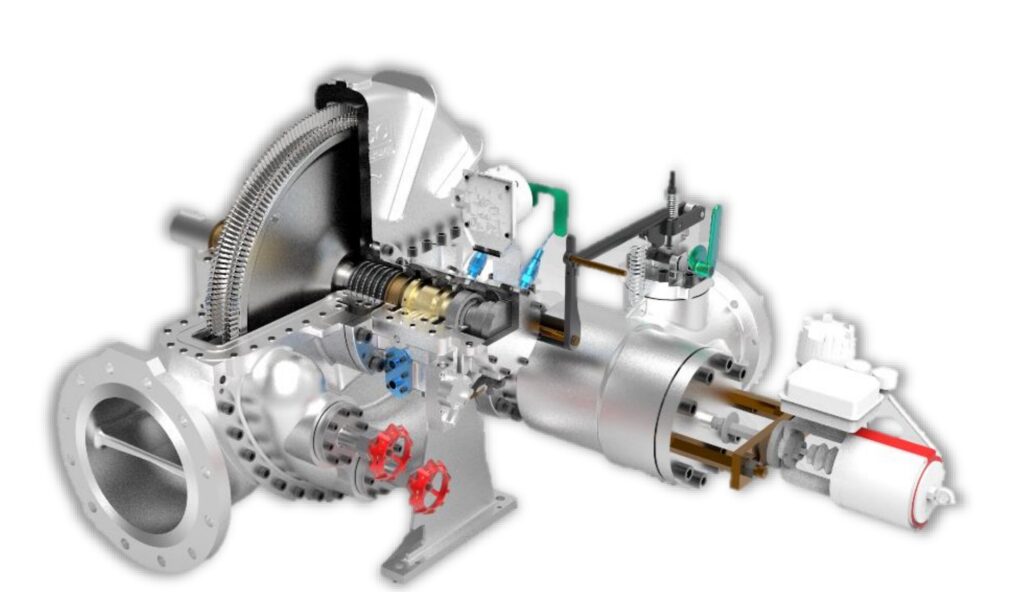
Cogeneration, or combined heat and power (CHP), is one of the most efficient ways to utilize steam turbines. In a conventional power generation system, a large portion of the energy in fuel is lost as waste heat. However, in a cogeneration system, steam turbines generate electricity while also supplying useful steam for industrial processes, district heating, or other thermal applications. This dual-purpose approach significantly improves overall energy efficiency.
A well-designed cogeneration system using a steam turbine can achieve energy utilization rates of 70% to 90%, compared to 30% to 40% in traditional power plants. This is because, instead of simply condensing exhaust steam at low pressure (wasting heat), steam turbines in CHP applications extract or exhaust steam at useful pressure levels for process heating, drying, sterilization, or other industrial needs.
Industries such as refineries, paper mills, food processing plants, and chemical industries benefit greatly from this setup. In these industries, steam is an essential part of operations, and using a steam turbine in a cogeneration system ensures that both mechanical power and thermal energy are fully utilized. Additionally, cogeneration reduces fuel consumption, lowers energy costs, and cuts greenhouse gas emissions by avoiding separate production of electricity and heat.
By integrating steam turbines in cogeneration applications, industries can improve their sustainability while maintaining a reliable and cost-effective energy supply. This makes steam turbines a preferred choice for facilities looking to enhance efficiency, reduce environmental impact, and optimize fuel utilization.
Fuel Flexibility
One of the key advantages of steam turbines is their ability to operate on a wide variety of fuel sources, making them highly adaptable across different industries and energy systems. Unlike internal combustion engines or gas turbines, which require specific fuels like natural gas or diesel, steam turbines generate power from steam, which can be produced using multiple heat sources. This flexibility allows industries to choose fuels based on availability, cost, and environmental considerations.
Types of Fuels Used in Steam Turbines
- Fossil Fuels – Steam turbines can be powered by coal, natural gas, or oil, making them suitable for large-scale power plants and industrial operations. Despite the shift toward cleaner energy, many existing power plants still rely on these fuels due to their high energy density and reliability.
- Biomass and Waste Fuels – Industries with access to biomass (wood chips, agricultural waste, bagasse) or industrial waste heat can use steam turbines to convert these renewable sources into electricity and process steam. This is particularly beneficial in sugar mills, paper mills, and waste-to-energy plants, where byproducts can be used as fuel.
- Geothermal Energy – Steam turbines are widely used in geothermal power plants, where high-pressure steam from underground reservoirs drives the turbine without the need for fuel combustion. This provides a clean and sustainable source of electricity with minimal emissions.
- Solar Thermal Energy – Concentrated solar power (CSP) plants use mirrors to focus sunlight and generate high-temperature steam, which then drives a steam turbine. This allows for renewable electricity generation without direct fuel consumption.
- Hydrogen and Synthetic Fuels – Emerging technologies are exploring hydrogen-fired boilers to produce steam for turbines, offering a potential low-carbon alternative to fossil fuels in the future. Additionally, synthetic fuels and ammonia-based systems are being developed to further enhance sustainability.
Advantages of Fuel Flexibility
- Cost Optimization – Industries can select the most economical fuel source based on market prices, reducing operational expenses.
- Energy Security – The ability to switch between fuels ensures continued operation even if one fuel source becomes scarce or expensive.
- Environmental Benefits – Using renewable or waste-based fuels can significantly lower carbon emissions and improve sustainability.
- Long-Term Viability – Steam turbines remain relevant in energy transitions, as they can gradually shift from fossil fuels to renewable sources without requiring major modifications.
This flexibility makes steam turbines a highly adaptable and future-proof solution for power generation and industrial energy systems, ensuring long-term efficiency and reliability.
Reliable and Durable Operation
Steam turbines are renowned for their reliability and durability, which is one of the primary reasons they are favored in large-scale industrial and power generation applications. The design and construction of steam turbines ensure they can withstand harsh operating conditions and provide long-term, trouble-free operation with minimal downtime. Here’s a closer look at what makes steam turbines such reliable and durable machines:
1. Robust Design and Construction
Steam turbines are engineered with heavy-duty materials capable of withstanding the extreme pressures and temperatures involved in steam expansion. The rotor and stator components are typically made from high-strength alloys, often treated with specialized coatings to prevent wear and corrosion. This ensures that the turbine can operate reliably in high-stress environments, such as refineries, chemical plants, and power stations, for many years.
2. Fewer Moving Parts
Unlike other types of engines or turbines, steam turbines have relatively few moving parts. This minimizes the risk of mechanical failure and reduces the need for frequent maintenance. The main moving parts, such as the rotor and blades, are designed for optimal performance and long-term use. Additionally, since there is no direct contact between moving and stationary parts (aside from bearings), friction is minimized, further enhancing the turbine’s durability.
3. Long Operational Lifespan
With proper maintenance, steam turbines are capable of running continuously for decades. Many steam turbines in industrial plants have been in operation for over 30 years, still performing reliably. Their extended lifespan makes them a cost-effective choice for industries looking for long-term energy solutions. In fact, most steam turbines are designed to handle hundreds of thousands of hours of operation before needing major overhauls or replacements.
4. Resistance to Harsh Conditions
Steam turbines are highly resistant to the high temperatures and pressure conditions that are often present in industrial environments. Whether used in power generation, chemical production, or refining, they are designed to handle extreme temperature fluctuations and high-pressure steam without compromising efficiency or safety.
5. Predictable and Proven Performance
Steam turbines have been used for over a century and are well-understood in terms of operation, maintenance, and failure modes. Their performance is highly predictable, and their operational behavior can be closely monitored to ensure reliability. Advances in digital monitoring, vibration analysis, and condition-based monitoring systems further enhance turbine reliability by identifying issues early and allowing for proactive maintenance.
6. Low Maintenance Needs
While steam turbines do require routine maintenance (such as lubrication, cleaning, and periodic inspections), their simple mechanical design means that maintenance is typically less frequent and less intensive compared to other types of power generation equipment. Many components, such as bearings and seals, have been designed for easy replacement, reducing downtime during scheduled maintenance.
7. Performance in Various Environments
Steam turbines are not only reliable in traditional industrial settings but are also used in more challenging environments, such as offshore oil rigs and remote geothermal power plants. Their ability to perform reliably under such conditions makes them ideal for industries that require consistent, continuous operation in a variety of locations and environments.
8. Redundancy and Backup Systems
In large-scale operations, it’s common to have multiple steam turbines operating in parallel, providing an added layer of reliability. If one turbine experiences issues, others can continue functioning, minimizing the impact on operations. Additionally, modern steam turbine systems can be integrated with smart control systems that monitor performance in real-time, providing an early warning system for potential failures.
Benefits of Reliability and Durability:
- Minimized Downtime – Reduced likelihood of unplanned shutdowns and disruptions.
- Cost-Effectiveness – Less frequent need for expensive repairs or replacements.
- Operational Consistency – Continuous, steady output of mechanical power and steam, essential for industrial processes.
- Long-Term Investment – A reliable and durable turbine ensures ongoing efficiency and performance, making it a sound investment for facilities looking to maximize operational life and energy output.
The combination of rugged construction, fewer moving parts, and predictable performance makes steam turbines a trusted choice for industries demanding high reliability and long-term durability in their energy systems.
Process Steam Integration
Process steam integration is one of the primary advantages of using steam turbines in industrial applications. Steam is a critical component in many manufacturing and processing industries for heating, drying, sterilization, and power generation. Steam turbines offer an efficient and reliable means to meet these process steam demands while also providing mechanical power. This integration enhances operational efficiency and reduces overall energy consumption.
1. Dual Purpose: Power Generation and Steam Supply
Steam turbines in process applications are designed to meet both power generation and process steam needs simultaneously. Unlike turbines in purely power plants, which focus solely on electricity generation, turbines in industrial settings are designed to produce both mechanical energy and thermal energy (steam) at the appropriate pressures for different processes.
For example, in a paper mill, steam is essential for drying paper sheets, while electricity is needed to power equipment like pumps and motors. A steam turbine can simultaneously generate electricity to power the mill and supply the necessary steam at a regulated pressure to the drying machines, making the entire system more efficient.
2. Efficient Use of Energy
In industrial settings, energy is often wasted in the form of excess heat or unused steam. Steam turbines help recover and optimize this energy by utilizing the high-pressure steam to generate power while also supplying steam for heating or other processes. This cogeneration or combined heat and power (CHP) system reduces the need for separate power plants and boilers, making the overall system more efficient.
For instance, in chemical plants, a steam turbine may extract energy from high-pressure steam generated in boilers to drive compressors or generators while also providing the right pressure steam for chemical reactions or distillation processes. This minimizes waste and maximizes energy utilization.
3. Flexible Pressure and Temperature Control
The ability to control steam pressure and temperature is crucial in process industries, where specific conditions are necessary for efficient operations. Steam turbines can be designed to handle multiple stages of steam expansion, enabling pressure regulation and temperature control. In systems like refineries or food processing, different processes may require steam at different pressures (e.g., high-pressure steam for distillation, low-pressure steam for heating).
Steam turbines can provide this flexibility, allowing for steam extraction at different points in the turbine cycle (in the case of extraction turbines) or using back-pressure turbines to exhaust steam at a specific, consistent pressure for process needs. This flexibility ensures that steam is always available at the right conditions for each part of the operation.
4. Integration with Waste Heat Recovery
Many industries generate significant amounts of waste heat as part of their operations. By integrating steam turbines with waste heat recovery systems, such as heat recovery steam generators (HRSG), industries can reuse this excess heat to generate steam and power. For instance, steel mills, cement plants, or refineries produce large amounts of waste heat that can be captured and converted into useful steam energy.
By recovering this waste heat, industries reduce their reliance on external fuel sources, improve overall efficiency, and reduce emissions. This approach is particularly beneficial in cogeneration systems, where the combined production of electricity and steam maximizes the utilization of the energy in the system, minimizing waste and cutting costs.
5. Reducing Fuel Consumption and Costs
Using steam turbines to integrate process steam into industrial systems also helps reduce fuel consumption and costs. By effectively using the same steam for both power generation and heating, industries can eliminate the need for separate steam generation units or boilers for power production. This is especially true for back-pressure turbines, which provide mechanical energy while also delivering steam at a pressure suitable for the process.
In facilities that rely heavily on steam, such as textile mills, food processors, or chemical plants, this integration reduces the need to burn additional fuel, lowers operational costs, and improves the economic sustainability of operations.
6. Industry-Specific Applications
- Paper and Pulp Mills: Steam is used for drying the paper, powering pulping machinery, and providing heat for other processes like bleaching. Steam turbines in these mills help meet both steam demand for drying and mechanical power needs.
- Refineries: Refineries need various steam pressures for distillation, cracking, and other chemical processes. Steam turbines enable the recovery of energy from high-pressure steam while providing process steam at different pressures, optimizing energy use.
- Food Processing: Steam is widely used in food sterilization, pasteurization, and drying. A steam turbine can meet the heating requirements while generating electricity for the facility’s operations.
7. Environmental Benefits
Process steam integration also has notable environmental advantages. By improving energy efficiency and reducing the need for additional fuel sources, steam turbines contribute to lower greenhouse gas emissions. Additionally, steam turbines integrated with waste heat recovery can reduce the amount of fuel burned and decrease the facility’s carbon footprint, which is increasingly important in industries facing stringent environmental regulations.
Benefits of Process Steam Integration
- Cost Reduction – Efficient use of steam reduces the need for additional fuel and separate steam generation systems, lowering operational costs.
- Increased Energy Efficiency – By integrating both power generation and process steam supply, industries can optimize their overall energy consumption.
- Operational Flexibility – Steam turbines can supply steam at different pressures and temperatures, making them adaptable to various industrial processes.
- Environmental Sustainability – Waste heat recovery and energy optimization contribute to reducing emissions and fuel consumption.
- Continuous Operation – Process steam turbines are designed to provide continuous, reliable steam and power, ensuring smooth and uninterrupted operations.
Conclusion
Process steam integration with steam turbines plays a vital role in improving the energy efficiency, operational flexibility, and cost-effectiveness of industrial operations. By generating both mechanical power and process steam simultaneously, steam turbines help industries optimize their energy use, reduce fuel consumption, and support sustainable practices, making them a cornerstone of modern industrial energy systems.
Environmental and Cost Benefits
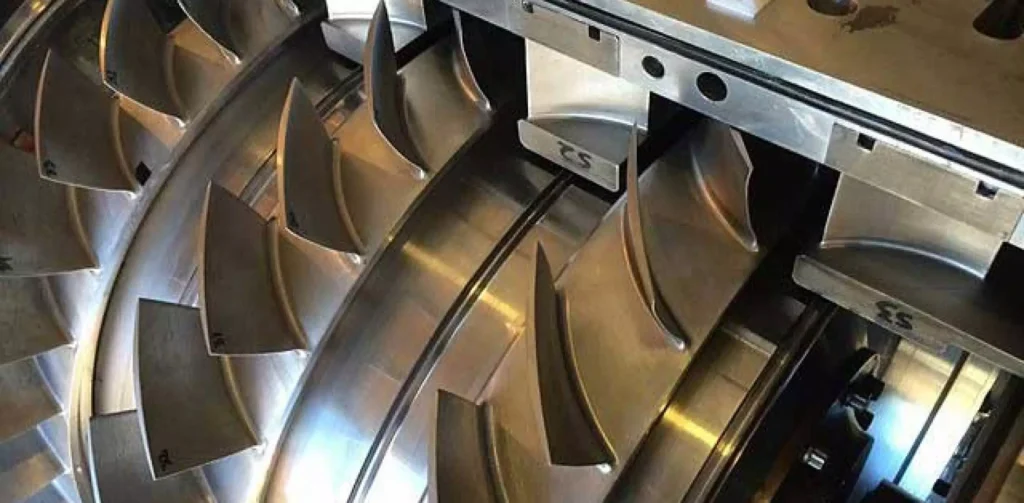
Steam turbines offer both environmental and economic advantages, making them an increasingly attractive option in industries seeking to improve energy efficiency, reduce operational costs, and minimize their environmental footprint. Below are the key environmental and cost benefits of using steam turbines in industrial and power generation applications:
1. Reduced Fuel Consumption and Cost
One of the primary benefits of steam turbines is their fuel efficiency. By using steam turbines in combined heat and power (CHP) systems, industries can reduce the need for separate fuel-burning equipment to produce electricity and heat. Instead, the same steam can be used for both mechanical power generation and process heating, resulting in a significant reduction in fuel consumption. This integrated approach optimizes fuel usage, reducing costs while ensuring a reliable supply of both electricity and steam.
For instance, in cogeneration systems, a single fuel source (e.g., natural gas, biomass, or waste) generates both electricity and steam for industrial use, ensuring that energy is produced at maximum efficiency and without waste. This leads to lower fuel bills, which is particularly advantageous for industries that require large amounts of steam, such as paper mills, chemical plants, and refineries.
2. Lower Greenhouse Gas Emissions
By improving energy efficiency and reducing the need for additional fuel consumption, steam turbines help to lower carbon emissions and minimize the environmental impact of industrial operations. Cogeneration systems that integrate steam turbines are particularly effective in reducing emissions, as they harness the full potential of the fuel used, converting it into both power and steam instead of losing energy as waste heat.
In traditional power plants without cogeneration, much of the energy produced is wasted as excess heat, contributing to higher emissions. However, by recovering this waste heat in cogeneration systems, steam turbines help mitigate these emissions and support a more sustainable and environmentally responsible approach to energy production.
Moreover, renewable energy sources like biomass and waste-derived fuels can be used in steam turbines to further reduce greenhouse gas emissions. Using biomass from agricultural waste or wood products instead of fossil fuels provides a carbon-neutral energy source, further decreasing the environmental footprint of industrial operations.
3. Waste Heat Recovery and Energy Efficiency
Steam turbines can be integrated with waste heat recovery systems, allowing industries to capture and repurpose excess heat from operations. This means that even byproducts like exhaust gases or heat from industrial furnaces can be used to generate steam and mechanical power, effectively reducing the need to burn additional fuel.
For example, industries like steel mills, cement plants, and refineries produce large amounts of waste heat. By integrating steam turbines into Heat Recovery Steam Generators (HRSGs), the waste heat is captured and converted into usable steam. This reduces the need for additional fuel to generate steam or electricity, improving the overall efficiency of the system and decreasing fuel costs and emissions.
This circular use of energy—where waste heat is converted back into useful steam—creates a closed-loop system that maximizes energy utilization while minimizing waste.
4. Cost-Effective Operations
While the initial investment in a steam turbine system may be high, the long-term cost savings far outweigh the upfront costs. The efficient use of steam turbines in cogeneration systems reduces the overall fuel requirements, leading to lower operational costs. The fuel savings, combined with lower maintenance and long lifespan, make steam turbines a cost-effective choice in the long run.
Additionally, steam turbines can be integrated with existing infrastructure, allowing industries to update their energy systems without the need for complete overhauls. This retrofit potential allows plants to optimize their energy use without incurring excessive capital expenses, further improving the return on investment.
The operational longevity of steam turbines also helps reduce maintenance and replacement costs over time. With proper maintenance, steam turbines can operate for decades with minimal repairs, leading to fewer downtime events and lower maintenance costs.
5. Reduced Dependence on External Energy Suppliers
Steam turbines that utilize local fuels (e.g., biomass or waste heat) or renewable energy sources reduce the reliance on external electricity providers or fossil fuel imports. This energy independence is particularly advantageous for industries operating in regions where energy prices are volatile or where access to fuel sources is limited.
By producing energy onsite through steam turbines, industries can reduce their exposure to fuel price fluctuations and ensure a more stable, predictable energy cost structure. This can be especially important in remote locations, where energy delivery can be expensive or unreliable.
6. Compliance with Environmental Regulations
As industries face increasingly stringent environmental regulations, using steam turbines for cogeneration and energy recovery helps companies comply with these standards. By improving energy efficiency and reducing emissions, steam turbines can help industries meet environmental targets and regulations, such as carbon emissions caps or clean energy mandates.
Industries that invest in energy-efficient technologies, such as steam turbines, may also benefit from government incentives or subsidies aimed at promoting sustainable practices. These financial incentives can help offset initial installation costs and improve the overall economics of steam turbine systems.
7. Contribution to Sustainability Goals
The use of steam turbines supports broader sustainability initiatives. Many industries are increasingly committed to reducing their environmental footprint as part of corporate social responsibility (CSR) and sustainable development goals (SDGs). By leveraging steam turbines for efficient power and steam generation, companies can contribute to global goals like reducing carbon emissions, minimizing energy waste, and promoting renewable energy use.
Conclusion
The environmental and cost benefits of steam turbines are substantial. They not only reduce fuel consumption and greenhouse gas emissions but also enhance energy efficiency through cogeneration and waste heat recovery. These turbines offer industries a way to lower operating costs, improve energy security, and comply with environmental regulations, all while contributing to sustainability efforts. By optimizing energy use and reducing environmental impact, steam turbines play a crucial role in helping industries transition to more efficient and eco-friendly energy systems.
4o mini
Şunu dedin:
long text without sections about Steam turbines for floating power stations
ChatGPT:
ChatGPT
Steam turbines are widely used in floating power stations due to their ability to generate both electricity and thermal energy efficiently in remote or offshore locations. Floating power stations, which are typically built on ships or barges, are designed to provide energy to areas that may lack access to a stable land-based grid or for applications where mobility and flexibility are crucial. These stations often operate in challenging environments, such as offshore oil rigs, islands, or maritime zones, where conventional energy infrastructure may not be feasible.
The integration of steam turbines into floating power stations offers several distinct advantages, starting with their fuel flexibility. Steam turbines can operate on a wide variety of fuel sources, including fossil fuels like coal, oil, and natural gas, as well as renewable sources like biomass, waste, and even geothermal or solar thermal energy. This versatility is particularly useful for floating power stations, as they may have access to different fuel sources depending on their location. For example, in offshore regions, the turbine could be powered by natural gas extracted from nearby wells or by biomass from local resources. The flexibility to switch between fuels based on availability, cost, and environmental considerations is a key feature that makes steam turbines ideal for floating power stations.
The reliability and durability of steam turbines also make them an excellent choice for these mobile power plants. Floating power stations must operate in harsh environments, with extreme weather conditions and challenging logistical constraints. Steam turbines, due to their robust design, are capable of withstanding the high pressures and temperatures generated in such environments. The turbines are built to endure continuous operation over long periods with minimal maintenance, making them particularly valuable for offshore power generation where access for maintenance is limited. Many steam turbines in industrial and offshore applications have operational lifespans of over 30 years, which ensures long-term, stable performance for floating power stations that are expected to operate for extended periods without frequent overhauls.
One of the key reasons steam turbines are used in floating power stations is their efficiency in generating both power and process steam. In many offshore applications, steam is not only required for power generation but also for industrial processes like desalination, heating, or even oil recovery. Steam turbines allow these floating stations to supply both the mechanical power needed for electricity generation and the thermal energy required for these additional processes. This dual functionality enhances the overall efficiency of the station, ensuring that the energy produced serves multiple purposes. This is particularly beneficial in offshore oil and gas fields, where steam can be used for enhanced oil recovery (EOR) techniques or in desalination plants to provide potable water for offshore workers.
Floating power stations are also often smaller scale compared to land-based plants, which makes the compact, modular design of steam turbines a perfect fit for these environments. Steam turbines can be integrated into various system sizes, from small-scale units suitable for isolated offshore locations to large-scale units capable of powering entire islands or regions. The ability to provide significant energy output in a compact form factor is an essential advantage in these floating setups, where space is at a premium.
Additionally, environmental sustainability is a growing concern in floating power station design. While traditional fossil fuel-powered plants have a significant environmental footprint, steam turbines in these settings can help mitigate some of the environmental impact through waste heat recovery and the potential to integrate renewable fuel sources. For instance, a floating power station using steam turbines can incorporate waste heat recovery systems that capture excess heat from power generation and use it to produce additional steam, improving fuel efficiency and reducing the overall fuel consumption. Moreover, using renewable fuels such as biomass or biofuels in steam turbines can significantly reduce greenhouse gas emissions, aligning floating power stations with global efforts to reduce carbon footprints and increase sustainability.
The ability to adapt to varying energy demands is another reason steam turbines are suitable for floating power stations. Depending on the location, a floating power station may need to adjust its energy output in response to fluctuating energy demands. Steam turbines can be easily adjusted to provide varying levels of power by controlling the steam pressure and flow, offering significant operational flexibility. This adaptability makes them highly suitable for areas with intermittent or seasonal energy needs, such as in offshore drilling rigs or remote islands that experience variable loads.
Moreover, steam turbines in floating power stations are often integrated with advanced monitoring systems that ensure efficient and reliable operation. These systems track performance metrics such as turbine speed, temperature, pressure, and vibration, enabling operators to detect potential issues early and perform predictive maintenance. This is particularly valuable in offshore environments where downtime can be costly and difficult to manage. The ability to remotely monitor and optimize turbine performance ensures that the floating power station continues to operate at peak efficiency without requiring frequent human intervention, which can be challenging in these locations.
Another benefit of using steam turbines in floating power stations is their relatively low environmental footprint when compared to other power generation methods. Unlike gas turbines or diesel engines, which often produce high levels of emissions, steam turbines can be equipped with emission control systems that significantly reduce pollutants such as sulfur dioxide, nitrogen oxides, and particulate matter. This is important for floating power stations operating in sensitive or protected marine environments, where environmental regulations may be stringent.
In conclusion, the use of steam turbines in floating power stations is a reliable and efficient solution for providing both electricity and process steam in remote or offshore locations. Their fuel flexibility, efficiency, and durability make them an ideal choice for these challenging environments. The ability to generate energy from various fuels, combined with their environmental sustainability, ensures that steam turbines remain a crucial technology in the future of floating power generation. As the demand for offshore energy increases, steam turbines will continue to play a central role in powering remote industries, supporting energy independence, and promoting sustainability.
The use of steam turbines in floating power stations also aligns well with the growing demand for energy independence and security in regions that are geographically isolated or have unreliable access to land-based power grids. Floating power stations, often stationed near offshore oil rigs, remote islands, or regions with limited infrastructure, provide a flexible and scalable solution to meet local power needs. The integration of steam turbines in these stations ensures that the energy generation is not dependent on external power supplies, reducing vulnerabilities to grid disruptions or reliance on centralized energy infrastructure.
Floating power stations equipped with steam turbines are particularly valuable in off-grid applications where traditional power infrastructure is either not available or is cost-prohibitive. For instance, in remote offshore oil platforms or small island communities, steam turbines can be the main power source, providing both electricity and process steam for a wide range of applications. Whether it’s powering equipment, providing heat for industrial processes, or generating desalinated water for drinking, steam turbines offer the versatility needed in such settings.
The mobility of floating power stations is another key advantage, especially in regions where energy demand is seasonal or fluctuates. These floating units can be relocated to areas with higher energy needs, making them a dynamic energy solution. Steam turbines, with their modular design and proven efficiency, allow these floating stations to scale their operations according to the local demand. If the energy needs increase or shift due to seasonal or economic factors, these turbines can be adjusted to provide a steady and reliable energy supply.
Maintenance and operational flexibility are also integral to the success of floating power stations. While remote locations pose logistical challenges for maintenance, modern steam turbines are designed for ease of servicing with fewer moving parts compared to other types of turbines. With advances in predictive maintenance and remote monitoring, steam turbines in floating power stations can be continuously monitored for performance metrics, allowing operators to identify potential problems before they cause a system failure. This ensures maximum uptime and operational efficiency, which is crucial in environments where downtime can lead to significant operational losses.
Moreover, floating power stations with steam turbines often incorporate advanced energy storage systems, such as batteries or thermal storage, which help to manage energy production during periods of low demand. These systems store excess energy generated by the turbines during off-peak periods, making it available for use when demand spikes. This feature allows the floating power station to operate at maximum capacity during high-demand periods, without wasting energy during lower-demand phases, further improving efficiency and reducing fuel consumption.
As floating power stations evolve, hybrid systems are becoming increasingly popular, where steam turbines are combined with other technologies, such as gas turbines or renewable energy sources like solar or wind power. This integration allows for even greater fuel flexibility and reduces reliance on fossil fuels, further reducing emissions and improving the sustainability of floating power stations. In offshore oil and gas operations, for example, the use of both steam turbines and natural gas or solar power can create a cleaner and more resilient energy system that can be more easily adapted to local fuel availability and environmental conditions.
In addition, steam turbines are an excellent choice for long-term energy projects where consistent, reliable power is required. The long lifespan and low maintenance requirements of steam turbines mean that floating power stations can continue to operate effectively for many years with minimal disruption. This is especially important in industries like oil and gas, where operational continuity is paramount for maximizing output and minimizing downtime.
Furthermore, with the push for sustainability and cleaner energy, floating power stations using steam turbines can help companies and governments achieve carbon neutrality goals. Through the use of biofuels, carbon capture and storage technologies, and other green energy solutions, steam turbines can play a pivotal role in reducing the carbon footprint of offshore energy production. In this regard, floating power stations can serve as a model for integrating renewable and sustainable practices into the energy industry, even in remote and offshore locations.
In conclusion, the use of steam turbines in floating power stations offers numerous advantages, including fuel flexibility, environmental sustainability, reliability, and cost-effectiveness. As the demand for energy continues to grow in remote and offshore regions, steam turbines will play an increasingly important role in providing efficient and flexible energy solutions. With their ability to operate on various fuels, recover waste heat, and meet both electrical and thermal energy needs, steam turbines are poised to remain a key technology in floating power generation for the foreseeable future.
In addition to the advantages already discussed, the ongoing development of advanced steam turbine technology further enhances their suitability for use in floating power stations. Innovations in turbine design, materials, and efficiency improvements continue to make steam turbines more adaptable to the specific challenges posed by floating power applications. These improvements include more efficient steam cycles, advanced alloys that can withstand higher temperatures and pressures, and automated control systems that allow for more precise operation. These technological advancements contribute to greater fuel efficiency and reduced emissions, further increasing the overall sustainability of floating power stations.
The integration of advanced control and automation systems in steam turbines has also revolutionized the operation of floating power stations. These systems enable the turbines to adjust to changing load demands automatically, ensuring optimal performance at all times. Operators can remotely monitor turbine performance, analyze data in real time, and make adjustments to optimize fuel consumption and emissions. In floating power stations, this automation is critical, as personnel may be limited, and human intervention might not always be feasible due to the station’s offshore location. This level of automation ensures that the turbines operate within optimal parameters, maximizing both energy output and fuel efficiency.
Another benefit of using steam turbines in floating power stations is their ability to handle load variations. Floating power stations are often deployed in regions where the energy demand can fluctuate significantly depending on time of day, weather conditions, or seasonal changes. Steam turbines offer excellent flexibility in responding to these variations, as their output can be adjusted according to the demand for electricity or process steam. This adaptability is crucial in environments where energy needs are not constant and can change rapidly, such as offshore oil platforms or areas with varying industrial activity.
The economic feasibility of floating power stations powered by steam turbines also becomes more attractive over time due to the declining cost of fuel and technology. As renewable energy sources like biomass, solar thermal, or geothermal energy become more affordable and efficient, they can be integrated into steam turbine systems, reducing operational costs and decreasing reliance on expensive imported fuels. Additionally, as technologies related to carbon capture and storage (CCS) improve, steam turbines in floating power stations can further mitigate their environmental impact. CCS technologies can capture and store the carbon emissions generated by the combustion of fossil fuels, making it possible for floating power stations to operate while adhering to strict emission regulations and contributing to broader decarbonization goals.
Hybrid energy systems combining steam turbines with other technologies, such as wind, solar, or battery storage, are gaining traction in floating power stations. These hybrid systems can provide a stable and reliable energy supply, even in the most challenging environmental conditions. For example, wind and solar power can supplement steam turbine operations during periods of high wind or sunlight, reducing the need for fossil fuels and lowering the overall carbon footprint. In turn, steam turbines can provide reliable, continuous power when wind or solar energy production is low, ensuring a consistent and uninterrupted energy supply.
Moreover, energy storage systems such as large-scale batteries or thermal energy storage can be used in conjunction with steam turbines to ensure the floating power station can meet energy demand during off-peak times. Excess energy generated during times of low demand can be stored and released during peak demand periods, ensuring that the power station operates efficiently at all times. This makes floating power stations even more reliable, reducing the risk of power shortages or blackouts in remote or offshore locations.
The growing importance of environmental and regulatory compliance further enhances the appeal of steam turbines in floating power stations. Stringent environmental regulations are being enforced globally, particularly in sensitive maritime and offshore environments, where emissions and pollution could have significant ecological impacts. Steam turbines, when equipped with advanced emission controls and the ability to operate on renewable fuels, can meet these increasingly stringent regulations while still providing a reliable source of energy. Additionally, their ability to run on biofuels or waste products helps mitigate the environmental impact associated with conventional fossil fuels.
As the demand for offshore power generation continues to rise, particularly in industries like oil and gas extraction, maritime shipping, and desalination, steam turbines are likely to play an even more prominent role in floating power stations. These industries require constant, reliable energy for their operations, and floating power stations with steam turbines offer an ideal solution for meeting those energy needs. With the added benefit of generating both electricity and steam, these stations can support diverse industrial processes, from powering production equipment to supplying steam for enhanced oil recovery, desalinating water, or driving industrial heating processes.
Finally, the long-term sustainability of floating power stations powered by steam turbines is further supported by the growing interest in decentralized energy systems. Floating power stations represent a shift away from traditional centralized power grids toward more localized, distributed energy solutions. This trend, combined with the flexibility, reliability, and efficiency of steam turbines, positions floating power stations as a key component in the future of energy production. These systems can reduce the pressure on land-based grids, ease the burden on energy infrastructure in remote locations, and help meet the energy demands of industries operating in isolated or offshore environments.
In conclusion, the use of steam turbines in floating power stations provides a highly efficient, flexible, and environmentally sustainable solution for generating power in remote, offshore, or challenging locations. Through innovations in turbine design, integration with renewable energy sources, and the ability to provide both electricity and process steam, steam turbines help optimize fuel use, reduce emissions, and improve energy security. As floating power stations continue to evolve, the role of steam turbines will remain central to delivering reliable, cost-effective energy to industries and regions that require it most.
In addition to the core advantages already outlined, the evolving role of steam turbines in floating power stations is further enhanced by their compatibility with emerging technologies and their potential to contribute to broader global energy goals. As the global energy landscape continues to shift towards renewable energy, floating power stations utilizing steam turbines can serve as key players in helping countries transition to more sustainable energy systems while also meeting the growing demands of industrial and maritime sectors.
One of the key aspects of future developments in floating power stations is the integration with renewable energy technologies. With the rise of offshore wind farms and solar power installations, steam turbines can be paired with these sources to create hybrid systems that balance the intermittent nature of renewable energy with the constant and reliable generation capabilities of steam turbines. For instance, when wind speeds are high, or sunlight is abundant, excess energy can be stored or used directly, reducing the need for fuel consumption in the steam turbine. When wind or solar energy production dips, the steam turbines can continue to generate energy, ensuring a stable power supply. This hybrid approach not only enhances the reliability and resilience of floating power stations but also minimizes the use of fossil fuels, making the energy produced more environmentally friendly.
As energy storage technologies improve, steam turbines can also benefit from better integration with large-scale storage systems. For example, advancements in battery storage or thermal energy storage systems could allow floating power stations to store energy produced during periods of low demand and use it during peak consumption times. This would eliminate the need for power stations to rely solely on constant fuel input for base-load generation, improving both the efficiency and economics of operation. When combined with energy storage, steam turbines will be able to operate at their most efficient levels, minimizing fuel consumption and lowering operational costs over time.
Furthermore, steam turbines’ inherent scalability is another critical factor driving their use in floating power stations. The modular nature of steam turbines allows for flexible system design, which can be scaled to meet the changing needs of different locations. For example, a floating power station designed to supply a small island or remote oil rig may require smaller turbines, while a larger system could be deployed to support larger, high-demand industrial complexes or offshore fields. This scalability means that floating power stations can be tailored to fit a wide variety of energy needs, providing a solution that can grow or shrink with the requirements of the site or operation. The flexibility in scaling up or down allows companies and governments to deploy the right-sized system for the task at hand, ensuring cost-effective operation while maintaining energy security.
Technological innovation in steam turbines is also driving improved performance and efficiency. Manufacturers are continuously refining turbine designs to enhance their operational efficiency, reliability, and longevity. The introduction of supercritical and ultra-supercritical steam turbines, which operate at higher pressures and temperatures than traditional turbines, leads to greater thermal efficiency. This results in more power being generated from the same amount of fuel, reducing the carbon footprint of the floating power station while lowering operational costs. Moreover, advancements in materials science are enabling the production of turbines that can withstand even higher temperatures and pressures, further boosting their performance and lifespan.
As global efforts to combat climate change intensify, floating power stations with steam turbines are becoming a viable option to help industries meet their emission reduction targets. Many governments around the world are enacting stricter environmental regulations and policies aimed at reducing greenhouse gas emissions. Floating power stations equipped with steam turbines that can run on biomass, waste, or synthetic fuels can significantly reduce the carbon intensity of offshore operations, helping companies comply with environmental standards. In regions where traditional fossil fuels are used, advanced steam turbine systems can be retrofitted with carbon capture technologies, which capture and store the carbon emissions generated by combustion processes. This makes floating power stations a more sustainable option, particularly in industries like offshore oil and gas extraction, where demand for energy is high, and reducing emissions is essential to meeting international climate goals.
The modular design of floating power stations also allows for greater adaptability in response to changing energy demands and shifting political, economic, and environmental landscapes. For instance, a floating power station could be relocated or reconfigured to meet new energy needs in different regions. As renewable energy infrastructure improves and new technology becomes more widely available, floating power stations can be adapted to incorporate new energy sources, keeping pace with evolving industry demands. This flexibility will be especially important as energy consumption patterns evolve with the growth of electric vehicles, increasing data centers, and the industrial shift towards cleaner manufacturing processes.
The cost-effectiveness of steam turbines in floating power stations is another important consideration as energy markets evolve. Although the initial capital investment required for steam turbine systems can be significant, their operational efficiency and long lifespan often lead to lower levelized cost of electricity (LCOE) over time. In addition, the ability of floating power stations to produce both electricity and process steam creates additional revenue opportunities for operators. For example, in remote regions or offshore platforms, steam can be used for various industrial purposes such as desalination, enhanced oil recovery, or cooling systems, contributing to the station’s overall economic viability.
The ability to create hybrid power generation systems, combining wind, solar, and steam turbines, allows for diverse revenue streams in floating power stations, ensuring that energy production can continue regardless of environmental conditions. Furthermore, the redundancy built into these hybrid systems ensures that even if one energy source is unavailable, the others can continue generating power, further enhancing operational resilience.
Economic incentives in many regions also make the use of steam turbines in floating power stations increasingly attractive. Governments are offering subsidies, tax incentives, and support for clean energy projects, which can offset the initial investment in these systems. Moreover, as energy markets continue to move toward more decentralized power generation, floating power stations are well-positioned to provide localized energy solutions that are both economically viable and environmentally sustainable.
In conclusion, the integration of steam turbines into floating power stations offers significant benefits in terms of reliability, efficiency, fuel flexibility, and environmental sustainability. As advancements in technology continue to improve turbine performance and integration with renewable energy sources, steam turbines will play an increasingly important role in meeting the global demand for offshore power generation. With their ability to provide both electricity and steam, coupled with their adaptability, scalability, and efficiency, steam turbines will remain a central component of the future of energy in floating power stations. Whether used in remote industrial applications, offshore oil platforms, or renewable energy integration, steam turbines offer a versatile and sustainable solution for powering our growing energy needs in challenging environments.
Steam Turbines for Carbon Capture Plants
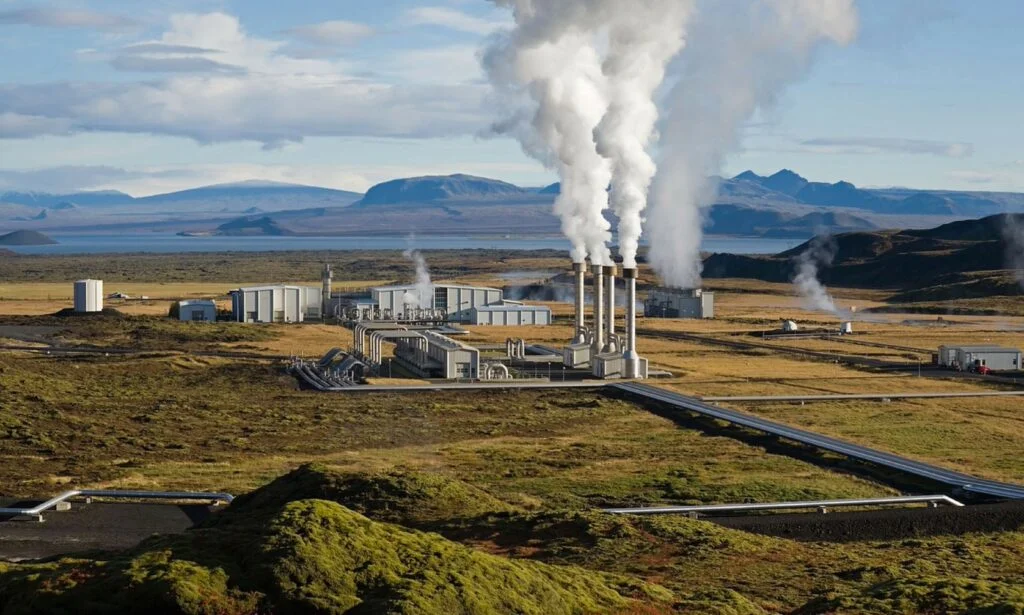
Steam turbines play a significant role in carbon capture plants, offering a reliable and efficient method for integrating power generation with carbon capture and storage (CCS) technologies. As the global focus shifts towards reducing carbon emissions to combat climate change, carbon capture plants have become crucial in helping industries meet emission reduction targets, particularly in sectors such as power generation, cement, and steel manufacturing. Steam turbines in these plants serve as the backbone of power generation while also supporting the energy-intensive processes required for carbon capture.
The primary role of steam turbines in carbon capture plants is in providing the necessary mechanical power and thermal energy to drive various components of the CCS process, including amine-based absorption systems, compression units, and pumping systems. These systems are typically powered by steam generated through fossil fuel combustion or biomass burning, and steam turbines are used to convert this thermal energy into electricity, which powers the plant’s operations.
Carbon capture plants require substantial amounts of energy, and steam turbines are well-suited for this task because of their ability to efficiently convert heat into mechanical power. In many cases, carbon capture processes are energy-intensive, particularly in post-combustion capture, where amines or other solvents are used to absorb CO2 from flue gases. This process requires a significant amount of thermal energy to regenerate the solvents, which is where steam turbines come into play. The steam turbines, powered by heat from burning fossil fuels or from waste heat recovery systems, provide the high-pressure steam necessary for the regeneration of the solvents.
Moreover, steam turbines can also integrate with combined heat and power (CHP) systems, where the heat generated from power production is used not only to drive the turbines but also to support the energy demands of the CCS process. This synergy significantly enhances overall plant efficiency, as both electricity and process heat are generated simultaneously, reducing the plant’s reliance on external energy sources and minimizing operating costs.
One of the key challenges in carbon capture is managing the energy penalty associated with the additional energy requirements for capturing and compressing CO2. The carbon capture process typically consumes between 20-30% more energy than conventional power generation, depending on the capture method and the type of fuel used. Steam turbines can help mitigate this energy penalty by improving overall plant efficiency through advanced turbine technologies such as regenerative cycles and supercritical steam cycles. These innovations improve the efficiency of steam turbines, reducing the amount of fuel required to generate the necessary steam for both power generation and carbon capture.
Another benefit of using steam turbines in carbon capture plants is their flexibility in terms of operational adjustments. Carbon capture plants often face fluctuations in CO2 emissions due to variations in industrial operations or external factors. Steam turbines can be adjusted to match these changes in energy demand, providing stable and reliable power generation. Their ability to adjust to different operational conditions helps ensure that the carbon capture plant remains efficient and cost-effective, even when emission levels vary.
The integration of carbon capture and storage with steam turbines is also supported by the use of waste heat recovery systems. In many cases, steam turbines can utilize waste heat from industrial processes, such as those found in cement or steel production, to generate the steam needed for the carbon capture process. This makes steam turbines particularly valuable for industrial carbon capture where energy recovery from waste heat can offset the additional energy demands of CCS, improving overall plant efficiency and reducing the need for additional fuel consumption.
In addition to supporting carbon capture in post-combustion systems, steam turbines also play a role in pre-combustion capture and oxy-fuel combustion technologies. In pre-combustion capture, steam turbines are used to provide power for the gasification process, which converts fossil fuels into hydrogen and carbon dioxide. The hydrogen is then burned for energy production, and the CO2 is captured before combustion occurs. Steam turbines provide the necessary power and heat to maintain the high temperatures required for gasification, contributing to the efficient capture of carbon.
Oxy-fuel combustion, where fossil fuels are burned in pure oxygen rather than air to produce a concentrated CO2 stream, also relies on steam turbines to drive the oxygen production systems and support the overall power generation process. Steam turbines are used in conjunction with cryogenic air separation units to produce the oxygen needed for combustion, and the steam generated during this process can also be used for carbon capture and compression.
In addition to energy generation, steam turbines in carbon capture plants can be configured to support carbon dioxide compression, which is necessary for transporting the captured CO2 to underground storage sites. Compressing CO2 requires significant amounts of energy, and steam turbines are often used to power the compression units that increase the pressure of the CO2 before it is injected into geological formations for long-term storage. The use of steam turbines for CO2 compression ensures that the capture plant operates at a high level of efficiency while maintaining the capacity to safely store the captured CO2.
As the economic and environmental pressures on industries to reduce carbon emissions continue to rise, carbon capture plants powered by steam turbines are likely to become increasingly important. The ability of steam turbines to increase efficiency, reduce fuel consumption, and support renewable energy integration makes them a vital component in the development of low-carbon energy systems. They are also highly adaptable, capable of operating on a range of fuels, including biomass, waste, and natural gas, providing greater fuel flexibility and supporting the transition to cleaner energy sources.
The growing importance of energy efficiency in carbon capture plants will continue to drive innovations in steam turbine technology. Supercritical steam cycles, advanced materials, and digital control systems are expected to further enhance the performance of steam turbines in CCS applications. These innovations will improve the overall efficiency of carbon capture plants, reduce their operational costs, and help industry leaders meet the ambitious carbon reduction goals set by governments worldwide.
In conclusion, steam turbines play an essential role in the functioning of carbon capture plants. Their ability to provide both mechanical power and thermal energy supports the complex energy requirements of carbon capture processes, while their efficiency and adaptability allow for the optimization of fuel use and the reduction of emissions. As global efforts to mitigate climate change intensify, steam turbines will continue to be a key technology in advancing carbon capture and storage, helping industries achieve their carbon reduction targets and contribute to a more sustainable energy future.
As the demand for carbon capture and storage (CCS) technologies grows, steam turbines will continue to be integral to optimizing plant efficiency, improving energy management, and reducing the overall carbon footprint of industrial processes. The increasing need to meet stringent climate goals and environmental regulations is pushing industries toward cleaner technologies, and steam turbines are ideally positioned to support this transition.
A crucial aspect of integrating steam turbines into CCS plants is their contribution to the overall energy balance. Carbon capture systems are typically energy-intensive and require both electricity and thermal energy. Steam turbines, especially when paired with combined cycle power plants, can provide a reliable and efficient method to meet these dual energy demands. By utilizing waste heat recovery systems and regenerative steam cycles, steam turbines improve the overall energy efficiency of the plant, reducing fuel consumption and operating costs. These energy-saving capabilities are essential in mitigating the energy penalty of carbon capture processes, which can consume a significant portion of the electricity generated by the plant.
The reliability of steam turbines is another critical factor in their continued use within carbon capture plants. CCS facilities often operate continuously under harsh conditions, and unplanned shutdowns or maintenance issues can lead to delays in carbon capture and storage processes. Steam turbines, known for their durability and long operational lifespans, offer the reliability needed for such demanding operations. Additionally, advancements in monitoring and predictive maintenance technologies are further enhancing the performance and uptime of steam turbines. These systems can provide early warning of potential issues, allowing for preventative maintenance and minimizing downtime, which is especially important in continuous processes like carbon capture.
An emerging trend in CCS technology is the growing focus on decarbonizing existing industrial operations. Many industries, such as cement, steel, and chemical production, are some of the largest emitters of carbon dioxide. Incorporating carbon capture systems into these plants can significantly reduce their emissions. Steam turbines, with their ability to operate on a wide variety of fuels, including biomass and syngas, can help retrofit existing power plants or industrial facilities to support carbon capture processes. These retrofitting opportunities allow industries to continue operations while meeting new environmental standards, without the need for completely new infrastructure. This is particularly valuable in industrial sectors where establishing new carbon-neutral facilities would be cost-prohibitive.
The growing potential for biomass and waste-to-energy systems to contribute to carbon neutrality is another area where steam turbines in CCS plants shine. Biomass, when used in combination with carbon capture technologies, offers a carbon-neutral energy source, making it an ideal fuel for reducing net emissions in power generation. Steam turbines can run on biomass and waste fuels with high efficiency, capturing the carbon produced from the combustion process and storing it underground. This integration of renewable and low-carbon fuels with CCS technologies is a key component in developing net-zero emissions energy systems and reducing dependence on fossil fuels.
Furthermore, advanced turbine technology is helping to overcome some of the limitations of traditional steam turbine systems in CCS applications. For example, supercritical and ultra-supercritical steam turbines are designed to operate at much higher temperatures and pressures than conventional turbines, allowing them to extract more energy from the steam cycle. This increased thermal efficiency helps reduce the energy consumption of the carbon capture process, improving the economic viability of CCS and reducing the additional cost burden of implementing these systems in power plants and industrial facilities.
The integration of digital technologies is also playing a significant role in enhancing the performance of steam turbines in CCS applications. Smart grids, predictive analytics, and advanced monitoring systems are being used to optimize the performance of both power generation and carbon capture systems. By constantly analyzing data from the turbine, capture systems, and plant operations, these digital tools can adjust operating parameters in real time to improve efficiency and minimize energy losses. Predictive maintenance algorithms can also help anticipate any potential failures or performance issues before they occur, reducing downtime and improving the overall operational lifespan of the turbines and the carbon capture systems they support.
Hydrogen production is another area where steam turbines can significantly contribute to carbon capture efforts. Hydrogen is increasingly being recognized as a clean fuel that can replace fossil fuels in various industrial processes, including steel production, power generation, and transportation. Steam methane reforming (SMR), a process used to produce hydrogen from natural gas, is energy-intensive and requires high-pressure steam. By integrating steam turbines into these processes, energy can be recovered and used efficiently to drive the reforming process, reducing both energy consumption and CO2 emissions.
Looking toward the future, carbon capture plants will need to become more cost-competitive to meet growing global demands and to align with the decarbonization goals set forth by international agreements like the Paris Agreement. As a result, continued advancements in steam turbine technology will be necessary to help reduce the overall cost per ton of CO2 captured. Efforts to improve turbine efficiency, fuel flexibility, and integration with other low-carbon technologies are expected to play a key role in making CCS technologies more accessible and economically feasible.
Collaboration between steam turbine manufacturers, energy companies, and government agencies will be crucial in scaling up carbon capture solutions. Government incentives, subsidies, and research funding will help to reduce initial investment costs and encourage the widespread adoption of CCS technology. This will, in turn, create more opportunities for industrial decarbonization and allow for the further development of steam turbines tailored specifically to the needs of carbon capture applications.
In conclusion, steam turbines are not only essential for the reliable and efficient operation of carbon capture plants, but they also offer a pathway for reducing the energy penalty of capturing CO2 and for optimizing the overall performance of these systems. With advancements in turbine efficiency, energy recovery, and integration with renewable energy sources, steam turbines are well-positioned to play a pivotal role in achieving net-zero emissions goals. By providing both power generation and the energy required for the carbon capture process, steam turbines support the transition to a more sustainable energy future, making them an indispensable component in the global effort to combat climate change.
As the global energy landscape continues to evolve with an increasing focus on decarbonization, the role of steam turbines in carbon capture plants is becoming even more critical. Continued innovations in turbine technology are expected to further drive down costs, increase efficiency, and enhance the overall sustainability of these systems. Looking ahead, there are several key trends and advancements that will shape the future of steam turbines in carbon capture applications.
One of the primary factors influencing the development of steam turbines in CCS plants is the shift towards greener and more sustainable fuels. With a growing emphasis on hydrogen, biomass, and waste-derived fuels in the global energy mix, steam turbines will increasingly be designed to operate on a wider variety of low-carbon and renewable fuels. Hydrogen, in particular, holds significant promise as a clean energy source. As green hydrogen production scales up, steam turbines will need to be adapted to handle the specific requirements of hydrogen combustion, which operates at higher temperatures and requires more precise control to ensure efficiency and emissions reduction.
The use of bioenergy with carbon capture and storage (BECCS) is another promising avenue for reducing the atmospheric CO2 concentration. BECCS combines the benefits of biomass combustion, which absorbs CO2 during growth, with carbon capture technologies. Steam turbines that operate in BECCS plants will play an important role by generating the necessary steam and mechanical energy to support the combustion and carbon capture processes. Since biomass combustion can vary in its energy content, turbines will need to be adaptable to different types of biomass fuels, ensuring reliable and efficient power generation for both energy production and CO2 capture.
Additionally, hybrid energy systems that combine steam turbines with renewable energy sources are becoming increasingly viable as part of a broader effort to integrate low-carbon technologies. In such systems, steam turbines could be powered by a combination of solar, wind, or geothermal energy, with excess renewable power being used to support the carbon capture process when demand for electricity is low. This integration helps balance the variability of renewable energy sources with the reliability of steam turbines, reducing the need for additional fossil fuel inputs.
Another significant trend is the rise of advanced steam cycle configurations, such as supercritical and ultra-supercritical steam cycles, in the context of carbon capture. These configurations allow steam turbines to operate at higher pressures and temperatures, resulting in increased thermal efficiency and lower fuel consumption. The improved efficiency reduces the amount of energy needed to capture and compress CO2, which is essential for mitigating the energy penalty associated with carbon capture processes. Furthermore, next-generation turbines will likely incorporate advanced materials designed to withstand the extreme conditions associated with supercritical steam cycles, ensuring longevity and reliability in CCS applications.
Digitalization will also play a crucial role in the future of steam turbines for carbon capture. The integration of Internet of Things (IoT) sensors, advanced analytics, and AI-powered optimization algorithms into turbine operations can significantly improve the performance and efficiency of both power generation and carbon capture systems. Real-time data from turbine sensors can monitor performance, detect issues before they occur, and enable predictive maintenance that minimizes unplanned downtime and reduces operational costs. By leveraging big data and machine learning, operators can optimize the entire CCS process, from power generation to CO2 compression, and improve overall energy efficiency.
Cost reduction remains one of the most significant challenges in carbon capture technologies. As steam turbines continue to evolve, they will need to become more cost-competitive to meet global emissions reduction goals. Efforts to standardize turbine designs and components, combined with advancements in manufacturing processes, can help lower initial capital costs for CCS projects. Additionally, government incentives, policy support, and carbon pricing mechanisms will be essential in driving investment into CCS technologies, making them economically viable for industries and power plants to adopt.
Collaboration between industry players, government agencies, and research institutions will also be crucial in advancing steam turbine technology for carbon capture applications. Public-private partnerships will provide the necessary funding for research and development to explore new turbine designs, better energy recovery systems, and more efficient integration with carbon capture processes. As the demand for carbon capture increases, there will be greater opportunities to implement large-scale CCS projects, especially in sectors where emissions are hard to eliminate, such as cement production and heavy industry.
In parallel, global supply chains for turbine manufacturing and associated equipment will need to become more resilient to meet the demands of large-scale CCS deployments. The need for highly specialized turbines that can operate under the unique conditions of carbon capture plants — such as fluctuating pressure, temperature, and fuel types — will drive the development of more robust supply chains and encourage the localization of production for greater efficiency.
Additionally, as carbon pricing mechanisms, such as carbon taxes and emissions trading systems, continue to be implemented globally, industries will be incentivized to adopt carbon capture technologies. The growing cost of carbon emissions will make CCS more attractive as a means of offsetting emissions and avoiding the financial penalties associated with exceeding carbon limits. Steam turbines, being the cornerstone of energy generation in many CCS plants, will help make these plants more economically viable by providing reliable and cost-effective power generation while supporting the carbon capture process.
Finally, public awareness and societal acceptance of carbon capture will play a significant role in shaping the future of steam turbines in these applications. As the understanding of the need for climate action increases, there will be greater support for technologies that contribute to reducing carbon emissions. By demonstrating the critical role that steam turbines play in driving the success of CCS projects and reducing the cost of decarbonization, industries and governments can build public support for the large-scale deployment of these technologies.
In conclusion, the future of steam turbines in carbon capture plants is promising, as ongoing technological advancements, efficiency improvements, and better integration with renewable energy sources continue to position steam turbines as a key technology in the battle against climate change. By continuing to innovate and adapt to the evolving energy landscape, steam turbines will play a vital role in enabling sustainable, cost-effective, and scalable carbon capture solutions that support the transition to a low-carbon global economy. With the right investments, policy frameworks, and technological developments, steam turbines will help shape a future where carbon capture and storage become a widespread tool for mitigating the effects of climate change.
Looking to the future, steam turbines for carbon capture plants will continue to evolve and adapt in response to changing market demands, technological advancements, and global efforts to address climate change. Some of the most exciting developments and opportunities lie in the areas of advanced materials, modularization, integration with renewable energy, and the global scaling of carbon capture technologies.
Advanced Materials for Enhanced Performance
The ongoing push to improve efficiency and durability in steam turbines, particularly in the context of carbon capture, is leading to innovations in advanced materials. Steam turbines need to operate at high temperatures and pressures, often in challenging environments that can cause wear and corrosion over time. To address these challenges, turbine manufacturers are developing superalloys and coatings that can withstand more extreme operating conditions, extending the lifespan of the turbine and improving its overall performance.
One key area of focus is the development of materials capable of handling the demands of supercritical and ultra-supercritical steam cycles, which operate at even higher pressures and temperatures. These materials are crucial for improving thermal efficiency in carbon capture plants, as turbines that operate in these cycles can extract more energy from the steam, reducing fuel consumption and emissions. Materials like ceramic matrix composites and high-performance nickel-based alloys are being explored for their potential to increase the operational limits of turbines while also reducing maintenance needs and downtime.
Modularization and Flexibility in Design
As the demand for carbon capture plants grows, the need for scalable and flexible turbine solutions will become even more pronounced. One approach to meeting this need is modularization, where turbines and other components are designed to be easily assembled and integrated into various plant configurations. Modular steam turbines allow for greater flexibility in carbon capture plant design, as different modules can be added or removed based on the specific energy requirements and carbon capture needs of the facility.
This modular approach can be particularly beneficial for retrofit projects, where existing power plants or industrial facilities are being upgraded to incorporate carbon capture technologies. In these cases, a modular turbine can be used to replace older, less efficient units without requiring a complete overhaul of the entire system. This not only reduces the capital cost of retrofitting but also shortens the implementation timeline, allowing companies to bring carbon capture capabilities online more quickly and start reducing their emissions.
Integration with Renewable Energy Systems
The increasing integration of renewable energy sources such as solar, wind, and geothermal energy into the global grid is creating new opportunities for steam turbines to contribute to low-carbon power generation. In many cases, carbon capture systems are best suited to operate alongside renewable energy technologies in hybrid power plants. Steam turbines in these settings can help provide consistent, reliable power while renewable sources like wind and solar fluctuate throughout the day.
In solar thermal power plants, for example, steam turbines are often used in combination with concentrated solar power (CSP) technologies. In these systems, mirrors concentrate sunlight to produce high-temperature steam, which is then used to drive steam turbines and generate electricity. If these plants are coupled with carbon capture technologies, steam turbines can support the additional energy needs for CO2 capture, while also benefiting from the low-carbon nature of solar energy.
Similarly, offshore wind farms and geothermal energy plants are increasingly being paired with steam turbines to create integrated systems that both produce clean energy and reduce carbon emissions. By leveraging the consistent and reliable output of these renewable sources, steam turbines can help stabilize grid operations while supporting the energy-intensive demands of carbon capture systems.
Global Scaling of Carbon Capture Technologies
As the world faces growing pressure to reduce emissions, the scaling up of carbon capture is imperative. One of the challenges in achieving large-scale deployment of carbon capture plants is the significant upfront investment required. Steam turbines will play a critical role in making these projects viable by driving cost reductions and enhancing the economic feasibility of large-scale carbon capture installations.
One area where steam turbines are expected to contribute is in the global scaling of CCS technologies, particularly in industries that are traditionally difficult to decarbonize, such as cement, steel, and chemical production. These industries emit large amounts of CO2 during production, and steam turbines can help provide the power and thermal energy needed to capture this CO2 efficiently. By integrating carbon capture systems with industrial processes and providing reliable energy for the capture and compression steps, steam turbines make it possible for industries to meet emissions regulations and achieve carbon neutrality goals.
Furthermore, as carbon storage infrastructure becomes more widespread, steam turbines will support the increased need for CO2 compression. The captured CO2 must be compressed to high pressures before being transported to storage sites, which requires significant amounts of energy. Steam turbines are well-suited to power CO2 compression units, ensuring that captured carbon can be safely and effectively stored underground for the long term.
Carbon Capture in Hard-to-Decarbonize Sectors
In the coming years, industries with challenging carbon footprints, such as refining, chemical production, and heavy industry, will likely be major areas of focus for carbon capture technologies. Steam turbines are already playing a key role in these sectors, providing power for energy-intensive processes and supporting post-combustion and pre-combustion capture techniques. As these sectors seek to meet emissions reduction targets, steam turbines will be essential in ensuring that the energy demands of carbon capture systems are met efficiently, without exacerbating the sector’s carbon footprint.
Additionally, some industries are beginning to explore the potential for direct air capture (DAC), which involves capturing CO2 directly from the atmosphere. Steam turbines are expected to play a role in powering DAC facilities, which require significant energy inputs to drive the chemical processes that remove CO2 from the air. By using steam turbines to power these systems, DAC plants will be able to operate more efficiently and contribute to larger-scale carbon removal strategies.
Public Policy and Market Drivers
The development and implementation of steam turbines for carbon capture will also depend heavily on public policy and market drivers. Increasing carbon pricing, government subsidies for clean energy technologies, and emission reduction mandates will all help to incentivize the adoption of CCS technologies and increase the demand for efficient, reliable steam turbines.
Governments around the world are expected to continue investing in research and development to lower the costs of carbon capture and incentivize its widespread adoption. Through policy frameworks, governments can stimulate private-sector investment in low-carbon technologies and help create a favorable business environment for the deployment of carbon capture plants and the necessary steam turbines.
Conclusion
The future of steam turbines in carbon capture applications is bright, with numerous opportunities for technological advancements, global scaling, and integration with renewable energy sources. By continuing to improve turbine efficiency, fuel flexibility, and adaptability to evolving energy systems, steam turbines will play an increasingly pivotal role in decarbonizing the global energy sector. As industries and governments around the world intensify efforts to mitigate climate change, steam turbines will continue to be an indispensable component in the development of sustainable and cost-effective carbon capture solutions, helping to achieve global emissions reduction goals and support the transition to a cleaner, more resilient energy future.
Steam turbines are an integral component in the production of ammonia, particularly within large-scale industrial operations. Ammonia is a key chemical used primarily in fertilizers, but it also plays an important role in other sectors such as chemical manufacturing, explosives, refrigeration, and energy storage. The production of ammonia is highly energy-intensive, with the Haber-Bosch process being the most common method for synthesizing ammonia. Steam turbines support this process by providing mechanical power and electricity, essential for the production cycle. Their role in power generation, heat recovery, and process integration is pivotal to the efficient, reliable, and cost-effective operation of ammonia plants.
Power Generation in Ammonia Production
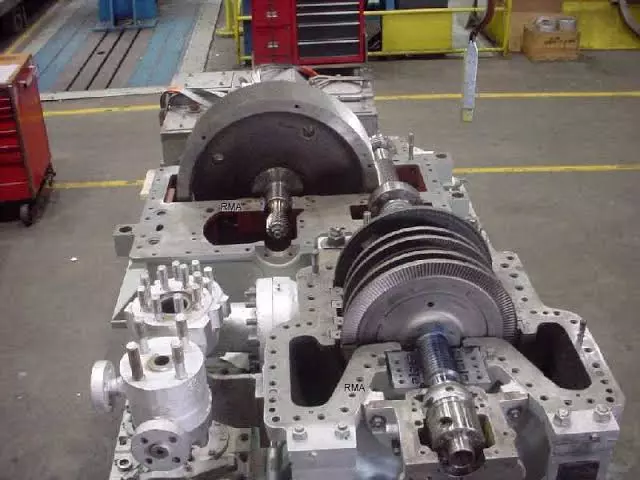
The Haber-Bosch process requires significant amounts of energy, primarily in the form of heat and electricity. In traditional ammonia plants, natural gas is often used as the primary feedstock for hydrogen production, which is a key reactant in ammonia synthesis. The natural gas is reformed to produce hydrogen, and the process itself requires high-pressure steam to drive the chemical reactions.
Steam turbines are typically used in these plants to generate power and provide thermal energy. In combined cycle plants, steam turbines operate alongside gas turbines, creating an efficient system for both power generation and heat recovery. The heat generated from the gas turbine exhaust can be recovered and used to produce steam, which is then expanded through the steam turbine to generate additional electricity. This combination allows for more efficient use of the natural gas feedstock, improving overall energy efficiency in the ammonia production process.
Energy Recovery and Efficiency
A critical component of modern ammonia plants is the energy recovery system. Steam turbines are often coupled with heat recovery steam generators (HRSGs) to capture waste heat from various parts of the ammonia production process. HRSGs are used to recover heat from the exhaust gases of gas turbines, reformers, and other high-temperature processes within the plant. The recovered heat is then converted into steam, which drives a steam turbine to generate electricity or provide mechanical power for the plant’s operations.
By recovering waste heat, steam turbines help improve the overall energy efficiency of the ammonia plant. This cogeneration capability reduces the need for external electricity sources, lowers fuel consumption, and ultimately helps to reduce the carbon footprint of ammonia production. The efficiency improvements are particularly important given the high energy costs associated with ammonia production.
Supporting High-Pressure Systems
Ammonia synthesis plants require high-pressure systems to drive the Haber-Bosch reaction, where hydrogen reacts with nitrogen to produce ammonia. The reaction occurs at high temperatures (around 450–500°C) and pressures (150–300 atmospheres), which are critical for achieving optimal reaction rates and yields.
Steam turbines play an essential role in maintaining these high-pressure environments by supplying the necessary mechanical energy to the compressors that pressurize the gases. The steam generated by the turbine can be used to power large compressor units, ensuring that the feedstock gases (hydrogen and nitrogen) are compressed to the appropriate pressures for the synthesis reaction. In addition, steam-driven mechanical drive systems are often used to power pumps, fans, and other essential equipment, making steam turbines a crucial part of the plant’s infrastructure.
Integration with Carbon Capture and Other Technologies
As sustainability and carbon reduction become more important in the industrial sector, the ammonia production industry is increasingly adopting carbon capture technologies to reduce CO2 emissions. Steam turbines will be integral to the integration of these carbon capture systems. The capture of carbon dioxide from ammonia plants typically requires significant amounts of energy to compress and transport the captured CO2. Steam turbines, especially when coupled with combined heat and power (CHP) or combined cycle systems, can help provide the necessary energy to drive the compression and liquefaction of CO2, making the entire carbon capture process more efficient.
Moreover, ammonia plants are also exploring hydrogen-based production routes as an alternative to natural gas reforming, such as green hydrogen produced by electrolysis. As green hydrogen production technologies mature, steam turbines may also be used to integrate hydrogen production and ammonia synthesis processes, supporting the transition toward a more sustainable, low-carbon ammonia production industry.
Reducing Operational Costs
As energy efficiency plays a major role in the cost-effectiveness of ammonia production, steam turbines help to reduce operational costs by improving plant efficiency and minimizing energy consumption. In many ammonia plants, steam turbines help offset the need for purchased electricity, allowing for greater cost control. The integration of steam turbines into combined heat and power (CHP) systems enables the plant to recover and use excess thermal energy to generate power, further reducing reliance on external energy sources and lowering operating expenses.
By improving plant efficiency and reducing energy consumption, steam turbines also help companies mitigate the impact of energy price fluctuations and ensure stable operational costs. This is particularly important in regions where energy prices are volatile or where ammonia production faces increased competition from alternative suppliers.
Fuel Flexibility and Sustainability
The ammonia production process is moving toward greater fuel flexibility and sustainability, and steam turbines are playing a key role in this shift. With the increasing adoption of renewable energy sources, ammonia plants are beginning to explore the use of biomass or waste-derived fuels as feedstocks for hydrogen production. Steam turbines can operate on a variety of fuels, including these low-carbon alternatives, ensuring the plant’s energy needs are met while reducing its carbon footprint.
Furthermore, hydrogen produced from renewable sources such as wind or solar power can be used in ammonia production, with steam turbines supporting the compression and conversion processes. In the future, steam turbines are expected to play an even more significant role in green ammonia production, where ammonia is synthesized using low-carbon hydrogen, offering a cleaner alternative to traditional ammonia production methods.
Reliability and Durability
Given the complex and energy-intensive nature of ammonia production, the reliability and durability of steam turbines are essential. Ammonia plants often operate around the clock, and any downtime can result in significant losses in production and revenue. Steam turbines are known for their long operational lifespans and their ability to withstand demanding conditions over extended periods.
Additionally, predictive maintenance technologies are improving the performance of steam turbines in ammonia production by allowing for early detection of wear or performance degradation. This enables plant operators to conduct timely maintenance, ensuring the turbines remain in optimal condition and preventing unexpected downtime.
Conclusion
Steam turbines play a critical role in ammonia production, supporting key processes such as power generation, energy recovery, and maintaining high-pressure systems essential for the Haber-Bosch process. As the industry moves toward greater energy efficiency, sustainability, and carbon reduction, steam turbines will continue to be integral to improving the performance, cost-effectiveness, and environmental footprint of ammonia plants. Their role in integrating with renewable energy sources, supporting carbon capture, and enhancing fuel flexibility will be increasingly important as the global ammonia industry adapts to the growing demand for cleaner, more sustainable production methods. With continued innovation and development, steam turbines will remain a cornerstone of the ammonia production process, helping the industry meet future energy and environmental challenges.
As the global demand for ammonia continues to grow, particularly for agricultural fertilizers, the need for more efficient and sustainable production methods becomes increasingly important. Steam turbines are playing a key role in achieving these objectives by providing the mechanical power and electricity necessary for ammonia synthesis and improving the overall energy efficiency of ammonia plants. The importance of steam turbines goes beyond just power generation; they are integral in heat recovery systems, fuel flexibility, and reducing the environmental impact of ammonia production.
In traditional ammonia plants, natural gas is used to produce hydrogen through steam methane reforming (SMR), which is then combined with nitrogen to create ammonia via the Haber-Bosch process. Steam turbines are essential in providing the power needed to drive the compressors, pumps, and other essential equipment in this energy-intensive process. Additionally, these turbines help recover energy from exhaust gases and process heat, converting it into useful steam that can be used to generate electricity or to drive mechanical equipment. This integration of power generation with heat recovery, known as cogeneration, improves the plant’s overall efficiency and helps reduce its reliance on external energy sources.
The ability of steam turbines to handle waste heat is especially important as ammonia plants often operate at high temperatures and pressures. The heat recovery steam generators (HRSGs) connected to steam turbines help capture heat from exhaust gases and convert it into steam for use in other parts of the plant. This recovered energy can be used for power generation or to maintain the high-temperature conditions required for ammonia synthesis, improving the energy efficiency of the entire plant. By recovering waste heat, steam turbines significantly reduce the amount of fuel required for the production process, which translates to lower operating costs and a reduced carbon footprint.
In recent years, there has been a growing focus on sustainability within the ammonia production industry. Efforts are being made to reduce the environmental impact of ammonia plants by incorporating carbon capture and storage (CCS) technologies. As these systems become more prevalent, steam turbines will play an important role in providing the energy needed to compress and transport the captured CO2. They will also be vital in supporting the integration of green hydrogen production methods, which use renewable energy sources like wind and solar to produce hydrogen via electrolysis. As ammonia production increasingly moves toward green ammonia, where low-carbon hydrogen replaces fossil fuels, steam turbines will help facilitate these advancements by providing the necessary mechanical power to the process.
The development of advanced turbine technologies will also drive improvements in the ammonia production process. New materials, such as high-performance alloys, will enable turbines to operate at even higher temperatures and pressures, increasing their efficiency and durability. Additionally, innovations in digitalization, including predictive maintenance and real-time monitoring, will help optimize turbine performance and minimize downtime, ensuring reliable operation in the demanding environment of ammonia production plants.
Fuel flexibility is another key area where steam turbines contribute to more sustainable ammonia production. As the world shifts towards biomass and waste-derived fuels, steam turbines are being adapted to operate on a broader range of fuels, which helps reduce dependence on natural gas and other fossil fuels. This adaptability allows ammonia plants to become more resilient to fluctuations in fuel prices and supports the broader transition to a circular economy, where waste products are used as resources in industrial processes.
Given the energy-intensive nature of ammonia production, the ability to reduce operational costs is crucial for maintaining competitiveness in the global market. Steam turbines help achieve this by improving the overall efficiency of the plant and reducing the amount of energy purchased from external sources. Through combined heat and power (CHP) systems, ammonia plants can maximize their energy recovery and reduce the need for additional fuel inputs, making the entire production process more cost-effective. Furthermore, by enabling ammonia plants to produce their own power, steam turbines help mitigate the impact of energy price volatility.
As the ammonia industry evolves, steam turbines will continue to be a critical technology in helping plants meet both economic and environmental goals. Their role in improving energy efficiency, reducing carbon emissions, and enabling the adoption of renewable and sustainable energy sources will be crucial as the industry works to meet the challenges of the future. Additionally, as ammonia plays an increasingly important role in green energy systems, such as hydrogen storage and carbon capture, steam turbines will be vital in supporting these applications and ensuring that ammonia production can continue to contribute to a cleaner, more sustainable world. The ongoing innovation in steam turbine design, efficiency, and operational flexibility ensures that they will remain an indispensable part of the ammonia production process for years to come.
The role of steam turbines in ammonia production will continue to evolve as the industry faces increasing pressures to reduce its environmental footprint while maintaining high levels of production efficiency. As global regulations become stricter and the demand for low-carbon ammonia grows, technological advancements in steam turbine design and integration will be essential in achieving these goals. One of the main driving forces will be the increasing integration of renewable energy sources, which will change how ammonia plants operate, and steam turbines will be key in making this integration seamless and efficient.
Integration with renewable energy is a major shift in the ammonia industry. Traditional ammonia production has heavily relied on natural gas or other fossil fuels. However, the rising push for sustainable energy has led many ammonia producers to explore ways to incorporate renewable sources such as wind, solar, and hydropower into their operations. Steam turbines are well-positioned to play a significant role in these changes, as they can be used to convert energy from various renewable sources into steam, which is essential for the ammonia synthesis process.
For example, concentrated solar power (CSP) can be used to generate high-temperature steam for ammonia plants, which can then be expanded through steam turbines to produce electricity or mechanical power. Additionally, offshore wind and solar farms are increasingly being used in hybrid setups with ammonia plants. In such setups, steam turbines are employed to ensure a steady supply of power when renewable energy sources fluctuate, maintaining plant operations without relying on fossil fuels. This hybrid approach allows ammonia plants to reduce their carbon emissions while enhancing energy resilience.
In parallel with renewable energy integration, ammonia production processes are also exploring electrification. Electrification involves replacing traditional combustion-based systems with electricity-driven processes, such as using green hydrogen produced from renewable electricity via electrolysis. Steam turbines can complement these innovations by integrating them into electrical power systems. For instance, electricity generated from renewable sources can be converted into mechanical power or steam through steam turbines, which can then drive compressors and other mechanical systems in the ammonia plant.
As the world focuses more on carbon capture, steam turbines will continue to provide the energy necessary for post-combustion CO2 capture technologies. These technologies require significant power to separate and compress the CO2, and steam turbines can be integrated into the carbon capture systems to provide that power. For ammonia plants pursuing carbon capture, utilization, and storage (CCUS), steam turbines are essential to ensure that the captured CO2 is compressed to the necessary pressures for transport and storage. Additionally, integrating steam turbines with CCUS can help improve the overall energy efficiency of the plant and reduce the additional energy consumption associated with CO2 capture.
Another area of improvement for ammonia plants is the pursuit of circular economy principles. Waste-to-energy technologies, where organic waste is used as a feedstock for hydrogen production, are becoming increasingly viable. Steam turbines are being adapted to run on biomass, waste oils, and other renewable fuels that contribute to more sustainable ammonia production. This shift is critical in reducing the carbon footprint of ammonia plants and ensuring that energy and raw materials are used efficiently throughout the production process. With steam turbines able to handle a wide range of fuels, ammonia plants can diversify their energy sources and minimize their environmental impact.
Technological advances in turbine design will also play a significant role in improving ammonia production. Newer turbine models designed with advanced materials and higher thermal efficiencies will be critical in enhancing the performance of ammonia plants. For example, turbines that operate at higher temperatures and pressures can increase the energy conversion efficiency, allowing plants to extract more energy from the same amount of fuel or renewable energy. This means less fuel is needed, lowering the operational costs and reducing emissions. In addition, new digital technologies, such as machine learning and predictive analytics, will allow operators to optimize turbine performance in real-time, reducing maintenance needs and improving the overall reliability of ammonia production systems.
Looking toward the future, modular ammonia plants could become more widespread. These smaller, more flexible systems can be built to fit specific regional needs and easily scaled up or down as demand fluctuates. Steam turbines can be designed to fit into these modular plants, providing the necessary power in a compact form. This flexibility is especially useful in remote or offshore locations where traditional large-scale ammonia production is not feasible.
As global demand for green ammonia grows, particularly for use in carbon-free shipping, energy storage, and sustainable fertilizers, the ammonia production industry will continue to push for cleaner and more efficient processes. Steam turbines will be central to the continued evolution of ammonia production, supporting both green hydrogen integration and carbon capture technologies. In particular, the role of ammonia in the energy transition is expected to increase, with ammonia serving as both an energy carrier and a low-carbon alternative in various applications.
In conclusion, the role of steam turbines in ammonia production will only grow as the industry continues to innovate and adapt to changing market demands and environmental concerns. Their ability to integrate with renewable energy, support carbon capture, and improve plant efficiency makes them an essential part of the ammonia production process. As the industry moves toward greener, more sustainable practices, steam turbines will continue to be crucial in meeting these goals, providing the mechanical power and electricity necessary to ensure that ammonia production can keep pace with the future needs of the global economy.
As ammonia production continues to evolve with an increasing focus on sustainability, steam turbines will remain central to addressing some of the industry’s most pressing challenges. One of the key drivers for change in ammonia production is the global push toward reducing greenhouse gas emissions. Ammonia, traditionally produced through fossil fuel-based processes, is energy-intensive and accounts for a significant portion of global industrial CO2 emissions. With a rising demand for green ammonia, which can be produced with low-carbon hydrogen or from renewable sources, steam turbines will play a vital role in the energy systems that enable this shift.
The transition to green ammonia will require substantial adjustments in the energy systems of ammonia plants. One of the critical components of this transition is the use of electrolyzers to produce hydrogen through water electrolysis powered by renewable electricity. Steam turbines can assist in this transition by providing backup or auxiliary power when renewable energy sources are intermittent. These turbines can also integrate hydrogen production with ammonia synthesis, especially in hybrid systems where renewable electricity can directly supply the electrolyzers while steam turbines handle the energy needs for compression, heat recovery, and power generation in the plant.
Further, the ammonia industry is expected to witness greater decarbonization through the adoption of carbon-neutral energy sources. For instance, biomass and biogas are renewable feedstocks that can replace fossil fuels in ammonia production. Steam turbines will be adapted to run efficiently on these alternative fuels, enabling ammonia plants to reduce their reliance on natural gas or coal. The ability to switch fuels without compromising turbine efficiency will be particularly important as ammonia production plants aim to meet stringent carbon reduction targets set by governments and regulatory bodies.
As circular economy principles gain traction in the chemical industry, steam turbines can play an integral role in promoting waste valorization and resource efficiency. Waste heat recovery and energy integration systems, which are at the core of many modern ammonia plants, will increasingly rely on steam turbines to optimize the energy balance of the entire process. By harnessing waste heat from various plant operations, steam turbines can convert excess thermal energy into usable electricity or mechanical power, reducing the overall energy demand of the plant. This kind of system is becoming more common in integrated refinery-ammonia complexes, where the steam turbines are used to recover heat from multiple industrial processes within the facility.
Another crucial aspect of modern ammonia production is the efficient handling of water resources. Steam turbines, especially when combined with desalination plants, can play a significant role in reducing the plant’s water consumption, which is a critical concern in regions facing water scarcity. Ammonia production requires substantial amounts of water for the production of steam, and efficient water management systems, supported by steam turbines, will be essential in minimizing waste and ensuring that plants operate sustainably. In regions where freshwater resources are limited, reverse osmosis desalination systems powered by steam turbines can help meet the plant’s water requirements.
Furthermore, hydrogen storage and ammonia as an energy carrier are gaining attention as possible solutions to the challenges posed by intermittent renewable energy production. Ammonia can serve as an efficient medium for storing hydrogen, which can later be used in fuel cells, combustion engines, or even as an energy source for other sectors such as transportation. In these applications, ammonia plants need to produce ammonia with a much lower carbon footprint than traditional processes. Steam turbines will be instrumental in ensuring that these plants operate at peak efficiency, enabling ammonia to act as an effective energy storage medium while reducing its carbon emissions.
In terms of the ammonia plant’s operation and energy demands, digitalization and smart technologies will also play a significant role in improving the performance of steam turbines. Sensors and advanced control systems can help optimize turbine operation by continuously monitoring parameters like temperature, pressure, and rotational speed. This real-time data can be used to predict maintenance needs, troubleshoot performance issues, and reduce downtime. Moreover, advances in artificial intelligence (AI) and machine learning are enabling predictive maintenance strategies, which can significantly reduce the costs associated with unplanned repairs and improve the lifespan of steam turbines.
The integration of steam turbines into modular ammonia production plants is another potential development. These smaller-scale plants, which can be deployed in different regions based on local demand, will benefit from the flexibility and scalability of steam turbine systems. These modular plants can be designed to optimize energy recovery and power generation based on local energy sources and requirements. Steam turbines, which can be scaled down for smaller plants, will enable efficient energy use even in these more compact systems. In addition, the ability to operate modular plants independently, or as part of a wider network, will allow ammonia production to be more resilient to supply chain disruptions, making it easier to respond to shifting demand.
Moreover, as ammonia plays an increasingly important role in hydrogen-based energy systems, steam turbines will be crucial in both hydrogen production and storage. As ammonia is used as a hydrogen carrier, steam turbines will help generate the power needed for processes such as ammonia cracking (breaking ammonia into hydrogen and nitrogen), which is vital for releasing hydrogen from ammonia to fuel vehicles, power plants, and industrial systems. Steam turbines will be key to driving the necessary processes in both ammonia synthesis and hydrogen extraction, making the ammonia-hydrogen cycle a more efficient and sustainable solution.
Ultimately, the ammonia industry’s transition toward more sustainable practices will require a concerted effort to optimize every aspect of the production process. Steam turbines, with their ability to handle diverse energy sources, improve energy efficiency, and support sustainable technologies like carbon capture, hydrogen storage, and renewable energy integration, will continue to be indispensable. Their role in integrated energy systems will be vital as ammonia production moves from traditional fossil-fuel-intensive methods to more environmentally friendly, energy-efficient technologies. The ongoing advancements in steam turbine design, efficiency, and operational flexibility will ensure that they remain a crucial part of the global effort to decarbonize industrial sectors and enable a sustainable future for ammonia production.
Steam Turbines in Metallurgical Plants
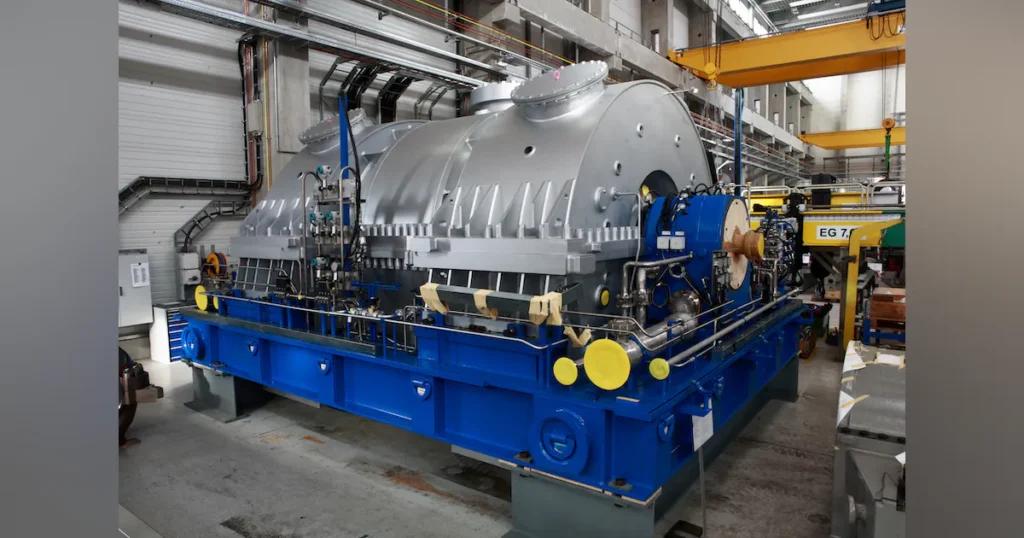
Steam turbines have long been a critical technology in metallurgical plants, playing a vital role in improving energy efficiency and supporting the high-energy demands of various processes. Metallurgical operations, particularly in industries such as steel production, aluminum refining, and copper processing, are known for their significant energy consumption, making energy optimization a priority. In these plants, steam turbines help convert waste heat and excess thermal energy into useful power, reducing the need for external energy sources and improving the overall cost-effectiveness of operations. As the metallurgical industry increasingly focuses on sustainability and carbon reduction, steam turbines will remain integral to achieving these goals while maintaining operational efficiency.
Metallurgical plants are typically large, energy-intensive facilities that rely on high-temperature processes such as smelting, refining, and casting. These processes produce significant amounts of waste heat, which can be captured and converted into useful energy using steam turbines. By integrating cogeneration systems (also known as combined heat and power systems, or CHP), steam turbines enable metallurgical plants to recover this excess heat, convert it into steam, and then use that steam to generate electricity or mechanical power for other parts of the plant. This makes the entire operation more energy-efficient, as it reduces the need for additional fuel consumption to meet power demands.
In the context of steel production, steam turbines are especially important. The steelmaking process, which involves blast furnaces or electric arc furnaces, requires enormous amounts of energy to melt metal ores, heat metals to high temperatures, and maintain the necessary conditions for the conversion of raw materials into finished products. Steel mills often generate excess heat through these processes, which can be captured using heat recovery steam generators (HRSGs) and directed toward steam turbines for power generation. This reduces the need for external energy supplies and helps minimize the carbon emissions associated with steel production, which is one of the most energy-intensive industries worldwide.
The integration of steam turbines into metallurgical plants allows for more sustainable operations by enhancing energy recovery, reducing fuel consumption, and lowering overall emissions. In many cases, plants are converting traditional energy sources like coal and natural gas into a more efficient form by generating power locally with steam turbines. This shift helps mitigate reliance on fossil fuels and improves the plant’s overall carbon footprint. In regions with abundant renewable energy, metallurgical plants are also exploring hybrid energy systems, where steam turbines support the integration of renewable power sources such as solar, wind, and hydropower into the plant’s energy mix.
In addition to energy recovery, steam turbines are also important in reducing operational costs and enhancing plant reliability. Metallurgical plants are often located in remote areas where access to the power grid may be limited or unreliable. By generating their own electricity using steam turbines, these plants can ensure a stable and continuous power supply, independent of external energy sources. This can be particularly valuable in critical operations, such as smelting and refining, where interruptions in power supply can result in significant production losses and delays.
Another advantage of using steam turbines in metallurgical plants is their ability to support waste-to-energy initiatives. Biomass, waste oils, and scrap materials are increasingly being used as alternative fuel sources in these plants. Steam turbines can be adapted to run on these renewable fuels, reducing the environmental impact of metallurgical operations and decreasing dependence on traditional fossil fuels. This flexibility in fuel choice supports the circular economy and helps make metallurgical plants more resilient to fuel price fluctuations.
As the metallurgical industry faces mounting pressure to reduce its environmental impact, the implementation of carbon capture and storage (CCS) technologies is becoming increasingly important. Steam turbines will continue to play a critical role in supporting the energy requirements of CCS systems by providing the necessary power for compression and transportation of captured CO2. Additionally, combined heat and power (CHP) systems in metallurgical plants can be used to improve the energy efficiency of carbon capture systems, making the process more cost-effective and sustainable.
The role of steam turbines in aluminum production is similarly significant. In the production of aluminum, the Hall-Héroult process requires the use of large amounts of electricity to extract aluminum from its ore, bauxite. Steam turbines can support this process by providing the power needed for various stages, including smelting, casting, and refining. In aluminum smelters, the use of steam turbines helps recover heat from the process and convert it into usable energy, improving the overall efficiency of the plant and lowering operational costs.
In terms of technology advancements, steam turbines continue to evolve to meet the demands of the metallurgical industry. Newer turbine models are designed with higher efficiency and reduced maintenance needs, ensuring that metallurgical plants can operate more reliably and at a lower cost. Innovations in turbine design, such as advanced materials that can withstand higher temperatures and pressures, are helping steam turbines operate more efficiently and increase their lifespan, even in the harsh conditions of metallurgical processes. Additionally, the adoption of digital technologies such as predictive maintenance, real-time monitoring, and artificial intelligence allows plant operators to optimize steam turbine performance, reduce downtime, and enhance overall system efficiency.
Looking to the future, the integration of smart grids and energy storage systems in metallurgical plants will further enhance the role of steam turbines in providing reliable, sustainable energy. With the rise of electric arc furnaces and other energy-efficient technologies, metallurgical plants will continue to innovate in their energy systems, and steam turbines will play a crucial role in these advancements. By enabling more flexible energy use, improving power generation from renewable sources, and reducing emissions, steam turbines will help make the metallurgical industry more sustainable, efficient, and cost-effective in the years to come.
In conclusion, steam turbines will remain an essential component in the energy systems of metallurgical plants, enabling more efficient and sustainable operations. By harnessing waste heat, supporting renewable energy integration, and providing reliable power generation, steam turbines help metallurgical plants reduce fuel consumption, lower emissions, and minimize operating costs. With advancements in turbine technology and growing emphasis on sustainability, steam turbines will continue to play a key role in transforming the metallurgical industry into a more energy-efficient and environmentally responsible sector.
As the metallurgical industry moves towards more sustainable practices, steam turbines will increasingly serve as an integral technology for achieving higher levels of energy efficiency, reduced emissions, and cost-effectiveness. In the pursuit of decarbonization goals, the pressure on metallurgical plants to adopt cleaner and more sustainable energy solutions is intensifying. Steam turbines, with their ability to operate efficiently across a variety of energy sources, are key to enabling this shift.
One of the main ways steam turbines contribute to decarbonization in metallurgical plants is through their ability to integrate with alternative energy sources, particularly renewable power generation. As many countries and industries work to reduce their carbon footprints, there is a growing push toward greener energy sources. Solar, wind, and hydroelectric power are increasingly being considered as viable options for supplementing or replacing fossil fuels in energy-intensive industries like metallurgy. Steam turbines can help in this transition by providing flexibility in meeting fluctuating power demands. For example, in plants where renewable energy may not be consistently available, steam turbines can complement renewable power by converting heat generated from biomass or other waste fuels into usable energy.
In particular, waste-to-energy systems are gaining attention as part of efforts to optimize energy use and reduce the environmental impact of metallurgical processes. Steam turbines can be powered by waste materials, including scrap metals, biomass, and industrial byproducts, providing a source of renewable energy while reducing the amount of waste that would otherwise be sent to landfills. This waste-to-energy integration allows metallurgical plants to produce cleaner, more sustainable energy without relying on traditional fossil fuels. The flexibility to switch between various fuel types, while maintaining high efficiency, is a significant advantage of using steam turbines in modern metallurgical operations.
In addition to their energy-generating capabilities, steam turbines are integral to improving overall plant energy efficiency. Through heat recovery and cogeneration systems, steam turbines can make use of the waste heat generated by industrial processes, which would otherwise be lost. Metallurgical processes such as blast furnace operations, arc furnaces, and casting generate substantial amounts of thermal energy, much of which is traditionally wasted. By installing heat recovery systems, metallurgical plants can capture this waste heat and use it to generate additional power through steam turbines, reducing the need to purchase energy from external sources and making the operation more energy-efficient overall.
Moreover, with the rise of electrification in industrial processes, steam turbines can contribute to integrating electricity into metallurgical operations. Electrification involves replacing traditional combustion-based systems with electrically driven processes, which can include electric arc furnaces (EAF) for steelmaking or electrochemical processes for aluminum refining. The electricity required for these operations can be produced more efficiently by steam turbines, which can convert thermal energy into mechanical power or electricity, providing a more sustainable and flexible approach to energy generation.
Another important application for steam turbines in the metallurgical industry is their role in carbon capture and storage (CCS). Steel and other metals are responsible for a significant portion of global industrial CO2 emissions, and as countries implement stricter environmental regulations, the implementation of CCS systems is becoming essential. Steam turbines can be used to generate the energy needed to operate CO2 capture systems, which involve the separation, compression, and transportation of CO2 from industrial processes. By incorporating steam turbines into these systems, metallurgical plants can ensure that carbon capture processes run efficiently, allowing them to meet emission reduction targets while maintaining production levels.
The continued innovation in turbine design also plays a significant role in improving the performance and efficiency of steam turbines in metallurgical plants. Advanced turbine technologies such as high-temperature turbines, low-pressure turbines, and hybrid designs enable plants to handle the high demands of modern industrial processes while improving energy efficiency. These new turbine models are designed to extract more energy from the same amount of fuel, allowing plants to operate at optimal efficiency, even in challenging environments. Additionally, the materials science advancements that allow turbines to operate at higher temperatures and pressures will enable metallurgical plants to use a broader range of fuels, enhancing operational flexibility and reducing energy consumption.
As digitalization continues to transform industries, metallurgical plants are increasingly adopting smart technologies for better monitoring and optimization. In steam turbine systems, real-time performance monitoring using sensors and predictive analytics helps ensure the turbines are operating at peak efficiency. Advanced diagnostic tools and artificial intelligence (AI) can predict maintenance needs, detect anomalies, and optimize turbine performance, reducing downtime and extending the lifespan of critical equipment. By integrating these digital tools, metallurgical plants can make data-driven decisions that improve the efficiency of their steam turbines and, by extension, their overall energy systems.
Modularization is another trend that could transform the way metallurgical plants use steam turbines. With the rise of modular plants that can be deployed in regions with varying energy availability and demand, steam turbines can be adapted to smaller, more flexible setups. These smaller, self-contained systems can provide reliable energy for specific metallurgical operations without requiring large, centralized power plants. As the demand for localized and decentralized energy solutions grows, steam turbines will continue to be a key component in the energy systems of these modular plants, offering scalability and adaptability.
In conclusion, steam turbines will remain central to the future of metallurgical plants, particularly as the industry strives for greater energy efficiency, carbon reduction, and sustainability. Their ability to integrate with renewable energy, waste-to-energy systems, carbon capture technologies, and electrification initiatives makes them indispensable in meeting the growing demands of the metallurgical industry. Advances in steam turbine design, combined with the rise of digital technologies and circular economy principles, will ensure that these turbines continue to drive innovation and efficiency in the sector. Ultimately, steam turbines will help metallurgical plants operate more sustainably, reduce their carbon emissions, and remain competitive in an increasingly eco-conscious global marketplace.
As the metallurgical industry continues to evolve, globalization and increasing competition in the marketplace are driving companies to adopt more efficient, cost-effective solutions. The increasing demand for high-quality metals, coupled with the need for rapid production, means that metallurgical plants are under constant pressure to optimize their processes and minimize energy waste. Steam turbines provide a crucial technological advantage in helping plants meet these pressures by improving power generation, reducing operating costs, and enhancing plant reliability.
Integration with Combined Heat and Power (CHP) Systems
One of the most notable benefits of steam turbines in metallurgical plants is their ability to integrate seamlessly into Combined Heat and Power (CHP) systems, which are widely used in energy-intensive industries like steelmaking. In these systems, waste heat from industrial processes is captured and converted into usable energy through steam turbines. This significantly improves the overall thermal efficiency of the plant by turning what would otherwise be waste heat into valuable electricity or mechanical power.
For instance, steel mills and foundries that rely on high-temperature processes such as rolling mills, annealing furnaces, and casting can capture excess heat from these operations and use steam turbines to generate power for other parts of the plant. In some cases, the steam produced by turbines can also be used for heating processes that require steam, such as hot-dip galvanizing, rolling, or pickling. This results in a more sustainable energy system and significantly reduces the need for purchasing external electricity, leading to cost savings and a reduced carbon footprint.
Furthermore, the flexibility of steam turbines allows them to support different plant configurations. Whether it’s a centralized energy generation system or a distributed generation system, steam turbines can adapt to various layouts to maximize energy efficiency. In plants that operate in multiple shifts or across large facilities, this flexibility ensures that plants can meet their energy needs even during periods of peak demand without relying solely on external grid power.
Reducing Operating Costs through Fuel Efficiency
In many metallurgical plants, fuel costs represent a substantial portion of overall operational expenses. As fuel prices fluctuate, the cost of production becomes harder to predict, making energy efficiency even more critical. Steam turbines help mitigate this issue by improving fuel efficiency and reducing the amount of fuel needed to meet power demands.
By recovering waste heat from furnaces, kilns, and smelting operations, steam turbines can reduce the need for additional fuel input. This waste heat is captured and converted into electricity or mechanical power, which directly offsets the cost of purchased fuel. In some advanced systems, the recovered energy is also used to drive compressors or support other mechanical processes within the plant, further reducing the need for external energy sources.
For metallurgical plants using coal or natural gas as their primary fuel, the use of steam turbines can improve energy conversion efficiency, allowing the plant to get more out of each unit of fuel. The combined effect of waste heat recovery and fuel efficiency improvements makes steam turbines a valuable investment, particularly in industries with high fuel consumption and volatile fuel prices.
Enhancing Plant Reliability and Reducing Downtime
Reliability is a critical factor in metallurgical plants, where even minor equipment failures can lead to significant production losses and financial consequences. Steam turbines, known for their reliable operation, contribute to plant uptime and consistent power generation.
The introduction of predictive maintenance and digital monitoring systems has further enhanced the reliability of steam turbines in metallurgical plants. By monitoring key performance indicators such as turbine speed, vibration, pressure, and temperature, operators can detect potential issues before they lead to failures. This proactive approach to maintenance reduces the likelihood of unplanned downtime, lowers maintenance costs, and extends the operational life of the turbines.
In energy-intensive operations like steel or aluminum production, where the production cycle can be disrupted by even short periods of downtime, the role of steam turbines in maintaining uninterrupted power supply is vital. The ability to stabilize the power grid, particularly in plants that have variable power requirements, helps smooth production processes and avoid costly stoppages.
Meeting Regulatory Compliance and Environmental Standards
The metallurgical industry is facing increasing pressure from governments and environmental regulators to reduce its environmental impact, particularly in terms of greenhouse gas (GHG) emissions. As one of the largest industrial contributors to global CO2 emissions, the adoption of cleaner technologies is essential for maintaining regulatory compliance and addressing climate change concerns.
Steam turbines help metallurgical plants meet emissions reduction targets by enabling the use of carbon-neutral fuels, such as biomass and biofuels. Many modern steam turbines can operate on renewable fuels, providing metallurgical plants with the flexibility to switch between fossil fuels and renewable sources depending on availability and cost. This flexibility helps plants adapt to changing fuel markets while also minimizing their environmental impact.
In addition, waste heat recovery systems powered by steam turbines allow metallurgical plants to significantly reduce their carbon emissions. By using energy more efficiently, plants reduce the amount of fuel they burn and, consequently, their GHG emissions. This makes steam turbines a key part of the strategy to meet carbon neutrality and sustainable development goals.
Advancements in Turbine Efficiency and Technology
As the metallurgical industry moves toward more sustainable and energy-efficient practices, advancements in turbine technology are playing a crucial role in maximizing the potential of steam turbines. New turbine designs, including high-efficiency turbines, compact turbines, and multi-stage turbines, are improving performance and providing better energy conversion efficiency.
Materials innovations are also contributing to the longevity and efficiency of modern steam turbines. Advanced high-temperature alloys allow turbines to withstand more extreme operational conditions, leading to increased durability and improved heat recovery. As the metallurgical industry demands more from its energy systems, these innovations will be essential in maintaining the reliability and performance of steam turbines in challenging environments.
Digital Integration and Smart Turbines
The integration of digital technologies into steam turbine operations is another exciting development in the metallurgical industry. Smart turbines equipped with Internet of Things (IoT) sensors and advanced control systems allow operators to monitor turbine performance in real-time. These digital tools provide insights into efficiency, wear and tear, and maintenance schedules, helping to optimize turbine operation and improve decision-making.
For example, machine learning algorithms can predict potential failures or inefficiencies by analyzing historical data from turbines and other plant equipment. This predictive capability enables more accurate scheduling of maintenance, reducing downtime and optimizing plant performance.
As the metallurgical industry adopts these digital advancements, the ability to remotely monitor and control steam turbine systems will enhance operational efficiency, reduce the need for on-site inspections, and help improve the accuracy of energy consumption forecasts.
Conclusion
In summary, steam turbines will continue to play a central role in improving energy efficiency, reducing emissions, and increasing cost-effectiveness in the metallurgical industry. As the sector transitions to more sustainable and energy-efficient practices, steam turbines will be key enablers of these changes, from waste heat recovery and fuel flexibility to carbon capture and renewable energy integration. With advancements in turbine technology and the adoption of digital monitoring and predictive maintenance, steam turbines will support the growing demand for sustainable practices in metallurgy, contributing to a more energy-efficient, reliable, and environmentally friendly industry. Through cogeneration systems, alternative fuel options, and improved operational reliability, steam turbines will remain a critical component in the drive toward greener and more cost-effective metallurgical processes.
As the metallurgical industry continues to face increasing demands for sustainability and energy efficiency, the role of steam turbines in supporting these goals will only expand. With advances in technology, the capabilities of steam turbines are constantly improving, enabling metallurgical plants to operate with higher efficiency, greater environmental responsibility, and enhanced competitiveness. Here are several ways steam turbines will continue to play a critical role in the evolution of metallurgical operations:
Advanced Turbine Designs for Higher Efficiency
The ongoing development of advanced steam turbine designs will continue to drive improvements in efficiency across the metallurgical sector. These new turbine models are being optimized to operate at higher temperatures, pressures, and rotational speeds, leading to better energy extraction from the same amount of fuel. High-efficiency turbines designed with advanced aerodynamic blade profiles and low-friction materials will maximize the energy conversion efficiency of steam turbines, further enhancing the overall efficiency of metallurgical plants.
In steel production, for example, where massive amounts of heat are generated during iron smelting and steelmaking processes, high-efficiency turbines can play a key role in recovering waste heat and converting it into usable power. This recovered energy can be used to power various stages of steel production or be sold back to the grid, reducing the plant’s operational costs and carbon footprint.
Moreover, the modular turbine designs that allow for smaller, more compact systems will also play an increasingly important role. These turbines offer greater flexibility, making them ideal for smaller plants or those operating in regions with varying power demand. This adaptability to different plant sizes and configurations ensures that steam turbines will remain relevant for a variety of metallurgical operations, from large integrated mills to smaller, specialized production facilities.
Energy Storage Integration
The integration of energy storage systems is expected to become more prevalent in metallurgical plants as the need for reliable, uninterrupted power grows. Steam turbines, in combination with energy storage solutions such as batteries or pumped hydro storage, will help ensure a steady power supply even when external power sources, such as renewables, are intermittent. By storing energy produced during periods of excess generation, steam turbines can ensure that metallurgical plants continue to operate smoothly during periods of high demand or low renewable generation.
Energy storage systems can be especially important for plants that rely on variable power sources like wind or solar. In cases where these sources cannot meet demand, steam turbines can supplement the grid by releasing stored energy, maintaining optimal plant operations without relying solely on external power grids. As energy storage technologies improve and become more cost-effective, this integration will play a pivotal role in enhancing the resilience and energy independence of metallurgical plants.
Supporting Industry 4.0 and Smart Manufacturing
The ongoing transformation of industrial processes through Industry 4.0 technologies will also influence the way steam turbines are integrated into metallurgical plants. Smart manufacturing, powered by artificial intelligence (AI), machine learning, the Internet of Things (IoT), and advanced data analytics, will enhance the monitoring, control, and optimization of steam turbines. By integrating sensor networks and predictive maintenance systems, plants can ensure that turbines operate at peak performance, reducing inefficiencies, unplanned downtime, and energy wastage.
For example, advanced sensors can provide real-time data on turbine vibration, temperature, pressure, and rotational speed, which can be fed into predictive maintenance software to forecast potential failures before they occur. This allows plant operators to schedule maintenance during non-peak times, reducing production downtime and avoiding expensive emergency repairs. Additionally, smart sensors can track turbine efficiency and make automatic adjustments to optimize energy consumption in response to changes in plant operations.
The ability to use AI and machine learning algorithms to analyze large amounts of operational data and make real-time adjustments will help metallurgical plants achieve new levels of operational efficiency and energy optimization. By using these technologies to continuously monitor turbine performance, metallurgical plants will be better positioned to improve efficiency and reduce their environmental impact.
Environmental Benefits and Emissions Reduction
The pressure on industries to meet stricter environmental regulations and carbon reduction targets will continue to drive the demand for more efficient energy solutions in metallurgical plants. Steam turbines, through their high efficiency and waste heat recovery capabilities, will be a critical part of reducing greenhouse gas emissions and lowering operational costs.
Carbon capture and storage (CCS) systems, which are essential for industries like metallurgy that produce high levels of CO2, can be supported by steam turbines. These systems require substantial amounts of energy to compress, transport, and store captured CO2, and steam turbines can provide the necessary power for these energy-intensive tasks. By utilizing excess heat from metallurgical processes to fuel these systems, steam turbines can make the entire carbon capture process more cost-effective and efficient, supporting the plant’s overall decarbonization efforts.
Moreover, as biofuels and renewable energy sources become more prominent in the metallurgical industry, steam turbines will continue to evolve to accommodate these new fuels. With the ability to run on a range of fuels, including biomass and waste-derived fuels, steam turbines offer the flexibility needed to transition to more sustainable energy sources, helping plants achieve carbon neutrality while maintaining reliable power generation capabilities.
Increasing Use of Waste-to-Energy Technologies
The move toward a circular economy is expected to accelerate in the coming years, with metallurgical plants increasingly looking for ways to reduce waste and recover value from byproducts. Steam turbines will be a key technology in facilitating this transition by enabling metallurgical plants to convert waste materials into usable energy through waste-to-energy systems.
For example, the recycling of scrap metal or the use of waste gases from metallurgical processes can be harnessed to generate steam, which is then used to power steam turbines. Additionally, other waste materials such as biomass, plastics, and industrial byproducts can be used to generate energy, providing a sustainable fuel source for metallurgical operations. This waste-to-energy integration reduces both the plant’s dependence on fossil fuels and its environmental impact by recycling materials and reducing landfill waste.
Cost Reduction and Operational Optimization
Finally, the role of steam turbines in metallurgical plants will remain critical in driving cost reductions through greater operational optimization. As energy costs account for a significant portion of total operating expenses in the metallurgical sector, improving energy efficiency is one of the most effective ways to reduce costs and increase profitability. Steam turbines, with their ability to recover and convert waste heat, provide a significant opportunity to cut down on external energy purchases and reduce overall fuel consumption.
By integrating heat recovery and cogeneration systems into metallurgical operations, steam turbines contribute to a more cost-effective energy strategy that minimizes waste, improves energy utilization, and enhances the financial performance of the plant. Additionally, advanced turbine monitoring and control technologies will continue to help metallurgical plants make real-time adjustments to optimize their energy usage, reducing costs while maximizing throughput and productivity.
Conclusion
As the metallurgical industry adapts to the demands of sustainability, energy efficiency, and regulatory compliance, steam turbines will play an increasingly central role. Through waste heat recovery, fuel flexibility, and advanced turbine technology, they will continue to support the industry’s transition toward greener, more efficient operations. Furthermore, the ongoing integration of smart technologies, renewable energy sources, and energy storage systems will allow steam turbines to provide greater flexibility and resilience to metallurgical plants, enabling them to meet the evolving challenges of the global marketplace.
By improving energy efficiency, reducing emissions, and enhancing cost-effectiveness, steam turbines will help metallurgical plants remain competitive while also contributing to the broader goals of sustainable development and carbon reduction. As these plants continue to embrace technological advancements and energy innovation, steam turbines will remain an essential tool for ensuring their future success in a rapidly changing industrial landscape.
Portable steam turbines are an increasingly valuable solution for industries and applications that require flexible, mobile, and reliable power generation. These turbines offer significant advantages in scenarios where traditional, fixed power plants are impractical or too costly. Portable steam turbines are designed to be modular and easily transportable, providing the flexibility to be relocated as needed for a wide range of applications, from temporary power generation at construction sites to emergency backup power during grid outages.
Key Features of Portable Steam Turbines
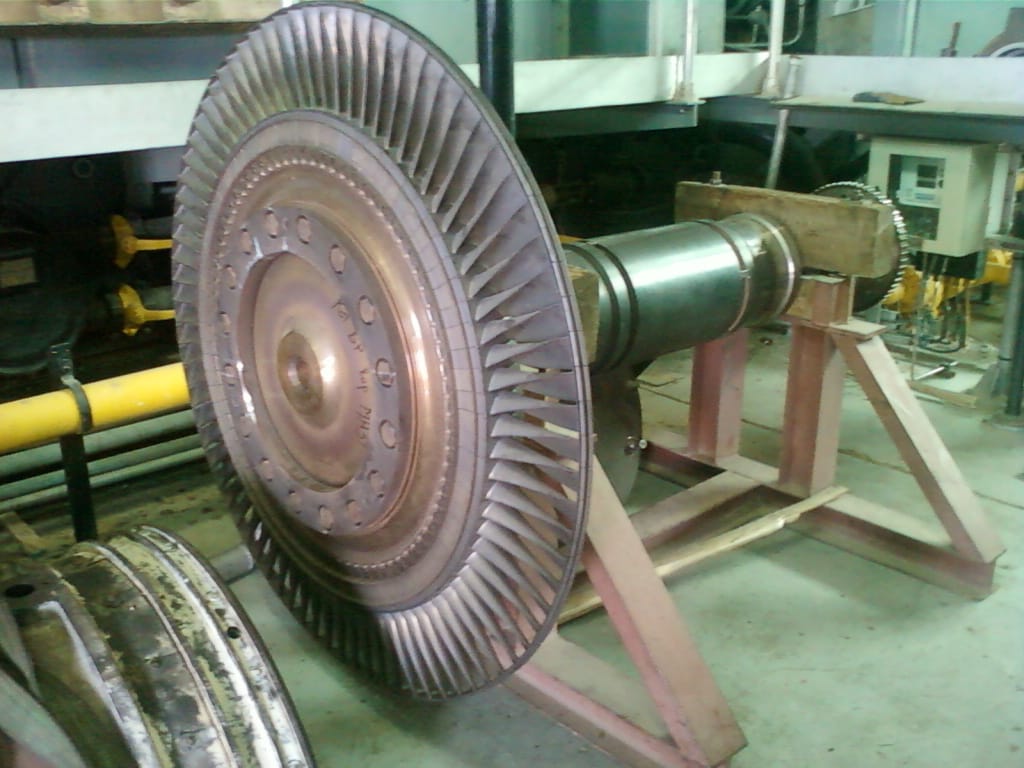
Portable steam turbines are designed to be compact and easy to transport, typically mounted on mobile platforms such as trailer-based units or self-contained containers. These turbines are capable of producing significant amounts of power and can operate using a variety of fuels, including natural gas, diesel, biomass, or even waste heat. Their modular design allows them to be scaled to meet specific power demands, making them highly adaptable for different operational environments.
Additionally, portable turbines are often designed with plug-and-play capabilities, meaning they can be quickly set up and integrated into existing systems without extensive infrastructure changes. This is particularly important in emergency situations, where rapid deployment is essential to restore power.
Applications of Portable Steam Turbines
- Emergency Power Supply: One of the most important applications for portable steam turbines is in providing backup power during emergencies or power outages. In situations where a grid failure or natural disaster has disrupted the local power supply, portable steam turbines can be deployed quickly to restore essential services to critical infrastructure, such as hospitals, water treatment plants, and communication networks. Their quick mobilization and self-contained units allow them to be operational in a short time frame.
- Temporary Power for Construction and Industrial Sites: Construction sites, mining operations, and other industrial applications often require a reliable power source for machinery and equipment. In such cases, portable steam turbines provide a temporary solution until a more permanent power generation system is established. The ability to use waste heat from on-site industrial processes to fuel these turbines makes them especially valuable in industrial environments, where power demand can fluctuate based on the project’s stage.
- Field Operations in Remote Areas: Portable steam turbines are particularly useful in remote or off-grid locations where establishing a permanent power plant is either too expensive or not feasible. In oil and gas exploration, mining, or military field operations, these turbines can be used to generate power for lighting, heating, electrical equipment, and communication systems. Their ability to run on flexible fuels such as diesel or biomass makes them versatile and adaptable to different environmental conditions.
- Disaster Recovery and Humanitarian Aid: In regions affected by natural disasters, where infrastructure has been damaged and electricity is unavailable, portable steam turbines can provide critical power for relief efforts. These turbines can power water pumps, food storage units, and mobile medical units, ensuring that humanitarian aid operations can continue even in the absence of a stable grid power supply. Their ability to operate in difficult conditions and be relocated quickly makes them ideal for these applications.
- Event Power Generation: For large-scale outdoor events like festivals, exhibitions, and temporary installations, portable steam turbines offer a reliable power source that can be easily scaled to meet fluctuating energy demands. Their mobility ensures that power generation is not tied to the local grid, making them an excellent choice for temporary venues and outdoor activities.
Advantages of Portable Steam Turbines
- Flexibility and Mobility: One of the primary benefits of portable steam turbines is their flexibility. These turbines can be quickly moved from one location to another, making them ideal for operations that require temporary or mobile power generation. Whether for emergency response, construction, or remote industrial operations, their ability to be redeployed as needed gives companies the ability to adapt to changing conditions.
- Ease of Installation and Operation: Portable steam turbines are often designed with user-friendly controls and minimal setup requirements, making them easy to install and operate. In emergency or temporary situations, minimizing the time required for installation is critical, and portable turbines are engineered to meet this need. In many cases, a turbine can be operational within a few hours of being delivered to the site.
- Reduced Capital Investment: The modular nature of portable steam turbines means that companies can avoid the capital costs associated with building a permanent power plant. This is particularly beneficial for temporary projects or remote operations where a permanent infrastructure investment may not be justified. Additionally, the ability to scale up or down depending on the power needs helps optimize costs.
- Energy Efficiency and Waste Heat Recovery: Portable steam turbines, like their stationary counterparts, can be integrated into waste heat recovery systems, allowing them to utilize heat from industrial processes or engines to generate power. This makes them an energy-efficient solution for industries that produce excess heat, such as in mining, oil and gas operations, and chemical plants. By recovering waste heat and converting it into electricity, portable steam turbines help reduce fuel consumption and improve overall system efficiency.
- Fuel Flexibility: Portable steam turbines are designed to run on a variety of fuels, offering significant flexibility in terms of fuel availability and cost. Whether powered by natural gas, diesel, biomass, or waste heat, these turbines can adapt to the local fuel supply, making them suitable for a wide range of geographic locations and operational scenarios.
Challenges and Considerations
Despite their many advantages, portable steam turbines do come with certain challenges that need to be considered before their deployment.
- Fuel Availability: The performance of portable steam turbines depends on a reliable supply of fuel. In remote areas or emergency situations, ensuring access to the right type of fuel can be a challenge. Some portable turbines can operate on multiple fuels, but logistical challenges related to fuel delivery and storage can complicate their use in certain environments.
- Maintenance and Durability: While portable steam turbines are designed to be durable and reliable, their mobility means that they are subject to wear and tear from frequent transportation and exposure to harsh environments. Regular maintenance and inspection are crucial to ensure that these turbines continue to operate efficiently and reliably over time. Depending on the operating conditions, the turbines may require more frequent servicing compared to stationary systems.
- Space Requirements: Even though portable steam turbines are designed to be compact, they still require a certain amount of space for installation. For very constrained sites, such as those in urban environments or locations with limited access, the space needed for setup and operation may be a limitation.
- Noise and Emissions: Portable steam turbines, especially those powered by diesel or other fossil fuels, may produce noise and emissions. In applications such as field hospitals or residential areas, managing noise levels and adhering to environmental regulations can present challenges. The environmental impact of emissions should be considered when choosing a fuel source, especially in areas with stringent regulatory standards.
Future Trends in Portable Steam Turbines
As the demand for sustainable and flexible power generation continues to rise, portable steam turbines are expected to evolve. Technological advances in fuel flexibility, efficiency, and digital monitoring are likely to further improve the performance and versatility of these systems. Additionally, the growing focus on renewable energy sources may lead to innovations in turbine designs that can better integrate with solar, wind, or biomass power generation, making portable steam turbines even more adaptable to changing energy needs.
Moreover, as industries continue to prioritize energy independence, cost reduction, and emission reductions, portable steam turbines are expected to play a growing role in meeting these objectives. Their ability to provide mobile, scalable, and reliable power generation makes them an essential part of the future energy landscape, particularly for industries and applications that require temporary or backup power solutions.
Conclusion
Portable steam turbines offer a unique solution for power generation in industries and scenarios where traditional power plants are impractical or too costly. Their flexibility, ease of installation, and fuel adaptability make them a versatile and reliable option for providing power in emergency situations, remote locations, construction sites, and temporary installations. While challenges such as fuel availability and maintenance must be addressed, the ongoing advancement of portable steam turbines is expected to make them even more efficient, cost-effective, and environmentally friendly. As industries continue to prioritize sustainability and energy independence, portable steam turbines will remain an essential tool for meeting these goals, offering a reliable, adaptable, and efficient power generation solution wherever it is needed.
Portable steam turbines continue to gain importance across a variety of industries, offering a practical solution for those in need of temporary or mobile power generation. Their flexibility, combined with the capacity to utilize multiple fuels, makes them ideal for dynamic environments where the energy demand fluctuates or where the infrastructure for permanent power plants is not available. In cases of emergency power supply, such as during grid failures or natural disasters, these turbines provide a quick-response power source, capable of restoring electricity to critical services without requiring a long installation period.
Moreover, in construction or mining operations, where reliable power is needed but a permanent facility would be too costly or impractical, portable steam turbines provide a valuable alternative. The turbine’s modular design means it can be easily transported to different locations, making it a versatile option for industrial sites with temporary or seasonal energy needs. These turbines can run on a range of fuels, making them adaptable to different operational environments. Whether powered by natural gas, diesel, or even waste heat, they can help industries reduce reliance on external energy sources and lower operational costs.
Their use in remote and off-grid locations is another key advantage, especially for oil and gas exploration or military applications. In these scenarios, access to a stable power grid is not always available, so portable steam turbines step in to provide energy for equipment, communication systems, and lighting. Their ability to run on a variety of fuels ensures they can be deployed effectively in many different environments, from rural and remote areas to disaster-stricken zones, offering a reliable power solution when the grid infrastructure is down or nonexistent.
The future of portable steam turbines is closely tied to technological advancements that enhance their performance and fuel efficiency. With the development of cleaner fuels, including biomass and renewable energy sources, portable steam turbines can support industries aiming to reduce their carbon footprints and improve their sustainability. As the world continues to move towards energy independence and cost-effective energy solutions, the portability and adaptability of steam turbines will continue to be in high demand. The integration of advanced monitoring systems, smart controls, and predictive maintenance will further extend the operational life and efficiency of these turbines, making them an even more attractive option for industries seeking reliable, on-demand power.
Portable steam turbines, with their modular design and ability to generate power rapidly and efficiently, will remain a cornerstone in providing temporary power solutions, supporting industries from construction and mining to emergency services and military operations. Their ability to reduce energy costs, improve operational flexibility, and adapt to a wide range of fuel sources will make them a key player in meeting the energy needs of a rapidly evolving global market.
As industries continue to evolve, the demand for portable steam turbines is expected to grow, driven by their unique capabilities to provide energy security and reliability in diverse applications. Their role in disaster recovery and humanitarian aid efforts is particularly important, as these turbines can provide quick-response power to critical infrastructure like hospitals, water treatment facilities, and communication centers in the aftermath of natural disasters. In areas where traditional grid power is unavailable or has been compromised, portable turbines offer an essential lifeline, helping to restore vital services and support relief operations until the infrastructure is rebuilt or power grids are restored.
In the military sector, where power is needed in the field for communication, equipment, and temporary bases, portable steam turbines are invaluable. Their mobility allows them to be deployed wherever needed, from combat zones to remote military bases, ensuring that troops have access to reliable energy. Furthermore, their ability to run on a variety of fuels makes them adaptable to situations where fuel availability may vary, offering flexibility in supply logistics. This mobility and adaptability provide a crucial advantage for forces operating in locations with limited or no access to established power grids.
Moreover, portable steam turbines are playing an increasing role in event power generation. For large-scale outdoor events such as festivals, exhibitions, or concerts, the ability to provide reliable, scalable power without relying on local grid infrastructure is a major advantage. These turbines can support everything from lighting and sound systems to catering facilities and exhibit spaces, ensuring that the event runs smoothly. The flexibility of portable turbines allows event organizers to scale power production according to the event’s specific needs, reducing the risk of power shortages or disruptions.
As energy efficiency continues to be a global priority, portable steam turbines are also evolving to integrate with renewable energy sources. Hybrid solutions combining steam turbines with solar or wind energy systems are becoming more popular, allowing industries and temporary installations to maximize energy generation while reducing reliance on fossil fuels. By integrating waste heat recovery systems and improving turbine design for higher efficiency, portable steam turbines are becoming an even more cost-effective and environmentally friendly solution for temporary power generation.
The future of portable steam turbines lies in their continued ability to meet diverse energy needs with increased efficiency, environmental sustainability, and flexibility. As technology advances, portable steam turbines will become even more fuel-efficient, compact, and powerful, allowing them to meet the growing demand for reliable, on-the-go power generation. With the ongoing emphasis on reducing carbon emissions, sustainable power generation, and energy resilience, portable steam turbines will remain a critical solution in addressing the energy challenges faced by industries and communities worldwide.
As the demand for sustainable energy solutions grows, portable steam turbines are evolving to play an even larger role in decarbonization efforts, especially when integrated with renewable energy sources and waste heat recovery systems. Their flexibility in fuel choice allows industries to reduce reliance on traditional fossil fuels, and the growing focus on circular economies means that portable steam turbines can contribute to sustainability goals by using waste energy and biofuels. In particular, their ability to convert waste heat from industrial processes into power is a powerful asset for industries looking to optimize their energy usage and minimize environmental impact. This ability to harness low-grade heat that would otherwise be wasted and turn it into useful electricity offers a significant advantage in sectors like chemicals, metallurgy, and manufacturing, where waste heat is abundant.
The industrial Internet of Things (IIoT) and smart technology are also transforming portable steam turbines. The integration of sensors, predictive maintenance algorithms, and real-time performance data into these turbines allows for more efficient operation and reduced downtime. By using data-driven insights, companies can monitor the performance of the turbines and anticipate issues before they arise, thereby reducing the need for manual inspections and enhancing the overall lifespan of the equipment. Remote monitoring capabilities also enable operators to control turbines from a distance, allowing for more streamlined management, particularly in remote locations.
Additionally, the adoption of hybrid energy systems involving portable steam turbines is growing in popularity. These systems combine conventional fuel sources with renewable energy sources like solar, wind, or biomass to reduce the carbon footprint of power generation. The flexibility of portable steam turbines in such hybrid setups is a key driver in industries aiming to balance cost, reliability, and sustainability. In regions where the power grid is unreliable or absent, such hybrid solutions are essential for providing continuous and reliable power while minimizing environmental impact.
The role of portable steam turbines is also expanding in the off-grid energy market. As remote regions, islands, and isolated communities seek to become less dependent on external energy sources, portable turbines are increasingly used as standalone solutions or in combination with renewable technologies to provide reliable, locally sourced power. Their ability to operate in these environments with limited infrastructure makes them a critical tool in promoting energy independence and energy access to underserved populations.
Looking ahead, portable steam turbines are likely to continue to evolve as technologies such as advanced materials and micro-turbines become more prevalent. These innovations could lead to even more compact, efficient, and cost-effective turbines, enabling industries to generate power in increasingly flexible and distributed ways. This could contribute to the decentralization of energy production, further empowering communities and industries to produce their own clean, reliable energy.
In conclusion, portable steam turbines are poised to remain at the forefront of temporary power generation solutions due to their mobility, fuel adaptability, efficiency, and growing role in sustainability. Their ability to operate in diverse settings—from remote industrial operations to disaster recovery efforts—ensures that they will continue to be a vital tool for meeting both short-term and long-term energy needs. As industries, governments, and communities continue to prioritize reliability, resilience, and environmental responsibility, portable steam turbines will be integral in driving a sustainable energy future.
Customized Industrial Turbines
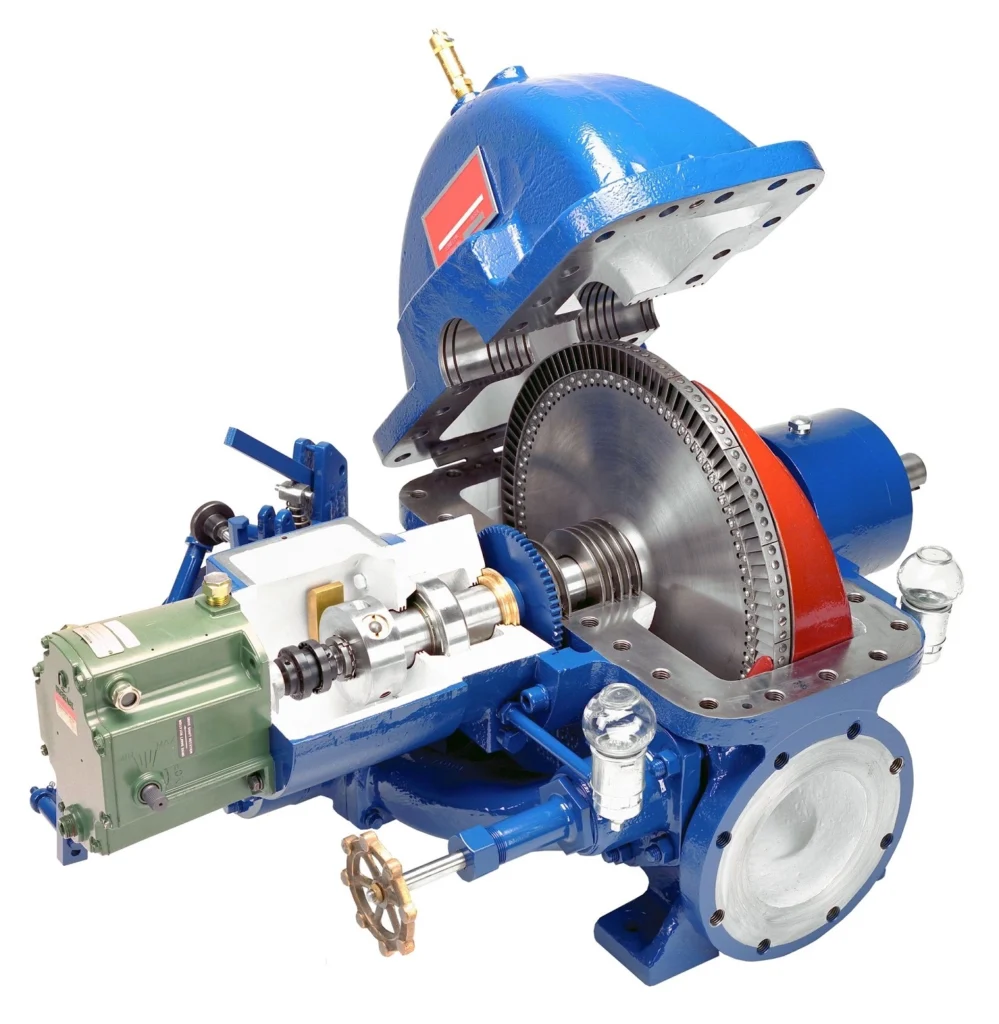
Customized industrial turbines are increasingly being utilized across various industries to meet specific power generation needs, optimize operational efficiency, and support sustainability goals. These turbines are designed and engineered to fit the unique requirements of individual businesses, offering tailored solutions for applications ranging from power generation to process steam and mechanical drive. By customizing the turbine’s design, materials, and operational parameters, industries can achieve greater performance, reduce operational costs, and improve reliability, ultimately enhancing their productivity.
The key to customized industrial turbines is their ability to be adapted to the specific conditions and demands of each application. Unlike off-the-shelf turbines, which are designed to meet general industry standards, customized turbines are engineered to handle unique operational conditions, including specific fuel types, operating pressures, temperatures, and duty cycles. For example, in industries where the process requires handling high temperatures or extreme pressures, customized turbines are built to withstand these challenging environments while maintaining high efficiency. These turbines can also be configured to run on a range of fuels, such as natural gas, biomass, or even waste heat, depending on the available resources at the site.
In the context of power generation, customized industrial turbines can be designed to suit particular grid requirements or operate in off-grid locations. For instance, industries with remote operations like mining, oil and gas, or forestry often face unique challenges related to power supply. Customized turbines can be designed to integrate with existing power systems and infrastructure, ensuring reliable energy production in these isolated environments. The ability to tailor the turbine to the site’s specific power needs, as well as adapt to the local fuel supply, significantly improves efficiency and reduces the need for additional infrastructure investment.
Another area where customized industrial turbines excel is in process industries such as chemical, petrochemical, and metallurgical plants. These industries often have highly specialized energy requirements due to the need for constant steam supply, mechanical power for equipment, and precise thermal management. Customized turbines designed for these industries are built to deliver the required output while ensuring efficiency and reliability. In petrochemical plants, for example, turbines are customized to handle the specific pressures and temperature variations involved in refining processes. Similarly, in metallurgical plants, turbines can be designed to integrate with electric arc furnaces or blast furnaces, optimizing the energy required for operations.
The use of customized turbines is also critical in the growing field of cogeneration and combined heat and power (CHP) systems, where both electrical power and thermal energy are produced simultaneously. Customized industrial turbines can be integrated with existing plant systems to capture waste heat and convert it into usable energy, improving the overall efficiency of the operation. This is especially valuable in industries with a high demand for both electricity and process steam, such as paper mills, food processing plants, and refineries. By optimizing the turbine to meet both the electrical and thermal energy requirements, companies can drastically reduce fuel consumption and improve their environmental footprint.
A significant advantage of customized turbines is their ability to meet environmental standards and regulations. As governments and regulatory bodies enforce stricter emissions limits and sustainability goals, industries are increasingly turning to customized solutions to ensure compliance. Turbines can be designed to operate with lower emissions, incorporating advanced combustion technologies, exhaust gas treatment systems, and energy recovery features to reduce the environmental impact. For example, turbines for biomass power plants can be customized to run efficiently on renewable fuels, significantly lowering their carbon footprint and supporting the transition to green energy.
Customized turbines are also essential in industries where space limitations or site-specific constraints must be considered. In certain industrial applications, the available physical space for turbines is limited, requiring the design of more compact units that can deliver the desired power output without taking up excessive space. Similarly, in areas with difficult access or extreme weather conditions, turbines may need to be designed with enhanced durability and weather resistance, ensuring they remain operational in challenging environments. This is especially important for industries in remote locations, such as offshore oil rigs or mountainous mining operations, where turbines must withstand harsh conditions while continuing to perform at high efficiency.
One of the key factors that make customized industrial turbines an attractive option is their ability to be integrated with advanced control systems and digital technologies. These turbines can be equipped with sensors, smart controls, and predictive maintenance tools, enabling operators to monitor performance in real time and identify potential issues before they become problems. Through the integration of IoT-based solutions, turbines can be continuously optimized to ensure they are running at peak efficiency, helping to reduce fuel consumption, minimize downtime, and extend the service life of the equipment. Digital systems also allow for more precise control over turbine operations, enabling industries to fine-tune the turbine’s performance to match changing demands.
Another major advantage of customized turbines is their scalability. As industries grow or require adjustments in their energy needs, customized turbines can be upgraded or expanded to meet increased demand. In many cases, additional turbines can be integrated into an existing system, expanding the power generation capacity or improving the overall efficiency of the operation. This scalability is especially important for industries experiencing fluctuating energy requirements, where the ability to scale power production quickly and efficiently can lead to significant cost savings and enhanced operational flexibility.
Customized industrial turbines also support cost optimization. While the initial investment in a tailored turbine system may be higher than a standard model, the ability to design a turbine that meets specific needs often leads to significant cost savings in the long run. The efficiency gains from having a turbine optimized for a particular operation can reduce fuel consumption, maintenance costs, and downtime, making the overall lifecycle cost of the turbine more economical. Furthermore, the customized approach ensures that the turbine operates at its highest possible efficiency, improving the financial performance of the facility.
As industries continue to face increasing pressure to reduce costs, improve efficiency, and meet sustainability targets, customized industrial turbines will remain a crucial part of the energy landscape. The flexibility, adaptability, and efficiency offered by customized turbines allow industries to tackle unique energy challenges, whether related to fuel use, operational conditions, or environmental regulations. With advances in materials science, digital technology, and engineering design, the future of customized turbines looks promising, offering even greater levels of performance, reliability, and environmental sustainability.
In conclusion, customized industrial turbines offer industries the ability to meet their specific energy needs with optimal efficiency, flexibility, and sustainability. Whether in power generation, process industries, or off-grid applications, these turbines provide tailored solutions that support both operational goals and environmental commitments. With their capacity to handle unique operational challenges, integrate with advanced technologies, and scale with growing energy demands, customized turbines are poised to remain a cornerstone of industrial energy systems, delivering reliable, cost-effective power well into the future.
Customized industrial turbines also play a significant role in enhancing the reliability and resilience of industrial operations. By tailoring turbines to specific operational needs, industries can mitigate risks associated with power disruptions or system failures. In critical industries like pharmaceuticals, food and beverage, and semiconductors, where consistent power supply is essential to maintain production quality and process integrity, customized turbines provide a solution that ensures continuous operation. With specialized designs that account for variables such as load fluctuations, maintenance schedules, and emergency backup, these turbines help minimize downtime and safeguard against unexpected shutdowns, which can result in costly production losses or equipment damage.
Customization also improves turbine performance in terms of load management. Industrial processes often experience fluctuations in demand, and turbines that are not optimized for such fluctuations may struggle to maintain stable output. Customized turbines, however, can be designed to adjust to these changes seamlessly, providing the right amount of power when needed without overloading the system. This capacity for dynamic load handling enhances overall system stability, prevents unnecessary wear and tear on the equipment, and optimizes fuel consumption by ensuring that the turbine operates within its most efficient performance range.
Moreover, the growing emphasis on digital twin technology and advanced simulation tools further enhances the customization of industrial turbines. By creating a digital replica of a turbine’s design, operators can simulate real-world conditions and predict how the turbine will perform under different operational scenarios. This allows for even more precise adjustments to be made during the design phase, ensuring that the turbine can perform optimally under a wide range of conditions. In addition, operators can use the digital twin to test various modifications and upgrades before implementing them, reducing the risk of unforeseen complications during operation and improving overall cost-efficiency.
The use of customized industrial turbines in smart grid systems is also becoming more prominent. These systems, which allow for real-time energy distribution and demand response, can greatly benefit from the integration of turbines that are tailored to meet specific grid requirements. Customized turbines that are compatible with smart grid technology can provide a flexible and responsive source of power that adjusts according to fluctuating grid demands. This ensures that industrial operations can continue smoothly while supporting the overall stability of the energy grid. Additionally, the predictive analytics used in these systems enable turbines to adjust their operations based on forecasted grid demand, further enhancing energy efficiency.
The long-term sustainability of customized industrial turbines is also enhanced by innovations in material science. Advances in corrosion-resistant alloys, high-temperature resistant materials, and lightweight components allow turbines to operate more efficiently in extreme conditions. These materials not only improve the turbine’s performance but also extend its lifespan, reducing the frequency of repairs or replacements and minimizing the associated costs. In industries where harsh environments are the norm, such as offshore oil platforms or waste-to-energy plants, turbines designed with these advanced materials offer a distinct advantage in terms of both durability and efficiency.
The future of customized industrial turbines is likely to be driven by the increasing need for energy efficiency, reliability, and environmental responsibility. As industries are under growing pressure to meet strict emissions regulations and sustainability targets, customized turbines that are specifically designed to reduce fuel consumption, optimize combustion, and minimize emissions will play a critical role in helping companies achieve their environmental goals. These turbines will be equipped with the latest emission control technologies, such as low-NOx combustion systems and carbon capture integration, to help industries meet governmental regulations and reduce their carbon footprints.
In conclusion, customized industrial turbines provide industries with a flexible and cost-effective solution for addressing a wide range of power generation and operational challenges. Whether enhancing reliability, optimizing efficiency, integrating with renewable energy, or supporting sustainability goals, these turbines are tailored to meet the specific demands of each operation. By offering long-term benefits in terms of cost savings, reduced downtime, and improved performance, customized turbines are an essential component of industrial energy systems. As technology continues to advance, these turbines will continue to evolve, providing even more efficient, reliable, and environmentally sustainable solutions for industries around the world.
Customized industrial turbines are also becoming increasingly important in addressing the challenge of energy security. Many industries, especially those that rely on large-scale, continuous power generation—such as steel, cement, and chemical production—must ensure that their turbines are specifically tailored to avoid vulnerabilities in their energy supply. Customized turbines offer enhanced protection against power outages and grid instabilities, ensuring that operations can continue without disruption. In regions where the power grid is unreliable or prone to outages, companies can rely on tailored turbines to provide backup power or even operate independently, ensuring that critical processes remain uninterrupted.
Moreover, as industries seek to optimize their overall energy mix, customized turbines can be designed to integrate seamlessly into hybrid systems that combine fossil fuels, renewables, and waste heat recovery. These systems help to achieve a balance between cost, reliability, and environmental impact. For example, in a cogeneration system, a customized turbine can harness both electricity and thermal energy, improving the overall efficiency of the system. By using a mix of renewable and conventional energy sources, companies can reduce their reliance on a single fuel type, ensuring that they are better equipped to handle fluctuations in energy availability and prices.
Another important factor driving the demand for customized turbines is the need for advanced automation and digital integration. With increasing reliance on automation and AI-powered optimization, the turbine control systems are becoming more sophisticated. Customized turbines can be equipped with smart sensors, real-time diagnostics, and remote monitoring capabilities, enabling operators to track performance metrics, detect inefficiencies, and plan for maintenance proactively. This digitalization allows for data-driven decision-making, making it easier for companies to adapt to changing energy demands, manage fuel costs, and fine-tune turbine operations for peak performance.
Customization also plays a critical role in enhancing the operational flexibility of turbines. In certain industries, production schedules can change frequently, and power needs might fluctuate as a result. A customized turbine can be designed to respond quickly to these changes, scaling its output up or down efficiently and maintaining stable operations even during transitions in load demand. In textile, food processing, and paper manufacturing, where the energy needs may vary depending on production cycles, the ability to adjust turbine output in real time can significantly improve energy efficiency and reduce waste.
Additionally, as industries seek to meet stricter environmental standards, customized turbines are increasingly designed to incorporate carbon capture and low-carbon technologies. These turbines can be equipped with advanced features like post-combustion capture systems, carbon capture and storage (CCS) integration, and no-carbon fuels (such as biogas or synthetic fuels). By incorporating these technologies, companies can reduce their greenhouse gas emissions and adhere to increasingly stringent regulations on air quality and climate change mitigation.
Customized turbines can also support industries in high-growth sectors, such as hydrogen production and battery manufacturing, which require clean power generation to maintain competitive advantage and meet rising energy demands. The flexibility of customized turbines means they can be integrated into these emerging industries to provide efficient and clean power. In hydrogen plants, turbines can be customized to generate power using clean sources, or in hybrid configurations where hydrogen is used as part of the energy mix, supporting the plant’s production process while maintaining environmental standards.
Scalability is another key benefit of customized turbines. As industries grow or face increased demand for energy, customized turbines can be designed to expand or scale with ease. For example, in large-scale manufacturing plants, energy needs often increase as production ramps up. Customized turbines can be built to handle this growth, either by adding more units or optimizing existing turbines to provide additional power without compromising efficiency. Similarly, for small- to medium-sized operations, turbines can be designed to be scalable, with the flexibility to meet the needs of today while planning for future energy requirements.
Furthermore, the ability to integrate with other power systems makes customized turbines an attractive solution for multi-fuel and microgrid systems. In these setups, turbines can be paired with solar, wind, or storage technologies, ensuring a stable energy supply even when renewable sources are intermittent. The combination of a customized turbine with storage solutions, such as batteries, allows for power to be stored during periods of excess generation and used when demand exceeds supply, offering a reliable and cost-efficient power solution.
Finally, the long-term reliability and extended operational life of customized turbines cannot be overstated. These turbines are designed with the specific challenges of each operation in mind, including factors such as high heat, high pressure, and abrasive fuels. By tailoring turbines to the demands of the application, manufacturers can ensure that their turbines will endure the test of time and provide continuous service with minimal downtime. As a result, companies can optimize their return on investment (ROI) over the lifespan of the turbine, reducing the total cost of ownership (TCO) and ensuring that the system remains effective over the long term.
In conclusion, customized industrial turbines are essential for industries aiming to improve energy efficiency, operational flexibility, and sustainability. By offering solutions that are tailored to meet specific industry needs, these turbines help companies reduce operational costs, enhance reliability, and achieve compliance with environmental standards. With advances in smart technology, fuel flexibility, and digital integration, the future of customized turbines looks promising, offering industries the tools they need to meet both present and future energy demands efficiently and sustainably. As industries evolve, customized turbines will continue to play a pivotal role in ensuring that businesses remain competitive, resilient, and sustainable in a rapidly changing energy landscape.
As we look further into the future of customized industrial turbines, it’s clear that their role will be increasingly influenced by advancements in energy storage and advanced materials. Energy storage systems, such as batteries and thermal storage, are becoming essential components of modern industrial energy systems, especially as renewable energy sources like wind and solar become more widely adopted. Customized turbines can be designed to integrate seamlessly with these storage systems, enabling the smooth transition between power generation and storage. This ensures that energy can be captured when supply exceeds demand and used during periods of high demand or low renewable energy availability.
By incorporating advanced materials into their design, customized turbines can become even more efficient and durable. High-performance materials that are resistant to corrosion, high temperatures, and wear are crucial in industries where turbines are exposed to harsh operating conditions. For example, superalloys, ceramic coatings, and composite materials are increasingly being used to improve turbine blades and other critical components, extending their operational lifespan and maintaining performance in extreme conditions. These materials not only increase the efficiency of the turbines but also make them more cost-effective over time by reducing maintenance needs and enhancing fuel efficiency.
Artificial intelligence (AI) and machine learning are also transforming the way customized industrial turbines are designed, operated, and maintained. With AI-powered predictive maintenance tools, turbines can be monitored continuously to detect signs of wear and tear before they result in system failures. Machine learning algorithms can analyze large amounts of operational data to identify patterns that may not be immediately apparent to human operators. This allows for proactive interventions that can optimize turbine performance and prevent unplanned downtime. Additionally, AI can help design turbines that are specifically tailored to the unique needs of each operation, using real-time data to make adjustments and improvements in turbine settings.
Customized turbines also offer an exciting opportunity to align energy generation with sustainability initiatives at the corporate and industry level. With growing concerns about climate change and the increasing demand for carbon-neutral solutions, many industries are seeking ways to integrate renewable energy technologies into their operations. Customized turbines can be designed to run efficiently on renewable fuels such as biomass, biogas, and even hydrogen, providing industries with the flexibility to reduce their carbon footprint. Furthermore, turbines that are optimized for carbon capture and energy recovery can help industrial facilities meet net-zero emissions targets by reducing the amount of CO2 released into the atmosphere.
In line with these trends, customized turbines are expected to become an integral part of decarbonization strategies for industries such as steel, cement, paper, and chemical manufacturing. These industries, which are traditionally some of the most energy-intensive and carbon-heavy, can greatly benefit from turbines that are specifically designed to work with low-carbon fuels and sustainable energy systems. For example, a customized turbine could be optimized for use in a hydrogen-based power generation system, providing a clean, efficient source of energy that supports a company’s green energy goals.
Decentralized power generation is another trend that is shaping the future of customized industrial turbines. As more industries and businesses seek to reduce their reliance on centralized power grids, the need for reliable, on-site power generation is growing. Customized turbines are particularly well-suited for this purpose, as they can be scaled to meet the specific energy needs of a given facility or operation. These turbines can be integrated with microgrids to create self-sufficient energy systems that provide stable, uninterrupted power to critical processes, even in remote or off-grid locations. By incorporating renewable energy sources like solar or wind, these microgrids can be further optimized to reduce reliance on fossil fuels and improve the sustainability of energy generation.
The growing demand for modular and scalable energy systems is also fueling interest in customized turbines. Modular turbines, which can be added or removed based on changing energy requirements, offer flexibility in adapting to evolving production needs. Industries can start with smaller turbines that meet their immediate power requirements and later scale up to larger systems as their operations grow. This modular approach is particularly attractive for industries with fluctuating energy demands or those operating in rapidly developing markets. Customized turbines can be designed to fit seamlessly into these modular systems, ensuring that each component works together efficiently to meet overall energy goals.
Furthermore, the globalization of manufacturing means that turbines must be adaptable to a wide range of local conditions and regulatory requirements. Customized turbines are particularly well-suited for meeting these challenges, as they can be engineered to comply with regional emissions standards, fuel availability, and economic considerations. For example, a customized turbine designed for a southeast Asian facility may need to be built to handle specific fuels available in the region, such as coal, biomass, or natural gas, while a turbine for a European facility may need to focus on high-efficiency combined heat and power (CHP) systems to comply with local sustainability mandates.
The evolution of clean technologies and circular economy principles is another key driver for customized industrial turbines. As industries strive to move toward more sustainable, closed-loop systems, turbines that are capable of integrating with waste-to-energy or energy recovery systems will become even more critical. Customized turbines can be designed to harness waste heat from industrial processes, biomass from agricultural or forestry waste, or byproducts from manufacturing, creating a more sustainable and cost-efficient energy generation model. By reducing waste and converting it into useful energy, these turbines support the transition to a more sustainable, circular economy.
Lastly, the growing focus on energy efficiency and cost-effectiveness continues to drive the demand for customized industrial turbines. As energy costs rise and industries face pressure to improve their bottom line, the ability to optimize turbine performance to reduce fuel consumption and increase operational uptime becomes a major priority. With their tailored designs, customized turbines can provide significant savings in energy usage, maintenance costs, and fuel consumption, delivering a solid return on investment over the long term.
In conclusion, customized industrial turbines are at the forefront of energy generation solutions, offering unmatched flexibility, efficiency, and sustainability. As industries continue to face challenges related to energy demand, environmental regulations, and cost optimization, customized turbines provide the tools needed to meet these demands while supporting future energy goals. With advancements in digital technologies, energy storage, renewable fuels, and smart grid integration, customized turbines will continue to evolve, playing a pivotal role in transforming the energy landscape and supporting industries in their quest for sustainable and efficient power generation.
Modular Power Block Steam Turbines
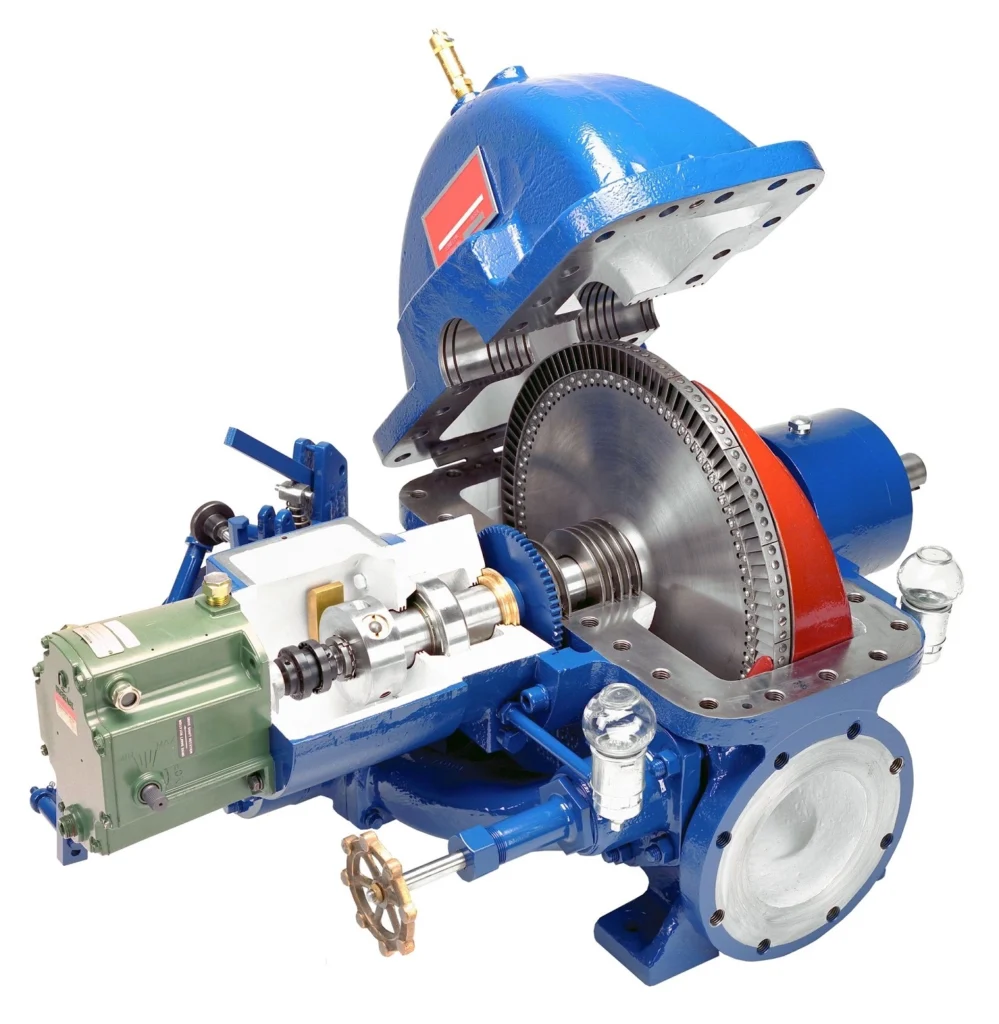
Modular power block steam turbines are an innovative solution for industries and power plants that require flexibility, scalability, and ease of installation in their energy generation systems. These turbines are designed as modular units, which means that they can be easily assembled, disassembled, or expanded to meet changing energy demands. This modular approach offers a range of benefits, including reduced capital investment, quicker commissioning, and the ability to integrate into a variety of operational settings.
One of the key advantages of modular power block steam turbines is their flexibility in scaling. As energy needs grow or fluctuate, modular turbines can be added or removed without significant downtime or disruption to operations. For example, a facility that initially requires a smaller turbine for its energy needs can start with a single modular unit and later expand the system by adding additional turbines to accommodate increased demand. This scalability is especially valuable for industries with fluctuating power requirements or those located in areas where demand for energy is growing rapidly.
In addition to flexibility, modular steam turbines offer quicker installation times compared to traditional, large-scale turbine systems. Since each module is pre-fabricated and tested in a controlled environment, the time spent on-site for assembly is significantly reduced. This can be especially advantageous in remote locations or facilities with limited downtime windows, such as industrial plants, offshore platforms, or floating power stations. The modular approach simplifies the commissioning process, leading to faster deployment and the ability to begin energy generation sooner.
Another significant benefit of modular steam turbines is their cost-effectiveness. By breaking the turbine into smaller, pre-engineered modules, manufacturers can reduce the overall capital expenditure for energy generation systems. The modular design allows for economies of scale in manufacturing, leading to reduced production costs, which can then be passed on to the end-user. Additionally, since modular turbines are easier to install and maintain, operational and maintenance costs are often lower compared to conventional turbine systems. This makes modular steam turbines an attractive option for industries that are seeking to optimize their energy costs while maintaining high performance and reliability.
Modular power block turbines are also an excellent fit for cogeneration and combined heat and power (CHP) applications. These turbines can be paired with waste heat recovery systems to produce both electricity and useful thermal energy for industrial processes. This dual-generation capability allows industries to make more efficient use of their energy resources, reducing waste and improving overall system efficiency. In industries like chemical manufacturing, food processing, and pulp and paper, where both electrical and thermal energy are essential, modular turbines provide a highly adaptable solution.
For renewable energy integration, modular steam turbines offer an ideal platform for coupling with renewable technologies such as biomass, solar thermal, or geothermal energy. In a hybrid system, these turbines can be used to generate power from renewable sources while maintaining grid stability. For instance, a modular turbine could be used in a biomass power plant, where it is fueled by plant-based materials, offering a sustainable, low-emission energy solution. The ability to scale these systems as renewable energy capacity increases further enhances their value.
The reliability of modular power block steam turbines is another factor that makes them particularly appealing. Since each module is individually tested and validated before installation, there is a reduced risk of operational failures or system malfunctions once the units are in place. The modular design also allows for easier maintenance and repairs, as individual modules can be serviced or replaced without the need to shut down the entire system. This helps to reduce downtime and ensures that power generation remains uninterrupted, a critical consideration in mission-critical operations like healthcare, data centers, and manufacturing plants.
Furthermore, modular turbines are often designed to be highly efficient, utilizing the latest technologies to ensure that fuel consumption is minimized and performance is maximized. For example, high-efficiency turbine blades, advanced heat exchangers, and digital control systems can be integrated into the modular units to optimize the performance of the turbine. These turbines are capable of running on a variety of fuels, from traditional natural gas to more sustainable options like biogas or hydrogen, making them versatile in meeting energy needs while also adhering to environmental standards.
Transportability is another significant feature of modular power block steam turbines. Due to their compact design, these turbines can be transported to various locations with relative ease. This is especially useful for mobile power generation or for facilities that need temporary power solutions, such as those found in construction, mining, or disaster relief efforts. The modular turbines can be quickly deployed and connected to the existing infrastructure, providing a reliable source of power during emergencies or peak demand periods.
From a sustainability perspective, modular turbines contribute to reducing the environmental impact of energy generation. By improving energy efficiency and enabling the use of renewable or low-carbon fuels, these turbines help to lower emissions and minimize the ecological footprint of power generation. The modular design also means that turbines can be more easily adapted or upgraded as new technologies emerge, allowing them to continue meeting future environmental standards.
In conclusion, modular power block steam turbines are a versatile and cost-effective solution for industries looking for reliable, flexible, and scalable energy generation. Whether used in industrial cogeneration, renewable energy applications, or remote locations, these turbines offer significant advantages in terms of performance, installation speed, operational cost, and sustainability. As energy demands continue to evolve and industries strive for greater efficiency and environmental responsibility, modular power block steam turbines will remain a key component in the global transition toward a more sustainable and resilient energy infrastructure.
In addition to the numerous advantages already highlighted, modular power block steam turbines offer several other compelling features that make them a preferred choice for modern energy generation systems. One of the key features is their adaptability to different operational environments. These turbines can be configured to meet the unique needs of various sectors, from heavy industrial plants to remote energy installations. The modular nature of the turbines allows them to be customized for a wide range of applications, including industries that require high-temperature, high-pressure, or low-emission operations. This adaptability ensures that modular turbines can effectively meet specific energy demands without compromising on performance or efficiency.
Moreover, modular turbines are designed to integrate easily with existing power systems, making them an excellent choice for retrofit projects. Many older power plants are looking for ways to modernize their systems and improve their overall energy efficiency. Instead of replacing entire power generation systems, modular turbines can be integrated into the existing infrastructure, providing a cost-effective way to enhance performance. This ability to seamlessly integrate with older systems reduces the need for major overhauls, minimizing downtime and installation costs while maximizing the utility of existing equipment.
Digitalization is another area where modular turbines are gaining traction. The growing trend toward smart power generation systems means that modular turbines are increasingly equipped with advanced sensor technologies, real-time data collection, and advanced analytics. This enables operators to monitor the performance of turbines remotely, gather insights into operational efficiency, and make informed decisions about maintenance, optimization, and system upgrades. Additionally, predictive maintenance and machine learning tools can be applied to modular turbines to forecast potential issues before they occur, improving reliability and minimizing unplanned downtime. These digital capabilities also enable better load management and more efficient energy use across the entire system.
As industries strive to become more carbon-conscious and environmentally responsible, modular power block steam turbines also offer a pathway to green energy solutions. These turbines can be designed to run on a variety of clean fuels—including biomass, hydrogen, and even synthetic fuels—which significantly reduce their carbon footprint compared to traditional fossil-fuel-based turbines. In cogeneration systems, modular turbines can recover waste heat and convert it into usable power, further enhancing the system’s efficiency and reducing the environmental impact of energy production. By enabling industries to integrate renewable energy sources into their power generation mix, modular turbines support broader sustainability goals and help companies comply with stricter environmental regulations.
Another emerging trend is the use of modular steam turbines in hybrid power systems. By combining modular turbines with renewable energy sources, such as solar or wind, industries can create hybrid systems that provide reliable and sustainable energy. These hybrid systems are particularly useful in regions with intermittent renewable energy resources, where turbines can fill the gaps in energy supply when solar or wind energy is unavailable. In such configurations, the modular turbines work in tandem with energy storage solutions (e.g., batteries or thermal storage) to ensure that power generation is constant and reliable. Hybrid systems are proving to be an ideal solution for industries seeking to reduce reliance on grid power and lower operational costs while still supporting their sustainability goals.
Modular turbines also offer an opportunity for off-grid and distributed energy solutions. In remote areas or locations without access to the main power grid, modular turbines can be deployed to provide independent, reliable power. This is particularly important for industries such as mining, oil and gas, and military applications, where a consistent energy supply is critical for maintaining operations. With modular turbines, these industries can generate their own power locally, reducing their dependence on external energy suppliers and mitigating risks associated with power outages or grid instability.
Additionally, the modular design enables the turbines to be transported and deployed to a variety of locations with minimal logistical challenges. Given their compact size and efficient use of space, these turbines can be used in both land-based and floating power plants. Floating power plants, for instance, can be used in offshore oil and gas platforms, ship-based power generation units, or even as part of marine-based renewable energy systems. This mobility is a key feature for industries that need flexible and portable energy solutions.
Finally, the long-term operational flexibility of modular steam turbines makes them an attractive choice for industries dealing with seasonal or cyclical energy demands. For example, in regions with significant seasonal variations in energy needs (e.g., cooling demands in summer or heating needs in winter), modular turbines can be easily ramped up or down to match power requirements. This capability helps industries avoid overproduction of energy during low-demand periods while ensuring that energy generation capacity remains available when demand surges.
In summary, modular power block steam turbines offer a versatile, efficient, and scalable solution for a wide range of energy generation needs. Their adaptability, cost-effectiveness, and flexibility make them ideal for industries seeking to optimize their energy production while reducing their environmental impact. As the energy landscape continues to evolve, these turbines will play an increasingly important role in providing reliable and sustainable power for a variety of applications, from industrial cogeneration to renewable energy integration and off-grid systems. With their ability to scale, adapt, and integrate into hybrid systems, modular turbines represent the future of efficient, flexible, and sustainable power generation.
Building on the numerous benefits already mentioned, the future of modular power block steam turbines looks even more promising, particularly as advancements in technology and global energy trends continue to evolve. Here are some additional aspects of modular steam turbines that will shape their role in the power generation sector in the coming years.
One key trend is the integration of digital technologies that enhance both operational efficiency and system reliability. As power generation systems become increasingly data-driven, modular turbines will leverage advanced control systems, real-time monitoring, and predictive analytics to optimize performance. By incorporating Internet of Things (IoT) devices and big data analytics, operators can monitor turbines in real-time, gather critical operational data, and make immediate adjustments to optimize energy production. These digital technologies not only improve operational efficiency but also enable the identification of potential issues before they escalate into major problems, minimizing downtime and maximizing the lifespan of the turbines.
In line with the trend of automation and intelligent power management, modular turbines will also be integrated into smart grids and microgrids. This will provide the ability to balance energy supply and demand more efficiently, especially in regions with fluctuating or intermittent renewable energy production. Modular turbines, working in conjunction with energy storage systems like batteries, can act as dynamic assets in these decentralized energy grids. These turbines can help smooth out renewable energy fluctuations, ensuring that energy is available when needed and optimizing the overall energy mix.
Furthermore, as the global push toward carbon neutrality intensifies, modular turbines will continue to evolve to meet stricter emissions regulations and sustainability goals. With the growing adoption of green fuels and renewable energy sources, the modular turbines will be designed to accommodate a broader range of fuels, including biomass, hydrogen, and even synthetic fuels derived from waste products. The ability to operate on low-carbon or carbon-neutral fuels is becoming increasingly essential in sectors such as steel production, chemical manufacturing, and electricity generation, where achieving carbon reductions is a top priority.
Hydrogen-based power generation is one area where modular turbines are expected to play a significant role in the near future. Hydrogen, as a clean fuel, has the potential to revolutionize the energy landscape, particularly in industries looking to reduce their carbon footprint. Modular steam turbines can be designed to run on green hydrogen, which is produced using renewable energy sources like wind and solar, making them an excellent fit for the growing demand for sustainable energy solutions. By integrating hydrogen into modular turbine systems, industries can reduce their reliance on traditional fossil fuels and move toward a more carbon-free energy future.
Another area of growth for modular power block turbines is the integration with waste-to-energy systems. In today’s economy, where circular economy principles are gaining traction, the ability to turn waste materials into usable energy is becoming an increasingly attractive solution. Modular turbines can be designed to run on biogas or waste-derived fuels, which not only help to reduce the environmental impact of waste but also generate clean, renewable energy. This is particularly relevant in industries like waste management, agriculture, and food processing, where there is an abundance of organic waste that can be converted into energy.
As global demand for energy storage technologies grows, modular steam turbines are likely to play an important role in energy storage systems as well. With their ability to store energy generated by renewable sources, such as solar or wind, modular turbines can be used in tandem with thermal energy storage systems to provide a consistent, reliable energy supply. For instance, excess energy from solar or wind farms can be stored as heat, which can then be used by modular turbines to generate electricity when renewable energy sources are not available. This thermal energy storage capability enables modular turbines to be part of a low-carbon, resilient energy infrastructure, capable of meeting both baseload and peak demand efficiently.
The increased adoption of modular power block steam turbines also aligns with the growing trend toward decentralized power generation. As industries and municipalities look for more localized energy solutions, modular turbines are well-suited to provide on-site power generation. This is particularly relevant for remote or off-grid locations, where bringing in power from the national grid is not feasible. Modular turbines can be deployed in these locations to generate electricity and thermal energy, making them ideal for mining operations, military bases, and disaster relief zones where reliable and immediate power is essential.
Additionally, modular turbines offer a significant advantage in terms of upgradability. As energy technologies continue to advance, modular turbines can be easily upgraded or modified with new components, digital systems, or fuel flexibility options to enhance performance and meet evolving energy requirements. For instance, as energy efficiency standards become more stringent or new low-carbon fuels become available, modular turbines can be adapted to accommodate these changes, providing long-term value for energy producers. This capability allows businesses to future-proof their energy infrastructure, ensuring that they are prepared to meet both regulatory changes and market demands as they evolve.
Finally, modular steam turbines will continue to serve as an important solution in emergency power generation. Whether for backup power in the case of grid failure, or for temporary power generation during peak demand or in response to disasters, modular turbines offer a flexible and reliable option for industries in need of critical energy. Their ability to be quickly deployed and integrated into existing systems makes them ideal for emergency response scenarios, particularly in industries such as oil and gas, construction, and telecommunications, where any interruption in power can lead to costly downtime and service disruptions.
In conclusion, modular power block steam turbines represent a cutting-edge solution for industries seeking reliable, efficient, and scalable energy generation. As global energy systems continue to shift toward decarbonization, renewable energy, and distributed generation, modular turbines will play a crucial role in enabling these transitions. Their adaptability to a wide range of fuels, ability to integrate with renewable energy sources, and contribution to energy storage systems make them a cornerstone of future energy infrastructure. Whether used in industrial applications, remote power generation, or hybrid energy systems, modular turbines offer a flexible, cost-effective, and sustainable solution for the evolving energy landscape.
As the world continues to prioritize sustainability and the need for low-carbon energy solutions, modular power block steam turbines are likely to see even greater demand in the coming decades. The broader trend toward decarbonization, energy resilience, and advanced manufacturing will drive innovations in modular turbine technology, making them increasingly valuable across various industries. Let’s explore further how these turbines will continue to evolve and integrate into the global energy landscape.
Continued Innovation in Turbine Materials and Design
One area of continued advancement in modular steam turbines is the development of new materials and advanced engineering techniques that improve the turbine’s efficiency and lifespan. As pressure to reduce energy costs and environmental impact intensifies, turbine manufacturers are focusing on materials that can withstand higher temperatures and pressures, which leads to improved performance and reduced energy consumption.
For example, superalloys and ceramic materials are becoming more common in high-performance turbine designs. These materials can endure the extreme operating conditions of modern steam turbines while maintaining structural integrity. Advanced coatings and corrosion-resistant materials are also being developed to prolong the life of turbines in harsh environments. These innovations will allow modular turbines to run more efficiently and require less maintenance, resulting in lower operating costs and a longer useful lifespan.
The aerodynamic design of modular turbines will also continue to improve. Enhanced blade designs, which reduce drag and maximize efficiency, are being explored in both steam turbines and combined-cycle systems. As computational fluid dynamics (CFD) modeling becomes more advanced, manufacturers can optimize the design of turbines to achieve higher performance while reducing energy losses.
Automation and Remote Monitoring
Automation in the form of smart control systems and remote monitoring will become increasingly critical in the operation of modular turbines. In industries that require continuous power generation, like chemical manufacturing, oil and gas, or mining, it is vital to ensure turbines are operating at peak efficiency. The integration of artificial intelligence (AI) and machine learning (ML) into turbine control systems allows for real-time diagnostics and performance optimization.
Through the use of sensors and cloud-based monitoring platforms, operators will be able to track the performance of turbines remotely, analyze data trends, and proactively address any issues. Predictive analytics tools will enable operators to schedule maintenance only when needed, based on real-time data, rather than relying on fixed schedules. This predictive approach not only extends the lifespan of the turbines but also ensures that potential faults are identified before they cause a complete shutdown, reducing downtime and increasing operational efficiency.
This level of autonomous operation will help industries achieve a higher level of reliability, with turbines operating more efficiently and with fewer interruptions. Moreover, it also helps to reduce the need for human intervention, reducing labor costs and mitigating risks associated with human error, especially in hazardous environments.
Hybrid Systems for Enhanced Flexibility
Modular power block steam turbines are already highly flexible, but as renewable energy sources like wind, solar, and hydropower grow in prominence, there will be an increasing need for hybrid power systems that combine renewable sources with traditional or backup power generation systems. The integration of energy storage technologies, such as batteries or thermal storage, alongside modular turbines, will allow for more dynamic energy systems.
In hybrid energy setups, modular steam turbines can act as a backup or peak-shaving resource when renewable energy generation fluctuates. For example, if solar panels experience a drop in output during cloudy weather, a modular turbine could step in to provide additional power, ensuring a constant energy supply. This type of integration could become especially useful in microgrids or in remote areas where energy security is a priority, allowing for more reliable energy while reducing dependence on centralized grids.
Furthermore, as the grid becomes increasingly decentralized, modular turbines will help to stabilize the grid in areas where renewable sources are inconsistent. This will be critical for regions experiencing high penetration of renewables or areas that are prone to energy disruptions. The modular turbine, with its ability to be quickly deployed or scaled, will act as a key enabler of distributed energy systems, further enhancing grid resilience.
Global Market Expansion
Modular steam turbines are likely to experience significant growth in emerging markets, particularly in regions where industrialization is accelerating, and energy demand is rising. Countries in Asia, Africa, and Latin America, which are seeing rapid urbanization and industrial expansion, will increasingly turn to modular turbines as a solution for both centralized and distributed power generation.
For instance, in Africa, where access to reliable power is still a challenge in many regions, modular turbines can be used to provide local, off-grid power in remote villages or industrial zones. In Asia, where nations like China and India are striving for a clean energy transition, modular turbines can be integrated into waste-to-energy systems, helping to address both energy demand and waste management simultaneously.
As these regions look for more affordable and flexible power generation options, modular turbines provide a solution that can be easily adapted to the local context. Their scalability makes them especially attractive for developing economies with fluctuating energy needs or limited infrastructure. Moreover, the ability to generate both electricity and heat through combined cogeneration or CHP systems is highly beneficial for industries in these regions, providing greater efficiency and energy savings.
Role in Offshore and Marine Applications
The use of modular steam turbines in offshore applications is another area where growth is expected. Floating power stations, offshore oil rigs, and marine-based platforms all require reliable, efficient power generation systems. Modular turbines, with their compact and scalable design, are particularly suited for these applications.
For offshore oil and gas platforms, where access to grid power is limited or non-existent, modular steam turbines offer an opportunity for energy independence. They can run on a variety of fuels, including natural gas and biogas, which makes them flexible enough to operate in the harsh conditions of offshore installations. Modular turbines used in offshore power plants can also be used to support desalination processes to provide fresh water for the platform, making them a versatile energy solution for maritime industries.
In addition, the emerging field of marine-based renewable energy—such as wave and tidal power—could benefit from the integration of modular turbines. These turbines can be deployed to harvest energy from ocean currents or wave motion, providing a reliable and sustainable power source for offshore operations. As marine energy technologies mature, modular turbines will likely become an essential component in delivering power to offshore wind farms or other renewable energy infrastructure.
Conclusion
The modular power block steam turbine market is poised for continued growth and innovation. With its flexibility, cost-effectiveness, and ability to integrate with renewable energy systems, modular turbines will continue to serve as a cornerstone for industries and power plants seeking to adapt to an increasingly decentralized, renewable-driven energy landscape.
As we look to the future, these turbines will not only support the transition to a low-carbon economy but will also help industrial sectors meet the growing demand for energy while ensuring that operations remain efficient, cost-effective, and environmentally responsible. Whether used in hybrid power systems, remote locations, or industrial applications, the modular turbine represents the future of scalable, adaptable, and resilient energy generation, making it an essential part of tomorrow’s power solutions.
Steam Turbines for Utility-scale Power Plants
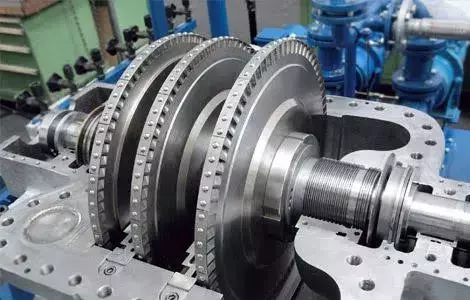
Utility-scale power plants are some of the most significant consumers of energy generation equipment, including steam turbines, due to their ability to produce large amounts of electricity efficiently and reliably. Steam turbines have long been the cornerstone of conventional power plants, including coal, natural gas, and nuclear plants, as well as cogeneration and combined-cycle power plants. They provide critical, high-output electricity generation for the grid, supporting both base load and peak demand needs. The following explores the role of steam turbines in utility-scale power plants, the factors driving their development, and how these turbines are adapting to meet the challenges of modern energy systems.
Core Functionality and Efficiency
The primary function of steam turbines in utility-scale power plants is to convert thermal energy into mechanical energy, which can then be converted into electrical energy by a generator. The efficiency of a steam turbine is vital to the overall performance of the power plant, as it directly impacts how much fuel is required to produce a unit of electricity. Over the years, steam turbines have evolved to meet ever-increasing demands for efficiency and reliability in utility-scale applications.
One of the major developments in steam turbine technology for utility-scale power plants is the enhancement of combined-cycle systems, where a steam turbine works in tandem with a gas turbine. In these systems, the gas turbine generates electricity using the exhaust gases from combustion, which are then used to generate steam to drive a steam turbine. This combined-cycle approach improves overall plant efficiency by using the waste heat from the gas turbine to produce additional electricity via the steam turbine. These systems can reach efficiency levels of 60% or higher, compared to the 33-40% efficiency of conventional steam-only plants.
This increase in efficiency is important as fuel costs and environmental concerns push for more energy-efficient and environmentally friendly power generation technologies. Combined-cycle power plants, which rely on both steam and gas turbines, are a critical aspect of the evolution of utility-scale power generation.
Fuel Flexibility and Adaptation to Changing Energy Mix
Utility-scale power plants have traditionally relied on fossil fuels, such as coal and natural gas, to generate steam. However, with the growing shift toward renewable energy and decarbonization efforts, utility plants are increasingly adopting fuel-flexible steam turbines. These turbines are designed to handle a wide range of fuels, including biomass, waste-derived fuels, hydrogen, and even solar thermal energy.
For example, in biomass power plants, steam turbines are used to convert organic matter into electricity. In these cases, the biomass—often wood chips, agricultural waste, or municipal solid waste—is burned to generate heat, which produces steam to power the turbine. The adaptability of steam turbines allows them to work in a carbon-neutral context when running on biomass, helping power plants reduce their overall carbon emissions.
Similarly, in hydrogen-fueled power plants, steam turbines can run on green hydrogen, a low-carbon fuel produced using renewable energy sources like wind and solar. By incorporating hydrogen into utility-scale power plants, steam turbines provide a solution for carbon-free power generation, supporting the global transition toward clean energy.
Fuel flexibility also extends to the integration of coal-to-gas transitions. In many power plants, coal turbines can be retrofitted to run on natural gas, allowing for significant reductions in greenhouse gas emissions. Steam turbines are typically capable of being modified to accommodate this shift in fuel use, which is critical for the transition away from coal-based power generation.
Integration with Renewable Energy and Storage Systems
As the global energy mix shifts toward greater reliance on renewable energy sources such as wind and solar, steam turbines are increasingly being integrated into systems that support the intermittent nature of these sources. Utility-scale plants must balance renewable energy generation with traditional fossil-fuel-based generation to ensure a constant supply of electricity to the grid. Steam turbines can play a vital role in this balancing act.
In solar thermal power plants, for example, mirrors or lenses concentrate sunlight to heat a working fluid, typically molten salt, which generates steam that drives a steam turbine. These plants provide a reliable form of dispatchable renewable energy, meaning they can generate power on demand, even when the sun is not shining. The efficiency of steam turbines in these settings ensures that the energy produced can be used effectively to supply the grid, regardless of fluctuations in solar energy availability.
Additionally, thermal energy storage systems can be coupled with steam turbines to store excess heat produced by solar or geothermal plants for later use. This stored energy can then be converted into electricity when demand spikes or renewable energy generation is insufficient. By using steam turbines to convert stored thermal energy into electricity, utility-scale power plants can provide reliable and flexible energy that complements renewable power generation.
Grid Stability and Reliability
Utility-scale power plants with steam turbines also play a critical role in ensuring grid stability. Power grids require a constant balance between supply and demand to avoid blackouts and maintain system stability. Steam turbines, particularly those in base load power plants, provide a steady and reliable source of power, capable of running for extended periods without interruptions.
Modern steam turbines are designed with the capability to quickly adjust their output to respond to fluctuations in demand. This ability to load-follow, or adjust output based on changing energy needs, makes steam turbines valuable for both peak shaving and back-up power applications. In times of high electricity demand, steam turbines can ramp up production to ensure the grid is adequately supplied with power. Conversely, during low-demand periods, steam turbines can reduce their output, helping to balance energy consumption across the grid.
In addition, steam turbines in utility plants can be used in black start operations, where the turbine can provide an essential power supply to restart the grid after a failure. This ability to operate independently and provide vital support during emergencies is a key advantage of steam turbines in large-scale power generation.
Environmental and Emissions Considerations
Environmental concerns and carbon emissions are increasingly important factors in the design and operation of utility-scale power plants. Steam turbines have been developed with lower emissions in mind, particularly in combined-cycle and cogeneration systems, where waste heat recovery and fuel switching can reduce the overall environmental impact. The latest designs in steam turbine technology incorporate advanced materials and coatings that can improve turbine performance and reduce fuel consumption, helping power plants to meet stringent environmental regulations.
Furthermore, steam turbines running on renewable fuels, such as biomass or hydrogen, offer a significant opportunity to reduce emissions while maintaining high efficiency. By using these clean fuels, power plants can contribute to the transition toward a carbon-neutral energy future, reducing their reliance on fossil fuels while still providing reliable and scalable energy to the grid.
Future of Steam Turbines in Utility-Scale Power Plants
The role of steam turbines in utility-scale power plants is evolving rapidly as technology advances and the global energy transition continues. As energy systems increasingly incorporate clean energy sources and focus on achieving carbon reduction targets, steam turbines are adapting to work with a broader range of fuels and to integrate seamlessly into hybrid energy systems.
The future of steam turbines will likely see further advancements in efficiency, reliability, and flexibility, with the ability to run on new low-carbon fuels, integrate with energy storage systems, and provide backup power during grid disruptions. Additionally, the growing focus on digitalization and automation will enhance the operation and maintenance of steam turbines, allowing for real-time monitoring, predictive maintenance, and optimized performance.
In conclusion, steam turbines will continue to be a vital component of utility-scale power plants, providing both reliable energy and flexibility in an increasingly complex and renewable-driven energy landscape. They will play a key role in ensuring grid stability, efficient energy use, and environmental sustainability as the world transitions to a more sustainable energy future.
As utility-scale power plants continue to adapt to evolving energy demands and environmental pressures, steam turbines are likely to become even more integral to modern energy systems. Looking ahead, several key trends will shape the future role of steam turbines in these plants, and the ways in which they are utilized will continue to advance alongside innovations in energy technology.
Advances in Turbine Design and Materials
To meet the increasing demand for more efficient and cost-effective power generation, steam turbines will continue to evolve in terms of design and materials. Modern turbines are being designed to run at higher temperatures and pressures, which boosts the overall efficiency of power plants. By increasing thermal efficiency, steam turbines can convert more heat into useful electrical energy, helping to reduce fuel consumption and lower emissions.
The development of advanced alloys and composite materials will be critical to ensuring that steam turbines can operate at these elevated temperatures and pressures. These materials will also make turbines more durable, extending their operational lifespan and reducing maintenance costs. Additionally, advancements in supercritical and ultra-supercritical steam cycles, which operate at higher pressures and temperatures than traditional cycles, are likely to increase turbine efficiency even further, allowing power plants to achieve greater outputs with the same amount of fuel.
One example is the supercritical steam turbine used in combined-cycle plants, which operates at pressures above 3,200 psi and temperatures over 1,000°F. These turbines are significantly more efficient than traditional subcritical steam turbines, with the potential to achieve efficiencies above 45%, making them well-suited for the growing demand for efficient, large-scale power generation.
Integration with Smart Grid Technology
The rise of the smart grid is expected to drive changes in how steam turbines are integrated into power plants and how they interact with the broader energy grid. Smart grid technologies allow for real-time communication between power generation sources, distribution networks, and consumers. Steam turbines in utility-scale plants will need to be increasingly compatible with smart grid systems, ensuring that they can respond quickly to fluctuations in energy demand and integrate seamlessly with renewable energy sources.
For example, steam turbines will likely become more involved in demand response programs, where they can be dispatched or reduced in response to signals from the grid operator. This flexibility will help utilities manage the variability of renewable energy sources like solar and wind, ensuring that excess energy is used efficiently and that power is available when demand peaks. By integrating steam turbines with smart grid systems, power plants will be able to optimize performance and efficiency, while also ensuring grid stability and reliability.
Moreover, predictive analytics and machine learning will play a more significant role in turbine operation. By analyzing data from turbines in real time, smart grid systems can predict potential failures and recommend preventative maintenance, ensuring that turbines run at peak efficiency and preventing costly downtimes.
Decarbonization and the Role of Carbon Capture
The ongoing global push for decarbonization is a significant factor in the future of steam turbines in utility-scale power plants. As countries strive to meet climate goals, utility plants that rely on fossil fuels are under increasing pressure to reduce their carbon emissions. This is where steam turbines, in conjunction with carbon capture technologies, can play a crucial role.
Carbon capture, utilization, and storage (CCUS) technologies can be retrofitted to existing steam turbines in power plants to capture the carbon dioxide (CO₂) produced during combustion. The captured CO₂ can either be stored underground or used in other industries, such as in the production of synthetic fuels or for enhanced oil recovery. By integrating CCUS with steam turbines, power plants can continue to use fossil fuels while reducing their carbon footprint, contributing to the transition to a low-carbon energy economy.
Furthermore, steam turbines in power plants that utilize biomass, waste-to-energy, or hydrogen can also support decarbonization efforts. These alternative fuels produce fewer emissions compared to conventional fossil fuels, and in the case of green hydrogen, they can offer carbon-free power generation. As more utility-scale plants adopt these cleaner energy sources, steam turbines will evolve to meet the unique requirements of these fuels, offering flexibility and reducing the environmental impact of power generation.
Distributed Generation and the Role of Steam Turbines
While utility-scale power plants will continue to be a primary source of electricity for large regions, distributed generation—the production of electricity close to where it is used—will become an increasingly important part of the energy mix. Steam turbines, particularly those used in combined heat and power (CHP) systems, can be deployed in smaller-scale, distributed applications to provide both electricity and useful heat for industries, communities, and even commercial buildings.
These decentralized systems can operate alongside renewable energy sources, providing backup power when wind or solar energy is not available. In addition to providing reliable electricity, steam turbines in CHP applications offer high overall efficiency by capturing and utilizing waste heat that would otherwise be lost. This makes them ideal for industrial applications, such as in chemical plants, refineries, and food processing, where both electricity and heat are required in large quantities.
Furthermore, as microgrids become more common in remote locations or in areas prone to power outages, steam turbines may play a key role in ensuring the reliability and resilience of local energy systems. By providing a flexible, efficient, and reliable energy source, steam turbines in microgrids can help support both local communities and critical infrastructure, making them an essential part of a decentralized energy future.
Expanding Use in Emerging Markets
As developing countries continue to industrialize and urbanize, there will be an increased demand for reliable, scalable, and affordable power generation solutions. In many emerging markets, steam turbines are expected to play a pivotal role in meeting growing energy needs. With their proven reliability and flexibility, steam turbines will continue to be a cornerstone technology for utility-scale plants in these regions.
In places like Africa, Asia, and Latin America, where access to electricity is still limited, steam turbines can be deployed in both centralized and distributed power generation systems. They can work with a variety of fuel sources, including coal, natural gas, biomass, and even renewable fuels, providing countries with a reliable energy source to meet their economic and industrial growth needs.
Moreover, as investment in infrastructure grows in these regions, there will be an opportunity to integrate cleaner technologies like carbon capture, cogeneration, and renewable energy integration into new steam turbine installations, supporting a more sustainable energy future.
Conclusion
Steam turbines will continue to be a vital part of utility-scale power plants, providing reliable, efficient, and flexible energy generation solutions. Their role will evolve as they adapt to higher efficiency standards, carbon reduction goals, and a growing integration with renewable energy sources. Whether employed in combined-cycle systems, hybrid power plants, or distributed generation systems, steam turbines will remain central to the global energy transition, balancing the demand for affordable, dispatchable energy with the need for sustainable, low-carbon power generation. As technology continues to improve, these turbines will play an even more prominent role in ensuring the world’s power systems remain resilient, efficient, and environmentally responsible.
As utility-scale power plants continue to evolve to meet the demands of a changing energy landscape, steam turbines will continue to play a central role in ensuring that global energy systems remain efficient, flexible, and capable of supporting the transition to cleaner energy. In the coming years, several emerging technologies and strategies are likely to shape the development of steam turbines in utility-scale applications. These developments will help ensure that steam turbines remain a viable and important component of future power generation, contributing to a more sustainable, resilient, and flexible energy infrastructure.
Adaptation to Hybrid Energy Systems
One of the key future trends for utility-scale power plants is the integration of hybrid energy systems. Hybrid systems combine various energy generation technologies—such as steam turbines, gas turbines, solar, wind, and energy storage systems—into a single plant to provide both reliable and clean electricity. Steam turbines, in these settings, will play a critical role in ensuring system stability and optimizing the dispatch of power.
For example, in a hybrid solar-thermal and gas-fired power plant, steam turbines will be responsible for converting the heat produced by the solar collectors into steam, which drives the turbine. Additionally, when solar energy is not available due to cloud cover or nighttime, the gas-fired component of the plant can provide backup energy, with the steam turbine handling both energy sources. The ability to adjust the operation of steam turbines to accommodate varying energy inputs from different sources makes them ideal for such hybrid systems.
In other hybrid applications, steam turbines may work in tandem with battery storage or pumped hydro storage systems. When renewable energy sources like wind and solar generate excess power, that energy can be stored for later use. During periods of low renewable generation or high demand, the stored energy can be converted back into electricity by steam turbines operating in a thermal power plant, ensuring a steady and flexible energy supply to the grid.
The continued evolution of hybrid energy systems, which combine the strengths of multiple power generation technologies, will further underscore the versatility and importance of steam turbines in meeting the future energy needs of the world.
Advances in Digitalization and Automation
In the future, steam turbines in utility-scale power plants will increasingly benefit from the ongoing trend toward digitalization and automation. As power plants adopt smart technologies, steam turbines will be equipped with advanced sensors and monitoring systems to gather real-time data on their performance. This data will be analyzed using artificial intelligence (AI) and machine learning algorithms to optimize turbine performance, predict potential failures, and enable predictive maintenance.
One significant advancement in this area is the development of digital twins for steam turbines. A digital twin is a virtual representation of a physical asset that is updated in real time with data from the actual turbine. By creating a digital twin of a steam turbine, operators can simulate and analyze different operating conditions, identify potential inefficiencies, and test scenarios without affecting the actual turbine’s performance. This technology can improve the overall reliability of turbines, reduce downtime, and increase efficiency by allowing for better decision-making in real time.
Additionally, remote monitoring and control systems will enable power plant operators to manage turbines from a distance, ensuring that any issues can be addressed promptly, even if the turbine is located in a remote or hard-to-reach area. With the integration of these advanced technologies, steam turbines will operate more efficiently, with a lower risk of unexpected breakdowns and reduced maintenance costs.
The Shift Toward Modular and Scalable Systems
As global energy demands fluctuate and markets evolve, there is a growing interest in more modular and scalable energy solutions. Steam turbines are increasingly being designed to be modular, allowing them to be deployed in a wide variety of settings, from utility-scale plants to smaller-scale, decentralized systems. This modularity offers several advantages, including the ability to build power plants that are tailored to specific energy needs and to adjust the scale of operations as demand grows.
In modular combined-cycle power plants, for example, steam turbines can be deployed alongside gas turbines and other energy systems in a highly flexible and scalable manner. These plants can start with smaller capacities and expand as needed, offering a cost-effective way to meet increasing energy demand without building massive infrastructure upfront.
Furthermore, modular steam turbine designs allow for easy integration with distributed generation systems, which can be important for providing power to remote areas or smaller industrial facilities. Modular steam turbines provide greater flexibility for utilities and developers to meet specific local energy needs while reducing the upfront costs associated with large, centralized power plants.
This shift toward modular systems will make steam turbines even more adaptable to a range of applications and markets, from large-scale power generation to industrial cogeneration and microgrids.
Role in Decentralized Energy Systems
While utility-scale power plants remain a critical component of the global energy mix, there is a significant push toward decentralized energy systems. These systems involve the generation of electricity closer to where it is consumed, reducing transmission losses, improving energy security, and supporting local economies.
Steam turbines, particularly in combined heat and power (CHP) configurations, are well-suited for these decentralized systems. CHP systems use a single energy source to produce both electricity and thermal energy, which is especially valuable in industrial applications, such as chemical plants, refineries, and food processing. These decentralized systems can operate independently or in tandem with the grid, providing flexible energy options for smaller communities or industries.
The rise of microgrids is another key factor contributing to the growth of decentralized energy systems. Microgrids are localized energy networks that can operate autonomously or be connected to the main grid. Steam turbines in these systems will continue to play a crucial role, particularly in providing reliable backup power during grid outages or for remote communities that lack direct access to centralized electricity sources. By integrating steam turbines with renewable energy sources, battery storage, and other energy technologies, microgrids can ensure a consistent and sustainable energy supply.
International and Regional Collaboration
As the need for cleaner energy and more sustainable power generation solutions grows, international and regional collaborations will become increasingly important. Steam turbines will continue to be a key area of focus in such efforts, particularly as countries work together to meet climate change goals and share knowledge about best practices in energy generation.
Countries with abundant renewable energy resources, such as wind and solar, may collaborate with others that have extensive natural gas, biomass, or geothermal resources to develop hybrid systems that combine various energy sources and technologies. Steam turbines will play a central role in facilitating this energy sharing, providing a reliable method for converting thermal energy into electricity. Additionally, the ability to use renewable and low-carbon fuels in steam turbines, such as biomass or green hydrogen, will help facilitate these international collaborations and contribute to a global transition to cleaner energy.
Closing Thoughts: The Future of Steam Turbines in Power Generation
As the global energy landscape evolves, steam turbines will continue to be essential components in the transition toward a more sustainable, reliable, and flexible power generation infrastructure. Their adaptability, fuel flexibility, and role in optimizing energy efficiency make them well-suited to meet the growing challenges of modern energy systems.
From utility-scale plants to decentralized microgrids, steam turbines will play a pivotal role in supporting the energy needs of both today and tomorrow. Their continued integration with renewable energy sources, storage technologies, and smart grid systems will ensure they remain relevant in the increasingly complex and dynamic world of energy production. Whether driven by the need for higher efficiency, the desire for cleaner fuels, or the push for grid stability and flexibility, steam turbines will remain a cornerstone of global power generation for years to come.
As we look toward the future, steam turbines will continue to evolve in response to the ongoing challenges and opportunities within the energy sector. Their role in utility-scale power generation will be shaped by several factors, from technological advancements to changes in regulatory frameworks and global energy demand. As a key technology for balancing the world’s growing need for electricity with the drive for more sustainable and cleaner energy sources, steam turbines are poised to play a major part in shaping the energy landscape of the 21st century.
Advances in Hybrid Power Plants and Energy Storage Integration
A key area of future development for steam turbines in utility-scale power plants lies in their integration with energy storage technologies and hybrid power systems. The combination of renewable energy sources like solar and wind with energy storage and steam turbines will enable power plants to offer dispatchable power—the ability to supply electricity on-demand—despite the intermittent nature of renewable generation.
Energy storage systems, such as batteries, pumped hydro, and compressed air storage, can store excess electricity produced during periods of high renewable generation and release that energy when demand is high or renewable sources are unavailable. By incorporating steam turbines into these hybrid systems, plants can ensure a reliable, steady supply of power while optimizing the use of renewable energy.
In solar thermal plants, steam turbines play an essential role by converting the heat captured from solar collectors into steam. In the event that solar energy is insufficient due to cloudy weather or nighttime, stored thermal energy can continue to drive the steam turbine, ensuring uninterrupted electricity generation. Similarly, hybrid plants combining natural gas, biomass, or geothermal energy with renewable power sources can increase their operational flexibility and efficiency, balancing the energy mix and reducing reliance on fossil fuels.
As battery storage technologies advance, steam turbines can be integrated into energy systems where battery storage complements turbine operation, allowing for smoother transitions between renewable energy generation and steam-driven power production. This hybrid approach will further increase the resilience of the grid while enabling power plants to adjust to changing demand and weather conditions.
Focus on Sustainability and Decarbonization
The transition to a low-carbon energy future will significantly impact the role of steam turbines in utility-scale power plants. As the global push for carbon neutrality intensifies, utilities and power generation companies are increasingly looking for ways to decarbonize their energy production while maintaining high reliability and efficiency.
One of the most promising ways steam turbines contribute to this transition is through the adoption of carbon capture and storage (CCS) technologies. These systems are designed to capture carbon dioxide (CO₂) emissions produced during combustion processes, preventing them from entering the atmosphere. Steam turbines used in fossil fuel plants can be paired with CCS systems to capture and store CO₂, helping to reduce the overall carbon footprint of power generation. This technology could become critical for existing steam turbine plants that continue to rely on coal or natural gas while transitioning toward cleaner energy sources.
Hydrogen as a fuel is also emerging as a game-changer in decarbonization efforts. As the technology for green hydrogen production—using renewable energy to split water into hydrogen and oxygen—advances, steam turbines can be used to produce electricity from hydrogen combustion. Since hydrogen does not produce carbon emissions when burned, it represents a carbon-free fuel that can significantly reduce the environmental impact of power generation. The integration of hydrogen into steam turbine cycles will be particularly beneficial in power plants seeking to balance a transition to a zero-emission energy mix while maintaining reliable, continuous power generation.
The increasing emphasis on biomass and waste-to-energy as alternative fuels will also influence steam turbine design and operation. Biomass, which includes organic materials like wood chips and agricultural waste, can be burned in steam turbines to generate electricity. These renewable fuels offer a more sustainable option compared to fossil fuels, reducing the carbon intensity of power generation. Steam turbines designed to handle a wider range of biomass feedstocks will be integral to meeting renewable energy targets and reducing reliance on coal and natural gas.
Digitalization and AI-Powered Optimization
Another transformative factor in the future of steam turbines in utility-scale power plants is the ongoing shift toward digitalization. The integration of smart technologies and artificial intelligence (AI) will allow steam turbines to operate more efficiently, improve predictive maintenance, and reduce costs.
Sensors embedded within steam turbines can continuously monitor various parameters, including temperature, pressure, vibration, and efficiency. These data points can be collected and analyzed in real time to detect potential issues before they lead to equipment failure. Advanced AI algorithms can use this data to make predictive recommendations, enabling operators to perform maintenance only when necessary and optimize turbine performance.
One of the most exciting developments in this area is the creation of digital twins for steam turbines. A digital twin is a virtual model of the turbine that mirrors its physical counterpart, allowing operators to simulate various operational conditions and identify potential inefficiencies without interrupting turbine operation. By using digital twins, utilities can improve turbine design, test performance under different scenarios, and enhance reliability.
Additionally, steam turbines will become an integral part of smart grids that enable more efficient distribution and consumption of electricity. These systems will optimize power flow based on real-time data from turbines, renewable energy sources, and energy storage, ensuring that power is distributed where it is needed most and minimizing waste. Steam turbines equipped with digital control systems can quickly adjust their output based on grid requirements, making them more adaptable to fluctuating energy supply and demand.
Global Expansion and Economic Growth
As the global population continues to grow, especially in developing regions, the demand for electricity will rise significantly. In many parts of the world, steam turbines will remain a primary solution for meeting these growing energy needs. Countries that are industrializing rapidly, such as those in Africa, Asia, and Latin America, will rely on steam turbines for both large-scale power generation and industrial applications.
For example, many developing countries are seeking to increase their industrial output and economic growth, both of which require reliable and affordable electricity. Steam turbines, with their ability to run on a variety of fuels—including coal, natural gas, biomass, and hydropower—are highly versatile and can be deployed in a range of geographic and economic contexts. As such, steam turbines will continue to be essential for powering the industrial sectors of these regions while contributing to economic development.
However, as these regions look to expand their energy infrastructure, they will also be mindful of the growing demand for clean energy solutions. Clean coal technologies, carbon capture, and biomass power plants are likely to be part of the energy mix in many emerging markets, ensuring that power generation remains economically viable while addressing environmental concerns.
Resilience in the Face of Climate Change
The increasing impacts of climate change, such as extreme weather events, rising temperatures, and shifting patterns of energy demand, will require power plants to become more resilient and capable of responding to unpredictable conditions. Steam turbines, particularly when integrated with backup power systems and hybrid technologies, can provide a reliable source of electricity during extreme events like heatwaves, droughts, or grid disruptions.
Moreover, the resilience of steam turbines will be enhanced by advances in modular and distributed generation systems, allowing them to be deployed in smaller, more flexible configurations that can continue operating in the face of localized power failures or energy shortages. In times of crisis, steam turbines will be able to step in to provide emergency power for critical services, communities, and industries.
Conclusion
Steam turbines will continue to be a foundational technology for utility-scale power plants, adapting to meet the challenges of decarbonization, energy reliability, and technological advancements. As the energy sector evolves to incorporate more renewable energy, advanced materials, hybrid systems, and smart technologies, steam turbines will remain a critical piece of the puzzle in ensuring a sustainable and resilient energy future. With their adaptability, fuel flexibility, and ongoing technological improvements, steam turbines will be instrumental in meeting the world’s energy demands while contributing to a cleaner, more efficient, and more sustainable power generation landscape.
Steam Turbines for Backup Power Generation
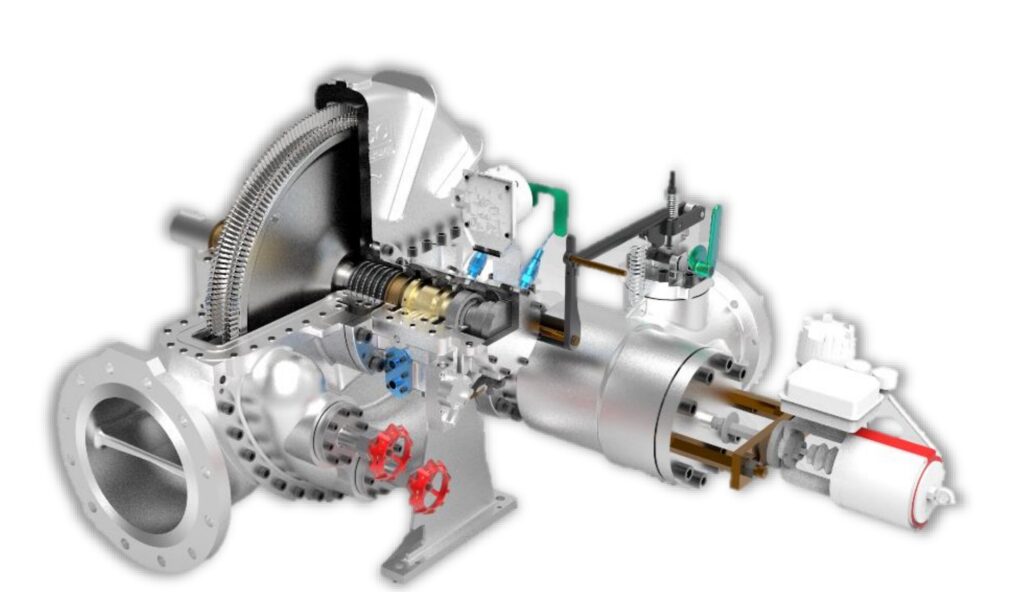
Steam turbines are increasingly being recognized for their essential role in backup power generation across a variety of industries and regions. As the demand for reliable electricity grows, especially in the face of increasing climate change events, grid instability, and supply disruptions, steam turbines provide a dependable solution for maintaining electricity supply when the main grid fails or when there is a need for rapid demand response. Their ability to offer flexibility, fuel variety, and long-term reliability makes steam turbines an ideal choice for backup power, even in remote areas or high-demand applications.
The importance of backup power generation continues to grow, with critical infrastructure, including hospitals, data centers, telecommunications, industrial plants, and military installations, all requiring a constant, uninterrupted power supply. Steam turbines in backup generation scenarios serve as an effective way to ensure that these critical services and operations can continue functioning without disruption, even during grid failures or extreme weather conditions.
Unlike other forms of backup power, such as batteries or diesel generators, steam turbines offer a much higher level of efficiency and long-term viability. They can generate power for extended periods and can be paired with a wide range of fuels. Whether the backup system uses biomass, natural gas, or renewable sources, the ability to rely on steam turbines during emergencies or critical times makes them a key component of ensuring energy security in the face of increasingly uncertain conditions.
One of the advantages of steam turbines as backup power sources is their ability to provide both electricity and thermal energy. In many industrial and process-driven operations, both forms of energy are required, and steam turbines can simultaneously provide heat and power. This is particularly beneficial for industries that rely on combined heat and power (CHP) systems, such as those in chemical manufacturing, food processing, or large-scale district heating systems. When integrated into a combined-cycle or co-generation system, steam turbines can operate as part of a multi-functional backup power solution that meets both electrical and heating needs.
Another key advantage is the fuel flexibility of modern steam turbines, which can be adapted to run on a variety of fuels, including conventional fuels like coal and natural gas, as well as renewable fuels like biomass, waste-to-energy, or even green hydrogen. This flexibility ensures that backup power generation can remain operational in regions where traditional fuel sources may be limited, or where fuel availability fluctuates.
Moreover, steam turbines are highly reliable, having been a cornerstone technology in energy generation for over a century. Their design allows them to function optimally for long periods, with minimal downtime. In backup generation scenarios, this level of reliability is critical, as power interruptions must be avoided at all costs. The ability of steam turbines to operate continuously, particularly when linked with energy storage or renewable technologies, ensures that they provide a dependable source of backup power when grid outages occur, whether caused by weather events, natural disasters, or infrastructure failures.
While steam turbines excel at providing long-duration backup power, their integration with advanced grid management systems and energy storage solutions increases their overall efficiency and responsiveness. For example, coupling steam turbines with battery storage systems allows for quicker recovery from disruptions, with the turbines coming online to provide steady power while the battery systems can supply energy at higher rates for shorter durations. The hybridization of steam turbines with these technologies can ensure that backup power systems are both effective and efficient, minimizing waste and optimizing energy use.
The growing trend toward microgrids and distributed generation also highlights the role of steam turbines in ensuring that backup power can be deployed in smaller, more localized settings. In areas that are off-grid or in developing regions where the main grid infrastructure is unreliable, steam turbines can operate as part of decentralized energy systems, providing electricity to communities or industries that might otherwise be vulnerable to power shortages. These small-scale systems, whether powered by biomass, solar thermal, or other energy sources, can be quickly scaled up or adjusted to meet changing demand, further enhancing energy resilience.
Another exciting development in the use of steam turbines for backup power is the increasing interest in hybrid and modular power systems. These systems combine multiple power generation technologies—such as gas turbines, renewable energy sources, and steam turbines—into a single, highly flexible unit. By leveraging steam turbines in these hybrid systems, operators can ensure a balance of continuous, on-demand power alongside intermittent energy sources, such as wind or solar. The combination of technologies allows for greater adaptability to fluctuations in energy demand and availability, ensuring that backup power is provided with minimal downtime or disruption.
In addition to grid-scale backup power generation, steam turbines also serve important roles in emergency preparedness and military applications. Military bases, for example, often require reliable, rapid-response power systems that can operate independently of the national grid. Steam turbines, especially in portable or modular configurations, can be deployed to provide crucial power in emergency situations, from military operations in remote locations to humanitarian efforts during natural disasters. In these cases, the combination of portability, fuel adaptability, and long operational lifetimes makes steam turbines an attractive option for backup power in critical, time-sensitive scenarios.
The backup power market is expanding rapidly, with demand driven by the need for energy security and resilience across a range of sectors. As the world becomes more interconnected and reliant on continuous electricity, ensuring that backup power systems can provide reliable, long-lasting solutions will become increasingly important. With their proven technology, fuel flexibility, and ability to integrate into hybrid energy systems, steam turbines are well-positioned to meet these demands, providing the dependable, scalable power necessary to keep essential services and industries running, even in the most challenging situations.
As global infrastructure continues to grow and climate-related disruptions become more frequent, the role of steam turbines in backup power generation will only become more prominent. Their integration with modern energy systems, advanced fuels, and storage technologies will enhance their utility as a reliable, efficient, and sustainable solution for ensuring that critical services have access to the power they need when they need it most. This will help ensure that energy security remains a top priority, and that we can meet the challenges of the future, with steam turbines continuing to serve as a cornerstone of backup power solutions.
As backup power solutions become an even greater priority, especially in light of growing global uncertainties, the role of steam turbines will continue to expand. One area where they will be particularly impactful is in high-demand regions where grid stability is frequently compromised. In such areas, steam turbines can be part of a larger energy resilience strategy, ensuring uninterrupted power during natural disasters, extreme weather events, or unexpected grid failures.
By using distributed generation systems, steam turbines can provide a reliable power source that operates independently or in conjunction with the main grid. This is particularly important in remote locations, industrial zones, or off-grid areas, where connection to a centralized grid may not be feasible or is unreliable. In these scenarios, steam turbines integrated into microgrids allow for energy autonomy, reducing the need to rely on external power sources and ensuring that essential services like healthcare, communications, and critical infrastructure remain operational.
One of the key advantages of steam turbines in backup power systems is their scalability. They can be customized to meet the specific power needs of a region or industry. Whether the requirement is for a small-scale backup generator for a hospital or a large-scale solution for an industrial plant, steam turbines can be sized accordingly to provide the necessary amount of electricity. Additionally, because steam turbines can operate efficiently on a variety of fuels, this adaptability allows them to be deployed in a wide range of environments, from industrial facilities to remote island communities where traditional power sources might not be accessible.
Another important aspect of steam turbines in backup power systems is their ability to provide combined heat and power (CHP) solutions. Many industries that rely on continuous, high-demand energy production, such as chemical plants, refineries, and paper mills, also require significant amounts of heat. Steam turbines can be used to generate both electricity and heat, enhancing the overall efficiency of the power system. This makes them particularly attractive for industries looking to reduce energy waste and improve the sustainability of their operations while ensuring they have a reliable backup power supply.
In co-generation plants, steam turbines not only support electricity generation during power outages, but they can also provide a source of thermal energy for industrial processes. This dual-purpose capability is especially beneficial in industrial settings where downtime can be extremely costly. The integration of steam turbines into backup power networks ensures that these plants remain operational, even during grid disruptions, while minimizing energy consumption and reducing their carbon footprint.
As we look ahead, sustainability will be a key driver for the future of backup power generation systems. Increasingly, governments, industries, and organizations are seeking solutions that reduce their environmental impact. Steam turbines powered by biomass, waste-to-energy, or green hydrogen provide a cleaner alternative to traditional fossil-fuel-based backup power sources like diesel generators. These renewable energy solutions can reduce the carbon footprint of backup power generation, making steam turbines a key technology in efforts to mitigate climate change.
The integration of advanced sensors, artificial intelligence (AI), and smart grid technology will also play a critical role in enhancing the efficiency of steam turbines in backup power systems. Smart sensors will monitor the performance of steam turbines in real time, providing operators with actionable data to optimize performance and predict maintenance needs before failures occur. This predictive maintenance capability ensures that backup systems are always ready to respond in times of crisis.
By integrating steam turbines with digital control systems and machine learning algorithms, backup power solutions can become even more responsive to dynamic energy demands. AI can help manage energy flow, balance supply and demand, and adjust power generation levels in real-time, ensuring that backup turbines operate efficiently and provide the necessary support during grid failures or high-demand periods.
In the energy transition era, where industries are increasingly turning to renewable energy sources, steam turbines will also become more closely integrated with other forms of clean power generation. For instance, combining steam turbines with solar thermal plants, geothermal energy, or hydrogen-fueled systems creates a hybrid system that ensures steady, dispatchable power even when the renewable energy sources are intermittent. These hybrid systems will be essential for balancing the grid, as renewable sources like wind and solar do not always align with peak demand.
In terms of global deployment, steam turbines are poised to play a significant role in developing nations and emerging markets, where energy infrastructure is still being built or upgraded. These regions, which often face unstable power grids and unreliable access to electricity, will benefit from the use of steam turbines in microgrids or off-grid systems. Their fuel flexibility and ability to work with both traditional and renewable energy sources make them an ideal choice for meeting the growing electricity demands in these areas.
The ability to deploy steam turbines as part of a modular or containerized power plant offers additional advantages. These portable, scalable systems can be rapidly deployed in areas that need immediate backup power, such as in the aftermath of a natural disaster or in remote military operations. This flexibility and speed of deployment make steam turbines a critical tool for emergency preparedness.
As energy security and resilience continue to be top priorities for governments and industries worldwide, steam turbines will remain a cornerstone of backup power systems. Their ability to provide high-capacity, long-duration power during emergencies or high-demand periods ensures that essential services, infrastructure, and industries are safeguarded. Moving forward, steam turbines will continue to evolve to meet the challenges of a rapidly changing energy landscape, integrating with new technologies and fueling the transition toward a more sustainable and reliable energy future.
In conclusion, the importance of steam turbines for backup power generation is undeniable. With their ability to operate on diverse fuels, provide combined heat and power, and integrate with modern grid technologies, steam turbines will continue to be an indispensable tool for ensuring uninterrupted electricity supply. As the world increasingly focuses on energy resilience, clean power, and sustainability, steam turbines will adapt and play a pivotal role in supporting global infrastructure, emergency systems, and critical applications.
As the demand for resilient and sustainable energy solutions continues to rise, steam turbines will become even more integral in addressing the evolving needs of backup power generation. The transition toward decarbonized energy sources, paired with the growing integration of renewables, makes steam turbines a versatile and adaptable technology for ensuring power supply during grid disturbances or emergencies.
An exciting trend is the increasing use of combined-cycle systems, where steam turbines are paired with gas turbines to maximize efficiency in both generation and backup scenarios. When these systems are used in backup power applications, the gas turbine provides quick-start capabilities to meet peak demands, while the steam turbine takes over to provide long-duration power. This hybrid approach ensures that backup systems not only meet immediate needs but also provide a stable, continuous supply when required. This synergy between steam and gas turbines provides a powerful solution for hybrid backup systems, particularly in industries with diverse energy needs.
Fuel versatility also continues to be a key factor in the deployment of steam turbines in backup power. While natural gas has traditionally been a common fuel for steam turbines, there is growing interest in biomass, waste-to-energy, and renewable hydrogen as alternative fuels for backup generation. For instance, steam turbines powered by biomass not only provide energy security but also support sustainability by reducing greenhouse gas emissions compared to fossil fuels. Biomass-fueled turbines are a particularly valuable option for areas where waste materials can be utilized for power generation, reducing waste and contributing to a circular economy.
Waste-to-energy technology is particularly significant in urban settings, where large amounts of waste are produced daily. By using steam turbines to convert municipal solid waste (MSW) into electricity, cities can address both waste disposal and backup power needs in one integrated system. This solution is particularly beneficial in locations facing landfill overcapacity or waste management challenges, providing a sustainable, clean method for handling waste while generating energy for local use during power disruptions.
The integration of green hydrogen into steam turbine systems further strengthens their viability as a backup power solution. Hydrogen, when produced through electrolysis using renewable electricity, is considered one of the most promising energy carriers for a decarbonized future. Steam turbines fueled by green hydrogen can provide a virtually carbon-free backup power option. This is especially relevant in industries or regions aiming to achieve net-zero emissions. Hydrogen’s high energy density and storage capacity make it an ideal solution for long-duration power supply, which is a key feature for backup applications, especially in industrial plants or remote communities.
Another promising development is the growing use of modular steam turbine systems for backup power generation. These systems are compact, easily scalable, and can be deployed rapidly to meet energy needs in emergency situations. Modular turbines offer several advantages, including easier transportation, reduced installation times, and the ability to adjust power output as demand fluctuates. For regions prone to natural disasters or areas with frequently disrupted grid access, modular backup turbines provide a robust, ready-to-deploy solution.
In industrial applications, steam turbines used for backup power provide an additional layer of security, ensuring that critical operations continue even in the event of a power outage. For instance, in chemical and pharmaceutical manufacturing, where precise control of power is vital for both production and safety, having steam turbines on standby ensures that production lines are not interrupted. By pairing these turbines with energy storage technologies such as batteries or flywheels, industries can ensure that power is immediately available when needed.
For data centers, where downtime can result in significant financial losses and disruptions to services, steam turbines play an important role in maintaining the continuity of operations. These centers require highly reliable, always-on power to prevent damage to servers, network equipment, and critical IT systems. In such cases, steam turbines provide both the reliability and capacity required for uninterrupted power, ensuring that the vast amounts of data stored in these facilities remain protected from power outages.
As more governments and organizations focus on energy resilience and climate change mitigation, the role of steam turbines in backup power systems will be increasingly important in developing strategies for sustainable energy storage. Long-duration energy storage systems, when paired with steam turbines, can create a reliable backup power system that bridges the gap between renewable energy generation and demand. This is especially important in areas where renewable generation (like solar and wind) can be intermittent. By utilizing steam turbines to provide backup generation during periods of low renewable output, energy systems can maintain stability without relying on fossil fuels.
Moreover, the rise of smart grids and demand response technologies presents new opportunities for optimizing steam turbines in backup power applications. Smart grid systems can intelligently manage power flows, adjusting to fluctuations in demand and available generation. In backup scenarios, this technology enables steam turbines to be deployed more efficiently, ensuring that they are used only when necessary and reducing overall operational costs. These systems can be integrated with energy management platforms to provide real-time data and control, further enhancing the reliability and responsiveness of backup power solutions.
Steam turbines will continue to evolve in the context of decentralized power generation as more businesses, communities, and even residential areas explore energy independence. In these smaller-scale, localized systems, steam turbines can be deployed as part of a distributed generation network, where they complement other forms of local power generation, such as solar panels or wind turbines, to ensure continuous power availability. These networks are more flexible, allowing for rapid response to power outages and load fluctuations, making them especially effective in areas where centralized grid infrastructure is unreliable or costly.
As we look ahead, the future of steam turbines in backup power generation is clear. They will continue to provide reliable, flexible, and sustainable solutions to ensure that critical operations, industries, and communities can maintain energy supply in the face of increasingly volatile power grids. By integrating steam turbines with advanced technologies like energy storage, smart grids, and renewable energy sources, the potential for these systems to contribute to a greener, more resilient energy future is immense. As energy resilience becomes a growing priority for governments and industries, the strategic deployment of steam turbines in backup power systems will be an essential tool for safeguarding our power infrastructure and ensuring continuity in an uncertain energy landscape.
The continued integration of advanced control systems and digital technologies in steam turbines for backup power generation will also be a major factor in their evolution. As Industry 4.0 continues to take shape, the addition of real-time monitoring, predictive analytics, and remote diagnostics will enhance the performance and efficiency of steam turbines in backup power applications. These innovations enable operators to quickly identify potential issues before they become critical, minimizing downtime and extending the life cycle of the turbines.
Digital twins, virtual models of physical assets, are already being used to simulate the behavior of steam turbines under various operating conditions. In backup power systems, digital twins can be employed to model turbine performance during grid disturbances, helping operators predict the optimal response time and efficiency. This proactive approach allows for data-driven decisions, ensuring that turbines are functioning at their peak capacity when they are needed the most.
Another benefit of digital technologies is the integration of artificial intelligence (AI) to optimize turbine operations. AI can analyze vast amounts of real-time operational data to adjust parameters such as fuel consumption, steam flow, and temperature, ensuring the turbine operates with maximum efficiency. The application of AI can also assist in automating the startup process, reducing the response time of steam turbines and allowing them to ramp up quickly during an emergency. AI-driven systems can make the backup power process more seamless and responsive, a key feature for industries or regions where immediate power restoration is critical.
As the global energy landscape shifts toward renewables, the need for reliable, long-duration backup power becomes even more pronounced. Renewable energy sources like solar and wind are inherently intermittent, meaning that they cannot always provide a consistent, reliable source of power. Steam turbines can bridge this gap by supplying power when renewable generation is insufficient, ensuring grid stability and reducing dependency on fossil fuels. In regions with a high penetration of renewables, steam turbines can act as a backup during periods of low solar or wind activity, enabling the continued flow of electricity without relying on more polluting energy sources like coal or oil.
Moreover, the role of steam turbines in microgrids is becoming more significant as the shift toward decentralized energy systems gains traction. Microgrids, which are localized energy networks that can operate independently of the main grid, rely on a combination of energy sources—such as solar, wind, and biomass—to meet local energy demand. Steam turbines can be integrated into microgrids to provide backup power during periods of grid instability or high demand. This capability is especially valuable for remote communities, island nations, or critical infrastructure that needs continuous, reliable energy, regardless of broader grid conditions.
Hybrid power systems, which combine steam turbines with other renewable or conventional power sources, are also gaining popularity. By incorporating steam turbines into these systems, energy providers can ensure a seamless transition between different power sources, maintaining grid stability and reliability. For example, steam turbines can be paired with solar thermal energy or biomass plants, where they act as a steady backup during times of low renewable energy generation, such as cloudy days or windless periods. These hybrid systems are particularly well-suited for remote or off-grid applications where energy supply must be constant and reliable.
As backup power systems continue to evolve, there is an increasing focus on environmental sustainability. As governments and industries around the world set ambitious goals to reduce carbon emissions and meet net-zero targets, steam turbines fueled by renewable energy sources will play a crucial role. For instance, in places where waste-to-energy plants are prevalent, steam turbines offer a sustainable way to generate power from organic waste. This form of energy generation not only provides backup power during emergencies but also helps to address waste management issues and reduce landfills.
In district heating applications, steam turbines are also being integrated to provide both heat and power. District heating systems are used in densely populated urban areas to supply hot water or steam to homes and businesses. By using steam turbines to generate electricity and heat simultaneously, these systems can deliver efficient and reliable energy while also serving as a backup during power disruptions. This dual functionality is especially important in regions with harsh winters or high heating demands, as it ensures both electricity and heating are available during grid outages.
One of the most promising developments in the use of steam turbines for backup power is the growing interest in long-duration storage solutions. Energy storage technologies, such as pumped hydro, compressed air energy storage (CAES), and advanced battery systems, are increasingly being paired with steam turbines to create hybrid systems that can store energy generated during times of high demand or low renewable output. When energy storage is combined with steam turbines, these systems can provide backup power for extended periods, even up to several hours or days, without relying on grid power.
Microgrids and energy islands are becoming an increasingly attractive solution for islands and remote regions that face energy security challenges. In these areas, steam turbines can be deployed alongside other renewable energy sources and storage systems to form an isolated, self-sustaining power system. In the event of a grid failure, steam turbines provide the necessary power to keep the island or remote community functioning until normal grid conditions are restored. These islands of energy independence are crucial in addressing the unique energy challenges of remote populations, whether on islands, rural communities, or in the Arctic regions, where extreme weather and distance from the grid make traditional power generation systems less viable.
The continued adoption of modular and containerized steam turbines for backup power applications offers even greater flexibility and cost-effectiveness. These systems are pre-assembled in a factory and can be rapidly deployed on-site, making them an excellent option for emergency situations or rapidly expanding operations. The modular nature of these systems allows them to be easily scaled up or down based on demand, ensuring that backup power can be tailored to specific needs. The portability and ease of installation also make these systems ideal for industries such as construction, military operations, or temporary installations, where speed and flexibility are essential.
Finally, as the global energy transition continues, steam turbines for backup power generation will be an essential component of efforts to create a clean, sustainable, and resilient energy system. The ability to integrate steam turbines into hybrid power systems, renewable energy projects, microgrids, and energy storage solutions ensures they will remain a reliable backup option in a variety of applications, from urban centers to remote areas and industrial plants. With their long operational life, high efficiency, and flexibility across fuels, steam turbines will continue to be a cornerstone of resilient energy infrastructure, ensuring that power disruptions and grid instability do not compromise critical services and infrastructure.
In conclusion, steam turbines will continue to evolve in response to the growing demand for reliable backup power, especially in the face of a shifting energy landscape. Their ability to integrate with renewable energy, fuel flexibility, and adaptability to both large-scale and decentralized applications makes them an ideal solution for meeting backup power needs in a world increasingly reliant on sustainable and resilient energy systems.
Steam Turbines for Energy Storage
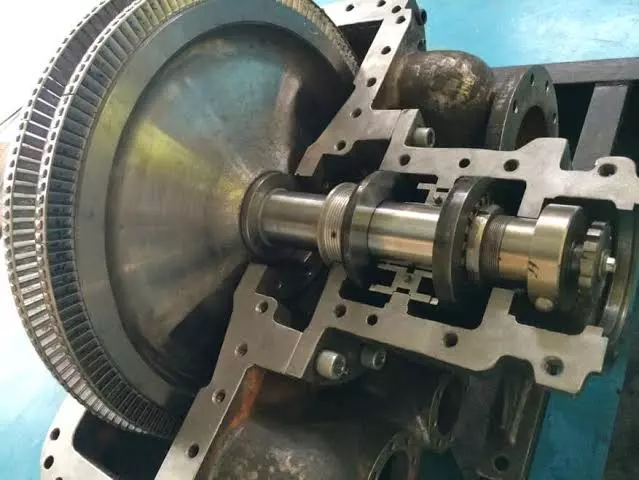
Steam turbines are emerging as a key component in energy storage systems, offering solutions for addressing the challenges of intermittent renewable energy sources such as wind and solar. As the world transitions to a more sustainable energy future, energy storage becomes increasingly important in stabilizing the grid and ensuring a constant supply of power, particularly during periods of high demand or when renewable energy generation is insufficient. Steam turbines can play a significant role in this process, particularly in pumped hydro storage, compressed air energy storage (CAES), and thermal energy storage systems. These technologies rely on steam turbines to generate electricity from stored energy, making them a reliable and efficient solution for long-duration energy storage.
One of the most common energy storage systems where steam turbines are used is pumped hydro energy storage (PHES). This technology involves pumping water to an elevated reservoir when electricity demand is low and then releasing the water to flow downhill, driving turbines to generate electricity during peak demand periods. Steam turbines are used in combination with conventional hydro turbines to increase the efficiency of this process, particularly in systems where high-temperature steam is used to improve turbine performance. In pumped hydro systems, the steam turbine can serve as an efficient method of converting stored water energy into electrical power, which is released to the grid when renewable energy generation is low or grid stability is needed.
In compressed air energy storage (CAES) systems, energy is stored by compressing air and storing it in underground caverns or containers. When electricity demand peaks, the compressed air is released, passing through turbines to generate electricity. Steam turbines are often integrated into CAES systems to improve the efficiency of the air expansion process. By using steam to further expand the air, steam turbines increase the energy output of the system, enabling it to generate more electricity from the same amount of stored compressed air. This hybrid system combines the benefits of compressed air storage with the power generation capabilities of steam turbines, offering a reliable and efficient solution for energy storage and backup power.
Thermal energy storage is another area where steam turbines can be used effectively. In this system, excess electricity generated during times of high renewable output is used to heat a medium, such as molten salt or water, to store thermal energy. When energy is needed, the stored heat is converted back into steam, which drives a steam turbine to generate electricity. Steam turbines in thermal storage systems provide a reliable method for converting stored heat into electrical power, which can be dispatched to the grid as needed. This approach is particularly beneficial in concentrated solar power (CSP) plants, where steam turbines are already used to generate power from solar-thermal energy. By combining thermal energy storage with steam turbines, CSP plants can offer long-duration energy storage that is highly efficient and scalable.
One of the key advantages of steam turbines in energy storage systems is their high efficiency and long operational life. Unlike traditional battery storage systems, which can degrade over time and require costly replacements, steam turbines are highly durable and can operate for decades with proper maintenance. Their efficiency in converting thermal or mechanical energy into electricity makes them an ideal choice for energy storage applications that require reliable and long-lasting solutions. Furthermore, steam turbines can be scaled to meet the specific needs of large-scale energy storage projects, ensuring that they can be deployed in a variety of settings, from utility-scale facilities to smaller, distributed generation systems.
The ability of steam turbines to operate on a variety of fuels also makes them versatile in energy storage systems. While traditional storage systems rely on specific types of energy, steam turbines can be fueled by a range of sources, including renewable fuels, natural gas, or biomass. This flexibility allows energy storage systems to be customized based on regional resources and energy needs. In areas with abundant biomass or waste materials, for example, steam turbines can convert stored thermal energy into electricity while using renewable fuels, further enhancing the sustainability of the energy storage system. Additionally, steam turbines can be integrated into waste-to-energy systems, where they provide backup power during periods when renewable energy generation is low, using waste heat to drive turbines and generate electricity.
As grid stability becomes a more pressing concern, especially with the increasing share of variable renewable energy sources, steam turbines offer an effective means of ensuring that energy storage systems can respond rapidly to fluctuations in supply and demand. Steam turbines, when integrated with energy storage systems, can provide the necessary grid support to balance fluctuations, ensuring a stable power supply. Fast-ramping capabilities of steam turbines allow them to quickly respond to sudden changes in electricity demand or generation, making them well-suited for backup power applications during peak hours or when renewable generation drops unexpectedly.
In the future, advanced steam turbines will play a pivotal role in enhancing energy storage capabilities, particularly in hybrid storage systems that combine thermal, mechanical, and chemical energy storage. By integrating steam turbines with battery storage systems, for instance, hybrid systems can provide both short-term, rapid response and long-duration power supply, optimizing energy storage capacity. Additionally, steam turbines can be combined with emerging technologies such as green hydrogen, where hydrogen can be used as a medium for storing energy that can be converted into steam for turbine power generation when required. These hybrid systems will offer a more comprehensive and flexible solution for storing and dispatching electricity, ensuring that energy storage can meet the varying demands of the grid and consumer needs.
Another area of development in steam turbines for energy storage is their integration with smart grid technologies. As energy grids become more decentralized and complex, smart grids are needed to monitor and manage energy flows in real-time. Steam turbines, when integrated with smart grid systems, can respond dynamically to grid conditions, adjusting power output based on demand signals or renewable energy generation forecasts. These systems can also improve the efficiency of energy storage systems by better managing the timing of turbine operations, ensuring that stored energy is used most effectively to maintain grid stability.
Modular steam turbines are increasingly being deployed in energy storage applications, providing flexibility and ease of installation. These compact, scalable units can be installed quickly, making them ideal for both new energy storage projects and retrofitting existing facilities. Their modular nature also allows for easy maintenance and upgrades, ensuring that energy storage systems remain efficient and reliable over time. This scalability is particularly beneficial for distributed energy storage systems, where smaller turbines can be used in conjunction with other local storage solutions to provide backup power to communities or industries.
As more countries and organizations commit to achieving net-zero carbon emissions and expanding their renewable energy capacity, steam turbines will play a crucial role in decarbonizing energy storage systems. By integrating steam turbines with carbon-neutral fuels, such as biomethane, green hydrogen, and renewable natural gas, energy storage can be made more sustainable, reducing the overall carbon footprint of the energy system. These efforts will support the ongoing transition toward a cleaner, more resilient energy future, where energy storage plays a central role in balancing supply and demand and ensuring a stable, reliable power grid.
In conclusion, steam turbines are emerging as a critical technology in energy storage systems, providing high-efficiency, long-duration storage solutions that are essential for maintaining grid stability as renewable energy becomes a more dominant source of electricity. With their versatility, scalability, and ability to integrate with various storage technologies, steam turbines offer a robust and sustainable approach to energy storage. As global energy systems become increasingly reliant on renewables, the integration of steam turbines into energy storage systems will be essential for ensuring that power generation remains reliable, efficient, and adaptable to changing energy demands.
The role of steam turbines in energy storage will continue to evolve with advancements in both technology and energy market needs. As renewable energy sources like solar and wind become more prevalent, their intermittent nature creates challenges for grid operators in balancing supply and demand. Steam turbines offer a reliable solution by providing long-duration storage and the ability to generate power on demand. This is especially important in grid-scale energy storage applications, where long periods of energy backup are required to support critical infrastructure and large-scale power systems.
Steam turbines’ integration with energy storage and generation hybrid systems is one of the most exciting developments in this space. These systems can combine steam turbines with battery storage, thermal storage, and other forms of energy storage to offer a more flexible, robust solution to energy challenges. In a hybrid setup, the steam turbine can either serve as the primary power generation unit or act as a backup to batteries or other renewable resources. For instance, batteries can provide fast response power, while steam turbines can supply long-term, sustained energy when needed, especially during extended periods of low renewable generation or high demand.
As steam turbines continue to be deployed in thermal storage systems, advanced heat storage technologies are being developed to increase their capacity. Molten salt storage, for example, allows for heat to be stored efficiently and used to generate steam, which drives turbines to produce electricity. This form of storage can be especially valuable in solar thermal plants, where steam turbines are used to generate electricity even after the sun has set, making the energy supply more reliable.
Moreover, geothermal energy is an emerging source of renewable power that integrates seamlessly with steam turbines. In geothermal plants, steam extracted from deep underground reservoirs is used to drive turbines and generate electricity. By combining geothermal energy with energy storage systems, such as pumped hydro or compressed air, steam turbines can play an even greater role in balancing grid supply and ensuring continuous power availability, especially in regions where geothermal resources are abundant.
The digitalization of steam turbine technology is another critical factor in enhancing their role in energy storage systems. Advanced sensors, real-time monitoring, and predictive analytics can be employed to optimize the operation and efficiency of steam turbines in energy storage applications. With the help of machine learning algorithms, turbines can operate more efficiently, adjusting their performance based on fluctuating energy demands, fuel availability, and grid conditions. This intelligent operation not only reduces energy wastage but also extends the lifespan of the turbines by ensuring that they are running at optimal conditions.
In addition to automation and digital monitoring, remote-controlled operation is becoming increasingly viable for steam turbines in energy storage systems. This technology allows operators to control turbines from anywhere, improving flexibility and reducing the need for on-site personnel. Such capability is especially beneficial for remote energy storage installations, such as those in off-grid areas or island nations, where constant human supervision may not be practical.
As countries increasingly shift toward a low-carbon economy, steam turbines in energy storage systems will also become more integrated with carbon capture and storage (CCS) technologies. Some energy storage projects, particularly those that utilize fossil fuels or biomass, will be designed to capture and store carbon emissions generated during turbine operations. In these applications, steam turbines could serve as the power generation component, while carbon capture technologies help minimize the environmental impact. By incorporating CCS systems, steam turbines can contribute to achieving net-zero emissions while still playing a critical role in providing backup power and grid stability.
Another key consideration in the future of steam turbines for energy storage is their integration with microgrids. Microgrids, which operate as self-contained energy systems, are gaining popularity as communities seek more localized and resilient solutions for power generation and distribution. Steam turbines can be an essential component in these systems, providing backup power during times of grid instability or renewable generation shortfalls. Microgrids powered by steam turbines can operate independently from the main grid, ensuring continuous power supply for critical infrastructure such as hospitals, military bases, and remote communities.
The continued innovation in steam turbine design will also lead to increased operational flexibility. The trend toward smaller, modular steam turbines allows for more precise control over power generation, enabling systems to scale more effectively based on storage capacity and demand. This modularity also reduces capital expenditure costs and installation time, making energy storage solutions with steam turbines more accessible for various industries and regions.
Looking toward the future, there is significant potential for hybrid energy storage systems to be more integrated with emerging technologies, such as artificial intelligence (AI) and blockchain. These technologies can help optimize energy storage and turbine operations by forecasting energy generation patterns, analyzing demand fluctuations, and streamlining power distribution. For instance, AI-driven systems could automatically optimize when to release stored energy to the grid based on real-time data, weather predictions, and grid needs. Similarly, blockchain technology can help streamline the transaction and tracking of energy credits, facilitating the sale of stored power in decentralized energy markets.
The need for sustainable and reliable backup power and long-duration energy storage will drive the growing demand for steam turbines in the coming decades. As energy storage systems become more integral to the decarbonization of the energy sector, steam turbines will continue to evolve in terms of both performance and environmental impact. Their ability to work with a wide range of energy storage technologies makes them a versatile, reliable, and efficient solution for managing energy supply and demand in the future. The potential for steam turbines to be used in hybrid storage systems, microgrids, and renewable energy integration will play a vital role in ensuring a stable, sustainable, and carbon-free energy future.
Looking ahead, the integration of steam turbines in energy storage systems will increasingly involve collaboration between different energy storage technologies. The convergence of thermal energy storage, electrochemical storage (batteries), and mechanical energy storage systems will provide a more holistic and flexible approach to managing energy. Steam turbines will be pivotal in such systems, particularly for applications requiring long-duration, high-capacity energy storage. For example, hybrid storage systems that combine thermal storage, such as molten salt, with steam turbines, will allow for storing and generating energy over extended periods, providing power during prolonged periods of high demand or when renewable energy generation is low.
The ability of steam turbines to work effectively with geothermal energy also opens up new possibilities in energy storage and generation. By utilizing the Earth’s natural heat to create steam, turbines can convert stored geothermal energy into electricity when needed. In regions where geothermal resources are abundant, steam turbines could serve as a backbone for local energy storage systems, ensuring a reliable and consistent power supply while helping reduce the reliance on fossil fuels. This could be especially beneficial in countries looking to integrate more renewable energy into their grids without sacrificing stability.
As smart grids continue to develop and evolve, steam turbines will be better able to interact with the grid in real time. Smart grid systems are designed to manage the distribution of power more efficiently and reliably, incorporating renewable energy sources, energy storage, and other distributed generation assets. Steam turbines in energy storage systems can be controlled dynamically to adjust their output based on the current grid demand, helping balance supply and demand. Through smart grid integration, steam turbines can also participate in demand response programs, where their operation is adjusted to accommodate fluctuations in demand, ensuring that grid stability is maintained during peak hours or when there is a shortfall in renewable generation.
One of the notable trends for the future of energy storage is the growing interest in long-duration energy storage (LDES) systems. Steam turbines are particularly well-suited for these applications, as they can provide sustained power over long periods, making them ideal for systems where energy needs to be stored for extended times before being released. LDES solutions, such as thermal energy storage or compressed air energy storage, paired with steam turbines, offer a potential solution for seasonal storage, where energy generated during peak production periods can be stored and released during off-peak or demand-heavy seasons.
Additionally, advanced steam turbines will likely be designed to work with a variety of non-fossil fuel sources to minimize carbon emissions and maximize the overall sustainability of energy storage systems. For example, steam turbines could be paired with green hydrogen, a clean fuel produced through electrolysis using renewable energy. In this scenario, steam turbines would convert hydrogen’s chemical energy into electricity, providing grid support and backup power. Green hydrogen, combined with steam turbines, holds significant promise for both energy storage and carbon-neutral power generation, aligning with global goals for net-zero emissions.
The development of modular and scalable steam turbines also allows for customized energy storage solutions that can be adapted to a variety of settings. These turbines can be easily integrated into different energy storage applications, from small-scale distributed systems to large utility-scale projects. The modular nature of these turbines allows for incremental capacity expansion, ensuring that energy storage systems can grow as demand for storage increases, without requiring massive upfront capital investment. The scalability also enhances the feasibility of retrofitting existing energy infrastructure with steam turbines, improving their energy storage and backup power capabilities.
Furthermore, the need for decentralized energy storage will continue to grow as microgrids become more common. Steam turbines in microgrid applications can provide resilient power generation during times of grid failure or instability, ensuring that local communities and industries have reliable power even when the main grid is down. This is particularly important for critical infrastructure, such as hospitals, military installations, and data centers, where uninterrupted power is essential for maintaining operations.
Economic incentives for renewable energy adoption, such as government subsidies, tax credits, and regulatory frameworks promoting the reduction of greenhouse gas emissions, will further stimulate the adoption of steam turbines for energy storage. Governments and utilities around the world are increasingly investing in renewable energy infrastructure, recognizing that energy storage is crucial for integrating renewable power sources like wind and solar into the grid. As part of this transition, steam turbines will play an essential role in enhancing grid resilience, enabling more flexible and efficient power systems that reduce dependence on fossil fuels.
In the longer term, steam turbines are expected to become an integral part of global energy transition strategies. As technologies such as advanced energy storage, hybrid systems, and smart grids continue to evolve, steam turbines will remain at the forefront of efforts to balance energy generation, storage, and consumption. Their ability to integrate with other power generation systems and provide long-term, sustainable energy storage makes them a key technology in achieving global energy security and reducing the environmental impact of power generation.
As energy storage needs grow, innovations in materials and turbine design will further enhance the performance and efficiency of steam turbines. The development of supercritical and ultra-supercritical steam turbines will allow for higher efficiencies in energy conversion, making steam turbines even more effective for use in energy storage systems. These advancements will help to optimize energy storage processes, reduce operational costs, and make steam turbines more competitive with other energy storage technologies, such as batteries and pumped hydro storage.
Lastly, as the focus on sustainability continues to drive the energy industry, life-cycle assessments (LCAs) of steam turbines will increasingly factor into their adoption in energy storage applications. The ability to minimize environmental impact throughout the turbine’s life— from manufacture to decommissioning— will be a key consideration for utilities and businesses investing in energy storage systems. Steam turbines, with their long lifespan, low operational costs, and fuel flexibility, are well-positioned to meet these demands, particularly in a future energy landscape where the focus will be on circular economy principles and the sustainable use of resources.
In conclusion, steam turbines are poised to become a critical technology in the world of energy storage, offering reliable, long-duration, and efficient solutions for both grid stability and backup power. As energy storage needs become more complex, steam turbines will continue to evolve, providing flexible, scalable, and sustainable solutions that can integrate seamlessly with renewable energy systems. With advanced turbine designs, digital optimization, and hybrid energy storage systems, steam turbines will help lead the way toward a cleaner, more resilient energy future.
As the global energy landscape continues to evolve, steam turbines for energy storage will increasingly be integrated into global decarbonization efforts, playing a pivotal role in supporting the transition to renewable energy sources while ensuring grid stability and power reliability. The growing emphasis on energy storage solutions will drive the continued innovation and application of steam turbines in both long-duration storage and power generation systems. These turbines, paired with advanced energy storage technologies, will help address challenges such as intermittent renewable generation, grid flexibility, and the need for backup power during periods of high demand.
In particular, the combination of energy storage and carbon-neutral technologies will be essential for achieving long-term sustainability goals. Steam turbines integrated into green hydrogen production and storage systems offer a compelling solution for decarbonizing energy storage and power generation. Green hydrogen, produced using renewable energy through electrolysis, can be stored and later converted into electricity using steam turbines. This method provides an effective means of energy storage that supports both grid stability and net-zero carbon emissions.
Moreover, steam turbines in hybrid energy storage systems will provide the flexibility needed to manage varying levels of renewable energy input. In these systems, steam turbines can complement other forms of energy storage, such as batteries and pumped hydro, by offering the ability to deliver long-duration power. Batteries are excellent for short-duration storage and fast response, but steam turbines excel at delivering sustained power over long periods. By combining these two technologies, hybrid systems can ensure that energy storage infrastructure meets both immediate and extended-duration energy needs, providing more comprehensive solutions for the grid.
The application of steam turbines will also evolve as the role of distributed energy resources (DERs) grows. These smaller, localized energy systems are becoming more popular as they offer flexibility and resilience, particularly in areas where grid reliability is a concern. Steam turbines used in microgrids or community-based energy storage systems can provide a reliable source of power during grid outages or periods of high demand. By integrating steam turbines with local renewable energy sources, these systems can help communities become more energy self-sufficient and reduce reliance on the central grid, improving both energy security and grid resilience.
As energy storage technologies continue to diversify, steam turbines will remain a strong contender in providing both scalability and economic viability. The modularity of steam turbines makes them suitable for a wide range of applications, from small-scale systems that serve individual buildings or communities to large, utility-scale facilities that provide grid support. Modular systems are also easier to install and maintain, allowing for faster deployment and cost-effective expansion. This makes them ideal for markets that require scalable and adaptable energy storage solutions, particularly in developing countries and remote regions where energy access is limited.
A key advantage of steam turbines in energy storage systems is their fuel flexibility, which provides an opportunity to integrate renewable, low-carbon fuels into the power generation process. For example, steam turbines can be operated on biomass, biogas, or renewable natural gas, allowing for a clean and sustainable means of generating electricity. This capability will be crucial in regions where renewable fuel availability is abundant but grid infrastructure is limited. By leveraging biofuels and other renewable resources, steam turbines can play a role in decarbonizing both the power generation sector and industrial processes, helping to accelerate the move toward a carbon-neutral future.
With the continued advancement of digital technologies, steam turbines are becoming smarter and more efficient. The integration of artificial intelligence (AI) and machine learning into turbine operations will enhance their ability to optimize performance and reduce maintenance costs. Predictive maintenance, for instance, uses sensors and data analytics to identify potential issues before they result in equipment failure, extending the lifespan of turbines and improving their overall reliability. These technologies will also allow steam turbines to more effectively interact with smart grids, ensuring that stored energy is distributed efficiently to where it is needed most.
In the context of grid-scale energy storage, the use of supercritical and ultra-supercritical steam turbines will become more common. These advanced turbines operate at higher temperatures and pressures, which increases their thermal efficiency and power output. By improving the efficiency of steam turbines in energy storage systems, these technologies can lower operational costs and reduce emissions, contributing to the overall goals of energy decarbonization and economic sustainability. Furthermore, steam turbines can be paired with thermal energy storage systems to create more efficient and cost-effective solutions for storing and generating electricity over extended periods.
The ongoing development of hybrid storage technologies—such as integrating steam turbines with battery storage and pumped hydro systems—will continue to expand the capabilities of energy storage. As storage systems become more sophisticated and interconnected, steam turbines will serve as the backbone for long-duration energy storage, offering the power generation capacity needed to maintain grid stability. These hybrid systems are designed to meet the full spectrum of energy needs, from providing rapid response to immediate power shortages to ensuring long-duration storage during periods of low renewable energy generation.
Lastly, as the demand for renewable energy continues to rise, steam turbines will increasingly play a role in integrating solar, wind, and geothermal energy sources into the power grid. By providing energy storage solutions that work seamlessly with renewable generation, steam turbines can smooth out the variability of these power sources, ensuring that energy is available when demand peaks. This will be particularly important as more countries move toward 100% renewable energy goals, requiring reliable and scalable energy storage systems that can support a renewable-dominant grid.
In conclusion, steam turbines are poised to play a central role in the future of energy storage and power generation. Their efficiency, fuel flexibility, and reliability make them well-suited for addressing the challenges posed by renewable energy integration, intermittent power generation, and long-duration energy storage needs. As energy storage systems evolve and hybrid technologies emerge, steam turbines will continue to offer flexible, scalable, and economically viable solutions that ensure grid stability and energy reliability. Their role in the decarbonization of the energy sector, combined with their ability to support sustainable power generation, positions steam turbines as a key technology in the transition to a cleaner, more resilient energy future.
Steam Turbines in Textile Industry
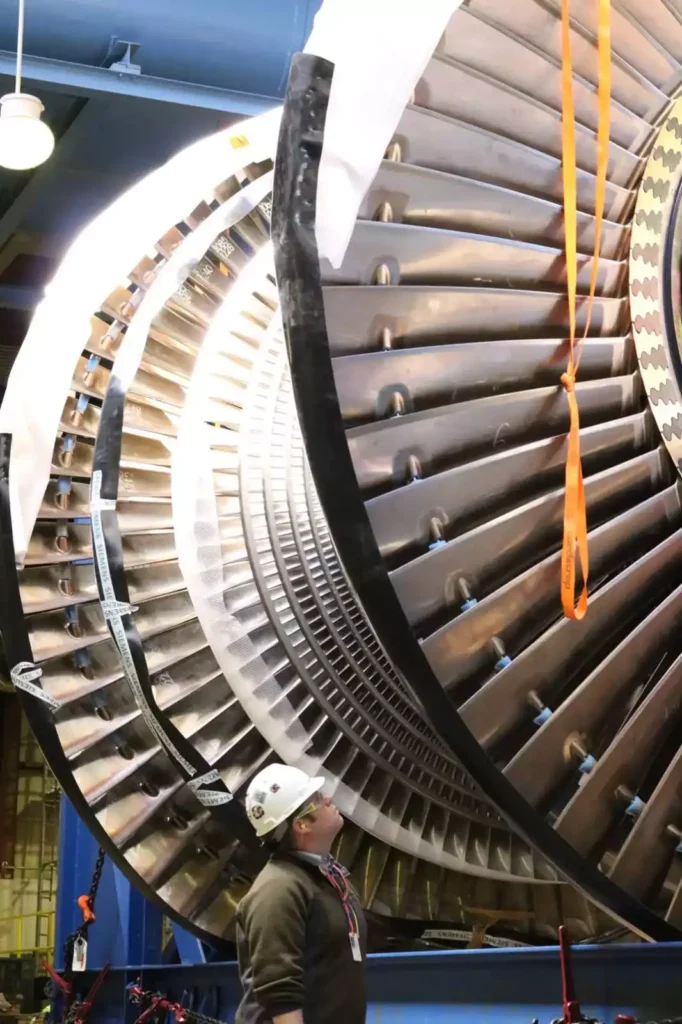
Steam turbines play a crucial role in the textile industry by providing reliable, efficient power for a wide range of processes, including spinning, weaving, dyeing, finishing, and other manufacturing stages. The textile industry, with its high energy demand, especially for heat, mechanical power, and electricity, benefits significantly from steam turbines due to their efficiency and fuel flexibility. These turbines are employed to generate the necessary mechanical energy that powers the various textile machines and to supply process steam, which is integral to many aspects of textile manufacturing.
One of the primary uses of steam turbines in the textile industry is in combined heat and power (CHP) systems, which produce both electricity and steam from a single fuel source. This is particularly advantageous in the textile sector, where both electrical power and steam are required in large quantities. Steam is essential for heating water, drying fabrics, dyeing, and finishing processes, while electricity is used to run machinery, control systems, and other plant operations. CHP systems offer a highly efficient solution by simultaneously meeting both electricity and heat demands, reducing energy costs and improving operational efficiency.
In many textile plants, steam turbines are integrated with boilers that convert various fuels, such as natural gas, biomass, or coal, into steam. The steam generated is then used to drive turbines, which in turn generate electricity. The power generated can either be used on-site to meet the factory’s needs or exported to the grid, providing additional revenue streams. By adopting CHP systems, textile manufacturers can significantly lower energy consumption and reduce operational costs.
Steam turbines are also used to drive mechanical equipment in textile plants. They are particularly effective for powering heavy machinery in textile mills, such as spinning machines, loom drives, and dyeing machines. The mechanical power provided by the steam turbines allows for efficient, high-speed production, contributing to increased throughput and improved productivity. Steam turbines, when used in conjunction with variable speed drives and advanced controls, can be finely tuned to match the specific power requirements of different processes, further enhancing energy efficiency and minimizing waste.
Another key benefit of steam turbines in the textile industry is their fuel flexibility. While many textile mills rely on traditional fuels like natural gas or coal, the trend is shifting toward using renewable fuels, such as biomass or waste materials from textile production itself. For example, the use of waste fabrics or wood chips as fuel sources can help reduce reliance on fossil fuels and lower overall carbon emissions. Steam turbines are highly adaptable to different types of fuels, allowing textile manufacturers to use a variety of feedstocks while still maintaining efficient and reliable power generation.
The energy efficiency of steam turbines is another reason they are favored in the textile industry. Steam turbines are capable of achieving high levels of thermal efficiency, particularly in combined-cycle or regenerative systems, where the waste heat from the turbine is used to generate additional steam or power. These systems help to maximize energy use, reduce fuel consumption, and lower operating costs. The ability to recover and reuse heat from the steam turbine exhaust is especially valuable in industries like textiles, where energy consumption is a significant portion of operational costs.
Moreover, steam turbines contribute to the sustainability efforts in the textile industry. With increasing regulatory pressure to reduce energy consumption and emissions, steam turbines provide a way to meet these requirements while also improving the bottom line. By using steam turbines for power generation and process steam, textile manufacturers can reduce their carbon footprint and energy intensity, contributing to a more sustainable operation. This is particularly important in the context of growing consumer demand for environmentally responsible products and sustainable manufacturing practices.
The textile industry also benefits from the reliability and durability of steam turbines. These turbines are designed for long service life and can handle the continuous, heavy-duty operation often required in industrial settings. The ability of steam turbines to operate reliably under fluctuating loads and varying operating conditions is crucial for maintaining production schedules and ensuring minimal downtime in textile mills.
In addition, steam turbines can be part of a cogeneration system in the textile industry, where excess steam or power can be used for other purposes within the facility. For example, surplus electricity from the turbine can be used for cooling systems or other equipment that require electricity, helping to further optimize energy use across the plant. Similarly, excess heat from the turbine can be directed toward other processes in the mill, such as water treatment or drying, further reducing energy consumption.
Lastly, with the digitization of industrial processes, advanced monitoring and control systems are being implemented in steam turbines to ensure optimal performance. Real-time data from sensors and machine learning algorithms can help predict maintenance needs, monitor efficiency, and optimize steam turbine operations. These innovations not only reduce the likelihood of unexpected failures but also enhance the overall energy efficiency of the system.
Overall, steam turbines are an integral part of the textile industry’s energy infrastructure. Their ability to provide both mechanical power and process steam through combined heat and power systems offers significant cost savings, increased energy efficiency, and enhanced sustainability. As the industry continues to move toward more environmentally friendly and energy-efficient practices, steam turbines will remain a vital technology in helping textile manufacturers meet their energy needs while reducing their environmental impact.
In addition to their role in power generation and process steam, steam turbines in the textile industry are also playing an increasingly important part in enhancing resource management and waste minimization strategies. By implementing closed-loop systems or cogeneration setups, textile manufacturers can optimize energy usage while minimizing waste. For example, excess heat from the steam turbines can be captured and reused for heating or cooling within the facility, reducing the need for external energy sources and making the plant more self-sufficient. This process not only increases energy efficiency but also helps in lowering fuel consumption and reducing greenhouse gas emissions.
Energy recovery through steam turbines can also be critical for textile mills that handle a variety of processes, including dyeing, washing, and finishing. These operations often require significant amounts of water and energy, leading to high costs and environmental concerns related to water treatment and waste discharge. By incorporating steam turbines into energy recovery systems, textile manufacturers can reuse heat from various parts of the production process, significantly lowering their operational costs and improving sustainability metrics.
Another growing area of importance is the ability to integrate renewable energy sources with steam turbine systems. With the global push toward carbon neutrality, textile plants are increasingly turning to biomass or biofuels to power steam turbines. Biomass—such as agricultural waste, sawdust, or textile production byproducts—can be burned to generate steam, creating a sustainable closed-loop system. This reduces reliance on fossil fuels and helps textile companies reduce their carbon emissions. Many textile plants are also exploring the potential of solar thermal energy or geothermal energy to produce steam, thus integrating a more diverse range of renewable sources into their operations.
Steam turbines can also contribute to enhancing the overall efficiency of textile mills by enabling greater automation in the energy management systems. With advanced controls and predictive maintenance systems, steam turbines can be fine-tuned to optimize performance, adapt to varying load conditions, and reduce energy waste. This means that turbines can automatically adjust their output based on the demand for both steam and electricity, ensuring that the plant operates efficiently without overproducing or consuming excessive resources. For example, if energy demand decreases during non-peak hours, the system can adjust the steam turbine’s output, ensuring that only the necessary amount of energy is being used.
Another innovative area where steam turbines are gaining traction is in off-grid or decentralized textile production. Many small-scale textile mills, particularly in developing regions, struggle with inconsistent access to grid electricity. Steam turbines can be used in these settings to provide both reliable power generation and process steam, often in a modular or containerized form that can be quickly deployed. By using locally available biomass or waste materials as fuel, these smaller plants can operate independently of the central grid, reducing energy costs and promoting local economic development. This decentralized model also helps reduce reliance on fossil fuels, contributing to a greener supply chain.
With the increasing focus on product traceability and supply chain transparency, steam turbines can help textile manufacturers meet sustainability goals that align with both consumer demand and regulatory requirements. As governments around the world tighten regulations on carbon emissions and environmental impact, manufacturers who adopt energy-efficient systems like steam turbines may gain an edge in the marketplace. These sustainable practices not only help reduce operational costs but also improve the brand image, making textile manufacturers more attractive to environmentally conscious consumers.
As global sustainability targets become more stringent, textile mills are facing pressure to improve water management and reduce the environmental impact of their waste, especially when it comes to chemical treatment and water use. Steam turbines, when combined with advanced water treatment technologies, can play a vital role in reducing water consumption and improving the recycling of water used in textile processes. By recovering heat from steam turbine exhausts, textile mills can reduce the need for additional water treatment and lower energy costs associated with heating water for industrial use.
Finally, the future of steam turbines in the textile industry is likely to involve more innovation around smart technology and digitalization. The rise of Industry 4.0, characterized by IoT (Internet of Things) sensors, data analytics, and cloud computing, means that steam turbines will become even more efficient and integrated into overall plant operations. By using real-time monitoring and machine learning algorithms, manufacturers will be able to optimize turbine performance, reduce wear and tear, and predict maintenance needs before they occur. These advancements will enable mills to maximize uptime, minimize production delays, and further reduce costs while ensuring a sustainable operation.
In conclusion, steam turbines are not only essential for meeting the textile industry’s power and steam demands but are also an integral part of a sustainable, energy-efficient, and environmentally responsible future. By enabling combined heat and power systems, supporting renewable energy integration, optimizing energy use, and contributing to waste minimization, steam turbines offer textile manufacturers an opportunity to enhance both their economic performance and their environmental footprint. The ongoing development of advanced steam turbine technologies, coupled with digitalization and automation, will continue to shape the future of textile production, creating new opportunities for cost savings, sustainability, and energy efficiency.
As the textile industry continues to face mounting pressure to reduce its environmental impact while maintaining competitiveness, steam turbines are increasingly seen as a solution that aligns with both economic efficiency and sustainable practices. The integration of steam turbines with advanced power generation systems, including combined-cycle plants or regenerative systems, is expected to further optimize energy use and ensure that the industry meets emerging carbon reduction goals.
Steam turbines can also be utilized to optimize waste heat recovery, a crucial step in minimizing energy losses. Many textile processes, especially dyeing, drying, and finishing, generate large amounts of excess heat. This heat, often discarded as waste, can be captured and converted into useful energy, either to power the steam turbine or to be used for heating and cooling purposes elsewhere in the plant. Heat exchangers and heat recovery systems are designed to capture this waste heat, further improving the overall thermal efficiency of the plant. By integrating these systems with steam turbines, textile manufacturers can increase energy efficiency by up to 30%, reducing their reliance on external energy sources and lowering overall operational costs.
In textile mills, where the production processes can operate 24/7, consistent and reliable power is a fundamental requirement. Steam turbines, known for their durability, long service life, and reliable performance under varying loads, provide an ideal solution to meet these needs. With their robust design and low-maintenance requirements, steam turbines offer textile mills a reliable means of generating continuous power and steam without compromising on performance. This reliability is particularly important in an industry where production interruptions can lead to costly downtimes and potential delays in fulfilling customer orders.
As the demand for more sustainable fabrics and eco-friendly production practices grows, textile manufacturers are also turning to steam turbines as part of their broader corporate sustainability strategies. Sustainable textiles, including organic cotton, recycled fabrics, and low-impact dyes, often require energy-intensive processing. By utilizing efficient steam turbine systems powered by biomass, solar, or wind energy, textile manufacturers can reduce the carbon intensity of their production, aligning with eco-conscious consumer trends and meeting the growing demand for responsibly sourced fabrics.
One of the key benefits of integrating biomass-powered steam turbines into textile manufacturing is the potential to close the loop on waste. By utilizing waste fibers, organic waste from production, or other renewable biomass materials, textile mills can produce their own energy on-site, making the production process more circular and less dependent on external fuel sources. This can help reduce waste sent to landfills while simultaneously lowering energy costs and improving sustainability. Additionally, the use of renewable fuels in steam turbines can help textile manufacturers meet sustainability certifications and improve their reputation as green companies, which is increasingly becoming a competitive advantage in the marketplace.
The importance of resource efficiency in the textile industry cannot be overstated. From water and energy usage to the reduction of chemical waste and other pollutants, every aspect of textile manufacturing contributes to environmental impacts. Steam turbines can play a pivotal role in minimizing energy usage and reducing emissions by enabling more efficient thermal management. Furthermore, the ability to recover waste heat through integrated systems allows for greater resource recovery, helping companies make the most of every unit of energy consumed. These capabilities are particularly significant in regions where resource scarcity, such as water or electricity shortages, can pose a major challenge to industrial operations.
As the industry embraces smart manufacturing, steam turbines will become even more intelligent and adaptable. The integration of advanced monitoring systems, artificial intelligence, and data analytics will allow for precise management of steam turbine operations, identifying inefficiencies or potential issues before they become significant problems. This will lead to greater uptime, better performance optimization, and improved cost control. Smart technologies will also help operators track energy usage patterns, which can be used to further optimize the entire production process for greater energy conservation and lower costs.
Looking forward, the evolution of steam turbine technology in the textile industry is likely to focus on smaller, modular turbine designs that can be easily scaled according to a facility’s specific needs. As demand for decentralized and off-grid systems grows, the ability to quickly deploy compact steam turbine systems will offer textile manufacturers in remote or developing regions a feasible means of power generation and energy independence. Modular systems are also easier to integrate into existing infrastructure, minimizing disruption and lowering installation costs. This adaptability makes steam turbines ideal for the growing trend of small-scale, localized textile production.
Steam turbines are also set to play an important role in the global push for energy decarbonization. As the textile industry seeks to reduce its reliance on fossil fuels and move toward net-zero emissions goals, steam turbines powered by renewable fuels or green hydrogen will become increasingly important. Steam turbines’ ability to efficiently generate electricity and process steam from renewable sources positions them as a key enabler of the energy transition, allowing textile manufacturers to maintain high production rates while adhering to global environmental targets.
In conclusion, steam turbines will continue to be a cornerstone of the textile industry’s energy infrastructure, offering both economic and environmental benefits. Their ability to provide reliable power and process steam, integrate with renewable energy sources, and optimize resource efficiency will make them an invaluable tool for textile manufacturers aiming to reduce operational costs and carbon footprints. As the industry increasingly prioritizes sustainability, steam turbines will play a critical role in helping companies meet both regulatory standards and consumer demand for eco-friendly textiles. Their long-term potential for improving energy efficiency, coupled with innovations in fuel flexibility, smart technology, and waste heat recovery, ensures that steam turbines will remain at the forefront of industrial energy solutions in the textile sector for many years to come.
Looking into the future of steam turbines in the textile industry, we can expect a continued focus on optimization and innovation to enhance both efficiency and sustainability. As textile production becomes more energy-intensive due to evolving market demands for higher-quality and specialty fabrics, steam turbines will remain essential in enabling manufacturers to meet these challenges while minimizing costs and their environmental footprint.
Emerging Technologies will further enhance the role of steam turbines in the textile industry. One such innovation is the development of supercritical and ultra-supercritical steam turbines, which operate at higher pressures and temperatures, achieving even greater thermodynamic efficiency. These advanced turbines allow for more efficient conversion of heat into energy, meaning textile mills could achieve higher performance with lower fuel input. This could significantly improve the energy efficiency of the overall textile manufacturing process and contribute to reducing operating expenses and carbon emissions.
Furthermore, as the push for decarbonization strengthens, the adoption of green hydrogen as a fuel source for steam turbines in textile mills will become more feasible. Hydrogen can be used to produce steam, and when paired with turbines, it can help reduce the carbon intensity of textile operations. Green hydrogen, produced via the electrolysis of water using renewable energy, holds particular promise for the textile industry, as it offers a clean fuel alternative that can be used without contributing to air pollution or greenhouse gas emissions.
The evolution of control systems in steam turbines will also be vital for maximizing energy efficiency in textile production. Advanced sensors, machine learning algorithms, and predictive analytics are expected to be increasingly integrated into steam turbines, enabling them to operate more effectively and with minimal waste. These technologies will allow for real-time monitoring of turbine performance, optimizing their output to match fluctuations in demand and ensuring that energy is only used when needed, without excess consumption. Such smart capabilities also allow manufacturers to conduct proactive maintenance, avoiding costly downtimes and enhancing the longevity of turbines.
As the global textile industry faces increasing pressure to improve supply chain transparency, ethically sourced materials, and low-carbon production, steam turbines will play an integral role in ensuring that these commitments can be met while maintaining economic competitiveness. Through the use of steam turbines, textile manufacturers can align their operations with environmental, social, and governance (ESG) criteria, responding to the growing demand from both consumers and regulators for more sustainable products and processes. Eco-labeling certifications, which require adherence to specific sustainability standards, are increasingly being linked to energy efficiency and emissions reduction. By utilizing energy-efficient steam turbines, textile manufacturers can meet these requirements, improve their marketability, and respond effectively to the rising consumer demand for sustainable textiles.
Moreover, as the circular economy continues to evolve, steam turbines may become an integral component of closed-loop systems within textile manufacturing. The ability to recover, reuse, and repurpose materials—whether through recycling waste fibers, water reuse, or the integration of renewable energy sources—requires energy-efficient technologies that can optimize overall resource utilization. Steam turbines not only provide power for these systems but can also enable the recovery of heat that would otherwise be lost in traditional processes, further enhancing the circularity of textile production.
In regions where the textile industry is expanding rapidly—particularly in developing countries—distributed energy solutions that rely on steam turbines could help address energy access issues. Many of these areas face challenges in accessing a stable power grid, and steam turbines, often powered by locally available biomass or waste, could offer a more sustainable and reliable solution for decentralized power generation. This would allow textile plants to remain operational without being dependent on unreliable grid infrastructure, providing economic benefits while also reducing environmental impact.
The development of modular steam turbine systems will also offer significant advantages to the textile industry. Modular solutions, where turbines are designed to be smaller and scalable, allow textile manufacturers to expand or downsize their systems as their needs evolve. These systems can be quickly deployed and installed without the complexity of large-scale infrastructure changes, making them ideal for dynamic production settings. Additionally, the flexibility of modular systems can accommodate future upgrades or expansions, ensuring that textile manufacturers are well-prepared for the growing demand for more sustainable and efficient textile products.
Finally, as the industry increasingly embraces digital transformation, the role of data-driven decisions will become crucial. Textile manufacturers can leverage big data and IoT connectivity to monitor energy consumption across their entire operations. By collecting and analyzing data from steam turbines, boilers, and other equipment, companies can make informed decisions about energy management, optimizing energy use, reducing waste, and achieving better operational performance. This data can also support broader corporate sustainability goals by tracking carbon emissions and other environmental impacts in real time, allowing manufacturers to make adjustments quickly and efficiently.
In conclusion, steam turbines in the textile industry are set to evolve from a reliable, energy-efficient solution to a cornerstone of the industry’s sustainability and energy transition strategies. As the demand for greener, more efficient textile production increases, steam turbines will play an indispensable role in improving energy efficiency, reducing carbon emissions, and enabling innovative production methods. From the continued integration of renewable energy and waste heat recovery to the development of smart control systems and decentralized energy solutions, steam turbines will help drive the textile industry’s shift toward a more sustainable and economically efficient future. The ability to combine energy efficiency, resource recovery, and sustainability goals through steam turbines will make them a critical tool in shaping the next generation of textile manufacturing.
Steam Turbines in Pulp and Paper Mills
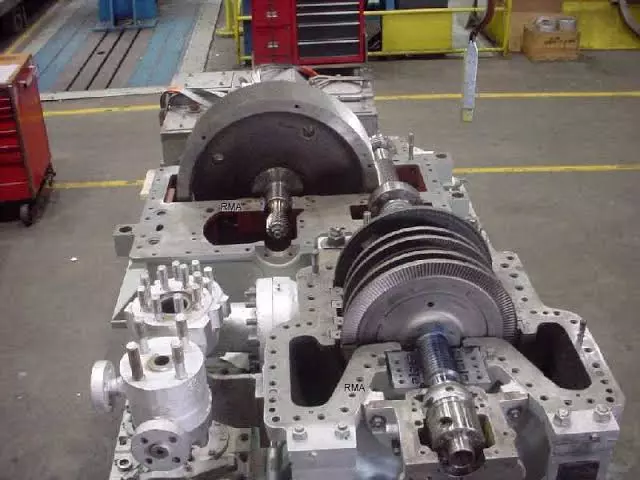
Steam turbines are a critical component in the pulp and paper industry, playing a vital role in power generation, process steam production, and overall plant efficiency. Pulp and paper mills typically require significant amounts of both electricity and process steam for their operations, including for pulping, drying, and finishing paper products. Steam turbines, by providing reliable power generation and heat recovery, contribute to reducing energy costs and improving the sustainability of the pulp and paper industry.
In pulp and paper mills, process steam is used extensively in several stages of production, such as for cooking wood chips during the pulping process, drying paper sheets, and bleaching pulp. Steam turbines can generate electricity while also producing steam that can be integrated into the mill’s internal energy system, enabling a combined heat and power (CHP) solution. This integration makes it possible to efficiently utilize the energy generated from the combustion of biomass, black liquor, or other waste materials produced by the mill. The implementation of a CHP system through steam turbines allows mills to maximize their energy recovery and reduce reliance on external energy sources, resulting in significant cost savings.
One of the major advantages of using steam turbines in pulp and paper mills is their ability to generate power from renewable sources, particularly biomass. Pulp and paper mills often have access to large quantities of biomass feedstock, such as wood chips, bark, or paper sludge, which can be used as fuel to fire boilers and produce steam. Steam turbines can convert the heat from these renewable fuels into electrical energy and process steam, creating a closed-loop system that reduces the mill’s reliance on fossil fuels and minimizes greenhouse gas emissions. By incorporating biomass as a fuel source, pulp and paper mills can improve their sustainability profile and meet the growing demand for eco-friendly production processes.
Another key benefit of steam turbines in the pulp and paper industry is their efficiency. The process of converting heat into electricity and steam through steam turbines can be highly efficient, especially when paired with advanced turbine designs and optimized system configurations. For example, high-efficiency steam turbines designed to operate at supercritical or ultra-supercritical pressures can achieve higher thermal efficiency, resulting in greater energy output with less fuel input. By improving energy efficiency, steam turbines help mills reduce fuel consumption, lower operational costs, and decrease their overall carbon footprint.
Beyond improving operational efficiency, steam turbines also play a crucial role in reducing water consumption in pulp and paper mills. Water is used extensively in various stages of production, from pulping to paper drying, and the management of water resources is a key consideration for sustainability. By using steam turbines in cogeneration and waste heat recovery systems, pulp and paper mills can optimize the use of water in their processes. Excess heat from the steam turbine can be used to pre-heat water before it is used in the plant, reducing the amount of water required for heating and minimizing water waste. Moreover, steam turbines can contribute to water treatment efforts by facilitating the recovery of condensate from the steam system, which can be purified and reused, reducing the need for fresh water intake.
The integration of steam turbines with advanced automation systems and predictive maintenance technologies can further enhance the performance and reliability of pulp and paper mills. Through the use of IoT sensors and data analytics, steam turbines can be monitored in real time, allowing operators to track performance metrics, identify potential issues, and perform predictive maintenance before equipment failures occur. By reducing downtime and ensuring optimal operation, these systems help mills achieve better performance, reduce repair costs, and extend the lifespan of their equipment.
Additionally, steam turbines can contribute to the pulp and paper industry’s efforts to meet regulatory requirements and environmental standards. The increasing focus on sustainability and the need to reduce carbon emissions have led to stricter environmental regulations for industrial sectors, including the pulp and paper industry. By incorporating steam turbines into their operations, mills can improve their energy efficiency, lower greenhouse gas emissions, and meet emission reduction targets. Steam turbines also offer the flexibility to be integrated with carbon capture technologies that can capture CO2 emissions from the mill’s flue gases, further enhancing the mill’s sustainability credentials.
Steam turbines can also be used to provide backup power during times of grid instability or during scheduled maintenance. In remote areas or locations where the power grid is unreliable, steam turbines offer a reliable backup power source to ensure continuous operations. This is particularly important in pulp and paper mills, where production interruptions can be costly and lead to delays in order fulfillment. By having a steam turbine system in place, mills can ensure that power is available when needed, even during unexpected disruptions to the grid.
The future of steam turbines in pulp and paper mills will likely involve further innovations in turbine design and system integration. As the industry continues to focus on digital transformation, advancements in smart manufacturing and advanced analytics will enable pulp and paper mills to optimize their steam turbine systems even further. Artificial intelligence (AI) and machine learning can be used to analyze data from steam turbines and other plant equipment to identify trends, predict maintenance needs, and optimize energy use in real-time. These technologies will help mills improve their overall productivity and sustainability while reducing operational costs and energy waste.
In conclusion, steam turbines are essential for driving efficiency and sustainability in the pulp and paper industry. Through their ability to provide combined heat and power, use renewable fuels like biomass, and optimize energy recovery, steam turbines enable pulp and paper mills to improve cost efficiency, reduce environmental impact, and meet regulatory requirements. As the industry continues to evolve, the integration of advanced technologies such as predictive maintenance and smart manufacturing will further enhance the role of steam turbines in supporting sustainable and efficient operations. Ultimately, the continued development of steam turbines will help the pulp and paper industry meet the growing demand for eco-friendly production while remaining competitive in an increasingly sustainability-conscious global market.
As the pulp and paper industry moves toward more sustainable practices, the integration of steam turbines into production processes becomes even more critical. Future developments will likely include more efficient turbine designs that not only increase energy output but also minimize environmental impact. With rising energy prices and stricter environmental regulations, pulp and paper mills are under increasing pressure to reduce energy consumption while maintaining high production rates.
One of the key areas of innovation in the use of steam turbines will be the integration with renewable energy sources. In addition to biomass, steam turbines in pulp and paper mills could also be paired with solar or wind power to provide an even more sustainable energy mix. These hybrid systems would allow mills to operate on renewable energy during times of high availability, reducing the reliance on non-renewable fuels. The ability to integrate renewable sources with traditional biomass-fueled systems will provide a flexible and adaptable energy solution that can help mills meet both financial goals and environmental commitments.
Moreover, as the global focus on carbon neutrality intensifies, pulp and paper mills will likely invest more in carbon capture and storage (CCS) technologies. Steam turbines can play an important role in supporting these efforts. By working in tandem with CCS systems, steam turbines can help capture and store carbon dioxide (CO2) emissions produced during biomass combustion. The captured CO2 can be transported and stored underground or utilized in other industries, such as for enhanced oil recovery or for the production of sustainable chemicals. Integrating carbon capture with steam turbines allows mills to reduce their carbon footprint and demonstrate a commitment to sustainability.
Another promising development is the potential for advanced steam turbine technology that incorporates artificial intelligence (AI) and machine learning to predict the best operational conditions for optimal performance. By analyzing large volumes of data from sensors and monitoring systems, AI can identify patterns in turbine efficiency and suggest adjustments that can improve energy consumption or detect issues before they cause a system failure. Predictive maintenance tools powered by AI can reduce unplanned downtime and help mills avoid costly repairs by addressing potential problems early. This technology will also make it easier for operators to run systems at maximum efficiency, saving on fuel and improving overall plant performance.
The future role of steam turbines in the pulp and paper industry also aligns with the increasing trend toward circular economy principles. As pulp and paper mills focus on reducing waste and improving resource recovery, steam turbines can be integral to creating a closed-loop system. By utilizing waste materials, such as wood chips, paper sludge, or other biomass waste products, mills can convert what would otherwise be discarded into valuable energy. The use of waste-to-energy technologies, including steam turbines, helps mills reduce their waste streams while simultaneously meeting energy demands. This circular approach not only helps improve profitability but also lowers environmental impact by decreasing landfill contributions and minimizing the need for external energy sources.
Additionally, modular steam turbine systems will likely gain more traction as the pulp and paper industry seeks to become more agile and adaptable. Smaller, modular turbines can be easily scaled to meet fluctuating demands, allowing mills to better manage their energy use and make cost-effective upgrades as production needs evolve. The ability to add or remove modules without significant downtime allows mills to maintain continuous operations while optimizing energy production. This flexibility is especially valuable for regional mills or those operating in emerging markets, where the ability to adjust capacity as production demands change can lead to cost savings and a more responsive manufacturing process.
The integration of energy storage with steam turbines could also offer a significant benefit to pulp and paper mills, particularly for those mills that operate in regions with intermittent power supply or fluctuating energy prices. Energy storage systems, such as batteries or thermal storage technologies, could store excess energy produced during periods of low demand or high turbine efficiency. This energy could then be used during peak demand times, reducing the need to purchase expensive grid electricity or to operate backup generators. By coupling energy storage with steam turbines, pulp and paper mills could significantly improve their energy resilience and further reduce operating costs.
Energy recovery technologies, including heat exchangers and waste heat boilers, will continue to be an essential part of steam turbine integration in pulp and paper mills. Steam turbines can be paired with heat recovery systems to capture and repurpose excess heat from other parts of the mill. This recovered energy can be used to power additional operations or heat water, reducing the need for external energy sources and improving overall thermal efficiency. With the growing importance of energy efficiency in the pulp and paper sector, steam turbines will be at the center of efforts to reduce energy consumption across the industry.
Lastly, as the push toward digital transformation accelerates, cloud-based energy management platforms will provide greater visibility into steam turbine operations. These platforms will enable operators to monitor steam turbine performance remotely and analyze data from across the plant to identify areas for improvement. By having access to detailed analytics, plant managers can make better decisions about energy use, improve operational efficiency, and meet sustainability targets. Moreover, real-time performance data will help prevent issues before they arise, increasing plant uptime and decreasing maintenance costs.
In conclusion, steam turbines will continue to be indispensable to the pulp and paper industry’s efforts to improve energy efficiency, reduce environmental impact, and enhance operational resilience. As the industry evolves, we will see greater adoption of renewable energy sources, advanced turbine designs, and smart technologies to maximize turbine performance. Whether through biomass energy, circular economy practices, or advanced automation and energy storage, steam turbines will help pulp and paper mills meet the growing demand for sustainable production while remaining economically viable in a rapidly changing global market. With a continued focus on technological innovation and energy efficiency, steam turbines will remain a cornerstone of the industry’s drive toward more sustainable, cost-effective, and environmentally responsible manufacturing.
Looking ahead, steam turbines in the pulp and paper industry will increasingly serve as a linchpin for the sector’s decarbonization goals and its overall push toward sustainability. As the global focus on climate change intensifies and industries are pressured to reduce their carbon emissions, the pulp and paper sector must explore innovative methods to decarbonize operations. Steam turbines are poised to play a critical role in this transformation by enabling mills to improve energy efficiency, minimize waste, and transition to renewable and low-carbon energy sources.
One avenue for further reducing emissions is the increasing use of biomass-based fuels in combination with steam turbines. Pulp and paper mills have access to significant quantities of biomass materials from wood waste, paper sludge, and other byproducts generated during production. By converting these waste products into energy, mills can significantly reduce the need for fossil fuels, thereby lowering their carbon footprint. The continued development of advanced combustion technologies paired with steam turbines will enable more efficient conversion of these renewable fuels into process steam and electricity, further advancing carbon-neutral operations.
A key focus in improving the performance of steam turbines in the pulp and paper sector will be on enhancing their operational flexibility. As renewable energy sources like solar and wind become more prevalent, the ability to adjust steam turbine operations in response to fluctuations in renewable energy production will be increasingly important. This flexibility will allow pulp and paper mills to integrate renewable energy more effectively while maintaining a reliable power supply, even during periods of low renewable generation. Steam turbines can act as a balancing force that helps stabilize power output when there are variations in renewable energy availability, ensuring that mills maintain consistent operations without relying solely on grid electricity.
In addition to renewable energy, steam turbines in pulp and paper mills will likely integrate with energy storage solutions, which can help balance the intermittent nature of renewable energy sources. Thermal energy storage systems could capture excess heat generated by steam turbines and store it for later use. This stored heat can be used during periods of high demand or when renewable energy sources are insufficient. Similarly, electrical energy storage systems, such as batteries, could store excess electricity generated during times of low mill demand. By integrating these energy storage systems, steam turbines will help optimize the energy use within the pulp and paper plant, reducing costs and ensuring a stable and sustainable energy supply.
The need for smart factory technologies will also drive the evolution of steam turbines in the pulp and paper industry. As more mills embrace the digital transformation of their operations, the use of advanced monitoring systems, AI-based predictive analytics, and IoT technologies will enable steam turbines to operate at peak efficiency. By collecting and analyzing data from turbines, boilers, and other components in real time, pulp and paper mills can make more informed decisions on maintenance, performance tuning, and resource optimization. This data-driven approach can extend the lifespan of steam turbines, reduce energy consumption, and avoid unplanned downtime, all of which contribute to improving cost-effectiveness and sustainability.
Furthermore, modular turbine designs will become more attractive in the pulp and paper industry as mills look for scalable solutions to match their production needs. These modular systems offer the flexibility to expand or reduce capacity as required, making them ideal for mills that experience fluctuations in production demand or are located in regions where energy requirements change seasonally. By allowing for easy scalability, these turbines provide an adaptable solution that fits well with the growing trend of more customized and dynamic production processes in the pulp and paper industry. The ability to scale the power generation system without requiring major infrastructure changes helps mills meet energy needs more efficiently, even as their production volumes fluctuate.
Additionally, the continued push toward zero-waste operations in the pulp and paper sector will further drive the integration of steam turbines in resource recovery efforts. By optimizing the heat recovery from turbines, mills can further improve their energy utilization, reusing steam and other byproducts within the plant. This closed-loop system reduces the need for external energy inputs, lowers operational costs, and minimizes environmental impact. The ability to recover and reuse energy generated from the steam turbine process also aligns with the increasing adoption of circular economy principles within the industry, where materials and energy are continuously reused and recycled to minimize waste.
Steam turbines will also contribute to regulatory compliance as the industry faces stricter environmental standards. Many countries are implementing regulations aimed at reducing industrial emissions and promoting more energy-efficient manufacturing processes. By integrating advanced steam turbine technology, pulp and paper mills can meet stringent emissions standards while optimizing their operations. The transition to low-carbon fuels, coupled with the use of carbon capture technologies (such as post-combustion capture systems for CO2), will enable mills to continue operating within regulatory frameworks while contributing to the global push for carbon neutrality.
Finally, the importance of energy independence will continue to grow, particularly for mills located in remote areas or regions where grid electricity is unreliable. Steam turbines can be used to generate power locally, ensuring continuous mill operations even during power outages or disruptions. This decentralization of power generation enhances energy resilience and allows mills to operate with greater autonomy. Additionally, distributed power systems powered by steam turbines and fueled by biomass or other locally available resources can reduce transportation and fuel costs, providing economic benefits to pulp and paper mills, especially in regions where access to the central power grid is limited.
In conclusion, the role of steam turbines in the pulp and paper industry will become even more integral as the sector shifts towards sustainable, energy-efficient, and carbon-neutral operations. With their ability to integrate renewable fuels, energy storage, smart technologies, and circular economy practices, steam turbines will remain a cornerstone in the efforts to optimize energy use, reduce emissions, and improve the economic viability of pulp and paper mills. By leveraging advanced turbine designs, data-driven solutions, and renewable energy sources, steam turbines will help pulp and paper mills meet the challenges of a rapidly changing global market while improving their environmental footprint and operational efficiency. The future of the pulp and paper industry is undoubtedly intertwined with the evolution of steam turbine technology, enabling manufacturers to meet growing global demand for sustainable products in an increasingly competitive and eco-conscious marketplace.
As the pulp and paper industry continues to evolve, steam turbines will play an even more significant role in enhancing the sector’s ability to meet both economic and environmental challenges. With the growing demand for sustainable practices and green manufacturing, the integration of steam turbines into the production process will drive further innovations in how the industry utilizes energy, manages waste, and adopts eco-friendly technologies. Several emerging trends and innovations will likely shape the future of steam turbines in the pulp and paper industry:
One of the emerging trends is the advancement in turbine materials and technology. Researchers and manufacturers are continually developing new materials that improve the performance, efficiency, and lifespan of steam turbines. Materials that are more resistant to wear, corrosion, and high temperatures will allow steam turbines to operate at higher pressures and temperatures, leading to even better energy efficiency. Alloy coatings and ceramic-based materials are examples of such innovations that can enhance the durability and performance of turbines, reducing the frequency of maintenance and extending the overall service life of the turbines. This not only improves the cost-effectiveness of the turbines but also contributes to the long-term sustainability of pulp and paper mills.
Additionally, hybrid steam turbine systems could become a significant area of development. These systems would combine steam turbines with other energy-generation technologies, such as gas turbines, solar panels, or wind turbines, to create a more flexible and resilient energy supply. By integrating multiple energy sources, pulp and paper mills can better manage fluctuations in energy availability and optimize their energy output to meet varying production demands. For example, during times of high renewable energy generation, such as sunny or windy days, solar or wind power could supplement the steam turbines, reducing the reliance on biomass or fossil fuels. This hybrid approach could lead to significant reductions in carbon emissions and improved overall energy efficiency.
The future of steam turbines in the pulp and paper industry will also be closely linked to the advancement of smart grid systems. Smart grids allow for more efficient energy distribution and the integration of renewable energy sources into the overall grid. Steam turbines in pulp and paper mills can be connected to these grids, enabling the plant to both consume and produce energy more effectively. For instance, during periods of excess energy production from renewable sources, excess power generated by steam turbines can be fed back into the grid, helping stabilize the energy supply. Conversely, when energy demand spikes, the mill can draw power from the grid, ensuring continuous operations without the need for expensive backup generators. The ability to interact with the grid will allow pulp and paper mills to become part of the larger energy ecosystem, further improving their energy management capabilities and reducing energy costs.
Energy storage technology will continue to play a critical role in the future of steam turbines in the pulp and paper industry. As renewable energy sources become more common, energy storage solutions will be needed to address their inherent intermittency. Steam turbines can be integrated with thermal energy storage systems, which store excess heat produced during turbine operation for later use. This stored thermal energy can be used when there is a demand for steam or electricity, reducing the reliance on non-renewable energy sources and improving the overall efficiency of the energy system. Additionally, battery storage systems can be used in conjunction with steam turbines to store electrical energy for future use, further improving energy resilience and cost-effectiveness.
Decentralized energy systems powered by steam turbines could also gain prominence as a solution for pulp and paper mills looking for energy independence. In remote locations, where access to the main power grid may be limited or unreliable, steam turbines can provide a self-sufficient power generation system. Using locally sourced biomass or waste products as fuel, these turbines can generate both electricity and process steam without relying on external power suppliers. This not only reduces energy costs for mills but also enhances their energy security by providing a reliable and localized energy source. Moreover, decentralized systems can be optimized to meet the specific energy needs of a particular mill, ensuring that the energy generated is used as efficiently as possible.
As part of the broader push for resource efficiency, waste heat recovery will continue to be a key area of focus for steam turbines in the pulp and paper industry. Recovery of excess heat from turbine exhaust can be used to pre-heat water or generate additional steam, further improving the energy efficiency of the plant. This is particularly important for mills that operate in areas where energy costs are high or where there is a strong push for sustainability. The ability to recover waste heat and convert it into useful energy helps reduce the mill’s overall energy consumption and lowers its environmental impact. Steam turbines, when integrated into a comprehensive waste heat recovery system, can significantly improve the thermal efficiency of the entire plant, making operations more sustainable and cost-effective.
Automation and digitalization will also continue to enhance the performance of steam turbines. The use of sensors, IoT devices, and data analytics allows mills to gather real-time information about turbine performance and detect potential issues before they result in equipment failure. By employing predictive maintenance techniques, mills can avoid unexpected downtime and reduce the costs associated with emergency repairs. Machine learning algorithms can analyze historical and real-time data to optimize turbine operations, making them more energy-efficient and less prone to breakdowns. As these digital tools evolve, the level of control and optimization that pulp and paper mills can achieve over their steam turbine systems will increase, leading to higher efficiency, better resource utilization, and reduced operational costs.
Lastly, the implementation of carbon capture and storage (CCS) technologies will become more widespread in the pulp and paper industry. By capturing CO2 emissions from the combustion of biomass or other fuels used to generate steam, mills can reduce their carbon footprint and contribute to global efforts to mitigate climate change. Steam turbines, when integrated with CCS technologies, can help pulp and paper mills achieve carbon-neutral operations. This will not only allow mills to comply with increasingly stringent environmental regulations but also position them as leaders in sustainable manufacturing practices.
In conclusion, the future of steam turbines in the pulp and paper industry is filled with potential for innovation and growth. With advancements in turbine materials, hybrid energy systems, energy storage, smart grids, and waste heat recovery, steam turbines will continue to play a central role in improving energy efficiency, reducing emissions, and driving sustainable practices. By integrating smart technologies, embracing renewable energy sources, and optimizing resource recovery, pulp and paper mills will be able to meet the growing demand for eco-friendly and energy-efficient products. Ultimately, steam turbines will help the industry navigate its transition to a more sustainable and carbon-conscious future, while remaining economically competitive in a global market.
Steam Turbines in Petrochemical Plants
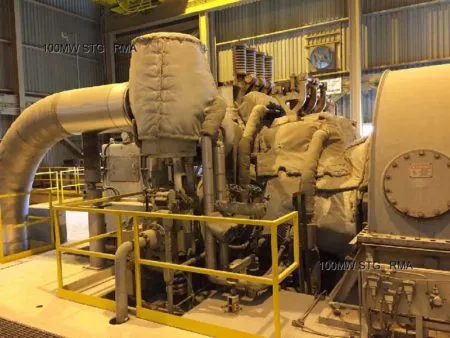
Steam turbines play a crucial role in petrochemical plants, where they are employed for a variety of functions to optimize energy generation, improve operational efficiency, and ensure sustainable production. Petrochemical plants are energy-intensive facilities that process natural gas, crude oil, and other raw materials into essential chemicals, plastics, and synthetic materials. Steam turbines, as an integral part of these plants, provide the required mechanical power for the plants’ processes while also helping to manage energy consumption and reduce environmental impact.
One of the primary functions of steam turbines in petrochemical plants is to generate electricity and process steam. These turbines are often connected to boilers, which convert the energy from combustion of fuels like natural gas, oil, or other industrial byproducts into high-pressure steam. The steam is then passed through the turbine, which converts the thermal energy into mechanical energy, driving the turbine shaft to generate electricity or provide mechanical power for pumps, compressors, and other essential equipment within the plant. This combination of electrical power generation and mechanical power makes steam turbines a versatile and efficient solution for petrochemical operations.
In addition to their primary role in electricity generation, steam turbines in petrochemical plants are often part of a larger cogeneration system or combined heat and power (CHP) system. These systems are designed to simultaneously generate electricity and useful thermal energy (such as steam) for industrial processes. Cogeneration systems allow petrochemical plants to optimize their energy use by utilizing waste heat, thus improving the overall efficiency of the plant. The integration of steam turbines into these systems reduces fuel consumption, lowers greenhouse gas emissions, and enhances the overall sustainability of the facility.
Energy efficiency is a critical consideration in petrochemical plants, given the high energy demands of the industry. Steam turbines can significantly improve energy efficiency by recovering waste heat from the combustion process and other stages of production. Heat recovery steam generators (HRSGs) can capture the waste heat from exhaust gases and utilize it to generate additional steam, which is then fed back into the steam turbine system. This closed-loop system reduces the need for additional fuel and minimizes energy losses. By maximizing the utilization of available energy, steam turbines help petrochemical plants lower their operational costs and meet environmental sustainability targets.
The integration of biomass and alternative fuels with steam turbines in petrochemical plants is another area of growth. As the industry works to transition toward more sustainable practices, the use of renewable fuels such as biomass, biofuels, or waste-derived fuels in place of traditional fossil fuels becomes increasingly important. These fuels can be burned in boilers to produce steam for the turbines, reducing the carbon footprint of the plant. Petrochemical plants using biomass-derived steam turbines can significantly reduce carbon emissions, making them a key part of the industry’s move towards greener production.
Another area where steam turbines contribute to the sustainability of petrochemical plants is through the adoption of carbon capture, utilization, and storage (CCUS) technologies. These technologies aim to capture carbon dioxide (CO2) emissions from the combustion process and other sources within the plant and store or utilize them in a way that prevents their release into the atmosphere. Steam turbines, by being part of the energy generation process, are inherently tied to CCUS efforts. By incorporating CCUS systems into their operations, petrochemical plants can significantly reduce their greenhouse gas emissions and move toward a more carbon-neutral future.
Modular steam turbine systems offer another important advantage in the petrochemical industry. These modular systems are designed to be easily scaled up or down to meet the changing energy demands of the plant. By offering flexibility in capacity and output, modular turbines help plants optimize energy generation while maintaining operational efficiency. For petrochemical facilities with varying production demands or those looking to add new units, modular turbines provide an efficient solution without the need for major infrastructure overhauls.
In refinery operations, steam turbines also help ensure a continuous supply of process steam for critical operations, such as distillation, cracking, and hydroprocessing. Steam is often used in these processes to provide the necessary heat for chemical reactions and to maintain temperature control. The integration of steam turbines helps regulate the supply of steam to these critical processes, maintaining consistent performance while avoiding disruptions that could compromise the quality or yield of products.
The growing focus on digitalization and the use of smart technologies will continue to enhance the role of steam turbines in petrochemical plants. Advanced condition monitoring, predictive analytics, and machine learning algorithms allow operators to monitor turbine performance in real time and optimize operations. Sensors installed on steam turbines provide data on key performance indicators such as temperature, pressure, vibrations, and flow rates, which can be analyzed to detect any anomalies or inefficiencies. With predictive maintenance tools, operators can identify potential problems before they lead to unplanned downtime, minimizing disruptions and reducing maintenance costs.
Moreover, digital twins, a simulation of the physical steam turbine system, enable engineers to test scenarios and make informed decisions about operation and optimization. These digital tools, powered by real-time data, can help streamline maintenance schedules, improve system performance, and ensure that turbines are running at optimal efficiency. The integration of AI and automation into turbine operations can further increase reliability and improve efficiency across the petrochemical plant.
Steam turbines in petrochemical plants also play a significant role in supporting backup power generation. In the event of a power outage or emergency shutdown, steam turbines can provide the necessary power to maintain critical operations and ensure that safety systems are functional. This is particularly important in petrochemical facilities where the interruption of power can lead to costly and hazardous incidents. By ensuring that steam turbines are designed for both power generation and backup power supply, petrochemical plants can maintain operational resilience in the face of unforeseen disruptions.
Finally, steam turbines contribute to the overall cost-effectiveness of petrochemical plants. Although the initial investment in steam turbine systems can be significant, their long-term benefits in terms of energy efficiency, reduced fuel consumption, and lower operational costs make them a valuable asset. With rising energy prices and increasing regulatory pressures, steam turbines enable petrochemical plants to stay competitive while improving their environmental performance. By optimizing energy generation and minimizing waste, petrochemical plants can enhance their profitability while contributing to global sustainability goals.
In conclusion, steam turbines are a critical component of petrochemical plants, supporting energy generation, process steam supply, and overall operational efficiency. As the industry continues to evolve, steam turbines will play an increasingly important role in enabling sustainable practices, improving energy efficiency, and reducing carbon emissions. Whether through cogeneration, the use of biomass fuels, the adoption of carbon capture technologies, or the integration of smart systems, steam turbines will continue to help petrochemical plants meet the challenges of a rapidly changing energy landscape while driving the industry’s transition toward greener and more efficient production methods.
As petrochemical plants face increasing pressure to reduce carbon emissions and improve energy efficiency, the role of steam turbines will continue to grow. With the ongoing push toward sustainability, steam turbines are being seen not just as power generators, but as essential components in the broader strategy for decarbonization and energy transition. Petrochemical facilities, traditionally reliant on fossil fuels for power and heat, are increasingly turning to renewable energy sources and waste heat recovery to meet their needs. Steam turbines, when integrated with these new systems, allow these plants to operate with lower emissions and improved energy profiles.
The adaptation of steam turbines to handle a variety of alternative fuels is crucial in this transition. As petrochemical plants look for cleaner fuel sources, turbines must be capable of running on fuels such as bio-oils, syngas, or even hydrogen. Hydrogen, in particular, presents a promising opportunity for the petrochemical industry as a clean energy source. Since hydrogen combustion produces only water vapor as a byproduct, its use in steam turbine systems has the potential to dramatically reduce carbon emissions. By investing in advanced combustion technologies and turbine modifications, petrochemical plants can adapt their steam turbines to hybrid or hydrogen-rich fuels, leading to more sustainable operations.
In addition to adapting to cleaner fuels, steam turbines in petrochemical plants can be further optimized through integrated energy systems that combine power generation with thermal management. For instance, systems that capture and store excess heat from the turbine exhaust to supply the plant’s heating needs can improve overall efficiency. Combined-cycle systems that integrate steam turbines with gas turbines can also be deployed, offering even higher levels of efficiency by utilizing both gas and steam cycles in tandem. These systems allow for the utilization of waste heat from the gas turbine exhaust to generate additional steam, which is then used to drive a steam turbine, further enhancing the overall energy conversion efficiency.
Energy integration with renewable sources will also play an increasingly important role in future petrochemical operations. Solar thermal systems, for instance, could supplement steam turbine systems in locations with abundant sunlight, reducing the reliance on fossil fuels. Similarly, wind power and geothermal energy could work in concert with steam turbines to provide consistent, low-carbon power to petrochemical facilities. By diversifying the energy sources that power steam turbines, petrochemical plants can not only reduce their carbon footprint but also enhance their resilience to energy price volatility and fuel supply disruptions.
In line with global efforts to move toward a circular economy, steam turbines can also support waste-to-energy technologies. Municipal solid waste and industrial byproducts, such as plastic waste or scrap tires, can be converted into bioenergy or syngas to fuel steam turbines. This not only reduces the environmental impact of waste disposal but also provides a renewable source of power and heat. In addition, by using carbon-neutral fuels, such as biomass or waste-derived gases, petrochemical plants can further reduce their greenhouse gas emissions and contribute to the reduction of the global carbon footprint.
The integration of smart technology is another key factor in optimizing steam turbine performance within petrochemical plants. Advanced sensors, IoT devices, and real-time monitoring systems can provide operators with detailed insights into turbine performance, allowing for immediate adjustments to improve efficiency. These tools also enable predictive maintenance, which helps prevent breakdowns and reduce unplanned downtime. Furthermore, through the integration of AI and machine learning, operators can gain insights into the most efficient ways to operate steam turbines, such as adjusting operating conditions to optimize fuel consumption or ensuring that turbines operate within their optimal performance range.
As energy demands in petrochemical plants continue to rise, the role of steam turbines in energy storage is also becoming more prominent. For instance, thermal energy storage (TES) systems can be used to store excess heat generated by steam turbines during periods of low demand. This stored energy can then be utilized during peak demand times or when renewable energy sources are unavailable, reducing the need for conventional fossil fuel-based power generation. This type of energy storage can also support grid stability by providing dispatchable energy when needed most.
Water treatment and steam quality are additional areas in which steam turbines contribute to the efficiency and reliability of petrochemical plants. Maintaining high-quality steam is critical to prevent damage to turbines and other equipment in the plant. Water treatment systems, such as demineralization and reverse osmosis, are often used in conjunction with steam turbines to ensure that the steam produced is free from impurities that can cause scale buildup, corrosion, or operational inefficiencies. High-quality steam not only improves turbine performance but also extends the life of equipment, reduces maintenance costs, and ensures that the plant operates reliably and efficiently.
Additionally, as part of the green chemistry movement, steam turbines are being used in innovative ways to support the sustainable production of chemicals and materials. For example, in the production of bio-based plastics, green solvents, and other bio-derived chemicals, steam turbines are used to provide the necessary heat and power for these energy-intensive processes. By utilizing biomass or biogas as fuel sources, petrochemical plants can produce chemicals in a way that is both economically viable and environmentally sustainable. This alignment with green chemistry principles will be critical as the industry seeks to reduce its reliance on petroleum-based feedstocks.
The future of steam turbines in petrochemical plants lies in their ability to adapt to the evolving demands of energy efficiency, sustainability, and cleaner production. By integrating these turbines into advanced energy systems, utilizing renewable fuels, and leveraging the latest digital technologies, petrochemical plants can ensure that they remain competitive in an increasingly environmentally-conscious market. Moreover, the continued development of steam turbine technologies will contribute to achieving global climate goals, allowing petrochemical plants to play a pivotal role in the energy transition and the creation of a more sustainable future.
As the petrochemical industry continues to evolve, steam turbines will increasingly be a cornerstone of the transition to a more sustainable, efficient, and resilient energy landscape. The ongoing push for lower-carbon emissions and greater energy efficiency means that steam turbines will not only remain integral to petrochemical operations but will also become more advanced and versatile in their capabilities.
The ongoing development of advanced materials for steam turbines is helping improve their efficiency and durability, even under demanding conditions. High-temperature alloys, ceramic coatings, and superalloys are being researched and incorporated into turbine designs to enhance performance and extend the lifespan of turbines. This is particularly important in the context of using alternative fuels, such as biomass or syngas, which may have different combustion properties and can lead to higher temperatures or more corrosive exhaust gases. By adopting these materials, petrochemical plants can increase their operational flexibility and reliability, ensuring that steam turbines can handle a wider range of fuels and environmental conditions.
Another key area of development is the integration of steam turbines with digital technologies. The ongoing adoption of Industry 4.0 technologies in the petrochemical sector is enabling the creation of “smart” steam turbines that can not only optimize performance in real-time but also predict potential issues before they become critical. These turbines can be equipped with advanced sensors and analytics that monitor turbine health, detect wear and tear, and provide actionable insights for maintenance teams. By incorporating predictive algorithms and machine learning, operators can improve efficiency, reduce energy waste, and prevent costly unplanned outages.
In addition, steam turbines will likely become more modular in design, making them easier to scale up or down based on the specific needs of the petrochemical facility. This modularity allows for the flexible configuration of turbines, enabling plants to adapt to changing production demands without making major capital investments in new infrastructure. Modular turbines can also provide more customized solutions for different types of petrochemical plants, whether they are focused on refining, chemical production, or plastics manufacturing.
Energy efficiency remains one of the most important considerations for petrochemical plants, especially given the industry’s reliance on large amounts of energy. As steam turbines are already a key component in cogeneration systems, efforts to further integrate these turbines into district heating or multi-plant systems will be crucial for maximizing energy utilization. By connecting multiple facilities to a shared steam turbine system, energy can be distributed more efficiently across a network, reducing overall energy consumption and improving the economic viability of the entire operation.
In the future, energy storage solutions will become increasingly important in balancing energy demand and supply within the petrochemical industry. Steam turbines could play a critical role in this by supporting thermal energy storage systems, where excess heat produced during periods of low demand is stored and then utilized during high-demand periods. This ability to store energy in the form of heat and release it when needed will improve the stability of energy supply, reduce reliance on the grid, and make petrochemical plants more resilient to energy price fluctuations.
Hydrogen, which is emerging as a key alternative fuel in the energy transition, will continue to be an important focus for steam turbine manufacturers. The ability to burn hydrogen directly in turbines opens up possibilities for zero-emission energy generation, helping petrochemical plants reduce their carbon footprint. Since hydrogen combustion produces only water vapor as a byproduct, turbines running on hydrogen could provide a cleaner alternative to traditional fossil fuels. Moreover, hydrogen can also be produced from renewable sources like wind, solar, or biomass, creating a closed-loop, low-carbon energy system for petrochemical operations. Hydrogen-ready turbines are already under development, and these turbines could serve as the foundation for future fuel-switching capabilities, enabling plants to transition seamlessly to hydrogen without significant new investments.
Another significant development is the growing integration of steam turbines with carbon capture and storage (CCS) technologies. As governments and industries push for net-zero emissions, the ability to capture and store carbon dioxide emissions from industrial processes becomes increasingly critical. Steam turbines can be integrated with CCS systems to help separate and compress CO2, reducing the carbon footprint of petrochemical operations. These technologies are especially important in plants that rely heavily on fossil fuels for heat and power. By combining energy generation with carbon capture, petrochemical plants can continue operating while reducing their environmental impact.
Flexibility in operations is another important trend for the future of steam turbines in petrochemical plants. As the demand for energy becomes more dynamic, petrochemical plants must be able to quickly adjust to changes in production schedules or energy prices. Steam turbines, when integrated with advanced control systems and automated processes, can provide the necessary flexibility to accommodate fluctuations in energy demand, reducing energy waste and improving overall cost efficiency. This operational flexibility will also allow plants to incorporate renewable energy sources and adjust to intermittent power generation from solar and wind.
Moreover, as the industry faces regulatory pressure to meet stringent environmental standards, steam turbines will be essential in helping petrochemical plants comply with these regulations. Turbine manufacturers are increasingly designing systems that meet or exceed emissions standards for NOx, SOx, and particulate matter, reducing the environmental impact of petrochemical operations. Additionally, electrification of steam generation processes, where steam turbines are driven by electric motors instead of combustion, can reduce the reliance on fossil fuels and contribute to cleaner production processes.
Lastly, the global move toward decarbonization and sustainable production in the petrochemical industry will increase the demand for energy-efficient steam turbine systems that are capable of working in tandem with alternative fuels, renewable energy, and waste heat recovery technologies. As these systems evolve, their role in driving the energy transition will become more prominent, helping petrochemical plants meet climate goals while maintaining cost-competitive operations.
In conclusion, the future of steam turbines in petrochemical plants will be shaped by innovation in technology, sustainability, and energy integration. As these plants look to reduce emissions, improve energy efficiency, and meet the demands of a rapidly changing energy landscape, steam turbines will remain an essential part of their infrastructure. By embracing new fuels, digital technologies, and energy storage solutions, petrochemical facilities can continue to thrive in a low-carbon future while driving forward the industry’s transition to greener production methods.
As the petrochemical industry faces increasing demands for sustainability, energy efficiency, and reduced emissions, steam turbines will play an increasingly critical role in supporting these transitions. Innovations in turbine technology and their integration with renewable energy sources, energy storage, and carbon capture systems will ensure that petrochemical plants can continue to meet both operational and environmental goals.
One major avenue of development for steam turbines in petrochemical plants is the integration of smart grid technologies and energy management systems. By linking steam turbines with a smart grid, petrochemical plants can better manage energy generation, consumption, and distribution across multiple sites or systems. These grids use real-time data to make decisions about when and where energy should be used, optimizing both power generation and efficiency. The ability to dynamically adjust turbine operations based on demand patterns and grid requirements will help petrochemical facilities become more responsive and adaptive to changing energy needs.
Additionally, the ongoing digitalization of petrochemical operations will have a significant impact on the management of steam turbines. With real-time monitoring, predictive analytics, and digital twins — virtual representations of physical assets — operators can gain deeper insights into turbine performance, identifying potential inefficiencies or failure points long before they become issues. This data-driven approach will enable predictive maintenance, reducing downtime, and improving the lifespan of turbines. These advancements will also support the remote operation of steam turbines, allowing operators to monitor and control turbine performance from any location, improving flexibility and operational efficiency.
The continued push toward circular economy principles in the petrochemical sector also suggests an expanded role for steam turbines in waste-to-energy applications. Steam turbines are already being employed in biomass and biogas plants to generate power from renewable feedstocks. However, the scope of this application is likely to increase, with the development of more advanced waste conversion technologies such as pyrolysis and gasification. These processes can convert plastic waste, municipal solid waste, and other non-recyclable materials into syngas or biofuels, which can then be used to power steam turbines. This integration of waste-to-energy systems not only provides an alternative power source but also contributes to solving the issue of waste management, which remains a major environmental challenge.
In addition to enhancing the sustainability of petrochemical plants, steam turbines can also support the efficiency of plant-wide energy systems. The trend toward combined heat and power (CHP) or cogeneration systems, which integrate steam turbines with heat recovery systems, will continue to be a focus for many petrochemical operations. By capturing and reusing waste heat for power generation or industrial processes, CHP systems maximize the overall energy efficiency of the plant. This not only reduces fuel consumption and operating costs but also reduces the carbon footprint of petrochemical production.
Another key development area is the increased decentralization of energy generation. As companies explore on-site power generation or localized energy systems, steam turbines will become part of microgrids or decentralized energy networks, allowing petrochemical plants to operate more independently and reduce their reliance on the grid. This decentralization can help improve the security of the plant’s power supply, especially in regions where grid stability is a concern, while also optimizing energy costs by sourcing power directly from renewable or low-carbon energy sources.
At the same time, modular steam turbine systems are gaining traction, particularly in smaller petrochemical plants or in areas with fluctuating energy demand. These systems are more flexible and scalable, allowing for easier adjustment of turbine capacity in response to changing production needs. This adaptability will be especially useful for petrochemical facilities that deal with seasonal fluctuations in demand or need to rapidly adjust to market conditions. The ability to scale operations up or down with modular systems reduces capital costs and improves the economic efficiency of turbine installation and operation.
The development of hybrid steam turbine systems is also gaining interest, particularly in the context of energy transition. These systems combine traditional steam turbine technology with other power generation sources, such as gas turbines, solar thermal, or wind energy. Hybrid systems allow for a more flexible energy mix, ensuring continuous and reliable energy supply even when renewable energy sources are intermittent. By using multiple sources of energy, plants can smooth out power fluctuations and reduce their reliance on fossil fuels, moving toward a cleaner, more sustainable energy model.
As hydrogen adoption continues to grow as a major fuel for the energy transition, steam turbines will need to evolve to handle the unique properties of hydrogen combustion. Unlike traditional fossil fuels, hydrogen has a higher combustion temperature and a different energy density, which requires adaptations in turbine design to optimize performance and efficiency. The use of hydrogen-enriched fuels and the development of hydrogen-fired turbines are expected to become increasingly widespread in petrochemical plants, enabling them to achieve lower emissions while continuing to provide reliable power and heat for industrial processes.
Furthermore, carbon capture, utilization, and storage (CCUS) technologies will become more deeply integrated with steam turbine systems in petrochemical plants. These technologies allow plants to capture CO2 emissions from the combustion process and either store them underground or use them in other industrial processes. Steam turbines, particularly in power plants that rely on fossil fuels, are often the primary source of CO2 emissions. Therefore, integrating carbon capture systems with these turbines will be critical in helping petrochemical plants meet stringent emission regulations and contribute to global decarbonization goals.
Looking forward, steam turbines will also need to integrate more effectively with advanced power generation technologies, such as advanced nuclear reactors. Although nuclear power has historically had limited application in petrochemical plants, the development of small modular reactors (SMRs) and other next-generation nuclear technologies may offer a viable, low-carbon alternative to traditional fossil fuel-powered turbines. As these technologies evolve, petrochemical plants may explore the integration of steam turbines with nuclear power, potentially offering a stable and sustainable energy source for the industry’s most energy-intensive processes.
Lastly, as governments and industries continue to push for net-zero emissions, steam turbines will play a key role in helping petrochemical plants reduce their reliance on carbon-intensive fuels and switch to low-carbon alternatives. The transition will involve more than just adopting cleaner energy sources — it will also require optimizing existing turbine systems to ensure they operate with minimal emissions. This will include not just improving efficiency and performance but also retrofitting existing turbines with carbon-capture technologies, as well as developing new turbine designs that can run efficiently on biofuels, synthetic fuels, or green hydrogen.
In conclusion, the role of steam turbines in petrochemical plants will continue to expand as the industry embraces new energy sources, more efficient technologies, and sustainable practices. Whether through the integration of renewable energy, the development of hydrogen-fired turbines, the incorporation of smart technologies, or the optimization of energy systems through combined heat and power, steam turbines will remain an essential part of the petrochemical industry’s drive for greater efficiency, lower emissions, and a more sustainable future.
Steam Turbines for Marine Propulsion
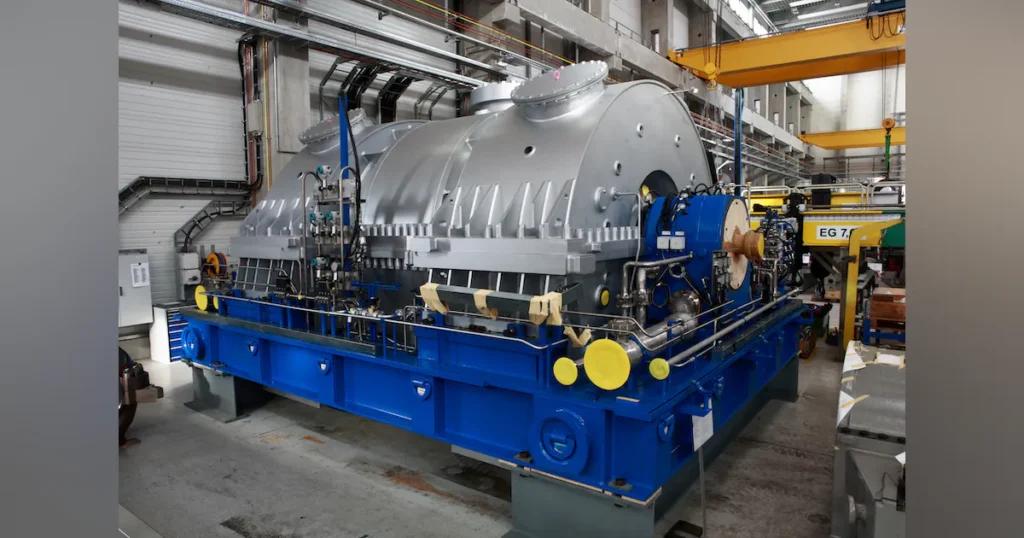
Steam turbines have a long history of being used for marine propulsion, particularly in large ships such as cruise liners, naval vessels, cargo ships, and icebreakers. Their ability to deliver high power output and operate efficiently for extended periods in challenging maritime conditions has made them a preferred choice for many types of ships, especially in the past century. While modern propulsion technologies such as diesel engines and gas turbines have become more common, steam turbines still have a significant presence in certain segments of the maritime industry due to their reliability, fuel flexibility, and adaptability in specific applications.
In the context of marine propulsion, steam turbines work by converting the thermal energy of steam into mechanical power, which is then used to drive a propeller or shaft. These turbines are typically powered by boilers that generate steam by burning fossil fuels, although in some cases, nuclear reactors can provide the heat necessary for steam generation. In this way, steam turbines continue to serve as a highly reliable and powerful propulsion system for various classes of ships.
One of the primary advantages of steam turbines for marine propulsion is their ability to produce high power output relative to their size. Steam turbines can be designed to operate at very high efficiencies and power levels, making them ideal for large vessels that require significant power for propulsion. This is particularly evident in naval ships and large cargo vessels, where the need for continuous power generation and propulsion capabilities is critical for long-duration missions, heavy loads, and rapid speeds.
Fuel flexibility is another significant advantage of steam turbines in marine propulsion. While oil-based fuels such as bunkered fuel are most commonly used, steam turbines can also be fueled by a wide range of other sources, including coal, liquefied natural gas (LNG), and even nuclear energy. This flexibility allows for operational adaptability, enabling ships to switch between different fuels based on availability, cost, and environmental regulations. For instance, in some military and civilian applications, nuclear-powered vessels, such as aircraft carriers and submarines, rely on steam turbines to generate power from nuclear reactors.
Another benefit of steam turbines for marine propulsion is their proven reliability and durability over time. These turbines are designed to withstand extreme operating conditions, including high-speed maneuvers, sustained high loads, and exposure to harsh marine environments. As a result, steam turbines are often used in naval applications where reliability is critical for the safety and success of military operations. For example, the U.S. Navy has operated nuclear-powered aircraft carriers, which use steam turbines driven by nuclear reactors, for decades. These ships are capable of remaining at sea for long periods without refueling, thanks to the high energy density of nuclear fuel and the efficiency of the steam turbine system.
In addition to large naval vessels and cruise ships, steam turbines are also used in commercial shipping and luxury liners. Many luxury cruise ships rely on steam turbines to provide both propulsion and onboard power for services such as lighting, air conditioning, and cooking. The high power output of steam turbines allows these ships to meet the demands of large passenger and crew populations while maintaining high levels of comfort and reliability.
In terms of efficiency, steam turbines are particularly well-suited for large ships with constant, high-speed propulsion needs. This is because steam turbines operate most efficiently at their optimal speeds, which align well with the continuous operating conditions of large vessels. Steam turbines also benefit from their ability to operate with minimal vibration and noise, contributing to smoother and quieter operations — a key factor for passenger ships and naval vessels.
In nuclear-powered vessels, steam turbines play an integral role by converting heat from nuclear fission into steam, which drives the turbines to produce propulsion and onboard power. This technology is primarily seen in military ships, such as aircraft carriers and submarines, where the need for extended endurance and independence from fuel resupply is paramount. Nuclear-powered ships equipped with steam turbines can operate for years without needing to refuel, which gives them a distinct strategic advantage for long-term operations.
In addition to conventional steam turbines, there has been ongoing research into advanced steam turbine designs to improve efficiency, reduce emissions, and allow greater operational flexibility in marine applications. Superheated steam turbines, for example, allow for more efficient conversion of thermal energy into mechanical power, while combined-cycle steam turbine systems (which pair steam turbines with gas turbines or other technologies) can further optimize fuel consumption and reduce environmental impact.
Moreover, with the rise of environmental regulations aimed at reducing emissions from ships, there has been a growing interest in hybrid propulsion systems that combine steam turbines with electric motors and renewable energy sources. Hybrid systems allow for greater operational efficiency and can be powered by low-emission fuels such as LNG or hydrogen. These systems also reduce the environmental impact of maritime transportation, making them particularly attractive in the context of global decarbonization goals.
For commercial maritime vessels operating in environmentally sensitive areas or with stringent emissions requirements, the development of zero-emission steam turbine systems is a possibility. These turbines could be powered by renewable energy sources such as solar thermal or geothermal energy to generate steam, eliminating the reliance on fossil fuels. While still in the conceptual or experimental stages, these technologies could transform the way steam turbines are used in marine propulsion by supporting a shift toward a more sustainable and green maritime industry.
In the future, digitalization and the integration of smart technologies into marine steam turbine systems will enable more effective monitoring, performance optimization, and predictive maintenance. These advancements allow for more efficient turbine operation and ensure the vessels can operate at peak efficiency throughout their lifespan. Sensors, data analytics, and machine learning can be employed to track turbine health, predict potential failures, and adjust operational parameters in real-time. This will not only improve the overall reliability and safety of steam turbine systems but also optimize fuel usage and reduce operational costs for vessel owners.
Modular steam turbine systems may also gain popularity for smaller vessels or for those needing flexible power configurations. These modular systems would allow for easier upgrades or replacements, ensuring that steam turbines can meet the specific needs of various types of ships without extensive re-engineering.
Overall, steam turbines will continue to be an important part of marine propulsion for large vessels, especially where high power output, fuel flexibility, reliability, and extended endurance are key requirements. The ongoing evolution of turbine technologies, including efficiency improvements, environmental innovations, and hybrid integration, will ensure that steam turbines remain a viable and valuable option for marine propulsion for the foreseeable future. Whether in the context of nuclear-powered vessels, luxury cruise ships, or military ships, the contribution of steam turbines to the maritime industry will continue to play an essential role in global transportation systems, particularly as the industry moves toward more sustainable and energy-efficient practices.
As the maritime industry continues to evolve, there is an increasing emphasis on the sustainability and environmental impact of shipping. Steam turbines, traditionally known for their efficiency in large vessels, are now being explored in the context of new, cleaner technologies that can further reduce the carbon footprint of maritime operations. Hybrid propulsion systems combining steam turbines with electric motors, fuel cells, or renewable energy sources like wind and solar are becoming a viable option for both commercial shipping and passenger vessels. This shift is driven by stricter environmental regulations, such as the IMO 2020 sulfur cap and future IMO decarbonization targets, which are pushing the industry toward greener and more energy-efficient solutions.
Hybrid systems that incorporate steam turbines can use battery storage to support energy needs, ensuring that ships can operate with reduced emissions, particularly in port areas or during low-load conditions. The ability to switch seamlessly between steam turbine power, electric motor propulsion, and auxiliary power systems based on demand can optimize fuel usage and ensure a more environmentally friendly operation, especially in regions where strict environmental standards are enforced.
One of the most promising innovations in the use of steam turbines for sustainable marine propulsion is the potential for LNG-powered ships equipped with steam turbines. LNG, being a cleaner alternative to traditional marine fuels like heavy fuel oil, emits significantly fewer pollutants such as sulfur oxides (SOx), nitrogen oxides (NOx), and particulate matter (PM). When used in combination with a steam turbine system, LNG offers an efficient, lower-emission fuel option for vessels, and it is becoming more prevalent as a result of the global push for reducing the maritime industry’s impact on climate change.
In terms of technological advances, supercritical steam turbine cycles are showing potential for improving the efficiency of steam turbines in marine propulsion. In a supercritical cycle, steam is heated to temperatures and pressures above its critical point, making it more efficient at converting heat to work. These advanced cycles can allow steam turbines to operate more efficiently with lower fuel consumption, which in turn reduces emissions and operational costs. Implementing these systems in future marine applications could further reduce the maritime industry’s dependence on fossil fuels.
Additionally, energy recovery systems are being integrated with steam turbines to harness the excess heat generated during normal operations. This recovered energy can be repurposed to improve overall efficiency, reduce fuel consumption, and power auxiliary systems aboard ships. By recovering heat from exhaust gases or other waste heat sources within the vessel, steam turbines can contribute to more efficient energy use across the entire vessel. This integration of heat recovery systems not only boosts efficiency but also aligns with broader goals of reducing fuel usage and cutting down on harmful emissions.
Another forward-thinking development is the use of steam turbines in hybrid renewable-powered vessels, particularly those exploring wind-assisted propulsion. By combining steam turbines with kite sails, rotor sails, or wing sails, vessels can harness natural forces to reduce fuel consumption. The role of steam turbines in this hybrid system would be to maintain steady propulsion when wind conditions are unfavorable or when high power is needed for certain operations, ensuring reliability and reducing the need for additional fuel.
Battery-electric power systems are also becoming a potential future complement to steam turbines in maritime applications. In the future, steam turbines could play a role in recharging the batteries of hybrid vessels, particularly in deep-sea vessels that require high-powered engines for extended periods. The ability to efficiently charge batteries using steam turbine systems could provide the required power boost for vessels during high-demand phases, like when a ship is departing from or entering a port. This dual-use of steam turbines — both for propulsion and battery recharging — may enhance operational flexibility and help meet both energy efficiency and zero-emission goals.
The integration of digitalization into steam turbine technology is another key factor in advancing marine propulsion. Through digital monitoring and predictive analytics, turbine operators can continuously assess the performance of the steam turbines, identifying potential issues before they arise. By using sensor networks and real-time data analytics, operators can optimize turbine performance for maximum efficiency and extend the lifespan of the turbines by scheduling proactive maintenance. This approach reduces unexpected failures, ensures continuous operation, and minimizes fuel consumption.
Moreover, modular steam turbine designs are expected to become more popular in smaller vessels or specialized applications. These modular systems allow for easier scaling of power capacity depending on the specific needs of the vessel, which is particularly advantageous for container ships, research vessels, and specialized marine vessels with fluctuating power demands. The flexibility of modular systems also means that ships can be more easily adapted or retrofitted to meet changing energy regulations or operational needs, further extending the life cycle of steam turbine systems.
Lastly, as global demand for offshore wind energy and floating platforms increases, steam turbines will likely play a role in hybrid energy systems for floating energy storage units or energy platforms. These platforms could combine steam turbines with renewable energy generation systems like wind turbines and solar panels to generate, store, and distribute energy in offshore environments. Steam turbines could help regulate energy distribution and supply in these settings, particularly when other renewable sources are unavailable or inconsistent.
In conclusion, steam turbines will remain a core technology in marine propulsion systems well into the future, especially as the industry focuses on improving fuel efficiency, reducing emissions, and embracing renewable energy. The continued evolution of steam turbine technologies — including integration with hybrid systems, advanced fuel options, heat recovery, and battery support systems — will contribute to cleaner, more efficient operations on the water. Whether in nuclear-powered vessels, LNG-powered ships, or hybrid renewable-powered vessels, steam turbines will help pave the way toward a more sustainable and energy-efficient maritime industry.
As steam turbine technology continues to evolve in the maritime industry, there are several more trends and innovations that are shaping their future use for marine propulsion. One of the most significant areas of development is the growing integration of advanced materials and coating technologies that are improving the efficiency and durability of steam turbines in the harsh marine environment. High temperatures, saltwater exposure, and the constant vibration of ships place considerable strain on turbine components. Advances in materials science, such as the use of ceramic coatings, corrosion-resistant alloys, and superalloys, are helping extend the lifespan of steam turbines while reducing maintenance costs and the need for frequent repairs.
Ceramic coatings in particular offer high resistance to corrosion and wear, which is crucial for the long-term reliability of turbines operating in marine environments. The application of these advanced coatings to turbine blades, casings, and other critical components can help reduce the impact of saltwater corrosion, increase heat resistance, and improve the overall performance of steam turbines. These improvements in material durability can also enhance the turbines’ efficiency over time, ensuring they continue to perform optimally despite the challenging operational conditions at sea.
Additionally, additive manufacturing, or 3D printing, is being explored for manufacturing complex turbine components. This technology allows for the production of highly customized, precision-engineered parts with reduced lead times and cost. In the case of steam turbines, additive manufacturing can enable the creation of optimized turbine blades and other parts that are lightweight, durable, and specifically designed for high-efficiency operation in marine settings. This technology also offers the potential for faster repairs, as turbine components could be printed on-demand, reducing downtime and improving vessel availability.
As the global maritime industry is under increasing pressure to reduce its carbon emissions and environmental impact, carbon capture and carbon-neutral technologies are gaining traction in maritime operations. Steam turbines, especially those powered by nuclear energy, could play a crucial role in the development of carbon-neutral ships. By integrating carbon capture technologies with steam turbines, ships could potentially capture and store CO2 emissions produced during their operations, significantly lowering their environmental impact. For example, advanced scrubbing systems could be used to filter CO2 emissions from the exhaust gases produced by steam turbines. These technologies could be paired with renewable energy sources to create a truly zero-emission propulsion system.
Green hydrogen is another fuel that is starting to attract attention in the maritime industry as a clean alternative to traditional marine fuels. Steam turbines could be used in conjunction with hydrogen-powered systems, either by using hydrogen to generate steam in boilers or by integrating hydrogen fuel cells alongside the turbines. This would allow ships to operate with zero emissions while maintaining the high power output necessary for long-distance travel. Although still in the early stages of development, hydrogen-powered vessels equipped with steam turbines could play a key role in the future of green shipping.
The future of steam turbines in the maritime sector is also likely to see greater automation and digital integration. As ships become more technologically advanced, the need for human intervention in the operation of steam turbines will decrease. By integrating automation systems, artificial intelligence (AI), and machine learning algorithms, steam turbines can operate with greater efficiency and adapt to changing conditions in real time. For instance, AI could help optimize steam flow and turbine speeds based on factors such as sea conditions, load demands, and fuel availability. Predictive analytics could also help anticipate maintenance needs, reducing the likelihood of failures and downtime.
Smart turbines that are connected to the internet of things (IoT) could continuously monitor turbine performance, sending data back to shore-based operations centers for analysis. This data could be used to identify trends, optimize fuel usage, and improve overall fleet performance. The growing capabilities of big data analytics, combined with cloud computing, will allow for more informed decision-making about turbine operations and fleet management. With these technological advancements, steam turbines in the maritime industry will not only become more efficient but also safer and more reliable.
As the maritime industry moves toward greater digitalization, smart cities, and intelligent ports, the role of steam turbines will be increasingly integrated into the broader ecosystem of smart maritime operations. The connectivity between vessels, ports, and shipping companies will enable real-time optimization of routes, energy use, and operational strategies. Steam turbines could potentially be part of an interconnected system where power demand is balanced across a fleet of ships, ensuring that each vessel operates at maximum efficiency and contributing to overall energy savings.
On a larger scale, floating steam turbine platforms could become a reality in the future as part of offshore energy solutions. These platforms could use steam turbines to generate power from renewable sources, such as offshore wind farms or tidal energy, and provide power to ships or coastal communities. Such systems would help address the growing demand for offshore renewable energy while contributing to cleaner, more sustainable marine energy production. Additionally, these floating platforms could be used to charge or support electric vessels by providing energy for batteries, further enhancing the transition to cleaner marine propulsion systems.
In conclusion, steam turbines will continue to evolve in response to the changing demands of the maritime industry. From their application in large naval vessels and commercial ships to their integration with sustainable fuels, renewable energy sources, and advanced digital technologies, steam turbines are poised to remain a crucial component in marine propulsion systems for years to come. Innovations in materials science, carbon capture, automation, and digital integration will ensure that steam turbines remain competitive and adaptable to the industry’s growing sustainability goals. With continued investment in green technologies and hybrid propulsion systems, steam turbines could play a key role in shaping a cleaner, more efficient, and more technologically advanced maritime industry.
As we continue to explore the future role of steam turbines in maritime propulsion, there are even more advancements on the horizon that could redefine their capabilities and applications within the sector. One area that holds significant promise is the use of advanced turbine designs that optimize steam generation and energy conversion processes to maximize efficiency and minimize environmental impact.
High-efficiency steam turbines are being designed to work in conjunction with newer, more advanced boiler systems, such as supercritical steam cycles and ultra-supercritical cycles, which operate at higher pressures and temperatures than traditional boilers. These advanced systems can generate steam at much higher efficiencies, which directly translates into better fuel economy and reduced emissions. When paired with steam turbines, they can provide more power while consuming less fuel, making them an ideal solution for vessels operating on long journeys, such as container ships, tankers, and cargo vessels.
Furthermore, advanced control systems are being integrated into steam turbine technology to further enhance efficiency. These systems enable real-time optimization of turbine performance by constantly adjusting operational parameters, such as steam pressure, temperature, and flow rates, to match the varying demands of the vessel. The use of smart sensors and real-time data analysis can ensure that the turbine operates at its optimal performance levels, reducing wear and tear, minimizing fuel consumption, and improving overall operational efficiency. This will not only lead to reduced fuel costs but also help meet global regulatory targets for emissions reductions.
An exciting development is the potential for closed-loop steam systems, which could revolutionize the way steam turbines are used in marine propulsion. In a closed-loop system, water is continuously cycled within the system without being released into the environment. This system could improve energy efficiency by ensuring that the steam is used in the most optimal way possible and reduce the need for fresh water intake, which is especially important for ships operating in areas with limited access to fresh water sources. These closed-loop systems also reduce the environmental impact of using large amounts of seawater for cooling purposes, as they eliminate the need for discharge of hot water into the ocean, which can disrupt marine ecosystems.
The integration of energy storage technologies alongside steam turbines could also play a crucial role in the future of marine propulsion. Energy storage systems, such as lithium-ion batteries or flow batteries, could be used to store excess energy generated by the turbine during periods of low demand or high energy output. This stored energy could then be used during peak load periods when additional power is needed, helping to stabilize energy use and ensure that vessels can operate efficiently at all times. In this scenario, steam turbines would not only provide propulsion but also contribute to the ship’s overall energy management system, enabling a more integrated and flexible energy usage model.
One particularly innovative approach to increasing the energy efficiency of steam turbines in maritime applications involves the use of combined heat and power (CHP) systems. CHP systems utilize the waste heat produced by the steam turbine to generate electricity, which can then be used to power auxiliary systems aboard the vessel, such as lighting, air conditioning, or refrigeration. By capturing and reusing waste heat, CHP systems can improve the overall fuel efficiency of the vessel, reduce fuel consumption, and lower operational costs, all while minimizing emissions.
Additionally, waste heat recovery systems are becoming a key feature in many modern steam turbines for marine propulsion. These systems capture heat from exhaust gases and other sources that would otherwise be wasted, redirecting it to power auxiliary systems or boost the efficiency of the steam turbine itself. This is particularly useful in scenarios where steam turbines are used in hybrid power systems that combine conventional turbines with electric propulsion or renewable energy sources. Waste heat recovery helps to make these systems even more efficient by ensuring that all available energy is used optimally, reducing overall fuel consumption and greenhouse gas emissions.
Another exciting avenue is the development of hybrid electric-steam propulsion systems that integrate steam turbines with electric motors. These systems would allow ships to alternate between steam turbine propulsion and electric-powered propulsion, depending on operational conditions. For example, steam turbines could be used for long-distance propulsion, where high power output is needed, while electric motors could be employed during port operations or at low speeds, reducing fuel consumption and emissions during these phases. This kind of hybrid approach could be particularly effective in reducing the carbon footprint of vessels that spend significant time in environmentally sensitive regions, such as coastal areas or near marine protected zones.
Moreover, the concept of floating steam turbine power generation platforms is emerging as a viable solution to address the growing demand for renewable energy, especially in offshore environments. These platforms could combine offshore wind turbines or wave energy converters with steam turbines to produce electricity, which can then be used to power both ships and coastal grids. These floating systems could help reduce the dependency on traditional power sources and provide a sustainable energy option for vessels operating in remote locations or offshore areas, where access to conventional power generation systems may be limited.
Lastly, the integration of steam turbines with autonomous shipping technologies could reshape the way vessels are operated in the future. Autonomous ships, which are equipped with advanced sensors, machine learning algorithms, and automated control systems, could be powered by steam turbines that are fully integrated into the vessel’s automation systems. These turbines would be able to adapt to changing conditions in real-time, adjusting power output and operational parameters to ensure optimal performance without the need for human intervention. By combining steam turbines with autonomous navigation and decision-making systems, ships could become more energy-efficient and environmentally friendly while reducing the risks associated with human error.
In conclusion, steam turbines will continue to evolve in the maritime industry, driven by advancements in materials science, fuel efficiency, digitalization, and sustainability. From high-efficiency turbine designs and advanced control systems to hybrid propulsion and energy storage integration, the future of steam turbines in marine propulsion looks promising. These innovations will ensure that steam turbines remain a crucial component of maritime power systems, helping the industry reduce emissions, improve energy efficiency, and transition toward a more sustainable future. The role of steam turbines in nuclear-powered vessels, green hydrogen applications, waste heat recovery, and autonomous shipping technologies will shape the next generation of maritime propulsion, making ships smarter, greener, and more efficient in their operations across the globe’s oceans.
Steam Turbines in Combined Heat and Power Systems
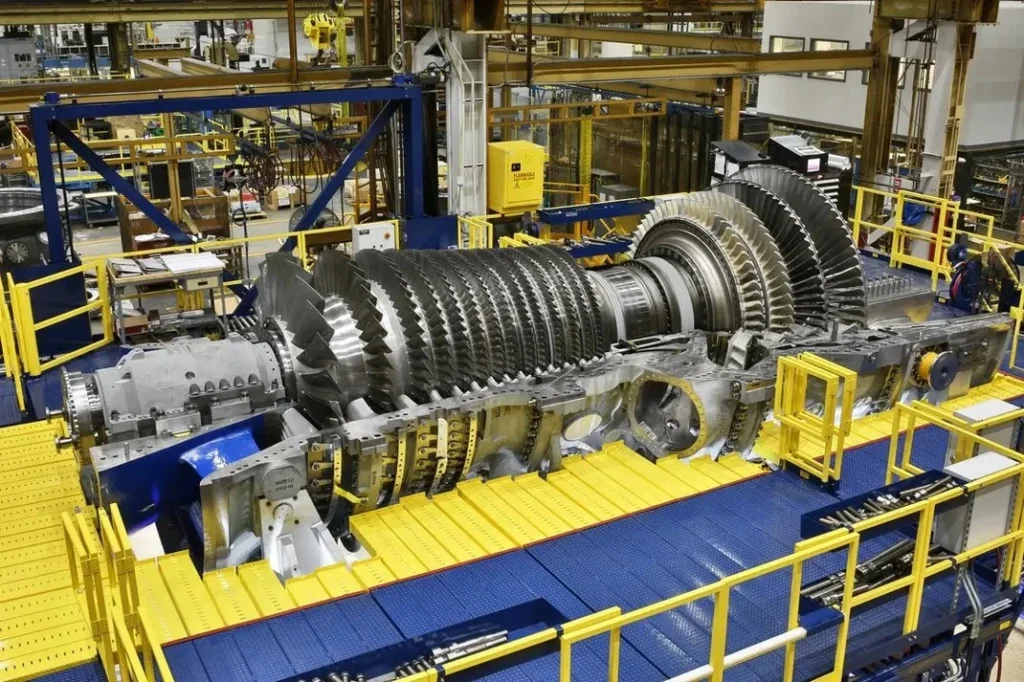
Steam turbines in combined heat and power (CHP) systems represent a highly efficient method of utilizing fuel to meet both electricity and thermal energy needs. By integrating power generation and heat recovery into a single process, CHP systems maximize energy utilization, reduce waste, and improve overall efficiency. Steam turbines are ideal for this role due to their ability to convert heat into mechanical energy and, ultimately, electricity.
In a typical CHP system, steam turbines are used to generate electricity, while simultaneously providing thermal energy in the form of steam or hot water for industrial processes, district heating, or other applications. This dual-function capability allows for a higher overall energy efficiency than traditional separate systems for power generation and heating. The waste heat produced by the steam turbine, instead of being lost to the atmosphere or cooling systems, is captured and used to meet thermal demand, whether in industrial operations like chemical manufacturing, food processing, or paper mills, or in district heating networks that provide warmth to residential and commercial buildings.
One of the key benefits of incorporating steam turbines into CHP systems is the ability to achieve high efficiency levels, typically around 80-90% compared to the 30-50% efficiency of conventional power generation systems. This efficiency improvement stems from the fact that the waste heat, which would otherwise be discarded in a traditional power plant, is effectively utilized. With steam turbines, the system essentially captures and uses the energy twice — once for electricity generation and once for heating, which makes the overall process much more resource-efficient.
Flexibility in Fuel Use
Steam turbines used in CHP systems are highly adaptable when it comes to fuel sources. They can operate with a variety of fuels, including natural gas, biomass, coal, or even waste heat from industrial processes. Natural gas is the most common fuel used in modern CHP systems, but the increasing focus on renewable energy and sustainable practices has led to more interest in utilizing biomass and other renewable fuels. Biomass CHP systems, for instance, utilize organic materials, such as wood chips, agricultural waste, or dedicated energy crops, to generate heat and power. This helps reduce reliance on fossil fuels and can contribute to a lower carbon footprint.
In the case of waste heat recovery in industrial processes, steam turbines can capture the heat produced by operations such as furnaces, incinerators, or refineries, which would otherwise be lost. This recovered energy can then be fed back into the system, increasing the overall efficiency of the process and decreasing the need for additional energy sources. Industrial CHP systems that utilize waste heat recovery are particularly beneficial because they reduce the overall energy consumption and associated costs for industries that require substantial amounts of heat, such as in the cement or chemical industries.
Industrial Applications
One of the most common applications of steam turbines in CHP systems is in industrial manufacturing. Industries that have high demand for both electricity and heat — such as paper mills, food processing plants, and chemical factories — can benefit greatly from a CHP system powered by steam turbines. The heat generated in these plants is used to maintain specific process temperatures, sterilize materials, or power dryers, while the electricity generated can power the plant’s operations, equipment, and machinery. By utilizing steam turbines, these industries can reduce their reliance on external power sources and improve energy efficiency.
For example, in a paper mill, steam is generated to power the pulping process, dry the paper, and provide heat for the chemical recovery cycle. The steam turbine drives a generator that produces electricity to power other equipment in the mill. This integrated approach allows the plant to reduce its energy costs and make better use of the heat already being produced in the process. Similarly, in a food processing plant, the steam generated by the boiler system can be used to cook, pasteurize, and sterilize products, while the electricity generated by the turbine powers the factory’s operations.
District Heating and Urban Energy Systems
Steam turbines in CHP systems also play a crucial role in district heating networks. These networks distribute thermal energy to urban or suburban areas, providing a reliable source of heat for residential, commercial, and institutional buildings. The steam produced by a CHP system is often transported through a network of insulated pipes to heat buildings, supply hot water, and provide space heating. This method of district heating is particularly effective in areas with dense populations or where centralized energy production can offer greater operational efficiency and reduced emissions.
For example, in cold climates where heating demand is high, using a CHP system to provide both electricity and heat to a district can significantly reduce the cost and energy consumption compared to heating individual homes or buildings with separate systems. By using steam turbines for CHP, these systems can be more energy-efficient, contributing to lower greenhouse gas emissions and helping meet sustainability goals.
Environmental Benefits
One of the most significant advantages of steam turbines in CHP systems is their positive impact on the environment. By utilizing both the electrical and thermal energy generated in a single system, CHP systems reduce overall fuel consumption, which in turn lowers the emissions of greenhouse gases (GHGs) and other pollutants. The ability to recover and utilize waste heat reduces the demand for additional fuel sources, further decreasing the carbon footprint.
In the case of biomass CHP systems, steam turbines can help support the circular economy by converting organic waste into energy. Biomass is considered a renewable fuel, and the CO2 emitted during combustion is offset by the CO2 absorbed by the plants during their growth. As a result, biomass CHP systems can be carbon-neutral, making them a valuable part of efforts to combat climate change and transition to renewable energy sources.
Moreover, CHP systems are highly scalable and can be deployed at a variety of sizes, from small distributed energy systems providing heat and power for individual buildings to large industrial-scale systems supplying entire neighborhoods or factory complexes. This scalability allows for greater flexibility in meeting energy demands and ensures that CHP systems can be tailored to suit specific energy needs and environmental targets.
Future Trends
Looking forward, several technological advancements are likely to further enhance the performance and efficiency of steam turbines in CHP systems. The development of advanced turbine materials that can withstand higher temperatures and pressures could allow for even greater efficiency. New turbine designs, such as micro-turbines and modular systems, may offer even greater flexibility in industrial applications, while the integration of digital technologies could provide real-time monitoring and control, allowing for optimized energy use and predictive maintenance.
The growing trend toward decentralized energy systems and smart grids may also see steam turbines playing a more significant role in local power generation. By pairing steam turbines with renewable energy sources like solar and wind, CHP systems could help provide stable and reliable power while reducing the reliance on fossil fuels. In addition, the increased use of energy storage technologies in CHP systems could allow for better integration of intermittent renewable energy, ensuring that excess power generated during periods of high production can be stored and used during peak demand periods.
In conclusion, steam turbines in combined heat and power systems offer a powerful and efficient solution for meeting both electricity and heating needs in industrial, commercial, and residential settings. The ability to recover waste heat and utilize it for thermal applications leads to substantial energy savings, reduced emissions, and lower operational costs. Whether in industrial applications, district heating, or biomass-powered systems, the combination of steam turbines and CHP technology will remain a critical component of efforts to improve energy efficiency, reduce environmental impact, and transition to a more sustainable energy future.
The integration of steam turbines in combined heat and power (CHP) systems is becoming increasingly important in various industrial sectors due to its ability to reduce energy consumption and environmental impact while optimizing operational costs. One key area where steam turbines in CHP systems are proving invaluable is in district heating networks. These networks provide centralized heat and, in some cases, electricity to large urban areas, where it is difficult to install and maintain individual heating systems for every building. Using steam turbines in such networks significantly improves efficiency by utilizing waste heat for heating purposes, allowing the energy that would otherwise be lost to be repurposed.
Furthermore, industrial symbiosis is another emerging trend where multiple industries work together to create energy loops using CHP systems. For example, one factory’s waste heat could be used to generate power or heat for another, leading to more efficient use of energy and reduced emissions across several industries. This concept relies heavily on the use of steam turbines to capture and redistribute waste heat in ways that would otherwise be wasted. Such collaborations can result in not only energy savings but also improved relationships between industries that benefit from shared resources.
The importance of energy recovery through CHP systems has also been magnified by the increasing focus on energy independence. Countries and regions that are aiming to reduce their reliance on imported fuels can benefit greatly from these systems, which make the most out of locally available fuels, especially in areas with abundant biomass, geothermal, or industrial waste heat. As many countries continue to seek ways to bolster energy security and sustainability, the widespread adoption of CHP systems powered by steam turbines offers a way to meet energy needs locally while reducing reliance on global supply chains.
Steam turbines also provide an efficient way to integrate renewable energy sources into traditional energy systems. For instance, solar thermal plants can generate heat to drive steam turbines for electricity production. In locations with abundant sunlight, this is a particularly promising avenue for CHP systems, as the heat from solar collectors can be used to generate steam, which powers turbines to create electricity. This renewable source of energy can complement CHP systems that are fueled by more conventional sources like natural gas or biomass, helping to further reduce carbon footprints and increase energy efficiency.
Another important development is the growing use of low-emission fuels in CHP systems. As the focus shifts toward cleaner energy sources, many industries are switching to low-carbon or carbon-neutral fuels such as biogas, hydrogen, or synthetic fuels produced from renewable sources. When used in conjunction with steam turbines, these fuels help further decrease the emissions produced during energy generation. For example, hydrogen-powered CHP systems could be a key component of net-zero emissions goals for industrial and urban energy systems. Hydrogen’s potential for use in steam turbines offers a clean alternative to conventional fossil fuels, with the added benefit of producing only water vapor as a byproduct.
To optimize the operation of steam turbines in CHP systems, digitalization plays a crucial role. The integration of smart technologies such as sensors, advanced monitoring systems, and AI-powered analytics enables real-time monitoring and management of energy production. This allows for the efficient use of steam turbines by dynamically adjusting operations to respond to changing energy demands and improving maintenance schedules. Predictive maintenance, powered by these technologies, also helps reduce downtime and prolongs the life of the turbines by identifying potential issues before they result in failures. This level of operational sophistication can significantly improve the economic viability of CHP systems, ensuring that they remain reliable and cost-effective over the long term.
In addition to industrial and residential energy needs, district cooling is gaining traction as another area where steam turbines in CHP systems are playing a role. District cooling systems, which are used to provide air conditioning for large urban areas or industrial zones, can benefit from steam turbine-driven systems that use excess heat or electricity from a CHP plant. This creates a highly efficient cooling solution for buildings and industrial processes, reducing the demand for electricity-intensive air conditioning units. By capturing and redistributing waste heat for cooling, steam turbines make it possible to meet both cooling and heating needs from the same system, further enhancing overall system efficiency.
As the world continues to shift toward more sustainable energy practices, the role of steam turbines in CHP systems will continue to grow. Their ability to offer high-efficiency performance, fuel flexibility, and the potential for integrating renewable energy sources make them a critical part of the transition to a low-carbon future. With their ability to generate both electricity and heat simultaneously, steam turbines contribute to more efficient use of resources, reducing waste, emissions, and operational costs. Whether in industrial, district, or renewable energy applications, steam turbines remain a key enabler of sustainable energy systems across multiple sectors, contributing to more resilient, efficient, and environmentally friendly energy solutions.
The ongoing advancements in steam turbine technology continue to play a pivotal role in enhancing the efficiency and environmental performance of combined heat and power (CHP) systems. As industries and municipalities aim to meet sustainability goals, steam turbines are evolving to meet the demands of modern energy systems. The key to their growing importance lies in their ability to drive energy transformation through the integration of various technologies and fuels, ensuring better performance in increasingly complex energy landscapes.
One of the primary focuses in enhancing steam turbine performance for CHP systems is improving thermodynamic efficiency. This can be achieved through the development of advanced materials and design innovations that allow turbines to operate at higher temperatures and pressures, ultimately leading to more efficient energy conversion. For instance, the use of superalloy materials that can withstand extreme conditions, such as higher steam temperatures and pressures, has significantly increased the efficiency and lifespan of steam turbines. These improvements result in better heat recovery and higher electrical output, which in turn makes the overall CHP system more cost-effective and capable of supporting larger, more energy-intensive operations.
In addition, new turbine designs, such as modular and microturbines, are making it easier to deploy CHP systems in a wider range of applications, including in remote locations or for smaller-scale industrial operations. These smaller systems offer a high level of flexibility, as they can be easily scaled up or down to meet specific energy demands. They can also be integrated with various energy sources, from geothermal and solar thermal to biomass or waste heat recovery. The ability to integrate these small-scale, modular turbines with decentralized renewable energy systems ensures greater energy independence and resilience.
Moreover, the transition to hydrogen as a fuel in CHP systems powered by steam turbines is a promising avenue for reducing carbon emissions. Hydrogen, when produced from renewable sources (often referred to as green hydrogen), can be used in place of fossil fuels to power turbines. This reduces the reliance on traditional carbon-based fuels, while providing a reliable and clean energy source for both electricity and heating applications. The ability of steam turbines to burn hydrogen without creating harmful emissions, such as carbon dioxide (CO₂), positions them as a cornerstone for achieving net-zero emissions and supporting carbon-neutral energy strategies.
Additionally, the growing focus on circular economy principles is driving industries to adopt waste heat recovery technologies in combination with steam turbines in CHP systems. By using energy that would otherwise be discarded, these systems not only reduce energy consumption but also help businesses minimize waste and emissions. In industries such as steel production, cement manufacturing, or chemical processing, where large amounts of waste heat are generated, steam turbines can be used to capture and repurpose this energy for both power generation and heating. This reduces reliance on external energy sources, decreases operational costs, and helps industries achieve their sustainability objectives.
Another important advancement is the growing integration of digital technologies to enhance the efficiency and reliability of steam turbines in CHP systems. The incorporation of Internet of Things (IoT) sensors, artificial intelligence (AI), and machine learning into turbine operations allows for predictive maintenance and real-time performance optimization. These innovations enable operators to monitor turbines remotely, anticipate mechanical issues, and schedule maintenance before failures occur. Predictive maintenance also helps optimize turbine performance by adjusting operations to meet changing energy demands, thus improving fuel efficiency and minimizing downtime.
Additionally, the advent of smart grids is enhancing the value of steam turbines in CHP systems. Smart grids enable better communication and coordination between power plants, distribution networks, and end-users, which improves energy efficiency across the system. By integrating steam turbines into these smart grid systems, electricity generation and distribution can be dynamically adjusted to match real-time energy demand. This leads to more stable energy supply, reduces grid congestion, and helps balance the integration of renewable energy sources with traditional power generation methods.
Steam turbines are also playing a key role in the development of energy storage systems. Thermal energy storage (TES) is an emerging technology that stores excess thermal energy, often generated by CHP systems, for later use. When coupled with steam turbines, TES allows for stored heat to be used to generate steam during peak energy demand periods. This provides a buffer against fluctuating energy needs, ensuring a continuous and reliable supply of power and heat. Such storage solutions are particularly important in regions with high penetration of intermittent renewable energy sources, like wind and solar, where the availability of power can vary depending on weather conditions.
The implementation of steam turbines in industrial-scale CHP systems also leads to the localization of energy production. By generating energy close to where it is consumed, these systems reduce the need for long-distance transmission, which is not only more energy-efficient but also more resilient in case of power outages. This localized approach to energy generation and consumption is increasingly becoming an integral part of energy resilience strategies, particularly in remote areas or emergency situations where the grid may be unreliable.
Another significant factor that is driving the adoption of steam turbines in CHP systems is the increased pressure on industries to reduce their carbon footprints. Governments worldwide are imposing stricter regulations on energy efficiency and emissions, and industries are seeking ways to comply with these requirements while keeping costs under control. CHP systems with steam turbines enable industries to reduce their reliance on carbon-intensive grid electricity, decrease the overall carbon footprint of their operations, and improve their environmental performance. These systems also enable industries to take advantage of various financial incentives, such as tax credits, subsidies, and renewable energy certificates (RECs), which can help offset the upfront costs of installation.
Looking ahead, steam turbines in CHP systems will continue to evolve, offering solutions to meet the growing demand for energy while reducing the environmental impact of energy production. With the increasing integration of renewable energy, energy storage, and digital technologies, steam turbines are expected to remain a cornerstone in achieving global sustainability targets. As industries, municipalities, and power providers seek to optimize energy production and reduce emissions, CHP systems powered by steam turbines will continue to play a critical role in shaping the future of energy generation and distribution.
The future of steam turbines in combined heat and power (CHP) systems will likely be shaped by further advancements in sustainability, efficiency, and technological integration. As global energy demands continue to rise and industries strive for carbon neutrality, the role of steam turbines in CHP systems will only become more prominent, offering the potential for a cleaner, more reliable, and cost-effective energy future.
Carbon capture and storage (CCS) technologies are increasingly being integrated with CHP systems that use steam turbines, helping to reduce the carbon dioxide (CO₂) emissions associated with energy production. In this context, steam turbines are not only central to efficient energy generation but also contribute to mitigating the environmental impact of fossil fuel-based energy systems. By combining CCS with steam turbines in CHP plants, industries can significantly reduce their carbon footprint while still meeting the heating and power demands of the facility. This approach aligns with global climate goals, as CCS can capture large amounts of CO₂, making steam turbines an even more integral part of a sustainable energy ecosystem.
Furthermore, hybrid CHP systems—which combine different energy sources such as natural gas, renewables, and even waste heat—are becoming a more common application for steam turbines. These hybrid systems allow for greater flexibility and adaptability in energy production, enabling operators to take advantage of the best available fuel sources at any given time. This is especially valuable in regions where renewable energy generation, such as solar or wind, may be intermittent. In such systems, steam turbines can play a critical role in smoothing out energy supply fluctuations by providing consistent and reliable heat and power. The combination of renewables with steam turbines allows for decarbonized electricity production, reducing dependency on fossil fuels.
Another area where steam turbines are set to make a significant impact is in the use of green hydrogen for CHP applications. As hydrogen production becomes more cost-effective and scalable, steam turbines can be adapted to run on hydrogen-rich fuels. Green hydrogen, produced from renewable electricity via electrolysis, can serve as a clean fuel source for steam turbines, providing a zero-emission alternative to fossil fuels. The ability to generate both heat and electricity using hydrogen in CHP systems positions steam turbines as a key player in decarbonizing industrial energy consumption. This technology is particularly beneficial for industries with high heat demand, such as steel, cement, and chemicals, where traditional fossil fuels are often used.
As energy decentralization continues to gain traction, steam turbines in CHP systems are becoming an increasingly viable solution for microgrids and distributed energy networks. Microgrids, which are small-scale, self-sufficient energy systems that can operate independently or in tandem with the larger grid, benefit from the use of steam turbines to provide consistent and high-quality energy. In a microgrid setting, steam turbines can be powered by a variety of fuels, including waste heat, biogas, or even solar thermal energy, and integrated with other renewable sources such as wind and solar. This decentralized energy production helps increase resilience and security by reducing dependence on centralized power plants and providing backup energy in case of grid outages.
The rise of digital twins and predictive analytics is also enhancing the operation of steam turbines in CHP systems. A digital twin is a virtual representation of a physical system that allows operators to monitor, simulate, and optimize turbine performance in real-time. By using big data and machine learning algorithms, operators can model how turbines will behave under various conditions and adjust operations to maximize energy efficiency and reduce wear and tear. These predictive capabilities enable more accurate scheduling of maintenance, ensuring that turbines run at peak performance for longer periods. Additionally, AI-driven analytics can help improve operational decision-making by optimizing load distribution and identifying the most efficient energy production methods.
The integration of advanced energy storage systems with steam turbine-driven CHP plants is another promising development. Thermal storage systems, for example, allow surplus heat generated during low-demand periods to be stored and used during peak demand. This provides an efficient way to shave peak loads and stabilize energy production while maintaining the performance of the CHP system. Steam turbines can leverage this stored heat to continue generating electricity or provide heating during periods when other energy sources may not be available. Furthermore, the ability to integrate energy storage systems, such as molten salt storage or compressed air energy storage, with steam turbines is further extending the operational flexibility and efficiency of CHP systems.
As energy efficiency regulations become stricter across the globe, the demand for high-performance steam turbines will grow. As part of this, turbines must be designed to meet increasingly stringent emission limits while still delivering the necessary energy output. Hybrid steam turbine systems, which combine steam turbine technology with advanced heat recovery technologies, will play a critical role in achieving these stringent goals. These systems can capture more waste heat, reduce overall energy consumption, and lower emissions compared to traditional methods.
Additionally, cross-sector collaboration will continue to drive innovation in steam turbine technology for CHP systems. Industries such as chemicals, agriculture, textiles, and refining are exploring synergies to share energy, waste heat, and other resources to optimize energy generation and minimize environmental impacts. For example, waste heat from one facility can be used to generate electricity and provide heating for another. This industrial symbiosis encourages the efficient use of resources, reduces overall energy demand, and fosters collaboration across sectors. Steam turbines play a vital role in connecting these industries by making it possible to transform waste heat into useful energy, benefiting the environment and improving energy efficiency.
As global investment in clean energy continues to rise, the economic viability of steam turbines in CHP systems will further increase. The cost of renewable energy, particularly solar and wind, continues to fall, and many countries and regions are providing substantial incentives to support the adoption of renewable technologies. Steam turbines, when paired with renewable energy sources and advanced energy storage systems, will become more competitive in the energy market, offering industries a means to reduce costs, improve sustainability, and meet regulatory demands.
In conclusion, the role of steam turbines in combined heat and power systems is set to expand as industries and power producers seek to meet evolving energy demands and sustainability goals. With innovations in hydrogen use, energy storage, digital technologies, and hybrid systems, steam turbines will continue to play a crucial role in the transition to more sustainable, efficient, and decentralized energy systems. As these technologies evolve and integrate more seamlessly with renewable sources and advanced storage solutions, steam turbines will remain an essential part of achieving net-zero emissions and ensuring long-term energy resilience.
Steam Turbines in Sugar Mills
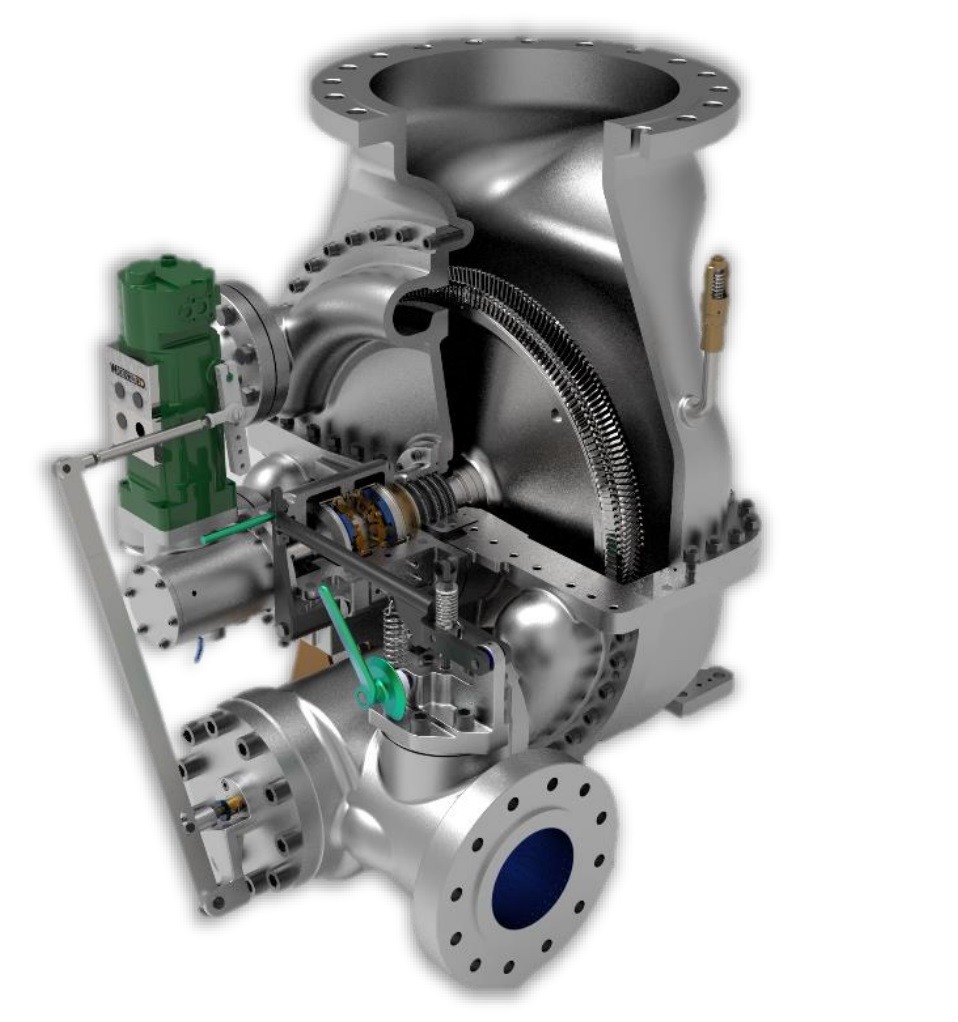
Steam turbines in sugar mills play a crucial role in enhancing the energy efficiency of sugar production processes. Sugar milling is a highly energy-intensive operation, and optimizing energy use can significantly reduce operational costs while improving sustainability. Steam turbines, integrated into the power generation systems of sugar mills, enable them to utilize the waste heat from the milling process to generate both electricity and steam for the mill’s operations. This approach reduces the need for external energy inputs, making sugar mills more self-sufficient and cost-effective.
Sugar production typically involves the extraction of juice from sugarcane or sugar beet, followed by a series of boiling and evaporation steps to concentrate the juice into a syrup. This process generates a substantial amount of waste heat, which can be harnessed through steam turbines for power generation. In this context, steam turbines in sugar mills serve as combined heat and power (CHP) systems, which provide both electricity for the mill’s operations and process steam for the boiling and evaporation stages.
The main advantages of using steam turbines in sugar mills are centered around energy efficiency and cost reduction. Since steam turbines can utilize the excess heat generated during sugar production, the mill does not need to rely on external electricity sources. This significantly reduces energy costs, which can account for a large portion of the operational expenses in sugar milling. Additionally, the steam generated by the turbines can be used to drive the mill’s industrial processes, providing the necessary heat for drying sugar, melting the raw sugar, or refining it. This integration of electricity and steam production improves overall efficiency and reduces the environmental impact of sugar mills by lowering the amount of energy consumed from external sources.
Bagasse, the fibrous material left over after sugarcane is crushed to extract juice, is a key source of biomass energy in sugar mills. Bagasse is often burned in boilers to produce steam, which is then used to drive steam turbines. This process is an excellent example of a sustainable energy model, as it allows sugar mills to generate power from a renewable and waste-derived resource. The use of bagasse for energy generation makes sugar mills more energy-independent and helps reduce the need for fossil fuels. In fact, many sugar mills can generate more electricity than they need for their own operations, enabling them to export surplus power to the local grid, providing an additional revenue stream and helping to support local energy needs.
In addition to bagasse, sugar mills are increasingly using other forms of biomass, such as wood chips and agricultural waste, to fuel steam turbines. This further enhances the environmental sustainability of the sugar mill’s operations, reducing reliance on non-renewable energy sources and contributing to a circular economy by utilizing waste materials for energy generation. Biomass-based energy systems are also considered carbon-neutral, as the carbon dioxide (CO₂) released during the combustion of biomass is offset by the carbon dioxide absorbed by the plants during their growth cycle.
Steam turbines in sugar mills also benefit from the integration of advanced control systems that optimize the operation of turbines and boilers. These systems use real-time data and analytics to adjust operations based on fluctuations in energy demand, ensuring that steam turbines operate efficiently and reduce the risk of energy waste. Predictive maintenance technologies, powered by digital tools such as IoT sensors and AI algorithms, help identify potential issues before they lead to breakdowns, ensuring consistent performance and minimizing downtime. This predictive approach helps prolong the lifespan of steam turbines and reduces operational disruptions, contributing to the mill’s overall productivity.
The increased focus on energy efficiency and emissions reduction has also spurred the development of high-efficiency steam turbines for sugar mills. Modern turbines are designed to operate at higher pressures and temperatures, increasing their thermodynamic efficiency. By improving efficiency, sugar mills can generate more electricity with the same amount of fuel, reducing fuel consumption and associated emissions. Additionally, improvements in turbine design have led to lower maintenance costs and longer operational lifespans, further enhancing the economic viability of steam turbines in sugar mills.
The growing interest in carbon capture and storage (CCS) technologies also presents an opportunity for sugar mills to further reduce their environmental impact. By integrating CCS technologies with the steam turbine systems, sugar mills can capture CO₂ emissions from the combustion of biomass fuels such as bagasse and store it underground or use it for industrial purposes, such as enhancing the production of greenhouses. This can help sugar mills achieve net-zero emissions and comply with tightening environmental regulations while continuing to operate efficiently.
In countries with high levels of solar radiation, the integration of solar thermal energy with steam turbines in sugar mills is becoming more popular. Solar collectors can capture sunlight and convert it into heat, which can then be used to generate steam that drives the turbine. This not only reduces the dependence on fossil fuels but also helps sugar mills lower their carbon emissions and make use of renewable energy sources. Additionally, solar-powered steam turbines could provide a backup energy solution for sugar mills during periods when biomass availability is low or when energy demand peaks.
Another significant trend is the increasing adoption of energy storage technologies in sugar mills. Thermal energy storage systems can store excess heat generated during periods of low energy demand, allowing the mill to use it later when energy needs increase. These systems ensure that steam turbines can operate at optimal efficiency, even during fluctuating production periods. By storing energy in this way, sugar mills can enhance the reliability and flexibility of their operations, reducing energy costs and providing more consistent power.
The development of modular steam turbines is also benefiting sugar mills, especially those with varying production capacities. Modular turbines can be easily scaled to meet the changing needs of the mill, offering flexibility in terms of energy generation capacity. These turbines are also more easily maintained and can be replaced or upgraded without significant downtime or disruptions to the mill’s operations. This modular approach allows sugar mills to adapt to growth or changes in energy demand over time, ensuring long-term sustainability and operational flexibility.
Finally, the growing trend of industrial symbiosis is opening new opportunities for steam turbines in sugar mills. In this model, energy, water, and other resources are shared between different industries to increase efficiency and reduce waste. For example, energy from a nearby sugar mill’s steam turbine could be used to power a neighboring facility, such as a distillery, that also requires steam for its production processes. This collaborative approach to resource sharing helps reduce operational costs for all parties involved while contributing to more sustainable industrial practices.
In conclusion, the use of steam turbines in sugar mills offers numerous benefits, from improving energy efficiency and reducing costs to enhancing sustainability and promoting the use of renewable energy. As sugar mills continue to seek ways to optimize their operations, steam turbines will play an increasingly important role in achieving these goals. With the integration of advanced technologies such as predictive maintenance, energy storage, and solar thermal energy, as well as the growing focus on carbon-neutral energy production, steam turbines in sugar mills will continue to evolve and contribute to more sustainable, cost-effective, and resilient energy systems in the sugar industry.
As sugar mills continue to face growing pressure to reduce costs and improve sustainability, steam turbines will play an even greater role in shaping their future operations. The ability of steam turbines to enhance energy efficiency through the effective use of waste heat—whether from bagasse combustion, process heating, or other sources—means that sugar mills can dramatically reduce energy expenses. With rising fuel costs and stricter environmental regulations, steam turbines enable mills to minimize their reliance on external power sources, which helps lower the financial burden of production.
Furthermore, the drive for resource optimization is influencing how steam turbines are integrated into broader mill operations. By recovering waste heat and maximizing its use through highly efficient turbines, sugar mills are enhancing their overall energy balance. For example, the surplus steam or electricity generated by the turbine can be used for additional processes, such as water desalination or cooling. In this way, steam turbines not only contribute to electricity generation but also play a role in the broader energy and resource management strategy of the mill. This not only increases overall mill productivity but also contributes to reducing its environmental footprint by reducing the demand for external energy.
The evolution of steam turbine design has also made them more adaptable to the specific needs of sugar mills. Advances in materials technology and turbine efficiency mean that modern turbines are able to operate at higher temperatures and pressures, further improving their energy conversion efficiency. These developments are essential as sugar mills look to maximize output while minimizing waste, and they align with the broader trend of higher-efficiency industrial equipment that is helping industries meet ambitious energy and carbon reduction targets.
As digitization continues to transform industrial operations, the integration of smart technologies with steam turbines is unlocking new opportunities for optimization and monitoring. By using sensors, real-time data, and predictive analytics, mills can monitor the performance of turbines more effectively, anticipate issues before they lead to breakdowns, and adjust operations for maximum efficiency. Condition-based monitoring systems can track turbine health, detect performance degradation, and help plan maintenance cycles more effectively. This reduces the likelihood of unplanned downtime, extending the lifespan of the turbine and reducing operational disruptions. Additionally, digital tools can help optimize energy production, ensuring that turbines operate at peak performance while minimizing energy waste.
The role of steam turbines in decarbonizing the sugar industry is also becoming increasingly important. Many sugar mills are located in regions where governments have set ambitious decarbonization goals, and they are looking for ways to transition to greener energy solutions. By utilizing renewable energy sources such as biomass and solar thermal energy, sugar mills can power steam turbines without relying on fossil fuels. This transition not only helps mills meet regulatory standards but also boosts their public image by demonstrating a commitment to sustainability. As carbon emissions reduction becomes a top priority for industries worldwide, the ability of steam turbines to generate electricity from renewable sources aligns well with both market demands and global sustainability trends.
Additionally, economic incentives from governments and international organizations can further support the adoption of steam turbines in sugar mills. These incentives may come in the form of tax credits, grants, or subsidies for energy-efficient technologies, including steam turbine installations. Such financial support can offset initial capital investment and make steam turbines more accessible to sugar mills looking to modernize their energy systems. As the demand for renewable and low-carbon energy technologies rises, governments are increasingly recognizing the role of steam turbines in promoting energy efficiency and climate action, making the case for their integration even stronger.
In regions where water scarcity is a significant issue, steam turbines can also help sugar mills improve water management. Water is an essential resource in sugar production, particularly during the refining and processing stages. By using steam turbines to generate electricity and heat from waste materials, sugar mills can reduce their water usage by decreasing their reliance on water-intensive power sources. This is increasingly important as water conservation becomes a key focus for industries, especially those located in areas where water is a limited resource. Through closed-loop water systems and improved heat recovery, sugar mills can use less fresh water while still maintaining their production capacity.
Lastly, as global sugar markets evolve, sugar mills are under pressure to improve cost-effectiveness and competitiveness. By adopting advanced steam turbine technologies, mills can not only optimize their energy use but also improve their market position. Mills that are able to reduce their operating costs through energy savings and sustainability initiatives can offer more competitive pricing on their products, benefiting from reduced production expenses while maintaining environmental integrity. In a market where sustainability is increasingly valued by consumers, adopting energy-efficient technologies like steam turbines can be a differentiator, helping mills align with consumer expectations for sustainable sourcing and low-carbon products.
In conclusion, steam turbines offer a wide range of benefits to sugar mills, from improving energy efficiency and reducing operational costs to promoting sustainability and environmental responsibility. As the industry continues to modernize, steam turbines will remain a key technology for optimizing energy use, reducing emissions, and ensuring long-term profitability. With the ongoing development of more efficient turbines, the integration of renewable energy, and the implementation of smart technologies, the future of steam turbines in sugar mills is poised to support the industry’s transformation into a more sustainable and economically viable sector.
As the sugar industry faces increasing pressure to meet sustainability and profitability goals, steam turbines are proving to be an integral part of the transition to more efficient and eco-friendly operations. The role of steam turbines in energy efficiency will continue to expand, especially as sugar mills look for innovative ways to minimize energy waste and maximize the utilization of available resources. For example, advanced steam turbine technology is enabling dual-mode operations in which turbines can switch between generating electricity and producing heat depending on demand. This flexibility allows sugar mills to optimize their energy systems for various production scenarios, adjusting for seasonal fluctuations in sugar production or energy requirements.
Moreover, the rise of smart grids is encouraging more sugar mills to integrate steam turbines with wider energy networks. Through advanced energy management systems, turbines can interact with the grid, enabling mills to supply surplus power when they have excess generation capacity and draw from the grid during periods of high energy demand. This type of integration further enhances the reliability and resilience of the mill’s energy system, making the facility more adaptable to changing operational needs. By participating in a broader energy exchange, sugar mills can create new revenue streams while contributing to the stability of the local or regional grid.
Another promising trend is the integration of steam turbines with district heating systems. These systems are particularly useful in areas where multiple industries or communities can benefit from shared thermal energy. By connecting a sugar mill’s steam turbine to a district heating network, the mill can provide steam or hot water to nearby industrial facilities or residential areas, further improving its energy efficiency and reducing energy costs across multiple sectors. This collaboration promotes the circular economy by ensuring that no excess energy goes to waste, providing a more sustainable solution for both the mill and the surrounding community.
Energy storage is also gaining traction in the sugar milling industry. As sugar mills strive for grid independence and energy security, technologies such as thermal energy storage (TES) are being incorporated into steam turbine systems. These storage systems allow steam turbines to store excess energy in the form of heat, which can later be used to produce steam when needed. For example, in times of low electricity demand, a sugar mill may produce excess steam that can be stored for future use. This stored thermal energy can be dispatched quickly to meet high-energy demands or during peak times, enhancing the overall efficiency of the energy system. Such energy storage solutions make steam turbines more responsive to fluctuating demand, improving the economic stability of the mill’s operations.
The continued integration of digital twin technology and artificial intelligence (AI) will help sugar mills optimize the operation of their steam turbines. A digital twin is a virtual replica of the steam turbine and its environment, which can be used to simulate different operational scenarios. AI-based analytics and machine learning algorithms can be applied to the digital twin to predict performance degradation and optimize maintenance schedules, further improving the lifespan of turbines and minimizing unexpected breakdowns. This approach allows sugar mills to reduce maintenance costs, improve reliability, and achieve predictive maintenance, which is becoming a standard practice across industries. The ability to continuously monitor and optimize steam turbine performance, in real-time, allows mills to reduce costs associated with unplanned downtime and lost production.
The customization of steam turbines to meet the unique needs of sugar mills is another key factor driving their adoption. Turbine manufacturers are increasingly offering bespoke solutions, which can be tailored to match the specific energy requirements of a sugar mill. For example, some turbines are designed for low-pressure, high-flow applications, making them ideal for mills with high steam demands but lower steam pressures. Others may be suited for combined heat and power (CHP) configurations, where steam turbines are paired with other technologies, such as boilers, to achieve the most energy-efficient configuration possible for the mill’s needs.
With the increasing awareness of the need to minimize emissions and reduce carbon footprints, sugar mills are focusing on more sustainable fuel options to support their steam turbines. As part of their transition to renewable energy, many mills are adopting co-generation systems that combine steam turbines with biomass-based power generation. Bagasse, a by-product of sugarcane processing, remains a key source of renewable fuel, but mills are also experimenting with other waste-to-energy strategies. For example, they may utilize agricultural waste, such as rice husks or corn stover, in combination with bagasse for steam generation, making the mill even more energy-efficient and environmentally friendly.
In addition to using biomass for fuel, some sugar mills are exploring the potential of biofuels and biogas as alternative sources of energy to drive steam turbines. The transition to biofuels can reduce the dependence on fossil fuels and lower the associated environmental impact. For instance, ethanol production, a key activity in sugar mills, generates bioethanol, which could be used as a supplemental fuel source for steam turbines, providing a sustainable loop in the energy cycle.
Furthermore, as regulations on emissions become more stringent, steam turbines are being designed with advanced emission control technologies. These innovations can help mills meet the growing demand for low-emission or even carbon-neutral solutions. Advanced filtration systems, flue gas desulfurization, and nitrogen oxide (NOx) reduction technologies are becoming standard features in steam turbine installations in sugar mills, ensuring compliance with environmental standards and contributing to the industry’s commitment to reducing its environmental footprint.
The development of high-efficiency steam turbines is leading to a reduction in the overall carbon intensity of sugar milling operations. These advanced turbines are designed with superior thermodynamic cycles, including regenerative heating and reheat systems, which allow for improved performance, even at lower fuel inputs. This makes sugar mills more competitive in a global market where energy costs are a key factor in the profitability of operations. In addition, lower emissions and higher efficiency contribute to a more sustainable and responsible image for the mill, helping companies meet both regulatory and market-driven sustainability goals.
The shift toward sustainability and green manufacturing in the sugar industry is also shaping consumer perceptions. Green-certified sugar mills that adopt steam turbines for clean energy generation will find that their products are increasingly valued by consumers who are seeking sustainably produced goods. The ability to demonstrate a commitment to environmentally conscious production can improve the mill’s market share, attract environmentally aware consumers, and bolster the mill’s reputation in a competitive marketplace.
In conclusion, steam turbines in sugar mills continue to play a vital role in improving energy efficiency, reducing costs, and enhancing sustainability. Their ability to recover and utilize waste heat, generate renewable energy, and support advanced technologies for predictive maintenance and digital optimization positions them as a cornerstone of modern sugar production. As the industry evolves, the use of steam turbines will continue to drive cost-effective, energy-efficient, and environmentally responsible practices in sugar mills, ensuring their competitiveness in an increasingly sustainable and energy-conscious global market.
As the sugar industry looks toward the future, the importance of steam turbines in transforming operations becomes even more evident. One area of increasing significance is the integration of steam turbines with renewable energy systems. The industry’s shift toward net-zero emissions requires the exploration of various energy sources that can be used to fuel steam turbines while minimizing environmental impact. Solar-thermal energy, geothermal, and wind energy have become viable options for steam turbine integration. For instance, solar-thermal power systems can be used to preheat water for steam generation, reducing the fuel load required for the turbine and enhancing overall efficiency. This hybrid approach between renewable energy and steam turbines reduces reliance on fossil fuels, lowers emissions, and boosts the sustainability of sugar mills.
Energy integration and smart technology will be key enablers in improving operational efficiency. The development of advanced energy management systems (EMS) for sugar mills will allow them to operate in a way that optimizes energy use across the facility. By connecting turbines, boilers, and other equipment into a single intelligent network, these systems will continuously monitor performance and automatically adjust operations to reduce waste and maximize energy savings. These technologies, including artificial intelligence (AI) and machine learning algorithms, will offer a higher level of control and foresight over the turbine’s performance and energy usage, allowing mills to make adjustments on the fly.
The adoption of advanced turbine designs that allow for greater operational flexibility will also play a central role. Variable-speed turbines, which can operate efficiently under varying load conditions, will enable sugar mills to adjust their energy production as needed. This is especially useful in sugar mills that experience fluctuating operational demands. For example, during seasonal peaks in sugar production, turbines can work at higher capacities, while at other times, they can operate at lower capacities without losing efficiency. These advancements help sugar mills achieve greater adaptability to market conditions, ensuring they are not overproducing or wasting energy when demand is low.
The growing trend of sustainability certifications is also creating a more competitive landscape for sugar mills. Mills that utilize steam turbines powered by renewable sources are better positioned to meet the requirements of global sustainability standards and qualify for green certifications such as Fair Trade or Rainforest Alliance. These certifications are becoming more critical as consumers demand greater transparency in the products they purchase, especially in industries such as food and beverages. The ability to demonstrate the sustainable operation of a sugar mill through energy-efficient technologies like steam turbines can give mills a distinct market advantage.
Additionally, the rise of local and decentralized energy production is influencing the design of steam turbine systems. As more sugar mills operate in rural or off-grid locations, there is a growing need for turbines that can function independently, without relying on the external grid for support. By utilizing steam turbines powered by renewable or waste-based fuels, these mills can generate their own electricity, significantly lowering energy costs and providing greater energy security. This off-grid capability is particularly beneficial for mills operating in remote regions where energy access might be limited or unreliable.
The benefits of steam turbines also extend to their long-term cost-effectiveness. Although the initial investment in a steam turbine system can be high, the operational cost savings from increased energy efficiency and lower fuel requirements can lead to significant payback over time. Furthermore, steam turbines have a long lifespan and are relatively easy to maintain with proper care and predictive maintenance practices. This durability ensures that sugar mills can rely on their turbines for decades, making them a wise investment for long-term sustainability.
The role of waste-to-energy processes will continue to grow in sugar mills, as waste by-products such as bagasse or biomass are increasingly used as fuel sources for steam turbines. By integrating these renewable fuel sources into the power generation process, sugar mills can reduce their dependence on external fuel suppliers, while also contributing to the reduction of greenhouse gas emissions. This circular economy approach, where waste is converted into valuable energy, enhances the overall sustainability of the mill and adds value to by-products that were previously discarded.
As the sugar industry becomes more focused on sustainability, there will also be greater attention paid to the environmental impact of steam turbine manufacturing and installation. Manufacturers will continue to focus on producing more eco-friendly turbines, utilizing advanced materials that reduce emissions during the manufacturing process. Additionally, the push for carbon-neutral manufacturing will lead to more sustainable production methods, which will further enhance the overall environmental benefits of steam turbines. By minimizing the carbon footprint of turbine production, the industry can ensure that the entire lifecycle of the turbines, from manufacturing to operation, remains in line with global sustainability objectives.
The increasing demand for alternative energy sources in the sugar industry, including biogas and waste-to-energy technologies, will likely increase the adoption of steam turbines that can operate efficiently on these renewable fuels. For example, biogas from sugarcane processing can be used to power steam turbines, providing a clean and renewable source of energy that reduces waste and lowers the carbon footprint of operations. As sugar mills explore more low-carbon solutions, steam turbines will play an important role in meeting sustainability targets and providing a reliable and flexible means of generating energy.
Finally, as global energy markets shift towards more decentralized and renewable energy solutions, the role of steam turbines will become even more critical. Sugar mills that adopt these technologies early on will not only benefit from energy savings but will also be well-positioned to participate in emerging energy markets. These may include local energy exchanges, where mills can sell surplus energy back to the grid or trade with other industries to optimize energy use. By becoming energy producers rather than just consumers, sugar mills can create new revenue streams, improve operational resilience, and solidify their position in a sustainable energy economy.
In summary, steam turbines are set to play a pivotal role in the future of the sugar industry by driving energy efficiency, reducing operational costs, and supporting sustainability goals. Through advanced technologies, integration with renewable energy systems, and the growing emphasis on resource recovery, steam turbines will continue to be a central component in the transformation of sugar mills into more sustainable, efficient, and competitive enterprises. As the industry embraces these advancements, steam turbines will be essential in enabling sugar mills to meet the challenges of a rapidly changing global market while contributing to the broader goals of environmental responsibility and energy resilience.
Steam Turbines in Refineries
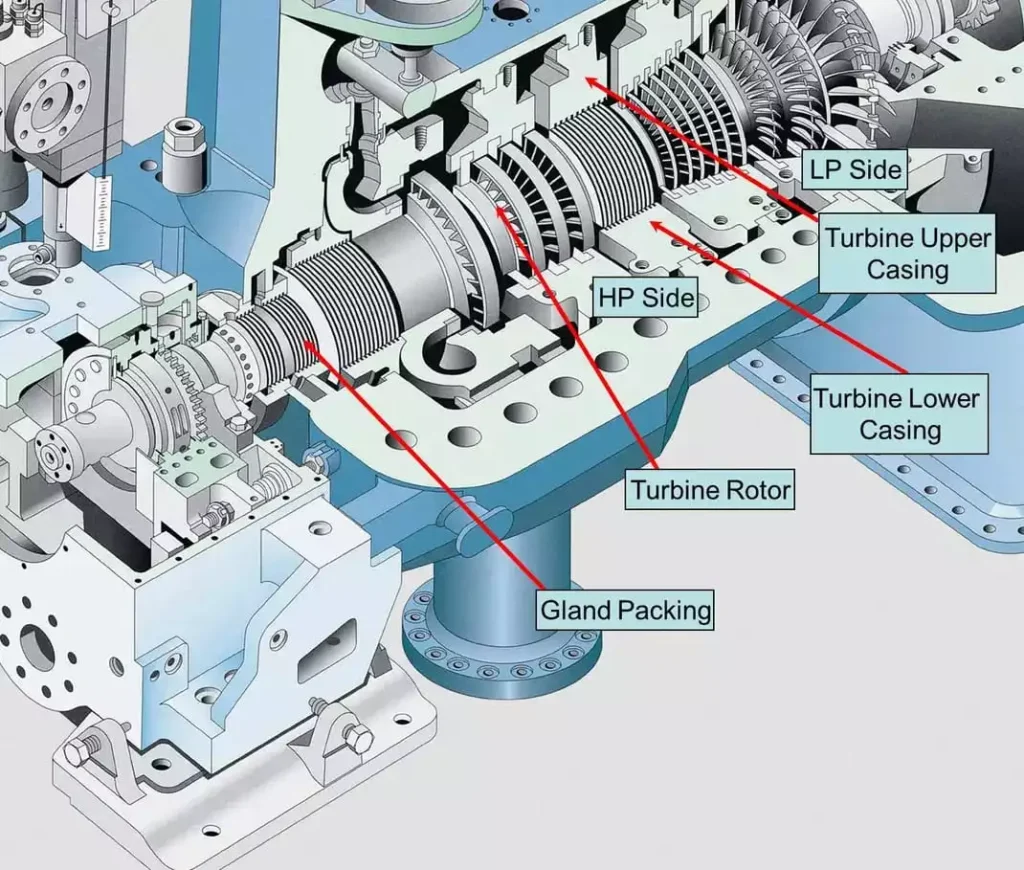
In refineries, steam turbines are crucial components of energy systems, used to convert the thermal energy from steam into mechanical energy for driving equipment or generating electricity. As refineries operate under intense energy demands for various processes such as distillation, cracking, and hydroprocessing, steam turbines provide an efficient means of harnessing waste heat and transforming it into usable power. This results in improved operational efficiency, reduced fuel consumption, and enhanced overall performance. The primary advantage of using steam turbines in refineries is their ability to maximize energy recovery from the processes already in place, thus enabling the refinery to become more energy-independent and cost-effective.
One of the primary uses of steam turbines in refineries is in cogeneration systems, where they are paired with boilers to generate both electricity and process steam. The combination of electricity production and process steam generation allows refineries to meet their own power needs while also optimizing fuel use. The integration of steam turbines into these systems enables refineries to take advantage of waste heat recovery. When waste heat from processes like furnaces or reactors is collected, it can be used to produce steam that drives turbines for power generation, reducing the need for external energy sources. This type of combined heat and power (CHP) system reduces operational costs by cutting energy purchases and helps refineries to achieve self-sufficiency.
Steam turbines in refineries are typically powered by steam produced from fuel combustion or other high-temperature processes, including furnace stacks and reformer units. This steam is then fed into turbines, which can be used for various functions, including driving compressors, pumps, and generators. By integrating steam turbines with other mechanical systems in refineries, the overall efficiency of the plant is increased, reducing the need for external power sources and lowering the overall energy consumption.
Another key advantage of steam turbines in refineries is their role in maintaining stable energy supplies. Refineries operate around the clock, and consistent energy availability is essential for smooth operations. Steam turbines help to balance energy demands, ensuring that the refinery can meet both peak and off-peak power needs without relying solely on the grid. When energy demand is high, steam turbines can ramp up production to meet the increased load, while during periods of low demand, they can operate more efficiently to provide the necessary amount of energy without overloading the system.
The increased focus on environmental responsibility within the refinery sector has spurred the development of advanced, low-emission steam turbine technology. Many refineries are now focusing on using renewable energy sources such as biomass, biogas, or hydrogen to fuel their turbines, contributing to a reduction in carbon emissions. The use of sustainable fuels also enhances the environmental footprint of refineries, helping them to meet tightening regulatory standards and societal demands for cleaner operations.
In addition to environmental concerns, refineries are increasingly adopting digital technologies and predictive analytics to optimize steam turbine performance. By integrating sensor networks and data analysis tools, refineries can monitor the performance of their turbines in real-time, predicting potential failures or performance degradation before they occur. This predictive approach not only extends the life of steam turbines but also reduces unplanned downtime and enhances the refinery’s overall reliability. Predictive maintenance ensures that turbines remain in top operational condition, minimizing disruption to the refining process and improving overall operational efficiency.
Steam turbines are also increasingly being customized to meet the specific needs of different refinery processes. For instance, refineries that handle heavier feedstocks or more complex chemical processes may require turbines with special configurations to handle the unique energy demands. Turbine manufacturers offer tailored solutions, such as turbines designed to operate in high-pressure or high-temperature environments, ensuring optimal efficiency in these challenging settings. These customized solutions allow for greater flexibility and adaptability, ensuring that turbines can perform at their best across a variety of operational scenarios.
The trend toward modular systems in modern refineries is another development that benefits the use of steam turbines. Modular power blocks, which consist of self-contained units that can be added or removed from the overall energy system, make it easier for refineries to scale their power production up or down depending on changing energy needs. Modular systems also make it easier to incorporate backup power capabilities, ensuring that steam turbines can continue to operate even if the main power supply fails. This level of flexibility and resilience is essential in maintaining the refinery’s operations without disruption, especially in critical areas such as distillation towers or catalytic cracking units.
Additionally, steam turbines for refineries help increase the reliability and resilience of power systems in the face of rising global energy demands. By being able to generate power on-site, refineries can protect themselves from potential grid instability or energy shortages. The refinery’s on-site generation of electricity through steam turbines also reduces its exposure to volatile energy prices, offering a more stable energy cost structure. This financial predictability is especially important in the highly competitive refining market, where maintaining low operational costs is essential to profitability.
Steam turbines also have the advantage of being highly reliable over the long term. Their proven durability and ability to operate continuously for extended periods without major issues make them ideal for the demanding environment of a refinery. Routine maintenance and monitoring ensure that turbines remain in peak condition, while the use of advanced materials in turbine construction extends their service life and reduces wear and tear.
In refineries, the use of steam turbines can significantly enhance energy recovery from the processing of crude oil. Hydrocracking, for example, generates a significant amount of waste heat, which can be used to produce steam for turbines. By capturing this waste heat and converting it into usable energy, refineries are able to improve their overall energy efficiency and reduce fuel consumption. This not only benefits the refinery financially but also improves its sustainability by reducing its reliance on external energy supplies.
Steam turbines also support the flexible use of energy within refineries, which is essential as energy demands fluctuate with changes in production schedules or market conditions. For example, in periods of high demand for refined products, steam turbines can be pushed to their maximum efficiency to generate additional power, while during lower-demand periods, turbines can be used more conservatively to reduce energy production costs. This dynamic energy management capability ensures that the refinery is always operating at its optimal energy output, minimizing waste and maximizing profitability.
The future potential of steam turbines in refineries lies in their integration with new technologies such as carbon capture, energy storage, and green hydrogen production. As refineries move toward reducing their carbon footprint, steam turbines will play a central role in capturing excess heat for use in carbon capture systems, improving the overall energy recovery process. Additionally, integrating steam turbines with energy storage solutions, such as thermal storage systems, will enable refineries to store excess energy for use during peak demand times or in case of emergencies, further enhancing their energy resilience.
In conclusion, steam turbines are integral to the operation of modern refineries, providing significant benefits in terms of energy efficiency, cost reduction, and environmental responsibility. Whether through the integration of cogeneration systems, the use of renewable fuels, or the incorporation of smart technologies, steam turbines continue to evolve as essential components in refinery operations. Their ability to harness waste heat, reduce dependence on external energy sources, and provide reliable, flexible power generation ensures that refineries will remain competitive and sustainable in the years to come.
As refineries continue to evolve in response to increasing energy demands, regulatory pressures, and the push for greater sustainability, the role of steam turbines becomes even more critical. One emerging trend is the integration of steam turbines into advanced refining technologies aimed at improving both operational efficiency and environmental performance. For example, the transition to hydrogenation processes and other advanced catalytic methods often generates significant waste heat, which can be recovered and converted into useful energy through steam turbines. This enhances the energy efficiency of these processes, reduces fuel consumption, and minimizes the carbon footprint of refinery operations.
The ability of steam turbines to operate in extreme conditions also makes them particularly valuable in refining processes that involve high pressures and temperatures, such as those in heavy oil and bitumen upgrading. These processes often require large amounts of energy to extract and refine valuable fuels from less conventional sources, and steam turbines are well-suited to handle the challenging conditions while maintaining reliability and efficiency. By recovering and utilizing waste heat from these processes, steam turbines play a central role in ensuring that refineries can meet stringent environmental standards without sacrificing production capacity.
In light of the increasing importance of sustainable refining practices, the integration of steam turbines with carbon capture technologies is becoming an essential feature of next-generation refineries. As part of the carbon capture, utilization, and storage (CCUS) strategy, steam turbines can facilitate the process by providing the necessary power for compression systems and other carbon capture equipment. By capturing CO2 emissions at the source and converting them into useful products or securely storing them underground, refineries can significantly reduce their environmental impact, helping to meet future emissions targets and climate goals.
Furthermore, steam turbines are also playing an increasingly important role in integrated refinery systems, where they support a variety of synergistic processes. The heat and power generated by steam turbines can be used in multiple refinery units, from desulfurization to distillation, creating a highly efficient and interconnected energy system that minimizes energy loss and maximizes the recovery of heat across the entire facility. This integrated approach reduces fuel costs, lowers emissions, and ensures that energy is used in the most effective manner possible.
The need for flexible and resilient energy sources in the face of changing energy markets and potential disruptions is another driving force behind the use of steam turbines in refineries. Many refineries are now exploring the possibility of incorporating renewable energy sources into their power systems, such as biomass and solar-thermal energy. When coupled with steam turbines, these renewable energy sources can provide refineries with an even more sustainable and cost-effective way to generate the heat and power needed for their operations. This diversified energy mix helps ensure that refineries are less reliant on fossil fuels and external energy suppliers, reducing both costs and carbon emissions.
Additionally, steam turbines contribute to refineries’ overall sustainability goals by facilitating the use of waste-to-energy processes. For instance, refineries that generate large quantities of organic waste, such as sludges or residual oils, can use this waste as fuel for steam generation. This process not only helps to dispose of waste materials in an environmentally responsible manner but also provides a renewable source of energy that can be harnessed by steam turbines. By converting waste into valuable energy, refineries can operate with a circular economy approach, where the by-products of refining become a resource rather than a liability.
In summary, steam turbines are an indispensable part of refinery operations, offering a wide range of benefits from energy efficiency and cost savings to supporting sustainability initiatives and enhancing environmental performance. As the industry continues to innovate and pursue cleaner technologies, the role of steam turbines will only grow in importance. By enabling refineries to optimize energy use, reduce emissions, and integrate renewable energy sources, steam turbines contribute significantly to the ongoing transformation of the refining sector, helping to meet the evolving energy demands of the modern world while working toward a low-carbon future.
Steam turbines are also central to the shift toward digitization and smart refinery operations. As refineries become more reliant on data analytics, Internet of Things (IoT) devices, and advanced control systems, steam turbines are being integrated into these smart systems for real-time monitoring and optimization. By using sensors to track performance metrics such as vibration, temperature, and pressure, refineries can continuously assess the health of their turbines and predict potential failures before they occur. This predictive maintenance approach not only reduces unplanned downtime but also helps in extending the life of turbines, optimizing their efficiency, and ensuring safe operation.
The integration of artificial intelligence (AI) and machine learning algorithms further enhances the capabilities of steam turbines in refineries. These technologies can analyze vast amounts of operational data to identify trends, optimize performance, and even suggest process adjustments that would enhance overall refinery efficiency. For example, AI can help fine-tune turbine settings in response to fluctuations in energy demand, ensuring that turbines operate at peak performance while maintaining a balance with the refinery’s other energy needs. This intelligent control improves the flexibility and efficiency of steam turbines, allowing refineries to adapt quickly to changes in demand or shifts in energy availability.
In addition to improving operational efficiency, the sustainability aspect of steam turbines continues to grow in importance. Refineries are increasingly focusing on reducing their carbon footprints and enhancing their environmental stewardship, which aligns with the growing demand for green technologies and clean energy solutions. Steam turbines help to achieve these goals by reducing reliance on conventional fossil fuels and enabling the integration of renewable energy sources. Solar, wind, and biomass energy, when used to generate steam or electricity, can be converted into mechanical power using turbines, leading to a reduced environmental impact. This aligns with global initiatives aimed at reducing carbon emissions, and steam turbines can play a pivotal role in meeting these targets by lowering greenhouse gas emissions and helping refineries transition to more sustainable energy systems.
Steam turbines also contribute to the economic competitiveness of refineries. In many cases, refineries are facing pressure from rising energy costs, volatile fuel prices, and increasing regulatory compliance requirements. Steam turbines allow refineries to improve their energy self-sufficiency, making them less dependent on the grid and more resilient to energy price fluctuations. By generating their own power from waste heat and optimizing their energy recovery systems, refineries can significantly lower their operational costs, which is a key factor in maintaining profitability in an increasingly competitive market. Furthermore, steam turbines’ long operational lifespans and low maintenance costs enhance the overall financial viability of the refinery by offering a low cost of ownership over time.
As refineries look for innovative ways to meet sustainability and efficiency goals, the use of steam turbines is expanding to include new technological applications. For example, cogeneration systems are becoming more sophisticated, with turbines now being used in combined cycle configurations to enhance overall energy recovery. These systems can use both gas turbines and steam turbines to produce power, increasing the total energy recovery from a given set of fuel inputs. This combined-cycle approach improves the overall thermal efficiency of the refinery and significantly reduces its environmental impact.
Steam turbines are also critical in supporting the shift toward hydrogen production, especially as green hydrogen emerges as a promising alternative to fossil fuels. The production of hydrogen typically involves steam methane reforming (SMR) or electrolysis, both of which require significant amounts of heat and power. Steam turbines can be integrated into these processes to enhance energy recovery and optimize production, making hydrogen a more feasible and cost-effective solution. As the demand for clean hydrogen increases, steam turbines will be essential in supporting refineries’ efforts to produce hydrogen from renewable sources, further advancing the green energy transition.
Refineries are also embracing more modular and flexible power generation solutions, and steam turbines are at the forefront of these innovations. Modular power blocks, which can be easily scaled up or down, offer refineries a way to meet fluctuating energy demands without the need for significant capital investment in large, fixed infrastructure. These systems allow refineries to adapt to changes in production levels or shifts in market conditions by adding or removing modules as needed. This scalability ensures that steam turbines can be part of energy systems that evolve with the refinery’s operational needs, maintaining both efficiency and cost-effectiveness over time.
Another emerging trend is the hybridization of steam turbine systems with energy storage technologies. As renewable energy sources like solar and wind power become more prevalent, the ability to store energy for later use is becoming increasingly important. Steam turbines, when integrated with thermal storage systems, can help refineries manage energy demand fluctuations by storing excess energy during low-demand periods and using it when demand peaks. This ability to store and release energy on demand enhances the refinery’s energy security, ensuring that it has a reliable power supply even when external sources are unstable or unavailable.
The role of steam turbines in the refinery industry is also evolving with the increasing focus on carbon capture and storage (CCS). As refineries face growing regulatory pressures to reduce carbon emissions, steam turbines play a vital role in facilitating CCS operations. The compression systems and separation units used in CCS processes require significant power, which steam turbines can provide. By coupling steam turbines with CCS technology, refineries can not only improve their environmental performance but also play an active role in mitigating climate change by capturing and storing CO2 emissions rather than releasing them into the atmosphere.
In conclusion, steam turbines in refineries offer a broad range of advantages, from improving energy efficiency and reducing costs to supporting sustainability initiatives and enabling smart energy systems. With advancements in digital technologies, renewable energy integration, and predictive maintenance, steam turbines will continue to play a key role in ensuring that refineries can meet the evolving challenges of the energy transition. By maximizing energy recovery, reducing emissions, and improving energy resilience, steam turbines will remain a central element in the refining industry’s efforts to operate more sustainably, efficiently, and profitably in the years to come.
The continued evolution of steam turbines in the refining industry is also driven by the need for greater energy resilience in the face of natural disasters, geopolitical instability, and other unforeseen disruptions. Refineries, particularly those located in areas vulnerable to extreme weather events or supply chain interruptions, must be able to maintain stable operations under a wide range of conditions. Steam turbines, with their ability to utilize diverse energy sources, provide a robust solution to these challenges. Their flexibility in fuel choice allows refineries to pivot quickly in response to supply chain disruptions, such as fluctuations in the availability of natural gas or crude oil, ensuring that the plant remains operational during critical periods.
Decentralized energy generation using steam turbines is also becoming an increasingly important strategy for enhancing refinery resilience. By implementing smaller, modular turbine systems, refineries can distribute their energy generation capabilities across the facility. This decentralized approach minimizes the risk of total system failure in case of a localized issue and can allow a refinery to continue functioning even if one part of its power generation infrastructure is compromised. This level of flexibility enhances the security of supply for essential refining processes and ensures that refineries can meet their production and environmental goals, even during times of crisis.
In line with the move toward more sustainable and resilient operations, steam turbines also play an important role in the broader energy transition. Many refineries are exploring options to reduce their reliance on fossil fuels by integrating renewable power into their energy mix. In this context, steam turbines offer a valuable pathway for utilizing energy from renewable sources, such as solar thermal or biomass energy, to generate steam. By combining renewable energy with traditional fuel sources in a hybrid system, refineries can reduce their carbon emissions and contribute to broader efforts aimed at achieving net-zero emissions. This transition to greener energy not only helps refineries comply with increasingly stringent regulations but also improves their long-term competitiveness in a world increasingly focused on sustainability.
Another important application of steam turbines in refineries is their role in reducing water usage through the effective management of cooling and steam generation processes. Refineries are increasingly being held accountable for their water consumption due to the pressures of sustainability and regulatory compliance. By using steam turbines in conjunction with advanced closed-loop cooling systems and waste heat recovery technologies, refineries can significantly reduce their water footprint. These innovations ensure that steam turbines are integral to helping refineries not only manage their energy consumption but also optimize their water resources, contributing to the overall sustainability of the operation.
Furthermore, steam turbines are evolving alongside the wider electrification trend within the refining industry. As electrification becomes a key strategy for reducing emissions and improving operational efficiency, steam turbines are increasingly being integrated into electrical generation systems, such as combined cycle plants. By combining steam and gas turbine technologies, refineries can achieve higher thermal efficiency and reduce their carbon emissions per unit of energy produced. This synergistic effect allows for even better energy use and supports refineries’ goals to meet both financial and environmental targets. It also provides the flexibility to integrate renewable energy more easily into the grid, enabling a smoother transition to a more sustainable energy system.
Steam turbines in refineries also offer long-term benefits in terms of reliability and maintenance optimization. One of the advantages of steam turbines is their durability, with some turbines operating for several decades with minimal performance degradation when properly maintained. Refineries benefit from the extended operational lifespans of steam turbines by avoiding the high capital expenditure required to replace power generation systems frequently. Additionally, predictive maintenance technologies can help identify potential issues before they result in system failures, ensuring that steam turbines continue to operate efficiently over the long term. This contributes to overall operational stability and cost-efficiency, allowing refineries to keep energy costs down while maximizing production.
In addition to their role in energy generation, steam turbines in refineries are also key players in hydroprocessing and other high-energy-demand processes. Processes such as hydrotreating and hydrocracking require significant amounts of heat and pressure to break down complex hydrocarbons. Steam turbines contribute to these processes by recovering waste heat and converting it into useful power, enhancing both the efficiency of these reactions and the overall profitability of the refinery. By optimizing the heat-to-power conversion process, refineries can reduce the need for external energy sources and lower the overall operational cost of these demanding processes.
Global regulatory frameworks and climate policies are another driving force behind the widespread adoption of steam turbines in refineries. Governments around the world are setting ambitious targets for carbon emissions reductions, and refineries must comply with these mandates to remain competitive. Steam turbines support this effort by enabling energy recovery and efficiency improvements, which directly translate into lower emissions and reduced fuel consumption. As governments continue to incentivize low-carbon technologies and penalize high-emission practices, refineries are increasingly turning to steam turbines as a means of staying ahead of regulatory changes while optimizing their operations.
Lastly, steam turbines are contributing to the transition of refineries into integrated energy hubs. Rather than simply serving as facilities for processing crude oil and producing refined products, refineries are evolving into multifunctional energy centers that generate and distribute electricity, hydrogen, and other valuable products. Steam turbines are an integral part of this transformation, providing reliable power generation and supporting the integration of alternative fuels. This new role allows refineries to diversify their energy portfolios and minimize risk by tapping into multiple sources of energy and offering new products to the market.
In conclusion, steam turbines will continue to play a critical role in the future of the refining industry. As refineries navigate the challenges of the energy transition, sustainability, and economic competitiveness, steam turbines provide the flexibility, efficiency, and reliability necessary for success. Their ability to integrate with advanced technologies such as carbon capture, renewable energy systems, and intelligent control platforms ensures that refineries remain resilient, adaptive, and prepared to meet the evolving demands of the energy market. With their long-standing reputation for durability and performance, steam turbines are well-positioned to remain a key component in the energy transformation of refineries for years to come.
Steam Turbines for Fertilizer Plants
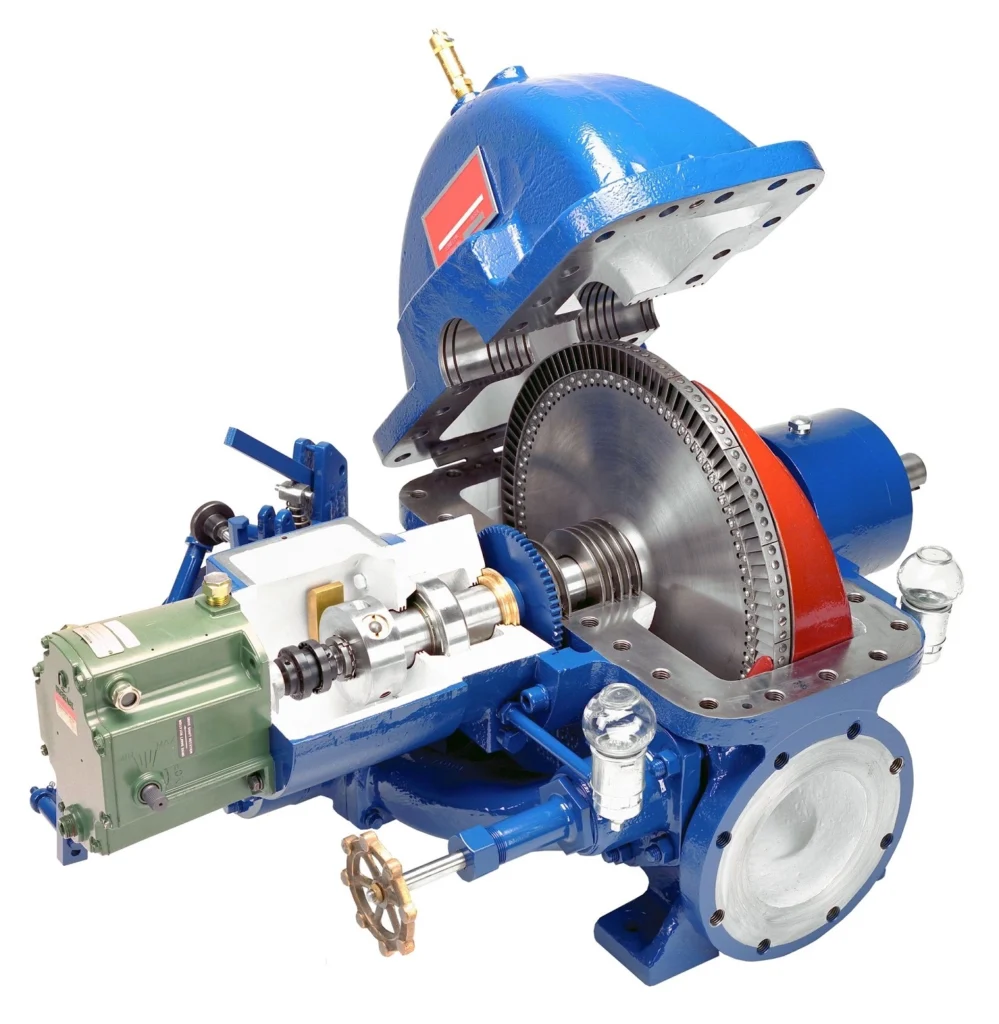
Steam turbines play a vital role in fertilizer plants by enhancing energy efficiency, supporting sustainability, and ensuring reliable operations. Fertilizer production, particularly the ammonia and urea manufacturing processes, requires substantial amounts of energy, both in the form of thermal energy and mechanical power. Steam turbines are central to optimizing energy use in these plants, where they are employed to recover waste heat, generate electricity, and drive mechanical processes. By integrating steam turbines into the power generation and heat recovery systems, fertilizer plants can achieve significant energy savings, reduce operational costs, and improve overall plant efficiency.
One of the primary applications of steam turbines in fertilizer plants is in the combined heat and power (CHP) systems, where steam generated from natural gas or other fuel sources is used to power steam turbines. These turbines then generate electricity and provide heat for the various stages of fertilizer production. Ammonia synthesis, for example, is a highly energy-intensive process, requiring large amounts of heat and pressure. Steam turbines enable fertilizer plants to recover and utilize waste heat from the ammonia production process, which can be used for steam generation or other power needs. This reduces the need for additional fuel inputs, contributing to lower energy costs and increased environmental sustainability.
Steam turbines also help fertilizer plants meet the growing demand for sustainable energy solutions by integrating renewable energy sources. Many fertilizer plants are exploring ways to incorporate biomass or solar-thermal energy into their energy mix. Steam turbines are well-suited to utilize renewable energy to produce steam, which can then be used to generate power or drive mechanical processes. Biomass-fired steam turbines, for example, use organic materials such as agricultural residues or waste to generate steam, turning what would otherwise be waste products into valuable energy. This not only improves the sustainability of fertilizer production but also helps plants comply with environmental regulations related to carbon emissions.
In addition to renewable energy integration, steam turbines in fertilizer plants play a crucial role in improving energy resilience and self-sufficiency. Fertilizer plants are often located in regions with variable access to the electrical grid or where power supply interruptions can significantly disrupt production. By using steam turbines in cogeneration or standalone power generation systems, plants can ensure a more reliable and stable energy supply. This is particularly important during periods of high demand or when local energy infrastructure is under strain. With steam turbines generating power on-site, fertilizer plants can reduce their dependence on the grid, minimizing the impact of power shortages or price fluctuations.
Another significant benefit of steam turbines is their ability to contribute to the decarbonization efforts of fertilizer plants. Fertilizer production, especially ammonia synthesis, is a major source of greenhouse gas emissions, primarily due to the use of natural gas in the steam reforming process. By integrating carbon capture, utilization, and storage (CCUS) systems, steam turbines can support efforts to reduce carbon emissions. The power generated by steam turbines can be used to compress and separate CO2 emissions captured from the ammonia production process, enabling the plant to store or repurpose the carbon. This not only helps plants comply with climate regulations but also contributes to a low-carbon economy by capturing CO2 that would otherwise be released into the atmosphere.
In addition to supporting carbon capture, steam turbines help fertilizer plants optimize their water use through the recovery of waste heat from cooling systems. Fertilizer plants typically require large amounts of water for cooling purposes, but by using steam turbines in conjunction with heat recovery systems, plants can reduce their overall water consumption. The recovered heat can be used to generate steam, which in turn powers turbines, reducing the need for water-intensive cooling processes. This contributes to the plant’s overall sustainability by lowering both water and energy consumption, which are key factors in meeting environmental standards and improving operational efficiency.
Steam turbines also contribute to the economic competitiveness of fertilizer plants by enabling them to reduce operational costs. As energy costs rise, optimizing the use of steam and electricity becomes increasingly important. By recovering waste heat and utilizing it to generate power, fertilizer plants can reduce the need for expensive purchased electricity and lower their fuel consumption. The cost savings generated from these improvements can be significant, helping plants stay competitive in a market where margins are often thin.
In the context of fertilizer plant modernization, steam turbines are essential in improving plant operations and facilitating the transition to more advanced and energy-efficient technologies. Many plants are upgrading their infrastructure to meet stricter environmental regulations and improve the efficiency of their processes. Steam turbines, along with other advanced technologies, are being integrated into these upgrades to maximize energy recovery, minimize emissions, and reduce the environmental impact of fertilizer production. By modernizing their energy systems with steam turbines, fertilizer plants can achieve higher levels of performance and sustainability, which is essential in an industry facing increasing pressure to meet global sustainability goals.
The flexibility of steam turbines also enables fertilizer plants to adapt to changing market conditions and energy demands. Fertilizer production is highly cyclical, with demand fluctuating based on factors such as agricultural seasons and commodity prices. By utilizing steam turbines in flexible power generation systems, plants can adjust their energy output to match changes in demand without incurring excessive costs. This scalability ensures that fertilizer plants can operate efficiently and sustainably, even during periods of market uncertainty or fluctuating production levels.
As fertilizer plants continue to focus on resource efficiency, waste minimization, and energy optimization, steam turbines will remain an integral part of their energy strategy. The ongoing push for green technologies and sustainable practices means that steam turbines will be essential in enabling plants to recover waste energy, integrate renewable sources, and reduce their carbon footprint. Additionally, advancements in turbine technology and digital systems will further enhance the capabilities of steam turbines, allowing fertilizer plants to operate more efficiently, reliably, and sustainably.
In conclusion, steam turbines are critical to the modernization and sustainability of fertilizer plants. They provide a reliable, flexible, and cost-effective solution to the energy-intensive demands of fertilizer production. By integrating steam turbines into combined heat and power systems, renewable energy configurations, and carbon capture processes, fertilizer plants can enhance energy efficiency, reduce emissions, and improve overall plant performance. With their role in energy recovery, renewable integration, carbon reduction, and economic competitiveness, steam turbines will continue to be an essential technology in the evolving fertilizer industry, helping plants meet both operational and environmental goals.
Steam turbines will continue to be pivotal in the fertilizer industry as the sector adapts to global trends in sustainability, resource optimization, and technological innovation. The need for fertilizer production to be both energy-efficient and environmentally friendly has led to increasing reliance on steam turbines for a variety of applications. As fertilizer production facilities increasingly look for ways to reduce their carbon footprint and operational costs, steam turbines provide a viable solution for generating the necessary power and heat while minimizing energy consumption.
Fertilizer plants are integrating steam turbines in cogeneration systems to not only meet their thermal and power needs but also to enhance overall energy recovery. By capturing waste heat from their processes and converting it into usable steam, these plants are improving their energy efficiency significantly. This capability is especially beneficial during the ammonia production process, which consumes a large amount of energy. Steam turbines can utilize this waste heat to produce both electricity and process steam, reducing the need for external electricity sources and optimizing overall energy use.
As fertilizer plants continue to focus on reducing their operational costs, steam turbines also provide opportunities for operational flexibility. Fertilizer plants often experience fluctuations in energy demand due to seasonal production cycles or market conditions. Steam turbines offer the ability to scale power output up or down based on production needs, enabling plants to better align energy usage with changing demands. This flexibility helps reduce fuel consumption during periods of lower energy needs, while still ensuring reliable power generation during peak times.
Furthermore, steam turbines can also support fertilizer plants’ efforts to meet their sustainability goals by enhancing their ability to integrate renewable energy sources into the production process. For example, some fertilizer plants are increasingly turning to biomass and waste-to-energy systems to generate steam, using organic materials as a fuel source. Steam turbines can effectively convert the energy generated from these renewable sources into electricity and steam, reducing dependence on fossil fuels. This not only contributes to sustainability but also provides the plants with an opportunity to become more energy self-sufficient.
In addition to renewable energy integration, the implementation of advanced control systems and digitalization is further optimizing steam turbine performance in fertilizer plants. With the advent of Industry 4.0 technologies, plant operators can monitor steam turbine efficiency in real-time, using predictive maintenance techniques and advanced analytics to detect inefficiencies or faults before they lead to costly downtime. This enhanced operational oversight ensures that steam turbines are always running at their optimal efficiency, minimizing energy waste and ensuring continuous, reliable performance.
The ongoing focus on carbon reduction and environmental responsibility is pushing fertilizer plants to explore more sustainable energy generation methods. Steam turbines, when paired with carbon capture technologies, offer a viable solution to capture and compress carbon dioxide (CO2) emissions from the production process. This technology allows plants to prevent significant emissions of greenhouse gases into the atmosphere while continuing their operations. With governments and regulatory bodies increasing pressure on industries to reduce their carbon footprint, steam turbines offer fertilizer plants a means to comply with stringent environmental regulations and mitigate the impact of their activities on the climate.
Furthermore, fertilizer plants are increasingly adopting closed-loop water systems to reduce their water consumption. Steam turbines contribute to this effort by enabling the use of waste heat recovery systems that reduce the need for additional water usage in cooling processes. Through these systems, the recovered steam is reintroduced into the production process or used for power generation, significantly reducing the overall water footprint of the plant. This is especially important in regions facing water scarcity, where efficient water use is critical to ensuring the sustainability of operations.
As fertilizer plants work towards increasing their operational efficiency, steam turbines will continue to be a key driver of energy recovery and overall process optimization. The ability to harness waste heat, generate electricity on-site, and use renewable energy sources for steam generation will allow plants to lower their operational costs and achieve a greener, more sustainable production model. With technological advancements in turbine efficiency and integration with other systems, steam turbines will remain an indispensable part of fertilizer plant operations as they evolve to meet the challenges of the future.
In summary, steam turbines offer numerous benefits to fertilizer plants by improving energy efficiency, reducing emissions, supporting renewable energy integration, and enhancing plant reliability. Their ability to recover waste heat, generate both electricity and process steam, and provide energy flexibility makes them a critical component in the push for more sustainable and cost-effective fertilizer production. As fertilizer plants continue to navigate the complexities of the global energy transition, steam turbines will be central to achieving their goals of efficiency, sustainability, and economic competitiveness.
As fertilizer plants evolve and focus on optimizing their energy consumption, steam turbines are becoming even more integral to achieving the industry’s goals of sustainability, cost reduction, and operational resilience. A growing focus on reducing carbon emissions is prompting fertilizer plants to adopt low-carbon technologies, and steam turbines are key in this transition. By implementing carbon capture systems, fertilizer plants can reduce the amount of CO2 released during the ammonia production process, a major emitter in the industry. The power needed to compress and transport the captured carbon is often provided by steam turbines, ensuring that the plant can continue producing fertilizers without adding to its carbon footprint.
Additionally, the shift towards electrification of industrial processes is another area where steam turbines are playing a pivotal role in fertilizer plants. Many plants are now incorporating electrical power generation alongside traditional steam generation methods, which increases the flexibility of their energy production. By pairing steam turbines with renewable energy sources such as solar or wind, fertilizer plants can reduce their reliance on fossil fuels, further lowering their carbon footprint. Steam turbines also offer a flexible power solution by adapting to intermittent renewable energy sources, providing a more stable and reliable energy supply.
The integration of advanced digital technologies is further transforming the way steam turbines are used in fertilizer plants. Condition monitoring systems, powered by real-time data analytics, are allowing plant operators to optimize turbine performance, predict maintenance needs, and improve overall operational efficiency. By continuously monitoring critical parameters such as turbine efficiency, vibrations, and temperature, these systems can identify issues before they lead to costly downtime, helping to extend the lifespan of the turbine while maximizing its operational performance.
Additionally, the modular design of some steam turbines is enabling fertilizer plants to achieve greater operational flexibility. In modular systems, smaller, more efficient turbines can be added as needed, allowing for scalability in response to changing energy demands. For instance, when fertilizer plants experience seasonal peaks in production, modular turbines provide the flexibility to increase power generation capacity without the need for a massive investment in new infrastructure. This adaptability ensures that plants are well-positioned to meet fluctuating market conditions and energy demands, enhancing their competitiveness in the global market.
Another critical aspect of steam turbines in fertilizer plants is their role in optimizing the use of steam within the plant. The efficiency of steam utilization is a key factor in reducing energy consumption and operational costs. By recovering waste heat and converting it back into steam for use in the production process, steam turbines contribute to reducing the plant’s overall energy consumption. The integration of heat recovery steam generators (HRSG) with steam turbines allows for maximum use of waste heat, significantly increasing the plant’s energy efficiency.
Steam turbines also support the diversification of energy sources in fertilizer plants. As energy supply chains become more unpredictable due to geopolitical instability or fluctuations in commodity prices, having diverse energy sources helps plants maintain a stable and reliable energy supply. Steam turbines can operate on various fuels, including natural gas, biomass, and even industrial waste, allowing fertilizer plants to maintain operational stability and reduce dependence on a single source of energy. This diversification strategy can be especially important for fertilizer plants located in regions with volatile energy markets.
The use of steam turbines also contributes to fertilizer plants’ efforts to optimize overall process efficiency. In addition to providing power and steam, these turbines can help regulate the temperature and pressure within the various chemical reactors and equipment in the production process. This allows for more consistent and efficient reactions, resulting in improved product quality and reduced production costs. Moreover, the precise control of steam pressure helps to optimize the rate of ammonia synthesis, ensuring higher yields and better energy efficiency.
As the global demand for fertilizers continues to rise, steam turbines will remain a crucial technology for fertilizer plants striving to meet this demand while staying competitive and environmentally responsible. These turbines provide the necessary flexibility, efficiency, and sustainability that modern fertilizer plants require to thrive in an increasingly energy-conscious and regulation-driven industry.
With growing pressure from governments, consumers, and industry stakeholders to reduce carbon emissions, fertilizer plants are leveraging steam turbines as part of their strategy for a more sustainable and resilient future. As part of this ongoing transition, the integration of digital technologies to monitor and optimize steam turbine performance will continue to evolve, leading to more energy-efficient and cost-effective fertilizer production processes. This, in turn, will allow fertilizer plants to meet global food production demands while contributing to a more sustainable agricultural supply chain.
In conclusion, steam turbines are playing a crucial role in helping fertilizer plants navigate the challenges of energy efficiency, carbon reduction, renewable energy integration, and operational flexibility. Their ability to recover waste heat, generate both electricity and steam, and integrate renewable energy sources makes them essential in meeting the evolving needs of the fertilizer industry. As fertilizer plants continue to prioritize sustainability and operational resilience, steam turbines will remain a key technology, enabling plants to reduce emissions, lower costs, and improve overall performance while helping to meet the global demand for fertilizers.
As fertilizer plants continue to innovate and strive for operational excellence, steam turbines will evolve alongside these advancements to further optimize resource utilization, energy recovery, and environmental performance. The integration of steam turbines into advanced energy management systems is another area where they are poised to make a significant impact. These systems use sophisticated algorithms and real-time data analytics to optimize the entire energy infrastructure of the plant, ensuring that steam turbines are operating at peak efficiency at all times. By continuously adjusting turbine output in response to changes in demand and energy availability, these systems can maximize both power generation and heat recovery, ensuring that fertilizer plants are consuming energy as efficiently as possible.
One important trend in the fertilizer industry is the increasing push toward circular economy principles, which seek to reduce waste, maximize resource use, and create more sustainable production systems. Steam turbines contribute to this vision by enabling waste heat recovery and improving energy efficiency throughout the plant. By recovering energy from processes like ammonia synthesis, drying, and granulation, steam turbines ensure that fertilizer plants are using less external energy and making better use of their resources. The ability to capture and reuse energy not only helps lower operating costs but also minimizes the environmental impact of fertilizer production by reducing the need for additional energy sources.
Steam turbines are also central to the growing focus on energy resilience within fertilizer plants. As global energy markets face volatility and disruptions, having an energy backup system in place is crucial to ensure the continuity of production. In this regard, steam turbines can operate in conjunction with backup boilers, battery storage systems, or combined heat and power (CHP) units to provide a more flexible and resilient energy solution. This level of resilience is particularly important for fertilizer plants located in remote areas or regions where power disruptions can cause significant downtime. The ability of steam turbines to provide reliable and sustainable power, even during periods of energy instability, further underscores their importance in maintaining uninterrupted production and meeting critical fertilizer demand.
Additionally, steam turbines are playing an increasingly significant role in the decarbonization efforts of fertilizer plants. As global pressure mounts to reduce greenhouse gas emissions, steam turbines are integral to enabling plants to reduce their reliance on carbon-intensive fossil fuels. For example, in the case of ammonia production, steam turbines are often used in integrated gasification combined cycle (IGCC) systems, where they help convert fossil fuels or biomass into cleaner forms of energy, such as synthesized gas (syngas). This process reduces the carbon intensity of the energy used to produce ammonia, aligning with the industry’s broader goals of reducing the environmental impact of fertilizer production.
Another area where steam turbines contribute significantly to sustainability is through their role in the optimization of water management. Fertilizer plants, particularly those involved in ammonia and urea production, require substantial amounts of water for cooling and process operations. By integrating steam turbines into water-cooled systems, plants can reduce their overall water consumption. The waste heat from steam turbines can be used to drive thermal desalination systems, converting seawater or brackish water into fresh water, which can be used for cooling or in the production process. This is a particularly valuable solution in regions facing water scarcity, allowing fertilizer plants to continue operating without putting undue strain on local water resources.
With ongoing technological advancements in steam turbine efficiency and control systems, plants can achieve even greater levels of performance and sustainability. Next-generation steam turbines will likely be even more efficient, compact, and adaptable to a range of operating conditions, helping to future-proof fertilizer plants against evolving energy demands and regulatory frameworks. For example, advancements in high-efficiency steam turbines will enable plants to generate more power from the same amount of fuel, reducing both costs and emissions. Moreover, digital twin technologies are expected to play an increasingly important role in the operation of steam turbines. These technologies create virtual models of the turbine systems, allowing operators to simulate various scenarios and optimize performance before making real-world changes, further enhancing plant efficiency.
As the industry faces mounting pressures to transition to cleaner, more sustainable energy solutions, steam turbines will continue to play an essential role in ensuring fertilizer plants remain competitive and meet environmental regulations. Their integration with renewable energy sources, advanced control systems, and sustainable practices will help reduce costs, lower carbon footprints, and improve overall plant performance.
Furthermore, steam turbines are a critical component of the global transition to renewable energy. With increasing investment in solar, wind, and geothermal energy, steam turbines can help integrate these renewable energy sources into the fertilizer production process. For example, steam turbines can be used in concentrated solar power (CSP) systems, where mirrors focus sunlight to generate steam, which in turn drives turbines to produce power. By integrating renewable energy into the production cycle, fertilizer plants can significantly reduce their dependency on non-renewable sources and further decarbonize their operations.
Finally, as the global population continues to grow, the demand for fertilizers is expected to rise significantly. At the same time, there is a growing need for fertilizer production to become more energy-efficient and sustainable. Steam turbines will remain a cornerstone of this transformation, offering a reliable, efficient, and flexible solution for addressing the challenges of increasing energy demands, carbon reduction, and resource conservation. As technological innovation continues to advance, steam turbines will become even more capable of helping fertilizer plants achieve their sustainability goals, making them an indispensable part of the industry’s future.
In conclusion, steam turbines will continue to be a critical technology for fertilizer plants striving to optimize energy use, reduce carbon emissions, and improve overall sustainability. Through their role in energy recovery, carbon capture, water management, and integration with renewable energy sources, steam turbines provide a powerful tool for improving the efficiency and environmental performance of fertilizer production. As the fertilizer industry moves toward a more sustainable future, steam turbines will remain a key enabler of innovation, helping plants meet global challenges while ensuring the availability of essential nutrients for food production.
Steam Turbines for Chemical Processing
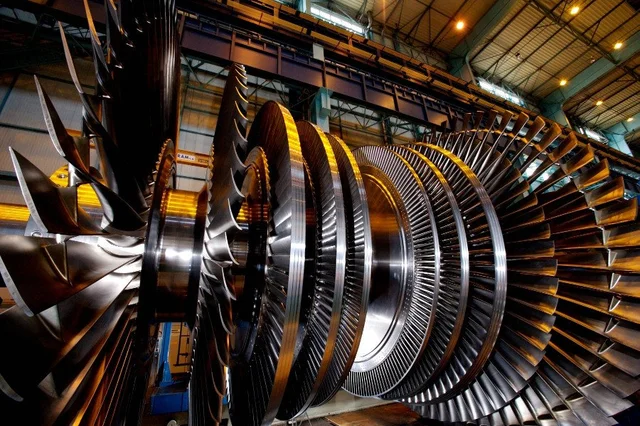
Steam turbines play a critical role in chemical processing industries by providing an efficient means of power generation, heat recovery, and energy management. Chemical plants, which involve complex processes such as synthesis, separation, purification, and reaction engineering, require a continuous and reliable supply of energy to ensure smooth operations. In this context, steam turbines serve as essential components in optimizing energy use, minimizing operational costs, and enhancing environmental performance.
In many chemical processing plants, steam is a key utility for driving chemical reactions, maintaining temperature and pressure conditions, and providing heat for distillation, evaporation, or drying processes. Steam turbines enable cogeneration systems, where they generate both electricity and process steam. By recovering waste heat from various stages of the chemical process, such as from reactor vessels, distillation columns, or heat exchangers, steam turbines can transform this thermal energy into usable power, significantly improving overall energy efficiency. This helps reduce reliance on external energy sources, lower operational costs, and decrease the plant’s environmental impact.
One significant advantage of using steam turbines in chemical processing is their ability to integrate with combined heat and power (CHP) systems. In such systems, steam turbines produce both electricity and steam, with the steam being used for industrial processes and the electricity providing power for plant operations. This dual output maximizes the use of available fuel, reducing waste and improving energy recovery. In many chemical plants, this form of energy efficiency is particularly valuable as it reduces both fuel consumption and emissions, making the plant more economically and environmentally sustainable.
Moreover, energy flexibility is another benefit that steam turbines bring to chemical processing plants. The demand for power and steam can vary depending on the plant’s operational cycles, the types of chemicals being produced, and market conditions. Steam turbines allow for better management of these fluctuations by adjusting the power generation to match the plant’s demand. By maintaining a steady supply of steam and electricity during peak demand periods, steam turbines help avoid disruptions in chemical production, while still providing operational flexibility during low-demand phases. This makes them essential for plants that operate in a dynamic environment.
Steam turbines also contribute to sustainability efforts in chemical processing by enabling the integration of renewable energy sources. As the chemical industry moves toward reducing its dependence on fossil fuels, steam turbines can be used to generate power from renewable sources such as biomass, geothermal energy, or waste heat. Biomass, for example, is increasingly being used in some chemical plants to produce steam that drives turbines. By converting organic waste materials into energy, steam turbines help reduce the chemical plant’s carbon footprint and contribute to a more sustainable energy system. In addition, integrating renewable energy into the energy mix allows plants to lower their reliance on non-renewable resources and meet regulatory goals related to greenhouse gas emissions.
The flexibility of steam turbines extends beyond just fuel choices; they can also be adapted to work with waste heat recovery systems. In chemical processing, excess heat from one process can be captured and repurposed to drive steam turbines, reducing the need for additional external energy sources. By recovering heat from reactions that occur at high temperatures, such as in exothermic processes (e.g., polymerization or cracking), steam turbines provide a way to capture valuable energy that would otherwise be lost. These heat recovery steam generators (HRSGs) can improve the overall efficiency of the chemical plant and lower operating costs while reducing energy waste.
Steam turbines are also essential for power backup and emergency systems in chemical processing plants. Many chemical plants operate with highly sensitive processes that require continuous power. Interruptions in electricity supply can lead to production stoppages, safety risks, or even hazardous situations. By incorporating steam turbines into backup power generation systems, plants can maintain reliable power supply during grid failures or equipment downtime. These turbines provide a secure and stable energy source, ensuring that critical processes continue uninterrupted, which is especially important in high-risk environments where safety is paramount.
Process control and monitoring are further areas where steam turbines contribute to chemical processing plants’ efficiency. Advanced digital technologies allow for continuous performance monitoring of steam turbines, enabling operators to detect early signs of wear and optimize the turbines’ operating conditions. Predictive maintenance based on real-time data analysis can prevent unnecessary downtime and extend the operational life of the turbines. This proactive approach to maintenance helps to optimize the availability of turbines, reducing costs related to unplanned shutdowns and improving the overall reliability of the plant.
Furthermore, modular steam turbine systems are increasingly used in chemical plants to provide scalable power solutions. Modular turbines can be installed in smaller increments, enabling plants to match turbine capacity with the exact power and steam requirements of each specific stage of the chemical process. As production needs fluctuate, steam turbines can be added or removed with minimal disruption, allowing for scalable energy solutions that can be adjusted according to demand.
As environmental regulations become more stringent and the push for carbon neutrality increases, steam turbines continue to provide an effective tool for chemical plants to reduce their carbon footprint. By enhancing energy recovery, increasing efficiency, and integrating renewable energy sources, steam turbines support chemical processing plants in achieving their sustainability goals. The ability to integrate with carbon capture technologies further reduces the impact of the chemical industry’s emissions, ensuring that plants remain compliant with environmental standards while continuing to operate efficiently.
In conclusion, steam turbines are crucial in optimizing energy use, improving operational efficiency, and ensuring sustainability within chemical processing industries. By providing reliable power and steam generation, enabling waste heat recovery, and supporting integration with renewable energy sources, steam turbines help chemical plants reduce their reliance on external energy and improve their overall energy footprint. They are also key in enhancing flexibility, reducing costs, and ensuring continuous and stable operations. As the chemical industry increasingly focuses on meeting global sustainability targets, steam turbines will continue to play a central role in enabling more energy-efficient, environmentally friendly, and cost-effective chemical production processes.
As chemical processing plants face increasing pressure to improve operational efficiency while reducing environmental impact, the role of steam turbines becomes even more crucial. These turbines are integral not only to power generation but also to optimizing the way energy is utilized across various plant operations. One of the key advantages of steam turbines is their ability to work alongside advanced automation and control systems to deliver precise control over steam production and electrical generation. These systems allow for dynamic adjustments based on real-time demand, ensuring that turbines are always operating at their peak efficiency, regardless of fluctuations in power or steam requirements.
This capacity for real-time optimization is particularly beneficial in complex chemical processes where the balance between energy input and output is critical. For example, in processes like distillation or drying, maintaining a steady supply of steam at the right temperature and pressure is essential for consistent product quality and energy efficiency. Steam turbines, in this context, enable chemical plants to fine-tune steam delivery, ensuring optimal reaction conditions while minimizing energy waste.
Moreover, energy recovery via steam turbines contributes to overall plant efficiency by reducing the need for additional energy inputs. Chemical plants often produce waste heat during various stages of their operations, such as in exothermic reactions or heat exchangers. Instead of allowing this heat to dissipate, steam turbines can capture and convert it into electricity and usable steam. This process of heat integration significantly reduces energy consumption and greenhouse gas emissions by maximizing the utility of the energy already within the system.
The integration of steam turbines with heat recovery steam generators (HRSGs) is a key strategy in this regard. These systems capture waste heat from flue gases or high-temperature processes and use it to generate steam that drives turbines. The recovered energy can be redirected back into the plant’s processes, reducing the demand for additional fuel inputs and allowing the plant to operate with less reliance on external energy sources. This closed-loop approach is especially valuable in industries like pharmaceuticals, plastics, and petrochemicals, where energy use is a significant portion of operational costs.
Steam turbines also facilitate fuel flexibility, enabling chemical plants to adapt to changing fuel supply conditions. Many plants are transitioning toward more sustainable and renewable sources of energy, such as biomass or waste-derived fuels, and steam turbines are capable of operating efficiently on a wide range of fuel types. This versatility helps mitigate risks related to fluctuating fuel prices or disruptions in supply, allowing chemical plants to maintain stable operations even in the face of energy market volatility.
The use of steam turbines in combined heat and power (CHP) systems is particularly valuable for chemical plants operating in regions where energy prices are high or where the local electricity grid may be unreliable. CHP systems enable the plant to generate electricity for its own use while simultaneously providing heat for processes. The integration of steam turbines into CHP systems also provides a way to reduce energy costs and improve energy independence, which is a crucial consideration for chemical plants located in remote areas or regions with unstable power grids.
Furthermore, as the industry moves toward decarbonization, the role of steam turbines becomes even more prominent in helping chemical plants meet their carbon reduction goals. Renewable energy integration, coupled with improved turbine efficiency, supports plants in transitioning to cleaner energy sources. Steam turbines can operate on fuels that produce lower carbon emissions, such as hydrogen or synthetic fuels produced from renewable sources. When paired with carbon capture technologies, steam turbines can further reduce the carbon footprint of chemical plants by helping to capture and sequester CO2 emissions from industrial processes.
Another emerging area for steam turbine technology in chemical processing is the digitalization of plant operations. By leveraging IoT (Internet of Things) sensors, big data, and AI (artificial intelligence), chemical plants can monitor turbine performance in real-time and apply predictive maintenance strategies. These systems can detect early signs of wear, optimize operational parameters, and predict the remaining lifespan of components like rotors and bearings, allowing operators to avoid costly downtime and unplanned maintenance. This data-driven approach leads to enhanced reliability, reduces maintenance costs, and ultimately improves the plant’s overall profitability.
In terms of energy security, steam turbines are an indispensable part of chemical plants’ efforts to ensure stable operations. In the event of power outages or supply interruptions, steam turbines can provide a reliable source of backup energy, allowing chemical processes to continue without disruption. This backup capability is particularly important in high-stakes industries like pharmaceutical manufacturing, where continuous operation is essential to ensure both product quality and safety. Steam turbines are typically integrated into the emergency power generation systems that are designed to keep critical systems running during power failures, ensuring that chemical plants can resume normal operations quickly after an outage.
Additionally, as global competition increases in the chemical processing sector, efficiency becomes a key differentiator. Steam turbines offer the potential to reduce overall energy costs, improve operational efficiency, and allow companies to offer competitive pricing while meeting stringent environmental standards. For example, as energy efficiency regulations become more stringent in many regions, steam turbines help chemical plants comply with these regulations while maintaining profitability. Their role in reducing fuel consumption and lowering emissions positions them as a critical asset in the industry’s ongoing drive for sustainability and cost-effectiveness.
Finally, steam turbines are also becoming more important in global supply chain optimization. The chemical industry is increasingly interconnected across regions, and steam turbines can help plants respond to changes in energy demand and supply in real time. By generating their own power and recovering waste heat, plants can become more self-sufficient, reducing their reliance on external suppliers and mitigating risks associated with energy supply disruptions. This autonomy is particularly advantageous for plants in regions where energy security is a concern or where grid infrastructure is unreliable.
In conclusion, steam turbines are a cornerstone technology in chemical processing plants, offering numerous benefits in terms of energy efficiency, cost savings, environmental performance, and operational reliability. Their ability to generate both electricity and steam from various energy sources, integrate with renewable energy, recover waste heat, and provide backup power positions them as a critical component in modernizing chemical plant operations. As chemical plants continue to pursue sustainability goals and tackle the challenges of energy efficiency and carbon reduction, steam turbines will remain an essential tool for achieving greater resilience, reducing emissions, and improving overall profitability.
Steam turbines in chemical processing continue to evolve as a central technology in the quest for greater efficiency and sustainability. As the chemical industry embraces more advanced process technologies, steam turbines are increasingly integrated into multi-tiered systems that enable optimized energy use, improve product yield, and support the transition to more sustainable practices. One such innovation is the development of integrated multi-fuel systems, which allow steam turbines to operate on a combination of conventional fossil fuels, biofuels, and even hydrogen. These systems contribute to the energy diversification of chemical plants, enabling them to be more flexible and adaptive to changes in energy availability, price fluctuations, and regulatory requirements.
In line with the industry’s move toward zero-emission goals, steam turbines are being paired with green technologies like electrification and energy storage. These combinations create hybrid systems that can provide additional flexibility to chemical plants in managing their energy use. By linking steam turbines with battery energy storage systems or green hydrogen production, chemical plants can store excess power generated during periods of low demand or use renewable electricity to power turbines during high-demand periods. This hybrid approach is particularly valuable as chemical plants work toward decarbonizing their operations without compromising performance or output.
An exciting area for steam turbines in the chemical sector is waste-to-energy technology. As chemical plants look for ways to reduce their reliance on conventional fuels and lower their carbon footprint, the ability to use industrial waste materials—such as plastic waste, sludge, and other organic waste—as a source of energy is gaining attention. Steam turbines play a critical role in these systems by converting waste heat from incineration or anaerobic digestion into usable steam and electricity. By transforming waste into energy, chemical plants not only reduce landfill contributions but also contribute to a circular economy model, where materials are continuously repurposed and reused.
The flexibility of steam turbines also supports the modular design of chemical plants, a trend that allows for quicker scalability and better adaptation to market changes. Modular plants can be expanded incrementally, adding capacity as demand grows without the need for large, upfront investments in infrastructure. Steam turbines, in this context, offer a modular approach to power generation, where smaller turbines can be installed as needed, with each module providing optimal steam and electricity for different parts of the plant. This scalable, decentralized approach allows chemical plants to remain agile, quickly responding to new demands or changes in production needs.
As the industry moves toward smarter operations, digital technologies such as predictive analytics, machine learning, and AI are increasingly being applied to optimize steam turbine performance in real time. These technologies use vast amounts of data collected from plant operations to continuously adjust turbine settings and improve energy efficiency. For instance, by analyzing patterns in energy demand, steam consumption, and operational stress, predictive maintenance tools can forecast potential failures and recommend specific maintenance actions, thereby reducing unplanned downtime and extending the lifespan of critical turbine components.
This type of advanced monitoring also allows for a more precise balance between energy generation and consumption. Chemical plants often face significant fluctuations in energy demand depending on the production schedule or external market conditions. Steam turbines equipped with real-time monitoring and predictive capabilities allow for quick adjustments to steam output, ensuring that only the necessary amount of energy is produced, reducing excess consumption, and improving overall plant efficiency.
In addition to improving operational efficiency, steam turbines in chemical processing plants contribute to reducing the environmental impact of operations. As energy efficiency improves, chemical plants consume fewer raw materials, such as coal, oil, or natural gas, leading to reduced emissions and overall environmental footprint. The use of cleaner fuels, such as biomass or waste heat, alongside steam turbines, helps reduce the plant’s carbon intensity, thus supporting the global push for lower greenhouse gas emissions.
Furthermore, by recovering waste heat and providing a constant, reliable energy source, steam turbines help chemical plants avoid the inefficiencies associated with purchasing external power from the grid, which may come from non-renewable sources. This autonomy not only enhances energy resilience but also contributes to economic savings, as the need to purchase external energy is minimized. In regions with volatile energy prices, steam turbines ensure that chemical plants remain economically competitive by insulating them from fluctuations in fuel and electricity costs.
Looking toward the future, steam turbines are likely to become even more integrated into digitally connected ecosystems that optimize energy performance across multiple plants or sectors. As industries and manufacturing processes become more interconnected through the Industrial Internet of Things (IIoT), steam turbines in chemical plants could be part of broader smart grids or energy management systems that help balance demand across multiple facilities. This will allow chemical plants to operate even more efficiently by sharing resources, such as excess steam or power, across a network of plants.
Cross-sector collaboration also holds great potential for the use of steam turbines in chemical processing. As companies in sectors like automotive, food production, and pharmaceuticals strive for net-zero emissions, sharing best practices and technologies, such as steam turbines, can accelerate the transition to cleaner, more efficient operations across industries. The implementation of energy-efficient technologies in one sector can often lead to innovations and cost reductions that can be replicated in others. As part of this collaborative push toward decarbonization, steam turbines play a central role in helping chemical plants align with global sustainability targets and meet international emissions reduction commitments.
Finally, as the regulatory landscape around industrial emissions becomes more stringent, steam turbines will continue to help chemical plants stay ahead of compliance requirements. By improving energy efficiency, recovering waste heat, and integrating renewable energy sources, chemical plants can meet emission reduction standards and avoid costly penalties. Steam turbines, in combination with other sustainable technologies, allow chemical plants to not only comply with regulations but also contribute positively to broader environmental and economic goals.
In summary, steam turbines in chemical processing plants provide a comprehensive solution to improving energy efficiency, reducing environmental impact, and supporting sustainable industrial practices. With their ability to recover waste heat, enable combined heat and power (CHP) systems, and integrate with renewable energy sources, steam turbines remain a cornerstone of energy-efficient chemical production. As the chemical industry moves toward smarter, cleaner, and more resilient operations, steam turbines will continue to be a key technology in achieving cost savings, environmental sustainability, and energy resilience.
As steam turbines continue to play an essential role in chemical processing plants, there is also growing interest in utilizing them for decentralized power generation. In this context, steam turbines can provide independent power to smaller or remote chemical processing facilities that may not have access to a reliable grid supply. By using localized energy generation, plants in remote areas can avoid the disruptions that often accompany central grid power sources, such as power outages or energy price hikes. This autonomy also allows for more cost-effective and reliable operations, especially in regions with unstable infrastructure or where energy access is limited.
Another key development is the role of steam turbines in helping chemical plants manage intermittent renewable energy sources, such as solar or wind power. While these sources provide environmentally friendly energy, their production is often erratic and dependent on weather conditions. Steam turbines, when integrated with thermal storage or combined systems using hydrogen, can ensure that chemical plants have a steady supply of energy even when renewable sources are unavailable. For example, excess solar or wind energy can be stored as heat or hydrogen and used later to generate steam for turbine-driven power generation. This integration of renewable energy into steam turbine systems helps smooth out the variability of clean power sources and supports a more resilient energy grid.
Waste heat recovery remains one of the most significant benefits of steam turbines in chemical processing. As chemical plants often operate at high temperatures, they produce large amounts of waste heat during their processes. Rather than allowing this valuable energy to escape, many plants use steam turbines to capture and convert the waste heat into useful steam or electricity. This reduces the need for external energy sources and lowers the overall environmental impact of the plant. This process also plays an important role in reducing greenhouse gas emissions, since it decreases the amount of fuel required to generate steam and power, thus lowering the carbon footprint of the plant.
In an effort to improve overall energy consumption, chemical plants are increasingly adopting a holistic approach to energy management. This involves the strategic integration of steam turbines with other energy-saving technologies, such as combined cycle systems, absorption chillers, and cogeneration. By pairing steam turbines with technologies that allow for both electricity and useful heat to be generated, chemical plants can achieve higher overall energy efficiency, which leads to significant cost savings. This is particularly valuable in energy-intensive processes, such as in the production of pharmaceuticals and fine chemicals, where precision, temperature control, and energy usage are crucial factors.
Another important consideration is the reliability and durability of steam turbines in chemical plants. These turbines are built to withstand the harsh conditions often present in industrial environments, such as high temperatures, high pressures, and corrosive substances. With proper maintenance and advanced monitoring systems, steam turbines can operate efficiently for long periods with minimal downtime. In high-demand plants, reducing maintenance costs and avoiding unexpected failures is critical, and steam turbines provide a solid foundation for ensuring the plant’s long-term operational reliability.
In terms of fuel flexibility, steam turbines are adaptable to a variety of feedstocks, including both traditional fuels such as natural gas and coal, as well as biomass, waste-derived fuels, and syngas. This fuel flexibility allows chemical plants to take advantage of changing energy markets, and in some cases, reduce their reliance on fossil fuels. Using renewable or low-carbon fuels can significantly reduce emissions, making the plant more sustainable and less dependent on non-renewable resources. Furthermore, with the rise of green hydrogen as a potential clean fuel, steam turbines can be adapted to run on hydrogen or hydrogen-rich gases, further contributing to the decarbonization of the chemical industry.
As part of a broader push for energy transition, steam turbines are being increasingly used in hybrid systems alongside other renewable and low-carbon technologies. For instance, steam turbines can work in conjunction with biogas plants or geothermal systems to provide consistent, stable power, while simultaneously reducing greenhouse gas emissions. When integrated into a clean energy ecosystem, steam turbines offer a path toward achieving carbon-neutral production in the chemical industry.
Process optimization is another area where steam turbines can make a substantial impact. By using advanced sensors and control systems, steam turbines can be integrated into a plant’s digital infrastructure. Real-time monitoring of turbine performance, steam production, and power consumption enables chemical plants to make data-driven decisions that enhance energy management. For example, adjusting turbine settings to meet varying levels of steam demand helps reduce energy waste and optimize overall efficiency, which is critical when operating in markets where energy costs are high. These digital tools also enable predictive maintenance strategies, which allow plants to identify potential issues before they become serious problems, minimizing downtime and reducing maintenance costs.
As chemical plants embrace more sustainable practices in their operations, steam turbines play an increasingly important role in improving resource efficiency. Not only do they enable the efficient generation of power and steam, but they also support circular economy models by utilizing waste heat and renewable energy sources. By adopting steam turbines, chemical plants can continue to improve their bottom line, reduce their environmental impact, and enhance their operational resilience.
The future of steam turbines in chemical processing also holds promise with the ongoing development of next-generation turbine technologies. These innovations include improved materials, advanced coatings, and design modifications that increase the turbines’ efficiency, reliability, and lifespan, even under more extreme operational conditions. Additionally, as artificial intelligence (AI) and machine learning become more prevalent, they will further enhance the capabilities of steam turbines in optimizing plant operations. AI-driven algorithms can monitor real-time performance data, predict demand fluctuations, and make dynamic adjustments to turbine operation, ensuring that energy use is always optimized.
In conclusion, steam turbines are a critical technology in the chemical processing industry, providing a flexible and efficient solution to the growing demands for energy optimization, sustainability, and cost savings. Their ability to recover waste heat, integrate with renewable energy sources, and adapt to a range of fuels ensures that chemical plants can operate more sustainably and profitably. As the industry moves toward greener and smarter solutions, steam turbines will continue to play a central role in shaping the future of energy use in the chemical sector. With advancements in technology, digitalization, and fuel flexibility, steam turbines will remain at the forefront of efforts to achieve net-zero emissions, improve energy efficiency, and reduce environmental impacts across chemical processing plants.
EMS Power Machines
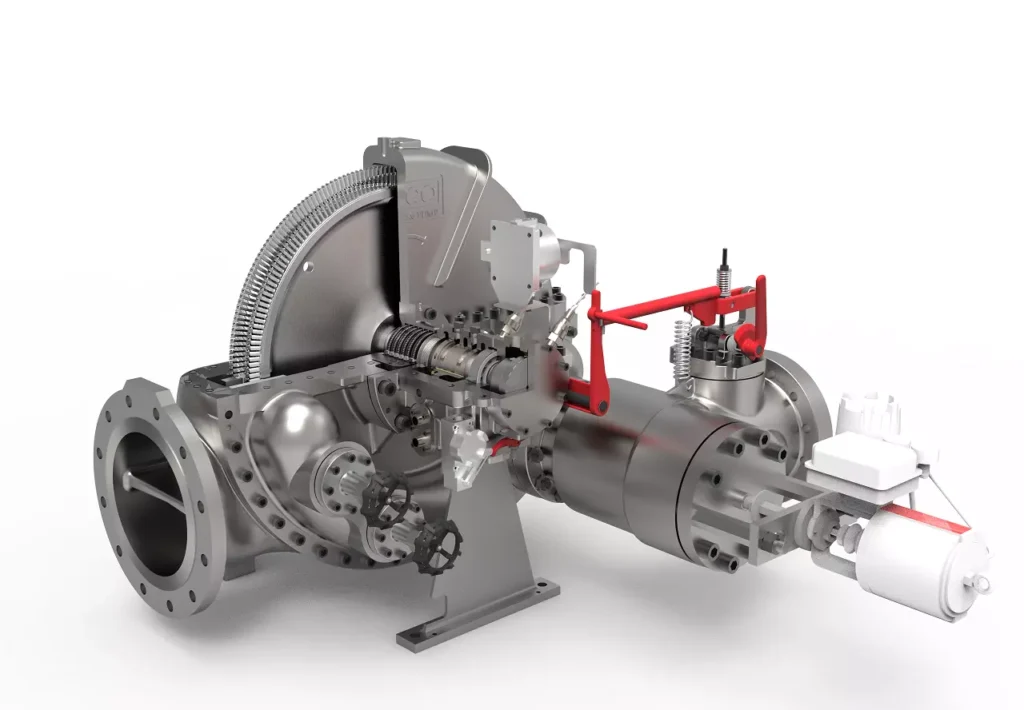
We design, manufacture and assembly Power Machines such as – diesel generators, electric motors, vibration motors, pumps, steam engines and steam turbines
EMS Power Machines is a global power engineering company, one of the five world leaders in the industry in terms of installed equipment. The companies included in the company have been operating in the energy market for more than 60 years.
EMS Power Machines manufactures steam turbines, gas turbines, hydroelectric turbines, generators, and other power equipment for thermal, nuclear, and hydroelectric power plants, as well as for various industries, transport, and marine energy.
EMS Power Machines is a major player in the global power industry, and its equipment is used in power plants all over the world. The company has a strong track record of innovation, and it is constantly developing new and improved technologies.
Here are some examples of Power Machines’ products and services:
- Steam turbines for thermal and nuclear power plants
- Gas turbines for combined cycle power plants and industrial applications
- Hydroelectric turbines for hydroelectric power plants
- Generators for all types of power plants
- Boilers for thermal power plants
- Condensers for thermal power plants
- Reheaters for thermal power plants
- Air preheaters for thermal power plants
- Feedwater pumps for thermal power plants
- Control systems for power plants
- Maintenance and repair services for power plants
EMS Power Machines is committed to providing its customers with high-quality products and services. The company has a strong reputation for reliability and innovation. Power Machines is a leading provider of power equipment and services, and it plays a vital role in the global power industry.
EMS Power Machines, which began in 1961 as a small factory of electric motors, has become a leading global supplier of electronic products for different segments. The search for excellence has resulted in the diversification of the business, adding to the electric motors products which provide from power generation to more efficient means of use.