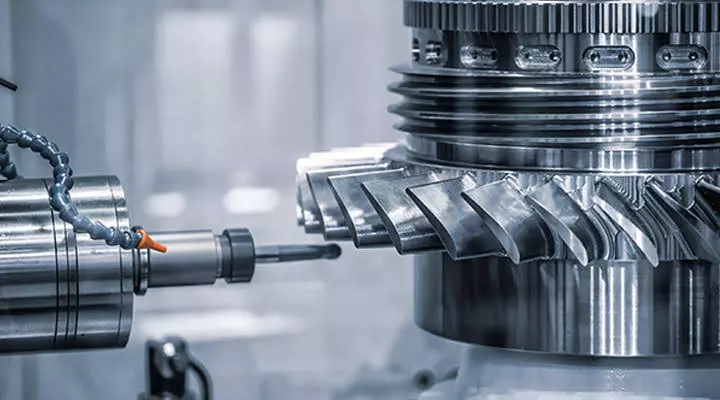
Steam Turbine Blade Manufacturers: Steam turbines are devices that convert thermal energy from steam into mechanical energy, driving generators to produce electricity. Blades are a critical component of steam turbines as they interact with the steam to extract energy efficiently. Proper blade design significantly impacts the turbine’s performance, reliability, and efficiency.
Types of Steam Turbine Blades
Impulse Blades
Impulse blades operate by redirecting steam flow. Steam is directed at the blades at high speed, and the energy is transferred primarily by a change in the steam’s direction. The pressure of the steam remains constant across the blade, making these blades suitable for high-pressure stages.
Applications: Often used in the high-pressure section of turbines where the steam velocity is very high.
Reaction Blades
In reaction blades, energy is extracted from both the pressure and the velocity of the steam. The blades are designed to create a pressure drop as steam passes over them, causing the blades to experience a reactive force. These blades are typically found in low-pressure sections of the turbine.
Applications: Commonly used in low to medium pressure stages.
Difference Between Impulse and Reaction Blades
- Impulse Blades: Operate mainly through changes in steam velocity. Suitable for high-pressure sections.
- Reaction Blades: Use both velocity and pressure drop. Suitable for lower pressure sections.
- Key Design Difference: Impulse blades have simpler designs compared to reaction blades, which are more aerodynamically complex.
Blade Materials
The choice of material for turbine blades is critical because they must withstand extreme conditions, including high temperatures, pressures, and potential corrosion from steam impurities.
Common Materials:
- Nickel-based Superalloys: Excellent heat resistance and strength.
- Titanium Alloys: Lightweight and strong, used where corrosion resistance is needed.
- Stainless Steel: Affordable and widely used in many parts of the turbine.
Material Selection Criteria:
- Heat Resistance
- Corrosion Resistance
- Strength and Durability
- Cost-effectiveness
Manufacturing Technologies for Steam Turbine Blades
Forging
Process: Heating metal to a high temperature and shaping it using a press or hammer. Advantages: Strong, high-quality components with good grain structure. Challenges: Costly for complex designs.
Casting
Process: Molten metal is poured into a mold that shapes the blade. Types:
- Sand Casting: Good for larger, less intricate blades.
- Investment Casting: Allows for precise and complex designs. Advantages: Economical for mass production. Applications: Suitable for both impulse and reaction blades.
Machining
Process: CNC machines precisely cut and finish the blade from a solid piece of metal. Benefits: High precision, smooth surface finishes. Drawbacks: Material wastage can be a concern.
Additive Manufacturing (3D Printing)
Process: Building blades layer by layer using powdered metals. Benefits: Design flexibility, reduced material waste, and quick prototyping. Future Potential: Suitable for rapid production and custom designs.
Coating and Surface Treatment
Coatings enhance blade performance by adding protective layers to resist corrosion, erosion, and heat.
Common Techniques:
- Plasma Spraying: Forms a protective layer.
- Thermal Spray Coating: Adds thermal resistance.
- Importance: Extends blade life and maintains efficiency.
Quality Control and Testing
Ensuring the integrity of turbine blades is vital due to the harsh operating conditions. Quality control involves various Non-Destructive Testing (NDT) methods:
- Ultrasonic Testing: Detects internal flaws.
- X-ray Inspection: Checks for defects inside the material.
- Surface Crack Testing: Ensures the blade’s surface is free from cracks.
Future Trends in Turbine Blade Manufacturing
- Advanced Materials: Research into lighter, stronger composite materials and new superalloys.
- Smart Manufacturing: Automation, AI, and real-time monitoring.
- Computational Design: Use of simulation to optimize blade shape, efficiency, and cooling.
Conclusion
Steam turbine blades are the cornerstone of efficient energy generation. With continued advancements in materials, design, and manufacturing technologies, turbine blades will become more efficient, durable, and cost-effective, ensuring a steady supply of energy for future generations.
Introduction to Steam Turbine Blades
Steam turbines are one of the most critical components in power generation systems, playing a vital role in converting thermal energy from steam into mechanical energy. This mechanical energy can then be used to drive electrical generators, pumps, and other machinery. A key component within a steam turbine is its blades, which are responsible for extracting energy from the high-pressure, high-temperature steam that flows through the turbine. Without well-designed and precisely manufactured blades, steam turbines cannot operate efficiently or reliably.
Understanding the Role of Steam Turbine Blades
Steam turbine blades are carefully engineered structures designed to interact with high-velocity steam to extract kinetic energy. As steam flows through the turbine, it strikes the blades, causing them to rotate and, in turn, drive a connected shaft. The energy transformation in a steam turbine involves two major steps:
- Steam Expansion: The pressurized steam is allowed to expand, converting its pressure energy into kinetic energy.
- Energy Extraction: The blades extract this kinetic energy, causing the rotor to spin.
The efficiency and performance of a steam turbine are directly influenced by the design and arrangement of its blades. The blades must be capable of withstanding extreme conditions, including high temperatures, pressures, and sometimes corrosive environments. Therefore, the design, material selection, and manufacturing process for turbine blades are crucial aspects that determine the overall success and longevity of the turbine system.
The Importance of Blade Design in Turbine Efficiency
Blades are the core functional elements that determine the efficiency of energy conversion in a steam turbine. The design of these blades has a significant impact on how effectively the turbine can convert steam energy into mechanical energy. Key factors influencing blade design include:
- Aerodynamics: Efficient aerodynamic design ensures that steam flows smoothly over the blades, reducing turbulence and energy losses. Streamlined blade profiles help in maximizing the energy extracted from the steam.
- Mechanical Strength: Blades need to endure high levels of mechanical stress due to the centrifugal forces at high rotational speeds. Therefore, they must be designed to be strong and durable.
- Thermal Efficiency: Since turbines operate at high temperatures, blade materials must maintain their integrity without deforming or melting. Proper cooling mechanisms are sometimes integrated into the blade design to prevent overheating.
- Corrosion and Erosion Resistance: Steam can contain impurities that may cause corrosion or erosion of blades over time. The material and coatings used for blades play a key role in minimizing these effects.
A well-designed blade ensures that the turbine operates with high efficiency, minimizing energy losses and maximizing power output. Conversely, poor blade design can lead to inefficiencies, higher operational costs, and potential mechanical failures.
Types of Steam Turbine Blades
Steam turbine blades can be classified into two main types: impulse blades and reaction blades. Each type is suited to different stages within the turbine, based on the specific energy conversion requirements.
3.1 Impulse Blades
Impulse blades operate on the principle of impulse, where steam jets are directed onto the blades at high velocity. The blades extract energy by changing the direction of the steam flow, resulting in a reactionary force that rotates the turbine rotor. Impulse blades are typically used in the high-pressure stages of the turbine because they can handle the high velocities and forces involved.
Key Characteristics:
- Steam pressure remains constant as it passes over the blade.
- Energy is extracted by changing the steam’s direction.
- Simple blade design, which is easier to manufacture.
- Typically found at the front (high-pressure) stages of the turbine.
3.2 Reaction Blades
Reaction blades work on the principle of both pressure drop and velocity change. Unlike impulse blades, reaction blades extract energy from steam through a gradual expansion process, where both the pressure and velocity of the steam change as it passes over the blade. These blades are used in the low-pressure stages of the turbine, where steam pressure has already been reduced.
Key Characteristics:
- Pressure drops as steam passes over the blade, causing a reactive force.
- More complex aerodynamic design compared to impulse blades.
- Found in the low to medium-pressure stages of the turbine.
- Require precise manufacturing to ensure smooth operation.
Design Considerations for Steam Turbine Blades
The design of turbine blades involves several considerations to optimize performance, durability, and cost-efficiency. Some of the key aspects are:
4.1 Aerodynamic Efficiency
Blades must be designed to ensure maximum energy extraction from the steam flow. This requires a deep understanding of fluid dynamics to minimize losses caused by turbulence, drag, and steam leakage. Modern blade designs often incorporate features such as twisted profiles to optimize the angle of attack and reduce energy losses.
4.2 Structural Integrity and Mechanical Stress
The high rotational speeds of steam turbines subject blades to significant mechanical stresses, particularly centrifugal forces. If not properly designed, these forces can lead to deformation, cracking, or even catastrophic failure. Blades must, therefore, be designed with sufficient mechanical strength, often using sophisticated finite element analysis (FEA) to predict stress distribution and identify potential failure points.
4.3 Thermal Resistance
Operating temperatures in steam turbines can exceed 600°C (1112°F), which can cause metal blades to soften or warp. The materials used for turbine blades must maintain their mechanical properties under these high temperatures. In some designs, cooling passages are integrated within the blades to dissipate heat, preventing overheating and thermal fatigue.
4.4 Corrosion and Erosion Protection
Steam can carry moisture and impurities, leading to corrosion and erosion of the blades over time. These effects can degrade blade performance and reduce the lifespan of the turbine. To counteract this, blades are often made from corrosion-resistant alloys or coated with protective materials that guard against wear and chemical attack.
Materials Used for Steam Turbine Blades
The choice of material for turbine blades is essential to ensure durability and reliability. The materials must possess a unique combination of properties, including high strength, corrosion resistance, and thermal stability. Common materials include:
5.1 Nickel-Based Superalloys
Nickel-based superalloys are among the most commonly used materials for turbine blades, especially in high-temperature sections. These alloys maintain their strength at high temperatures and are resistant to oxidation and corrosion. Examples include Inconel and Waspaloy.
5.2 Titanium Alloys
Titanium alloys are valued for their excellent strength-to-weight ratio and corrosion resistance, making them ideal for low-pressure, high-velocity sections of the turbine where reduced blade weight can improve efficiency.
5.3 Stainless Steels
Stainless steels are a more cost-effective option, often used in lower temperature and lower-stress sections of the turbine. They offer a good balance of strength, corrosion resistance, and cost, making them suitable for less demanding applications.
5.4 Ceramic-Matrix Composites (CMCs)
Recent advancements have introduced ceramic-matrix composites, which can operate at higher temperatures than metal alloys. Although still in experimental and limited commercial use, CMCs hold the potential to significantly improve turbine efficiency by allowing for higher operational temperatures without the risk of material degradation.
6. Manufacturing Processes for Steam Turbine Blades
Manufacturing turbine blades involves precision processes to ensure exact specifications and high-quality finishes. Typical manufacturing methods include:
6.1 Forging
Forging involves shaping metal under high pressure, producing strong and durable blades. It is particularly useful for creating high-strength components that can withstand significant mechanical stresses.
6.2 Casting
Casting allows for the production of complex blade geometries by pouring molten metal into molds. Investment casting, in particular, is a preferred method for reaction blades, where precise shapes and smooth surface finishes are essential for performance.
6.3 Machining
Machining processes, including CNC (Computer Numerical Control) milling, are used to achieve precise blade dimensions and fine surface finishes. This process is crucial for final shaping and trimming to ensure aerodynamic efficiency.
6.4 Additive Manufacturing
Additive manufacturing, or 3D printing, has emerged as a cutting-edge technology for producing turbine blades. It allows for the creation of intricate designs that are difficult to achieve through traditional manufacturing. While still not widespread, additive manufacturing holds promise for rapid prototyping and production of customized blade designs.
7. The Future of Steam Turbine Blade Technology
The design and manufacturing of steam turbine blades continue to evolve, with ongoing research aimed at improving efficiency, reducing costs, and extending operational life. Future trends include:
- Advanced Materials: Development of new alloys and composite materials that can withstand even higher temperatures and pressures.
- Coating Innovations: Improved coatings that offer better protection against corrosion, erosion, and thermal degradation.
- Digital Twins and Simulation: The use of digital twins to simulate blade performance under various conditions, enabling engineers to optimize designs before manufacturing.
- Smart Manufacturing: Integration of AI and machine learning in the manufacturing process for real-time quality control and defect detection.
Conclusion
Steam turbine blades are fundamental to the operation of modern power generation systems, responsible for converting thermal energy into mechanical energy with high efficiency. The intricate design and precise manufacturing of these blades require a careful balance of aerodynamics, material science, and mechanical engineering. With advancements in material technology and manufacturing processes, the future of steam turbine blades looks promising, with improvements aimed at enhancing performance, reducing maintenance needs, and enabling cleaner, more sustainable energy production.
Understanding the complexities behind blade design and manufacturing highlights the importance of continuous innovation, ensuring that steam turbines remain a reliable source of power for years to come.
Types of Steam Turbine Blades
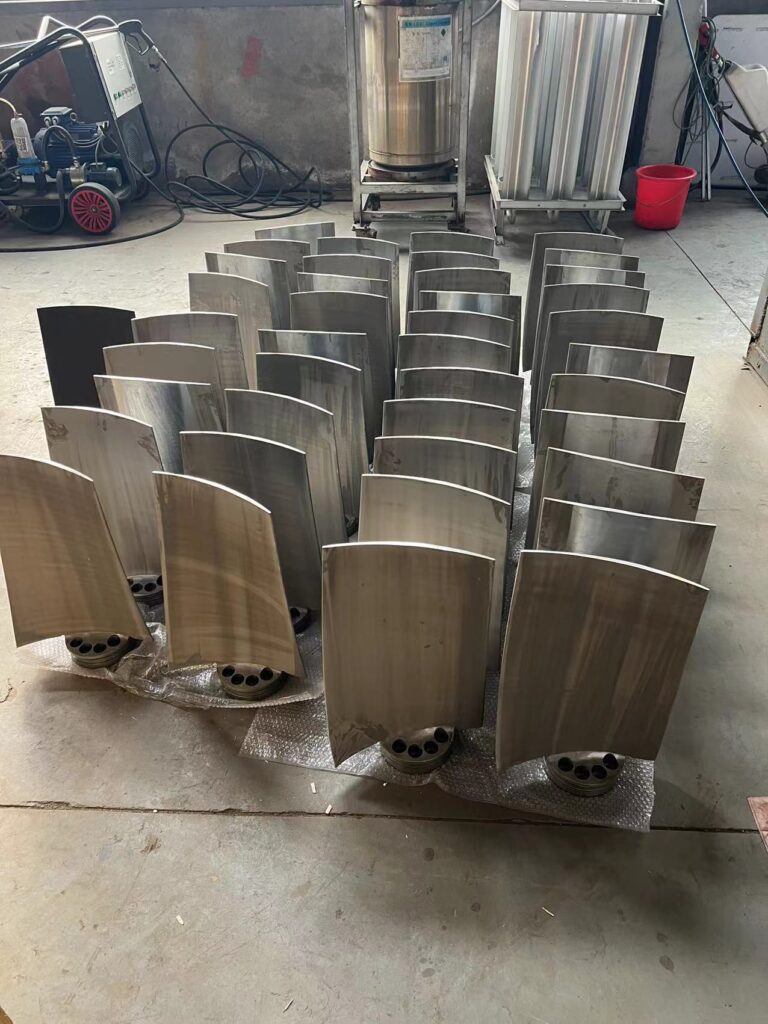
Steam turbine blades are the critical components responsible for converting thermal energy from steam into mechanical energy. The design and configuration of these blades are pivotal in determining the efficiency, performance, and operational characteristics of a steam turbine. Broadly, steam turbine blades are classified into two major types: impulse blades and reaction blades. This classification is based on the principles of operation and the way they extract energy from the steam.
This detailed exploration will cover the different types of blades, their operational principles, design considerations, and applications within the turbine system. By understanding the distinctions between these blade types, it becomes easier to appreciate their specific uses, advantages, and how they contribute to the overall performance of a steam turbine.
1. The Role of Steam Turbine Blades in Energy Conversion
Before diving into the types of blades, it’s essential to understand their role in the turbine’s energy conversion process. Steam turbines operate on the principle of expanding high-pressure, high-temperature steam to extract energy. This expansion process occurs through a series of stages, where the blades play a key role:
- Energy Extraction: Blades interact with the steam to convert its kinetic energy into mechanical rotation. This rotational motion drives a generator, producing electricity.
- Efficient Energy Use: The design and arrangement of blades are crucial to maximize energy extraction while minimizing losses, turbulence, and inefficiency.
- Pressure and Velocity Management: Through careful design, blades manage the steam’s pressure and velocity, ensuring optimal performance across different stages of the turbine.
Steam turbines are often divided into high-pressure, intermediate-pressure, and low-pressure sections, with different types of blades used in each section to handle varying energy levels and steam characteristics.
2. Impulse Blades
2.1 Operating Principle
Impulse blades operate based on the impulse principle, where the kinetic energy of high-velocity steam is used to rotate the turbine rotor. In an impulse turbine, steam is directed at the blades through nozzles, converting the steam’s pressure energy into kinetic energy. As the high-speed jet of steam strikes the impulse blades, it changes direction, causing a force that turns the rotor. Importantly, the pressure of the steam remains constant as it passes over the blades; only the velocity changes.
2.2 Design Characteristics
- Shape and Structure: Impulse blades are bucket-shaped, designed to capture and redirect the steam flow. They are often symmetrical, with a concave surface to catch the steam effectively.
- Fixed Blade and Moving Blade Arrangement: In an impulse turbine, steam first passes through fixed nozzles, which guide the steam onto the moving blades. The fixed nozzles are not part of the rotor, while the moving blades are mounted on the rotor shaft.
- Energy Distribution: The energy extracted by impulse blades comes solely from the kinetic energy of the steam, with no change in pressure. This requires high precision in blade design to minimize losses due to turbulence and steam leakage.
2.3 Advantages of Impulse Blades
- Simple Design: The straightforward shape of impulse blades makes them easier to manufacture compared to more complex designs.
- High Efficiency at High Pressure: Impulse blades are efficient at handling high-pressure steam, making them ideal for the high-pressure sections of a turbine.
- Ease of Maintenance: Due to their simplicity, impulse blades are easier to inspect, maintain, and replace, reducing operational costs.
2.4 Applications
Impulse blades are primarily used in the high-pressure stages of a turbine. This is because they are well-suited to handle the high-velocity steam generated at the beginning of the energy conversion process. Their design allows them to extract energy efficiently even when the steam pressure is very high, which is common in the initial stages of steam expansion.
3. Reaction Blades
3.1 Operating Principle
Reaction blades operate on the principle of both impulse and reaction forces. Unlike impulse blades, reaction blades utilize a continuous pressure drop across the blades to extract energy. As steam passes through the blades, it expands and accelerates, creating a reactive force that pushes the blades and rotates the rotor. This process involves both a change in pressure and velocity, unlike the impulse system where only velocity changes.
3.2 Design Characteristics
- Aerodynamic Shape: Reaction blades are more aerodynamically complex than impulse blades. They are designed with a profile that allows steam to expand and accelerate as it flows over the surface, creating lift-like forces.
- Fixed and Moving Blade Rows: Similar to impulse turbines, reaction turbines also have fixed and moving blade rows. However, in this case, both sets contribute to energy extraction. The fixed blades act as guides, causing the steam to change direction and accelerate onto the moving blades.
- Pressure Distribution: In reaction blades, the pressure decreases as steam moves over the blades, which differentiates them from impulse blades. This pressure drop across the blades contributes to the generation of mechanical force.
3.3 Advantages of Reaction Blades
- Higher Energy Extraction: Since reaction blades utilize both pressure and velocity changes, they can extract more energy from steam than impulse blades in certain situations.
- Smooth and Continuous Operation: The design of reaction blades allows for smoother operation, as the energy conversion is more gradual. This can lead to improved efficiency in the low-pressure stages.
- Efficiency Across Pressure Ranges: Reaction blades can be adapted to operate efficiently across different pressure ranges, making them versatile within the turbine system.
3.4 Applications
Reaction blades are typically found in the intermediate and low-pressure sections of a turbine. As the steam pressure drops throughout the turbine, reaction blades continue to extract energy efficiently. Their design is particularly beneficial where the steam pressure and velocity are lower, and a smooth, continuous conversion of energy is desired.
4. Comparative Analysis: Impulse vs. Reaction Blades
To better understand the distinctions between impulse and reaction blades, it is useful to compare their operational characteristics, design features, and typical uses within a turbine system.
Feature | Impulse Blades | Reaction Blades |
---|---|---|
Operating Principle | Utilizes kinetic energy from high-velocity steam. | Uses both pressure and velocity changes. |
Pressure Change | No change in pressure across the blades. | Pressure drops as steam moves over the blades. |
Design Complexity | Relatively simple and bucket-shaped. | More complex, aerodynamically designed. |
Energy Extraction | Extracts energy primarily from velocity. | Extracts energy from both velocity and pressure. |
Preferred Pressure Stage | High-pressure stages of turbines. | Low and intermediate-pressure stages. |
Maintenance | Easier to maintain and replace. | Requires more precise manufacturing and maintenance. |
5. Special Blade Configurations and Hybrid Designs
In modern steam turbines, there are also configurations that combine the principles of both impulse and reaction designs to optimize performance across varying steam conditions. These are often called “hybrid” or “compound” turbines and are designed to handle different stages of steam expansion more efficiently.
5.1 Compound Staging
- Combination Approach: In a compound turbine, high-pressure sections may utilize impulse blades to handle the intense kinetic energy of the initial steam flow. As the steam pressure drops, reaction blades take over to continue the energy extraction process more smoothly.
- Enhanced Efficiency: This approach allows the turbine to maintain high efficiency across a wide range of operational conditions, accommodating both high and low-pressure steam effectively.
5.2 Curtis Stage (Multi-Stage Impulse)
- Design Description: The Curtis stage is a multi-stage impulse design, often used as a part of the high-pressure stage of a turbine. Instead of a single set of impulse blades, multiple sets are arranged in series, allowing for a gradual reduction in steam velocity.
- Applications: This design is used to improve efficiency when dealing with very high-velocity steam, making it suitable for large, high-capacity power plants.
6. Key Design Considerations for Turbine Blades
6.1 Aerodynamic Efficiency
Both impulse and reaction blades must be designed to ensure smooth steam flow, minimizing drag and turbulence. This is especially critical for reaction blades, where the aerodynamic profile is more complex.
6.2 Material Strength and Durability
Given the high-speed rotation and the extreme conditions under which turbine blades operate, material selection is crucial. Both types of blades are subject to stress, but impulse blades face more intense impact forces, while reaction blades endure a combination of pressure and shear forces.
6.3 Precision Manufacturing
Impulse blades are simpler in shape, making them easier to manufacture. However, reaction blades require higher precision in both design and manufacturing due to their aerodynamic complexity and need to handle gradual pressure drops without losing efficiency.
7. Advances in Blade Design and Future Trends
The field of turbine blade design continues to evolve, driven by the demand for higher efficiency, lower emissions, and greater operational flexibility. Future advancements are likely to include:
- 3D Printed Blades: Offering more intricate designs that improve aerodynamics and efficiency.
- Advanced Materials: Development of new alloys and composites that can withstand even higher temperatures and pressures.
- Adaptive Blade Designs: Innovations in blade shapes that can adjust to varying steam conditions, further optimizing performance across different operational modes.
Conclusion
Steam turbine blades, whether impulse or reaction, are fundamental components that enable efficient energy conversion in power plants. The choice between impulse and reaction blades, or a combination of both, depends on the specific application and the operating conditions of the turbine. Understanding the principles, advantages, and design characteristics of each blade type is essential for designing turbines that operate efficiently, reliably, and with minimal maintenance. As technology continues to advance, the future of turbine blade design looks to become even more innovative, leading to cleaner, more sustainable, and more efficient power generation systems.
Impulse Blades in Steam Turbines: An In-Depth Exploration
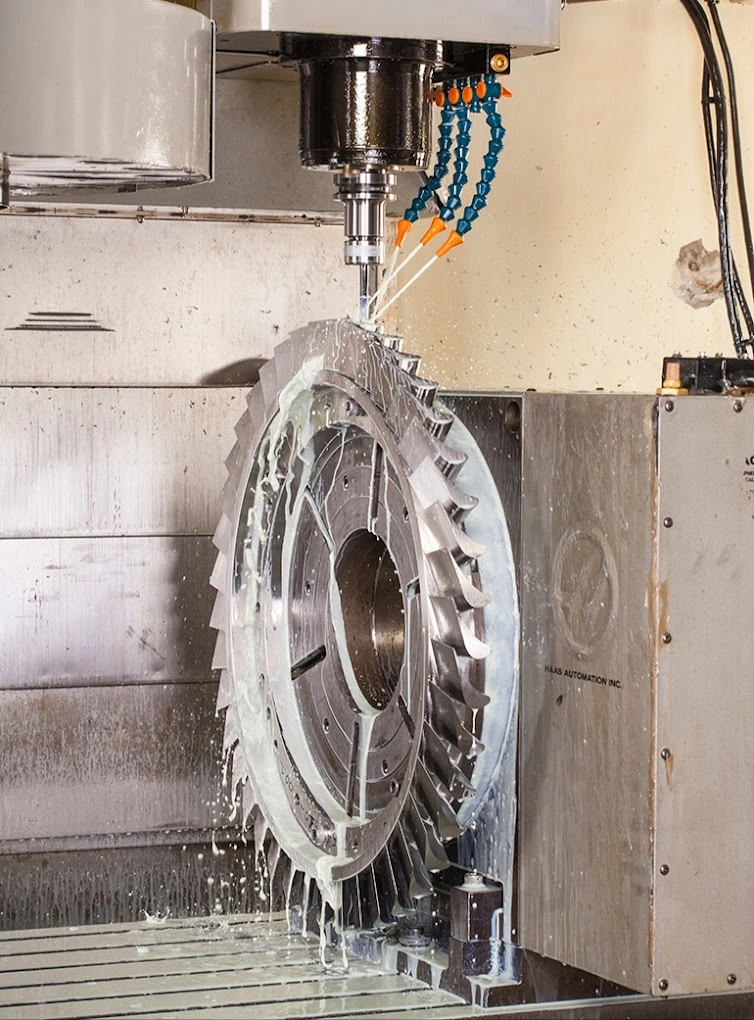
Impulse blades are one of the two primary types of blades used in steam turbines, and they play a crucial role in the conversion of steam’s kinetic energy into mechanical energy. These blades are designed to harness high-velocity steam to drive the turbine rotor, generating power. In this comprehensive exploration, we will delve into the design, operating principles, material considerations, applications, and manufacturing techniques of impulse blades, along with their advantages and challenges.
1. Understanding Impulse Turbines and Their Blades
Impulse turbines are characterized by their unique method of energy conversion. Unlike reaction turbines, where energy extraction involves a gradual pressure drop across the blades, impulse turbines convert the steam’s pressure energy into kinetic energy before it reaches the blades. This high-velocity steam then strikes the impulse blades, causing them to rotate.
1.1 Operating Principle of Impulse Blades
The operating principle of impulse blades is based on the impulse force, which is the result of steam jets striking the blades at high speeds. Here’s how it works:
- Steam Expansion in Nozzles: The pressurized steam is expanded in nozzles before it reaches the impulse blades. The nozzles convert the pressure energy of the steam into high-velocity jets. By the time the steam exits the nozzles, most of its pressure energy has been converted into kinetic energy.
- Kinetic Energy Transfer: As the steam jet strikes the impulse blades, it changes direction, creating a force (impulse) that pushes the blades. The steam’s pressure remains constant throughout this process; only its velocity changes. The resulting impulse force rotates the rotor, converting kinetic energy into mechanical energy.
- Mechanical Rotation: The blades are mounted on a rotor, and as they turn, they drive the connected shaft. This shaft is connected to a generator, which ultimately converts the mechanical energy into electrical energy.
This method of energy extraction allows impulse turbines to operate efficiently at high steam pressures, making them ideal for the initial stages of steam turbines where the pressure is at its peak.
2. Design Characteristics of Impulse Blades
The design of impulse blades is crucial to their function. These blades must be shaped and arranged in a way that maximizes energy extraction from the steam while minimizing energy losses. Key design characteristics include:
2.1 Blade Shape and Geometry
- Bucket Shape: Impulse blades are often designed with a “bucket” or “cup” shape. This design allows the blades to catch the steam effectively and redirect it, generating the maximum impulse force.
- Symmetrical Design: The blades are typically symmetrical, allowing for a uniform distribution of force and ensuring balanced rotation of the rotor. The symmetrical design also helps to minimize wear and tear, leading to improved longevity.
- Curvature and Angle: The curvature of the blades is carefully designed to change the direction of the steam flow without causing excessive turbulence or drag. The angle at which the blades are positioned ensures that the steam strikes them at the optimal point, maximizing energy transfer.
2.2 Fixed and Moving Blade Arrangement
Impulse turbines typically utilize a combination of fixed nozzles and moving blades:
- Fixed Nozzles: These are stationary components that direct the steam onto the moving blades. They play a crucial role in converting the steam’s pressure energy into high-velocity jets.
- Moving Blades: Mounted on the rotor, the moving blades receive the steam from the nozzles and extract kinetic energy from it. The rotor rotates due to the impulse force generated by the change in the steam’s direction.
2.3 Stage Configuration
Impulse turbines can be designed with multiple stages to enhance energy extraction. In a single-stage impulse turbine, all the energy is extracted in one go, which may not be efficient. Multi-stage impulse turbines, like the Curtis stage, utilize multiple rows of nozzles and blades, allowing for gradual energy extraction. This staged approach reduces the velocity of the steam in increments, improving overall efficiency and minimizing mechanical stress on the blades.
3. Advantages of Impulse Blades
Impulse blades offer several benefits that make them a preferred choice for certain stages of steam turbines. Some of these advantages include:
3.1 High Efficiency at High Pressure
Impulse blades are well-suited for high-pressure steam because they convert the steam’s pressure energy into kinetic energy before the steam reaches the blades. This makes them efficient in the initial stages of the turbine where steam pressure is highest.
3.2 Simplicity of Design
The design of impulse blades is relatively simple compared to reaction blades. This simplicity translates to easier manufacturing and maintenance. The straightforward design reduces manufacturing costs and simplifies the process of inspection and repair, making impulse blades a cost-effective option for turbine operators.
3.3 Adaptability to Varying Conditions
Impulse blades can operate effectively under varying steam conditions without significant loss of efficiency. This adaptability makes them useful in applications where steam conditions may fluctuate, such as in industrial power generation.
3.4 Ease of Maintenance and Replacement
Since impulse blades are designed to handle high-impact forces and do not experience pressure drops, they are typically less susceptible to damage from wear and tear. Additionally, their simpler design means that they can be easily inspected, maintained, and replaced if necessary, minimizing downtime during maintenance activities.
4. Applications of Impulse Blades in Steam Turbines
Impulse blades are primarily used in the high-pressure stages of steam turbines. In these sections, the steam pressure is at its peak, and the goal is to convert this pressure into kinetic energy as efficiently as possible. Impulse blades are also used in certain industrial turbines where conditions may vary, but high efficiency is still required.
4.1 Power Plants
In large-scale power plants, impulse blades are typically found in the high-pressure stages of the turbine, where they are responsible for extracting energy from steam that is fresh out of the boiler. The blades can handle the high pressure and temperature conditions effectively, ensuring efficient energy conversion right from the start.
4.2 Industrial Applications
Many industries use steam turbines for driving equipment like compressors, pumps, and blowers. Impulse blades are commonly used in these applications because they can handle varying loads and pressures, providing reliable performance across a range of operating conditions.
4.3 Marine Propulsion
Impulse turbines have also been used in the marine industry to drive ship propellers. The turbines convert the high-pressure steam produced in the boiler into mechanical energy, which then drives the ship’s propeller shaft, propelling the vessel forward.
5. Materials Used in Impulse Blade Manufacturing
The materials used for impulse blades must withstand harsh conditions, including high temperatures, high pressures, and exposure to steam and other elements. Key material properties include thermal resistance, strength, corrosion resistance, and durability. Some of the common materials used include:
5.1 Stainless Steel
Stainless steel is widely used due to its strength, durability, and resistance to corrosion. It is capable of withstanding the high temperatures and pressures encountered in the high-pressure stages of turbines. Additionally, stainless steel is relatively cost-effective, making it a popular choice for many turbine manufacturers.
5.2 Nickel-Based Superalloys
Nickel-based superalloys, such as Inconel and Waspaloy, are often used in high-performance applications where extreme temperatures are a concern. These alloys retain their mechanical properties at high temperatures and are resistant to oxidation and corrosion. However, they are more expensive than stainless steel.
5.3 Titanium Alloys
Titanium alloys are valued for their high strength-to-weight ratio, which makes them ideal for applications where reduced weight is an advantage. These alloys also offer excellent resistance to corrosion, which is beneficial in environments where the steam may contain impurities.
6. Manufacturing Technologies for Impulse Blades
The production of impulse blades requires precision engineering to ensure they meet exact specifications. Manufacturing technologies include:
6.1 Forging
Forging involves shaping metal under high pressure to produce strong, durable blades. This process is often used for the production of high-strength components that need to endure significant mechanical stress. Forging helps achieve a robust grain structure, enhancing the blade’s strength and durability.
6.2 Machining
After the initial forging, the blades are typically machined to achieve the precise shapes and dimensions required for optimal performance. CNC (Computer Numerical Control) machining is commonly used for this purpose, as it allows for high precision and control over the blade’s final form.
6.3 Investment Casting
For more complex blade geometries, investment casting is often used. This process involves creating a wax model of the blade, which is then coated in a ceramic shell. Once the wax is melted out, molten metal is poured into the ceramic mold to form the blade. Investment casting allows for the production of intricate designs with smooth finishes, which are critical for minimizing energy losses.
7. Challenges and Future Trends in Impulse Blade Design
7.1 Challenges in Impulse Blade Operation
- Erosion and Corrosion: Impulse blades can suffer from erosion and corrosion due to the high-speed impact of steam, especially if the steam contains impurities. This can lead to gradual wear and a decrease in efficiency over time.
- Thermal Stress: The blades operate under high-temperature conditions, leading to thermal stress that can cause material fatigue and cracking if not properly managed.
- Noise and Vibration: High-speed operation can lead to noise and vibration, which may require damping mechanisms to minimize wear and improve performance.
7.2 Future Trends in Impulse Blade Technology
- Advanced Materials: Ongoing research is focused on developing new materials that can withstand higher temperatures and pressures, improving turbine efficiency. Superalloys and ceramic-matrix composites (CMCs) are among the materials being explored for future applications.
- Additive Manufacturing: Also known as 3D printing, additive manufacturing offers the potential to create complex blade geometries that are difficult to achieve with traditional methods. This could lead to more efficient designs and faster production times.
- Improved Coating Technologies: Enhanced coating technologies can improve the blades’ resistance to erosion and corrosion, extending their lifespan and reducing maintenance costs. Thermal barrier coatings (TBCs) are particularly promising for high-temperature applications.
Conclusion
Impulse blades are fundamental to the operation of steam turbines, especially in the high-pressure stages. Their design and function are based on the principle of impulse, where kinetic energy from high-velocity steam is converted into mechanical energy. The simplicity of their design, combined with their ability to handle high-pressure conditions, makes them an essential component in power generation, industrial, and marine applications.
Advancements in material science, manufacturing technologies, and design engineering are continuously improving the performance and durability of impulse blades. As the demand for more efficient and reliable power generation continues to grow, the role of impulse blades in steam turbines will remain crucial, driving innovation and development in this field.
Reaction Blades in Steam Turbines: An In-Depth Exploration
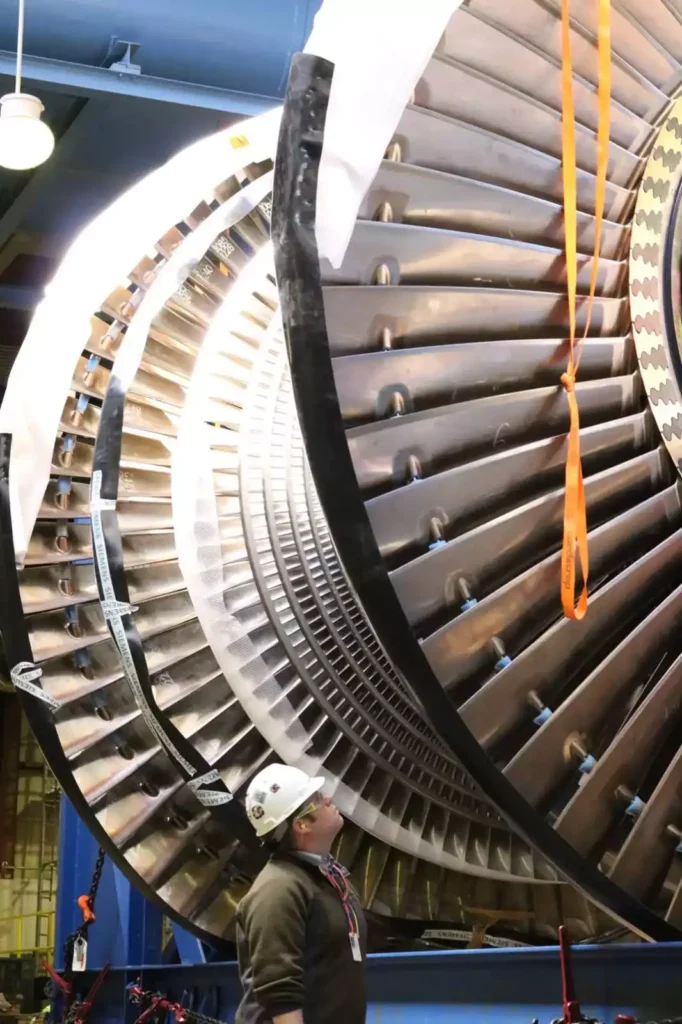
Reaction blades are a fundamental component of steam turbines, especially in the low to medium-pressure stages. Unlike impulse blades, which rely solely on changes in the velocity of steam to generate mechanical force, reaction blades harness both pressure and velocity changes. This makes them essential for the efficient extraction of energy from steam as it expands and loses pressure within the turbine. In this comprehensive exploration, we will delve into the design, principles of operation, materials, applications, manufacturing techniques, and future trends of reaction blades.
1. Understanding Reaction Turbines and Their Blades
Reaction turbines operate on a combined principle of impulse and reaction. As steam passes over the blades, it experiences a drop in both pressure and velocity, causing the blades to move. This dual-action method of energy extraction allows for a smoother and more gradual transfer of energy, making reaction turbines highly efficient across varying steam pressures.
1.1 Operating Principle of Reaction Blades
The operating principle of reaction blades is based on Newton’s Third Law of Motion, which states that for every action, there is an equal and opposite reaction. Here’s how it works:
- Energy Conversion: Unlike impulse turbines, where energy is mainly converted in the nozzles before reaching the blades, reaction turbines use blades that act as both nozzles and energy extractors. Steam accelerates as it passes over the blades, expanding and losing pressure. This creates a reactive force that drives the rotor.
- Pressure Drop Across the Blades: As steam flows over the reaction blades, it expands, resulting in a pressure drop. This pressure drop occurs gradually, allowing for a smoother and continuous extraction of energy.
- Reactive Force and Rotor Motion: The steam’s acceleration creates a reactive force that propels the blades forward, turning the rotor. The rotor’s motion then drives the connected shaft, converting the extracted energy into mechanical work, which can then be used to generate electricity.
Because the energy extraction involves changes in both pressure and velocity, reaction blades are typically used in stages where the steam pressure is lower and has already undergone some expansion.
2. Design Characteristics of Reaction Blades
The design of reaction blades is more complex compared to impulse blades because they need to accommodate both pressure and velocity changes. This complexity ensures that the turbine operates efficiently and extracts maximum energy from the steam.
2.1 Blade Shape and Geometry
- Aerofoil Design: Reaction blades have a more aerodynamic, aerofoil-like shape. This design is crucial for guiding the steam smoothly over the blade surface, allowing it to expand and accelerate without creating excessive turbulence or energy losses.
- Twisted Profile: The blades often feature a twisted or contoured profile. This design helps optimize the steam’s angle of attack as it flows through different sections of the blade, improving efficiency. The twisting also allows the blades to handle variations in steam velocity and pressure more effectively.
- Fixed and Moving Blade Rows: Reaction turbines consist of alternating rows of fixed blades (stator blades) and moving blades (rotor blades). The fixed blades direct the steam onto the moving blades, causing it to accelerate and expand. The moving blades then convert this energy into mechanical motion.
2.2 Gradual Pressure Drop Across Stages
- Energy Extraction Across Multiple Stages: Unlike impulse turbines, where the energy is extracted in discrete bursts, reaction turbines operate over multiple stages, with a gradual decrease in pressure across each stage. This staged approach allows for a smoother, more controlled energy transfer, reducing mechanical stress on the blades.
- Staggered Blade Arrangement: The blades are arranged in a staggered pattern to ensure efficient steam flow. This arrangement helps maintain continuous energy extraction across each stage, minimizing disruptions in the steam flow and improving overall turbine efficiency.
3. Advantages of Reaction Blades
Reaction blades offer several benefits that make them suitable for specific applications in steam turbines. Some of the key advantages include:
3.1 High Efficiency in Low to Medium-Pressure Stages
Reaction blades are particularly effective in the low and medium-pressure sections of a steam turbine, where the steam has already undergone significant expansion. The gradual energy extraction ensures that even when the steam pressure is lower, the turbine can still operate efficiently, making the most of the remaining energy in the steam.
3.2 Smooth and Continuous Energy Conversion
The design of reaction blades allows for a continuous and smooth energy conversion process. By gradually extracting energy across multiple stages, reaction turbines minimize mechanical shocks and vibrations, which can lead to more stable and reliable operation. This smooth operation also contributes to less wear and tear, enhancing the lifespan of the turbine components.
3.3 Adaptability Across Pressure Ranges
Reaction blades can handle a wide range of steam pressures, making them versatile and adaptable. This flexibility is especially beneficial in power plants that operate under varying load conditions, as the turbine can maintain efficiency across different operational settings.
3.4 Enhanced Aerodynamic Performance
The aerodynamic design of reaction blades reduces drag and turbulence, which helps improve the overall efficiency of the turbine. By minimizing aerodynamic losses, the blades can extract more energy from the steam, leading to higher performance levels.
4. Applications of Reaction Blades in Steam Turbines
Reaction blades are primarily used in the medium to low-pressure stages of steam turbines. Their ability to handle gradual energy extraction makes them ideal for these sections, where the steam has expanded and the pressure is lower. Some of the typical applications include:
4.1 Power Generation Plants
In power plants, reaction blades are found in the latter stages of the turbine, where the steam has already passed through high-pressure sections. The blades continue to extract energy efficiently from the steam as it expands further, ensuring that no energy is wasted.
4.2 Industrial and Mechanical Drives
In industrial applications, such as in factories and manufacturing plants, reaction turbines are used to drive mechanical equipment. The smooth operation and efficiency of reaction blades make them suitable for industrial processes that require consistent, reliable power.
4.3 Marine Propulsion Systems
Reaction turbines are sometimes used in marine propulsion systems, where efficiency and smooth operation are critical. The gradual energy extraction process of reaction blades helps maintain steady propulsion, even when the steam pressure varies.
5. Materials Used in Reaction Blade Manufacturing
The choice of materials for reaction blades is essential due to the challenging operating conditions, including exposure to high temperatures, moisture, and corrosive elements. Key properties include thermal resistance, strength, corrosion resistance, and durability. Some of the common materials used for reaction blades include:
5.1 Stainless Steel
Stainless steel is widely used due to its balance of strength, durability, and resistance to corrosion. It can withstand high temperatures and provides reliable performance in the low-pressure stages of the turbine. Additionally, stainless steel is relatively affordable, making it a practical choice for many turbine designs.
5.2 Nickel-Based Superalloys
Nickel-based superalloys, such as Hastelloy and Inconel, are used in high-performance turbines where higher operating temperatures and more demanding conditions are expected. These materials retain their mechanical properties at high temperatures and are resistant to oxidation and corrosion, making them ideal for long-term use in reaction blades.
5.3 Titanium Alloys
Titanium alloys offer a high strength-to-weight ratio and excellent corrosion resistance, making them suitable for applications where reduced weight is advantageous. They are particularly effective in low-pressure stages where the steam has cooled, and lightweight components can improve overall efficiency.
6. Manufacturing Technologies for Reaction Blades
The manufacturing of reaction blades requires precision and expertise to ensure that the blades meet exact specifications and can operate efficiently. Some of the common manufacturing techniques include:
6.1 Precision Casting
Casting, particularly investment casting, is a popular method for manufacturing reaction blades. This process involves creating a detailed wax model of the blade, which is then coated in a ceramic shell. Once the wax is melted out, molten metal is poured into the mold to form the blade. Investment casting allows for the production of intricate shapes and smooth surfaces, which are critical for aerodynamic efficiency.
6.2 CNC Machining
Computer Numerical Control (CNC) machining is used to refine the blades after casting. This process ensures that the blades have precise dimensions and smooth surfaces, which are necessary for optimal aerodynamic performance. CNC machining also allows for customization, enabling engineers to fine-tune blade designs for specific applications.
6.3 Additive Manufacturing (3D Printing)
Additive manufacturing is an emerging technology that offers the potential to produce complex blade geometries that are difficult to achieve with traditional methods. This technique allows for rapid prototyping and the creation of customized blade designs, improving flexibility and reducing production times. Though still not widespread in commercial turbine manufacturing, 3D printing holds promise for future developments.
7. Challenges and Future Trends in Reaction Blade Design
7.1 Challenges in Reaction Blade Operation
- Corrosion and Erosion: Reaction blades are exposed to steam that may contain impurities, leading to corrosion and erosion over time. This can degrade blade performance and reduce the efficiency of the turbine.
- Thermal Fatigue: Operating at high temperatures for extended periods can cause thermal fatigue, leading to material degradation. Engineers must carefully select materials that can withstand these conditions without losing mechanical integrity.
- Precision Manufacturing Requirements: The aerodynamic complexity of reaction blades makes them challenging to manufacture. Any imperfections can lead to reduced efficiency, making precision manufacturing essential.
7.2 Future Trends in Reaction Blade Technology
- Advanced Materials and Coatings: Research is ongoing into new materials and coatings that can withstand higher temperatures, improve corrosion resistance, and reduce wear. Advanced ceramics and superalloys are being explored as potential materials for future reaction blades.
- Smart Blades: With the rise of digital technologies, there is potential for the development of “smart” blades that can monitor their own performance in real time. Sensors embedded within the blades could provide data on temperature, stress, and wear, enabling predictive maintenance and enhancing reliability.
- Improved Aerodynamic Designs: Computational fluid dynamics (CFD) and simulation tools are being used to refine the aerodynamic designs of reaction blades. These tools allow engineers to optimize the blade shapes and profiles for better performance, even under varying operating conditions.
Conclusion
Reaction blades are integral to the operation of steam turbines, especially in the medium to low-pressure stages where the steam has already expanded. Their design, which leverages both pressure and velocity changes, allows for efficient, smooth, and continuous energy extraction. The complex aerodynamic shape of these blades, combined with the need for durable, high-performance materials, makes them one of the most challenging yet essential components of turbine engineering.
Advancements in materials science, precision manufacturing, and aerodynamic design continue to improve the efficiency and reliability of reaction blades. As the demand for more efficient power generation grows, the role of reaction blades will become even more significant, driving innovation and ensuring the sustainable production of energy. With future trends pointing toward smart, adaptable, and high-performance designs, reaction blades will likely remain at the forefront of steam turbine technology for years to come.
Differences Between Impulse and Reaction Blades in Steam Turbines: A Comprehensive Exploration
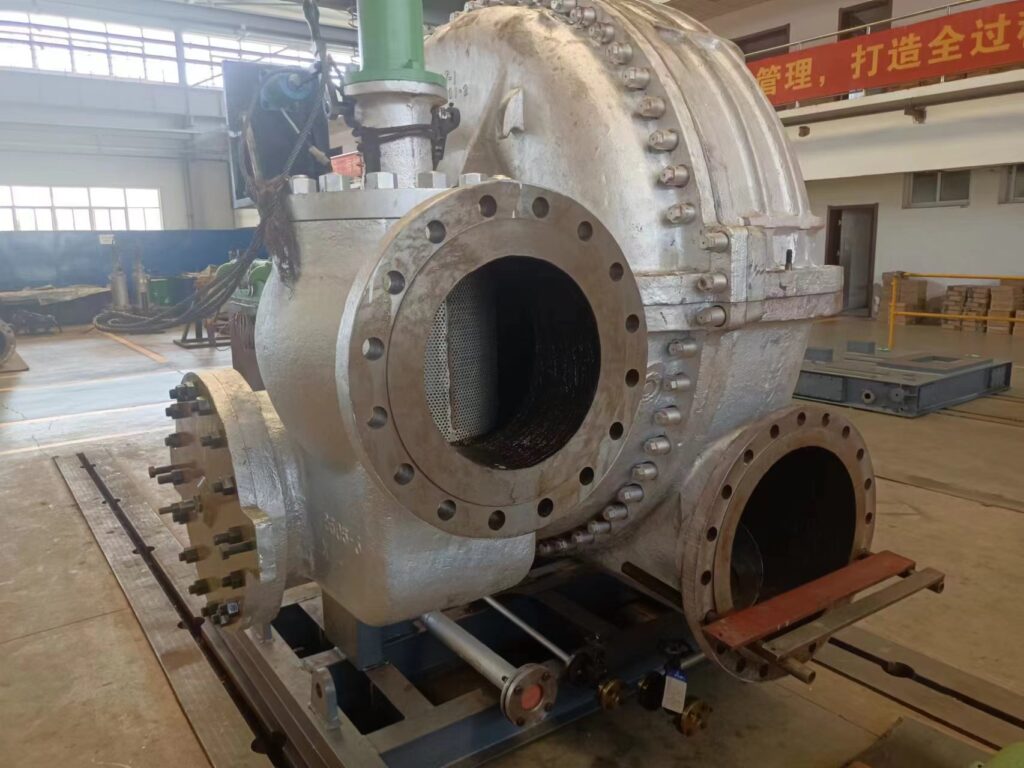
Steam turbines are a crucial part of power generation systems, transforming thermal energy from steam into mechanical energy that drives electrical generators. The efficiency of this energy conversion depends largely on the design of the turbine blades. There are two primary types of blades used in steam turbines: impulse blades and reaction blades. Each type operates on distinct principles and is suited to different stages of the turbine. This comprehensive exploration will delve into the key differences between impulse and reaction blades, including their operating principles, design characteristics, material considerations, applications, and advantages. Understanding these distinctions is essential for optimizing turbine performance and improving overall energy efficiency.
1. Operating Principles
The fundamental difference between impulse and reaction blades lies in how they convert steam energy into mechanical motion. The distinction arises from the way each type of blade handles the pressure and velocity of steam.
1.1 Impulse Blades:
- Impulse Principle: Impulse blades operate on the principle of converting the kinetic energy of high-velocity steam into mechanical motion. Steam is first expanded and accelerated in stationary nozzles, where its pressure energy is converted into kinetic energy. The high-speed steam then strikes the impulse blades, causing them to rotate. The blades themselves do not cause a change in steam pressure; instead, they redirect the steam, changing its velocity and generating an impulse force that drives the rotor.
- Constant Pressure Across the Blades: As steam flows over impulse blades, its pressure remains constant, but its velocity changes. This results in an impulse force that rotates the turbine.
1.2 Reaction Blades:
- Reaction Principle: Reaction blades, on the other hand, utilize both pressure and velocity changes to generate mechanical motion. Steam expands and accelerates directly as it passes over the blades, experiencing a gradual drop in pressure. This process generates a reactive force, much like the thrust produced by a rocket engine. The combination of pressure drop and change in steam velocity creates a continuous driving force on the blades.
- Pressure Drop Across the Blades: Unlike impulse blades, reaction blades cause the steam to experience a pressure drop as it flows over them. The energy conversion process is continuous, and the reactive force generated by the pressure change drives the turbine.
2. Design Characteristics
The design of impulse and reaction blades reflects their distinct operating principles. These design differences are crucial for maximizing efficiency and ensuring smooth operation in different stages of the turbine.
2.1 Impulse Blade Design:
- Bucket-Shaped Blades: Impulse blades are typically bucket-shaped or cup-shaped, designed to catch and redirect the steam flow. The shape allows for efficient conversion of the kinetic energy of the steam into mechanical energy.
- Symmetrical Design: The blades are often symmetrical, with a concave profile that ensures uniform force distribution, minimizing wear and tear. The design also helps in reducing turbulence and energy losses.
- Fixed and Moving Blade Arrangement: Impulse turbines use a combination of fixed nozzles (or stators) and moving blades. The nozzles are stationary components that direct steam onto the moving blades, which are mounted on the rotor shaft. Energy is extracted as the steam changes direction upon striking the moving blades.
2.2 Reaction Blade Design:
- Aerofoil-Shaped Blades: Reaction blades are more aerodynamic and resemble an aerofoil shape. This shape is essential for allowing the steam to expand and accelerate smoothly over the surface, facilitating both pressure drop and velocity change.
- Twisted Profile: Reaction blades often feature a twisted or contoured profile to optimize the steam’s angle of attack and ensure smooth flow. This design minimizes drag and turbulence, increasing efficiency.
- Alternating Fixed and Moving Blade Rows: Reaction turbines consist of alternating rows of fixed and moving blades. The fixed blades, or stators, direct the steam onto the moving blades, causing it to expand and accelerate. Both sets of blades play a role in energy conversion, unlike in impulse turbines where only the moving blades are responsible for extracting energy.
3. Energy Conversion Process
The way impulse and reaction blades convert energy highlights another key difference between the two. The efficiency and application of each blade type are directly influenced by their respective energy conversion mechanisms.
3.1 Impulse Energy Conversion:
- Discrete Energy Transfer: In impulse turbines, energy is transferred in a discrete manner. Steam’s pressure energy is converted entirely into kinetic energy in the nozzles before it reaches the blades. The blades extract energy by redirecting the steam, causing a change in momentum and producing mechanical rotation.
- High-Pressure Operation: Impulse turbines are ideal for high-pressure stages, where the steam has not yet expanded significantly. The high velocity of the steam jets allows for efficient energy extraction even when the steam pressure is high.
3.2 Reaction Energy Conversion:
- Continuous Energy Transfer: In reaction turbines, energy transfer is continuous. As steam passes over the blades, it undergoes a pressure drop and accelerates, providing a continuous reactive force. This gradual energy extraction ensures smooth and efficient operation, especially at lower steam pressures.
- Low to Medium-Pressure Operation: Reaction turbines are most effective in low to medium-pressure stages, where the steam has already expanded and its pressure has decreased. The ability to extract energy continuously from the expanding steam makes reaction blades suitable for these conditions.
4. Applications Within the Steam Turbine
The differences in operating principles and design characteristics mean that impulse and reaction blades are used in different sections of a steam turbine. Each blade type is suited to specific conditions, enhancing overall turbine performance.
4.1 Impulse Blade Applications:
- High-Pressure Stages: Impulse blades are primarily used in the high-pressure stages of the turbine. Here, steam pressure is at its peak, and the goal is to convert this pressure into kinetic energy as efficiently as possible. The impulse design allows for effective energy extraction from high-speed steam jets.
- Industrial and Mechanical Turbines: Due to their ability to handle high-pressure, high-velocity steam, impulse turbines are also common in mechanical drives and industrial applications, such as driving compressors, pumps, and blowers.
4.2 Reaction Blade Applications:
- Medium to Low-Pressure Stages: Reaction blades are typically found in the medium and low-pressure sections of a turbine. These blades continue to extract energy from the steam as it expands and its pressure drops. The gradual energy extraction process makes reaction turbines suitable for handling the remaining energy in the steam efficiently.
- Power Generation and Marine Propulsion: Reaction turbines are commonly used in power plants and marine propulsion systems, where continuous and smooth energy conversion is necessary for stable operation.
5. Advantages and Disadvantages
The unique characteristics of impulse and reaction blades come with their own sets of advantages and challenges. Understanding these can help determine the most appropriate application for each blade type.
5.1 Advantages of Impulse Blades:
- Simple Design: The straightforward, bucket-shaped design of impulse blades makes them easier to manufacture and maintain. This simplicity translates to lower production costs and simpler maintenance procedures.
- Effective High-Pressure Performance: Impulse blades are efficient at converting the kinetic energy of high-velocity steam jets, making them ideal for high-pressure stages where steam pressure is still high.
- Ease of Maintenance: The simple design allows for easy inspection, maintenance, and replacement, reducing downtime during repairs.
5.2 Disadvantages of Impulse Blades:
- Less Efficient at Lower Pressures: Impulse blades are less effective in extracting energy from steam at lower pressures, limiting their application to high-pressure stages.
- Mechanical Stress: The high-speed impact of steam on impulse blades can cause mechanical stress, which can lead to wear over time.
5.3 Advantages of Reaction Blades:
- High Efficiency Across Pressure Ranges: Reaction blades can operate efficiently across a range of pressures, making them versatile and adaptable. They can continue to extract energy from steam even when the pressure is lower.
- Smooth and Continuous Energy Conversion: The gradual energy extraction process ensures a smoother operation with less mechanical vibration, improving the longevity of the turbine components.
- Aerodynamic Design: The aerodynamic shape reduces drag and turbulence, leading to better efficiency and performance.
5.4 Disadvantages of Reaction Blades:
- Complex Design and Manufacturing: The aerodynamic and twisted design of reaction blades requires precise engineering, making them more difficult and expensive to manufacture compared to impulse blades.
- Maintenance Challenges: Due to their complex design, reaction blades can be harder to inspect, maintain, and replace, leading to potential maintenance challenges.
6. Material Considerations for Impulse and Reaction Blades
Both impulse and reaction blades must be made from materials that can withstand extreme conditions, including high temperatures, pressures, and exposure to moisture and corrosion. However, their specific operating environments can influence material choices.
6.1 Impulse Blades:
- Materials for High-Impact Forces: Impulse blades are subject to high-impact forces from steam jets, so they require materials with high tensile strength and resistance to impact. Stainless steel and nickel-based superalloys are commonly used due to their ability to maintain structural integrity at high temperatures.
- Corrosion Resistance: As these blades operate in high-pressure environments, materials must also resist corrosion and oxidation to prevent degradation.
6.2 Reaction Blades:
- Materials for Aerodynamic Performance: Reaction blades require materials that maintain their shape under thermal stress to ensure aerodynamic efficiency. Nickel-based superalloys and titanium alloys are often used because of their high-temperature resistance, strength, and corrosion resistance.
- Lightweight Options: In lower-pressure stages, where reducing the weight of the blades can improve efficiency, materials like titanium alloys are preferred due to their strength-to-weight ratio.
7. Future Trends and Technological Advancements
As technology advances, the design and efficiency of both impulse and reaction blades continue to improve. Future trends include:
7.1 Advanced Materials:
- Ceramic-Matrix Composites (CMCs): New materials, such as CMCs, offer high-temperature resistance and reduced weight, which could improve the performance of both impulse and reaction blades. These materials allow turbines to operate at higher temperatures, increasing overall efficiency.
7.2 Smart Manufacturing Techniques:
- Additive Manufacturing: 3D printing and additive manufacturing enable the production of complex blade geometries that are difficult to achieve with traditional methods. This allows for more aerodynamic designs and quicker production times.
- Precision Machining: Advances in CNC machining and computer-aided design (CAD) enable the production of more precise and efficient blade shapes, optimizing steam flow and energy conversion.
7.3 Integrated Sensors and Monitoring:
- Smart Blades: Future blades may integrate sensors that monitor temperature, pressure, and stress in real time. This data can help detect potential issues early, allowing for predictive maintenance and reducing the risk of unexpected failures.
Conclusion
Impulse and reaction blades are integral to the efficient operation of steam turbines, each serving specific roles within the turbine’s energy conversion process. Impulse blades excel in high-pressure environments by converting kinetic energy into mechanical motion, while reaction blades offer continuous energy extraction across medium and low-pressure stages. The differences in their design, operating principles, and material requirements reflect their distinct functions and highlight the need for tailored solutions in turbine engineering.
Understanding these differences is essential for optimizing turbine performance, ensuring reliable operation, and advancing the technology behind power generation systems. As research continues to push the boundaries of material science and manufacturing techniques, the future of turbine blade design promises even greater efficiency, durability, and adaptability, driving the next generation of energy solutions.
Design Considerations for Steam Turbine Blades: A Comprehensive Exploration
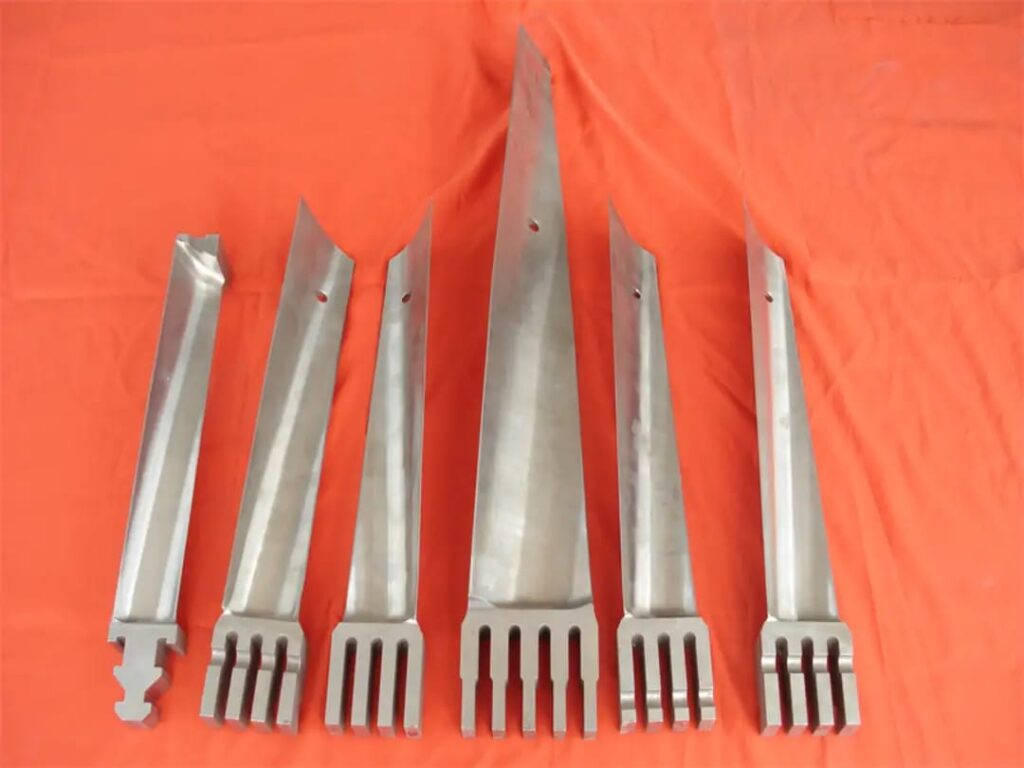
Steam turbine blades are the heart of a steam turbine system, playing a pivotal role in converting thermal energy from steam into mechanical energy. The design of these blades has a direct impact on the efficiency, performance, and reliability of the turbine. Proper blade design is essential for minimizing energy losses, reducing maintenance costs, and ensuring long-term operational stability. This comprehensive guide will explore the key design considerations for steam turbine blades, covering aspects such as aerodynamics, mechanical strength, thermal efficiency, material selection, and manufacturing processes. By understanding these factors, engineers can optimize blade performance and enhance overall turbine efficiency.
1. Aerodynamic Efficiency
Aerodynamic design is one of the most critical considerations for steam turbine blades. Efficient aerodynamic profiles minimize energy losses, improve steam flow, and enhance overall turbine performance.
1.1 Streamlined Blade Profiles
- Minimizing Drag and Turbulence: The shape of the blades must be optimized to allow smooth steam flow, minimizing drag and turbulence. Poorly designed blades can cause steam flow separation, leading to energy losses. Streamlined, aerofoil-shaped blades help in maintaining laminar flow, which reduces friction and improves efficiency.
- Blade Curvature and Twist: Turbine blades often feature a curved, twisted design to ensure that steam strikes the blades at an optimal angle, known as the angle of attack. This curvature helps in maintaining consistent steam velocity across the blade surface, leading to better energy extraction. Twisting also compensates for the varying radius of the blade from the hub to the tip, ensuring efficient steam flow along the entire blade length.
- Importance of Leading and Trailing Edges: The design of the blade’s leading and trailing edges is crucial. A sharp leading edge reduces resistance when steam first strikes the blade, while a smooth trailing edge minimizes wake and turbulence, ensuring efficient steam exit.
1.2 Blade Angle and Pitch
- Optimizing Steam Flow: The pitch and angle of the blades must be carefully designed to optimize the direction and velocity of steam flow. If the angle is too steep, it may cause steam to bounce off, reducing energy extraction. Conversely, a shallow angle may lead to steam passing over without sufficient interaction, resulting in energy loss.
- Variable Blade Angle Designs: Modern turbines sometimes employ variable blade angles, allowing the blades to adjust based on steam conditions. This adaptability can improve efficiency under varying load conditions.
2. Mechanical Strength and Durability
Mechanical integrity is another critical factor in blade design. Steam turbine blades must withstand high rotational speeds, mechanical stresses, and forces generated by steam flow, all while maintaining structural integrity.
2.1 Centrifugal Forces
- High Rotational Speeds: Steam turbine blades rotate at extremely high speeds, subjecting them to significant centrifugal forces. These forces increase towards the blade tips, potentially causing deformation or failure if not properly managed. Blades must be designed with sufficient mechanical strength to withstand these forces without bending or cracking.
- Stress Distribution: Engineers use finite element analysis (FEA) to assess stress distribution across the blade. The goal is to design a blade that can evenly distribute stress, reducing the likelihood of weak points that could lead to failure. Proper material selection and blade geometry play a crucial role in achieving this balance.
2.2 Blade Vibration and Resonance
- Avoiding Harmful Vibrations: The high-speed operation of turbines can lead to vibrations, which, if not controlled, can cause fatigue and blade damage over time. Blade designs must account for natural frequencies to avoid resonance conditions, where the blade’s natural frequency matches the operational frequency, leading to amplified vibrations.
- Damping Mechanisms: Incorporating damping mechanisms in blade design can help mitigate vibrations. This can include internal damping features or external damping systems, reducing the stress on the blades and enhancing their longevity.
2.3 Blade Length and Aspect Ratio
- Balancing Performance and Strength: The length and aspect ratio of turbine blades affect both their aerodynamic performance and mechanical strength. Longer blades can capture more energy, but they are also more susceptible to bending and mechanical stress. Designers must balance these factors, considering the specific operating conditions of the turbine.
3. Thermal Efficiency and Cooling Mechanisms
Steam turbines operate at high temperatures, especially in the high-pressure sections. Blade materials must retain their mechanical properties at elevated temperatures without deforming or melting.
3.1 Thermal Resistance and Heat Tolerance
- High-Temperature Operation: Steam turbine blades in high-pressure stages can face temperatures exceeding 600°C (1112°F). The design must ensure that the blades can withstand these conditions without compromising their mechanical strength. The choice of materials and coatings is crucial in achieving this.
- Thermal Expansion Management: Different parts of a blade can expand at different rates when exposed to heat. If not properly managed, thermal expansion can lead to deformation or even cracking. Blade design must account for thermal expansion, incorporating features that allow for controlled and uniform expansion.
3.2 Cooling Systems for Blades
- Internal Cooling Passages: For blades operating at very high temperatures, especially in gas turbines, internal cooling passages can be integrated into the design. These passages allow cool air to flow through the blade, reducing the temperature and preventing overheating. While more common in gas turbines, similar cooling technologies can be adapted for steam turbines.
- Thermal Barrier Coatings (TBCs): Applying thermal barrier coatings to the blade surfaces can improve their thermal resistance. These coatings act as an insulating layer, reducing the amount of heat that penetrates the blade material. This helps to maintain the blade’s structural integrity and extends its operational life.
4. Material Selection
The choice of material is fundamental to blade performance, impacting durability, heat tolerance, corrosion resistance, and cost-effectiveness. Material selection depends on the specific requirements of the turbine stage and operating conditions.
4.1 Common Blade Materials
- Nickel-Based Superalloys: These alloys are commonly used in high-temperature sections due to their excellent heat resistance and mechanical strength. Superalloys such as Inconel and Waspaloy maintain their properties at high temperatures, making them ideal for high-pressure, high-temperature environments.
- Stainless Steel: Stainless steel is often used for blades in lower-temperature sections of the turbine. It offers a good balance of strength, corrosion resistance, and affordability, making it suitable for a variety of applications.
- Titanium Alloys: Titanium alloys are valued for their high strength-to-weight ratio and corrosion resistance. They are particularly useful in situations where reducing blade weight is advantageous, such as in low-pressure stages where longer blades can improve efficiency.
4.2 Corrosion and Erosion Resistance
- Corrosive Environments: Steam can contain impurities that cause corrosion over time, weakening the blades. Material selection must consider the likelihood of corrosion, especially in wet steam regions or in environments where the steam quality may vary.
- Erosion Protection: The high-velocity impact of steam can lead to erosion, gradually wearing away the blade surfaces. To combat this, materials are selected for their erosion resistance, and coatings may be applied to enhance protection. Tungsten carbide coatings, for instance, are sometimes used to shield blades from erosive wear.
5. Manufacturing Processes and Quality Control
The manufacturing process of turbine blades must ensure precise dimensions, smooth surfaces, and structural integrity. Advanced manufacturing techniques help achieve these goals, while quality control is essential for ensuring that each blade meets the required specifications.
5.1 Precision Casting and Forging
- Investment Casting: Investment casting is a popular method for producing turbine blades, allowing for complex geometries and smooth surface finishes. This process involves creating a wax model of the blade, which is then coated with a ceramic shell. Once the wax is melted out, molten metal is poured into the shell, forming the blade.
- Forging: Forging involves shaping metal under high pressure, resulting in blades with excellent mechanical properties. Forging can produce strong, durable blades with a robust grain structure that enhances their resistance to stress and deformation.
5.2 CNC Machining
- Precision and Surface Finish: After casting or forging, blades may undergo CNC (Computer Numerical Control) machining to achieve precise dimensions and fine surface finishes. This process ensures that the blades are aerodynamic and fit perfectly within the turbine assembly.
- Customization and Prototyping: CNC machining also allows for customization and rapid prototyping, enabling engineers to test different blade designs and optimize performance before mass production.
5.3 Quality Control and Non-Destructive Testing (NDT)
- Ensuring Blade Integrity: Quality control is essential throughout the manufacturing process to ensure that each blade meets stringent specifications. Non-destructive testing methods, such as ultrasonic testing, X-ray inspection, and dye penetrant testing, are used to detect internal and surface defects without damaging the blades.
- Dimensional Accuracy and Tolerance: Maintaining dimensional accuracy is critical for blade performance. Even minor deviations from the design can lead to inefficiencies, turbulence, or mechanical failure. Quality control processes verify that the blades are manufactured to exact tolerances.
6. Advanced Design Techniques and Computational Tools
Modern steam turbine blade design has been greatly enhanced by the use of advanced computational tools, allowing engineers to simulate and optimize blade performance before physical prototypes are produced.
6.1 Computational Fluid Dynamics (CFD)
- Simulating Steam Flow: CFD tools allow engineers to simulate how steam flows over the blades, enabling them to analyze and optimize aerodynamic performance. By visualizing steam flow patterns, engineers can identify areas of turbulence or drag and make design adjustments to improve efficiency.
- Thermal Analysis: CFD tools can also be used for thermal analysis, simulating how heat interacts with the blades and assessing the effectiveness of cooling mechanisms or thermal barrier coatings.
Materials Used for Steam Turbine Blades: A Comprehensive Exploration
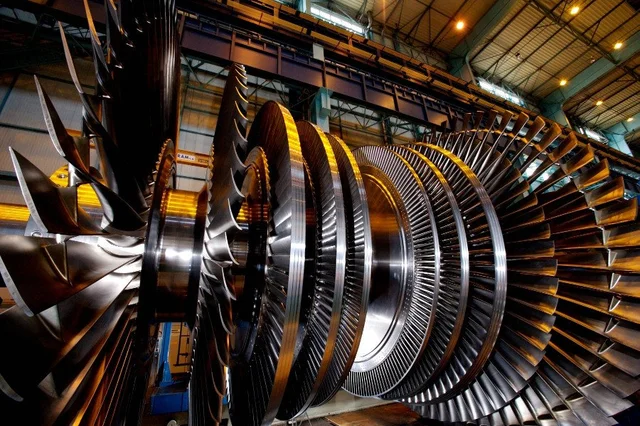
Steam turbine blades are exposed to harsh operating conditions, including high temperatures, high pressures, and potential corrosive environments. Therefore, the selection of materials for these blades is critical to ensure performance, reliability, and longevity. The materials must possess a combination of properties, such as high strength, thermal stability, corrosion resistance, and durability. This section will delve into the various materials used for steam turbine blades, exploring their properties, advantages, and applications in different sections of the turbine.
1. Key Properties Required for Steam Turbine Blade Materials
Steam turbine blades must meet a range of stringent requirements to operate efficiently under harsh conditions. Some of the essential properties include:
1.1 High-Temperature Strength
Blades in the high-pressure stages of a turbine operate at extremely high temperatures, often exceeding 600°C (1112°F). The material must retain its strength and structural integrity at these elevated temperatures without softening, deforming, or failing.
1.2 Corrosion and Oxidation Resistance
Steam can contain impurities that cause corrosion over time, weakening the blades and reducing their efficiency. Therefore, materials must resist oxidation and corrosion, especially in sections where steam quality may vary or where blades are exposed to moisture (in low-pressure sections).
1.3 Creep Resistance
Prolonged exposure to high temperatures can lead to creep, which is the gradual deformation of the material under stress. Turbine blades need to withstand creep to maintain their shape and performance over long periods.
1.4 Fatigue Resistance
The high-speed rotation of turbine blades subjects them to cyclic mechanical stresses, which can cause fatigue over time. Materials must have good fatigue resistance to endure these repeated stress cycles without cracking or failure.
2. Common Materials for Steam Turbine Blades
2.1 Nickel-Based Superalloys
Nickel-based superalloys are widely regarded as one of the best materials for steam turbine blades, particularly in the high-pressure and high-temperature sections. These alloys, such as Inconel, Waspaloy, and Rene alloys, are known for their exceptional heat resistance and strength at elevated temperatures.
Key Properties:
- High strength and resistance to deformation at temperatures up to 900°C (1652°F).
- Excellent oxidation and corrosion resistance.
- Good fatigue and creep resistance, ensuring long-term stability.
Applications:
- High-pressure turbine stages where temperatures and pressures are at their peak.
- Environments where corrosion due to impurities in steam is a concern.
2.2 Titanium Alloys
Titanium alloys, such as Ti-6Al-4V, are used for turbine blades where strength, corrosion resistance, and low weight are crucial. These alloys are not as heat-resistant as nickel-based superalloys but offer an excellent strength-to-weight ratio.
Key Properties:
- Lightweight with high strength, reducing the load on the rotor.
- Excellent corrosion resistance, especially to steam and moisture.
- Good fatigue resistance, though less effective at extremely high temperatures compared to superalloys.
Applications:
- Low to medium-pressure stages of the turbine, where the steam has already cooled, and reducing the weight of blades can enhance efficiency.
- Situations where improved corrosion resistance is needed without the need for extreme heat resistance.
2.3 Stainless Steels
Stainless steels, including martensitic and austenitic grades, are popular materials for turbine blades due to their balance of strength, cost-effectiveness, and corrosion resistance. While not as heat-resistant as nickel alloys, stainless steels can be effective in less demanding sections of the turbine.
Key Properties:
- Good mechanical strength and resistance to wear.
- Corrosion and oxidation resistance in various environments.
- Cost-effective compared to more exotic materials like superalloys.
Applications:
- Low-pressure sections of the turbine where the temperatures are relatively lower.
- Industrial and mechanical turbines that operate under less extreme conditions.
2.4 Cobalt-Based Alloys
Cobalt-based alloys, such as Stellite, are known for their excellent wear resistance and ability to maintain mechanical properties at high temperatures. These alloys are sometimes used in situations where wear and corrosion resistance are more critical than the need for extreme heat resistance.
Key Properties:
- High resistance to wear, making them suitable for environments with abrasive particles.
- Good high-temperature stability, though not as effective as nickel-based superalloys.
- Strong resistance to oxidation and corrosion.
Applications:
- Components exposed to abrasive conditions or where wear resistance is critical.
- High-wear sections of the turbine, often in industrial or mechanical applications.
3. Emerging Materials for Steam Turbine Blades
3.1 Ceramic Matrix Composites (CMCs)
Ceramic Matrix Composites (CMCs) are an emerging class of materials that offer high-temperature resistance and low weight. While still being developed and refined for widespread commercial use, CMCs have the potential to operate at temperatures higher than those tolerated by metal alloys.
Key Properties:
- Extremely high heat resistance, allowing operation at temperatures exceeding 1000°C (1832°F).
- Lightweight, which can improve efficiency by reducing the rotational inertia of the blades.
- Resistant to oxidation and corrosion.
Applications:
- Future high-temperature turbine designs, especially in gas turbines, with potential adaptation for steam turbines.
- Situations where reducing weight and increasing temperature tolerance can lead to significant efficiency gains.
3.2 Superalloy Development and High-Entropy Alloys (HEAs)
Continuous research into advanced superalloys and new materials, such as high-entropy alloys (HEAs), aims to push the boundaries of what turbine blades can endure. HEAs are composed of multiple principal elements, providing a balance of strength, durability, and heat resistance.
Key Properties:
- Improved heat resistance and mechanical strength.
- Potential for tailored properties to match specific operational needs.
- Ongoing research may lead to more cost-effective and durable materials.
Applications:
- High-temperature and high-stress sections of the turbine.
- Future turbine designs requiring enhanced performance.
Manufacturing Processes for Steam Turbine Blades: A Detailed Exploration
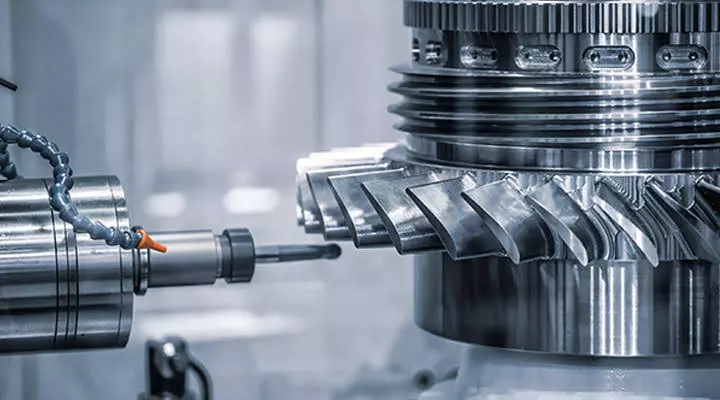
The manufacturing of steam turbine blades requires precision, advanced engineering, and high-quality materials to meet stringent performance standards. The processes used must ensure that the blades are aerodynamically efficient, mechanically strong, and capable of withstanding extreme conditions. This section explores the key manufacturing processes for steam turbine blades, including forging, casting, machining, and emerging technologies like additive manufacturing.
1. Precision Forging
1.1 Process Overview
Forging is a process where metal is shaped by applying compressive forces, typically through hammering or pressing. In the case of steam turbine blades, precision forging is used to produce components that are robust, durable, and have excellent mechanical properties.
Advantages:
- Produces strong, dense materials with good grain structures, enhancing fatigue and creep resistance.
- Ideal for high-stress components, such as those in the high-pressure sections of the turbine.
- Allows for the production of blades with specific mechanical properties tailored to their operational conditions.
Applications:
- High-pressure turbine blades that need to withstand significant mechanical stress.
- Situations where the structural integrity and mechanical strength of the blades are crucial.
1.2 Precision Die Forging
Precision die forging is used to create complex shapes with tight tolerances. By using precise dies, manufacturers can produce blades that require minimal finishing, reducing costs and ensuring consistency.
2. Investment Casting
2.1 Process Overview
Investment casting, also known as lost-wax casting, is one of the most common methods for producing turbine blades. The process involves creating a wax model of the blade, which is then coated in a ceramic shell. Once the wax is melted out, molten metal is poured into the mold, forming the blade.
Advantages:
- Capable of producing complex geometries with smooth surface finishes.
- High precision, allowing for intricate designs that improve aerodynamic efficiency.
- Suitable for materials that are difficult to machine, such as superalloys and titanium alloys.
Applications:
- Production of blades for both high-pressure and low-pressure stages.
- Manufacturing components that require precise aerodynamic profiles and complex shapes.
3. CNC Machining
3.1 Process Overview
CNC (Computer Numerical Control) machining is used to refine turbine blades after they have been cast or forged. This process involves cutting, milling, and shaping the blades to achieve precise dimensions and smooth surfaces.
Advantages:
- High precision and control over the final shape, ensuring aerodynamic efficiency.
- Allows for customization and rapid prototyping, enabling engineers to test different designs.
- Effective at producing intricate details that improve the blade’s performance.
Applications:
- Refining and finishing blades for high-performance turbine applications.
- Prototyping new designs to optimize efficiency and test different configurations.
4. Additive Manufacturing (3D Printing)
4.1 Process Overview
Additive manufacturing, or 3D printing, is an emerging technology that offers new possibilities for turbine blade production. The process involves building blades layer by layer using powdered metals or metal wires. While still in its early stages for large-scale production, it has significant potential.
Advantages:
- Allows for complex, intricate designs that are difficult to achieve with traditional methods.
- Reduces material waste, as only the necessary material is used.
- Enables rapid prototyping, speeding up the design and testing process.
Applications:
- Production of customized, small-batch turbine blades for specific applications.
- Prototyping new designs and testing innovative blade configurations.
5. Quality Control and Non-Destructive Testing (NDT)
5.1 Ensuring Blade Integrity
Quality control is essential throughout the manufacturing process to ensure that each blade meets stringent performance and safety standards. Non-destructive testing (NDT) methods are commonly used to detect defects without damaging the blades.
NDT Techniques:
- Ultrasonic Testing: Detects internal flaws, such as cracks or voids, by using high-frequency sound waves.
- X-Ray Inspection: Provides detailed images of the blade’s internal structure, identifying any defects that may not be visible on the surface.
- Dye Penetrant Testing: Reveals surface cracks by applying a dye to the blade, which seeps into any imperfections and highlights them under UV light.
Conclusion
The design and production of steam turbine blades rely heavily on the careful selection of materials and precise manufacturing processes. Nickel-based superalloys, titanium alloys, and stainless steels are the primary materials used, each chosen for their specific properties, such as heat resistance, corrosion resistance, and strength. Meanwhile, forging, casting, machining, and emerging technologies like additive manufacturing ensure that these materials are shaped into precise, efficient, and durable blades. With continuous advancements in material science and manufacturing, the future of steam turbine blade production promises even greater efficiency, reliability, and performance.
Understanding the Role of Steam Turbine Blades: A Comprehensive Exploration
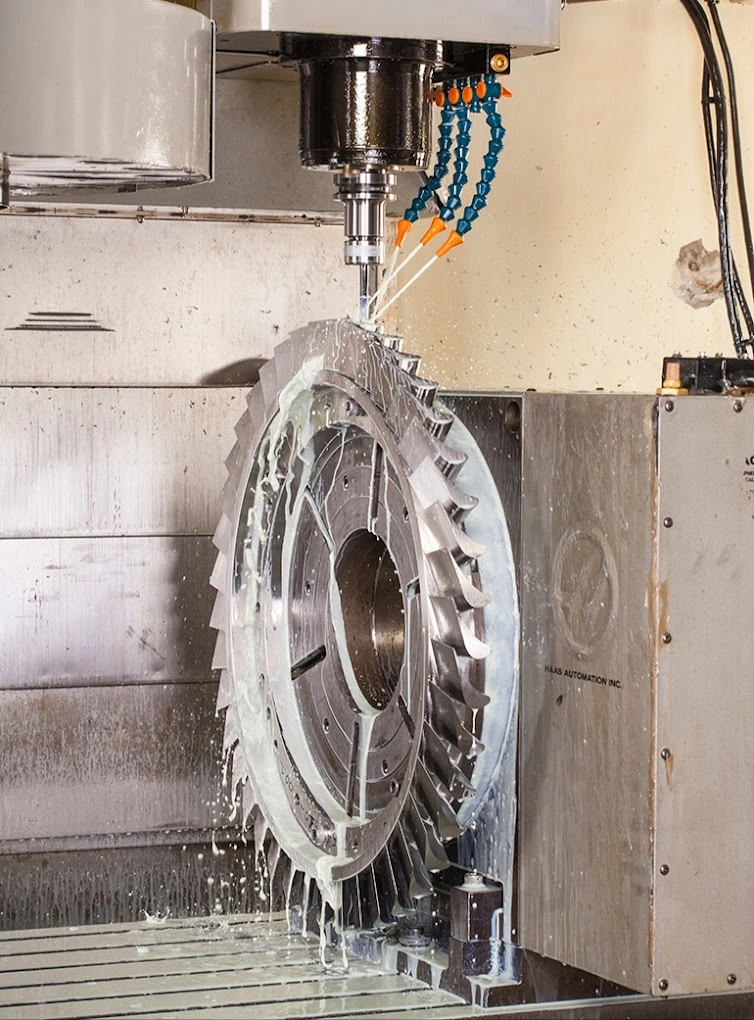
Steam turbines are a crucial component in power generation systems, responsible for converting thermal energy from steam into mechanical energy, which is then used to generate electricity. At the heart of this process are the turbine blades, which play a pivotal role in harnessing the kinetic energy of steam. The design, efficiency, and operation of these blades directly influence the performance of the entire turbine. This detailed exploration will provide an in-depth understanding of the role of steam turbine blades, covering their function, design principles, types, operating conditions, and the factors influencing their performance. We will also examine the impact of blade technology on overall turbine efficiency and the advancements shaping the future of steam turbine blades.
1. Introduction to Steam Turbines and Blade Function
Steam turbines have been a primary technology for electricity generation for over a century, utilizing the thermal energy of steam to drive a rotor connected to a generator. The basic principle behind a steam turbine is to allow high-pressure steam to expand and convert its energy into rotational motion, which drives the generator to produce electricity.
1.1 The Role of Blades in Energy Conversion
The turbine blades are the components that interact directly with the steam, making them the key players in energy conversion. As steam flows through the turbine, it passes over multiple sets of blades arranged in stages. Each set of blades extracts energy from the steam, causing the rotor to spin. This rotation drives the generator shaft, converting mechanical energy into electrical energy.
- Kinetic Energy Extraction: The blades are designed to capture the kinetic energy of the steam and convert it into mechanical work. The efficient design of blades ensures that as much energy as possible is extracted from the steam at each stage.
- Pressure Management: Blades also help manage the expansion of steam and the associated pressure drop, which is crucial for efficient energy conversion. The process involves transforming high-pressure steam into a lower-pressure state while maintaining the momentum necessary to drive the turbine.
2. Key Functions of Steam Turbine Blades
Steam turbine blades perform several essential functions within the turbine system. These include:
2.1 Energy Extraction
The primary function of turbine blades is to extract energy from the high-velocity, high-pressure steam that enters the turbine. The efficiency with which the blades can capture this energy determines the overall performance of the turbine. The design of the blades, including their shape, angle, and surface finish, is crucial for maximizing energy extraction.
- Impulse Blades: These blades extract energy by redirecting the steam flow, causing a change in its velocity. Impulse blades are used in high-pressure stages where the steam enters the turbine at high speeds.
- Reaction Blades: Reaction blades operate by utilizing both the pressure drop and velocity change of the steam as it expands over the blades. These blades are used in low to medium-pressure stages where the steam has already undergone some expansion.
2.2 Directional Control of Steam Flow
Turbine blades also play a key role in directing the flow of steam through the turbine. Proper directional control ensures that the steam maintains its velocity and does not cause turbulence or energy losses. The smooth transition of steam between different stages of blades is essential for maintaining high efficiency and minimizing wear.
2.3 Pressure Drop Management
The expansion of steam within the turbine involves a series of pressure drops across each stage. The blades must be designed to manage these pressure changes without causing excessive energy loss. Efficient pressure management allows for better energy conversion and helps in sustaining the mechanical work output of the turbine.
3. Types of Steam Turbine Blades and Their Roles
Steam turbines use two main types of blades, each serving a specific purpose based on their position within the turbine and the characteristics of the steam at that stage.
3.1 Impulse Blades
Impulse blades are designed to convert the kinetic energy of steam into mechanical energy by redirecting its flow. Steam enters the turbine through nozzles that convert the pressure energy into high-velocity jets. These jets strike the impulse blades, changing direction and transferring kinetic energy to the rotor.
- High-Pressure Stages: Impulse blades are typically used in the high-pressure stages of a turbine where the steam is moving at high velocities. Their design allows for effective energy extraction from fast-moving steam.
- Simple Blade Design: The design of impulse blades is relatively straightforward, often with a bucket or cup shape that allows for efficient redirection of steam.
3.2 Reaction Blades
Reaction blades work by extracting energy from both the pressure drop and the velocity change of the steam. As steam expands and flows over these blades, it accelerates, creating a reactive force that drives the turbine rotor. This process involves a continuous energy transfer, making reaction blades suitable for stages where the steam has expanded and its pressure has decreased.
- Low to Medium-Pressure Stages: Reaction blades are found in the low and medium-pressure stages of turbines. They are designed to handle steam that has already expanded, extracting energy continuously as it flows over the blades.
- Aerodynamic Design: The design of reaction blades is more complex, often featuring an aerofoil shape to facilitate smooth steam flow and gradual pressure changes.
4. Design Considerations for Steam Turbine Blades
The design of turbine blades is critical to their function and overall turbine performance. Several factors must be considered to ensure efficient operation and durability under harsh conditions.
4.1 Aerodynamics and Blade Geometry
- Efficient Steam Flow: The aerodynamic design of the blades ensures that steam flows smoothly over the surface, minimizing drag and turbulence. Blade geometry must be optimized to maximize the energy captured from the steam while reducing losses.
- Blade Angle and Twist: The angle and curvature of the blades must be carefully engineered to maintain the optimal angle of attack for the steam. Twisting the blades allows for better interaction with the steam across different stages, improving energy extraction.
4.2 Mechanical Strength and Durability
- High-Speed Operation: Turbine blades must withstand high rotational speeds without deforming or failing. Mechanical strength is essential to resist the centrifugal forces generated during operation.
- Resistance to Wear and Corrosion: Steam can contain impurities that cause wear and corrosion over time. The material of the blades must be chosen to resist these conditions, ensuring longevity and consistent performance.
4.3 Thermal Management
- Heat Resistance: The high-pressure stages of a turbine can reach temperatures exceeding 600°C (1112°F). Blade materials must retain their mechanical properties at these elevated temperatures without warping or degrading.
- Thermal Expansion Control: Differences in thermal expansion between different parts of the turbine can cause stress and potential damage. Blades must be designed to accommodate thermal expansion, ensuring that they remain stable across a range of operating temperatures.
5. Factors Influencing Blade Performance
Several factors influence the performance of turbine blades, and understanding these can help improve overall turbine efficiency.
5.1 Steam Quality
- Superheated vs. Wet Steam: The quality of the steam affects how it interacts with the blades. Superheated steam, which contains no water droplets, is ideal for efficient energy transfer. Wet steam, on the other hand, can cause erosion and reduce efficiency, especially in the low-pressure stages of the turbine.
- Steam Flow Rate: The flow rate of steam must be optimized to match the design of the blades. Too much steam can cause turbulence and inefficiencies, while too little steam can lead to underperformance.
5.2 Blade Material Selection
- Nickel-Based Superalloys: Commonly used in high-temperature sections due to their heat resistance and strength. These materials maintain their properties even under extreme conditions, making them ideal for high-pressure blades.
- Titanium and Stainless Steel: Used in lower temperature sections, these materials offer a good balance of strength, corrosion resistance, and cost-effectiveness.
6. Impact of Blade Technology on Turbine Efficiency
The design and efficiency of turbine blades have a direct impact on the overall efficiency of the turbine. Advances in blade technology can lead to significant improvements in power output and fuel economy.
6.1 Improved Aerodynamics for Higher Efficiency
Advancements in computational fluid dynamics (CFD) have allowed engineers to simulate steam flow and optimize blade designs for better aerodynamic performance. By refining the shape and profile of the blades, manufacturers can reduce drag, minimize turbulence, and improve energy capture.
6.2 Enhanced Materials for Durability and Performance
The development of advanced materials, such as nickel-based superalloys and ceramic matrix composites (CMCs), has enabled turbine blades to operate at higher temperatures and pressures without degrading. These materials enhance the durability of the blades, reducing maintenance needs and extending the operational life of the turbine.
6.3 Integration of Cooling Systems
In high-pressure stages where temperatures are extremely high, cooling systems can be integrated into the blade design. These systems help dissipate heat, preventing the blades from overheating and losing their structural integrity. Advanced cooling techniques are crucial for improving the efficiency and reliability of turbines operating under extreme conditions.
7. Future Trends in Steam Turbine Blade Technology
The evolution of turbine blade technology continues to drive improvements in power generation. Several emerging trends and technologies are shaping the future of steam turbine blades.
7.1 Additive Manufacturing (3D Printing)
Additive manufacturing is enabling the production of complex blade geometries that were previously difficult or impossible to achieve with traditional manufacturing methods. This technology allows for rapid prototyping, customized designs, and reduced material waste, making it a promising tool for the future of turbine blade production.
7.2 Smart Blades with Integrated Sensors
The integration of sensors into turbine blades can provide real-time data on temperature, pressure, and mechanical stress. This information can be used to monitor blade performance, predict maintenance needs, and optimize turbine operation, reducing the risk of unexpected failures.
7.3 Development of Advanced Coatings
Advanced coatings are being developed to improve the wear and corrosion resistance of turbine blades. These coatings can extend the lifespan of the blades, reduce maintenance costs, and improve efficiency by ensuring smoother steam flow over the blade surfaces.
Conclusion
Steam turbine blades are the critical components that enable the efficient conversion of steam energy into mechanical energy. Understanding their role involves recognizing the importance of their design, material selection, and operational conditions. From managing steam flow to withstanding high temperatures and pressures, the blades’ performance directly affects the efficiency and reliability of the turbine.
Advancements in blade technology, including improved materials, aerodynamic designs, and emerging manufacturing techniques, are driving the future of power generation. By focusing on the development of more efficient, durable, and adaptable blades, engineers can continue to improve turbine performance, ensuring that steam turbines remain a viable and sustainable solution for global energy needs
Nickel-Based Superalloys: A Comprehensive Exploration
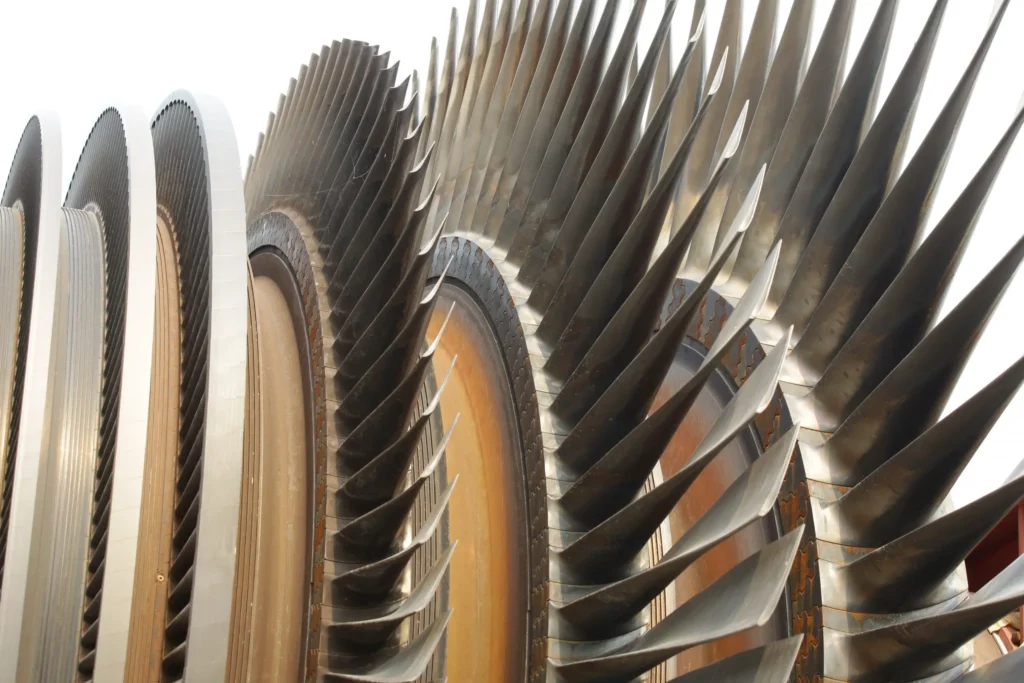
Nickel-based superalloys are a class of high-performance materials known for their exceptional strength, heat resistance, and ability to withstand harsh operating environments. These alloys are primarily used in applications that require materials to perform reliably under extreme conditions, such as in steam and gas turbines, jet engines, and power plants. The combination of mechanical properties, thermal stability, and resistance to corrosion and oxidation makes nickel-based superalloys an essential component in high-temperature technologies. This comprehensive exploration will cover the composition, properties, applications, manufacturing processes, challenges, and future trends associated with nickel-based superalloys.
1. Introduction to Nickel-Based Superalloys
Nickel-based superalloys are metallic alloys that have been engineered to maintain high strength, toughness, and corrosion resistance at elevated temperatures, often exceeding 1,000°C (1,832°F). The primary element in these alloys is nickel, but they also contain other metals such as chromium, cobalt, aluminum, titanium, molybdenum, and tantalum. Each of these elements contributes to specific properties that enhance the overall performance of the alloy.
1.1 Defining Characteristics
- High-Temperature Strength: Nickel-based superalloys retain their mechanical properties at high temperatures, making them suitable for components exposed to extreme heat.
- Oxidation and Corrosion Resistance: These alloys form a protective oxide layer that shields them from corrosive environments, ensuring longevity and reliability.
- Resistance to Creep: Creep is the tendency of a material to deform slowly under stress, especially at high temperatures. Nickel-based superalloys are designed to resist creep, maintaining their structural integrity over long periods.
2. Composition and Alloying Elements
The remarkable properties of nickel-based superalloys stem from their complex composition, which includes a variety of alloying elements. Each element serves a specific function, enhancing particular properties of the base alloy.
2.1 Key Alloying Elements
- Chromium (Cr): Chromium is essential for providing oxidation and corrosion resistance. It forms a stable oxide layer on the surface of the alloy, protecting it from degradation.
- Cobalt (Co): Cobalt enhances the alloy’s strength and stability at high temperatures. It also improves resistance to thermal fatigue.
- Aluminum (Al) and Titanium (Ti): Both elements contribute to the formation of the γ’ (gamma prime) phase, which strengthens the alloy by impeding dislocation movement. This phase precipitation is crucial for maintaining the material’s mechanical strength at high temperatures.
- Molybdenum (Mo) and Tungsten (W): These elements improve the alloy’s resistance to creep, adding to its strength by solid-solution hardening.
- Tantalum (Ta) and Niobium (Nb): These refractory metals enhance high-temperature stability and improve resistance to oxidation and corrosion.
2.2 Microstructure of Nickel-Based Superalloys
The microstructure of nickel-based superalloys is a key factor in their performance. They are generally characterized by two primary phases:
- γ (Gamma) Phase: This is the continuous matrix phase, primarily made of nickel. It provides a base for the alloy’s structure.
- γ’ (Gamma Prime) Phase: The γ’ phase is an intermetallic compound that precipitates within the γ matrix. It is critical for the alloy’s strength, as it prevents the movement of dislocations, a mechanism that would otherwise lead to material deformation.
The combination of these phases allows nickel-based superalloys to maintain their strength even at elevated temperatures, where most other materials would fail.
3. Properties of Nickel-Based Superalloys
The properties of nickel-based superalloys make them ideal for demanding applications. Some of the most important properties include:
3.1 High-Temperature Strength
Nickel-based superalloys maintain their mechanical strength at temperatures where other materials would soften or melt. This property is achieved through the addition of alloying elements that form stable phases, resisting dislocation movement even under thermal stress.
3.2 Resistance to Oxidation and Corrosion
The ability to resist oxidation and corrosion is essential for materials exposed to hot, reactive environments. Nickel-based superalloys develop a thin, adherent oxide layer (primarily chromium oxide) that acts as a protective barrier, preventing further degradation.
3.3 Creep Resistance
Creep, or slow deformation under constant stress, is a major concern for materials operating at high temperatures. Nickel-based superalloys are designed to resist creep by utilizing a microstructure that hinders the movement of atoms, effectively locking the material’s shape and structure.
3.4 Fatigue Resistance
High-temperature components, such as turbine blades, experience cyclical loading, which can lead to fatigue over time. Nickel-based superalloys have excellent fatigue resistance, allowing them to endure repeated stress cycles without cracking or failing.
4. Applications of Nickel-Based Superalloys
Nickel-based superalloys are used in a variety of high-temperature, high-stress applications across several industries, including aerospace, power generation, and chemical processing.
4.1 Steam and Gas Turbines
- Turbine Blades and Vanes: The high strength and heat resistance of nickel-based superalloys make them ideal for turbine blades, which must operate in high-temperature environments. These alloys allow turbines to run at higher temperatures, improving efficiency and reducing fuel consumption.
- Combustor Liners and Casings: Nickel-based superalloys are used in combustors where they can withstand the intense heat and corrosive gases produced during fuel combustion.
4.2 Aerospace Industry
- Jet Engine Components: Nickel-based superalloys are essential for jet engines, where they are used in turbine blades, discs, and combustion chambers. The ability of these alloys to withstand high temperatures and stresses is critical for engine performance and reliability.
- Spacecraft: The high thermal and mechanical stability of nickel-based superalloys make them suitable for parts exposed to extreme conditions in space, such as heat shields and structural components.
4.3 Power Generation
- Nuclear Power Plants: In nuclear reactors, nickel-based superalloys are used for components that must endure high temperatures, radiation, and corrosive environments, such as heat exchangers and control rods.
- Fossil Fuel Power Plants: These alloys are used in various components within boilers and turbines, enabling them to operate at higher temperatures, which improves efficiency.
4.4 Chemical Processing
- Heat Exchangers and Reactors: Nickel-based superalloys are used in chemical plants where materials need to resist corrosion, oxidation, and thermal stress. Their durability makes them suitable for reactors, piping, and other equipment that handle aggressive chemicals and extreme temperatures.
5. Manufacturing Processes for Nickel-Based Superalloys
The manufacturing of nickel-based superalloys is complex and requires precise control over composition and microstructure. The most common methods include casting, forging, and advanced techniques like additive manufacturing.
5.1 Investment Casting
Investment casting, or lost-wax casting, is widely used for producing complex shapes such as turbine blades. The process involves creating a wax model, coating it with a ceramic shell, and then melting out the wax. Molten nickel-based alloy is then poured into the mold to create the component.
Advantages:
- Allows for intricate designs and complex geometries.
- Produces smooth surface finishes, reducing the need for additional machining.
- Suitable for high-performance components that require precise specifications.
5.2 Forging
Forging involves shaping the alloy under high pressure and temperature, creating a dense, high-strength material with a refined grain structure. This process is used for producing parts that need excellent mechanical properties, such as turbine discs and structural components.
Advantages:
- Produces high-strength components with excellent fatigue and creep resistance.
- Enhances the grain structure, improving mechanical performance.
- Suitable for components exposed to extreme stress.
5.3 Additive Manufacturing (3D Printing)
Additive manufacturing is an emerging technology that enables the production of components layer by layer, using powdered nickel-based superalloys. This process is gaining popularity for its ability to produce complex geometries and reduce material waste.
Advantages:
- Allows for rapid prototyping and production of complex, customized parts.
- Reduces lead times and material wastage.
- Enables the creation of lightweight, optimized structures that are difficult to manufacture using traditional methods.
6. Challenges in Using Nickel-Based Superalloys
While nickel-based superalloys are invaluable in high-temperature applications, they come with their own set of challenges.
6.1 Cost
Nickel-based superalloys are expensive to produce due to the high cost of raw materials and the complexity of the manufacturing processes. The presence of rare elements like tantalum and rhenium can drive up costs further, making these materials less economical for certain applications.
6.2 Difficult Machinability
The high strength and hardness of nickel-based superalloys make them challenging to machine. Special tools and machining techniques are required to cut, shape, and finish these materials, adding to the manufacturing cost and complexity.
6.3 Material Degradation
Although these superalloys are designed to resist oxidation, corrosion, and creep, they can still degrade over long periods, especially under extreme operating conditions. Understanding and mitigating this degradation is critical for ensuring the longevity and reliability of components made from these materials.
7. Future Trends in Nickel-Based Superalloys
The development of nickel-based superalloys continues to evolve, driven by the demand for higher performance, efficiency, and durability in challenging environments.
7.1 Development of New Alloys
Researchers are continually exploring new compositions to enhance the properties of nickel-based superalloys. By experimenting with different alloying elements and microstructures, scientists aim to develop materials that can operate at even higher temperatures and resist more extreme conditions. This includes the exploration of high-entropy alloys (HEAs), which consist of multiple principal elements and offer unique combinations of properties.
7.2 Additive Manufacturing Innovations
Advancements in additive manufacturing (AM) technology are allowing for the creation of more complex and efficient components. AM enables engineers to design parts with internal cooling channels and optimized geometries that were previously impossible to manufacture using conventional methods. This technology holds the promise of reducing costs, improving performance, and enabling faster production times.
7.3 Recycling and Sustainability
Given the high cost of producing nickel-based superalloys, there is a growing focus on recycling and reusing these materials. Developing efficient recycling processes can help reduce waste, lower production costs, and conserve valuable resources. Additionally, sustainable practices in the extraction and processing of raw materials are being explored to reduce the environmental impact of producing superalloys.
Conclusion
Nickel-based superalloys are among the most advanced and versatile materials used in high-temperature, high-stress applications. Their ability to maintain strength, resist corrosion, and endure extreme conditions makes them indispensable in industries such as aerospace, power generation, and chemical processing. Despite challenges like high costs and difficult machinability, ongoing research and technological advancements are driving the development of new alloys and manufacturing techniques.
As industries continue to push the limits of what is possible, nickel-based superalloys will play a crucial role in enabling the next generation of high-performance technologies. From more efficient turbines to lighter, stronger aerospace components, these superalloys will remain at the forefront of materials science, shaping the future of engineering and manufacturing.
Titanium Alloys: A Comprehensive Exploration
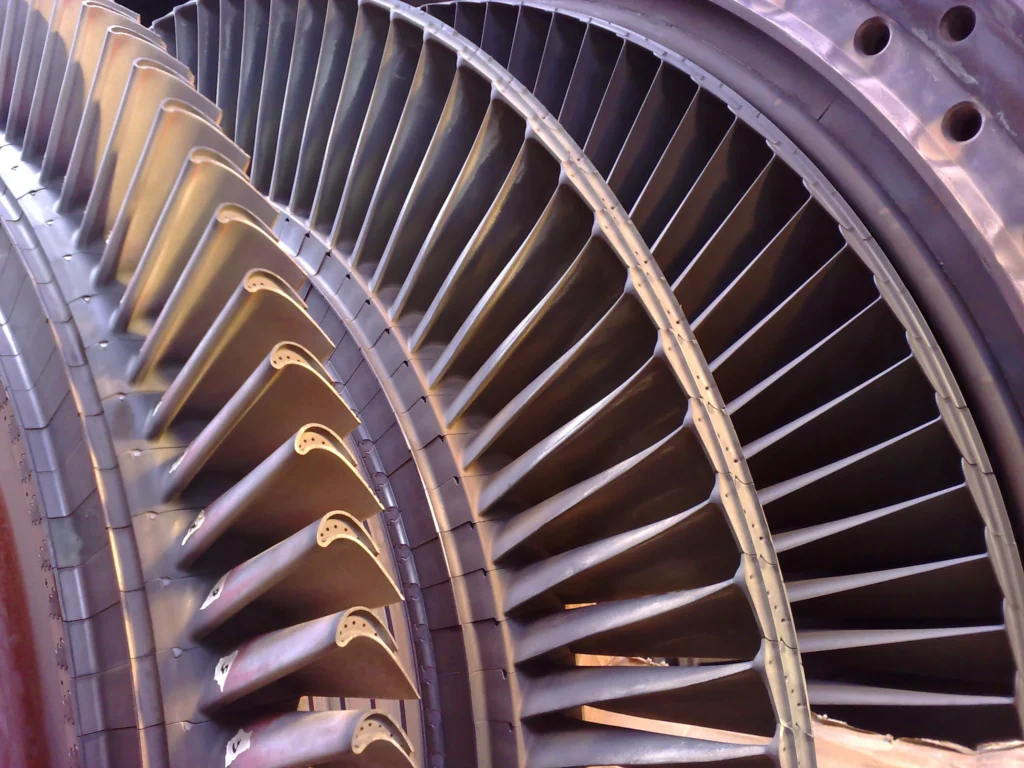
Titanium alloys are a class of metals that combine titanium with other elements to improve specific properties, such as strength, corrosion resistance, and high-temperature stability. Known for their excellent strength-to-weight ratio, corrosion resistance, and biocompatibility, titanium alloys are used across various industries, including aerospace, automotive, medical, and power generation. This comprehensive exploration will delve into the composition, properties, applications, manufacturing processes, challenges, and future trends associated with titanium alloys.
1. Introduction to Titanium Alloys
Titanium is a metallic element that is renowned for its low density and high strength. Its alloys retain these characteristics while adding other desirable properties, such as improved resistance to corrosion and greater ductility. Titanium alloys are categorized based on their microstructure into three main groups: alpha alloys, beta alloys, and alpha-beta alloys. Each type has distinct properties, making them suitable for different applications.
1.1 Defining Characteristics
- High Strength-to-Weight Ratio: Titanium alloys are as strong as steel but much lighter, making them ideal for applications where weight savings are critical.
- Excellent Corrosion Resistance: Titanium naturally forms a thin oxide layer that protects it from corrosion in most environments, including seawater and acidic conditions.
- Biocompatibility: Titanium alloys are non-toxic and compatible with human tissue, making them ideal for medical implants.
2. Composition and Classification of Titanium Alloys
Titanium alloys are generally classified based on their microstructure, which is determined by the alloying elements added to the titanium base. These classifications help in understanding the properties and potential applications of each type.
2.1 Alpha Alloys
Alpha alloys are primarily composed of titanium with small amounts of aluminum, tin, and other elements that stabilize the alpha phase. These alloys are non-heat treatable, meaning they cannot be strengthened by heat treatment but maintain their properties at high temperatures.
Key Properties:
- Excellent corrosion resistance, even at high temperatures.
- Moderate strength with good weldability and ductility.
- Retain strength and stability up to 600°C (1112°F).
Applications:
- Aerospace components, such as jet engine casings and airframes.
- Chemical processing equipment due to their corrosion resistance.
- Power generation, especially in environments where heat resistance is critical.
2.2 Beta Alloys
Beta alloys contain elements such as molybdenum, vanadium, and chromium, which stabilize the beta phase. These alloys are heat treatable and can be strengthened by heat treatment to achieve high strength.
Key Properties:
- High strength and toughness, especially after heat treatment.
- Good formability, making them easier to machine and shape.
- Less resistant to high temperatures compared to alpha alloys but still strong at room temperature.
Applications:
- Aerospace components that require high strength, such as landing gear and fasteners.
- Automotive parts, particularly in performance and racing vehicles.
- Medical devices, including surgical instruments and orthopedic implants.
2.3 Alpha-Beta Alloys
Alpha-beta alloys are the most widely used type of titanium alloys, containing a balanced mix of alpha and beta stabilizers. They combine the advantages of both alpha and beta alloys, offering a balance of strength, corrosion resistance, and heat treatability.
Key Properties:
- High strength and good ductility.
- Heat treatable, allowing for increased strength through processing.
- Good corrosion resistance across various environments.
Applications:
- Aircraft components, such as turbine blades and compressor disks.
- Marine applications, including propeller shafts and submarine parts.
- Medical implants, including dental implants and joint replacements.
3. Properties of Titanium Alloys
The properties of titanium alloys make them ideal for demanding applications. Some of the key properties include:
3.1 Strength and Lightweight
Titanium alloys are as strong as most steels but are about 40% lighter, making them ideal for applications where reducing weight is critical without compromising strength. This strength-to-weight ratio is one of the most significant advantages of titanium alloys.
3.2 Corrosion Resistance
One of the standout features of titanium alloys is their excellent resistance to corrosion. Titanium naturally forms a passive oxide layer that protects it from rusting or corroding, even in harsh environments such as seawater, chlorine, and acidic conditions.
3.3 Biocompatibility
Titanium alloys are highly biocompatible, meaning they do not react adversely with human tissues. This property makes them an excellent choice for medical implants, such as bone plates, screws, and joint replacements, as the body readily accepts them without allergic reactions or other complications.
3.4 High Temperature Stability
Certain titanium alloys can maintain their mechanical properties at elevated temperatures, making them suitable for high-temperature applications. However, they are not as heat-resistant as nickel-based superalloys and are primarily used where moderate high-temperature performance is required.
4. Applications of Titanium Alloys
Titanium alloys are versatile materials used in a wide range of industries, from aerospace to medicine. Some of the most common applications include:
4.1 Aerospace Industry
- Aircraft Structural Components: The aerospace industry relies heavily on titanium alloys for structural components, such as frames, wings, and landing gear, due to their high strength and low weight.
- Engine Parts: Titanium alloys are used in jet engine components, such as turbine blades and compressor discs, where they can withstand high temperatures and stresses while remaining lightweight.
- Spacecraft: The combination of strength, corrosion resistance, and light weight makes titanium alloys ideal for use in space exploration, including parts for rockets, satellites, and space stations.
4.2 Automotive Industry
- Performance and Racing Cars: Titanium alloys are used in high-performance automotive components, such as connecting rods, valves, and exhaust systems, where reducing weight and increasing strength can enhance performance and fuel efficiency.
- Motorcycle Parts: In racing and performance motorcycles, titanium alloys are used for exhaust systems, frames, and fasteners, providing durability without adding unnecessary weight.
4.3 Medical and Dental Applications
- Orthopedic Implants: Titanium alloys are commonly used in hip and knee replacements, bone screws, and spinal implants due to their biocompatibility and strength. They can withstand the stresses within the human body while remaining inert and safe.
- Dental Implants: The material’s resistance to corrosion and biocompatibility make it ideal for dental implants, where it can integrate with bone tissue without causing adverse reactions.
4.4 Marine and Chemical Processing
- Marine Hardware: Titanium alloys are used in propeller shafts, pumps, and other marine hardware because they resist corrosion in seawater, making them more durable than traditional materials.
- Chemical Processing Equipment: In the chemical industry, titanium alloys are used for valves, heat exchangers, and piping systems because they can withstand corrosive substances, reducing maintenance costs and downtime.
5. Manufacturing Processes for Titanium Alloys
The production of titanium alloys involves various sophisticated manufacturing processes, each chosen based on the application and desired properties of the final product.
5.1 Extraction and Refining
- Kroll Process: Most titanium is produced using the Kroll process, which involves converting titanium ore (typically ilmenite or rutile) into titanium tetrachloride and then reducing it with magnesium. This produces pure titanium sponge, which can be melted and alloyed with other elements to create titanium alloys.
5.2 Forging and Forming
- Hot Forging: Titanium alloys are often forged at high temperatures to achieve the desired shapes and enhance mechanical properties. The forging process improves the alloy’s grain structure, leading to increased strength and toughness.
- Cold Forming: For applications where tight tolerances and smooth finishes are required, cold forming can be used. Although more challenging due to the hardness of titanium, cold forming results in components with excellent surface finishes.
5.3 Casting
- Investment Casting: Investment casting is used to produce complex shapes, such as turbine blades, that would be difficult to create through machining or forging. This process allows for precision and detail, making it suitable for components with intricate designs.
5.4 Additive Manufacturing (3D Printing)
- Selective Laser Melting (SLM) and Electron Beam Melting (EBM): Additive manufacturing is gaining popularity for producing titanium alloy components. Technologies like SLM and EBM build parts layer by layer, allowing for complex geometries and reduced material waste. This process is particularly useful for creating custom parts in aerospace and medical applications.
6. Challenges in Using Titanium Alloys
Despite their many advantages, titanium alloys come with several challenges that need to be addressed to optimize their use.
6.1 High Cost
The production of titanium alloys is expensive due to the complex extraction and refining process. The cost of raw materials and energy-intensive manufacturing steps, such as forging and machining, makes titanium alloys less economical for widespread use compared to other metals.
6.2 Difficult Machinability
Titanium alloys are difficult to machine because of their hardness and low thermal conductivity, which can lead to tool wear and overheating. Specialized tools and techniques are required to machine titanium alloys, adding to the production costs.
6.3 Susceptibility to Hydrogen Embrittlement
Titanium alloys can absorb hydrogen from the environment, leading to a phenomenon called hydrogen embrittlement. This condition makes the material brittle and prone to cracking, which can be a critical issue in high-stress applications.
7. Future Trends in Titanium Alloy Development
As industries continue to demand lighter, stronger, and more durable materials, the development of titanium alloys is advancing. Researchers are exploring new ways to improve existing alloys and create new ones with enhanced properties.
7.1 Development of Lower-Cost Titanium Alloys
Efforts are underway to reduce the cost of titanium alloy production by refining extraction methods and developing new alloys that use less expensive alloying elements. These advances could make titanium alloys more accessible for a broader range of applications, including construction and consumer goods.
7.2 Enhanced Additive Manufacturing Techniques
The rise of additive manufacturing has the potential to revolutionize the production of titanium alloys. New 3D printing techniques are being developed to improve precision, reduce material waste, and allow for the creation of more complex and customized parts. This technology is especially promising for aerospace and medical applications, where bespoke components are often required.
7.3 Alloy Design for Improved Properties
Researchers are also working on creating new titanium alloys with enhanced properties, such as increased strength, better corrosion resistance, and improved machinability. By fine-tuning the composition and processing methods, new alloys can be developed to meet the specific demands of emerging technologies.
Conclusion
Titanium alloys are indispensable in industries that require materials with a high strength-to-weight ratio, corrosion resistance, and biocompatibility. Their use spans across aerospace, automotive, medical, and marine sectors, where they have proven to be reliable, durable, and efficient. However, the challenges of high costs and difficult machinability limit their widespread adoption.
With ongoing advancements in manufacturing technologies, such as additive manufacturing, and the development of new, lower-cost alloys, the future of titanium alloys looks promising. As industries continue to push the boundaries of performance and efficiency, titanium alloys will play a crucial role in enabling the next generation of engineering solutions.
Stainless Steels: A Comprehensive Exploration
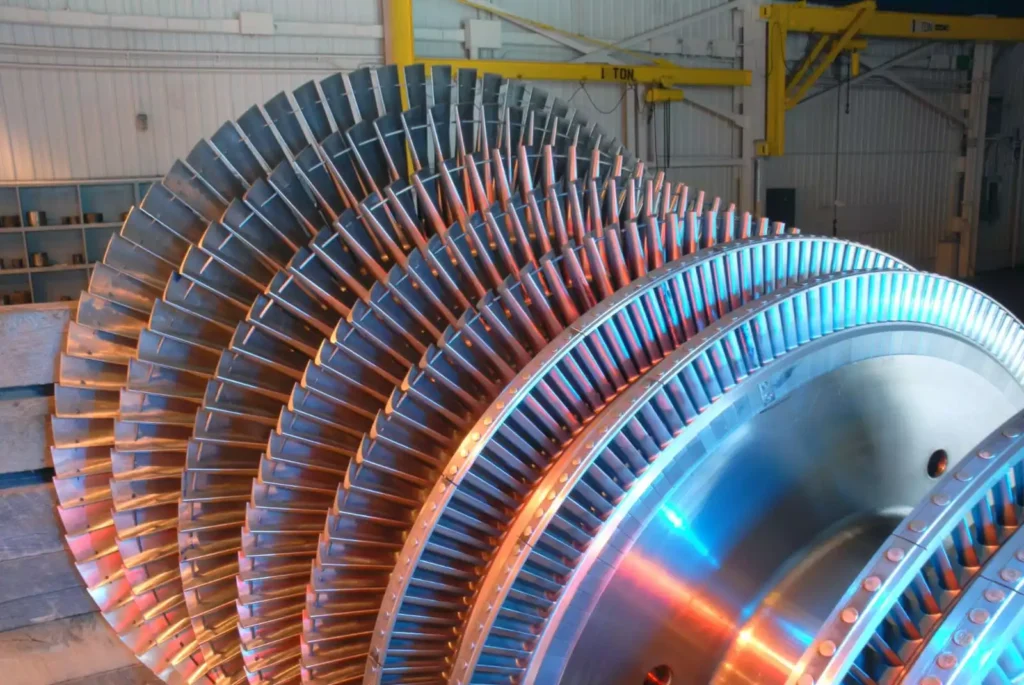
Stainless steels are a group of iron-based alloys known for their corrosion resistance, strength, and versatility. Their unique properties make them one of the most widely used materials in industries ranging from construction and automotive to medical and food processing. Stainless steels are characterized by the addition of chromium, which imparts resistance to rusting and corrosion, setting them apart from ordinary carbon steels. This comprehensive exploration will cover the composition, types, properties, applications, manufacturing processes, challenges, and future trends associated with stainless steels.
1. Introduction to Stainless Steels
Stainless steel was first developed in the early 20th century and has since become a material of choice for a vast range of applications due to its durability, aesthetic appeal, and resistance to environmental and chemical factors. The term “stainless” refers to its ability to resist staining, corrosion, and rusting, a property achieved through the addition of chromium and other alloying elements.
1.1 Defining Characteristics
- Corrosion Resistance: The standout feature of stainless steel is its ability to resist rust and corrosion, even when exposed to moisture, chemicals, and harsh environments.
- High Strength and Durability: Stainless steels offer a combination of high tensile strength and durability, making them suitable for structural applications.
- Aesthetic Appeal: The bright, shiny surface of stainless steel adds to its aesthetic appeal, which is why it is often used in architectural and decorative applications.
2. Composition and Classification of Stainless Steels
Stainless steels are primarily iron alloys with a minimum of 10.5% chromium content, which forms a passive oxide layer on the surface, protecting it from corrosion. Other elements, such as nickel, molybdenum, carbon, and manganese, are added to enhance specific properties. Based on their microstructure and composition, stainless steels are classified into five main types:
2.1 Austenitic Stainless Steels
Austenitic stainless steels are the most widely used type, known for their excellent corrosion resistance, good formability, and weldability. They are characterized by a face-centered cubic (FCC) crystal structure, which remains stable across a wide range of temperatures.
Key Properties:
- High corrosion resistance, particularly in acidic and chloride environments.
- Non-magnetic in annealed condition.
- Excellent toughness, even at low temperatures.
Common Grades:
- 304 Stainless Steel: The most common grade, known for its versatility and balance of properties.
- 316 Stainless Steel: Contains added molybdenum for improved corrosion resistance in chloride-rich environments.
Applications:
- Food processing equipment, chemical plants, kitchen utensils, and medical devices.
2.2 Ferritic Stainless Steels
Ferritic stainless steels have a body-centered cubic (BCC) crystal structure, similar to carbon steels. They offer good corrosion resistance and are less expensive than austenitic steels, but they have lower toughness and are more difficult to weld.
Key Properties:
- Moderate corrosion resistance.
- Magnetic and less ductile than austenitic steels.
- Lower cost compared to austenitic grades.
Common Grades:
- 430 Stainless Steel: Known for good corrosion resistance and formability, often used in automotive trim.
- 409 Stainless Steel: Used in automotive exhaust systems due to its heat resistance and cost-effectiveness.
Applications:
- Automotive parts, home appliances, and architectural components.
2.3 Martensitic Stainless Steels
Martensitic stainless steels are known for their high strength and hardness, which is achieved through heat treatment. They have a body-centered tetragonal (BCT) structure and are less corrosion-resistant than austenitic and ferritic steels.
Key Properties:
- High hardness and strength.
- Moderate corrosion resistance.
- Can be heat-treated for improved mechanical properties.
Common Grades:
- 410 Stainless Steel: Used for cutlery, tools, and valves, offering a balance of hardness and corrosion resistance.
- 420 Stainless Steel: Known as “surgical steel,” used in medical instruments and razor blades.
Applications:
- Cutlery, surgical instruments, fasteners, and machine components.
2.4 Duplex Stainless Steels
Duplex stainless steels have a mixed microstructure of austenite and ferrite, combining the best properties of both types. They offer higher strength than austenitic steels and improved corrosion resistance compared to ferritic steels.
Key Properties:
- High strength and excellent corrosion resistance, particularly to chloride-induced stress corrosion cracking.
- Good weldability and toughness.
- Magnetic due to the presence of ferrite.
Common Grades:
- 2205 Duplex Stainless Steel: Offers excellent corrosion resistance and high strength.
- 2507 Super Duplex Stainless Steel: Known for even higher resistance to corrosion and improved mechanical properties.
Applications:
- Oil and gas industry, chemical processing, desalination plants, and marine applications.
2.5 Precipitation-Hardening (PH) Stainless Steels
Precipitation-hardening stainless steels can be heat-treated to achieve high strength while maintaining good corrosion resistance. They are often used in aerospace and industrial applications where high performance is required.
Key Properties:
- High strength and good corrosion resistance.
- Can be hardened through aging heat treatments.
- Excellent mechanical properties.
Common Grades:
- 17-4 PH Stainless Steel: Widely used for its combination of high strength, toughness, and moderate corrosion resistance.
- 15-5 PH Stainless Steel: Similar to 17-4 PH but with improved toughness.
Applications:
- Aerospace components, valves, pumps, and gears.
3. Properties of Stainless Steels
The properties of stainless steels are what make them a versatile and valuable material across many industries. Some of the key properties include:
3.1 Corrosion Resistance
Stainless steels are highly resistant to corrosion due to the passive oxide layer formed by chromium. This layer prevents rusting and protects the metal from damage when exposed to moisture, chemicals, and other corrosive environments. The addition of elements like molybdenum and nickel can further enhance corrosion resistance.
3.2 Strength and Toughness
Stainless steels offer a range of strength and toughness, depending on their composition and heat treatment. Martensitic and precipitation-hardening steels can be heat-treated to achieve high hardness, while austenitic and duplex steels provide excellent toughness, even at low temperatures.
3.3 Formability and Weldability
Austenitic stainless steels, in particular, are known for their good formability and weldability, making them suitable for complex shapes and structures. Ferritic and duplex stainless steels are also formable, but care must be taken during welding to prevent issues such as cracking.
3.4 Temperature Resistance
Stainless steels can withstand both high and low temperatures. Austenitic grades maintain their toughness at cryogenic temperatures, while ferritic and martensitic steels can endure elevated temperatures, making them suitable for applications involving thermal cycling.
4. Applications of Stainless Steels
The versatility of stainless steels makes them suitable for a broad range of applications across various industries.
4.1 Construction and Architecture
- Building Facades and Roofing: Stainless steel is used in architectural projects for its aesthetic appeal, durability, and corrosion resistance. It can be polished, brushed, or textured to achieve different finishes, making it a popular choice for modern designs.
- Structural Components: Stainless steels are used in the construction of bridges, railway stations, and other infrastructure due to their strength and resistance to weathering.
4.2 Food and Beverage Industry
- Processing Equipment: Stainless steels are used to manufacture tanks, pipes, and other equipment in food processing plants because they do not corrode or react with food products. Grades like 304 and 316 are commonly used for this purpose.
- Kitchen Utensils: Cutlery, cookware, and kitchen appliances are often made from stainless steel due to its hygienic properties, ease of cleaning, and resistance to rusting.
4.3 Automotive and Transportation
- Exhaust Systems: Stainless steels are used in exhaust systems because they can withstand high temperatures and resist corrosion from exhaust gases. Grades like 409 and 304 are typical choices.
- Structural Parts and Fasteners: Stainless steel fasteners and structural parts are used in vehicles, ships, and trains for their strength and corrosion resistance.
4.4 Medical and Pharmaceutical
- Surgical Instruments and Implants: Stainless steels, particularly 316L and 420, are used to manufacture surgical instruments, implants, and medical devices because they are biocompatible, easy to sterilize, and resistant to corrosion.
- Pharmaceutical Equipment: Tanks, mixers, and piping systems used in pharmaceutical manufacturing are often made from stainless steel to ensure cleanliness and prevent contamination.
5. Manufacturing Processes for Stainless Steels
The production of stainless steels involves several key processes, including melting, casting, forming, and finishing.
5.1 Melting and Alloying
The process begins with melting scrap stainless steel and raw materials in an electric arc furnace. Alloying elements like chromium, nickel, and molybdenum are added to achieve the desired composition. After melting, the molten metal is refined and cast into slabs or billets.
5.2 Hot and Cold Rolling
- Hot Rolling: The steel is heated and passed through rollers to reduce its thickness and shape it into sheets, plates, or coils. This process improves the material’s ductility and workability.
- Cold Rolling: After hot rolling, the steel can undergo cold rolling, where it is further processed at room temperature to improve surface finish, strength, and dimensional accuracy.
5.3 Annealing and Heat Treatment
Annealing involves heating the steel to a specific temperature and then cooling it slowly. This process relieves internal stresses, enhances ductility, and restores the material’s microstructure. Heat treatment is also used to harden certain grades, such as martensitic and precipitation-hardening steels.
5.4 Surface Finishing
Stainless steel can be finished in various ways, including polishing, brushing, and electroplating. Surface finishing enhances the material’s appearance and can provide additional resistance to corrosion. Common finishes include mirror polish, satin, and matte.
6. Challenges in Using Stainless Steels
Despite their advantages, stainless steels come with a set of challenges that need to be addressed.
6.1 Cost
The cost of alloying elements like chromium, nickel, and molybdenum makes stainless steels more expensive than carbon steels. Efforts to reduce costs include using leaner compositions with lower nickel and higher nitrogen content.
6.2 Difficulties in Machining
Certain grades of stainless steel are challenging to machine due to their hardness and work-hardening properties. This can lead to tool wear and increased production costs.
6.3 Welding Challenges
Some stainless steels, particularly ferritic and martensitic grades, can be difficult to weld because of issues like cracking and loss of corrosion resistance in the heat-affected zone. Special techniques and filler materials are often required to ensure proper weld quality.
7. Future Trends in Stainless Steel Development
Ongoing research and innovation in stainless steel production are focused on improving properties, sustainability, and cost-effectiveness.
7.1 Development of Lean Duplex Stainless Steels
Lean duplex stainless steels offer a balance of strength, corrosion resistance, and lower cost by reducing the amount of expensive alloying elements. These materials are being developed to meet the growing demand for affordable, high-performance stainless steels.
7.2 Advancements in Additive Manufacturing
Additive manufacturing, or 3D printing, is being used to create complex stainless steel components that would be difficult to produce using traditional methods. This technology allows for greater design flexibility and reduced material waste.
7.3 Sustainable Production Practices
The stainless steel industry is moving towards more sustainable practices, including recycling, energy-efficient production, and reducing emissions. Stainless steel is already highly recyclable, and advancements in green manufacturing processes will further reduce its environmental impact.
Conclusion
Stainless steels are among the most versatile and widely used materials in the world, known for their excellent corrosion resistance, strength, and durability. From architectural structures to medical devices, they play a vital role in various sectors due to their unique properties. Although challenges such as high costs and machining difficulties exist, ongoing developments in alloy design and manufacturing techniques continue to expand their applications.
As industries seek more efficient, cost-effective, and sustainable solutions, the future of stainless steel will likely include new compositions, advanced processing methods, and a greater emphasis on recycling and sustainability. Stainless steel remains a material of choice for the future, offering reliability, performance, and longevity in countless applications worldwide.
Cobalt-Based Alloys: A Comprehensive Exploration
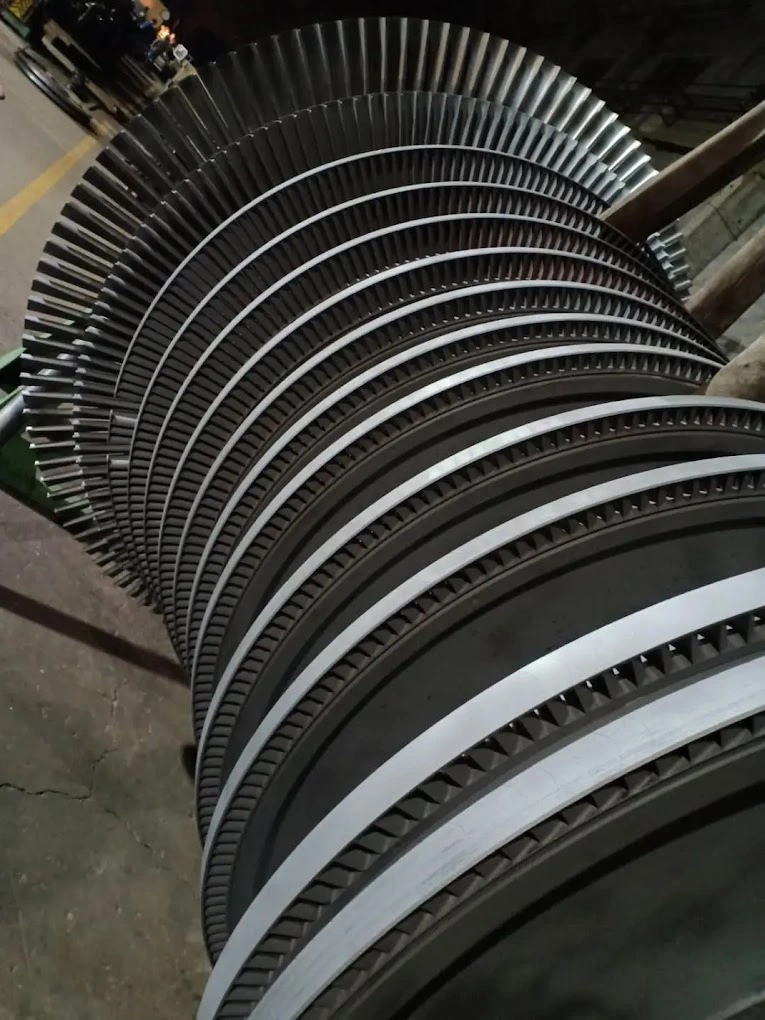
Cobalt-based alloys are a class of high-performance materials known for their excellent wear resistance, corrosion resistance, and ability to maintain mechanical properties at elevated temperatures. These alloys are extensively used in demanding environments such as aerospace, energy, medical, and industrial applications. Their unique combination of strength, toughness, and resistance to extreme conditions makes them indispensable in sectors where materials face high stress, abrasion, and heat. This comprehensive exploration will cover the composition, properties, applications, manufacturing processes, challenges, and future trends associated with cobalt-based alloys.
1. Introduction to Cobalt-Based Alloys
Cobalt-based alloys, often simply referred to as cobalt alloys, are metallic materials where cobalt is the primary element. These alloys are specifically designed to perform in environments where resistance to wear, corrosion, and high temperatures is critical. The most well-known family of cobalt-based alloys is Stellite, a trademark name for alloys that were developed early in the 20th century for cutting tools and wear-resistant applications.
1.1 Defining Characteristics
- High Wear Resistance: Cobalt alloys are renowned for their exceptional resistance to abrasion, erosion, and galling, making them ideal for cutting tools, valve seats, and bearings.
- Excellent Corrosion Resistance: Cobalt-based alloys resist corrosion in various environments, including acids, seawater, and other aggressive chemicals.
- Retention of Mechanical Properties at High Temperatures: Unlike many other alloys, cobalt alloys maintain their strength, toughness, and hardness even when exposed to high temperatures, making them suitable for aerospace and industrial turbine components.
2. Composition and Classification of Cobalt-Based Alloys
Cobalt-based alloys are typically composed of cobalt as the base element, with the addition of chromium, tungsten, molybdenum, nickel, and other elements. The choice and proportion of these alloying elements influence the specific properties of the alloy.
2.1 Key Alloying Elements
- Chromium (Cr): Chromium enhances the corrosion resistance of cobalt-based alloys. It forms a stable, protective oxide layer on the alloy’s surface, preventing oxidation and degradation in harsh environments.
- Tungsten (W) and Molybdenum (Mo): These elements improve the high-temperature strength and wear resistance of the alloys. They contribute to solid-solution strengthening and carbide formation, which enhances hardness and durability.
- Nickel (Ni): Nickel improves the alloy’s toughness and ductility. It also aids in corrosion resistance, making cobalt alloys suitable for use in environments exposed to acids and salts.
- Carbon (C): Carbon is used in controlled amounts to form hard carbides within the alloy, significantly improving wear resistance. However, excessive carbon can make the material brittle.
2.2 Classification of Cobalt-Based Alloys
Cobalt-based alloys can be broadly categorized into three main types based on their microstructure: cobalt-chromium, cobalt-chromium-tungsten, and cobalt-chromium-molybdenum alloys.
- Cobalt-Chromium Alloys: These alloys are known for their excellent corrosion resistance and are commonly used in medical implants and dental prosthetics. The addition of chromium provides superior resistance to oxidation and chemical attack.
- Cobalt-Chromium-Tungsten Alloys: The presence of tungsten makes these alloys incredibly hard and wear-resistant. They are often used in cutting tools, industrial valves, and engine components where durability is critical.
- Cobalt-Chromium-Molybdenum Alloys: These alloys offer a balance of strength, wear resistance, and corrosion resistance. They are often used in the aerospace sector, as well as in medical applications where biocompatibility is essential.
3. Properties of Cobalt-Based Alloys
The properties of cobalt-based alloys make them suitable for use in extreme conditions where other materials might fail. Some of the most important properties include:
3.1 High-Temperature Strength and Stability
Cobalt alloys retain their mechanical properties at high temperatures, often exceeding 800°C (1472°F). This makes them ideal for components that operate in extreme heat, such as gas turbines, jet engines, and industrial furnaces. Unlike nickel-based superalloys, which may lose strength at high temperatures, cobalt-based alloys can maintain hardness and resistance to creep.
3.2 Superior Wear and Abrasion Resistance
One of the most notable characteristics of cobalt alloys is their ability to resist wear, abrasion, and erosion. This is due to the formation of hard carbides within the alloy, which provide resistance to scratching, galling, and other forms of surface damage. This property is critical for components that are subject to constant friction, such as cutting tools and industrial machinery parts.
3.3 Excellent Corrosion and Oxidation Resistance
Cobalt-based alloys exhibit excellent corrosion resistance, especially in environments that are acidic or contain chloride ions. The chromium content in the alloy forms a passive oxide film on the surface, protecting the metal from further corrosion. This property makes cobalt alloys suitable for use in chemical processing, marine environments, and medical implants.
3.4 Magnetic Properties
Cobalt alloys can exhibit ferromagnetic properties, making them useful in applications where magnetic properties are desired, such as in electric motors and magnetic sensors.
4. Applications of Cobalt-Based Alloys
Due to their unique combination of properties, cobalt-based alloys are utilized in a wide range of industries. Some of the key applications include:
4.1 Aerospace and Power Generation
- Gas Turbine Components: The high-temperature strength and creep resistance of cobalt alloys make them suitable for turbine blades, vanes, and combustor liners in jet engines and power generation turbines. These components operate under extreme temperatures and mechanical stress, where the alloy’s ability to maintain its properties is crucial.
- Rocket Engines: Cobalt alloys are used in rocket engine components due to their ability to withstand high temperatures and corrosive gases, ensuring reliable performance during launches.
4.2 Cutting Tools and Industrial Machinery
- Cutting Tools: Cobalt-based alloys, such as Stellite, are widely used in cutting tools because of their wear resistance. These tools can maintain sharpness and resist wear even when cutting through hard or abrasive materials.
- Valve Seats and Bearings: Cobalt alloys are ideal for valve seats, bearings, and other components that require high wear resistance. They can withstand the constant friction and mechanical stress seen in industrial machines, oil drilling equipment, and automotive parts.
4.3 Medical and Dental Applications
- Orthopedic Implants: The biocompatibility and corrosion resistance of cobalt-chromium alloys make them ideal for use in orthopedic implants, such as hip and knee replacements. These materials do not corrode within the human body and are well-tolerated by tissues.
- Dental Prosthetics: Cobalt alloys are also used in dental prosthetics, including crowns, bridges, and orthodontic brackets. Their strength, wear resistance, and ability to maintain shape over time make them suitable for long-term use in dental applications.
4.4 Chemical Processing and Marine Industry
- Chemical Processing Equipment: Cobalt alloys are used in chemical reactors, pumps, and piping systems where exposure to corrosive substances is a concern. Their resistance to acids and other aggressive chemicals ensures long-lasting performance.
- Marine Components: Due to their excellent corrosion resistance, cobalt alloys are also employed in marine applications, such as propeller shafts and underwater equipment, where they can resist the corrosive effects of seawater.
5. Manufacturing Processes for Cobalt-Based Alloys
The production of cobalt-based alloys involves various sophisticated manufacturing processes to ensure that the final product meets the required standards of strength, durability, and performance.
5.1 Investment Casting
- Lost-Wax Casting: Investment casting is a common method for producing cobalt alloy components with complex geometries, such as turbine blades and orthopedic implants. The process involves creating a wax model, coating it with a ceramic shell, and then melting out the wax. Molten cobalt alloy is poured into the ceramic mold, forming the desired component.
- Advantages: Investment casting allows for precise control over the shape and dimensions of the final product, making it ideal for parts that require intricate designs and tight tolerances.
5.2 Powder Metallurgy
- Sintering Process: Powder metallurgy involves compressing cobalt alloy powder into a desired shape and then sintering it at high temperatures to create a solid, dense component. This process is suitable for producing parts that need to be extremely hard and wear-resistant, such as cutting tools and bearings.
- Advantages: Powder metallurgy allows for the creation of components with specific microstructures and properties that might be difficult to achieve through traditional casting methods.
5.3 Hot and Cold Forging
- Forging: Forging involves shaping the alloy under high pressure and temperature to improve the material’s grain structure and enhance its mechanical properties. Forged cobalt alloys exhibit excellent strength and wear resistance, making them suitable for high-stress applications.
- Cold Forging: For components that require a smooth surface finish and precise dimensions, cold forging can be used. This process improves the strength of the alloy by work-hardening it, resulting in a more durable product.
6. Challenges in Using Cobalt-Based Alloys
Despite their many advantages, cobalt-based alloys come with a set of challenges that need to be addressed to optimize their use.
6.1 High Cost
The cost of cobalt is relatively high compared to other metals, such as iron or aluminum. This is due to the limited supply and the expense of mining and refining cobalt. The high cost of cobalt can make products made from cobalt-based alloys expensive, limiting their widespread use.
6.2 Difficult Machinability
Cobalt alloys are hard and wear-resistant, but these properties make them difficult to machine. Specialized tools and techniques are often required to cut, shape, and finish these alloys, adding to the manufacturing cost and complexity.
6.3 Supply Chain and Ethical Concerns
A significant portion of the world’s cobalt supply comes from the Democratic Republic of Congo (DRC), where concerns about human rights, child labor, and environmental issues have been raised. Ensuring a sustainable and ethical supply chain for cobalt is a critical challenge for industries relying on cobalt-based alloys.
7. Future Trends in Cobalt-Based Alloy Development
Research and innovation are driving the development of new cobalt-based alloys with enhanced properties and more sustainable production methods.
7.1 Development of New Alloy Compositions
Scientists are exploring new alloy compositions that can improve the performance of cobalt-based alloys, such as adding rare earth elements to enhance high-temperature stability or using alternative alloying elements to reduce costs without compromising quality. These innovations aim to expand the range of applications for cobalt-based alloys.
7.2 Advances in Additive Manufacturing
Additive manufacturing, or 3D printing, is being used to produce complex cobalt alloy components with reduced material waste. This technology enables the creation of custom, intricate designs that are difficult to achieve with traditional methods. For example, the aerospace industry can benefit from 3D-printed turbine blades that offer improved aerodynamic performance and reduced weight.
7.3 Sustainable Sourcing and Recycling
Given the ethical and environmental concerns surrounding cobalt mining, there is a growing emphasis on finding sustainable and ethical sources of cobalt. Recycling cobalt from end-of-life batteries and other products is one strategy to reduce reliance on primary mining. Researchers are also exploring ways to reduce or replace cobalt in certain applications where alternatives can provide similar performance.
Conclusion
Cobalt-based alloys are among the most versatile and durable materials used in high-performance applications. Their ability to maintain mechanical properties at elevated temperatures, resist wear and corrosion, and offer biocompatibility makes them invaluable in industries such as aerospace, medical, and chemical processing. However, challenges such as high costs, machining difficulties, and ethical concerns about cobalt sourcing need to be addressed.
The future of cobalt-based alloys lies in the development of new compositions, advanced manufacturing techniques, and sustainable sourcing practices. As industries continue to push the boundaries of performance and efficiency, cobalt alloys will play a critical role in enabling the next generation of engineering solutions. By overcoming existing challenges and leveraging new technologies, cobalt-based alloys will remain at the forefront of material science, offering reliable and robust solutions for the most demanding environments.
Manufacturing Technologies for Steam Turbine Blades: A Comprehensive Exploration
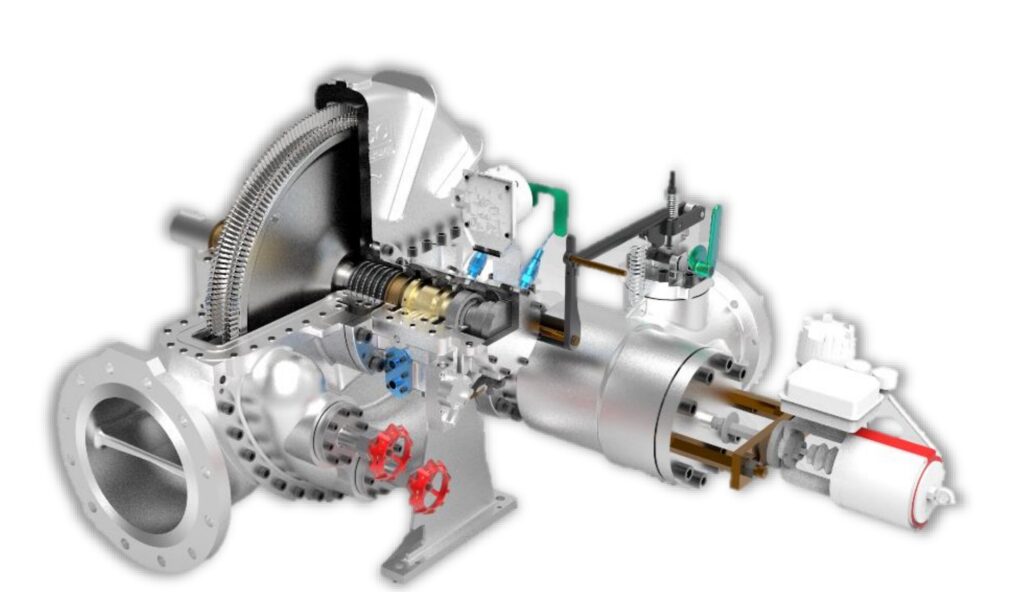
Steam turbine blades are critical components that play a central role in the energy conversion process within a steam turbine. The performance, efficiency, and reliability of a steam turbine heavily depend on the quality and precision of its blades. Due to the extreme operating conditions—high temperatures, pressures, and rotational speeds—manufacturing these blades requires a high level of engineering expertise and precision. This comprehensive guide will explore the various manufacturing technologies used to produce steam turbine blades, including casting, forging, machining, additive manufacturing, and advanced quality control techniques.
1. Importance of Manufacturing Quality in Steam Turbine Blades
The efficiency of a steam turbine largely depends on the aerodynamic, mechanical, and thermal performance of its blades. Poor manufacturing quality can lead to inefficiencies, premature wear, and potential failures, causing significant economic losses and safety hazards. Therefore, precision in the manufacturing process is crucial to ensure:
- Dimensional Accuracy: Correct blade geometry ensures smooth steam flow and efficient energy conversion.
- Material Integrity: High mechanical strength, fatigue resistance, and corrosion resistance are necessary to withstand harsh operating conditions.
- Surface Finish: Smooth blade surfaces reduce drag, turbulence, and energy losses, leading to improved turbine efficiency.
2. Materials Used in Steam Turbine Blades and Their Impact on Manufacturing
The choice of material plays a crucial role in determining the manufacturing process for steam turbine blades. Common materials include:
- Nickel-Based Superalloys: Used in high-pressure turbine stages due to their excellent high-temperature strength and resistance to oxidation and creep.
- Titanium Alloys: Valued for their high strength-to-weight ratio, typically used in low-pressure sections.
- Stainless Steels: Widely used in lower temperature sections of the turbine due to their good balance of strength, corrosion resistance, and cost-effectiveness.
The properties of these materials, such as hardness and heat resistance, impact how they can be processed and shaped during manufacturing. Harder materials, for example, may require more specialized tooling and machining techniques.
3. Manufacturing Processes for Steam Turbine Blades
3.1 Investment Casting
Investment casting, also known as lost-wax casting, is one of the most common methods for producing steam turbine blades, especially those with complex geometries. This process involves creating a wax model of the blade, which is then coated with a ceramic shell. Once the wax is melted out, molten metal is poured into the mold to form the blade.
Process Overview:
- Wax Pattern Creation: A model of the blade is created using wax. This wax pattern represents the exact shape of the final blade.
- Shell Building: The wax pattern is dipped into a ceramic slurry and coated with ceramic sand. This process is repeated until a thick ceramic shell forms around the wax model.
- Wax Removal: The wax is melted out, leaving a hollow ceramic mold.
- Metal Pouring: Molten metal (such as a nickel-based superalloy) is poured into the ceramic mold, filling the cavity left by the wax.
- Cooling and Shell Removal: After the metal has solidified, the ceramic shell is broken away, and the rough blade is retrieved.
- Finishing: The blade undergoes further processing, such as machining and polishing, to achieve the desired final dimensions and surface finish.
Advantages:
- Complex Geometries: Investment casting allows for the production of blades with intricate shapes and internal cooling channels, which are difficult to achieve through other methods.
- Precision: High dimensional accuracy and surface finish, reducing the need for extensive machining.
Challenges:
- Cost: The process can be expensive due to the need for precise molds and high-quality ceramic materials.
- Time-Consuming: Building the ceramic shell and cooling the molten metal takes time, making it less suitable for rapid production.
3.2 Forging
Forging is a manufacturing process that involves shaping metal under high pressure, typically by hammering or pressing. This process is used to produce high-strength steam turbine blades with excellent mechanical properties and a refined grain structure.
Process Overview:
- Heating the Metal: The raw metal, often in the form of billets or ingots, is heated to a high temperature to make it malleable.
- Shaping: The hot metal is placed between two dies, which are then pressed together to shape the blade. Forging can be done using open-die (for larger components) or closed-die (for more precise shaping) methods.
- Cooling: The forged part is allowed to cool, solidifying the refined grain structure and increasing the mechanical strength of the blade.
- Heat Treatment: Additional heat treatment processes, such as annealing or quenching, may be applied to enhance the mechanical properties of the blade.
- Machining and Finishing: The forged blade undergoes machining to achieve the desired final shape and smooth surface finish.
Advantages:
- Strength and Durability: Forging enhances the grain structure, making blades stronger and more resistant to fatigue and wear.
- Material Integrity: Forging reduces the risk of internal defects, such as porosity, that can weaken the blade.
Challenges:
- Complexity: Forging is less suitable for producing complex blade shapes, particularly those with intricate cooling channels.
- Cost: High tooling costs can make forging expensive, especially for low production volumes.
3.3 Machining
Machining involves the removal of material from a workpiece using cutting tools to create the final shape of the turbine blade. This process is often used after casting or forging to achieve precise dimensions and surface finishes.
Process Overview:
- CNC Machining: Computer Numerical Control (CNC) machines are used to mill, drill, and grind the blade to the desired shape. CNC technology allows for high precision and repeatability.
- Surface Finishing: Additional processes, such as polishing or grinding, are used to improve the surface finish and aerodynamic properties of the blade.
- Inspection and Quality Control: Advanced inspection techniques, such as laser scanning and coordinate measuring machines (CMMs), are used to ensure the blade meets all design specifications.
Advantages:
- Precision: Machining allows for tight tolerances, ensuring that blades fit perfectly within the turbine assembly.
- Flexibility: CNC machining can produce complex shapes and profiles, making it suitable for both prototype and mass production.
Challenges:
- Material Waste: Machining often involves cutting away significant amounts of material, leading to waste.
- Tool Wear: Hard materials, such as nickel-based superalloys, can cause rapid wear on cutting tools, increasing production costs.
3.4 Additive Manufacturing (3D Printing)
Additive manufacturing, or 3D printing, is an emerging technology that offers the potential to revolutionize the production of steam turbine blades. Unlike traditional subtractive manufacturing methods, additive manufacturing builds components layer by layer, allowing for greater design flexibility.
Process Overview:
- Design and Slicing: A digital model of the blade is created using CAD software. The model is then sliced into thin layers.
- Layer-by-Layer Fabrication: The 3D printer uses metal powder or wire, melting and depositing it layer by layer to build the blade. Techniques such as Selective Laser Melting (SLM) and Electron Beam Melting (EBM) are commonly used for metal parts.
- Post-Processing: The printed blade may undergo additional heat treatment, machining, and finishing to achieve the desired final properties.
Advantages:
- Design Flexibility: Additive manufacturing enables the creation of complex geometries, such as internal cooling channels, which are difficult to produce using traditional methods.
- Reduced Waste: Unlike machining, additive manufacturing minimizes material waste, as only the necessary material is used.
- Rapid Prototyping: 3D printing allows for quick production of prototypes, enabling faster design iterations and testing.
Challenges:
- Material Limitations: Not all materials are suitable for additive manufacturing, and achieving consistent quality can be difficult.
- Cost: 3D printing technology, especially for metals, is still relatively expensive, making it less viable for mass production.
4. Advanced Techniques in Blade Manufacturing
4.1 Hot Isostatic Pressing (HIP)
Hot Isostatic Pressing is a process used to improve the quality of cast or additive-manufactured turbine blades by eliminating internal porosity. The blade is placed in a high-pressure, high-temperature environment, which compresses the material and removes any voids or defects.
Advantages:
- Improved Material Density: HIP ensures that the material is fully dense, improving mechanical properties and resistance to fatigue.
- Extended Lifespan: The removal of internal defects reduces the risk of cracks and other failures, extending the lifespan of the blade.
4.2 Laser Cladding
Laser cladding involves melting a thin layer of material onto the surface of the blade using a laser. This process can be used to add protective coatings or repair worn or damaged blades.
Advantages:
- Enhanced Surface Properties: Laser cladding can add wear-resistant or corrosion-resistant coatings, improving the performance and durability of the blade.
- Repair and Refurbishment: This technique allows for the repair of expensive turbine blades, reducing the need for complete replacement.
5. Quality Control and Inspection Techniques
Ensuring the quality of steam turbine blades is critical for safe and efficient turbine operation. Advanced inspection and quality control techniques are used throughout the manufacturing process.
5.1 Non-Destructive Testing (NDT)
Non-destructive testing methods are used to inspect the internal and external quality of blades without damaging them. Common NDT techniques include:
- Ultrasonic Testing: Uses high-frequency sound waves to detect internal defects, such as cracks or voids.
- X-Ray Inspection: Provides detailed images of the internal structure, revealing any hidden flaws or inconsistencies.
- Dye Penetrant Testing: A dye is applied to the blade surface, which seeps into any cracks, making them visible under UV light.
5.2 Coordinate Measuring Machines (CMM)
CMMs are used to measure the dimensions of turbine blades with high precision. The machine uses a probe to touch various points on the blade surface, comparing the measurements to the original design specifications.
Advantages:
- High Accuracy: Ensures that blades meet tight tolerances and fit perfectly within the turbine assembly.
- Automated Inspection: CMMs can be programmed for automated inspection, reducing the need for manual measurement and improving consistency.
6. Future Trends in Steam Turbine Blade Manufacturing
The future of steam turbine blade manufacturing is set to be shaped by advances in materials science, automation, and digital technologies. Some of the key trends include:
6.1 Development of Advanced Materials
Ongoing research into new materials, such as ceramic matrix composites (CMCs) and high-entropy alloys (HEAs), could lead to blades that are lighter, stronger, and more heat-resistant. These materials could improve turbine efficiency and enable operation at higher temperatures.
6.2 Integration of Digital Twins and AI
Digital twins, which are virtual replicas of physical assets, allow manufacturers to simulate and optimize blade performance before production. Combined with AI, digital twins can predict potential issues, optimize design, and enhance the efficiency of the manufacturing process.
6.3 Automation and Robotics
Automation is becoming increasingly important in blade manufacturing. Robotics can handle tasks such as machining, polishing, and inspection, reducing labor costs, improving consistency, and speeding up production.
Conclusion
The manufacturing of steam turbine blades involves a combination of traditional and advanced technologies, each with its own strengths and challenges. From investment casting and forging to additive manufacturing and laser cladding, these processes enable the production of high-quality blades that are essential for efficient and reliable turbine operation. Advanced inspection techniques and quality control ensure that every blade meets stringent standards, minimizing the risk of failures and maximizing efficiency.
As technology continues to advance, the future of steam turbine blade manufacturing will see further integration of digital tools, new materials, and automated processes, leading to improvements in performance, cost-efficiency, and sustainability. By overcoming the challenges and embracing new innovations, manufacturers can continue to produce blades that drive the next generation of energy solutions.
The Importance of Manufacturing Quality in Steam Turbine Blades: A Comprehensive Exploration
Steam turbine blades are at the heart of power generation systems, converting thermal energy from steam into mechanical energy, which in turn drives generators to produce electricity. The efficiency, reliability, and longevity of steam turbines are highly dependent on the quality of the turbine blades. Given the extreme operating conditions they endure—such as high temperatures, pressures, and rotational speeds—manufacturing quality is critical. Poorly manufactured blades can lead to inefficiencies, increased maintenance costs, and catastrophic failures. This comprehensive exploration will delve into the importance of manufacturing quality for steam turbine blades, covering the factors that influence quality, the challenges of manufacturing, quality control processes, and the implications of poor-quality blades.
1. Role of Steam Turbine Blades in Power Generation
Before discussing the importance of manufacturing quality, it is essential to understand the role of steam turbine blades within a turbine. Steam turbines convert the thermal energy of high-pressure steam into rotational mechanical energy. This energy is transferred to a generator that produces electricity. The blades are the key components that interact directly with the steam, playing a crucial role in energy conversion.
1.1 Energy Conversion and Efficiency
Turbine blades must be precisely manufactured to ensure they convert as much energy from the steam as possible. High manufacturing quality ensures that blades are aerodynamically optimized, which leads to higher efficiency. Any deviation from the optimal design can result in energy losses, reducing the overall efficiency of the power plant.
1.2 Mechanical Strength and Reliability
Blades are exposed to intense mechanical forces due to high-speed rotation. They must be robust enough to handle these forces without deforming or failing. High-quality manufacturing processes ensure that blades have the necessary mechanical properties, such as strength, toughness, and resistance to wear and tear.
2. Factors Influencing Manufacturing Quality in Steam Turbine Blades
Achieving high manufacturing quality for steam turbine blades involves several critical factors, ranging from material selection and precision engineering to surface finish and inspection.
2.1 Material Selection and Processing
The choice of material has a direct impact on the performance and durability of turbine blades. Common materials used include nickel-based superalloys, titanium alloys, and stainless steels. The material must be able to withstand high temperatures, resist corrosion, and maintain mechanical integrity under stress. Proper material processing, such as heat treatment, is also crucial to ensure the blade achieves the desired properties.
2.2 Precision Engineering and Dimensional Accuracy
Blades must be manufactured to precise dimensions to ensure they fit perfectly within the turbine assembly. Dimensional accuracy affects the flow of steam through the turbine. Even slight deviations can lead to turbulence, energy losses, and reduced efficiency. Precision engineering also ensures that blades maintain aerodynamic profiles, which is essential for optimal performance.
2.3 Surface Finish
The surface finish of turbine blades plays a vital role in reducing drag and turbulence, which can affect efficiency. Smooth surfaces allow steam to flow over the blades without causing excessive friction, leading to higher efficiency. A poor surface finish can lead to increased energy losses, higher fuel consumption, and reduced overall turbine performance.
3. Challenges in Manufacturing High-Quality Steam Turbine Blades
The manufacturing of steam turbine blades involves several complex processes, each of which must be carefully managed to ensure high quality. These processes include casting, forging, machining, and sometimes additive manufacturing. Each of these methods comes with its own set of challenges.
3.1 Complexity of Blade Geometry
Turbine blades are designed with complex geometries to optimize the conversion of steam energy into mechanical motion. This complexity can make the manufacturing process difficult, especially when precise tolerances must be maintained. Intricate designs may also include internal cooling channels, which are essential for blades operating in high-temperature environments. Producing these designs with high accuracy requires advanced manufacturing techniques.
3.2 Material Challenges
The materials used for turbine blades, such as nickel-based superalloys, are known for their high strength and resistance to heat. However, these same properties can make the materials challenging to work with. For example, superalloys are difficult to machine due to their hardness, which can lead to increased tool wear and higher production costs. Ensuring that the material is processed correctly—through methods like heat treatment and coating—is essential for achieving the desired mechanical properties.
3.3 Manufacturing Defects and Their Impact
Defects in the manufacturing process can have serious consequences. Common defects include cracks, voids, inclusions, and dimensional deviations. These defects can compromise the mechanical strength of the blade, lead to premature wear, and increase the risk of catastrophic failures. Quality control processes, such as non-destructive testing (NDT), are essential to identify and address these defects before the blades are installed.
4. Importance of Quality Control in Manufacturing Processes
Given the challenges associated with manufacturing turbine blades, rigorous quality control is essential throughout the production process. Quality control ensures that each blade meets the required specifications, minimizing the risk of failures and optimizing turbine performance.
4.1 Non-Destructive Testing (NDT)
NDT methods are critical for inspecting turbine blades without causing damage. These methods include:
- Ultrasonic Testing: Uses high-frequency sound waves to detect internal defects such as cracks or voids. This method is especially useful for identifying flaws that are not visible on the surface.
- X-Ray Inspection: Provides detailed images of the internal structure of the blade, revealing any inconsistencies or defects. X-ray inspection is often used for complex geometries where other testing methods may not be effective.
- Dye Penetrant Testing: Involves applying a dye to the blade surface, which seeps into any cracks, making them visible under ultraviolet light. This method is effective for detecting surface defects.
4.2 Precision Measurement Tools
Precision measurement tools, such as Coordinate Measuring Machines (CMMs), are used to ensure that blades are manufactured to exact specifications. CMMs can measure the dimensions of a blade with high accuracy, ensuring that it conforms to the design tolerances. This precision is crucial for maintaining the aerodynamic efficiency of the blade.
4.3 Statistical Process Control (SPC)
SPC involves using statistical methods to monitor and control the manufacturing process. By analyzing data from production, manufacturers can identify trends and address issues before they lead to defects. SPC helps in maintaining consistent quality and reducing variability in the production process.
5. Implications of Poor Manufacturing Quality
The consequences of poor manufacturing quality in steam turbine blades can be severe, affecting not only the efficiency of the turbine but also the safety and reliability of the entire power generation system.
5.1 Reduced Efficiency and Higher Operating Costs
Poorly manufactured blades can lead to inefficiencies in the turbine, reducing the overall power output. If the blades are not aerodynamically optimized, steam will not flow smoothly, leading to turbulence and energy losses. This can result in higher fuel consumption and increased operating costs, as the turbine requires more steam to generate the same amount of electricity.
5.2 Increased Maintenance and Downtime
Blades that are not manufactured to high standards are more likely to experience wear and tear, leading to increased maintenance requirements. Frequent maintenance not only adds to the operational costs but also results in downtime, which can affect the reliability of the power supply. In severe cases, damaged blades may need to be replaced entirely, leading to significant expenses.
5.3 Risk of Catastrophic Failure
The failure of a turbine blade during operation can have catastrophic consequences, including damage to the turbine and the surrounding infrastructure. Blade failure can occur due to fatigue, creep, or the presence of defects such as cracks or voids. In addition to causing mechanical damage, blade failure can lead to safety hazards, posing risks to personnel and equipment.
6. Case Studies Highlighting the Importance of Manufacturing Quality
6.1 Improved Efficiency Through Precision Engineering
A leading power plant manufacturer implemented advanced CNC machining and precision measurement techniques in the production of its turbine blades. By ensuring tighter tolerances and smoother surface finishes, the company was able to reduce energy losses, resulting in a 5% increase in turbine efficiency. This improvement translated to significant cost savings over the lifetime of the turbine.
6.2 Addressing Defects with Advanced NDT
A turbine blade manufacturer experienced issues with cracks forming in blades during operation. After conducting a thorough analysis, the company implemented ultrasonic testing as part of its quality control process. By identifying and addressing defects during production, the company reduced the incidence of blade failures and improved the reliability of its turbines.
6.3 Preventing Failures with Material Improvements
A power plant suffered a catastrophic failure when a turbine blade broke during operation, causing extensive damage. Investigations revealed that the blade material had microstructural defects that led to fatigue. As a result, the plant implemented stricter material processing protocols, including improved heat treatment and quality control measures, to prevent future failures.
7. Future Trends in Manufacturing Quality for Steam Turbine Blades
As technology continues to evolve, new advancements are shaping the future of turbine blade manufacturing, enabling higher quality and greater efficiency.
7.1 Additive Manufacturing (3D Printing)
Additive manufacturing, or 3D printing, offers the potential to produce turbine blades with complex geometries that were previously difficult to manufacture. This technology allows for the integration of internal cooling channels and other design features that can improve efficiency. Additionally, 3D printing can reduce waste and lower production costs by using only the necessary material.
7.2 Digital Twins and Simulation
Digital twins—virtual models of physical components—are being used to simulate and analyze the performance of turbine blades before they are manufactured. By testing different designs in a digital environment, engineers can optimize blade performance and reduce the risk of defects. Digital twins also allow for real-time monitoring of blades during operation, enabling predictive maintenance.
7.3 Advances in Material Science
The development of new materials, such as ceramic matrix composites (CMCs) and high-entropy alloys (HEAs), has the potential to improve the performance of turbine blades. These materials offer greater strength, heat resistance, and durability, enabling turbines to operate at higher temperatures and pressures. Advanced coatings are also being developed to enhance wear resistance and reduce corrosion.
8. Strategies to Enhance Manufacturing Quality in Steam Turbine Blades
To ensure high manufacturing quality, companies can adopt several best practices:
8.1 Implementing Lean Manufacturing Principles
Lean manufacturing focuses on reducing waste and improving efficiency throughout the production process. By streamlining operations and eliminating non-value-added activities, manufacturers can improve product quality and reduce production costs.
8.2 Continuous Training and Skill Development
Manufacturing turbine blades requires a high level of expertise. Continuous training and skill development ensure that workers are proficient in the latest technologies and techniques, leading to better-quality products. Skilled technicians are better equipped to identify potential issues and implement solutions.
8.3 Investment in Advanced Machinery and Technology
Investing in state-of-the-art machinery, such as CNC machines, 3D printers, and advanced inspection tools, enables manufacturers to produce turbine blades with greater precision and consistency. Automated systems can also reduce the risk of human error, leading to higher quality outcomes.
Conclusion
The manufacturing quality of steam turbine blades is critical to the efficiency, reliability, and safety of power generation systems. High-quality manufacturing processes ensure that blades have the necessary aerodynamic, mechanical, and thermal properties to withstand extreme operating conditions. Poor manufacturing quality can lead to inefficiencies, increased maintenance costs, and even catastrophic failures, emphasizing the importance of rigorous quality control.
As technology advances, new methods such as additive manufacturing, digital twins, and advanced materials are enhancing the capabilities of turbine blade manufacturing. By adopting these innovations and maintaining a focus on quality, manufacturers can produce turbine blades that deliver optimal performance, reducing costs and improving the sustainability of energy production.
In a world increasingly reliant on efficient and reliable energy, the importance of manufacturing quality in steam turbine blades cannot be overstated. High standards in production processes not only ensure the safety and longevity of turbines but also contribute to the overall efficiency and environmental sustainability of power generation.
Materials Used in Steam Turbine Blades and Their Impact on Manufacturing: A Comprehensive Exploration
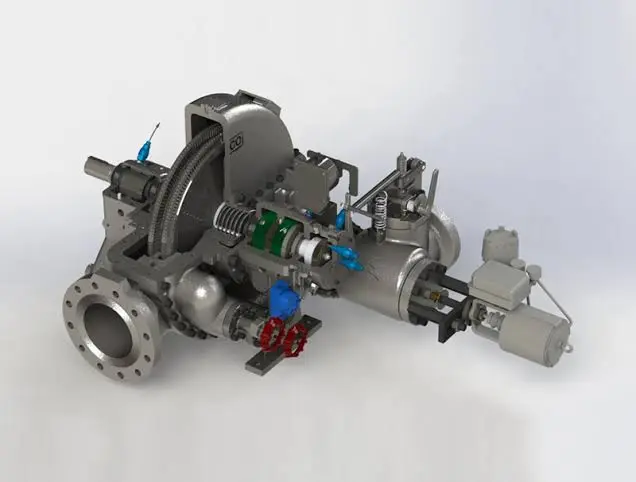
Steam turbine blades are critical components in power generation systems, responsible for converting thermal energy from steam into mechanical energy. To ensure efficiency, reliability, and longevity, these blades must withstand extreme operating conditions, including high temperatures, pressures, and rotational speeds. The choice of materials for steam turbine blades is crucial as it affects not only the blade’s performance but also the manufacturing process. This comprehensive exploration will cover the various materials used in steam turbine blades, their properties, applications, and how these materials influence manufacturing techniques.
1. Importance of Material Selection in Steam Turbine Blades
Steam turbine blades operate under extreme conditions, such as high temperatures (up to 600°C or higher), high pressures, and significant centrifugal forces due to high rotational speeds. They also encounter steam that may carry impurities, causing corrosion and erosion over time. Therefore, the materials selected for turbine blades must have specific properties to ensure optimal performance and longevity. These properties include:
- High-Temperature Strength: The material must maintain its mechanical integrity under elevated temperatures.
- Resistance to Creep and Fatigue: Prolonged exposure to stress and high temperatures can lead to creep (slow deformation) and fatigue (repeated stress-induced cracking). The material should resist these conditions.
- Corrosion and Oxidation Resistance: The material must withstand corrosion from steam and oxidation at high temperatures.
- Thermal Conductivity and Expansion: The material’s thermal properties should allow it to handle temperature changes without significant expansion or contraction, which could cause stress and damage.
2. Common Materials Used in Steam Turbine Blades
Several materials are used for steam turbine blades, each chosen based on the operating conditions of different stages of the turbine. Common materials include nickel-based superalloys, titanium alloys, stainless steels, and, more recently, advanced ceramics and composites. Each of these materials offers unique advantages and challenges, affecting the manufacturing process in different ways.
2.1 Nickel-Based Superalloys
Nickel-based superalloys are some of the most widely used materials in the high-pressure and high-temperature sections of steam turbines. These alloys are designed to maintain strength, toughness, and resistance to oxidation and creep even at temperatures exceeding 800°C.
Key Properties:
- High-Temperature Strength: Nickel-based superalloys retain their strength at temperatures where most other metals would fail. This makes them suitable for high-pressure turbine blades.
- Oxidation and Corrosion Resistance: These alloys can form a stable oxide layer that protects them from oxidation and corrosion, prolonging their service life.
- Creep Resistance: Their microstructure, often containing precipitates such as γ’ (gamma prime) phases, helps resist creep.
Common Grades:
- Inconel (e.g., Inconel 718): Known for its excellent high-temperature performance and resistance to oxidation.
- Nimonic (e.g., Nimonic 90): Offers high strength and creep resistance, ideal for blades in high-stress environments.
Impact on Manufacturing:
- Challenges in Machining: Nickel-based superalloys are difficult to machine due to their hardness. Specialized cutting tools and techniques are needed, increasing production costs.
- Precision Casting: Investment casting is often used for these alloys to create complex blade geometries. Precision is key to ensuring high-quality blades with minimal defects.
- Heat Treatment: Post-casting heat treatments are necessary to optimize the microstructure for high-temperature performance.
2.2 Titanium Alloys
Titanium alloys are used in the low-pressure sections of steam turbines, where their high strength-to-weight ratio and excellent corrosion resistance make them an attractive choice. Titanium is significantly lighter than nickel and can reduce the overall weight of the turbine, which improves efficiency.
Key Properties:
- High Strength-to-Weight Ratio: Titanium alloys are strong yet lightweight, which reduces the centrifugal forces acting on the blades.
- Corrosion Resistance: Titanium is highly resistant to corrosion, especially in environments containing moisture or impurities.
- Good Fatigue Resistance: Titanium can endure cyclic loading without significant fatigue, making it ideal for blades that undergo repeated stress.
Common Grades:
- Ti-6Al-4V: One of the most popular titanium alloys, used extensively due to its excellent combination of strength, weight, and corrosion resistance.
Impact on Manufacturing:
- Complex Machining: Titanium alloys are known for their poor machinability. They are prone to work hardening and can cause tool wear, necessitating specialized machining techniques.
- Forging: Due to the difficulty of machining, titanium turbine blades are often forged. Forging enhances the grain structure, improving strength and durability.
- Additive Manufacturing: Advances in 3D printing technology have enabled the production of titanium components with complex geometries, offering new possibilities for blade design.
2.3 Stainless Steels
Stainless steels are commonly used in low to medium-temperature sections of steam turbines. They offer a good balance of mechanical strength, corrosion resistance, and cost-effectiveness.
Key Properties:
- Corrosion Resistance: Stainless steels are resistant to rust and corrosion, especially in wet steam environments.
- Good Mechanical Strength: They can maintain adequate strength at moderate temperatures and pressures.
- Cost-Effective: Compared to superalloys and titanium, stainless steels are less expensive and easier to process.
Common Grades:
- Martensitic Stainless Steels (e.g., 410, 420): Known for their hardness and strength, used in low-temperature sections of turbines.
- Austenitic Stainless Steels (e.g., 316, 304): Offer good corrosion resistance and are easier to fabricate, but have lower strength compared to martensitic grades.
Impact on Manufacturing:
- Ease of Machining and Fabrication: Stainless steels are relatively easier to machine and weld, reducing production costs.
- Casting and Forging: Both casting and forging are viable methods for producing stainless steel blades, depending on the required properties and applications.
- Heat Treatment: Heat treatment can enhance the mechanical properties of martensitic grades, making them stronger and more durable.
2.4 Advanced Ceramics and Composites
Recent advancements have introduced the use of advanced ceramics and ceramic matrix composites (CMCs) in turbine blades. These materials offer extreme temperature resistance and light weight, which can significantly improve turbine efficiency.
Key Properties:
- Ultra-High Temperature Resistance: Ceramics can withstand temperatures that would cause metals to melt, making them ideal for next-generation turbines.
- Lightweight: Ceramic materials are much lighter than metals, reducing the overall mass and improving efficiency.
- Wear and Corrosion Resistance: Ceramics are inherently resistant to wear and corrosion, extending the life of the blades.
Common Types:
- Silicon Carbide (SiC): Often used in CMCs for high-temperature applications due to its stability and strength.
- Alumina (Al2O3): A traditional ceramic known for its hardness and thermal resistance.
Impact on Manufacturing:
- Difficult Processing: Ceramics are challenging to process due to their brittleness. Advanced manufacturing techniques, such as additive manufacturing and hot isostatic pressing (HIP), are often required.
- Complex Shaping: Traditional methods like machining can be difficult with ceramics, so near-net-shape manufacturing processes are preferred to minimize post-processing.
- High Production Costs: The production of ceramic turbine blades is currently expensive, limiting their widespread adoption. However, ongoing research aims to make these processes more cost-effective.
3. Manufacturing Processes for Steam Turbine Blades
The choice of material affects the manufacturing process of turbine blades. Below are some common manufacturing techniques and how they are influenced by material properties.
3.1 Investment Casting
Investment casting is commonly used for producing blades from superalloys and stainless steels. This process is ideal for complex geometries and allows for precise control over dimensions.
Material Impact:
- Nickel-Based Superalloys: Investment casting allows for the creation of intricate cooling channels that are essential for high-temperature performance. Superalloys’ properties can make casting challenging, requiring precise temperature control and post-casting heat treatments.
- Stainless Steels: Stainless steels are easier to cast than superalloys, making the process less costly and complex.
3.2 Forging
Forging involves shaping heated metal using compressive forces. This process is used for high-strength materials like titanium alloys and certain grades of stainless steel.
Material Impact:
- Titanium Alloys: Forging helps enhance the grain structure of titanium, improving its mechanical properties. However, due to its poor machinability, precision forging is necessary to minimize the need for further machining.
- Stainless Steels: Forging is often used for martensitic stainless steels, which are then heat-treated to achieve the desired hardness and strength.
3.3 Machining
Machining processes such as milling, grinding, and turning are used to achieve precise dimensions and smooth surface finishes.
Material Impact:
- Superalloys and Titanium: Both materials are difficult to machine due to their hardness. This requires the use of specialized cutting tools (such as carbide or ceramic tools) and techniques to reduce tool wear and prevent overheating.
- Stainless Steels: Stainless steels are easier to machine, particularly austenitic grades. This reduces the overall production time and cost.
3.4 Additive Manufacturing
Additive manufacturing, or 3D printing, is an emerging technology that allows for the production of complex geometries with minimal waste. This technique is gaining popularity for manufacturing turbine blades, especially prototypes and small batches.
Material Impact:
- Titanium and Superalloys: Additive manufacturing enables the production of intricate internal structures, such as cooling channels, that would be challenging to create through traditional methods. However, the high melting points of these materials require advanced 3D printing technologies like Electron Beam Melting (EBM) or Selective Laser Melting (SLM).
- Ceramics and Composites: 3D printing allows for precise control over ceramic shapes and internal structures, which can be beneficial for high-temperature applications. However, it is still an emerging field and has high production costs.
4. Quality Control and Testing of Turbine Blade Materials
Quality control is essential in the manufacturing of turbine blades, as even minor defects can lead to failure under extreme operating conditions. Common testing methods include:
4.1 Non-Destructive Testing (NDT)
- Ultrasonic Testing: Used to detect internal defects in materials like superalloys and titanium.
- X-Ray Inspection: Provides images of the blade’s internal structure to check for voids or cracks.
- Dye Penetrant Testing: Effective for surface defect detection, especially in forged stainless steels and titanium alloys.
4.2 Mechanical Testing
- Creep Testing: Assesses how the material will behave under constant stress at high temperatures, critical for superalloys.
- Fatigue Testing: Determines the material’s resistance to repeated stress cycles, essential for titanium alloys and stainless steels.
4.3 Microstructure Analysis
- Scanning Electron Microscopy (SEM): Used to examine the microstructure of superalloys and titanium alloys, ensuring the heat treatment and processing have achieved the desired grain structure.
5. Future Trends in Turbine Blade Material Development
Advances in materials science and manufacturing technology are driving the development of new materials and techniques for steam turbine blades.
5.1 High-Entropy Alloys (HEAs)
HEAs are a new class of materials composed of multiple principal elements that offer a balance of strength, toughness, and thermal resistance. They have the potential to improve turbine efficiency at high temperatures.
5.2 Ceramic Matrix Composites (CMCs)
CMCs, such as silicon carbide composites, are lightweight and can withstand ultra-high temperatures, making them ideal for future high-performance turbines.
5.3 Nano-Coatings and Surface Treatments
Advanced coatings are being developed to improve the corrosion and wear resistance of existing materials. Nano-coatings can provide a thin but highly durable layer, enhancing the longevity of turbine blades.
Conclusion
The choice of materials for steam turbine blades is critical to achieving efficient, reliable, and durable turbine operation. Nickel-based superalloys, titanium alloys, stainless steels, and advanced ceramics each offer unique advantages and challenges, impacting the manufacturing process, from casting and forging to machining and quality control. As technology advances, the development of new materials, such as high-entropy alloys and ceramic matrix composites, along with innovations in additive manufacturing and surface treatments, promises to further enhance the performance of turbine blades.
The ongoing improvement in turbine blade materials will contribute to higher efficiency and lower operational costs in power generation, making the choice of materials and manufacturing processes essential considerations for the future of energy production.
The Importance of Material Selection in Steam Turbine Blades: A Comprehensive Analysis
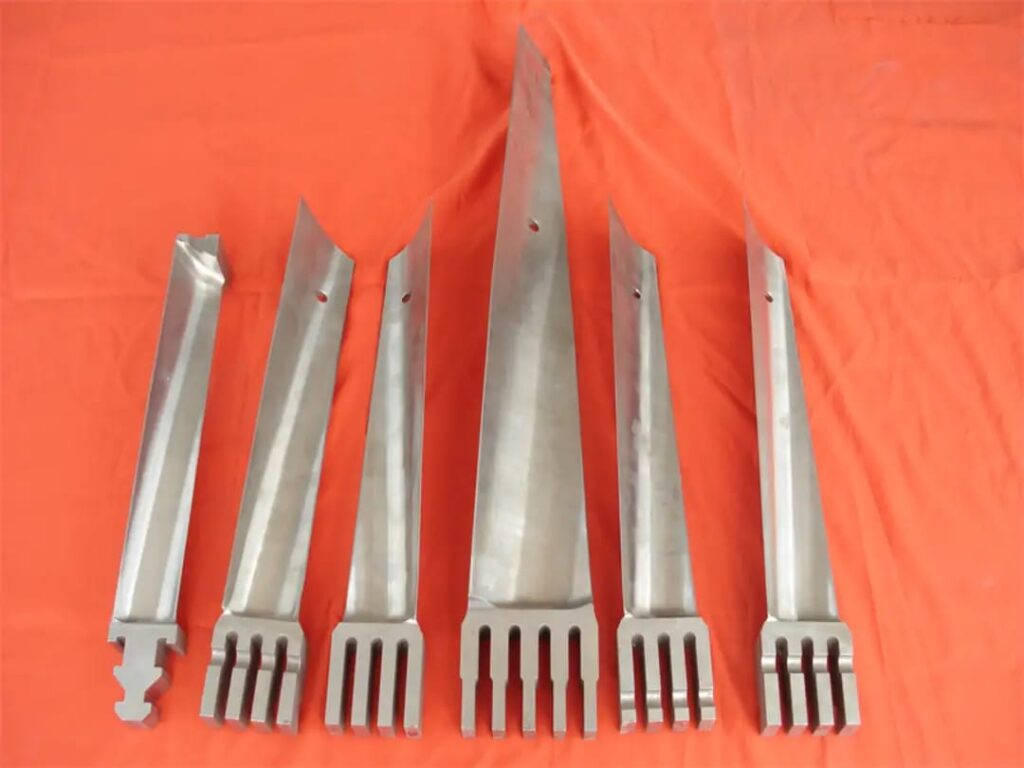
Steam turbine blades are the backbone of power generation systems, tasked with converting thermal energy from steam into mechanical energy, which is then used to generate electricity. Operating in extremely challenging environments, these blades are subjected to high temperatures, immense pressures, and substantial rotational speeds. Consequently, selecting the right material for steam turbine blades is essential for optimizing performance, efficiency, and durability. Material choice affects blade strength, resistance to wear and corrosion, creep behavior, and manufacturing viability. This comprehensive analysis will explore why material selection is crucial in steam turbine blades, covering the primary material properties required, common materials used, and the long-term impacts of appropriate material selection.
1. Key Challenges Faced by Steam Turbine Blades
Steam turbine blades must endure harsh operational conditions, which include:
- High Temperatures: Blades in high-pressure turbine sections operate at temperatures exceeding 600°C (1112°F), which can weaken materials over time and reduce their resistance to deformation.
- High Pressure and Centrifugal Forces: As turbine blades rotate at high speeds, they experience immense centrifugal forces, especially in the outer blades of the turbine, necessitating materials that can withstand high stress without deforming.
- Corrosive Environments: Steam may contain impurities, causing corrosion and oxidation over time. This effect is intensified in high-temperature, high-humidity environments, making corrosion resistance a critical material property.
- Wear and Erosion: The flow of steam and any entrained particles can lead to erosion of the blade surface, impacting the efficiency and lifespan of the turbine blades.
2. Essential Material Properties for Steam Turbine Blades
Selecting the right material for steam turbine blades requires balancing several properties to ensure the blades can withstand operational stresses while maintaining efficiency. Key material properties include:
2.1 High-Temperature Strength and Creep Resistance
- Importance: High-temperature strength ensures that the blade material can withstand the mechanical stresses at elevated temperatures without losing its structural integrity. Creep resistance is essential to prevent gradual deformation under prolonged high-temperature exposure.
- Impact of Inadequate Strength: Without sufficient high-temperature strength, blades may deform, leading to inefficient energy conversion and increased risk of blade failure.
2.2 Fatigue Resistance
- Importance: Turbine blades experience cyclic stresses due to the rotational motion and fluctuating pressure conditions. Fatigue resistance is crucial to prevent cracks and fractures caused by these repetitive stress cycles.
- Impact of Poor Fatigue Resistance: Materials with low fatigue resistance may develop microscopic cracks, leading to premature failures and potential turbine downtime.
2.3 Corrosion and Oxidation Resistance
- Importance: Turbine blades often operate in high-moisture environments and are exposed to impurities that can corrode the material over time. Oxidation resistance is also essential at elevated temperatures to prevent deterioration.
- Impact of Low Corrosion Resistance: Blades that are susceptible to corrosion can deteriorate faster, reducing their lifespan and necessitating frequent repairs or replacements.
2.4 Thermal Conductivity and Expansion
- Importance: Thermal conductivity helps dissipate heat more effectively, while low thermal expansion ensures that the blade maintains its shape and fit within the turbine as temperatures change.
- Impact of High Thermal Expansion: Materials with high thermal expansion may warp or become misaligned, leading to inefficient operation and potential contact with surrounding turbine components.
2.5 Wear and Erosion Resistance
- Importance: High-speed steam, especially when containing small abrasive particles, can erode the blade surface over time. Erosion resistance ensures that the blade surface remains intact and aerodynamic.
- Impact of Poor Erosion Resistance: Eroded blades have reduced efficiency due to changes in shape and surface roughness, which can increase drag and reduce the turbine’s power output.
3. Common Materials Used in Steam Turbine Blades
The materials chosen for steam turbine blades are typically optimized to address the various operational challenges. Common materials include nickel-based superalloys, titanium alloys, stainless steels, and emerging ceramic matrix composites. Each of these materials offers unique properties suited to different turbine sections.
3.1 Nickel-Based Superalloys
Nickel-based superalloys are commonly used in the high-pressure, high-temperature sections of turbines due to their excellent high-temperature strength, creep resistance, and oxidation resistance. These alloys typically contain nickel as the base element, along with chromium, cobalt, and aluminum to enhance specific properties.
- Advantages: Superior high-temperature performance, resistance to oxidation, and good creep resistance.
- Limitations: High cost and difficulty in machining, which requires specialized tooling and manufacturing techniques.
3.2 Titanium Alloys
Titanium alloys, known for their high strength-to-weight ratio and corrosion resistance, are used in lower-pressure stages of turbines where temperatures are lower. These alloys help reduce the overall weight of the turbine, contributing to improved efficiency and performance.
- Advantages: Lightweight, good fatigue resistance, and corrosion resistance.
- Limitations: Titanium is difficult to machine and can be costly, particularly for large components.
3.3 Stainless Steels
Stainless steels, particularly martensitic and austenitic grades, are often used in lower-temperature sections of the turbine. These steels offer a balance of mechanical strength, corrosion resistance, and cost-effectiveness.
- Advantages: Cost-effective, relatively easy to machine, and good corrosion resistance.
- Limitations: Limited performance at very high temperatures compared to superalloys and ceramics.
3.4 Advanced Ceramics and Ceramic Matrix Composites (CMCs)
Ceramics, such as silicon carbide, are increasingly being explored for use in turbine blades. These materials offer extreme temperature resistance and excellent wear properties, making them ideal for high-performance turbines.
- Advantages: High-temperature stability, excellent wear resistance, and lightweight.
- Limitations: Brittle nature and difficulty in shaping and machining make ceramics challenging to work with.
4. How Material Selection Affects Turbine Blade Performance
The material selected for turbine blades has a direct impact on their performance, affecting overall efficiency, durability, and operating costs.
4.1 Efficiency
- Aerodynamic Profiles: The choice of material allows for precise blade shapes and profiles, reducing drag and turbulence. High-quality materials enable thin, streamlined designs that enhance aerodynamic efficiency.
- Thermal Efficiency: Materials with high thermal conductivity help dissipate heat quickly, maintaining blade shape and reducing the risk of thermal expansion. This allows for higher turbine operating temperatures, increasing thermal efficiency.
4.2 Durability and Reliability
- Resistance to Creep and Fatigue: High-strength materials like nickel superalloys and titanium alloys prevent deformation, cracking, and material failure under cyclic stresses, enhancing the reliability of the turbine.
- Corrosion Resistance: Materials resistant to corrosion, such as stainless steels and nickel superalloys, are more durable, reducing maintenance frequency and downtime.
4.3 Maintenance and Lifecycle Costs
- Longer Service Life: Materials with high creep resistance, fatigue resistance, and corrosion resistance require less frequent replacements, lowering lifecycle costs.
- Reduced Maintenance Needs: Durable materials reduce the need for repairs and replacements, leading to lower maintenance costs and fewer operational interruptions.
5. Impact of Material Selection on Manufacturing Processes
Material selection influences the manufacturing processes required to produce turbine blades, as each material presents unique challenges in terms of machining, casting, and finishing.
5.1 Casting and Forging
- Nickel-Based Superalloys: Due to their high melting points and complex compositions, superalloys require investment casting processes, often followed by hot isostatic pressing (HIP) to eliminate porosity. Forging is less common for superalloys due to their brittleness at lower temperatures.
- Titanium Alloys: Titanium alloys are often forged to improve their strength and grain structure. Precision forging techniques are necessary to achieve the desired mechanical properties while minimizing waste.
- Stainless Steels: Stainless steels can be either forged or cast, depending on the specific grade and application requirements. Martensitic stainless steels are commonly heat-treated to enhance hardness and durability.
5.2 Machining and Surface Finishing
- Nickel-Based Superalloys and Titanium: Both of these materials are challenging to machine due to their hardness and high strength, requiring specialized cutting tools and techniques to prevent tool wear and overheating.
- Ceramics: Ceramic blades are particularly difficult to shape and machine due to their brittleness. Near-net-shape manufacturing and laser cutting are often used to minimize post-processing.
- Additive Manufacturing: Advanced manufacturing techniques, such as 3D printing, are increasingly used for complex materials like superalloys and ceramics. Additive manufacturing allows for complex internal cooling structures, which are essential for efficient thermal management in high-temperature applications.
5.3 Quality Control
High-quality materials require rigorous quality control processes to detect potential defects such as cracks, voids, and inclusions, which can compromise the integrity of the blades. Non-destructive testing methods, such as ultrasonic testing, X-ray inspection, and dye penetrant testing, are essential to ensure each blade meets stringent quality standards.
6. Future Trends in Material Development for Steam Turbine Blades
As turbine technology evolves to meet increasing demands for efficiency and durability, the development of new materials and advanced coatings continues to play a crucial role in enhancing blade performance.
6.1 High-Entropy Alloys (HEAs)
High-entropy alloys are a new class of materials composed of multiple principal elements. They offer an innovative approach to improving high-temperature stability and resistance to wear and corrosion. HEAs are being researched for use in turbine blades as they offer potential improvements over traditional superalloys.
6.2 Ceramic Matrix Composites (CMCs)
CMCs, especially silicon carbide-based composites, have emerged as promising materials for turbine blades due to their lightweight and ultra-high-temperature resistance. CMCs can operate at temperatures exceeding those of superalloys, potentially increasing turbine efficiency by allowing for higher operating temperatures.
6.3 Nano-Coatings and Thermal Barrier Coatings
Advanced coatings, such as nano-coatings and thermal barrier coatings, are being developed to enhance the surface properties of turbine blades. These coatings protect the blade surface from oxidation, corrosion, and wear, extending the lifespan of the material. Thermal barrier coatings, in particular, help insulate the blade, allowing for operation at higher temperatures.
7. The Long-Term Benefits of Selecting the Right Material
Proper material selection is an investment in the long-term performance and reliability of steam turbine blades. The right material choice leads to:
- Increased Efficiency: Materials with high thermal conductivity, oxidation resistance, and wear resistance help maintain the aerodynamic efficiency of the blades, leading to improved turbine performance.
- Extended Operational Lifespan: Blades made from high-quality, durable materials require fewer replacements, reducing maintenance costs and turbine downtime.
- Enhanced Safety and Reliability: Selecting the right materials minimizes the risk of material failures, contributing to safer, more reliable power generation systems.
Conclusion
Material selection for steam turbine blades is a critical factor that influences every aspect of turbine performance, from efficiency and durability to maintenance and manufacturing complexity. Nickel-based superalloys, titanium alloys, stainless steels, and advanced ceramics each offer unique properties that make them suitable for different turbine sections, each with specific operational demands. As the demand for higher efficiency and reliability continues to grow, innovations in material science will drive advancements in turbine blade design, enabling more sustainable and cost-effective energy production.
The importance of material selection in steam turbine blades cannot be overstated. By carefully choosing materials that offer the best combination of strength, resistance to wear and corrosion, and high-temperature performance, manufacturers can produce turbine blades that enhance power generation systems, reduce operational costs, and contribute to a more reliable energy infrastructure.
Common Materials Used in Steam Turbine Blades
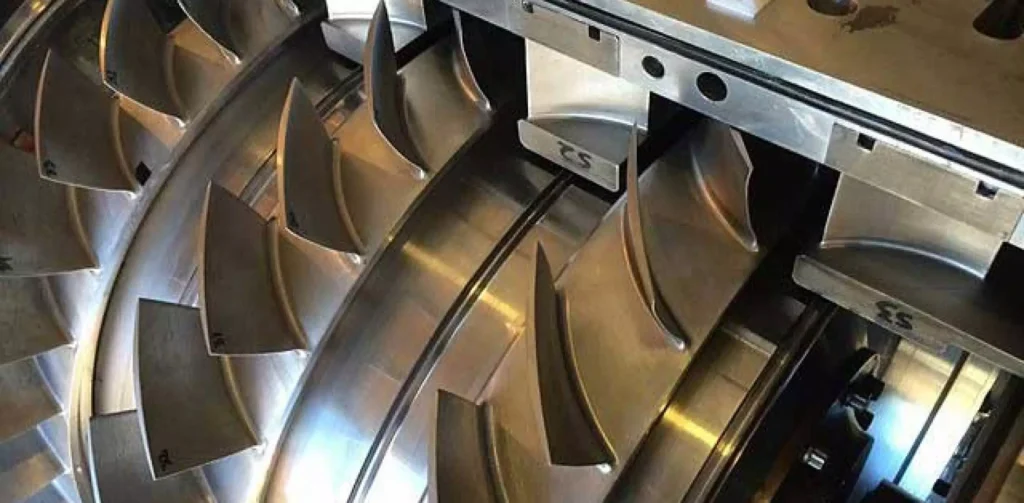
Steam turbine blades are essential components in power generation systems, and the materials used in their construction are chosen to withstand extreme conditions, including high temperatures, high pressures, and corrosive environments. Each material used in turbine blades offers a unique combination of properties that enhances performance, durability, and efficiency. Here’s an overview of the most common materials used in steam turbine blades and why they are selected for different sections of a turbine.
1. Nickel-Based Superalloys
Nickel-based superalloys are widely used in the high-temperature, high-stress sections of steam turbines, particularly in high-pressure turbine stages where the blades face extreme temperatures and high centrifugal forces.
Properties:
- High-Temperature Strength: These superalloys maintain their strength and structural integrity at temperatures exceeding 800°C (1472°F).
- Creep Resistance: Nickel superalloys are highly resistant to creep (slow deformation under stress) due to their microstructure, which often includes precipitates like the γ’ (gamma prime) phase.
- Oxidation and Corrosion Resistance: The chromium content in nickel-based superalloys forms a protective oxide layer, shielding the material from oxidation and corrosion in high-temperature environments.
Common Alloys:
- Inconel (e.g., Inconel 718): Known for excellent high-temperature performance and resistance to oxidation.
- Nimonic (e.g., Nimonic 90): Provides high strength and creep resistance, ideal for high-stress environments.
Applications:
Nickel-based superalloys are typically used in the high-pressure stages of turbines where temperatures and stresses are highest, and they are often investment cast to create complex cooling channels for thermal management.
2. Titanium Alloys
Titanium alloys are used in turbine sections where lower temperatures prevail, typically in the intermediate and low-pressure stages. Their high strength-to-weight ratio and excellent corrosion resistance make them ideal for turbine blades in these areas.
Properties:
- High Strength-to-Weight Ratio: Titanium alloys offer strength similar to that of steel but at a significantly lower weight, reducing centrifugal forces and improving efficiency.
- Corrosion Resistance: Titanium alloys resist corrosion from steam and impurities, extending the operational lifespan of the blades.
- Good Fatigue Resistance: Titanium’s resistance to cyclic loading makes it ideal for turbine blades that experience repetitive stresses.
Common Alloys:
- Ti-6Al-4V: One of the most popular titanium alloys, known for its excellent combination of strength, corrosion resistance, and fatigue performance.
Applications:
Titanium alloys are typically used in the intermediate and low-pressure stages of turbines, where reducing blade weight is beneficial and temperatures are within titanium’s operational range.
3. Stainless Steels
Stainless steels, particularly martensitic and austenitic grades, are commonly used in low to medium-temperature sections of steam turbines. They offer a good balance of mechanical strength, corrosion resistance, and cost-effectiveness, making them suitable for use in lower-temperature, lower-stress regions of the turbine.
Properties:
- Corrosion Resistance: Stainless steels form a natural chromium oxide layer that protects them from corrosion, even in moist environments.
- Good Mechanical Strength: These steels maintain adequate strength at moderate temperatures and pressures.
- Cost-Effective: Stainless steels are generally more affordable than superalloys and titanium, making them a cost-effective choice for sections with lower operational demands.
Common Grades:
- Martensitic Stainless Steels (e.g., 410, 420): Known for their hardness and strength, suitable for low-temperature sections of turbines.
- Austenitic Stainless Steels (e.g., 316, 304): Offer good corrosion resistance and are easier to fabricate, although they have lower strength compared to martensitic grades.
Applications:
Stainless steels are used in the lower-temperature sections of turbines where high strength is still required, but extreme temperatures and pressures are not a primary concern.
4. Advanced Ceramics and Ceramic Matrix Composites (CMCs)
Ceramic matrix composites (CMCs) are increasingly being explored for high-performance turbine blades, especially in cutting-edge turbine designs where high temperatures are a significant factor.
Properties:
- Ultra-High Temperature Resistance: Ceramics can withstand temperatures that would cause metals to soften or melt, making them ideal for advanced, high-temperature turbines.
- Lightweight: Ceramic materials are much lighter than metals, reducing the overall mass of the turbine and improving efficiency.
- Wear and Corrosion Resistance: Ceramics are resistant to wear and corrosion, especially in harsh environments, which can extend blade life.
Common Types:
- Silicon Carbide (SiC) Composites: Often used in ceramic matrix composites due to their stability, strength, and resistance to oxidation at high temperatures.
- Alumina (Al2O3): Known for its hardness and thermal stability, though more brittle than silicon carbide.
Applications:
CMCs and advanced ceramics are primarily used in experimental or high-efficiency turbine designs, such as in the aerospace industry, where extreme operating conditions require ultra-high temperature and wear resistance.
5. Cobalt-Based Alloys
Cobalt-based alloys, such as Stellite, are valued for their high wear resistance and ability to retain strength at moderately high temperatures. Although they are not as widely used as nickel superalloys, they serve specific applications where wear and corrosion resistance are critical.
Properties:
- Wear and Abrasion Resistance: Cobalt-based alloys are highly resistant to surface wear, making them suitable for components exposed to constant friction or abrasion.
- Good Corrosion Resistance: The chromium content in cobalt alloys provides resistance to corrosion in steam and harsh environments.
- Moderate High-Temperature Stability: While not as heat-resistant as nickel superalloys, cobalt alloys maintain their properties at elevated temperatures.
Common Alloys:
- Stellite: Known for its extreme hardness and wear resistance, often used in cutting tools and valve seats.
Applications:
Cobalt-based alloys are generally used in components where wear and erosion are primary concerns, such as valve seats and other parts of turbines that experience high friction.
6. High-Entropy Alloys (HEAs) and Future Materials
High-entropy alloys (HEAs) are a newer class of materials composed of multiple principal elements, which can provide unique properties suited for turbine applications. Although still under research, they offer potential improvements in high-temperature strength and corrosion resistance.
Properties:
- Enhanced Strength and Toughness: HEAs are engineered to maintain strength at high temperatures while resisting wear and fatigue.
- High Corrosion Resistance: Certain HEAs have shown improved corrosion resistance in high-temperature environments.
- Thermal Stability: HEAs can maintain stable microstructures at elevated temperatures, making them suitable for turbine applications.
Applications:
Currently, high-entropy alloys are primarily experimental but are being tested for use in high-performance turbine blades and other high-temperature applications.
Conclusion
The materials used in steam turbine blades—nickel-based superalloys, titanium alloys, stainless steels, cobalt-based alloys, and emerging materials like CMCs and HEAs—are each selected based on the specific demands of turbine operation. The right material choice ensures that the blades can withstand extreme temperatures, high pressures, corrosive environments, and the constant mechanical stress of rotation, all of which contribute to the efficiency, longevity, and reliability of the turbine.
In the future, as demands for energy efficiency and performance increase, advancements in materials science will continue to play a crucial role in improving turbine blade materials. This could include new compositions and manufacturing techniques that allow for even higher operating temperatures, improved corrosion resistance, and greater durability, helping to meet the energy demands of tomorrow while minimizing maintenance and operational costs.
Nickel-Based Superalloys: A Comprehensive Overview
Nickel-based superalloys are a class of high-performance materials designed to withstand extreme environments, especially those involving high temperatures, intense mechanical stress, and corrosive conditions. These alloys, often simply called “superalloys,” are primarily composed of nickel and strengthened by a complex combination of alloying elements such as chromium, cobalt, aluminum, titanium, and molybdenum. Due to their exceptional strength and stability at high temperatures, nickel-based superalloys are essential in industries like aerospace, power generation, and petrochemical processing. This comprehensive overview will explore the composition, properties, applications, manufacturing processes, and future advancements of nickel-based superalloys.
1. Introduction to Nickel-Based Superalloys
Nickel-based superalloys were developed during the 1940s as materials capable of withstanding the high temperatures and stresses of jet engines. Since then, they have become critical materials in any high-temperature application, particularly in steam turbines, gas turbines, jet engines, and nuclear reactors. These alloys are engineered to maintain mechanical properties at temperatures often exceeding 700°C (1292°F), where other metals would fail.
1.1 Defining Characteristics
- High-Temperature Strength: These alloys maintain their structural integrity and resist deformation even at high temperatures.
- Oxidation and Corrosion Resistance: Nickel superalloys resist oxidation and corrosion due to the formation of a protective oxide layer.
- Creep and Fatigue Resistance: These alloys resist long-term deformation (creep) under stress and can endure repetitive thermal and mechanical loading.
2. Composition and Alloying Elements
Nickel-based superalloys consist primarily of nickel, but they contain a range of alloying elements to enhance specific properties. The unique microstructure and composition of these alloys allow them to perform under extreme conditions.
2.1 Key Alloying Elements
- Chromium (Cr): Adds oxidation and corrosion resistance by forming a stable oxide layer on the surface.
- Cobalt (Co): Enhances strength and thermal stability, especially at elevated temperatures.
- Aluminum (Al) and Titanium (Ti): These elements form the γ’ (gamma prime) phase, which is crucial for strengthening the alloy and inhibiting dislocation movement.
- Molybdenum (Mo) and Tungsten (W): Improve high-temperature strength and resistance to creep through solid-solution strengthening.
- Tantalum (Ta) and Niobium (Nb): Enhance high-temperature stability and creep resistance, while adding to oxidation and corrosion resistance.
2.2 Microstructure of Nickel-Based Superalloys
Nickel-based superalloys have a complex microstructure with two primary phases:
- γ (Gamma) Matrix: A continuous nickel-rich matrix that provides ductility and toughness.
- γ’ (Gamma Prime) Precipitates: An intermetallic phase that forms a cubic lattice and contributes to strength. The γ’ phase hinders dislocation movement, providing creep resistance and high-temperature strength.
The unique microstructure of nickel-based superalloys allows them to retain their mechanical properties at elevated temperatures where other materials would soften and fail.
3. Properties of Nickel-Based Superalloys
The properties of nickel-based superalloys make them ideal for high-temperature and high-stress applications.
3.1 High-Temperature Strength
Nickel-based superalloys maintain their mechanical strength at temperatures above 800°C (1472°F). The γ’ precipitates within the matrix inhibit dislocation movement, preventing plastic deformation even under high stress.
3.2 Oxidation and Corrosion Resistance
The alloying elements in nickel-based superalloys, such as chromium, aluminum, and tantalum, enable the formation of a protective oxide layer that shields the material from oxidation and corrosion. This property is essential in environments where high-temperature gases and corrosive elements are present.
3.3 Creep and Fatigue Resistance
Creep, or slow deformation under prolonged stress, is a concern at high temperatures. The microstructure of nickel-based superalloys resists creep, ensuring that the material remains stable and reliable under continuous high-temperature operation. The fatigue resistance of these alloys is also critical in applications involving repeated stress cycles, such as jet engines and turbines.
3.4 Thermal Stability and Low Thermal Expansion
Nickel-based superalloys have low thermal expansion, reducing the risk of warping or misalignment at high temperatures. Their thermal stability ensures that they retain their properties under fluctuating thermal loads.
4. Applications of Nickel-Based Superalloys
Due to their exceptional properties, nickel-based superalloys are used in applications requiring high durability, reliability, and resistance to extreme conditions.
4.1 Aerospace Industry
- Jet Engine Components: Nickel-based superalloys are used in turbine blades, vanes, combustion chambers, and exhaust systems in jet engines. They can withstand the high temperatures and stresses associated with aircraft propulsion.
- Spacecraft: Components exposed to extreme heat during re-entry, such as heat shields and exhaust nozzles, use nickel-based superalloys for their heat resistance and structural integrity.
4.2 Power Generation
- Gas Turbines: Nickel-based superalloys are essential in gas turbines for power plants, where they are used in the high-temperature sections. This enables turbines to operate at higher temperatures, improving efficiency and power output.
- Steam Turbines: These superalloys are used in steam turbine blades and other components subjected to high temperatures and corrosive environments.
4.3 Oil and Gas Industry
- Chemical Processing Equipment: Nickel-based superalloys are used in pumps, valves, and piping systems where exposure to corrosive substances is common.
- Drilling Components: The wear resistance of these superalloys makes them ideal for downhole tools and drilling equipment that operate under high stress and in abrasive environments.
4.4 Nuclear Power
Nickel-based superalloys are used in reactor components, particularly in high-temperature zones where materials must resist radiation damage and maintain structural integrity under prolonged stress.
5. Manufacturing Processes for Nickel-Based Superalloys
The complex composition and microstructure of nickel-based superalloys make their manufacturing challenging. Various methods are employed to produce components with high dimensional accuracy, strength, and durability.
5.1 Investment Casting
Investment casting, also known as lost-wax casting, is commonly used to create intricate shapes such as turbine blades. The process involves creating a wax model of the component, coating it in ceramic, and then melting out the wax to leave a mold. Molten nickel-based alloy is poured into the mold, forming the component after cooling.
- Advantages: Allows for complex geometries and intricate cooling channels.
- Challenges: Requires precise control over temperature and alloy composition to avoid defects like porosity.
5.2 Forging
Forging involves shaping the alloy under high pressure and temperature, resulting in components with high strength and improved grain structure. Forged parts are denser and have better mechanical properties, making them suitable for high-stress applications.
- Advantages: Produces strong, durable components with improved grain structure.
- Challenges: Limited to simpler shapes; requires subsequent machining for complex geometries.
5.3 Powder Metallurgy
In powder metallurgy, alloy powders are compressed and sintered (heated below melting point) to create components. This method allows for precise control over the composition and properties of the alloy.
- Advantages: Enables production of components with tailored properties and reduced material waste.
- Challenges: Limited in producing larger components due to porosity concerns.
5.4 Additive Manufacturing (3D Printing)
Additive manufacturing allows for layer-by-layer construction of components, particularly beneficial for creating complex geometries. Technologies like Selective Laser Melting (SLM) and Electron Beam Melting (EBM) are used to manufacture parts from nickel-based superalloy powders.
- Advantages: Allows for complex, lightweight designs and rapid prototyping.
- Challenges: Quality control is difficult; porosity and anisotropy (variation in properties) can occur in printed parts.
6. Challenges in Using Nickel-Based Superalloys
While nickel-based superalloys are invaluable in high-temperature applications, they present unique challenges.
6.1 High Cost
The complex alloying elements used in superalloys, such as tantalum and rhenium, are expensive, contributing to the high cost of these materials. The intricate manufacturing processes also add to production costs.
6.2 Difficult Machinability
The hardness and strength of nickel-based superalloys make them difficult to machine, requiring specialized tools and techniques. This increases manufacturing time and costs and necessitates stringent quality control.
6.3 Environmental and Ethical Concerns
Certain alloying elements, such as cobalt, are mined in regions with environmental and ethical concerns. As a result, industries are seeking sustainable practices and alternatives to reduce reliance on rare elements.
7. Future Developments in Nickel-Based Superalloys
Advancements in materials science and manufacturing technology continue to push the boundaries of nickel-based superalloy performance, with ongoing research focused on improving their efficiency and reducing costs.
7.1 High-Entropy Alloys (HEAs)
High-entropy alloys, which consist of multiple principal elements, are being studied as potential alternatives to traditional superalloys. HEAs offer unique mechanical and thermal properties and have shown promise for use in high-temperature applications.
7.2 Nano-Coatings and Surface Treatments
Nano-coatings and advanced surface treatments are being developed to enhance the oxidation, corrosion, and wear resistance of nickel-based superalloys. These coatings can improve surface properties without compromising the alloy’s mechanical properties.
Titanium Alloys: A Comprehensive Overview
Titanium alloys are a group of metallic materials primarily composed of titanium, combined with other elements such as aluminum, vanadium, tin, and molybdenum to enhance specific properties. Known for their exceptional strength-to-weight ratio, corrosion resistance, and biocompatibility, titanium alloys are widely used across various industries, including aerospace, medical, automotive, and chemical processing. This overview will cover the composition, properties, types, applications, manufacturing processes, and challenges associated with titanium alloys.
1. Key Characteristics of Titanium Alloys
Titanium alloys are particularly valued for their unique combination of properties that make them suitable for demanding applications. Some of the most significant characteristics include:
1.1 High Strength-to-Weight Ratio
- Importance: Titanium alloys offer strength comparable to that of steel but at a fraction of the weight. This property is essential in applications where reducing weight is a priority, such as in aerospace and automotive engineering.
- Impact: The reduced weight allows for lighter and more fuel-efficient designs without compromising structural integrity.
1.2 Excellent Corrosion Resistance
- Importance: Titanium naturally forms a protective oxide layer, which gives it superior resistance to corrosion, especially in environments exposed to seawater, chemicals, and acids.
- Impact: This makes titanium alloys highly suitable for applications in marine, chemical processing, and medical implants, where corrosion resistance is critical.
1.3 Biocompatibility
- Importance: Titanium alloys are non-toxic and well-tolerated by the human body, making them ideal for biomedical applications such as implants and surgical tools.
- Impact: Titanium is widely used in medical devices and implants, including joint replacements, dental implants, and bone plates.
1.4 High Temperature Stability
- Importance: Certain titanium alloys maintain their strength at elevated temperatures, although their temperature resistance is lower than that of nickel-based superalloys. This property makes them suitable for some aerospace and industrial applications where moderate high-temperature performance is required.
- Impact: These alloys are used in aircraft engines and other high-temperature environments where moderate heat resistance is sufficient.
2. Types of Titanium Alloys
Titanium alloys are classified into three main categories based on their microstructure: alpha alloys, beta alloys, and alpha-beta alloys. Each type offers a distinct balance of properties that make them suitable for different applications.
2.1 Alpha Alloys
Alpha alloys contain titanium with small additions of elements such as aluminum and tin. These alloys are non-heat-treatable but offer good strength, toughness, and corrosion resistance, especially at high temperatures.
- Properties: Excellent corrosion resistance and good high-temperature stability up to 600°C (1112°F).
- Applications: Used in jet engine casings, airframes, and chemical processing equipment due to their high-temperature resistance and good corrosion performance.
2.2 Beta Alloys
Beta alloys contain transition metals like molybdenum, vanadium, and chromium, which stabilize the beta phase. These alloys are heat-treatable, meaning they can be strengthened by heat treatment, and are generally more ductile and formable.
- Properties: High strength and toughness, good formability, but less resistant to high temperatures compared to alpha alloys.
- Applications: Commonly used in applications that require high strength, such as landing gear, fasteners, and springs in the aerospace and automotive industries.
2.3 Alpha-Beta Alloys
Alpha-beta alloys contain a mix of alpha and beta stabilizing elements, providing a balance of both phases. These alloys are also heat-treatable and offer a combination of strength, ductility, and corrosion resistance.
- Properties: Good strength, excellent toughness, and corrosion resistance, and can be heat-treated to achieve desired properties.
- Common Grade: Ti-6Al-4V is the most widely used titanium alloy and represents the balance of alpha and beta phases, offering good formability, weldability, and strength.
- Applications: Used extensively in aerospace, marine, and medical applications due to its versatility and overall performance.
3. Properties of Titanium Alloys
The properties of titanium alloys are what make them versatile and valuable in various industries. Some of the key properties include:
3.1 Mechanical Strength and Lightweight
Titanium alloys are as strong as most steels but are about 40% lighter, making them highly desirable in industries that prioritize weight savings without sacrificing durability, such as aerospace and automotive.
3.2 Corrosion and Oxidation Resistance
Titanium alloys are resistant to rust and corrosion due to the oxide layer that forms on the surface. This property is beneficial for applications in harsh environments, such as marine or chemical processing.
3.3 Biocompatibility
Titanium alloys are non-toxic and compatible with human tissue, which makes them suitable for medical implants. The body readily accepts titanium without causing allergic reactions or other adverse effects, making it an ideal material for orthopedic and dental implants.
3.4 Heat Resistance
Some titanium alloys can withstand temperatures up to 600°C (1112°F), which, while not as high as nickel-based superalloys, makes them useful for moderate high-temperature applications in aerospace and industrial environments.
4. Applications of Titanium Alloys
The versatility of titanium alloys makes them suitable for a wide range of applications across various industries.
4.1 Aerospace and Defense
- Aircraft Structures: Titanium alloys are extensively used in airframes, wings, landing gear, and fasteners due to their high strength-to-weight ratio and corrosion resistance.
- Jet Engine Components: Titanium is used in compressor blades and discs, where moderate high-temperature performance is required, but excessive weight would affect engine efficiency.
- Spacecraft: The lightweight and corrosion-resistant nature of titanium makes it ideal for space exploration, including parts for satellites, rockets, and space stations.
4.2 Medical and Dental
- Orthopedic Implants: Titanium alloys, particularly Ti-6Al-4V, are commonly used in hip and knee replacements, spinal implants, and bone screws due to their biocompatibility and strength.
- Dental Implants: Titanium’s compatibility with human tissue makes it ideal for dental implants, where it can integrate with the jawbone and provide long-lasting performance.
- Surgical Instruments: Titanium is non-magnetic and can be easily sterilized, making it suitable for surgical tools and instruments.
4.3 Automotive and Motorsports
- Performance Parts: Titanium alloys are used in high-performance automotive components, such as exhaust systems, connecting rods, and valves, where reducing weight and increasing durability enhance performance.
- Motorcycles: In racing and performance motorcycles, titanium alloys are used in exhaust systems, frames, and fasteners for their strength and reduced weight, which improves speed and fuel efficiency.
4.4 Marine and Chemical Processing
- Marine Hardware: Titanium alloys are used in marine environments, such as propeller shafts, heat exchangers, and pumps, due to their corrosion resistance, especially in seawater.
- Chemical Processing Equipment: Titanium is resistant to many corrosive chemicals, making it ideal for valves, pipes, and vessels in chemical plants.
5. Manufacturing Processes for Titanium Alloys
Titanium alloys require specialized manufacturing processes due to their unique properties, such as high strength, corrosion resistance, and poor machinability.
5.1 Extraction and Refining
- Kroll Process: Most titanium is produced using the Kroll process, which involves converting titanium ore into titanium tetrachloride and then reducing it with magnesium to produce titanium sponge. The sponge is then melted and alloyed with other elements to form titanium alloys.
5.2 Forging and Forming
- Hot Forging: Titanium alloys are often hot-forged to improve their grain structure, which enhances strength and toughness. The forging process also allows for complex shapes, which are common in aerospace and automotive components.
- Cold Forming: Cold forming improves surface finish and maintains tighter tolerances, though it is more challenging due to titanium’s hardness and the risk of work-hardening.
5.3 Machining
Machining titanium alloys can be challenging due to their hardness and low thermal conductivity, which can cause tools to overheat and wear out quickly. Specialized cutting tools, coolants, and machining techniques are required to produce titanium parts without damaging tools or the material.
5.4 Additive Manufacturing (3D Printing)
- Selective Laser Melting (SLM) and Electron Beam Melting (EBM): Additive manufacturing is increasingly used to produce titanium alloy components. 3D printing allows for complex geometries and reduced material waste, particularly useful in aerospace and medical applications.
6. Challenges in Using Titanium Alloys
Despite their advantages, titanium alloys present certain challenges that must be addressed in manufacturing and design.
6.1 High Cost
Titanium alloys are expensive due to the complex extraction and refining process. The cost of raw materials and manufacturing methods limits the widespread use of titanium, particularly in industries where cost-effectiveness is a priority.
6.2 Poor Machinability
Titanium is difficult to machine due to its hardness and low thermal conductivity, which can cause overheating and increased tool wear. Specialized tools and techniques are required to machine titanium, adding to production costs.
6.3 Susceptibility to Hydrogen Embrittlement
Titanium can absorb hydrogen, leading to hydrogen embrittlement, which makes the material brittle and prone to cracking. Care must be taken to prevent hydrogen exposure during processing and application to maintain the alloy’s integrity.
7. Future Trends in Titanium Alloy Development
Ongoing research in materials science and manufacturing is driving new advancements in titanium alloys.
7.1 Low-Cost Titanium Alloys
Efforts are being made to reduce the cost of titanium production, such as improving the Kroll process or developing alternative extraction methods. These advancements could make titanium alloys more affordable and accessible for broader applications.
7.2 Enhanced Additive Manufacturing Techniques
Additive manufacturing technology for titanium alloys is evolving, allowing for the production of lightweight and complex designs with internal structures that improve strength and reduce weight. These advancements are particularly beneficial for aerospace and medical applications.
7.3 Improved Surface Treatments and Coatings
Advanced coatings, such as titanium nitride, can enhance the wear resistance and surface hardness of titanium alloys, extending their applications in high-wear environments like cutting tools and engine components.
Conclusion
Titanium alloys are among the most versatile and valuable materials used in modern engineering. Their unique combination of high strength-to-weight ratio, corrosion resistance, and biocompatibility makes them ideal for demanding applications in aerospace, medical, automotive, and marine industries. Despite challenges such as high costs and poor machinability, advances in manufacturing techniques and materials science continue to expand the use of titanium alloys.
The future of titanium alloys lies in reducing production costs, improving machining techniques, and exploring additive manufacturing to produce complex, lightweight structures. By leveraging these developments, titanium alloys will remain at the forefront of material technology, enabling more efficient, durable, and innovative designs across various industries.
Stainless Steels: A Comprehensive Overview
Stainless steels are a versatile group of iron-based alloys characterized by their high resistance to corrosion and rust. The defining feature of stainless steel is the presence of chromium, which forms a passive oxide layer on the surface, protecting it from corrosion and wear. With excellent mechanical properties and adaptability, stainless steels are used in diverse industries, including construction, automotive, medical, and food processing. This overview will cover the composition, properties, types, applications, manufacturing processes, and challenges associated with stainless steels.
1. Key Characteristics of Stainless Steels
Stainless steels are widely appreciated for a combination of properties that make them suitable for applications where corrosion resistance, durability, and aesthetics are essential. Key characteristics include:
1.1 Corrosion Resistance
- Importance: The chromium content in stainless steel reacts with oxygen to form a thin, stable oxide layer that protects against corrosion, even in wet and humid conditions.
- Impact: Stainless steels maintain their appearance and strength in various environments, from kitchen settings to corrosive industrial processes.
1.2 Strength and Durability
- Importance: Stainless steels have a range of strengths, from moderate to high, depending on the alloy and heat treatment. This strength makes them suitable for structural and load-bearing applications.
- Impact: This strength and durability make stainless steel a preferred choice in industries requiring long-lasting materials, such as construction and heavy equipment manufacturing.
1.3 Aesthetic Appeal
- Importance: Stainless steels can be polished to a high gloss or brushed to achieve various finishes, adding aesthetic value to architectural and decorative applications.
- Impact: The smooth, reflective surface enhances visual appeal, making stainless steel popular for modern building facades, sculptures, and kitchen appliances.
2. Types of Stainless Steels
Stainless steels are divided into different types based on their microstructure and alloying elements, each offering unique properties and advantages. The primary types are austenitic, ferritic, martensitic, duplex, and precipitation-hardening stainless steels.
2.1 Austenitic Stainless Steels
Austenitic stainless steels are the most commonly used type, known for their excellent corrosion resistance, formability, and weldability. They contain high levels of chromium and nickel and have a face-centered cubic (FCC) crystal structure.
- Properties: Excellent corrosion resistance, non-magnetic, and good toughness, even at low temperatures.
- Common Grades: 304 Stainless Steel (versatile and widely used) and 316 Stainless Steel (improved corrosion resistance with added molybdenum).
- Applications: Used in food processing, chemical plants, medical equipment, and kitchen utensils.
2.2 Ferritic Stainless Steels
Ferritic stainless steels have a body-centered cubic (BCC) structure and contain moderate chromium with little or no nickel. They offer good corrosion resistance and are less expensive than austenitic steels but have lower toughness.
- Properties: Magnetic, good corrosion resistance, and moderate strength, but lower weldability and ductility.
- Common Grades: 430 Stainless Steel (used in automotive trim) and 409 Stainless Steel (used in exhaust systems).
- Applications: Used in automotive, home appliances, and architectural components.
2.3 Martensitic Stainless Steels
Martensitic stainless steels are characterized by high strength and hardness, achieved through heat treatment. They have a body-centered tetragonal (BCT) crystal structure and contain chromium with limited nickel and carbon content.
- Properties: High hardness and strength, moderate corrosion resistance, and magnetic.
- Common Grades: 410 Stainless Steel (used for cutlery) and 420 Stainless Steel (used in surgical instruments).
- Applications: Used in cutlery, surgical tools, valves, and other applications requiring high hardness.
2.4 Duplex Stainless Steels
Duplex stainless steels have a microstructure that combines austenitic and ferritic phases, offering higher strength than austenitic stainless steels and improved corrosion resistance, especially against chloride-induced stress corrosion cracking.
- Properties: High strength, good weldability, excellent corrosion resistance, and magnetic.
- Common Grades: 2205 Duplex Stainless Steel and 2507 Super Duplex Stainless Steel (for extreme corrosion resistance).
- Applications: Used in the oil and gas industry, chemical processing, and marine applications.
2.5 Precipitation-Hardening (PH) Stainless Steels
Precipitation-hardening stainless steels can be strengthened through a heat treatment process called aging, providing high strength and moderate corrosion resistance.
- Properties: High strength, excellent toughness, and good corrosion resistance.
- Common Grades: 17-4 PH Stainless Steel (used for its high strength and corrosion resistance) and 15-5 PH Stainless Steel.
- Applications: Used in aerospace, valves, gears, and high-performance components.
3. Properties of Stainless Steels
The properties of stainless steels vary depending on the type, but some common properties make them ideal for a wide range of applications.
3.1 Corrosion and Oxidation Resistance
Stainless steels resist corrosion due to their chromium content, which forms a passive oxide layer on the surface. This property is essential in environments where exposure to moisture, acids, and chemicals is common.
3.2 Strength and Toughness
Depending on the alloy and heat treatment, stainless steels offer a range of strengths. Martensitic and precipitation-hardening grades, for example, can achieve high hardness and strength through heat treatment.
3.3 Formability and Weldability
Austenitic stainless steels, in particular, are known for their excellent formability and weldability, making them suitable for complex shapes and assemblies. Ferritic and duplex grades are less formable and require careful welding to prevent cracking.
3.4 Temperature Resistance
Certain stainless steels can withstand both high and low temperatures. Austenitic grades retain toughness at cryogenic temperatures, while martensitic grades offer good performance at moderately elevated temperatures.
4. Applications of Stainless Steels
Stainless steels are used across a wide range of industries due to their durability, aesthetic appeal, and versatility.
4.1 Construction and Architecture
- Building Facades and Roofing: Stainless steel is used in architectural projects for its durability and aesthetic appeal, often with a polished or brushed finish for a modern look.
- Structural Components: Stainless steels are used in bridges, railway stations, and other infrastructure for their resistance to corrosion and strength.
4.2 Food and Beverage Industry
- Processing Equipment: Stainless steels are widely used in food processing equipment like tanks, pipes, and conveyor systems due to their corrosion resistance and ease of cleaning.
- Kitchen Utensils: Cutlery, cookware, and appliances are often made from stainless steel due to its hygiene, durability, and ease of maintenance.
4.3 Automotive and Transportation
- Exhaust Systems: Stainless steels, especially ferritic grades, are used in exhaust systems due to their corrosion resistance and ability to withstand high temperatures.
- Structural Parts and Fasteners: Stainless steel fasteners and structural parts are used in vehicles, ships, and trains for strength and corrosion resistance.
4.4 Medical and Pharmaceutical
- Surgical Instruments and Implants: Stainless steels, especially 316L and 420, are used in surgical instruments, implants, and medical devices for their biocompatibility and corrosion resistance.
- Pharmaceutical Equipment: Tanks, mixers, and piping used in pharmaceutical manufacturing are often made of stainless steel for cleanliness and to avoid contamination.
5. Manufacturing Processes for Stainless Steels
The production of stainless steels involves melting, alloying, forming, and finishing processes, each tailored to achieve the desired properties.
5.1 Melting and Alloying
- Electric Arc Furnace (EAF): Stainless steel production typically starts with melting raw materials in an electric arc furnace. Alloying elements like chromium, nickel, and molybdenum are added to achieve the desired properties.
5.2 Hot and Cold Rolling
- Hot Rolling: The steel is heated and passed through rollers to achieve the desired shape and thickness. Hot rolling improves ductility and is often followed by cold rolling for improved surface finish.
- Cold Rolling: Used for thinner and more precise products, cold rolling provides a better surface finish, strength, and tighter tolerances.
5.3 Annealing and Heat Treatment
Annealing is used to soften stainless steel and relieve internal stresses, enhancing ductility and making the material easier to form and weld. Certain grades, such as martensitic and precipitation-hardening stainless steels, require additional heat treatments to achieve high strength and hardness.
5.4 Surface Finishing
Stainless steel surfaces can be finished in various ways, including polishing, brushing, and electroplating. Surface finishing enhances appearance and corrosion resistance, with finishes ranging from mirror polish to satin and matte.
6. Challenges in Using Stainless Steels
Despite their advantages, stainless steels present some challenges.
6.1 Cost of Alloying Elements
The cost of alloying elements like chromium, nickel, and molybdenum makes stainless steels more expensive than carbon steels. Efforts to reduce costs include developing lean compositions with lower nickel and higher nitrogen content.
6.2 Difficulties in Machining and Welding
Certain grades of stainless steel are challenging to machine due to their hardness and work-hardening properties, leading to increased tool wear and production costs. Ferritic and martensitic grades can be difficult to weld and may crack if proper welding techniques are not used.
6.3 Susceptibility to Stress Corrosion Cracking
While stainless steels resist corrosion, certain grades are susceptible to stress corrosion cracking (SCC) in chloride-rich environments, limiting their use in certain applications. Duplex stainless steels are more resistant to SCC, offering a better alternative in such conditions.
7. Future Trends in Stainless Steel Development
The stainless steel industry continues to evolve with new compositions, manufacturing technologies, and sustainable practices.
7.1 Development of Lean Duplex Stainless Steels
Lean duplex stainless steels, which have lower nickel content, offer a cost-effective alternative with a balance of strength and corrosion resistance. These materials are designed to meet the growing demand for affordable, high-performance stainless steels.
7.2 Advanced Additive Manufacturing
Additive manufacturing, or 3D printing, is being used to create complex stainless steel components that are challenging to produce with traditional methods. This technology provides greater design flexibility and reduces material waste.
7.3 Sustainable Production and Recycling
The stainless steel industry is moving toward sustainable practices, including recycling and energy-efficient production methods. Stainless steel is already highly recyclable, and advancements in green manufacturing processes further reduce its environmental impact.
Conclusion
Stainless steels are among the most widely used materials worldwide, offering an excellent combination of corrosion resistance, strength, durability, and aesthetic appeal. Their versatility makes them indispensable across various industries, from construction and food processing to medical and automotive.
While stainless steels face challenges such as high costs and machining difficulties, ongoing innovations in materials science and manufacturing technology continue to expand their capabilities. The future of stainless steel will likely include new alloy compositions, advancements in additive manufacturing, and a focus on sustainability.
By leveraging these advancements, stainless steels will remain at the forefront of material technology, enabling more efficient, cost-effective, and environmentally friendly applications across multiple sectors.
EMS Power Machines
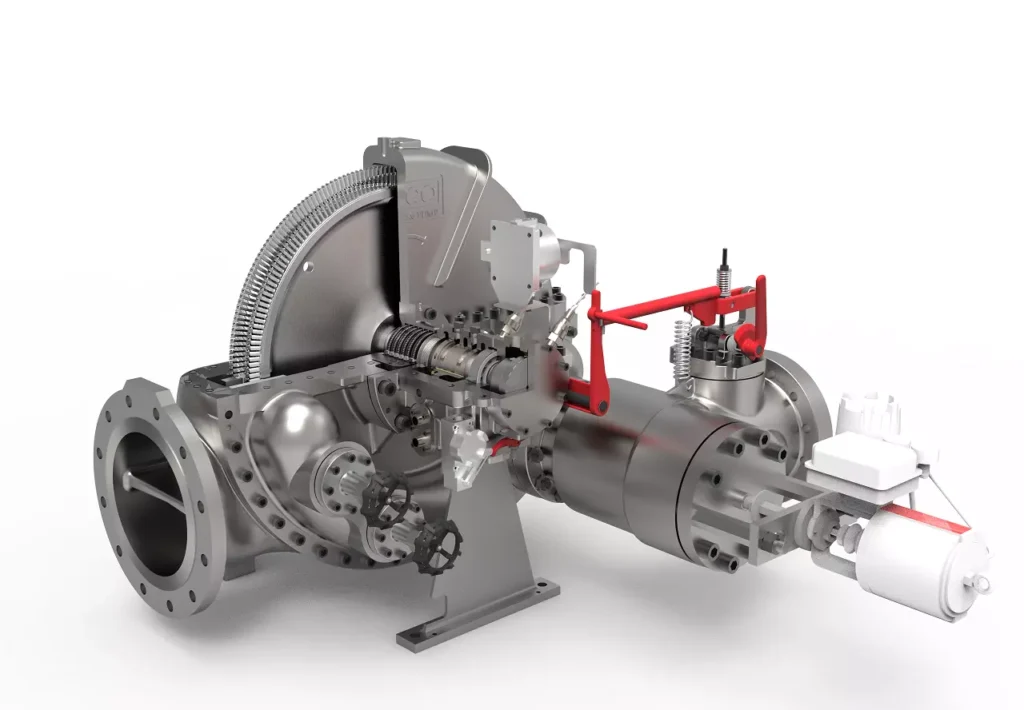
We design, manufacture and assembly Power Machines such as – diesel generators, electric motors, vibration motors, pumps, steam engines and steam turbines
EMS Power Machines is a global power engineering company, one of the five world leaders in the industry in terms of installed equipment. The companies included in the company have been operating in the energy market for more than 60 years.
EMS Power Machines manufactures steam turbines, gas turbines, hydroelectric turbines, generators, and other power equipment for thermal, nuclear, and hydroelectric power plants, as well as for various industries, transport, and marine energy.
EMS Power Machines is a major player in the global power industry, and its equipment is used in power plants all over the world. The company has a strong track record of innovation, and it is constantly developing new and improved technologies.
Here are some examples of Power Machines’ products and services:
- Steam turbines for thermal and nuclear power plants
- Gas turbines for combined cycle power plants and industrial applications
- Hydroelectric turbines for hydroelectric power plants
- Generators for all types of power plants
- Boilers for thermal power plants
- Condensers for thermal power plants
- Reheaters for thermal power plants
- Air preheaters for thermal power plants
- Feedwater pumps for thermal power plants
- Control systems for power plants
- Maintenance and repair services for power plants
EMS Power Machines is committed to providing its customers with high-quality products and services. The company has a strong reputation for reliability and innovation. Power Machines is a leading provider of power equipment and services, and it plays a vital role in the global power industry.
EMS Power Machines, which began in 1961 as a small factory of electric motors, has become a leading global supplier of electronic products for different segments. The search for excellence has resulted in the diversification of the business, adding to the electric motors products which provide from power generation to more efficient means of use.