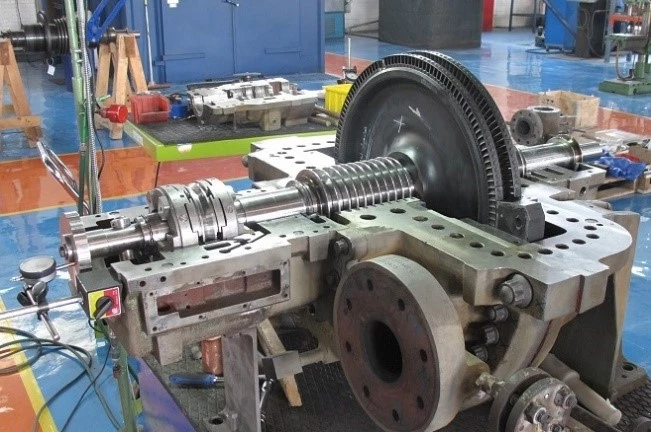
Modern Steam Engines for Sale: Steam turbines and engines have been at the heart of power generation for over a century. From the early days of industrialization to the modern era, these machines have evolved significantly in design, efficiency, and application. A steam turbine is a device that converts the thermal energy of steam into mechanical work, which can then be used to generate electricity or drive mechanical processes.
Turbine Machine: The basic principle behind a turbine machine is the conversion of energy. In a steam turbine, this involves converting high-pressure, high-temperature steam into rotational energy through a series of blades or vanes. This rotational energy is then used to drive a generator, which produces electricity.
Turbine Generator Working Principle: The working principle of a turbine generator is straightforward yet complex. As steam passes through the turbine, it causes the blades to spin. This spinning motion drives the generator’s rotor, producing electricity through electromagnetic induction. The efficiency of this process depends on various factors, including the design of the turbine, the pressure and temperature of the steam, and the quality of the generator.
Types of Steam Turbines
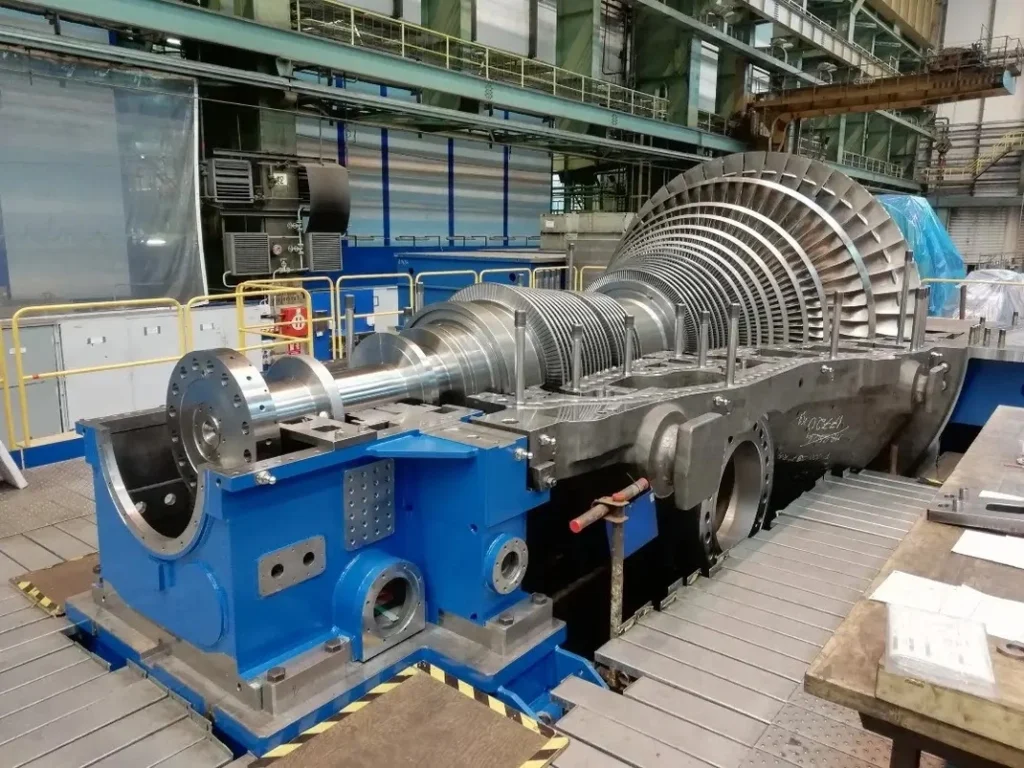
Steam turbines come in various types, each designed for specific applications and operating conditions. The two primary categories are impulse and reaction turbines.
Impulse Turbine Definition and Operation: An impulse turbine operates by directing steam through nozzles at high velocity onto the turbine blades. The steam pressure drops across the nozzles, converting potential energy into kinetic energy. The Curtis stage turbine is a common example of an impulse turbine, utilizing multiple stages to extract energy more efficiently.
Curtis Stage Turbine: Named after its inventor, Charles G. Curtis, this turbine uses a series of rotating and stationary blades to gradually reduce the steam’s energy, maximizing efficiency. The Curtis stage turbine is particularly effective in applications where a significant reduction in steam pressure is required.
Impulse Reaction Turbine: In contrast to impulse turbines, reaction turbines operate on the principle that steam expands and accelerates as it passes through both stationary and moving blades. The difference in design leads to variations in efficiency, maintenance requirements, and ideal operating conditions.
Steam Cycle and Its Components
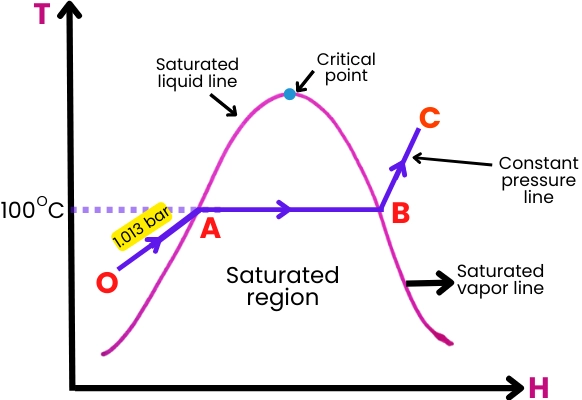
The steam cycle, often referred to as the Rankine cycle, is the fundamental thermodynamic process that underpins the operation of steam turbines in power generation. Understanding the steam cycle and its components is crucial for optimizing the efficiency and performance of thermal power plants. This section delves into the intricacies of the steam cycle diagram, the role of steam condensers, and the function of steam nozzle converts in energy conversion within turbines.
The Steam Cycle Diagram Explained
At its core, the steam cycle diagram illustrates the sequential processes that steam undergoes to generate mechanical and electrical energy. The primary stages include heating, expansion, condensation, and pumping. Here’s a step-by-step breakdown:
- Water Pumping (Pumping Stage):
- Function: The cycle begins with water being pumped from a low-pressure reservoir into a high-pressure boiler.
- Process: The pump increases the pressure of the water, preparing it for efficient heating. Although pumps consume energy, their role is vital in maintaining the cycle’s continuity.
- Boiling (Heating Stage):
- Function: High-pressure water is heated in the boiler to produce steam.
- Process: Heat is supplied to the water, typically through the combustion of fossil fuels or other energy sources, elevating its temperature and pressure until it becomes saturated or superheated steam.
- Expansion in the Turbine (Expansion Stage):
- Function: The high-pressure steam expands through the turbine, converting thermal energy into mechanical work.
- Process: As steam passes through the turbine blades, it loses pressure and temperature while gaining velocity, driving the turbine rotor to generate rotational energy.
- Condensation (Condensation Stage):
- Function: After expansion, the steam enters the condenser, where it is cooled and condensed back into water.
- Process: The condenser removes residual heat from the steam, often using cooling water from a nearby source. This phase change from gas to liquid is essential for maintaining a vacuum and enhancing the turbine’s efficiency.
- Recirculation (Return to Pumping Stage):
- Function: The condensed water is returned to the pump, completing the cycle.
- Process: By recycling the water, the system ensures a continuous flow of the working fluid, sustaining the power generation process.
The steam cycle diagram provides a visual representation of these stages, highlighting the flow of energy and the transformation of water into steam and back. Key points on the diagram typically include the boiler, turbine, condenser, and pump, each connected by lines indicating the flow of steam and water.
Role of Steam Condensers
Steam condensers play a pivotal role in the efficiency of the steam cycle. Their primary function is to convert exhaust steam from the turbine back into liquid water, enabling the cycle to repeat. Several critical aspects highlight the importance of condensers:
- Heat Rejection:
- Function: Condensers reject the residual heat carried by the steam after it has passed through the turbine.
- Process: By removing this heat, condensers help maintain a low-pressure environment at the turbine’s exhaust, which is essential for maximizing the turbine’s efficiency.
- Maintaining Vacuum:
- Function: Creating a vacuum in the condenser reduces the back pressure on the turbine.
- Process: A lower exhaust pressure allows the turbine to extract more energy from the steam during expansion, improving overall performance.
- Water Recovery:
- Function: Condensers facilitate the recovery of water for reuse in the cycle.
- Process: By condensing the steam back into water, condensers ensure that the working fluid remains within the system, minimizing water consumption and operational costs.
- Types of Condensers:
- Surface Condensers: Use cooling water to absorb heat from the steam without direct contact.
- Jet Condensers: Introduce a spray of cooling water directly into the steam, allowing for rapid heat transfer.
- Air-Cooled Condensers: Utilize ambient air to cool and condense the steam, reducing dependency on water sources.
The efficiency of a steam condenser directly impacts the overall efficiency of the power plant. Advanced materials and design innovations continue to enhance condenser performance, contributing to more sustainable and cost-effective power generation.
Steam Nozzle Converts: Energy Conversion in Turbines
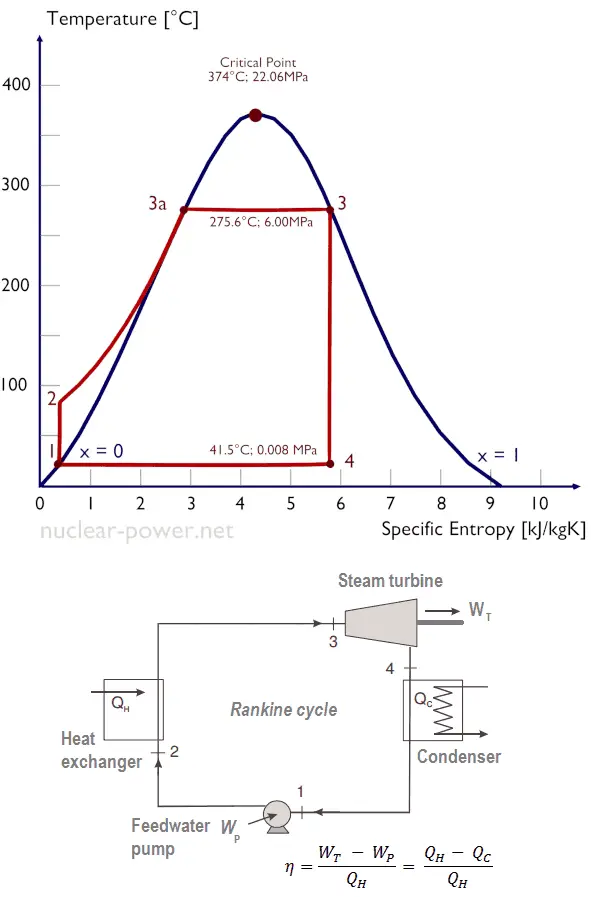
Steam nozzle converts are integral components within steam turbines, responsible for the precise conversion of thermal energy into kinetic energy. Their design and operation significantly influence the turbine’s efficiency and performance. Here’s an in-depth look at their functionality:
- Function of Steam Nozzles:
- Energy Conversion: Steam nozzles accelerate the steam to high velocities, directing it onto the turbine blades with optimal force.
- Pressure Reduction: As steam passes through the nozzles, its pressure drops, facilitating the conversion of pressure energy into kinetic energy.
- Types of Steam Nozzles:
- Convergent Nozzles: Narrow towards the exit, suitable for subsonic steam velocities.
- Convergent-Divergent Nozzles: Narrow at the throat and widen towards the exit, enabling supersonic steam velocities, crucial for high-efficiency turbines.
- Design Considerations:
- Shape and Geometry: The nozzle’s shape must ensure smooth acceleration of steam, minimizing turbulence and energy losses.
- Material Selection: High-temperature-resistant materials are essential to withstand the harsh conditions within the turbine.
- Operational Impact:
- Blade Loading: Properly designed nozzles ensure uniform steam distribution across turbine blades, preventing uneven loading and mechanical stress.
- Efficiency Optimization: Efficient steam nozzles maximize the conversion of thermal energy into mechanical work, enhancing the turbine’s overall efficiency.
- Advanced Technologies:
- Variable Geometry Nozzles: Allow for adjustments in nozzle shape and size based on operating conditions, providing flexibility and maintaining optimal performance across varying loads.
- Aerodynamic Enhancements: Incorporating aerodynamic features reduces energy losses and improves steam flow characteristics.
The steam nozzle converts are thus critical in ensuring that the energy within the steam is effectively harnessed by the turbine. Innovations in nozzle design continue to drive improvements in turbine efficiency, contributing to more sustainable and powerful energy generation systems.
Integration of Components in the Steam Cycle
The seamless integration of the steam cycle’s components—boiler, turbine, condenser, and pump—is essential for maintaining a stable and efficient power generation process. Each component interacts dynamically, responding to changes in load demands and operational conditions.
- Thermodynamic Efficiency:
- The efficiency of the steam cycle is influenced by the temperature and pressure differences between the boiler and condenser.
- Maximizing the temperature and pressure at the boiler while minimizing the condenser pressure enhances the cycle’s efficiency.
- Heat Exchange Optimization:
- Effective heat exchange in the boiler and condenser ensures that energy is utilized optimally, reducing waste and improving performance.
- Advanced heat exchanger designs, such as economizers and superheaters, further enhance thermal efficiency.
- Control Systems:
- Automated control systems regulate the flow of steam, water, and cooling agents, maintaining optimal operating conditions.
Expansion in the Turbine (Expansion Stage):
- Function: The high-pressure steam enters the turbine, where it expands and loses pressure. This expansion drives the turbine blades, converting the steam’s thermal energy into mechanical work.
- Process: The steam’s pressure and temperature drop significantly as it passes through multiple stages of the turbine, each stage designed to extract as much energy as possible. The mechanical work generated by the turbine is then used to drive an electrical generator, producing electricity.
- Condensation (Condensation Stage):
- Function: After passing through the turbine, the low-pressure steam enters a condenser, where it is cooled and converted back into water.
- Process: In the condenser, the steam releases its remaining thermal energy and condenses into water. This process is typically aided by cooling water from a nearby river, lake, or cooling tower. The condensation process is crucial for maintaining the efficiency of the steam cycle, as it allows the water to be recycled back into the boiler.
- Feedwater Heating (Optional):
- Function: Before the condensed water returns to the boiler, it may pass through a series of feedwater heaters.
- Process: Feedwater heaters use extracted steam from various turbine stages to preheat the water. This increases the overall efficiency of the cycle by reducing the amount of fuel required to heat the water to its boiling point.
Role of Steam Condensers
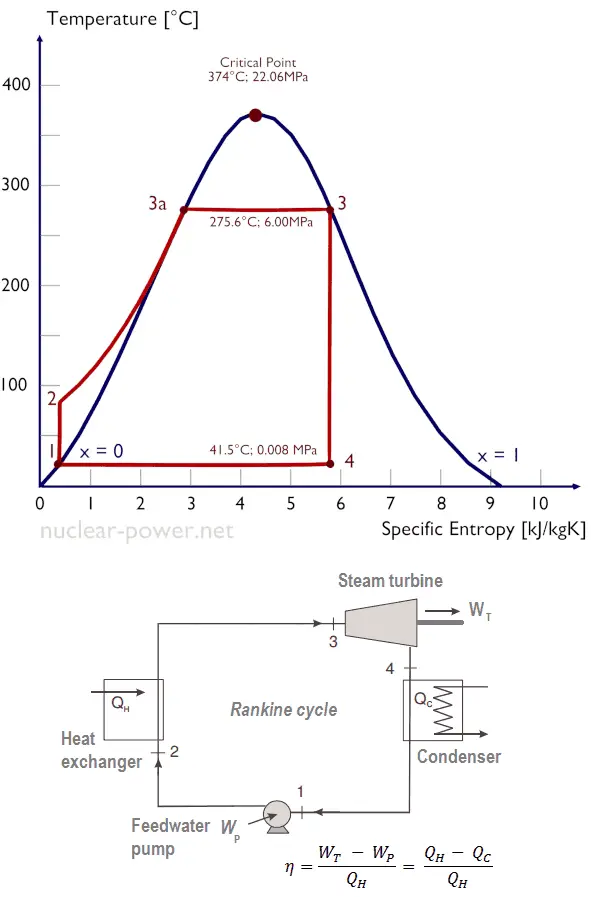
Steam condensers play a vital role in the efficiency of the steam cycle by facilitating the condensation of steam back into water. Their primary functions include:
- Maintaining Vacuum Pressure: By condensing steam and creating a vacuum, condensers reduce the back pressure on the turbine, allowing it to operate more efficiently.
- Heat Rejection: Condensers remove waste heat from the cycle, typically transferring it to a cooling medium like water or air.
- Water Recovery: By converting steam back into water, condensers enable the reuse of water in the cycle, reducing the need for fresh water and minimizing environmental impact.
There are several types of condensers, including surface condensers and evaporative condensers, each suited to different operational conditions and plant designs. The choice of condenser type affects the overall efficiency and maintenance requirements of the power plant.
Steam Nozzle Converts: Energy Conversion in Turbines
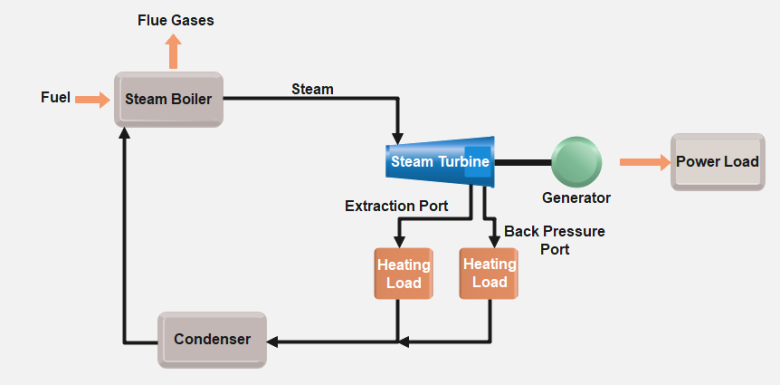
Steam nozzles are critical components in the energy conversion process within turbines. They convert the thermal energy of steam into kinetic energy, which drives the turbine blades. The key functions and types of steam nozzles include:
- Energy Conversion: Steam nozzles accelerate steam to high velocities, converting its thermal energy into kinetic energy. This high-velocity steam then impinges on the turbine blades, causing them to rotate.
- Types of Nozzles:
- Convergent Nozzles: These nozzles are used when the steam flow needs to be accelerated, typically in impulse turbines.
- Divergent Nozzles: Used when the steam flow needs to be decelerated, though less common in steam turbines.
- Convergent-Divergent Nozzles: Often used in high-pressure applications, these nozzles initially converge to accelerate steam and then diverge to manage pressure drops.
The design and efficiency of the steam nozzles significantly impact the overall performance of the turbine, affecting both power output and operational efficiency.
Low Pressure Turbines in Thermal Power Plants
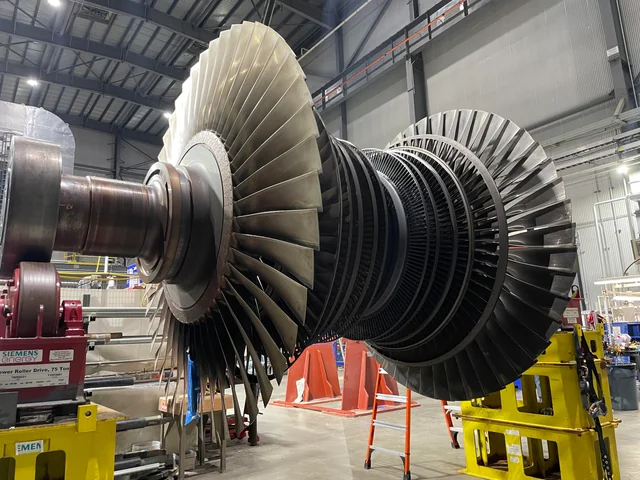
Low-pressure turbines (LPTs) are crucial components in thermal power plants, particularly in the later stages of the steam cycle where the steam pressure is significantly reduced after passing through the high-pressure and intermediate-pressure turbines. This section explores the role of LPTs, their design considerations, and their interaction with intermediate-pressure (IP) steam.
Role and Importance of Low Pressure Turbines
Low-pressure turbines handle steam that has already expanded through high-pressure (HP) and intermediate-pressure (IP) turbines. The key functions of LPTs include:
- Energy Extraction: Even at low pressure, steam still possesses significant energy. LPTs extract the remaining energy from the steam, converting it into mechanical work that can drive a generator.
- Operational Efficiency: LPTs contribute to the overall efficiency of the power plant by maximizing the energy extracted from steam before it is condensed in the condenser. They are designed to operate efficiently at low pressures and temperatures, often dealing with steam that is only slightly above saturation.
Design and Efficiency Considerations
Designing low-pressure turbines involves several unique challenges:
- Blade Design: LPT blades are typically longer and larger in diameter compared to HP and IP turbine blades. This design allows for efficient energy extraction from the low-pressure steam. However, the larger blades also introduce mechanical stresses, making material selection and aerodynamic design critical.
- Moisture Handling: As steam expands in the LPT, it often reaches saturation, leading to moisture formation. This moisture can cause erosion on the turbine blades if not properly managed. Therefore, LPTs are designed with features that minimize moisture-related damage.
- Thermal Expansion: The large size and operating conditions of LPTs necessitate careful management of thermal expansion. Turbine casings and blades must be designed to accommodate expansion without causing misalignment or mechanical failure.
Interaction with IP Steam Pressure
Low-pressure turbines operate in conjunction with intermediate-pressure turbines in a coordinated manner:
- Steam Routing: After passing through the IP turbine, the steam is directed into the LPT. The pressure and temperature of the steam at this point are critical for optimizing the performance of the LPT. IP steam pressure must be carefully managed to ensure that the LPT operates within its design parameters.
- Efficiency Optimization: By carefully controlling the IP steam pressure and temperature, power plant operators can optimize the performance of both the IP and LPT stages. This optimization often involves fine-tuning the reheating process and managing the flow rate of steam between the turbine stages.
Control and Regulation in Steam Turbines
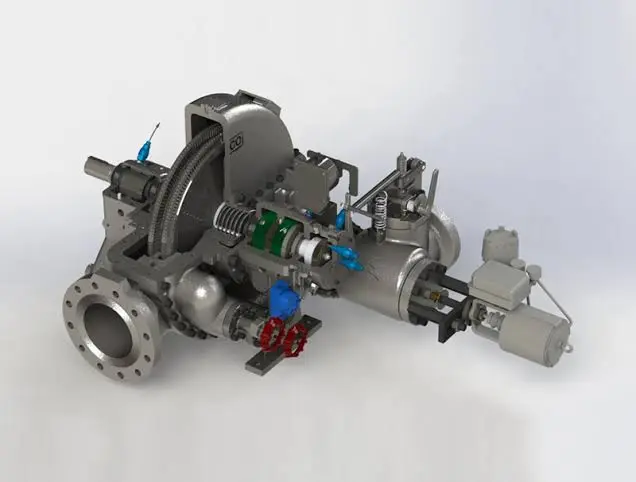
The efficient operation of steam turbines depends not only on their design but also on sophisticated control and regulation systems. These systems ensure that the turbine operates safely, reliably, and efficiently under varying load conditions. This section discusses the role of steam governors, control mechanisms, and safety features.
What is a Steam Governor?
A steam governor is a device used to regulate the speed and output of a steam turbine by controlling the flow of steam into the turbine. The main functions of a steam governor include:
- Speed Regulation: The governor adjusts the steam flow to maintain a constant turbine speed, regardless of changes in load demand. This is crucial for stable power generation, as fluctuations in turbine speed can lead to frequency variations in the electrical grid.
- Load Matching: By regulating the steam flow, the governor ensures that the turbine’s power output matches the load demand. This helps in maintaining grid stability and preventing overloading of the turbine.
- Safety Control: Governors also serve as a safety mechanism by preventing the turbine from overspeeding. In case of a sudden drop in load, the governor quickly reduces the steam flow to avoid mechanical damage to the turbine.
Steam Turbine Control Mechanisms
Steam turbine control systems are complex and involve various mechanisms that work together to ensure efficient and safe operation. Key components of turbine control systems include:
- Throttle Valves: These valves control the flow of steam into the turbine. By adjusting the opening of the throttle valves, the control system regulates the amount of steam entering the turbine, thereby controlling its speed and power output.
- Extraction Control: In some turbines, steam is extracted at intermediate stages for heating or other processes. The extraction control system manages the amount of steam diverted from the turbine, balancing power generation with other operational needs.
- Reheat Control: In power plants with reheat cycles, the control system manages the reheating process, ensuring that steam re-entering the turbine at intermediate stages is at the optimal temperature and pressure.
- Emergency Stop Systems: In case of a malfunction or emergency, the turbine control system includes mechanisms to rapidly shut down the turbine. This might involve closing throttle valves and activating brakes to quickly bring the turbine to a stop.
Safety Features and Efficiency Improvements
Modern steam turbines are equipped with various safety features and efficiency enhancements, including:
- Overspeed Protection: To prevent damage due to overspeeding, turbines are fitted with sensors and automatic shutdown mechanisms that activate if the turbine exceeds its maximum safe speed.
- Vibration Monitoring: Continuous monitoring of turbine vibrations helps detect imbalances or mechanical faults early, allowing for timely maintenance and preventing catastrophic failures.
- Load-Shedding Capability: In case of a grid disturbance, turbines can be designed to quickly reduce load or shut down to protect both the turbine and the electrical grid.
- Advanced Control Algorithms: Modern control systems use sophisticated algorithms to optimize turbine operation, improving efficiency by fine-tuning steam flow, temperature, and pressure in real-time.
Modern Steam Engines and Small-scale Applications
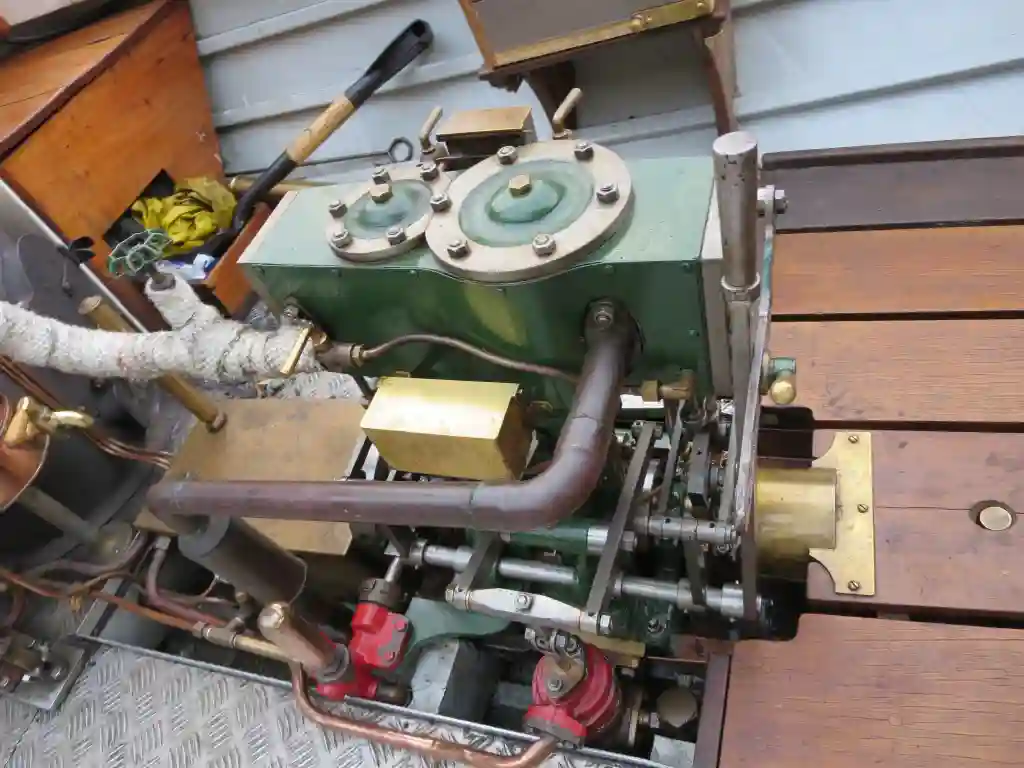
While large-scale steam turbines dominate the power generation industry, modern steam engines still find applications in smaller-scale, specialized contexts. This section explores the features, advantages, and applications of small-scale steam engines, including those available for sale today.
10 hp Steam Engine for Sale: Applications and Advantages
A 10 hp steam engine represents a small, versatile power source that can be used in various applications, particularly where electricity is not readily available or in off-grid settings. Key features and benefits include:
- Portability: These engines are compact and can be transported to remote locations, making them ideal for agricultural operations, sawmills, and other off-grid applications.
- Fuel Flexibility: Small steam engines can run on a variety of fuels, including wood, coal, and biomass, providing flexibility in resource-limited areas.
- Reliability: With fewer moving parts compared to internal combustion engines, steam engines are robust and require less maintenance, making them suitable for long-term, unattended operation.
- Educational Use: These engines are also used in educational settings to demonstrate the principles of thermodynamics and mechanical engineering.
Modern Steam Engines for Sale: Advances in Design and Efficiency
Modern steam engines, available for sale today, have incorporated numerous technological advancements to improve their efficiency and reduce environmental impact. These advancements include:
- Improved Materials: Modern steam engines use advanced materials that can withstand higher pressures and temperatures, resulting in better efficiency and durability.
- Compact Designs: Advances in engineering have led to more compact and lightweight designs, making these engines easier to install and operate.
- Enhanced Control Systems: Modern steam engines often come equipped with digital control systems that optimize fuel use, monitor engine performance, and reduce emissions.
- Renewable Fuel Options: Some modern steam engines are designed to run on renewable fuels, such as wood chips or other biomass, aligning with sustainability goals.
These engines are used in niche applications, including small-scale power generation, marine propulsion, and hobbyist or educational projects.
High-Power and Industrial Applications
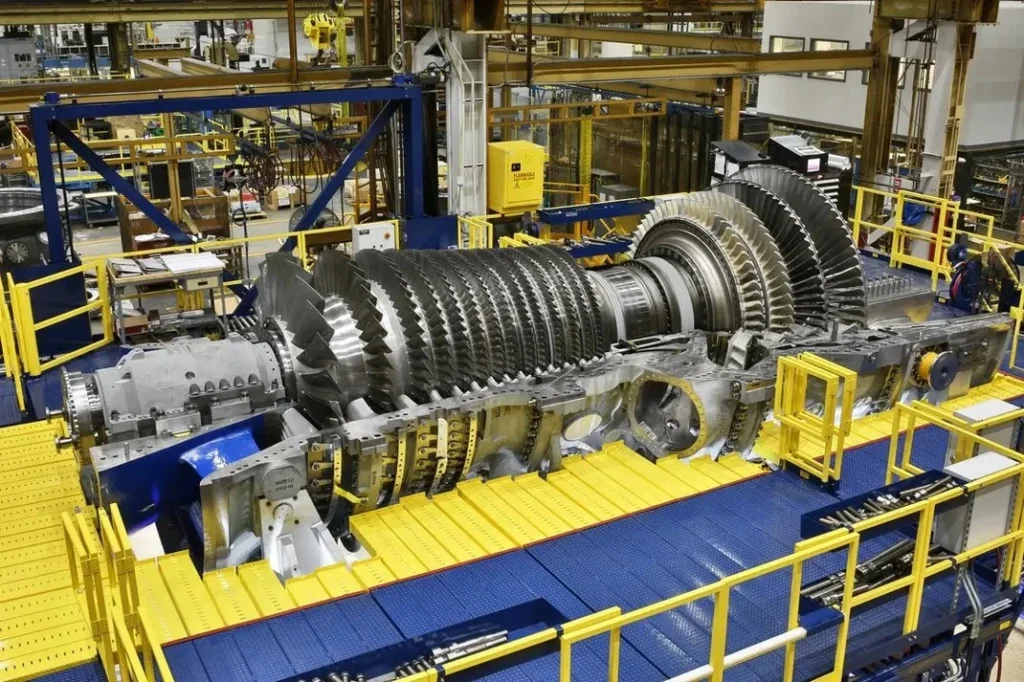
Steam turbines are also critical in high-power and industrial applications, where their ability to generate large amounts of energy efficiently is highly valued. This section explores the use of 50kW steam turbines and turbine propellers in industrial contexts.
50kW Steam Turbine: Use Cases and Performance
A 50kW steam turbine is a mid-sized power generation unit suitable for various industrial applications. Key use cases include:
- Industrial Process Heat: In many industries, such as chemical manufacturing and food processing, steam is required not just for power generation but also for process heat. A 50kW steam turbine can be integrated into these processes, providing both electricity and steam for heating.
- Combined Heat and Power (CHP) Systems: In CHP systems, steam turbines are used to generate electricity while the waste heat is captured and used for heating, significantly improving overall energy efficiency.
- Off-Grid Power Generation: For remote industrial sites, a 50kW steam turbine can provide a reliable source of power, particularly when paired with a biomass boiler or other renewable energy sources.
Integration in Industrial Power Generation
The integration of steam turbines in industrial power generation involves several key considerations:
- Fuel Source: The choice of fuel—whether biomass, coal, or natural gas—affects the design and operation of the turbine. Biomass-fueled turbines are increasingly popular due to their renewable nature and lower carbon footprint.
- Load Matching: Industrial sites often have varying power demands. Steam turbines must be able to adjust their output to match these fluctuations efficiently, often requiring sophisticated control systems.
- Environmental Impact: Modern steam turbines are designed with environmental considerations in mind. This includes minimizing emissions, improving fuel efficiency, and incorporating technologies like carbon capture and storage (CCS).
Wood Gasification and Wood-burning Engines
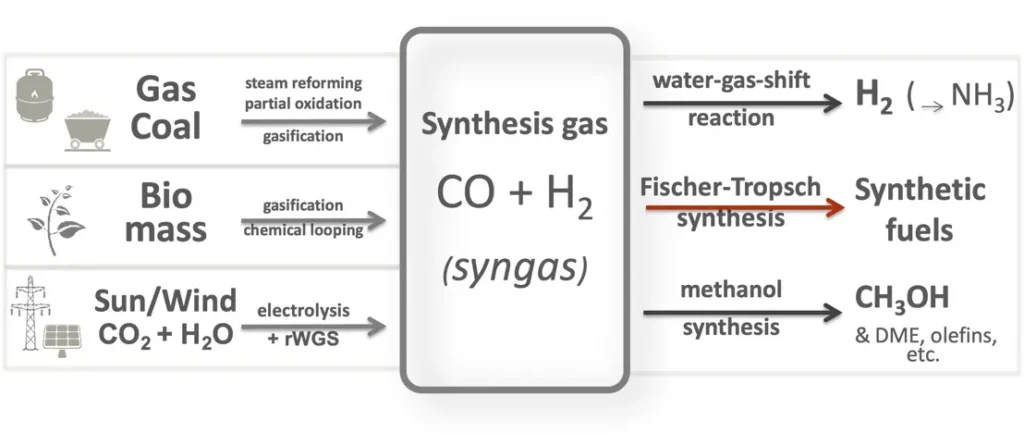
Wood gasification and wood-burning engines represent a sustainable approach to power generation, particularly in areas with abundant biomass resources. This section explains the wood gasification process, explores wood-burning engine technology, and discusses the use of wood gas electric generators.
The Wood Gasification Process: From Biomass to Energy
Wood gasification is a process that converts biomass into a combustible gas mixture known as producer gas or syngas. The key steps in the wood gasification process include:
- Pyrolysis: Wood is heated in the absence of oxygen, causing it to decompose into charcoal and volatile gases. This stage produces a mix of hydrogen, carbon monoxide, methane, and other hydrocarbons.
- Combustion: A small portion of the biomass is combusted in a controlled environment to provide the heat necessary for pyrolysis and the subsequent reactions.
- Reduction: The volatile gases produced in the pyrolysis stage pass through a bed of hot charcoal, where they react to form a cleaner gas mixture. This mixture consists primarily of carbon monoxide, hydrogen, and traces of methane.
- Gas Cleaning: The producer gas is then cleaned to remove tar, particulates, and other impurities, making it suitable for use in internal combustion engines, turbines, or for direct combustion in boilers.
The wood gasification process is highly efficient, with the potential to convert a significant portion of the energy content of biomass into usable gas. This gas can be used to generate electricity, heat, or as a chemical feedstock.
Wood-burning Engine Technology and Applications
Wood-burning engines, also known as wood gas engines, are designed to run on the producer gas generated from wood gasification. Key features and applications include:
- Engine Design: These engines are typically modified internal combustion engines that can burn a mix of producer gas and air. They are often used in rural areas or off-grid locations where wood is readily available as a fuel source.
- Applications: Wood-burning engines are used in various applications, including power generation, agricultural machinery, and as backup generators. They offer a renewable energy solution in areas where conventional fuels are expensive or unavailable.
- Advantages: The use of wood as a fuel is carbon-neutral, meaning that the carbon dioxide released during combustion is offset by the carbon absorbed during the growth of the trees. This makes wood-burning engines an environmentally friendly option.
Wood Gas Electric Generator: A Sustainable Power Source
Wood gas electric generators convert the producer gas from wood gasification into electricity. These generators are particularly useful in decentralized power generation systems where sustainability and fuel availability are key considerations. Key aspects include:
- Generator Efficiency: The efficiency of wood gas electric generators depends on the quality of the producer gas and the design of the generator. Modern designs have improved efficiency and reliability, making them suitable for continuous operation.
- Renewable Energy: By using biomass as a fuel, wood gas electric generators offer a renewable and sustainable source of energy, reducing reliance on fossil fuels and decreasing greenhouse gas emissions.
- Community Power Solutions: In remote or rural areas, wood gas generators can provide a reliable source of electricity, supporting local economies and improving the quality of life.
Self-sustaining Power Systems
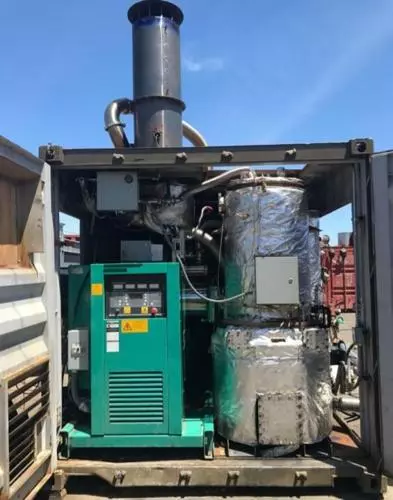
Self-sustaining power systems are designed to operate independently, generating and maintaining their own energy without relying on external power sources. This section examines self-sustaining power generators and discusses the innovations in renewable energy technologies that make such systems possible.
Understanding Self-sustaining Power Generators
A self-sustaining power generator is a system that generates its own energy continuously, often using renewable resources, with minimal external input. Key characteristics include:
- Renewable Energy Sources: These generators typically harness renewable energy sources such as solar, wind, hydro, or biomass to maintain continuous operation.
- Energy Storage: Self-sustaining systems often include energy storage solutions, such as batteries or flywheels, to store excess energy produced during periods of high generation for use during periods of low generation.
- Automation and Control: Advanced control systems monitor the performance of self-sustaining generators, optimizing their operation and ensuring they respond effectively to changes in energy demand or resource availability.
Innovations in Renewable Energy Technologies
Recent advancements in renewable energy technologies have made self-sustaining power systems more efficient and viable. Innovations include:
- Improved Solar Panels: New materials and designs have increased the efficiency of solar panels, allowing for more energy capture from the same amount of sunlight.
- Wind Turbine Advances: Modern wind turbines are more efficient and capable of generating electricity at lower wind speeds, making wind power more accessible and reliable.
- Energy Storage Breakthroughs: Developments in battery technology, such as solid-state batteries, have improved energy storage capacity and efficiency, enabling longer periods of self-sustaining operation.
- Hybrid Systems: Combining multiple renewable energy sources, such as solar and wind, in a single system increases reliability and ensures continuous power generation even when one resource is unavailable.
Self-sustaining power systems represent the future of energy, offering a sustainable solution for off-grid communities, remote industrial operations, and areas with unreliable grid access.
Turbine Generators: Working Principle and Operation
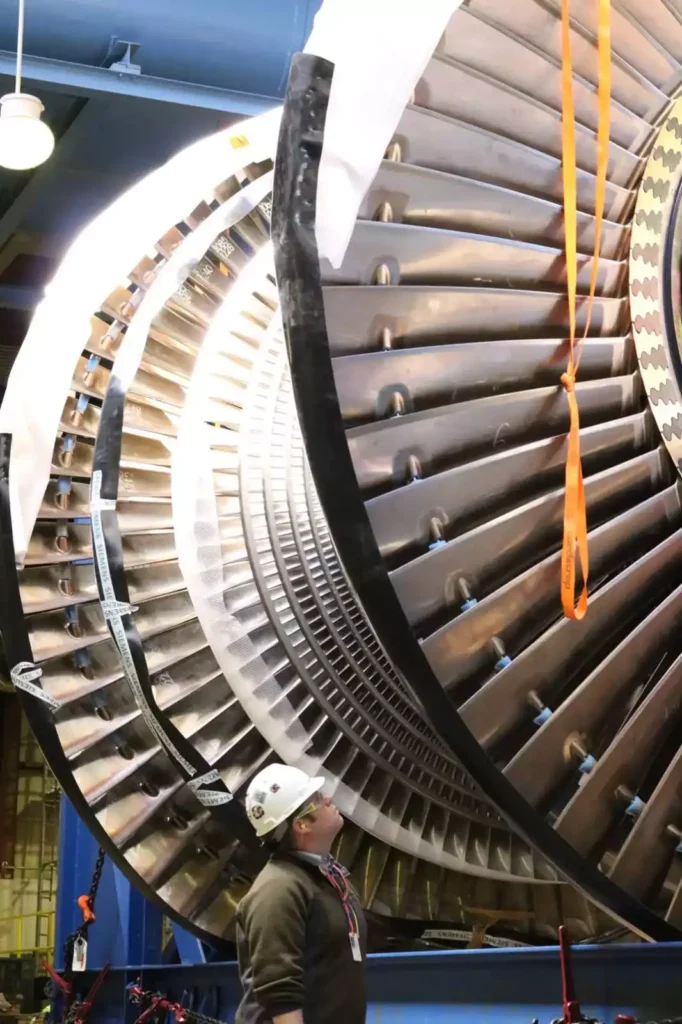
Turbine generators are essential components of power generation systems, converting mechanical energy from turbines into electrical energy. This section explains the working principle of turbine generators, discusses efficiency considerations, and explores the integration of turbines and generators in power plants.
How Turbine Generators Work
The basic working principle of a turbine generator involves the conversion of mechanical energy from a turbine into electrical energy through electromagnetic induction. The process includes:
- Mechanical Energy Input: The turbine, driven by steam, water, or wind, rotates a shaft connected to the generator.
- Electromagnetic Induction: Inside the generator, the rotating shaft turns a rotor, which is surrounded by a magnetic field. The movement of the rotor within this magnetic field induces an electric current in the stator windings, generating electricity.
- Power Output: The electrical energy generated is then transmitted to the power grid or used to power equipment directly. The amount of power generated depends on the speed of the turbine, the strength of the magnetic field, and the efficiency of the generator.
Efficiency and Power Output Considerations
The efficiency of a turbine generator is influenced by several factors:
- Turbine Efficiency: The efficiency of the turbine itself plays a significant role in determining the overall efficiency of the generator. Factors such as blade design, steam pressure, and temperature affect how effectively the turbine converts energy.
- Generator Design: Modern generators are designed to minimize losses through advanced materials, cooling systems, and precision engineering. High-efficiency generators reduce the amount of mechanical energy lost as heat, increasing the overall power output.
- Operational Conditions: The conditions under which the turbine generator operates, including temperature, humidity, and load demand, also impact efficiency. Proper maintenance and monitoring are essential to maintaining optimal performance.
Case Studies and Real-world Applications
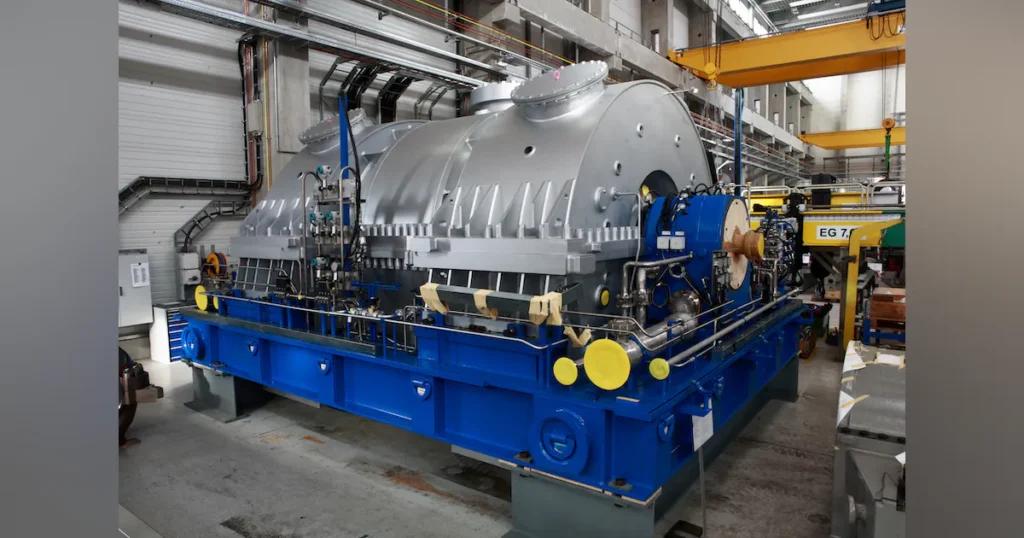
Real-world applications of steam turbines and generators demonstrate the versatility and efficiency of these technologies in various industries. This section presents case studies of steam turbines in modern power plants, comparing different turbine technologies and their performance.
Examples of Steam Turbines in Modern Power Plants
Case studies provide insights into the practical applications of steam turbines, highlighting their role in power generation:
- Coal-fired Power Plant: A large coal-fired power plant uses a combination of high-pressure, intermediate-pressure, and low-pressure steam turbines to maximize energy extraction from steam. The plant’s use of advanced steam cycle technology and efficient turbines results in a high overall efficiency.
- Nuclear Power Plant: In a nuclear power plant, steam turbines are used to convert the thermal energy from nuclear fission into mechanical energy. The use of multiple turbine stages and reheating processes ensures that as much energy as possible is extracted from the steam, contributing to the plant’s base-load power generation.
- Biomass Power Plant: A biomass power plant utilizes a 50kW steam turbine to generate electricity from wood chips. The turbine’s integration with a wood gasification system allows the plant to operate sustainably, reducing its carbon footprint and reliance on fossil fuels.
Comparative Analysis of Different Turbine Technologies
Comparing different turbine technologies reveals the strengths and weaknesses of various approaches:
- Impulse vs. Reaction Turbines: Impulse turbines, like the Curtis stage turbine, are efficient at high-pressure stages, while reaction turbines are better suited for lower pressure stages where steam expands gradually. The choice between these technologies depends on the specific requirements of the power plant.
- Single-stage vs. Multi-stage Turbines: Single-stage turbines are simpler and less expensive but less efficient than multi-stage turbines, which extract more energy from the steam. Multi-stage turbines are typically used in large-scale power generation, where efficiency is paramount.
- Renewable vs. Conventional Fuel Turbines: Steam turbines powered by renewable fuels, such as biomass or geothermal energy, offer environmental benefits but may require more complex fuel handling and processing systems compared to conventional fuel turbines.
Future Trends and Innovations in Turbine Technology
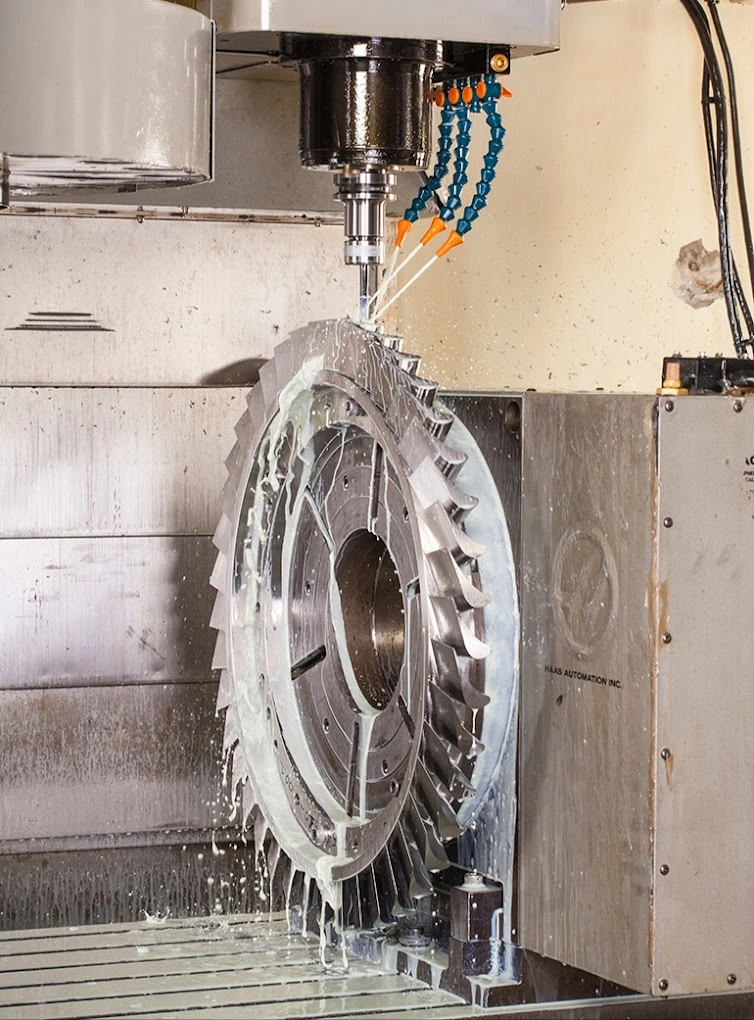
The future of turbine technology is shaped by emerging trends and innovations aimed at improving efficiency, reducing environmental impact, and expanding the range of applications. This section explores these trends and their implications for the power generation industry.
Emerging Technologies in Turbine Design
Several emerging technologies are poised to revolutionize turbine design:
- Supercritical CO2 Turbines: These turbines use supercritical carbon dioxide as a working fluid instead of steam. They offer higher efficiency and smaller size compared to traditional steam turbines, making them ideal for compact power generation systems.
- Advanced Blade Materials: New materials, such as ceramic composites and high-temperature alloys, are being developed to withstand higher temperatures and stresses, improving turbine efficiency and longevity.
- Additive Manufacturing (3D Printing): Additive manufacturing allows for the creation of complex turbine components with precise tolerances and optimized designs, reducing manufacturing costs and improving performance.
Sustainability and Environmental Considerations
As environmental concerns become increasingly important, turbine technology is evolving to address these challenges:
- Carbon Capture Integration: Steam turbines in fossil fuel power plants are being integrated with carbon capture and storage (CCS) systems to reduce greenhouse gas emissions. This technology captures carbon dioxide from the flue gases before it is released into the atmosphere.
- Hybrid Energy Systems: Hybrid systems that combine steam turbines with renewable energy sources, such as solar thermal or wind power, are being developed to provide a more stable and sustainable power supply.
- Waste Heat Recovery: Innovations in waste heat recovery technologies are enabling more efficient use of the thermal energy produced in industrial processes, reducing overall energy consumption and emissions.
Conclusion
In conclusion, steam turbines and related technologies continue to play a vital role in power generation, offering a reliable and efficient means of producing electricity. From large-scale power plants to small-scale, off-grid applications, these machines have proven their versatility and efficiency over decades of use.
The advancements in turbine design, control systems, and materials are pushing the boundaries of what steam turbines can achieve, making them more efficient, environmentally friendly, and adaptable to a wide range of energy sources, including renewable fuels like biomass and wood gas.
As the world moves toward a more sustainable future, steam turbines will remain at the forefront of power generation technology, integrating with new innovations and continuing to provide a stable foundation for the global energy infrastructure.
This text serves as a comprehensive overview of the key concepts, technologies, and trends in the field of steam turbines, engines, and renewable energy systems. By exploring these topics, readers can gain a deeper understanding of how these systems work, their applications, and their importance in modern power generation.
Outline for Additional Sections
- Advanced Steam Turbine Technologies
- Innovations in turbine blade design
- High-efficiency steam turbines: Concepts and benefits
- Integration of AI and machine learning in turbine operation
- Keywords: advanced steam turbines, turbine blade design, AI in turbine control
- Turbine Maintenance and Reliability
- Predictive maintenance techniques for turbines
- Common turbine failures and how to prevent them
- Importance of regular inspection and servicing
- Keywords: turbine maintenance, predictive maintenance, turbine reliability
- Environmental Impact and Sustainability
- Reducing carbon footprint in steam turbine operation
- Sustainable fuel alternatives: Biomass, hydrogen, and more
- Life cycle assessment of steam turbines
- Keywords: steam turbine sustainability, reducing carbon footprint, sustainable fuels
- Steam Turbine Applications in Industry
- Use of steam turbines in the chemical and petrochemical industries
- Steam turbines in food processing and pharmaceuticals
- Industrial cogeneration and combined heat and power (CHP) systems
- Keywords: steam turbines in industry, industrial cogeneration, CHP systems
- Case Studies in Renewable Energy Integration
- Case study: Biomass-fired steam turbines in power generation
- Geothermal steam turbines: Case studies from Iceland and other countries
- Small-scale steam turbine installations in developing regions
- Keywords: biomass-fired turbines, geothermal steam turbines, small-scale turbines
- Economic Analysis of Steam Power Generation
- Cost-benefit analysis of steam turbines vs. other power generation technologies
- Economic viability of small-scale steam engines and turbines
- Financing and funding options for steam power projects
- Keywords: economic analysis of steam turbines, cost-benefit of steam power, financing steam power
- Future of Steam Turbine Technology
- Emerging trends in steam turbine research and development
- Potential for hybrid steam-electric systems
- The role of steam turbines in a hydrogen economy
- Keywords: future of steam turbines, hybrid steam systems, hydrogen economy
- Steam Turbine Safety and Standards
- Global safety standards for steam turbine operation
- Training and certification for turbine operators
- Risk assessment and management in steam power plants
- Keywords: steam turbine safety, turbine operation standards, risk management in steam plants
- Comparison with Other Power Generation Technologies
- Comparing steam turbines with gas turbines and internal combustion engines
- Advantages and disadvantages of steam turbines in various applications
- Role of steam turbines in decentralized and grid-connected systems
- Keywords: steam vs. gas turbines, decentralized power generation, grid-connected turbines
- Steam Turbines in Marine and Aerospace Applications
- Use of steam turbines in naval vessels
- Historical and modern uses of steam turbines in ships
- Potential applications of steam turbines in space exploration
- Keywords: steam turbines in ships, naval steam turbines, aerospace steam turbines
Advanced Steam Turbine Technologies
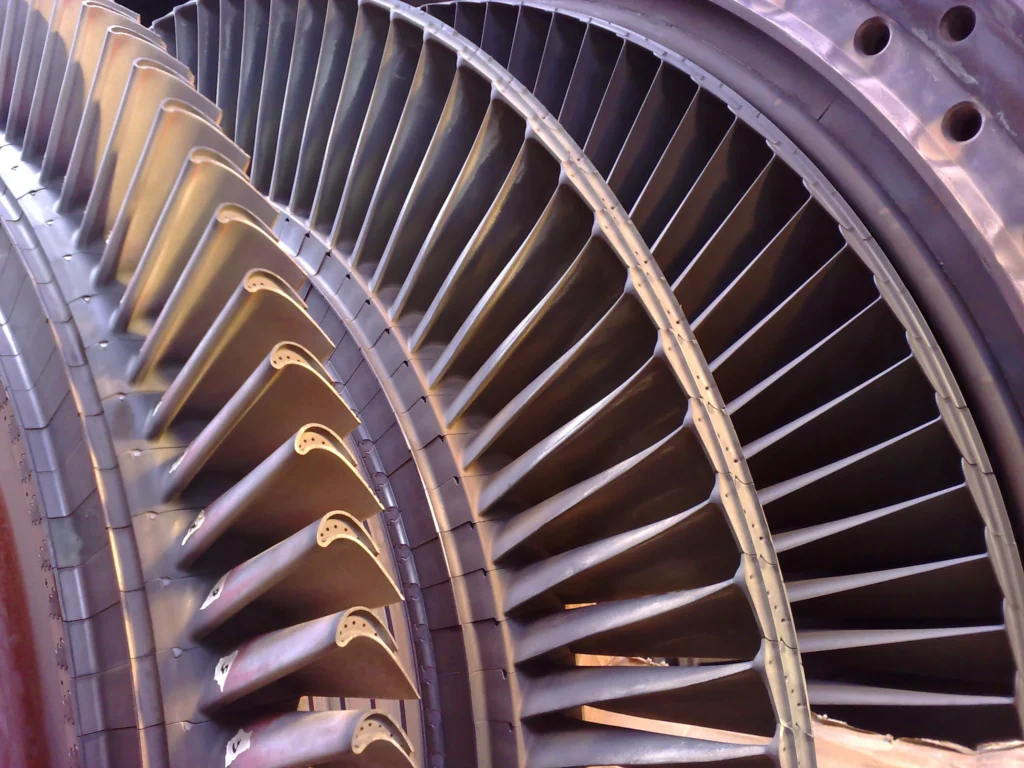
Innovations in Turbine Blade Design
Turbine blades are critical components in steam turbines, determining the efficiency, reliability, and performance of the machine. Over the years, significant innovations have been made in turbine blade design to enhance their effectiveness:
- Aerodynamic Optimization: Modern turbine blades are designed using advanced aerodynamic principles to minimize drag and maximize the conversion of steam energy into mechanical work. Computational Fluid Dynamics (CFD) simulations are often used in the design process to optimize blade shape and size.
- Material Advances: The development of new materials, such as high-temperature alloys and ceramic composites, has allowed turbine blades to withstand higher temperatures and stresses, leading to improved efficiency and longer lifespans. These materials are particularly important in high-pressure turbines where conditions are extreme.
- Cooling Technologies: Advanced cooling techniques, such as internal cooling channels and thermal barrier coatings, have been integrated into turbine blades to manage the intense heat generated during operation. These technologies prevent overheating and extend the life of the blades.
- Adaptive Blades: Some modern turbines feature adaptive or flexible blades that can adjust their angle or curvature in response to changing operating conditions. This adaptability helps maintain optimal efficiency across a wide range of loads.
These innovations have led to the development of high-efficiency steam turbines that are capable of delivering more power while consuming less fuel and producing fewer emissions.
High-efficiency Steam Turbines: Concepts and Benefits
High-efficiency steam turbines represent the next generation of power generation technology, offering significant improvements over traditional designs. The concepts behind these turbines include:
- Supercritical and Ultra-supercritical Steam: By operating at supercritical or ultra-supercritical steam conditions, these turbines achieve higher thermal efficiencies. Supercritical steam turbines operate at temperatures and pressures above the critical point of water, resulting in a more efficient steam cycle and reduced fuel consumption.
- Combined Cycle Systems: High-efficiency steam turbines are often used in combined cycle power plants, where they work in conjunction with gas turbines. The waste heat from the gas turbine is used to generate steam, which drives the steam turbine, thereby maximizing the overall efficiency of the plant.
- Heat Recovery Steam Generators (HRSG): In combined cycle plants, HRSG units capture waste heat from gas turbines to produce steam. This steam is then used to drive high-efficiency steam turbines, further improving the plant’s efficiency.
- Advanced Control Systems: High-efficiency turbines are equipped with state-of-the-art control systems that optimize operation in real-time. These systems adjust steam flow, temperature, and pressure to ensure maximum efficiency under varying load conditions.
The benefits of high-efficiency steam turbines include lower operating costs, reduced greenhouse gas emissions, and increased power output from the same amount of fuel. These turbines are particularly valuable in large-scale power generation, where even small efficiency gains can lead to significant cost savings and environmental benefits.
Integration of AI and Machine Learning in Turbine Operation
Artificial intelligence (AI) and machine learning (ML) are increasingly being integrated into turbine operation to enhance performance, reliability, and maintenance:
- Predictive Maintenance: AI algorithms can analyze data from sensors placed on turbines to predict when maintenance is needed. By identifying potential issues before they lead to failures, predictive maintenance reduces downtime and repair costs.
- Performance Optimization: Machine learning models can be used to optimize turbine operation by analyzing historical data and identifying patterns that lead to improved efficiency. These models continuously learn and adapt, ensuring that turbines operate at peak efficiency under all conditions.
- Fault Detection and Diagnosis: AI-powered systems can detect anomalies in turbine operation that may indicate mechanical issues or inefficiencies. Early detection allows operators to address problems before they escalate, improving the reliability of the turbine.
- Remote Monitoring and Control: AI and ML enable remote monitoring of turbines, allowing operators to manage multiple turbines from a centralized location. This capability is particularly valuable in large power plants or offshore installations where on-site monitoring may be challenging.
The integration of AI and ML in turbine operation represents a significant step forward in the evolution of steam turbine technology, offering new possibilities for efficiency, reliability, and cost-effectiveness.
Turbine Maintenance and Reliability
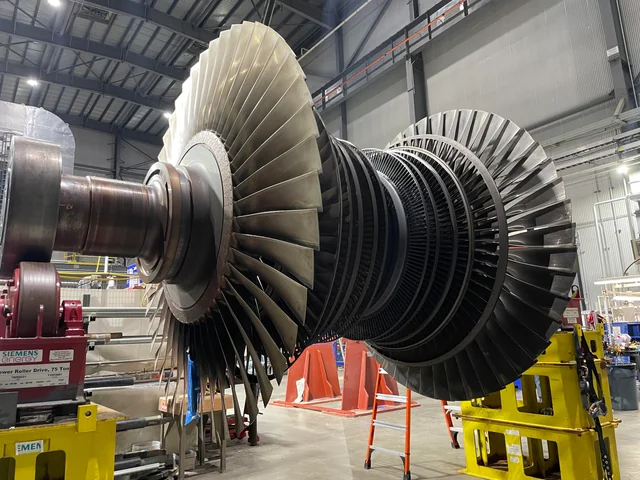
Predictive Maintenance Techniques for Turbines
Predictive maintenance is a proactive approach to turbine maintenance that uses data analytics and sensor technology to predict when a turbine is likely to need maintenance. Key techniques include:
- Vibration Analysis: By monitoring the vibrations of turbine components, predictive maintenance systems can detect imbalances, misalignments, and bearing wear before they lead to failure. Vibration data is analyzed to identify patterns that indicate potential issues.
- Thermography: Infrared thermography is used to detect hot spots in turbine components, which can indicate problems such as insulation breakdown or overheating. By identifying these issues early, operators can prevent damage to the turbine.
- Oil Analysis: The condition of lubricating oil in a turbine is a critical indicator of the turbine’s health. Predictive maintenance involves regular analysis of oil samples to detect contaminants, wear particles, and chemical changes that could signal impending problems.
- Acoustic Emissions: Acoustic monitoring systems detect high-frequency sounds that are often associated with cracks, leaks, or other mechanical issues. By capturing these emissions, operators can identify and address issues before they become critical.
Predictive maintenance not only improves turbine reliability but also reduces maintenance costs by minimizing unplanned downtime and extending the life of turbine components.
Common Turbine Failures and How to Prevent Them
Despite the robust design of steam turbines, they are still susceptible to various types of failures. Common failures and prevention strategies include:
- Blade Erosion: Blade erosion, often caused by the presence of moisture in the steam, can reduce the efficiency and lifespan of a turbine. Preventive measures include using high-quality materials, improving steam quality, and regularly inspecting blades for signs of wear.
- Bearing Failure: Bearings are critical components that support the rotating parts of a turbine. Common causes of bearing failure include inadequate lubrication, contamination, and misalignment. Preventing bearing failure involves regular lubrication, monitoring bearing temperatures, and ensuring proper alignment during installation.
- Corrosion: Steam turbines can be susceptible to corrosion, especially in the presence of impurities in the steam or in environments with high humidity. Corrosion prevention strategies include using corrosion-resistant materials, maintaining proper water chemistry, and applying protective coatings to vulnerable components.
- Rotor Cracks: The turbine rotor is subjected to high stresses and temperatures, which can lead to the development of cracks over time. Regular non-destructive testing (NDT) methods such as ultrasonic testing and magnetic particle inspection are essential for detecting rotor cracks early.
Preventing these common turbine failures requires a combination of proper design, regular maintenance, and the use of advanced monitoring techniques.
Importance of Regular Inspection and Servicing
Regular inspection and servicing of steam turbines are essential for maintaining their reliability and efficiency. Key benefits of regular inspection include:
- Early Detection of Issues: Regular inspections allow operators to detect and address potential issues before they lead to significant failures. This proactive approach minimizes downtime and reduces repair costs.
- Extended Equipment Life: Routine maintenance, including cleaning, lubrication, and the replacement of worn components, helps extend the life of the turbine and ensures it operates efficiently throughout its service life.
- Compliance with Safety Standards: Regular servicing ensures that turbines comply with industry safety standards, reducing the risk of accidents and ensuring safe operation.
- Optimization of Performance: During servicing, technicians can make adjustments to optimize the turbine’s performance, ensuring it operates at peak efficiency.
Regular inspection and servicing are critical components of a comprehensive turbine maintenance strategy, contributing to the overall reliability and performance of steam turbines.
Environmental Impact and Sustainability
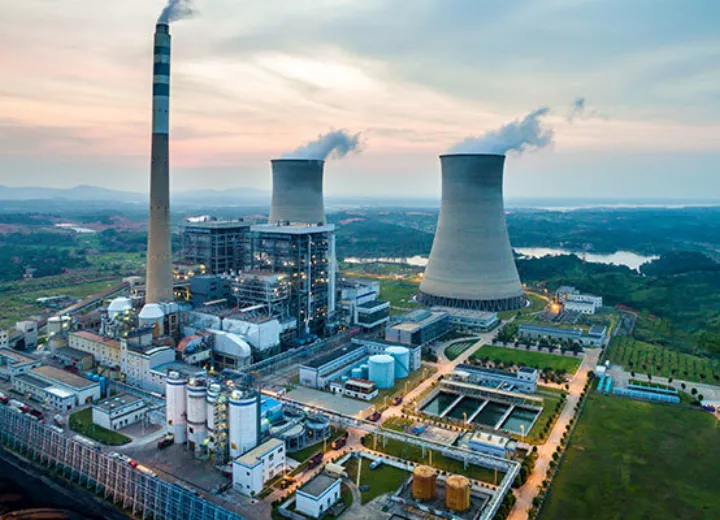
Reducing Carbon Footprint in Steam Turbine Operation
Steam turbines play a crucial role in power generation, but they also contribute to carbon emissions, particularly when powered by fossil fuels. Strategies to reduce the carbon footprint of steam turbine operation include:
- Fuel Switching: Transitioning from coal or oil to lower-carbon fuels such as natural gas, biomass, or hydrogen can significantly reduce carbon emissions. Biomass and hydrogen, in particular, offer the potential for near-zero carbon emissions when sourced sustainably.
- Efficiency Improvements: Improving the efficiency of steam turbines reduces the amount of fuel needed to generate electricity, thereby lowering carbon emissions. This can be achieved through advanced turbine designs, better control systems, and the integration of supercritical and ultra-supercritical steam conditions.
- Carbon Capture and Storage (CCS): CCS technologies capture carbon dioxide emissions from steam turbines and store them underground or use them in industrial processes. By capturing and storing carbon emissions, CCS can make steam turbines part of a low-carbon energy solution.
- Combined Heat and Power (CHP): CHP systems use the waste heat from steam turbines for heating or industrial processes, improving overall energy efficiency and reducing the need for additional fuel consumption.
Implementing these strategies can help reduce the environmental impact of steam turbines and contribute to global efforts to combat climate change.
Sustainable Fuel Alternatives: Biomass, Hydrogen, and More
Sustainable fuel alternatives are critical to reducing the environmental impact of steam turbines. Key alternatives include:
- Biomass: Biomass, such as wood chips, agricultural waste, and energy crops, is a renewable fuel source that can be used in steam turbines. When sustainably sourced, biomass is carbon-neutral, as the carbon dioxide released during combustion is offset by the carbon absorbed during the growth of the biomass.
- Hydrogen: Hydrogen is a clean fuel that produces only water when burned. Steam turbines can be adapted to run on hydrogen, either alone or in combination with other fuels. The development of green hydrogen, produced using renewable energy, offers the potential for zero-carbon power generation.
- Waste-to-Energy: Waste-to-energy plants use steam turbines to generate electricity from municipal solid waste, industrial waste, and other non-recyclable materials. This approach not only reduces waste but also provides a source of renewable energy.
- Geothermal Energy: Geothermal steam, generated from the Earth’s heat, is a renewable and sustainable energy source. Geothermal steam turbines have a low environmental impact and can provide a stable source of power, particularly in regions with significant geothermal resources.
These sustainable fuel alternatives offer viable pathways for reducing the carbon footprint of steam turbines and transitioning to a more sustainable energy future.
Life Cycle Assessment of Steam Turbines
Life cycle assessment (LCA) is a method used to evaluate the environmental impact of steam turbines throughout their entire life cycle, from raw material extraction to disposal. Key stages of LCA include:
- Material Extraction and Manufacturing: The environmental impact of extracting raw materials, such as metals and alloys, and manufacturing turbine components is assessed. This includes energy consumption, greenhouse gas emissions, and resource depletion.
- Operation and Maintenance: The environmental impact during the operation phase includes fuel consumption, emissions, and waste generation. Maintenance activities, such as the replacement of worn components and lubrication, also contribute to the overall impact.
- End-of-Life Disposal: The disposal or recycling of turbine components at the end of their service life is considered. Recycling reduces the environmental impact by recovering valuable materials, while disposal in landfills can contribute to environmental pollution.
LCA provides a comprehensive view of the environmental impact of steam turbines and helps identify opportunities for improvement in design, operation, and disposal practices.
Steam Turbine Applications in Industry
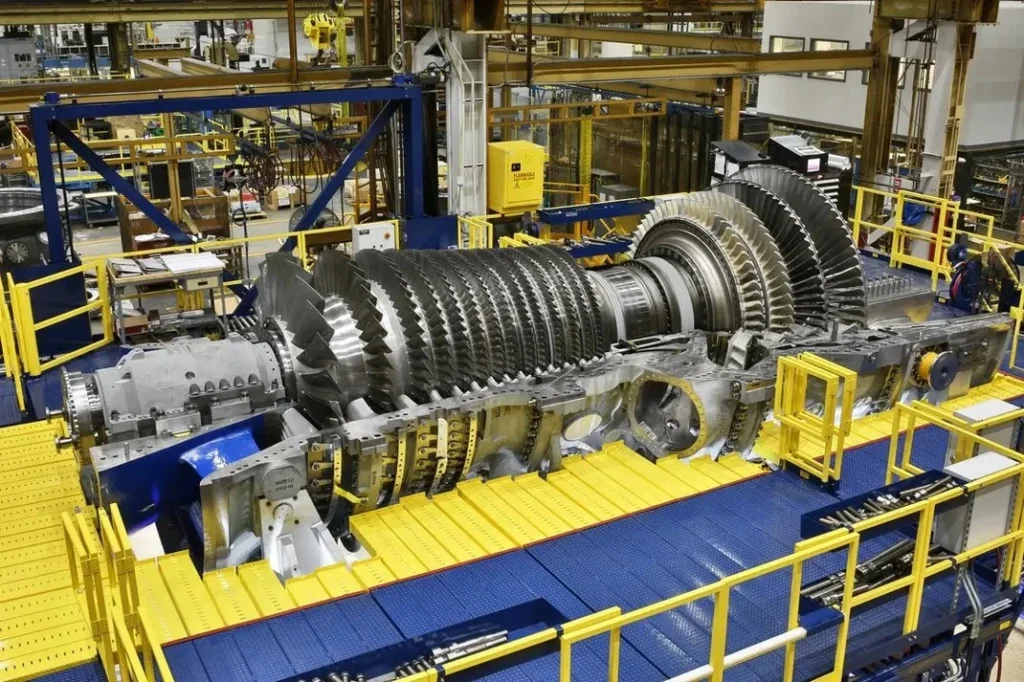
Use of Steam Turbines in the Chemical and Petrochemical Industries
Steam turbines are widely used in the chemical and petrochemical industries for both power generation and mechanical drive applications. Key roles include:
- Power Generation: Many chemical plants use steam turbines to generate electricity on-site, providing a reliable and efficient source of power. The use of combined heat and power (CHP) systems allows these plants to utilize waste heat for process heating, further improving energy efficiency.
- Mechanical Drives: Steam turbines are used to drive pumps, compressors, and other equipment in chemical and petrochemical plants. Their ability to handle high pressures and temperatures makes them ideal for these demanding applications.
- Steam Integration: Steam is often an integral part of chemical processes, such as in the production of ammonia, methanol, and ethylene. Steam turbines help optimize the use of steam within these processes, improving overall plant efficiency.
The use of steam turbines in the chemical and petrochemical industries contributes to the efficient and reliable operation of these plants, supporting the production of essential chemicals and fuels.
Steam Turbines in Food Processing and Pharmaceuticals
In the food processing and pharmaceutical industries, steam turbines are used for power generation, process heating, and mechanical drives. Key applications include:
- Power Generation: Many food processing plants and pharmaceutical facilities generate their own electricity using steam turbines, ensuring a reliable power supply and reducing dependence on the grid. This is particularly important in facilities where power interruptions can lead to significant product losses.
- Process Heating: Steam is used for cooking, sterilization, and other processes in food processing and pharmaceuticals. Steam turbines provide an efficient means of generating the necessary steam, often as part of a combined heat and power (CHP) system.
- Sterilization and Drying: In pharmaceutical manufacturing, steam is essential for sterilization and drying processes. Steam turbines ensure a steady supply of high-quality steam, supporting the production of safe and effective medicines.
The integration of steam turbines in these industries enhances operational efficiency, product quality, and energy sustainability.
Industrial Cogeneration and Combined Heat and Power (CHP) Systems
Cogeneration, or combined heat and power (CHP), systems use steam turbines to generate electricity and useful heat simultaneously. Key benefits and applications include:
- Increased Efficiency: CHP systems capture and utilize waste heat from electricity generation, achieving overall efficiencies of 60% to 80%, compared to 30% to 50% for conventional power plants.
- Industrial Applications: CHP systems are widely used in industries with significant heat and power demands, such as chemical manufacturing, food processing, and paper production. These systems provide both electricity and process steam, reducing energy costs and emissions.
- District Heating: In addition to industrial applications, CHP systems can provide district heating, supplying hot water or steam to buildings and homes in a community. This approach improves energy efficiency and reduces greenhouse gas emissions.
Industrial cogeneration and CHP systems are a proven means of improving energy efficiency, reducing costs, and minimizing environmental impact in a wide range of industries.
Case Studies in Renewable Energy Integration
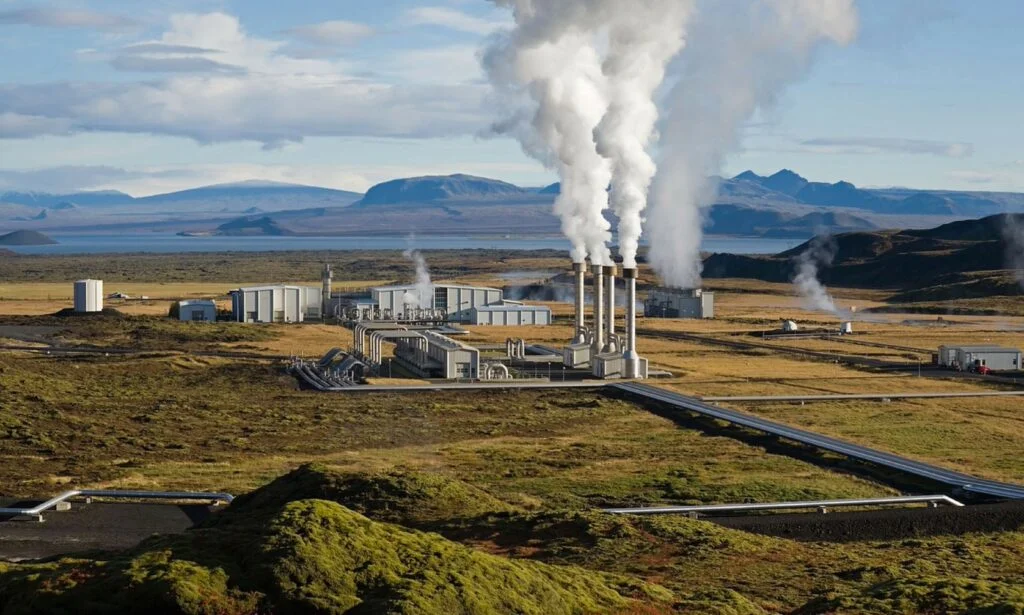
Case Study: Biomass-fired Steam Turbines in Power Generation
Biomass-fired steam turbines are used in power plants that burn organic materials, such as wood chips, agricultural waste, and energy crops, to generate electricity. A case study of a biomass power plant might highlight:
- Fuel Source and Sustainability: The power plant uses sustainably sourced biomass, such as locally harvested wood chips or agricultural residues, to fuel its steam turbine. The use of renewable biomass reduces the plant’s carbon footprint and supports local economies.
- Turbine Design and Efficiency: The steam turbine is designed to handle the unique characteristics of biomass combustion, such as lower steam temperatures and potential contaminants. Advanced materials and coatings are used to prevent corrosion and fouling, ensuring reliable operation.
- Environmental Impact: The plant’s use of biomass as a fuel source results in near-zero net carbon emissions, as the carbon dioxide released during combustion is offset by the carbon absorbed during the growth of the biomass. The plant may also implement emissions control technologies, such as particulate filters and scrubbers, to minimize air pollution.
This case study demonstrates the viability of biomass-fired steam turbines as a sustainable and renewable source of electricity.
Geothermal Steam Turbines: Case Studies from Iceland and Other Countries
Geothermal steam turbines generate electricity using steam produced from the Earth’s natural heat. Case studies from geothermal power plants, such as those in Iceland, illustrate:
- Geothermal Resource Utilization: The power plant harnesses steam from deep geothermal reservoirs, where water is heated by the Earth’s natural geothermal energy. This steam drives the turbines to generate electricity with minimal environmental impact.
- Turbine Technology: The steam turbines used in geothermal power plants are designed to handle the specific conditions of geothermal steam, which may contain corrosive gases and minerals. The turbines are made from materials that resist corrosion and fouling, ensuring long-term reliability.
- Sustainability and Economic Impact: Geothermal power plants provide a reliable and sustainable source of electricity, contributing to Iceland’s goal of achieving 100% renewable energy. The plants also support local economies by providing jobs and attracting investment.
These case studies highlight the potential of geothermal steam turbines to provide clean, renewable energy in regions with geothermal resources.
Small-scale Steam Turbine Installations in Developing Regions
Small-scale steam turbine installations are being used in developing regions to provide decentralized power generation. A case study of such an installation might focus on:
- Community Impact: The small-scale steam turbine provides reliable electricity to a rural community, powering homes, schools, and businesses. The turbine may be fueled by locally available biomass, such as wood or agricultural waste, supporting energy independence.
- Technology and Design: The turbine is designed for simplicity and ease of maintenance, making it suitable for use in areas with limited technical expertise. It may be part of a hybrid system that includes solar panels or wind turbines to ensure a stable power supply.
- Economic Benefits: The availability of reliable electricity enables local businesses to operate more efficiently, leading to economic growth and improved quality of life for the community.
This case study illustrates the potential of small-scale steam turbines to provide sustainable and decentralized power solutions in developing regions.
Economic Analysis of Steam Power Generation
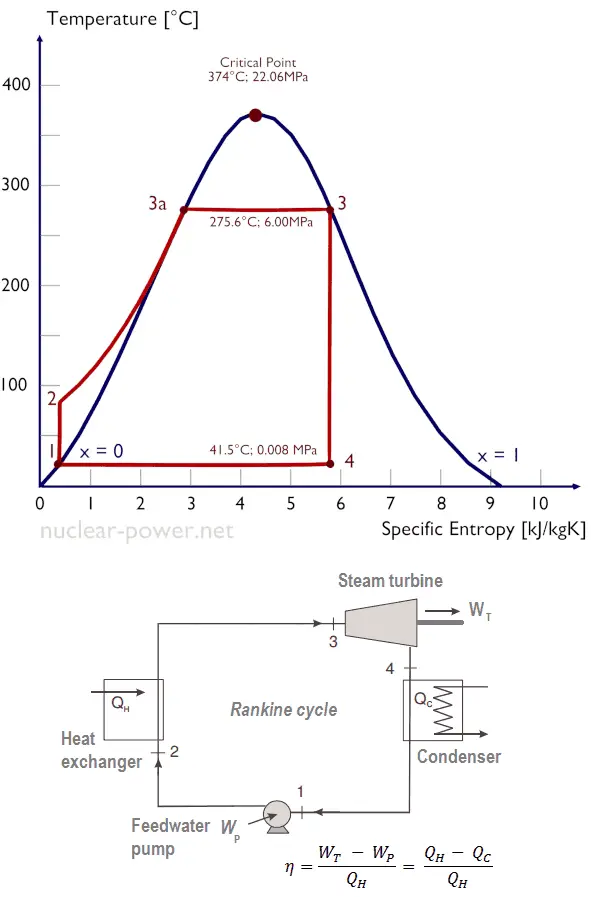
Cost-benefit Analysis of Steam Turbines vs. Other Power Generation Technologies
A cost-benefit analysis compares the economic viability of steam turbines with other power generation technologies, such as gas turbines, wind turbines, and solar panels. Key considerations include:
- Capital Costs: Steam turbines typically have higher upfront capital costs compared to other technologies, particularly when accounting for the cost of boilers and associated infrastructure. However, these costs can be offset by the long service life and high efficiency of steam turbines.
- Operating Costs: Operating costs for steam turbines include fuel costs, maintenance, and labor. These costs can vary depending on the fuel source (e.g., coal, biomass, natural gas) and the efficiency of the turbine. Steam turbines generally have lower operating costs than gas turbines due to their higher efficiency and lower fuel consumption.
- Environmental Costs: The environmental impact of steam turbines depends on the fuel source. Biomass and geothermal steam turbines have lower environmental costs compared to coal-fired turbines, due to lower carbon emissions and reduced air pollution.
- Return on Investment (ROI): The ROI of steam turbines is influenced by factors such as fuel availability, electricity prices, and government incentives for renewable energy. In regions with high electricity demand and stable fuel supplies, steam turbines can provide a strong ROI.
This analysis helps decision-makers evaluate the economic feasibility of steam turbines in various power generation scenarios.
Economic Viability of Small-scale Steam Engines and Turbines
Small-scale steam engines and turbines offer unique economic opportunities in niche applications. An economic analysis might consider:
- Capital and Operating Costs: Small-scale steam engines typically have lower capital costs compared to large-scale turbines, making them accessible to small businesses, farms, and off-grid communities. Operating costs are influenced by the availability of low-cost fuels, such as wood or agricultural waste.
- Market Potential: The market for small-scale steam engines includes remote areas, hobbyists, and industries with specific power needs, such as sawmills and agricultural processing. The economic viability of these engines depends on the availability of customers and the ability to compete with other off-grid power solutions.
- Subsidies and Incentives: Government subsidies and incentives for renewable energy projects can enhance the economic viability of small-scale steam engines. These incentives may include grants, tax credits, and low-interest loans for renewable energy installations.
Small-scale steam engines can provide a cost-effective and sustainable power solution for specific applications, particularly in areas where other power generation options are limited.
Financing and Funding Options for Steam Power Projects
Financing and funding are critical to the success of steam power projects, particularly for large-scale installations. Key financing options include:
- Project Financing: Project financing involves raising capital for steam power projects based on the projected revenue from the sale of electricity. This financing structure is often used for large-scale power plants and involves a combination of debt and equity financing.
- Government Grants and Loans: Governments may offer grants, low-interest loans, or loan guarantees to support the development of steam power projects, particularly those that use renewable fuels or contribute to energy security.
- Public-Private Partnerships (PPPs): PPPs involve collaboration between government entities and private companies to develop steam power projects. In these partnerships, the government may provide land, infrastructure, or financial support, while the private sector handles project development and operation.
- Green Bonds: Green bonds are a type of financing specifically designed to support environmentally sustainable projects, including renewable energy projects that use steam turbines. Investors in green bonds are typically interested in supporting projects that have a positive environmental impact.
Understanding the various financing and funding options available can help project developers secure the necessary capital to bring steam power projects to fruition.
Future of Steam Turbine Technology
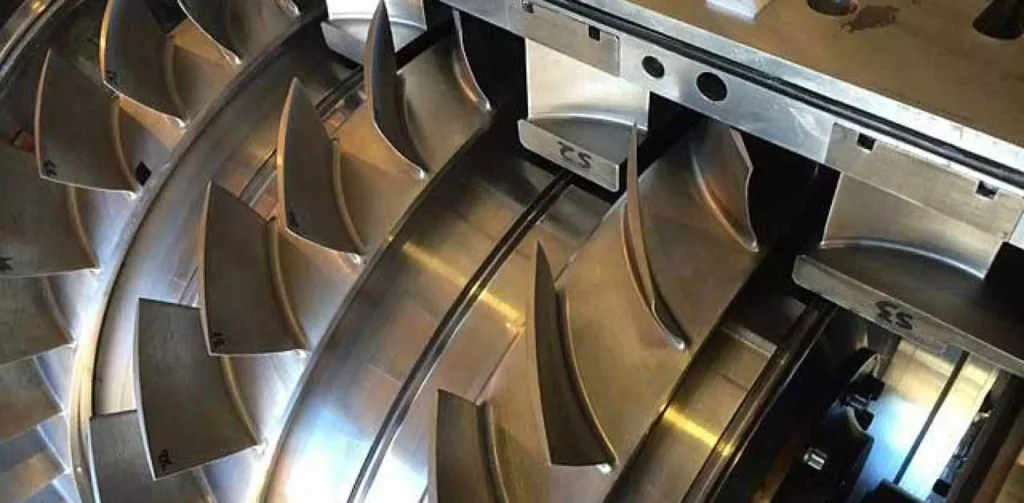
Emerging Trends in Steam Turbine Research and Development
Research and development in steam turbine technology are focused on improving efficiency, reducing emissions, and expanding the range of applications. Key emerging trends include:
- Supercritical and Ultra-supercritical Steam Cycles: Researchers are exploring the use of supercritical and ultra-supercritical steam cycles to achieve higher thermal efficiencies. These cycles operate at temperatures and pressures above the critical point of water, allowing for more efficient energy conversion and reduced fuel consumption.
- Carbon Capture Integration: The integration of carbon capture and storage (CCS) technologies with steam turbines is an area of active research. By capturing and storing carbon dioxide emissions from steam power plants, CCS can help reduce the environmental impact of fossil fuel-based power generation.
- Small Modular Steam Turbines: The development of small modular steam turbines is aimed at providing flexible, scalable power solutions for decentralized and off-grid applications. These turbines can be easily transported and assembled, making them suitable for remote or rapidly growing areas.
- Hybrid Steam-Electric Systems: Hybrid systems that combine steam turbines with other power generation technologies, such as solar or wind, are being developed to provide more reliable and sustainable energy solutions. These systems can optimize the use of renewable energy sources while maintaining the stability of the power grid.
These trends indicate a promising future for steam turbine technology, with continued advancements expected to enhance their efficiency, sustainability, and versatility.
Potential for Hybrid Steam-Electric Systems
Hybrid steam-electric systems combine the benefits of steam turbines with other power generation technologies to create more resilient and efficient energy systems. Key features and benefits include:
- Enhanced Reliability: By integrating steam turbines with renewable energy sources such as solar or wind, hybrid systems can provide a more reliable power supply. When solar or wind generation is low, the steam turbine can compensate by increasing its output, ensuring a continuous supply of electricity.
- Increased Efficiency: Hybrid systems can optimize energy use by utilizing waste heat from steam turbines in other processes, such as heating or additional power generation. This approach improves the overall efficiency of the system and reduces fuel consumption.
- Flexibility in Fuel Use: Hybrid steam-electric systems can be designed to run on a variety of fuels, including biomass, natural gas, and hydrogen. This flexibility allows operators to switch between different energy sources based on availability, cost, and environmental impact.
The development of hybrid steam-electric systems is a key area of focus for the future of power generation, offering a way to integrate renewable energy sources with traditional power generation technologies.
The Role of Steam Turbines in a Hydrogen Economy
As the world moves towards a hydrogen economy, steam turbines are expected to play a significant role in hydrogen-based power generation. Key aspects include:
- Hydrogen-fueled Steam Turbines: Steam turbines can be adapted to run on hydrogen, either through direct combustion or by using hydrogen in combination with other fuels. Hydrogen-fueled steam turbines produce only water vapor as a byproduct, making them a zero-emission power generation option.
- Hydrogen Production via Electrolysis: Steam turbines can be used to power electrolyzers that produce hydrogen from water. The hydrogen can then be stored and used as a fuel for power generation or other industrial processes. This approach supports the development of a hydrogen economy by providing a reliable source of clean hydrogen.
- Integration with Renewable Energy: Steam turbines can be integrated with renewable energy sources, such as wind or solar, to produce green hydrogen. During periods of excess renewable energy production, the steam turbine can generate electricity to power electrolyzers, producing hydrogen that can be stored and used later.
The transition to a hydrogen economy presents significant opportunities for steam turbines, offering a pathway to zero-emission power generation and supporting the development of a sustainable energy system.
Steam Turbine Safety and Standards
Global Safety Standards for Steam Turbine Operation
Safety is a critical consideration in the operation of steam turbines, with global standards established to ensure safe and reliable operation. Key standards and regulations include:
- ISO Standards: The International Organization for Standardization (ISO) has established several standards related to the design, operation, and maintenance of steam turbines. These standards cover aspects such as safety, efficiency, and environmental impact, and are widely adopted by manufacturers and operators around the world.
- ASME Standards: The American Society of Mechanical Engineers (ASME) provides standards for the design and operation of pressure vessels, boilers, and steam turbines. ASME standards are particularly important in industries where steam turbines are used for critical applications, such as power generation and chemical processing.
- IEC Standards: The International Electrotechnical Commission (IEC) sets standards for the electrical components of steam turbines, including generators, control systems, and safety devices. These standards ensure that steam turbines operate safely within electrical systems and comply with global electrical safety regulations.
- National and Regional Regulations: In addition to international standards, steam turbines must comply with national and regional safety regulations. These regulations may include specific requirements for emissions, noise levels, and workplace safety, and vary depending on the location of the turbine.
Compliance with these safety standards is essential for the safe and efficient operation of steam turbines, reducing the risk of accidents and ensuring long-term reliability.
Training and Certification for Turbine Operators
Proper training and certification are essential for steam turbine operators to ensure safe and efficient operation. Key aspects of training and certification include:
- Operator Training Programs: Training programs for steam turbine operators cover topics such as turbine operation, maintenance, safety procedures, and troubleshooting. These programs may be offered by turbine manufacturers, technical schools, or industry associations.
- Certification Requirements: Certification requirements for steam turbine operators vary by region and industry. Operators may need to obtain certification from a recognized authority, such as a government agency or industry association, to demonstrate their competence and knowledge of turbine operation.
- Continuing Education: Steam turbine operators are often required to participate in continuing education to keep their skills up to date with the latest technologies and safety practices. Continuing education may include advanced training courses, workshops, and seminars on new developments in turbine technology.
Proper training and certification are critical for ensuring that steam turbines are operated safely and efficiently, reducing the risk of accidents and optimizing performance.
Risk Assessment and Management in Steam Power Plants
Risk assessment and management are essential components of steam power plant operation, helping to identify and mitigate potential hazards. Key aspects of risk assessment and management include:
- Hazard Identification: The first step in risk assessment is identifying potential hazards associated with steam turbine operation. These hazards may include mechanical failures, high-pressure steam leaks, electrical faults, and environmental risks such as emissions and noise.
- Risk Analysis: Once hazards have been identified, they are analyzed to determine the likelihood and potential impact of each risk. This analysis helps prioritize risks and identify areas where additional safety measures may be needed.
- Risk Mitigation: Based on the results of the risk analysis, risk mitigation strategies are developed to reduce the likelihood and impact of identified risks. These strategies may include engineering controls, such as safety devices and alarms, as well as administrative controls, such as safety procedures and training programs.
- Emergency Response Planning: In addition to risk mitigation, steam power plants must have emergency response plans in place to address potential accidents or incidents. These plans outline the steps to be taken in the event of an emergency, including evacuation procedures, communication protocols, and first aid measures.
Effective risk assessment and management are essential for maintaining the safety and reliability of steam power plants, protecting both workers and the environment.
Comparison with Other Power Generation Technologies
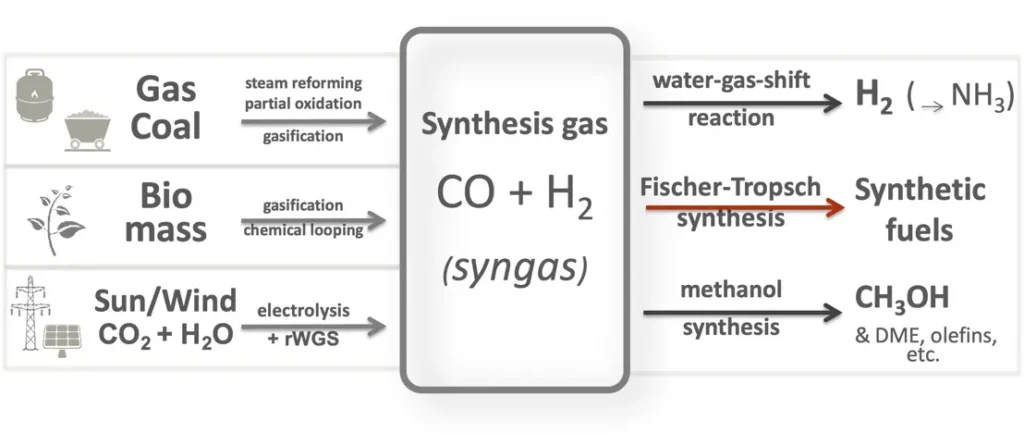
Comparing Steam Turbines with Gas Turbines and Internal Combustion Engines
Steam turbines, gas turbines, and internal combustion engines are all widely used for power generation, each with its own advantages and disadvantages. Key comparisons include:
- Efficiency: Steam turbines generally have higher thermal efficiency than internal combustion engines but lower efficiency than combined cycle gas turbines. Combined cycle gas turbines achieve higher efficiency by capturing and utilizing waste heat from the gas turbine to produce additional electricity.
- Fuel Flexibility: Steam turbines are highly versatile in terms of fuel use, capable of running on a variety of fuels including coal, natural gas, biomass, and waste heat. Gas turbines are typically optimized for natural gas but can also burn other fuels with modifications. Internal combustion engines are commonly used with liquid fuels such as diesel and gasoline but can also run on natural gas.
- Environmental Impact: The environmental impact of each technology depends on the fuel used. Steam turbines powered by coal or oil have higher emissions compared to gas turbines and internal combustion engines. However, steam turbines running on renewable fuels such as biomass or geothermal steam have lower environmental impacts. Gas turbines have relatively low emissions when using natural gas, but their environmental impact increases when using liquid fuels.
- Capital and Operating Costs: Steam turbines generally have higher capital costs compared to gas turbines and internal combustion engines, due to the need for boilers and other infrastructure. Operating costs vary depending on fuel prices and maintenance requirements. Gas turbines have lower capital costs and are often preferred for applications where quick start-up and shutdown are important. Internal combustion engines have the lowest capital costs but are typically used for smaller-scale power generation.
This comparison highlights the trade-offs between different power generation technologies and helps decision-makers choose the best option for their specific needs.
Advantages and Disadvantages of Steam Turbines in Various Applications
Steam turbines offer several advantages and disadvantages depending on the application. Key points include:
- Advantages:
- High Efficiency: Steam turbines are highly efficient, particularly in large-scale power generation and combined heat and power (CHP) applications.
- Fuel Flexibility: Steam turbines can run on a wide range of fuels, including fossil fuels, biomass, waste heat, and geothermal steam, making them versatile for various applications.
- Reliable and Long-lasting: Steam turbines have a proven track record of reliability and longevity, with many turbines operating for decades with proper maintenance.
- High Power Output: Steam turbines are capable of generating large amounts of electricity, making them suitable for base-load power generation in large power plants.
- Disadvantages:
- High Capital Costs: The capital costs of steam turbines are higher than those of gas turbines and internal combustion engines, particularly due to the need for boilers and other infrastructure.
- Complex Operation: Steam turbines require complex systems for steam generation, control, and maintenance, which can increase operational complexity and costs.
- Slow Start-up and Shutdown: Steam turbines typically require longer start-up and shutdown times compared to gas turbines and internal combustion engines, making them less suitable for applications that require rapid response to changes in power demand.
Understanding these advantages and disadvantages can help operators select the appropriate power generation technology for their specific application.
Role of Steam Turbines in Decentralized and Grid-connected Systems
Steam turbines play a vital role in both decentralized and grid-connected power generation systems. Key roles include:
- Decentralized Power Generation: In decentralized systems, steam turbines provide power to off-grid or remote locations, such as industrial sites, rural communities, and islands. These systems often use renewable fuels, such as biomass or geothermal steam, to generate electricity locally, reducing reliance on centralized power grids and improving energy security.
- Grid-connected Power Generation: In grid-connected systems, steam turbines are used in large power plants to generate electricity for distribution through the electrical grid. These plants may use a variety of fuels, including coal, natural gas, biomass, and waste heat, to provide reliable base-load power to the grid.
- Combined Heat and Power (CHP): Steam turbines are commonly used in CHP systems, where they generate both electricity and useful heat. These systems can be used in both decentralized and grid-connected settings, improving overall energy efficiency and reducing greenhouse gas emissions.
- Peaking and Backup Power: While steam turbines are typically used for base-load power generation, they can also be used as peaking or backup power sources in grid-connected systems. This is particularly true for turbines that run on renewable fuels or waste heat, which can provide a sustainable source of backup power during periods of high demand.
The versatility of steam turbines makes them suitable for a wide range of power generation applications, from large-scale grid-connected plants to small decentralized systems.
Steam Turbines in Marine and Aerospace Applications
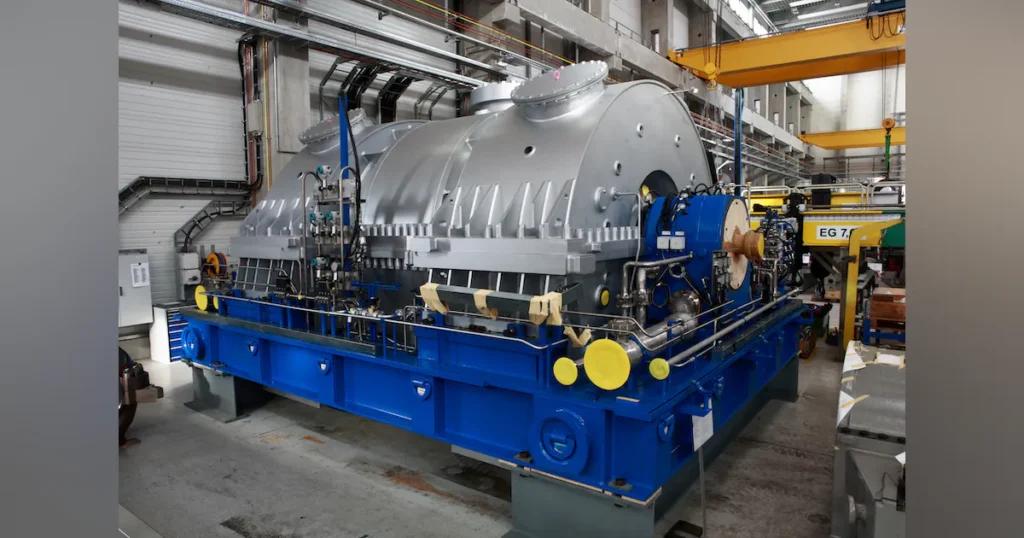
Use of Steam Turbines in Naval Vessels
Steam turbines have a long history of use in naval vessels, where their reliability and high power output are essential for propulsion and power generation. Key aspects of steam turbines in naval vessels include:
- Propulsion Systems: Steam turbines are used to drive the propellers of naval vessels, providing the necessary power for high-speed and long-distance travel. Turbine propulsion systems are known for their reliability and ability to operate under harsh conditions.
- Nuclear-powered Vessels: Many naval vessels, particularly submarines and aircraft carriers, are powered by nuclear reactors that generate steam to drive the turbines. Nuclear-powered steam turbines provide the vessels with virtually unlimited range and the ability to operate for extended periods without refueling.
- Marine Steam Turbine Design: The design of steam turbines for naval vessels is optimized for efficiency, durability, and low maintenance. Special materials and coatings are used to withstand the corrosive effects of seawater, and the turbines are designed to operate efficiently at a range of speeds.
Steam turbines continue to play a crucial role in naval propulsion, supporting the operation of some of the most advanced and powerful vessels in the world.
Historical and Modern Uses of Steam Turbines in Ships
Steam turbines have been used in ships for over a century, with historical and modern applications including:
- Early Steam Turbine Ships: The first steam turbine-powered ship, the SS Turbinia, was launched in 1894, demonstrating the superior speed and efficiency of steam turbines compared to traditional reciprocating steam engines. This led to the widespread adoption of steam turbines in commercial and military vessels in the early 20th century.
- World War II and Post-war Era: During World War II, steam turbines powered many of the largest and fastest warships, including battleships, aircraft carriers, and cruisers. In the post-war era, steam turbines continued to be used in commercial ships, such as ocean liners and cargo vessels.
- Modern LNG Carriers: In recent years, steam turbines have been used in liquefied natural gas (LNG) carriers, where the boil-off gas from the LNG cargo is used to generate steam and power the turbines. These ships are designed for long-haul voyages and benefit from the efficiency and reliability of steam turbines.
The use of steam turbines in ships has evolved over time, with modern applications focusing on efficiency, sustainability, and the use of alternative fuels.
Potential Applications of Steam Turbines in Space Exploration
While steam turbines are not currently used in space exploration, there is potential for their application in future space missions. Possible applications include:
- Spacecraft Power Generation: Steam turbines could be used to generate electricity for spacecraft by harnessing heat from nuclear reactors or solar thermal systems. The turbines would convert the heat into mechanical energy, which could then be used to generate electricity for propulsion, life support, and other spacecraft systems.
- In-situ Resource Utilization (ISRU): Steam turbines could play a role in ISRU on the Moon or Mars, where local resources such as water ice could be converted into steam to power turbines. This could provide a sustainable source of power for lunar or Martian bases, reducing the need for energy supplies from Earth.
- Thermal Energy Storage: Steam turbines could be integrated with thermal energy storage systems on space missions, storing excess heat generated during periods of high energy production and releasing it to generate electricity during periods of low energy availability.
While still in the conceptual stage, the potential applications of steam turbines in space exploration highlight their versatility and adaptability to a wide range of power generation challenges.
EMS Power Machines
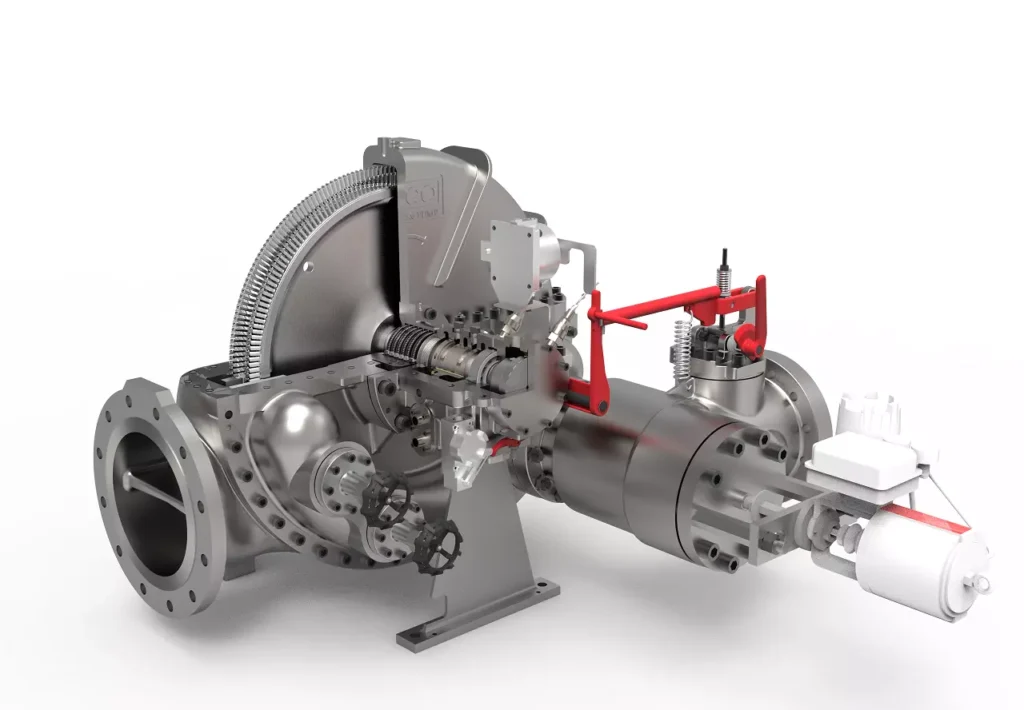
We design, manufacture and assembly Power Machines such as – diesel generators, electric motors, vibration motors, pumps, steam engines and steam turbines
EMS Power Machines is a global power engineering company, one of the five world leaders in the industry in terms of installed equipment. The companies included in the company have been operating in the energy market for more than 60 years.
EMS Power Machines manufactures steam turbines, gas turbines, hydroelectric turbines, generators, and other power equipment for thermal, nuclear, and hydroelectric power plants, as well as for various industries, transport, and marine energy.
EMS Power Machines is a major player in the global power industry, and its equipment is used in power plants all over the world. The company has a strong track record of innovation, and it is constantly developing new and improved technologies.
Here are some examples of Power Machines’ products and services:
- Steam turbines for thermal and nuclear power plants
- Gas turbines for combined cycle power plants and industrial applications
- Hydroelectric turbines for hydroelectric power plants
- Generators for all types of power plants
- Boilers for thermal power plants
- Condensers for thermal power plants
- Reheaters for thermal power plants
- Air preheaters for thermal power plants
- Feedwater pumps for thermal power plants
- Control systems for power plants
- Maintenance and repair services for power plants
EMS Power Machines is committed to providing its customers with high-quality products and services. The company has a strong reputation for reliability and innovation. Power Machines is a leading provider of power equipment and services, and it plays a vital role in the global power industry.
EMS Power Machines, which began in 1961 as a small factory of electric motors, has become a leading global supplier of electronic products for different segments. The search for excellence has resulted in the diversification of the business, adding to the electric motors products which provide from power generation to more efficient means of use.