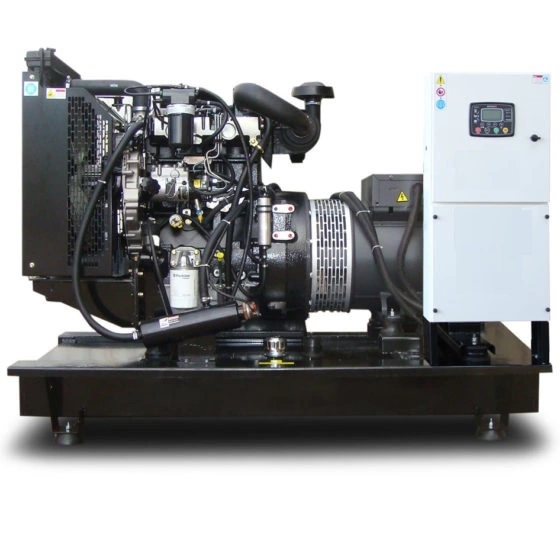
Here you will find some brief information about the marine diesel generator working principle and its application areas. High quality and low price
Marine Diesel Generator Working Principle
Marine diesel generators work based on the principle of internal combustion engines. They use diesel fuel to generate mechanical energy, which is then converted into electrical energy through a generator. Here is a simplified explanation of the working principle:
- Fuel Injection: The process starts with the injection of diesel fuel into the combustion chamber of the engine. This is typically done through a fuel injection system that sprays fuel into the cylinder at a precise moment.
- Compression Stroke: The piston inside the cylinder moves upwards, compressing the air inside the combustion chamber. The compression increases the temperature and pressure of the air.
- Ignition: Once the air is compressed, the fuel injected into the cylinder is ignited by a spark plug or by the high temperature and pressure in the chamber. The combustion of the fuel-air mixture creates a rapid expansion of gases, pushing the piston downward.
- Power Stroke: As the piston moves downward, it transfers the energy from the combustion process to the connecting rod, which converts the linear motion into rotary motion.
- Crankshaft Rotation: The rotary motion of the connecting rod is transmitted to the crankshaft, which converts the linear motion into a rotating motion.
- Generator Operation: The rotating crankshaft is connected to the generator, which consists of a rotor and stator. The rotating motion of the crankshaft induces an electromagnetic field in the stator, which generates electricity through electromagnetic induction.
- Electrical Output: The electrical energy produced by the generator is then available for use to power various electrical systems and equipment on the marine vessel.
The process described above repeats in a continuous cycle, with the combustion of fuel and the movement of the pistons driving the rotation of the crankshaft and the generation of electricity. Marine diesel generators are designed to provide a reliable source of electrical power for various applications on board ships and boats.
Fuel Injection
Fuel injection is a process used in internal combustion engines, including marine diesel generators, to deliver the precise amount of fuel to the combustion chamber at the right time. It plays a crucial role in optimizing fuel efficiency, performance, and emissions control. Here’s an overview of how fuel injection works:
- Fuel Supply: The fuel, typically diesel in the case of marine diesel generators, is stored in a fuel tank. It is then drawn from the tank by a fuel pump and delivered to the fuel injection system.
- Fuel Injection System: The fuel injection system consists of several components, including a fuel pump, fuel injectors, and control mechanisms. The fuel pump pressurizes the fuel and delivers it to the injectors.
- Timing and Quantity Control: The timing and quantity of fuel injection are precisely controlled by the engine’s electronic control unit (ECU) or a mechanical system. The ECU monitors various engine parameters, such as speed, load, and temperature, to determine the optimal timing and fuel quantity for each combustion cycle.
- Injection Process: When the ECU signals the fuel injectors, they open to spray a fine mist of fuel into the combustion chamber. The injectors are typically positioned near the intake valves or directly into the combustion chamber. The spray pattern and atomization of the fuel help ensure efficient combustion.
- Combustion: The fuel mixes with the compressed air inside the combustion chamber. As the piston reaches the top of its compression stroke, the fuel-air mixture is ignited by a spark plug or by the high temperature and pressure in the chamber, depending on the engine type.
- Combustion Efficiency: Fuel injection allows for precise control over the fuel-air mixture, resulting in better combustion efficiency compared to older carburetor systems. This leads to improved fuel economy, reduced emissions, and increased power output.
- System Monitoring and Adjustment: The fuel injection system continuously monitors engine conditions and adjusts the fuel injection parameters accordingly. This adaptive control helps optimize performance and emissions in real-time.
Overall, fuel injection in marine diesel generators provides more precise control over the fuel delivery process, resulting in improved efficiency, reduced emissions, and better engine performance compared to traditional carburetor systems.
Compression Stroke
The compression stroke is one of the four strokes in a four-stroke internal combustion engine cycle, including marine diesel generators. It is the second stroke in the cycle and plays a crucial role in the combustion process. Here’s an overview of the compression stroke:
- Intake Stroke: Before the compression stroke, the engine goes through the intake stroke. During this stroke, the intake valve opens, allowing a mixture of air and fuel (in the case of a spark-ignited engine) or just air (in the case of a compression-ignited engine) to enter the combustion chamber. The piston moves downward, creating a vacuum that draws the air or air-fuel mixture into the cylinder.
- Compression Stroke: After the intake stroke, the intake valve closes, and the piston starts moving upward. This upward movement compresses the air or air-fuel mixture trapped inside the cylinder. As the piston moves toward the top of the cylinder, the volume of the combustion chamber decreases, causing the pressure and temperature of the mixture to increase.
- Ignition: Near the end of the compression stroke, the fuel-air mixture is ignited in a spark-ignited engine by a spark plug. In a compression-ignited engine, the high temperature and pressure in the combustion chamber cause the injected fuel to ignite spontaneously.
- Power Stroke: After the combustion of the fuel-air mixture, the power stroke follows. This stroke is characterized by the rapid expansion of the burning gases, which forces the piston back down with significant force. The downward movement of the piston generates the power that drives the engine.
- Exhaust Stroke: Finally, after the power stroke, the exhaust stroke occurs. The exhaust valve opens, and the piston moves upward, pushing the burned gases out of the cylinder and into the exhaust system. This prepares the cylinder for the next intake stroke.
During the compression stroke, the air or air-fuel mixture is compressed to a high pressure and temperature, creating the ideal conditions for efficient combustion. By compressing the mixture, the engine maximizes the power output and fuel efficiency. The compression ratio, which is the ratio of the cylinder volume at bottom dead center (BDC) to the cylinder volume at top dead center (TDC), plays a significant role in determining the engine’s performance characteristics. Higher compression ratios generally result in better efficiency and power output.
Overall, the compression stroke is a critical part of the engine cycle, where the fuel-air mixture is compressed to create the conditions necessary for efficient combustion and power generation in a marine diesel generator.
Ignition
Ignition is a crucial step in the operation of a marine diesel generator or any internal combustion engine. It refers to the process of initiating the combustion of the fuel-air mixture inside the engine’s cylinders. In a marine diesel generator, ignition occurs in two main types: spark ignition and compression ignition.
- Spark Ignition: In spark-ignited engines, such as gasoline engines, the ignition process is initiated by a spark plug. During the compression stroke, as the piston nears the top of the cylinder, an electrical spark is generated by the spark plug. This spark ignites the fuel-air mixture, which results in the rapid combustion and expansion of the gases. The spark plug produces the necessary high-voltage electrical discharge to ignite the air-fuel mixture and initiate the combustion process.
- Compression Ignition: Marine diesel generators typically use compression-ignited engines, commonly known as diesel engines. In these engines, ignition occurs due to the high temperature and pressure resulting from the compression of the air in the combustion chamber. During the compression stroke, the air is compressed to a high pressure, which leads to a significant rise in temperature. At a specific point in the compression stroke, fuel is injected into the combustion chamber, usually by a fuel injector. The heat and pressure in the chamber cause the fuel to ignite spontaneously, without the need for a spark plug. This process is often referred to as “autoignition” or “self-ignition.” The ignition timing, which determines when the fuel is injected, is carefully controlled to ensure efficient and reliable combustion.
The ignition process is critical for starting the combustion reaction that produces the power needed to drive the marine diesel generator. It needs to be accurately timed and controlled to ensure efficient combustion, power generation, and overall engine performance. Proper ignition timing and the right fuel-air mixture are essential for achieving optimal engine efficiency, power output, and emissions control.
It’s important to note that marine diesel generators require a reliable and consistent ignition system to ensure smooth and reliable operation. The ignition system, whether spark-ignition or compression-ignition, needs to be properly maintained and periodically inspected to ensure proper functioning. Regular maintenance, including checking spark plugs (for spark-ignition engines) or fuel injectors (for compression-ignition engines), is essential to maintain optimal ignition performance.
Power Stroke
The power stroke is a crucial phase in the operation of a marine diesel generator or any internal combustion engine. It is the phase where the combustion of the fuel-air mixture generates high-pressure gases that exert force on the piston, resulting in the generation of power.
In a marine diesel generator, the power stroke occurs after the ignition of the fuel-air mixture. Here’s an overview of the power stroke process:
- Ignition: After the compression stroke, where the air-fuel mixture is compressed inside the cylinder, the fuel is ignited either by a spark plug (spark-ignition engines) or through autoignition (compression-ignition engines). The ignition causes the rapid combustion of the fuel, generating high-pressure gases.
- Expansion: The combustion of the fuel-air mixture produces a rapid increase in pressure. The high-pressure gases expand, forcing the piston to move downward. As the expanding gases push against the piston, the reciprocating motion is converted into rotational motion through the crankshaft.
- Power Generation: The downward movement of the piston, driven by the force of the expanding gases, is transferred to the crankshaft. The rotating motion of the crankshaft generates mechanical power. This power is then transmitted to the generator, which converts it into electrical power.
During the power stroke, the combustion process is carefully controlled to ensure efficient power generation. Factors such as fuel-air mixture ratio, injection timing (in compression-ignition engines), and combustion chamber design play a crucial role in optimizing power output, fuel efficiency, and emissions control.
It’s important to note that the power stroke is only one phase of the four-stroke cycle in a marine diesel generator. The other three phases include the intake stroke (air intake), compression stroke (compression of the air-fuel mixture), and exhaust stroke (expulsion of exhaust gases).
Efficient power stroke operation is essential for the overall performance of a marine diesel generator. Proper maintenance, including regular inspection of fuel systems, combustion chamber cleanliness, and fuel quality, is crucial to ensure smooth and reliable power stroke operation and maximize the generator’s performance and longevity.
Crankshaft Rotation
The rotation of the crankshaft is a fundamental aspect of the operation of a marine diesel generator or any internal combustion engine. The crankshaft converts the linear motion of the piston into rotational motion, which ultimately drives the generator to produce electricity.
Here’s an overview of how the crankshaft rotation occurs in a marine diesel generator:
- Power Stroke: During the power stroke, the high-pressure gases produced by the combustion of the fuel-air mixture push the piston downward. The connecting rod, which is connected to the piston, transfers this linear motion to the crankshaft.
- Crankshaft Design: The crankshaft consists of a series of offset crank throws or journals. The connecting rod is attached to one of these crank throws, usually through a piston pin or wrist pin. As the piston moves downward during the power stroke, it rotates the crankshaft due to the connection between the connecting rod and the crank throw.
- Rotation Direction: The rotation direction of the crankshaft depends on the engine design. In most marine diesel generators, the crankshaft rotates in a clockwise direction (when viewed from the front). This rotation direction is often referred to as the “normal” or “right-hand” rotation.
- Flywheel and Generator Connection: The crankshaft is connected to the flywheel, which helps to maintain the rotational momentum and smooth out any variations in the power delivery. The flywheel is also connected to the generator shaft, transmitting the rotational motion to the generator, which then converts it into electrical power.
The crankshaft rotation is synchronized with the engine’s combustion cycle and the generator’s electrical output requirements. The speed of the crankshaft rotation, measured in revolutions per minute (RPM), is controlled by the engine’s throttle and governor system. This allows for the regulation of the generator’s output power and maintains the desired operational speed.
Proper maintenance and lubrication of the crankshaft and its associated components are essential to ensure smooth and efficient rotation. Regular inspections, lubricant checks, and maintenance procedures are performed to maintain the integrity and performance of the crankshaft, ensuring reliable operation of the marine diesel generator.
Diesel Engine of the Generators
“EMS Power Machines” uses diesel engines that are manufactured with the latest technology, in accordance with ISO3046 standards, and designed for generator sets. The diesel engines used; are designed for low fuel consumption, with 4-stroke type, direct injection, with all needed limiting and level sensors, with diesel electronic or mechanical type governor mounted on the fuel pump for sensitive speed adjustment or regulation.
The engines used, may have oil, air, or water-type cooling systems, depending on customer request and the diesel engine. There are also oil, fuel, and air filters that are designed for heavy operation conditions, which provide the engine with a long lifetime with high performance. All the equipment that is needed for the diesel engine for operating safely and reliably, is provided along with the generator set.
EMS Power Machines can provide a base frame fuel tank or free-standing fuel tank dependent on the model preferences of the customer. Larger sets require free-standing fuel tanks due to the need for high fuel capacity.
Fuel tanks are manufactured of plate steel or other suitable materials.
Teksan ensures that the fuel tanks are all manufactured in accordance with relevant standards. EMS Power Machines fuel tanks are equipped with:
- Filling cap
- Tank ventilation
- Fuel outlet valve
- Fuel return connections
- Tank drainage plug
- Sediment trapping section
- Level gauge pipe
- Float switches (Optional)
- Automatic filling (Optional)
It is highly recommended to install a fuel filter and/or a water separator on the outlet line of these fuel tanks.
Engine Brands of Diesel Generators for Sale
- Perkins Engines
- Cummins Engines
- Ricardo Engines
- Baudoin Engines
- Shanghai Dongfeng Engines
- Volvo Engines
- Yangdong Engines
We use any of the above-mentioned diesel engines for the production of our diesel generators according to the customers’ requests.
Perkins engines are manufactured in the UK and are very common in the generator production market.
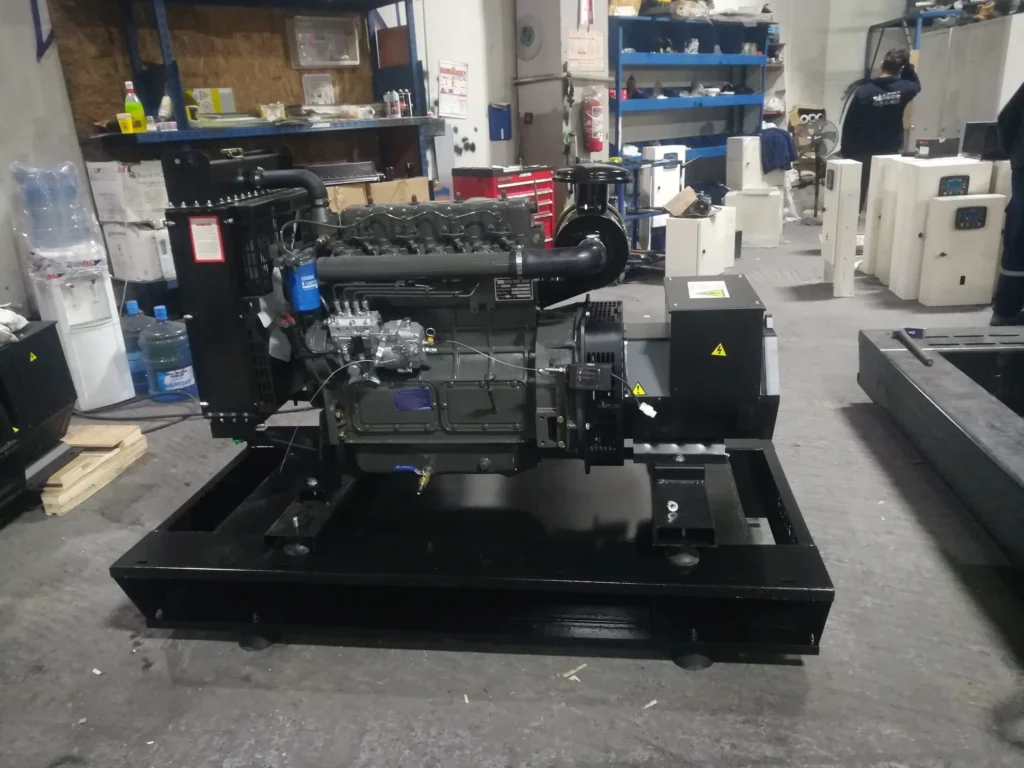
Ricardo engines are manufactured in China and have a very high market share in the generator manufacturing market.
Base Frame of the Generators
The base frame on which the generator set is placed has been manufactured using proper steel plates or special profiles based on the necessary dynamic, static, and vibration calculations in order for providing high resistance. EMS Power Machines produces the base frames for all ranges in accordance with international standards.
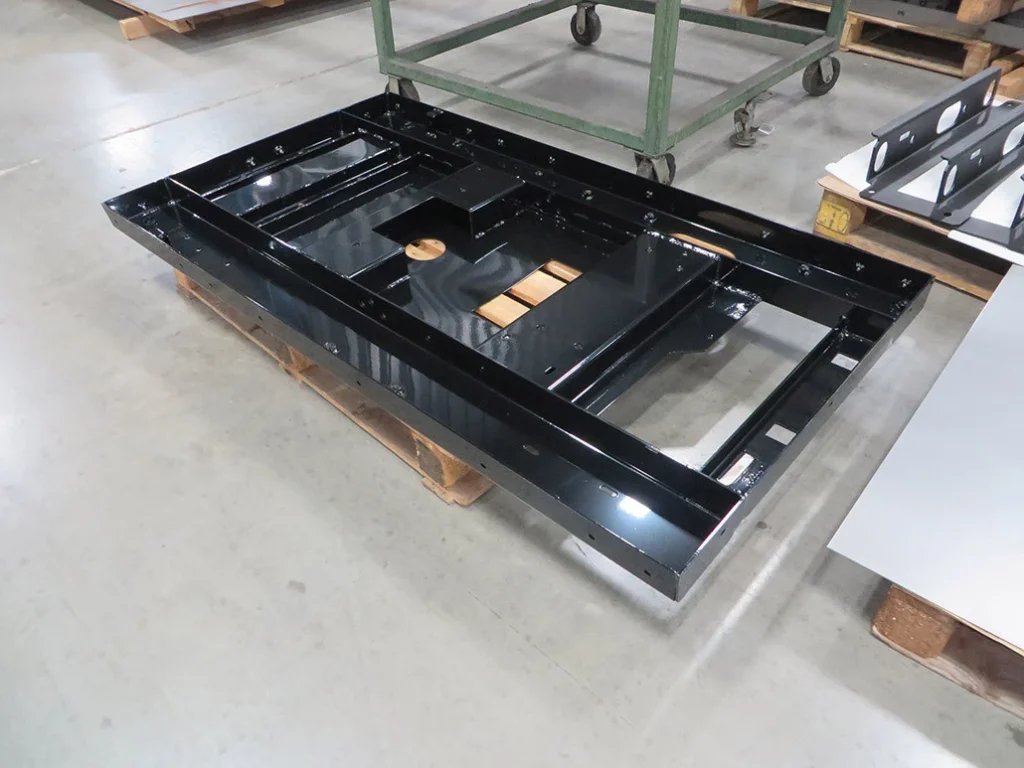
The base frame of a generator, often referred to as the generator skid or chassis, is a crucial structural component that provides support, stability, and a foundation for the entire generator set. It plays a key role in ensuring the proper functioning, safety, and longevity of the generator. Here are some key aspects related to the base frame of generators:
Functions and Features
- Support Structure:
- The base frame serves as the primary support structure for the generator set, providing a stable foundation to hold all the components together.
- Engine and Alternator Mounting:
- The engine and alternator, the two main components of a generator set, are securely mounted on the base frame. Proper alignment and secure mounting are essential for efficient operation and to minimize vibrations.
- Vibration Isolation:
- Many base frames incorporate features to isolate vibrations produced during the operation of the generator. This helps reduce noise and ensures that vibrations do not impact the performance or structural integrity of the generator.
- Fuel Tank Support:
- In some generator sets, the fuel tank is integrated into or mounted on the base frame. This provides a secure and stable location for the fuel tank.
- Cooling System Support:
- The cooling system components, such as radiators and cooling fans, are often mounted on or integrated into the base frame to ensure proper airflow and cooling.
- Lifting Points:
- Base frames are designed with lifting points or provisions for lifting equipment. This facilitates ease of transportation, installation, and maintenance of the generator set.
- Weatherproofing:
- Depending on the design, the base frame may provide some level of protection against environmental elements, such as rain and dust, to ensure the longevity of the generator set.
- Accessibility:
- The base frame is designed to allow easy access to key components for maintenance and service tasks. This includes access panels and doors for routine inspections and repairs.
- Corrosion Resistance:
- Base frames are often constructed from materials that offer corrosion resistance to withstand environmental conditions and ensure a longer service life.
Considerations
- Material Selection:
- Base frames are commonly made of steel, but the type and quality of the steel used can vary. The choice of materials depends on factors such as environmental conditions, weight considerations, and corrosion resistance.
- Size and Dimensions:
- The size and dimensions of the base frame are determined by the overall size of the generator set. It should provide adequate space for all components and ensure proper ventilation.
- Site Conditions:
- The design of the base frame should consider the specific site conditions where the generator will be installed. This includes factors such as seismic requirements, soil conditions, and available space.
- Transportation:
- The base frame design should facilitate ease of transportation, considering factors such as size, weight, and lifting points.
- Regulatory Compliance:
- The design and construction of the base frame should comply with relevant safety and construction standards set by regulatory authorities.
The base frame is a critical element in the overall design and functionality of a generator set. Its design and construction should align with the specific requirements of the generator and the intended application. Manufacturers often provide detailed specifications for the base frame in the generator set documentation. When selecting or installing a generator set, it’s important to follow the manufacturer’s guidelines and consider any site-specific requirements.
Vibration Isolators
Vibration isolators, also known as vibration mounts or isolating mounts, are components used in diesel generators to reduce the transmission of vibrations and noise generated during the operation of the engine. These isolators play a crucial role in enhancing the overall performance, stability, and comfort of the generator set. Here are key aspects related to the vibration isolators of diesel generators:
Functions and Features
- Vibration Reduction:
- The primary function of vibration isolators is to reduce the transmission of vibrations generated by the diesel engine to the surrounding structure. This helps minimize the impact of vibrations on adjacent equipment and structures.
- Noise Reduction:
- In addition to reducing vibrations, isolators also contribute to noise reduction. They help isolate the generator set from its surroundings, preventing the transmission of noise to nearby areas.
- Component Protection:
- Vibration isolators protect various components of the generator set, including the engine, alternator, and other critical parts, from the potentially damaging effects of excessive vibrations.
- Structural Integrity:
- By reducing vibrations, isolators contribute to maintaining the structural integrity of the generator set and the surrounding infrastructure. Excessive vibrations can lead to wear and tear on components and may compromise the overall stability of the generator.
- Isolation from External Vibrations:
- Isolators not only prevent the transmission of internal vibrations but also isolate the generator set from external vibrations, such as those from nearby machinery or environmental factors.
- Adjustability:
- Some vibration isolators are designed to be adjustable, allowing for fine-tuning to achieve optimal vibration isolation based on the specific operating conditions and requirements.
Types of Vibration Isolators
- Spring Mounts:
- Spring mounts use metal springs to isolate vibrations. They are effective in reducing both high and low-frequency vibrations.
- Rubber Mounts:
- Rubber mounts, or elastomeric mounts, use rubber or other elastomeric materials to absorb and dampen vibrations. They are effective for isolating high-frequency vibrations.
- Air Springs:
- Air springs use compressed air to provide isolation. They are effective in isolating low-frequency vibrations and are often used in large and heavy machinery.
- Viscous Dampers:
- Viscous dampers use hydraulic fluid to absorb and dissipate vibrations. They are effective in isolating both high and low-frequency vibrations.
- Active Isolation Systems:
- Active isolation systems use sensors and actuators to actively counteract vibrations in real-time. These systems can provide dynamic and adaptive vibration control.
Considerations
- Application Specifics:
- The selection of vibration isolators should consider the specific application, environmental conditions, and the frequency spectrum of vibrations generated by the diesel generator.
- Load Capacity:
- The isolators should be selected based on the load capacity of the generator set to ensure proper support and isolation.
- Installation and Maintenance:
- Proper installation and regular maintenance of the vibration isolators are crucial to ensure their effectiveness over time.
- Regulatory Compliance:
- Compliance with relevant safety and regulatory standards should be considered when selecting vibration isolators.
- Manufacturer Recommendations:
- Follow the manufacturer’s recommendations for the type and specification of vibration isolators suitable for a particular generator model.
Vibration isolators are integral components that contribute to the smooth and reliable operation of diesel generators while minimizing the impact on surrounding structures and environments. When selecting or maintaining vibration isolators, it’s essential to consider the specific requirements of the generator set and follow the guidelines provided by the generator manufacturer.
Vibration insulators are used in order to decrease the negative effects of vibrations caused by the rotational movement of the engine and alternator. These insulators which also prevent the vibration to be transferred from
the base frame to the ground, are placed between the engine/alternator and the base frame. Specially chosen vibration isolators are mounted between the engine, alternator, and base frame. Alternatively, in bigger generator sets, vibration isolators are mounted between the base frame and floor.
Exhaust System and Silencer
An exhaust system should be designed to decrease the noise coming from the exhaust manifold and dispel the exhaust gases into the atmosphere. The exhaust system consists of a flexible compensator that absorbs vibration and expansion, steel pipes, bend, silencer, and mounting equipment. Further details on exhaust systems can be found in the “Installation” section of this manual.
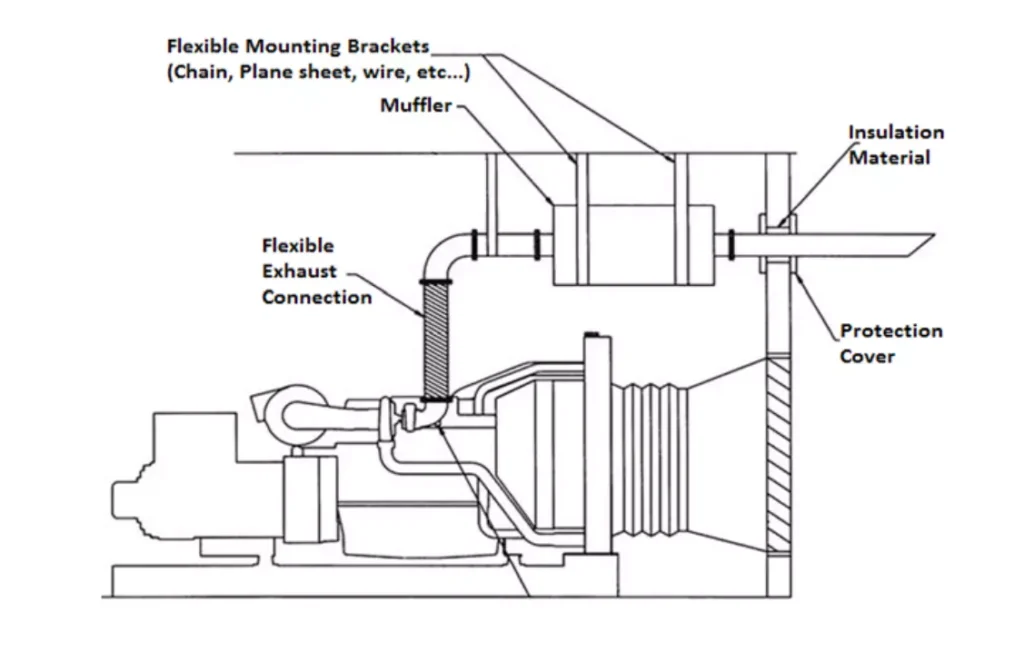
The exhaust system and silencer of a diesel generator play a crucial role in managing and reducing the noise and emissions produced during the operation of the generator. Here are key aspects related to the exhaust system and silencer of diesel generators:
Exhaust System
- Exhaust Manifold:
- The exhaust manifold collects exhaust gases from the engine cylinders and directs them to the exhaust system.
- Turbocharger (if applicable):
- In some diesel generators, especially those with larger engines, a turbocharger may be used to increase the efficiency of exhaust gas evacuation.
- Piping:
- Exhaust piping carries the hot gases from the engine to the other components of the exhaust system. It is designed to withstand high temperatures and is often insulated to prevent heat dissipation.
- After-Treatment Devices:
- Modern diesel generators often incorporate after-treatment devices such as diesel particulate filters (DPF) and selective catalytic reduction (SCR) systems to reduce emissions and comply with environmental regulations.
Silencer
- Purpose:
- The silencer, or muffler, is designed to reduce the noise generated by the exhaust gases as they exit the generator. It helps in creating a more tolerable and quieter operating environment.
- Design:
- Silencers are typically designed with sound-absorbing materials and internal baffles to attenuate and dissipate sound energy. The design may vary based on the specific noise reduction requirements.
- Inlet and Outlet:
- Silencers have inlet and outlet ports that are connected to the exhaust piping. The exhaust gases enter the silencer through the inlet and exit through the outlet.
- Materials:
- Silencers are constructed using materials that can withstand high temperatures and corrosion, given the harsh environment of exhaust gases.
- Resonators (if applicable):
- Some silencers may incorporate resonators to further dampen specific frequencies of sound and enhance noise reduction.
- Spark Arrestor (if applicable):
- In certain applications, especially in environments where the risk of fire is a concern, a spark arrestor may be included in the silencer to prevent sparks from exiting the exhaust.
Considerations
- Noise Regulations:
- Compliance with local noise regulations is a critical consideration when selecting or designing the exhaust system and silencer. Different regions may have specific noise level requirements that need to be met.
- Emission Regulations:
- Ensure that the exhaust system, including any after-treatment devices, complies with emissions regulations applicable to the generator’s location.
- Engine Efficiency:
- The design of the exhaust system should not compromise the efficiency of the engine. It should allow for proper evacuation of exhaust gases without causing backpressure.
- Maintenance:
- Regular inspection and maintenance of the exhaust system and silencer are essential to ensure proper functioning and longevity. This includes checking for leaks, corrosion, and damage.
- Installation:
- Proper installation of the exhaust system and silencer is crucial for optimal performance. Consider factors such as proper clearances, support structures, and heat dissipation.
- Manufacturer Recommendations:
- Follow the recommendations provided by the generator manufacturer regarding the selection, installation, and maintenance of the exhaust system and silencer.
The exhaust system and silencer are critical components that contribute to the safe and environmentally friendly operation of diesel generators. When selecting or maintaining these components, it’s important to consider both regulatory requirements and the specific operational needs of the generator. Consulting with the generator manufacturer or a qualified professional can help ensure that the exhaust system is designed and maintained to meet the necessary standards.
Control System
The control system of a diesel generator is a crucial component that governs and manages the operation of the generator set. It includes a range of components and features designed to monitor, control, and protect the generator during various operating conditions. Here are key aspects related to the control system of diesel generators:
Components of the Control System
- Control Panel:
- The control panel is the interface through which operators interact with the generator. It typically includes displays, buttons, switches, and indicators for monitoring and controlling various parameters.
- Controller:
- The controller is the central processing unit responsible for monitoring and regulating the generator’s functions. It may be a microprocessor-based controller that processes data from sensors and issues commands to different components.
- Sensors:
- Various sensors are deployed throughout the generator to measure critical parameters such as engine speed, oil pressure, coolant temperature, voltage, and current. These sensors provide real-time data to the controller.
- Automatic Voltage Regulator (AVR):
- The AVR is responsible for maintaining a stable and consistent voltage output from the generator. It adjusts the excitation current to the generator’s alternator to control the voltage level.
- Engine Control Module (ECM):
- The ECM monitors and controls the diesel engine’s operation. It manages fuel injection, air intake, exhaust emissions, and other parameters to optimize engine performance and efficiency.
- Governor:
- The governor regulates the speed of the engine by controlling the fuel injection. It helps maintain a constant speed under varying loads.
- Protection System:
- The protection system safeguards the generator against abnormal conditions such as overloading, overheating, low oil pressure, and over-speeding. It can initiate automatic shutdowns to prevent damage.
- Data Logging and Communication:
- Some control systems feature data logging capabilities to record operational data over time. Communication interfaces may allow for remote monitoring and control.
Features and Functions
- Start/Stop Control:
- The control system initiates the start and stop sequences of the generator based on manual or automatic commands.
- Load Sharing (Parallel Operation):
- In parallel operation scenarios where multiple generators are connected, the control system ensures proper load sharing and synchronization.
- Synchronization:
- The control system facilitates synchronization when connecting the generator to an electrical grid or other generators, ensuring a seamless connection without disturbances.
- Emergency Shutdown:
- The control system includes emergency shutdown features that can be triggered in response to critical faults or unsafe conditions to protect the generator.
- Remote Monitoring and Control:
- Advanced control systems may allow remote monitoring and control of the generator, providing real-time information and the ability to make adjustments from a distance.
- Diagnostic and Fault Analysis:
- The control system can diagnose faults, provide alerts or alarms, and perform self-diagnostics to aid in troubleshooting and maintenance.
Considerations
- Compatibility:
- Ensure that the control system is compatible with the generator set and any additional components, especially if the generator is part of a larger power system.
- Scalability:
- Consider the scalability of the control system to accommodate future upgrades or additions to the generator system.
- User Interface:
- Evaluate the user interface of the control panel for ease of use and accessibility, especially for operators who need to monitor and manage the generator.
- Integration with Power Systems:
- If the generator is part of a larger power distribution system, ensure that the control system can seamlessly integrate with other power management components.
- Training and Documentation:
- Adequate training and documentation should be provided for operators to effectively use and troubleshoot the control system.
The control system is a critical aspect of diesel generators, ensuring reliable and efficient operation while providing essential protection features. When selecting a generator, it’s important to understand the capabilities of the control system and how well it aligns with the specific requirements of the intended application. Manufacturers typically provide detailed specifications and documentation related to the control system for each generator model.
Various control systems are developed for ensuring the protection of the generator set against failures, load transfers, and the reliability of the operation of the generator set. Control system designs can vary according to the customer requirements and assembling requirements. The main
types of control systems are Manual, Automatic, Standby, and Parallel working systems.
All control systems are mounted on steel panels containing a lockable door for easy reaching and service. Further technical information about the control systems of the generator sets can be found in the “Control Systems” section of this manual and the manual of the controller.
Installation of Generators
The installation of generators is a critical process that involves several steps to ensure proper functionality, safety, and compliance with regulations. Whether installing a standby generator for backup power or a prime power generator for continuous operation, following best practices is essential. Here is a general guide for the installation of generators:
1. Site Selection
- Regulatory Compliance:
- Ensure compliance with local building codes, zoning regulations, and environmental requirements. Obtain any necessary permits before starting the installation.
- Space and Clearance:
- Select a location with sufficient space for the generator and its accessories. Allow for proper clearance around the generator for maintenance and ventilation.
- Ventilation:
- Ensure adequate ventilation to dissipate heat generated by the generator. Generators typically require space for air intake and exhaust.
- Accessibility:
- Choose a location that allows easy access for installation, maintenance, and potential repairs. Consider factors such as crane access and pathways for transporting equipment.
2. Foundation and Mounting
- Foundation Construction:
- Prepare a stable foundation for the generator. The foundation should be level, sturdy, and capable of supporting the generator’s weight.
- Vibration Isolation:
- If applicable, install vibration isolators or mounts to minimize the transmission of vibrations from the generator to the foundation and surrounding structures.
- Anchor the Generator:
- Anchor the generator securely to the foundation to prevent movement or shifting during operation or external forces.
3. Electrical Connections
- Transfer Switch Installation:
- Install an automatic transfer switch (ATS) to facilitate seamless switching between the main power source and the generator during power outages.
- Wiring:
- Connect the generator to the electrical distribution system following local electrical codes and regulations. Ensure proper sizing of conductors and adherence to safety standards.
- Grounding:
- Establish proper grounding for the generator as per electrical codes. A grounding electrode system helps ensure safety and proper functioning.
- Voltage Configuration:
- Verify that the generator’s voltage configuration matches the requirements of the connected loads. Adjust settings if necessary.
4. Fuel System
- Fuel Storage:
- If the generator has an internal fuel tank, ensure it is filled with the appropriate fuel. For external fuel tanks, connect and test the fuel supply system.
- Fuel Quality:
- Ensure that the fuel supply meets the specifications recommended by the generator manufacturer. Use clean and high-quality fuel.
5. Exhaust System
- Exhaust Piping:
- Install the exhaust piping in compliance with local codes and regulations. Ensure proper venting of exhaust gases away from occupied spaces.
- Silencer Installation:
- If a silencer is included, install it in the exhaust system to reduce noise emissions. Follow the manufacturer’s recommendations for placement and installation.
6. Control System
- Control Panel Wiring:
- Connect the control panel to the generator and ensure proper wiring. Verify the functionality of control features such as start/stop, monitoring, and protection systems.
- Testing:
- Conduct thorough testing of the control system to ensure all functions operate as intended. Test automatic start/stop sequences, alarms, and safety shutdowns.
7. Commissioning and Testing
- Load Testing:
- Conduct load tests to ensure the generator can handle the expected loads. Verify the generator’s performance under varying load conditions.
- System Integration:
- Integrate the generator into the overall power system. If multiple generators are used, ensure proper synchronization and load sharing.
- Commissioning Procedures:
- Follow the commissioning procedures provided by the generator manufacturer. This may include adjusting settings, verifying alarms, and ensuring all systems are operational.
8. Documentation
- As-Built Documentation:
- Prepare as-built documentation that includes detailed drawings, specifications, and records of the installation. This documentation is valuable for future maintenance and reference.
- Operation and Maintenance Manuals:
- Provide the end user with comprehensive operation and maintenance manuals. Include information on routine maintenance, troubleshooting, and emergency procedures.
9. Training
- Operator Training:
- Provide training for operators on how to start, stop, and operate the generator safely. Ensure they are familiar with the control panel and understand basic troubleshooting procedures.
- Maintenance Training:
- Train maintenance personnel on routine maintenance tasks, including oil changes, filter replacements, and inspections. Emphasize the importance of following the manufacturer’s maintenance schedule.
10. Compliance
- Final Inspection:
- Conduct a final inspection to ensure compliance with all applicable codes, regulations, and safety standards.
- Certifications:
- Obtain any necessary certifications or approvals from local authorities or regulatory bodies.
- Record Keeping:
- Keep detailed records of the installation, testing, and commissioning processes. This documentation may be required for compliance audits and warranty support.
11. Ongoing Monitoring and Maintenance
- Monitoring Systems:
- Implement continuous monitoring systems for key parameters, such as fuel levels, oil pressure, and coolant temperature. Consider remote monitoring options for quick response to issues.
- Scheduled Maintenance:
- Establish a scheduled maintenance program and adhere to the manufacturer’s recommendations. Regular maintenance is essential for the reliability and longevity of the generator.
- Emergency Response Plan:
- Develop and communicate an emergency response plan outlining procedures to follow in the event of a generator malfunction or failure.
Conclusion
The installation of generators is a multifaceted process that requires careful planning, attention to detail, and compliance with various standards and regulations. Collaboration with experienced professionals, including electrical engineers, mechanical contractors, and generator technicians, can contribute to a successful installation. Additionally, consulting with the generator manufacturer and following their guidelines is essential to ensure optimal performance and longevity of the generator system.
The selection and preparation of the location where the generator set will be placed is the most important step of installation. So please make sure that the generator set is installed at a place that is selected and prepared fully in conformity with the instructions in this manual.
Also, remember that you can call us for any further information or confirmation about this issue. If the generator will be placed on an upper floor, not the basement or ground, the responsibility of static load distribution belongs to the customer. The customer should get approval from an authority about this issue before installation.
Environmental Conditions
Install the generator set in such a place that it will not be directly exposed to harsh environmental conditions such as rain, snow, hail, flood, humidity, excessive sunlight, extremely low or high temperature, dust, soil, sand or wind. The place where the generator set will be installed must be, clean, dry, well illuminated and ventilated, free of corrosive or conductive pollutant substances like dust, lint, smoke, oil vapor, exhaust smoke, etc…
Be sure to leave enough blank space around the generator set, in order to ease future maintenance or repair activities Remember that it can be necessary to disassemble the main parts like the engine, alternator, or base frame in some cases. The base ground where the generator will be settled must be clean dry and must have a good drainage system. Put the generator set in such a place that nobody unauthorized can access it, or at least take necessary precautions about it.
Place generator sets in such places that they will not be affected by the operation of any other machines. Do not install or run the generator set at any place that has any possibility of risk in terms of safety of operation.
Also, provide the necessary precautions (canopy option) or protections against bad weather conditions if it will be placed outside.
The doors of the room that the generator set will be placed in, must be at enough size for the main parts (engine, alternator, radiator, etc…) to pass through. Also, ventilation windows can be built portable or mobile for
this purpose.
Diesel Generator
A diesel generator is a device that converts diesel fuel into electricity. Diesel generators are typically used as backup power sources in the event of a power outage, but they can also be used as primary power sources in remote areas where there is no grid electricity available.
Diesel generators work by using a diesel engine to turn a generator. The diesel engine burns diesel fuel to create mechanical energy, which is then converted into electrical energy by the generator.
Diesel generators are available in a variety of sizes and power outputs. Some diesel generators are small enough to be portable, while others are large enough to power entire buildings or communities.
Diesel generators are a reliable and efficient way to generate electricity. They are also relatively easy to operate and maintain.
Here are some examples of where diesel generators are used:
- Hospitals and other critical facilities: Diesel generators are used to provide backup power in hospitals, data centers, and other critical facilities. This ensures that these facilities continue to operate even in the event of a power outage.
- Construction sites: Diesel generators are used to provide power for construction tools and equipment at construction sites. This allows construction work to continue even in remote areas where there is no grid electricity available.
- Emergency services: Diesel generators are used to provide power for emergency services, such as ambulances and fire trucks. This ensures that these services can continue to operate even in the event of a power outage.
- Remote areas: Diesel generators are used to provide primary power in remote areas where there is no grid electricity available. This allows people living in these areas to have access to electricity for lighting, cooking, and other essential needs.
Diesel generators are a valuable tool for generating electricity in a variety of situations. They are reliable, efficient, and easy to operate and maintain.
Diesel Generator Outputs
The output of a diesel generator is measured in kilowatts (kW). The output of a diesel generator is limited by the size and power of the diesel engine that it uses. Diesel generators are available in a variety of sizes and power outputs, ranging from small portable generators that produce a few kW of power to large industrial generators that produce thousands of kW of power.
The output of a diesel generator is also affected by a number of other factors, including:
- Fuel quality: The quality of the diesel fuel used in a generator can affect its output. Lower quality diesel fuel can produce less power and can also damage the generator.
- Air quality: The quality of the air that the generator is operating in can also affect its output. Operating a generator in thin air or in hot weather can reduce its output.
- Maintenance: Proper maintenance of a diesel generator is essential to ensure its optimal performance. A generator that is not properly maintained may produce less power and may also be more likely to break down.
Here are some examples of the power outputs of different types of diesel generators:
- Small portable generator: 1-5 kW
- Medium-sized generator: 5-10 kW
- Large generator: 10-100 kW
- Industrial generator: 100 kW and up
The power output of a diesel generator is an important factor to consider when choosing a generator for a particular application. The generator should have enough power output to meet the needs of the devices and appliances that will be connected to it.
It is also important to note that the power output of a diesel generator is not the same as its efficiency. The efficiency of a diesel generator is the percentage of the fuel energy that is converted into electrical energy. A more efficient generator will produce more electrical energy for a given amount of fuel.
Diesel Generators
Diesel generators are a type of backup or standby power source that uses a diesel engine to generate electricity. These generators are widely used in various applications where a reliable and continuous power supply is crucial. Here are key aspects related to diesel generators:
Components of Diesel Generators
- Diesel Engine:
- The diesel engine is the primary component responsible for converting diesel fuel into mechanical energy. This mechanical energy is then used to turn a generator to produce electricity.
- Generator (Alternator):
- The generator, or alternator, converts the mechanical energy from the diesel engine into electrical energy. It consists of a rotor and a stator, and as the rotor turns within the stator’s magnetic field, it induces an electric current.
- Fuel System:
- The fuel system stores and delivers diesel fuel to the engine for combustion. It typically includes a fuel tank, fuel pump, and fuel injectors.
- Cooling System:
- Diesel generators have a cooling system to maintain optimal operating temperatures. This system may include a radiator, cooling fans, and a water or air cooling mechanism.
- Exhaust System:
- The exhaust system is responsible for expelling the combustion gases produced during the diesel engine’s operation. It usually includes a muffler and may incorporate emission control devices.
- Control Panel:
- The control panel houses the generator’s control and monitoring systems. It allows operators to start or stop the generator, monitor performance, and sometimes control other parameters such as voltage and frequency.
- Voltage Regulator:
- The voltage regulator maintains a stable output voltage by adjusting the excitation current to the generator’s rotor.
- Battery Charger:
- Diesel generators often have a battery or set of batteries to start the engine. A battery charger ensures that the batteries remain charged and ready to start the generator when needed.
- Automatic Transfer Switch (ATS):
- An ATS is a crucial component for standby generators. It automatically switches the electrical load from the main power source to the generator when it detects a power outage and vice versa when the main power is restored.
Working Principle:
- Combustion: Diesel fuel is injected into the combustion chamber, and the heat generated by the compression of air ignites the fuel.
- Mechanical Energy: The combustion process produces high-pressure gases that expand, creating mechanical energy. This energy is used to rotate the engine’s crankshaft.
- Electricity Generation: The rotating crankshaft is connected to the generator, causing it to spin. As the generator’s rotor rotates within the stator, it induces an electric current, generating electricity.
Applications:
- Emergency Power:
- Diesel generators are commonly used for emergency backup power in critical facilities such as hospitals, data centers, and telecommunications facilities.
- Construction Sites:
- They are used on construction sites to power tools and equipment where a reliable grid connection may not be available.
- Industrial Facilities:
- Diesel generators provide backup power for industrial plants and manufacturing facilities to prevent production disruptions.
- Remote Locations:
- In remote or off-grid locations, where a stable power supply from the grid is not feasible, diesel generators can provide a reliable source of electricity.
- Mining Operations:
- Diesel generators are often used in mining operations to power equipment in remote and rugged environments.
- Agriculture:
- Farms may use diesel generators to power irrigation systems, machinery, and other agricultural equipment.
Advantages:
- Fuel Availability:
- Diesel fuel is widely available, making diesel generators suitable for various locations.
- Fuel Efficiency:
- Diesel generators are known for their fuel efficiency, providing a cost-effective solution for standby power.
- Durability:
- Diesel generators are generally robust and durable, capable of handling heavy loads and providing long service life.
- High Torque:
- Diesel engines provide high torque, making them suitable for applications with varying load conditions.
Limitations:
- Noise and Emissions:
- Diesel generators can be noisy, and their combustion process produces emissions. However, advancements in technology have led to quieter and more environmentally friendly models.
- Maintenance:
- Regular maintenance is essential to ensure the proper functioning of diesel generators.
- Initial Cost:
- Diesel generators may have a higher upfront cost compared to some other types of generators.
Diesel generators are a reliable and widely used solution for providing backup or primary power in various settings. The choice of a diesel generator depends on factors such as power requirements, environmental considerations, and the specific needs of the application.
Diesel generators are machines that convert the chemical energy of diesel fuel into mechanical energy, which is then used to generate electricity. They are a popular choice for a variety of applications, including prime power for remote locations, backup power for businesses, and emergency power for hospitals and other critical infrastructure.
Diesel generators are available in a wide range of sizes, from small portable generators that can be used to power a few appliances to large stationary generators that can power entire buildings or even small towns.
Diesel generators are typically powered by four-stroke diesel engines. Diesel engines are known for their reliability and fuel efficiency, making them a good choice for applications where long-term operation is required.
Diesel generators work by burning diesel fuel in the engine, which drives a generator to produce electricity. The electricity generated by the generator can then be used to power lights, appliances, and other electrical devices.
Diesel generators are a valuable source of backup power in the event of a power outage. They can also be used as a primary source of power in remote locations where there is no access to the electrical grid.
Here are some of the benefits of using a diesel generator:
- Reliable: Diesel generators are very reliable and can operate for long periods of time without any problems.
- Fuel-efficient: Diesel generators are fuel-efficient, which can save you money on operating costs.
- Durable: Diesel generators are built to last and can withstand harsh operating conditions.
- Versatile: Diesel generators can be used in a variety of applications, from prime power for remote locations to backup power for businesses and critical infrastructure.
If you are considering purchasing a diesel generator, be sure to do your research and choose a generator that is the right size and type for your needs. You should also consider the cost of fuel and maintenance when making your decision.
EMS Power Machines
We design, manufacture and assembly Power Machines such as – diesel generators, electric motors, vibration motors, pumps, steam engines and steam turbines
EMS Power Machines is a global power engineering company, one of the five world leaders in the industry in terms of installed equipment. The companies included in the company have been operating in the energy market for more than 60 years.
EMS Power Machines manufactures steam turbines, gas turbines, hydroelectric turbines, generators, and other power equipment for thermal, nuclear, and hydroelectric power plants, as well as for various industries, transport, and marine energy.
EMS Power Machines is a major player in the global power industry, and its equipment is used in power plants all over the world. The company has a strong track record of innovation, and it is constantly developing new and improved technologies.
Here are some examples of Power Machines’ products and services:
- Steam turbines for thermal and nuclear power plants
- Gas turbines for combined cycle power plants and industrial applications
- Hydroelectric turbines for hydroelectric power plants
- Generators for all types of power plants
- Boilers for thermal power plants
- Condensers for thermal power plants
- Reheaters for thermal power plants
- Air preheaters for thermal power plants
- Feedwater pumps for thermal power plants
- Control systems for power plants
- Maintenance and repair services for power plants
EMS Power Machines is committed to providing its customers with high-quality products and services. The company has a strong reputation for reliability and innovation. Power Machines is a leading provider of power equipment and services, and it plays a vital role in the global power industry.
EMS Power Machines, which began in 1961 as a small factory of electric motors, has become a leading global supplier of electronic products for different segments. The search for excellence has resulted in the diversification of the business, adding to the electric motors products which provide from power generation to more efficient means of use.