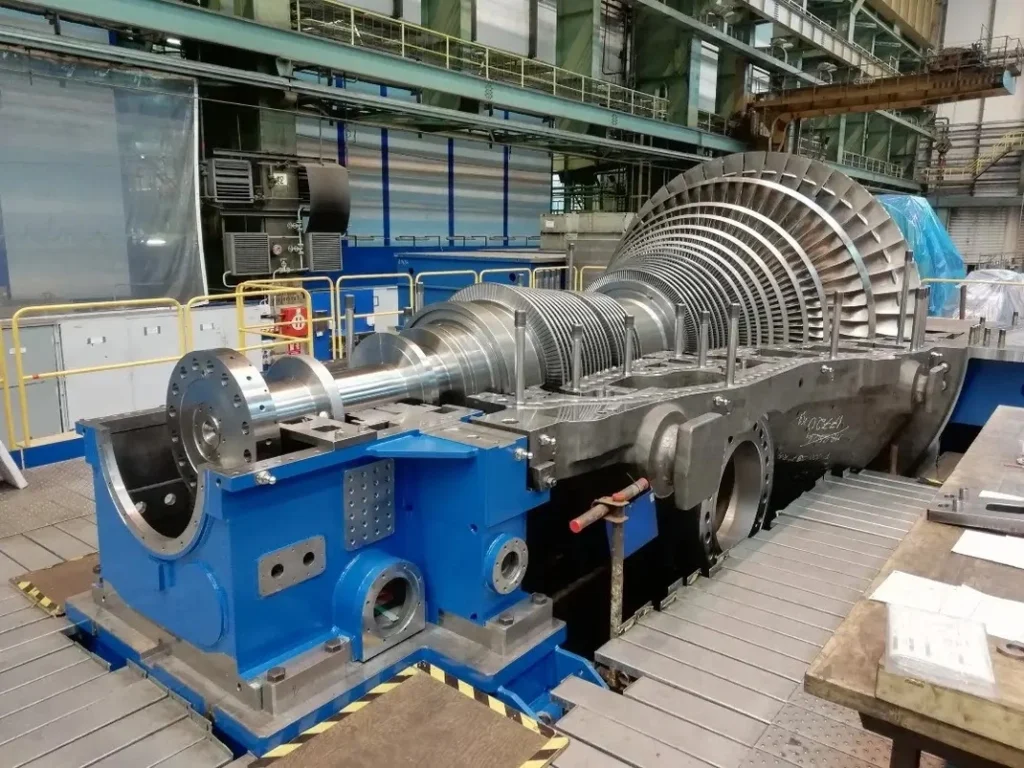
Key Terminology in Steam Turbines: Heat energy is one of the most fundamental forms of energy that powers industries and economies around the world. It can be converted into mechanical energy, electrical energy, or other forms of usable power through various processes, with one of the most effective methods being steam generation and expansion in turbines. The process begins with the conversion of a fuel source, such as coal, natural gas, or nuclear energy, into heat through combustion or other reactions. This heat energy is then used to raise the temperature of water to produce steam, which can be directed through a turbine to generate mechanical power. The power is subsequently converted into electrical energy through a generator, creating an efficient means of producing electricity.
In a steam turbine system, heat energy is used to convert water into high-pressure steam, which is then directed through a series of turbine blades. These blades are designed to extract energy from the steam, causing the turbine to spin. As the steam flows over the blades, it loses pressure and temperature, and the mechanical energy generated by the turbine is used to drive a generator that produces electricity. The efficiency of this process is largely dependent on the quality of the heat source, the design of the steam cycle, and the turbine itself.
Steam turbines operate on the principle of thermodynamics, specifically the Rankine cycle, which describes the process of converting heat energy into mechanical work. In this cycle, water is heated in a boiler to produce steam. The high-pressure steam is then expanded through a turbine, where it loses both temperature and pressure. As the steam expands, it causes the turbine blades to spin, driving a shaft connected to an electrical generator. After passing through the turbine, the steam is cooled and condensed back into water in a condenser, where it is then returned to the boiler to repeat the cycle.
Condensate and back-pressure turbines are two common types of steam turbines used in different applications. In a condensate turbine, steam that has been expanded in a turbine and then condensed into water is returned to the boiler for reheating and reuse in the cycle. These turbines are typically used in power plants where maximizing efficiency and minimizing energy losses is a priority. By recovering heat from the exhaust steam, condensate turbines can improve the overall energy conversion efficiency of the system.
Back-pressure turbines, on the other hand, are designed to allow the steam to exit the turbine at a lower pressure, typically for use in industrial processes that require lower-pressure steam. These turbines are often used in cogeneration systems, where both electricity and useful heat are produced. In these systems, the turbine drives a generator to produce electricity, while the exhaust steam is used for heating or other processes in the industrial facility. The ability to extract energy from steam at different pressure levels makes back-pressure turbines versatile and efficient for a wide range of industrial applications.
The efficiency of a steam turbine is influenced by several factors, including the temperature and pressure of the steam entering the turbine, the condition of the turbine blades, and the effectiveness of the condenser. High-pressure, high-temperature steam is more effective at generating power because it contains more energy. Additionally, the design of the turbine blades plays a significant role in the efficiency of energy extraction from the steam. Blades that are carefully designed to optimize the flow of steam through the turbine can increase the overall efficiency of the system. The condenser, which cools the steam after it passes through the turbine, must also be designed for optimal heat transfer to ensure that the steam is effectively condensed back into water.
In recent years, advances in steam turbine technology have focused on improving efficiency, reducing emissions, and enabling greater flexibility in operation. Modern turbines are designed with more advanced materials and manufacturing techniques, allowing them to operate at higher temperatures and pressures, thereby increasing efficiency. Additionally, technologies like combined cycle power plants, where steam turbines are combined with gas turbines to maximize energy production, have become increasingly popular due to their improved efficiency and lower environmental impact.
Overall, heat energy and steam turbines are integral to the generation of electrical power in many industries around the world. As technology continues to evolve, steam turbines will play a key role in meeting the world’s energy demands in a more efficient and sustainable manner.
Steam Turbines
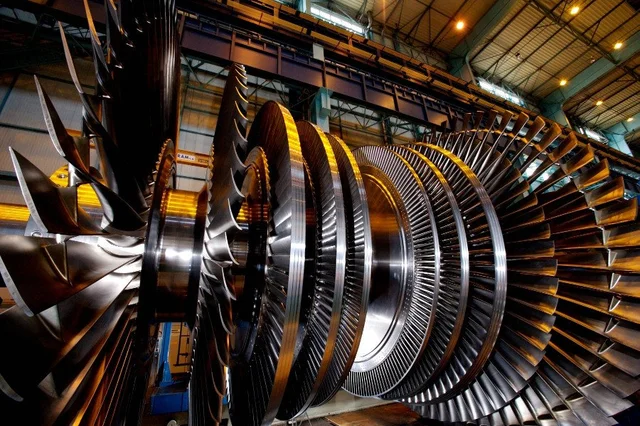
As the demand for cleaner, more sustainable energy sources continues to grow, steam turbine technology is evolving to meet these challenges. Advances in material science have allowed for the development of turbines capable of withstanding higher temperatures and pressures, which leads to greater thermal efficiency. By utilizing advanced alloys and coatings, turbines can now operate at temperatures well above traditional limits, thereby improving their efficiency and performance. This is particularly important in the context of combined heat and power (CHP) systems, where maximizing the use of steam energy for both electricity generation and industrial heating is crucial.
One such advancement is the integration of supercritical and ultra-supercritical steam cycles. These cycles use steam at higher pressures and temperatures than traditional subcritical cycles, which improves the overall efficiency of the process. Supercritical steam turbines operate at a pressure greater than 22.1 megapascals (MPa) and a temperature above 374°C (705°F), allowing them to extract more energy from the steam. Ultra-supercritical turbines push these boundaries even further, operating at temperatures of 600°C (1,112°F) or higher. These high-efficiency systems reduce fuel consumption and lower greenhouse gas emissions, making them an essential part of the shift toward cleaner energy production.
Another promising development in steam turbine technology is the incorporation of digitalization and advanced monitoring systems. By integrating sensors and real-time data analytics into turbine operations, engineers can monitor performance, predict failures, and optimize the turbine’s operation. This predictive maintenance approach helps to extend the lifespan of the equipment, reduce downtime, and prevent costly repairs. Moreover, digital tools can be used to simulate turbine performance under different conditions, allowing operators to fine-tune the turbine’s settings for optimal efficiency under varying loads and environmental conditions.
The role of steam turbines is also expanding beyond traditional power generation plants. In the field of renewable energy, steam turbines are being integrated into geothermal and concentrated solar power (CSP) systems. In geothermal plants, steam produced from deep-earth reservoirs is directed to turbines, where it drives generators to produce electricity. CSP plants use mirrors or lenses to concentrate sunlight onto a receiver, which generates heat to produce steam. This steam is then used to drive turbines in a similar way to conventional fossil-fuel-based plants. Both of these technologies leverage the basic principles of steam turbine operation but in more environmentally friendly ways, contributing to the diversification of energy sources and the global transition to renewable energy.
Another innovative approach is the use of steam turbines in hybrid power plants. These systems combine conventional steam turbines with renewable energy sources, such as wind or solar power. During times when renewable energy production is low, steam turbines can help to stabilize the grid by generating electricity from stored thermal energy. In contrast, when renewable generation is high, the turbines can operate at lower levels or even be idled to reduce emissions. Hybrid systems allow for greater grid flexibility and energy security, ensuring that a consistent power supply is available even when renewable sources are intermittent.
Despite these advances, challenges remain in the steam turbine industry. The need for improved efficiency must be balanced with the economic and environmental costs of developing new technologies. Additionally, the aging infrastructure in many regions requires modernization to keep up with evolving energy demands. Older turbines may need to be upgraded with more efficient components or replaced entirely, which can be a costly and time-consuming process. However, these investments are crucial for maintaining the reliability and sustainability of energy systems.
The future of steam turbines is likely to be shaped by the increasing demand for decarbonized energy, advances in digital technology, and the integration of renewable sources into the energy mix. The continuing development of high-efficiency turbines, coupled with the ability to monitor and optimize their performance, will be key to meeting global energy needs in a more sustainable manner. Furthermore, the versatility of steam turbines, particularly in cogeneration and hybrid applications, will help to meet the evolving requirements of industries that depend on both electricity and heat.
In conclusion, heat energy and steam turbines remain foundational to modern power generation, offering a highly efficient means of converting thermal energy into mechanical work. With ongoing advancements in turbine design, materials, and operational strategies, steam turbines will continue to play an essential role in the global energy landscape, providing a reliable, adaptable, and increasingly eco-friendly solution for power production in the coming decades. As technologies continue to improve and new applications are developed, the potential for steam turbines to support the world’s transition to a low-carbon, energy-efficient future is vast.
As the energy landscape evolves, the integration of steam turbines into more sustainable and flexible energy systems will be increasingly important. One key area of development is the combination of steam turbine technology with carbon capture, utilization, and storage (CCUS) systems. These systems are designed to capture carbon dioxide (CO2) emissions from industrial processes, including those from power generation, and either store it underground or convert it into useful products. By coupling steam turbines with CCUS, power plants can reduce their carbon footprint while still providing reliable electricity. This could be particularly valuable for industries where complete decarbonization is difficult, such as cement and steel production, or in areas where renewable energy generation is not feasible due to geography or economic factors.
The demand for low-emission power generation systems will also drive the development of hybrid turbine technologies. These could integrate steam turbines with emerging technologies, such as hydrogen combustion turbines, where hydrogen is burned to generate steam or directly drive a turbine. Hydrogen is a clean-burning fuel that, when used in turbines, produces only water vapor as a byproduct, making it an attractive option for decarbonizing the energy sector. Turbines capable of running on a mix of hydrogen and natural gas (or even pure hydrogen) are being tested and developed, offering a pathway toward cleaner and more flexible energy systems.
Furthermore, the global push toward energy storage solutions is likely to affect the role of steam turbines in power generation. In traditional power plants, steam turbines are used to generate electricity on-demand, but energy storage systems, such as battery storage or pumped hydro storage, can help smooth the intermittency of renewable energy sources. In hybrid setups, excess renewable energy could be stored during times of high generation and released as needed to drive a steam turbine. For instance, thermal energy storage, which stores heat for later use, could be integrated with steam turbines in concentrated solar power (CSP) systems, allowing the turbines to operate even when sunlight is not available.
Advancements in the digitalization of steam turbine operations are also expected to lead to more intelligent, automated systems. With the increased integration of Internet of Things (IoT) devices, machine learning algorithms, and artificial intelligence (AI), turbines will be able to continuously adjust their operation for optimal performance. These technologies will allow for predictive maintenance, reducing the need for scheduled downtime, and improving the overall reliability of turbines. Smart sensors will monitor factors such as vibration, temperature, and pressure, alerting operators to potential issues before they lead to failures. This proactive approach not only extends the lifespan of turbines but also reduces operational costs by preventing expensive breakdowns.
The renewable energy transition will also see the expansion of district heating systems, which are increasingly using steam turbines for heat and power generation. District heating involves the centralized production of heat, usually from a combined heat and power (CHP) plant, which is then distributed to homes and businesses. These systems are particularly popular in colder climates, where heating demands are high, as they offer an efficient way to meet both heating and electrical needs. By using back-pressure turbines, CHP plants can extract energy from steam and distribute it in the form of heat to nearby buildings while still generating electricity for the grid.
In the maritime industry, steam turbines will continue to be used in large ships and vessels, such as cruise ships, oil tankers, and cargo ships. Steam turbines have been a reliable choice for propulsion in these vessels due to their ability to deliver high power output and efficiency. Although some modern ships have adopted gas turbines or diesel engines, steam turbines remain the preferred option for many large-scale ships because of their proven reliability and the ability to operate on a variety of fuels, including nuclear power in certain naval applications. The use of steam turbines in marine propulsion systems is expected to continue evolving with the growing interest in hybrid systems and cleaner fuels.
In the context of industrial applications, steam turbines are also being explored for use in more niche areas. For example, in the petrochemical industry, turbines are used to power various chemical production processes. Similarly, in the food and beverage industry, steam turbines help power operations such as sterilization, drying, and pasteurization. The flexibility of steam turbines makes them a key component in industries requiring a reliable source of both electricity and heat. Furthermore, as energy efficiency becomes a priority in industrial operations, turbines are being adapted to operate at optimal conditions, reducing energy consumption and improving productivity.
Looking toward the future, the next generation of steam turbines will likely be even more efficient, adaptable, and environmentally friendly. The integration of renewable energy, advances in turbine design, and the implementation of smart technologies will ensure that steam turbines remain a cornerstone of the global energy landscape. As industries and governments continue to prioritize sustainability, steam turbines will play a pivotal role in meeting these goals, providing reliable, efficient, and clean energy solutions across a wide range of applications.
In summary, the future of steam turbines is intertwined with the global energy transition, with their role expanding beyond traditional power plants to support renewable energy, hybrid systems, and industrial applications. Their ability to convert heat energy into useful mechanical work efficiently makes them an essential part of the energy mix, and as technology progresses, they will continue to evolve in ways that support sustainability, flexibility, and innovation in power generation.
As we continue to move toward a more sustainable and decentralized energy landscape, the adaptability of steam turbines will be crucial in integrating diverse energy sources into the grid. Their versatility in handling different types of fuel, from fossil fuels to renewable energy sources such as biomass, hydrogen, and even geothermal heat, positions them as a bridge between conventional and renewable power generation methods. As more countries work toward reducing their reliance on fossil fuels, the challenge lies in ensuring that the power grid remains stable and reliable, especially as renewable energy sources like wind and solar power fluctuate due to weather patterns. Steam turbines can help stabilize the grid by providing backup power and load-balancing capabilities, especially in hybrid or combined systems that leverage multiple energy sources.
One emerging area where steam turbines can contribute is in the growing concept of microgrids. Microgrids are small, localized energy systems that can operate independently or in tandem with the larger grid. In off-grid or remote locations, steam turbines can be used as part of microgrids, providing a reliable, self-contained source of electricity and heat. For example, in island nations or areas with unreliable grid infrastructure, steam turbines, especially those integrated with renewable sources like biomass or waste heat recovery, can provide a more stable and sustainable energy supply. These systems are capable of responding quickly to local energy demands, making them particularly effective in areas where grid-connected power might be inconsistent.
Waste heat recovery is another significant area where steam turbines will play a role in energy conservation and efficiency. In many industrial processes, large amounts of heat are generated as a byproduct, yet this heat is often wasted. By capturing and converting this waste heat into usable energy through steam turbines, industries can improve their overall energy efficiency and reduce their carbon footprint. For example, in the chemical, steel, or cement industries, where high-temperature processes generate substantial heat, steam turbines can harness this excess thermal energy and convert it into additional electricity, contributing to both energy savings and reduced environmental impact.
The push for decarbonization is also influencing how steam turbines are designed for the future. The International Energy Agency (IEA) and other regulatory bodies are setting increasingly stringent emissions standards, pushing manufacturers to develop turbines that can operate efficiently with minimal carbon emissions. As countries implement carbon pricing mechanisms and set ambitious net-zero goals, the demand for turbines that can operate with low-emission fuels will rise. Turbines designed to run on hydrogen, ammonia, or even synthetic fuels—produced through processes like carbon capture and utilization—are already being explored. Hydrogen-powered steam turbines, for example, offer the promise of a completely zero-emission energy system when hydrogen is produced through renewable means like electrolysis using green electricity.
Additionally, as the digital revolution continues to reshape industries, the role of steam turbines will be heavily influenced by the increasing connectivity of power systems. With the rise of smart grids, the integration of steam turbines into broader energy networks will become more seamless, allowing for real-time data sharing, system optimization, and demand-response capabilities. The ability to monitor and adjust turbine performance in real-time will lead to more efficient operations, lower operating costs, and improved reliability. Artificial intelligence and machine learning will enable predictive analytics to optimize turbine operations based on historical data, weather patterns, and energy demand forecasts.
Another aspect to consider in the future of steam turbines is the potential role of artificial intelligence (AI) and machine learning in the design process itself. As computational power continues to grow, AI can be used to design more efficient, durable, and cost-effective turbine blades and components. Using simulation models and genetic algorithms, engineers can optimize the aerodynamics of turbine blades, predict material fatigue, and even design blades that can better handle specific operational conditions, such as variable steam pressures and temperatures. By leveraging AI for both the design and operational optimization of steam turbines, manufacturers can push the boundaries of efficiency and performance even further.
In addition to these technological innovations, the environmental and regulatory landscape will continue to influence the development of steam turbine technology. Governments worldwide are implementing policies to reduce emissions and encourage the adoption of cleaner technologies. For example, the European Union’s Green Deal and similar initiatives in other parts of the world are pushing industries toward cleaner and more sustainable energy systems. These policies are likely to create an even stronger market demand for advanced steam turbines that can operate on renewable fuels or integrate into low-carbon systems. Carbon taxes and emissions trading systems could make fossil-fuel-based power generation less economically viable, increasing the incentive for industries to adopt technologies like steam turbines running on hydrogen or waste heat.
Moreover, the adoption of steam turbines in offshore energy generation is gaining attention. Offshore wind farms, for example, have the potential to generate large amounts of electricity. While most offshore wind projects currently rely on electricity generation directly from turbines, there is growing interest in converting offshore wind energy into thermal energy, which could then be used to generate steam and drive steam turbines. This technology, although still in the early stages, could enable energy storage and conversion systems that complement the variability of wind energy and provide more consistent power to the grid.
One of the key drivers of these innovations is the push for energy security and resilience. Recent events, such as the energy crisis caused by geopolitical tensions and the COVID-19 pandemic, have highlighted the importance of robust and flexible energy systems. Steam turbines, with their ability to work across a wide range of fuel sources and operate in various system configurations, provide a level of redundancy and flexibility that can enhance the resilience of energy systems, especially when combined with renewables, storage, and other advanced technologies.
As the world continues to prioritize sustainability and efficiency, steam turbines will undoubtedly play a significant role in the energy systems of the future. Their ability to adapt to new fuels, operate in hybrid systems, and integrate with renewable sources makes them an essential part of the global effort to achieve carbon neutrality. By embracing the full potential of steam turbine technology—through improvements in materials, design, efficiency, and digitalization—the energy industry can create a future where reliable, clean energy is accessible to all.
In conclusion, the future of steam turbines is one of continued innovation and adaptation. As the world transitions to a more sustainable energy system, steam turbines will be at the forefront, enabling the integration of renewable sources, reducing emissions, and improving energy efficiency across industries. Whether used in power plants, microgrids, industrial applications, or hybrid systems, steam turbines will remain a cornerstone of global energy infrastructure, helping to power a cleaner, more resilient future.
Key Factors in Turbine Design
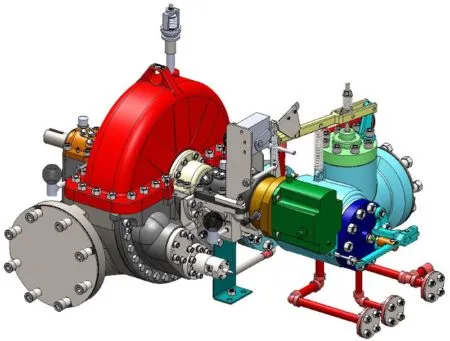
The design of a steam turbine is a complex and multifaceted process, requiring a careful balance of efficiency, durability, and performance. Several key factors influence the design of turbines, and each of these elements must be optimized to achieve the desired outcomes in power generation, industrial applications, or any other setting where turbines are used. From the thermodynamic properties of steam to the materials used for construction, turbine design involves an intricate understanding of fluid mechanics, mechanical engineering, and thermodynamics. Below are some of the most important factors that shape turbine design:
1. Thermodynamics of the Steam Cycle
The thermodynamic principles that govern the Rankine cycle are foundational to turbine design. The efficiency of a steam turbine is heavily dependent on the pressure and temperature of the steam entering the turbine, as well as how effectively the turbine extracts energy from the steam. The steam’s temperature and pressure dictate how much energy is available to drive the turbine, and optimizing the turbine’s design to maximize energy extraction is essential. High-pressure, high-temperature steam results in higher energy conversion efficiency, but designing turbines that can handle these extreme conditions without suffering material degradation is a significant challenge.
The design of the steam path through the turbine, including stages of expansion and the geometry of the blades, is determined by thermodynamic considerations. For example, in supercritical and ultra-supercritical steam cycles, turbines must be engineered to handle the higher pressures and temperatures involved. Moreover, as steam expands and loses energy through the turbine, it must do so efficiently in order to minimize energy losses.
2. Turbine Blade Design
Turbine blades are critical components in steam turbines because they extract mechanical energy from the steam. Blade design involves both aerodynamic and material considerations. The shape, size, and number of blades affect the turbine’s efficiency, as do factors such as the angle of attack and the flow path through the blades. The blades must be designed to withstand the forces exerted by high-velocity steam, which can vary across different stages of the turbine. Additionally, the blades must be resistant to erosion, corrosion, and thermal stresses, all of which can affect performance over time.
Blade materials need to be chosen for their ability to endure high temperatures and pressures while maintaining their strength and flexibility. Modern steam turbines often use advanced alloys, such as stainless steel and nickel-based alloys, which can handle the extreme operating conditions without degrading. Advances in coating technologies also play a crucial role in protecting the blades from corrosion and improving their lifespan. The optimization of blade geometry is also essential to ensure that the steam flow remains as smooth as possible, which reduces energy losses and maximizes efficiency.
3. Efficiency and Heat Transfer
The efficiency of a steam turbine is not solely dependent on the quality of the steam entering the turbine but also on the turbine’s ability to efficiently convert thermal energy into mechanical energy. A key factor in turbine design is minimizing losses due to friction, heat loss, and irreversibilities in the thermodynamic cycle. The steam must undergo multiple expansions in a multi-stage turbine, and each stage must be designed to extract the maximum possible energy from the steam.
In addition to the blade design, the configuration of the steam path and the number of stages are optimized to ensure that the expansion of the steam occurs gradually, with minimal energy loss. Efficient heat transfer systems, such as the condenser and heat exchangers, are also critical components in turbine systems. The condenser cools the steam after it has passed through the turbine, returning it to water form, which is then pumped back into the boiler to be reheated. Effective heat transfer in the condenser improves the overall cycle efficiency, and any inefficiencies here can drastically reduce the performance of the turbine.
4. Materials and Durability
Material selection is one of the most important aspects of turbine design, as the materials used must withstand the high temperatures, pressures, and stresses encountered during operation. Steam turbines often operate in environments where temperatures can exceed 600°C (1,100°F), and the materials must retain their mechanical properties over long periods without degradation. Turbines made of advanced materials such as titanium alloys, stainless steel, and high-temperature resistant alloys can ensure that the blades, casing, and other components remain durable over extended periods of high-stress operation.
In addition to high-temperature resistance, materials must also be resistant to corrosion and erosion. The steam in a turbine contains trace amounts of impurities, including salts and oxygen, which can cause corrosion and erosion of the turbine blades. Special coatings or surface treatments are often applied to enhance material durability and extend turbine life.
5. Thermal Stress and Fatigue
Thermal stress and mechanical fatigue are important factors in turbine design. As steam turbines operate at extremely high temperatures, the components experience significant thermal cycling—where parts are heated and cooled repeatedly. This can cause thermal expansion and contraction, leading to the potential for material fatigue over time. Engineers must design turbines to minimize these stresses by using materials that can absorb these fluctuations and by ensuring the turbine components are properly cooled and ventilated.
Moreover, the thermal stresses on the blades and other components must be carefully managed to prevent warping, cracking, or failure. Design features such as thermal barriers, cooling channels, and optimized blade shapes can help mitigate these stresses.
6. Bearing and Shaft Design
Turbines rely on a series of bearings to support the rotating shaft, which transmits the mechanical energy to the generator. The bearing design is crucial to ensuring smooth turbine operation and minimizing friction. Bearings need to be capable of supporting the turbine’s weight and rotational forces while ensuring minimal energy loss. They must also be durable enough to withstand extreme temperatures, pressures, and lubrication conditions.
The shaft itself is designed for strength, stability, and efficiency, often made from high-strength alloys that are resistant to deformation under the mechanical load. Precision in shaft alignment and rotor dynamics is critical to ensuring the turbine operates at peak efficiency and to preventing vibrations or mechanical failure.
7. Vibration Control and Noise Reduction
Vibration is a natural consequence of rotating machinery, but excessive vibration can lead to mechanical failure, damage to the components, and inefficiency in energy conversion. Designing a steam turbine to minimize vibrations requires careful attention to rotor balance, bearing support, and turbine casing design. Vibration analysis is often performed during the design process to ensure the turbine operates smoothly throughout its lifecycle.
Noise reduction is also an important consideration, especially for turbines that are used in urban or residential areas. Noise can be a byproduct of steam flow, mechanical friction, and rotor interactions with the air. Engineers work to minimize these effects through the use of sound-dampening materials, optimized turbine casing designs, and vibration-damping technologies.
8. Control Systems and Automation
Modern steam turbines are equipped with sophisticated control systems that allow operators to monitor and adjust performance in real-time. Automation and digital controls are essential for optimizing turbine operation, ensuring that the system operates efficiently across a range of conditions. These control systems can adjust parameters such as steam pressure, temperature, and turbine speed, automatically optimizing the system’s performance.
Advanced turbine designs incorporate sensors that monitor parameters like temperature, pressure, vibration, and exhaust conditions. These sensors feed data into centralized control systems, enabling operators to identify inefficiencies, predict failures, and perform maintenance only when necessary. Automation systems help extend the life of the turbine, improve reliability, and ensure optimal operation under varying load conditions.
9. Maintenance and Accessibility
A turbine’s design must also take into account ease of maintenance and repair. Components like bearings, blades, and seals must be easily accessible for inspection and maintenance to ensure the long-term performance of the system. The design should facilitate the removal and replacement of components, minimizing downtime during maintenance. For turbines that operate in remote locations or offshore, ease of maintenance can greatly influence operational costs and reliability.
Conclusion
Turbine design is a multifaceted process that requires careful consideration of thermodynamics, materials science, mechanical engineering, and operational efficiency. Each component of the turbine, from the blades to the bearings to the control systems, must be optimized for durability, efficiency, and reliability. As technology advances, the role of steam turbines in power generation, industrial applications, and renewable energy systems will continue to evolve, and the design considerations discussed here will remain crucial in maximizing their performance and sustainability. By focusing on optimizing these key factors, engineers can create turbines that are not only efficient but also capable of meeting the energy demands of the future.
Turbine design is a dynamic process that evolves with advancements in technology and the ever-changing needs of energy production. The key to successful turbine performance lies in optimizing the interaction between steam and the mechanical components that convert thermal energy into usable power. This optimization spans many aspects, including the thermodynamics, materials used, and the structural integrity of the turbine. The efficiency of a steam turbine is closely linked to its ability to manage the complex forces exerted by steam as it expands through the turbine stages. Turbines must extract as much energy as possible from the steam while minimizing losses that occur due to friction, heat loss, and other factors that decrease the overall performance.
The process of steam expansion within the turbine is fundamental to maximizing energy conversion, and a well-designed turbine can maintain high efficiency over a long period of operation. The material selection for turbine components, including blades, casings, and bearings, is of paramount importance to ensure that the turbine can withstand the high temperatures and pressures typically involved in steam power generation. Turbines operate under extreme conditions, and the materials chosen must be resistant to thermal stress, corrosion, and erosion. Over time, high temperatures can lead to material fatigue and degradation, making the use of advanced alloys and special coatings critical to the turbine’s longevity and performance. The blade design is particularly crucial, as it directly affects the turbine’s ability to capture and convert steam energy into mechanical power.
Turbine blades are subjected to significant mechanical and thermal stress, and their design must optimize the steam flow and maintain structural integrity. Aerodynamic design principles come into play to ensure that the steam flows smoothly over the blades, minimizing energy losses. Additionally, the blades must be resistant to factors like cavitation, erosion, and corrosion to ensure a long operational lifespan. As turbines operate in varying conditions, including fluctuations in load demand, efficiency can also be influenced by the design of the steam path and the number of turbine stages. Multi-stage turbines are often used to capture as much energy as possible from the steam by gradually expanding it across different stages.
This staged expansion reduces the likelihood of energy loss at each stage and improves overall turbine efficiency. Moreover, the turbine design must address issues like vibration control and noise reduction, both of which can affect turbine performance and operational safety. Vibration, in particular, can lead to mechanical failures, while noise can be a byproduct of steam flow and mechanical friction. Engineers design turbines with special vibration-damping technologies, optimizing the alignment and balance of rotating components to minimize vibrations that can cause damage or reduce efficiency. Alongside mechanical design, control systems have become integral to turbine operation, allowing for real-time monitoring and adjustments.
These automated systems help maintain optimal operating conditions, adjusting parameters such as steam pressure and temperature to keep the turbine performing at peak efficiency. Sensors embedded within the turbine provide continuous data on factors like temperature, pressure, and vibration, feeding this information into centralized control systems that can predict failures and adjust operations accordingly. These advances in automation and data analytics not only improve operational efficiency but also help extend the lifespan of turbines by facilitating timely maintenance and repairs. Turbine design also has to consider the ease of maintenance, ensuring that components can be accessed and serviced without excessive downtime.
Maintenance strategies are built into the design, allowing for the replacement of worn-out parts like blades, seals, and bearings. In some designs, modular components are used to simplify repairs and replacement processes, reducing the need for extensive downtime during maintenance periods. Turbines designed for industrial or power generation purposes often have features built in to address different fuel types, waste heat recovery, or hybrid operations with renewable sources. For example, turbines that can handle both hydrogen and natural gas or utilize waste heat are becoming increasingly important as energy systems shift toward decarbonization. These hybrid systems help reduce emissions while maintaining reliable energy generation.
The integration of turbines into microgrids and combined heat and power systems further increases their versatility, allowing them to operate efficiently in distributed energy setups or with varying energy sources. In the future, turbines are expected to continue evolving in response to new technological developments, such as the use of hydrogen or ammonia as fuels, advances in additive manufacturing, and the growth of renewable energy sources. Advanced turbine designs will focus on improving thermal efficiency, reducing emissions, and enhancing overall performance, ensuring that they remain a crucial component in meeting global energy demands. As energy generation becomes more complex, steam turbine technology will continue to be at the forefront of innovations that support a sustainable, resilient, and efficient power grid for the future.
As the world increasingly shifts towards cleaner energy systems, the role of steam turbines will evolve in tandem with new power generation methods, especially as industries seek to reduce their carbon footprints. One of the most promising developments in turbine technology is the transition to low-carbon and renewable fuel sources. Hydrogen, for example, has emerged as a potential alternative to traditional fossil fuels, and turbines capable of operating on hydrogen offer the possibility of near-zero emissions power generation. While the technology is still in its early stages, the ability of steam turbines to adapt to hydrogen combustion presents an exciting opportunity for industries looking to decarbonize.
The challenge, however, lies in modifying existing turbine designs to handle the combustion properties of hydrogen, which differs from natural gas in terms of temperature, flame speed, and energy density. Turbine blades and components will need to be carefully designed to withstand these new operating conditions while ensuring that the turbine’s performance remains optimal. Moreover, the storage, distribution, and production of hydrogen at scale are issues that need to be addressed to make hydrogen-fired turbines viable on a larger scale.
Another key area of innovation is the integration of steam turbines with renewable energy sources, such as solar and wind power. Steam turbines are not only limited to traditional fossil fuel-based power plants; they are increasingly being incorporated into hybrid systems where they work in tandem with renewable sources. For instance, concentrated solar power (CSP) systems use mirrors or lenses to focus sunlight and generate steam, which can then drive a turbine. This hybrid approach allows renewable energy to be stored and used on demand, providing a more reliable and consistent source of power compared to intermittent solar or wind generation alone.
Similarly, waste heat recovery is an area where steam turbines are poised to make a significant impact. Many industries produce excess heat as a byproduct of their operations—heat that often goes to waste. By capturing this waste heat and using it to generate steam, industries can improve their overall energy efficiency and reduce emissions. This not only helps businesses lower their operational costs but also aligns with global efforts to reduce waste and enhance sustainability.
In the context of energy storage, steam turbines have potential applications in systems designed to store excess energy for later use. One of the most promising technologies in this area is thermal energy storage, where surplus energy (often from renewable sources) is used to generate heat that can later be converted into steam to drive a turbine. This stored energy can then be released during periods of high demand, helping to stabilize the grid and ensuring a reliable energy supply. The ability to store energy in this way is particularly valuable in areas with high renewable penetration, where fluctuations in supply can be a challenge.
In addition to energy storage, the growing emphasis on decentralized and distributed energy systems further elevates the importance of steam turbines. Microgrids, which are localized energy networks that can operate independently or in conjunction with the main grid, are becoming more common, especially in remote areas or regions with unreliable grid infrastructure. Steam turbines can play a critical role in these systems, providing backup power or serving as the primary power source in combination with renewable generation. Their ability to operate in a flexible, modular manner makes them well-suited for integration into microgrid setups.
The increasing use of digital technologies is also transforming steam turbine design and operation. The application of sensors, real-time monitoring, and data analytics allows for enhanced control over turbine performance. Predictive maintenance, made possible by artificial intelligence (AI) and machine learning, enables turbines to operate more efficiently and with fewer unexpected breakdowns. Through constant monitoring of key parameters such as pressure, temperature, and vibration, operators can adjust turbine settings in real-time, preventing inefficiencies and extending the turbine’s operational life. These smart turbines can also communicate with the wider energy system, enabling them to respond dynamically to changes in energy demand and supply.
Moreover, the digitalization of steam turbine operations extends beyond individual machines and into the broader energy ecosystem. Smart grids, which use advanced communication and control technologies to optimize the flow of electricity, will rely on turbines that can seamlessly integrate into the grid and respond to fluctuations in demand. By leveraging real-time data and predictive analytics, steam turbines can be part of an intelligent grid that automatically adjusts generation based on immediate needs, improving efficiency and reliability while lowering costs.
Beyond these technological advances, the environmental impact of steam turbines will remain a central consideration in their design and application. As governments around the world enact stricter emissions regulations, turbine manufacturers will face increasing pressure to design machines that operate with minimal carbon emissions. The development of cleaner and more sustainable fuels, such as biogas, synthetic fuels, and ammonia, will be essential for ensuring that turbines meet these emissions standards.
To meet these challenges, engineers will need to focus on creating turbines that are not only more efficient but also more adaptable to various fuel types and operating conditions. This adaptability will be critical in supporting the transition to a low-carbon economy, where power generation is increasingly decentralized, fuel-diverse, and intermittent.
The future of steam turbine design will likely involve a combination of improving the efficiency of traditional steam cycles, adapting turbines to new fuels, and integrating them with emerging technologies such as energy storage and smart grid systems. With the growing need for clean, reliable energy and the expansion of renewable energy sources, steam turbines will continue to play a vital role in the energy transition. By embracing new materials, digital technologies, and advanced fuel options, steam turbines will remain an essential component of the global energy infrastructure, helping to power a sustainable future while meeting the world’s increasing energy demands.
In conclusion, the ongoing development and innovation in steam turbine design will continue to shape the future of energy production. Whether it’s through integrating with renewable energy systems, adopting new low-carbon fuels, or embracing digital technologies for smarter operation, steam turbines are poised to remain a cornerstone of energy generation. As the energy landscape evolves, so too will turbine technology, ensuring that steam turbines will play a crucial role in supporting a clean, efficient, and resilient energy future.
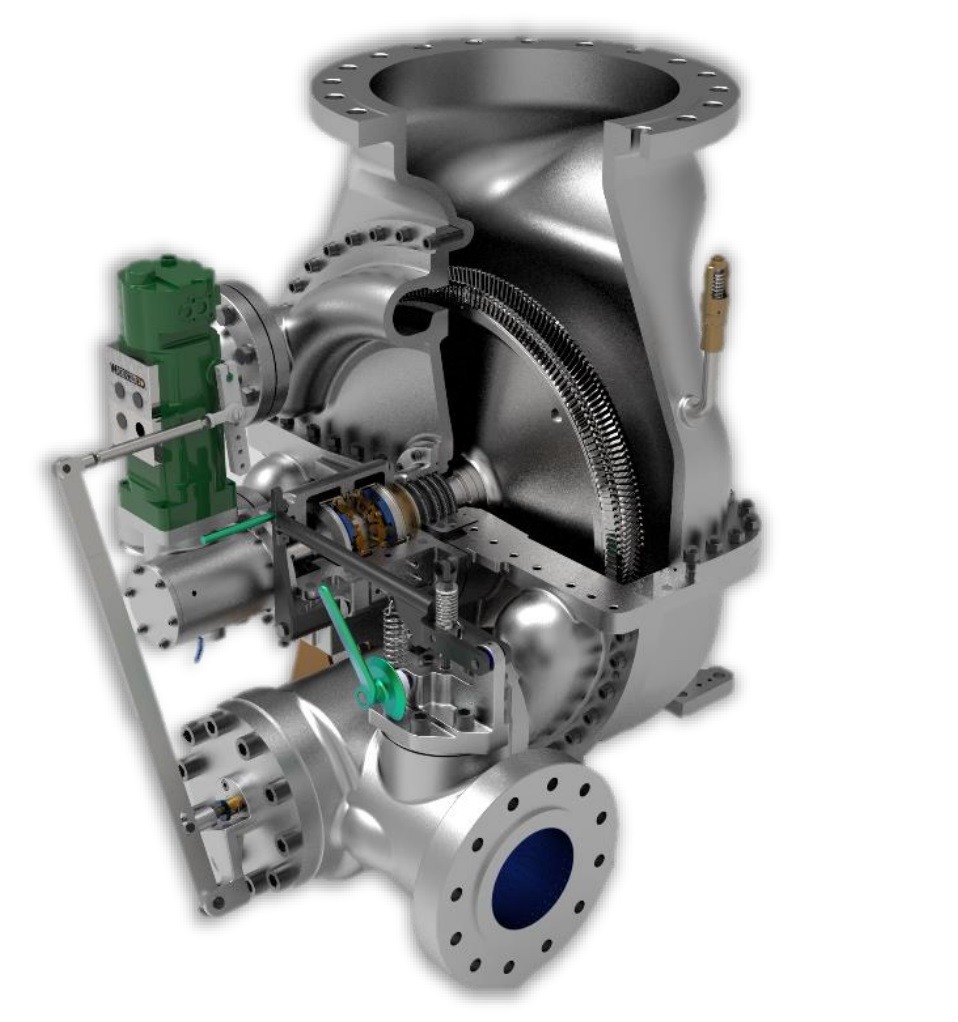
As we move further into the 21st century, the future of steam turbine technology will be shaped by an increasingly complex set of demands, ranging from the need for higher efficiency and lower emissions to the integration of advanced control systems and alternative energy sources. The growing emphasis on sustainability will continue to drive innovation in turbine design, ensuring that they remain a critical part of energy production in both traditional and emerging markets.
One area where steam turbines are expected to have a significant impact is in the field of carbon capture and storage (CCS). CCS technologies are being developed to capture carbon dioxide (CO₂) emissions from industrial processes and power generation, preventing them from entering the atmosphere and contributing to climate change. In the case of steam turbines, integrating CCS with conventional fossil-fuel-based power plants could provide a pathway to significantly reduce emissions from these plants. However, the capture, compression, and storage of CO₂ require energy, and steam turbines could be used to supply this energy in a way that minimizes additional emissions.
Furthermore, the decarbonization of the power sector is increasingly focusing on electrifying various industries, from transportation to heating, to reduce reliance on fossil fuels. Steam turbines are likely to play a pivotal role in this shift, especially in combination with the growing demand for renewable electricity. Their efficiency, adaptability to various fuels, and ability to integrate with energy storage systems make them well-suited to meet the demands of a low-carbon future. With power plants becoming more flexible and capable of rapidly ramping up or down to accommodate intermittent renewable generation, turbines will continue to be central to balancing supply and demand.
Another emerging trend is the use of hybrid systems, where steam turbines are integrated with other types of generation technologies, such as gas turbines, wind turbines, and even nuclear reactors. In combined-cycle power plants, for example, gas turbines and steam turbines work together to maximize the overall efficiency of the power generation process. The waste heat from the gas turbine is used to produce steam, which then drives the steam turbine to generate additional electricity. These hybrid systems can improve the fuel efficiency of power plants, reduce emissions, and increase the overall reliability of the energy system.
Advanced nuclear power plants, particularly those designed with a focus on smaller, modular designs (known as small modular reactors or SMRs), also present a potential area for steam turbines. SMRs have the advantage of being more flexible and adaptable to a variety of applications, from industrial power generation to remote or off-grid installations. These systems will likely rely on steam turbines to convert the heat generated by nuclear fission into electrical power, and advances in turbine design will be necessary to meet the unique requirements of these plants, including handling high temperatures and varying operating conditions.
The drive toward a more decentralized and flexible grid will also require steam turbines to adapt to new configurations. Microgrids, which are localized energy networks capable of operating independently or in conjunction with larger grids, will benefit from steam turbines designed for modular and adaptable deployment. These turbines must be able to handle varying input sources, such as renewable generation from wind and solar, as well as backup power from traditional fossil or nuclear sources. The ability of turbines to quickly ramp up or down in response to shifting energy demands will be increasingly important in such decentralized systems.
Additionally, the need for steam turbines to support the growing role of intermittent renewable energy sources, such as wind and solar, will necessitate the development of new hybrid power systems. Wind and solar energy are variable, meaning that their generation does not always match the demand for electricity. By coupling steam turbines with renewable generation technologies, it is possible to provide backup power when renewable sources are not available, ensuring a reliable supply of electricity. Furthermore, steam turbines can play a key role in grid stabilization by compensating for fluctuations in renewable energy generation, smoothing out the variability in supply.
As the energy transition progresses, innovation in turbine technology will also be driven by advances in digitalization, automation, and artificial intelligence. Smart grid technologies, which enable real-time monitoring and control of energy flows, will become more sophisticated, and steam turbines will need to be compatible with these systems. By integrating advanced sensors, control systems, and machine learning algorithms, turbines will be able to automatically adjust their performance based on real-time data, optimizing efficiency and reducing wear and tear on components.
Moreover, digital twins—virtual replicas of physical turbines—will allow engineers to simulate turbine performance under various conditions, predicting potential issues before they occur and identifying opportunities for optimization. These digital models can be used to test new materials, improve designs, and refine operating parameters without the need for costly physical prototypes or extensive trial-and-error testing.
The future of turbine technology will also involve greater use of advanced manufacturing techniques, such as 3D printing and additive manufacturing. These methods allow for the creation of more complex, lightweight, and durable turbine components that are not possible with traditional manufacturing processes. 3D printing could enable the production of custom turbine parts with intricate geometries and materials optimized for specific operating conditions, which would lead to improvements in both performance and efficiency.
Turbine technology will likely evolve towards systems that are more flexible, efficient, and compatible with a variety of fuels and power generation methods. The potential for steam turbines to support a diverse array of energy sources, from traditional fossil fuels to renewables and nuclear power, makes them an essential part of the future energy mix. Furthermore, advances in materials science, digitalization, and hybridization with other technologies will allow turbines to operate more efficiently, reduce their environmental impact, and provide a more reliable energy supply.
As global energy demands continue to rise and the need for low-carbon solutions becomes more urgent, steam turbines will remain a cornerstone of power generation. Through continued innovation, adaptation to new fuels, and integration with emerging technologies, steam turbines will contribute to the development of a more sustainable, resilient, and efficient global energy system. In doing so, they will play a vital role in the energy transition and help pave the way for a cleaner, more reliable future.
Basic Construction of Steam Turbines
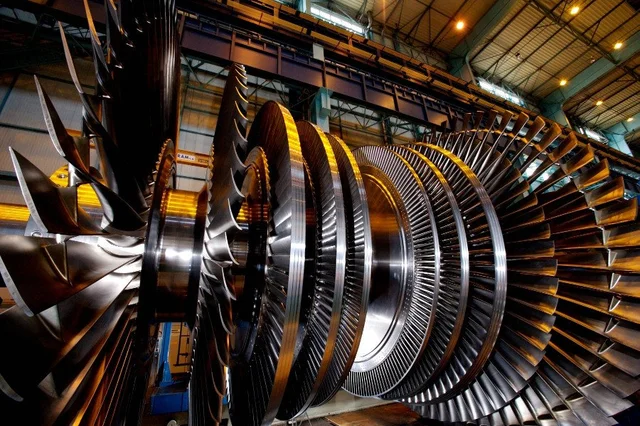
The basic construction of steam turbines involves a series of components and mechanisms designed to efficiently convert thermal energy from steam into mechanical power. This process happens within a relatively simple yet highly engineered system that must operate under extreme conditions. While the complexity can vary based on the turbine’s design and application, most steam turbines share core structural elements.
At the heart of a steam turbine’s design is the rotor, which is the rotating part of the turbine responsible for transforming the steam’s thermal energy into rotational motion. The rotor consists of a shaft, blades, and disks that are all attached in such a way that they can rotate freely within the casing. The rotor is powered by the steam that flows through the turbine’s stages, with the force of the steam pushing against the blades and causing them to turn. The shaft is the central part of the rotor and connects the turbine blades to the generator or mechanical device that is being powered by the turbine.
The blades themselves are one of the most critical components of the turbine. They are designed to extract energy from the steam as it passes over them, and their shape and material are crucial for the turbine’s efficiency. Steam turbine blades are typically made from high-strength materials capable of withstanding the high temperatures and pressures encountered in the system. These blades are attached to disks, which are mounted on the shaft. The arrangement of blades on the disks is done in such a way that the steam flows through multiple stages, allowing for incremental energy extraction.
The casing, or outer shell of the turbine, is another key element of its construction. The casing is designed to contain the steam as it flows through the turbine stages, directing it in a controlled manner across the blades. It also serves as a protective barrier, keeping steam and other internal components safely enclosed. The casing helps manage steam pressure and temperature while providing support for various internal components. Inside the casing, there is a series of fixed blades or nozzles, which direct the steam flow to the rotor blades in an optimized manner. These nozzles are designed to convert the thermal energy of steam into kinetic energy, accelerating the steam before it hits the turbine blades.
The steam that powers a turbine is produced in a boiler, where water is heated until it becomes steam at high pressure and temperature. The steam then enters the turbine through the steam inlet and passes through the nozzles before it reaches the blades. After expanding through the turbine stages, the steam exits the turbine as exhaust, and it is typically sent to a condenser where it is cooled and turned back into water.
In addition to the core components of the rotor, blades, casing, and nozzles, steam turbines also include several auxiliary systems that help maintain their operation. One such system is the lubrication system, which ensures that the rotor shaft and other moving components are adequately lubricated to reduce friction and wear. Cooling systems, seals, and vibration-damping systems are also integral to the construction of a steam turbine, all designed to maintain the turbine’s performance and prolong its lifespan.
The design of the turbine is generally divided into stages, with each stage consisting of both moving and fixed blades. As the steam passes through each stage, it expands and loses some of its thermal energy, which is then converted into rotational energy by the moving blades. The fixed blades (or stator blades) direct the steam into the moving blades and help guide the flow. A multi-stage turbine allows for more efficient energy extraction from the steam by gradually reducing the steam’s pressure and temperature over several stages, rather than extracting all the energy in a single stage.
Turbine stages can be either impulse or reaction stages, depending on how the steam’s energy is extracted. In an impulse stage, the steam is accelerated through nozzles before striking the moving blades, converting its velocity into rotational energy. In a reaction stage, the steam expands and accelerates as it passes over both the fixed and moving blades, creating a pressure difference that drives the rotor. Both types of stages are used in various configurations to balance efficiency and performance.
The exhaust from a steam turbine typically flows into a condenser, where the steam is cooled down and condensed back into water, ready to be returned to the boiler for reuse. The condenser may operate under vacuum conditions, helping to reduce the exhaust pressure and increase the efficiency of the turbine. After the steam has been condensed, the water is pumped back into the boiler to continue the cycle.
The entire steam turbine assembly is mounted on a foundation, and the components are designed to withstand the stresses of high-speed rotation and the forces exerted by the steam. This requires careful engineering of the bearings and supports that hold the rotor shaft in place, ensuring that the turbine remains stable and operates smoothly. Bearings, often made from materials like babbitt metal, are used to support the rotor shaft while minimizing friction and wear.
To prevent overheating and ensure the longevity of the turbine, advanced cooling systems are also employed. These systems circulate cool water or air around the turbine components, helping to regulate temperatures and prevent thermal damage. Cooling systems can also help maintain the required pressure differential between the different stages of the turbine, contributing to the overall performance and efficiency of the machine.
The structural components of a steam turbine, including the casing, rotor, blades, and shaft, are subjected to rigorous testing during the manufacturing process to ensure they can withstand the extreme operating conditions. Materials used in the construction of steam turbines must have high resistance to corrosion, erosion, and fatigue, which are common problems when turbines are exposed to high temperatures and pressures over long periods. Advanced alloys and coatings are often used to enhance the durability of these components.
As technology advances, steam turbines continue to become more efficient and reliable. New materials, coatings, and manufacturing techniques allow for turbines that can operate at higher temperatures and pressures, extracting more energy from the steam. The development of more efficient seals, bearings, and cooling systems also helps improve the overall performance of steam turbines, reducing energy losses and increasing reliability.
In conclusion, the basic construction of a steam turbine involves a highly engineered system with several interconnected components, each playing a vital role in ensuring that thermal energy is efficiently converted into mechanical power. The rotor, blades, casing, and nozzles are essential for the turbine’s operation, while auxiliary systems like lubrication, cooling, and vibration control further enhance performance. Advances in materials science and manufacturing continue to drive improvements in turbine efficiency, making them an integral part of modern power generation and industrial processes.
As steam turbine technology advances, several innovations continue to improve their design, efficiency, and durability. Key areas of development include materials, cooling techniques, and advanced manufacturing processes, which all work together to make modern turbines more efficient and cost-effective.
One of the primary challenges in steam turbine construction is the material selection, as the components must withstand extreme operational conditions such as high temperatures, pressures, and thermal stresses. Over the years, advancements in metallurgy have led to the development of advanced alloys that are better suited to handle these challenges. For instance, turbine blades are often made from high-strength, heat-resistant alloys like nickel-based superalloys, which are capable of withstanding temperatures above 1,000°C (1,832°F) without losing their structural integrity. These alloys also exhibit excellent resistance to oxidation, corrosion, and erosion, all of which are common issues in turbines exposed to high-pressure steam over long periods of time.
In addition to the materials used for the turbine blades, the casing, shaft, and other components also benefit from the use of advanced materials. The casing, for example, is typically constructed from steel alloys that provide strength and durability while maintaining the necessary resistance to heat and pressure. In some cases, advanced coatings are applied to these components to further enhance their resistance to wear, oxidation, and corrosion, ensuring that the turbine continues to operate effectively for many years.
Cooling techniques have also seen significant improvements in recent years. As turbines operate at higher temperatures, efficient cooling becomes essential for maintaining performance and preventing overheating. Modern steam turbines often use sophisticated cooling systems that circulate water or air through the casing, rotor, and other components to dissipate heat and maintain optimal operating temperatures. These systems are designed to be highly effective, with some turbines featuring closed-loop cooling circuits that allow for the reuse of cooling water, improving overall efficiency and reducing water consumption.
Along with traditional cooling methods, advanced heat exchangers and heat recovery systems are being integrated into steam turbine designs. These systems capture waste heat from the turbine exhaust and convert it back into useful energy, either by preheating the steam before it enters the turbine or by generating electricity through other means such as thermoelectric generators. Heat recovery helps to reduce the overall energy consumption of the turbine, improving its efficiency and reducing the environmental impact of its operation.
Additive manufacturing, or 3D printing, is another area that is revolutionizing steam turbine construction. This technology allows for the creation of complex, custom-designed turbine components that would be difficult or impossible to manufacture using traditional methods. For example, turbine blades can be 3D printed with intricate internal cooling channels that improve heat dissipation and enhance performance. This approach not only allows for more efficient designs but also reduces material waste and manufacturing time, making it a highly cost-effective solution.
In addition to these advancements in materials and manufacturing, the control and monitoring systems of modern steam turbines have become more sophisticated. Digital control systems enable real-time monitoring of turbine performance, providing operators with valuable data on parameters such as pressure, temperature, vibration, and rotor speed. This data is used to optimize turbine operation, adjusting settings in real time to maintain peak efficiency and prevent damage to the turbine components. Predictive maintenance tools powered by artificial intelligence (AI) and machine learning can analyze data trends and detect potential issues before they result in failures, allowing for proactive maintenance and reducing downtime.
The integration of smart sensors and data analytics is also improving the operation of steam turbines in industrial and power generation applications. Sensors embedded in the turbine components provide continuous feedback on performance, which is then processed by advanced algorithms to identify patterns and optimize operation. This level of real-time insight allows operators to make more informed decisions, improving efficiency, reducing fuel consumption, and extending the lifespan of the turbine.
In addition to performance optimization, these digital systems also contribute to the maintenance and safety of steam turbines. For example, vibration sensors monitor the health of the rotor and detect any imbalances or irregularities that may indicate potential failures. Pressure and temperature sensors provide data on the steam flow, allowing operators to adjust settings for optimal performance. These sensors are often connected to a central control system, allowing for automated adjustments to ensure that the turbine operates within safe limits.
As steam turbine technology continues to evolve, one of the key challenges is adapting turbines to a broader range of fuel sources. The increasing emphasis on renewable energy and low-carbon technologies means that steam turbines must be able to operate with fuels such as biomass, synthetic fuels, hydrogen, and even waste heat from industrial processes. This requires modifications to the turbine design, including changes to the combustion system, steam cycle, and materials used in the construction of components like the blades and casings. These adjustments ensure that the turbines remain efficient and reliable when operating with alternative fuels, contributing to the overall shift towards a more sustainable energy system.
Another area where steam turbines are seeing innovation is in their integration with renewable energy technologies. Steam turbines can be coupled with solar thermal power systems, where concentrated solar power (CSP) is used to generate steam, which then drives the turbine to generate electricity. This hybrid approach allows for renewable energy to be stored and used on demand, overcoming the intermittent nature of solar power. Similarly, steam turbines are being integrated into combined heat and power (CHP) systems, where they generate both electricity and useful heat for industrial processes or district heating, further improving the efficiency of power generation.
Steam turbines are also becoming more flexible in terms of their ability to operate in combined-cycle plants. In these plants, both gas and steam turbines work together to maximize efficiency. The gas turbine generates electricity by burning natural gas, while the waste heat from the gas turbine is used to generate steam, which then drives the steam turbine to generate additional power. This combined-cycle approach significantly improves the overall efficiency of the power plant, reducing fuel consumption and emissions while producing more electricity.
In conclusion, the construction of steam turbines has evolved significantly over the years, with advancements in materials, cooling technologies, manufacturing techniques, and digital systems all contributing to higher efficiency, reliability, and performance. As steam turbines continue to adapt to new fuel sources, hybrid power systems, and renewable energy technologies, they will remain a vital part of the global energy landscape, playing a key role in the transition to a cleaner, more sustainable future. The ongoing development of turbine technology will ensure that steam turbines continue to meet the growing demands for efficient, low-carbon power generation in a wide range of applications, from large-scale power plants to decentralized energy systems.
As the future of steam turbines unfolds, the ongoing technological advancements promise to further enhance the capabilities of these machines, making them more adaptable, efficient, and environmentally friendly. Key trends and developments will continue to shape their role in the global energy landscape, ensuring that steam turbines remain vital in both traditional and emerging applications.
One area of future development for steam turbines is their integration with carbon capture and storage (CCS) technologies. As the need for reducing carbon emissions intensifies, steam turbines will increasingly be employed in power plants equipped with CCS systems. In these systems, carbon dioxide is captured from the flue gas and stored underground, preventing it from being released into the atmosphere. Steam turbines play a critical role in providing the necessary power for compressing and transporting CO₂ in CCS systems, further enhancing the overall energy efficiency of power plants. The integration of CCS with steam turbines can significantly reduce the carbon footprint of fossil-fuel-based power generation, aligning with global efforts to combat climate change.
The growing role of hydrogen as a clean energy carrier presents another exciting opportunity for steam turbine development. Hydrogen, when used as a fuel source, produces only water vapor as a byproduct, making it a promising alternative to traditional fossil fuels. In steam turbines, hydrogen can be used to generate high-temperature steam, which drives the turbine to produce electricity. The combustion of hydrogen, however, presents unique challenges, particularly in terms of ensuring turbine materials can withstand the extreme temperatures and pressures generated by hydrogen combustion. Research and development efforts are focused on optimizing turbine components, including blades, nozzles, and casings, to handle these new operating conditions, making steam turbines compatible with hydrogen and other clean fuels.
Additionally, the transition to renewable energy sources such as solar, wind, and geothermal power is reshaping the role of steam turbines. In hybrid systems, steam turbines can work in conjunction with these renewable energy sources, either by using their waste heat or by integrating them into combined heat and power (CHP) systems. For instance, concentrated solar power (CSP) systems use mirrors or lenses to focus sunlight onto a central receiver, creating extremely high temperatures that generate steam. This steam can then drive a steam turbine to generate electricity. The combination of renewable generation with steam turbines offers the advantage of reliable, baseload power generation while mitigating the intermittent nature of solar and wind power.
Geothermal energy, another renewable source, has also become a promising application for steam turbines. In geothermal power plants, steam is extracted from the Earth’s crust, where it has been heated by the planet’s internal heat. This steam is used to drive a steam turbine, generating electricity. Geothermal power is renewable, reliable, and has a low environmental impact, making it a key player in the energy transition. Steam turbines used in geothermal applications are designed to handle the high temperatures and potentially corrosive properties of geothermal steam, requiring specialized materials and components that can withstand these challenging conditions.
The development of supercritical and ultra-supercritical steam cycles represents another significant advancement in steam turbine technology. These cycles operate at higher pressures and temperatures than traditional steam cycles, enabling steam turbines to achieve higher efficiencies. By using supercritical steam, where water is heated beyond its critical point (where it no longer behaves as a liquid or gas), power plants can extract more energy from the same amount of fuel, reducing the need for fuel and lowering emissions. These advanced cycles require steam turbines to be designed with materials capable of withstanding the extreme conditions associated with supercritical steam, and manufacturers are continuously developing new alloys and coatings to meet these demands.
As power grids around the world become increasingly decentralized and reliant on renewable sources, steam turbines will need to adapt to more dynamic and flexible operating conditions. The ability to quickly respond to fluctuations in energy demand and supply is essential in the context of intermittent renewable generation. Steam turbines are well-suited to provide grid stability, particularly when combined with energy storage systems that can store excess energy produced during periods of low demand and release it when demand spikes. This capability to ramp up and down quickly, known as “cycling,” will be increasingly important in ensuring a stable and reliable energy supply. The ability to integrate steam turbines with energy storage systems, such as batteries or pumped hydro storage, will allow turbines to work in tandem with renewable generation to smooth out the variability in supply.
The role of steam turbines in microgrids and off-grid applications is also expected to grow. Microgrids are small, localized energy systems that can operate independently of the main grid. In remote areas or developing regions, microgrids can provide reliable electricity where traditional grid infrastructure is not available or economically viable. Steam turbines, particularly in combination with renewable energy sources and energy storage systems, can offer a reliable and flexible solution for these decentralized energy networks. The ability of steam turbines to operate in a range of configurations, including small-scale, modular setups, makes them ideal for microgrid applications.
Finally, as digitalization continues to transform the energy sector, steam turbines will benefit from advancements in smart monitoring, predictive maintenance, and automation. The integration of IoT (Internet of Things) sensors and data analytics into turbine design allows for real-time monitoring of turbine performance, helping to optimize efficiency and reduce operational costs. Predictive maintenance, powered by artificial intelligence (AI) and machine learning, can anticipate potential failures before they occur, reducing downtime and maintenance costs while increasing the lifespan of turbine components. By continuously analyzing data from sensors, operators can make data-driven decisions to improve turbine performance, identify inefficiencies, and optimize energy output.
Automation and advanced control systems will also enhance the operation of steam turbines, making them more adaptable to changing conditions and better integrated into smart grids. These systems can automatically adjust turbine settings to maintain optimal performance based on real-time data, ensuring that the turbine operates efficiently regardless of fluctuations in steam pressure, temperature, or power demand.
In conclusion, the future of steam turbines is bright, with a host of innovations driving improvements in efficiency, sustainability, and adaptability. From hydrogen-powered turbines to advanced materials and digital control systems, steam turbines will continue to play a central role in the global energy transition. By adapting to new fuel sources, integrating with renewable energy systems, and embracing cutting-edge technologies, steam turbines will remain essential in providing reliable, low-carbon energy for a rapidly changing world. As the energy landscape evolves, steam turbines will evolve with it, helping to meet the growing demand for clean, efficient, and sustainable power.
As the energy landscape continues to evolve, the integration of steam turbines into future power systems will increasingly reflect the global shift towards sustainability and decarbonization. Innovations in turbine design, fuel flexibility, and digital technologies will not only enhance the operational efficiency of steam turbines but also help to mitigate the environmental impacts of power generation. Let’s look deeper into some of the key areas where steam turbines are set to play an even more pivotal role in the coming years.
Decarbonization and Low-Carbon Fuels: The drive for decarbonization in the energy sector is a major factor shaping the future of steam turbines. With global commitments to net-zero emissions by mid-century, the role of fossil fuels must be reduced significantly. This shift necessitates the adoption of low-carbon and renewable fuels, such as hydrogen, biofuels, and synthetic fuels, that can be used in steam turbines to produce clean energy.
Hydrogen, in particular, holds great promise as a clean fuel for steam turbines. When combusted, hydrogen produces only water vapor, making it an ideal candidate for reducing greenhouse gas emissions in power generation. However, the combustion of hydrogen presents unique challenges, such as higher flame temperatures and different combustion dynamics compared to natural gas or coal. Turbine manufacturers are investing heavily in developing turbines that can burn hydrogen efficiently and reliably, with specialized combustors, advanced materials, and cooling technologies to handle the high thermal loads associated with hydrogen combustion.
Additionally, steam turbines are being adapted to work with biofuels and synthetic fuels derived from biomass, waste, and other sustainable feedstocks. These fuels are considered carbon-neutral because the carbon released during combustion is roughly equivalent to the amount absorbed by the biomass during its growth cycle. By using steam turbines in conjunction with these biofuels, power plants can produce renewable energy while minimizing their carbon footprint.
Flexibility and Grid Support: The growing integration of renewable energy sources such as wind and solar into the power grid is one of the most significant changes in the energy sector. However, the intermittent nature of these sources – they only generate power when the wind is blowing or the sun is shining – can cause challenges for grid stability. This has placed greater emphasis on the need for flexible and reliable backup power systems, which steam turbines can provide.
Steam turbines can be configured to provide flexible and rapid response to fluctuations in grid demand, making them an essential part of modern, renewable-rich grids. By combining steam turbines with energy storage systems such as batteries or pumped hydro storage, the power generated from intermittent renewable sources can be stored during periods of high generation and used during periods of high demand. This ability to “cycle” or ramp up and down quickly ensures that steam turbines can be seamlessly integrated into a grid that relies on variable renewable energy sources.
Additionally, combined-cycle power plants (CCPP), which combine gas turbines with steam turbines, offer high operational flexibility and exceptional efficiency. In these plants, the gas turbine generates electricity, and the waste heat from the gas turbine is used to generate steam that drives a steam turbine, producing more electricity. Combined-cycle plants can quickly adjust output to meet changes in demand, making them ideal for stabilizing grids with high shares of renewable energy.
Microgrids and Distributed Energy Systems: Microgrids, which are localized energy systems that can operate independently of the main grid, are becoming increasingly important in both developed and developing regions. Microgrids can provide reliable electricity to remote areas, islands, or regions with unreliable grid infrastructure. In these systems, steam turbines play a key role in ensuring a steady and reliable power supply, especially when integrated with renewable energy sources such as solar or wind, and energy storage systems.
Steam turbines used in microgrids need to be compact, modular, and highly efficient to meet the specific needs of small-scale, decentralized power systems. The growing demand for clean, decentralized energy solutions has driven the development of smaller, more versatile steam turbines that can be easily integrated into microgrids. These smaller turbines can operate on a variety of fuels, including waste heat, biomass, and synthetic fuels, offering further flexibility for off-grid or isolated communities.
Steam turbines in microgrids are also used to provide combined heat and power (CHP) for industrial and residential applications. CHP systems generate both electricity and useful heat from the same fuel source, making them highly efficient. In industrial settings, steam turbines can be coupled with process heat to provide a reliable energy solution that improves overall energy efficiency and reduces emissions.
Advanced Control Systems and Automation: One of the most exciting developments in the steam turbine sector is the increasing use of advanced control systems and automation technologies. The advent of digitalization in the energy industry has led to the development of more sophisticated turbine monitoring and control systems that can significantly improve turbine performance, efficiency, and safety.
Real-time monitoring of turbine parameters such as temperature, pressure, vibrations, and rotor speed allows operators to make informed decisions and adjust turbine settings to optimize performance. This data can be analyzed using artificial intelligence (AI) and machine learning algorithms to detect patterns, predict maintenance needs, and identify potential issues before they result in costly failures. These predictive maintenance techniques can reduce downtime, extend turbine life, and lower maintenance costs by allowing operators to perform maintenance only when necessary, rather than on a fixed schedule.
Automation is also improving turbine control, allowing for more precise adjustments in response to changes in steam flow, temperature, and pressure. Automated systems can optimize turbine performance without the need for constant manual intervention, ensuring that the turbine operates within its optimal performance parameters. This reduces the risk of human error and ensures the turbine operates at peak efficiency, contributing to overall energy savings.
Cybersecurity and Digital Resilience: As steam turbines become more connected and integrated into digital systems, cybersecurity becomes an increasingly important consideration. Modern steam turbines are often equipped with sensors, communication networks, and control systems that are vulnerable to cyberattacks. A cyberattack on a turbine or its associated control systems could lead to operational disruptions, equipment damage, or even safety risks.
Ensuring the digital resilience of steam turbines is crucial as more utilities and power plants adopt digital technologies and automation. Robust cybersecurity protocols, including encryption, firewalls, and multi-factor authentication, will be essential in protecting steam turbines from cyber threats. Furthermore, as turbines become more connected to broader energy management systems and smart grids, the implementation of secure communication channels and intrusion detection systems will be vital to maintaining the integrity of the overall grid.
Sustainability in Manufacturing: The environmental impact of steam turbine manufacturing is another consideration as the industry strives to meet sustainability goals. The extraction of raw materials, the energy-intensive manufacturing processes, and the eventual disposal of turbine components can contribute to the carbon footprint of turbine production. To address this, manufacturers are exploring ways to reduce the environmental impact of turbine construction through improved material recycling, the use of sustainable materials, and more energy-efficient production methods.
For example, the development of new, lightweight materials and advanced manufacturing techniques such as additive manufacturing (3D printing) can reduce material waste and improve the efficiency of turbine construction. Additive manufacturing allows for the creation of highly complex turbine components with minimal material usage, enabling more efficient designs and reducing manufacturing energy consumption.
Furthermore, the use of sustainable practices in turbine production, including the use of renewable energy in manufacturing facilities and the recycling of materials, can help reduce the overall environmental impact of steam turbines. As the demand for low-carbon technologies continues to grow, manufacturers will increasingly prioritize sustainability throughout the lifecycle of steam turbines.
Conclusion: The future of steam turbines is characterized by innovation, adaptability, and a focus on sustainability. As power systems transition toward renewable and low-carbon energy sources, steam turbines will continue to evolve, integrating with new fuels, digital technologies, and advanced manufacturing techniques to meet the demands of a changing energy landscape. Whether in large-scale power plants, hybrid systems, microgrids, or renewable energy integration, steam turbines will remain a central component of the global energy mix, providing reliable, efficient, and clean power well into the future. Their ongoing development and adoption will be critical in achieving the world’s decarbonization goals and ensuring a sustainable and resilient energy system for generations to come.
Overview of steam turbine systems
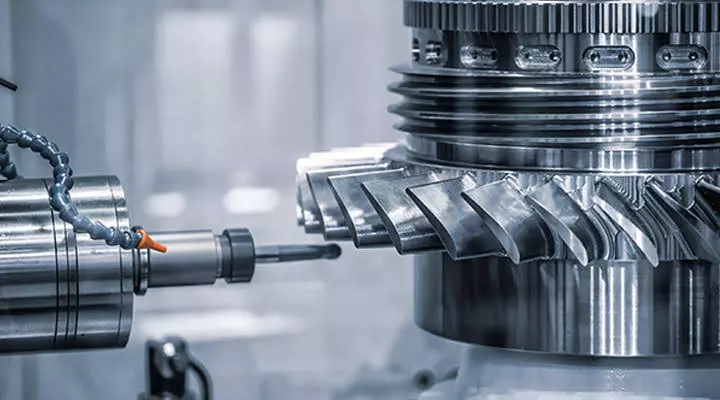
Steam turbine systems play a critical role in the production of electrical power, industrial processes, and various mechanical applications. These systems are designed to convert thermal energy from steam into mechanical energy, which is then used to generate electricity or perform mechanical work. The fundamental components of a steam turbine system include the boiler, turbine, condenser, and associated control and auxiliary systems. Over the years, steam turbine technology has evolved to become more efficient, reliable, and flexible, enabling its use in a wide range of applications across industries and power plants.
Basic Principles of Steam Turbine Systems:
At its core, a steam turbine system operates on the principle of thermodynamics, specifically the conversion of heat energy from steam into mechanical energy through the expansion of steam in a turbine. The process begins in the boiler, where water is heated to produce high-pressure steam. This steam is then directed into the turbine, where it flows through a series of blades mounted on a rotor shaft. As the steam passes through the blades, it causes the rotor to spin, converting the thermal energy into mechanical energy. This spinning rotor is then connected to a generator or other mechanical systems to produce electricity or perform useful work.
The steam that exits the turbine is typically cooled and condensed back into water in a condenser before being sent back to the boiler to repeat the cycle. This closed-loop process, known as the Rankine cycle, is the fundamental operating cycle of steam turbine systems. The efficiency of a steam turbine system depends on how effectively it can convert thermal energy into mechanical energy, as well as how efficiently the steam is condensed and recycled.
Key Components of Steam Turbine Systems:
- Boiler: The boiler is the heart of the steam generation process, where fuel (such as coal, natural gas, or biomass) is burned to produce heat, which then heats water to produce steam. Modern boilers are designed to operate at high pressures and temperatures to maximize the energy output of the steam, and they can be adapted to burn a variety of fuels. The design of the boiler must ensure efficient heat transfer and minimal energy losses to achieve optimal performance.
- Turbine: The steam turbine itself consists of a rotor with blades, a casing, and a series of stages that facilitate the expansion of steam. Steam enters the turbine at high pressure and temperature, causing the blades to rotate and convert the thermal energy into mechanical energy. The turbine can be divided into several stages, each with a set of fixed blades and moving blades that extract energy from the steam. The number of stages and the design of the blades influence the efficiency and power output of the turbine.
- Condenser: After steam passes through the turbine and does work, it exits the turbine as low-pressure steam and enters the condenser. The condenser cools the steam by transferring the heat to a cooling medium (usually water or air), causing the steam to condense into water. The condensed water is then pumped back into the boiler to be reheated, completing the Rankine cycle. The efficiency of the condenser is critical to the overall efficiency of the steam turbine system, as poor heat exchange can result in higher operating temperatures and reduced performance.
- Generator: In most steam turbine systems, the rotor of the turbine is connected to a generator, which converts the mechanical energy of the rotating turbine into electrical energy. The generator consists of a rotating rotor and a stationary stator, with the rotor being driven by the turbine’s mechanical power. As the rotor spins, it induces a magnetic field that generates alternating current (AC) electricity in the stator. The output of the generator is then fed into the electrical grid or used for industrial purposes.
- Auxiliary Systems: In addition to the core components, steam turbine systems include various auxiliary systems that support operation and ensure safe, efficient performance. These may include feedwater pumps, cooling systems, steam valves, lubrication systems, and control systems. These systems work together to regulate the flow of steam, monitor turbine performance, and provide the necessary cooling and lubrication to prevent overheating or wear of the turbine components.
Types of Steam Turbine Systems:
Steam turbine systems can be classified into several types based on their design, application, and configuration. The most common types include:
- Condensing Steam Turbines: These turbines are typically used in power plants to generate electricity. In a condensing steam turbine system, the steam exhaust is condensed in a condenser to produce a vacuum, which increases the efficiency of the turbine. This type of system is often used in large-scale power plants where maximum energy conversion is desired.
- Back-Pressure Steam Turbines: Back-pressure turbines are commonly used in industrial applications where both electricity and useful process steam are required. In these systems, the exhaust steam from the turbine is used for heating or industrial processes, rather than being condensed. The turbine operates at a higher pressure than in condensing turbines, making it suitable for applications where steam is needed for other purposes.
- Extraction Steam Turbines: Extraction turbines are used when steam needs to be extracted from the turbine at various points along its flow path. These turbines allow steam to be used for multiple applications, such as district heating, while still producing electricity. The steam is extracted at specific stages to meet the demands of the industrial process or heating network, making this type of turbine versatile for combined heat and power (CHP) systems.
- Combined-Cycle Systems: In combined-cycle systems, both gas and steam turbines are used to maximize efficiency. In this setup, a gas turbine generates electricity using the heat from burning natural gas, and the waste heat from the gas turbine is used to produce steam to drive a steam turbine, which generates additional electricity. This configuration can significantly increase the overall efficiency of a power plant by utilizing the waste heat from the gas turbine.
Efficiency and Performance Factors:
The performance of a steam turbine system is largely determined by its efficiency, which depends on several factors, including:
- Steam Conditions: The temperature and pressure of the steam entering the turbine directly affect the efficiency of the system. Higher steam temperatures and pressures allow for more energy to be extracted from the steam, improving efficiency. However, these conditions also require the turbine components to be made from advanced materials that can withstand the extreme heat and pressures without deteriorating.
- Turbine Design: The number of stages in the turbine, the size and shape of the blades, and the rotor speed all influence how effectively the turbine extracts energy from the steam. Advances in turbine blade design, such as the use of high-strength alloys and improved aerodynamic shapes, have contributed to significant efficiency gains in modern steam turbines.
- Heat Recovery: The efficiency of a steam turbine system can be further enhanced by implementing heat recovery systems, such as combined-cycle or cogeneration setups. These systems capture waste heat from the turbine exhaust or from industrial processes to generate additional steam or electricity, reducing overall energy consumption.
- Condensation Efficiency: The effectiveness of the condenser in cooling and condensing the steam is another critical factor. Efficient heat transfer and minimal losses in the condenser help to maintain low exhaust temperatures, which in turn improves the overall efficiency of the turbine.
- Maintenance and Monitoring: Regular maintenance and real-time monitoring of turbine components are essential for maintaining optimal performance. Advances in digitalization, such as the use of sensors and data analytics, have enabled better monitoring of turbine conditions and predictive maintenance, reducing downtime and improving efficiency.
Emerging Trends and Technologies in Steam Turbine Systems:
As the demand for cleaner, more efficient energy sources increases, steam turbine systems are evolving to meet new challenges and applications. Some of the key trends include:
- Integration with Renewable Energy: Steam turbines are being adapted for use in hybrid systems that integrate renewable energy sources such as solar or wind. For example, concentrated solar power (CSP) systems use mirrors or lenses to focus sunlight and generate steam, which is then used to drive a steam turbine. This approach allows for renewable energy to be stored and used on demand, overcoming the intermittent nature of solar and wind power.
- Higher Efficiency Cycles: Supercritical and ultra-supercritical steam cycles, which operate at higher pressures and temperatures than conventional steam cycles, are being developed to improve efficiency. These cycles allow steam turbines to extract more energy from the same amount of fuel, reducing fuel consumption and emissions while increasing electricity output.
- Hydrogen-Fueled Turbines: The increasing use of hydrogen as a clean fuel is driving the development of hydrogen-compatible steam turbines. Hydrogen combustion produces only water vapor, making it an ideal fuel for decarbonizing the energy sector. Researchers are exploring new materials and turbine designs that can handle the unique properties of hydrogen, such as its high flame temperature and low energy density.
- Digitalization and Smart Turbines: Advances in digital technologies are enabling steam turbines to become “smarter” and more efficient. Real-time monitoring, predictive maintenance, and advanced control systems are helping operators optimize turbine performance, extend the lifespan of components, and reduce maintenance costs.
Conclusion:
Steam turbine systems are a cornerstone of modern power generation and industrial processes, providing a reliable and efficient means of converting thermal energy into mechanical work. As the world shifts toward renewable energy and decarbonization, steam turbines will continue to evolve, integrating new fuels, advanced materials, and digital technologies to meet the demands of a cleaner, more sustainable energy future. Whether used in traditional power plants, hybrid systems, or microgrids, steam turbines will remain a critical component of the global energy mix for many years to come.
Steam turbine systems play a central role in modern power generation, industrial processes, and even some transport applications. Their fundamental purpose is to convert thermal energy from steam into mechanical energy, which can then be used to generate electricity or perform mechanical work in various industries. These systems are vital in both conventional and renewable energy sectors, and they serve as the backbone for many large-scale energy operations due to their reliability and efficiency.
The core process begins in a boiler, where water is heated to generate high-pressure steam. This steam then travels to the turbine, where it passes through blades attached to a rotor. As the steam flows over the blades, it causes them to rotate, transforming the thermal energy of the steam into mechanical energy. The rotor is connected to a generator, which converts this mechanical energy into electrical energy. After the steam has passed through the turbine, it is cooled and condensed in a condenser, typically using water or air, before being pumped back to the boiler to repeat the cycle.
Efficiency in a steam turbine system is a function of several factors, including the temperature and pressure of the steam entering the turbine. The higher the temperature and pressure, the more energy the steam can carry, thus improving the efficiency of the turbine. Modern steam turbines operate at higher pressures and temperatures, thanks to advancements in materials and turbine design. These improvements allow turbines to extract more energy from the steam, which leads to greater efficiency and power output. Furthermore, as the demand for cleaner energy grows, steam turbines are increasingly being adapted to work with a variety of renewable fuels, such as hydrogen or biomass, further enhancing their relevance in the transition to a low-carbon energy future.
The role of steam turbines has evolved to accommodate the growing integration of renewable energy sources. As wind and solar power become more prevalent, the ability to store energy and respond to fluctuations in demand becomes essential. Steam turbines, particularly in combined-cycle plants, can help balance intermittent renewable energy by providing flexible and reliable backup power. This capability makes them an important part of the energy transition, as they can help stabilize grids and ensure a steady supply of power when renewable generation is low.
Recent technological advances have also enabled steam turbines to become more flexible and adaptable to changing operating conditions. For example, modern steam turbines can quickly adjust their output to meet shifts in energy demand, ensuring that they can maintain stable operation alongside fluctuating renewable sources. Additionally, predictive maintenance and real-time monitoring using advanced sensors and data analytics allow operators to optimize turbine performance and minimize downtime. These technologies not only improve turbine efficiency but also extend the lifespan of critical components by allowing for more precise and timely maintenance.
The integration of steam turbines into combined heat and power (CHP) systems further enhances their utility by providing both electricity and useful heat. CHP systems are used in industrial applications, district heating, and large-scale power generation, offering significant energy savings and reducing emissions. In such systems, steam turbines can harness waste heat from industrial processes or other sources to generate steam, which is then used to produce electricity, making these systems highly efficient. This approach not only reduces fuel consumption but also minimizes environmental impacts by using energy more effectively.
As the energy landscape continues to shift toward sustainability, steam turbines are adapting to accommodate new challenges, such as the need for decarbonization and increased reliance on low-carbon fuels. The development of hydrogen-compatible turbines is one example of how steam turbines are evolving to meet these demands. Hydrogen can be burned in steam turbines to produce energy without the carbon emissions associated with traditional fossil fuels, and research is underway to develop turbines that can operate efficiently with hydrogen, which requires special design considerations due to its unique combustion properties. In addition to hydrogen, other renewable fuels, such as biofuels, are also being used in steam turbine systems, allowing for a more diverse energy mix and supporting efforts to reduce the carbon footprint of power generation.
The future of steam turbine systems will likely be shaped by continued innovation in materials, digital technologies, and system integration. The use of advanced materials, such as superalloys and ceramics, will allow turbines to operate at even higher temperatures and pressures, improving their overall efficiency. Furthermore, digitalization is transforming the way turbines are operated and maintained, with technologies like artificial intelligence (AI) and machine learning enabling more precise control and predictive capabilities. These technologies can help identify potential issues before they lead to failures, reducing maintenance costs and improving the reliability of steam turbine systems.
As the global energy sector undergoes significant transformation, steam turbine systems will continue to play a critical role in power generation and industrial processes. Their ability to operate efficiently with a wide range of fuels, provide flexible backup power, and integrate into complex energy systems positions them as a key technology for the future. Whether in conventional power plants, hybrid renewable systems, or microgrids, steam turbines will remain a crucial component in ensuring a stable, sustainable, and low-carbon energy future.
As energy demands increase and the need for a transition to cleaner energy systems intensifies, steam turbines are expected to evolve even further. Advances in turbine efficiency, fuel flexibility, and system integration will continue to shape the future role of steam turbines in the global energy landscape. One of the driving forces behind this evolution is the rising need for carbon capture and storage (CCS) technologies, which are becoming an essential part of efforts to mitigate greenhouse gas emissions from fossil-fuel-based power plants.
Steam turbines are being incorporated into integrated systems that combine both power generation and CCS technologies. In these systems, steam turbines can continue to generate electricity, while the CO2 produced from the combustion of fossil fuels is captured, compressed, and stored underground or repurposed for industrial use. This combination of energy production and carbon capture is vital for ensuring that power generation remains a viable option even as countries push toward net-zero emissions targets. The role of steam turbines in these CCS systems will be pivotal, as their flexibility and efficiency allow them to work in tandem with technologies that help reduce the environmental impact of fossil fuels.
The evolution of steam turbine systems also comes with a focus on optimizing their lifecycle costs. Given that steam turbines are long-term investments with multi-decade lifespans, ensuring their economic viability over time is crucial. As such, turbine manufacturers are focusing on improving the overall performance, reliability, and durability of turbines through better materials, manufacturing techniques, and design. Components such as turbine blades, bearings, and seals are undergoing continuous development to reduce wear and increase the lifespan of turbines, which in turn reduces the need for costly repairs and replacements.
Moreover, the increasing use of digital tools and data analytics has allowed operators to extract even more value from steam turbines. Real-time data from sensors embedded in various turbine components is analyzed to optimize performance, identify anomalies, and predict future maintenance needs. By using advanced data analytics, operators can improve operational efficiency, reduce fuel consumption, and lower maintenance costs, all while increasing the lifespan and reliability of turbine systems. In this regard, “smart turbines” are becoming a reality, incorporating IoT sensors, automated control systems, and machine learning algorithms to continuously refine performance. This approach helps avoid unplanned outages and ensures that turbines are operating at optimal levels at all times.
The growing complexity of the global energy mix means that steam turbines are increasingly used in hybrid systems, where they are integrated with other energy sources, such as renewable technologies, gas turbines, or even energy storage solutions. For example, steam turbines can be paired with large-scale solar or wind power plants, where they can operate as backup power sources when renewable generation is insufficient. This hybrid approach offers the flexibility to draw from multiple sources of power, reducing reliance on any single form of generation and increasing the overall resilience of the energy grid. In particular, hybrid systems with steam turbines and energy storage are becoming attractive options for regions with high shares of variable renewable energy, as they provide a way to store excess energy when renewable generation is high and discharge that energy when demand spikes or generation decreases.
Steam turbines are also becoming an important component in distributed energy systems, where small-scale, localized generation systems are deployed to meet the needs of specific regions or industries. Microgrids, for example, can use steam turbines in combination with renewable energy sources, batteries, or even fuel cells to provide reliable, sustainable power to communities or industrial facilities. In these applications, steam turbines need to be highly adaptable, efficient, and capable of operating in a decentralized manner. Their ability to respond to local power needs while being integrated with renewable energy sources ensures that steam turbines will remain relevant in an increasingly decentralized energy landscape.
In addition to power generation, steam turbines are also used in a variety of industrial applications, including process industries such as chemicals, pharmaceuticals, and oil refining. In these industries, steam turbines are often part of combined heat and power (CHP) systems, where both electricity and process heat are produced from a single fuel source. This approach maximizes efficiency by ensuring that the waste heat from the steam turbine is used for industrial processes, reducing energy consumption and emissions. As industries continue to embrace sustainable practices, steam turbines are likely to see an increase in demand for their ability to deliver both electricity and useful heat in a single integrated system.
As the push for sustainability becomes more pressing, steam turbines will likely be designed to be even more fuel-agnostic, allowing them to operate with a wider range of renewable fuels. Some turbines are being developed with a greater ability to burn hydrogen and other green fuels like ammonia, which can be produced with little to no carbon emissions. These turbines could be deployed in a wide variety of applications, from large-scale power plants to smaller industrial processes, helping to decarbonize sectors that are otherwise challenging to electrify.
Moreover, the global transition to a circular economy could have significant implications for the steam turbine industry. As more focus is placed on resource efficiency, waste minimization, and the recycling of materials, the lifecycle of steam turbines will likely evolve. Manufacturers may increasingly prioritize the use of recyclable and sustainably sourced materials, ensuring that turbines can be more easily decommissioned and their components repurposed once they reach the end of their service life. The shift toward circular manufacturing processes will align with global efforts to reduce waste, carbon emissions, and reliance on finite resources, contributing to a more sustainable industrial future.
In the longer term, the development of new materials, such as advanced alloys, composites, and even coatings designed for high-performance environments, will enhance the ability of steam turbines to withstand more extreme operating conditions. These innovations will improve efficiency, reduce maintenance requirements, and increase the overall operational life of turbines, making them more economically viable in the face of growing energy demands.
Finally, steam turbines will play a significant role in maintaining grid stability as the energy mix continues to diversify. Grid operators are increasingly integrating diverse energy sources into the grid, including wind, solar, and other renewables, as well as traditional thermal plants. Steam turbines, with their ability to operate in both base-load and peaking scenarios, will continue to be a critical asset in maintaining grid reliability. Their ability to provide backup power during periods of low renewable generation or sudden demand spikes will help ensure that grids remain stable and resilient.
In conclusion, steam turbine systems are integral to the energy infrastructure of the future, offering flexibility, efficiency, and the ability to integrate with renewable and low-carbon technologies. As energy systems evolve and face new challenges, steam turbines will adapt through innovations in design, materials, and technology. Whether used in traditional fossil-fuel plants, combined-cycle systems, renewable hybrid plants, microgrids, or industrial applications, steam turbines will continue to be a cornerstone of the global energy transition. Their ongoing development will ensure that they remain an essential part of a cleaner, more sustainable, and reliable energy future.
As the world continues its push toward decarbonization, steam turbines will also evolve to meet the growing emphasis on reducing environmental impact. One of the critical aspects of this transformation is improving the environmental footprint of steam turbines themselves. While the turbines themselves are not inherently polluting, the fuels used to generate steam and the processes surrounding their operation can contribute to greenhouse gas emissions. As such, significant efforts are being made to develop cleaner steam generation methods, improve the efficiency of turbine systems, and integrate carbon capture and storage (CCS) technology into existing systems.
The integration of carbon capture with steam turbines can help drastically reduce emissions from power plants, especially those still reliant on fossil fuels. By capturing CO2 from exhaust gases before they are released into the atmosphere, CCS technologies can effectively mitigate the environmental impact of steam turbines that run on coal or natural gas. However, these systems require significant investment and technological innovation, particularly to improve the efficiency and cost-effectiveness of CO2 capture and storage processes. As the cost of carbon capture decreases and the technology improves, steam turbines integrated into CCS systems will become more widespread, further promoting the transition to a low-carbon economy.
Another area of focus in reducing the environmental impact of steam turbines is in the reduction of water usage. Traditional steam turbine systems require significant amounts of water for cooling, especially in large-scale power plants. This can put pressure on local water resources, particularly in regions experiencing water scarcity. To address this challenge, many modern turbines are being designed to operate with closed-loop cooling systems, which recycle and reuse water, significantly reducing water consumption. Additionally, air-cooled condensers are being developed and deployed in certain locations, eliminating the need for water-based cooling altogether. These innovations are helping to make steam turbines more sustainable and less reliant on water resources, particularly in areas where water conservation is a pressing concern.
In addition to these environmental improvements, the future of steam turbines is closely tied to the advancement of digital technologies. The increasing use of sensors, predictive maintenance, and digital twins (virtual representations of physical systems) will allow for even greater optimization of turbine performance. Digital twins, in particular, are a powerful tool for simulating the behavior of steam turbines in real-time, allowing engineers and operators to assess and predict how a turbine will perform under different conditions, without physically testing the equipment. This technology can be used to detect potential issues before they cause failures, enabling more proactive maintenance and reducing downtime.
As digitalization continues to improve, steam turbine operators will be able to fine-tune operational parameters such as steam pressure, temperature, and flow rates to maximize efficiency and reduce fuel consumption. With real-time monitoring, operators can adjust these variables based on the current conditions and energy demand, ensuring that turbines are always running at their optimal performance. Moreover, data analytics will provide insights into operational patterns, allowing for continuous improvement and better decision-making in both operation and maintenance schedules.
The growing trend toward distributed energy systems, including microgrids and decentralized power generation, is another key factor shaping the future of steam turbines. Microgrids, which are small, localized grids capable of operating independently from the main power grid, are becoming increasingly popular in regions with unreliable or underserved power supplies. Steam turbines in microgrids can provide backup power or serve as the main source of energy when renewable generation is insufficient. The flexibility and reliability of steam turbines make them ideal for these types of decentralized systems, where maintaining power supply reliability is critical.
Furthermore, as the energy sector becomes more interconnected, steam turbines are increasingly being integrated into hybrid power plants that combine multiple technologies to meet varying power demands. These hybrid plants can use a combination of steam, gas, solar, and energy storage systems to create more resilient and efficient energy solutions. For example, steam turbines can complement gas turbines in combined-cycle plants, where waste heat from the gas turbine is used to generate steam, improving the overall efficiency of the system. In renewable-based hybrid plants, steam turbines can be used to provide baseload or backup power, helping to stabilize intermittent renewable energy sources like wind and solar.
In industrial settings, steam turbines will continue to play a key role in combined heat and power (CHP) applications, where they provide both electricity and process heat. These systems are highly efficient, as they capture waste heat from the turbine to be used for industrial processes, reducing overall energy consumption and emissions. As industries work to meet stricter environmental regulations and lower their carbon footprints, CHP systems powered by steam turbines will remain an essential part of industrial energy solutions. Innovations in turbine technology, such as the ability to run on cleaner fuels like hydrogen or biogas, will further enhance the sustainability of these systems.
The versatility of steam turbines, along with their proven track record of reliability and efficiency, means they will remain central to energy production in the coming decades. Their adaptability to new fuels, including renewable sources and hydrogen, ensures that they will continue to contribute to decarbonization efforts across various sectors, from power generation to industrial applications. As the global energy mix evolves, steam turbines will play an indispensable role in ensuring a stable, reliable, and low-carbon energy future.
Moreover, as nations work to implement the Paris Agreement and achieve net-zero emissions by mid-century, steam turbines will become a key technology in the global effort to reduce carbon emissions. This will require both continued innovation in turbine design and materials, as well as greater integration with renewable energy systems, carbon capture technologies, and energy storage solutions. The development of steam turbines capable of utilizing green hydrogen, advanced biofuels, and other sustainable energy sources will ensure that these systems remain relevant in a decarbonized world.
Finally, international collaboration and knowledge sharing will be crucial in advancing steam turbine technology. By pooling resources, expertise, and research efforts, companies, governments, and academic institutions can accelerate the development of new technologies that improve turbine efficiency, reduce costs, and minimize environmental impact. As the transition to cleaner energy continues, the global community will need to work together to harness the full potential of steam turbines, ensuring that they remain a vital part of the world’s energy infrastructure for years to come.
In conclusion, the future of steam turbines is shaped by the ongoing evolution of energy systems, technological advancements, and environmental priorities. With an emphasis on efficiency, flexibility, and sustainability, steam turbines will continue to play a pivotal role in meeting the world’s energy needs while addressing the challenges of climate change and environmental degradation. Their ability to adapt to new fuels, integrate with renewable energy sources, and optimize performance through digitalization ensures that steam turbines will remain a cornerstone of the global energy transition.
Primary Uses of Steam Turbines
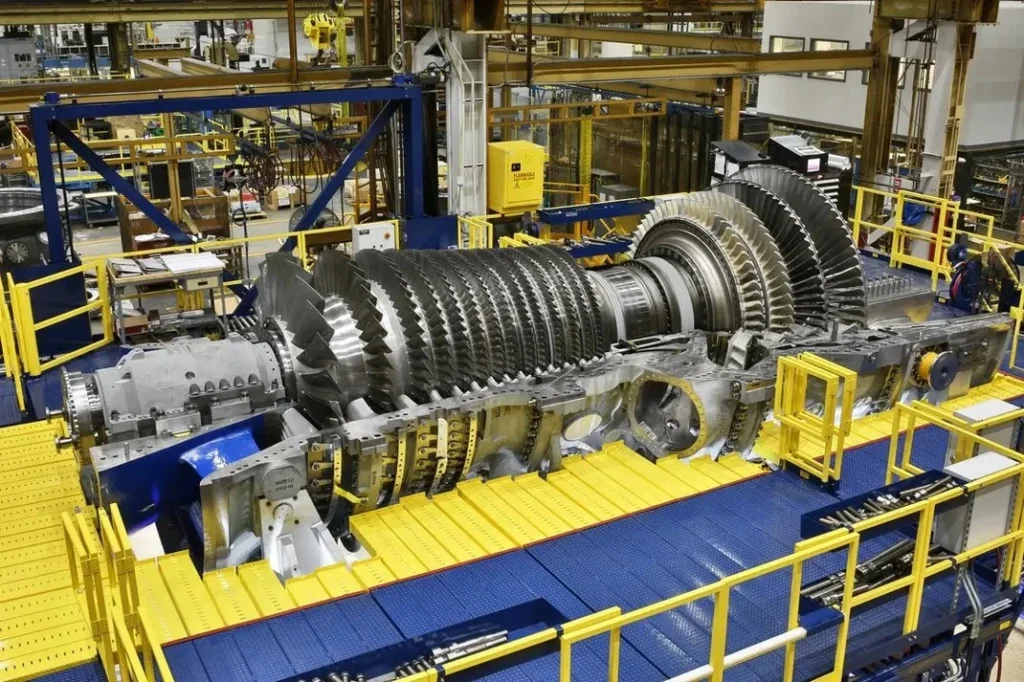
Steam turbines have a wide array of primary uses across various industries, primarily in the generation of electricity, but also in mechanical drive applications for industries like oil and gas, chemical processing, and manufacturing. These versatile machines play a critical role in power generation, helping to produce both large-scale electricity in central power plants and smaller-scale power in industrial applications. The combination of high efficiency, reliability, and adaptability ensures that steam turbines continue to be a key technology in both conventional and emerging energy systems.
The most common and well-known use of steam turbines is in power plants, where they generate electricity by converting thermal energy into mechanical energy. In these plants, steam turbines are used in thermal power generation, where heat is produced from burning fossil fuels (such as coal, natural gas, or oil), nuclear reactions, or renewable fuels like biomass. Steam generated from these processes drives the turbines, which then convert the steam’s energy into mechanical energy that is coupled to a generator. The generator, in turn, produces electricity. These power plants are typically large-scale operations, designed to supply electricity to national or regional grids.
One of the significant advantages of steam turbines in power generation is their efficiency. Modern steam turbines are designed to operate at extremely high temperatures and pressures, allowing them to extract more energy from steam and achieve greater overall efficiency. The use of combined-cycle plants, where steam turbines are paired with gas turbines, further increases efficiency by capturing and utilizing waste heat. These plants are able to achieve efficiency levels above 60%, which is a considerable improvement over earlier steam turbine designs.
Another primary use of steam turbines is in combined heat and power (CHP) systems. In CHP, also known as cogeneration, steam turbines are used to generate both electricity and useful heat simultaneously. This application is commonly found in industrial and commercial facilities that require both electrical power and heat for manufacturing processes, district heating, or other uses. By utilizing waste heat from the turbine for heating purposes, CHP systems dramatically improve the overall efficiency of energy use. These systems are particularly advantageous in industries like chemicals, food processing, and paper production, where both electrical power and heat are in constant demand.
Steam turbines are also used in industries that require mechanical drive systems to power machinery, pumps, compressors, and other equipment. In these applications, steam turbines are used to drive mechanical equipment instead of generating electricity. For example, in the oil and gas industry, steam turbines are often used to power pumps and compressors that are essential for the extraction, processing, and transportation of oil and gas. In chemical manufacturing, steam turbines can drive compressors for refrigeration, air conditioning, or other cooling processes. The mechanical drive capabilities of steam turbines allow them to serve as a reliable and efficient power source in industries that rely on high levels of mechanical energy.
In the maritime industry, steam turbines were historically used to power ships, and while gas turbines and diesel engines have largely replaced them in modern vessels, steam turbines are still employed in some large ships, such as aircraft carriers and certain cargo vessels. Steam turbines provide efficient propulsion, especially in naval applications, where power and reliability are crucial. They operate by heating water to generate steam, which drives a turbine connected to a propeller shaft. The turbines in these ships typically operate using heat produced by nuclear reactors, ensuring that they can remain at sea for extended periods without needing to refuel.
In addition to power generation and mechanical drive applications, steam turbines are used in district heating systems, where they generate both electricity and thermal energy for heating homes, businesses, and other buildings. In these systems, a steam turbine is used to generate electricity, while the heat produced as a byproduct of the steam generation process is piped into local buildings for space heating. This dual-purpose approach to energy generation is particularly efficient in areas where heating demand is significant and where electricity generation and heating can be combined in a single system.
Steam turbines are also an important part of renewable energy systems, particularly in the utilization of concentrated solar power (CSP). In CSP plants, mirrors or lenses are used to focus sunlight onto a central receiver, where it is used to generate steam. The steam then drives a steam turbine, which is connected to a generator to produce electricity. CSP plants can operate even when the sun is not shining, as they often include thermal storage systems to retain the heat collected during the day. Steam turbines are essential to these systems, as they help to convert the stored thermal energy into electricity, providing a renewable energy solution with the ability to supply power when sunlight is unavailable.
In the food and beverage industry, steam turbines are used to power large-scale equipment such as industrial boilers, dryers, and evaporators. Steam turbines in these applications can help improve energy efficiency by utilizing waste heat or providing the mechanical energy required for the production of food and beverages. Given the high energy consumption of food processing operations, using steam turbines to drive essential equipment ensures that energy use is optimized while maintaining the desired production output.
In chemical plants and petrochemical facilities, steam turbines are used to drive a wide variety of mechanical systems, including compressors, pumps, and refrigeration units. These industries rely on the consistent and reliable operation of steam turbines to support their production processes. The ability to generate both electricity and mechanical power from steam allows chemical and petrochemical facilities to reduce their reliance on external electricity sources and operate more independently.
In addition to their use in traditional power generation and industrial applications, steam turbines are also employed in some small-scale or off-grid power systems, such as those used in remote areas or specific industrial sites where centralized power distribution is not feasible. These decentralized systems can be powered by a variety of fuels, including natural gas, biomass, or even waste heat from industrial processes. Steam turbines in these applications help provide reliable and efficient power without the need for a connection to a larger power grid.
In the geothermal energy industry, steam turbines play a critical role in harnessing the energy stored in the Earth’s subsurface. Geothermal power plants use steam extracted from underground reservoirs to drive steam turbines, which are connected to generators to produce electricity. This renewable energy source is particularly attractive in regions with abundant geothermal resources, and steam turbines are key to capturing and converting the heat energy from these sources into electricity.
One of the emerging uses of steam turbines is in the hydrogen economy. Hydrogen can be used as a clean fuel for steam turbines, with the combustion of hydrogen producing steam that drives the turbine. This application has the potential to play a significant role in decarbonizing power generation and industrial processes, as hydrogen can be produced from renewable sources and burned without emitting CO2. As the technology for hydrogen production and storage continues to improve, steam turbines may become an important part of the infrastructure needed to support a hydrogen-based economy.
In summary, steam turbines are used in a wide range of applications beyond just electricity generation, serving critical roles in industries ranging from chemical manufacturing to oil and gas, food processing, and beyond. Their ability to efficiently convert thermal energy into mechanical energy makes them indispensable in various sectors, whether for power generation, mechanical drive systems, or combined heat and power applications. The versatility of steam turbines, coupled with advancements in technology, ensures that they will continue to be a key component of energy production systems worldwide, particularly as industries and countries transition toward more sustainable and low-carbon energy solutions.
As the demand for cleaner, more sustainable energy solutions grows, steam turbines are expected to play an even more prominent role in supporting the global transition to a low-carbon economy. In the context of decarbonization, steam turbines will increasingly be integrated into systems that use renewable energy sources, such as solar, wind, and biomass, or hybrid systems that combine traditional and renewable sources.
In the case of wind and solar power, steam turbines are increasingly being used in hybrid systems to provide grid stability and backup power. Since these renewable sources can be intermittent, with power output varying depending on weather conditions and time of day, steam turbines can complement them by providing a consistent and reliable source of electricity when renewable energy production is low. For example, in a combined-cycle power plant, a steam turbine can work alongside a gas turbine, where the waste heat from the gas turbine is used to generate steam. This hybrid approach helps optimize fuel usage and increase overall efficiency, especially when renewable energy supply fluctuates.
Biomass, as a renewable fuel source, is another area where steam turbines are finding new applications. In biomass power plants, organic materials such as wood chips, agricultural waste, or even algae are burned to generate heat, which is then used to produce steam. The steam drives a turbine connected to a generator to produce electricity. Biomass can be a particularly attractive solution in regions with abundant agricultural or forestry resources, as it provides a sustainable way to generate energy while reducing the environmental impact of waste products. Steam turbines in these plants help optimize energy production, ensuring that biomass is utilized efficiently and that the electricity generated is both reliable and environmentally friendly.
As the world’s energy grid continues to evolve, steam turbines will increasingly be employed in smaller, decentralized applications, such as microgrids and localized energy systems. These systems are particularly useful in remote or off-grid areas, where traditional grid infrastructure may be lacking or impractical. By integrating steam turbines with renewable energy sources, such as solar or wind, microgrids can provide reliable and sustainable energy solutions that are less dependent on centralized power generation. Steam turbines in these systems may also be used in conjunction with energy storage technologies, such as batteries, to provide backup power during times when renewable generation is insufficient.
Steam turbines are also expected to play a significant role in energy storage systems, particularly in applications that use thermal energy storage. In these systems, excess energy produced during periods of low demand or high renewable output is stored as heat and later converted back into electricity using steam turbines. For example, in concentrated solar power (CSP) plants, mirrors or lenses focus sunlight onto a central receiver, which stores the heat in a thermal storage medium. When electricity is needed, the stored heat is used to generate steam, which drives a steam turbine and produces electricity. This process allows renewable energy plants to operate even when the sun isn’t shining, providing a reliable source of power even during nighttime or cloudy conditions.
In addition to their use in power generation, steam turbines will continue to be critical in industrial applications, particularly in sectors that require both heat and power, such as chemical manufacturing, paper production, and food processing. These industries typically rely on combined heat and power (CHP) systems, where steam turbines generate both electricity and the thermal energy needed for production processes. By optimizing energy usage, these systems help reduce overall fuel consumption and greenhouse gas emissions while providing a reliable and cost-effective source of power and heat.
For example, in the pulp and paper industry, steam turbines are used in CHP systems to generate the steam required for the paper manufacturing process, while also producing electricity for the plant’s operations. Similarly, in the chemical industry, steam turbines power compressors and other equipment, while also providing heat for processes such as distillation and drying. These applications highlight the versatility of steam turbines in industrial settings, where energy efficiency is key to minimizing costs and environmental impact.
In the petrochemical and oil refining sectors, steam turbines continue to be used to drive compressors, pumps, and other critical equipment. These industries require a large and consistent supply of power, and steam turbines offer a reliable solution to meet their energy demands. In these settings, steam turbines often operate in conjunction with other power generation technologies, such as gas turbines, to provide a stable and flexible power supply. The combination of these systems allows for better utilization of waste heat and improved overall efficiency, particularly in plants that require both electricity and heat for refining processes.
In the context of decarbonization, steam turbines may also see increased use in systems that run on hydrogen. Hydrogen, which can be produced from renewable sources, such as wind and solar, offers a clean alternative to traditional fuels. When used in steam turbines, hydrogen generates steam through combustion, with the byproduct being water vapor instead of carbon dioxide. This makes hydrogen-powered steam turbines a promising solution for power generation, particularly in sectors that are difficult to electrify. As the technology for hydrogen production, storage, and distribution improves, steam turbines could become a key component in a hydrogen-based energy system.
The hydrogen economy presents significant opportunities for steam turbine technology, as hydrogen can be used in a variety of applications, from large-scale power plants to industrial processes. Furthermore, hydrogen has the potential to decarbonize sectors such as transportation, heating, and heavy industry, and steam turbines could play an integral role in supporting this transformation. The ability to operate on hydrogen or a mix of hydrogen and natural gas will help steam turbines continue to provide a reliable source of power while reducing the carbon footprint of energy production.
In addition to the ongoing development of hydrogen-powered turbines, the integration of digital technologies will continue to improve the efficiency and performance of steam turbines. The adoption of advanced monitoring systems, predictive maintenance, and artificial intelligence will help operators optimize turbine performance, minimize downtime, and reduce the need for costly repairs. These technologies enable steam turbines to operate more efficiently and with greater precision, contributing to reduced fuel consumption and lower operational costs.
Looking ahead, steam turbines will continue to be integral to both centralized and decentralized power systems, providing reliable and efficient energy solutions in a variety of contexts. Their flexibility, efficiency, and ability to integrate with renewable energy sources and other technologies make them a key component in the ongoing transition to a low-carbon energy future. Whether in large-scale power plants, industrial applications, or hybrid renewable systems, steam turbines will play an essential role in ensuring the continued reliability, sustainability, and resilience of the global energy infrastructure.
In summary, the primary uses of steam turbines are diverse and far-reaching, extending well beyond traditional electricity generation. From industrial and mechanical drive applications to combined heat and power systems, steam turbines are used in a variety of sectors, including power generation, chemicals, food processing, and oil and gas. As the global energy landscape continues to evolve, steam turbines will play an increasingly important role in decarbonization efforts, renewable energy integration, and energy efficiency. By adapting to new fuels, technologies, and applications, steam turbines will remain a vital part of the world’s energy systems for years to come.
As the energy sector continues to evolve with the integration of renewable technologies and the drive for decarbonization, steam turbines are likely to remain a cornerstone in the global energy landscape. Their flexibility, combined with innovations that allow for the use of alternative fuels, advanced operational techniques, and integration with renewable systems, positions them well for continued relevance in both traditional and emerging energy systems.
The transition to renewable energy sources such as wind, solar, and geothermal brings challenges of intermittency and variability in power supply. This is where steam turbines will remain pivotal, particularly in hybrid power plants that combine both renewable sources and traditional thermal generation. For example, a solar thermal power plant can store heat during the day and generate steam at night using the stored thermal energy, ensuring a steady power supply. Steam turbines in these plants help maintain grid stability and provide a reliable power source even when sunlight is not available. Similarly, in wind and solar power systems, steam turbines can be paired with energy storage technologies to ensure that excess renewable energy is captured and converted to electricity when demand peaks or renewable generation is low.
The ability to utilize various forms of thermal energy—whether from biomass, geothermal sources, or even nuclear fission—ensures that steam turbines remain versatile and adaptable to a wide range of applications. Biomass power plants, which generate electricity by burning organic materials, use steam turbines to convert thermal energy from the combustion process into mechanical power. Geothermal power plants, similarly, harness the heat from beneath the Earth’s surface to produce steam that drives turbines and generates electricity. Both of these energy sources are renewable and, when combined with efficient steam turbines, contribute to a low-carbon and sustainable energy mix.
Another critical development is the potential role of steam turbines in hydrogen-based power systems. Hydrogen, particularly green hydrogen produced via renewable electricity (such as wind or solar), presents an exciting avenue for decarbonizing power generation. Hydrogen combustion produces water vapor as a byproduct, making it a clean energy source. Steam turbines running on hydrogen are capable of converting this hydrogen-derived steam into mechanical power for electricity generation. This can significantly reduce the carbon footprint of power plants, especially in heavy industrial sectors that traditionally rely on fossil fuels for energy production.
In addition, the trend toward smaller, decentralized power systems is reshaping the role of steam turbines. Microgrids, which operate independently or in conjunction with the larger grid, are becoming more common in both developed and emerging economies. Steam turbines, paired with renewable energy sources and energy storage systems, can provide the necessary backup power to these microgrids, ensuring consistent and reliable electricity supply in remote or off-grid locations. These systems are especially valuable in areas where grid infrastructure is unreliable or unavailable, making steam turbines an essential part of energy resilience in both urban and rural settings.
In the industrial sector, steam turbines continue to provide mechanical drive for key operations, including in petrochemical plants, refineries, and manufacturing facilities. They drive compressors, pumps, and other heavy machinery that are integral to the production process. The reliability and efficiency of steam turbines in these settings are key to reducing operational costs, improving energy efficiency, and enhancing sustainability. As industries move toward greener processes, steam turbines can also be used in combined heat and power (CHP) configurations to provide both electricity and process heat, reducing the need for external energy sources and optimizing energy use.
Further, the integration of digital technologies will continue to enhance the operation of steam turbines, making them smarter, more efficient, and easier to maintain. Predictive analytics, powered by real-time data collected from turbine sensors, can predict maintenance needs and optimize turbine performance. By analyzing trends in turbine operation and identifying potential issues before they occur, operators can reduce downtime and improve the lifespan of turbines. Moreover, digital twins—virtual models that replicate the physical turbine—can simulate the behavior of turbines under different conditions and help engineers optimize design and performance before implementing changes in the field. This digital transformation is essential for improving the efficiency and reliability of steam turbine systems in modern energy operations.
As the demand for more efficient and cleaner technologies grows, governments and industries are increasingly looking for ways to reduce emissions and increase the environmental sustainability of their operations. Steam turbines can contribute to this shift by providing a flexible platform for integrating various low-carbon technologies. For instance, hybrid power plants, combining steam turbines with carbon capture and storage (CCS) technology, could significantly reduce the carbon footprint of traditional fossil fuel-based power generation. Steam turbines can also play an important role in providing grid stabilization services when there are high penetrations of variable renewable energy sources, such as wind and solar, which do not produce a constant energy supply.
The ongoing improvements in turbine design—such as the development of more advanced materials, better heat-resistant alloys, and improved cooling technologies—will further enhance the efficiency and longevity of steam turbines, enabling them to operate at higher temperatures and pressures. These advancements will allow turbines to operate more efficiently, maximizing the energy extracted from steam and reducing the need for fuel consumption. Furthermore, advancements in turbine coatings, which reduce friction and wear, will further increase the operational life of turbines while reducing maintenance costs.
In terms of future developments, the integration of steam turbines with carbon capture technologies represents one of the most promising avenues for reducing carbon emissions from large-scale power plants. By capturing CO2 emissions before they are released into the atmosphere, carbon capture and storage (CCS) technologies can significantly mitigate the environmental impact of power generation. For example, when integrated into a steam turbine-based power plant, CCS can remove up to 90% of the carbon dioxide emissions generated, thereby helping power plants meet stricter environmental regulations and achieve decarbonization targets. While the initial cost of implementing CCS is high, the long-term environmental benefits and regulatory advantages make it an increasingly attractive option for fossil fuel-based power generation.
The role of steam turbines in reducing global emissions also extends to industrial applications. For instance, steam turbines in CHP systems used in industrial processes such as refining, chemical production, and steel manufacturing can help reduce energy consumption by utilizing waste heat. The greater efficiency of these systems allows industries to reduce their reliance on external energy sources and cut greenhouse gas emissions. By optimizing energy use within the industrial sector, steam turbines contribute to the overall decarbonization of manufacturing processes, aligning with the global push toward more sustainable and energy-efficient industries.
In conclusion, steam turbines will remain a fundamental technology in power generation and industrial applications for the foreseeable future. As energy systems become increasingly diversified, steam turbines will play a key role in enabling a low-carbon, resilient, and efficient energy infrastructure. From their traditional role in large-scale power plants to their emerging applications in renewable energy, hydrogen, and hybrid power systems, steam turbines will continue to evolve and adapt to the changing needs of the energy sector. With advances in digitalization, fuel flexibility, and efficiency, steam turbines will contribute significantly to the decarbonization of the energy landscape, ensuring a sustainable and reliable energy future for the world.
As the global energy transition accelerates, steam turbines will likely continue to evolve, integrating even more advanced technologies that improve their performance, efficiency, and environmental impact. While their core function of converting thermal energy into mechanical energy will remain unchanged, the adaptation to emerging technologies and new fuel sources will enable steam turbines to play a more dynamic role in the power sector and beyond. Here are a few more ways in which steam turbines will continue to shape the energy landscape in the coming years:
Flexibility in Fuel Sources
One of the most significant developments in steam turbine technology is the increasing flexibility in fuel use. Historically, steam turbines were primarily associated with fossil fuels, but they are now being adapted to run on a variety of alternative, cleaner fuels. In addition to natural gas, which is widely used today, steam turbines can be modified to operate on hydrogen, ammonia, or biofuels, which are low-carbon alternatives. These fuels are particularly important in the context of decarbonization, as they have the potential to significantly reduce the carbon footprint of power generation.
For instance, hydrogen-powered steam turbines are an exciting frontier in clean energy technology. As hydrogen is seen as a key solution to achieving net-zero emissions, steam turbines running on hydrogen could become integral to decarbonizing the electricity generation sector. The combustion of hydrogen produces water vapor instead of carbon dioxide, making it a clean fuel for turbine systems. Although hydrogen is currently more expensive and less widely available, ongoing advances in green hydrogen production technologies and the expansion of hydrogen infrastructure could help steam turbines become a critical component of a carbon-free energy future.
Moreover, steam turbines are increasingly being used in combined heat and power (CHP) systems that run on renewable fuels such as biomass. Biomass power plants, which convert organic materials into heat or electricity, can leverage steam turbines to generate both power and heat, contributing to an efficient and sustainable energy system. Biomass-derived energy can be considered carbon-neutral, especially when sourced from sustainably managed forests or agricultural waste. Steam turbines, when combined with biomass systems, contribute to a circular and renewable energy economy by utilizing what would otherwise be waste products.
Technological Integration with Digital and AI Tools
The integration of digital technologies, including artificial intelligence (AI), the Internet of Things (IoT), and machine learning, will continue to revolutionize the operation and maintenance of steam turbines. These innovations can enhance turbine performance, reduce downtime, and provide real-time monitoring of turbine health.
With IoT sensors embedded throughout the turbine and its components, operators can gain valuable insights into the condition and efficiency of the system. Real-time data can monitor vibration levels, temperature, pressure, and other key metrics that affect turbine performance. AI-powered analytics can predict when a turbine is likely to fail or need maintenance, allowing operators to perform preventative measures before issues escalate into major failures. This predictive maintenance reduces operational costs, extends the life of the turbine, and improves overall reliability.
Furthermore, digital twins—virtual representations of physical systems—are helping engineers and operators simulate turbine behavior in various conditions. These digital models enable engineers to test different scenarios and operational changes, such as load variations or environmental conditions, without affecting the physical turbine. This ability to model and predict turbine performance before implementing changes in the real world allows for more efficient design optimization and decision-making.
Role in Hybrid Systems and Energy Storage
Hybrid energy systems that combine renewable energy sources with thermal power generation will play a crucial role in the future grid. Steam turbines are key components of these hybrid systems, which help balance the intermittency of renewable power sources like wind and solar. For example, in a combined cycle power plant, a gas turbine is paired with a steam turbine, improving efficiency by using the waste heat from the gas turbine to generate steam for the steam turbine.
These hybrid systems can also incorporate energy storage technologies, such as battery storage or thermal storage, to address variability in renewable generation. In a thermal energy storage system, excess energy generated by solar or wind during peak production hours can be stored as heat in a molten salt or other heat-storage medium. Later, when electricity demand is high or renewable output is low, the stored heat can be converted into steam and used to drive a steam turbine for power generation. This capability for energy storage allows steam turbines to play an essential role in stabilizing grids that rely heavily on renewable energy.
Additionally, steam turbines will likely become a central component of “dispatchable” renewable power generation systems. These systems can store energy during periods of low demand or high renewable output and release it during times of high demand or low renewable availability. This flexibility ensures that renewable energy can be reliably integrated into the grid, allowing for a smoother transition to a cleaner, more resilient energy system.
Decentralization and Microgrids
The trend toward decentralized energy systems and microgrids, especially in remote or off-grid regions, presents a significant opportunity for steam turbines to play a crucial role in local power generation. Microgrids are localized energy systems that can operate independently or in coordination with the larger grid. These systems are particularly useful in areas where the central power grid is unreliable or unavailable.
Steam turbines, often paired with renewable energy sources and energy storage systems, can provide reliable backup power in these microgrids. For example, a microgrid might include solar panels, wind turbines, and a steam turbine powered by biomass or waste heat. The steam turbine would act as a backup generator to ensure that the system remains operational during periods of low renewable output or high demand. This decentralized model of energy production offers a more resilient and sustainable solution to energy needs in remote or underserved areas.
Integration with Carbon Capture, Utilization, and Storage (CCUS)
As the world continues to grapple with the urgent need to reduce greenhouse gas emissions, steam turbines will increasingly be integrated into carbon capture, utilization, and storage (CCUS) systems. CCUS technologies capture carbon dioxide (CO2) emissions from power plants and industrial processes and either store them underground or repurpose them for commercial use, such as in the production of synthetic fuels or chemicals.
Steam turbines can play a key role in this process, particularly in power plants where CO2 emissions are captured. The capture process often requires additional energy, which can be provided by a steam turbine operating in a combined-cycle or CHP configuration. For example, steam turbines can be used to generate electricity and supply heat to the CO2 capture units, improving the overall efficiency of the system. While integrating CCUS with steam turbines presents some technical challenges, such as maintaining efficiency while capturing emissions, it is expected to be a crucial part of efforts to decarbonize heavy industry and power generation.
The Future of Steam Turbines in a Sustainable Energy Economy
Looking ahead, steam turbines are poised to remain a core technology in the pursuit of a sustainable energy economy. As global efforts to combat climate change intensify, steam turbines will be instrumental in achieving the goals of decarbonization. Their adaptability to a variety of fuels—whether natural gas, biomass, hydrogen, or geothermal—will ensure they continue to play a role in a diverse and resilient energy system.
Steam turbines will also continue to serve as a reliable and efficient technology in industrial sectors, where the demand for both power and heat is integral to production. Their ability to operate efficiently in combined heat and power systems will remain essential in reducing the carbon footprint of industrial operations and improving energy utilization.
Furthermore, the ongoing advancements in turbine design, digitalization, hybrid energy systems, and energy storage integration will enhance their efficiency, reliability, and ability to integrate with renewable energy sources. As steam turbines continue to adapt to the needs of a rapidly changing energy landscape, they will play an essential role in powering a cleaner, more sustainable, and resilient global economy.
In summary, steam turbines will continue to be a cornerstone of power generation and industrial processes, contributing to energy efficiency, sustainability, and decarbonization. With advancements in fuel flexibility, digital technologies, energy storage integration, and carbon capture, steam turbines will remain central to the transition to a low-carbon energy future.
General Characteristics of Steam Turbines
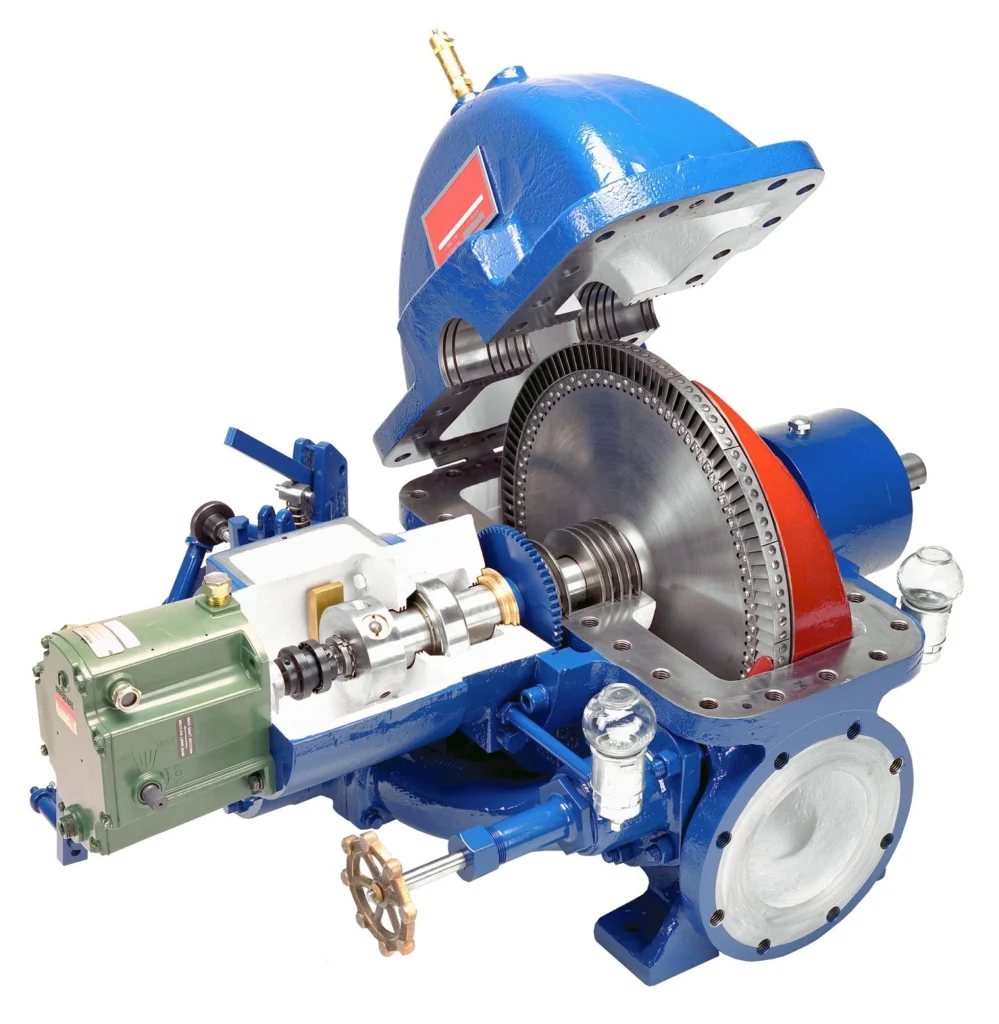
Steam turbines are one of the most widely used technologies for converting thermal energy into mechanical energy in various applications, particularly in power generation, industrial processes, and mechanical drive systems. Their ability to efficiently generate power has made them a cornerstone of modern energy production. The general characteristics of steam turbines highlight their versatility, efficiency, and wide range of applications. Here, we explore these characteristics in detail, focusing on the key aspects that define steam turbines and their operation.
Efficiency
One of the primary characteristics of steam turbines is their high efficiency in converting heat into mechanical energy. This efficiency is particularly enhanced when steam turbines are used in combined cycle systems, where waste heat from a gas turbine is used to produce steam for the turbine. Combined-cycle plants can achieve thermal efficiencies upwards of 60%, significantly higher than traditional steam-only power plants. The efficiency of a steam turbine is influenced by various factors, including the temperature and pressure of the steam, the turbine design, and the operational conditions.
In addition to thermal efficiency, steam turbines are capable of performing at high operational reliability over extended periods. Their ability to operate continuously for years with proper maintenance makes them a dependable choice for power generation, especially in base-load plants where consistent and uninterrupted power is required.
Power Generation Capacity
Steam turbines come in a wide range of sizes and power capacities, from small units used in industrial applications to large-scale turbines used in utility-scale power plants. The power output of a steam turbine is typically measured in megawatts (MW), and large turbines can generate hundreds of megawatts of electricity. The power generation capacity of a steam turbine is directly related to its size, the steam pressure, and the temperature conditions under which it operates. Larger turbines are designed to handle higher pressures and temperatures, which improves their efficiency and power output.
In industrial applications, smaller steam turbines are used to generate both power and heat in combined heat and power (CHP) systems, where they are integrated into processes that require both electrical energy and thermal energy, such as in chemical, paper, or food processing plants. These turbines are typically in the range of a few megawatts and can help reduce energy costs by utilizing waste heat for industrial processes.
Versatility in Fuel Use
Steam turbines are highly versatile and can operate on a variety of fuels. Traditionally, steam turbines have been fueled by coal, oil, and natural gas. However, with the increasing shift toward renewable energy and the need for decarbonization, steam turbines are now being adapted to operate on alternative fuels, such as biomass, hydrogen, and geothermal energy. Biomass plants, for example, burn organic materials like wood chips, agricultural waste, or other plant-based fuels to generate steam that powers a turbine.
Hydrogen, as a clean alternative fuel, has also become an area of focus for steam turbine development. Hydrogen combustion produces only water vapor as a byproduct, making it an environmentally friendly fuel for turbines. Steam turbines can be modified to handle hydrogen combustion, which may help reduce the carbon emissions of power plants while utilizing renewable energy sources for hydrogen production.
Geothermal energy is another important renewable resource that can be used to generate steam for turbines. In geothermal plants, steam is extracted from underground reservoirs of hot water and used to drive turbines for power generation. This energy source provides a constant, renewable supply of heat, making steam turbines a key component of geothermal power plants.
Design and Configuration Flexibility
Steam turbines come in various configurations and designs, allowing for a high degree of flexibility in application. The two primary types of steam turbines are:
- Impulse Turbines: In impulse turbines, the steam is directed at the turbine blades under high pressure, causing the blades to move and generate mechanical power. The steam loses some of its pressure as it moves through the turbine, but its velocity increases. Impulse turbines are typically used in smaller turbines and are commonly found in low- and medium-pressure steam systems.
- Reaction Turbines: In reaction turbines, steam flows over the blades in a way that generates both pressure and velocity changes. This creates a reaction force on the blades, which drives the turbine. Reaction turbines are used in larger steam turbine systems, where the steam pressure is high, and are typically employed in higher pressure and temperature environments.
Additionally, steam turbines can be designed for specific applications, such as regenerative or reheat systems, where steam is passed through the turbine in multiple stages to improve efficiency. Regenerative systems use the exhaust steam to preheat incoming steam, reducing the fuel needed for steam production. Reheat systems are used in large power plants to further improve thermal efficiency by reheating steam between turbine stages, increasing the overall output of the turbine.
Operating Conditions and Performance
The performance of a steam turbine is greatly influenced by operating conditions, such as steam pressure, temperature, and flow rate. Higher steam pressure and temperature generally lead to higher efficiency and power output, as more thermal energy can be converted into mechanical energy. However, there are practical limits to the pressure and temperature that a turbine can handle, as these factors can affect the materials and components used in turbine construction.
Modern steam turbines, especially those in supercritical or ultra-supercritical power plants, operate at very high pressures and temperatures, often exceeding 300 bar and 600°C (1,200°F). These advanced turbines are designed to optimize the thermodynamic cycle and extract the maximum amount of energy from the steam. The use of advanced materials, such as high-strength alloys, is critical for ensuring that turbines can withstand these extreme conditions and operate efficiently over long periods.
Maintenance and Reliability
Steam turbines are known for their reliability and long operational lifespans. With proper maintenance, they can operate continuously for decades. Routine maintenance typically includes inspections of key components, such as the blades, seals, bearings, and rotors. Regular monitoring of turbine performance using sensors and diagnostic tools is essential to detect potential issues before they become major problems.
Predictive maintenance technologies, enabled by digital sensors and analytics, are increasingly being used to enhance the reliability of steam turbines. By analyzing data from the turbine’s operation, operators can predict when components are likely to fail, reducing unplanned downtime and extending the service life of the turbine. These advancements in monitoring and maintenance practices improve the overall performance and cost-effectiveness of steam turbines.
Environmental Impact and Sustainability
Steam turbines themselves are relatively low in environmental impact when compared to other thermal power generation technologies. However, their environmental footprint is primarily dependent on the type of fuel used to produce steam. For example, steam turbines powered by fossil fuels such as coal or natural gas contribute to greenhouse gas emissions, which have significant environmental consequences.
To reduce the environmental impact of steam turbines, a growing focus is on integrating them into renewable and low-carbon energy systems. Biomass, geothermal, and hydrogen are all environmentally friendly fuels that can be used with steam turbines to reduce carbon emissions. Furthermore, the integration of carbon capture and storage (CCS) technology in steam turbine systems can significantly reduce the carbon dioxide emissions from fossil-fuel-based power plants, helping mitigate climate change.
Additionally, steam turbines used in combined heat and power (CHP) systems help improve overall energy efficiency by utilizing both the electrical and thermal outputs for industrial processes. This reduces waste and increases energy savings in applications such as district heating, chemical production, and food processing, contributing to a more sustainable energy model.
Application in Various Industries
Steam turbines are used in a wide range of industries, both for power generation and mechanical drive applications. In power generation, steam turbines are found in utility-scale power plants, including fossil fuel, nuclear, and renewable energy plants. They are used to generate electricity from steam produced by the combustion of fuel or by utilizing geothermal heat or solar thermal energy.
In addition to power generation, steam turbines are used extensively in industrial applications. They drive mechanical equipment such as compressors, pumps, and blowers in industries such as oil and gas, chemicals, and paper production. These turbines are often part of CHP systems, where they produce both electricity and process heat, making them an integral part of many manufacturing processes. The ability to provide both power and heat from a single system makes steam turbines an efficient and cost-effective solution for industrial operations.
Conclusion
In conclusion, steam turbines possess a wide array of characteristics that make them versatile, efficient, and reliable components in power generation and industrial applications. From their ability to generate large amounts of power to their flexibility in fuel use and design configurations, steam turbines remain at the heart of the global energy infrastructure. With advancements in fuel flexibility, digital monitoring, and maintenance practices, steam turbines will continue to play an essential role in the ongoing transformation toward cleaner, more sustainable energy systems. Their adaptability to new technologies and their proven track record of reliability make them an enduring and crucial element of the modern energy landscape.
As the demand for cleaner, more sustainable energy solutions grows, steam turbines will continue to evolve and adapt to meet the challenges of the future. Their role in the global energy transition is expected to expand, particularly as technology advances, energy systems become more integrated, and new sources of power generation come into play. The following points highlight additional characteristics and trends shaping the future of steam turbines:
Integration with Renewable Energy
As renewable energy sources such as wind, solar, and hydropower become more prominent, the role of steam turbines will be pivotal in balancing supply and demand. Steam turbines, particularly in combined cycle and combined heat and power (CHP) systems, are being adapted to work alongside renewable energy technologies. For example, hybrid systems that combine steam turbines with solar thermal or biomass can provide reliable and consistent power when renewable generation is intermittent.
In solar thermal plants, mirrors or lenses concentrate sunlight to generate high-temperature steam, which drives a steam turbine. This integration allows for the generation of power during daylight hours while maintaining efficiency even when sunlight is not constant. Similarly, biomass systems that use organic waste as fuel, often in combination with a steam turbine, contribute to the broader mix of renewable and low-carbon technologies.
Moreover, geothermal energy, which is inherently stable and reliable, presents another opportunity for steam turbines to contribute to the energy mix. Steam turbines used in geothermal plants can generate power continuously, with minimal environmental impact, as long as geothermal resources remain available. As the world moves towards greater reliance on renewable energy, steam turbines will continue to play a key role in the success of hybrid energy systems and the integration of renewable power into the grid.
Contribution to Grid Stability and Flexibility
Steam turbines are increasingly important in maintaining grid stability, especially in systems with high shares of renewable energy. The variable nature of renewable generation, particularly from wind and solar, necessitates the use of dispatchable power sources to ensure a steady and reliable energy supply. Steam turbines can be a crucial part of this equation by providing the flexibility needed to balance the grid during periods of low renewable output or high demand.
Steam turbines can be designed for fast start-up times, enabling them to respond quickly to fluctuations in power demand. This makes them suitable for grid balancing applications, where they can step in to provide power when renewable generation falls short. Combined cycle plants, which use both gas and steam turbines, are particularly effective in this regard, as the steam turbine can be used to absorb excess heat from the gas turbine, improving overall system efficiency and reducing fuel consumption.
In addition, steam turbines integrated with energy storage systems, such as thermal or battery storage, offer a way to store excess energy generated during peak renewable output periods and release it when needed. This ability to store and dispatch energy helps smooth out the fluctuations in power availability from renewable sources, ensuring a reliable and stable energy supply.
Advances in Materials and Technology
Advancements in materials and manufacturing technologies will continue to drive the evolution of steam turbines. Higher temperatures and pressures, which improve the efficiency of steam turbines, can place significant stress on turbine components. As such, the development of new materials that can withstand extreme conditions is essential to pushing the limits of steam turbine performance.
Advanced alloys, ceramics, and coatings are being developed to improve the heat resistance, strength, and durability of turbine blades, rotors, and other key components. For instance, nickel-based superalloys are increasingly being used in high-temperature environments because of their excellent thermal resistance and ability to maintain structural integrity under stress. These materials allow steam turbines to operate more efficiently at higher temperatures, thereby increasing their overall power output and reducing emissions.
Additive manufacturing, or 3D printing, is also beginning to play a role in the production of turbine components. This technology allows for the creation of complex, highly specialized parts that are more difficult or expensive to manufacture using traditional methods. By reducing waste and enabling the production of lighter, stronger components, additive manufacturing can help further improve turbine efficiency and performance.
Hybrid Power Plants and Distributed Energy Systems
The growing trend towards decentralized energy systems, including microgrids, further highlights the value of steam turbines in the energy landscape. Microgrids, which are local energy systems capable of operating independently from the main grid, are increasingly incorporating steam turbines in combined heat and power (CHP) configurations. These systems are especially useful in remote areas, industrial facilities, and other locations where access to the main power grid may be unreliable or unavailable.
Steam turbines can serve as both a power generation and heat production source in these systems, contributing to both electricity and thermal energy needs. When coupled with renewable energy sources such as wind, solar, or biomass, microgrids with steam turbines can provide a reliable, sustainable, and cost-effective solution for local energy generation.
In hybrid power plants, where multiple generation technologies are used in conjunction, steam turbines complement other sources like gas turbines, wind, solar, and energy storage. These hybrid plants are designed to optimize efficiency, reduce emissions, and provide reliable power across a wide range of conditions. Steam turbines, in particular, can provide stable base-load power and serve as an efficient backup to intermittent renewable sources.
Technological Integration with Artificial Intelligence (AI) and Machine Learning
The future of steam turbine operation and maintenance is increasingly being shaped by artificial intelligence (AI) and machine learning technologies. By collecting data from sensors embedded in steam turbines, operators can monitor performance in real-time, detect anomalies, and predict potential failures before they occur. AI algorithms analyze this data to identify patterns that would be difficult for human operators to detect, improving both operational efficiency and reliability.
Machine learning models can also optimize turbine performance by adjusting operational parameters in real time to match changing conditions, such as fluctuations in fuel quality or demand. This level of automation reduces the need for manual intervention, improving efficiency and reducing the risk of human error.
Predictive maintenance powered by AI and machine learning allows for more effective scheduling of maintenance activities. By predicting when parts are likely to wear out or fail, operators can take proactive measures to replace or repair components before a breakdown occurs, reducing downtime and extending the life of the turbine. This leads to significant cost savings and improves the overall reliability of the system.
Decarbonization and Carbon Capture Integration
As part of the broader effort to reduce carbon emissions, steam turbines are increasingly being integrated with carbon capture, utilization, and storage (CCUS) technologies. In these systems, carbon dioxide (CO2) emissions from steam turbine power plants are captured, transported, and stored underground, preventing them from being released into the atmosphere. The integration of CCUS technologies allows steam turbines to continue operating in fossil fuel power plants while reducing their carbon footprint.
Additionally, steam turbines can play a role in the utilization of captured CO2. For example, the CO2 captured from a power plant can be used in processes such as enhanced oil recovery or the production of synthetic fuels and chemicals. By converting CO2 into valuable products, these technologies help close the carbon loop, contributing to a more sustainable and circular economy.
Conclusion
In the coming decades, steam turbines will remain an essential technology in both traditional and renewable energy systems. Their ability to operate across a wide range of fuels, efficiencies, and operating conditions ensures their continued relevance in an evolving energy landscape. With advancements in materials science, digital technologies, hybrid systems, and carbon capture integration, steam turbines will play an increasingly important role in providing reliable, flexible, and low-carbon power. Their adaptability and proven track record of performance make them a cornerstone technology in the ongoing transition to a cleaner, more sustainable energy future.
Steam turbines are an integral part of the energy landscape, and their evolution continues to meet the growing demand for cleaner, more sustainable, and efficient power generation. The future of steam turbines will likely see even more integration with emerging technologies, ensuring their continued relevance across various industries. One of the key drivers for the future of steam turbines will be the push towards zero-emission power generation. In line with global efforts to reduce greenhouse gas emissions and mitigate climate change, the development of steam turbines that can operate on low-carbon fuels, such as hydrogen, will become increasingly important. Hydrogen, when used as a fuel, produces only water vapor as a byproduct, making it an ideal candidate for decarbonizing steam turbine systems. The ability to integrate hydrogen into existing steam turbine infrastructure or design new turbines specifically for hydrogen combustion will be a game-changer in the energy sector.
Moreover, the combination of renewable energy sources with steam turbines will see continued innovation. For example, the use of concentrated solar power (CSP) systems, where solar energy is harnessed to create high-temperature steam, will increasingly be paired with steam turbines to generate electricity. The ability of steam turbines to work with intermittent renewable resources, like wind and solar, by acting as backup power generators or as part of hybrid power plants, is another area where advancements are expected. As these renewable technologies continue to mature and become more integrated into power grids, steam turbines will play an essential role in ensuring the stability and reliability of electricity supply, especially in regions that rely heavily on variable renewable sources.
The growth of distributed energy systems and microgrids, which allow localized energy production and consumption, will also drive demand for steam turbines. These systems can be powered by various sources, including renewable energy, natural gas, or biomass, with steam turbines providing both electricity and thermal energy in combined heat and power (CHP) applications. Microgrids, which can operate independently or in coordination with the main power grid, are gaining popularity in remote locations, industrial facilities, and critical infrastructure, where energy reliability is a top priority. The use of steam turbines in such applications allows for more efficient energy use, reducing the need for separate heating and power systems and minimizing fuel consumption.
In the realm of energy storage, steam turbines may become increasingly integrated with advanced storage technologies such as thermal storage or battery systems. For example, excess electricity generated from renewable sources can be used to heat a storage medium, which can then be converted back into steam when needed. This approach allows for energy to be stored and dispatched when demand is high, providing grid stability and ensuring a consistent power supply. The integration of storage systems with steam turbines will likely be essential as more renewable energy sources are added to the grid.
In addition to technological advancements, steam turbines will also benefit from the ongoing development of digital tools and artificial intelligence. Advanced monitoring systems, powered by digital sensors and machine learning algorithms, will enhance the efficiency and reliability of steam turbines. These systems can detect anomalies, optimize operational settings in real-time, and predict maintenance needs, reducing unplanned downtime and extending the lifespan of turbine components. With these innovations, steam turbines will not only become more efficient but also smarter, capable of adapting to changing operating conditions and improving performance based on real-time data analysis.
As the global energy transition continues, steam turbines will play a crucial role in meeting both energy demand and sustainability goals. Their adaptability to different fuels, integration with renewable energy systems, and ability to provide reliable power will ensure that they remain an essential technology in the years to come. With advancements in fuel flexibility, materials science, and digital technologies, the steam turbine will continue to evolve, helping shape a cleaner, more resilient, and sustainable energy future for generations to come.
The continued innovation in steam turbine technology is poised to enhance the overall performance of power plants and improve the sustainability of the energy sector. One of the significant areas of focus for future development is the reduction of operational costs while increasing the efficiency of steam turbines. The growing need to optimize energy production in the face of fluctuating fuel prices and regulatory pressures will likely lead to the implementation of advanced turbine designs and operational strategies. For instance, improvements in heat recovery and thermodynamic cycles will contribute to higher efficiencies, reducing the amount of fuel needed for the same amount of energy generation. These advancements will not only drive down operational costs but will also reduce the carbon footprint of power plants, helping to meet global emission reduction targets.
The integration of digital technologies, particularly the Internet of Things (IoT), will further transform the operation of steam turbines. IoT-enabled sensors and connected devices will allow operators to remotely monitor turbine health, gather real-time data on performance metrics, and make adjustments as needed. This interconnected approach will streamline operations, optimize turbine performance, and improve energy output while minimizing downtime. IoT applications could also be extended to predictive maintenance, enabling operators to forecast the wear and tear of turbine components and avoid unplanned shutdowns or costly repairs.
In addition to these operational efficiencies, steam turbines will increasingly be used in the context of decentralized and off-grid energy systems. As the world continues to move towards localized energy production, steam turbines will be deployed in microgrids, islanded systems, and rural areas where access to the main power grid is limited. These systems, often based on renewable energy sources like biomass, solar thermal, and geothermal, can utilize steam turbines to provide power and heat to local communities, industrial operations, or critical infrastructure. In remote or off-grid locations, steam turbines can offer a reliable and efficient solution for power generation, enabling energy independence and enhancing energy security.
As steam turbines evolve to meet these new demands, the role of hydrogen will become even more significant. In addition to being used as a fuel for electricity generation, hydrogen can also serve as a long-term storage solution, facilitating the storage of excess energy generated by renewable sources. By using excess renewable electricity to produce hydrogen through electrolysis, it can be stored and then used to generate steam for turbines when needed. This ability to produce, store, and consume hydrogen provides an important pathway to decarbonizing energy systems and integrating more renewable energy sources.
The adoption of hydrogen as a primary fuel for steam turbines will require advancements in both turbine design and fuel infrastructure. For example, steam turbines must be engineered to handle hydrogen combustion at scale, and new fueling systems will be necessary to ensure a continuous supply of hydrogen. This transition will require substantial investment in research and development as well as infrastructure development to support hydrogen production, storage, and distribution networks.
As the global energy sector undergoes a shift towards greater electrification and decarbonization, steam turbines will play an increasingly central role in ensuring reliable and sustainable energy production. With their proven capabilities in large-scale power generation and their flexibility to adapt to new fuels and technologies, steam turbines are expected to remain a cornerstone of the energy mix for many years to come.
Moreover, as steam turbines become more integrated with other advanced technologies, such as artificial intelligence, energy storage systems, and hybrid plants, they will continue to evolve as dynamic and responsive elements in the power grid. By leveraging cutting-edge technologies and new fuel sources, steam turbines will contribute to a more resilient and sustainable global energy system.
In conclusion, the future of steam turbines looks promising, with numerous opportunities for innovation and improvement. The technology will continue to evolve in response to the global push for cleaner, more efficient energy production. As part of a broader shift towards renewable energy and a more sustainable energy future, steam turbines will remain an essential and versatile component of the energy landscape, supporting the transition to a low-carbon economy while providing reliable and efficient power generation. Their adaptability, combined with ongoing advancements in digital technologies, materials, and fuel flexibility, will ensure that steam turbines remain a key player in shaping the energy systems of tomorrow.
Fundamentals of Steam Turbine Mechanics
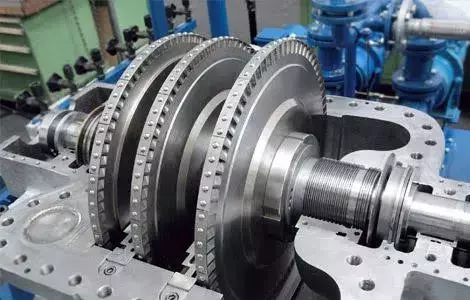
The fundamental mechanics of steam turbines are built around the principles of thermodynamics and fluid dynamics, focusing on converting thermal energy from steam into mechanical energy for useful work. The operation of a steam turbine is a direct application of these principles, where high-pressure steam is expanded through turbine blades to produce rotational motion that drives machinery, such as generators, pumps, and compressors.
Steam turbines operate based on the basic thermodynamic process known as the Rankine cycle, which consists of four primary stages: heating the water, converting it to steam, expanding the steam through the turbine, and then condensing it back into water. The cycle is designed to extract the maximum possible energy from the steam by allowing it to expand in a controlled manner, transferring thermal energy into mechanical energy.
The steam enters the turbine at high pressure and temperature and is directed into nozzles, which convert thermal energy into kinetic energy by accelerating the steam. The high-speed steam then strikes the blades of the turbine, causing the rotor to rotate. The design of the blades, the arrangement of stages, and the geometry of the turbine’s internal components are all critical to optimizing the transfer of energy from steam to mechanical motion.
The turbine is made up of multiple stages, with each stage consisting of stationary blades (or nozzles) and rotating blades (or rotors). The steam enters the turbine through the nozzles, which direct the flow of steam onto the rotating blades. The steam expands as it moves through each stage, gradually losing pressure and temperature while transferring its energy to the blades. This results in the rotational motion of the turbine, which is then transmitted to a shaft connected to a generator or other machinery.
In a typical steam turbine, multiple stages are arranged in a series to allow for greater energy extraction from the steam. The number of stages in a turbine determines its efficiency and the degree of expansion that can be achieved. In larger turbines, additional stages are added to ensure the steam is expanded over a longer path, extracting more energy before it exits the system. The design of these stages is also influenced by the desired output, with different configurations of blades and nozzles used depending on the application.
As the steam moves through the turbine, it undergoes a drop in pressure and temperature. This expansion of the steam causes a corresponding increase in volume, which pushes the blades of the turbine, generating mechanical energy. The greater the pressure differential between the steam entering the turbine and the steam exiting it, the more energy can be extracted.
In the operation of steam turbines, efficiency plays a critical role in maximizing energy production. The efficiency of a steam turbine is influenced by various factors, including the quality of steam, the pressure and temperature of the steam entering the turbine, the number of stages in the turbine, and the design of the turbine blades. High-efficiency turbines are designed to ensure that as much energy as possible is converted into mechanical motion while minimizing energy losses due to heat dissipation, friction, and turbulence within the turbine.
Steam turbines are typically classified based on their operation, design, and application. There are several key types of turbines, including impulse turbines and reaction turbines. Impulse turbines operate by converting the steam’s kinetic energy into mechanical energy through the impact of high-velocity steam jets on blades. In contrast, reaction turbines generate mechanical energy through the reaction forces created as steam passes over the turbine blades. Reaction turbines typically operate at higher pressure and are more commonly used in large-scale power generation applications.
The design of the turbine blades is crucial to ensuring the turbine’s efficiency. Blades are often constructed from high-strength alloys that can withstand the extreme temperatures and pressures found within the turbine. Additionally, the geometry of the blades is optimized to ensure that the steam flow is directed in a way that maximizes the energy transfer. The angle of the blades, the spacing between them, and their surface area all contribute to the efficiency of the turbine.
The rotor, which is the central shaft connected to the turbine blades, plays a key role in transferring mechanical energy to the generator or other equipment. As the rotor spins, it creates a torque that can be harnessed to produce electricity or drive mechanical systems. The rotor is usually connected to a shaft that transfers the rotational energy to a generator or other machinery, where it is converted into usable power.
The efficiency of a steam turbine is not solely determined by the mechanical design of the blades and rotor. The operational environment, including factors such as steam quality, temperature, and pressure, significantly impacts turbine performance. For example, steam that is not superheated or is too saturated may lead to reduced turbine efficiency, as the steam will not have enough thermal energy to drive the blades effectively.
Lubrication and cooling systems are essential components that help maintain the mechanical integrity of the turbine during operation. High temperatures and pressures can lead to wear and tear on the turbine’s components, which is why proper lubrication and cooling are necessary to reduce friction and prevent overheating. In many steam turbines, the rotor is supported by bearings that require continuous lubrication to minimize friction and ensure smooth operation.
Another key factor in steam turbine operation is the management of condensate. After steam has passed through the turbine and delivered its energy, it is condensed back into water in the condenser. The condensate is then pumped back to the boiler to be re-heated and converted into steam once again. Effective management of the condensate system is essential for maintaining the efficiency of the Rankine cycle, as it ensures the turbine operates with the proper input of steam pressure and temperature.
To maintain peak performance, steam turbines are regularly monitored and maintained to address potential issues, such as erosion, corrosion, and mechanical fatigue. The rotor, blades, and bearings are particularly susceptible to wear and require periodic inspection and maintenance. Advances in digital monitoring technologies and sensors have enabled more accurate tracking of turbine performance, allowing for predictive maintenance and early detection of issues before they lead to catastrophic failures.
In summary, the mechanics of steam turbines are a complex interplay of thermodynamic and fluid dynamics principles that work together to convert thermal energy into mechanical energy. By optimizing the flow of steam, the design of blades and rotors, and managing system conditions such as pressure and temperature, steam turbines are able to produce reliable, efficient power. While advancements in materials and digital technologies continue to improve turbine performance, the fundamental mechanics of steam turbines remain rooted in the principles of energy conversion, fluid flow, and thermodynamics. These principles will continue to guide the development of steam turbines as they evolve to meet the changing needs of modern power generation and industrial applications.
As steam turbines continue to evolve, their mechanics will be influenced by several emerging technologies and strategies aimed at improving efficiency, flexibility, and sustainability. The integration of advanced materials, for instance, plays a critical role in addressing the challenges posed by high temperatures and pressures. New materials, such as superalloys and ceramics, are being developed to withstand the extreme conditions inside the turbine while maintaining their structural integrity and resistance to wear. These materials not only allow steam turbines to operate at higher temperatures and pressures, thus improving their overall efficiency, but they also help reduce the overall maintenance costs and extend the turbine’s lifespan.
In addition to materials advancements, the growing implementation of computational fluid dynamics (CFD) tools is revolutionizing the design and optimization of steam turbines. CFD simulations allow engineers to model the flow of steam through the turbine in great detail, helping them identify areas where energy is being lost due to turbulence, friction, or inefficient steam expansion. These insights lead to more precise blade designs, optimized nozzle geometries, and more efficient stage configurations, all contributing to higher overall performance and energy extraction from the steam.
Furthermore, digital twin technology is emerging as a valuable tool in steam turbine operation and maintenance. A digital twin is a virtual replica of the physical turbine, created using real-time data collected from sensors embedded in the system. By simulating the turbine’s behavior under various operating conditions, digital twins allow operators to predict how the turbine will respond to different stresses and optimize its operation. The digital twin can also be used to model potential failure scenarios, enabling predictive maintenance strategies that reduce downtime and enhance the overall reliability of the turbine.
One of the key areas of focus for steam turbine development is increasing their flexibility in terms of fuel and operating conditions. As global power grids evolve to accommodate more variable renewable energy sources, such as wind and solar, the ability of steam turbines to adapt quickly to changes in demand and fuel availability will be crucial. New designs are being developed to make steam turbines more responsive to fluctuations in steam flow, enabling them to ramp up or down more quickly without sacrificing efficiency. This increased flexibility also includes the potential to use a wider range of fuels, including hydrogen, synthetic fuels, and biomass, in addition to traditional fossil fuels. By allowing steam turbines to run on alternative fuels, the energy sector can reduce its reliance on carbon-intensive energy sources and move toward a more sustainable future.
Steam turbines will also continue to play an essential role in the decarbonization of the energy sector. The integration of carbon capture, utilization, and storage (CCUS) technologies with steam turbine power plants is one of the most promising ways to reduce the carbon footprint of fossil fuel-based power generation. In these systems, CO2 emissions produced during the combustion of fossil fuels are captured, transported, and stored underground, preventing them from entering the atmosphere. Although the combination of CCUS and steam turbines comes with its own set of technical challenges, including energy penalties associated with capturing and compressing CO2, it represents a significant opportunity for reducing emissions while still relying on existing steam turbine infrastructure.
Moreover, steam turbines are expected to remain an essential component in hybrid power systems that combine different energy generation technologies. In these systems, steam turbines work alongside gas turbines, renewable energy sources, and energy storage systems to create a more reliable and efficient energy mix. For example, in combined cycle power plants, steam turbines are paired with gas turbines, using the waste heat from the gas turbine to generate steam, which drives the steam turbine. This increases the overall efficiency of the system by capturing and utilizing heat that would otherwise be wasted.
The role of steam turbines in distributed energy systems is also expected to expand. As microgrids and off-grid energy systems become more prevalent, steam turbines will be deployed to provide localized, reliable power generation. These systems are especially important in areas where grid access is limited or where energy security is a priority. In these applications, steam turbines can operate in conjunction with renewable energy sources, such as biomass, geothermal, or concentrated solar power (CSP), to provide continuous power even when renewable generation is intermittent.
As steam turbines evolve, their role in industrial applications will continue to be vital. In industries such as petrochemicals, chemicals, and refining, steam turbines are commonly used to generate electricity and provide mechanical power for various processes. These industries require high levels of reliability and efficiency in their power generation systems, and steam turbines offer a proven solution. As industrial processes become more energy-intensive, the demand for efficient and flexible steam turbine systems will grow, driving the need for innovations in turbine design, materials, and operational strategies.
In conclusion, the fundamentals of steam turbine mechanics will continue to provide the foundation for the development of more efficient, flexible, and sustainable power generation technologies. As steam turbines evolve to meet the demands of a changing energy landscape, advancements in materials, computational tools, and fuel flexibility will help optimize their performance. The integration of steam turbines with renewable energy, energy storage, and carbon capture technologies will enable them to play a crucial role in the global transition to cleaner energy systems. With ongoing innovation and adaptation, steam turbines will remain a cornerstone of power generation, ensuring that they continue to provide reliable, efficient, and environmentally responsible energy solutions for decades to come.
As the future of steam turbine technology unfolds, one of the key areas of focus will be the continued optimization of their efficiency through the implementation of advanced manufacturing processes and precision engineering. Technologies such as additive manufacturing (3D printing) are beginning to play a role in turbine design, allowing for the creation of more complex and optimized geometries that were previously difficult or impossible to achieve with traditional manufacturing methods. This can lead to improved aerodynamic and thermodynamic efficiency, especially in the blades and rotor sections, where the flow of steam is most critical. Additive manufacturing allows for the production of parts with intricate internal cooling channels or optimized surface structures, improving heat dissipation and reducing energy losses.
In parallel with the development of advanced manufacturing technologies, the role of digital technologies in steam turbine operation will continue to grow. The use of artificial intelligence (AI) and machine learning (ML) will enable steam turbines to become even more autonomous and intelligent. For example, AI algorithms can be used to predict and optimize turbine performance based on real-time data collected from sensors. These algorithms can analyze trends and patterns, identifying the most efficient operating parameters for the turbine under varying conditions. Additionally, machine learning can help identify potential faults or areas of inefficiency before they become major issues, enabling a proactive approach to maintenance and performance optimization.
This shift toward intelligent turbines will be supported by the rise of the Industrial Internet of Things (IIoT), where interconnected devices and sensors collect vast amounts of data from turbines and other components in real-time. This data is used to continuously monitor the health of the turbine, providing operators with insights into its performance and alerting them to any abnormalities. By leveraging predictive analytics and advanced data analytics, operators can optimize turbine performance, improve uptime, and reduce the frequency of unplanned maintenance activities.
The growing emphasis on sustainability will also drive the integration of steam turbines into the circular economy. As industries and power plants aim to reduce waste and increase resource efficiency,
steam turbines can play a crucial role by enabling the recovery and reuse of energy that would otherwise be lost. For example, the integration of steam turbines into waste-to-energy (WTE) plants and industrial processes that generate significant amounts of waste heat could dramatically improve energy efficiency. In these systems, excess heat from processes like cement production, steel manufacturing, or chemical processes could be captured and converted into steam, which in turn drives a turbine to generate additional electricity. This not only reduces energy consumption but also reduces the environmental impact of industrial operations.
Another emerging area of focus for steam turbines is the development of “green” hydrogen, which is produced through water electrolysis using renewable electricity. The integration of hydrogen into steam turbine systems is gaining traction as a way to further decarbonize the energy sector. Hydrogen can be used to generate steam for turbines, and since its combustion produces no carbon emissions, it offers a path toward cleaner power generation. Hydrogen turbines will need to be developed to handle the specific characteristics of hydrogen as a fuel, including its lower energy density compared to natural gas, and the fact that hydrogen combustion may create different thermal expansion and material challenges. Nevertheless, as hydrogen infrastructure expands and becomes more cost-effective, steam turbines designed for hydrogen combustion will likely play an increasingly important role in the global energy transition.
Furthermore, hybrid systems combining steam turbines with renewable sources such as geothermal energy are becoming increasingly relevant. Geothermal power plants already use steam turbines to generate electricity by tapping into the Earth’s natural heat, and as geothermal resources become more accessible in regions previously considered non-viable, the potential for combining geothermal energy with steam turbines will grow. This renewable energy source offers baseload power generation, which is especially valuable for stabilizing the grid as intermittent renewable sources like solar and wind become more dominant.
In addition to their application in power generation, steam turbines are also becoming increasingly important in industrial cogeneration (combined heat and power, or CHP) systems. In CHP plants, steam turbines can be used to generate both electricity and useful heat for industrial processes. This dual-use approach maximizes efficiency by capturing waste heat from power generation and reusing it for other purposes. The growing demand for CHP systems, driven by industrial sectors seeking to improve energy efficiency and reduce emissions, will keep steam turbines integral to industrial energy systems.
As energy storage technologies mature, steam turbines may also be incorporated into hybrid energy systems that combine thermal storage with traditional steam turbine technology. These systems use stored heat to generate steam and power turbines when renewable energy sources are not producing electricity, thus improving grid reliability and facilitating higher renewable energy penetration. In regions with large-scale renewable power generation, such hybrid systems could provide a reliable backup that ensures a steady power supply even when wind or sunlight is not available.
Steam turbines are also finding new applications in the field of district energy systems, where they can be used in conjunction with waste heat recovery systems to provide electricity and heating to entire neighborhoods or urban areas. These systems provide an efficient way to capture and use waste heat generated by power plants, industrial facilities, or other sources. By converting waste heat into electricity through steam turbines, district energy systems not only reduce the overall energy consumption of urban areas but also help lower emissions and improve energy security.
With the continued advancement of technologies such as carbon capture and storage (CCS), steam turbines will be able to operate within systems designed to remove CO2 from the atmosphere or industrial processes. In CCS systems, steam turbines could be used to drive compressors and pumps that assist in capturing, transporting, and storing carbon dioxide. While the integration of CCS with steam turbines presents its own challenges, such as the additional energy requirements for capturing CO2, it offers a promising pathway for reducing emissions from fossil-fuel-based power plants and industrial sources.
Finally, the importance of maintaining the mechanical integrity of steam turbines cannot be overstated. Over time, turbines are subjected to significant wear and tear, with components like blades and rotors experiencing fatigue, erosion, and corrosion. Ongoing research into advanced coatings, surface treatments, and corrosion-resistant materials will help ensure that turbines remain durable and efficient throughout their operational lifespans. Additionally, improvements in turbine diagnostics, including the use of real-time data and advanced sensors, will enable more accurate tracking of turbine health, leading to more effective maintenance practices and longer operational lifespans.
In conclusion, the fundamentals of steam turbine mechanics will continue to be refined and advanced in the face of changing technological, economic, and environmental challenges. From the integration of digital technologies and AI to the growing use of renewable fuels and hybrid systems, the steam turbine will remain a cornerstone of global power generation and industrial processes. As we move toward a more sustainable and efficient energy future, the role of steam turbines will expand to include innovative applications across multiple sectors, from renewable energy integration to waste heat recovery, and even in emerging sectors like hydrogen power generation and carbon capture. Their ability to adapt to new fuels, materials, and technologies will ensure that steam turbines continue to be a vital part of the energy mix for decades to come.
Looking toward the future, steam turbines will continue to adapt and integrate with emerging energy technologies to meet the challenges of a rapidly evolving energy landscape. One of the most significant advancements in steam turbine technology is their potential role in the transition to a low-carbon economy. As governments and industries around the world strive to meet ambitious emissions reduction targets, steam turbines will need to evolve to work seamlessly with renewable energy sources and carbon-neutral fuels. The integration of steam turbines into new hybrid and multi-energy systems will be essential for ensuring the reliable and efficient operation of power plants and industrial facilities as they move toward greater sustainability.
A key development in this transition is the potential use of steam turbines in combination with energy storage solutions. Energy storage technologies, such as large-scale batteries and thermal energy storage, are becoming increasingly critical for addressing the intermittency of renewable energy sources like solar and wind. In these systems, steam turbines can be used to convert stored thermal energy into mechanical power when renewable generation is low. This kind of synergy between steam turbines and energy storage will enhance grid stability, ensuring that electricity is available when demand is high or renewable generation is insufficient.
The concept of microgrids and decentralized energy systems is also gaining traction, particularly in regions where access to the main electricity grid is limited or unreliable. Steam turbines will play an essential role in these systems, providing reliable power generation that can be synchronized with renewable sources like solar or wind. In isolated or remote communities, steam turbines powered by biomass, geothermal, or waste heat could provide a self-sufficient and sustainable source of electricity and heat, enabling these areas to reduce their dependence on fossil fuels and imported energy.
In addition to these technological advancements, steam turbines will also benefit from improved operational practices driven by the growing use of automation, AI, and machine learning in power plant management. By integrating predictive analytics and real-time performance monitoring, operators will be able to detect and resolve issues before they result in equipment failure or significant downtime. AI-driven systems can optimize turbine performance in real time, adjusting operating parameters such as steam pressure, temperature, and flow rates to maximize efficiency and reduce energy losses. This level of operational intelligence will also allow for better coordination with other power generation assets, such as gas turbines, wind farms, and solar plants, ensuring a seamless and cost-effective operation of the entire energy system.
While digitalization and advanced analytics will undoubtedly enhance the performance of steam turbines, continued innovation in turbine design and materials will remain essential for improving efficiency and reliability. For example, improvements in blade coatings and surface treatments can help reduce the impact of high-temperature steam and minimize the wear and tear that typically occurs over time. Advances in additive manufacturing, which enable the production of complex parts with intricate geometries, will allow for the creation of more efficient turbine blades that optimize steam flow, reduce friction, and improve heat transfer.
At the same time, the development of more advanced cooling systems will be crucial for extending the life of steam turbines and improving their operational efficiency. Cooling systems are essential for managing the high temperatures that steam turbines operate under, and innovations in cooling technology could allow turbines to operate at even higher temperatures, leading to greater efficiency. Furthermore, technologies such as dry cooling, which eliminates the need for large volumes of water, could reduce the environmental footprint of steam turbines, particularly in regions facing water scarcity.
Another area where steam turbines could see further innovation is in the use of supercritical and ultra-supercritical steam conditions. Supercritical steam, which operates at temperatures and pressures above the critical point of water, allows for much higher efficiency compared to conventional steam conditions. Ultra-supercritical conditions, which take this concept even further, have the potential to achieve efficiencies that were once thought impossible. The challenge for steam turbines is to develop materials and designs that can withstand the extreme temperatures and pressures involved in these high-efficiency processes. However, the potential for significantly reducing fuel consumption and emissions makes this an exciting area for future turbine development.
The integration of steam turbines with carbon capture and storage (CCS) systems will also be an important aspect of their role in decarbonizing the energy sector. As steam turbines continue to be used in fossil fuel-based power plants, CCS technologies can be applied to capture the carbon dioxide emissions produced during combustion. Steam turbines could be used to drive the compressors and pumps that help transport and store CO2, allowing these plants to operate with significantly lower emissions. Although CCS still faces challenges in terms of cost and efficiency, its integration with steam turbine systems could enable power plants to continue operating while meeting stringent environmental regulations.
In the long term, the development of hybrid power plants that combine steam turbines with nuclear power could play a significant role in providing baseload power generation with minimal emissions. Advanced nuclear technologies, such as small modular reactors (SMRs) or thorium reactors, are being developed with the potential to provide cleaner, safer, and more flexible energy solutions. In these systems, steam turbines could play a critical role by generating electricity using steam produced by the nuclear process. This hybrid approach could combine the benefits of steam turbine technology with the low-carbon characteristics of nuclear power, offering a sustainable and reliable source of energy for the future.
Lastly, as the global energy mix continues to diversify and shift toward more decentralized and renewable sources, the importance of maintaining steam turbine infrastructure will grow. While renewable energy sources such as solar, wind, and geothermal are becoming more prevalent, steam turbines will still be required to provide reliable backup power and to operate in conjunction with these technologies. Ensuring that steam turbine systems are well-maintained and capable of operating in diverse environments, with varying fuels and fluctuating grid demands, will be crucial to maintaining grid stability and ensuring energy security.
In conclusion, steam turbines will continue to be a fundamental component of power generation and industrial processes, but their role will evolve significantly as they adapt to the challenges and opportunities presented by new energy technologies and sustainability goals. By leveraging advancements in materials, digital technologies, and hybrid systems, steam turbines will help meet the growing demand for efficient, flexible, and low-carbon power generation. With their ability to integrate with renewable energy sources, improve energy efficiency, and support carbon capture efforts, steam turbines will remain a cornerstone of the energy sector, providing reliable and sustainable solutions for decades to come.
Key Terminology in Steam Turbines
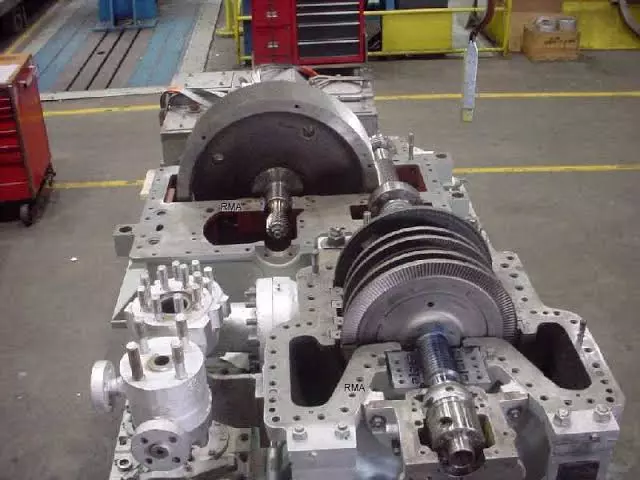
The world of steam turbines comes with a unique set of technical terms and concepts that are essential for understanding how these machines operate. Here is a breakdown of some of the key terminology in steam turbine technology:
- Steam: The vaporized form of water, which is used to transfer thermal energy to the turbine. Steam is produced by heating water in a boiler, and its pressure and temperature are crucial in determining the efficiency and power output of the turbine.
- Turbine Blade: The individual components that form part of the rotor of a steam turbine. These blades are designed to capture the energy from the high-pressure steam and convert it into mechanical energy as they rotate. The design and materials used in blades are key to turbine performance.
- Rotor: The rotating part of the turbine that is connected to the turbine shaft. The rotor is responsible for converting the energy from the steam into rotational mechanical energy.
- Stator: The stationary component of the turbine that contains the fixed blades or nozzles, which direct the steam flow onto the rotating blades of the rotor. The stator plays an important role in regulating the steam’s energy as it enters the rotor.
- Nozzle: A device that accelerates and directs the flow of steam onto the turbine blades. Nozzles control the speed and direction of steam, ensuring it strikes the blades at the correct angle for maximum efficiency.
- Condensation: The process by which steam cools and turns back into liquid water after passing through the turbine and losing its energy. The condenser is typically used to remove heat and cause condensation by reducing steam pressure, creating a vacuum that allows the turbine to operate efficiently.
- Regenerative Cycle: A thermodynamic cycle that utilizes steam turbines and heat exchangers to capture waste heat from the turbine exhaust to preheat the incoming feedwater, increasing the overall efficiency of the system.
- Back Pressure Turbine: A type of steam turbine that operates at a lower pressure at the exhaust side, used in applications where the exhaust steam is needed for heating purposes or other processes, rather than being condensed.
- Condensing Turbine: A type of steam turbine where the exhaust steam is cooled down to a liquid state (condensed) in a condenser. This type of turbine operates at lower exhaust pressures, which typically leads to higher efficiency compared to back-pressure turbines.
- Thermodynamic Cycle: The series of processes that convert thermal energy into mechanical energy in a steam turbine. The most common cycle is the Rankine cycle, which involves the heating, expansion, and condensation of steam to produce work.
- Pressure Ratio: The ratio of the steam pressure at the inlet of the turbine to the pressure at the exhaust. This ratio is important because it helps determine the efficiency and power output of the turbine. Higher pressure ratios generally lead to more efficient turbines.
- Isentropic Efficiency: A measure of the efficiency of a steam turbine based on the assumption that the expansion of steam through the turbine is reversible and occurs without any entropy increase. The actual performance is compared to the ideal, isentropic expansion.
- Stage: Refers to one set of rotor and stator blades in the turbine. A multi-stage steam turbine uses several stages in sequence to extract more energy from the steam, with each stage performing part of the expansion process.
- Specific Steam Consumption (SSC): The amount of steam required to produce a unit of power output, typically expressed in kilograms of steam per kilowatt-hour (kg/kWh). Lower SSC values indicate more efficient turbines, as they use less steam to generate the same amount of power.
- Exhaust: The steam that has passed through the turbine and is discharged from the system. The quality and pressure of the exhaust steam can impact the efficiency of the turbine, as well as the design of the condenser and cooling systems.
- Heat Rate: A measure of the efficiency of a steam turbine in converting fuel into electricity. It is the amount of fuel energy required to produce one kilowatt-hour of electricity, typically measured in British thermal units (BTU) per kilowatt-hour.
- Superheated Steam: Steam that has been heated beyond its boiling point, typically to higher temperatures and pressures. Superheating increases the energy content of the steam and improves the efficiency of the turbine.
- Subcritical, Supercritical, and Ultra-supercritical: Terms used to describe the pressure and temperature conditions of steam in the system. Subcritical steam operates at pressures below the critical point (374°C and 22.1 MPa), while supercritical and ultra-supercritical conditions refer to steam above this threshold, allowing for more efficient power generation.
- Thermal Efficiency: The ratio of useful work output to the total energy input, expressed as a percentage. In steam turbines, thermal efficiency is a measure of how effectively the system converts the heat energy from steam into mechanical energy.
- Centrifugal Force: The force that acts on the steam turbine blades as the rotor spins. The blades are subjected to this force, which helps them maintain their shape and remain attached to the rotor during high-speed operation.
- Choking: A phenomenon that occurs when steam velocity exceeds a critical limit, causing the flow to become restricted, which can reduce efficiency. Proper design of the nozzles and rotor blades is required to avoid choking.
- Blade Tip Losses: Losses in turbine efficiency that occur due to the flow of steam at the blade tips. This phenomenon is due to steam leakage and the inefficiency created by the steam not fully interacting with the blade surface.
- Erosion: The gradual wearing away of turbine blades due to high-velocity steam and particulate matter within the steam flow. Over time, erosion can cause surface damage, reducing turbine efficiency and requiring maintenance.
- Vibration: Vibrations in steam turbines can occur due to imbalances, misalignment, or irregularities in steam flow. Excessive vibration can lead to mechanical failures and is closely monitored to ensure the turbine remains within safe operational limits.
- Overload: Operating a steam turbine beyond its rated capacity, which can lead to excessive wear, damage, or efficiency loss. Operating within the specified load range is critical for turbine longevity and optimal performance.
- Reheat: A process where steam is heated again after passing through the first stage of expansion in the turbine, improving efficiency by increasing the temperature of the steam before it enters the next turbine stage.
- Load: The amount of electrical or mechanical output produced by a steam turbine at any given time. Load fluctuations can affect turbine performance, and the turbine must be designed to handle varying loads without compromising efficiency.
- Generator: The device attached to the steam turbine that converts the mechanical energy produced by the turbine into electrical energy. The efficiency and size of the generator are important factors in determining the overall performance of a steam turbine system.
- Saturated Steam: Steam at its boiling point, where any additional heat would result in the steam becoming superheated. Saturated steam has a fixed temperature and pressure, and its energy content is typically lower than that of superheated steam.
- Thermodynamic Efficiency: This refers to the effectiveness with which a steam turbine converts thermal energy into mechanical energy. It is influenced by factors like the temperature and pressure of steam, design characteristics, and the overall system configuration.
Understanding these key terms is critical for anyone working with steam turbines, as they describe the fundamental concepts and mechanisms that govern turbine operation. These terms lay the foundation for discussing turbine design, performance, and troubleshooting, and mastering them is crucial for optimizing turbine efficiency, longevity, and reliability.
The development of steam turbines over the years has been marked by a continuous focus on increasing their efficiency, reliability, and adaptability to changing energy systems. One of the most important aspects of steam turbine operation is the careful management of the steam conditions—pressure, temperature, and flow rate—since these factors directly impact the turbine’s efficiency and output. The interaction between the high-pressure steam and the turbine blades is a critical part of the energy conversion process. The efficiency of a steam turbine is heavily influenced by how effectively the steam is expanded through the turbine stages and how well the exhaust steam is managed, often through a condenser or a back-pressure turbine system.
The process begins with the generation of steam in a boiler, where water is heated to produce steam at high pressure. This steam is then directed into the turbine, where it undergoes expansion through a series of stages. As the steam moves through each stage, it loses pressure and temperature, releasing energy that causes the turbine blades to rotate. The rotor, attached to the blades, converts this energy into mechanical work, which is typically used to drive generators or other machinery. The efficiency of the turbine is closely linked to the conditions under which the steam expands. For example, superheating the steam before it enters the turbine allows for higher energy conversion, as it ensures the steam maintains its energy content for longer before condensing.
Once the steam passes through the turbine and loses its energy, it exits at a lower pressure. This exhaust steam is either directed to a condenser, where it is cooled and condensed back into water, or to a process in a back-pressure turbine. In back-pressure systems, the exhaust steam is used for heating purposes or in industrial processes, such as district heating or chemical production, instead of being condensed. This is especially common in cogeneration plants, where the turbine serves a dual purpose of generating electricity and supplying heat.
The thermal efficiency of steam turbines is also influenced by their design, especially the blade configuration and the materials used in the construction of turbine components. Advances in materials science have led to the development of blades that can withstand higher temperatures and pressures, enabling turbines to operate at more efficient thermodynamic cycles. Supercritical and ultra-supercritical steam conditions, for instance, push the limits of temperature and pressure, allowing turbines to achieve higher efficiencies by extracting more energy from the steam. These turbines are particularly useful in large-scale power plants, where the demand for efficiency is paramount.
Another significant aspect of steam turbine operation is the need for regular maintenance and monitoring to ensure long-term reliability. Steam turbines experience significant mechanical stress, particularly in the blades and rotor, where high rotational speeds and thermal stresses can lead to wear and damage over time. Monitoring technologies, such as vibration sensors, temperature probes, and strain gauges, are often used to detect any signs of irregularities or potential failures before they lead to costly downtime or catastrophic failures. The integration of digital technologies, including AI and machine learning, is improving predictive maintenance by analyzing real-time data and identifying performance trends that could indicate issues before they manifest.
The growing interest in renewable energy sources is pushing the development of steam turbine systems that can operate efficiently alongside technologies like solar, wind, and biomass. Hybrid power plants, which combine steam turbines with renewable energy sources, aim to create flexible, low-carbon energy systems that can respond to fluctuating energy demands. In such systems, steam turbines might serve as backup power generators, running on renewable fuels such as biomass or even hydrogen, ensuring grid stability when renewable sources are not producing sufficient energy.
Moreover, the evolving role of hydrogen in the energy sector has gained attention due to its potential as a clean fuel for power generation. Steam turbines can be adapted to run on hydrogen, either in pure form or as a blended fuel with natural gas. Hydrogen combustion produces only water vapor as a byproduct, making it an ideal candidate for decarbonizing power plants that rely on steam turbines. The challenge, however, lies in designing turbines that can handle hydrogen’s unique properties, such as its lower energy density compared to natural gas, and its potential to cause higher rates of material degradation due to its chemical reactivity. Despite these challenges, the prospect of hydrogen-powered steam turbines represents an exciting direction for future energy systems.
In addition to their applications in large-scale power generation, steam turbines are also finding increasing use in smaller, decentralized energy systems, such as microgrids and industrial cogeneration plants. These systems often require turbines that can operate efficiently at varying loads, depending on the energy demand. For example, in industrial processes, steam turbines can be used to generate electricity while simultaneously providing heat for manufacturing processes, resulting in significant energy savings and reduced emissions. The ability to use steam turbines in smaller-scale applications demonstrates their versatility and importance in meeting a wide range of energy needs.
The integration of steam turbines into waste heat recovery systems is another area where they are playing an increasingly important role. Many industrial processes, such as cement production, steel manufacturing, and chemical refining, generate large amounts of waste heat. Steam turbines can be used to capture this waste heat and convert it into electricity, increasing the overall energy efficiency of these operations. This process, known as combined heat and power (CHP) or cogeneration, can significantly reduce the carbon footprint of industrial facilities while simultaneously lowering energy costs.
As energy systems continue to evolve and become more complex, the role of steam turbines in ensuring reliable and efficient power generation will remain essential. Their ability to integrate with diverse fuel sources, advanced technologies, and energy systems will make them a key component in the global transition to a low-carbon energy future. Whether as part of large-scale power plants, hybrid systems with renewable energy sources, or smaller industrial cogeneration units, steam turbines will continue to play a crucial role in meeting the world’s growing energy demands while minimizing environmental impact.
As the energy sector undergoes significant transformations, particularly with the push towards decarbonization and renewable energy integration, steam turbines will need to evolve to meet new challenges. Their ability to work flexibly with varying fuel sources, alongside innovations in turbine materials, design, and system integration, will be critical to maintaining their relevance. One of the key areas of development lies in the use of steam turbines in combined-cycle systems, which pair steam turbines with gas turbines for higher efficiency and reduced emissions.
In a combined-cycle system, gas turbines generate electricity by combusting fuel and driving a generator, producing exhaust gases that are typically very hot. These exhaust gases are then used to produce steam in a heat recovery steam generator (HRSG), which is sent to the steam turbine. The steam turbine generates additional power by extracting energy from the steam, further improving the overall efficiency of the power plant. The integration of steam turbines into such systems can achieve efficiency rates of over 60%, significantly higher than those of traditional standalone steam turbine or gas turbine plants.
Additionally, the development of advanced steam cycle technologies, such as the use of integrated carbon capture and storage (CCS) systems, offers another avenue for improving the environmental performance of steam turbines. CCS technologies capture carbon dioxide (CO2) emissions before they can be released into the atmosphere and store them underground or repurpose them for industrial applications. By coupling CCS with steam turbines, power plants can continue to operate while significantly reducing their greenhouse gas emissions, making them more sustainable and helping to meet global climate goals.
Another trend that is shaping the future of steam turbines is the growing emphasis on digitalization and automation. The integration of digital technologies in turbine operation and maintenance can enhance performance, reduce downtime, and lower operating costs. For example, real-time data collection and predictive analytics can help optimize turbine performance by adjusting operating parameters based on changing conditions, such as variations in steam pressure or temperature. Additionally, machine learning algorithms can be used to predict when maintenance is needed, reducing the need for manual inspections and minimizing unplanned outages. This level of predictive maintenance not only improves the reliability of turbines but also extends their operational lifespan by preventing the need for costly repairs.
The role of steam turbines in hybrid and multi-energy systems is another exciting area of growth. As energy grids transition towards incorporating a mix of renewable sources like solar, wind, and hydropower, steam turbines can play a critical role in balancing grid stability. These systems often require backup power generation to account for fluctuations in renewable energy production. Steam turbines, particularly those powered by biomass, hydrogen, or geothermal energy, can be used as a flexible and reliable backup, ensuring that the grid remains stable even when renewable sources are not generating enough electricity.
For instance, the ability to burn renewable fuels such as biomass or even hydrogen in steam turbines could make them an essential part of the energy transition. Biomass power plants have already demonstrated their potential for producing electricity with lower carbon emissions compared to fossil fuels, and hydrogen, when produced using renewable energy, can serve as a clean fuel option. As hydrogen production technologies advance, steam turbines may be able to operate more efficiently with hydrogen as a fuel, enabling them to contribute to the decarbonization of the energy sector.
Moreover, steam turbines in the form of modular, scalable units are also being explored for use in smaller-scale applications. For example, small modular reactors (SMRs), a next-generation nuclear technology, could pair well with steam turbines to produce reliable, low-carbon energy in distributed energy systems. These smaller, modular plants offer the advantage of being able to provide power to remote areas or to supplement larger grid systems without requiring the massive infrastructure of traditional nuclear plants.
Microgrids and decentralized energy systems are also gaining traction, particularly in areas where access to a central electricity grid is limited. Steam turbines, when coupled with renewable sources or local thermal generation, can provide reliable electricity and heat, contributing to local energy resilience. In these applications, steam turbines could operate efficiently at lower capacities while still contributing to overall energy security.
The future of steam turbines also involves ongoing research into improving their material science and design to withstand the extreme operating conditions associated with new energy sources and high-efficiency processes. For example, turbines must be able to operate at higher temperatures and pressures without compromising their performance or durability. The development of advanced alloys and coatings that can resist corrosion, erosion, and high-temperature wear will play a crucial role in enabling turbines to run efficiently over long operational lifespans. Additionally, the use of 3D printing and additive manufacturing techniques could allow for the production of complex turbine components that improve steam flow and reduce mechanical losses, further enhancing efficiency.
Lastly, the evolution of steam turbines is intrinsically linked to global efforts to combat climate change. The need for low-carbon power generation is pushing industries to explore new avenues for using steam turbines in environmentally friendly ways. In the long term, steam turbines may be key enablers of a low-carbon future, particularly as energy storage and renewable generation technologies continue to develop. Their ability to work seamlessly with renewable energy sources, store excess energy, and provide reliable backup power will help create a more resilient and sustainable energy grid.
The transformation of steam turbines is not just a technical challenge but also an opportunity to reshape how the world generates and consumes energy. As renewable energy technologies, hydrogen, and carbon capture continue to evolve, steam turbines will remain at the heart of power generation, contributing to a more sustainable, flexible, and energy-efficient future. With ongoing innovations in turbine design, materials, and integration with digital technologies, steam turbines will continue to serve as a cornerstone of global energy systems, playing a pivotal role in the shift toward clean and efficient power generation.
As the world transitions toward more sustainable energy systems, the role of steam turbines will continue to evolve. One of the key challenges for the future is the need for steam turbines to be adaptable to different energy sources and grid configurations. The rise of distributed energy systems, which integrate various forms of energy generation (such as solar, wind, and biomass), requires turbines to be highly flexible in how they operate, including handling fluctuations in demand and supply.
One of the potential solutions for improving the integration of steam turbines with renewables is the development of hybrid systems. Hybrid power plants combine renewable energy sources, such as solar or wind, with conventional power generation methods, including steam turbines. This combination allows the steam turbine to operate as a backup or a baseload power generator while renewable sources provide intermittent energy. In hybrid systems, steam turbines may either operate in a load-following capacity, adjusting their output to match changes in renewable generation, or they may serve as a stabilizing force on the grid during periods when renewable generation is low.
Another emerging trend is the use of steam turbines in small, decentralized energy production systems. These systems are particularly valuable in remote or off-grid locations where connecting to a central power grid is not feasible. By using local sources of heat or renewable fuels (such as biomass, biogas, or even waste heat), small steam turbines can provide reliable, cost-effective power. This concept is particularly relevant in developing regions or in industrial facilities where a constant and independent energy supply is needed for continuous operation.
Advanced manufacturing techniques, such as 3D printing, have the potential to revolutionize the construction of steam turbines by allowing for the production of more complex and efficient components at a reduced cost. For example, 3D printing can create turbine blades and other critical parts with intricate designs that are not possible with traditional manufacturing methods. This could lead to improved steam flow, reduced mechanical losses, and higher efficiency overall. Furthermore, the ability to produce parts on demand could help reduce downtime and maintenance costs, ensuring that turbines remain operational for longer periods.
The growing importance of hydrogen in the global energy mix presents another significant opportunity for steam turbines. Hydrogen is considered a clean fuel because its combustion produces only water vapor, making it an ideal candidate for decarbonizing various sectors, including power generation. The use of hydrogen as a fuel in steam turbines is particularly promising because hydrogen can be generated from renewable sources, such as wind or solar energy, and stored for later use. Hydrogen-powered steam turbines could help stabilize grids that rely heavily on renewable energy by providing dispatchable power whenever needed. As hydrogen production technologies continue to scale up, and as storage and transportation methods improve, hydrogen could become a significant contributor to future energy systems, and steam turbines will play a key role in its use.
Another important aspect of the future of steam turbines is the continued focus on improving their environmental performance. While steam turbines are generally more efficient than many other forms of power generation, there is always room for improvement. One avenue for achieving better environmental outcomes is through the adoption of advanced carbon capture, utilization, and storage (CCUS) technologies. These technologies capture carbon dioxide emissions from power plants before they can be released into the atmosphere, storing or repurposing the captured CO2 for industrial use. Integrating CCUS with steam turbines could significantly reduce the carbon footprint of conventional power plants, making them more compatible with global climate targets.
In the context of power plant design, steam turbines will continue to benefit from advances in computer modeling and simulation technologies. The use of computational fluid dynamics (CFD) allows engineers to design more efficient turbines by simulating steam flow and heat transfer within the turbine components. This enables the identification of design improvements before physical prototypes are built, reducing the time and cost associated with turbine development. Moreover, the ability to model various operating conditions and simulate the impact of different fuel sources will allow for the optimization of turbine performance across a range of energy systems.
The evolving role of steam turbines also raises questions about the future of centralized and decentralized energy grids. While traditional large-scale power plants have relied heavily on centralized grids, there is a shift toward more localized, flexible energy systems. In these systems, steam turbines could be deployed in modular units that are smaller, more efficient, and easier to integrate with renewable energy sources. These smaller, distributed turbines can be located closer to where the energy is needed, reducing transmission losses and enhancing overall grid stability. Microgrids, which are localized grids that can operate independently or in conjunction with the larger grid, are becoming increasingly important in this regard. Steam turbines, when coupled with renewable generation sources and energy storage, can provide the reliability and flexibility needed for microgrids to function effectively.
One final area of innovation for steam turbines is their integration with emerging energy storage technologies. Energy storage systems, such as batteries or thermal storage, are key to managing the intermittent nature of renewable energy sources. By storing excess energy when renewable generation is high and releasing it when demand peaks or renewable generation drops, these systems can help smooth out fluctuations and ensure a stable power supply. Steam turbines could be integrated into energy storage systems, where they help generate electricity from stored thermal energy. This could involve capturing and storing heat from renewable sources during periods of high generation and then converting it into electricity through the steam turbine when needed.
The future of steam turbines is exciting and holds immense potential to contribute to the global transition toward sustainable, low-carbon energy systems. Their adaptability to new fuels, advanced technologies, and hybrid energy systems makes them a crucial component in modern energy infrastructure. Whether used in large-scale power plants, decentralized energy systems, or as part of advanced combined-cycle and hybrid systems, steam turbines will continue to evolve to meet the demands of a cleaner, more efficient energy future. As technological innovations progress, and as new challenges emerge, steam turbines will remain at the forefront of power generation, delivering reliable, efficient, and environmentally responsible energy solutions for years to come.
Steam Turbine Designs for Power Plants
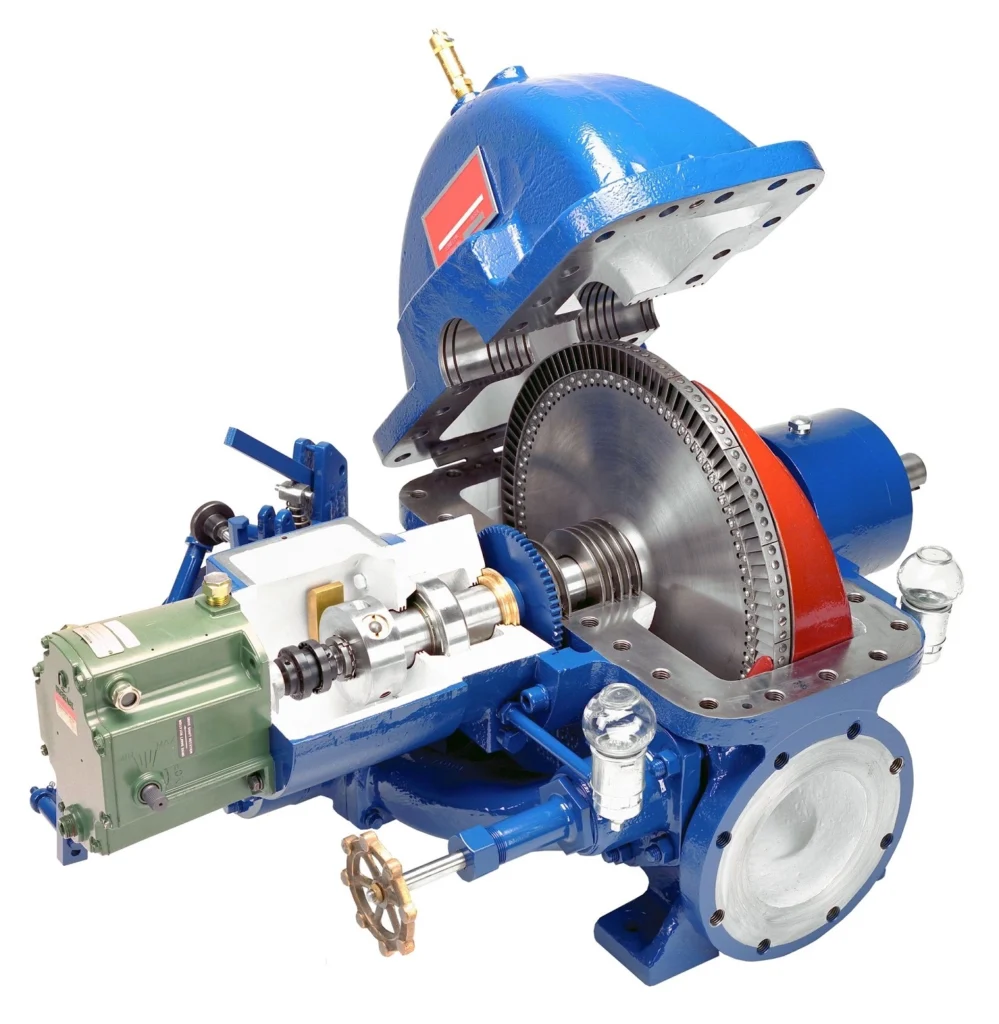
Steam turbine designs for power plants are critical in ensuring that power generation is efficient, reliable, and adaptable to various operational conditions. The design of steam turbines is influenced by a number of factors, including the scale of the plant, the type of fuel used, the operational flexibility required, and the specific energy efficiency goals of the plant. While the basic principles of steam turbine design have remained largely consistent over time, ongoing advances in materials, technology, and system integration continue to push the boundaries of what is possible. As a result, the design of steam turbines has evolved to meet the diverse needs of modern power plants, especially as the energy sector moves toward cleaner, more sustainable solutions.
A key consideration in steam turbine design is the thermodynamic cycle in which the turbine operates. The most common cycle for power generation is the Rankine cycle, in which water is heated to produce steam that drives a turbine. The steam expands through a series of stages in the turbine, and the energy released in the expansion process is converted into mechanical power. The steam is then condensed and pumped back to the boiler to be reheated. The efficiency of the Rankine cycle is primarily determined by the steam pressure and temperature, and the design of the turbine must maximize the energy extraction from the steam while minimizing energy losses.
The design of a steam turbine for a power plant typically consists of several key components: the rotor, the stator, the blades, the casing, and the bearings. The rotor is the central rotating shaft to which the blades are attached, while the stator contains stationary blades or nozzles that direct the steam flow onto the rotor blades. The blades are designed to extract as much energy as possible from the expanding steam by converting its thermal energy into mechanical motion. The casing houses the rotor and stator and helps direct the steam flow through the turbine stages. Bearings support the rotor and allow it to rotate with minimal friction. Each of these components must be designed to handle the high temperatures and pressures associated with modern steam turbine operations.
Over the years, significant advancements have been made in the materials used to construct steam turbines. Early turbines were primarily made of low-strength materials, which limited their operational capabilities. However, modern steam turbines are made from advanced alloys and composite materials that are capable of withstanding the extreme temperatures and pressures found in power plants. These materials not only allow for more efficient turbines but also help reduce maintenance costs and extend the operational lifespan of the turbine. For example, superalloys made from nickel and cobalt are commonly used in the blades and rotor of high-temperature turbines because they offer exceptional resistance to heat and corrosion.
Another important factor in turbine design is the number of stages in the turbine. In a single-stage turbine, steam passes through only one set of blades before being exhausted. However, in most power plants, multi-stage turbines are used to maximize efficiency. In a multi-stage turbine, steam passes through a series of stages, with each stage consisting of a rotor and stator. As steam passes through each stage, it loses pressure and temperature, and the energy is extracted in increments. This staged process helps to ensure that the turbine operates at the most efficient thermodynamic conditions for as long as possible. The number of stages required depends on the steam pressure and temperature at the inlet and the desired output of the turbine.
The design of steam turbines is also closely tied to the type of power plant in which they will be used. In fossil-fuel power plants, steam turbines are typically designed to handle steam produced by burning coal, natural gas, or oil in a boiler. In these plants, the steam is often produced at relatively high pressures and temperatures, which requires turbines that are built to handle these extreme conditions. The design of the turbine in this context also considers factors such as fuel efficiency, emissions control, and the need for flexibility in responding to changes in fuel input and operational conditions.
In contrast, in nuclear power plants, steam turbines are used to convert heat generated by nuclear fission into mechanical power. Nuclear reactors operate at high temperatures and pressures, and the design of the steam turbine must accommodate these conditions while ensuring safety and efficiency. Nuclear power plants require turbines that can operate in a highly controlled environment, and turbine designs often incorporate features that help to minimize the risk of failure, such as redundant systems and safety mechanisms. Additionally, because nuclear plants often operate at a steady state with little variation in output, steam turbines in these plants are designed for stable, continuous operation with minimal load-following requirements.
The integration of renewable energy sources is also influencing steam turbine design. For example, in combined-cycle plants, steam turbines are used alongside gas turbines to improve efficiency. In these systems, a gas turbine generates electricity by combusting fuel, and the exhaust gases are used to produce steam that drives the steam turbine. The integration of steam turbines into these hybrid systems allows for better utilization of the energy produced by the gas turbine, leading to higher overall efficiency. Additionally, the ability of steam turbines to work with renewable fuels, such as biomass or hydrogen, is becoming increasingly important as the global energy mix shifts toward cleaner sources of energy. Steam turbines are being designed to handle these fuels in a way that maintains efficiency while reducing carbon emissions.
Another area where steam turbine design is evolving is in the context of low-carbon and zero-carbon power generation. The increasing emphasis on decarbonization has led to the development of steam turbines that can operate with carbon capture and storage (CCS) systems, which capture CO2 emissions and prevent them from entering the atmosphere. Integrating CCS into steam turbine systems requires careful design to ensure that the turbines continue to operate efficiently while dealing with the additional heat and pressure demands associated with carbon capture processes. Moreover, there is growing interest in using steam turbines with hydrogen as a fuel, which has the potential to further reduce emissions and provide a clean, sustainable source of energy.
The design of steam turbines for power plants must also account for the need for flexibility in operation. Power plants today are often required to operate in a more dynamic and responsive manner due to the increasing integration of intermittent renewable energy sources like wind and solar power. Steam turbines must be designed to handle changes in load, ramping up or down quickly in response to fluctuations in renewable generation. This requires advanced control systems and turbine designs that can handle frequent start-ups, shut-downs, and load changes without compromising efficiency or reliability.
In addition to these technical considerations, the economic aspects of steam turbine design play a crucial role in determining the overall cost-effectiveness of power plants. The initial capital cost of steam turbines, as well as the operating and maintenance costs over their lifetime, must be carefully evaluated to ensure that the plant remains competitive in the energy market. The efficiency improvements resulting from advanced turbine designs can help offset these costs by reducing fuel consumption and lowering operating expenses over time. Furthermore, the design of steam turbines must also consider their environmental impact, particularly in terms of emissions and resource consumption. Sustainable turbine designs, such as those that incorporate recyclable materials or energy-efficient components, are becoming increasingly important as the global demand for environmentally responsible power generation grows.
Overall, the design of steam turbines for power plants is a highly complex and dynamic field that involves a combination of engineering, materials science, and economic considerations. As power plants continue to evolve to meet the demands of cleaner, more flexible energy systems, steam turbines will play a critical role in achieving these goals. Whether used in traditional fossil-fuel plants, nuclear plants, or renewable energy systems, the design of steam turbines will continue to be a key factor in determining the efficiency, reliability, and environmental impact of modern power generation.
Looking ahead, the future of steam turbine designs will be shaped by advancements in several critical areas. As the global energy landscape continues to shift toward cleaner, more sustainable power generation, the development of steam turbines will be influenced by technological innovations, market demands, and regulatory requirements. To meet these challenges, steam turbine designs will need to prioritize flexibility, efficiency, and adaptability to new fuels and energy systems.
One of the most promising advancements in steam turbine design is the integration of advanced materials that can withstand extreme operating conditions. Modern steam turbines operate at higher temperatures and pressures than ever before, and this trend is expected to continue. To maximize efficiency and minimize wear, manufacturers are turning to new alloys, coatings, and composite materials that offer improved resistance to heat, corrosion, and fatigue. For example, advanced superalloys, ceramic materials, and coatings such as thermal barrier coatings (TBCs) are being developed for use in turbine blades and other critical components. These materials allow turbines to operate at higher temperatures without suffering from degradation, leading to better thermal efficiency and longer operational lifespans.
The design of turbine blades is particularly critical in enhancing turbine efficiency. As steam expands through the turbine, the energy is converted into mechanical motion by the blades. The design of these blades—such as their shape, material properties, and surface coatings—directly affects how efficiently energy is extracted from the steam. Blade design is evolving to incorporate more aerodynamically optimized shapes, better heat resistance, and improved stress distribution to increase performance and reduce maintenance needs. Additionally, the use of computational fluid dynamics (CFD) software has allowed engineers to simulate steam flow through turbines in unprecedented detail, leading to more efficient blade designs that maximize energy extraction while minimizing mechanical losses.
Another key area of development is turbine efficiency in combined-cycle systems. As previously mentioned, combined-cycle power plants use both gas turbines and steam turbines to increase overall plant efficiency by utilizing the waste heat from the gas turbine to produce steam for the steam turbine. Steam turbine designs in these plants must be optimized for quick response times, as gas turbines can experience fluctuations in output depending on factors such as fuel quality or grid demand. Advanced turbine controls, digital monitoring, and real-time data analysis will allow for greater flexibility in operating steam turbines in combined-cycle configurations, enabling them to ramp up or down efficiently to meet the varying energy demands of the grid.
Further progress in steam turbine design will be influenced by the increasing reliance on renewable energy sources, especially wind, solar, and biomass. Steam turbines can play a vital role in integrating these renewables into the grid, particularly when used in hybrid systems or when paired with energy storage solutions. For instance, steam turbines can be employed in biomass power plants to convert organic matter into steam and generate electricity. Similarly, the ability to burn hydrogen in steam turbines is emerging as a promising option for reducing carbon emissions. Hydrogen, when produced from renewable energy sources, can be used as a low-carbon fuel in turbines, providing a clean alternative to traditional fossil fuels. This flexibility in fuel options will make steam turbines an even more integral part of the energy transition as they can easily be adapted to work with hydrogen or other low-carbon fuels.
As the use of hydrogen grows, steam turbine manufacturers will need to design turbines that can handle the unique properties of hydrogen as a fuel. Hydrogen combustion creates higher temperatures and different pressure dynamics compared to traditional fossil fuels, which can affect turbine performance. Research is already underway to develop turbines that are optimized for hydrogen combustion, and as this technology matures, we can expect to see more widespread use of hydrogen-powered steam turbines in both power generation and industrial applications.
The role of steam turbines in carbon capture and storage (CCS) technology will also play a significant role in their design evolution. As governments and industries seek to reduce carbon emissions from existing power plants, CCS technology is emerging as a critical solution. Steam turbines that operate in power plants with integrated CCS systems will need to be designed with the additional energy requirements of capturing and compressing CO2. This may involve modifying the turbine design to account for the extra heat or pressure demands, as well as optimizing the turbine’s performance to ensure minimal efficiency loss when operating alongside CCS systems.
The ongoing digital transformation of the energy sector will have a profound impact on steam turbine design and operation. Digital technologies, such as Internet of Things (IoT) sensors, data analytics, machine learning, and predictive maintenance, will enable power plants to operate more efficiently and with fewer disruptions. For steam turbines, this means better monitoring of critical components, real-time performance tracking, and predictive analytics that can identify potential issues before they lead to failure. Turbine designs will incorporate more sensors and diagnostic systems, allowing operators to optimize turbine performance and reduce downtime. For example, real-time data on steam flow, temperature, pressure, and vibration can be used to fine-tune turbine operations, improving efficiency and extending the lifespan of components.
Automation and advanced control systems will also enhance the ability of steam turbines to operate in a more flexible and responsive manner. As renewable energy sources, such as solar and wind, become a larger part of the energy mix, steam turbines will need to operate with greater flexibility to match fluctuations in energy production. Advanced control systems that can quickly adjust turbine operations in response to changes in grid demand or the availability of renewable energy will allow power plants to provide reliable baseload power while adapting to the variable nature of renewable generation.
In addition to enhancing operational flexibility, the design of steam turbines for power plants must also take into account sustainability and environmental impact. The pressure is mounting for the power generation sector to reduce greenhouse gas emissions and minimize the environmental footprint of power plants. Innovations in turbine design, such as the use of recyclable materials, energy-efficient coatings, and reduced emissions technologies, will be key in helping power plants meet these targets. Steam turbines must continue to evolve to operate more efficiently, reduce waste heat, and minimize their carbon footprint. Incorporating sustainability considerations into turbine design will be essential in making the energy sector more environmentally friendly and in meeting global climate goals.
Finally, the growing focus on energy resilience and security will shape the future of steam turbine designs. As global power grids become more complex and interconnected, the need for reliable and flexible power generation technologies will increase. Steam turbines, particularly in decentralized or microgrid configurations, can provide stable, reliable energy even in the face of grid disturbances or interruptions in renewable energy supply. Steam turbine designs for small-scale, distributed systems will be crucial in enhancing energy security, particularly in remote regions or areas with limited access to centralized grids.
In conclusion, the future of steam turbine designs for power plants is marked by continuous innovation, with a focus on increasing efficiency, flexibility, and sustainability. As the energy sector embraces cleaner fuels, renewable energy integration, and advanced technologies, steam turbines will remain a vital component in power generation. Whether used in large-scale power plants, combined-cycle systems, or hybrid renewable energy setups, steam turbines will play an essential role in the transition to a low-carbon, flexible, and resilient energy future.
The continuous evolution of steam turbine technology in response to modern challenges will involve a wide array of interdisciplinary advancements. One key development will be the integration of steam turbines with next-generation power generation technologies such as advanced nuclear reactors and supercritical CO2 cycles.
Advanced Nuclear Reactors and Steam Turbines: Advanced nuclear reactors, such as small modular reactors (SMRs) and next-generation fission reactors, will likely become more prominent in the future energy landscape. These reactors offer significant advantages in terms of scalability, safety, and reduced environmental impact. However, their integration with steam turbines will require new turbine designs to handle different heat sources, pressures, and operational characteristics compared to traditional nuclear reactors.
For example, some next-generation nuclear reactors operate at higher temperatures than current reactors, which could lead to the need for steam turbines that are capable of handling these elevated temperatures while maintaining efficiency and material integrity. Innovations in heat exchangers and turbine materials—such as ceramics and other heat-resistant composites—will be essential in ensuring steam turbines can maximize energy conversion while enduring the extreme operating conditions of advanced reactors.
Supercritical CO2 (sCO2) Cycles and Turbines: Another area where steam turbine technology is expected to undergo significant changes is in the development of supercritical CO2 cycles. In these cycles, CO2 is used as the working fluid instead of water, and it operates at supercritical pressures and temperatures. This approach offers higher thermal efficiencies than traditional Rankine cycles, especially in power plants utilizing fossil fuels, nuclear energy, or renewable heat sources.
For steam turbines, the integration of sCO2 cycles will necessitate new designs that can handle CO2’s unique thermodynamic properties, such as its density and heat transfer characteristics. sCO2 turbines are expected to operate at higher efficiencies than traditional steam turbines, and they offer the potential for lower costs and reduced emissions when applied in various power generation contexts. The adaptation of steam turbine designs to sCO2 cycles will require innovative engineering solutions, such as redesigned blades, seals, and heat exchangers, to optimize performance under these conditions.
Hybrid Energy Systems and Steam Turbine Flexibility: As the global energy mix increasingly includes renewable energy sources such as wind, solar, and geothermal, the role of steam turbines will evolve within hybrid energy systems. Hybrid plants that combine steam turbines with gas turbines or renewable energy sources, such as biomass and concentrated solar power (CSP), will become more common.
These hybrid systems allow for optimized efficiency by utilizing the strengths of each energy source. For instance, in a CSP system, solar thermal energy is used to heat a working fluid, which then drives a steam turbine. In the event of cloudy weather or at night, natural gas or biomass can be used to maintain continuous power generation. In these hybrid applications, steam turbines must be designed to handle varying steam flow rates and temperatures, allowing them to operate efficiently under dynamic conditions.
In addition, steam turbines will be required to work in a more load-following capacity, meaning they must be able to rapidly adjust their output in response to fluctuations in renewable generation. This operational flexibility will be crucial in balancing supply and demand as intermittent renewable sources dominate the energy mix.
Digitalization and Smart Turbine Systems: The digitalization of power plants is accelerating, with technologies such as artificial intelligence (AI), machine learning (ML), and the Internet of Things (IoT) playing an increasingly important role in optimizing turbine operations. These technologies enable power plant operators to monitor turbine health in real time, predict maintenance needs, and optimize performance without the need for manual intervention.
For steam turbines, smart systems can collect data from sensors embedded in turbine components, such as blades, bearings, and casings. This data can then be analyzed to predict when maintenance is required, identify potential failure points, and optimize the operation of the turbine to reduce energy losses. Machine learning algorithms can also be used to adjust turbine operations dynamically based on grid demand, ensuring that turbines operate at peak efficiency while reducing wear and tear.
Moreover, digital twin technology—a virtual replica of a turbine—could be used to simulate turbine performance in various operating conditions, helping engineers optimize turbine design and operation before physical changes are made. This capability can improve both design and operational reliability, reducing downtime and maintenance costs.
Sustainable and Green Materials: As sustainability becomes a more prominent focus in all sectors of the economy, steam turbine designs will likely incorporate greener materials and manufacturing processes. For example, turbine manufacturers may turn to sustainable and recyclable materials to reduce the environmental impact of production and disposal. These materials might include advanced composites or bio-based alloys that offer the same strength and heat resistance as traditional materials but with a lower carbon footprint.
Furthermore, turbine designs will need to incorporate energy-efficient production techniques. Additive manufacturing (3D printing) could allow for more precise and customized components, reducing material waste and improving turbine efficiency by creating parts with complex geometries that are difficult to produce with conventional methods. As demand for sustainability grows, the materials used in steam turbines must not only meet the performance requirements but also align with the broader goals of reducing the environmental impact of energy production.
Modular Steam Turbines for Distributed Generation: The push for decentralized energy production is another factor influencing steam turbine design. Modular, smaller-scale steam turbines will be more widely used in distributed generation systems, where energy is produced closer to the point of use, reducing the need for long-distance power transmission. These systems can operate in remote locations, such as off-grid areas, or in urban environments, where local energy generation can reduce pressure on centralized grids.
Modular steam turbines will also be integrated into microgrids, which can operate independently of the main power grid. Microgrids are expected to play a key role in providing resilient and reliable power in areas susceptible to natural disasters or grid instability. Steam turbines designed for these applications must be compact, efficient, and capable of quickly responding to fluctuations in demand, whether it is a surge in local energy consumption or a drop in renewable generation.
In addition, these smaller turbines may need to operate on a variety of renewable fuels, such as biogas, waste heat, or hydrogen, further increasing their adaptability and ensuring they remain viable in a changing energy landscape.
Global Impact of Turbine Design Innovations: The advances in steam turbine design will not only shape the energy landscape in developed countries but will also have significant implications for emerging economies. In many parts of the world, there is an increasing demand for reliable, affordable, and clean energy. Steam turbines, particularly those adapted for smaller-scale, decentralized, and renewable energy applications, will be pivotal in addressing these needs.
In developing countries, where access to centralized energy infrastructure is often limited, small-scale, off-grid steam turbines can provide a reliable energy source. These turbines can be fueled by locally available resources, such as agricultural waste, biomass, or even small-scale geothermal energy, offering a cost-effective and sustainable power solution.
At the same time, as countries in the developing world industrialize and their energy needs grow, efficient and flexible steam turbines will be essential to meet the increasing demand for electricity while minimizing environmental impact. By adopting advanced steam turbine technologies that are optimized for low-carbon fuels and integrated into hybrid or combined-cycle systems, these countries can leapfrog to more sustainable energy systems.
Conclusion: The future of steam turbine designs is poised to be shaped by several factors, including advancements in materials, fuel flexibility, digital technologies, and environmental sustainability. As the world transitions toward cleaner, more resilient, and decentralized energy systems, steam turbines will continue to play a central role in power generation. Whether in large-scale combined-cycle plants, small modular systems, hybrid energy setups, or microgrids, steam turbines will evolve to meet the ever-changing demands of the global energy landscape.
By embracing these innovations, steam turbines will help facilitate the energy transition, contributing to more efficient, reliable, and environmentally responsible power generation. With continued research and development, the next generation of steam turbines will not only push the boundaries of efficiency but also ensure that power plants worldwide can adapt to the demands of a cleaner, more dynamic, and sustainable energy future.
As we look further into the future of steam turbine technology, additional trends and considerations will further define the role these turbines play in the energy sector. Some of these developments are rooted in the broader transformations within the global energy system, as well as in new engineering paradigms that will push steam turbine capabilities to new heights.
Flexibility in Power Generation Systems: One of the driving forces behind innovation in steam turbines will be the increasing need for flexible and responsive power generation systems. This is especially important as renewable energy sources such as wind and solar continue to gain market share. These sources, while crucial for reducing carbon emissions, are inherently intermittent, requiring backup generation systems that can rapidly ramp up or down to balance supply and demand.
Steam turbines, which have traditionally been part of baseload power plants, are being redesigned to operate more dynamically in these mixed-generation systems. Manufacturers are developing turbines that can quickly adjust their power output, which may require innovative control systems and modifications to turbine components. This flexibility will ensure steam turbines remain relevant in grid systems that are more variable and unpredictable.
This shift toward flexible operation has led to the development of combined heat and power (CHP) systems, where steam turbines not only generate electricity but also supply useful heat for industrial processes or district heating systems. Such systems can provide efficient, near-continuous power while addressing the need for heat, further boosting the overall efficiency and value of steam turbines in an increasingly integrated energy system.
Hydrogen Economy and Steam Turbines: The growing interest in hydrogen as a clean alternative to fossil fuels presents an exciting opportunity for steam turbines. Hydrogen, when burned, produces water vapor as the primary byproduct, making it a highly attractive fuel in the transition toward a low-carbon economy. Hydrogen can be produced via electrolysis using renewable electricity, thus offering a carbon-free fuel source when combined with renewable energy technologies.
Steam turbines are already being adapted to use hydrogen as a fuel in certain industrial settings, particularly where high temperatures are required for steam generation, such as in steel production or refining. In the future, hydrogen could be used more broadly in power plants to generate steam, further reducing emissions from fossil-fuel-based plants. However, adapting steam turbines to burn hydrogen requires specialized components that can handle the high temperatures associated with hydrogen combustion and address any unique operational challenges that hydrogen may pose, such as its lower energy density and higher combustion temperatures.
As the hydrogen economy evolves, turbine manufacturers will continue to refine turbine designs to operate on blends of hydrogen and natural gas, eventually moving toward 100% hydrogen combustion. This transition could significantly reduce the carbon footprint of steam turbine operations, making them more compatible with net-zero energy goals.
Advanced Manufacturing Techniques: Manufacturing techniques themselves will be revolutionized in the design and production of steam turbines. Advanced manufacturing, such as additive manufacturing (3D printing), is poised to revolutionize turbine production. By enabling the creation of highly customized and geometrically complex components that would be difficult or impossible to manufacture through traditional methods, 3D printing could reduce material waste, improve performance, and shorten lead times for turbine components.
Moreover, additive manufacturing allows for the creation of parts with optimized internal geometries, such as cooling channels or complex lattice structures, which could reduce the weight of the turbine while enhancing thermal performance. These innovations could lead to more efficient, cost-effective, and durable steam turbines that meet the demanding operational conditions of modern power plants.
In addition to 3D printing, precision casting, and other advanced manufacturing techniques are also being explored to produce high-performance alloys with superior material properties. These techniques will help engineers overcome the limitations posed by existing manufacturing methods and ensure steam turbines can meet the increasing demands for higher temperatures and pressures, improving their overall efficiency and lifespan.
Improved Maintenance and Lifecycle Management: With increasing digitalization, steam turbine maintenance is becoming more predictive rather than reactive. Advanced sensors, combined with machine learning algorithms, are enabling operators to predict when specific components will fail, thus reducing the need for costly downtime and minimizing the likelihood of unexpected failures. This predictive maintenance not only reduces operational disruptions but also extends the overall lifecycle of steam turbines.
Smart systems integrated with turbine components allow for real-time monitoring of temperature, pressure, vibration, and stress levels. By collecting this data continuously, machine learning models can analyze trends, anticipate potential failures, and recommend proactive maintenance. This system reduces both the frequency and the severity of turbine failures, ultimately leading to greater reliability and lower operating costs.
For steam turbines, this shift in maintenance strategy can lead to increased service life by ensuring that parts are replaced or repaired before they fail, and operating conditions are constantly optimized. Operators will have more data-driven insights into when to perform maintenance and how to adjust operations to minimize wear, which translates into lower overall lifecycle costs for turbine assets.
Integration with Energy Storage Systems: Another exciting development for steam turbines lies in their integration with energy storage systems. As intermittent renewable sources like wind and solar become more prevalent, energy storage technologies such as batteries, pumped hydro storage, or thermal storage systems will be essential for balancing supply and demand. Steam turbines can be paired with thermal energy storage systems, where excess renewable energy is used to heat a working fluid, which can later be used to generate steam for power production.
This hybrid approach allows for greater grid stability and efficiency by providing a reliable source of power even when renewable generation is low. Steam turbines paired with energy storage systems have the potential to become key assets in the emerging market for long-duration energy storage, ensuring that power generation remains consistent even during periods of low renewable output.
International Collaboration and Standards: As steam turbine technology continues to evolve, international collaboration and the establishment of common standards will be essential. Steam turbine manufacturers, research institutions, and governments must work together to create harmonized standards that ensure turbines are designed for optimal efficiency, safety, and environmental sustainability.
Global partnerships between countries and industries will help share knowledge, facilitate technology transfer, and accelerate the development of next-generation steam turbines. This will be particularly important in regions that are transitioning away from coal-based power generation to cleaner energy sources, as the development of steam turbine designs that are adaptable to both conventional and renewable fuels will be critical in meeting climate goals.
Conclusion: The ongoing evolution of steam turbine technology presents a promising future for the global energy sector. Whether addressing the challenges posed by renewable energy integration, hydrogen fuel adoption, or advanced manufacturing, steam turbines will continue to be a cornerstone of efficient power generation. By leveraging innovations in materials science, digitalization, energy storage, and flexible operation, the next generation of steam turbines will be more efficient, adaptable, and sustainable than ever before.
As the world moves toward a more resilient, low-carbon energy future, steam turbines will remain central to meeting the growing demand for electricity, balancing energy supply with sustainability, and supporting the transition to renewable energy sources. Through technological advancements and global collaboration, steam turbine systems will continue to evolve, ensuring they remain a vital and reliable component in the ever-changing landscape of power generation.
Functionality of Steam Turbines
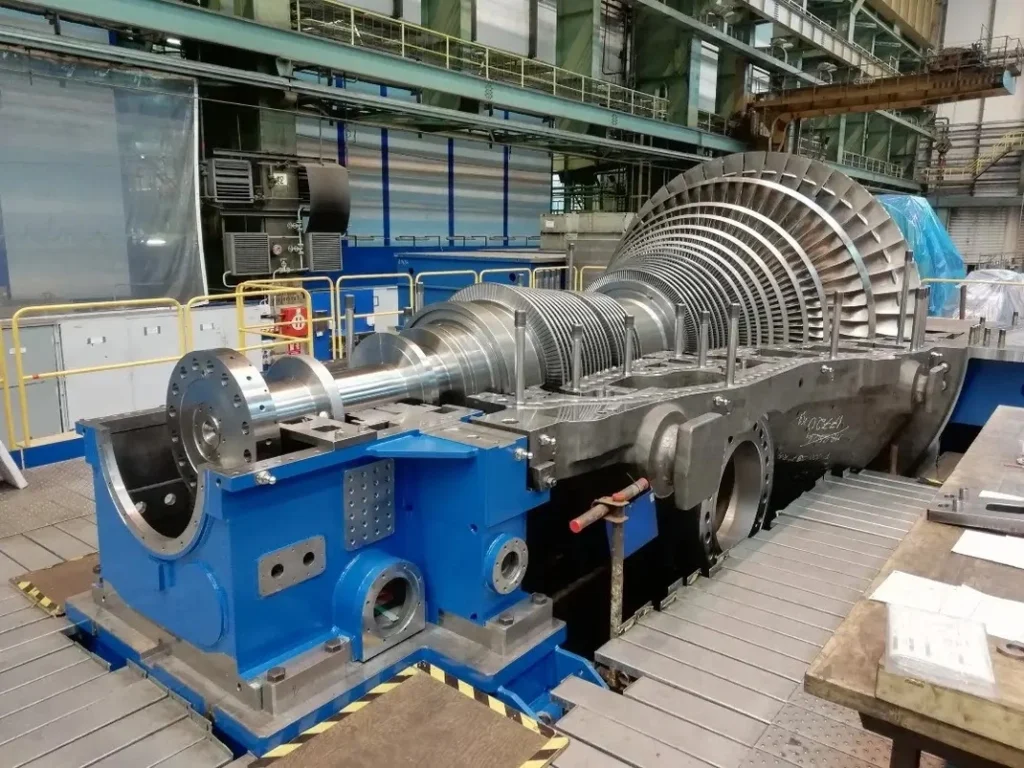
The functionality of steam turbines is intricately tied to their ability to convert thermal energy from steam into mechanical energy, which is then used to generate electricity or perform mechanical work. Understanding how steam turbines function involves delving into several key components, processes, and mechanisms that drive their operation, along with the factors that influence their efficiency and overall performance.
At the core of steam turbine functionality lies the principle of thermodynamics, which dictates how steam—created by heating water under pressure—transfers energy to the turbine blades, causing the turbine rotor to spin. This spinning motion is harnessed to generate electricity through the connected generator or to drive mechanical processes in industrial applications.
Thermodynamic Principles: Steam turbines operate primarily based on the Rankine cycle, which is a thermodynamic cycle involving the heating of water to create steam, followed by the expansion of this steam in the turbine to do mechanical work. The cycle involves the following steps: water is heated under pressure, converting it into steam; the steam then enters the turbine, where it expands, doing work on the turbine blades and causing the rotor to spin; and finally, the steam exits the turbine and is condensed back into water to repeat the process.
The expansion of steam in the turbine causes a reduction in pressure and temperature, which releases energy in the form of kinetic energy. This kinetic energy is converted into rotational mechanical energy as the steam flows over the blades of the turbine. The efficiency of this conversion depends on several factors, including the temperature and pressure of the steam entering the turbine, the speed at which the steam passes over the blades, and the design of the turbine itself.
Energy Conversion: In a steam turbine, thermal energy is converted into mechanical energy through the motion of steam. The process begins when high-pressure steam is directed onto the turbine blades. As the steam passes over the blades, it imparts its energy, causing the blades to move. This rotational motion of the blades is transferred to the shaft, which is connected to the turbine generator. The rotating shaft then drives the generator to produce electricity.
The steam’s kinetic energy is gradually transferred to the blades as the steam expands from high pressure to lower pressure through various stages of the turbine. In multi-stage turbines, steam passes through several sets of blades that progressively extract energy at different pressure levels. This staged expansion maximizes the efficiency of the energy conversion process and ensures that the steam turbine operates at optimal efficiency under a wide range of conditions.
Blade Design and Aerodynamics: The blades of a steam turbine are critical to its functionality. Their design is based on the aerodynamic principle of converting the kinetic energy of steam into rotational motion. As steam enters the turbine, it is directed onto stationary blades known as nozzles. These nozzles direct the steam flow onto the moving blades in a controlled manner, ensuring that the steam interacts with the blades at an optimal angle.
The blades are designed to efficiently capture the energy of the steam and convert it into rotational movement. The shape, material, and construction of the blades are optimized to withstand the high temperatures and pressures of steam while minimizing energy losses. Turbine blades are often made from advanced alloys that can resist thermal stress, corrosion, and erosion, ensuring long-term durability and consistent performance.
The efficiency of the energy conversion process is significantly influenced by the blade design. A turbine with more advanced and optimized blades can extract more energy from the steam, thus improving the turbine’s overall efficiency. Blade materials and design are particularly important in high-performance turbines used in combined-cycle or supercritical steam turbine systems, where operating conditions can be extreme.
Steam Flow Control: Controlling the flow of steam is essential for maximizing the functionality and efficiency of the turbine. Steam flow control involves regulating the pressure, temperature, and volume of steam entering the turbine. The control of steam flow ensures that the turbine operates at the optimal point of the Rankine cycle, where energy conversion is most efficient.
Steam is typically produced in a boiler, which heats water to high temperatures using a variety of heat sources such as burning fossil fuels, nuclear reactions, or renewable energy like geothermal energy. The steam is then fed into the turbine through valves that control the flow and pressure. These valves can adjust the amount of steam entering the turbine depending on the desired output and operational conditions, allowing the turbine to operate across a range of load demands.
In advanced turbine systems, steam flow is monitored and adjusted using sophisticated sensors and digital control systems. These systems provide real-time feedback on the performance of the turbine and adjust steam flow and operational parameters to optimize efficiency. For example, if the turbine is operating at a suboptimal load, the steam flow can be increased or decreased to match the optimal operating conditions.
Steam Expansion and Work Extraction: The primary function of the steam turbine is to expand steam from high pressure to low pressure, extracting work from the steam during the expansion process. The steam enters the turbine at high pressure and high temperature, where it passes through several stages of expansion. As the steam expands, it loses pressure and temperature, but its volume increases.
Each stage of the turbine contains a set of blades designed to extract energy from the steam. The steam transfers its energy to the blades, causing the blades to spin, which in turn drives the rotor and shaft. In multi-stage turbines, the steam undergoes expansion in several stages, which allows for a more gradual reduction in pressure and temperature. By spreading the energy extraction over multiple stages, the turbine can maintain higher efficiency and minimize the loss of energy.
The number of stages and the design of each stage depend on the operating conditions and the specific application of the turbine. In higher-capacity or high-efficiency turbines, such as those used in combined-cycle power plants, multiple stages are often used to ensure maximum energy extraction and minimize energy losses.
Condensing and Non-Condensing Systems: There are two main types of steam turbine systems: condensing and non-condensing turbines. The key difference between them lies in the way the exhaust steam is managed after it passes through the turbine.
In a condensing turbine system, steam is allowed to expand to a low pressure at the end of the turbine, causing it to cool and condense into water in a condenser. This water is then pumped back into the boiler to be reheated. Condensing turbines are commonly used in large-scale power plants where the turbine is part of a larger Rankine cycle, and the efficiency of energy conversion is maximized by extracting as much energy as possible from the steam.
In a non-condensing turbine, also known as a back-pressure turbine, the steam is allowed to exit the turbine at a higher pressure, which means that some of the energy remains in the steam for use in other processes. Non-condensing turbines are often used in industrial applications where both electricity and heat are needed, such as in chemical processing or district heating systems. These systems are more energy-efficient in applications that require both power and heat simultaneously.
Turbine Efficiency and Performance Factors: The efficiency of a steam turbine is a key factor in its functionality and operational costs. Several factors affect turbine efficiency, including steam quality, blade design, materials used, operational conditions, and system maintenance. The steam quality, which refers to the dryness of the steam and the absence of liquid water droplets, is critical to ensuring that the turbine blades do not suffer from erosion or corrosion, which would reduce efficiency.
Additionally, the turbine’s operational speed plays a role in how efficiently it can convert steam energy into mechanical energy. The steam turbine must operate at a speed that allows the blades to extract energy without exceeding the mechanical limits of the turbine components. Similarly, the turbine’s load-following capabilities and the ability to adjust to changing energy demands are crucial to ensuring continuous, efficient operation.
As turbine designs continue to improve with the adoption of advanced materials, higher efficiency levels are achieved. These improvements result in turbines that can operate at higher pressures and temperatures, extract more energy from the steam, and ultimately reduce the operational costs of the power plant or industrial process.
Conclusion: The functionality of steam turbines is built upon a series of carefully optimized processes that convert thermal energy into mechanical work. Through the principles of thermodynamics, steam expansion, energy conversion, and advanced blade design, steam turbines generate power in a highly efficient manner. The functionality of these turbines is continually evolving to meet the needs of modern power generation, integrating new technologies such as digital control systems, advanced materials, and greater fuel flexibility.
As steam turbines evolve, their role in supporting a cleaner, more sustainable energy future will only grow. Whether they are used in large-scale power plants, hybrid systems, or industrial applications, their ability to convert thermal energy into mechanical power will continue to be a cornerstone of energy generation worldwide. Their ongoing development, in terms of both efficiency and adaptability, will ensure they remain a critical component in the global transition to a low-carbon energy landscape.
As the demand for cleaner and more efficient energy sources increases, steam turbines continue to adapt to the evolving energy landscape. Their functionality is being enhanced through the integration of new technologies, materials, and innovative designs that improve both their performance and environmental impact. These developments are essential as industries and utilities aim to meet stricter emissions regulations and push toward a more sustainable future.
Digitalization and Automation: The rise of digital technologies, particularly in the realm of automation and data analytics, is reshaping how steam turbines are monitored and operated. The integration of smart sensors and real-time data analytics allows operators to gather detailed insights into turbine performance. By continuously collecting data on parameters such as pressure, temperature, vibration, and rotational speed, operators can make more informed decisions on turbine operations, detecting potential issues before they escalate into failures.
Predictive maintenance, driven by artificial intelligence (AI) and machine learning, is becoming increasingly common in turbine systems. By analyzing historical data, these technologies can predict when certain turbine components are likely to need maintenance or replacement, thereby minimizing unplanned downtime. This level of automation ensures turbines operate at peak efficiency and reduces operating costs by extending the life of critical components.
Digital control systems are also enabling more precise regulation of steam flow, temperature, and pressure, which directly influences turbine efficiency. These systems can respond dynamically to shifts in energy demand, adjusting the turbine’s operation in real time to ensure that it remains within its optimal performance range.
Carbon Capture and Storage (CCS) Integration: Another area where steam turbine functionality is evolving is in its integration with carbon capture and storage (CCS) technologies. In many power plants, particularly those relying on fossil fuels, steam turbines remain a core component of power generation. However, with the growing emphasis on reducing greenhouse gas emissions, there is increasing pressure on industries to capture and store carbon dioxide (CO₂) emissions.
While steam turbines themselves do not directly contribute to carbon emissions, their operation is often part of larger systems that rely on fossil fuels for steam generation. To meet global climate goals, many plants are adopting CCS systems that capture CO₂ from the exhaust gases of combustion processes before it enters the atmosphere. These systems often require additional energy to operate, which means that integrating CCS with steam turbines must be done efficiently to avoid significant losses in power generation capacity.
One method being explored is the use of steam turbines to drive the compressors that are essential to CO₂ capture and transportation. By integrating the turbine’s mechanical energy into the carbon capture process, the overall efficiency of the system can be improved. This synergy between steam turbines and CCS technologies helps reduce the carbon footprint of traditional power plants and plays a crucial role in achieving net-zero emissions targets.
Combined Heat and Power (CHP) Systems: Steam turbines continue to be integral to combined heat and power (CHP) systems, which offer a highly efficient way to use energy. In a CHP system, a steam turbine not only generates electricity but also provides useful heat for industrial processes or district heating. This dual-purpose approach maximizes energy utilization by capturing waste heat that would otherwise be lost in conventional power plants.
In industries such as chemical manufacturing, paper production, or food processing, where both electricity and heat are required, steam turbines in CHP systems can provide substantial cost savings and improve overall energy efficiency. The heat generated by the turbine can be used for a wide variety of processes, such as drying, heating, or powering mechanical equipment.
As global energy markets continue to evolve, CHP systems are becoming an increasingly popular solution for reducing energy consumption and emissions, particularly in areas where district heating infrastructure is already in place. By integrating steam turbines into these systems, industries can reduce their dependence on external power sources while simultaneously lowering their carbon footprint.
High-Efficiency and Supercritical Steam Turbines: Advances in materials science, particularly the development of heat-resistant alloys, are enabling steam turbines to operate at higher pressures and temperatures, further improving their efficiency. Supercritical steam turbines, which operate at pressures and temperatures above the critical point of water (374°C and 22.06 MPa), are at the forefront of this trend.
These high-efficiency turbines can achieve significantly higher thermal efficiency than conventional subcritical turbines, which operate at lower pressures and temperatures. Supercritical turbines extract more energy from the steam before it is exhausted, thus maximizing the conversion of thermal energy into mechanical energy. As a result, power plants utilizing supercritical steam turbines are able to produce more electricity from the same amount of fuel, reducing fuel consumption and lowering emissions.
Ultracritical turbines, which operate at even higher pressures and temperatures, are also being explored for use in next-generation power plants. These turbines represent the cutting edge of steam turbine design and hold the promise of even greater efficiency gains.
Sustainability and Green Energy Transitions: As the global energy industry shifts toward greener, more sustainable sources, steam turbines are evolving to support the transition to renewable energy. One of the most promising areas of development is in the adaptation of steam turbines for use with renewable fuels such as biomass, waste-to-energy technologies, and hydrogen.
For biomass-fired power plants, steam turbines are already a critical part of the system. Biomass can be used as a renewable fuel source that produces steam through combustion, which is then used to drive steam turbines. In such systems, turbines must be adapted to handle the potentially variable quality of biomass fuels and the associated particulate matter. However, the ability of steam turbines to run on biomass makes them an important technology in the context of achieving sustainable energy goals.
Hydrogen, a clean energy carrier, is also becoming an attractive alternative to fossil fuels. Steam turbines can be adapted to burn hydrogen, either as a pure fuel or as part of a blend with natural gas. In this configuration, hydrogen’s combustion produces only water vapor, significantly reducing carbon emissions from steam turbine operations.
Challenges in Steam Turbine Functionality: Despite all the advances in steam turbine technology, several challenges remain. One of the primary obstacles is the degradation of turbine components due to high thermal and mechanical stresses over time. As turbines operate at increasingly higher pressures and temperatures, components such as blades, seals, and bearings are subjected to significant wear and tear. Ensuring the durability and longevity of these parts is essential for minimizing downtime and reducing maintenance costs.
Another challenge is the need for greater flexibility in turbine operation. In modern energy systems, where demand can fluctuate rapidly and renewable generation is intermittent, steam turbines must be capable of starting up and shutting down quickly without compromising their efficiency. Traditional steam turbines, which were designed for steady, baseload operation, need to be re-engineered to handle these demands. Manufacturers are addressing this challenge by designing turbines that can handle more frequent cycling and ramping operations, without compromising their overall performance and longevity.
Future Outlook: The functionality of steam turbines will continue to evolve as part of the broader effort to meet the world’s energy needs sustainably and efficiently. Innovations in turbine design, materials, and operational flexibility will ensure that steam turbines remain an integral part of the global energy mix. Whether in traditional power plants, renewable energy systems, or industrial applications, steam turbines will play a vital role in converting thermal energy into mechanical work, driving progress toward a more sustainable future.
As technologies such as digitalization, hydrogen combustion, carbon capture, and energy storage become more widespread, steam turbines will adapt to ensure they remain at the forefront of efficient energy conversion. This adaptability, combined with advancements in efficiency and sustainability, will allow steam turbines to continue to meet the demands of a rapidly changing energy landscape, driving cleaner, more reliable, and cost-effective power generation.
Looking ahead, steam turbines will continue to play an important role in both traditional and emerging energy sectors, with several promising advancements set to enhance their capabilities and broaden their applications.
Integration with Hybrid Energy Systems: One of the growing trends in energy generation is the integration of multiple energy sources into hybrid systems. These systems combine steam turbines with other forms of power generation, such as solar, wind, and natural gas, to create a more flexible, resilient, and sustainable energy infrastructure.
For example, in solar thermal power plants, mirrors or lenses concentrate sunlight to heat a fluid, often water, which is then used to generate steam. This steam is passed through a steam turbine to generate electricity. By integrating solar energy with steam turbines, these systems can provide baseload power generation with a renewable source of energy. Steam turbines in these setups help to smooth out the intermittent nature of solar power, enabling continuous electricity generation, especially during cloudy days or at night when sunlight is unavailable.
In wind power hybrid systems, steam turbines can be coupled with wind energy to manage fluctuations in wind speed and maintain stable power output. Wind turbines often experience variable power generation due to changes in wind velocity. By pairing steam turbines with wind generation, operators can use steam turbine-based plants to compensate for these fluctuations and provide more consistent energy output to the grid.
Enhanced Materials for Durability and Performance: Material science advancements are crucial in pushing the boundaries of steam turbine functionality, especially as turbines are subjected to ever-increasing operational demands. The high temperature, pressure, and corrosive conditions in which steam turbines operate place substantial stress on turbine components. The development of advanced materials that can withstand these extreme environments while maintaining structural integrity is essential for improving turbine efficiency and reducing maintenance costs.
New materials, such as ceramic matrix composites and superalloys, offer enhanced resistance to heat, corrosion, and mechanical fatigue. These materials allow turbines to operate at higher temperatures and pressures, leading to greater efficiency. In addition, new coatings can help prevent wear and tear, extending the life of turbine blades and other components. This progress in materials science is critical for supporting the future of high-efficiency steam turbines that are capable of meeting the rigorous demands of modern power plants and industrial processes.
Advancements in Hybrid Fuel Systems: The future of steam turbines will also see innovations in the use of hybrid fuel systems. Hybrid systems combine multiple types of fuel to improve the flexibility and sustainability of power generation. One promising example is the combination of biogas and natural gas in steam turbines. This allows for cleaner energy production by incorporating renewable fuel sources, such as methane captured from landfills or agricultural waste, into traditional natural gas-powered plants.
Hydrogen is also emerging as a key fuel for the future of steam turbines. The combustion of hydrogen produces only water vapor as a byproduct, making it a clean alternative to fossil fuels. As hydrogen infrastructure grows and the cost of hydrogen production decreases, steam turbines will likely play a pivotal role in utilizing hydrogen for power generation. Hydrogen can be blended with natural gas in existing turbines or used in its pure form in specially designed systems.
Flexible Operation and Grid Integration: As renewable energy sources, like solar and wind, increase in prominence, the need for flexible power generation systems becomes more critical. Steam turbines are being redesigned to accommodate frequent cycling and rapid load-following capabilities. This means turbines must be able to start up and shut down quickly, adjust to varying power demand, and operate efficiently across a wide range of loads.
In these scenarios, steam turbines need to work in harmony with energy storage solutions like batteries or thermal storage systems. For instance, when renewable energy generation is high, excess energy can be stored and used to produce steam when generation is low, maintaining a steady supply of power. This integration between renewable energy, energy storage, and steam turbines will enable a more stable and reliable grid that can accommodate the fluctuating nature of renewable power sources.
Global Shift Toward Decentralized Energy Generation: The ongoing shift from centralized to decentralized energy systems is reshaping how steam turbines are used. Instead of large, centralized power plants, smaller distributed energy systems are becoming increasingly common. These systems allow energy to be generated closer to where it is consumed, reducing transmission losses and improving energy security. Steam turbines can be adapted for smaller-scale applications such as combined heat and power (CHP) systems for industrial facilities, district heating systems, or even standalone power generation for remote communities.
These decentralized systems offer flexibility and allow for more efficient energy use in urban and rural settings. In industrial settings, the integration of steam turbines in CHP systems ensures that both electricity and heat are used in the most efficient manner, while reducing the environmental impact of fossil fuel consumption.
Environmental Impact Reduction: The future of steam turbines is deeply connected to efforts aimed at reducing the environmental impact of power generation. While steam turbines themselves are relatively clean compared to other mechanical technologies, their associated power generation systems—especially those that burn fossil fuels—are significant sources of carbon emissions. To address this, many utilities and industries are investing in carbon capture and storage (CCS) technologies to capture CO₂ emissions from the combustion process before they enter the atmosphere.
CCS, when integrated with steam turbines in coal or natural gas plants, can help reduce the overall carbon footprint of electricity generation. Though CCS still faces challenges in terms of cost and scalability, its integration with steam turbines holds great potential for reducing emissions from existing infrastructure.
Additionally, waste heat recovery systems are becoming increasingly important in minimizing the environmental impact of steam turbine systems. By capturing waste heat from industrial processes or power plants, steam turbines can convert this otherwise wasted energy into useful electricity or mechanical work, improving the overall energy efficiency of the system.
R&D and Future Innovations: Research and development in steam turbine technology will continue to push the boundaries of what is possible in terms of efficiency, sustainability, and performance. This includes innovations in advanced control systems that enable turbines to respond in real-time to grid demands, developments in advanced alloys and materials for longer-lasting turbine components, and improvements in turbine design to reduce noise, vibration, and other mechanical stresses.
The future of steam turbines is also intertwined with the development of next-generation power plants that combine steam turbines with advanced technologies like molten salt storage and supercritical CO₂ cycles. By utilizing new methods of energy conversion and storage, these next-gen plants could enhance the performance and environmental sustainability of steam turbines.
Conclusion: As the energy sector evolves toward greater sustainability, steam turbines remain a cornerstone of efficient energy conversion. Their ability to generate reliable, cost-effective power will continue to be essential as the world moves towards a more decentralized, flexible, and environmentally conscious energy grid.
The development of hybrid systems, the incorporation of renewable fuels, advancements in materials, and the integration of smart technologies all contribute to the ongoing evolution of steam turbines. They are not just adapting to the future of energy—they are driving it forward, helping to meet the growing global demand for cleaner, more efficient, and more flexible energy systems. With these advances, steam turbines will continue to be a vital technology in the transition to a low-carbon energy future, ensuring that power generation remains reliable, sustainable, and adaptable in an ever-changing world.
Looking even further into the future, the evolution of steam turbines will be influenced by a variety of factors including technological innovation, shifting global energy priorities, and the urgent need for sustainable development. There are several key areas where steam turbine technology will likely continue to evolve, making them even more integral to the global energy mix.
The Role of Steam Turbines in the Circular Economy
As industries increasingly embrace the circular economy model, where resources are reused, recycled, and repurposed to reduce waste and optimize resource efficiency, steam turbines will have an important role to play. For example, steam turbines can be integrated into systems designed to capture waste heat from industrial processes and use it for other operations, whether that’s for heating, cooling, or generating electricity. This further reduces the demand for new resources and decreases energy consumption. In particular, the recovery and use of waste heat can be enhanced by implementing combined heat and power (CHP) systems, which maximize the utility of steam turbines by generating both electrical and thermal energy from the same fuel source.
Additionally, steam turbines can be integrated into waste-to-energy technologies that repurpose municipal solid waste, agricultural waste, and other forms of waste biomass to produce steam, which can then be used to drive turbines and generate electricity. By utilizing waste as a fuel source, power generation becomes more sustainable, reducing the need for raw materials and decreasing the volume of waste sent to landfills.
Decarbonization and the Role of Green Hydrogen
One of the most promising trends for the future of steam turbines is the increasing focus on green hydrogen. Produced by electrolyzing water using renewable electricity, green hydrogen offers a carbon-neutral fuel source that can be used in steam turbines as a replacement for fossil fuels. The ability to use hydrogen in steam turbines aligns with global efforts to decarbonize the energy sector and mitigate climate change.
Hydrogen-powered steam turbines could play an essential role in gas-fired power plants by replacing or blending hydrogen with natural gas to create lower-emission power generation systems. The challenge remains, however, in scaling up hydrogen production and ensuring that it can be delivered at a low enough cost for widespread use. Nevertheless, with growing investment in hydrogen infrastructure and ongoing advancements in electrolyzer technologies, green hydrogen may become a significant contributor to power generation in the coming decades, potentially fueling steam turbines for the production of clean, baseload electricity.
Integration with Energy Storage Systems
As the share of intermittent renewable energy sources like wind and solar continues to grow, the integration of energy storage technologies with steam turbines will become increasingly important. By coupling steam turbines with advanced energy storage systems, such as battery storage, pumped hydro storage, or thermal energy storage, power plants will be able to store excess energy generated during periods of low demand or high renewable generation. This stored energy can then be used to produce steam and power turbines when demand spikes or renewable generation drops.
Thermal energy storage works by storing excess heat in materials like molten salts or solid media, which can be converted back into steam to drive turbines. This form of storage is particularly well-suited for large-scale power plants that use steam turbines, allowing for more flexible and reliable operations, while also enhancing the plant’s ability to integrate renewable energy sources.
By effectively integrating energy storage with steam turbines, power plants can become more resilient, flexible, and able to support the transition to a renewable-powered energy system.
High-Temperature and High-Pressure Steam Turbines
The increasing demand for efficiency in power generation means that steam turbines will continue to operate at higher temperatures and pressures than ever before. As turbine designers strive for maximum efficiency, the potential to use supercritical steam conditions will continue to expand. Supercritical steam operates at pressures and temperatures beyond the critical point of water, where it exhibits unique thermodynamic properties that result in higher efficiency when driving turbines.
Advancements in supercritical and ultracritical steam turbines will allow for even greater heat-to-power conversion efficiency, reducing fuel consumption and emissions in the process. These high-efficiency turbines are expected to be crucial for achieving decarbonization goals in both conventional and renewable energy contexts.
For example, combined-cycle power plants that use a combination of gas and steam turbines will benefit from supercritical steam cycles. This hybrid system maximizes efficiency by using the waste heat from gas turbines to generate steam, which then powers steam turbines. Such plants are some of the most efficient in the world, but further advancements in high-temperature steam turbine technology could push efficiency levels even higher.
Optimizing Energy Systems with AI and Machine Learning
The future of steam turbine technology will be increasingly intertwined with artificial intelligence (AI) and machine learning. These advanced technologies will enable power plants to better optimize turbine performance, anticipate maintenance needs, and enhance operational efficiency. By incorporating AI into turbine design and operations, systems can adapt to changing conditions in real time, ensuring that turbines operate within their optimal parameters.
Machine learning algorithms can predict wear and tear on turbine components by analyzing vast amounts of data collected from sensors embedded in the turbine system. These systems can identify early signs of mechanical failure or performance degradation, allowing operators to carry out preventive maintenance before expensive breakdowns occur. AI can also help with the optimization of turbine load management, ensuring that the turbine operates efficiently across a range of variable operating conditions, such as fluctuating demand or changes in fuel quality.
Furthermore, machine learning could be used to dynamically adjust turbine settings in response to grid demand, improving overall system reliability and responsiveness. By helping optimize steam turbine operations through digital transformation, AI and machine learning will make steam turbines more efficient, cost-effective, and reliable.
Resilience in the Face of Climate Change
As climate change continues to impact global weather patterns, the ability of steam turbines to perform in extreme conditions will become increasingly important. Extreme weather events, such as heatwaves, hurricanes, floods, and droughts, can disrupt the operation of traditional power plants. In some cases, high temperatures can cause water sources to become too warm for effective cooling, while flooding and storms may damage infrastructure. Steam turbines will need to be resilient enough to operate in these increasingly challenging conditions.
One way to address this is by developing modular steam turbine systems that can be quickly deployed in remote or affected areas, offering flexibility and backup power capabilities. Additionally, resilient cooling systems are being developed to enable turbines to continue operating under challenging conditions, such as those caused by heatwaves or water shortages. By enhancing the resilience of steam turbines, they can continue to provide reliable power even in the face of extreme weather events linked to climate change.
Conclusion
The future of steam turbines is bright, with a myriad of technological advancements and growing demands for clean energy and efficiency paving the way for their continued importance in power generation and industrial applications. Through the integration of renewable energy, energy storage, hybrid fuels, digital technologies, and advanced materials, steam turbines will remain essential to a sustainable energy future.
As global energy systems continue to shift toward lower-carbon alternatives, steam turbines will be adaptable to new fuel sources such as hydrogen, biomass, and waste materials. Innovations in turbine design, automation, and smart monitoring will further improve their efficiency and reliability, ensuring that steam turbines continue to meet the energy demands of the future.
Ultimately, steam turbines will remain at the heart of the energy transition—enabling cleaner, more flexible, and more efficient power generation. Their role in supporting the decarbonization of the energy sector, improving industrial efficiency, and integrating renewable energy will continue to be critical as the world strives to build a sustainable and resilient energy system for future generations.
Steam Turbine Power Output Analysis
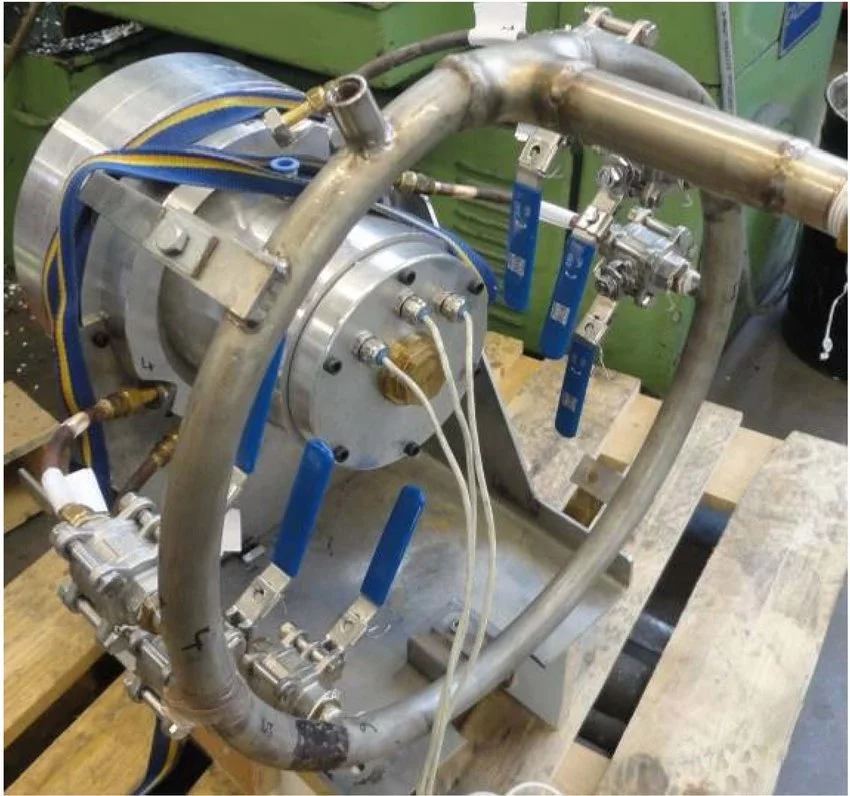
The analysis of steam turbine power output is a critical component in the design, operation, and optimization of steam turbines. It involves evaluating various factors that influence the efficiency, performance, and overall energy conversion capacity of the turbine. The power output of a steam turbine is typically a function of several key variables, including steam pressure, temperature, flow rate, and turbine design. Understanding these factors, and how they interact, is essential for maximizing the efficiency of power plants and industrial systems that rely on steam turbines.
Thermodynamics and Power Output
The thermodynamic principles that govern steam turbine performance are rooted in the laws of energy conversion, particularly the conversion of thermal energy (from steam) into mechanical energy (to drive the turbine rotor). This process is influenced by thermodynamic cycles, most commonly the Rankine cycle, which is the fundamental operating cycle for steam turbines. The efficiency of the steam turbine in converting thermal energy to mechanical energy depends largely on the steam conditions—primarily temperature and pressure—and the turbine’s operational parameters.
In an ideal Rankine cycle, steam is heated in a boiler to generate high-pressure, high-temperature steam. This steam is then expanded through the turbine, where it loses pressure and temperature, transferring energy to the turbine blades, which rotate and drive a generator to produce electrical power. The efficiency of this energy conversion process is determined by the temperature difference between the steam entering the turbine and the steam exiting it. The larger this difference, the more work can be extracted, and the greater the potential power output.
To calculate the theoretical power output of a steam turbine, several key thermodynamic relationships are used:
- Turbine Power Output Equation:P=m˙×(h1−h2)P = \dot{m} \times (h_1 – h_2)P=m˙×(h1−h2)Where:
- PPP is the power output (in watts or megawatts),
- m˙\dot{m}m˙ is the mass flow rate of steam (in kg/s),
- h1h_1h1 is the enthalpy of the steam entering the turbine (in kJ/kg),
- h2h_2h2 is the enthalpy of the steam exiting the turbine (in kJ/kg).
- Efficiency Considerations: The efficiency of a steam turbine is the ratio of useful power output to the total energy input from the steam. Real turbines, however, do not operate in an ideal thermodynamic environment, and losses due to friction, heat dissipation, and mechanical inefficiencies reduce their effectiveness. These losses are factored into the overall isentropic efficiency of the turbine, which is a measure of how close the turbine’s actual performance is to the theoretical ideal.Isentropic efficiency is calculated as:\eta = \frac{h_1 – h_2_{ideal}}{h_1 – h_2_{actual}}Where:
- h_2_{ideal} is the enthalpy at the ideal (isentropic) exit state,
- h_2_{actual} is the enthalpy at the actual exit state.
Key Factors Affecting Steam Turbine Power Output
- Steam Temperature and Pressure: The temperature and pressure of the steam entering the turbine are perhaps the most important factors in determining the power output. Higher temperature and pressure typically result in higher enthalpy, which leads to more energy being available for conversion into mechanical work. However, increasing the steam temperature and pressure requires the use of advanced materials that can withstand higher stresses, and such turbines need to be designed for high-temperature operation, typically using superalloys and advanced coatings.
- Steam Quality and Flow Rate: The steam quality, defined as the fraction of the steam that is in the vapor phase (as opposed to being a mixture of liquid and vapor), directly affects the turbine’s performance. Higher quality steam ensures that the turbine operates more efficiently by reducing the potential for erosion and cavitation, which can reduce power output over time. The flow rate of steam, or the mass of steam entering the turbine per unit of time, is another crucial parameter. A higher flow rate means more steam is available to produce power, thus increasing the overall output of the turbine.
- Turbine Efficiency and Mechanical Losses: In practice, turbines experience a variety of mechanical losses due to friction, vibration, and imperfections in blade design. These losses are inevitable but can be minimized with precise engineering and maintenance. Turbine efficiency decreases when mechanical losses increase, reducing the total power output for a given steam input.
- Turbine Design and Configuration: The design and configuration of the turbine play a critical role in its power output. Different types of turbines, such as impulse turbines and reaction turbines, have different characteristics. Impulse turbines, for example, convert the kinetic energy of steam into mechanical energy by directing the steam jets onto blades, while reaction turbines rely on the pressure difference between the steam inlet and exhaust. The choice of turbine design impacts how efficiently the turbine extracts energy from steam and influences the overall power output.
- Exhaust Pressure: The exhaust pressure, or the pressure at which steam leaves the turbine, also affects the power output. A lower exhaust pressure (often achieved using a condenser) allows the steam to expand more fully and extract more energy, thereby increasing the power output. The efficiency of the condenser and the ability to maintain low exhaust pressure are important factors for ensuring maximum energy extraction from the steam.
- Partial Load Operation: Steam turbines are often designed to operate at a specific capacity, but in real-world applications, they may be required to operate at partial load conditions. When operating at less than full load, the turbine’s power output will decrease proportionally, and there may be additional losses due to suboptimal efficiency at lower operating levels. In these situations, turbine performance analysis helps identify ways to improve efficiency or minimize losses during partial load operation.
Power Output Optimization
To optimize steam turbine power output, power plants can implement various strategies that maximize efficiency and minimize losses. These strategies may include:
- Reheating and Regeneration: Reheating steam between stages of expansion can increase the power output by maintaining higher steam temperatures throughout the turbine. Additionally, regenerative feedwater heating, which recovers heat from the turbine exhaust and uses it to preheat the feedwater entering the boiler, can improve overall cycle efficiency.
- Control and Monitoring Systems: Modern steam turbines are equipped with advanced monitoring systems that allow operators to adjust operational parameters in real time to maintain optimal performance. Sensors and control systems can detect changes in steam pressure, temperature, and flow rate, enabling operators to make adjustments that enhance efficiency and prevent operational issues that could impact power output.
- Upgrades and Retrofits: In older turbines, upgrading or retrofitting key components, such as blades, nozzles, and seals, can improve performance and increase power output. Advances in materials and manufacturing processes have made it possible to enhance turbine efficiency by improving the aerodynamics and thermal resistance of key turbine components.
Conclusion
The power output of a steam turbine is influenced by a complex interplay of thermodynamic, mechanical, and design factors. By understanding these factors and optimizing turbine operations, operators can maximize the efficiency and performance of steam turbines, leading to higher power output and more sustainable energy generation. Whether in traditional fossil fuel-based power plants, nuclear power stations, or renewable energy systems, steam turbines remain a cornerstone of modern power generation, and the ongoing analysis of their power output is critical for ensuring that they operate at peak efficiency.
The power output of a steam turbine is influenced by a variety of factors, all of which need to be optimized for maximum efficiency and performance. At its core, the steam turbine converts thermal energy from steam into mechanical energy by exploiting the difference in pressure and temperature as steam expands across the turbine blades. The basic thermodynamic principles driving this conversion are governed by the Rankine cycle, which is the foundation for most steam turbine operations. By understanding the relationship between steam conditions—such as pressure, temperature, flow rate, and quality—and turbine design, operators can effectively predict and enhance the power output of the system.
When analyzing steam turbine power output, the key consideration is the enthalpy difference between the steam entering and exiting the turbine. The greater the difference in enthalpy, the more work can be extracted by the turbine. This is typically achieved by maximizing the temperature and pressure of the steam entering the turbine. However, it’s essential to balance this with the need for advanced materials capable of withstanding the high stresses and heat involved in such operations. Materials like superalloys and ceramic coatings are employed to handle the extreme conditions found in high-temperature turbines.
Another critical factor in steam turbine power output is the mass flow rate of steam. The more steam flowing through the turbine, the greater the amount of energy available for conversion into mechanical work. However, the quality of the steam—how much of it is in a gaseous versus a liquid state—also plays a significant role in determining turbine efficiency. If the steam quality is low (e.g., when steam is too saturated with water), it can lead to mechanical issues such as erosion and reduced efficiency in the turbine.
In addition to steam conditions, turbine design is paramount. Different types of turbines (impulse vs. reaction) operate on distinct principles, impacting how efficiently they convert energy from the steam. For example, impulse turbines convert kinetic energy into mechanical energy through high-speed steam jets, while reaction turbines rely on the pressure drop across the blades to generate power. Each design has its benefits depending on the operational requirements, and the choice of turbine can greatly influence the total power output.
The operation of the turbine is also impacted by the exhaust pressure, or the pressure at which the steam exits the turbine. Lower exhaust pressure allows for a greater expansion of steam, which leads to a higher energy extraction and more power output. Condenser systems that maintain low exhaust pressure are often used to achieve this effect, improving overall performance. Conversely, higher exhaust pressures can limit energy extraction, resulting in reduced power output.
A critical aspect of real-world turbine operation is managing partial load conditions. Many steam turbines are designed for maximum efficiency at full load, but in practice, they often operate at less than optimal conditions. During these times, there are often additional mechanical losses due to suboptimal operating parameters, and these can reduce the power output of the turbine. The ability to adapt to such changes, optimize turbine settings, and prevent efficiency losses during partial load conditions is a key aspect of effective steam turbine power output management.
Furthermore, optimizing power output often involves improving the efficiency of the steam cycle through technological innovations. For example, reheating the steam between turbine stages can help maintain higher temperatures and pressures, thereby increasing the amount of energy extracted. Similarly, regenerative feedwater heating is another technique where heat from the turbine’s exhaust is used to preheat the water entering the boiler, reducing fuel consumption and improving the overall thermodynamic efficiency of the cycle.
Modern steam turbines also benefit from advanced control and monitoring systems that provide real-time data on operational conditions such as steam flow, temperature, pressure, and mechanical integrity. By continuously monitoring these parameters, turbine operators can make adjustments to maintain the turbine’s performance at optimal levels. These systems can also help predict when maintenance is needed, preventing unplanned downtime and ensuring that the turbine operates efficiently over time.
Another avenue for improving steam turbine power output is through the retrofit and upgrade of key turbine components. As turbines age or as new technological advances become available, components such as blades, nozzles, seals, and bearings can be replaced with more efficient versions. Modern materials and manufacturing techniques can significantly improve turbine performance by increasing thermal resistance, enhancing the aerodynamic properties of blades, and reducing mechanical losses from friction and wear.
In summary, optimizing steam turbine power output involves a comprehensive approach that includes maximizing the energy conversion efficiency of the thermodynamic cycle, selecting appropriate turbine designs, managing steam quality and flow rates, and maintaining low exhaust pressures. Additionally, technological advances, such as reheating, regenerative feedwater heating, and upgrades to turbine components, contribute to increasing efficiency and power output. With continuous improvements in turbine design, monitoring, and material technology, steam turbines will remain central to efficient power generation for a wide variety of applications, from traditional fossil fuel plants to emerging renewable energy systems.
To continue enhancing steam turbine power output, advancements in materials science and turbine design are expected to play a major role. As the push for higher efficiency and greater sustainability intensifies, innovations in both material durability and turbine architecture are becoming increasingly important. Higher operating temperatures and pressures demand new materials capable of maintaining strength and integrity under extreme conditions. For example, ceramic matrix composites and superalloys are already being used in turbine blades and other critical components, offering improved resistance to thermal stresses, oxidation, and corrosion. These materials can withstand the intense heat and mechanical stresses within a turbine, enabling more efficient energy conversion at higher temperatures and pressures.
In parallel, improvements in aerodynamics and thermodynamics of the turbine blades are also being pursued. The shape and design of the blades significantly influence the efficiency with which steam energy is converted into mechanical power. Advances in computational fluid dynamics (CFD) and blade design optimization techniques allow for more precise engineering, leading to blades that can extract more energy from steam while minimizing losses due to turbulence, friction, and vibration. By improving blade geometry and materials, steam turbines can achieve greater mechanical output with the same or even lower steam input, leading to higher power generation efficiency.
Moreover, digitalization and smart monitoring are transforming the way turbines are operated and maintained. Sensors embedded in turbines can continuously collect real-time data on parameters such as temperature, pressure, vibration, and steam quality. This data can be used to optimize turbine performance, detect anomalies before they lead to failure, and adjust operational settings in real time to maintain optimal power output. Machine learning algorithms can be applied to this data to predict maintenance needs, identify efficiency gaps, and optimize operational parameters. For example, AI-based systems can analyze patterns in turbine performance and suggest adjustments to steam flow, exhaust pressure, or other operational settings to enhance power output.
The ability to predict and address potential failures before they occur is another critical benefit of digitalization. By leveraging predictive maintenance strategies, operators can prevent unplanned downtime, reduce repair costs, and extend the lifespan of the turbine. This proactive approach minimizes disruptions in power generation and ensures that turbines remain in peak condition, consistently delivering high power output.
The integration of renewable energy sources into steam turbine systems is another area where advancements will have a significant impact on power output analysis. As renewable energy sources like wind and solar power become more prevalent, steam turbines are increasingly being paired with energy storage systems to provide a reliable and flexible power generation solution. For example, thermal energy storage systems can store excess energy generated by renewables during periods of high generation and release it as heat to generate steam when demand is high. This stored energy can then drive steam turbines to provide power when renewable sources are less available, helping to stabilize the grid and maintain consistent power output.
Additionally, hybrid systems that combine steam turbines with other power generation technologies, such as gas turbines or solar thermal energy, are gaining traction. In such systems, steam turbines can operate in tandem with other energy sources to optimize the overall efficiency and power output. For example, in a combined-cycle power plant, the waste heat from a gas turbine can be used to generate steam, which in turn drives a steam turbine, creating a more efficient and flexible power generation system. This approach maximizes the use of available energy and reduces the overall environmental footprint of the system.
As the energy industry continues to evolve, flexibility in steam turbine operations will become increasingly important. Modern turbines are being designed with the capability to ramp up and down more quickly, enabling them to respond to fluctuations in grid demand and variations in renewable energy output. This flexibility is particularly crucial for supporting intermittent energy sources like wind and solar, which can experience fluctuations in generation based on weather conditions. Steam turbines that are able to quickly adjust their output can help balance the grid and provide a reliable source of baseload power, ensuring the stability and reliability of the energy system.
In the context of carbon reduction and decarbonization, steam turbines will continue to be essential in the transition to cleaner energy. By improving the efficiency of steam cycles, integrating renewable energy sources, and utilizing low-carbon fuels such as hydrogen or biofuels, steam turbines will play a central role in reducing the carbon footprint of the power generation sector. The development of hydrogen-powered steam turbines represents a significant opportunity to decarbonize heavy industries and power generation, offering a path toward cleaner, more sustainable energy systems.
The role of steam turbines in distributed energy systems is also gaining prominence. As power generation becomes more decentralized and localized, smaller-scale steam turbines will be used in applications such as combined heat and power (CHP) systems for industrial processes, district heating, and remote communities. These distributed systems allow for more efficient and localized energy production, reducing transmission losses and enhancing energy security.
As we look to the future of steam turbines, their role in sustainability and energy resilience will continue to evolve. Advancements in turbine design, materials, control systems, and integration with renewable energy sources will all contribute to improving the power output of steam turbines. By maximizing efficiency, reducing emissions, and increasing flexibility, steam turbines will remain a cornerstone of the global energy landscape, helping to meet growing demand for power while supporting the transition to a more sustainable and resilient energy system.
In conclusion, steam turbines will continue to be a critical technology for power generation in the coming decades. The increasing demand for efficiency, sustainability, and flexibility will drive innovations in turbine design, materials, and operational strategies. From improving thermodynamic cycles and optimizing energy conversion to leveraging digital technologies for predictive maintenance and performance enhancement, steam turbines are well-positioned to remain at the forefront of the global energy transition. Whether in large-scale power plants, renewable energy integration, or distributed energy systems, steam turbines will continue to play a key role in providing reliable, efficient, and clean power to meet the needs of a rapidly changing world.
As the demand for energy continues to grow and the world shifts toward cleaner, more sustainable energy systems, steam turbines will evolve in response to new challenges and opportunities. The integration of digital technologies, advanced materials, and hybrid systems will play a pivotal role in enhancing the performance and efficiency of steam turbines. One of the key developments on the horizon is the transition to low-carbon fuels, such as hydrogen, biofuels, and synthetic fuels, which can be used in place of conventional fossil fuels in steam turbines. This transition offers a path toward reducing the carbon footprint of power generation while maintaining the efficiency and reliability of steam turbines.
Hydrogen, in particular, holds great promise as a clean fuel for steam turbines. When burned or used in fuel cells, hydrogen produces only water vapor as a byproduct, making it an ideal fuel for reducing greenhouse gas emissions. In hydrogen-powered steam turbines, hydrogen can be combusted to generate steam, which then drives the turbine. This process, when coupled with advanced turbine designs and efficient thermodynamic cycles, can help achieve near-zero emissions in power generation. Hydrogen can also be produced using renewable energy sources through electrolysis, creating a closed-loop system where clean energy is used to produce fuel, which in turn powers turbines with minimal environmental impact.
In addition to hydrogen, biofuels are gaining traction as a renewable energy source for steam turbines. Biofuels, derived from organic materials such as plant matter, algae, and waste products, can be used to generate steam in a similar way to conventional fuels. When sourced sustainably, biofuels can provide a low-carbon alternative to fossil fuels, contributing to a circular economy and reducing the environmental impact of power generation. Many power plants are already experimenting with co-firing biofuels alongside traditional fuels to reduce emissions and enhance sustainability.
Another promising area of innovation for steam turbines is their integration with thermal energy storage systems. Thermal energy storage allows excess energy to be stored as heat during periods of low demand or when renewable energy generation is high. This stored thermal energy can then be used to generate steam when demand rises or when renewable sources are less available, helping to balance the grid and provide a reliable source of power. Technologies such as molten salt storage, phase-change materials, and high-temperature thermal storage are being developed to improve the efficiency and scalability of thermal energy storage systems, providing greater flexibility in power generation.
The role of steam turbines in distributed energy systems is also becoming more important. As the world moves toward a more decentralized energy grid, smaller-scale steam turbines are being used in a variety of applications, such as combined heat and power (CHP) systems for industrial facilities, district heating systems, and remote off-grid communities. These distributed systems allow for more efficient and localized energy production, reducing transmission losses and enhancing energy resilience. In areas where the electrical grid is unreliable or non-existent, steam turbines can provide a crucial source of power for essential services and industries.
The growing emphasis on resilience in the energy sector also presents an opportunity for steam turbines. As extreme weather events and natural disasters become more frequent, there is an increasing need for power generation systems that are robust, flexible, and capable of quickly responding to disruptions. Steam turbines, with their ability to operate at various scales and integrate with other forms of energy, are well-suited for meeting these needs. Their ability to provide baseload power while also being adaptable to changing conditions makes them a key component of resilient energy systems.
In addition, the development of advanced control systems and artificial intelligence (AI) will continue to shape the future of steam turbine operation. AI-based systems can analyze vast amounts of data collected from sensors embedded in turbines, allowing operators to predict performance issues, optimize operating conditions, and schedule maintenance more efficiently. For instance, predictive algorithms can anticipate when a turbine is likely to experience a decrease in efficiency or failure, enabling proactive maintenance to minimize downtime and extend the turbine’s lifespan. These smart systems will not only help reduce costs but also improve overall system performance by ensuring that turbines operate at their peak efficiency for longer periods.
Furthermore, energy efficiency programs and policy frameworks are likely to play a significant role in driving the future development of steam turbines. Governments and regulatory bodies are increasingly focused on incentivizing the adoption of low-carbon technologies and improving the energy efficiency of power generation. Policies such as carbon pricing, emissions trading, and renewable energy targets can encourage the deployment of advanced steam turbine technologies that maximize efficiency and minimize environmental impact. International collaborations and investments in research and development will also be essential for advancing steam turbine technology and facilitating the transition to sustainable energy systems.
As the global energy landscape continues to evolve, the role of steam turbines will expand to encompass not only traditional power generation but also emerging technologies such as carbon capture and storage (CCS) and small modular reactors (SMRs). In CCS systems, steam turbines are often used to drive compressors and other equipment needed for capturing and storing carbon emissions from power plants. In SMRs, which are small-scale nuclear reactors, steam turbines can be used to convert heat from the reactor into electricity. These innovations will allow steam turbines to contribute to a wide range of decarbonization efforts and clean energy solutions.
Looking further ahead, fusion energy could also have a profound impact on the future of steam turbine technology. Although fusion power is still in the experimental stages, if it becomes commercially viable, it will produce vast amounts of heat that could be harnessed to generate steam and drive turbines. The potential for fusion-powered steam turbines would provide a nearly unlimited source of clean energy, revolutionizing the global power generation industry.
In conclusion, the future of steam turbines is marked by a convergence of technological innovations, sustainable energy solutions, and evolving power generation needs. As steam turbines continue to evolve in response to the challenges of decarbonization, renewable energy integration, and grid flexibility, they will remain a cornerstone of modern power generation. By improving turbine efficiency, adopting low-carbon fuels, integrating renewable energy sources, and leveraging digital technologies, steam turbines will play a vital role in creating a more sustainable, resilient, and flexible global energy system. As the world strives toward a cleaner, more efficient energy future, steam turbines will remain at the forefront of this transition, providing reliable and flexible power to meet the needs of future generations.
Differences Between Impulse and Reaction Steam Turbines
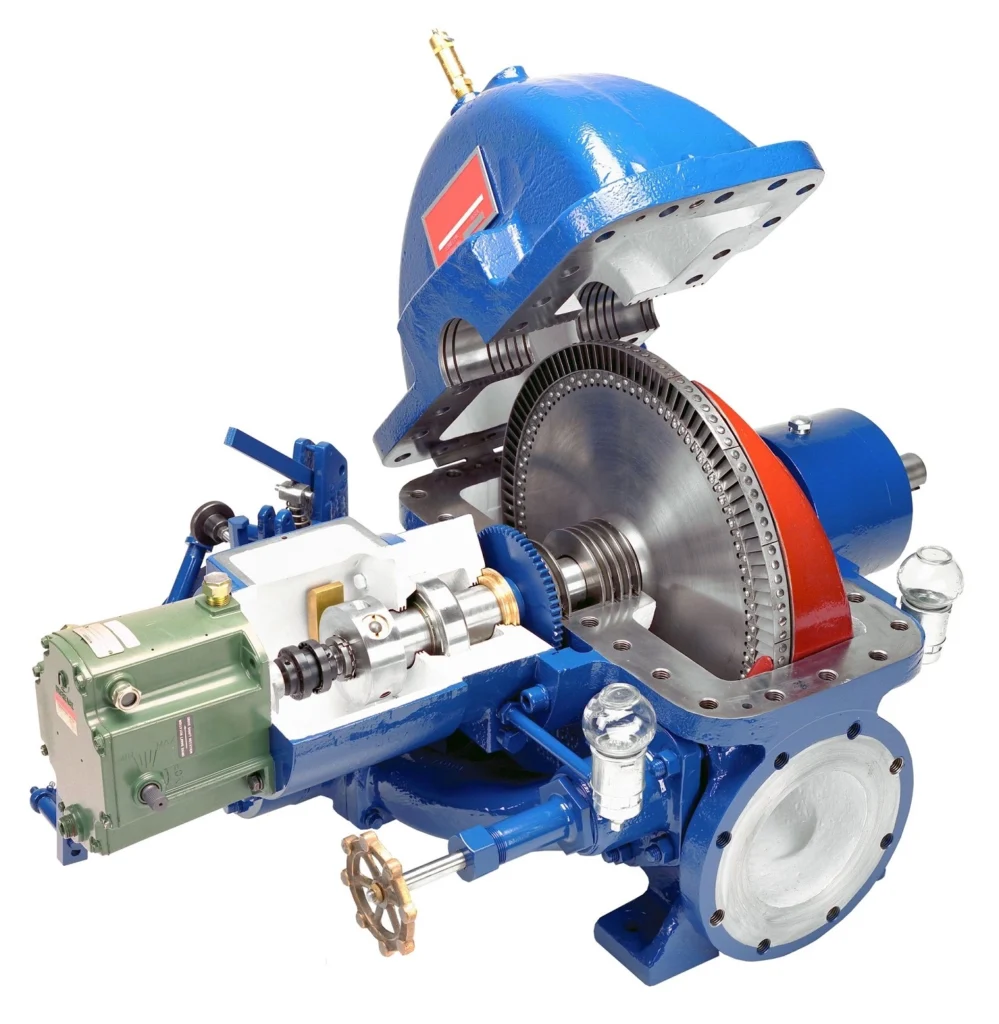
Impulse and reaction steam turbines are two of the most commonly used types of turbines in the power generation industry, and while they both convert thermal energy from steam into mechanical energy, they do so using different principles and designs. These differences significantly influence their efficiency, performance, and suitable applications. Understanding the key distinctions between impulse and reaction turbines can provide a clearer picture of how they operate and what makes each type suitable for various industrial uses.
Impulse Steam Turbines
Impulse turbines operate on the principle of impulse, which involves converting the kinetic energy of the steam into mechanical energy by directing high-velocity steam jets onto blades. In an impulse turbine, the steam is first expanded through a nozzle, where its pressure is reduced and velocity increases. The high-speed steam is then directed at the turbine blades, causing the blades to rotate. The turbine blades themselves do not affect the steam’s pressure directly, but rather the steam’s velocity and kinetic energy. The steam pressure drops entirely in the nozzles before it strikes the blades, and the only energy that drives the turbine comes from the kinetic energy of the steam jets.
The key features of an impulse turbine include:
- Energy Conversion: The turbine blades are designed to convert the kinetic energy of the steam directly into mechanical work. This results in a rapid transfer of energy.
- Design: Impulse turbines are typically made of multiple stages, with each stage containing nozzles and blades that further convert steam energy.
- Pressure Drop: The pressure drop of steam occurs solely in the nozzles, with the steam entering the turbine blades at constant pressure.
- Applications: Impulse turbines are best suited for high-pressure steam conditions, where the steam enters the turbine with high velocity. They are often used in applications like small to medium-sized power plants and in systems where steam pressure is already high.
One of the advantages of impulse turbines is their simple design and ability to handle high-velocity steam with relatively low thermal stress. They are often more cost-effective than reaction turbines and are used in applications with lower steam flow rates or where simplicity and reliability are critical.
Reaction Steam Turbines
Reaction turbines, on the other hand, operate on the principle of reaction, where steam pressure drops gradually across each stage of the turbine. In this design, the steam is expanded not just in the nozzles, but across the turbine blades as well. As the steam passes over the blades, both the pressure and velocity of the steam decrease. The reaction turbine relies on the reaction force from the steam’s pressure drop across the blades to generate rotational energy. Essentially, the blades themselves are shaped in such a way that as steam passes over them, the change in pressure causes the blades to move.
Key features of reaction turbines include:
- Energy Conversion: The steam pressure is dropped continuously across both the nozzles and blades. The turbine blades are designed to produce motion through both velocity and pressure changes in the steam.
- Design: Reaction turbines typically feature rotating blades and stationary blades arranged in multiple stages. Each stage contains nozzles and blades, and steam expands progressively across each stage.
- Pressure Drop: The pressure of the steam drops gradually through each stage as it moves through the turbine, leading to an increase in velocity and a gradual expansion of steam.
- Applications: Reaction turbines are often used in large-scale power generation and situations where consistent steam quality and efficient expansion are required. They are more common in large power plants where the steam flow rate is high.
The reaction turbine’s design enables higher efficiency at lower steam velocities, making them suitable for lower-pressure steam where more uniform expansion is needed. They are often favored in applications where efficiency and smooth power output are more important than handling extreme pressure variations.
Key Differences Between Impulse and Reaction Steam Turbines
- Energy Conversion Mechanism:
- In impulse turbines, the energy is converted primarily through the kinetic energy of the steam jets, with pressure dropping entirely in the nozzles before steam strikes the blades.
- In reaction turbines, energy conversion happens through a combination of pressure drop and velocity change across the turbine blades.
- Pressure Drop:
- Impulse turbines experience a single pressure drop in the nozzles, with constant pressure steam entering the turbine blades.
- Reaction turbines experience a gradual pressure drop across both the nozzles and blades, leading to a more continuous energy conversion process.
- Blade Design:
- Impulse turbines feature blades that convert the kinetic energy of steam into rotational energy through steam jets.
- Reaction turbines feature blades that use the reaction force of expanding steam to generate mechanical energy, with blades designed to optimize the pressure drop over each stage.
- Efficiency:
- Impulse turbines are often simpler, with lower efficiency compared to reaction turbines, particularly at higher steam flow rates or when the turbine needs to operate with varying steam conditions.
- Reaction turbines generally provide higher efficiency, especially in larger plants with constant steam pressure and flow rates.
- Suitability for Steam Conditions:
- Impulse turbines are better suited for high-pressure and high-velocity steam, where steam expansion in nozzles is sufficient to generate the necessary kinetic energy.
- Reaction turbines are designed to handle lower-pressure steam and larger volumes of steam, making them more efficient in large-scale applications.
- Applications:
- Impulse turbines are typically used in smaller power plants or where simplicity is preferred, as they are effective at high-pressure conditions and generally handle moderate steam flow rates.
- Reaction turbines are more common in large power plants where steam conditions are less volatile, and efficiency is prioritized, particularly where large steam flow and gradual pressure drop are key to optimal performance.
- Mechanical Complexity:
- Impulse turbines have a simpler mechanical structure because the steam’s pressure is dropped only in the nozzles, leading to fewer moving parts and simpler maintenance.
- Reaction turbines are more complex mechanically, with multiple stages of pressure and velocity conversion that require more detailed engineering and precise blade design for efficient operation.
- Cost:
- Impulse turbines are typically cheaper to manufacture due to their simpler design and fewer components.
- Reaction turbines tend to be more expensive due to their intricate design, more components, and more complex engineering.
Conclusion
The choice between impulse and reaction turbines depends on a range of factors, including steam pressure, flow rates, and specific application needs. Impulse turbines are ideal for smaller-scale applications where high-velocity steam and a simpler, cost-effective solution are required, while reaction turbines excel in large-scale power plants where efficiency, gradual expansion, and high steam flow rates are crucial for optimal performance. Both types of turbines have their unique advantages, and their application is determined by the specific operational requirements of the power generation facility or industrial process.
The choice between impulse and reaction turbines ultimately depends on the specific requirements of the power generation process, including steam conditions, efficiency goals, and the scale of the operation. Impulse turbines are generally better suited for smaller-scale power plants or applications where the steam is high-pressure and high-velocity, as they can handle such conditions efficiently while maintaining a simpler design. They are favored when low initial cost, fewer moving parts, and ease of maintenance are prioritized. In contrast, reaction turbines are more complex but provide higher efficiency and performance at large scales, especially where there is a need for more gradual steam expansion across the turbine stages. They work well in large power plants where constant, steady steam flow is crucial and where maximizing energy conversion efficiency is a primary concern.
The mechanical differences between the two types of turbines influence their ability to handle various operational conditions. Impulse turbines, with their simpler design, tend to be less sensitive to variations in steam pressure and velocity, making them more suitable for applications where the steam conditions are more volatile or variable. The design allows them to effectively convert the kinetic energy of the steam into mechanical work, without requiring extensive modifications to handle fluctuating steam conditions. However, this also means that impulse turbines might not operate as efficiently in conditions where steam must expand progressively across the turbine blades, as is the case in large power plants or more continuous, steady-state applications.
In contrast, reaction turbines rely on a continuous pressure drop that occurs not just in the nozzles, but also across each turbine blade. This gradual expansion of steam allows for more controlled energy extraction, making them ideal for larger systems that require a high degree of efficiency and where energy production needs to be smooth and consistent. The interaction between the steam and the turbine blades in reaction turbines results in both pressure and velocity changes, and this process optimizes energy conversion, especially in plants with larger steam volumes and where the steam is continuously expanded through multiple stages. However, the complexity of reaction turbines makes them more expensive to produce and maintain, as they require detailed engineering to manage both pressure and velocity drops in each stage.
Given their higher efficiency and greater ability to handle large steam volumes, reaction turbines are typically found in larger power plants, industrial applications, and processes where maintaining high efficiency over extended periods is essential. They provide a more uniform output over time and can manage larger systems more effectively, whereas impulse turbines are often used in smaller, more straightforward applications where simplicity and cost are the primary considerations.
Additionally, the choice between the two types of turbines also depends on the desired operational flexibility. Impulse turbines, with their simpler design, are easier to control and can adapt more readily to changes in operational conditions. Reaction turbines, with their more intricate blade designs and more gradual pressure expansion, might require more precise adjustments to optimize performance, but they provide higher overall efficiency when operating under ideal conditions.
In conclusion, while both impulse and reaction turbines are fundamental technologies in steam power generation, they are suited to different operational needs. Impulse turbines are ideal for smaller, less complex applications where cost and simplicity are key, whereas reaction turbines excel in larger power plants where high efficiency, sustained energy output, and the ability to handle larger steam flow rates are necessary. The trade-offs between complexity, cost, efficiency, and scale are central to selecting the right turbine technology for a given application. By understanding the principles and characteristics of each type of turbine, engineers can design more effective and optimized steam power systems that meet the specific needs of their projects.
As the energy sector continues to evolve, the role of steam turbines in power generation remains critical, with both impulse and reaction turbines contributing in different ways to meet the growing demand for electricity. Despite their differences, both types of turbines share the common goal of efficiently converting thermal energy from steam into mechanical work, but how they do this can have significant implications for the design and operation of power plants.
One of the driving factors for choosing between impulse and reaction turbines is operational efficiency. Over time, the efficiency of steam turbines, particularly reaction turbines, has been greatly improved through advances in materials, turbine design, and cooling techniques. Materials that can withstand higher temperatures and pressures, such as superalloys and ceramic coatings, have allowed turbines to operate in more extreme conditions, improving their overall thermal efficiency. This is particularly important in reaction turbines, where the gradual expansion of steam over multiple stages results in more energy being extracted from the steam. The improvements in aerodynamic design and blading technology have also played a significant role in enhancing the performance of reaction turbines, making them the preferred choice for large-scale power plants.
Moreover, efficiency gains in reaction turbines can translate into better fuel economy and lower operational costs over time. As energy costs continue to rise globally, the ability to generate more power from less fuel is crucial for maintaining the economic viability of large-scale power plants. Reaction turbines, due to their superior efficiency in large systems, can help reduce fuel consumption while simultaneously increasing the output of power plants, making them a more sustainable choice for the future of energy generation. This has led to the widespread adoption of reaction turbines in modern coal, nuclear, and natural gas power stations, where maximizing output and minimizing costs is essential.
Another consideration for the use of steam turbines is maintenance and reliability. While reaction turbines offer higher efficiency, they are also more complex to maintain due to the intricate design of their blades and the gradual pressure drop across multiple stages. This can make reaction turbines more prone to mechanical wear and tear, especially in harsh operating conditions. In contrast, impulse turbines, with their simpler design and fewer moving parts, are easier to maintain and have lower operational downtime. This can be especially advantageous in smaller power plants or industries where reliability and cost-effectiveness are paramount, and where frequent maintenance might be difficult to manage.
In addition, the importance of renewable energy integration into the power grid is pushing for more flexible and adaptive steam turbine technologies. Both impulse and reaction turbines can play a role in supporting hybrid energy systems that combine steam turbines with renewable sources such as solar, wind, and geothermal. In such systems, steam turbines might need to operate in fluctuating conditions, and their efficiency and responsiveness to changing energy inputs become crucial. Reaction turbines, due to their ability to efficiently manage high steam volumes and sustained energy production, are more suited to integrating into grid systems where a steady and consistent power supply is required. On the other hand, impulse turbines, with their simpler control systems and faster response times, may be better suited for smaller-scale or backup power systems where flexibility is needed to support intermittent renewable energy sources.
Looking forward, the continued development of advanced turbine control systems will enhance the operation and efficiency of both impulse and reaction turbines. The integration of digital controls, artificial intelligence (AI), and machine learning can enable turbines to automatically adjust to changing steam conditions, predict potential failures, and optimize their performance in real time. For instance, AI algorithms can monitor key turbine parameters such as steam pressure, temperature, and flow rate, adjusting operational settings to maximize efficiency and minimize wear and tear on the turbine components. Predictive maintenance systems, enabled by sensor data, will also be crucial in identifying issues before they cause downtime or performance degradation, reducing costs associated with unplanned outages and repairs.
As the global focus on decarbonization intensifies, steam turbines will also need to adapt to operate efficiently with alternative and cleaner fuels. The integration of hydrogen and biofuels into steam turbine systems is an area of active research. Hydrogen in particular presents a significant opportunity to decarbonize steam turbine operations, as it burns cleanly without releasing carbon emissions. For both impulse and reaction turbines, adapting to hydrogen combustion will require modifications to the burner and nozzle systems, as hydrogen has different combustion characteristics compared to traditional fossil fuels. Research is ongoing to determine how the turbine blades and nozzles can be optimized for hydrogen to ensure efficient energy conversion while minimizing the risk of corrosion and material degradation.
Furthermore, thermal energy storage systems paired with steam turbines are expected to play an increasing role in ensuring grid stability and energy reliability. As renewable energy sources like wind and solar can fluctuate throughout the day, steam turbines connected to thermal storage can store excess energy in the form of heat, which can be later converted into electricity as needed. This would enable a more reliable and consistent supply of electricity from renewable sources, ensuring that energy is available when demand is high. Impulse turbines, with their rapid response times, may be particularly useful in such systems for providing quick bursts of power, while reaction turbines could be used for maintaining a steady flow of power over longer periods.
In conclusion, the evolution of steam turbines, both impulse and reaction types, will continue to be shaped by advancements in materials, fuel types, digital technologies, and energy storage solutions. As the demand for cleaner, more efficient energy grows, the need for highly adaptable and flexible turbine systems that can integrate into a diverse and evolving energy mix will become even more important. While impulse turbines are likely to remain the turbine of choice for smaller, simpler, and cost-effective systems, reaction turbines will continue to dominate in large-scale power plants where efficiency, reliability, and high-performance are required. With ongoing innovations in turbine technology and a greater focus on sustainability, both impulse and reaction turbines will play critical roles in shaping the future of global energy generation, contributing to a more sustainable, efficient, and flexible energy landscape.
As the global energy landscape shifts towards more sustainable and cleaner energy solutions, steam turbines—whether impulse or reaction—will continue to play a vital role in bridging the gap between traditional power generation and the renewable energy future. The increasing integration of renewable energy sources such as solar, wind, and geothermal into the grid requires that steam turbines adapt to more dynamic, variable energy production systems. In this context, steam turbines may not only be used in traditional power plants, but also as key components in hybrid systems and grid stabilization solutions that combine both renewable and conventional energy sources.
The ability to operate flexibly and adjust to fluctuating steam pressures, temperatures, and flow rates will be essential for turbines in these advanced energy systems. As steam turbines are employed in more diverse environments, it will be critical to continue improving their adaptability, especially when dealing with more intermittent and variable energy sources like wind and solar. This will lead to the development of advanced control algorithms, smart sensors, and predictive maintenance tools that ensure turbines operate at optimal efficiency despite changes in energy supply or demand. Smart monitoring systems will make it possible for turbines to respond in real-time to fluctuations in steam flow or pressure, helping balance supply and demand on the grid.
In addition to grid stability, steam turbines are expected to be central to the development of combined heat and power (CHP) systems, which can increase the overall efficiency of energy production. These systems use the waste heat generated by steam turbines to produce both electricity and useful thermal energy for industrial processes, district heating, or other applications. With the demand for greater energy efficiency increasing worldwide, the ability to utilize steam turbines in CHP setups will be a major factor in improving the sustainability of industrial processes, reducing emissions, and cutting energy costs. These systems will also become increasingly important as industries look for ways to decarbonize while maintaining competitive energy prices.
The pursuit of cleaner energy generation will also drive innovation in steam turbine designs to accommodate alternative fuels such as biomass or hydrogen. Biomass power plants, which burn organic materials to generate steam, will benefit from turbines designed to handle the variations in fuel quality and combustion characteristics that biomass can present. Likewise, hydrogen’s potential as a clean fuel for power generation requires steam turbines to be optimized for the high temperatures and pressures associated with hydrogen combustion. While hydrogen combustion produces no CO2 emissions, it does introduce new challenges in turbine material science, including the need to mitigate hydrogen embrittlement and corrosion in turbine components. Engineers will continue to innovate around turbine materials and coatings to withstand these challenges, ensuring turbines can operate efficiently in hydrogen-powered systems.
As global efforts to meet net-zero emissions targets intensify, the use of steam turbines in carbon capture and storage (CCS) applications will also become increasingly important. CCS technologies capture carbon dioxide produced during the combustion of fossil fuels, preventing it from entering the atmosphere. In these systems, steam turbines are often used to drive the compression and pumping of CO2 captured from flue gases. Steam turbines’ role in this process is crucial, as efficient power conversion can help minimize the energy required for CO2 capture, making the entire CCS process more economically viable.
Furthermore, the technological advancements in materials science, particularly high-temperature alloys, ceramic materials, and superconductors, will allow steam turbines to operate at higher efficiencies and with greater resilience in extreme environments. High-temperature alloys, for example, can withstand the stresses associated with higher steam pressures and temperatures, leading to increased thermal efficiency. This will be especially beneficial for reaction turbines, which rely on gradual pressure drops and the conversion of both pressure and velocity in each stage. The continued development of these materials will open up new possibilities for steam turbines to operate in more demanding conditions, improving their overall performance and contributing to the broader goals of cleaner, more efficient energy generation.
In the near future, the integration of advanced manufacturing techniques such as 3D printing (additive manufacturing) will revolutionize turbine design and production. 3D printing can allow for the creation of turbine components with high precision, enabling complex geometries that were previously difficult or expensive to produce using traditional methods. This technology could be particularly useful in the production of turbine blades, which require extreme precision to optimize performance and efficiency. By using 3D printing, manufacturers could create blades with intricate internal cooling channels to better manage the heat produced by the steam, or tailor the shape of blades to minimize aerodynamic losses, leading to further improvements in efficiency.
Additionally, modular turbine designs may become more prevalent, offering the flexibility to scale turbine capacity up or down based on demand. This approach would allow for greater customization in turbine installation, enabling power plants to more easily adjust their energy production capacity as needed without a complete overhaul of existing systems. Modular designs could also facilitate maintenance and repairs, as individual turbine modules could be replaced or serviced without taking the entire turbine offline. This could reduce both operational downtime and maintenance costs, increasing the overall efficiency and reliability of steam turbine-powered plants.
As steam turbines continue to evolve, the need for sustainable energy practices and the integration of emission-reducing technologies will only grow. The development of turbines that are not only more efficient but also capable of operating with low-carbon or carbon-neutral fuels, coupled with the advancements in turbine materials and manufacturing, promises a more sustainable and energy-efficient future.
The global transition to cleaner energy will shape the future of steam turbine technology, with emphasis on optimizing performance, reducing environmental impact, and increasing flexibility. As industries and energy systems work toward decarbonization, steam turbines will remain a critical piece of the energy puzzle—adapting to new fuels, enhancing efficiency, and helping to stabilize the grid, all while maintaining their essential role in large-scale power generation. Whether in hybrid systems, combined heat and power solutions, or renewable energy integration, the ongoing innovation in turbine technology ensures that steam turbines will continue to be indispensable in the journey toward a more sustainable, resilient, and energy-efficient world.
Looking further into the future, the role of steam turbines in energy production will be shaped by the growing importance of energy storage technologies and grid modernization. As the demand for electricity continues to increase globally, and as more renewable energy sources come online, the need for advanced methods to store and manage energy will become even more crucial. Steam turbines, particularly in combined-cycle plants, can work synergistically with energy storage systems to balance fluctuations in renewable energy generation, such as the variability seen in wind and solar power. These storage systems, including battery storage, pumped hydro storage, and compressed air energy storage (CAES), allow excess energy generated during periods of high renewable production to be stored and later converted back into electricity when demand is high, or when renewable generation dips. Steam turbines can play a vital role in these systems by using stored energy to produce steam and generate electricity as needed.
As the energy grid itself evolves to accommodate smart grids and distributed energy resources (DERs), steam turbines will be increasingly integrated into more decentralized, flexible systems that offer greater resilience and adaptability. A smart grid relies on digital communication and advanced control systems to manage the flow of electricity across a network, allowing for more efficient distribution and the integration of diverse energy sources. Steam turbines, particularly those in small modular nuclear reactors (SMRs) or microgrids, will need to be able to respond to changing demands in real time. This requires highly responsive turbine control systems that can make instant adjustments to steam parameters and output in response to grid conditions or fluctuations in renewable energy supply. Such adaptability will be essential as the energy market moves towards more distributed and decentralized forms of energy generation.
The rise of digital twins in turbine technology also promises to revolutionize the operation and maintenance of steam turbines. A digital twin is a virtual model of a physical turbine that simulates its performance, behavior, and condition in real time. By using sensors embedded in the turbine and collecting data about its operational state, the digital twin can predict when maintenance is needed, optimize performance, and even simulate different operational scenarios to test the turbine’s response to various conditions. This can help engineers identify inefficiencies, predict failures before they occur, and ultimately reduce maintenance costs and downtime. In addition to improving turbine reliability, digital twins will also allow for the fine-tuning of turbine design in the development phase, enabling engineers to optimize performance based on real-world data before the turbines are physically built.
Moreover, artificial intelligence (AI) and machine learning (ML) are expected to play an increasing role in predictive maintenance and performance optimization. By analyzing historical data from turbines, AI systems can learn patterns of behavior and identify subtle signs of wear and tear, allowing for early intervention to prevent costly failures. Machine learning algorithms can also be used to continually adjust turbine settings for optimal performance based on varying conditions, ensuring that steam turbines operate at peak efficiency at all times. This technology could extend the lifespan of turbines, reduce operating costs, and increase the reliability of power generation systems.
Carbon capture, utilization, and storage (CCUS) will also become an increasingly important application for steam turbines in the transition to a carbon-neutral energy system. As global carbon emissions become a focal point for climate change mitigation, steam turbines will be integrated into carbon capture processes that collect CO2 emissions from power plants and industrial facilities. Supercritical and ultra-supercritical steam turbines, which operate at higher pressures and temperatures, will be critical in improving the efficiency of these processes, ensuring that the energy required to capture and compress CO2 is minimized. Steam turbines will need to be optimized for this task, both in terms of thermal efficiency and in their ability to withstand the stresses of prolonged operation in CCUS environments.
The ongoing global decarbonization efforts and growing environmental awareness will also result in stricter regulations for power plant emissions. To meet these stringent emissions targets, power plant operators will have to integrate new technologies into their existing systems to reduce their carbon footprint. In this environment, steam turbines with advanced combustion and exhaust systems, designed to maximize energy output while minimizing environmental impact, will become more common. The adoption of low-emission combustion systems, such as those used in natural gas combined cycle (NGCC) plants or biomass-based power plants, will help reduce the carbon emissions of power generation while ensuring that steam turbines maintain their high levels of efficiency.
At the same time, small modular reactors (SMRs), which are compact nuclear power systems, could revolutionize the use of steam turbines in power generation. SMRs have the potential to provide low-carbon, reliable power in smaller, distributed plants that are more flexible and easier to integrate with renewable energy sources. Steam turbines in these systems would need to be highly adaptable and capable of responding quickly to changes in reactor output. The modular design of SMRs also means that smaller, scalable turbines could be used, reducing capital costs and making nuclear energy more accessible to a broader range of markets.
Looking even further into the future, the development of fusion energy may introduce another paradigm shift in steam turbine applications. Nuclear fusion, which promises to provide virtually limitless and clean energy, could lead to the creation of steam at extremely high temperatures and pressures, creating new challenges and opportunities for steam turbine technology. Fusion reactors would likely require turbines capable of handling higher steam conditions than current technologies allow. The research and development of such high-performance turbines may push the boundaries of materials science and mechanical engineering, potentially leading to breakthroughs in turbine technology that could benefit both traditional and renewable energy sources.
Ultimately, the future of steam turbines is one of constant evolution, with advancements in materials, digital technologies, and system integration opening up new opportunities for more efficient, sustainable, and flexible power generation. The ongoing drive for clean energy, grid reliability, and sustainable industrial processes will continue to shape the development of turbine technology. As the energy industry becomes increasingly complex and interconnected, steam turbines will remain at the heart of many of the most innovative solutions, ensuring that they continue to contribute to global energy needs in a cleaner, more efficient, and adaptable manner.
Through these advancements, steam turbines will play a pivotal role in supporting the transition to a low-carbon economy, offering high-performance solutions that address the pressing need for clean, reliable, and sustainable energy systems. As new technologies emerge, the role of steam turbines will continue to evolve, ensuring their place in the energy landscape for many decades to come.
Steam Turbine Performance Basics
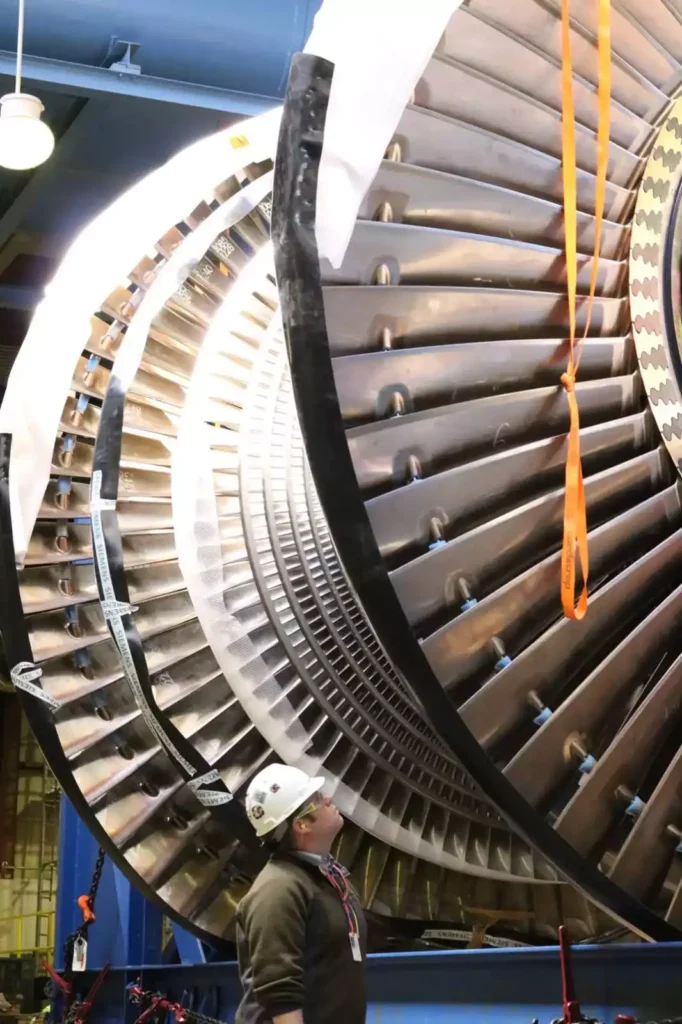
Steam turbine performance is a critical aspect of power generation, as it directly influences the efficiency, reliability, and economic viability of power plants. The performance of a steam turbine is largely determined by its ability to convert the thermal energy from steam into mechanical energy and, eventually, electrical energy. Understanding the basics of steam turbine performance involves examining various factors such as efficiency, power output, steam conditions, and the specific design of the turbine itself.
One of the primary indicators of steam turbine performance is thermal efficiency. This refers to the turbine’s ability to convert the thermal energy contained in steam into mechanical energy. The higher the thermal efficiency, the more energy the turbine can extract from the steam, leading to a higher power output for the same amount of fuel or heat input. Thermal efficiency is heavily influenced by the operating conditions of the steam turbine, including steam pressure, temperature, and flow rate, as well as the quality of the steam. The efficiency of a steam turbine is typically measured by comparing the energy it produces to the energy it consumes. In modern steam turbines, thermal efficiency has been significantly improved with advances in materials and design, allowing for higher operational temperatures and pressures.
The isentropic efficiency of a steam turbine is another important performance metric. It compares the actual performance of the turbine to the ideal or isentropic process, where the steam undergoes an ideal expansion with no losses in energy. The closer the actual performance is to the ideal isentropic efficiency, the more efficiently the turbine is converting thermal energy into mechanical work. The difference between the ideal and actual efficiencies is often due to friction, turbine blade erosion, heat losses, and other mechanical losses. Isentropic efficiency is typically calculated for each stage of the turbine, as different stages can experience varying levels of loss.
Power output is a key measure of turbine performance and is determined by the mass flow rate of steam passing through the turbine and the expansion of steam in the turbine stages. It is typically expressed in megawatts (MW) or kilowatts (kW) and represents the amount of mechanical energy produced by the turbine. Power output is affected by the steam conditions, such as pressure, temperature, and flow rate, as well as the turbine’s size and design. High-pressure steam entering the turbine expands and loses energy as it moves through the turbine stages, converting its thermal energy into mechanical energy. The more steam that can be passed through the turbine, and the higher the steam conditions, the greater the power output. Power output can also be adjusted based on the operational needs of the plant, making steam turbines an essential component in adjusting to demand fluctuations.
Steam conditions such as temperature and pressure are fundamental to understanding steam turbine performance. High steam pressure and temperature are essential for maximizing the thermal energy available for conversion into mechanical power. Superheated steam—steam that is heated beyond its boiling point—has a higher energy content, making it more efficient for turbine operation. As the steam enters the turbine, it expands and loses both temperature and pressure. Steam turbine performance can be optimized by maintaining high steam quality and minimizing any losses in the steam system. Steam conditions are typically controlled and monitored through pressure regulators, temperature sensors, and flow meters to ensure that the turbine operates at its most efficient point.
Another important aspect of steam turbine performance is the pressure ratio—the ratio of the steam pressure at the turbine inlet to the pressure at the outlet. A higher pressure ratio generally leads to higher power output, but it also places greater demands on the turbine and may require more advanced materials and design techniques to handle the increased pressure and temperature. The pressure ratio directly impacts the expansion ratio of the steam as it passes through the turbine, affecting the turbine’s overall efficiency. Multistage turbines, where steam passes through several stages of expansion, are used to improve the overall pressure ratio and maximize energy extraction. The performance of each stage is determined by the expansion process and the degree to which the steam is allowed to expand and cool as it passes through the turbine blades.
Mechanical losses, such as friction and turbulence within the turbine, also play a role in turbine performance. While steam turbines are designed to minimize these losses, factors like bearing friction, turbine blade drag, and sealing losses can reduce the overall efficiency of the turbine. Advanced turbine designs, such as aerodynamically optimized blades and precision bearings, can reduce mechanical losses, enhancing overall performance. Regular maintenance, including inspection and lubrication of bearings, replacement of worn-out turbine blades, and sealing, is necessary to ensure optimal mechanical efficiency.
Another factor that influences steam turbine performance is vibration. Excessive vibration can reduce the efficiency of a turbine, cause mechanical stress, and ultimately lead to premature failure. Monitoring vibration levels using advanced sensors is essential for diagnosing problems such as imbalance or misalignment in the turbine’s rotating components. Vibration can also be a sign of wear or degradation of turbine components, which can negatively impact overall performance.
The operating range of a steam turbine is another important consideration. While turbines are typically designed to operate efficiently within a certain range of steam conditions, their ability to adapt to varying conditions over time—such as fluctuations in load, pressure, and temperature—is a critical aspect of performance. Modern turbines are designed to be more adaptable, with the ability to handle transient conditions and adjust to changes in steam supply and power demand without sacrificing performance.
The efficiency of heat recovery systems also impacts the overall performance of steam turbines. In many modern power plants, heat recovery steam generators (HRSGs) are used to capture waste heat from the exhaust gases of combustion turbines or other processes. This captured heat is then used to produce steam for use in steam turbines, improving the overall thermal efficiency of the system. The integration of heat recovery systems allows steam turbines to operate in a more combined-cycle fashion, where both the steam turbine and a gas turbine work together to generate electricity from a single fuel source, resulting in higher overall plant efficiency.
Lastly, the maintenance practices employed on steam turbines significantly influence their long-term performance. Regular inspections, performance monitoring, and predictive maintenance schedules help identify issues before they lead to catastrophic failure. For example, monitoring vibration levels, blade wear, steam leaks, and thermal efficiency can provide valuable insight into the turbine’s condition. Predictive maintenance tools powered by artificial intelligence and machine learning are becoming more common, allowing operators to analyze trends in turbine performance and schedule maintenance proactively. Proper alignment, lubrication, and cooling are key to maintaining turbine efficiency over time.
In conclusion, steam turbine performance is influenced by numerous factors, from steam conditions to mechanical design, operating range, and maintenance practices. Thermal efficiency, power output, pressure ratio, and operating conditions such as temperature and steam quality are all critical in determining how well a steam turbine converts thermal energy into mechanical work. By optimizing these factors, improving turbine designs, and integrating advanced technologies such as predictive maintenance, steam turbines can continue to provide reliable, efficient power generation for a wide range of applications, from large-scale power plants to industrial operations and renewable energy systems. As the energy sector continues to evolve, understanding and improving steam turbine performance will remain central to achieving greater energy efficiency, sustainability, and grid reliability.
As the demand for energy efficiency and sustainability increases, the need for optimizing steam turbine performance will continue to drive innovation and technological advancements. This will include not only enhancing the fundamental design of steam turbines but also integrating them more effectively into modern energy systems that rely on both conventional and renewable sources of power.
Advanced materials will play a significant role in improving turbine performance. As turbines operate at higher pressures and temperatures to extract more energy from steam, they require materials that can withstand the extreme conditions without degrading. The development of high-temperature alloys and ceramic coatings has already allowed turbines to achieve greater thermal efficiency. These materials are essential for maintaining performance and longevity, especially in ultra-supercritical and combined-cycle systems where both steam temperature and pressure are significantly higher than in traditional setups. Innovations in nanotechnology and composite materials may further enhance turbine components, providing better heat resistance and reducing material fatigue.
The integration of digital technologies in turbine systems will revolutionize their performance monitoring and optimization. The use of sensors that measure parameters like pressure, temperature, vibration, and steam quality in real time will become more sophisticated. These sensors, coupled with big data analytics, will allow for the continuous tracking of a turbine’s performance. With this wealth of data, machine learning algorithms can predict potential failures or inefficiencies before they happen, allowing for predictive maintenance that reduces downtime and extends the life of the equipment. This digital approach will also enable more dynamic optimization, where turbines can adjust their operation based on real-time data, ensuring they are always running at peak performance.
Additionally, artificial intelligence (AI) will help refine steam turbine operations by automatically adjusting control systems to optimize energy production. AI can analyze vast amounts of data from turbines, identifying patterns and correlations that might not be immediately apparent to human operators. This can help with everything from load optimization to the detection of early signs of wear, enhancing both the turbine’s efficiency and reliability.
Hybrid systems that combine steam turbines with other energy generation technologies will also become more common. For instance, gas-steam combined-cycle plants are already widely used due to their higher efficiency, as the waste heat from gas turbines is used to generate steam for steam turbines. This combination significantly improves overall thermal efficiency. In the future, the integration of renewable energy sources like wind, solar, or even geothermal with steam turbines could create highly efficient and flexible energy systems. These hybrid systems can adapt to the variability of renewable energy production, providing stable baseload power while also utilizing carbon-neutral fuels such as hydrogen or biofuels to minimize emissions.
Steam turbines used in renewable applications are expected to play a crucial role in the evolving energy mix. For example, concentrated solar power (CSP) plants use mirrors or lenses to focus sunlight onto a receiver, generating steam that can then be used in steam turbines. In these applications, optimizing the performance of steam turbines to work with varying solar conditions, while ensuring energy storage capabilities, will be key. Similarly, geothermal energy, which produces steam from the earth’s heat, will also benefit from turbine designs tailored to the unique properties of geothermal steam, which can vary in pressure, temperature, and chemical composition.
As the demand for distributed energy systems grows, smaller, modular steam turbines will become increasingly important. These smaller systems, sometimes used in microgrids or remote applications, will need to be highly adaptable, cost-effective, and easy to maintain. They will be able to generate power from a variety of sources, including waste heat, renewable energy, and even small-scale nuclear reactors, while offering high efficiency and low emissions. The ability to use modular turbine designs for these smaller systems could enable rapid deployment and scaling, allowing energy production to be more localized, flexible, and resilient.
The development of steam turbine systems for carbon capture and storage (CCS) will also contribute significantly to performance optimization. Steam turbines can be used to power the compression of CO2 captured from flue gases in power plants. As the focus on carbon mitigation technologies intensifies, steam turbines designed to operate with carbon capture processes will need to achieve high efficiency while minimizing energy losses. Research into turbine materials that can handle the high pressures and temperatures associated with CO2 compression will play a crucial role in reducing the overall energy penalty of these systems.
In the realm of steam turbine operation and load management, flexible operation will become increasingly important. Modern power plants are expected to be more responsive to changes in grid demand, particularly as renewable energy sources introduce variability in power supply. Steam turbines that can adjust their output quickly in response to fluctuations in energy demand or changes in renewable generation will be essential for grid stability. Turbines that can ramp up or down in output without compromising efficiency or longevity will be in high demand as part of energy systems that require flexible, on-demand power.
Another key trend is the increasing demand for sustainability in turbine design. Environmental concerns and regulations are pushing the development of turbines that are not only more efficient but also more environmentally friendly. Advances in environmentally friendly materials, such as non-toxic coatings and more sustainable manufacturing methods, will reduce the environmental footprint of turbines. Furthermore, the use of clean fuels such as hydrogen, biofuels, or even green ammonia in power plants could reduce emissions and allow steam turbines to play a central role in decarbonizing the energy sector.
The life cycle assessment (LCA) of steam turbines is an important factor in their long-term sustainability. Understanding the environmental impact of steam turbine production, operation, and disposal will guide the development of turbines that minimize waste, energy use, and emissions. Recyclability and the use of circular economy principles in turbine design will ensure that turbines remain relevant in the growing push for sustainable manufacturing practices. This could involve designing turbines to be more easily disassembled and repurposed at the end of their life, which could help reduce waste and further decrease the environmental impact of turbine technology.
Ultimately, the performance of steam turbines is tied to their ability to meet the challenges of an evolving energy landscape. As the world increasingly moves toward clean, sustainable, and flexible energy systems, steam turbines will continue to be a critical technology. Their role in improving energy efficiency, enabling grid stability, reducing carbon emissions, and supporting renewable energy integration will remain essential. With ongoing advancements in materials, digital technologies, hybrid systems, and carbon capture, steam turbines are poised to continue playing a key role in powering a low-carbon, resilient future.
As we look further into the future of steam turbine technology, it’s clear that ongoing advancements will push the boundaries of efficiency, adaptability, and sustainability. One important area of development is the advancement of hybrid power plants that integrate steam turbines with other forms of power generation, such as gas turbines and renewable energy sources like solar and wind. Hybrid power systems are designed to optimize the strengths of different energy sources while minimizing their individual limitations. For instance, steam turbines paired with solar thermal power or wind power can improve the overall efficiency of the power generation process by leveraging diverse and sometimes complementary energy inputs. The optimization of steam turbines within these hybrid systems will be crucial for maximizing the use of available energy resources while minimizing operational costs and environmental impact.
As the global push for net-zero emissions intensifies, steam turbines will be an integral part of low-carbon energy solutions. The integration of carbon capture, utilization, and storage (CCUS) technologies with steam turbines will offer one of the most promising avenues for reducing the carbon footprint of fossil fuel-based power generation. When applied in coal or natural gas power plants, steam turbines can help in compressing and transporting the CO2 captured from flue gases, preventing its release into the atmosphere. Similarly, renewable natural gas or biomass can be used in steam turbine-driven power plants as a cleaner alternative to conventional fossil fuels. These technologies, paired with steam turbines, can play a central role in creating a more sustainable energy mix by reducing the environmental impact of energy generation without sacrificing efficiency or performance.
The integration of steam turbines with energy storage systems is another exciting development. As renewable energy sources like wind and solar are inherently intermittent, efficient energy storage is key to maintaining a stable and reliable power supply. By pairing steam turbines with advanced battery storage systems or pumped hydro storage, power plants can store excess energy produced during periods of low demand and use it during high-demand periods, ensuring grid stability. This integration will enhance the flexibility of power plants, allowing steam turbines to not only serve as baseload generation units but also provide peak shaving and load-following capabilities. Steam turbines that can efficiently transition between various operating modes and optimize energy storage processes will be in high demand for modern, resilient power grids.
Flexible and fast-ramping steam turbines will become more prevalent as utilities increasingly rely on them for grid stabilization. With the rise of renewable energy, there is a growing need for turbines that can quickly respond to fluctuations in electricity demand and supply, especially during the integration of variable sources like wind and solar power. Fast-ramping steam turbines can efficiently increase or decrease their output in response to changes in grid conditions, offering significant value to power operators who need to balance intermittent generation with consistent demand. These turbines will require improvements in control systems and faster steam conditioning processes to minimize any lag in power output adjustments.
Another potential area for growth is the application of steam turbines in small-scale, decentralized energy systems. Microgrids and distributed energy resources (DERs) are gaining popularity due to their ability to provide localized, independent power generation, particularly in remote or off-grid locations. Steam turbines in these systems must be designed to operate with higher flexibility, lower capital costs, and minimal environmental impact. Small, modular steam turbines designed for waste heat recovery or biomass could become increasingly popular for industrial applications, offering sustainable and efficient solutions for distributed energy generation. The ability to scale these turbines based on the specific needs of the microgrid or industrial plant will further enhance their economic feasibility.
Digitalization and automation are transforming how steam turbines are operated and maintained. With advances in Internet of Things (IoT) technologies, steam turbines are now being equipped with smart sensors that monitor and collect vast amounts of operational data in real time. This data is then analyzed using cloud computing and artificial intelligence (AI) to provide deep insights into turbine performance. The insights gained from this digital approach can help operators make more informed decisions regarding maintenance schedules, operational adjustments, and efficiency optimizations. For example, predictive maintenance algorithms can anticipate when parts such as turbine blades, bearings, or seals may wear out, allowing for targeted interventions before costly failures occur. Furthermore, automated turbine control systems can optimize turbine output and performance based on real-time demand signals, improving overall system efficiency.
One of the most transformative innovations on the horizon is the development of advanced manufacturing techniques such as additive manufacturing (3D printing), which may revolutionize the way turbine components are designed and produced. 3D printing offers the potential to create more complex and efficient turbine blades, parts, and casings, with reduced waste and faster production times. This technology could lead to the creation of turbines with improved aerodynamics and material properties, enhancing their efficiency and performance. Additive manufacturing also opens the door to more customized turbine solutions, where parts can be optimized for specific operating conditions or for unique applications such as geothermal power generation or small-scale distributed energy systems.
As global energy demand continues to rise, the need for increased power output from steam turbines will persist. At the same time, the focus will remain on improving efficiency and reducing emissions. The implementation of next-generation steam turbines that leverage cutting-edge materials, digital technologies, hybrid systems, and enhanced manufacturing techniques will provide a pathway to achieving these goals. These turbines will be more capable of handling varying operational demands, integrating with renewable energy sources, and optimizing energy storage, all while contributing to the global transition toward a low-carbon economy.
Lastly, the development of steam turbines will continue to focus on improving safety and reliability. As turbines are subjected to extreme temperatures, pressures, and mechanical stresses, ensuring their safety and long-term durability is paramount. Ongoing research into material science, safety standards, and failure prediction technologies will play a vital role in reducing the risks associated with steam turbine operation. These measures will ensure that steam turbines not only perform efficiently but also remain a safe and reliable component in the energy infrastructure of the future.
In conclusion, the future of steam turbines is bright, with ongoing advancements in technology, materials, and integration into modern energy systems. Their role in enabling efficient, flexible, and sustainable power generation will be crucial to meeting the growing global demand for energy. By combining state-of-the-art manufacturing, advanced digital technologies, and a focus on sustainability, steam turbines will continue to be at the heart of energy generation for years to come, playing an essential role in creating a low-carbon, resilient, and efficient energy future.
As the global energy landscape continues to evolve, steam turbines will play an essential role in addressing some of the most pressing challenges, including the integration of renewable energy, the decarbonization of industries, and the development of more efficient and resilient power generation systems.
One of the major trends shaping the future of steam turbines is their ability to integrate with renewable energy systems. As countries around the world strive to meet ambitious climate goals, renewable sources such as solar, wind, and geothermal are becoming increasingly important. However, the intermittency of renewable energy presents a challenge for grid operators, who need to balance supply and demand effectively. Steam turbines, particularly in combined-cycle power plants, offer an ideal solution for ensuring grid stability by providing baseload power and peak shaving capabilities. When integrated with renewables, steam turbines can help smooth out fluctuations in energy production, ensuring that the grid remains reliable even when the sun isn’t shining or the wind isn’t blowing.
To further enhance the flexibility of steam turbines, advanced steam turbine designs will likely focus on improving efficiency at partial load operations. In the past, steam turbines were typically designed to operate at full load for optimal efficiency. However, with the increasing importance of integrating variable renewable energy sources, turbines must be able to operate effectively at part-load conditions, adjusting their output in real-time based on fluctuating demand. This development is critical for making steam turbines more adaptable to grid management in systems that rely on a higher share of renewable energy sources.
In line with the shift towards decarbonization, advanced steam turbines will need to operate with lower carbon-intensive fuels. The rise of green hydrogen as an energy carrier is expected to have a significant impact on the future of steam turbines. Green hydrogen, produced via electrolysis using renewable electricity, can be used as a clean fuel for power generation, especially in hydrogen-fired power plants that incorporate steam turbines. By transitioning from fossil fuels to hydrogen, steam turbines can play a central role in reducing carbon emissions from the power sector, while still maintaining high efficiency and power output.
The integration of carbon capture, utilization, and storage (CCUS) technologies with steam turbines will become increasingly important as part of the global effort to reduce greenhouse gas emissions. Steam turbines are used in post-combustion CO2 capture systems, where they help power the compression of CO2, making the carbon capture process more energy-efficient. Research is ongoing to develop steam turbines specifically optimized for low-carbon and zero-emissions power plants that utilize both CCUS and renewable energy sources.
The concept of district heating, in which heat generated by power plants is distributed to residential and industrial areas for space heating and hot water, is another application where steam turbines can have a significant impact. Combined heat and power (CHP) systems, where steam turbines generate both electricity and heat, are increasingly popular in regions with high demand for heating. As cities continue to grow, the need for more sustainable and efficient heating solutions will drive the demand for steam turbines that can operate in CHP systems. By optimizing these systems to use low-carbon or renewable energy sources, steam turbines will continue to be an integral part of sustainable urban infrastructure.
To achieve these goals, research and development in steam turbine technology will focus on several key areas:
- Material science advancements: New materials capable of withstanding higher temperatures, pressures, and stresses will enable steam turbines to operate more efficiently and last longer. Ceramic materials and high-temperature alloys are expected to play a key role in allowing turbines to handle extreme conditions, which will be especially important in future systems utilizing supercritical and ultra-supercritical steam.
- Automation and control systems: The use of advanced digital technologies such as artificial intelligence (AI), machine learning, and predictive analytics will enhance the performance of steam turbines. These technologies will allow for real-time monitoring of turbine performance, enabling predictive maintenance, performance optimization, and more efficient load-following operations in response to varying energy demand.
- Hybrid power generation: The future of steam turbines may also lie in the development of hybrid energy systems that combine steam turbines with other energy sources such as solar, wind, biomass, and geothermal. These hybrid systems can provide more consistent and reliable power generation while also reducing the environmental impact of fossil-fuel-based generation. For example, solar thermal power plants that generate steam for turbines are expected to become more widespread as solar power technologies advance.
- Modular and small-scale turbines: The growing trend toward decentralized power generation and microgrids calls for the development of smaller, more modular steam turbines. These turbines can be deployed in remote areas or on a smaller scale, such as for industrial applications, where they can utilize waste heat or other localized energy sources. The flexibility of these small-scale systems will make them more cost-effective and adaptable, especially in off-grid or rural applications.
- Environmental impact reduction: As the environmental impact of energy generation becomes an even higher priority, steam turbines will need to be designed with sustainability in mind. This includes improving energy efficiency to reduce fuel consumption, integrating carbon-neutral fuels, and ensuring end-of-life recyclability for turbine components. Future turbines will be designed to minimize their overall carbon footprint, from manufacturing to disposal, supporting a circular economy approach to power generation.
- Enhanced performance for industrial applications: Beyond power generation, steam turbines will continue to be used in industrial settings where they help drive mechanical processes, such as in chemical plants, oil refineries, and paper mills. The demand for efficient, reliable turbines in these applications will drive the development of turbines that can operate in challenging environments and handle a wide range of operational conditions, while also reducing emissions.
- Public policy and regulatory influence: As the role of steam turbines in renewable energy systems and low-carbon technologies increases, public policy and regulatory frameworks will be critical in shaping their future. Governments and industry leaders must collaborate to create the right incentives for research and development in turbine technology and to ensure that renewable energy integration is incentivized at the policy level. Policies that support decarbonization, renewable energy investment, and emissions reductions will drive the future direction of steam turbine technology, ensuring that turbines play a central role in achieving climate goals.
In conclusion, the future of steam turbines is inextricably linked to the broader transition toward a sustainable, low-carbon energy future. Steam turbines will remain a cornerstone of power generation for decades to come, providing the foundation for efficient, resilient, and clean energy systems that integrate renewable sources, support decarbonization efforts, and contribute to a more sustainable world. By embracing cutting-edge materials, digital innovation, and flexible, hybrid power generation systems, steam turbines will continue to evolve to meet the demands of an ever-changing energy landscape, ensuring their place as a key technology in the global pursuit of sustainable energy.
Steam Turbines in Energy Efficiency
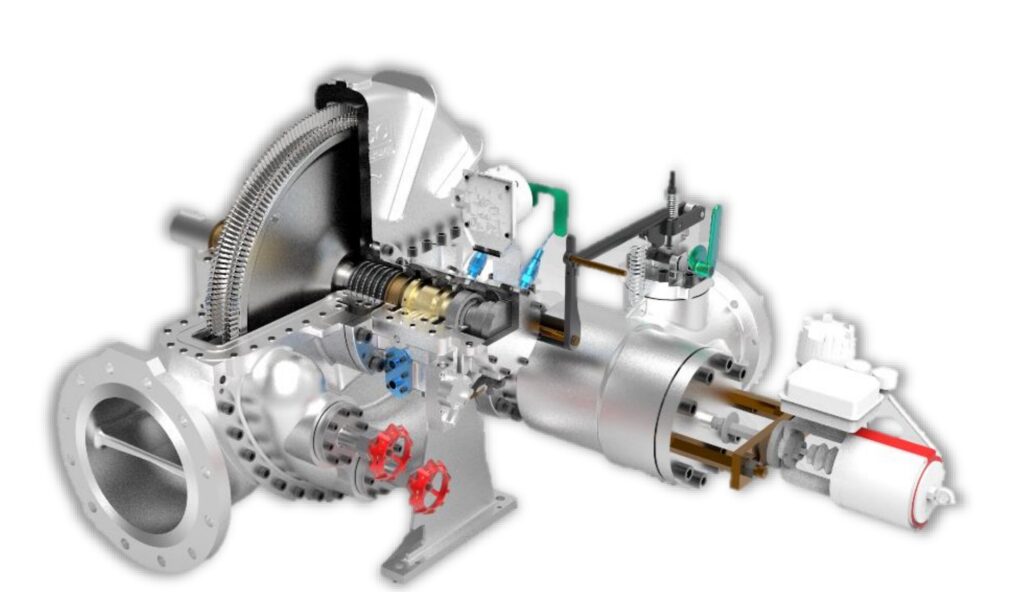
Steam turbines play a pivotal role in enhancing energy efficiency in both industrial and power generation applications. As global energy consumption continues to rise, improving the efficiency of energy systems is more crucial than ever. Steam turbines offer a highly effective means of optimizing energy use, minimizing waste, and driving sustainability in a range of industries. Their design, functionality, and integration into energy systems make them an essential component in achieving better energy efficiency, especially in applications that involve heat conversion and combined heat and power (CHP) systems.
One of the most notable ways steam turbines improve energy efficiency is through their ability to convert thermal energy into mechanical energy with high precision. The core efficiency of a steam turbine depends on its ability to extract useful energy from steam at high pressure and temperature, then convert that energy into rotational mechanical power. The efficiency of steam turbines has steadily increased over the years, thanks to innovations in turbine materials, blade design, and cooling technologies. High-efficiency turbines can convert a higher percentage of the available heat energy into useful work, thus reducing fuel consumption and increasing the overall efficiency of the power generation process.
Supercritical and ultra-supercritical steam turbines are a key part of the movement toward more energy-efficient power plants. These turbines operate at much higher temperatures and pressures than traditional turbines, enabling them to extract more energy from the steam and increase overall plant efficiency. In supercritical systems, steam is heated to a point where it does not change phase (from liquid to gas) when subjected to high pressure, allowing for more energy to be extracted as it expands through the turbine. Ultra-supercritical steam turbines, which operate at even higher temperatures and pressures, can achieve efficiency levels above 45%, a significant improvement over conventional subcritical systems.
The ability of steam turbines to operate in combined-cycle power plants also greatly contributes to energy efficiency. In these plants, steam turbines are paired with gas turbines to take advantage of both the high-temperature exhaust gases from the gas turbine and the waste heat that would otherwise be lost in traditional power generation systems. This combination allows for the generation of both electricity and useful heat, which can be utilized for district heating, industrial processes, or even converted into additional power. Combined-cycle systems can achieve efficiencies of over 60%, far exceeding the efficiency of traditional steam turbine-based power plants.
Another key area where steam turbines significantly enhance energy efficiency is through their role in combined heat and power (CHP) systems. CHP systems use the waste heat produced during power generation to provide heating and cooling for residential, industrial, or commercial buildings. By capturing and reusing waste heat, these systems can achieve overall energy efficiencies of up to 80%, as opposed to the 30-40% efficiency typical of conventional separate power and heating systems. Steam turbines, when used in CHP applications, help maximize the use of thermal energy, reducing the need for additional fuel and lowering overall emissions.
In industrial applications, steam turbines are used to recover waste heat from processes and convert it into usable mechanical energy, which can then be used for mechanical work or to generate electricity. Industries such as chemical manufacturing, oil refining, paper and pulp production, and steelmaking generate large amounts of waste heat during production processes. By installing steam turbines and heat recovery systems, these industries can recapture this waste heat and significantly improve their energy efficiency. The recovered energy can be used to power plant equipment, reducing the need to purchase additional electricity and improving the overall economics of the production process.
Furthermore, waste heat recovery steam turbines are an increasingly popular choice for improving energy efficiency in facilities that operate at high temperatures. These turbines can be used to recover heat from exhaust gases, flue gases, or other high-temperature sources, converting it into useful power or energy. Industries that burn fuels, such as biomass, coal, or natural gas, often have excess heat that can be captured and put to work. By installing a waste heat recovery steam turbine system, the overall energy consumption of a facility can be reduced, helping businesses achieve cost savings while also minimizing environmental impacts.
The integration of digitalization and advanced control systems in steam turbines has further boosted their ability to enhance energy efficiency. The use of real-time monitoring, predictive maintenance, and AI-based optimization enables operators to fine-tune turbine performance, detect inefficiencies, and optimize energy usage. Advanced sensors and IoT technologies can provide operators with a continuous stream of performance data, which can be analyzed to identify opportunities for improvement. Predictive algorithms can also anticipate when maintenance is needed, helping to prevent unexpected failures and ensuring that the turbine is always operating at its highest possible efficiency.
Materials innovation has also played a significant role in improving the energy efficiency of steam turbines. The development of new high-temperature alloys, ceramic materials, and composite materials has allowed turbines to operate at higher temperatures and pressures without compromising their structural integrity. These materials help turbines withstand the extreme operating conditions associated with modern, high-efficiency systems, which in turn contributes to a reduction in energy losses due to friction, heat, and material fatigue. Moreover, these materials help reduce the need for frequent maintenance and increase the lifespan of steam turbines, leading to long-term energy efficiency gains.
Another factor contributing to the enhanced energy efficiency of steam turbines is the ability to utilize alternative fuels and sustainable energy sources. Steam turbines are highly adaptable and can be designed to operate on biomass, green hydrogen, natural gas, or even waste-derived fuels, offering more sustainable alternatives to traditional coal and oil-based power plants. By incorporating renewable fuels into their operation, steam turbines can help reduce carbon emissions while improving energy efficiency, supporting the global transition to a more sustainable energy mix.
In district heating systems, steam turbines can provide both electricity and heat to urban areas, significantly reducing energy waste. These systems rely on the capture of waste heat from power generation or industrial processes to provide heating for buildings, schools, hospitals, and businesses. By efficiently distributing heat through pipes and using steam turbines to generate electricity at the same time, the overall energy efficiency of district heating systems is greatly enhanced. This integration can lead to more affordable and reliable energy for urban populations, while also contributing to reduced CO2 emissions in cities.
Looking ahead, energy efficiency innovations in steam turbine technology will likely continue to focus on enhancing their operational flexibility. As energy grids increasingly incorporate intermittent renewable sources like solar and wind, steam turbines will need to be capable of adjusting their output quickly to match demand, even at partial load or during periods of low demand. Advances in digital control systems, turbo-machinery design, and energy storage solutions will help steam turbines meet these challenges, further boosting their efficiency in future energy systems.
In conclusion, steam turbines will remain a key technology in improving energy efficiency across a wide range of applications. From power plants to industrial facilities and district heating systems, steam turbines are integral to optimizing energy use, reducing emissions, and enhancing the performance of both conventional and renewable energy systems. As new materials, designs, and digital innovations continue to drive improvements, steam turbines will continue to be a cornerstone in achieving global energy efficiency goals, supporting sustainability and cost savings while meeting the world’s growing demand for reliable and clean energy.
Looking to the future, the role of steam turbines in energy efficiency will only continue to grow as the world pushes toward decarbonization and increased reliance on renewable energy sources. While the primary focus has traditionally been on improving steam turbine efficiency in traditional power generation, there is increasing emphasis on integrating these turbines into emerging energy systems to optimize their use in diverse contexts, from smart grids to microgrids.
As the global energy landscape shifts, flexibility will be one of the key attributes of future steam turbines. The growing share of variable renewable energy sources such as wind and solar means that energy demand patterns are becoming more unpredictable. To accommodate this, steam turbines will need to adapt to frequent load fluctuations. A more dynamic approach to turbine design, where systems can quickly ramp up or down in response to changes in demand, will become more important. For example, steam turbines designed to operate at part load with minimal efficiency loss will be more common. This flexibility will help ensure that steam turbines remain integral to the energy mix, especially as energy markets become more decentralized and more responsive to local demand.
Moreover, fuel diversification will be a significant factor in enhancing energy efficiency. Steam turbines are being designed to operate with a variety of alternative fuels, such as biomass, synthetic fuels, and renewable hydrogen. This fuel flexibility ensures that turbines can be used in a wide range of applications that support a low-carbon economy. As the technology for producing these alternative fuels becomes more advanced, the ability to transition to cleaner sources without sacrificing energy output or efficiency will be increasingly important. This shift will reduce reliance on fossil fuels, leading to lower emissions while maintaining high-efficiency performance levels.
Hybrid power systems that combine steam turbines with other energy sources will also play a significant role in boosting energy efficiency. For instance, in hybrid systems combining solar thermal or geothermal energy with steam turbines, heat generated from renewable sources can be converted into mechanical power through steam turbines. These systems not only increase the overall efficiency of power generation but also reduce the carbon footprint by leveraging clean energy sources for heating purposes.
Energy storage systems, particularly those designed to store thermal energy, will likely be integrated with steam turbines to enhance operational flexibility and efficiency. Thermal energy storage technologies, such as molten salt storage in concentrated solar power plants or battery storage in hybrid setups, can store excess energy generated during peak production periods and release it when demand spikes or renewable generation drops. By coupling these storage solutions with steam turbines, energy producers can smooth out fluctuations and optimize turbine operation, ensuring higher overall efficiency even during intermittent power generation.
At the same time, continued advancements in control systems and sensor technologies will allow for even more precise and efficient operation. Advanced monitoring systems, coupled with AI and machine learning, will enable real-time optimization of turbine performance. These technologies will not only predict the best operating conditions but also identify potential areas for improvement in real time, resulting in a continuous feedback loop of optimization. Predictive maintenance techniques will reduce downtime and ensure that turbines operate at peak efficiency for longer periods, reducing energy waste and unnecessary fuel consumption.
The digital transformation of the energy sector, including the widespread use of digital twins and big data analytics, will also play a major role in improving steam turbine performance. By creating a virtual replica of a turbine, operators can simulate various scenarios, test different operating conditions, and analyze the impact of different fuel types on efficiency. This approach allows for the identification of design flaws, maintenance needs, and opportunities for improvements before any physical changes are made, optimizing the lifecycle of turbines and enhancing their overall contribution to energy efficiency.
As environmental regulations become stricter, steam turbines will need to be designed to meet emissions standards while maintaining their efficiency. Advances in carbon capture technologies integrated with steam turbine systems could provide a significant boost to their ability to help decarbonize the power sector. Carbon capture processes can capture CO2 produced during combustion, preventing it from entering the atmosphere, and steam turbines can be used to compress and process the captured carbon. Combined with renewable and carbon-neutral energy sources, this integration will be key to meeting climate targets while maintaining operational efficiency.
Furthermore, modular steam turbines will become more prevalent as energy producers move toward decentralized and distributed energy systems. Smaller, more modular steam turbines can be deployed in local, off-grid power systems or in microgrids to support communities and industries that are remote or less connected to the central grid. These smaller turbines can be scaled up or down based on local demand, ensuring high efficiency even in smaller, more flexible applications. This trend will be particularly relevant in regions where energy infrastructure is lacking or unreliable, allowing for more resilient and self-sufficient energy systems.
Finally, steam turbines will continue to be an integral part of efforts to enhance energy security. As nations look to diversify their energy sources and reduce reliance on fossil fuels, turbines that are capable of utilizing locally available resources, including waste heat, biomass, and renewables, will support more resilient energy systems. These turbines will help ensure that energy systems remain stable and efficient, even during periods of disruption or peak demand.
In conclusion, the future of steam turbines in energy efficiency is bright and full of potential. As the world moves toward a more sustainable energy future, steam turbines will continue to evolve, becoming more flexible, adaptable, and efficient. Whether used in large-scale power plants, industrial applications, or decentralized microgrids, steam turbines will be key to achieving higher efficiency, lower emissions, and greater sustainability in the global energy landscape. By embracing innovative technologies, alternative fuels, and digital advancements, steam turbines will remain a cornerstone of efficient energy production for years to come.
As steam turbines continue to evolve, the integration of advanced materials and cutting-edge manufacturing techniques will be crucial in pushing the boundaries of efficiency and performance. The ongoing development of super alloys, ceramic composites, and nanotechnology can lead to steam turbines capable of operating at even higher temperatures and pressures. These materials will help turbines endure the extreme conditions typical of modern, high-efficiency power plants, allowing them to extract even more energy from steam. Furthermore, 3D printing and other advanced manufacturing processes will enable the production of highly optimized turbine components with precision and cost-efficiency, further improving overall turbine efficiency while reducing maintenance needs.
The rise of smart grids will also enhance the efficiency of steam turbines by enabling them to interact with more sophisticated energy systems. Smart grids use advanced information and communication technology to monitor, control, and optimize the flow of electricity. By incorporating steam turbines into these systems, operators can dynamically adjust turbine output based on real-time data, ensuring that energy is generated and distributed in the most efficient manner. This will be especially important as renewable energy sources like wind and solar become more prominent, requiring power systems to balance variable generation with demand. Demand-side management technologies that use real-time data to adjust energy usage will further optimize the role of steam turbines in balancing supply and demand, leading to improved overall system efficiency.
One area that holds significant promise for enhancing steam turbine performance is hybridization with renewable energy sources. Solar thermal systems, for example, capture solar energy to generate heat, which can then be used to create steam that powers a steam turbine. This process can help decarbonize energy production by reducing the need for fossil fuels, offering a more sustainable and efficient solution. Geothermal energy, another renewable source, can be harnessed in steam turbines for baseload power generation. The consistent temperature of geothermal reservoirs allows for the continuous operation of steam turbines, offering a reliable and sustainable power source. The combination of these renewable sources with steam turbine technology will play a pivotal role in reducing the carbon intensity of power plants and improving overall energy efficiency.
In addition, district energy systems, where steam turbines provide both electricity and thermal energy for heating or cooling, offer a highly efficient way to use steam turbines in urban settings. These systems reduce energy waste by using the excess heat produced during power generation for other purposes, such as space heating or industrial processes. By providing integrated energy services—electricity, heat, and sometimes cooling—steam turbines in district energy systems can achieve very high overall efficiencies, potentially approaching 80% or more. This integrated approach to energy delivery is ideal for cities, which consume large amounts of energy and often experience seasonal peaks in demand for heating and cooling.
The global transition to decarbonized energy systems presents both challenges and opportunities for steam turbines. As renewable energy sources continue to grow, steam turbines will likely become a critical technology in the hybridization of grids, providing stability, flexibility, and backup power for intermittent renewable generation. Their ability to operate efficiently with a variety of fuels, including green hydrogen, synthetic fuels, and biomass, will be essential for facilitating the transition away from fossil fuel dependency.
Looking beyond electricity generation, steam turbines will also play a key role in industrial decarbonization efforts. Many heavy industries, such as cement manufacturing, steel production, and chemical processing, rely on steam as a heat source for various processes. By implementing energy-efficient steam turbines alongside carbon capture, storage technologies, and renewable heat sources, these industries can reduce their carbon emissions while improving energy efficiency. This will be critical in meeting both national and international emissions reduction targets and enabling industries to comply with increasingly stringent environmental regulations.
Furthermore, steam turbines will continue to serve as key components in combined heat and power (CHP) systems, which are increasingly seen as a means to increase energy efficiency in both industrial and residential applications. In CHP systems, steam turbines can generate both electricity and useful heat, such as hot water or steam, for residential heating, industrial processes, or other applications. By maximizing the use of energy and minimizing waste, CHP systems achieve high levels of energy efficiency and can be deployed in a variety of settings, from small-scale operations to large cities.
Flexibility in operation will continue to be a defining characteristic of the next generation of steam turbines. As energy systems evolve to integrate more renewable energy and face fluctuating demand patterns, steam turbines must adapt to provide reliable, on-demand power and support grid stability. High-efficiency turbines designed for fast-ramping operation, capable of quickly adjusting to grid fluctuations, will be essential for maintaining balance in grids with a high proportion of renewable generation. Additionally, turbines that can seamlessly operate at both partial load and full load conditions will further optimize their efficiency and reduce the need for costly backups.
At the same time, carbon-neutral fuels will drive the future of steam turbine design. For example, green hydrogen has garnered significant attention as a clean, renewable fuel source for the power sector. Steam turbines capable of burning green hydrogen without producing carbon emissions could significantly reduce the environmental impact of power generation. As the hydrogen economy grows, turbines designed for this fuel will play a central role in reducing the carbon footprint of power generation while maintaining high levels of energy efficiency.
Lastly, steam turbines are also being adapted for use in modular power systems. These systems offer a flexible and scalable approach to power generation, where smaller turbines are used in remote or distributed settings. These modular turbines can be integrated into microgrids to provide power to rural communities, off-grid installations, or mobile applications. By enabling power generation at the point of demand, modular steam turbines contribute to a more resilient and efficient energy infrastructure, especially in areas where traditional grid access is unavailable or unreliable.
In summary, the future of steam turbines is closely linked to advancements in technology, fuel flexibility, and digitalization. With ongoing improvements in turbine materials, control systems, and operational flexibility, steam turbines will remain a cornerstone of energy efficiency across a broad range of applications. Their ability to harness a variety of energy sources—fossil, renewable, and even waste heat—ensures their continued relevance in an evolving energy landscape. As the world moves toward a more sustainable, decarbonized future, steam turbines will play a key role in reducing energy consumption, minimizing waste, and providing reliable, efficient power across industries, cities, and energy systems.
As we look forward to the continued evolution of steam turbines, several important factors will shape their future development, making them an even more integral part of the energy landscape. The pursuit of greater efficiency, combined with the integration of renewable energy sources, will continue to be a primary focus for turbine manufacturers and energy producers alike. The advancements in material science will allow turbines to withstand higher temperatures and pressures, further pushing the boundaries of efficiency while reducing the environmental footprint.
A particularly exciting area of development is the integration of steam turbines with energy storage systems. As renewable energy sources like wind and solar become more prominent, their intermittent nature presents challenges for energy grids. Energy storage technologies, such as battery storage, thermal storage, and hydrogen storage, can help address these challenges by storing excess energy during periods of high production and releasing it when demand peaks or renewable output decreases. By coupling steam turbines with storage systems, energy producers can ensure a steady, reliable supply of power while improving the efficiency of both the turbine and the grid as a whole.
The role of steam turbines in power-to-x technologies is also growing. Power-to-x refers to technologies that convert excess renewable electricity into other forms of energy or raw materials, such as green hydrogen, ammonia, and synthetic fuels. These technologies often rely on electrolysis or other chemical processes, but steam turbines can be used to harness the energy generated from these processes. As the demand for green hydrogen and sustainable fuels increases, steam turbines will serve as key components in power generation systems that support these emerging sectors.
Moreover, heat recovery from industrial processes is expected to become a more prevalent application for steam turbines in the future. Many industries, such as steel production, chemical manufacturing, and oil refining, generate vast amounts of waste heat. By utilizing this waste heat in a steam turbine, industries can convert this thermal energy into useful electricity, significantly increasing their overall energy efficiency. This form of cogeneration or combined heat and power (CHP) systems can reduce energy costs for industries while contributing to lower greenhouse gas emissions.
In addition to industrial applications, steam turbines will continue to be used in the growing field of district energy systems. These systems, which distribute energy for heating, cooling, and electricity generation across multiple buildings or even entire districts, are increasingly seen as an efficient and sustainable solution for urban environments. Steam turbines used in district energy systems can help optimize energy usage by generating both electricity and useful heat at high efficiencies. These systems not only help reduce the overall energy consumption of urban areas but also enhance energy security by providing reliable and localized power, particularly in densely populated regions where energy demand is high.
A future trend that will have a significant impact on steam turbines is the move toward decarbonizing heavy industries. Industries like cement, steel, and chemical production are notoriously difficult to decarbonize due to their reliance on high-temperature processes and the substantial energy required for production. By integrating steam turbines into these processes, particularly in carbon capture systems, heavy industries can reduce their reliance on fossil fuels, enhance energy efficiency, and lower their carbon emissions. In these applications, steam turbines can convert waste heat from industrial processes into electricity, helping to reduce the carbon intensity of these sectors and play a critical role in meeting global decarbonization goals.
Digital innovation is another area that will continue to influence the efficiency and effectiveness of steam turbines. The increasing use of data analytics, artificial intelligence, and machine learning in the power generation sector will allow operators to optimize turbine performance in real-time. By collecting data on turbine operation, analyzing performance trends, and predicting maintenance needs, operators can achieve higher levels of reliability and efficiency while minimizing the risk of downtime. Predictive maintenance will reduce the need for costly and disruptive repairs, extending the lifespan of turbines and maximizing the return on investment. Digital twins (virtual representations of physical turbines) will also allow for simulations of turbine performance under various conditions, helping engineers identify opportunities for further optimization.
The smart grid revolution will further enhance the performance of steam turbines. These grids use digital communication technologies to automatically adjust energy supply and demand, allowing for more efficient and flexible energy use. Steam turbines can be integrated into these systems, enabling them to adjust their output based on real-time demand signals from the grid. This flexibility will be critical as grids become increasingly decentralized and rely more on renewable energy sources. Steam turbines that can quickly ramp up or down in response to grid requirements will be essential for balancing the intermittency of solar and wind generation while maintaining stable grid operation.
The push for sustainable infrastructure in cities and green building standards will also drive demand for more efficient steam turbines. District heating and cooling systems that use steam turbines to generate both electricity and thermal energy will be a key part of the green building movement, reducing energy consumption and improving the environmental performance of urban areas. As cities continue to grow and the demand for energy-efficient solutions increases, steam turbines will play a central role in reducing urban carbon footprints and optimizing energy use.
Finally, the global transition toward renewable energy will increasingly involve the use of hybrid power plants, where steam turbines work in tandem with solar, wind, and battery storage systems. These hybrid setups can improve overall system efficiency by reducing reliance on fossil fuel-based power while maintaining grid stability. By combining multiple energy sources in a single plant, these hybrid systems can leverage the complementary strengths of each source, providing a stable, reliable, and efficient energy supply. Steam turbines will continue to serve as an integral part of these hybrid power plants, contributing to the decarbonization of the energy sector.
In conclusion, the future of steam turbines is a dynamic and exciting one. As technology continues to advance, steam turbines will become more flexible, efficient, and adaptable, playing a crucial role in the decarbonization of the global energy system. Whether in large-scale power plants, industrial settings, district energy systems, or hybrid energy configurations, steam turbines will be central to achieving greater energy efficiency and lower emissions. With innovations in materials, fuel types, digital technology, and integrated energy systems, steam turbines will remain a cornerstone of energy production, making significant contributions to a sustainable, efficient, and decarbonized future.
Steam Turbines in Mechanical Drives
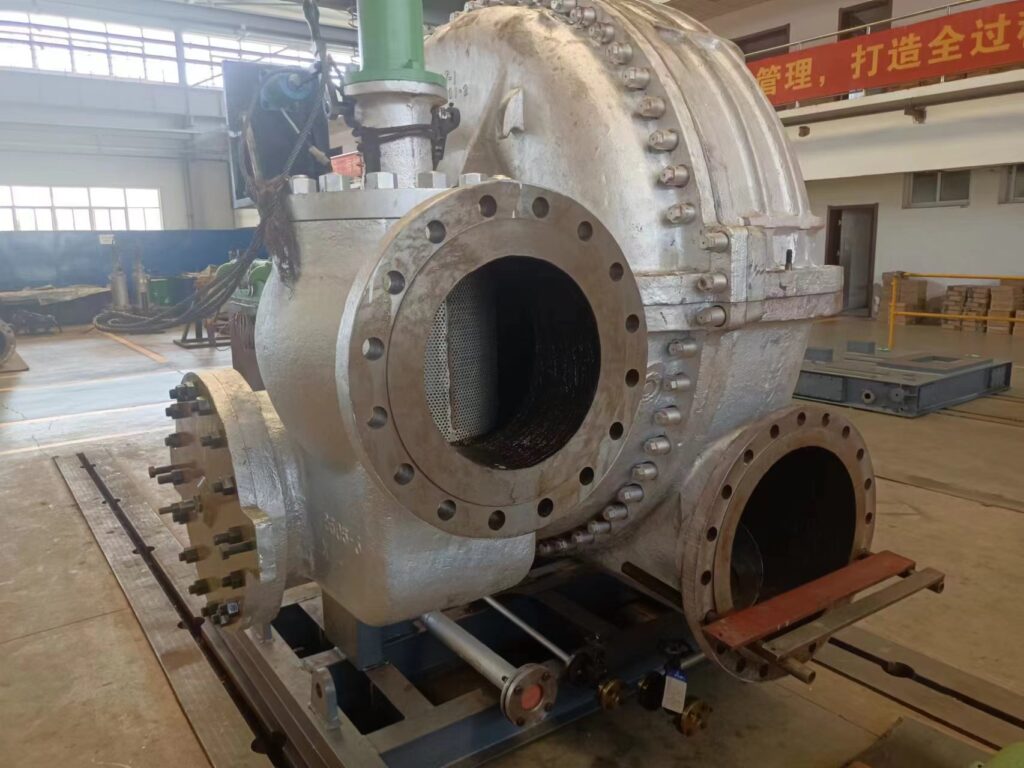
Steam turbines are a vital component in mechanical drives, offering reliable and efficient power for a wide range of industrial applications. Unlike their primary role in power generation, where steam turbines are used to convert heat energy into electricity, mechanical drives utilize steam turbines to provide direct rotational energy to mechanical equipment, such as pumps, compressors, fans, and other machinery. This versatile use of steam turbines spans a broad spectrum of industries, including petrochemical, chemical, mining, cement, and paper manufacturing, among others.
In mechanical drive applications, steam turbines operate by using the high-pressure steam produced in a boiler or other heat source. This steam passes through the turbine’s rotor blades, causing them to spin. The rotating rotor then drives a connected piece of machinery, transmitting mechanical energy directly from the steam turbine to the equipment. This method of energy conversion is extremely effective, as steam turbines can operate under high loads, providing consistent and stable power for industrial operations.
One of the key benefits of using steam turbines for mechanical drives is their ability to maintain a high level of reliability and efficiency over long periods of continuous operation. These turbines are capable of running 24/7 in industrial environments without significant performance degradation. The robust design and engineering of steam turbines allow them to handle extreme operational conditions, including high-temperature and high-pressure environments, which are common in many industrial processes.
Steam turbines in mechanical drives are particularly advantageous in process industries where continuous and uninterrupted power is necessary. For example, in the chemical industry, steam turbines drive compressors that maintain the flow of gases and liquids throughout the production process. In oil refineries, steam turbines are used to power pumps and blowers that move fluids and gases throughout the system. The efficiency of steam turbines helps to reduce energy consumption, which is crucial in industries that rely heavily on energy for their operations.
Another important application of steam turbines in mechanical drives is in the pumping stations used in water treatment and sewage systems. These turbines provide the rotational power needed to pump water through pipelines and ensure the continuous operation of water treatment facilities. In such applications, the reliability and energy efficiency of steam turbines are critical for maintaining operations without interruption.
In addition to industrial applications, steam turbines are also used in marine propulsion systems, where they drive propellers and other mechanical systems on ships. Steam turbines in marine vessels have been used for decades to provide reliable propulsion power, especially in large ships and naval vessels. In these applications, the compact size of steam turbines relative to their power output is a major advantage, as it allows for efficient propulsion systems without occupying excessive space in the ship.
The efficiency of steam turbines in mechanical drive systems is further enhanced by their ability to be integrated into cogeneration systems, where they can produce both mechanical energy and electricity simultaneously. Cogeneration systems are widely used in industries that require both power and heat for their operations. For example, in the paper industry, steam turbines are used to power mechanical drives while simultaneously generating electricity and providing heat for the drying processes. This dual-purpose use of steam turbines helps to optimize energy consumption and improve overall system efficiency.
Fuel flexibility is another feature of steam turbines in mechanical drive applications. These turbines can operate on a variety of fuels, including natural gas, biomass, and waste heat. This flexibility allows for more sustainable operations, as industries can choose fuel sources that align with their environmental goals or local availability. Additionally, the ability to use waste heat, such as heat generated from industrial processes, to power steam turbines further enhances the efficiency of mechanical drive systems and reduces the need for external fuel inputs.
As industries continue to focus on sustainability and energy efficiency, the demand for low-emission and high-efficiency steam turbines will increase. In this context, steam turbines can be integrated into hybrid systems where they work alongside renewable energy sources, such as solar or wind, to provide mechanical power for industrial processes. The combination of renewable energy and steam turbines will reduce carbon emissions while maintaining reliable and efficient mechanical drive capabilities.
Digitalization and smart technology are also playing an increasing role in enhancing the performance of steam turbines in mechanical drives. By integrating advanced sensors, data analytics, and predictive maintenance technologies, operators can optimize the performance of steam turbines in real-time. These technologies allow for continuous monitoring of turbine performance, identifying potential issues before they result in downtime, and ensuring that the turbine operates at peak efficiency. Machine learning algorithms can be used to predict future maintenance needs and optimize the overall operation of the mechanical drive system, leading to cost savings and extended turbine lifespans.
One area where steam turbines are expected to play a larger role in the future is in decentralized power generation. In such systems, steam turbines can be used in microgrids to provide mechanical power to local industries or communities. These smaller, modular turbines can be powered by renewable sources or biomass and used to provide power for mechanical drives in specific applications, such as water pumping, refrigeration, or industrial manufacturing. This decentralized approach to power generation is particularly beneficial in remote or off-grid locations, where access to the main electricity grid is limited or unavailable.
Looking to the future, the integration of advanced materials and manufacturing techniques will continue to enhance the efficiency and performance of steam turbines used in mechanical drives. Advanced alloys and ceramic materials will allow turbines to operate at even higher pressures and temperatures, further improving their efficiency and power output. Additionally, additive manufacturing (3D printing) could allow for the production of turbine components with more intricate designs and better thermal performance, reducing material waste and enhancing the overall durability of the system.
Hybrid energy systems will continue to be a key development area for steam turbines in mechanical drives. As industries increasingly adopt green technologies and renewable fuels, steam turbines will be used in conjunction with solar and wind power to provide continuous and reliable mechanical energy. The combination of renewable and steam turbine power will help industrial sectors transition to a more sustainable energy model while maintaining the high reliability and efficiency that steam turbines are known for.
In conclusion, steam turbines in mechanical drives will remain a crucial technology in various industries, offering reliable, efficient, and flexible solutions for powering industrial equipment. From process industries to water treatment, marine propulsion to cogeneration systems, steam turbines continue to provide vital mechanical energy in a wide range of applications. With ongoing advancements in fuel flexibility, digitalization, and material science, steam turbines will continue to evolve, improving energy efficiency and supporting the global transition to a more sustainable and low-carbon future. Their ability to operate with a variety of fuels, integrate with renewable energy sources, and provide high-efficiency mechanical power ensures that steam turbines will remain a key component in the energy landscape for years to come.
As industries continue to innovate and seek more sustainable solutions, the role of steam turbines in mechanical drives will evolve in tandem with these advancements. The increasing emphasis on energy efficiency and cost reduction across industries will drive the demand for more advanced turbine designs that maximize performance while minimizing environmental impact.
One notable trend is the growing interest in combined heat and power (CHP) systems. These systems are becoming more prevalent in industrial settings, where both mechanical power and thermal energy are required for the manufacturing processes. By using steam turbines in CHP systems, industries can significantly increase overall efficiency by utilizing waste heat from their operations. The steam turbines convert this thermal energy into mechanical power for driving equipment, while simultaneously providing electricity for other processes, making the system far more efficient than traditional energy production methods.
Steam turbines are also expected to become an integral part of district energy systems, where mechanical power is needed for heating, cooling, and electricity generation for communities or industrial parks. These systems provide a centralized approach to energy generation, reducing overall infrastructure costs and improving the energy resilience of the region. The steam turbines in these setups provide a flexible and reliable source of mechanical energy for pumps, compressors, and other equipment, making them a valuable component of modern urban energy infrastructure.
In the biomass energy sector, steam turbines have the potential to play an even larger role in renewable energy generation. Biomass, derived from organic materials such as agricultural waste, forest residues, or even municipal solid waste, can be converted into steam to drive turbines. This process reduces the reliance on fossil fuels and offers an environmentally friendly alternative for producing both electricity and mechanical power. As the demand for renewable energy sources increases, steam turbines powered by biomass will contribute to reducing greenhouse gas emissions and provide industries with a cleaner source of mechanical power.
The concept of “green” mechanical drives will further promote steam turbines in industries that seek to minimize their carbon footprints. For example, in the paper and pulp industries, which have traditionally relied on fossil fuels for power generation, integrating steam turbines powered by renewable energy sources, such as biomass or waste heat, can dramatically reduce emissions. The adoption of steam turbines as part of a more circular economy will encourage companies to make use of waste energy, improving sustainability in manufacturing processes while maintaining efficiency.
Steam turbines will also see growing adoption in energy-efficient industrial automation systems, where they are used to power automated equipment for processes such as material handling, machinery operations, and assembly lines. These systems rely on consistent and reliable mechanical power to ensure smooth and uninterrupted operations. As manufacturing becomes more automated, the demand for turbines to provide high-performance mechanical energy will increase, pushing innovation in turbine design and control systems to meet the new demands of industry.
Moreover, modular steam turbine systems are likely to see expanded use in industrial environments. These smaller, more flexible turbines can be deployed in various operational settings where smaller and more localized sources of mechanical power are needed. Modular systems can be customized to fit the specific needs of the operation, whether it’s providing power to a single pump or a whole set of equipment. This modular approach provides industries with the flexibility to scale operations up or down, optimizing the performance of the mechanical drive system and increasing overall efficiency.
The integration of smart grid technology with steam turbines will also be critical in optimizing industrial energy use. These advanced grids, which use digital communication technologies to manage energy distribution, will enable steam turbines to operate more efficiently and flexibly. The ability to monitor turbine performance and adjust operations in real-time, based on demand signals from the grid, will ensure that energy is used optimally and that mechanical drives are functioning at peak efficiency. This integration can help to reduce operational costs and improve the sustainability of industrial processes.
Looking ahead, additive manufacturing (3D printing) has the potential to revolutionize the production of steam turbines for mechanical drive applications. By using advanced printing technologies to create turbine components, manufacturers can design more intricate and optimized parts that are lighter, more efficient, and more cost-effective than traditional manufacturing methods allow. This could result in turbines that are better suited to specific applications, such as high-temperature environments or areas where space is limited, further expanding the versatility of steam turbines.
The demand for reducing downtime and improving the reliability of mechanical drive systems will continue to spur innovations in steam turbine maintenance. With advancements in predictive analytics, IoT (Internet of Things) sensors, and remote monitoring technologies, operators can more accurately predict when turbines need maintenance or repair, reducing costly unscheduled downtime. By using real-time data to monitor turbine conditions and performance, operators can detect potential problems early, allowing for proactive maintenance that extends the life of the turbine and improves its long-term reliability.
As industries shift toward greener technologies, steam turbines used in mechanical drives will also benefit from growing regulatory pressure to reduce carbon emissions. Governments worldwide are imposing stricter emissions standards, and industries are being encouraged to adopt more sustainable technologies. This will likely lead to greater adoption of renewable fuels, such as biogas, hydrogen, and biomass, to power steam turbines, enabling them to remain compliant with new emissions regulations while providing mechanical power.
As steam turbines become increasingly integrated into smart industrial ecosystems, the ability to provide adaptable mechanical drive systems will allow manufacturers to enhance their flexibility and response times. The rapid changes in supply chains and the increasing demand for customized products will require industries to be more agile. Steam turbines, with their ability to provide highly efficient, scalable, and adaptable mechanical power, will play a key role in meeting these challenges. These turbines can easily adapt to changing production schedules and fluctuating power needs, making them invaluable in a world where industrial flexibility and cost competitiveness are paramount.
In summary, the future of steam turbines in mechanical drives is one of continuous innovation and expansion. As industries strive for greater efficiency, sustainability, and adaptability, steam turbines will evolve to meet the demands of modern manufacturing processes, from automated systems to renewable energy integration and energy-efficient district energy systems. Their reliability, efficiency, and versatility in providing both mechanical and electrical energy ensure that steam turbines will remain a key player in industrial energy solutions, supporting the global transition to a more sustainable and energy-efficient future. Through advancements in materials, digitalization, and hybrid energy systems, steam turbines will continue to enhance the performance and sustainability of mechanical drive systems, delivering reliable, high-efficiency solutions for industries across the world.
As we continue to look toward the future of steam turbines in mechanical drives, further advancements in control systems will enhance turbine performance. The integration of advanced control technologies such as variable speed drives (VSDs) and automatic load regulation will allow steam turbines to operate with greater precision and adaptability. These technologies enable turbines to adjust to varying power needs in real time, ensuring that the mechanical drive systems can operate efficiently under fluctuating conditions. By optimizing the turbine’s speed and power output, industries can reduce energy consumption and improve system efficiency, resulting in cost savings and a more sustainable energy model.
The flexibility of steam turbines in handling diverse steam sources will also be a key consideration in future mechanical drive applications. As industries increasingly move toward using waste heat or waste steam to power mechanical drives, steam turbines will become more versatile in accepting a variety of steam conditions. Whether utilizing low-pressure steam from industrial processes or high-temperature steam from advanced boilers, steam turbines will be optimized for a broad range of applications. This flexibility enhances their utility in settings where waste heat recovery is critical, such as in chemical processing, petroleum refineries, and power plants that have cogeneration capabilities.
Another important area of development is advanced monitoring systems that enable predictive and condition-based maintenance. Through the use of sensors and real-time data analytics, steam turbines can be equipped with systems that continuously monitor key performance metrics, such as vibration, temperature, pressure, and rotational speed. These systems can analyze data to identify potential issues before they cause failures, ensuring that maintenance activities are performed only when necessary. By shifting from reactive to proactive maintenance, industries can reduce operational downtime and extend the life of their steam turbines, leading to significant cost savings and reduced maintenance expenses.
The focus on energy decentralization and local power generation will further drive the adoption of steam turbines in mechanical drives. Distributed energy systems, powered by renewable resources such as solar, wind, or biomass, are becoming more common, especially in remote or off-grid locations. Steam turbines can play a crucial role in these systems, providing mechanical power to local industries or communities. By pairing turbines with renewable energy sources, these systems can offer continuous mechanical power for industrial applications without relying on traditional energy grids. This decentralization of energy generation also helps enhance energy security, especially in regions where access to the central grid may be limited or unreliable.
Furthermore, energy storage solutions, such as battery systems and thermal storage, will enhance the role of steam turbines in future energy systems. In cogeneration plants and hybrid energy systems, steam turbines can be used to store excess energy during periods of low demand and release it during peak periods. For example, thermal storage systems can store heat generated by steam turbines and release it later when mechanical power is needed. This ability to store and release energy will improve the overall efficiency of mechanical drives and further contribute to sustainable industrial practices.
Steam turbines are also expected to play a more significant role in hydrogen production. As the global energy transition accelerates, hydrogen is gaining attention as a clean energy source. Green hydrogen, produced using renewable energy, can be used as a fuel for steam turbines in mechanical drives. Hydrogen combustion produces zero carbon emissions, making it an ideal solution for industries seeking to decarbonize their operations. By utilizing hydrogen as a fuel source, steam turbines can contribute to a low-carbon economy, providing mechanical power for various industrial applications while helping companies meet emissions reduction targets.
With the growing interest in advanced materials, steam turbines are likely to incorporate new materials that enhance both their performance and longevity. For instance, superalloys and ceramic materials are being developed to withstand higher temperatures and pressures, increasing the efficiency of steam turbines. These materials improve the turbines’ resistance to corrosion and erosion, enabling them to operate for longer periods without requiring frequent repairs or replacements. Such improvements will increase the lifespan of steam turbines in mechanical drives, making them an even more cost-effective option for industrial applications.
In addition to material innovations, manufacturing techniques like additive manufacturing (3D printing) are transforming the production of turbine components. With the ability to create more complex geometries and optimize designs, 3D printing allows for more efficient, lightweight components that enhance the overall performance of steam turbines. This will be especially beneficial for turbines operating in specialized environments where traditional manufacturing methods fall short. The increased precision and efficiency offered by 3D printing could reduce energy losses, improve system reliability, and lower manufacturing costs.
One of the most exciting developments in the future of steam turbines for mechanical drives is their potential integration with artificial intelligence (AI) and machine learning (ML). These technologies can help optimize turbine performance by analyzing vast amounts of operational data. AI algorithms can predict when a turbine is likely to experience a malfunction, enabling predictive maintenance that minimizes downtime. Additionally, machine learning can be used to continuously improve the efficiency of steam turbines, automatically adjusting their operations to meet changing demand or environmental conditions. By leveraging AI and ML, industrial operators can achieve greater levels of automation, leading to increased operational efficiency and cost savings.
Moreover, the integration of steam turbines with digital twins—virtual replicas of physical systems—will provide valuable insights into turbine performance and optimization. Digital twins use real-time data to simulate how a steam turbine will perform under different conditions, allowing operators to make data-driven decisions about turbine operations. This can be especially helpful in industries that require fine-tuned control over their mechanical systems, such as aerospace, automotive, and high-precision manufacturing.
Finally, collaborative technologies that involve industry partnerships will further accelerate the adoption of steam turbines in mechanical drives. Collaboration between turbine manufacturers, energy providers, and end-users can lead to the development of tailored turbine solutions that address the unique needs of specific industries. Custom-built turbines can be designed to meet the particular demands of various industrial sectors, whether it’s for enhanced durability, improved energy efficiency, or adaptability to specific fuel types. These partnerships will also drive innovation in areas like digitalization, automation, and system integration, ensuring that steam turbines remain at the forefront of mechanical drive technology for years to come.
In conclusion, the future of steam turbines in mechanical drives is bright, driven by advancements in materials, digital technology, and sustainable energy practices. As industries continue to demand higher efficiency, reduced emissions, and flexible energy solutions, steam turbines will evolve to meet these challenges, providing reliable, efficient, and adaptable power for mechanical systems across a wide range of applications. From industrial automation to hybrid energy systems, steam turbines will remain an indispensable component of modern manufacturing and energy production, contributing to a more sustainable and energy-efficient world.
Looking further into the future, steam turbines in mechanical drives will continue to evolve alongside emerging technological trends in both energy generation and industrial processes. Their versatility and ability to adapt to a wide range of fuels and energy systems will enable them to stay relevant in an increasingly diversified energy landscape.
As industries continue to push the envelope on sustainability, waste-to-energy technologies will become more prevalent. Steam turbines can play a key role in waste management systems by converting municipal waste, industrial byproducts, or even non-recyclable materials into useful energy. This will help reduce landfill waste while producing clean energy for mechanical drives, contributing to the circular economy model. In this context, turbines will not only provide mechanical power for industrial processes but also help tackle one of the most pressing global challenges—waste reduction.
In the realm of industrial decarbonization, steam turbines will be central to many carbon capture and storage (CCS) systems. These systems are designed to capture carbon dioxide emissions from industrial processes, preventing them from entering the atmosphere. By integrating steam turbines into CCS systems, industries can capture waste heat from power generation and use it to drive turbines that produce mechanical power for other processes. This innovative integration will further support the transition to low-carbon technologies and promote carbon-neutral operations across many sectors.
Global industrial trends, such as Industry 4.0 and the Internet of Things (IoT), will shape the future role of steam turbines in mechanical drives. As more connected devices enter industrial environments, turbines will be monitored and controlled through sophisticated networks, allowing for greater optimization and predictive maintenance. Data collected from IoT sensors embedded in turbines will feed into centralized control systems, allowing for real-time adjustments to performance and the early detection of issues. This capability will reduce downtime, extend turbine life, and enhance overall operational efficiency.
Moreover, with the growing shift toward digital twins—virtual representations of physical systems—steam turbines will benefit from real-time simulations that reflect their current operating conditions. By using digital twins, engineers and operators can simulate different operating scenarios to determine the most efficient and cost-effective way to run turbines. This predictive capability will be especially useful for optimizing steam turbine performance under varying operational demands, whether in manufacturing, power generation, or oil and gas industries.
As the demand for clean energy continues to grow, steam turbines will also be utilized in a broader array of renewable energy systems. For example, steam turbines powered by geothermal energy or solar thermal power are already proving to be viable options in certain regions. These systems generate steam using the heat of the Earth’s core or concentrated solar energy to drive turbines that produce mechanical power or electricity. As renewable energy sources continue to scale globally, steam turbines will be key players in hybrid renewable energy systems, where they can integrate with other green technologies to maximize efficiency and reliability.
The continued development of hydrogen-based energy systems will also boost the role of steam turbines in mechanical drives. Hydrogen has the potential to serve as a clean fuel source for steam turbines, especially in industrial sectors like steel production, cement manufacturing, and chemical processing, where high temperatures and mechanical power are necessary. As the technology for green hydrogen production advances and becomes more economically viable, steam turbines powered by hydrogen could offer a sustainable alternative to traditional fossil-fuel-driven mechanical drives.
In parallel with these technological advancements, advanced turbine designs will emerge to address the growing need for more compact, efficient, and customizable systems. For example, compact turbines that can operate at smaller scales will open new opportunities for steam turbines in off-grid energy solutions and small-scale industrial applications. These systems will be more affordable and adaptable to localized power generation needs, such as in remote mining operations, agricultural facilities, or smaller factories that do not have access to large power grids. The ability to produce mechanical power on-site, from renewable or waste sources, will reduce reliance on centralized energy infrastructures and enhance energy security in these settings.
In the future, we are likely to see a greater emphasis on high-performance materials that enable steam turbines to function at higher efficiencies in extreme environments. Supercritical and ultra-supercritical steam cycles—where steam temperatures and pressures exceed typical levels—will require turbines capable of withstanding higher stresses and operating conditions. These higher-efficiency turbines will produce more power with less fuel, helping industries reduce their environmental footprint while maintaining operational effectiveness.
As the world continues to experience increased pressure to adopt sustainable technologies and reduce emissions, steam turbines will also evolve to handle the challenges associated with the integration of multiple energy sources. The future of industrial energy will likely be characterized by hybrid systems that combine renewable and conventional power sources to ensure reliable, continuous operations. Steam turbines will be critical in helping industries adapt to these evolving energy portfolios, ensuring that mechanical drives are available to power systems, even when renewable energy sources such as solar or wind are intermittent.
Furthermore, with the growing focus on circular economy principles, steam turbines could be increasingly incorporated into closed-loop systems that allow industries to reuse energy and minimize waste. For instance, steam turbines could be part of energy recovery systems in chemical plants or refineries, where waste heat from one process can be captured and used to generate steam to drive turbines that power other equipment. By reusing energy within industrial processes, companies can reduce the need for external energy inputs and improve overall system efficiency.
Finally, in response to increasing global energy demands and the call for resilient energy systems, steam turbines will continue to be an essential component of large-scale power plants, particularly in combination with renewable energy systems. Their ability to provide stable, continuous mechanical power to critical infrastructure will be indispensable, especially as the demand for renewable energy integration increases. With their long-established reliability, steam turbines will be an enduring cornerstone of modern power generation, providing mechanical drive systems that enhance the efficiency and flexibility of energy production across various sectors.
In conclusion, steam turbines will continue to play an indispensable role in mechanical drives well into the future. As energy systems become more complex, interconnected, and environmentally conscious, steam turbines will evolve to meet the demands of industrial efficiency, energy resilience, and sustainability. Whether integrated with renewable energy, smart grids, hydrogen-based systems, or advanced manufacturing technologies, steam turbines will remain a cornerstone of modern industrial operations. The continued development of more efficient, adaptable, and environmentally friendly turbine technologies will ensure that steam turbines remain an essential tool for powering a wide range of mechanical systems across industries worldwide.
Medium-pressure Steam Turbines
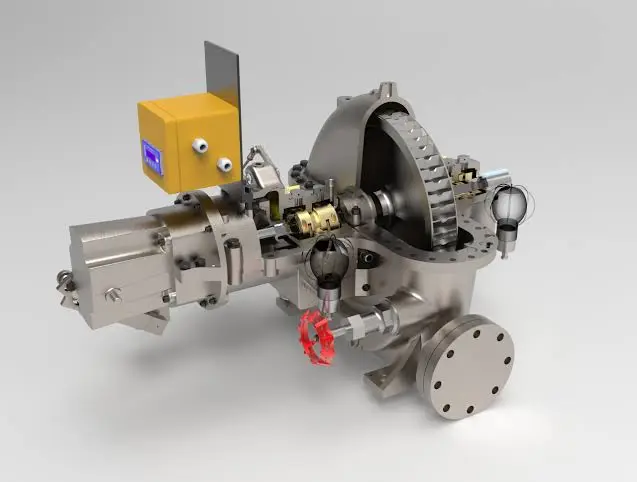
Medium-pressure steam turbines are essential components in industrial applications that require a balance between performance, efficiency, and operational cost-effectiveness. These turbines operate at moderate pressure levels, typically in the range of 10 to 30 bar, and are used in a variety of industries, including chemical processing, petrochemical industries, cogeneration plants, and food production facilities, among others. Medium-pressure steam turbines are particularly favored in systems where the steam available is neither too high in pressure nor too low to generate sufficient mechanical power.
The primary function of medium-pressure steam turbines is to convert the energy from steam into mechanical work, which can be used to drive equipment such as compressors, pumps, or electric generators. These turbines operate efficiently when coupled with other systems, such as heat exchangers, steam boilers, or waste-heat recovery units, to maximize their energy conversion capabilities.
In terms of performance characteristics, medium-pressure steam turbines are designed to handle moderate steam conditions and provide a balance between energy output and efficiency. They offer several advantages over both low-pressure and high-pressure turbines, especially in industrial environments where the steam supply fluctuates in pressure or where cost-effective operation is crucial. These turbines are generally less complex than high-pressure systems, which makes them easier to maintain and less expensive to operate while still offering robust performance.
One of the key advantages of medium-pressure steam turbines is their ability to operate in a wide range of conditions. They can handle variations in steam pressure and temperature while maintaining consistent performance, making them ideal for applications where the pressure and temperature of steam are not always constant, such as in cogeneration or district heating systems. This flexibility allows medium-pressure turbines to accommodate steam from various sources, including industrial boilers, waste-heat recovery systems, and biomass plants.
Medium-pressure steam turbines are often designed to work in combined heat and power (CHP) systems, where both electricity generation and thermal energy are required. In these systems, the medium-pressure turbine is used to generate power, while the exhaust steam is used for heating purposes, such as in district heating networks or industrial processes that require steam for various heating applications. The combination of power generation and heat recovery improves overall energy efficiency and reduces operational costs, making these systems a sustainable solution for energy-intensive industries.
Another notable feature of medium-pressure steam turbines is their ability to provide mechanical drive power for heavy-duty industrial equipment. In industries such as paper manufacturing, mining, and chemical production, steam turbines are often used to power equipment like conveyors, agitators, or centrifuges. The mechanical power generated by the turbine is transmitted to these machines through a shaft, allowing them to perform work in processes that require significant power, such as mixing, separating, or heating.
From a design standpoint, medium-pressure steam turbines typically feature a simple yet robust structure that is well-suited for continuous operation in demanding industrial environments. The turbines are often designed with several stages of expansion to efficiently extract energy from steam at different pressure levels. This staged expansion allows for the controlled conversion of thermal energy into mechanical work, improving the overall efficiency of the turbine. Additionally, these turbines can be designed with multiple inlet nozzles to distribute steam evenly across the rotor blades, ensuring smoother operation and enhanced performance.
In terms of energy efficiency, medium-pressure steam turbines are typically designed for optimal thermal efficiency, meaning they extract as much useful energy as possible from the available steam. This efficiency can be further optimized by using regenerative feedwater heating, which recovers heat from the exhaust steam to preheat the incoming feedwater before it enters the boiler. This process reduces fuel consumption and improves overall system efficiency. Medium-pressure turbines can also be integrated with condensing systems that allow the turbine to extract more energy from the exhaust steam, which is then condensed and returned to the system.
In maintenance, medium-pressure steam turbines are relatively easy to service due to their straightforward design and modular components. This reduces the need for expensive downtime and allows for faster repairs, which is critical in industries that rely on continuous operation. Furthermore, these turbines are often equipped with advanced monitoring systems that provide real-time data on operational performance, allowing operators to detect any potential issues before they lead to major failures. This predictive maintenance capability ensures that the turbines remain in optimal working condition and extend their operational lifespan.
As the demand for clean energy and sustainability increases, medium-pressure steam turbines will continue to evolve. These turbines are ideal for use in renewable energy systems, particularly in biomass and waste-to-energy plants, where steam pressure is generally moderate. The ability of medium-pressure turbines to handle varying steam qualities, such as low-pressure steam or steam with impurities, makes them a flexible choice for environmentally friendly energy systems. The continued development of advanced materials and high-efficiency designs will further enhance the performance of these turbines, enabling them to operate at even higher efficiencies while meeting stricter environmental standards.
Additionally, with the growing focus on energy decentralization and local power generation, medium-pressure steam turbines are becoming increasingly important for microgrids and off-grid power systems. These systems provide reliable, localized power generation, often using renewable energy sources or waste heat. Medium-pressure steam turbines are well-suited for these applications because of their flexibility, cost-effectiveness, and ability to operate with a wide range of steam pressures. As energy systems become more decentralized, these turbines will be vital in providing reliable power to communities, industries, and remote areas.
The use of medium-pressure steam turbines in industrial waste heat recovery systems is also growing. Many industrial processes, such as steel manufacturing or chemical production, generate large amounts of waste heat, which can be captured and converted into usable steam. This steam can then be used to drive medium-pressure turbines, which generate mechanical power for equipment or electricity. By recovering waste heat, industries can reduce their dependence on traditional energy sources, lower emissions, and improve overall efficiency.
In conclusion, medium-pressure steam turbines offer a versatile, efficient, and cost-effective solution for a wide range of industrial applications. Their ability to operate with moderate steam pressures, provide mechanical power, and integrate into cogeneration systems makes them ideal for industries looking to improve energy efficiency and sustainability. As the demand for renewable energy, energy recovery, and cost-effective power generation grows, medium-pressure steam turbines will continue to play a crucial role in modern industrial energy systems. With continued advancements in turbine technology and design, medium-pressure steam turbines will remain at the forefront of energy-efficient mechanical drive solutions.
The future of medium-pressure steam turbines is deeply linked to ongoing trends in energy efficiency and sustainability. As industries across the world increasingly embrace the energy transition and seek to meet more stringent environmental regulations, medium-pressure steam turbines are poised to become even more integral in driving industrial processes with minimal environmental impact. Their ability to work seamlessly with renewable energy sources and waste heat recovery systems positions them as versatile components in the transition toward a low-carbon economy.
As renewable energy sources such as solar, wind, and biomass grow in prominence, medium-pressure turbines will continue to be vital in hybrid energy systems. These systems combine traditional energy sources with renewables to provide a stable and reliable energy supply. Medium-pressure steam turbines are especially well-suited for biomass power plants, where the steam produced from burning organic materials can be converted into mechanical energy. Their relatively moderate pressure ratings make them ideal for operating with the fluctuating steam conditions often found in biomass energy systems.
Similarly, the development of combined cycle power plants will benefit from the integration of medium-pressure turbines. These plants typically use gas turbines to generate electricity, followed by the recovery of waste heat to generate steam that drives a steam turbine. By using a medium-pressure steam turbine in the second phase of power generation, such systems can significantly improve their overall efficiency, providing both electricity and heat while minimizing fuel consumption and emissions.
The expanding need for district heating systems is another area where medium-pressure steam turbines will continue to play a critical role. District heating involves the centralized production of heat, which is then distributed to multiple buildings or industrial complexes. In these systems, medium-pressure steam turbines can be used to generate mechanical power or electricity while also providing thermal energy for heating purposes. The ability to produce both power and heat from a single energy source makes these systems highly efficient, reducing overall energy consumption and carbon footprints.
In industrial sectors like chemical processing and petrochemical production, where consistent and reliable steam is required for various manufacturing processes, medium-pressure steam turbines will be essential. As these industries strive to reduce operational costs and increase sustainability, the efficiency and flexibility of medium-pressure turbines make them an attractive option. They can be integrated into cogeneration systems that meet both the electricity and steam needs of a facility, ensuring a more efficient use of energy resources.
Another emerging trend is the use of digital technologies to enhance the performance and reliability of medium-pressure steam turbines. The integration of IoT sensors, data analytics, and machine learning will enable real-time monitoring of turbine performance. Operators can use these insights to optimize operations, predict maintenance needs, and improve overall system efficiency. By leveraging these technologies, industries can reduce downtime, lower maintenance costs, and extend the service life of their turbines.
As manufacturers focus on cost-effectiveness, medium-pressure steam turbines are becoming more compact and modular. This trend is important for smaller-scale industrial operations, particularly those in remote locations or in sectors that don’t require large-scale power generation. By offering modular turbines that can be scaled to meet the specific needs of a business, turbine manufacturers are providing cost-effective solutions for industries with variable energy demands. These smaller-scale turbines can be tailored to suit specific applications, ensuring efficient energy conversion while minimizing capital expenditure.
Furthermore, the use of advanced materials will continue to play a key role in improving the efficiency and durability of medium-pressure steam turbines. High-strength alloys, ceramic coatings, and corrosion-resistant materials will allow turbines to operate at higher temperatures and pressures, improving overall performance while reducing wear and tear over time. These innovations will help extend the lifespan of medium-pressure turbines and ensure they remain competitive in the face of increasingly demanding industrial standards.
The industrial trend toward decarbonization is also pushing medium-pressure steam turbines to evolve. Many industries are now exploring ways to incorporate hydrogen as a clean fuel source. Hydrogen-powered turbines are expected to gain traction in the coming years as industries seek alternative ways to reduce their carbon emissions. Medium-pressure steam turbines that can run on hydrogen-rich steam or blended hydrogen-steam mixtures will contribute to the energy transition by offering a viable, low-emission alternative to traditional fossil-fuel-based turbines.
Moreover, as industries become more energy-conscious, the role of medium-pressure steam turbines in demand-side management will increase. With the ability to efficiently convert steam into mechanical power or electricity, medium-pressure turbines will be used to help manage energy demand during peak periods. By shifting energy consumption to off-peak times, industries can reduce their overall energy costs and contribute to a more stable energy grid.
As global demand for clean energy and resource efficiency intensifies, medium-pressure steam turbines will continue to be an integral part of a wide range of industries. Their combination of flexibility, efficiency, and cost-effectiveness makes them ideal for industrial applications that rely on moderate steam pressures. Whether used in cogeneration systems, district heating networks, or biomass energy plants, these turbines will remain a cornerstone of modern energy systems.
Finally, the continuous evolution of steam turbine technology, driven by advancements in materials science, digital control systems, and energy management, will further enhance the performance of medium-pressure steam turbines. Their future will likely involve even more precise control systems for optimizing energy use and adapting to variable energy supply. With their ability to work efficiently in a wide range of applications and environments, medium-pressure steam turbines will play a critical role in meeting the global challenges of energy efficiency, sustainability, and economic growth.
As we move further into the 21st century, the role of medium-pressure steam turbines is becoming even more crucial in a rapidly evolving energy landscape. Global energy challenges, including the need to decarbonize industries, increase energy efficiency, and integrate renewable energy, will continue to influence the development of these turbines. In this context, medium-pressure steam turbines will not only remain an important part of industrial energy systems but will also adapt to new demands and technologies.
One area where medium-pressure steam turbines will likely see significant advancements is in their adaptation to hybrid energy systems. As the world shifts toward more decentralized energy production, medium-pressure turbines will increasingly be integrated into systems that combine both renewable and conventional energy sources. This hybridization could involve the use of turbines alongside solar power, wind energy, and battery storage systems to ensure a reliable and steady supply of energy, especially in regions with fluctuating renewable energy availability. The flexibility of medium-pressure turbines to work with variable steam pressures and temperatures makes them well-suited for such applications, where energy sources are intermittently available and need to be stored or adjusted to meet demand.
The modular design of modern medium-pressure steam turbines is also a key factor in their continued relevance. As industries continue to seek more flexible, adaptable, and cost-effective energy solutions, modular turbines provide the scalability and versatility required to meet specific operational needs. By offering turbines that can be scaled up or down depending on the size of the operation, businesses can better align their energy infrastructure with variable production demands and changing market conditions. This modularity also supports faster installation times, making turbines easier to deploy in new industrial plants or upgraded facilities.
With the growing emphasis on sustainability, medium-pressure steam turbines will also become more efficient in terms of resource utilization. Improvements in turbine efficiency will allow industries to extract more energy from the same amount of steam, leading to lower fuel consumption, reduced emissions, and less waste. Advanced turbine blades, optimized nozzles, and improved thermodynamic cycles will contribute to these efficiency gains. Additionally, turbine manufacturers are likely to integrate waste heat recovery systems into medium-pressure turbines to make better use of heat energy that would otherwise be lost to the environment. This waste heat can be repurposed for use in other industrial processes or converted into electricity.
Another growing area of focus for medium-pressure steam turbines is their integration with carbon capture and storage (CCS) technologies. As part of efforts to mitigate climate change, many industries are looking into CCS to reduce the carbon dioxide (CO₂) emissions from their operations. Medium-pressure turbines can be adapted to support these technologies by using cleaner energy sources and incorporating systems that capture and store CO₂ emissions generated during the steam cycle. The synergy between turbine technology and CCS could offer an effective way for industrial facilities to decarbonize while maintaining the reliable and efficient power generation that medium-pressure turbines provide.
In addition to their role in carbon capture, medium-pressure steam turbines are also likely to be used in bioenergy systems. The production of energy from biomass, biogas, and other organic materials is seen as a key solution for reducing greenhouse gas emissions and supporting sustainable energy goals. By using medium-pressure steam turbines in bioenergy plants, industries can convert biomass into steam, which is then used to generate electricity or mechanical power for industrial processes. This process not only provides a renewable energy source but also supports the circular economy by making use of organic waste materials.
As industries become more digitally integrated, medium-pressure steam turbines will also benefit from the growing use of industrial Internet of Things (IoT) technologies. The real-time monitoring of turbine performance, coupled with predictive maintenance, will help operators avoid downtime, increase the longevity of turbines, and optimize energy use. By integrating sensors and data analytics into the turbines, operators can track parameters such as vibration, temperature, and pressure to identify potential issues before they result in failures. Additionally, predictive maintenance tools will allow for better scheduling of maintenance activities, reducing the need for costly emergency repairs and increasing the efficiency of turbine operations.
The development of advanced computational models and simulation tools will also play a crucial role in improving medium-pressure steam turbine performance. By using computer-aided design (CAD) and computational fluid dynamics (CFD), engineers can optimize the design of turbine components such as blades, nozzles, and rotors to enhance efficiency and reduce wear. These simulations allow for more accurate predictions of turbine performance under various operating conditions, enabling manufacturers to refine their designs before construction. This results in turbines that are not only more efficient but also more durable and easier to maintain.
Medium-pressure steam turbines will also remain critical in cogeneration and combined heat and power (CHP) systems. These systems are increasingly popular in industries where both heat and power are required for operations. By using medium-pressure steam turbines, businesses can efficiently generate electricity while also utilizing the exhaust steam for industrial heating applications, such as drying, distillation, or heating buildings. This dual-use of energy improves overall system efficiency, reduces fuel consumption, and minimizes waste, contributing to the overall sustainability of the operation.
As the global population grows and the demand for energy increases, medium-pressure steam turbines will continue to be vital for providing reliable, sustainable, and cost-effective power in industrial applications. Their ability to adapt to changing energy needs, work with renewable energy sources, and improve overall efficiency ensures that they will remain a critical component of the energy infrastructure. The future of medium-pressure steam turbines will likely involve further technological innovations, including improvements in energy storage, flexible fuel systems, and integration with emerging renewable energy technologies. These advancements will ensure that medium-pressure steam turbines continue to meet the demands of a rapidly evolving energy landscape, helping industries achieve their sustainability goals and contribute to a greener, more efficient future.
High-pressure Steam Turbines
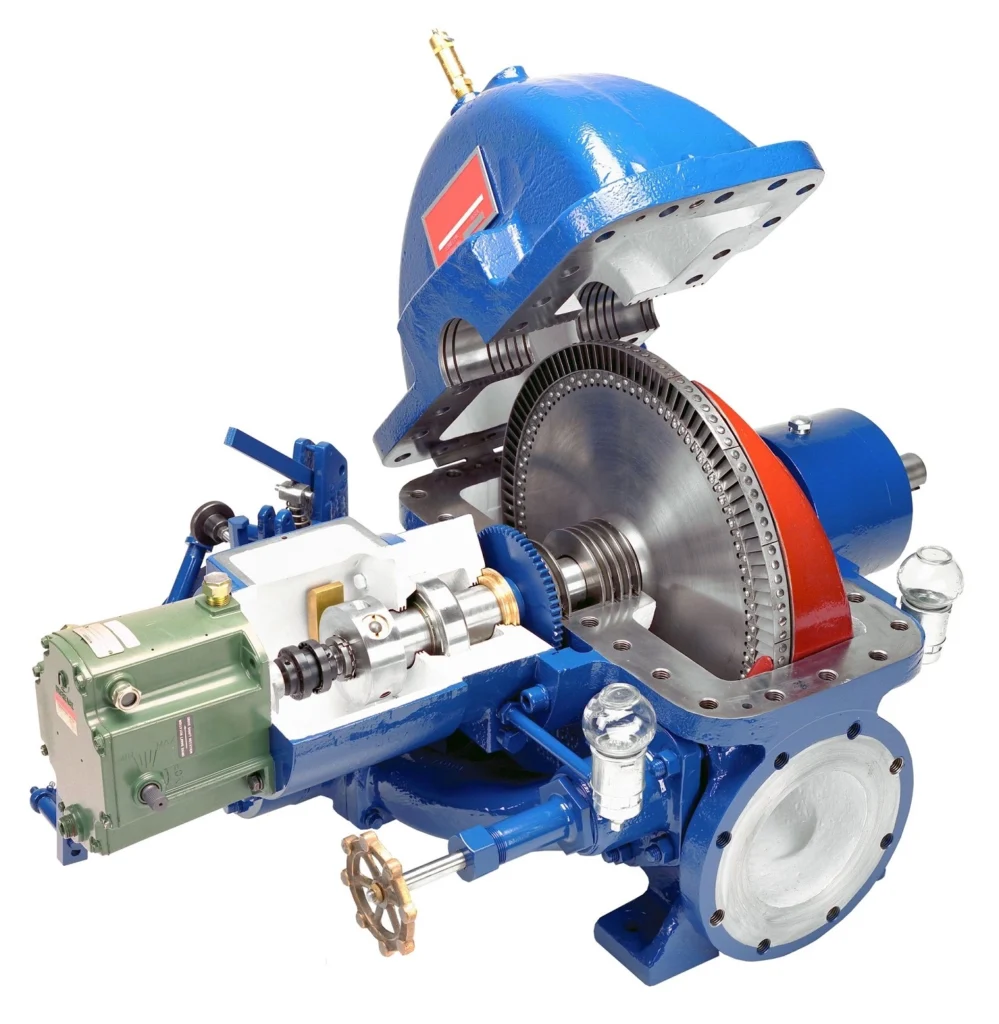
High-pressure steam turbines are a crucial part of many energy systems, especially in large-scale power generation and industrial applications. These turbines are designed to operate with steam at pressures exceeding 30 bar (often in the range of 50 to 150 bar) and temperatures that can reach up to 600°C or more. High-pressure steam turbines are typically used in power plants, refineries, and chemical plants, where the generation of large amounts of power or mechanical energy is required.
The primary function of high-pressure steam turbines is to convert the thermal energy in high-pressure steam into mechanical energy, which is then used to drive electric generators, industrial machinery, or mechanical drives. The energy conversion process in high-pressure steam turbines is highly efficient due to the high energy content of the steam, making them ideal for electric power generation in fossil fuel, nuclear, or geothermal power plants. These turbines are also essential in combined-cycle power plants, where the heat from gas turbines is used to produce steam that drives the high-pressure turbine.
High-pressure steam turbines are designed to operate with steam at high temperatures and high pressures, which makes them highly efficient at extracting energy from steam. The high-pressure steam is expanded in stages through a series of rotors and stators, where the thermal energy of the steam is converted into mechanical work. As the steam expands, it loses pressure and temperature, and this energy is used to rotate the turbine’s rotor, which is connected to a shaft. The mechanical work generated by the rotor is then used to power a generator or drive industrial equipment.
The design of high-pressure steam turbines is optimized for maximum efficiency and performance. This involves careful attention to thermodynamic cycles, flow control, and mechanical materials that can withstand the high temperatures and pressures encountered during operation. High-pressure turbines typically consist of multiple stages of expansion to allow for gradual pressure reduction, thereby maximizing energy extraction. The design of the blades and nozzles is critical to ensuring that steam flows smoothly and efficiently through the turbine, minimizing energy losses due to turbulence or friction.
A key feature of high-pressure steam turbines is their ability to operate efficiently in combined-cycle power generation. In these systems, the exhaust gases from a gas turbine are used to produce steam that drives a high-pressure steam turbine. The high-efficiency operation of this combined cycle results in higher overall efficiency, as it allows for the cogeneration of electricity and thermal energy. The use of high-pressure steam turbines in such systems maximizes energy output while minimizing fuel consumption, making them an important tool in the pursuit of energy efficiency.
High-pressure steam turbines are also commonly used in nuclear power plants, where they are used to convert the heat produced by nuclear fission into mechanical work. In these plants, steam is generated by pressurized water reactors (PWRs) or boiling water reactors (BWRs), and the steam is directed to high-pressure turbines to generate electricity. The high pressure and temperature of the steam make the turbines efficient at converting heat into electrical energy.
The materials used in high-pressure steam turbines are designed to withstand the extreme conditions of high-pressure steam, including high thermal stresses, corrosion, and erosion. Superalloys and high-strength steel are often used for turbine components such as blades, disks, and shafts. These materials are designed to retain their strength and integrity at elevated temperatures, ensuring long-term reliability and performance. Advanced coatings are also applied to critical components to improve their resistance to oxidation and corrosion, extending the lifespan of the turbine.
In terms of performance, high-pressure steam turbines are capable of achieving very high levels of efficiency. The conversion of thermal energy into mechanical work is optimized through the use of advanced thermodynamic cycles and precise engineering. High-pressure steam turbines are typically used in settings where large amounts of electricity need to be generated continuously, such as in large power plants. Their performance is often characterized by their ability to operate at high load factors, ensuring that they can provide a steady and reliable supply of power over long periods.
The integration of high-pressure steam turbines into cogeneration and combined heat and power (CHP) systems is also common in industries where both electricity and heat are needed. These systems allow industries to maximize their energy use by simultaneously generating electricity and providing thermal energy for processes such as heating, drying, distillation, and chemical processing. In such systems, the high-pressure steam turbine drives the generator to produce electricity, while the exhaust steam can be used for industrial heating applications, contributing to improved energy efficiency and reduced operational costs.
The role of high-pressure steam turbines in the energy transition cannot be understated. As countries and industries strive to reduce carbon emissions and transition to more sustainable energy systems, high-pressure steam turbines are likely to play a key role in the development of carbon capture and storage (CCS) technologies. High-pressure steam turbines can be integrated with CCS systems to recover and capture CO2 emissions from industrial processes. This would allow industries to continue using high-pressure turbines in power generation while mitigating their environmental impact.
In the context of renewable energy integration, high-pressure steam turbines are often used in biomass power plants and waste-to-energy facilities. In these plants, biomass materials such as wood chips, agricultural waste, and even municipal solid waste are burned to produce steam that drives a high-pressure turbine. The high-pressure steam extracted from these renewable sources is then converted into mechanical energy, which can be used for electricity generation or mechanical drives. This process allows for the conversion of renewable organic matter into useful energy, contributing to sustainable power generation.
Another important application for high-pressure steam turbines is in heavy industrial processes, such as petrochemical and chemical production. These industries often require high-pressure steam for heating and power generation to support complex manufacturing processes. High-pressure steam turbines can be used to provide both mechanical power for equipment and electricity for the facility, improving overall energy efficiency while reducing reliance on external power sources.
Maintenance and reliability are crucial considerations for high-pressure steam turbines, as they are subjected to high thermal stresses and mechanical loads during operation. The turbine components must be regularly inspected and maintained to ensure that they continue to operate at peak performance. The development of predictive maintenance systems that use real-time monitoring and sensor data will play a major role in ensuring the reliability of high-pressure steam turbines, enabling operators to anticipate potential failures and reduce downtime.
Future innovations in high-pressure steam turbine technology will likely focus on improving efficiency, increasing operational flexibility, and reducing environmental impacts. New materials and design concepts, such as the development of ultra-supercritical steam cycles (where steam is heated to even higher temperatures and pressures), could push the boundaries of turbine performance, allowing for even greater efficiency in power generation. Furthermore, advanced controls and digital technologies will continue to improve the operation and monitoring of high-pressure steam turbines, helping to optimize their performance, reduce emissions, and improve overall system efficiency.
As global energy needs continue to rise, high-pressure steam turbines will remain a critical part of the energy mix. Whether used in conventional power plants, combined-cycle systems, nuclear plants, or renewable energy installations, these turbines will continue to provide reliable, efficient, and sustainable power generation. Their ability to handle high-pressure steam, convert thermal energy into mechanical work, and operate efficiently in a wide range of applications ensures that high-pressure steam turbines will remain a cornerstone of modern energy systems for years to come.
Looking ahead, the role of high-pressure steam turbines will be further defined by their integration into emerging energy systems and their adaptation to meet global energy demands in a sustainable and efficient manner. As we continue to face climate change and the urgent need for decarbonization, high-pressure steam turbines will play an instrumental part in the transition to cleaner energy solutions, even as their design and operation evolve.
One significant trend is the shift towards more flexible operations for high-pressure steam turbines. Traditionally designed to operate at a steady, continuous rate, these turbines are now being adapted to respond more dynamically to changes in energy demand. The growing integration of intermittent renewable energy sources, such as wind and solar power, into the grid creates the need for flexible backup power systems. High-pressure steam turbines can be designed to ramp up and down more quickly to provide support when renewable energy generation is low or demand peaks. This flexibility makes them an essential tool in balancing energy supply and demand, ensuring grid reliability while supporting the integration of renewable sources.
A major focus for the future of high-pressure steam turbines is improving their thermal efficiency through innovations in advanced cycles and high-temperature materials. As we push the boundaries of efficiency, ultra-supercritical steam cycles—which involve steam temperatures and pressures that far exceed current conventional limits—are becoming a key area of research and development. These systems allow steam turbines to extract more energy from the same amount of fuel, contributing to lower operational costs and reduced environmental impact. This will be particularly important in sectors such as coal and natural gas-fired power plants, where minimizing emissions and improving efficiency is essential for meeting international climate targets.
Another promising advancement is the development of integrated systems that combine high-pressure steam turbines with other forms of energy generation, such as geothermal, biomass, and even hydrogen. By pairing steam turbines with renewable heat sources, these systems can offer an effective way to decarbonize industries that traditionally rely on fossil fuels. For instance, in biomass-to-power plants, the combustion of organic materials can produce high-pressure steam that drives turbines, offering a renewable alternative to coal-fired power generation. Similarly, hydrogen-fueled power plants could use high-pressure steam turbines to convert the heat produced from burning hydrogen into electricity, providing a clean source of power that produces zero carbon emissions.
High-pressure steam turbines are also set to play a pivotal role in cogeneration and district heating systems, especially in urban areas. In these systems, waste heat from the turbine’s exhaust steam can be used for heating buildings, industrial processes, and even greenhouses. This use of waste heat recovery increases the overall efficiency of energy systems by utilizing thermal energy that would otherwise be wasted. Moreover, as urbanization continues and more cities around the world require efficient heating solutions, high-pressure steam turbines will contribute to reducing the carbon footprint of urban energy consumption.
Digitalization will continue to enhance the operation and maintenance of high-pressure steam turbines. The integration of Internet of Things (IoT) technologies and data analytics into turbine operations allows for real-time performance monitoring, predictive maintenance, and optimization of turbine performance. Through the use of sensors, operators can track a wide range of parameters—such as vibration, temperature, pressure, and rotational speed—to ensure the turbine is operating within optimal conditions. In the event of a potential issue, predictive algorithms can alert operators to take preventative action, reducing the risk of unexpected downtime and expensive repairs.
The next-generation materials being developed for high-pressure steam turbines will also enhance their performance and longevity. Materials that can withstand higher temperatures and pressures, such as advanced ceramics and superalloys, will help increase the turbine’s operating range and reduce the wear and tear associated with high-pressure steam. These materials are also more resistant to corrosion, which is a significant challenge in steam turbines, especially in plants that use aggressive fuels or chemicals. Innovations in coating technologies will further enhance the resistance of turbine components to oxidation and erosion, ensuring a longer lifespan and improved reliability.
As the demand for decarbonization increases, high-pressure steam turbines will also see expanded applications in industries that require high-temperature and high-pressure steam, such as petrochemical and chemical manufacturing. These industries traditionally rely on fossil fuels to generate the necessary steam for their operations, but in the future, cleaner and more sustainable methods, including the use of high-pressure turbines powered by renewable energy, will become more prevalent. The combination of biomass, waste heat recovery, and carbon capture could enable high-pressure steam turbines to support decarbonization efforts while continuing to meet the energy needs of these energy-intensive industries.
In nuclear power plants, high-pressure steam turbines will remain a cornerstone of clean power generation. Even as the energy sector moves toward renewable sources, nuclear power offers a consistent, low-carbon energy source that can complement the variability of wind and solar energy. High-pressure steam turbines, combined with pressurized water reactors (PWRs) or boiling water reactors (BWRs), will continue to provide large-scale, reliable electricity generation. The efficiency of high-pressure turbines in these plants will become even more critical as efforts are made to extend the operational lifespan of nuclear reactors and improve overall plant efficiency.
With increasing demand for cleaner and more sustainable power, the future of high-pressure steam turbines will be shaped by innovations in carbon-neutral technologies and system integration. By integrating these turbines with advanced grid systems, smart energy management, and carbon capture technologies, industries and power plants will be able to achieve maximum efficiency and reduce their environmental impact. As energy systems become more digitally integrated, automated, and decentralized, high-pressure steam turbines will evolve to become more flexible and adaptable, allowing them to continue meeting the complex energy demands of the future.
In conclusion, high-pressure steam turbines will remain a vital component of modern energy systems, adapting to the evolving needs of the energy landscape. Through continuous advancements in efficiency, flexibility, and integration with renewable energy and carbon capture technologies, these turbines will continue to provide reliable, sustainable, and cost-effective power to industries worldwide. As the global focus on sustainability and energy efficiency intensifies, high-pressure steam turbines will evolve to meet these challenges, helping industries reduce emissions and optimize energy use for a cleaner, more sustainable future.
As we continue to explore the potential of high-pressure steam turbines, several emerging trends and innovations are shaping their future applications, performance, and contribution to global energy systems.
One of the most promising areas for high-pressure steam turbines is their role in energy storage systems. As renewable energy sources like wind and solar generate electricity intermittently, there is an increasing need for efficient ways to store energy for times when generation is low or demand is high. High-pressure steam turbines, integrated into thermal energy storage systems (such as concentrated solar power plants or molten salt storage systems), can play a key role in storing thermal energy and converting it back into mechanical work when needed. This would allow for dispatchable renewable power, helping to stabilize the grid and reduce reliance on fossil-fuel-based peaking plants.
The development of hydrogen-based energy systems is another area where high-pressure steam turbines will find new applications. As the world seeks to decarbonize and transition to hydrogen economies, high-pressure steam turbines can be used in hydrogen power plants or hydrogen-based cogeneration systems. Hydrogen can be burned to generate heat, which is used to produce steam that drives high-pressure turbines. Since hydrogen combustion produces no CO2 emissions, this method of power generation would significantly reduce the environmental impact of traditional fossil fuel-based power plants.
Further innovations in advanced steam cycles are also underway. The development of supercritical and ultra-supercritical steam cycles can improve the performance of high-pressure steam turbines by operating at higher pressures and temperatures, thereby increasing the overall thermodynamic efficiency of the plant. By pushing the limits of the Rankine cycle and utilizing advanced materials capable of withstanding extreme conditions, engineers can design steam turbines that deliver even higher efficiencies. Combined supercritical and ultra-supercritical cycles are likely to become more widespread in both fossil-fuel plants and renewable hybrid systems, ensuring more efficient power generation with less fuel consumption.
Moreover, the use of artificial intelligence (AI) and machine learning (ML) in the design, monitoring, and maintenance of high-pressure steam turbines will continue to transform the industry. AI-powered optimization tools can help improve turbine design by simulating a wider range of operating conditions and identifying potential issues before they arise. Predictive maintenance using machine learning algorithms can analyze real-time data from sensors installed on turbines to detect patterns and predict failures before they lead to costly downtime. This is especially important in industrial applications where steam turbines operate in continuous, high-demand environments, and any disruption can lead to significant losses.
With increased emphasis on sustainability and carbon emissions reduction, high-pressure steam turbines will likely become a key part of the circular economy. By integrating turbines with waste heat recovery systems, industrial symbiosis, and resource recovery technologies, turbines will help optimize energy use across industries. For example, the waste heat from one industrial process can be used to generate steam that drives a high-pressure turbine in another, creating a symbiotic relationship between facilities. This approach not only improves energy efficiency but also reduces the amount of waste and emissions generated by industrial operations.
High-pressure steam turbines will also be essential in carbon capture and storage (CCS) systems. In these systems, CO2 emissions produced during combustion or industrial processes are captured, transported, and stored underground to prevent them from entering the atmosphere. Steam turbines integrated into these CCS systems can be used to provide mechanical power for the compression and injection of CO2, as well as to drive the capture process itself. By combining high-pressure turbines with CCS technology, industries can significantly reduce their carbon footprint while continuing to produce energy.
As part of the hydropower and tidal energy sectors, high-pressure steam turbines are also being evaluated for their potential to optimize energy conversion in marine-based renewable energy systems. For example, tidal energy plants generate electricity by harnessing the power of tidal flows. The combination of high-pressure steam turbines with offshore energy storage systems could provide an efficient and environmentally friendly way to generate and store electricity from these renewable sources.
Finally, as global demand for clean energy solutions continues to rise, high-pressure steam turbines will be an essential part of meeting the increasing need for grid stability and distributed power generation. In particular, small- to medium-scale combined heat and power (CHP) systems and microgrids can benefit from the use of high-pressure turbines. These systems can offer localized, reliable power to remote communities, data centers, and industrial parks while reducing transmission losses and providing the necessary backup power in case of grid instability.
Research into new steam technologies such as magnetic steam turbines or new steam expansion techniques could further optimize the performance of high-pressure turbines. These new technologies could lead to turbines that are lighter, more efficient, and less prone to mechanical wear, contributing to even greater energy savings and cost reductions.
In conclusion, the evolution of high-pressure steam turbines is closely tied to the ongoing energy transition and the global pursuit of sustainable and efficient energy systems. With continuous advancements in technology, design, materials, and integration with emerging renewable energy solutions, high-pressure steam turbines will continue to play a central role in both conventional and low-carbon power generation systems. By improving operational efficiency, enhancing performance, and reducing emissions, high-pressure steam turbines will remain essential tools in addressing the world’s growing energy demands while supporting the transition to a low-carbon future.
As the demand for cleaner, more efficient energy systems increases globally, the role of high-pressure steam turbines in driving decarbonization and energy transition efforts will only become more crucial. These turbines are not just confined to traditional applications in coal and natural gas-fired power plants; they are increasingly being integrated into hybrid renewable energy systems and clean technology innovations that are revolutionizing the energy sector.
The continued development of next-generation turbine designs will focus heavily on improving efficiency and reliability. One of the key areas of innovation is the integration of additive manufacturing (3D printing) into turbine production. 3D printing can allow for the creation of more complex turbine components that are lighter, stronger, and more resistant to wear and corrosion. For example, 3D-printed turbine blades can be designed with intricate geometries that optimize airflow, reduce material use, and improve thermal efficiency. This technology could enable turbines to be customized for specific environments and applications, further enhancing their flexibility and adaptability.
In addition to 3D printing, the development of smart materials such as shape-memory alloys and self-healing coatings will further enhance the performance and longevity of high-pressure steam turbines. Shape-memory alloys, which can change shape in response to temperature fluctuations, can be used in components that undergo significant thermal stresses. Similarly, self-healing coatings will help prevent corrosion and erosion, extending the turbine’s operational lifespan and reducing the need for maintenance.
Looking toward the future, energy storage integration will become even more critical as the world increases its reliance on renewable energy sources. High-pressure steam turbines will likely play an important role in thermal energy storage systems, where excess electricity generated from renewable sources is used to heat a fluid that can later be used to produce steam. This stored steam can then drive turbines, providing dispatchable power when renewable generation is low. In this way, high-pressure steam turbines can contribute to grid stability and load balancing, helping integrate renewable energy into power grids and ensuring reliable power supply.
Another area where high-pressure steam turbines are expected to grow is in cogeneration and district energy systems. These systems, which produce both electricity and useful heat from a single energy source, are becoming increasingly popular in urban areas, industries, and large-scale commercial applications. High-pressure steam turbines in cogeneration systems can provide both electrical power and thermal energy for district heating, which delivers hot water or steam to multiple buildings or industrial facilities. By utilizing waste heat and improving overall energy efficiency, cogeneration systems can reduce energy costs, lower emissions, and increase the sustainability of energy infrastructure.
Moreover, as the world moves toward decentralized energy systems, high-pressure steam turbines will have an important role in microgrids and distributed generation systems. Microgrids, which can operate independently of the central grid or in coordination with it, are becoming increasingly popular in remote areas, critical infrastructure, and military applications. High-pressure steam turbines integrated into these systems will provide a reliable and scalable power source, improving energy security and reducing dependence on centralized fossil fuel-based power plants.
High-pressure steam turbines will also continue to be central to the industrial decarbonization efforts. Industries such as steel, cement, and chemical manufacturing, which have historically relied heavily on fossil fuels, are under increasing pressure to reduce their carbon emissions. High-pressure steam turbines, when integrated with renewable energy sources, biomass, or waste heat recovery, will enable these industries to generate clean, reliable power on-site while reducing their carbon footprint. In particular, biomass-fired steam turbines present an opportunity for these industries to transition to more sustainable energy sources while maintaining high levels of energy efficiency.
The role of high-pressure steam turbines in nuclear power generation will continue to evolve as nuclear plants around the world seek to increase efficiency, extend operating lifespans, and reduce costs. Small modular reactors (SMRs) and advanced nuclear reactors are becoming an area of intense research, and high-pressure steam turbines will likely play a role in these systems. SMRs, which are smaller and more flexible than traditional nuclear reactors, can be deployed in a variety of applications, including remote areas or to complement renewable energy systems. High-pressure steam turbines in these next-generation nuclear plants will be designed to operate at higher temperatures and pressures, maximizing energy extraction and improving overall system efficiency.
Finally, global collaboration in research and development will be essential in driving the future of high-pressure steam turbines. As countries and regions work toward achieving net-zero emissions and energy security, cross-border collaboration on energy technologies will be key to accelerating the adoption of clean technologies. By pooling resources and expertise, countries can share the costs and risks associated with developing new turbine technologies, ensuring that the next generation of high-pressure steam turbines is both technologically advanced and economically viable.
In summary, high-pressure steam turbines will continue to play an essential role in the global energy landscape. Through technological advancements in design, materials, and integration with emerging energy systems, they will contribute to more efficient, flexible, and sustainable power generation. Whether through their integration into renewable energy systems, cogeneration, energy storage, or industrial decarbonization, high-pressure steam turbines are set to be a cornerstone of the clean energy transition, ensuring that industries and power plants continue to meet the world’s growing energy needs while reducing their environmental impact. As energy systems evolve, high-pressure steam turbines will remain a vital tool in the pursuit of cleaner, smarter, and more resilient energy systems.
The Role of Steam Turbines in Energy Conversion
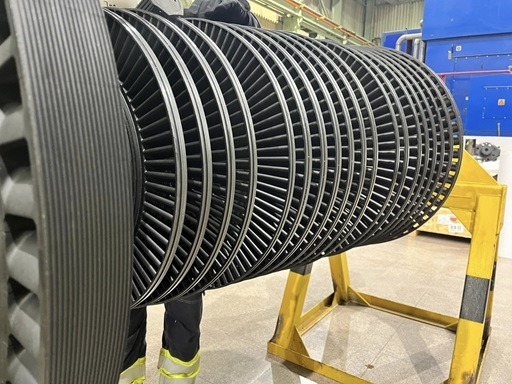
The role of steam turbines in energy conversion is fundamental to the generation of electrical power, particularly in thermal power plants and cogeneration systems. Steam turbines convert the thermal energy of steam into mechanical energy, which is then used to drive generators for electricity production. This conversion process is essential for both traditional fossil fuel-based power plants and emerging renewable energy systems, offering a reliable and scalable means of generating electricity. As the world seeks to transition to cleaner and more efficient energy systems, the role of steam turbines in energy conversion remains critical in meeting global power demands.
Conversion of Thermal Energy into Mechanical Energy
The core principle behind the functioning of a steam turbine is the conversion of thermal energy (produced by burning fuel, nuclear reactions, or capturing waste heat) into mechanical energy. The process begins when water is heated to produce steam, which is then expanded through a series of blades in the turbine. As steam flows over the blades, it causes the turbine to spin, converting the energy from the steam’s pressure and temperature into rotational mechanical energy.
This mechanical energy is then transferred to a generator, which converts it into electrical energy. The efficiency of this energy conversion is crucial for the overall performance of a power plant, and steam turbines play a vital role in maximizing this efficiency. Factors such as steam pressure, temperature, and turbine design all influence the conversion efficiency, making the optimization of steam turbines an ongoing area of research and development.
Steam Turbines in Fossil Fuel and Nuclear Power Generation
Traditionally, steam turbines have been the backbone of fossil fuel power plants (coal, oil, and natural gas), where they convert the heat generated from burning fuel into electrical energy. The steam is typically produced in a boiler, where the fuel is burned to produce high-pressure steam, which is then passed through the turbine to generate power. In nuclear power plants, the process is similar, except that the heat is produced by nuclear reactions in the reactor instead of burning fossil fuels. This conversion process is central to how large-scale power plants generate the electricity needed to meet industrial and residential demand.
In these systems, steam turbines are designed to operate at high temperatures and pressures, which maximizes the efficiency of the conversion process. Over the years, advances in supercritical and ultra-supercritical steam cycles have allowed power plants to operate at even higher pressures and temperatures, resulting in increased efficiency and a reduction in the amount of fuel required to generate electricity. By improving the efficiency of steam turbines, these plants can produce more electricity while using less fuel, which not only reduces costs but also lowers carbon emissions.
Steam Turbines in Renewable Energy Systems
The role of steam turbines is expanding beyond traditional fossil-fuel-based power plants into renewable energy systems. In concentrated solar power (CSP) plants, for example, mirrors or lenses are used to focus sunlight onto a fluid, which is then heated to produce high-pressure steam. This steam is passed through a steam turbine, which drives a generator to produce electricity. In this way, steam turbines enable the conversion of solar thermal energy into electrical power.
Similarly, in biomass power plants, steam turbines are used to convert the heat produced from burning organic materials into mechanical energy. Biomass, which includes materials such as wood chips, agricultural waste, and other organic matter, can be used as a renewable fuel source to generate electricity. The steam produced from the combustion of biomass fuels drives the turbine, which then generates electrical energy in a similar manner to fossil fuel plants but with the added benefit of using a renewable fuel source.
Geothermal power plants also rely on steam turbines to convert thermal energy from the Earth’s heat into electrical power. In geothermal systems, water is heated by the Earth’s natural heat sources, forming steam that is directed through turbines to generate electricity. This process offers a sustainable and low-carbon way to produce electricity, as geothermal energy is a constant and reliable source of thermal energy.
Steam Turbines in Cogeneration Systems
Another critical area where steam turbines play a significant role in energy conversion is in cogeneration or combined heat and power (CHP) systems. These systems simultaneously produce electrical energy and useful heat from a single energy source. Steam turbines in cogeneration systems are used to convert heat generated from the combustion of fuels into steam, which drives the turbine to produce electricity. In parallel, the waste heat from the steam turbine is recovered and used for industrial processes, district heating, or hot water production.
Cogeneration systems offer a more efficient alternative to conventional power generation by utilizing the waste heat that would otherwise be lost. This increases the overall energy efficiency of the system and reduces the amount of fuel required to generate the same amount of energy. As energy efficiency becomes an increasingly important factor in sustainability efforts, cogeneration systems powered by steam turbines are expected to play a larger role in both industrial and residential energy systems.
Steam Turbines in Emerging Energy Technologies
As part of the growing emphasis on clean energy technologies, steam turbines are also expected to play an important role in emerging energy conversion systems. One such example is hydrogen-based power generation. High-pressure steam turbines can be used to convert heat produced from hydrogen combustion into steam, which in turn drives turbines to generate electricity. Since hydrogen combustion produces no carbon emissions, this form of power generation offers a cleaner alternative to traditional fossil fuel-based systems. Similarly, hydrogen can be used in combined cycle systems, where steam turbines complement gas turbines to maximize energy efficiency and minimize emissions.
Waste heat recovery is another area where steam turbines are increasingly being used for energy conversion. Industrial facilities that generate large amounts of waste heat, such as cement plants, steel mills, and chemical plants, can integrate steam turbines into their operations to capture and convert this waste heat into electrical power. By using steam turbines to recover waste heat, these industries can improve their energy efficiency, lower their operating costs, and reduce their environmental impact.
Advanced Technologies and Future Trends
The future of steam turbines in energy conversion will be shaped by advancements in both turbine design and system integration. Supercritical and ultra-supercritical steam cycles will continue to push the boundaries of efficiency, enabling power plants to generate more electricity from the same amount of fuel. Moreover, advanced materials, such as superalloys and composite materials, will allow turbines to operate at higher temperatures and pressures, further improving energy conversion efficiency.
In addition, digitalization and smart grid integration will increasingly play a role in optimizing the operation of steam turbines. The use of IoT sensors, machine learning algorithms, and predictive maintenance techniques will help ensure that steam turbines operate at peak efficiency, minimize downtime, and extend their service life. Real-time monitoring and performance analysis can help operators identify areas for improvement and optimize energy conversion processes, making steam turbines more efficient and reliable.
The role of steam turbines in energy conversion will continue to evolve as energy systems become more diverse, interconnected, and sustainable. Whether in traditional power plants, renewable energy systems, cogeneration plants, or emerging technologies like hydrogen power generation, steam turbines will remain a cornerstone of energy conversion for the foreseeable future. By improving efficiency, flexibility, and sustainability, steam turbines will play a critical role in the global shift toward cleaner, more reliable, and more efficient energy systems. As such, steam turbines will continue to contribute significantly to meeting the world’s growing energy demands while reducing environmental impact and supporting global sustainability goals.
The ongoing development of steam turbines in energy conversion technologies highlights their indispensable role in modern power generation and the transition to sustainable energy systems. These turbines, which are central to the conversion of thermal energy into mechanical energy, have evolved with advancements in materials science, turbine design, and operational processes to optimize their efficiency, performance, and environmental impact. From traditional coal, gas, and nuclear plants to emerging renewable systems like solar thermal and biomass, steam turbines provide a reliable means of generating electricity.
In traditional power generation, steam turbines are crucial for converting heat into electrical energy. In fossil fuel-based plants, the process begins with the combustion of coal, oil, or natural gas to produce heat. This heat converts water into steam, which is then directed through the turbine, causing it to spin and generate mechanical energy. This energy is transferred to a generator that produces electrical power. Similarly, in nuclear power plants, steam turbines are used to harness heat from nuclear fission reactions. With continued advancements in turbine materials, such as superalloys and ceramic coatings, modern steam turbines can operate at higher temperatures and pressures, significantly improving overall efficiency.
In addition to traditional uses, steam turbines are increasingly integrated into renewable energy systems. In concentrated solar power (CSP) plants, sunlight is focused onto a fluid to produce steam that drives a turbine for electricity generation. Biomass power plants also utilize steam turbines by burning organic materials like wood chips, agricultural residues, and waste to create steam. These renewable applications offer a cleaner alternative to fossil fuels, as they generate electricity with reduced carbon emissions, contributing to the decarbonization of the energy sector.
Steam turbines are also playing an important role in cogeneration or combined heat and power (CHP) systems. These systems not only generate electricity but also capture the waste heat from the turbine to be used in industrial processes or district heating. This increases the overall efficiency of the system by utilizing energy that would otherwise be wasted, making cogeneration an attractive solution for industries looking to reduce their energy consumption and carbon footprint.
Emerging technologies in energy conversion are also benefiting from steam turbine advancements. Hydrogen-based power generation is one example, where steam turbines could play a key role in converting the heat from hydrogen combustion into electricity. Hydrogen is gaining attention as a clean fuel because it produces no carbon emissions when burned, making it a promising alternative to fossil fuels. Similarly, in waste heat recovery applications, steam turbines are used to capture and convert excess heat from industrial processes, turning it into usable electricity. This approach contributes to improving the efficiency of industrial facilities and reducing their environmental impact.
Looking ahead, steam turbines are expected to play a critical role in the future of energy conversion as part of a broader strategy to achieve global sustainability goals. The development of advanced turbine designs, such as supercritical and ultra-supercritical steam cycles, is pushing the boundaries of thermal efficiency. These advancements will allow steam turbines to operate at even higher pressures and temperatures, extracting more energy from the same amount of fuel. Digitalization and advanced monitoring systems will further optimize steam turbine operations, enabling real-time performance analysis, predictive maintenance, and efficiency improvements.
As energy systems become more decentralized and interconnected, the role of steam turbines will continue to evolve. In microgrids and distributed energy systems, where power generation is closer to where it is consumed, steam turbines will be key components in ensuring stable and reliable electricity production. Hybrid systems that combine renewable energy sources, such as wind and solar, with steam turbines will help provide dispatchable power, ensuring that energy needs are met even when the availability of renewable sources fluctuates.
In addition to their role in power generation, steam turbines are also integral to industrial decarbonization efforts. Industries that have historically been heavily reliant on fossil fuels, such as steel, cement, and chemicals, are seeking ways to reduce their carbon emissions. Steam turbines, when integrated with biomass or waste heat recovery systems, can help these industries transition to cleaner energy sources while maintaining high levels of energy efficiency. These turbines offer a practical solution for large-scale energy conversion needs, balancing energy production with reduced environmental impact.
With the increasing focus on sustainability, renewable energy, and carbon reduction, the role of steam turbines in energy conversion will continue to expand. The integration of steam turbines into next-generation energy systems, including thermal energy storage, green hydrogen production, and circular economy principles, will contribute significantly to the energy transition. As countries around the world strive to meet net-zero emissions targets, steam turbines will remain a central technology in enabling the efficient, reliable, and clean conversion of energy from various sources.
The future of steam turbines will be shaped by ongoing research and technological advancements aimed at improving their efficiency, reducing their environmental impact, and ensuring their continued relevance in a rapidly evolving energy landscape. As these turbines become more adaptable, versatile, and efficient, they will play a pivotal role in transforming global energy systems and contributing to a more sustainable future. Through their ability to convert heat into mechanical energy and their integration with renewable and low-carbon technologies, steam turbines will remain an essential part of the global effort to create a cleaner, more efficient energy future.
As steam turbines continue to evolve, their role in modern power generation and energy systems will only become more critical in addressing the growing global demand for sustainable energy. The ongoing transition toward a more decarbonized and resilient energy infrastructure presents both challenges and opportunities for steam turbine technology. One of the key factors driving innovation in this field is the push for higher energy efficiency, which directly impacts both environmental sustainability and operational costs.
With global energy consumption expected to rise over the next few decades, particularly in emerging economies, there is a strong incentive to maximize the output of each unit of fuel consumed. To this end, steam turbines are being designed to operate at even more extreme conditions, such as ultra-supercritical pressures and temperatures. This allows for greater energy extraction, reducing fuel requirements while simultaneously lowering carbon emissions. These advancements are critical for industries, utilities, and governments seeking to meet climate goals without compromising energy supply.
In parallel, digital technologies and smart grid integration are transforming the way steam turbines are monitored and operated. The use of real-time data from sensors embedded in turbine components enables operators to optimize performance and identify potential issues before they lead to downtime or inefficiencies. Advanced predictive maintenance techniques are helping extend the lifespan of steam turbines by accurately forecasting when maintenance or repairs are needed. This ensures that turbines remain in optimal working condition, reducing unplanned outages and lowering overall operational costs.
Incorporating advanced materials is another area where steam turbine performance is significantly improving. Materials such as ceramic coatings and composite alloys are being developed to withstand higher temperatures and reduce wear from extreme operating conditions. These materials help increase the durability and efficiency of turbines, making them more suited to modern power plants and renewable energy applications that require constant performance under fluctuating operational conditions.
As renewable energy technologies, including wind, solar, and geothermal, become more prominent, steam turbines are increasingly being integrated into hybrid power systems. These systems combine renewable energy sources with steam turbine-driven power generation to ensure that electricity can be produced consistently, even when the availability of renewable resources is intermittent. For example, in concentrated solar power (CSP) systems, steam turbines are used to convert the thermal energy stored in mirrors or lenses into mechanical energy, ensuring that power can be generated even after the sun sets. Similarly, biomass-fired steam turbines can help stabilize the power grid by providing a reliable power source that complements the variability of other renewable technologies.
Waste-to-energy technologies also stand to benefit from the continued development of steam turbines. By converting waste materials into useful energy, these systems help reduce landfill waste while providing a sustainable power source. Steam turbines in these applications convert the heat generated from the combustion of waste into electricity, making them a valuable tool in managing both waste and energy needs. As urbanization increases, the integration of waste-to-energy systems in cities will become more important, making steam turbines even more relevant for sustainable urban planning.
In industrial applications, steam turbines continue to serve as a critical component of cogeneration and combined heat and power (CHP) systems. By capturing and reusing waste heat, these systems improve overall efficiency and reduce the demand for external power sources. Industries such as refining, chemical production, and paper mills are increasingly turning to steam turbines to meet their power and thermal energy requirements in a more sustainable and cost-effective manner.
As the world moves toward net-zero emissions, there is growing interest in using steam turbines in combination with carbon capture technologies. In power plants and industrial facilities, steam turbines can be integrated into systems that capture and store carbon dioxide emissions, helping to mitigate the environmental impact of fossil fuel use. This combination of steam turbines and carbon capture technologies will be vital in decarbonizing hard-to-abate sectors such as heavy industry and long-distance transportation.
In terms of future energy production, hydrogen is emerging as a promising clean fuel, and steam turbines are poised to play a key role in its utilization. Hydrogen combustion produces only water vapor as a byproduct, making it an ideal option for reducing carbon emissions. In hydrogen-fired power plants, steam turbines will be used to convert the heat from hydrogen combustion into mechanical energy. Additionally, green hydrogen, produced using renewable energy sources, could be used in combination with steam turbines to create a zero-emissions power generation system.
One of the exciting prospects for the future of steam turbines is their integration into advanced nuclear reactors, particularly small modular reactors (SMRs). These reactors, which are smaller, safer, and more flexible than traditional nuclear plants, will likely use steam turbines to generate electricity. As the global demand for clean energy increases, the role of nuclear power, alongside renewables, is expected to grow, and steam turbines will be central to these next-generation energy systems.
The future of steam turbines will also see their continued integration into smart grids, which will help optimize energy distribution and reduce losses. Steam turbines in distributed energy systems, such as microgrids, will allow for greater flexibility and reliability, ensuring that power can be generated and used locally, even during grid failures or natural disasters. This localized energy generation is essential for improving energy security and ensuring that power can be delivered where it is needed most.
Finally, the role of steam turbines in the global transition to sustainable energy will be shaped by increasing collaboration between governments, industry stakeholders, and research institutions. As countries and regions work toward achieving their climate targets and reducing their carbon footprints, the continued development of steam turbines will be essential in providing the energy infrastructure needed to support clean energy systems. By pooling resources, knowledge, and expertise, international cooperation will accelerate the pace of innovation, ensuring that steam turbines remain a key technology in the future energy landscape.
In conclusion, steam turbines will continue to be a fundamental part of energy conversion technologies for decades to come. Whether in traditional power plants, renewable energy systems, waste-to-energy applications, or emerging technologies like hydrogen and nuclear, steam turbines will play an indispensable role in ensuring the efficient and sustainable generation of electricity. With ongoing advancements in materials, design, and digital technologies, steam turbines will evolve to meet the challenges of the modern energy landscape, driving global efforts toward a cleaner, more sustainable energy future.
As we continue to explore the future of steam turbines, several emerging trends and developments point to the expanding role of these devices in the energy sector. These trends suggest that the next few decades will see steam turbines become even more integral to global energy systems, especially as the world strives to meet climate goals and achieve net-zero emissions.
Decarbonization of Industrial Processes:
Steam turbines are poised to become critical players in decarbonizing energy-intensive industrial sectors. Industries such as cement, steel, and chemical manufacturing are responsible for a significant portion of global carbon emissions. Integrating steam turbines with biomass, waste heat recovery, and carbon capture systems in industrial plants can substantially reduce emissions. These industries can leverage steam turbines to not only generate electricity but also to produce heat for their processes, ensuring that waste energy is captured and used effectively. Over time, these systems will become more efficient and flexible, enabling industries to decarbonize without sacrificing productivity or profitability.
Decentralized and Distributed Energy Systems:
The development of microgrids and distributed energy resources (DERs) will play a crucial role in future energy systems. Steam turbines, particularly smaller and more modular models, will be essential for powering these systems. Distributed steam turbines can be integrated into local renewable energy projects and combined heat and power (CHP) setups, offering a sustainable and efficient energy solution at the local level. This approach increases energy resilience, reduces transmission losses, and ensures that communities can generate and consume energy close to where it is needed. Additionally, steam turbines in distributed systems can be used to balance supply and demand, complementing intermittent renewable sources like wind and solar power.
Energy Storage Solutions and Hybrid Systems:
As energy storage technologies continue to advance, steam turbines will become even more adaptable in hybrid energy systems. The combination of steam turbines with thermal storage, battery storage, or pumped hydro storage offers a flexible solution to ensure grid stability. Thermal energy storage systems, for example, can store excess heat generated by renewable sources or waste heat from industrial processes, which can later be used to drive steam turbines for electricity generation. This makes energy more accessible during peak demand periods or when renewable energy sources are unavailable, reducing reliance on fossil fuels and enhancing the sustainability of the energy system.
Advanced Digitalization and Automation:
The ongoing integration of artificial intelligence (AI), machine learning (ML), and advanced analytics into steam turbine operations will drastically improve efficiency and performance. Digital tools that monitor turbine health, predict potential failures, and optimize performance in real-time are already becoming common. In the future, the use of smart sensors and digital twins will enable more precise control over turbine performance. These technologies will help operators minimize downtime, reduce maintenance costs, and extend turbine lifespans. By providing real-time data, operators will be able to optimize turbine performance to align with fluctuating energy demand, ensuring greater operational flexibility and energy efficiency.
Environmental Impact and Sustainability Considerations:
One of the key driving forces behind the continued evolution of steam turbines is the need to minimize environmental impacts. As pressure mounts to reduce greenhouse gas emissions, turbine manufacturers are focusing on cleaner, more sustainable designs. Improvements in material science, such as the development of superalloys and high-performance coatings, will allow steam turbines to operate at higher temperatures and pressures, improving efficiency and reducing fuel consumption. Additionally, the use of steam turbines in combination with carbon capture and energy recovery systems is vital for capturing and storing carbon emissions from industrial sources.
Further, there is growing attention on life-cycle analysis (LCA) of steam turbines to assess their environmental footprint throughout their production, operation, and decommissioning. Efforts are being made to ensure that the manufacturing and disposal of steam turbines are more sustainable, including recycling critical materials and reducing waste during production. The implementation of circular economy principles in turbine design—such as using reusable components or repurposing parts for other uses—will be essential in ensuring that steam turbines contribute to a more sustainable future.
Steam Turbines in Next-Generation Nuclear Power:
Small modular reactors (SMRs) and advanced nuclear reactors are expected to become key contributors to the future of low-carbon electricity generation. Steam turbines will play a critical role in converting the thermal energy produced by nuclear fission into electricity. The ongoing development of these advanced reactors is focused on making them safer, more cost-effective, and flexible enough to integrate with renewable energy sources. Steam turbines will be designed to work in harmony with integrated energy systems where nuclear power supports renewable energy by providing dispatchable power. Additionally, these systems are being optimized for hydrogen production through electrolysis, further positioning steam turbines as crucial components in the future energy mix.
Hydrogen and Clean Fuel Utilization:
As the global energy sector explores green hydrogen as a solution for decarbonizing hard-to-abate sectors, steam turbines are expected to play an integral role in hydrogen-based power generation. Steam turbines can be adapted to run on hydrogen fuel, producing zero-emissions power by combusting hydrogen instead of fossil fuels. This innovation could drastically reduce carbon emissions across the power generation sector and beyond. Furthermore, hydrogen gas turbines are already being used in various applications to generate power, and the integration of steam turbines will likely enhance the overall flexibility and efficiency of these systems.
In hydrogen-based cogeneration systems, steam turbines can not only produce electricity but also provide necessary heat for industrial processes or district heating. As hydrogen infrastructure grows, the integration of steam turbines into hydrogen hubs will further support the transition to a hydrogen economy, offering cleaner energy solutions for both electricity generation and industrial applications.
Role in Global Energy Security:
Steam turbines also contribute significantly to energy security by ensuring the stability and reliability of power generation in a variety of systems. As energy production increasingly shifts toward more localized and decentralized solutions, steam turbines offer an excellent balance of efficiency, reliability, and versatility. In emergency backup systems or off-grid power plants, steam turbines can serve as a critical source of energy when conventional sources are unavailable or compromised. Their adaptability to different types of fuel, including biomass, waste, renewable sources, and fossil fuels, ensures they can provide continuous power even under challenging circumstances.
The Global Impact of Steam Turbines:
As countries around the world pursue sustainable energy goals and work toward carbon neutrality, steam turbines will remain a vital technology for meeting electricity demand while reducing environmental impact. Whether as part of traditional power generation systems, hybrid renewable solutions, cogeneration facilities, or hydrogen-based applications, the role of steam turbines will continue to evolve and adapt to the changing needs of the global energy landscape. Innovations in steam turbine design, materials, and integration with renewable technologies will ensure their continued relevance in the effort to combat climate change and build a cleaner, more resilient energy future. The versatility of steam turbines, combined with their ongoing development, positions them as a cornerstone of the energy transition in the years to come.
In sum, as steam turbines become more advanced, they will not only drive energy production but also contribute to shaping the future of sustainable, low-carbon, and efficient global energy systems. The integration of emerging technologies and strategies will propel these turbines to meet the challenges of modern energy demands while mitigating the environmental impact of traditional power generation, ensuring that they remain indispensable tools in the ongoing energy transformation.
Steam Turbine Innovations
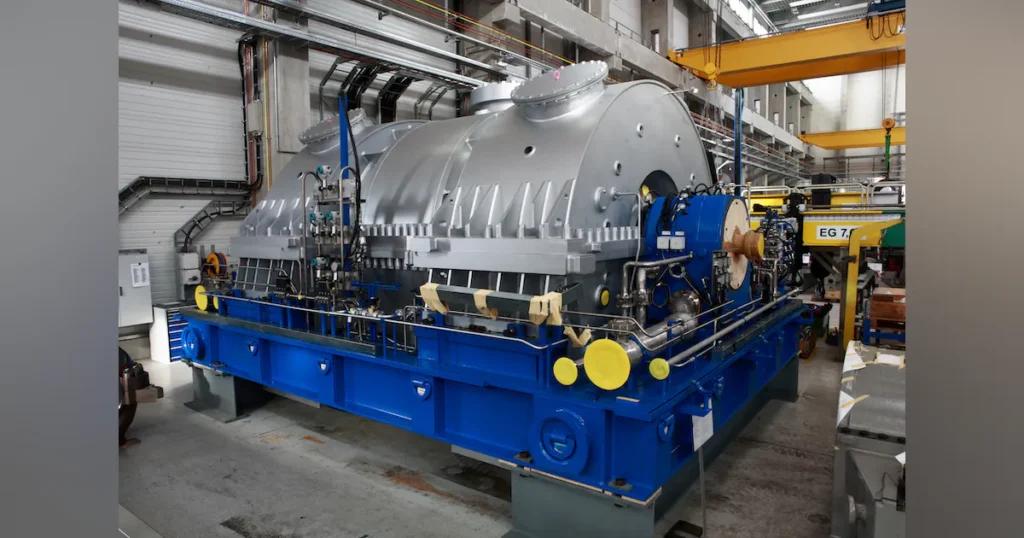
Steam turbine technology has experienced continuous innovation over the years, and as the energy sector shifts toward more sustainable and efficient solutions, steam turbines are evolving in ways that will define the future of power generation. These innovations aim to improve efficiency, reduce environmental impact, and enhance the adaptability of turbines to various energy sources and applications. From advanced materials to digitalization and integration with renewable energy systems, the field of steam turbine design is rapidly advancing, with significant implications for energy production worldwide.
One of the major drivers behind steam turbine innovation is the demand for higher thermal efficiency. To meet the growing need for low-carbon energy while minimizing fuel consumption, manufacturers are designing turbines that can operate under ultra-supercritical (USC) and advanced supercritical conditions, where both the temperature and pressure of steam are elevated beyond conventional limits. These advances allow for greater energy extraction from the same amount of fuel, improving the overall efficiency of the power generation process. As a result, plants using these turbines can produce more electricity with less fuel, reducing emissions and contributing to global efforts to decarbonize energy production.
High-temperature materials play a critical role in enabling these innovations. Advances in ceramic coatings, superalloys, and turbine blade materials have allowed for higher operating temperatures and pressures without compromising the turbine’s structural integrity. By using these advanced materials, turbines can withstand harsher conditions, which improves performance, reliability, and efficiency over the long term. These materials also extend the lifespan of steam turbines, allowing plants to operate at higher efficiency for extended periods without significant degradation.
Another area of innovation is the development of modular steam turbines. These turbines are designed to be more flexible and scalable, allowing them to be easily integrated into distributed energy systems or combined heat and power (CHP) plants. This modular approach makes steam turbines more adaptable for small-scale power generation, which is becoming increasingly important in decentralized energy systems. These modular turbines can be used in industries, remote locations, or off-grid applications, offering a flexible and efficient solution to meet localized energy needs.
The integration of digital technologies into steam turbine systems is transforming how turbines are monitored, operated, and maintained. The use of Internet of Things (IoT) sensors and real-time data analytics is improving the operational efficiency of steam turbines by providing insights into performance metrics, wear patterns, and potential failures. Predictive maintenance tools, powered by artificial intelligence (AI) and machine learning, can predict turbine failures before they occur, minimizing downtime and extending the turbine’s service life. This reduces maintenance costs and ensures that turbines operate at peak efficiency. Moreover, turbine operators can adjust operational parameters in real-time, optimizing performance in response to fluctuating energy demand or grid conditions.
Hybrid systems combining steam turbines with renewable energy sources are another key area of innovation. Steam turbines are increasingly being integrated into concentrated solar power (CSP) plants, where mirrors or lenses concentrate sunlight to produce heat, which is then used to generate steam. This heat can be stored and converted into electricity even when the sun is not shining, ensuring continuous power generation. Similarly, in biomass-fired power plants, steam turbines are used to convert organic waste into electricity, providing a renewable and sustainable energy source. These hybrid systems improve the overall efficiency of renewable energy generation and help stabilize energy supply from intermittent renewable sources like wind and solar.
Additionally, steam turbines are becoming more integrated with hydrogen production and storage technologies. As hydrogen is increasingly seen as a clean fuel for a decarbonized future, steam turbines will play a pivotal role in hydrogen-powered plants. Green hydrogen, produced using renewable energy sources, can be used to fuel steam turbines in combined-cycle plants, producing zero-emissions power. Turbines can be adapted to burn hydrogen, which produces only water vapor as a byproduct. This transition to hydrogen fuel will be particularly important for decarbonizing industries and sectors that are difficult to electrify, such as steel production and heavy transportation.
The integration of steam turbines in energy storage systems is also being explored. Technologies like thermal energy storage and battery storage are being coupled with steam turbines to enhance grid reliability and flexibility. In thermal storage systems, excess energy from renewable sources can be stored as heat and later converted into steam to drive turbines when demand peaks or when renewable energy production is low. Similarly, in battery storage systems, steam turbines can be used in hybrid systems that convert stored electricity back into mechanical energy when needed.
Steam turbines are also being innovated for use in advanced nuclear power systems. Small modular reactors (SMRs), which are compact and scalable, offer a promising solution for low-carbon, flexible energy generation. These reactors often use steam turbines to convert thermal energy into mechanical energy, and their smaller, safer design opens up new possibilities for decentralized nuclear power. Next-generation nuclear reactors, such as molten salt reactors and high-temperature gas reactors, also utilize steam turbines to generate electricity. The fusion of advanced nuclear technologies with steam turbine design is expected to be a key area of development for meeting global energy needs in the coming decades.
The waste-to-energy sector is another field where steam turbines are evolving. Steam turbines are commonly used in power plants that convert municipal solid waste, industrial waste, or biomass into electricity. As the waste-to-energy industry grows, the efficiency and environmental impact of steam turbines will continue to improve, with advanced turbines capable of extracting more energy from less waste. These turbines are being optimized for lower emissions and greater fuel flexibility, allowing for cleaner, more sustainable power generation from waste materials.
Energy efficiency standards and regulatory pressure are driving innovation in steam turbines as well. With stringent emissions regulations and international agreements on climate change, turbine manufacturers are being pushed to develop technologies that reduce both fuel consumption and greenhouse gas emissions. This is leading to the development of more efficient steam cycles, combined-cycle systems, and carbon capture integration. In particular, carbon capture and storage (CCS) technologies are being integrated with steam turbine plants to trap and store carbon emissions produced during power generation, significantly reducing the environmental impact of fossil-fuel-fired plants.
The ongoing trend toward global decarbonization and the pursuit of net-zero emissions goals has also sparked innovation in integrating steam turbines with other low-carbon technologies. For example, steam turbines are being used in conjunction with geothermal energy systems, where heat from the Earth is converted into steam to drive turbines. Similarly, in tidal power and wave energy systems, steam turbines are being adapted to generate electricity from the movement of water. These technologies provide consistent, renewable energy that can complement wind and solar power.
In conclusion, the future of steam turbines is defined by continuous innovation that aims to enhance efficiency, flexibility, and sustainability. These turbines are evolving to meet the demands of the modern energy landscape, from integrating with renewable energy systems to enabling the use of clean fuels like hydrogen. The development of advanced materials, digital technologies, and hybrid power systems will ensure that steam turbines remain a key part of the energy transition in the decades to come. Whether in industrial processes, renewable energy integration, or emerging energy technologies, the role of steam turbines will remain central to achieving a sustainable, low-carbon energy future.
As the steam turbine industry continues to innovate and evolve, it is becoming increasingly clear that the turbines of the future will not only be more efficient and sustainable but also more adaptable to a wider range of energy sources and applications. Several key developments and trends are shaping the future of steam turbines, ensuring their ongoing relevance in the global energy transition.
One of the most promising innovations is the development of high-efficiency hybrid systems, where steam turbines are combined with other forms of energy generation to optimize performance and reduce emissions. These hybrid systems can include combinations of gas turbines, renewable energy sources, and battery storage to provide a more flexible and resilient power generation system. By integrating steam turbines with renewable technologies like solar thermal power, wind energy, and bioenergy, it is possible to create more reliable and consistent energy output, overcoming the intermittency of renewable sources. Hybrid systems also improve grid stability by offering a dispatchable power supply, which is crucial for maintaining energy reliability in regions with high renewable energy penetration.
Another significant innovation in the steam turbine sector is the rise of low-carbon and zero-carbon fuels. In particular, the use of green hydrogen as a fuel source for steam turbines is gaining traction. Hydrogen, when produced through renewable means (i.e., electrolysis using renewable energy), is a carbon-neutral fuel, making it an ideal candidate for replacing fossil fuels in power generation. Steam turbines can be adapted to burn hydrogen, either alone or in blends with natural gas, allowing existing plants to transition to cleaner energy sources without requiring complete overhauls. This flexibility is a critical aspect of steam turbine innovation, enabling power plants to adopt cleaner fuels and reduce their carbon footprints.
Additionally, the integration of energy storage technologies with steam turbines will play an increasingly important role in future power systems. Thermal energy storage, which involves capturing excess heat generated by renewable sources or industrial processes and storing it for later use, can be paired with steam turbines to ensure continuous power generation. For example, in concentrated solar power (CSP) systems, mirrors or lenses concentrate sunlight to produce heat, which is stored in thermal energy storage tanks. This stored heat is then converted into steam to drive turbines and generate electricity. These systems allow renewable energy plants to provide power even when sunlight is not available, thus addressing the intermittent nature of solar power.
Geothermal energy is another area where steam turbines are making a significant impact. Geothermal power plants use heat from the Earth’s core to produce steam, which drives turbines and generates electricity. As geothermal technology continues to advance, steam turbines will play a key role in unlocking more of the Earth’s geothermal potential, especially in regions that have previously been considered less viable for geothermal development. By harnessing enhanced geothermal systems (EGS), where water is injected into deep underground reservoirs to produce steam, steam turbines can help provide a consistent, renewable energy source that is not dependent on weather conditions or time of day.
The development of modular steam turbines is also a critical advancement in steam turbine innovation. These modular turbines can be easily scaled up or down to meet varying energy demands, making them ideal for smaller, decentralized power plants or applications where space is limited. Modular designs allow for quicker installation and more flexible energy solutions, especially in remote areas, islands, or industrial facilities that require reliable power generation without relying on large centralized plants. Additionally, these turbines can be used in microgrids, helping to provide localized energy solutions that can be more resilient to grid disruptions and tailored to specific community or industrial needs.
The digitalization of steam turbines is another transformative trend that is shaping the future of turbine technology. The use of advanced sensors, predictive analytics, and artificial intelligence (AI) in turbine operations allows for real-time monitoring and performance optimization. Smart sensors embedded in steam turbines can continuously measure key operational parameters, such as temperature, pressure, and vibration, and transmit this data to operators for analysis. By leveraging machine learning algorithms, these sensors can detect early signs of wear or failure, enabling predictive maintenance and reducing costly downtime. Digital tools can also optimize the turbine’s operational settings in real-time, adjusting parameters based on grid conditions, energy demand, and fuel availability to maximize efficiency and minimize fuel consumption.
One of the key benefits of this digital revolution is the ability to perform remote diagnostics and performance monitoring, allowing operators to manage turbine operations from anywhere in the world. This capability is particularly valuable in large or remote power plants where on-site personnel may be limited. Remote monitoring systems can provide operators with real-time alerts and diagnostic information, enabling them to respond to potential issues quickly and make informed decisions to optimize turbine performance.
Advanced materials continue to play a significant role in steam turbine innovation. Research into new materials, such as ceramic composites, nanomaterials, and superalloys, is enhancing the turbines’ resistance to high temperatures, pressures, and corrosive environments. These materials enable turbines to operate more efficiently at higher temperatures, resulting in increased energy extraction and better fuel utilization. Innovations in coatings and corrosion-resistant materials also extend the lifespan of turbine components, reducing maintenance costs and improving overall plant reliability. The development of these advanced materials ensures that steam turbines remain durable and cost-effective, even in the most demanding operating conditions.
The trend toward flexible and adaptive turbines is another key focus of innovation. As the energy sector shifts to more renewable and decentralized energy sources, steam turbines must be able to operate across a wide range of conditions and adapt to different fuel types. This includes the ability to burn a variety of fuels, such as biomass, waste, or hydrogen, and to operate in hybrid configurations with renewable energy sources. Flexible turbines can quickly adjust to changes in power demand or shifts in fuel availability, ensuring that power generation remains stable and efficient, even as the grid becomes more dynamic.
Finally, global regulatory trends and the push for carbon neutrality are driving innovation in steam turbine technology. As countries commit to reducing greenhouse gas emissions and meeting international climate goals, there is increasing pressure on power plants to adopt more sustainable and low-carbon technologies. This regulatory pressure is spurring the development of turbines that not only meet efficiency and performance standards but also adhere to stringent environmental regulations. Innovations such as carbon capture and storage (CCS), combined heat and power (CHP), and waste heat recovery systems are being integrated into steam turbine designs to help plants reduce their carbon emissions and operate in a more environmentally responsible manner.
In conclusion, steam turbine innovations are transforming the way power is generated and distributed across the globe. From the integration of renewable energy systems to the development of more efficient, flexible, and adaptable turbines, these innovations are playing a pivotal role in advancing the energy transition. As the world moves toward sustainable, low-carbon energy solutions, steam turbines will continue to evolve, ensuring that they remain a key technology for meeting future energy demands while reducing environmental impact. The continued development of smart technologies, advanced materials, and hybrid systems will allow steam turbines to operate more efficiently, reliably, and sustainably in the energy systems of tomorrow.
As the development of steam turbine technology continues to advance, several emerging trends will shape its role in the energy landscape, particularly in response to global energy demands, the transition to renewable energy sources, and sustainability goals. These turbines are evolving not only in terms of efficiency and reliability but also in their ability to integrate with cutting-edge energy systems and support the goals of net-zero emissions and climate resilience. The future of steam turbines is deeply connected to the broader transformation of the energy sector, especially with the ongoing push for decarbonization, energy security, and a more sustainable power grid.
One significant area of development is the collaboration between steam turbines and emerging grid technologies. As the energy mix diversifies with more distributed generation from renewable sources like wind and solar, power grids are becoming increasingly complex and dynamic. Steam turbines will need to adapt to fluctuating energy supply and demand patterns by operating in more flexible and responsive ways. This could include shifting from base-load power generation to providing peak-load or backup power during periods of high demand or when renewable generation is low. By integrating with smart grids, steam turbines can help stabilize the power grid and ensure a consistent energy supply.
The concept of grid resilience will be central to future steam turbine design. Modern turbines must be able to quickly ramp up or down in response to grid fluctuations, especially as more intermittent renewable sources are introduced. Energy storage systems, like battery storage or pumped hydro storage, will likely work in conjunction with steam turbines to smooth out energy supply. These systems can store excess power generated during periods of high renewable output and then release it during periods of lower production. Steam turbines in such systems can enhance the stability and flexibility of these hybrid plants, contributing to a more resilient and adaptable energy infrastructure.
Furthermore, there is growing interest in the integration of carbon capture, utilization, and storage (CCUS) technologies in steam turbine systems. CCUS is increasingly seen as a key solution for reducing the carbon footprint of existing fossil-fuel power plants and achieving climate neutrality. Steam turbines are being incorporated into combined cycle plants with CCUS to capture carbon emissions from fossil-fuel combustion and prevent them from entering the atmosphere. This innovation could significantly extend the lifespan of existing power plants while lowering their environmental impact, contributing to efforts to combat climate change. In these setups, steam turbines would work in concert with post-combustion capture technologies to absorb and store CO2 produced during the energy generation process.
Another important development is the move toward decarbonized industrial applications. Industrial processes, such as those in the chemical, cement, steel, and refining industries, have traditionally been significant sources of carbon emissions. In these industries, steam turbines are increasingly being used to generate electricity and reclaim waste heat, making these operations more energy-efficient and less reliant on fossil fuels. Moreover, with the development of green hydrogen production via electrolysis, steam turbines can play a key role in supporting industrial decarbonization by providing a reliable energy source for hydrogen plants, which are critical to low-carbon fuel development.
Hybrid renewable energy systems are also becoming a core focus in steam turbine innovation. As countries move toward more sustainable energy systems, there is a rising need for power plants that combine conventional energy sources with renewable technologies such as solar, wind, and geothermal energy. Steam turbines are ideally suited for integration with these technologies, offering flexibility and adaptability for combined heat and power (CHP) systems, renewable power stations, and energy storage systems. By combining the strengths of steam turbines with renewable energy sources, these hybrid systems can deliver cleaner, more efficient, and reliable energy solutions. The ability to store energy from intermittent renewable sources like wind and solar in the form of heat allows for more consistent power generation, even when conditions are less favorable for those sources.
Steam turbines are also being designed with an increasing focus on compactness and portability, catering to off-grid and remote applications. Smaller-scale modular turbines that can be installed in smaller plants or mobile setups are ideal for areas with limited access to large-scale infrastructure or for industries that require localized power solutions. These portable turbines, often referred to as micro turbines, are already being used in industrial applications, military operations, and remote areas where access to traditional power grids is not possible. The ongoing development of mobile turbine units can support both stand-alone and distributed energy systems, helping provide power to remote locations or mobile operations.
The use of low-temperature steam turbines in waste heat recovery processes is another promising area of innovation. Waste heat from various industrial processes, such as cement production, steel manufacturing, or even data centers, can be harnessed using low-temperature steam turbines to generate additional power. This allows industries to maximize energy recovery from their existing processes and reduce their reliance on external energy sources. In some cases, steam turbines could even be used to convert waste heat from renewable energy generation, like solar or geothermal energy, into usable electricity.
There is also an increasing trend toward customized turbine designs, where steam turbines are being tailored to the specific needs of individual applications. Whether for combustion optimization, low-emission operations, or hybrid energy integration, manufacturers are designing turbines to meet precise requirements in terms of fuel type, load capacity, and operating conditions. This trend is particularly important as industries and utilities look for ways to integrate alternative fuels, renewable energy, and emissions-reduction technologies without the need for expensive, large-scale infrastructure changes.
Finally, digital twin technology is becoming a powerful tool in steam turbine design and operation. A digital twin is a virtual replica of a physical system that can be used to simulate and analyze turbine performance under various operating conditions. These virtual models allow engineers to experiment with different configurations, optimize turbine design, and predict potential issues before they occur. By simulating real-time conditions, a digital twin can provide insights into how turbines perform in real-world scenarios, helping to identify performance bottlenecks, reduce fuel consumption, and extend turbine life. This integration of simulation and digital modeling into turbine design will undoubtedly play a crucial role in advancing the performance and sustainability of steam turbines.
As we look toward the future, the role of steam turbines will remain integral to the global energy landscape. Their adaptability, efficiency, and capability to integrate with renewable energy sources, energy storage solutions, and sustainable fuels ensure that they will continue to be a cornerstone of power generation. The continuous innovation in materials science, digital technology, and energy systems integration is propelling steam turbines into new areas of application, from industrial plants to decentralized, renewable energy systems. With these advancements, steam turbines will play a pivotal role in achieving carbon-neutral energy systems and helping to meet global sustainability targets.
As the global energy landscape evolves, the future of steam turbines will be deeply intertwined with the continuous growth of emerging technologies, environmental policy shifts, and the need for energy systems that are resilient, adaptable, and sustainable. There are several additional trends and innovations that are set to shape the ongoing role of steam turbines in the energy mix.
One of the most exciting prospects for steam turbines lies in their potential to support the integration of emerging energy storage technologies. As the world moves toward intermittent renewable energy sources like solar and wind, there is a growing need for systems that can store energy when production exceeds demand and release it when supply is low. Steam turbines, when combined with thermal energy storage (TES), can act as a crucial component in renewable energy storage solutions. The process typically involves storing excess energy in the form of heat, which can then be converted back into steam to drive turbines, generating electricity. This type of energy storage is seen as an effective solution to mitigate the challenges of renewable intermittency and can complement battery storage by providing long-duration energy storage solutions that last for hours or even days.
Thermal storage systems, such as those used in concentrated solar power (CSP) plants, can store vast amounts of heat, which is then used to produce steam for turbine operation. These systems can offer a continuous power supply, even during periods when sunlight or wind conditions are not optimal. As the technology matures and becomes more widely deployed, steam turbines integrated with thermal energy storage will play an increasingly important role in providing grid stability and helping to balance energy supply with demand.
Another growing area of innovation is in district heating systems, where steam turbines are used to generate electricity and provide heat for residential, commercial, and industrial buildings. These systems are particularly beneficial in densely populated areas, where central heating and power generation can be shared across multiple buildings. By using waste heat recovery from industrial processes or from renewable energy sources, steam turbines in district heating plants can provide both electrical power and thermal energy, optimizing fuel use and reducing emissions. District heating, especially when combined with combined heat and power (CHP) systems, offers significant energy efficiency benefits, reducing the need for separate heating and electricity generation.
As the demand for low-carbon energy solutions grows, steam turbines are also increasingly being designed to work with a variety of alternative fuels. One major area of interest is the use of biomass and biofuels in steam turbines. Biomass, such as agricultural waste, wood pellets, and other organic materials, can be used to produce steam and electricity. Similarly, biofuels—sustainable alternatives to fossil fuels—can also be utilized in steam turbines. These fuels help to close the carbon loop by absorbing CO2 during growth and releasing it when burned, potentially offering a carbon-neutral solution for power generation. The versatility of steam turbines in adapting to different fuel sources ensures that they remain relevant in a world shifting towards cleaner and more sustainable energy systems.
Additionally, advanced turbine technology continues to evolve to meet the demands of modern power systems. Innovations like high-efficiency materials, superheated steam, and low-emission combustion technologies are improving the performance of steam turbines. New alloy compositions are being developed to withstand higher temperatures and pressures, allowing for more efficient energy extraction from heat sources. Advanced coatings and corrosion-resistant materials are enhancing the durability of turbine components, extending their operational life and reducing maintenance needs. These materials enable turbines to operate at supercritical and ultra-supercritical pressures—conditions that yield higher efficiency, increased power output, and lower fuel consumption.
The digitalization of steam turbines is another significant advancement that promises to reshape the way turbines are designed, operated, and maintained. IoT-enabled sensors, predictive analytics, and artificial intelligence are allowing for real-time monitoring and predictive maintenance in turbine systems. By continuously collecting data on turbine performance, operators can gain a deeper understanding of the turbine’s condition and make data-driven decisions to optimize efficiency. Predictive algorithms can forecast when maintenance is needed, minimizing downtime and preventing costly repairs. Furthermore, digital models, such as digital twins, can simulate various operating scenarios, helping engineers and operators optimize turbine configurations before they are implemented in real-world operations. This ongoing use of big data and AI-driven optimization is setting the stage for the next generation of highly efficient, reliable, and cost-effective steam turbines.
There is also a growing trend toward flexibility in operation for steam turbines, enabling them to function in a more integrated energy ecosystem. As the grid becomes more complex, turbines will be required to provide not only base-load power but also to support grid balancing, peak shaving, and frequency regulation. Steam turbines are already capable of ramping up or down in response to changing grid conditions, but ongoing advancements in their ability to operate in hybrid configurations with renewables and energy storage will enhance their role as a flexible and reliable source of power in the grid. This is particularly important in regions with high renewable penetration, where steam turbines can provide backup generation and stabilize grid fluctuations caused by variable renewable energy production.
The modularity of steam turbine designs is another area of innovation that will drive future growth. Modular steam turbines allow for greater flexibility in scale, making it possible to adapt turbine configurations to smaller or distributed power generation plants. These turbines can be used in a variety of applications, from industrial cogeneration plants to microgrids in remote areas. This modular approach not only makes turbine installation and maintenance more cost-effective but also offers the opportunity for scalable power solutions, particularly in regions with evolving energy needs. Modular systems can be expanded over time as demand grows, reducing the initial capital investment and making energy more accessible to a wider range of consumers.
Finally, global energy policies and the growing focus on sustainable development goals (SDGs) are accelerating the adoption of steam turbines in emerging markets, where reliable and affordable electricity is in high demand. Steam turbines are especially attractive in countries looking to diversify their energy sources and improve energy access while maintaining environmental responsibility. These regions are increasingly investing in cleaner technologies like combined-cycle gas turbines, geothermal plants, and biomass plants, where steam turbines are integral to energy generation. International cooperation, financial support for clean energy technologies, and a push toward reducing energy poverty will continue to drive the adoption of steam turbines worldwide.
In conclusion, the future of steam turbines is marked by ongoing technological innovation, sustainability-driven advances, and the increasing demand for flexible, low-carbon, and efficient energy systems. As the global energy landscape shifts towards cleaner and more decentralized energy solutions, steam turbines will remain a key player in providing reliable, efficient, and adaptable power generation. With developments in advanced materials, digital technologies, hybrid energy systems, and alternative fuels, steam turbines will continue to evolve and play a vital role in meeting the world’s energy demands in the face of growing environmental challenges.
Steam Turbine-driven Generators
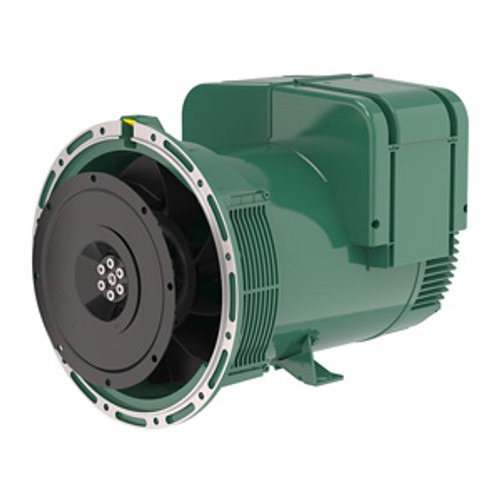
Steam turbine-driven generators play a central role in electricity generation, transforming thermal energy into electrical power through a well-established mechanical process. These systems have been integral to industrial and utility-scale power generation for over a century, and they continue to be indispensable as a reliable and efficient means of generating electricity. The fundamental principle behind steam turbine-driven generators involves the conversion of steam energy, typically generated by burning fossil fuels, nuclear fission, or using renewable sources such as geothermal energy, into mechanical energy, which is then used to drive an electrical generator.
The design and performance of steam turbine-driven generators are closely linked to the characteristics of the steam turbine itself, with both components being critical to the system’s overall efficiency, reliability, and capacity. As with any turbine system, the steam turbine converts the thermal energy from the steam into rotational motion. This motion drives the shaft connected to the generator, which then produces electricity through electromagnetic induction. The efficiency of this conversion is dependent on several factors, including the pressure and temperature of the steam, the design of the turbine blades, and the generator’s characteristics, including the number of poles and the type of cooling used.
The role of steam turbine-driven generators in large-scale power plants cannot be overstated. In fossil-fuel plants, nuclear power stations, and combined heat and power (CHP) systems, steam turbines are typically coupled with generators to produce electricity for the grid. These plants use heat energy generated by burning coal, natural gas, or through nuclear reactions to convert water into steam, which then expands and drives the turbine. In many cases, the same steam is used in heat recovery systems, either in a direct or combined cycle to enhance energy efficiency.
Efficiency in steam turbine-driven generators has always been a critical focus for both engineers and plant operators. The turbines themselves are designed to maximize the energy extracted from steam while minimizing losses. As steam turbines continue to evolve, improvements in material science, fluid dynamics, and turbine blade design allow turbines to operate at higher efficiencies, especially at higher pressures and temperatures. In this context, innovations in ultra-supercritical and supercritical steam cycles are providing turbines with the ability to generate electricity at higher efficiencies, reducing the amount of fuel needed to produce a given amount of power and lowering emissions.
Combined cycle power plants offer one of the most efficient ways to produce electricity with steam turbine-driven generators. In these plants, a gas turbine is used in tandem with a steam turbine to capture and utilize the waste heat from the gas turbine exhaust. The waste heat is used to produce steam, which drives the steam turbine and generator, resulting in significantly improved efficiency when compared to traditional power generation systems. These plants are becoming more common due to their higher energy conversion rates and their ability to produce reliable power while reducing emissions and fuel consumption.
Beyond large power plants, steam turbine-driven generators are also used in industrial cogeneration systems, where they serve dual purposes: providing electricity and utilizing waste heat for process heating or other industrial functions. Cogeneration plants are popular in industries such as chemical production, oil refining, and food processing, where the need for both electricity and heat can be met simultaneously. This reduces overall energy costs and makes better use of the fuel consumed by the plant, which is key in industries where energy consumption is a significant operating expense.
Steam turbine-driven generators also play an important role in geothermal power plants, where steam is directly sourced from the earth’s natural heat. In these plants, hot water or steam from deep within the earth’s crust is brought to the surface, where it drives the turbine to produce electricity. This form of energy generation is seen as one of the most sustainable, as it relies on an almost limitless and renewable resource. In these systems, the steam turbine system is optimized for a lower temperature steam than in traditional fossil-fuel plants but still plays a central role in electricity generation.
The maintenance and longevity of steam turbine-driven generators are also crucial for the performance of power plants. Over time, turbines are subject to wear and tear, particularly in high-temperature and high-pressure systems, where components like turbine blades, seals, and bearings can degrade. Regular monitoring systems, such as vibration analysis, thermal imaging, and performance diagnostics, help detect issues before they cause significant damage. Through predictive maintenance and the use of advanced monitoring techniques, operators can reduce unplanned outages and extend the operational life of the turbines and generators, ensuring they operate at optimal efficiency for many years.
Steam turbine-driven generators are not only used for base-load power generation but are also increasingly integrated into renewable energy systems. As hybrid power systems gain traction, steam turbines are being coupled with technologies like solar power and wind energy to create more sustainable and reliable energy solutions. For example, in concentrated solar power (CSP) systems, solar energy is used to heat a fluid, which is then used to produce steam that drives a turbine-generator set. Similarly, hybrid wind-solar-steam systems are being explored to provide a more continuous and stable energy output by blending intermittent renewable sources with thermal energy storage and steam turbines.
Advanced turbine and generator technologies are enhancing the performance of steam turbine-driven generators in several ways. New turbine designs feature more efficient blade geometries, improved aerodynamics, and advanced coatings that reduce friction, improve heat resistance, and prolong the turbine’s operational life. Moreover, supercritical and ultra-supercritical turbine systems, which operate at much higher temperatures and pressures than conventional turbines, are pushing the boundaries of power generation efficiency. These turbines generate more power from less fuel, which is particularly advantageous in efforts to reduce carbon emissions and move toward net-zero energy systems.
Another innovation is the use of digital technologies in turbine-generator systems. The rise of digital twin technology, which creates a virtual model of the turbine and generator for real-time simulation and monitoring, is helping operators fine-tune performance and extend the lifespan of equipment. By continuously collecting data from sensors embedded in the turbines, engineers can monitor vibration, temperature, pressure, and other factors that could indicate problems. This real-time data analysis allows for the early detection of potential issues, predictive maintenance, and overall better management of steam turbine-driven generators.
As power plants transition to low-carbon or decarbonized systems, steam turbine-driven generators are being incorporated into technologies like carbon capture and storage (CCS). In these systems, steam turbines play a role in powering the equipment needed to capture CO2 emissions from power plants and store them underground. The integration of CCS technology with steam turbines is essential for mitigating the environmental impact of fossil fuel-based power generation during the transition to more sustainable energy sources.
With increasing global demands for clean energy, there is a clear emphasis on efficiency and sustainability in steam turbine-driven generator designs. Whether for large utility-scale power plants or smaller industrial cogeneration systems, these generators continue to evolve, offering cleaner, more efficient, and reliable power solutions. As new challenges in the energy sector arise, the development of more flexible and efficient steam turbine-generator systems will be essential for providing stable power while addressing the growing need for renewable energy integration, decarbonization, and climate change mitigation. These innovations will help ensure that steam turbine-driven generators continue to be a cornerstone of the global energy infrastructure for years to come.
The ongoing developments in steam turbine-driven generators point toward a future where these systems are integral not just in large centralized power plants but also in distributed generation systems. The rise of microgrids—small-scale, localized energy systems that can operate independently or in conjunction with the larger grid—is driving new applications for steam turbine generators. In these settings, steam turbines, often paired with alternative or renewable heat sources such as biomass, waste heat recovery, or geothermal energy, are becoming key components for energy independence, reliability, and local sustainability.
Microgrids are particularly beneficial in regions where the power infrastructure is unreliable, such as in remote communities or areas with developing economies. By providing on-site generation and storage capabilities, these smaller-scale steam turbine systems help reduce dependence on central grid power, enhance energy resilience during outages, and lower transmission losses. The flexibility of steam turbine generators also supports their use in hybrid power systems that combine renewable energy sources with thermal backup generation, ensuring that power is available even when solar or wind resources are unavailable.
The global push for energy security and a transition toward resilient, decentralized energy systems further underscores the importance of steam turbine-driven generators in the evolving energy landscape. These generators can be used to harness energy from a variety of local resources, providing reliable power that can be utilized for industrial, residential, and critical infrastructure purposes. Additionally, these systems can be designed to operate in high-availability modes, ensuring that essential services such as hospitals, water treatment plants, and emergency services have an uninterrupted power supply.
Efficiency optimization continues to be a major area of focus. As power systems become more interconnected and complex, smart grids and demand-side management technologies are offering new opportunities to integrate steam turbine-driven generators into energy markets. By providing not just electricity but also frequency regulation and voltage support, these generators can contribute to the overall stability of the grid. They also have the potential to become key players in demand response programs, where operators can adjust turbine output in response to real-time grid needs, enhancing both the economic and environmental efficiency of power generation.
Looking forward, steam turbine-driven generators will play a central role in the hydrogen economy. As hydrogen production technologies advance, especially green hydrogen made from water through electrolysis powered by renewable energy, steam turbines could be integrated into systems that convert excess renewable energy into hydrogen. When needed, this hydrogen can be used as a fuel for gas turbines or converted back into electricity using fuel cells, with steam turbines providing backup generation or grid stabilization during peak demand. The ability to use steam turbines in hydrogen-based energy systems could help address one of the major challenges of renewable energy—how to store and use excess power when it’s not needed.
Furthermore, as climate change mitigation efforts intensify, steam turbines will be key to the development of carbon capture technologies. Power plants using steam turbines, particularly those fueled by fossil fuels, are increasingly incorporating carbon capture, utilization, and storage (CCUS) systems. These systems capture CO2 emissions before they are released into the atmosphere and store them underground or use them in various industrial applications. By integrating CCUS technologies with steam turbine-driven generators, it is possible to significantly reduce the carbon footprint of fossil fuel power generation while still maintaining the reliable and efficient output that these systems are known for.
On the technological front, the advancements in additive manufacturing (3D printing) and robotics are starting to play a role in steam turbine design and maintenance. These technologies are enhancing the ability to produce complex turbine components that are lightweight, stronger, and more resistant to heat and stress. Through the use of 3D printing, turbines can be designed with geometries that were previously difficult or impossible to manufacture, leading to improvements in efficiency and performance. Moreover, robotic systems can assist in the maintenance of steam turbines by carrying out tasks like inspections, repairs, and replacements in environments that are too hazardous or difficult for humans to enter.
The environmental impact of steam turbine-driven generators is also being addressed through increased focus on their integration into circular economy models. In this context, turbines, generators, and associated components are designed to be reused, refurbished, and recycled, reducing waste and extending the lifespan of these high-cost assets. When a turbine reaches the end of its life, its parts can be repurposed or recycled, contributing to a more sustainable approach to energy generation. Similarly, advances in sustainable materials are allowing for more eco-friendly manufacturing processes and reducing the environmental impact of both turbines and generators.
With the global demand for electricity continuing to rise, particularly in rapidly growing economies, steam turbine-driven generators will remain a key solution in meeting these needs. The flexibility of these systems, coupled with innovations in fuel use, energy storage, and system integration, ensures that steam turbines will continue to evolve and adapt to meet the challenges of modern power generation. Whether used in large-scale power plants, distributed energy systems, or as part of hybrid renewable energy solutions, steam turbine-driven generators will remain central to global efforts to provide clean, reliable, and affordable energy for all.
In summary, steam turbine-driven generators are evolving alongside advancements in energy technology, digitalization, sustainability, and efficiency. Their role in renewable integration, hybrid power systems, microgrids, and energy storage ensures their relevance in future power generation strategies. Coupled with carbon capture, hydrogen production, and digital optimization, these systems are poised to remain a cornerstone of energy infrastructure, contributing to cleaner, more resilient, and more efficient energy systems in the decades ahead. As the world transitions to a low-carbon future, steam turbine-driven generators will continue to play a pivotal role in shaping the global energy landscape.
The future of steam turbine-driven generators is intrinsically tied to the broader transformation of the global energy sector. As the demand for sustainable and adaptable power generation grows, these systems are being redesigned to align with modern energy priorities. This involves not only optimizing their traditional roles but also exploring innovative integrations into new and emerging energy infrastructures. The versatility of steam turbines ensures their continued relevance, particularly as hybrid and flexible systems become the backbone of a decentralized, low-carbon energy grid.
Energy storage integration is one area where steam turbine-driven generators are finding new applications. With the proliferation of variable renewable energy sources such as wind and solar, which are inherently intermittent, there is a pressing need for systems that can balance supply and demand. Steam turbines are increasingly being combined with thermal energy storage systems that capture excess heat during periods of low demand and release it when needed. This enables turbines to generate electricity more consistently, acting as a stabilizing force in grids with high renewable penetration. The ability to use stored heat for extended periods also positions steam turbines as a valuable component of long-duration energy storage solutions, which are critical for grid reliability.
Additionally, waste heat recovery is gaining traction as industries strive to improve energy efficiency and reduce emissions. Many industrial processes generate significant amounts of waste heat that can be repurposed to produce steam for turbines, thereby generating electricity without additional fuel consumption. This approach is being adopted in cement production, steel manufacturing, and even data centers, where cooling requirements generate heat that can be captured and utilized. Waste heat recovery systems, combined with steam turbines, not only improve overall system efficiency but also contribute to significant cost savings and environmental benefits for industrial operators.
In terms of fuel flexibility, the adaptability of steam turbines is being harnessed to support the transition to renewable and alternative fuels. Traditional fossil fuels like coal and natural gas are increasingly being supplemented or replaced by biomass, waste-derived fuels, and synthetic fuels such as those produced from captured carbon dioxide and hydrogen. Steam turbines are particularly well-suited to these applications, as they can handle a wide range of steam conditions and compositions. This capability makes them a cornerstone technology for power plants that are diversifying their fuel sources to reduce their carbon footprint and comply with stringent environmental regulations.
The role of steam turbines in desalination is another promising area of development. In regions with limited freshwater resources, turbines can be integrated into dual-purpose plants that generate electricity while producing potable water through thermal desalination processes. These systems use the low-pressure steam exiting the turbine to drive desalination units, making efficient use of thermal energy that would otherwise go to waste. This approach is particularly valuable in arid regions, where the need for both energy and water is critical. The coupling of steam turbines with desalination technologies highlights their potential to address not only energy challenges but also global water scarcity.
Digital transformation is rapidly reshaping the operation and maintenance of steam turbine-driven generators. Advanced machine learning algorithms and IoT (Internet of Things) sensors are enabling real-time monitoring and predictive maintenance, reducing unplanned downtime and extending the operational lifespan of these systems. Digital twins, in particular, are becoming a standard tool for operators, allowing them to simulate turbine performance under various conditions and identify inefficiencies or potential failures before they occur. By leveraging these technologies, operators can achieve peak performance while minimizing maintenance costs and maximizing the return on investment.
As power systems grow more complex, grid interactivity is emerging as a key capability for steam turbine-driven generators. In a future dominated by smart grids, these turbines will play an active role in grid stabilization, offering ancillary services such as voltage regulation, reactive power support, and black start capabilities. Their ability to ramp up or down quickly in response to grid demands makes them ideal for balancing intermittent renewable energy sources. This grid interactivity ensures that steam turbines remain a vital part of the energy ecosystem, even as renewable technologies become more prevalent.
From a policy and economic perspective, government incentives and regulatory frameworks are shaping the adoption and evolution of steam turbine-driven generators. Investments in research and development, as well as subsidies for clean energy technologies, are accelerating the deployment of advanced turbine systems that meet higher efficiency and emission standards. For instance, incentives for carbon-neutral technologies are driving innovations in turbines that can operate effectively with hydrogen or other low-carbon fuels. Similarly, regulations aimed at reducing emissions are encouraging the retrofitting of existing turbines with modern components and systems to improve their environmental performance.
The global energy transition is also spurring greater collaboration between public and private sectors to develop next-generation steam turbine technologies. Partnerships between turbine manufacturers, research institutions, and energy companies are fostering innovation in areas such as material science, thermodynamics, and aerodynamics. These collaborations are leading to breakthroughs in turbine efficiency, durability, and adaptability, ensuring that steam turbines remain competitive in a rapidly evolving energy market.
Looking further ahead, the role of steam turbine-driven generators in space exploration and off-world energy systems is beginning to be explored. Concepts for lunar or Martian colonies often include energy systems that rely on thermal energy conversion, and steam turbines could serve as a reliable technology for generating electricity in these extreme environments. Their robustness and ability to operate under varying conditions make them a promising option for long-term, sustainable energy solutions beyond Earth.
In conclusion, the evolution of steam turbine-driven generators reflects the broader trends and challenges of the modern energy landscape. These systems are adapting to meet the demands of a world that prioritizes efficiency, sustainability, and flexibility. By integrating with advanced technologies, diversifying fuel sources, and expanding into new applications, steam turbines are poised to remain a cornerstone of global energy systems. Their ability to balance traditional power generation with emerging renewable and hybrid systems ensures their continued relevance as the energy sector transitions toward a cleaner, more sustainable future. Whether in large-scale power plants, industrial facilities, or innovative hybrid systems, steam turbine-driven generators will continue to play a pivotal role in shaping the energy solutions of tomorrow.
As steam turbine-driven generators continue to evolve, their integration into emerging technologies and global energy frameworks promises to redefine their role in the energy ecosystem. One of the most transformative areas is their potential role in carbon-negative energy systems. As carbon capture, utilization, and storage (CCUS) technologies advance, steam turbines are being integrated into facilities designed to actively remove carbon dioxide from the atmosphere. These systems, often referred to as bioenergy with carbon capture and storage (BECCS), use biomass as a fuel source to generate electricity, with the resulting carbon emissions captured and stored underground. By pairing steam turbines with BECCS systems, it becomes possible to produce power while achieving a net reduction in atmospheric CO2, offering a scalable solution to combat climate change.
Another exciting development is the use of steam turbines in supercritical and ultra-supercritical power plants, which operate at extremely high temperatures and pressures to achieve higher efficiencies. These advanced systems push the boundaries of materials science and engineering, as they require components that can withstand extreme operating conditions without compromising performance or longevity. The higher efficiency of supercritical and ultra-supercritical turbines reduces fuel consumption and emissions, making them a preferred choice for modern power plants striving to meet stricter environmental standards. These technologies represent a significant leap forward in the efficiency and sustainability of steam power generation.
The application of artificial intelligence (AI) in optimizing steam turbine performance is also becoming increasingly widespread. AI-driven algorithms are being used to analyze vast amounts of operational data, identifying patterns and anomalies that can inform better decision-making. For example, AI can predict when a turbine component is likely to fail, allowing operators to schedule maintenance proactively and avoid costly unplanned outages. Additionally, AI can optimize turbine operation in real time, adjusting parameters such as steam flow, pressure, and temperature to maximize efficiency under varying load conditions. This digital transformation enhances the reliability, efficiency, and economic viability of steam turbines, ensuring their competitiveness in a rapidly changing energy market.
The use of closed-loop systems is another area where steam turbine technology is advancing. These systems recycle steam after it has passed through the turbine, condensing it back into water to be reheated and reused. This approach not only improves the efficiency of the turbine but also significantly reduces water consumption, which is a critical consideration in regions facing water scarcity. Closed-loop systems are particularly advantageous in industries and power plants where environmental regulations require strict water usage and discharge controls. By minimizing water wastage and improving overall system sustainability, these systems make steam turbines more environmentally friendly and economically attractive.
Steam turbines are also being adapted for use in micro steam power plants, which are small-scale systems designed for localized energy production. These micro plants are ideal for applications in remote areas, small industries, or facilities that require dedicated power sources. The compact design and flexibility of these turbines allow them to be customized for specific needs, such as combined heat and power (CHP) applications, where both electricity and thermal energy are produced simultaneously. By enabling on-site energy generation, micro steam power plants reduce reliance on centralized grids and enhance energy resilience, particularly in off-grid or underserved regions.
In the renewable energy sector, steam turbines are finding innovative applications in geothermal energy production. Geothermal power plants use heat from the Earth’s interior to generate steam, which drives the turbines. Unlike solar or wind energy, geothermal energy provides a stable and continuous power supply, making it an ideal complement to intermittent renewable sources. Advances in turbine technology are enabling these systems to operate efficiently across a wider range of temperatures and pressures, expanding the feasibility of geothermal energy in regions with moderate geothermal resources. This diversification of renewable energy sources underscores the adaptability and relevance of steam turbines in a decarbonized energy future.
Furthermore, the modularization of steam turbine systems is gaining traction, allowing for easier transportation, installation, and scalability. Modular turbines can be assembled on-site from pre-fabricated components, reducing construction time and costs. This approach is particularly beneficial for distributed energy projects and facilities in remote locations, where traditional turbine installations may be logistically challenging. Modular systems also offer the flexibility to scale up as energy demands grow, providing a cost-effective and future-proof solution for a wide range of applications.
In the broader context of global energy equity, steam turbines are playing a crucial role in bringing reliable and affordable electricity to developing regions. By utilizing locally available resources, such as biomass or geothermal energy, steam turbines can help bridge the energy gap in areas where infrastructure for traditional energy sources is lacking. These systems not only support economic development but also contribute to social progress by enabling access to education, healthcare, and other essential services powered by electricity.
As the energy sector continues to evolve, the role of steam turbine-driven generators will extend beyond traditional electricity generation to encompass a wide array of innovative applications. Their versatility, coupled with ongoing advancements in materials science, digital technologies, and system integration, ensures that they will remain a cornerstone of global energy systems. Whether in powering cities, supporting industries, or enabling renewable energy solutions, steam turbines will continue to adapt and thrive in the face of emerging challenges and opportunities. Their enduring importance lies not only in their historical contributions to energy generation but also in their potential to shape a cleaner, more sustainable, and equitable energy future.
EMS Power Machines
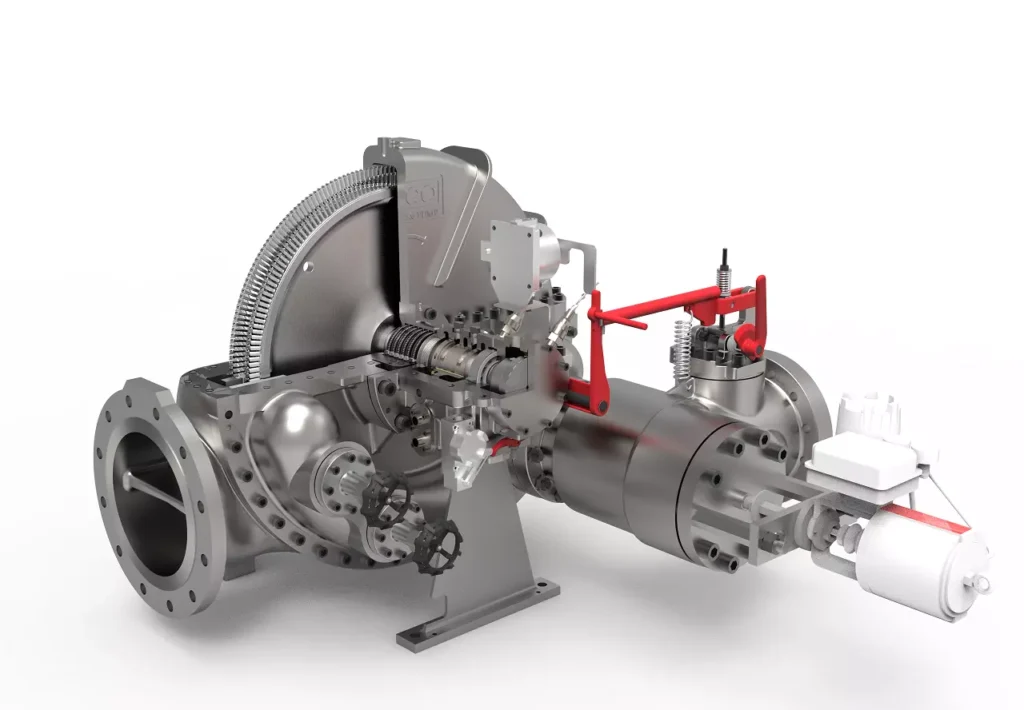
We design, manufacture and assembly Power Machines such as – diesel generators, electric motors, vibration motors, pumps, steam engines and steam turbines
EMS Power Machines is a global power engineering company, one of the five world leaders in the industry in terms of installed equipment. The companies included in the company have been operating in the energy market for more than 60 years.
EMS Power Machines manufactures steam turbines, gas turbines, hydroelectric turbines, generators, and other power equipment for thermal, nuclear, and hydroelectric power plants, as well as for various industries, transport, and marine energy.
EMS Power Machines is a major player in the global power industry, and its equipment is used in power plants all over the world. The company has a strong track record of innovation, and it is constantly developing new and improved technologies.
Here are some examples of Power Machines’ products and services:
- Steam turbines for thermal and nuclear power plants
- Gas turbines for combined cycle power plants and industrial applications
- Hydroelectric turbines for hydroelectric power plants
- Generators for all types of power plants
- Boilers for thermal power plants
- Condensers for thermal power plants
- Reheaters for thermal power plants
- Air preheaters for thermal power plants
- Feedwater pumps for thermal power plants
- Control systems for power plants
- Maintenance and repair services for power plants
EMS Power Machines is committed to providing its customers with high-quality products and services. The company has a strong reputation for reliability and innovation. Power Machines is a leading provider of power equipment and services, and it plays a vital role in the global power industry.
EMS Power Machines, which began in 1961 as a small factory of electric motors, has become a leading global supplier of electronic products for different segments. The search for excellence has resulted in the diversification of the business, adding to the electric motors products which provide from power generation to more efficient means of use.