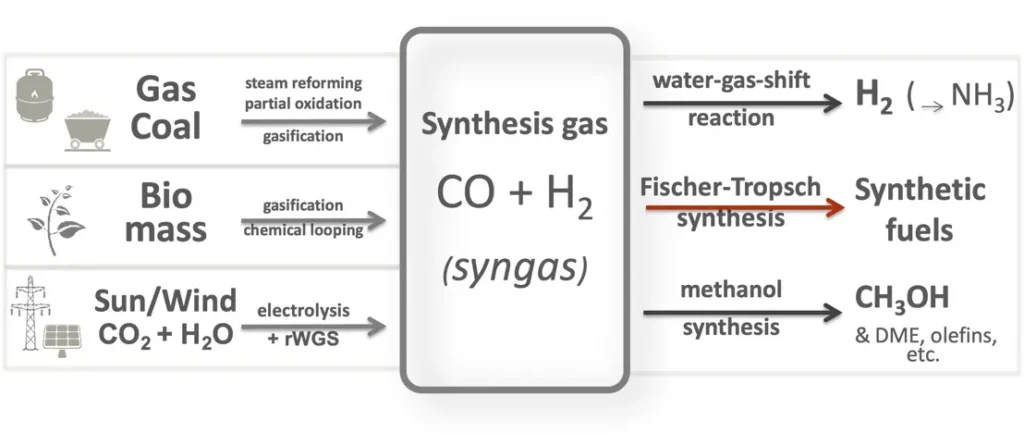
Gasification: Gasification is a thermochemical process that converts carbonaceous materials, such as biomass, coal, or organic waste, into synthesis gas (syngas) consisting mainly of hydrogen (H2), carbon monoxide (CO), and methane (CH4). The process occurs in a gasifier, where the feedstock is subjected to high temperatures (>700°C) and controlled amounts of oxygen or steam in a low-oxygen environment. Gasification involves several key reactions, including pyrolysis, oxidation, and reduction, leading to the production of a clean and versatile fuel gas that can be used for power generation, chemical synthesis, hydrogen production, and other industrial applications. Gasification offers advantages such as high energy efficiency, low emissions, and flexibility in feedstock selection, making it a promising technology for sustainable energy production and waste management.
Gasification
- Pyrolysis: Pyrolysis is a thermal decomposition process that converts biomass or organic materials into biochar, bio-oil, and syngas in the absence of oxygen or with limited oxygen supply. During pyrolysis, the feedstock is heated to temperatures typically ranging from 300°C to 800°C, causing the breakdown of complex organic molecules into simpler compounds. The pyrolysis products can vary depending on the temperature, heating rate, and residence time, with biochar being the solid residue, bio-oil being the liquid fraction, and syngas consisting of gaseous components such as hydrogen, carbon monoxide, and methane. Pyrolysis offers several advantages, including the production of biochar for soil amendment, bio-oil for biofuel production, and syngas for energy generation, making it a versatile technology for biomass utilization and waste valorization.
- Combustion: Combustion is a chemical reaction in which a fuel reacts with oxygen to produce heat, light, and combustion products such as carbon dioxide (CO2), water vapor (H2O), and other gases. In the context of thermal conversion, combustion refers to the controlled burning of biomass, coal, or waste materials to generate heat or energy. Combustion processes typically occur in boilers, furnaces, or power plants, where the fuel is burned in the presence of air or oxygen to produce steam for electricity generation, heat for industrial processes, or hot water for heating applications. Combustion technologies range from traditional stoker-fired boilers to advanced fluidized bed combustors and gasification-combustion systems, offering efficient and reliable solutions for energy production with varying fuel types and quality.
- Incineration: Incineration is a thermal treatment process that involves the combustion of solid, liquid, or gaseous waste materials to reduce their volume, destroy hazardous components, and recover energy. In incineration plants, waste materials are combusted at high temperatures (>800°C) in specially designed furnaces or kilns equipped with pollution control devices to minimize emissions of pollutants such as particulate matter, dioxins, and heavy metals. The heat generated during incineration can be recovered in the form of steam or hot gases for electricity generation, district heating, or industrial processes, providing a sustainable and environmentally sound method for waste management and resource recovery.
- Torrefaction: Torrefaction is a mild pyrolysis process that involves the thermal treatment of biomass in the absence of oxygen at temperatures typically ranging from 200°C to 300°C. During torrefaction, biomass undergoes partial decomposition and removal of volatile compounds, resulting in a dry, brittle, and energy-dense solid fuel known as torrefied biomass or biocoal. Torrefied biomass exhibits improved properties such as higher energy density, lower moisture content, and enhanced grindability and storability compared to raw biomass, making it suitable for combustion, gasification, or co-firing with coal in power plants. Torrefaction offers benefits such as reduced transportation costs, improved biomass logistics, and increased utilization of renewable biomass resources for energy production.
- Carbonization: Carbonization is a thermal conversion process that transforms organic materials such as wood, peat, or agricultural residues into carbon-rich char or charcoal through the elimination of volatile components. The process occurs at temperatures typically ranging from 300°C to 700°C in the absence of oxygen or with limited oxygen supply, preventing complete combustion and promoting the formation of carbonaceous residues. Carbonization can be achieved through various methods, including traditional kiln carbonization, retort carbonization, or modern pyrolysis technologies. The resulting charcoal can be used as a solid fuel for cooking, heating, or metallurgical processes, as a soil amendment for agriculture, or as a precursor for activated carbon production, providing valuable products and environmental benefits through the conversion of biomass into stable carbonaceous materials.
- Biomass-to-energy: Biomass-to-energy refers to the process of converting biomass feedstocks such as wood, agricultural residues, energy crops, or organic waste into heat, electricity, or biofuels through thermal conversion technologies such as combustion, gasification, or pyrolysis. Biomass-to-energy systems utilize the energy stored in biomass materials to generate power or heat for industrial, commercial, or residential applications, offering renewable and sustainable alternatives to fossil fuels. Biomass-to-energy technologies play a crucial role in decentralized energy production, rural development, and climate change mitigation by harnessing the carbon-neutral energy potential of biomass resources while reducing greenhouse gas emissions and dependence on non-renewable energy sources.
- Waste-to-energy: Waste-to-energy involves the conversion of municipal solid waste (MSW), industrial waste, or other waste materials into heat, electricity, or fuels through thermal conversion processes such as incineration, gasification, or pyrolysis. Waste-to-energy facilities provide an environmentally sustainable solution for waste management by reducing the volume of waste, recovering energy from organic materials, and minimizing the environmental impact of landfills. Waste-to-energy technologies contribute to resource recovery, energy production, and renewable energy generation while addressing waste disposal challenges and promoting circular economy principles through the utilization of waste as a valuable resource for energy production and resource conservation.
- Biochar production: Biochar production involves the thermal conversion of biomass feedstocks into a stable carbonaceous material known as biochar through processes such as pyrolysis or carbonization. Biochar is a porous, carbon-rich material that retains nutrients, enhances soil fertility, and improves soil structure and water retention when applied to agricultural soils. Biochar production offers several benefits, including carbon sequestration, soil carbon storage, and climate change mitigation, by converting biomass into a stable form of organic carbon that can persist in the soil for centuries. Biochar also provides opportunities for sustainable agriculture, bioenergy production, and waste management through the utilization of biomass resources for soil improvement and environmental remediation.
- Thermal depolymerization: Thermal depolymerization is a thermochemical process that converts organic waste materials such as plastics, rubber, or organic sludge into liquid hydrocarbons, gases, and solid residues through the application of heat and pressure in the presence of water or steam. During thermal depolymerization, complex organic polymers are broken down into smaller hydrocarbon molecules, which can be further refined into fuels, chemicals, or feedstocks for various industrial applications. Thermal depolymerization offers a promising solution for waste valorization and resource recovery by converting non-recyclable waste materials into
Gasification:
Gasification is a thermochemical process that transforms carbonaceous materials into a mixture of gases known as synthesis gas (syngas) by subjecting them to high temperatures and controlled amounts of oxygen or steam in a low-oxygen environment. This process typically occurs in a gasifier, where solid, liquid, or gaseous feedstocks such as biomass, coal, or waste materials are converted into a combustible gas containing hydrogen, carbon monoxide, methane, and other hydrocarbons.
The gasification process involves several key steps. Firstly, the feedstock is introduced into the gasifier, where it undergoes drying and devolatilization, releasing volatile components such as water, tar, and organic compounds. These volatiles then undergo further decomposition through pyrolysis, resulting in the formation of char, which serves as a porous matrix for subsequent gasification reactions.
Next, the char undergoes gasification reactions, where it reacts with oxygen or steam to produce syngas. Depending on the gasification conditions, various gasification agents can be employed, including air, oxygen, steam, or a combination thereof. The choice of gasification agent influences the composition and properties of the resulting syngas, with oxygen-blown gasification typically yielding higher hydrogen content, while steam-blown gasification favors higher carbon monoxide production.
Gasification offers several advantages over traditional combustion processes. Firstly, it allows for the utilization of a wide range of feedstocks, including low-quality or waste materials that are unsuitable for direct combustion. Additionally, gasification facilitates the production of a clean and versatile fuel gas that can be used for power generation, heating, or as a feedstock for chemical synthesis processes. Furthermore, gasification can be integrated with other energy conversion technologies such as combined heat and power (CHP) systems or fuel cells to achieve higher overall efficiency and energy utilization.
Overall, gasification represents a promising pathway towards sustainable energy production and waste management, offering a flexible and efficient means of converting diverse feedstocks into valuable energy products while minimizing environmental impact and resource depletion. As research and development efforts continue to advance gasification technologies, its potential applications in both stationary and mobile energy systems are expected to expand, contributing to the transition towards a more sustainable and resilient energy future.
Pyrolysis:
Pyrolysis is a thermochemical process that decomposes organic materials in the absence of oxygen or with limited oxygen supply, resulting in the production of biochar, bio-oil, and syngas. This process involves heating the biomass feedstock to elevated temperatures (typically between 300°C and 800°C), causing it to undergo thermal degradation and break down into volatile gases, liquids, and solid char.
During pyrolysis, the biomass feedstock undergoes several stages of decomposition. Initially, the moisture content of the biomass is removed through drying, followed by the release of volatile compounds such as organic acids, aldehydes, and ketones during the pyrolysis reactions. These volatile components are then condensed to form bio-oil, a dark, viscous liquid with energy content comparable to conventional petroleum fuels.
Simultaneously, solid carbonaceous residues, known as biochar or charcoal, are formed as the non-volatile fraction of the biomass undergoes carbonization. Biochar is a stable, carbon-rich material that retains the skeletal structure of the original biomass and contains high levels of fixed carbon, making it suitable for applications such as soil amendment, carbon sequestration, and water filtration.
In addition to biochar and bio-oil, pyrolysis also produces a mixture of gases known as syngas, which typically consists of hydrogen, carbon monoxide, methane, and other hydrocarbons. Syngas can be utilized as a renewable fuel for power generation, heating, or as a feedstock for chemical synthesis processes, offering versatility and flexibility in energy applications.
Pyrolysis technologies can be classified based on the heating rate, residence time, and operating conditions. Fast pyrolysis processes, characterized by rapid heating rates and short residence times, favor the production of bio-oil, while slow pyrolysis processes, with slower heating rates and longer residence times, result in higher biochar yields. Intermediate pyrolysis processes offer a compromise between biochar and bio-oil production, providing a balanced output of both products.
Overall, pyrolysis represents a promising pathway for converting biomass into valuable energy products and bio-based materials, offering environmental benefits such as carbon sequestration, waste reduction, and renewable energy production. As research and development efforts continue to advance, pyrolysis technologies are expected to play an increasingly important role in the transition towards a sustainable and low-carbon economy.
Combustion:
Combustion is a chemical reaction between a fuel and an oxidizing agent, typically oxygen, that results in the rapid release of heat and light energy. In the context of thermal conversion, combustion refers to the controlled burning of solid, liquid, or gaseous fuels to generate heat or produce power.
The combustion process involves several key steps. Firstly, the fuel and oxidizer are brought into contact and mixed to ensure efficient combustion. In the case of solid fuels such as biomass or coal, they are typically pulverized or shredded to increase the surface area available for combustion. Liquid fuels such as oil or ethanol are atomized into fine droplets, while gaseous fuels such as natural gas or hydrogen are mixed with air or oxygen in the proper stoichiometric ratio.
Once the fuel and oxidizer are mixed, they are ignited, initiating the combustion reaction. During combustion, the fuel molecules break apart and react with oxygen molecules to form carbon dioxide (CO2), water vapor (H2O), and other combustion products such as nitrogen oxides (NOx) and sulfur dioxide (SO2), depending on the fuel composition and combustion conditions.
The heat released during combustion raises the temperature of the surrounding environment, which can be utilized for various applications such as space heating, water heating, steam generation, or electricity production. Combustion processes can be classified based on the type of fuel used (solid, liquid, or gaseous), the combustion technology employed (e.g., fluidized bed combustion, pulverized coal combustion), and the combustion system’s design and operating parameters.
Combustion technologies have been widely used for centuries to meet human energy needs, from heating and cooking to industrial processes and power generation. While combustion provides a convenient and reliable source of energy, it also produces emissions such as CO2, NOx, SO2, and particulate matter, which can have negative environmental and health impacts if not properly controlled. As a result, efforts are underway to develop cleaner and more efficient combustion technologies, such as advanced flue gas cleaning systems, low-emission burners, and integrated gasification combined cycle (IGCC) plants, to minimize environmental pollution and mitigate climate change.
Incineration:
Incineration is a thermal treatment process that involves the controlled combustion of waste materials to convert them into ash, flue gases, and heat. This process is typically carried out in specially designed facilities called incinerators, which are equipped with combustion chambers, flue gas treatment systems, and energy recovery units.
The incineration process begins with the collection and preparation of waste materials, which may include municipal solid waste (MSW), hazardous waste, medical waste, or industrial waste. The waste is then transported to the incineration facility, where it undergoes sorting and shredding to remove contaminants and optimize combustion efficiency.
Once prepared, the waste is fed into the combustion chamber of the incinerator, where it is burned at high temperatures (typically between 800°C and 1,200°C) in the presence of excess air or oxygen. During combustion, organic materials in the waste are oxidized to carbon dioxide (CO2) and water vapor (H2O), while inorganic materials are converted into ash.
The heat generated during incineration is recovered through heat exchangers or boiler systems, where it is used to produce steam for electricity generation, district heating, or industrial processes. This process, known as waste-to-energy (WTE) or energy recovery, helps offset the energy consumption of the incineration facility and provides a renewable energy source.
In addition to energy recovery, incineration also serves to reduce the volume of waste and destroy hazardous components such as pathogens, organic pollutants, and toxic chemicals. Modern incineration facilities are equipped with advanced pollution control technologies, such as bag filters, electrostatic precipitators, and scrubbers, to capture and neutralize harmful emissions such as particulate matter, heavy metals, dioxins, and furans.
While incineration offers several benefits, including waste volume reduction, energy recovery, and pollution control, it also raises concerns about air emissions, ash disposal, and public health impacts. To address these concerns, stringent regulations and emission standards have been implemented to ensure the safe and environmentally sound operation of incineration facilities. Additionally, efforts are underway to promote waste minimization, recycling, and alternative waste treatment technologies to complement and reduce the reliance on incineration for waste management.
Gas Cleaning:
Gas cleaning is a crucial step in thermal conversion processes, particularly those involving combustion, gasification, and pyrolysis, where the generated gases may contain impurities, pollutants, and particulate matter that need to be removed before discharge or utilization. Gas cleaning technologies aim to minimize emissions, improve air quality, and ensure compliance with environmental regulations.
Several methods are employed for gas cleaning, depending on the type and concentration of contaminants present in the gas stream. Some of the common gas cleaning techniques include:
- Particulate Removal: Particulate matter, such as ash, soot, and dust, can be removed from the gas stream using devices like electrostatic precipitators, fabric filters (baghouses), cyclones, or wet scrubbers. These devices use different mechanisms, such as electrostatic forces, filtration, centrifugal force, or wet scrubbing, to capture and remove particulates from the gas stream.
- Acid Gas Removal: Acid gases, including sulfur dioxide (SO2), hydrogen chloride (HCl), and hydrogen fluoride (HF), can be removed from the gas stream through processes such as wet scrubbing, dry scrubbing, or chemical absorption. Wet scrubbers use a liquid absorbent (e.g., water, lime slurry) to chemically react with and remove acid gases, while dry scrubbers employ solid sorbents (e.g., lime, limestone) to adsorb or react with the acid gases.
- Mercury Removal: Mercury emissions from thermal conversion processes can be controlled using specialized sorbent injection systems or activated carbon injection (ACI) systems. These systems inject sorbents or activated carbon into the gas stream, where they adsorb mercury vapor and remove it from the gas phase.
- Particulate Matter Control: Advanced technologies such as catalytic converters and ceramic filters can be used to control particulate emissions from thermal conversion processes. Catalytic converters employ catalysts to promote the oxidation of organic pollutants, while ceramic filters utilize porous ceramic materials to capture and remove particulate matter from the gas stream.
- NOx Reduction: Nitrogen oxides (NOx) emissions can be reduced using selective catalytic reduction (SCR) or selective non-catalytic reduction (SNCR) systems. SCR systems use a catalyst to convert NOx into nitrogen (N2) and water vapor (H2O) using ammonia as a reducing agent, while SNCR systems inject urea or ammonia directly into the flue gas stream to chemically reduce NOx emissions.
Overall, gas cleaning technologies play a crucial role in mitigating the environmental impact of thermal conversion processes by removing harmful pollutants and ensuring compliance with regulatory standards. Continued research and development efforts are focused on improving the efficiency, effectiveness, and cost-effectiveness of gas cleaning technologies to address emerging environmental challenges and promote sustainable energy production.
Catalytic Conversion:
Catalytic conversion is a chemical process that involves the use of catalysts to facilitate the transformation of reactants into desired products at lower temperatures and pressures compared to traditional thermal conversion methods. This process is widely used in various industries, including petroleum refining, chemical synthesis, and environmental remediation, to produce high-value products, reduce energy consumption, and minimize environmental impact.
In catalytic conversion, a catalyst is a substance that accelerates the rate of chemical reactions by providing an alternative reaction pathway with lower activation energy. Catalysts do not undergo permanent chemical changes during the reaction and can be used repeatedly, making them highly efficient and cost-effective for large-scale industrial processes.
There are two main types of catalytic conversion processes:
- Heterogeneous Catalysis: In heterogeneous catalysis, the catalyst exists in a different phase from the reactants and products. Typically, solid catalysts are used, and the reactants are in the gas or liquid phase. The catalytic reaction occurs on the surface of the catalyst, where the reactant molecules adsorb onto active sites, undergo chemical transformations, and desorb as products. Examples of heterogeneous catalytic processes include catalytic cracking in petroleum refining, selective catalytic reduction (SCR) of nitrogen oxides (NOx) in exhaust gases, and Fischer-Tropsch synthesis for producing synthetic fuels from syngas.
- Homogeneous Catalysis: In homogeneous catalysis, both the catalyst and the reactants are in the same phase, usually in solution. Homogeneous catalysis often involves transition metal complexes or organometallic compounds that can undergo reversible coordination or redox reactions with the reactants. Homogeneous catalytic processes are particularly useful for organic synthesis, where precise control over reaction conditions and selectivity is desired. Examples of homogeneous catalytic reactions include hydrogenation, oxidation, and hydroformylation reactions.
Catalytic conversion offers several advantages over traditional thermal conversion methods. Firstly, catalytic processes operate under milder conditions, resulting in lower energy consumption, reduced equipment corrosion, and improved selectivity towards desired products. Additionally, catalytic conversion enables the utilization of renewable feedstocks, such as biomass-derived sugars or oils, for the production of biofuels, chemicals, and materials, contributing to sustainability and resource conservation efforts.
Overall, catalytic conversion plays a critical role in modern industrial processes by enabling efficient and selective chemical transformations, driving innovation in energy production, environmental protection, and sustainable development. Continued research and development efforts are focused on designing novel catalysts, optimizing reaction conditions, and scaling up catalytic processes to meet the growing demand for cleaner, more efficient, and sustainable technologies.
Carbonization:
Carbonization is a thermochemical process that involves the conversion of organic materials into carbon-rich char or carbonaceous residue through heating in the absence of oxygen or with limited oxygen supply. This process is commonly used to produce charcoal from biomass feedstocks such as wood, agricultural residues, or organic waste.
During carbonization, the organic material is subjected to elevated temperatures (typically between 300°C and 700°C) in a low-oxygen environment, such as a kiln, retort, or pyrolysis reactor. As the temperature increases, volatile components such as water, tar, and other organic compounds are driven off, leaving behind a solid residue composed primarily of carbon.
The carbonization process can be divided into several stages:
- Drying: In the initial stage, moisture present in the biomass is evaporated and removed from the material. This helps reduce energy consumption during subsequent heating and prevents steam explosions or excessive pressure buildup within the carbonization vessel.
- Pyrolysis: As the temperature continues to rise, the biomass undergoes pyrolysis, a thermal decomposition process where organic compounds break down into volatile gases and liquid products. This stage is characterized by the release of tar, methane, hydrogen, and other volatile hydrocarbons, which are typically collected and used as fuel or chemical feedstock.
- Carbonization: In the final stage, the remaining solid residue is subjected to further heating, causing it to undergo carbonization. During this process, the organic material decomposes further, with the formation of char or carbonaceous residue rich in fixed carbon. The carbonization temperature and residence time influence the properties of the resulting charcoal, including its carbon content, porosity, and mechanical strength.
Carbonization is a key step in the production of charcoal, a valuable energy source and raw material used in various applications, including metallurgy, cooking, and filtration. Charcoal is prized for its high carbon content, low ash content, and long burning time, making it an efficient and versatile fuel for heating and cooking in both domestic and industrial settings.
In addition to charcoal production, carbonization also plays a role in the production of activated carbon, a highly porous form of carbon used for water purification, air filtration, and environmental remediation. Activated carbon is produced by further processing charcoal through physical or chemical activation methods, which increase its surface area and adsorption capacity.
Overall, carbonization is a fundamental process in biomass conversion, enabling the production of valuable carbonaceous materials for energy, industry, and environmental applications. Continued research and development efforts are focused on optimizing carbonization processes, improving charcoal quality, and exploring novel applications for carbonaceous materials in emerging technologies such as carbon capture and storage (CCS) and renewable energy storage.
Gasification:
Gasification is a thermochemical process that converts carbonaceous feedstocks, such as coal, biomass, or municipal solid waste, into a synthesis gas (syngas) containing hydrogen, carbon monoxide, methane, and other gaseous components. This process occurs in a controlled environment with a limited supply of oxygen or steam, typically at elevated temperatures ranging from 600°C to 1,500°C.
The gasification process involves several key steps:
- Feedstock Preparation: The carbonaceous feedstock, such as coal, wood chips, or agricultural residues, is first prepared by drying and grinding to a suitable particle size. This increases the surface area and facilitates the conversion process.
- Feedstock Gasification: The prepared feedstock is then fed into a gasifier, where it undergoes thermochemical reactions in the presence of a gasification agent, typically steam, oxygen, or a combination of both. The feedstock reacts with the gasification agent at high temperatures, leading to the production of syngas.
- Syngas Generation: The gasification reactions produce a mixture of gases, including hydrogen (H2), carbon monoxide (CO), methane (CH4), carbon dioxide (CO2), and other trace gases. The composition of the syngas depends on factors such as the feedstock type, gasification conditions, and the choice of gasification agent.
- Tar and Particulate Removal: Gasification of biomass feedstocks can produce tar and particulate matter, which need to be removed to prevent equipment fouling and ensure downstream process efficiency. Various tar removal technologies, such as scrubbers, filters, and catalytic converters, are employed to clean the syngas before it is used or further processed.
- Syngas Utilization: The syngas produced during gasification can be utilized for various applications, including power generation, heat production, hydrogen production, and chemical synthesis. Syngas can be burned directly in gas turbines, boilers, or engines to generate electricity or heat. Alternatively, it can be further processed to separate and purify individual gas components for use in chemical processes or as fuel for hydrogen fuel cells.
Gasification offers several advantages over traditional combustion processes, including higher energy efficiency, lower emissions, and greater fuel flexibility. It enables the conversion of a wide range of feedstocks, including low-quality coal, biomass residues, and waste materials, into a clean and versatile energy carrier. Gasification also facilitates carbon capture and storage (CCS) technologies by producing a concentrated stream of CO2, which can be captured and sequestered to mitigate greenhouse gas emissions.
Overall, gasification represents a promising pathway for sustainable energy production and resource utilization, offering a versatile and efficient technology for converting diverse feedstocks into valuable fuels, chemicals, and energy products. Continued research and development efforts are focused on improving gasification processes, increasing process efficiency, and expanding the range of feedstocks and applications for gasification technology.
Syngas:
Syngas, short for synthesis gas, is a mixture of gases primarily composed of hydrogen (H2) and carbon monoxide (CO), along with lesser amounts of methane (CH4), carbon dioxide (CO2), and other trace gases. It is produced through the gasification of carbonaceous feedstocks such as coal, biomass, or municipal solid waste in a controlled environment with a limited supply of oxygen or steam.
The composition of syngas depends on several factors, including the type of feedstock, gasification conditions (temperature, pressure, residence time), and the choice of gasification agent (oxygen, steam, air). Typically, syngas has a H2/CO ratio ranging from 1:1 to 3:1, which can be adjusted depending on the desired end-use applications.
Syngas is a versatile energy carrier with a wide range of applications across various industries:
- Power Generation: Syngas can be burned directly in gas turbines, boilers, or internal combustion engines to generate electricity or heat. Combined cycle power plants utilize syngas as a fuel source to maximize energy efficiency by capturing waste heat for additional power generation.
- Hydrogen Production: Syngas can be used as a precursor for hydrogen production through a process called water-gas shift reaction. In this reaction, CO reacts with steam (H2O) to produce CO2 and H2. The resulting hydrogen-rich syngas can be further purified to produce high-purity hydrogen for fuel cells, ammonia production, or industrial processes.
- Chemical Synthesis: Syngas serves as a feedstock for the production of a wide range of chemicals and fuels through catalytic processes such as Fischer-Tropsch synthesis, methanol synthesis, and hydrocarbon synthesis. These processes utilize the H2 and CO present in syngas to produce valuable products such as methanol, ammonia, synthetic fuels, and olefins.
- Biorefining: Syngas produced from biomass gasification can be integrated into biorefinery processes for the production of biofuels and biochemicals. Biomass-derived syngas can be converted into biofuels such as ethanol, biodiesel, or synthetic diesel through thermochemical or biochemical conversion pathways.
- Carbon Capture and Utilization (CCU): Syngas can be used as a feedstock for carbon capture and utilization (CCU) technologies to produce value-added products while reducing greenhouse gas emissions. CO2 captured from syngas can be utilized for the production of chemicals, polymers, or construction materials through processes such as carbonation or mineralization.
Syngas offers several advantages as an energy carrier, including its flexibility, abundance of feedstock sources, and potential for carbon capture and utilization. However, challenges such as gas cleanup, gas quality control, and process efficiency optimization need to be addressed to fully realize the potential of syngas for sustainable energy production and resource utilization. Continued research and development efforts are focused on advancing gasification technologies, improving syngas conversion processes, and exploring novel applications for syngas in the transition towards a low-carbon economy.
Biomass Gasification:
Biomass gasification is a thermochemical process that converts biomass feedstocks into a combustible gas mixture called syngas. This process occurs in a gasifier, where biomass materials such as wood chips, agricultural residues, or organic waste are subjected to high temperatures and a controlled supply of oxygen, steam, or a combination of both. The gasification reactions produce a synthesis gas (syngas) containing hydrogen, carbon monoxide, methane, and other gaseous components, along with tar, char, and ash residues.
The biomass gasification process involves several key steps:
- Feedstock Preparation: Biomass feedstocks are first prepared by drying and grinding to a suitable particle size. This increases the surface area and facilitates the conversion process in the gasifier.
- Gasification Reactions: The prepared biomass feedstock is fed into the gasifier, where it undergoes thermochemical reactions in a low-oxygen environment at temperatures typically ranging from 700°C to 1,200°C. The biomass reacts with the gasification agent (oxygen, steam, or a combination) to produce syngas through a series of endothermic and exothermic reactions, including pyrolysis, oxidation, and reduction.
- Syngas Cleanup: The raw syngas produced from biomass gasification contains impurities such as tar, particulate matter, and contaminants that need to be removed to meet quality specifications for downstream applications. Various gas cleanup technologies, including cyclones, scrubbers, filters, and catalytic converters, are employed to remove impurities and improve syngas quality.
- Syngas Utilization: The cleaned syngas can be utilized for various energy and chemical applications, including power generation, heat production, hydrogen production, and chemical synthesis. Syngas can be burned directly in gas turbines, boilers, or engines to generate electricity or heat. Alternatively, it can be further processed to separate and purify individual gas components for use in chemical processes or as fuel for hydrogen fuel cells.
Biomass gasification offers several advantages over traditional combustion-based energy systems, including higher energy efficiency, lower emissions, and greater fuel flexibility. It enables the conversion of a wide range of biomass feedstocks, including agricultural residues, forestry waste, energy crops, and organic waste materials, into a clean and versatile energy carrier. Biomass gasification also promotes resource conservation and environmental sustainability by utilizing renewable feedstocks and reducing reliance on fossil fuels.
Overall, biomass gasification represents a promising technology for sustainable energy production and waste management, offering a renewable and environmentally friendly pathway for generating heat, power, and fuels from biomass resources. Continued research and development efforts are focused on improving gasification processes, increasing process efficiency, and expanding the range of biomass feedstocks and applications for biomass gasification technology.
Gasifier Design:
Gasifier design refers to the engineering and configuration of gasification systems used to convert carbonaceous feedstocks into synthesis gas (syngas) through thermochemical processes. Gasifier design plays a crucial role in determining the efficiency, performance, and reliability of gasification systems for various applications, including power generation, heat production, and chemical synthesis.
Key aspects of gasifier design include:
- Reactor Configuration: Gasifiers can be classified based on their reactor configuration, including fixed-bed, fluidized-bed, entrained-flow, and downdraft gasifiers. Each type has unique characteristics and operating conditions that influence gasification performance, syngas quality, and process efficiency.
- Feedstock Handling: Gasifier design must accommodate the characteristics of the feedstock, including particle size, moisture content, and ash composition. Systems for feedstock preparation, handling, and feeding into the gasifier are designed to ensure uniform fuel distribution, efficient heating, and optimal gasification performance.
- Gasification Agent: Gasifiers can use various gasification agents, including air, oxygen, steam, or a combination, to facilitate the thermochemical reactions during gasification. The choice of gasification agent influences syngas composition, gasification efficiency, and process economics.
- Temperature and Pressure Control: Gasifier design includes provisions for controlling operating parameters such as temperature, pressure, and residence time to optimize gasification performance and syngas quality. Temperature control is critical to ensure proper biomass conversion, minimize tar formation, and maximize gasification efficiency.
- Syngas Cleanup: Gasifier design may incorporate syngas cleanup systems to remove impurities such as tar, particulate matter, and contaminants from the raw syngas. Various cleanup technologies, including cyclones, scrubbers, filters, and catalytic converters, are integrated into the gasification system to improve syngas quality and meet downstream requirements.
- Heat Management: Gasifier design includes provisions for managing heat transfer within the system to maintain optimal operating temperatures and thermal efficiency. Heat recovery systems may be incorporated to capture and utilize waste heat for preheating feedstock, generating steam, or providing process heat for other applications.
- Safety and Reliability: Gasifier design prioritizes safety and reliability by incorporating features such as gas leak detection, pressure relief systems, and emergency shutdown mechanisms to prevent accidents and ensure system integrity during operation.
Gasifier design is a multidisciplinary endeavor that integrates principles of chemical engineering, mechanical engineering, materials science, and process control. Advanced computational modeling and simulation techniques are employed to optimize gasifier design, predict performance, and guide system improvements.
Overall, effective gasifier design is essential for the successful deployment of gasification technology in diverse applications, offering sustainable solutions for energy production, waste management, and resource utilization. Continued research and development efforts are focused on advancing gasifier design methodologies, enhancing system performance, and expanding the range of feedstocks and applications for gasification technology.
Biomass Conversion:
Biomass conversion refers to the process of transforming biomass feedstocks into useful energy carriers, chemicals, materials, and products through various thermochemical, biochemical, and physicochemical processes. Biomass, derived from organic sources such as plants, forestry residues, agricultural crops, and organic waste, represents a renewable and abundant resource that can be utilized to meet energy needs and reduce dependence on fossil fuels.
There are several pathways for biomass conversion, each with its own advantages, limitations, and applications:
- Thermochemical Conversion:
- Gasification: Biomass gasification converts solid biomass into synthesis gas (syngas) through thermochemical reactions in a controlled environment with limited oxygen or steam. Syngas can be used for power generation, heat production, hydrogen production, and chemical synthesis.
- Pyrolysis: Biomass pyrolysis involves heating biomass in the absence of oxygen to produce bio-oil, biochar, and syngas. Bio-oil can be upgraded to produce transportation fuels, while biochar can be used as a soil amendment or carbon sequestration agent.
- Combustion: Biomass combustion involves burning biomass directly to produce heat, steam, or electricity. It is commonly used in residential, commercial, and industrial heating applications, as well as in biomass-fired power plants.
- Biochemical Conversion:
- Anaerobic Digestion: Biomass can undergo anaerobic digestion, where microorganisms break down organic matter in the absence of oxygen to produce biogas (a mixture of methane and carbon dioxide) and digestate (a nutrient-rich fertilizer).
- Fermentation: Biomass fermentation utilizes microorganisms to convert sugars and starches present in biomass feedstocks into biofuels such as ethanol and butanol. It is commonly used in the production of bioethanol from sugarcane, corn, and cellulosic biomass.
- Physicochemical Conversion:
- Hydrothermal Processing: Biomass can be converted into biofuels and chemicals through hydrothermal processing, which involves heating biomass in the presence of water at high temperatures and pressures. This process can produce bio-oil, biochar, and syngas.
- Torrefaction: Biomass torrefaction involves heating biomass in the absence of oxygen at temperatures between 200°C and 300°C to produce a dry, energy-dense solid fuel called torrefied biomass or bio-coal.
Biomass conversion technologies offer numerous environmental and economic benefits, including reduced greenhouse gas emissions, waste reduction, rural development, and energy security. However, challenges such as feedstock availability, process efficiency, product quality, and economic viability need to be addressed to realize the full potential of biomass conversion for sustainable energy production and resource utilization.
Research and development efforts are focused on advancing biomass conversion technologies, improving process efficiency, developing new feedstock sources, and exploring integrated biorefinery concepts to maximize the value and sustainability of biomass-derived products. Continued innovation and investment in biomass conversion are essential for transitioning towards a more sustainable and renewable energy future.
Biomass Gasification Plant:
A biomass gasification plant is a facility that converts biomass feedstocks into synthesis gas (syngas) through the thermochemical process of gasification. These plants play a crucial role in the utilization of renewable biomass resources for energy production, offering a sustainable alternative to fossil fuels and contributing to the reduction of greenhouse gas emissions.
Key components and processes of a biomass gasification plant include:
- Feedstock Handling and Preparation: Biomass feedstocks such as wood chips, agricultural residues, forestry waste, or energy crops are received, stored, and prepared for gasification. This may involve drying, grinding, and sizing the feedstock to ensure uniformity and optimize gasification performance.
- Gasification Reactor: The heart of the biomass gasification plant is the gasifier, where biomass feedstocks undergo thermochemical reactions in a controlled environment with limited oxygen or steam. Gasifiers can be of various types, including fixed-bed, fluidized-bed, entrained-flow, or downdraft gasifiers, each with its unique characteristics and operating conditions.
- Gasification Process: In the gasification reactor, biomass feedstocks are subjected to high temperatures (typically between 700°C and 1,200°C) and a controlled supply of gasification agent (oxygen, steam, or a combination) to produce syngas. The gasification process involves several chemical reactions, including pyrolysis, oxidation, and reduction, leading to the conversion of biomass into syngas.
- Syngas Cleanup: The raw syngas produced from biomass gasification contains impurities such as tar, particulate matter, and contaminants that need to be removed to meet quality specifications for downstream applications. Syngas cleanup systems, including cyclones, scrubbers, filters, and catalytic converters, are employed to remove impurities and improve syngas quality.
- Syngas Utilization: The cleaned syngas can be utilized for various energy and chemical applications, including power generation, heat production, hydrogen production, and chemical synthesis. Syngas can be burned directly in gas turbines, boilers, or engines to generate electricity or heat. Alternatively, it can be further processed to separate and purify individual gas components for use in chemical processes or as fuel for hydrogen fuel cells.
- Waste Management: Biomass gasification plants may produce by-products such as ash, char, and wastewater during the gasification process. Proper waste management and disposal practices are implemented to handle these by-products safely and minimize environmental impacts.
Biomass gasification plants offer several advantages over conventional combustion-based energy systems, including higher energy efficiency, lower emissions, and greater fuel flexibility. They enable the utilization of a wide range of biomass feedstocks, including agricultural residues, forestry waste, energy crops, and organic waste materials, for clean and sustainable energy production.
Continued research and development efforts are focused on advancing biomass gasification technology, improving process efficiency, enhancing syngas cleanup systems, and exploring integrated biorefinery concepts to maximize the value and sustainability of biomass-derived products. Biomass gasification plants represent a promising pathway towards a more sustainable and renewable energy future, contributing to energy security, environmental protection, and rural development.
Syngas Generator:
A syngas generator, also known as a gas generator or gasifier, is a device or system that produces synthesis gas (syngas) through the gasification of carbonaceous feedstocks such as coal, biomass, or municipal solid waste. Syngas generators play a vital role in converting these feedstocks into a versatile energy carrier that can be utilized for various applications, including power generation, heat production, chemical synthesis, and hydrogen production.
Key components and processes of a syngas generator include:
- Gasification Reactor: The gasification reactor is the core component of the syngas generator, where carbonaceous feedstocks undergo thermochemical reactions in a controlled environment with a limited supply of oxygen, steam, or a combination of both. Gasification reactors can be of different designs, including fixed-bed, fluidized-bed, entrained-flow, or downdraft gasifiers, each offering unique advantages and operating characteristics.
- Feedstock Handling and Preparation: Carbonaceous feedstocks such as coal, biomass, or municipal solid waste are received, stored, and prepared for gasification. Feedstock preparation may involve drying, shredding, grinding, and sizing to optimize gasification performance and ensure uniform fuel distribution in the gasifier.
- Gasification Process: In the gasification reactor, carbonaceous feedstocks are subjected to high temperatures (typically between 700°C and 1,200°C) and a controlled supply of gasification agent (oxygen, steam, or air) to produce syngas. The gasification process involves several thermochemical reactions, including pyrolysis, oxidation, and reduction, leading to the conversion of carbonaceous feedstocks into syngas.
- Syngas Cleanup: The raw syngas produced from the gasification process contains impurities such as tar, particulate matter, sulfur compounds, and contaminants that need to be removed to meet quality specifications for downstream applications. Syngas cleanup systems, including cyclones, scrubbers, filters, and catalytic converters, are employed to remove impurities and improve syngas quality.
- Syngas Utilization: The cleaned syngas can be utilized for various energy and chemical applications, including power generation, heat production, hydrogen production, and chemical synthesis. Syngas can be burned directly in gas turbines, boilers, or engines to generate electricity or heat. Alternatively, it can be further processed to separate and purify individual gas components for use in chemical processes or as fuel for hydrogen fuel cells.
Syngas generators offer several advantages over conventional combustion-based energy systems, including higher energy efficiency, lower emissions, and greater fuel flexibility. They enable the utilization of a wide range of carbonaceous feedstocks, including coal, biomass, agricultural residues, and municipal solid waste, for clean and sustainable energy production.
Continued research and development efforts are focused on advancing syngas generator technology, improving process efficiency, enhancing syngas cleanup systems, and exploring novel applications for syngas in the transition towards a low-carbon economy. Syngas generators represent a promising pathway towards a more sustainable and renewable energy future, contributing to energy security, environmental protection, and economic development.
Gasification Process:
The gasification process is a thermochemical conversion method that transforms carbonaceous feedstocks, such as coal, biomass, or municipal solid waste, into a gaseous mixture known as synthesis gas (syngas). This process occurs in a gasifier, where feedstocks are subjected to high temperatures and a controlled supply of oxygen, steam, or a combination of both, in a low-oxygen environment. The gasification process involves several key steps and reactions:
- Pyrolysis: The initial stage of the gasification process involves heating the carbonaceous feedstock in the absence of oxygen to temperatures typically ranging from 500°C to 800°C. This thermochemical decomposition, known as pyrolysis, breaks down complex organic molecules in the feedstock into smaller hydrocarbons, volatile gases, and char.
- Oxidation: Once the feedstock is heated and partially decomposed, a controlled supply of oxygen, steam, or air is introduced into the gasifier to initiate the oxidation reactions. These reactions involve the combustion of carbonaceous material with oxygen or the reaction of carbon with steam to produce carbon monoxide and hydrogen. The overall reactions can be represented as follows:
- C + O2 → CO2
- C + H2O → CO + H2
- Reduction: As the carbonaceous material reacts with oxygen or steam, the temperature in the gasifier increases, and the resulting carbon dioxide and water vapor interact with the remaining carbon to produce additional syngas components through reduction reactions:
- CO2 + C → 2CO
- H2O + C → CO + H2
- Tar and Char Formation: During the gasification process, some of the carbonaceous material may undergo incomplete conversion, leading to the formation of tar and char residues. Tar consists of complex hydrocarbons that can condense on surfaces and equipment, while char is the solid residue remaining after pyrolysis and gasification reactions.
- Syngas Composition: The composition of the syngas produced from gasification depends on factors such as the feedstock type, gasification conditions, and gasifier design. Typical syngas composition includes hydrogen (H2), carbon monoxide (CO), carbon dioxide (CO2), methane (CH4), and trace amounts of other gases such as nitrogen (N2), hydrogen sulfide (H2S), and ammonia (NH3).
The syngas produced from the gasification process is a versatile energy carrier that can be utilized for various applications, including power generation, heat production, chemical synthesis, and hydrogen production. Syngas can be burned directly in gas turbines, boilers, or engines to generate electricity or heat, or further processed to separate and purify individual gas components for use in chemical processes or as fuel for hydrogen fuel cells.
Gasification offers several advantages over conventional combustion-based energy systems, including higher energy efficiency, lower emissions, and greater fuel flexibility. It enables the utilization of a wide range of carbonaceous feedstocks for clean and sustainable energy production, contributing to energy security, environmental protection, and economic development. Continued research and development efforts are focused on advancing gasification technology, improving process efficiency, and exploring novel applications for syngas in the transition towards a low-carbon economy.
Gasification Plant Design and Operation:
Gasification plants are complex facilities designed to efficiently convert various carbonaceous feedstocks into valuable synthesis gas (syngas) through the process of gasification. The design and operation of gasification plants involve numerous considerations to ensure optimal performance, reliability, and safety. Here are some key aspects of gasification plant design and operation:
- Feedstock Selection and Preparation: Gasification plants can utilize a wide range of feedstocks, including coal, biomass, municipal solid waste, and industrial residues. The selection of feedstock depends on factors such as availability, cost, energy content, and environmental impact. Feedstock preparation involves handling, sizing, drying, and sometimes pre-treatment to optimize gasification efficiency and feedstock utilization.
- Gasification Reactor Design: Gasification reactors are the core components of gasification plants, where feedstocks undergo thermochemical reactions to produce syngas. Reactor design considerations include reactor type (e.g., fixed-bed, fluidized-bed, entrained-flow), operating temperature and pressure, residence time, gasification agent (oxygen, air, steam), and feedstock feeding mechanism. The choice of reactor design depends on factors such as feedstock characteristics, gasification process requirements, and desired syngas composition.
- Gasification Process Control: Gasification plants require robust process control systems to monitor and regulate various parameters such as temperature, pressure, gas flow rates, feedstock feeding rates, and gas composition. Advanced control strategies, including feedback and feedforward control loops, are employed to maintain stable and efficient operation, optimize performance, and ensure safety.
- Syngas Cleanup and Conditioning: The raw syngas produced from the gasification process contains impurities such as tar, particulate matter, sulfur compounds, and contaminants that need to be removed to meet quality specifications for downstream applications. Syngas cleanup systems, including cyclones, scrubbers, filters, and catalytic converters, are employed to remove impurities and improve syngas quality. Syngas conditioning processes such as cooling, drying, and compression may also be required to prepare syngas for further processing and utilization.
- Syngas Utilization and Integration: The cleaned syngas can be utilized for various energy and chemical applications, including power generation, heat production, hydrogen production, and chemical synthesis. Gasification plants may be integrated with other processes such as combined heat and power (CHP) systems, gas-to-liquid (GTL) processes, or integrated biorefineries to maximize resource utilization, energy efficiency, and product value.
- Safety and Environmental Considerations: Gasification plant design and operation must comply with strict safety regulations and environmental standards to minimize risks to personnel, communities, and ecosystems. Measures such as process safety management, risk assessment, emissions monitoring, and waste management are implemented to ensure safe and environmentally responsible operation.
Overall, the successful design and operation of gasification plants require interdisciplinary expertise in engineering, chemistry, process control, and environmental science. Continued research and development efforts are focused on advancing gasification technology, improving process efficiency, and reducing environmental impacts to realize the full potential of gasification for sustainable energy production and resource utilization.
Gasification Plant Economics and Feasibility Analysis:
Gasification plants represent significant investments in capital, operation, and maintenance costs. Conducting thorough economic and feasibility analyses is crucial to evaluate the financial viability of such projects and make informed investment decisions. Here’s an overview of the key aspects involved in assessing the economics and feasibility of gasification plants:
- Cost Estimation: The first step in economic analysis is estimating the capital costs associated with designing, constructing, and commissioning the gasification plant. This includes costs for equipment, materials, labor, engineering services, permitting, and land acquisition. Operational costs, including feedstock procurement, labor, maintenance, utilities, and waste disposal, are also estimated.
- Revenue Generation: Gasification plants generate revenue through the sale of syngas and other by-products such as heat, electricity, chemicals, or biofuels. Revenue streams depend on market prices for syngas and by-products, as well as demand dynamics, regulatory incentives, and competition. Long-term contracts, off-take agreements, or feedstock supply agreements may secure revenue streams and mitigate market risks.
- Financial Modeling: Financial modeling involves projecting cash flows, revenues, expenses, and returns over the project’s lifecycle. Discounted cash flow (DCF) analysis, net present value (NPV), internal rate of return (IRR), payback period, and profitability indices are commonly used metrics to assess project economics and compare investment alternatives. Sensitivity analysis helps evaluate the impact of uncertain variables such as feedstock prices, energy prices, and regulatory changes on project returns.
- Risk Assessment: Gasification projects entail various risks that may affect their economic viability, including technical risks (e.g., technology performance, reliability, scalability), market risks (e.g., commodity prices, demand uncertainty), financial risks (e.g., capital cost overruns, financing costs), regulatory risks (e.g., environmental compliance, policy changes), and operational risks (e.g., feedstock availability, equipment downtime). Risk assessment and mitigation strategies, such as insurance, hedging, contingency planning, and diversification, are essential to manage project risks and enhance financial resilience.
- Market Analysis: Market analysis involves assessing the demand for syngas and by-products, identifying potential customers and end-users, understanding market dynamics, and evaluating competitive landscape and pricing trends. Market studies help validate revenue projections, identify market opportunities, and formulate marketing and sales strategies to maximize project profitability.
- Regulatory Compliance: Gasification projects must comply with local, state, and federal regulations governing environmental, health, safety, and land use aspects. Permitting requirements, emissions standards, waste disposal regulations, and financial incentives such as tax credits or subsidies may impact project economics and feasibility. Engaging with regulatory authorities, conducting environmental impact assessments, and obtaining necessary permits are essential steps in project development.
- Social and Environmental Impact Assessment: Gasification projects may have social and environmental impacts on local communities, ecosystems, and stakeholders. Conducting social and environmental impact assessments (SEIA) helps identify potential risks, assess mitigation measures, and incorporate sustainability considerations into project planning and decision-making. Stakeholder engagement, community consultation, and corporate social responsibility (CSR) initiatives are integral to building trust, managing reputational risks, and ensuring sustainable development outcomes.
Overall, conducting comprehensive economic and feasibility analyses is essential to evaluate the financial, technical, market, regulatory, and social aspects of gasification projects and make informed investment decisions. Collaboration with multidisciplinary teams, stakeholders, financial institutions, and industry partners can help address challenges, mitigate risks, and optimize project outcomes for successful project development and implementation.
Gasification Plant Environmental Impact:
Gasification plants offer numerous benefits in terms of energy production, resource utilization, and waste management. However, they also have environmental impacts that need to be carefully assessed, managed, and mitigated to ensure sustainable development and minimize adverse effects on ecosystems, air quality, and human health. Here are some key environmental considerations associated with gasification plants:
- Greenhouse Gas Emissions: Gasification of carbonaceous feedstocks produces carbon dioxide (CO2) emissions, although typically at lower levels compared to conventional combustion processes. However, gasification can also produce methane (CH4) emissions, particularly if not properly managed. Methane is a potent greenhouse gas with a higher global warming potential than CO2, so controlling methane emissions is essential to minimize the plant’s overall greenhouse gas footprint.
- Particulate Matter and Air Quality: Gasification processes can generate particulate matter (PM), sulfur dioxide (SO2), nitrogen oxides (NOx), volatile organic compounds (VOCs), and other air pollutants, depending on the feedstock composition and gasification conditions. These pollutants can contribute to local air quality degradation, respiratory illnesses, and environmental damage. Implementing effective emissions control technologies such as electrostatic precipitators, scrubbers, and catalytic converters is essential to reduce emissions and protect air quality.
- Ash Disposal and Waste Management: Gasification produces ash and other solid residues as by-products, which require proper handling, storage, and disposal to prevent environmental contamination. Ash disposal methods include landfilling, recycling for beneficial use in construction materials or agriculture, and thermal treatment to reduce volume and toxicity. Effective waste management practices minimize the risk of soil and water contamination, groundwater pollution, and ecosystem degradation.
- Water Usage and Pollution: Gasification plants require water for cooling, steam generation, syngas cleaning, and other process-related activities. Water consumption and wastewater discharge can affect local water resources, aquatic ecosystems, and downstream water quality. Implementing water conservation measures, recycling and reusing process water, and treating wastewater to meet regulatory standards help minimize water usage and pollution impacts.
- Land Use and Habitat Impact: Gasification plants require land for site development, construction, and operation, which may result in habitat loss, ecosystem fragmentation, and biodiversity impacts. Land use planning, environmental impact assessments, and habitat restoration measures are essential to minimize land use conflicts, protect sensitive habitats, and preserve biodiversity. Incorporating green infrastructure, landscaping, and vegetation buffers can enhance site aesthetics and ecological value.
- Noise and Visual Impact: Gasification plants can generate noise and visual disturbances during construction and operation, which may affect nearby communities and wildlife habitats. Implementing noise abatement measures such as sound barriers, acoustic enclosures, and operational controls help reduce noise levels and mitigate community annoyance. Visual screening, landscaping, and aesthetic design considerations can minimize visual impacts and integrate the plant into the surrounding landscape.
- Climate Change Mitigation and Adaptation: Despite their environmental impacts, gasification plants can contribute to climate change mitigation by displacing fossil fuel-based energy sources, reducing greenhouse gas emissions, and supporting the transition to a low-carbon economy. Implementing carbon capture and storage (CCS) technologies can further enhance the plant’s climate change mitigation potential by capturing and sequestering CO2 emissions underground.
Overall, assessing and managing the environmental impacts of gasification plants require comprehensive environmental monitoring, regulatory compliance, stakeholder engagement, and continuous improvement initiatives. Integrating environmental considerations into project planning, design, and operation helps minimize adverse impacts, enhance environmental performance, and promote sustainable development of gasification projects.
Gasification Plant Safety and Risk Management:
Gasification plants are complex industrial facilities that involve high temperatures, pressures, and potentially hazardous materials. Ensuring safety and managing risks is paramount to protect personnel, communities, and the environment. Here are key aspects of gasification plant safety and risk management:
- Process Safety Management (PSM): Gasification plants implement rigorous process safety management systems to identify, evaluate, and control hazards associated with gasification processes. This includes conducting process hazard analyses (PHA), risk assessments, and safety reviews to identify potential hazards, assess their likelihood and consequences, and implement risk mitigation measures.
- Safety Instrumented Systems (SIS): Gasification plants utilize safety instrumented systems to automatically detect and respond to abnormal conditions or process upsets to prevent accidents and protect personnel and equipment. Safety systems such as emergency shutdown systems (ESD), fire and gas detection systems, and pressure relief devices are designed to activate and mitigate hazards before they escalate.
- Emergency Response Planning: Gasification plants develop comprehensive emergency response plans (ERP) to address potential accidents, spills, fires, or other emergencies. ERP includes procedures for personnel evacuation, emergency communication, first aid, firefighting, spill containment, and coordination with local emergency services. Regular emergency drills and training exercises ensure preparedness and response effectiveness.
- Occupational Health and Safety (OHS): Gasification plants prioritize occupational health and safety to protect workers from workplace hazards and ensure a safe working environment. This includes implementing safety training programs, providing personal protective equipment (PPE), conducting job hazard analyses (JHA), and promoting a culture of safety awareness and accountability among employees.
- Hazardous Materials Management: Gasification plants handle and process potentially hazardous materials such as flammable gases, toxic chemicals, and combustible dusts. Proper handling, storage, labeling, and disposal of hazardous materials are essential to prevent accidents, spills, leaks, and environmental contamination. Material safety data sheets (MSDS), chemical inventories, and spill response procedures help manage hazardous materials safely.
- Fire Protection and Prevention: Gasification plants implement fire protection and prevention measures to minimize the risk of fires and explosions. This includes installing fire detection and suppression systems, maintaining fire hydrants and extinguishers, conducting fire risk assessments, and implementing hot work permits and fire safety protocols.
- Security and Access Control: Gasification plants implement security measures to protect critical infrastructure, equipment, and personnel from unauthorized access, sabotage, terrorism, or vandalism. Security measures may include perimeter fencing, access controls, surveillance cameras, security patrols, and cybersecurity protocols to safeguard plant operations and data systems.
- Environmental Risk Management: Gasification plants assess and manage environmental risks associated with air emissions, water usage, waste disposal, and ecosystem impacts. This includes monitoring and controlling emissions, implementing spill prevention and response measures, managing waste streams, and conducting environmental impact assessments (EIA) to minimize environmental liabilities and comply with regulatory requirements.
By implementing robust safety management systems, risk assessment methodologies, and emergency response procedures, gasification plants can effectively mitigate hazards, protect personnel and assets, and ensure safe and sustainable operation throughout the plant lifecycle. Continuous monitoring, evaluation, and improvement of safety performance are essential to maintain a high level of safety culture and resilience in the face of evolving risks and challenges.
Gasification Plant Commissioning and Operations:
Gasification plant commissioning and operations involve a series of critical steps and ongoing activities to ensure the efficient and reliable production of syngas while maintaining safety, environmental compliance, and economic performance. Here’s an overview of key aspects of gasification plant commissioning and operations:
- Commissioning Planning: Prior to startup, a comprehensive commissioning plan is developed to systematically test and verify the performance of all plant systems and equipment. This includes pre-commissioning activities such as equipment inspections, system flushing, and mechanical integrity testing, followed by functional testing, performance testing, and final acceptance testing.
- Startup Procedures: Gasification plant startup involves gradually bringing the plant online, starting with non-critical systems and gradually ramping up to full operation. Startup procedures include equipment warm-up, system pressurization, fuel feeding, ignition, and synchronization of auxiliary systems such as air and steam supply. Startup is conducted in accordance with established procedures and under close supervision to ensure safe and controlled operation.
- Process Optimization: Once the plant is operational, ongoing process optimization efforts are undertaken to maximize efficiency, productivity, and product quality while minimizing energy consumption, emissions, and operating costs. This may involve adjusting operating parameters such as temperature, pressure, feedstock composition, and gasification agent flow rates to optimize syngas yield and composition.
- Maintenance and Reliability: Gasification plant maintenance programs are implemented to ensure the reliability and availability of critical equipment and systems. This includes preventive maintenance activities such as equipment inspections, lubrication, cleaning, and replacement of worn components, as well as predictive maintenance techniques such as condition monitoring, vibration analysis, and thermography to identify and address potential issues before they lead to downtime or failure.
- Safety Management: Safety remains a top priority during plant operations, with stringent safety protocols, procedures, and training programs in place to protect personnel, equipment, and the environment. Safety audits, inspections, and incident investigations are conducted regularly to identify hazards, assess risks, and implement corrective actions to prevent accidents and ensure compliance with regulatory requirements.
- Environmental Compliance: Gasification plant operations are subject to environmental regulations governing air emissions, water discharge, waste management, and other environmental aspects. Continuous emissions monitoring, effluent testing, and environmental reporting are conducted to ensure compliance with permit limits and regulatory standards. Pollution control technologies such as scrubbers, filters, and catalytic converters are employed to minimize emissions and mitigate environmental impacts.
- Quality Control: Syngas quality is monitored and controlled to meet specified product specifications and end-user requirements. Analytical instrumentation and process control systems are utilized to measure key parameters such as gas composition, heating value, sulfur content, and particulate emissions. Quality assurance measures are implemented to ensure consistent product quality and performance.
- Training and Skills Development: Gasification plant personnel receive comprehensive training and skills development to operate and maintain the plant safely and efficiently. Training programs cover plant operations, safety procedures, emergency response protocols, environmental compliance, and equipment maintenance. Ongoing skills development initiatives ensure that operators and maintenance personnel remain proficient in their roles and capable of adapting to evolving technologies and operational challenges.
By implementing effective commissioning, startup, and operational practices, gasification plants can achieve reliable, safe, and environmentally responsible production of syngas for various energy and chemical applications. Continuous monitoring, optimization, and improvement efforts are essential to maximize plant performance, minimize risks, and ensure long-term viability and competitiveness in the evolving energy landscape.
Biomass to Energy
Biomass Feedstock:
Biomass feedstock refers to the organic materials used as raw inputs for biomass-to-energy processes. These materials are derived from various renewable sources such as agricultural residues, forestry residues, energy crops, animal waste, municipal solid waste, and organic industrial waste. Biomass feedstock can be classified into different categories based on their origin, composition, and physical properties.
Agricultural residues, including crop residues (such as straw, husks, and stalks) and processing residues (such as bagasse and pomace), are abundant sources of biomass feedstock. Forestry residues, such as logging residues, sawdust, and wood chips, are generated during forest harvesting and processing activities. Energy crops, such as switchgrass, miscanthus, and willow, are cultivated specifically for biomass production and can be harvested annually or on a rotational basis.
Animal waste, including manure from livestock operations and poultry farms, contains organic matter that can be converted into biogas through anaerobic digestion processes. Municipal solid waste (MSW) and organic industrial waste, such as food processing residues and paper mill sludge, represent urban biomass resources that can be diverted from landfills and incinerators for energy recovery.
The selection of biomass feedstock depends on various factors, including availability, cost, energy content, moisture content, ash content, and sustainability considerations. Feedstock preprocessing may be required to remove impurities, reduce particle size, and enhance energy density for efficient handling, storage, and conversion. Biomass feedstock sustainability involves assessing its environmental, social, and economic impacts throughout its lifecycle, including land use, water use, greenhouse gas emissions, biodiversity, and socioeconomic benefits.
Overall, biomass feedstock plays a critical role in biomass-to-energy processes, providing renewable and sustainable sources of fuel and energy for power generation, heat production, biofuels production, and other applications. Effective management of biomass feedstock resources is essential to ensure efficient, reliable, and environmentally responsible utilization of biomass for energy purposes.
Anaerobic Digestion:
Anaerobic digestion is a biological process that converts organic materials into biogas and organic residues in the absence of oxygen. It is a natural process that occurs in anaerobic environments, such as landfills, wetlands, and the digestive systems of animals. In controlled environments, anaerobic digestion is widely used to treat organic waste and produce renewable energy in the form of biogas.
The anaerobic digestion process involves a series of biochemical reactions carried out by a diverse community of microorganisms, including bacteria, archaea, and fungi. These microorganisms break down complex organic compounds present in the feedstock into simpler molecules, such as volatile fatty acids, hydrogen, and carbon dioxide. Methanogenic archaea then metabolize these intermediate products to produce methane (CH4) and carbon dioxide (CO2) through a process known as methanogenesis.
Anaerobic digestion can be divided into four main stages: hydrolysis, acidogenesis, acetogenesis, and methanogenesis. During hydrolysis, complex organic molecules are broken down into soluble compounds by hydrolytic enzymes. In the acidogenesis stage, acid-forming bacteria further break down these compounds into volatile fatty acids, alcohols, and other organic acids. Acetogenic bacteria then convert these compounds into acetic acid, hydrogen, and carbon dioxide during acetogenesis. Finally, methanogenic archaea convert acetic acid, hydrogen, and carbon dioxide into methane and carbon dioxide during methanogenesis.
Biogas produced through anaerobic digestion typically consists of 50-70% methane (CH4) and 30-50% carbon dioxide (CO2), along with trace amounts of other gases such as hydrogen sulfide (H2S) and ammonia (NH3). Biogas can be used as a renewable fuel for electricity generation, heat production, vehicle fuel, or upgraded to biomethane for injection into natural gas pipelines or use as a transportation fuel.
In addition to biogas, anaerobic digestion also produces digestate, which is the organic residue remaining after digestion. Digestate can be used as a nutrient-rich fertilizer or soil amendment for agricultural purposes, completing the nutrient cycling process and closing the loop on organic waste management.
Overall, anaerobic digestion offers a sustainable waste management solution that simultaneously reduces organic waste disposal, produces renewable energy, and generates valuable by-products for agricultural and environmental applications. As a versatile and environmentally friendly technology, anaerobic digestion plays a key role in the transition towards a circular economy and the decarbonization of energy systems.
Biogas Production:
Biogas production is the process of generating methane-rich gas, known as biogas, through the anaerobic digestion of organic materials. This renewable energy source is produced from a variety of organic feedstocks, including agricultural residues, animal manure, food waste, sewage sludge, and energy crops. Biogas production offers numerous environmental, economic, and social benefits, making it an increasingly popular alternative to fossil fuels.
The biogas production process occurs in anaerobic digesters, which are sealed tanks or chambers where organic materials undergo decomposition in the absence of oxygen. Microorganisms break down the complex organic compounds present in the feedstock into simpler molecules, primarily methane (CH4) and carbon dioxide (CO2), through a series of biochemical reactions.
Several factors influence biogas production, including the composition and characteristics of the feedstock, temperature, pH, hydraulic retention time, and the design and operation of the anaerobic digester. Optimal conditions for biogas production typically involve maintaining a neutral pH (around 7), a temperature range of 35-55°C (mesophilic digestion) or 55-65°C (thermophilic digestion), and sufficient mixing and retention time to maximize microbial activity.
Biogas composition varies depending on the feedstock and the efficiency of the anaerobic digestion process. Typically, biogas consists of 50-70% methane, 30-50% carbon dioxide, and trace amounts of other gases such as hydrogen sulfide, ammonia, and water vapor. Biogas can be used directly as a fuel for heating, electricity generation, or vehicle fuel, or it can be upgraded to biomethane through purification processes such as pressure swing adsorption or membrane separation for injection into natural gas pipelines or use as a transportation fuel.
Biogas production offers several environmental benefits, including the reduction of greenhouse gas emissions by capturing and utilizing methane, a potent greenhouse gas, from organic waste streams. It also helps to mitigate odor emissions from manure management and wastewater treatment facilities and reduces reliance on fossil fuels, contributing to climate change mitigation and energy security.
Furthermore, biogas production supports sustainable waste management practices by diverting organic waste from landfills and incinerators, reducing methane emissions from anaerobic decomposition in these disposal sites. It also generates valuable by-products such as digestate, a nutrient-rich fertilizer, which can be used to improve soil health and fertility in agricultural applications.
Overall, biogas production offers a versatile and sustainable energy solution that addresses multiple environmental, social, and economic challenges. By harnessing the energy potential of organic waste streams, biogas production contributes to a circular economy, renewable energy transition, and climate change mitigation efforts.
Biofuel:
Biofuel is a type of renewable fuel derived from organic materials, also known as biomass, that can be used to replace or supplement conventional fossil fuels in various applications, including transportation, heating, and electricity generation. Biofuels are considered carbon-neutral or low-carbon alternatives to fossil fuels because the carbon dioxide (CO2) released during combustion is offset by the carbon dioxide absorbed during the growth of the biomass feedstock.
There are several types of biofuels, each produced through different conversion processes and derived from different biomass feedstocks:
- First-Generation Biofuels: These biofuels are produced from food crops or edible oils, such as corn, sugarcane, soybean, and palm oil. The most common first-generation biofuels include biodiesel, produced from vegetable oils or animal fats through a process called transesterification, and ethanol, produced from fermenting sugars or starches found in crops such as corn, sugarcane, and wheat.
- Second-Generation Biofuels: Also known as advanced biofuels, these biofuels are produced from non-food biomass feedstocks, such as agricultural residues, forestry residues, energy crops, and algae. Second-generation biofuels include cellulosic ethanol, produced from lignocellulosic biomass through enzymatic hydrolysis and fermentation processes, and renewable diesel, produced from hydrotreating or pyrolysis of biomass feedstocks.
- Third-Generation Biofuels: These biofuels are produced from microalgae, which have high oil content and can be cultivated in various aquatic environments, including ponds, bioreactors, and open ocean systems. Algal biofuels offer potential advantages such as high productivity, minimal land use requirements, and the ability to utilize non-arable land and wastewater for cultivation.
- Biogasoline and Biobutanol: These biofuels are produced through advanced biochemical or thermochemical conversion processes that can directly replace gasoline or be blended with conventional fuels in existing engines and infrastructure. Biogasoline is produced from the fermentation of sugars or syngas derived from biomass, while biobutanol is produced through the fermentation of sugars by certain microorganisms.
Biofuels offer several environmental and economic benefits compared to fossil fuels, including reduced greenhouse gas emissions, enhanced energy security, and support for rural economies and agricultural communities. However, challenges remain in terms of feedstock availability, land use competition, technological development, and market penetration. Continued research, development, and deployment of biofuel technologies are essential to realizing the full potential of biofuels as a sustainable and scalable energy solution in the transition to a low-carbon economy.
Pyrolysis:
Pyrolysis is a thermochemical conversion process that decomposes organic materials into biochar, bio-oil, and syngas in the absence of oxygen. This process involves heating biomass feedstock to high temperatures (typically between 300°C and 800°C) in a controlled environment, such as a reactor or kiln, to induce thermal decomposition.
During pyrolysis, biomass undergoes a series of complex chemical reactions, including dehydration, decarboxylation, and depolymerization, leading to the formation of three main products:
- Biochar: Biochar is a carbon-rich solid residue that remains after the volatile components of biomass are driven off during pyrolysis. It is a stable form of carbon that can improve soil fertility, enhance water retention, and sequester carbon in agricultural and environmental applications.
- Bio-oil: Bio-oil, also known as pyrolysis oil or bio-crude, is a dark, viscous liquid that contains a mixture of oxygenated hydrocarbons, phenolic compounds, and other organic compounds. Bio-oil can be further processed into transportation fuels, specialty chemicals, and other value-added products through upgrading processes such as hydrotreating, hydrodeoxygenation, and fractional distillation.
- Syngas: Syngas, or synthesis gas, is a mixture of hydrogen (H2), carbon monoxide (CO), carbon dioxide (CO2), methane (CH4), and other gases produced during pyrolysis. Syngas can be used as a fuel for heat and power generation, or it can be further processed into hydrogen, ammonia, methanol, or synthetic hydrocarbons through catalytic conversion or gasification processes.
Pyrolysis offers several advantages as a biomass conversion technology, including high energy efficiency, flexibility in feedstock selection, and the production of multiple valuable products. It can utilize a wide range of biomass feedstocks, including agricultural residues, forestry residues, energy crops, and organic waste, making it a versatile and scalable technology for biomass valorization.
However, challenges remain in terms of optimizing pyrolysis process parameters, such as temperature, residence time, and heating rate, to maximize product yields and quality. Additionally, the economic viability of pyrolysis depends on factors such as feedstock availability, processing costs, and market demand for biochar, bio-oil, and syngas products.
Research and development efforts are ongoing to improve pyrolysis technology, enhance product yields and quality, reduce environmental impacts, and increase the competitiveness of biochar, bio-oil, and syngas in the global energy market. Overall, pyrolysis holds significant potential as a sustainable and carbon-neutral pathway for converting biomass into renewable fuels, chemicals, and materials, contributing to the transition to a low-carbon economy.
Biochar:
Biochar is a carbon-rich solid material produced through the process of pyrolysis, which involves heating biomass feedstock in the absence of oxygen. It is a type of charcoal that is used primarily as a soil amendment to improve soil fertility, enhance crop productivity, and sequester carbon in terrestrial ecosystems. Biochar is characterized by its porous structure, high surface area, and stable carbon content, making it an effective tool for soil carbon sequestration and climate change mitigation.
The production of biochar involves heating biomass feedstock, such as agricultural residues, forestry residues, energy crops, or organic waste, at temperatures ranging from 300°C to 800°C in a pyrolysis reactor. During pyrolysis, volatile components of the biomass, including water, organic acids, and gases, are driven off, leaving behind a carbon-rich solid residue, i.e., biochar.
Biochar has several beneficial properties that make it an attractive soil amendment:
- Soil Fertility: Biochar improves soil fertility by enhancing nutrient retention, promoting soil aggregation, and providing a habitat for beneficial microorganisms. Its porous structure and high surface area allow it to adsorb and retain nutrients, such as nitrogen, phosphorus, and potassium, reducing nutrient leaching and improving nutrient availability to plants.
- Soil Water Management: Biochar improves soil water retention and infiltration by increasing soil porosity and reducing soil compaction. Its porous structure acts as a sponge, absorbing and holding moisture in the soil, thereby reducing irrigation requirements and increasing drought resilience in agricultural systems.
- Soil Carbon Sequestration: Biochar is a stable form of carbon that can persist in soils for hundreds to thousands of years, effectively sequestering carbon from the atmosphere and mitigating climate change. By converting biomass into biochar, carbon that would otherwise be released into the atmosphere as carbon dioxide during decomposition is stored in the soil, contributing to long-term carbon storage and climate change mitigation efforts.
- Soil pH Modification: Biochar can modify soil pH and buffer soil acidity by adsorbing and releasing hydrogen ions. Depending on the feedstock and pyrolysis conditions, biochar may have alkaline properties that can help neutralize acidic soils and improve soil pH for optimal plant growth.
- Contaminant Remediation: Biochar has the ability to adsorb and immobilize contaminants, such as heavy metals, organic pollutants, and pesticides, in soil and water systems. Its porous structure and high surface area provide ample binding sites for adsorbing contaminants, reducing their bioavailability and potential for leaching into groundwater or uptake by plants.
Overall, biochar represents a promising and sustainable soil amendment with multifaceted benefits for soil health, crop productivity, and environmental sustainability. Its widespread adoption in agricultural and land management practices has the potential to enhance soil resilience, increase food security, and mitigate climate change on a global scale. However, further research is needed to optimize biochar production processes, assess its long-term effects on soil quality and ecosystem functioning, and develop practical guidelines for its application in diverse agricultural and land-use contexts.
Carbonization:
Carbonization is a thermochemical process that converts organic materials, such as biomass, coal, or organic waste, into carbon-rich solids, gases, and liquids through the application of heat in the absence of oxygen or with limited oxygen supply. This process involves heating the organic material to high temperatures (typically between 400°C and 900°C) in a controlled environment, such as a retort, kiln, or reactor, to induce chemical reactions that drive off volatile components and leave behind a carbonaceous residue.
During carbonization, organic materials undergo several complex chemical and physical transformations, including dehydration, devolatilization, polymerization, and graphitization, resulting in the production of three main products:
- Charcoal: Charcoal is a carbon-rich solid residue produced from the carbonization of biomass, wood, or other organic materials. It is primarily composed of carbon, with small amounts of ash and volatile matter. Charcoal is widely used as a fuel for cooking, heating, and industrial processes due to its high energy density, low moisture content, and clean-burning properties.
- Pyrolysis Gas: Pyrolysis gas, also known as pyrolysis oil, syngas, or producer gas, is a mixture of gases produced during the carbonization process. It typically consists of hydrogen (H2), methane (CH4), carbon monoxide (CO), carbon dioxide (CO2), and various hydrocarbons, depending on the feedstock and process conditions. Pyrolysis gas can be used as a fuel for heat and power generation or further processed into liquid fuels and chemicals through gasification or catalytic conversion processes.
- Tar and Condensates: Tar and condensates are liquid by-products formed during the cooling and condensation of volatile gases released during carbonization. They contain a mixture of organic compounds, including phenols, hydrocarbons, and oxygenated compounds, with varying degrees of complexity and chemical composition. Tar and condensates can be further processed into valuable chemicals, solvents, or fuel additives through distillation, fractionation, or chemical refining processes.
Carbonization is used in various industrial applications, including charcoal production, biochar production, coke manufacturing, and waste-to-energy conversion. It offers several advantages as a biomass conversion technology, including the production of high-quality solid, liquid, and gaseous fuels, energy recovery from organic waste streams, and the potential for carbon sequestration and climate change mitigation through the production of biochar.
However, challenges remain in terms of optimizing carbonization processes to maximize product yields, quality, and energy efficiency, as well as minimizing environmental impacts, such as air pollution and greenhouse gas emissions. Continued research, development, and deployment of carbonization technologies are essential to realizing the full potential of biomass as a sustainable and renewable energy source in the transition to a low-carbon economy.
Thermochemical Conversion:
Thermochemical conversion refers to a set of processes that transform biomass, organic waste, or fossil fuels into useful energy carriers, such as heat, electricity, biofuels, or chemicals, through the application of heat and chemical reactions. Unlike biochemical conversion processes that involve biological organisms, thermochemical conversion relies on physical and chemical mechanisms to break down and transform the molecular structure of feedstocks.
There are several thermochemical conversion technologies, each with its own specific process conditions, feedstock requirements, and product outputs:
- Pyrolysis: Pyrolysis is a process that decomposes biomass or organic waste in the absence of oxygen at elevated temperatures (typically between 300°C and 800°C), resulting in the production of biochar, bio-oil, and syngas. Biochar is a carbon-rich solid residue, bio-oil is a liquid product, and syngas is a mixture of hydrogen, carbon monoxide, methane, and other gases.
- Gasification: Gasification involves converting biomass or fossil fuels into a synthesis gas (syngas) through the partial oxidation of feedstocks at high temperatures (typically between 700°C and 1,500°C) and with a controlled amount of oxygen or steam. Syngas can be used as a fuel for heat and power generation, or further processed into liquid fuels, chemicals, or hydrogen.
- Combustion: Combustion is a process that oxidizes biomass or fossil fuels in the presence of oxygen at high temperatures (typically above 700°C), releasing heat energy and producing carbon dioxide, water vapor, and ash as by-products. Combustion is commonly used for heat and power generation in boilers, furnaces, and power plants.
- Torrefaction: Torrefaction is a mild pyrolysis process that thermally treats biomass at temperatures between 200°C and 300°C in the absence of oxygen. It removes moisture and volatile components from biomass, resulting in a dry, energy-dense solid called torrefied biomass. Torrefied biomass has improved grindability, energy density, and storage stability compared to raw biomass, making it suitable for co-firing with coal or as a feedstock for gasification or pyrolysis.
- Hydrothermal Carbonization (HTC): HTC is a process that converts wet biomass or organic waste into hydrochar through hydrothermal treatment at elevated temperatures (typically between 180°C and 250°C) and pressures. Hydrochar is a carbonaceous solid with properties similar to coal or biochar, and it can be used as a soil amendment, energy carrier, or feedstock for further processing.
Thermochemical conversion technologies offer several advantages, including high energy efficiency, versatility in feedstock utilization, and the production of multiple value-added products. They can also help mitigate greenhouse gas emissions, reduce dependence on fossil fuels, and support sustainable waste management practices. However, challenges such as feedstock availability, technology scale-up, economic viability, and environmental impacts need to be addressed to realize the full potential of thermochemical conversion in the transition to a low-carbon and sustainable energy future.
Biomass Gasification:
Biomass gasification is a thermochemical process that converts biomass feedstock into a synthesis gas (syngas) consisting mainly of hydrogen (H2), carbon monoxide (CO), carbon dioxide (CO2), and methane (CH4) through the partial oxidation of organic materials at elevated temperatures. Unlike combustion, which fully oxidizes biomass in the presence of oxygen, gasification occurs in a controlled environment with limited oxygen or air supply, allowing for the production of a combustible gas mixture.
The biomass gasification process typically involves several steps:
- Drying: The biomass feedstock, which may include agricultural residues, forestry residues, energy crops, or organic waste, is first dried to reduce its moisture content. Low moisture content is essential to ensure efficient gasification and prevent energy loss during the heating process.
- Pyrolysis: The dried biomass is then subjected to pyrolysis, where it is heated in the absence of oxygen to temperatures between 400°C and 800°C. Pyrolysis breaks down the biomass into volatile components, such as gases, tars, and char, without complete combustion.
- Gasification: The pyrolysis products are then introduced into a gasification reactor, along with a controlled amount of air, oxygen, or steam. In the gasification reactor, the volatile components react with the oxidizing agent to produce a synthesis gas (syngas) containing hydrogen, carbon monoxide, methane, and other gases. The composition of the syngas depends on factors such as the feedstock, operating conditions, and gasification technology.
- Gas Cleaning: The raw syngas produced in the gasification reactor may contain impurities, such as particulates, tars, sulfur compounds, and trace contaminants. Gas cleaning processes, such as filtration, scrubbing, and catalytic conversion, are employed to remove impurities and improve the quality of the syngas before it is used for downstream applications.
- Utilization: The purified syngas can be utilized for various energy applications, including heat and power generation, hydrogen production, synthesis of liquid fuels and chemicals, and industrial processes. Syngas can be combusted directly in gas engines, turbines, or boilers to generate electricity and heat, or it can be further processed into biofuels, such as ethanol, methanol, or synthetic diesel, through catalytic conversion or Fischer-Tropsch synthesis.
Biomass gasification offers several advantages as a renewable energy technology, including high energy efficiency, fuel flexibility, and potential for carbon sequestration. It enables the utilization of a wide range of biomass feedstocks, including low-quality and waste materials, for energy production, contributing to sustainable resource utilization and waste management. However, challenges such as feedstock availability, gasification process efficiency, and economic viability need to be addressed to realize the full potential of biomass gasification as a clean and renewable energy solution. Ongoing research and development efforts are focused on improving gasification technologies, reducing costs, and increasing the competitiveness of biomass-derived syngas in the global energy market.
Syngas:
Syngas, short for synthesis gas, is a versatile mixture of gases primarily composed of hydrogen (H2) and carbon monoxide (CO), along with varying amounts of carbon dioxide (CO2), methane (CH4), water vapor (H2O), and other trace gases. It is produced through thermochemical processes such as biomass gasification, coal gasification, or steam reforming of hydrocarbons.
Syngas has several important properties that make it a valuable intermediate in various industrial processes and energy applications:
- Fuel: Syngas is a combustible gas mixture that can be used as a fuel for heat and power generation in gas engines, gas turbines, or boilers. Its high hydrogen content provides a clean-burning fuel with low emissions of pollutants such as sulfur dioxide (SO2), nitrogen oxides (NOx), and particulate matter.
- Feedstock: Syngas serves as a feedstock for the production of a wide range of valuable products, including liquid fuels, chemicals, and synthetic materials. Through processes such as Fischer-Tropsch synthesis, methanol synthesis, or hydroformylation, syngas can be converted into fuels such as synthetic diesel, gasoline, or aviation fuel, as well as chemicals such as methanol, ammonia, and olefins.
- Hydrogen Production: Syngas can be further processed to produce high-purity hydrogen gas through water-gas shift reactions or membrane separation technologies. Hydrogen derived from syngas is used as a clean fuel for fuel cells, hydrogenation reactions, or industrial processes, contributing to the decarbonization of energy systems and reducing greenhouse gas emissions.
- Chemical Feedstock: Syngas is a versatile chemical feedstock for the synthesis of a wide range of organic compounds and materials. It can be used to produce basic chemicals such as methanol, ammonia, and hydrogen cyanide, which serve as building blocks for the production of plastics, fertilizers, pharmaceuticals, and other industrial products.
- Carbon Capture and Utilization (CCU): Syngas derived from biomass or carbonaceous feedstocks can be used in carbon capture and utilization (CCU) processes to produce carbon-negative fuels and products. By capturing and storing carbon dioxide emissions from syngas production and utilization, CCU technologies can contribute to mitigating climate change and reducing the carbon footprint of industrial processes.
Syngas production from renewable feedstocks, such as biomass or biogas, offers environmental benefits compared to syngas derived from fossil fuels, as it reduces dependence on finite resources, mitigates greenhouse gas emissions, and promotes sustainable energy production. However, challenges such as feedstock availability, process efficiency, and economic viability need to be addressed to realize the full potential of syngas as a clean and renewable energy carrier in the transition to a low-carbon economy. Ongoing research and development efforts are focused on improving syngas production technologies, optimizing downstream processes, and advancing CCU strategies to enhance the sustainability and competitiveness of syngas-based energy systems.
Biomass Power Plant:
A biomass power plant is a facility that generates electricity by burning biomass feedstocks, such as wood, agricultural residues, energy crops, or organic waste, in a boiler to produce steam. The steam is then used to drive a turbine connected to a generator, converting the thermal energy into electrical power. Biomass power plants play a crucial role in the transition to renewable energy sources, offering a sustainable alternative to fossil fuels for electricity generation.
The operation of a biomass power plant involves several key components and processes:
- Feedstock Handling: Biomass feedstocks, such as wood chips, sawdust, or agricultural residues, are delivered to the power plant and stored in large piles or silos. Feedstock handling equipment, such as conveyors, grinders, and storage bins, is used to transport, process, and prepare the biomass for combustion.
- Combustion: The biomass feedstock is fed into a boiler, where it is burned in the presence of air or oxygen to produce heat. The combustion process releases energy in the form of heat, which is used to convert water into steam.
- Steam Generation: The heat generated from biomass combustion is transferred to water circulating through tubes in the boiler, producing high-pressure steam. The steam is then directed to a steam turbine through pipes, where it expands and exerts pressure on the turbine blades.
- Electricity Generation: The steam turbine is connected to a generator, which converts the mechanical energy from the turbine into electrical energy. As the turbine blades rotate, they turn the generator rotor, producing alternating current (AC) electricity.
- Cooling and Condensation: After passing through the turbine, the steam is condensed back into water using a condenser, releasing latent heat in the process. The condensed water is then returned to the boiler to be reheated and reused in the steam cycle.
- Pollution Control: Biomass combustion releases pollutants such as particulate matter, nitrogen oxides (NOx), sulfur dioxide (SO2), and volatile organic compounds (VOCs) into the atmosphere. To comply with environmental regulations and minimize air emissions, biomass power plants are equipped with pollution control technologies, such as electrostatic precipitators, bag filters, selective catalytic reduction (SCR), and flue gas desulfurization (FGD) systems.
- Ash Handling: After combustion, the remaining ash and residues from the biomass feedstock are collected in ash hoppers or cyclones and removed from the boiler. Depending on the composition and characteristics of the ash, it may be reused as a soil amendment, construction material, or disposed of in landfills.
Biomass power plants offer several advantages, including renewable and sustainable fuel supply, carbon neutrality, and potential for decentralized energy production. They can also help mitigate greenhouse gas emissions, reduce dependence on fossil fuels, and promote rural economic development through biomass supply chains. However, challenges such as feedstock availability, biomass logistics, and technology optimization need to be addressed to realize the full potential of biomass power generation as a reliable and environmentally friendly energy solution. Ongoing research, development, and deployment efforts are focused on improving biomass conversion technologies, increasing efficiency, and enhancing environmental performance to support the transition to a low-carbon energy future.
Gasification Plant:
A gasification plant is a facility that converts carbonaceous feedstocks, such as coal, biomass, or waste materials, into a synthesis gas (syngas) through the partial oxidation of feedstock at elevated temperatures and with a controlled amount of oxygen or steam. Gasification is a thermochemical process that breaks down the molecular structure of the feedstock, producing a combustible gas mixture that can be used for various energy and chemical applications.
The operation of a gasification plant involves several key stages:
- Feedstock Preparation: Carbonaceous feedstocks, such as coal, wood chips, agricultural residues, or municipal solid waste, are prepared and processed to achieve the desired size, moisture content, and chemical composition. Depending on the feedstock characteristics, size reduction, drying, and sorting may be required before gasification.
- Gasification Reactor: The prepared feedstock is introduced into a gasification reactor, along with a controlled amount of air, oxygen, or steam. The gasification reactor operates at high temperatures (typically between 700°C and 1,500°C) and pressures, promoting the thermochemical conversion of the feedstock into syngas.
- Chemical Reactions: In the gasification reactor, several chemical reactions occur between the feedstock and the oxidizing agent (air, oxygen, or steam), resulting in the production of syngas. The primary reactions include:
- Pyrolysis: Thermal decomposition of the feedstock at high temperatures in the absence of oxygen, producing volatile compounds, char, and tar.
- Partial Oxidation: Oxidation of the volatile compounds and char with a limited supply of oxygen or steam, generating carbon monoxide (CO) and hydrogen (H2) through gasification reactions.
- Water-Gas Shift: Conversion of carbon monoxide (CO) and water vapor (H2O) into carbon dioxide (CO2) and additional hydrogen (H2) through water-gas shift reactions, increasing the hydrogen content of the syngas.
- Syngas Cleanup: The raw syngas produced in the gasification reactor may contain impurities such as tars, sulfur compounds, ammonia, and particulates. Syngas cleanup processes, including filtration, scrubbing, catalytic conversion, and tar cracking, are employed to remove impurities and improve the quality of the syngas for downstream applications.
- Utilization: The purified syngas can be utilized for various energy and chemical applications, including:
- Heat and Power Generation: Syngas can be combusted directly in gas engines, gas turbines, or boilers to produce heat and electricity for industrial processes, district heating, or power generation.
- Liquid Fuels Production: Syngas can be further processed through Fischer-Tropsch synthesis, methanol synthesis, or hydrocarbon reforming to produce liquid fuels such as synthetic diesel, gasoline, or jet fuel.
- Chemical Synthesis: Syngas serves as a versatile feedstock for the production of chemicals and materials, including methanol, ammonia, hydrogen cyanide, synthetic natural gas (SNG), and olefins.
Gasification plants offer several advantages over conventional combustion technologies, including higher energy efficiency, lower emissions of pollutants, and greater flexibility in feedstock utilization. They can also help address waste management challenges by converting organic waste materials into valuable energy products. However, challenges such as feedstock availability, technology complexity, and economic viability need to be addressed to realize the full potential of gasification as a clean and sustainable energy solution. Ongoing research, development, and deployment efforts are focused on improving gasification technologies, reducing costs, and increasing the competitiveness of syngas-based energy systems in the global energy market.
Biomass Gasification Plant:
A biomass gasification plant is a facility designed to convert biomass feedstocks into a synthesis gas (syngas) through the process of gasification. Unlike combustion, which involves burning biomass in the presence of oxygen to produce heat and energy, gasification converts biomass into a combustible gas mixture by partially oxidizing it at high temperatures and with a limited supply of oxygen or steam. Biomass gasification plants play a crucial role in the utilization of renewable biomass resources for energy production and contribute to reducing greenhouse gas emissions and dependence on fossil fuels.
The operation of a biomass gasification plant involves several key components and processes:
- Feedstock Handling and Preparation: Biomass feedstocks, such as wood chips, agricultural residues, energy crops, or organic waste, are delivered to the gasification plant and processed to remove contaminants, reduce moisture content, and achieve the desired particle size. Feedstock handling equipment, such as conveyors, grinders, and drying systems, is used to prepare the biomass for gasification.
- Gasification Reactor: The prepared biomass feedstock is introduced into a gasification reactor, where it undergoes thermochemical conversion at high temperatures (typically between 700°C and 1,500°C) and with a controlled amount of air, oxygen, or steam. The gasification reactor can operate in various configurations, including fixed-bed, fluidized bed, or entrained flow, depending on the feedstock characteristics and process requirements.
- Chemical Reactions: Inside the gasification reactor, several chemical reactions occur between the biomass feedstock and the oxidizing agent, resulting in the production of syngas. The primary reactions involved in biomass gasification include:
- Pyrolysis: Thermal decomposition of the biomass feedstock at high temperatures in the absence of oxygen, producing volatile compounds, char, and tar.
- Partial Oxidation: Oxidation of the volatile compounds and char with a limited supply of oxygen or steam, generating carbon monoxide (CO) and hydrogen (H2) through gasification reactions.
- Water-Gas Shift: Conversion of carbon monoxide (CO) and water vapor (H2O) into carbon dioxide (CO2) and additional hydrogen (H2) through water-gas shift reactions, increasing the hydrogen content of the syngas.
- Syngas Cleanup: The raw syngas produced in the gasification reactor may contain impurities such as tars, sulfur compounds, ammonia, and particulates. Syngas cleanup processes, including filtration, scrubbing, catalytic conversion, and tar cracking, are employed to remove impurities and improve the quality of the syngas for downstream applications.
- Utilization: The purified syngas can be utilized for various energy and chemical applications, including heat and power generation, liquid fuels production, and chemical synthesis. Syngas can be combusted directly in gas engines, turbines, or boilers to produce heat and electricity, or it can be further processed into biofuels, such as ethanol, methanol, or synthetic diesel, through catalytic conversion or Fischer-Tropsch synthesis.
Biomass gasification plants offer several advantages, including high energy efficiency, fuel flexibility, and potential for carbon sequestration. They enable the utilization of a wide range of biomass feedstocks for energy production, contributing to sustainable resource utilization and waste management. However, challenges such as feedstock availability, gasification process efficiency, and economic viability need to be addressed to realize the full potential of biomass gasification as a clean and renewable energy solution. Ongoing research, development, and deployment efforts are focused on improving gasification technologies, reducing costs, and increasing the competitiveness of biomass-derived syngas in the global energy market.
Gasification Process:
Gasification is a thermochemical process that converts carbonaceous materials, such as coal, biomass, or waste, into a synthesis gas (syngas) containing hydrogen (H2), carbon monoxide (CO), carbon dioxide (CO2), and other trace gases. It involves the partial oxidation of the feedstock at high temperatures (typically between 700°C and 1,500°C) and with a controlled amount of oxygen, air, or steam. The gasification process can be carried out in various reactor configurations, including fixed-bed, fluidized bed, entrained flow, or downdraft gasifiers, depending on the feedstock characteristics and process requirements.
The gasification process consists of several key steps:
- Drying: In the initial stage of gasification, the feedstock undergoes drying to remove moisture and achieve the desired moisture content for efficient gasification. Moisture content in the feedstock can significantly affect the gasification process by requiring additional energy input for vaporization and reducing the overall efficiency of syngas production.
- Pyrolysis: As the feedstock is heated to high temperatures in the absence of oxygen, it undergoes pyrolysis, a thermal decomposition process that breaks down complex organic compounds into volatile gases, char, and tar. Pyrolysis occurs at temperatures above 300°C and leads to the release of volatile hydrocarbons, including methane, ethylene, and other light hydrocarbons, which contribute to the formation of syngas during gasification.
- Gasification Reactions: In the gasification reactor, the pyrolyzed volatiles and char react with the oxidizing agent (oxygen, air, or steam) to produce syngas through several chemical reactions, including:
- Partial Oxidation: The oxidation of carbonaceous compounds (char and volatile hydrocarbons) with a limited supply of oxygen or steam, resulting in the production of carbon monoxide (CO) and hydrogen (H2) through gasification reactions: 2C+H2O→CO+H2 2C+O2→CO2
- Water-Gas Shift Reaction: The conversion of carbon monoxide (CO) and water vapor (H2O) into carbon dioxide (CO2) and additional hydrogen (H2) through water-gas shift reactions, increasing the hydrogen content of the syngas: 2CO+H2O→CO2+H2
- Syngas Cleanup: The raw syngas produced in the gasification reactor contains impurities such as tars, sulfur compounds, ammonia, and particulates, which need to be removed to improve the quality of the syngas for downstream applications. Syngas cleanup processes, including filtration, scrubbing, catalytic conversion, and tar cracking, are employed to remove impurities and enhance the purity and composition of the syngas.
- Utilization: The purified syngas can be utilized for various energy and chemical applications, including heat and power generation, liquid fuels production, and chemical synthesis. Syngas can be combusted directly in gas engines, turbines, or boilers to produce heat and electricity, or it can be further processed into biofuels, such as ethanol, methanol, or synthetic diesel, through catalytic conversion or Fischer-Tropsch synthesis.
Gasification offers several advantages over conventional combustion technologies, including higher energy efficiency, lower emissions of pollutants, and greater flexibility in feedstock utilization. It enables the conversion of a wide range of carbonaceous materials into valuable energy products, contributing to the transition to a sustainable and low-carbon energy future. However, challenges such as feedstock availability, gasification process efficiency, and economic viability need to be addressed to realize the full potential of gasification as a clean and renewable energy solution. Ongoing research, development, and deployment efforts are focused on improving gasification technologies, reducing costs, and increasing the competitiveness of syngas-based energy systems in the global energy market.
Biomass Energy:
Biomass energy refers to the renewable energy derived from organic materials, such as wood, crop residues, agricultural waste, and organic municipal solid waste. It is produced through various processes, including combustion, gasification, fermentation, and biochemical conversion, and can be utilized for heat, electricity, and transportation fuels. Biomass energy plays a significant role in the transition to a sustainable energy future by reducing greenhouse gas emissions, promoting rural development, and diversifying energy sources.
The utilization of biomass for energy dates back thousands of years, with early humans using wood as their primary source of heat and cooking fuel. Today, biomass energy technologies have evolved to include advanced conversion processes that enhance efficiency, reduce emissions, and expand the range of biomass feedstocks that can be utilized.
The key processes for biomass energy conversion include:
- Combustion: Biomass combustion involves burning organic materials in the presence of oxygen to produce heat and energy. It is the most common and widely used method for biomass energy production, with applications ranging from residential heating and cooking to industrial-scale power generation. Biomass combustion systems include stoves, boilers, and power plants, which can be designed to burn various biomass feedstocks, including wood chips, pellets, agricultural residues, and municipal solid waste.
- Gasification: Biomass gasification is a thermochemical process that converts biomass feedstocks into a synthesis gas (syngas) containing hydrogen (H2), carbon monoxide (CO), carbon dioxide (CO2), and other trace gases. It involves the partial oxidation of biomass at high temperatures and with a controlled amount of oxygen or steam. Syngas produced from biomass gasification can be utilized for heat and power generation, as well as for the production of liquid fuels and chemicals.
- Fermentation: Biomass fermentation is a biological process that converts sugars and starches present in biomass feedstocks into ethanol and other biofuels through microbial fermentation. It is commonly used in the production of bioethanol from crops such as corn, sugarcane, and wheat. Biomass fermentation processes can also produce biogas, a renewable natural gas composed primarily of methane (CH4) and carbon dioxide (CO2), through anaerobic digestion of organic materials.
- Biochemical Conversion: Biomass biochemical conversion involves the use of enzymes and microorganisms to break down complex organic compounds in biomass feedstocks into sugars, which can then be fermented into biofuels such as ethanol and biodiesel. Biochemical conversion processes, such as enzymatic hydrolysis and microbial fermentation, offer potential advantages in terms of feedstock flexibility, process efficiency, and environmental sustainability.
Biomass energy offers several advantages over fossil fuels, including renewable availability, carbon neutrality, and potential for waste reduction and resource utilization. It can help mitigate climate change by reducing greenhouse gas emissions and dependence on finite fossil fuel resources. However, challenges such as feedstock availability, technological development, and economic competitiveness need to be addressed to realize the full potential of biomass energy as a sustainable and scalable energy solution. Ongoing research, development, and deployment efforts are focused on improving biomass energy technologies, increasing efficiency, and reducing costs to accelerate the transition to a low-carbon and resilient energy system.
Renewable Energy:
Renewable energy refers to energy derived from natural resources that are replenished continuously or within a relatively short period, making them virtually inexhaustible on human timescales. These energy sources include sunlight, wind, water, geothermal heat, and biomass. Unlike fossil fuels, which are finite and contribute to environmental pollution and climate change, renewable energy sources offer sustainable alternatives that can reduce greenhouse gas emissions, enhance energy security, and promote economic development.
The main sources of renewable energy include:
- Solar Energy: Solar energy is derived from the sunlight that reaches the Earth’s surface and can be converted into electricity or heat using photovoltaic (PV) panels or solar thermal systems, respectively. Solar power is abundant, widely distributed, and increasingly cost-competitive, making it one of the fastest-growing sources of renewable energy globally.
- Wind Energy: Wind energy is generated by harnessing the kinetic energy of wind through wind turbines, which convert it into electricity. Wind power is a mature and rapidly expanding renewable energy technology, with onshore and offshore wind farms contributing significantly to electricity generation in many countries around the world.
- Hydropower: Hydropower, or hydroelectric power, is generated by capturing the energy of flowing water and converting it into electricity using turbines and generators. It is one of the oldest and most widely used forms of renewable energy, with large-scale hydropower plants providing a significant portion of global electricity supply.
- Geothermal Energy: Geothermal energy is derived from the heat stored beneath the Earth’s surface and can be used for heating, cooling, and electricity generation. Geothermal power plants extract heat from underground reservoirs of hot water or steam and convert it into electricity through turbines and generators.
- Biomass Energy: Biomass energy is produced from organic materials such as wood, crop residues, agricultural waste, and organic municipal solid waste. It can be utilized for heat, electricity, and transportation fuels through processes such as combustion, gasification, fermentation, and biochemical conversion.
Renewable energy technologies offer numerous environmental, economic, and social benefits, including:
- Climate Mitigation: Renewable energy sources produce little to no greenhouse gas emissions during operation, helping to mitigate climate change and reduce air pollution.
- Energy Security: Renewable energy diversifies the energy mix and reduces dependence on imported fossil fuels, enhancing energy security and resilience to supply disruptions.
- Economic Development: The deployment of renewable energy technologies creates jobs, stimulates economic growth, and fosters innovation and investment in clean energy industries.
- Environmental Sustainability: Renewable energy minimizes environmental impacts, preserves natural resources, and protects ecosystems and biodiversity.
Despite these advantages, the widespread adoption of renewable energy faces challenges such as intermittency, grid integration, and cost competitiveness. Continued research, development, and deployment efforts are needed to overcome these barriers and accelerate the transition to a sustainable energy future powered by renewable resources. Government policies, financial incentives, and international cooperation play crucial roles in driving the deployment of renewable energy technologies and achieving global energy sustainability goals.
Carbon Neutrality:
Carbon neutrality, also known as net-zero carbon emissions or climate neutrality, refers to achieving a balance between the amount of greenhouse gases (GHGs) emitted into the atmosphere and the amount removed or offset through various mitigation measures. In essence, carbon neutrality involves reducing carbon dioxide (CO2) emissions to the point where they are equal to or less than the amount sequestered or offset, resulting in no net increase in atmospheric CO2 concentrations.
Achieving carbon neutrality is essential for mitigating climate change and limiting global warming to well below 2 degrees Celsius above pre-industrial levels, as outlined in the Paris Agreement. It involves comprehensive strategies and actions across multiple sectors to reduce emissions, enhance carbon sinks, and promote sustainable development practices.
Key elements of carbon neutrality include:
- Emission Reductions: The primary objective of carbon neutrality is to reduce anthropogenic emissions of greenhouse gases, particularly CO2, methane (CH4), and nitrous oxide (N2O), which are the main drivers of climate change. Emission reduction strategies include improving energy efficiency, transitioning to renewable energy sources, decarbonizing transportation and industry, and implementing sustainable land use and waste management practices.
- Carbon Offsetting: In cases where it is not feasible to eliminate all emissions, carbon offsetting can be used to compensate for residual emissions by investing in projects that remove or reduce equivalent amounts of CO2 from the atmosphere. Carbon offset projects may include afforestation and reforestation initiatives, renewable energy projects, energy efficiency programs, and methane capture from landfills or agricultural activities.
- Carbon Sequestration: Carbon sequestration involves capturing and storing CO2 emissions from industrial processes, power plants, and other point sources to prevent their release into the atmosphere. Carbon capture and storage (CCS) technologies, including carbon capture and utilization (CCU), geological storage, and enhanced oil recovery (EOR), are employed to capture CO2 emissions and permanently store them underground or utilize them for industrial processes.
- Natural Carbon Sinks: Natural ecosystems, including forests, wetlands, and oceans, act as carbon sinks, absorbing CO2 from the atmosphere through photosynthesis and storing it in biomass, soils, and sediments. Protecting and restoring natural carbon sinks, such as through forest conservation, reforestation, and sustainable land management practices, can enhance their capacity to sequester carbon and contribute to carbon neutrality efforts.
- Lifecycle Assessment: Assessing the lifecycle emissions of products, services, and processes is essential for identifying opportunities to reduce emissions across the entire supply chain. Lifecycle assessment (LCA) analyzes the environmental impacts of a product or activity from raw material extraction to end-of-life disposal, enabling informed decisions to minimize emissions and maximize resource efficiency.
Achieving carbon neutrality requires collective action and collaboration among governments, businesses, communities, and individuals to transition to low-carbon and resilient economies. It involves setting ambitious emissions reduction targets, implementing effective policies and regulations, investing in clean technologies and infrastructure, and fostering a culture of sustainability and environmental stewardship. By embracing carbon neutrality, societies can mitigate climate risks, enhance economic prosperity, and safeguard the planet for future generations.
Gasification Plant:
A gasification plant is a facility that utilizes gasification technology to convert carbonaceous feedstocks, such as coal, biomass, or waste, into synthesis gas (syngas) for various energy and chemical applications. Gasification plants play a crucial role in the transition to a sustainable energy future by enabling the efficient utilization of diverse feedstocks and reducing greenhouse gas emissions compared to conventional combustion processes.
Key components and processes in a gasification plant include:
- Feedstock Handling and Preparation: Carbonaceous feedstocks, such as coal, biomass, or waste, are received, stored, and prepared for gasification. Feedstock preparation may involve drying, shredding, grinding, and size reduction to optimize the feedstock properties and facilitate feeding into the gasification reactor.
- Gasification Reactor: The gasification reactor is the heart of the gasification plant, where the carbonaceous feedstock undergoes thermochemical conversion at high temperatures and with a controlled amount of oxygen, air, or steam. Gasification reactors can be of various types, including fixed-bed, fluidized bed, entrained flow, or downdraft gasifiers, depending on the feedstock characteristics and process requirements.
- Gas Cleanup and Conditioning: The raw syngas produced in the gasification reactor contains impurities such as tars, sulfur compounds, ammonia, and particulates, which need to be removed or reduced to improve the quality of the syngas for downstream applications. Gas cleanup and conditioning processes, including filtration, scrubbing, catalytic conversion, and tar cracking, are employed to remove impurities and enhance the purity and composition of the syngas.
- Syngas Utilization: The purified syngas can be utilized for various energy and chemical applications, including heat and power generation, liquid fuels production, and chemical synthesis. Syngas can be combusted directly in gas engines, turbines, or boilers to produce heat and electricity, or it can be further processed into biofuels, such as ethanol, methanol, or synthetic diesel, through catalytic conversion or Fischer-Tropsch synthesis.
- Waste Management: Gasification plants may also incorporate waste management systems to handle by-products and residues generated during the gasification process. Ash, char, and other solid residues can be recovered and utilized as by-products or disposed of in an environmentally responsible manner, minimizing waste and maximizing resource utilization.
Gasification plants offer several advantages over conventional combustion technologies, including higher energy efficiency, lower emissions of pollutants, and greater flexibility in feedstock utilization. They enable the conversion of a wide range of carbonaceous materials into valuable energy products, contributing to the diversification of energy sources and the reduction of dependence on fossil fuels. However, challenges such as feedstock availability, gasification process efficiency, and economic viability need to be addressed to realize the full potential of gasification as a clean and renewable energy solution. Ongoing research, development, and deployment efforts are focused on improving gasification technologies, reducing costs, and increasing the competitiveness of syngas-based energy systems in the global energy market.
Syngas Generator:
A syngas generator, also known as a gasifier, is a device or system that converts carbonaceous feedstocks, such as coal, biomass, or waste, into synthesis gas (syngas) through thermochemical processes. Syngas generators play a vital role in various energy and chemical applications, providing a versatile and efficient means of utilizing diverse feedstocks for heat, power, and fuel production.
Key components and operation of a syngas generator include:
- Feedstock Handling and Preparation: The syngas generator receives carbonaceous feedstocks, which may include solid, liquid, or gaseous materials. Feedstocks are prepared and processed to optimize their physical and chemical properties for efficient conversion in the gasification process. This may involve drying, shredding, grinding, and size reduction of solid feedstocks, or pre-treatment of liquid and gaseous feedstocks to remove impurities.
- Gasification Reactor: The gasification reactor is where the thermochemical conversion of feedstock into syngas occurs. Gasification processes typically involve heating the feedstock to high temperatures in a controlled environment with a limited supply of oxygen, air, or steam. Various types of gasification reactors exist, including fixed-bed, fluidized bed, entrained flow, and downdraft gasifiers, each offering unique advantages and suited to different feedstock types and process requirements.
- Syngas Cleanup and Conditioning: The raw syngas produced in the gasification reactor contains impurities such as tars, sulfur compounds, ammonia, and particulates, which must be removed or reduced to improve the quality of the syngas for downstream applications. Syngas cleanup and conditioning processes, such as filtration, scrubbing, catalytic conversion, and tar cracking, are employed to purify the syngas and enhance its composition and properties.
- Syngas Utilization: The purified syngas can be utilized for various energy and chemical applications, including heat and power generation, liquid fuels production, and chemical synthesis. Syngas can be combusted directly in gas engines, turbines, or boilers to produce heat and electricity, or it can be further processed into biofuels, such as ethanol, methanol, or synthetic diesel, through catalytic conversion or Fischer-Tropsch synthesis.
- Waste Management: Syngas generators may incorporate waste management systems to handle by-products and residues generated during the gasification process. Ash, char, and other solid residues can be recovered and utilized as by-products or disposed of in an environmentally responsible manner, minimizing waste and maximizing resource utilization.
Syngas generators offer several advantages over conventional energy technologies, including higher energy efficiency, lower emissions of pollutants, and greater flexibility in feedstock utilization. They enable the conversion of a wide range of carbonaceous materials into valuable energy products, contributing to the diversification of energy sources and the reduction of dependence on fossil fuels. However, challenges such as feedstock availability, gasification process efficiency, and economic viability need to be addressed to realize the full potential of syngas generators as clean and renewable energy solutions. Ongoing research, development, and deployment efforts are focused on improving gasification technologies, reducing costs, and increasing the competitiveness of syngas-based energy systems in the global energy market.
Clean Energy
Renewable Energy:
Renewable energy refers to energy derived from natural resources that are replenished continuously or within a relatively short period, making them virtually inexhaustible on human timescales. These energy sources include sunlight, wind, water, geothermal heat, and biomass. Unlike fossil fuels, which are finite and contribute to environmental pollution and climate change, renewable energy sources offer sustainable alternatives that can reduce greenhouse gas emissions, enhance energy security, and promote economic development.
The main sources of renewable energy include:
- Solar Energy: Solar energy is derived from the sunlight that reaches the Earth’s surface and can be converted into electricity or heat using photovoltaic (PV) panels or solar thermal systems, respectively. Solar power is abundant, widely distributed, and increasingly cost-competitive, making it one of the fastest-growing sources of renewable energy globally.
- Wind Energy: Wind energy is generated by harnessing the kinetic energy of wind through wind turbines, which convert it into electricity. Wind power is a mature and rapidly expanding renewable energy technology, with onshore and offshore wind farms contributing significantly to electricity generation in many countries around the world.
- Hydropower: Hydropower, or hydroelectric power, is generated by capturing the energy of flowing water and converting it into electricity using turbines and generators. It is one of the oldest and most widely used forms of renewable energy, with large-scale hydropower plants providing a significant portion of global electricity supply.
- Geothermal Energy: Geothermal energy is derived from the heat stored beneath the Earth’s surface and can be used for heating, cooling, and electricity generation. Geothermal power plants extract heat from underground reservoirs of hot water or steam and convert it into electricity through turbines and generators.
- Biomass Energy: Biomass energy is produced from organic materials such as wood, crop residues, agricultural waste, and organic municipal solid waste. It can be utilized for heat, electricity, and transportation fuels through processes such as combustion, gasification, fermentation, and biochemical conversion.
Renewable energy technologies offer numerous environmental, economic, and social benefits, including:
- Climate Mitigation: Renewable energy sources produce little to no greenhouse gas emissions during operation, helping to mitigate climate change and reduce air pollution.
- Energy Security: Renewable energy diversifies the energy mix and reduces dependence on imported fossil fuels, enhancing energy security and resilience to supply disruptions.
- Economic Development: The deployment of renewable energy technologies creates jobs, stimulates economic growth, and fosters innovation and investment in clean energy industries.
- Environmental Sustainability: Renewable energy minimizes environmental impacts, preserves natural resources, and protects ecosystems and biodiversity.
Despite these advantages, the widespread adoption of renewable energy faces challenges such as intermittency, grid integration, and cost competitiveness. Continued research, development, and deployment efforts are needed to overcome these barriers and accelerate the transition to a sustainable energy future powered by renewable resources. Government policies, financial incentives, and international cooperation play crucial roles in driving the deployment of renewable energy technologies and achieving global energy sustainability goals.
Solar Power:
Solar power is a renewable energy technology that harnesses sunlight to generate electricity or heat. It is derived from the conversion of sunlight into usable energy through photovoltaic (PV) panels or solar thermal systems. Solar power is one of the fastest-growing sources of clean energy globally, offering numerous environmental, economic, and social benefits.
Key components and processes involved in solar power generation include:
- Photovoltaic (PV) Panels: PV panels consist of semiconductor materials, typically silicon, that convert sunlight directly into electricity through the photovoltaic effect. When sunlight strikes the PV cells, it generates an electric current by freeing electrons from the atoms in the material, creating a flow of electricity.
- Solar Thermal Systems: Solar thermal systems use sunlight to heat a fluid, such as water or oil, which then generates steam to drive turbines and produce electricity. Solar thermal power plants may employ different technologies, including parabolic troughs, solar towers, and dish/engine systems, to concentrate sunlight and generate heat for power generation.
- Inverters: In solar PV systems, inverters convert the direct current (DC) electricity generated by the PV panels into alternating current (AC) electricity suitable for use in homes, businesses, and the grid. Inverters also regulate the voltage and frequency of the electricity to ensure compatibility with the electrical grid.
- Mounting Structures: PV panels are mounted on structures, such as rooftops, ground-mounted arrays, or solar tracking systems, to optimize their exposure to sunlight and maximize energy production. Mounting structures may be fixed or adjustable to track the sun’s movement throughout the day for increased efficiency.
- Balance of System Components: Solar power systems include various balance of system (BOS) components, such as wiring, junction boxes, combiner boxes, fuses, circuit breakers, and monitoring equipment, to ensure safe and efficient operation of the system.
Solar power offers several advantages over conventional energy sources, including:
- Abundant Resource: Solar energy is abundant, widely available, and inexhaustible, making it a sustainable and environmentally friendly alternative to fossil fuels.
- Reduced Emissions: Solar power generates electricity without emitting greenhouse gases or air pollutants, helping to mitigate climate change and reduce air pollution.
- Energy Independence: Solar power enables individuals, businesses, and communities to generate their own electricity and reduce reliance on imported fossil fuels, enhancing energy security and resilience.
- Job Creation: The solar industry creates jobs in manufacturing, installation, operation, maintenance, and research, contributing to economic growth and job creation in local communities.
Despite these advantages, challenges such as intermittency, energy storage, grid integration, and cost competitiveness remain barriers to the widespread adoption of solar power. Continued research, development, and deployment efforts are needed to overcome these challenges and realize the full potential of solar energy as a clean and sustainable energy source for the future. Government policies, financial incentives, technological innovation, and public awareness campaigns play critical roles in driving the transition to a solar-powered energy system and achieving global sustainability goals.
Wind Energy:
Wind energy is a renewable energy technology that harnesses the kinetic energy of wind to generate electricity. It is one of the oldest and most widely deployed forms of renewable energy, with wind turbines converting wind power into electrical power through a series of mechanical and electrical processes. Wind energy offers numerous environmental, economic, and social benefits, making it a key component of the transition to a sustainable energy future.
Key components and processes involved in wind energy generation include:
- Wind Turbines: Wind turbines are the primary technology used to capture wind energy and convert it into electricity. Modern wind turbines consist of three main components: the rotor blades, the nacelle (housing the generator and other components), and the tower. As the wind blows, it causes the rotor blades to spin, turning the kinetic energy of the wind into mechanical energy.
- Generators: Within the nacelle, the mechanical energy from the rotating blades is converted into electrical energy by a generator. Most wind turbines use electromagnetic generators, which produce alternating current (AC) electricity when the rotor shaft rotates. The generator is connected to the power grid via power electronics and transformers to deliver the electricity to consumers.
- Control Systems: Wind turbines are equipped with control systems that monitor wind speed, direction, and other factors to optimize performance and ensure safe operation. Pitch control systems adjust the angle of the rotor blades to maximize energy capture and prevent damage in high winds, while yaw control systems orient the turbine to face into the wind for optimal efficiency.
- Grid Connection: The electricity generated by wind turbines is transmitted to the power grid through underground or overhead power lines. Wind farms are typically connected to the grid at a substation, where the electricity is converted to higher voltages for efficient transmission over long distances and distributed to end-users.
- Wind Resource Assessment: Before installing wind turbines, developers conduct wind resource assessments to determine the suitability and potential energy yield of a site. This involves collecting data on wind speed, direction, turbulence, and other meteorological parameters using meteorological towers, remote sensing devices, and computer modeling.
Wind energy offers several advantages over conventional energy sources, including:
- Abundant Resource: Wind energy is abundant and widely distributed, with vast potential for deployment in both onshore and offshore locations around the world.
- Zero Emissions: Wind power generates electricity without emitting greenhouse gases or air pollutants, helping to mitigate climate change and reduce air pollution.
- Low Operating Costs: Once installed, wind turbines have relatively low operating costs and can produce electricity at competitive prices compared to fossil fuel-based power plants.
- Job Creation: The wind energy industry creates jobs in manufacturing, construction, installation, operation, maintenance, and research, contributing to economic growth and job creation in local communities.
Despite these advantages, challenges such as intermittency, grid integration, land use conflicts, and visual impacts remain barriers to the widespread adoption of wind energy. Continued research, development, and deployment efforts are needed to overcome these challenges and realize the full potential of wind energy as a clean and sustainable energy source for the future. Government policies, financial incentives, technological innovation, and public engagement play critical roles in driving the transition to a wind-powered energy system and achieving global sustainability goals.
Hydropower:
Hydropower, also known as hydroelectric power, is a renewable energy technology that harnesses the energy of flowing water to generate electricity. It is one of the oldest and most widely used forms of renewable energy, with hydroelectric power plants operating in various sizes and capacities around the world. Hydropower offers numerous environmental, economic, and social benefits, making it a key component of the global energy mix.
Key components and processes involved in hydropower generation include:
- Dam and Reservoir: Hydropower plants typically utilize dams to impound water and create reservoirs, which serve as storage reservoirs to regulate water flow and ensure continuous power generation. The height of the dam and the volume of water stored in the reservoir determine the potential energy available for electricity generation.
- Intake Structure: Water is drawn from the reservoir through intake structures, such as gates, screens, or tunnels, and directed to the turbines for power generation. Intake structures may incorporate trash racks to prevent debris and sediment from entering the turbines and causing damage.
- Turbines: Turbines are the primary components used to convert the kinetic energy of flowing water into mechanical energy. Different types of turbines, including Francis, Kaplan, and Pelton turbines, are employed depending on factors such as water flow rate, head (height difference), and power output requirements.
- Generators: The mechanical energy produced by the turbines is transmitted to generators, where it is converted into electrical energy. Generators are typically coupled directly to the turbines and use electromagnetic induction to produce alternating current (AC) electricity.
- Transformer and Transmission Lines: The electricity generated by hydropower plants is stepped up to higher voltages using transformers for efficient transmission over long distances. Transmission lines transmit the electricity from the power plant to distribution networks, substations, and end-users.
- Tailrace: After passing through the turbines, the water, now with reduced energy, is discharged back into the river or downstream water body through the tailrace. Tailrace channels may include energy dissipation structures, such as stilling basins or energy dissipators, to reduce erosion and minimize environmental impacts.
Hydropower offers several advantages over conventional energy sources, including:
- Clean and Renewable: Hydropower generates electricity without emitting greenhouse gases or air pollutants, making it a clean and environmentally friendly energy source.
- Baseload Power: Hydropower plants can operate continuously or with minimal downtime, providing reliable baseload power to meet electricity demand, stabilize the grid, and support the integration of variable renewable energy sources.
- Water Management: Hydropower plants offer opportunities for water management, including flood control, irrigation, and water supply, enhancing water security and resilience to climate change impacts.
- Energy Storage: Some hydropower plants can store excess energy by pumping water back into reservoirs during periods of low demand, effectively acting as energy storage facilities to balance supply and demand on the grid.
Despite these advantages, hydropower development can have significant environmental and social impacts, including habitat alteration, ecosystem disruption, and displacement of communities. Sustainable hydropower planning and management practices, environmental mitigation measures, and stakeholder engagement are essential to minimize these impacts and ensure the responsible and equitable development of hydropower resources. Ongoing research, innovation, and collaboration are also needed to address emerging challenges and optimize the contribution of hydropower to global energy sustainability goals.
Geothermal Energy:
Geothermal energy is a renewable energy technology that harnesses heat from the Earth’s interior to generate electricity or provide heating and cooling for buildings and industrial processes. It is derived from the natural heat stored within the Earth’s crust, primarily from the decay of radioactive elements and residual heat from the planet’s formation. Geothermal energy offers a reliable, continuous, and environmentally friendly source of power with minimal greenhouse gas emissions and air pollution.
Key components and processes involved in geothermal energy utilization include:
- Geothermal Reservoirs: Geothermal energy is extracted from underground reservoirs of hot water or steam located in geological formations such as volcanic regions, geothermal hot spots, or areas with high heat flow. These reservoirs may be located at varying depths within the Earth’s crust and can range in temperature from moderately warm to extremely hot.
- Well Drilling: Wells are drilled into the geothermal reservoirs to extract the hot water or steam for energy production. Geothermal wells can be categorized as production wells, injection wells, or monitoring wells, depending on their specific functions within the geothermal system.
- Production Facilities: Geothermal production facilities consist of surface infrastructure, including steam separators, heat exchangers, turbines, and generators, that extract heat from the geothermal fluid and convert it into electricity. The type of production facility varies depending on the temperature and composition of the geothermal fluid.
- Binary Cycle Power Plants: Binary cycle power plants are commonly used to generate electricity from low to moderate temperature geothermal resources. In a binary cycle system, the hot geothermal fluid is passed through a heat exchanger to vaporize a secondary working fluid with a lower boiling point, such as isobutane or ammonia. The vaporized working fluid then drives a turbine to generate electricity before being condensed and returned to the heat exchanger.
- Flash Steam Power Plants: Flash steam power plants are utilized for high-temperature geothermal resources where the geothermal fluid is at or near boiling point. In a flash steam system, the high-pressure geothermal fluid is released into a flash tank, causing it to rapidly vaporize or “flash” into steam. The steam is then used to drive turbines connected to generators to produce electricity.
- Direct Use Applications: In addition to electricity generation, geothermal energy can be directly utilized for heating and cooling purposes in buildings, greenhouses, and industrial processes. Direct use applications typically involve circulating geothermal fluid through heat exchangers or utilizing hot water or steam directly from geothermal wells.
Geothermal energy offers several advantages over conventional energy sources, including:
- Reliability and Baseload Power: Geothermal power plants can operate continuously, providing reliable baseload power to meet electricity demand and complement intermittent renewable energy sources like wind and solar.
- Low Environmental Impact: Geothermal energy production emits minimal greenhouse gases and air pollutants, resulting in lower environmental impacts compared to fossil fuel-based power generation.
- Local Resource: Geothermal resources are often found in close proximity to areas of electricity demand, reducing the need for long-distance transmission and enhancing energy security and resilience.
- Long-Term Sustainability: Geothermal reservoirs can sustainably produce energy for decades to centuries with proper management and reservoir engineering techniques, offering long-term energy security and economic benefits to host communities.
Despite these advantages, geothermal energy development faces challenges such as high upfront costs, resource uncertainty, and geological constraints. Continued research, development, and investment are needed to overcome these challenges and unlock the full potential of geothermal energy as a clean, reliable, and sustainable energy source for the future. Government policies, financial incentives, and international cooperation play essential roles in supporting geothermal development and achieving global energy sustainability goals.
Solar Energy:
Solar energy is a renewable energy technology that harnesses sunlight to generate electricity or provide thermal energy for heating and cooling. It is derived from the electromagnetic radiation emitted by the Sun, which contains photons that can be converted into usable energy through various photovoltaic and solar thermal technologies. Solar energy offers abundant, clean, and sustainable power with minimal environmental impact, making it a key contributor to the transition to a low-carbon energy system.
Key components and processes involved in solar energy utilization include:
- Photovoltaic (PV) Panels: Photovoltaic panels, commonly known as solar panels, are the primary technology used to convert sunlight directly into electricity through the photovoltaic effect. Solar cells within the panels are made of semiconductor materials, such as silicon, that absorb photons from sunlight and release electrons, generating direct current (DC) electricity.
- Inverters: The DC electricity generated by solar panels is converted into alternating current (AC) electricity using inverters. AC electricity is the standard form of electricity used in homes, businesses, and the power grid, making inverters essential for connecting solar energy systems to the grid or standalone applications.
- Mounting Structures: Solar panels are mounted on supporting structures, such as rooftops, ground-mounted racks, or solar tracking systems, to optimize their exposure to sunlight and maximize energy capture throughout the day. Mounting structures may include tilt and azimuth adjustments to optimize panel orientation for maximum solar irradiance.
- Balance of System Components: In addition to solar panels and inverters, solar energy systems require balance of system (BOS) components such as wiring, connectors, junction boxes, and mounting hardware to safely and efficiently connect, support, and protect the solar array.
- Solar Thermal Collectors: Solar thermal collectors utilize sunlight to heat a fluid (such as water or a heat transfer fluid) directly or indirectly, producing thermal energy for heating water, space heating, or industrial processes. Solar thermal systems may use flat-plate collectors, evacuated tube collectors, or concentrating solar collectors, depending on the application and temperature requirements.
- Storage Systems: Solar energy systems can be integrated with energy storage systems, such as batteries or thermal storage tanks, to store excess energy generated during periods of high sunlight for use during periods of low sunlight or high energy demand. Energy storage enhances the reliability, flexibility, and resilience of solar energy systems and facilitates their integration into the grid.
Solar energy offers several advantages over conventional energy sources, including:
- Abundant Resource: Solar energy is abundant and widely available, with the potential to meet global energy demand many times over.
- Zero Emissions: Solar power generates electricity without emitting greenhouse gases or air pollutants, helping to mitigate climate change and reduce air pollution.
- Decentralized Generation: Solar energy systems can be deployed at various scales, from small rooftop installations to utility-scale solar farms, enabling decentralized electricity generation and increasing energy resilience and security.
- Scalability and Modularity: Solar energy systems can be easily scaled up or down to meet specific energy needs, making them suitable for a wide range of applications, from off-grid residential systems to grid-connected utility-scale installations.
Despite these advantages, solar energy deployment faces challenges such as intermittency, variability, and intermittency. Continued research, development, and deployment efforts are needed to overcome these challenges and unlock the full potential of solar energy as a clean, reliable, and affordable energy source for the future. Government policies, financial incentives, technological innovation, and public engagement play critical roles in accelerating the adoption of solar energy and achieving global sustainability goals.
Wind Energy:
Wind energy is a renewable energy technology that harnesses the kinetic energy of wind to generate electricity. It is one of the fastest-growing sources of renewable energy globally, with wind turbines deployed in diverse environments ranging from onshore and offshore locations to remote and urban areas. Wind energy offers numerous environmental, economic, and social benefits, making it a key component of the transition to a low-carbon energy system.
Key components and processes involved in wind energy utilization include:
- Wind Turbines: Wind turbines are the primary technology used to convert the kinetic energy of wind into mechanical energy. Modern wind turbines consist of several key components, including the tower, rotor blades, nacelle, gearbox, generator, and control systems. As the wind flows over the rotor blades, it causes them to rotate, driving the generator to produce electricity.
- Tower: The tower provides structural support for the wind turbine and elevates the rotor blades to capture higher wind speeds at greater heights. Towers can vary in height depending on the site conditions, wind resource, and turbine size, with taller towers generally enabling access to stronger and more consistent winds.
- Rotor Blades: Rotor blades are aerodynamically designed to capture the maximum amount of wind energy and convert it into rotational motion. Blade length, shape, and material composition are optimized to enhance efficiency, reduce drag, and withstand varying wind conditions.
- Nacelle: The nacelle houses critical components of the wind turbine, including the gearbox, generator, and control systems. It is positioned atop the tower and rotates to align with the direction of the wind, enabling optimal wind capture and energy production.
- Generator: The generator converts the mechanical energy produced by the rotating rotor blades into electrical energy. Most modern wind turbines use synchronous generators or permanent magnet generators to produce alternating current (AC) electricity, which is then transmitted to the grid or stored for later use.
- Control Systems: Control systems monitor wind speed, direction, turbine operation, and grid conditions to optimize energy production, ensure safe operation, and protect the turbine from damage due to high winds or other adverse conditions. Advanced control algorithms enable variable-speed operation and active yaw control to maximize energy capture and minimize loads on the turbine components.
- Grid Connection: Electricity generated by wind turbines is typically transmitted to the grid via underground or overhead power lines. Grid connection infrastructure may include substations, transformers, and transmission lines to transport electricity from wind farms to end-users, ensuring reliable and efficient integration into the electrical grid.
Wind energy offers several advantages over conventional energy sources, including:
- Clean and Renewable: Wind energy generates electricity without emitting greenhouse gases or air pollutants, making it a clean and environmentally friendly energy source.
- Abundant Resource: Wind energy is abundant and widely distributed, with significant potential for expansion in both onshore and offshore environments.
- Low Operating Costs: Once installed, wind turbines have relatively low operating and maintenance costs compared to fossil fuel-based power plants, resulting in long-term cost savings and price stability for electricity consumers.
- Job Creation and Economic Development: Wind energy development creates jobs and stimulates economic growth in local communities through investments in manufacturing, construction, operation, and maintenance of wind farms.
Despite these advantages, wind energy deployment faces challenges such as intermittency, grid integration, and land use conflicts. Continued innovation, research, and collaboration are needed to overcome these challenges and realize the full potential of wind energy as a sustainable and scalable solution to global energy needs. Government policies, financial incentives, technological advancements, and public engagement play critical roles in supporting wind energy development and achieving climate and energy sustainability goals.
Hydropower:
Hydropower, also known as hydroelectric power, is a renewable energy technology that harnesses the energy of flowing water to generate electricity. It is one of the oldest and most widely used sources of renewable energy, with hydropower plants located on rivers, streams, and reservoirs around the world. Hydropower offers numerous environmental, economic, and social benefits, making it a key component of the global energy mix.
Key components and processes involved in hydropower utilization include:
- Dam and Reservoir: Hydropower plants typically require a dam to impound water and create a reservoir, which serves as a storage facility for water. The dam controls the flow of water and regulates the release of water downstream to generate electricity and manage water resources for irrigation, flood control, and other purposes.
- Intake Structure: The intake structure is located at the base of the dam and allows water to flow from the reservoir into the power plant. It may include gates, screens, and trash racks to control debris and sediment and protect the turbines and other equipment from damage.
- Penstock: The penstock is a large pipe or conduit that carries water from the intake structure to the turbine(s) inside the power plant. The penstock is typically made of steel or reinforced concrete and may include valves or gates to regulate the flow of water and control turbine operation.
- Turbine: The turbine is the primary component of the hydropower plant that converts the energy of flowing water into mechanical energy. Turbines may be of various types, including Francis, Kaplan, Pelton, or Crossflow turbines, depending on the hydraulic conditions and design requirements of the site.
- Generator: The generator is connected to the turbine and converts the mechanical energy produced by the turbine into electrical energy. Most hydropower plants use synchronous generators to produce alternating current (AC) electricity, which is then transmitted to the grid for distribution to consumers.
- Transformer and Transmission Lines: The electricity generated by the hydropower plant is typically stepped up in voltage using transformers and transmitted to the grid via overhead or underground transmission lines. Transmission infrastructure may include substations, switchgear, and distribution lines to transport electricity from the power plant to end-users.
Hydropower offers several advantages over conventional energy sources, including:
- Clean and Renewable: Hydropower generates electricity without emitting greenhouse gases or air pollutants, making it a clean and environmentally friendly energy source.
- Reliability and Baseload Power: Hydropower plants can operate continuously and provide reliable baseload power to meet electricity demand, complementing intermittent renewable energy sources like wind and solar.
- Energy Storage: Some hydropower plants incorporate pumped storage facilities that store excess electricity during periods of low demand and release it during periods of high demand, providing grid stability and balancing services.
- Water Management: Hydropower projects can provide multiple benefits beyond electricity generation, including water supply, flood control, irrigation, navigation, and recreational opportunities.
Despite these advantages, hydropower development faces challenges such as environmental and social impacts, habitat alteration, and sedimentation. Continued research, planning, and stakeholder engagement are needed to optimize the benefits and minimize the negative impacts of hydropower projects. Integrated water resource management, environmental assessment, and multi-stakeholder collaboration are essential for sustainable hydropower development and achieving global energy and water sustainability goals.
Geothermal Energy:
Geothermal energy is a renewable energy technology that harnesses the heat stored beneath the Earth’s surface to generate electricity or provide direct heating and cooling. It utilizes the natural heat flux from the Earth’s interior, which originates from radioactive decay and residual heat from the planet’s formation. Geothermal energy is abundant and widely distributed, with potential for deployment in various geological settings, including volcanic regions, tectonic plate boundaries, and deep sedimentary basins.
Key components and processes involved in geothermal energy utilization include:
- Geothermal Reservoir: Geothermal reservoirs are underground formations containing hot water or steam trapped within permeable rock formations, such as fractured volcanic rocks or sedimentary aquifers. These reservoirs vary in temperature, depth, and fluid composition, depending on geological conditions and regional tectonic activity.
- Geothermal Wells: Geothermal wells are drilled into the Earth’s crust to access the hot fluids or steam contained within geothermal reservoirs. Production wells are used to extract the hot fluid or steam to the surface, while injection wells are used to reinject cooled fluids or wastewater back into the reservoir to maintain pressure and sustain production.
- Production Equipment: Production equipment, such as pumps, separators, and heat exchangers, is used to extract, separate, and utilize the hot fluids or steam produced from geothermal wells. Depending on the temperature and fluid composition, various technologies, such as flash steam, binary cycle, or direct use systems, may be employed to convert geothermal energy into usable forms of heat and electricity.
- Power Plant: Geothermal power plants are facilities that convert the thermal energy contained in geothermal fluids or steam into electricity. There are several types of geothermal power plants, including dry steam, flash steam, and binary cycle plants, each suited to different temperature and fluid conditions. Power plants may also incorporate heat exchangers, turbines, generators, and condensers to optimize energy conversion efficiency and power output.
- Direct Use Applications: Geothermal energy can be utilized directly for heating and cooling applications without the need for electricity generation. Direct use applications include district heating, space heating, greenhouse heating, aquaculture, industrial processes, and spa and recreational activities. Direct use systems typically involve the circulation of geothermal fluids through heat exchangers or distribution networks to transfer heat to end-users.
Geothermal energy offers several advantages over conventional energy sources, including:
- Baseload Power: Geothermal power plants can provide continuous, reliable baseload power that is not subject to intermittency or variability, making them well-suited for meeting base load electricity demand.
- Low Emissions: Geothermal power generation produces minimal greenhouse gas emissions and air pollutants, contributing to climate change mitigation and air quality improvement.
- Long-Term Resource Availability: Geothermal reservoirs are naturally replenished by ongoing heat flux from the Earth’s interior, providing a sustainable and long-term source of energy with minimal environmental impact.
- Local Economic Development: Geothermal projects can stimulate economic growth and create jobs in regions with abundant geothermal resources, fostering local investment, infrastructure development, and technology innovation.
Despite these advantages, geothermal energy deployment faces challenges such as resource exploration and characterization, drilling costs, and subsurface uncertainty. Continued research, technology development, and policy support are needed to overcome these challenges and unlock the full potential of geothermal energy as a reliable, sustainable, and cost-effective energy source for the future. Public-private partnerships, regulatory frameworks, and international cooperation can accelerate geothermal development and contribute to global energy security and environmental sustainability goals.
Solar Energy:
Solar energy is a renewable energy technology that harnesses sunlight to generate electricity or provide heat for various applications. It is one of the most abundant and widely available sources of renewable energy, with the potential to meet a significant portion of global energy demand. Solar energy technologies utilize photovoltaic (PV) cells or solar thermal collectors to convert sunlight into usable forms of energy.
Key components and processes involved in solar energy utilization include:
- Photovoltaic (PV) Cells: PV cells, also known as solar cells, are semiconductor devices that convert sunlight directly into electricity through the photovoltaic effect. When sunlight strikes the surface of a PV cell, it generates an electric current by exciting electrons in the semiconductor material. PV cells are typically made of silicon, although other materials such as cadmium telluride and thin-film materials are also used.
- Solar Panels: Solar panels consist of multiple PV cells interconnected and encapsulated within a frame to form a solar module or panel. Solar panels are designed to capture sunlight and convert it into electricity efficiently. They are available in various sizes, shapes, and configurations to suit different applications, from rooftop installations to utility-scale solar farms.
- Inverter: Inverters are devices that convert the direct current (DC) electricity generated by solar panels into alternating current (AC) electricity suitable for use in buildings, appliances, and the electrical grid. Inverters also perform power management functions, such as voltage regulation, frequency control, and grid synchronization, to ensure safe and reliable operation of solar power systems.
- Mounting Structures: Mounting structures provide support and orientation for solar panels, ensuring optimal sunlight exposure and system efficiency. Mounting options include roof-mounted systems, ground-mounted arrays, tracking systems, and building-integrated photovoltaics (BIPV), which integrate solar panels into building materials such as windows, facades, and roofing tiles.
- Balance of System (BOS) Components: BOS components include wiring, connectors, junction boxes, combiner boxes, inverters, monitoring systems, and other auxiliary equipment required to interconnect, monitor, and control solar power systems. BOS components play a critical role in system performance, reliability, and safety.
- Solar Thermal Collectors: Solar thermal collectors are devices that capture sunlight to heat a fluid or medium for space heating, water heating, industrial processes, or electricity generation through concentrated solar power (CSP) systems. Solar thermal collectors may use flat-plate, evacuated tube, parabolic trough, or dish concentrator designs, depending on the application and temperature requirements.
- Storage Systems: Solar energy storage systems, such as batteries, thermal storage tanks, or molten salt storage, store excess energy generated during periods of sunlight abundance for use during periods of low or no sunlight. Energy storage enhances the reliability, stability, and resilience of solar power systems, enabling increased integration of solar energy into the grid and off-grid applications.
Solar energy offers several advantages over conventional energy sources, including:
- Abundant Resource: Solar energy is abundant and widely available, with the potential to meet a significant portion of global energy demand.
- Clean and Renewable: Solar energy generates electricity without emitting greenhouse gases or air pollutants, making it a clean and environmentally friendly energy source.
- Modularity and Scalability: Solar power systems are modular and scalable, allowing for flexible deployment in diverse environments and applications, from small-scale residential installations to utility-scale solar farms.
- Cost-Competitive: The cost of solar photovoltaic (PV) technology has declined significantly in recent years, making solar energy increasingly cost-competitive with conventional energy sources in many regions.
Despite these advantages, solar energy deployment faces challenges such as intermittency, grid integration, land use, and material availability. Continued research, innovation, policy support, and investment are needed to overcome these challenges and unlock the full potential of solar energy as a key contributor to global energy transition and sustainability goals.
Wind Energy:
Wind energy is a renewable energy technology that harnesses the kinetic energy of moving air to generate electricity. It is one of the fastest-growing sources of renewable energy globally, with wind turbines installed on land and offshore to capture the energy of the wind and convert it into electricity. Wind energy offers numerous environmental, economic, and social benefits, making it a key component of the transition to a low-carbon and sustainable energy future.
Key components and processes involved in wind energy utilization include:
- Wind Turbines: Wind turbines are the primary devices used to convert wind energy into electricity. Modern wind turbines consist of three main components: the rotor, nacelle, and tower. The rotor contains the blades, which capture the wind and convert its kinetic energy into rotational mechanical energy. The nacelle houses the generator, gearbox, and other critical components responsible for converting the rotational energy into electricity. The tower provides structural support and elevates the rotor to capture higher wind speeds at greater heights.
- Rotor Blades: Rotor blades are aerodynamic structures that capture the kinetic energy of the wind and convert it into rotational motion. Modern wind turbine blades are typically made of fiberglass-reinforced composites or carbon fiber, designed to maximize efficiency and durability while minimizing weight and cost. Blade design, length, and shape influence the turbine’s performance, power output, and operational characteristics.
- Generator: The generator is housed within the nacelle and converts the rotational motion of the rotor into electrical energy. Most modern wind turbines use synchronous or asynchronous generators to produce alternating current (AC) electricity, which is then transmitted to the grid for distribution to consumers. The generator is connected to the rotor shaft via a gearbox or direct-drive system, which increases rotational speed and optimizes power generation efficiency.
- Yaw System: The yaw system allows the wind turbine to align itself with the prevailing wind direction to maximize energy capture and optimize power output. Yaw motors and sensors automatically adjust the orientation of the nacelle and rotor relative to the wind direction, ensuring optimal performance under varying wind conditions and changing wind directions.
- Control Systems: Control systems monitor and regulate various aspects of wind turbine operation, including rotor speed, blade pitch angle, yaw angle, and power output. Advanced control algorithms and sensors optimize turbine performance, maximize energy capture, and ensure safe and reliable operation under different wind conditions, grid requirements, and operational scenarios.
- Tower: The tower provides structural support for the wind turbine components and elevates the rotor to capture higher wind speeds and reduce turbulence. Towers are typically made of steel or concrete and vary in height depending on site-specific wind conditions, terrain, and regulatory requirements. Taller towers allow wind turbines to access stronger and more consistent winds at higher altitudes, increasing energy capture and efficiency.
Wind energy offers several advantages over conventional energy sources, including:
- Abundant Resource: Wind energy is abundant and widely available, with significant potential for deployment in regions with favorable wind conditions, both onshore and offshore.
- Clean and Renewable: Wind energy generates electricity without emitting greenhouse gases or air pollutants, making it a clean and environmentally friendly energy source.
- Cost-Competitive: The cost of wind energy has declined significantly in recent years, making it increasingly competitive with conventional energy sources in many regions. Continued technological advancements, economies of scale, and policy support are driving further cost reductions and market expansion.
Despite these advantages, wind energy deployment faces challenges such as intermittency, grid integration, land use, and visual and noise impacts. Continued research, innovation, policy support, and stakeholder engagement are needed to overcome these challenges and maximize the contribution of wind energy to global energy transition and sustainability goals.
Hydropower:
Hydropower, also known as hydroelectric power, is a renewable energy technology that harnesses the energy of flowing water to generate electricity. It is one of the oldest and most widely used forms of renewable energy, with hydropower plants installed on rivers, streams, and dams around the world. Hydropower offers numerous environmental, economic, and social benefits, making it a key component of the global energy mix and a cornerstone of sustainable development.
Key components and processes involved in hydropower utilization include:
- Hydraulic Structures: Hydraulic structures, such as dams, weirs, and intake structures, are built to control the flow of water and create reservoirs or water storage facilities. Dams are typically constructed across rivers or streams to impound water and create artificial lakes or reservoirs. Weirs and intake structures regulate the flow of water into hydropower plants and ensure optimal operation and efficiency.
- Turbines: Turbines are devices that convert the kinetic energy of flowing water into mechanical energy. There are several types of turbines used in hydropower plants, including Francis, Kaplan, Pelton, and Crossflow turbines, each suited to different flow conditions and hydraulic characteristics. Turbines are connected to generators, which convert the mechanical energy into electrical energy through electromagnetic induction.
- Generators: Generators are electrical machines that convert mechanical energy into electrical energy through electromagnetic induction. In hydropower plants, generators are typically connected to turbines and driven by the rotational motion of the turbine shaft. Generators produce alternating current (AC) electricity, which is transmitted to the grid for distribution to consumers or used to power local communities and industries.
- Penstocks: Penstocks are large pipes or conduits that convey water from the reservoir or intake structure to the turbines in hydropower plants. Penstocks are designed to withstand high pressures and flow rates and are often made of steel or reinforced concrete. They play a critical role in controlling the flow of water and optimizing the performance of the turbines.
- Transformer and Electrical Infrastructure: Transformer and electrical infrastructure, such as switchyards, transformers, and transmission lines, are used to step up the voltage of the electricity generated by hydropower plants for transmission and distribution to consumers. High-voltage transmission lines transport the electricity over long distances to population centers and industrial areas, where it is distributed through local distribution networks to homes, businesses, and facilities.
Hydropower offers several advantages over conventional energy sources, including:
- Clean and Renewable: Hydropower generates electricity without emitting greenhouse gases or air pollutants, making it a clean and environmentally friendly energy source.
- Baseload Power: Hydropower plants can provide continuous, reliable baseload power, complementing intermittent renewable energy sources such as solar and wind.
- Flexible Operation: Hydropower plants can adjust their output quickly to respond to changes in electricity demand, grid requirements, and market conditions, providing valuable flexibility and stability to the grid.
Despite these advantages, hydropower deployment faces challenges such as environmental and social impacts, regulatory constraints, and limited site availability. Continued research, innovation, and stakeholder engagement are needed to address these challenges and maximize the contribution of hydropower to global energy transition and sustainability goals. Sustainable hydropower development requires careful planning, integrated resource management, and consideration of environmental, social, and economic factors to ensure the long-term viability and resilience of hydropower projects.
Geothermal Energy:
Geothermal energy is a renewable energy technology that harnesses heat from the Earth’s interior to generate electricity or provide direct heating and cooling for various applications. It is derived from the natural heat stored beneath the Earth’s surface, primarily in the form of hot water or steam trapped in geothermal reservoirs. Geothermal energy offers significant potential as a clean, reliable, and sustainable energy source, particularly in regions with high geothermal resources and active tectonic activity.
Key components and processes involved in geothermal energy utilization include:
- Geothermal Reservoirs: Geothermal reservoirs are underground formations of hot water, steam, or rock heated by the Earth’s internal heat. These reservoirs occur naturally in regions with volcanic activity, tectonic plate boundaries, or hot spots where heat from the Earth’s mantle rises to the surface. Geothermal reservoirs are characterized by their temperature, depth, permeability, and fluid chemistry, which determine their suitability for geothermal energy extraction.
- Geothermal Wells: Geothermal wells are drilled into the Earth’s crust to access geothermal reservoirs and extract hot water or steam for energy production. There are two main types of geothermal wells: production wells, which extract hot water or steam from the reservoir, and injection wells, which re-inject cooled water or spent steam back into the reservoir to maintain pressure and sustainability. Geothermal wells may extend thousands of meters below the Earth’s surface and require specialized drilling equipment and techniques.
- Production Facilities: Geothermal production facilities, also known as power plants or geothermal plants, are designed to extract heat from geothermal reservoirs and convert it into electricity. There are several types of geothermal power plants, including flash steam plants, binary cycle plants, and dry steam plants, each suited to different reservoir conditions and fluid characteristics. These plants typically include steam separators, turbines, generators, condensers, and other auxiliary equipment to produce electricity efficiently.
- Binary Cycle Technology: Binary cycle technology is a type of geothermal power generation that utilizes low-to-medium temperature geothermal resources to produce electricity. In binary cycle plants, hot geothermal fluid is passed through a heat exchanger to transfer its heat to a secondary working fluid with a lower boiling point, such as isobutane or pentane. The vaporized working fluid then drives a turbine-generator to produce electricity, while the cooled geothermal fluid is re-injected into the reservoir.
- Direct Use Applications: In addition to electricity generation, geothermal energy can be used directly for heating, cooling, and industrial processes. Direct use applications include district heating systems, greenhouses, aquaculture, spas, and industrial processes such as food drying, lumber drying, and mineral extraction. Geothermal heat pumps are also used for residential and commercial heating and cooling by transferring heat between the Earth and buildings through underground pipes.
Geothermal energy offers several advantages over conventional energy sources, including:
- Renewable and Sustainable: Geothermal energy is renewable and sustainable, as it relies on heat from the Earth’s interior that is continuously replenished by natural processes such as radioactive decay and heat convection.
- Low Emissions: Geothermal power generation produces minimal greenhouse gas emissions and air pollutants compared to fossil fuels, making it a clean and environmentally friendly energy source.
- Reliable and Baseload Power: Geothermal power plants can provide continuous, reliable baseload power, complementing intermittent renewable energy sources such as solar and wind.
Despite these advantages, geothermal energy deployment faces challenges such as resource availability, exploration and development costs, regulatory constraints, and environmental considerations. Continued research, innovation, and investment are needed to overcome these challenges and unlock the full potential of geothermal energy as a key contributor to global energy transition and sustainability goals. Sustainable geothermal development requires careful resource assessment, technology development, and stakeholder engagement to ensure responsible and equitable use of this valuable energy resource.
Bioenergy:
Bioenergy is a renewable energy technology that utilizes organic materials, such as biomass, to produce heat, electricity, biofuels, and other forms of energy. It encompasses a wide range of organic feedstocks, including agricultural residues, forestry waste, energy crops, organic waste, and animal manure, which are converted into usable energy through various processes such as combustion, gasification, anaerobic digestion, and biochemical conversion. Bioenergy plays a significant role in global energy systems, providing a versatile and sustainable source of energy for heating, electricity generation, transportation, and industrial applications.
Key components and processes involved in bioenergy utilization include:
- Biomass Feedstock: Biomass feedstock refers to organic materials derived from plants, animals, or organic waste streams that can be used as fuel or feedstock for bioenergy production. Common biomass feedstocks include wood chips, agricultural residues (such as corn stover, wheat straw, and rice husks), energy crops (such as switchgrass, miscanthus, and sugarcane), organic waste (such as municipal solid waste, sewage sludge, and food waste), and animal manure.
- Combustion: Biomass combustion is a widely used method for converting solid biomass into heat and electricity. In combustion systems, biomass feedstock is burned in boilers or furnaces to produce steam, which is then used to drive turbines and generate electricity. Heat produced during combustion can also be used for district heating, industrial processes, and residential heating applications. Advanced combustion technologies, such as fluidized bed combustion and biomass co-firing with coal, improve efficiency, reduce emissions, and enhance fuel flexibility.
- Gasification: Biomass gasification is a thermochemical process that converts solid biomass into syngas (synthetic gas), a mixture of hydrogen, carbon monoxide, carbon dioxide, and methane. Gasification involves heating biomass feedstock in a low-oxygen environment to produce a combustible gas, which can be used for electricity generation, heat production, or conversion into biofuels such as bioethanol or biodiesel. Gasification technologies include fixed-bed gasifiers, fluidized bed gasifiers, and entrained flow gasifiers, each offering different advantages in terms of feedstock flexibility, gas quality, and process efficiency.
- Anaerobic Digestion: Anaerobic digestion is a biological process that converts organic waste and biomass into biogas through microbial decomposition in the absence of oxygen. In anaerobic digesters, organic feedstock is broken down by anaerobic bacteria to produce biogas, a mixture of methane and carbon dioxide. Biogas can be used directly for heat and electricity generation or upgraded to biomethane for injection into natural gas pipelines or use as a transportation fuel. Anaerobic digestion also produces digestate, a nutrient-rich fertilizer that can be used to enhance soil health and fertility.
- Biochemical Conversion: Biochemical conversion involves the use of enzymes, bacteria, or other microorganisms to convert biomass feedstock into biofuels such as ethanol, biodiesel, and biobutanol. Biochemical processes include fermentation, enzymatic hydrolysis, and microbial fermentation, which break down complex carbohydrates and sugars in biomass into simpler molecules that can be converted into liquid fuels. Biochemical conversion technologies are used in the production of biofuels from crops such as corn, sugarcane, and soybeans, as well as lignocellulosic biomass from agricultural residues, forestry waste, and energy crops.
Bioenergy offers several advantages over conventional energy sources, including:
- Renewable and Sustainable: Bioenergy is derived from organic materials that can be replenished through natural processes such as photosynthesis and organic waste decomposition, making it renewable and sustainable in the long term.
- Carbon Neutral: Biomass feedstocks used for bioenergy production absorb carbon dioxide from the atmosphere during growth, offsetting emissions from combustion or conversion processes and making bioenergy carbon neutral or even carbon negative when combined with carbon capture and storage (CCS) technologies.
- Resource Diversity: Bioenergy relies on a diverse range of feedstocks, including agricultural residues, forestry waste, energy crops, and organic waste, which can be sourced locally, regionally, or globally, enhancing energy security and reducing dependence on fossil fuels.
Despite these advantages, bioenergy deployment faces challenges such as feedstock availability, land use competition, environmental impacts, and technology costs. Sustainable bioenergy development requires careful resource management, land use planning, and stakeholder engagement to ensure responsible and equitable use of biomass resources while maximizing the environmental, economic, and social benefits of bioenergy production. Continued research, innovation, and policy support are needed to overcome these challenges and realize the full potential of bioenergy as a key contributor to global energy transition and sustainability goals.
Carbon Capture and Storage (CCS):
Carbon capture and storage (CCS) is a technology that captures carbon dioxide (CO2) emissions from industrial processes, power plants, and other large point sources, transports it to a storage site, and injects it deep underground for long-term storage or geological sequestration. CCS plays a critical role in mitigating climate change by reducing CO2 emissions from fossil fuel combustion and industrial processes, thereby helping to limit global warming and meet greenhouse gas reduction targets.
Key components and processes involved in CCS include:
- Capture: The capture stage involves capturing CO2 emissions from industrial sources such as power plants, refineries, cement plants, and steel mills before they are released into the atmosphere. There are three main types of CO2 capture technologies: post-combustion capture, pre-combustion capture, and oxy-fuel combustion. Post-combustion capture involves removing CO2 from flue gases using chemical solvents or sorbents. Pre-combustion capture involves separating CO2 from syngas produced by gasification of fossil fuels. Oxy-fuel combustion involves burning fossil fuels in a high-purity oxygen environment to produce a concentrated stream of CO2 for capture.
- Transport: After capture, CO2 is compressed into a dense, supercritical fluid for transportation via pipelines, ships, or trucks to suitable storage sites. CO2 pipelines are the most common mode of transportation for large-scale CCS projects, with dedicated pipelines designed to transport CO2 from capture facilities to storage sites. CO2 can also be transported by ship or truck for shorter distances or in regions where pipeline infrastructure is not available.
- Storage: The storage stage involves injecting CO2 deep underground into geological formations for long-term storage or sequestration. Suitable storage formations include deep saline aquifers, depleted oil and gas reservoirs, and unmineable coal seams, which provide porous and permeable rock formations capable of trapping and retaining CO2 over geological timescales. Injection wells are drilled into the storage formations, and CO2 is injected into the subsurface under high pressure to ensure proper distribution and containment.
- Monitoring and Verification: Once CO2 is injected underground, monitoring and verification efforts are implemented to ensure the integrity and safety of the storage site and confirm that CO2 remains trapped and contained over time. Monitoring techniques include seismic surveys, pressure monitoring, geochemical analysis, and remote sensing technologies, which provide real-time data on CO2 movement, storage capacity, and potential leakage risks. Regular monitoring and verification are essential for regulatory compliance, risk management, and public acceptance of CCS projects.
- Risk Assessment and Management: CCS projects undergo comprehensive risk assessment and management to identify and mitigate potential risks associated with CO2 storage, such as leakage, induced seismicity, groundwater contamination, and ecosystem impacts. Risk assessment includes site characterization, geomechanical modeling, and probabilistic analysis to evaluate storage site suitability, integrity, and long-term stability. Risk management strategies may include well design and construction, injection rate optimization, pressure monitoring, and contingency planning to address potential hazards and uncertainties.
CCS offers several advantages as a climate mitigation technology, including:
- Emissions Reduction: CCS can significantly reduce CO2 emissions from industrial processes and power generation, helping to mitigate climate change and achieve greenhouse gas reduction targets.
- Carbon Removal: CCS can remove CO2 from the atmosphere and store it underground, effectively reversing emissions from fossil fuel combustion and industrial activities.
- Fossil Fuel Use: CCS enables continued use of fossil fuels for power generation and industrial processes while reducing associated emissions, providing a bridge to a low-carbon energy future.
Despite these advantages, CCS deployment faces challenges such as high costs, regulatory barriers, public acceptance, and limited storage capacity. Continued research, innovation, and policy support are needed to overcome these challenges and accelerate the deployment of CCS as a key technology for achieving climate goals and transitioning to a sustainable low-carbon energy system.
Renewable Energy Integration:
Renewable energy integration refers to the process of incorporating renewable energy sources, such as solar, wind, hydroelectric, and biomass, into existing energy systems to meet electricity demand while minimizing reliance on fossil fuels and reducing greenhouse gas emissions. As the share of renewable energy in the global energy mix continues to grow, integrating renewable energy into electricity grids and energy systems poses technical, economic, and regulatory challenges, as well as opportunities for enhancing system flexibility, reliability, and sustainability.
Key components and processes involved in renewable energy integration include:
- Grid Integration: Grid integration involves integrating renewable energy sources into electricity grids and balancing supply and demand to ensure grid stability and reliability. This includes upgrading and expanding grid infrastructure, such as transmission lines, substations, and grid control systems, to accommodate variable and distributed generation from renewable sources. Smart grid technologies, energy storage systems, demand response programs, and flexible grid management strategies are also deployed to optimize renewable energy integration and maximize system efficiency.
- Intermittency Management: Renewable energy sources such as solar and wind are inherently intermittent, as their generation depends on weather conditions and natural variability. Intermittency management involves forecasting renewable energy output, scheduling generation, and dispatching resources to balance supply and demand in real time. This may involve deploying energy storage systems, flexible generation assets, demand-side management, and grid balancing services to smooth fluctuations in renewable energy output and maintain grid stability.
- Flexibility Mechanisms: Flexibility mechanisms enable the efficient integration of renewable energy by providing flexibility in generation, demand, and grid operation. This includes flexible generation technologies such as natural gas-fired power plants, hydroelectric dams, and energy storage systems that can ramp up or down quickly to accommodate fluctuations in renewable energy output. Demand-side flexibility, through demand response programs, time-of-use pricing, and smart appliances, allows consumers to adjust electricity consumption in response to price signals and grid conditions.
- Market Design: Renewable energy integration requires market mechanisms and regulatory frameworks that incentivize investment in renewable energy infrastructure, promote competition, and facilitate efficient operation of electricity markets. This includes designing market rules, tariffs, and incentives that value renewable energy generation, provide revenue certainty for renewable energy projects, and encourage grid flexibility and innovation. Market reforms such as capacity markets, carbon pricing, and renewable energy mandates can also support renewable energy integration and decarbonization objectives.
- Policy Support: Policy support is essential for renewable energy integration, providing the regulatory certainty, financial incentives, and market signals needed to drive investment and innovation in renewable energy technologies. This includes renewable energy targets, feed-in tariffs, tax credits, renewable portfolio standards, and other policy instruments that promote renewable energy deployment, grid modernization, and energy transition. Regulatory reforms, capacity market mechanisms, and cross-border cooperation can also facilitate renewable energy integration across regions and countries.
Renewable energy integration offers several benefits, including:
- Decarbonization: Renewable energy integration reduces reliance on fossil fuels and helps mitigate climate change by reducing greenhouse gas emissions from electricity generation.
- Energy Security: Renewable energy diversifies the energy mix, enhances energy security, and reduces dependence on imported fossil fuels, enhancing energy resilience and geopolitical stability.
- Economic Growth: Renewable energy integration stimulates economic growth, creates jobs, and fosters innovation in renewable energy technologies, grid infrastructure, and energy services, driving economic development and competitiveness.
Despite these benefits, renewable energy integration faces challenges such as grid constraints, system reliability, curtailment of renewable energy, and market barriers. Addressing these challenges requires coordinated efforts from policymakers, regulators, grid operators, utilities, and industry stakeholders to develop and implement effective strategies for integrating renewable energy into energy systems and accelerating the transition to a sustainable low-carbon energy future.
Renewable Energy Storage:
Renewable energy storage is a key technology that enables the capture, storage, and utilization of energy generated from renewable sources such as solar, wind, hydroelectric, and biomass, providing flexibility, reliability, and resilience to energy systems. Energy storage systems store excess energy when renewable sources are abundant and release it when needed, helping to balance supply and demand, stabilize grids, and integrate intermittent renewable energy into electricity systems effectively.
Key components and processes involved in renewable energy storage include:
- Battery Storage: Battery storage systems use electrochemical reactions to store and release energy in the form of electricity. Lithium-ion batteries are the most commonly used battery technology for renewable energy storage due to their high energy density, fast response times, and long cycle life. Other types of battery technologies include lead-acid batteries, sodium-ion batteries, flow batteries, and solid-state batteries, each offering different advantages in terms of cost, performance, and scalability. Battery storage systems are deployed at various scales, from residential and commercial installations to utility-scale projects, to provide grid stabilization, peak shaving, load shifting, and backup power services.
- Pumped Hydro Storage: Pumped hydro storage is the oldest and most widely deployed form of grid-scale energy storage, using surplus electricity to pump water from a lower reservoir to a higher reservoir during periods of low demand. When electricity demand increases, water is released from the upper reservoir through turbines to generate electricity. Pumped hydro storage systems offer high efficiency, long cycle life, and large storage capacity, making them suitable for bulk energy storage and grid balancing services. However, pumped hydro storage requires suitable topography and water resources, limiting its deployment to specific geographic locations.
- Thermal Energy Storage: Thermal energy storage systems store heat energy from renewable sources such as solar thermal collectors, concentrating solar power plants, and biomass-fired boilers for later use in heating, cooling, or power generation applications. Thermal energy storage technologies include sensible heat storage, latent heat storage, and thermochemical storage, which store heat in solid, liquid, or chemical form, respectively. Thermal energy storage systems are used in residential, commercial, industrial, and utility-scale applications to enhance energy efficiency, reduce energy costs, and support renewable energy integration.
- Flywheel Energy Storage: Flywheel energy storage systems store kinetic energy in a spinning rotor and convert it back to electricity when needed. Flywheels consist of a rotating mass suspended in a vacuum chamber, supported by magnetic bearings to minimize friction and energy losses. When electricity is fed into the system, the flywheel accelerates, storing energy as rotational kinetic energy. When electricity is required, the flywheel decelerates, converting kinetic energy back into electricity. Flywheel energy storage systems offer fast response times, high efficiency, and long cycle life, making them suitable for grid stabilization, frequency regulation, and short-duration energy storage applications.
- Compressed Air Energy Storage (CAES): Compressed air energy storage systems use excess electricity to compress air and store it in underground caverns or aboveground pressure vessels. When electricity demand increases, the stored air is released and expanded through turbines to generate electricity. CAES systems can be configured as conventional adiabatic CAES, which relies on underground caverns for air storage, or as advanced isothermal CAES, which uses thermal energy storage to improve efficiency and performance. CAES systems offer large storage capacity, long-duration discharge, and rapid response times, making them suitable for grid-scale energy storage and renewable energy integration.
Renewable energy storage offers several benefits, including:
- Grid Stability: Renewable energy storage enhances grid stability by balancing supply and demand, smoothing fluctuations in renewable energy output, and providing grid ancillary services such as frequency regulation, voltage control, and black start capability.
- Energy Flexibility: Renewable energy storage provides flexibility in energy production and consumption, allowing renewable energy to be stored and dispatched when needed, regardless of weather conditions or time of day.
- Renewable Energy Integration: Renewable energy storage facilitates the integration of intermittent renewable energy sources such as solar and wind into electricity grids, enabling higher penetration levels of renewables and reducing curtailment of renewable energy.
Despite these benefits, renewable energy storage faces challenges such as high costs, technology maturity, regulatory barriers, and market structures. Continued research, development, and deployment of energy storage technologies, along with supportive policies and incentives, are needed to overcome these challenges and unlock the full potential of renewable energy storage for a sustainable low-carbon energy future.
Microgrid Integration:
Microgrid integration refers to the integration of distributed energy resources (DERs), including renewable energy sources, energy storage systems, and demand-side resources, into localized energy systems known as microgrids. Microgrids are small-scale, localized electricity grids that can operate independently or in conjunction with the main grid, providing reliable, resilient, and sustainable energy supply to specific communities, campuses, industrial facilities, or remote areas.
Key components and processes involved in microgrid integration include:
- DER Deployment: Microgrid integration begins with the deployment of distributed energy resources (DERs) such as solar photovoltaic (PV) panels, wind turbines, biomass generators, combined heat and power (CHP) systems, and energy storage systems (ESS). These DERs provide on-site generation, storage, and management of electricity, heat, and cooling, reducing reliance on centralized generation and enhancing energy independence and resilience.
- Control and Management Systems: Microgrids require sophisticated control and management systems to coordinate the operation of DERs, optimize energy generation and consumption, and maintain grid stability and reliability. Advanced microgrid controllers, energy management systems (EMS), and supervisory control and data acquisition (SCADA) systems are deployed to monitor and control DERs in real-time, manage energy flows, and respond to changes in grid conditions and energy demand.
- Grid Interconnection: Microgrids can operate in island mode, disconnected from the main grid, or in grid-connected mode, interacting with the main grid to import or export electricity as needed. Grid interconnection enables microgrids to exchange energy with the main grid, access backup power during emergencies, and participate in energy markets for revenue generation or cost savings. Grid interconnection requires bi-directional inverters, protective relays, and communication protocols to ensure seamless integration and grid stability.
- Energy Management Strategies: Microgrid integration involves developing energy management strategies to optimize the use of DERs, balance supply and demand, and maximize system efficiency and resilience. Energy management strategies may include demand response programs, load shifting, peak shaving, energy arbitrage, and energy trading, which allow microgrids to adjust energy consumption and generation in response to grid conditions, market prices, and user preferences.
- Resilience and Reliability: Microgrid integration enhances energy resilience and reliability by providing backup power, voltage and frequency regulation, and islanding capability during grid outages or emergencies. Microgrids can automatically disconnect from the main grid and continue to operate autonomously using local DERs, ensuring uninterrupted energy supply to critical loads such as hospitals, military bases, and data centers. Redundant components, energy storage systems, and emergency response protocols are deployed to enhance microgrid resilience and reliability.
Microgrid integration offers several benefits, including:
- Energy Independence: Microgrid integration reduces dependence on centralized generation and enhances energy independence by utilizing local renewable energy resources and distributed generation assets.
- Resilience: Microgrid integration enhances energy resilience by providing backup power, islanding capability, and self-healing functionality during grid outages or emergencies, ensuring uninterrupted energy supply to critical facilities and communities.
- Sustainability: Microgrid integration promotes sustainable energy use and environmental stewardship by leveraging renewable energy sources, reducing greenhouse gas emissions, and supporting local energy production and consumption.
Despite these benefits, microgrid integration faces challenges such as high upfront costs, regulatory barriers, technical complexity, and interoperability issues. Overcoming these challenges requires collaboration among stakeholders, supportive policies and incentives, and technological innovation to accelerate the deployment and adoption of microgrids as a key strategy for enhancing energy resilience, sustainability, and reliability in diverse energy systems and communities.
Gasification Process
- Gasification Process: Gasification is a thermochemical conversion process that converts organic materials such as biomass, coal, or municipal solid waste into synthesis gas (syngas) through partial oxidation in a controlled environment.
- Syngas Production: Syngas, or synthesis gas, is a mixture of carbon monoxide (CO), hydrogen (H2), carbon dioxide (CO2), methane (CH4), and other trace gases produced by gasification. Syngas can be used as a fuel for power generation, heat production, or chemical synthesis.
- Biomass Gasification: Biomass gasification is the process of converting biomass feedstocks such as wood chips, agricultural residues, or energy crops into syngas using heat, steam, and a controlled oxygen supply in a gasifier reactor.
- Coal Gasification: Coal gasification is the process of converting coal into syngas by reacting coal with steam and oxygen at high temperatures and pressures in a gasifier reactor. Coal gasification enables cleaner and more efficient utilization of coal for power generation, hydrogen production, or chemical synthesis.
- Syngas Cleanup: Syngas produced by gasification typically contains impurities such as tars, particulates, sulfur compounds, and trace metals, which must be removed through syngas cleanup processes such as gas cooling, scrubbing, filtration, and catalytic conversion to meet quality specifications for downstream applications.
- Gasifier Reactor: The gasifier reactor is the core component of a gasification system where biomass, coal, or other feedstocks are converted into syngas through thermochemical reactions. Gasifier reactors can be classified based on their operating temperature, pressure, feedstock type, and gasification process (e.g., fixed-bed, fluidized-bed, entrained-flow).
- Feedstock Flexibility: Gasification systems offer flexibility in feedstock selection, allowing a wide range of organic materials to be converted into syngas, including biomass, coal, municipal solid waste, industrial waste, and agricultural residues. Feedstock flexibility enhances resource utilization, waste management, and energy security.
- Tar Reforming: Tar reforming is a syngas cleanup process that converts tar compounds present in raw syngas into lighter hydrocarbons and gases through catalytic or thermal reactions. Tar reforming improves syngas quality, reduces equipment fouling, and enhances downstream process efficiency.
- Gasification Efficiency: Gasification systems offer high energy conversion efficiency compared to conventional combustion technologies, as they can extract energy from both the carbon and hydrogen content of feedstocks and utilize waste heat for process integration or cogeneration applications.
- Integrated Gasification Combined Cycle (IGCC): IGCC is a power generation technology that combines coal or biomass gasification with a combined cycle power plant to produce electricity with high efficiency and low emissions. IGCC systems offer advantages such as fuel flexibility, carbon capture potential, and improved environmental performance.
- Sustainability: Gasification systems contribute to sustainable development by enabling the use of renewable and low-carbon feedstocks, reducing greenhouse gas emissions, promoting energy efficiency, and supporting circular economy principles through waste-to-energy conversion and resource recovery.
- Gasification Residue Management: Gasification produces solid residues such as char, ash, and slag, which must be managed properly to minimize environmental impacts and maximize resource recovery. Residue management techniques include ash disposal, utilization in construction materials, soil amendment, and carbon sequestration.
- Syngas Utilization: Syngas produced by gasification can be utilized for various applications, including power generation, heat production, hydrogen production, synthetic fuel synthesis (e.g., Fischer-Tropsch synthesis), chemical production (e.g., methanol, ammonia), and industrial processes (e.g., steelmaking, glass manufacturing).
- Flexibility in Energy Conversion: Gasification systems offer flexibility in energy conversion pathways, allowing syngas to be converted into electricity, heat, or hydrogen through different technologies such as internal combustion engines, gas turbines, fuel cells, or chemical reactors depending on the application requirements and market conditions.
- Gasification Plant Design: Gasification plant design involves the selection of gasifier technology, syngas cleanup equipment, syngas utilization processes, and overall system configuration to meet specific project objectives, feedstock characteristics, environmental regulations, and economic considerations.
- Gasification Economics: Gasification economics depend on factors such as feedstock costs, plant capital investment, operating and maintenance expenses, energy market prices, policy incentives, and financing options. Economic feasibility studies and lifecycle assessments are conducted to evaluate the viability of gasification projects and optimize investment decisions.
- Modular Gasification Systems: Modular gasification systems are compact, scalable, and prefabricated units that can be deployed rapidly at various scales, from small-scale distributed energy applications to large-scale industrial installations. Modular gasification systems offer advantages such as cost savings, flexibility, and ease of deployment, especially in remote or decentralized settings.
- Gasification Heat Integration: Gasification heat integration involves recovering and utilizing waste heat from gasification processes for heating, cooling, or power generation applications through heat exchangers, steam turbines, or organic Rankine cycles. Heat integration improves energy efficiency, reduces operating costs, and enhances overall system performance.
- Carbon Capture and Utilization (CCU): Gasification enables carbon capture and utilization (CCU) by capturing carbon dioxide (CO2) emissions from syngas and converting them into valuable products such as synthetic fuels, chemicals, building materials, or mineral carbonates. CCU technologies mitigate greenhouse gas emissions, promote carbon circular
Gasification Process:
The gasification process is a thermochemical conversion method that transforms organic materials, such as biomass, coal, or municipal solid waste, into synthesis gas, also known as syngas. This process occurs in a gasifier, which operates under controlled conditions of temperature, pressure, and oxygen supply.
In the gasification process, the organic feedstock undergoes several chemical reactions, including pyrolysis, oxidation, and reduction. Initially, the feedstock is subjected to pyrolysis, where it is heated in the absence of oxygen to produce volatile compounds such as tars, oils, and gases. These volatile compounds are then partially oxidized by introducing a controlled amount of oxygen or steam into the gasifier, resulting in the formation of carbon monoxide (CO) and hydrogen (H2), along with carbon dioxide (CO2) and water vapor (H2O). Finally, the carbon monoxide and hydrogen undergo further reactions to produce a mixture of gases with varying compositions, depending on the feedstock and gasification conditions.
The syngas produced by the gasification process typically consists of carbon monoxide, hydrogen, carbon dioxide, methane, and other trace gases. The composition of the syngas can be adjusted by controlling the gasification parameters, such as temperature, pressure, residence time, and feedstock composition, to meet specific requirements for downstream applications.
Gasification offers several advantages over conventional combustion technologies, including higher energy efficiency, lower emissions, and greater fuel flexibility. Syngas produced from gasification can be used as a fuel for power generation, heat production, or chemical synthesis, offering a versatile energy source that can be tailored to meet various energy needs.
Overall, the gasification process plays a crucial role in converting organic waste materials into valuable energy products, contributing to energy security, environmental sustainability, and resource efficiency. Continuous advancements in gasification technology are further enhancing its efficiency, reliability, and applicability across a wide range of industries and applications.
Syngas Production:
Syngas, short for synthesis gas, is a versatile fuel produced through the gasification process, where organic feedstocks such as biomass, coal, or municipal solid waste are converted into a mixture of gases. Syngas production involves a series of thermochemical reactions that occur in a gasifier under controlled conditions.
The composition of syngas typically includes carbon monoxide (CO), hydrogen (H2), carbon dioxide (CO2), methane (CH4), and trace amounts of other gases. The exact composition of syngas varies depending on factors such as the feedstock used, gasification process parameters, and gasifier design.
During gasification, the organic feedstock undergoes pyrolysis, oxidation, and reduction reactions. Initially, the feedstock is heated in the absence of oxygen, causing it to decompose into volatile compounds through pyrolysis. These volatile compounds are then partially oxidized by introducing a controlled amount of oxygen or steam into the gasifier, leading to the formation of CO and H2, along with CO2 and H2O.
The syngas produced by gasification has several advantages over traditional fuels. It can be produced from a variety of feedstocks, including renewable biomass sources, providing an environmentally friendly alternative to fossil fuels. Syngas can also be used as a fuel for power generation, heat production, or chemical synthesis, offering versatility in its applications.
Furthermore, syngas can serve as a feedstock for the production of valuable chemicals and fuels through processes such as Fischer-Tropsch synthesis, methanol synthesis, or ammonia synthesis. These processes allow syngas to be converted into liquid fuels, such as synthetic diesel or gasoline, as well as commodity chemicals like methanol and hydrogen.
Overall, syngas production plays a vital role in enabling the efficient utilization of organic waste materials and renewable biomass resources for energy generation and chemical production. As research and development efforts continue to improve gasification technology, syngas is poised to play an increasingly important role in the transition to a more sustainable and resource-efficient energy economy.
Biomass Gasification:
Biomass gasification is a thermochemical process that converts biomass feedstocks into syngas, a mixture of carbon monoxide, hydrogen, carbon dioxide, and methane, along with other trace gases. This process offers a sustainable and environmentally friendly way to utilize biomass resources for energy production and chemical synthesis.
The biomass gasification process typically involves four main steps: drying, pyrolysis, combustion, and gasification. In the drying stage, moisture is removed from the biomass feedstock to improve the efficiency of subsequent processes. Next, the dried biomass undergoes pyrolysis, where it is heated in the absence of oxygen, leading to the release of volatile organic compounds and the formation of char.
The volatile compounds produced during pyrolysis are then partially oxidized in the combustion zone of the gasifier, where a controlled amount of oxygen is introduced. This partial oxidation reaction generates heat and converts a portion of the biomass into carbon dioxide and water vapor. The heat generated in the combustion zone provides the energy required for the subsequent gasification reactions.
In the gasification zone of the gasifier, the remaining char and volatile compounds react with steam and additional oxygen to produce syngas. This gasification reaction occurs at elevated temperatures, typically between 700°C and 1000°C, and under controlled pressure conditions. The syngas produced in the gasification zone exits the gasifier and can be further processed and utilized for various applications.
Biomass gasification offers several advantages over traditional combustion-based methods of biomass utilization. It allows for the efficient conversion of biomass into a clean and versatile energy carrier, syngas, which can be used for power generation, heat production, and the synthesis of valuable chemicals and fuels. Additionally, biomass gasification can help reduce greenhouse gas emissions and dependence on fossil fuels, contributing to environmental sustainability and energy security.
Research and development efforts in biomass gasification technology continue to improve process efficiency, reduce costs, and expand the range of biomass feedstocks that can be effectively utilized. As a result, biomass gasification holds significant potential as a key technology for enabling the transition to a more sustainable and resource-efficient energy system
Coal Gasification:
Coal gasification is a thermochemical process that converts coal into syngas, a mixture of carbon monoxide, hydrogen, carbon dioxide, and other gases, through a series of chemical reactions. This process offers a cleaner and more efficient way to utilize coal for energy production compared to conventional combustion methods.
In coal gasification, coal is subjected to high temperatures and pressures in the presence of steam and controlled amounts of oxygen or air. The process occurs in a gasifier reactor, where coal undergoes several sequential reactions, including pyrolysis, oxidation, and gasification.
During the pyrolysis stage, coal is heated in the absence of oxygen, leading to the release of volatile organic compounds and the formation of char. These volatile compounds are then partially oxidized in the oxidation zone of the gasifier, where oxygen or air is introduced, generating heat and producing carbon dioxide and water vapor.
In the gasification zone of the gasifier, the remaining char and volatile compounds react with steam and additional oxygen to produce syngas. This gasification reaction occurs at high temperatures, typically between 700°C and 1000°C, and under controlled pressure conditions. The syngas produced in the gasification zone contains carbon monoxide and hydrogen, along with other gases, and can be further processed and utilized for various applications.
Coal gasification offers several advantages over traditional coal combustion methods. It allows for the efficient conversion of coal into a clean and versatile energy carrier, syngas, which can be used for power generation, heat production, and the synthesis of valuable chemicals and fuels. Additionally, coal gasification enables the capture and sequestration of carbon dioxide emissions, reducing the environmental impact of coal-based energy production.
Research and development efforts in coal gasification technology continue to improve process efficiency, reduce costs, and enhance environmental performance. As a result, coal gasification holds significant potential as a key technology for enabling the transition to a more sustainable and low-carbon energy system, particularly in regions with abundant coal reserves.
Biomass-to-Energy:
Biomass-to-energy refers to the process of converting biomass feedstocks into useful forms of energy, such as heat, electricity, or liquid fuels. This process plays a crucial role in harnessing renewable energy sources and reducing reliance on fossil fuels, thereby mitigating greenhouse gas emissions and promoting sustainable development.
The biomass-to-energy conversion process typically involves various technologies, including combustion, gasification, pyrolysis, and anaerobic digestion, each offering unique advantages and applications depending on the characteristics of the biomass feedstock and desired energy output.
- Combustion: Biomass combustion involves burning organic materials such as wood, agricultural residues, or dedicated energy crops to produce heat. This heat can be used directly for space heating, industrial processes, or converted into electricity through steam turbines or other heat-to-power technologies.
- Gasification: Biomass gasification converts biomass feedstocks into syngas, a mixture of carbon monoxide, hydrogen, and other gases, through a thermochemical process. Syngas can be used as a fuel for power generation, heat production, or further processed into liquid fuels or chemicals.
- Pyrolysis: Biomass pyrolysis involves heating biomass in the absence of oxygen to produce biochar, bio-oil, and syngas. Biochar can be used as a soil amendment to improve soil fertility and sequester carbon, while bio-oil can be further processed into transportation fuels or specialty chemicals.
- Anaerobic Digestion: Biomass anaerobic digestion utilizes microorganisms to break down organic materials in the absence of oxygen, producing biogas, primarily methane and carbon dioxide. Biogas can be used as a renewable fuel for heat, electricity generation, or vehicle fuel, while the residual digestate can be used as a fertilizer.
Biomass-to-energy technologies offer numerous environmental and economic benefits, including reducing greenhouse gas emissions, diverting organic waste from landfills, and promoting rural development through the utilization of locally available biomass resources. As renewable energy policies and technological advancements continue to drive the deployment of biomass-to-energy systems, they play an increasingly important role in the transition to a sustainable and low-carbon energy future.
Gasification Plant:
A gasification plant is an industrial facility designed to convert carbonaceous feedstocks, such as coal, biomass, or waste materials, into syngas through a thermochemical process known as gasification. These plants play a crucial role in producing clean and versatile energy carriers that can be used for power generation, heat production, or the synthesis of fuels and chemicals.
Gasification plants typically consist of several key components, including:
- Gasifier: The gasifier is the heart of the gasification plant, where the feedstock undergoes thermochemical reactions to produce syngas. Gasifiers can vary in design and configuration, including fixed-bed, fluidized-bed, or entrained-flow gasifiers, depending on the specific requirements of the feedstock and desired syngas composition.
- Feedstock Handling System: This system includes equipment for receiving, storing, and preparing the feedstock for gasification. Depending on the feedstock type, it may involve processes such as shredding, drying, or size reduction to optimize gasification performance.
- Gas Cleanup System: The gas produced in the gasifier contains impurities such as tar, particulates, sulfur compounds, and trace metals, which need to be removed to meet quality specifications for downstream applications. Gas cleanup systems typically include processes such as cooling, scrubbing, filtration, and catalytic conversion to remove contaminants and ensure syngas purity.
- Syngas Conditioning and Treatment: After cleanup, the syngas may undergo additional treatment to adjust its composition and properties for specific end uses. This may include processes such as water-gas shift reaction, hydrogen sulfide removal, carbon dioxide capture, and adjustment of syngas heating value.
- Syngas Utilization Systems: The purified and conditioned syngas can be used directly as a fuel for power generation, heat production, or as a feedstock for the production of synthetic fuels, chemicals, or hydrogen. Gasification plants may incorporate various syngas utilization technologies, such as gas turbines, internal combustion engines, fuel cells, or chemical reactors, depending on the intended application.
Gasification plants offer several advantages over conventional combustion-based energy systems, including higher efficiency, lower emissions, and greater fuel flexibility. They can utilize a wide range of feedstocks, including coal, biomass, agricultural residues, and municipal solid waste, making them versatile and adaptable to different regional resource availability and energy needs.
Overall, gasification plants play a critical role in the transition to a more sustainable and low-carbon energy future by enabling the efficient utilization of carbonaceous feedstocks and the production of clean and renewable energy resources. Continued advancements in gasification technology and process integration are driving further improvements in efficiency, economics, and environmental performance, ensuring their continued relevance and importance in the global energy landscape.
Syngas Generator:
A syngas generator is a device or system designed to produce syngas, a versatile fuel, from various carbonaceous feedstocks such as coal, biomass, or waste materials. Syngas generators play a vital role in providing a clean and flexible energy source for a wide range of applications, including power generation, heat production, and chemical synthesis.
Syngas generators employ thermochemical processes, such as gasification or reforming, to convert solid, liquid, or gaseous feedstocks into syngas. The specific design and operation of a syngas generator depend on factors such as the type of feedstock, desired syngas composition, and intended application.
Gasification is one of the most common methods used in syngas generators, where feedstocks are heated in a controlled environment with limited oxygen or steam. This thermochemical process breaks down the feedstock into its constituent gases, primarily carbon monoxide (CO) and hydrogen (H2), along with carbon dioxide (CO2) and methane (CH4), depending on the feedstock composition and gasification conditions.
Syngas generators typically consist of several key components:
- Gasifier: The gasifier is the core component of the syngas generator, where the gasification process takes place. Gasifiers can vary in design, including fixed-bed, fluidized-bed, or entrained-flow gasifiers, depending on the feedstock and process requirements.
- Feedstock Handling System: This system includes equipment for feeding and preparing the feedstock for gasification. Depending on the feedstock type, it may involve processes such as drying, size reduction, and feedstock conditioning to optimize gasification performance.
- Gas Cleanup System: The syngas produced in the gasifier contains impurities such as tar, particulates, sulfur compounds, and trace metals, which need to be removed to meet quality specifications for downstream applications. Gas cleanup systems typically include processes such as cooling, scrubbing, filtration, and catalytic conversion to remove contaminants and ensure syngas purity.
- Syngas Conditioning and Treatment: After cleanup, the syngas may undergo additional treatment to adjust its composition and properties for specific end uses. This may include processes such as water-gas shift reaction, hydrogen sulfide removal, carbon dioxide capture, and adjustment of syngas heating value.
- Syngas Utilization Systems: The purified and conditioned syngas can be used directly as a fuel for power generation, heat production, or as a feedstock for the production of synthetic fuels, chemicals, or hydrogen. Syngas generators may incorporate various utilization technologies, such as gas turbines, internal combustion engines, fuel cells, or chemical reactors, depending on the intended application.
Syngas generators offer several advantages, including fuel flexibility, reduced greenhouse gas emissions, and the ability to utilize a wide range of feedstocks, including renewable biomass and waste materials. Continued advancements in syngas generator technology are driving improvements in efficiency, reliability, and environmental performance, making syngas an increasingly important component of the transition to a sustainable and low-carbon energy future.
Gasification System:
A gasification system is a technological platform designed to convert carbonaceous feedstocks, such as coal, biomass, or waste materials, into a synthesis gas (syngas) through a thermochemical process known as gasification. Gasification systems play a pivotal role in enabling the efficient utilization of diverse feedstocks for energy production, chemical synthesis, and waste management.
Gasification involves subjecting the feedstock to high temperatures and controlled amounts of oxygen, steam, or a combination of both in a gasifier reactor. This thermochemical process breaks down the complex hydrocarbons present in the feedstock into simpler molecules, primarily carbon monoxide (CO) and hydrogen (H2), along with carbon dioxide (CO2) and methane (CH4), depending on the feedstock composition and gasification conditions.
The key components of a gasification system include:
- Gasifier: The gasifier is the central unit where the gasification reactions occur. Gasifiers come in various configurations, including fixed-bed, fluidized-bed, and entrained-flow designs, each offering different advantages in terms of feedstock flexibility, operating conditions, and syngas composition.
- Feedstock Preparation System: This system involves the preparation and handling of the feedstock before it enters the gasifier. Depending on the feedstock type and characteristics, it may include processes such as drying, size reduction, and feedstock conditioning to optimize gasification performance.
- Gas Cleaning and Conditioning: The syngas produced in the gasifier contains impurities such as tar, particulates, sulfur compounds, and trace metals, which need to be removed to meet quality specifications for downstream applications. Gas cleaning and conditioning systems typically include processes such as cooling, scrubbing, filtration, and catalytic conversion to remove contaminants and ensure syngas purity.
- Syngas Utilization: The purified and conditioned syngas can be utilized for various applications, including power generation, heat production, and chemical synthesis. Gasification systems may incorporate different utilization technologies, such as gas turbines, internal combustion engines, fuel cells, or chemical reactors, depending on the desired end use and economic considerations.
Gasification systems offer several advantages over conventional combustion-based energy systems, including higher efficiency, lower emissions, and greater feedstock flexibility. They can utilize a wide range of feedstocks, including coal, biomass, agricultural residues, and municipal solid waste, making them versatile and adaptable to different regional resource availability and energy needs.
Overall, gasification systems play a crucial role in the transition to a more sustainable and low-carbon energy future by enabling the efficient conversion of carbonaceous feedstocks into clean and versatile syngas, thereby reducing greenhouse gas emissions and promoting energy security and resilience. Continued advancements in gasification technology and process integration are driving further improvements in efficiency, economics, and environmental performance, ensuring their continued relevance and importance in the global energy landscape
Thermal Conversion:
Thermal conversion refers to a set of processes that harness heat to transform various organic materials into useful products such as energy, fuels, and chemicals. These processes rely on the application of heat to initiate and drive chemical reactions, leading to the conversion of feedstocks into desired end products.
There are several key thermal conversion technologies, each offering unique advantages and applications:
- Combustion: Combustion is a widely used thermal conversion process that involves burning organic materials in the presence of oxygen to release heat energy. This process is commonly used in boilers, furnaces, and power plants to produce steam for electricity generation or heat for industrial processes.
- Gasification: Gasification is a thermochemical process that converts carbonaceous feedstocks, such as coal, biomass, or waste materials, into a mixture of gases known as syngas. This process occurs in a gasifier at high temperatures and in the absence of oxygen or with limited oxygen supply. Syngas can be used as a fuel for power generation, heat production, or as a feedstock for the production of chemicals and fuels.
- Pyrolysis: Pyrolysis is a thermal decomposition process that breaks down organic materials into solid char, liquid bio-oil, and gases (syngas) in the absence of oxygen or with limited oxygen supply. The specific products generated depend on the temperature and residence time during pyrolysis. Bio-oil produced from pyrolysis can be further processed into transportation fuels or chemicals.
- Liquefaction: Liquefaction is a process that converts solid or gaseous feedstocks into liquid fuels through the application of heat and pressure. This process is commonly used in the production of biofuels from biomass feedstocks, such as lignocellulosic materials or algae.
- Torrefaction: Torrefaction is a mild pyrolysis process that thermally treats biomass at temperatures between 200°C and 300°C in the absence of oxygen. This process removes moisture and volatile compounds from biomass, resulting in a dry and energy-dense material known as torrefied biomass. Torrefied biomass can be used as a renewable fuel in combustion and gasification processes.
- Hydrothermal Carbonization (HTC): HTC is a thermal conversion process that utilizes water at elevated temperatures and pressures to convert wet biomass feedstocks into hydrochar, a carbon-rich solid material. HTC can effectively process wet and high-moisture biomass streams, such as sewage sludge, organic waste, and agricultural residues, into a stable and energy-dense biochar product.
Thermal conversion technologies offer numerous benefits, including the production of renewable energy, the valorization of biomass and waste resources, and the reduction of greenhouse gas emissions. These processes play a crucial role in the transition to a more sustainable and low-carbon energy future by enabling the efficient utilization of diverse feedstocks and the production of clean and renewable energy carriers. Continued research and development efforts are focused on improving the efficiency, economics, and environmental performance of thermal conversion technologies to accelerate their adoption and deployment on a global scale.
Carbon-Neutral Power:
Carbon-neutral power refers to electricity generation methods that produce minimal or zero net carbon dioxide (CO2) emissions over their entire lifecycle, effectively balancing the amount of CO2 released into the atmosphere with an equivalent amount of CO2 removed or offset. This concept is essential for mitigating climate change and reducing the carbon footprint associated with energy production.
Several key technologies and approaches enable the generation of carbon-neutral power:
- Renewable Energy Sources: Renewable energy sources such as solar, wind, hydroelectric, and geothermal power generate electricity without emitting CO2 during operation. These technologies harness naturally occurring energy flows or heat from the Earth’s core and convert them into electricity, providing clean and sustainable power generation options.
- Biomass Energy: Biomass energy involves the combustion or gasification of organic materials such as wood, agricultural residues, and bioenergy crops to produce heat or electricity. When sustainably managed, biomass energy can be considered carbon-neutral because the CO2 emitted during combustion is balanced by the CO2 absorbed by plants during photosynthesis.
- Carbon Capture and Storage (CCS): CCS technologies capture CO2 emissions from power plants or industrial facilities and transport them to underground geological formations for long-term storage or utilization. By preventing CO2 from entering the atmosphere, CCS can significantly reduce the carbon footprint of fossil fuel-based power generation, enabling carbon-neutral or even carbon-negative power production.
- Bioenergy with Carbon Capture and Storage (BECCS): BECCS combines biomass energy generation with CCS to achieve carbon-negative emissions. Biomass feedstocks absorb CO2 from the atmosphere as they grow, and when converted into energy and coupled with CCS, the process can result in a net removal of CO2 from the atmosphere, making it a potent tool for carbon dioxide mitigation.
- Hydropower Reservoir Management: Proper management of hydropower reservoirs can optimize power generation while minimizing methane emissions, a potent greenhouse gas released from decomposing organic matter in flooded areas. Strategies such as run-of-river hydropower or reducing the extent of reservoir flooding can help mitigate these emissions, contributing to carbon-neutral power production.
- Nuclear Power: Nuclear power plants generate electricity through nuclear fission reactions, which do not emit CO2 during operation. While nuclear power is not strictly renewable, it provides a low-carbon baseload electricity source that can help reduce greenhouse gas emissions compared to fossil fuel-based power generation.
Achieving carbon-neutral power requires a combination of renewable energy deployment, energy efficiency improvements, and the widespread adoption of low-carbon technologies such as CCS and BECCS. Policy support, technological innovation, and international collaboration are essential for accelerating the transition to a carbon-neutral energy system and combating climate change effectively.
Sustainable Energy:
Sustainable energy refers to energy sources and practices that meet present needs without compromising the ability of future generations to meet their own needs. It encompasses a broad range of technologies, policies, and strategies aimed at reducing environmental impacts, promoting economic development, and ensuring social equity in energy access and use.
Key components of sustainable energy include:
- Renewable Energy Sources: Renewable energy sources such as solar, wind, hydroelectric, geothermal, and biomass provide clean and abundant energy without depleting finite resources or emitting greenhouse gases. These sources harness natural energy flows and can be replenished over time, making them sustainable alternatives to fossil fuels.
- Energy Efficiency: Improving energy efficiency across all sectors, including buildings, transportation, industry, and agriculture, is essential for reducing energy consumption and minimizing waste. Energy-efficient technologies, building design, transportation systems, and industrial processes can significantly reduce energy demand while maintaining or improving service levels and productivity.
- Decentralized Energy Systems: Decentralized energy systems empower communities to generate, distribute, and manage their energy locally, reducing reliance on centralized power plants and transmission infrastructure. Distributed generation technologies such as rooftop solar panels, small wind turbines, and micro-hydropower systems enhance energy resilience, promote energy independence, and support local economic development.
- Energy Access: Ensuring universal access to modern, reliable, and affordable energy services is fundamental to sustainable development. Access to electricity and clean cooking fuels improves living standards, enhances health outcomes, fosters economic opportunities, and empowers communities, particularly in rural and underserved areas.
- Electrification of Transport: Electrifying transportation systems by transitioning from fossil fuel-powered vehicles to electric vehicles (EVs) reduces greenhouse gas emissions, air pollution, and reliance on imported oil. Integrating EVs with renewable energy sources and smart grid technologies enhances energy efficiency and grid stability while supporting the transition to sustainable mobility.
- Smart Grids and Energy Storage: Smart grid technologies enable the integration of renewable energy sources, demand response programs, and energy storage systems to optimize energy use, enhance grid reliability, and facilitate the transition to a more flexible and resilient energy system. Energy storage technologies such as batteries, pumped hydro, and thermal storage play a crucial role in balancing supply and demand and integrating variable renewable energy sources into the grid.
- Policy and Regulation: Effective policies, regulations, and incentives are essential for promoting sustainable energy deployment and investment, addressing market barriers, and internalizing the social and environmental costs of energy production and consumption. Policy measures such as renewable energy targets, carbon pricing mechanisms, energy efficiency standards, and financial incentives for clean energy investments can accelerate the transition to sustainable energy systems.
Sustainable energy represents a holistic approach to addressing energy challenges while advancing environmental stewardship, economic prosperity, and social equity. By embracing sustainable energy solutions, societies can create a more resilient, equitable, and environmentally sustainable energy future for generations to come.
Carbon Neutrality:
Carbon neutrality refers to achieving a balance between the amount of carbon dioxide (CO2) emissions released into the atmosphere and the amount of CO2 removed or offset from the atmosphere, resulting in a net-zero carbon footprint. This concept is crucial for mitigating climate change by reducing the accumulation of greenhouse gases in the atmosphere, which contribute to global warming and associated environmental impacts.
Achieving carbon neutrality involves several key strategies and initiatives:
- Emissions Reduction: The primary goal of carbon neutrality efforts is to minimize CO2 emissions across all sectors of society, including energy production, transportation, industry, agriculture, and buildings. This involves implementing energy efficiency measures, transitioning to renewable energy sources, adopting low-carbon technologies, and improving industrial processes to reduce emissions intensity.
- Renewable Energy Transition: Transitioning from fossil fuel-based energy sources to renewable energy sources such as solar, wind, hydroelectric, and geothermal power is essential for decarbonizing the energy sector. Renewable energy technologies generate electricity without emitting CO2 during operation, thereby reducing reliance on fossil fuels and mitigating emissions from electricity generation.
- Carbon Capture and Storage (CCS): CCS technologies capture CO2 emissions from industrial processes, power plants, and other stationary sources and store them underground or utilize them for industrial applications. By preventing CO2 from entering the atmosphere, CCS can significantly reduce emissions from sectors where complete decarbonization is challenging, such as cement production, steel manufacturing, and natural gas processing.
- Afforestation and Reforestation: Forests act as natural carbon sinks, absorbing CO2 from the atmosphere through photosynthesis and storing it in biomass and soil. Afforestation (planting trees in areas that were previously devoid of forests) and reforestation (restoring degraded or deforested areas) initiatives can enhance carbon sequestration capacity, offsetting emissions from other sources and contributing to carbon neutrality goals.
- Carbon Offsetting: Carbon offsetting involves investing in projects that reduce or remove CO2 emissions elsewhere to compensate for emissions generated by specific activities or operations. This may include funding renewable energy projects, forest conservation initiatives, methane capture projects, or community-based sustainable development projects that deliver verifiable emission reductions.
- Energy Efficiency and Conservation: Improving energy efficiency and promoting conservation practices help reduce energy consumption and associated emissions across residential, commercial, and industrial sectors. This includes implementing energy-efficient technologies, upgrading building insulation, optimizing transportation systems, and promoting sustainable land use and urban planning.
- Sustainable Agriculture Practices: Adopting sustainable agriculture practices, such as conservation tillage, crop rotation, and agroforestry, can enhance soil carbon sequestration, reduce emissions from fertilizer use and livestock, and promote biodiversity conservation. Sustainable land management practices contribute to carbon neutrality by minimizing emissions and enhancing carbon sinks in agricultural landscapes.
- Public Awareness and Education: Raising awareness about the importance of carbon neutrality, climate change, and sustainable development is essential for fostering public support and engagement. Education campaigns, outreach initiatives, and community-based programs can empower individuals, businesses, and policymakers to take action and support carbon neutrality efforts.
Overall, achieving carbon neutrality requires a comprehensive and coordinated approach involving government policies, private sector initiatives, technological innovation, and individual actions. By transitioning to a low-carbon economy and embracing sustainable practices, societies can mitigate climate change, protect ecosystems, and create a more resilient and equitable future for all.
Carbon Offsetting:
Carbon offsetting is a mechanism used to compensate for carbon dioxide (CO2) emissions generated from human activities by investing in projects that reduce or remove an equivalent amount of CO2 from the atmosphere. This approach is based on the principle of “carbon neutrality,” aiming to balance the emissions produced with equivalent reductions or removals elsewhere, effectively mitigating the overall impact on climate change.
Key aspects of carbon offsetting include:
- Project Types: Carbon offset projects encompass a wide range of activities designed to reduce greenhouse gas emissions or enhance carbon sequestration. Common project types include renewable energy projects (such as wind farms, solar parks, and hydroelectric dams), energy efficiency initiatives (such as retrofitting buildings with energy-efficient technologies), afforestation and reforestation efforts, methane capture from landfills or agricultural operations, and sustainable land management practices.
- Additionality: A crucial criterion for carbon offset projects is additionality, which means that the emissions reductions or removals achieved would not have occurred without the financial support generated by the sale of carbon offsets. Projects must demonstrate that they are going beyond business as usual and implementing measures that result in verifiable emission reductions or removals.
- Measurement and Verification: Rigorous measurement, reporting, and verification (MRV) protocols are essential for ensuring the credibility and integrity of carbon offset projects. Independent third-party organizations assess project eligibility, monitor emissions reductions or removals, and verify that the claimed carbon credits are legitimate and accurately reflect the project’s impact.
- Certification Standards: Various certification standards and programs have been established to govern carbon offset markets and ensure transparency, consistency, and environmental integrity. Leading standards include the Verified Carbon Standard (VCS), the Gold Standard, the Climate Action Reserve (CAR), and the Clean Development Mechanism (CDM) under the Kyoto Protocol. These standards provide guidelines for project development, validation, verification, and issuance of carbon credits.
- Co-Benefits: In addition to carbon mitigation, many offset projects deliver co-benefits such as improved air and water quality, biodiversity conservation, sustainable livelihoods, and social and economic development. Projects that contribute to broader sustainable development goals can attract additional support and enhance their overall environmental and social impact.
- Market Mechanisms: Carbon offsetting operates within voluntary and compliance markets. In voluntary markets, businesses, organizations, and individuals voluntarily purchase carbon offsets to reduce their carbon footprint and demonstrate environmental stewardship. Compliance markets, on the other hand, are regulated by government mandates or carbon pricing mechanisms, such as emissions trading systems (cap-and-trade) or carbon taxes, which require certain entities to offset a portion of their emissions.
- Criticism and Challenges: While carbon offsetting can play a role in climate mitigation strategies, it is not without criticism and challenges. Critics argue that offsetting may allow polluters to avoid taking meaningful action to reduce emissions at the source, leading to a false sense of environmental responsibility or “greenwashing.” Ensuring the environmental integrity and long-term effectiveness of offset projects requires robust standards, transparent accounting practices, and ongoing monitoring and evaluation.
Overall, carbon offsetting can be a valuable tool for achieving carbon neutrality and advancing global efforts to address climate change, provided that projects are carefully selected, rigorously evaluated, and transparently implemented to deliver meaningful emissions reductions and sustainable development benefits.
Bioenergy:
Bioenergy refers to energy derived from biomass, organic materials derived from plants, animals, and organic wastes, which can be converted into heat, electricity, or liquid fuels. It is a renewable energy source that plays a significant role in reducing greenhouse gas emissions, promoting energy security, and supporting rural development. Bioenergy systems utilize various conversion technologies to transform biomass into usable forms of energy, contributing to a more sustainable and diversified energy mix.
Key aspects of bioenergy include:
- Biomass Feedstocks: Bioenergy can be derived from a wide range of biomass feedstocks, including agricultural residues (such as crop residues and straw), forestry residues (such as wood chips and sawdust), energy crops (such as switchgrass and miscanthus), organic wastes (such as municipal solid waste and sewage sludge), and dedicated energy crops grown specifically for energy production.
- Conversion Technologies: Biomass can be converted into energy through several conversion technologies, including combustion, gasification, pyrolysis, anaerobic digestion, and fermentation. Combustion involves burning biomass directly to produce heat or electricity, while gasification converts biomass into a combustible gas (syngas) that can be used for power generation or as a feedstock for producing biofuels. Pyrolysis involves heating biomass in the absence of oxygen to produce bio-oil, biochar, and syngas. Anaerobic digestion utilizes microorganisms to break down organic matter in the absence of oxygen, producing biogas (a mixture of methane and carbon dioxide) that can be used for heat, power, or transportation fuel. Fermentation processes convert biomass into liquid biofuels such as ethanol and biodiesel.
- Energy Applications: Bioenergy can be used for various energy applications, including heat generation for residential, commercial, and industrial purposes; electricity generation through biomass-fired power plants; and transportation fuel production, including ethanol for blending with gasoline and biodiesel for diesel engines. Bioenergy systems can be integrated with conventional energy infrastructure or deployed as standalone systems, depending on local resource availability, energy demand, and technological considerations.
- Environmental Benefits: Bioenergy offers environmental benefits compared to fossil fuels, including reduced greenhouse gas emissions, improved air quality, and enhanced carbon sequestration potential. Biomass-derived energy sources are considered carbon-neutral or carbon-negative when accounting for the carbon dioxide absorbed by biomass during growth, effectively offsetting emissions from combustion or conversion processes. Additionally, bioenergy production can help mitigate forest fires and reduce the accumulation of organic wastes in landfills, contributing to ecosystem health and resilience.
- Sustainability Considerations: The sustainable production and use of biomass for energy purposes require careful consideration of environmental, social, and economic factors. Sustainable biomass management practices ensure the protection of biodiversity, soil and water resources, and ecosystem services while promoting social equity, land tenure rights, and rural livelihoods. Certification schemes, voluntary sustainability standards, and lifecycle assessments help assess and mitigate potential environmental and social impacts associated with bioenergy production and supply chains.
- Policy Support and Market Development: Governments, international organizations, and private sector stakeholders play key roles in supporting bioenergy development through policy incentives, research and development funding, market incentives, and capacity-building initiatives. Renewable energy targets, feed-in tariffs, tax incentives, and carbon pricing mechanisms promote investment in bioenergy projects and stimulate market demand for sustainable biofuels and bioproducts. International collaboration and knowledge sharing facilitate technology transfer, best practices dissemination, and the harmonization of bioenergy standards and regulations across regions.
Overall, bioenergy represents a versatile and renewable energy source with significant potential to contribute to climate mitigation, energy security, and sustainable development objectives. By leveraging biomass resources sustainably and deploying advanced conversion technologies, bioenergy can play a vital role in transitioning to a low-carbon, resilient, and inclusive energy system.
Biomass Gasification:
Biomass gasification is a thermochemical process that converts biomass feedstocks into a combustible gas mixture called synthesis gas or syngas. This versatile energy carrier can be used for various applications, including heat and power generation, transportation fuel production, and industrial processes. Biomass gasification offers several advantages over traditional combustion technologies, including higher energy efficiency, lower emissions, and greater fuel flexibility.
Key aspects of biomass gasification include:
- Feedstock Selection: Biomass gasification can utilize a wide range of feedstocks, including wood chips, agricultural residues, energy crops, forestry residues, municipal solid waste, and organic wastes. The choice of feedstock depends on factors such as availability, cost, energy content, and environmental considerations.
- Gasification Process: The gasification process involves heating biomass feedstocks in a controlled environment with limited oxygen (substoichiometric conditions) to produce a mixture of gases, primarily carbon monoxide (CO), hydrogen (H2), carbon dioxide (CO2), methane (CH4), and trace amounts of other gases. The gasification reactions typically occur in three stages: drying and pyrolysis (thermal decomposition of biomass into volatile compounds), gasification (partial oxidation of volatiles to produce syngas), and char conversion (oxidation of residual char to release additional gases).
- Gasifier Design: Biomass gasifiers come in various designs, including fixed-bed, fluidized-bed, entrained-flow, and downdraft gasifiers, each with unique operating characteristics and applications. Fixed-bed gasifiers pass biomass feedstock through a stationary bed of hot inert material (e.g., sand or ceramic) to facilitate gasification reactions. Fluidized-bed gasifiers suspend biomass particles in a stream of gas (air, steam, or recycled syngas) to improve heat and mass transfer and enhance reaction kinetics. Entrained-flow gasifiers pulverize biomass into fine particles and introduce them into a high-temperature reactor with a stream of oxidizing gas to achieve rapid gasification. Downdraft gasifiers introduce biomass from the top of a vertical reactor and allow it to descend through a zone of drying, pyrolysis, and gasification, with syngas exiting from the bottom.
- Syngas Composition and Cleanup: The composition of syngas produced from biomass gasification depends on factors such as feedstock type, gasifier design, operating conditions, and process parameters. Syngas typically contains varying concentrations of CO, H2, CO2, CH4, tars, particulates, and trace contaminants such as sulfur and nitrogen compounds. Syngas cleanup technologies remove impurities and contaminants to meet specific end-use requirements, including gas cooling and quenching, particulate removal, tar cracking and reforming, sulfur and nitrogen removal, and gas conditioning (e.g., moisture removal and temperature adjustment).
- Syngas Utilization: Syngas can be utilized through various conversion pathways, including combustion in internal combustion engines, gas turbines, or boilers for heat and power generation; catalytic synthesis for production of liquid fuels (e.g., methanol, ethanol, Fischer-Tropsch diesel) and chemicals (e.g., ammonia, hydrogen); and biological conversion to produce biofuels (e.g., biohydrogen, biomethane) or biochemicals (e.g., ethanol, organic acids). Integrated gasification combined cycle (IGCC) systems combine gasification with steam turbine and combined cycle technologies to achieve high overall energy efficiency and low emissions.
- Environmental and Economic Considerations: Biomass gasification offers several environmental benefits, including reduced greenhouse gas emissions, improved air quality (due to lower emissions of sulfur dioxide, nitrogen oxides, and particulates), and enhanced waste management through utilization of organic residues and wastes. However, gasification also poses challenges related to feedstock availability and logistics, technology complexity and reliability, capital and operating costs, and regulatory and policy considerations. Life cycle assessments (LCAs) and techno-economic analyses (TEAs) help evaluate the environmental and economic performance of biomass gasification systems and inform decision-making regarding technology deployment and investment.
In summary, biomass gasification represents a promising pathway for converting renewable biomass resources into clean and versatile energy carriers, offering significant potential to contribute to sustainable energy production, climate mitigation, and rural development objectives. Continued research, development, and deployment efforts are essential to overcome technical, economic, and institutional barriers and realize the full potential of biomass gasification technologies.
Gasification Plant:
A gasification plant is a facility that utilizes gasification technology to convert various feedstocks, such as biomass, coal, petroleum coke, or municipal solid waste, into a synthesis gas (syngas) that can be used for heat, power, or chemical production. Gasification plants play a crucial role in the transition to a more sustainable and low-carbon energy system by enabling the utilization of diverse feedstocks and reducing greenhouse gas emissions compared to conventional combustion technologies.
Key aspects of gasification plants include:
- Feedstock Preparation: Gasification plants require feedstocks with specific characteristics to ensure efficient operation and high-quality syngas production. Feedstock preparation involves size reduction (e.g., grinding or shredding) to increase surface area and facilitate conversion reactions, moisture removal to improve gasification efficiency and reduce energy consumption, and feedstock blending to optimize process performance and syngas composition. Depending on the feedstock type and availability, gasification plants may source feedstocks from various suppliers or integrate with upstream biomass processing facilities.
- Gasification Reactors: Gasification plants employ various types of gasification reactors, including fixed-bed, fluidized-bed, entrained-flow, and plasma gasifiers, each with distinct operating principles and performance characteristics. Fixed-bed gasifiers pass feedstock through a stationary bed of hot inert material (e.g., sand or ceramic) to promote gasification reactions and syngas production. Fluidized-bed gasifiers suspend feedstock particles in a stream of gas (air, steam, or recycled syngas) to enhance heat and mass transfer and improve reaction kinetics. Entrained-flow gasifiers pulverize feedstock into fine particles and introduce them into a high-temperature reactor with a stream of oxidizing gas to achieve rapid gasification. Plasma gasifiers utilize electrical plasma arcs to generate high temperatures and break down feedstock molecules into syngas components.
- Syngas Cleanup and Conditioning: The syngas produced by gasification reactors typically contains impurities such as tars, particulates, sulfur compounds, nitrogen compounds, and trace contaminants, which must be removed or reduced to meet specific end-use requirements. Syngas cleanup and conditioning technologies include gas cooling and quenching, particulate removal (e.g., cyclones, filters), tar cracking and reforming (e.g., catalytic tar reforming, thermal cracking), sulfur and nitrogen removal (e.g., desulfurization, denitrification), moisture removal (e.g., condensation, absorption), and gas composition adjustment (e.g., hydrogen-to-carbon monoxide ratio adjustment).
- Syngas Utilization: Cleaned and conditioned syngas can be utilized through various conversion pathways to produce heat, power, fuels, and chemicals. Common syngas utilization options include combustion in internal combustion engines, gas turbines, or boilers for heat and power generation; catalytic synthesis for production of liquid fuels (e.g., methanol, Fischer-Tropsch diesel) and chemicals (e.g., ammonia, hydrogen); and biological conversion to produce biofuels (e.g., biohydrogen, biomethane) or biochemicals (e.g., ethanol, organic acids). Integrated gasification combined cycle (IGCC) systems combine gasification with steam turbine and combined cycle technologies to achieve high overall energy efficiency and low emissions.
- Environmental and Economic Considerations: Gasification plants offer several environmental and economic benefits compared to conventional combustion technologies, including higher energy efficiency, lower greenhouse gas emissions, reduced air pollution, and improved waste management. However, gasification also poses challenges related to feedstock availability and logistics, technology complexity and reliability, capital and operating costs, and regulatory and policy considerations. Life cycle assessments (LCAs) and techno-economic analyses (TEAs) help evaluate the environmental and economic performance of gasification plants and inform decision-making regarding technology deployment and investment.
In summary, gasification plants represent a versatile and environmentally friendly approach to converting diverse feedstocks into valuable energy products, supporting the transition to a more sustainable and resilient energy system. Continued research, development, and deployment efforts are essential to overcome technical, economic, and institutional barriers and realize the full potential of gasification technologies in addressing energy and environmental challenges.
Gasification System:
A gasification system is a comprehensive engineering solution that integrates various components and processes to convert solid, liquid, or gaseous feedstocks into a synthesis gas (syngas) suitable for a wide range of energy and chemical applications. Gasification systems play a vital role in the utilization of renewable and alternative feedstocks, such as biomass, coal, waste, and other organic materials, by transforming them into a clean and versatile energy carrier.
Key components and processes of a gasification system include:
- Feedstock Handling and Preparation: Gasification systems require suitable feedstock handling and preparation facilities to receive, store, and process feedstocks before they enter the gasification reactor. Depending on the feedstock type and characteristics, this may involve size reduction (e.g., grinding, shredding), drying to remove moisture, blending to achieve desired composition, and feedstock conditioning to optimize gasification performance.
- Gasification Reactor: The heart of a gasification system is the gasification reactor, where feedstocks undergo thermochemical conversion in a controlled environment to produce syngas. Gasification reactors come in various configurations, including fixed-bed, fluidized-bed, entrained-flow, and plasma gasifiers, each offering unique advantages and operating characteristics. These reactors utilize heat, pressure, and a controlled supply of oxidizing agent (e.g., air, oxygen, steam) to initiate gasification reactions and generate syngas.
- Syngas Cleanup and Conditioning: The syngas produced by the gasification reactor contains impurities such as tars, particulates, sulfur compounds, nitrogen compounds, and trace contaminants, which must be removed or reduced to meet specific quality requirements for downstream utilization. Syngas cleanup and conditioning technologies include gas cooling and quenching, particulate removal (e.g., cyclones, filters), tar cracking and reforming (e.g., catalytic tar reforming, thermal cracking), sulfur and nitrogen removal (e.g., desulfurization, denitrification), moisture removal (e.g., condensation, absorption), and gas composition adjustment (e.g., hydrogen-to-carbon monoxide ratio adjustment).
- Syngas Utilization: Cleaned and conditioned syngas can be utilized through various conversion pathways to produce heat, power, fuels, and chemicals. Common syngas utilization options include combustion in internal combustion engines, gas turbines, or boilers for heat and power generation; catalytic synthesis for production of liquid fuels (e.g., methanol, Fischer-Tropsch diesel) and chemicals (e.g., ammonia, hydrogen); and biological conversion to produce biofuels (e.g., biohydrogen, biomethane) or biochemicals (e.g., ethanol, organic acids). Integrated gasification combined cycle (IGCC) systems combine gasification with steam turbine and combined cycle technologies to achieve high overall energy efficiency and low emissions.
- Control and Monitoring Systems: Gasification systems require sophisticated control and monitoring systems to ensure safe and efficient operation, optimize process performance, and comply with regulatory requirements. These systems typically include sensors, actuators, controllers, and software interfaces that monitor key process parameters (e.g., temperature, pressure, flow rates), adjust operating conditions in real-time, and provide operators with real-time data and insights to support decision-making and troubleshooting.
- Environmental and Economic Considerations: Gasification systems offer several environmental and economic benefits compared to conventional combustion technologies, including higher energy efficiency, lower greenhouse gas emissions, reduced air pollution, and improved waste management. However, gasification also poses challenges related to feedstock availability and logistics, technology complexity and reliability, capital and operating costs, and regulatory and policy considerations. Life cycle assessments (LCAs) and techno-economic analyses (TEAs) help evaluate the environmental and economic performance of gasification systems and inform decision-making regarding technology deployment and investment.
In summary, gasification systems represent a versatile and environmentally sustainable approach to converting a wide range of feedstocks into valuable energy products, supporting the transition to a more resilient and low-carbon energy system. Continued innovation, research, and collaboration are essential to overcome technical, economic, and institutional barriers and realize the full potential of gasification technologies in addressing global energy and environmental challenges.
Gasification System:
A gasification system is a complex engineering arrangement designed to convert various feedstocks into a gaseous mixture called synthesis gas or syngas. This process involves the partial oxidation of the feedstock at elevated temperatures in a controlled environment. Gasification systems are versatile and can utilize a wide range of feedstocks, including coal, biomass, municipal solid waste, and petroleum coke, to produce syngas, which can be used for power generation, heat production, and the synthesis of valuable chemicals and fuels.
Here’s a detailed overview of the components and processes involved in a typical gasification system:
- Feedstock Preparation: Before entering the gasification reactor, feedstocks undergo preparation to optimize their suitability for the gasification process. This may involve grinding, shredding, drying, and sizing to reduce particle size, moisture content, and increase surface area for efficient gasification.
- Gasification Reactor: The gasification reactor is the core component of the system where the actual gasification process takes place. Various types of gasification reactors exist, including fixed-bed, fluidized-bed, entrained-flow, and plasma gasifiers. These reactors operate at high temperatures and pressures, typically ranging from 700°C to 1500°C, and use a controlled supply of oxygen, air, or steam to initiate chemical reactions that convert the feedstock into syngas.
- Syngas Cleanup and Conditioning: The syngas produced in the gasification reactor contains impurities such as tars, particulates, sulfur compounds, and nitrogen compounds, which must be removed or reduced to meet quality standards for downstream applications. Syngas cleanup and conditioning processes involve cooling, filtration, scrubbing, and chemical treatment to remove contaminants and adjust the composition of the syngas.
- Syngas Utilization: Cleaned and conditioned syngas can be utilized through various pathways to produce energy or chemicals. Common syngas utilization methods include combustion in gas turbines or boilers to generate heat and electricity, conversion to liquid fuels through Fischer-Tropsch synthesis or methanol synthesis, and production of hydrogen or ammonia for industrial applications.
- Heat Recovery: Gasification systems often incorporate heat recovery mechanisms to maximize energy efficiency. Heat recovered from syngas cooling and cleanup processes can be used to preheat feedstock or generate steam for power generation or other industrial processes.
- Control and Monitoring Systems: Gasification systems rely on sophisticated control and monitoring systems to maintain optimal operating conditions and ensure safe and efficient operation. These systems include sensors, actuators, and control algorithms to monitor process parameters, adjust operating parameters, and provide real-time feedback to operators.
- Environmental Considerations: Gasification systems offer several environmental benefits compared to conventional combustion technologies, including lower greenhouse gas emissions, reduced air pollution, and potential for carbon capture and storage. However, environmental considerations such as emissions of criteria pollutants, management of ash and by-products, and potential impacts on air and water quality must be addressed to ensure sustainable operation.
- Economic Viability: The economic viability of gasification systems depends on factors such as feedstock availability and cost, capital investment, operating expenses, and revenue from syngas and by-product sales. Techno-economic analysis is often used to evaluate the financial feasibility of gasification projects and identify opportunities for cost optimization.
In summary, gasification systems offer a flexible and efficient means of converting diverse feedstocks into valuable products while minimizing environmental impacts. Continued research and development are essential to further improve the performance, reliability, and cost-effectiveness of gasification technologies for widespread deployment in the transition to a low-carbon energy future.
Gasification System:
Gasification systems are intricate engineering setups designed to convert various carbonaceous feedstocks into a gaseous mixture known as syngas, which is rich in hydrogen and carbon monoxide. This process occurs under controlled conditions of temperature, pressure, and oxygen supply to facilitate the chemical reactions necessary for gasification. Let’s delve into the components and functions of a gasification system:
- Feedstock Handling and Preparation: This stage involves receiving, storing, and preparing the feedstock for gasification. Depending on the feedstock type (biomass, coal, waste), preparation may include shredding, drying, and size reduction to enhance its suitability for the gasification process.
- Gasification Reactor: At the core of the system lies the gasification reactor, where the actual conversion of feedstock into syngas takes place. Various types of gasifiers exist, including fixed-bed, fluidized-bed, and entrained-flow gasifiers, each with unique characteristics and operating conditions. Gasification reactions occur in the presence of a controlled amount of oxygen or steam at high temperatures, typically ranging from 700°C to 1500°C.
- Syngas Cleanup and Conditioning: The syngas produced in the reactor contains impurities such as tars, particulates, sulfur compounds, and nitrogen compounds, which need to be removed or reduced to meet quality standards. Syngas cleanup involves processes like cooling, filtration, scrubbing, and catalytic conversion to remove contaminants and adjust the composition of the syngas to meet downstream requirements.
- Heat Recovery: Gasification systems often incorporate heat recovery mechanisms to maximize energy efficiency. Heat generated during syngas cooling and cleanup processes can be recovered and utilized for various purposes such as preheating feedstock, generating steam, or supplying heat to industrial processes.
- Syngas Utilization: The cleaned and conditioned syngas can be utilized through various pathways depending on the intended application. Common utilization routes include combustion in gas turbines or boilers for power generation, conversion to liquid fuels or chemicals via catalytic processes like Fischer-Tropsch synthesis or methanol synthesis, and production of hydrogen or ammonia for industrial purposes.
- Control and Monitoring Systems: Gasification systems require sophisticated control and monitoring systems to ensure safe and efficient operation. These systems include sensors, actuators, and control algorithms that monitor key process parameters, adjust operating conditions in real-time, and provide feedback to operators to optimize performance and maintain system integrity.
- Environmental Considerations: Gasification offers several environmental benefits compared to conventional combustion technologies, including lower greenhouse gas emissions, reduced air pollution, and potential for carbon capture and storage. However, environmental considerations such as emissions of criteria pollutants, management of by-products like ash and slag, and potential impacts on local air and water quality must be addressed to ensure sustainable operation.
- Economic Viability: The economic viability of gasification systems depends on factors such as feedstock availability and cost, capital investment, operating expenses, and revenue from syngas and by-product sales. Techno-economic analysis is often employed to evaluate the financial feasibility of gasification projects and identify opportunities for cost optimization and risk mitigation.
In summary, gasification systems represent a promising technology for converting a wide range of feedstocks into valuable products while minimizing environmental impacts. Continued research, innovation, and collaboration are crucial to further improve the efficiency, reliability, and cost-effectiveness of gasification processes for widespread adoption in the transition to a sustainable energy future.
Gasification System:
Gasification systems are advanced engineering solutions designed to convert various carbonaceous feedstocks into a valuable energy carrier known as syngas or synthesis gas. These systems operate through a series of thermochemical processes that involve the partial oxidation of feedstocks at high temperatures in a controlled environment. Here’s an in-depth look at the components and functions of a typical gasification system:
- Feedstock Handling and Preparation: Gasification begins with the handling and preparation of the feedstock, which can include biomass, coal, municipal solid waste, or even organic residues. Feedstock preparation involves size reduction, drying, and sometimes pelletization to optimize its physical and chemical properties for efficient gasification.
- Gasification Reactor: The heart of the gasification system is the gasification reactor, where the actual conversion of feedstock into syngas occurs. Gasification reactors come in various configurations such as fixed-bed, fluidized-bed, entrained-flow, and plasma gasifiers, each offering unique advantages in terms of feedstock flexibility, residence time, and temperature control. Within the reactor, feedstock undergoes thermochemical reactions in the presence of a controlled amount of oxygen, air, or steam, resulting in the production of syngas.
- Syngas Cleanup and Conditioning: The raw syngas produced in the gasification reactor contains impurities such as tars, particulates, sulfur compounds, and trace contaminants that need to be removed or reduced to meet quality standards for downstream applications. Syngas cleanup and conditioning processes involve cooling, filtration, scrubbing, and chemical treatment to purify the syngas and adjust its composition to desired specifications.
- Heat Recovery: Gasification systems often incorporate heat recovery mechanisms to maximize energy efficiency and minimize waste heat. Heat recovered from syngas cooling and cleanup processes can be utilized for various purposes such as preheating feedstock, generating steam for power generation, or supplying heat to industrial processes, thereby improving overall system efficiency.
- Syngas Utilization: Cleaned and conditioned syngas can be utilized through various pathways to produce heat, power, fuels, and chemicals. Common syngas utilization routes include combustion in gas turbines or boilers for electricity generation, conversion to liquid fuels through Fischer-Tropsch synthesis or methanol synthesis, and production of hydrogen or ammonia for industrial applications.
- Control and Monitoring Systems: Gasification systems rely on sophisticated control and monitoring systems to ensure safe and efficient operation. These systems include sensors, actuators, and control algorithms that continuously monitor process parameters such as temperature, pressure, flow rates, and composition, and make automatic adjustments to maintain optimal operating conditions.
- Environmental Considerations: While gasification offers several environmental benefits compared to conventional combustion technologies, such as lower greenhouse gas emissions and reduced air pollution, it also poses environmental challenges related to emissions of criteria pollutants, management of by-products like ash and slag, and potential impacts on local air and water quality. Effective environmental management strategies are essential to mitigate these impacts and ensure the sustainability of gasification systems.
- Economic Viability: The economic viability of gasification systems depends on factors such as feedstock availability and cost, capital investment, operating expenses, and revenue from syngas and by-product sales. Techno-economic analysis plays a crucial role in assessing the financial feasibility of gasification projects and identifying opportunities for cost optimization and risk mitigation.
In conclusion, gasification systems represent a versatile and sustainable technology for converting diverse feedstocks into valuable products while minimizing environmental impacts. Continued research, innovation, and collaboration are essential to further improve the efficiency, reliability, and cost-effectiveness of gasification processes for widespread adoption in the global energy landscape.
EMS Power Machines
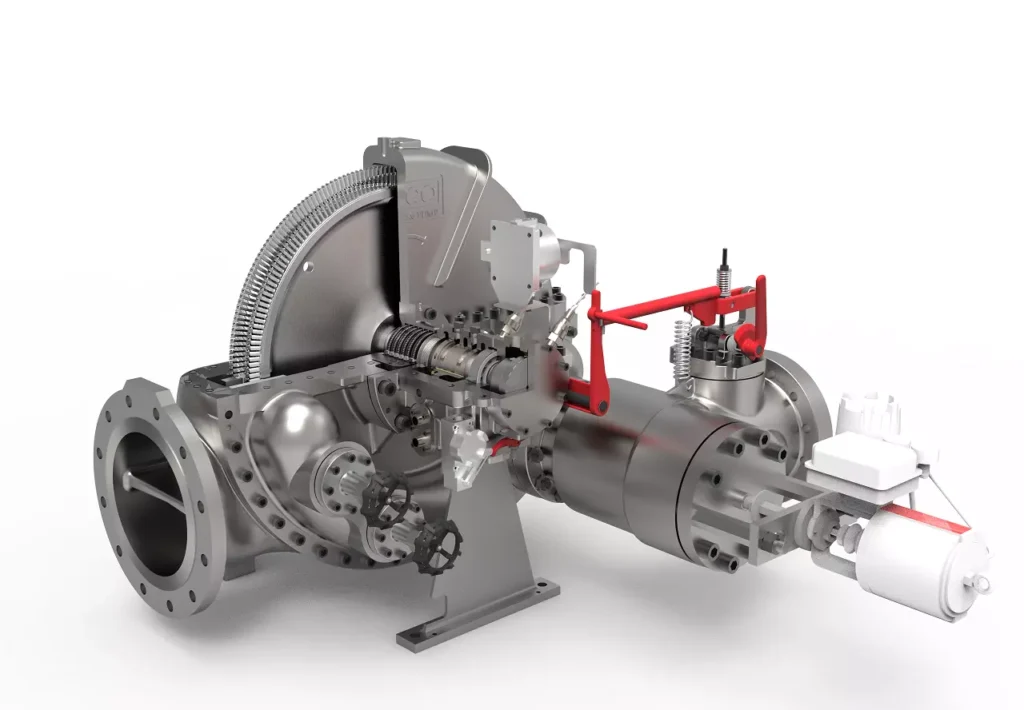
We design, manufacture and assembly Power Machines such as – diesel generators, electric motors, vibration motors, pumps, steam engines and steam turbines
EMS Power Machines is a global power engineering company, one of the five world leaders in the industry in terms of installed equipment. The companies included in the company have been operating in the energy market for more than 60 years.
EMS Power Machines manufactures steam turbines, gas turbines, hydroelectric turbines, generators, and other power equipment for thermal, nuclear, and hydroelectric power plants, as well as for various industries, transport, and marine energy.
EMS Power Machines is a major player in the global power industry, and its equipment is used in power plants all over the world. The company has a strong track record of innovation, and it is constantly developing new and improved technologies.
Here are some examples of Power Machines’ products and services:
- Steam turbines for thermal and nuclear power plants
- Gas turbines for combined cycle power plants and industrial applications
- Hydroelectric turbines for hydroelectric power plants
- Generators for all types of power plants
- Boilers for thermal power plants
- Condensers for thermal power plants
- Reheaters for thermal power plants
- Air preheaters for thermal power plants
- Feedwater pumps for thermal power plants
- Control systems for power plants
- Maintenance and repair services for power plants
EMS Power Machines is committed to providing its customers with high-quality products and services. The company has a strong reputation for reliability and innovation. Power Machines is a leading provider of power equipment and services, and it plays a vital role in the global power industry.
EMS Power Machines, which began in 1961 as a small factory of electric motors, has become a leading global supplier of electronic products for different segments. The search for excellence has resulted in the diversification of the business, adding to the electric motors products which provide from power generation to more efficient means of use.