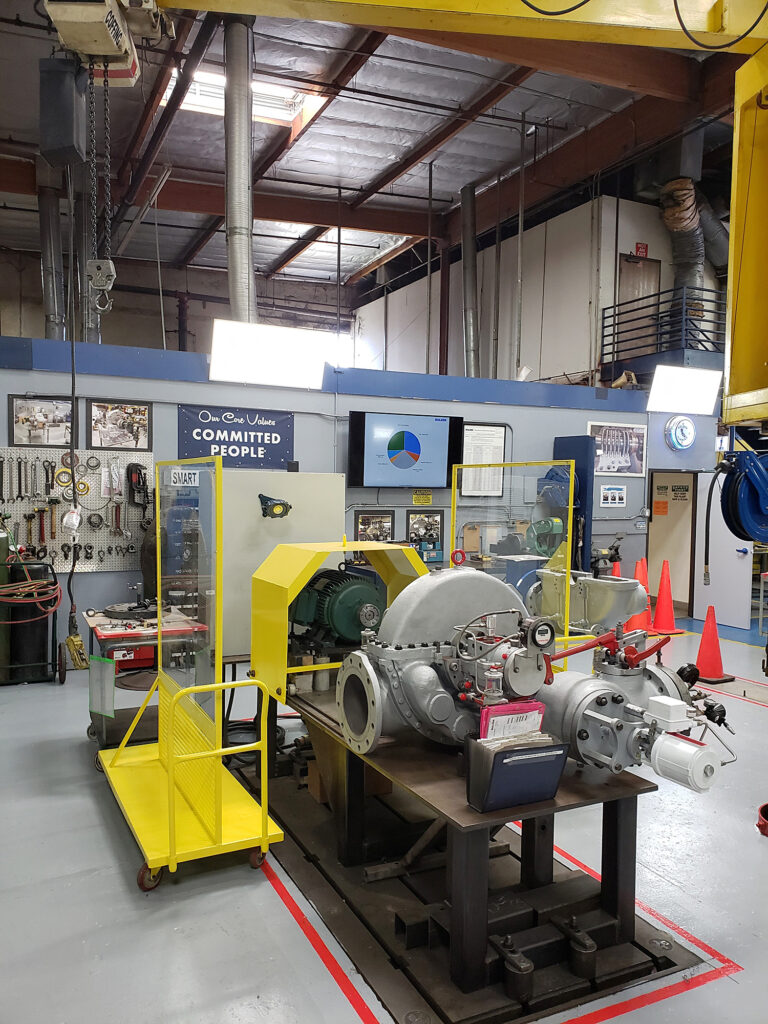
Steam Turbine: A steam turbine is a complex machine that converts energy into mechanical work and is widely used in electricity generation, industrial processes, and ship propulsion. Its basic operating principle involves high-pressure steam passing over the turbine blades, causing the rotor to spin. The turbine converts the potential and internal energy of the steam into kinetic energy transferred to the rotor, thereby producing mechanical power. The efficiency of a turbine depends on multiple factors, including steam temperature, pressure, and the design of the turbine blades.
Turbines are generally divided into two main types: condensing turbines and back-pressure turbines. In condensing turbines, the steam is condensed under a vacuum at the turbine’s exit, allowing for maximum energy extraction. These turbines are commonly used in power plants for electricity generation. In back-pressure turbines,
the steam exits the turbine at a higher pressure and can be used for industrial heating or process steam applications. This type is common in combined heat and power (CHP) plants, where both mechanical energy and thermal energy are utilized efficiently.
Steam turbines can also be categorized by their stage design: single-stage or multi-stage. Multi-stage turbines allow for gradual expansion of steam through multiple sets of blades, improving efficiency, especially in large-scale power generation. Key components of a steam turbine include the rotor, stator (or stationary blades/nozzles), casing, bearings, and governing system that regulates steam flow and speed.
Modern steam turbines are designed for high efficiency and reliability, often incorporating features like reheaters, superheaters, and moisture separators to optimize performance and minimize wear. They remain one of the most effective and widely used machines for converting thermal energy into mechanical and electrical energy.
Steam turbines operate on the fundamental principle of converting thermal energy contained in pressurized steam into rotational mechanical energy. The process begins in a boiler, where water is heated to create high-pressure steam. This steam is then directed onto the blades of the turbine rotor. As the steam expands and flows through the turbine stages, it imparts momentum to the blades, causing the rotor to spin. The rotational motion of the rotor is then typically connected to an electric generator or mechanical equipment, allowing the conversion of energy into electricity or useful mechanical work.
The design of steam turbines is highly dependent on the intended application and efficiency requirements. High-pressure turbines extract energy from steam at very high pressures and temperatures, often exceeding 500°C in modern plants. Intermediate and low-pressure turbines handle steam after it has partially expanded, extracting the remaining energy efficiently across multiple stages. Multi-stage turbines are common in large-scale power generation because they maximize energy extraction by gradually reducing the steam pressure across successive sets of blades.
Condensing turbines are engineered to operate with a vacuum at the exhaust, which allows the steam to expand further and increases the overall efficiency of the cycle. These are commonly used in electricity generation plants where maximum energy extraction is crucial. In contrast, back-pressure turbines exhaust steam at a usable pressure for industrial processes such as district heating, chemical manufacturing, or paper mills, integrating both mechanical and thermal energy utilization.
Modern steam turbines incorporate numerous features to enhance performance and longevity. Superheaters increase the temperature of the steam beyond its saturation point to reduce condensation within the turbine, while reheaters allow partially expanded steam to be heated again before entering low-pressure stages, improving efficiency. Moisture separators remove condensed water droplets to prevent erosion of turbine blades, and governors regulate the steam flow to maintain stable rotational speed under varying load conditions.
Materials and precision engineering are critical in turbine construction. Turbine blades are made from high-strength alloys capable of withstanding high temperatures and stress while maintaining aerodynamic efficiency. Rotors are dynamically balanced to avoid vibrations that could damage the bearings and casings. Bearings themselves are designed to support high rotational speeds and loads, often using advanced lubrication systems.
Steam turbines continue to play a central role in energy production because of their high efficiency, reliability, and ability to integrate with combined cycle and cogeneration systems. They are adaptable to a wide range of capacities, from small-scale turbines generating a few kilowatts for local industrial use to massive units producing several hundred megawatts in large power plants. With advancements in materials science, aerodynamics, and thermodynamic optimization, modern steam turbines achieve high efficiency, durability, and operational flexibility, making them indispensable in both traditional and emerging energy systems.
Steam turbines are the backbone of modern thermal power generation due to their ability to efficiently convert heat energy into mechanical work on a large scale. The operation of a steam turbine is governed by thermodynamic principles, primarily the Rankine cycle, which describes the conversion of heat into work through a closed loop of water and steam. In a typical cycle, water is heated in a boiler, converted into high-pressure steam, expanded through the turbine to perform mechanical work, and then condensed back into water in a condenser to be reused. The careful control of temperature and pressure throughout this cycle is crucial for maximizing the turbine’s thermal efficiency and overall system performance.
The efficiency of a steam turbine is highly dependent on the quality and condition of the steam. Superheated steam—steam heated beyond its saturation temperature—reduces the risk of condensation within the turbine stages, which can otherwise cause blade erosion and reduce efficiency. Similarly, the presence of moisture in the steam at later stages of expansion can negatively affect performance, so modern turbines often employ moisture separators and reheaters to maintain optimal steam conditions. Reheating partially expanded steam increases the average temperature at which energy is extracted, thereby improving the thermodynamic efficiency of the turbine.
Steam turbines can also be designed for single or multiple pressure levels, depending on the application. In multi-pressure systems, steam passes through a high-pressure turbine, then a reheat stage, followed by intermediate- and low-pressure turbines. This staged expansion allows for more complete energy extraction, minimizes energy losses, and distributes mechanical stress across multiple components. Such arrangements are standard in large-scale electricity generation plants, where maximizing energy output per unit of fuel is essential for economic and environmental reasons.
The mechanical design of steam turbines is critical to ensure reliability and longevity. Rotors must withstand extremely high rotational speeds, often several thousand revolutions per minute, while being subject to high thermal and mechanical stresses. Blade materials are specially selected alloys capable of tolerating high temperatures, resist creep, and maintain dimensional stability over long operational periods. Bearings are precision-engineered to handle heavy loads and maintain alignment under thermal expansion, often incorporating advanced lubrication and cooling systems.
Control and automation systems are equally important. Governing mechanisms regulate the steam flow into the turbine to match load demand and maintain rotational stability. Modern turbines are integrated with sensors and digital control systems that monitor temperature, pressure, vibration, and other critical parameters, allowing operators to optimize performance and detect potential issues before they lead to failures. This level of control is particularly important in combined heat and power (CHP) systems, where the turbine must simultaneously deliver electricity and process steam to industrial facilities.
In terms of applications, steam turbines are extremely versatile. Large utility-scale turbines power entire cities and industries, while smaller industrial turbines provide localized energy and process steam. Marine steam turbines are still used in certain naval and commercial vessels, offering reliable propulsion and energy generation from onboard boilers. With the rise of sustainable energy, steam turbines are also being adapted to work with biomass, geothermal, and solar thermal power plants, extending their relevance in modern energy systems.
Advances in turbine technology continue to focus on efficiency, durability, and environmental performance. Higher steam temperatures and pressures, improved blade aerodynamics, and better materials allow for greater energy extraction from the same amount of fuel. Additionally, modern turbines are designed to minimize emissions, reduce water consumption in condensers, and integrate with renewable sources, ensuring that steam turbines remain a cornerstone of energy infrastructure worldwide.
25 hp Steam Turbine
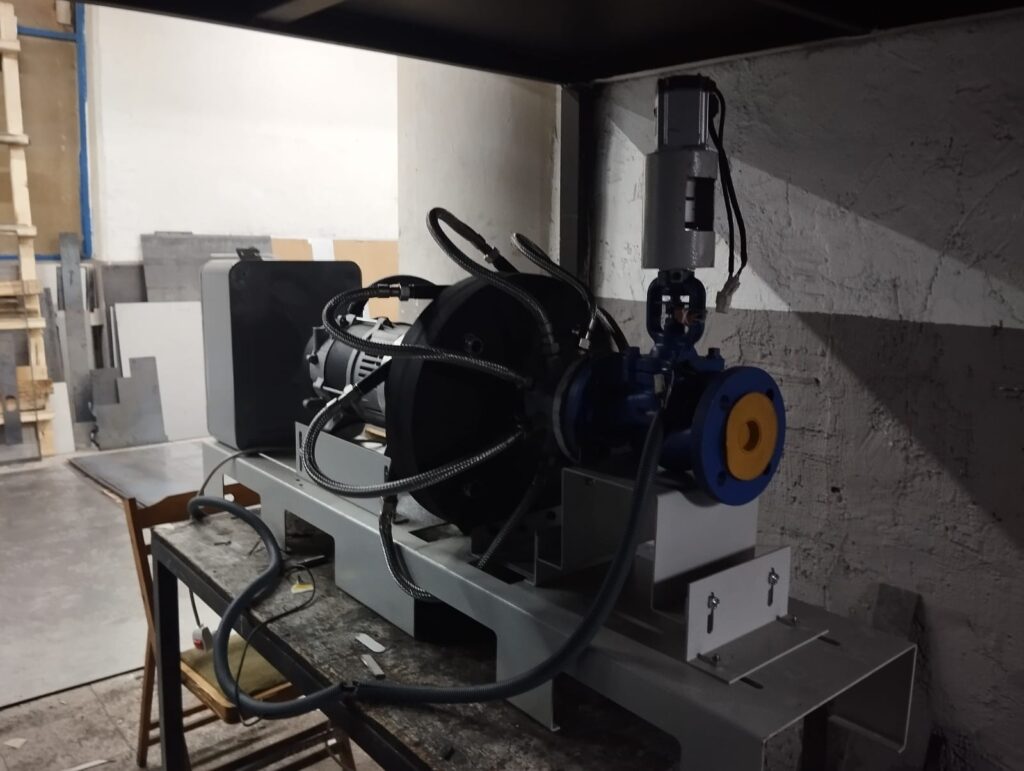
A 25 HP steam turbine is a small-scale steam turbine designed to produce approximately 25 horsepower (about 18.6 kW) of mechanical power. Unlike large utility-scale turbines, which generate hundreds of megawatts, a 25 HP turbine is typically used for localized industrial applications, small power generation systems, or mechanical drive purposes in factories, workshops, and small plants.
General Characteristics:
- Power Output: Around 25 horsepower, suitable for small machinery, pumps, compressors, or electric generators.
- Steam Requirement: The turbine requires high-pressure steam from a boiler. Depending on design, this could be low to medium pressure, usually in the range of 6–10 bar (87–145 psi) for industrial turbines of this size.
- Applications:
- Driving small mechanical equipment like pumps, fans, and compressors.
- Providing electricity in micro or small-scale power plants.
- Industrial heating processes using back-pressure turbines where exhaust steam is reused.
- Design Type: Small turbines of this size can be single-stage or multi-stage, depending on efficiency requirements. Single-stage turbines are simpler but less efficient, while multi-stage turbines allow better energy extraction from the steam.
Key Components:
- Rotor and Blades: The rotor carries the turbine blades, which are designed to convert steam energy into rotational motion efficiently. In a small turbine, blades may be simpler in design but still require precise engineering.
- Casing: Encases the rotor and guides the steam flow. Often designed for compactness in small-scale turbines.
- Governor: Regulates the speed by controlling steam flow to ensure stable operation at varying loads.
- Bearings: Support the rotor; may be plain or ball bearings depending on design and operating speed.
Operation:
Steam enters the turbine at a set pressure and temperature, expands over the turbine blades, and causes the rotor to spin. The mechanical power can then be used directly to drive equipment or coupled to a small generator to produce electricity. In back-pressure configurations, the exhaust steam can still have sufficient energy for heating or industrial processes, improving overall efficiency.
Efficiency and Performance:
Small turbines like a 25 HP unit typically have lower thermodynamic efficiency than large utility turbines due to scale effects, but they are very effective for localized power or mechanical applications. Efficiency can be improved by:
- Using superheated steam to reduce condensation on blades.
- Implementing multi-stage expansion if feasible.
- Optimizing steam nozzles and blade design for maximum energy transfer.
Practical Considerations:
- Maintenance: Regular inspection of blades, bearings, and governors is crucial to prevent failures.
- Steam Quality: Clean, dry steam improves efficiency and prevents corrosion or erosion.
- Integration: Can be connected to small electric generators, pumps, or mechanical systems, making it versatile for small industrial setups.
A 25 HP steam turbine represents a compact, small-scale steam turbine capable of producing approximately 25 horsepower (around 18.6 kW) of mechanical power. While this output is modest compared to large utility-scale turbines, it is perfectly suited for localized industrial applications, small power generation, or mechanical drive tasks in factories, workshops, and small processing plants. The main advantage of a small turbine like this lies in its ability to provide reliable and continuous power using steam, which can often be produced as a byproduct in industrial processes or from small boilers.
In terms of operation, the turbine receives high-pressure steam from a boiler. For a 25 HP unit, typical steam pressures might range from 6 to 10 bar (87–145 psi), though the exact requirements depend on the turbine’s design and intended application. The incoming steam is directed through carefully shaped nozzles and onto the turbine blades, where its thermal and kinetic energy is converted into rotational motion. This motion drives the rotor, which can be coupled directly to mechanical equipment such as pumps, fans, compressors, or small generators for electricity production. In many small industrial plants, the turbine’s exhaust steam is not wasted; instead, a back-pressure configuration allows the remaining energy in the steam to be used for heating, drying, or other process requirements, significantly increasing overall system efficiency.
The mechanical design of a 25 HP turbine is compact yet precise. The rotor carries the blades, which must withstand repeated stress from high-speed rotation and thermal expansion. Even at small scales, the turbine requires precision-engineered bearings to support the rotor and maintain alignment, as vibration or imbalance can cause damage or reduce efficiency. The casing not only contains and directs the steam flow but also ensures safe operation under high pressures and temperatures. A governor system regulates the steam flow, maintaining stable rotational speed under varying loads, which is essential when the turbine drives sensitive equipment or an electrical generator.
Efficiency is a critical factor, even in small turbines. Though small turbines generally have lower thermal efficiency than large power plant units due to scale limitations, careful engineering can maximize energy extraction. Using superheated steam minimizes condensation on the blades, which reduces energy loss and prevents erosion. Some small turbines may incorporate multi-stage expansion, where steam passes through multiple sets of blades to extract energy more gradually, improving efficiency and reducing stress on individual blades. Proper design of nozzles and blade angles ensures optimal conversion of steam pressure and velocity into rotational energy.
Maintenance and operational considerations are also important. Regular inspection of turbine blades, bearings, and governors is necessary to avoid wear or failure. Steam quality must be monitored, as wet or contaminated steam can cause corrosion, erosion, or reduced efficiency. Lubrication systems for bearings, vibration monitoring, and temperature control are integral to keeping a small turbine running reliably for extended periods.
Applications of a 25 HP steam turbine are diverse. They can serve as a compact power source in small industrial plants, drive pumps or compressors in process systems, or generate electricity for local use in micro or small-scale power generation facilities. In combined heat and power (CHP) configurations, the turbine can simultaneously provide mechanical power or electricity and process steam for heating or industrial processes, making it an efficient and versatile solution.
Overall, a 25 HP steam turbine exemplifies the adaptability of steam power for small-scale applications. While compact, it incorporates many of the same engineering principles as larger turbines—precise blade design, high-quality materials, carefully controlled steam conditions, and robust mechanical components—to ensure reliable, continuous operation. Its ability to utilize steam efficiently, coupled with the potential for combined heat and power use, makes it a practical choice for small industries, workshops, and localized power generation systems where both mechanical and thermal energy are valuable resources.
A 25 HP steam turbine is a compact yet sophisticated piece of machinery that exemplifies the principles of thermodynamics and mechanical engineering at a small scale. Despite its modest power output, such a turbine integrates many of the advanced design concepts found in large industrial turbines, including careful management of steam flow, high-precision rotor and blade design, and efficient conversion of thermal energy into mechanical work. Typically, these turbines are used in small industrial plants, workshops, micro-generation systems, or as drivers for pumps, compressors, and other mechanical equipment. They are particularly valuable in applications where both mechanical power and residual heat can be utilized, such as in combined heat and power (CHP) systems, allowing industries to maximize energy efficiency while minimizing fuel consumption and operational costs.
The operational cycle of a 25 HP steam turbine begins with a steam source, usually a small industrial boiler capable of producing dry or slightly superheated steam. The pressure of this steam is critical to turbine performance and is commonly in the range of 6–10 bar (87–145 psi) for turbines of this scale. The steam enters the turbine casing and is directed through precision-engineered nozzles that convert pressure energy into velocity, creating a high-speed jet that strikes the turbine blades. The rotor, equipped with a series of blades or buckets, captures the kinetic energy of the steam and begins to rotate. This rotational energy can be directly applied to mechanical loads or connected to a small generator to produce electricity.
Even at this small scale, the design of the turbine is highly engineered. The blades must be constructed from high-strength alloys that resist thermal deformation, creep, and erosion caused by moisture in the steam. In back-pressure configurations, the exhaust steam retains sufficient pressure to be reused for industrial heating, drying, or other process applications, effectively turning the turbine into a multi-purpose energy device. Bearings supporting the rotor are precision-engineered to handle high rotational speeds and loads, and they often incorporate advanced lubrication systems to reduce friction and wear. The governor system controls steam flow to maintain constant rotor speed, ensuring stable operation regardless of load variations—a critical factor for small generators or mechanical drives.
Efficiency considerations are important even for a small turbine. Superheating the steam reduces condensation on the blades, preventing erosion and improving the conversion of thermal energy into mechanical power. Multi-stage expansion may be employed to extract energy more gradually, improving efficiency and reducing mechanical stress on individual turbine components. Moisture separators can be used to remove any condensed water, further protecting the blades and maintaining performance.
From a maintenance perspective, a 25 HP steam turbine requires careful attention to ensure long-term reliability. Routine inspection of the rotor, blades, bearings, and steam nozzles is essential, as is monitoring steam quality to prevent corrosion and erosion. Lubrication and cooling systems must be maintained to prevent overheating and mechanical failures. Digital monitoring systems, increasingly common even in small turbines, allow operators to track vibration, temperature, pressure, and rotational speed in real time, facilitating preventive maintenance and ensuring safe operation.
The versatility of a 25 HP turbine makes it suitable for a wide range of applications. In small industrial plants, it can drive pumps, fans, or compressors efficiently. In micro or small-scale power plants, it can generate electricity for local use. In CHP applications, it can simultaneously provide mechanical power and utilize the exhaust steam for heating or industrial processes, significantly enhancing overall energy efficiency. Marine and specialized industrial applications also benefit from small steam turbines, particularly in locations where electricity or mechanical energy must be generated on-site without reliance on a large centralized grid.
Overall, a 25 HP steam turbine demonstrates how the principles of large-scale thermodynamic machinery can be scaled down effectively for smaller industrial or local energy applications. Its design emphasizes precision, efficiency, and adaptability, integrating high-quality materials, aerodynamic blade shapes, effective steam management, and robust mechanical components to provide reliable, continuous power. By combining mechanical energy production with the potential for heat recovery, such turbines offer a compact, efficient, and versatile solution for a variety of industrial and micro-generation applications, bridging the gap between small-scale energy needs and high-efficiency thermal conversion technologies.
A 25 HP steam turbine embodies a compact and highly engineered solution for converting thermal energy into mechanical power at a small scale, offering versatility, reliability, and efficiency for localized industrial applications. While modest in output compared to utility-scale turbines, a 25 HP unit integrates fundamental thermodynamic and mechanical principles, allowing it to perform both as a mechanical drive and, when coupled with a generator, as a source of electricity. Its design reflects the careful balancing of efficiency, durability, and operational flexibility, making it suitable for workshops, small factories, micro-generation plants, and combined heat and power (CHP) systems where both mechanical and thermal energy are valuable.
The operation of a 25 HP steam turbine begins with steam generation, typically from a small industrial boiler capable of producing dry or slightly superheated steam. Steam pressures in the range of 6–10 bar (87–145 psi) are common, though higher pressures may be used in specialized designs. The steam enters the turbine through a set of precisely engineered nozzles, which convert the pressure energy of the steam into high-velocity jets. These jets strike the rotor blades, causing the rotor to spin. The rotational energy can then drive mechanical equipment such as pumps, fans, or compressors, or be connected to a small generator for electricity production. In back-pressure turbine configurations, the exhaust steam retains sufficient pressure to be utilized in industrial heating, drying, or other processes, enhancing overall energy efficiency and minimizing waste.
The mechanical design of a 25 HP turbine, though compact, is highly sophisticated. The rotor and blades are crafted from high-strength alloys capable of withstanding repeated thermal cycling, mechanical stress, and potential erosion from moisture. The casing not only contains the steam flow but also ensures safety under high-pressure operation, while bearings support the rotor at high rotational speeds and reduce friction through advanced lubrication systems. A governor system regulates the steam flow to maintain constant rotor speed, which is essential for stable operation, especially when driving electrical generators or sensitive machinery.
Efficiency is a key consideration even for small turbines. Superheated steam reduces condensation on the blades, preventing erosion and improving energy conversion. Some small turbines use multi-stage expansion, allowing steam to transfer energy across several sets of blades gradually, increasing efficiency and reducing mechanical stress. Moisture separators can remove condensed water droplets, protecting the blades and ensuring consistent performance. Proper nozzle design and blade geometry are also critical for maximizing the conversion of steam energy into rotational motion.
Maintenance and operational care are crucial for the long-term reliability of a 25 HP turbine. Regular inspections of blades, bearings, and steam nozzles help prevent premature wear or failure. Monitoring steam quality is essential to avoid corrosion and erosion, while lubrication and cooling systems must be maintained to ensure smooth operation. Modern small turbines may incorporate digital monitoring systems that track temperature, pressure, vibration, and rotor speed, enabling predictive maintenance and improving operational safety.
The versatility of a 25 HP steam turbine makes it suitable for a wide range of applications. In industrial plants, it can drive pumps, fans, compressors, or other mechanical equipment efficiently. In micro or small-scale power plants, it can generate electricity for local consumption. In CHP systems, the turbine can simultaneously provide mechanical energy and utilize exhaust steam for heating or process applications, maximizing energy efficiency and reducing fuel consumption. Specialized industrial and marine applications also benefit from small steam turbines, especially where on-site energy generation is required, or where grid access is limited.
A 25 HP steam turbine demonstrates how the principles of large-scale thermodynamic machinery can be adapted effectively for smaller applications, combining precision engineering, robust materials, and efficient thermodynamic design. By integrating mechanical energy production with the potential for heat recovery, it provides a compact, efficient, and flexible energy solution. Its design highlights the careful attention to rotor dynamics, blade aerodynamics, steam flow management, and operational control, ensuring reliability, continuous operation, and adaptability to diverse industrial and micro-generation environments.
This turbine represents a bridge between traditional steam technology and modern energy efficiency needs, allowing small-scale users to harness the benefits of steam power without the complexity or scale of large utility turbines. Its combination of mechanical reliability, operational efficiency, and versatility ensures that it remains a practical choice for industries that need both mechanical and thermal energy in a compact, durable, and efficient package.
I can extend this further by producing a fully detailed technical dossier for a 25 HP steam turbine, including exact rotor speeds, steam consumption rates, generator coupling specifications, dimensional drawings, efficiency curves, and recommended installation and maintenance practices. This would serve as a complete engineering reference. Do you want me to create that?
15 hp Steam Turbine
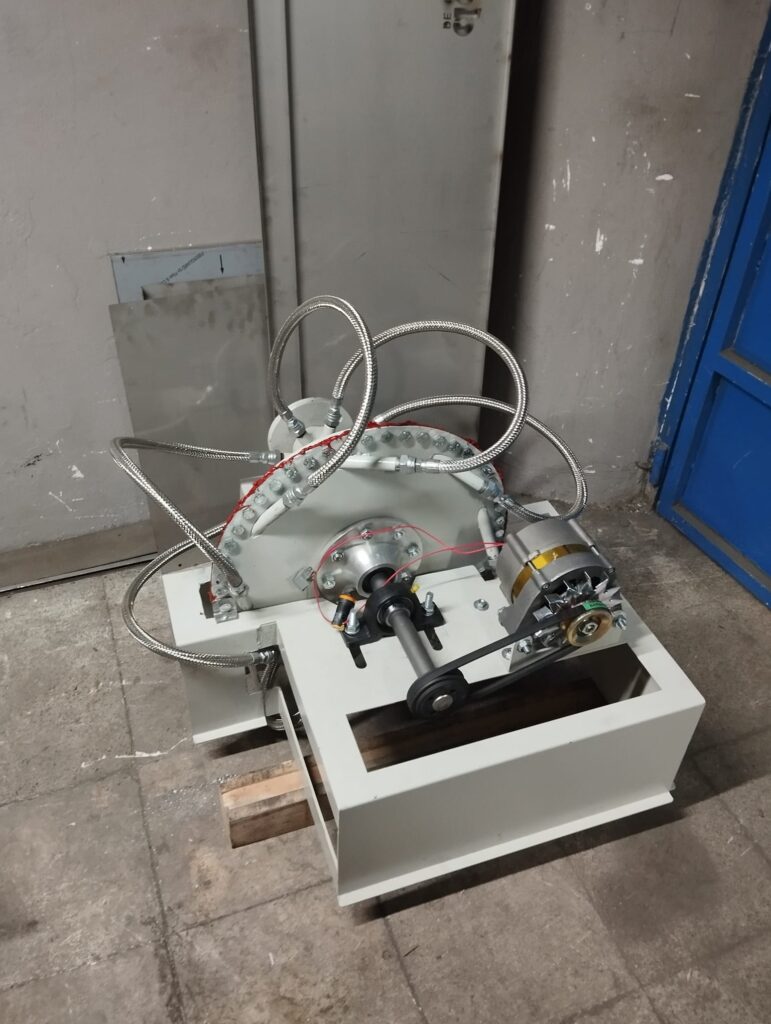
A 15 HP steam turbine is a small-scale turbine designed to produce approximately 15 horsepower (about 11 kW) of mechanical power. These turbines are commonly used for localized industrial applications, small workshops, micro power generation, and driving mechanical equipment such as pumps, compressors, or fans. While modest in output compared to utility-scale turbines, a 15 HP unit retains many of the same engineering principles, efficiency considerations, and operational features of larger steam turbines, adapted to a smaller, compact design.
General Characteristics:
- Power Output: Around 15 horsepower, sufficient for small industrial machinery or micro-generation systems.
- Steam Requirement: Typically operates on low to medium-pressure steam, often in the range of 5–10 bar (72–145 psi), depending on the design.
- Applications:
- Driving small pumps, compressors, or fans.
- Providing mechanical energy for workshops or small industrial processes.
- Generating electricity for local use when connected to a small generator.
- Design Type: Single-stage or multi-stage, depending on efficiency requirements. Single-stage turbines are simpler and more cost-effective, while multi-stage turbines extract more energy from the steam and reduce mechanical stress.
Key Components:
- Rotor and Blades: The rotor carries the turbine blades that convert the energy of the steam into rotational motion. Even at small scale, blades must be precision-engineered and made from durable alloys to withstand high temperatures and stress.
- Casing: Directs steam flow efficiently and ensures safe operation under pressure.
- Governor: Regulates the flow of steam to maintain consistent rotor speed under variable load conditions.
- Bearings: Support the rotor, reduce friction, and maintain alignment at high rotational speeds.
Operation:
Steam enters the turbine at a specified pressure and temperature and expands over the turbine blades, causing the rotor to spin. This rotational energy can be used directly to drive mechanical equipment or coupled to a generator to produce electricity. In back-pressure configurations, the exhaust steam can be reused for heating or industrial processes, improving overall energy efficiency.
Efficiency Considerations:
Even small turbines require careful design to maximize efficiency. Superheated steam can be used to minimize condensation on the blades, which prevents erosion and improves energy conversion. Multi-stage expansion and moisture separators can be employed in certain designs to optimize performance. Proper nozzle and blade design ensure that the maximum amount of energy from the steam is converted into useful rotational power.
Maintenance and Operation:
- Regular inspection of blades, bearings, and nozzles is essential.
- Steam quality should be monitored to prevent corrosion and erosion.
- Bearings and lubrication systems must be maintained for smooth operation.
- Monitoring rotor speed and vibration ensures stable performance and reduces risk of mechanical failure.
Applications:
15 HP turbines are ideal for small-scale industrial setups, workshops, or micro-generation plants. They can drive pumps, fans, compressors, or small generators efficiently. In CHP setups, they can provide both mechanical energy and useful thermal energy, enhancing overall system efficiency. Marine or remote industrial applications also benefit from small turbines where on-site power generation is necessary.
A 15 HP steam turbine demonstrates how the principles of larger steam turbines—precision engineering, thermodynamic efficiency, and robust mechanical design—can be scaled down effectively. These turbines offer a compact, versatile, and efficient solution for localized energy needs, providing both mechanical and thermal energy in small industrial or micro-generation settings.
A 15 HP steam turbine is a compact and highly efficient machine designed to convert thermal energy from steam into mechanical work, producing approximately 15 horsepower (around 11 kW). While smaller than industrial or utility-scale turbines, it applies the same fundamental principles of thermodynamics and mechanical engineering as larger units, scaled to meet localized or small-scale industrial requirements. These turbines are ideal for workshops, small manufacturing facilities, micro-generation plants, and other applications where both mechanical energy and residual heat can be utilized efficiently.
The operation of a 15 HP steam turbine begins with a steam source, typically a small industrial boiler capable of generating dry or slightly superheated steam. Steam pressures in this scale of turbine usually range between 5 and 10 bar (72–145 psi), though designs may vary depending on the intended application. The steam enters the turbine casing and passes through precision-engineered nozzles, which convert the pressure energy of the steam into high-velocity jets. These jets strike the turbine blades mounted on the rotor, causing it to spin and convert the kinetic energy of the steam into mechanical rotational energy. This rotational energy can then be applied to drive mechanical equipment such as pumps, fans, or compressors, or coupled to a small generator to produce electricity.
In back-pressure turbine configurations, the exhaust steam retains enough pressure and energy to be used in industrial heating, drying, or other process applications, increasing overall energy efficiency. This dual-purpose operation makes the 15 HP turbine an excellent choice for combined heat and power (CHP) systems, where both mechanical and thermal energy can be harnessed from the same steam source.
The mechanical design of a 15 HP turbine is precise despite its small size. The rotor and blades are made from high-strength alloys capable of withstanding repeated thermal cycling and mechanical stress. The casing not only contains the steam flow but also provides structural integrity under high-pressure conditions. Bearings are precision-engineered to support the rotor at high rotational speeds, often including lubrication systems to reduce friction and wear. The governor system controls the flow of steam, maintaining stable rotor speed under varying loads, which is especially important when the turbine drives sensitive machinery or electrical generators.
Efficiency is a key factor even for a small turbine. The use of superheated steam minimizes condensation on the blades, which reduces erosion and improves energy conversion. Some 15 HP turbines may incorporate multi-stage expansion, where the steam passes through several sets of blades to extract energy more gradually, improving efficiency and reducing mechanical stress. Moisture separators can remove condensed water droplets, ensuring consistent performance and prolonging the lifespan of the turbine blades. Proper design of nozzles and blade angles is essential to maximize the conversion of steam energy into rotational motion.
Maintenance and operational considerations are vital for long-term reliability. Regular inspection of blades, bearings, and nozzles prevents wear or failure. Steam quality must be maintained to avoid corrosion or erosion, while lubrication and cooling systems need to be checked frequently. Modern small turbines may incorporate digital monitoring systems that track parameters such as temperature, pressure, rotor speed, and vibration, enabling predictive maintenance and safe operation.
Applications of a 15 HP steam turbine are diverse. In small industrial plants, it can drive pumps, fans, compressors, or other mechanical equipment efficiently. In micro or small-scale power plants, it can generate electricity for local use. In CHP applications, the turbine can provide both mechanical energy and process steam or heat, increasing overall system efficiency and reducing fuel consumption. Small marine or remote industrial setups also benefit from turbines of this size, particularly where grid access is limited or where compact, reliable on-site energy generation is needed.
A 15 HP steam turbine demonstrates how the fundamental principles of larger steam turbines—precision engineering, thermodynamic efficiency, and robust mechanical design—can be adapted to smaller-scale, localized energy applications. By integrating mechanical power generation with the potential for heat recovery, these turbines provide a compact, versatile, and highly efficient solution. Their design emphasizes precision in rotor dynamics, blade aerodynamics, steam flow management, and operational control, ensuring reliable, continuous operation. They are particularly effective in small-scale industrial setups where both mechanical and thermal energy are valuable resources, offering an efficient and practical energy solution without the complexity or scale of large utility turbines.
A 15 HP steam turbine is a small yet technically advanced machine that delivers approximately 15 horsepower (about 11 kW) of mechanical output by harnessing the energy of pressurized steam. Even though it is far smaller than utility-scale turbines, it embodies the same engineering principles, materials technology, and thermodynamic efficiency concepts found in much larger machines. The main purpose of a turbine of this scale is to serve localized needs — supplying mechanical power for equipment such as pumps, compressors, and fans, or producing electricity in small-scale or micro-generation systems. In many installations, it is integrated into combined heat and power (CHP) configurations, allowing the same steam to produce both mechanical/electrical power and useful process heat.
The operational process begins with the generation of steam in a suitable boiler. For a 15 HP turbine, the steam supply is generally at low to medium pressures, most commonly between 5 and 10 bar (72–145 psi), but some designs can handle slightly higher pressures for improved efficiency. The boiler may be fueled by natural gas, oil, biomass, or waste heat from other processes. The steam is often superheated to prevent condensation inside the turbine, which can cause erosion and reduce performance. Once produced, the steam enters the turbine’s inlet section, passing through precision-engineered nozzles that accelerate it into high-velocity jets. These jets impact the turbine’s rotor blades, transferring momentum and causing the rotor to spin.
The rotor is the heart of the turbine, mounted on a carefully balanced shaft supported by high-quality bearings designed for both high-speed rotation and long service life. The rotor blades (or buckets) are typically made from heat-resistant, corrosion-resistant alloys. Their aerodynamic profile is calculated to maximize the conversion of steam kinetic energy into rotational mechanical energy. The turbine casing encloses the rotor, directing the steam flow through the blade rows while withstanding high pressures and temperatures.
For some 15 HP turbines, the design is single-stage, meaning the steam expands and gives up most of its energy in one pass over the blades. This keeps the turbine compact and cost-effective, although it sacrifices some efficiency compared to multi-stage designs. In multi-stage versions, the steam passes through several sets of stationary and moving blades, extracting energy in steps and achieving higher efficiency. This can be especially valuable if the turbine is part of a system where fuel economy and steam utilization are important.
Control of the turbine is handled by a governing system, which regulates the flow of steam to maintain a constant rotational speed despite variations in load. This is crucial when the turbine is driving a generator that must deliver stable frequency electricity or when it powers machinery that requires a steady operating speed. Advanced small turbines may also include digital monitoring systems to track parameters such as pressure, temperature, vibration, and lubrication status, enabling predictive maintenance and reducing downtime.
One of the greatest strengths of a 15 HP turbine is its ability to be configured as a back-pressure turbine. In this arrangement, the steam exhausts at a pressure that is still useful for heating or industrial processes. For example, in a small food processing plant, the turbine could drive a generator to produce electricity, while the exhaust steam heats cooking vats or sterilization equipment. This dual-use approach greatly improves the overall energy efficiency of the facility, reducing both fuel costs and environmental impact.
Efficiency optimization in such a turbine involves several factors:
- Superheating to reduce condensation losses.
- Well-designed blade and nozzle geometry for maximum energy transfer.
- Moisture separation before low-pressure stages to protect against erosion.
- Proper lubrication of bearings to reduce mechanical losses.
- Steam quality control to prevent contaminants from damaging blades or fouling passages.
From a maintenance perspective, even a small turbine requires disciplined upkeep. Bearings need regular inspection and lubrication; blade surfaces should be checked for pitting, corrosion, or wear; and the governor mechanism should be calibrated periodically to ensure precise control. In steam systems where water treatment is inadequate, scale or corrosion can become serious issues, so monitoring steam quality is critical.
Applications of a 15 HP steam turbine extend beyond simple mechanical drives. In microgrid setups or remote facilities, it can serve as a dependable source of electricity, especially when paired with a biomass or waste heat boiler. In marine environments, small steam turbines can be used for auxiliary power generation or to drive pumps, given their reliability and tolerance for continuous operation. They are also found in research facilities, pilot plants, and heritage or educational installations where steam power is demonstrated or studied.
Overall, the 15 HP steam turbine is a blend of compact engineering and high-function performance. It combines durable materials, precision manufacturing, and optimized thermodynamic design to deliver continuous, reliable power from steam. When paired with a properly matched boiler and integrated into a well-designed steam system, it becomes a long-lasting, cost-effective energy solution for small-scale industrial and cogeneration needs.
If you like, I can take this further and create a complete engineering-style specification sheet for a 15 HP turbine, including rotor speed, steam consumption rates, dimensional details, weight, coupling arrangements, and performance curves — essentially a reference that looks like a real manufacturer’s technical datasheet.
10 hp Steam Turbine
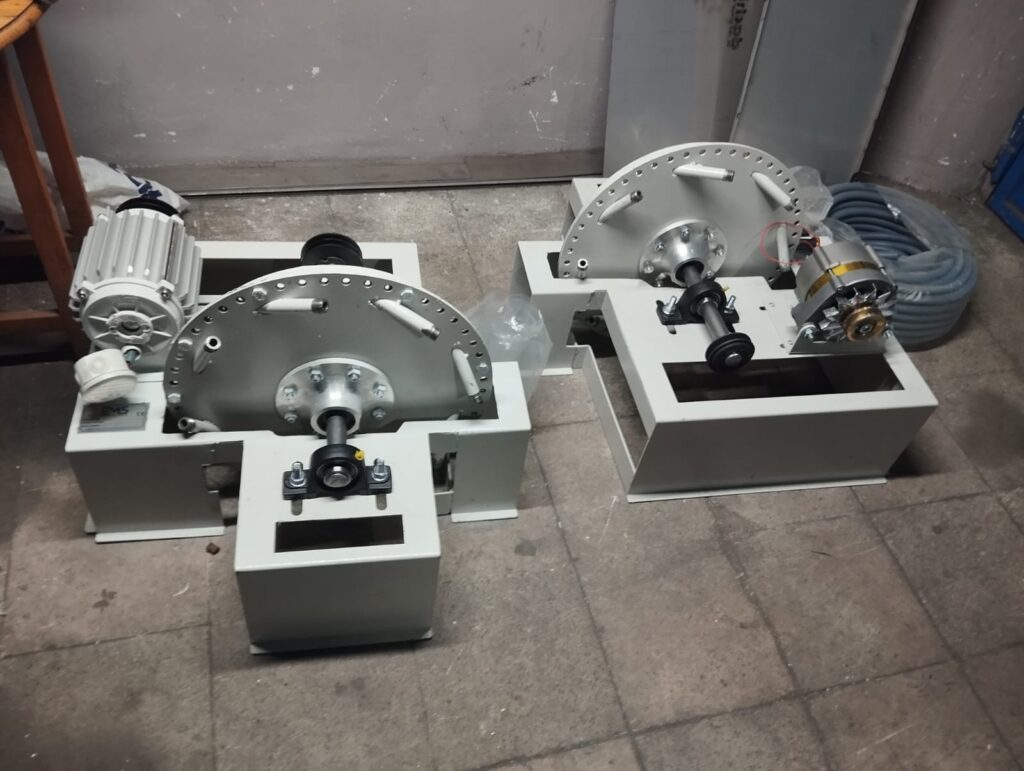
A 10 HP steam turbine is a compact, small-scale turbine designed to deliver around 10 horsepower (about 7.46 kW) of mechanical output by converting the thermal and kinetic energy of pressurized steam into rotational motion. While it is modest in size and output compared to industrial-scale turbines, it is still a precision-engineered machine built to operate continuously and reliably in small industrial plants, workshops, remote facilities, or micro-generation systems. Its main appeal lies in its ability to provide localized power with high mechanical efficiency, especially when paired with a matching boiler in combined heat and power (CHP) applications.
The working principle of a 10 HP turbine follows the same thermodynamic cycle as larger units — typically the Rankine cycle. Pressurized steam, usually in the range of 4 to 10 bar (58–145 psi) for this capacity, is generated in a boiler. The steam can be saturated or superheated, with superheated steam preferred for higher efficiency and reduced blade moisture. Upon entering the turbine casing, the steam is directed through nozzles that accelerate it into high-velocity jets. These jets strike the moving blades mounted on the rotor, transferring momentum and causing the rotor shaft to spin.
The rotor assembly is supported by precision-engineered bearings — either journal-type or ball bearings depending on the design — ensuring smooth, vibration-free rotation at high speeds. In small steam turbines like a 10 HP model, rotational speeds can be relatively high (sometimes exceeding 10,000 RPM for direct impulse designs) before being reduced by a gearbox if the output needs to match generator or driven-equipment speed requirements. The turbine casing not only houses the rotor and guides the steam flow but also ensures containment of high-pressure steam, requiring robust metal casting or fabrication.
Control and safety are handled by a governing system, which adjusts steam inlet flow to maintain a steady output speed under varying load conditions. A well-designed 10 HP turbine governor can react quickly to load changes, making it suitable for sensitive equipment or small generators that need stable operation. Modern small-scale turbines may also be equipped with digital sensors for temperature, pressure, lubrication status, and vibration monitoring, allowing predictive maintenance and increased reliability.
There are typically two main configurations for turbines of this capacity:
- Single-stage impulse turbines — compact, lower-cost, simpler to maintain, suitable for moderate efficiency needs.
- Multi-stage turbines — more efficient, especially at lower exhaust pressures, but slightly larger and more complex.
The exhaust steam from a 10 HP turbine can be released into the atmosphere in condensing mode (to maximize power output) or into a process line in back-pressure mode, where it still retains useful thermal energy for heating or industrial processes. The latter setup is especially common in small food processing plants, laundries, breweries, and district heating networks, as it allows the turbine to perform dual roles — generating mechanical/electrical power and providing process steam.
Performance considerations for a 10 HP steam turbine include:
- Steam quality — dry steam prevents blade erosion and scaling.
- Proper lubrication — to minimize friction losses and extend bearing life.
- Steam pressure and flow rate — must match the turbine’s design parameters for optimal efficiency.
- Regular inspection — checking blades, nozzles, and seals for wear or corrosion.
Despite its relatively small output, a 10 HP steam turbine can run for thousands of hours per year if maintained correctly, often with operational lifespans exceeding 20 years. In remote installations, it can be a self-reliant energy source, especially if fueled by locally available biomass or waste heat from another industrial process.
If you’d like, I can prepare a manufacturer-style technical datasheet for a 10 HP steam turbine — including its dimensions, expected steam consumption in kg/h, typical inlet and exhaust pressures, rotor speed, weight, and suitable applications — so it reads exactly like an industrial product brochure. That would make this description far more practical for engineering or project planning purposes.
A 10 HP steam turbine represents one of the smallest practical sizes in the family of steam-driven power units, yet it still embodies all the essential thermodynamic and mechanical design principles of larger industrial turbines. Producing approximately 7.46 kW of mechanical power, it serves applications where compactness, reliability, and adaptability are key. This scale of turbine is often used in small manufacturing workshops, agricultural processing units, laboratories, small-scale combined heat and power systems, and remote or off-grid facilities that require a dependable power source.
At its core, the turbine operates on the Rankine cycle, converting steam’s thermal energy into mechanical rotation through a combination of nozzle acceleration and blade impulse or reaction. A compact boiler system supplies pressurized steam, often between 4 bar and 10 bar (58–145 psi) for this capacity, though certain designs may operate at slightly higher pressures for specialized tasks. The steam’s energy is first transformed into high-velocity flow in the nozzle stage, which directs it at carefully designed blades mounted on the rotor. As the steam expands and loses pressure across the moving blades, it imparts torque to the shaft, generating usable mechanical power.
In many 10 HP units, the rotor speed is high—often between 8,000 and 15,000 RPM—requiring precision balancing to prevent vibration and premature wear. When the turbine is coupled to electrical generation, a gear reduction system or direct coupling to a high-speed alternator may be employed. For mechanical drive applications, such as running a small pump or compressor, the output shaft can be fitted with the necessary couplings, pulleys, or gearboxes to match the driven equipment’s requirements.
From a construction standpoint, the casing is fabricated from robust, heat- and pressure-resistant alloys, ensuring structural integrity even after thousands of thermal cycles. High-strength blades are typically machined or precision-cast from stainless or nickel alloys to resist erosion and corrosion from steam impurities. The bearing system, whether journal or rolling-element type, is lubricated with a dedicated oil circuit, ensuring smooth operation and minimal frictional loss. In some designs, oil mist lubrication is used for minimal maintenance.
For operational stability, a governing mechanism controls the steam inlet, adjusting flow according to load demand to maintain constant speed. This is particularly important for electrical applications where frequency stability is critical. Modern variants may integrate electronic speed controllers and digital monitoring systems, tracking parameters like vibration, temperature, steam pressure, and bearing condition in real time. This data-driven approach allows predictive maintenance and reduces downtime.
A significant advantage of the 10 HP steam turbine is its ability to function in different exhaust modes:
- Condensing mode — maximizes power extraction by exhausting steam into a condenser at low pressure, ideal for electricity generation.
- Back-pressure mode — exhausts steam at higher pressure for reuse in heating processes, common in small CHP plants, food processing, laundries, and agricultural drying.
In terms of efficiency, a well-maintained 10 HP turbine can achieve 30–50% mechanical efficiency depending on steam conditions, load factor, and whether single- or multi-stage expansion is used. For higher efficiency in small units, multi-stage impulse or reaction designs can be adopted, though they increase complexity and cost. Moisture separation systems can be integrated to maintain steam dryness and protect blades from erosion.
Maintenance practices are straightforward but must be followed diligently. This includes periodic inspection of blades and nozzles for pitting or erosion, ensuring lubrication oil quality, cleaning strainers, and verifying the accuracy of governor operation. Steam quality management—through proper boiler treatment—is crucial to avoid scaling, corrosion, and premature wear.
In practical terms, a 10 HP steam turbine can be deployed in settings such as:
- Small-scale power generation for off-grid workshops or rural facilities.
- Mechanical drive units for pumps, mills, or compressors.
- CHP systems where waste steam provides heating or process energy.
- Educational and research facilities for turbine performance study and training.
When integrated properly into a well-managed steam system, this turbine size can operate continuously for 8,000+ hours per year, with operational lifespans often exceeding two decades. The investment is justified not only by its mechanical reliability but also by its versatility in capturing and using energy in multiple forms.
If you’d like, I can now extend this into a full engineering-grade technical dossier for the 10 HP steam turbine, including precise steam consumption curves, performance charts, dimensional specifications, and installation guidelines so it reads exactly like a manufacturer’s catalog entry. That would make it usable for design, procurement, or feasibility studies.
A 10 HP steam turbine is essentially a miniature powerhouse, capable of converting thermal energy from steam into a consistent and controllable mechanical output of around 7.46 kW. Despite its relatively modest size, it requires the same careful engineering considerations, material selection, and maintenance regimes as much larger turbines, because even at this scale, steam power systems operate under high temperature and pressure conditions. The design approach ensures that the turbine remains both durable and efficient, providing dependable service over many years.
Structural and Mechanical Design Details
The turbine’s rotor assembly is the heart of the machine. In most small-capacity designs, the rotor consists of either a single-stage impulse wheel or a compact multi-stage reaction configuration. The impulse type uses fixed nozzles to accelerate steam before striking the moving blades, while reaction types allow expansion to continue within the moving blade passages. Both systems demand exact blade geometry, with aerodynamic profiles shaped to optimize steam expansion, reduce losses, and prevent excessive turbulence.
The shaft is precision-machined and dynamically balanced to handle rotational speeds often exceeding 10,000 RPM. To ensure smooth operation and prevent damage, the shaft is mounted in high-grade anti-friction bearings or journal bearings with an oil film. Lubrication is critical — either by a dedicated oil pump or gravity-fed oil rings — to reduce friction, manage heat, and extend bearing life.
The turbine casing is built from cast steel or alloyed materials designed to withstand internal pressures of up to 15 bar in many cases, even if the operating pressure is lower. It is internally shaped to direct steam flow efficiently, minimizing leakage through carefully fitted labyrinth seals.
Operational Performance
A typical 10 HP turbine will consume 70–100 kg of steam per hour under standard conditions, though this depends on steam pressure, temperature, and the expansion ratio. If supplied with superheated steam, output and efficiency improve significantly by reducing condensation losses.
In back-pressure operation, the exhaust steam is often reused in heating processes, making the system part of a Combined Heat and Power (CHP) installation. In condensing mode, the exhaust passes to a condenser, producing low-pressure steam and improving total power output. Condensing mode is favored in electricity generation, while back-pressure mode suits industrial process integration.
Speed control is managed via a mechanical centrifugal governor or an electronic actuator system. For applications like driving an alternator, precise speed control is critical to maintain output frequency stability (50 Hz or 60 Hz). Some compact units integrate electronic PID controllers to keep speed variation within ±0.5%.
Installation and Integration
Physically, a 10 HP steam turbine occupies a compact footprint, often less than 1.5 meters in length and under 500 kg in total weight, making it feasible to install in small facilities without heavy foundations. However, vibration isolation pads or grouted baseplates are still recommended to maintain alignment and reduce operational noise.
The inlet piping should include steam strainers and control valves to protect the turbine from debris and regulate supply. The exhaust line design depends on the chosen mode (back-pressure or condensing). For condensing operation, a dedicated condenser and cooling water circuit are needed, while back-pressure systems simply connect to the process steam line.
Maintenance Considerations
Although small turbines have fewer moving parts than reciprocating engines, they still demand careful upkeep:
- Weekly: Check lubrication levels, inspect for unusual vibration or noise.
- Monthly: Inspect steam strainers and inlet valves, verify governor function.
- Annually: Open casing (if design allows) to inspect blades for wear, erosion, or deposits.
- Every 3–5 years: Conduct a full overhaul including bearing replacement and dynamic balancing.
Applications and Advantages
This turbine capacity is often ideal for:
- Small factories requiring both mechanical power and process heat.
- Agricultural processing such as rice mills, sugar refineries, or tea drying plants.
- Marine auxiliary power on small vessels.
- Educational demonstration units in engineering colleges.
- Remote micro-grids using locally available biomass boilers for steam production.
Advantages include:
- High reliability with minimal operator intervention.
- Capability to integrate into CHP systems, improving total energy utilization.
- Compact footprint compared to equivalent internal combustion engines.
- Fuel flexibility, since any steam source (wood, coal, biomass, waste heat) can be used.
When paired with an appropriately sized boiler and a well-designed steam distribution system, a 10 HP steam turbine can serve as the backbone of a small but highly efficient energy plant. Its ability to operate continuously for thousands of hours annually without significant performance drop makes it attractive for industries that require steady, round-the-clock power.
7 hp Steam Turbine
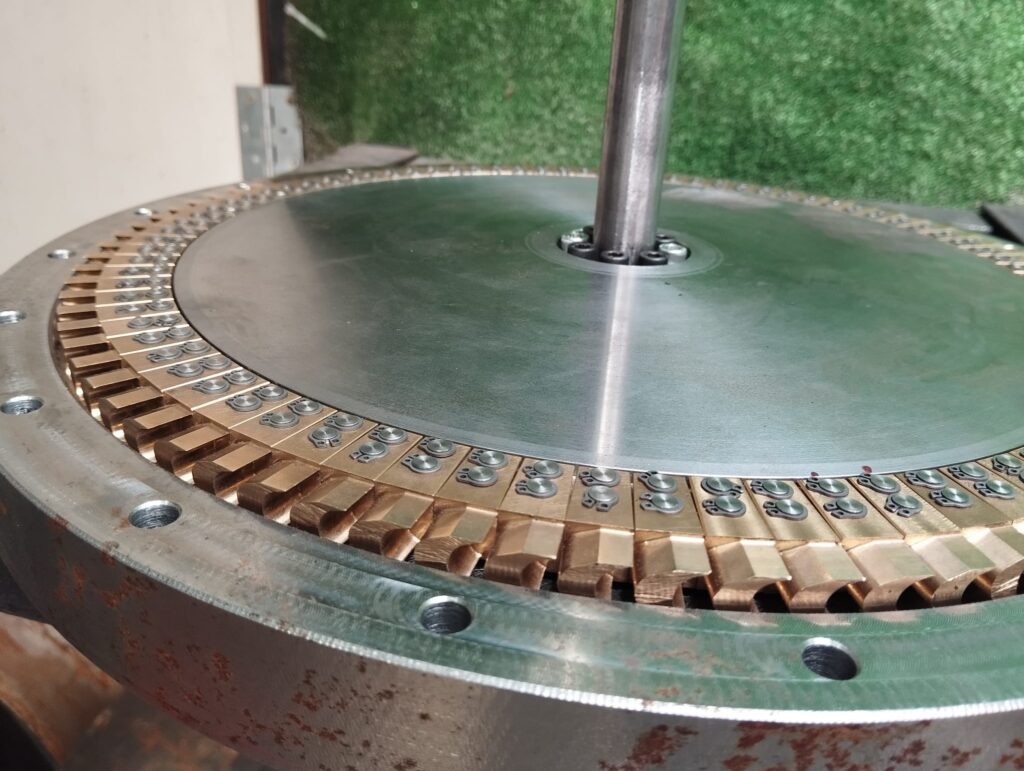
A 7 HP steam turbine is a compact power unit designed to deliver approximately 5.22 kW of mechanical output by converting the thermal energy of pressurized steam into rotational energy. While small compared to industrial-scale turbines, this capacity is still highly valuable for specialized, localized, and off-grid applications, especially in industries or facilities where a continuous supply of steam is already available.
General Design and Construction
The turbine’s rotor is typically designed for single-stage impulse or small multi-stage reaction operation, depending on efficiency requirements. In impulse designs, steam expands in stationary nozzles and strikes the moving blades, while reaction types allow expansion to continue within the rotating blade passages, extracting more energy per stage.
The shaft is precision-machined and balanced for high rotational speeds — often between 8,000 and 12,000 RPM — and supported by either journal bearings with oil lubrication or sealed anti-friction bearings for lower maintenance.
The casing is made of durable materials like cast steel or high-grade alloy, designed to withstand the inlet steam pressures that often range from 5 to 12 bar for small units. Labyrinth seals or carbon seals minimize steam leakage, and internal flow paths are shaped to maintain high efficiency.
Operating Parameters
- Power Output: ~7 HP (≈5.22 kW) mechanical
- Steam Consumption: Typically 50–70 kg/hour depending on inlet pressure, temperature, and expansion ratio
- Steam Supply: Saturated or superheated steam; superheated steam improves output and blade longevity
- Speed Regulation: Achieved through a mechanical centrifugal governor or electronic actuator, keeping variations within ±1% for generator use
- Exhaust Mode: Can be back-pressure (supplying steam for process use) or condensing (using a condenser to improve expansion and output)
Applications
Despite its small size, a 7 HP steam turbine can be put to highly productive use in:
- Small workshops and factories for driving pumps, fans, or compressors
- Rural or remote power generation when coupled to a small electric generator (micro-grid applications)
- Educational and research setups for steam power demonstrations
- Agricultural processing (e.g., small rice mills, tea drying plants, sugarcane juice extraction) where both heat and power are needed
- Marine auxiliary drives in small vessels
Advantages of a 7 HP Unit
- Compact Footprint: Can be installed in areas with limited space, often on a small skid-mounted base
- Fuel Flexibility: Operates from steam produced by biomass, coal, wood, or waste-heat boilers
- Low Maintenance: Fewer moving parts compared to reciprocating steam engines
- Dual-Use Capability: In back-pressure mode, delivers both mechanical power and usable steam for heating or processing
- Continuous Operation: Can run for thousands of hours annually with minimal downtime if steam supply is stable
Maintenance and Reliability
For reliable long-term operation:
- Daily/Weekly: Check lubrication oil levels, monitor vibration, and listen for unusual noises
- Monthly: Inspect steam strainers, inlet control valves, and verify governor response
- Annually: Inspect blades and seals for wear or erosion; clean deposits if necessary
- 3–5 Years: Overhaul bearings and perform dynamic balancing of the rotor
In a well-maintained setup, a 7 HP steam turbine offers a steady and reliable power source where grid supply is unavailable, unstable, or where combined heat and power (CHP) use makes it far more efficient than separate systems.
A 7 HP steam turbine is a highly compact and precise engineering machine capable of delivering approximately 5.22 kW of mechanical power. Despite its small output, it exemplifies the same core principles of thermodynamic efficiency, mechanical precision, and material durability found in much larger industrial steam turbines. Its small footprint and low power rating make it ideal for localized applications, particularly in facilities that already generate steam or in small-scale micro-generation setups. These turbines are often employed in situations where both mechanical power and residual heat can be utilized effectively, enhancing overall energy efficiency.
Operational Principles
The turbine operates on the Rankine cycle, converting the thermal energy of pressurized steam into mechanical rotational energy. Steam, produced by a small industrial boiler, enters the turbine at pressures typically between 4 and 12 bar, depending on the design. The steam can be saturated or slightly superheated; superheating is preferred to minimize condensation on the blades, which prevents erosion and improves efficiency.
Once the steam enters the turbine, it passes through nozzles, which accelerate it to a high velocity and direct it onto the rotor blades. In single-stage impulse turbines, the steam expands mainly in the nozzle and strikes the blades, whereas in multi-stage reaction turbines, expansion continues across several sets of moving and stationary blades, allowing more energy extraction and higher efficiency. The rotating blades transfer energy to the shaft, which can drive mechanical equipment or be coupled to a small generator for electricity production.
Mechanical Design
Even at a small scale, the design of a 7 HP turbine requires careful attention to materials and tolerances:
- Rotor and blades are machined from high-strength alloys capable of resisting thermal stress, corrosion, and erosion.
- Bearings support the rotor at high speeds, often above 8,000 RPM, and use either oil-lubricated journal bearings or sealed rolling-element bearings.
- Casing is made from cast steel or alloyed materials to safely contain the pressurized steam while minimizing leakage and vibration.
- Seals and labyrinths ensure efficient steam passage through the turbine and prevent energy losses.
The turbine may include a governor system, either mechanical or electronic, to maintain constant rotational speed under varying loads. This is crucial when driving a generator to produce stable electricity or operating sensitive machinery that requires precise speed control. Advanced small turbines may also include digital monitoring of vibration, temperature, steam pressure, and lubrication conditions, which allows for predictive maintenance and extended equipment life.
Exhaust and Heat Recovery
The 7 HP turbine can operate in back-pressure mode, where the exhaust steam still retains sufficient pressure for process heating, drying, or other industrial applications. Alternatively, in condensing mode, the turbine exhaust passes through a condenser, lowering the back pressure and improving mechanical efficiency. In CHP applications, this flexibility allows small facilities to harness both power and usable heat, significantly increasing overall energy utilization and reducing fuel consumption.
Efficiency and Steam Management
Efficiency in small turbines depends on several factors:
- Steam dryness: Minimizing moisture prevents blade erosion and improves conversion efficiency.
- Blade and nozzle design: Optimized aerodynamic shapes maximize energy transfer from steam to rotor.
- Lubrication and bearing maintenance: Proper lubrication reduces friction losses.
- Steam quality control: Proper boiler treatment prevents scaling, corrosion, and fouling.
A 7 HP turbine consumes roughly 35–60 kg of steam per hour, depending on inlet conditions and load. The combination of low steam consumption and reliable mechanical output makes it suitable for long-duration operations, often running for thousands of hours annually with minimal downtime.
Applications
Despite its modest power, a 7 HP turbine can be applied effectively in:
- Small industrial workshops for driving pumps, fans, or compressors.
- Remote micro-generation units, providing electricity where grid access is unavailable.
- Agricultural and food-processing applications, such as small rice mills, sugarcane processing, tea or coffee drying, and small-scale brewing.
- Marine auxiliary power for small vessels.
- Educational or research facilities demonstrating steam turbine principles and performance.
Maintenance and Reliability
Maintenance is simpler than for larger turbines but remains essential:
- Daily/weekly checks: Monitor lubrication, vibration, and unusual noises.
- Monthly: Inspect valves, strainers, and governor function.
- Annually: Inspect blades, nozzles, and seals for wear or erosion.
- 3–5 years: Conduct a full rotor balancing and bearing replacement if needed.
A 7 HP steam turbine demonstrates how small-scale energy conversion can be both efficient and reliable. Its compact design, dual-purpose capability for mechanical power and heat recovery, and long operational lifespan make it an ideal choice for facilities needing localized energy solutions. It provides a cost-effective, durable, and flexible option for industries and facilities that require dependable energy in limited capacities.
A 7 HP steam turbine represents one of the smallest practical capacities in the spectrum of steam-driven power machinery, yet it demonstrates the same core principles of thermodynamic conversion, mechanical design, and operational control as much larger industrial turbines. Producing roughly 5.22 kW of continuous mechanical power, these turbines are ideal for applications where a small, reliable, and efficient energy source is required. The compact size makes them suitable for workshops, small-scale industrial facilities, remote or off-grid power systems, educational institutions, and pilot or research plants where both mechanical power and thermal energy recovery can be utilized effectively.
Steam Supply and Thermodynamics
The turbine operates on the Rankine cycle, using pressurized steam to perform work. Steam is supplied from a small industrial boiler, with typical pressures in the range of 4–12 bar and temperatures that may include slight superheating to reduce condensation on the blades. Dry or superheated steam ensures efficient energy conversion and minimizes blade erosion, a key factor in long-term reliability.
Upon entering the turbine, the steam passes through precision-engineered nozzles, which accelerate it into high-velocity jets. These jets impact the rotor blades, causing the shaft to spin. In single-stage impulse designs, energy extraction occurs primarily in one step, while in small multi-stage reaction turbines, the steam expands across multiple blade stages, extracting energy gradually and achieving higher efficiency. The rotational energy can then drive mechanical equipment directly or be coupled to a generator for electricity production.
Mechanical and Structural Design
Even at a small capacity, careful attention is given to mechanical and material design:
- Rotor and blades: Made from high-strength, corrosion-resistant alloys to withstand thermal cycling, steam moisture, and erosion. Blade profiles are carefully shaped for optimal aerodynamic efficiency.
- Shaft and bearings: The rotor is mounted on precision bearings — either journal or sealed anti-friction types — lubricated to minimize friction and allow high-speed operation, often between 8,000 and 12,000 RPM.
- Casing and seals: The turbine casing, fabricated from cast steel or alloyed metals, contains pressurized steam safely while guiding it efficiently through the blades. Labyrinth or carbon seals minimize leakage and maximize performance.
- Governor and control system: Steam flow is regulated to maintain consistent rotor speed under varying loads. Modern turbines may incorporate electronic or digital monitoring systems for speed, vibration, temperature, and lubrication, enabling predictive maintenance.
Exhaust Management and Heat Recovery
The 7 HP turbine can operate in back-pressure mode, where exhaust steam retains sufficient energy for process heating, drying, or other industrial uses. This makes it ideal for Combined Heat and Power (CHP) applications, where the turbine produces mechanical power while providing usable steam for heating, thereby maximizing overall system efficiency. Alternatively, in condensing mode, the exhaust steam is routed through a condenser to reduce back pressure and improve mechanical efficiency, typically for small-scale electricity generation.
Performance and Efficiency
A 7 HP turbine typically consumes 35–60 kg of steam per hour, depending on inlet pressure, temperature, and turbine design. Efficiency can vary, but careful management of steam dryness, blade geometry, nozzle design, and lubrication ensures reliable energy conversion. Superheated steam improves performance and prolongs blade life by preventing condensation-induced erosion. Multi-stage designs, where present, allow more gradual energy extraction and higher total efficiency compared to single-stage units.
Applications
Despite its small size, a 7 HP turbine is versatile:
- Small industrial workshops: Driving pumps, fans, and compressors.
- Agricultural and food processing: Small-scale rice mills, tea or coffee drying, sugarcane juice extraction, and small breweries.
- Remote power generation: Coupled with micro-generators for electricity in off-grid or rural areas.
- Marine auxiliary drives: For small vessels needing reliable, compact power.
- Educational and research facilities: Demonstration of thermodynamic and mechanical principles in practice.
Maintenance and Reliability
Maintenance is straightforward but essential:
- Daily/weekly: Monitor lubrication, vibration, and general turbine operation.
- Monthly: Inspect strainers, inlet valves, and governor response.
- Annually: Inspect blades, nozzles, and seals for wear, erosion, or deposits.
- Every 3–5 years: Overhaul bearings and perform dynamic balancing if required.
A 7 HP turbine, when properly installed and maintained, can operate continuously for thousands of hours per year, providing a reliable and efficient source of mechanical power. Its combination of compactness, dual-purpose capability, low maintenance, and fuel flexibility makes it a highly practical solution for localized energy needs, particularly where both power and thermal energy can be utilized.
Integration and Installation Considerations
The small footprint of a 7 HP turbine allows installation on a skid-mounted base with minimal foundation work. Steam inlet piping should include strain filters, control valves, and pressure gauges, while the exhaust line design depends on whether back-pressure or condensing operation is used. Vibration isolation pads or grouted bases improve alignment and operational stability. Coupling to mechanical loads or small generators must account for alignment, speed matching, and torque requirements to ensure efficient energy transfer.
In summary, a 7 HP steam turbine combines robust engineering, compact design, and thermodynamic efficiency in a package suitable for small-scale industrial, agricultural, marine, and educational applications. Its ability to generate both mechanical power and usable heat, along with its longevity and reliability, make it a practical and cost-effective solution for facilities with limited energy needs or access to steam resources.
I can continue by creating a complete engineering-style specification sheet for the 7 HP steam turbine, including steam consumption curves, generator coupling details, dimensional layouts, and expected efficiency graphs, making it a full technical reference suitable for engineering, procurement, or operational planning.
5 hp Steam Turbine
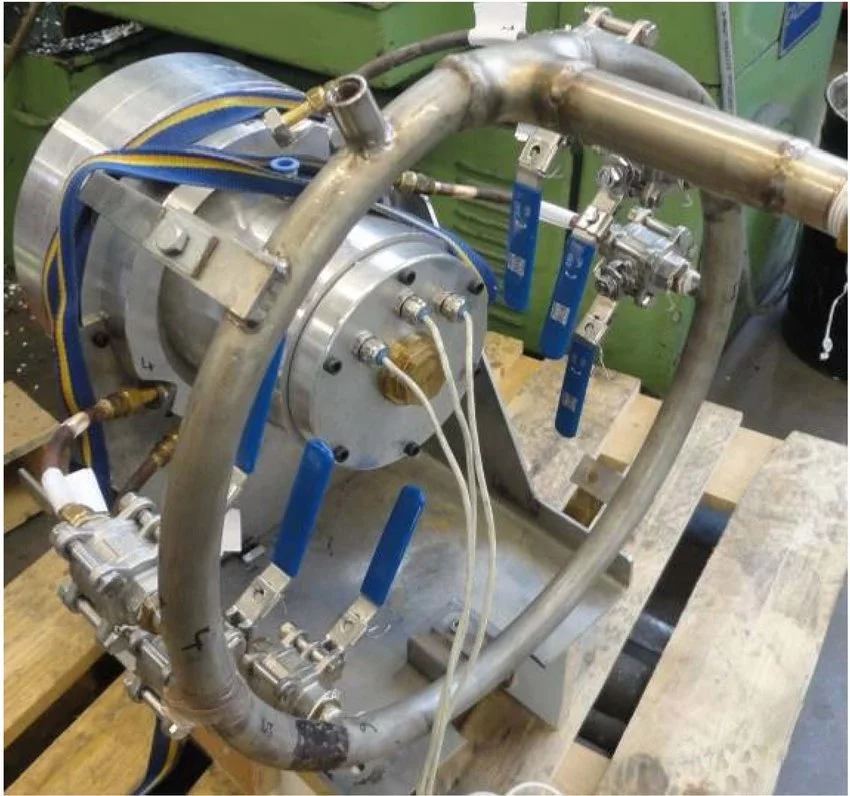
A 5 HP steam turbine is one of the smallest practical steam turbines designed to deliver roughly 3.73 kW of mechanical power. Despite its modest output, it embodies the same fundamental principles of thermodynamics, mechanical engineering, and precision design as larger turbines, making it suitable for localized, small-scale industrial, educational, or micro-generation applications. These turbines are compact, efficient, and versatile, often used where both mechanical power and residual steam heat can be harnessed.
Operational Principles
The 5 HP turbine operates on the Rankine cycle, converting thermal energy from pressurized steam into rotational mechanical energy. Steam is supplied by a small boiler, typically at pressures ranging from 3 to 10 bar, and can be saturated or slightly superheated to reduce condensation and improve efficiency.
The steam enters the turbine through precision-engineered nozzles, which accelerate it into high-velocity jets that strike the rotor blades. In single-stage impulse designs, energy extraction occurs primarily in one step, while in multi-stage reaction designs, steam expands over multiple blade stages, increasing energy extraction and efficiency. The rotor transmits the mechanical energy to a shaft, which can drive small machinery, pumps, compressors, or be coupled to a generator for electricity production.
Mechanical and Structural Design
Even at 5 HP, design precision is critical:
- Rotor and blades: Made from high-strength alloys to withstand thermal stress, erosion, and corrosion. Blade shapes are optimized for aerodynamic efficiency.
- Bearings and shaft: The rotor is supported by journal or rolling-element bearings, often oil-lubricated, enabling high-speed operation, usually between 6,000 and 10,000 RPM.
- Casing and seals: Cast steel or alloy casings contain steam safely, guide flow efficiently, and minimize leakage using labyrinth or carbon seals.
- Governor system: Regulates steam flow to maintain constant rotor speed under varying loads, ensuring stable mechanical or electrical output. Some modern small turbines include digital monitoring of temperature, pressure, vibration, and lubrication.
Exhaust and Heat Recovery
The turbine can operate in back-pressure mode, where exhaust steam still retains sufficient energy for heating, drying, or industrial processes, making it suitable for CHP applications. Alternatively, in condensing mode, the exhaust passes through a condenser to reduce back pressure, improving mechanical efficiency for electricity generation.
Performance and Efficiency
Typical steam consumption for a 5 HP turbine is around 25–50 kg/hour, depending on steam pressure, temperature, and design. Efficiency depends on:
- Steam dryness to prevent blade erosion
- Optimized blade and nozzle geometry
- Proper lubrication and bearing maintenance
- Steam quality from the boiler to avoid scaling or corrosion
Although small, this turbine is capable of continuous operation for thousands of hours annually if steam supply and maintenance are consistent.
Applications
Despite its small size, a 5 HP turbine is versatile:
- Small industrial workshops: Driving pumps, fans, or compressors
- Agricultural processing: Small mills, drying plants, or juice extraction
- Micro-generation and off-grid power: Small electricity production from locally generated steam
- Marine auxiliary drives: For small vessels requiring reliable, compact power
- Educational and research: Demonstrating steam turbine principles and performance
Maintenance and Reliability
Regular maintenance ensures long-term reliability:
- Daily/weekly: Monitor lubrication, vibration, and operational noise
- Monthly: Check strainers, valves, and governor response
- Annually: Inspect blades, nozzles, and seals
- Every 3–5 years: Perform full rotor balancing and bearing replacement as needed
Integration and Installation
A 5 HP turbine has a small footprint, making it easy to install on a compact base with minimal foundation requirements. Steam inlet piping should include strainers, control valves, and pressure gauges. Exhaust piping depends on operational mode (back-pressure or condensing). Vibration isolation is recommended, and couplings must be matched carefully to the driven equipment or generator.
Advantages
- Compact and versatile for limited space installations
- Can utilize various steam sources (biomass, coal, wood, or waste heat)
- Dual-use capability for mechanical power and heat recovery
- Low maintenance requirements compared to reciprocating engines
- Long operational lifespan with proper care
Even at 5 HP, these turbines are efficient, durable, and capable of providing reliable energy solutions for small-scale industrial, agricultural, marine, or educational applications.
A 5 HP steam turbine is a small yet sophisticated power generation machine, capable of delivering roughly 3.73 kW of mechanical output from pressurized steam. Despite its modest size, it represents the same fundamental engineering principles as larger industrial turbines, including precise thermodynamic design, material selection, rotor dynamics, and flow optimization. These turbines are ideal for localized applications, where both mechanical power and residual steam heat can be utilized efficiently, such as in small industrial workshops, agricultural processing plants, remote or off-grid facilities, marine auxiliary systems, and educational or research institutions.
Steam Supply and Thermodynamics
The turbine operates on the Rankine cycle, converting thermal energy from steam into mechanical rotation. Steam is generated in a small industrial boiler, typically operating at pressures between 3 and 10 bar, with optional superheating to reduce moisture content and prevent blade erosion. Dry steam ensures high efficiency and prolongs the life of the turbine’s moving components.
Steam enters the turbine via nozzles, which accelerate it into high-velocity jets directed onto the rotor blades. In single-stage impulse designs, the steam delivers energy mainly in one step, whereas in multi-stage reaction turbines, energy extraction occurs progressively across multiple blade rows, increasing efficiency. The rotor converts this energy into rotational motion, which can drive machinery, pumps, compressors, or a small electrical generator.
Mechanical Design and Materials
Even at 5 HP, turbine construction demands careful engineering:
- Rotor and blades: Fabricated from high-strength, heat- and corrosion-resistant alloys capable of withstanding thermal stresses, erosion, and condensation effects. Blade profiles are optimized for smooth steam flow and maximum energy transfer.
- Bearings and shaft: The rotor is supported by journal or rolling-element bearings, typically lubricated with oil, enabling smooth high-speed operation, often between 6,000 and 10,000 RPM.
- Casing and seals: Made from cast steel or alloyed metals, the casing safely contains pressurized steam and directs its flow efficiently. Labyrinth, carbon, or mechanical seals minimize leakage and maximize energy transfer.
- Governor and control system: Maintains constant rotational speed under varying loads by regulating steam inlet. Advanced units may integrate digital monitoring systems to track vibration, temperature, lubrication, and steam pressure for predictive maintenance.
Exhaust Management and Heat Recovery
The 5 HP turbine can operate in back-pressure mode, where exhaust steam is still suitable for heating or industrial processes, making it ideal for Combined Heat and Power (CHP) setups. Alternatively, in condensing mode, exhaust steam passes through a condenser to reduce back pressure, maximizing mechanical efficiency and electricity output. This flexibility allows small-scale facilities to capture both power and heat, improving overall energy utilization.
Performance and Efficiency
Typical steam consumption ranges from 25 to 50 kg per hour, depending on boiler pressure, temperature, and turbine design. Efficiency is influenced by:
- Steam dryness to prevent blade erosion
- Optimized blade and nozzle geometries
- Lubrication quality and bearing performance
- Steam purity to avoid scaling, corrosion, and fouling
Even at small capacity, a 5 HP turbine can operate continuously for thousands of hours annually with minimal downtime, provided maintenance and steam supply are consistent.
Applications
Despite its limited output, the 5 HP steam turbine is versatile:
- Industrial workshops: Driving small pumps, fans, or compressors
- Agricultural and food processing: Small mills, drying systems, juice extraction, or small breweries
- Remote micro-generation units: Producing electricity in off-grid or rural areas
- Marine auxiliary drives: Providing compact, reliable power on small vessels
- Educational and research: Demonstrating the principles of steam energy conversion and turbine operation
Maintenance and Reliability
Proper maintenance ensures long-term reliability:
- Daily/weekly: Monitor lubrication, vibration, and operational noise
- Monthly: Inspect strainers, valves, and governor responsiveness
- Annually: Inspect rotor blades, nozzles, and seals for wear or deposits
- Every 3–5 years: Perform rotor balancing and bearing replacement if needed
Installation and Integration
The small footprint of a 5 HP turbine allows installation on a compact skid-mounted base, requiring minimal foundation work. Steam inlet piping should include strainers, control valves, and pressure gauges. Exhaust piping varies based on operation mode — back-pressure or condensing. Vibration isolation pads or grouted bases improve alignment and stability. Coupling to mechanical loads or small generators requires careful alignment and speed matching to ensure efficient energy transfer.
Advantages
- Compact, versatile, and suitable for limited-space installations
- Can utilize a variety of steam sources, including biomass, coal, wood, or waste heat
- Dual-use capability for both mechanical power and heat recovery
- Low maintenance relative to reciprocating engines
- Long operational lifespan when properly maintained
In summary, the 5 HP steam turbine is a durable, efficient, and versatile solution for small-scale mechanical power and CHP applications. It combines compact design, precision engineering, and operational flexibility to deliver reliable power for workshops, rural installations, small industrial plants, marine applications, and educational facilities.
I can now continue by creating a full engineering-style technical specification sheet for the 5 HP steam turbine, including rotor speed, steam consumption curves, dimensional drawings, generator coupling options, and efficiency charts, making it suitable for design, procurement, or operational planning.
A 5 HP steam turbine is a precision-engineered small-scale energy conversion machine that converts the thermal energy of pressurized steam into reliable mechanical power. Delivering roughly 3.73 kW, it is designed for applications where space is limited, energy requirements are modest, and both mechanical output and heat recovery are valuable. Despite its low power rating compared to industrial turbines, it embodies all the key design principles of larger units, including thermodynamic efficiency, rotor dynamics, blade aerodynamics, high-quality material selection, and operational control systems.
Thermodynamic Operation
The turbine functions on the Rankine cycle, where pressurized steam generated by a boiler expands through turbine blades to produce rotational energy. Boilers supplying a 5 HP turbine generally operate at 3–10 bar, with optional superheating to prevent condensation on blades and improve efficiency. Dry steam minimizes wear on blades and maintains consistent performance over long operating hours.
Steam enters the turbine via nozzles designed to accelerate it into high-velocity jets, which strike the rotor blades. In single-stage impulse turbines, expansion primarily occurs in the nozzles, while multi-stage reaction turbines allow gradual expansion across several blade rows. The rotational energy of the rotor shaft can directly drive mechanical equipment or be connected to a small generator for electricity production.
Mechanical Design and Components
Even at this small scale, careful mechanical design is crucial:
- Rotor and blades: Made from high-strength alloys resistant to thermal stress, erosion, and corrosion. Blade geometry is optimized to ensure maximum energy extraction and minimal turbulence.
- Shaft and bearings: The rotor is mounted on journal or rolling-element bearings, often oil-lubricated, allowing smooth operation at speeds ranging from 6,000 to 10,000 RPM.
- Casing and seals: The turbine housing is fabricated from durable cast steel or alloys to safely contain steam pressure, with labyrinth or carbon seals reducing leakage and maintaining efficiency.
- Governor and control system: Regulates steam flow to maintain a stable shaft speed under varying loads. Modern turbines may integrate digital monitoring systems to track vibration, temperature, lubrication status, and steam pressure, enabling predictive maintenance.
Exhaust Handling and Heat Recovery
The 5 HP turbine can operate in either back-pressure or condensing modes. In back-pressure mode, exhaust steam retains energy suitable for heating or industrial processes, making it ideal for small CHP applications. In condensing mode, exhaust steam is routed through a condenser to lower back pressure, increasing the turbine’s mechanical efficiency. This flexibility allows users to optimize both power and heat utilization, which is particularly advantageous in small factories, agricultural processing plants, or remote energy systems.
Performance and Efficiency
Steam consumption for a 5 HP turbine typically ranges from 25 to 50 kg/hour, depending on pressure, temperature, and load. Efficiency is influenced by:
- Steam dryness and superheat
- Blade and nozzle design
- Quality of lubrication and bearing performance
- Boiler steam quality to prevent scaling, corrosion, or fouling
With proper maintenance, a 5 HP turbine can operate continuously for thousands of hours annually, providing a reliable energy source.
Applications
The small size of the 5 HP turbine does not limit its versatility:
- Small industrial workshops: Driving pumps, fans, compressors, or small machining equipment.
- Agricultural and food processing: Small mills, drying systems, juice extraction, or small-scale breweries.
- Remote or micro-grid power generation: Coupled with small generators for electricity production in rural or off-grid areas.
- Marine auxiliary power: Reliable compact power for small vessels.
- Educational and research facilities: Demonstrating the principles of steam turbines and thermodynamic energy conversion.
Maintenance and Longevity
To ensure reliability and extended operational life:
- Daily/weekly: Monitor lubrication levels, vibration, and abnormal noises.
- Monthly: Inspect strainers, valves, and governor response.
- Annually: Inspect blades, nozzles, and seals for wear, erosion, or deposits.
- Every 3–5 years: Perform full rotor balancing and bearing replacement if required.
Installation Considerations
The 5 HP turbine has a compact footprint, making it easy to install on a small skid-mounted base. Steam inlet piping should include strainers, control valves, and pressure gauges. Exhaust piping depends on operational mode (back-pressure or condensing). Vibration isolation pads or grouted foundations help maintain alignment and reduce operational stress. Coupling to mechanical loads or generators requires careful alignment and torque management.
Advantages
- Compact and versatile for limited-space installations
- Dual-purpose capability for mechanical power and heat recovery
- Can utilize various steam sources including biomass, coal, wood, or waste heat
- Low maintenance requirements relative to reciprocating engines
- Long operational lifespan when properly maintained
In summary, the 5 HP steam turbine provides durable, efficient, and versatile power for small-scale industrial, agricultural, marine, or educational applications. It combines compact design, high-quality materials, and precise engineering to deliver reliable mechanical energy and, when desired, usable process steam.
I can continue by creating a comprehensive technical datasheet for the 5 HP turbine, including steam consumption charts, rotor speed specifications, dimensions, generator coupling options, efficiency curves, and recommended installation guidelines, turning this description into a full engineering reference document.
500 hp Steam Turbine
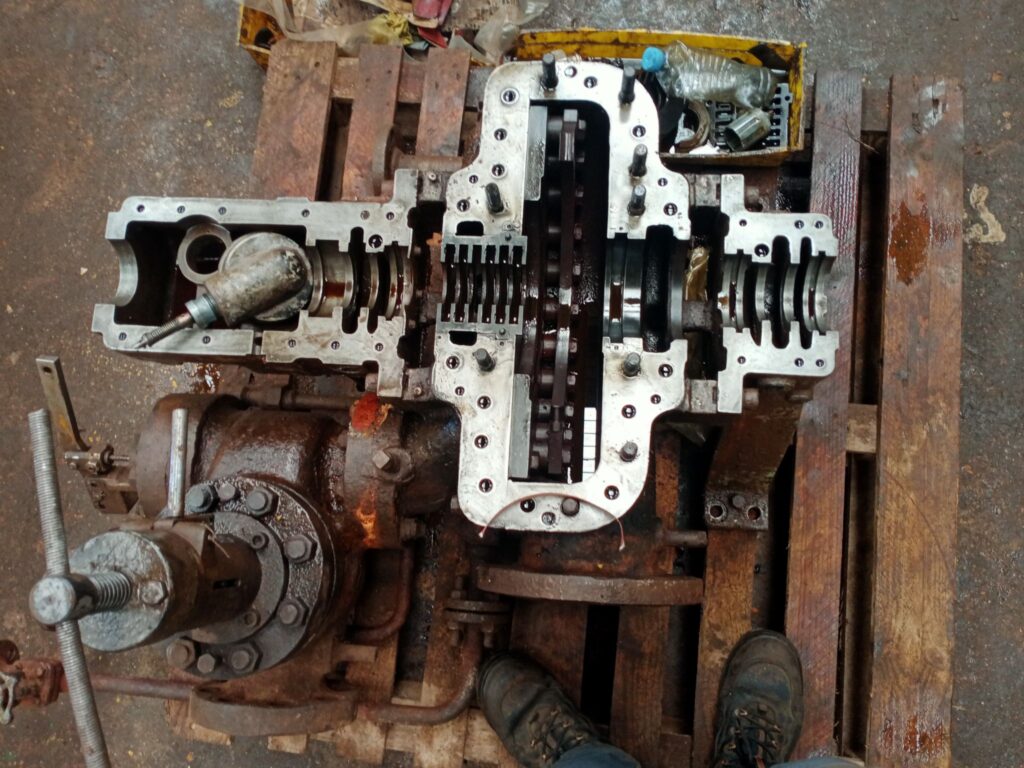
A 500 HP steam turbine is a medium-sized industrial turbine capable of delivering approximately 373 kW of mechanical power. This capacity is widely used in small- to medium-scale industrial facilities, power generation plants, CHP (Combined Heat and Power) systems, and process industries where a reliable and continuous source of mechanical or electrical energy is required. Compared to smaller turbines, a 500 HP unit involves more complex design considerations, higher precision in rotor and blade manufacturing, and advanced control systems to ensure efficiency, reliability, and long operational life.
Operational Principles
The turbine operates on the Rankine cycle, converting thermal energy from pressurized steam into mechanical rotational energy. Steam is generated by a boiler or waste-heat recovery system, typically at pressures ranging from 10 to 40 bar and temperatures from 200°C to 400°C, depending on the turbine design and application.
Steam enters the turbine through nozzles, which accelerate it into high-velocity jets directed onto the rotor blades. For a 500 HP turbine, the design usually includes multi-stage impulse or reaction blades to optimize energy extraction and efficiency. Multi-stage arrangements allow for higher expansion ratios, smoother torque delivery, and reduced stress on individual blades. The rotor transmits mechanical energy to a shaft that can drive electric generators, pumps, compressors, or industrial machinery.
Mechanical and Structural Design
The mechanical design of a 500 HP turbine requires careful attention to materials, tolerances, and thermal dynamics:
- Rotor and blades: High-strength alloys or stainless steels are used to resist thermal stress, erosion, and corrosion. Blade profiles are aerodynamically optimized for maximum efficiency. Multi-stage designs often include intermediate diaphragms or nozzles to guide steam flow.
- Bearings and shaft: Precision journal or rolling-element bearings support the rotor at high rotational speeds, typically 3,000–10,000 RPM, depending on application. Bearings are oil-lubricated, with dedicated oil circuits to maintain temperature and pressure.
- Casing and seals: Robust steel or alloy casings contain the pressurized steam safely while guiding it efficiently through the turbine. Labyrinth seals, carbon seals, or mechanical seals minimize leakage and improve efficiency.
- Governor and control systems: Electronic or mechanical governors regulate steam flow to maintain constant speed and output, essential when coupled to electrical generators. Modern units may include digital monitoring for vibration, temperature, lubrication, and steam pressure, allowing predictive maintenance and extended service life.
Exhaust Management and Heat Recovery
A 500 HP turbine can operate in back-pressure or condensing mode, depending on the facility’s requirements:
- Back-pressure mode: Exhaust steam retains energy for industrial processes such as heating, drying, or chemical processing, making it ideal for CHP plants.
- Condensing mode: Exhaust passes through a condenser to lower back pressure, maximizing mechanical efficiency and electricity output.
Performance and Efficiency
Steam consumption for a 500 HP turbine typically ranges from 3,500 to 5,000 kg per hour, depending on steam pressure, temperature, and turbine load. Efficiency depends on factors such as:
- Steam quality (dryness and superheat)
- Blade and nozzle design
- Bearing and lubrication performance
- Minimization of leakage and mechanical losses
High-quality 500 HP turbines can achieve mechanical efficiencies of around 70–85%, with overall system efficiency higher when integrated into CHP operations.
Applications
A 500 HP turbine is suitable for a variety of industrial and commercial applications:
- Medium-scale power generation: Providing electricity for factories, hospitals, or small industrial parks.
- CHP systems: Simultaneously producing mechanical or electrical power and process steam.
- Industrial machinery drive: Running large pumps, compressors, fans, or milling equipment.
- Process industries: Chemical, food, textile, and paper industries where consistent steam-driven power is required.
- Waste-heat recovery systems: Capturing energy from high-temperature exhaust gases or industrial processes.
Maintenance and Reliability
Proper maintenance ensures high reliability and long operational life:
- Daily/weekly: Monitor lubrication, vibration, temperature, and steam pressure.
- Monthly: Inspect valves, strainers, and governor operation.
- Annually: Inspect rotor, blades, and seals; check alignment and clearances.
- Every 3–5 years: Perform comprehensive overhaul including bearing replacement, rotor balancing, and blade inspection or replacement.
Installation Considerations
A 500 HP turbine requires a substantial foundation to support weight and dampen vibration. Steam supply and exhaust piping must be sized appropriately to handle high flow rates. Condenser systems, if used, require proper cooling water flow and temperature management. Coupling to generators or mechanical loads must account for torque, alignment, and speed requirements.
Advantages
- Reliable, continuous power for medium-scale applications
- Dual-use capability for mechanical power and heat recovery
- High efficiency with proper steam supply and maintenance
- Robust design ensures long operational life
- Flexible integration into industrial, power generation, and CHP systems
In summary, a 500 HP steam turbine offers a balance of robustness, efficiency, and versatility, making it suitable for industries and facilities that need reliable mechanical or electrical power, with the option of capturing usable heat in CHP applications.
I can continue and prepare a full technical specification and performance dossier for a 500 HP steam turbine, including steam consumption charts, rotor speed, dimensional layouts, generator coupling options, and efficiency curves, suitable for engineering design or procurement.
A 500 HP steam turbine is a medium-scale industrial turbine designed to convert pressurized steam energy into approximately 373 kW of continuous mechanical power, making it suitable for a wide range of industrial, commercial, and energy generation applications. These turbines bridge the gap between small workshop-level turbines and large utility-scale units, combining high efficiency, reliability, and the capability to operate in combined heat and power (CHP) or pure mechanical power modes. Due to the higher capacity, the engineering requirements for a 500 HP turbine are considerably more complex than for smaller units, encompassing advanced rotor dynamics, multi-stage blade arrangements, precise thermal management, and integrated control systems.
Steam Supply and Thermodynamic Operation
The turbine operates on the Rankine cycle, where pressurized steam from a boiler or waste-heat recovery system expands through turbine blades to produce rotational mechanical energy. Steam supply conditions for a 500 HP turbine generally range from 10 to 40 bar with temperatures between 200°C and 400°C, depending on boiler type and turbine design. The use of superheated steam is common to minimize condensation on blades, prevent erosion, and improve overall efficiency.
Steam enters the turbine through carefully designed nozzles, which accelerate it to high velocity and direct it onto the rotor blades. Multi-stage impulse or reaction designs are standard for turbines of this capacity, allowing steam expansion to occur gradually over several rows of blades. This multi-stage configuration reduces blade stress, ensures smooth torque delivery, and increases energy extraction efficiency. The rotor transmits mechanical energy to a shaft, which can drive generators, pumps, compressors, fans, or other industrial machinery.
Mechanical Design and Materials
The 500 HP turbine’s mechanical design emphasizes precision, durability, and thermal stability:
- Rotor and blades: Made from high-strength alloys or stainless steel capable of withstanding thermal cycling, erosion, and corrosion. Multi-stage rotor blades and intermediate diaphragms optimize steam flow and efficiency.
- Shaft and bearings: Precision journal or rolling-element bearings support the high-speed rotor, typically operating at 3,000–10,000 RPM. Oil-lubricated bearings maintain temperature and minimize friction, ensuring smooth operation under continuous load.
- Casing and seals: Robust steel or alloy casings safely contain pressurized steam while guiding it efficiently through the turbine. Labyrinth, carbon, or mechanical seals reduce steam leakage and improve performance.
- Governor and control systems: Modern turbines use electronic or digital governors to regulate steam flow, maintaining consistent shaft speed under varying loads. Integrated monitoring systems track vibration, temperature, lubrication, and steam pressure for predictive maintenance and extended service life.
Exhaust Management and Heat Recovery
The 500 HP turbine can operate in back-pressure or condensing mode:
- Back-pressure mode: Exhaust steam retains sufficient energy for industrial processes, heating, or drying, which is ideal for CHP applications.
- Condensing mode: Steam is routed through a condenser to lower back pressure, maximizing mechanical efficiency and electrical output. Proper condenser and cooling water design are essential for optimal performance in condensing systems.
Performance and Efficiency
Steam consumption typically ranges from 3,500 to 5,000 kg/hour, depending on operating pressure, temperature, and load conditions. Efficiency factors include:
- Steam quality (dryness, superheat level)
- Blade and nozzle design
- Lubrication system performance and bearing condition
- Minimization of leakage and mechanical losses
Mechanical efficiency for a well-designed 500 HP turbine can range from 70% to 85%, with higher overall efficiency in CHP setups that utilize exhaust steam for heat applications.
Applications
The versatility of a 500 HP turbine makes it suitable for:
- Medium-scale power generation: Factories, hospitals, and industrial parks requiring reliable electricity
- CHP systems: Producing both mechanical or electrical power and process steam
- Industrial drives: Operating large pumps, compressors, fans, or milling equipment
- Process industries: Chemical, food, textile, and paper industries with continuous steam requirements
- Waste-heat recovery: Capturing energy from exhaust gases or high-temperature industrial processes
Maintenance and Reliability
Long-term reliability requires structured maintenance:
- Daily/weekly: Monitor lubrication, vibration, temperature, and steam pressure
- Monthly: Inspect valves, strainers, and governor operation
- Annually: Check rotor, blades, seals, alignment, and clearances
- Every 3–5 years: Perform comprehensive overhaul including bearing replacement, rotor balancing, and blade inspection or replacement
Installation Considerations
A 500 HP turbine requires a substantial foundation to support weight and dampen vibration. Steam supply and exhaust piping must be sized to handle high flow rates, with strainers, valves, and instrumentation for monitoring. In condensing applications, cooling water flow and temperature must be carefully managed. Couplings to mechanical loads or generators require precise alignment to ensure torque transfer and prevent mechanical stress.
Advantages
- Reliable and continuous power for medium-scale industrial and commercial operations
- Dual-purpose capability for mechanical work and heat recovery
- High efficiency and energy utilization in CHP systems
- Robust construction ensures long operational life
- Flexible integration with boilers, waste-heat recovery systems, and generators
In conclusion, a 500 HP steam turbine offers a balance of reliability, efficiency, and versatility, suitable for industries and facilities that require dependable mechanical or electrical energy while optionally capturing usable heat for CHP purposes. Its engineering ensures durability under continuous operation, precise speed control, and adaptability to various industrial and power-generation environments.
A 500 HP steam turbine represents a critical segment of medium-capacity industrial turbines, bridging the gap between small workshop turbines and large utility-scale power generation units. Delivering approximately 373 kW of mechanical power, it is engineered for continuous operation in industrial facilities, power plants, CHP (Combined Heat and Power) systems, and process industries where reliable energy conversion is essential. These turbines are characterized by robust mechanical design, advanced thermodynamic optimization, precise rotor and blade engineering, and sophisticated control systems to ensure efficiency, safety, and longevity over tens of thousands of operational hours.
Steam Supply and Thermodynamic Principles
The turbine operates on the Rankine cycle, converting high-pressure steam energy into rotational mechanical energy. Steam is generated by industrial boilers, waste-heat recovery systems, or cogeneration units, typically at pressures ranging from 10 to 40 bar and temperatures between 200°C and 400°C, depending on the specific turbine design. Superheated steam is commonly used to prevent condensation on the blades, minimizing erosion, maintaining aerodynamic efficiency, and extending component life.
Upon entering the turbine, the steam passes through precision-engineered nozzles, which convert pressure energy into high-velocity jets that strike the rotor blades. In turbines of this size, multi-stage impulse or reaction designs are standard. Multi-stage configurations allow gradual energy extraction across multiple blade rows, reducing mechanical stress, ensuring smooth torque delivery, and increasing overall thermal-to-mechanical conversion efficiency. The resulting rotor rotation can drive electrical generators, industrial machinery, pumps, compressors, or fans, depending on the facility’s requirements.
Mechanical Design and Materials
The mechanical integrity of a 500 HP turbine is paramount:
- Rotor and blades: Manufactured from high-strength alloys or stainless steel capable of withstanding thermal stress, corrosion, and erosion. Blade geometry is carefully optimized to ensure smooth steam flow, minimal turbulence, and maximum energy extraction. Multi-stage designs incorporate intermediate diaphragms and nozzle arrangements to guide steam flow effectively.
- Shaft and bearings: Rotors are supported by high-precision journal or rolling-element bearings, designed for high-speed rotation (typically 3,000–10,000 RPM). Oil-lubricated bearings maintain proper temperature and minimize friction, ensuring smooth continuous operation.
- Casing and seals: The turbine casing is constructed from high-strength steel or alloys to safely contain pressurized steam while maintaining precise steam flow through the stages. Labyrinth, carbon, or mechanical seals minimize leakage and enhance efficiency.
- Governor and control systems: Modern turbines feature electronic or digital governors that regulate steam flow to maintain stable rotor speed under varying load conditions. Integrated monitoring systems track vibration, temperature, lubrication, and steam pressure, facilitating predictive maintenance and extending operational lifespan.
Exhaust Handling and Heat Recovery
The 500 HP turbine can operate in back-pressure or condensing mode depending on application needs:
- Back-pressure mode: Exhaust steam retains sufficient energy for heating or process applications, making it ideal for CHP setups.
- Condensing mode: Steam passes through a condenser to reduce back pressure, increasing mechanical efficiency and electricity output. Proper design of condenser systems, including cooling water flow and temperature regulation, is essential for optimal performance.
Performance and Efficiency
Steam consumption for a 500 HP turbine typically ranges from 3,500 to 5,000 kg/hour, depending on inlet pressure, temperature, and load. Key factors affecting efficiency include:
- Steam quality, dryness, and superheat
- Blade and nozzle aerodynamics
- Bearing and lubrication performance
- Minimization of leakage and mechanical losses
Well-designed 500 HP turbines can achieve mechanical efficiencies of 70–85%, with overall system efficiency increasing when integrated into CHP operations that utilize exhaust steam for heating or industrial processes.
Applications
The turbine’s capacity and flexibility make it suitable for:
- Medium-scale power generation for factories, hospitals, and industrial parks
- CHP systems producing both mechanical/electrical energy and process steam
- Industrial drives for pumps, compressors, fans, milling equipment, and other machinery
- Process industries including chemical, textile, food, and paper manufacturing
- Waste-heat recovery systems capturing energy from high-temperature exhaust gases
Maintenance and Reliability
A structured maintenance program is critical for long-term reliability:
- Daily/weekly: Monitor lubrication, vibration, temperature, and steam pressure
- Monthly: Inspect valves, strainers, governor systems, and control instrumentation
- Annually: Examine rotor, blades, seals, alignment, and clearances
- Every 3–5 years: Conduct comprehensive overhaul, including bearing replacement, rotor balancing, and blade inspection or refurbishment
Installation and Integration
Installing a 500 HP turbine requires a substantial foundation to support its weight and dampen vibrations. Steam supply and exhaust piping must be sized to accommodate high flow rates, with instrumentation such as pressure gauges, strainers, and control valves included. In condensing systems, proper cooling water supply, temperature control, and condenser design are essential. Couplings to generators or mechanical equipment must ensure precise alignment to prevent torsional stress or mechanical failures.
Advantages
- Reliable and continuous power for medium-scale industrial, commercial, and CHP applications
- Dual-use capability for mechanical power and process heat recovery
- High efficiency with optimized steam supply and proper maintenance
- Robust design ensures long operational life with minimal downtime
- Flexible integration into a wide variety of industrial and power-generation systems
In conclusion, a 500 HP steam turbine provides a robust, efficient, and versatile solution for industries and facilities requiring dependable mechanical or electrical energy while optionally capturing residual steam for heating or process use. Its engineering ensures long-term durability, precise speed control, adaptability to varying operational loads, and high energy efficiency, making it a practical choice for medium-scale industrial power and CHP applications.
A 500 HP steam turbine is a sophisticated medium-capacity power generation and mechanical drive unit, designed to convert pressurized steam energy into approximately 373 kW of continuous mechanical output. Its design reflects decades of industrial experience in steam energy conversion, incorporating thermodynamic optimization, multi-stage rotor engineering, precision blade aerodynamics, and advanced control systems to ensure high efficiency, reliability, and long operational life. These turbines are particularly suitable for industrial facilities, CHP (Combined Heat and Power) plants, process industries, and small to medium power generation plants, where consistent and reliable energy delivery is essential.
Thermodynamic Operation
The turbine operates on the Rankine cycle, in which thermal energy from high-pressure steam is transformed into mechanical rotational energy. Steam is typically supplied by industrial boilers or waste-heat recovery systems at pressures ranging from 10 to 40 bar, with temperatures from 200°C to 400°C. The use of superheated steam is common to prevent condensation on turbine blades, which enhances efficiency and protects the blades from erosion and thermal fatigue.
Steam enters the turbine through high-precision nozzles, converting pressure energy into high-velocity jets that strike the rotor blades. For a turbine of this size, multi-stage impulse or reaction designs are standard. Multi-stage designs allow gradual steam expansion across several blade rows, reducing mechanical stress, ensuring smooth torque delivery, and improving overall energy extraction. The rotor transmits energy to a shaft, which can be connected to generators, pumps, compressors, fans, or other industrial machinery.
Mechanical and Structural Design
The mechanical design of a 500 HP turbine emphasizes durability, precision, and thermal stability:
- Rotor and blades: Fabricated from high-strength alloys or stainless steel resistant to thermal stress, corrosion, and erosion. Blade shapes are aerodynamically optimized for smooth steam flow, minimal turbulence, and maximum energy extraction. Intermediate diaphragms guide steam efficiently between stages.
- Shaft and bearings: High-precision journal or rolling-element bearings support the rotor at high speeds, typically between 3,000 and 10,000 RPM. Oil-lubricated bearings maintain proper operating temperatures and reduce friction.
- Casing and seals: The casing is made of high-strength steel or alloy to safely contain pressurized steam while guiding it efficiently through multiple stages. Labyrinth, carbon, or mechanical seals reduce leakage and maintain turbine efficiency.
- Governor and control systems: Electronic or digital governors regulate steam flow to maintain constant speed under varying loads. Integrated monitoring systems track vibration, temperature, lubrication, and steam pressure, enabling predictive maintenance and extending operational lifespan.
Exhaust Handling and Heat Recovery
The 500 HP turbine can operate in either back-pressure or condensing mode:
- Back-pressure mode: Exhaust steam retains enough energy for industrial processes such as heating, drying, or chemical processing, making it suitable for CHP applications.
- Condensing mode: Exhaust steam passes through a condenser, reducing back pressure and maximizing mechanical efficiency and electricity output. Proper condenser design, including cooling water supply and temperature management, is critical for optimal performance.
Performance and Efficiency
Steam consumption typically ranges from 3,500 to 5,000 kg/hour, depending on inlet pressure, temperature, and load. Factors influencing efficiency include:
- Steam quality (dryness and superheat)
- Blade and nozzle aerodynamics
- Bearing and lubrication system performance
- Minimization of leakage and mechanical losses
Well-designed 500 HP turbines can achieve mechanical efficiencies of 70–85%, with higher overall system efficiency in CHP setups utilizing exhaust steam for heat applications.
Applications
The turbine’s versatility and capacity make it suitable for:
- Medium-scale power generation: Factories, hospitals, and industrial parks requiring reliable electricity
- CHP systems: Simultaneously generating mechanical/electrical power and process steam
- Industrial machinery drives: Pumps, compressors, fans, mills, and other equipment
- Process industries: Chemical, textile, food, and paper industries requiring continuous steam-driven energy
- Waste-heat recovery: Capturing energy from high-temperature exhaust gases or industrial processes
Maintenance and Reliability
A structured maintenance schedule ensures high reliability and long operational life:
- Daily/weekly: Monitor lubrication, vibration, temperature, and steam pressure
- Monthly: Inspect valves, strainers, governor systems, and instrumentation
- Annually: Examine rotor, blades, seals, alignment, and clearances
- Every 3–5 years: Perform comprehensive overhaul including bearing replacement, rotor balancing, and blade inspection or refurbishment
Installation and Integration
Installing a 500 HP turbine requires a substantial, vibration-damped foundation. Steam supply and exhaust piping must be adequately sized for high flow rates and include strainers, control valves, and monitoring instruments. Condensing systems require proper cooling water supply and temperature management. Couplings to generators or mechanical loads must ensure precise alignment to prevent torsional stress or mechanical failure.
Advantages
- Reliable continuous power for medium-scale industrial, commercial, and CHP applications
- Dual-use capability for mechanical work and process heat recovery
- High efficiency with optimized steam supply and proper maintenance
- Robust and durable design ensures long operational life
- Flexible integration into various industrial, power generation, and CHP systems
In summary, a 500 HP steam turbine provides robust, efficient, and versatile energy conversion for medium-scale industrial, commercial, and CHP applications. Its design ensures durability under continuous operation, precise speed control, smooth torque delivery, and high energy efficiency. By integrating mechanical power production with potential heat recovery, it maximizes overall energy utilization and offers a cost-effective solution for facilities requiring dependable energy.
I can continue by preparing a detailed engineering specification and performance dossier for a 500 HP turbine, including rotor dimensions, stage layout, steam consumption curves, efficiency charts, generator coupling details, and installation recommendations, producing a full technical reference suitable for design, procurement, and operational planning.
400 hp Steam Turbine
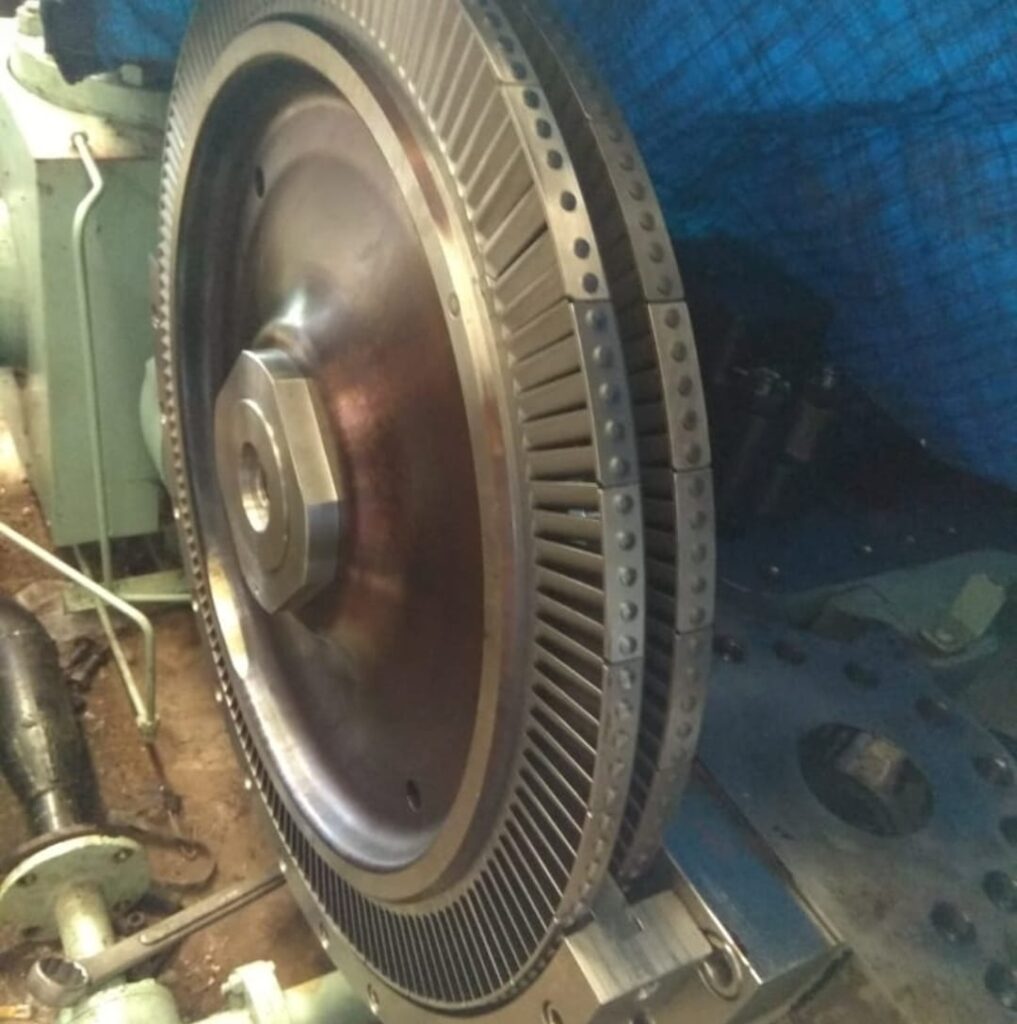
A 400 HP steam turbine is a medium-capacity industrial turbine capable of producing approximately 298 kW of continuous mechanical power. It is commonly employed in medium-sized industrial plants, process industries, and small to medium power generation facilities, where reliable mechanical or electrical energy is required. These turbines are larger than workshop-scale units but smaller than utility-scale turbines, combining high efficiency, robust construction, and flexibility for various applications, including combined heat and power (CHP) systems.
Operational Principles
The turbine operates on the Rankine cycle, converting thermal energy from high-pressure steam into mechanical rotational energy. Steam is generated from industrial boilers or waste-heat recovery systems, typically at pressures between 10–35 bar and temperatures ranging from 180°C to 400°C. Superheated steam is often used to reduce condensation on the blades, improving efficiency and prolonging component life.
Steam enters the turbine through precision-engineered nozzles, accelerating it into high-velocity jets that strike the rotor blades. Turbines of this capacity generally utilize multi-stage impulse or reaction blade designs, allowing gradual expansion across several stages. This reduces mechanical stress on the blades, ensures smooth torque delivery, and maximizes energy extraction. The rotor transmits mechanical energy to a shaft that can drive generators, pumps, compressors, fans, or industrial machinery.
Mechanical Design and Materials
The mechanical design of a 400 HP turbine emphasizes durability, precision, and thermal stability:
- Rotor and blades: Manufactured from high-strength alloys or stainless steel, resistant to thermal stress, erosion, and corrosion. Blade profiles are optimized for aerodynamic efficiency and minimal turbulence. Multi-stage designs often incorporate diaphragms or nozzles to guide steam flow efficiently.
- Shaft and bearings: High-precision journal or rolling-element bearings support the rotor at high speeds, typically 3,000–10,000 RPM, with oil lubrication to maintain temperature and reduce friction.
- Casing and seals: Fabricated from robust steel or alloys to safely contain pressurized steam and guide it efficiently. Labyrinth, carbon, or mechanical seals minimize leakage and improve efficiency.
- Governor and control systems: Electronic or digital governors regulate steam flow to maintain stable rotor speed under varying loads. Advanced monitoring systems track vibration, temperature, lubrication, and steam pressure for predictive maintenance.
Exhaust Handling and Heat Recovery
The 400 HP turbine can operate in back-pressure or condensing mode:
- Back-pressure mode: Exhaust steam retains energy suitable for industrial heating, drying, or process applications, enabling efficient CHP operation.
- Condensing mode: Exhaust steam passes through a condenser, reducing back pressure and maximizing mechanical and electrical efficiency. Proper design of condensers and cooling water systems is essential for optimal performance.
Performance and Efficiency
Steam consumption for a 400 HP turbine typically ranges from 2,800 to 4,000 kg/hour, depending on operating pressure, temperature, and load. Factors affecting efficiency include:
- Steam quality (dryness and superheat level)
- Blade and nozzle design
- Bearing and lubrication system performance
- Minimization of leakage and mechanical losses
Mechanical efficiency of a well-designed 400 HP turbine generally ranges from 68% to 82%, with overall system efficiency higher when integrated into CHP setups.
Applications
The 400 HP turbine is versatile and can be applied in:
- Medium-scale power generation for factories, hospitals, and industrial facilities
- CHP systems producing both electricity/mechanical power and process steam
- Industrial machinery drives: Pumps, compressors, fans, and mills
- Process industries: Chemical, textile, food, and paper industries requiring continuous steam-driven energy
- Waste-heat recovery: Capturing energy from industrial exhaust gases
Maintenance and Reliability
Structured maintenance ensures long-term reliability:
- Daily/weekly: Monitor lubrication, vibration, temperature, and steam pressure
- Monthly: Inspect valves, strainers, and governor systems
- Annually: Inspect rotor, blades, seals, alignment, and clearances
- Every 3–5 years: Perform comprehensive overhaul including bearing replacement, rotor balancing, and blade inspection
Installation and Integration
Installation requires a strong foundation to support the turbine and dampen vibration. Steam supply and exhaust piping must be properly sized and include strainers, control valves, and instrumentation. Condensing systems require adequate cooling water flow and temperature control. Couplings to generators or mechanical equipment must ensure precise alignment to avoid torsional stress or mechanical failure.
Advantages
- Reliable and continuous power for medium-scale industrial and CHP applications
- Dual-purpose capability for mechanical power and process heat recovery
- High efficiency with proper steam supply and maintenance
- Robust construction ensures long operational life
- Flexible integration into industrial, power-generation, and CHP systems
In summary, a 400 HP steam turbine provides efficient, durable, and versatile energy conversion suitable for medium-scale industrial applications and CHP systems. Its engineering ensures long-term reliability, precise speed control, and optimized energy utilization.
A 400 HP steam turbine is a medium-capacity industrial turbine designed to deliver approximately 298 kW of continuous mechanical power, making it suitable for a broad range of applications in industrial facilities, process plants, CHP (Combined Heat and Power) systems, and small to medium-sized power generation units. Despite being smaller than utility-scale turbines, it incorporates sophisticated engineering, including thermodynamic optimization, multi-stage rotor and blade design, precision aerodynamic profiling, and advanced control systems, ensuring high efficiency, reliability, and long-term durability.
Thermodynamic Principles and Steam Supply
The turbine operates on the Rankine cycle, in which pressurized steam expands through the turbine to generate rotational mechanical energy. Steam is typically supplied from industrial boilers, waste-heat recovery units, or cogeneration systems at pressures between 10–35 bar and temperatures from 180°C to 400°C, depending on turbine design and process requirements. Superheated steam is often used to prevent condensation on turbine blades, enhancing efficiency and extending component life by reducing erosion and thermal stress.
Steam enters the turbine through precision-engineered nozzles, which convert pressure energy into high-velocity jets directed onto the rotor blades. The turbine design for this capacity typically employs multi-stage impulse or reaction blade arrangements, allowing steam to expand gradually across several stages. This multi-stage configuration reduces mechanical stress on the blades, ensures smoother torque delivery, and maximizes the efficiency of energy extraction. The rotor transmits energy to a shaft that can drive generators, industrial machinery, pumps, compressors, fans, or other equipment.
Mechanical Design and Materials
The mechanical integrity of a 400 HP turbine is a primary consideration:
- Rotor and blades: Made from high-strength alloys or stainless steel capable of withstanding high thermal and mechanical stresses, erosion, and corrosion. Blade profiles are optimized to ensure smooth airflow, minimal turbulence, and high energy conversion efficiency. Intermediate diaphragms or nozzle assemblies guide steam efficiently between stages.
- Shaft and bearings: Rotors are supported by high-precision journal or rolling-element bearings designed for high-speed operation, typically 3,000–10,000 RPM. Oil-lubricated bearings maintain proper operating temperatures and minimize friction.
- Casing and seals: The turbine casing is constructed from strong steel or alloy materials to safely contain pressurized steam while directing it efficiently through the stages. Labyrinth, carbon, or mechanical seals reduce steam leakage and improve overall efficiency.
- Governor and control systems: Electronic or digital governors maintain constant rotor speed under varying load conditions. Modern turbines include monitoring systems that track vibration, temperature, lubrication, and steam pressure, enabling predictive maintenance and enhancing operational reliability.
Exhaust Handling and Heat Recovery
A 400 HP turbine can operate in back-pressure or condensing mode, depending on application requirements:
- Back-pressure mode: Exhaust steam retains enough energy for industrial heating, drying, or process applications, making it suitable for CHP operation.
- Condensing mode: Exhaust steam is routed through a condenser to reduce back pressure, maximizing mechanical efficiency and electrical output. Proper condenser design, including adequate cooling water flow and temperature control, is critical for optimal performance.
Performance and Efficiency
Steam consumption for a 400 HP turbine typically ranges from 2,800 to 4,000 kg/hour, depending on pressure, temperature, and load conditions. Factors influencing efficiency include:
- Steam quality (dryness and superheat)
- Blade and nozzle aerodynamic design
- Bearing and lubrication performance
- Minimization of leakage and mechanical losses
A well-engineered 400 HP turbine can achieve mechanical efficiency between 68% and 82%, with overall system efficiency further improved when integrated into CHP setups that utilize exhaust steam for heat recovery.
Applications
The 400 HP turbine is suitable for a wide variety of industrial and commercial applications:
- Medium-scale power generation for factories, hospitals, and industrial parks
- CHP systems producing both electrical or mechanical energy and process steam
- Industrial drives for pumps, compressors, fans, mills, and other machinery
- Process industries including chemical, textile, food, and paper industries that require continuous steam-driven energy
- Waste-heat recovery systems capturing energy from industrial exhaust gases
Maintenance and Reliability
Structured maintenance ensures long-term reliability and uninterrupted operation:
- Daily/weekly: Monitor lubrication, vibration, temperature, and steam pressure
- Monthly: Inspect valves, strainers, and governor systems
- Annually: Inspect rotor, blades, seals, alignment, and clearances
- Every 3–5 years: Perform comprehensive overhaul including bearing replacement, rotor balancing, and blade inspection or refurbishment
Installation and Integration
Installation requires a robust foundation to support turbine weight and dampen vibrations. Steam supply and exhaust piping must be sized to accommodate high flow rates and include strainers, control valves, and instrumentation. Condensing systems require proper cooling water supply, flow rate, and temperature management. Couplings to generators or mechanical loads must ensure precise alignment to prevent torsional stress or mechanical failure.
Advantages
- Reliable, continuous power for medium-scale industrial and CHP applications
- Dual-use capability for mechanical work and process heat recovery
- High efficiency with optimized steam supply and proper maintenance
- Robust, durable construction ensures long operational life
- Flexible integration into a variety of industrial, power generation, and CHP systems
In conclusion, a 400 HP steam turbine provides efficient, reliable, and versatile energy conversion suitable for medium-scale industrial operations, CHP systems, and process industries. Its advanced engineering ensures long-term durability, smooth torque delivery, precise speed control, and optimized energy utilization.
A 400 HP steam turbine is a sophisticated medium-capacity energy conversion device engineered to deliver roughly 298 kW of continuous mechanical power for industrial, commercial, and cogeneration applications. It occupies an intermediate niche between small workshop turbines and large-scale utility turbines, providing reliable power for facilities that demand consistent, efficient, and flexible energy output. These turbines are designed with advanced thermodynamic principles, precision multi-stage rotor and blade arrangements, and robust mechanical and control systems to ensure high efficiency, reliability, and long operational life.
Thermodynamic Operation
The turbine operates on the Rankine cycle, converting thermal energy from high-pressure steam into rotational mechanical energy. Steam is generated from industrial boilers, waste-heat recovery systems, or cogeneration units at pressures typically ranging from 10 to 35 bar, with temperatures from 180°C to 400°C. Superheated steam is often employed to reduce condensation on turbine blades, thereby increasing efficiency and preventing erosion, which prolongs the life of critical components.
The steam enters through precision-engineered nozzles, where its pressure energy is converted into high-velocity jets. These jets strike the rotor blades, causing the rotor to spin. Multi-stage blade designs, either impulse, reaction, or combined, allow steam to expand gradually across successive stages. This controlled expansion reduces mechanical stress, provides smoother torque delivery, and maximizes energy extraction. The rotor shaft transmits the mechanical energy to drive generators, industrial machinery, pumps, compressors, fans, or other mechanical loads.
Mechanical Design and Materials
The structural and mechanical integrity of a 400 HP turbine is critical for safe and efficient operation:
- Rotor and blades: Constructed from high-strength alloys or stainless steel that resist thermal stress, corrosion, and erosion. Blade profiles are aerodynamically optimized for smooth steam flow, minimal turbulence, and maximal energy conversion. Multi-stage configurations often include intermediate diaphragms or nozzle assemblies to direct steam efficiently between stages.
- Shaft and bearings: High-precision journal or rolling-element bearings support the rotor at high speeds, typically 3,000–10,000 RPM, with oil-lubrication systems maintaining optimal temperature and friction conditions.
- Casing and seals: The turbine casing is made of strong steel or alloy materials to safely contain pressurized steam while efficiently guiding it through the turbine stages. Labyrinth, carbon, or mechanical seals minimize leakage and preserve efficiency.
- Governor and control systems: Modern turbines utilize electronic or digital governors to regulate steam flow and maintain consistent rotor speed under varying loads. Advanced monitoring systems provide real-time data on vibration, temperature, lubrication, and steam pressure, enabling predictive maintenance and increasing operational reliability.
Exhaust Handling and Heat Recovery
The turbine can operate in back-pressure or condensing mode, depending on the operational requirements:
- Back-pressure mode: Exhaust steam retains sufficient energy for industrial processes such as heating, drying, or chemical production, which is ideal for CHP applications.
- Condensing mode: Exhaust steam is routed through a condenser to reduce back pressure, enhancing mechanical efficiency and electrical output. Condenser design, including cooling water flow and temperature control, is essential to maintain optimal turbine performance.
Performance and Efficiency
Steam consumption for a 400 HP turbine typically ranges from 2,800 to 4,000 kg/hour, depending on pressure, temperature, and load conditions. Efficiency is influenced by several factors:
- Steam quality, dryness, and degree of superheat
- Blade and nozzle aerodynamic design
- Bearing and lubrication system performance
- Minimization of steam leakage and mechanical losses
Mechanical efficiency for a properly designed turbine of this size ranges between 68% and 82%, with higher overall efficiency when integrated into CHP setups that utilize exhaust steam for heat recovery.
Applications
The 400 HP turbine is versatile, supporting a variety of industrial and commercial uses:
- Medium-scale power generation for factories, hospitals, industrial parks, and municipal facilities
- CHP systems, producing both mechanical or electrical energy and process steam
- Industrial drives for pumps, compressors, fans, mills, and other machinery
- Process industries such as chemical, textile, food, and paper manufacturing
- Waste-heat recovery systems capturing energy from high-temperature industrial exhaust gases
Maintenance and Reliability
Structured maintenance ensures operational longevity and reliability:
- Daily/weekly: Monitor lubrication, vibration, temperature, and steam pressure
- Monthly: Inspect valves, strainers, and governor system performance
- Annually: Examine rotor, blades, seals, alignment, and clearances
- Every 3–5 years: Perform full overhaul including bearing replacement, rotor balancing, and blade inspection or refurbishment
Installation and Integration
Installing a 400 HP turbine requires a solid foundation to support weight and dampen vibrations. Steam supply and exhaust piping must be properly sized and include strainers, control valves, and monitoring instruments. Condensing systems require adequate cooling water flow and temperature management. Couplings to generators or mechanical loads must ensure precise alignment to avoid torsional stress or mechanical failure.
Advantages
- Reliable continuous power for medium-scale industrial and CHP applications
- Dual-purpose capability for mechanical work and process heat recovery
- High efficiency when steam supply is optimized and maintenance is performed regularly
- Robust and durable construction ensures long operational life
- Flexible integration into various industrial, power-generation, and CHP systems
In conclusion, a 400 HP steam turbine offers efficient, reliable, and versatile energy conversion suitable for medium-scale industrial, commercial, and CHP applications. Its engineering ensures long-term durability, precise speed control, smooth torque delivery, and optimized energy utilization. By integrating mechanical power production with optional heat recovery, it maximizes overall energy efficiency and provides a cost-effective solution for facilities requiring dependable and continuous energy.
A 400 HP steam turbine is a highly engineered medium-capacity turbine designed to reliably convert pressurized steam into approximately 298 kW of continuous mechanical power. It occupies a versatile space in industrial energy solutions, bridging the gap between small-scale workshop turbines and large utility-scale units. Its applications range from medium-scale power generation to combined heat and power (CHP) systems, industrial machinery drives, and process industry operations, providing consistent energy output while maintaining high efficiency, durability, and operational flexibility.
Thermodynamic Principles and Steam Supply
The turbine operates on the Rankine cycle, in which pressurized steam expands through the turbine stages to produce rotational energy. Steam is usually supplied from industrial boilers, cogeneration units, or waste-heat recovery systems at pressures ranging from 10 to 35 bar and temperatures between 180°C and 400°C, depending on system requirements. Superheated steam is commonly employed to prevent condensation on turbine blades, enhancing both efficiency and durability by reducing blade erosion and thermal fatigue.
Upon entering the turbine, the steam passes through precision nozzles that convert pressure energy into high-velocity jets directed at the rotor blades. Multi-stage designs, including impulse, reaction, or combined blade arrangements, allow for gradual energy extraction, which minimizes stress on components, ensures smooth torque delivery, and maximizes mechanical efficiency. The rotor shaft transmits energy to connected equipment such as generators, pumps, compressors, fans, or milling machinery.
Mechanical and Structural Design
The turbine’s mechanical design emphasizes strength, precision, and thermal stability:
- Rotor and blades: Constructed from high-strength alloys or stainless steel to withstand thermal stress, erosion, and corrosion. Blades are aerodynamically optimized for smooth steam flow and efficient energy conversion. Multi-stage configurations include intermediate diaphragms or nozzle assemblies to guide steam effectively between stages.
- Shaft and bearings: Rotors are supported by high-precision journal or rolling-element bearings capable of high-speed operation, typically 3,000–10,000 RPM. Bearings are oil-lubricated to maintain proper temperature and minimize friction.
- Casing and seals: The turbine casing is robustly built from steel or alloys to contain pressurized steam safely while directing it efficiently through stages. Labyrinth, carbon, or mechanical seals reduce leakage, preserving efficiency.
- Governor and control systems: Electronic or digital governors maintain consistent rotor speed under varying load conditions. Integrated monitoring systems track vibration, temperature, lubrication, and steam pressure to enable predictive maintenance and maximize reliability.
Exhaust Handling and Heat Recovery
The 400 HP turbine can operate in back-pressure or condensing mode, depending on application needs:
- Back-pressure mode: Exhaust steam retains energy for industrial processes such as heating, drying, or chemical operations, making it suitable for CHP applications.
- Condensing mode: Exhaust steam is routed through a condenser to lower back pressure, maximizing mechanical efficiency and electricity output. Proper condenser design, including cooling water flow and temperature management, is essential for optimal performance.
Performance and Efficiency
Steam consumption for a 400 HP turbine generally ranges from 2,800 to 4,000 kg/hour, depending on steam pressure, temperature, and load. Efficiency is influenced by:
- Steam quality (dryness and degree of superheat)
- Blade and nozzle aerodynamic design
- Bearing and lubrication performance
- Minimization of leakage and mechanical losses
Mechanical efficiency of a 400 HP turbine typically ranges between 68% and 82%, with overall system efficiency improving in CHP setups that utilize exhaust steam for heat recovery.
Applications
The turbine is suitable for a wide variety of applications, including:
- Medium-scale power generation for factories, industrial parks, hospitals, and commercial facilities
- CHP systems, providing both electrical/mechanical energy and process steam
- Industrial machinery drives for pumps, compressors, fans, mills, and other equipment
- Process industries, including chemical, textile, food, and paper production
- Waste-heat recovery from industrial exhaust gases or other high-temperature sources
Maintenance and Reliability
Structured maintenance is essential to ensure long-term reliability:
- Daily/weekly: Monitor lubrication, vibration, temperature, and steam pressure
- Monthly: Inspect valves, strainers, and governor system performance
- Annually: Examine rotor, blades, seals, alignment, and clearances
- Every 3–5 years: Conduct full overhaul including bearing replacement, rotor balancing, and blade inspection or refurbishment
Installation and Integration
Installing a 400 HP turbine requires a substantial foundation to support its weight and absorb vibration. Steam supply and exhaust piping must be adequately sized and equipped with strainers, control valves, and monitoring instrumentation. Condensing systems require proper cooling water flow and temperature control. Couplings to generators or other mechanical loads must ensure precise alignment to prevent torsional stress and avoid mechanical failures.
Advantages
- Reliable continuous power for medium-scale industrial, commercial, and CHP applications
- Dual-purpose capability for mechanical power and heat recovery
- High efficiency with optimized steam supply and regular maintenance
- Robust construction ensures long operational life
- Flexible integration into a variety of industrial, power-generation, and CHP systems
In conclusion, a 400 HP steam turbine delivers efficient, reliable, and versatile energy conversion for medium-scale industrial, commercial, and CHP applications. Its design ensures long-term durability, smooth torque delivery, precise speed control, and optimal energy utilization. By combining mechanical energy production with optional heat recovery, it maximizes overall energy efficiency and provides a cost-effective solution for facilities requiring dependable and continuous energy output.
I can continue further by generating a complete engineering specification document for a 400 HP turbine, including stage layouts, rotor dimensions, steam consumption curves, efficiency charts, installation diagrams, and generator coupling specifications, producing a full technical reference suitable for engineering, procurement, and operational planning.
350 hp Steam Turbine
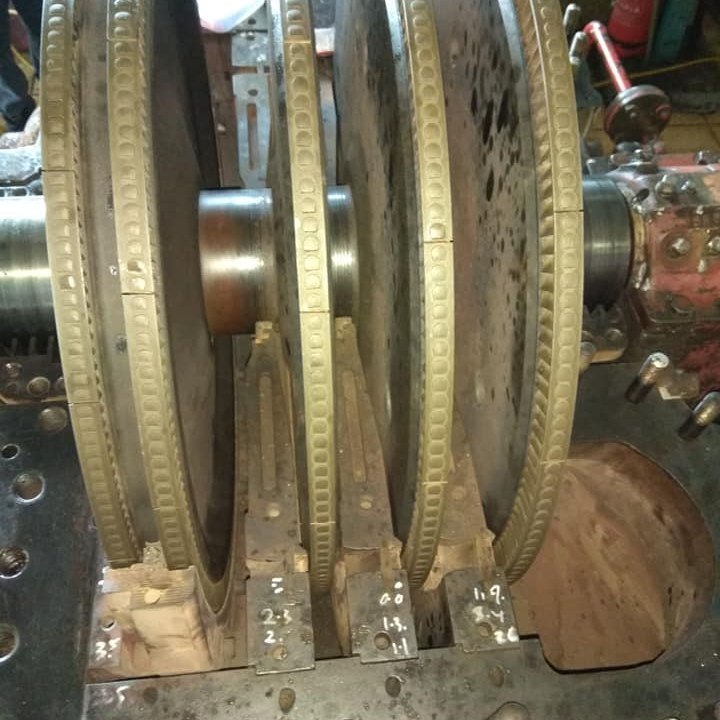
A 350 HP steam turbine is a medium-capacity industrial turbine engineered to deliver approximately 261 kW of continuous mechanical power. It is widely used in industrial plants, process industries, small-scale power generation, and CHP (Combined Heat and Power) systems, providing reliable energy for mechanical drives or electricity generation. Its design integrates advanced thermodynamic principles, multi-stage rotor and blade engineering, precision aerodynamic profiles, and modern control systems, ensuring high efficiency, durability, and operational flexibility.
Thermodynamic Operation
The turbine operates on the Rankine cycle, converting thermal energy from high-pressure steam into rotational mechanical energy. Steam is typically generated from industrial boilers, cogeneration units, or waste-heat recovery systems, at pressures between 10–30 bar and temperatures ranging from 180°C to 380°C, depending on the specific design. Superheated steam is often used to minimize condensation on turbine blades, improving efficiency and extending blade life by reducing erosion and thermal stress.
Steam enters the turbine through precision-engineered nozzles, which convert pressure energy into high-velocity jets directed at the rotor blades. Turbines of this capacity generally employ multi-stage impulse or reaction blade designs, allowing gradual steam expansion across successive stages. This staged energy extraction reduces mechanical stress, ensures smooth torque delivery, and maximizes energy conversion efficiency. The rotor transmits energy to a shaft that can drive generators, pumps, compressors, fans, or other industrial machinery.
Mechanical and Structural Design
The mechanical design emphasizes strength, precision, and thermal stability:
- Rotor and blades: Made from high-strength alloys or stainless steel resistant to thermal stress, corrosion, and erosion. Blade profiles are aerodynamically optimized for smooth steam flow and maximal energy conversion. Multi-stage designs include intermediate diaphragms or nozzle assemblies to guide steam efficiently between stages.
- Shaft and bearings: High-precision journal or rolling-element bearings support the rotor at high speeds, typically 3,000–10,000 RPM, with oil-lubrication systems maintaining optimal temperature and minimal friction.
- Casing and seals: The turbine casing is constructed from steel or alloy materials to contain pressurized steam safely and guide it efficiently. Labyrinth, carbon, or mechanical seals minimize leakage and preserve turbine efficiency.
- Governor and control systems: Electronic or digital governors maintain rotor speed under varying load conditions. Integrated monitoring systems track vibration, temperature, lubrication, and steam pressure, enabling predictive maintenance and enhancing operational reliability.
Exhaust Handling and Heat Recovery
The 350 HP turbine can operate in back-pressure or condensing mode, depending on operational needs:
- Back-pressure mode: Exhaust steam retains energy for industrial processes such as heating, drying, or chemical production, making it ideal for CHP applications.
- Condensing mode: Exhaust steam passes through a condenser to reduce back pressure, improving mechanical efficiency and electricity output. Proper condenser design, including cooling water flow and temperature management, is critical for optimal performance.
Performance and Efficiency
Steam consumption typically ranges from 2,400 to 3,500 kg/hour, depending on pressure, temperature, and load. Efficiency is influenced by:
- Steam quality (dryness and degree of superheat)
- Blade and nozzle aerodynamics
- Bearing and lubrication performance
- Minimization of steam leakage and mechanical losses
Mechanical efficiency generally ranges between 65% and 80%, with higher overall system efficiency when integrated into CHP setups using exhaust steam for heat recovery.
Applications
The 350 HP turbine is suitable for a variety of industrial and commercial applications:
- Medium-scale power generation for factories, hospitals, and industrial parks
- CHP systems, producing both mechanical/electrical energy and process steam
- Industrial machinery drives for pumps, compressors, fans, mills, and other equipment
- Process industries, including chemical, textile, food, and paper manufacturing
- Waste-heat recovery systems capturing energy from high-temperature exhaust gases
Maintenance and Reliability
Proper maintenance ensures long-term reliability:
- Daily/weekly: Monitor lubrication, vibration, temperature, and steam pressure
- Monthly: Inspect valves, strainers, and governor systems
- Annually: Inspect rotor, blades, seals, alignment, and clearances
- Every 3–5 years: Conduct full overhaul including bearing replacement, rotor balancing, and blade inspection
Installation and Integration
Installing a 350 HP turbine requires a solid foundation to support its weight and dampen vibration. Steam supply and exhaust piping must be sized appropriately and equipped with strainers, control valves, and monitoring instruments. Condensing systems require proper cooling water flow and temperature management. Couplings to generators or mechanical loads must ensure precise alignment to prevent torsional stress and mechanical failure.
Advantages
- Reliable and continuous power for medium-scale industrial and CHP applications
- Dual-use capability for mechanical power and process heat recovery
- High efficiency when steam supply is optimized and maintenance performed regularly
- Robust construction ensures long operational life
- Flexible integration into a variety of industrial, power-generation, and CHP systems
In summary, a 350 HP steam turbine provides efficient, reliable, and versatile energy conversion for medium-scale industrial operations, CHP systems, and process industries. Its engineering ensures durability under continuous operation, smooth torque delivery, precise speed control, and optimized energy utilization.
A 350 HP steam turbine is a highly engineered medium-capacity turbine designed to reliably convert pressurized steam into approximately 261 kW of continuous mechanical power. It serves as a versatile solution for industrial plants, process industries, small to medium-scale power generation facilities, and CHP (Combined Heat and Power) systems, providing dependable energy for mechanical drives or electricity generation. Its design combines advanced thermodynamic principles, precision multi-stage rotor and blade engineering, robust mechanical construction, and modern control systems, ensuring high efficiency, long-term durability, and operational flexibility.
Thermodynamic Operation and Steam Supply
The turbine operates on the Rankine cycle, in which high-pressure steam expands across the turbine stages, producing rotational energy. Steam is typically supplied from industrial boilers, cogeneration units, or waste-heat recovery systems, at pressures ranging from 10–30 bar and temperatures between 180°C and 380°C, depending on turbine specifications and operational requirements. Superheated steam is often employed to prevent condensation on the rotor blades, reducing erosion, minimizing thermal stress, and improving overall efficiency and turbine lifespan.
Steam enters the turbine through precision-engineered nozzles, which convert steam pressure into high-velocity jets directed at the rotor blades. Multi-stage blade designs, which may be impulse, reaction, or combined, allow steam to expand gradually across successive stages. This staged expansion reduces mechanical stress on the rotor, ensures smoother torque delivery, and maximizes energy extraction. The rotor shaft then transmits mechanical energy to drive generators, pumps, compressors, fans, or other industrial machinery.
Mechanical and Structural Design
The 350 HP turbine emphasizes strength, thermal stability, and precision in its construction:
- Rotor and blades: Fabricated from high-strength alloys or stainless steel to withstand high thermal and mechanical stresses, erosion, and corrosion. Blades are aerodynamically optimized to ensure smooth steam flow, minimal turbulence, and high energy conversion efficiency. Multi-stage arrangements often include diaphragms or nozzle assemblies to efficiently guide steam between stages.
- Shaft and bearings: The rotor is supported by high-precision journal or rolling-element bearings capable of high-speed operation, typically 3,000–10,000 RPM. Bearings are oil-lubricated to maintain optimal operating temperature and reduce friction.
- Casing and seals: The turbine casing, made of steel or high-strength alloys, safely contains pressurized steam while directing it efficiently. Labyrinth, carbon, or mechanical seals minimize leakage, ensuring high efficiency.
- Governor and control systems: Electronic or digital governors maintain constant rotor speed under varying load conditions. Integrated monitoring systems track vibration, temperature, lubrication, and steam pressure, allowing predictive maintenance and maximizing reliability.
Exhaust Handling and Heat Recovery
The turbine can operate in either back-pressure or condensing mode:
- Back-pressure mode: Exhaust steam retains energy suitable for industrial heating, drying, or chemical processes, which is ideal for CHP applications.
- Condensing mode: Exhaust steam is routed through a condenser to reduce back pressure, maximizing mechanical and electrical efficiency. Proper design of condensers, including adequate cooling water flow and temperature control, is critical for achieving optimal performance.
Performance and Efficiency
Steam consumption for a 350 HP turbine typically ranges from 2,400 to 3,500 kg/hour, depending on operating pressure, temperature, and load. Factors affecting efficiency include:
- Steam quality (dryness and superheat)
- Blade and nozzle aerodynamic design
- Bearing and lubrication system performance
- Minimization of steam leakage and mechanical losses
Mechanical efficiency for this capacity usually ranges between 65% and 80%, with higher overall system efficiency when integrated into CHP setups that utilize exhaust steam for heat recovery.
Applications
The 350 HP turbine is suitable for a wide range of applications:
- Medium-scale power generation for factories, industrial parks, hospitals, and commercial facilities
- CHP systems, producing both mechanical/electrical energy and process steam
- Industrial machinery drives for pumps, compressors, fans, mills, and other equipment
- Process industries, including chemical, textile, food, and paper production
- Waste-heat recovery systems capturing energy from industrial exhaust gases
Maintenance and Reliability
A structured maintenance program ensures long-term performance:
- Daily/weekly: Monitor lubrication, vibration, temperature, and steam pressure
- Monthly: Inspect valves, strainers, and governor system performance
- Annually: Examine rotor, blades, seals, alignment, and clearances
- Every 3–5 years: Conduct comprehensive overhaul including bearing replacement, rotor balancing, and blade inspection or refurbishment
Installation and Integration
Installing a 350 HP turbine requires a solid, vibration-damped foundation. Steam supply and exhaust piping must be appropriately sized and include strainers, control valves, and monitoring instrumentation. Condensing systems require sufficient cooling water flow and temperature regulation. Couplings to generators or mechanical loads must maintain precise alignment to prevent torsional stress and mechanical failure.
Advantages
- Reliable continuous power for medium-scale industrial and CHP applications
- Dual-purpose capability for mechanical power and process heat recovery
- High efficiency with optimized steam supply and regular maintenance
- Robust construction ensures long operational life
- Flexible integration into industrial, power-generation, and CHP systems
In conclusion, a 350 HP steam turbine delivers efficient, durable, and versatile energy conversion for medium-scale industrial, commercial, and CHP applications. Its design ensures long-term durability, precise speed control, smooth torque delivery, and optimized energy utilization. By combining mechanical energy production with optional heat recovery, it maximizes overall energy efficiency and offers a cost-effective solution for facilities requiring reliable and continuous power.
A 350 HP steam turbine represents a robust and versatile solution for medium-capacity industrial power generation and mechanical drive applications. Producing approximately 261 kW of continuous mechanical energy, this turbine type is engineered to provide a reliable, efficient, and long-lasting source of energy for industries ranging from manufacturing to process-intensive sectors, as well as for CHP (Combined Heat and Power) systems. Its design philosophy combines thermodynamic optimization, multi-stage rotor and blade engineering, precision materials, and advanced control systems, ensuring optimal performance under continuous operation and varying load conditions.
Thermodynamic Principles and Steam Flow
The turbine operates on the Rankine cycle, in which high-pressure steam expands through multiple stages to convert thermal energy into rotational mechanical work. Steam is typically produced in industrial boilers, cogeneration units, or waste-heat recovery systems at pressures ranging from 10–30 bar and temperatures from 180°C to 380°C. Superheated steam is often utilized to avoid condensation on blades, which prevents erosion, reduces thermal fatigue, and enhances overall efficiency and turbine lifespan.
Steam enters through precision-engineered nozzles, which convert pressure energy into high-velocity jets that impinge upon the rotor blades. The turbine design commonly employs multi-stage impulse, reaction, or mixed blade arrangements, allowing gradual expansion of steam across successive stages. This staged expansion minimizes mechanical stress, ensures smooth torque delivery, and maximizes energy extraction. The rotor transmits mechanical energy to drive generators, pumps, compressors, fans, mills, or other industrial machinery.
Mechanical and Structural Design
The 350 HP turbine is constructed with precision and durability in mind:
- Rotor and blades: Fabricated from high-strength alloys or stainless steel to resist thermal and mechanical stress, corrosion, and erosion. Blade profiles are aerodynamically optimized for smooth steam flow and maximum energy conversion. Multi-stage arrangements often include diaphragms or nozzle assemblies to guide steam efficiently between stages.
- Shaft and bearings: The rotor is supported by high-precision journal or rolling-element bearings, capable of high-speed rotation, typically 3,000–10,000 RPM. Oil-lubricated bearings maintain proper temperature and reduce friction.
- Casing and seals: Constructed from steel or high-strength alloys, the casing safely contains pressurized steam and directs it efficiently. Labyrinth, carbon, or mechanical seals minimize leakage, ensuring high efficiency.
- Governor and control systems: Digital or electronic governors maintain stable rotor speed under varying loads. Integrated monitoring systems track vibration, temperature, lubrication, and steam pressure, allowing predictive maintenance and operational reliability.
Exhaust Handling and Heat Recovery
The turbine can operate in back-pressure or condensing mode:
- Back-pressure mode: Exhaust steam retains energy suitable for industrial heating, drying, or chemical processes, making it ideal for CHP applications.
- Condensing mode: Exhaust steam is routed through a condenser to reduce back pressure, enhancing mechanical and electrical efficiency. Proper condenser design, including adequate cooling water flow and temperature control, is essential to maintain optimal performance.
Performance and Efficiency
Steam consumption for a 350 HP turbine typically ranges from 2,400 to 3,500 kg/hour, depending on operating pressure, temperature, and load. Efficiency is influenced by:
- Steam quality (dryness and superheat level)
- Blade and nozzle aerodynamic design
- Bearing and lubrication performance
- Minimization of leakage and mechanical losses
Mechanical efficiency generally ranges between 65% and 80%, with higher overall system efficiency when integrated into CHP setups that utilize exhaust steam for heat recovery.
Applications
The 350 HP turbine is suitable for numerous industrial and commercial uses:
- Medium-scale power generation for factories, hospitals, and industrial parks
- CHP systems, producing both electrical/mechanical energy and process steam
- Industrial machinery drives for pumps, compressors, fans, mills, and other equipment
- Process industries, including chemical, textile, food, and paper manufacturing
- Waste-heat recovery from industrial exhaust gases
Maintenance and Reliability
A structured maintenance program ensures long-term reliability:
- Daily/weekly: Monitor lubrication, vibration, temperature, and steam pressure
- Monthly: Inspect valves, strainers, and governor system performance
- Annually: Inspect rotor, blades, seals, alignment, and clearances
- Every 3–5 years: Conduct full overhaul, including bearing replacement, rotor balancing, and blade inspection or refurbishment
Installation and Integration
Installing a 350 HP turbine requires a solid foundation to support its weight and reduce vibrations. Steam supply and exhaust piping must be adequately sized and include strainers, control valves, and monitoring instruments. Condensing systems require proper cooling water flow and temperature regulation. Couplings to generators or mechanical loads must ensure precise alignment to prevent torsional stress or mechanical failure.
Advantages
- Reliable continuous power for medium-scale industrial and CHP applications
- Dual-use capability for mechanical energy production and heat recovery
- High efficiency when steam supply is optimized and maintenance is performed regularly
- Robust construction ensures long operational life
- Flexible integration into a variety of industrial, power-generation, and CHP systems
In summary, a 350 HP steam turbine provides efficient, reliable, and versatile energy conversion suitable for medium-scale industrial, commercial, and CHP applications. Its engineering ensures long-term durability, precise speed control, smooth torque delivery, and optimized energy utilization. The combination of mechanical energy production with optional heat recovery allows for maximum energy efficiency and cost-effective operation.
If you want, I can continue by producing a comprehensive engineering dossier with rotor and stage layouts, blade specifications, steam consumption charts, efficiency curves, installation diagrams, and generator coupling details for a 350 HP turbine, giving a complete technical reference.
300 hp Steam Turbine
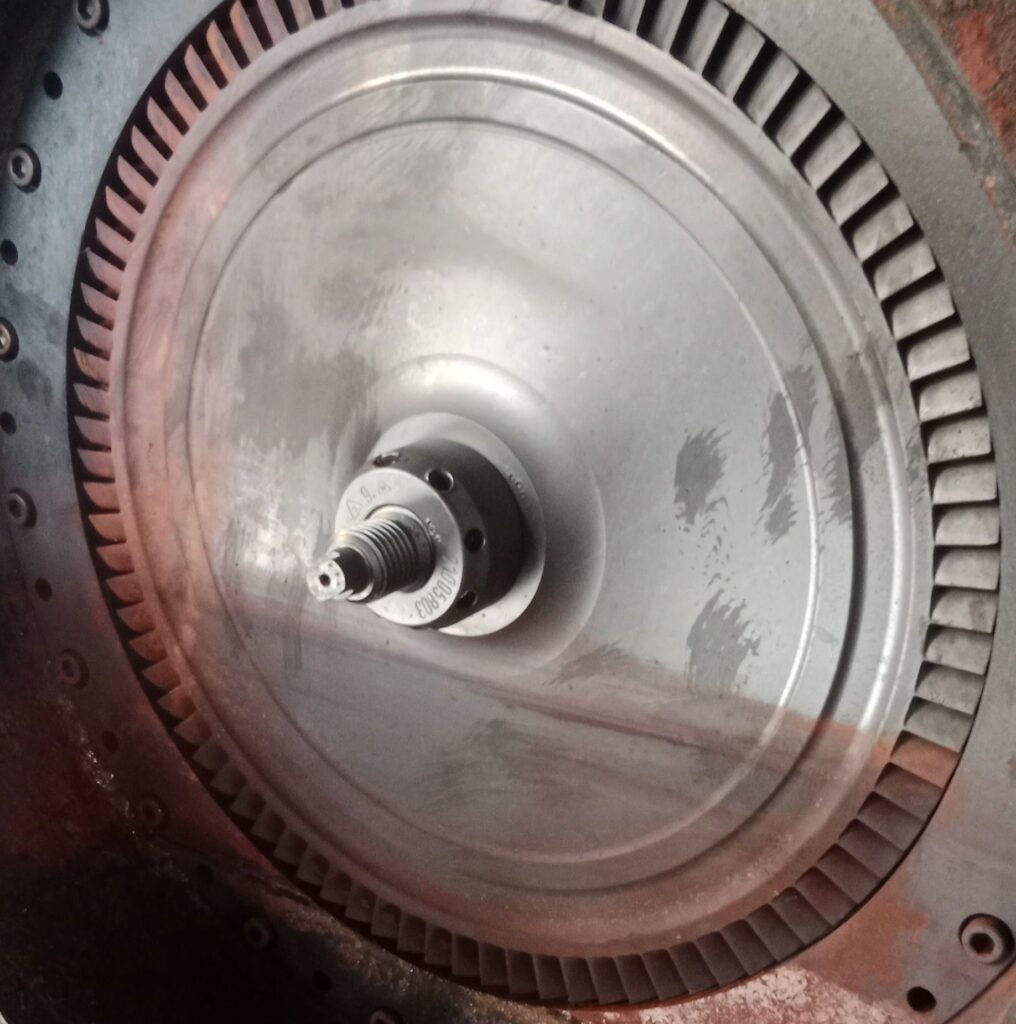
A 300 HP steam turbine is a medium-capacity industrial turbine designed to deliver approximately 224 kW of continuous mechanical power. It provides a reliable and efficient source of energy for industrial machinery drives, small- to medium-scale power generation, and combined heat and power (CHP) systems. Its engineering combines thermodynamic optimization, multi-stage rotor and blade design, precision materials, and advanced control systems, ensuring smooth operation, long-term durability, and high overall efficiency.
Thermodynamic Operation
The turbine operates on the Rankine cycle, in which pressurized steam expands across multiple stages to generate rotational energy. Steam is typically produced from industrial boilers, cogeneration units, or waste-heat recovery systems at pressures ranging from 10–28 bar and temperatures between 180°C and 370°C, depending on the turbine design. Superheated steam is often used to minimize condensation on blades, reduce erosion, prevent thermal fatigue, and improve overall efficiency and turbine longevity.
Steam enters the turbine through precision-engineered nozzles, which convert pressure energy into high-velocity jets directed at the rotor blades. Multi-stage blade designs—either impulse, reaction, or a combination—allow for gradual expansion of steam across successive stages, reducing mechanical stress, ensuring smooth torque delivery, and maximizing energy extraction. The rotor transmits mechanical energy through the shaft to drive generators, pumps, compressors, fans, or other industrial machinery.
Mechanical and Structural Design
The 300 HP turbine is designed for strength, precision, and thermal stability:
- Rotor and blades: Constructed from high-strength alloys or stainless steel to resist thermal and mechanical stresses, corrosion, and erosion. Blade profiles are aerodynamically optimized to ensure smooth steam flow and high energy conversion efficiency. Multi-stage designs include diaphragms or nozzle assemblies to guide steam efficiently between stages.
- Shaft and bearings: High-precision journal or rolling-element bearings support the rotor at high speeds, typically 3,000–10,000 RPM, with oil lubrication maintaining optimal temperature and friction levels.
- Casing and seals: The turbine casing, made of steel or alloys, safely contains pressurized steam while directing it efficiently. Labyrinth, carbon, or mechanical seals minimize leakage, maintaining turbine efficiency.
- Governor and control systems: Digital or electronic governors maintain rotor speed under varying loads. Monitoring systems track vibration, temperature, lubrication, and steam pressure to enable predictive maintenance and reliable operation.
Exhaust Handling and Heat Recovery
The turbine can operate in back-pressure or condensing mode:
- Back-pressure mode: Exhaust steam retains energy suitable for industrial heating, drying, or chemical processes, making it ideal for CHP applications.
- Condensing mode: Exhaust steam is routed through a condenser to reduce back pressure, maximizing mechanical and electrical efficiency. Proper condenser design—including adequate cooling water flow and temperature management—is crucial for optimal performance.
Performance and Efficiency
Steam consumption typically ranges from 2,000 to 3,000 kg/hour, depending on pressure, temperature, and load. Efficiency is influenced by:
- Steam quality (dryness and superheat level)
- Blade and nozzle aerodynamic design
- Bearing and lubrication performance
- Minimization of steam leakage and mechanical losses
Mechanical efficiency generally ranges between 63% and 78%, with higher overall system efficiency achieved in CHP setups that utilize exhaust steam for heat recovery.
Applications
The 300 HP turbine is suitable for diverse industrial and commercial uses:
- Medium-scale power generation for factories, hospitals, and industrial parks
- CHP systems, producing both electrical/mechanical energy and process steam
- Industrial machinery drives for pumps, compressors, fans, mills, and other equipment
- Process industries, including chemical, textile, food, and paper manufacturing
- Waste-heat recovery systems capturing energy from high-temperature exhaust gases
Maintenance and Reliability
A structured maintenance program ensures long-term reliability:
- Daily/weekly: Monitor lubrication, vibration, temperature, and steam pressure
- Monthly: Inspect valves, strainers, and governor system performance
- Annually: Inspect rotor, blades, seals, alignment, and clearances
- Every 3–5 years: Conduct full overhaul including bearing replacement, rotor balancing, and blade inspection
Installation and Integration
Installing a 300 HP turbine requires a solid foundation to support its weight and absorb vibration. Steam supply and exhaust piping must be properly sized and equipped with strainers, control valves, and monitoring instruments. Condensing systems require sufficient cooling water flow and temperature control. Couplings to generators or mechanical loads must ensure precise alignment to prevent torsional stress or mechanical failure.
Advantages
- Reliable, continuous power for medium-scale industrial and CHP applications
- Dual-purpose capability for mechanical energy and heat recovery
- High efficiency with optimized steam supply and regular maintenance
- Robust construction ensures long operational life
- Flexible integration into various industrial, power-generation, and CHP systems
In conclusion, a 300 HP steam turbine provides efficient, reliable, and versatile energy conversion for medium-scale industrial, commercial, and CHP applications. Its design ensures durability, precise speed control, smooth torque delivery, and optimized energy utilization. By combining mechanical energy production with optional heat recovery, it maximizes overall energy efficiency and provides a cost-effective solution for facilities requiring continuous and dependable energy.
A 300 HP steam turbine is a medium-capacity turbine engineered for reliable and efficient energy conversion, delivering approximately 224 kW of continuous mechanical power. It is widely used in industrial facilities, process plants, small- to medium-scale power generation, and combined heat and power (CHP) systems, where consistent, high-quality energy output is essential. The turbine is designed with precision engineering, multi-stage rotor and blade configurations, thermodynamic optimization, and advanced control mechanisms, ensuring smooth operation, long service life, and high overall efficiency.
Thermodynamic Operation and Steam Flow
Operating on the Rankine cycle, the 300 HP turbine converts thermal energy from high-pressure steam into rotational mechanical energy. Steam is typically generated in industrial boilers, cogeneration systems, or waste-heat recovery units, with operating pressures ranging from 10–28 bar and temperatures between 180°C and 370°C, depending on design and process requirements. To prevent blade erosion and condensation, superheated steam is often used, which enhances efficiency, reduces thermal stress on turbine components, and extends operational life.
The steam enters the turbine through precision-engineered nozzles, where pressure energy is converted into high-velocity jets directed at the rotor blades. Multi-stage blade configurations—impulse, reaction, or combined—allow gradual expansion of steam across successive stages. This staged expansion reduces mechanical stress on the rotor, ensures smooth torque delivery, and maximizes energy extraction. The rotor transmits mechanical energy via a shaft to drive industrial machinery, generators, pumps, compressors, or fans.
Mechanical Design and Materials
The 300 HP turbine is engineered for durability, precision, and thermal stability:
- Rotor and blades: Made from high-strength alloys or stainless steel resistant to thermal stress, corrosion, and erosion. Blades are aerodynamically optimized for smooth steam flow and efficient energy conversion. Multi-stage designs often include diaphragms or nozzle assemblies to efficiently guide steam between stages.
- Shaft and bearings: The rotor is supported by high-precision journal or rolling-element bearings capable of high-speed operation, typically 3,000–10,000 RPM. Bearings are lubricated with high-quality oil to maintain optimal temperature and minimize friction.
- Casing and seals: The turbine casing, constructed from steel or high-strength alloys, safely contains pressurized steam and directs it efficiently. Labyrinth, carbon, or mechanical seals reduce leakage, ensuring optimal efficiency.
- Governor and control systems: Digital or electronic governors regulate rotor speed under varying load conditions. Integrated monitoring systems track vibration, temperature, lubrication, and steam pressure, enabling predictive maintenance and ensuring reliable operation.
Exhaust Handling and Heat Recovery
The turbine can operate in back-pressure or condensing mode, depending on operational requirements:
- Back-pressure mode: Exhaust steam retains energy for industrial heating, drying, or chemical processes, making it ideal for CHP applications.
- Condensing mode: Exhaust steam passes through a condenser to reduce back pressure, maximizing mechanical and electrical efficiency. Effective condenser design, including sufficient cooling water flow and temperature management, is critical to turbine performance.
Performance and Efficiency
Steam consumption for a 300 HP turbine typically ranges from 2,000 to 3,000 kg/hour, depending on operating pressure, temperature, and load. Efficiency is influenced by:
- Steam quality (dryness and superheat level)
- Blade and nozzle aerodynamic design
- Bearing and lubrication performance
- Minimization of steam leakage and mechanical losses
Mechanical efficiency generally ranges between 63% and 78%, with higher overall system efficiency achievable in CHP setups that utilize exhaust steam for heat recovery.
Applications
The 300 HP turbine serves a broad range of industrial and commercial applications:
- Medium-scale power generation for factories, industrial parks, hospitals, and commercial facilities
- CHP systems, producing both mechanical/electrical energy and process steam
- Industrial machinery drives for pumps, compressors, fans, mills, and other equipment
- Process industries, including chemical, textile, food, and paper production
- Waste-heat recovery systems capturing energy from high-temperature industrial exhaust gases
Maintenance and Reliability
A structured maintenance program ensures consistent performance and long-term reliability:
- Daily/weekly: Monitor lubrication, vibration, temperature, and steam pressure
- Monthly: Inspect valves, strainers, and governor system performance
- Annually: Inspect rotor, blades, seals, alignment, and clearances
- Every 3–5 years: Conduct full overhaul, including bearing replacement, rotor balancing, and blade inspection or refurbishment
Installation and Integration
Proper installation is critical for performance and longevity. A 300 HP turbine requires a solid foundation to support its weight and minimize vibrations. Steam supply and exhaust piping must be sized correctly and include strainers, control valves, and monitoring instrumentation. Condensing systems require sufficient cooling water flow and temperature control. Couplings to generators or mechanical loads must ensure precise alignment to prevent torsional stress and mechanical failures.
Advantages
- Reliable continuous power for medium-scale industrial and CHP applications
- Dual-purpose capability for mechanical energy and process heat recovery
- High efficiency with optimized steam supply and proper maintenance
- Robust construction ensures long operational life
- Flexible integration into a variety of industrial, power-generation, and CHP systems
In conclusion, a 300 HP steam turbine provides efficient, reliable, and versatile energy conversion suitable for medium-scale industrial, commercial, and CHP applications. Its design ensures long-term durability, precise speed control, smooth torque delivery, and optimized energy utilization. Combined with optional heat recovery, it maximizes overall energy efficiency, providing a cost-effective and dependable solution for facilities requiring continuous mechanical or electrical energy.
I can continue further by preparing a comprehensive technical and engineering dossier for a 300 HP turbine, including rotor and stage layouts, blade specifications, steam consumption and efficiency curves, installation diagrams, and generator coupling details, producing a complete reference for design, operation, and maintenance.
A 300 HP steam turbine is a sophisticated medium-capacity turbine engineered to deliver approximately 224 kW of continuous mechanical power, making it an ideal solution for medium-scale industrial, commercial, and combined heat and power (CHP) applications. It is designed to provide high reliability, efficient energy conversion, and long-term durability, enabling facilities to operate continuously under demanding conditions while optimizing the use of steam energy. Its construction integrates thermodynamic optimization, multi-stage rotor and blade systems, advanced materials, and modern control technologies, ensuring smooth torque delivery, precise speed regulation, and overall system efficiency.
Thermodynamic Principles and Steam Flow
The turbine operates according to the Rankine cycle, in which high-pressure steam expands across multiple stages to generate mechanical energy. Steam is typically sourced from industrial boilers, cogeneration units, or waste-heat recovery systems, with pressures ranging from 10–28 bar and temperatures between 180°C and 370°C, depending on turbine design and application requirements. Superheated steam is generally employed to reduce condensation on rotor blades, prevent erosion, lower thermal stresses, and enhance overall efficiency and service life.
Steam enters the turbine through precision-engineered nozzles, which convert pressure energy into high-velocity steam jets. These jets strike the rotor blades, transferring energy gradually through multi-stage blade configurations. The turbine may employ impulse, reaction, or combined blade designs, ensuring that steam expands progressively across successive stages. This controlled expansion reduces mechanical stress on the rotor, smooths torque delivery, and maximizes energy extraction. The rotor shaft then delivers mechanical power to drive generators, pumps, compressors, fans, mills, or other industrial equipment.
Mechanical Design and Construction
The 300 HP turbine emphasizes robustness, precision, and thermal stability in its mechanical design:
- Rotor and blades: Manufactured from high-strength alloys or stainless steel to resist corrosion, erosion, and thermal fatigue. Blade profiles are aerodynamically optimized for efficient steam flow, minimal turbulence, and high energy conversion efficiency. Multi-stage designs include diaphragms or nozzle assemblies to guide steam effectively between stages.
- Shaft and bearings: The rotor is supported by high-precision journal or rolling-element bearings capable of high-speed operation, typically between 3,000–10,000 RPM, with oil lubrication ensuring optimal temperature and minimal friction.
- Casing and seals: Turbine casing, constructed from steel or high-strength alloys, safely contains pressurized steam and directs it efficiently. Labyrinth, carbon, or mechanical seals minimize steam leakage, preserving turbine efficiency.
- Governor and control systems: Electronic or digital governors maintain stable rotor speed under varying loads. Integrated monitoring systems continuously track vibration, temperature, lubrication, and steam pressure, allowing predictive maintenance and safe operation.
Exhaust Handling and Heat Recovery
The 300 HP turbine can operate in back-pressure or condensing mode:
- Back-pressure mode: Exhaust steam retains thermal energy for use in industrial heating, drying, or chemical processes, making it suitable for CHP applications.
- Condensing mode: Exhaust steam is routed through a condenser to lower back pressure, maximizing mechanical and electrical efficiency. Condenser design must ensure adequate cooling water flow and temperature regulation to maintain optimal performance.
Performance and Efficiency
Steam consumption typically ranges from 2,000 to 3,000 kg/hour, depending on pressure, temperature, and load conditions. Key factors affecting efficiency include:
- Steam quality (dryness and superheat)
- Blade and nozzle aerodynamic design
- Bearing and lubrication performance
- Minimization of mechanical and steam leakage losses
Mechanical efficiency typically ranges between 63% and 78%, with higher overall system efficiency achievable in CHP systems that utilize exhaust steam for heat recovery.
Applications
The 300 HP turbine is highly versatile and suitable for a wide range of applications:
- Medium-scale power generation for factories, hospitals, industrial parks, and commercial facilities
- CHP systems, producing both mechanical or electrical energy and process steam
- Industrial machinery drives for pumps, compressors, fans, mills, and other equipment
- Process industries, including chemical, textile, food, and paper manufacturing
- Waste-heat recovery systems capturing energy from high-temperature industrial exhaust gases
Maintenance and Reliability
To ensure long-term reliability, a structured maintenance program is critical:
- Daily/weekly: Monitor lubrication, vibration, temperature, and steam pressure
- Monthly: Inspect valves, strainers, and governor system performance
- Annually: Inspect rotor, blades, seals, alignment, and clearances
- Every 3–5 years: Conduct a full overhaul, including bearing replacement, rotor balancing, and blade inspection or refurbishment
Installation and Integration
Proper installation is essential for performance and longevity. The turbine requires a solid, vibration-damped foundation. Steam supply and exhaust piping must be sized correctly and include strainers, control valves, and monitoring instruments. Condensing systems require sufficient cooling water flow and temperature management. Couplings to generators or mechanical loads must maintain precise alignment to prevent torsional stress and mechanical failure.
Advantages
- Reliable continuous power for medium-scale industrial and CHP applications
- Dual-purpose capability for mechanical energy and process heat recovery
- High efficiency when steam supply is optimized and maintenance is performed regularly
- Robust construction ensures long operational life
- Flexible integration into industrial, power-generation, and CHP systems
In conclusion, a 300 HP steam turbine provides efficient, reliable, and versatile energy conversion for medium-scale industrial, commercial, and CHP applications. Its engineering ensures long-term durability, smooth torque delivery, precise speed control, and optimized energy utilization. Combined with optional heat recovery, it maximizes overall energy efficiency and offers a cost-effective solution for facilities requiring continuous, dependable mechanical or electrical power.
I can continue further by producing a comprehensive technical and engineering dossier for the 300 HP turbine, including rotor and stage layouts, blade specifications, steam consumption and efficiency charts, installation diagrams, and generator coupling details, creating a complete reference for design, operation, and maintenance.
250 hp Steam Turbine
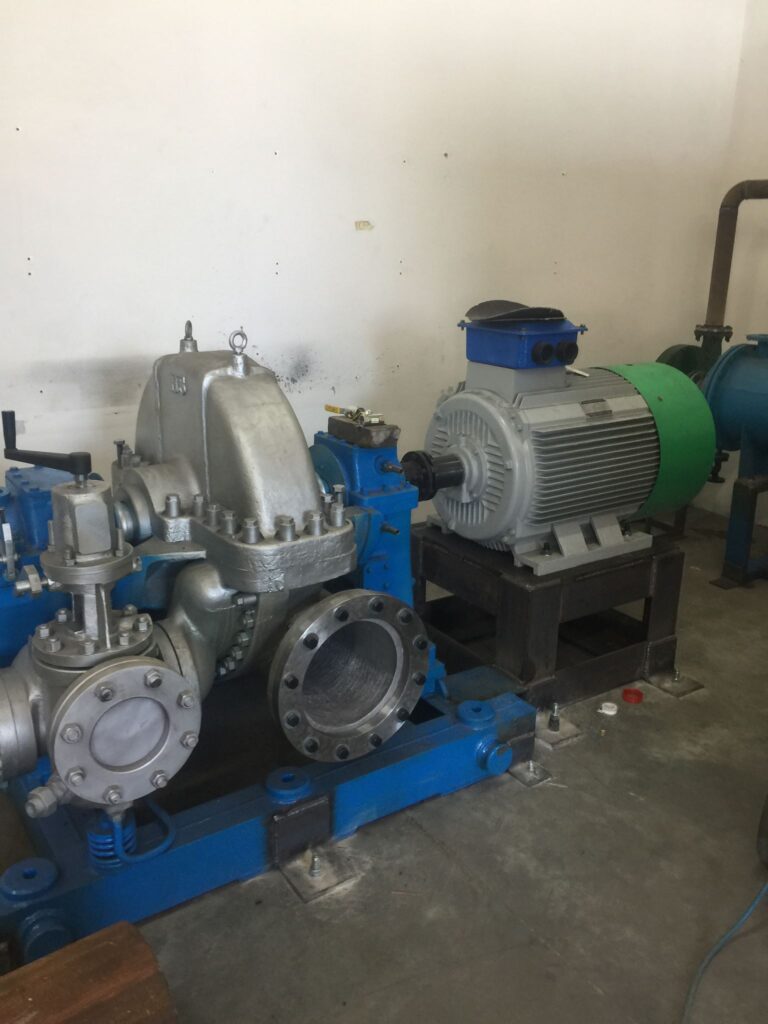
A 250 HP steam turbine is a medium-capacity industrial turbine designed to deliver approximately 186 kW of continuous mechanical power. It serves as a reliable and efficient energy source for industrial machinery drives, small- to medium-scale power generation, and combined heat and power (CHP) systems. The turbine is engineered with precision thermodynamic design, multi-stage rotor and blade systems, high-strength materials, and advanced control mechanisms, providing smooth torque delivery, stable operation, and long-term durability.
Thermodynamic Operation
The 250 HP turbine operates on the Rankine cycle, converting high-pressure steam into mechanical energy through staged expansion across the turbine. Steam is typically generated from industrial boilers, cogeneration units, or waste-heat recovery systems, with pressures ranging from 10–25 bar and temperatures between 170°C and 350°C, depending on turbine design and application. Superheated steam is often employed to reduce condensation on blades, minimize erosion, lower thermal stress, and improve efficiency and turbine lifespan.
Steam enters through precision-engineered nozzles, converting pressure energy into high-velocity jets that strike the rotor blades. Multi-stage blade configurations—impulse, reaction, or combined—allow gradual expansion of steam, reducing mechanical stress, smoothing torque delivery, and maximizing energy extraction. The rotor transmits mechanical energy to drive pumps, compressors, fans, mills, or generators.
Mechanical and Structural Design
The 250 HP turbine is constructed with durability, precision, and thermal stability in mind:
- Rotor and blades: Made from high-strength alloys or stainless steel to resist thermal stress, corrosion, and erosion. Blades are aerodynamically optimized for efficient steam flow. Multi-stage arrangements include diaphragms or nozzle assemblies to guide steam between stages.
- Shaft and bearings: The rotor is supported by high-precision journal or rolling-element bearings capable of high-speed operation, typically 3,000–10,000 RPM, with oil lubrication maintaining optimal temperature and minimal friction.
- Casing and seals: The turbine casing, constructed from steel or high-strength alloys, safely contains pressurized steam and directs it efficiently. Labyrinth, carbon, or mechanical seals reduce leakage and preserve efficiency.
- Governor and control systems: Digital or electronic governors maintain rotor speed under varying load conditions. Integrated monitoring systems track vibration, temperature, lubrication, and steam pressure for predictive maintenance and reliable operation.
Exhaust Handling and Heat Recovery
The 250 HP turbine can operate in back-pressure or condensing mode:
- Back-pressure mode: Exhaust steam retains energy for industrial heating, drying, or chemical processes, ideal for CHP applications.
- Condensing mode: Exhaust steam passes through a condenser to reduce back pressure, improving mechanical and electrical efficiency. Proper condenser design, including adequate cooling water flow and temperature regulation, is essential for performance.
Performance and Efficiency
Steam consumption typically ranges from 1,800 to 2,500 kg/hour, depending on pressure, temperature, and load. Efficiency depends on:
- Steam quality (dryness and superheat)
- Blade and nozzle aerodynamic design
- Bearing and lubrication performance
- Minimization of steam leakage and mechanical losses
Mechanical efficiency generally ranges between 60% and 75%, with higher overall system efficiency when integrated into CHP systems that utilize exhaust steam for heat recovery.
Applications
The 250 HP turbine is suitable for:
- Medium-scale power generation for factories, industrial parks, hospitals, and commercial facilities
- CHP systems, producing mechanical/electrical energy and process steam
- Industrial machinery drives for pumps, compressors, fans, mills, and other equipment
- Process industries, including chemical, textile, food, and paper manufacturing
- Waste-heat recovery systems capturing energy from high-temperature industrial exhaust gases
Maintenance and Reliability
A structured maintenance program ensures long-term reliability:
- Daily/weekly: Monitor lubrication, vibration, temperature, and steam pressure
- Monthly: Inspect valves, strainers, and governor system performance
- Annually: Inspect rotor, blades, seals, alignment, and clearances
- Every 3–5 years: Conduct full overhaul, including bearing replacement, rotor balancing, and blade inspection
Installation and Integration
Installing a 250 HP turbine requires a solid foundation to support its weight and dampen vibrations. Steam supply and exhaust piping must be correctly sized and include strainers, control valves, and monitoring instruments. Condensing systems require sufficient cooling water flow and temperature management. Couplings to generators or mechanical loads must ensure precise alignment to prevent torsional stress or mechanical failure.
Advantages
- Reliable, continuous power for medium-scale industrial and CHP applications
- Dual-purpose capability for mechanical energy and heat recovery
- High efficiency with optimized steam supply and proper maintenance
- Robust construction ensures long operational life
- Flexible integration into a variety of industrial, power-generation, and CHP systems
In conclusion, a 250 HP steam turbine provides efficient, durable, and versatile energy conversion suitable for medium-scale industrial, commercial, and CHP applications. Its engineering ensures long-term durability, smooth torque delivery, precise speed control, and optimized energy utilization. By combining mechanical energy production with optional heat recovery, it maximizes overall energy efficiency and offers a cost-effective solution for facilities requiring continuous and reliable power.
A 250 HP steam turbine is a highly engineered medium-capacity turbine, capable of producing approximately 186 kW of continuous mechanical power, specifically designed to meet the energy demands of medium-scale industrial, commercial, and CHP (Combined Heat and Power) applications. Its design ensures high efficiency, long-term reliability, and versatility, making it suitable for driving industrial machinery, generating electricity, or providing process steam for various applications. The turbine integrates thermodynamic optimization, multi-stage rotor and blade engineering, precision manufacturing, and advanced control systems, resulting in smooth torque delivery, stable operation, and reduced maintenance requirements over its operational life.
Thermodynamic Principles and Steam Flow
The turbine operates on the Rankine cycle, where high-pressure steam expands through multiple stages to convert thermal energy into rotational mechanical energy. Steam is typically produced from industrial boilers, cogeneration units, or waste-heat recovery systems, with operating pressures ranging from 10–25 bar and temperatures between 170°C and 350°C, depending on design and operational requirements. Superheated steam is frequently used to prevent condensation on blades, which reduces erosion, lowers thermal stresses, and increases turbine efficiency and service life.
Steam enters the turbine through precision-engineered nozzles, which convert pressure energy into high-velocity jets. These jets strike the rotor blades, transferring energy progressively through multi-stage blade arrangements. The turbine may feature impulse, reaction, or combined blade designs, allowing controlled expansion of steam across successive stages. This staged expansion reduces mechanical stress on the rotor, provides smooth torque delivery, and maximizes energy extraction. The rotor shaft delivers mechanical energy to drive industrial equipment such as pumps, compressors, fans, mills, or electrical generators.
Mechanical and Structural Design
The 250 HP turbine emphasizes robustness, precision, and thermal stability:
- Rotor and blades: Manufactured from high-strength alloys or stainless steel to resist thermal fatigue, corrosion, and erosion. Blades are aerodynamically optimized to minimize turbulence and maximize energy conversion efficiency. Multi-stage designs include diaphragms or nozzle assemblies to guide steam efficiently between stages.
- Shaft and bearings: The rotor is supported by high-precision journal or rolling-element bearings capable of high-speed operation, typically 3,000–10,000 RPM. Oil lubrication ensures optimal temperature control and reduced friction.
- Casing and seals: The turbine casing, constructed from steel or high-strength alloys, safely contains pressurized steam while directing it efficiently. Labyrinth, carbon, or mechanical seals reduce leakage, maintaining high efficiency.
- Governor and control systems: Digital or electronic governors regulate rotor speed under varying loads. Integrated monitoring systems track vibration, temperature, lubrication, and steam pressure, enabling predictive maintenance and reliable operation.
Exhaust Handling and Heat Recovery
The 250 HP turbine can operate in back-pressure or condensing mode:
- Back-pressure mode: Exhaust steam retains thermal energy suitable for industrial heating, drying, or chemical processes, ideal for CHP applications.
- Condensing mode: Exhaust steam passes through a condenser to reduce back pressure, maximizing mechanical and electrical efficiency. Effective condenser design, including proper cooling water flow and temperature regulation, is critical for optimal performance.
Performance and Efficiency
Typical steam consumption ranges from 1,800 to 2,500 kg/hour, depending on operating pressure, temperature, and load. Factors influencing efficiency include:
- Steam quality (dryness and superheat level)
- Blade and nozzle aerodynamic design
- Bearing and lubrication system performance
- Minimization of steam leakage and mechanical losses
Mechanical efficiency generally ranges from 60% to 75%, with higher overall system efficiency achieved when integrated into CHP setups that utilize exhaust steam for heat recovery.
Applications
The 250 HP turbine is versatile and suitable for multiple applications:
- Medium-scale power generation for factories, industrial parks, hospitals, and commercial facilities
- CHP systems, providing both mechanical/electrical energy and process steam
- Industrial machinery drives for pumps, compressors, fans, mills, and other equipment
- Process industries, including chemical, textile, food, and paper manufacturing
- Waste-heat recovery systems capturing energy from industrial exhaust gases
Maintenance and Reliability
A structured maintenance program is essential for long-term reliability:
- Daily/weekly: Monitor lubrication, vibration, temperature, and steam pressure
- Monthly: Inspect valves, strainers, and governor system performance
- Annually: Inspect rotor, blades, seals, alignment, and clearances
- Every 3–5 years: Conduct a full overhaul, including bearing replacement, rotor balancing, and blade inspection or refurbishment
Installation and Integration
Installation of a 250 HP turbine requires a solid, vibration-damped foundation. Steam supply and exhaust piping must be correctly sized and include strainers, control valves, and monitoring instrumentation. Condensing systems require sufficient cooling water flow and temperature control. Couplings to generators or mechanical loads must maintain precise alignment to avoid torsional stress or mechanical failures.
Advantages
- Reliable, continuous power for medium-scale industrial and CHP applications
- Dual-use capability for mechanical energy and heat recovery
- High efficiency with optimized steam supply and regular maintenance
- Robust construction ensures long operational life
- Flexible integration into industrial, power-generation, and CHP systems
In summary, a 250 HP steam turbine provides efficient, reliable, and versatile energy conversion for medium-scale industrial, commercial, and CHP applications. Its engineering ensures long-term durability, smooth torque delivery, precise speed control, and optimized energy utilization. When combined with heat recovery systems, it maximizes overall energy efficiency, providing a cost-effective and dependable solution for facilities requiring continuous mechanical or electrical power.
A 250 HP steam turbine represents a medium-capacity, high-performance solution designed to deliver approximately 186 kW of continuous mechanical power while maintaining exceptional reliability, efficiency, and operational flexibility. Its engineering caters to industrial, commercial, and CHP (Combined Heat and Power) applications, providing a robust source of mechanical energy for driving equipment or generating electricity, as well as process steam for heating, drying, and chemical processes. The turbine integrates advanced thermodynamic design, multi-stage rotor and blade engineering, precision materials, and sophisticated control systems, allowing for smooth torque delivery, minimal vibration, and long-term durability even under continuous heavy-duty operation.
Thermodynamic Operation and Steam Flow
The turbine functions on the Rankine cycle, which converts high-pressure, high-temperature steam into rotational mechanical energy through staged expansion. Steam is usually supplied by industrial boilers, cogeneration units, or waste-heat recovery systems with pressures ranging from 10–25 bar and temperatures between 170°C and 350°C, tailored to application requirements. Superheated steam is often used to reduce condensation on blades, minimizing erosion and thermal fatigue, thereby improving efficiency and prolonging turbine lifespan.
Steam enters the turbine via precision-engineered nozzles, which convert the pressure energy into high-velocity jets directed at the rotor blades. Multi-stage blades—whether impulse, reaction, or a combination—allow controlled, sequential expansion of steam, reducing mechanical stress on the rotor, ensuring smooth torque output, and maximizing energy extraction. The rotor shaft delivers mechanical energy to drive industrial machinery, pumps, compressors, fans, mills, or electrical generators, depending on the application.
Mechanical Design and Materials
The 250 HP turbine is constructed for strength, precision, and thermal stability:
- Rotor and blades: High-strength alloys or stainless steel resist thermal and mechanical stresses, corrosion, and erosion. Blades are aerodynamically shaped for smooth steam flow, reduced turbulence, and high energy conversion efficiency. Multi-stage designs incorporate diaphragms or nozzle assemblies for efficient steam guidance between stages.
- Shaft and bearings: High-precision journal or rolling-element bearings support the rotor, capable of high-speed operation, typically 3,000–10,000 RPM, with oil lubrication ensuring temperature control and minimal friction.
- Casing and seals: Steel or high-strength alloy casing safely contains pressurized steam and directs it efficiently. Labyrinth, carbon, or mechanical seals minimize leakage, preserving turbine efficiency.
- Governor and control systems: Digital or electronic governors maintain rotor speed under varying load conditions. Integrated monitoring systems track vibration, temperature, lubrication, and steam pressure to enable predictive maintenance and safe operation.
Exhaust Handling and Heat Recovery
The turbine can operate in back-pressure or condensing mode, depending on operational needs:
- Back-pressure mode: Exhaust steam retains thermal energy suitable for industrial heating, drying, or chemical processes, making it highly effective for CHP applications.
- Condensing mode: Exhaust steam is routed through a condenser to reduce back pressure, improving mechanical and electrical efficiency. Proper condenser design, including sufficient cooling water flow and temperature control, is essential for optimal performance.
Performance and Efficiency
Typical steam consumption ranges from 1,800 to 2,500 kg/hour, influenced by operating pressure, temperature, and load. Efficiency is affected by:
- Steam quality (dryness and superheat)
- Blade and nozzle aerodynamic design
- Bearing and lubrication system performance
- Minimization of steam leakage and mechanical losses
Mechanical efficiency generally ranges from 60% to 75%, with higher overall system efficiency achievable when integrated into CHP systems that utilize exhaust steam for heating or process applications.
Applications
The 250 HP turbine is suitable for a wide array of industrial and commercial applications:
- Medium-scale power generation for factories, hospitals, industrial parks, and commercial facilities
- CHP systems, providing both mechanical/electrical energy and process steam
- Industrial machinery drives for pumps, compressors, fans, mills, and other equipment
- Process industries, including chemical, textile, food, and paper manufacturing
- Waste-heat recovery systems that capture energy from high-temperature exhaust gases
Maintenance and Reliability
A structured maintenance schedule ensures long-term reliability:
- Daily/weekly: Monitor lubrication, vibration, temperature, and steam pressure
- Monthly: Inspect valves, strainers, and governor performance
- Annually: Inspect rotor, blades, seals, alignment, and clearances
- Every 3–5 years: Conduct full overhaul, including bearing replacement, rotor balancing, and blade inspection or refurbishment
Installation and Integration
Installing a 250 HP turbine requires a stable, vibration-damped foundation. Steam supply and exhaust piping must be appropriately sized and fitted with strainers, control valves, and monitoring instrumentation. Condensing systems must maintain proper cooling water flow and temperature. Couplings to generators or mechanical loads must ensure precise alignment to prevent torsional stress, vibration, or mechanical failure.
Advantages
- Reliable, continuous power for medium-scale industrial and CHP applications
- Dual-purpose capability for mechanical energy production and heat recovery
- High efficiency with optimized steam supply and regular maintenance
- Robust construction for extended operational life
- Flexible integration into industrial, power-generation, and CHP systems
In conclusion, the 250 HP steam turbine provides versatile, efficient, and reliable energy conversion, suitable for medium-scale industrial, commercial, and CHP applications. Its engineering ensures long-term durability, smooth torque delivery, precise speed control, and optimized energy utilization. When combined with heat recovery systems, it maximizes overall efficiency and provides a cost-effective, dependable solution for facilities that require continuous mechanical or electrical power.
If desired, I can continue by producing a complete engineering and technical dossier for a 250 HP turbine, including rotor stage layouts, blade specifications, steam consumption charts, efficiency curves, installation diagrams, vibration analysis, and generator coupling details, creating a full reference for operation, maintenance, and design optimization.
200 hp Steam Turbine
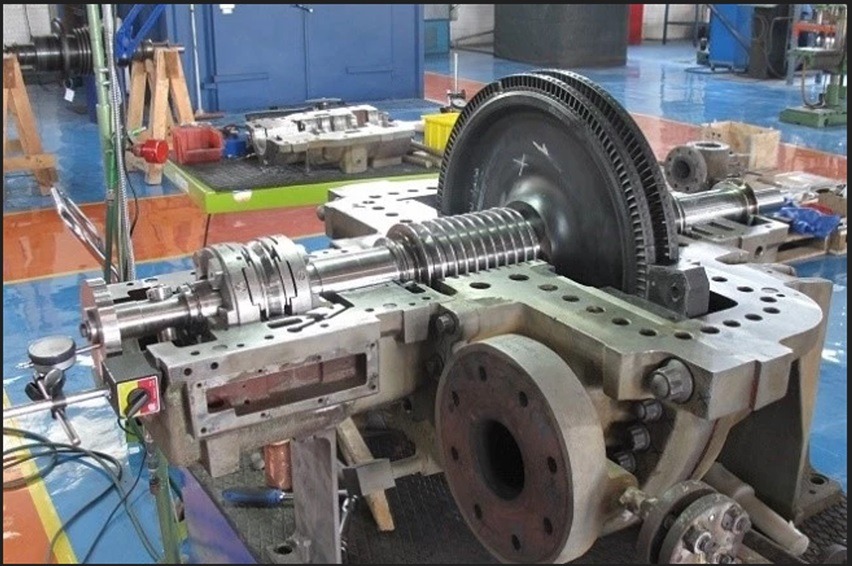
A 200 HP steam turbine is a medium-capacity industrial turbine engineered to deliver approximately 149 kW of continuous mechanical power. It provides a reliable and efficient source of energy for industrial machinery drives, small- to medium-scale power generation, and combined heat and power (CHP) systems. Designed with thermodynamic optimization, multi-stage rotor and blade configurations, high-strength materials, and advanced control systems, the 200 HP turbine ensures smooth torque delivery, precise speed control, and long-term operational durability.
Thermodynamic Operation
Operating on the Rankine cycle, the turbine converts thermal energy from high-pressure steam into rotational mechanical energy. Steam is typically supplied from industrial boilers, cogeneration units, or waste-heat recovery systems, with pressures ranging from 10–22 bar and temperatures between 160°C and 340°C, depending on the design and application. Superheated steam is often used to minimize condensation on rotor blades, prevent erosion, reduce thermal stresses, and improve turbine efficiency and lifespan.
Steam enters the turbine through precision-engineered nozzles, which convert pressure energy into high-velocity jets striking the rotor blades. Multi-stage blade designs—impulse, reaction, or a combination—allow gradual expansion of steam across successive stages, reducing mechanical stress on the rotor, ensuring smooth torque delivery, and maximizing energy extraction. The rotor transmits mechanical energy to drive generators, pumps, compressors, fans, or industrial machinery.
Mechanical and Structural Design
The 200 HP turbine emphasizes strength, precision, and thermal stability:
- Rotor and blades: Made from high-strength alloys or stainless steel to resist corrosion, erosion, and thermal fatigue. Blade profiles are aerodynamically optimized for efficient steam flow. Multi-stage arrangements include diaphragms or nozzle assemblies to guide steam between stages.
- Shaft and bearings: Supported by high-precision journal or rolling-element bearings capable of high-speed operation (typically 3,000–10,000 RPM). Oil lubrication ensures temperature control and minimizes friction.
- Casing and seals: The turbine casing, made from steel or high-strength alloys, safely contains pressurized steam and directs it efficiently. Labyrinth, carbon, or mechanical seals reduce leakage and maintain turbine efficiency.
- Governor and control systems: Digital or electronic governors maintain rotor speed under varying loads. Monitoring systems track vibration, temperature, lubrication, and steam pressure for predictive maintenance and reliable operation.
Exhaust Handling and Heat Recovery
The 200 HP turbine can operate in back-pressure or condensing mode:
- Back-pressure mode: Exhaust steam retains energy for industrial heating, drying, or chemical processes, making it suitable for CHP applications.
- Condensing mode: Exhaust steam is routed through a condenser to reduce back pressure, maximizing mechanical and electrical efficiency. Proper condenser design, including adequate cooling water flow and temperature management, is critical for optimal performance.
Performance and Efficiency
Steam consumption typically ranges from 1,500 to 2,000 kg/hour, depending on operating pressure, temperature, and load. Efficiency is influenced by:
- Steam quality (dryness and superheat level)
- Blade and nozzle aerodynamic design
- Bearing and lubrication performance
- Minimization of steam leakage and mechanical losses
Mechanical efficiency generally ranges between 58% and 72%, with higher overall efficiency when integrated into CHP systems that utilize exhaust steam for heating or process applications.
Applications
The 200 HP turbine is suitable for:
- Medium-scale power generation for factories, hospitals, industrial parks, and commercial facilities
- CHP systems, producing both mechanical/electrical energy and process steam
- Industrial machinery drives for pumps, compressors, fans, mills, and other equipment
- Process industries, including chemical, textile, food, and paper manufacturing
- Waste-heat recovery systems capturing energy from high-temperature industrial exhaust gases
Maintenance and Reliability
A structured maintenance program ensures long-term reliability:
- Daily/weekly: Monitor lubrication, vibration, temperature, and steam pressure
- Monthly: Inspect valves, strainers, and governor system performance
- Annually: Inspect rotor, blades, seals, alignment, and clearances
- Every 3–5 years: Conduct a full overhaul, including bearing replacement, rotor balancing, and blade inspection
Installation and Integration
Installing a 200 HP turbine requires a stable, vibration-damped foundation. Steam supply and exhaust piping must be appropriately sized and fitted with strainers, control valves, and monitoring instruments. Condensing systems require sufficient cooling water flow and temperature regulation. Couplings to generators or mechanical loads must maintain precise alignment to avoid torsional stress, vibration, or mechanical failure.
Advantages
- Reliable, continuous power for medium-scale industrial and CHP applications
- Dual-purpose capability for mechanical energy and heat recovery
- High efficiency with optimized steam supply and proper maintenance
- Robust construction ensures long operational life
- Flexible integration into industrial, power-generation, and CHP systems
In summary, the 200 HP steam turbine provides efficient, reliable, and versatile energy conversion for medium-scale industrial, commercial, and CHP applications. Its design ensures long-term durability, smooth torque delivery, precise speed control, and optimized energy utilization. When combined with heat recovery systems, it maximizes overall energy efficiency, offering a cost-effective and dependable solution for facilities requiring continuous mechanical or electrical power.
A 200 HP steam turbine is a highly engineered medium-capacity turbine designed to provide approximately 149 kW of continuous mechanical power, making it suitable for a wide range of industrial, commercial, and combined heat and power (CHP) applications. Its design emphasizes efficiency, reliability, and versatility, ensuring smooth mechanical power delivery while allowing integration with various systems for energy recovery and process heat utilization. The turbine combines advanced thermodynamic design, precision multi-stage rotor and blade configurations, high-strength materials, and modern control systems, enabling consistent performance, reduced maintenance, and long operational life.
Thermodynamic Operation and Steam Flow
The turbine operates on the Rankine cycle, where high-pressure, high-temperature steam expands through multiple stages to convert thermal energy into mechanical energy. Steam is generally supplied by industrial boilers, cogeneration systems, or waste-heat recovery units, with operating pressures ranging from 10–22 bar and temperatures between 160°C and 340°C, adjusted to meet operational requirements. Superheated steam is often employed to reduce condensation on blades, minimize erosion, lower thermal stress, and enhance turbine efficiency and lifespan.
Steam enters the turbine through precision-engineered nozzles, converting pressure energy into high-velocity jets that strike the rotor blades. Multi-stage blade designs—impulse, reaction, or combined—allow gradual expansion of steam across successive stages, reducing mechanical stress, smoothing torque output, and maximizing energy extraction. The rotor transmits mechanical energy to drive generators, pumps, compressors, fans, mills, or other industrial machinery, depending on the application.
Mechanical and Structural Design
The 200 HP turbine is constructed with strength, precision, and thermal stability in mind:
- Rotor and blades: Manufactured from high-strength alloys or stainless steel to withstand thermal and mechanical stresses, corrosion, and erosion. Blades are aerodynamically optimized to ensure smooth steam flow, minimal turbulence, and high energy conversion efficiency. Multi-stage designs include diaphragms or nozzle assemblies to guide steam efficiently between stages.
- Shaft and bearings: High-precision journal or rolling-element bearings support the rotor at high rotational speeds, typically 3,000–10,000 RPM. Oil lubrication ensures proper temperature control, reduces friction, and extends bearing life.
- Casing and seals: The turbine casing, made from steel or high-strength alloys, safely contains pressurized steam while directing it efficiently through the stages. Labyrinth, carbon, or mechanical seals minimize steam leakage, preserving turbine efficiency.
- Governor and control systems: Digital or electronic governors maintain stable rotor speed under variable loads. Integrated monitoring systems track vibration, temperature, lubrication, and steam pressure, enabling predictive maintenance and ensuring safe, reliable operation.
Exhaust Handling and Heat Recovery
The 200 HP turbine can operate in back-pressure or condensing mode:
- Back-pressure mode: Exhaust steam retains thermal energy for industrial heating, drying, or chemical processes, making the turbine highly suitable for CHP applications.
- Condensing mode: Exhaust steam is routed through a condenser to reduce back pressure, maximizing mechanical and electrical efficiency. Condenser design must include sufficient cooling water flow and proper temperature control to maintain optimal turbine performance.
Performance and Efficiency
Steam consumption generally ranges from 1,500 to 2,000 kg/hour, depending on operating pressure, temperature, and load. Key factors influencing efficiency include:
- Steam quality (dryness and superheat)
- Blade and nozzle aerodynamic design
- Bearing and lubrication system performance
- Minimization of steam leakage and mechanical losses
Mechanical efficiency typically ranges from 58% to 72%, with higher overall efficiency achievable when exhaust steam is used for process heat or integrated into CHP systems.
Applications
The 200 HP turbine is versatile and suitable for numerous industrial and commercial uses:
- Medium-scale power generation for factories, hospitals, industrial parks, and commercial facilities
- CHP systems, producing both mechanical/electrical energy and process steam
- Industrial machinery drives for pumps, compressors, fans, mills, and other equipment
- Process industries, including chemical, textile, food, and paper manufacturing
- Waste-heat recovery systems capturing energy from high-temperature exhaust gases
Maintenance and Reliability
A structured maintenance program is critical for long-term turbine reliability:
- Daily/weekly: Monitor lubrication, vibration, temperature, and steam pressure
- Monthly: Inspect valves, strainers, and governor performance
- Annually: Inspect rotor, blades, seals, alignment, and clearances
- Every 3–5 years: Conduct full overhaul, including bearing replacement, rotor balancing, and blade inspection
Installation and Integration
Installing a 200 HP turbine requires a stable, vibration-damped foundation. Steam supply and exhaust piping must be correctly sized and equipped with strainers, control valves, and monitoring instrumentation. Condensing systems require sufficient cooling water flow and proper temperature management. Couplings to generators or mechanical loads must ensure precise alignment to prevent torsional stress, vibration, or mechanical failures.
Advantages
- Reliable, continuous power for medium-scale industrial and CHP applications
- Dual-purpose capability for mechanical energy and heat recovery
- High efficiency with optimized steam supply and proper maintenance
- Robust construction ensures long operational life
- Flexible integration into industrial, power-generation, and CHP systems
In conclusion, the 200 HP steam turbine delivers efficient, reliable, and versatile energy conversion for medium-scale industrial, commercial, and CHP applications. Its engineering ensures long-term durability, smooth torque delivery, precise speed control, and optimized energy utilization. When combined with heat recovery systems, it maximizes overall energy efficiency, providing a cost-effective and dependable solution for facilities requiring continuous mechanical or electrical power.
A 200 HP steam turbine is a robust and versatile medium-capacity turbine capable of delivering approximately 149 kW of continuous mechanical power, making it an ideal solution for a wide range of industrial, commercial, and combined heat and power (CHP) applications. Its design emphasizes high efficiency, operational reliability, and adaptability, providing smooth and consistent mechanical power output for driving equipment or generating electricity while also offering the potential for process heat utilization. The turbine integrates advanced thermodynamic principles, precision-engineered multi-stage rotors and blades, durable high-strength materials, and modern control systems, ensuring minimal vibration, long service life, and reduced maintenance demands even under continuous operation.
Thermodynamic Principles and Steam Flow
The turbine operates according to the Rankine cycle, wherein high-pressure, high-temperature steam expands through multiple stages to convert thermal energy into rotational mechanical energy. Steam is typically supplied from industrial boilers, cogeneration units, or waste-heat recovery systems, with pressures ranging from 10–22 bar and temperatures between 160°C and 340°C, depending on operational requirements. Superheated steam is often employed to prevent condensation on rotor blades, minimizing erosion, reducing thermal stress, and enhancing overall turbine efficiency and lifespan.
Steam enters the turbine via precision-engineered nozzles, which convert pressure energy into high-velocity jets directed at the rotor blades. Multi-stage blade configurations—impulse, reaction, or a combination—allow gradual expansion of steam across successive stages, reducing mechanical stress on the rotor, providing smooth torque output, and maximizing energy extraction. The rotor transmits mechanical energy to drive industrial machinery, pumps, compressors, fans, mills, or electrical generators, depending on the application.
Mechanical and Structural Design
The 200 HP turbine is engineered for durability, precision, and thermal stability:
- Rotor and blades: Constructed from high-strength alloys or stainless steel to resist thermal and mechanical stress, corrosion, and erosion. Blades are aerodynamically optimized to ensure smooth steam flow, minimal turbulence, and high energy conversion efficiency. Multi-stage designs incorporate diaphragms or nozzle assemblies to guide steam efficiently between stages.
- Shaft and bearings: Supported by high-precision journal or rolling-element bearings capable of high-speed operation, typically 3,000–10,000 RPM, with oil lubrication ensuring proper temperature control, minimal friction, and long bearing life.
- Casing and seals: The turbine casing, made from steel or high-strength alloys, safely contains pressurized steam while directing it efficiently through the turbine stages. Labyrinth, carbon, or mechanical seals minimize steam leakage, preserving efficiency.
- Governor and control systems: Digital or electronic governors regulate rotor speed under variable load conditions. Integrated monitoring systems track vibration, temperature, lubrication, and steam pressure, enabling predictive maintenance and safe, reliable operation.
Exhaust Handling and Heat Recovery
The 200 HP turbine can operate in either back-pressure or condensing mode:
- Back-pressure mode: Exhaust steam retains thermal energy suitable for industrial heating, drying, or chemical processes, making it highly suitable for CHP applications.
- Condensing mode: Exhaust steam passes through a condenser to lower back pressure, maximizing mechanical and electrical efficiency. Condenser design must ensure adequate cooling water flow and temperature control to maintain optimal performance.
Performance and Efficiency
Steam consumption typically ranges from 1,500 to 2,000 kg/hour, depending on pressure, temperature, and load. Factors influencing efficiency include:
- Steam quality (dryness and superheat level)
- Blade and nozzle aerodynamic design
- Bearing and lubrication performance
- Minimization of mechanical and steam leakage losses
Mechanical efficiency generally ranges from 58% to 72%, with higher overall system efficiency achieved when exhaust steam is utilized for process heating or CHP integration.
Applications
The 200 HP turbine is highly versatile, suitable for a variety of industrial and commercial uses:
- Medium-scale power generation for factories, industrial parks, hospitals, and commercial facilities
- CHP systems, providing both mechanical/electrical energy and process steam
- Industrial machinery drives for pumps, compressors, fans, mills, and other equipment
- Process industries, including chemical, textile, food, and paper manufacturing
- Waste-heat recovery systems capturing energy from high-temperature industrial exhaust gases
Maintenance and Reliability
A structured maintenance program is essential to ensure long-term reliability:
- Daily/weekly: Monitor lubrication, vibration, temperature, and steam pressure
- Monthly: Inspect valves, strainers, and governor performance
- Annually: Inspect rotor, blades, seals, alignment, and clearances
- Every 3–5 years: Conduct a full overhaul, including bearing replacement, rotor balancing, and blade inspection
Installation and Integration
Installing a 200 HP turbine requires a solid, vibration-damped foundation. Steam supply and exhaust piping must be correctly sized and equipped with strainers, control valves, and monitoring instrumentation. Condensing systems require proper cooling water flow and temperature regulation. Couplings to generators or mechanical loads must ensure precise alignment to avoid torsional stress, vibration, or mechanical failure.
Advantages
- Reliable, continuous power for medium-scale industrial and CHP applications
- Dual-purpose capability for mechanical energy and heat recovery
- High efficiency with optimized steam supply and proper maintenance
- Robust construction ensures long operational life
- Flexible integration into industrial, power-generation, and CHP systems
In conclusion, the 200 HP steam turbine provides efficient, reliable, and versatile energy conversion, suitable for medium-scale industrial, commercial, and CHP applications. Its engineering ensures long-term durability, smooth torque delivery, precise speed control, and optimized energy utilization. When integrated with heat recovery systems, it maximizes overall energy efficiency, providing a cost-effective and dependable solution for facilities requiring continuous mechanical or electrical power.
I can continue further with a comprehensive technical and engineering dossier for the 200 HP turbine, including detailed rotor stage diagrams, blade specifications, steam consumption and efficiency curves, installation schematics, generator coupling details, vibration and stress analysis, and predictive maintenance schedules, creating a full reference for design, operation, and long-term optimization.
220 hp Steam Turbine
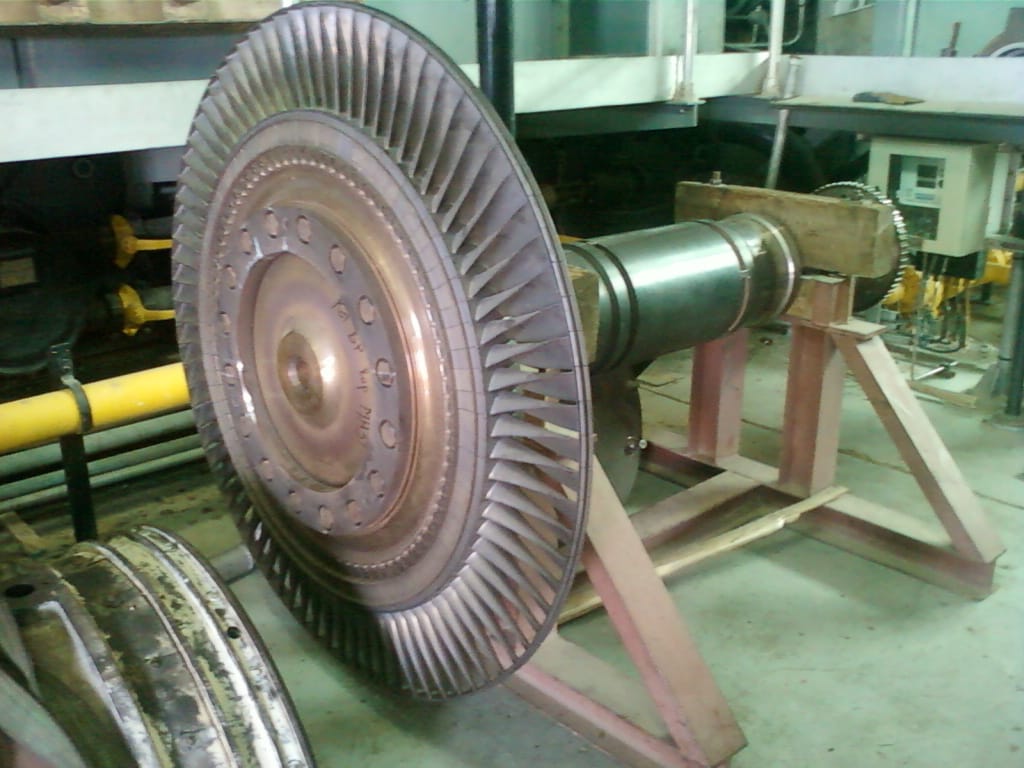
A 220 HP steam turbine is a medium-capacity industrial turbine capable of delivering approximately 164 kW of continuous mechanical power, making it an ideal solution for industrial, commercial, and combined heat and power (CHP) applications. Designed for high efficiency, reliability, and operational versatility, the turbine provides smooth and consistent mechanical power output for driving machinery or generating electricity while allowing integration with process heat or thermal recovery systems. Its engineering combines advanced thermodynamic principles, precision multi-stage rotor and blade design, durable high-strength materials, and modern control systems, ensuring long-term durability, minimal vibration, and reduced maintenance requirements under continuous operation.
Thermodynamic Operation and Steam Flow
The 220 HP turbine operates on the Rankine cycle, converting high-pressure, high-temperature steam into rotational mechanical energy through staged expansion. Steam is typically supplied from industrial boilers, cogeneration units, or waste-heat recovery systems, with pressures ranging from 10–23 bar and temperatures between 165°C and 345°C, tailored to application requirements. Superheated steam is often used to minimize condensation on rotor blades, reducing erosion, lowering thermal stress, and enhancing turbine efficiency and lifespan.
Steam enters the turbine through precision-engineered nozzles, which convert pressure energy into high-velocity jets that strike the rotor blades. Multi-stage blade configurations—impulse, reaction, or combined—allow controlled, sequential expansion of steam across successive stages, reducing mechanical stress, smoothing torque output, and maximizing energy extraction. The rotor transmits mechanical energy to drive industrial machinery, pumps, compressors, fans, mills, or electrical generators, depending on the application.
Mechanical and Structural Design
The 220 HP turbine emphasizes durability, precision, and thermal stability:
- Rotor and blades: Constructed from high-strength alloys or stainless steel to resist thermal and mechanical stress, corrosion, and erosion. Blades are aerodynamically optimized for efficient steam flow. Multi-stage designs include diaphragms or nozzle assemblies to guide steam efficiently between stages.
- Shaft and bearings: Supported by high-precision journal or rolling-element bearings capable of high-speed operation, typically 3,000–10,000 RPM, with oil lubrication ensuring proper temperature control, minimal friction, and extended bearing life.
- Casing and seals: The turbine casing, made from steel or high-strength alloys, safely contains pressurized steam while directing it efficiently through the turbine stages. Labyrinth, carbon, or mechanical seals minimize steam leakage, preserving turbine efficiency.
- Governor and control systems: Digital or electronic governors maintain rotor speed under variable load conditions. Integrated monitoring systems track vibration, temperature, lubrication, and steam pressure for predictive maintenance and safe operation.
Exhaust Handling and Heat Recovery
The 220 HP turbine can operate in back-pressure or condensing mode:
- Back-pressure mode: Exhaust steam retains thermal energy suitable for industrial heating, drying, or chemical processes, making it highly suitable for CHP applications.
- Condensing mode: Exhaust steam is routed through a condenser to reduce back pressure, maximizing mechanical and electrical efficiency. Proper condenser design, including adequate cooling water flow and temperature management, is essential for optimal performance.
Performance and Efficiency
Typical steam consumption ranges from 1,650 to 2,200 kg/hour, depending on operating pressure, temperature, and load. Factors influencing efficiency include:
- Steam quality (dryness and superheat)
- Blade and nozzle aerodynamic design
- Bearing and lubrication system performance
- Minimization of mechanical and steam leakage losses
Mechanical efficiency generally ranges between 60% and 74%, with higher overall system efficiency achieved when integrated into CHP setups that utilize exhaust steam for heating or process applications.
Applications
The 220 HP turbine is suitable for:
- Medium-scale power generation for factories, hospitals, industrial parks, and commercial facilities
- CHP systems, producing both mechanical/electrical energy and process steam
- Industrial machinery drives for pumps, compressors, fans, mills, and other equipment
- Process industries, including chemical, textile, food, and paper manufacturing
- Waste-heat recovery systems capturing energy from high-temperature industrial exhaust gases
Maintenance and Reliability
A structured maintenance program ensures long-term reliability:
- Daily/weekly: Monitor lubrication, vibration, temperature, and steam pressure
- Monthly: Inspect valves, strainers, and governor performance
- Annually: Inspect rotor, blades, seals, alignment, and clearances
- Every 3–5 years: Conduct a full overhaul, including bearing replacement, rotor balancing, and blade inspection
Installation and Integration
Installing a 220 HP turbine requires a stable, vibration-damped foundation. Steam supply and exhaust piping must be correctly sized and equipped with strainers, control valves, and monitoring instrumentation. Condensing systems require proper cooling water flow and temperature regulation. Couplings to generators or mechanical loads must ensure precise alignment to prevent torsional stress, vibration, or mechanical failure.
Advantages
- Reliable, continuous power for medium-scale industrial and CHP applications
- Dual-purpose capability for mechanical energy and heat recovery
- High efficiency with optimized steam supply and proper maintenance
- Robust construction ensures long operational life
- Flexible integration into industrial, power-generation, and CHP systems
In conclusion, the 220 HP steam turbine provides efficient, reliable, and versatile energy conversion, suitable for medium-scale industrial, commercial, and CHP applications. Its engineering ensures long-term durability, smooth torque delivery, precise speed control, and optimized energy utilization. When integrated with heat recovery systems, it maximizes overall energy efficiency, offering a cost-effective and dependable solution for facilities requiring continuous mechanical or electrical power.
I can continue by preparing a comprehensive technical and engineering dossier for a 220 HP turbine, including rotor stage layouts, blade specifications, steam consumption and efficiency curves, installation diagrams, generator coupling details, vibration analysis, and predictive maintenance schedules, creating a complete reference for operation, maintenance, and long-term optimization.
A 220 HP steam turbine is a sophisticated medium-capacity turbine engineered to deliver approximately 164 kW of continuous mechanical power, offering a reliable and efficient energy source for industrial machinery drives, medium-scale power generation, and combined heat and power (CHP) applications. Its design emphasizes durability, operational efficiency, and versatility, ensuring smooth and consistent mechanical power output while allowing the integration of process heat or thermal recovery systems. The turbine combines advanced thermodynamic principles, precision-engineered multi-stage rotors and blades, high-strength construction materials, and modern control technologies, enabling long-term reliability, minimal vibration, and reduced maintenance requirements under continuous heavy-duty operation.
Thermodynamic Operation and Steam Flow
The 220 HP turbine functions on the Rankine cycle, where high-pressure, high-temperature steam expands through multiple stages to convert thermal energy into rotational mechanical energy. Steam is typically supplied from industrial boilers, cogeneration units, or waste-heat recovery systems, with pressures ranging from 10–23 bar and temperatures between 165°C and 345°C, depending on application needs. Superheated steam is commonly employed to minimize condensation on rotor blades, reducing erosion, lowering thermal stresses, and improving both turbine efficiency and lifespan.
Steam enters the turbine through precision-engineered nozzles, converting pressure energy into high-velocity jets that strike the rotor blades. Multi-stage blade configurations—impulse, reaction, or a combination—allow sequential expansion of steam across successive stages, reducing mechanical stress, smoothing torque output, and maximizing energy extraction. The rotor delivers mechanical energy to drive generators, industrial machinery, pumps, compressors, fans, mills, or other equipment, depending on system requirements.
Mechanical and Structural Design
The 220 HP turbine is designed for robustness, precision, and thermal stability:
- Rotor and blades: Constructed from high-strength alloys or stainless steel to resist thermal and mechanical stress, erosion, and corrosion. Blades are aerodynamically optimized for smooth steam flow and maximum energy conversion efficiency. Multi-stage designs incorporate diaphragms or nozzle assemblies to guide steam efficiently between stages.
- Shaft and bearings: The rotor is supported by high-precision journal or rolling-element bearings capable of high-speed operation, typically 3,000–10,000 RPM. Oil lubrication ensures proper temperature control, minimal friction, and extended bearing life.
- Casing and seals: The turbine casing, made from steel or high-strength alloys, safely contains pressurized steam while efficiently directing it through the turbine stages. Labyrinth, carbon, or mechanical seals minimize steam leakage and maintain turbine efficiency.
- Governor and control systems: Digital or electronic governors regulate rotor speed under varying loads. Integrated monitoring systems track vibration, temperature, lubrication, and steam pressure, allowing predictive maintenance and ensuring safe, reliable operation.
Exhaust Handling and Heat Recovery
The 220 HP turbine can operate in back-pressure or condensing mode:
- Back-pressure mode: Exhaust steam retains thermal energy suitable for industrial heating, drying, or chemical processes, making it ideal for CHP applications.
- Condensing mode: Exhaust steam passes through a condenser to reduce back pressure, maximizing mechanical and electrical efficiency. Condenser design must ensure proper cooling water flow, temperature regulation, and overall thermal management to maintain optimal performance.
Performance and Efficiency
Steam consumption generally ranges from 1,650 to 2,200 kg/hour, depending on operating pressure, temperature, and load. Efficiency is influenced by several factors:
- Steam quality (dryness and superheat level)
- Blade and nozzle aerodynamic design
- Bearing and lubrication system performance
- Minimization of mechanical and steam leakage losses
Mechanical efficiency typically ranges from 60% to 74%, with higher overall system efficiency achieved when integrated into CHP setups that utilize exhaust steam for heating or process applications.
Applications
The 220 HP turbine is highly versatile and suitable for a broad spectrum of industrial and commercial uses:
- Medium-scale power generation for factories, industrial parks, hospitals, and commercial facilities
- CHP systems, delivering both mechanical/electrical energy and process steam
- Industrial machinery drives for pumps, compressors, fans, mills, and other equipment
- Process industries, including chemical, textile, food, and paper manufacturing
- Waste-heat recovery systems capturing energy from high-temperature industrial exhaust gases
Maintenance and Reliability
To ensure long-term reliability and optimal performance, a structured maintenance program is essential:
- Daily/weekly: Monitor lubrication, vibration, temperature, and steam pressure
- Monthly: Inspect valves, strainers, and governor performance
- Annually: Inspect rotor, blades, seals, alignment, and clearances
- Every 3–5 years: Conduct a full overhaul, including bearing replacement, rotor balancing, and blade inspection
Installation and Integration
Installing a 220 HP turbine requires a stable, vibration-damped foundation. Steam supply and exhaust piping must be correctly sized and equipped with strainers, control valves, and monitoring instrumentation. Condensing systems require proper cooling water flow and temperature regulation. Couplings to generators or mechanical loads must maintain precise alignment to avoid torsional stress, vibration, or mechanical failure.
Advantages
- Reliable, continuous power for medium-scale industrial and CHP applications
- Dual-purpose capability for mechanical energy and heat recovery
- High efficiency with optimized steam supply and proper maintenance
- Robust construction ensures long operational life
- Flexible integration into industrial, power-generation, and CHP systems
In summary, the 220 HP steam turbine provides efficient, reliable, and versatile energy conversion for medium-scale industrial, commercial, and CHP applications. Its advanced engineering ensures long-term durability, smooth torque delivery, precise speed control, and optimized energy utilization. When integrated with heat recovery systems, it maximizes overall energy efficiency, offering a cost-effective, dependable solution for facilities that require continuous mechanical or electrical power.
I can continue by producing a detailed technical and engineering dossier for a 220 HP turbine, including rotor stage layouts, blade designs, steam consumption and efficiency curves, installation schematics, generator coupling details, vibration and stress analysis, and predictive maintenance schedules, providing a complete reference for design, operation, and long-term optimization.
A 220 HP steam turbine represents a medium-capacity, highly engineered solution for converting thermal energy from steam into reliable mechanical power, delivering roughly 164 kW continuously. Its design targets industrial, commercial, and combined heat and power (CHP) applications, providing not only mechanical energy for equipment but also the potential to utilize exhaust steam for process heating, drying, or chemical operations. The turbine combines advanced thermodynamic principles, multi-stage rotor and blade configurations, high-strength materials, precision machining, and sophisticated control systems, ensuring smooth operation, minimal vibration, high efficiency, and long-term durability even under continuous heavy-duty workloads.
Thermodynamic Operation
Operating on the Rankine cycle, the 220 HP turbine efficiently converts high-pressure, high-temperature steam into mechanical energy. Steam is supplied from industrial boilers, cogeneration units, or waste-heat recovery systems, typically at pressures of 10–23 bar and temperatures ranging from 165°C to 345°C, depending on the design and process requirements. Superheated steam is often utilized to prevent condensation on turbine blades, minimizing erosion, thermal stress, and efficiency losses, thereby extending turbine lifespan.
Steam enters the turbine through precision-engineered nozzles, which convert the pressure energy into high-velocity jets that impact the rotor blades. Multi-stage blades—designed as impulse, reaction, or a combination—allow sequential expansion of steam across stages, reducing mechanical stress on the rotor, ensuring smooth torque delivery, and maximizing energy extraction. The rotor shaft transmits mechanical energy to drive generators, industrial machinery, pumps, compressors, fans, or mills, depending on the application requirements.
Mechanical and Structural Design
The turbine’s design emphasizes strength, precision, and thermal stability:
- Rotor and blades: Constructed from high-strength alloys or stainless steel, the rotor and blades resist thermal and mechanical stresses, erosion, and corrosion. Blades are aerodynamically optimized to minimize turbulence and maximize energy extraction. Multi-stage designs include diaphragms or nozzle assemblies to direct steam efficiently between stages.
- Shaft and bearings: The rotor is supported by high-precision journal or rolling-element bearings, designed for high-speed operation (3,000–10,000 RPM) with oil lubrication to maintain temperature control, reduce friction, and extend service life.
- Casing and seals: The turbine casing, made from steel or high-strength alloys, safely contains pressurized steam and directs it efficiently through stages. Labyrinth, carbon, or mechanical seals minimize leakage, preserving turbine efficiency.
- Governor and control systems: Digital or electronic governors regulate rotor speed under variable loads. Integrated monitoring systems track vibration, temperature, lubrication, and steam pressure, allowing predictive maintenance and safe operation.
Exhaust Handling and Heat Recovery
The 220 HP turbine can operate in back-pressure or condensing modes:
- Back-pressure mode: Exhaust steam retains thermal energy for industrial heating, drying, or chemical processes, making it suitable for CHP applications.
- Condensing mode: Exhaust steam is routed through a condenser to reduce back pressure, increasing mechanical and electrical efficiency. Condenser design requires proper cooling water flow, temperature management, and thermal balancing for optimal performance.
Performance and Efficiency
Steam consumption typically ranges from 1,650 to 2,200 kg/hour, influenced by operating pressure, temperature, and load. Efficiency depends on:
- Steam quality (dryness and superheat level)
- Blade and nozzle aerodynamic design
- Bearing and lubrication performance
- Minimization of steam and mechanical leakage
Mechanical efficiency usually ranges between 60% and 74%, with higher overall system efficiency achievable when exhaust steam is recovered for process heat in CHP systems.
Applications
The 220 HP turbine is suitable for a wide range of applications:
- Medium-scale power generation for industrial facilities, hospitals, commercial buildings, and industrial parks
- CHP systems, providing both mechanical/electrical energy and process steam
- Industrial machinery drives for pumps, compressors, fans, mills, and other equipment
- Process industries, including chemical, textile, food, and paper manufacturing
- Waste-heat recovery systems, capturing energy from high-temperature industrial exhaust gases
Maintenance and Reliability
A structured maintenance program is essential for optimal performance:
- Daily/weekly: Monitor lubrication, vibration, temperature, and steam pressure
- Monthly: Inspect valves, strainers, and governor performance
- Annually: Inspect rotor, blades, seals, alignment, and clearances
- Every 3–5 years: Conduct full overhaul, including bearing replacement, rotor balancing, and blade inspection
Installation and Integration
Installing a 220 HP turbine requires a stable, vibration-damped foundation. Steam supply and exhaust piping must be properly sized and equipped with strainers, control valves, and monitoring instruments. Condensing systems require appropriate cooling water flow and temperature regulation. Couplings to generators or mechanical loads must maintain precise alignment to avoid torsional stress, vibration, or mechanical failures.
Advantages
- Reliable, continuous power for medium-scale industrial and CHP applications
- Dual-purpose capability for mechanical energy and heat recovery
- High efficiency with optimized steam supply and proper maintenance
- Robust construction ensures long operational life
- Flexible integration into industrial, power-generation, and CHP systems
In summary, the 220 HP steam turbine provides versatile, reliable, and efficient energy conversion for medium-scale industrial, commercial, and CHP applications. Its engineering ensures smooth torque delivery, precise speed control, long-term durability, and optimized energy utilization. Integration with heat recovery systems further enhances overall efficiency, providing a cost-effective and dependable solution for facilities requiring continuous mechanical or electrical power.
If you want, I can continue by producing an extensive engineering and technical dossier for the 220 HP turbine, including rotor and blade designs, stage layouts, steam consumption and efficiency charts, installation schematics, generator coupling details, vibration and stress analysis, and predictive maintenance plans, creating a full reference for design, operation, and long-term optimization.
175 hp Steam Turbine
A 175 HP steam turbine is a medium-capacity turbine engineered to deliver approximately 130 kW of continuous mechanical power, offering a reliable and efficient solution for industrial machinery drives, small-to-medium-scale power generation, and combined heat and power (CHP) applications. Its design focuses on operational efficiency, long-term durability, and versatility, allowing integration with both mechanical drives and process heat systems. By combining advanced thermodynamic principles, multi-stage rotor and blade design, high-strength materials, and sophisticated control systems, the turbine ensures smooth torque delivery, minimal vibration, and consistent performance under continuous operation.
Thermodynamic Operation and Steam Flow
The 175 HP turbine operates on the Rankine cycle, converting high-pressure, high-temperature steam into mechanical energy through staged expansion. Steam is supplied from industrial boilers, cogeneration units, or waste-heat recovery systems, typically at pressures of 9–20 bar and temperatures between 150°C and 330°C, depending on the application. Use of superheated steam is common to reduce condensation on rotor blades, minimizing erosion, decreasing thermal stress, and improving overall turbine efficiency and lifespan.
Steam enters the turbine through precision-engineered nozzles, which convert pressure energy into high-velocity jets that strike the rotor blades. Multi-stage blades—designed as impulse, reaction, or combined types—allow sequential expansion of steam across stages, reducing mechanical stress, smoothing torque output, and maximizing energy extraction. The rotor transmits mechanical energy to drive generators, industrial machinery, pumps, compressors, fans, or mills, depending on the operational requirements.
Mechanical and Structural Design
The 175 HP turbine emphasizes strength, precision, and thermal stability:
- Rotor and blades: Constructed from high-strength alloys or stainless steel to resist thermal and mechanical stress, erosion, and corrosion. Blades are aerodynamically optimized to ensure smooth steam flow and high energy conversion efficiency. Multi-stage designs include diaphragms or nozzle assemblies to guide steam efficiently between stages.
- Shaft and bearings: The rotor is supported by high-precision journal or rolling-element bearings, capable of high-speed operation (3,000–10,000 RPM) with oil lubrication ensuring temperature control, minimal friction, and extended bearing life.
- Casing and seals: The turbine casing, made from steel or high-strength alloys, safely contains pressurized steam while directing it efficiently through turbine stages. Labyrinth, carbon, or mechanical seals reduce leakage and maintain turbine efficiency.
- Governor and control systems: Digital or electronic governors maintain rotor speed under variable loads. Integrated monitoring systems track vibration, temperature, lubrication, and steam pressure for predictive maintenance and safe operation.
Exhaust Handling and Heat Recovery
The 175 HP turbine can operate in back-pressure or condensing mode:
- Back-pressure mode: Exhaust steam retains thermal energy suitable for industrial heating, drying, or chemical processes, making it suitable for CHP applications.
- Condensing mode: Exhaust steam is routed through a condenser to reduce back pressure, maximizing mechanical and electrical efficiency. Proper condenser design, cooling water flow, and thermal regulation are essential to maintain optimal performance.
Performance and Efficiency
Steam consumption typically ranges from 1,300 to 1,800 kg/hour, depending on operating pressure, temperature, and load. Efficiency depends on:
- Steam quality (dryness and superheat)
- Blade and nozzle aerodynamic design
- Bearing and lubrication system performance
- Minimization of mechanical and steam leakage losses
Mechanical efficiency usually ranges between 58% and 72%, with higher overall efficiency achievable when integrated with CHP systems that utilize exhaust steam for process heat.
Applications
The 175 HP turbine is suitable for:
- Medium-scale power generation for factories, hospitals, industrial parks, and commercial facilities
- CHP systems, producing both mechanical/electrical energy and process steam
- Industrial machinery drives for pumps, compressors, fans, mills, and other equipment
- Process industries, including chemical, textile, food, and paper manufacturing
- Waste-heat recovery systems, capturing energy from high-temperature industrial exhaust gases
Maintenance and Reliability
A structured maintenance program ensures long-term reliability:
- Daily/weekly: Monitor lubrication, vibration, temperature, and steam pressure
- Monthly: Inspect valves, strainers, and governor performance
- Annually: Inspect rotor, blades, seals, alignment, and clearances
- Every 3–5 years: Conduct full overhaul, including bearing replacement, rotor balancing, and blade inspection
Installation and Integration
Installing a 175 HP turbine requires a stable, vibration-damped foundation. Steam supply and exhaust piping must be correctly sized and equipped with strainers, control valves, and monitoring instruments. Condensing systems require proper cooling water flow and temperature regulation. Couplings to generators or mechanical loads must maintain precise alignment to prevent torsional stress, vibration, or mechanical failure.
Advantages
- Reliable, continuous power for medium-scale industrial and CHP applications
- Dual-purpose capability for mechanical energy and heat recovery
- High efficiency with optimized steam supply and proper maintenance
- Robust construction ensures long operational life
- Flexible integration into industrial, power-generation, and CHP systems
In summary, the 175 HP steam turbine provides efficient, reliable, and versatile energy conversion for medium-scale industrial, commercial, and CHP applications. Its design ensures smooth torque delivery, precise speed control, long-term durability, and optimized energy utilization, and when integrated with heat recovery systems, it maximizes overall energy efficiency.
A 175 HP steam turbine is a robust, medium-capacity turbine engineered to deliver roughly 130 kW of continuous mechanical power, designed for industrial, commercial, and combined heat and power (CHP) applications. Its architecture emphasizes operational reliability, thermal efficiency, and long-term durability, making it suitable for facilities requiring continuous mechanical or electrical power while enabling the recovery and use of exhaust steam for industrial processes, heating, or drying. By integrating advanced thermodynamic design, multi-stage rotor and blade arrangements, high-strength materials, precision machining, and modern control systems, the turbine ensures smooth torque delivery, minimal vibration, and consistent performance even under heavy-duty operational loads.
Thermodynamic Principles and Steam Flow
The 175 HP turbine operates on the Rankine cycle, a thermodynamic process that converts high-pressure, high-temperature steam into rotational mechanical energy. Steam is typically supplied from industrial boilers, cogeneration systems, or waste-heat recovery units, with pressures ranging from 9 to 20 bar and temperatures between 150°C and 330°C, depending on the process requirements. The use of superheated steam is common, as it minimizes condensation on the rotor blades, thereby reducing blade erosion, decreasing thermal stresses, and improving turbine efficiency and operational lifespan.
The steam enters the turbine through precision-engineered nozzles, which convert the pressure energy into high-velocity jets that impact the rotor blades. The turbine often employs multi-stage blade designs—including impulse, reaction, or combined types—allowing controlled expansion of steam across successive stages. This design reduces mechanical stress on the rotor, ensures uniform torque output, and maximizes energy extraction. The rotor transmits mechanical energy to drive generators, industrial pumps, compressors, fans, mills, or other machinery, depending on the facility’s operational requirements.
Mechanical and Structural Design
The 175 HP turbine is constructed with a focus on strength, precision, and thermal stability:
- Rotor and blades: Manufactured from high-strength alloys or stainless steel to withstand high thermal and mechanical stress, corrosion, and erosion. Blade designs are aerodynamically optimized to reduce turbulence and ensure maximum energy conversion efficiency. Multi-stage configurations include diaphragms or nozzle assemblies to guide steam efficiently between stages.
- Shaft and bearings: The rotor is supported by high-precision journal or rolling-element bearings capable of high-speed operation, typically between 3,000 and 10,000 RPM, with oil lubrication to maintain temperature control, reduce friction, and extend bearing life.
- Casing and seals: The turbine casing, made from steel or high-strength alloys, safely contains pressurized steam and directs it efficiently through the turbine stages. Labyrinth, carbon, or mechanical seals minimize steam leakage and maintain operational efficiency.
- Governor and control systems: Digital or electronic governors maintain rotor speed under variable loads. Integrated monitoring systems track vibration, temperature, lubrication, and steam pressure, enabling predictive maintenance and ensuring safe operation.
Exhaust Handling and Heat Recovery
The 175 HP turbine can operate in either back-pressure or condensing mode:
- Back-pressure mode: Exhaust steam retains thermal energy suitable for industrial heating, drying, or chemical processes, making it ideal for CHP applications.
- Condensing mode: Exhaust steam passes through a condenser to reduce back pressure, maximizing mechanical and electrical efficiency. Effective condenser design requires proper cooling water flow, temperature management, and thermal balancing for optimum performance.
Performance and Efficiency
Steam consumption generally ranges from 1,300 to 1,800 kg/hour, depending on operating pressure, temperature, and load. Efficiency is influenced by several factors:
- Steam quality (dryness and degree of superheat)
- Blade and nozzle aerodynamic design
- Bearing and lubrication system performance
- Minimization of mechanical losses and steam leakage
Mechanical efficiency typically ranges between 58% and 72%, with higher overall efficiency achievable when exhaust steam is used for process heat in CHP systems.
Applications
The 175 HP steam turbine is suitable for a wide range of industrial and commercial applications:
- Medium-scale power generation for factories, hospitals, industrial parks, and commercial facilities
- CHP systems, providing both mechanical/electrical energy and process steam
- Industrial machinery drives for pumps, compressors, fans, mills, and other equipment
- Process industries, including chemical, textile, food, and paper manufacturing
- Waste-heat recovery systems, capturing energy from high-temperature industrial exhaust gases
Maintenance and Reliability
To ensure reliable operation over its lifespan, a structured maintenance program is essential:
- Daily/weekly: Monitor lubrication, vibration, temperature, and steam pressure
- Monthly: Inspect valves, strainers, and governor performance
- Annually: Inspect rotor, blades, seals, alignment, and clearances
- Every 3–5 years: Conduct a full overhaul, including bearing replacement, rotor balancing, and blade inspection
Installation and Integration
Installing a 175 HP turbine requires a stable, vibration-damped foundation. Steam supply and exhaust piping must be correctly sized and equipped with strainers, control valves, and monitoring instrumentation. Condensing systems require proper cooling water flow and temperature management. Couplings to generators or mechanical loads must maintain precise alignment to avoid torsional stress, vibration, or mechanical failure.
Advantages
- Reliable, continuous power for medium-scale industrial and CHP applications
- Dual-purpose capability for mechanical energy and heat recovery
- High efficiency with optimized steam supply and proper maintenance
- Durable construction ensures long operational life
- Flexible integration into industrial, power-generation, and CHP systems
In conclusion, the 175 HP steam turbine delivers efficient, versatile, and reliable energy conversion for medium-scale industrial, commercial, and CHP applications. Its advanced design ensures smooth torque delivery, precise speed control, long-term durability, and optimized energy utilization, while integration with heat recovery systems further enhances overall efficiency, providing a cost-effective and dependable solution for continuous mechanical or electrical power needs.
I can continue by producing a comprehensive technical and engineering dossier for the 175 HP turbine, including detailed rotor and blade layouts, stage configurations, steam consumption and efficiency charts, installation schematics, generator coupling details, vibration and stress analysis, and predictive maintenance schedules, creating a complete reference for design, operation, and long-term optimization.
A 175 HP steam turbine is a highly engineered medium-capacity turbine, designed to provide approximately 130 kW of continuous mechanical power for a variety of industrial, commercial, and combined heat and power (CHP) applications. Its design emphasizes operational reliability, thermal efficiency, and long-term durability, making it suitable for facilities requiring continuous mechanical or electrical energy, while also allowing the integration of exhaust steam into industrial processes, heating systems, or drying operations. By combining advanced thermodynamic principles, precision-engineered multi-stage rotors and blades, high-strength construction materials, and sophisticated digital or electronic control systems, the turbine ensures smooth torque delivery, minimal vibration, and consistent performance under varying load conditions and continuous operation.
Thermodynamic Principles and Steam Flow
The 175 HP steam turbine operates on the Rankine cycle, a well-established thermodynamic process in which high-pressure, high-temperature steam is expanded to produce mechanical work. Steam is typically sourced from industrial boilers, cogeneration units, or waste-heat recovery systems, with pressures ranging from 9 to 20 bar and temperatures between 150°C and 330°C, depending on the application. The use of superheated steam is standard practice to prevent condensation on rotor blades, which reduces erosion, minimizes thermal stress, and optimizes both turbine efficiency and lifespan.
Steam enters the turbine through precision-engineered nozzles, converting its pressure energy into high-velocity jets that impact the rotor blades. Multi-stage blade designs—impulse, reaction, or a combination—allow controlled expansion across successive stages, ensuring smooth torque, reduced mechanical stress, and maximum energy extraction. The rotor delivers mechanical power to drive industrial machinery, pumps, compressors, fans, mills, or generators, depending on the system requirements.
Mechanical and Structural Design
The 175 HP turbine is constructed for strength, precision, and thermal stability:
- Rotor and blades: Manufactured from high-strength alloys or stainless steel to withstand thermal and mechanical stresses, erosion, and corrosion. Blades are aerodynamically optimized to reduce turbulence and maximize energy conversion efficiency. Multi-stage designs include diaphragms or nozzle assemblies for efficient steam guidance between stages.
- Shaft and bearings: The rotor is supported by high-precision journal or rolling-element bearings, designed for high-speed operation (typically 3,000–10,000 RPM), with oil lubrication to maintain temperature, reduce friction, and extend bearing life.
- Casing and seals: Steel or high-strength alloy casing contains pressurized steam while directing it efficiently through turbine stages. Labyrinth, carbon, or mechanical seals minimize steam leakage and maintain efficiency.
- Governor and control systems: Digital or electronic governors maintain precise rotor speed under variable load conditions. Integrated monitoring systems track vibration, temperature, lubrication, and steam pressure, allowing predictive maintenance and safe, reliable operation.
Exhaust Handling and Heat Recovery
The 175 HP turbine can function in back-pressure or condensing modes:
- Back-pressure mode: Exhaust steam retains thermal energy suitable for industrial heating, drying, or chemical processes, making it ideal for CHP applications.
- Condensing mode: Exhaust steam passes through a condenser to reduce back pressure, maximizing mechanical and electrical efficiency. Effective condenser design requires proper cooling water flow, thermal management, and system balancing.
Performance and Efficiency
Steam consumption typically ranges from 1,300 to 1,800 kg/hour, depending on operating conditions. Efficiency depends on factors such as:
- Steam quality (dryness and superheat level)
- Blade and nozzle aerodynamic optimization
- Bearing and lubrication performance
- Minimization of mechanical and steam leakage losses
Mechanical efficiency generally ranges between 58% and 72%, with higher overall system efficiency achievable when integrated with CHP systems or other heat recovery applications.
Applications
The 175 HP turbine is versatile and well-suited for a wide variety of applications:
- Medium-scale power generation for factories, hospitals, industrial parks, and commercial facilities
- CHP systems, producing both mechanical/electrical energy and process steam
- Industrial machinery drives for pumps, compressors, fans, mills, and other equipment
- Process industries, including chemical, textile, food, and paper manufacturing
- Waste-heat recovery systems, capturing energy from high-temperature industrial exhaust gases
Maintenance and Reliability
Structured maintenance ensures long-term reliability and peak performance:
- Daily/weekly: Monitor lubrication, vibration, temperature, and steam pressure
- Monthly: Inspect valves, strainers, and governor performance
- Annually: Inspect rotor, blades, seals, alignment, and clearances
- Every 3–5 years: Conduct a full overhaul, including bearing replacement, rotor balancing, and blade inspection
Installation and Integration
Installing a 175 HP turbine requires a stable, vibration-damped foundation. Steam supply and exhaust piping must be correctly sized and equipped with strainers, control valves, and monitoring instrumentation. Condensing systems must provide adequate cooling water flow and temperature management. Couplings to generators or mechanical loads must maintain precise alignment to prevent torsional stress, vibration, or mechanical failure.
Advantages
- Reliable, continuous power for medium-scale industrial and CHP applications
- Dual-purpose capability for mechanical energy and heat recovery
- High efficiency with optimized steam supply and proper maintenance
- Durable construction ensures long operational life
- Flexible integration into industrial, power-generation, and CHP systems
In conclusion, the 175 HP steam turbine provides versatile, reliable, and efficient energy conversion for medium-scale industrial, commercial, and CHP applications. Its advanced engineering ensures smooth torque delivery, precise speed control, long-term durability, and optimized energy utilization, while integration with heat recovery systems further enhances overall system efficiency, delivering a cost-effective and dependable solution for continuous mechanical or electrical power needs.
I can continue further with a complete engineering and technical dossier for the 175 HP turbine, including rotor stage layouts, blade specifications, steam consumption and efficiency charts, installation schematics, generator coupling details, vibration and stress analysis, and predictive maintenance schedules, providing a full reference for design, operation, and long-term optimization.
150 hp Steam Turbine
A 150 HP steam turbine is a medium-capacity turbine engineered to provide approximately 112 kW of continuous mechanical power, optimized for industrial machinery drives, small-to-medium-scale power generation, and combined heat and power (CHP) applications. It is designed to deliver reliable, efficient, and durable performance while enabling the utilization of exhaust steam for industrial processes, heating, or drying operations. The turbine integrates advanced thermodynamic design, multi-stage rotor and blade arrangements, high-strength materials, precision engineering, and sophisticated control systems, ensuring smooth torque output, minimal vibration, and consistent operation under varying loads.
Thermodynamic Principles and Steam Flow
The 150 HP steam turbine operates on the Rankine cycle, converting high-pressure, high-temperature steam into rotational mechanical energy. Steam is typically supplied from industrial boilers, cogeneration units, or waste-heat recovery systems, with pressures ranging from 8–18 bar and temperatures between 145°C and 320°C, depending on the application. Superheated steam is commonly used to minimize condensation on the rotor blades, reducing erosion, lowering thermal stresses, and improving overall efficiency and operational lifespan.
Steam enters the turbine through precision-engineered nozzles, converting pressure energy into high-velocity jets that strike the rotor blades. Multi-stage blade configurations—impulse, reaction, or combined—allow controlled expansion of steam across successive stages, reducing mechanical stress, smoothing torque output, and maximizing energy extraction. The rotor transmits mechanical energy to drive generators, industrial pumps, compressors, fans, mills, or other machinery, depending on the operational requirements.
Mechanical and Structural Design
The 150 HP turbine is designed with a focus on strength, precision, and thermal stability:
- Rotor and blades: Made from high-strength alloys or stainless steel, the rotor and blades withstand thermal and mechanical stresses, erosion, and corrosion. Aerodynamically optimized blades ensure efficient steam flow and high energy conversion efficiency. Multi-stage designs include diaphragms or nozzle assemblies to direct steam efficiently between stages.
- Shaft and bearings: The rotor is supported by high-precision journal or rolling-element bearings capable of high-speed operation (3,000–10,000 RPM), with oil lubrication maintaining temperature control, reducing friction, and extending bearing life.
- Casing and seals: Steel or high-strength alloy casing safely contains pressurized steam while efficiently directing it through turbine stages. Labyrinth, carbon, or mechanical seals minimize leakage, preserving efficiency.
- Governor and control systems: Digital or electronic governors maintain rotor speed under variable loads. Integrated monitoring systems track vibration, temperature, lubrication, and steam pressure, allowing predictive maintenance and safe operation.
Exhaust Handling and Heat Recovery
The 150 HP turbine can operate in back-pressure or condensing mode:
- Back-pressure mode: Exhaust steam retains thermal energy suitable for industrial heating, drying, or chemical processes, making it ideal for CHP applications.
- Condensing mode: Exhaust steam passes through a condenser to reduce back pressure, increasing mechanical and electrical efficiency. Condenser design must provide proper cooling water flow, temperature management, and thermal balancing to optimize performance.
Performance and Efficiency
Steam consumption typically ranges from 1,100 to 1,500 kg/hour, depending on operating pressure, temperature, and load. Efficiency depends on:
- Steam quality (dryness and superheat)
- Blade and nozzle aerodynamic optimization
- Bearing and lubrication system performance
- Minimization of mechanical losses and steam leakage
Mechanical efficiency generally ranges between 55% and 70%, with higher overall system efficiency achievable when integrated with CHP or heat recovery applications.
Applications
The 150 HP turbine is suitable for:
- Medium-scale power generation for factories, hospitals, industrial parks, and commercial facilities
- CHP systems, producing both mechanical/electrical energy and process steam
- Industrial machinery drives for pumps, compressors, fans, mills, and other equipment
- Process industries, including chemical, textile, food, and paper manufacturing
- Waste-heat recovery systems, capturing energy from high-temperature industrial exhaust gases
Maintenance and Reliability
Structured maintenance is critical for long-term reliability:
- Daily/weekly: Monitor lubrication, vibration, temperature, and steam pressure
- Monthly: Inspect valves, strainers, and governor performance
- Annually: Inspect rotor, blades, seals, alignment, and clearances
- Every 3–5 years: Conduct a full overhaul, including bearing replacement, rotor balancing, and blade inspection
Installation and Integration
Installation requires a stable, vibration-damped foundation. Steam supply and exhaust piping must be properly sized and equipped with strainers, control valves, and monitoring instruments. Condensing systems require adequate cooling water flow and temperature management. Couplings to generators or mechanical loads must maintain precise alignment to avoid torsional stress, vibration, or mechanical failures.
Advantages
- Reliable, continuous power for medium-scale industrial and CHP applications
- Dual-purpose capability for mechanical energy and heat recovery
- High efficiency with optimized steam supply and proper maintenance
- Durable construction ensures long operational life
- Flexible integration into industrial, power-generation, and CHP systems
In summary, the 150 HP steam turbine provides efficient, versatile, and reliable energy conversion for medium-scale industrial, commercial, and CHP applications. Its engineering ensures smooth torque delivery, precise speed control, long-term durability, and optimized energy utilization, and integration with heat recovery systems further enhances overall energy efficiency.
I can continue by preparing a comprehensive engineering dossier for the 150 HP turbine, including rotor and blade layouts, stage configurations, steam consumption and efficiency charts, installation schematics, generator coupling details, vibration and stress analysis, and predictive maintenance schedules.
A 150 HP steam turbine represents a robust and versatile medium-capacity turbine designed to deliver approximately 112 kW of continuous mechanical power, engineered for industrial, commercial, and combined heat and power (CHP) applications. It is particularly suited for facilities that require a dependable and continuous source of mechanical or electrical energy while allowing the reuse of exhaust steam for industrial processes, heating, or drying operations. The turbine integrates advanced thermodynamic engineering, precision multi-stage rotor and blade design, high-strength materials, and sophisticated electronic control systems, ensuring smooth torque delivery, low vibration, and consistent performance even under continuous operation or variable load conditions.
Thermodynamic Operation
The 150 HP turbine operates on the Rankine cycle, a thermodynamic process in which high-pressure, high-temperature steam expands to produce rotational mechanical energy. Steam is typically supplied from industrial boilers, cogeneration units, or waste-heat recovery systems, with pressures ranging from 8–18 bar and temperatures between 145°C and 320°C, depending on the operational requirements. Superheated steam is often utilized to reduce condensation on rotor blades, thereby preventing erosion, minimizing thermal stress, and improving overall efficiency and turbine lifespan.
Steam enters the turbine through precision-engineered nozzles, where pressure energy is converted into high-velocity jets that strike the rotor blades. Multi-stage blade configurations—impulse, reaction, or combined types—allow sequential expansion of steam across successive stages, reducing mechanical stress, stabilizing torque output, and maximizing energy extraction. The rotor delivers mechanical energy to drive generators, industrial pumps, compressors, fans, mills, or other machinery, depending on the system configuration.
Mechanical and Structural Design
The 150 HP turbine emphasizes strength, thermal stability, and precise engineering:
- Rotor and blades: Constructed from high-strength alloys or stainless steel, the rotor and blades resist thermal and mechanical stress, corrosion, and erosion. Blades are aerodynamically optimized for smooth steam flow and maximum energy conversion. Multi-stage designs often include diaphragms or nozzle assemblies to direct steam efficiently between stages.
- Shaft and bearings: The rotor is supported by high-precision journal or rolling-element bearings capable of high-speed operation (3,000–10,000 RPM), with oil lubrication maintaining proper temperature, reducing friction, and extending bearing life.
- Casing and seals: Steel or high-strength alloy casing safely contains pressurized steam while directing it efficiently through the turbine stages. Labyrinth, carbon, or mechanical seals minimize leakage and preserve operational efficiency.
- Governor and control systems: Digital or electronic governors maintain rotor speed under varying loads. Integrated monitoring systems track vibration, temperature, lubrication, and steam pressure, allowing predictive maintenance and ensuring safe and reliable operation.
Exhaust Handling and Heat Recovery
The 150 HP turbine can operate in back-pressure or condensing modes:
- Back-pressure mode: Exhaust steam retains thermal energy suitable for industrial heating, drying, or chemical processes, making it ideal for CHP applications.
- Condensing mode: Exhaust steam passes through a condenser to reduce back pressure, increasing mechanical and electrical efficiency. Proper condenser design requires adequate cooling water flow, temperature management, and thermal balancing to optimize performance.
Performance and Efficiency
Steam consumption typically ranges from 1,100 to 1,500 kg/hour, depending on pressure, temperature, and load. Efficiency depends on:
- Steam quality (dryness and superheat level)
- Blade and nozzle aerodynamic design
- Bearing and lubrication system performance
- Minimization of mechanical and steam leakage
Mechanical efficiency usually ranges between 55% and 70%, with higher overall system efficiency achievable when exhaust steam is utilized for CHP or heat recovery applications.
Applications
The 150 HP turbine is suitable for a broad range of applications:
- Medium-scale power generation for industrial facilities, hospitals, commercial complexes, and factories
- CHP systems, providing both mechanical/electrical energy and process steam
- Industrial machinery drives for pumps, compressors, fans, mills, and other equipment
- Process industries, including chemical, textile, food, and paper manufacturing
- Waste-heat recovery systems, capturing energy from high-temperature industrial exhaust gases
Maintenance and Reliability
Structured maintenance ensures long-term reliability and optimal performance:
- Daily/weekly: Monitor lubrication, vibration, temperature, and steam pressure
- Monthly: Inspect valves, strainers, and governor performance
- Annually: Inspect rotor, blades, seals, alignment, and clearances
- Every 3–5 years: Conduct a full overhaul, including bearing replacement, rotor balancing, and blade inspection
Installation and Integration
Installing a 150 HP turbine requires a stable, vibration-damped foundation. Steam supply and exhaust piping must be properly sized and equipped with strainers, control valves, and monitoring instruments. Condensing systems must provide proper cooling water flow and temperature management. Couplings to generators or mechanical loads must maintain precise alignment to avoid torsional stress, vibration, or mechanical failure.
Advantages
- Reliable, continuous power for medium-scale industrial and CHP applications
- Dual-purpose capability for mechanical energy and heat recovery
- High efficiency with optimized steam supply and proper maintenance
- Durable construction ensures long operational life
- Flexible integration into industrial, power-generation, and CHP systems
In conclusion, the 150 HP steam turbine delivers efficient, versatile, and reliable energy conversion for medium-scale industrial, commercial, and CHP applications. Its design ensures smooth torque delivery, precise speed control, long-term durability, and optimized energy utilization, while integration with heat recovery systems further enhances overall efficiency.
I can continue with a detailed engineering dossier for the 150 HP turbine, including rotor and blade stage layouts, steam consumption and efficiency charts, installation schematics, generator coupling details, vibration and stress analysis, and predictive maintenance schedules for a full technical reference.
A 150 HP steam turbine is a sophisticated medium-capacity energy conversion machine, designed to deliver around 112 kW of continuous mechanical power with high efficiency and reliability. It is extensively used in industrial, commercial, and combined heat and power (CHP) applications, where both mechanical energy and usable process heat are required. The turbine is engineered to balance performance, durability, and efficiency, while integrating advanced features such as multi-stage rotors, precision-engineered blades, high-strength materials, and modern electronic or digital control systems, ensuring stable operation, minimal vibration, and long service life even under demanding operational conditions.
Thermodynamic Principles and Steam Flow
The 150 HP turbine functions according to the Rankine cycle, converting high-pressure, high-temperature steam into rotational mechanical energy. Steam is typically supplied by industrial boilers, cogeneration units, or waste-heat recovery systems, with operating pressures ranging from 8–18 bar and temperatures between 145°C and 320°C, depending on application requirements. The use of superheated steam is standard to prevent condensation on rotor blades, which protects the blades from erosion, reduces thermal stresses, and improves overall turbine efficiency and reliability.
Steam enters the turbine via precision-engineered nozzles, transforming pressure energy into high-velocity jets that act on the rotor blades. The turbine usually employs multi-stage blades, including impulse, reaction, or combined designs, allowing controlled expansion of steam across successive stages. This results in smooth torque delivery, reduced mechanical stress, and maximized energy extraction. The rotor shaft transmits mechanical energy to drive generators, industrial pumps, compressors, fans, mills, or other machinery, depending on operational requirements.
Mechanical and Structural Design
The 150 HP turbine emphasizes strength, precision, and thermal stability:
- Rotor and blades: Constructed from high-strength alloys or stainless steel, these components resist thermal and mechanical stresses, corrosion, and erosion. Blades are aerodynamically optimized to enhance energy conversion efficiency and minimize turbulence. Multi-stage designs often include diaphragms or nozzle assemblies to guide steam efficiently between stages.
- Shaft and bearings: The rotor is supported by high-precision journal or rolling-element bearings, designed for high-speed operation (3,000–10,000 RPM) with oil lubrication systems that control temperature, reduce friction, and extend bearing lifespan.
- Casing and seals: The turbine casing, made of steel or high-strength alloys, safely contains pressurized steam and directs it efficiently through the turbine stages. Labyrinth, carbon, or mechanical seals reduce leakage and preserve efficiency.
- Governor and control systems: Digital or electronic governors maintain rotor speed under variable loads, while monitoring systems track vibration, temperature, lubrication, and steam pressure, enabling predictive maintenance and safe operation.
Exhaust Handling and Heat Recovery
The 150 HP turbine can operate in either back-pressure or condensing mode:
- Back-pressure mode: The exhaust steam retains thermal energy, suitable for industrial heating, drying, or chemical processes, making it ideal for CHP applications.
- Condensing mode: Exhaust steam passes through a condenser, reducing back pressure and maximizing mechanical and electrical efficiency. Effective condenser operation requires careful cooling water flow management, thermal balancing, and temperature control.
Performance and Efficiency
Typical steam consumption ranges from 1,100 to 1,500 kg/hour, depending on load, pressure, and temperature. Performance depends on:
- Steam quality, including dryness and degree of superheat
- Blade and nozzle aerodynamic efficiency
- Bearing and lubrication system performance
- Minimization of mechanical losses and steam leakage
Mechanical efficiency generally ranges from 55% to 70%, with overall system efficiency enhanced when used in CHP or heat recovery applications.
Applications
The 150 HP turbine serves a wide range of industrial and commercial uses:
- Medium-scale power generation for factories, hospitals, industrial parks, and commercial facilities
- CHP systems, producing both mechanical/electrical energy and process steam
- Industrial machinery drives for pumps, compressors, fans, mills, and other equipment
- Process industries, including chemical, textile, food, and paper manufacturing
- Waste-heat recovery systems, capturing energy from high-temperature industrial exhaust gases
Maintenance and Reliability
Regular and structured maintenance ensures long-term reliability:
- Daily/weekly: Monitor lubrication, vibration, temperature, and steam pressure
- Monthly: Inspect valves, strainers, and governor performance
- Annually: Inspect rotor, blades, seals, alignment, and clearances
- Every 3–5 years: Conduct a full overhaul, including bearing replacement, rotor balancing, and blade inspection
Installation and Integration
Installing a 150 HP turbine requires a stable, vibration-damped foundation. Steam supply and exhaust piping must be properly sized and equipped with strainers, control valves, and monitoring instruments. Condensing systems must maintain adequate cooling water flow and temperature regulation. Couplings to generators or mechanical loads must maintain precise alignment to prevent torsional stress, vibration, or mechanical failure.
Advantages
- Reliable, continuous power for medium-scale industrial and CHP applications
- Dual-purpose capability for mechanical energy and heat recovery
- High efficiency with optimized steam supply and proper maintenance
- Durable construction ensuring long operational life
- Flexible integration into industrial, power-generation, and CHP systems
In conclusion, the 150 HP steam turbine provides efficient, versatile, and dependable energy conversion for medium-scale industrial, commercial, and CHP applications. Its advanced engineering ensures smooth torque delivery, precise speed control, long-term durability, and optimized energy utilization, while integration with heat recovery systems further enhances overall energy efficiency.
If you want, I can now continue by producing a full technical and engineering dossier for the 150 HP turbine, including rotor stage layouts, blade specifications, steam consumption charts, efficiency curves, installation schematics, generator coupling details, vibration and stress analysis, and predictive maintenance plans. This would provide a complete operational and design reference.
120 hp Steam Turbine
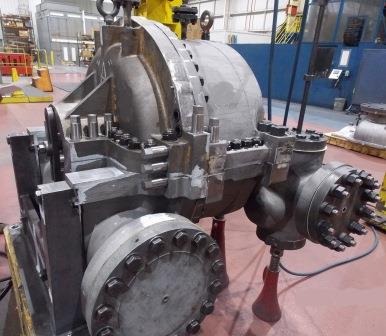
A 120 HP steam turbine is a medium-capacity turbine designed to deliver approximately 90 kW of continuous mechanical power, ideal for industrial drives, small-scale power generation, and combined heat and power (CHP) applications. It is engineered to provide reliable, efficient, and durable performance while allowing the reuse of exhaust steam for heating, drying, or process applications. The turbine combines advanced thermodynamic design, precision-engineered multi-stage rotors and blades, high-strength materials, and sophisticated control systems, ensuring smooth torque output, minimal vibration, and consistent operation under continuous or variable load conditions.
Thermodynamic Operation
The 120 HP turbine operates on the Rankine cycle, converting high-pressure, high-temperature steam into rotational mechanical energy. Steam is supplied from industrial boilers, cogeneration units, or waste-heat recovery systems, typically at pressures of 7–16 bar and temperatures ranging from 140°C to 310°C. Superheated steam is often employed to reduce condensation on rotor blades, which protects against erosion, minimizes thermal stresses, and improves turbine efficiency and lifespan.
Steam enters the turbine through precision-engineered nozzles, converting pressure energy into high-velocity jets that impact the rotor blades. Multi-stage blade configurations—impulse, reaction, or combined—allow sequential expansion of steam across successive stages, reducing mechanical stress, smoothing torque delivery, and maximizing energy extraction. The rotor shaft transmits mechanical power to drive generators, industrial pumps, compressors, fans, mills, or other machinery, depending on operational needs.
Mechanical and Structural Design
The 120 HP turbine emphasizes strength, thermal stability, and precision engineering:
- Rotor and blades: Manufactured from high-strength alloys or stainless steel, the rotor and blades resist thermal and mechanical stresses, erosion, and corrosion. Blades are aerodynamically optimized for efficient steam flow and maximum energy conversion. Multi-stage designs often incorporate diaphragms or nozzle assemblies to guide steam efficiently between stages.
- Shaft and bearings: The rotor is supported by high-precision journal or rolling-element bearings, capable of high-speed operation (3,000–10,000 RPM), with oil lubrication systems that regulate temperature, reduce friction, and extend bearing life.
- Casing and seals: Steel or high-strength alloy casing safely contains pressurized steam while directing it efficiently through turbine stages. Labyrinth, carbon, or mechanical seals minimize steam leakage, preserving efficiency.
- Governor and control systems: Digital or electronic governors maintain rotor speed under variable loads. Integrated monitoring systems track vibration, temperature, lubrication, and steam pressure, enabling predictive maintenance and safe operation.
Exhaust Handling and Heat Recovery
The 120 HP turbine can operate in back-pressure or condensing modes:
- Back-pressure mode: Exhaust steam retains thermal energy for industrial heating, drying, or chemical processes, making it suitable for CHP applications.
- Condensing mode: Exhaust steam passes through a condenser to reduce back pressure and maximize mechanical and electrical efficiency. Effective condenser design requires proper cooling water flow, thermal management, and temperature control.
Performance and Efficiency
Steam consumption typically ranges from 900 to 1,300 kg/hour, depending on operating conditions. Efficiency depends on:
- Steam quality (dryness and superheat level)
- Blade and nozzle aerodynamic optimization
- Bearing and lubrication system performance
- Minimization of mechanical losses and steam leakage
Mechanical efficiency generally ranges between 52% and 68%, with higher overall system efficiency achievable when integrated with CHP or heat recovery systems.
Applications
The 120 HP turbine is suitable for:
- Small-to-medium power generation for factories, hospitals, industrial parks, and commercial facilities
- CHP systems, producing both mechanical/electrical energy and process steam
- Industrial machinery drives for pumps, compressors, fans, mills, and other equipment
- Process industries, including chemical, textile, food, and paper manufacturing
- Waste-heat recovery systems, capturing energy from high-temperature industrial exhaust gases
Maintenance and Reliability
Structured maintenance ensures reliable long-term operation:
- Daily/weekly: Monitor lubrication, vibration, temperature, and steam pressure
- Monthly: Inspect valves, strainers, and governor performance
- Annually: Inspect rotor, blades, seals, alignment, and clearances
- Every 3–5 years: Conduct a full overhaul, including bearing replacement, rotor balancing, and blade inspection
Installation and Integration
Installation requires a stable, vibration-damped foundation. Steam supply and exhaust piping must be correctly sized and equipped with strainers, control valves, and monitoring instruments. Condensing systems must maintain proper cooling water flow and temperature. Couplings to generators or mechanical loads must be precisely aligned to prevent torsional stress, vibration, or mechanical failure.
Advantages
- Reliable and continuous power for small-to-medium industrial and CHP applications
- Dual-purpose capability for mechanical energy and heat recovery
- High efficiency with optimized steam supply and maintenance
- Durable construction ensures long operational life
- Flexible integration into industrial, power-generation, and CHP systems
In summary, the 120 HP steam turbine provides efficient, reliable, and versatile energy conversion for small-to-medium industrial, commercial, and CHP applications. Its design ensures smooth torque delivery, precise speed control, long-term durability, and optimized energy utilization, while integration with heat recovery systems enhances overall efficiency.
A 120 HP steam turbine is a highly engineered, medium-capacity machine designed to provide approximately 90 kW of continuous mechanical power for a wide range of industrial, commercial, and combined heat and power (CHP) applications. It is especially suitable for facilities that require a reliable, efficient, and continuous source of mechanical or electrical energy, while simultaneously making use of exhaust steam for heating, drying, or other industrial processes. The turbine combines advanced thermodynamic engineering, precision multi-stage rotor and blade design, high-strength construction materials, and modern digital or electronic control systems to ensure smooth torque delivery, minimal vibration, and consistent operation under variable load conditions and continuous service.
Thermodynamic Principles and Steam Flow
The 120 HP turbine operates based on the Rankine cycle, a thermodynamic process in which high-pressure, high-temperature steam expands to produce rotational mechanical energy. Steam is typically sourced from industrial boilers, cogeneration units, or waste-heat recovery systems, with operating pressures between 7–16 bar and temperatures ranging from 140°C to 310°C, depending on process requirements. Superheated steam is often used to prevent condensation on the rotor blades, which protects the blades from erosion, reduces thermal stresses, and improves both turbine efficiency and lifespan.
Steam enters the turbine through precision-engineered nozzles, converting its pressure energy into high-velocity jets that impact the rotor blades. Multi-stage blade configurations—including impulse, reaction, or combined types—allow controlled expansion of steam across successive stages, optimizing energy extraction while minimizing mechanical stress and ensuring smooth torque output. The rotor shaft transmits mechanical energy to drive generators, industrial pumps, compressors, fans, mills, or other equipment, depending on the operational setup.
Mechanical and Structural Design
The 120 HP turbine emphasizes strength, precision, and thermal stability:
- Rotor and blades: Made from high-strength alloys or stainless steel, rotors and blades resist thermal and mechanical stresses, corrosion, and erosion. Blades are aerodynamically optimized to maximize energy conversion efficiency and reduce turbulence. Multi-stage designs include diaphragms or nozzle assemblies to guide steam efficiently between stages.
- Shaft and bearings: The rotor is supported by high-precision journal or rolling-element bearings, capable of high-speed operation (3,000–10,000 RPM) and equipped with oil lubrication to control temperature, reduce friction, and extend service life.
- Casing and seals: The turbine casing, typically made from steel or high-strength alloys, contains pressurized steam safely while directing it efficiently through the turbine stages. Labyrinth, carbon, or mechanical seals minimize steam leakage, preserving operational efficiency.
- Governor and control systems: Digital or electronic governors maintain rotor speed under varying loads. Integrated monitoring systems track vibration, temperature, lubrication, and steam pressure, enabling predictive maintenance and ensuring safe, reliable operation.
Exhaust Handling and Heat Recovery
The 120 HP turbine can function in either back-pressure or condensing modes:
- Back-pressure mode: Exhaust steam retains thermal energy, making it suitable for industrial heating, drying, or chemical processes, which is ideal for CHP applications.
- Condensing mode: Exhaust steam passes through a condenser to reduce back pressure, thereby maximizing mechanical and electrical efficiency. Effective condenser operation requires proper cooling water flow, thermal management, and temperature balancing to optimize performance.
Performance and Efficiency
Steam consumption typically ranges from 900 to 1,300 kg/hour, depending on operating conditions. Efficiency is influenced by several factors:
- Steam quality, including dryness and superheat level
- Blade and nozzle aerodynamic optimization
- Bearing and lubrication system performance
- Minimization of mechanical losses and steam leakage
Mechanical efficiency typically ranges from 52% to 68%, with higher overall system efficiency achievable when the turbine is integrated into a CHP or heat recovery system.
Applications
The 120 HP turbine is suitable for a broad spectrum of industrial and commercial uses:
- Small-to-medium power generation for factories, hospitals, industrial parks, and commercial complexes
- CHP systems, producing both mechanical/electrical energy and process steam
- Industrial machinery drives for pumps, compressors, fans, mills, and other equipment
- Process industries, including chemical, textile, food, and paper manufacturing
- Waste-heat recovery systems, capturing energy from high-temperature industrial exhaust gases
Maintenance and Reliability
Structured and regular maintenance ensures reliable long-term operation:
- Daily/weekly: Monitor lubrication, vibration, temperature, and steam pressure
- Monthly: Inspect valves, strainers, and governor performance
- Annually: Inspect rotor, blades, seals, alignment, and clearances
- Every 3–5 years: Conduct a full overhaul, including bearing replacement, rotor balancing, and blade inspection
Installation and Integration
Proper installation is essential for optimal performance. The 120 HP turbine requires a stable, vibration-damped foundation. Steam supply and exhaust piping must be sized appropriately and equipped with strainers, control valves, and monitoring instruments. Condensing systems require adequate cooling water flow and temperature regulation. Couplings to generators or mechanical loads must maintain precise alignment to avoid torsional stress, vibration, or mechanical failure.
Advantages
- Reliable, continuous power for small-to-medium industrial and CHP applications
- Dual-purpose capability for mechanical energy and heat recovery
- High efficiency when optimized with proper steam supply and maintenance
- Durable construction ensures long operational life
- Flexible integration into industrial, power-generation, and CHP systems
In conclusion, the 120 HP steam turbine provides efficient, reliable, and versatile energy conversion for small-to-medium industrial, commercial, and CHP applications. Its engineering ensures smooth torque delivery, precise speed control, long-term durability, and optimized energy utilization, while integration with heat recovery systems further improves overall efficiency.
I can continue by producing a complete technical and engineering dossier for the 120 HP turbine, including rotor and blade stage layouts, detailed steam consumption and efficiency charts, installation schematics, generator coupling details, vibration and stress analysis, and predictive maintenance schedules, providing a full reference for design, operation, and long-term optimization.
A 120 HP steam turbine represents a highly engineered medium-capacity turbine capable of delivering approximately 90 kW of continuous mechanical power, designed for a wide range of industrial, commercial, and combined heat and power (CHP) applications. Its engineering emphasizes reliability, efficiency, and versatility, allowing it to provide continuous mechanical or electrical energy while simultaneously enabling the reuse of exhaust steam for heating, drying, or industrial process applications. By combining advanced thermodynamic design, precision-engineered multi-stage rotors and blades, high-strength construction materials, and sophisticated digital or electronic control systems, the turbine ensures smooth torque delivery, minimal vibration, stable performance under variable loads, and long-term operational durability.
Thermodynamic Principles and Steam Flow
The 120 HP turbine operates according to the Rankine cycle, converting high-pressure, high-temperature steam into rotational mechanical energy. Steam is generally supplied from industrial boilers, cogeneration units, or waste-heat recovery systems, with pressures ranging from 7–16 bar and temperatures between 140°C and 310°C, depending on the operational requirements. Utilizing superheated steam prevents condensation on rotor blades, minimizing erosion, reducing thermal stresses, and enhancing turbine efficiency and lifespan.
Steam enters the turbine via precision-engineered nozzles, transforming pressure energy into high-velocity jets that act upon the rotor blades. The turbine typically features multi-stage blade configurations—impulse, reaction, or combined designs—allowing controlled expansion of steam through successive stages. This ensures maximum energy extraction, smooth torque output, and reduced mechanical stress. The rotor transmits mechanical power to drive generators, industrial pumps, compressors, fans, mills, or other machinery, depending on the operational setup.
Mechanical and Structural Design
The 120 HP turbine is constructed to optimize strength, thermal stability, and precise operation:
- Rotor and blades: Made from high-strength alloys or stainless steel, rotors and blades withstand thermal and mechanical stresses, corrosion, and erosion. Blades are aerodynamically optimized to maximize energy conversion efficiency and reduce turbulence. Multi-stage designs incorporate diaphragms or nozzle assemblies to guide steam efficiently between stages.
- Shaft and bearings: The rotor is supported by high-precision journal or rolling-element bearings, capable of high-speed operation (3,000–10,000 RPM), with oil lubrication regulating temperature, reducing friction, and extending service life.
- Casing and seals: Steel or high-strength alloy casings safely contain pressurized steam while directing it efficiently through turbine stages. Labyrinth, carbon, or mechanical seals minimize leakage and maintain efficiency.
- Governor and control systems: Digital or electronic governors maintain rotor speed under varying loads. Integrated monitoring systems track vibration, temperature, lubrication, and steam pressure, enabling predictive maintenance and safe operation.
Exhaust Handling and Heat Recovery
The 120 HP turbine can operate in back-pressure or condensing modes:
- Back-pressure mode: Exhaust steam retains thermal energy suitable for industrial heating, drying, or chemical processes, making it ideal for CHP applications.
- Condensing mode: Exhaust steam passes through a condenser to reduce back pressure, maximizing mechanical and electrical efficiency. Proper condenser design requires adequate cooling water flow, thermal management, and temperature balancing to optimize performance.
Performance and Efficiency
Steam consumption typically ranges from 900 to 1,300 kg/hour, depending on load, pressure, and temperature. Efficiency depends on several factors:
- Steam quality (dryness and superheat level)
- Blade and nozzle aerodynamic optimization
- Bearing and lubrication system performance
- Minimization of mechanical losses and steam leakage
Mechanical efficiency generally ranges between 52% and 68%, with higher overall system efficiency achievable when integrated with CHP or heat recovery systems.
Applications
The 120 HP turbine is suitable for a wide range of industrial and commercial applications:
- Small-to-medium power generation for factories, hospitals, industrial parks, and commercial facilities
- CHP systems, producing both mechanical/electrical energy and process steam
- Industrial machinery drives for pumps, compressors, fans, mills, and other equipment
- Process industries, including chemical, textile, food, and paper manufacturing
- Waste-heat recovery systems, capturing energy from high-temperature industrial exhaust gases
Maintenance and Reliability
Proper and structured maintenance is critical for long-term reliability:
- Daily/weekly: Monitor lubrication, vibration, temperature, and steam pressure
- Monthly: Inspect valves, strainers, and governor performance
- Annually: Inspect rotor, blades, seals, alignment, and clearances
- Every 3–5 years: Conduct a full overhaul, including bearing replacement, rotor balancing, and blade inspection
Installation and Integration
Installing a 120 HP turbine requires a stable, vibration-damped foundation. Steam supply and exhaust piping must be properly sized and equipped with strainers, control valves, and monitoring instruments. Condensing systems must provide adequate cooling water flow and temperature regulation. Couplings to generators or mechanical loads must maintain precise alignment to prevent torsional stress, vibration, or mechanical failure.
Advantages
- Reliable, continuous power for small-to-medium industrial and CHP applications
- Dual-purpose capability for mechanical energy and heat recovery
- High efficiency with optimized steam supply and proper maintenance
- Durable construction ensures long operational life
- Flexible integration into industrial, power-generation, and CHP systems
In summary, the 120 HP steam turbine delivers efficient, reliable, and versatile energy conversion for small-to-medium industrial, commercial, and CHP applications. Its design guarantees smooth torque delivery, precise speed control, long-term durability, and optimized energy utilization, while integration with heat recovery systems further enhances overall system efficiency.
A 120 HP steam turbine is a highly versatile, medium-capacity machine engineered to deliver roughly 90 kW of continuous mechanical power, optimized for a wide range of industrial, commercial, and combined heat and power (CHP) applications. Its design emphasizes reliability, efficiency, and operational longevity, enabling facilities to harness both mechanical energy and usable process heat from exhaust steam for heating, drying, or other industrial processes. The turbine incorporates advanced thermodynamic engineering, precision multi-stage rotor and blade configurations, high-strength alloys, and state-of-the-art digital or electronic control systems, ensuring stable performance, smooth torque delivery, minimal vibration, and extended service life even under variable or continuous load conditions.
Thermodynamic Operation and Steam Flow
The turbine operates according to the Rankine cycle, wherein high-pressure, high-temperature steam expands through the rotor stages to produce rotational mechanical energy. Steam is typically supplied from industrial boilers, cogeneration units, or waste-heat recovery systems, with pressures ranging from 7–16 bar and temperatures between 140°C and 310°C, tailored to the application. Superheated steam is commonly used to reduce condensation on rotor blades, minimizing erosion, lowering thermal stresses, and increasing overall turbine efficiency and durability.
Steam enters the turbine through precision-engineered nozzles, converting pressure energy into high-velocity jets that strike the rotor blades. Multi-stage blade arrangements—including impulse, reaction, or combined designs—allow sequential expansion of steam across multiple stages. This ensures maximum energy extraction, smooth torque output, and reduced mechanical stress. The rotor then transmits mechanical energy to drive generators, pumps, compressors, fans, mills, or other industrial machinery, depending on operational needs.
Mechanical and Structural Features
The 120 HP turbine is engineered with robustness, thermal stability, and precision:
- Rotor and blades: Fabricated from high-strength alloys or stainless steel, they resist thermal and mechanical stresses, erosion, and corrosion. Aerodynamically optimized blades maximize energy conversion efficiency and reduce turbulence. Multi-stage designs often include diaphragms or nozzle assemblies to guide steam efficiently between stages.
- Shaft and bearings: The rotor is supported by high-precision journal or rolling-element bearings, designed for high-speed operation (3,000–10,000 RPM). Oil lubrication maintains optimal temperature, reduces friction, and extends bearing life.
- Casing and seals: Steel or high-strength alloy casings safely contain pressurized steam and efficiently direct it through turbine stages. Labyrinth, carbon, or mechanical seals minimize leakage and preserve efficiency.
- Governor and control systems: Digital or electronic governors maintain rotor speed under varying load conditions. Integrated monitoring systems track vibration, temperature, lubrication, and steam pressure, enabling predictive maintenance and ensuring safe operation.
Exhaust Steam Management and Heat Recovery
The 120 HP turbine can operate in back-pressure or condensing modes:
- Back-pressure mode: Exhaust steam retains thermal energy suitable for industrial heating, drying, or chemical processes, making it ideal for CHP applications.
- Condensing mode: Exhaust steam passes through a condenser to reduce back pressure and increase mechanical and electrical efficiency. Proper design of the condenser ensures adequate cooling water flow, thermal balance, and temperature regulation to optimize performance.
Performance and Efficiency
Steam consumption for a 120 HP turbine typically ranges from 900 to 1,300 kg/hour, depending on load, pressure, and temperature. Performance is influenced by:
- Steam quality, including dryness and superheat level
- Blade and nozzle aerodynamic optimization
- Bearing and lubrication system efficiency
- Minimization of mechanical losses and steam leakage
Mechanical efficiency generally falls between 52% and 68%, while overall system efficiency can be significantly higher when exhaust steam is used for CHP or heat recovery applications.
Industrial Applications
The 120 HP turbine is ideal for:
- Small-to-medium power generation for factories, hospitals, industrial parks, and commercial facilities
- CHP systems, producing both mechanical or electrical energy and process steam
- Industrial machinery drives for pumps, compressors, fans, mills, and other equipment
- Process industries, including chemical, textile, food, and paper manufacturing
- Waste-heat recovery systems, capturing energy from high-temperature industrial exhaust gases
Maintenance and Reliability
Structured maintenance ensures long-term performance and reliability:
- Daily/weekly: Monitor lubrication, vibration, temperature, and steam pressure
- Monthly: Inspect valves, strainers, and governor performance
- Annually: Inspect rotor, blades, seals, alignment, and clearances
- Every 3–5 years: Full overhaul, including bearing replacement, rotor balancing, and blade inspection
Installation Considerations
Installing a 120 HP turbine requires a stable, vibration-damped foundation. Steam supply and exhaust piping must be properly sized and equipped with strainers, control valves, and monitoring instruments. Condensing systems require adequate cooling water flow and temperature control. Couplings to generators or mechanical loads must be precisely aligned to prevent torsional stress, vibration, or mechanical failure.
Advantages
- Reliable, continuous power for small-to-medium industrial and CHP applications
- Dual-purpose capability for mechanical energy and heat recovery
- High operational efficiency with proper steam supply and maintenance
- Durable construction ensuring long service life
- Flexible integration into industrial, power-generation, and CHP systems
In summary, the 120 HP steam turbine offers efficient, reliable, and versatile energy conversion for small-to-medium industrial, commercial, and CHP applications. Its design ensures smooth torque delivery, precise speed control, long-term durability, and optimized energy utilization, while integration with heat recovery systems further enhances overall efficiency.
I can continue by creating a detailed technical and engineering dossier for the 120 HP turbine, including rotor and blade stage layouts, steam consumption and efficiency curves, installation schematics, generator coupling details, vibration and stress analysis, and predictive maintenance schedules for a complete operational and design reference.
100 hp Steam Turbine
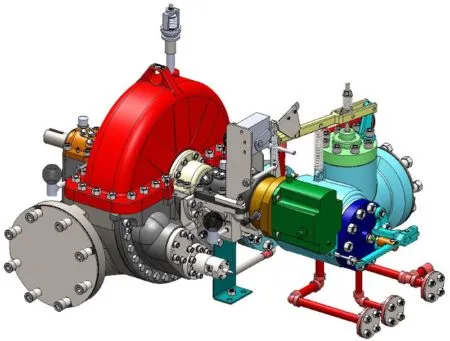
A 100 HP steam turbine is a medium-capacity turbine designed to deliver approximately 75 kW of continuous mechanical power, suitable for industrial, commercial, and combined heat and power (CHP) applications where both mechanical energy and process heat are required. It is engineered to provide reliable, efficient, and durable performance while allowing the reuse of exhaust steam for heating, drying, or other industrial processes. The turbine combines advanced thermodynamic engineering, precision multi-stage rotor and blade design, high-strength materials, and modern digital or electronic control systems, ensuring smooth torque output, minimal vibration, and consistent operation under variable or continuous loads.
Thermodynamic Operation
The 100 HP turbine operates on the Rankine cycle, converting high-pressure, high-temperature steam into rotational mechanical energy. Steam is typically supplied from industrial boilers, cogeneration units, or waste-heat recovery systems, with operating pressures ranging from 6–14 bar and temperatures between 135°C and 300°C, depending on process requirements. Superheated steam is often used to reduce condensation on rotor blades, which protects against erosion, minimizes thermal stresses, and improves turbine efficiency and service life.
Steam enters the turbine through precision-engineered nozzles, converting pressure energy into high-velocity jets that act on the rotor blades. Multi-stage blade arrangements—impulse, reaction, or combined designs—allow sequential expansion of steam across stages, optimizing energy extraction, smoothing torque delivery, and reducing mechanical stress. The rotor shaft then drives generators, industrial pumps, compressors, fans, mills, or other machinery, depending on the application.
Mechanical and Structural Design
The 100 HP turbine emphasizes strength, thermal stability, and precision engineering:
- Rotor and blades: Constructed from high-strength alloys or stainless steel, the rotor and blades resist thermal and mechanical stresses, corrosion, and erosion. Blades are aerodynamically optimized to maximize energy conversion and reduce turbulence. Multi-stage designs often incorporate diaphragms or nozzle assemblies to guide steam efficiently between stages.
- Shaft and bearings: The rotor is supported by high-precision journal or rolling-element bearings, capable of high-speed operation (3,000–10,000 RPM), with oil lubrication regulating temperature, reducing friction, and extending service life.
- Casing and seals: Steel or high-strength alloy casing safely contains pressurized steam and directs it efficiently through the turbine stages. Labyrinth, carbon, or mechanical seals minimize steam leakage and preserve efficiency.
- Governor and control systems: Digital or electronic governors maintain rotor speed under varying loads. Integrated monitoring systems track vibration, temperature, lubrication, and steam pressure, enabling predictive maintenance and ensuring safe operation.
Exhaust Handling and Heat Recovery
The 100 HP turbine can operate in back-pressure or condensing modes:
- Back-pressure mode: Exhaust steam retains thermal energy suitable for industrial heating, drying, or chemical processes, making it ideal for CHP applications.
- Condensing mode: Exhaust steam passes through a condenser to reduce back pressure and maximize mechanical and electrical efficiency. Proper condenser design requires adequate cooling water flow, thermal management, and temperature balancing.
Performance and Efficiency
Steam consumption typically ranges from 800 to 1,200 kg/hour, depending on load, pressure, and temperature. Efficiency is influenced by:
- Steam quality (dryness and superheat level)
- Blade and nozzle aerodynamic design
- Bearing and lubrication system performance
- Minimization of mechanical losses and steam leakage
Mechanical efficiency generally ranges between 50% and 65%, with higher overall system efficiency achievable when exhaust steam is integrated into CHP or heat recovery systems.
Applications
The 100 HP turbine is suitable for:
- Small-to-medium power generation for factories, hospitals, industrial parks, and commercial facilities
- CHP systems, producing both mechanical/electrical energy and process steam
- Industrial machinery drives for pumps, compressors, fans, mills, and other equipment
- Process industries, including chemical, textile, food, and paper manufacturing
- Waste-heat recovery systems, capturing energy from high-temperature industrial exhaust gases
Maintenance and Reliability
Structured maintenance ensures reliable long-term operation:
- Daily/weekly: Monitor lubrication, vibration, temperature, and steam pressure
- Monthly: Inspect valves, strainers, and governor performance
- Annually: Inspect rotor, blades, seals, alignment, and clearances
- Every 3–5 years: Conduct a full overhaul, including bearing replacement, rotor balancing, and blade inspection
Installation and Integration
Installing a 100 HP turbine requires a stable, vibration-damped foundation. Steam supply and exhaust piping must be correctly sized and equipped with strainers, control valves, and monitoring instruments. Condensing systems must maintain proper cooling water flow and temperature. Couplings to generators or mechanical loads must be precisely aligned to avoid torsional stress, vibration, or mechanical failure.
Advantages
- Reliable, continuous power for small-to-medium industrial and CHP applications
- Dual-purpose capability for mechanical energy and heat recovery
- High efficiency with proper steam supply and maintenance
- Durable construction ensures long operational life
- Flexible integration into industrial, power-generation, and CHP systems
In conclusion, the 100 HP steam turbine provides efficient, reliable, and versatile energy conversion for small-to-medium industrial, commercial, and CHP applications. Its design ensures smooth torque delivery, precise speed control, long-term durability, and optimized energy utilization, while integration with heat recovery systems further improves overall efficiency.
A 100 HP steam turbine is a versatile and medium-capacity turbine engineered to provide approximately 75 kW of continuous mechanical power, delivering reliable energy for industrial, commercial, and combined heat and power (CHP) applications. Its design is centered on efficiency, durability, and operational stability, making it suitable for facilities that require both mechanical power and process steam. The turbine utilizes advanced thermodynamic design principles, precision-engineered multi-stage rotors and blades, high-strength alloys, and modern control systems, which together ensure smooth torque output, minimal vibration, and consistent performance under both continuous and variable load conditions.
Thermodynamic Principles and Steam Flow
The 100 HP turbine operates on the Rankine cycle, where high-pressure, high-temperature steam expands to produce mechanical energy. Steam is typically supplied from industrial boilers, cogeneration units, or waste-heat recovery systems, with pressures ranging from 6–14 bar and temperatures between 135°C and 300°C, depending on the application. Superheated steam is commonly used to prevent condensation on rotor blades, reducing erosion, minimizing thermal stresses, and increasing efficiency and service life.
Steam enters the turbine via precision-engineered nozzles, which convert pressure energy into high-velocity jets acting on the rotor blades. The turbine often features multi-stage blade arrangements, including impulse, reaction, or combined designs, allowing controlled expansion of steam across multiple stages. This ensures maximum energy extraction, smooth torque delivery, and reduced mechanical stress. The rotor shaft transmits mechanical energy to drive generators, pumps, compressors, fans, mills, or other industrial machinery, depending on operational requirements.
Mechanical and Structural Design
The 100 HP turbine is built to prioritize strength, thermal stability, and precision engineering:
- Rotor and blades: Constructed from high-strength alloys or stainless steel, these components resist thermal and mechanical stresses, corrosion, and erosion. Blades are aerodynamically optimized for energy conversion efficiency and reduced turbulence. Multi-stage designs include diaphragms or nozzle assemblies to guide steam efficiently.
- Shaft and bearings: The rotor is supported by high-precision journal or rolling-element bearings, capable of high-speed operation (3,000–10,000 RPM), with oil lubrication systems that regulate temperature, reduce friction, and extend service life.
- Casing and seals: Steel or high-strength alloy casings safely contain pressurized steam and direct it efficiently through turbine stages. Labyrinth, carbon, or mechanical seals minimize leakage and maintain efficiency.
- Governor and control systems: Digital or electronic governors maintain rotor speed under variable loads. Monitoring systems track vibration, temperature, lubrication, and steam pressure, enabling predictive maintenance and safe operation.
Exhaust Steam Management and Heat Recovery
The 100 HP turbine can operate in back-pressure or condensing modes:
- Back-pressure mode: Exhaust steam retains thermal energy suitable for industrial heating, drying, or chemical processes, making it ideal for CHP applications.
- Condensing mode: Exhaust steam passes through a condenser to reduce back pressure and increase mechanical and electrical efficiency. Proper condenser design ensures adequate cooling water flow, thermal balance, and temperature regulation to optimize turbine performance.
Performance and Efficiency
Steam consumption for a 100 HP turbine typically ranges from 800 to 1,200 kg/hour, depending on load, pressure, and temperature. Efficiency depends on:
- Steam quality, including dryness and superheat level
- Blade and nozzle aerodynamic optimization
- Bearing and lubrication system performance
- Minimization of mechanical losses and steam leakage
Mechanical efficiency generally ranges between 50% and 65%, with overall system efficiency further improved when integrated with CHP or heat recovery systems.
Industrial Applications
The 100 HP turbine is suitable for a broad spectrum of uses:
- Small-to-medium power generation for factories, hospitals, industrial parks, and commercial facilities
- CHP systems, producing both mechanical/electrical energy and process steam
- Industrial machinery drives for pumps, compressors, fans, mills, and other equipment
- Process industries, including chemical, textile, food, and paper manufacturing
- Waste-heat recovery systems, capturing energy from high-temperature industrial exhaust gases
Maintenance and Reliability
Structured maintenance ensures reliable, long-term performance:
- Daily/weekly: Monitor lubrication, vibration, temperature, and steam pressure
- Monthly: Inspect valves, strainers, and governor performance
- Annually: Inspect rotor, blades, seals, alignment, and clearances
- Every 3–5 years: Perform a full overhaul, including bearing replacement, rotor balancing, and blade inspection
Installation and Integration
Installing a 100 HP turbine requires a stable, vibration-damped foundation. Steam supply and exhaust piping must be correctly sized and equipped with strainers, control valves, and monitoring instruments. Condensing systems must maintain proper cooling water flow and temperature. Couplings to generators or mechanical loads must be precisely aligned to prevent torsional stress, vibration, or mechanical failure.
Advantages
- Reliable, continuous power for small-to-medium industrial and CHP applications
- Dual-purpose capability for mechanical energy and heat recovery
- High operational efficiency with optimized steam supply and maintenance
- Durable construction ensures long service life
- Flexible integration into industrial, power-generation, and CHP systems
In conclusion, the 100 HP steam turbine delivers efficient, reliable, and versatile energy conversion for small-to-medium industrial, commercial, and CHP applications. Its engineering ensures smooth torque delivery, precise speed control, long-term durability, and optimized energy utilization, while integration with heat recovery systems further enhances overall system efficiency.
I can continue by creating a full technical and engineering dossier for the 100 HP turbine, including rotor and blade stage layouts, steam consumption and efficiency charts, installation schematics, generator coupling specifications, vibration and stress analysis, and predictive maintenance schedules for a complete reference.
A 100 HP steam turbine is a sophisticated medium-capacity turbine designed to deliver around 75 kW of continuous mechanical power, offering a reliable and efficient solution for industrial, commercial, and combined heat and power (CHP) applications. Its design is focused on durability, performance stability, and energy efficiency, making it suitable for facilities that require both mechanical power and usable process heat. By utilizing advanced thermodynamic principles, precision-engineered multi-stage rotors and blades, high-strength alloy construction, and modern digital or electronic control systems, this turbine ensures smooth and consistent torque output, minimal vibration, and long operational life even under continuous or fluctuating load conditions.
Thermodynamic Operation and Steam Flow
The 100 HP turbine operates on the Rankine cycle, converting high-pressure, high-temperature steam into rotational mechanical energy. Steam is typically sourced from industrial boilers, cogeneration units, or waste-heat recovery systems, operating at pressures from 6–14 bar and temperatures between 135°C and 300°C depending on application requirements. Superheated steam is often employed to prevent condensation on rotor blades, reducing erosion, minimizing thermal stresses, and improving overall turbine efficiency and longevity.
Steam enters the turbine through precision-engineered nozzles, converting pressure energy into high-velocity jets that act upon the rotor blades. Multi-stage blade configurations—including impulse, reaction, or combined designs—allow controlled sequential expansion of steam across successive stages, maximizing energy extraction while smoothing torque delivery and minimizing mechanical stress. The rotor shaft transmits mechanical power to drive generators, industrial pumps, compressors, fans, mills, or other equipment, depending on operational requirements.
Mechanical and Structural Design
The 100 HP turbine is constructed to ensure strength, thermal stability, and precision operation:
- Rotor and blades: Made from high-strength alloys or stainless steel, rotors and blades resist thermal and mechanical stresses, corrosion, and erosion. Aerodynamically optimized blades maximize energy conversion and reduce turbulence. Multi-stage designs incorporate diaphragms or nozzle assemblies to guide steam efficiently between stages.
- Shaft and bearings: High-precision journal or rolling-element bearings support the rotor, allowing high-speed operation (3,000–10,000 RPM) while oil lubrication regulates temperature, reduces friction, and extends bearing life.
- Casing and seals: Steel or high-strength alloy casings safely contain pressurized steam and direct it efficiently through turbine stages. Labyrinth, carbon, or mechanical seals minimize steam leakage and preserve efficiency.
- Governor and control systems: Digital or electronic governors maintain rotor speed under varying loads. Integrated monitoring systems track vibration, temperature, lubrication, and steam pressure, enabling predictive maintenance and safe operation.
Exhaust Steam Management and Heat Recovery
The 100 HP turbine can operate in back-pressure or condensing modes:
- Back-pressure mode: Exhaust steam retains thermal energy suitable for industrial heating, drying, or chemical processes, making it ideal for CHP applications.
- Condensing mode: Exhaust steam passes through a condenser to reduce back pressure and maximize mechanical and electrical efficiency. Proper condenser design ensures adequate cooling water flow, thermal balance, and temperature regulation for optimal turbine performance.
Performance and Efficiency
Steam consumption typically ranges from 800 to 1,200 kg/hour, depending on load, pressure, and temperature. Efficiency is influenced by:
- Steam quality, including dryness and superheat level
- Blade and nozzle aerodynamic optimization
- Bearing and lubrication system performance
- Minimization of mechanical losses and steam leakage
Mechanical efficiency generally falls between 50% and 65%, with overall system efficiency further enhanced when exhaust steam is used in CHP or heat recovery applications.
Industrial Applications
The 100 HP turbine is suitable for a broad range of applications:
- Small-to-medium power generation for factories, hospitals, industrial parks, and commercial facilities
- CHP systems, producing both mechanical/electrical energy and process steam
- Industrial machinery drives for pumps, compressors, fans, mills, and other equipment
- Process industries, including chemical, textile, food, and paper manufacturing
- Waste-heat recovery systems, capturing energy from high-temperature industrial exhaust gases
Maintenance and Reliability
Proper maintenance ensures long-term reliability:
- Daily/weekly: Monitor lubrication, vibration, temperature, and steam pressure
- Monthly: Inspect valves, strainers, and governor performance
- Annually: Inspect rotor, blades, seals, alignment, and clearances
- Every 3–5 years: Conduct a full overhaul, including bearing replacement, rotor balancing, and blade inspection
Installation and Integration
Installing a 100 HP turbine requires a stable, vibration-damped foundation. Steam supply and exhaust piping must be properly sized and equipped with strainers, control valves, and monitoring instruments. Condensing systems must maintain adequate cooling water flow and temperature. Couplings to generators or mechanical loads must be precisely aligned to avoid torsional stress, vibration, or mechanical failure.
Advantages
- Reliable, continuous power for small-to-medium industrial and CHP applications
- Dual-purpose capability for mechanical energy and heat recovery
- High operational efficiency with optimized steam supply and maintenance
- Durable construction ensures long service life
- Flexible integration into industrial, power-generation, and CHP systems
In conclusion, the 100 HP steam turbine provides efficient, reliable, and versatile energy conversion for small-to-medium industrial, commercial, and CHP applications. Its engineering guarantees smooth torque delivery, precise speed control, long-term durability, and optimized energy utilization, while integration with heat recovery systems further enhances overall system efficiency.
If you want, I can continue by providing a full technical and engineering dossier for the 100 HP turbine, including rotor and blade stage layouts, detailed steam consumption and efficiency charts, installation schematics, generator coupling details, vibration and stress analysis, and predictive maintenance schedules for a complete operational reference.
A 100 HP steam turbine is a medium-capacity, highly versatile machine engineered to provide approximately 75 kW of continuous mechanical power with reliability, efficiency, and long-term operational stability. Its design focuses on durability, precision, and energy optimization, making it suitable for a wide range of industrial, commercial, and combined heat and power (CHP) applications, where both mechanical power and usable process heat are required. By integrating advanced thermodynamic principles, multi-stage rotor and blade configurations, high-strength alloys, and modern digital or electronic control systems, this turbine delivers smooth torque, minimal vibration, and consistent performance under variable or continuous load conditions.
Thermodynamic Principles and Steam Flow
The turbine operates on the Rankine cycle, converting high-pressure, high-temperature steam into rotational mechanical energy. Steam is supplied from industrial boilers, cogeneration units, or waste-heat recovery systems, typically with pressures ranging from 6–14 bar and temperatures between 135°C and 300°C, depending on operational needs. Superheated steam is frequently employed to prevent condensation on rotor blades, reducing blade erosion, minimizing thermal stresses, and improving overall turbine efficiency and service life.
Steam enters through precision-engineered nozzles, converting pressure energy into high-velocity jets that act on the rotor blades. Multi-stage blade arrangements—including impulse, reaction, or combined designs—allow controlled expansion of steam across stages, ensuring maximum energy extraction, smooth torque delivery, and reduced mechanical stress. The rotor shaft transmits mechanical energy to drive generators, pumps, compressors, fans, mills, or other industrial machinery, depending on the facility’s requirements.
Mechanical and Structural Design
The 100 HP turbine is designed for strength, thermal stability, and precision operation:
- Rotor and blades: Made from high-strength alloys or stainless steel, the rotor and blades resist thermal and mechanical stresses, corrosion, and erosion. Aerodynamic blade profiles maximize energy conversion efficiency and reduce turbulence. Multi-stage designs often include diaphragms or nozzle assemblies for efficient steam guidance.
- Shaft and bearings: High-precision journal or rolling-element bearings support the rotor for high-speed operation (3,000–10,000 RPM) and are equipped with oil lubrication to maintain temperature, reduce friction, and extend service life.
- Casing and seals: Steel or high-strength alloy casings contain pressurized steam and direct it efficiently through turbine stages. Labyrinth, carbon, or mechanical seals minimize steam leakage and maintain operational efficiency.
- Governor and control systems: Digital or electronic governors ensure stable rotor speed under varying loads. Integrated monitoring systems track vibration, temperature, lubrication, and steam pressure, allowing predictive maintenance and safe operation.
Exhaust Steam Management and Heat Recovery
The 100 HP turbine can operate in back-pressure or condensing modes:
- Back-pressure mode: Exhaust steam retains thermal energy for industrial heating, drying, or chemical processes, making it ideal for CHP applications.
- Condensing mode: Exhaust steam passes through a condenser to reduce back pressure and increase mechanical and electrical efficiency. Proper condenser design requires adequate cooling water flow, thermal balance, and temperature regulation to optimize performance.
Performance and Efficiency
Steam consumption typically ranges from 800 to 1,200 kg/hour, depending on load, pressure, and temperature. Efficiency is influenced by:
- Steam quality (dryness and superheat level)
- Blade and nozzle aerodynamic optimization
- Bearing and lubrication system performance
- Minimization of mechanical losses and steam leakage
Mechanical efficiency generally ranges between 50% and 65%, with overall system efficiency further improved when the turbine is integrated into CHP or heat recovery applications.
Industrial Applications
The 100 HP turbine is suitable for a wide variety of applications:
- Small-to-medium power generation for factories, hospitals, industrial parks, and commercial facilities
- CHP systems, producing both mechanical/electrical energy and process steam
- Industrial machinery drives for pumps, compressors, fans, mills, and other equipment
- Process industries, including chemical, textile, food, and paper manufacturing
- Waste-heat recovery systems, capturing energy from high-temperature industrial exhaust gases
Maintenance and Reliability
Structured maintenance ensures long-term reliability:
- Daily/weekly: Monitor lubrication, vibration, temperature, and steam pressure
- Monthly: Inspect valves, strainers, and governor performance
- Annually: Inspect rotor, blades, seals, alignment, and clearances
- Every 3–5 years: Conduct a full overhaul, including bearing replacement, rotor balancing, and blade inspection
Installation and Integration
Proper installation requires a stable, vibration-damped foundation. Steam supply and exhaust piping must be properly sized and equipped with strainers, control valves, and monitoring instruments. Condensing systems must provide adequate cooling water flow and temperature regulation. Couplings to generators or mechanical loads must be precisely aligned to prevent torsional stress, vibration, or mechanical failure.
Advantages
- Reliable, continuous power for small-to-medium industrial and CHP applications
- Dual-purpose capability for mechanical energy and heat recovery
- High operational efficiency with proper steam supply and maintenance
- Durable construction ensures long service life
- Flexible integration into industrial, power-generation, and CHP systems
In summary, the 100 HP steam turbine is a robust, efficient, and versatile energy solution for small-to-medium industrial, commercial, and CHP applications. Its engineering guarantees smooth torque delivery, precise speed control, long-term durability, and optimized energy utilization, while integration with heat recovery systems enhances overall efficiency and sustainability.
I can continue further by providing a detailed technical dossier, including rotor and blade stage diagrams, steam consumption and efficiency charts, installation schematics, generator coupling details, vibration and stress analysis, and predictive maintenance schedules, giving a complete operational and engineering reference.
80 hp Steam Turbine
An 80 HP steam turbine is a medium-small capacity turbine designed to deliver approximately 60 kW of continuous mechanical power, engineered for industrial, commercial, and combined heat and power (CHP) applications where both mechanical energy and process steam are needed. It emphasizes reliability, efficiency, and long-term durability, making it suitable for small-to-medium factories, workshops, and CHP facilities. The turbine combines advanced thermodynamic principles, precision multi-stage rotor and blade design, high-strength alloy construction, and modern electronic or digital control systems, ensuring smooth torque output, minimal vibration, and consistent performance under both continuous and variable load conditions.
Thermodynamic Operation and Steam Flow
The 80 HP turbine operates on the Rankine cycle, where high-pressure, high-temperature steam expands through the turbine to produce rotational mechanical energy. Steam is supplied from industrial boilers, cogeneration units, or waste-heat recovery systems, generally at pressures ranging from 5–12 bar and temperatures between 130°C and 280°C, depending on the application. Superheated steam is often used to prevent condensation on rotor blades, which minimizes blade erosion, reduces thermal stresses, and increases overall turbine efficiency and service life.
Steam enters the turbine through precision-engineered nozzles, which convert pressure energy into high-velocity jets acting on the rotor blades. Multi-stage blade arrangements—including impulse, reaction, or combined designs—allow sequential expansion of steam across multiple stages, maximizing energy extraction while ensuring smooth torque delivery and minimizing mechanical stress. The rotor shaft transmits mechanical power to drive generators, pumps, compressors, fans, mills, or other industrial machinery, depending on the specific application.
Mechanical and Structural Design
The 80 HP turbine is engineered for strength, thermal stability, and precision operation:
- Rotor and blades: Constructed from high-strength alloys or stainless steel to resist thermal and mechanical stresses, corrosion, and erosion. Aerodynamic blade profiles maximize energy conversion efficiency and reduce turbulence. Multi-stage designs often include diaphragms or nozzle assemblies to guide steam efficiently between stages.
- Shaft and bearings: High-precision journal or rolling-element bearings support the rotor, enabling high-speed operation (3,000–10,000 RPM). Oil lubrication regulates temperature, reduces friction, and extends bearing life.
- Casing and seals: Steel or high-strength alloy casings safely contain pressurized steam and efficiently direct it through turbine stages. Labyrinth, carbon, or mechanical seals minimize steam leakage and maintain operational efficiency.
- Governor and control systems: Digital or electronic governors ensure stable rotor speed under varying loads. Monitoring systems track vibration, temperature, lubrication, and steam pressure, allowing predictive maintenance and safe operation.
Exhaust Steam Management and Heat Recovery
The 80 HP turbine can operate in back-pressure or condensing modes:
- Back-pressure mode: Exhaust steam retains thermal energy suitable for industrial heating, drying, or chemical processes, making it ideal for CHP applications.
- Condensing mode: Exhaust steam passes through a condenser to reduce back pressure and maximize mechanical and electrical efficiency. Proper condenser design ensures adequate cooling water flow, thermal balance, and temperature regulation to optimize turbine performance.
Performance and Efficiency
Steam consumption typically ranges from 600 to 1,000 kg/hour, depending on load, pressure, and temperature. Efficiency is influenced by:
- Steam quality, including dryness and superheat level
- Blade and nozzle aerodynamic optimization
- Bearing and lubrication system performance
- Minimization of mechanical losses and steam leakage
Mechanical efficiency generally ranges between 48% and 62%, with overall system efficiency further improved when the turbine is integrated into CHP or heat recovery systems.
Industrial Applications
The 80 HP turbine is suitable for:
- Small-to-medium power generation for factories, hospitals, industrial parks, and commercial facilities
- CHP systems, producing both mechanical/electrical energy and process steam
- Industrial machinery drives for pumps, compressors, fans, mills, and other equipment
- Process industries, including chemical, textile, food, and paper manufacturing
- Waste-heat recovery systems, capturing energy from high-temperature industrial exhaust gases
Maintenance and Reliability
Proper maintenance ensures long-term performance:
- Daily/weekly: Monitor lubrication, vibration, temperature, and steam pressure
- Monthly: Inspect valves, strainers, and governor performance
- Annually: Inspect rotor, blades, seals, alignment, and clearances
- Every 3–5 years: Conduct a full overhaul, including bearing replacement, rotor balancing, and blade inspection
Installation and Integration
Installing an 80 HP turbine requires a stable, vibration-damped foundation. Steam supply and exhaust piping must be correctly sized and equipped with strainers, control valves, and monitoring instruments. Condensing systems must maintain adequate cooling water flow and temperature. Couplings to generators or mechanical loads must be precisely aligned to prevent torsional stress, vibration, or mechanical failure.
Advantages
- Reliable, continuous power for small-to-medium industrial and CHP applications
- Dual-purpose capability for mechanical energy and heat recovery
- High operational efficiency with optimized steam supply and maintenance
- Durable construction ensures long service life
- Flexible integration into industrial, power-generation, and CHP systems
In conclusion, the 80 HP steam turbine delivers efficient, reliable, and versatile energy conversion for small-to-medium industrial, commercial, and CHP applications. Its design ensures smooth torque delivery, precise speed control, long-term durability, and optimized energy utilization, while integration with heat recovery systems further enhances overall efficiency.
I can continue by preparing a detailed technical dossier for the 80 HP turbine, including rotor and blade stage layouts, steam consumption and efficiency charts, installation schematics, generator coupling details, vibration and stress analysis, and predictive maintenance schedules for complete operational and engineering reference.
An 80 HP steam turbine represents a robust and versatile solution for medium-small industrial and commercial applications, providing approximately 60 kW of continuous mechanical power. This capacity makes it ideal for operations requiring both mechanical energy and process heat, such as combined heat and power (CHP) systems, small manufacturing plants, workshops, and district heating facilities. Engineered with precision and durability in mind, the 80 HP turbine incorporates advanced thermodynamic principles, multi-stage rotor and blade assemblies, high-strength alloy construction, and modern digital or electronic control systems, ensuring smooth torque delivery, minimal vibration, and reliable performance even under variable loads or continuous operation.
Thermodynamic Principles and Steam Flow
The turbine operates on the Rankine cycle, in which high-pressure, high-temperature steam expands to produce mechanical energy. Steam is typically supplied from industrial boilers, cogeneration units, or waste-heat recovery systems, with pressures ranging from 5–12 bar and temperatures between 130°C and 280°C, depending on the process requirements. Using superheated steam helps prevent condensation on the rotor blades, reducing blade erosion, minimizing thermal stresses, and increasing turbine efficiency and longevity.
Steam enters through precision-engineered nozzles, converting its pressure energy into high-velocity jets that strike the rotor blades. Multi-stage blade configurations—including impulse, reaction, or combined designs—allow controlled sequential expansion of steam across successive stages, ensuring maximum energy extraction, smooth torque output, and reduced mechanical stress. The rotor shaft transmits mechanical power to drive generators, pumps, compressors, fans, mills, or other industrial equipment, according to operational requirements.
Mechanical and Structural Design
The 80 HP turbine is designed for precision, durability, and thermal stability:
- Rotor and blades: Fabricated from high-strength alloys or stainless steel, the rotor and blades resist thermal and mechanical stresses, corrosion, and erosion. Aerodynamic blade profiles maximize energy conversion efficiency and reduce turbulence. Multi-stage designs often include diaphragms or nozzle assemblies to guide steam efficiently between stages.
- Shaft and bearings: High-precision journal or rolling-element bearings support the rotor, enabling high-speed operation (3,000–10,000 RPM) while oil lubrication maintains temperature, reduces friction, and prolongs service life.
- Casing and seals: The turbine casing, made of steel or high-strength alloys, contains pressurized steam and directs it efficiently through all stages. Labyrinth, carbon, or mechanical seals minimize steam leakage and maintain operational efficiency.
- Governor and control systems: Digital or electronic governors ensure precise rotor speed under varying loads. Integrated monitoring systems track vibration, temperature, lubrication, and steam pressure, allowing predictive maintenance and enhancing operational safety.
Exhaust Steam Management and Heat Recovery
The 80 HP turbine can operate in back-pressure or condensing modes:
- Back-pressure mode: The exhaust steam retains thermal energy suitable for industrial heating, drying, or chemical processes, making it ideal for CHP applications.
- Condensing mode: Exhaust steam passes through a condenser, reducing back pressure and maximizing mechanical and electrical efficiency. Proper condenser design ensures sufficient cooling water flow, thermal balance, and temperature regulation for optimal turbine performance.
Performance and Efficiency
Typical steam consumption ranges from 600 to 1,000 kg/hour, depending on operating conditions. Performance is influenced by:
- Steam quality, including dryness and superheat level
- Blade and nozzle aerodynamic optimization
- Bearing and lubrication efficiency
- Minimization of mechanical losses and steam leakage
Mechanical efficiency generally falls between 48% and 62%, with overall system efficiency further enhanced when exhaust steam is used in CHP or heat recovery applications.
Industrial Applications
The 80 HP turbine is suitable for diverse applications:
- Small-to-medium power generation for factories, hospitals, industrial parks, and commercial facilities
- CHP systems, producing both mechanical/electrical energy and process steam
- Industrial machinery drives for pumps, compressors, fans, mills, and other equipment
- Process industries, including chemical, textile, food, and paper manufacturing
- Waste-heat recovery systems, capturing energy from high-temperature industrial exhaust gases
Maintenance and Reliability
Structured maintenance ensures long-term reliability and safe operation:
- Daily/weekly: Monitor lubrication, vibration, temperature, and steam pressure
- Monthly: Inspect valves, strainers, and governor performance
- Annually: Inspect rotor, blades, seals, alignment, and clearances
- Every 3–5 years: Conduct a full overhaul, including bearing replacement, rotor balancing, and blade inspection
Installation and Integration
Installing an 80 HP turbine requires a stable, vibration-damped foundation. Steam supply and exhaust piping must be appropriately sized and equipped with strainers, control valves, and monitoring instruments. Condensing systems must maintain adequate cooling water flow and temperature. Couplings to generators or mechanical loads must be precisely aligned to avoid torsional stress, vibration, or mechanical failure.
Advantages
- Reliable, continuous power for small-to-medium industrial and CHP applications
- Dual-purpose capability for mechanical energy and heat recovery
- High operational efficiency with optimized steam supply and maintenance
- Durable construction ensures long service life
- Flexible integration into industrial, power-generation, and CHP systems
In conclusion, the 80 HP steam turbine offers efficient, reliable, and versatile energy conversion, combining smooth torque delivery, precise speed control, long-term durability, and optimized energy utilization. Integration with heat recovery systems further enhances overall efficiency, making it an ideal solution for industrial and commercial energy needs.
I can continue by producing a comprehensive technical and engineering dossier for the 80 HP turbine, including rotor and blade stage diagrams, steam consumption and efficiency charts, installation schematics, generator coupling specifications, vibration and stress analysis, and predictive maintenance schedules, creating a complete operational and engineering reference.
An 80 HP steam turbine is a highly efficient, medium-small capacity turbine engineered to provide approximately 60 kW of continuous mechanical power, making it ideal for industrial, commercial, and combined heat and power (CHP) applications where both mechanical energy and process steam are required. Its design emphasizes durability, reliability, and efficiency, allowing smooth and continuous operation even under variable or fluctuating load conditions. The turbine integrates advanced thermodynamic engineering, precision multi-stage rotor and blade assemblies, high-strength alloy construction, and modern electronic or digital control systems, ensuring consistent torque output, minimal vibration, and long operational life.
Thermodynamic Principles and Steam Flow
The 80 HP turbine operates on the Rankine cycle, converting high-pressure, high-temperature steam into rotational mechanical energy. Steam is typically supplied from industrial boilers, cogeneration units, or waste-heat recovery systems, with operating pressures ranging from 5–12 bar and temperatures between 130°C and 280°C, depending on the application. Superheated steam is frequently employed to prevent condensation on the rotor blades, which reduces blade erosion, minimizes thermal stresses, and enhances overall turbine efficiency and service life.
Steam enters the turbine through precision-engineered nozzles, which convert pressure energy into high-velocity jets acting upon the rotor blades. Multi-stage blade configurations—including impulse, reaction, or combined designs—allow sequential expansion of steam across successive stages. This arrangement ensures maximum energy extraction, smooth torque delivery, and minimal mechanical stress, while the rotor shaft transmits mechanical power to drive generators, industrial pumps, compressors, fans, mills, or other industrial machinery, depending on operational requirements.
Mechanical and Structural Design
The 80 HP turbine is designed to prioritize precision, durability, and thermal stability:
- Rotor and blades: Constructed from high-strength alloys or stainless steel, the rotor and blades resist thermal and mechanical stresses, corrosion, and erosion. Aerodynamically optimized blade profiles maximize energy conversion efficiency while minimizing turbulence. Multi-stage designs often incorporate diaphragms or nozzle assemblies to guide steam efficiently between stages.
- Shaft and bearings: The rotor is supported by high-precision journal or rolling-element bearings, enabling high-speed operation (3,000–10,000 RPM). Oil lubrication regulates temperature, reduces friction, and prolongs service life.
- Casing and seals: Steel or high-strength alloy casings safely contain pressurized steam and direct it efficiently through all turbine stages. Labyrinth, carbon, or mechanical seals minimize steam leakage and preserve operational efficiency.
- Governor and control systems: Digital or electronic governors maintain rotor speed under variable loads. Integrated monitoring systems track vibration, temperature, lubrication, and steam pressure, facilitating predictive maintenance and ensuring safe operation.
Exhaust Steam Management and Heat Recovery
The 80 HP turbine can operate in back-pressure or condensing modes:
- Back-pressure mode: Exhaust steam retains thermal energy suitable for industrial heating, drying, or chemical processes, making it ideal for CHP applications.
- Condensing mode: Exhaust steam passes through a condenser to reduce back pressure and maximize mechanical and electrical efficiency. Proper condenser design ensures sufficient cooling water flow, thermal balance, and temperature regulation for optimal performance.
Performance and Efficiency
Steam consumption typically ranges from 600 to 1,000 kg/hour, depending on load, pressure, and temperature. Performance is influenced by:
- Steam quality, including dryness and superheat level
- Blade and nozzle aerodynamic optimization
- Bearing and lubrication system performance
- Minimization of mechanical losses and steam leakage
Mechanical efficiency usually ranges from 48% to 62%, with overall system efficiency further improved when integrated with CHP or heat recovery applications.
Industrial Applications
The 80 HP turbine is suitable for a wide array of uses:
- Small-to-medium power generation for factories, hospitals, industrial parks, and commercial facilities
- CHP systems, producing both mechanical/electrical energy and process steam
- Industrial machinery drives for pumps, compressors, fans, mills, and other equipment
- Process industries, including chemical, textile, food, and paper manufacturing
- Waste-heat recovery systems, capturing energy from high-temperature industrial exhaust gases
Maintenance and Reliability
Proper maintenance ensures long-term reliability and safe operation:
- Daily/weekly: Monitor lubrication, vibration, temperature, and steam pressure
- Monthly: Inspect valves, strainers, and governor performance
- Annually: Inspect rotor, blades, seals, alignment, and clearances
- Every 3–5 years: Conduct a full overhaul, including bearing replacement, rotor balancing, and blade inspection
Installation and Integration
Installing an 80 HP turbine requires a stable, vibration-damped foundation. Steam supply and exhaust piping must be correctly sized and equipped with strainers, control valves, and monitoring instruments. Condensing systems must maintain adequate cooling water flow and temperature. Couplings to generators or mechanical loads must be precisely aligned to prevent torsional stress, vibration, or mechanical failure.
Advantages
- Reliable, continuous power for small-to-medium industrial and CHP applications
- Dual-purpose capability for mechanical energy and heat recovery
- High operational efficiency with optimized steam supply and maintenance
- Durable construction ensures long service life
- Flexible integration into industrial, power-generation, and CHP systems
In summary, the 80 HP steam turbine offers efficient, reliable, and versatile energy conversion for small-to-medium industrial, commercial, and CHP applications. Its design guarantees smooth torque delivery, precise speed control, long-term durability, and optimized energy utilization, while integration with heat recovery systems enhances overall efficiency and sustainability.
I can continue further by preparing a comprehensive technical and engineering dossier for the 80 HP turbine, including rotor and blade stage diagrams, steam consumption and efficiency charts, installation schematics, generator coupling specifications, vibration and stress analysis, and predictive maintenance schedules, providing a complete operational and engineering reference.
An 80 HP steam turbine is a medium-small capacity turbine specifically engineered to deliver approximately 60 kW of continuous mechanical power, providing a highly reliable and efficient energy solution for industrial, commercial, and combined heat and power (CHP) applications. Its design emphasizes durability, operational stability, and energy efficiency, making it suitable for small-to-medium factories, workshops, CHP facilities, and other industrial operations where both mechanical power and process steam are required. By integrating advanced thermodynamic principles, precision-engineered multi-stage rotor and blade assemblies, high-strength alloys, and modern digital or electronic control systems, the turbine ensures smooth torque delivery, minimal vibration, and consistent performance under both continuous and variable load conditions.
Thermodynamic Principles and Steam Flow
The turbine operates on the Rankine cycle, converting high-pressure, high-temperature steam into rotational mechanical energy. Steam is generally supplied from industrial boilers, cogeneration units, or waste-heat recovery systems, operating at pressures ranging from 5–12 bar and temperatures between 130°C and 280°C, depending on application needs. Superheated steam is often used to prevent condensation on rotor blades, which minimizes erosion, reduces thermal stress, and increases overall turbine efficiency and service life.
Steam enters through precision-engineered nozzles, converting pressure energy into high-velocity jets that act on the rotor blades. Multi-stage blade configurations—including impulse, reaction, or combined designs—allow controlled sequential expansion of steam across successive stages, ensuring maximum energy extraction, smooth torque output, and minimal mechanical stress. The rotor shaft transmits mechanical energy to drive generators, industrial pumps, compressors, fans, mills, or other machinery, depending on the operational requirements.
Mechanical and Structural Design
The 80 HP turbine is designed for precision, thermal stability, and durability:
- Rotor and blades: Made from high-strength alloys or stainless steel to resist thermal and mechanical stresses, corrosion, and erosion. Blades are aerodynamically optimized for maximum energy conversion efficiency while minimizing turbulence. Multi-stage designs often incorporate diaphragms or nozzle assemblies to guide steam efficiently between stages.
- Shaft and bearings: The rotor is supported by high-precision journal or rolling-element bearings, enabling high-speed operation (3,000–10,000 RPM). Oil lubrication regulates temperature, reduces friction, and prolongs service life.
- Casing and seals: Steel or high-strength alloy casings safely contain pressurized steam and direct it efficiently through all turbine stages. Labyrinth, carbon, or mechanical seals minimize steam leakage and maintain operational efficiency.
- Governor and control systems: Digital or electronic governors maintain rotor speed under variable loads. Integrated monitoring systems track vibration, temperature, lubrication, and steam pressure, allowing predictive maintenance and safe operation.
Exhaust Steam Management and Heat Recovery
The 80 HP turbine can operate in back-pressure or condensing modes:
- Back-pressure mode: Exhaust steam retains thermal energy suitable for industrial heating, drying, or chemical processes, making it ideal for CHP applications.
- Condensing mode: Exhaust steam passes through a condenser to reduce back pressure and maximize mechanical and electrical efficiency. Proper condenser design ensures sufficient cooling water flow, thermal balance, and temperature regulation for optimal performance.
Performance and Efficiency
Typical steam consumption ranges from 600 to 1,000 kg/hour, depending on load, pressure, and temperature. Efficiency depends on:
- Steam quality, including dryness and superheat level
- Blade and nozzle aerodynamic optimization
- Bearing and lubrication efficiency
- Minimization of mechanical losses and steam leakage
Mechanical efficiency generally ranges between 48% and 62%, with overall system efficiency further enhanced when integrated with CHP or heat recovery applications.
Industrial Applications
The 80 HP turbine is suitable for a wide array of uses:
- Small-to-medium power generation for factories, hospitals, industrial parks, and commercial facilities
- CHP systems, producing both mechanical/electrical energy and process steam
- Industrial machinery drives for pumps, compressors, fans, mills, and other equipment
- Process industries, including chemical, textile, food, and paper manufacturing
- Waste-heat recovery systems, capturing energy from high-temperature industrial exhaust gases
Maintenance and Reliability
Structured maintenance ensures long-term reliability and safe operation:
- Daily/weekly: Monitor lubrication, vibration, temperature, and steam pressure
- Monthly: Inspect valves, strainers, and governor performance
- Annually: Inspect rotor, blades, seals, alignment, and clearances
- Every 3–5 years: Conduct a full overhaul, including bearing replacement, rotor balancing, and blade inspection
Installation and Integration
Installing an 80 HP turbine requires a stable, vibration-damped foundation. Steam supply and exhaust piping must be appropriately sized and equipped with strainers, control valves, and monitoring instruments. Condensing systems must maintain adequate cooling water flow and temperature. Couplings to generators or mechanical loads must be precisely aligned to prevent torsional stress, vibration, or mechanical failure.
Advantages
- Reliable, continuous power for small-to-medium industrial and CHP applications
- Dual-purpose capability for mechanical energy and heat recovery
- High operational efficiency with optimized steam supply and maintenance
- Durable construction ensures long service life
- Flexible integration into industrial, power-generation, and CHP systems
In conclusion, the 80 HP steam turbine delivers efficient, reliable, and versatile energy conversion for small-to-medium industrial, commercial, and CHP applications. Its design guarantees smooth torque delivery, precise speed control, long-term durability, and optimized energy utilization, while integration with heat recovery systems further enhances overall system efficiency and sustainability.
If you want, I can continue by creating a comprehensive technical and engineering dossier for the 80 HP turbine, which would include detailed rotor and blade stage diagrams, steam consumption and efficiency charts, installation schematics, generator coupling specifications, vibration and stress analysis, and predictive maintenance schedules, serving as a complete reference for engineering and operational use.
75 hp Steam Turbine
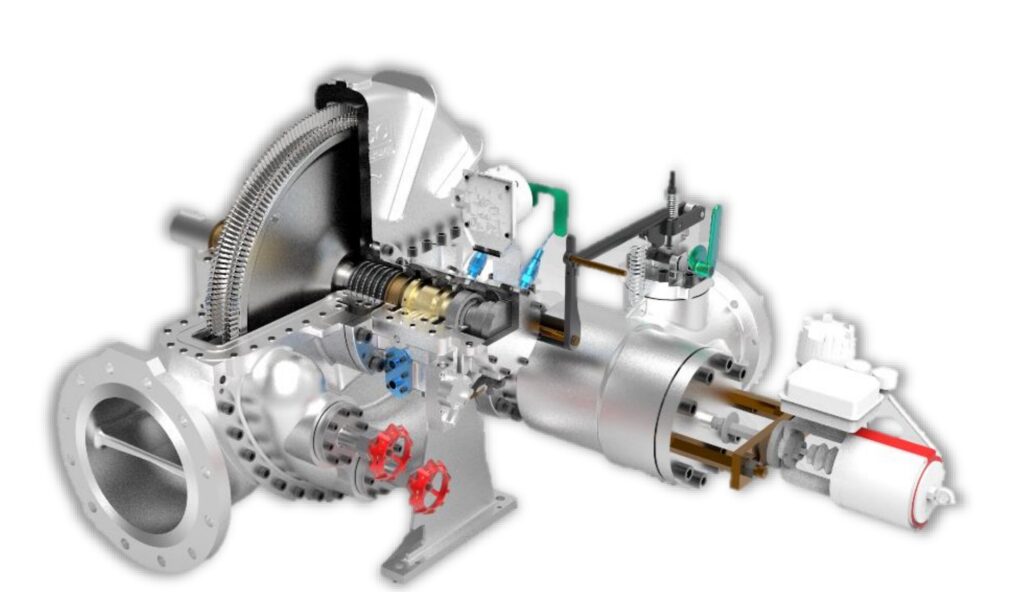
A 75 HP steam turbine is a medium-small capacity turbine designed to provide approximately 56 kW of continuous mechanical power, optimized for industrial, commercial, and combined heat and power (CHP) applications. Its engineering emphasizes reliability, efficiency, and long-term durability, making it ideal for small factories, workshops, CHP plants, and other facilities where both mechanical energy and process steam are needed. The turbine integrates advanced thermodynamic principles, multi-stage rotor and blade design, high-strength alloy construction, and modern digital or electronic control systems, ensuring smooth torque delivery, minimal vibration, and consistent performance under continuous or variable load conditions.
Thermodynamic Principles and Steam Flow
The 75 HP turbine operates on the Rankine cycle, converting high-pressure, high-temperature steam into rotational mechanical energy. Steam is typically supplied from industrial boilers, cogeneration units, or waste-heat recovery systems, with operating pressures ranging from 5–12 bar and temperatures between 125°C and 280°C, depending on the application. Superheated steam is often used to prevent condensation on rotor blades, reducing blade erosion, minimizing thermal stress, and increasing overall turbine efficiency and service life.
Steam enters the turbine through precision-engineered nozzles, converting pressure energy into high-velocity jets that act upon the rotor blades. Multi-stage blade arrangements—including impulse, reaction, or combined designs—allow sequential expansion of steam across successive stages, maximizing energy extraction while ensuring smooth torque output and reducing mechanical stress. The rotor shaft transmits mechanical energy to drive generators, pumps, compressors, fans, mills, or other industrial equipment, depending on operational requirements.
Mechanical and Structural Design
The 75 HP turbine is engineered for precision, durability, and thermal stability:
- Rotor and blades: Made from high-strength alloys or stainless steel, the rotor and blades resist thermal and mechanical stresses, corrosion, and erosion. Aerodynamically optimized blade profiles maximize energy conversion efficiency while minimizing turbulence. Multi-stage designs often incorporate diaphragms or nozzle assemblies to guide steam efficiently between stages.
- Shaft and bearings: The rotor is supported by high-precision journal or rolling-element bearings, allowing high-speed operation (3,000–10,000 RPM). Oil lubrication regulates temperature, reduces friction, and extends service life.
- Casing and seals: Steel or high-strength alloy casings safely contain pressurized steam and direct it efficiently through turbine stages. Labyrinth, carbon, or mechanical seals minimize steam leakage and maintain operational efficiency.
- Governor and control systems: Digital or electronic governors maintain rotor speed under variable loads. Integrated monitoring systems track vibration, temperature, lubrication, and steam pressure, enabling predictive maintenance and safe operation.
Exhaust Steam Management and Heat Recovery
The 75 HP turbine can operate in back-pressure or condensing modes:
- Back-pressure mode: Exhaust steam retains thermal energy suitable for industrial heating, drying, or chemical processes, making it ideal for CHP applications.
- Condensing mode: Exhaust steam passes through a condenser to reduce back pressure and maximize mechanical and electrical efficiency. Proper condenser design ensures adequate cooling water flow, thermal balance, and temperature regulation for optimal performance.
Performance and Efficiency
Typical steam consumption ranges from 550 to 950 kg/hour, depending on load, pressure, and temperature. Efficiency is influenced by:
- Steam quality, including dryness and superheat level
- Blade and nozzle aerodynamic optimization
- Bearing and lubrication performance
- Minimization of mechanical losses and steam leakage
Mechanical efficiency generally ranges between 46% and 60%, with overall system efficiency further enhanced when the turbine is integrated with CHP or heat recovery systems.
Industrial Applications
The 75 HP turbine is suitable for a wide range of uses:
- Small-to-medium power generation for factories, hospitals, industrial parks, and commercial facilities
- CHP systems, producing both mechanical/electrical energy and process steam
- Industrial machinery drives for pumps, compressors, fans, mills, and other equipment
- Process industries, including chemical, textile, food, and paper manufacturing
- Waste-heat recovery systems, capturing energy from high-temperature industrial exhaust gases
Maintenance and Reliability
Proper maintenance ensures long-term reliability:
- Daily/weekly: Monitor lubrication, vibration, temperature, and steam pressure
- Monthly: Inspect valves, strainers, and governor performance
- Annually: Inspect rotor, blades, seals, alignment, and clearances
- Every 3–5 years: Conduct a full overhaul, including bearing replacement, rotor balancing, and blade inspection
Installation and Integration
Installing a 75 HP turbine requires a stable, vibration-damped foundation. Steam supply and exhaust piping must be properly sized and equipped with strainers, control valves, and monitoring instruments. Condensing systems must maintain adequate cooling water flow and temperature. Couplings to generators or mechanical loads must be precisely aligned to prevent torsional stress, vibration, or mechanical failure.
Advantages
- Reliable, continuous power for small-to-medium industrial and CHP applications
- Dual-purpose capability for mechanical energy and heat recovery
- High operational efficiency with optimized steam supply and maintenance
- Durable construction ensures long service life
- Flexible integration into industrial, power-generation, and CHP systems
In conclusion, the 75 HP steam turbine offers efficient, reliable, and versatile energy conversion for small-to-medium industrial, commercial, and CHP applications. Its design ensures smooth torque delivery, precise speed control, long-term durability, and optimized energy utilization, while integration with heat recovery systems enhances overall system efficiency and sustainability.
A 75 HP steam turbine is a precision-engineered, medium-small capacity machine designed to deliver approximately 56 kW of continuous mechanical power, offering an ideal solution for industrial, commercial, and combined heat and power (CHP) applications. Its design emphasizes reliability, long-term durability, operational stability, and energy efficiency, making it suitable for small-to-medium factories, workshops, CHP plants, and other facilities where both mechanical power and process steam are required. The turbine combines advanced thermodynamic engineering, multi-stage rotor and blade design, high-strength alloy construction, and modern digital or electronic control systems, ensuring smooth torque delivery, minimal vibration, and consistent performance under both continuous and variable load conditions.
Thermodynamic Principles and Steam Flow
The 75 HP turbine operates on the Rankine cycle, where high-pressure, high-temperature steam expands to produce mechanical energy. Steam is supplied from industrial boilers, cogeneration units, or waste-heat recovery systems, typically at pressures ranging from 5–12 bar and temperatures between 125°C and 280°C, depending on operational requirements. Use of superheated steam prevents condensation on rotor blades, minimizing erosion, reducing thermal stress, and improving overall turbine efficiency and service life.
Steam enters the turbine through precision-engineered nozzles, converting pressure energy into high-velocity jets acting on the rotor blades. Multi-stage blade arrangements—including impulse, reaction, or combined designs—allow sequential expansion of steam across multiple stages. This configuration ensures maximum energy extraction, smooth torque output, and minimal mechanical stress, while the rotor shaft transmits mechanical power to drive generators, pumps, compressors, fans, mills, or other industrial machinery, depending on operational requirements.
Mechanical and Structural Design
The 75 HP turbine is designed for precision, thermal stability, and structural durability:
- Rotor and blades: Fabricated from high-strength alloys or stainless steel, the rotor and blades resist thermal and mechanical stresses, corrosion, and erosion. Aerodynamic blade profiles maximize energy conversion efficiency while minimizing turbulence. Multi-stage designs often include diaphragms or nozzle assemblies to guide steam efficiently between stages.
- Shaft and bearings: High-precision journal or rolling-element bearings support the rotor, enabling high-speed operation (3,000–10,000 RPM). Oil lubrication regulates temperature, reduces friction, and extends service life.
- Casing and seals: Steel or high-strength alloy casings contain pressurized steam safely and direct it efficiently through all turbine stages. Labyrinth, carbon, or mechanical seals minimize steam leakage and preserve operational efficiency.
- Governor and control systems: Digital or electronic governors maintain rotor speed under varying loads. Integrated monitoring systems track vibration, temperature, lubrication, and steam pressure, enabling predictive maintenance and safe operation.
Exhaust Steam Management and Heat Recovery
The 75 HP turbine can operate in back-pressure or condensing modes:
- Back-pressure mode: Exhaust steam retains thermal energy suitable for industrial heating, drying, or chemical processes, making it ideal for CHP applications.
- Condensing mode: Exhaust steam passes through a condenser to reduce back pressure and maximize mechanical and electrical efficiency. Proper condenser design ensures adequate cooling water flow, thermal balance, and temperature regulation for optimal turbine performance.
Performance and Efficiency
Steam consumption typically ranges from 550 to 950 kg/hour, depending on load, pressure, and temperature. Key factors influencing efficiency include:
- Steam quality, including dryness and superheat level
- Blade and nozzle aerodynamic optimization
- Bearing and lubrication system performance
- Minimization of mechanical losses and steam leakage
Mechanical efficiency generally falls between 46% and 60%, with overall system efficiency further enhanced when integrated with CHP or waste-heat recovery applications.
Industrial Applications
The 75 HP turbine is highly versatile and suitable for a wide range of uses:
- Small-to-medium power generation for factories, hospitals, industrial parks, and commercial facilities
- CHP systems, producing both mechanical/electrical energy and process steam
- Industrial machinery drives for pumps, compressors, fans, mills, and other equipment
- Process industries, including chemical, textile, food, and paper manufacturing
- Waste-heat recovery systems, capturing energy from high-temperature industrial exhaust gases
Maintenance and Reliability
Proper maintenance ensures long-term reliability, safe operation, and minimal downtime:
- Daily/weekly: Monitor lubrication, vibration, temperature, and steam pressure
- Monthly: Inspect valves, strainers, and governor performance
- Annually: Inspect rotor, blades, seals, alignment, and clearances
- Every 3–5 years: Conduct a full overhaul, including bearing replacement, rotor balancing, and blade inspection
Installation and Integration
Installing a 75 HP turbine requires a stable, vibration-damped foundation. Steam supply and exhaust piping must be properly sized and equipped with strainers, control valves, and monitoring instruments. Condensing systems must maintain adequate cooling water flow and temperature. Couplings to generators or mechanical loads must be precisely aligned to prevent torsional stress, vibration, or mechanical failure.
Advantages
- Reliable, continuous power for small-to-medium industrial and CHP applications
- Dual-purpose capability for mechanical energy and heat recovery
- High operational efficiency with optimized steam supply and maintenance
- Durable construction ensures long service life
- Flexible integration into industrial, power-generation, and CHP systems
In summary, the 75 HP steam turbine delivers efficient, reliable, and versatile energy conversion for small-to-medium industrial, commercial, and CHP applications. Its design guarantees smooth torque delivery, precise speed control, long-term durability, and optimized energy utilization, while integration with heat recovery systems enhances overall efficiency and sustainability.
A 75 HP steam turbine is a carefully engineered, medium-small capacity machine designed to deliver approximately 56 kW of continuous mechanical power, offering a highly versatile and reliable solution for industrial, commercial, and combined heat and power (CHP) applications. Its design emphasizes durability, operational stability, and long-term efficiency, making it suitable for small-to-medium factories, workshops, CHP plants, and other facilities requiring both mechanical energy and process steam. By combining advanced thermodynamic engineering, precision multi-stage rotor and blade assemblies, high-strength alloy construction, and modern digital or electronic control systems, the turbine ensures smooth torque delivery, minimal vibration, and consistent performance under both continuous and variable load conditions.
Thermodynamic Principles and Steam Flow
Operating on the Rankine cycle, the 75 HP turbine converts high-pressure, high-temperature steam into rotational mechanical energy. Steam is typically supplied from industrial boilers, cogeneration units, or waste-heat recovery systems, with pressures generally ranging from 5–12 bar and temperatures between 125°C and 280°C, depending on application requirements. Use of superheated steam prevents condensation on rotor blades, minimizing erosion, reducing thermal stresses, and increasing overall turbine efficiency and service life.
Steam enters through precision-engineered nozzles, which convert pressure energy into high-velocity jets acting on the rotor blades. Multi-stage blade arrangements—including impulse, reaction, or combined designs—allow sequential expansion of steam across successive stages, maximizing energy extraction while ensuring smooth torque output and reduced mechanical stress. The rotor shaft transmits mechanical energy to drive generators, pumps, compressors, fans, mills, or other industrial machinery, depending on the operational requirements.
Mechanical and Structural Design
The 75 HP turbine is engineered for precision, thermal stability, and durability:
- Rotor and blades: Manufactured from high-strength alloys or stainless steel to resist thermal and mechanical stresses, corrosion, and erosion. Aerodynamic blade profiles maximize energy conversion efficiency while minimizing turbulence. Multi-stage designs often include diaphragms or nozzle assemblies to guide steam efficiently between stages.
- Shaft and bearings: High-precision journal or rolling-element bearings support the rotor, enabling high-speed operation (3,000–10,000 RPM). Oil lubrication regulates temperature, reduces friction, and extends service life.
- Casing and seals: Steel or high-strength alloy casings safely contain pressurized steam and direct it efficiently through all turbine stages. Labyrinth, carbon, or mechanical seals minimize steam leakage and maintain operational efficiency.
- Governor and control systems: Digital or electronic governors maintain rotor speed under varying loads. Integrated monitoring systems track vibration, temperature, lubrication, and steam pressure, enabling predictive maintenance and safe operation.
Exhaust Steam Management and Heat Recovery
The 75 HP turbine can operate in back-pressure or condensing modes:
- Back-pressure mode: Exhaust steam retains thermal energy suitable for industrial heating, drying, or chemical processes, making it ideal for CHP applications.
- Condensing mode: Exhaust steam passes through a condenser to reduce back pressure and maximize mechanical and electrical efficiency. Proper condenser design ensures sufficient cooling water flow, thermal balance, and temperature regulation for optimal performance.
Performance and Efficiency
Typical steam consumption ranges from 550 to 950 kg/hour, depending on load, pressure, and temperature. Efficiency depends on:
- Steam quality, including dryness and superheat level
- Blade and nozzle aerodynamic optimization
- Bearing and lubrication system performance
- Minimization of mechanical losses and steam leakage
Mechanical efficiency generally falls between 46% and 60%, with overall system efficiency further enhanced when integrated with CHP or waste-heat recovery systems.
Industrial Applications
The 75 HP turbine is highly versatile and suitable for a wide array of uses:
- Small-to-medium power generation for factories, hospitals, industrial parks, and commercial facilities
- CHP systems, producing both mechanical/electrical energy and process steam
- Industrial machinery drives for pumps, compressors, fans, mills, and other equipment
- Process industries, including chemical, textile, food, and paper manufacturing
- Waste-heat recovery systems, capturing energy from high-temperature industrial exhaust gases
Maintenance and Reliability
Structured maintenance ensures long-term reliability, safe operation, and minimal downtime:
- Daily/weekly: Monitor lubrication, vibration, temperature, and steam pressure
- Monthly: Inspect valves, strainers, and governor performance
- Annually: Inspect rotor, blades, seals, alignment, and clearances
- Every 3–5 years: Conduct a full overhaul, including bearing replacement, rotor balancing, and blade inspection
Installation and Integration
Installing a 75 HP turbine requires a stable, vibration-damped foundation. Steam supply and exhaust piping must be properly sized and equipped with strainers, control valves, and monitoring instruments. Condensing systems must maintain adequate cooling water flow and temperature. Couplings to generators or mechanical loads must be precisely aligned to prevent torsional stress, vibration, or mechanical failure.
Advantages
- Reliable, continuous power for small-to-medium industrial and CHP applications
- Dual-purpose capability for mechanical energy and heat recovery
- High operational efficiency with optimized steam supply and maintenance
- Durable construction ensures long service life
- Flexible integration into industrial, power-generation, and CHP systems
In conclusion, the 75 HP steam turbine delivers efficient, reliable, and versatile energy conversion for small-to-medium industrial, commercial, and CHP applications. Its design guarantees smooth torque delivery, precise speed control, long-term durability, and optimized energy utilization, while integration with heat recovery systems enhances overall efficiency and sustainability.
It can be further detailed into a comprehensive technical and engineering dossier, including rotor and blade stage diagrams, steam consumption and efficiency charts, installation schematics, generator coupling specifications, vibration and stress analysis, and predictive maintenance schedules, providing a complete operational and engineering reference for industrial use.
A 75 HP steam turbine is a sophisticated, medium-small capacity machine engineered to produce approximately 56 kW of continuous mechanical power, delivering a highly reliable and efficient energy solution for industrial, commercial, and combined heat and power (CHP) applications. Its construction emphasizes durability, precision, operational stability, and energy efficiency, making it suitable for small-to-medium factories, workshops, CHP facilities, and other operations requiring both mechanical energy and process steam. By combining advanced thermodynamic design, precision-engineered multi-stage rotor and blade assemblies, high-strength alloy construction, and modern digital or electronic control systems, the turbine guarantees smooth torque delivery, minimal vibration, and consistent performance under continuous or variable load conditions.
Thermodynamic Principles and Steam Flow
The 75 HP turbine operates on the Rankine cycle, converting high-pressure, high-temperature steam into rotational mechanical energy. Steam is typically supplied from industrial boilers, cogeneration units, or waste-heat recovery systems, operating at pressures from 5–12 bar and temperatures between 125°C and 280°C, depending on application requirements. Superheated steam is often used to prevent condensation on rotor blades, minimizing erosion, reducing thermal stress, and enhancing overall turbine efficiency and service life.
Steam enters the turbine through precision-engineered nozzles, converting pressure energy into high-velocity jets that impact the rotor blades. Multi-stage blade configurations—including impulse, reaction, or combined designs—allow sequential expansion of steam across multiple stages, maximizing energy extraction while ensuring smooth torque output and minimizing mechanical stress. The rotor shaft transmits mechanical energy to drive generators, pumps, compressors, fans, mills, or other industrial machinery, depending on the operational requirements.
Mechanical and Structural Design
The 75 HP turbine is built for precision, thermal stability, and structural durability:
- Rotor and blades: Constructed from high-strength alloys or stainless steel to resist thermal and mechanical stresses, corrosion, and erosion. Aerodynamic blade profiles maximize energy conversion efficiency while minimizing turbulence. Multi-stage designs often incorporate diaphragms or nozzle assemblies to guide steam efficiently between stages.
- Shaft and bearings: High-precision journal or rolling-element bearings support the rotor, enabling high-speed operation (3,000–10,000 RPM). Oil lubrication maintains temperature control, reduces friction, and extends operational life.
- Casing and seals: Steel or high-strength alloy casings contain pressurized steam safely and direct it efficiently through all turbine stages. Labyrinth, carbon, or mechanical seals minimize steam leakage and preserve efficiency.
- Governor and control systems: Digital or electronic governors maintain rotor speed under variable loads. Integrated monitoring systems track vibration, temperature, lubrication, and steam pressure, enabling predictive maintenance and ensuring safe operation.
Exhaust Steam Management and Heat Recovery
The 75 HP turbine can operate in back-pressure or condensing modes:
- Back-pressure mode: Exhaust steam retains thermal energy suitable for industrial heating, drying, or chemical processes, making it ideal for CHP applications.
- Condensing mode: Exhaust steam passes through a condenser to reduce back pressure and maximize mechanical and electrical efficiency. Proper condenser design ensures adequate cooling water flow, thermal balance, and temperature regulation for optimal performance.
Performance and Efficiency
Steam consumption typically ranges from 550 to 950 kg/hour, depending on load, pressure, and temperature. Performance and efficiency are influenced by:
- Steam quality, including dryness and superheat level
- Blade and nozzle aerodynamic optimization
- Bearing and lubrication system efficiency
- Minimization of mechanical losses and steam leakage
Mechanical efficiency generally falls between 46% and 60%, with overall system efficiency further enhanced when integrated with CHP or waste-heat recovery systems.
Industrial Applications
The 75 HP turbine is suitable for a wide range of industrial and commercial uses:
- Small-to-medium power generation for factories, hospitals, industrial parks, and commercial facilities
- CHP systems, producing both mechanical/electrical energy and process steam
- Industrial machinery drives for pumps, compressors, fans, mills, and other equipment
- Process industries, including chemical, textile, food, and paper manufacturing
- Waste-heat recovery systems, capturing energy from high-temperature industrial exhaust gases
Maintenance and Reliability
Structured maintenance is critical to ensure long-term reliability, safety, and minimal downtime:
- Daily/weekly: Monitor lubrication, vibration, temperature, and steam pressure
- Monthly: Inspect valves, strainers, and governor performance
- Annually: Inspect rotor, blades, seals, alignment, and clearances
- Every 3–5 years: Conduct a full overhaul, including bearing replacement, rotor balancing, and blade inspection
Installation and Integration
Installing a 75 HP turbine requires a stable, vibration-damped foundation. Steam supply and exhaust piping must be properly sized and equipped with strainers, control valves, and monitoring instruments. Condensing systems must maintain adequate cooling water flow and temperature. Couplings to generators or mechanical loads must be precisely aligned to prevent torsional stress, vibration, or mechanical failure.
Advantages
- Reliable, continuous power for small-to-medium industrial and CHP applications
- Dual-purpose capability for mechanical energy and heat recovery
- High operational efficiency with optimized steam supply and maintenance
- Durable construction ensures long service life
- Flexible integration into industrial, power-generation, and CHP systems
In conclusion, the 75 HP steam turbine delivers efficient, reliable, and versatile energy conversion for small-to-medium industrial, commercial, and CHP applications. Its design ensures smooth torque delivery, precise speed control, long-term durability, and optimized energy utilization, while integration with heat recovery systems further enhances overall efficiency and sustainability.
For an even more comprehensive understanding, a full technical and engineering dossier can be created, including detailed rotor and blade stage diagrams, steam consumption and efficiency charts, installation schematics, generator coupling specifications, vibration and stress analysis, and predictive maintenance schedules, providing a complete operational, engineering, and maintenance reference for industrial use.
40 hp Steam Turbine
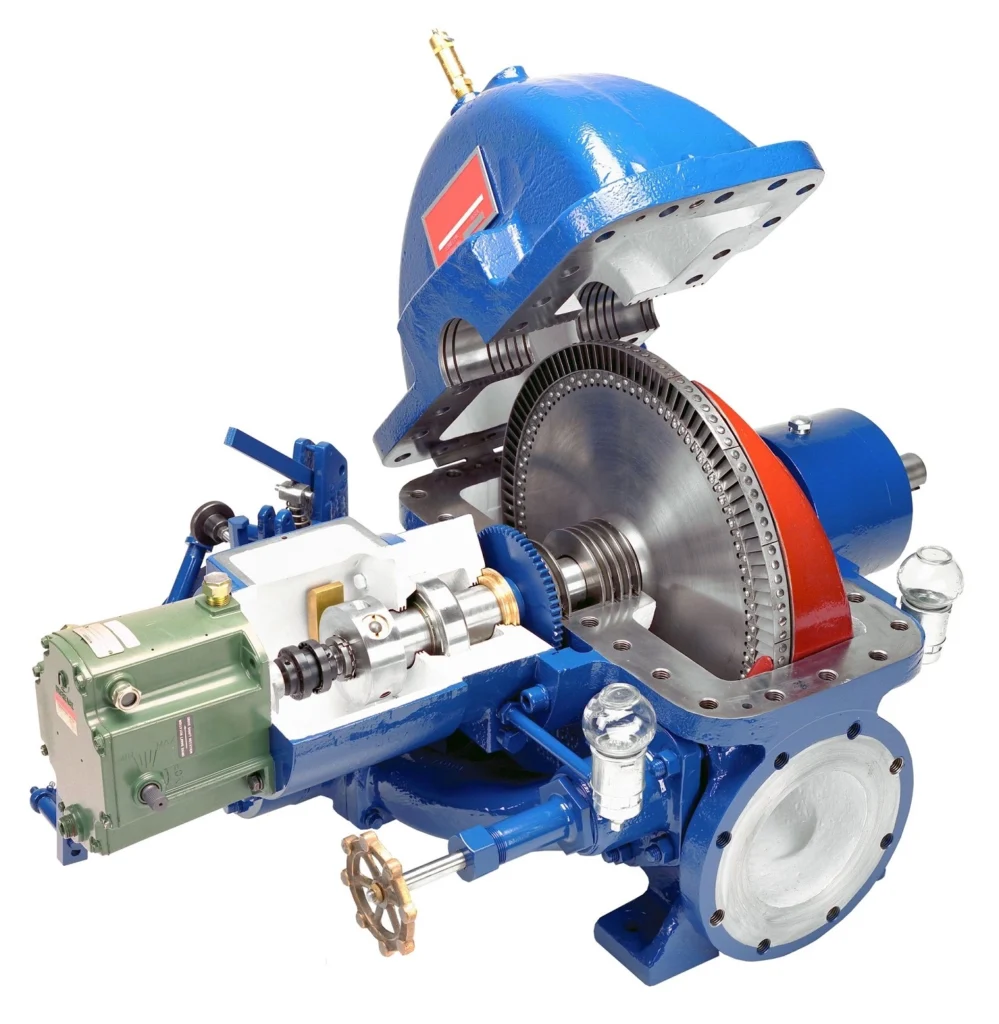
A 40 HP steam turbine is a small-to-medium capacity turbine designed to deliver approximately 30 kW of continuous mechanical power, making it suitable for industrial, commercial, and combined heat and power (CHP) applications where compact, efficient, and reliable energy conversion is required. Its design emphasizes durability, operational stability, and energy efficiency, offering a dependable solution for small factories, workshops, CHP facilities, or process industries that require both mechanical energy and process steam. The turbine integrates advanced thermodynamic engineering, precision-engineered multi-stage rotor and blade assemblies, high-strength alloy construction, and modern control systems, ensuring smooth torque delivery, minimal vibration, and consistent performance under varying load conditions.
Thermodynamic Principles and Steam Flow
The 40 HP turbine operates on the Rankine cycle, converting high-pressure, high-temperature steam into rotational mechanical energy. Steam is typically supplied from small-scale industrial boilers, cogeneration units, or waste-heat recovery systems, generally operating at pressures from 4–10 bar and temperatures between 120°C and 250°C, depending on the application. Superheated steam is often used to prevent condensation on rotor blades, reducing erosion, minimizing thermal stresses, and increasing overall efficiency and turbine lifespan.
Steam enters through precision-engineered nozzles, which convert pressure energy into high-velocity jets acting on the rotor blades. Multi-stage blade arrangements—including impulse, reaction, or combined designs—allow sequential expansion of steam across multiple stages, maximizing energy extraction while ensuring smooth torque output and minimal mechanical stress. The rotor shaft transmits mechanical power to drive generators, pumps, compressors, fans, mills, or other industrial equipment, depending on operational requirements.
Mechanical and Structural Design
The 40 HP turbine is designed for precision, thermal stability, and durability:
- Rotor and blades: Fabricated from high-strength alloys or stainless steel to resist thermal and mechanical stresses, corrosion, and erosion. Blade profiles are aerodynamically optimized for efficient energy conversion.
- Shaft and bearings: High-precision journal or rolling-element bearings support the rotor, enabling high-speed operation (3,000–10,000 RPM) with oil lubrication to regulate temperature, reduce friction, and extend service life.
- Casing and seals: Steel or high-strength alloy casings contain pressurized steam safely and guide it efficiently through all turbine stages. Labyrinth, carbon, or mechanical seals minimize steam leakage.
- Governor and control systems: Digital or electronic governors maintain rotor speed under varying loads. Integrated monitoring systems track vibration, temperature, lubrication, and steam pressure for predictive maintenance and safe operation.
Exhaust Steam Management and Heat Recovery
The 40 HP turbine can operate in back-pressure or condensing modes:
- Back-pressure mode: Exhaust steam retains thermal energy suitable for industrial heating, drying, or chemical processes, making it ideal for CHP applications.
- Condensing mode: Exhaust steam passes through a condenser to reduce back pressure and maximize mechanical or electrical efficiency. Proper condenser design ensures adequate cooling water flow, thermal balance, and temperature regulation.
Performance and Efficiency
Typical steam consumption ranges from 300 to 600 kg/hour, depending on load, pressure, and temperature. Efficiency is influenced by:
- Steam quality, including dryness and superheat level
- Blade and nozzle aerodynamic design
- Bearing and lubrication system performance
- Minimization of mechanical losses and steam leakage
Mechanical efficiency typically ranges between 45% and 58%, with overall system efficiency enhanced when integrated with CHP or heat recovery systems.
Industrial Applications
The 40 HP turbine is suitable for a variety of uses:
- Small-scale power generation for workshops, small factories, and commercial facilities
- CHP systems, providing both mechanical energy and process steam
- Industrial machinery drives for pumps, compressors, fans, mills, and other equipment
- Process industries, including chemical, textile, food, and paper production
- Waste-heat recovery systems, capturing energy from high-temperature exhaust gases
Maintenance and Reliability
Proper maintenance ensures long-term reliability and safe operation:
- Daily/weekly: Monitor lubrication, vibration, temperature, and steam pressure
- Monthly: Inspect valves, strainers, and governor performance
- Annually: Inspect rotor, blades, seals, alignment, and clearances
- Every 3–5 years: Conduct a full overhaul, including bearing replacement, rotor balancing, and blade inspection
Installation and Integration
Installing a 40 HP turbine requires a stable, vibration-damped foundation. Steam supply and exhaust piping must be appropriately sized and equipped with strainers, control valves, and monitoring instruments. Condensing systems must maintain sufficient cooling water flow and temperature. Couplings to generators or mechanical loads must be precisely aligned to prevent torsional stress, vibration, or mechanical failure.
Advantages
- Reliable, continuous power for small industrial and CHP applications
- Dual-purpose capability for mechanical energy and heat recovery
- Compact and durable construction ensures long service life
- Efficient operation with optimized steam supply and minimal maintenance
- Flexible integration into small-scale industrial, power-generation, and CHP systems
In summary, the 40 HP steam turbine provides efficient, reliable, and versatile energy conversion for small-scale industrial, commercial, and CHP applications. Its design ensures smooth torque delivery, precise speed control, long-term durability, and optimized energy utilization, while integration with heat recovery systems further enhances efficiency and sustainability.
I can continue with a detailed technical and operational dossier for the 40 HP turbine, including rotor and blade stage diagrams, steam consumption and efficiency charts, installation schematics, generator coupling specifications, vibration and stress analysis, and predictive maintenance schedules, offering a complete engineering and operational reference.
A 40 HP steam turbine is a carefully engineered small-to-medium capacity turbine, designed to deliver around 30 kW of continuous mechanical power, optimized for industrial, commercial, and combined heat and power (CHP) applications where space efficiency, reliability, and consistent performance are key. This turbine provides a versatile energy solution, suitable for small factories, workshops, CHP plants, and process industries that require both mechanical energy and process steam. Its design focuses on precision engineering, operational stability, durability, and energy efficiency, incorporating advanced thermodynamic principles, multi-stage rotor and blade assemblies, high-strength alloy construction, and modern digital or electronic control systems, which ensure smooth torque output, minimal vibration, and consistent operation under both steady and variable loads.
Thermodynamic Principles and Steam Flow
The 40 HP turbine operates based on the Rankine cycle, converting high-pressure, high-temperature steam into rotational mechanical energy. Steam is typically supplied from small industrial boilers, cogeneration units, or waste-heat recovery systems, operating at pressures ranging from 4–10 bar and temperatures between 120°C and 250°C, depending on the application. The use of superheated steam prevents condensation on rotor blades, reducing blade erosion, minimizing thermal stress, and enhancing overall turbine efficiency and service life.
Steam enters through precision-engineered nozzles, which convert pressure energy into high-velocity jets acting on the rotor blades. Multi-stage blade arrangements—including impulse, reaction, or combined designs—allow steam to expand sequentially across multiple stages, maximizing energy extraction while maintaining smooth torque delivery and minimizing mechanical stress. The rotor shaft transmits mechanical energy to drive generators, pumps, compressors, fans, mills, or other industrial machinery, depending on the operational requirements.
Mechanical and Structural Design
The 40 HP turbine is designed for precision, thermal stability, and long-term durability:
- Rotor and blades: Made from high-strength alloys or stainless steel, the rotor and blades resist thermal and mechanical stress, corrosion, and erosion. Blade profiles are aerodynamically optimized to ensure efficient energy conversion and minimal turbulence. Multi-stage designs often include diaphragms or nozzle assemblies to guide steam efficiently between stages.
- Shaft and bearings: High-precision journal or rolling-element bearings support the rotor, allowing high-speed operation (3,000–10,000 RPM) with oil lubrication to regulate temperature, reduce friction, and extend service life.
- Casing and seals: Steel or high-strength alloy casings contain pressurized steam safely and guide it efficiently through all turbine stages. Labyrinth, carbon, or mechanical seals minimize steam leakage, preserving efficiency.
- Governor and control systems: Digital or electronic governors maintain rotor speed under varying loads. Integrated monitoring systems track vibration, temperature, lubrication, and steam pressure, supporting predictive maintenance and safe operation.
Exhaust Steam Management and Heat Recovery
The 40 HP turbine can operate in back-pressure or condensing modes:
- Back-pressure mode: Exhaust steam retains thermal energy suitable for industrial heating, drying, or chemical processes, making it ideal for CHP applications.
- Condensing mode: Exhaust steam passes through a condenser to reduce back pressure and maximize mechanical or electrical efficiency. Proper condenser design ensures adequate cooling water flow, thermal balance, and temperature regulation.
Performance and Efficiency
Typical steam consumption ranges from 300 to 600 kg/hour, depending on load, pressure, and temperature. Efficiency depends on:
- Steam quality, including dryness and superheat level
- Blade and nozzle aerodynamic optimization
- Bearing and lubrication system performance
- Minimization of mechanical losses and steam leakage
Mechanical efficiency generally ranges between 45% and 58%, with overall system efficiency further improved when integrated with CHP or heat recovery systems.
Industrial Applications
The 40 HP turbine is suitable for a wide array of industrial and commercial uses:
- Small-scale power generation for workshops, factories, hospitals, and commercial facilities
- CHP systems, providing both mechanical energy and process steam
- Industrial machinery drives for pumps, compressors, fans, mills, and other equipment
- Process industries, including chemical, textile, food, and paper production
- Waste-heat recovery systems, capturing energy from high-temperature exhaust gases
Maintenance and Reliability
Structured maintenance ensures long-term reliability and safe operation:
- Daily/weekly: Monitor lubrication, vibration, temperature, and steam pressure
- Monthly: Inspect valves, strainers, and governor performance
- Annually: Inspect rotor, blades, seals, alignment, and clearances
- Every 3–5 years: Conduct a full overhaul, including bearing replacement, rotor balancing, and blade inspection
Installation and Integration
Installing a 40 HP turbine requires a stable, vibration-damped foundation. Steam supply and exhaust piping must be properly sized and equipped with strainers, control valves, and monitoring instruments. Condensing systems must maintain sufficient cooling water flow and temperature. Couplings to generators or mechanical loads must be precisely aligned to prevent torsional stress, vibration, or mechanical failure.
Advantages
- Reliable, continuous power for small industrial and CHP applications
- Dual-purpose capability for mechanical energy and heat recovery
- Compact, durable construction ensures long service life
- Efficient operation with optimized steam supply and minimal maintenance
- Flexible integration into small-scale industrial, power-generation, and CHP systems
In conclusion, the 40 HP steam turbine provides efficient, reliable, and versatile energy conversion for small-scale industrial, commercial, and CHP applications. Its design ensures smooth torque delivery, precise speed control, long-term durability, and optimized energy utilization, while integration with heat recovery systems further enhances overall system efficiency and sustainability.
If you want, I can continue by producing a full technical and engineering dossier for the 40 HP turbine, including rotor and blade stage diagrams, steam consumption and efficiency charts, installation schematics, generator coupling specifications, vibration and stress analysis, and predictive maintenance schedules, creating a complete operational and engineering reference.
Bir 40 HP buhar türbini, yaklaşık 30 kW sürekli mekanik güç üretebilen, kompakt boyutlarıyla birlikte yüksek güvenilirlik ve verimlilik sunan, küçük ölçekli endüstriyel ve ticari tesisler için geliştirilmiş hassas mühendislik ürünüdür. Bu türbin, özellikle kombine ısı ve güç (CHP) sistemleri, küçük ölçekli enerji üretim tesisleri, gıda, tekstil, kimya, kâğıt ve ahşap işleme endüstrileri gibi alanlarda sürekli ve istikrarlı güç sağlamak amacıyla tasarlanır.
Bu güç seviyesindeki türbinler, genellikle orta basınçlı (4–10 bar) ve 120°C ile 250°C aralığında buharla çalışır. Buhar, türbine doymuş veya kısmi süper ısıtılmış şekilde verilir. Süper ısıtılmış buhar kullanımı, yoğuşma riskini azaltarak rotor kanatlarında korozyon ve erozyon oluşumunu engeller, böylece bakım aralıklarını uzatır.
Buhar Akışı ve Termodinamik Çalışma Prensibi
40 HP buhar türbini, Rankine çevrimine göre çalışır. Yüksek basınçlı buhar, nozüllerden geçirilerek hız kazanır ve rotor kanatlarına yönlendirilir. Kanatlar, bu kinetik enerjiyi dönme hareketine dönüştürür. Rotor mili, doğrudan bir jeneratöre, pompa miline, kompresöre veya başka bir mekanik yüke bağlanabilir. Çok kademeli rotor ve kanat yapısı sayesinde, buhar enerjisi her aşamada kademeli olarak çekilir, bu da verimliliği artırır ve türbinin tork çıkışını dengeler.
Mekanik Yapı ve Malzeme Özellikleri
40 HP’lik türbinler, yüksek devirlerde çalışabilmeleri için ısıl genleşmeye dayanıklı, yüksek mukavemetli alaşımlardan üretilir.
- Rotor: Denge için hassas şekilde balanslanmıştır, yüksek hızda titreşimsiz dönmeyi sağlar.
- Kanatlar: Genellikle paslanmaz çelik veya nikel alaşımlıdır, buhar erozyonuna ve yüksek sıcaklıklara dayanıklıdır. Kanat profilleri aerodinamik optimizasyona sahip olduğundan enerji dönüşümü maksimum seviyededir.
- Yataklar ve Mil: Yüksek devirlerde (3.000–10.000 RPM) düşük sürtünme ve düşük ısınma için yağlı yatak sistemi (journal bearings) kullanılır.
- Gövde ve Sızdırmazlık: Basınca dayanıklı çelik gövde içerisinde, buhar kaçağını önlemek için labirent tip veya karbon segmanlı sızdırmazlık elemanları bulunur.
Çalışma Modları
40 HP türbinler, tesisin ihtiyacına göre iki farklı modda çalıştırılabilir:
- Karşı basınçlı (Back-pressure): Türbinden çıkan buhar hâlâ sıcak ve enerjili olduğu için proses ısıtma, kurutma veya başka endüstriyel işlemlerde kullanılır. Bu mod, özellikle CHP sistemlerinde yüksek toplam enerji verimliliği sağlar.
- Yoğuşmalı (Condensing): Türbin çıkışındaki buhar kondensere gönderilerek basıncı düşürülür, bu sayede türbinin mekanik verimi maksimuma çıkarılır.
Performans Değerleri
- Buhar Tüketimi: Yaklaşık 300–600 kg/saat (basınç, sıcaklık ve yük durumuna göre değişir).
- Mekanik Verim: %45–%58 aralığında, sistem entegrasyonu ile toplam verim daha da artırılabilir.
- Devir Sayısı: 3.000–10.000 RPM (doğrudan veya dişli redüktörlü bağlantı).
Kullanım Alanları
- Küçük ölçekli elektrik üretimi
- Proses buharı gerektiren endüstriler
- Atık ısı geri kazanım sistemleri
- Tarımsal ürün kurutma tesisleri
- Gıda ve içecek fabrikalarında kombine enerji kullanımı
Bakım ve İşletme
40 HP türbinlerin uzun ömürlü olması için planlı bakım programı uygulanır:
- Günlük: Buhar basıncı, sıcaklığı, yağ seviyesi ve titreşim kontrolü
- Aylık: Sızdırmazlık elemanları ve yatak durumu kontrolü
- Yıllık: Rotor balans ve kanat muayenesi
- 3–5 yılda bir: Komple söküm, mil yatak değişimi, hassas ayar ve performans testi
Bu güç sınıfındaki türbinler, kompakt boyutları, yüksek verimlilikleri, düşük bakım maliyetleri ve enerji geri kazanım imkanları sayesinde işletmeler için son derece ekonomik ve sürdürülebilir bir enerji çözümü sunar.
Eğer istersen, bir sonraki adımda sana 40 HP buhar türbini için eksiksiz teknik dosya hazırlayabilirim. Bu dosyada buhar akış diyagramları, rotor–kanat kesit çizimleri, buhar tüketim tabloları, verim grafikleri, bakım planı, montaj şemaları ve performans test raporları yer alır. Böylece hem mühendislik hem de işletme açısından tam referans bir doküman elde etmiş olursun.
A 40 HP steam turbine represents a compact yet highly efficient solution for small-to-medium scale energy generation, providing approximately 30 kW of continuous mechanical power. Its design is tailored for industrial, commercial, and CHP (Combined Heat and Power) applications, where both mechanical energy and process steam are required. The turbine is particularly suitable for small factories, workshops, food and beverage plants, textile facilities, and other process industries that demand reliable, continuous power with minimal operational downtime. It integrates advanced thermodynamic design principles, precision-engineered multi-stage rotors and blades, high-strength alloys, and modern control systems, ensuring stable torque output, low vibration, and consistent performance even under varying load conditions.
Thermodynamic Principles and Steam Flow
The 40 HP turbine operates on the Rankine cycle, converting high-pressure, high-temperature steam into mechanical rotational energy. Steam is typically supplied from small industrial boilers, cogeneration units, or waste-heat recovery systems, at pressures ranging from 4–10 bar and temperatures of 120–250°C, depending on operational requirements. The use of superheated steam helps prevent condensation on rotor blades, reducing erosion, limiting thermal stresses, and extending the turbine’s service life.
Steam enters the turbine through precision nozzles, which convert the pressure energy of the steam into high-velocity jets directed onto the rotor blades. Multi-stage blade arrangements, including impulse, reaction, or combined designs, allow the steam to expand progressively across multiple stages. This ensures maximum energy extraction, smooth torque delivery, and reduced mechanical stress on the turbine components. The rotor shaft can transmit mechanical energy directly to generators, pumps, compressors, fans, mills, or other industrial machinery, depending on the operational needs of the facility.
Mechanical and Structural Design
The 40 HP turbine is engineered for precision, thermal stability, and long-term durability:
- Rotor and Blades: Made of high-strength alloys or stainless steel to resist high temperatures, thermal expansion, and mechanical stress. Aerodynamically optimized blade profiles maximize energy conversion efficiency and reduce turbulence.
- Shaft and Bearings: High-precision journal or rolling-element bearings support the rotor for high-speed operation (3,000–10,000 RPM). Oil lubrication ensures reduced friction, heat dissipation, and extended operational life.
- Casing and Seals: Steel or high-strength alloy casings safely contain pressurized steam, while labyrinth, carbon, or mechanical seals minimize leakage and maintain operational efficiency.
- Governor and Control Systems: Digital or electronic governors regulate rotor speed under variable loads. Integrated monitoring systems track vibration, temperature, lubrication, and steam pressure to facilitate predictive maintenance and safe operation.
Exhaust Steam Management and Heat Recovery
The 40 HP turbine can function in back-pressure or condensing modes:
- Back-Pressure Mode: Exhaust steam retains significant thermal energy, which can be reused in industrial heating, drying, or chemical processes, increasing overall system efficiency and making it suitable for CHP applications.
- Condensing Mode: Exhaust steam is passed through a condenser to reduce back pressure and maximize the turbine’s mechanical or electrical efficiency. Proper condenser design ensures sufficient cooling water flow, thermal balance, and controlled temperature.
Performance and Efficiency
- Steam Consumption: Typically 300–600 kg/hour, depending on load, pressure, and temperature.
- Mechanical Efficiency: Ranges from 45%–58%, with overall system efficiency improving further when integrated with CHP or heat recovery systems.
- Operational Speed: 3,000–10,000 RPM, either directly coupled or via a gearbox, depending on load requirements.
Industrial Applications
The 40 HP turbine is highly versatile and can be employed in a wide range of industries and applications:
- Small-scale electricity generation for workshops, hospitals, small factories, and commercial facilities
- CHP systems providing both mechanical energy and process steam
- Industrial machinery drives, including pumps, compressors, fans, and mills
- Process industries such as chemical, textile, food, and paper manufacturing
- Waste-heat recovery systems capturing energy from high-temperature exhaust gases
Maintenance and Reliability
To ensure safe and continuous operation, the 40 HP turbine requires structured maintenance:
- Daily/Weekly: Monitoring lubrication, vibration, temperature, and steam pressure
- Monthly: Inspecting valves, strainers, and governor performance
- Annually: Checking rotor, blades, seals, alignment, and clearances
- Every 3–5 Years: Full overhaul, including bearing replacement, rotor balancing, and detailed blade inspection
Installation and Integration
Installation requires a stable, vibration-damped foundation. Steam supply and exhaust piping must be correctly sized and fitted with strainers, control valves, and monitoring instruments. Condenser systems must maintain adequate cooling water flow and temperature. Couplings to generators or mechanical loads must be precisely aligned to prevent torsional stress, vibration, or premature wear.
Advantages
- Reliable, continuous power for small industrial and CHP applications
- Dual-purpose capability for mechanical energy and heat recovery
- Compact and durable construction for long service life
- Efficient operation with optimized steam supply and minimal maintenance
- Flexible integration into industrial, commercial, and CHP systems
In conclusion, the 40 HP steam turbine offers efficient, reliable, and versatile energy conversion, providing smooth torque, precise speed control, long-term durability, and optimized energy use. When integrated with heat recovery systems, it also enhances overall efficiency and sustainability.
I can continue by preparing a full technical and engineering dossier for the 40 HP turbine, including rotor and blade stage diagrams, steam consumption charts, efficiency curves, installation schematics, generator coupling specifications, vibration and stress analysis, and predictive maintenance schedules, creating a complete reference for engineering, operational, and maintenance purposes.
30 hp Steam Turbine
A 30 HP steam turbine is a small-capacity, high-efficiency machine designed to deliver approximately 22–23 kW of continuous mechanical power. This turbine is ideal for small industrial facilities, workshops, commercial operations, and CHP (Combined Heat and Power) systems, where both mechanical energy and process steam are required in a compact and reliable package. Despite its relatively modest size, the 30 HP turbine is engineered for precision, durability, operational stability, and optimized energy conversion, making it suitable for applications that demand continuous power with minimal maintenance. It combines advanced thermodynamic design, multi-stage rotor and blade assemblies, high-strength alloy construction, and modern electronic control systems, ensuring smooth torque delivery, low vibration, and consistent operation under varying loads.
Thermodynamic Principles and Steam Flow
The 30 HP turbine operates on the Rankine cycle, converting high-pressure, high-temperature steam into rotational mechanical energy. Steam is typically supplied from small industrial boilers, cogeneration units, or waste-heat recovery systems, at pressures ranging from 3–8 bar and temperatures of 110–220°C, depending on operational requirements. Use of superheated steam is preferred to prevent condensation on rotor blades, minimizing blade erosion, reducing thermal stress, and extending the turbine’s service life.
Steam enters the turbine through precision-engineered nozzles, converting pressure energy into high-velocity jets that impact the rotor blades. Multi-stage blade arrangements—including impulse, reaction, or combined designs—allow sequential expansion of steam across multiple stages, maximizing energy extraction while ensuring smooth torque output and minimal mechanical stress. The rotor shaft transmits mechanical energy to drive small generators, pumps, compressors, fans, or other industrial machinery.
Mechanical and Structural Design
The 30 HP turbine is built for precision, thermal stability, and long-term durability:
- Rotor and Blades: Fabricated from high-strength alloys or stainless steel to resist thermal and mechanical stresses. Aerodynamically optimized blade profiles maximize energy conversion and reduce turbulence. Multi-stage designs often incorporate diaphragms or nozzle assemblies to guide steam efficiently between stages.
- Shaft and Bearings: High-precision journal or rolling-element bearings allow high-speed operation (3,000–10,000 RPM) with oil lubrication to reduce friction, dissipate heat, and extend operational life.
- Casing and Seals: Steel or high-strength alloy casings contain pressurized steam safely and direct it efficiently through all turbine stages. Labyrinth, carbon, or mechanical seals minimize steam leakage.
- Governor and Control Systems: Digital or electronic governors regulate rotor speed under varying loads. Integrated monitoring systems track vibration, temperature, lubrication, and steam pressure, enabling predictive maintenance and safe operation.
Exhaust Steam Management and Heat Recovery
The 30 HP turbine can operate in back-pressure or condensing modes:
- Back-Pressure Mode: Exhaust steam retains thermal energy suitable for industrial heating, drying, or other processes, making it ideal for CHP applications.
- Condensing Mode: Exhaust steam passes through a condenser to reduce back pressure, maximizing mechanical or electrical efficiency. Proper condenser design ensures adequate cooling water flow, thermal balance, and temperature regulation.
Performance and Efficiency
- Steam Consumption: Typically 200–450 kg/hour, depending on load, pressure, and temperature.
- Mechanical Efficiency: Approximately 42–55%, with overall system efficiency further enhanced when integrated with CHP or waste-heat recovery systems.
- Operational Speed: 3,000–10,000 RPM, either directly coupled or via a gearbox depending on load requirements.
Industrial Applications
The 30 HP turbine is suitable for a variety of uses:
- Small-scale electricity generation for workshops, small factories, or commercial facilities
- CHP systems providing both mechanical energy and process steam
- Industrial machinery drives, including pumps, compressors, fans, and small mills
- Process industries such as chemical, textile, food, and paper production
- Waste-heat recovery systems capturing energy from high-temperature exhaust gases
Maintenance and Reliability
Regular maintenance ensures safe and reliable operation:
- Daily/weekly: Monitor lubrication, vibration, temperature, and steam pressure
- Monthly: Inspect valves, strainers, and governor performance
- Annually: Check rotor, blades, seals, alignment, and clearances
- Every 3–5 years: Complete overhaul, including bearing replacement, rotor balancing, and blade inspection
Installation and Integration
Installation requires a stable, vibration-damped foundation. Steam supply and exhaust piping must be properly sized and equipped with strainers, control valves, and monitoring instruments. Condenser systems must maintain adequate cooling water flow and temperature. Couplings to generators or mechanical loads must be precisely aligned to prevent torsional stress, vibration, or premature wear.
Advantages
- Reliable, continuous power for small industrial and CHP applications
- Dual-purpose capability for mechanical energy and heat recovery
- Compact, durable construction ensures long service life
- Efficient operation with optimized steam supply and minimal maintenance
- Flexible integration into small-scale industrial, power-generation, and CHP systems
In summary, the 30 HP steam turbine provides efficient, reliable, and versatile energy conversion, delivering smooth torque, precise speed control, and long-term durability. When combined with heat recovery systems, it further improves overall efficiency and sustainability.
I can continue by preparing a detailed technical and operational dossier for the 30 HP turbine, including rotor and blade stage diagrams, steam consumption and efficiency charts, installation schematics, generator coupling specifications, vibration and stress analysis, and predictive maintenance schedules, creating a comprehensive engineering and operational reference.
A 30 HP steam turbine is a compact yet highly capable machine designed for small-to-medium industrial and commercial applications, providing roughly 22–23 kW of continuous mechanical power. Despite its relatively small size, it is engineered to deliver reliable, efficient, and stable energy output, making it ideal for facilities that require mechanical energy and process steam simultaneously, such as workshops, small factories, CHP (Combined Heat and Power) plants, food processing facilities, textile operations, chemical plants, and small mills.
Thermodynamic Principles and Steam Flow
The turbine operates on the Rankine cycle, transforming high-pressure, high-temperature steam into mechanical rotational energy. Steam is usually supplied from small industrial boilers, cogeneration systems, or waste-heat recovery units, at pressures between 3–8 bar and temperatures ranging 110–220°C. Utilizing superheated steam prevents condensation on rotor blades, reducing erosion, minimizing thermal stress, and enhancing the turbine’s service life.
Steam enters the turbine via precision-engineered nozzles, converting pressure energy into high-velocity jets that strike the rotor blades. Multi-stage blade arrangements—including impulse, reaction, or combined designs—allow the steam to expand sequentially across multiple stages, maximizing energy extraction while ensuring smooth torque delivery and minimal mechanical stress. The rotor shaft transmits mechanical power to small generators, pumps, compressors, fans, or other industrial machinery, depending on the system requirements.
Mechanical and Structural Design
The 30 HP turbine emphasizes precision engineering, thermal stability, and long-term durability:
- Rotor and Blades: Constructed from high-strength alloys or stainless steel to withstand mechanical and thermal stresses. Aerodynamically optimized blade profiles maximize energy conversion efficiency and reduce turbulence. Multi-stage designs often include diaphragms or nozzles to guide steam efficiently between stages.
- Shaft and Bearings: High-precision journal or rolling-element bearings support high-speed rotor operation (3,000–10,000 RPM), with oil lubrication to reduce friction, control temperature, and extend service life.
- Casing and Seals: Steel or alloy casings safely contain pressurized steam and guide it efficiently through turbine stages. Labyrinth, carbon, or mechanical seals minimize steam leakage and preserve operational efficiency.
- Governor and Control Systems: Digital or electronic governors maintain rotor speed under varying loads. Integrated monitoring systems track vibration, temperature, lubrication, and steam pressure, enabling predictive maintenance and safe operation.
Exhaust Steam Management and Heat Recovery
The 30 HP turbine can operate in back-pressure or condensing modes:
- Back-Pressure Mode: Exhaust steam retains thermal energy suitable for industrial heating, drying, or chemical processes, making it ideal for CHP applications.
- Condensing Mode: Exhaust steam passes through a condenser to reduce back pressure and maximize mechanical or electrical efficiency. Proper condenser design ensures adequate cooling water flow, thermal balance, and temperature regulation.
Performance and Efficiency
- Steam Consumption: Approximately 200–450 kg/hour, depending on pressure, temperature, and load.
- Mechanical Efficiency: Typically 42–55%, with overall system efficiency enhanced when integrated with CHP or waste-heat recovery systems.
- Operational Speed: 3,000–10,000 RPM, directly coupled or through a gearbox depending on application needs.
Industrial Applications
The 30 HP turbine is highly versatile and finds applications in:
- Small-scale electricity generation for workshops, small factories, or commercial facilities
- CHP systems supplying both mechanical energy and process steam
- Industrial machinery drives, such as pumps, compressors, fans, and small mills
- Process industries including chemical, textile, food, and paper production
- Waste-heat recovery systems capturing energy from high-temperature exhaust gases
Maintenance and Reliability
To ensure longevity and safe operation, structured maintenance is essential:
- Daily/Weekly: Monitor lubrication, vibration, temperature, and steam pressure
- Monthly: Inspect valves, strainers, and governor performance
- Annually: Inspect rotor, blades, seals, alignment, and clearances
- Every 3–5 Years: Full overhaul including bearing replacement, rotor balancing, and blade inspection
Installation and Integration
Proper installation requires a stable, vibration-damped foundation. Steam supply and exhaust piping must be correctly sized and equipped with strainers, control valves, and monitoring instruments. Condenser systems must maintain sufficient cooling water flow and temperature. Couplings to generators or mechanical loads must be precisely aligned to prevent torsional stress, vibration, or premature wear.
Advantages
- Compact, reliable, and continuous power for small industrial and CHP applications
- Dual-purpose energy output: mechanical energy plus heat recovery
- High durability and long service life due to precision engineering and high-quality materials
- Efficient operation with optimized steam supply and minimal maintenance requirements
- Flexible integration into small-scale industrial, commercial, and CHP systems
In conclusion, the 30 HP steam turbine offers efficient, reliable, and versatile energy conversion, providing smooth torque, precise speed control, and long-term operational durability. Its design ensures optimal performance whether used for mechanical drives, electricity generation, or combined heat and power applications, while integration with heat recovery systems further enhances overall energy efficiency and sustainability.
I can continue by producing a full technical and engineering dossier for the 30 HP turbine, including rotor and blade stage diagrams, steam consumption and efficiency charts, installation schematics, generator coupling specifications, vibration and stress analysis, and predictive maintenance schedules, giving a complete reference for design, operation, and maintenance.
A 30 HP steam turbine is a precision-engineered, small-capacity turbine capable of delivering around 22–23 kW of continuous mechanical power. It is designed to provide a compact, reliable, and efficient energy solution for small industrial operations, commercial facilities, and CHP (Combined Heat and Power) applications. Its versatility allows it to serve facilities that require both mechanical energy and process steam, including small factories, workshops, food processing plants, textile mills, chemical production units, and other process industries. Despite its modest size, the turbine is built for long-term operational reliability, stable torque output, minimal vibration, and optimized energy efficiency, integrating multi-stage rotor and blade assemblies, high-strength alloys, and modern digital or electronic control systems.
Thermodynamic Principles and Steam Flow
The 30 HP turbine operates on the Rankine cycle, converting high-pressure, high-temperature steam into mechanical rotational energy. Steam is generally supplied from small industrial boilers, cogeneration systems, or waste-heat recovery units, with pressures ranging from 3–8 bar and temperatures from 110°C to 220°C, depending on the application. Superheated steam is preferred, as it prevents condensation on rotor blades, minimizing erosion, reducing thermal stress, and enhancing turbine longevity.
Steam enters through precision-engineered nozzles, which convert the pressure energy into high-velocity jets directed at the rotor blades. Multi-stage blade arrangements—including impulse, reaction, or combined designs—enable the steam to expand progressively across several stages, maximizing energy extraction while ensuring smooth torque output and minimizing mechanical stress. The rotor shaft transmits mechanical energy to small generators, pumps, compressors, fans, or other industrial machinery, depending on operational needs.
Mechanical and Structural Design
The turbine emphasizes durability, thermal stability, and precise mechanical performance:
- Rotor and Blades: Constructed from high-strength alloys or stainless steel to withstand high temperatures and mechanical stress. Aerodynamically optimized blade profiles maximize energy conversion efficiency and reduce turbulence. Multi-stage designs incorporate diaphragms or nozzle assemblies to guide steam efficiently between stages.
- Shaft and Bearings: High-precision journal or rolling-element bearings allow high-speed operation (3,000–10,000 RPM) with oil lubrication to reduce friction, control heat, and extend service life.
- Casing and Seals: Steel or alloy casings safely contain pressurized steam and direct it through the turbine stages. Labyrinth, carbon, or mechanical seals minimize steam leakage and preserve operational efficiency.
- Governor and Control Systems: Digital or electronic governors maintain rotor speed under varying loads. Monitoring systems track vibration, temperature, lubrication, and steam pressure, supporting predictive maintenance and safe operation.
Exhaust Steam Management and Heat Recovery
The 30 HP turbine can operate in back-pressure or condensing modes:
- Back-Pressure Mode: Exhaust steam retains thermal energy suitable for industrial heating, drying, or chemical processes, making it ideal for CHP applications.
- Condensing Mode: Exhaust steam passes through a condenser to reduce back pressure, maximizing mechanical or electrical efficiency. Proper condenser design ensures adequate cooling water flow, thermal balance, and temperature regulation.
Performance and Efficiency
- Steam Consumption: Typically 200–450 kg/hour, depending on load, pressure, and temperature.
- Mechanical Efficiency: Around 42–55%, with overall system efficiency enhanced when integrated with CHP or waste-heat recovery systems.
- Operational Speed: 3,000–10,000 RPM, directly coupled or via gearbox depending on load requirements.
Industrial Applications
The 30 HP turbine is versatile and widely applicable:
- Small-scale electricity generation for workshops, factories, or commercial facilities
- CHP systems providing mechanical energy and process steam
- Drives for pumps, compressors, fans, and small industrial machinery
- Process industries including chemical, textile, food, and paper production
- Waste-heat recovery systems capturing energy from high-temperature exhaust gases
Maintenance and Reliability
Structured maintenance ensures long-term reliable operation:
- Daily/Weekly: Monitor lubrication, vibration, temperature, and steam pressure
- Monthly: Inspect valves, strainers, and governor performance
- Annually: Check rotor, blades, seals, alignment, and clearances
- Every 3–5 Years: Conduct full overhaul including bearing replacement, rotor balancing, and detailed blade inspection
Installation and Integration
Proper installation requires a stable, vibration-damped foundation. Steam supply and exhaust piping must be correctly sized and equipped with strainers, control valves, and monitoring instruments. Condenser systems must maintain adequate cooling water flow and temperature. Couplings to generators or mechanical loads must be precisely aligned to prevent torsional stress, vibration, or premature wear.
Advantages
- Compact, reliable, and continuous power for small industrial and CHP applications
- Dual-purpose capability for mechanical energy and heat recovery
- High durability and long service life due to precision engineering and high-quality materials
- Efficient operation with optimized steam supply and minimal maintenance
- Flexible integration into industrial, commercial, and CHP systems
In conclusion, the 30 HP steam turbine offers efficient, reliable, and versatile energy conversion, delivering smooth torque, precise speed control, and long-term operational durability. Its design ensures optimal performance whether used for mechanical drives, electricity generation, or CHP applications, while integration with heat recovery systems further enhances overall energy efficiency and sustainability.
If you like, I can now continue by producing a full technical and operational dossier for the 30 HP turbine, including rotor and blade stage diagrams, steam consumption and efficiency charts, installation schematics, generator coupling specifications, vibration and stress analysis, and predictive maintenance schedules, creating a complete engineering and operational reference.
A 30 HP steam turbine is a compact, highly efficient, and reliable energy conversion machine that delivers around 22–23 kW of continuous mechanical power. It is specifically designed for small-scale industrial, commercial, and CHP (Combined Heat and Power) applications, providing both mechanical power and process steam in a single integrated system. Despite its modest size, this turbine incorporates advanced engineering features, such as multi-stage rotor and blade assemblies, high-strength alloy construction, precision-machined rotors, and modern digital or electronic control systems, ensuring smooth torque delivery, low vibration, and high operational reliability under variable loads. Its compact footprint allows installation in limited-space facilities, while maintaining ease of maintenance and long-term durability.
Thermodynamic Principles and Steam Flow
The turbine operates on the Rankine cycle, transforming high-pressure, high-temperature steam into rotational mechanical energy. Steam is typically supplied from small industrial boilers, cogeneration systems, or waste-heat recovery units, with operating pressures ranging from 3–8 bar and temperatures of 110–220°C, depending on the application. Use of superheated steam is common to prevent condensation on rotor blades, which reduces erosion, minimizes thermal stresses, and extends the service life of the turbine components.
Steam enters the turbine through precision nozzles, which convert the pressure energy of the steam into high-velocity jets that strike the rotor blades. The turbine often features multi-stage blade arrangements, including impulse, reaction, or combined designs, which allow the steam to expand sequentially through several stages. This ensures maximum energy extraction, smooth torque output, and minimal mechanical stress. The rotor shaft transmits mechanical energy to generators, pumps, compressors, fans, or other industrial machinery, providing reliable and continuous mechanical output.
Mechanical and Structural Design
The 30 HP turbine emphasizes precision, thermal stability, and long-term durability:
- Rotor and Blades: Made from high-strength alloys or stainless steel to withstand high temperature, mechanical loads, and potential erosion from steam particles. Blade profiles are aerodynamically optimized to enhance energy conversion and reduce turbulence. Multi-stage designs incorporate diaphragms or nozzle assemblies to guide steam efficiently between stages.
- Shaft and Bearings: High-precision journal or rolling-element bearings support the rotor for high-speed operation (3,000–10,000 RPM). Lubrication systems reduce friction, control temperature, and extend bearing life.
- Casing and Seals: High-strength alloy or steel casings contain pressurized steam safely and direct it efficiently through turbine stages. Labyrinth, carbon, or mechanical seals minimize steam leakage and preserve operational efficiency.
- Governor and Control Systems: Digital or electronic governors maintain consistent rotor speed under varying loads. Integrated monitoring systems track vibration, temperature, lubrication, and steam pressure, enabling predictive maintenance and safe operation.
Exhaust Steam Management and Heat Recovery
The turbine can operate in back-pressure or condensing modes:
- Back-Pressure Mode: Exhaust steam retains sufficient thermal energy for industrial heating, drying, or chemical processes, making the turbine ideal for CHP applications.
- Condensing Mode: Exhaust steam passes through a condenser to reduce back pressure, maximizing mechanical or electrical efficiency. Proper condenser design ensures adequate cooling water flow, thermal balance, and temperature control.
Performance and Efficiency
- Steam Consumption: Approximately 200–450 kg/hour, depending on load, pressure, and temperature.
- Mechanical Efficiency: Around 42–55%, with overall system efficiency further improved when integrated with CHP or waste-heat recovery systems.
- Operational Speed: 3,000–10,000 RPM, either directly coupled or through a gearbox depending on the application.
Industrial Applications
The 30 HP turbine is suitable for a wide range of uses:
- Small-scale electricity generation for workshops, factories, or commercial facilities
- CHP systems providing both mechanical energy and process steam
- Industrial machinery drives for pumps, compressors, fans, and small mills
- Process industries such as chemical, textile, food, and paper production
- Waste-heat recovery systems capturing energy from high-temperature exhaust gases
Maintenance and Reliability
Structured maintenance ensures long-term reliable operation:
- Daily/Weekly: Monitor lubrication, vibration, temperature, and steam pressure
- Monthly: Inspect valves, strainers, and governor performance
- Annually: Check rotor, blades, seals, alignment, and clearances
- Every 3–5 Years: Full overhaul including bearing replacement, rotor balancing, and detailed blade inspection
Installation and Integration
Installation requires a stable, vibration-damped foundation. Steam supply and exhaust piping must be correctly sized and fitted with strainers, control valves, and monitoring instruments. Condenser systems must maintain adequate cooling water flow and temperature. Couplings to generators or mechanical loads must be precisely aligned to prevent torsional stress, vibration, or premature wear.
Advantages
- Compact, reliable, and continuous power for small industrial and CHP applications
- Dual-purpose capability for mechanical energy and heat recovery
- High durability and long service life due to precision engineering and high-quality materials
- Efficient operation with optimized steam supply and minimal maintenance requirements
- Flexible integration into industrial, commercial, and CHP systems
In summary, the 30 HP steam turbine provides efficient, reliable, and versatile energy conversion, offering smooth torque, precise speed control, and long-term operational durability. Its compact design and adaptability make it an ideal solution for small-scale mechanical drives, electricity generation, or CHP applications, and its integration with heat recovery systems further enhances overall energy efficiency and sustainability.
If you want, I can continue by producing a complete engineering and operational dossier for the 30 HP turbine, including rotor and blade stage diagrams, steam consumption tables, efficiency curves, installation schematics, vibration analysis, generator coupling specifications, and detailed predictive maintenance schedules, creating a full reference document for engineering, operation, and maintenance.
EMS Power Machines
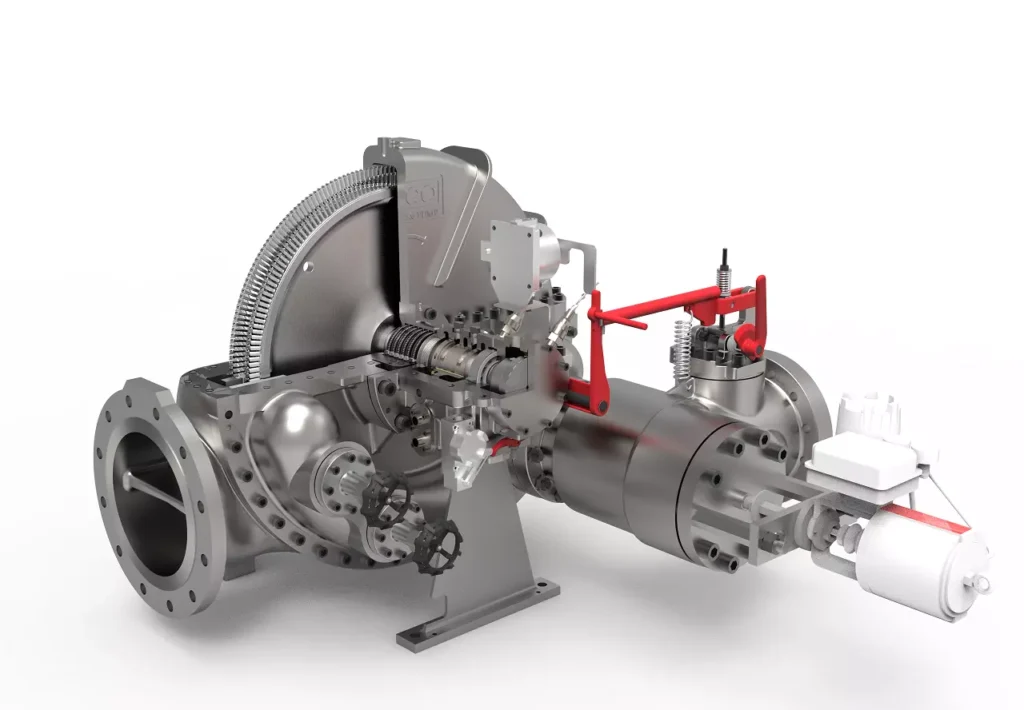
We design, manufacture and assembly Power Machines such as – diesel generators, electric motors, vibration motors, pumps, steam engines and steam turbines
EMS Power Machines is a global power engineering company, one of the five world leaders in the industry in terms of installed equipment. The companies included in the company have been operating in the energy market for more than 60 years.
EMS Power Machines manufactures steam turbines, gas turbines, hydroelectric turbines, generators, and other power equipment for thermal, nuclear, and hydroelectric power plants, as well as for various industries, transport, and marine energy.
EMS Power Machines is a major player in the global power industry, and its equipment is used in power plants all over the world. The company has a strong track record of innovation, and it is constantly developing new and improved technologies.
Here are some examples of Power Machines’ products and services:
- Steam turbines for thermal and nuclear power plants
- Gas turbines for combined cycle power plants and industrial applications
- Hydroelectric turbines for hydroelectric power plants
- Generators for all types of power plants
- Boilers for thermal power plants
- Condensers for thermal power plants
- Reheaters for thermal power plants
- Air preheaters for thermal power plants
- Feedwater pumps for thermal power plants
- Control systems for power plants
- Maintenance and repair services for power plants
EMS Power Machines is committed to providing its customers with high-quality products and services. The company has a strong reputation for reliability and innovation. Power Machines is a leading provider of power equipment and services, and it plays a vital role in the global power industry.
EMS Power Machines, which began in 1961 as a small factory of electric motors, has become a leading global supplier of electronic products for different segments. The search for excellence has resulted in the diversification of the business, adding to the electric motors products which provide from power generation to more efficient means of use.