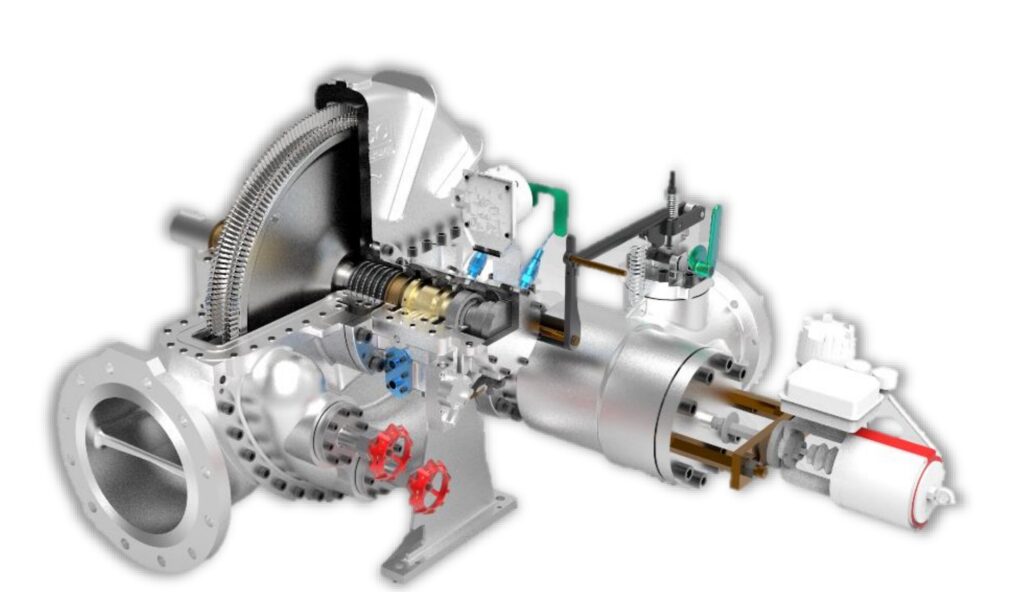
Steam Turbine for Educational Purposes: A Steam Power Plant Trainer is a specialized system used for educational or industrial training purposes to simulate the operation of a real steam power plant
A Steam Power Plant Trainer is a specialized system used for educational or industrial training purposes to simulate the operation of a real steam power plant. These trainers can be hardware-based units installed in laboratories or software-based simulators designed for teaching thermodynamic cycles, system controls, and power generation operations. In academic environments, such trainers often consist of scaled-down physical systems including a boiler, turbine, condenser, generator, feedwater pump, and associated control instruments.
They are used in engineering colleges, vocational training centers, and research institutions to demonstrate the Rankine cycle, component behavior, safety procedures, and energy conversion efficiency. Some systems are fully automated and include data acquisition systems, PLC control, SCADA interfaces, and real-time monitoring panels. Trainers may allow experimentation with varying parameters such as steam pressure, load, cooling water flow, and turbine speed to help students understand dynamic responses. Manufacturers like Armfield, TecQuipment, Edibon, and GUNT offer compact educational steam plant trainers designed with visualization windows, transparent pipes, and cutaway models.
These help learners see internal steam flow, turbine rotor movement, and condensation processes in real-time. In more advanced training facilities or industrial simulators, software-based platforms simulate the full operation of utility-scale power plants using high-fidelity dynamic models. These include emergency scenarios, startup and shutdown sequences, and turbine trip events. Such simulators are often used in power utility training centers to certify operators and ensure regulatory compliance. Steam power plant trainers also serve R&D purposes where researchers test new turbine blade designs, superheater arrangements, or control strategies. The goal of these trainers is to bridge the gap between theoretical thermodynamics and practical engineering.
Depending on complexity, some trainers simulate basic steam circuits while others support combined heat and power (CHP) schemes, regenerative feedwater heating, and steam extraction. Institutions may integrate trainers into hybrid systems with solar preheating or waste heat recovery to teach modern energy technologies. Educational trainers may run on electricity and generate simulated steam, or include a small electric boiler producing real low-pressure steam. Safety features such as pressure relief valves, temperature cut-offs, and emergency stops are typically standard. Maintenance practices, fault diagnosis, and instrumentation calibration are also often included in the training syllabus. The use of steam power plant trainers improves hands-on skills, operational awareness, and engineering intuition in students and technicians. They help future power engineers visualize abstract cycle diagrams and perform real experiments involving enthalpy calculations and energy balances.
Many modern steam power plant trainers are modular, allowing instructors to add or remove components such as economizers, superheaters, reheaters, or feedwater heaters to demonstrate different cycle configurations. This flexibility enables users to model basic or advanced Rankine cycles and compare their thermal efficiencies. Some trainers include digital twin integration where real-time data from the physical trainer is mirrored on a computer for simulation-based analysis. This dual-mode approach helps learners correlate theoretical simulation results with physical system behavior.
In software-based platforms, the interface usually mimics real DCS or SCADA environments, allowing trainees to practice navigating alarms, adjusting setpoints, and handling unexpected disturbances. Graphical user interfaces display process variables such as steam temperature, turbine RPM, generator voltage, and condenser pressure. Trainers designed for energy auditing education also include measurement devices like flow meters, thermocouples, wattmeters, and pressure transducers for analyzing energy losses and efficiency improvements.
For institutions teaching power engineering fundamentals, the trainer often includes curriculum support such as manuals, lab sheets, and experiment protocols aligned with ABET or other educational standards. These setups are highly useful in courses covering power plant technology, thermal engineering, instrumentation, control systems, and mechanical operations. In industrial settings, full-scale digital steam plant simulators are used for training control room operators on large utility boilers and steam turbines under realistic load-following or peak-shaving conditions. These systems use real-time modeling engines capable of simulating fluid dynamics, heat transfer, and control logic. In some training centers, operators practice on a 1:1 replica of the control room panel where touchscreen interfaces replicate physical buttons and dials.
This immersive approach helps reinforce operator reflexes and decision-making in high-pressure scenarios. In academic projects, steam trainers also serve as testbeds for research on renewable integration, hybrid cycle optimization, and advanced fault detection algorithms. They are sometimes used in postgraduate thesis work or industrial collaborations. Depending on the supplier, steam plant trainers may come as turnkey solutions with installation, training, and after-sales support. Customizable models allow universities or companies to align the system with their curriculum or process standards. In recent years, some trainers have begun incorporating augmented reality (AR) or virtual reality (VR) for more immersive learning, allowing trainees to explore plant components virtually and conduct simulated walk-throughs. Overall, steam power plant trainers play a vital role in bridging theory and practice by creating a safe, controlled, and repeatable environment for understanding complex energy systems and real-world plant behavior.
In addition to educational benefits, steam power plant trainers help build familiarity with operational procedures, safety interlocks, and emergency handling, which are critical for preventing accidents in actual power plants. Students and trainees learn how to respond to scenarios such as boiler overpressure, turbine overspeed, condenser vacuum loss, or generator overloads—each scenario mimicked by the trainer with corresponding alarms and system responses. This hands-on learning reduces human error risks and enhances readiness for field operations. Instructors can also intentionally introduce faults or malfunctions—like blocked steam lines, feedwater pump failures, or sensor inaccuracies—so trainees can diagnose and correct issues, reinforcing problem-solving skills. Some advanced trainers come with cloud connectivity, allowing remote monitoring, data logging, and integration with learning management systems (LMS), which is especially useful for blended learning or online education environments.
Another key feature in many trainers is the ability to simulate energy conversion paths in detail. From fuel input or electrical heating to steam generation, mechanical rotation, and electricity production, the trainer helps visualize where energy losses occur. Learners can calculate thermal efficiency, analyze turbine performance curves, study heat rate, and observe how variations in load or steam pressure affect output. Trainers also teach how regenerative feed heating improves efficiency by reducing fuel consumption, or how a condenser maintains low exhaust pressure to extract more energy from steam. These details provide practical reinforcement of thermodynamic laws, particularly the first and second laws of thermodynamics.
For sustainability education, some steam power plant trainers are integrated with biomass boilers, solar-assisted heating, or waste heat recovery systems to illustrate low-carbon or hybrid generation methods. These hybrid configurations show students how renewable sources can assist traditional thermal systems, an important concept in today’s energy transition. Trainers can also compare open and closed-loop cycles, dry vs. wet cooling methods, and different turbine configurations such as impulse and reaction stages. In lab settings, students may disassemble turbine models to see rotor blades, nozzle arrangements, shaft alignment, and bearing housings—deepening mechanical understanding.
Many trainers include graphical trend recording to show changes in pressure, temperature, and flow over time. This supports lessons in dynamic systems, control loop tuning, and transient analysis. PID control behavior can be studied directly by adjusting control parameters and observing system stability or oscillation. Some trainers also allow interface with MATLAB, LabVIEW, or other simulation environments for custom control algorithm development or academic experiments. These integrations make the trainer more than just a demonstration unit—it becomes a complete experimental and research platform.
Ultimately, steam power plant trainers are essential for building competent engineers and technicians in power generation industries. Whether used for operator licensing, undergraduate labs, or control system research, they provide a critical bridge between classroom theory and real-world application.
Steam power plant trainers also play an important role in familiarizing users with energy management systems and utility economics. Trainees can observe how fuel consumption relates to electrical output, and how changes in operating parameters can impact cost, emissions, and efficiency. Some trainer systems include modules to simulate fuel types—such as coal, gas, or biomass—so users can compare their thermal efficiencies and emission profiles. Environmental modules may include emission sensors for NOx, CO2, and particulate matter to demonstrate the environmental impact of different operational strategies. These features are especially valuable for training in sustainable energy production, regulatory compliance, and emissions reduction techniques.
In technical training programs, trainers are also used to explain auxiliary systems of steam plants, such as feedwater treatment, deaerators, lube oil systems, cooling towers, and condensate extraction. Understanding these subsystems is critical, as the reliability of the whole plant often depends on the proper functioning of these supporting components. For example, learners can simulate and troubleshoot problems in condensate pumps or air ingress in condensers, which are common failure points in actual power plants. In advanced trainers, students may also learn about turbine governing systems, including mechanical, hydraulic, and electronic governors, and explore how these systems maintain speed and stability under load variations.
Moreover, steam power plant trainers often include electrical generation and synchronization modules. These simulate how generators are connected to a grid, including control of voltage, frequency, and phase matching during synchronization. Learners can practice black start procedures, island mode operation, and grid connection steps in a low-risk environment. Protection devices such as circuit breakers, overload relays, and fuses are typically included, enabling users to study electrical faults and apply protective relaying principles. This adds a valuable layer of electrical engineering education to the mechanical and thermodynamic learning objectives.
For vocational education, especially in technical colleges or industrial training institutes, steam trainers can be tailored to focus on job-specific skills such as valve operation, flange fitting, insulation techniques, or instrumentation calibration. Real tools, gauges, and control valves are incorporated so that students develop the tactile skills needed in field maintenance roles. Modular trainers can even be mounted on wheeled frames for mobility between classrooms or to accommodate multiple training stations in a single lab.
Manufacturers of these systems often provide training programs for instructors, ensuring they can operate, maintain, and teach with the trainer effectively. These may include online tutorials, certification courses, and access to user communities for sharing experiment ideas or troubleshooting tips. Some institutions even collaborate with the trainer manufacturers to develop new modules or integrate emerging technologies like hydrogen combustion, carbon capture simulation, or small modular reactor (SMR) interfaces.
As the global energy landscape evolves, the importance of well-trained personnel who understand both classical and modern power generation technologies continues to grow. Steam power plant trainers help meet this need by offering controlled, repeatable, and safe environments where complex systems can be explored in detail, knowledge can be retained through practice, and future engineers can gain the confidence to manage real-world power plants with competence and care.
Small Size Steam Power Plant Models
Small size steam power plant models are designed to replicate the basic operation and principles of full-scale thermal power plants on a compact, safe, and manageable scale. These models are widely used in engineering colleges, vocational schools, and training institutes for hands-on learning and demonstration of the Rankine cycle. Most small-scale models include a boiler, steam turbine or reciprocating engine, condenser, feedwater system, and a basic electrical generator. The boiler is often electrically heated or LPG-fired to produce low-pressure steam suitable for classroom use. The turbine is usually a single-stage impulse type or a small reciprocating piston engine coupled to a dynamometer or generator for mechanical or electrical output measurement. These setups allow learners to observe how heat energy is converted into mechanical energy and then into electricity.
Small steam plant models are typically mounted on a steel base or frame with transparent panels and labeled piping to visualize flow direction. Instrumentation such as pressure gauges, thermocouples, flow meters, tachometers, and wattmeters are included for monitoring system performance and conducting experiments. Some systems come with data acquisition software that allows real-time plotting of performance curves, enthalpy-entropy diagrams, and efficiency calculations. Many units have mimic diagrams on the front panel, showing component arrangement and process flow for educational clarity. Trainers may include variable loads such as resistive bulbs or small motors to simulate real load changes on the system and study the turbine or engine response.
In laboratory conditions, these models allow students to carry out structured experiments like measuring boiler efficiency, turbine output versus steam pressure, heat balance around each component, and system response to load variations. Advanced models may include features like regenerative feedwater heating, superheaters, and condensate recovery tanks to simulate more complex cycle variations. Some are equipped with safety valves, cutoffs, and alarms to reinforce training on safe plant operation and emergency procedures. For technical training, students also learn how to start up and shut down the system, identify leaks or faults, and maintain water level and pressure within safe operating ranges.
Manufacturers such as Fabotronix, Sci-tech Didactic, Essom, GUNT, TecQuipment, and Kouei Trading offer a variety of models tailored to specific learning levels—from basic cycle visualization to advanced instrumentation and PLC-based control. Reciprocating engine-based models are often used to demonstrate mechanical linkages, crankshaft motion, and engine torque measurement, while turbine-based models are used to analyze velocity profiles, nozzle function, and turbine efficiency. Some models simulate real power plants with scaled-down versions of control panels, steam traps, pumps, and sensors to provide an industrial training environment. For electrical engineering applications, students can measure output voltage, current, power factor, and frequency of the generated electricity, and study synchronization principles with a simulated grid.
These small steam power plant models offer an interactive and realistic platform for energy education, helping learners build a comprehensive understanding of thermal systems, thermodynamics, energy conversion, and plant operation. They are often used as a foundation for final-year projects, research on energy systems, or as a test bench for developing control algorithms and fault detection systems. Their compact size allows use in typical laboratory spaces, and with appropriate ventilation and safety practices, they provide an effective and practical tool for training the next generation of power engineers.
Some small steam power plant models also incorporate transparent or open-frame components that allow users to see the internal workings of turbines, engines, or pumps during operation. This visual accessibility enhances comprehension of key mechanical principles, such as expansion in turbine blades, piston movement in reciprocating engines, or steam condensation inside shell-and-tube heat exchangers. Educational trainers often use color-coded piping and simplified flow diagrams to reinforce the identification of steam lines, feedwater returns, exhaust, and condensate paths. These features support intuitive learning and help students correlate physical layout with thermodynamic flow paths seen in textbooks.
In more advanced versions, programmable logic controllers (PLCs) and touchscreens are integrated to simulate the automatic control of real power plants. Trainees can observe how the system reacts when steam flow is increased or when the feedwater pump fails, and they can manually adjust parameters such as valve positions or electrical load. This kind of interactivity fosters deeper understanding of control strategies and system dynamics. With PLC or SCADA integration, users can simulate various scenarios, perform remote operation, and visualize data trends over time. This makes small-scale steam power plant trainers highly valuable not only for mechanical engineering training but also for those specializing in automation, process control, and instrumentation.
Additionally, modular systems are increasingly common, allowing individual components—like the boiler, turbine, condenser, or generator—to be disconnected or swapped out. This is especially helpful in educational environments where different groups may focus on specific components or want to test the impact of individual system changes. For instance, replacing a single-stage turbine with a multi-nozzle type allows investigation of nozzle angle effects or partial admission operation. Similarly, different condenser types—air-cooled, water-cooled, or spray condensers—can be tested to analyze their impact on back pressure and efficiency.
Some models support hybrid energy learning by integrating solar water heaters or biomass combustion chambers for preheating feedwater. This integration demonstrates how renewable sources can complement steam-based systems. Water treatment modules may also be included to show the effect of feedwater quality on boiler life and overall plant performance. In research-focused institutions, these small power plant models are sometimes used to test new control algorithms, low-grade heat recovery strategies, or small-scale combined heat and power (CHP) systems using steam as the working medium.
In terms of safety and maintenance education, these trainers are also invaluable. Students can perform mock maintenance procedures such as replacing gaskets, checking insulation, lubricating bearings, or inspecting steam traps. Simulated faults like steam leaks, low water level, or bearing overheating can be introduced to train users on diagnosis and corrective actions. This prepares them for real-world maintenance practices and encourages a proactive approach to plant reliability and efficiency.
Despite their small scale, these models can generate enough data to perform full thermodynamic cycle analysis. By logging parameters like inlet and outlet temperatures, pressures, rotational speed, steam consumption, and electrical load, learners can construct actual T-s and h-s diagrams and compare experimental results with theoretical expectations. This ability to bridge theoretical and practical understanding is a core strength of these educational systems.
Because of their simplicity and manageable scale, these trainers are also well-suited for public demonstrations, science museums, or awareness campaigns where basic energy conversion principles are introduced to a broader audience. They provide a clear and tangible illustration of how steam, as a working fluid, can convert thermal energy into mechanical and electrical power. This is particularly useful in developing educational infrastructure or promoting STEM subjects to younger students.
In conclusion, small-size steam power plant models are not just scaled-down systems—they are powerful educational tools that condense decades of engineering knowledge into a hands-on platform. They help students, technicians, and engineers understand how steam systems function, how energy efficiency can be measured and improved, and how each subsystem contributes to overall plant operation. Their compact size, safety features, modular design, and integration with digital tools make them ideal for modern teaching and research environments focused on energy systems and power generation.
Beyond teaching fundamentals, small steam power plant models serve as test platforms for innovative energy concepts. For example, researchers use them to trial low-pressure steam cycles optimized for waste heat recovery or geothermal applications where steam availability is limited. By adjusting boiler parameters or turbine configurations on these models, they evaluate how to maximize output under constrained conditions. This flexibility supports experimentation with superheating, reheat cycles, or combined cycles integrating gas and steam turbines at miniature scale.
In industrial training centers, these models help prepare operators for real plant control rooms by simulating startup, shutdown, and emergency protocols. Trainees learn sequencing, interlock functions, and alarm responses within a physically interactive setup. Some trainers include real control panel replicas or digital interfaces reflecting actual plant software, bridging the gap between classroom and plant floor. This reduces training time and operational errors when transitioning to full-scale power plants.
Furthermore, small models often double as platforms for control systems development. Students or engineers can program PLCs or microcontrollers to automate boiler firing rates, control feedwater levels, or regulate turbine speed in response to load changes. This hands-on approach enhances understanding of feedback loops, PID control, and system stability. Coupling mechanical and control education fosters multidisciplinary skills essential for modern power plant operation.
From an environmental perspective, these models enable demonstration of emission control measures such as scrubbers or catalytic converters adapted for small-scale combustion. They also allow study of condenser types and cooling methods to minimize thermal pollution. Educational modules can highlight the impact of operational choices on fuel consumption and greenhouse gas emissions, promoting sustainable engineering practices.
Moreover, small steam power plant models contribute to the development of renewable and hybrid energy systems. For instance, integrating solar thermal preheaters or biomass boilers with conventional steam cycles allows exploration of cleaner energy pathways and carbon reduction strategies. This aligns training with global trends towards decarbonization and energy transition.
Finally, these models support public outreach and STEM engagement activities. Their visible steam flow, rotating turbines, and electrical output provide compelling demonstrations that make thermodynamics tangible and exciting. By fostering curiosity and hands-on interaction, they inspire future generations to pursue careers in energy and engineering fields.
In essence, small steam power plant models are versatile tools that extend well beyond simple classroom demonstrations. They empower education, research, innovation, and industry training by delivering practical, scalable, and adaptable platforms for mastering steam power technology.
Small steam power plant models also provide an accessible means to explore economic and operational optimization techniques. Users can experiment with varying fuel types, steam pressures, and load profiles to analyze how these variables affect fuel consumption, operating costs, and plant efficiency. This practical exposure to cost-benefit trade-offs teaches learners about the economic realities of power generation, including fuel sourcing, maintenance expenses, and downtime impacts.
Additionally, these models support the study of system reliability and availability by allowing simulation of common faults or failures such as boiler tube leaks, valve malfunctions, or turbine blade damage. By deliberately inducing faults, trainees develop diagnostic skills and learn corrective maintenance procedures in a safe environment. This proactive fault management training helps minimize unplanned outages and improves overall plant resilience.
For those interested in environmental compliance, small-scale models can be equipped with sensors to monitor emissions such as carbon dioxide, nitrogen oxides, or particulate matter, demonstrating how operational adjustments impact environmental performance. This hands-on approach promotes an understanding of environmental regulations and the importance of pollution control technologies.
Integration with digital technologies like IoT sensors and cloud-based monitoring platforms is increasingly common, even in small trainers. This facilitates remote monitoring, real-time data analysis, and predictive maintenance exercises, preparing trainees for the growing digitalization of power plants worldwide. It also allows educators to incorporate data science and analytics into traditional engineering curricula.
In research contexts, these compact models enable the testing of innovative materials, coatings, or surface treatments on turbine blades or boiler components to improve efficiency or reduce wear. They serve as physical testbeds to validate computational models or simulate aging effects over accelerated cycles.
Overall, small steam power plant models embody a holistic educational ecosystem. They bridge the gap between theory and practice, enable experimentation with mechanical, electrical, and control systems, and foster skills essential for modern, sustainable power generation. Their versatility makes them valuable assets across academia, industry, and public outreach, equipping users to meet current and future energy challenges confidently.
These small steam power plant models also provide an ideal platform for exploring advanced thermodynamic cycles beyond the simple Rankine cycle. For example, users can investigate regenerative cycles where steam is extracted at intermediate pressures to preheat feedwater, improving overall plant efficiency. By incorporating feedwater heaters or reheaters into the model, learners see firsthand how these modifications impact temperature and pressure profiles, fuel consumption, and net output.
Combined cycles, which integrate gas turbines with steam turbines to utilize exhaust heat, can also be simulated on modular small-scale systems. This allows trainees to understand how multiple cycles can be linked to boost efficiency and reduce emissions, reflecting trends in modern power generation technology. Hybrid configurations combining renewable inputs—like solar thermal or biomass—with conventional steam cycles are increasingly studied using these models, illustrating pathways toward decarbonized energy systems.
The hands-on nature of these models helps demystify complex processes like phase changes, entropy changes, and exergy analysis by letting users visualize and measure parameters during real operation. For instance, observing steam expanding in the turbine blades or condensing in the heat exchanger turns abstract thermodynamic concepts into concrete experience. This approach significantly improves retention and comprehension, especially for students new to thermal sciences.
Another educational benefit is the exposure to instrumentation and measurement techniques. Trainees learn how to properly install, calibrate, and interpret data from sensors such as thermocouples, pressure transducers, flow meters, and tachometers. These skills are critical for accurate plant monitoring, control, and diagnostics. Some trainers include built-in fault simulation to help users identify erroneous sensor readings or troubleshoot instrumentation failures.
In addition to mechanical and electrical aspects, small steam power plant models often incorporate fluid dynamics lessons by illustrating flow behavior through nozzles, valves, pipes, and condensers. Observing pressure drops, velocity changes, and phase transitions helps users appreciate the complexities of steam flow and heat transfer in power plants.
Maintenance training is also enhanced by the manageable size and accessibility of these models. Students can practice disassembly, inspection, cleaning, lubrication, and reassembly of critical components such as turbines, pumps, and valves. This hands-on experience is invaluable for developing mechanical aptitude and understanding the physical demands of plant operation.
Finally, the compactness and safety features of these models make them suitable for a wide range of settings, from university laboratories and technical colleges to corporate training centers and public science exhibits. They offer a scalable, interactive, and engaging way to build foundational knowledge and practical skills in steam power generation, supporting workforce development and innovation in the energy sector.
Educational Steam Turbine Setups
Educational steam turbine setups are specially designed systems used in academic and training environments to teach the principles, operation, and maintenance of steam turbines. These setups range from small-scale bench models to sophisticated simulators that replicate real-world power plant conditions. The primary aim is to provide hands-on experience with turbine components, steam flow dynamics, energy conversion, and control systems in a safe, manageable format.
Typically, educational steam turbine setups include a boiler or steam source that produces low to moderate pressure steam, a turbine unit (often impulse or reaction type), a generator or dynamometer to measure mechanical output, and a condenser or cooling system to complete the cycle. The turbine may be single or multi-stage, depending on the complexity of the setup and learning objectives. These systems are equipped with pressure gauges, temperature sensors, flow meters, tachometers, and load devices to monitor performance parameters and analyze efficiency.
Some setups use electric heaters or small fuel burners to generate steam, allowing safe indoor use with proper ventilation. Others may connect to external steam supplies in advanced labs. Transparent or cutaway turbine casings and piping often enhance visibility of internal parts, helping students visualize steam paths, blade action, and rotor movement.
In more advanced educational environments, turbine setups integrate programmable logic controllers (PLCs) and human-machine interfaces (HMIs) to simulate real plant control and automation systems. Trainees learn startup and shutdown sequences, load changes, speed regulation, and emergency procedures, improving operational skills and situational awareness.
Software-based turbine simulators complement physical setups by providing dynamic modeling of turbine behavior under varying conditions. These allow virtual experimentation with parameters like steam temperature, pressure, nozzle configurations, and load variations without the need for physical steam generation.
Educational steam turbine setups support experiments such as measuring turbine output, determining isentropic efficiency, evaluating performance curves, studying vibration and noise, and understanding thermodynamic cycles. They also enable maintenance training, including disassembly, inspection, lubrication, and troubleshooting of components.
Suppliers like Armfield, TecQuipment, GUNT, and others offer a variety of steam turbine training rigs tailored for university labs, vocational schools, and industrial training centers. These systems vary in power rating, instrumentation sophistication, and control integration, catering to different educational needs and budgets.
Overall, educational steam turbine setups provide an essential bridge between theoretical knowledge and practical skills, preparing students and trainees for careers in power generation, mechanical engineering, and plant operation.
Educational steam turbine setups offer students the opportunity to observe and analyze the conversion of thermal energy from steam into mechanical work. By controlling steam pressure and flow, learners can study how these variables influence turbine speed, torque, and output power. The setups typically allow measurement of input and output parameters to calculate efficiencies, losses, and performance characteristics, helping reinforce thermodynamic and mechanical engineering principles. Many rigs include adjustable nozzles or variable steam admission to simulate partial load conditions and study turbine response.
In some setups, the turbine rotor is mounted on precision bearings with vibration sensors to teach students about rotor dynamics and the importance of balancing. This aids understanding of mechanical stresses and maintenance requirements in real turbines. Noise measurement features may also be present, demonstrating the acoustic impact of steam expansion and blade geometry.
Educational setups frequently incorporate condensers or cooling systems to simulate the full Rankine cycle and demonstrate how reducing exhaust pressure increases turbine efficiency. Condensate recovery and feedwater heating components may also be part of the system, illustrating regenerative cycle benefits and the importance of water treatment to prevent corrosion and scaling.
For operational training, systems are often equipped with control panels or software interfaces that replicate real turbine control rooms. Trainees can practice startup, load changes, speed control, and emergency shutdown procedures in a controlled environment. Some setups connect to programmable logic controllers (PLCs) and human-machine interfaces (HMIs), allowing hands-on experience with automation and process control used in modern power plants.
Disassembly and maintenance exercises are an integral part of educational steam turbine setups. Students learn to identify and handle turbine components such as blades, seals, shafts, bearings, and casings. They practice inspection techniques for wear, corrosion, and alignment issues. This practical knowledge is critical for preparing technicians and engineers for field maintenance roles.
In addition to mechanical and thermodynamic lessons, these setups support electrical engineering education by coupling turbines with generators or dynamometers. Learners can analyze electrical output parameters, synchronization methods, and generator load responses. This multidisciplinary approach enhances understanding of the complete power generation process.
Many educational steam turbine setups are modular and scalable, allowing institutions to expand systems with additional components like reheaters, superheaters, or advanced control modules. This flexibility enables progressive learning from basic principles to complex plant operation scenarios.
Safety features are integral to these setups, including pressure relief valves, emergency stops, and interlocks to ensure safe operation during experiments. Comprehensive manuals and structured lab exercises guide students through theory, operation, data collection, and analysis.
By combining physical models, instrumentation, control systems, and software simulation, educational steam turbine setups provide a comprehensive, hands-on learning environment. They equip students with practical skills and deep understanding necessary for careers in power generation, mechanical design, and energy systems engineering.
Some educational steam turbine setups also include advanced diagnostic tools such as thermal imaging cameras, laser vibrometers, and strain gauges to analyze heat distribution, mechanical stresses, and deformation under operational conditions. These tools allow students and researchers to study turbine performance in greater detail, identify potential failure points, and optimize maintenance schedules. Integrating such instrumentation helps bridge the gap between theoretical knowledge and real-world engineering challenges.
In recent years, many setups have incorporated digital twin technology, creating virtual replicas of the physical turbine system that run in parallel with real-time data collection. This allows users to simulate “what-if” scenarios, perform predictive maintenance, and test control strategies without risking hardware damage. Virtual twins can be accessed remotely, supporting distance learning and collaborative research projects.
Educational turbine rigs often come with software packages that provide detailed cycle analysis, performance evaluation, and data visualization tools. These packages enable students to compare experimental results against theoretical models, fostering critical thinking and analytical skills. The software may also simulate fault conditions, such as blade erosion or steam leakage, enhancing troubleshooting exercises.
Some setups allow exploration of various turbine designs, such as impulse versus reaction turbines, axial versus radial flow, or single-stage versus multi-stage arrangements. This hands-on comparison helps learners understand how design choices affect efficiency, power output, and mechanical complexity. By experimenting with interchangeable turbine components, students gain insight into the engineering trade-offs involved in turbine design.
In industrial training environments, steam turbine setups may be linked with boiler simulators, condensate systems, and electrical grid simulators to create comprehensive power plant mockups. This integrated approach gives trainees a holistic understanding of plant operation, from steam generation through electricity production and distribution. Operators learn to coordinate multiple systems, manage load fluctuations, and respond to emergencies effectively.
Educational steam turbine setups are increasingly used for research on emerging technologies, such as supercritical steam cycles, hydrogen-fueled boilers, and carbon capture integration. By adapting these models, researchers can investigate performance improvements, environmental impacts, and control strategies on a manageable scale before applying findings to full-scale plants.
Overall, educational steam turbine setups are evolving to meet modern engineering demands by combining mechanical, electrical, digital, and environmental learning components. They serve as vital tools in developing the next generation of power engineers, operators, and researchers equipped to innovate in the rapidly changing energy sector.
Educational steam turbine setups also emphasize the importance of safety protocols and operational best practices. Trainees are taught how to interpret safety alarms, handle emergency shutdowns, and follow lockout-tagout procedures during maintenance. These safety lessons help reduce the risk of accidents when working with high-pressure steam and rotating machinery in real plants. Training often includes simulated fault scenarios like over-speed conditions, steam leaks, or loss of condenser vacuum, allowing learners to practice swift and correct responses in a controlled environment.
To deepen understanding, setups may feature instrumentation that monitors vibration, temperature gradients, and bearing lubrication conditions in real time. Students learn to analyze these parameters to detect early signs of mechanical wear or imbalance, fostering proactive maintenance approaches. This condition monitoring training is crucial for minimizing downtime and extending turbine life.
Many institutions integrate their steam turbine training with power system courses, where students study grid connection, load balancing, and power quality. Hands-on experiments with synchronization, voltage regulation, and frequency control help bridge mechanical turbine operation with electrical grid demands. This multidisciplinary training prepares engineers to manage the interface between generation and distribution systems effectively.
As renewable energy grows, educational setups increasingly demonstrate how steam turbines can be integrated into hybrid plants using solar thermal, biomass, or geothermal sources. This allows students to explore sustainable energy solutions and the challenges of integrating variable renewable inputs with steady steam cycles. It also fosters innovation in designing flexible, efficient, and low-carbon power generation systems.
Finally, the portability and modularity of many modern steam turbine trainers facilitate their use beyond traditional labs—in outreach programs, technical fairs, and remote training centers. This flexibility helps spread practical steam turbine knowledge to diverse audiences, supporting workforce development and public awareness of energy technologies.
In summary, educational steam turbine setups combine mechanical training, control system education, safety instruction, and sustainability awareness. They offer a rich, interactive environment that equips learners with the knowledge and skills needed for careers in power generation, energy management, and engineering innovation.
Educational steam turbine setups often incorporate real-time data logging and analytics capabilities, allowing users to record, visualize, and analyze performance metrics over extended periods. This feature enables detailed study of transient behaviors such as startup dynamics, load changes, and response to control inputs. By examining trends in temperature, pressure, vibration, and output power, students learn to identify patterns indicative of optimal operation or emerging faults. This long-term data approach is invaluable for developing skills in performance optimization and predictive maintenance.
Integration with simulation software is also common, providing a virtual environment where learners can test hypothetical scenarios before applying changes on the physical setup. This synergy between simulation and hands-on experimentation helps reinforce theoretical concepts and develop problem-solving skills. For example, students can simulate the effect of changing steam inlet temperature on turbine efficiency, then validate predictions through actual measurements.
Some advanced educational setups feature multi-turbine arrangements or combined cycles, demonstrating how steam turbines can be used in series or parallel configurations to maximize energy extraction. These complex arrangements provide insights into real-world plant design challenges, such as managing steam reheating, extraction for feedwater heating, and balancing mechanical loads across turbines.
Training programs using these setups often include comprehensive curricula covering thermodynamics, fluid mechanics, materials science, control systems, electrical engineering, and environmental impacts. This multidisciplinary approach ensures students understand the interconnected nature of steam power plants and prepares them for diverse roles in the energy sector.
Furthermore, these setups support research on new materials and blade designs aimed at increasing efficiency and durability under high temperatures and stresses. By testing prototype components on educational turbines, researchers can collect valuable performance data and identify potential improvements before scaling to commercial applications.
In public outreach, educational steam turbine models serve as engaging demonstrations illustrating how thermal energy converts to mechanical and electrical power. Their visual and interactive nature makes complex energy concepts accessible to non-experts, fostering interest in STEM fields and awareness of energy production technologies.
Overall, educational steam turbine setups combine hands-on training, simulation, research capabilities, and outreach potential, making them versatile and essential tools in the evolving landscape of energy education and innovation.
Educational steam turbine setups also provide a practical framework for teaching energy efficiency and sustainability principles in real-world engineering contexts. Through carefully designed experiments, students can quantify where energy is lost in a steam cycle—such as in the boiler, through friction losses in piping, or in the turbine exhaust—and identify strategies for improving overall efficiency. These could include adding insulation, optimizing steam admission, adjusting condenser pressure, or recovering waste heat.
Moreover, these setups allow learners to explore real thermodynamic trade-offs. For example, they can observe how lowering condenser pressure increases turbine efficiency but requires more effective cooling, or how superheating the steam raises cycle efficiency but also imposes more stress on turbine materials. These trade-offs are key to understanding the design choices and constraints in full-scale plants.
Some setups simulate off-design conditions, helping users understand how turbines perform under fluctuating load, partial steam supply, or cooling water shortages. These simulations are vital for preparing students to operate and manage power systems under dynamic and unpredictable real-world conditions. Users also gain insight into the behavior of auxiliary systems like feedwater pumps, vacuum ejectors, and lubrication systems that support turbine function but are often overlooked in classroom theory.
The growing focus on decarbonization and flexible energy systems is also shaping how educational steam turbine setups are used. Many programs now encourage students to develop and test innovative control strategies aimed at integrating turbines into grids dominated by intermittent renewable sources. These may include automated load-following controls, demand-response algorithms, or coordination of steam turbines with battery storage and solar PV.
Educational setups that include emissions monitoring modules help reinforce environmental awareness. Students can study how combustion conditions affect pollutants like CO₂ and NOₓ and test the impact of operational decisions on emission levels. Some setups go further by allowing simulation of post-combustion capture systems or exhaust heat utilization, supporting education in sustainable plant design.
In research institutions, educational steam turbines are often used to test low-boiling-point working fluids, organic Rankine cycles (ORC), and advanced sealing technologies. They also support experimental validation of CFD models, materials testing under steam erosion and corrosion, and investigation of startup optimization to reduce thermal shock and energy waste.
Finally, educational steam turbine setups promote teamwork and technical communication. Students working in lab groups must coordinate roles, follow technical procedures, analyze results, write reports, and present findings—skills directly transferable to industry environments. The blend of manual operation, data interpretation, digital tools, and system-level thinking makes these setups ideal platforms for developing competent, adaptable, and safety-conscious engineers ready for the challenges of modern energy systems.
General Estimations:
- Condensing Steam Turbine (Efficient Plant)
- Steam Consumption: 3 – 5 tons per MW
- Efficiency: 30 – 40%
- Conditions: High-pressure steam (e.g., 100 bar, 540°C)
- Back-Pressure Steam Turbine (CHP or Process Steam)
- Steam Consumption: 5 – 8 tons per MW
- Efficiency: Lower because some energy remains in the exhaust steam
- Used where process steam is needed (e.g., industrial applications)
- Older, Less Efficient Plants
- Steam Consumption: 7 – 10 tons per MW
- Efficiency: Below 30%
- Lower steam parameters and older technology result in higher consumption.
Formula-Based Approach:
For a rough estimate, we use:m˙=Pη⋅hsteam\dot{m} = \frac{P}{\eta \cdot h_{\text{steam}}}m˙=η⋅hsteamP
Where:
- m˙\dot{m}m˙ = Steam mass flow rate (kg/s)
- PPP = Power output (W)
- η\etaη = Turbine efficiency (typically 30-40%)
- hsteamh_{\text{steam}}hsteam = Enthalpy drop across the turbine (kJ/kg)
For high-efficiency plants with superheated steam (e.g., 100 bar, 540°C), the enthalpy drop is about 1,200 – 1,800 kJ/kg. Using 35% efficiency:m˙=1,000,0000.35×1,500≈1.9 kg/s=6.8 tons/hr\dot{m} = \frac{1,000,000}{0.35 \times 1,500} \approx 1.9 \, \text{kg/s} = 6.8 \, \text{tons/hr}m˙=0.35×1,5001,000,000≈1.9kg/s=6.8tons/hr
- Modern condensing turbine: 3-5 tons of steam per MW
- Back-pressure turbine (process use): 5-8 tons of steam per MW
- Older plants: 7-10 tons of steam per MW
Detailed Breakdown for a Modern Condensing Steam Turbine
A modern condensing steam turbine operates with high-efficiency parameters, typically using superheated steam at 100 bar and 540°C and exhausting into a vacuum (condenser pressure around 0.1 bar or lower). These conditions maximize the enthalpy drop across the turbine, improving efficiency.
Step 1: Steam Parameters and Enthalpy Calculation
From standard steam tables:
- At 100 bar, 540°C (superheated steam):
- Enthalpy h1h_1h1 ≈ 3,400 kJ/kg
- Entropy s1s_1s1 ≈ 6.6 kJ/kg·K
- At condenser pressure 0.1 bar (saturated steam at vacuum):
- Saturated liquid enthalpy hfh_fhf ≈ 191 kJ/kg
- Enthalpy of saturated vapor hgh_ghg ≈ 2,600 kJ/kg
- Isentropic expansion (using entropy s1=s2s_1 = s_2s1=s2):
- Assuming a quality of ~80-85%, we get an estimated enthalpy h2h_2h2 ≈ 2,200 kJ/kg
Step 2: Work Done by Steam
The enthalpy drop across the turbine is:Δh=h1−h2=3400−2200=1200 kJ/kg\Delta h = h_1 – h_2 = 3400 – 2200 = 1200 \text{ kJ/kg}Δh=h1−h2=3400−2200=1200 kJ/kg
Since 1 MW = 1,000 kJ/s, the required steam mass flow rate is:m˙=1,000η×Δh\dot{m} = \frac{1,000}{\eta \times \Delta h}m˙=η×Δh1,000
Assuming a turbine efficiency η\etaη of 35%:m˙=1,0000.35×1200=1,000420≈2.38 kg/s\dot{m} = \frac{1,000}{0.35 \times 1200} = \frac{1,000}{420} \approx 2.38 \text{ kg/s}m˙=0.35×12001,000=4201,000≈2.38 kg/s
Converting to tons per hour:2.38×3600/1000=8.57 tons/hour2.38 \times 3600 / 1000 = 8.57 \text{ tons/hour}2.38×3600/1000=8.57 tons/hour
Step 3: Typical Range
For a well-optimized modern plant, the actual steam consumption varies between:
- 3 to 5 tons per MW-hour (depending on efficiency and exact parameters).
Detailed Breakdown for a Back-Pressure Steam Turbine
A back-pressure steam turbine is commonly used in cogeneration (CHP) plants or industrial applications, where the exhaust steam is utilized for process heating instead of being condensed. The key difference from a condensing turbine is that the exhaust pressure is much higher, which means less energy is extracted per unit of steam.
Step 1: Steam Parameters and Enthalpy Calculation
Typical operating conditions:
- Inlet steam:
- Pressure = 40 bar
- Temperature = 450°C
- Enthalpy (h1h_1h1) ≈ 3,270 kJ/kg
- Entropy (s1s_1s1) ≈ 6.6 kJ/kg·K
- Exhaust steam (back-pressure for process use):
- Pressure = 5 bar (saturated)
- Enthalpy (h2h_2h2) ≈ 2,750 kJ/kg
Step 2: Work Done by Steam
The enthalpy drop across the turbine:Δh=h1−h2=3270−2750=520 kJ/kg\Delta h = h_1 – h_2 = 3270 – 2750 = 520 \text{ kJ/kg}Δh=h1−h2=3270−2750=520 kJ/kg
Since 1 MW = 1,000 kJ/s, the required steam mass flow rate is:m˙=1,000η×Δh\dot{m} = \frac{1,000}{\eta \times \Delta h}m˙=η×Δh1,000
Assuming a turbine efficiency (η\etaη) of 35%:m˙=1,0000.35×520=1,000182≈5.5 kg/s\dot{m} = \frac{1,000}{0.35 \times 520} = \frac{1,000}{182} \approx 5.5 \text{ kg/s}m˙=0.35×5201,000=1821,000≈5.5 kg/s
Converting to tons per hour:5.5×3600/1000=19.8 tons/hour5.5 \times 3600 / 1000 = 19.8 \text{ tons/hour}5.5×3600/1000=19.8 tons/hour
Step 3: Typical Range
For a back-pressure turbine, the actual steam consumption varies between:
- 5 to 8 tons per MW-hour, depending on the exhaust pressure and efficiency.
Key Differences Compared to a Condensing Turbine
Parameter | Condensing Turbine | Back-Pressure Turbine |
---|---|---|
Exhaust Pressure | Vacuum (~0.1 bar) | Medium (e.g., 3-10 bar) |
Steam Consumption | 3-5 tons/MWh | 5-8 tons/MWh |
Efficiency | Higher (~35-40%) | Lower (~25-35%) |
Use Case | Electricity generation | Cogeneration (CHP), process heat |
Detailed Breakdown for an Older, Less Efficient Steam Turbine
Older steam turbines, especially those used in low-efficiency power plants, operate with lower steam pressures and temperatures, leading to higher steam consumption per MW generated. These are typically found in older thermal power plants, smaller industrial units, or systems using saturated steam instead of superheated steam.
Step 1: Steam Parameters and Enthalpy Calculation
Typical operating conditions for an older plant:
- Inlet steam:
- Pressure = 20 bar
- Temperature = 350°C
- Enthalpy (h1h_1h1) ≈ 3,050 kJ/kg
- Exhaust steam (to condenser at vacuum, 0.1 bar):
- Enthalpy (h2h_2h2) ≈ 2,100 kJ/kg
Step 2: Work Done by Steam
The enthalpy drop across the turbine:Δh=h1−h2=3050−2100=950 kJ/kg\Delta h = h_1 – h_2 = 3050 – 2100 = 950 \text{ kJ/kg}Δh=h1−h2=3050−2100=950 kJ/kg
Since 1 MW = 1,000 kJ/s, the required steam mass flow rate is:m˙=1,000η×Δh\dot{m} = \frac{1,000}{\eta \times \Delta h}m˙=η×Δh1,000
Assuming a turbine efficiency (η\etaη) of 30% (lower than modern turbines):m˙=1,0000.30×950=1,000285≈3.5 kg/s\dot{m} = \frac{1,000}{0.30 \times 950} = \frac{1,000}{285} \approx 3.5 \text{ kg/s}m˙=0.30×9501,000=2851,000≈3.5 kg/s
Converting to tons per hour:3.5×3600/1000=12.6 tons/hour3.5 \times 3600 / 1000 = 12.6 \text{ tons/hour}3.5×3600/1000=12.6 tons/hour
Step 3: Typical Steam Consumption for Older Plants
For a low-efficiency plant, the actual steam consumption varies between:
- 7 to 10 tons per MW-hour, depending on factors like cycle degradation, turbine age, and operating conditions.
Comparison with Modern Turbines
Parameter | Modern Condensing Turbine | Older Condensing Turbine |
---|---|---|
Steam Pressure | ~100 bar | ~20 bar |
Steam Temperature | ~540°C | ~350°C |
Exhaust Pressure | Vacuum (~0.1 bar) | Vacuum (~0.1 bar) |
Steam Consumption | 3-5 tons/MWh | 7-10 tons/MWh |
Efficiency | 35-40% | ~25-30% |
Use Case | Modern power plants | Old/inefficient power plants |
How much electricity does a steam turbine generate
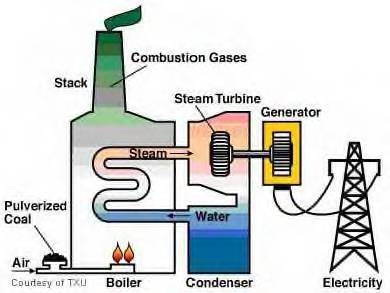
The electricity generated by a steam turbine depends on several factors, including steam flow rate, inlet steam conditions (pressure & temperature), turbine efficiency, and cycle configuration. Here’s a breakdown of how to estimate power generation.
1. Basic Power Calculation
The power output of a steam turbine can be estimated using the formula:P=m˙×η×ΔhP = \dot{m} \times \eta \times \Delta hP=m˙×η×Δh
Where:
- PPP = Power output (kW)
- m˙\dot{m}m˙ = Steam mass flow rate (kg/s)
- η\etaη = Turbine efficiency (typically 30-40%)
- Δh\Delta hΔh = Enthalpy drop across the turbine (kJ/kg)
Example Calculation
Let’s assume:
- Inlet steam: 100 bar, 540°C → h1=3400h_1 = 3400h1=3400 kJ/kg
- Exhaust (condenser at 0.1 bar): h2=2200h_2 = 2200h2=2200 kJ/kg
- Enthalpy drop: Δh=3400−2200=1200\Delta h = 3400 – 2200 = 1200Δh=3400−2200=1200 kJ/kg
- Efficiency: 35%
- Steam flow rate: 10 kg/s
P=10×0.35×1200P = 10 \times 0.35 \times 1200P=10×0.35×1200P=4,200 kW=4.2 MWP = 4,200 \text{ kW} = 4.2 \text{ MW}P=4,200 kW=4.2 MW
Thus, 10 kg/s of steam produces ~4.2 MW in an efficient steam turbine.
2. Typical Power Generation by Steam Flow Rate
Steam Flow Rate | Approx. Power Output |
---|---|
1 kg/s | 0.4 – 0.5 MW |
5 kg/s | 2 – 2.5 MW |
10 kg/s | 4 – 5 MW |
50 kg/s | 20 – 25 MW |
100 kg/s | 40 – 50 MW |
500 kg/s | 200 – 250 MW |
3. Power Generation for Different Turbine Types
Turbine Type | Typical Power Output per Ton of Steam |
---|---|
Condensing Turbine | 0.7 – 1.2 MW per ton of steam |
Back-Pressure Turbine | 0.3 – 0.6 MW per ton of steam |
Older, Inefficient Turbines | 0.2 – 0.5 MW per ton of steam |
4. Factors Affecting Power Output
- Steam Parameters: Higher pressure & temperature = more power
- Turbine Efficiency: Modern turbines (up to 40% efficiency) produce more power
- Back-Pressure vs. Condensing: Back-pressure turbines produce less power since they retain energy in the exhaust steam
- Reheat and Regeneration: Adding reheating & feedwater heaters improves efficiency
Detailed Breakdown for Power Generation by Steam Flow Rate
The power output of a modern condensing steam turbine depends on steam flow rate, inlet steam conditions, and turbine efficiency. Here, we analyze the electricity generated per unit of steam flow.
1. Steam Turbine Power Formula
P=m˙×η×ΔhP = \dot{m} \times \eta \times \Delta hP=m˙×η×Δh
Where:
- PPP = Power output (kW)
- m˙\dot{m}m˙ = Steam mass flow rate (kg/s)
- η\etaη = Turbine efficiency (typically 35-40%)
- Δh\Delta hΔh = Enthalpy drop across the turbine (kJ/kg)
2. Steam Conditions and Enthalpy Drop
Assume a modern condensing turbine with:
- Inlet steam: 100 bar, 540°C → h1=3400h_1 = 3400h1=3400 kJ/kg
- Exhaust steam (condenser pressure ~0.1 bar, saturated): h2=2200h_2 = 2200h2=2200 kJ/kg
- Enthalpy drop:
Δh=h1−h2=3400−2200=1200 kJ/kg\Delta h = h_1 – h_2 = 3400 – 2200 = 1200 \text{ kJ/kg}Δh=h1−h2=3400−2200=1200 kJ/kg
- Efficiency: 35% (η=0.35\eta = 0.35η=0.35)
Now, let’s calculate power for different steam flow rates.
3. Power Output at Different Steam Flow Rates
Steam Flow Rate (m˙\dot{m}m˙) | Power Output (MW) |
---|---|
1 kg/s | 0.42 MW |
5 kg/s | 2.1 MW |
10 kg/s | 4.2 MW |
20 kg/s | 8.4 MW |
50 kg/s | 21 MW |
100 kg/s | 42 MW |
500 kg/s | 210 MW |
This means that for every 1 kg/s of steam flow, a modern condensing turbine can generate approximately 0.4-0.5 MW of power.
4. Power Output Per Ton of Steam
To express in tons per hour (tph):1 ton/hour=10003600≈0.28 kg/s1 \text{ ton/hour} = \frac{1000}{3600} \approx 0.28 \text{ kg/s}1 ton/hour=36001000≈0.28 kg/s
Using the same efficiency and enthalpy drop:
Steam Flow Rate (tons/hour) | Power Output (MW) |
---|---|
1 tph | 0.12 MW |
5 tph | 0.6 MW |
10 tph | 1.2 MW |
50 tph | 6 MW |
100 tph | 12 MW |
500 tph | 60 MW |
So, a modern condensing steam turbine generates 0.7 – 1.2 MW per ton of steam, depending on efficiency and steam conditions.
5. Factors That Improve Power Output
- Higher inlet pressure & temperature → More enthalpy drop → More power
- Better turbine efficiency (modern turbines reach up to 40%)
- Reheat cycles → Additional expansion stages for increased power
- Lower condenser pressure → Higher enthalpy drop
Conclusion
- Condensing steam turbines generate about 0.7-1.2 MW per ton of steam.
- For every 1 kg/s of steam flow, around 0.4-0.5 MW is produced.
- Increasing steam pressure, temperature, and turbine efficiency leads to higher power generation.
Detailed Breakdown for Power Generation in a Back-Pressure Steam Turbine
A back-pressure steam turbine is widely used in cogeneration (CHP) systems, where the exhaust steam is used for process heating rather than being condensed. This results in lower power output per ton of steam compared to a condensing turbine because less energy is extracted.
1. Steam Turbine Power Formula
P=m˙×η×ΔhP = \dot{m} \times \eta \times \Delta hP=m˙×η×Δh
Where:
- PPP = Power output (kW)
- m˙\dot{m}m˙ = Steam mass flow rate (kg/s)
- η\etaη = Turbine efficiency (typically 25-35%)
- Δh\Delta hΔh = Enthalpy drop across the turbine (kJ/kg)
2. Steam Conditions and Enthalpy Drop
Assume a back-pressure turbine with:
- Inlet steam: 40 bar, 450°C → h1=3270h_1 = 3270h1=3270 kJ/kg
- Exhaust steam (5 bar, saturated): h2=2750h_2 = 2750h2=2750 kJ/kg
- Enthalpy drop:
Δh=h1−h2=3270−2750=520 kJ/kg\Delta h = h_1 – h_2 = 3270 – 2750 = 520 \text{ kJ/kg}Δh=h1−h2=3270−2750=520 kJ/kg
- Efficiency: 30% (η=0.30\eta = 0.30η=0.30)
Now, let’s calculate power for different steam flow rates.
3. Power Output at Different Steam Flow Rates
Steam Flow Rate (m˙\dot{m}m˙) | Power Output (MW) |
---|---|
1 kg/s | 0.16 MW |
5 kg/s | 0.8 MW |
10 kg/s | 1.6 MW |
20 kg/s | 3.2 MW |
50 kg/s | 8 MW |
100 kg/s | 16 MW |
500 kg/s | 80 MW |
This means that for every 1 kg/s of steam flow, a back-pressure turbine generates approximately 0.15-0.3 MW, significantly lower than a condensing turbine (0.4-0.5 MW per kg/s).
4. Power Output Per Ton of Steam
To express in tons per hour (tph):1 ton/hour=10003600≈0.28 kg/s1 \text{ ton/hour} = \frac{1000}{3600} \approx 0.28 \text{ kg/s}1 ton/hour=36001000≈0.28 kg/s
Using the same efficiency and enthalpy drop:
Steam Flow Rate (tons/hour) | Power Output (MW) |
---|---|
1 tph | 0.05 MW |
5 tph | 0.3 MW |
10 tph | 0.6 MW |
50 tph | 3 MW |
100 tph | 6 MW |
500 tph | 30 MW |
So, a back-pressure steam turbine generates 0.3 – 0.6 MW per ton of steam, depending on efficiency and steam conditions.
5. Why Does a Back-Pressure Turbine Generate Less Power?
- Higher exhaust pressure (5-10 bar instead of vacuum) → Less enthalpy drop
- Process steam retains energy for industrial use
- Used in CHP plants where both heat & power are needed
6. Comparison with a Condensing Turbine
Parameter | Condensing Turbine | Back-Pressure Turbine |
---|---|---|
Exhaust Pressure | Vacuum (~0.1 bar) | 3-10 bar |
Power Output per ton of steam | 0.7 – 1.2 MW | 0.3 – 0.6 MW |
Efficiency | Higher (~35-40%) | Lower (~25-35%) |
Best Use Case | Power plants | CHP & industrial heating |
7. Conclusion
- Back-pressure turbines generate less power (~0.3 – 0.6 MW per ton of steam) because the exhaust steam is still usable for heating.
- Every 1 kg/s of steam flow produces about 0.15-0.3 MW, depending on efficiency.
- Best for industrial applications where both heat and electricity are needed.
Detailed Breakdown for Power Generation in an Older, Less Efficient Steam Turbine
Older steam turbines, especially those in low-efficiency power plants, operate with lower steam pressures and temperatures, leading to higher steam consumption per MW. These turbines may also suffer from mechanical losses, outdated design, and poor steam quality, all of which reduce power output.
1. Steam Turbine Power Formula
P=m˙×η×ΔhP = \dot{m} \times \eta \times \Delta hP=m˙×η×Δh
Where:
- PPP = Power output (kW)
- m˙\dot{m}m˙ = Steam mass flow rate (kg/s)
- η\etaη = Turbine efficiency (typically 25-30% for older units)
- Δh\Delta hΔh = Enthalpy drop across the turbine (kJ/kg)
2. Steam Conditions and Enthalpy Drop
For an older condensing turbine (e.g., in a 1960s-era thermal power plant):
- Inlet steam: 20 bar, 350°C → h1=3050h_1 = 3050h1=3050 kJ/kg
- Exhaust steam (condenser at 0.1 bar): h2=2100h_2 = 2100h2=2100 kJ/kg
- Enthalpy drop:
Δh=h1−h2=3050−2100=950 kJ/kg\Delta h = h_1 – h_2 = 3050 – 2100 = 950 \text{ kJ/kg}Δh=h1−h2=3050−2100=950 kJ/kg
- Efficiency: 30% (η=0.30\eta = 0.30η=0.30)
3. Power Output at Different Steam Flow Rates
Steam Flow Rate (m˙\dot{m}m˙) | Power Output (MW) |
---|---|
1 kg/s | 0.28 MW |
5 kg/s | 1.4 MW |
10 kg/s | 2.8 MW |
20 kg/s | 5.6 MW |
50 kg/s | 14 MW |
100 kg/s | 28 MW |
500 kg/s | 140 MW |
This means that for every 1 kg/s of steam flow, an older condensing turbine generates approximately 0.25-0.3 MW, which is lower than a modern condensing turbine (0.4-0.5 MW per kg/s).
4. Power Output Per Ton of Steam
To express in tons per hour (tph):1 ton/hour=10003600≈0.28 kg/s1 \text{ ton/hour} = \frac{1000}{3600} \approx 0.28 \text{ kg/s}1 ton/hour=36001000≈0.28 kg/s
Using the same efficiency and enthalpy drop:
Steam Flow Rate (tons/hour) | Power Output (MW) |
---|---|
1 tph | 0.08 MW |
5 tph | 0.4 MW |
10 tph | 0.8 MW |
50 tph | 4 MW |
100 tph | 8 MW |
500 tph | 40 MW |
So, an older steam turbine generates only 0.2 – 0.5 MW per ton of steam, depending on its efficiency and condition.
5. Why Does an Older Steam Turbine Generate Less Power?
- Lower Steam Pressure & Temperature: Less energy per kg of steam
- Lower Efficiency (~25-30%) due to outdated design & wear
- Higher Mechanical & Steam Leakage Losses
- Less Advanced Turbine Staging & Control
6. Comparison with Modern & Back-Pressure Turbines
Parameter | Modern Condensing Turbine | Older Condensing Turbine | Back-Pressure Turbine |
---|---|---|---|
Exhaust Pressure | Vacuum (~0.1 bar) | Vacuum (~0.1 bar) | 3-10 bar |
Power Output per ton of steam | 0.7 – 1.2 MW | 0.2 – 0.5 MW | 0.3 – 0.6 MW |
Efficiency | 35-40% | 25-30% | 25-35% |
Best Use Case | Power plants | Older power plants | CHP & industrial heating |
7. Conclusion
- Older turbines generate less power (~0.2 – 0.5 MW per ton of steam) due to lower efficiency and steam conditions.
- Every 1 kg/s of steam flow produces about 0.25-0.3 MW, compared to 0.4-0.5 MW in modern turbines.
- Upgrading older turbines to higher-pressure, higher-temperature steam cycles significantly improves power generation.
Steam Turbine Propulsion System
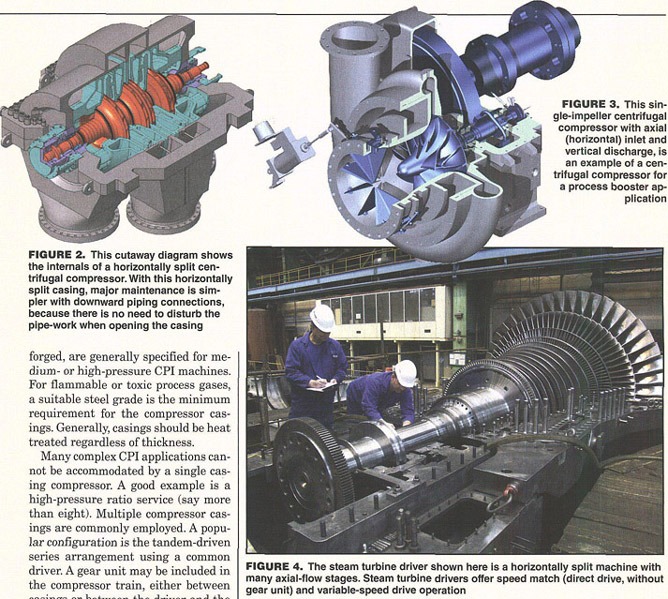
A steam turbine propulsion system is used in marine vessels, power plants, and industrial applications where mechanical power or electrical power is required. It converts thermal energy from steam into mechanical energy to drive propellers, generators, or pumps.
1. Working Principle of a Steam Turbine Propulsion System
The propulsion system follows a Rankine cycle with key stages:
- Boiler/Steam Generator
- Fuel (coal, oil, or nuclear energy) heats water to generate high-pressure steam.
- Steam Turbine
- High-pressure steam expands through turbine blades, converting thermal energy into rotational energy.
- Reduction Gearing (if needed)
- In marine propulsion, turbines operate at high RPM (3000–5000 RPM), while ship propellers require low RPM (80–250 RPM).
- Reduction gears match turbine speed to propeller speed.
- Propeller Shaft
- The rotating shaft transfers power to the propeller, creating thrust to move the vessel.
- Condenser
- Exhaust steam from the turbine is condensed into water using seawater cooling.
- This allows efficient reuse of water.
- Feed Pump
- The condensed water is pumped back into the boiler to complete the cycle.
2. Types of Steam Turbine Propulsion Systems
A. Direct Drive Steam Turbine
- High-speed turbines directly drive the propeller.
- Used in early warships and commercial vessels.
- Disadvantages: Inefficient at low speeds, complex control.
B. Geared Steam Turbine
- Uses reduction gears to slow turbine speed to match the propeller.
- More efficient than direct drive.
- Found in battleships, aircraft carriers, and merchant ships.
C. Turbo-Electric Propulsion
- Steam turbine drives an electric generator instead of a propeller shaft.
- The generated electricity powers electric motors connected to the propeller.
- Used in cruise ships, icebreakers, and submarines.
D. Nuclear Steam Turbine Propulsion
- Nuclear reactors produce heat to generate steam.
- Used in naval submarines and aircraft carriers.
- Advantage: Unlimited range and high endurance.
3. Advantages of Steam Turbine Propulsion
✅ Smooth & Vibration-Free Operation (vs. diesel engines)
✅ High Power Output – Suitable for large vessels
✅ Reliable & Durable – Less maintenance
✅ Can Use Multiple Fuel Types (coal, oil, nuclear)
4. Disadvantages of Steam Turbine Propulsion
❌ Lower Efficiency compared to diesel engines
❌ Slow Startup Time – Takes time to generate steam
❌ Bulky System – Requires space for boilers, turbines, and condensers
5. Applications of Steam Turbine Propulsion
🚢 Naval Ships – Aircraft carriers, destroyers, submarines
🛳 Cruise Ships & Icebreakers – Turbo-electric propulsion
⚓ LNG Carriers – Steam turbine propulsion for gas carriers
🔬 Nuclear-Powered Vessels – Submarines, aircraft carriers
1. Detailed Components of a Steam Turbine Propulsion System
A steam turbine propulsion system consists of multiple components working together to convert thermal energy from steam into mechanical power to drive a propeller. Below is a detailed breakdown of each component and its function.
1.1. Boiler/Steam Generator
- Function: Generates high-pressure steam by heating water.
- Types:
- Fire-tube boilers (smaller vessels, low pressure)
- Water-tube boilers (large ships, high pressure)
- Nuclear reactors (naval applications)
🔹 Example: A marine water-tube boiler produces steam at 60–100 bar and 500°C.
1.2. Steam Turbine
- Function: Converts thermal energy of steam into rotational mechanical energy.
- Types of Marine Steam Turbines:
- High-Pressure (HP) Turbine → First stage, extracts initial energy.
- Intermediate-Pressure (IP) Turbine → Second expansion stage.
- Low-Pressure (LP) Turbine → Final stage before exhaust.
🔹 Example: A large marine turbine operates at 3000–5000 RPM.
1.3. Reduction Gearing
- Function: Reduces high RPM from turbines to suitable propeller RPM (80–250 RPM).
- Types:
- Single-Reduction Gear → Used for moderate-speed turbines.
- Double-Reduction Gear → Used for high-speed turbines.
- Locked Train Reduction Gear → Used in warships for efficiency.
🔹 Example: A Naval Aircraft Carrier may use double-reduction gears to reduce turbine speed (3500 RPM) to propeller speed (150 RPM).
1.4. Shafting System
- Function: Transfers power from turbine to propeller.
- Components:
- Thrust Bearings → Absorb axial thrust from propeller.
- Line Shaft Bearings → Support long shaft length.
- Stern Tube & Seals → Prevents water ingress.
🔹 Example: Large naval ships use a hollow shaft to reduce weight.
1.5. Propeller
- Function: Converts rotational energy into thrust.
- Types:
- Fixed-Pitch Propeller (FPP) → Simple, efficient, but non-adjustable.
- Controllable-Pitch Propeller (CPP) → Adjustable blades for speed control.
🔹 Example: A cruise ship propeller has a diameter of 5–9 meters and operates at 80–150 RPM.
1.6. Condenser
- Function: Converts exhaust steam back into water by cooling it with seawater.
- Types:
- Surface Condenser → Used in large ships, most common.
- Jet Condenser → Simple, but less efficient.
🔹 Example: A surface condenser can handle 100+ tons of steam per hour.
1.7. Feedwater System
- Function: Pumps and preheats condensed water before returning to the boiler.
- Components:
- Deaerator → Removes dissolved gases to prevent corrosion.
- Feedwater Pump → Pressurizes water for boiler.
- Economizer → Preheats water using exhaust gases.
🔹 Example: A high-pressure feed pump operates at 150–200 bar.
1.8. Control & Automation System
- Function: Monitors steam flow, pressure, temperature, and turbine speed.
- Key Features:
- Governor System → Controls turbine speed.
- Emergency Shutdown (ESD) → Protects against failures.
- Remote Monitoring → Used in modern vessels for efficiency tracking.
🔹 Example: Modern steam turbine ships use PLC-based automation systems for real-time monitoring.
Conclusion
- A steam turbine propulsion system consists of boilers, turbines, reduction gears, shafting, and condensers working in a cycle.
- Efficiency is improved through gearing, preheating systems, and automation.
- Used in naval ships, cruise liners, LNG carriers, and nuclear submarines.
2. Detailed Breakdown of Steam Turbine Propulsion System Types
There are several different types of steam turbine propulsion systems used in various applications such as naval ships, commercial vessels, and industrial plants. Below is a detailed exploration of each type and its unique advantages and applications.
2.1. Direct Drive Steam Turbine Propulsion
- Function: The steam turbine directly drives the propeller, converting thermal energy into mechanical energy without the need for a reduction gearbox.
- Applications: Primarily used in older naval ships and smaller vessels where efficiency is not as critical.
- Design:
- High-Speed Turbine: These turbines operate at 3000-5000 RPM, which is high compared to the required low RPM of the propeller (typically 80-250 RPM).
- Disadvantages:
- Inefficiency at lower speeds: The turbine must operate at a constant high speed, which leads to inefficiency when the ship is moving at lower speeds.
- Vibration & noise: The high rotational speeds can lead to vibrations and noise.
🔹 Example: Early 20th-century naval vessels, such as WWI destroyers, used direct drive turbines.
2.2. Geared Steam Turbine Propulsion
- Function: Uses a reduction gear to lower the RPM of the turbine to match the optimal RPM of the propeller.
- Applications: Commonly found in modern naval ships, large commercial vessels, and passenger ships.
- Design:
- Turbine Types: Consists of high-pressure (HP), intermediate-pressure (IP), and low-pressure (LP) turbines arranged in stages.
- Reduction Gears: Reduces the turbine’s high RPM (3000-5000 RPM) down to the desired propeller speed (80-250 RPM).
- Advantages:
- Improved efficiency at various speeds, especially when vessels operate at cruising speed.
- Better fuel efficiency: Suitable for larger ships, allowing for a more balanced operation.
- Disadvantages:
- Mechanical complexity: Requires complex gearing systems.
- Maintenance: More moving parts lead to more maintenance and potential failure points.
🔹 Example: Royal Navy Aircraft Carriers, like the HMS Ark Royal, employ geared steam turbines for efficient propulsion.
2.3. Turbo-Electric Propulsion
- Function: In turbo-electric systems, the steam turbine drives an electric generator, which then powers an electric motor connected to the propeller shaft.
- Applications: Used in large cruise ships, icebreakers, and submarines.
- Design:
- Steam-to-Electric Conversion: The steam turbine drives an alternator that converts mechanical energy into electrical power.
- Electric Motors: The electricity is used to power electric propulsion motors connected to the propeller.
- Advantages:
- Flexibility: Multiple electric motors can be used for better maneuverability and speed control.
- Better distribution of power: Allows the use of multiple smaller motors, which increases redundancy.
- Reduced mechanical complexity: Fewer direct mechanical linkages between turbine and propeller.
- Disadvantages:
- Lower efficiency compared to direct drive or geared systems.
- Complexity and cost: Higher initial cost and sophisticated control systems.
🔹 Example: Modern Cruise Ships like the Oasis of the Seas use turbo-electric propulsion for improved fuel efficiency and better control of the vessel’s motion.
2.4. Nuclear Steam Turbine Propulsion
- Function: Uses the heat generated by nuclear reactors to produce steam, which then powers a steam turbine to propel the vessel.
- Applications: Primarily used in naval submarines, aircraft carriers, and large icebreakers.
- Design:
- Nuclear Reactor: The heat generated from a nuclear fission process in a pressurized reactor or boiling water reactor produces high-pressure steam.
- Turbine Stages: The steam expands through HP, IP, and LP turbines to generate power.
- Advantages:
- Unrestricted range: Nuclear propulsion allows for virtually unlimited endurance, as the ship can operate for months without refueling.
- Energy efficiency: High-efficiency conversion of nuclear heat to mechanical power.
- Stealth: Submarines with nuclear propulsion do not need to surface frequently, enhancing stealth capabilities.
- Disadvantages:
- High cost: Nuclear reactors and associated infrastructure are expensive.
- Complexity: Requires highly skilled personnel for operation and maintenance.
- Environmental concerns: Waste disposal and safety concerns regarding radioactive materials.
🔹 Example: The USS Nimitz and other nuclear-powered aircraft carriers rely on nuclear steam turbines for propulsion.
2.5. Integrated Electric Propulsion (IEP)
- Function: A more advanced system where electric motors and gas turbines are integrated to drive the propellers, often using steam turbines for auxiliary power generation.
- Applications: Used in modern naval vessels, such as destroyers and corvettes.
- Design:
- Steam Turbine Drives Generator: The steam turbine generates electrical power, which is fed to electric motors connected to the propellers.
- Hybrid Power Sources: Uses a combination of gas turbines, diesel engines, and electric generators to meet varying power demands.
- Advantages:
- Fuel efficiency and operational flexibility.
- Reduced emissions: With the potential to switch between fuel sources for operational efficiency.
- Better power management: By integrating gas and steam turbines into the propulsion system.
- Disadvantages:
- Complex control systems: Requires advanced software for optimal power management.
- High cost: More expensive due to the integration of multiple power sources.
🔹 Example: The Royal Navy’s Type 45 Destroyers use an integrated electric propulsion system.
Conclusion
The steam turbine propulsion system is versatile and has been adapted over time to fit the needs of different maritime industries, ranging from military applications to commercial vessels. Each system—whether direct drive, geared turbine, turbo-electric, or nuclear-powered—offers unique advantages and is suited to particular vessel types and operational requirements.
3. Comparison of Steam Turbine Propulsion System with Diesel and Gas Turbine Propulsion
Steam turbines, diesel engines, and gas turbines are the primary propulsion systems used in modern ships, each offering different advantages depending on the vessel’s size, purpose, and operational requirements. Below is a detailed comparison of these three systems.
3.1. Steam Turbine Propulsion vs. Diesel Engine Propulsion
Efficiency
- Steam Turbines:
- Lower thermal efficiency: Steam turbines generally have lower efficiency compared to modern diesel engines, especially at low load.
- Best at higher loads: Steam turbines are more efficient at constant high speeds, which is why they are often used in large ships like aircraft carriers or merchant ships that operate at relatively constant cruising speeds.
- Diesel Engines:
- Higher thermal efficiency: Diesel engines are typically more efficient than steam turbines, with efficiency often ranging from 40-50%.
- Flexible operation: Diesel engines perform well at varying loads and speeds, making them ideal for vessels that require flexibility in their power output.
Power-to-Weight Ratio
- Steam Turbines:
- Heavy and bulky: Steam turbines are relatively heavy and require more space due to the size of the boiler, condenser, and auxiliary systems.
- Diesel Engines:
- Compact and lighter: Diesel engines are more compact and provide a higher power-to-weight ratio, making them ideal for smaller vessels or for those that need more space for cargo.
Maintenance and Operating Costs
- Steam Turbines:
- Higher maintenance costs: Steam turbines require frequent maintenance, especially for the high-temperature steam components. Components such as boilers and condensers need constant monitoring.
- Longer operational life: When maintained well, steam turbines can run for decades, especially in marine applications.
- Diesel Engines:
- Lower maintenance requirements: Diesel engines require less frequent maintenance than steam turbines and have fewer components that wear out over time.
- Higher fuel consumption: Diesel engines burn fuel directly, making them less efficient compared to steam turbines that utilize a multi-stage conversion process (fuel to heat to steam to mechanical power).
Startup Time
- Steam Turbines:
- Longer startup time: It takes time to heat up the boiler and generate steam, which means steam turbines are slower to start. This can be a disadvantage in situations that require rapid acceleration.
- Diesel Engines:
- Quick startup: Diesel engines start almost immediately, making them ideal for applications that need to reach full power quickly (e.g., in smaller vessels or ships in harbor).
Operational Flexibility
- Steam Turbines:
- Limited at low speeds: Steam turbines tend to be less efficient at low speeds and are less versatile when handling variable speeds.
- More suitable for constant high-speed operation: Steam turbines are great for ships that cruise at a consistent speed, such as military ships, cruise liners, and large merchant vessels.
- Diesel Engines:
- Good at varying speeds: Diesel engines are ideal for vessels that need to frequently change speed or operate in variable conditions, such as fishing boats, small cargo ships, and tugs.
3.2. Steam Turbine Propulsion vs. Gas Turbine Propulsion
Efficiency
- Steam Turbines:
- More efficient at steady high loads: As mentioned earlier, steam turbines perform well when the ship operates at a steady cruising speed.
- Lower thermal efficiency at variable speeds: At lower loads or speeds, steam turbines are less efficient compared to gas turbines.
- Gas Turbines:
- Higher thermal efficiency at high speeds: Gas turbines are highly efficient at higher speeds and are used in applications where maximum power and speed are necessary, such as in military vessels.
- Lower efficiency at lower loads: Gas turbines experience significant efficiency drops when operating at lower loads, making them less ideal for vessels that spend a lot of time at cruising or low speeds.
Power-to-Weight Ratio
- Steam Turbines:
- Larger and bulkier: As mentioned before, steam turbines are large and require considerable space for the boiler and steam plant components.
- Gas Turbines:
- Lightweight and compact: Gas turbines have a higher power-to-weight ratio than steam turbines, making them more suitable for vessels where space and weight are limited, such as naval destroyers, high-speed ferries, and fast patrol boats.
Startup Time
- Steam Turbines:
- Longer startup: The time required to generate steam means that steam turbines are slower to start, which is a disadvantage in situations requiring rapid movement.
- Gas Turbines:
- Very fast startup: Gas turbines can start almost instantly and reach full power quickly, which is why they are used in military applications, such as jet engines and naval ships that require high-speed performance.
Fuel Consumption
- Steam Turbines:
- Fuel flexibility: Steam turbines can use a variety of fuels (coal, oil, nuclear energy) to produce steam, which makes them flexible in terms of fuel choice, particularly in coal-fired power plants.
- Gas Turbines:
- Higher fuel efficiency than steam turbines but are typically optimized for liquid fuels (diesel, aviation gas, or even natural gas). Gas turbines are highly optimized for speed and power rather than fuel variety.
Applications
- Steam Turbines:
- Best suited for large vessels with steady operational profiles, such as aircraft carriers, cruise ships, merchant vessels, and oil tankers. They are also ideal for nuclear-powered ships, where fuel is less of a concern.
- Gas Turbines:
- Used in military applications and fast vessels like naval destroyers, frigates, and high-speed ferries. They are ideal for applications that require speed, maneuverability, and rapid response.
3.3. Key Takeaways
Aspect | Steam Turbine | Diesel Engine | Gas Turbine |
---|---|---|---|
Efficiency | Lower, best at steady high speeds | Higher, flexible at various speeds | High, but drops at lower speeds |
Power-to-Weight | Heavy and bulky | Compact and light | Very lightweight and compact |
Startup Time | Slow (requires time to generate steam) | Fast (instant power on startup) | Very fast startup |
Fuel Type | Flexible (coal, oil, nuclear) | Diesel, light fuels | Typically liquid fuels (diesel, natural gas) |
Maintenance | High (boilers, condensers, etc.) | Moderate (fewer moving parts) | High (complex machinery) |
Best for | Large, steady-speed vessels (aircraft carriers) | Small to medium vessels (fishing boats, tugs) | High-speed and military applications |
Conclusion
Each propulsion system has its strengths and weaknesses depending on the type of vessel and operational needs.
- Steam turbines excel in large, steady-speed ships with a constant operational profile.
- Diesel engines are more suitable for flexible, medium-to-small vessels requiring lower fuel consumption and faster startups.
- Gas turbines are perfect for high-speed vessels like naval ships and fast ferries that prioritize rapid acceleration and compact design.
Steam Turbine for Educational Purposes
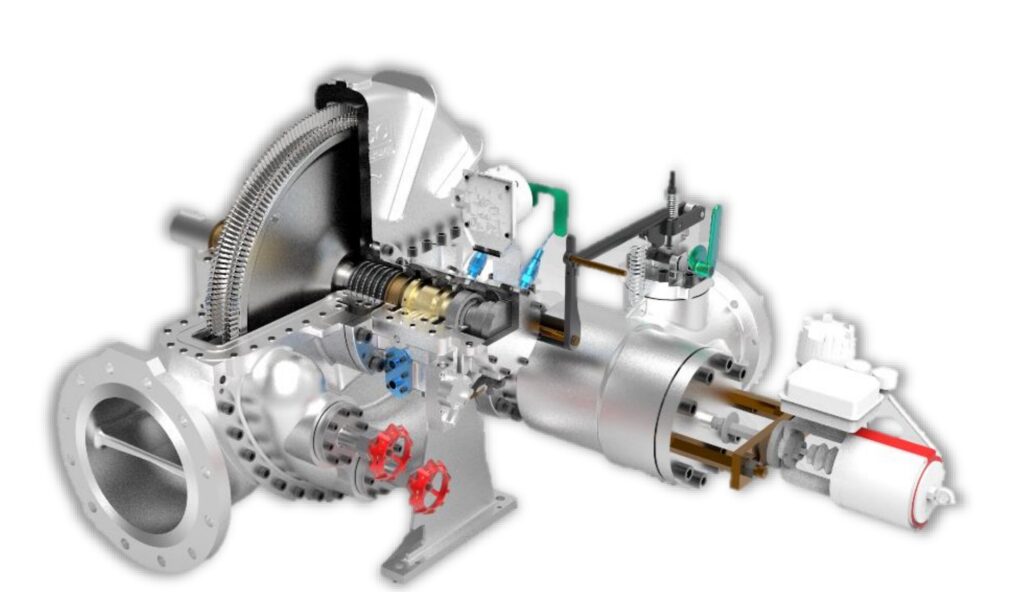
Steam turbines are a great topic for educational purposes, as they offer a practical application of various scientific principles, such as thermodynamics, fluid mechanics, and energy conversion. Below is a detailed explanation of how steam turbines work and how they can be used in an educational setting.
1. Introduction to Steam Turbines for Education
A steam turbine is a device that converts thermal energy from steam into mechanical energy. In a steam turbine, high-pressure steam is directed over blades attached to a rotating shaft, causing it to spin and create mechanical power. This mechanical power can then be used to generate electricity or provide propulsion, depending on the system.
Key Concepts to Understand in an Educational Setting:
- Thermodynamics: The study of energy transformations, especially how heat energy is converted into mechanical work.
- Energy Conversion: How heat energy in steam is converted into rotational mechanical energy.
- Fluid Mechanics: The study of steam flow, pressure, and velocity as it interacts with the blades of the turbine.
- Efficiency: Understanding how efficiently a steam turbine converts thermal energy into mechanical power.
2. Steam Turbine Working Principle
The operation of a steam turbine is based on expansion of steam. Here’s a step-by-step explanation that can be used for educational purposes:
- Heating Water: Water is heated in a boiler until it turns into high-pressure steam.
- Steam Expansion: The high-pressure steam is directed into the nozzle of the steam turbine, where it is accelerated.
- Blade Rotation: The high-speed steam passes through multiple stages of blades, where it loses pressure and transfers kinetic energy to the blades.
- Mechanical Power: The blades are attached to a shaft, and as the steam pushes against them, it causes the shaft to rotate, producing mechanical power.
- Exhaust Steam: After passing through the turbine, the steam exits as low-pressure steam and can be condensed back into water for reuse (in a closed-loop system).
3. Basic Components of a Steam Turbine for Educational Demonstrations
For educational purposes, you can explore the following key components:
- Boiler: Heats water to produce steam.
- Purpose in Education: Demonstrates how heat is used to generate energy in a system.
- Turbine Blades: Rotating blades that convert the kinetic energy of steam into mechanical work.
- Purpose in Education: Demonstrates the conversion of energy from one form to another (from heat energy to mechanical energy).
- Condenser: Condenses the exhaust steam back into water.
- Purpose in Education: Demonstrates energy conservation in a closed system and the concept of heat exchange.
- Governor: Regulates the turbine’s speed.
- Purpose in Education: Teaches the concept of feedback mechanisms in maintaining a constant system performance.
- Generator (optional): Converts mechanical energy into electrical energy.
- Purpose in Education: Allows students to learn about electrical generation from mechanical motion.
4. Educational Activities with Steam Turbines
4.1. Model Demonstrations
Building or using a steam turbine model can help students visualize the process. Small models can be bought or made in the classroom to demonstrate basic principles.
- Model Steam Turbine Kit: A small, simple steam turbine kit can help students understand how steam flow creates rotational motion. You can use hot water and simple parts like a small turbine wheel to demonstrate basic operations.
- Demonstrating Power Output: You could show how the turbine’s rotational speed increases with higher steam pressure or flow rate, illustrating concepts of energy and work.
4.2. Thermodynamic Cycle
Introduce students to the Rankine Cycle, which is the fundamental thermodynamic cycle for steam turbines.
- Boiler (heat addition) → Turbine (work output) → Condenser (heat rejection) → Pump (work input).
- Use diagrams to show the heat exchange, pressure, and temperature changes throughout the cycle.
5. Steam Turbine Efficiency and Applications
Discuss the efficiency of steam turbines in real-world applications. You can show the importance of heat-to-power conversion and how it relates to thermodynamics in a more practical sense.
- Efficiency Factors: Discuss factors that affect turbine efficiency, such as steam pressure, temperature, and the design of the turbine blades.
- Applications in Real Life: Explain how large steam turbines are used in power plants, ships, and industries for electricity generation and propulsion. You can introduce examples like nuclear-powered submarines, coal-fired power plants, or hydroelectric dams that often use steam turbines.
Discussion Points for Students:
- Why is steam used in turbines? Discuss the properties of steam (energy capacity, pressure, and temperature) that make it ideal for mechanical work.
- How does steam pressure affect power generation? Introduce the concept of pressure and volume in the Rankine Cycle.
- Energy Efficiency: Ask students to calculate the efficiency of a steam turbine and understand the loss of energy at various stages of the cycle.
6. Hands-On Projects & Demonstrations for Students
6.1. Simple Steam Turbine Model
Create a simple steam turbine using household materials or a DIY kit. For example:
- Materials: A small metal turbine, tubing, and a heat source (like a kettle or electric heater).
- Objective: Students can heat water to produce steam, which will turn the turbine, demonstrating energy transfer.
6.2. Rankine Cycle Simulation
Use a computer simulation or online calculator to show the Rankine Cycle at different operating points. Tools like Thermodynamic Property Charts (Mollier or T-s diagrams) can show students how heat energy is converted into work in a steam turbine system.
7. Safety Considerations
When working with steam turbines, safety is critical. If students are involved in building models or experiments with heat sources, emphasize:
- Handling hot water or steam: Steam can cause burns or injuries, so proper care must be taken when working with pressurized or hot steam.
- Proper equipment: Ensure that pressure gauges, safety valves, and other controls are in place to prevent accidents.
Conclusion
Steam turbines offer an engaging way to teach students about energy conversion, thermodynamics, and mechanical engineering principles. From small hands-on models to theoretical concepts like the Rankine Cycle, steam turbines provide rich material for interactive learning and are relevant to many real-world applications. This makes them an ideal subject for educational settings ranging from high school science classes to university engineering programs.
1. Introduction to Steam Turbines for Education (Continued)
Steam turbines are a fascinating and valuable topic for educational purposes because they integrate several scientific disciplines, including thermodynamics, fluid dynamics, mechanical engineering, and energy conversion. Understanding how steam turbines operate can give students insights into how power plants, ships, and even aerospace systems generate energy.
1.1. Basic Concept of a Steam Turbine
A steam turbine is a device that converts thermal energy from steam into mechanical energy through a series of blades and stages. The general concept of a steam turbine can be broken down into:
- Energy Input: Heat is used to convert water into steam. The steam is generated under high pressure in a boiler.
- Energy Conversion: The high-pressure steam flows into the turbine, where it hits blades mounted on a shaft. The force of the steam causes the blades to rotate, turning the shaft.
- Mechanical Power Output: The rotating shaft is connected to a generator or propeller, which either generates electricity or propels a ship, airplane, or other machinery.
1.2. Components of a Steam Turbine
To better understand the working of a steam turbine, it is important to know its key components. Here are the basic parts involved in the operation of a steam turbine:
- Boiler:
- Function: Heats water to produce steam.
- Educational Purpose: Students can learn how thermal energy is transferred to water and how steam is generated.
- Learning Opportunity: Demonstrates heat transfer and phase changes (liquid to gas).
- Turbine Blades:
- Function: The high-pressure steam flows through these blades, transferring its energy to the shaft.
- Educational Purpose: This is where kinetic energy from steam is converted into rotational mechanical energy.
- Learning Opportunity: Shows how fluid dynamics and force transfer work in machinery.
- Turbine Shaft:
- Function: The shaft rotates as steam moves through the blades, producing mechanical work.
- Educational Purpose: Students can observe how torque and rotational motion are generated.
- Learning Opportunity: Helps understand the conversion of force into rotational motion.
- Condenser:
- Function: Cool the steam after it has passed through the turbine and turns it back into water.
- Educational Purpose: Demonstrates how energy is released from steam and condensed into water.
- Learning Opportunity: Teach about heat rejection, phase change, and closed-loop systems.
- Governor:
- Function: Controls the turbine’s rotational speed.
- Educational Purpose: Students can learn about feedback control and how to maintain a stable operation.
- Learning Opportunity: Demonstrates the importance of control systems in mechanical engineering.
1.3. Educational Models of Steam Turbines
To make the study of steam turbines more interactive and engaging, students can be introduced to small-scale models. These models help demonstrate the key principles without the complexity of full-scale turbines.
- Miniature Steam Turbine Kits: These kits can be assembled in the classroom and powered by a small heat source like hot water or steam from a kettle. The students can watch how steam flows over blades and produces rotational motion.
- DIY Steam Engine: You can use materials like a small motor or even a model boiler to simulate how steam turns a turbine. This can be done with simple materials, such as a can for a boiler and pins or blades for the turbine.
- Steam-Driven Mini Generator: If available, a small turbine connected to a generator can show how steam power is used to generate electricity, allowing students to see energy conversion in real-time.
1.4. Energy Conversion in a Steam Turbine
The principle of energy conversion is central to understanding how steam turbines work. The energy input to the turbine comes in the form of heat energy provided by steam, which is a high-energy gas. This steam is used to do work by rotating the turbine blades.
Energy Conversion Process:
- Thermal Energy (Heat): Water is heated in the boiler, causing it to vaporize into steam.
- Kinetic Energy (Steam Movement): The high-pressure steam flows through nozzles and blades. The energy from the steam’s movement pushes the turbine blades, creating kinetic energy.
- Mechanical Energy: The kinetic energy of the steam is converted into mechanical energy through the rotation of the turbine shaft.
- Electricity (if applicable): If the turbine is connected to a generator, the mechanical energy of the rotating shaft is converted into electrical energy.
1.5. Steam Turbine Working Cycle (Rankine Cycle)
The Rankine Cycle is the thermodynamic cycle that is most commonly used to describe the operation of steam turbines. This cycle is an important part of thermodynamics and is a great way to explain the heat-to-work conversion in turbines.
Key Stages of the Rankine Cycle:
- Boiler (Heat Addition): Heat is added to water, converting it into high-pressure steam.
- Turbine (Work Extraction): Steam expands in the turbine, transferring its energy to the turbine blades, which rotate and do work.
- Condenser (Heat Rejection): The steam is cooled and condensed back into liquid water, releasing the heat energy to the surroundings.
- Pump (Work Input): A pump is used to increase the pressure of the liquid water before it enters the boiler to be heated again.
1.6. Applications of Steam Turbines in Education
Understanding the practical applications of steam turbines can help students appreciate their significance and broaden their knowledge. Steam turbines are used in a variety of real-world applications that demonstrate the transfer of energy from heat to work:
- Power Plants: Steam turbines are commonly used in both fossil fuel (coal, oil, natural gas) and nuclear power plants. These turbines convert heat energy into mechanical energy to drive generators that produce electricity.
- Marine Propulsion: Large ships, including aircraft carriers, merchant vessels, and cruise liners, often use steam turbines for propulsion. In this case, the mechanical energy produced by the turbine is used to rotate propellers, propelling the ship forward.
- Industry: In some industrial applications, steam turbines drive large machines or compressors used in manufacturing processes.
1.7. Conclusion
The steam turbine is a versatile device that not only helps us understand basic principles of energy conversion but also links multiple scientific concepts into practical applications. Whether it’s producing electricity in power plants, propelling ships, or driving industrial machinery, steam turbines are central to many technological fields.
In an educational setting, steam turbines provide an excellent way to teach concepts like thermodynamics, energy conversion, fluid dynamics, and mechanical work. By building models, using simulations, and studying real-world applications, students can gain hands-on experience and deepen their understanding of energy systems.
Next Steps for Educational Projects
- Classroom Experiment: Set up a small steam turbine model and let students control variables like steam pressure and blade angles to see how these affect performance.
- Rankine Cycle Simulation: Use software or apps that simulate the Rankine Cycle to show students the relationship between temperature, pressure, and energy conversion.
- Field Trip: Arrange a visit to a power plant or ship with steam turbines to show students how turbines are used in the real world.
2. Steam Turbine Working Principle
The working principle of a steam turbine revolves around converting the thermal energy of steam into mechanical energy, which can then be used for various applications such as generating electricity, propulsion in ships, and in industrial machinery. Here’s a deeper dive into how this process works, with a focus on thermodynamics and fluid dynamics:
2.1. Steam Generation (Boiler Phase)
Before the steam turbine can operate, high-pressure steam needs to be generated. This step involves heating water in a boiler to convert it into steam. Here’s what happens:
- Water Heating: Water is fed into a boiler, which is typically powered by burning fossil fuels (coal, oil, or natural gas) or by using nuclear energy. In some systems, solar or geothermal energy may also be used.
- Phase Change: As heat is applied, the water absorbs thermal energy, increasing its temperature and pressure until it reaches its boiling point. At this point, it vaporizes into steam.
- Superheating: The steam can be further superheated to increase its energy, which makes the steam more effective at driving the turbine. Superheated steam has a higher temperature and energy content, allowing for more efficient energy transfer.
2.2. Steam Expansion (Turbine Phase)
Once the steam is generated, it is directed into the turbine where the real work of energy conversion occurs. The process is based on the expansion of steam as it passes through the turbine blades.
- Nozzle and Pressure Drop: The high-pressure steam enters the turbine through a nozzle, which accelerates the steam, causing it to move at very high speeds. As steam moves through the nozzle, it undergoes a pressure drop and a corresponding increase in velocity.
- Blade Interaction: The high-speed steam enters multiple stages of blades attached to a rotating shaft. The turbine blades are designed to convert the kinetic energy of the steam into rotational motion. As steam hits the blades, the pressure of the steam decreases, transferring its energy to the blades.
- Mechanical Energy: The rotating blades turn a shaft, converting the kinetic energy of the steam into mechanical energy. This rotation can either drive a generator to produce electricity or provide mechanical power to drive a pump, fan, or other machinery.
- Multi-Stage Expansion: In most turbines, steam expands over multiple stages of blades, known as stages of the turbine, to extract as much energy as possible. Each stage reduces the pressure and temperature of the steam, while the blades convert more energy into mechanical work.
2.3. Exhaust Steam and Heat Rejection
Once the steam has passed through the turbine, it is at a lower pressure and temperature and is no longer useful for generating work. This exhaust steam is then passed to a condenser, where it is cooled and condensed back into water for reuse.
- Condenser Operation: The steam entering the condenser is cooled by water or air, causing it to lose energy and return to its liquid state. This liquid water is then pumped back into the boiler to be reheated, completing the closed-loop cycle.
- Energy Rejection: The process of cooling the steam and condensing it back into water involves the rejection of heat to the environment. The amount of heat rejected is a key factor in determining the efficiency of the turbine and the overall system.
2.4. The Rankine Cycle in Steam Turbine Operation
A fundamental thermodynamic cycle that describes the operation of a steam turbine is the Rankine Cycle. The Rankine Cycle involves the following key processes:
- Heat Addition (Boiler): Heat is added to the water in the boiler, causing it to convert into steam at high pressure.
- Work Extraction (Turbine): The high-pressure steam expands in the turbine, where it performs work (either generating electricity or mechanical work).
- Heat Rejection (Condenser): The steam is cooled and condensed back into water in the condenser, rejecting waste heat to the environment.
- Work Input (Pump): The liquid water is pumped back into the boiler, increasing its pressure and preparing it for reheating. The pump does this with the smallest amount of energy input, as the water is already at a low temperature and pressure.
In a perfect Rankine Cycle, the goal is to maximize work output and minimize the energy losses due to heat rejection and inefficiencies in the components.
2.5. Thermodynamic Efficiency of a Steam Turbine
The efficiency of a steam turbine is influenced by several factors, including the temperature and pressure of the steam, as well as how effectively the energy is converted into mechanical power.
- Thermal Efficiency: The thermal efficiency of the Rankine Cycle is affected by the difference in temperature between the boiler (where steam is generated) and the condenser (where heat is rejected). The greater the temperature difference, the more efficient the cycle.
- Isentropic Efficiency: This refers to the idealized thermodynamic process where the steam undergoes expansion in the turbine without any entropy increase (i.e., without any energy loss). In reality, steam turbines cannot achieve perfect isentropic efficiency due to losses like friction, heat losses, and turbulence.
- Improvements to Efficiency: Steam turbine efficiency can be improved by using higher pressures and higher temperatures of steam, and by incorporating reheat cycles, where steam is reheated after partial expansion to restore its energy.
2.6. Mechanical Power Output
The mechanical power output of a steam turbine depends on several variables, including steam flow rate, pressure, and temperature:
- Power Equation: The mechanical power produced by the steam turbine is given by:P=m˙×hinlet−houtletP = \dot{m} \times h_{\text{inlet}} – h_{\text{outlet}}P=m˙×hinlet−houtletWhere:
- PPP is the mechanical power output.
- m˙\dot{m}m˙ is the mass flow rate of steam (in kg/s).
- hinleth_{\text{inlet}}hinlet and houtleth_{\text{outlet}}houtlet are the enthalpies of the steam at the turbine’s inlet and outlet (in kJ/kg), which depend on the steam pressure and temperature.
The higher the mass flow rate of steam and the greater the difference in enthalpy between the steam entering and exiting the turbine, the higher the mechanical power output.
2.7. Power Conversion to Electricity (Generator)
If the turbine is connected to a generator, the mechanical energy from the rotating shaft is converted into electrical energy:
- Generator Operation: The rotating shaft turns the rotor inside the generator, which produces a magnetic field. This induces an electrical current in the surrounding stator coils, thus generating electricity.
- Electricity Output: The electrical output of a steam turbine generator depends on the mechanical power being transferred to the generator and the design of the generator itself.
- Grid Connection: The generated electrical power is then transmitted to the electrical grid, providing power for homes, businesses, and industries.
Conclusion of Steam Turbine Working Principle
In summary, steam turbines operate on the principle of converting thermal energy from steam into mechanical energy through the expansion of steam in a series of rotating blades. This mechanical energy can then be used to generate electricity, drive machinery, or propel vehicles.
By understanding the basic working principles of steam turbines, including their thermodynamic cycles, efficiency, and power conversion processes, students and engineers can design, optimize, and improve steam turbine systems for various industrial and energy applications.
3. Types of Steam Turbines and Their Applications (Continued)
Steam turbines come in different configurations depending on the application, operating conditions, and desired efficiency. Understanding the various types of steam turbines is crucial for determining which design is most suitable for specific applications. Here we explore the main types of steam turbines, their characteristics, and their typical uses.
3.1. Types of Steam Turbines
- Impulse Turbine
- Working Principle: In an impulse turbine, steam is expanded through nozzles that convert pressure into kinetic energy. The high-speed steam then strikes the blades, causing the turbine to rotate. The key characteristic of an impulse turbine is that the pressure drop occurs entirely in the nozzles, and the turbine blades only change the direction of the steam flow, not its pressure.
- Characteristics:
- Simple design with relatively fewer parts.
- High-speed operation.
- Efficient in low-pressure and high-velocity steam conditions.
- Applications: Impulse turbines are often used in small-scale applications, such as small power plants and pumps, where high-speed, low-pressure steam is available.
- Reaction Turbine
- Working Principle: A reaction turbine works on the principle of pressure and velocity changes across the blades. As the steam passes over the blades, the pressure drops gradually while its velocity increases. The blades act as reaction forces, and the steam expands within the blades themselves. This means that both the nozzles and blades are involved in the pressure drop and work conversion process.
- Characteristics:
- More efficient than impulse turbines at higher pressures and large-scale operations.
- Blade design can be more complex due to the pressure drop occurring throughout the turbine.
- Typically used in larger systems with higher steam flow rates.
- Applications: Large power plants (both fossil fuel and nuclear), where higher pressure and steam flow are used, typically use reaction turbines for their efficiency and scalability.
- Combined Impulse-Reaction Turbine
- Working Principle: Some steam turbines combine the best of both impulse and reaction turbines. This design utilizes impulse stages for high-pressure steam and reaction stages for lower-pressure steam. This combination allows for more efficient operation over a broader range of conditions.
- Characteristics:
- Flexibility to handle a range of steam pressures.
- Higher efficiency at varying operational conditions.
- Applications: These turbines are often used in large-scale industrial applications and in power plants where a wide range of steam pressures is generated.
3.2. Applications of Steam Turbines
The applications of steam turbines are vast and can be categorized into various industries, each requiring different designs based on steam pressure, temperature, and flow rate. Here are some of the primary applications of steam turbines:
3.2.1. Power Generation
- Electricity Generation: The most common use of steam turbines is in power plants, where they are used to generate electricity. Fossil fuel (coal, natural gas) and nuclear power plants use steam turbines to convert heat energy into mechanical energy and then into electrical energy.
- Efficiency Improvements: Modern power plants often use combined cycle systems, where the exhaust steam from the turbine is used to produce additional energy. For example, the combined gas-steam cycle uses the hot gases from a gas turbine to produce steam for a steam turbine, enhancing the overall efficiency.
3.2.2. Marine and Ship Propulsion
- Ship Propulsion: Large vessels, such as aircraft carriers, container ships, and cruise ships, use steam turbines to generate mechanical power for propulsion. These turbines are often driven by nuclear reactors in large ships, especially military and energy-efficient vessels.
- Marine Turbines: The steam turbines in ships are designed for high-efficiency and to operate continuously under heavy load conditions, providing high thrust for long durations.
3.2.3. Industrial Applications
- Mechanical Drive: In industries like petrochemical, chemical, and paper production, steam turbines are often used to drive large machines like compressors, fans, and pumps. These turbines are powered by the waste steam from the production process, making them highly efficient for energy recovery.
- Cogeneration Systems: Steam turbines in industrial settings are sometimes part of a cogeneration system, where they produce both electricity and usable heat (such as hot water or steam) for heating purposes. This system maximizes energy use and minimizes waste.
3.2.4. Cogeneration and Combined Heat and Power (CHP)
- Cogeneration Systems: In a cogeneration system, a steam turbine produces electricity while simultaneously providing thermal energy (such as hot water or steam) for industrial or residential heating. This process increases energy efficiency by utilizing both electrical and thermal energy from the same fuel source.
- CHP Plants: Steam turbines are commonly used in CHP (combined heat and power) plants, where both electricity and thermal energy are produced simultaneously. These plants typically operate in industries that have a high demand for both electricity and heat, such as in chemical manufacturing, food production, and district heating.
3.2.5. Nuclear Power Plants
- Nuclear Steam Turbines: Nuclear power plants use nuclear reactors to produce heat, which generates steam to drive a steam turbine. The turbines in nuclear plants are similar to those in fossil-fuel plants, but the energy source is different. The steam is produced by nuclear fission reactions in the reactor core.
- Safety and Control: Steam turbines in nuclear plants must be designed with high levels of safety, as the turbines are used in a controlled, high-energy environment. The turbines are designed to withstand high-pressure steam and operate safely under continuous operation.
3.2.6. Air Conditioning and Refrigeration
- Mechanical Refrigeration: Steam turbines are also used in mechanical refrigeration systems, where steam drives compressors in the cooling cycle. This process is seen in certain large-scale industrial cooling systems, such as in air conditioning for commercial buildings, where steam turbines help drive cooling compressors efficiently.
3.2.7. Waste-to-Energy Plants
- Waste Incineration: In waste-to-energy (WTE) plants, steam turbines are used to convert the heat from incinerating waste into electricity. The heat from burning municipal solid waste or other types of organic waste is used to produce steam, which drives a steam turbine to generate power.
- Environmental Benefits: WTE plants provide an alternative method of waste disposal while generating electricity, reducing the volume of landfilled waste, and recovering energy.
3.3. Special Considerations in Steam Turbine Design and Operation
Several factors must be considered when designing and operating steam turbines for different applications:
- Steam Conditions: The temperature, pressure, and quality of steam entering the turbine significantly impact the design of the turbine. For example:
- Superheated steam requires turbines with specific materials to handle higher temperatures.
- Low-pressure steam may be used in smaller turbines or for cogeneration systems.
- Thermal Efficiency: High-efficiency turbines often employ multi-stage expansion, where the steam expands over several turbine stages. This process minimizes the loss of thermal energy and maximizes work output.
- Load Fluctuations: The turbine must be designed to handle fluctuating loads. In power generation, this means the turbine should operate efficiently under various electricity demand levels, and in industrial applications, it must handle varying machine loads.
- Maintenance and Reliability: Steam turbines must be regularly maintained to prevent wear on the blades, bearings, and seals. Turbines in critical applications like nuclear power plants or military ships require high reliability and redundancy.
- Environmental Impact: Environmental factors, such as emissions from the combustion process in fossil fuel plants or heat dissipation in nuclear plants, need to be carefully managed. Many modern systems incorporate closed-loop cooling and carbon capture technologies to reduce their environmental footprint.
3.4. Conclusion
Steam turbines are versatile and critical devices in modern energy systems. Their various types (impulse, reaction, and combined systems) are tailored for different operational needs, from small-scale industrial applications to large power plants and marine propulsion. Steam turbines also play a key role in cogeneration systems, nuclear energy, and waste-to-energy plants, where they enhance overall system efficiency and contribute to sustainable energy solutions.
By understanding the different types and applications of steam turbines, engineers and operators can choose the most appropriate turbine for each application, optimizing performance and reducing energy consumption.
Steam Turbine Bucket: A steam turbine generator is a device that converts thermal energy from steam into mechanical energy using a steam turbine and then converts that mechanical energy into electrical energy using a generator. It is a key component in power generation systems, commonly found in power plants, industrial facilities, and cogeneration systems.
Main Components of a Steam Turbine Generator
- Steam Turbine – Converts thermal energy of steam into rotational mechanical energy.
- Impulse Turbine: Uses high-velocity steam jets to rotate the blades.
- Reaction Turbine: Uses steam expansion through fixed and moving blades to generate motion.
- Generator – Converts mechanical energy from the turbine into electrical energy via electromagnetic induction.
- Condenser (for condensing turbines) – Condenses exhaust steam to improve efficiency by creating a vacuum.
- Boiler (External Component) – Generates high-pressure steam by heating water.
- Steam Control Valves – Regulate steam flow into the turbine.
- Lubrication System – Ensures smooth turbine operation by reducing friction.
- Cooling System – Maintains the temperature of components to prevent overheating.
Types of Steam Turbine Generators
- Condensing Steam Turbine Generator
- Utilized in power plants.
- Steam exhausts into a condenser, creating a vacuum for maximum energy extraction.
- Back-Pressure Steam Turbine Generator
- Used in industrial and cogeneration applications.
- Exhaust steam is used for heating or industrial processes.
- Extraction Steam Turbine Generator
- Allows steam extraction at different stages for industrial or heating use.
- Can be designed for partial condensing or back-pressure operation.
Working Principle of a Steam Turbine Generator
- Steam Production: High-pressure steam is generated in a boiler.
- Steam Expansion: Steam enters the turbine, expanding through nozzles and causing blades to rotate.
- Mechanical Energy Transfer: The rotating turbine shaft drives the generator.
- Electrical Power Generation: The generator converts mechanical energy into electricity through electromagnetic induction.
- Steam Exhaust: Steam exits either to a condenser (for a condensing turbine) or for industrial use (for a back-pressure turbine).
Applications of Steam Turbine Generators
- Power Plants: Coal, nuclear, biomass, and combined cycle plants.
- Industrial Cogeneration: Paper mills, chemical plants, refineries.
- Geothermal Power Plants: Uses steam from underground reservoirs.
- Marine Propulsion: Some ships use steam turbines for power generation.
A steam turbine generator is a machine that converts steam energy into electrical power. It consists of two main parts:
- Steam Turbine – This is where high-pressure steam enters and pushes the blades, causing the rotor to spin. The turbine works by either impulse or reaction principles.
- Generator – The spinning turbine shaft connects to a generator, which produces electricity through electromagnetic induction.
How It Works
- Water is heated in a boiler to produce steam.
- High-pressure steam enters the turbine and expands, causing the blades to rotate.
- The rotating shaft drives a generator, converting mechanical energy into electrical energy.
- The steam then exits the turbine—either to a condenser (in condensing turbines) or for industrial use (in back-pressure turbines).
Types of Steam Turbine Generators
- Condensing Turbines – Used in power plants; exhaust steam is condensed to improve efficiency.
- Back-Pressure Turbines – Used in industries where the exhaust steam is needed for heating or processing.
- Extraction Turbines – Steam is extracted at intermediate stages for industrial use while still generating power.
Applications
- Power generation in thermal power plants (coal, nuclear, biomass, geothermal).
- Industrial cogeneration (paper mills, chemical plants, refineries).
- Marine propulsion (some ships use steam turbines).
Efficiency and Performance of Steam Turbine Generators
The efficiency of a steam turbine generator depends on several factors, including steam conditions, turbine design, and energy losses.
Factors Affecting Efficiency
- Steam Pressure and Temperature – Higher steam pressure and temperature increase efficiency by extracting more energy.
- Turbine Blade Design – Optimized blade profiles improve energy conversion.
- Multiple Stages – Using high, intermediate, and low-pressure stages enhances efficiency.
- Reheating and Regeneration – Preheating feedwater using extracted steam improves cycle efficiency.
- Condenser Vacuum – A lower condenser pressure (deep vacuum) increases energy extraction.
Typical Efficiency Levels
- Simple steam turbines: 30–40% thermal efficiency.
- Advanced steam cycles (with reheating and regeneration): 40–45%.
- Combined cycle power plants (steam + gas turbines): 55–60%.
Maintenance and Reliability
Regular maintenance ensures longevity and performance. Key aspects include:
- Lubrication System Checks – Prevents friction damage to bearings and rotating parts.
- Blade Inspection – Detects erosion, corrosion, or cracking.
- Steam Quality Control – Avoids deposits and corrosion inside the turbine.
- Generator Cooling System – Prevents overheating of electrical components.
- Vibration Monitoring – Identifies imbalances and potential failures early.
Advantages of Steam Turbine Generators
✔ High efficiency for large-scale power generation.
✔ Long operational lifespan with proper maintenance.
✔ Suitable for a wide range of fuels (coal, biomass, nuclear, geothermal).
✔ Can be integrated with industrial processes for cogeneration.
Types of Steam Turbines in Detail
Steam turbines can be classified based on their operating principles and applications.
1. Based on Energy Conversion Principle
- Impulse Turbine – Steam expands through nozzles, converting pressure energy into kinetic energy. The high-speed steam jets strike the blades, causing rotation. Example: De Laval Turbine.
- Reaction Turbine – Steam expands gradually through both fixed and moving blades, generating reaction forces that drive rotation. Example: Parsons Turbine.
2. Based on Exhaust Conditions
- Condensing Turbine – Common in power plants; steam exhausts into a condenser, creating a vacuum that maximizes energy extraction.
- Back-Pressure Turbine – Used in cogeneration systems; exhaust steam is utilized in industrial processes, improving overall efficiency.
- Extraction Turbine – Allows steam to be extracted at intermediate stages for heating or industrial use while still generating power.
- Bleed Turbine – Similar to an extraction turbine but with uncontrolled steam extraction for feedwater heating.
3. Based on Flow Direction
- Axial Flow Turbine – Steam moves along the shaft axis; widely used in power generation.
- Radial Flow Turbine – Steam flows radially inward or outward; used in small-scale applications.
Steam Turbine Generator Operation Modes
- Base Load Operation – The turbine runs continuously at high efficiency, supplying steady power. Used in coal, nuclear, and large-scale thermal plants.
- Peak Load Operation – The turbine is operated only when demand is high. More common in smaller or supplementary power plants.
- Cogeneration Mode – Generates electricity while supplying steam for industrial processes, maximizing efficiency.
Common Challenges in Steam Turbine Operation
- Blade Erosion and Corrosion – Caused by moisture and impurities in steam.
- Thermal Stress and Fatigue – Due to frequent start-stop cycles or temperature fluctuations.
- Steam Quality Issues – Poor steam quality leads to deposits, scaling, and reduced efficiency.
- Generator Overheating – Requires effective cooling mechanisms like hydrogen or water cooling.
- Vibration and Imbalance – Can cause mechanical failures if not monitored.
Future Trends in Steam Turbine Technology
- Supercritical and Ultra-Supercritical Steam Cycles – Operating at higher pressures and temperatures to improve efficiency.
- Integrated Renewable Hybrid Systems – Combining steam turbines with solar or biomass energy for sustainable power generation.
- Advanced Materials and Coatings – Using high-temperature-resistant alloys to enhance turbine lifespan.
- Digital Monitoring and AI-Based Predictive Maintenance – Improving reliability through real-time performance tracking and automated diagnostics.
Steam Turbine Manufacturing Process
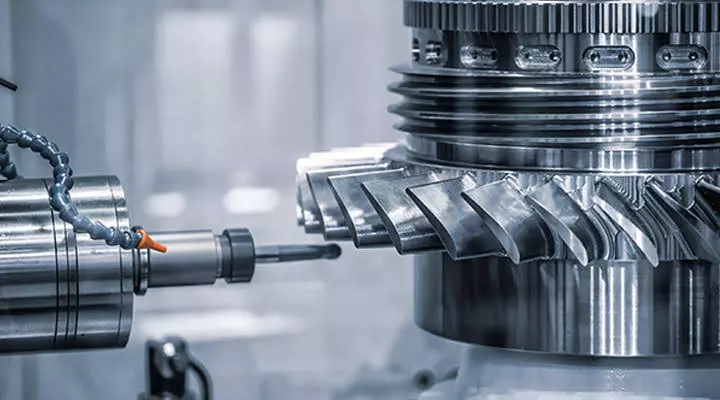
The manufacturing of steam turbines is a complex, high-precision process that involves several stages, from material selection to final assembly and testing. Below is a detailed breakdown of the process.
Design and Engineering
Before manufacturing begins, engineers design the steam turbine based on the intended application, steam conditions, and efficiency requirements.
- Thermodynamic Analysis – Determines steam flow, pressure, and temperature requirements.
- Structural Design – Ensures the turbine casing, rotor, and blades can withstand operational stresses.
- Material Selection – High-strength alloys are used to resist high temperatures and pressures.
- Computer-Aided Design (CAD) & Computational Fluid Dynamics (CFD) – Optimize turbine blade profiles for maximum efficiency.
Material Selection and Procurement
Steam turbines operate under extreme conditions, so high-quality materials are essential.
- Rotor & Casing: Forged from high-strength steel alloys (e.g., chromium-molybdenum-vanadium steel).
- Blades: Made from stainless steel or nickel-based superalloys to resist corrosion and high temperatures.
- Bearings & Seals: High-precision alloys or composite materials ensure smooth operation.
Component Manufacturing
a) Rotor Manufacturing
- Forged steel billets are heated and forged into the rotor shape.
- Precision machining on CNC (Computer Numerical Control) machines ensures accurate dimensions.
- Heat treatment (quenching, tempering) improves strength and toughness.
- Balancing and inspection are performed to minimize vibration.
b) Blade Manufacturing
- Steam turbine blades are forged or cast depending on size and material.
- CNC machining creates the aerodynamic profile.
- Surface coatings (like thermal barrier coatings) enhance durability.
- Quality checks ensure proper fit and performance.
c) Casing and Other Structural Components
- The turbine casing is cast or fabricated from heavy-duty steel.
- Machining and drilling ensure accurate alignment with the rotor and steam inlets.
- Welding and assembly of internal components are performed with precision.
Assembly and Integration
- The rotor is mounted inside the casing with precise tolerances.
- Blades are attached using rivets or fir-tree root designs.
- Bearings, seals, and lubrication systems are installed.
- The generator is coupled to the turbine shaft for power conversion.
Quality Control and Testing
a) Non-Destructive Testing (NDT)
- Ultrasonic Testing (UT): Detects internal flaws in turbine components.
- Magnetic Particle Testing (MPT): Identifies surface cracks in rotor and blades.
- X-ray and Radiographic Testing: Ensures weld integrity.
b) Mechanical and Performance Testing
- Rotor Balancing: Ensures smooth operation and minimizes vibration.
- Pressure & Leak Tests: Check for steam leakage under high pressure.
- Full Load Testing: Simulates real-world operating conditions to verify performance.
Final Assembly and Shipping
- After successful testing, the turbine is disassembled into transportable sections.
- It is packaged and shipped to the power plant or industrial facility for installation.
- On-site installation includes foundation mounting, alignment, and commissioning.
The manufacturing of steam turbines begins with the design and engineering phase, where engineers determine the turbine’s specifications based on its intended application. This includes analyzing steam pressure, temperature, and flow rates while optimizing the blade profiles for maximum efficiency using computer simulations. High-strength materials such as chromium-molybdenum-vanadium steel for the rotor and nickel-based superalloys for the blades are selected to withstand extreme conditions.
The rotor is forged from a steel billet, then precision-machined and heat-treated to improve strength. Blades are either cast or forged, shaped using CNC machines, and coated to enhance durability. The turbine casing is cast or fabricated from heavy-duty steel, then machined for precise alignment. Bearings, seals, and other critical components are also manufactured with high precision.
During assembly, the rotor is installed in the casing, and the blades are attached using secure mounting techniques. The generator is coupled to the turbine shaft, and all components are aligned carefully. Quality control involves rigorous non-destructive testing methods such as ultrasonic and X-ray inspections to detect flaws. Performance tests, including rotor balancing and full-load testing, ensure the turbine operates efficiently and reliably.
After final assembly, the turbine is disassembled into transportable sections, shipped to the installation site, and reassembled for commissioning. Leading manufacturers of steam turbines include Siemens, General Electric, Mitsubishi Power, Toshiba, Doosan Škoda, BHEL, and Harbin Electric. Each company specializes in different turbine types, including those used in power plants, cogeneration systems, and industrial applications.
Once the steam turbine is manufactured and assembled, it undergoes extensive quality control and performance testing before being deployed for industrial or power generation use. Testing begins with non-destructive evaluation techniques such as ultrasonic testing to detect internal defects, magnetic particle testing to identify surface cracks, and radiographic X-ray inspections to ensure weld integrity. These tests help verify that the turbine components can withstand high pressures and temperatures without failure.
Rotor balancing is a critical step to ensure smooth operation and minimize vibration. Any imbalance can cause excessive wear on bearings and reduce the lifespan of the turbine. Pressure and leak tests are also conducted to check for steam leakage and ensure that all seals and joints perform as expected under real operating conditions. Full-load performance testing is carried out by running the turbine at different speeds and loads to evaluate efficiency, power output, and thermal stability.
After passing all quality checks, the turbine is prepared for shipment. Since turbines are often too large to transport in one piece, they are disassembled into sections, securely packaged, and transported to the power plant or industrial facility. Upon arrival, installation begins with precise alignment on a reinforced foundation. Engineers reassemble the turbine, connect it to the generator and steam supply system, and conduct final inspections before commissioning.
During commissioning, engineers gradually increase the turbine’s load while monitoring parameters like temperature, pressure, rotational speed, and vibration levels. Control systems are tested, safety mechanisms are verified, and operational fine-tuning is performed to achieve optimal performance. Once everything is confirmed to be working as expected, the turbine is put into full operation, providing reliable power generation or steam for industrial processes.
Once the steam turbine is fully operational, continuous monitoring and maintenance are essential to ensure long-term reliability and efficiency. Operators use advanced monitoring systems to track critical parameters such as steam temperature, pressure, rotational speed, vibration, and lubrication conditions. Any irregularities in these readings can indicate potential issues, allowing for preventive maintenance before serious damage occurs.
Routine maintenance includes inspecting turbine blades for erosion or corrosion, checking seals and bearings for wear, and ensuring proper lubrication to reduce friction. Over time, deposits can accumulate on turbine blades due to impurities in steam, reducing efficiency. Periodic cleaning and surface treatment help restore optimal performance. The generator also requires regular maintenance, including cooling system checks and insulation testing to prevent electrical failures.
Predictive maintenance technologies, such as vibration analysis and thermal imaging, help identify early signs of mechanical stress, misalignment, or overheating. Many modern turbines are equipped with AI-driven diagnostic systems that analyze real-time data and provide predictive failure alerts, minimizing downtime and costly repairs.
Despite rigorous maintenance, some turbine components have a finite lifespan and require periodic overhauls. Major overhauls involve disassembling the turbine, replacing worn-out parts, and rebalancing the rotor. In large power plants, these overhauls are scheduled during planned outages to avoid disruption to power supply.
As steam turbine technology evolves, manufacturers are developing new materials, coatings, and digital monitoring solutions to extend turbine lifespans and improve efficiency. Ultra-supercritical steam turbines, for example, operate at higher temperatures and pressures, increasing power output while reducing fuel consumption. Advances in automation and remote monitoring also enable operators to optimize turbine performance in real time, further enhancing reliability and operational flexibility.
Construction of steam turbine
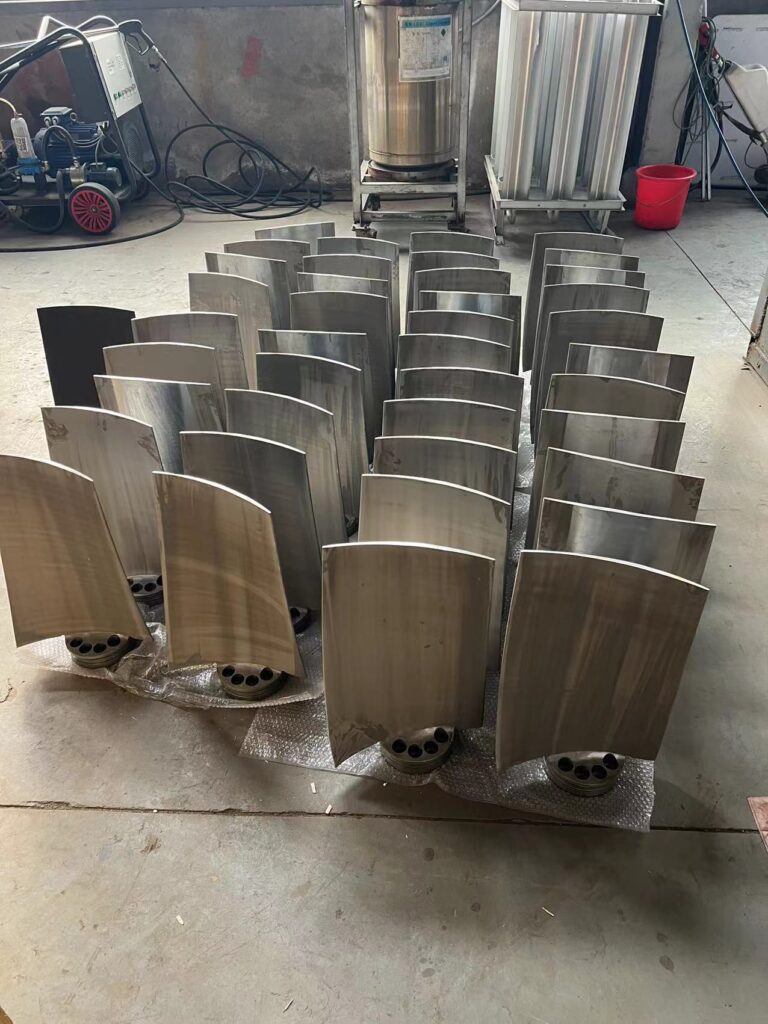
The construction of a steam turbine involves multiple high-precision components designed to efficiently convert thermal energy from steam into mechanical power. Each component is engineered to withstand extreme temperatures, pressures, and rotational forces while maintaining efficiency and durability.
Main Components of a Steam Turbine
- Rotor (Shaft) – The central rotating component that carries the blades and transmits mechanical power to the generator. It is typically made of high-strength forged steel to handle high-speed rotation and stress.
- Blades – Steam turbine blades are mounted on the rotor and are responsible for extracting energy from steam. They are made of heat-resistant alloys and designed aerodynamically to maximize efficiency. Blades can be categorized as:
- Moving blades (rotor blades): Attached to the rotating shaft and convert steam energy into rotational motion.
- Fixed blades (stator blades or nozzles): Stationary blades that direct and accelerate steam onto the moving blades.
- Casing (Housing) – The outer structure that encloses the turbine and contains the steam. It is typically made of cast steel or welded steel plates and designed to withstand high pressures.
- Steam Inlet and Control Valves – These regulate the flow of high-pressure steam entering the turbine. The valves help control power output by adjusting the steam supply.
- Bearings and Lubrication System – Bearings support the rotor and reduce friction. The lubrication system ensures smooth operation by supplying oil to bearings, preventing overheating and wear.
- Seals and Glands – Prevent steam leakage at high-speed rotating parts. These seals help maintain efficiency by ensuring steam remains in the desired flow path.
- Condenser (for condensing turbines) – In a condensing steam turbine, the exhaust steam is directed to a condenser, where it is cooled and converted back into water to improve efficiency.
- Extraction or Exhaust System – In some turbines, part of the steam is extracted at intermediate stages for industrial heating or further processing, while the remaining steam continues expansion for power generation.
Construction Process
- Material Selection – High-strength steel alloys and corrosion-resistant materials are chosen for turbine components.
- Forging and Machining – The rotor and blades are forged and precisely machined using CNC technology.
- Casting and Fabrication – The turbine casing is cast or fabricated to withstand high pressures.
- Blade Assembly – Blades are mounted on the rotor using specialized fastening techniques such as fir-tree root fixing or welding.
- Final Assembly – The rotor, bearings, seals, and other components are assembled within the casing.
- Balancing and Testing – The assembled turbine undergoes rigorous testing to ensure smooth operation, vibration control, and steam tightness.
- Installation and Commissioning – The turbine is transported, installed on-site, connected to the generator and steam system, and tested before full operation.
The construction of a steam turbine involves assembling high-precision components designed to withstand extreme pressures, temperatures, and rotational forces while ensuring maximum efficiency and durability. The central component is the rotor, a high-strength forged steel shaft that carries the turbine blades and transmits mechanical power to the generator. The blades, made from heat-resistant alloys, are mounted on the rotor and play a crucial role in extracting energy from steam. These blades are designed aerodynamically to maximize efficiency, with moving blades attached to the rotor and stationary blades directing steam flow.
The turbine casing, made of cast or welded steel, encloses the rotor and blades while containing high-pressure steam. Steam enters through control valves that regulate its flow and adjust power output. Bearings support the rotor and minimize friction, while a lubrication system ensures smooth operation and prevents overheating. Specialized seals prevent steam leakage at rotating parts, maintaining efficiency by keeping steam within the designated flow path. In condensing turbines, a condenser cools and converts exhaust steam back into water to improve the cycle’s efficiency, whereas in extraction turbines, part of the steam is extracted for industrial heating or further processing.
The manufacturing process begins with selecting high-strength steel alloys and corrosion-resistant materials. The rotor and blades are forged and precisely machined using CNC technology, while the casing is cast or fabricated to withstand operational stresses. Blades are securely mounted onto the rotor using fir-tree root fixing or welding techniques. During final assembly, the rotor, blades, bearings, seals, and auxiliary systems are integrated within the casing, ensuring proper alignment. The turbine undergoes rigorous balancing and performance testing to eliminate vibrations, check for leaks, and verify operational efficiency. After passing quality control, it is transported to the installation site, mounted on a foundation, connected to the generator and steam supply, and commissioned for operation. The entire construction process ensures long-term reliability and efficiency in power generation and industrial applications.
Once the steam turbine is installed and commissioned, its operation relies on precise coordination between various components to ensure efficient energy conversion. Steam is introduced into the turbine at high pressure and temperature through the control valves, which regulate its flow based on power demand. As the steam passes through the stationary blades, it is directed onto the rotating blades, where it expands and loses pressure while transferring kinetic energy to the rotor. This rotational energy is transmitted to the generator, converting mechanical power into electricity. The process continues across multiple turbine stages, with each stage extracting additional energy from the steam.
The efficiency of a steam turbine depends on several factors, including the quality of steam, blade design, and operating conditions. Over time, factors like erosion, corrosion, and deposits from impurities in steam can affect performance, making regular maintenance essential. Bearings and lubrication systems are monitored continuously to prevent excessive wear and overheating, while vibration sensors detect potential misalignment or imbalance in the rotor. Advanced monitoring systems use real-time data to analyze operational efficiency and predict maintenance needs, reducing unexpected failures and improving reliability.
In condensing turbines, exhaust steam is directed to a condenser, where it is cooled and converted back into water before being pumped back to the boiler, creating a closed-loop system that enhances efficiency. In back-pressure or extraction turbines, a portion of the steam is diverted for industrial heating or other applications while the remaining steam continues expansion for power generation. This versatility makes steam turbines a critical component in power plants, cogeneration systems, and industrial processes.
As technology advances, modern steam turbines incorporate high-temperature-resistant materials, optimized blade geometries, and digital control systems to improve efficiency and extend operational life. Supercritical and ultra-supercritical turbines operate at even higher pressures and temperatures, reducing fuel consumption and emissions. Ongoing research in materials science and automation continues to enhance turbine performance, ensuring their role remains vital in energy generation and industrial applications.
As steam turbine technology continues to evolve, improvements in materials, design, and digital monitoring systems are enhancing efficiency, reliability, and sustainability. Advanced alloys and thermal coatings are being developed to withstand higher temperatures and pressures, allowing turbines to operate in ultra-supercritical conditions with increased efficiency and reduced fuel consumption. Computational fluid dynamics (CFD) simulations help optimize blade geometries to improve steam flow and energy extraction, minimizing losses and extending component lifespans.
Digitalization plays a key role in modern turbine operation, with smart sensors and AI-driven analytics enabling real-time monitoring of critical parameters such as temperature, pressure, vibration, and steam flow. Predictive maintenance systems analyze operational data to identify potential issues before they cause failures, reducing unplanned downtime and maintenance costs. Remote monitoring capabilities allow operators to make adjustments and optimize performance without direct intervention, increasing flexibility and responsiveness in power generation.
In addition to efficiency gains, environmental concerns drive advancements in steam turbine integration with renewable energy sources. Hybrid power plants combine steam turbines with solar thermal, biomass, or waste heat recovery systems to maximize energy utilization and reduce greenhouse gas emissions. Carbon capture and storage (CCS) technologies are also being integrated into steam power plants to mitigate environmental impact.
Looking ahead, research in advanced manufacturing techniques, such as additive manufacturing (3D printing), could revolutionize steam turbine production by allowing for complex, high-efficiency blade designs with reduced material waste. As global energy demands continue to grow, steam turbines remain a crucial component in electricity generation, industrial processes, and combined heat and power (CHP) systems. Their adaptability, durability, and potential for further efficiency improvements ensure they will continue to play a vital role in the future of energy production.
Characteristics of steam turbine
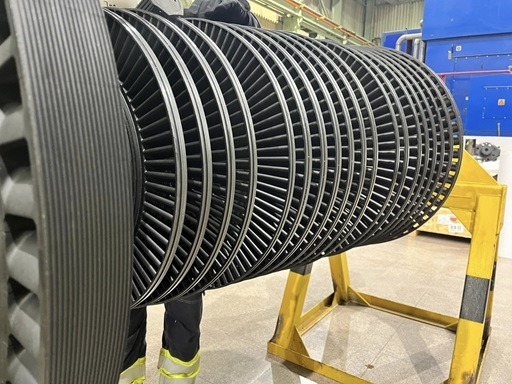
Steam turbines have several key characteristics that define their performance, efficiency, and suitability for various applications. They are widely used in power generation, industrial processes, and cogeneration systems due to their ability to convert thermal energy from steam into mechanical power with high efficiency and reliability.
One of the primary characteristics of a steam turbine is its high thermal efficiency, especially in large-scale power plants where superheated or ultra-supercritical steam conditions are used. The efficiency of a steam turbine depends on factors such as steam pressure, temperature, expansion ratio, and blade design. Multi-stage turbines, which consist of multiple sets of rotating and stationary blades, extract energy from steam more effectively by allowing gradual expansion and pressure reduction.
Steam turbines operate with a continuous rotary motion, unlike reciprocating engines, which experience cyclic motion. This results in smoother operation, reduced mechanical stress, and lower vibration levels, contributing to longer operational life and lower maintenance requirements. Their high-speed rotation allows them to be directly coupled to electrical generators, enabling efficient power generation with minimal mechanical losses.
The power output of a steam turbine can be controlled by regulating the steam flow through inlet control valves, allowing flexible operation to match varying power demands. In condensing steam turbines, the exhaust steam is directed to a condenser, where it is cooled and converted back into water for reuse in a closed-loop system, maximizing efficiency. In back-pressure and extraction turbines, steam is partially or fully extracted at intermediate stages for industrial heating or other applications, demonstrating their versatility in combined heat and power (CHP) systems.
Steam turbines are designed to handle high pressures and temperatures, often exceeding 500°C and 100 bar in modern power plants. Advanced materials, coatings, and precision engineering ensure that components can withstand thermal stress, corrosion, and erosion over long periods. The reliability of steam turbines is one of their strongest characteristics, with many units operating continuously for years with minimal downtime. Predictive maintenance technologies, such as vibration analysis and real-time monitoring, further enhance reliability by detecting early signs of wear or misalignment.
Another important characteristic is scalability. Steam turbines can be designed for small industrial applications or large-scale power generation, with capacities ranging from a few megawatts to over 1,000 megawatts in the case of nuclear and supercritical coal power plants. Their ability to integrate with different heat sources, including fossil fuels, nuclear energy, and renewable sources like biomass and solar thermal, makes them highly adaptable in diverse energy systems.
Overall, steam turbines are characterized by high efficiency, smooth continuous operation, flexible power control, durability, and the ability to operate under extreme conditions. Their advanced design, combined with modern digital monitoring and predictive maintenance systems, ensures their continued role as a reliable and efficient solution for large-scale energy conversion and industrial applications.
Steam turbines are known for their ability to operate at high efficiency under a wide range of conditions, making them a preferred choice for power generation and industrial applications. Their ability to extract maximum energy from steam depends on the thermodynamic cycle they operate within, typically the Rankine cycle, where high-pressure steam expands through multiple stages to convert thermal energy into mechanical work. This expansion process is optimized using multi-stage blade arrangements, where steam progressively loses pressure while transferring its kinetic energy to the rotor.
The rotational speed of a steam turbine is another defining characteristic. High-speed operation, often in the range of 3,000 to 3,600 RPM for power generation applications, allows them to be directly coupled with electrical generators, ensuring efficient energy conversion. Some turbines, particularly in specialized applications, can operate at even higher speeds, requiring reduction gears to match generator frequency. The smooth and continuous rotary motion minimizes mechanical wear and contributes to the long service life of steam turbines, often exceeding 30 years with proper maintenance.
The adaptability of steam turbines to various operating conditions is another key characteristic. They can function in condensing or non-condensing (back-pressure) configurations, depending on whether the exhaust steam is fully utilized or condensed back into water for reuse. Condensing turbines maximize efficiency by extracting the maximum possible energy from steam before it exits at low pressure, while back-pressure turbines are used where steam is needed for industrial heating or process applications. Extraction turbines further enhance flexibility by allowing steam withdrawal at intermediate stages for combined heat and power applications.
Modern steam turbines incorporate advanced materials and coatings to withstand extreme temperatures and pressures. Nickel-based superalloys, stainless steel, and thermal barrier coatings protect turbine blades from corrosion, erosion, and thermal fatigue, ensuring long-term reliability. Computational fluid dynamics (CFD) and finite element analysis (FEA) are used in blade design to optimize steam flow, minimize losses, and enhance performance. Digital monitoring systems equipped with smart sensors provide real-time diagnostics, predictive maintenance insights, and remote operational control, further improving efficiency and reliability.
Steam turbines continue to evolve with advancements in ultra-supercritical and high-efficiency designs, reducing fuel consumption and emissions. Their integration with renewable energy sources, such as biomass and solar thermal power, further expands their role in sustainable energy systems. As a result, they remain a cornerstone of global power generation, providing stable and efficient electricity in both traditional and modern energy infrastructure.
The ability of steam turbines to operate efficiently under varying conditions makes them highly versatile for different energy applications. Their efficiency is influenced by factors such as steam pressure, temperature, and the number of expansion stages. In modern power plants, ultra-supercritical steam turbines operate at pressures above 250 bar and temperatures exceeding 600°C, significantly increasing thermal efficiency and reducing fuel consumption. The integration of reheaters, which reheat steam after partial expansion, further improves efficiency by reducing moisture content and increasing energy extraction in later stages of the turbine.
Another key characteristic is the turbine’s durability and long operational life. Properly maintained steam turbines can operate continuously for years with minimal downtime. The robust design, use of high-quality materials, and advanced sealing technologies prevent steam leakage and ensure consistent performance. Bearings, lubrication systems, and rotor balancing play a crucial role in minimizing wear and vibration, extending the service life of the turbine. Routine inspections using non-destructive testing methods such as ultrasonic and thermal imaging help detect early signs of material fatigue, enabling proactive maintenance and preventing costly failures.
Steam turbines also offer flexible load-following capabilities, allowing them to adjust power output based on demand. While they are most efficient when operating at full load, modern control systems enable part-load operation with optimized steam flow regulation. In combined cycle power plants, steam turbines work alongside gas turbines, utilizing waste heat from the gas turbine to generate additional power through a heat recovery steam generator (HRSG), improving overall plant efficiency.
In industrial applications, steam turbines are widely used for mechanical drive purposes, powering compressors, pumps, and other equipment in oil refineries, chemical plants, and district heating systems. Their ability to utilize various steam sources, including waste heat from industrial processes, enhances energy efficiency and cost savings. Extraction and back-pressure turbines further increase operational flexibility by providing steam at different pressures for process heating, desalination, and other industrial uses.
As technology advances, digital monitoring and automation play an increasingly important role in steam turbine operations. Smart sensors collect real-time data on temperature, pressure, vibration, and efficiency, feeding into AI-driven predictive maintenance systems. These technologies help optimize performance, reduce maintenance costs, and extend turbine life by detecting issues before they lead to major failures. Remote monitoring and control allow operators to adjust turbine settings from centralized locations, improving operational efficiency and responsiveness.
Looking ahead, research into new materials, including ceramic-based coatings and additive manufacturing (3D printing) for turbine components, is expected to further enhance performance and efficiency. The continued development of carbon capture and storage (CCS) technologies in steam power plants aims to reduce environmental impact, making steam turbines a crucial part of the transition to cleaner energy systems. Their proven reliability, adaptability, and efficiency ensure they will continue to play a key role in global energy production for decades to come.
Steam turbines remain a dominant technology in large-scale power generation due to their ability to provide stable and efficient energy conversion. Their adaptability to different fuel sources, including coal, natural gas, nuclear, biomass, and even concentrated solar power, makes them an integral part of the global energy mix. In nuclear power plants, steam turbines operate using high-temperature steam generated from nuclear reactors, where their long service life and high reliability are essential for continuous electricity production. Similarly, in fossil-fuel power plants, advanced steam cycles with supercritical and ultra-supercritical parameters continue to improve efficiency while reducing emissions.
One of the most significant developments in steam turbine technology is the integration of hybrid and renewable energy systems. In solar thermal power plants, steam turbines are used to convert heat energy collected from mirrors and heliostats into electricity. Biomass-fired steam turbines provide a sustainable alternative to fossil fuels, utilizing organic waste materials for steam generation. Industrial cogeneration systems, which produce both electricity and usable heat, have also become increasingly popular due to their ability to achieve overall efficiencies of 80% or more by utilizing steam for both power generation and industrial processes.
Advancements in turbine design focus on improving aerodynamics, reducing energy losses, and increasing operational flexibility. Computational fluid dynamics (CFD) modeling is widely used to refine blade profiles, optimize steam flow, and minimize turbulence. The introduction of variable-pressure turbines allows for improved efficiency at part-load conditions, making them better suited for fluctuating power demands. Additionally, low-pressure last-stage blade designs are continuously evolving to reduce losses and increase the energy extracted from exhaust steam.
Automation and digitalization have transformed steam turbine operation and maintenance. Advanced control systems, utilizing machine learning algorithms and AI-driven analytics, optimize performance by adjusting steam flow, pressure, and temperature in real time. Digital twins—virtual models of turbines—are now used to simulate operating conditions, predict wear patterns, and suggest maintenance strategies before actual issues arise. This predictive approach minimizes unplanned downtime, extends equipment life, and reduces operational costs.
Looking forward, the role of steam turbines will continue to evolve as global energy priorities shift toward sustainability and efficiency. The development of advanced materials, such as ceramic matrix composites and corrosion-resistant alloys, will further enhance turbine durability and efficiency. Carbon capture and storage (CCS) technologies are expected to become more integrated with steam power plants, reducing their carbon footprint. As energy systems modernize, steam turbines will remain a key player, whether in traditional power plants, hybrid renewable systems, or future energy innovations that demand reliable, high-efficiency power generation.
Development of steam turbine
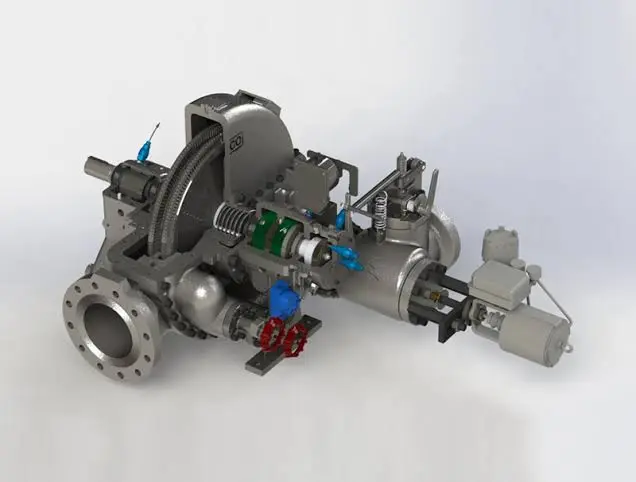
The development of steam turbines has been a gradual process spanning several centuries, driven by advancements in engineering, materials science, and thermodynamics. From early experimental designs to the high-efficiency turbines used in modern power plants, steam turbine technology has continuously evolved to meet increasing demands for power generation, industrial applications, and efficiency improvements.
The concept of using steam to produce mechanical work dates back to the first century AD, with Hero of Alexandria’s primitive steam-powered device, the aeolipile. However, practical steam power did not emerge until the 17th and 18th centuries. The development of early steam engines by Thomas Savery and Thomas Newcomen provided the foundation for steam power, though these devices operated with low efficiency and were primarily used for pumping water. James Watt’s improvements to the steam engine in the late 18th century introduced the separate condenser, significantly increasing efficiency and making steam power more viable for industrial use.
The transition from reciprocating steam engines to rotary steam turbines was a major breakthrough in the late 19th century. In 1884, Charles Parsons invented the first practical steam turbine, using a multi-stage reaction principle to achieve continuous rotary motion with much greater efficiency than previous steam engines. Almost simultaneously, Gustaf de Laval developed an impulse turbine, which used high-velocity steam jets directed onto turbine blades. These innovations revolutionized power generation by enabling high-speed, high-efficiency energy conversion, leading to widespread adoption in electricity production and naval propulsion.
Throughout the 20th century, steam turbine technology advanced rapidly, with improvements in blade design, steam conditions, and manufacturing processes. The introduction of superheated steam significantly increased efficiency by reducing moisture content and improving energy extraction. Multi-stage turbines, reheat cycles, and condensing systems further enhanced performance, making steam turbines the dominant technology in large-scale power plants. The expansion of fossil-fuel and nuclear power plants in the mid-20th century further drove the development of high-capacity steam turbines, with units exceeding 1,000 megawatts in output.
In recent decades, research has focused on increasing efficiency and sustainability. The development of ultra-supercritical and advanced ultra-supercritical steam turbines, operating at pressures above 250 bar and temperatures over 600°C, has pushed efficiency levels beyond 45%, reducing fuel consumption and emissions. Modern computational fluid dynamics (CFD) and finite element analysis (FEA) are now used to optimize blade aerodynamics and reduce energy losses. Digital monitoring and AI-driven predictive maintenance have further improved reliability, reducing operational costs and extending turbine lifespans.
Looking ahead, future developments in steam turbine technology will focus on integrating renewable energy sources, improving materials through advanced coatings and additive manufacturing, and enhancing environmental performance through carbon capture and storage (CCS) systems. As global energy demand continues to evolve, steam turbines remain a cornerstone of efficient power generation, with continuous innovation ensuring their role in both traditional and sustainable energy systems.
The continuous development of steam turbines has been driven by the need for higher efficiency, durability, and adaptability in power generation and industrial applications. One of the key factors in this evolution has been the improvement of materials used in turbine construction. Early steam turbines relied on carbon steel, but as steam conditions became more extreme, high-strength alloys, stainless steel, and nickel-based superalloys were introduced to withstand high temperatures and pressures. Modern turbines utilize advanced coatings, such as thermal barrier coatings, to protect blades from erosion, corrosion, and thermal fatigue, extending their operational lifespan.
Another major advancement has been the refinement of blade design and steam flow optimization. The introduction of computational fluid dynamics (CFD) has allowed engineers to create highly efficient blade profiles that maximize energy extraction while minimizing losses. In multi-stage turbines, carefully designed reaction and impulse blades work together to ensure a smooth and efficient transfer of kinetic energy from steam to the rotor. The development of longer last-stage blades has also improved the performance of low-pressure sections, allowing more energy to be extracted from exhaust steam before it reaches the condenser.
Reheat and regenerative cycles have played a crucial role in increasing the efficiency of steam turbines. In a reheat cycle, steam is expanded in the high-pressure turbine, reheated in the boiler, and then expanded further in the intermediate and low-pressure turbines. This process reduces moisture content in the later stages, improving efficiency and preventing blade erosion. Regenerative feedwater heating, where steam is extracted from intermediate stages to preheat the feedwater, also enhances overall plant efficiency by reducing the fuel required to generate steam.
Automation and digital monitoring systems have revolutionized steam turbine operation and maintenance. Real-time data collection through smart sensors allows for precise control of steam flow, pressure, and temperature, ensuring optimal performance under varying load conditions. Predictive maintenance techniques, enabled by machine learning and artificial intelligence, analyze operational data to detect potential failures before they occur, reducing unplanned downtime and maintenance costs. Digital twins, virtual models of steam turbines, are now used to simulate different operating scenarios, optimize performance, and improve reliability.
These continuous advancements in materials, blade design, thermodynamic cycles, and digital monitoring have made modern steam turbines more efficient and reliable than ever before. As the global energy industry shifts toward cleaner and more sustainable technologies, steam turbines are evolving to integrate with renewable energy sources, carbon capture systems, and hybrid power generation solutions. Their long history of innovation ensures they will remain a key technology in energy production for decades to come.
The efficiency improvements and technological advancements in steam turbines have also been driven by the increasing demand for sustainable and cleaner energy solutions. One of the most significant developments in recent years has been the move toward ultra-supercritical (USC) and advanced ultra-supercritical (A-USC) steam conditions. These turbines operate at pressures above 300 bar and temperatures exceeding 700°C, significantly improving thermal efficiency beyond 45%, reducing fuel consumption, and lowering carbon emissions. The materials used in these high-temperature turbines include nickel-based alloys and advanced ceramics, which can withstand extreme thermal stresses and prolong operational life.
The integration of steam turbines with renewable energy sources has expanded their role in modern power generation. In biomass and waste-to-energy plants, steam turbines convert heat from combustion into electricity, providing a sustainable alternative to fossil fuels. Similarly, in solar thermal power plants, steam turbines use heat collected from concentrated solar energy to generate electricity, improving efficiency and grid stability. Hybrid power plants, which combine steam turbines with other energy sources such as gas turbines or solar energy, offer flexible and efficient energy solutions by optimizing heat utilization across multiple systems.
Another key development in steam turbine technology is the implementation of highly flexible operational strategies to accommodate varying energy demands. Traditionally, steam turbines operate most efficiently at full load, but modern control systems allow them to adjust to partial load conditions without significant efficiency losses. This is particularly important in power grids with high levels of intermittent renewable energy, where steam turbines must ramp up or down to balance fluctuations in wind and solar power. Fast-start turbines and sliding-pressure operation techniques have been developed to enhance the load-following capabilities of steam turbines, making them more adaptable to modern energy grids.
The role of digitalization in steam turbine operation continues to expand, with advanced monitoring systems enabling real-time optimization and predictive maintenance. Digital twin technology, which creates a virtual replica of a turbine, allows engineers to simulate operating conditions, predict performance trends, and optimize maintenance schedules. AI-driven analytics assess sensor data to detect early signs of wear, misalignment, or inefficiencies, allowing operators to take corrective action before failures occur. Remote monitoring and control systems enable plant operators to manage turbine performance from centralized locations, improving efficiency and reducing the need for on-site interventions.
As global energy priorities shift toward sustainability and efficiency, steam turbines are being integrated with carbon capture and storage (CCS) technologies to reduce greenhouse gas emissions from fossil-fuel power plants. These systems capture CO₂ from flue gases before it is released into the atmosphere, allowing steam power plants to operate with a lower environmental impact. Research into closed-loop supercritical CO₂ (sCO₂) cycles, which use CO₂ instead of steam as a working fluid, is also gaining attention as a potential next-generation alternative to traditional steam cycles, offering higher efficiency and lower emissions.
With ongoing innovations in materials, digital technologies, and hybrid energy systems, steam turbines continue to evolve to meet the demands of a changing energy landscape. Their ability to integrate with renewable sources, operate under extreme conditions, and provide reliable power generation ensures that they will remain a critical component of global energy infrastructure for decades to come.
The future of steam turbine technology is centered around continued advancements in efficiency, flexibility, and environmental sustainability. One of the key areas of development is in supercritical carbon dioxide (sCO₂) cycles, which offer a potential breakthrough in energy conversion efficiency. Unlike traditional steam cycles, sCO₂ operates at high pressures and densities, allowing for more compact and efficient turbine designs. These systems have the potential to increase efficiency by 5–10% compared to conventional Rankine cycles, while also reducing water consumption—a major advantage in arid regions where water-intensive cooling systems are a concern.
In addition to sCO₂, hydrogen co-firing and ammonia-based combustion systems are being explored as low-carbon alternatives for steam generation. By integrating hydrogen or ammonia as fuels in power plants, steam turbines can operate with significantly reduced CO₂ emissions while maintaining high efficiency. These developments align with global decarbonization efforts and the transition toward cleaner energy sources. Hybrid power plants, where steam turbines work in tandem with renewable energy sources like solar thermal and geothermal, further enhance their role in sustainable energy systems.
The evolution of steam turbine materials and manufacturing techniques is another major area of innovation. Advanced ceramic coatings, additive manufacturing (3D printing), and new high-temperature alloys are being developed to extend turbine lifespan and improve resistance to wear, erosion, and thermal fatigue. 3D printing enables the production of complex turbine blade geometries that optimize aerodynamics and heat resistance, allowing for higher efficiency and lower maintenance costs.
Automation and AI-driven optimization are also transforming how steam turbines operate. Real-time performance monitoring, powered by digital twins and IoT-connected sensors, enables predictive maintenance and continuous efficiency improvements. AI algorithms analyze operating conditions and suggest adjustments to optimize steam flow, load distribution, and temperature control, reducing energy losses and extending component life. These technologies are making steam turbines more adaptable to dynamic power grid demands, ensuring their continued relevance in modern energy systems.
Looking further into the future, research into closed-loop high-efficiency energy systems, such as combined Brayton-Rankine cycles and waste heat recovery solutions, is gaining momentum. These systems aim to recover and utilize as much waste heat as possible, maximizing overall plant efficiency. Coupled with carbon capture technologies, steam turbines will play a crucial role in bridging the gap between current energy infrastructure and a low-carbon future.
As global energy needs evolve, steam turbines remain at the forefront of power generation innovation. Whether through advanced thermodynamic cycles, improved materials, or AI-driven optimization, these machines will continue to adapt to new challenges and play a vital role in providing reliable, efficient, and sustainable energy worldwide.
How do steam power plants work
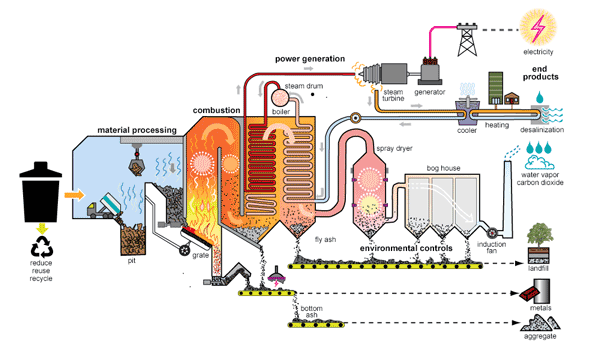
Steam power plants generate electricity by converting thermal energy from fuel combustion into mechanical energy using steam turbines. The process follows the Rankine cycle, a thermodynamic cycle that efficiently converts heat into work. The key components and working principles of a steam power plant are as follows:
1. Fuel Combustion and Steam Generation
The process begins with a boiler or steam generator, where fuel (coal, natural gas, biomass, or nuclear energy) is burned to produce heat. In nuclear power plants, heat is generated by nuclear fission rather than combustion. The heat converts water into high-pressure, high-temperature steam. Superheaters may be used to further increase steam temperature, improving efficiency and reducing moisture content in later stages.
2. Expansion in the Steam Turbine
The high-pressure steam is directed to a steam turbine, where it expands and pushes turbine blades, causing the rotor to spin. This conversion of thermal energy into mechanical work is highly efficient in multi-stage turbines, where steam passes through high-pressure (HP), intermediate-pressure (IP), and low-pressure (LP) turbine stages before exiting. The rotational motion of the turbine shaft is used to drive a generator to produce electricity.
3. Electricity Generation
The turbine is connected to an electric generator, which converts mechanical energy into electrical energy using electromagnetic induction. The spinning turbine shaft rotates a coil of wire within a magnetic field, generating alternating current (AC) electricity, which is then sent to a transformer for voltage regulation and distribution.
4. Steam Condensation and Recycling
After passing through the turbine, the low-pressure steam enters a condenser, where it is cooled using a cooling system (air-cooled or water-cooled). The steam condenses back into water and is collected in a hot well. This condensate is then pumped back to the boiler by a feedwater pump, completing the closed-loop cycle. In many power plants, feedwater heaters improve efficiency by preheating the water using steam extracted from the turbine.
5. Waste Heat Management and Environmental Controls
Steam power plants generate waste heat, which is either released into the atmosphere or utilized in cogeneration (CHP) systems, where excess heat is used for district heating, desalination, or industrial processes. Modern power plants also employ pollution control technologies, such as electrostatic precipitators, scrubbers, and carbon capture systems, to reduce emissions and improve environmental performance.
Efficiency Enhancements
Modern steam power plants implement several strategies to increase efficiency:
- Supercritical and ultra-supercritical steam cycles operate at extremely high pressures and temperatures to maximize thermal efficiency.
- Reheating and regenerative feedwater heating reduce steam moisture content and improve heat utilization.
- Digital monitoring and automation optimize plant operations, enabling real-time performance adjustments and predictive maintenance.
Applications and Importance
Steam power plants play a crucial role in global electricity generation, providing reliable base-load power for grids. They are used in fossil-fuel, biomass, geothermal, solar thermal, and nuclear power stations. As technology advances, steam power plants are being integrated with renewable energy and carbon capture systems to enhance sustainability and reduce their environmental impact.
The efficiency and reliability of steam power plants have been continuously improved through advancements in technology, thermodynamic cycle enhancements, and material innovations. One of the most significant developments in modern steam power plants is the use of supercritical and ultra-supercritical (USC) steam conditions. Unlike conventional subcritical power plants, where steam exists as a mixture of liquid and gas, supercritical power plants operate at pressures above 22.1 MPa (the critical point of water), where steam directly transitions into a high-energy gas phase. Ultra-supercritical plants push these limits even further, with operating temperatures exceeding 600°C. These advancements significantly increase thermal efficiency, reducing fuel consumption and greenhouse gas emissions.
Reheat and regenerative cycles also play a crucial role in improving efficiency. In a reheat cycle, steam is expanded in the high-pressure turbine, reheated in the boiler, and then sent to the intermediate and low-pressure turbines for further expansion. This reduces steam moisture content and prevents blade erosion while improving overall energy extraction. Regenerative feedwater heating, where some steam is extracted from intermediate turbine stages to preheat the feedwater before it enters the boiler, further enhances efficiency by reducing the energy required for steam generation.
Material advancements have been critical to enabling these high-efficiency power plants. Nickel-based superalloys, high-chromium steels, and ceramic coatings have been developed to withstand extreme temperatures and pressures, increasing the durability and reliability of turbine components. Advanced blade design and computational fluid dynamics (CFD) modeling allow for optimized steam flow, reducing aerodynamic losses and increasing overall turbine performance. Longer last-stage blades have also been introduced in low-pressure sections to improve energy extraction from exhaust steam.
Automation and digital monitoring systems have transformed steam power plant operation and maintenance. Internet of Things (IoT) sensors continuously monitor critical parameters such as steam temperature, pressure, and turbine vibration, providing real-time data to plant operators. AI-driven predictive maintenance detects early signs of wear and inefficiencies, reducing downtime and maintenance costs. The use of digital twins—virtual models of steam power plants—allows engineers to simulate operating conditions and optimize performance before making real-world adjustments.
In terms of environmental impact, modern steam power plants are increasingly adopting carbon capture and storage (CCS) technologies to reduce CO₂ emissions. By capturing and storing carbon emissions from flue gases, these plants can continue to provide reliable electricity while minimizing their contribution to climate change. Integrated gasification combined cycle (IGCC) technology, which converts coal into synthetic gas before combustion, further enhances efficiency and reduces pollutant emissions.
Looking ahead, the integration of steam turbines with renewable energy sources such as biomass, solar thermal, and geothermal power is expanding their role in sustainable energy generation. Hybrid systems, where steam turbines operate alongside gas turbines or renewable energy sources, allow for greater flexibility in power generation, improving grid stability. Additionally, emerging technologies like supercritical CO₂ (sCO₂) cycles promise to further enhance efficiency and reduce environmental impact by using CO₂ instead of water as the working fluid.
With continuous advancements in thermodynamics, materials science, and digitalization, steam power plants remain a cornerstone of global energy infrastructure. As new technologies emerge, their efficiency, flexibility, and environmental performance will continue to improve, ensuring their relevance in the evolving energy landscape.
The future of steam power plants is being shaped by cutting-edge advancements in efficiency, sustainability, and flexibility. One of the most promising developments is the adoption of supercritical carbon dioxide (sCO₂) power cycles, which offer significant advantages over traditional steam cycles. Unlike water-based steam cycles, sCO₂ operates at higher densities and pressures, allowing for more compact turbine designs and higher thermal efficiency. This technology reduces energy losses, enhances power plant flexibility, and minimizes water consumption, making it particularly valuable in regions with water scarcity. Research is ongoing to integrate sCO₂ cycles into next-generation power plants, including nuclear and solar thermal applications.
The use of hydrogen as a fuel source is also gaining attention in steam power generation. Hydrogen can be co-fired with fossil fuels or used as a primary fuel in modified boilers, producing steam with little to no carbon emissions. Hydrogen-based steam power plants could become a key component of decarbonized energy systems, particularly in conjunction with renewable hydrogen production via electrolysis. Ammonia-fueled power plants are another emerging concept, as ammonia can be used as a hydrogen carrier and combusted to generate heat for steam production while minimizing carbon emissions.
Hybrid power plants, which combine steam turbines with other energy sources, are becoming more common as energy grids transition toward renewable energy. In solar thermal power plants, steam turbines convert heat from concentrated solar energy into electricity, allowing for energy storage and grid stability. Geothermal power plants use naturally occurring steam or hot water from deep underground reservoirs to drive turbines, providing a continuous and renewable energy source. Hybrid gas-steam plants, utilizing combined-cycle configurations, optimize fuel usage by running both gas and steam turbines from a single fuel source, improving overall efficiency.
Another key area of innovation is advanced waste heat recovery systems. Many industrial processes produce large amounts of unused heat, which can be captured and used to generate steam for power production. Organic Rankine Cycle (ORC) systems allow low-temperature waste heat to be converted into electricity using organic working fluids instead of water, enabling power generation from sources that were previously considered inefficient. Waste heat recovery is especially valuable in industries such as steel manufacturing, cement production, and chemical processing, where excess heat is abundant.
As energy demand fluctuates due to increased renewable energy integration, modern steam power plants are adopting flexible operating strategies to enhance grid reliability. Sliding pressure operation, fast-start technologies, and variable load adjustments allow steam turbines to ramp up or down quickly in response to changing energy demands. This adaptability makes steam power plants crucial for balancing renewable energy fluctuations, ensuring a stable power supply even when solar or wind generation varies.
The role of digitalization and artificial intelligence (AI) in optimizing steam power plant performance continues to grow. AI-driven control systems analyze real-time data from IoT-connected sensors to optimize fuel combustion, steam flow, and turbine efficiency. Digital twins simulate plant operations, allowing engineers to test different scenarios, predict maintenance needs, and improve overall performance without disrupting actual plant operations. These technologies help reduce downtime, lower maintenance costs, and extend the lifespan of critical components.
Looking ahead, carbon capture, utilization, and storage (CCUS) technologies will play an essential role in making steam power plants more sustainable. By capturing CO₂ emissions from flue gases and either storing it underground or converting it into useful products, CCUS can significantly reduce the environmental footprint of fossil-fuel-based steam power plants. The combination of CCUS with biomass power generation (Bioenergy with Carbon Capture and Storage, or BECCS) even has the potential to create carbon-negative power plants, removing more CO₂ from the atmosphere than they emit.
With continuous advancements in high-efficiency materials, hybrid energy systems, digital monitoring, and carbon reduction technologies, steam power plants are evolving to meet the needs of a cleaner and more flexible energy future. While traditional coal-fired plants are being phased out in many regions, next-generation steam power technologies will remain a critical part of the global energy mix, ensuring efficiency, reliability, and sustainability in an increasingly decarbonized world.
As steam power plants continue to evolve, several emerging technologies and research areas are shaping their future. One of the most promising developments is closed-loop supercritical CO₂ (sCO₂) power cycles, which can operate at much higher efficiencies than traditional Rankine cycles. These systems use CO₂ instead of water as the working fluid, allowing for more compact turbines, reduced water usage, and improved thermal efficiency. Research is ongoing to integrate sCO₂ cycles into both fossil-fuel and renewable energy systems, particularly in nuclear power plants, solar thermal plants, and waste heat recovery applications.
Another transformative advancement is the integration of advanced energy storage technologies with steam power plants. Thermal energy storage (TES) systems allow excess heat to be stored in materials such as molten salts or phase-change materials, which can later be used to generate steam when electricity demand is high. This makes steam power plants more flexible and better suited for balancing intermittent renewable energy sources like solar and wind. Pumped heat energy storage (PHES) is also being explored, where excess electricity is converted into heat and stored in solid materials before being converted back into steam-based electricity when needed.
Artificial intelligence (AI) and machine learning (ML) are playing an increasing role in improving steam power plant performance. AI-driven algorithms analyze real-time data from turbines, boilers, and condensers to optimize energy efficiency, predict equipment failures, and automate operational adjustments. Self-learning control systems can dynamically optimize steam pressure, temperature, and fuel combustion, ensuring that power plants run at peak efficiency under varying load conditions. Digital twin technology, which creates virtual models of power plants, allows operators to test different scenarios, optimize performance, and predict maintenance needs without disrupting actual plant operations.
In the pursuit of sustainability, zero-emission steam power plants are being explored using hydrogen combustion, ammonia-based fuels, and biomass gasification. Hydrogen-fueled steam turbines are gaining attention due to their ability to produce steam without carbon emissions. Similarly, ammonia—a hydrogen carrier—can be burned in high-temperature steam boilers with minimal greenhouse gas emissions. Biomass-based steam power plants, when combined with carbon capture technologies (BECCS), offer the potential for negative carbon emissions, meaning they can remove CO₂ from the atmosphere while generating electricity.
Hybridization with renewable energy sources is also expanding. Geothermal and solar thermal power plants use steam turbines in conjunction with naturally occurring heat sources, providing low-carbon and continuous power generation. Hybrid gas-steam combined cycle plants maximize efficiency by utilizing waste heat from gas turbines to generate steam for additional power generation. These hybrid approaches are being designed to work with renewable hydrogen, waste heat recovery, and concentrated solar power (CSP) systems to create fully decarbonized energy solutions.
Advancements in steam turbine materials and manufacturing techniques are further pushing efficiency boundaries. The use of nickel-based superalloys, advanced ceramic coatings, and additive manufacturing (3D printing) enables turbine components to withstand extreme temperatures and pressures, extending their operational lifespan and reducing maintenance costs. Aerodynamic blade design improvements, made possible through computational fluid dynamics (CFD) simulations, are optimizing steam flow and reducing energy losses.
As power grids continue to evolve, flexible steam turbine operation is becoming increasingly important. Traditionally, steam turbines operated best at full load, but modern designs now allow for fast start-up, sliding pressure operation, and rapid load changes to accommodate variable renewable energy generation. These features make steam power plants more adaptable to modern grid requirements, improving overall system stability.
With ongoing innovations in advanced thermodynamic cycles, energy storage, digitalization, and clean energy integration, steam power plants are positioned to remain a key player in the global energy transition. As new technologies continue to emerge, the next generation of steam power plants will be more efficient, environmentally sustainable, and better suited for a flexible and decarbonized energy landscape.
Main parts of turbine
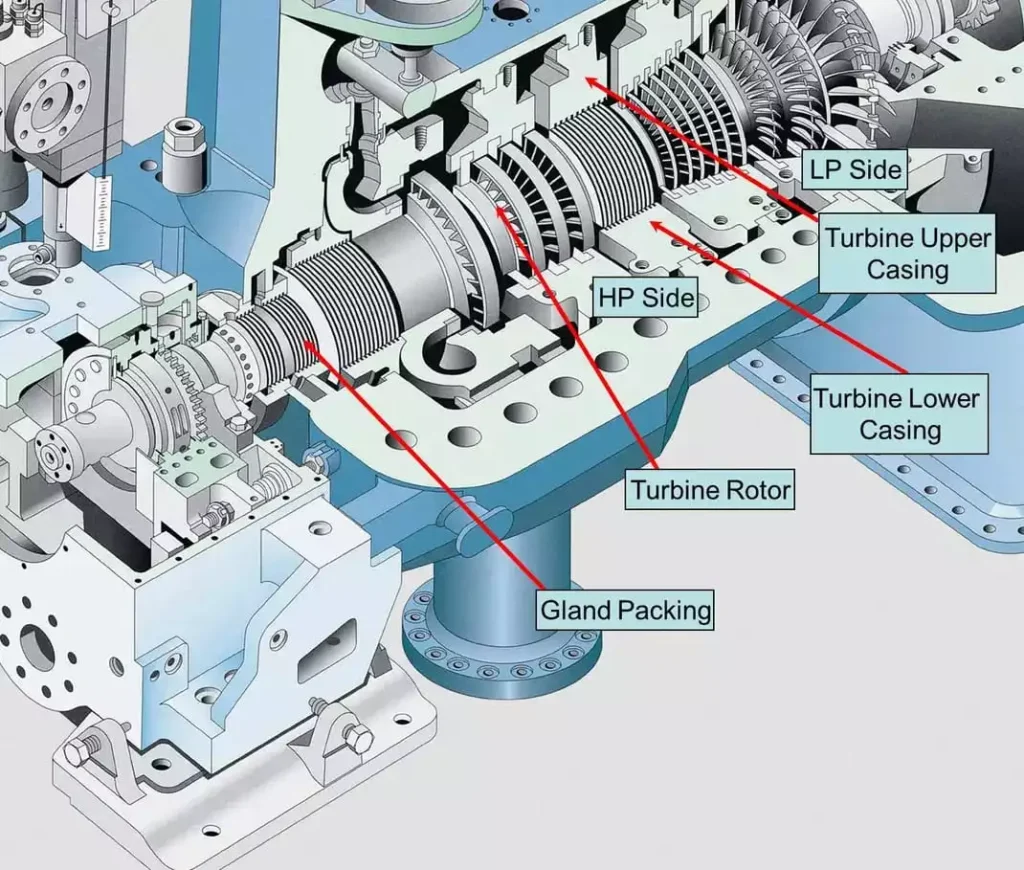
A steam turbine consists of several key components, each playing a critical role in converting thermal energy from steam into mechanical power. The main parts of a steam turbine include:
1. Rotor
The rotor is the rotating component of the turbine that carries the turbine blades and is connected to the generator shaft. It converts the kinetic energy of steam into rotational mechanical energy. The rotor must be precisely balanced to ensure smooth operation and minimize vibration.
2. Blades (Buckets)
Turbine blades, also called buckets, are mounted on the rotor and are responsible for extracting energy from high-pressure steam. They come in two main types:
- Impulse blades: Used in impulse turbines, these blades change the direction of high-velocity steam jets, causing the rotor to spin.
- Reaction blades: Used in reaction turbines, these blades experience both steam pressure and velocity changes, producing additional rotational force.
3. Casing (Cylinder)
The casing encloses the rotor and blades, directing steam flow through the turbine. It is typically divided into high-pressure, intermediate-pressure, and low-pressure sections. The casing must withstand high temperatures and pressures while minimizing heat losses.
4. Nozzles
Nozzles are responsible for directing and accelerating the steam onto the turbine blades. They convert thermal energy into kinetic energy by reducing the steam pressure and increasing velocity before it reaches the rotor. Nozzles are used mainly in impulse turbines.
5. Bearings
Bearings support the turbine rotor and allow it to rotate smoothly. There are two main types:
- Journal bearings: Support radial loads and help maintain shaft alignment.
- Thrust bearings: Absorb axial forces and prevent the rotor from moving along its axis.
6. Shaft
The shaft transmits rotational energy from the rotor to the generator or mechanical load. It must be precisely machined to ensure efficient power transfer with minimal friction losses.
7. Steam Chest and Control Valves
The steam chest is the section where steam enters the turbine. It contains control valves, which regulate steam flow and pressure to ensure optimal turbine performance. Control valves include stop valves, which shut off steam flow, and governor valves, which adjust steam input based on load demand.
8. Glands and Seals
To prevent steam leakage and maintain efficiency, turbines use gland seals at shaft entry and exit points. These seals prevent high-pressure steam from escaping while also keeping air from entering low-pressure sections. Labyrinth seals and carbon ring seals are commonly used in steam turbines.
9. Exhaust System and Condenser
After expanding through the turbine, low-pressure steam exits through the exhaust system and enters the condenser, where it is cooled and converted back into water. The condenser improves efficiency by maintaining a low back-pressure at the turbine exhaust.
10. Governor System
The governor system automatically controls the steam flow to maintain a constant turbine speed, adjusting for load variations. It prevents overspeed conditions and ensures stable operation by modulating the control valves.
11. Coupling
The coupling connects the turbine shaft to the generator or driven equipment, transmitting mechanical power. It must be flexible enough to accommodate slight misalignments while maintaining efficient power transfer.
Each of these components plays a crucial role in the operation and efficiency of a steam turbine, ensuring reliable power generation in various industrial and power plant applications.
The performance and reliability of a steam turbine depend on the precise design, material selection, and maintenance of its key components. Each part undergoes significant mechanical, thermal, and aerodynamic stresses during operation, requiring careful engineering and monitoring.
Rotor and Blades
The rotor is typically made from high-strength alloy steels to withstand the immense rotational forces and thermal stresses. It is machined to extremely tight tolerances to ensure balance and smooth operation. The blades, often made from nickel-based superalloys or titanium alloys, must endure high temperatures and steam velocities without deformation or fatigue. To enhance performance, modern turbines use shrouded blades (connected at the tips) or free-standing blades depending on efficiency requirements. Last-stage blades (LSBs) in low-pressure turbines are the longest and most crucial, designed aerodynamically to handle high-speed exhaust steam while minimizing energy losses.
Casing and Sealing Systems
The casing, usually constructed from cast steel or welded steel plates, contains steam at different pressure levels. It is insulated to reduce heat losses and maintain efficiency. The casing also incorporates expansion joints to accommodate thermal expansion and contraction during load variations. Sealing systems, such as labyrinth seals and brush seals, prevent steam leakage along the rotor shaft. In high-performance turbines, advanced sealing materials, such as carbon fiber composites, improve efficiency by minimizing leakage losses.
Bearings and Shaft
Bearings support the rotor’s weight and maintain alignment. Hydrodynamic bearings, lubricated with oil, reduce friction and dissipate heat generated during operation. Magnetic bearings are being explored in modern designs for even lower friction and improved performance. The shaft, made from forged steel, must be perfectly aligned with the generator to prevent excessive vibrations and ensure smooth power transmission.
Steam Chest and Control Valves
The steam chest directs incoming steam to the turbine through precisely controlled stop valves and governor valves. These components regulate steam pressure and flow, ensuring stable turbine speed under varying load conditions. Fast-acting emergency stop valves (ESVs) are critical safety features that shut off steam supply in case of an overspeed event or system failure.
Condenser and Exhaust System
The exhaust system directs low-pressure steam to the condenser, where it is cooled and converted back into water for reuse in the boiler. The condenser operates under vacuum conditions, created by air ejectors or vacuum pumps, to maximize turbine efficiency. Cooling water circulation systems maintain optimal condensation temperatures, using either natural water sources (once-through cooling) or cooling towers for recirculated cooling.
Governor System and Automation
The governor system is an essential control mechanism that adjusts steam flow to match electrical load demand. Modern turbines use electronic and hydraulic governors integrated with programmable logic controllers (PLCs) for precise speed and load control. Advanced power plants use AI-driven predictive analytics to optimize governor responses, reducing fluctuations and improving grid stability.
Maintenance and Performance Optimization
Regular maintenance is crucial to ensure long-term turbine efficiency. Condition monitoring systems (CMS) use vibration analysis, temperature sensors, and acoustic emissions to detect early signs of wear or misalignment. Remote monitoring technologies, connected through Industrial Internet of Things (IIoT) platforms, provide real-time data on turbine health, allowing predictive maintenance and minimizing unplanned downtime.
Future Innovations
Emerging 3D-printed turbine components and ceramic matrix composites (CMCs) are being developed to withstand higher temperatures and improve overall efficiency. Additionally, supercritical CO₂ turbines and hydrogen-compatible steam turbines are being explored as part of the transition to cleaner energy sources. These innovations aim to push turbine efficiency beyond current limits while reducing operational costs and emissions.
With continued advancements in materials, digitalization, and energy integration, steam turbines remain at the core of global power generation, adapting to the needs of a more sustainable and efficient energy future.
The evolution of steam turbine technology continues to drive improvements in efficiency, reliability, and sustainability. With ongoing research and the integration of advanced materials, digital monitoring, and hybrid energy systems, modern steam turbines are more sophisticated than ever.
Advanced Materials and Manufacturing Techniques
One of the most significant advancements in steam turbine design is the use of high-performance materials that can withstand extreme temperatures and pressures. Nickel-based superalloys, titanium alloys, and ceramic matrix composites (CMCs) are being increasingly used in turbine blades and rotors to improve thermal resistance and reduce component wear. These materials allow turbines to operate at higher temperatures, increasing efficiency.
Additive manufacturing (3D printing) is also revolutionizing turbine production. Complex components, including optimized blade geometries and cooling structures, can now be fabricated with greater precision and reduced material waste. This technology allows for the rapid prototyping of new blade designs and the on-site manufacturing of replacement parts, minimizing downtime and maintenance costs.
Steam Turbine Digitalization and Smart Monitoring
The integration of Industrial Internet of Things (IIoT) and artificial intelligence (AI) in steam turbines is enhancing performance monitoring and predictive maintenance. Smart sensors installed on turbine components collect real-time data on temperature, pressure, vibration, and steam flow. This data is analyzed using machine learning algorithms to detect early signs of wear, misalignment, or inefficiencies before they lead to failures.
Digital twin technology is becoming a key tool in steam turbine management. A digital twin is a virtual replica of a physical turbine that continuously updates based on live operational data. Engineers use these models to simulate different operating conditions, predict maintenance needs, and optimize performance without disrupting actual plant operations.
Hybrid Steam Turbine Power Plants
As the energy landscape shifts toward greater renewable integration, steam turbines are being adapted for hybrid power generation.
- Solar thermal power plants use steam turbines to convert heat from concentrated solar energy into electricity. Advanced thermal energy storage (TES) systems, such as molten salt storage, allow steam turbines to operate even when sunlight is unavailable.
- Geothermal power plants use naturally occurring steam from underground reservoirs to drive turbines, providing continuous and carbon-free electricity.
- Combined-cycle power plants (CCPPs) integrate gas turbines and steam turbines, utilizing waste heat from gas turbines to generate additional steam power, significantly increasing overall efficiency.
- Hydrogen-powered steam turbines are under development, allowing for cleaner energy production by using hydrogen as a fuel source in modified boilers.
Enhancements in Steam Flow and Efficiency
Modern steam turbines feature improved blade aerodynamics for more efficient energy extraction. Advanced computational fluid dynamics (CFD) modeling helps engineers design blades with optimal steam flow paths, reducing energy losses and enhancing power output. Variable geometry turbines, where blade angles adjust dynamically based on load demand, are also improving efficiency and flexibility.
Supercritical and ultra-supercritical steam conditions are now standard in high-efficiency power plants. By operating at temperatures above 600°C and pressures above 300 bar, these turbines achieve thermal efficiencies exceeding 45%, significantly reducing fuel consumption and emissions. Future supercritical CO₂ (sCO₂) power cycles aim to push efficiencies even further, utilizing dense-phase CO₂ as a working fluid instead of steam.
Sustainability and Carbon Reduction Technologies
To meet global decarbonization goals, steam turbine technology is being paired with carbon capture, utilization, and storage (CCUS) systems. By capturing and storing CO₂ emissions from steam power plants, net-zero and even carbon-negative electricity generation can be achieved. Additionally, bioenergy with carbon capture and storage (BECCS) is gaining traction, where steam turbines powered by biomass can actively remove CO₂ from the atmosphere.
Future Outlook
With continuous advancements in high-efficiency steam cycles, AI-driven monitoring, hydrogen compatibility, and hybrid energy integration, steam turbines remain a cornerstone of the global energy mix. The future will see more flexible, efficient, and environmentally sustainable steam turbines that can adapt to a rapidly evolving energy landscape while providing reliable power generation.
Next-Generation Innovations in Steam Turbine Technology
As the energy industry transitions toward higher efficiency and lower emissions, steam turbine technology is advancing in several critical areas. From breakthrough thermodynamic cycles to artificial intelligence (AI)-driven optimization, the next generation of steam turbines will be more efficient, flexible, and sustainable.
Supercritical CO₂ (sCO₂) Power Cycles
One of the most promising innovations is the supercritical carbon dioxide (sCO₂) power cycle, which replaces steam with CO₂ in a closed-loop system. Unlike traditional Rankine cycles, sCO₂ turbines operate at higher pressures and densities, leading to:
- Higher thermal efficiency (above 50%) due to reduced energy losses
- Smaller and more compact turbines, reducing equipment footprint
- Lower cooling water requirements, making them ideal for arid regions
Research is ongoing to integrate sCO₂ cycles into coal, nuclear, concentrated solar power (CSP), and waste heat recovery systems. These turbines are expected to revolutionize the efficiency of next-generation power plants.
Hydrogen-Compatible Steam Turbines
The push for zero-carbon energy is driving research into hydrogen-fueled boilers for steam turbines. By replacing fossil fuels with hydrogen, power plants can generate electricity without carbon emissions. Key challenges include:
- Developing high-temperature-resistant turbine materials for hydrogen combustion
- Designing hydrogen storage and distribution infrastructure
- Integrating hydrogen co-firing with existing steam plants for gradual transition
Some leading manufacturers are already testing 100% hydrogen-fired steam turbines, with commercial deployment expected in the near future.
AI-Driven Predictive Maintenance and Automation
Modern steam turbines are integrating AI and machine learning (ML) to enhance real-time monitoring and predictive maintenance. AI-driven systems analyze operational data, including:
- Vibration patterns to detect bearing or rotor imbalances
- Temperature fluctuations to predict material fatigue
- Steam flow and pressure variations to optimize efficiency
Using digital twin technology, operators can simulate different load scenarios and prevent failures before they occur, reducing unplanned downtime and improving plant availability.
Hybrid Power Plants and Grid Flexibility
Steam turbines are evolving to support grid flexibility and renewable energy integration:
- Hybrid gas-steam plants use gas turbines alongside steam turbines to improve load response times.
- Solar-assisted steam plants use concentrated solar energy to heat water, reducing fuel consumption.
- Energy storage integration with molten salt or phase-change materials (PCMs) allows excess heat to be stored for later use, increasing plant efficiency.
As power grids incorporate more intermittent renewables, steam turbines with rapid start-up capabilities and sliding pressure control will become crucial for grid stability.
Carbon Capture and Waste Heat Recovery
To reduce emissions, modern steam turbines are being paired with carbon capture, utilization, and storage (CCUS) systems. These technologies allow CO₂ to be captured and either stored underground or used for enhanced oil recovery (EOR), synthetic fuel production, or industrial applications. Additionally, waste heat recovery steam turbines are being deployed in industrial settings to convert low-grade heat into electricity, improving overall efficiency.
Future Outlook
The steam turbines of the future will be smaller, more efficient, and environmentally sustainable. Innovations in supercritical cycles, AI optimization, hydrogen co-firing, and hybrid energy integration will ensure that steam turbines remain a vital component of the global power industry for decades to come. As energy demands shift, steam turbines will continue evolving to meet the challenges of a decarbonized and flexible energy grid.
Steam Turbine Parts Drawing
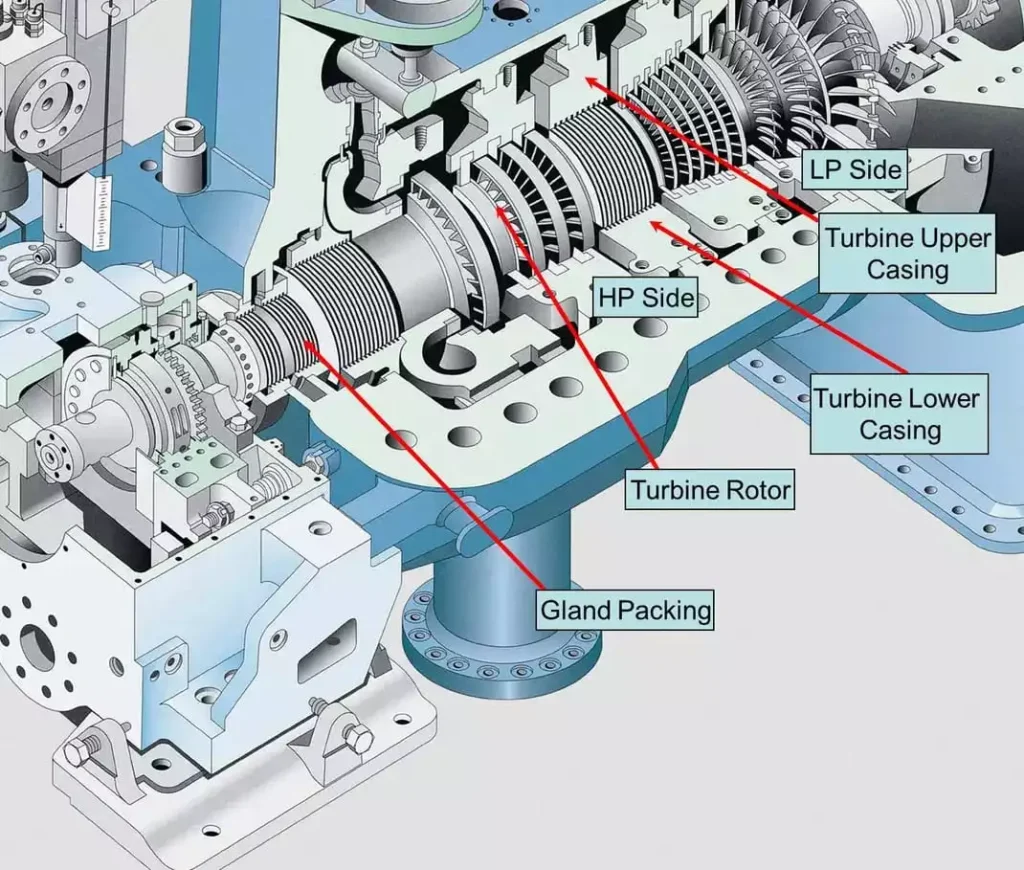
1. Rotor
The rotor is the central rotating shaft that carries the turbine blades. It is typically made of high-strength alloy steel to withstand high-speed rotation, thermal stress, and mechanical loads. The rotor converts the kinetic energy of steam into rotational mechanical energy, which is then transmitted to a generator for electricity production.
2. Stator
The stator is the stationary part of the turbine, which houses the nozzle and guide vanes. It directs the steam flow onto the blades in an efficient manner to maximize energy extraction. The stator also supports the bearings and seals that ensure smooth rotor operation.
3. Turbine Blades
The blades are crucial for converting steam energy into mechanical energy. They are divided into:
- Fixed blades (nozzles): These guide the high-pressure steam onto the moving blades.
- Moving blades: These rotate as steam passes over them, driving the rotor.
Blades are typically made from stainless steel, nickel-based superalloys, or titanium alloys for high-temperature and corrosion resistance.
4. Steam Inlet and Control Valves
The steam inlet is where high-pressure steam enters the turbine. Control valves regulate the steam flow to maintain turbine speed and power output. Types of valves include:
- Stop valves: Completely shut off steam flow in emergencies.
- Governor valves: Adjust the steam flow to control speed and load.
5. Bearings
Bearings support the rotor and allow smooth rotation. The main types are:
- Journal bearings: Support radial loads.
- Thrust bearings: Absorb axial loads and keep the rotor in position.
Most steam turbines use hydrodynamic bearings, lubricated with oil to reduce friction and wear.
6. Casing
The casing encloses the turbine, containing high-pressure steam and directing it through the blades. It is usually made from cast or welded steel to withstand extreme operating conditions.
7. Seals and Glands
Seals prevent steam leakage from the casing and rotor. Labyrinth seals and carbon ring seals are commonly used to reduce efficiency losses.
8. Condenser
After passing through the last stage of the turbine, the steam is cooled in the condenser, converting it back into water. This maintains a vacuum at the turbine exhaust, increasing efficiency.
9. Exhaust System
The exhaust system directs low-pressure steam from the turbine to the condenser. Efficient exhaust design minimizes back pressure, improving performance.
10. Governing System
The governing system controls turbine speed and adjusts load variations by regulating steam flow through the governor valves. Modern turbines use electronic and hydraulic governors for precise control.
11. Lubrication System
The lubrication system provides oil to bearings and moving parts to reduce friction and dissipate heat. It includes an oil pump, filters, and coolers.
12. Heat Exchangers and Reheaters
- Heat exchangers recover waste heat from the exhaust steam to improve efficiency.
- Reheaters heat partially expanded steam before entering the next turbine stage, increasing power output.
13. Extraction Ports
Steam extraction ports remove steam at intermediate pressure stages for use in industrial processes or feedwater heating.
These components work together to ensure the efficient conversion of thermal energy into mechanical energy, making steam turbines a key technology for power generation. Let me know if you need more details!
14. Steam Chests
The steam chest is the section where high-pressure steam is introduced and controlled before entering the turbine stages. It contains stop valves and control valves, ensuring precise regulation of steam flow to optimize turbine performance and prevent overspeeding or damage due to excessive pressure.
15. Diaphragms and Nozzle Rings
In multi-stage turbines, diaphragms separate the high-pressure and low-pressure stages. They contain nozzles or stationary guide vanes that direct steam onto the moving blades efficiently. Nozzle rings are similar but are often used in impulse turbines to convert steam energy into high-velocity jets before hitting the rotor blades.
16. Shaft Couplings
Steam turbines are often connected to generators, compressors, or mechanical drives through shaft couplings. These couplings ensure the smooth transmission of mechanical power while accommodating slight misalignments. Types include:
- Rigid couplings for fixed alignment
- Flexible couplings to absorb minor misalignments and thermal expansion
17. Gland Steam System
The gland steam system prevents air from leaking into the turbine at low-pressure points and stops steam from escaping at high-pressure points. It consists of gland seals, which use either labyrinth seals or carbon rings to control leakage and maintain efficiency.
18. Drain System
A drain system removes condensed steam (water droplets) that can form inside the turbine casing or piping. Accumulated condensate can damage blades through water hammer effects. The drain system ensures proper removal of moisture to prevent erosion and maintain efficiency.
19. Turning Gear
The turning gear is a small motor-driven mechanism that slowly rotates the turbine shaft when the turbine is shut down. This prevents shaft bending due to uneven cooling, ensuring smooth startup and operation when the turbine is restarted.
20. Cooling System
Steam turbines operate at extremely high temperatures, so they require effective cooling systems. Cooling methods include:
- Hydrogen cooling in generators coupled with turbines, increasing efficiency
- Oil coolers to regulate bearing temperature
- Water or air-cooled condensers to enhance heat dissipation
21. Bypass System
A bypass system allows steam to be diverted around the turbine during startup, shutdown, or emergencies. This prevents sudden pressure build-up and allows gradual turbine warm-up, reducing thermal stress.
22. Exhaust Hood and Diffuser
The exhaust hood directs the steam leaving the last stage of the turbine to the condenser. The diffuser reduces steam velocity, lowering back pressure and improving turbine efficiency.
23. Blade Root and Blade Fixing Mechanisms
Turbine blades are attached to the rotor using blade roots, which ensure secure mounting and allow for expansion due to temperature changes. Common blade root designs include:
- Fir-tree root: A multi-tooth interlocking design providing high strength and resistance to centrifugal forces.
- Dovetail root: A simple slot-and-tab design for easy installation and replacement.
Blades in high-speed turbines are often secured using locking pins or shroud bands to prevent movement and reduce vibrations.
24. Last-Stage Blades (LSB) and Tip-Timing Sensors
The last-stage blades (LSBs) in low-pressure turbines are the longest and most critical, as they handle high steam volumes at low pressure. LSBs are designed for maximum aerodynamic efficiency and may include:
- Twisted profiles to reduce turbulence
- Damping wires to minimize vibration
- Tip shrouds to limit losses
Modern turbines use tip-timing sensors to monitor blade vibrations and detect early signs of fatigue or failure.
25. Thermal Insulation and Expansion Joints
To minimize heat losses and protect surrounding components, turbine casings and piping are covered with thermal insulation. Materials include ceramic fibers, mineral wool, or composite insulation coatings.
Expansion joints accommodate thermal growth and contraction, preventing excessive stress on turbine casing and pipework. These joints are typically made from flexible metal bellows or sliding plates.
26. Shaft Seals and Steam Leakage Control
High-speed steam turbines require shaft seals to prevent steam leakage along the rotor. Common types include:
- Labyrinth seals: A series of narrow, stepped grooves that reduce steam leakage by creating pressure drops.
- Carbon ring seals: Graphite-based rings that provide tight sealing for smaller turbines.
- Brush seals: High-performance seals using fine wire bristles for better sealing with reduced friction.
A vacuum sealing system is also used in condensing turbines to maintain low back pressure and prevent air ingress.
27. Steam Reheat and Moisture Separator Reheater (MSR)
In high-efficiency turbines, steam is reheated between stages to prevent excessive moisture buildup. This is done using:
- Steam reheaters (in double or triple pressure turbines) to increase steam temperature before entering the next turbine stage.
- Moisture Separator Reheaters (MSRs) in nuclear and large thermal plants, which remove water droplets and reheat steam for improved efficiency and reduced blade erosion.
28. Auxiliary Systems (Fire Protection, Emergency Shutdown, and Instrumentation)
Modern steam turbines rely on various auxiliary systems to ensure safety and optimal performance:
- Fire protection systems use CO₂ or water mist to protect the turbine area from potential oil fires.
- Emergency shutdown (ESD) systems rapidly cut off steam flow in case of overspeed, high vibration, or mechanical failure.
- Instrumentation and sensors continuously monitor parameters such as steam pressure, temperature, rotor speed, blade stress, and vibration levels to optimize performance and detect faults early.
29. Lube Oil System
The lubrication system ensures smooth operation of the bearings and moving parts by supplying oil at the correct temperature and pressure. Key components include:
- Main oil pump: Driven by the turbine shaft, it supplies oil during normal operation.
- Auxiliary oil pump: Operates during startup or shutdown when the main pump is inactive.
- Emergency oil pump: A backup system that activates if other pumps fail, preventing damage to the bearings.
- Oil coolers and filters: Maintain proper oil temperature and cleanliness to prevent wear and overheating.
30. Jacking Oil System
Large turbines require a jacking oil system to lift the rotor slightly before startup, reducing friction and allowing smooth rotation. This system operates at high pressure to inject oil between the bearing surfaces before the shaft gains full speed.
31. Turbine Drains and Warm-Up Lines
Before startup, residual condensate in the turbine must be removed to prevent water hammer and blade damage. The drain system directs water away from the turbine casing and piping.
Warm-up lines help preheat the turbine gradually, reducing thermal stress and preventing cracks in metal components.
32. Load Gear and Gearbox (for Mechanical Drives)
In steam turbines driving mechanical equipment (like pumps or compressors), a gearbox is used to match the turbine’s high-speed rotation with the required operating speed of the driven equipment. These gears are:
- Single-stage reduction gears for moderate speed adjustments.
- Multi-stage planetary gears for higher reductions and efficiency.
33. Steam Admission Systems (Throttle and Partial Arc Admission)
Modern turbines use different steam admission techniques for efficiency and load control:
- Full-arc admission: Steam enters all nozzles at once, ideal for base-load power plants.
- Partial-arc admission: Steam is admitted through selected nozzles to improve efficiency at part loads.
- Throttle governing: Adjusts steam pressure entering the turbine to regulate power output.
34. Exhaust Hood Spray System
To prevent overheating in the last-stage blades (LSB), a cooling spray system injects water into the exhaust hood. This reduces temperature and protects the turbine from thermal damage during low-load conditions.
35. Start-Up and Run-Down Monitoring System
A start-up monitoring system ensures that the turbine accelerates smoothly from rest to operating speed by controlling steam admission and rotor warm-up rates. Similarly, a run-down system monitors rotor deceleration after shutdown, preventing thermal shock and excessive bearing loads.
36. Hydrogen and Stator Water Cooling (for Turbine-Driven Generators)
In steam turbine-driven generators, cooling is critical:
- Hydrogen cooling: The generator is filled with hydrogen gas, which reduces windage losses and efficiently removes heat from the rotor and stator.
- Stator water cooling: A closed-loop deionized water system cools the generator windings, ensuring safe operation at high power outputs.
37. Exhaust Expansion Joints and Condenser Neck
The exhaust expansion joint absorbs thermal expansion and vibrations between the turbine and condenser. The condenser neck is a large-diameter pipe that connects the turbine exhaust to the condenser, ensuring smooth steam flow and minimal pressure loss.
38. Steam Turbine Acoustic and Vibration Monitoring
High-speed turbines generate vibrations and noise, which must be monitored to prevent failures. Advanced systems include:
- Acoustic monitoring to detect leaks and steam flow disturbances.
- Vibration sensors to track shaft alignment and blade conditions.
- Online condition monitoring for real-time performance analysis and predictive maintenance.
Main Parts of a Steam Turbine
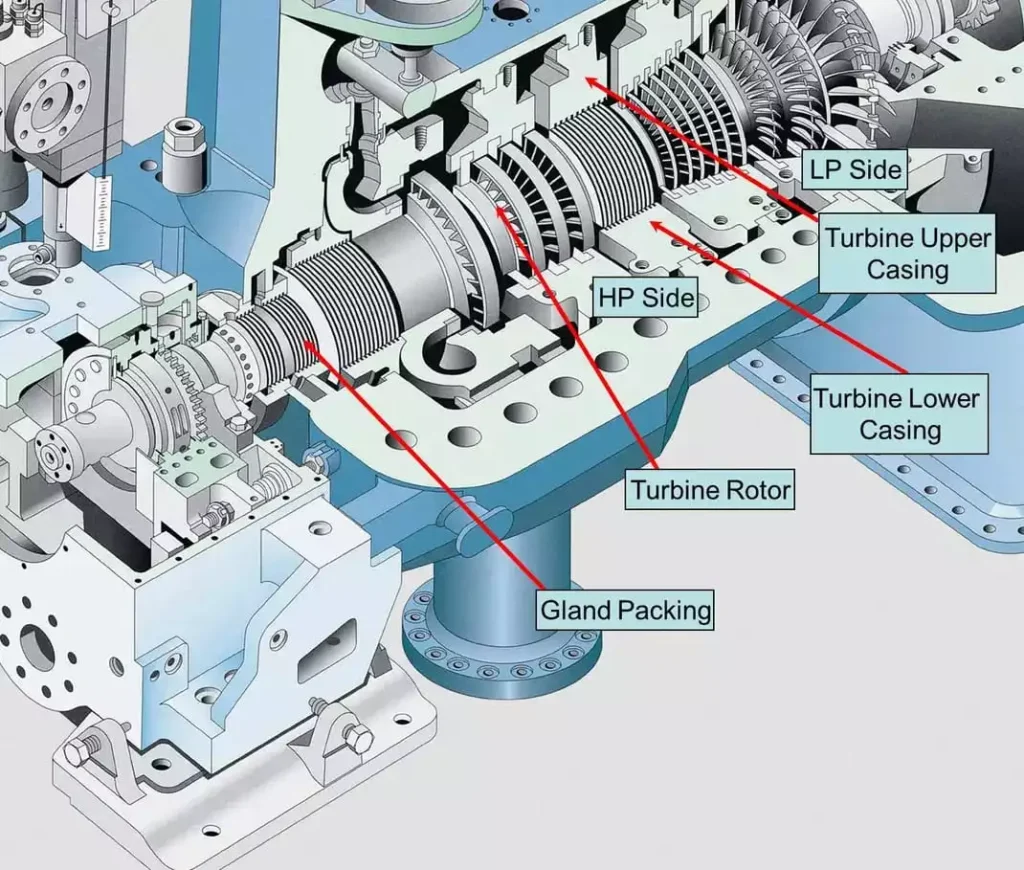
- Rotor – The rotating shaft that carries the turbine blades and transmits mechanical energy to the generator or driven equipment.
- Stator – The stationary part that houses guide vanes and nozzle rings to direct steam onto the blades efficiently.
- Turbine Blades – Convert steam energy into rotational motion. They are divided into:
- Fixed (Nozzle) Blades – Direct high-pressure steam onto moving blades.
- Moving Blades – Rotate under steam force to drive the rotor.
- Steam Inlet and Control Valves – Regulate the flow and pressure of steam entering the turbine. Includes:
- Stop Valves – Shut off steam supply during emergencies.
- Governor Valves – Control the turbine speed and load.
- Bearings – Support the rotor and reduce friction.
- Journal Bearings – Support radial loads.
- Thrust Bearings – Prevent axial movement of the rotor.
- Casing – The outer shell that contains steam and supports the turbine structure.
- Seals and Glands – Prevent steam leakage at high-pressure points and air ingress at low-pressure points.
- Condenser – Converts exhaust steam back into water to improve efficiency.
- Exhaust System – Directs low-pressure steam from the turbine to the condenser.
- Governing System – Controls the turbine speed and adjusts load variations.
- Lubrication System – Supplies oil to bearings and moving parts for cooling and friction reduction.
- Heat Exchangers and Reheaters – Recover waste heat and improve efficiency by reheating steam between stages.
- Extraction Ports – Remove intermediate-pressure steam for industrial use or feedwater heating.
- Steam Chests – Contain the valves and passages that direct steam into the turbine stages.
- Diaphragms and Nozzle Rings – Separate turbine stages and direct steam flow.
- Shaft Couplings – Connect the turbine shaft to the generator or driven equipment.
- Gland Steam System – Prevents steam leakage and maintains proper sealing.
- Drain System – Removes condensed steam to prevent damage.
- Turning Gear – A small motor that slowly rotates the rotor during shutdown to prevent bending.
- Cooling System – Regulates temperature in turbine components.
- Bypass System – Allows controlled steam diversion during startup and shutdown.
- Exhaust Hood and Diffuser – Reduce steam velocity and improve efficiency.
- Blade Root and Fixing Mechanisms – Secure blades to the rotor.
- Thermal Insulation and Expansion Joints – Protect against heat loss and accommodate expansion.
- Shaft Seals and Steam Leakage Control – Minimize losses and maintain efficiency.
- Steam Reheat and Moisture Separator Reheater (MSR) – Improve efficiency by removing moisture and reheating steam.
- Fire Protection, Emergency Shutdown, and Instrumentation – Ensure operational safety.
- Lube Oil and Jacking Oil Systems – Provide lubrication and assist in smooth startup.
- Load Gear and Gearbox – Adjust speed when driving mechanical loads.
- Steam Admission Systems (Throttle and Partial Arc Admission) – Optimize steam control for efficiency.
- Start-Up and Run-Down Monitoring Systems – Ensure controlled acceleration and deceleration.
- Hydrogen and Stator Water Cooling (for Turbine-Driven Generators) – Maintain temperature in power generation applications.
- Exhaust Expansion Joints and Condenser Neck – Absorb thermal expansion and connect to the condenser.
- Acoustic and Vibration Monitoring – Detect faults and ensure reliable operation.
The rotor is the rotating shaft that carries the turbine blades and transmits mechanical energy to the generator or other driven equipment. The stator is the stationary part of the turbine, housing guide vanes and nozzle rings that direct steam onto the moving blades efficiently. Turbine blades are divided into fixed (nozzle) blades, which direct high-pressure steam onto moving blades, and moving blades, which rotate under the force of the steam to drive the rotor.
Steam enters the turbine through steam inlet and control valves, which regulate flow and pressure. Stop valves shut off the steam supply during emergencies, while governor valves control the turbine speed and load. Bearings provide support and reduce friction, with journal bearings supporting radial loads and thrust bearings preventing axial movement of the rotor.
The casing is the outer shell that contains the steam and provides structural support. Seals and glands prevent steam leakage at high-pressure points and air ingress at low-pressure points. The exhaust system directs low-pressure steam from the turbine into the condenser, which converts exhaust steam back into water, improving efficiency.
The governing system controls the turbine speed and adjusts to load variations. The lubrication system supplies oil to bearings and moving parts, reducing friction and cooling components. Heat exchangers and reheaters recover waste heat and improve efficiency by reheating steam between turbine stages. Extraction ports remove intermediate-pressure steam for feedwater heating or industrial use.
Steam chests house the valves and steam passages leading into the turbine. Diaphragms and nozzle rings separate turbine stages and direct steam flow. Shaft couplings connect the turbine shaft to the generator or any driven equipment. The gland steam system prevents steam leakage and maintains sealing efficiency.
Drain systems remove condensed steam to prevent water hammer and blade damage. The turning gear is a small motor that slowly rotates the rotor during shutdown to prevent shaft bending due to uneven cooling. The cooling system regulates temperature in various turbine components, with methods including oil coolers, air-cooled condensers, and water cooling.
A bypass system allows controlled steam diversion during startup, shutdown, or emergencies, preventing sudden pressure build-up. The exhaust hood and diffuser guide the steam leaving the turbine to the condenser while reducing velocity and improving efficiency. Blade roots and fixing mechanisms secure the blades to the rotor and accommodate thermal expansion.
Thermal insulation and expansion joints help minimize heat loss and absorb expansion stress. Shaft seals and steam leakage control systems minimize energy losses and maintain turbine efficiency. Steam reheat and moisture separator reheaters enhance performance by removing moisture and reheating steam between stages.
Fire protection, emergency shutdown systems, and advanced instrumentation ensure safe operation. Lube oil and jacking oil systems provide lubrication and reduce startup friction. Load gears and gearboxes adjust speed when the turbine drives mechanical equipment.
Steam admission systems, such as throttle and partial arc admission, optimize steam flow for efficiency. Startup and rundown monitoring systems ensure controlled acceleration and deceleration of the turbine. Hydrogen and stator water cooling are used in turbine-driven generators to manage high temperatures.
Exhaust expansion joints and condenser necks accommodate thermal expansion and ensure smooth steam flow into the condenser. Acoustic and vibration monitoring systems help detect potential faults, improve reliability, and prevent failures. These components collectively ensure efficient and safe turbine operation, maximizing energy conversion from steam to mechanical power.
The rotor, a crucial component of the steam turbine, is responsible for carrying the turbine blades and transmitting mechanical energy to the generator or other connected equipment. The stator, which remains stationary, contains guide vanes and nozzle rings that direct steam flow efficiently onto the moving blades. The turbine blades play a critical role in energy conversion, with fixed (nozzle) blades directing high-pressure steam and moving blades harnessing this energy to drive the rotor.
Steam enters the turbine through a series of inlet and control valves, which regulate both flow and pressure. Stop valves serve as a safety feature by shutting off the steam supply in emergency situations, while governor valves continuously adjust the turbine’s speed and load conditions. Bearings, essential for smooth operation, support the rotor and reduce friction, with journal bearings handling radial loads and thrust bearings preventing axial movement.
The turbine casing encloses the entire system, providing containment and structural support. Seals and glands ensure minimal steam leakage at high-pressure points and prevent air ingress in low-pressure sections. The exhaust system facilitates the removal of low-pressure steam, directing it toward the condenser, where it is converted back into water to enhance the cycle’s efficiency.
A governing system continuously monitors and regulates the turbine’s speed, ensuring stable performance across varying load conditions. The lubrication system supplies oil to critical components, reducing wear and dissipating heat. Heat exchangers and reheaters improve thermal efficiency by recovering waste heat and reheating steam before it enters subsequent turbine stages. Extraction ports allow controlled steam removal for feedwater heating or industrial applications.
Steam chests house the necessary valves and channels for distributing steam efficiently across turbine stages. Diaphragms and nozzle rings help direct steam flow and separate different pressure zones within the turbine. Shaft couplings provide a secure connection between the turbine shaft and the generator or other driven machinery. The gland steam system prevents unnecessary steam loss while maintaining an effective seal.
Drain systems ensure that condensed steam is promptly removed, preventing damage from water hammer effects. The turning gear, a slow-speed motor, rotates the rotor during shutdown periods to prevent shaft deformation due to uneven cooling. The cooling system plays a significant role in regulating turbine component temperatures, employing various methods such as oil coolers, water-cooled condensers, and air-based cooling solutions.
A bypass system offers controlled steam diversion, particularly during startup and shutdown operations, to avoid abrupt pressure fluctuations. The exhaust hood and diffuser ensure efficient steam discharge, reducing velocity before directing it into the condenser. Blade root and fixing mechanisms provide secure attachment of blades to the rotor, accommodating thermal expansion and high centrifugal forces.
Thermal insulation minimizes heat loss and enhances turbine efficiency, while expansion joints accommodate material expansion due to temperature variations. Shaft seals and steam leakage control mechanisms further optimize efficiency by reducing unwanted energy loss. Steam reheat and moisture separator reheaters play a vital role in improving performance, preventing excessive moisture accumulation, and increasing overall efficiency.
To enhance operational safety, turbines are equipped with fire protection systems, emergency shutdown mechanisms, and comprehensive instrumentation that continuously monitors parameters such as vibration, temperature, and pressure. Lubrication and jacking oil systems support smooth operation, particularly during startup when the rotor requires assistance to overcome static friction.
For applications where the turbine drives mechanical loads, load gears and gearboxes adjust rotational speeds as needed. Steam admission techniques, such as throttle and partial arc admission, optimize steam control to maximize efficiency across varying load conditions. Startup and rundown monitoring systems facilitate controlled acceleration and deceleration, protecting the turbine from undue stress.
Hydrogen and stator water cooling methods are commonly employed in generator-driven turbines to manage temperature rise and prevent overheating. Exhaust expansion joints and the condenser neck absorb thermal expansion and ensure efficient steam flow into the condenser.
Advanced acoustic and vibration monitoring systems are integrated to detect potential mechanical issues, enhancing reliability and preventing failures. Collectively, these components and subsystems ensure that the steam turbine operates efficiently, safely, and with minimal energy loss, maximizing power generation and performance.
The rotor is the central rotating component of the steam turbine, carrying the turbine blades and transmitting mechanical energy to the generator or other driven machinery. The stator remains stationary and contains guide vanes and nozzle rings that direct steam flow efficiently onto the moving blades. Turbine blades are divided into fixed (nozzle) blades, which direct high-pressure steam onto the moving blades, and moving blades, which convert the energy from steam into rotational motion to drive the rotor.
Steam enters the turbine through inlet and control valves, which regulate both flow and pressure. Stop valves act as safety devices, shutting off the steam supply in emergency situations, while governor valves adjust turbine speed and load conditions. Bearings provide crucial support, ensuring smooth rotation and reducing friction. Journal bearings handle radial loads, while thrust bearings prevent axial movement of the rotor.
The casing encloses the turbine, providing structural support and containing the high-pressure steam. Seals and glands prevent steam leakage at high-pressure sections and stop air from entering in low-pressure zones. The exhaust system directs low-pressure steam from the turbine to the condenser, where it is converted back into water, improving overall efficiency.
The governing system continuously monitors and controls turbine speed, ensuring stable operation under varying load conditions. The lubrication system provides oil to critical components, reducing wear and dissipating heat. Heat exchangers and reheaters recover waste heat and reheat steam before it enters later stages, increasing efficiency. Extraction ports remove intermediate-pressure steam for industrial processes or to preheat feedwater.
Steam chests contain valves and passages that distribute steam effectively to different turbine stages. Diaphragms and nozzle rings help control steam direction and separate various pressure zones within the turbine. Shaft couplings provide a secure connection between the turbine shaft and the generator or other driven equipment. The gland steam system prevents steam loss while ensuring proper sealing at critical locations.
Drain systems remove condensed steam to prevent damage caused by water hammer. The turning gear, a slow-speed motor, rotates the rotor during shutdown to prevent deformation due to uneven cooling. The cooling system regulates temperature in turbine components, using methods such as oil coolers, air-cooled condensers, and water-based cooling.
A bypass system allows controlled steam diversion during startup, shutdown, or emergency conditions to prevent sudden pressure fluctuations. The exhaust hood and diffuser guide steam out of the turbine, reducing its velocity and improving efficiency. Blade root and fixing mechanisms securely attach blades to the rotor while accommodating thermal expansion and centrifugal forces.
Thermal insulation reduces heat loss, improving efficiency, while expansion joints accommodate material expansion due to temperature fluctuations. Shaft seals and steam leakage control mechanisms minimize energy losses. Steam reheat and moisture separator reheaters improve performance by preventing excessive moisture buildup and optimizing steam quality for later turbine stages.
To ensure safe operation, fire protection systems, emergency shutdown mechanisms, and instrumentation continuously monitor parameters such as vibration, temperature, and pressure. Lubrication and jacking oil systems help maintain smooth operation, with jacking oil assisting in lifting the rotor during startup to minimize friction.
When the turbine drives mechanical equipment, load gears and gearboxes adjust rotational speeds accordingly. Steam admission techniques, such as throttle and partial arc admission, optimize steam flow for efficiency across different load conditions. Startup and rundown monitoring systems ensure smooth acceleration and deceleration, preventing excessive stress on turbine components.
Hydrogen and stator water cooling methods are used in generator-driven turbines to manage temperature and prevent overheating. Exhaust expansion joints and condenser necks absorb thermal expansion and facilitate smooth steam flow into the condenser.
Acoustic and vibration monitoring systems detect potential mechanical issues early, improving reliability and preventing failures. All these components and systems work together to ensure that the steam turbine operates efficiently, safely, and with minimal energy loss, maximizing its power generation capability.
Steam Turbine Rotor
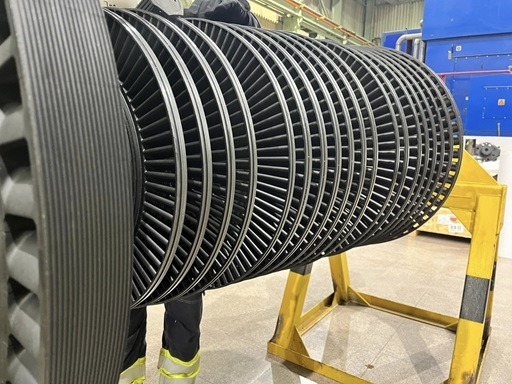
The steam turbine rotor is the central rotating component that converts thermal energy from steam into mechanical energy. It is a critical part of the turbine assembly, responsible for carrying the moving blades and transmitting power to the generator or other driven machinery.
The rotor consists of a solid or built-up shaft onto which turbine blades are mounted. It is designed to withstand high rotational speeds, extreme temperatures, and mechanical stresses. The materials used for rotor construction are typically high-strength alloy steels with excellent thermal and fatigue resistance.
The rotor operates under high centrifugal forces due to the attached blades, requiring precision balancing to minimize vibrations. It is supported by journal bearings that handle radial loads and thrust bearings that control axial movement. Shaft couplings connect the rotor to other mechanical components, such as the generator or gearbox.
To maintain efficiency and reliability, the rotor undergoes rigorous testing, including ultrasonic inspections and non-destructive evaluations. Cooling mechanisms, such as internal air or steam cooling, are often integrated to prevent overheating and prolong the rotor’s operational life.
Rotor designs vary based on the type of steam turbine, with single-shaft and multi-shaft configurations used in different applications. Advanced rotor designs may include integral shrouds or lacing wires to improve blade stability and reduce vibration.
The performance of the rotor directly impacts the efficiency and longevity of the steam turbine, making its precise design and maintenance crucial in power generation and industrial applications.
The steam turbine rotor is the primary rotating element in a steam turbine, converting the energy from high-pressure steam into mechanical motion. It consists of a long shaft with multiple stages of rotating blades attached, which interact with stationary blades to extract energy from the steam efficiently. The rotor must withstand high speeds, elevated temperatures, and significant mechanical stress, requiring precision engineering and high-strength materials such as nickel-chromium-molybdenum alloy steel.
The rotor is typically forged as a single piece or assembled from multiple sections, depending on the turbine size and design. In high-capacity turbines, the rotor may be a monoblock construction for strength and reliability, while smaller turbines might use a shrunk-on disc design, where individual discs with blades are fitted onto the shaft. It is designed to operate at extremely high speeds, often reaching thousands of revolutions per minute (RPM), which necessitates precise balancing to prevent excessive vibration.
One of the key features of the rotor is its blade attachment system. Moving blades are secured to the rotor using root designs such as fir-tree, dovetail, or pinned configurations, allowing for thermal expansion while maintaining structural integrity. To reduce stress and vibration, blade tips may be connected with lacing wires or integral shrouds.
The rotor is supported by bearings, which help maintain smooth rotation and minimize wear. Journal bearings support radial loads, ensuring the rotor remains centered, while thrust bearings handle axial forces, preventing movement along the shaft’s length. Proper lubrication of these bearings is essential to ensure the rotor’s long-term operation and reliability.
Steam sealing is another crucial aspect of rotor design. Gland seals are used at both ends of the rotor to prevent steam leakage from high-pressure sections and to avoid air ingress in low-pressure sections. These seals typically use labyrinth, carbon ring, or brush-type configurations to maintain efficiency.
Thermal expansion is a critical consideration in rotor operation. As the turbine heats up during operation, the rotor expands, requiring careful alignment with stationary components to prevent excessive stress. Advanced turbines incorporate flexible or multi-bearing rotor designs to accommodate expansion and avoid excessive thermal stresses.
Cooling mechanisms may also be integrated into rotor designs to maintain optimal operating temperatures. Some large turbines use internally cooled rotors, where cooling steam or air flows through channels within the shaft to dissipate excess heat.
The rotor is connected to the generator or mechanical load via a coupling system, which must be precisely aligned to prevent misalignment-related failures. Flexible or rigid couplings are used depending on the application and the level of torque transmission required.
To ensure operational safety and efficiency, rotors undergo rigorous testing, including high-speed balancing, ultrasonic inspections, and non-destructive testing methods to detect material defects. Vibration monitoring systems continuously assess rotor behavior to identify potential issues before they lead to failure.
Rotor maintenance involves periodic inspections, realignment, and blade replacement if wear or damage is detected. The lifespan of a well-maintained rotor can extend for decades, but operational factors such as thermal cycling, steam quality, and mechanical loads affect its durability.
The efficiency and reliability of a steam turbine heavily depend on the rotor’s precision design, quality of materials, and maintenance practices. Modern rotors incorporate advanced manufacturing techniques such as precision forging, 3D profiling, and computational fluid dynamics (CFD) optimization to enhance performance and longevity.
The steam turbine rotor is the core rotating component that converts steam energy into mechanical motion. It consists of a central shaft with multiple stages of rotating blades, interacting with stationary blades to extract maximum energy from steam expansion. Designed to operate under extreme conditions, the rotor must withstand high rotational speeds, elevated temperatures, and significant mechanical stresses. To achieve this, it is manufactured from high-strength alloy steels such as nickel-chromium-molybdenum alloys, which offer excellent thermal and fatigue resistance.
The rotor’s design varies depending on the turbine type and application. In high-capacity turbines, the rotor is typically a monoblock forging to ensure strength and structural integrity, while in smaller or modular turbines, a built-up construction with shrunk-on discs may be used. The high-speed nature of steam turbines, often reaching thousands of revolutions per minute (RPM), requires precise balancing to minimize vibration and mechanical stress.
Turbine blades are securely attached to the rotor using specialized root designs such as fir-tree, dovetail, or pinned configurations. These attachment methods allow for thermal expansion while maintaining structural stability. Blade tips may be reinforced with shrouds or lacing wires to improve aerodynamic efficiency and reduce vibration. Each stage of the rotor is designed for specific pressure and velocity conditions, ensuring optimal steam energy extraction.
Bearings play a crucial role in rotor stability. Journal bearings support the rotor radially, keeping it aligned, while thrust bearings absorb axial forces generated by steam pressure imbalances. These bearings require a continuous supply of lubrication to minimize friction and dissipate heat, preventing premature wear or failure.
To prevent steam leakage and maintain efficiency, gland seals are installed at both ends of the rotor. These seals use labyrinth, carbon ring, or brush configurations to reduce steam loss in high-pressure sections and prevent air ingress in low-pressure areas. Proper sealing is critical to maintaining turbine performance and efficiency.
Thermal expansion is a major consideration in rotor design. As the turbine reaches operating temperature, the rotor expands, necessitating precise clearances between moving and stationary components. Advanced turbine designs incorporate flexible rotor arrangements or multi-bearing support systems to accommodate thermal stresses and prevent excessive loads on turbine casings and bearings.
Cooling mechanisms are sometimes integrated into the rotor to regulate temperature and enhance durability. Large turbines may feature internally cooled rotors with steam or air channels that dissipate excess heat, preventing material degradation and prolonging service life.
The rotor connects to the generator or mechanical load via a coupling system that must be carefully aligned to avoid misalignment-related failures. Depending on the application, flexible or rigid couplings are used to transmit torque efficiently while compensating for minor alignment deviations.
To ensure safe and reliable operation, steam turbine rotors undergo rigorous quality control and testing. High-speed balancing, ultrasonic inspections, and non-destructive evaluation techniques are used to detect material defects or imbalances. Advanced vibration monitoring systems continuously assess rotor performance, identifying potential issues before they lead to catastrophic failures.
Maintenance of the rotor is essential for long-term turbine reliability. Regular inspections, alignment checks, and blade replacements help extend its lifespan, which can reach several decades under proper operating conditions. Factors such as steam quality, thermal cycling, and mechanical loads influence the rotor’s durability, making preventive maintenance critical.
Modern rotor designs incorporate advanced computational fluid dynamics (CFD) simulations, precision forging techniques, and 3D profiling to optimize efficiency and aerodynamics. These innovations contribute to higher performance, reduced energy losses, and extended operational life, making steam turbine rotors a vital component in power generation and industrial applications.
The steam turbine rotor is the essential rotating element responsible for converting steam energy into mechanical power. It is designed to operate at high speeds while withstanding extreme temperatures and mechanical stresses. The rotor consists of a shaft with multiple stages of rotating blades, interacting with stationary blades to extract maximum energy from steam expansion. It is typically made from high-strength alloy steel, such as nickel-chromium-molybdenum alloys, to ensure durability, resistance to thermal fatigue, and structural integrity.
The rotor’s construction depends on the turbine type and application. In large, high-power turbines, the rotor is usually forged as a single monoblock piece to maintain structural strength and reliability. In smaller turbines, a built-up design with shrunk-on discs may be used, where individual rotor discs are fitted onto the shaft. Each approach offers specific advantages in terms of stress distribution, thermal expansion handling, and ease of maintenance.
Blade attachment is a critical aspect of rotor design. Moving blades are secured using fir-tree, dovetail, or pinned roots, ensuring they remain in place despite high centrifugal forces. To reduce vibration and improve aerodynamic efficiency, blades may be equipped with shrouds or lacing wires that provide additional structural support. The length and profile of the blades vary across turbine stages, with longer blades in low-pressure sections to accommodate expanding steam.
The rotor is supported by journal bearings that maintain its radial alignment and thrust bearings that absorb axial forces generated by steam pressure differentials. These bearings require a continuous supply of lubricating oil to minimize friction, dissipate heat, and prevent wear. Advanced bearing systems include tilting-pad designs to enhance rotor stability and reduce vibration.
To maintain efficiency, steam sealing mechanisms such as labyrinth seals, carbon rings, or brush seals are installed at both ends of the rotor. These prevent steam leakage in high-pressure sections and block air ingress in low-pressure zones. Proper sealing minimizes energy losses and protects turbine performance.
Thermal expansion management is a crucial design consideration. As the rotor heats up, it expands, requiring precise clearances between the rotor and stationary components to prevent excessive stress. Flexible coupling arrangements and multi-bearing support systems help accommodate thermal growth while maintaining proper alignment.
Some high-performance turbines incorporate internal cooling mechanisms, where cooling steam or air circulates within the rotor to regulate temperatures. This prevents overheating, reduces thermal stresses, and extends the rotor’s service life.
The rotor is connected to the generator or driven machinery through a coupling system, which must be precisely aligned to avoid misalignment-induced failures. Depending on the load requirements, either flexible or rigid couplings are used to efficiently transmit torque while allowing for slight alignment deviations.
Rotor reliability is ensured through rigorous testing and monitoring. High-speed balancing is performed to minimize vibration, and non-destructive testing methods such as ultrasonic and radiographic inspections detect potential material defects. Vibration monitoring systems continuously track rotor behavior, identifying anomalies before they lead to major failures.
Routine maintenance is crucial for rotor longevity. Inspections, realignment, and periodic blade replacements help extend the operational lifespan, which can exceed several decades under optimal conditions. Factors such as steam quality, cyclic loading, and thermal stresses influence rotor wear, making preventive maintenance essential.
Advanced rotor designs incorporate computational fluid dynamics (CFD) simulations, precision forging techniques, and optimized blade profiles to enhance aerodynamic efficiency and reduce energy losses. These innovations contribute to improved turbine performance, extended service life, and increased power generation efficiency, making the rotor a vital component in steam turbines used for power plants and industrial applications.
Steam Turbine Materials
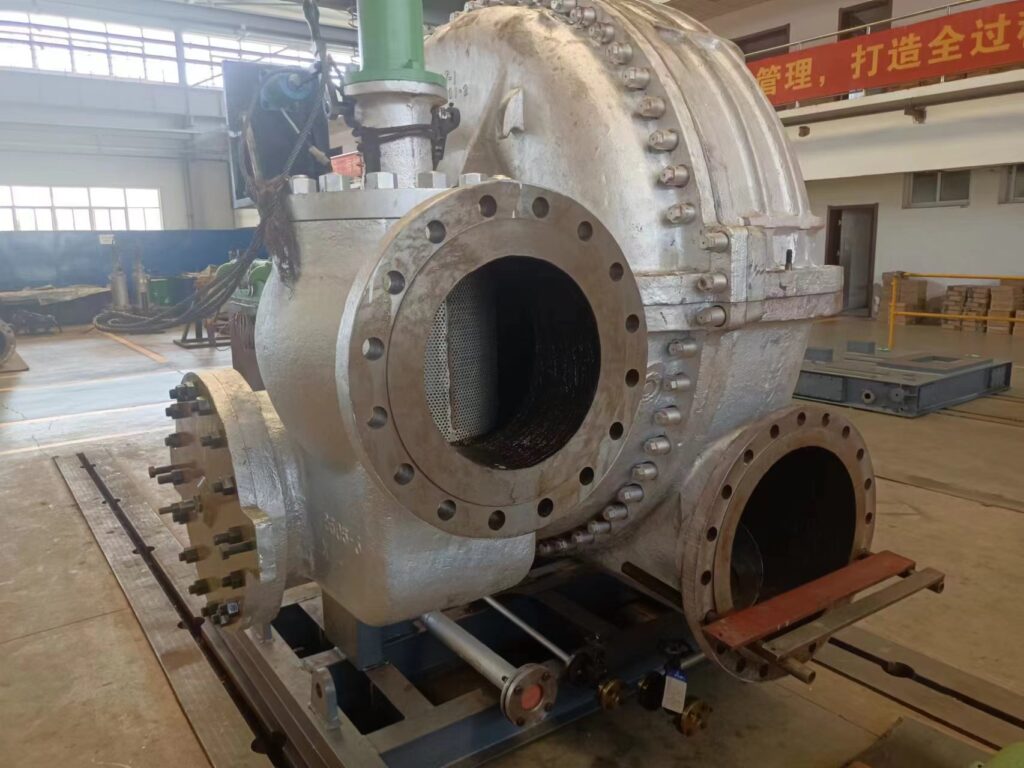
Steam turbines operate under extreme conditions of high temperature, pressure, and rotational speed, requiring materials with exceptional mechanical strength, thermal stability, and corrosion resistance. The selection of materials depends on the turbine’s operating conditions, including the steam temperature and pressure levels.
Rotor Materials
The rotor is subjected to high centrifugal forces and thermal stresses, requiring materials with excellent strength, toughness, and fatigue resistance. Common materials include:
- Low-Alloy Steels (Cr-Mo, Ni-Cr-Mo Steels) – Used for rotors operating at moderate temperatures. Examples include ASTM A470 and A471.
- High-Alloy Steels (9-12% Cr Steels) – Suitable for high-temperature applications in advanced steam turbines, providing better creep resistance and oxidation protection.
- Nickel-Based Alloys (Inconel, Nimonic) – Used in ultra-supercritical turbines where temperatures exceed 600°C, offering superior creep and corrosion resistance.
Blade Materials
Turbine blades experience high thermal and mechanical stresses, requiring materials that balance strength, corrosion resistance, and resistance to creep and fatigue.
- Stainless Steels (12% Cr Steels, 17-4 PH, 403 SS, 410 SS) – Commonly used for high-pressure and intermediate-pressure blades due to their good corrosion and erosion resistance.
- Titanium Alloys (Ti-6Al-4V) – Used for low-pressure blades in some applications due to their high strength-to-weight ratio and corrosion resistance.
- Nickel-Based Superalloys (Inconel 718, Udimet 720, Nimonic 80A) – Found in advanced turbines with high steam temperatures to withstand extreme conditions.
Casing and Shell Materials
The turbine casing must endure high internal steam pressure while maintaining structural stability.
- Cast Carbon Steel (ASTM A216 WCB, ASTM A105) – Used for low and medium-pressure casings.
- Cr-Mo Steel (ASTM A182 F22, ASTM A387 Gr. 22) – Used for high-pressure casings due to improved thermal and mechanical properties.
- High-Nickel and Creep-Resistant Alloys – Used in ultra-supercritical turbines where temperatures exceed 600°C.
Bearing and Shaft Materials
Bearings and shafts require materials with excellent wear resistance and fatigue strength.
- Bearing Steels (AISI 52100, M50, and 440C Stainless Steel) – Provide high hardness and wear resistance.
- High-Nickel and Chromium Alloys – Used for high-temperature applications to prevent oxidation.
Seal and Gasket Materials
Seals and gaskets prevent steam leakage and require materials resistant to heat and pressure.
- Graphite and Carbon-Based Seals – Used in gland seals due to their low friction and self-lubricating properties.
- Metallic Seals (Stainless Steel, Inconel) – Provide better longevity in high-temperature zones.
Fasteners and Bolting Materials
Bolts, nuts, and fasteners hold turbine components together under extreme conditions.
- High-Strength Alloy Steels (ASTM A193 B7, B16, A286) – Used for high-temperature, high-stress applications.
- Nickel-Based Alloys (Inconel 718, Hastelloy X) – Provide superior strength and corrosion resistance in advanced turbines.
Material Selection Factors
- Temperature and Pressure Resistance – Materials must withstand high steam temperatures and pressures.
- Creep and Fatigue Resistance – Components must resist long-term deformation under constant stress.
- Corrosion and Erosion Resistance – Steam impurities can cause corrosion and erosion, requiring robust materials.
- Manufacturability and Cost – High-performance materials must also be cost-effective and manufacturable.
The use of advanced materials, including high-alloy steels, nickel-based superalloys, and titanium, has significantly improved the efficiency, durability, and performance of modern steam turbines, particularly in high-efficiency power plants such as supercritical and ultra-supercritical systems.
Steam turbines operate under extreme conditions, requiring materials that can withstand high temperatures, pressures, and mechanical stresses. The choice of materials is crucial for ensuring efficiency, longevity, and reliability. Each component of the turbine, including the rotor, blades, casing, bearings, and seals, is made from materials specifically chosen for their mechanical properties, thermal stability, and resistance to corrosion and wear.
The rotor is one of the most critical parts of the turbine, as it experiences high centrifugal forces and thermal stresses. It is typically made from high-strength alloy steels such as nickel-chromium-molybdenum (Ni-Cr-Mo) alloys or 9-12% chromium steels, which provide excellent resistance to creep and fatigue. For ultra-supercritical steam turbines operating at extreme temperatures, nickel-based superalloys such as Inconel 718 or Nimonic alloys may be used due to their superior thermal resistance.
Turbine blades require materials that can withstand high steam velocities, thermal expansion, and erosion from water droplets in lower pressure stages. Stainless steels, particularly 12% chromium alloys (403 SS, 410 SS, and 17-4 PH stainless steel), are commonly used in high-pressure and intermediate-pressure stages due to their corrosion and oxidation resistance. In the low-pressure stages, where blades are longer and exposed to significant forces, titanium alloys such as Ti-6Al-4V may be used to reduce weight while maintaining strength. Some advanced turbines use nickel-based superalloys like Nimonic 80A or Inconel 718, which provide excellent high-temperature performance and creep resistance.
The casing of a steam turbine serves as a pressure vessel that contains and directs the steam flow. It must withstand high steam pressures while maintaining structural integrity. For low and medium-pressure casings, cast carbon steels like ASTM A216 WCB or ASTM A105 are commonly used. For high-pressure and high-temperature casings, chromium-molybdenum steels such as ASTM A182 F22 or ASTM A387 Gr. 22 are preferred due to their improved creep strength and oxidation resistance. In ultra-supercritical steam turbines, casings may be made from high-nickel alloys to withstand extreme operating conditions.
Bearings and shafts in a steam turbine require materials with high wear resistance and fatigue strength. Journal bearings and thrust bearings typically use high-carbon and chromium-bearing steels, such as AISI 52100 or M50 tool steel, which offer excellent hardness and durability. In high-temperature applications, nickel-based or cobalt-based alloys may be used to prevent oxidation and wear.
Seals and gaskets are essential for preventing steam leakage and ensuring efficiency. Graphite-based seals and carbon rings are commonly used in gland sealing systems due to their self-lubricating properties. Metallic seals, including those made from stainless steel or Inconel, offer higher durability and are often used in high-temperature sections.
Bolts, fasteners, and couplings in steam turbines must withstand extreme thermal expansion and mechanical loads. High-strength alloy steels such as ASTM A193 B7 and B16 are commonly used for bolting applications. In high-temperature sections, nickel-based alloys like Inconel 718 or Hastelloy X provide superior strength and oxidation resistance.
Material selection is driven by factors such as temperature and pressure resistance, creep and fatigue resistance, corrosion and erosion resistance, and cost-effectiveness. Advances in metallurgy, including the use of powder metallurgy, precision forging, and thermal barrier coatings, have enhanced the performance of modern steam turbines. These innovations help improve efficiency, reduce maintenance costs, and extend the lifespan of turbine components, making them more reliable for power generation applications.
Steam turbines require materials that can withstand extreme temperatures, high rotational speeds, and mechanical stress while maintaining efficiency and durability. The selection of materials is based on their ability to resist thermal expansion, corrosion, creep, and fatigue, ensuring long-term operational reliability. Different components of the turbine are made from specialized materials tailored to their specific functions.
The rotor is a critical component, subjected to high centrifugal forces and temperature fluctuations. It is commonly made from high-strength alloy steels, such as nickel-chromium-molybdenum (Ni-Cr-Mo) alloys, which provide excellent resistance to thermal fatigue and creep. In high-performance turbines, especially ultra-supercritical systems, nickel-based superalloys like Inconel 718 or Nimonic alloys are used due to their superior thermal resistance and mechanical strength. The rotor must be precisely manufactured and balanced to minimize vibration and ensure stability during operation.
Turbine blades experience high steam velocities and temperatures, requiring materials with excellent creep resistance and fatigue strength. For high-pressure stages, stainless steels such as 12% chromium alloys (403 SS, 410 SS, and 17-4 PH stainless steel) are commonly used due to their oxidation and corrosion resistance. Low-pressure stages often use titanium alloys, such as Ti-6Al-4V, which offer a high strength-to-weight ratio while reducing centrifugal forces. In extreme conditions, nickel-based superalloys like Nimonic 80A or Inconel 718 are employed to withstand high thermal stress and prevent material degradation over time.
The casing of a steam turbine acts as a pressure vessel and must be capable of withstanding high steam pressures and temperature variations. For low and medium-pressure turbines, cast carbon steels like ASTM A216 WCB or ASTM A105 are typically used. High-pressure turbines require materials with greater thermal and mechanical stability, such as chromium-molybdenum steels (ASTM A182 F22, ASTM A387 Gr. 22), which provide better creep resistance. In ultra-supercritical turbines, casings may incorporate high-nickel alloys to handle extreme steam conditions without deformation.
Bearings and shafts must endure constant rotational motion while minimizing friction and wear. Journal bearings and thrust bearings are typically made from high-carbon and chromium-bearing steels, such as AISI 52100 or M50 tool steel, known for their hardness and durability. To improve longevity in high-temperature applications, nickel-based and cobalt-based alloys are sometimes used to prevent oxidation and wear. Bearings require continuous lubrication to prevent overheating and ensure smooth operation.
Seals and gaskets prevent steam leakage and maintain turbine efficiency. Graphite-based seals and carbon rings are commonly used due to their low friction properties and thermal resistance. Metallic seals, made from stainless steel or Inconel, provide better durability and are often used in high-temperature turbine sections to prevent loss of steam pressure.
Bolts, fasteners, and couplings must be able to withstand thermal expansion and high mechanical loads. High-strength alloy steels (ASTM A193 B7, B16) are commonly used for fastening turbine components. For extreme operating conditions, nickel-based alloys, such as Inconel 718 or Hastelloy X, offer superior strength, oxidation resistance, and long-term stability.
Material selection is influenced by key factors such as thermal and mechanical properties, resistance to corrosion and erosion, creep resistance, and cost-effectiveness. Modern steam turbines benefit from advanced materials and manufacturing techniques such as precision forging, powder metallurgy, and thermal barrier coatings, which enhance their performance and efficiency. These advancements contribute to longer turbine lifespans, reduced maintenance costs, and increased overall energy efficiency, making steam turbines more reliable and effective in power generation applications.
Steam turbines operate under extreme conditions, requiring materials that can withstand high temperatures, pressures, and mechanical stresses while maintaining long-term reliability. The selection of materials for various components is crucial to ensure high efficiency, durability, and minimal maintenance.
The rotor is a critical rotating component that experiences high centrifugal forces and thermal stresses. It is typically made from high-strength alloy steels, such as nickel-chromium-molybdenum (Ni-Cr-Mo) alloys, which offer excellent resistance to fatigue and creep. For high-temperature applications, particularly in ultra-supercritical turbines, nickel-based superalloys such as Inconel 718 and Nimonic 80A are used due to their superior heat resistance and structural integrity. The rotor must be precisely balanced to minimize vibrations and ensure smooth operation.
Turbine blades are subjected to high steam velocities, thermal expansion, and erosion from water droplets, especially in the low-pressure stages. Blades in high-pressure sections are often made from 12% chromium stainless steels (403 SS, 410 SS, and 17-4 PH stainless steel), which provide good corrosion and oxidation resistance. For low-pressure blades, where weight reduction is crucial, titanium alloys (Ti-6Al-4V) are used due to their high strength-to-weight ratio and resistance to corrosion. In advanced turbines operating at extreme temperatures, nickel-based superalloys (Nimonic, Udimet, Inconel) provide excellent high-temperature strength and creep resistance.
The casing of the turbine acts as a pressure vessel, containing and directing the steam flow. It must withstand both high steam pressures and temperature fluctuations. Cast carbon steels (ASTM A216 WCB, ASTM A105) are commonly used for low and medium-pressure casings, while high-pressure sections require chromium-molybdenum steels (ASTM A182 F22, ASTM A387 Gr. 22) due to their superior creep resistance and thermal stability. Ultra-supercritical turbines may use high-nickel alloys to handle extreme operating conditions.
Bearings and shafts require materials that provide excellent wear resistance and fatigue strength to withstand continuous motion and heavy loads. Journal bearings and thrust bearings are often made from high-carbon and chromium-bearing steels (AISI 52100, M50 tool steel), which offer high hardness and durability. In high-temperature applications, nickel-based and cobalt-based alloys are used to prevent oxidation and wear. Bearings are also lubricated with high-quality oils to reduce friction and extend their lifespan.
Seals and gaskets play a vital role in preventing steam leakage and ensuring the turbine operates efficiently. Graphite-based seals and carbon rings are widely used due to their self-lubricating properties and ability to withstand high temperatures. Metallic seals, made from stainless steel or Inconel, offer higher durability and are preferred in high-temperature sections where steam pressures are extreme.
Bolts, fasteners, and couplings hold various turbine components together and must endure thermal expansion and mechanical stresses. High-strength alloy steels (ASTM A193 B7, B16) are commonly used for bolting applications. In high-temperature zones, nickel-based alloys (Inconel 718, Hastelloy X) provide superior strength and oxidation resistance, ensuring long-term structural stability.
The selection of materials is based on key factors such as temperature resistance, mechanical strength, corrosion resistance, and cost-effectiveness. Modern steam turbines benefit from advanced manufacturing processes such as precision forging, powder metallurgy, and thermal barrier coatings, which improve material performance and efficiency. These innovations enhance turbine durability, reduce maintenance costs, and increase overall energy output, making them essential for modern power generation applications.
A steam turbine bucket, commonly referred to as a blade, is a crucial component in a steam turbine that extracts energy from high-pressure and high-temperature steam. Buckets are responsible for converting the kinetic energy of steam into mechanical energy by directing and controlling the steam flow across the turbine’s stages. They are designed to withstand extreme forces, including centrifugal forces, high temperatures, corrosion, and erosion caused by steam and water droplets.
Material Selection for Steam Turbine Buckets
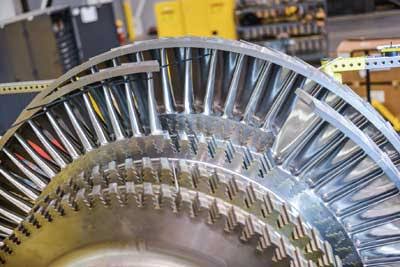
Steam turbine buckets must be made from materials that provide high strength, resistance to creep, corrosion, and fatigue, and maintain stability at elevated temperatures. The choice of material depends on the turbine’s operating conditions, including pressure and temperature.
- High-Pressure Stage Blades: Typically made from stainless steels such as 12% chromium alloys (403 SS, 410 SS, 17-4 PH stainless steel) due to their excellent oxidation and corrosion resistance.
- Intermediate-Pressure Stage Blades: Often made from chromium-molybdenum steels or precipitation-hardened stainless steels, which provide a balance between strength and ductility.
- Low-Pressure Stage Blades: Subjected to steam condensation, requiring titanium alloys (Ti-6Al-4V) or nickel-based superalloys (Nimonic 80A, Inconel 718) to prevent corrosion and erosion while maintaining high mechanical strength.
Types of Steam Turbine Buckets
Steam turbine buckets are categorized based on their function and design:
- Impulse Blades: Found in impulse turbines, these buckets have a simple curved profile and work by changing the direction of high-velocity steam jets. The kinetic energy of steam is converted into rotational motion with minimal pressure drop across the blade.
- Reaction Blades: Used in reaction turbines, these buckets have an airfoil shape that utilizes both steam velocity and pressure drop across the blade surface, generating additional lift and improving efficiency.
Key Features of Steam Turbine Buckets
- Shrouded or Unshrouded Designs: Shrouded buckets have an outer band connecting them to reduce vibration and leakage losses, while unshrouded blades allow for easier cooling and are used in high-speed applications.
- Root Attachments: The bucket root, or dovetail, secures the blade to the rotor disk. Various attachment designs, such as fir-tree, dovetail, or pinned connections, ensure mechanical stability and prevent dislodging under high centrifugal forces.
- Erosion and Corrosion Protection: Low-pressure stage blades are coated with special materials, such as cobalt-based or nickel-based coatings, to resist erosion from water droplets in wet steam conditions.
Manufacturing and Performance Enhancements
- Precision Forging & Machining: Ensures uniform grain structure and strength.
- Shot Peening & Surface Treatments: Improves fatigue resistance.
- Hollow or Cooled Buckets: Used in high-temperature applications to prevent overheating and material degradation.
Steam turbine buckets are engineered for high efficiency and durability, playing a key role in the performance and longevity of a turbine. Their design and material selection are continually improved through advanced metallurgy and aerodynamics to maximize energy conversion and reliability in power generation applications.
Steam turbine buckets, or blades, are one of the most critical components in a turbine, responsible for efficiently extracting energy from high-pressure and high-temperature steam. Their design, material composition, and manufacturing techniques directly impact the performance, efficiency, and durability of the turbine.
Material Selection
The choice of material for turbine buckets depends on operating conditions such as temperature, pressure, and exposure to corrosion or erosion. Materials must possess high mechanical strength, resistance to thermal expansion, and the ability to withstand long-term fatigue stresses.
- High-Pressure Stage Blades: Made from stainless steels, particularly 12% chromium alloys (403 SS, 410 SS, 17-4 PH stainless steel), which offer excellent oxidation resistance and mechanical strength at high temperatures.
- Intermediate-Pressure Stage Blades: Often manufactured using chromium-molybdenum steels or precipitation-hardened stainless steels, providing an optimal balance between strength and flexibility.
- Low-Pressure Stage Blades: These blades are more susceptible to erosion due to steam condensation. Titanium alloys (Ti-6Al-4V) or nickel-based superalloys (Nimonic 80A, Inconel 718) are used to improve corrosion resistance and maintain strength in wet steam conditions.
Types of Steam Turbine Buckets
Buckets are designed to maximize energy conversion from steam to mechanical power. The two main types are:
- Impulse Buckets: Used in impulse turbines, these blades deflect high-velocity steam jets, converting kinetic energy into rotational energy with minimal pressure loss across the stage. The steam impacts the blade and changes direction, causing rotation.
- Reaction Buckets: Used in reaction turbines, these blades utilize both steam velocity and pressure drop to generate motion. The steam expands within the blade passage, creating additional lift and improving efficiency.
Design Considerations
The performance of turbine buckets depends on several key design features:
- Shrouded vs. Unshrouded Buckets: Shrouded blades are connected by a cover band to reduce vibration and leakage, improving efficiency and longevity. Unshrouded blades, commonly used in high-speed applications, reduce weight and allow better cooling.
- Root Attachments: The bucket root connects the blade to the rotor disk using dovetail, fir-tree, or pinned designs to prevent movement or dislodging under high centrifugal forces.
- Coatings for Protection: In low-pressure and high-temperature conditions, blades are coated with erosion-resistant materials such as cobalt-based or nickel-based alloys to improve durability.
Manufacturing and Performance Enhancements
To achieve optimal performance, steam turbine buckets undergo advanced manufacturing processes:
- Precision Forging & Machining: Ensures a uniform grain structure for increased strength.
- Shot Peening & Surface Treatments: Enhances fatigue resistance and longevity.
- Hollow or Cooled Buckets: In high-temperature applications, hollow designs allow internal cooling to prevent thermal degradation.
Steam turbine bucket design and materials are continuously evolving to improve turbine efficiency and reliability. Modern advancements in metallurgy, aerodynamics, and computational simulations contribute to better energy conversion, reduced wear, and extended service life in power generation applications.
Steam turbine buckets, or blades, are essential for converting thermal energy from high-pressure steam into mechanical energy that drives the turbine rotor. These components operate under extreme conditions, including high temperatures, pressures, and rotational speeds, requiring precise design and material selection to ensure efficiency and durability.
Material Selection
The materials used for steam turbine buckets must have high mechanical strength, resistance to thermal expansion, corrosion resistance, and the ability to withstand fatigue and creep over long periods. The selection varies depending on the turbine stage.
- High-Pressure Stage Blades are typically made from stainless steels such as 403 SS, 410 SS, and 17-4 PH stainless steel, which offer excellent oxidation resistance, high-temperature strength, and durability.
- Intermediate-Pressure Stage Blades require a balance between toughness and resistance to creep. Chromium-molybdenum steels and precipitation-hardened stainless steels are commonly used in this section.
- Low-Pressure Stage Blades face issues like steam condensation, leading to erosion and corrosion. These blades often use titanium alloys (Ti-6Al-4V) or nickel-based superalloys (Nimonic 80A, Inconel 718), which provide superior mechanical properties and corrosion resistance.
Types of Steam Turbine Buckets
There are two primary types of turbine buckets based on the energy conversion method:
- Impulse Buckets: These blades are used in impulse turbines, where steam is expanded through nozzles and directed at high velocity onto the buckets. The change in momentum generates rotational motion. These blades experience minimal pressure drop.
- Reaction Buckets: In reaction turbines, the blades have an aerodynamic profile, allowing steam to expand through the blade passages. The pressure drop across the blade results in additional lift, increasing efficiency.
Key Features and Design Considerations
- Shrouded vs. Unshrouded Buckets:
- Shrouded buckets have a cover band that reduces vibration and leakage, improving efficiency.
- Unshrouded buckets are lighter and allow for better cooling, often used in high-speed applications.
- Root Attachments: Buckets are attached to the rotor using fir-tree, dovetail, or pinned connections to ensure a secure fit and prevent failure due to centrifugal forces.
- Erosion and Corrosion Protection: Low-pressure blades are more prone to water droplet erosion. Protective coatings, such as cobalt-based or nickel-based coatings, help increase blade lifespan.
Manufacturing Techniques and Performance Enhancements
Modern steam turbine buckets are produced using advanced manufacturing techniques to improve their efficiency and reliability.
- Precision Forging & Machining: Ensures uniform grain structure and mechanical strength.
- Shot Peening & Surface Treatments: Increases fatigue resistance and extends service life.
- Hollow or Internally Cooled Buckets: Used in high-temperature applications to prevent thermal stress and improve operational stability.
Turbine buckets are continuously improved through advancements in metallurgy, aerodynamics, and computational fluid dynamics (CFD) simulations, leading to enhanced performance, higher efficiency, and longer service life in power generation applications.
A steam chest in a steam turbine is a critical component that acts as an intermediary between the steam supply and the turbine inlet. It regulates the flow of high-pressure steam to the turbine blades, ensuring controlled expansion and efficient energy conversion. The steam chest is designed to handle extreme temperatures and pressures while maintaining smooth operation and preventing steam leakage.
Function of the Steam Chest
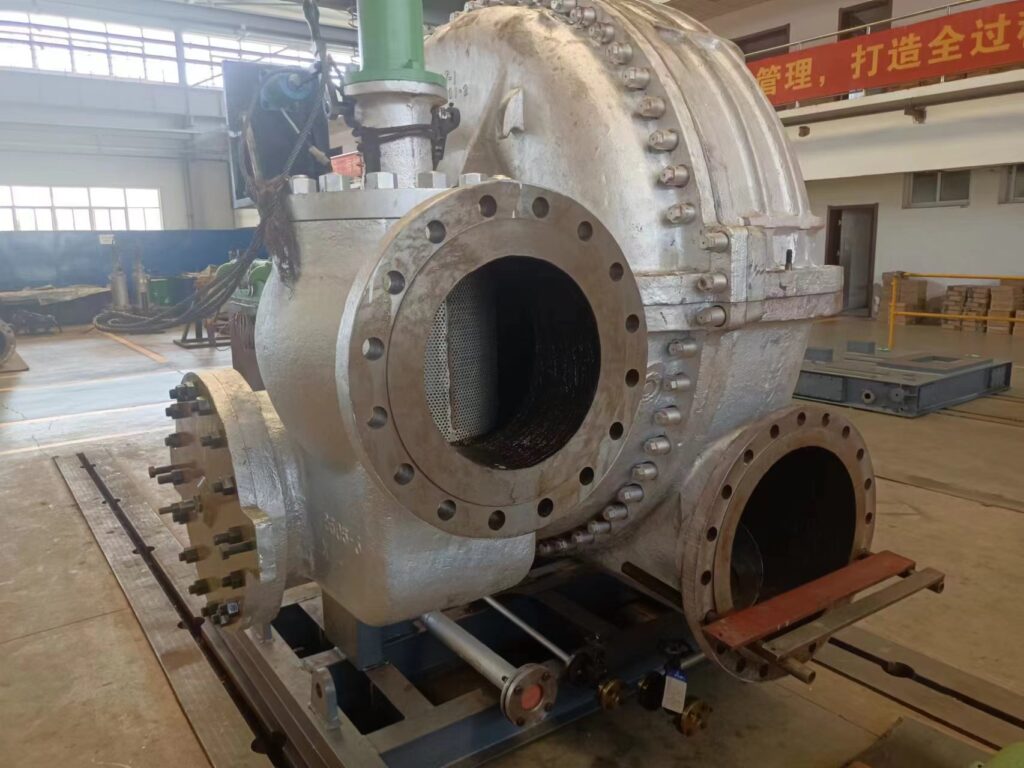
The primary functions of the steam chest in a steam turbine include:
- Regulating Steam Flow: The steam chest houses control valves that manage the amount of steam entering the turbine, preventing excessive pressure fluctuations and ensuring efficient turbine operation.
- Pressure and Temperature Control: It maintains the required pressure and temperature of the steam before it enters the turbine, optimizing energy conversion.
- Steam Distribution: It evenly distributes steam to the turbine stages, ensuring uniform flow and preventing thermal imbalances.
- Preventing Water Ingress: The steam chest design helps separate water droplets from steam, reducing erosion and wear on turbine blades.
Components of a Steam Chest
A steam chest typically consists of the following key parts:
- Main Steam Valves: Control the flow of steam from the boiler to the turbine. These may include stop valves and control valves, which regulate the steam pressure and flow rate.
- Valve Actuators: Mechanisms that control the opening and closing of the steam valves, either mechanically, hydraulically, or electrically.
- Steam Piping and Nozzles: Directs the steam efficiently from the steam chest into the turbine stages.
- Casing: A high-strength, heat-resistant enclosure made of chromium-molybdenum steels or nickel-based alloys, designed to withstand high pressures and temperatures.
Types of Steam Chests
- Single Steam Chest: Found in small or medium turbines, where a single chamber regulates steam flow.
- Double Steam Chest: Used in larger turbines, where multiple inlets help distribute steam more evenly, reducing thermal stresses and improving efficiency.
Material and Construction
Since the steam chest operates under extreme conditions, it is made from materials such as carbon steel, chromium-molybdenum steel, or high-temperature nickel-based alloys. These materials provide thermal stability, corrosion resistance, and mechanical strength to withstand high-pressure steam environments.
Importance in Steam Turbine Performance
A well-designed steam chest ensures stable turbine operation by preventing thermal shocks, reducing wear on blades, and optimizing steam expansion. Proper maintenance and monitoring of steam chests help enhance turbine efficiency, extend service life, and minimize operational downtime in power plants and industrial applications.
The steam chest in a steam turbine serves as a critical control and distribution system, ensuring the proper regulation of high-pressure steam before it enters the turbine blades. It plays a vital role in maintaining efficiency, safety, and performance under extreme operating conditions.
Function of the Steam Chest
The steam chest regulates the pressure, temperature, and flow rate of steam entering the turbine. It houses key control components, including stop valves and control valves, which adjust steam delivery based on load demand. By maintaining a stable steam supply, the steam chest prevents pressure surges and minimizes mechanical stress on the turbine.
In addition to controlling steam flow, the steam chest helps manage thermal expansion and ensures an even distribution of steam across the turbine inlet. This prevents localized overheating, which can lead to material fatigue and efficiency losses.
Key Components of a Steam Chest
- Stop Valves: These are safety devices that shut off steam flow in case of an emergency or during maintenance. They prevent steam from entering the turbine when it is not in operation.
- Control Valves: These regulate the amount of steam entering the turbine, ensuring optimal energy conversion and efficiency. The valves can be operated mechanically, hydraulically, or electrically based on turbine design.
- Casing: The steam chest casing is made of high-strength, heat-resistant alloys that can withstand high pressures and temperatures. Common materials include chromium-molybdenum steel and nickel-based alloys.
- Steam Nozzles and Piping: These direct steam from the chest to the turbine blades, ensuring smooth expansion and minimal turbulence.
Types of Steam Chests
Depending on the turbine’s size and operating conditions, different types of steam chests are used:
- Single Steam Chest: Found in smaller turbines, where a single chamber regulates steam flow.
- Double Steam Chest: Used in larger turbines with multiple steam inlets, allowing better steam distribution and reducing thermal stresses.
Material and Design Considerations
The materials used in a steam chest must resist thermal expansion, high-pressure stress, and corrosion from high-temperature steam. Chromium-molybdenum steels and nickel-based alloys are commonly used due to their high mechanical strength and resistance to thermal fatigue.
Proper steam chest design and maintenance are essential for ensuring safe and efficient turbine operation. A well-maintained steam chest minimizes wear and tear on turbine blades, prevents steam leakage, and enhances overall power plant efficiency.
The steam chest of a steam turbine is a crucial component responsible for controlling and distributing high-pressure steam before it enters the turbine blades. It ensures efficient energy conversion, protects turbine components, and maintains stable operating conditions under high temperatures and pressures.
Functions of the Steam Chest
The steam chest plays several important roles in turbine operation:
- Regulating Steam Flow: It houses control valves that manage the amount of steam entering the turbine, preventing sudden pressure fluctuations and ensuring optimal efficiency.
- Maintaining Pressure and Temperature Stability: The steam chest ensures that steam is delivered at the correct pressure and temperature to maximize energy conversion without causing thermal stress on turbine components.
- Steam Distribution: It ensures uniform steam flow across the turbine’s first stage, preventing uneven thermal expansion and reducing efficiency losses.
- Protecting Against Water Ingress: The steam chest design helps separate any residual water droplets in the steam, preventing erosion and damage to turbine blades.
Key Components of a Steam Chest
- Stop Valves: These act as emergency shut-off devices, preventing steam from entering the turbine during shutdowns or maintenance.
- Control Valves: These regulate the precise amount of steam entering the turbine, adjusting for varying load demands. They may be operated mechanically, hydraulically, or electrically.
- Casing: The outer enclosure, made of high-strength materials like chromium-molybdenum steel or nickel-based alloys, is designed to withstand extreme conditions.
- Steam Nozzles and Piping: These guide steam from the chest into the turbine stages in a controlled manner to optimize expansion and energy transfer.
Types of Steam Chests
- Single Steam Chest: Found in smaller turbines, where one chamber controls steam entry.
- Double Steam Chest: Used in larger turbines with multiple inlets for better steam distribution and reduced thermal stresses.
Material and Design Considerations
Since the steam chest operates in a high-pressure and high-temperature environment, it must be built from materials that resist thermal expansion, stress, and corrosion. Nickel-based alloys and chromium-molybdenum steels are commonly used due to their strength and durability.
Importance in Steam Turbine Performance
A well-designed steam chest enhances turbine performance by:
- Ensuring stable turbine operation through controlled steam flow.
- Preventing thermal shock and material fatigue.
- Reducing erosion and corrosion, extending the turbine’s lifespan.
Proper maintenance of the steam chest is essential to prevent leaks, optimize efficiency, and ensure safe and reliable operation in power generation and industrial applications.
The steam chest in a steam turbine is a key component that regulates and distributes high-pressure steam before it enters the turbine blades. It ensures efficient steam expansion, protects turbine components from sudden pressure fluctuations, and optimizes energy conversion.
Functions of the Steam Chest
The steam chest serves multiple functions:
- Steam Flow Regulation: It houses control valves that adjust the amount of steam entering the turbine, ensuring smooth and efficient operation under varying load conditions.
- Pressure and Temperature Control: It maintains stable steam pressure and temperature, preventing excessive thermal stress on turbine components.
- Uniform Steam Distribution: It directs steam evenly to the turbine inlet, preventing localized overheating and efficiency losses.
- Erosion and Corrosion Prevention: By removing excess moisture from steam, it protects turbine blades from erosion and prolongs their lifespan.
Main Components of a Steam Chest
- Stop Valves: Emergency shut-off valves that block steam flow when needed, such as during shutdowns or maintenance.
- Control Valves: These regulate the steam flow rate, adjusting turbine power output based on load demand. They can be operated mechanically, hydraulically, or electrically.
- Casing: Made of heat-resistant materials like chromium-molybdenum steel or nickel-based alloys, it withstands high-pressure and high-temperature conditions.
- Steam Nozzles and Passages: These direct the steam from the chest into the turbine stages in a controlled manner to ensure efficient expansion.
Types of Steam Chests
- Single Steam Chest: Used in smaller turbines, where a single inlet controls steam entry.
- Double Steam Chest: Found in larger turbines, allowing better steam distribution and reducing thermal stress.
Material Selection and Design
The steam chest must withstand extreme operating conditions, requiring materials with high mechanical strength, thermal stability, and corrosion resistance. Common materials include nickel-based superalloys and chromium-molybdenum steels, which provide excellent durability.
Impact on Steam Turbine Performance
A well-designed steam chest enhances turbine efficiency by:
- Ensuring stable and controlled steam flow to optimize energy conversion.
- Reducing thermal shock and material fatigue, extending turbine life.
- Minimizing steam leakage and improving overall plant efficiency.
Regular maintenance of the steam chest is essential to prevent operational issues, maintain efficiency, and ensure long-term reliability in steam turbine applications.
Steam turbine parts name
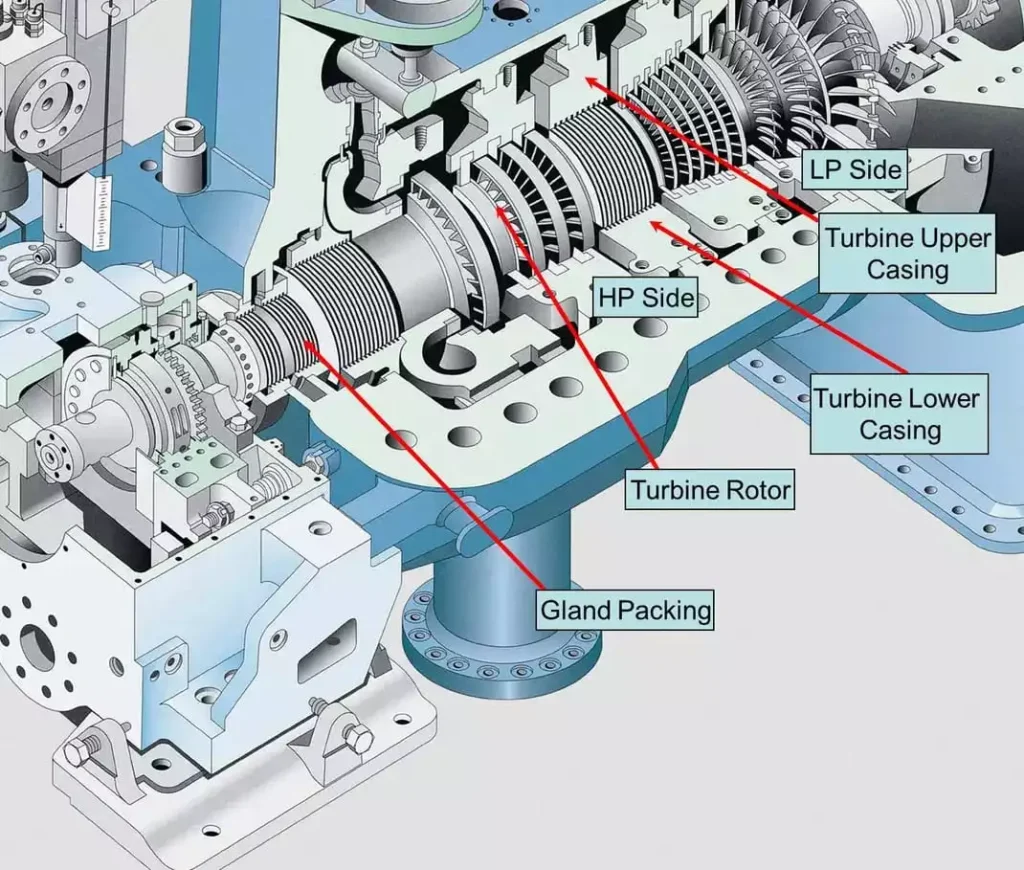
A steam turbine consists of several essential components that work together to convert thermal energy from steam into mechanical energy. The main parts of a steam turbine include:
- Rotor: The rotating shaft that carries the turbine blades and converts steam energy into mechanical work.
- Blades (Buckets): Fixed and moving blades that direct and expand the steam, generating rotational force.
- Casing: The outer shell that encloses the turbine, containing the steam and maintaining pressure.
- Steam Chest: The chamber where steam is regulated before entering the turbine.
- Nozzles: Direct and accelerate steam onto the turbine blades for efficient energy conversion.
- Bearings: Support the rotor and ensure smooth rotation with minimal friction.
- Governing System: Controls steam flow to regulate turbine speed and power output.
- Coupling: Connects the turbine to the generator or mechanical load.
- Thrust Bearings: Absorb axial forces and prevent rotor movement along its axis.
- Seals (Labyrinth Seals): Prevent steam leakage between high- and low-pressure areas.
- Condenser: Cools and condenses exhaust steam into water for reuse in the cycle.
- Extraction Ports: Remove steam at intermediate stages for heating or industrial processes.
- Lubrication System: Ensures smooth operation of bearings and moving parts.
Each of these components plays a crucial role in ensuring efficient turbine performance and long-term reliability.
A steam turbine consists of several essential components that work together to efficiently convert thermal energy from steam into mechanical energy. The rotor is the main rotating component that carries the turbine blades and transfers mechanical energy to the connected load. The blades, also known as buckets, are arranged in stages and play a crucial role in directing and expanding the steam to generate rotational force. The casing is the outer shell that encloses the turbine, containing the high-pressure steam and maintaining structural integrity under extreme operating conditions. The steam chest is responsible for regulating and distributing steam before it enters the turbine blades, ensuring controlled flow and optimal performance.
Nozzles are used to direct and accelerate steam onto the turbine blades, increasing kinetic energy for efficient energy transfer. Bearings support the rotor, reducing friction and ensuring smooth operation, while thrust bearings absorb axial forces and prevent unwanted movement along the rotor’s axis. The governing system controls steam flow and regulates turbine speed to match power demand and maintain stability. Couplings connect the turbine to the generator or mechanical load, ensuring efficient power transmission.
Seals, including labyrinth seals, prevent steam leakage between high- and low-pressure sections, maintaining efficiency and preventing pressure losses. The condenser is a vital component in the steam cycle, where exhaust steam is cooled and condensed back into water for reuse in the system. Extraction ports allow steam to be drawn from intermediate turbine stages for industrial heating or feedwater heating applications, improving overall efficiency. The lubrication system provides continuous lubrication to bearings and moving parts, reducing wear and ensuring reliable turbine operation. Each of these components plays an essential role in maintaining the efficiency, durability, and overall performance of the steam turbine system.
A steam turbine is composed of several interconnected parts that work together to efficiently convert thermal energy from steam into mechanical power. The rotor is the central rotating shaft that carries the turbine blades and transmits mechanical energy to the connected generator or machinery. The blades, also called buckets, are arranged in rows and play a crucial role in directing and expanding the steam flow to generate rotational motion. The casing serves as the external shell, enclosing the turbine and maintaining the required pressure while withstanding high temperatures. The steam chest is where steam is regulated and controlled before it enters the turbine, ensuring a steady and optimized flow.
Nozzles are responsible for accelerating the steam and directing it precisely onto the turbine blades to maximize energy transfer. Bearings provide support to the rotor, ensuring smooth rotation with minimal friction, while thrust bearings specifically counteract axial forces to prevent unwanted movement along the rotor’s axis. The governing system controls steam admission to regulate turbine speed and maintain stable power output according to demand. The coupling connects the turbine to the generator or other driven equipment, ensuring efficient power transmission.
Seals, such as labyrinth seals, help prevent steam leakage between different pressure sections, improving efficiency and reducing energy loss. The condenser cools the exhaust steam and condenses it back into water for reuse in the system, forming a closed-loop cycle. Extraction ports are positioned at various turbine stages to remove steam for industrial applications or to improve efficiency by preheating feedwater. The lubrication system ensures that bearings and other moving components remain properly lubricated, reducing wear and enhancing reliability. These components collectively contribute to the efficient and continuous operation of a steam turbine, ensuring its durability and performance in power generation and industrial applications.
A steam turbine is made up of several key components that work together to convert the energy from steam into mechanical power. The rotor is the main rotating shaft that carries the turbine blades and transfers mechanical energy to a connected generator or other machinery. The blades, also known as buckets, are arranged in multiple stages and play a critical role in directing and expanding the steam to produce rotational movement. The casing encloses the turbine, maintaining pressure and protecting internal components from external conditions. The steam chest regulates and distributes steam before it enters the turbine blades, ensuring a controlled and efficient flow.
Nozzles are used to accelerate and direct steam onto the turbine blades, increasing its velocity for efficient energy transfer. Bearings provide support to the rotor, reducing friction and ensuring smooth operation, while thrust bearings counteract axial forces and prevent the rotor from moving along its axis. The governing system regulates steam admission to control turbine speed and power output, adapting to changes in load demand. The coupling connects the turbine to the generator or another driven system, allowing for seamless energy transmission.
Seals, such as labyrinth seals, prevent steam from leaking between high- and low-pressure sections, maintaining efficiency and minimizing energy loss. The condenser cools and condenses exhaust steam back into water, enabling it to be reused in the cycle. Extraction ports remove steam at intermediate stages for industrial heating applications or to improve efficiency by preheating feedwater. The lubrication system provides oil to bearings and other moving parts, reducing friction and wear while ensuring long-term reliability.
Each of these components plays a vital role in ensuring the efficiency, durability, and performance of a steam turbine in power generation and industrial applications. Proper maintenance and precise control of these parts are essential for reliable operation and maximum energy output.
Steam turbine performance curve
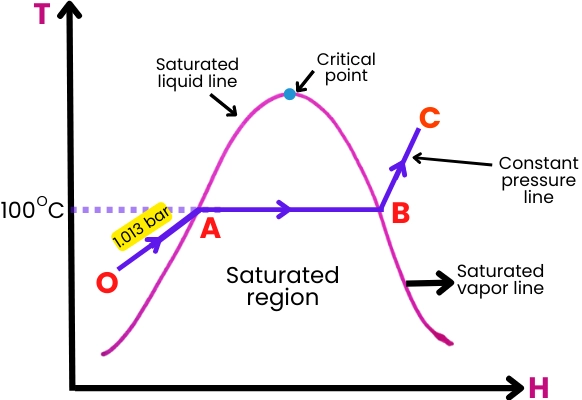
The performance curve of a steam turbine is a graphical representation that illustrates the relationship between various operational parameters, such as power output, efficiency, steam flow rate, and pressure. These curves help in analyzing turbine behavior under different load conditions and optimizing its performance for maximum efficiency.
Types of Steam Turbine Performance Curves
- Power Output vs. Steam Flow Curve
- This curve shows how turbine power output varies with steam flow rate.
- Typically, power output increases with steam flow up to a certain limit, after which efficiency losses may occur due to excessive steam consumption.
- Heat Rate vs. Load Curve
- The heat rate represents the amount of heat energy required to generate a unit of electrical power (typically in kJ/kWh or BTU/kWh).
- As the load increases, the heat rate initially decreases, indicating improved efficiency, but at very high loads, heat rate may rise due to increased inefficiencies.
- Efficiency vs. Load Curve
- This curve shows the variation of turbine efficiency with load.
- Efficiency is typically highest at a specific load known as the design load and decreases at both lower and higher loads due to steam flow inefficiencies and losses.
- Exhaust Pressure vs. Load Curve
- This curve indicates how the exhaust pressure changes with varying load conditions.
- For condensing turbines, a lower exhaust pressure improves efficiency by increasing available expansion work.
- For back-pressure turbines, the exhaust pressure remains nearly constant depending on process steam requirements.
- Speed vs. Load Curve (for Variable Speed Turbines)
- This curve represents the relationship between turbine speed and load demand, mainly for mechanical drive applications where speed adjustments are needed.
Key Factors Affecting Steam Turbine Performance
- Steam inlet conditions: Higher inlet pressure and temperature improve efficiency.
- Load variations: Efficiency drops at partial load due to throttling losses and leakage.
- Exhaust conditions: Lower condenser pressure in condensing turbines increases output.
- Blade and nozzle condition: Erosion, fouling, and wear affect efficiency.
- Governing system response: Accurate control of steam flow optimizes performance.
Understanding and analyzing these performance curves help in optimizing steam turbine operations, improving fuel efficiency, and extending equipment life.
The performance curve of a steam turbine represents the relationship between key operational parameters such as power output, efficiency, steam flow rate, and pressure. These curves help operators analyze turbine behavior under different conditions and optimize performance for maximum efficiency and reliability.
One of the most important performance curves is the power output vs. steam flow curve, which illustrates how the turbine’s power output changes as the steam flow rate varies. Typically, as steam flow increases, power output also increases, but beyond a certain point, efficiency losses occur due to excessive steam consumption and mechanical limitations. This curve helps determine the optimal steam flow rate for a given turbine load.
Another key curve is the heat rate vs. load curve, which shows how much thermal energy (in kJ/kWh or BTU/kWh) is required to produce a unit of electrical power. At lower loads, heat rate tends to be high due to inefficient steam expansion and increased losses. As the load increases, the heat rate decreases, reaching an optimal level at the design load. However, at very high loads, the heat rate starts rising again due to increased steam and mechanical inefficiencies.
The efficiency vs. load curve demonstrates how turbine efficiency changes with varying load. Steam turbines typically achieve their highest efficiency at design load, where steam expansion and energy conversion are optimized. At lower or higher loads, efficiency drops due to increased throttling losses, leakage, and non-ideal steam expansion. Operators use this curve to determine the most efficient operating range of the turbine.
For exhaust pressure vs. load, condensing turbines show a decrease in exhaust pressure as load increases, improving efficiency by maximizing available expansion work. In contrast, back-pressure turbines maintain a relatively constant exhaust pressure depending on downstream steam requirements. Managing exhaust pressure correctly is essential for maintaining turbine efficiency.
In variable-speed applications, the speed vs. load curve helps illustrate the relationship between turbine speed and power demand. This is especially important in mechanical drive applications where steam turbines power pumps, compressors, or fans that require varying speeds.
Several factors influence the shape of these curves, including steam inlet pressure and temperature, load variations, exhaust conditions, blade condition, and governing system efficiency. By analyzing performance curves, operators can fine-tune steam flow, optimize load settings, and ensure long-term efficiency and reliability of the turbine.
The performance curve of a steam turbine provides valuable insights into its efficiency, power output, steam consumption, and operating behavior under different conditions. These curves are essential for optimizing turbine operation, improving energy efficiency, and ensuring reliable performance in power generation and industrial applications.
The power output vs. steam flow curve illustrates how the turbine’s power output changes with varying steam flow rates. As steam flow increases, power output rises proportionally up to the turbine’s design limit. Beyond this point, additional steam flow results in diminishing efficiency gains due to steam saturation, mechanical losses, and increased thermal stress on turbine components.
The heat rate vs. load curve is crucial for evaluating the turbine’s fuel efficiency. The heat rate represents the amount of thermal energy required to generate one unit of electrical power, usually measured in kJ/kWh or BTU/kWh. At low loads, the heat rate is high due to inefficient steam expansion and losses. As the load increases, the heat rate improves, reaching an optimal level at the design load. However, at very high loads, the heat rate starts increasing again due to excessive steam consumption and operational inefficiencies.
The efficiency vs. load curve shows how turbine efficiency changes with load variations. Steam turbines typically achieve maximum efficiency at the design load, where steam expansion and mechanical energy conversion are optimized. At partial loads, efficiency drops due to throttling losses, increased leakage, and non-ideal steam expansion. Running a turbine outside its optimal load range for extended periods results in higher operating costs and reduced lifespan.
The exhaust pressure vs. load curve is particularly important for condensing and back-pressure turbines. In condensing turbines, exhaust pressure decreases as load increases, enhancing efficiency by maximizing available expansion work. In contrast, back-pressure turbines maintain a nearly constant exhaust pressure, as they supply process steam to industrial applications. Managing exhaust conditions effectively ensures optimal energy utilization and prevents steam wastage.
For turbines used in mechanical drive applications, the speed vs. load curve shows how turbine speed varies with power demand. While many power generation turbines operate at a fixed speed, variable-speed steam turbines adjust their speed based on load requirements, making them suitable for driving pumps, compressors, and other industrial equipment.
Several operational factors influence turbine performance, including steam inlet pressure and temperature, load fluctuations, exhaust conditions, blade and nozzle condition, and the efficiency of the governing system. By analyzing performance curves, operators can fine-tune steam flow rates, adjust load settings, and implement maintenance strategies to enhance efficiency, reduce fuel consumption, and ensure the turbine operates reliably within its design parameters.
The performance curve of a steam turbine is a graphical representation of how the turbine operates under different conditions. It helps engineers and operators understand the relationship between key parameters such as power output, efficiency, steam flow, and pressure. These curves are essential for optimizing turbine operation and improving overall efficiency.
The power output vs. steam flow curve shows the correlation between the amount of steam supplied to the turbine and the power it produces. At lower steam flows, power output increases proportionally. However, beyond a certain point, additional steam does not result in a proportional power increase due to efficiency losses caused by steam saturation, mechanical constraints, and thermal inefficiencies.
The heat rate vs. load curve represents the amount of thermal energy required to produce one unit of electrical energy. The heat rate is highest at low loads due to inefficiencies in steam expansion and energy conversion. As the load increases, the heat rate decreases, reaching its lowest point at the design load, where the turbine operates most efficiently. At very high loads, the heat rate begins to rise again due to increased steam consumption and mechanical losses.
The efficiency vs. load curve demonstrates how efficiently the turbine converts steam energy into mechanical power at different loads. Maximum efficiency is achieved at the design load, where steam expansion is optimal. At lower or higher loads, efficiency declines due to throttling losses, increased leakage, and off-design steam flow patterns. Running the turbine outside its optimal range for extended periods can result in excessive fuel consumption and wear on components.
The exhaust pressure vs. load curve varies depending on the type of turbine. In condensing turbines, exhaust pressure typically decreases as load increases, allowing for greater energy extraction from steam expansion. In back-pressure turbines, exhaust pressure remains relatively stable, as steam is used for industrial heating or other processes. Proper management of exhaust pressure is essential for maintaining efficiency and avoiding excessive steam losses.
For turbines used in mechanical drive applications, the speed vs. load curve shows how the turbine’s rotational speed changes with power demand. While most power generation turbines operate at a fixed speed, mechanical drive turbines may vary their speed to match the requirements of connected equipment such as pumps or compressors.
Several factors influence turbine performance, including steam inlet conditions, load variations, exhaust conditions, blade and nozzle wear, and the effectiveness of the governing system. By analyzing these performance curves, operators can adjust steam flow, optimize load distribution, and implement maintenance strategies to maximize efficiency and reliability while reducing operating costs.
Highest efficiency steam turbine
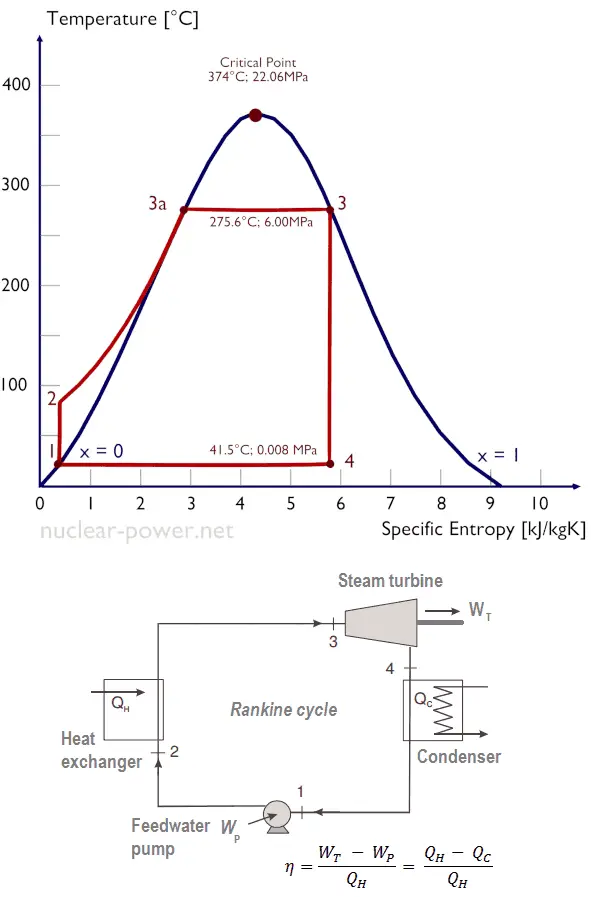
The highest efficiency steam turbines are those designed to minimize energy losses and maximize the conversion of thermal energy from steam into mechanical work. The efficiency of a steam turbine is influenced by multiple factors, including steam conditions, turbine design, cycle configuration, and operational parameters. The most efficient steam turbines typically operate in modern ultra-supercritical and combined-cycle power plants, where advanced technologies are used to enhance thermal efficiency.
Factors Contributing to High Efficiency in Steam Turbines:
- High Steam Parameters (Supercritical and Ultra-Supercritical Steam)
- Steam turbines achieve the highest efficiency when operating at supercritical (above 22.1 MPa) and ultra-supercritical (above 25 MPa, 600–620°C) conditions.
- Higher steam pressures and temperatures improve thermal efficiency by increasing the enthalpy drop across the turbine.
- Multi-Stage Expansion
- High-efficiency steam turbines use multiple stages to extract maximum energy from steam.
- These turbines typically have high-pressure (HP), intermediate-pressure (IP), and low-pressure (LP) stages to optimize expansion.
- In reheat cycles, steam is reheated between stages to reduce moisture content and improve efficiency.
- Advanced Blade Design
- 3D-aerofoil blades, optimized for minimal aerodynamic losses, improve efficiency.
- Long last-stage blades in low-pressure sections reduce steam exit velocity losses.
- Reaction and impulse blading combination ensures maximum energy extraction.
- Regenerative Feedwater Heating
- High-efficiency turbines use regenerative feedwater heating, where extracted steam preheats feedwater before entering the boiler.
- This improves Rankine cycle efficiency by reducing the fuel needed to reach operating temperature.
- Low Exhaust Pressure (Condensing Turbines)
- Condensing steam turbines operate with very low exhaust pressure (vacuum conditions), maximizing enthalpy drop and power output.
- Modern plants use efficient condensers to maintain vacuum levels below 0.1 bar absolute.
- Combined Cycle Integration
- In combined-cycle power plants (CCPPs), high-efficiency steam turbines are used alongside gas turbines.
- Waste heat from the gas turbine is used to generate steam, improving overall plant efficiency to 60% or more.
- Advanced Materials and Coatings
- High-alloy steels and nickel-based superalloys withstand extreme temperatures and pressures, reducing wear and increasing efficiency.
- Thermal barrier coatings minimize heat losses.
Examples of the Most Efficient Steam Turbines:
- GE SteamH (GE Vernova)
- Used in ultra-supercritical power plants.
- Efficiency exceeds 50% in standalone steam cycles.
- Siemens SST-5000 Series
- Found in modern combined-cycle and supercritical plants.
- Combined-cycle plant efficiency can reach over 60%.
- Mitsubishi Power Ultra-Supercritical Turbines
- Installed in high-efficiency coal power plants.
- Steam cycle efficiency of around 45-50%.
Conclusion
The highest efficiency steam turbines operate at ultra-supercritical steam conditions, utilize multi-stage expansion, integrate reheating and regenerative heating, and are optimized for minimal losses through advanced blade design and materials. The most efficient power plants combine steam turbines with gas turbines in a combined-cycle configuration, achieving efficiencies exceeding 60%.
The highest efficiency steam turbines are designed to extract the maximum possible energy from steam while minimizing losses. These turbines are used in modern power plants, particularly in ultra-supercritical and combined-cycle configurations, where high temperatures, pressures, and advanced engineering techniques improve overall performance.
One of the most critical factors for high efficiency is steam conditions. Turbines operating at ultra-supercritical pressures (above 25 MPa) and temperatures (600–620°C) achieve much greater thermal efficiency compared to subcritical or supercritical turbines. The higher the inlet steam temperature and pressure, the greater the energy extracted per unit of steam mass, improving the Rankine cycle efficiency.
Another key factor is multi-stage expansion, where steam passes through several turbine stages, including high-pressure (HP), intermediate-pressure (IP), and low-pressure (LP) sections. The use of multiple stages allows for more complete energy extraction and minimizes losses. Additionally, reheat cycles—where steam is reheated after initial expansion—prevent excessive moisture formation and improve turbine performance.
Blade design plays a significant role in increasing efficiency. 3D-aerofoil blades with optimized profiles reduce aerodynamic losses and improve steam flow dynamics. Long last-stage blades in the low-pressure section help reduce exit velocity losses, increasing the power extracted from the steam. Modern turbines also combine impulse and reaction blading, ensuring efficient energy transfer throughout different pressure stages.
Regenerative feedwater heating further boosts efficiency by using extracted steam to preheat the feedwater before it enters the boiler. This reduces the fuel required to achieve operating temperature, thereby improving the overall cycle efficiency. Most high-efficiency steam turbines incorporate multiple feedwater heaters to maximize this effect.
For condensing turbines, maintaining a low exhaust pressure is essential for high efficiency. A well-designed condenser system operates under vacuum conditions, typically below 0.1 bar absolute, maximizing the enthalpy drop across the turbine. The lower the exhaust pressure, the greater the work extracted from steam expansion.
In combined-cycle power plants (CCPPs), steam turbines work alongside gas turbines, using the waste heat from gas turbines to generate steam. This combined approach significantly enhances overall plant efficiency, often exceeding 60%, compared to standalone steam power plants, which typically achieve 45-50%.
Modern steam turbines also benefit from advanced materials and coatings. High-alloy steels and nickel-based superalloys enable turbines to withstand extreme conditions without degradation. Thermal barrier coatings and erosion-resistant materials further extend turbine life and efficiency by reducing thermal and mechanical stresses.
Some of the most efficient steam turbines available today include GE’s SteamH series, Siemens SST-5000 series, and Mitsubishi Power ultra-supercritical turbines. These turbines, particularly in combined-cycle configurations, achieve industry-leading efficiency levels, with some power plants reaching an overall thermal efficiency of over 60%.
The combination of ultra-supercritical steam conditions, optimized multi-stage expansion, reheating, regenerative feedwater heating, and advanced materials allows modern steam turbines to achieve the highest possible efficiency, making them crucial for high-performance power generation.
The highest efficiency steam turbines are designed to extract the maximum energy from steam while minimizing losses. They are primarily used in ultra-supercritical (USC) power plants and combined-cycle power plants (CCPPs), where they achieve exceptional efficiency levels through advanced technology and optimized thermodynamic cycles.
Key Factors Influencing Steam Turbine Efficiency
1. Ultra-Supercritical Steam Parameters
High-efficiency turbines operate at ultra-supercritical conditions, meaning steam pressures above 25 MPa and temperatures exceeding 600°C. The higher the steam temperature and pressure, the greater the expansion work available, leading to improved thermal efficiency. Some advanced turbines now operate at 700°C+ with experimental advanced ultra-supercritical (A-USC) technology.
2. Multi-Stage Expansion & Reheat Cycles
The most efficient steam turbines use multi-stage expansion, including high-pressure (HP), intermediate-pressure (IP), and low-pressure (LP) turbines. The steam expands progressively through each stage, extracting maximum energy.
- Reheat cycles further boost efficiency by reheating the steam between expansion stages, preventing excessive moisture formation and maintaining high enthalpy.
- Double or triple reheat cycles (used in some ultra-efficient plants) enhance performance by recovering additional energy from the steam.
3. Advanced Blade Design
Turbine efficiency is heavily influenced by aerodynamic blade design. Modern turbines use:
- 3D-aerofoil blades, optimized to reduce aerodynamic losses.
- Long last-stage blades, especially in the LP section, to maximize power extraction.
- Impulse and reaction blading, strategically combined for optimal energy conversion.
4. Low Exhaust Pressure (Condensing Turbines)
In condensing turbines, efficiency is maximized by maintaining vacuum conditions in the condenser, typically below 0.1 bar absolute. A lower exhaust pressure increases the enthalpy drop, improving power output.
5. Regenerative Feedwater Heating
Modern high-efficiency steam turbines use regenerative feedwater heaters, where extracted steam preheats the boiler feedwater. This process reduces the fuel needed for heating and improves the overall Rankine cycle efficiency. Plants with multiple stages of feedwater heating achieve better fuel economy and performance.
6. Combined-Cycle Power Plants (CCPPs)
The highest efficiency steam turbines are often integrated into combined-cycle configurations, where a gas turbine generates power first, and its waste heat is used to produce steam for the steam turbine. This heat recovery steam generator (HRSG) process allows CCPPs to achieve thermal efficiencies exceeding 60%, compared to standalone steam plants, which typically range from 45-50%.
7. Advanced Materials & Coatings
Steam turbines operating under extreme conditions require high-strength materials.
- Nickel-based superalloys and high-chromium steels withstand high temperatures and pressures.
- Thermal barrier coatings protect blades from heat damage, improving longevity and maintaining efficiency.
- Erosion-resistant coatings on last-stage blades prevent wear from steam condensation and impurities.
Leading High-Efficiency Steam Turbines
Some of the most advanced steam turbines with industry-leading efficiency include:
- GE SteamH Series – Used in ultra-supercritical power plants, achieving over 50% efficiency in standalone steam cycles.
- Siemens SST-5000 Series – Found in combined-cycle and ultra-supercritical plants, contributing to 60%+ plant efficiency in CCPPs.
- Mitsubishi Power Ultra-Supercritical Turbines – Used in modern coal and biomass power plants, achieving around 45-50% efficiency.
Conclusion
The highest efficiency steam turbines operate at ultra-supercritical conditions, use multiple expansion stages, integrate reheating and regenerative heating, and employ advanced blade technology. Combined-cycle configurations further enhance efficiency, making modern steam turbines crucial for sustainable and high-performance power generation.
The mechanical efficiency of a steam turbine is a measure of how effectively the turbine converts the thermal energy in steam into mechanical energy (usually rotational energy) to do work. It can be expressed as the ratio of the useful mechanical power output of the turbine to the total energy supplied by the steam.
Mechanical Efficiency Formula:
ηmech=PmechPinput=Pmechm⋅h\eta_{mech} = \frac{P_{mech}}{P_{input}} = \frac{P_{mech}}{m \cdot h}ηmech=PinputPmech=m⋅hPmech
Where:
- ηmech\eta_{mech}ηmech = Mechanical efficiency
- PmechP_{mech}Pmech = Mechanical power output of the turbine (in watts or horsepower)
- PinputP_{input}Pinput = Energy supplied by the steam (in watts or horsepower)
- mmm = Mass flow rate of steam (in kg/s)
- hhh = Enthalpy of steam at the inlet (in kJ/kg)
Key Factors Affecting Mechanical Efficiency:
- Steam Quality: Higher steam quality (superheated steam) typically leads to better efficiency since it reduces the moisture content in the exhaust steam, which can lead to energy losses.
- Turbine Design: The design of the turbine blades, the number of stages, and the overall configuration of the turbine play a significant role in the mechanical efficiency. Multi-stage turbines generally tend to be more efficient than single-stage ones.
- Temperature and Pressure: Higher inlet temperature and pressure usually improve the efficiency, as the enthalpy of the steam is higher, which translates to more usable energy.
- Mechanical Losses: These include losses due to friction in bearings, seals, and other moving parts, as well as losses due to the conversion of energy to vibrations, heat, and sound.
- Energy Conversion Losses: Some energy may be lost as steam expands and cools within the turbine, particularly in the exhaust stages.
Typical Mechanical Efficiency Range:
- Modern steam turbines can achieve mechanical efficiencies ranging from 85% to 95% under optimal conditions. The efficiency may be lower at lower pressures and temperatures or when the system is not operating optimally.
1. Steam Quality:
Steam quality refers to the proportion of steam that is in the vapor phase, as opposed to the liquid phase (or “wet steam”). The quality of the steam directly impacts the performance of the turbine.
What is Steam Quality?
Steam quality is often expressed as a percentage that indicates the amount of steam that is in the vapor phase compared to the total amount of steam (vapor + liquid). For example, if the steam quality is 95%, this means that 95% of the steam is in the vapor phase, and the remaining 5% is liquid water (or condensate).
- Dry Steam (Steam Quality = 100%): This is ideal for turbine performance. It contains no moisture or liquid water and is entirely in the vapor phase. Dry steam minimizes energy loss due to condensation and allows the turbine blades to operate at peak efficiency.
- Wet Steam (Steam Quality < 100%): Wet steam contains a certain amount of liquid water, which can cause significant energy losses. As the steam expands and cools inside the turbine, the water droplets can impact the turbine blades, reducing the mechanical efficiency by increasing friction and causing erosion or damage to the blades.
Impact of Steam Quality on Mechanical Efficiency:
- Energy Losses: When steam is wet, the presence of liquid droplets reduces the effective energy conversion within the turbine. Liquid water doesn’t expand and perform useful work as steam does, so it reduces the turbine’s mechanical output. The energy that should have gone into rotation is instead absorbed in converting the water droplets to steam.
- Turbine Blade Damage: Moisture in the steam leads to corrosion and erosion of the turbine blades. The water droplets can strike the blades with high velocity, damaging their surfaces and reducing their ability to convert thermal energy into mechanical energy efficiently. This damage can further reduce the turbine’s efficiency over time, especially if the steam is consistently wet.
- Thermal Efficiency Reduction: As steam quality decreases (i.e., as the steam becomes wetter), the energy required to vaporize the liquid water increases. This added energy requires more fuel or higher-pressure steam to maintain the same output, reducing the overall efficiency of the system. In systems with wet steam, the thermal efficiency is also lower due to the lower specific heat capacity of wet steam compared to dry steam.
- Superheating: One way to improve steam quality is through superheating, which involves raising the steam temperature above its saturation point. Superheated steam has no moisture, which makes it much more effective in driving the turbine and ensures better energy conversion.
Ideal Conditions for Steam Quality:
- To maximize turbine efficiency, dry, superheated steam is ideal. This type of steam minimizes moisture-related losses and enables efficient energy conversion.
- The steam quality should be close to 100% to ensure minimal liquid water content and reduce losses due to condensation.
In practical terms, steam turbines are often designed to work with specific steam qualities, and systems may include equipment like moisture separators or superheaters to ensure that the steam quality remains high and optimal for turbine operation.
Summary of Steam Quality’s Impact:
- High steam quality means better energy conversion, fewer mechanical losses, and improved efficiency.
- Wet steam, on the other hand, can cause mechanical damage, energy losses, and lower turbine efficiency.
2. Turbine Design:
The design of the steam turbine plays a crucial role in determining its overall mechanical efficiency. Key design factors include the number of stages, the blade geometry, the material choice, and the turbine configuration. Each of these factors influences how effectively the turbine converts the thermal energy from steam into mechanical energy.
Key Elements of Turbine Design:
- Number of Stages:
- Single-stage Turbines: These turbines have one set of blades and are typically used for lower power applications where steam pressure and temperature are moderate. While they can be efficient in specific cases, their overall performance is limited when compared to multi-stage turbines.
- Multi-stage Turbines: Most large steam turbines are multi-stage. This means the steam goes through several stages of expansion, with each stage featuring a set of blades. In these turbines, the steam expands in stages (or steps), with each stage gradually extracting energy from the steam.
- Advantages:
- Better Energy Extraction: Each stage helps extract more energy from the steam, making multi-stage turbines much more efficient at converting thermal energy into mechanical energy.
- Improved Pressure and Temperature Management: By dividing the expansion process into multiple stages, the steam can be expanded more efficiently, with better control over the pressure and temperature at each stage. This reduces energy losses and helps optimize the turbine’s performance.
- Disadvantages: Multi-stage turbines are more complex and expensive to build and maintain than single-stage turbines. They also require more precise control and balancing.
- Advantages:
- Blade Geometry:
- The shape and size of the turbine blades are essential in converting the thermal energy of steam into mechanical energy. The design of the blades determines how efficiently they interact with the steam flow.
- Impulse Blades: These blades are used in impulse turbines, where the steam’s pressure is converted into kinetic energy as the steam impacts the blades. The energy is transferred to the blades through this impact, causing the turbine to spin. These turbines are simple in design but are less efficient at very high pressures.
- Reaction Blades: In reaction turbines, the steam expands in the nozzle and then strikes the blades, creating a reaction force that causes rotation. These turbines are more complex but tend to be more efficient, especially in large-scale applications. They utilize the steam’s kinetic energy more effectively.
- Blade Design Characteristics: The geometry of the blades (such as their width, angle, and curvature) affects the efficiency of the energy transfer from steam to mechanical power. Properly designed blades ensure smooth steam flow and reduce energy losses caused by turbulence, vibration, or drag.
- The shape and size of the turbine blades are essential in converting the thermal energy of steam into mechanical energy. The design of the blades determines how efficiently they interact with the steam flow.
- Blade Materials:
- High-temperature materials are used in turbine blades to withstand the high temperatures and stresses imposed by the steam. Materials like superalloys are commonly used in modern steam turbines because they maintain their strength and resistance to corrosion and erosion at high temperatures.
- The durability of the materials also affects the long-term efficiency of the turbine. High-quality materials ensure less wear and tear, less energy loss due to surface degradation, and a longer operational lifespan.
- Turbine Configuration:
- Condensing vs. Non-Condensing Turbines:
- Condensing turbines operate with a vacuum at the exhaust side of the turbine, which allows for more energy extraction from the steam. The steam is condensed into water after passing through the turbine, and the pressure difference across the turbine is maximized.
- Non-condensing turbines release steam at higher pressure (without condensation), which is typically used in back-pressure turbines or turbines that drive compressors.
- Condensing vs. Non-Condensing Turbines:
- Turbine Size:
- Larger turbines generally have higher efficiency due to economies of scale. The larger the turbine, the better it can handle larger steam volumes, and the more efficiently it can extract energy. However, there’s a point of diminishing returns as the turbine size increases, and at very large scales, mechanical losses due to friction and vibrations can increase.
- Cooling and Lubrication Systems:
- Effective cooling systems help maintain the proper operational temperature of the turbine, ensuring it operates efficiently without overheating.
- The lubrication system ensures that friction between moving parts is minimized, reducing mechanical losses and improving overall efficiency. Bearings, seals, and other moving components are kept well-lubricated to reduce wear and tear, preventing efficiency losses from friction.
Key Advantages of Efficient Turbine Design:
- Better Heat Conversion: A well-designed turbine allows the steam to expand efficiently through each stage, extracting maximum energy.
- Lower Friction Losses: A smooth interaction between steam and turbine blades reduces friction losses and ensures the turbine remains efficient.
- Reduced Maintenance: Efficient blade and material design reduce the likelihood of mechanical damage, meaning that maintenance needs are lower, and efficiency is maintained over a longer lifespan.
Summary of Turbine Design’s Impact:
- Multi-stage turbines are generally more efficient than single-stage turbines, especially at high pressures and large scale operations.
- The blade geometry and material selection significantly affect how effectively energy is transferred from steam to the turbine shaft, reducing losses and improving efficiency.
- Turbine configuration, such as condensing versus non-condensing, influences how efficiently the turbine can extract energy and convert it to mechanical work.
- The design must also consider long-term maintenance, cooling, and lubrication systems to ensure the turbine operates efficiently and with minimal wear over time.
3. Temperature and Pressure:
The temperature and pressure of steam play a critical role in determining the efficiency of a steam turbine. Both of these factors directly influence the enthalpy (total heat content) of the steam, which is crucial in the process of converting thermal energy into mechanical energy. The higher the temperature and pressure, the more energy is contained in the steam, and the more effectively it can drive the turbine blades.
Influence of Pressure:
- Steam Pressure and Energy Content:
- High Pressure: The pressure of the steam influences its density and specific volume. When steam is generated at higher pressures, it has a higher energy content per unit mass, as the enthalpy (heat content) of the steam increases. The higher pressure allows the steam to expand more gradually as it moves through the turbine, extracting more energy at each stage.
- Low Pressure: Lower steam pressures reduce the enthalpy of the steam, meaning there is less energy available to do mechanical work in the turbine. As a result, turbines that operate at lower pressures generally have lower efficiencies because the steam doesn’t carry as much energy to convert into mechanical power.
- Expansion Process:
- As steam expands through the turbine, the pressure drops. High-pressure steam expands more effectively because the pressure drop in each stage is optimized for efficient energy extraction. If the steam pressure is too low, the expansion becomes too rapid, leading to energy losses and reduced efficiency.
- Exhaust Pressure:
- The exhaust pressure (the pressure of the steam leaving the turbine) is another important factor. A lower exhaust pressure (such as in condensing turbines, where the steam is condensed into water) creates a larger pressure differential between the inlet and the exhaust, allowing more energy to be extracted from the steam. Conversely, a higher exhaust pressure (such as in back-pressure turbines) reduces the available energy for extraction, as the pressure differential is smaller.
Influence of Temperature:
- Superheating Steam:
- Superheated Steam: Superheating involves raising the temperature of steam above its saturation point, which removes moisture and increases the steam’s energy content. Superheated steam has a higher enthalpy, meaning it contains more energy that can be converted into mechanical power. The higher the temperature of the steam, the greater the energy available for conversion into mechanical work.
- Advantages of Superheated Steam:
- More Efficient Energy Transfer: Since superheated steam contains more energy and is drier, it reduces mechanical losses due to condensation or wet steam.
- Increased Turbine Efficiency: Superheated steam allows the turbine to extract more energy, improving the overall efficiency of the turbine.
- Reduced Corrosion and Erosion: Superheated steam avoids the moisture issues that can lead to turbine blade erosion and corrosion, resulting in longer turbine lifespan and consistent efficiency.
- Disadvantages: Superheating requires additional equipment (such as a superheater), which increases the complexity and cost of the system. It also requires more fuel or heat energy to maintain the higher temperature, but the benefits in efficiency generally outweigh the additional costs.
- Advantages of Superheated Steam:
- Superheated Steam: Superheating involves raising the temperature of steam above its saturation point, which removes moisture and increases the steam’s energy content. Superheated steam has a higher enthalpy, meaning it contains more energy that can be converted into mechanical power. The higher the temperature of the steam, the greater the energy available for conversion into mechanical work.
- Effect of High-Temperature Steam:
- Higher steam temperatures generally result in greater energy efficiency because they allow for a more gradual and efficient expansion of the steam in the turbine. As the steam is expanded through the turbine stages, the energy available for conversion into mechanical energy is maximized when the steam is hot.
- Temperature Gradient: The greater the difference in temperature between the steam entering the turbine and the exhaust steam, the more energy can be extracted. However, there is a practical limit to how high the steam temperature can be raised due to material constraints (the turbine blades, for example, need to withstand extreme temperatures).
- Temperature and Efficiency:
- Steam that is too hot can cause problems such as turbine blade erosion, fatigue, and degradation of materials. Therefore, while higher temperatures improve efficiency, they also introduce challenges related to the durability of turbine materials, which must be capable of withstanding these extreme conditions.
- Conversely, lower temperatures reduce the energy available in the steam and result in lower mechanical efficiency since the turbine cannot extract as much energy from the steam.
The Relationship Between Pressure and Temperature:
- The Rankine cycle, which is the basic thermodynamic cycle used in steam turbines, shows the relationship between pressure, temperature, and efficiency. In this cycle, steam is heated and pressurized, and then expanded through the turbine. The higher the initial pressure and temperature of the steam, the more efficient the Rankine cycle becomes because it allows for a greater temperature drop (and thus more energy extraction) as the steam expands.
- Supercritical Boilers: In modern high-efficiency plants, supercritical steam (steam at pressures above the critical point, where it no longer behaves as a liquid or gas) is used to achieve even higher efficiencies. These systems operate at pressures and temperatures above the normal saturation point, significantly improving the efficiency of steam turbines. Supercritical steam systems achieve efficiencies of 40% or more, which is much higher than traditional subcritical systems.
Practical Considerations:
- Thermal Limits of Materials:
- As the steam temperature and pressure increase, turbine blades and other components need to be made of advanced materials that can handle these extreme conditions without failing. Modern turbines use materials like nickel-based superalloys that retain their strength and durability at high temperatures.
- Energy Efficiency of Steam Cycles:
- The efficiency of the overall steam cycle (including the turbine) depends on the temperature and pressure of the steam, but also on how effectively the system can handle waste heat, control exhaust pressures, and maintain a stable temperature profile throughout the process. Regenerative heating (using feedwater heaters) and reheat cycles (where steam is reheated between stages of expansion) are often employed to optimize temperature and pressure profiles for better efficiency.
Summary of the Impact of Temperature and Pressure:
- High pressure and temperature steam (superheated steam) generally improves the mechanical efficiency of the turbine by providing more energy for conversion into mechanical power.
- Steam expansion in turbines is more efficient when the temperature and pressure are optimized, allowing for more gradual energy extraction and less energy loss.
- Superheating steam ensures that it remains dry, reducing losses from condensation and improving overall efficiency.
- Material limitations prevent the temperature and pressure from being raised infinitely, but advancements in turbine materials and design continue to push the boundaries of what’s possible.
Would you like to explore more about how steam temperature and pressure are managed in real-world turbine systems, or discuss any specific component used to optimize these factors?
A 1000 kW steam turbine generator refers to a steam turbine driving a generator that produces 1000 kilowatts (1 MW) of electrical power. Such systems are typically used in various industrial, commercial, or utility applications where a reliable source of power is required. Let’s break down the main components, working principles, and key considerations involved in such a system.
Main Components of a 1000 kW Steam Turbine Generator:
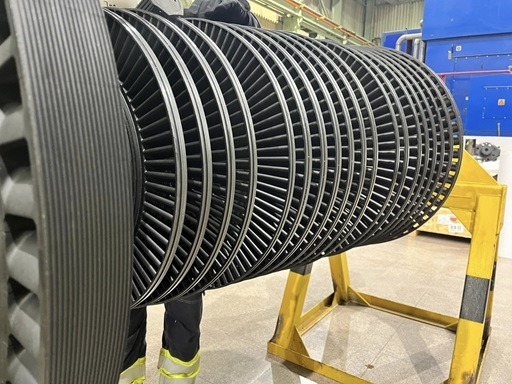
- Steam Boiler:
- Purpose: The steam boiler generates high-pressure steam by heating water using a fuel source (such as coal, natural gas, oil, or biomass).
- Type: The boiler can be a fire-tube or water-tube type, depending on the application and the capacity required. For 1000 kW turbines, water-tube boilers are typically more common because they are more efficient at higher pressures and temperatures.
- Steam Turbine:
- Type: This turbine could be an impulse turbine, a reaction turbine, or a combination of both (depending on the design and application).
- Impulse Turbine: The steam jets directly hit the turbine blades, transferring kinetic energy to the turbine.
- Reaction Turbine: The steam flow changes the pressure as it moves through the blades, causing a reaction force that turns the turbine.
- Power Output: The turbine is sized to produce 1 MW (1000 kW) of mechanical power. This is the power generated by the turbine’s rotor and is used to drive the generator.
- Steam Quality: Ideally, the turbine would use superheated steam for higher efficiency, reducing moisture-related losses and improving energy extraction.
- Type: This turbine could be an impulse turbine, a reaction turbine, or a combination of both (depending on the design and application).
- Generator:
- Function: The generator is connected to the turbine shaft. It converts the mechanical energy from the turbine into electrical energy using electromagnetic induction.
- Type: A synchronous generator is typically used in steam turbine systems, as it operates at a constant speed that is synchronized with the grid frequency (50 Hz or 60 Hz depending on the region).
- Condenser (in a condensing steam turbine system):
- Purpose: The condenser cools the exhaust steam after it passes through the turbine, converting it back into water. It creates a vacuum at the exhaust side of the turbine, maximizing the pressure difference and improving energy extraction.
- Cooling: It usually uses cooling water or air as a medium to condense the steam. In larger systems, a surface condenser is used to maintain high efficiency.
- Feedwater Pump and Heater:
- Feedwater Pump: The pump sends the condensed water from the condenser back into the boiler for re-evaporation.
- Feedwater Heater: Some systems use a feedwater heater to preheat the water before it enters the boiler, improving overall system efficiency by recovering waste heat.
- Control and Protection Systems:
- Control System: Ensures proper synchronization between the turbine, generator, and the grid. It also adjusts steam input based on power demand.
- Protection System: Includes safety mechanisms to protect the turbine and generator from overloads, high temperatures, or pressures, as well as low water levels.
Working Principle of the System:
- Steam Generation: Water is heated in the boiler to produce steam at high pressure (typically 40-80 bar) and high temperature (400-600°C, depending on the turbine design).
- Steam Expansion: The high-pressure steam enters the turbine and expands through multiple stages. The energy from the steam causes the turbine blades to rotate, converting thermal energy into mechanical energy.
- Mechanical Power Conversion: The rotating turbine shaft is connected to the generator, which converts the mechanical energy into electrical energy through electromagnetic induction.
- Power Output: The generator produces 1000 kW of electrical power. The system is designed to deliver this power at a stable output, ensuring the voltage and frequency match the requirements of the connected grid or load.
- Condensation: After passing through the turbine, the exhaust steam enters the condenser, where it is cooled and condensed back into water, completing the cycle.
- Water Recycling: The condensed water is pumped back into the boiler to be reheated, creating a closed-loop system.
Key Performance Considerations for a 1000 kW Steam Turbine Generator:
- Thermal Efficiency:
- Efficiency depends on several factors, including steam quality, temperature, and pressure. Steam turbines operating with superheated steam at high pressures achieve better thermal efficiency.
- Rankine Cycle: The steam turbine generator operates based on the Rankine Cycle, and increasing the temperature and pressure of the steam leads to better overall efficiency and power output.
- Steam Quality:
- Dry steam (with little to no moisture) improves the efficiency of the turbine by ensuring minimal energy loss due to condensation or moisture in the exhaust steam.
- Superheating the steam further reduces moisture content, improving turbine efficiency and reducing wear on turbine blades.
- Exhaust Pressure:
- Lower exhaust pressure (via a condenser) allows the steam to expand more fully, extracting more energy from the steam. A vacuum at the exhaust side helps optimize the expansion, leading to higher efficiency.
- Operational Flexibility:
- The 1000 kW steam turbine generator is typically designed for continuous operation at a specific load. However, many modern systems can adjust output based on demand. For example, the turbine can operate in load-following mode to adjust its power output as per the varying needs of the grid.
- Maintenance and Lifespan:
- Regular maintenance is crucial for maintaining the efficiency and reliability of the turbine generator. This includes inspections of the turbine blades, bearings, seals, and cooling system.
- Over time, components like the turbine blades and bearings may wear due to heat, friction, and erosion, which can reduce overall efficiency. Therefore, preventive maintenance is important for ensuring long-term efficiency.
- Fuel Type:
- Fuel Efficiency: The choice of fuel (coal, oil, natural gas, or biomass) affects the overall efficiency and environmental impact of the system. Combined-cycle systems (where waste heat from the turbine is used to generate additional power) can improve efficiency.
Applications of 1000 kW Steam Turbine Generators:
- Industrial Power Plants:
- They are commonly used in large industrial operations, such as chemical plants, refineries, or paper mills, where both electrical power and process heat are required.
- Combined Heat and Power (CHP) Systems:
- Steam turbines in CHP plants generate both electricity and useful heat for industrial or commercial applications, making them highly efficient.
- Renewable Energy:
- Some biomass power plants use steam turbines to generate power from organic materials, contributing to renewable energy generation.
- District Heating:
- In areas where district heating is provided, a steam turbine generator can also be part of a larger system that distributes heat to residential or commercial areas.
Conclusion:
A 1000 kW steam turbine generator is a reliable and efficient way to convert thermal energy from steam into electrical power. The key to its efficient operation lies in maintaining optimal steam pressure, temperature, and quality. Proper design, maintenance, and fuel management are essential for achieving the desired power output and ensuring long-term operational efficiency.
1. Steam Boiler: The Heart of the Steam Turbine System
The steam boiler is the key component that generates steam by converting water into high-temperature, high-pressure steam, which then drives the turbine to produce mechanical power. The performance and efficiency of the steam boiler directly influence the overall efficiency of the turbine system.
Key Functions of the Steam Boiler:
- Water Heating: The primary function of the steam boiler is to heat water to its boiling point using an external heat source. The heat source could be combustion of fuel (such as coal, natural gas, or oil) or waste heat recovery from other industrial processes.
- Steam Generation: The boiler is designed to generate steam at high pressure (typically in the range of 40-80 bar) and temperature (usually between 400-600°C for superheated steam). This high-pressure steam carries a significant amount of energy, which will be transferred to the turbine for mechanical work.
- Steam Quality: The quality of steam produced in the boiler—whether it is dry or saturated—is important. Superheated steam (steam that has been heated beyond its saturation point) is preferred because it ensures more efficient expansion in the turbine, minimizing moisture-related damage to the turbine blades and improving energy transfer.
Types of Boilers for a 1000 kW Steam Turbine Generator:
- Fire-Tube Boilers:
- Structure: These boilers consist of a set of tubes through which hot gases pass, while water surrounds them in a shell. The heat from the gases transfers to the water, producing steam.
- Advantages: Simple design, suitable for small to medium capacities, and relatively inexpensive.
- Disadvantages: Less efficient at higher pressures and temperatures compared to water-tube boilers, making them less common in larger industrial applications like a 1000 kW turbine generator.
- Water-Tube Boilers:
- Structure: In water-tube boilers, water circulates through tubes that are heated externally by the combustion gases. This design allows the boiler to operate at higher pressures and temperatures.
- Advantages: More efficient at higher pressures and temperatures. They can handle higher steam capacities and are ideal for large-scale applications like industrial plants and steam turbine generators.
- Disadvantages: More complex design and higher initial costs compared to fire-tube boilers, but the improved efficiency justifies the investment.
- Combined Heat and Power (CHP) Boilers:
- In some applications, boilers are integrated into combined heat and power systems, where both electricity and useful heat are generated. These boilers are often highly efficient and can use fuels like natural gas, biomass, or waste heat.
- Superheated Steam Boilers:
- These boilers are specifically designed to generate superheated steam. They include additional equipment such as superheaters, which further heat the steam to increase its energy content before it enters the turbine.
- Importance for a 1000 kW Steam Turbine Generator: Superheating improves the turbine efficiency by providing drier steam, which is crucial for larger turbines that require consistent energy input.
Boiler Design and Efficiency Factors:
- Boiler Pressure and Temperature:
- The higher the pressure and temperature of the steam, the more energy it contains. For a 1000 kW steam turbine generator, boilers typically operate at pressures around 40-80 bar.
- Superheating the steam to temperatures of 400-600°C ensures that the steam is both dry and contains a high energy content. Superheated steam is particularly important for modern, high-efficiency turbines.
- Boiler Efficiency:
- Thermal efficiency of the boiler is crucial because it determines how much of the energy from the fuel is converted into usable steam. Modern high-efficiency boilers can achieve thermal efficiencies of 85% or higher.
- Fuels: The type of fuel used also impacts boiler efficiency. For instance, natural gas-fired boilers tend to have higher efficiency compared to coal-fired ones, but the latter is more economical in large-scale power plants.
- Combustion Process: The efficiency of the boiler’s combustion system (burner design, air-fuel mixture, etc.) directly affects the energy output. Flue gas recirculation and air preheating are techniques used to improve combustion efficiency.
- Heat Recovery:
- Many modern boilers incorporate heat recovery systems to utilize exhaust gases and improve efficiency. For example, a regenerative air heater can recover some of the heat from the exhaust gases and use it to preheat the incoming combustion air, thus reducing the amount of fuel required.
- In larger systems, economizers (devices that preheat feedwater using exhaust gases) can be used to reduce fuel consumption and increase overall efficiency.
- Boiler Control Systems:
- Modern boilers are equipped with advanced control systems that monitor and adjust parameters like fuel flow, air-fuel ratio, water temperature, and pressure. These systems ensure that the boiler operates optimally and maintains the required steam pressure and temperature for the turbine.
- Automatic Control systems allow for real-time adjustments, reducing human intervention and improving system reliability.
- Feedwater Treatment:
- Water quality is important for efficient boiler operation. Impurities in the feedwater can cause scaling and corrosion within the boiler tubes, reducing heat transfer efficiency and potentially damaging the system.
- Water treatment involves removing contaminants such as dissolved salts, minerals, and oxygen before the water enters the boiler. This is done using water softeners, demineralizers, and deoxygenators.
Boiler Selection for a 1000 kW Steam Turbine Generator:
- Steam Output Requirements:
- A 1000 kW steam turbine generator typically requires steam at a rate that corresponds to the power output. Depending on the steam pressure and temperature, the boiler capacity must be matched to ensure it can generate the required steam output to drive the turbine at the specified load.
- Superheating Requirements:
- Since superheated steam is preferred for efficiency, the boiler must be designed to produce steam at the necessary temperature and pressure. The superheater within the boiler will increase the steam temperature before it enters the turbine, improving energy conversion efficiency.
- Efficiency and Reliability:
- The boiler’s efficiency should be high to minimize fuel consumption and operating costs. The boiler must also be designed for reliability, with robust materials capable of withstanding high pressure and temperature for extended periods.
- Fuel Type:
- The choice of fuel (coal, natural gas, biomass, or other fuels) will affect the boiler design, efficiency, and operating costs. Natural gas is commonly used for large-scale turbines due to its efficiency and cleaner combustion properties compared to coal.
Maintenance and Monitoring:
- Regular Inspection:
- Boilers should undergo regular inspections to check for signs of wear, corrosion, and scaling. This helps maintain high efficiency and prevent operational issues.
- Water Chemistry Control:
- Maintaining proper water chemistry is essential for minimizing corrosion and scaling within the boiler. Periodic testing and treatment are required to ensure the water quality is optimal.
- Performance Monitoring:
- Continuous monitoring of key parameters such as pressure, temperature, fuel consumption, and steam output is critical for optimizing boiler performance and preventing issues like inefficiency or downtime.
Conclusion:
The steam boiler is a critical component in a 1000 kW steam turbine generator system. It needs to produce high-pressure, high-temperature steam in a manner that is efficient, reliable, and capable of meeting the turbine’s needs. Proper design, maintenance, and optimization of the boiler are essential for maximizing the overall efficiency of the system and ensuring consistent power output.
2. Steam Turbine: Converting Thermal Energy to Mechanical Power
The steam turbine is the key component in the power generation process. It uses steam, produced by the boiler, to generate mechanical energy by rotating the turbine blades. This mechanical energy is transferred to the generator to produce electrical power.
Key Components of a Steam Turbine:
- Turbine Rotor:
- The rotor consists of a shaft and a set of blades attached to it. The rotor is connected directly to the generator, so when the rotor turns, the generator also turns, producing electricity.
- Blade Materials: Turbine blades are made from materials that can withstand high temperatures and pressures, such as stainless steel, nickel alloys, and titanium.
- Blade Design: Blades are designed to extract energy efficiently from the steam. They can be impulse blades (which receive steam jets) or reaction blades (which rely on steam pressure change).
- Turbine Stator:
- The stator is a set of stationary blades or nozzles that direct steam onto the moving blades (rotor). The stator is designed to convert pressure energy into kinetic energy.
- Stage Design: Steam turbines usually operate in multiple stages, each consisting of a set of rotor blades and stator blades. Steam passes through the stages, expanding and losing pressure and temperature, which causes the rotor to spin.
- Steam Nozzles:
- Steam is injected through nozzles in the stator to direct it onto the blades with the appropriate velocity and direction. The nozzle design ensures efficient energy transfer from steam to the turbine blades.
- Governors and Control Mechanisms:
- The governor regulates the steam flow into the turbine based on load demand, controlling the turbine’s speed and output.
- Variable nozzle control: In advanced systems, the nozzles may be variable to adjust the steam flow, allowing the turbine to operate efficiently across a range of operating conditions.
- Turbine Shaft:
- The turbine shaft is connected to the generator and transmits mechanical power generated by the turbine blades to the electrical generator. The shaft is designed to withstand high rotational speeds and mechanical stress.
- Bearings and Seals:
- Bearings support the turbine rotor, ensuring smooth rotation. Seals prevent steam leakage and maintain pressure within the turbine stages, improving efficiency.
- Exhaust System:
- The exhaust system removes the low-pressure steam after it passes through the turbine. This exhaust steam is typically directed to the condenser, where it is cooled and condensed back into water to be recycled in the boiler.
Types of Steam Turbines Used in Power Generation:
- Impulse Turbines:
- In impulse turbines, steam enters through nozzles and strikes the blades with high velocity. The change in velocity imparts kinetic energy to the blades, causing them to rotate.
- These turbines are generally used in smaller systems or where steam pressure is relatively low.
- Advantages: Simple design, efficient at higher speeds.
- Reaction Turbines:
- In reaction turbines, the steam pressure decreases as it flows through the turbine, creating a reaction force that causes the blades to rotate. As steam flows through the blades, its pressure drops, and this change in pressure imparts energy to the rotor.
- Reaction turbines are commonly used in larger-scale power plants due to their efficiency at converting high-pressure steam into mechanical power.
- Condensing and Non-Condensing Turbines:
- Condensing turbines: These turbines exhaust steam into a vacuum condenser, allowing for a significant reduction in exhaust pressure, which increases turbine efficiency by maximizing the steam expansion.
- Non-condensing turbines: In these turbines, exhaust steam is directly sent to a process or used in heating systems, and no condenser is needed.
- Back-Pressure Turbines:
- Back-pressure turbines are a type of non-condensing turbine where the exhaust steam pressure is controlled to provide process heat at a lower pressure. The steam is used for both generating power and for industrial heating purposes.
- These turbines are ideal for combined heat and power (CHP) systems, where both electricity and heat are needed.
Operation of a Steam Turbine in a 1000 kW Generator System:
- Steam Admission:
- High-pressure steam is admitted to the turbine through nozzles. The steam enters the turbine stages and moves over the turbine blades, causing them to rotate.
- The energy transfer from steam to the blades is mainly in the form of kinetic energy, which drives the turbine’s rotor.
- Energy Conversion:
- In each turbine stage, the steam loses pressure as it expands, converting the thermal energy into kinetic energy. This process continues as the steam passes through subsequent stages of blades in the turbine.
- The mechanical energy generated from the rotating rotor is transferred to the generator through the turbine shaft.
- Exhaust Steam:
- After passing through the turbine blades, the steam exits the turbine as low-pressure steam and enters the condenser in a condensing turbine system.
- The steam is condensed back into water to be reused in the boiler.
- Speed Regulation:
- The turbine’s speed is controlled by adjusting the steam flow through the governor system. The speed of the turbine must be synchronized with the generator’s output frequency, ensuring the correct voltage and frequency of the electricity produced.
- Power Generation:
- As the turbine rotor turns, it drives the synchronous generator, which converts the mechanical energy into electrical energy. The generator produces 1000 kW of electrical power, which can be fed into the grid or used for local consumption.
Key Performance Parameters of a Steam Turbine:
- Efficiency:
- Steam turbine efficiency depends on how well the system converts thermal energy from steam into mechanical energy. Efficient turbines can operate at thermal efficiencies of 40-50% in typical power plants, though this depends on factors such as steam pressure, temperature, and quality.
- Steam Flow Rate:
- The steam flow rate is critical in determining the power output. For a 1000 kW steam turbine, the required steam flow rate will depend on the pressure and temperature of the steam. High-pressure, superheated steam will require less flow to produce the same power compared to saturated steam.
- Turbine Pressure Ratio:
- The pressure ratio (the ratio of steam pressure at the turbine inlet to the exhaust pressure) plays a crucial role in determining the turbine’s efficiency. A higher pressure ratio typically results in higher efficiency, especially when using a condensing turbine system with a vacuum at the exhaust.
- Mechanical Stress and Vibration:
- Turbine blades experience significant mechanical stress from the steam flow, and regular maintenance is needed to check for signs of wear, corrosion, and vibration issues. Proper balance and alignment are essential for efficient operation.
- Speed and Load Regulation:
- The turbine must maintain a constant speed (usually synchronous speed) while adjusting to changing loads. Load-following capability allows the turbine to match power output with demand fluctuations.
Key Maintenance Considerations:
- Blade Inspection:
- Regular inspection of the turbine blades is necessary to detect erosion, corrosion, and fatigue from high-pressure steam. Blade replacements may be required periodically, depending on operational conditions.
- Seals and Bearings:
- Seals around the rotor must be regularly checked to prevent steam leakage, which can reduce efficiency. Bearings must also be checked to ensure smooth operation and minimize vibration.
- Lubrication:
- Proper lubrication is crucial for reducing friction in the turbine shaft and bearings. Maintenance should include checking the lubrication system and replacing lubricants regularly to avoid breakdowns.
- Rotor Alignment:
- Ensuring proper alignment of the turbine rotor is essential for preventing excessive wear on bearings and seals. Misalignment can cause efficiency losses and increase maintenance costs.
Conclusion:
The steam turbine is a highly efficient component in a 1000 kW generator system, capable of converting thermal energy from steam into mechanical energy. It involves a complex system of nozzles, rotor blades, stators, and control mechanisms that must work in harmony to generate consistent power. Proper maintenance, high-quality steam, and efficient design are key factors in achieving optimal performance.
3. Electrical Generator: Converting Mechanical Power to Electrical Power
The electrical generator is where the mechanical energy from the steam turbine is transformed into electrical energy, typically in the form of alternating current (AC). The generator operates based on the principle of electromagnetic induction, where mechanical motion (the turning of the turbine) induces a flow of current in a coil of wire.
Key Components of the Electrical Generator:
- Rotor:
- The rotor is the rotating part of the generator and is directly connected to the steam turbine shaft. It typically contains large electromagnets or permanent magnets, which rotate inside a stationary stator.
- Excitation System: The rotor can be either a synchronous rotor (with a wound coil) or a permanent magnet rotor. In large-scale generators, the rotor is usually excited by a DC current supplied by an external source or brushless exciter.
- Stator:
- The stator is the stationary part of the generator, composed of a set of coils or windings that are arranged around the rotor. When the rotor turns, it induces a changing magnetic field, which induces an electric current in the stator windings.
- The stator typically consists of three-phase windings, designed to produce three-phase AC power, which is commonly used for large-scale power generation.
- Shaft:
- The shaft connects the turbine rotor to the generator rotor. As the turbine turns, it drives the generator’s rotor through the shaft, transferring mechanical energy.
- Bearings and Cooling System:
- The generator’s rotor and shaft are supported by bearings, which need to be regularly lubricated and maintained to avoid mechanical failure.
- A cooling system is crucial to maintain optimal operating temperatures. Large generators often have a cooling system based on air or water to dissipate heat generated during power conversion.
- Commutator (for DC generators):
- Some older generators use a commutator to reverse the current direction in the rotor windings. However, modern generators often use brushless exciter systems that eliminate the need for commutators.
- Exciter System:
- In many modern generators, the exciter provides the DC power necessary to create the magnetic field in the rotor. The brushless exciter eliminates the need for brushes and commutators, offering greater reliability and less maintenance.
- Voltage Regulator:
- The voltage regulator is responsible for maintaining a constant output voltage from the generator, regardless of fluctuations in load or speed. It adjusts the excitation current to regulate the generator’s output voltage within desired limits.
How a Steam Turbine Powers a Generator:
- Turbine and Generator Coupling:
- The steam turbine rotor is directly connected to the generator rotor through a coupling. The turbine spins the generator’s rotor at a high speed (typically at synchronous speed), causing the generator to produce electrical power.
- Electromagnetic Induction:
- As the rotor spins inside the stator, it creates a magnetic field that moves across the coils in the stator. This motion induces an electromotive force (EMF) in the stator windings according to Faraday’s Law of Induction.
- The induced EMF causes an electric current to flow in the stator windings, producing electrical power.
- Power Conversion:
- The electrical current generated in the stator is typically alternating current (AC), and for industrial power generation, it’s usually three-phase AC. Three-phase power is efficient for transmission and distribution, providing consistent energy flow and reducing losses in the system.
- Synchronous Speed:
- The generator rotor must rotate at a specific speed known as synchronous speed for the generator to produce AC power at the correct frequency. In most power systems, this is 50 Hz or 60 Hz, depending on the region.
- The synchronous speed depends on the number of poles in the generator and the frequency of the electrical system. For example, in a 4-pole generator, the synchronous speed at 50 Hz would be 1500 rpm.
- Voltage Regulation:
- The excitation system maintains the rotor’s magnetic field strength, ensuring the generator produces the correct voltage. The voltage regulator adjusts the excitation to compensate for changes in load and ensure a steady voltage output, even as the turbine’s speed or load varies.
Key Performance Parameters of a Generator:
- Power Output:
- The generator output is the amount of electrical power produced, which for a 1000 kW turbine generator would be 1000 kW (1 MW). This is typically measured in kilowatts (kW) or megawatts (MW) for large-scale generators.
- Efficiency:
- The electrical efficiency of the generator refers to the proportion of mechanical energy from the turbine that is converted into usable electrical energy. In modern generators, this efficiency typically ranges from 95% to 99%, depending on the design, load conditions, and cooling systems.
- Voltage and Frequency:
- The generator produces three-phase AC power, typically at voltages of 11 kV, 6.6 kV, or 415 V for industrial applications. The voltage is regulated by the excitation system and voltage regulator to meet grid or load requirements.
- The frequency of the AC power is maintained at 50 Hz or 60 Hz, depending on regional standards. A generator must synchronize its output with the grid frequency for smooth power integration.
- Power Factor:
- The power factor indicates how effectively the generator’s output is being used by the load. It’s a measure of the phase difference between voltage and current. A power factor close to 1 indicates efficient use of electrical power.
- Power factor correction may be required in systems with inductive loads (like motors), and generators must often be equipped with equipment to manage this.
- Load Response:
- Load-following capability refers to the ability of the generator to adjust its output based on variations in the demand for power. Generators are designed to handle load changes smoothly and efficiently, maintaining stable operation without significant fluctuations in voltage or frequency.
Generator Types for a 1000 kW Steam Turbine System:
- Synchronous Generators:
- Synchronous generators are the most commonly used in large-scale power generation, including steam turbine systems. These generators rotate at a speed that is synchronized with the grid frequency, meaning they produce stable, reliable AC power.
- Induction Generators:
- Induction generators are less common in turbine systems but can be used in some cases, especially in small-scale or off-grid applications. They work by converting mechanical power into electrical power without the need for synchronization with the grid. However, they require reactive power for operation, which must be supplied externally.
- Brushless Generators:
- Many modern generators use brushless excitation systems to eliminate the need for brushes and slip rings. These generators are more reliable, require less maintenance, and have longer operational lifespans.
- Integrated CHP Generators:
- In some systems, the generator is part of a combined heat and power (CHP) system, where the steam turbine generates both electricity and heat. These systems are highly efficient and often used in industrial applications where both electrical and thermal energy are needed.
Generator Maintenance Considerations:
- Regular Inspections:
- Regular inspections of the rotor, stator, bearings, and excitation system are essential to ensure optimal operation and prevent breakdowns. Inspections should focus on checking for wear, overheating, and mechanical alignment issues.
- Cooling Systems:
- The generator’s cooling system (either air or water-based) must be maintained to prevent overheating, which can degrade efficiency and cause damage. Regular cleaning and monitoring of the cooling system are crucial.
- Lubrication:
- Bearings and the shaft need proper lubrication to reduce friction and wear. Regular oil changes and checks are needed to ensure smooth operation.
- Excitation System Monitoring:
- The excitation system must be regularly monitored and calibrated to ensure the generator produces the correct voltage under various load conditions.
- Vibration Monitoring:
- Excessive vibration can be a sign of mechanical issues such as misalignment or imbalanced rotors. Vibration monitoring systems are often used to detect and diagnose these problems early.
Conclusion:
The electrical generator plays a pivotal role in converting the mechanical energy from the steam turbine into electrical energy. By relying on principles of electromagnetic induction, the generator produces three-phase AC power, which is regulated and stabilized by the excitation system and voltage regulator. Proper maintenance, including regular inspections and cooling system management, is crucial to ensure high efficiency and reliable performance over the generator’s lifetime.
Characteristics of Small Steam Turbine Generators:
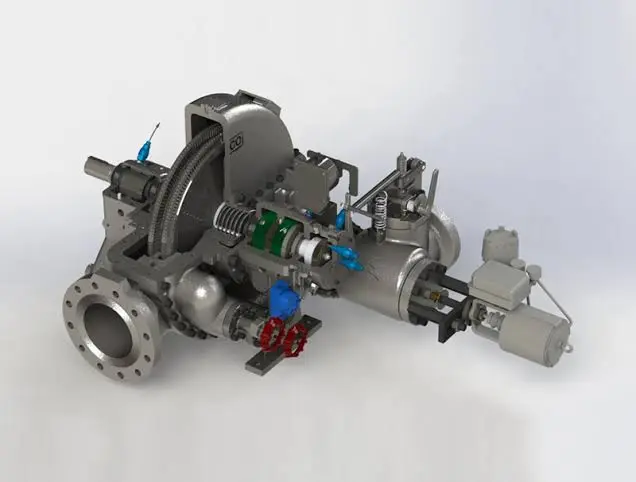
- Power Output:
- Small steam turbine generators can produce from a few kW up to around 10 MW of electrical power, but the smallest units are typically in the range of 1 kW to 500 kW.
- These units are commonly used for industrial cogeneration (CHP systems), remote power generation, or backup systems in areas where large grid connections are impractical.
- Compact Design:
- Small steam turbines have a compact design to fit within limited spaces and can be directly coupled to a generator.
- The rotor and stator are smaller in size, and materials are chosen to provide efficiency while reducing weight and physical size.
- Steam Supply:
- Small steam turbines can operate using saturated steam, superheated steam, or even low-pressure steam depending on the application.
- The steam required can be generated from various sources like biomass boilers, waste heat recovery, solar thermal systems, or fossil fuel boilers.
- Efficiency:
- The efficiency of small steam turbine generators generally falls between 20% to 40%, but this depends on the specific design, load, and steam quality.
- Efficiency may be lower compared to larger turbines due to scale losses and the lower pressure/temperature operating conditions in small systems.
- Design Types:
- Impulse Turbines: Often used for smaller units, impulse turbines use high-velocity jets of steam that strike the blades to generate power.
- Reaction Turbines: These turbines use both pressure and velocity changes in the steam to generate energy, and they are often found in medium-sized systems.
- Back-Pressure Turbines: Used for small-scale cogeneration, these turbines exhaust steam at a pressure that is useful for industrial heating, making them ideal for process steam applications.
Example Applications of Small Steam Turbine Generators:
- Remote Power Generation:
- In remote or off-grid locations, small steam turbine generators can be used to provide electricity. These systems may rely on locally sourced fuel or renewable energy like biomass to create steam.
- Backup and Emergency Power:
- Small steam turbines can serve as reliable backup power systems for critical facilities, such as hospitals, data centers, or military installations.
- Cogeneration (Combined Heat and Power):
- In industrial settings, small steam turbines are often integrated with boilers to produce both electricity and process heat, making them efficient for facilities with high thermal demand.
- Waste Heat Recovery:
- Some small turbines are designed to use waste heat from industrial processes, exhaust gases from combustion engines, or from combined-cycle systems to generate electricity.
Manufacturers and Small Steam Turbine Generators:
- Turboden:
- Specializes in small-scale organic Rankine cycle (ORC) systems, which use heat from low-temperature sources like geothermal or industrial waste heat. These can be thought of as smaller, less conventional steam turbines.
- Siemens:
- Known for producing steam turbines across a range of sizes, Siemens also offers smaller turbines for cogeneration and renewable energy applications, typically starting around 500 kW.
- Turbine Manufacturers for Industrial Use:
- Mitsubishi Heavy Industries and General Electric also provide turbines, including some in the lower kW range (small industrial units or backup systems).
Specific Examples:
- 1-5 kW Steam Turbine Generator:
- These are used for very small power generation applications, such as in small industrial plants, microgrids, or research and development projects.
- Example: Small-scale biomass or waste heat recovery systems using saturated steam.
- 20 kW to 100 kW Steam Turbine Generator:
- These sizes are commonly used in cogeneration systems or for smaller commercial applications that need both power and process heat.
- Example: Small combined heat and power (CHP) plants in agricultural facilities or small factories.
- 200 kW to 500 kW Steam Turbine Generator:
- A popular size for industrial cogeneration where a significant amount of both power and heat are needed. Often integrated into biomass or waste-to-energy plants.
- Example: A 300 kW steam turbine could power a small textile factory while providing heat for the dyeing process.
Key Factors for Small Steam Turbine Generator Systems:
- Cost:
- Small steam turbines can be more expensive on a per-kW basis compared to larger systems due to the relatively higher cost of manufacturing small-scale turbines and the infrastructure needed to support them.
- Efficiency Considerations:
- The operating efficiency may vary depending on the quality of steam, the pressure and temperature conditions, and the application (i.e., electricity only or combined heat and power).
- Maintenance:
- Smaller turbines tend to have lower maintenance costs compared to larger industrial turbines, but regular monitoring of components like the rotor, bearings, and seals is still essential.
Conclusion:
The smallest steam turbine generators are typically in the range of 1 kW to 500 kW and are used for remote power generation, backup power, and cogeneration. They are suitable for applications where electricity and/or heat are needed in smaller quantities, such as in industrial plants, rural areas, and remote locations. These turbines often rely on biomass, waste heat, or fossil fuels to generate steam and produce power.
1-5 kW Steam Turbine Generators: Compact and Niche Applications
These small steam turbines are compact, and their use cases are highly specialized. They are generally used in areas where large-scale power generation is not necessary, and the focus is on localized or off-grid power systems. The design of these turbines is tailored to provide an efficient energy conversion process while remaining physically small and relatively simple in construction.
Key Features of 1-5 kW Steam Turbine Generators:
- Compact Size:
- The 1-5 kW turbines are designed to fit into compact spaces, which makes them suitable for locations where floor space is limited or where portability is a concern.
- These turbines can be found in mobile systems or remote installations such as agricultural operations, small industrial plants, or backup power systems.
- Low Operating Pressure:
- Small steam turbine generators often operate at low pressure steam (saturated or slightly superheated) rather than high-pressure steam. This makes the system simpler and more cost-effective for smaller outputs.
- These turbines may run efficiently on steam produced by small-scale boilers or waste heat recovery systems that don’t need high pressure to be effective.
- Types of Fuel Sources:
- Biomass: In rural or agricultural settings, small turbines can be used in biomass power plants, where organic matter like wood chips, agricultural waste, or other biomass sources are burned to create steam.
- Waste Heat: These small turbines can also be powered by waste heat recovery systems, such as those found in industrial plants, where excess heat from furnaces, engines, or other machinery is captured and converted into usable steam.
- Fossil Fuels: For small backup power systems, fossil fuels like natural gas or oil may be used to generate the steam required for operation.
- Cogeneration (CHP) Capability:
- Many 1-5 kW steam turbines are designed to work in cogeneration systems where both electricity and heat are needed. For example, they may be used to provide electricity for a small factory while also supplying heat for the production process or for space heating.
- Simplicity and Durability:
- These turbines are designed for ease of operation with minimal complexity. They typically have fewer components than larger turbines and require less maintenance. Durability is important as they are often used in off-grid or industrial settings where service might be infrequent.
Applications of 1-5 kW Steam Turbine Generators:
- Remote Power Generation:
- In remote regions, especially in developing countries or isolated areas, small steam turbines can be used to power basic infrastructure, such as homes, schools, and small businesses.
- These systems are often powered by locally sourced biomass, which can be sustainably sourced from agricultural waste, wood, or even municipal solid waste.
- Backup or Emergency Power:
- Small steam turbines are sometimes used in backup or emergency power systems for critical infrastructure. They are more reliable and cost-effective than battery-powered systems for certain applications, especially where heat is also needed.
- For example, a small steam turbine generator could serve as a backup for a hospital or communications tower where both power and heat are essential.
- Small Industrial or Commercial Applications:
- Small steam turbines are well-suited for cogeneration in industrial processes with a low power demand. For instance, a small food processing plant could use a 1-5 kW turbine to generate electricity for its operations and heat for its production process.
- They can be integrated into small manufacturing facilities where they provide a steady source of energy without requiring connection to a large electrical grid.
- Agriculture and Farming:
- Small steam turbine generators can be used in agricultural settings, where they may be integrated with biomass boilers that utilize crop waste or wood from the farm itself as fuel.
- The electricity generated could power irrigation systems, small machinery, or refrigeration units, while the waste heat could be used for drying crops or providing warmth for greenhouses.
- Off-Grid and Hybrid Energy Systems:
- Small steam turbines can be part of hybrid renewable energy systems, combining them with solar, wind, or hydroelectric systems. These hybrid systems provide a consistent power supply by compensating for the intermittent nature of renewable sources like solar and wind.
- Such systems are ideal for remote or off-grid locations, ensuring a constant power supply where conventional grid infrastructure may not be available.
Design and Operational Considerations:
- Boiler Sizing:
- The steam generator or boiler must be appropriately sized for the turbine. Small turbines often use compact, low-pressure boilers that can quickly produce steam and are easy to maintain.
- The thermal efficiency of the boiler and turbine combination directly affects the system’s overall performance and fuel consumption. Boilers designed for small turbines typically operate at sub-critical pressures, making them simpler and more cost-effective.
- Steam Quality:
- Small turbines generally operate on saturated steam or slightly superheated steam. It’s important that the steam quality is maintained to avoid damaging the turbine blades and to ensure efficient energy conversion.
- The pressure and temperature of the steam are usually regulated using pressure-reducing valves and temperature controllers.
- Heat Recovery:
- Small steam turbine systems are often paired with waste heat recovery systems. For instance, excess heat from industrial processes (like exhaust from engines, furnaces, or dryers) can be used to generate steam for the turbine.
- This not only improves the overall efficiency of the system but also reduces the need for additional fuel, making the system more environmentally friendly and cost-effective.
- Grid Integration:
- While most small turbines are standalone systems, they can also be integrated into the local grid in some cases. For example, small power plants or community grids can connect multiple small steam turbine generators to provide distributed energy in a localized area.
- The system must ensure synchronization with the grid’s frequency and voltage requirements to prevent power quality issues.
Maintenance and Reliability:
- Routine Inspections: Even though small steam turbines are relatively low-maintenance compared to larger units, regular checks are essential. Inspections should cover steam flow rates, pressure levels, and temperature control systems to ensure that the turbine is operating within optimal parameters.
- Lubrication and Sealing: Bearings, seals, and other moving parts should be regularly lubricated to prevent wear and tear. Proper sealing of the system prevents steam loss and ensures efficient operation.
- Cleaning: Components like the turbine blades and exhaust system should be kept clean to avoid build-up of debris or scaling, which can reduce efficiency.
- Monitoring: Small turbines often incorporate sensors and control systems to monitor key parameters like temperature, pressure, and vibration, ensuring that any issues are detected early before they lead to costly breakdowns.
Examples of 1-5 kW Steam Turbine Generators:
- Micro Steam Turbines: These turbines are designed specifically for low-power, off-grid applications, and can often be found in small biomass power systems or waste heat recovery projects. Manufacturers like Turboden (focused on organic Rankine cycles) or Turbine Technologies provide these small-scale turbines.
- Portable Steam Turbines: In some cases, companies build portable steam turbines that can be moved and used for temporary installations or in emergency situations. These are commonly employed in disaster relief efforts or for military use where mobility and flexibility are needed.
Conclusion:
1-5 kW steam turbine generators are versatile and compact power sources that serve niche applications where both electricity and heat are needed. These systems are ideal for remote power generation, backup power, small-scale cogeneration, and waste heat recovery applications. By using biomass or waste heat, they provide a sustainable and reliable energy source, especially in off-grid or rural locations.
20-100 kW Steam Turbine Generators: Intermediate Power Generation for Various Applications
These 20-100 kW turbines are often used for small industrial cogeneration (CHP) systems, where both power and heat are needed. They strike a balance between cost, complexity, and output, providing an efficient solution for commercial and industrial entities that don’t need large-scale power generation but still require a reliable and consistent energy supply.
Key Features of 20-100 kW Steam Turbine Generators:
- Intermediate Power Output:
- 20-100 kW turbines are perfect for mid-sized operations like small factories, food processing plants, textile industries, and agriculture operations that require both electrical power and process heat.
- This size is ideal for cogeneration systems (combined heat and power), where electricity is generated to power operations, and the waste heat is used for industrial processes such as drying, heating, or water treatment.
- Steam Supply and Operating Pressure:
- These turbines typically use saturated steam or slightly superheated steam, and they may operate at medium pressure (up to 30 bar) depending on the steam quality and boiler configuration.
- The boiler feeding the turbine may range from low-pressure steam boilers to medium-pressure systems that can generate steam for multiple applications, including heating.
- Fuel Sources:
- These turbines can run on a variety of fuel sources, depending on availability and efficiency requirements:
- Biomass: Small industrial facilities often rely on biomass (wood chips, agricultural residues) to power small steam turbines. These systems are highly sustainable and suited for industries in rural areas.
- Fossil Fuels: Some systems run on natural gas or oil, especially in regions where biomass may not be readily available. These fuel sources are more convenient and may be used in conjunction with gas boilers to provide high-efficiency steam generation.
- Waste Heat: Waste heat recovery is also a common option for turbines of this size, using heat from industrial processes, exhaust gases from engines, or other sources of thermal energy.
- These turbines can run on a variety of fuel sources, depending on availability and efficiency requirements:
- Cogeneration (CHP) Applications:
- In this power range, turbines are most commonly used in cogeneration systems where both power and heat are used by the host facility. The electricity produced is used for internal needs (e.g., powering equipment, lighting, etc.), and the exhaust steam is used for heating or industrial processes.
- For example, a small chemical plant may use a 50 kW steam turbine to generate electricity while using the heat for distillation or heating reactors.
- Grid Connection and Off-Grid Options:
- While many 20-100 kW turbines are designed for grid-connected systems, they can also be used in off-grid applications. For example, in isolated areas or industrial sites, these turbines could serve as a standalone power system.
- These systems may be integrated into the local electrical grid, providing distributed generation to reduce reliance on centralized power plants and increase the reliability of energy supply.
Applications of 20-100 kW Steam Turbine Generators:
- Small Industrial Cogeneration (CHP):
- This is one of the most common applications for steam turbines in the 20-100 kW range. CHP systems are particularly beneficial for industries where both electricity and heat are required.
- For example:
- Food processing plants: Where electricity is needed to power equipment like mixers and conveyors, and heat is required for cooking, drying, or pasteurizing products.
- Textile industries: Where power is used to run machinery, and steam heat is required for dyeing or pressing fabrics.
- Agricultural Applications:
- Small steam turbines can be used in agricultural settings where both electricity and heat are required. In greenhouses, for example, turbines can provide both power for lighting and heat for maintaining optimal growing conditions.
- Biomass cogeneration is especially useful in rural agricultural settings, where wood or crop residues can be used to power steam turbines.
- Waste Heat Recovery:
- Many industrial processes generate excess heat that can be recovered and converted into useful power with a steam turbine. For instance, cogeneration systems in factories, refineries, or chemical plants often make use of waste heat for electricity generation and process heating.
- A steel mill or cement factory could use waste heat from its kilns or furnaces to generate steam, which powers a turbine for electricity production and provides process heat.
- Renewable Energy Systems:
- Small steam turbines can also be part of renewable energy systems, especially in applications such as biomass power generation or geothermal plants. For example, biomass plants convert organic materials (wood, agricultural waste) into steam, which drives a turbine to produce electricity.
- Geothermal systems use steam from deep underground reservoirs to drive turbines and generate electricity. These systems are more common in areas with significant geothermal resources.
- District Heating Systems:
- In some cases, a small steam turbine may be used as part of a district heating system, where steam or hot water is generated in a central plant and distributed to nearby buildings or facilities for heating.
- In these systems, the steam turbine generates electricity, while the heat from the turbine’s exhaust can be used for space heating or industrial heating.
Design and Operational Considerations:
- Boiler Sizing and Steam Generation:
- The boiler feeding a 20-100 kW steam turbine must be capable of producing steam at the correct pressure and temperature for efficient turbine operation. Medium-pressure boilers are typically used for turbines in this range.
- Proper steam regulation ensures that the steam is delivered to the turbine at the required flow rate and pressure, maximizing turbine efficiency.
- Efficiency:
- The overall efficiency of the system depends on factors like boiler efficiency, turbine efficiency, and how effectively the system recovers heat. Typical overall efficiency for steam turbine systems in this size range can range from 60% to 80%, depending on the quality of steam and design considerations.
- These systems are designed to maximize the use of available thermal energy, with some systems incorporating heat recovery steam generators (HRSGs) to capture waste heat and improve system performance.
- Grid Synchronization:
- For grid-connected systems, the small steam turbine must be equipped with a synchronization system that ensures the turbine’s output is in phase with the grid’s frequency and voltage requirements.
- Control systems are also used to manage load and ensure the turbine operates within safe parameters under variable demand.
- Maintenance and Monitoring:
- These turbines are generally low maintenance compared to larger turbines, but periodic inspections are necessary to check for wear and tear, particularly in components like rotors, bearings, and seals.
- Regular vibration monitoring, steam flow checks, and oil lubrication should be part of the maintenance program.
- Cost Considerations:
- The initial capital cost for these systems is a key consideration for businesses. While small steam turbines are less expensive than large utility turbines, the total cost includes the boiler system, installation, and maintenance.
- However, the long-term savings from lower energy costs (especially when using biomass or waste heat) can offset the initial investment over time.
Example Manufacturers of 20-100 kW Steam Turbine Generators:
- Siemens:
- Siemens manufactures small and medium-sized steam turbines, including those in the 20-100 kW range. They provide highly efficient and customizable systems for cogeneration, biomass power, and waste heat recovery applications.
- Turboden:
- Known for their work in organic Rankine cycles (ORC), Turboden specializes in renewable energy systems, offering turbines for small and medium-scale installations. They work with applications such as biomass, geothermal, and waste heat recovery.
- Mitsubishi Heavy Industries:
- Mitsubishi offers small steam turbine generators, some in the 30-100 kW range, which are commonly used for cogeneration in commercial and industrial applications.
- HSTT (Hansen Steam Turbine Technology):
- They offer custom steam turbine solutions for small and medium-sized systems, including turbines in the 50-100 kW range, suitable for cogeneration, biomass, and waste heat recovery applications.
Conclusion:
20-100 kW steam turbine generators provide reliable power and heat for a wide range of small industrial and commercial applications. These turbines are particularly effective in cogeneration systems, biomass power generation, and waste heat recovery projects. They offer a balance of power output, efficiency, and cost-effectiveness, making them ideal for mid-sized operations that need both electrical power and thermal energy.
100 kW to 1 MW Steam Turbine Generators: Larger Scale Power Generation for Industrial and Commercial Use
100 kW to 1 MW steam turbines are typically used in medium-sized industries, biomass power plants, and cogeneration systems (CHP) where both electricity and thermal energy are needed. These turbines are more commonly found in waste heat recovery, renewable energy, and combined heat and power (CHP) applications, and serve a diverse range of industries such as manufacturing, food processing, and small district heating plants.
Key Features of 100 kW to 1 MW Steam Turbine Generators:
- Higher Power Output:
- These turbines are capable of producing 100 kW to 1 MW of electricity, making them ideal for small-to-medium-sized industries that need a reliable power source. This range of turbines can serve the power needs of small factories, commercial buildings, agriculture operations, and even district heating networks.
- A system in this power range can handle larger loads and is typically more integrated into existing infrastructure than smaller turbines.
- Medium-High Pressure Steam:
- Turbines in the 100 kW to 1 MW range often require medium-pressure steam, typically in the range of 15-40 bar (220-580 psi), to achieve their higher power output. This pressure is necessary to provide enough energy for the turbine to operate efficiently while ensuring that heat recovery or cogeneration functions well.
- Steam is typically superheated to improve efficiency, although saturated steam may still be used depending on the application.
- Flexible Fuel Sources:
- These turbines can run on a variety of fuel types, including:
- Biomass: Ideal for use in biomass power plants, especially in industries that produce organic waste (such as wood chips, agricultural residues, and other biomass materials).
- Natural Gas: Can also be powered by natural gas or other fossil fuels in cases where biomass is not available or a reliable local supply of organic material is lacking.
- Waste Heat Recovery: These turbines are frequently used in waste heat recovery systems, where heat from industrial processes or exhaust gases is used to generate steam, which drives the turbine to generate power.
- These turbines can run on a variety of fuel types, including:
- Cogeneration (CHP):
- As with smaller turbines, many 100 kW to 1 MW turbines are used in cogeneration (CHP) systems. In these setups, electricity is generated for the facility’s internal use, while the exhaust steam is used for heating or process purposes.
- This is particularly advantageous in industries with significant thermal energy needs, such as food processing, chemical manufacturing, and paper mills, where both power and heat are essential for operations.
- Grid Integration:
- These turbines are often connected to the local electrical grid to provide distributed power generation. In some cases, they can also work in off-grid settings, supplying power to remote or isolated facilities.
- Grid synchronization is an important factor in these systems. They require advanced controls to ensure that the turbine output matches the frequency and voltage requirements of the grid.
- Control and Automation:
- Steam turbine systems in this range are generally equipped with advanced control systems to regulate steam flow, pressure, temperature, and turbine speed. These systems help optimize efficiency, manage load fluctuations, and ensure safe and reliable operation.
Applications of 100 kW to 1 MW Steam Turbine Generators:
- Industrial Cogeneration (CHP):
- Many industries use 100 kW to 1 MW turbines for cogeneration purposes. The steam produced can be used for both power generation and heating, making it highly efficient. Examples include:
- Food Processing: In food processing plants where heat is required for cooking or drying, these turbines generate electricity while providing the necessary steam for heating processes.
- Textile Manufacturing: In textile factories, electricity is used to power machines, while steam provides energy for dyeing, washing, and finishing processes.
- Paper Mills: In paper mills, steam is used for drying and processing, while turbines generate electricity for the plant’s equipment.
- Many industries use 100 kW to 1 MW turbines for cogeneration purposes. The steam produced can be used for both power generation and heating, making it highly efficient. Examples include:
- Biomass Power Plants:
- Biomass plants often utilize 100 kW to 1 MW steam turbines to generate electricity from organic waste. This range of turbines is typically found in small-scale or decentralized biomass power stations that serve small communities, agricultural businesses, or even remote industrial facilities.
- For example, a biomass cogeneration system could convert wood chips into electricity for a sawmill while providing waste heat for drying wood or heating the facility.
- Waste Heat Recovery:
- Waste heat recovery systems use excess heat from industrial processes or exhaust gases from engines, furnaces, or boilers to generate steam for turbine operation. This not only improves the overall efficiency of the system but also reduces the carbon footprint by capturing and reusing waste energy.
- Chemical plants, refineries, and steel mills are common examples where 100 kW to 1 MW turbines are used in waste heat recovery systems.
- District Heating Systems:
- Small-scale district heating systems often employ steam turbines in the 100 kW to 1 MW range to provide both electricity and heat to residential or commercial buildings in a localized area.
- These systems can be fueled by biomass, natural gas, or waste heat, making them flexible and sustainable solutions for heating in urban areas or industrial parks.
- Renewable Energy Systems:
- Steam turbines in this size range are used in renewable energy systems, particularly in biomass and geothermal energy production. In geothermal power plants, steam is produced naturally from the Earth’s heat and used to generate electricity through turbines.
- These systems are well-suited for areas with geothermal resources or in applications where biomass is readily available.
- Backup Power:
- In some cases, a 100 kW to 1 MW steam turbine generator can be used as backup power for critical facilities such as hospitals, data centers, or communications hubs. The turbine can be fueled by biomass or waste heat, ensuring both power and thermal energy are available during grid outages.
Design and Operational Considerations:
- Boiler Sizing and Steam Quality:
- The boiler must be able to provide high-quality steam (superheated or saturated) at the correct pressure and temperature for the turbine. Proper sizing is essential to ensure that the system operates at maximum efficiency.
- Boiler systems typically have a capacity slightly higher than the turbine’s maximum steam demand to account for fluctuations in steam usage.
- Efficiency:
- The efficiency of 100 kW to 1 MW steam turbine generators can range from 70% to 85%, depending on factors like steam quality, system design, and operational conditions. Heat recovery systems can further enhance efficiency by capturing exhaust steam for process heating or district heating applications.
- The integration of feedwater heaters and economizers can also improve overall system efficiency by reducing energy waste.
- Maintenance:
- Maintenance requirements are slightly more intensive than those of smaller turbines, but still manageable. Routine checks for steam leakage, vibration levels, lubrication, and inspections of seals and bearings are necessary.
- Regular inspections of steam generators and turbine performance ensure that the system operates at peak performance and that downtime due to mechanical issues is minimized.
- Grid Synchronization:
- For grid-connected turbines, synchronization with the grid is vital. Modern automatic synchronization systems ensure that the turbine’s output is in phase with the local electrical grid’s frequency and voltage.
- Additionally, the turbine control systems must be equipped to manage fluctuations in power demand to maintain stable grid integration.
- Environmental Impact:
- While biomass and waste heat recovery systems have a lower environmental impact compared to fossil fuel-powered turbines, it is essential to monitor emissions and ensure compliance with local environmental regulations. The use of flue gas treatment systems such as scrubbers or filter systems may be necessary to meet emissions standards.
Example Manufacturers of 100 kW to 1 MW Steam Turbine Generators:
- Siemens:
- Siemens manufactures turbines that cater to small- to medium-sized cogeneration plants and waste heat recovery systems. Their turbines in this range are highly customizable and can be used for a variety of fuel sources and applications.
- Turboden:
- Turboden specializes in organic Rankine cycle (ORC) systems that incorporate steam turbines. They offer turbines for biomass, geothermal, and waste heat recovery applications, often in the 100 kW to 1 MW range.
- Mitsubishi Heavy Industries:
- Mitsubishi provides steam turbines for medium-sized industrial operations. Their turbines are often used in cogeneration and biomass power generation projects.
- Man Turbo:
- Man Turbo offers turbines in the 100 kW to 1 MW range suitable for combined heat and power (CHP) applications. These turbines are used in industries such as chemicals, food processing, and textiles.
Conclusion:
100 kW to 1 MW steam turbine generators serve as an excellent solution for mid-sized industrial and commercial applications, particularly in cogeneration, biomass, and waste heat recovery systems. These turbines provide both electricity and thermal energy, making them ideal for small industrial plants, district heating systems, and renewable energy projects. They are capable of running on various fuel types, including biomass, natural gas, and waste heat, and can be integrated into both grid-connected and off-grid systems.
The smallest steam turbine generators typically have power outputs in the range of 1-10 kW and are used in highly specialized or small-scale applications. These turbines are designed for very low power needs and are often found in applications where compact size, portability, or cost-effectiveness is a priority. They are ideal for remote installations, research and development, or small commercial applications where both electricity and heat are required.
Smallest Steam Turbine Generators (1-10 kW): Compact and Low-Cost Power Generation
These tiny turbines can generate enough power for small industrial processes, research labs, small cottages, or remote locations. Below are some of the key details and applications of these small-scale turbines.
Key Features of Small Steam Turbine Generators (1-10 kW):
- Very Low Power Output:
- The power range of 1-10 kW is ideal for small-scale applications where the energy demand is minimal.
- These turbines are typically used in locations that do not require large amounts of electricity, such as small workshops, laboratories, or backup systems for remote homes or cabins.
- Compact Size:
- These turbines are often compact and designed to occupy minimal space, making them easy to transport or install in constrained environments.
- The small size allows for easy integration into custom systems, where space and weight limitations are a concern.
- Low Steam Flow Requirements:
- 1-10 kW turbines generally require low steam flow rates and operate at low to medium pressures. This means they can be powered by relatively small boilers or steam sources.
- These turbines typically operate with saturated steam or slightly superheated steam at pressures around 3-15 bar (43-217 psi), depending on the design.
- Fuel Flexibility:
- Small turbines can be powered by a variety of low-cost fuels, such as biomass, natural gas, or even waste heat from small-scale industrial processes.
- They are often part of small biomass plants or renewable energy systems where cost-effective and locally sourced fuels (like wood chips or agricultural waste) are available.
- Off-Grid and Remote Applications:
- 1-10 kW steam turbine generators are ideal for off-grid applications, providing electricity in remote areas or backup power for facilities with limited access to grid power.
- In remote homes, research stations, or small villages, these turbines can be used to generate power in conjunction with other renewable energy sources (such as solar or wind).
Applications of 1-10 kW Steam Turbine Generators:
- Small-Scale Cogeneration (CHP):
- Even in the low power range, small steam turbines can be part of cogeneration (CHP) systems where both electricity and heat are generated.
- In small industries or research labs, the steam produced can be used for heating or process heating (such as for drying or sterilizing), while the turbine generates electricity for internal use.
- Example: A small food processing facility may use a small steam turbine to power equipment while utilizing waste heat to cook or dry products.
- Renewable Energy and Biomass Power Generation:
- Biomass plants that utilize organic materials such as wood chips, crop residues, or agricultural waste can incorporate small steam turbines for efficient power generation.
- For example, a small farm or agricultural business may use a small steam turbine generator to convert waste biomass into usable energy.
- Off-Grid Power Generation:
- In remote locations, small steam turbines can provide off-grid power generation for small communities, remote homes, or scientific outposts.
- These turbines can be part of hybrid systems that combine multiple energy sources, such as solar or wind, along with steam-based generation.
- Laboratory and Research Applications:
- Small steam turbines are often used in research labs or university projects for educational purposes or for testing and developing new steam turbine technologies.
- These turbines are compact enough to be easily moved between different setups and used in controlled environments to simulate real-world conditions.
- Backup and Emergency Power:
- Small turbines can serve as backup power in applications where a constant and reliable power supply is critical but only small-scale power is required.
- In emergency situations, such as for hospitals, data centers, or remote research stations, small steam turbines can be deployed as part of a distributed generation system.
Design and Operational Considerations:
- Steam Generation:
- For 1-10 kW steam turbine generators, the boiler system must be small and efficient enough to provide sufficient steam at the right pressure and temperature.
- Small-scale boilers are typically used, and these can be either electric, biomass-powered, or fueled by natural gas.
- Steam is typically saturated, but slightly superheated steam can be used for greater efficiency if required.
- Efficiency:
- The efficiency of these small turbines generally ranges from 50% to 70%, depending on factors like steam quality and the efficiency of the boiler and turbine system.
- Heat recovery can be incorporated into the system to improve overall efficiency by capturing exhaust heat and reusing it for space heating or industrial processes.
- Cost-Effectiveness:
- Small steam turbines are relatively inexpensive compared to larger systems, making them a good option for small businesses, remote applications, or small-scale cogeneration plants.
- However, the upfront cost of the boiler and installation can be a significant part of the overall system cost.
- Maintenance:
- Small steam turbines require periodic maintenance, including inspections of bearings, seals, and vibration monitoring.
- These turbines are typically simpler than larger systems, and thus require less frequent or complex maintenance.
Example Manufacturers of Small Steam Turbine Generators:
- Siemens:
- Siemens offers compact steam turbines in various sizes, including turbines designed for small-scale power generation, biomass cogeneration, and off-grid installations.
- Turboden:
- Turboden offers small steam turbine solutions for biomass and waste heat recovery applications, including turbines with low output capacities for compact, distributed power generation.
- Hansen:
- Hansen Steam Turbine Technology (HSTT) designs small, high-efficiency steam turbines in the 1-10 kW range, suitable for biomass, waste heat, and industrial applications.
- Wuxi:
- Wuxi Steam Turbine Co. manufactures small steam turbines for applications such as biomass and small industrial plants, offering turbines with outputs in the low kW range.
Conclusion:
The smallest steam turbine generators (1-10 kW) are compact and cost-effective solutions for low-power generation needs. They are ideal for off-grid installations, small cogeneration systems, biomass power plants, and remote applications. Despite their small size, they can be highly efficient when integrated into distributed generation systems, offering flexibility in both fuel sources and operational applications. Their relatively low capital costs make them accessible for small businesses, research stations, or residential power generation systems that need both electricity and heat.
Small Steam Turbine Generators (1-10 kW) – Applications and Use Cases
1. Small-Scale Cogeneration (CHP) Systems
Small steam turbines can be effectively integrated into cogeneration systems (CHP), which are used to provide both electricity and heat for industrial or commercial processes.
- Process Heating: Small businesses, such as textile manufacturers, breweries, or food processing plants, often require heat for their operations. By installing a 1-10 kW steam turbine system, they can generate both electricity for internal use and heat for processing or drying.Example: A brewery could use the steam turbine to generate electricity for lighting, refrigeration, and other electrical equipment, while using the waste heat for heating water and sterilizing brewing equipment.
- Power Supply for Remote Locations: Small-scale cogeneration systems are particularly useful for remote industrial operations that are off the grid. A cottage industry or a small manufacturing facility located far from the main power supply can benefit from small steam turbines powered by locally available fuels like biomass or natural gas.Example: A small sawmill in a rural area could use a small steam turbine running on wood chips to generate electricity and provide heat for drying timber.
2. Off-Grid and Remote Applications
Small steam turbines (1-10 kW) are ideal for off-grid applications, where the electricity grid is inaccessible or impractical. These turbines provide an independent source of power and can be used in various settings, such as remote communities, research stations, or island-based systems.
- Remote Homes and Communities: Small turbine generators powered by biomass or waste heat can be used to power homes or small communities in areas where extending the power grid is not feasible. By using wood pellets, agricultural waste, or landfill gas, these systems provide both electricity and hot water for heating or cooking.Example: A remote village could use small turbines connected to a biomass boiler to generate electricity for homes while using the exhaust steam to heat water for residents.
- Emergency and Backup Power: Small turbines can be used as a backup power source for critical facilities in remote areas or locations prone to power outages. These turbines provide reliable power during grid failures, ensuring uninterrupted operation for essential services like hospitals, data centers, or military outposts.Example: A research station in an isolated location might use a small steam turbine to ensure constant power for sensitive experiments and equipment during power outages.
3. Waste Heat Recovery
Small steam turbines are particularly useful for waste heat recovery systems, where they capture excess heat from industrial processes and convert it into usable electricity. This type of system reduces energy waste and improves overall energy efficiency in industrial settings.
- Industries with High Heat Generation: Industries such as chemical processing, steel manufacturing, and refining generate significant amounts of waste heat. Small steam turbines can capture this heat and convert it into electricity to power their own operations, thereby improving energy efficiency and reducing the need for external power sources.Example: A paper mill could use waste heat from its drying process to generate steam, which would then drive a small turbine to generate electricity. The process could also supply hot water for other parts of the operation.
- Industrial Plants with Flue Gas Heat: For industrial plants using boilers or combustion engines, waste heat from exhaust gases or flue gas can be used to generate steam for a small turbine system. This reduces the energy consumption of the plant by recovering energy that would otherwise be lost.Example: A cement plant could capture heat from its kiln and use it to produce steam for a small turbine generator, reducing the amount of grid-supplied electricity needed for its operations.
4. Biomass Power Generation
Small steam turbines are frequently used in biomass power generation systems, especially in applications where locally available biomass fuels such as wood chips, agricultural residues, or municipal solid waste are abundant.
- Biomass Cogeneration Plants: In biomass cogeneration systems, a small steam turbine is powered by biomass boilers that burn organic materials. These turbines can generate electricity while the exhaust steam can be used for heating. This provides a dual benefit of reducing waste and generating renewable energy.Example: A small bioenergy plant located near agricultural operations can use crop residues like straw or corn stalks to fuel a small steam turbine for power generation while providing heat to nearby facilities.
- Sustainable and Renewable Energy: Biomass-based small steam turbine systems offer an environmentally sustainable solution by converting organic waste into energy, helping to reduce reliance on fossil fuels and contributing to carbon neutrality goals.
5. Educational and Research Applications
Small steam turbines are also used in educational settings and research institutions to demonstrate the principles of thermodynamics, energy conversion, and mechanical systems. They provide hands-on learning experiences for students and researchers interested in steam turbine technology and energy systems.
- Training and Simulation: Engineering students or energy professionals can use small steam turbines to simulate real-world systems, understand energy generation, and study thermal efficiency in a controlled environment.Example: A university might use small steam turbines in labs to teach students how energy conversion works and to explore the potential of steam as an energy source in renewable systems.
- Prototype Development: Researchers and companies working on new energy technologies may use small steam turbines to prototype advanced systems that require energy conversion for testing. This can include waste heat recovery systems or new turbine designs that operate more efficiently at small scales.
6. Backup and Peak Load Power for Small Industrial Operations
For small businesses, industrial facilities, or even manufacturing units, a 1-10 kW steam turbine generator can serve as a reliable backup or peak-load power source, especially when the primary grid power supply is unreliable or fluctuates.
- Powering Small Machines: In industries with intermittent power requirements, small steam turbines can generate electricity to run small machines and equipment. This ensures that operations continue smoothly, even if the local power grid fails or fluctuates.Example: A textile factory could use a small steam turbine as a backup power source for sewing machines or other equipment during periods when grid power is unavailable or unstable.
Design and Operational Considerations for Small Steam Turbines (1-10 kW)
- Boiler Selection and Steam Quality:
- Small steam turbines require a low to medium-pressure steam supply, typically in the range of 3-15 bar (43-217 psi), depending on the design of the turbine.
- The boiler system must be small, compact, and capable of producing high-quality steam with minimal loss. Boilers for small turbines are often fuel-efficient, especially when powered by biomass or waste heat.
- System Integration:
- Small steam turbines must be designed with a focus on compactness and ease of integration into existing systems. Many of these turbines come as modular units that can be easily combined with other energy systems such as solar, wind, or battery storage to create hybrid energy solutions.
- Efficiency Improvements:
- Small steam turbines can be integrated with heat recovery systems to increase overall efficiency. The turbine can generate electricity from excess heat, while exhaust steam can be reused for industrial processes, space heating, or even desalination in some cases.
- Control and Automation:
- Even at small scales, control systems are critical to ensuring that the turbine operates within optimal parameters. Advanced automatic control systems help monitor and adjust steam flow, turbine speed, and output to maintain efficient and safe operation.
- Maintenance and Longevity:
- Maintenance is generally less intensive for small steam turbines compared to larger units, but periodic checks of bearings, seals, and vibration levels are necessary to ensure long-term reliability and prevent failure. These turbines tend to have lower maintenance costs, making them an attractive option for smaller operations.
Conclusion
Small steam turbine generators (1-10 kW) are versatile, cost-effective solutions for off-grid power generation, biomass plants, small cogeneration systems, and waste heat recovery applications. Their compact design and ability to run on a variety of fuels (biomass, natural gas, waste heat) make them ideal for remote locations, educational purposes, and small-scale industries. By generating both electricity and heat, they offer a sustainable energy solution that can reduce reliance on fossil fuels and enhance energy efficiency in industrial operations.
Design Considerations for Small Steam Turbine Generators (1-10 kW)
When designing or selecting a small steam turbine generator, there are several key considerations to ensure that the system operates efficiently, safely, and cost-effectively. These considerations include:
1. Steam Flow and Pressure Requirements
For small steam turbines (1-10 kW), the steam flow rate and steam pressure are crucial to ensuring the turbine operates efficiently.
- Steam Pressure: Small turbines typically operate at low to medium pressure, often in the range of 3-15 bar (43-217 psi), though some turbines may operate at slightly higher pressures (up to 20 bar) to increase efficiency. The design of the turbine and boiler system must ensure that steam is produced at the correct pressure, as too high or low a pressure can significantly affect efficiency.
- Steam Flow Rate: The turbine’s steam flow rate is directly proportional to its electrical output. For small turbines, the required steam flow is relatively low, and it’s essential that the system be designed to produce enough steam to match the turbine’s needs without excessive fuel consumption.
- Steam Quality: The quality of steam—whether it is saturated or superheated—also impacts turbine performance. Superheated steam (steam that is heated above its boiling point) can increase efficiency and allow the turbine to operate at higher speeds. However, for very small turbines, saturated steam is typically adequate for efficient operation and simplifies the boiler design.
2. Fuel Source Flexibility
One of the standout features of small steam turbine generators is their fuel flexibility. Small turbines can be adapted to run on a variety of fuels, which is essential for making these systems viable in different geographic locations or industries.
- Biomass: Small steam turbines can run on biomass fuels, such as wood chips, agricultural residues, straw, or biogas. Biomass is often locally available and renewable, making it a cost-effective and environmentally friendly option for small-scale power generation. Biomass boilers are paired with the steam turbines, where the biomass is burned to generate steam.
- Natural Gas: In regions where natural gas is readily available, small steam turbines can also run on natural gas. Natural gas can provide a steady and reliable source of steam generation, making it an option for more urban or industrial applications where biomass may not be feasible.
- Waste Heat: Small steam turbines can also be powered by waste heat from industrial processes, such as heat recovery from combustion engines, furnaces, or chemical reactors. These systems capture waste heat that would otherwise be lost to the environment and convert it into useful electricity. Waste heat recovery is an efficient way to improve energy utilization in industries with high thermal output.
3. Size and Integration
Given their small size, small steam turbines are designed to fit into compact spaces while still maintaining high performance. This makes them suitable for industries and applications where space is limited or where a modular system approach is required.
- Modular Systems: Small steam turbines are often integrated into modular energy systems that can be scaled up or down based on energy needs. These systems can be installed in a containerized format for easy shipping and installation in remote areas. Modular systems are particularly useful for off-grid applications, where installation may need to be done in stages.
- Integration with Other Energy Sources: Small turbines are often used in hybrid systems, where they work alongside other energy technologies such as solar or wind power. For instance, a small steam turbine can act as a backup power source for a solar or wind-powered system during cloudy or calm periods, ensuring uninterrupted power supply.
- Cogeneration (CHP): As mentioned earlier, small turbines are ideal for cogeneration systems. These systems produce both electricity and usable heat, which makes them highly efficient in industries that require both. The design must consider dual-purpose heat recovery (for hot water or process heating) in addition to electrical generation.
4. Efficiency and Performance
- Thermal Efficiency: Efficiency is paramount in steam turbine design. Small steam turbines typically have an efficiency range of 50% to 70%, but this can vary based on steam quality, turbine design, and the integration of waste heat recovery systems. Some turbines use regenerative systems to improve efficiency by recycling exhaust steam.
- Mechanical and Electrical Efficiency: The mechanical efficiency of the turbine (how well the turbine converts steam energy into mechanical energy) and electrical efficiency (how well the turbine generator converts mechanical energy into electricity) both affect the overall performance. Small steam turbines generally exhibit lower mechanical efficiency compared to larger turbines, due to their compact size and operational constraints.
- Startup and Load Response: Small steam turbines are designed to be flexible, with the ability to start up quickly and respond to changing loads, which is particularly important in distributed energy systems. They can be used as part of load-following systems, where their output is adjusted based on demand.
5. Maintenance and Durability
- Maintenance Intervals: Small steam turbines are generally easier to maintain than larger turbines. Since they are designed for lower outputs, their components are less stressed, leading to fewer breakdowns. However, regular inspections of seals, bearings, vibration levels, and steam flow control are still required to maintain performance.
- Long-Term Durability: Proper maintenance is essential for ensuring long-term operation. Wear and tear on parts such as rotors and bearings can reduce turbine efficiency over time. Preventive maintenance and monitoring systems can help extend the turbine’s lifespan and prevent downtime.
Applications of Small Steam Turbine Generators (1-10 kW) – Continued
6. Small-Scale Industrial Power Generation
- Small Manufacturing Plants: Small steam turbines can be used to power small-scale industrial plants that have continuous or semi-continuous energy needs. For example, textile mills, food processing plants, or small chemical factories can use a small steam turbine to generate electricity for machinery while also utilizing waste heat for drying or heating.
- Waste Heat Recovery in Industrial Settings: Industries like steel mills, refineries, and paper mills can install small steam turbines for waste heat recovery. These turbines help convert low-quality exhaust heat into electricity, improving overall energy efficiency. This is especially true in industries where high levels of waste heat are generated and can be effectively captured.
7. Combined Heat and Power for Small Municipal Facilities
Small steam turbines can be used in district heating or municipal cogeneration systems to provide heat and power to small towns or communities.
- District Heating: In cold climates or areas where centralized heating systems are needed, small steam turbines can be used to provide both electricity and heat. The electricity can be supplied to homes or businesses, while the heat is used for residential heating or hot water supply.
- Energy Security for Small Communities: In areas that are isolated or prone to power outages, small steam turbines can enhance energy security by providing a reliable and sustainable power source. These turbines can be powered by locally sourced biomass or waste materials, creating a more resilient and self-sufficient energy grid.
8. Research and Development
- Energy Systems Research: Small steam turbines play an important role in the research and development of new energy systems and technologies. Researchers use small turbines to simulate and test energy conversion systems, study steam thermodynamics, and develop more efficient turbine designs. Small-scale turbines are ideal for experimental setups due to their manageable size and cost-effectiveness.
- Prototyping New Turbine Technologies: Manufacturers and developers of new turbine technologies often use small steam turbines as test platforms. For instance, they may prototype turbine blades or rotor designs that maximize efficiency or explore new materials for turbine components to reduce wear and increase lifespan.
9. Hybrid and Backup Power Systems
For both commercial and residential applications, small steam turbine generators can serve as a backup power source, ensuring reliability and continuity in case of grid outages. When integrated with solar or wind power, small steam turbines provide:
- Reliability During Interruptions: In regions where grid power is unreliable or where power outages are frequent, a small steam turbine can provide power backup, either as a standalone unit or integrated into a hybrid system with solar or wind energy. This is particularly useful for critical applications such as data centers or remote health clinics.
- Energy Storage Systems: Small steam turbines can also be linked with energy storage systems (like batteries) to provide power when the primary energy source is insufficient or intermittent. This enhances the system’s overall resilience and reliability.
Conclusion
Small steam turbine generators (1-10 kW) are highly versatile and efficient solutions for a range of applications. They are well-suited for small-scale power generation, cogeneration, off-grid setups, and waste heat recovery systems. Their compact design, fuel flexibility, and reliable performance make them ideal for industries, remote communities, and distributed generation systems.
By considering factors like steam flow, fuel type, and integration with other systems, these turbines offer a path toward more sustainable and cost-effective energy generation, particularly in areas with limited access to the traditional power grid. Whether used for biomass energy, waste heat recovery, or small industrial applications, small steam turbines present a scalable, adaptable solution for both existing and emerging energy needs.
3. Economic Benefits of Small Steam Turbine Generators (1-10 kW)
Small steam turbines (1-10 kW) can offer a range of economic benefits for various industries and applications. Below are some of the key financial advantages:
1. Reduced Energy Costs
- Fuel Efficiency: When compared to grid power or diesel generators, small steam turbines can significantly reduce energy costs, especially if they are powered by renewable fuels such as biomass or waste heat. These turbines convert thermal energy into electricity more efficiently than many other forms of small-scale power generation, leading to lower fuel expenses over time.
- Cogeneration: By providing both electricity and usable heat in cogeneration systems, small steam turbines allow businesses and industries to avoid purchasing separate heating and power solutions. This means businesses save on both electricity bills and heating costs (e.g., for water, space heating, or industrial processes).Example: A small factory could use a biomass-powered small steam turbine to generate electricity and provide process heating, reducing their reliance on grid power for electricity and natural gas for heating.
2. Energy Independence and Resilience
- Off-Grid and Backup Power: Small steam turbines provide energy independence for businesses and communities in remote areas or those prone to grid instability. They reduce dependence on external energy providers, which can result in long-term savings and more stable energy pricing. These turbines are especially useful in remote communities where extending the grid is impractical.
- Backup Power: In regions with frequent power outages, small steam turbines can act as a backup power source, avoiding costly downtime or reliance on expensive diesel generators. By using local, renewable fuel sources (such as biomass or waste heat), businesses can lower fuel costs and avoid expensive repairs associated with diesel engines.
3. Government Incentives and Support
Many governments offer incentives, subsidies, or tax credits for renewable energy projects, including biomass energy and waste heat recovery systems. These incentives can make the installation of small steam turbines more affordable, reducing initial capital expenditures. In some cases, businesses may be able to apply for grants or low-interest loans to fund small-scale turbine systems.
- Renewable Energy Credits (RECs): In some regions, businesses or municipalities that generate power from renewable sources like biomass or waste heat can sell RECs to utilities, which are required to meet renewable energy mandates. This can help recoup part of the initial investment and offset ongoing operating costs.
- Tax Incentives: Tax credits for renewable energy systems are often available for businesses investing in clean energy technologies. These credits reduce the overall financial burden of installing small steam turbine systems.
4. Long-Term Savings
- Lower Maintenance Costs: Small steam turbines are generally easier and less expensive to maintain than large turbines or other backup power systems. The simplicity of their design and their typically low operating pressure means they experience less wear and tear compared to larger turbines.
- Durability and Longevity: Small steam turbines, if properly maintained, can last for decades with minimal repairs. Over the long term, this can lead to significant savings in comparison to other power generation solutions that may require frequent servicing or replacement.
5. Job Creation and Economic Development
In rural or underdeveloped areas, small-scale steam turbine systems, particularly those powered by biomass, can help foster local economies. These systems may create jobs in fuel supply, maintenance, and installation, as well as generating opportunities for local industries to capitalize on renewable energy resources.
Example: A small biomass-to-power plant could create local employment opportunities, from wood chipping and fuel handling to ongoing turbine maintenance and system management.
4. Challenges in Implementing Small Steam Turbine Generators (1-10 kW)
While small steam turbine systems offer numerous benefits, there are also challenges that must be addressed during installation, operation, and long-term maintenance:
1. High Initial Capital Cost
The upfront cost of installing a small steam turbine system can be significant, particularly for biomass-powered systems or waste heat recovery systems. This includes costs for the turbine itself, boiler systems, control systems, and the infrastructure for fuel handling (e.g., biomass storage). These costs can be a barrier for small businesses or remote communities that are on tight budgets.
- Financing Options: However, many companies or governments offer financing options such as subsidies, grants, or low-interest loans that can help offset the initial cost of installation. Businesses may need to conduct a thorough financial analysis to determine the payback period and justify the investment.
2. Fuel Availability and Storage
- Biomass Fuel Supply: Small steam turbines that run on biomass face the challenge of ensuring a consistent, reliable supply of fuel. Biomass fuels like wood chips, agricultural residues, or wood pellets can be difficult to source and store in sufficient quantities, particularly in regions without abundant agricultural activity. Ensuring that an adequate fuel supply is in place year-round is critical to the success of these systems.
- Fuel Transportation: In some remote areas, the transportation of biomass fuel can add to the operational costs. Additionally, fuel storage and handling systems must be maintained to prevent spoilage, pests, or inefficient combustion.
3. Limited Expertise
Small steam turbines may require specialized expertise to install, maintain, and operate. Finding skilled personnel, especially in remote areas or developing regions, can be a challenge. Training programs or partnerships with local engineers can help address this issue, but it requires an upfront investment in human resources.
4. Regulation and Permitting
In some regions, small steam turbines—especially those powered by biomass or waste heat—may require specific permits, inspections, or compliance with local regulations, such as emissions standards and environmental impact assessments. This can complicate the installation process and increase time-to-market, especially in areas with strict environmental policies.
- Environmental Impact: Though biomass and waste heat recovery are renewable and generally considered low-carbon, small turbines still produce emissions that need to be regulated, especially in densely populated areas or regions with air quality restrictions.
5. Integration into Existing Infrastructure
Small steam turbines must often be integrated into existing systems, such as industrial boilers, power grids, or district heating networks. Ensuring seamless integration and compatibility can sometimes be complex, requiring upgraded electrical systems, heat exchangers, and control systems.
- Hybrid Systems: Small steam turbines are often used in hybrid systems, which means they need to be integrated with other power generation sources (like solar or wind), battery storage, or diesel generators. This can increase the complexity of the installation and require sophisticated smart grid and energy management solutions.
5. Future Potential and Technological Developments
1. Advancements in Efficiency and Design
Research and development in the field of small steam turbines is likely to lead to improvements in efficiency, particularly in miniaturized turbines that are optimized for low-pressure, small-scale operations. Potential advancements include:
- Materials Innovation: New, lightweight, and durable materials may be used to construct turbine blades, rotors, and casings, improving the thermal efficiency and long-term durability of the turbines.
- Improved Turbine Blades: Advances in turbine blade design—such as more aerodynamic shapes or advanced coatings to reduce wear—could boost the turbine’s efficiency and reduce maintenance requirements.
- Hybrid Energy Systems: As demand for renewable energy solutions increases, small steam turbines will likely be integrated into hybrid energy systems, where they work alongside solar, wind, and storage technologies. This allows for continuous power generation in regions with intermittent renewable resources.
2. Growth in Biomass Energy and Waste Heat Recovery
As interest in renewable energy grows, so will the adoption of biomass and waste heat recovery systems, which are ideal for driving small steam turbines. Many industries, especially those that generate waste heat (like steel mills or chemical plants), are increasingly focused on energy recovery solutions.
- Circular Economy: Small steam turbines that use biomass or waste materials support a circular economy, where waste is reused and converted into valuable energy. As more industries adopt waste-to-energy technologies, small steam turbines will become more integral to reducing overall carbon footprints and enhancing energy efficiency.
3. Decentralized Energy Networks
The trend toward decentralized energy—with small-scale power generation systems located near the point of use—will continue to rise. Small steam turbines fit well into these distributed energy networks, offering local energy generation that is resilient, sustainable, and cost-effective.
- Energy Resilience: In response to power grid vulnerabilities (such as natural disasters or cyberattacks), small turbines are expected to play a critical role in building more resilient energy infrastructure at the local level, reducing dependency on centralized power generation.
Conclusion
Small steam turbine generators (1-10 kW) represent a promising technology for a variety of applications, including cogeneration, waste heat recovery, biomass energy generation, and off-grid power systems. While challenges exist in terms of fuel supply, initial investment, and integration, the benefits—such as lower energy costs, energy independence, and economic resilience—make them an attractive solution for many industries and communities.
With continued advancements in technology, efficiency, and sustainability, small steam turbine systems will become even more cost-effective and widespread, playing a crucial role in the transition toward renewable energy and decentralized power solutions.
EMS Power Machines
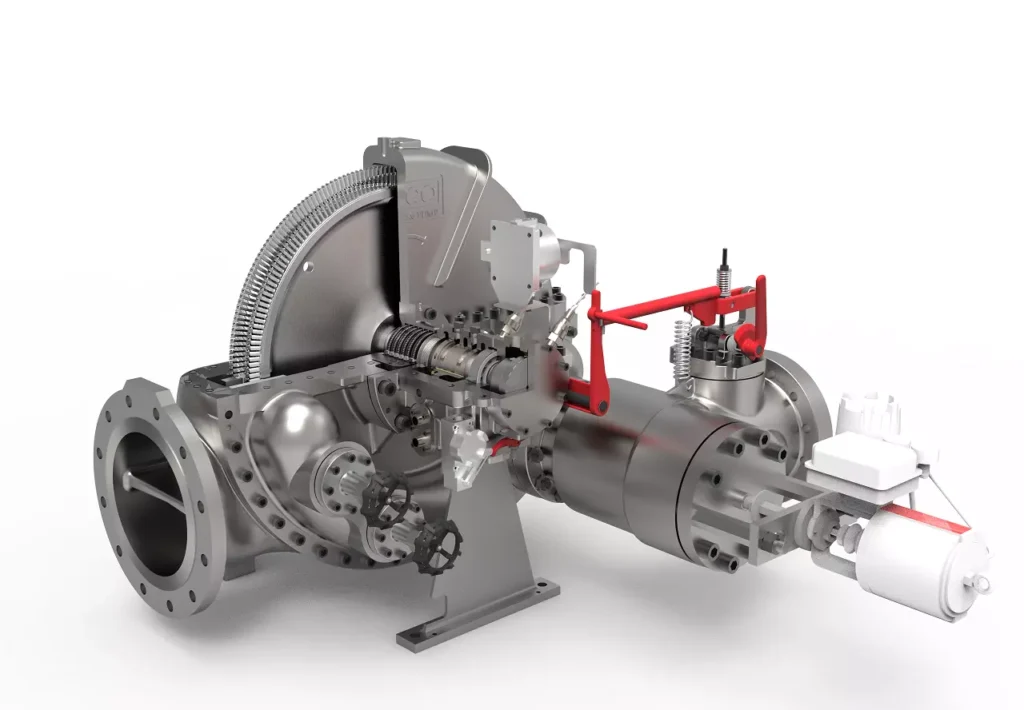
We design, manufacture and assembly Power Machines such as – diesel generators, electric motors, vibration motors, pumps, steam engines and steam turbines
EMS Power Machines is a global power engineering company, one of the five world leaders in the industry in terms of installed equipment. The companies included in the company have been operating in the energy market for more than 60 years.
EMS Power Machines manufactures steam turbines, gas turbines, hydroelectric turbines, generators, and other power equipment for thermal, nuclear, and hydroelectric power plants, as well as for various industries, transport, and marine energy.
EMS Power Machines is a major player in the global power industry, and its equipment is used in power plants all over the world. The company has a strong track record of innovation, and it is constantly developing new and improved technologies.
Here are some examples of Power Machines’ products and services:
- Steam turbines for thermal and nuclear power plants
- Gas turbines for combined cycle power plants and industrial applications
- Hydroelectric turbines for hydroelectric power plants
- Generators for all types of power plants
- Boilers for thermal power plants
- Condensers for thermal power plants
- Reheaters for thermal power plants
- Air preheaters for thermal power plants
- Feedwater pumps for thermal power plants
- Control systems for power plants
- Maintenance and repair services for power plants
EMS Power Machines is committed to providing its customers with high-quality products and services. The company has a strong reputation for reliability and innovation. Power Machines is a leading provider of power equipment and services, and it plays a vital role in the global power industry.
EMS Power Machines, which began in 1961 as a small factory of electric motors, has become a leading global supplier of electronic products for different segments. The search for excellence has resulted in the diversification of the business, adding to the electric motors products which provide from power generation to more efficient means of use.