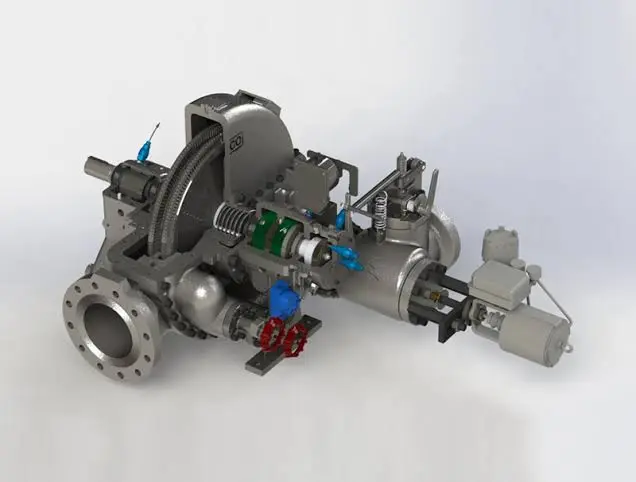
Used Micro Turbine for Sale: Steam turbines are mechanical devices that extract thermal energy from pressurized steam and convert it into mechanical work, typically used to drive electrical generators in power plants. The basic operation of a steam turbine involves the expansion of steam through a series of blades or vanes that are mounted on a rotating shaft. As the steam expands and cools, it transfers its energy to the turbine blades, causing the rotor to spin. This mechanical motion is then used to generate electricity or drive other machinery.
Steam turbines come in various designs, depending on the specific application and the requirements of the power generation system. The two main types of steam turbines are condensing and back-pressure turbines. Condensing turbines are used in large-scale power plants where the exhaust steam is condensed into water in a condenser, usually by cooling with water or air. This process allows for more efficient energy extraction from the steam, as it can be expanded to a lower pressure, resulting in a higher thermal efficiency.
Back-pressure turbines, on the other hand, do not condense the exhaust steam. Instead, the steam exits the turbine at a higher pressure and is often used for heating or industrial processes. This type of turbine is commonly found in combined heat and power (CHP) systems, where both electricity and heat are needed. The advantage of back-pressure turbines is that they allow for the utilization of the exhaust steam, improving the overall efficiency of the system by providing useful heat in addition to electricity.
The design and operation of steam turbines involve several key components, including the rotor, stator, blades, nozzles, and casing. The rotor is the central shaft that holds the blades and rotates to convert steam energy into mechanical energy. The stator contains stationary blades or nozzles that direct the steam flow onto the rotor blades at the optimal angle to maximize energy transfer. The blades are designed to withstand high temperatures and pressures, and they are typically made from materials that can resist corrosion and wear.
Steam turbines operate under varying load conditions, and their efficiency can be affected by factors such as steam temperature, pressure, and quality. To optimize performance, modern steam turbines are equipped with control systems that adjust the steam flow and pressure based on the demand for electricity or heat. These control systems use sensors and actuators to monitor and regulate the turbine’s operation, ensuring safe and efficient performance.
Maintenance and reliability are critical aspects of steam turbine operation. Regular inspections and maintenance are required to prevent issues such as blade erosion, fouling, and mechanical wear. Advanced diagnostic tools and techniques, such as vibration analysis and thermography, are used to detect potential problems early and avoid unplanned outages.
Steam turbines play a crucial role in power generation, especially in fossil fuel and nuclear power plants. They are also used in renewable energy applications, such as geothermal and biomass power plants. The ongoing development of advanced materials, coatings, and control systems continues to improve the efficiency and reliability of steam turbines, making them an essential component of the modern energy landscape.
Steam Turbines
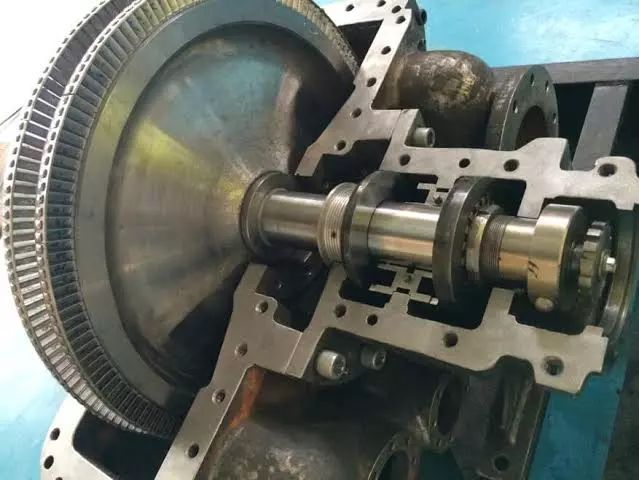
In the context of energy generation, steam turbines are integral to the efficiency and reliability of various power systems. Their versatility allows them to be used across a wide range of scales, from small industrial facilities to large power plants producing hundreds of megawatts. The thermodynamic process that underpins steam turbine operation is the Rankine cycle, which involves the boiling of water into steam, expansion of steam through the turbine, condensation of the steam back into water, and then reheating to complete the cycle.
The efficiency of a steam turbine is largely influenced by the inlet steam conditions—namely, its temperature and pressure. Higher inlet steam temperatures and pressures generally lead to higher efficiencies because they allow the steam to do more work as it expands through the turbine. However, there are practical and material limitations to how high these parameters can be set, as the components must be able to withstand the extreme conditions without degradation over time.
Another factor that plays a significant role in turbine efficiency is the exhaust pressure, which is directly influenced by the design of the condenser in a condensing turbine system. The lower the exhaust pressure, the more work can be extracted from the steam. In practice, this means maintaining a vacuum in the condenser, which helps in drawing the steam through the turbine more effectively. Effective heat exchange in the condenser is crucial for maintaining this vacuum and, consequently, the overall efficiency of the system.
In addition to efficiency, another critical aspect of steam turbine operation is the load-following capability. This refers to the ability of the turbine to adjust its output to match the fluctuating demand for electricity. This capability is particularly important in modern energy grids, which incorporate a significant amount of variable renewable energy sources such as wind and solar power. Steam turbines in these systems must be able to ramp up or down quickly and efficiently to ensure grid stability and reliability.
Steam turbines are also used in cogeneration, or combined heat and power (CHP) systems, where both electricity and useful heat are produced from the same energy source. These systems are highly efficient because they make use of the thermal energy that would otherwise be wasted in a traditional power plant setup. In industrial applications, steam turbines can be found in refineries, chemical plants, and paper mills, where they drive pumps, compressors, and other equipment.
The design of steam turbines continues to evolve, driven by the need for greater efficiency, reduced emissions, and improved reliability. Advances in materials science have led to the development of new alloys and coatings that can withstand higher temperatures and pressures, thus improving the efficiency of the turbines. Additionally, innovations in blade design, such as three-dimensional profiling and advanced aerodynamic shaping, help reduce losses and improve performance.
Modern steam turbines are also increasingly incorporating digital technologies for monitoring and control. Sensors placed throughout the turbine provide real-time data on temperatures, pressures, vibrations, and other critical parameters. This data is analyzed using advanced algorithms and machine learning techniques to predict maintenance needs, optimize performance, and prevent failures before they occur.
Overall, steam turbines are a mature technology that continues to see significant improvements, making them a cornerstone of global electricity generation. Their ability to efficiently convert thermal energy into mechanical work is unparalleled, and their role in the transition to more sustainable energy systems remains crucial. As the world moves towards decarbonization, steam turbines are expected to play a vital role in hybrid systems that combine traditional and renewable energy sources, ensuring a stable and efficient supply of electricity.
Steam Turbine Manufacturing
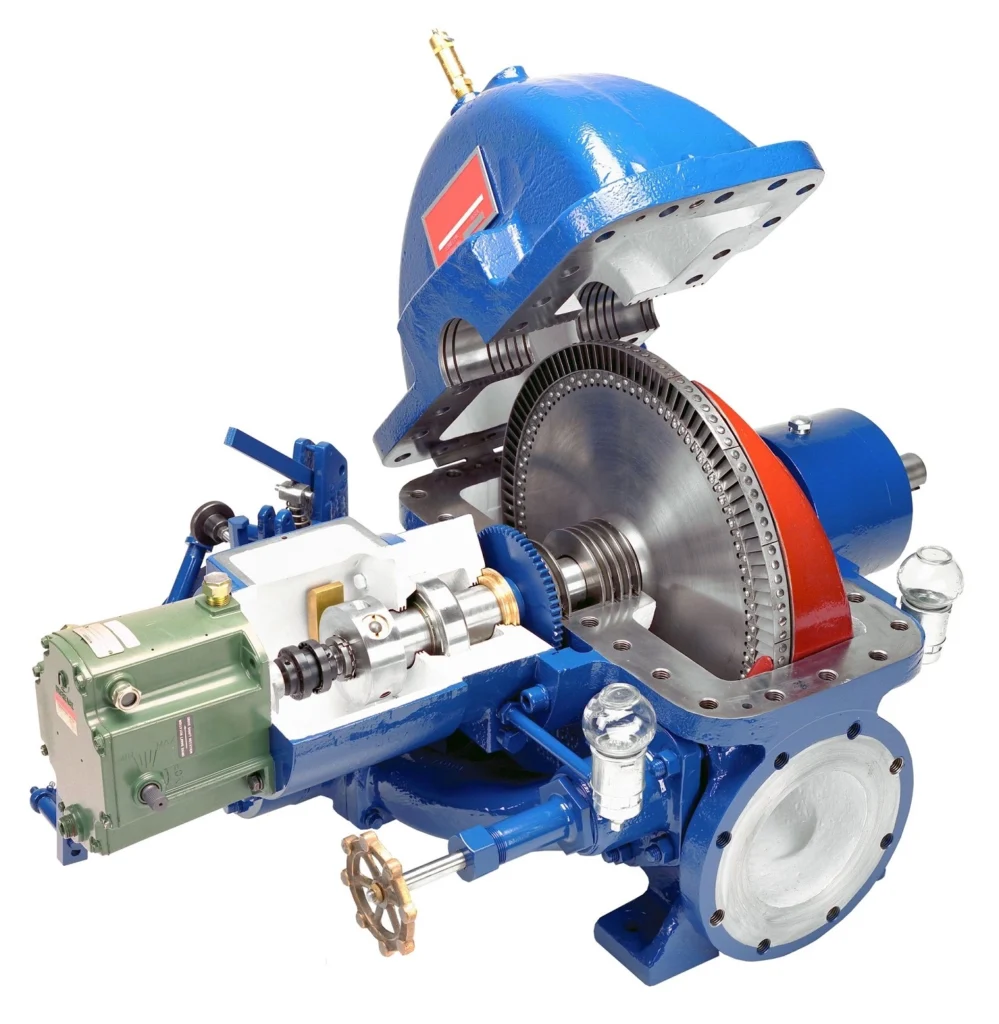
The manufacturing of steam turbines is a complex and precise process that requires a deep understanding of materials science, engineering principles, and advanced manufacturing techniques. Given the critical role of steam turbines in power generation, the manufacturing process is designed to ensure high reliability, efficiency, and longevity. Several key stages define the process of steam turbine manufacturing:
Design and Engineering
Before manufacturing begins, extensive design and engineering work is required. Engineers use advanced computer-aided design (CAD) software to create detailed models of the turbine, including its blades, rotor, casing, and other components. Computational fluid dynamics (CFD) and finite element analysis (FEA) are used to simulate the performance of the turbine under various operating conditions, helping to optimize the design for efficiency and durability. The design process also involves selecting materials that can withstand high temperatures, pressures, and corrosive environments typical in steam turbine operation.
Material Selection and Procurement
Steam turbines are typically made from high-strength alloys capable of withstanding the harsh conditions inside the turbine. Common materials include stainless steel, titanium alloys, and nickel-based superalloys. These materials are chosen for their strength, corrosion resistance, and ability to maintain structural integrity at high temperatures. Sourcing high-quality raw materials is critical to ensure the reliability of the final product. Manufacturers often work closely with suppliers to obtain materials that meet stringent specifications.
Casting and Forging
Key components of a steam turbine, such as the rotor and casing, are often produced through casting or forging processes. Forging involves shaping the metal using compressive forces, which results in components with superior mechanical properties, such as increased strength and toughness. Casting involves pouring molten metal into molds to create the desired shapes. Precision in these processes is essential, as any defects can compromise the performance and safety of the turbine.
Machining
Once the basic shapes are formed, precision machining is used to create the intricate details of the turbine components. Computer numerical control (CNC) machines are commonly used for this purpose, allowing for high precision and repeatability. Machining processes include milling, drilling, and grinding, which shape the turbine blades and other components to their final dimensions. The tolerances in steam turbine manufacturing are extremely tight, as even minor deviations can affect performance and efficiency.
Blade Manufacturing
The blades of a steam turbine are one of its most critical components, as they directly interact with the steam to extract energy. Blades are manufactured using precision forging and machining processes, followed by surface finishing to achieve the required aerodynamic profiles. Advanced blade designs may involve complex three-dimensional shapes to optimize the flow of steam and reduce losses. After manufacturing, blades are subjected to rigorous quality control checks, including dimensional inspection and non-destructive testing to ensure there are no internal defects.
Assembly
The assembly of a steam turbine involves carefully fitting all components together, including the rotor, blades, casing, and ancillary systems. This process requires high precision to ensure that all parts align correctly and that the turbine operates smoothly. During assembly, components are often tested for balance and alignment to prevent vibrations and mechanical stresses during operation. Any imbalance in the rotor, for example, can lead to severe operational issues.
Testing and Quality Assurance
Before a steam turbine is shipped to the customer, it undergoes a series of tests to verify its performance and reliability. These tests include hydrostatic testing to check for leaks, performance testing to measure efficiency and output, and mechanical testing to assess the turbine’s ability to operate under load. Non-destructive testing methods, such as ultrasonic and radiographic inspections, are used to detect any internal defects that could compromise safety.
Shipping and Installation
Once testing is complete, the turbine is disassembled for shipping. Components are carefully packaged to protect them from damage during transit. Upon arrival at the installation site, the turbine is reassembled and installed, often with the assistance of engineers from the manufacturing company. Installation involves precise alignment and connection to the power plant’s steam and electrical systems. After installation, the turbine undergoes further testing to ensure it operates correctly within the plant’s specific conditions.
After-Sales Support and Maintenance
Manufacturers typically provide ongoing support to ensure the long-term performance of the turbine. This includes regular maintenance services, parts replacement, and technical support. Some manufacturers offer remote monitoring services, where the turbine’s performance is continuously tracked to detect potential issues early and prevent unplanned outages.
The manufacturing of steam turbines is a highly specialized field that combines advanced engineering, precision manufacturing, and rigorous quality control. The goal is to produce turbines that operate reliably for decades, delivering efficient and sustainable power generation. As technology evolves, steam turbine manufacturing continues to innovate, incorporating new materials, designs, and digital tools to enhance performance and meet the demands of a changing energy landscape.
Design and Engineering
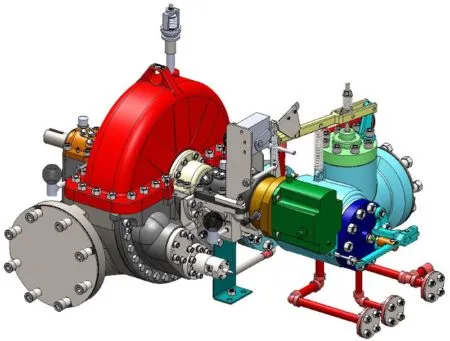
Design and engineering for steam turbines is a highly specialized field that involves careful planning, innovation, and technical expertise. The process begins with defining the specifications for the turbine based on its intended application, which can range from large-scale power generation plants to smaller industrial facilities. Engineers consider numerous factors during the design phase, including the type of fuel or heat source, the desired efficiency, the operational conditions, and the specific requirements of the power grid or industrial system.
The design of a steam turbine is a delicate balance between thermal efficiency, mechanical reliability, and cost-effectiveness. Engineers use advanced computer-aided design (CAD) software to create detailed models of every component, from the rotor and blades to the casing and control systems. CAD models allow engineers to visualize the turbine in three dimensions, which helps to identify potential issues early in the process and optimize the design for performance. These models are often accompanied by simulations that predict how the turbine will behave under various operational conditions. Computational fluid dynamics (CFD) plays a crucial role in these simulations, as it allows engineers to study the flow of steam through the turbine and refine the design of the blades, nozzles, and other key components to maximize energy extraction and minimize losses.
Finite element analysis (FEA) is another critical tool in the design process. It helps engineers evaluate how the turbine will respond to stresses, vibrations, and thermal expansion. This analysis is essential for ensuring the structural integrity of the turbine, as it must withstand extreme temperatures and pressures while maintaining efficient operation. FEA can simulate the impact of different materials, geometries, and operational scenarios, allowing engineers to fine-tune the design to achieve the best performance and durability. The use of these advanced simulation tools has revolutionized steam turbine design, enabling manufacturers to create more efficient, reliable, and cost-effective turbines.
The materials used in steam turbine construction are carefully chosen to meet the demanding operational conditions. High-strength alloys, such as stainless steel, nickel-based superalloys, and titanium, are selected for their ability to resist corrosion, fatigue, and high temperatures. The materials must not only withstand the stresses of rotating at high speeds but also the corrosive effects of steam, which can lead to erosion and material degradation over time. Material selection is a crucial aspect of the design process, as the right choice of alloys can significantly impact the turbine’s longevity and efficiency.
The design also takes into account the turbine’s ability to operate across a wide range of load conditions. Steam turbines are designed to handle varying steam flow rates, pressures, and temperatures while maintaining stable and efficient operation. Engineers use sophisticated control systems to monitor and adjust the turbine’s performance in real time, ensuring that it responds effectively to changes in demand. The ability to operate efficiently across different load conditions is particularly important in modern power plants, which often need to ramp up or down quickly in response to fluctuating electricity demand or the integration of renewable energy sources like wind and solar power.
Turbine designers must also address the issue of vibration and mechanical resonance. Since turbines rotate at extremely high speeds, any imbalance or misalignment can lead to excessive vibrations that can damage the turbine and reduce its operational life. To mitigate these risks, the design process includes careful balancing of the rotor, ensuring that it is precisely aligned and that the rotor blades are evenly distributed. Vibration analysis is carried out throughout the design process to identify potential resonance frequencies and prevent them from aligning with the turbine’s operating speed.
The layout and configuration of the turbine system are also critical aspects of the design. Engineers must ensure that the various components, such as the rotor, stator, nozzles, and casing, fit together seamlessly and are arranged in a way that optimizes steam flow and minimizes energy losses. Turbine designers must also consider the integration of the turbine with the larger power plant system, including the condenser, heat exchangers, and electrical generator. The turbine must be able to operate in harmony with the rest of the plant, ensuring that steam is efficiently converted into mechanical energy and that the plant’s overall efficiency is maximized.
Another important aspect of turbine design is ensuring ease of maintenance. Steam turbines are complex machines, and over the course of their operational life, they will require regular maintenance to ensure optimal performance. Design engineers aim to make the turbine components accessible for inspections, repairs, and replacements. For example, the rotor and blades may be designed for easy removal and replacement, while the casing is often constructed with features that allow for quick access to critical components. The design process also incorporates redundancy and safety features to ensure that the turbine operates safely under all conditions and that any potential failure can be quickly detected and addressed.
Ultimately, the goal of the design and engineering process is to create a turbine that operates with maximum efficiency, reliability, and safety, while minimizing maintenance requirements and ensuring a long service life. This requires not only a deep understanding of thermodynamics and mechanical engineering but also a constant awareness of the practical challenges and constraints of real-world operation. The design of steam turbines continues to evolve, driven by advances in materials science, computational methods, and manufacturing technologies, as engineers work to meet the growing demand for more efficient and sustainable power generation solutions.
As the design and engineering of steam turbines progress, another key consideration is the integration of advancements in digital technologies. Modern steam turbine design increasingly incorporates digital tools to enhance both performance and reliability. For instance, digital twin technology is becoming an essential aspect of turbine engineering. A digital twin is a virtual replica of the turbine that allows engineers to simulate and monitor its performance throughout its lifecycle. By using real-time data from sensors installed on the turbine, the digital twin can provide insights into the turbine’s operation, predict potential failures, and suggest optimizations. This capability is vital for improving operational efficiency, reducing downtime, and extending the service life of the turbine.
Furthermore, the design process is heavily influenced by environmental and regulatory factors. With the growing emphasis on reducing the carbon footprint of power generation, steam turbines must be designed with fuel efficiency and emissions control in mind. For example, turbines may be optimized for use with alternative fuels or to capture and reduce emissions from the combustion process. Designers must also consider the plant’s water usage and the efficiency of the cooling system, as steam turbines typically require large amounts of water for cooling. In regions where water resources are scarce, turbines are designed to minimize water consumption or integrate more sustainable cooling technologies, such as air-cooled condensers.
Another critical design focus in steam turbine engineering is the ability to adapt to changing grid demands, particularly with the increasing penetration of renewable energy sources. Power plants equipped with steam turbines must be able to quickly adjust their output to respond to fluctuations in demand or the intermittency of renewable sources like wind and solar. This requires advanced control systems and turbine designs that allow for rapid load-following capabilities, where the turbine can seamlessly increase or decrease its output in response to changes in grid conditions. The trend toward flexible, high-performance turbines is becoming more pronounced as the global energy landscape shifts toward cleaner and more decentralized energy sources.
The advancement of steam turbine efficiency is also driven by improvements in thermodynamic cycles. Over the years, engineers have worked to enhance the Rankine cycle, which forms the basis of steam turbine operation. Innovations like supercritical and ultra-supercritical steam cycles, where steam is heated to extremely high temperatures and pressures before entering the turbine, have led to significant gains in efficiency. These cycles allow for higher temperature steam, which in turn improves the turbine’s ability to convert thermal energy into mechanical work. However, achieving the necessary materials and engineering standards to operate at these extreme conditions presents challenges, requiring continuous innovation in both turbine design and materials technology.
For turbines used in combined heat and power (CHP) systems, designers must ensure that the turbine is capable of efficiently utilizing both the electricity generation and heat production aspects of the system. This requires a nuanced approach to design, where the steam turbine is integrated into a larger system that can effectively harness waste heat, optimizing both electrical and thermal efficiency. The design of these systems must account for various factors, including the pressure and temperature of the steam, the flow rate of the working fluid, and the specific requirements for heating.
During the engineering process, steam turbine designers also focus on safety and operational resilience. Steam turbines operate under extremely high pressures and temperatures, which necessitate robust safety features. The engineering team must design for scenarios like pressure surges, mechanical failures, or unexpected operational conditions. Safety valves, pressure relief systems, and redundant mechanisms are incorporated to ensure that the turbine can operate safely and continue functioning even in the event of minor faults or anomalies. The material selection, stress analysis, and overall design must ensure that the turbine can withstand these extreme conditions without compromising the safety of the plant or its personnel.
Moreover, design engineers work closely with other stakeholders, including environmental specialists, electrical engineers, and system integrators, to ensure that the turbine fits seamlessly into the larger power plant or industrial system. This interdisciplinary approach helps optimize the overall system performance, ensuring that the turbine operates at its peak efficiency while meeting regulatory requirements and operational goals. In many cases, the design process is iterative, with prototypes and mockups being created and tested to identify areas for improvement before the final design is implemented.
As steam turbine technology continues to evolve, there is an increasing focus on modular and flexible designs. Modular turbines are designed for easy assembly and customization, making them suitable for a wide range of applications, from small-scale industrial projects to large power plants. These modular designs allow for easier maintenance, upgrades, and future scalability, accommodating changes in energy demand or the integration of newer technologies as they become available.
In summary, the design and engineering of steam turbines is a highly intricate process that requires careful consideration of a broad range of factors. From materials selection and thermodynamic optimization to advanced digital tools and environmental sustainability, engineers must balance numerous variables to create a turbine that meets the evolving needs of the energy industry. The ongoing advancements in design methodology, coupled with the development of new materials and technologies, will continue to drive improvements in steam turbine performance, efficiency, and sustainability, making them a cornerstone of modern energy systems for years to come.
Material Selection and Procurement
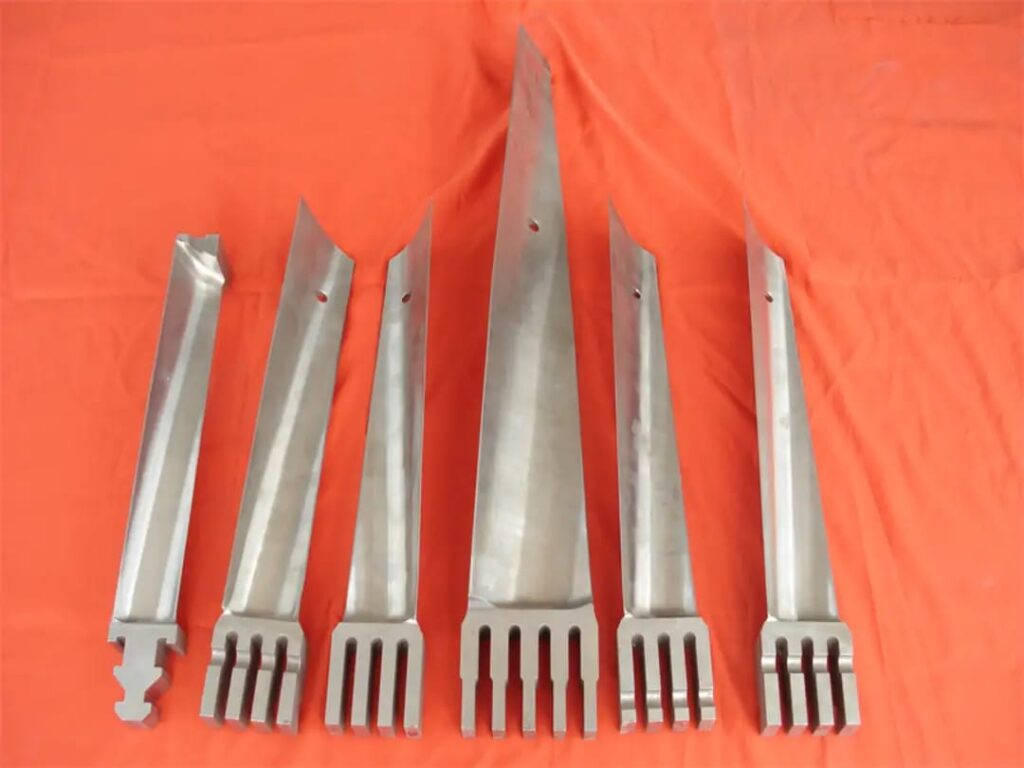
Material selection and procurement for steam turbines is one of the most critical aspects of their design and manufacturing process, as it directly affects the turbine’s performance, longevity, and reliability. Steam turbines operate under extreme conditions, including high temperatures, pressures, and mechanical stresses. Therefore, the materials used in their construction must possess specific properties that allow them to withstand these harsh environments while maintaining their structural integrity over the long term.
The first step in material selection is to identify the operating conditions of the turbine, such as the steam temperature, pressure, and flow rate, as well as the mechanical stresses that the components will experience. These factors are crucial for determining the type of material that will be used in different parts of the turbine, such as the rotor, blades, casing, and other critical components. The materials must be able to resist thermal degradation, mechanical fatigue, corrosion, and erosion, all of which can lead to premature failure if not properly addressed.
One of the most common materials used in the construction of steam turbines is high-strength steel, particularly stainless steel and nickel-based alloys. Stainless steel is favored for its excellent resistance to corrosion and its ability to withstand high temperatures. However, for more demanding applications, especially in modern high-efficiency turbines operating at supercritical or ultra-supercritical pressures and temperatures, higher-performance alloys, such as nickel-based superalloys, are often required. These alloys offer superior resistance to both thermal fatigue and corrosion, making them ideal for components that are exposed to the hottest parts of the turbine.
The turbine blades, in particular, are subjected to intense mechanical stresses and extreme temperatures as they interact with the high-pressure steam. To ensure optimal performance and durability, these blades are often made from advanced materials such as Inconel or Hastelloy, both of which are nickel-based superalloys known for their high-temperature strength and resistance to oxidation and corrosion. These materials are specifically designed to retain their mechanical properties at temperatures that can exceed 700°C, which is typical in modern, high-efficiency steam turbines.
The selection of materials for turbine components such as the rotor is equally important. The rotor must be able to handle both the mechanical stresses of rotating at high speeds and the thermal stresses caused by the temperature fluctuations within the turbine. Materials used for the rotor, therefore, need to have excellent tensile strength, fatigue resistance, and thermal conductivity. Forged steel and special alloys, such as carbon steels with added chromium or molybdenum, are often used in these applications. These materials provide the necessary strength while ensuring that the rotor can expand and contract with temperature changes without warping or cracking.
In addition to strength and resistance to thermal degradation, steam turbine components must also be resistant to erosion and corrosion caused by the high-speed steam flowing over the surfaces of the blades and other parts. Over time, steam can carry water droplets, dirt, and other particulates that cause wear and tear on turbine components. To mitigate this, materials such as chromium and other carbide-forming elements are often incorporated into the design to enhance wear resistance. The use of coatings and surface treatments, such as thermal spraying or the application of ceramic coatings, can further protect these surfaces from erosion and corrosion, extending the life of the turbine.
Beyond the performance properties, material selection also takes into account factors like cost, availability, and manufacturability. While high-performance alloys may offer superior properties, they are also more expensive and can be more challenging to process. Manufacturers must therefore balance the need for performance with the cost-effectiveness of the materials used. In many cases, the materials for less critical components, such as the casing, may be selected for their lower cost and ease of manufacturing, while more expensive and specialized materials are reserved for high-stress areas like the blades and rotor.
Once the appropriate materials are selected, the procurement process begins. Procurement involves sourcing raw materials from suppliers who can meet the strict specifications required for steam turbine construction. These materials must undergo thorough quality control checks to ensure they meet the required standards before they are used in manufacturing. This includes checking for impurities, verifying the material’s chemical composition, and ensuring that the material can withstand the expected operational stresses. The procurement process also involves managing the supply chain to ensure that materials are delivered on time, within budget, and in the quantities needed for the turbine’s construction.
One important consideration during procurement is the certification of materials, particularly for high-performance alloys and superalloys. These materials often need to be sourced from specialized suppliers who can provide documentation to verify their composition, heat treatment processes, and testing results. In some cases, turbine manufacturers may even work closely with material suppliers during the development stage to ensure that the materials meet the exact requirements for a specific turbine design.
In the context of steam turbine manufacturing, it is also essential to address environmental and sustainability considerations. The mining, processing, and disposal of raw materials can have significant environmental impacts. Manufacturers increasingly prioritize the use of recycled materials and sustainable practices in material sourcing. For example, some turbine manufacturers are exploring the use of advanced alloys that can be recycled more easily at the end of their lifecycle, reducing the environmental footprint of the turbine. Additionally, the focus on energy efficiency in modern steam turbines has led to the development of materials that enhance the performance of the turbine while minimizing energy consumption during their production and use.
To support long-term reliability and efficiency, manufacturers often implement robust material testing programs. This includes non-destructive testing methods such as ultrasonic testing, x-ray inspection, and magnetic particle testing to identify internal flaws or defects in the materials. Material samples may undergo accelerated aging tests to simulate years of service, allowing engineers to better understand how materials will behave over time under high-stress conditions. These testing methods help ensure that the selected materials will perform as expected throughout the turbine’s operational life, providing confidence that the turbine will meet the required safety and efficiency standards.
In conclusion, material selection and procurement are foundational to the design and performance of steam turbines. The materials chosen must be able to withstand the extreme conditions within the turbine, including high temperatures, pressures, and mechanical stresses, while also offering resistance to corrosion, erosion, and thermal degradation. The procurement process ensures that high-quality materials are sourced from reliable suppliers and are subject to rigorous testing to guarantee their performance. As steam turbine technology continues to evolve, innovations in material science and manufacturing techniques will play a vital role in improving turbine efficiency, durability, and sustainability, making material selection a key driver of the industry’s ongoing progress.
As steam turbine technology continues to advance, the ongoing development of materials plays a critical role in meeting the evolving demands of power generation. With growing concerns about energy efficiency, environmental sustainability, and the need to adapt to renewable energy sources, material selection remains a dynamic area of research and innovation. One major direction is the development of even more advanced high-temperature materials capable of withstanding the pressures and thermal stresses required for ultra-supercritical and advanced steam cycles.
Researchers and engineers are working on new alloys, including advanced ceramics and composites, that promise to push the boundaries of steam turbine efficiency. These materials are designed to offer superior thermal resistance, reduced wear, and improved mechanical strength while also being lighter and more cost-effective than their predecessors. The development of coatings that can be applied to turbine blades and other high-temperature components is another area of focus. For example, thermal barrier coatings (TBCs) are being studied for their ability to protect turbine components from extreme temperatures, thus extending their operational life and reducing the need for frequent maintenance.
Another key area of material innovation is in corrosion resistance. As steam turbines become more efficient, they are often required to operate at higher pressures and temperatures, which can increase the likelihood of corrosion due to the interaction with high-pressure steam, water droplets, and other particulates. Research into corrosion-resistant alloys and coatings that can prevent the formation of scale or corrosion on turbine components is ongoing. Advanced materials that can withstand both the corrosive effects of steam and the mechanical stresses of turbine operation will be vital to the continued performance and longevity of turbines in a wide range of applications, from traditional fossil fuel plants to modern systems designed to integrate with renewable energy sources.
The ongoing push for sustainability in the power generation industry also influences material selection. As environmental concerns regarding resource extraction and waste disposal continue to rise, the use of recycled materials and sustainable manufacturing processes is becoming increasingly important. Manufacturers are investigating the use of recycled high-performance alloys, which can significantly reduce the environmental impact of turbine production while maintaining the performance characteristics required for modern turbines. In addition, more stringent regulations around environmental impacts are driving innovation in material handling and disposal at the end of a turbine’s lifecycle, focusing on reducing waste and improving the recyclability of turbine components.
The procurement process itself is evolving to address these challenges. Manufacturers are increasingly collaborating with suppliers to ensure a more sustainable and efficient material supply chain. This involves not only ensuring the consistent quality and availability of materials but also ensuring that the environmental impacts of material production and transportation are minimized. Advanced supply chain management systems, along with improved material traceability, are helping manufacturers to track the environmental and social impacts of their material choices, which is critical for both regulatory compliance and corporate social responsibility initiatives.
Moreover, the role of material testing and certification continues to grow. As turbines operate under more extreme conditions, it is essential to test the materials under accelerated aging conditions, as well as to conduct detailed performance assessments in real-world environments. These tests often involve subjecting materials to conditions that simulate decades of wear and tear in a much shorter time frame, allowing engineers to identify potential issues and weaknesses before the turbine is deployed. Non-destructive testing methods, such as laser scanning and x-ray imaging, allow for the detailed inspection of turbine materials and components, ensuring that the turbine can perform safely and efficiently over the long term.
The importance of material selection and procurement cannot be overstated in the context of steam turbine reliability. High-performance materials are crucial for ensuring that turbines can withstand the intense mechanical and thermal stresses they experience, which is especially important in industries like power generation, where downtime is costly. Steam turbines are designed to run for decades, so the materials chosen must offer long-term durability and low maintenance requirements, reducing the need for frequent repairs or replacements.
Additionally, as the world shifts towards more flexible and decentralized energy systems, the role of steam turbines in power plants that integrate renewable energy sources will require turbines to operate efficiently across a wide range of conditions. This means that materials need to not only endure high temperatures and pressures but also be adaptable to a range of operational cycles. As plants move from baseload operation to load-following, materials that offer better thermal cycling performance—those that can withstand rapid heating and cooling cycles without degrading—will be increasingly important. This could lead to a greater emphasis on materials that can handle such stress without suffering from fatigue or cracking, ensuring reliable operation even as demand fluctuates.
In conclusion, material selection and procurement for steam turbines is a multifaceted process that involves selecting the right materials to ensure efficiency, durability, and sustainability. The continued evolution of turbine technology, including the shift toward more efficient and flexible systems, requires the development of materials that can withstand higher temperatures, pressures, and stresses while offering greater resistance to corrosion, erosion, and thermal fatigue. As the power generation industry seeks to meet global energy demands while minimizing environmental impact, advancements in material science will remain a cornerstone of steam turbine innovation, playing a critical role in improving turbine performance, extending service life, and reducing operational costs.
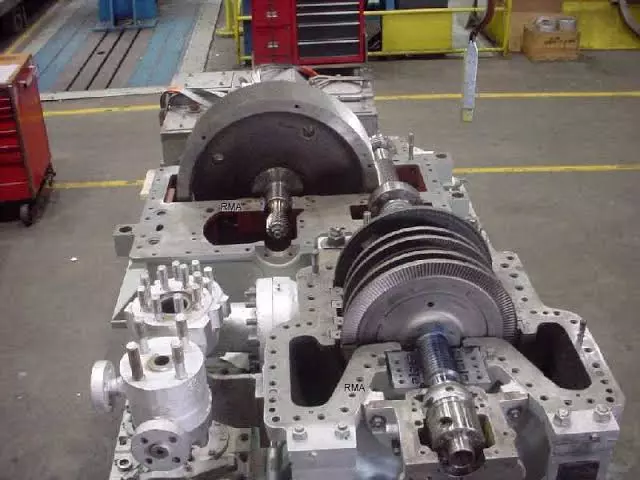
As the need for more efficient, sustainable, and adaptable steam turbines grows, material selection and procurement processes are expected to undergo further evolution. The increasing demand for renewable energy integration, combined with the need to meet stringent emissions regulations and operational flexibility, will continue to push the boundaries of material science. One key area of ongoing development is the creation of materials with enhanced resistance to thermal cycling. Modern steam turbines are often required to start up and shut down rapidly, especially in plants that complement intermittent renewable energy sources like wind and solar. These frequent cycling operations place tremendous stress on turbine components, particularly the materials used in the blades, rotor, and casings, which are exposed to high-temperature steam during operation.
Materials that can endure repeated heating and cooling cycles without developing cracks, warping, or other forms of fatigue are essential for these flexible power plants. Research into advanced composites and hybrid materials, such as ceramic-metal composites, is aimed at creating stronger, more resilient materials capable of withstanding these rapid temperature changes. These materials not only need to be thermally stable but also exhibit high mechanical strength and resistance to both thermal and mechanical fatigue. This research is vital to ensuring that turbines can efficiently meet the demands of a modern grid that requires more flexible, responsive power generation.
Another critical area of material innovation is the development of high-performance coatings and surface treatments to protect turbine components. As turbines are subjected to extremely high temperatures and pressures, and as they interact with corrosive steam, protective coatings can significantly extend their operational life. Advances in thermal barrier coatings (TBCs) and oxidation-resistant coatings help reduce material degradation by protecting the turbine’s surface from the damaging effects of high-temperature steam and the erosion caused by high-speed steam flow and particulate matter. These coatings not only extend the service life of turbine components but also contribute to improved efficiency by reducing energy losses due to surface degradation.
Nanotechnology is also playing an increasingly important role in steam turbine materials research. Nanomaterials, due to their unique properties at the atomic scale, offer the potential for greater strength, improved corrosion resistance, and better thermal conductivity compared to traditional materials. Research into the use of nanoparticles or nanostructured coatings for turbine blades and other components aims to create surfaces that are both harder and more resistant to the environmental conditions within the turbine. While the use of nanomaterials is still in the experimental stages, it holds promise for significantly improving turbine performance and longevity in the future.
The focus on reducing the environmental impact of steam turbine manufacturing and operation is also influencing material selection and procurement. As global sustainability initiatives become more prominent, turbine manufacturers are increasingly adopting green manufacturing practices. This includes the use of recycled materials and minimizing the carbon footprint of the materials themselves. The use of more sustainable and readily available raw materials, such as certain types of steel and alloys, is being prioritized, and some manufacturers are exploring alternative materials that could lower the environmental impact during both the production and operational phases of the turbine lifecycle.
Additionally, turbine manufacturers are exploring opportunities for the use of low-carbon and sustainable materials. For instance, certain bio-based composites and advanced polymers are being tested for use in less critical turbine components, where their properties may offer similar advantages to traditional materials at a lower environmental cost. While not yet widely adopted for high-performance turbine components, such research represents the growing trend of reducing reliance on traditional, resource-intensive materials.
The global supply chain for turbine materials is also undergoing significant changes. With growing demands for raw materials driven by the expanding global energy market, manufacturers are placing increased emphasis on ensuring the sustainability and reliability of their supply chains. The sourcing of rare materials, such as rare-earth elements used in high-performance alloys, has become more challenging. Turbine manufacturers are adopting strategies to mitigate supply chain risks, including working with a broader range of suppliers, investing in domestic production capabilities, and exploring alternatives to materials that are in short supply or subject to price volatility.
The procurement process is also evolving to incorporate more sophisticated methods for material traceability, quality control, and lifecycle management. This ensures that every material used in turbine manufacturing meets rigorous standards for performance and safety. By utilizing digital tools, such as blockchain or other tracking systems, turbine manufacturers can ensure that materials are sourced responsibly, with a transparent view of the entire supply chain. This also allows manufacturers to monitor the performance of materials throughout the turbine’s life, which can be useful for predictive maintenance and identifying potential issues before they lead to turbine failure.
In line with global trends in manufacturing efficiency, steam turbine manufacturers are increasingly looking toward additive manufacturing, or 3D printing, to complement traditional material procurement. Additive manufacturing techniques allow for the creation of complex turbine components with higher precision and reduced material waste. While still an emerging technology in turbine production, additive manufacturing has the potential to reduce manufacturing costs, improve the performance of turbine components, and even enable the production of highly customized parts. This is particularly useful for small-scale or specialized turbine applications where traditional manufacturing processes might be inefficient or cost-prohibitive.
Looking ahead, the focus on material selection and procurement in steam turbine technology is likely to center around increasing turbine performance while reducing costs and environmental impact. Innovations in material science, from next-generation alloys and coatings to new digital tools for procurement and quality control, will continue to shape the future of turbine manufacturing. As energy systems become increasingly complex and diverse, with greater emphasis on renewable energy integration and flexibility, the ability to select, source, and manufacture turbine materials that meet these evolving needs will be a key determinant of the industry’s success. Steam turbines, supported by cutting-edge material innovations, will continue to play a central role in achieving global energy goals, balancing the need for reliable power with the imperative for sustainability.
Casting and Forging
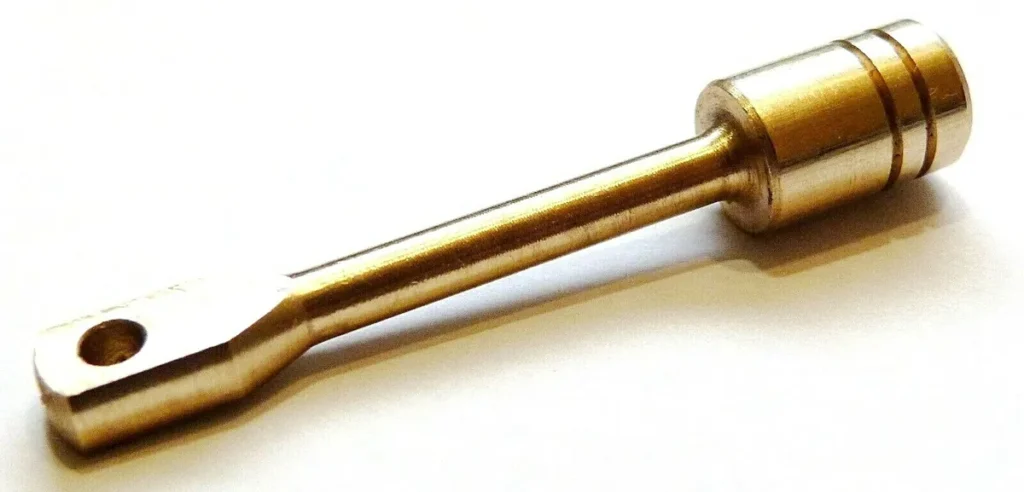
Casting and forging are two of the most fundamental manufacturing processes in the production of steam turbines, and both play a critical role in determining the performance, reliability, and longevity of turbine components. These processes are used to create the large and complex parts of the turbine, such as the rotor, casing, blades, and other critical components that must withstand extreme stresses and high temperatures during operation.
Casting is the process of pouring molten metal into a mold to create a solidified part in the shape of the mold. It is commonly used for producing intricate or complex components with relatively low to medium production volumes. In the context of steam turbines, casting is used for parts such as turbine casings, large valves, and other components that require specific shapes or geometries that are difficult to achieve with other manufacturing techniques. The casting process allows for the creation of parts with relatively intricate designs, making it an ideal choice for components that require complex internal passages or cavities, such as cooling channels within a turbine casing.
The casting process begins with the preparation of the mold, which can be made from a variety of materials, including sand, metal, or ceramic, depending on the type of metal being used and the desired properties of the final part. The metal to be cast is heated to its melting point, then poured into the mold, where it cools and solidifies into the desired shape. The resulting part may undergo further processing, such as heat treatment, machining, or surface finishing, to refine its properties and dimensions. In steam turbine manufacturing, precision is crucial, as any defects or deviations in the casting can compromise the performance and safety of the turbine. As such, quality control is a critical aspect of the casting process, with rigorous inspection techniques like x-ray imaging and ultrasonic testing used to identify internal defects or cracks that may not be visible to the naked eye.
Forging, on the other hand, is a process in which metal is shaped by applying compressive forces, typically using hammers or presses. It is often used to produce parts that require high strength and durability, as the forging process aligns the grain structure of the metal, making it stronger and more resistant to stress than cast materials. Forging is commonly used for producing turbine rotors, shafts, and other load-bearing components that must endure high mechanical stresses during operation. Because of its ability to create high-strength components, forging is an essential process for parts that need to withstand the rotational forces and thermal stresses experienced in a steam turbine.
Forging begins with the selection of the raw material, typically in the form of billets or bars of metal. These materials are heated to a temperature where they become malleable and can be shaped under pressure. The metal is then placed between dies, which apply compressive force to form the part into the desired shape. Depending on the specific design and the complexity of the component, multiple stages of forging may be required. The first stage involves rough forming, followed by more precise shaping and finishing in subsequent stages. This ensures that the final component meets the tight tolerances required for turbine operation.
One of the key benefits of forging is its ability to produce components with superior mechanical properties. The compressive forces used in forging refine the grain structure of the material, making it denser and stronger. This is particularly important for turbine rotors, which are subjected to high rotational forces and thermal stresses. Forged components are less likely to contain internal voids, cracks, or other defects, which can be common in cast materials. This makes forged parts ideal for critical applications where failure could result in significant damage or downtime, such as in the turbine’s rotating parts.
While casting is often used for producing larger, more complex parts with intricate shapes, forging is typically reserved for components that require high strength and precision, such as turbine blades, rotors, and shafts. The process also allows for a more controlled grain structure, which is essential for ensuring that the part can withstand the stresses and fatigue associated with high-speed rotation. The combination of casting and forging in turbine manufacturing allows manufacturers to take advantage of the unique benefits of each process, ensuring that every component is optimally designed for its specific function within the turbine.
In some cases, components may undergo both casting and forging. For example, a large turbine casing might be cast to form its basic shape, and then subjected to forging or other finishing processes to enhance its mechanical properties or to achieve more precise tolerances. This hybrid approach can be particularly useful for complex turbine parts that require both intricate geometry and superior strength.
One of the challenges in casting and forging turbine components lies in the need for material selection. The materials used for steam turbines must be able to withstand high temperatures, pressures, and corrosive environments, while also being capable of being processed through these manufacturing methods. High-strength steels, nickel-based alloys, and superalloys are commonly used in turbine manufacturing due to their excellent thermal stability, resistance to corrosion, and mechanical strength. However, the selection of the right material is crucial for ensuring that the casting or forging process will be successful and that the final part will meet the necessary performance standards.
In addition to material selection, both casting and forging processes require precise control of temperature, pressure, and time to ensure that the components meet the required specifications. In casting, for example, the cooling rate of the molten metal can affect the microstructure and properties of the final part, so it must be carefully controlled to prevent defects like porosity or cracking. Similarly, in forging, the temperature at which the material is worked and the amount of force applied must be closely monitored to ensure that the material is properly formed without damaging its structure.
Post-processing is another important aspect of casting and forging in turbine manufacturing. After casting or forging, parts often undergo heat treatment to further refine their properties. Heat treatment processes, such as annealing, hardening, or tempering, can improve the material’s strength, ductility, and resistance to fatigue. In some cases, the parts may also undergo surface treatments, such as coating or polishing, to enhance their durability and performance in the harsh conditions of a steam turbine.
Both casting and forging are essential to the manufacturing of steam turbines, each playing a key role in creating the robust components required for optimal turbine operation. By utilizing casting for complex shapes and forging for high-strength, load-bearing parts, manufacturers are able to produce steam turbines that can endure the intense stresses of modern power generation. Through careful material selection, process control, and post-processing, manufacturers ensure that turbine components meet the highest standards for reliability and performance, contributing to the long-term success of steam turbine technology in a rapidly evolving energy landscape.
As turbine technology continues to evolve, the methods of casting and forging are also advancing to keep pace with the increasing demands of efficiency, reliability, and cost-effectiveness. One significant trend is the continued refinement of both processes to produce more complex, higher-performance turbine components. Modern steam turbines operate at higher pressures and temperatures than ever before, and these enhanced operational conditions require parts that are both stronger and more resistant to wear, corrosion, and fatigue. This places even greater demands on the materials, casting molds, forging techniques, and finishing processes used in manufacturing.
In the realm of casting, there have been notable improvements in techniques such as investment casting, which is widely used for high-precision turbine components. Investment casting involves creating a detailed wax model of the part, coating it with a ceramic shell, and then melting away the wax to leave a hollow mold. The mold is then filled with molten metal to create the final part. This technique allows for the creation of highly detailed parts with complex geometries, such as turbine blades and intricate internal passages. It is especially useful for turbine components that require tight tolerances and smooth surface finishes. The ability to produce such detailed parts with investment casting has expanded the range of geometries that can be achieved, enabling the design of more efficient turbine blades that maximize steam flow and reduce energy loss.
Another significant advancement in casting is the use of 3D printing, also known as additive manufacturing, to create molds and even final components for turbines. In this process, layers of material are deposited one by one to build up a part. 3D printing has the potential to revolutionize turbine casting by enabling the creation of complex, customized parts that would be impossible or extremely expensive to produce using traditional methods. For example, intricate internal cooling channels in turbine blades that optimize the cooling of high-temperature surfaces can be created with great precision using 3D-printed molds or cores. The ability to print molds directly allows manufacturers to bypass some of the traditional limitations of mold-making, reducing both lead time and cost. Moreover, 3D printing enables the use of advanced materials that might otherwise be difficult to cast in traditional molds, including high-performance alloys or superalloys.
The advances in casting technology are paralleled by innovations in forging. One important development is the use of isothermal forging, a process in which the workpiece is heated to a uniform temperature, allowing it to be forged at a more controlled rate. This results in less distortion, reduced tool wear, and improved material properties, particularly in terms of grain structure. Isothermal forging can be particularly beneficial for creating turbine rotors and other high-strength components, as it allows for the production of parts with a more uniform structure, enhancing the mechanical properties of the material. This method ensures that the forged part maintains its integrity even under the high temperatures and stresses typically experienced in a steam turbine.
Another key advancement in forging is the use of precision forging, which employs highly sophisticated equipment to achieve even tighter tolerances and better control over the material’s final properties. Precision forging techniques have made it possible to produce components that are not only stronger and more reliable but also lighter, which is essential in modern turbine design. For example, reducing the weight of turbine blades or rotors can improve the overall efficiency of the turbine by reducing rotational inertia, allowing for faster response times and better fuel efficiency.
Along with these advanced forging and casting methods, manufacturers are increasingly incorporating automation and digital technologies into the production process. Computer numerical control (CNC) machines and robotics are being employed to perform precise machining and finishing of turbine components after casting or forging. These automated systems improve the consistency and accuracy of the manufacturing process, reducing the risk of human error and enabling the production of complex parts that would be difficult to achieve manually. Additionally, these technologies enable greater flexibility in turbine production, allowing manufacturers to quickly adjust to changing design requirements or custom orders.
The integration of digital twin technology is also making a significant impact on casting and forging in turbine manufacturing. A digital twin is a virtual representation of a physical object, and in the context of turbine manufacturing, it can be used to simulate the behavior of components during the casting or forging process. By using digital twins, manufacturers can predict potential issues, such as material defects, stress concentrations, or distortions, before they occur in the actual production process. This allows for more informed decision-making during the design and manufacturing stages, improving the overall quality of the turbine components and reducing waste.
Furthermore, advances in material science continue to influence both casting and forging practices. As the materials used in turbine manufacturing become more advanced, manufacturers are developing new processes to better handle these materials during the casting and forging stages. For example, newer nickel-based superalloys, which offer exceptional high-temperature strength and resistance to corrosion, require highly specialized casting and forging processes to ensure the parts meet the necessary performance standards. In response, manufacturers have refined their processes to accommodate these high-performance materials, ensuring that turbine components made from such alloys maintain their integrity and reliability during long-term operation.
The growing emphasis on sustainability is also shaping the future of casting and forging. As energy production becomes more environmentally focused, there is an increasing demand for sustainable manufacturing processes that minimize energy consumption and reduce waste. For example, the use of more energy-efficient furnaces, improved material recycling practices, and low-emission forging techniques are gaining traction in turbine manufacturing. The ability to recycle metals, particularly rare and expensive alloys, reduces the environmental impact of raw material extraction while also lowering production costs. This focus on sustainability is also driving the development of alternative manufacturing methods that could further reduce the ecological footprint of turbine component production.
Finally, the rise of advanced quality control techniques is essential in ensuring that turbine components meet the strict requirements of modern power generation. Non-destructive testing (NDT) methods, including ultrasonic testing, x-ray inspection, and eddy current testing, are employed to detect any potential flaws or imperfections in cast and forged components. These testing methods are critical for ensuring that turbine parts can perform safely and efficiently under the extreme conditions they will face in operation. Additionally, the increasing use of real-time data monitoring during the manufacturing process allows manufacturers to detect issues as they arise and make adjustments in real time, further improving the consistency and quality of the final product.
In conclusion, casting and forging are pivotal processes in the manufacturing of steam turbines, and their continued advancement is crucial to meeting the demands of modern energy production. With innovations in materials, automation, digital technologies, and sustainability, these manufacturing techniques are evolving to create turbine components that are stronger, more precise, and more efficient than ever before. As turbine manufacturers continue to push the boundaries of what is possible in terms of performance, reliability, and environmental responsibility, the role of casting and forging in turbine production will remain central to the development of the next generation of steam turbines.
Machining
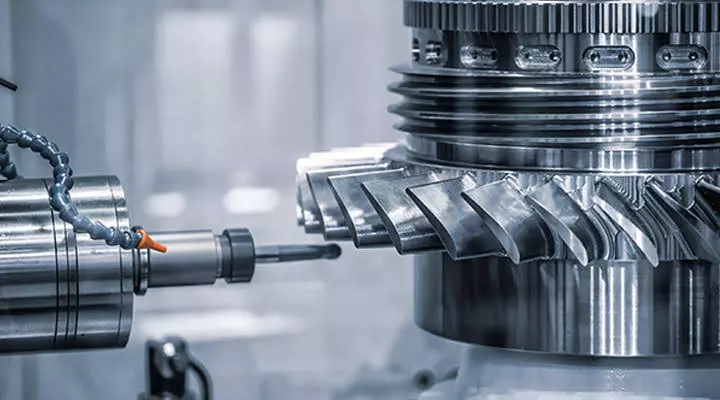
Machining is an essential part of the manufacturing process for steam turbines, enabling the production of highly precise components that meet the stringent requirements of performance, durability, and reliability. Steam turbines are complex machines that operate under extreme conditions, including high pressure, temperature, and rotational speed. The parts that make up a steam turbine must therefore be fabricated with exacting accuracy to ensure smooth operation and minimize the risk of failure. Machining processes are used to shape, refine, and finish turbine components after casting, forging, or other initial manufacturing steps. These processes are crucial for ensuring that the final parts meet the tight tolerances required for efficient and safe turbine operation.
The machining of steam turbine components typically involves several different techniques, each tailored to the specific needs of the part being produced. One of the most commonly used methods is milling, which involves the use of rotating cutting tools to remove material from a workpiece. Milling is often used for turbine blades, casings, and other complex components that require intricate surface geometries or fine detailing. High-speed milling can achieve precise tolerances and surface finishes, which are critical for ensuring that turbine blades, for example, are aerodynamically efficient and able to withstand the stresses placed on them during operation.
Turning is another important machining process that is often employed in turbine manufacturing. It involves rotating the workpiece while a cutting tool is applied to remove material and shape the part. This method is commonly used for creating round or cylindrical components, such as turbine shafts and rotors, which are subject to high rotational forces in operation. Turning allows for high precision in terms of dimensional accuracy and surface finish, both of which are essential for ensuring that turbine shafts rotate smoothly and without excessive wear or vibration.
Grinding is a precision machining process that uses abrasive wheels to remove material from a workpiece, resulting in a smooth surface finish. It is often used to achieve high-precision tolerances and tight dimensional control in turbine components. For example, grinding is frequently employed to refine the surface of turbine rotors and blades after casting or forging to ensure that they meet the strict geometric and surface finish specifications required for optimal performance. Grinding can also be used to remove any remaining imperfections from the surface of the material, improving the component’s ability to resist corrosion, wear, and other forms of degradation.
Electrical discharge machining (EDM) is a non-traditional machining method that uses electrical discharges to erode material from a workpiece. EDM is particularly useful for machining complex geometries or hard-to-reach areas that might be difficult to access using conventional machining techniques. This process is often used to create intricate features in turbine components, such as cooling channels within turbine blades, or to refine turbine parts made from hard, high-strength materials that are difficult to machine using traditional cutting tools. EDM can achieve very fine tolerances and surface finishes, making it an ideal process for turbine components that require intricate details or precision.
Laser machining is another advanced technique that has found increasing use in turbine manufacturing. This method involves using a high-powered laser beam to cut, drill, or etch materials with extreme precision. Laser machining can be used for creating small, intricate holes or patterns in turbine components, such as cooling holes in turbine blades, which help to regulate the temperature of the blade surfaces. The advantage of laser machining is its ability to produce high-quality cuts with minimal thermal distortion, which is crucial for maintaining the integrity of the turbine component, particularly in high-performance applications.
In addition to these individual machining processes, many steam turbine components undergo a combination of techniques to achieve the desired results. For example, a turbine blade might first be forged into a rough shape and then subjected to milling and grinding to achieve the precise geometry required. Afterward, it may undergo EDM or laser machining to create small features such as cooling channels. The choice of machining processes depends on the complexity of the component, the material being used, and the specific performance requirements of the turbine.
One of the key challenges in machining steam turbine components is working with the high-strength, heat-resistant materials commonly used in turbine manufacturing. Materials like high-performance alloys, nickel-based superalloys, and other exotic materials are often employed for their ability to withstand the extreme temperatures and stresses encountered in steam turbines. However, these materials can be difficult to machine due to their hardness and toughness. Specialized cutting tools, advanced cooling techniques, and optimized machining parameters are often required to achieve the desired results when working with these materials. For instance, the use of high-speed cutting tools made from carbide or other hard materials, along with advanced cooling techniques like through-tool coolant delivery, can help to reduce tool wear and improve cutting efficiency when machining tough materials.
Another important aspect of machining is ensuring that the turbine components are free from defects and meet the required quality standards. High-precision machining is critical for maintaining the integrity of the components and ensuring that they perform optimally in the turbine. Advanced inspection methods, such as laser scanning, coordinate measuring machines (CMM), and 3D imaging, are used to check the dimensions and surface quality of turbine components during and after machining. These technologies allow manufacturers to detect any deviations from the specified tolerances, ensuring that parts are produced with the utmost accuracy. Non-destructive testing (NDT) methods, such as ultrasonic testing and x-ray inspection, are also commonly used to detect internal defects, ensuring that the components are free from cracks or other weaknesses that could lead to failure during operation.
In modern turbine manufacturing, automation plays an increasingly important role in machining. The use of Computer Numerical Control (CNC) machines allows for highly precise and repeatable machining of turbine components. CNC machines are programmed with detailed specifications and can perform a wide range of machining operations with minimal human intervention. This increases the speed and efficiency of the manufacturing process while ensuring consistent quality. Additionally, robotic arms and automated loading systems are increasingly being used to handle turbine parts during machining, reducing the risk of human error and improving safety on the production floor.
One of the latest trends in machining technology is the integration of additive manufacturing or 3D printing with traditional machining processes. Additive manufacturing can be used to create prototypes or small quantities of turbine components, allowing manufacturers to test and refine designs before moving to full-scale production. While additive manufacturing is not yet widely used for large-scale turbine production, it holds promise for creating complex parts or features that would be difficult or impossible to machine using traditional methods. In some cases, additive manufacturing is used to produce customized tooling or fixtures that aid in the machining of turbine components.
As turbine technology continues to evolve, machining processes will play a key role in meeting the increasing demands for efficiency, performance, and sustainability. The continued development of advanced machining techniques, improved materials, and cutting-edge technologies will enable manufacturers to produce turbine components with even greater precision, durability, and performance. Through careful integration of machining methods, quality control, and material science, turbine manufacturers can ensure that each part is produced to the highest standards, contributing to the overall efficiency and longevity of steam turbine systems in modern power generation.
As steam turbine technology advances, the demands on machining processes continue to increase, pushing manufacturers to innovate and refine machining techniques further. The evolution of turbine designs, especially in terms of efficiency and performance, requires even greater precision and durability in the components produced. Machining, therefore, must evolve to accommodate these demands, particularly as turbines are pushed to operate at higher pressures, temperatures, and rotational speeds.
One of the key factors in improving the performance of steam turbines is the optimization of turbine blades. The design of these blades plays a critical role in determining the overall efficiency of the turbine, as they are responsible for converting steam energy into mechanical energy. Modern turbine blades are often made from high-performance alloys that offer superior resistance to heat and wear, such as nickel-based superalloys. These materials, while capable of withstanding extreme operational conditions, are also notoriously difficult to machine due to their hardness and toughness.
To address this challenge, the use of advanced machining techniques is becoming more prevalent. For example, high-velocity oxygen fuel (HVOF) coating is often applied to turbine blades to improve their resistance to wear and corrosion. This process involves spraying a high-velocity stream of particles onto the surface of the blade to create a hard, dense coating. After the coating is applied, the blade may undergo precision machining to remove any excess material and achieve the final shape and surface finish. The combination of HVOF coating and precise machining ensures that turbine blades remain resilient to erosion and fatigue, ultimately improving the lifespan of the turbine.
The role of thermal barrier coatings (TBCs) is also growing in importance. TBCs are applied to turbine blades to protect them from high-temperature steam. These coatings are typically made from ceramic materials and act as insulators, allowing the blades to operate at higher temperatures without experiencing thermal damage. Machining of turbine blades with TBCs is more challenging, as the coatings can be fragile and prone to cracking during processing. Specialized techniques, such as laser-based machining or abrasive water jet cutting, are often employed to preserve the integrity of the coatings while achieving the required precision.
In addition to blade machining, the increasing use of additive manufacturing in turbine production is opening up new possibilities for both component design and manufacturing efficiency. Additive manufacturing, particularly in the form of metal 3D printing, is being explored for the production of complex turbine components, such as nozzles, blading, and structural elements. These components can be fabricated layer by layer, with the ability to create intricate internal geometries, cooling channels, and other features that would be difficult or impossible to achieve through traditional machining methods. In turbine blades, for example, additive manufacturing allows for the creation of advanced cooling channels that maximize the efficiency of heat dissipation during operation.
While additive manufacturing offers considerable design flexibility, it is typically used in conjunction with traditional machining processes for finishing and refining parts. For instance, a turbine blade may be created using 3D printing, but it will still require machining to achieve the final shape, tolerances, and surface finish. This hybrid approach, combining additive manufacturing with traditional machining, enables turbine manufacturers to take full advantage of the strengths of both technologies. Additive manufacturing can be used to create complex geometries quickly and cost-effectively, while machining ensures that the final components meet the strict tolerances required for turbine operation.
The integration of robotics and automation into the machining process is another area of significant advancement. Automated systems are increasingly being used to handle turbine components throughout the machining process, reducing the need for human intervention and minimizing the risk of errors or defects. Robots equipped with advanced vision systems can inspect components in real time, allowing for immediate feedback on whether parts meet the required tolerances. This level of automation increases the consistency and accuracy of machining operations, reducing variability in the final products and ensuring that each component adheres to the exact specifications needed for optimal turbine performance.
CNC machining remains the cornerstone of precision manufacturing for steam turbine components. CNC machines are capable of executing highly intricate movements and cutting operations, allowing for tight tolerances and complex shapes to be created with minimal human oversight. The increased use of multi-axis CNC machines has expanded the capability to create even more complex geometries, such as those found in turbine blades with advanced airfoil shapes. These machines allow for the precise control of tool movement, ensuring that each pass removes material in a way that optimizes both part geometry and surface quality.
The importance of maintaining high surface quality in turbine components cannot be overstated. In high-performance applications, such as steam turbines, even minor surface imperfections can lead to significant problems, including stress concentration, fatigue failure, and corrosion. As a result, post-machining surface treatments, such as polishing, honing, or shot peening, are often applied to turbine components to enhance their durability and performance. These treatments improve surface finish, reduce surface roughness, and relieve residual stresses, ensuring that the turbine parts can withstand the harsh operating conditions they will face in service.
Surface coating technologies are also critical in improving the longevity of turbine components. For example, coatings that resist oxidation, corrosion, or wear are often applied to the surfaces of turbine blades, nozzles, and other components to enhance their resistance to the damaging effects of high temperatures, steam, and pressure. These coatings are typically applied using advanced methods like physical vapor deposition (PVD) or chemical vapor deposition (CVD), and after application, the parts often undergo machining to remove any excess coating and ensure a smooth, uniform finish.
Environmental concerns are also influencing machining processes in steam turbine manufacturing. As industries strive to become more sustainable, machining practices that minimize waste and energy consumption are increasingly in demand. For example, the use of dry machining techniques, which eliminate the need for cutting fluids and reduce environmental pollution, is gaining traction in turbine manufacturing. Additionally, advances in tool design and coatings have led to longer tool life and more efficient cutting, which reduces both material waste and the need for frequent tool replacements.
The combination of advanced machining techniques, automation, and material science is helping turbine manufacturers meet the growing demands for performance, efficiency, and sustainability. Through continuous innovation, machining processes are becoming more capable, enabling the production of turbine components that are stronger, more precise, and more durable than ever before. As the energy industry moves toward more efficient and environmentally friendly solutions, machining will continue to play a crucial role in ensuring the reliability and performance of steam turbines in power generation. The ongoing development of machining technologies will further enhance the precision and efficiency of turbine manufacturing, ultimately contributing to the success of modern power generation systems.
Blade Manufacturing
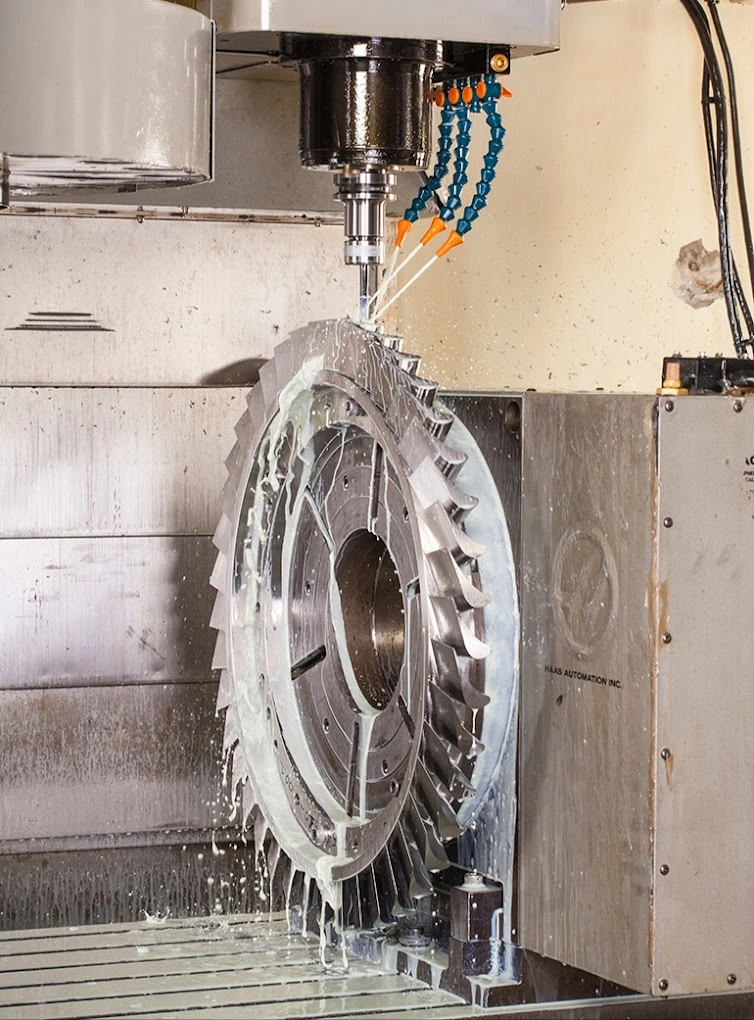
Blade manufacturing is one of the most critical aspects of steam turbine production, as turbine blades play a pivotal role in the turbine’s efficiency and overall performance. These blades are subjected to extreme forces, including high temperatures, pressures, and rotational speeds, which demand exceptional material strength and precision in their design and manufacture. The process of manufacturing turbine blades involves a combination of advanced materials, intricate manufacturing techniques, and precise quality control to ensure that the final blades can withstand these harsh operating conditions while maintaining their efficiency over time.
The manufacturing of turbine blades begins with careful material selection. The material chosen must be able to endure the high temperatures and stresses encountered within the turbine. For steam turbines, the most commonly used materials are high-performance alloys, such as nickel-based superalloys, which possess superior resistance to thermal degradation, oxidation, and corrosion. These materials are designed to retain their mechanical strength even at elevated temperatures, making them ideal for use in turbine blades. The selection of the right material is critical, as the blade material directly impacts the blade’s longevity, thermal resistance, and overall efficiency.
Once the material is selected, the next step is often casting, which is used to create the initial shape of the blade. Investment casting is one of the most widely employed techniques for producing turbine blades. In this process, a detailed wax or plastic model of the blade is created, coated with a ceramic shell, and then heated to remove the wax and harden the shell. The ceramic mold is then filled with molten metal to form the blade. Investment casting is particularly advantageous for turbine blades because it allows for the production of highly complex shapes with intricate geometries and fine details. This is essential for creating the highly optimized airfoil profiles and internal cooling channels that modern turbine blades require. The complexity of these designs is necessary to maximize the efficiency of the turbine by improving steam flow and heat dissipation.
After casting, the blades undergo various machining operations to refine their shape and dimensions. Machining is a crucial step in blade manufacturing, as it ensures that the blades meet the precise tolerances required for optimal performance. Common machining processes for turbine blades include milling, grinding, and turning. Milling is used to remove material and shape the blade, while grinding is often employed to achieve a smooth surface finish and to refine the blade’s aerodynamic profile. Blades may also undergo turning operations, especially if they have cylindrical features, such as root sections that fit into the turbine rotor. These processes are essential for achieving the exact geometry needed for the blade to perform efficiently in the turbine.
One of the most critical aspects of blade manufacturing is ensuring the internal cooling channels are correctly formed. Modern turbine blades are often designed with complex internal cooling systems that help regulate the temperature of the blade during operation. These cooling channels allow for the circulation of coolant, typically air or steam, to remove heat from the blade surfaces and maintain optimal performance. The cooling channels are particularly important in preventing thermal damage to the blades, which can occur due to the extreme temperatures of the steam entering the turbine. These channels are often intricate and difficult to form, and they may be created using advanced techniques like laser drilling, EDM, or 3D printing. These methods provide the precision required to create small, complex geometries inside the blades that are not achievable with traditional casting or machining techniques.
In addition to cooling, blades must be designed with aerodynamic profiles that maximize steam flow efficiency. The design of the airfoil, or blade shape, is optimized to convert the steam’s thermal energy into mechanical energy as efficiently as possible. This involves careful engineering to ensure that the blade maintains the appropriate angle of attack and airflow characteristics across its surface. Computational fluid dynamics (CFD) simulations are commonly used during the design process to predict and optimize the airflow around the blades, guiding the development of the airfoil shape. Once the blade design is finalized, it is then implemented in the manufacturing process, ensuring that the blade has the correct curvature, taper, and surface texture to achieve optimal performance.
After the blades are shaped and cooled, they undergo a series of heat treatments to enhance their mechanical properties. Heat treatment processes, such as solution treatment, aging, and annealing, are used to refine the microstructure of the blade material, improving its strength, toughness, and resistance to thermal degradation. These treatments alter the material’s grain structure and properties to enhance its ability to withstand the mechanical stresses and high temperatures encountered during turbine operation. Heat treatment is a critical step in blade manufacturing, as it directly impacts the blade’s durability and performance.
In addition to heat treatment, turbine blades may undergo surface treatments to improve their resistance to wear and corrosion. Techniques such as thermal spraying, shot peening, and coating are commonly applied to protect the blade surface. Thermal spraying involves the deposition of a protective coating onto the blade’s surface to improve its resistance to oxidation and corrosion. Shot peening is a process in which the blade surface is bombarded with small metal or ceramic particles to induce compressive stresses, which help to prevent fatigue and crack formation. Coatings, such as thermal barrier coatings (TBCs), are often applied to the surface of the blade to protect it from high-temperature steam and to reduce heat transfer to the blade material. These surface treatments play a crucial role in extending the lifespan of turbine blades and ensuring their continued performance under demanding operating conditions.
Once the blades have undergone all the necessary treatments, they are subjected to rigorous testing and inspection to ensure that they meet the required specifications. Non-destructive testing (NDT) methods, such as ultrasonic testing, X-ray inspection, and dye penetrant testing, are used to detect any potential internal defects or surface cracks that could compromise the blade’s structural integrity. These inspections are critical for ensuring that the blades are free from defects that could lead to failure during turbine operation. In addition to NDT, dimensional inspection is performed using high-precision measurement equipment, such as coordinate measuring machines (CMM), to verify that the blades meet the precise tolerances required for optimal performance.
Finally, the blades are carefully assembled into the turbine rotor, where they are fastened using highly precise and secure attachment methods. The process of attaching the blades to the rotor requires careful alignment and balancing to ensure that the turbine operates smoothly and efficiently. The blades are typically attached using dovetail or fir-tree joints, which provide a strong, secure connection while allowing for thermal expansion and contraction during turbine operation. Once the blades are assembled, the entire rotor is balanced to ensure that it spins evenly and without vibration, which is crucial for maintaining the efficiency and longevity of the turbine.
Throughout the entire process of turbine blade manufacturing, quality control is of paramount importance. Each blade must meet strict standards of material quality, precision, and performance to ensure that the turbine operates efficiently and safely. Advances in manufacturing technologies, including automation, robotics, and real-time monitoring systems, have made it possible to achieve higher levels of precision and consistency in blade production. These innovations help to reduce the risk of defects and ensure that turbine blades perform at their best over the course of their long operational life.
In conclusion, turbine blade manufacturing is a highly complex and precise process that involves multiple stages, including material selection, casting, machining, heat treatment, coating, and quality control. Each stage is critical for ensuring that the blades meet the high-performance standards required for steam turbines. Advances in manufacturing technologies and material science continue to push the boundaries of what is possible in blade design and production, leading to turbines that are more efficient, durable, and capable of operating under increasingly demanding conditions.
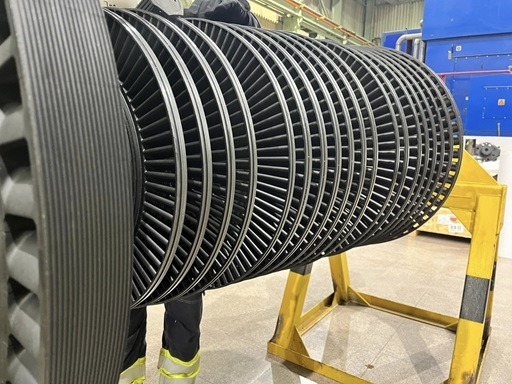
As turbine technology progresses, there are continuous advancements in turbine blade manufacturing to meet the growing demands of power generation, particularly as the focus shifts toward higher efficiency and sustainability. These developments are largely driven by the need for turbines that can operate at even higher temperatures, pressures, and rotational speeds while maintaining reliability and performance over extended periods. To address these challenges, manufacturers are employing innovative techniques and materials to further enhance turbine blade production and their operational capabilities.
One area where significant innovation is occurring is in the field of advanced materials for turbine blades. New alloys, composites, and coatings are being developed to increase the blades’ ability to withstand the harsh conditions within the turbine. For example, research into new high-temperature materials such as refractory metals and ceramic matrix composites (CMCs) is showing promise. CMCs, which combine ceramics with reinforcing fibers, offer high strength at elevated temperatures, corrosion resistance, and reduced weight compared to traditional superalloys. These materials may allow turbines to operate at even higher temperatures and improve their efficiency by enabling better heat conversion. The challenge with such materials lies in processing and manufacturing methods, as they are typically more difficult to work with than conventional metals. New approaches, such as advanced machining and additive manufacturing, are being explored to make these materials viable for turbine blade production.
In addition to material advancements, blade design continues to evolve. One of the key focuses of modern turbine blade design is improving aerodynamic efficiency. Turbine blades are shaped to optimize the flow of steam, thereby maximizing the amount of mechanical energy extracted from the steam. Computational fluid dynamics (CFD) plays a pivotal role in modern blade design, as it allows engineers to simulate steam flow patterns and refine blade shapes to achieve the best possible performance. These simulations help identify the most efficient airfoil geometries and cooling channel configurations, reducing energy losses due to drag and improving the efficiency of steam conversion.
Another area of focus in blade design is the integration of more advanced cooling techniques. As turbine blades are exposed to high-temperature steam, they must be kept cool to prevent thermal damage and maintain their structural integrity. Traditionally, turbine blades were cooled using air that was passed through internal cooling channels, but modern designs incorporate more complex cooling strategies. For instance, blades are increasingly being designed with enhanced internal cooling systems that use a combination of cooling air, steam, and even liquid coolant. The cooling channels inside the blades can be highly intricate, incorporating serpentine, pin-fin, or other advanced geometries that maximize cooling efficiency without compromising structural strength. These advanced cooling systems are critical for prolonging the life of the blades and improving turbine efficiency.
Additive manufacturing, or 3D printing, is another groundbreaking technology that has started to play a role in turbine blade production. Additive manufacturing allows for the creation of components layer by layer, which opens up new possibilities for producing complex blade designs with intricate internal cooling channels or unique surface geometries. Unlike traditional manufacturing methods, which often require expensive molds or complex tooling, additive manufacturing can produce turbine blades with geometries that would be difficult or even impossible to achieve using conventional methods. The use of additive manufacturing for turbine blades is still in its infancy, but it holds the potential to revolutionize blade design by enabling faster prototyping, reducing waste, and allowing for more customized solutions.
Moreover, as the push for cleaner and more sustainable energy sources continues, turbine blade manufacturers are focusing on improving blade longevity and resistance to degradation. One such method is through the use of coatings that enhance the blades’ resistance to oxidation, corrosion, and wear. Thermal barrier coatings (TBCs) are commonly applied to the surfaces of turbine blades to protect them from the extreme temperatures they are exposed to. These coatings act as insulators, allowing the blade material to remain at a lower temperature than the steam, reducing thermal stress and improving overall blade durability. Other coatings, such as oxidation-resistant coatings or coatings designed to reduce friction, are also used to protect blades from wear caused by the high-speed interaction with steam and particles in the turbine. The development of more advanced coatings and the ability to apply them more effectively are key areas of research in improving turbine blade performance.
Manufacturers are also focusing on reducing the environmental impact of turbine blade production. The energy-intensive nature of traditional blade manufacturing, including casting, forging, and machining, has prompted the industry to look for ways to reduce energy consumption and material waste. Technologies such as precision casting, which minimizes material waste during the initial casting phase, and advanced machining processes that use less energy, are being implemented to make turbine blade manufacturing more sustainable. Additionally, there is a growing interest in recycling and reusing materials from decommissioned turbine blades. This not only reduces waste but also contributes to the sustainability of the manufacturing process.
Quality control and testing remain integral to the production of turbine blades. As turbine blades operate in extreme conditions, their performance and reliability must be ensured at every step of the manufacturing process. Manufacturers use various non-destructive testing (NDT) techniques, such as ultrasonic testing, X-ray inspection, and eddy current testing, to detect any internal flaws or surface defects that could compromise the blade’s performance. These tests allow for early detection of potential issues, such as cracks, porosity, or inclusions, which could lead to blade failure during operation. In addition to NDT, blades are often subjected to rigorous mechanical testing, including fatigue testing and creep testing, to simulate the conditions the blades will face over their operational lifespan. These tests help verify the material properties and performance characteristics of the blades, ensuring that they meet the high standards required for safe and efficient turbine operation.
As the global energy landscape shifts towards renewable energy sources, steam turbines continue to play a crucial role in power generation, particularly in combined cycle power plants and other applications where efficiency is key. The ongoing development of more advanced turbine blades, with improved materials, design, cooling systems, and coatings, will be essential to meeting the increasing demand for energy while minimizing environmental impact. By adopting cutting-edge manufacturing technologies, optimizing designs, and incorporating more sustainable practices, manufacturers can continue to enhance turbine blade performance and support the transition to a more energy-efficient and sustainable future.
In conclusion, turbine blade manufacturing is a highly complex, specialized process that involves a combination of advanced materials, precision engineering, and rigorous testing. From the initial selection of materials to the final inspection of the blades, each step of the process is crucial for ensuring that the blades can perform optimally under the demanding conditions of steam turbines. As turbine technology continues to evolve, manufacturers are developing new materials, coatings, and manufacturing techniques to increase blade efficiency, longevity, and sustainability. These innovations will help drive the continued improvement of steam turbines, enabling more efficient and environmentally friendly power generation solutions for the future.
Assembly
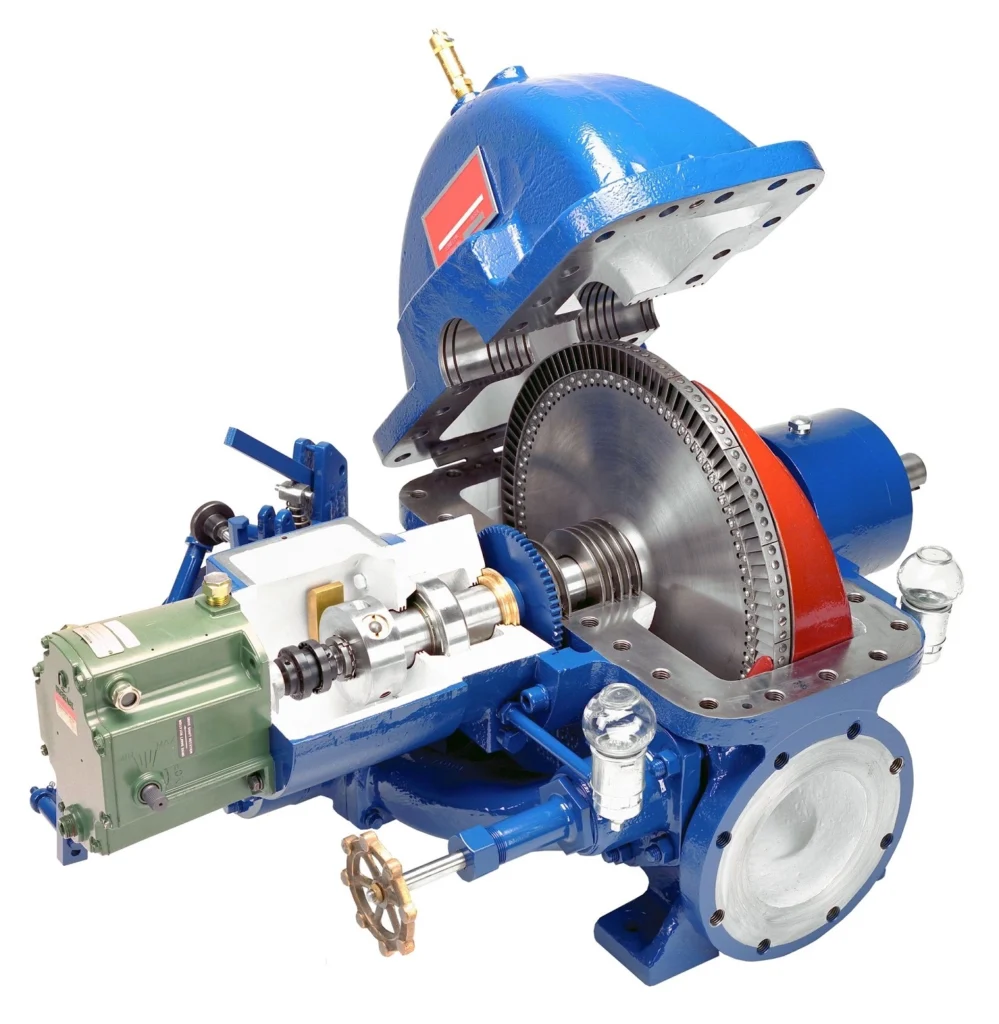
Assembly is a crucial stage in the steam turbine manufacturing process, where individual components such as blades, rotors, casings, and other critical parts are brought together to create the fully operational turbine. This stage requires precision, skill, and careful coordination, as the successful integration of these components determines the turbine’s overall efficiency, reliability, and safety during its operation. The assembly process is complex and often requires several steps, from the initial preparation of parts to final testing and alignment before the turbine is ready for installation.
The first step in the assembly of a steam turbine is the preparation of the individual components. These components are typically produced separately through casting, forging, machining, or additive manufacturing, depending on the part’s function and design. Once the components are ready, they are inspected for quality and dimensional accuracy. It is essential to ensure that all parts meet the strict tolerances required for turbine operation, as even slight deviations can lead to performance issues, vibrations, or mechanical failure. Non-destructive testing (NDT) methods, such as ultrasonic testing, X-ray, or magnetic particle inspection, are often employed at this stage to detect any internal flaws or surface imperfections that could compromise the turbine’s reliability.
After inspection, the components are cleaned and prepared for assembly. Cleaning is a critical step to ensure that there is no debris, oil, or other contaminants that could affect the turbine’s performance. High-precision cleaning techniques, such as ultrasonic cleaning or solvent-based cleaning, are often employed to remove any particles or residues from the surfaces of the components. This ensures that all parts fit together properly and minimizes the risk of damage during the assembly process.
Once the parts are prepared, the assembly process begins, starting with the rotor. The rotor is typically the central rotating component of the turbine, to which the turbine blades are attached. The rotor shaft is first aligned and carefully positioned within the turbine casing or housing, ensuring that it is correctly oriented for rotation. Precision alignment is critical, as any misalignment can result in vibrations, excessive wear, or premature failure of the rotor. Specialized equipment, such as laser alignment systems or dial indicators, is often used to ensure that the rotor is precisely aligned within the casing.
Once the rotor is positioned, the turbine blades are attached to the rotor, usually by means of dovetail or fir-tree joints, which provide secure attachment while allowing for thermal expansion and contraction during operation. The attachment of the blades requires careful attention to detail to ensure that they are securely fixed, balanced, and properly positioned. In many cases, the blades must be individually installed, with each one being inspected for proper fit and alignment before proceeding to the next.
In addition to the rotor and blades, other critical components, such as the nozzles, diaphragms, and seals, must also be carefully installed during assembly. Nozzles control the flow of steam into the turbine, while diaphragms help to direct steam flow across the blades. Seals are essential for preventing steam leakage, which could reduce the turbine’s efficiency. These components are typically installed with great precision to ensure that the steam flows smoothly and efficiently through the turbine, without any loss of energy or pressure.
During assembly, the casing or housing that encloses the turbine is also put in place. The casing serves to contain the rotor and blades, while also providing structural support and housing for the bearings and other critical components. It is essential that the casing is carefully aligned and sealed to prevent any loss of pressure or steam leakage. The casing must also be checked for proper clearance around the rotor and blades to ensure smooth rotation and prevent any interference between moving parts.
As the turbine is assembled, attention must also be paid to the installation of auxiliary systems, such as lubrication, cooling, and sealing systems. Lubrication is essential for reducing friction between moving parts and preventing wear, while cooling systems help maintain the turbine’s temperature within optimal limits. Sealing systems are designed to prevent steam leakage and maintain pressure within the turbine. Each of these systems must be carefully installed and tested to ensure proper operation.
One of the most critical aspects of turbine assembly is balancing. The turbine rotor, with all of its blades and other components, must be perfectly balanced to ensure smooth and stable operation. Any imbalance in the rotor can lead to vibrations, which can cause mechanical failure or reduced efficiency. Balancing is typically achieved through the addition or removal of small amounts of weight on the rotor, which is carefully measured and adjusted until the rotor is within the required balance tolerances. Dynamic balancing machines or computerized systems are often used for this process to achieve the level of precision needed.
Once the rotor, blades, and casing are assembled, the turbine undergoes a series of tests to ensure that everything is functioning correctly. These tests are typically performed under controlled conditions and may include functional tests, performance tests, and safety tests. Functional tests check that all components are working as intended, such as verifying that the blades rotate smoothly and that steam flows through the turbine efficiently. Performance tests are designed to measure the turbine’s output under simulated operating conditions, ensuring that it meets the specified power and efficiency requirements. Safety tests check for potential issues such as steam leaks, mechanical failure, or overheating, and ensure that the turbine can operate safely under extreme conditions.
During testing, any issues that arise are addressed immediately, and adjustments are made to the assembly as necessary. This could involve fine-tuning the rotor alignment, rebalancing the turbine, or replacing faulty components. The goal is to ensure that the turbine is operating at optimal efficiency and can withstand the stresses it will face during actual operation.
After the turbine has passed all tests and is deemed fully operational, the final step in the assembly process is packaging and shipping. Depending on the size and complexity of the turbine, this step may involve disassembling certain parts for transportation, then reassembling the turbine at its final installation site. In some cases, the turbine may be partially assembled on-site, with the remaining assembly completed once the turbine is positioned in place. This is especially common for large industrial turbines, which are often too large to transport fully assembled.
Once the turbine reaches its final destination, it undergoes final assembly and installation, where it is integrated into the power plant’s infrastructure. This includes connecting the turbine to the electrical grid, integrating control systems, and ensuring that all auxiliary systems, such as cooling and lubrication, are functioning properly. Final testing is conducted on-site to verify that the turbine is fully operational and ready for service. Once all systems are functioning correctly and the turbine is thoroughly tested, it is commissioned for full-scale operation.
In conclusion, the assembly of a steam turbine is a highly detailed and precision-driven process that involves the careful integration of various components to ensure that the turbine operates efficiently and reliably. From the rotor to the blades, casing, and auxiliary systems, each part must be meticulously assembled, tested, and adjusted to meet the strict performance standards required for turbine operation. The assembly process is not only about putting the parts together but also ensuring that every system is functioning as intended and that the turbine is properly aligned, balanced, and ready for service. As turbine technology continues to advance, the assembly process will continue to evolve, incorporating new materials, designs, and manufacturing techniques to improve performance, reliability, and sustainability.
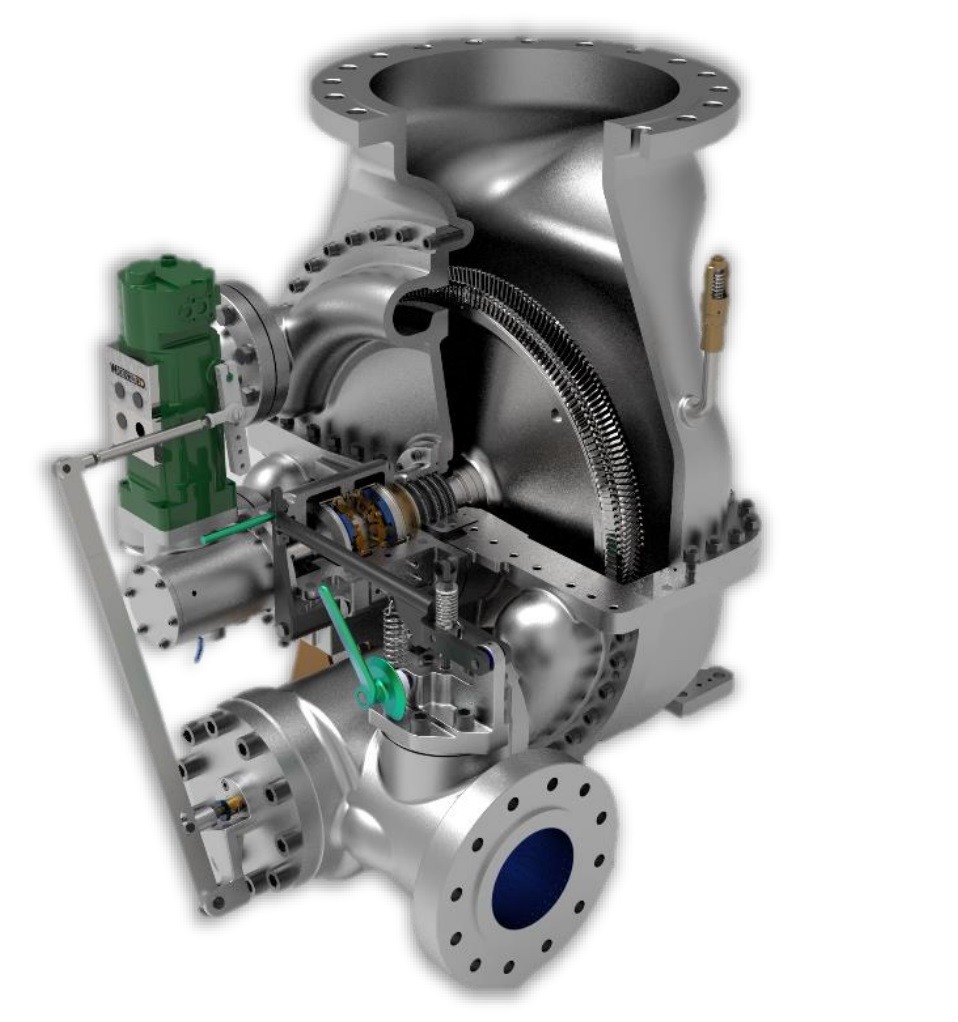
Once the turbine is fully assembled and ready for final testing, the focus shifts to ensuring the system operates as expected under actual working conditions. At this stage, final checks are performed on all interconnected systems, including electrical, mechanical, and control systems, to verify that they work seamlessly together. These final inspections and tests aim to confirm that the turbine can handle its intended operational loads and that all systems are functioning within the specified parameters.
A crucial part of the final testing process is the performance testing, where the turbine is put through a series of simulations to ensure it can operate efficiently under various conditions. This includes ramping up to full operational speeds and monitoring key performance metrics such as pressure, temperature, power output, and steam flow. Performance testing helps to confirm the turbine’s efficiency, reliability, and compliance with the design specifications. If any deviations from expected performance are noted, further adjustments are made to ensure the turbine can operate optimally once installed in the field.
Another vital component of the final testing process is the safety testing. During these tests, the turbine is subjected to scenarios that could potentially cause safety hazards, such as overpressure conditions, excessive temperatures, or power surges. Safety systems are rigorously checked to ensure that they function correctly, and the turbine is capable of responding to any emergency conditions. These systems often include pressure relief valves, emergency shutdown procedures, and temperature regulation mechanisms that help prevent catastrophic failure in the event of an abnormal condition. The goal of safety testing is to ensure that the turbine not only performs efficiently but can also protect against unforeseen failures that might compromise plant safety or turbine longevity.
Once performance and safety testing have been completed successfully, the next step is to conduct operational testing. In this phase, the turbine is tested in actual operating conditions, typically at a power plant or facility where it will be installed. The turbine is carefully monitored during this phase to ensure that all systems continue to function as intended under real-world loads and conditions. Engineers and technicians observe the turbine’s behavior, checking for any signs of vibration, noise, or unusual wear, and monitor critical parameters like bearing temperatures, steam flow, and pressure. If the turbine meets all operational requirements and passes this final round of testing, it is deemed ready for service.
Another significant aspect of final assembly is the integration of control and monitoring systems. Turbines are equipped with advanced control systems that monitor various parameters, such as temperature, pressure, vibration, and rotational speed, and adjust turbine operation to ensure optimal performance. These control systems are typically computer-based and are integrated with plant monitoring systems to allow real-time tracking of turbine performance. Control systems also include protective features, such as automatic shutdown procedures, to safeguard the turbine from damage under abnormal operating conditions.
The installation of sensors and diagnostic tools is also a key part of the assembly process. These tools are designed to continuously monitor the condition of critical components, providing real-time data that can be used for predictive maintenance, performance optimization, and troubleshooting. Sensors placed on bearings, blades, and rotors track parameters such as temperature, vibration, and stress levels, helping to identify potential issues before they lead to failure. This data can be sent to a centralized control room, allowing operators to take proactive measures to address any anomalies.
Once the turbine has undergone its final testing and is ready for commissioning, it is transported to its operational site if it hasn’t already been installed. Depending on the size and complexity of the turbine, this process may require disassembling large parts and transporting them by land, sea, or air. Upon arrival at the site, the turbine is reassembled and connected to the plant’s infrastructure, including steam pipes, generators, and electrical systems.
Installation of the turbine at the power plant involves further alignment and integration. The turbine is positioned within its designated housing, and various mechanical systems, such as cooling, lubrication, and exhaust systems, are connected. Final adjustments are made to the alignment of the rotor and the blades to ensure smooth operation. This often involves precision tools and equipment, such as laser alignment systems, to ensure that the rotor is perfectly centered within the casing and that there is no undue friction or wear during operation.
Once the turbine has been installed and integrated, another round of performance and safety checks is conducted on-site to ensure that the turbine can operate reliably under real-world conditions. Engineers will run the turbine at various speeds and loads to simulate different operating conditions and monitor its performance. This testing is done to confirm that the turbine will operate efficiently and reliably for the duration of its expected lifespan. If all tests pass successfully, the turbine is then ready for commercial operation.
Ongoing maintenance is critical to ensuring that the turbine continues to function at peak efficiency throughout its operational life. This includes scheduled inspections, part replacements, and performance monitoring. Over time, components such as bearings, seals, and blades may experience wear and need to be replaced. In some cases, turbines may undergo major overhauls or refurbishments to extend their operational life or improve efficiency. The assembly process is therefore not just about the initial setup but also involves planning for the turbine’s long-term maintenance and potential upgrades.
In conclusion, the assembly of a steam turbine is a multi-faceted and highly precise process that involves several stages of integration, alignment, testing, and adjustments. Each component, from the rotor and blades to the casing, seals, and cooling systems, must be carefully assembled to ensure the turbine operates efficiently, safely, and reliably. The process culminates in extensive performance and safety testing, both in the factory and on-site, to ensure the turbine meets its design specifications and operational requirements. With the turbine assembled, tested, and integrated into the power plant, it can provide reliable power generation, contributing to the plant’s efficiency and sustainability. Regular maintenance and monitoring ensure that the turbine continues to operate at its best over the long term, ensuring continued success and longevity in power generation applications.
Testing and Quality Assurance
Testing and quality assurance are fundamental components of the steam turbine manufacturing process, ensuring that each turbine meets the necessary performance, safety, and reliability standards before being put into service. As steam turbines are critical components in power generation, the consequences of failure can be significant, including energy production loss, potential damage to the turbine itself, and even safety hazards to plant personnel. Therefore, rigorous testing and quality control processes are implemented at every stage of manufacturing to guarantee that the turbine operates efficiently and reliably under a wide range of operating conditions.
The testing process begins early in the manufacturing stage, starting with individual components such as the rotor, blades, and casings. These components undergo detailed inspections to verify that they meet the design specifications and quality standards. The initial tests typically involve non-destructive testing (NDT) methods, such as ultrasonic testing, X-ray inspections, and magnetic particle testing, which help identify any internal defects, cracks, or material inconsistencies without damaging the parts. These inspections are essential for detecting problems that might not be visible to the naked eye but could potentially lead to catastrophic failure later in the turbine’s operation.
Once individual components pass their initial inspections, assembly testing begins. During the assembly phase, each part is carefully brought together, and the turbine is assembled under highly controlled conditions to ensure that all components fit together precisely. Alignment checks are critical during this stage, especially for the rotor and blades, to avoid issues such as excessive vibrations or friction once the turbine is in operation. The rotor, for instance, must be perfectly aligned within the casing, as even slight misalignments can lead to significant wear or failure. Special tools, such as laser alignment systems and dial indicators, are often used to ensure the accuracy of the rotor’s position and prevent any misalignment that could affect performance.
Another key aspect of assembly testing is the verification of the turbine’s mechanical integrity and balance. Balancing is an essential process to ensure that the turbine operates smoothly at high speeds. The rotor and blades must be perfectly balanced to prevent vibrations, which can cause damage to the turbine or reduce its operational life. Dynamic balancing machines or computerized systems are typically employed to measure and adjust the balance of the rotor and blades. The turbine undergoes several iterations of balancing, adjusting small weights as needed until it is balanced within the precise tolerances required for smooth and efficient operation.
Once the turbine is fully assembled, it undergoes a series of operational tests to simulate real-world conditions. These tests are typically conducted in a test facility, where the turbine is subjected to a range of scenarios that mimic the conditions it will face once installed at the power plant. The turbine is gradually ramped up to full operational speeds and subjected to various loads, pressures, and temperatures to evaluate its performance under different conditions. During these tests, key parameters such as steam flow, temperature, pressure, and power output are closely monitored to ensure that the turbine meets its design specifications and performs as expected.
Performance testing is critical, as it helps verify that the turbine will produce the required amount of power and operate efficiently throughout its lifespan. Turbines are designed to operate at specific pressure and temperature ranges, and performance testing ensures that these conditions are met. The turbine’s efficiency is measured by its ability to convert steam energy into mechanical energy and then into electrical power. Any discrepancies in performance at this stage could indicate potential issues with the design or assembly, such as leaks, inadequate sealing, or issues with steam flow dynamics. If any performance issues are detected during testing, adjustments are made to optimize the turbine’s operation.
In addition to performance testing, safety testing is a crucial aspect of the quality assurance process. Steam turbines operate under extreme pressure and temperature conditions, and ensuring that safety mechanisms are in place to protect the turbine and the surrounding infrastructure is paramount. During safety testing, the turbine is subjected to emergency scenarios, such as overpressure conditions or equipment failures, to verify that safety systems function as intended. Pressure relief valves, emergency shutdown systems, and other protective measures are thoroughly tested to ensure they will activate when needed to prevent catastrophic failure. These safety systems are crucial for protecting both the turbine and the plant operators from harm in the event of an emergency.
Once the turbine has passed all operational and safety tests, it undergoes final inspections before being shipped for installation. These inspections ensure that the turbine meets all regulatory and quality standards set by industry organizations and governing bodies. The final inspections often include visual checks, dimensional measurements, and a review of the test data to verify that all aspects of the turbine meet the required specifications. In addition to these standard inspections, manufacturers may also conduct endurance testing, where the turbine is run for extended periods under simulated load conditions to ensure that it can operate reliably over the long term without degradation.
To ensure the turbine’s continued reliability throughout its operational life, many manufacturers also implement predictive maintenance programs. These programs use sensors and monitoring systems installed in the turbine to track performance metrics such as vibration, temperature, and pressure. This data is continuously collected and analyzed to detect any anomalies that could indicate a potential issue. Predictive maintenance helps to identify issues before they become critical, allowing for proactive repairs or part replacements, which can help extend the turbine’s lifespan and reduce downtime.
Throughout the entire manufacturing process, quality assurance is a key focus, with stringent protocols in place to verify that every aspect of the turbine meets the highest standards of performance and safety. Manufacturers adhere to strict quality control procedures at each stage, from component fabrication and assembly to final testing and inspection. Quality assurance personnel are responsible for overseeing these processes, ensuring that every turbine is built to the highest standards. The aim is to minimize the risk of failure and ensure that the turbine will deliver reliable performance throughout its operational life.
In addition to internal quality control, third-party certifications and audits play an important role in verifying the turbine’s quality. Many turbines are subject to international standards and certifications, such as ISO 9001, which sets guidelines for quality management systems. These certifications ensure that the manufacturer adheres to best practices and maintains consistent quality throughout the production process. Independent testing and verification by external organizations provide an additional layer of assurance that the turbine meets global standards and regulations.
As part of the ongoing commitment to quality assurance, many manufacturers also focus on continuous improvement processes. These processes involve analyzing past production data, identifying areas for improvement, and implementing changes to enhance turbine design, manufacturing processes, and testing methods. By continually refining their practices and adopting new technologies, manufacturers can increase turbine efficiency, reduce manufacturing costs, and improve overall quality.
In conclusion, testing and quality assurance are vital to ensuring the performance, safety, and longevity of steam turbines. From initial component testing to final performance, safety, and operational checks, each stage of the process is designed to guarantee that the turbine will operate efficiently and reliably under a range of conditions. By employing rigorous testing procedures and maintaining stringent quality control standards, manufacturers ensure that their turbines can withstand the demanding environments in which they operate, providing reliable power generation for years to come.
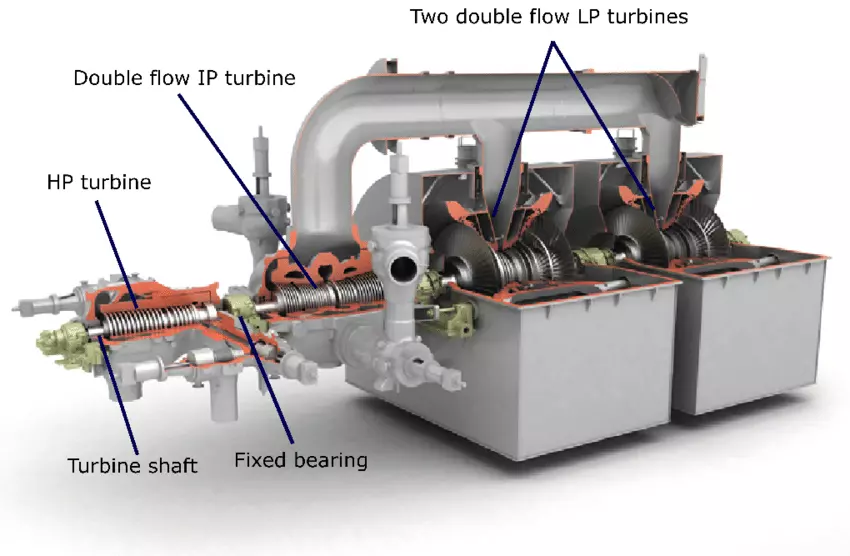
After the turbine passes all testing phases and is deemed fully operational, it enters the final stages of the commissioning process, where it is prepared for actual use at the power plant or installation site. However, testing and quality assurance don’t end with the delivery and installation of the turbine. Continuous monitoring and ongoing assessments are crucial to ensure that the turbine performs optimally throughout its service life.
Upon reaching the installation site, the turbine undergoes a series of final inspections and tests to ensure that it integrates seamlessly with the rest of the plant’s infrastructure. Installation tests focus on confirming that the turbine is correctly aligned, all auxiliary systems (such as cooling, lubrication, and steam control systems) are properly connected, and that the turbine is operating within the required parameters. These tests often include checking the clearance between rotating and stationary components, verifying pressure and temperature conditions, and conducting functional tests of the turbine’s control systems.
One important element of the final commissioning process is the system integration testing, where the turbine’s performance is evaluated alongside the rest of the plant’s systems. These tests ensure that the turbine operates efficiently with the power generation system, steam boiler, electrical generation equipment, and control systems. The integration tests check for correct synchronization with the grid and ensure that the turbine can maintain optimal performance under varying loads. Furthermore, any adjustments needed to align the turbine with the specific operating conditions of the power plant are made during this stage.
While commissioning tests verify that the turbine is working as designed, the importance of post-installation monitoring cannot be overstated. The performance of a steam turbine is subject to many variables, such as changes in steam conditions, plant operations, and load variations. Therefore, an ongoing monitoring and diagnostic program is essential to track the turbine’s health and optimize its performance over time. Remote monitoring systems, often integrated with a plant’s control center, collect and analyze data from various sensors embedded in the turbine. These systems track critical parameters like vibration levels, steam pressure, temperature gradients, and rotational speed. By analyzing this data, operators can spot potential problems early, such as bearing wear, misalignment, or efficiency drops.
Predictive maintenance is a key component of this ongoing monitoring. By analyzing historical performance data and current operational metrics, advanced algorithms and artificial intelligence can predict when specific components might need maintenance, based on trends and early warning signs. This allows operators to plan maintenance activities in advance, preventing unexpected breakdowns, reducing downtime, and extending the life of the turbine. Predictive maintenance can also help to optimize the turbine’s performance by identifying areas where efficiency gains can be made or where operational adjustments are necessary.
Another aspect of maintaining turbine reliability is periodic testing and inspection. Even though the turbine has passed its initial commissioning tests, ongoing inspections are necessary to ensure that it continues to operate efficiently and safely. These periodic checks often involve inspections of the turbine’s blades, seals, bearings, and rotors, as well as the systems that support turbine operation. Vibration analysis is often performed as part of these inspections to detect any imbalances that could indicate wear or misalignment. Thermography or infrared inspections can be used to detect temperature anomalies in critical components such as bearings, which may indicate early signs of failure. In addition, periodic testing of the turbine’s control systems ensures that the turbine is able to respond appropriately to operational changes and emergency situations.
In some cases, turbines may undergo major overhauls after a certain period of operation, usually every few years or based on operating hours. These overhauls involve disassembling the turbine for detailed inspections, replacing worn-out components, and performing upgrades to improve performance or efficiency. Overhauls are an opportunity to check for any wear on the blades, rotor, and other internal components, and to replace parts that have experienced fatigue. These major overhauls are often scheduled during planned plant downtime to minimize the impact on overall power generation.
One of the key goals of ongoing testing and maintenance is to ensure that the turbine operates within the parameters specified during its design and testing phases. If performance deviates from expected values, it could signal a potential issue with one or more turbine components, and corrective action can be taken before any significant damage occurs. Monitoring the turbine’s efficiency is particularly important, as even small losses in efficiency can result in higher operational costs and lower energy output.
Turbine upgrades may also be required over time. These can involve modifications to improve efficiency, such as installing new blades, enhancing cooling systems, or upgrading the control systems to take advantage of new technology. Technological advancements in materials, manufacturing methods, and digital controls often lead to opportunities to retrofit older turbines with more advanced components. Such upgrades can significantly extend the turbine’s operational life, improve fuel efficiency, and reduce emissions.
Finally, as part of the overall quality assurance strategy, manufacturers often provide ongoing support and service to the turbine owner throughout its operating life. This support can include regular maintenance services, remote monitoring, troubleshooting assistance, and availability of spare parts. Many manufacturers offer service contracts that include periodic inspections, performance audits, and access to technical expertise. By maintaining close communication with the turbine owner, manufacturers can ensure that any emerging issues are addressed promptly, and that the turbine continues to perform optimally over its entire service life.
In conclusion, testing and quality assurance are vital not only during the initial stages of turbine manufacturing and assembly but also throughout the turbine’s operational life. From comprehensive initial tests to ongoing performance monitoring and periodic inspections, these activities ensure that the turbine delivers reliable power generation, maximizes efficiency, and maintains safety throughout its service. Through predictive maintenance, remote monitoring, and periodic overhauls, steam turbines can operate efficiently for many years, meeting the evolving needs of the power generation industry while minimizing unexpected downtime and costly repairs.
Micro Turbine for Sale
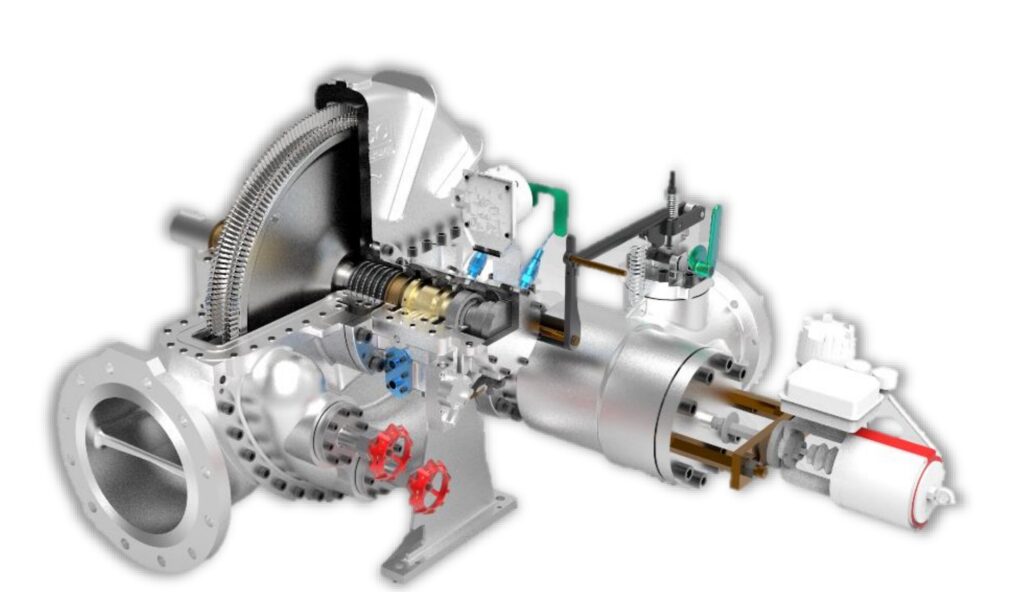
Micro turbines are compact, high-efficiency turbines designed for use in small-scale power generation applications. They have gained significant attention in recent years due to their ability to produce electricity efficiently in areas where traditional large-scale turbines or power plants may not be practical. These turbines are commonly used in distributed generation systems, offering a solution for off-grid power, remote locations, and backup power needs. With their small footprint, high efficiency, and potential for use with a variety of fuel sources, micro turbines have become an attractive option for businesses, homeowners, and organizations looking for reliable and cost-effective power generation.
Micro turbines are typically characterized by their small size, with power outputs ranging from a few kilowatts to several hundred kilowatts. This makes them ideal for applications such as powering small industrial facilities, residential homes, remote communications stations, and even electric vehicles. Their compact design allows for easy integration into existing infrastructure, and they are often used in conjunction with renewable energy sources such as solar panels or wind turbines to create hybrid systems. Additionally, micro turbines are well-suited for use in combined heat and power (CHP) systems, where they provide both electricity and thermal energy for heating or cooling.
One of the key advantages of micro turbines is their efficiency. These turbines can achieve high thermal efficiency, often exceeding 30% in electrical generation and up to 80% in combined heat and power systems, making them much more efficient than traditional internal combustion engines or diesel generators. Micro turbines are typically fueled by natural gas, propane, biogas, or even hydrogen, giving users a range of options for fuel selection based on availability and cost. Their ability to operate on different fuels makes them versatile and adaptable to various geographical locations and energy markets.
The compact design of micro turbines also contributes to their low environmental impact. They have lower emissions compared to conventional fossil-fuel-powered generators, producing fewer pollutants like nitrogen oxides (NOx) and carbon dioxide (CO2). Some micro turbines can even run on renewable gases such as biogas from organic waste, further reducing their environmental footprint. This makes them an attractive option for businesses and organizations looking to reduce their carbon footprint or meet sustainability goals.
Another important feature of micro turbines is their reliability. These turbines are designed to operate in harsh environments, and many are equipped with advanced control systems to ensure consistent performance over time. The turbines typically feature robust construction with high-quality materials, which helps to minimize wear and tear and extend their operational life. Additionally, micro turbines generally require less maintenance compared to other power generation technologies, thanks to their simple design, fewer moving parts, and the fact that they operate at lower temperatures.
In terms of pricing, micro turbines vary in cost depending on factors such as size, power output, and fuel type. The initial investment for a micro turbine can be higher than traditional backup generators, but the long-term savings in operational costs, energy efficiency, and reduced maintenance requirements can make them a cost-effective choice over the lifetime of the system. In some cases, government incentives and rebates for clean energy technologies may help offset the upfront costs, further improving the economic feasibility of micro turbine installations.
For businesses and organizations that require a continuous, reliable source of power, micro turbines are an appealing solution. Their ability to provide backup power during grid outages, or to supply base-load power for off-grid locations, is a significant advantage in regions with unreliable electricity infrastructure. Micro turbines are especially useful in remote or rural areas where the installation of larger, centralized power plants may be cost-prohibitive or logistically challenging. Additionally, micro turbines can be used as part of a larger distributed generation system, where multiple turbines are deployed to serve a community or industrial complex.
The growing interest in renewable energy and sustainable power generation has spurred the development of more advanced micro turbine technologies. Manufacturers are continuously working on improving the efficiency, reliability, and environmental performance of these turbines to meet the increasing demand for clean, affordable energy. As the technology evolves, micro turbines are expected to become even more efficient, with improved fuel flexibility, higher power outputs, and the ability to integrate seamlessly with other energy systems.
In terms of availability, micro turbines for sale can be found through a variety of suppliers, ranging from large-scale turbine manufacturers to specialized dealers. These turbines are sold both as standalone units or as part of integrated energy systems that include power electronics, control systems, and support infrastructure. Many suppliers offer installation and maintenance services to ensure that the turbines are properly integrated into existing power systems, with ongoing support for troubleshooting and repairs.
As the demand for decentralized, clean, and reliable power continues to rise, micro turbines will play a pivotal role in meeting these needs. Whether for residential, commercial, or industrial applications, these turbines offer a cost-effective, efficient, and environmentally friendly solution for small-scale power generation. The combination of high efficiency, low emissions, and versatility makes micro turbines an attractive option for those looking to reduce their dependence on traditional grid power and embrace sustainable energy solutions.
Micro turbines continue to evolve as part of the broader trend toward distributed energy resources (DERs). These technologies are becoming integral components of energy systems that are more decentralized, flexible, and resilient, particularly as global energy demands shift towards sustainability and self-sufficiency. Micro turbines, with their ability to provide power directly at the point of use, contribute significantly to this transition, supporting both residential and industrial sectors in their efforts to reduce energy costs, improve energy security, and reduce environmental impacts.
One area where micro turbines are gaining traction is in combined heat and power (CHP) applications. In CHP systems, micro turbines produce both electricity and usable heat, which can be harnessed for heating buildings, providing hot water, or even supporting industrial processes that require thermal energy. This dual-use capability boosts the overall efficiency of the system, making it a highly attractive solution for users looking to maximize energy savings. The efficiency benefits of CHP systems are particularly compelling in industrial applications, where there is a constant demand for both electricity and heat. Businesses in sectors such as food processing, chemical production, and pharmaceuticals can leverage micro turbines for CHP to optimize energy consumption, reduce waste, and enhance sustainability efforts.
The versatility of micro turbines extends to their ability to integrate with renewable energy systems. As the world moves towards more sustainable energy solutions, micro turbines are increasingly being paired with solar, wind, or biomass power sources to create hybrid energy systems. These hybrid systems can significantly improve energy reliability and reduce dependence on the grid, especially in remote locations or regions where energy infrastructure is lacking or unreliable. For example, in off-grid areas, micro turbines powered by renewable resources can provide a stable and reliable source of electricity, ensuring that local communities have access to the energy they need without relying on traditional fossil-fuel-based power generation.
Additionally, micro turbines are emerging as an essential technology for the emerging hydrogen economy. With the increasing focus on hydrogen as a clean energy carrier, micro turbines are being designed and optimized to run on hydrogen fuel. These turbines offer a high-efficiency, low-emission alternative to traditional internal combustion engines for generating electricity and heat from hydrogen. The ability to utilize hydrogen as a fuel source opens up new possibilities for decarbonizing industries such as transportation, manufacturing, and power generation. Micro turbines that run on hydrogen can play a pivotal role in this transition, contributing to a low-carbon future by reducing the reliance on conventional fossil fuels.
Furthermore, advancements in digital control systems are enhancing the capabilities of micro turbines. These systems enable real-time monitoring and management of turbine performance, optimizing efficiency, and providing valuable data for predictive maintenance. With sensors and analytics integrated into the turbines, operators can monitor critical parameters such as temperature, vibration, and pressure, which allows them to detect early signs of wear or potential issues before they lead to failures. This level of monitoring improves the reliability of the turbines, reduces downtime, and extends their operational life. Smart grid technology is also enabling micro turbines to work in conjunction with larger energy systems, offering a flexible and responsive solution to grid management, particularly as renewable energy sources like solar and wind, which are intermittent, become more common.
From a market perspective, the demand for micro turbines is expected to increase as industries and consumers alike look for reliable, efficient, and cost-effective energy solutions. Small-scale power generation is particularly appealing in regions with high energy costs, unstable power grids, or significant environmental concerns. As more people and businesses move toward self-sufficiency and carbon neutrality, micro turbines provide an efficient and scalable solution for achieving these goals. Government incentives and subsidies for renewable energy technologies are also helping to drive market growth, making micro turbines an even more attractive investment for those looking to adopt sustainable energy solutions.
In terms of installation, micro turbines offer significant advantages. Unlike large-scale power plants or traditional generators, they require minimal space, which makes them ideal for urban or confined settings. Their modular design allows them to be deployed in a variety of settings, from small residential properties to large commercial or industrial complexes. Furthermore, many micro turbines are designed with easy integration in mind, allowing them to be connected to existing infrastructure with minimal disruption. Installation and commissioning are typically streamlined processes, with many manufacturers providing turn-key solutions that include system design, installation, and maintenance.
While micro turbines offer many advantages, there are also challenges to consider. The initial capital cost for purchasing and installing micro turbines can still be relatively high compared to conventional backup generators or grid electricity. However, as the technology matures and economies of scale are achieved, prices are expected to decrease over time. Additionally, in some cases, regulatory or permitting requirements may delay the deployment of micro turbines, depending on local energy policies and environmental regulations. Nonetheless, as awareness of their benefits grows, and as renewable energy and energy efficiency policies continue to expand, the adoption of micro turbines is likely to accelerate.
In summary, micro turbines present a promising solution for small-scale, decentralized power generation. With their compact size, high efficiency, and ability to operate on a variety of fuels, including natural gas, biogas, and hydrogen, they are an increasingly popular choice for both residential and industrial applications. Their ability to provide both electricity and heat in combined heat and power systems further enhances their appeal. As part of a broader trend towards sustainability and distributed energy resources, micro turbines play a key role in the future of energy generation, helping users reduce costs, lower their carbon footprint, and achieve greater energy independence. Whether used alone or as part of a hybrid energy system, micro turbines offer a flexible, efficient, and environmentally friendly solution to meet the growing energy demands of the future.
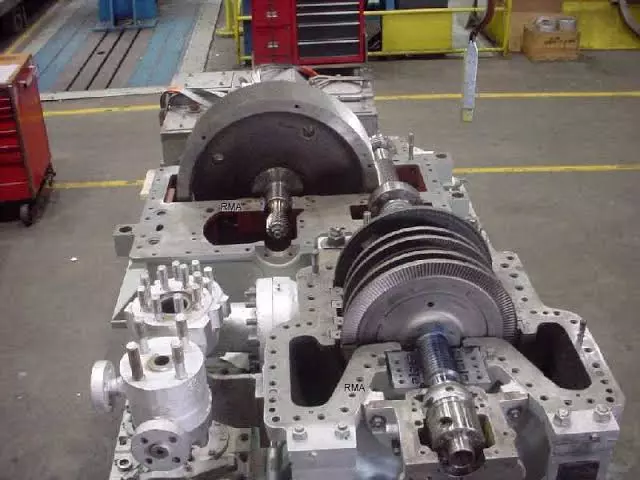
The future of micro turbines holds exciting potential, especially as the global energy landscape continues to shift toward greater sustainability and resilience. As technology advances, micro turbines are expected to become even more efficient, with innovations that improve fuel flexibility, enhance reliability, and integrate more seamlessly with renewable energy systems. For businesses, municipalities, and individuals seeking to reduce their reliance on traditional power grids and fossil fuels, micro turbines offer a promising avenue for achieving energy security, cost savings, and environmental goals.
One of the key areas of future development for micro turbines is their ability to operate with a broader range of fuels. While many micro turbines currently run on natural gas or propane, research and innovation are expanding the potential fuel options. For instance, the integration of biogas, which is produced from organic waste materials, not only offers a renewable fuel source but also provides a way to help reduce methane emissions from landfills and agricultural processes. This makes biogas-powered micro turbines a compelling option for environmentally conscious businesses and municipalities, especially in agricultural regions where organic waste is abundant.
Additionally, the ability to run on hydrogen is becoming increasingly important. As hydrogen production technology advances and becomes more widely available, micro turbines that use hydrogen as a fuel will play a significant role in reducing carbon emissions across various sectors. Hydrogen-powered micro turbines will support industries in transitioning to clean energy, with applications ranging from powering industrial plants to providing electricity for remote communities or off-grid locations. The integration of hydrogen into the broader energy ecosystem also facilitates a more diverse and resilient energy mix, which is essential for reducing vulnerability to supply disruptions.
The advancement of digital technologies will further enhance the capabilities of micro turbines. For example, the use of machine learning and advanced analytics can improve predictive maintenance strategies. With real-time data from sensors embedded in the turbine, operators can analyze operational patterns and make adjustments before issues escalate, optimizing performance and minimizing downtime. These technologies can also be linked to smart grids, enabling micro turbines to respond to changes in energy demand dynamically, contributing to a more balanced and flexible energy system.
Another area of focus for micro turbines is the potential for integration with energy storage solutions. As energy storage technologies improve, micro turbines can work in tandem with batteries or other storage systems to provide a more consistent and reliable energy supply. This integration is particularly valuable for intermittent renewable energy sources such as solar and wind, which can be unpredictable. By pairing micro turbines with energy storage, it becomes possible to store excess power generated during times of high production and release it when demand exceeds supply, thus ensuring a stable power supply even during periods of low renewable generation.
Micro turbines also have a critical role in the development of microgrids, small-scale, localized energy systems that can operate independently from the main grid. Microgrids, which can integrate various energy sources, such as solar, wind, and storage, with micro turbines, offer a robust solution for energy security in both rural and urban areas. Microgrids can be particularly beneficial in regions prone to natural disasters, where power outages are common. By utilizing micro turbines in these microgrids, communities can ensure that they have reliable power sources even in the event of grid failure, enhancing their resilience in the face of climate change and other challenges.
Additionally, micro turbines are increasingly being considered as part of urban infrastructure projects. As cities grow and face rising energy demands, micro turbines offer an opportunity for decentralized, efficient power generation. By incorporating micro turbines into district energy systems, urban areas can reduce their reliance on central grid infrastructure, lower carbon emissions, and optimize energy distribution. Furthermore, micro turbines can be used in combination with advanced building energy management systems (BEMS) to ensure that energy use is efficient and aligned with the specific needs of the building or district.
From a financial perspective, the ongoing development of micro turbines is expected to drive down costs and make these technologies more accessible to a wider range of customers. As manufacturers continue to innovate, the economies of scale will come into play, resulting in lower production costs, improved efficiency, and a reduction in the initial investment required for purchasing and installing micro turbines. Over time, the cost savings achieved through improved energy efficiency and reduced maintenance requirements will further enhance the attractiveness of micro turbines as a viable long-term energy solution.
Governments and regulatory bodies also play a vital role in shaping the future of micro turbines. With the global push for cleaner energy and the implementation of more stringent environmental regulations, micro turbines are positioned to benefit from policies and incentives that promote energy efficiency and carbon reduction. As governments continue to invest in renewable energy infrastructure and provide incentives for clean technologies, micro turbines will be an essential component of achieving national and international sustainability goals.
The growing market for micro turbines also opens opportunities for innovation and entrepreneurship. As the technology matures and demand increases, new companies are emerging to offer micro turbine products, services, and solutions tailored to specific market needs. This competitive landscape fosters innovation and the development of new applications for micro turbines, from small-scale residential units to large industrial systems.
In conclusion, the future of micro turbines is bright, driven by advances in technology, the growing demand for decentralized and sustainable energy solutions, and the integration of micro turbines into various energy systems. Their ability to provide reliable, efficient, and environmentally friendly power makes them an attractive choice for diverse applications, from homes and businesses to remote communities and industrial facilities. With the continued development of fuel flexibility, digital technologies, and integration with renewable energy sources and storage systems, micro turbines will be a cornerstone of the evolving energy landscape, contributing to a more sustainable and resilient global energy future.
Micro turbines
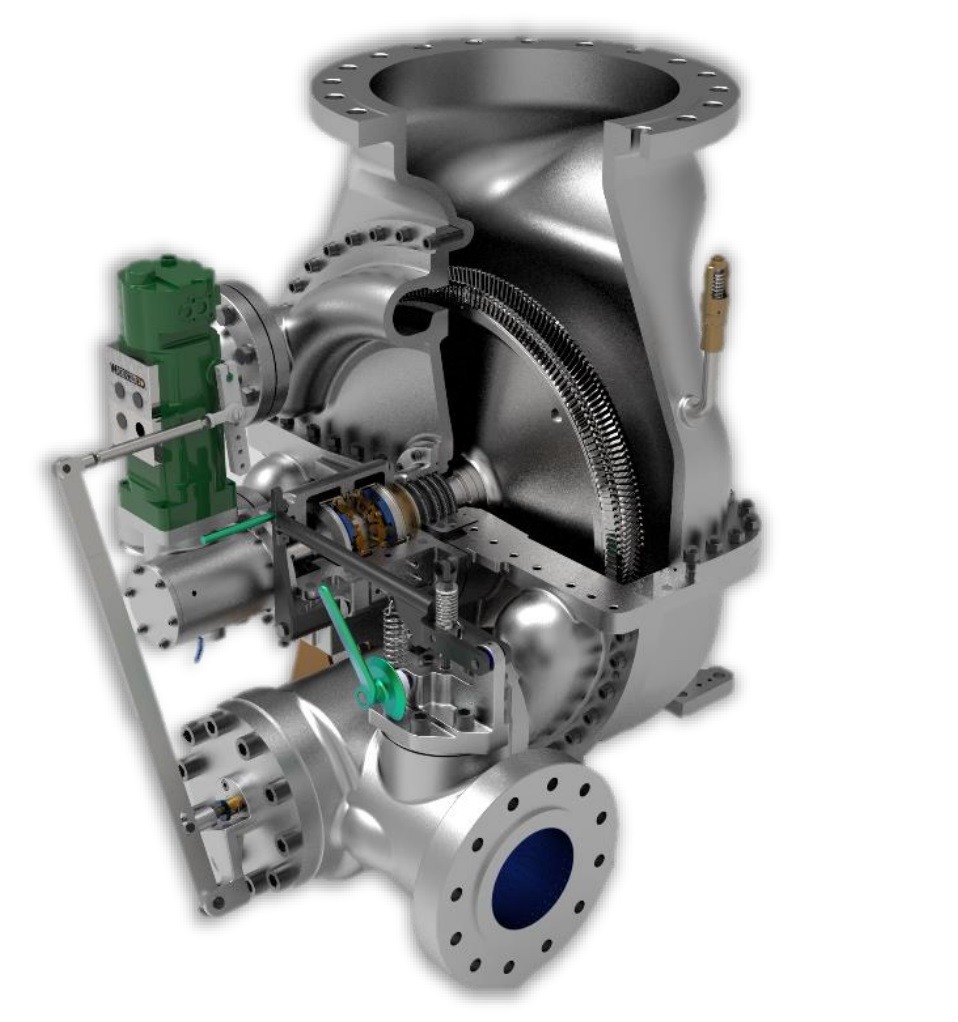
Micro turbines are small, high-efficiency turbines designed for compact and decentralized power generation. They are engineered to provide electricity and, in many cases, both electricity and heat through combined heat and power (CHP) systems. These turbines typically range in power output from a few kilowatts to several hundred kilowatts, making them ideal for small-scale applications, including residential homes, small industrial operations, remote facilities, and off-grid power generation.
One of the primary advantages of micro turbines is their compact size and versatility. Due to their small footprint, they can be easily installed in tight spaces or integrated into existing infrastructure. Micro turbines are used in various settings, from small businesses requiring reliable backup power to remote locations where connecting to the main grid would be cost-prohibitive or impractical. They are often used in conjunction with renewable energy sources such as solar or wind power to create hybrid systems, enhancing overall system efficiency and reliability.
Micro turbines are known for their high thermal efficiency, especially when used in CHP applications. A micro turbine can achieve significant energy savings by producing both electrical power and thermal energy. The thermal energy can be used for heating, hot water production, or industrial processes that require heat, reducing the need for separate heating systems and improving overall system efficiency. In CHP systems, the turbine’s electrical output is complemented by the heat it produces, often making it a cost-effective solution for businesses with continuous energy needs.
One of the major advantages of micro turbines is their ability to operate on a variety of fuels. They can run on natural gas, propane, biogas, or even hydrogen. This fuel flexibility allows them to be used in different geographical locations with varying fuel availability, making them a highly adaptable energy solution. For example, micro turbines running on biogas derived from organic waste offer a renewable and environmentally friendly energy option, further reducing greenhouse gas emissions.
In addition to their fuel flexibility, micro turbines are known for their reliability and ease of maintenance. Unlike traditional generators or combustion engines, micro turbines have fewer moving parts, which reduces the risk of mechanical failure. Their design typically includes advanced control systems that allow them to operate efficiently under a wide range of conditions. Moreover, they generally require less maintenance than other power generation technologies because they have fewer components subject to wear and tear. This reliability makes micro turbines an attractive option for applications where consistent performance is critical, such as in remote or off-grid locations, where access to maintenance services may be limited.
The low environmental impact of micro turbines is another key benefit. Compared to traditional fossil fuel-based generators, micro turbines produce fewer emissions, including lower levels of nitrogen oxides (NOx) and carbon dioxide (CO2). Some micro turbines are designed to run on renewable fuels, further reducing their carbon footprint. The relatively low emissions of micro turbines make them an appealing choice for businesses and organizations looking to meet sustainability goals and reduce their environmental impact.
Although micro turbines can have a higher initial cost compared to conventional generators, their long-term savings in operational costs, efficiency, and reduced maintenance needs can make them a cost-effective solution over time. The operating costs for micro turbines are typically lower due to their high efficiency, long service life, and reduced fuel consumption compared to other power generation technologies. Additionally, in some regions, government incentives or tax credits for clean energy technologies can help offset the initial investment, making micro turbines an even more attractive choice for businesses and homeowners looking to switch to renewable and efficient energy solutions.
Micro turbines also offer significant advantages in off-grid and backup power applications. In regions with unreliable or nonexistent access to the main grid, micro turbines can provide a stable and reliable source of power. These turbines are often used in remote areas where electricity is not readily available, such as rural villages, telecommunications towers, or research stations. Their ability to generate power locally reduces the need for long-distance transmission lines, which can be costly and prone to failure during storms or other disruptions. This decentralized approach to energy generation improves energy security, ensuring a more resilient power supply for critical operations.
The growing interest in micro turbines has spurred further technological advancements, improving their efficiency, performance, and integration with renewable energy systems. For instance, hybrid systems combining micro turbines with solar panels, wind turbines, or energy storage systems are becoming increasingly popular. These hybrid systems can optimize energy production and storage, ensuring that electricity is available when it is needed most. With the use of advanced power electronics and control systems, these systems can manage fluctuations in energy supply and demand, providing a seamless and reliable energy source.
The integration of micro turbines into microgrids is another area of significant growth. A microgrid is a small-scale energy system that can operate independently or in conjunction with the main grid. Micro turbines are well-suited for inclusion in microgrids because of their ability to generate power locally and efficiently. In remote areas or communities that experience frequent power outages, microgrids powered by micro turbines can ensure that critical infrastructure—such as hospitals, schools, and emergency services—remains operational even when the main grid fails. This contributes to overall energy resilience, which is becoming increasingly important in the face of climate change and natural disasters.
Micro turbines are also emerging as part of the broader push for hydrogen-powered energy systems. As the hydrogen economy develops, micro turbines can play a crucial role in utilizing hydrogen as a clean fuel for electricity generation. Hydrogen-powered micro turbines would produce electricity with zero carbon emissions, making them an important tool for decarbonizing various sectors, including transportation, industry, and power generation. As hydrogen production becomes more widespread and cost-effective, the demand for micro turbines that run on hydrogen is expected to grow, opening up new possibilities for clean, distributed energy systems.
In summary, micro turbines represent an increasingly important technology in the transition to cleaner, more efficient, and decentralized energy systems. Their ability to operate on various fuels, produce both electricity and heat, and offer high efficiency and reliability make them an attractive option for a wide range of applications. Whether for residential, commercial, or industrial use, micro turbines provide a flexible and sustainable energy solution. As technological advancements continue and the global demand for clean energy rises, micro turbines will play an essential role in shaping the future of power generation.
As micro turbine technology continues to evolve, further advancements are likely to unlock even more applications and efficiencies, broadening their potential impact across various industries. These advancements could drive additional adoption of micro turbines, especially as energy demand grows globally and environmental concerns become increasingly pressing.
One of the key areas of development for micro turbines is their ability to integrate seamlessly with smart grid technologies. Smart grids, which use advanced communication and monitoring systems to manage electricity distribution, can benefit greatly from the decentralized nature of micro turbines. By enabling micro turbines to communicate with the grid and adjust their output based on demand, they can help stabilize the grid, particularly as more intermittent renewable energy sources like solar and wind are integrated. The flexibility of micro turbines in a smart grid environment allows them to act as both a local power source and a balancing mechanism to ensure that energy is available when and where it is needed.
Furthermore, as the demand for cleaner energy solutions continues to rise, micro turbines will increasingly be seen as essential components in the development of sustainable energy systems. Their low emissions and ability to run on renewable fuels make them an attractive solution for businesses and communities aiming to reduce their carbon footprint. The incorporation of micro turbines into district energy systems is one example of how they can help create more energy-efficient and sustainable cities. In these systems, multiple micro turbines could be used to provide both electricity and heat to buildings in a localized area, reducing overall energy consumption and increasing energy efficiency.
Micro turbines also have potential in the transportation sector, particularly for applications such as hybrid electric vehicles (HEVs) or auxiliary power units (APUs) for trucks, ships, and airplanes. In these applications, micro turbines can serve as a compact and efficient energy source to supplement traditional propulsion systems. For example, in a hybrid vehicle, a micro turbine could generate electricity to charge batteries or power electric motors, extending the range of the vehicle and improving fuel efficiency. Similarly, in aviation or marine applications, micro turbines can provide auxiliary power for non-propulsion systems, reducing the load on primary engines and increasing overall efficiency.
In remote and off-grid areas, micro turbines can offer a critical solution for ensuring energy access. Many remote communities and industrial sites still rely on diesel generators or other polluting sources of energy, which are both costly and environmentally damaging. By switching to micro turbines powered by renewable fuels like biogas or hydrogen, these areas can reduce their dependence on fossil fuels while gaining access to more reliable, locally produced power. Micro turbines are particularly valuable in regions where traditional energy infrastructure is lacking or difficult to install, such as isolated islands or mountainous regions. Their ability to generate power locally can eliminate the need for expensive and vulnerable transmission lines, making them a more cost-effective and resilient solution.
The evolving role of micro turbines in energy storage and hybrid systems is another promising area. With the development of more efficient and affordable energy storage technologies, such as advanced batteries, micro turbines can be paired with these storage systems to optimize energy production and consumption. In these hybrid systems, the micro turbine can operate during periods of low energy demand, generating excess power that is stored for later use. This combination of micro turbines and energy storage ensures that electricity is available during times of peak demand or when renewable energy generation is insufficient, helping to stabilize the energy supply and reduce reliance on the grid.
In addition to their role in microgrids and hybrid systems, micro turbines are poised to contribute to the development of larger-scale distributed energy resources (DERs). Distributed energy refers to small-scale power generation technologies that are located close to the point of use, rather than relying on large, centralized power plants. Micro turbines are a key element of DERs, as they offer a decentralized, efficient, and flexible solution for local power generation. As part of a broader trend toward decentralization in energy production, micro turbines help reduce transmission and distribution losses and increase the overall resilience of energy systems.
The growing adoption of micro turbines will likely be supported by continued research and development. Innovations in materials science, turbine design, and control systems are expected to improve the efficiency, lifespan, and performance of micro turbines, further driving down costs and enhancing their appeal. As micro turbines become more technologically advanced, they will become an increasingly vital component of the clean energy transition, providing localized, low-emission power generation solutions to meet the growing demand for sustainable energy.
Finally, micro turbines’ scalability and modularity will continue to make them a versatile option for a wide range of applications. They can be deployed in small, standalone units for individual residential or commercial use or scaled up to form larger distributed energy networks. This scalability ensures that micro turbines can meet the needs of diverse customer bases, from homeowners and small businesses to large industrial complexes or even entire communities. Their ability to adapt to different power generation capacities and integrate with other technologies makes them a crucial part of the future energy mix.
In conclusion, micro turbines offer a highly efficient, flexible, and sustainable energy solution that is well-positioned to play a key role in the future of decentralized power generation. Their ability to operate on a variety of fuels, provide both electricity and heat, and integrate with renewable energy sources and storage systems makes them an attractive choice for a wide range of applications. With ongoing technological advancements and increased adoption across industries, micro turbines will continue to contribute to a cleaner, more resilient, and more sustainable energy future. Whether used for backup power, off-grid applications, hybrid energy systems, or district energy networks, micro turbines provide a reliable and efficient way to meet the growing global demand for cleaner energy.
As micro turbines continue to evolve, they will also play a critical role in the global push toward net-zero emissions. With governments, corporations, and communities setting ambitious climate targets, the need for clean, reliable, and locally generated power is more pressing than ever. Micro turbines, with their efficiency, low emissions, and fuel flexibility, are uniquely positioned to support these sustainability goals.
One area where micro turbines could have a significant impact is in the decarbonization of industries that are traditionally difficult to electrify, such as manufacturing, mining, and heavy transportation. These industries often rely on fossil fuels for power, and transitioning them to cleaner energy sources has been a major challenge. Micro turbines, especially those that can run on renewable fuels like biogas or hydrogen, offer a viable solution. By using these low-carbon fuels, micro turbines can help reduce emissions from industrial processes, supporting the transition to cleaner production while ensuring the reliability and availability of power.
As the world moves toward more sustainable practices, there is also an increasing focus on circular economy principles, which aim to reduce waste and maximize resource efficiency. Micro turbines can align with these principles in several ways. For instance, micro turbines powered by waste gases, such as flared natural gas or methane from landfills, provide a way to capture and use energy that would otherwise be wasted. This process not only reduces emissions but also contributes to the overall efficiency of the energy system. Additionally, the ability to run on renewable fuels like biogas or hydrogen made from waste materials further reduces the reliance on fossil fuels and minimizes environmental impact.
Micro turbines’ ability to integrate with renewable energy sources will also be crucial as the energy grid becomes more decentralized and diversified. In the future, energy grids will likely consist of a combination of traditional and renewable power generation, with renewable energy sources such as wind, solar, and geothermal playing a larger role. Micro turbines can complement these renewable sources by providing reliable, consistent power when renewable energy generation is intermittent or insufficient. This ability to fill in the gaps ensures that renewable energy can be used more effectively, reducing the reliance on fossil fuels and helping to stabilize the grid.
Moreover, micro turbines are increasingly being recognized for their potential in addressing energy poverty in developing regions. Many parts of the world, particularly in rural and remote areas, still lack reliable access to electricity. Micro turbines provide a cost-effective and sustainable solution for these regions. By utilizing local renewable resources, such as agricultural waste or small-scale biogas production, micro turbines can offer reliable off-grid power without the need for extensive infrastructure. This not only improves the quality of life in underserved communities but also supports economic development by providing reliable energy for businesses, schools, hospitals, and other essential services.
The trend toward greater energy resilience is another factor driving the adoption of micro turbines. As extreme weather events and natural disasters become more frequent due to climate change, the vulnerability of traditional power grids is becoming more evident. Power outages caused by storms, wildfires, or earthquakes can have devastating consequences for communities and businesses. Micro turbines, particularly when used in microgrids, offer a solution by providing localized and reliable power that can operate independently of the main grid. This ability to “island” during grid failures is a valuable feature, ensuring that critical services remain operational even when the broader electricity infrastructure is compromised.
The long-term cost-effectiveness of micro turbines will also continue to drive their adoption. While the initial investment for a micro turbine system may be higher than that for conventional backup generators, the operational savings over time can make them a more economical option. Micro turbines are typically more fuel-efficient and require less maintenance than traditional generators, leading to lower long-term operating costs. Additionally, their ability to run on a variety of fuels, including renewables and waste products, offers greater flexibility and cost control, particularly in areas where fuel prices may fluctuate.
A growing focus on decentralized energy generation also opens up opportunities for community-scale micro turbine projects. In some regions, communities are taking control of their energy production by investing in small-scale, locally managed microgrids powered by micro turbines. These community-based systems allow residents to benefit from cleaner, more affordable energy, while also providing the flexibility to prioritize energy sources that align with local needs and resources. By harnessing the power of micro turbines, these communities can reduce their reliance on centralized power grids, lower energy costs, and increase energy independence.
Moreover, the integration of micro turbines into electric vehicle (EV) charging infrastructure could help address some of the challenges associated with the growing demand for EVs. As the number of electric vehicles on the road increases, so too will the need for charging stations. Micro turbines could be deployed at these stations, providing clean and reliable power for charging while reducing the strain on the grid. In locations where grid access is limited or unreliable, micro turbines could enable off-grid charging, further supporting the adoption of electric vehicles and contributing to the decarbonization of the transportation sector.
Another emerging application for micro turbines is in data centers and critical infrastructure facilities. These facilities, which require a constant supply of power to operate their servers and equipment, are increasingly turning to micro turbines to provide backup power and ensure uninterrupted service. Micro turbines offer a reliable, high-efficiency solution for maintaining operations during grid failures, helping to prevent costly downtime and ensuring data security.
As the world continues to embrace renewable energy and move toward cleaner, more resilient energy systems, micro turbines will play a key role in this transition. With their ability to generate reliable power from a variety of fuels, including renewable and waste-derived sources, micro turbines will be integral to creating a more sustainable energy future. By providing a flexible, scalable, and efficient solution for decentralized power generation, micro turbines will support the transition to cleaner, more resilient energy systems, benefiting individuals, businesses, and communities around the world.
Distributed energy resources
Distributed energy resources (DERs) refer to small-scale power generation or storage systems that are located close to where the energy is used, rather than at a central plant. These resources can generate, store, or manage energy locally and are becoming increasingly important as the world moves toward cleaner, more resilient, and decentralized energy systems. DERs can include renewable energy sources, such as solar panels and wind turbines, as well as other technologies like micro turbines, batteries, and combined heat and power (CHP) systems. They are designed to provide power independently or in conjunction with the larger energy grid, allowing for greater flexibility, efficiency, and reliability in energy supply.
The primary advantage of DERs is their ability to decentralize power generation. Instead of relying on large, centralized power plants, DERs allow for localized generation, reducing the need for long-distance transmission lines, which can be expensive and prone to loss. By generating electricity closer to where it is needed, DERs can reduce transmission losses, improve grid stability, and reduce the environmental impact of long-distance energy transport. This is particularly important in areas with aging or unreliable infrastructure, where DERs can provide a more resilient and cost-effective alternative to traditional energy systems.
In addition to reducing transmission losses, DERs can contribute to greater energy efficiency. Technologies such as combined heat and power (CHP) systems and microgrids can simultaneously generate both electricity and useful heat, providing a higher overall efficiency compared to traditional energy systems that produce only electricity. For example, a CHP system can generate power and use the waste heat for space heating, hot water production, or industrial processes, improving overall system efficiency and reducing the need for additional energy resources. In regions with high heating demands, this can be a particularly effective way to optimize energy use.
One of the most significant benefits of DERs is their ability to integrate with renewable energy sources, such as solar, wind, or biomass. As the demand for clean energy increases, renewable energy technologies are being deployed at greater scales, and DERs can support this transition by allowing for localized generation of renewable power. Solar panels, wind turbines, and small-scale hydropower systems are all examples of renewable DERs that can provide clean, low-emission power to homes, businesses, and communities. By incorporating these renewable resources into the grid or using them in standalone systems, DERs can contribute to reducing the reliance on fossil fuels and lowering greenhouse gas emissions.
DERs also provide greater flexibility in terms of energy storage and load management. Batteries and other energy storage systems allow for the storing of excess energy generated by renewable sources, such as solar and wind, for use during times when generation is low or demand is high. This ability to store energy for later use helps to balance supply and demand, making renewable energy sources more reliable and ensuring a stable energy supply. Storage technologies can also help to reduce peak demand on the grid, lowering the need for expensive, carbon-intensive peaking power plants.
Microgrids, which are small, localized energy systems that can operate independently or in connection with the main grid, are another important aspect of distributed energy resources. Microgrids can include a variety of DERs, such as solar panels, wind turbines, batteries, and micro turbines, and can be used to power a specific area or community. They are particularly valuable in remote or off-grid locations where access to the main grid is limited or unreliable. Microgrids can also increase energy security by allowing critical infrastructure, such as hospitals or emergency services, to continue operating even during power outages or grid failures.
The rise of DERs is also helping to create more resilient and flexible energy systems. As extreme weather events and natural disasters become more frequent, the vulnerability of centralized energy infrastructure is becoming more apparent. Power outages caused by storms, wildfires, or other disruptions can have widespread consequences, especially for critical services like healthcare, water treatment, and telecommunications. By decentralizing power generation, DERs provide a way to ensure that power is available when it is needed most. In areas where power outages are common, businesses and homes can use DERs to maintain a reliable power supply during emergencies.
The adoption of DERs also aligns with the growing trend of energy independence. With the ability to generate and store energy locally, individuals, businesses, and communities can reduce their dependence on the larger energy grid and mitigate the impact of rising energy costs. In some cases, DERs can even allow for “energy independence,” where a home or business can generate enough power to meet its own needs without relying on external sources. This level of energy autonomy is becoming increasingly attractive to consumers who are seeking greater control over their energy usage and expenses.
As DERs become more widespread, they are being integrated into the larger energy grid through advanced grid technologies. Smart grids, which use digital communication and automation to manage the flow of electricity, are designed to accommodate a wide range of energy sources, including distributed resources like solar panels and microgrids. Through smart grid systems, DERs can communicate with the grid to adjust their output based on demand, providing a more dynamic and responsive energy system. This ability to integrate distributed resources into the grid helps to improve grid stability and ensure that electricity is available when and where it is needed.
The regulatory environment surrounding DERs is also evolving. In many countries, governments are implementing policies and incentives to encourage the adoption of distributed energy technologies. These policies can include subsidies for renewable energy installations, tax credits for energy storage systems, and financial support for microgrid projects. In some regions, utilities are beginning to embrace DERs as part of their long-term energy strategy, offering incentives for customers to install solar panels, batteries, or other distributed resources. The expansion of these policies is helping to drive further growth in the DER sector.
However, the widespread adoption of DERs also presents challenges. One of the key obstacles is the integration of distributed resources into existing energy infrastructure. While DERs can provide significant benefits in terms of efficiency, flexibility, and sustainability, they also require sophisticated management systems to ensure that they can work together seamlessly with the central grid. The increasing complexity of managing a grid with a large number of decentralized resources presents technical and regulatory challenges that will need to be addressed as DER adoption grows.
Another challenge is ensuring that DERs are accessible and affordable to a broad range of consumers. While the cost of renewable energy technologies, such as solar panels and batteries, has decreased significantly in recent years, initial installation costs can still be a barrier for some households and businesses. Innovative financing models, such as power purchase agreements (PPAs) or leasing options, are helping to make DERs more accessible, but further efforts will be needed to ensure that the benefits of distributed energy are available to all consumers.
Despite these challenges, the future of distributed energy resources looks promising. As technological advancements continue to improve the efficiency and cost-effectiveness of DERs, and as policy frameworks evolve to support their adoption, DERs will become an increasingly integral part of the global energy landscape. Whether in the form of rooftop solar panels, community-based microgrids, or advanced energy storage systems, distributed energy resources offer a flexible, sustainable, and resilient solution to the world’s growing energy needs. They are helping to transform the way we produce, consume, and manage energy, and they will play a critical role in the transition to a cleaner, more decentralized energy future.
As the adoption of distributed energy resources (DERs) grows, their potential to transform energy systems will expand significantly. The increasing focus on sustainability, resilience, and energy efficiency is driving innovation in DER technologies. Advances in energy storage, automation, and grid management will allow DERs to function more seamlessly within broader energy systems, enhancing their ability to provide reliable power in both urban and rural settings.
One of the key trends in the future development of DERs is the continued evolution of energy storage systems. As renewable energy sources such as wind and solar are intermittent, efficient storage solutions are critical for balancing supply and demand. New storage technologies, including advanced lithium-ion batteries, solid-state batteries, and flow batteries, are emerging to enhance the efficiency, capacity, and lifespan of energy storage. These innovations will allow DERs to store excess energy generated during periods of low demand or high renewable generation and discharge it when it is needed most, such as during peak hours or times when renewable generation is insufficient. Energy storage will also help to mitigate the intermittency of renewable energy, making it a more reliable and predictable power source.
In addition to improving energy storage, digital technologies will play a pivotal role in the future of DERs. The integration of smart meters, sensors, and advanced communication systems into the grid will enable real-time monitoring, optimization, and management of distributed resources. With the help of artificial intelligence (AI) and machine learning, the grid can predict energy demand, optimize the use of local energy resources, and efficiently distribute energy based on real-time data. Smart home technologies will also allow consumers to monitor and control their energy usage, creating opportunities for load shifting and demand response programs. This integration of digital technologies into DER systems will further enhance their efficiency, reliability, and integration with the central grid.
The increasing prevalence of virtual power plants (VPPs) is another trend that will accelerate the deployment of DERs. A VPP is a network of distributed energy resources, such as solar panels, batteries, and microgrids, that are aggregated and managed as a single entity. By pooling the resources of individual DERs, a VPP can operate like a traditional power plant, providing reliable and flexible electricity to the grid. VPPs can optimize the output of distributed resources and offer services such as frequency regulation, voltage control, and grid balancing. As more DERs are deployed, the development of VPPs will provide a way to harness the full potential of decentralized energy systems while maintaining grid stability.
The increasing demand for electric vehicles (EVs) is also driving the need for advanced DER solutions. As the number of EVs on the road grows, the demand for charging infrastructure will surge. Microgrids and distributed energy systems can play a key role in supporting this transition by providing decentralized, clean energy for EV charging stations. Microgrids powered by solar energy and storage can offer off-grid charging solutions, allowing EV owners to charge their vehicles in remote or underserved areas without relying on the central grid. Additionally, vehicle-to-grid (V2G) technologies could enable EVs to serve as mobile energy storage units, allowing electric vehicles to discharge energy back into the grid during periods of high demand, further enhancing grid flexibility and resilience.
Another critical area of development for DERs is the expansion of community-based energy systems. In both rural and urban settings, communities are coming together to invest in local energy solutions that reduce their reliance on the grid, lower energy costs, and support the transition to clean energy. Community solar projects, for example, allow multiple households or businesses to collectively invest in solar installations and share the benefits of renewable energy generation. Similarly, community-based microgrids can provide localized, resilient power to entire neighborhoods or towns, reducing the impact of power outages and providing an affordable and sustainable energy solution. By fostering greater energy autonomy, these community-driven initiatives can improve energy security and enhance social equity by making clean energy more accessible to low-income households.
The regulatory landscape for DERs will continue to evolve as governments around the world recognize the need to support decentralized energy systems. Policies and incentives that encourage the installation of solar panels, energy storage systems, and other DER technologies are expected to expand, helping to drive down installation costs and encourage the widespread adoption of clean energy solutions. Many governments are already offering tax credits, rebates, and other financial incentives for residential and commercial installations of solar panels and batteries, and these policies are likely to become more robust as the need for sustainable energy solutions grows. Additionally, regulatory frameworks that allow for greater flexibility in the integration of DERs with the grid will be essential for ensuring that these technologies can function effectively in a distributed energy landscape.
Despite the many benefits, there are still challenges to the widespread adoption of DERs. One major obstacle is the need for modernized grid infrastructure that can accommodate a large number of distributed energy resources. Traditional grids were designed to handle centralized power generation and one-way electricity flow from power plants to consumers. As more DERs are integrated into the grid, the infrastructure must evolve to support two-way power flows, manage distributed energy generation, and ensure grid stability. Utilities and grid operators will need to invest in smart grid technologies, advanced metering systems, and grid automation to ensure that DERs can operate in harmony with the larger grid.
Another challenge is the complexity of managing and coordinating a large number of small-scale energy resources. While the integration of DERs into the grid can offer many benefits, it also requires sophisticated coordination and management. This includes addressing issues such as balancing supply and demand, optimizing energy storage, and ensuring that distributed resources can respond to grid signals in real-time. Advanced grid management tools, AI, and machine learning algorithms will be essential for addressing these challenges and ensuring that DERs can operate effectively.
The cost of DER technologies is also a significant consideration for widespread adoption. While prices for renewable energy systems like solar panels and batteries have decreased significantly in recent years, initial installation costs can still be prohibitive for some consumers. Innovative financing models, such as leasing options or power purchase agreements (PPAs), are helping to make DERs more affordable, but more efforts will be needed to ensure that DER technologies are accessible to all income levels.
Despite these challenges, the future of distributed energy resources is promising. As technology advances, costs decrease, and policy frameworks become more supportive, DERs will become a central component of the global energy transition. Their ability to provide clean, reliable, and flexible power generation, coupled with their potential to enhance grid resilience and reduce energy costs, positions them as a key solution for the evolving energy landscape. With continued innovation and collaboration among stakeholders, DERs will play an essential role in creating a more sustainable, decentralized, and resilient energy future.
As we look to the future, the integration of distributed energy resources (DERs) into mainstream energy systems will be pivotal in addressing the challenges of climate change, energy security, and the ongoing transition to renewable energy. With the rapid advancements in technology, the increasing affordability of renewable energy systems, and the growing importance of energy independence, DERs will become more common in both residential and commercial settings.
The rise of electric vehicles (EVs) and their interaction with DERs is a significant trend that will continue to evolve. As EV adoption grows, so too does the potential for DERs to play a key role in providing charging infrastructure that is decentralized, renewable, and more resilient to grid disruptions. One exciting possibility is the role of vehicle-to-grid (V2G) technology, where EVs not only draw power from the grid but can also return electricity to the grid when demand is high, helping to stabilize the grid during peak times. This bi-directional flow of electricity creates an opportunity for EVs to serve as mobile energy storage devices, adding an additional layer of flexibility and efficiency to the grid. In this scenario, EVs can act as dynamic contributors to the power grid, enhancing the integration of intermittent renewable resources like solar and wind power.
Microgrids are another exciting application of DERs that will continue to grow in importance. Microgrids are small-scale, localized energy systems that can operate independently or in conjunction with the larger grid. These systems allow communities, businesses, and institutions to generate, store, and manage their own electricity. When coupled with renewable energy resources, such as solar panels or wind turbines, and storage solutions like batteries, microgrids provide a resilient and sustainable energy solution. In the event of a grid failure or natural disaster, microgrids can “island” and continue providing power, ensuring that critical infrastructure such as hospitals, schools, and emergency services remain operational. This ability to maintain an independent power supply during grid disruptions increases the resilience of communities and helps mitigate the impacts of extreme weather events, which are becoming more frequent due to climate change.
One of the advantages of microgrids and other DER systems is the potential for energy sharing. In some communities or regions, DERs are being deployed in such a way that they allow for peer-to-peer energy exchange. Through platforms that enable the buying and selling of excess energy, consumers can trade power with their neighbors or other members of the community. This decentralization of energy production and consumption can lower costs, increase energy access, and improve the overall efficiency of energy systems. For instance, a homeowner with excess solar power can sell their surplus electricity to neighbors or businesses that need it, contributing to a more decentralized and equitable energy economy.
The proliferation of DERs also encourages innovation in energy management software. As the number of small-scale energy systems increases, so too does the need for sophisticated digital tools that can monitor, manage, and optimize energy usage. These tools enable consumers, businesses, and grid operators to track energy production, consumption, and storage in real-time, helping to ensure the efficient operation of DERs. Advanced algorithms, powered by artificial intelligence (AI) and machine learning, will play an increasingly important role in this process, allowing for more precise load forecasting, demand response, and real-time grid balancing. Through this increased automation and digitalization, DERs will be better integrated into the broader grid system and can respond dynamically to changes in supply and demand.
Furthermore, as the world increasingly moves toward decentralized energy systems, the role of local energy governance will become more important. Communities, local governments, and cooperatives are increasingly taking control of their energy production and consumption. By creating and managing local energy markets, these entities can reduce their reliance on centralized power sources, lower energy costs, and support local economies. In some cases, these local energy markets are supported by legislation that enables the creation of energy cooperatives, where consumers come together to invest in and share the benefits of renewable energy projects.
A crucial aspect of the future of DERs is their contribution to energy equity and social inclusion. In many parts of the world, access to reliable and affordable electricity remains a significant challenge. DERs have the potential to bridge the energy gap in underserved communities, particularly in rural or remote areas that are not connected to the central grid. Off-grid DER systems, powered by renewable resources such as solar or wind, can provide a cost-effective and sustainable energy solution. In addition, as the cost of renewable energy technologies continues to decrease, DERs will become more accessible to low-income households, improving their quality of life and offering opportunities for economic development.
The growing importance of sustainability and the need for decarbonization will also drive the adoption of DERs. Governments, businesses, and individuals are increasingly aware of the need to reduce greenhouse gas emissions and transition to clean energy sources. DERs, particularly those powered by renewable energy, contribute to these goals by reducing the reliance on fossil fuels. Furthermore, as industries move toward net-zero emissions, DERs will be part of the broader strategy to decarbonize sectors such as manufacturing, transportation, and agriculture. The ability to use locally generated renewable power instead of relying on traditional grid electricity can help businesses reduce their carbon footprint and meet their sustainability targets.
However, despite their many advantages, widespread adoption of DERs still faces challenges. One of the main obstacles is the need for regulatory frameworks that can support the integration of distributed resources into existing energy systems. In many cases, traditional regulations and utility business models are not well-suited to accommodate decentralized energy generation, which can create barriers to the adoption of DERs. Policymakers will need to update regulations and incentive structures to facilitate the integration of DERs into the grid and ensure that the benefits of these technologies are accessible to all.
Another challenge is the need for significant investment in infrastructure. In order to support the widespread deployment of DERs, grids must be modernized to accommodate two-way power flows and the integration of a wide variety of energy sources. Smart grid technologies, advanced metering systems, and digital communication networks will be necessary to ensure that DERs can operate seamlessly within the broader energy system. Investments in energy storage solutions will also be crucial for ensuring that excess energy generated by renewable sources can be stored and used when needed.
Despite these challenges, the future of DERs remains bright. As technological innovations continue to reduce costs and improve the efficiency of energy storage, renewable generation, and energy management systems, DERs will become a central component of global energy infrastructure. The ability to decentralize energy generation, increase energy efficiency, reduce costs, and enhance resilience will make DERs an essential tool in addressing the challenges of climate change, energy security, and sustainability. The adoption of DERs will contribute to a cleaner, more flexible, and more resilient energy future, one that is powered by local, renewable energy and designed to meet the needs of communities, businesses, and individuals in a rapidly changing world.
Combined heat and power (CHP)
Combined Heat and Power (CHP), also known as cogeneration, is an energy-efficient technology that simultaneously produces electricity and useful heat from a single fuel source. It represents a highly efficient use of energy because it captures and utilizes heat that would otherwise be wasted in conventional power generation processes, where heat is typically discarded into the environment. By recovering this waste heat and converting it into usable thermal energy, CHP systems offer a way to achieve substantial improvements in energy efficiency, reduce greenhouse gas emissions, and lower operational costs.
The core principle behind CHP is the simultaneous generation of two forms of energy—electricity and heat—from one energy source, typically natural gas, biomass, coal, or even waste materials. The system is designed to operate in a way that makes use of the heat generated during the electricity production process, rather than letting it escape into the atmosphere. In a conventional power plant, the steam or hot gases used to generate electricity are often released into the environment without being utilized further. However, in a CHP system, this heat is captured and repurposed, which makes the system significantly more efficient.
CHP systems can vary greatly in size and scale, ranging from small-scale systems that serve individual buildings, to larger, district-level systems that can provide both heat and power to entire communities or industrial plants. The technology is applicable to a wide range of sectors, including residential, commercial, industrial, and institutional settings. CHP systems are particularly effective in locations where there is a high demand for both electricity and thermal energy, such as in hospitals, universities, industrial manufacturing plants, and large office buildings.
One of the key benefits of CHP is its ability to achieve a high level of efficiency compared to traditional, separate heat and power generation methods. In conventional systems, electricity is generated in a power plant, and heat is produced in separate boilers or furnaces. Each of these processes is typically less efficient individually, and significant energy losses occur during transmission and distribution. In contrast, CHP systems integrate both functions, maximizing the use of energy and minimizing waste. Depending on the design and operating conditions, CHP systems can achieve efficiencies of up to 80-90%, compared to the typical 30-40% efficiency of separate heat and power generation systems.
In terms of energy savings, CHP systems are particularly advantageous in environments where a consistent and reliable supply of both electricity and thermal energy is required. In industrial settings, for example, where steam and hot water are essential for various manufacturing processes, a CHP system can produce electricity for the plant while simultaneously providing heat for processes such as heating, drying, or chemical reactions. This integrated approach leads to significant cost savings, as the facility can meet its energy needs with a single, efficient system rather than relying on multiple energy sources.
For residential and commercial buildings, CHP systems can be used to supply both electricity and heating or cooling needs. In colder climates, where heating demands are high, a CHP system can be an especially efficient solution, as it provides heat directly to the building without needing to rely on separate heating systems. By generating power on-site and utilizing waste heat for space heating or water heating, building owners can reduce their reliance on the grid and lower energy bills. In addition to space heating, CHP systems can also support district heating networks, where heat is distributed to multiple buildings through an underground network of pipes, creating a highly efficient energy system at the neighborhood or city level.
Biomass is another fuel source that can be used in CHP systems, and its utilization further enhances the sustainability and environmental benefits of the technology. Biomass-fired CHP systems use organic materials such as wood chips, agricultural residues, or other plant-based materials as fuel to generate both heat and power. Biomass is considered a renewable energy source, as it can be replenished through sustainable agricultural practices, and it is also carbon-neutral when managed properly. The use of biomass in CHP systems can be an important step in reducing carbon emissions, particularly in industrial applications or communities that rely on fossil fuels for heat and power generation.
In addition to natural gas and biomass, CHP systems can also operate on waste fuels, including landfill gas, sewage gas, and waste oils. The use of waste fuels in CHP systems helps to address environmental challenges by diverting waste from landfills or incineration and repurposing it to produce useful energy. This form of waste-to-energy technology not only improves efficiency but also helps to mitigate the environmental impact of waste disposal.
Environmental benefits of CHP systems are particularly significant when considering their potential to reduce greenhouse gas emissions and reliance on fossil fuels. By improving energy efficiency and reducing the need for separate heat and power generation, CHP systems reduce the overall consumption of fuel and lower emissions of carbon dioxide (CO2), nitrogen oxides (NOx), and other pollutants. In regions where carbon pricing mechanisms are in place, CHP systems may offer additional financial incentives by helping to reduce a facility’s carbon footprint. Furthermore, by integrating renewable fuels such as biomass or waste into the system, CHP systems can further contribute to the decarbonization of energy production.
In addition to efficiency and environmental advantages, CHP systems offer increased energy reliability and resilience. Because CHP systems generate power locally, they can provide a reliable source of energy during grid outages or periods of peak demand. This is particularly important for critical facilities such as hospitals, data centers, and manufacturing plants, where uninterrupted energy supply is essential. CHP systems can also help to reduce the stress on the central grid by providing power at times when the grid is under strain, improving overall grid stability.
From a financial perspective, CHP systems offer significant savings in the long run. The initial capital investment for a CHP system can be substantial, depending on the size and complexity of the installation, but the operational savings achieved through increased efficiency and reduced energy consumption often result in a short payback period. In addition, many governments and utilities offer incentives, tax credits, or subsidies to encourage the adoption of CHP systems, which can help to offset the initial costs. These financial incentives, combined with the long-term savings in energy costs, make CHP systems an attractive investment for businesses and organizations looking to reduce their energy expenditures.
However, despite the many advantages of CHP systems, their adoption can be limited by certain factors. One of the main challenges is the high upfront capital cost associated with installing a CHP system. While the long-term operational savings can offset this investment, the initial cost may be prohibitive for some organizations, particularly small businesses or residential consumers. Financial incentives and grants can help mitigate this barrier, but the availability of such programs can vary by region. Additionally, CHP systems require specialized maintenance and expertise, which may pose challenges for facilities without access to the necessary technical support.
The installation of a CHP system also requires a consistent and reliable supply of fuel. In some regions, the availability of appropriate fuels such as natural gas or biomass may be limited, which can affect the feasibility of implementing a CHP system. Moreover, the ongoing operation of the system depends on fuel price stability, which can be volatile, especially in the case of natural gas.
Another challenge for the widespread adoption of CHP systems is the regulatory landscape. In some regions, existing energy policies and regulations may not be conducive to the widespread deployment of CHP technology. For example, utility grid access and interconnection standards may need to be updated to accommodate distributed energy systems like CHP. Furthermore, policymakers must create a regulatory environment that supports the financial incentives for CHP adoption and ensures that systems are operated safely and efficiently.
Despite these challenges, the future of CHP looks promising. As governments, industries, and communities increasingly prioritize energy efficiency, sustainability, and resilience, CHP technology will continue to play a key role in achieving these goals. The advancement of CHP systems, including the integration of renewable energy sources and waste fuels, will help reduce energy consumption, lower emissions, and create more reliable and cost-effective energy systems. With continued technological innovations, favorable regulatory frameworks, and financial incentives, CHP systems will remain a critical tool in the global transition toward cleaner and more efficient energy production.
As the demand for more sustainable and efficient energy solutions grows, Combined Heat and Power (CHP) systems will likely see increased deployment across various sectors. This growth will be driven by a combination of technological advances, economic pressures, and government policies aimed at reducing carbon emissions and improving energy efficiency. The integration of CHP systems into the energy landscape offers a flexible, reliable, and environmentally friendly option for power generation, particularly in settings where both heat and electricity are required.
The continued innovation in CHP technology will improve the economic and environmental performance of these systems. For instance, the integration of digital technologies and advanced control systems into CHP operations can further enhance efficiency by optimizing energy generation, improving maintenance schedules, and minimizing downtime. Digital solutions, including predictive analytics and real-time monitoring, allow operators to adjust settings and optimize performance to reduce energy waste, improve system longevity, and minimize operational costs. The ability to forecast energy demand and adjust CHP output accordingly will be crucial in maximizing the system’s efficiency.
Additionally, improvements in fuel flexibility are likely to play an important role in the future of CHP systems. Current systems are typically designed to run on specific fuels, such as natural gas or biomass. However, with the growing interest in renewable energy and sustainable fuel sources, CHP technology is evolving to utilize a broader range of feedstocks. For instance, biogas derived from organic waste, such as agricultural residues or wastewater, can be used to fuel CHP systems, offering a renewable alternative to fossil fuels. Similarly, hydrogen, which is emerging as a promising clean fuel, could be integrated into CHP systems to further reduce carbon emissions. These innovations will allow CHP systems to be more adaptable to various fuel sources, contributing to the transition toward a cleaner and more sustainable energy system.
Furthermore, CHP systems will continue to contribute to the development of decentralized energy networks, also known as distributed generation. As power grids become more complex and distributed, local energy production through CHP will be crucial in reducing the reliance on centralized power plants and minimizing transmission and distribution losses. With the increasing prevalence of microgrids, CHP systems can serve as the cornerstone of these local energy solutions, providing both power and heat while increasing energy resilience. Microgrids, often powered by renewable energy sources such as solar or wind, can integrate CHP as a backup power solution, allowing communities or businesses to remain self-sufficient even during grid outages or periods of high demand.
In industries such as manufacturing, where energy demand is high and the need for process heat is constant, CHP systems offer the potential for significant cost savings and energy security. Industries like paper and pulp, chemicals, food processing, and steel production, which require large amounts of heat and power for their operations, can benefit immensely from implementing CHP systems. These industries often operate in energy-intensive processes that generate substantial amounts of waste heat, which can be captured and reused by CHP units, reducing their overall fuel consumption. As industrial sectors become more focused on energy efficiency and sustainability, CHP systems will increasingly be viewed as an essential tool for achieving operational goals while minimizing environmental impact.
Additionally, the role of CHP systems in enhancing energy security cannot be overstated. For regions or nations that rely on imported fuels, such as natural gas, for electricity and heating, CHP offers a more energy-independent alternative. By producing both heat and power on-site, businesses and municipalities can reduce their dependence on external fuel sources, ensuring that they are less vulnerable to price volatility and supply disruptions. In areas prone to extreme weather events or natural disasters, the distributed nature of CHP systems offers a greater degree of resilience compared to centralized power generation. In these cases, CHP systems can operate independently or in isolation, providing continuous energy to critical infrastructure such as hospitals, emergency services, and data centers when the central grid goes down.
The combination of these advantages—improved energy efficiency, reduced environmental impact, enhanced resilience, and greater fuel flexibility—positions CHP as a key player in the global energy transition. However, to fully realize the potential of CHP systems, there must be a concerted effort from governments, utilities, and industry stakeholders to address the remaining barriers to widespread adoption. Key to this process is the creation of a favorable policy and regulatory framework that incentivizes investment in CHP technology and supports its integration into the energy market.
Governments can play a crucial role by offering financial incentives such as grants, tax credits, or subsidies to lower the initial capital cost of CHP installations. Many countries already have such incentives in place, but expanding these programs and offering long-term support would make CHP more accessible to businesses and communities that could benefit from it. Moreover, policymakers must consider the implementation of policies that encourage the use of renewable fuels in CHP systems, providing additional benefits for the environment and helping to meet renewable energy targets.
Another important consideration for the future of CHP is its integration with emerging technologies such as smart grids, energy storage systems, and demand-side management solutions. Smart grids, with their advanced communication and control systems, can optimize the operation of distributed energy resources like CHP, ensuring that energy is produced and consumed efficiently. CHP systems integrated with energy storage, such as batteries, could also help to smooth out fluctuations in power demand and supply, providing a reliable source of energy even when renewable generation is low. Demand-side management tools, which allow for better coordination between energy suppliers and consumers, could further enhance the value of CHP by helping to balance supply and demand across the grid.
The development of new business models and financing mechanisms will also be essential in driving the adoption of CHP systems, particularly for smaller-scale applications. As the technology becomes more accessible and cost-competitive, new financial models such as power purchase agreements (PPAs) or shared ownership schemes could help businesses and consumers who may not have the capital to invest in a full CHP system upfront. Under these models, third-party developers could install and maintain the CHP system, with the customer purchasing the energy produced at a reduced rate over time. This would allow more organizations, especially small and medium-sized enterprises, to take advantage of the cost savings and efficiency benefits offered by CHP.
In conclusion, the future of Combined Heat and Power (CHP) systems looks bright, with increasing opportunities for both energy savings and environmental benefits. By utilizing both heat and electricity from a single source, CHP systems are among the most efficient energy solutions available. As technological advances continue to improve the performance, affordability, and flexibility of CHP systems, they will become an even more important component of the energy landscape. From enhancing industrial efficiency to supporting resilient energy systems, CHP technology has the potential to contribute significantly to a sustainable, low-carbon energy future. However, to fully realize the benefits of CHP, concerted efforts are required to overcome barriers such as high upfront costs, regulatory challenges, and the need for appropriate infrastructure. With the right policies, investments, and innovation, CHP can be a powerful tool in achieving the global goals of energy efficiency, sustainability, and carbon reduction.
The ongoing evolution of Combined Heat and Power (CHP) systems will continue to be shaped by advancements in technology, energy policy, and market trends. As global attention increasingly turns toward sustainable energy solutions, CHP stands at the intersection of economic efficiency and environmental responsibility. Its capacity to simultaneously generate electricity and useful heat positions it as a key contributor to meeting global energy demands while reducing carbon emissions.
One significant aspect of the future growth of CHP systems is the growing emphasis on decarbonization. As countries set more ambitious targets for reducing greenhouse gas emissions, CHP systems can play a vital role in the transition to a low-carbon energy future. By efficiently using energy and minimizing waste, CHP helps to decrease the overall amount of fuel required for both electricity and heating. When paired with renewable fuels such as biomass, biogas, or hydrogen, CHP systems can contribute to achieving carbon-neutral energy generation. Additionally, CHP’s ability to integrate with renewable energy sources enhances the overall decarbonization efforts, providing a way to bridge the gap between intermittent renewable generation (such as wind and solar) and the consistent energy needs of industries and communities.
The widespread adoption of renewable energy technologies, such as wind, solar, and geothermal, has added a new layer of complexity to the energy grid. CHP systems can complement these renewable energy sources by providing consistent, baseload power when renewable generation is low. For instance, during periods of low sunlight or wind, CHP systems can generate electricity and heat from biomass or natural gas, helping to stabilize the grid and ensuring that energy demand is met. By acting as a flexible backup source, CHP helps to integrate variable renewable energy sources into the grid, making them more reliable and efficient.
In addition to renewables, the rise of green hydrogen is also poised to revolutionize the energy sector, and CHP systems can play a role in this transformation. Green hydrogen, produced using renewable electricity to split water molecules through electrolysis, can be used as a clean fuel in CHP systems. When used in a CHP unit, green hydrogen can generate both heat and power with virtually zero carbon emissions, providing a scalable and sustainable solution for industries, buildings, and communities looking to decarbonize their energy supply. The combination of CHP and green hydrogen holds the potential to decarbonize high-emission sectors such as heavy industry, transportation, and even residential heating, contributing to the global push toward net-zero emissions.
At the same time, CHP systems will need to continue evolving in terms of their technical design and operational efficiency. New materials and advanced manufacturing techniques are likely to improve the efficiency, lifespan, and environmental performance of CHP systems. For instance, the use of advanced heat exchangers, high-efficiency turbines, and more durable materials can enhance the performance of CHP units, allowing them to operate at higher temperatures and pressures, which results in greater thermal efficiency. Additionally, the integration of cutting-edge monitoring and control technologies, including artificial intelligence (AI) and machine learning algorithms, will enable more precise control of CHP systems, ensuring optimal operation and reducing energy losses.
As the market for CHP systems continues to expand, there will be increased collaboration between technology developers, utilities, and policy makers to create a supportive ecosystem for CHP adoption. Governments will continue to play a crucial role in promoting CHP through subsidies, tax incentives, and favorable regulations. In many cases, CHP will be included in broader energy efficiency and decarbonization programs aimed at reducing the carbon intensity of industrial operations and buildings. By incentivizing the deployment of CHP technology, policymakers can help industries meet their sustainability targets while also fostering innovation in the energy sector.
At the consumer level, the increased availability of small-scale, modular CHP units will make the technology more accessible to a wider range of customers, including small businesses and households. These smaller systems can be integrated with renewable energy technologies such as solar panels and wind turbines to create highly efficient, self-sufficient energy solutions. In some regions, particularly in off-grid or remote areas, small-scale CHP systems can provide a reliable and cost-effective way to meet both electricity and heating needs, reducing dependence on centralized energy infrastructure.
Furthermore, the rise of digitalization and the internet of things (IoT) will enable CHP systems to become even more intelligent and adaptable. Through IoT-connected sensors and real-time data analytics, operators will be able to track the performance of their CHP systems more accurately, identifying opportunities for improvement and proactively addressing maintenance needs. Advanced data analytics will also help optimize the interaction between CHP systems and the wider energy grid, improving the coordination between energy supply and demand. By leveraging big data and predictive analytics, operators can optimize energy production, reduce fuel consumption, and minimize emissions, ultimately driving cost savings and environmental benefits.
As demand for energy-efficient and sustainable solutions continues to rise, the role of CHP in achieving energy security and resilience will also be emphasized. In the face of global energy challenges such as rising fuel costs, geopolitical instability, and the need for grid resilience, decentralized and self-sufficient energy solutions like CHP offer a way to mitigate these risks. In critical facilities, such as hospitals, emergency services, and military bases, CHP systems can provide reliable power and heating, ensuring that operations continue even during power outages or disruptions in the energy supply. By reducing the reliance on external energy providers and enhancing the local generation of power, CHP systems increase energy independence and security.
The long-term outlook for CHP systems is one of continued growth and integration into the broader energy landscape. As the world works to address climate change and reduce its reliance on fossil fuels, CHP offers a viable and sustainable solution for meeting energy needs in both developed and emerging markets. With their ability to deliver high-efficiency energy, reduce emissions, and improve energy resilience, CHP systems are set to play a key role in the transformation of the global energy system.
In conclusion, the future of Combined Heat and Power (CHP) systems is promising, driven by technological innovation, growing demand for energy efficiency, and the global transition to a cleaner, more sustainable energy mix. As CHP systems evolve, they will become even more integral to meeting the world’s energy needs while reducing environmental impact. The integration of renewable energy, advances in system design, and the increased use of smart technologies will further enhance the benefits of CHP. By embracing CHP as part of the broader energy transition, businesses, communities, and nations can help create a more resilient, efficient, and sustainable energy future.
Hydrogen fuel
Hydrogen fuel is rapidly emerging as a critical component of the global effort to transition to a cleaner, more sustainable energy system. As one of the most abundant elements in the universe, hydrogen has the potential to replace fossil fuels in a wide range of applications, from power generation and transportation to industrial processes and residential heating. Hydrogen fuel, when produced and utilized through clean technologies, offers the promise of reducing carbon emissions, improving energy security, and providing an efficient energy storage solution to support the growing demand for renewable energy.
Hydrogen itself is not a primary energy source but rather an energy carrier, similar to electricity. It does not occur freely in nature but must be extracted from compounds such as water, natural gas, or biomass. The most common method of hydrogen production is through steam methane reforming (SMR), which involves extracting hydrogen from natural gas. While this process is widely used and cost-effective, it releases carbon dioxide (CO2) as a byproduct, making it less desirable in terms of environmental impact. However, with advances in technology, the carbon emissions associated with SMR can be captured and stored, making this process more sustainable.
Alternatively, hydrogen can be produced through electrolysis, a process that uses electricity to split water into hydrogen and oxygen. When the electricity used for electrolysis comes from renewable sources such as wind, solar, or hydropower, the resulting hydrogen is referred to as “green hydrogen.” This process is entirely clean and produces no carbon emissions, making it the most sustainable option for hydrogen production. Green hydrogen is seen as a key solution to decarbonizing industries and sectors that are otherwise difficult to electrify, such as heavy industry, long-haul transportation, and chemical production.
One of the primary advantages of hydrogen as a fuel is its versatility. It can be used in a variety of applications, including as a fuel for vehicles, in power plants, as a feedstock for industrial processes, and in residential heating systems. In the transportation sector, hydrogen fuel cells have the potential to replace gasoline and diesel in cars, trucks, buses, trains, and even ships. Hydrogen-powered vehicles (HPVs) are attractive because they offer long driving ranges, fast refueling times, and zero emissions, making them a clean alternative to traditional internal combustion engine vehicles. This is particularly important in addressing the limitations of battery electric vehicles (BEVs), which can suffer from range anxiety and long charging times.
In addition to its use in transportation, hydrogen can be used in power generation, either directly in fuel cells or in combustion turbines. Fuel cells generate electricity by combining hydrogen with oxygen, with the only byproduct being water vapor. This process is highly efficient and clean, making hydrogen a viable option for decentralized and large-scale power generation. In the context of renewable energy, hydrogen can serve as an energy storage solution. When renewable energy generation exceeds demand, excess electricity can be used to produce hydrogen through electrolysis. This hydrogen can then be stored and used later to generate electricity when demand is high or renewable generation is low. This capability to store and transport energy in the form of hydrogen addresses one of the main challenges associated with renewable energy—its intermittency.
Hydrogen also has significant potential in the industrial sector, particularly in heavy industries such as steelmaking, cement production, and refining, which are traditionally energy-intensive and carbon-emitting. Hydrogen can serve as a cleaner alternative to coal and natural gas in high-temperature industrial processes. In steel production, for example, hydrogen can be used to replace coke as a reducing agent in the blast furnace, leading to a significant reduction in CO2 emissions. Similarly, hydrogen can be used in chemical manufacturing, where it is already a key feedstock, to replace carbon-based raw materials and minimize environmental impact.
In the context of residential heating, hydrogen can be blended with natural gas in existing gas networks to reduce emissions from heating systems. A more ambitious approach involves converting buildings and heating systems to run entirely on hydrogen. This would eliminate carbon emissions from home heating, making it possible to decarbonize one of the largest sources of residential energy consumption. Hydrogen could also be used in combined heat and power (CHP) systems, which provide both heat and electricity, making it a flexible solution for residential and commercial energy needs.
One of the most significant challenges facing the widespread adoption of hydrogen as a fuel is the cost of production. Currently, green hydrogen produced through electrolysis is more expensive than hydrogen produced from natural gas, mainly due to the high cost of renewable electricity and the electrolysis process itself. However, costs are expected to fall as renewable energy prices continue to decrease, electrolyzer technology improves, and economies of scale are achieved. Governments around the world are investing heavily in hydrogen research and infrastructure, with the aim of reducing the cost of hydrogen production and making it more competitive with fossil fuels. In some regions, hydrogen production is already being incentivized through subsidies, tax credits, and policy support, further driving down costs and accelerating the commercialization of hydrogen technologies.
The development of hydrogen infrastructure is another key challenge. To support the widespread use of hydrogen as a fuel, significant investments are needed in hydrogen production, storage, and distribution networks. Hydrogen needs to be stored either as a compressed gas, liquid, or in solid form, each of which presents unique challenges in terms of storage and transportation. The development of a robust hydrogen infrastructure is critical to enabling the adoption of hydrogen-powered vehicles, industrial applications, and residential heating systems. Governments and private companies are working together to build the necessary infrastructure, with plans for hydrogen refueling stations, pipelines, and storage facilities.
Another challenge to hydrogen adoption is the need for a skilled workforce to develop, operate, and maintain hydrogen technologies. As the hydrogen economy grows, there will be a greater demand for engineers, technicians, and researchers who specialize in hydrogen production, storage, and utilization. Educational and training programs will need to be expanded to ensure that workers have the skills needed to support the hydrogen industry.
Hydrogen fuel also has the potential to create new economic opportunities. The global shift toward hydrogen presents the possibility of new industries, job creation, and economic growth, particularly in regions with abundant renewable energy resources. For example, countries with vast wind or solar potential could become major exporters of green hydrogen, creating a new global market for hydrogen fuel. Additionally, hydrogen can play a role in creating energy independence by reducing reliance on imported oil and gas, helping countries to diversify their energy mix and enhance their energy security.
International cooperation will also be essential to the success of the hydrogen economy. The production, storage, and distribution of hydrogen require collaboration between countries, industries, and research institutions. Global agreements on standards, regulations, and infrastructure will help create a cohesive hydrogen market that allows for the efficient exchange of hydrogen fuel across borders. Collaboration on research and development can also accelerate the commercialization of hydrogen technologies, making them more affordable and widely available.
In conclusion, hydrogen fuel holds immense potential to transform the global energy landscape. As a clean and versatile energy carrier, hydrogen can be used in a wide range of applications, from transportation and power generation to industrial processes and heating. When produced through renewable energy sources, hydrogen is a carbon-free fuel that can contribute significantly to decarbonizing hard-to-abate sectors and supporting the integration of renewable energy into the grid. While challenges such as cost, infrastructure development, and workforce training remain, ongoing technological advancements and government support are paving the way for hydrogen to become a mainstream energy solution. The future of hydrogen fuel is promising, and its role in achieving a sustainable, low-carbon energy future will only continue to grow as investments in hydrogen technology and infrastructure expand globally.
As the world moves toward a more sustainable energy future, the role of hydrogen in the global energy mix will continue to grow. Its unique properties as a clean, efficient, and versatile energy carrier position hydrogen as a key enabler in the transition to net-zero emissions. However, realizing the full potential of hydrogen fuel requires overcoming several technical, economic, and logistical challenges, many of which are currently being addressed through innovation, research, and collaboration across industries and governments.
The hydrogen economy is expected to evolve in stages, with early applications focusing on sectors where hydrogen can provide the most immediate benefits. Transportation, for example, is already seeing the adoption of hydrogen fuel cells in vehicles such as buses, trucks, and trains. These vehicles offer a compelling alternative to battery electric vehicles (BEVs), particularly in heavy-duty transport and long-distance travel. Hydrogen fuel cell vehicles (FCVs) are ideal for these applications because they offer a longer range and quicker refueling times than BEVs, addressing some of the key limitations of electric mobility. For long-haul trucking, where battery weight and recharging times are significant barriers, hydrogen provides an efficient and scalable solution. Similarly, hydrogen-powered trains are being developed to replace diesel-powered locomotives in regions where electrification of rail infrastructure is not feasible.
In the maritime and aviation sectors, hydrogen fuel is also gaining traction as a potential solution for reducing emissions. The shipping industry, which accounts for a significant portion of global CO2 emissions, is exploring the use of hydrogen in fuel cells and internal combustion engines. Hydrogen-powered ships can offer zero-emission solutions for both short-distance and long-distance voyages, and when combined with renewable energy sources, such as wind or solar, hydrogen-powered ships could provide a fully decarbonized shipping option. In aviation, hydrogen is being tested as a potential fuel for aircraft, especially for short-haul flights. The use of hydrogen in aviation could reduce the sector’s reliance on jet fuel and contribute to meeting the ambitious decarbonization targets set by international bodies such as the International Civil Aviation Organization (ICAO).
In addition to transportation, hydrogen’s role in power generation is increasingly recognized as a critical component of the energy transition. Hydrogen can be used in gas turbines for large-scale power plants or in smaller, distributed generation systems. When combined with renewable energy sources, hydrogen can help balance supply and demand by storing excess energy generated during times of high renewable output and using it to generate electricity when renewable generation is low. This “power-to-gas” approach is a promising way to store and distribute renewable energy, reducing the need for expensive and inefficient battery storage. Hydrogen can also be used in fuel cells for backup power and off-grid applications, offering a reliable, clean energy source for remote areas or critical infrastructure such as hospitals, data centers, and military bases.
Hydrogen can also play a central role in industrial decarbonization, where it is used to replace fossil fuels in energy-intensive processes such as steel production, cement manufacturing, and chemical production. For example, in steel manufacturing, hydrogen can be used to reduce iron ore into iron, eliminating the need for coal-based coke and significantly reducing carbon emissions. The chemical industry, which is a major consumer of hydrogen, can also benefit from green hydrogen, which can replace hydrogen derived from natural gas in processes such as ammonia production. Hydrogen’s versatility as both a feedstock and an energy source positions it as a key solution for decarbonizing sectors that are difficult to electrify through other means.
While hydrogen holds great promise, its widespread adoption will depend on a concerted effort to build the necessary infrastructure. A global hydrogen economy requires the development of hydrogen production, storage, and transportation networks. Hydrogen pipelines, storage tanks, and refueling stations will need to be established to support the large-scale use of hydrogen in transportation, industry, and power generation. For example, countries like Japan, Germany, and South Korea are already making significant investments in hydrogen infrastructure, including hydrogen fueling stations and pipeline networks. The construction of a robust infrastructure is critical to enabling the efficient distribution of hydrogen across regions and ensuring that hydrogen can be produced and delivered to where it is needed most.
Another key factor influencing hydrogen adoption is the cost of production. As mentioned earlier, green hydrogen, produced using renewable electricity, is currently more expensive than hydrogen derived from natural gas. However, the cost of renewable electricity has been falling steadily in recent years, and as electrolyzer technology advances, the cost of green hydrogen is expected to decrease. This trend is being supported by government policies and subsidies that incentivize the development of green hydrogen production projects. The increasing scale of renewable energy deployment, coupled with economies of scale in electrolyzer manufacturing, is likely to result in further reductions in hydrogen production costs.
Hydrogen fuel will also benefit from innovations in hydrogen storage technologies. Storing hydrogen in a safe and efficient manner is one of the major challenges to its widespread use, as hydrogen is a low-density gas that requires high-pressure storage or cryogenic cooling. Advances in materials science, such as the development of advanced hydrogen storage tanks and solid-state hydrogen storage methods, will improve the efficiency and safety of hydrogen storage systems. These innovations will make it easier and more cost-effective to store hydrogen for both short-term and long-term use, ensuring that it is available when and where it is needed.
The integration of hydrogen into the global energy system will require coordinated efforts among governments, industries, and research institutions. Policymakers will need to create a regulatory environment that supports hydrogen adoption by providing clear standards, incentives, and funding for hydrogen research and development. International collaboration on hydrogen production, storage, and distribution infrastructure will also be essential to ensuring that hydrogen can be traded and transported efficiently across borders. Public-private partnerships will play a crucial role in financing hydrogen projects, particularly those that involve large-scale infrastructure development.
In addition to the technical and economic challenges, public perception of hydrogen will also influence its adoption. The safety of hydrogen, which is highly flammable, is an important concern that needs to be addressed through rigorous safety standards, public education, and effective risk management. Overcoming these concerns and demonstrating the safety and reliability of hydrogen technologies will be key to gaining public trust and fostering widespread acceptance of hydrogen as a mainstream fuel.
As the hydrogen economy continues to evolve, it will likely become a central pillar of the global energy landscape, complementing other renewable energy sources and enabling the decarbonization of hard-to-abate sectors. Hydrogen offers a flexible, scalable, and clean energy solution that can be used in transportation, power generation, industrial processes, and heating. With continued technological advancements, policy support, and infrastructure development, hydrogen has the potential to play a pivotal role in achieving global climate goals and ensuring a sustainable energy future.
In conclusion, hydrogen fuel represents a promising solution for a wide range of energy challenges, from reducing greenhouse gas emissions to providing energy storage and balancing renewable energy generation. While significant hurdles remain, ongoing technological, economic, and policy innovations are driving the hydrogen economy forward. As hydrogen becomes more accessible and affordable, it will undoubtedly play an increasingly important role in shaping a cleaner, more resilient, and sustainable energy system. The future of hydrogen is bright, and its potential to transform industries, transportation, and power generation is immense.
As the hydrogen economy expands, its impact will be felt across numerous sectors, influencing both the global energy landscape and the way industries operate. Beyond the direct applications of hydrogen fuel in power generation, transportation, and industry, hydrogen offers a variety of ancillary benefits that are critical to achieving long-term sustainability and energy security goals.
One of the key aspects of hydrogen’s potential lies in its ability to enable sector coupling, or the integration of different energy sectors such as electricity, heat, and transport. This interconnection allows hydrogen to bridge the gap between intermittent renewable energy sources and the demand for reliable, dispatchable power. As more renewable energy, such as wind and solar, comes online, it can lead to periods of excess generation when supply exceeds demand. During these times, surplus renewable electricity can be used to produce hydrogen via electrolysis, which can then be stored for use in various sectors. The stored hydrogen can be converted back into electricity when demand is high or renewable generation is low, providing a flexible and efficient means of balancing the grid. This makes hydrogen an essential element in the broader energy system, helping to address the challenges posed by the increasing share of renewable energy in the grid.
Furthermore, hydrogen can help decarbonize industries that are difficult to electrify using traditional methods, such as heavy industry and shipping. As the world continues to address its emissions reduction targets, hydrogen can play a crucial role in sectors like steelmaking, cement production, and chemical manufacturing, where high temperatures are required and electrification is challenging. The use of hydrogen as a clean fuel in these industries will significantly reduce their carbon footprints, helping to decarbonize some of the most energy-intensive processes. For instance, in the steel industry, hydrogen-based direct reduction (H2-DR) processes have the potential to replace the carbon-intensive blast furnace method, which traditionally relies on coke as a fuel. This shift to hydrogen could make the steel industry far less polluting, contributing to the global effort to reduce industrial emissions.
In the maritime and aviation sectors, where heavy fuel use and long operational durations have traditionally made decarbonization efforts challenging, hydrogen is also gaining traction. Hydrogen-powered ships, both for cargo and passenger transport, can offer zero-emission alternatives to diesel-powered vessels, helping to reduce the carbon intensity of the shipping industry. In aviation, hydrogen fuel holds the potential to replace conventional jet fuel, which is a major contributor to greenhouse gas emissions in the transport sector. Hydrogen-powered aircraft would emit only water vapor as exhaust, significantly reducing aviation’s environmental impact. In addition to direct fuel substitution, hydrogen can also serve as a crucial fuel for powering on-board systems in electric aircraft, contributing to more sustainable aviation technologies.
In addition to its applications in energy production, transportation, and industry, hydrogen also has the potential to revolutionize energy storage. While batteries are well-suited for short-term storage of energy, hydrogen offers a more versatile and long-term storage solution. This is particularly important in regions with high seasonal fluctuations in renewable energy generation. Hydrogen can be produced during periods of surplus renewable energy generation, stored, and then used to generate power when renewable generation drops, such as during the winter months or on cloudy days. This capability makes hydrogen an essential part of efforts to provide year-round clean energy to grids and communities, even in regions with less consistent renewable energy availability.
The integration of hydrogen into national and global energy systems will be supported by advances in hydrogen infrastructure. Developing a widespread hydrogen infrastructure is critical for enabling the large-scale use of hydrogen across transportation, industry, and power generation. This will require the creation of hydrogen storage, distribution, and refueling networks that can transport and deliver hydrogen safely and efficiently. As hydrogen is produced and used at different locations, it will need to be transported via pipelines or by trucks, ships, and rail. The establishment of hydrogen pipelines, particularly in regions with high demand or significant hydrogen production, will facilitate the widespread use of hydrogen by making it easier to distribute and store.
Furthermore, hydrogen refueling stations, particularly for hydrogen-powered vehicles, will play a crucial role in increasing the adoption of hydrogen in transportation. Just as the network of gas stations allows for the widespread use of gasoline and diesel, hydrogen refueling stations will need to become ubiquitous in order to meet the needs of hydrogen-powered vehicles. The establishment of a global network of hydrogen refueling stations will be instrumental in accelerating the transition to hydrogen-powered transport, making it a more viable and attractive option for consumers and businesses.
The hydrogen economy also opens up new avenues for international cooperation and trade. As countries around the world seek to meet their emissions reduction targets, many are exploring the potential of hydrogen as a clean energy carrier. Hydrogen can be produced from renewable sources in regions with abundant wind, solar, or hydropower potential, and then exported to other regions where renewable resources are less abundant. For instance, countries in the Middle East, North Africa, and Australia, which have vast renewable energy resources, are already positioning themselves as potential exporters of green hydrogen to markets in Europe and Asia. The development of international hydrogen trade networks will not only help countries meet their energy needs but also foster collaboration and the sharing of technological expertise.
The advancement of hydrogen technologies will also create new economic opportunities. As the hydrogen economy grows, so too will the demand for research and development, manufacturing, and deployment of hydrogen-related technologies. This will drive job creation in sectors ranging from engineering and manufacturing to infrastructure development and maintenance. For example, the production of hydrogen electrolysis systems, fuel cells, and storage technologies will require a skilled workforce, creating new industries and opportunities for innovation. The transition to a hydrogen economy will also stimulate investment in green technologies, attracting both public and private sector capital.
As the hydrogen market matures, the establishment of global standards for hydrogen production, storage, and transportation will be critical to ensuring safety and consistency in the industry. International regulatory frameworks will help facilitate the safe and efficient use of hydrogen, allowing for the widespread adoption of hydrogen technologies across different regions. This will also ensure that hydrogen is produced and used in an environmentally responsible manner, with clear guidelines for reducing emissions and minimizing the environmental impact of hydrogen production.
At the same time, the public and private sectors must continue to collaborate in developing policies and incentives that promote the use of hydrogen fuel. Governments around the world are already setting ambitious targets for hydrogen adoption, with some countries offering financial incentives for the development of hydrogen infrastructure and technology. These policies will help create a favorable environment for hydrogen adoption, encouraging investment in research, production, and infrastructure development. They will also help drive down the costs of hydrogen production, making it more competitive with conventional fuels.
Public acceptance and understanding of hydrogen will also be a critical factor in the success of the hydrogen economy. Safety concerns, such as the flammability of hydrogen, must be addressed through proper regulation, safety protocols, and public education. Ensuring that communities are informed about the benefits and safety of hydrogen technologies will help build public trust and acceptance, which will be essential for the widespread deployment of hydrogen systems.
In conclusion, hydrogen fuel is poised to become a cornerstone of the future energy landscape. With its ability to decarbonize multiple sectors, provide flexible energy storage, and integrate with renewable energy sources, hydrogen presents a viable solution to the challenges posed by climate change and energy security. As technology advances, costs decrease, and infrastructure develops, hydrogen’s role in powering the global economy will only continue to grow. The hydrogen economy offers exciting opportunities for innovation, international cooperation, and job creation, all while contributing to a cleaner, more sustainable future. The widespread adoption of hydrogen technologies will be essential in achieving global climate goals and ensuring a resilient and sustainable energy system for future generations.
Energy storage integration
Energy storage integration is becoming a crucial component of the global transition to clean, renewable energy. As renewable energy sources such as solar, wind, and hydropower become more dominant, the need for reliable energy storage systems has intensified. These energy sources are intermittent, meaning they do not generate a consistent supply of electricity throughout the day or year. For example, solar energy is only available when the sun is shining, and wind energy depends on wind conditions. Energy storage helps solve this challenge by capturing excess energy during periods of high production and releasing it when demand is high or when renewable generation is low. This makes energy storage systems an essential part of the energy infrastructure for managing the variability of renewable energy and ensuring a reliable and stable power supply.
Energy storage systems work by storing energy in various forms, such as chemical, mechanical, or thermal energy, and then converting that stored energy back into electricity when needed. The most common form of energy storage is battery storage, which stores electricity chemically in batteries. Batteries, such as lithium-ion batteries, are widely used due to their high energy density, efficiency, and declining cost. These batteries can be deployed in a wide range of applications, from large-scale grid storage to smaller systems for residential use. However, other types of energy storage systems, including pumped hydro storage, compressed air energy storage, and thermal storage, are also important for different use cases.
Pumped hydro storage is one of the oldest and most established forms of large-scale energy storage. In this system, water is pumped from a lower reservoir to an upper reservoir using excess electricity. When electricity demand increases, water is released from the upper reservoir to flow back down through turbines, generating electricity. Pumped hydro storage is highly efficient and capable of providing large amounts of energy for extended periods, but its deployment is limited to areas with suitable topography, such as mountainous regions.
Compressed air energy storage (CAES) is another form of mechanical energy storage that uses compressed air to store energy. In a CAES system, excess electricity is used to compress air and store it in underground caverns or tanks. When energy is needed, the compressed air is released and passed through turbines to generate electricity. While CAES systems have been deployed in some regions, they are still in the early stages of development and are less common than other storage technologies. CAES systems are well-suited to large-scale energy storage applications and can provide grid stability over long durations.
Thermal energy storage (TES) systems capture and store heat for later use. These systems are typically used in conjunction with concentrated solar power (CSP) plants, where sunlight is concentrated to generate high temperatures that can be stored in materials such as molten salt. The stored thermal energy can be used to generate electricity during periods when sunlight is not available. TES can also be used for district heating and cooling, where excess heat is stored and then distributed to homes or businesses.
One of the key challenges in energy storage integration is the cost of these systems. Although the cost of energy storage, particularly battery storage, has decreased significantly in recent years, it is still a major factor that influences the economics of energy storage. High upfront costs for storage systems can be a barrier to widespread adoption, especially in regions where energy prices are low or where energy storage is not yet seen as economically viable. However, the cost of energy storage is expected to continue to decline as technology improves and economies of scale are achieved. Battery prices, for instance, have dropped by more than 80% over the past decade, and this trend is likely to continue as manufacturing capacity increases and technology advances.
Energy storage systems also need to be integrated into the existing energy infrastructure, which presents another set of challenges. The integration of large-scale energy storage into power grids requires careful planning and investment in transmission and distribution infrastructure. Energy storage systems must be able to communicate with grid operators to balance supply and demand, and they must be deployed in locations that optimize their effectiveness. In some cases, energy storage can be deployed in conjunction with renewable energy generation systems, such as solar or wind farms, to improve grid reliability and ensure that excess energy is captured and stored for later use.
The integration of energy storage also involves addressing technical challenges related to grid stability and the management of variable renewable energy sources. For example, as renewable energy generation increases, the grid will experience fluctuations in supply that need to be managed. Energy storage can help smooth out these fluctuations by providing a buffer for excess energy during periods of high generation and delivering energy when renewable generation is low. This type of flexibility is essential for maintaining grid stability, especially as the share of renewable energy in the global power mix continues to rise.
In addition to balancing supply and demand, energy storage plays an important role in supporting grid resilience and reliability. In regions prone to extreme weather events or other disruptions, energy storage systems can provide backup power in the event of outages, helping to ensure continuity of service for critical infrastructure such as hospitals, data centers, and emergency response facilities. Additionally, energy storage can help reduce the need for costly and environmentally damaging peaking power plants, which are often used to meet short-term spikes in electricity demand. By providing a clean and flexible source of backup power, energy storage contributes to the overall reliability and resilience of the energy grid.
The potential for energy storage to support renewable energy integration is further enhanced by the development of microgrids. Microgrids are localized networks of energy generation, storage, and distribution that can operate independently or in coordination with the main grid. By integrating energy storage with local renewable generation sources, microgrids can help communities become more energy independent and resilient. This is particularly important in remote areas, island communities, or areas with unreliable grid infrastructure. Microgrids can function autonomously during power outages or periods of grid instability, and the energy stored in these systems can be used to maintain local power supplies until the main grid is restored.
In addition to supporting the integration of renewable energy into the grid, energy storage also plays a role in facilitating the transition to a decentralized energy system. As more consumers install rooftop solar panels and become producers of their own energy, energy storage allows them to store excess electricity for later use, reducing their reliance on the grid and lowering their energy bills. This trend, known as “prosumers,” is transforming the way energy is produced, distributed, and consumed. Energy storage systems enable prosumers to store their self-generated electricity and use it when demand is highest, reducing the need to purchase electricity from the grid and improving the economics of residential and commercial solar energy systems.
One of the emerging areas of energy storage integration is the use of artificial intelligence (AI) and advanced data analytics to optimize the operation of storage systems. AI algorithms can analyze energy demand patterns, weather forecasts, and renewable energy generation data to predict when energy storage systems should charge and discharge. These algorithms can also help operators manage the use of energy storage in real time, ensuring that storage systems are being utilized as efficiently as possible. By incorporating AI into the operation of energy storage, grid operators can improve the flexibility and responsiveness of the energy system, making it easier to integrate higher levels of renewable energy.
In conclusion, energy storage integration is critical for the successful transition to a renewable, low-carbon energy system. It allows for the efficient use of renewable energy, helps maintain grid stability, supports the resilience of the energy infrastructure, and enables the growth of decentralized energy generation. As energy storage technology continues to advance and costs continue to decrease, it will become an increasingly important tool for managing the variability of renewable energy sources, ensuring a reliable and flexible power supply, and supporting the transition to a more sustainable and resilient energy future.
Steam Turbine Governing System
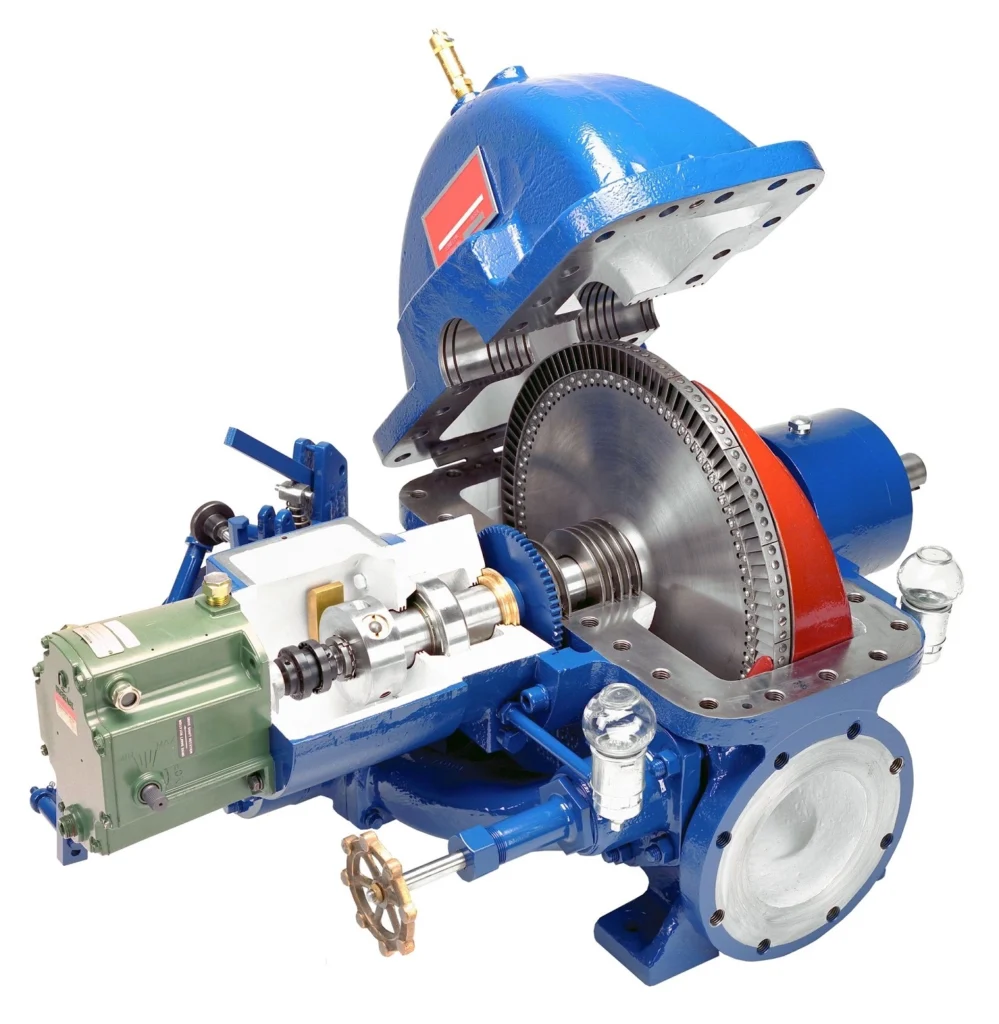
A steam turbine governing system is essential for regulating the speed and output of a steam turbine, ensuring that it operates efficiently and within its design specifications. The governing system is responsible for maintaining the turbine’s operational stability, particularly in response to varying loads and changing conditions within the power plant. This system typically involves a series of components designed to adjust the steam flow to the turbine’s rotor, maintaining the desired rotational speed and preventing the turbine from overspeeding or stalling.
The governing system is designed to manage the turbine’s speed by controlling the amount of steam that is allowed to enter the turbine. This is crucial because steam turbines are typically designed to operate at a specific rotational speed, which is dictated by the power generation requirements and the turbine’s mechanical characteristics. The system needs to respond to changes in electrical load, where the turbine must either increase or decrease its power output to match demand. In the case of an increase in load, the steam flow to the turbine must be increased, whereas a decrease in load requires reducing the steam supply. The governing system controls this adjustment by modifying the steam valves, ensuring that the turbine maintains its optimal operating conditions.
There are several different types of governing systems used in steam turbines, each with unique mechanisms for controlling the steam flow. One of the most common systems is the hydraulic governor, which uses hydraulic pressure to control the steam valves. The hydraulic system is powered by oil or water, which operates a series of pistons and actuators to regulate the valve positions in response to load changes. The hydraulic governor is sensitive and can make precise adjustments to steam flow, allowing the turbine to maintain a steady speed.
Another widely used governing system is the electronic governor, which relies on electrical signals to regulate the steam flow. These governors use sensors to measure the turbine’s speed and load, and then transmit these signals to a control system that adjusts the steam valves accordingly. Electronic governors offer a higher degree of precision and can respond more quickly to changing conditions than hydraulic governors. Furthermore, they often include advanced control algorithms that optimize turbine performance and efficiency, enhancing the overall operation of the turbine.
In modern steam turbine plants, digital control systems are increasingly being used to manage the governing system. These systems integrate sensors, actuators, and controllers into a centralized digital network, enabling real-time monitoring and control of the turbine. Digital governors offer numerous benefits, including improved speed control, better coordination with other plant systems, and the ability to fine-tune the turbine’s operation for maximum efficiency. Digital control systems can also provide detailed diagnostic data, allowing operators to predict maintenance needs and address potential issues before they lead to failures.
The steam turbine governing system also plays a crucial role in ensuring the protection of the turbine. One of the primary concerns is preventing overspeed, which occurs when the turbine’s rotational speed exceeds safe limits. Overspeed can cause catastrophic damage to the turbine, potentially leading to a failure of critical components such as the rotor or bearings. To prevent this, the governing system continuously monitors the turbine’s speed and adjusts the steam flow to keep the turbine within its safe operating range. In the event of an emergency, the governing system can take immediate action to reduce the steam flow or shut down the turbine if necessary.
Another important function of the governing system is the ability to maintain synchronization between the turbine and the generator. In a power plant, the turbine is connected to an electrical generator that produces electricity. The speed of the turbine must be carefully controlled to ensure that it matches the frequency of the electrical grid. If the turbine’s speed deviates too much from the grid frequency, it can lead to instability and potential damage to both the turbine and the electrical grid. The governing system adjusts the steam flow to ensure that the turbine remains synchronized with the generator and the grid, preventing frequency fluctuations and maintaining a stable power output.
To optimize the operation of the governing system, various auxiliary systems are often incorporated into the turbine’s design. These may include systems for lubrication, cooling, and steam pressure regulation, all of which help ensure that the governing system operates smoothly and efficiently. Proper maintenance of these auxiliary systems is vital for the continued performance and longevity of the governing system, as well as the turbine as a whole.
The turbine’s governing system also has an important role during startup and shutdown procedures. During startup, the governing system is responsible for gradually increasing the steam flow to bring the turbine up to speed in a controlled manner. This gradual increase prevents the turbine from experiencing mechanical stress and ensures that the turbine reaches its optimal operating speed safely. During shutdown, the governing system reduces the steam flow to slow the turbine down in a controlled manner, preventing damage to the turbine’s components.
In addition to these primary functions, modern steam turbine governing systems often incorporate features for remote monitoring and control. This allows operators to adjust settings and monitor the performance of the turbine from a central control room or even from remote locations. Remote control capabilities enhance the flexibility of turbine operation, allowing for more responsive adjustments and better overall management of plant operations.
The development of more advanced governing systems continues to evolve alongside improvements in turbine technology and plant automation. With the increasing emphasis on improving efficiency, reducing emissions, and ensuring plant reliability, new governing systems are being designed to meet these objectives. These systems incorporate advanced algorithms and artificial intelligence to optimize steam flow and turbine performance, further enhancing the efficiency of power plants.
In conclusion, the steam turbine governing system is a critical component of modern steam turbine operations, ensuring that the turbine operates safely, efficiently, and in synchronization with the generator and grid. Whether using hydraulic, electronic, or digital controls, the governing system plays a key role in managing steam flow, maintaining stable turbine speed, and preventing potential damage. As technology continues to advance, these systems are becoming more sophisticated, offering increased precision, better performance, and greater reliability. By continuously improving the governing system, operators can ensure that their turbines operate at peak efficiency, contributing to the overall performance and sustainability of the power generation industry.
The integration of advanced technologies into steam turbine governing systems continues to enhance the flexibility and efficiency of power plants. One of the most promising developments is the use of predictive maintenance and condition monitoring systems, which are often integrated into modern governing systems. These systems continuously monitor the performance of the turbine, detecting any deviations from normal operating conditions that may indicate wear or potential failures. By using sensors to measure parameters such as vibration, temperature, pressure, and speed, the system can provide real-time diagnostics and predict when maintenance is required. This allows operators to schedule maintenance activities proactively, reducing the risk of unplanned downtime and minimizing the overall maintenance costs.
In addition, artificial intelligence (AI) and machine learning (ML) technologies are becoming increasingly incorporated into steam turbine governing systems. These technologies enable more advanced data analysis and optimization, allowing the governing system to adapt to changing conditions in real time. AI and ML algorithms can analyze vast amounts of operational data to optimize steam flow and turbine speed, taking into account factors such as load fluctuations, steam pressure variations, and grid frequency adjustments. This ability to respond dynamically to varying conditions not only improves the efficiency of the turbine but also enhances the overall performance of the power plant.
The use of AI and ML in governing systems can also lead to improved fault detection and anomaly identification. By analyzing historical data and identifying patterns that precede failure events, these systems can learn to recognize early warning signs of potential problems. This predictive capability can lead to earlier intervention and more targeted repairs, reducing the likelihood of catastrophic turbine failures and extending the life of the equipment.
Moreover, with the ongoing shift toward more sustainable energy generation, steam turbine governing systems are increasingly being adapted to support the integration of renewable energy sources into the grid. As renewable energy generation becomes more prevalent, there is a growing need for power plants to be flexible and responsive to fluctuations in renewable output. Steam turbines equipped with advanced governing systems can quickly adjust to changes in renewable generation, allowing power plants to provide stable backup power when needed. In the case of wind or solar power generation, the grid can experience periods of excess or insufficient supply, which requires fast responses from conventional power sources like steam turbines. The governing system can quickly increase or decrease the steam flow to meet these changes, ensuring the grid remains stable and reliable.
The need for fast response times in the governing system has driven innovation in turbine design and control. Some modern turbines are designed to operate at partial load for extended periods without sacrificing efficiency. This is important in a grid that increasingly relies on variable renewable energy sources, where conventional thermal plants must be more adaptable and capable of providing power when renewables cannot meet demand. To achieve this, the governing system is able to rapidly adjust steam flow to meet both short-term and long-term fluctuations in demand, ensuring that the turbine operates efficiently even under varying load conditions.
In some cases, steam turbine governing systems are also being integrated with grid management software, which enables a more coordinated approach to energy distribution across the entire power network. Grid operators can monitor the status of multiple turbines and adjust their output as needed to maintain grid stability. These systems can optimize the distribution of power from different plants based on real-time data, ensuring that the correct mix of energy generation is used to meet demand while minimizing the environmental impact. The ability to integrate steam turbine governing systems with grid management software enables a more flexible, efficient, and environmentally friendly power generation model.
The expansion of hybrid power systems, which combine steam turbines with renewable energy sources or energy storage technologies, is another area where steam turbine governing systems are becoming increasingly important. Hybrid systems offer the potential to combine the benefits of both renewable and conventional energy sources, allowing for more reliable power generation and smoother integration of renewables into the grid. For example, a combined cycle plant that integrates a steam turbine with a gas turbine and energy storage system can take advantage of both fossil and renewable fuels, with the governing system optimizing the steam flow based on the available energy sources. This approach allows for more efficient use of resources and helps to maintain grid stability.
Additionally, steam turbine governing systems are being developed to address specific challenges posed by emerging energy markets, such as those focused on decarbonization and the reduction of greenhouse gas emissions. Many power plants are now being retrofitted with carbon capture technologies, which can remove CO2 emissions from the flue gas before they are released into the atmosphere. In these applications, the governing system may need to adjust steam flow to accommodate the additional energy demands required for the carbon capture process. The governing system can play a critical role in ensuring that the steam turbine continues to operate efficiently while supporting the carbon capture equipment, helping power plants achieve their emissions reduction goals.
As global efforts to address climate change intensify, steam turbines and their governing systems will play an essential role in the transition to cleaner energy systems. Many countries are increasing their reliance on natural gas, nuclear power, and renewable energy to reduce carbon emissions from coal-fired plants. Steam turbines, especially those in combined cycle configurations, are highly efficient and offer flexibility to operate with a variety of fuels. The integration of these turbines with advanced governing systems ensures that they can maintain high efficiency while supporting grid stability and helping to meet emissions reduction targets.
The ongoing advancements in steam turbine governing systems are also helping to improve overall operational safety. The ability to constantly monitor turbine conditions and adjust steam flow in response to real-time data helps prevent potential damage caused by mechanical stress, temperature fluctuations, or changes in steam pressure. Additionally, many modern governing systems incorporate multiple layers of protection, such as overspeed trips, steam pressure limiters, and temperature sensors, to ensure the turbine operates within safe parameters. This approach helps safeguard against accidents and ensures that turbines continue to operate at peak efficiency.
In conclusion, steam turbine governing systems are a critical element of modern power generation, ensuring that turbines operate efficiently, safely, and in sync with grid requirements. With advancements in digital control, AI, and predictive maintenance, these systems are becoming more sophisticated and responsive, providing greater operational flexibility and reliability. As renewable energy integration, hybrid systems, and decarbonization goals become increasingly important, steam turbine governing systems will continue to evolve to meet these challenges. By improving turbine performance, extending equipment lifespan, and contributing to the stability of the power grid, modern governing systems are helping to drive the transition to a more sustainable and efficient energy future.
As steam turbine governing systems continue to evolve, their role in enhancing operational efficiency and supporting the transition to cleaner energy becomes even more critical. With the global push toward reducing carbon emissions, steam turbines, and the systems that control them, are adapting to meet these new challenges. One important development is the growing trend of flexibility in turbine operation. In the past, steam turbines were predominantly used in base-load power plants, running at full capacity for extended periods. Today, however, with the increasing integration of renewable energy sources like wind and solar, steam turbines are being required to operate in more dynamic conditions, including frequent starts, stops, and varying load levels. This necessitates that governing systems become more sophisticated, with a greater focus on ensuring smooth transitions between different operating states.
Flexibility is not just about load-following capabilities but also involves maintaining the turbine’s operational efficiency across a range of conditions. For example, modern turbines may operate at reduced loads for longer periods without suffering from reduced performance or increased wear. This is important in regions where energy demand fluctuates due to seasonal variations or unexpected drops in renewable energy generation. The governing system plays a crucial role in optimizing steam flow under such circumstances to ensure that the turbine remains efficient and responsive without causing unnecessary strain on the components.
Another emerging trend in steam turbine operation is the integration of advanced sensors and monitoring technologies, which provide real-time data on various parameters such as vibration, temperature, pressure, and steam flow. These sensors allow operators to have a much more detailed view of turbine performance, enabling them to make more informed decisions regarding system adjustments and maintenance. By continuously tracking the health of the turbine components, such as bearings, blades, and seals, the governing system can anticipate potential problems and trigger preventive actions before they lead to a failure. This predictive capability reduces the need for expensive, unscheduled maintenance and helps improve the overall uptime of the turbine.
In addition to operational flexibility, governing systems are increasingly being designed with a focus on energy efficiency. By adjusting the steam flow to match the optimal operating conditions, the governing system can minimize energy waste. Modern systems can optimize steam admission to the turbine to ensure that the turbine’s efficiency is maximized across various load levels. This is particularly important as power plants face pressure to meet stricter emissions regulations and improve overall environmental performance. The ability to optimize steam flow also helps reduce fuel consumption, making turbines more economical and environmentally friendly.
The role of steam turbine governing systems is also expanding in distributed energy systems, such as microgrids and combined heat and power (CHP) plants. These systems are increasingly being deployed to provide localized energy solutions, particularly in remote areas or urban environments where energy demand is variable. In such applications, steam turbines must be able to respond to local energy needs, adjusting steam flow in real time to balance the supply of electricity with the demand. The governing system plays a critical role in managing these local energy fluctuations, ensuring that the turbine operates efficiently within the constraints of a decentralized energy environment.
As the integration of renewable energy and distributed energy systems becomes more widespread, steam turbine governing systems must also accommodate varying grid conditions. For example, turbines operating in regions with high levels of renewable energy penetration may need to respond rapidly to grid frequency fluctuations caused by sudden changes in renewable generation. In such cases, governing systems must be able to quickly adjust steam flow to either absorb excess power or provide backup power to the grid, depending on the situation. The ability to maintain grid stability during such fluctuations is essential for ensuring reliable energy supply.
Furthermore, the integration of energy storage technologies with steam turbine systems is another avenue that is being explored to enhance grid stability and flexibility. Energy storage systems, such as batteries or pumped hydro storage, can store excess energy when renewable generation is high and release it when generation is low. By integrating energy storage with steam turbine systems, it is possible to smooth out the intermittency of renewable energy sources, allowing the steam turbine to operate at more consistent load levels. The governing system can then work in tandem with the energy storage system to optimize steam flow, ensuring that the turbine operates efficiently while contributing to overall grid stability.
Additionally, the expansion of digitalization in power generation plants is driving the modernization of steam turbine governing systems. Digital twin technology, for example, creates a virtual replica of the steam turbine and its components, allowing operators to simulate various operating conditions and predict how the turbine will behave under different scenarios. This digital model can be used to optimize turbine performance, identify areas for improvement, and reduce downtime. By linking the governing system with these digital tools, operators can make data-driven decisions that lead to better turbine performance, greater efficiency, and more effective maintenance scheduling.
One of the most notable advancements in steam turbine technology is the transition to supercritical and ultra-supercritical steam turbines, which operate at higher temperatures and pressures than conventional steam turbines. These turbines are more efficient because they extract more energy from the steam, reducing fuel consumption and emissions. However, these advanced turbines require sophisticated governing systems that can handle the increased pressure and temperature levels. The governing system must ensure that steam flow is precisely controlled to prevent overheating, ensure stable operation, and protect the turbine components. As more plants adopt supercritical and ultra-supercritical turbines, the demand for advanced governing systems capable of managing these high-performance turbines will continue to rise.
The evolving regulatory landscape also plays a role in shaping the development of steam turbine governing systems. Governments and regulatory bodies around the world are setting stricter environmental standards, pushing power plants to reduce their carbon footprint and improve the efficiency of their operations. In response, governing systems must adapt to meet these regulations by ensuring that turbines operate at optimal efficiency levels and reduce emissions. Innovations in turbine design and governing system technologies are crucial for meeting these regulatory requirements while maintaining the economic viability of power plants.
In conclusion, the future of steam turbine governing systems is deeply intertwined with the broader energy transformation happening worldwide. As power plants adapt to more dynamic grid conditions, renewable energy integration, and stricter environmental standards, the role of the governing system becomes even more vital. Advanced technologies such as AI, machine learning, predictive maintenance, and digital twins are enhancing the performance and reliability of governing systems, enabling turbines to operate more efficiently and respond more flexibly to changing conditions. As steam turbines continue to evolve, their governing systems will play a central role in ensuring that these turbines contribute effectively to a more sustainable, flexible, and reliable energy future.
Steam Turbine
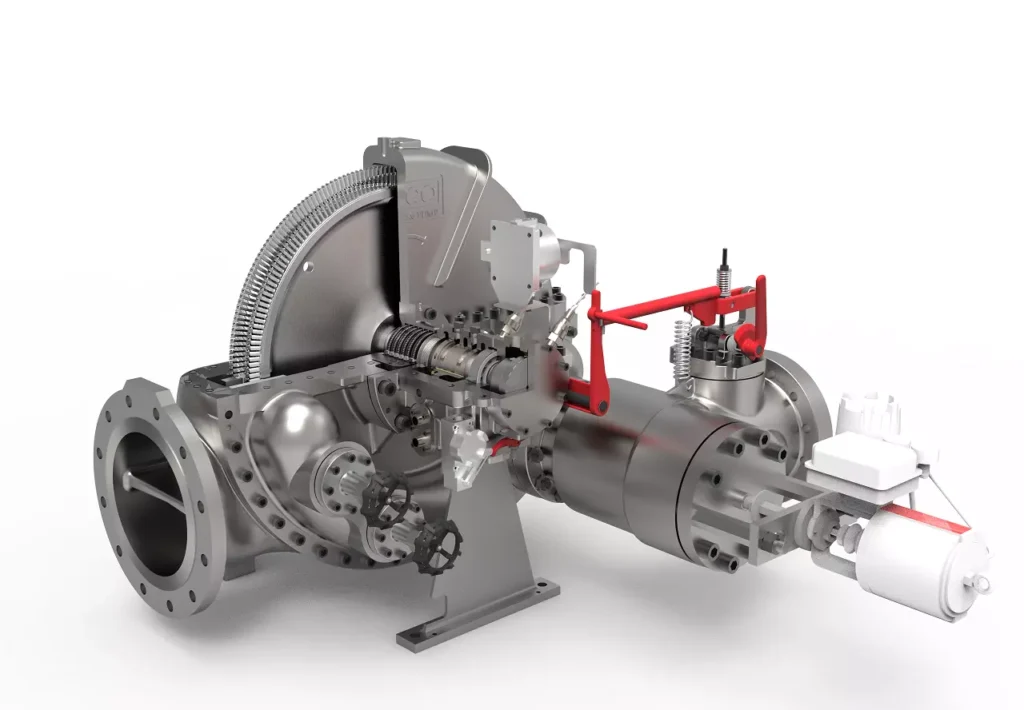
A steam turbine is a mechanical device that converts thermal energy from steam into rotational mechanical energy. This process plays a vital role in power generation, particularly in the context of large-scale power plants. The steam turbine operates on the principle of converting the pressure energy of steam into kinetic energy, which then turns a rotor attached to a generator, producing electricity. Steam turbines are commonly used in both industrial and electrical applications, where their ability to efficiently convert heat into work makes them an essential part of power generation infrastructure.
Steam turbines work based on the thermodynamic principles of the Rankine cycle, which involves the heating of water to produce steam that is then expanded through a series of blades or rotors. The steam is directed onto the turbine blades at high pressure, causing them to rotate. The rotational energy is transferred to the turbine shaft, which is connected to a generator to produce electrical power. After passing through the turbine, the steam is condensed back into water and returned to the boiler to begin the cycle anew. This continuous cycle of steam generation, expansion, and condensation is key to the operation of steam turbines.
The construction of a steam turbine is a complex process, involving a number of key components. The main parts include the rotor, stator, nozzles, and blades. The rotor is the central part of the turbine, consisting of a shaft and a series of blades. The stator houses the nozzles that direct steam onto the blades and serves as a stationary part of the turbine. The blades themselves are designed to capture the energy from the steam and convert it into rotational force. In addition to these components, steam turbines also include a series of seals, bearings, and other auxiliary systems to ensure smooth operation and prevent leakage of steam.
The performance of a steam turbine is influenced by various factors, including the pressure, temperature, and flow rate of the steam entering the turbine, as well as the design of the turbine itself. Higher pressure and temperature steam typically result in higher efficiency, as the turbine can extract more energy from the steam. Additionally, the efficiency of a steam turbine is influenced by the quality of the steam, which should be dry and free of impurities. Impurities such as water droplets or contaminants can cause erosion or damage to the turbine blades, reducing its efficiency and lifespan.
Steam turbines are available in a wide range of sizes and configurations to meet different power generation requirements. Smaller turbines are typically used in industrial applications, such as cogeneration plants or district heating systems, where they generate both electricity and heat. Larger turbines, on the other hand, are used in utility-scale power plants, where they generate electricity by expanding steam produced in large boilers. These turbines are typically coupled with generators and other power plant equipment to form a complete system that can produce a steady supply of electricity to the grid.
In addition to their use in power generation, steam turbines are also employed in other industries, including petrochemical, marine, and industrial applications. In the marine industry, steam turbines are used to power large ships, providing the necessary thrust to propel the vessel through the water. In petrochemical refineries, steam turbines are often used to drive compressors or other equipment, providing mechanical power for various processes. Industrial applications also make use of steam turbines in cogeneration systems, where both electricity and useful heat are produced for industrial processes.
As with any complex mechanical system, steam turbines require regular maintenance to ensure optimal performance and longevity. Common maintenance tasks include monitoring the turbine’s vibration levels, temperature, and pressure, as well as inspecting the blades and other components for signs of wear or damage. Over time, turbine blades can become eroded or cracked due to the high-pressure steam and mechanical stresses, which can reduce the turbine’s efficiency and increase the risk of failure. Routine inspection and maintenance are essential for preventing such issues and ensuring the continued reliable operation of the turbine.
One of the key factors driving the development of steam turbine technology is the ongoing push for higher efficiency and reduced environmental impact. As the demand for clean energy continues to grow, the efficiency of steam turbines has become a focal point in the design of modern power plants. Advanced steam turbines are being developed to operate at higher temperatures and pressures, allowing them to achieve greater efficiency and generate more electricity from less fuel. These advanced turbines are also designed to reduce emissions, making them an important part of the transition to cleaner, more sustainable energy systems.
To improve turbine efficiency, manufacturers have been incorporating new materials and technologies into steam turbine design. For example, the use of advanced alloys and coatings can help increase the turbine’s resistance to high temperatures and corrosive environments, allowing the turbine to operate more efficiently at higher temperatures. In addition, new blade designs and turbine configurations are being developed to maximize the energy extraction from the steam while minimizing losses due to friction and turbulence.
In recent years, steam turbines have also been adapted to accommodate the growing need for flexibility in power generation. As renewable energy sources such as wind and solar power become more prevalent, power plants must be able to respond quickly to fluctuations in energy demand. Steam turbines, once primarily used in base-load plants, are now being adapted for use in peaking plants, where they can quickly ramp up or down their output to meet changing grid conditions. This flexibility is essential for integrating renewable energy into the power grid, as it allows steam turbines to provide backup power when renewable sources are not generating enough electricity to meet demand.
One of the key advantages of steam turbines is their ability to operate in combined-cycle systems, where the waste heat from the turbine is used to generate additional power. In a combined-cycle plant, the exhaust steam from the turbine is passed through a heat recovery steam generator (HRSG), where it is used to produce steam that drives a second turbine, often a gas turbine. This configuration increases the overall efficiency of the power plant, as it allows for the capture and use of waste heat that would otherwise be lost. Combined-cycle plants are among the most efficient power generation systems in operation today, making them a popular choice for modern energy production.
Despite their advantages, steam turbines also face certain challenges. One of the primary challenges is the wear and tear on turbine components over time. The high temperatures, pressures, and mechanical stresses involved in turbine operation can cause significant damage to the blades, bearings, and other critical parts. While regular maintenance can help mitigate these issues, turbine downtime for repairs or replacements can be costly and disruptive to power generation operations. As such, manufacturers are continually working to improve the durability and longevity of steam turbines, developing new materials and designs that can withstand the harsh operating conditions.
Another challenge facing the steam turbine industry is the growing competition from alternative power generation technologies. Gas turbines, for example, have become increasingly popular in recent years due to their higher efficiency and faster response times. While steam turbines still offer advantages in terms of fuel flexibility and scalability, gas turbines are often seen as more suitable for meeting the growing demand for flexible, on-demand power generation. However, steam turbines remain a key part of the energy landscape, particularly in large-scale power plants and industrial applications.
In conclusion, steam turbines are a crucial technology for modern power generation, offering efficient and reliable means of converting thermal energy into mechanical work. They play a key role in both traditional and emerging energy systems, providing power to the grid and supporting industrial processes. As the demand for cleaner, more efficient energy grows, steam turbines will continue to evolve, with advancements in materials, design, and efficiency driving their development. Despite the challenges posed by alternative technologies, steam turbines remain an integral part of the global energy mix, helping to meet the world’s electricity needs while supporting efforts to reduce carbon emissions and transition to a more sustainable energy future.
Steam turbines will continue to evolve to meet the demands of modern power generation and industrial applications. With the increasing focus on reducing carbon emissions, innovations in steam turbine design are aimed at enhancing their efficiency, reliability, and adaptability. Research and development efforts are exploring ways to improve turbine performance by incorporating more advanced materials and optimizing blade and rotor designs. For example, the use of advanced coatings on turbine blades is becoming more prevalent, helping to reduce corrosion and wear caused by high temperatures and the corrosive nature of the steam. This not only increases the lifespan of the turbine but also helps maintain its efficiency over a longer period of time.
In addition to materials innovations, steam turbines are being designed with enhanced aerodynamics and thermodynamic efficiency. By reducing energy losses due to friction and turbulence, manufacturers can achieve higher power outputs with less fuel. This is particularly important as the global energy landscape shifts toward more sustainable power generation. Advanced steam turbines are designed to operate at higher pressures and temperatures, which increases the overall energy extracted from the steam and improves overall plant efficiency. These high-efficiency turbines are essential in maximizing the potential of both fossil fuels and renewable sources of energy, ensuring that power plants can continue to operate sustainably while minimizing environmental impacts.
As the power grid continues to modernize, steam turbines are also being adapted to work alongside emerging technologies, such as energy storage systems and hybrid power plants. The combination of steam turbines with energy storage solutions, such as battery storage or pumped hydro storage, can provide additional flexibility to meet fluctuating energy demands. For instance, when renewable generation is abundant, the excess energy can be stored and later used to supplement power generation during times when renewable resources are unavailable. This synergy allows steam turbines to play an active role in supporting grid stability, especially as renewable energy becomes an increasingly large part of the energy mix.
Moreover, the digitalization of the energy industry is transforming how steam turbines are monitored and managed. Digital twins, for example, offer a virtual representation of the turbine, allowing operators to monitor and simulate turbine performance in real-time. This advanced technology helps operators predict maintenance needs, optimize turbine performance, and identify potential issues before they lead to costly breakdowns. With integrated digital platforms, operators can analyze data from turbine sensors to improve decision-making and make real-time adjustments to optimize turbine operation. As the energy sector embraces more digital tools, steam turbine operators will have greater control over turbine efficiency and the ability to quickly respond to changes in demand or plant conditions.
In addition to performance enhancements, steam turbines are also becoming more adaptable to the integration of alternative fuels. The drive for a low-carbon future means that many steam turbines are being designed or retrofitted to accommodate fuels such as biomass, hydrogen, or synthetic gases. By adapting to these fuels, steam turbines can help power plants transition away from traditional fossil fuels like coal and natural gas, reducing greenhouse gas emissions and supporting the global effort to decarbonize the energy sector. The ability to burn alternative fuels in steam turbines also enhances fuel security and reduces reliance on a single energy source, making the overall power generation system more resilient.
The trend toward greater flexibility in power generation also means that steam turbines are increasingly being used in applications where fast ramp-up and ramp-down capabilities are necessary. While traditional steam turbines were often used in base-load plants that operated continuously at full capacity, modern steam turbines are being designed to handle more variable loads. These turbines can quickly adjust their output to meet sudden changes in electricity demand, allowing power plants to provide backup or peaking power when renewable energy generation fluctuates or during periods of high demand. This ability to rapidly respond to grid requirements is essential for maintaining the stability of the electrical grid as more renewable energy sources are integrated.
Steam turbines are also playing an important role in the development of carbon capture, utilization, and storage (CCUS) technologies. As governments and industries work toward reducing CO2 emissions, many power plants are being equipped with CCUS systems to capture carbon dioxide emissions before they are released into the atmosphere. The energy required for these systems is often provided by steam turbines, which can use the waste heat from the power generation process to drive the carbon capture equipment. This integration of steam turbines with CCUS helps make power generation more sustainable by reducing the carbon footprint of conventional power plants.
Despite the many advancements, challenges remain for the steam turbine industry. One of the primary challenges is the need for continuous innovation to keep pace with evolving energy demands and environmental regulations. As global energy consumption grows and the pressure to reduce emissions increases, the steam turbine industry must continue to develop more efficient and environmentally friendly solutions. Additionally, steam turbines must compete with newer technologies, such as gas turbines and renewables, which may offer faster response times or higher efficiencies in some applications. However, the versatility of steam turbines, particularly in combined-cycle plants, ensures that they will remain a valuable part of the energy mix for the foreseeable future.
As the energy industry undergoes a transformation toward decarbonization, steam turbines are being called upon to support the transition from conventional, fossil fuel-based power generation to cleaner, more sustainable systems. With advances in turbine design, materials, and digitalization, steam turbines are becoming more efficient, flexible, and adaptable. Their ability to provide reliable power generation while supporting the integration of renewable energy sources, energy storage, and carbon capture technologies positions steam turbines as a key technology in the future energy landscape. As the industry continues to evolve, steam turbines will remain integral to meeting the growing global demand for clean, reliable, and efficient energy.
The future of steam turbines lies in their continued ability to adapt to new technological, environmental, and economic challenges. With the ongoing evolution of energy systems worldwide, steam turbines are increasingly being integrated into hybrid power plants that combine multiple energy sources to optimize performance and efficiency. These plants can combine steam turbines with renewable energy sources like solar or wind, as well as energy storage systems, to provide a more flexible, reliable, and sustainable power supply. Hybridization of power plants ensures that when renewable energy is unavailable due to intermittency or weather conditions, steam turbines can quickly provide backup power, filling the gaps and maintaining grid stability.
As renewable energy capacity expands, the need for efficient energy storage solutions becomes more critical. Steam turbines can play a crucial role in facilitating energy storage by providing a reliable backup when storage systems are deployed. For instance, in concentrated solar power (CSP) plants, steam turbines are used to convert thermal energy from solar heat into electricity. In these setups, solar collectors capture and store heat during the day, which can then be used to generate steam that drives a turbine, enabling electricity generation even when the sun isn’t shining. This kind of hybrid system can bridge the gap between intermittent renewable generation and consistent energy demand, improving the overall reliability and efficiency of the energy grid.
Another area of development in steam turbine technology is the ongoing integration with the digital transformation of the energy sector. The use of advanced analytics, machine learning, and AI in turbine monitoring systems is providing operators with new insights into the health of the turbine, enabling predictive maintenance and real-time decision-making. By continuously gathering and analyzing data from sensors placed throughout the turbine, operators can detect early warning signs of potential failures, such as vibrations, overheating, or component degradation. These insights allow for more precise maintenance schedules, minimizing downtime and maximizing the lifespan of the turbine. Furthermore, digital twin technology allows for the creation of a virtual model of the turbine, which can simulate various operational conditions and provide a platform for optimization.
Digitalization is also making it possible to enhance the control and optimization of steam turbines. With the integration of advanced control algorithms, steam turbines can automatically adjust their operating parameters based on real-time feedback, ensuring that they are operating at their highest efficiency while maintaining grid stability. These control systems enable turbines to respond quickly to fluctuations in demand or supply, allowing them to maintain optimal performance even in a rapidly changing energy environment.
Steam turbines are also being integrated into decentralized energy systems, such as microgrids and off-grid power solutions. These smaller, localized energy systems are becoming increasingly popular due to their ability to provide reliable, renewable energy in areas with limited access to a centralized power grid. Steam turbines, particularly when combined with renewable energy sources like biomass or geothermal, can be used to generate electricity in these decentralized systems. Their adaptability allows them to handle the fluctuating demands of smaller-scale applications while contributing to a cleaner and more resilient energy system.
In terms of fuel flexibility, the ability of steam turbines to burn a variety of fuels, including biomass, natural gas, and even hydrogen, makes them highly adaptable to the needs of the energy sector. Biomass, as a renewable fuel source, offers the potential for carbon-neutral power generation when paired with steam turbines, making them an important tool for meeting global sustainability goals. Furthermore, as hydrogen energy becomes more viable and cost-effective, steam turbines can be retrofitted or designed to burn hydrogen as a fuel, reducing the overall carbon footprint of power plants. This capability positions steam turbines as versatile components in the transition to a low-carbon future, offering an essential bridge between current fossil fuel-based systems and more sustainable energy solutions.
The development of ultra-supercritical steam turbines is another significant advancement in the field. These turbines operate at much higher pressures and temperatures than traditional supercritical turbines, allowing for increased efficiency and reduced emissions. Ultra-supercritical turbines are becoming more common in new coal-fired power plants as they can extract more energy from the steam, resulting in less fuel consumption and lower greenhouse gas emissions. This technology is also being explored in other sectors, including gasification and integrated gasification combined cycle (IGCC) systems, which use a variety of feedstocks to produce electricity. These systems, when combined with advanced carbon capture technologies, can offer a pathway to decarbonized power generation while still utilizing fossil fuels.
In the broader context of energy transition, steam turbines also play a role in supporting the industrial sector’s shift toward cleaner energy. Many industries rely on steam turbines for combined heat and power (CHP) applications, where both electricity and useful heat are generated from the same source. CHP systems, which use steam turbines to produce electricity while simultaneously using the waste heat for industrial processes such as heating, drying, or chemical production, significantly improve energy efficiency. By using steam turbines in CHP configurations, industries can reduce their reliance on external power sources, lower energy costs, and reduce their carbon emissions.
The demand for higher efficiency, greater flexibility, and lower emissions is driving continued research and development in steam turbine technology. Manufacturers are focusing on improving turbine performance by developing advanced blade materials, enhancing steam conditions (temperature, pressure, and flow), and implementing better designs for minimizing energy losses. The ongoing trend toward automation and digitalization in power plants is improving turbine control, operation, and maintenance, making it possible to operate turbines with greater precision and reliability.
One of the most promising areas of innovation in steam turbine technology is the development of hybrid steam turbine systems. These systems combine the benefits of steam turbines with other energy conversion technologies, such as gas turbines, to improve overall plant efficiency. For instance, a combined cycle plant that integrates both steam and gas turbines can achieve much higher efficiencies than either turbine type operating alone. Gas turbines provide quick ramp-up times and high efficiencies at part-load operations, while steam turbines can operate efficiently at full load, taking advantage of the waste heat generated by the gas turbine. This integration of steam and gas turbines in hybrid plants is expected to become more widespread as energy demands become more variable and the need for flexible, high-efficiency power plants grows.
In conclusion, steam turbines continue to be a cornerstone of modern energy generation, supporting the production of electricity in both conventional and renewable energy systems. The ongoing development of steam turbine technology, combined with innovations in materials, control systems, and fuel flexibility, ensures that steam turbines will remain relevant in the transition to a cleaner, more sustainable energy future. Whether integrated into large-scale power plants, hybrid systems, or decentralized energy solutions, steam turbines are evolving to meet the demands of a rapidly changing energy landscape, providing reliable, efficient, and flexible power for generations to come.
The continuous development of steam turbine technology is increasingly focused on increasing efficiency, reducing emissions, and improving adaptability in response to the evolving global energy landscape. Innovations in design and material science are helping steam turbines operate at even higher levels of performance and sustainability. These advancements are especially crucial as the global push toward decarbonization intensifies, and the energy sector strives to balance increasing demand with lower environmental impact.
One of the key trends in steam turbine development is the pursuit of even higher efficiency levels. This is being achieved through innovations such as advanced heat exchangers, which improve the heat recovery process, and the introduction of new turbine blade designs. These blades are optimized to handle higher stress and temperature conditions, reducing energy losses and improving overall performance. High-efficiency turbines are particularly important in combined-cycle power plants, where waste heat from one turbine is used to generate additional power. In this way, advanced steam turbines are contributing significantly to reducing fuel consumption and emissions, making them an integral part of future energy systems.
The growing need for flexibility in energy generation is also pushing steam turbine technology forward. As renewable energy sources like wind and solar become more widespread, power plants must be able to accommodate the intermittent nature of these energy sources. Steam turbines, particularly those used in combined-cycle plants, offer the flexibility needed to respond quickly to fluctuations in renewable energy output. They can ramp up or down rapidly to meet changes in demand, providing backup power during periods of low renewable generation. This characteristic makes steam turbines a crucial component in maintaining grid stability as the share of renewable energy in the energy mix grows.
Another area of focus is the integration of steam turbines into emerging low-carbon technologies. Carbon capture, utilization, and storage (CCUS) are becoming increasingly important for mitigating the environmental impact of fossil fuel power plants. Steam turbines are often used to drive the systems that capture CO2 emissions, enabling power plants to operate more sustainably while reducing their carbon footprint. The use of steam turbines in CCUS applications aligns with the global effort to reduce greenhouse gas emissions and combat climate change, further solidifying their role in the future energy landscape.
As the energy sector shifts toward more decentralized and distributed systems, steam turbines are also finding new applications. Microgrids, which can operate independently or in conjunction with the main power grid, often rely on steam turbines to provide reliable, local power generation. These small-scale systems are especially useful in remote areas or regions with unreliable access to the central grid. By integrating steam turbines into these distributed systems, communities can achieve greater energy independence while reducing the need for long-distance transmission and distribution infrastructure.
The potential for using steam turbines in conjunction with alternative fuels is another exciting development. Biomass, hydrogen, and other renewable fuels are gaining traction as cleaner alternatives to fossil fuels. Steam turbines are highly adaptable and can be modified to burn these alternative fuels efficiently. Biomass power plants, for example, often use steam turbines to generate electricity by burning organic materials such as wood pellets, agricultural waste, or dedicated energy crops. These plants offer a way to reduce greenhouse gas emissions while providing a renewable source of energy. Likewise, hydrogen is becoming an increasingly important fuel source due to its clean-burning properties, and steam turbines are being adapted to handle hydrogen combustion, further expanding their versatility.
The role of steam turbines in the decarbonization of the global energy system is underscored by their ability to operate with fuels that produce zero or low emissions. When integrated into systems that utilize renewable fuels or even renewable hydrogen, steam turbines can help power plants operate with little to no carbon output. These technologies will become increasingly important in industries like heavy manufacturing and transportation, which are traditionally more difficult to decarbonize. In such contexts, steam turbines can be used in combination with other technologies to produce low-carbon industrial heat and power, further driving the transition to a greener economy.
The demand for reduced operational costs, improved uptime, and lower maintenance needs is also pushing steam turbine manufacturers to innovate. With the use of advanced monitoring and diagnostic systems, operators can better understand the condition of the turbine and predict potential failures before they happen. Predictive maintenance technologies are transforming the way steam turbines are serviced and managed. These systems rely on data analytics, sensors, and machine learning to monitor turbine performance in real time, providing operators with actionable insights to optimize performance, reduce energy waste, and prevent costly downtimes. By predicting when and where maintenance is needed, predictive maintenance can minimize the risk of catastrophic failures and extend the lifespan of the turbines, thereby reducing long-term operational costs.
Additionally, the digitalization of the energy industry has made it possible for operators to optimize steam turbine performance remotely. Through the use of digital twins, which are virtual replicas of the turbine, operators can simulate various operating conditions and test different parameters without physically adjusting the turbine. This not only allows for better optimization of performance but also enables more effective troubleshooting. The increasing reliance on digital platforms allows for more effective control, optimization, and operation of steam turbines in diverse environments, providing greater operational flexibility and reducing costs.
As the energy sector increasingly relies on a combination of renewable energy sources, energy storage, and advanced power generation systems, steam turbines are expected to remain an essential part of the global energy infrastructure. While new technologies, such as gas turbines and energy storage systems, may offer advantages in certain areas, steam turbines will continue to provide a proven, reliable, and flexible solution for both large-scale and small-scale power generation. Their ability to integrate with diverse energy systems, adapt to a range of fuel types, and provide a steady, reliable power output will keep steam turbines in demand for the foreseeable future.
The transition to a more sustainable energy system, driven by the need to reduce greenhouse gas emissions, will continue to shape the development of steam turbine technology. Advances in efficiency, fuel flexibility, and digitalization will ensure that steam turbines remain a key part of the energy mix, supporting the global shift toward cleaner, more resilient power generation. As these innovations unfold, steam turbines will continue to play a crucial role in providing reliable, cost-effective, and low-carbon energy to meet the needs of an ever-changing world.
Governing System
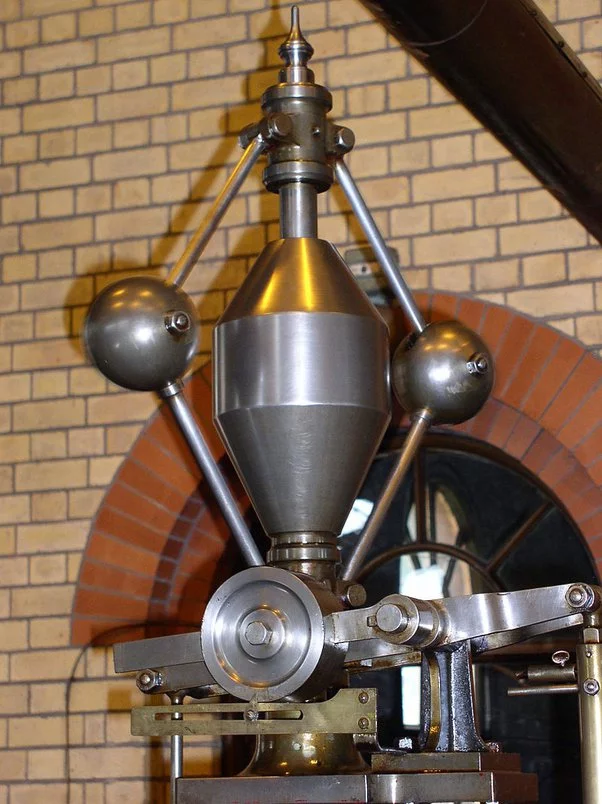
The governing system of a steam turbine is an integral component of its overall operation, ensuring that the turbine runs efficiently and reliably under varying load conditions. The purpose of a governing system is to maintain the speed of the turbine within prescribed limits, regardless of fluctuations in load, steam pressure, or other operational factors. This is achieved by adjusting the flow of steam into the turbine, either by controlling the steam valves or adjusting the nozzles, ensuring that the turbine speed stays consistent and that the generator or mechanical load attached to the turbine operates at the desired speed.
In its simplest form, a steam turbine governing system uses a mechanical governor, which is a device that senses changes in turbine speed and adjusts the steam flow accordingly. Traditionally, these systems were purely mechanical, relying on centrifugal force to detect speed variations. However, modern governing systems have evolved to incorporate advanced electronic control systems that provide greater precision and responsiveness. These modern systems rely on a variety of sensors, actuators, and control algorithms to maintain the turbine’s operational parameters and optimize performance.
The governing system works by continuously monitoring the turbine’s speed through speed sensors. If the turbine speed increases above the desired value, the system responds by reducing the steam flow, which in turn decreases the speed of the turbine. Conversely, if the speed drops below the set point, the system increases the steam flow to raise the speed. The key is to achieve a stable, continuous adjustment that maintains the correct speed despite changes in operational conditions. This is particularly important in power plants or industrial facilities where turbines need to operate under varying loads or with fluctuating steam pressure.
One of the most important functions of a governing system is to provide a stable output in response to changes in demand. In electricity generation, the governing system ensures that a steam turbine’s output matches the load requirements of the power grid, providing a stable supply of electricity to meet consumer demand. As grid demand increases, the governing system increases the steam input to the turbine to maintain the output, and as demand decreases, the system reduces steam flow to prevent oversupply. This balancing act is crucial for maintaining the reliability and stability of the power grid, especially in systems that rely on variable energy sources like wind or solar power.
Modern governing systems typically consist of several key components: speed sensors, control valves, actuator systems, and control mechanisms. The speed sensors constantly monitor the rotational speed of the turbine. The control valves are responsible for regulating the amount of steam entering the turbine. Actuators are used to adjust the control valves based on the information provided by the control system, which interprets the signals from the speed sensors and adjusts the steam flow accordingly. The control system, often based on a microprocessor or a digital controller, processes the data from the sensors and determines the appropriate response. It uses a feedback loop to maintain the turbine speed within a specified range.
The sophistication of modern governing systems allows for greater flexibility and efficiency in turbine operation. Many modern systems incorporate digital technology, such as programmable logic controllers (PLCs) or distributed control systems (DCS), which offer improved precision, real-time monitoring, and enhanced diagnostic capabilities. These systems can not only maintain the turbine speed but also monitor other key operational parameters, such as temperature, pressure, and vibration, to ensure optimal performance and safety. Advanced control algorithms can adjust the steam flow dynamically to optimize efficiency, taking into account factors like turbine load, steam quality, and environmental conditions.
In addition to controlling the turbine speed, the governing system can also play a role in protecting the turbine from operating outside of safe parameters. In situations where the turbine may experience sudden changes in load, steam quality, or pressure, the governing system can respond rapidly to prevent over-speed or overloading. This safety feature is essential in ensuring that the turbine operates within its mechanical and thermal limits, preventing damage to components or systems.
Another important aspect of governing systems is their integration with the overall power plant control system. The governing system must communicate with other systems in the plant, such as the boiler control system and the load management system, to ensure smooth and coordinated operation. For example, in a combined-cycle power plant, the governing system of the steam turbine needs to coordinate with the gas turbine’s governing system to ensure the two turbines operate in harmony, optimizing plant efficiency and minimizing fuel consumption. This requires precise synchronization of the steam and gas turbines, which is made possible by the governing system’s ability to adjust steam flow based on real-time plant conditions.
The development of advanced governing systems has also led to improvements in the overall energy efficiency of steam turbine-driven systems. By maintaining the turbine speed within an optimal range and adjusting steam input dynamically, modern governing systems help minimize energy waste, reduce fuel consumption, and optimize turbine performance. In turn, this contributes to the overall efficiency of the power generation process, which is essential in both reducing operational costs and minimizing environmental impacts.
As renewable energy integration becomes more prevalent in the power grid, governing systems will need to evolve to handle the increasing variability of power supply and demand. The ability of governing systems to respond rapidly and precisely to changes in demand or supply will be crucial in ensuring the stability and reliability of the grid. For example, when there is a sudden drop in renewable generation due to cloud cover or a sudden change in wind speed, the governing system must respond quickly to provide backup power from the steam turbine to maintain grid stability.
Furthermore, with the growing emphasis on digitalization in the energy sector, governing systems are becoming smarter, more automated, and capable of interacting with other systems in real time. The integration of Internet of Things (IoT) technology and machine learning algorithms allows governing systems to continuously optimize turbine performance by learning from historical data and real-time operational conditions. This not only improves turbine efficiency but also enhances the accuracy of predictive maintenance, helping to identify potential issues before they lead to failure.
For power plants that incorporate combined heat and power (CHP) systems, governing systems are critical in ensuring that both electricity and heat are produced efficiently. The governing system adjusts the steam flow to meet both the electrical and thermal demands of the plant, ensuring that both forms of energy are generated without compromising the performance of the turbine or the efficiency of the overall system. In industrial applications, where steam turbines are often used for mechanical drive or for powering compressors, pumps, and other equipment, the governing system ensures that the steam turbine operates in sync with the energy needs of the facility.
In conclusion, the governing system of a steam turbine plays a critical role in ensuring stable, efficient, and safe operation. Through its ability to maintain the turbine’s speed within a specified range, adjust steam flow in response to varying conditions, and protect the turbine from operational extremes, the governing system helps optimize turbine performance and contributes to the overall efficiency of power generation systems. As energy systems evolve and become more complex, governing systems will continue to advance, incorporating digital technologies and adaptive control strategies to meet the demands of modern power grids and industrial applications.
As the energy landscape evolves and increasingly incorporates renewable energy sources, the role of the governing system in steam turbines will continue to expand. With the integration of wind, solar, and other intermittent renewable sources, the grid’s supply becomes more unpredictable, making it essential for governing systems to respond more dynamically. This adaptability will ensure that steam turbines can smoothly balance fluctuations in grid demand, especially when renewable generation surges or drops unexpectedly. Steam turbines, with their ability to operate efficiently over a wide range of loads, are well-positioned to provide backup power when renewable sources falter, and governing systems will be essential in achieving that balance.
In modern power plants, the coordination between steam turbine governing systems and other plant systems is crucial. The plant-wide control systems, often digital in nature, help ensure that steam turbines operate efficiently by aligning their performance with that of other plant components, including the boiler, cooling system, and auxiliary equipment. Through advanced communications and control, the governing system can synchronize the turbine with the overall energy generation process, leading to improved system efficiency and reduced fuel consumption.
One significant advancement in turbine governing systems is the growing use of artificial intelligence (AI) and machine learning (ML) to enhance system performance. By collecting large amounts of operational data from turbines and analyzing it using AI and ML algorithms, operators can optimize the governing system’s responses to a variety of scenarios. These systems can learn from historical data and predict future turbine behavior under various conditions. As a result, governing systems become more proactive, detecting potential performance issues before they arise and adjusting control strategies in real time to maintain optimal turbine operation. This predictive capability helps reduce the risk of turbine failures, minimizes downtime, and ensures that turbines run at their most efficient levels.
Further advancements in digitalization, such as cloud-based systems and real-time data analysis, are making governing systems even more powerful and responsive. With cloud-based technologies, operators can monitor and control the turbine’s performance remotely, allowing for more flexibility and faster decision-making. These platforms can aggregate data from multiple turbines across different plants, providing insights into performance trends and potential areas for optimization. Cloud computing also enables better collaboration between operational teams, allowing for more coordinated and informed decision-making, improving overall plant management.
Additionally, as environmental regulations become more stringent, governing systems will need to play a larger role in ensuring that turbines comply with emission standards. For example, modern governing systems can adjust the turbine’s operating parameters to minimize emissions, ensuring that the plant stays within regulatory limits while maintaining high efficiency. This can involve adjusting steam flow, optimizing fuel consumption, or ensuring that combustion temperatures remain at the ideal levels to reduce NOx, SOx, and particulate emissions. The integration of the governing system with environmental monitoring systems will be crucial in meeting these demands and supporting the transition to cleaner, more sustainable energy production.
The development of hybrid power plants, which combine multiple forms of energy generation, also relies on the flexibility and responsiveness of governing systems. For example, plants that use both steam turbines and gas turbines or other renewable technologies need governing systems that can ensure these components operate in harmony. When one energy source is unavailable or in short supply, the governing system ensures that the other systems compensate for the loss. This hybrid operation helps ensure that power generation remains stable and efficient, reducing the risk of outages and allowing for more flexibility in the face of changing energy demands.
In industries such as oil, gas, and chemical manufacturing, where steam turbines are used for mechanical drive applications, the governing system plays an important role in ensuring that the turbine operates efficiently under varying load conditions. For example, in a refinery or petrochemical plant, steam turbines are often used to drive compressors, pumps, and other equipment that are critical to the production process. The governing system ensures that the turbine maintains the correct speed to drive these processes efficiently while preventing excessive wear on the turbine and reducing energy consumption. This helps keep production costs low and ensures that the plant remains competitive in a market that increasingly demands energy efficiency.
In addition to operational benefits, advanced governing systems can also help optimize the lifecycle costs of steam turbines. By ensuring that turbines operate within optimal parameters, governing systems can reduce wear and tear on turbine components, extending their operational lifespans. With predictive maintenance capabilities, governing systems help reduce the likelihood of catastrophic failures, which can result in expensive repairs and extended downtime. In turn, this reduces the total cost of ownership over the turbine’s life cycle and improves the return on investment for power plant operators.
The continuous advancements in turbine governing systems also support the trend toward smaller-scale, distributed power generation systems. Microgrids and local energy systems, which often rely on steam turbines for backup or base-load power, require governing systems that can manage the turbine’s performance efficiently in small, decentralized settings. The ability of governing systems to work seamlessly in these distributed applications helps ensure that even remote or off-grid locations can access reliable, efficient power generation.
In the future, as energy systems become more decentralized and interconnected, governing systems will become more important than ever. The ability to monitor, control, and adjust the operation of turbines will be key to maintaining grid stability and ensuring a reliable energy supply in a world increasingly dominated by renewable sources. Additionally, as the push for decarbonization continues, governing systems will play a vital role in optimizing turbines for low-carbon fuels such as hydrogen and biomass, ensuring that they can operate with minimal environmental impact.
In conclusion, the governing system of a steam turbine is a crucial component in ensuring its stable, efficient, and safe operation. From maintaining turbine speed to optimizing efficiency and reducing emissions, governing systems are critical to the smooth operation of power plants, industrial facilities, and other energy generation systems. With advancements in digitalization, artificial intelligence, and real-time data analysis, these systems are becoming smarter and more capable of adapting to the evolving needs of the energy sector. As energy demands increase, and the global energy landscape continues to shift toward more sustainable and decentralized solutions, the importance of an efficient and responsive governing system will only grow. Steam turbine governing systems are evolving alongside these changes, ensuring that turbines continue to play a vital role in the energy generation mix for years to come.
As the energy sector continues to innovate and evolve, the role of the governing system in steam turbines will become even more critical in ensuring the efficiency, sustainability, and flexibility of energy generation. The increasing integration of renewable energy, energy storage, and advanced grid management systems will necessitate that governing systems in steam turbines become more intelligent and adaptive. These systems must not only manage the basic operation of the turbine but also be capable of responding to complex grid conditions, supporting the integration of fluctuating renewable energy sources, and meeting increasingly stringent environmental regulations.
A key area of development is the incorporation of advanced control strategies that enable steam turbines to operate seamlessly with energy storage systems. As renewable energy sources like wind and solar power become more common, their intermittent nature can create challenges for grid stability. Steam turbines, with their ability to provide flexible, fast-response power generation, are well-suited to complement renewables. The governing system must be able to adjust the turbine’s performance in real time to match the variability of renewable energy generation, allowing the steam turbine to quickly ramp up or down to balance supply and demand. Additionally, the integration of energy storage technologies like batteries or pumped hydro storage can help smooth out the fluctuations of renewable energy, and the governing system can coordinate with these storage systems to optimize energy distribution and ensure grid stability.
In parallel with renewable integration, the global trend towards decentralized energy generation means that steam turbines are increasingly being used in smaller, distributed systems. This could involve microgrids, local combined heat and power (CHP) plants, or industrial applications where steam turbines provide reliable, on-site power generation. In these cases, governing systems must be able to handle a variety of operating scenarios, ensuring that turbines can function efficiently and reliably in small-scale or remote settings. Moreover, the governing system must interface with other systems within the local grid, enabling dynamic control and integration with distributed energy resources such as solar panels, battery storage, and demand response mechanisms.
As digital technologies continue to penetrate the energy industry, the governing systems of steam turbines will increasingly rely on advanced data analytics, artificial intelligence (AI), and machine learning (ML). These technologies will enable the system to predict potential issues before they arise, optimize the turbine’s performance across a wide range of operating conditions, and ensure the turbine operates at peak efficiency. AI algorithms, for example, can analyze large sets of operational data to identify patterns, anticipate performance degradation, and recommend maintenance actions. By continuously learning from real-time data, these intelligent governing systems can make adjustments to steam flow, speed, and other parameters in real time to keep the turbine running at optimal efficiency.
Another key area of development is the ability of governing systems to handle alternative fuels. As the world transitions towards cleaner energy sources, steam turbines must adapt to handle a variety of fuels, including biomass, hydrogen, and synthetic fuels. These fuels, which are often produced from renewable sources, require precise control and management during combustion to ensure optimal turbine performance. The governing system must be able to adjust the steam flow and combustion parameters to ensure the turbine operates efficiently and produces minimal emissions. For example, hydrogen combustion requires different operational parameters compared to natural gas or coal, and the governing system must be capable of adapting quickly to these changes.
The ability to operate with low-emission fuels also ties into the broader trend of decarbonization in the energy sector. Governments and industry leaders are increasingly focusing on reducing carbon emissions, and steam turbines are expected to play a significant role in this transition. By incorporating advanced emission control technologies into the governing system, steam turbines can help meet regulatory standards for greenhouse gases, particulate matter, and other pollutants. The governing system can optimize turbine operation to minimize NOx, CO2, and other harmful emissions, contributing to cleaner, more sustainable energy production.
The future of steam turbine governing systems will also be shaped by the growing importance of grid flexibility. As power grids become more complex, with the integration of both centralized and decentralized energy sources, the ability of governing systems to respond dynamically to changes in grid demand will be crucial. This may involve not just adjusting steam input to match load, but also coordinating with grid management systems to manage voltage, frequency, and other grid parameters. In some cases, governing systems may need to respond to signals from the grid operator, adjusting turbine output in response to changes in overall grid conditions or specific grid events, such as peak demand or faults.
With the increasing demand for high efficiency and low operational costs, predictive maintenance is becoming a vital aspect of steam turbine governance. Instead of relying on scheduled maintenance intervals, predictive maintenance systems use real-time data from sensors embedded in the turbine to assess the health of critical components. This data is analyzed to predict potential failures, such as bearing wear, blade degradation, or fuel system issues. By identifying problems before they cause unplanned downtime, operators can schedule maintenance during periods of low demand or optimize shutdown times, reducing both the costs and the risks associated with turbine failure. The integration of these predictive systems into governing systems helps ensure that turbines run more reliably and cost-effectively over their lifespan.
As the energy market becomes more competitive, operators are looking for ways to optimize not just the performance of individual turbines, but also the entire fleet of turbines within a power plant. Through digital twin technology, operators can create virtual models of steam turbines and simulate their behavior under various conditions. This allows them to optimize the governing system and predict how turbines will respond to different loads, fuels, and operating parameters. By analyzing the virtual model in real time, operators can adjust the governing system to optimize turbine performance, enhance efficiency, and ensure the plant operates as smoothly as possible.
The combination of digitalization, renewable energy integration, and advanced predictive technologies will transform steam turbine governing systems into highly adaptive, efficient, and reliable components of the modern energy landscape. These systems will be essential for maintaining grid stability, optimizing turbine performance, and ensuring that turbines continue to meet the demands of a rapidly changing energy world. As steam turbines become more integral to decarbonization efforts and the integration of renewables, the governing system will evolve to meet these new challenges, helping to create a more sustainable, flexible, and resilient global energy infrastructure.
In conclusion, the governing system in a steam turbine plays an indispensable role in maintaining optimal turbine operation. Through its ability to control steam flow, adjust speed, and ensure operational stability, the governing system ensures that steam turbines can deliver reliable, efficient, and clean power. As the energy industry continues to evolve with the introduction of more renewable sources, smarter grids, and cleaner fuels, governing systems will continue to advance, incorporating cutting-edge technologies such as artificial intelligence, machine learning, and predictive maintenance. These advancements will enhance the flexibility, efficiency, and sustainability of steam turbines, ensuring their continued relevance in the future of global energy production.
Renewable Energy
Renewable energy is a critical component in the transition to a sustainable energy future, as it offers a cleaner alternative to conventional fossil fuels, helping to reduce greenhouse gas emissions, mitigate climate change, and create a more resilient energy infrastructure. Renewable energy sources are derived from natural processes that are constantly replenished, such as sunlight, wind, rain, tides, geothermal heat, and even biomass. Unlike finite fossil fuels like coal, oil, and natural gas, renewable resources are abundant and can be harnessed repeatedly, making them a key element in long-term energy strategies.
Solar energy, one of the most widely adopted forms of renewable energy, harnesses sunlight through solar panels, which convert the sun’s radiation into electricity. Solar photovoltaic (PV) technology has seen significant advances in efficiency and cost reduction over the past few decades. Solar panels are used in a variety of applications, from residential rooftop installations to large-scale solar farms. Additionally, solar thermal systems are used to capture heat from the sun and can be used for applications like water heating or for generating electricity through concentrated solar power (CSP) plants. Solar power’s scalability, from small home systems to large utility-scale plants, makes it highly versatile and adaptable to different needs.
Wind energy, another key renewable resource, harnesses the power of wind to generate electricity. Wind turbines, typically installed in areas with high wind speeds, convert the kinetic energy of the wind into mechanical energy, which is then used to generate electricity. Wind farms can be located onshore, where land-based turbines are installed, or offshore, where turbines are placed in bodies of water to take advantage of stronger and more consistent winds. The cost of wind energy has decreased significantly in recent years, and its potential for growth is vast, particularly in regions with strong wind resources.
Hydropower, which generates electricity from the movement of water, is one of the oldest and most established forms of renewable energy. Hydropower plants can range from large dams that store water and release it through turbines to smaller run-of-river systems that do not require extensive reservoirs. While large-scale hydropower plants have been criticized for their environmental and social impacts, such as habitat destruction and displacement of communities, small-scale and micro-hydro systems offer more sustainable options that minimize ecological disruptions. Hydropower remains a crucial contributor to global renewable energy production and is particularly important in regions with significant river systems.
Geothermal energy taps into the heat stored beneath the Earth’s surface to generate electricity and provide heating. Geothermal power plants are typically located in regions with high geothermal activity, such as areas with active volcanoes or tectonic plate boundaries. These plants use steam or hot water from underground reservoirs to drive turbines that generate electricity. In addition to electricity generation, geothermal energy can also be used for district heating, providing a reliable and constant source of thermal energy. One of the advantages of geothermal energy is that it is available 24/7, unlike solar and wind, which are intermittent. However, its potential is geographically limited to areas with accessible geothermal resources.
Biomass energy involves the conversion of organic materials such as plant and animal waste, wood, or agricultural residues into energy. Biomass can be burned directly for heat or converted into biofuels like ethanol or biodiesel, which can be used as replacements for gasoline or diesel in transportation. Biomass power plants generate electricity by burning organic materials to produce steam, which drives turbines. In addition to biofuels, biogas, which is produced through the anaerobic digestion of organic waste, can also be used to generate electricity or heat. Biomass is considered a renewable resource, as the organic materials used can be regrown or replenished, making it a potentially sustainable energy source. However, the sustainability of biomass depends on factors such as land use, feedstock sourcing, and carbon emissions from combustion.
Ocean energy is an emerging form of renewable energy that captures the power of tides, waves, and ocean currents. Tidal energy systems use the rise and fall of tides to generate electricity, while wave energy technologies harness the motion of ocean waves. Ocean current turbines operate similarly to underwater wind turbines, using the flow of ocean currents to generate power. Although ocean energy has great potential, it is still in the early stages of development, and many of the technologies require further innovation and investment to become commercially viable on a large scale.
Renewable energy offers numerous advantages over traditional fossil fuels. It is abundant, widely distributed across the globe, and produces little to no greenhouse gas emissions during operation, making it a cornerstone of efforts to combat climate change. Additionally, renewable energy systems are becoming increasingly cost-competitive with fossil fuels. As technology advances and economies of scale are achieved, the cost of renewable energy generation has fallen significantly, making it a more affordable option for countries, businesses, and individuals.
Moreover, renewable energy contributes to energy security and resilience by diversifying the energy supply and reducing reliance on imported fossil fuels. Many countries with abundant renewable resources are leveraging this advantage to reduce their dependence on foreign energy sources, enhancing their energy independence and stability. In regions prone to natural disasters or supply disruptions, distributed renewable energy systems like rooftop solar panels, small wind turbines, and off-grid energy solutions can offer greater resilience and reduce the impact of power outages.
The integration of renewable energy into the global energy grid presents certain challenges, primarily due to the intermittent nature of some renewable resources like wind and solar. These sources are not available 24/7 and are subject to fluctuations in weather and time of day. As a result, managing grid stability and ensuring a constant, reliable supply of electricity becomes more complex as the share of renewables increases. To address this challenge, energy storage technologies, such as batteries and pumped storage, are essential. These systems store excess energy generated during periods of high renewable output and release it when demand is high or renewable generation is low. Additionally, advanced grid management techniques, such as demand response and smart grids, are being developed to better integrate renewable energy and balance supply and demand.
Another challenge is the need for infrastructure upgrades to accommodate the increased penetration of renewable energy. Traditional power grids were designed for centralized energy generation from fossil fuels, and integrating large amounts of distributed, variable renewable energy requires significant changes to grid infrastructure. These upgrades may include the expansion of transmission lines to connect renewable energy sources to population centers, the development of smart grid technologies that enable better communication and control, and the establishment of energy storage systems that can provide grid stabilization.
The growth of renewable energy also has significant economic and social implications. The renewable energy sector has created millions of jobs worldwide in manufacturing, installation, operation, and maintenance of renewable energy systems. In addition to job creation, renewable energy can drive economic development in rural areas, where resources like wind, solar, and biomass are often abundant. As renewable energy markets continue to grow, they also stimulate investment in clean technology, innovation, and research, fostering a new, sustainable economy.
Governments around the world have recognized the importance of renewable energy and have introduced policies, subsidies, and incentives to support its development. These efforts are part of broader strategies to reduce greenhouse gas emissions, meet climate targets, and transition to a low-carbon economy. The Paris Agreement, signed in 2015, set a global framework for limiting global warming to below 2°C and pursuing efforts to limit it to 1.5°C, with renewable energy playing a central role in achieving these goals.
Despite the many benefits, the widespread adoption of renewable energy faces barriers such as regulatory hurdles, financing challenges, and resistance from traditional fossil fuel industries. However, with continued technological innovation, supportive policies, and increasing public awareness of the need for sustainable energy, the growth of renewable energy is expected to accelerate in the coming decades. As the world moves towards a cleaner, more sustainable energy future, renewable energy will play a vital role in shaping the way we generate, distribute, and consume power.
As the renewable energy sector continues to expand, innovations in technology, policy, and finance will be crucial in overcoming existing barriers and accelerating the transition to a more sustainable energy system. One area of innovation is the development of next-generation renewable energy technologies that enhance efficiency and lower costs. For example, researchers are working on advanced solar panel technologies, such as tandem solar cells and perovskite-based materials, which could dramatically increase the efficiency of solar power generation while reducing production costs. Similarly, advancements in wind turbine design, such as larger blades and floating offshore turbines, are opening up new possibilities for harnessing wind energy in areas that were previously less viable.
In addition to technological advancements, the integration of renewable energy into existing grids will benefit from more sophisticated forecasting tools and digital technologies. Machine learning and artificial intelligence are being used to improve the accuracy of weather forecasts, which in turn helps grid operators predict renewable energy output more effectively. This predictive capability will be essential for optimizing the use of energy storage and adjusting grid operations to accommodate the variability of renewable resources.
Energy storage is one of the key enablers of a renewable-powered future. While lithium-ion batteries have become the standard for grid-scale storage, research is ongoing into alternative storage technologies that could offer greater efficiency, lower costs, and longer lifespans. Technologies like solid-state batteries, flow batteries, and compressed air energy storage (CAES) are being developed to address some of the limitations of traditional storage systems. These advances could help balance renewable energy supply and demand more effectively, enabling greater reliance on intermittent sources like solar and wind.
Another area where renewable energy can make a significant impact is in the electrification of other sectors, such as transportation, heating, and industrial processes. The use of renewable electricity to power electric vehicles (EVs) is already gaining traction, reducing dependence on fossil fuels in the transportation sector. Similarly, the electrification of heating and cooling systems in buildings, along with the use of heat pumps and other technologies, can reduce the need for natural gas and oil in residential and commercial applications. In the industrial sector, renewable electricity can replace fossil fuels in processes like steel production, cement manufacturing, and chemical production, helping to decarbonize some of the most energy-intensive industries.
Decentralized energy production and consumption will continue to grow in importance as communities, businesses, and individuals look for ways to take control of their energy supply. Small-scale renewable energy systems, such as rooftop solar panels, small wind turbines, and home battery storage, are becoming more affordable and accessible. The rise of microgrids, which are localized energy systems that can operate independently or in coordination with the main grid, is another trend that supports decentralization. These systems enable communities to generate, store, and consume their own energy, reducing reliance on the centralized grid and improving energy resilience, especially in remote or disaster-prone areas.
Policy and regulatory frameworks will be pivotal in shaping the future of renewable energy. Governments around the world have set ambitious renewable energy targets and implemented various incentives to promote clean energy. Feed-in tariffs, tax credits, subsidies, and renewable energy standards are among the mechanisms used to encourage investment in renewable energy projects. As renewable energy becomes a larger share of the global energy mix, policy-makers will need to ensure that the necessary infrastructure and market frameworks are in place to support its growth. This may involve revising existing laws to accommodate new technologies, such as energy storage, smart grids, and electric vehicles, and addressing challenges related to grid integration, system reliability, and equity.
International cooperation will also play a critical role in accelerating the global adoption of renewable energy. Many countries, particularly in the developing world, face challenges in accessing the capital, technology, and expertise needed to scale up renewable energy projects. Global partnerships, financing mechanisms, and knowledge-sharing platforms can help bridge these gaps and ensure that renewable energy benefits are shared equitably across regions. Initiatives like the Green Climate Fund and international renewable energy cooperatives are helping to mobilize investments and provide technical assistance to countries in need.
Public support and engagement are essential to driving the widespread adoption of renewable energy. As awareness of climate change and the environmental impacts of fossil fuels grows, public demand for clean energy solutions is increasing. Consumers are becoming more conscious of their energy choices, and many are actively seeking renewable energy options, whether through purchasing green energy plans from utilities or installing solar panels on their properties. This shift in consumer behavior is putting pressure on utilities and businesses to transition to renewable energy sources. In turn, this is driving further innovation and competition in the renewable energy market, leading to faster adoption and greater investment in clean energy technologies.
The economic opportunities associated with renewable energy are vast. The renewable energy industry has already created millions of jobs worldwide, spanning various sectors such as manufacturing, construction, engineering, research, and project development. As the market grows, so too does the potential for job creation, particularly in emerging economies that are investing in renewable infrastructure. The renewable energy transition also opens up new business opportunities for startups and established companies alike, ranging from solar panel manufacturers to energy storage developers and electric vehicle producers.
In conclusion, renewable energy is a key driver of the global transition to a sustainable energy future. With its vast potential, renewable energy can provide clean, abundant, and cost-effective power that can meet the world’s growing energy demands while reducing environmental impacts. However, realizing this potential requires continued technological innovation, policy support, infrastructure development, and international cooperation. As renewable energy technologies become more advanced, cost-competitive, and integrated into energy systems, the transition to a low-carbon economy will accelerate, offering new opportunities for economic growth, job creation, and environmental protection. The move toward renewable energy is not just an environmental necessity but also an economic and social imperative, shaping a cleaner, more resilient, and more equitable energy future for generations to come.
As we continue to advance in the development and adoption of renewable energy, several key factors will further define the trajectory of this global transition. One important aspect is the role of energy efficiency, which goes hand-in-hand with renewable energy development. By improving the efficiency of energy generation, transmission, and consumption, we can maximize the impact of renewable sources and reduce the overall demand for energy. Innovations in energy-efficient technologies, from high-performance building materials and lighting systems to advanced industrial processes and transportation, will enable society to get more out of every unit of energy, whether it is renewable or not.
Smart grids, another crucial development, are poised to play a major role in integrating renewable energy into the electricity grid. Traditional grids were designed to deliver electricity from a central power plant to consumers in a one-way flow, making it difficult to incorporate the variable nature of renewable sources like solar and wind. Smart grids, however, enable two-way communication between energy producers, storage systems, and consumers, which allows for real-time monitoring and optimization of energy distribution. This enhanced flexibility ensures that renewable energy can be more efficiently integrated into the grid, balancing supply and demand while maintaining system reliability. Furthermore, smart grids can facilitate the use of demand response programs, where consumers can adjust their energy usage in response to signals from the grid operator, contributing to greater grid stability and efficiency.
The development of advanced materials will also significantly impact the future of renewable energy. New materials that enhance the efficiency of solar cells, improve energy storage systems, or enable more efficient wind turbine designs could lead to breakthroughs in renewable energy technology. For example, the development of perovskite solar cells, which promise higher efficiency at a lower cost than traditional silicon-based cells, could revolutionize solar power production. In wind energy, lighter and stronger composite materials could lead to larger, more efficient turbines that can capture more wind energy, particularly in offshore locations.
The hydrogen economy is another area where renewable energy could play a transformative role. Hydrogen is a versatile energy carrier that can be produced from water using renewable electricity through a process called electrolysis. Once produced, hydrogen can be stored, transported, and used in a variety of applications, from powering vehicles to providing heat or electricity for industrial processes. It can even serve as a backup energy source, helping to balance supply and demand when renewable energy generation is low. The use of hydrogen as a clean fuel for transportation, industry, and electricity generation could dramatically reduce global reliance on fossil fuels and help decarbonize some of the hardest-to-electrify sectors. However, the widespread use of hydrogen requires continued advancements in production efficiency, storage technologies, and infrastructure development.
Public and private sector investment in research and development (R&D) will continue to be a driving force in advancing renewable energy technologies. Government funding, alongside private sector innovation, is essential for scaling up renewable energy solutions and addressing the technical, economic, and social challenges of the energy transition. Collaborative R&D efforts between governments, universities, research institutions, and private companies can accelerate the commercialization of emerging technologies, bringing new solutions to market more quickly. Furthermore, international cooperation in R&D can help ensure that renewable energy technologies are accessible and affordable for developing countries, supporting a global transition to clean energy.
One of the most significant challenges in the renewable energy transition is ensuring that the benefits are distributed equitably. While renewable energy offers vast potential, it also requires careful consideration of social, economic, and political factors. As the energy landscape shifts, some regions and communities may face challenges, such as job displacement in traditional energy sectors or limited access to clean energy technologies. It is essential that governments, businesses, and civil society work together to address these disparities by providing job training and reskilling opportunities for workers in fossil fuel industries, ensuring access to affordable renewable energy for all populations, and supporting the development of local renewable energy industries in developing countries.
Global cooperation on climate change and energy policy will also be crucial in driving the renewable energy transition. International agreements, such as the Paris Agreement, have set ambitious climate targets that are impossible to meet without a massive increase in renewable energy production. Countries must work together to establish common goals, share knowledge, and pool resources to tackle the complex and interconnected challenges of climate change, energy security, and sustainable development. Cooperation can also help to create international markets for renewable energy technologies, providing the economies of scale needed to further drive down costs and make clean energy more accessible.
In the coming decades, we will likely see a dramatic shift in how we produce, consume, and think about energy. Renewable energy will not only be the dominant source of power but will also serve as a catalyst for broader societal changes. As more industries, communities, and individuals embrace renewable energy, new business models will emerge that redefine traditional energy systems. For instance, the rise of prosumers—consumers who both produce and consume energy—will lead to new energy-sharing platforms and decentralized markets. This shift will empower individuals and communities to take control of their energy supply, reducing reliance on centralized utilities and providing opportunities for local economic development.
As renewable energy continues to grow, it will also be vital to address the environmental impacts associated with its production and deployment. While renewable energy technologies generally have lower environmental footprints compared to fossil fuels, there are still concerns related to land use, resource extraction, and waste management. For example, the mining of materials for solar panels and wind turbines, such as rare earth elements and lithium, raises environmental and ethical concerns. It will be important to develop sustainable sourcing practices, recycling programs, and circular economy models to minimize these impacts and ensure that renewable energy technologies are truly environmentally responsible.
The future of renewable energy is incredibly promising, with vast potential to meet the world’s energy needs while addressing climate change, improving energy security, and creating economic opportunities. However, realizing this potential will require continued innovation, investment, collaboration, and a commitment to inclusivity. Renewable energy technologies are advancing rapidly, and with the right policies, infrastructure, and support, they will become the cornerstone of a sustainable, low-carbon energy system. As we move toward this future, renewable energy will play a central role in shaping a more equitable, resilient, and sustainable global energy landscape.
Predictive Maintenance
Predictive maintenance is a proactive approach to equipment management that leverages data and advanced analytics to predict when machinery or assets are likely to fail. By identifying potential issues before they result in costly breakdowns, organizations can minimize downtime, optimize operational efficiency, and extend the lifespan of their equipment. Unlike traditional maintenance strategies, which rely on either scheduled maintenance (time-based) or reactive maintenance (repairing equipment after failure), predictive maintenance aims to anticipate problems and address them preemptively, ensuring smooth operations while reducing maintenance costs.
The foundation of predictive maintenance lies in the use of real-time data gathered from various sensors embedded in machines and equipment. These sensors monitor different parameters, such as temperature, vibration, pressure, and speed, and feed this data into a central system for analysis. By continuously monitoring these parameters, predictive maintenance systems can detect anomalies or patterns that suggest potential failures or wear and tear before they reach a critical point. For example, if a sensor detects unusual vibration in a motor, it may indicate that a bearing is deteriorating, allowing maintenance crews to replace the part before it causes a system failure.
Advanced data analytics plays a crucial role in predictive maintenance. Machine learning (ML) and artificial intelligence (AI) algorithms are used to analyze the large amounts of data collected by sensors. These algorithms can identify patterns and trends in the data that would be difficult for humans to detect, allowing maintenance teams to make data-driven decisions. By training models on historical maintenance data, AI systems can predict the likelihood of equipment failure and recommend the most effective course of action. For instance, an AI system might predict that a pump is likely to fail within the next two weeks based on historical data and current performance metrics, giving the maintenance team enough time to schedule the necessary repairs without disrupting operations.
The implementation of predictive maintenance offers a wide range of benefits to organizations across industries. One of the primary advantages is reduced downtime. By predicting when equipment is likely to fail, businesses can plan maintenance activities during scheduled downtime or at a convenient time, minimizing disruptions to operations. This proactive approach also helps prevent unplanned downtime, which can be costly in terms of lost production, repair expenses, and potential damage to surrounding equipment.
Another significant benefit is cost savings. Traditional time-based maintenance often leads to unnecessary repairs or replacements, as parts are replaced on a fixed schedule regardless of their actual condition. Predictive maintenance, on the other hand, allows businesses to replace or repair only the components that need attention, reducing unnecessary expenditures and improving resource allocation. Additionally, by catching issues early, predictive maintenance can help avoid the more expensive costs associated with major equipment failures, such as emergency repairs or the need for new equipment.
Predictive maintenance also contributes to improved asset lifespan and reliability. By identifying and addressing problems before they become severe, businesses can extend the life of their equipment and avoid premature replacement. The ability to optimize equipment use also ensures that assets perform at their best for as long as possible, which is particularly important for industries that rely on high-cost, high-value machinery, such as manufacturing, aviation, and energy.
For organizations looking to implement predictive maintenance, there are several key considerations. The first step is the installation of sensors and data collection systems. These sensors must be placed on critical components of machinery to monitor the relevant parameters, such as motor speed, temperature, and vibration. In addition to sensor installation, organizations must ensure they have the necessary infrastructure to store and process the vast amounts of data generated by these systems. Cloud computing and edge computing are often used to handle this data and enable real-time analysis, ensuring that maintenance teams receive timely notifications and recommendations.
Next, organizations need to invest in the necessary software and analytical tools to process and interpret the data collected from sensors. Advanced analytics platforms that use machine learning and AI are typically employed to detect patterns and predict failures. It’s important for businesses to work closely with data scientists and engineers to develop models that accurately reflect the performance of their specific equipment, taking into account historical performance data, environmental factors, and other relevant variables.
A successful predictive maintenance strategy also requires collaboration across departments. Maintenance teams, operations teams, and IT specialists must work together to ensure that data is being captured accurately and that maintenance schedules are optimized based on predictive insights. Furthermore, it’s essential that staff are trained to interpret the results of predictive analytics and take appropriate action. In some cases, predictive maintenance insights may suggest minor adjustments or repairs that can be handled by operators, while in other cases, more specialized maintenance may be required.
The integration of predictive maintenance into an organization’s broader operational strategy can be a significant cultural shift. Employees accustomed to reactive maintenance may need time to adjust to the idea of using data-driven insights to guide decision-making. Additionally, organizations must be prepared to invest in the technology and expertise required for successful implementation. While the initial investment in predictive maintenance tools and systems can be high, the long-term benefits—such as reduced downtime, extended equipment life, and cost savings—make it a worthwhile investment for many businesses.
The effectiveness of predictive maintenance also depends on the quality and accuracy of the data being collected. Inaccurate or incomplete data can lead to false predictions and unnecessary maintenance activities. As a result, organizations need to ensure that their sensors are properly calibrated and maintained, and that data collection processes are standardized to ensure consistency. Regular audits of sensor performance and data quality are essential to maintaining the reliability of predictive maintenance systems.
Predictive maintenance is not a one-size-fits-all solution; its success depends on the specific needs and characteristics of each organization. For industries with highly complex and expensive machinery, such as aerospace, oil and gas, or manufacturing, predictive maintenance can offer substantial benefits in terms of cost savings, increased efficiency, and extended asset lifespan. For less complex systems, predictive maintenance may offer fewer advantages but can still provide value by preventing unexpected failures and optimizing resource usage.
As technology continues to evolve, predictive maintenance systems are likely to become even more sophisticated. The integration of the Internet of Things (IoT), cloud computing, and 5G connectivity is expected to further enhance the capabilities of predictive maintenance, enabling more real-time insights, greater accuracy, and faster response times. In addition, advancements in AI and machine learning will continue to refine predictive models, allowing for more precise predictions and automated decision-making.
The growing adoption of predictive maintenance is also driving the development of new business models and service offerings. Companies that specialize in predictive maintenance technologies are offering subscription-based models, where businesses pay for access to software platforms and analytics tools, reducing the need for upfront capital investment. Additionally, some companies offer predictive maintenance as a service, where they manage the monitoring and analysis of equipment performance on behalf of businesses. This allows organizations to take advantage of predictive maintenance without needing to invest heavily in the technology and expertise themselves.
In conclusion, predictive maintenance represents a significant advancement in the way businesses manage their equipment and assets. By using real-time data, advanced analytics, and machine learning, organizations can predict potential failures before they occur, leading to reduced downtime, cost savings, improved reliability, and extended equipment lifespan. While implementing predictive maintenance requires an investment in technology, infrastructure, and expertise, the long-term benefits make it a valuable strategy for businesses looking to optimize their operations and reduce maintenance costs. As technology continues to evolve, predictive maintenance will become an even more integral part of industrial and manufacturing processes, helping businesses maintain their competitive edge in an increasingly data-driven world.
Energy Efficiency
Energy efficiency is a fundamental concept in the quest to reduce energy consumption, lower costs, and mitigate the environmental impact of human activities. It refers to using less energy to perform the same task or achieve the same result. By improving energy efficiency, organizations, households, and industries can significantly decrease their energy consumption, leading to both economic and environmental benefits. In an era of rising energy prices and growing concern about climate change, energy efficiency is becoming an increasingly critical element of sustainable energy practices.
At its core, energy efficiency is about optimizing the use of energy in every aspect of life. It involves using energy more intelligently by adopting technologies, practices, and behaviors that minimize energy waste. This can be achieved by improving the efficiency of various systems and devices, including lighting, heating and cooling systems, appliances, industrial machinery, transportation, and more. Energy-efficient technologies and practices not only help reduce energy consumption but also contribute to lowering greenhouse gas emissions, as the production of energy often involves the burning of fossil fuels, which release carbon dioxide (CO2) and other pollutants into the atmosphere.
One of the most significant areas where energy efficiency can make a difference is in buildings. Residential and commercial buildings account for a substantial portion of global energy consumption, primarily due to heating, cooling, lighting, and the use of electrical appliances. Implementing energy-efficient measures in buildings can lead to substantial energy savings and reduce the carbon footprint of the built environment. Simple measures like insulating buildings to reduce heat loss, upgrading windows, and using energy-efficient lighting (e.g., LED bulbs) can significantly lower energy consumption. In addition, advanced technologies such as smart thermostats, energy management systems, and automated building controls can optimize heating and cooling based on occupancy, weather conditions, and time of day, further enhancing energy efficiency.
In the industrial sector, energy efficiency improvements can have a transformative impact. Industries are often large consumers of energy, particularly in manufacturing processes that involve heating, cooling, and the operation of machinery. Adopting energy-efficient technologies, such as high-efficiency motors, variable speed drives, and heat recovery systems, can reduce the energy required to produce goods. In addition to upgrading equipment, energy management systems can help industries track their energy consumption, identify inefficiencies, and implement strategies for improvement. For example, using waste heat from industrial processes to generate power or preheat materials can reduce the need for external energy sources, leading to both cost savings and lower environmental impact.
Transportation is another sector where energy efficiency plays a crucial role. Vehicles, from cars to trucks to public transport, consume large amounts of fuel, and improving the efficiency of transportation systems can help reduce overall energy use and emissions. The adoption of electric vehicles (EVs) is one of the most significant advancements in transportation efficiency, as they require less energy to operate than traditional internal combustion engine vehicles. Additionally, innovations in vehicle design, such as lightweight materials, aerodynamics, and improved drivetrains, have made modern vehicles more energy-efficient. Beyond individual vehicles, improving the energy efficiency of public transportation systems, shipping, and logistics networks can help reduce fuel consumption and emissions on a larger scale.
The potential for energy efficiency extends to power generation as well. Although the production of electricity is inherently energy-intensive, improving the efficiency of power plants and the transmission and distribution of electricity can reduce energy losses. Modernizing aging power infrastructure, upgrading transmission lines, and using advanced power generation technologies, such as combined-cycle gas turbines, can help increase the overall efficiency of power production. Furthermore, integrating renewable energy sources like wind and solar into the grid can improve the efficiency of the overall energy system, as these sources typically have lower operational costs and environmental impacts compared to fossil-fuel-based power plants.
In addition to technological innovations, behavioral changes play a significant role in energy efficiency. Individuals and organizations can adopt energy-saving practices that reduce energy consumption without necessarily requiring significant investments in new technologies. Simple actions like turning off lights when not in use, using energy-efficient appliances, and reducing unnecessary heating or cooling can lead to measurable energy savings. Encouraging people to use energy more wisely is an essential part of a comprehensive approach to energy efficiency, and public awareness campaigns, education, and incentives can help drive widespread adoption of energy-saving behaviors.
Government policies and regulations have a significant influence on energy efficiency improvements. Many countries have implemented energy efficiency standards and regulations for buildings, appliances, vehicles, and industrial processes to ensure that energy use is optimized. For example, the introduction of appliance efficiency standards, such as ENERGY STAR in the United States, has led to the widespread adoption of more energy-efficient products. Similarly, building codes and standards that mandate insulation, energy-efficient windows, and efficient heating and cooling systems have made new construction more energy-efficient. Governments also offer incentives and tax breaks to encourage businesses and homeowners to invest in energy-efficient technologies, helping to make these solutions more affordable and accessible.
The role of energy efficiency in addressing climate change cannot be overstated. Energy efficiency is often considered the “first fuel” in efforts to reduce carbon emissions because it offers a cost-effective, immediate way to cut emissions. Reducing energy consumption means that less fossil fuel is burned to produce electricity, heat, or power vehicles, directly leading to lower greenhouse gas emissions. According to the International Energy Agency (IEA), energy efficiency improvements accounted for nearly half of the global reduction in energy-related CO2 emissions in recent years. As the world seeks to meet climate goals and transition to a low-carbon economy, energy efficiency will continue to be a critical tool in reducing emissions.
Energy efficiency also has significant economic benefits. In addition to reducing energy costs for consumers and businesses, it can stimulate job creation and economic growth. The development and deployment of energy-efficient technologies create jobs in manufacturing, construction, engineering, and services. Moreover, energy efficiency investments often yield a high return on investment, making them an attractive proposition for governments and businesses. For example, companies that invest in energy-efficient equipment and practices can reduce operating costs, improve their competitiveness, and achieve higher profit margins. Similarly, governments that promote energy efficiency can see economic benefits in the form of reduced energy expenditures, improved energy security, and job creation.
As energy efficiency technologies continue to advance, the potential for further improvements grows. The development of smart grids, advanced energy storage systems, and digital technologies such as the Internet of Things (IoT) will make it easier to monitor and optimize energy use across entire systems. IoT-enabled devices, for example, can provide real-time data on energy consumption, allowing for more precise control over energy use in homes, businesses, and industrial settings. Similarly, the integration of artificial intelligence (AI) and machine learning algorithms can improve energy management by predicting energy needs, optimizing energy distribution, and identifying inefficiencies.
Despite the many benefits of energy efficiency, challenges remain. One of the primary obstacles is the upfront cost of energy-efficient technologies, which can be a barrier to adoption, particularly in developing countries or among low-income households. To overcome this, innovative financing mechanisms, such as energy performance contracting and green financing, can help reduce the financial burden of energy efficiency investments. Additionally, the lack of awareness and education about energy efficiency can prevent many people from realizing the benefits of energy-saving practices. Public campaigns, incentives, and subsidies can help raise awareness and encourage widespread adoption of energy-efficient solutions.
In conclusion, energy efficiency is a cornerstone of sustainable energy practices, offering a range of benefits, from cost savings and job creation to reduced greenhouse gas emissions and energy consumption. By adopting energy-efficient technologies, practices, and behaviors, individuals, businesses, and governments can contribute to a more sustainable, low-carbon future. With ongoing advancements in technology and supportive policy frameworks, the potential for energy efficiency to transform the way we produce, use, and think about energy is immense. The future of energy lies in our ability to use energy more wisely, efficiently, and sustainably.
Biomass Energy Generator
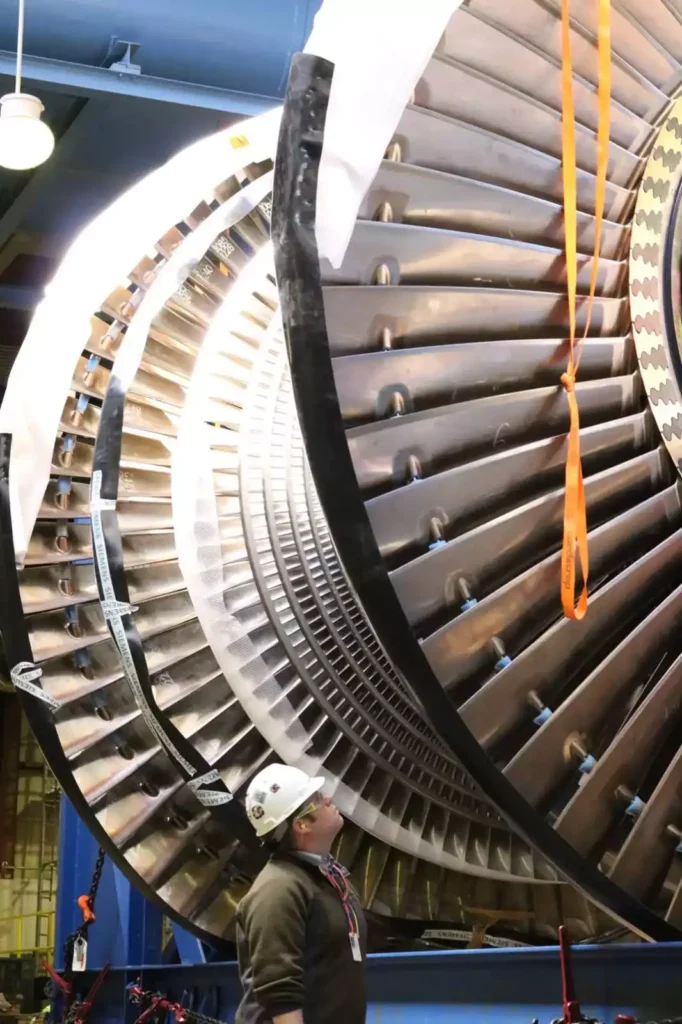
Biomass energy generation is a renewable energy technology that involves the use of organic materials, such as plant matter, animal waste, and other biodegradable materials, to produce heat, electricity, or fuel. Biomass energy has been harnessed for centuries, but modern biomass power generation has grown significantly in importance as the world looks for sustainable and cleaner alternatives to fossil fuels. Biomass is considered a carbon-neutral energy source because the carbon dioxide (CO2) released during the combustion or conversion of biomass materials is roughly equivalent to the CO2 that the plants absorbed during their growth. This makes biomass energy an attractive option for reducing greenhouse gas emissions, particularly when compared to conventional fossil fuels like coal, oil, and natural gas.
The biomass energy generation process typically involves the combustion, gasification, or anaerobic digestion of organic materials to release energy. Combustion, the most common method, involves burning biomass materials such as wood pellets, agricultural waste, or dedicated energy crops in a furnace or boiler to produce heat, which is then used to generate steam to power a turbine and produce electricity. Gasification, on the other hand, involves converting biomass into a synthetic gas (syngas) by heating it in a low-oxygen environment, which can then be used for electricity generation or as a fuel for internal combustion engines. Anaerobic digestion is a biological process in which microorganisms break down organic matter in the absence of oxygen, producing biogas, primarily methane, which can be used as a renewable fuel for heating, electricity generation, or transportation.
One of the main advantages of biomass energy generation is that it is renewable and abundant. Biomass feedstocks are widely available, especially in agricultural regions where crop residues, such as straw and corn stalks, are often underutilized. In addition, biomass can be derived from waste materials, such as sawdust, food waste, and even municipal solid waste, helping to reduce waste and provide an environmentally friendly way to dispose of organic materials. This makes biomass a particularly attractive energy source for rural and agricultural communities, where the potential for using locally available resources for energy generation is high.
Biomass power plants can vary in size and scale, from small-scale units that serve individual buildings or communities to large, utility-scale plants that supply power to the grid. In many cases, biomass power generation is integrated with other renewable energy technologies, such as wind or solar power, to provide a more reliable and consistent energy supply. Biomass power plants can operate continuously, providing baseload power generation, which is a key advantage over some intermittent renewable energy sources like wind and solar. This makes biomass an important component of a diverse energy mix, particularly in regions seeking to transition away from fossil fuels and reduce their dependence on non-renewable energy sources.
The efficiency of biomass power generation depends on several factors, including the type of biomass used, the conversion technology employed, and the design of the power plant. Different types of biomass materials have varying energy contents, which means that some feedstocks may be more efficient than others. For example, hardwoods like oak or maple have higher energy densities than softwoods like pine, meaning they produce more heat per unit of weight when burned. However, biomass feedstocks that are lower in energy content can be processed or pretreated to improve their efficiency, such as by pelletizing wood chips or drying agricultural residues to reduce moisture content. Similarly, advances in biomass conversion technologies are continually improving efficiency and reducing costs, helping to make biomass a more viable and competitive energy source.
Despite its many benefits, biomass energy generation also presents some challenges. One of the primary concerns is the potential environmental impact of large-scale biomass production. The demand for biomass feedstocks could lead to land-use changes, such as deforestation or the conversion of natural habitats into monoculture energy crops, which may have negative effects on biodiversity and ecosystems. Additionally, the transportation and processing of biomass materials can contribute to carbon emissions, potentially offsetting some of the carbon savings associated with the use of biomass energy. To address these concerns, it is important to ensure that biomass feedstocks are sourced sustainably and that the carbon lifecycle of biomass energy is carefully considered. This includes accounting for emissions associated with land-use changes, harvesting, transportation, and processing.
Another challenge of biomass energy generation is its competition with other land uses, such as food production, forestry, and conservation. The large-scale cultivation of biomass crops may put pressure on land and water resources, potentially leading to conflicts over land use. In some cases, the diversion of agricultural land for bioenergy production could result in higher food prices and food insecurity, particularly in developing countries. To mitigate these challenges, it is essential to balance the use of biomass for energy with other land uses and to prioritize the use of waste materials or non-food crops for energy generation. Additionally, research is ongoing into more sustainable and efficient forms of biomass production, such as the use of algae or fast-growing perennial grasses, which may offer lower environmental impacts and less competition with food production.
The carbon neutrality of biomass energy is another area of debate. While it is true that the CO2 released during biomass combustion is offset by the CO2 absorbed by plants during their growth, the overall carbon balance depends on various factors. For example, the carbon footprint of biomass energy can be influenced by the energy inputs required to grow, harvest, process, and transport biomass materials. In some cases, these energy inputs may result in carbon emissions that reduce the overall carbon neutrality of biomass. Additionally, the time frame over which biomass energy is considered carbon-neutral is also important. While the CO2 released during combustion is reabsorbed by plants over time, this cycle can take years or decades, meaning that the immediate environmental impact of biomass energy may be higher than that of other renewable energy sources like wind or solar.
Biomass energy generation also faces challenges related to infrastructure and market development. Biomass power plants require specialized equipment and infrastructure, such as boilers, turbines, and storage facilities, which can be expensive to build and maintain. Additionally, the supply chain for biomass feedstocks can be complex and variable, as the availability of biomass materials depends on factors like seasonal variation, crop yields, and transportation logistics. To ensure the long-term viability of biomass energy, it is essential to develop robust supply chains and improve the efficiency of biomass processing and transportation. Governments, industry stakeholders, and researchers are working to address these challenges by investing in research and development, as well as developing policies and incentives that promote the growth of the biomass energy sector.
Despite these challenges, biomass energy generation has considerable potential to contribute to a sustainable, low-carbon energy future. As part of the broader renewable energy mix, biomass can help reduce reliance on fossil fuels, decrease greenhouse gas emissions, and support energy security. In regions where biomass resources are abundant, biomass energy generation can provide a reliable and renewable source of power, especially when combined with other renewable energy technologies. The development of more efficient biomass conversion technologies, sustainable sourcing practices, and innovative feedstock options will help overcome current limitations and unlock the full potential of biomass as a renewable energy source.
In conclusion, biomass energy generation is a promising renewable energy technology that can provide a sustainable alternative to fossil fuels. By utilizing organic materials like wood, agricultural waste, and food scraps, biomass energy helps reduce waste, supports local economies, and provides a renewable energy source that can help mitigate climate change. However, like any energy source, biomass energy presents challenges related to environmental impact, land use, and carbon emissions. With careful management, ongoing technological advancements, and sustainable sourcing practices, biomass energy generation has the potential to play an important role in the transition to a cleaner, more sustainable energy system.
Biomass energy generation continues to evolve as researchers and engineers explore new ways to enhance its efficiency, sustainability, and overall impact. The ongoing development of advanced technologies is central to improving the economic and environmental performance of biomass as an energy source. For example, one area of focus is the optimization of conversion processes. While traditional methods like combustion and gasification have been in use for many years, innovations such as pyrolysis and hydrothermal liquefaction are gaining attention for their potential to extract more energy from biomass materials while producing fewer emissions.
Pyrolysis involves heating biomass materials in the absence of oxygen to break them down into bio-oil, syngas, and charcoal. This process has several advantages over direct combustion, as it can yield higher energy outputs and produce valuable byproducts, such as biochar, which can be used as a soil amendment to improve soil fertility and sequester carbon. Furthermore, bio-oil produced through pyrolysis can be refined into transportation fuels, creating a potential bridge between biomass energy and the transportation sector.
Hydrothermal liquefaction is another promising technology that converts biomass into liquid fuels by subjecting it to high temperatures and pressure in the presence of water. This process mimics the natural formation of fossil fuels and is capable of converting a wider range of biomass feedstocks, including wet organic materials like algae, food waste, and sewage sludge. Hydrothermal liquefaction could open new avenues for utilizing biomass resources that are difficult to process with traditional methods.
In addition to conversion technologies, advancements in biomass feedstock development are also key to improving the overall viability of biomass energy. Research is underway to explore the potential of non-food crops, such as switchgrass, miscanthus, and algae, for use in bioenergy production. These crops offer several advantages over traditional food crops, including faster growth rates, higher energy yields per acre, and reduced competition with food production. Algae, in particular, has garnered significant attention for its potential to produce biofuels due to its high oil content and ability to grow in a wide range of environments, including wastewater treatment systems.
Another area of development in biomass energy is the improvement of biomass supply chains. The transportation and storage of biomass materials can be expensive and logistically challenging, especially when large quantities are needed for power generation. To address these challenges, researchers are working on methods to increase the energy density of biomass feedstocks, making them easier and more cost-effective to transport and store. This includes processes like densification, where biomass materials are compressed into pellets, briquettes, or cubes, making them more compact and easier to handle. Additionally, efforts are being made to optimize harvesting and collection techniques to reduce waste and ensure a consistent and reliable supply of biomass materials.
In terms of policy and market development, governments and international organizations are increasingly recognizing the potential of biomass energy as part of their strategies for achieving clean energy targets. Several countries have established biomass energy incentives, subsidies, and renewable energy targets to encourage the growth of the sector. These policies can help reduce the financial barriers to investing in biomass energy infrastructure, making it more accessible to both developers and consumers. In many cases, biomass energy is being integrated into existing renewable energy programs, such as feed-in tariffs and renewable portfolio standards, to ensure a stable market for biomass-generated electricity and heat.
At the same time, efforts are being made to ensure the sustainability of biomass energy by promoting the use of feedstocks that do not harm ecosystems or food security. International sustainability certification programs, such as the Roundtable on Sustainable Biomaterials (RSB) and the Sustainable Biomass Program (SBP), help ensure that biomass energy production meets environmental, social, and economic criteria. These standards are designed to minimize the negative impacts of biomass production, such as deforestation, loss of biodiversity, and land-use changes that compete with food production. By certifying sustainable biomass sources, these programs help build consumer confidence in the environmental integrity of biomass energy.
In terms of market opportunities, biomass energy offers significant potential for rural development and job creation. The establishment of biomass power plants and biofuel production facilities can create employment opportunities in agriculture, forestry, and manufacturing. Additionally, the demand for locally sourced biomass feedstocks can provide economic benefits for farmers and landowners, encouraging sustainable land management practices. In rural areas where biomass resources are abundant, these opportunities can help revitalize local economies and reduce the economic challenges associated with fossil fuel dependence.
In conclusion, biomass energy generation has the potential to play a significant role in addressing the world’s energy needs while reducing the environmental impacts of fossil fuels. As technologies continue to evolve and markets develop, biomass energy is becoming an increasingly competitive and sustainable energy option. The key to unlocking its full potential lies in improving efficiency, ensuring sustainability, and developing robust supply chains that can meet the growing demand for renewable energy. While challenges remain, the continued research and innovation in biomass energy technology offer exciting prospects for a cleaner, more sustainable energy future.
The future of biomass energy generation is promising, with ongoing advancements in technology, sustainability practices, and market integration paving the way for its broader adoption. The transition to a low-carbon, renewable energy system requires a diversified approach, and biomass plays a critical role in complementing other renewable sources such as wind, solar, and hydropower. Biomass’s unique ability to provide reliable, baseload power makes it an essential part of the global effort to decarbonize energy systems and reduce dependence on fossil fuels.
One area where biomass energy can contribute to this transition is in the use of biomass for heat generation. Many industries and residential sectors rely on heat for various processes, from manufacturing to home heating. Biomass heating systems, such as biomass boilers and stoves, provide an alternative to natural gas, oil, or coal-based heating. These systems are increasingly being adopted in both developed and developing countries, offering a clean and cost-effective option for meeting heating needs. In regions with abundant biomass resources, such as forests or agricultural areas, biomass heating systems can be especially beneficial, providing localized energy solutions and reducing the need for imported fossil fuels.
Another emerging opportunity for biomass energy is in the production of bio-based chemicals and materials. Biomass can be converted into a wide variety of valuable chemicals that are traditionally derived from petroleum, such as plastics, solvents, and fertilizers. This shift from petroleum-based chemicals to bio-based alternatives can reduce the environmental impact of chemical production, as biomass feedstocks are renewable and often produce fewer greenhouse gas emissions during their lifecycle. Additionally, the use of biomass in the production of bio-based materials can help create a more circular economy, where renewable resources are continually cycled through the production process, reducing waste and resource depletion.
The growing interest in the bioeconomy is another factor driving the expansion of biomass energy generation. A bioeconomy focuses on utilizing renewable biological resources, such as plants, algae, and waste materials, to create products, energy, and services. Biomass energy generation is a central component of this bioeconomy, providing the energy necessary to support the sustainable production of bio-based goods. As governments and industries look to transition to more sustainable economic models, the development of biomass energy can help achieve broader environmental goals, including reducing carbon emissions, increasing energy security, and promoting rural economic development.
However, the path forward for biomass energy is not without challenges. One of the ongoing concerns is the potential competition for biomass resources between energy production, food production, and other uses such as forestry and animal feed. To address this, the focus is shifting toward the use of non-food biomass feedstocks, including agricultural residues, forest residues, and waste materials from the food, forestry, and agricultural industries. By tapping into these resources, biomass energy generation can avoid competing with food production, while still providing a valuable source of renewable energy. Additionally, research into more efficient and sustainable feedstock production methods, such as agroforestry or the cultivation of energy crops on marginal lands, is helping to alleviate concerns about land-use competition.
Carbon capture and storage (CCS) technologies are another potential avenue for improving the sustainability of biomass energy generation. Biomass energy systems are already considered carbon-neutral because the CO2 emitted during combustion is reabsorbed by the plants during their growth. However, capturing and storing the carbon emissions from biomass combustion could provide an additional layer of environmental benefit, making biomass a negative-carbon energy source. By integrating CCS with biomass power plants, the CO2 emissions could be captured and stored underground, further reducing the environmental impact and potentially even helping to reduce the concentration of CO2 in the atmosphere. Ongoing research is exploring the feasibility and scalability of combining biomass energy generation with carbon capture technologies.
International cooperation and policy frameworks will also play a crucial role in advancing biomass energy. Countries around the world are increasingly recognizing the need to transition to renewable energy sources and meet climate change targets. Biomass energy has a key role to play in this transition, particularly in countries with abundant biomass resources. International collaboration on research, technology development, and sustainability standards will help to ensure that biomass energy is deployed in an environmentally responsible and economically viable way. Multinational initiatives, such as the International Energy Agency (IEA) Bioenergy Technology Collaboration Programme, are helping to foster global cooperation and the sharing of best practices in biomass energy.
In terms of market trends, the growing demand for clean, renewable energy is likely to increase investment in biomass energy projects. Governments around the world are offering financial incentives and subsidies for biomass energy production, as part of broader renewable energy policies aimed at reducing carbon emissions and meeting climate goals. These incentives can help reduce the financial barriers to entry for biomass energy projects and stimulate the development of new infrastructure, such as biomass power plants and biofuel refineries. Furthermore, the price competitiveness of biomass energy relative to fossil fuels will improve as biomass conversion technologies continue to advance, making it a more attractive option for both investors and consumers.
Biomass energy is also gaining traction as an essential part of integrated, decentralized energy systems. As renewable energy technologies like solar and wind become more widespread, the need for energy storage and backup power systems has become more apparent. Biomass, with its ability to generate reliable baseload power, can complement intermittent renewable energy sources by providing a steady supply of energy when solar and wind power generation are low. This integration of biomass into a diverse energy mix helps create a more resilient and stable energy grid, capable of meeting the demands of modern society while reducing reliance on fossil fuels.
As the global demand for energy continues to rise and the impacts of climate change become more apparent, the need for clean, renewable energy sources will only increase. Biomass energy has the potential to play a significant role in the transition to a sustainable energy future, by providing a reliable and low-carbon source of power, heat, and biofuels. Ongoing research, technological innovations, and supportive policies will help to address the challenges facing biomass energy, making it a more viable and attractive option for meeting the world’s energy needs. As the biomass energy sector continues to grow and evolve, it will be an integral part of the global effort to reduce greenhouse gas emissions, improve energy security, and build a sustainable, low-carbon economy.
Biomass Energy
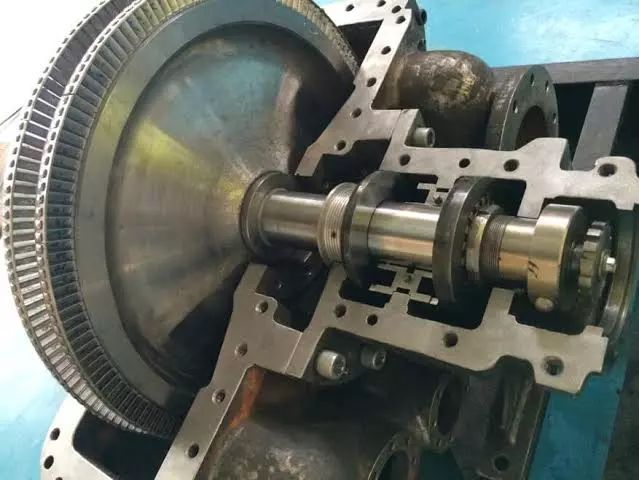
Biomass energy is a renewable energy source derived from organic materials such as wood, agricultural residues, and even waste products. Biomass has been utilized for thousands of years as a means of heating and cooking, but its role in modern energy production has evolved significantly. Today, biomass is recognized as a vital component of the renewable energy mix, offering a cleaner and more sustainable alternative to fossil fuels. The primary appeal of biomass energy lies in its ability to produce electricity, heat, and biofuels in a way that contributes to reducing carbon emissions and minimizing the environmental impact associated with conventional energy sources.
The fundamental concept behind biomass energy is the conversion of organic material into usable energy forms. Biomass can be burned directly to generate heat, which can be used in power plants to produce electricity or in industrial processes. Alternatively, biomass can undergo chemical or biological processes to produce gas or liquid fuels. The process of converting biomass into energy often involves combustion, gasification, or anaerobic digestion, each of which has unique advantages depending on the type of biomass and the intended energy output.
Combustion is the most common method for generating energy from biomass. In this process, organic materials such as wood chips, agricultural waste, or dedicated energy crops are burned to produce heat. The heat is used to generate steam, which drives a turbine connected to an electric generator. Biomass-fired power plants function similarly to conventional coal-fired power plants but emit fewer greenhouse gases because the carbon released during combustion is offset by the carbon absorbed by the plants during their growth. While combustion is effective and widely used, it has some limitations, such as the emission of particulate matter and the need for specialized equipment to handle different types of biomass materials.
Gasification is another process used to convert biomass into energy. This involves heating biomass in a low-oxygen environment to produce a synthetic gas, or “syngas,” composed primarily of hydrogen, carbon monoxide, and methane. The syngas can then be burned in a turbine or internal combustion engine to produce electricity or used as a fuel for other applications. Gasification offers several benefits over traditional combustion, including higher energy efficiency and the ability to process a wider range of biomass feedstocks, such as wet materials and waste products. Additionally, gasification reduces the formation of pollutants such as nitrogen oxides and sulfur compounds, making it a cleaner alternative to direct combustion.
Anaerobic digestion is a biological process that breaks down organic materials in the absence of oxygen, resulting in the production of biogas, primarily methane. This process occurs naturally in landfills, sewage treatment plants, and other environments where organic matter decomposes without oxygen. In anaerobic digestion systems, organic waste such as food scraps, manure, or sewage sludge is placed in a sealed container called a digester. Microorganisms break down the material, releasing biogas, which can be captured and used as a fuel for heating, electricity generation, or even as a transportation fuel. Anaerobic digestion is highly versatile and can be applied to a wide range of organic waste materials, making it a promising technology for waste management and energy generation.
The carbon neutrality of biomass energy is a key aspect of its environmental appeal. Biomass is considered carbon-neutral because the carbon dioxide released during the combustion or conversion of biomass materials is roughly equivalent to the carbon absorbed by the plants during their growth. This makes biomass an attractive alternative to fossil fuels, which release additional carbon into the atmosphere that has been sequestered for millions of years. However, it is important to note that biomass energy is not entirely without environmental impact. The carbon footprint of biomass depends on factors such as the type of biomass used, the energy required to grow, harvest, and process the feedstocks, and the transportation of biomass materials to power plants. To ensure biomass remains a sustainable energy source, it is critical to consider these factors in lifecycle assessments and adopt sustainable sourcing practices.
Biomass is also considered a renewable energy source because the feedstocks used to produce it can be replenished over time. Unlike fossil fuels, which take millions of years to form, biomass materials grow relatively quickly and can be harvested sustainably. Biomass feedstocks come from various sources, including forestry residues, agricultural waste, and dedicated energy crops such as switchgrass and miscanthus. The availability of biomass feedstocks is a key consideration for biomass energy generation, as consistent and reliable access to raw materials is essential for power plants and biofuel production facilities to operate efficiently. In some regions, biomass feedstocks are abundant, particularly in agricultural or forested areas, making biomass energy a promising option for rural development and energy independence.
The potential of biomass to reduce greenhouse gas emissions is another significant advantage. Biomass energy systems produce lower levels of carbon dioxide and other harmful pollutants compared to fossil fuel-based power generation. Additionally, when biomass is sourced from waste materials or sustainably managed forests, it can have a positive environmental impact by diverting waste from landfills and reducing the need for logging of old-growth forests. Moreover, the use of biomass for energy helps to displace fossil fuels, reducing the need for coal, oil, and natural gas, which are among the largest contributors to global warming and air pollution.
Despite its many advantages, there are some challenges associated with biomass energy generation. One of the main concerns is the land use required to produce biomass feedstocks. Large-scale biomass production may lead to competition with food production, particularly if energy crops are grown on land that could otherwise be used for food crops. Additionally, the cultivation of biomass crops may contribute to deforestation, habitat loss, and soil degradation if not managed responsibly. To address these issues, efforts are being made to develop sustainable biomass production practices that minimize environmental impacts and prioritize the use of non-food crops or waste materials.
Another challenge is the cost-effectiveness of biomass energy generation. While biomass is often cheaper than fossil fuels in some regions, the infrastructure required to convert biomass into energy, such as power plants, gasifiers, and digesters, can be expensive to build and maintain. Additionally, the transportation and storage of biomass materials can be costly due to their bulkiness and low energy density. To improve the economic viability of biomass energy, research is focused on increasing the energy efficiency of conversion processes, optimizing supply chains, and developing technologies that enhance the energy density of biomass feedstocks, such as pelletization or densification.
Biomass energy can also face competition from other renewable energy sources, such as wind, solar, and hydropower, which have lower operational costs and fewer environmental impacts. However, biomass offers unique benefits that make it an essential component of a diversified energy mix. Unlike intermittent sources like wind and solar, biomass can provide reliable, baseload power generation, making it a valuable complement to other renewables. Biomass can also be used in combined heat and power (CHP) systems, where both electricity and heat are generated from the same biomass fuel source, improving overall efficiency and reducing waste.
The future of biomass energy is promising, with ongoing advancements in technology and sustainable practices helping to address its challenges. Innovations in biomass conversion technologies, such as advanced gasification systems, pyrolysis, and biofuel production, continue to improve the efficiency and sustainability of biomass energy generation. Additionally, the growing demand for renewable energy and bio-based products presents new opportunities for biomass, including biofuels for transportation, bioplastics, and bio-based chemicals. As governments and industries continue to invest in research and development, biomass energy will play an increasingly important role in the transition to a clean, low-carbon energy future.
As biomass energy continues to develop, it will likely integrate more closely with other renewable energy sources, creating a more flexible and resilient energy system. One of the key advantages of biomass is its ability to generate baseload power, providing a consistent supply of energy when renewable sources like solar or wind are not producing electricity. This makes biomass a critical player in the push to decarbonize energy systems while ensuring grid reliability. Biomass can complement intermittent renewable energy sources by acting as a backup or providing energy storage through technologies like combined heat and power (CHP) systems, which increase the overall efficiency of biomass power generation.
The growing demand for clean and sustainable energy solutions is driving investments in the biomass sector, and governments around the world are increasingly recognizing biomass as an essential part of their renewable energy strategies. Many countries have implemented policies to encourage the use of biomass, including tax credits, renewable energy standards, and subsidies for biomass-based power generation and biofuel production. These policies help to lower the costs of biomass energy production and make it a more attractive option for utilities and industrial users.
In addition to its use in power generation and biofuel production, biomass energy has the potential to contribute to a circular economy. The concept of a circular economy emphasizes the importance of reducing waste, reusing materials, and recycling resources to create a sustainable, closed-loop system. Biomass, especially when sourced from waste materials, can play an important role in this system. Agricultural and forestry residues, food waste, and other organic materials can be converted into energy, reducing the amount of waste sent to landfills and decreasing the need for raw materials from natural resources. By diverting waste into productive energy uses, biomass energy contributes to a more sustainable and resource-efficient economy.
In the transportation sector, biofuels derived from biomass, such as ethanol and biodiesel, have gained popularity as cleaner alternatives to gasoline and diesel. These biofuels can be used in existing internal combustion engines with little or no modification, making them an easy option for reducing transportation-related emissions. Biofuels have the potential to significantly reduce greenhouse gas emissions from the transportation sector, which is one of the largest sources of carbon dioxide worldwide. Research into next-generation biofuels, such as algae-based fuels or cellulosic ethanol, is expected to improve the performance and sustainability of biofuels, further expanding their role in decarbonizing the transportation sector.
Another promising area for biomass energy is the development of advanced materials and chemicals from biomass feedstocks. The chemical industry has long relied on petroleum and natural gas as raw materials for the production of plastics, solvents, and other chemicals. Biomass offers the potential to replace fossil fuels in the production of these materials, reducing the environmental impact of the chemical industry. Biomass-derived chemicals, known as “biochemicals,” can be used to create biodegradable plastics, green solvents, and other sustainable products. This shift to bio-based chemicals aligns with the growing demand for more sustainable consumer products and reduces the chemical industry’s reliance on non-renewable resources.
As biomass energy continues to grow, sustainability will remain a key focus. It is essential that biomass production and energy generation processes minimize negative environmental impacts, such as deforestation, land-use changes, and competition with food production. Sustainable biomass sourcing practices, such as using waste products, non-food crops, and residues, help reduce these concerns and ensure that biomass energy is a responsible and environmentally friendly option. Certification programs and sustainability standards, such as the Roundtable on Sustainable Biomaterials (RSB) and the Sustainable Biomass Program (SBP), provide guidelines for ensuring that biomass energy production meets environmental and social criteria.
Global collaboration and investment in research and development will be crucial in unlocking the full potential of biomass energy. Innovations in biomass conversion technologies, feedstock development, and efficiency improvements will make biomass more competitive with other renewable energy sources. For example, research into more efficient gasification and pyrolysis technologies could enable the use of a broader range of feedstocks, such as municipal waste, and improve the energy yield from these materials. In addition, improvements in the logistics and transportation of biomass feedstocks, such as pelletization and densification, can help make biomass energy more cost-effective and scalable.
In conclusion, biomass energy plays a significant role in the global transition to renewable, low-carbon energy. It offers a flexible and reliable energy source that can be used for electricity generation, heating, and biofuel production. With ongoing technological advancements, research, and sustainability practices, biomass has the potential to meet a growing share of the world’s energy needs while contributing to a cleaner, more sustainable energy system. By reducing greenhouse gas emissions, supporting rural economies, and helping to create a circular economy, biomass energy offers numerous benefits and will continue to be a vital component of the renewable energy landscape for years to come.
As biomass energy technologies mature, their potential for creating a more resilient and decentralized energy system continues to expand. In many regions, especially rural and remote areas, biomass energy can provide a stable and locally sourced energy supply, reducing dependence on centralized grids and imported fuels. This decentralization can improve energy security, reduce transmission losses, and offer more affordable energy solutions in areas that are otherwise underserved by traditional energy infrastructure.
Small-scale biomass systems, such as residential biomass heating units or community-scale combined heat and power (CHP) plants, are becoming increasingly popular. These systems can provide localized, cost-effective solutions for heating, electricity generation, or combined heat and power production. In some cases, small-scale biomass projects can be tailored to specific needs, such as district heating for communities, which further enhances energy accessibility and efficiency. With further technological developments, these systems are expected to become more cost-competitive and capable of running on a wider range of feedstocks, making them an attractive solution for both developing and industrialized nations.
Another significant trend in biomass energy is the development of advanced biofuels that are more efficient, sustainable, and versatile than traditional biofuels. For example, cellulosic ethanol, derived from non-food biomass such as agricultural residues or woody biomass, is one of the most promising next-generation biofuels. Unlike first-generation biofuels made from food crops like corn or sugarcane, cellulosic ethanol does not compete with food production and can be made from a wide variety of feedstocks that would otherwise go to waste. The development of enzymes and microbes that can efficiently break down the cellulose in plant materials is a key focus of research in this area. As technology advances, cellulosic biofuels could play a major role in decarbonizing the transportation sector and reducing reliance on fossil fuels.
Similarly, algae-based biofuels are another exciting area of research. Algae can be grown in a wide range of conditions, including non-arable land, and has a high oil content, which makes it a promising source of biodiesel and jet fuel. Algae cultivation also has the potential to absorb carbon dioxide from the atmosphere, contributing to the reduction of greenhouse gas emissions. While the commercial viability of algae-based biofuels is still being explored, advancements in algae farming, processing, and biofuel extraction techniques suggest that they could become an important part of the biofuel market in the coming years.
In addition to fuel production, biomass energy can also contribute to the development of sustainable building materials. Biomass can be used to produce biocomposites, which are materials made from plant fibers or other renewable feedstocks. These biocomposites can be used in the construction of buildings, furniture, and automotive parts, replacing traditional materials like plastics, metals, and cement. The use of renewable materials in construction can significantly reduce the carbon footprint of buildings and infrastructure, providing an eco-friendly alternative to conventional building materials. Furthermore, biomass-based building materials are biodegradable and have a lower environmental impact throughout their lifecycle compared to non-renewable alternatives.
The integration of biomass energy with other technologies, such as carbon capture and storage (CCS), is another area that could enhance its sustainability. While biomass is considered carbon-neutral, combining biomass power plants with CCS technologies has the potential to create “negative emissions,” where more carbon dioxide is removed from the atmosphere than is emitted during energy generation. By capturing the CO2 produced during biomass combustion and storing it underground, these systems could help offset emissions from other sectors, contributing to climate change mitigation efforts. Research into the feasibility and scalability of biomass-CCS systems is ongoing, and while challenges remain, they could represent a significant breakthrough in efforts to combat global warming.
In the context of global climate change mitigation, biomass energy is increasingly seen as a critical part of the solution. The International Energy Agency (IEA) and other organizations have emphasized the role of biomass in achieving global decarbonization targets. In particular, the use of biomass for both power generation and the production of biofuels can help reduce emissions from the energy, transportation, and industrial sectors. Biomass energy also helps diversify energy portfolios, providing countries with greater energy security and resilience in the face of fluctuations in global fuel prices.
The international trade of biomass is another area where significant growth is expected. With biomass being a versatile energy source, countries with abundant biomass resources—such as the United States, Brazil, and Canada—are exploring export opportunities to meet the growing demand for renewable energy in other parts of the world. Biomass pellets, which are compacted forms of biomass that are easier to transport and store, have become an important commodity in global energy markets. Many European countries, including the United Kingdom and the Netherlands, import biomass pellets to replace coal in their power plants as part of their decarbonization efforts. This global trade in biomass presents both opportunities and challenges, including concerns about sustainability and the carbon footprint of biomass transportation, but it highlights the growing role of biomass in the global energy transition.
As the biomass energy sector continues to expand, governments and industry leaders must prioritize the development of sustainable biomass sourcing practices. This includes implementing policies that ensure responsible land management, reduce deforestation, and prioritize the use of waste materials and non-food crops. The long-term success of biomass as a renewable energy source depends on its ability to meet energy demands without compromising food security, biodiversity, or ecosystem health. Certification schemes, such as the Forest Stewardship Council (FSC) and the Roundtable on Sustainable Biomaterials (RSB), are essential for ensuring that biomass is sourced in an environmentally responsible manner and that its lifecycle impacts are minimized.
Public awareness and education about the benefits and challenges of biomass energy are also crucial. While biomass offers many environmental benefits, including reduced greenhouse gas emissions and waste diversion, it is not a one-size-fits-all solution. It is important for consumers, policymakers, and businesses to understand the trade-offs and complexities involved in biomass energy production and use. Encouraging informed decision-making, investing in sustainable biomass technologies, and fostering public-private partnerships will be key to realizing the full potential of biomass as a renewable energy source.
In summary, biomass energy is a versatile and renewable resource that can play a central role in the transition to a low-carbon energy future. Through continued innovation and sustainable practices, biomass energy can provide a reliable and environmentally friendly solution to meet the world’s energy needs, reduce greenhouse gas emissions, and support the development of bio-based products. The growth of biomass energy technologies, such as advanced biofuels, biochemicals, and decentralized energy systems, offers immense potential for both energy production and economic development. With thoughtful planning, collaboration, and investment, biomass energy will continue to be an important part of the global effort to build a sustainable, clean, and resilient energy system.
Renewable energy
Renewable energy refers to energy derived from natural sources that are replenished on a human timescale. These sources include sunlight, wind, rain, tides, geothermal heat, and more, offering sustainable alternatives to traditional fossil fuels. The shift toward renewable energy is driven by the need to reduce greenhouse gas emissions, decrease dependence on non-renewable resources, and mitigate the impacts of climate change. With growing concerns over environmental sustainability and the depletion of fossil fuel reserves, renewable energy has become a key component in the global effort to transition to a cleaner, more sustainable energy system.
Solar energy is one of the most widely recognized forms of renewable energy. It harnesses energy from the sun’s rays and can be converted into electricity using photovoltaic cells or concentrated solar power systems. Solar power has seen dramatic growth over the past few decades, driven by advances in technology, cost reductions, and favorable policy incentives. Solar panels can be deployed on rooftops, in large-scale solar farms, or integrated into building materials, making solar energy highly versatile and scalable. While solar energy production is intermittent and depends on weather conditions and the time of day, energy storage systems, such as batteries, can help address this challenge by storing excess energy for use during periods of low sunlight.
Wind energy is another major form of renewable energy. Wind turbines convert the kinetic energy of moving air into electricity. Onshore and offshore wind farms are increasingly common, and they are capable of generating large amounts of power. Wind energy is particularly effective in areas with high and consistent wind speeds, such as coastal regions and open plains. Similar to solar energy, wind energy is intermittent, meaning that wind turbines only generate electricity when the wind is blowing. However, advancements in grid integration and energy storage technologies are helping to make wind energy a more reliable and consistent source of power.
Hydropower, also known as hydroelectric power, is one of the oldest and most established forms of renewable energy. It involves the use of flowing water to generate electricity. The energy from falling or flowing water is harnessed by turbines, which are connected to generators that produce electricity. Hydropower can be classified into different types, including large-scale dams, run-of-river systems, and pumped storage hydropower. While large-scale dams can produce significant amounts of energy, they can also have environmental and social impacts, including habitat disruption, water quality degradation, and displacement of local communities. As a result, there is increasing interest in developing smaller, more environmentally friendly hydroelectric systems that can be more easily integrated into existing water systems with minimal disruption.
Geothermal energy taps into the heat stored beneath the Earth’s surface. It utilizes steam or hot water reservoirs located deep underground to generate electricity or provide direct heating. Geothermal power plants are typically located in areas with significant volcanic activity, such as parts of the United States, Iceland, and New Zealand. Geothermal energy is considered a reliable and consistent source of power, as the Earth’s internal heat is constant and not dependent on weather conditions. However, the initial costs of setting up geothermal plants can be high, and drilling deep wells can be technically challenging. Despite these challenges, geothermal energy remains a promising option for providing clean, baseload power.
Biomass energy, derived from organic materials such as wood, agricultural residues, and waste, is another key component of the renewable energy landscape. Biomass can be burned to generate heat or electricity, or it can be converted into biofuels, such as ethanol and biodiesel, for use in transportation. Biomass is considered carbon-neutral because the carbon dioxide released during combustion is offset by the carbon absorbed by the plants during their growth. However, the sustainability of biomass energy depends on the sourcing of feedstocks and the management of land use. The use of waste materials, such as agricultural residues and wood chips, is a more sustainable option than growing dedicated energy crops, which could compete with food production or lead to deforestation.
Ocean energy is an emerging field that harnesses the power of ocean tides, waves, and temperature differences to generate electricity. Tidal energy relies on the movement of tides to drive turbines, while wave energy captures the kinetic energy of ocean waves. Ocean thermal energy conversion (OTEC) uses temperature differences between warm surface water and cold deep water to produce electricity. While ocean energy has great potential, the technology is still in its infancy, and there are significant technical and environmental challenges to overcome. However, ocean energy could play an important role in the future of renewable energy, particularly in coastal areas where there is abundant access to the ocean.
One of the key benefits of renewable energy is its ability to reduce greenhouse gas emissions, helping to combat climate change. Unlike fossil fuels, which release large amounts of carbon dioxide (CO2) and other pollutants into the atmosphere when burned, renewable energy sources produce little or no direct emissions. The transition to renewable energy is essential for meeting global climate targets, such as those outlined in the Paris Agreement, which aims to limit global warming to well below 2°C above pre-industrial levels. By reducing emissions from power generation, transportation, and other sectors, renewable energy can significantly contribute to the reduction of global CO2 levels and help mitigate the impacts of climate change.
Renewable energy also offers energy security by diversifying energy sources and reducing dependence on imported fossil fuels. Many countries, especially those without significant domestic fossil fuel resources, rely heavily on oil, coal, and natural gas imports to meet their energy needs. By investing in renewable energy infrastructure, nations can reduce their reliance on foreign energy supplies and create a more resilient and self-sufficient energy system. Moreover, renewable energy systems are less vulnerable to price fluctuations and geopolitical tensions that often affect global fossil fuel markets.
In addition to environmental and energy security benefits, the renewable energy sector is a significant driver of economic growth and job creation. The renewable energy industry employs millions of people worldwide in manufacturing, installation, operation, and maintenance of renewable energy systems. The expansion of renewable energy markets also fosters innovation and technological advancements, creating new opportunities for businesses and entrepreneurs. As the cost of renewable energy technologies continues to decrease, particularly for solar and wind power, these industries are expected to grow even further, contributing to economic development and job creation, especially in rural and remote areas where many renewable energy projects are located.
Despite these advantages, there are several challenges to the widespread adoption of renewable energy. One of the main hurdles is the intermittency of certain renewable energy sources, such as solar and wind. Energy production from these sources fluctuates depending on weather conditions, time of day, and seasonal variations. To address this challenge, advances in energy storage technologies, such as batteries, pumped hydro storage, and thermal storage, are critical. These technologies can store excess energy produced during periods of high production for use when demand is higher or when renewable generation is low.
The integration of renewable energy into existing power grids is another challenge. Many power grids were originally designed to accommodate centralized, fossil-fuel-based power plants, and adapting them to handle decentralized, variable renewable energy sources requires significant upgrades. Smart grid technologies, which enable more flexible and efficient management of energy flows, are essential for integrating renewable energy into the grid. Additionally, the development of energy storage systems and demand response mechanisms can help balance supply and demand, ensuring a stable and reliable energy system.
Policy support and investment are also crucial for accelerating the transition to renewable energy. Governments play a key role in shaping the energy landscape through regulations, incentives, and subsidies that encourage the development and deployment of renewable energy technologies. The implementation of renewable energy targets, carbon pricing mechanisms, and green investment programs can stimulate private sector investment in renewable energy infrastructure and research. Global cooperation, through initiatives such as the United Nations Framework Convention on Climate Change (UNFCCC), can help align international efforts to promote renewable energy and tackle climate change on a global scale.
In conclusion, renewable energy is a vital part of the solution to the world’s energy challenges. It offers numerous benefits, including reduced greenhouse gas emissions, energy security, economic growth, and job creation. As technology advances and costs continue to fall, renewable energy will become increasingly accessible and affordable, helping to power the world in a sustainable, low-carbon future. The ongoing development of renewable energy technologies, alongside supportive policies and investments, will be essential to achieving a cleaner, greener energy system for future generations.
As the renewable energy sector continues to evolve, the global transition to sustainable energy systems will require collaboration across industries, governments, and communities. This collaborative effort will be essential not only in addressing technical and logistical challenges but also in ensuring that the benefits of renewable energy are distributed equitably across regions and populations. For example, many developing countries have abundant renewable energy resources, such as solar and wind, but face challenges in deploying these technologies due to financial constraints, lack of infrastructure, and limited technical expertise. International cooperation, knowledge sharing, and financial assistance can help bridge these gaps and ensure that renewable energy access is available to all, especially in regions where energy poverty is prevalent.
A growing focus on decentralization is also a key component of the renewable energy transition. Distributed energy resources (DERs), which are small-scale energy systems that generate, store, or manage electricity locally, offer a promising solution for enhancing energy access, particularly in remote or underserved areas. These systems can be based on renewable sources such as solar panels, small-scale wind turbines, or biogas plants, and can be integrated with battery storage to provide reliable, off-grid power. The ability to deploy renewable energy systems at a local level can improve energy resilience, reduce transmission and distribution losses, and reduce dependence on centralized power plants.
Along with technological advancements, the growth of renewable energy is driving the development of new financial models that support clean energy projects. Innovative financing mechanisms, such as green bonds, impact investing, and renewable energy auctions, have become key drivers of renewable energy development, especially in emerging markets. These financing mechanisms allow governments, corporations, and financial institutions to raise capital for renewable energy projects while offering attractive returns for investors. As the renewable energy market continues to grow, it is likely that these financial models will evolve to meet the increasing demand for clean energy investments.
The electrification of various sectors, such as transportation, heating, and industrial processes, is another major trend contributing to the renewable energy transition. As more industries and sectors adopt electric technologies, the demand for clean electricity will rise, making the need for renewable energy even more urgent. Electric vehicles (EVs), for example, have become increasingly popular as governments and consumers seek to reduce emissions from the transportation sector. EVs can be powered by renewable electricity, allowing them to further reduce their carbon footprint. Additionally, the adoption of heat pumps and electric heating systems in buildings can reduce the use of fossil fuels for heating, contributing to lower emissions from the residential and commercial sectors.
The integration of renewable energy into buildings and urban infrastructure is another promising development. The concept of “net-zero energy buildings” (NZEBs), which produce as much energy as they consume through the use of renewable energy systems, is gaining traction around the world. These buildings incorporate energy-efficient technologies, such as insulation, efficient lighting, and energy management systems, along with renewable energy sources like solar panels or small wind turbines. NZEBs are seen as a model for future urban development, helping to reduce the energy demand of buildings and contribute to broader sustainability goals.
As the renewable energy sector expands, new challenges will emerge. The intermittency of certain renewable energy sources, such as solar and wind, remains a significant concern for grid stability and reliability. While energy storage technologies, including batteries and pumped hydro storage, have made significant progress, they are still expensive and face scalability challenges. Additionally, the integration of large amounts of renewable energy into existing power grids will require smart grid technologies that can balance supply and demand, manage fluctuations, and provide real-time data to improve grid efficiency.
Hydrogen energy, produced from renewable sources through the process of electrolysis, is gaining attention as a potential solution to address the intermittency of renewable energy. Green hydrogen, which is generated using renewable electricity, can be stored and transported as a clean energy carrier, providing a means to store excess renewable energy produced during periods of high generation. Hydrogen can be used in a variety of applications, including transportation (hydrogen fuel cells for vehicles), industry (as a feedstock for manufacturing), and power generation (in gas turbines or fuel cells). The development of a hydrogen economy, where hydrogen is produced, stored, and used as a clean energy carrier, is seen as a critical step toward achieving a fully decarbonized energy system.
While the potential of renewable energy is vast, its success will depend on continued investment, innovation, and policy support. Governments and international organizations must play a leading role in providing incentives, creating supportive regulatory frameworks, and ensuring that renewable energy technologies are accessible and affordable. At the same time, private sector investment and innovation will drive technological advancements and help scale up renewable energy production. Public awareness and engagement are also essential for ensuring the success of renewable energy initiatives. Educating consumers, businesses, and policymakers about the benefits and challenges of renewable energy will help create a broad base of support for clean energy solutions.
The renewable energy revolution is not just about reducing emissions and providing sustainable energy; it is also about creating new economic opportunities, fostering innovation, and building a more resilient energy system. By shifting away from fossil fuels and embracing renewable technologies, we can build a future that is more sustainable, equitable, and prosperous. Renewable energy offers the promise of a cleaner, greener, and more connected world, where energy is generated and consumed in harmony with the planet’s natural systems.
In conclusion, renewable energy is essential to addressing the global challenges of climate change, energy security, and sustainable development. With advancements in technology, supportive policies, and increased investment, renewable energy has the potential to transform the global energy landscape. The transition to renewable energy is a complex process that will require collaboration, innovation, and a commitment to sustainability. As the world continues to embrace renewable energy, we are moving closer to a future where clean, sustainable, and accessible energy powers our homes, industries, and communities.
As the global energy landscape continues to evolve, the expansion of renewable energy technologies and the associated infrastructure is increasingly seen as a critical factor in achieving long-term sustainability. The push for renewable energy is not only about mitigating climate change but also about improving the efficiency, reliability, and affordability of energy systems across the world. The success of renewable energy hinges on both technological advancements and the collective efforts of governments, industries, and communities to create a low-carbon future.
One of the ongoing developments that are likely to shape the future of renewable energy is the concept of “smart cities.” Smart cities use advanced technology, data, and energy-efficient systems to enhance urban living, reduce energy consumption, and improve environmental sustainability. These cities integrate renewable energy into their design, use energy-efficient infrastructure, and encourage sustainable practices, such as reducing waste and promoting clean transportation. The adoption of smart grid technologies, energy storage, and distributed energy systems will be integral to making cities more energy-efficient and better equipped to integrate renewable energy sources at scale. Additionally, the idea of microgrids—small, localized grids that can operate independently of the main grid—can enhance the resilience of urban areas, allowing them to produce, store, and distribute renewable energy in response to local demand.
Energy efficiency remains one of the cornerstones of a renewable energy transition. Maximizing the use of energy through efficient systems and reducing energy waste in all sectors—such as residential, commercial, industrial, and transportation—is crucial for reducing overall energy consumption and minimizing the environmental impact of energy production. Energy-efficient appliances, buildings, and manufacturing processes can play an essential role in lowering energy demand while complementing the increased use of renewable energy. Moreover, energy efficiency measures can contribute to economic savings and help ensure that renewable energy resources are utilized in the most effective way possible.
The role of innovation cannot be overstated in the continued advancement of renewable energy. Research and development into new materials, processes, and energy generation techniques are accelerating the transition to cleaner energy. For instance, next-generation solar panels, such as perovskite solar cells, promise higher efficiency at lower production costs, making solar energy even more accessible. In wind energy, advancements in turbine design, including floating wind turbines, can unlock new offshore wind potential in deeper waters where traditional turbines are not feasible. Additionally, innovations in energy storage, such as solid-state batteries, and the growing potential of green hydrogen to act as an energy carrier, are vital to addressing the intermittency challenges associated with renewable energy.
Emerging technologies such as carbon capture and storage (CCS) also have the potential to complement renewable energy by reducing the carbon footprint of industrial activities. By capturing carbon emissions from industries and power plants and storing them underground or converting them into usable products, CCS technologies can provide a bridging solution until renewable energy sources fully replace fossil fuels. In parallel with the use of renewables, CCS can help limit the damage caused by unavoidable emissions in sectors that are more challenging to decarbonize, such as cement production and heavy industry.
One of the critical factors driving the renewable energy revolution is the growing recognition of the economic opportunities associated with clean energy. As fossil fuel prices fluctuate and become more volatile, renewable energy offers a more stable and predictable cost structure, making it an attractive option for investors, industries, and governments. The renewable energy sector already provides millions of jobs worldwide, from manufacturing to installation, maintenance, and operations. As renewable energy technologies continue to scale, even more opportunities for job creation, innovation, and economic growth will arise.
Energy democratization, which involves empowering communities and individuals to generate, store, and consume their energy, is another important aspect of the renewable energy movement. The rise of rooftop solar installations, small-scale wind turbines, and community solar projects enables households and local communities to become active participants in the energy system. This decentralized model not only provides greater control over energy consumption but also reduces reliance on centralized, fossil fuel-based power generation, helping to increase resilience and reduce emissions. Furthermore, energy cooperatives and community-owned renewable energy projects can foster social cohesion and allow local communities to share in the economic benefits of renewable energy.
One significant development in renewable energy adoption is the electrification of traditionally non-electric sectors. Transportation, for instance, is undergoing a transformation with the rapid growth of electric vehicles (EVs), powered by renewable electricity. EVs are not only more efficient than their gasoline and diesel counterparts, but they can also contribute to grid stability when used in conjunction with smart grids and vehicle-to-grid (V2G) technologies. Electric vehicles can store excess energy during periods of low demand and feed it back into the grid during peak demand, helping to balance electricity supply and demand. Additionally, with the advancement of charging infrastructure, the widespread adoption of EVs becomes increasingly feasible.
The global shift to renewable energy also intersects with the broader goals of sustainable development. Renewable energy supports the achievement of several of the United Nations’ Sustainable Development Goals (SDGs), particularly those related to affordable and clean energy, climate action, economic growth, and responsible consumption. By providing clean and sustainable energy, renewable sources help reduce the reliance on polluting fossil fuels, which disproportionately impact disadvantaged communities and contribute to environmental degradation. Furthermore, renewable energy plays a critical role in addressing energy poverty by providing affordable access to electricity in remote or underserved regions, empowering communities and improving quality of life.
Despite the overwhelming benefits, the renewable energy transition will require significant investment in infrastructure, research, and policy frameworks to scale up clean energy solutions. Governments around the world must continue to develop and implement policies that incentivize the growth of renewable energy, such as tax credits, subsidies, renewable energy targets, and carbon pricing mechanisms. These policies, alongside public and private investment, will help stimulate the necessary research and development, drive technological innovation, and reduce costs, enabling renewable energy to become the dominant source of power globally.
In summary, renewable energy represents the future of global energy systems, offering sustainable, low-carbon alternatives to traditional fossil fuels. The continued development and integration of renewable energy sources such as solar, wind, geothermal, biomass, and hydropower hold the potential to transform the way energy is generated, stored, and consumed. Overcoming the challenges of intermittency, storage, grid integration, and financing will be essential for realizing the full potential of renewable energy. However, through collaboration, technological innovation, and policy support, renewable energy can provide a pathway to a cleaner, more sustainable, and economically prosperous future. The renewable energy transition is not just an environmental imperative but a vast opportunity for building a sustainable global economy that benefits all.
Carbon neutrality
Carbon neutrality, also known as achieving net-zero carbon emissions, is the state in which the amount of carbon dioxide (CO2) and other greenhouse gases emitted into the atmosphere is balanced by the amount of emissions removed or offset. This concept is at the heart of global efforts to combat climate change, as it aims to stop the accumulation of greenhouse gases in the atmosphere, thereby stabilizing global temperatures and reducing the harmful impacts of global warming.
The need for carbon neutrality has never been more urgent. The consequences of unchecked carbon emissions, including rising global temperatures, extreme weather events, melting ice caps, sea-level rise, and disruptions to ecosystems, are already being felt around the world. To avoid the most catastrophic effects of climate change, scientists and policymakers agree that humanity must limit global warming to well below 2°C above pre-industrial levels, with efforts to aim for 1.5°C. Achieving carbon neutrality is a key part of meeting these goals.
Reaching carbon neutrality involves both reducing emissions and increasing efforts to absorb or offset the remaining emissions that cannot be eliminated. Carbon emissions come from various sources, with the primary contributors being the burning of fossil fuels for energy, industrial processes, transportation, deforestation, and agricultural activities. Reducing emissions requires significant changes to how energy is produced, how industries operate, how transportation is managed, and how land is used. This includes transitioning to renewable energy sources, improving energy efficiency, adopting sustainable agricultural practices, and protecting and restoring forests, which act as carbon sinks.
One of the most critical steps in achieving carbon neutrality is the transition to renewable energy. Fossil fuels, such as coal, oil, and natural gas, are the largest sources of carbon emissions globally, and replacing them with clean, renewable sources of energy—such as solar, wind, hydropower, and geothermal—is essential for reducing carbon output. Renewable energy technologies have seen significant advancements in recent years, making them more cost-competitive and accessible. Solar panels, wind turbines, and energy storage systems are rapidly becoming key components of the global energy infrastructure, helping to reduce dependence on fossil fuels.
Alongside the expansion of renewable energy, improving energy efficiency is another critical strategy for achieving carbon neutrality. By using energy more efficiently across sectors such as transportation, industry, and buildings, we can significantly reduce overall demand for energy and, in turn, decrease emissions. For example, enhancing the energy efficiency of buildings through better insulation, lighting, and heating systems can reduce energy consumption while also cutting costs. In transportation, the adoption of electric vehicles (EVs) and the shift towards public transportation and alternative fuels like hydrogen can reduce the emissions from fossil fuel-powered vehicles.
In addition to reducing emissions, offsetting is an important component of achieving carbon neutrality. Since certain sectors, such as heavy industry and aviation, may have difficulty completely eliminating their emissions in the near term, carbon offsetting allows for the neutralization of emissions by investing in projects that remove or reduce greenhouse gases elsewhere. These projects may include reforestation and afforestation, which capture CO2 from the atmosphere, or the development of carbon capture and storage (CCS) technologies that trap emissions from industrial processes and store them underground. Carbon credits are often used as a mechanism for offsetting, where companies or individuals can purchase credits to compensate for their emissions.
Another approach to offsetting emissions is through the use of negative emissions technologies (NETs), which aim to remove CO2 directly from the atmosphere. These include methods such as direct air capture (DAC), which uses machines to pull CO2 out of the air and store it, or soil carbon sequestration, where carbon is stored in soil through changes in agricultural practices. While these technologies show promise, they are still in the early stages of development and face challenges related to scalability, cost, and environmental impacts. However, they will play a role in the global effort to reach carbon neutrality, especially in sectors that are difficult to decarbonize.
The concept of carbon neutrality also extends to the corporate and national levels. Governments around the world are setting ambitious climate targets, with many committing to achieving carbon neutrality by mid-century. For example, the European Union has set a goal of becoming carbon-neutral by 2050, while countries such as the United Kingdom and Canada have established similar targets. These commitments are typically accompanied by a range of policies and regulations, such as carbon pricing, emissions trading systems, renewable energy mandates, and energy efficiency standards, designed to encourage the reduction of emissions across all sectors of the economy.
Corporations are also setting carbon neutrality goals, often in line with international climate agreements or in response to increasing pressure from consumers, investors, and regulators. Many companies are committing to reduce their emissions through energy efficiency improvements, transitioning to renewable energy, and adopting sustainable practices throughout their supply chains. Companies that achieve carbon neutrality often purchase carbon credits or engage in offset projects to neutralize the emissions they cannot eliminate. In addition to contributing to global climate goals, corporate carbon neutrality efforts can offer reputational benefits, reduce regulatory risks, and enhance brand loyalty among increasingly environmentally conscious consumers.
Achieving carbon neutrality is not only about addressing environmental concerns—it also presents significant economic and social opportunities. The transition to a low-carbon economy can stimulate innovation, create new industries, and generate jobs, particularly in sectors such as renewable energy, energy storage, sustainable agriculture, and electric transportation. It can also enhance energy security by reducing reliance on imported fossil fuels, while improving public health by reducing air pollution associated with the burning of coal and other fossil fuels.
Despite these opportunities, the path to carbon neutrality is not without challenges. One of the main obstacles is the need for large-scale infrastructure changes, such as the construction of renewable energy plants, the expansion of electric vehicle charging networks, and the retrofitting of buildings to improve energy efficiency. The transition to carbon-neutral systems will also require significant investment in research and development to make clean technologies more affordable and accessible, particularly in developing countries. Moreover, international collaboration and cooperation will be crucial in addressing global emissions, as climate change is a collective issue that requires coordinated action from all countries.
The role of governments, businesses, and individuals is pivotal in achieving carbon neutrality. Governments must provide strong leadership by implementing policies that support carbon reduction, setting clear targets, and creating incentives for clean energy investments. Businesses need to adopt sustainable practices and embrace innovation to drive emissions reductions and make sustainability an integral part of their operations. Individuals, too, can contribute by making environmentally conscious choices, such as reducing energy consumption, adopting sustainable transportation options, and supporting companies and policies that prioritize sustainability.
In conclusion, carbon neutrality is a critical objective in the global fight against climate change. By transitioning to renewable energy, improving energy efficiency, and investing in carbon offsetting and negative emissions technologies, we can work towards reducing the global carbon footprint. Governments, corporations, and individuals all have roles to play in this transition, and the collective efforts to achieve carbon neutrality will help ensure a sustainable and resilient future for generations to come. While the path to carbon neutrality presents challenges, it also offers immense opportunities for innovation, economic growth, and environmental preservation.
As we continue to advance towards carbon neutrality, the integration of circular economy principles will play an increasingly significant role in reducing carbon footprints and fostering sustainability. A circular economy focuses on reducing waste and making the most of available resources by encouraging the reuse, recycling, and refurbishment of products and materials. This approach contrasts with the traditional linear economy, which relies on a “take-make-dispose” model, where resources are extracted, used, and discarded. In a circular economy, resources remain in use for as long as possible, which can substantially reduce carbon emissions associated with resource extraction, production, and waste management.
One of the key areas where the circular economy can contribute to carbon neutrality is in the manufacturing sector. Industries such as electronics, textiles, and automotive production are responsible for a significant portion of global emissions due to the energy-intensive processes involved in creating new products. By focusing on designing products that are easier to repair, reuse, and recycle, manufacturers can lower emissions and reduce the demand for raw materials, which often involves energy-intensive extraction and processing. For instance, the automotive industry is increasingly adopting circular principles by designing vehicles with recyclable components and using recycled materials in the production process.
Similarly, the construction sector, which contributes significantly to global emissions, can benefit from circular practices. Reusing construction materials, such as steel, concrete, and wood, reduces the need for new raw materials, thereby cutting emissions from production and transportation. Additionally, retrofitting and refurbishing existing buildings, rather than demolishing them and constructing new ones, can help conserve energy and materials. By incorporating these circular practices, the construction industry can play a pivotal role in achieving carbon neutrality.
One of the challenges of achieving carbon neutrality is addressing the emissions associated with the more difficult-to-decarbonize sectors. For example, heavy industries such as steel, cement, and chemicals are among the largest emitters of carbon due to the chemical reactions and high heat required in their processes. While renewable energy can help reduce emissions from these sectors, other solutions, such as carbon capture, utilization, and storage (CCUS), will be necessary to achieve full decarbonization. CCUS technologies capture CO2 emissions from industrial processes and either store them underground or convert them into useful products. This approach has the potential to make a significant contribution to reducing emissions from hard-to-abate sectors.
The aviation and shipping industries also present substantial challenges in the push for carbon neutrality. Both sectors are highly dependent on fossil fuels and have few alternatives to reduce emissions in the short term. However, innovations in alternative fuels, such as biofuels and hydrogen, along with improvements in fuel efficiency and changes in operational practices, could help reduce emissions in these industries. For instance, sustainable aviation fuel (SAF), which is derived from renewable sources such as plants or waste materials, has the potential to reduce emissions in the aviation sector. In shipping, the development of wind-assisted propulsion technologies and the exploration of zero-emission vessels powered by hydrogen or ammonia are gaining momentum.
Another challenge to carbon neutrality is the need for a transition in the global agricultural sector. Agriculture is both a source of greenhouse gas emissions—primarily methane and nitrous oxide—and a significant land use contributor. The sector is responsible for a substantial portion of global emissions, particularly from livestock farming and fertilizer use. To achieve carbon neutrality, agriculture must adopt more sustainable practices, such as regenerative agriculture, which focuses on soil health, increased biodiversity, and carbon sequestration. Additionally, reducing food waste, adopting plant-based diets, and improving the efficiency of agricultural supply chains can help lower emissions in this sector.
One of the most important aspects of achieving carbon neutrality is global cooperation and a collective effort to tackle the climate crisis. While individual countries, industries, and businesses can take significant steps towards reducing emissions, the scale of the challenge requires coordinated action on an international level. The Paris Agreement, which was adopted by nearly every nation in 2015, set a global framework for addressing climate change by committing to limit global temperature rise and achieve net-zero emissions by the middle of the century. Continued international cooperation, including financial support for developing nations, will be critical for reaching the global carbon neutrality goal.
Carbon markets and international trade in carbon credits will also play a role in helping countries and companies meet their emissions reduction targets. By creating a system where carbon emissions are priced, carbon markets incentivize the reduction of emissions by allowing entities to buy and sell carbon allowances or credits. This approach can facilitate the flow of capital to carbon-reduction projects and stimulate investment in clean technologies. However, ensuring the integrity of carbon markets and ensuring that offsets represent genuine emissions reductions is vital for ensuring the effectiveness of this approach.
In addition to policy measures, financial innovations and the growing role of climate finance will support the transition to carbon neutrality. Financial instruments such as green bonds, impact investing, and climate funds are increasingly being used to fund clean energy projects, climate adaptation, and emissions reduction initiatives. As private sector investments in sustainability grow, it is essential to ensure that these financial flows are directed toward projects that have a real impact on reducing emissions and supporting the transition to a low-carbon economy.
Carbon neutrality also presents opportunities for innovation in new technologies, business models, and consumer behavior. The rise of renewable energy, energy storage, electric vehicles, and carbon capture technologies has already led to the creation of new industries and job opportunities. Similarly, the development of sustainable products, services, and business models focused on reducing environmental impact offers growth opportunities. For example, companies in the fashion and food industries are exploring sustainable practices such as circular design, plant-based products, and responsible sourcing to reduce their carbon footprints.
In conclusion, carbon neutrality is an essential goal for addressing the challenges of climate change and securing a sustainable future. It requires a holistic approach that includes reducing emissions through the transition to renewable energy, improving energy efficiency, implementing circular economy principles, and investing in carbon offsetting and negative emissions technologies. Achieving carbon neutrality will require collective action from governments, businesses, and individuals, along with the development of supportive policies, financial systems, and innovations. The transition to a low-carbon economy presents both challenges and opportunities, but with the right combination of technological advancements, policy frameworks, and global cooperation, carbon neutrality is achievable. The path to carbon neutrality not only promises to mitigate climate change but also offers the potential for economic growth, job creation, and a more sustainable and resilient world.
Bioeconomy
Bioeconomy refers to the use of biological resources, processes, and principles to produce goods, services, and energy in a sustainable manner, aiming to enhance economic growth, address societal challenges, and promote environmental sustainability. It encompasses a wide range of sectors, including agriculture, forestry, fisheries, food production, bioenergy, biotechnology, and industrial processes that utilize renewable biological resources. The central idea behind the bioeconomy is to shift from the traditional fossil-based economy, which relies heavily on non-renewable resources, to a more sustainable and circular economic model that harnesses the potential of natural biological systems.
The bioeconomy can be seen as a crucial component of the broader movement towards sustainability and resource efficiency. By replacing fossil fuels and other non-renewable resources with biological materials, the bioeconomy aims to reduce greenhouse gas emissions, conserve resources, and promote the circular use of materials. This is particularly important in the context of global climate change, where there is an urgent need to transition to sustainable production and consumption patterns. The bioeconomy can provide solutions to various environmental challenges, including reducing carbon footprints, minimizing waste, and promoting biodiversity conservation.
One of the key drivers of the bioeconomy is biotechnology, which enables the conversion of biological materials into a wide range of products and services. For example, biotechnology can be used to create biofuels, bioplastics, and bio-based chemicals that serve as sustainable alternatives to petroleum-based products. These innovations are increasingly important in industries such as transportation, packaging, and manufacturing, where the reliance on fossil fuels and non-renewable resources has significant environmental impacts. Advances in biotechnology also allow for the development of new medicines, vaccines, and treatments, making bioeconomy a critical field for improving health outcomes and addressing global health challenges.
The agricultural sector plays a vital role in the bioeconomy, as it provides the raw materials for many bio-based products, including food, fibers, and bioenergy. The sustainable management of agricultural systems is therefore essential to the success of the bioeconomy. This includes practices such as precision farming, agroecology, and sustainable land management, which aim to improve crop yields, enhance soil health, and reduce the environmental impacts of farming. The bioeconomy also promotes the use of waste and by-products from agriculture, such as crop residues, food waste, and animal manure, to produce bioenergy and other valuable products, thus reducing waste and creating new economic opportunities.
Forestry is another important sector within the bioeconomy, as forests provide renewable resources such as timber, wood products, and biomass for energy production. Sustainable forest management practices, such as reforestation, afforestation, and responsible harvesting, ensure that forest resources are used in a way that preserves biodiversity, mitigates climate change, and contributes to rural development. The bioeconomy encourages the use of wood and other forest products in a variety of applications, including bio-based chemicals, materials, and bioenergy, helping to reduce dependence on fossil fuels and promote sustainable growth in rural areas.
Bioenergy, which includes biofuels, biogas, and biomass, is a critical aspect of the bioeconomy. Bioenergy can be used to replace fossil fuels in sectors such as transportation, heating, and electricity generation. The production of biofuels, such as ethanol and biodiesel, from crops like corn, sugarcane, and algae, provides an alternative to petroleum-based fuels, reducing greenhouse gas emissions and enhancing energy security. Similarly, biogas, produced from the anaerobic digestion of organic waste, can be used to generate renewable electricity and heat, while also reducing the amount of waste sent to landfills. Biomass, including wood chips, agricultural residues, and dedicated energy crops, can be used for large-scale power generation or heating, contributing to a more sustainable energy mix.
The bioeconomy also has the potential to contribute to economic growth and job creation, particularly in rural and remote areas. By fostering innovation in the production of bio-based products and services, the bioeconomy can create new industries and market opportunities, from renewable energy production to sustainable agriculture and forestry. The development of bio-based products also provides opportunities for small and medium-sized enterprises (SMEs) to innovate and participate in global value chains. Furthermore, the bioeconomy can enhance food security by improving the efficiency of agricultural production and reducing food waste, while also contributing to rural development through the promotion of sustainable land use and resource management.
One of the challenges of the bioeconomy is ensuring that its growth is both sustainable and inclusive. While the bioeconomy offers significant potential for environmental and economic benefits, its development must be guided by principles of sustainability and equity. This includes ensuring that the production of bio-based products does not lead to deforestation, land degradation, or the depletion of natural resources. It is also essential to ensure that the benefits of the bioeconomy are distributed equitably, particularly in developing countries, where access to biotechnology, markets, and sustainable practices may be limited.
Policy frameworks and regulations are essential to fostering the growth of the bioeconomy. Governments play a key role in promoting research and innovation in biotechnology and bio-based industries, as well as providing incentives for the adoption of sustainable practices in agriculture, forestry, and energy production. Policy tools such as subsidies, tax incentives, and green procurement policies can encourage businesses to invest in bio-based solutions and promote the use of renewable resources. At the same time, regulatory frameworks must ensure that bioeconomy activities are carried out in an environmentally responsible manner, with safeguards in place to protect ecosystems, biodiversity, and human health.
International cooperation is also important for the development of the bioeconomy. Global challenges such as climate change, food security, and biodiversity loss require coordinated efforts between countries, industries, and research institutions. Sharing knowledge, best practices, and technological innovations across borders can accelerate the transition to a sustainable bioeconomy and help address common challenges. Additionally, international trade in bio-based products and services can open up new markets for bioeconomy industries, fostering economic growth and creating opportunities for sustainable development.
In conclusion, the bioeconomy represents a transformative approach to economic growth, sustainability, and resource management. By harnessing the potential of biological resources and processes, the bioeconomy offers solutions to some of the most pressing global challenges, including climate change, resource depletion, and food security. Through innovation in biotechnology, sustainable agriculture and forestry practices, and the development of bio-based products and energy sources, the bioeconomy has the potential to drive sustainable growth, create new industries, and promote environmental stewardship. However, the success of the bioeconomy depends on the adoption of sustainable practices, the development of supportive policies and regulations, and global cooperation to ensure that its benefits are shared equitably.
Energy conversion
Energy conversion refers to the process of changing one form of energy into another, typically with the goal of making energy more useful for specific applications. This process is fundamental to modern society, as it enables the generation of electricity, heating, cooling, and mechanical work from a variety of energy sources. Energy conversion occurs in many forms, from the combustion of fuels to the transformation of solar radiation into electrical energy, and it plays a crucial role in how we produce, distribute, and consume energy. The efficiency of energy conversion technologies is a critical factor in reducing energy consumption, minimizing environmental impacts, and enhancing the sustainability of energy systems.
One of the most common forms of energy conversion is the transformation of thermal energy into mechanical energy, which occurs in power plants that burn fossil fuels such as coal, oil, and natural gas. These plants operate on the principle of steam generation, where water is heated by burning fuel to produce steam, which then drives a turbine connected to a generator to produce electricity. Although fossil fuel-based power plants have been the dominant source of energy generation for many years, they are associated with high levels of greenhouse gas emissions, air pollution, and resource depletion, leading to growing interest in more sustainable energy conversion technologies.
Renewable energy sources, such as solar, wind, and hydropower, are increasingly becoming central to energy conversion processes due to their ability to produce clean and sustainable energy. Solar energy conversion is primarily achieved through photovoltaic (PV) cells, which capture sunlight and convert it directly into electrical energy through the photovoltaic effect. Wind energy conversion, on the other hand, involves the use of wind turbines to convert the kinetic energy of wind into mechanical energy, which is then used to generate electricity. Hydropower utilizes the potential and kinetic energy of water, often through dams or turbines, to produce mechanical energy that can be converted into electricity. These renewable energy sources offer significant advantages over fossil fuels, including lower emissions and the potential for infinite supply, but they also face challenges related to intermittency and variability, which necessitate the development of advanced energy storage and grid integration technologies.
In addition to electrical energy conversion, thermal energy conversion is also crucial in many industrial and residential applications. For example, natural gas boilers and furnaces convert chemical energy in natural gas into heat for space heating and hot water production. Similarly, geothermal energy, which harnesses the heat stored beneath the Earth’s surface, is increasingly used for both electricity generation and direct heating applications. This form of energy conversion is considered highly sustainable, as it relies on a renewable and consistent source of heat, although its geographic limitations restrict its widespread application.
Energy conversion technologies also include the use of chemical processes, such as those found in batteries and fuel cells, which convert chemical energy into electrical energy. In batteries, chemical reactions between the electrodes and electrolyte generate an electric current that can power devices such as smartphones, electric vehicles, and grid storage systems. Fuel cells operate on a similar principle, where hydrogen and oxygen react electrochemically to produce electricity, with water as the only byproduct. Fuel cells are considered a promising technology for clean energy conversion, particularly in transportation and stationary power generation, due to their high efficiency and low emissions.
One of the challenges of energy conversion is the issue of efficiency. Not all energy that is input into a system can be converted into useful work; some of it is inevitably lost as waste heat, friction, or other forms of energy dissipation. The efficiency of an energy conversion process is a measure of how effectively it transforms energy from one form to another, and improving this efficiency is a key goal in energy system design. For example, combined heat and power (CHP) systems, which simultaneously produce electricity and useful heat from a single fuel source, can achieve significantly higher overall efficiency compared to traditional systems that only generate electricity. Similarly, technological advances in energy storage, such as high-capacity batteries and thermal storage systems, are essential for improving the overall efficiency of energy conversion and ensuring that renewable energy sources can be more reliably integrated into the grid.
Energy conversion also plays a key role in reducing the environmental impacts associated with energy use. Conventional methods of energy conversion, particularly those that rely on fossil fuels, are major contributors to air pollution and climate change. The combustion of coal, oil, and natural gas releases carbon dioxide (CO2) and other greenhouse gases into the atmosphere, which trap heat and contribute to global warming. In contrast, renewable energy conversion technologies, such as wind, solar, and hydropower, produce little to no direct emissions, making them more environmentally friendly. In addition, advancements in carbon capture, utilization, and storage (CCUS) technologies are being explored as ways to reduce the carbon emissions associated with fossil fuel-based energy conversion, although these technologies are still in development and have not yet been widely deployed.
The integration of renewable energy sources into the broader energy grid presents both opportunities and challenges in the context of energy conversion. While renewable energy offers the potential for cleaner and more sustainable energy, it is often intermittent and variable, meaning that energy generation from sources like wind and solar may not always align with demand. As a result, energy conversion systems must be designed to manage these fluctuations, often through the use of energy storage systems, demand-side management, and grid balancing techniques. Smart grids, which use digital technology to monitor and manage electricity flow, are an important tool for optimizing energy conversion and distribution in a world with a growing share of renewable energy sources.
Another key area of innovation in energy conversion is the development of decentralized and off-grid systems, which can provide energy in remote or underserved regions. Off-grid systems, such as small-scale solar power systems, microgrids, and biogas generators, enable local communities to access reliable and affordable energy without relying on centralized power plants or long-distance transmission lines. These systems can also contribute to energy resilience, as they are less vulnerable to disruptions from natural disasters or infrastructure failures. The development of efficient and cost-effective energy conversion technologies for off-grid applications is crucial for achieving universal energy access and promoting sustainable development.
As global demand for energy continues to rise, the need for efficient, reliable, and sustainable energy conversion technologies becomes increasingly urgent. Innovations in energy conversion are essential for reducing dependence on fossil fuels, minimizing environmental impacts, and ensuring that energy systems can meet the needs of a growing and increasingly urbanized global population. The transition to a low-carbon energy future will require continued advancements in energy conversion technologies, as well as the development of supportive policies and investment in research and development. From renewable energy to advanced battery systems, energy conversion technologies will be at the forefront of efforts to create a more sustainable, equitable, and resilient energy future for all.
Steam Condensation
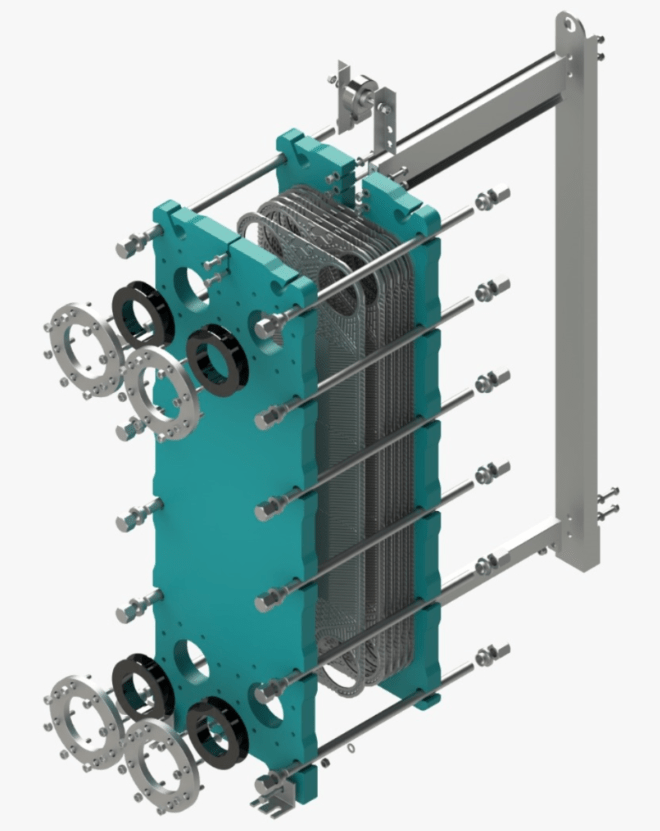
Superheated steam condensation is a crucial process in many industrial applications, particularly in steam turbines and heat exchangers, where steam is used to generate mechanical or electrical energy. The process involves the cooling and phase transition of steam from its superheated state back into liquid water, often under controlled conditions. Understanding the behavior of superheated steam during condensation is essential for designing efficient systems that maximize energy recovery while minimizing heat losses and damage to equipment.
Superheated steam refers to steam that has been heated beyond its boiling point, such that it is at a temperature higher than that required for the steam to exist in equilibrium with water at a given pressure. This superheating process increases the thermal energy of the steam and is typically achieved by adding heat to the steam after it has already reached its boiling point. Superheated steam is used in a variety of applications, including in steam turbines where its high temperature allows for a greater energy conversion efficiency as it expands and does mechanical work.
The condensation of superheated steam occurs when the steam is cooled down below its superheated temperature, typically by releasing heat to a surrounding medium such as air or water. As the steam cools, the temperature decreases, and the steam begins to lose its thermal energy. The condensation process is marked by a phase change, where steam, which is a gas, transforms back into water, which is a liquid. During this process, the temperature of the steam decreases until it reaches the saturation point, at which point the steam starts to condense rapidly, releasing latent heat in the process.
The phase change during condensation is a key feature of superheated steam condensation. Unlike sensible heat, which can be easily measured with a thermometer, latent heat refers to the energy required to change the phase of a substance without changing its temperature. During the condensation of superheated steam, the steam releases latent heat, which is transferred to the cooling medium. This transfer of heat is what allows steam condensers to efficiently recover thermal energy, making it available for reuse in industrial processes or power generation. For example, in a steam power plant, the heat released during condensation can be used to pre-heat water entering the boiler, thereby improving the overall thermal efficiency of the system.
Condensation of superheated steam is a complex process influenced by several factors, including the pressure, temperature, and flow characteristics of the steam, as well as the design and efficiency of the condenser. The rate at which superheated steam condenses depends on the temperature gradient between the steam and the cooling surface. A larger temperature difference generally leads to faster condensation, as more heat is transferred. However, excessive temperature differences can cause thermal stresses on equipment, leading to material fatigue or damage over time. Therefore, it is crucial to maintain optimal temperature gradients to ensure efficient condensation while preventing equipment damage.
In industrial applications, superheated steam condensation typically occurs within a steam condenser. The condenser is a heat exchanger that provides a surface for steam to come into contact with a cooling medium, usually water. The cooling water flows through the condenser tubes, and the steam surrounds them. As the steam loses its thermal energy, it condenses on the cooler surfaces of the tubes and turns back into water. The condensed steam, now referred to as condensate, is then collected and pumped back into the boiler or reused in the system, minimizing water loss and improving the overall efficiency of the operation.
In some systems, particularly in closed-loop cooling systems, the cooling water may undergo a heat exchange process before being used to cool the steam. In this case, the heat exchanger is designed to prevent contamination of the steam and cooling water. Superheated steam condensation in these systems requires careful management of the heat exchange process to ensure that the temperature and pressure of the steam are controlled effectively throughout the entire cycle.
The efficiency of superheated steam condensation is critical in many energy systems. In power plants, steam turbines that operate with superheated steam depend on efficient heat exchange during condensation to maintain their high efficiency. The condenser’s ability to remove heat efficiently from the steam allows the turbine to work at lower exhaust pressures, increasing the overall efficiency of the system. The use of large, highly effective condensers, often with enhanced heat transfer surfaces, is essential for improving the performance of steam turbines and ensuring that they operate at peak efficiency over time.
Aside from power generation, superheated steam condensation is also used in a variety of industrial processes such as chemical manufacturing, food processing, and desalination. In these industries, steam is used to heat or sterilize materials, and the condensation of superheated steam is an essential part of maintaining the temperature and pressure conditions required for these processes. For instance, in chemical processing, superheated steam may be used to drive chemical reactions, and the condensation process is carefully controlled to optimize reaction conditions and recovery of heat. In food processing, superheated steam is often employed in sterilization and pasteurization, and the condensation process helps ensure that products are heated efficiently and uniformly.
One of the challenges associated with superheated steam condensation is the potential for scaling or fouling of condenser surfaces. When steam condenses on the cooling surfaces, impurities present in the steam, such as minerals or chemicals, can deposit on the surface of the condenser tubes. This accumulation of material can impede heat transfer, reduce efficiency, and lead to maintenance issues. To prevent scaling, water treatment systems are often employed to remove impurities from the steam before it enters the condenser, and regular cleaning of the condenser tubes is necessary to maintain efficient operation.
Moreover, in high-pressure systems where superheated steam is involved, the design of the condenser must accommodate the high temperature and pressure conditions of the steam to prevent mechanical failure. Specialized materials that can withstand these harsh conditions are often used in the construction of condensers. Additionally, the potential for steam to condense unevenly due to local temperature variations requires advanced monitoring and control systems to regulate steam flow and temperature throughout the process.
In conclusion, superheated steam condensation is a vital process in many energy and industrial applications, where it allows for the efficient conversion of thermal energy into usable forms, such as electricity or heat. The process is governed by principles of heat transfer, latent heat, and phase change, and its efficiency is influenced by factors such as temperature gradients, system design, and cooling methods. Superheated steam condensation requires careful management to optimize energy recovery, prevent equipment damage, and maintain operational efficiency, making it an integral part of modern industrial systems, power generation, and thermal management.
The process of superheated steam condensation is not just important for improving efficiency in traditional power generation systems but also plays a significant role in the transition to more sustainable energy practices. As industries and power plants strive to reduce carbon emissions and adopt cleaner energy solutions, optimizing steam condensation processes is becoming even more critical. Technologies and innovations are being explored to further enhance the efficiency of steam condensation, particularly in systems that rely on renewable or low-carbon sources of energy.
For example, in concentrated solar power (CSP) plants, superheated steam is often used to drive turbines and generate electricity. In such applications, improving the heat recovery during condensation becomes even more important, as the overall efficiency of the CSP plant depends on how well it can retain and reuse thermal energy. Advanced cooling technologies, such as dry cooling or hybrid systems that combine both air and water cooling, are being investigated as ways to improve the heat exchange efficiency during superheated steam condensation while also reducing water consumption, which is crucial in water-scarce regions.
Additionally, in geothermal power plants, superheated steam derived from the Earth’s natural heat is used for electricity generation. The condensation process in geothermal plants is also vital for maintaining efficient energy conversion. Here, managing the temperature and pressure of the steam is crucial for both safety and efficiency. The condensate that is produced during the cooling process can be reinjected into the geothermal reservoir to maintain pressure levels, ensuring the long-term sustainability of the energy resource.
The integration of superheated steam condensation with carbon capture and storage (CCS) technologies also holds promise for reducing greenhouse gas emissions from fossil-fuel-powered plants. CCS systems capture CO2 emissions from power plant exhaust and prevent them from being released into the atmosphere. As superheated steam cools and condenses in a power plant, the residual heat can be harnessed to aid in the operation of CCS systems, improving their efficiency and reducing the overall energy penalty associated with carbon capture. This dual benefit of optimizing superheated steam condensation for both energy generation and emissions reduction is an area of active research and development.
Furthermore, the adoption of combined heat and power (CHP) systems in industries such as manufacturing, district heating, and commercial buildings is making efficient superheated steam condensation even more crucial. CHP systems simultaneously generate both electricity and useful heat from the same energy source, which is typically achieved by utilizing the waste heat from steam condensation. By improving the condensation process and optimizing heat recovery, CHP systems can operate at high efficiencies and significantly reduce overall energy consumption. This approach is a key strategy for enhancing energy efficiency in both urban and industrial settings.
In the context of space heating and cooling, district heating systems that use steam for thermal energy distribution can benefit from improved superheated steam condensation. These systems, often deployed in colder regions, can be more energy-efficient by utilizing advanced condensation technologies that minimize thermal losses during heat transfer. The development of more efficient steam condensation techniques can lead to lower operational costs and reduced environmental impacts associated with heating large urban areas.
The importance of superheated steam condensation extends to many sectors beyond energy generation, including chemical and food processing industries. In chemical manufacturing, steam is often used as a heat source for various reactions. The efficient recovery of heat from the condensation process can significantly reduce energy consumption and improve process economics. Similarly, in food processing, steam is used for sterilization, pasteurization, and drying processes, where the release of latent heat during condensation plays a vital role in maintaining product quality while reducing energy use.
Research into alternative materials and new cooling technologies for superheated steam condensation is also ongoing. For instance, materials with better thermal conductivity, such as advanced composites or novel alloys, may help improve the rate at which steam condenses, making heat transfer more efficient. Similarly, innovations in surface coatings, such as hydrophobic or nanostructured surfaces, could further enhance condensation efficiency by reducing frictional losses and encouraging faster phase changes.
Overall, superheated steam condensation is a critical component of many energy and industrial systems. As the demand for more sustainable energy solutions continues to grow, optimizing the condensation process will play an increasingly important role in improving energy efficiency, reducing operational costs, and minimizing environmental impacts. Continued technological advancements in heat recovery, cooling systems, and system integration will enhance the performance of superheated steam condensation processes, ensuring they remain a key part of efficient energy generation, industrial processes, and low-carbon energy solutions.
EMS Power Machines
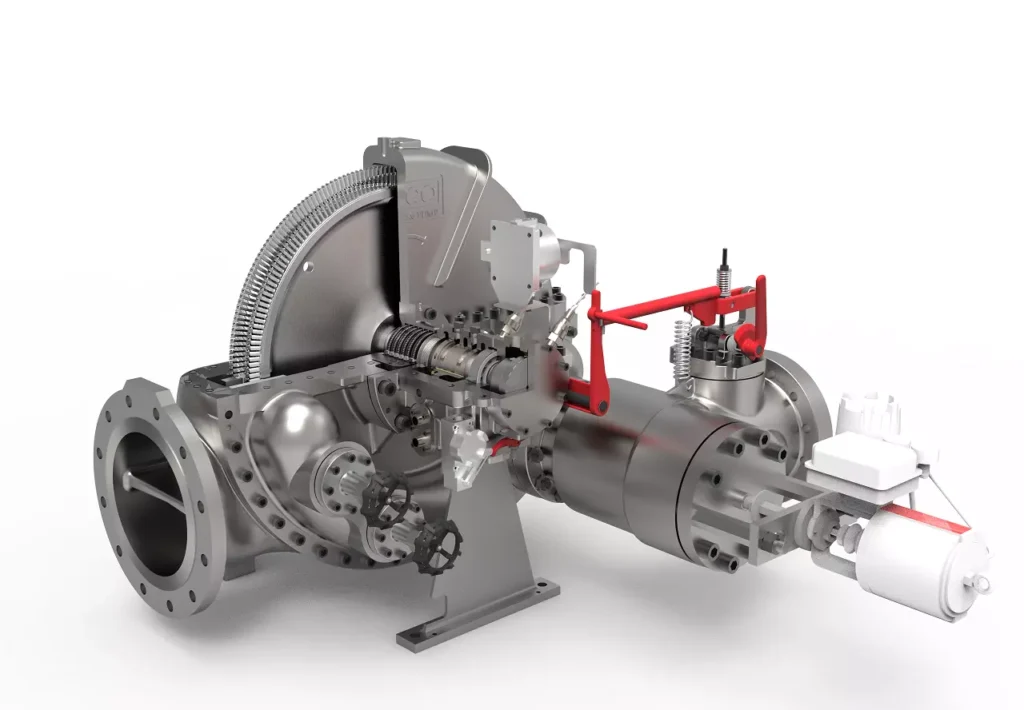
We design, manufacture and assembly Power Machines such as – diesel generators, electric motors, vibration motors, pumps, steam engines and steam turbines
EMS Power Machines is a global power engineering company, one of the five world leaders in the industry in terms of installed equipment. The companies included in the company have been operating in the energy market for more than 60 years.
EMS Power Machines manufactures steam turbines, gas turbines, hydroelectric turbines, generators, and other power equipment for thermal, nuclear, and hydroelectric power plants, as well as for various industries, transport, and marine energy.
EMS Power Machines is a major player in the global power industry, and its equipment is used in power plants all over the world. The company has a strong track record of innovation, and it is constantly developing new and improved technologies.
Here are some examples of Power Machines’ products and services:
- Steam turbines for thermal and nuclear power plants
- Gas turbines for combined cycle power plants and industrial applications
- Hydroelectric turbines for hydroelectric power plants
- Generators for all types of power plants
- Boilers for thermal power plants
- Condensers for thermal power plants
- Reheaters for thermal power plants
- Air preheaters for thermal power plants
- Feedwater pumps for thermal power plants
- Control systems for power plants
- Maintenance and repair services for power plants
EMS Power Machines is committed to providing its customers with high-quality products and services. The company has a strong reputation for reliability and innovation. Power Machines is a leading provider of power equipment and services, and it plays a vital role in the global power industry.
EMS Power Machines, which began in 1961 as a small factory of electric motors, has become a leading global supplier of electronic products for different segments. The search for excellence has resulted in the diversification of the business, adding to the electric motors products which provide from power generation to more efficient means of use.