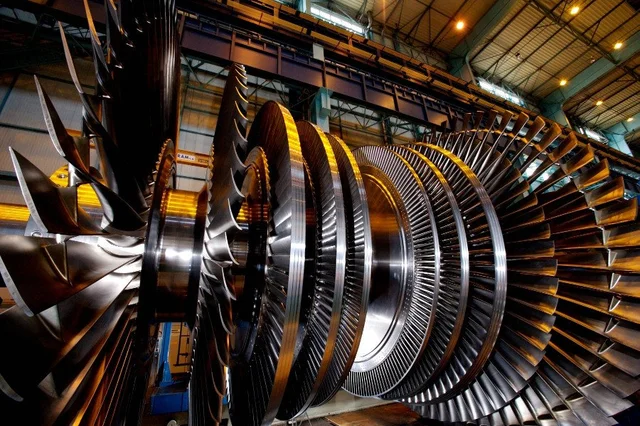
On Site Power Generator: Power generation from exhaust gas is an increasingly important method for improving energy efficiency and reducing emissions in various industries. Exhaust gas typically contains significant amounts of thermal energy, which, if not captured, is wasted into the environment. By harnessing this energy, industries can achieve dual benefits of reducing their energy costs and lowering greenhouse gas emissions.
The process of power generation from exhaust gas usually involves the use of waste heat recovery systems. These systems capture the heat energy in the exhaust gas from sources such as internal combustion engines, gas turbines, industrial furnaces, or boilers. The recovered heat can then be converted into electricity or used for other applications such as heating or cooling. The technology is widely used in industries like power generation, manufacturing, marine transportation, and oil and gas.
One of the most common technologies for generating power from exhaust gas is the Organic Rankine Cycle (ORC). In this process, a working fluid with a low boiling point is heated by the exhaust gas. The resulting vapor drives a turbine connected to a generator to produce electricity. The ORC is particularly suitable for applications involving low-temperature exhaust gases, making it a popular choice in industrial waste heat recovery.
Another widely used method is the use of heat recovery steam generators (HRSGs). These systems are commonly found in combined cycle power plants. Here, the exhaust gas from a gas turbine is directed to an HRSG, where it is used to produce steam. This steam then drives a steam turbine to generate additional electricity. Combined cycle power plants are highly efficient, as they utilize both the thermal and mechanical energy of the exhaust gases.
Thermoelectric generators (TEGs) are another promising technology for converting exhaust gas heat into electricity. These devices use thermoelectric materials that can directly convert temperature differences into electric voltage. While TEGs are currently less efficient than other methods, they have advantages such as compact size, no moving parts, and minimal maintenance. This makes them suitable for small-scale applications or remote locations where other systems may not be viable.
In the automotive sector, exhaust gas heat recovery systems are increasingly integrated into vehicle engines to improve fuel efficiency. For example, some modern vehicles use exhaust gas to power turbochargers or to generate electricity through thermoelectric devices, which can then be used to power auxiliary systems.
The use of exhaust gas for power generation also contributes to environmental sustainability. By capturing and reusing waste heat, industries can reduce their dependence on primary energy sources like fossil fuels. This leads to a decrease in carbon dioxide emissions and helps meet stricter environmental regulations. Moreover, such systems can contribute to the circular economy by transforming what was once considered waste into a valuable resource.
Despite the many advantages, there are challenges to implementing exhaust gas power generation systems. Initial capital costs can be high, and the economic viability often depends on the scale of the operation and the availability of exhaust gas. Furthermore, the efficiency of these systems is influenced by factors such as the temperature and flow rate of the exhaust gas, as well as the quality of the equipment used.
Advancements in materials science and engineering are helping to address these challenges. For instance, new high-temperature materials and improved thermoelectric materials are enhancing the performance and durability of waste heat recovery systems. Digital technologies such as advanced sensors and predictive maintenance are also playing a role in optimizing system performance and reducing operational costs.
In conclusion, power generation from exhaust gas is a critical strategy for enhancing energy efficiency and promoting sustainable industrial practices. With ongoing technological advancements and growing environmental awareness, the adoption of exhaust gas power generation systems is expected to increase across various sectors, contributing to a more sustainable energy future.
Power Generation
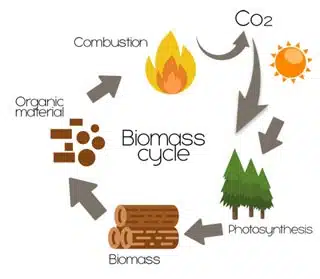
The future potential of power generation from exhaust gas lies in several key areas, including integration with renewable energy systems, development of decentralized energy solutions, and incorporation into smart grid technologies. By combining exhaust gas recovery systems with renewable energy sources such as solar or wind, hybrid energy systems can be developed. These systems improve overall energy reliability and efficiency by utilizing waste heat during periods of low renewable energy output. Such integration not only enhances the sustainability of power generation but also reduces dependency on fossil fuels, aligning with global decarbonization goals.
In industrial applications, the use of exhaust gas recovery can significantly improve the overall efficiency of production processes. Industries like cement, steel, and chemicals often produce vast amounts of high-temperature exhaust gases, which represent a valuable energy resource. Advanced waste heat recovery systems tailored to these industries can recover heat at various stages of the production process, ensuring minimal energy loss. Additionally, modular and scalable recovery systems are being developed, allowing smaller industrial facilities to adopt these technologies cost-effectively.
Marine transportation is another sector where exhaust gas power generation is gaining traction. Large ships powered by diesel engines produce substantial quantities of exhaust gas, which can be utilized to generate auxiliary power onboard. By installing waste heat recovery systems, ships can reduce their fuel consumption and comply with increasingly stringent maritime emission regulations. This also extends the operational range of vessels and reduces the frequency of refueling stops, contributing to operational efficiency.
The role of digitalization in exhaust gas power generation is becoming increasingly prominent. Smart sensors and control systems are being integrated into waste heat recovery setups, enabling real-time monitoring and optimization of system performance. Predictive maintenance powered by artificial intelligence (AI) and machine learning (ML) can identify potential issues before they lead to system failures, reducing downtime and maintenance costs. Digital twins, which create virtual replicas of physical systems, are being used to simulate and optimize the performance of exhaust gas recovery systems under different operating conditions.
Regulatory frameworks and government incentives play a critical role in accelerating the adoption of exhaust gas power generation technologies. Many governments offer tax breaks, subsidies, and grants to industries and businesses that implement energy-efficient and environmentally friendly technologies. These incentives not only make the adoption of such systems more economically viable but also drive innovation in the field.
Research and development efforts are continuously focused on overcoming the limitations of existing technologies. For instance, scientists are working on developing thermoelectric materials with higher conversion efficiencies and broader operational temperature ranges. Similarly, innovations in heat exchanger design are improving the ability to capture and transfer heat from exhaust gases, even under variable flow conditions. The development of compact, lightweight, and cost-effective systems is particularly important for expanding applications in sectors like automotive and aerospace, where space and weight constraints are critical.
In urban environments, exhaust gas power generation can contribute to the development of microgrids and decentralized energy systems. By capturing waste heat from local sources such as district heating plants, incinerators, or even large data centers, these systems can supply electricity and heating to nearby communities. This localized approach to energy generation reduces transmission losses and enhances energy security.
Another emerging application is in the realm of combined cooling, heat, and power (CCHP) systems. These systems utilize exhaust gas heat to provide not just electricity and heating, but also cooling through absorption chillers. Such multifunctional systems are particularly valuable in commercial and residential complexes, as they optimize energy use and reduce overall costs.
In summary, power generation from exhaust gas is a multifaceted solution with widespread applications across industries, transportation, and urban infrastructure. As technology continues to advance and the global focus on sustainability intensifies, the potential of exhaust gas recovery to transform energy systems will only grow. By converting waste into a resource, this technology represents a vital step toward a more efficient, sustainable, and resilient energy future.
The expansion of power generation from exhaust gas is also deeply intertwined with the global shift toward energy resilience and sustainability. With growing concerns about climate change and energy security, utilizing every available energy source, including waste heat from exhaust gas, has become an imperative. The ability to transform waste energy into usable power aligns with the broader objectives of reducing greenhouse gas emissions and achieving net-zero targets.
One promising area of innovation is the use of advanced materials and nanotechnology to enhance the efficiency of heat recovery systems. Materials with exceptional thermal conductivity, corrosion resistance, and durability are being developed to withstand the high temperatures and harsh conditions of exhaust gas environments. Nanostructured thermoelectric materials, for example, are showing significant promise in improving the performance of thermoelectric generators. These advancements not only increase the efficiency of energy conversion but also extend the lifespan of the equipment, thereby reducing operational costs over time.
The integration of exhaust gas power generation systems with energy storage technologies is another avenue for maximizing their potential. By coupling waste heat recovery with advanced battery systems or thermal energy storage, excess energy can be stored during periods of low demand and utilized during peak demand. This capability is especially valuable in industrial and commercial settings, where energy demand often fluctuates. Hybrid systems that combine waste heat recovery, renewable energy, and energy storage can provide a stable and reliable power supply while minimizing environmental impact.
Moreover, the role of policy and international cooperation cannot be overstated. Many countries have introduced stringent energy efficiency standards and carbon pricing mechanisms, which incentivize the adoption of waste heat recovery technologies. International organizations and trade bodies are also working to standardize practices and share best practices across borders. Collaborative research initiatives funded by governments and private entities are driving innovation and accelerating the deployment of these technologies.
In transportation, particularly in the automotive and aerospace industries, the push for electrification and fuel efficiency has highlighted the importance of capturing and utilizing exhaust gas energy. In hybrid and electric vehicles, waste heat from internal combustion engines can be used to generate electricity, which can then charge the battery or power auxiliary systems. Similarly, in aircraft, innovative waste heat recovery systems are being explored to reduce fuel consumption and enhance overall efficiency.
Marine vessels and off-road machinery also benefit from exhaust gas recovery systems. For instance, in large cargo ships, integrating waste heat recovery systems with the propulsion system can lead to substantial fuel savings and emissions reductions. Offshore oil and gas platforms are also adopting these technologies to reduce their reliance on diesel generators, thereby cutting operational costs and environmental impact.
The deployment of small-scale exhaust gas power generation systems in rural and remote areas represents a significant opportunity for decentralized energy access. In regions where grid infrastructure is limited or nonexistent, waste heat recovery can provide a reliable and sustainable source of power. For example, small biomass-powered generators often produce exhaust gas that can be harnessed to improve efficiency and meet the energy needs of local communities. This approach not only promotes energy equity but also contributes to rural development.
The role of education and workforce development is crucial for the widespread adoption of these technologies. As demand for skilled professionals in energy efficiency and waste heat recovery grows, educational institutions and training programs must adapt to equip the workforce with the necessary expertise. Engineers, technicians, and energy managers trained in the latest advancements in exhaust gas power generation will play a vital role in ensuring the successful implementation and maintenance of these systems.
In conclusion, the potential of power generation from exhaust gas extends far beyond energy efficiency. It represents a fundamental shift in how industries, transportation systems, and urban infrastructures perceive and utilize energy resources. By turning waste into value, exhaust gas recovery systems not only address environmental challenges but also provide economic benefits, making them an indispensable component of the global energy transition. As technology continues to evolve, and as regulatory and societal pressures mount, the adoption of these systems will likely become a standard practice across sectors, paving the way for a more sustainable and efficient energy future.
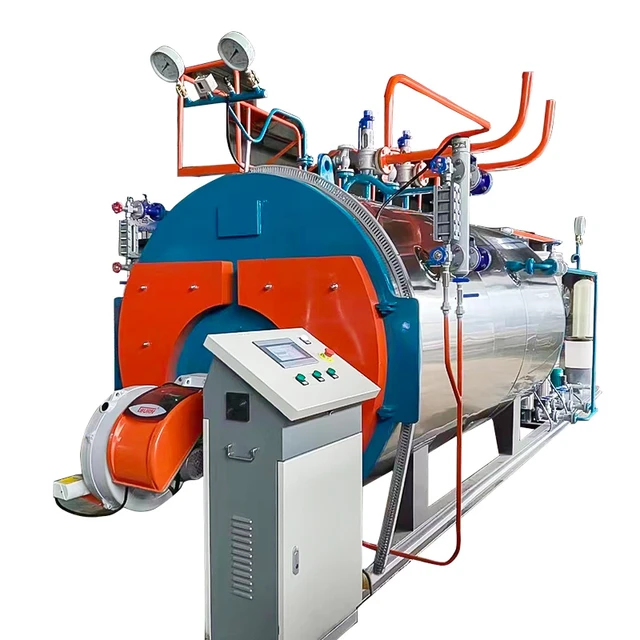
Looking further into the future, the integration of exhaust gas power generation with emerging technologies such as artificial intelligence (AI), the Internet of Things (IoT), and blockchain could revolutionize the way waste heat is captured, stored, and distributed. These technologies can play a significant role in improving the efficiency and functionality of waste heat recovery systems, making them smarter, more flexible, and better optimized for real-time conditions.
AI and machine learning algorithms, for example, can be employed to monitor and predict the behavior of exhaust gas recovery systems, enabling predictive maintenance and dynamic optimization of energy conversion processes. By analyzing historical data, AI can foresee potential system failures and recommend preventative actions before issues arise, significantly reducing downtime and maintenance costs. Additionally, AI can optimize the operation of waste heat recovery systems in response to varying loads, temperature fluctuations, and other variables, ensuring maximum efficiency at all times.
The IoT, which connects devices and systems through a network to share data, can enhance the performance of waste heat recovery systems by providing real-time feedback and remote control capabilities. Sensors embedded in the system can continuously monitor temperature, pressure, and other parameters, transmitting data to central control units for analysis. This allows operators to adjust system settings and identify potential inefficiencies remotely, improving system responsiveness and reliability.
Furthermore, the use of blockchain technology could facilitate the creation of decentralized energy markets, where individuals or businesses with waste heat recovery systems can trade the excess power they generate. Blockchain can ensure transparency, traceability, and security in energy transactions, providing a framework for microgrids or peer-to-peer energy sharing. This could lead to the emergence of localized energy markets where power generation from exhaust gas is not only a tool for efficiency but also an economic driver in communities and businesses.
The rise of digital twins, virtual replicas of physical systems, is another exciting development in the realm of waste heat recovery. A digital twin of an exhaust gas recovery system would allow engineers and operators to simulate, monitor, and test various configurations and parameters in a virtual environment before making changes to the physical system. This technology can improve decision-making and facilitate rapid troubleshooting, reducing the need for costly physical interventions and enhancing the overall efficiency of the system.
In addition to technological advancements, the societal and cultural acceptance of waste heat recovery systems will play a pivotal role in their future success. The increasing global awareness of environmental issues, such as climate change and resource depletion, has led to a greater emphasis on energy conservation and sustainability. As industries and governments commit to reaching net-zero emissions targets, there will likely be a heightened focus on technologies that help reduce energy consumption and minimize waste. Public and private sector collaboration will be key in driving the widespread adoption of these systems.
Moreover, the ongoing development of green financing mechanisms and carbon credit markets may further accelerate the implementation of exhaust gas power generation technologies. Financial incentives, such as low-interest loans for energy efficiency projects or the ability to sell carbon credits from waste heat recovery initiatives, can make the adoption of these systems more economically attractive for businesses. Governments and financial institutions could introduce subsidies or grants specifically targeted at companies investing in innovative waste heat recovery technologies, making these systems more accessible to a broader range of industries.
The integration of waste heat recovery into the circular economy model could also unlock new opportunities for resource efficiency and sustainability. By viewing waste heat not as a byproduct but as a valuable resource, companies can contribute to the broader effort to close the loop on material and energy flows. In sectors like manufacturing, where energy consumption is high, waste heat recovery systems can complement efforts to reduce raw material consumption and improve recycling rates, leading to reduced environmental impact and cost savings.
As waste heat recovery technologies evolve, the potential for hybrid systems that integrate exhaust gas with other energy generation methods is growing. For instance, hybrid systems that combine combustion engines, renewable energy sources, and waste heat recovery could achieve significantly higher efficiency than relying on any single technology. These systems would leverage the complementary strengths of each energy source, enabling industries to meet their energy needs while minimizing waste and emissions.
In the long term, the continuous development of global energy infrastructure will likely include waste heat recovery systems as a fundamental building block. From the design of energy-efficient buildings to the upgrading of industrial processes, waste heat recovery will be incorporated into a wide variety of applications. The transition to a low-carbon, sustainable energy future will require a multi-faceted approach that includes not only renewable energy generation but also innovative methods for recovering and reusing waste heat. By making use of what was once considered “waste,” industries and societies can move closer to achieving their energy and environmental goals.
In conclusion, power generation from exhaust gas is poised to become an integral part of the energy landscape. As technologies continue to advance, and as the global push for sustainability intensifies, the opportunities for utilizing waste heat for power generation will expand. The integration of digital technologies, hybrid systems, and decentralized energy solutions will further enhance the efficiency, scalability, and applicability of these systems across sectors. By capitalizing on the potential of exhaust gas, industries can reduce their environmental footprint, lower operating costs, and contribute to a more resilient and sustainable energy future.
Power Generation
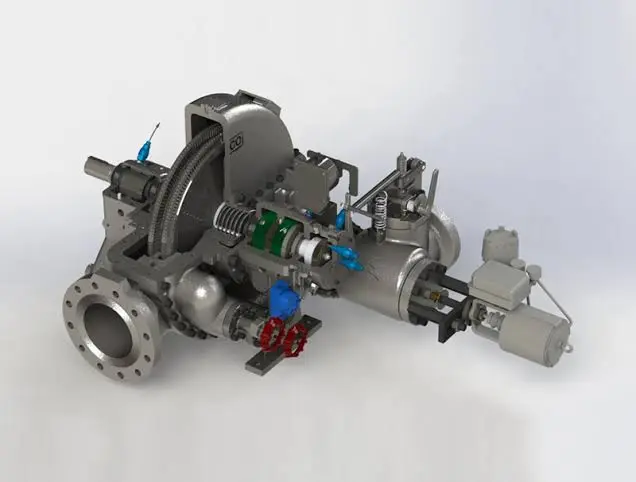
The evolution of power generation from exhaust gas is likely to intersect with other transformative trends in the energy sector, such as the transition to hydrogen-based systems, the proliferation of distributed energy resources (DERs), and the rise of energy-as-a-service (EaaS) business models. These developments, alongside advancements in waste heat recovery, will shape a more interconnected and efficient energy ecosystem.
Hydrogen, often referred to as the fuel of the future, offers a promising pathway for clean energy, and its integration with exhaust gas recovery systems could unlock significant synergies. In industrial processes or transportation systems where hydrogen is produced or consumed, waste heat is often generated as a byproduct. Capturing and utilizing this heat to produce electricity or support other thermal applications could significantly enhance the overall energy efficiency of hydrogen systems. For instance, in hydrogen electrolysis plants, the heat released during the production process could be captured using advanced heat recovery systems, thereby reducing the overall energy input required.
Distributed energy resources (DERs), which include small-scale power generation systems such as rooftop solar panels, wind turbines, and microturbines, can also benefit from waste heat recovery integration. In combined heat and power (CHP) configurations, small generators or engines used in DERs produce both electricity and heat. The heat can be recovered from the exhaust gases and used for space heating, cooling, or industrial processes. This localized, decentralized approach to energy generation reduces transmission losses and promotes energy self-sufficiency in communities and businesses.
The EaaS business model is another area where exhaust gas power generation could play a vital role. Companies adopting EaaS focus on providing energy solutions rather than just energy as a commodity. This model includes services such as energy management, optimization, and maintenance of energy systems. Waste heat recovery systems could be offered as part of comprehensive energy efficiency solutions, with providers handling the installation, operation, and optimization of the systems. This removes the upfront cost barrier for businesses while allowing them to benefit from reduced energy costs and lower emissions.
In urban planning, the role of exhaust gas power generation could expand through integration into smart cities and urban energy systems. District energy networks, for example, could leverage waste heat from local sources such as industrial plants, data centers, or transportation hubs to supply heating and cooling to residential and commercial buildings. With advanced sensors, data analytics, and AI-driven energy management systems, these networks can be optimized to balance supply and demand dynamically, ensuring efficient use of energy resources.
Another frontier for waste heat recovery is its application in advanced manufacturing technologies, including 3D printing and other additive manufacturing methods. These processes often involve localized high-temperature operations that release significant heat. By capturing this waste heat, manufacturers can improve the energy efficiency of their operations and reduce overall costs. The integration of heat recovery systems into smart factories equipped with IoT and AI technologies could further enhance operational efficiency and sustainability.
In the context of space exploration and off-world colonization, waste heat recovery systems could play a critical role in energy management. Spacecraft and planetary bases operate in resource-constrained environments where every watt of energy matters. Heat generated by onboard systems, engines, or reactors can be captured and reused to generate power or regulate temperatures, enhancing the sustainability of long-term space missions.
The potential for exhaust gas power generation also extends to the agriculture sector, where energy-intensive operations such as drying, heating, and greenhouse climate control are common. By integrating waste heat recovery systems with biogas plants or other agricultural machinery, farms can reduce their reliance on external energy sources and lower operating costs. Additionally, waste heat can support precision agriculture techniques by providing energy for sensors, monitoring equipment, and automated systems that optimize crop production.
To further accelerate the adoption of exhaust gas power generation, international collaboration in research, policy, and technology transfer will be essential. Sharing best practices and technological advancements across borders can help overcome barriers to implementation and ensure that both developed and developing regions can benefit from this technology. Public-private partnerships, international research consortia, and global standards for waste heat recovery systems will play pivotal roles in driving this progress.
Education and public awareness campaigns can also enhance the adoption and impact of waste heat recovery technologies. By informing stakeholders—ranging from policymakers to consumers—about the environmental and economic benefits of these systems, society can build the momentum needed to integrate waste heat recovery into mainstream energy strategies.
In conclusion, power generation from exhaust gas represents a convergence of technology, sustainability, and innovation. As the global energy system continues to evolve, the ability to harness waste heat will become increasingly important for industries, cities, and nations striving for efficiency and resilience. Whether through integration with hydrogen systems, support for decentralized energy models, or its role in space exploration, waste heat recovery is a versatile and indispensable component of the energy transition. By embracing this technology, humanity can move closer to a future where energy resources are utilized to their fullest potential, waste is minimized, and the environmental impact of energy generation is significantly reduced.
1. Introduction to Exhaust Gas Power Generation
- Overview of exhaust gas as a byproduct of industrial and mechanical processes.
- Importance of harnessing waste heat for energy efficiency and sustainability.
- Applications across industries and transportation.
2. Key Technologies for Waste Heat Recovery
- Organic Rankine Cycle (ORC).
- Heat Recovery Steam Generators (HRSG).
- Thermoelectric Generators (TEGs).
- Emerging technologies such as nanotechnology-enhanced systems.
3. Industrial Applications of Waste Heat Recovery
- Steel, cement, and chemical industries as key sectors.
- Case studies of energy savings and efficiency improvements.
- Integration with industrial processes.
4. Transportation Sector Applications
- Waste heat recovery in marine vessels for auxiliary power.
- Automotive applications like turbochargers and hybrid systems.
- Aerospace innovations for efficiency in flight.
5. Urban and Decentralized Energy Solutions
- Role of waste heat recovery in district heating and cooling.
- Microgrids and local energy markets leveraging waste heat.
- Integration into smart city infrastructure.
6. Technological Advancements and Innovation
- Advanced materials for heat exchangers and thermoelectric devices.
- Use of AI and IoT for system optimization and predictive maintenance.
- Development of hybrid energy systems combining renewables and waste heat.
7. Environmental and Economic Benefits
- Reduction in greenhouse gas emissions and carbon footprints.
- Cost savings for industries and consumers.
- Contribution to circular economy and resource optimization.
8. Challenges and Barriers to Adoption
- High initial costs and return on investment concerns.
- Technological limitations, such as efficiency of low-temperature heat recovery.
- Regulatory, logistical, and market-based barriers.
9. Policy, Incentives, and Global Collaboration
- Role of government subsidies, tax incentives, and carbon credits.
- International cooperation and knowledge sharing.
- Case studies of successful policy-driven implementations.
10. Future Directions and Emerging Applications
- Integration with hydrogen energy systems and renewables.
- Space exploration and off-world applications.
- Role in energy-as-a-service models and next-generation energy infrastructure.
Each section can be expanded with technical details, case studies, and real-world examples to provide a comprehensive exploration of the topic. Let me know if you’d like to develop or refine any specific section!
Introduction to Exhaust Gas Power Generation
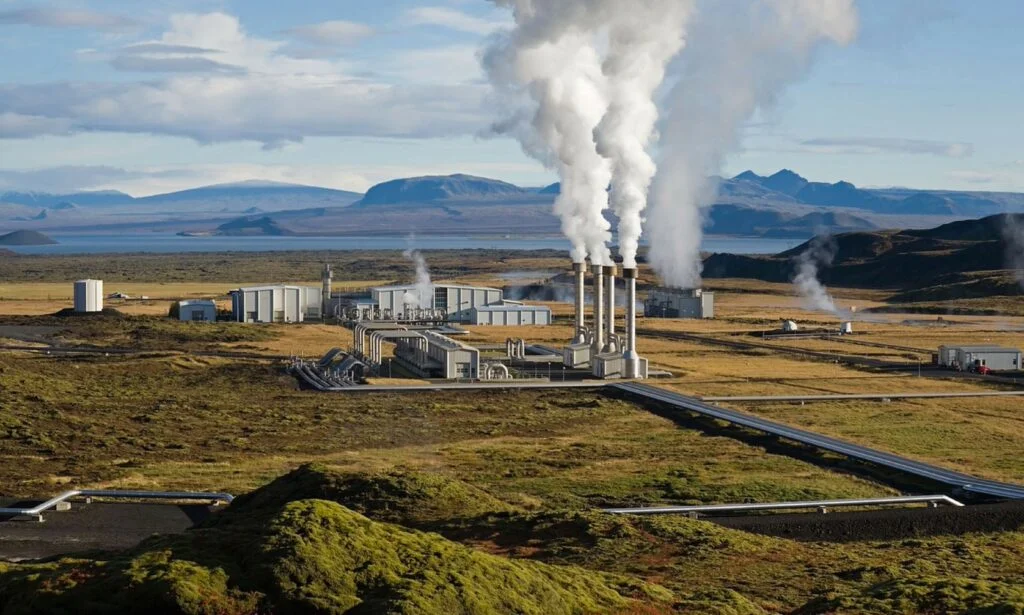
Exhaust gas power generation is a transformative approach to enhancing energy efficiency and reducing waste in a world increasingly focused on sustainability. Exhaust gases, typically a byproduct of combustion processes in industrial, transportation, and energy generation sectors, represent a significant source of untapped thermal energy. This waste energy, often vented into the atmosphere, contributes to inefficiencies and environmental challenges. By harnessing the thermal potential of exhaust gases, industries can convert waste heat into useful power, reducing energy consumption, lowering greenhouse gas emissions, and improving overall system efficiency.
The concept of recovering energy from exhaust gases is rooted in the fundamental principle of thermodynamics, which recognizes that no energy conversion process is perfectly efficient. During combustion, a substantial portion of the energy in fuels is lost as heat, primarily through exhaust gases. Depending on the application, exhaust gases can range in temperature from a few hundred degrees Celsius to well over a thousand degrees, making them a valuable resource for energy recovery. Capturing and utilizing this energy not only mitigates waste but also alleviates the demand for primary energy sources, contributing to both economic and environmental benefits.
Exhaust gas power generation finds application across a diverse range of industries and systems. In industrial settings, where processes such as steelmaking, cement production, and chemical manufacturing generate vast amounts of high-temperature exhaust gases, the potential for waste heat recovery is immense. These industries operate energy-intensive processes, and the ability to recover heat from exhaust streams allows them to improve energy efficiency and reduce operational costs. Similarly, in power plants, especially those using fossil fuels or biomass, the implementation of waste heat recovery systems can significantly enhance thermal efficiency, making energy generation more sustainable.
The transportation sector is another critical area where exhaust gas power generation is gaining traction. Internal combustion engines in automobiles, ships, and aircraft emit significant amounts of heat through exhaust systems. Technologies such as turbochargers and thermoelectric generators have been developed to capture this energy and convert it into useful power. Turbochargers, for instance, use exhaust gas energy to drive air compressors, improving engine efficiency and performance. Thermoelectric generators, on the other hand, can convert heat directly into electricity, providing power for auxiliary systems in vehicles or contributing to the overall energy balance.
The potential of exhaust gas power generation extends beyond industrial and transportation applications to urban infrastructure and decentralized energy systems. In urban environments, waste heat from sources like district heating plants, incinerators, or even large-scale data centers can be captured and utilized to supply electricity and heating to nearby buildings. This localized approach not only reduces energy waste but also enhances energy security and reliability by minimizing transmission losses. Moreover, in remote or off-grid areas, exhaust gas recovery systems integrated with small-scale generators can provide a reliable and sustainable source of power, improving energy access and supporting local development.
The development of advanced technologies has significantly improved the feasibility and efficiency of exhaust gas power generation. Heat recovery systems such as Heat Recovery Steam Generators (HRSGs), Organic Rankine Cycle (ORC) systems, and thermoelectric devices have emerged as viable solutions for capturing and converting waste heat. HRSGs are commonly used in power plants and industrial applications to produce steam from high-temperature exhaust gases, which can then drive turbines to generate electricity. ORC systems, which use organic fluids with lower boiling points than water, are particularly effective for recovering heat from lower-temperature exhaust gases, broadening the range of applications for waste heat recovery. Thermoelectric generators, though currently less efficient, offer the advantage of directly converting heat into electricity, making them ideal for compact and lightweight applications.
The adoption of exhaust gas power generation is driven not only by technological advancements but also by growing regulatory and economic pressures. Governments and international bodies have introduced stringent energy efficiency standards and emissions regulations, incentivizing industries to adopt waste heat recovery systems. Financial mechanisms such as tax credits, grants, and carbon pricing further encourage investment in these technologies, making them more accessible and economically viable. At the same time, rising energy costs and increasing awareness of the environmental impact of energy use are motivating industries and businesses to explore innovative solutions to reduce waste and improve sustainability.
Despite its many benefits, exhaust gas power generation also faces challenges. The high upfront cost of installing waste heat recovery systems can be a barrier for some businesses, particularly small and medium enterprises. Additionally, the variability in the quality and temperature of exhaust gases across different applications requires tailored solutions, which can add complexity and cost to system design and implementation. However, ongoing research and development efforts are addressing these challenges, with innovations in materials, system integration, and digitalization paving the way for more efficient, cost-effective, and versatile solutions.
In conclusion, exhaust gas power generation represents a critical step forward in the pursuit of energy efficiency and sustainability. By transforming waste into a resource, this approach not only reduces environmental impacts but also offers economic advantages, making it an attractive option for a wide range of applications. As technology continues to advance and the global focus on energy conservation intensifies, the role of exhaust gas power generation in shaping a more sustainable energy landscape will undoubtedly grow. Its potential to contribute to decarbonization, resource optimization, and energy resilience makes it a cornerstone of the transition to a cleaner, more efficient energy future.
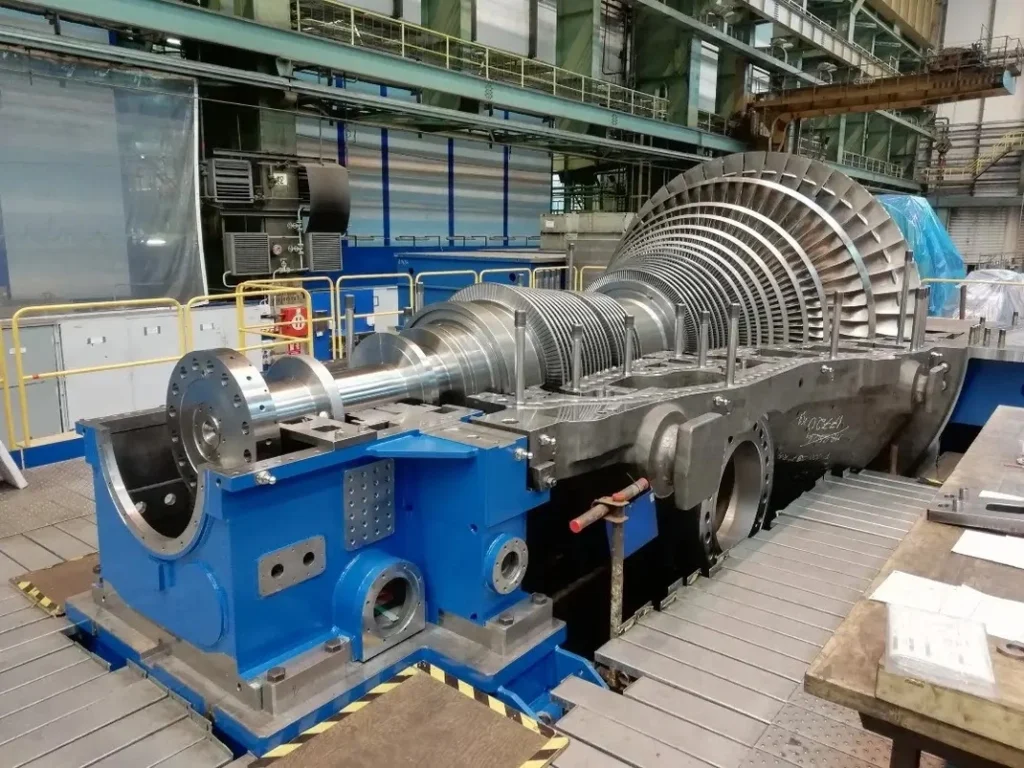
As the demand for more efficient energy systems intensifies, the scope of exhaust gas power generation is expected to broaden significantly. Emerging trends in energy systems design, coupled with advancements in materials science and data-driven technologies, are creating new opportunities to leverage waste heat as a valuable resource. The global energy transition, driven by the need to decarbonize and diversify energy sources, places exhaust gas power generation at the intersection of innovation and necessity.
One of the most promising developments in the field is the integration of waste heat recovery systems with renewable energy technologies. Solar and wind power, while crucial components of a sustainable energy future, are inherently intermittent. By incorporating exhaust gas power generation into hybrid systems, energy producers can mitigate the variability of renewables. For example, a combined cycle power plant that uses both gas turbines and a waste heat recovery system can provide a stable and reliable base load, while excess electricity generated during peak renewable output can be stored or redirected to other applications.
In industrial settings, the concept of energy cascading is gaining traction. This approach involves sequentially using waste heat at different temperature levels for multiple purposes, maximizing its utilization before it is finally discharged. High-temperature exhaust gases might first be used to generate electricity, followed by medium-temperature applications such as industrial heating, and finally, low-temperature processes like preheating water or space heating. This cascading use of energy significantly improves the overall efficiency of energy systems and aligns with the principles of a circular economy.
The role of digitalization in exhaust gas power generation cannot be overstated. Technologies such as artificial intelligence (AI), machine learning, and the Internet of Things (IoT) are transforming how waste heat recovery systems are monitored, maintained, and optimized. Smart sensors embedded within heat recovery systems can collect real-time data on temperature, pressure, and flow rates, which is then analyzed to identify inefficiencies or predict equipment failures. These insights allow operators to perform targeted maintenance and make adjustments to optimize performance, reducing downtime and operational costs.
Thermoelectric technology continues to hold potential for specific applications, particularly in scenarios where space is limited, or system simplicity is paramount. Advances in nanotechnology are enhancing the efficiency of thermoelectric materials, making it possible to convert waste heat into electricity with greater effectiveness. Research into novel materials such as skutterudites, half-Heusler compounds, and graphene-based composites is yielding promising results, potentially revolutionizing the use of thermoelectric generators in waste heat recovery.
In the transportation sector, the potential for exhaust gas power generation to contribute to decarbonization is vast. In automotive engineering, hybrid and electric vehicles (EVs) are increasingly being equipped with systems that recover waste heat from components such as the battery pack, motor, or power electronics. This recovered heat can be converted into electricity, extending the vehicle’s range and improving overall efficiency. Similarly, in heavy-duty applications such as shipping, waste heat recovery systems can play a significant role in reducing fuel consumption and emissions, making maritime transport more sustainable.
Global collaboration and policy support will be essential to fully realize the potential of exhaust gas power generation. International standards and protocols for the design, installation, and operation of waste heat recovery systems can help create a level playing field and promote widespread adoption. Furthermore, government incentives such as grants, subsidies, and tax breaks can lower the financial barriers to entry, particularly for small and medium-sized enterprises. Carbon trading schemes that reward companies for reducing emissions through waste heat recovery can also provide a powerful economic incentive.
Education and workforce development are critical components of scaling up exhaust gas power generation. As industries increasingly adopt these systems, there will be a growing demand for skilled professionals capable of designing, installing, and maintaining advanced waste heat recovery technologies. Universities, technical institutes, and vocational training programs must adapt their curricula to prepare the next generation of engineers, technicians, and energy managers with the necessary expertise.
Looking ahead, the role of exhaust gas power generation in global energy systems is poised to expand as technologies mature and the economic case for adoption becomes stronger. Its ability to enhance energy efficiency, reduce emissions, and complement renewable energy systems makes it a cornerstone of sustainable development. By transforming what was once regarded as waste into a valuable resource, exhaust gas power generation exemplifies the innovative approaches needed to address the dual challenges of energy demand and environmental impact. As this field continues to evolve, it will undoubtedly play a pivotal role in shaping a cleaner, more efficient, and more resilient energy future.
Key Technologies for Waste Heat Recovery
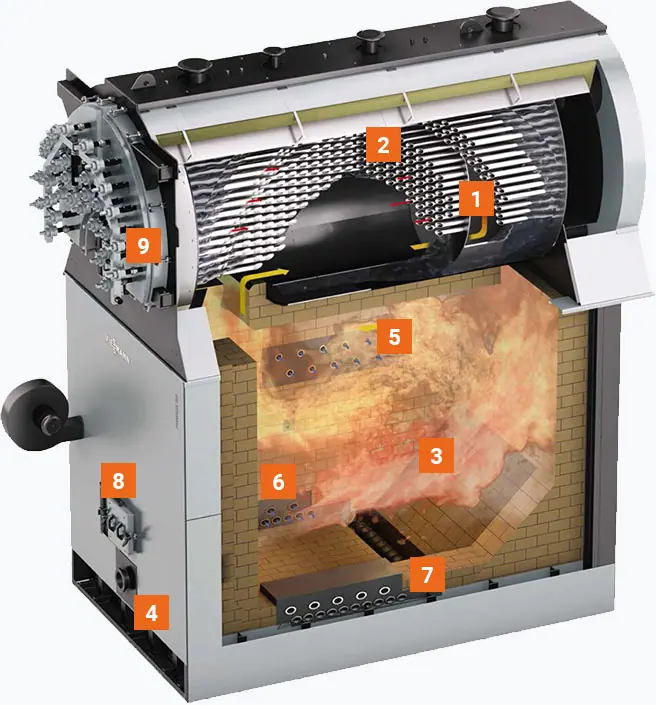
Key technologies for waste heat recovery are central to advancing energy efficiency and sustainability across various sectors. Waste heat, a byproduct of industrial, transportation, and energy processes, often escapes into the environment without being utilized. This heat represents a significant untapped resource that, if effectively captured and converted, can reduce energy consumption, lower emissions, and enhance economic performance. Over the years, numerous technologies have been developed to harness waste heat, each tailored to specific temperature ranges, industrial applications, and energy needs. These technologies have become increasingly sophisticated, driven by advances in materials science, engineering, and digitalization.
One of the most widely used technologies for waste heat recovery is the Heat Recovery Steam Generator (HRSG). HRSG systems are integral components of combined cycle power plants, where they capture exhaust heat from gas turbines to produce steam. This steam can then drive a steam turbine, generating additional electricity and significantly increasing the overall efficiency of the plant. HRSG systems are highly effective for high-temperature applications, typically operating in power plants and large industrial facilities. Their modular design allows customization to meet specific operational requirements, making them a versatile choice for industries seeking to optimize energy utilization.
For medium- and low-temperature waste heat, the Organic Rankine Cycle (ORC) has emerged as a highly efficient and adaptable solution. The ORC operates on the same principles as traditional steam cycles but uses organic fluids with lower boiling points instead of water. This makes ORC systems particularly suitable for capturing heat from sources with lower temperatures, such as industrial exhaust streams, geothermal energy, or even solar thermal systems. The use of organic working fluids allows ORC systems to operate at lower pressures and temperatures, reducing equipment stress and maintenance costs while maintaining high efficiency. ORC technology is widely used in industries such as cement, steel, and biomass power generation, where medium- to low-grade heat is abundant.
Another critical technology in waste heat recovery is the Regenerative Heat Exchanger. These systems are designed to transfer heat from hot exhaust gases to incoming cold streams, preheating them and reducing the energy required for subsequent processes. Regenerative heat exchangers are particularly effective in applications such as glass manufacturing, where maintaining consistent high temperatures is essential. The continuous exchange of heat minimizes energy wastage, lowering fuel consumption and operating costs. The design of these systems has advanced significantly, with innovations in materials and configurations allowing for greater heat transfer efficiency and durability.
Thermoelectric Generators (TEGs) represent a unique approach to waste heat recovery by directly converting heat into electricity using thermoelectric materials. These materials exploit the Seebeck effect, where a temperature difference across a material generates an electric voltage. TEGs are compact, lightweight, and require no moving parts, making them ideal for applications where space and simplicity are critical considerations. While their efficiency is currently lower than other waste heat recovery systems, ongoing research into advanced thermoelectric materials, such as skutterudites and half-Heusler compounds, promises to improve performance. TEGs are particularly useful in automotive applications, where they can harness waste heat from vehicle exhaust systems to power auxiliary systems, improving overall fuel efficiency.
For extremely high-temperature applications, Heat Pipes and Phase-Change Systems offer effective solutions. Heat pipes are highly efficient thermal conductors that transfer heat through the phase change of a working fluid within a sealed pipe. These systems are widely used in electronics cooling, aerospace applications, and high-temperature industrial processes. Phase-change systems, such as those using molten salts, can store and transfer heat at extremely high temperatures, making them suitable for concentrated solar power plants and high-temperature industrial furnaces.
The integration of Energy Storage Technologies with waste heat recovery systems is also gaining traction. Thermal energy storage (TES) systems, such as molten salt tanks or phase-change materials, allow the captured heat to be stored for later use. This is particularly advantageous in applications where there is a mismatch between the availability of waste heat and the demand for energy. By decoupling heat capture from its use, TES systems enhance the flexibility and reliability of waste heat recovery operations.
Digitalization and smart control systems are transforming waste heat recovery technologies, enabling more precise monitoring and optimization. IoT-enabled sensors, combined with advanced data analytics and machine learning algorithms, can monitor system performance in real-time, predict maintenance needs, and optimize operations for maximum efficiency. These advancements not only improve the effectiveness of waste heat recovery systems but also reduce operational costs and downtime.
Advanced Materials and Coatings are also playing a crucial role in improving the performance of waste heat recovery systems. High-performance materials with excellent thermal conductivity and corrosion resistance ensure the durability and efficiency of heat exchangers and other components operating in harsh environments. Innovations such as graphene-based coatings, ceramic composites, and high-temperature alloys are pushing the boundaries of what waste heat recovery systems can achieve.
Lastly, Hybrid Systems that combine multiple waste heat recovery technologies are becoming more common. For example, an industrial facility might use an ORC system to generate electricity from medium-grade heat, while simultaneously employing regenerative heat exchangers to preheat incoming process streams. Such hybrid approaches maximize the utilization of available heat, ensuring that energy recovery is as comprehensive and efficient as possible.
In summary, waste heat recovery technologies are diverse, each offering unique advantages tailored to specific applications and requirements. From HRSGs and ORCs to TEGs and advanced heat exchangers, these systems represent a critical component of modern energy strategies. As industries and governments continue to prioritize energy efficiency and sustainability, the development and deployment of these technologies will play a pivotal role in reducing waste, conserving resources, and mitigating the environmental impact of energy use. With ongoing research and innovation, the potential for waste heat recovery to transform energy systems is immense, paving the way for a more sustainable and efficient future.
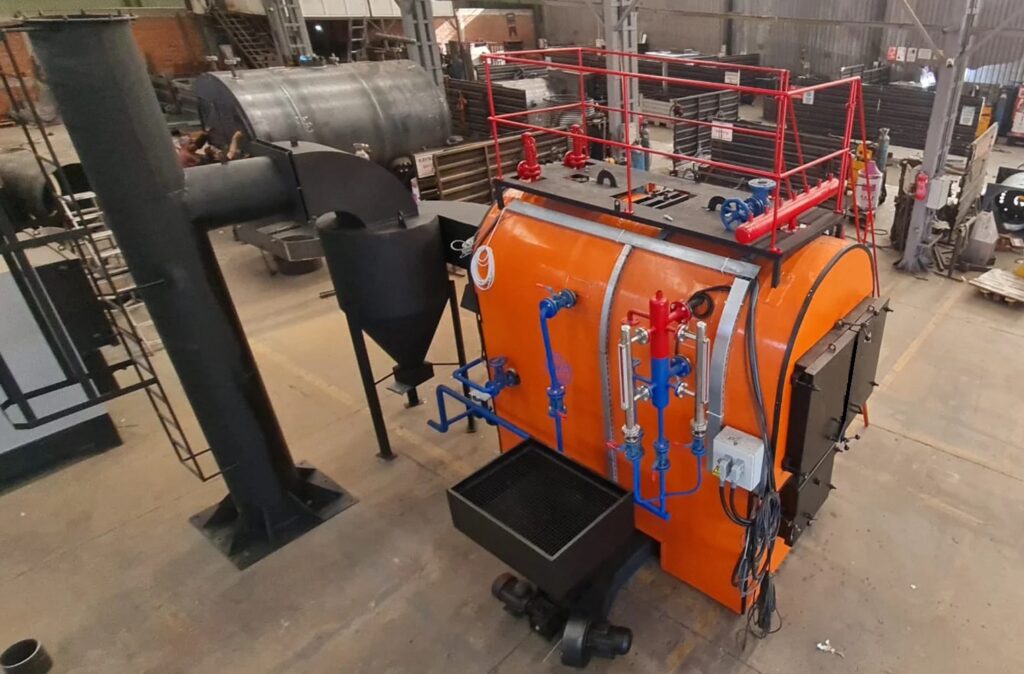
The future of waste heat recovery technologies is promising, as advancements in engineering, materials science, and system integration continue to push the boundaries of what these systems can achieve. Emerging technologies and innovative designs are addressing the limitations of current systems, opening new avenues for the utilization of waste heat across a wider range of industries and applications.
One area of significant interest is the development of supercritical CO₂ (sCO₂) cycles for waste heat recovery. These systems use supercritical carbon dioxide as the working fluid, which operates at a state between liquid and gas, offering superior thermodynamic properties compared to traditional steam or organic fluids. sCO₂ cycles are highly efficient at capturing and converting waste heat from high-temperature sources, such as gas turbines, into electricity. They require smaller equipment sizes due to the high density of supercritical CO₂, making them particularly suitable for compact or space-constrained environments. This technology has the potential to revolutionize power generation in industries such as aerospace, nuclear energy, and concentrated solar power.
Micro-scale and modular waste heat recovery systems are also emerging as a key focus of innovation. These smaller systems are designed to capture and utilize heat from distributed or low-capacity sources that were previously considered uneconomical to exploit. For instance, micro ORC systems are being developed for applications such as residential heating, small-scale industrial processes, and off-grid power generation. The modularity of these systems allows for scalability, enabling users to add or remove units based on changing energy needs. This approach enhances flexibility and lowers the barriers to entry for smaller businesses and communities seeking to implement waste heat recovery solutions.
In the context of urban environments, district energy systems are becoming a focal point for waste heat recovery applications. By integrating waste heat recovery systems with urban infrastructure, such as district heating and cooling networks, cities can harness heat from industrial plants, power stations, and even unconventional sources like data centers or wastewater treatment plants. This captured heat can be distributed through a network of insulated pipes to provide heating or cooling to residential and commercial buildings, significantly reducing energy consumption and greenhouse gas emissions in urban areas. Advanced heat exchangers and heat pumps play a critical role in these systems, enabling efficient transfer and utilization of heat across diverse applications.
Another promising avenue for waste heat recovery is its integration with hydrogen production technologies. Waste heat from industrial processes or power plants can be used to drive thermochemical or electrochemical reactions involved in hydrogen production. For example, high-temperature exhaust gases can provide the thermal energy needed for steam methane reforming (SMR) or solid oxide electrolysis cells (SOECs), improving the efficiency of these processes and lowering their overall energy demands. This synergy between waste heat recovery and hydrogen production supports the development of a hydrogen-based energy economy, offering a pathway toward decarbonizing sectors that are challenging to electrify.
Research into dynamic and adaptive systems is also advancing the field of waste heat recovery. These systems are designed to respond to fluctuating heat loads and variable operating conditions, ensuring consistent performance and energy capture. For instance, adaptive ORC systems can automatically adjust their working fluid composition or operating parameters based on real-time data, optimizing efficiency under different heat source conditions. Similarly, smart heat exchangers equipped with sensors and actuators can dynamically regulate heat transfer rates to match demand, enhancing the overall responsiveness and reliability of waste heat recovery systems.
Collaborative platforms and shared infrastructure are emerging as strategic approaches to optimize waste heat utilization across industrial clusters or regions. In such setups, multiple facilities with diverse heat requirements and sources can share a common waste heat recovery system or network. This allows high-grade heat from one facility to be used in processes requiring lower-grade heat in another, maximizing overall energy efficiency and reducing waste. These collaborative models are supported by advancements in data analytics, which enable precise matching of heat supply and demand across complex networks.
Environmental considerations are also driving innovation in waste heat recovery technologies. Systems are being designed with a focus on minimizing environmental impact, such as using non-toxic and environmentally friendly working fluids in ORC systems or developing heat exchangers that reduce fouling and corrosion, which can lead to hazardous waste. The integration of waste heat recovery with carbon capture and storage (CCS) technologies is another area of interest. By using recovered heat to power CCS processes, industries can reduce the energy penalty associated with capturing and storing CO₂ emissions, making these systems more economically viable and environmentally sustainable.
The role of waste heat recovery in supporting the transition to net-zero energy systems cannot be overstated. As industries, governments, and communities strive to decarbonize, waste heat recovery offers a practical and impactful solution to reduce reliance on primary energy sources and minimize carbon footprints. It complements renewable energy technologies, enhances the efficiency of existing systems, and provides a pathway for industries to meet stringent environmental and energy efficiency targets.
As we look to the future, waste heat recovery will continue to evolve and integrate with other advanced energy technologies. From hybrid systems that combine waste heat recovery with solar or wind power to novel applications in aerospace and space exploration, the potential applications of waste heat recovery are vast and varied. The ongoing convergence of innovation, policy support, and market demand ensures that waste heat recovery will remain a cornerstone of sustainable energy strategies, playing a vital role in creating a cleaner, more efficient, and resilient energy landscape.
Industrial Applications of Waste Heat Recovery
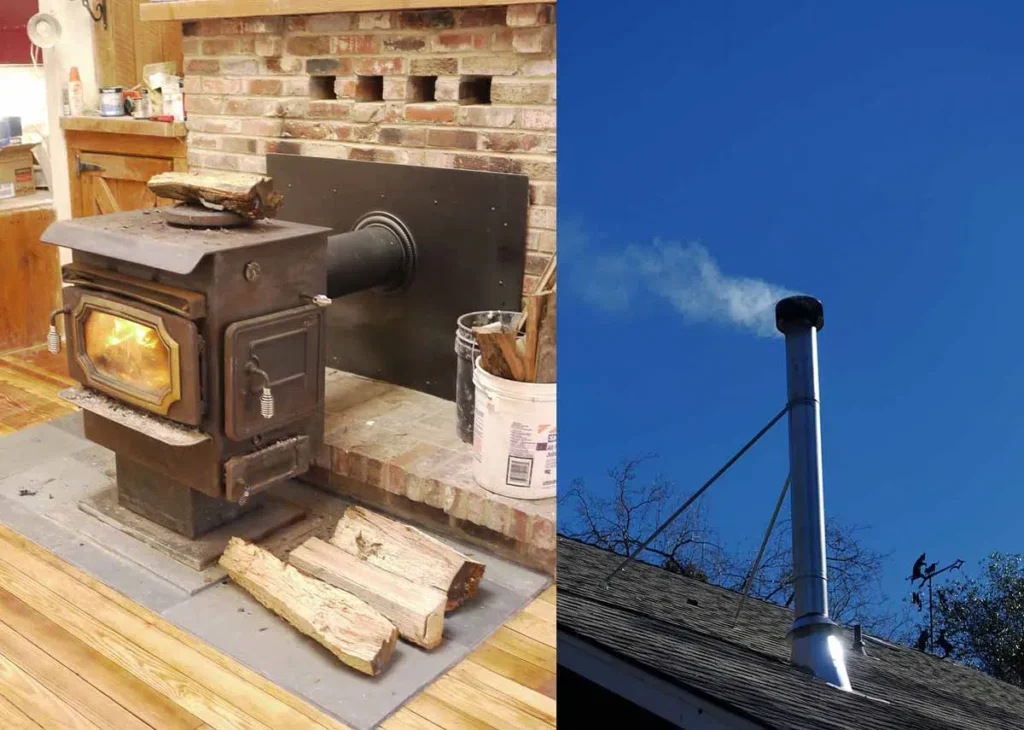
Industrial applications of waste heat recovery are critical for improving energy efficiency and sustainability in sectors that consume large amounts of energy. The industrial sector is responsible for a significant portion of global energy consumption, and much of this energy is wasted in the form of heat that escapes through exhaust gases, cooling systems, or other byproducts of industrial processes. The recovery and utilization of this waste heat not only helps reduce energy costs but also contributes to a reduction in greenhouse gas emissions, making it a key strategy in the transition toward more sustainable industrial practices.
Industries that rely heavily on high-temperature processes, such as steel manufacturing, cement production, and chemical processing, produce substantial amounts of waste heat. In the steel industry, for example, heat is generated during the smelting and refining processes, where temperatures often exceed 1,000°C. Capturing this waste heat and converting it into useful energy can have a profound impact on the overall energy efficiency of steel plants. Heat recovery systems, such as heat recovery steam generators (HRSGs), can capture heat from exhaust gases and produce steam, which can then be used to generate electricity or provide process heat for other parts of the plant. Similarly, in cement production, rotary kilns, which operate at extremely high temperatures, generate large amounts of heat that can be recovered and used in various ways, such as preheating raw materials or generating electricity.
The chemical industry is another sector where waste heat recovery is becoming increasingly important. Many chemical processes, such as distillation, cracking, and drying, involve high temperatures that produce large quantities of waste heat. By integrating waste heat recovery systems into these processes, chemical plants can improve their energy efficiency and reduce their reliance on external energy sources. Organic Rankine Cycle (ORC) systems, for instance, are widely used in the chemical industry to recover heat from lower temperature exhaust gases. These systems use organic fluids with lower boiling points than water, allowing them to capture heat from sources such as cooling towers, drying systems, or reaction vessels, and convert it into electricity or useful thermal energy.
In the food and beverage industry, heat recovery systems are used to capture waste heat from processes like drying, pasteurization, and cooking. For example, large-scale food processing plants often use steam or hot water for cooking and sterilization. The heat from exhaust gases and other hot surfaces can be recovered and used to preheat incoming water or air, reducing the need for additional energy input and lowering operating costs. In addition to reducing energy consumption, waste heat recovery in the food industry can also improve process control and reduce environmental impact by minimizing emissions of greenhouse gases and other pollutants.
Waste heat recovery is also essential in the refining and petrochemical sectors, where high-temperature reactions and distillation processes are routine. In oil refineries, excess heat is generated during the distillation of crude oil, the cracking of hydrocarbons, and the operation of furnaces and reactors. By integrating waste heat recovery systems, refineries can significantly reduce their energy costs and improve the overall efficiency of their operations. Heat exchangers and HRSG systems are commonly used in these industries to recover heat from flue gases and other exhaust streams, which can then be used to generate steam or provide thermal energy for other parts of the plant.
The manufacturing of glass, ceramics, and other high-temperature materials is another area where waste heat recovery plays a critical role. Glass production furnaces operate at temperatures that can exceed 1,500°C, generating vast amounts of waste heat. By employing heat recovery technologies such as regenerative heat exchangers, glass manufacturers can capture and reuse this heat to preheat raw materials or generate electricity. Similarly, in the ceramics industry, heat from kilns can be captured and used to dry raw materials or preheat combustion air, reducing the need for external energy inputs and improving overall energy efficiency.
In the textile industry, processes such as dyeing, drying, and finishing consume large amounts of energy, and waste heat recovery systems can help reduce the energy demands of these processes. Heat recovery can be implemented in various stages of textile production, from capturing heat from exhaust gases in drying machines to utilizing waste heat from chemical reactions during dyeing. The recovered energy can be used to preheat water, air, or materials, reducing the need for additional heating and lowering operating costs.
The automotive industry is increasingly adopting waste heat recovery technologies as part of its efforts to improve fuel efficiency and reduce emissions. One of the most common applications is the use of thermoelectric generators (TEGs), which convert heat from the engine’s exhaust gases directly into electricity. This electricity can power auxiliary systems, such as lighting, air conditioning, or infotainment, reducing the load on the vehicle’s main battery and improving overall fuel efficiency. Additionally, waste heat recovery technologies like turbochargers, which use exhaust gases to drive a compressor that forces more air into the engine, help improve engine performance and fuel efficiency, particularly in high-performance vehicles.
Waste heat recovery is not only beneficial for large-scale industrial facilities but also offers significant advantages in small and medium-sized enterprises (SMEs). In smaller manufacturing operations, where energy costs can represent a substantial portion of operational expenses, waste heat recovery systems provide a cost-effective way to reduce energy consumption and improve overall productivity. Modular systems, such as small-scale ORC units or heat pumps, can be easily integrated into existing infrastructure, offering flexible and scalable solutions for a wide range of applications.
Beyond reducing energy costs and improving efficiency, waste heat recovery technologies can also support broader sustainability goals. Many industries are under increasing pressure from governments, regulators, and consumers to reduce their environmental impact and lower carbon emissions. By capturing and reusing waste heat, industries can decrease their overall energy consumption and reduce the need for fossil fuel-based energy, which in turn reduces their carbon footprint. Furthermore, the integration of waste heat recovery systems can contribute to compliance with environmental regulations, such as those related to greenhouse gas emissions, and help companies meet sustainability targets set by investors or stakeholders.
Despite the clear benefits, the widespread adoption of waste heat recovery systems in industrial applications faces several challenges. The high upfront costs associated with installing these systems can be a barrier, particularly for smaller businesses that may not have the capital to invest in such technologies. Additionally, the technical complexity of integrating waste heat recovery into existing industrial processes can be a challenge, as it often requires customized solutions tailored to specific processes and operational conditions. However, with the continued advancement of technologies, such as more efficient heat exchangers, lower-cost ORC systems, and improved digital control systems, the economic case for waste heat recovery is becoming stronger. Moreover, incentives and subsidies provided by governments and regulatory bodies to encourage energy efficiency and reduce emissions are helping to offset these initial costs.
In conclusion, waste heat recovery is a vital component of modern industrial operations, offering significant energy savings, reduced environmental impact, and enhanced operational efficiency. By capturing and reusing waste heat, industries can improve their bottom lines while contributing to the global effort to reduce energy consumption and mitigate climate change. As technology continues to advance, the potential for waste heat recovery across a broader range of industries will only increase, making it an essential strategy for a sustainable industrial future.
As industries continue to face pressure to improve energy efficiency and reduce carbon emissions, waste heat recovery technologies are expected to play an even more significant role in the future. Advancements in digitalization, materials science, and system integration are opening new avenues for optimizing waste heat recovery systems and enabling their widespread deployment across diverse sectors.
One of the major trends shaping the future of waste heat recovery is the growing importance of digitalization and smart technologies. The integration of advanced sensors, data analytics, and Internet of Things (IoT) devices into waste heat recovery systems allows for real-time monitoring, predictive maintenance, and performance optimization. Smart systems can adjust operational parameters based on fluctuating energy demands, weather conditions, and other external factors, ensuring maximum efficiency. Predictive analytics, powered by machine learning algorithms, can identify patterns in energy consumption and detect inefficiencies before they result in costly downtime or system failures. This data-driven approach enhances the reliability and lifespan of waste heat recovery systems, reducing operational costs and improving overall system performance.
The role of artificial intelligence (AI) in waste heat recovery is also becoming more pronounced. AI can help optimize complex energy systems by modeling energy flows, simulating system behaviors, and recommending adjustments in real time. For example, AI algorithms can predict the amount of waste heat available from industrial processes, assess the most cost-effective ways to capture and use it, and determine the optimal balance between different waste heat recovery technologies (such as ORC, heat pumps, or thermoelectric generators). As AI systems learn from data over time, they can refine their predictions and recommendations, further enhancing energy efficiency and operational savings.
Another emerging development is the advancement of materials used in waste heat recovery systems. New materials with superior heat resistance, thermal conductivity, and corrosion resistance are being developed to improve the efficiency and durability of heat exchangers, heat recovery steam generators, and other components of waste heat recovery systems. For example, graphene-based materials are gaining attention for their excellent thermal properties, which could help improve the heat transfer efficiency of heat exchangers. Likewise, ceramic composites and advanced alloys are being researched for their ability to withstand the extreme temperatures and harsh environments found in high-temperature industrial processes, such as in steel production and glass manufacturing. These advanced materials could reduce maintenance costs and extend the operational life of waste heat recovery systems.
Hybrid systems that combine multiple waste heat recovery technologies are also an exciting development. For instance, combining heat recovery with renewable energy sources, such as solar or geothermal energy, could provide a more reliable and consistent energy supply. Hybrid systems can optimize the use of waste heat across a range of temperatures and applications, making them suitable for industries with diverse energy needs. For example, a combined ORC and heat pump system could efficiently recover heat from low- and medium-temperature exhaust gases while providing heating and cooling for industrial processes. Hybrid systems could also integrate energy storage solutions, such as thermal energy storage, allowing for heat recovery during periods of excess waste heat and storage for later use when demand is high or renewable energy sources are unavailable.
The development of modular and small-scale waste heat recovery systems is another key trend. These systems are being designed to meet the needs of smaller businesses, remote locations, and industries with decentralized energy requirements. Modular systems are flexible and scalable, allowing companies to add or remove units based on their changing needs. For example, small-scale ORC systems can be integrated into small manufacturing plants, agricultural operations, or even residential buildings to recover waste heat from processes such as cooking, drying, or space heating. These systems can provide cost-effective energy solutions for industries that may not have the resources to invest in large, centralized waste heat recovery installations.
The growing interest in circular economy principles is also driving innovation in waste heat recovery. The concept of a circular economy emphasizes the reuse, recycling, and repurposing of materials and energy to minimize waste and environmental impact. Waste heat recovery fits perfectly into this model by converting what would otherwise be discarded heat into valuable energy. In industries such as mining, forestry, and agriculture, the implementation of waste heat recovery systems can contribute to the sustainable management of resources and reduce the environmental footprint of operations. Additionally, the combination of waste heat recovery with other circular economy practices, such as material recycling and waste-to-energy technologies, can further optimize resource utilization and reduce reliance on fossil fuels.
Governments and regulatory bodies are also playing an increasingly important role in the adoption of waste heat recovery technologies. Many countries are implementing stricter energy efficiency regulations and offering financial incentives, such as tax credits, grants, and subsidies, to encourage the use of waste heat recovery systems. In addition, carbon pricing mechanisms, such as carbon taxes and cap-and-trade programs, are creating economic incentives for industries to reduce their greenhouse gas emissions. These policies are helping to drive the widespread adoption of waste heat recovery systems, making them more economically viable and attractive to businesses.
As industries continue to evolve and become more energy-conscious, the demand for sustainable energy solutions will grow. Waste heat recovery is positioned to play a crucial role in helping industries meet their sustainability goals by improving energy efficiency, reducing emissions, and lowering operational costs. By capturing and reusing waste heat, industries can reduce their dependence on traditional energy sources, lower their carbon footprints, and contribute to global efforts to combat climate change.
Looking forward, the adoption of waste heat recovery systems is expected to increase significantly across a wide range of industries. The convergence of advanced technologies, such as AI, smart systems, and advanced materials, along with favorable policies and incentives, is paving the way for a future where waste heat recovery is not just a niche technology but a mainstream solution for achieving sustainable, energy-efficient industrial operations. By continuing to invest in research, development, and deployment, waste heat recovery will play an instrumental role in the global transition to a more energy-efficient and environmentally responsible industrial sector.
Transportation Sector Applications
The transportation sector plays a vital role in global energy consumption and greenhouse gas emissions, with vehicles, trains, ships, and aircraft all contributing significantly to energy demand and environmental impact. As efforts to reduce carbon footprints and enhance energy efficiency intensify, the utilization of waste heat recovery technologies in transportation is gaining traction. By recovering and reusing the heat generated during operation, transportation systems can improve fuel efficiency, reduce emissions, and lower operational costs, making them an essential part of the industry’s transition to sustainable energy.
In road transportation, waste heat recovery is already being integrated into various types of vehicles, ranging from passenger cars to heavy-duty trucks. One of the most promising technologies in this area is the thermoelectric generator (TEG). TEGs work by converting waste heat from the engine’s exhaust gases directly into electricity, leveraging the Seebeck effect, where a temperature gradient generates electrical voltage. This recovered electricity can power auxiliary systems within the vehicle, such as air conditioning, lighting, and infotainment, thus reducing the load on the vehicle’s primary battery or alternator. By relieving the engine of the task of powering these systems, TEGs improve fuel efficiency and reduce overall energy consumption, contributing to a reduction in carbon emissions.
In hybrid and electric vehicles, waste heat recovery plays a critical role in further enhancing energy efficiency. While these vehicles are already more energy-efficient than traditional combustion-engine vehicles, waste heat recovery technologies offer an additional layer of optimization. Electric vehicles (EVs), for example, can use thermoelectric devices to recover heat generated by the battery, motor, and other components, converting it into usable electricity or thermal energy. This recovered energy can then be used to recharge the battery or for cabin heating, reducing the reliance on external energy sources and increasing the range and efficiency of the vehicle. Similarly, in hybrid vehicles, waste heat recovery can complement the powertrain by capturing and utilizing heat from the internal combustion engine, further extending the range and improving fuel economy.
In the realm of heavy-duty transport, such as trucks, buses, and trains, waste heat recovery technologies are becoming increasingly important for improving operational efficiency and reducing fuel consumption. For long-haul trucks, the engine’s exhaust gases contain substantial amounts of waste heat, which can be recovered using organic Rankine cycle (ORC) systems or heat exchangers. ORC systems are particularly useful for converting low- to medium-temperature exhaust heat into mechanical or electrical energy, which can then be used to drive the truck’s auxiliary systems or even contribute to propulsion. In buses, where fuel economy is a critical consideration due to the high frequency of stop-and-go driving, waste heat recovery can be employed to capture and reuse heat generated during braking or idling. This recovered energy can help power air conditioning, heating, and other electrical systems, reducing fuel consumption and emissions.
The maritime industry is another area where waste heat recovery has the potential to significantly improve energy efficiency and reduce emissions. Ships, particularly large cargo vessels, consume vast amounts of fuel and emit large quantities of greenhouse gases due to the inefficiencies inherent in their engines. Many modern ships are incorporating waste heat recovery systems to capture heat from the exhaust gases of the engine and repurpose it for other uses. For example, waste heat recovery steam generators (WHRSGs) can be installed to convert exhaust heat into steam, which can then be used to drive a steam turbine generator, producing electricity for the ship’s operations. This reduces the need for additional fuel to generate electricity, leading to significant fuel savings and lower emissions. Similarly, heat recovery systems can be integrated into the air conditioning and refrigeration systems of ships, further optimizing energy use.
In the aviation sector, waste heat recovery presents an opportunity to enhance fuel efficiency and reduce the environmental impact of air travel. Aircraft engines generate enormous amounts of heat during operation, much of which is lost through exhaust gases. While the aviation industry is known for its efforts to improve fuel efficiency through advanced propulsion technologies and aerodynamics, the potential to recover and reuse waste heat remains largely untapped. Emerging concepts, such as thermophotovoltaic (TPV) systems, aim to convert high-temperature exhaust heat from jet engines into electricity using semiconductors. This recovered electricity could potentially power various systems on the aircraft, such as lighting, avionics, and air conditioning, reducing the overall fuel consumption of the aircraft. Additionally, waste heat recovery could be integrated into auxiliary power units (APUs) on aircraft, reducing the need for fuel consumption during taxiing and ground operations.
The application of waste heat recovery in rail transportation is also gaining attention, especially in high-speed and freight trains. Trains operate at relatively high speeds, and the friction between the train wheels and tracks, as well as the heat generated by the engine and braking systems, result in substantial amounts of waste heat. In modern rail systems, technologies such as ORC systems and regenerative braking are being employed to recover and reuse this heat. ORC systems can convert exhaust heat from diesel or electric train engines into electrical energy, which can then be used to power onboard systems or even contribute to the train’s propulsion. Regenerative braking, a technology that has become common in electric trains, allows the energy generated during braking to be captured and stored in batteries, which can then be reused for acceleration or powering auxiliary systems.
One of the key challenges in transportation waste heat recovery is the integration of recovery technologies into existing infrastructure. Many vehicles and transport systems are designed with traditional powertrain configurations, where waste heat is not captured or reused. Retrofitting these systems with waste heat recovery technologies can be costly and technically challenging. However, as the demand for cleaner, more energy-efficient transportation grows, there is increasing pressure to innovate and integrate these technologies. Advances in materials science, energy conversion technologies, and system integration are driving the development of more compact, cost-effective, and efficient waste heat recovery solutions that can be easily incorporated into existing vehicles, ships, trains, and aircraft.
Governments and regulatory bodies around the world are also encouraging the adoption of waste heat recovery technologies in the transportation sector through incentives, standards, and regulations. Many countries have introduced stricter fuel efficiency standards for vehicles, vessels, and aircraft, which are pushing manufacturers to explore new technologies, including waste heat recovery, to meet these targets. Additionally, carbon pricing mechanisms and incentives for clean technologies are providing financial motivation for the transportation industry to invest in waste heat recovery systems. As technology continues to evolve and efficiency standards become more stringent, the integration of waste heat recovery technologies into the transportation sector will likely increase, resulting in lower energy consumption, reduced emissions, and a more sustainable transportation future.
In conclusion, the transportation sector’s adoption of waste heat recovery technologies is a critical step toward improving energy efficiency, reducing operational costs, and mitigating the environmental impact of various modes of transport. Whether through thermoelectric generators, ORC systems, regenerative braking, or other innovative solutions, the potential for recovering and reusing waste heat in transportation is vast. As industries and governments continue to prioritize sustainability and energy efficiency, waste heat recovery will play an increasingly central role in the transformation of the transportation sector into a more energy-efficient and environmentally responsible industry.
As the transportation sector continues to evolve, the ongoing research and development into advanced waste heat recovery technologies is expected to significantly improve their performance and applicability. Some of the key areas where innovation is likely to drive progress include the efficiency of thermoelectric materials, miniaturization of heat recovery systems, and the development of more integrated systems that combine waste heat recovery with other energy-saving technologies.
One of the major areas of focus is the improvement of thermoelectric materials used in waste heat recovery systems. Thermoelectric generators (TEGs) are particularly appealing for use in transportation because they can directly convert waste heat into electrical energy without the need for moving parts. However, the efficiency of these systems has been limited by the performance of the thermoelectric materials. Recent advancements in materials science, such as the development of nanostructured thermoelectric materials, are improving the efficiency of TEGs by enhancing their ability to convert heat into electricity. By increasing the efficiency of thermoelectric materials, it will be possible to recover more energy from waste heat, making these systems even more attractive for use in vehicles, ships, and aircraft.
Miniaturization of waste heat recovery systems is another key development that could expand the range of applications for these technologies. Many waste heat recovery systems, such as ORC units, are still relatively large and complex, making them less suitable for smaller vehicles, such as passenger cars or motorcycles. However, researchers are working on making these systems more compact and efficient, enabling them to be integrated into smaller and more diverse transportation platforms. For instance, small-scale ORC systems are already being designed to fit into heavy-duty trucks, but future innovations could make them small enough to be used in passenger vehicles, offering significant fuel savings and reducing the need for external energy sources.
Integrated energy systems that combine waste heat recovery with other energy-saving technologies are also likely to play a crucial role in the future of transportation. As more electric and hybrid vehicles hit the road, the integration of waste heat recovery with energy storage systems—such as advanced batteries and supercapacitors—will enable vehicles to store recovered energy more effectively. This stored energy could be used to power the vehicle’s propulsion system, reducing the reliance on the grid and increasing the overall efficiency of the vehicle. In addition, integrating waste heat recovery with energy-efficient HVAC (heating, ventilation, and air conditioning) systems could significantly reduce the energy required for climate control, which is a major energy demand in transportation.
In the shipping industry, the combination of waste heat recovery with carbon capture technologies is an exciting frontier. Ships are major contributors to global greenhouse gas emissions, and while waste heat recovery can help reduce fuel consumption, it may also play a role in reducing carbon emissions. Carbon capture technologies can be integrated into the exhaust systems of ships to capture CO2 before it is released into the atmosphere. The recovered waste heat could then be used to power the carbon capture process, making the entire system more energy-efficient and cost-effective. This type of integration could be key to making shipping more sustainable and compliant with increasingly stringent environmental regulations.
Hydrogen-powered vehicles are another potential area where waste heat recovery could make a significant impact. Hydrogen fuel cells produce heat as a byproduct of generating electricity, and this heat could be recovered and reused in a variety of ways. For example, the waste heat from fuel cells could be used to preheat the incoming hydrogen or air supply, improving the overall efficiency of the system. Similarly, waste heat could be used to provide cabin heating in vehicles, reducing the need for additional power and improving the vehicle’s overall energy performance.
As governments around the world continue to enforce stricter emission standards and promote sustainable transportation initiatives, waste heat recovery will be an increasingly valuable tool for achieving these goals. The European Union, for example, has introduced various regulations aimed at improving fuel efficiency and reducing emissions in the transport sector. Similarly, in China and the United States, policymakers are pushing for innovations that lower carbon emissions and improve the energy efficiency of vehicles, ships, and aircraft. Financial incentives, such as subsidies for electric vehicles and hybrid technologies, and carbon taxes aimed at reducing the environmental impact of transportation, will likely further encourage the development and deployment of waste heat recovery systems.
In conclusion, the application of waste heat recovery technologies in the transportation sector holds significant promise for reducing fuel consumption, enhancing energy efficiency, and lowering emissions across a variety of transportation modes. From improving the fuel efficiency of road vehicles and reducing the environmental footprint of maritime shipping to enhancing the performance of hybrid and electric vehicles, waste heat recovery is poised to play a central role in the future of sustainable transportation. As technological innovations continue to progress, the potential for recovering and reusing waste heat will expand, making these systems more effective and accessible for a wide range of applications. With the combined efforts of industry, research, and government, waste heat recovery will be an essential part of the global transition to cleaner, more energy-efficient transportation systems.
Urban and Decentralized Energy Solutions
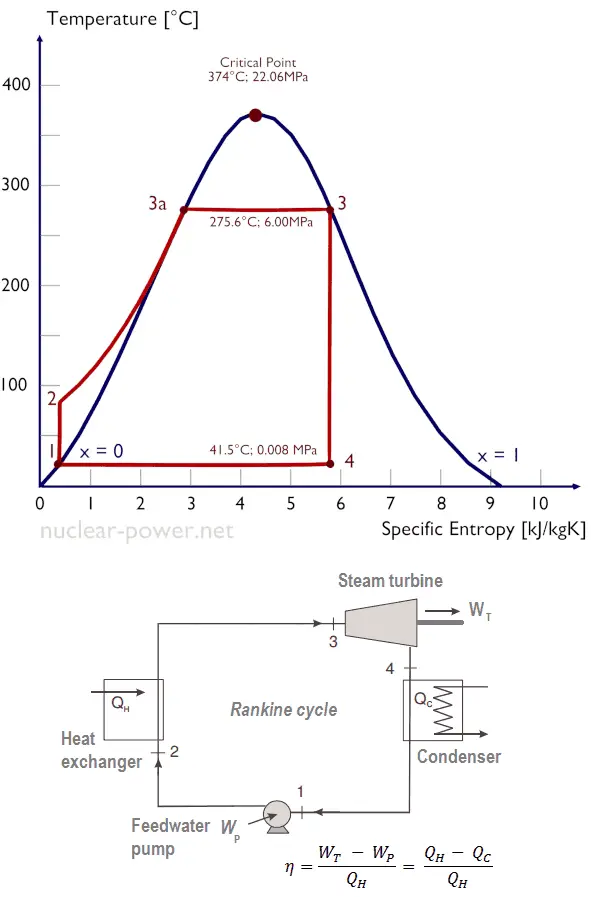
Urban areas are centers of high energy consumption, and as cities grow and become more densely populated, the demand for energy continues to increase. In parallel, the need to transition toward sustainable and decentralized energy solutions is becoming more critical in addressing the challenges of climate change, resource depletion, and energy security. Traditional centralized energy systems, reliant on fossil fuels and large-scale power plants, often result in inefficiencies, transmission losses, and environmental impacts. In contrast, decentralized energy solutions offer a more localized, efficient, and sustainable alternative that aligns with the goals of reducing carbon footprints and promoting energy independence.
One of the key aspects of urban and decentralized energy solutions is the ability to harness and optimize local energy resources. Urban environments often have access to a wide range of renewable energy sources that can be exploited to meet their energy needs. Solar power, for example, is increasingly being integrated into the urban landscape through rooftop solar panels, solar windows, and solar farms situated in urban outskirts. These distributed solar systems allow buildings and communities to generate their own electricity, reducing reliance on the central grid and decreasing the demand for fossil-fuel-based power generation. Advances in solar energy storage technologies, such as batteries and thermal storage systems, further enhance the viability of decentralized solar energy by allowing excess power to be stored and used when generation is low or demand is high.
Similarly, wind energy has found a place in urban and decentralized energy solutions. While large wind farms are typically located in rural areas, smaller-scale urban wind turbines are being integrated into the fabric of cities, particularly in places with high wind potential. These turbines can be installed on rooftops, in parking structures, or in open spaces within urban environments, where they can generate power to meet local needs. Though urban wind turbines face challenges, such as turbulence from surrounding buildings and noise, advances in turbine design and location optimization are helping to overcome these issues. In addition, microgrids—which are localized networks that can operate independently or in coordination with the larger grid—are emerging as a powerful solution for integrating renewable energy sources into urban energy systems. Microgrids can incorporate solar, wind, and other distributed generation sources, allowing neighborhoods or districts to become more energy resilient, especially during grid outages or emergencies.
Another promising approach in urban energy solutions is the use of waste heat recovery from buildings, factories, and other industrial facilities. In cities, heat generated by air conditioning, heating systems, and industrial processes can be captured and repurposed for useful applications, such as space heating, water heating, or even electricity generation. District heating systems, in which excess heat from power plants or industrial facilities is used to heat entire neighborhoods, are becoming increasingly common in urban areas. These systems can reduce the need for individual heating units in homes and buildings, lowering energy consumption and reducing greenhouse gas emissions. By integrating these systems into existing urban infrastructure, cities can make use of the waste heat produced in other sectors, creating a more efficient and circular energy system.
Biomass energy is another renewable resource with potential in urban and decentralized energy solutions. Biomass can be used to generate electricity or heat, and organic waste from urban areas—such as food scraps, agricultural residues, and wood chips—can be converted into biogas or used directly for energy production. Anaerobic digestion systems, which break down organic matter in the absence of oxygen to produce biogas, are gaining popularity in urban settings for their ability to process waste and generate clean energy simultaneously. In addition, biomass cogeneration systems, which produce both electricity and useful heat, are being deployed in urban districts to create sustainable energy systems that contribute to the city’s energy needs while minimizing waste.
Incorporating energy storage solutions into urban energy systems is critical for balancing supply and demand, especially with the intermittent nature of renewable energy sources like solar and wind. Battery storage systems are increasingly being installed in residential and commercial buildings, allowing energy generated during peak hours to be stored and used during periods of low production. Thermal energy storage is also becoming more prevalent in urban environments, where excess heat can be stored in insulated tanks and used for space heating, cooling, or hot water. The integration of energy storage with renewable energy sources and local microgrids allows cities to optimize their energy systems, ensuring a stable and reliable power supply, even as the share of renewable energy increases.
The concept of smart grids is essential to the effective management of decentralized energy solutions in urban areas. A smart grid incorporates digital technologies, sensors, and data analytics to optimize the flow of electricity throughout the grid. This allows utilities and consumers to monitor and adjust energy usage in real time, reducing waste and improving energy efficiency. In urban areas, smart grids can help manage the integration of renewable energy, energy storage, and decentralized power generation systems. For example, when solar or wind power generation exceeds demand, excess electricity can be stored in batteries or sold back to the grid, while energy deficits can be met by drawing from local renewable sources or stored energy. This flexibility enables urban areas to operate more efficiently, reduce costs, and minimize their environmental impact.
Electric vehicles (EVs) are an integral part of the shift toward decentralized urban energy systems. As the number of electric vehicles on the roads increases, cities are adapting their infrastructure to support EV charging and to enable vehicles to interact with the grid. EVs can serve as mobile energy storage units, helping to balance grid demand by supplying stored energy during peak periods. In turn, cities can encourage the use of EVs by offering incentives for their adoption and providing widespread charging infrastructure. Some urban areas are also exploring the idea of vehicle-to-grid (V2G) systems, where EVs can discharge electricity back to the grid during periods of high demand, further enhancing the flexibility and resilience of decentralized energy networks.
Another important aspect of urban and decentralized energy solutions is the promotion of energy efficiency across buildings and infrastructure. Retrofitting existing buildings with energy-efficient technologies, such as LED lighting, high-performance insulation, smart thermostats, and energy-efficient appliances, can significantly reduce energy consumption and enhance the overall efficiency of urban energy systems. New construction projects are increasingly incorporating energy-efficient designs, renewable energy generation, and waste heat recovery systems, resulting in “green buildings” that produce more energy than they consume. Building energy management systems (BEMS) enable the continuous monitoring and optimization of energy use in commercial and residential buildings, helping to reduce energy waste and cut down on operational costs.
Governments and policymakers are playing a crucial role in accelerating the adoption of urban and decentralized energy solutions. Many cities have set ambitious targets for reducing carbon emissions and transitioning to 100% renewable energy. Incentives, such as tax credits, subsidies, and grants, are being offered to support the deployment of renewable energy technologies, energy storage systems, and energy-efficient infrastructure. Policies that promote the circular economy, where resources are reused and waste is minimized, are driving the adoption of decentralized energy solutions that make use of local resources. International climate agreements and regional energy initiatives are further pushing cities toward sustainable energy transitions.
In conclusion, the shift toward urban and decentralized energy solutions is transforming the way cities generate, distribute, and consume energy. By leveraging renewable energy sources, waste heat recovery, energy storage, and advanced grid technologies, cities can create more resilient, efficient, and sustainable energy systems. As urbanization continues to rise and the demand for energy grows, decentralized energy solutions offer a promising path forward to meet the energy needs of future generations while reducing environmental impacts and promoting energy independence. The successful implementation of these technologies will require collaboration between governments, industries, and consumers to foster innovation, invest in infrastructure, and create policies that support the transition to a more sustainable urban energy future.
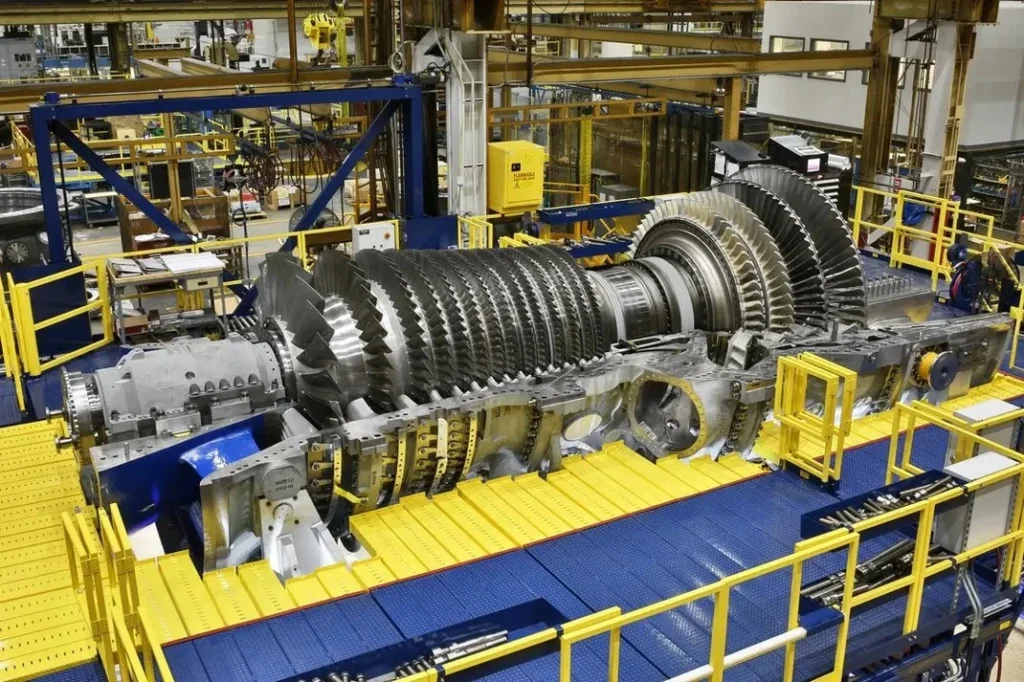
As cities continue to evolve into smarter, more sustainable hubs, urban and decentralized energy solutions will play an increasingly vital role in reshaping the global energy landscape. Community-based energy solutions are gaining prominence, wherein neighborhoods, districts, or entire communities come together to generate, manage, and share energy resources. These decentralized energy systems empower local communities, enabling them to take control of their energy supply, reduce costs, and enhance their resilience to energy disruptions.
A significant example of community-based energy solutions is energy cooperatives. These cooperatives allow individuals and organizations within a community to pool their resources and invest in renewable energy systems such as solar arrays, wind turbines, or biomass plants. The energy generated is either used locally or sold back to the grid, with profits being reinvested into the community or used to lower energy costs for members. This model not only promotes energy independence but also fosters a sense of collective responsibility for energy production and consumption, encouraging collaboration toward shared environmental goals.
In cities that are striving to integrate smart cities initiatives, urban and decentralized energy solutions are often interwoven with other smart technologies, such as smart meters, internet of things (IoT) devices, and artificial intelligence (AI). These systems can provide real-time data on energy consumption, enabling better demand forecasting and more precise energy distribution. For instance, AI algorithms can be used to predict when energy demand will peak, allowing for the optimization of energy storage and the seamless integration of renewable energy into the grid. Smart meters, which track energy use in real time, allow consumers to monitor and adjust their consumption patterns, contributing to energy savings and reducing peak load demands.
In addition to technological innovations, urban planning and design will increasingly play a critical role in the integration of decentralized energy solutions. Cities can be designed or retrofitted to facilitate the efficient deployment of renewable energy systems. For example, new developments can be built with solar panels integrated into the architecture, green roofs, and energy-efficient designs that reduce the overall demand for energy. Moreover, urban heat islands, where city environments are significantly warmer than surrounding rural areas due to human activities and dense infrastructure, can benefit from energy solutions that both mitigate these temperature effects and promote sustainable energy use. Green spaces, urban forests, and reflective building materials can all help reduce the urban heat island effect, while also improving overall environmental quality.
The role of digital platforms in urban energy management is also expanding. These platforms facilitate peer-to-peer (P2P) energy trading, allowing individuals and businesses to sell excess energy generated from rooftop solar panels or other sources to their neighbors or community members. By eliminating intermediaries, P2P energy trading helps reduce transaction costs, making energy sharing more affordable and accessible. Moreover, these platforms can incorporate blockchain technology to enhance transparency, traceability, and security in energy transactions. As the regulatory landscape around P2P energy trading evolves, it holds the potential to transform how cities and their residents interact with energy markets, further decentralizing energy generation and consumption.
The growing emphasis on resilience in urban energy systems is another factor driving the adoption of decentralized solutions. Natural disasters, such as hurricanes, wildfires, or floods, as well as geopolitical instability, can lead to disruptions in centralized energy supply chains. Decentralized energy solutions, particularly microgrids and community energy systems, offer enhanced resilience by allowing urban areas to function autonomously in the event of grid failures. These systems can operate independently, relying on local renewable energy generation and storage, providing critical energy services during emergencies, and allowing cities to recover more swiftly.
Furthermore, the convergence of decentralized energy solutions with electric mobility presents exciting possibilities for sustainable urban living. As the adoption of electric vehicles (EVs) continues to rise, urban areas are beginning to explore how these vehicles can contribute to decentralized energy systems. EVs can serve as mobile energy storage units, storing energy when demand is low and supplying it back to the grid when demand peaks. Vehicle-to-grid (V2G) technologies allow for bidirectional energy flow, enabling EV owners to sell excess stored energy back to the grid or share it with their neighbors. This not only helps balance the supply and demand of electricity but also provides EV owners with the potential for cost savings and incentives for participating in the grid.
The role of government policies and incentives remains crucial in supporting the growth of urban and decentralized energy solutions. Policy frameworks that encourage renewable energy investments, carbon reduction goals, and innovation in energy storage and distribution are essential for driving the transition to sustainable energy systems. Many cities are setting ambitious targets for reducing their carbon emissions and increasing their reliance on renewable energy sources. For instance, cities like Copenhagen, Vancouver, and Amsterdam have committed to becoming carbon-neutral in the coming decades. Incentive programs, such as subsidies, tax credits, and low-interest loans for renewable energy installations, energy-efficient upgrades, and EV adoption, can significantly reduce the financial barriers to implementing decentralized energy solutions.
Public-private partnerships (PPPs) also play an important role in advancing urban energy solutions. Governments, utilities, and private sector companies can collaborate to create innovative financing models, deploy smart grids, and integrate renewable energy systems into urban infrastructure. These partnerships can help scale decentralized energy solutions, making them more accessible to a wider range of urban residents and businesses.
As the global population continues to urbanize, cities will need to find creative solutions to meet their growing energy needs sustainably. Urban and decentralized energy solutions offer a promising path forward, enabling cities to reduce their reliance on fossil fuels, decrease carbon emissions, and enhance energy resilience. The integration of renewable energy sources, smart technologies, and energy-efficient practices will create urban environments that are not only more sustainable but also more livable, equitable, and energy-independent. The future of urban energy lies in the hands of citizens, industries, governments, and innovators working together to create systems that prioritize sustainability, efficiency, and community empowerment.
Ultimately, the success of decentralized energy solutions in urban areas will depend on continued technological advancements, supportive policy frameworks, and strong collaboration across sectors. By embracing these solutions, cities can play a central role in addressing global energy challenges while fostering a more sustainable, resilient, and equitable energy future.
Technological Advancements and Innovation
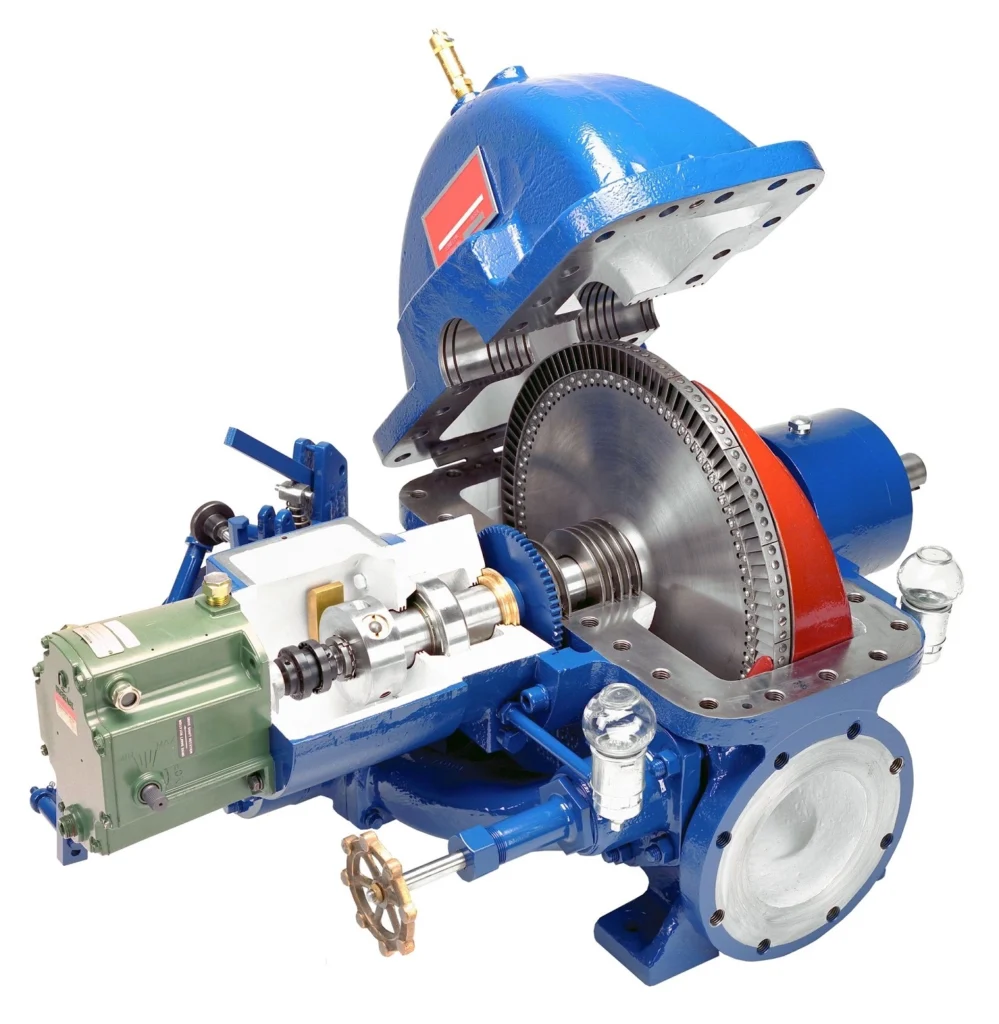
Technological advancements and innovation have long been driving forces in the transformation of energy systems across the globe. From the early adoption of electricity to the rise of renewable energy technologies, innovations in energy generation, storage, and distribution continue to shape the way we produce and consume power. These advancements not only enhance the efficiency of existing energy systems but also introduce new possibilities for the sustainable and decentralized generation of energy. As the world faces growing environmental challenges and an increasing demand for energy, the development of cutting-edge technologies plays a pivotal role in reshaping the energy landscape.
One of the most significant technological advancements in the energy sector has been in renewable energy technologies, particularly in solar, wind, and hydropower. Over the past few decades, solar photovoltaic (PV) technology has advanced dramatically, with efficiency improvements, cost reductions, and innovations in materials and manufacturing processes. Solar panels are now capable of converting more sunlight into electricity, and emerging technologies, such as solar cells made from perovskite materials, are showing even greater potential for higher efficiencies and lower production costs. The development of bifacial solar panels, which capture sunlight from both the front and back surfaces of the panel, is another innovation that maximizes energy capture and further reduces the cost of solar energy.
Similarly, advancements in wind turbine technology have led to larger, more efficient turbines capable of harnessing wind energy in a broader range of conditions. The development of floating wind turbines, which can be deployed in deeper waters far offshore, is a game-changer for wind energy. These turbines are not constrained by the shallow waters near coastlines, opening up vast areas for wind energy development. Additionally, innovations in turbine blade design, such as the use of lighter, stronger materials and improved aerodynamics, have led to greater power generation and increased lifespan for wind turbines. The evolution of distributed wind energy systems also allows for smaller-scale wind installations, making it easier to integrate wind power into rural and urban areas.
Energy storage technologies have undergone significant improvements in recent years, addressing one of the most critical challenges in renewable energy generation: the intermittent nature of solar and wind power. Battery storage systems, particularly lithium-ion batteries, have become more efficient and affordable, enabling excess energy generated during peak production times to be stored for later use. Innovations in solid-state batteries are pushing the boundaries of energy storage, offering higher energy densities, faster charging times, and longer lifespans than conventional lithium-ion batteries. Additionally, research into flow batteries and sodium-ion batteries is exploring alternatives that could offer more sustainable, cost-effective options for large-scale energy storage, further enhancing the flexibility and reliability of renewable energy grids.
The development of smart grid technology has revolutionized the way electricity is distributed and consumed. Smart grids use digital sensors, communication systems, and data analytics to optimize the flow of electricity, improve grid reliability, and enable more efficient energy use. One of the key innovations within smart grids is demand response technology, which allows utilities to better match energy supply with demand. By incentivizing consumers to reduce energy usage during peak demand times, smart grids help balance the load and prevent blackouts. Additionally, the integration of advanced metering infrastructure (AMI) enables consumers to monitor and adjust their energy consumption in real time, leading to more efficient energy use and cost savings.
Microgrids and decentralized energy systems represent another significant advancement in energy technology, allowing communities, businesses, and even individuals to generate and manage their own energy. These systems can operate independently from the main power grid, providing resilience in the event of grid disruptions caused by natural disasters or other emergencies. Microgrids often incorporate a combination of renewable energy sources, such as solar and wind, along with energy storage and backup power generation. The ability of microgrids to operate autonomously and integrate with local energy resources allows for greater energy security and supports the transition to a more decentralized, sustainable energy model.
Hydrogen technology is also seeing rapid advancements, particularly in the production of green hydrogen, which is generated using renewable energy sources. Hydrogen has long been recognized as a potential clean fuel for a variety of applications, from transportation to industrial processes. However, the challenge has been the production of hydrogen in an environmentally sustainable manner. Traditional hydrogen production methods, such as steam methane reforming, release significant amounts of carbon dioxide. Electrolysis, which uses electricity to split water molecules into hydrogen and oxygen, has become a more viable method of green hydrogen production, particularly when powered by renewable energy. The development of hydrogen fuel cells is enabling the use of hydrogen in transportation, particularly in hydrogen-powered vehicles like buses, trucks, and trains, which produce zero emissions at the point of use.
Carbon capture, utilization, and storage (CCUS) technologies are advancing as well, offering solutions to reduce carbon emissions from power plants and industrial processes. CCUS involves capturing carbon dioxide from the exhaust gases of fossil fuel power plants and either storing it underground or repurposing it for industrial uses, such as in the production of synthetic fuels or chemicals. Innovations in direct air capture (DAC) are pushing the boundaries of this technology by enabling the capture of carbon directly from the atmosphere. This could play a crucial role in achieving net-zero emissions goals by removing CO2 from the air and reducing the overall carbon footprint of industries and economies.
Another area of rapid technological development is energy efficiency technologies. Innovations in building materials, such as high-performance insulation, smart windows, and energy-efficient lighting, have led to dramatic reductions in the energy needed to heat, cool, and power buildings. Smart thermostats and building energy management systems (BEMS) enable real-time monitoring and optimization of energy use, ensuring that buildings consume only the energy they need. The development of passive house standards, which focus on designing buildings with minimal energy consumption through better insulation and natural ventilation, is also pushing the boundaries of energy-efficient construction.
Electric vehicles (EVs) and vehicle-to-grid (V2G) technologies are among the most exciting innovations in the transportation sector. The rapid adoption of EVs is reducing dependence on fossil fuels and contributing to a cleaner, greener transportation system. EVs also have the potential to serve as mobile energy storage units, with V2G technology allowing electric cars to return power to the grid during peak demand periods, helping to stabilize the grid and balance energy supply and demand. Advances in charging infrastructure are making it easier for consumers to adopt EVs, with fast-charging stations, wireless charging, and ultra-fast charging technologies reducing the time required to recharge vehicles.
Lastly, artificial intelligence (AI) and machine learning (ML) are becoming increasingly integrated into the energy sector, optimizing everything from energy production to consumption patterns. AI-powered predictive analytics can forecast energy demand, helping to optimize grid operations and improve energy efficiency. Machine learning algorithms are being used to develop more accurate models for energy consumption and to improve the efficiency of renewable energy generation systems. In combination with big data analytics, AI is enabling smarter decision-making and the creation of more adaptive, responsive energy systems that can efficiently manage fluctuating energy supply and demand.
In conclusion, technological advancements and innovations are revolutionizing the energy landscape, enabling more efficient, sustainable, and decentralized energy systems. From renewable energy technologies to energy storage, smart grids, and emerging solutions like hydrogen and carbon capture, these innovations are laying the foundation for a cleaner, more resilient energy future. As research and development continue to push the boundaries of what is possible, the energy sector is on the brink of a transformation that will drive significant environmental, economic, and social benefits. Through continued investment in technology, collaboration across industries, and supportive policy frameworks, these advancements will help to address the world’s energy challenges and contribute to a sustainable, low-carbon future.
As the energy transition continues to unfold, technological advancements are expected to play an even more critical role in shaping the future of energy systems. The emergence of new and improved technologies will not only facilitate the integration of renewable energy sources but also drive the creation of more sustainable, resilient, and efficient energy infrastructures.
The role of digitalization in energy systems is becoming increasingly important as new technologies are deployed. IoT devices embedded in energy infrastructure, such as smart meters, sensors, and actuators, allow for real-time monitoring and control of energy consumption and production. These devices enable better demand response management, allowing utilities to optimize energy distribution, prevent grid overloads, and reduce waste. Additionally, cloud computing and big data analytics are transforming the way energy systems are managed by enabling the collection, processing, and analysis of vast amounts of data from diverse sources. This helps utilities and energy providers predict energy demand, optimize grid operations, and make more informed decisions regarding the expansion and maintenance of energy infrastructure.
Blockchain technology is also beginning to make inroads into the energy sector, offering solutions for decentralized energy trading, data security, and transparency. Blockchain allows for peer-to-peer energy transactions, where consumers can trade excess energy generated from renewable sources, such as solar panels or wind turbines, directly with one another. By eliminating intermediaries, blockchain technology can help reduce transaction costs and make energy trading more efficient and accessible. Additionally, the use of blockchain can enhance security and transparency in energy markets, ensuring that transactions are recorded in an immutable and tamper-proof ledger.
The decarbonization of heavy industries, such as steel, cement, and chemicals, is another area where technological innovation is making significant strides. Industries that rely on energy-intensive processes are exploring new technologies to reduce their carbon emissions, such as electrification, green hydrogen, and carbon capture utilization and storage (CCUS). For example, the use of green hydrogen as a feedstock in the production of steel is gaining traction, as it can replace the use of coal and other fossil fuels in blast furnaces. The development of electric arc furnaces powered by renewable energy sources is also making steel production cleaner and more sustainable.
Moreover, the development of sustainable bioenergy technologies is creating new opportunities for renewable energy production, particularly in rural areas. Biomass energy can be generated from agricultural residues, wood, and organic waste, providing a renewable source of heat and electricity. Innovations in biofuels, such as advanced biofuels derived from algae, agricultural waste, or other non-food sources, are also being explored as alternatives to fossil fuels in the transportation and aviation sectors. These biofuels can be used in existing infrastructure and vehicles, making them a viable and sustainable option for reducing carbon emissions.
The integration of artificial intelligence (AI) and machine learning (ML) is helping to optimize energy consumption and improve efficiency across multiple sectors. AI is being used to predict energy demand, allowing for better grid management and more accurate forecasting of energy needs. Machine learning algorithms are also being applied to predictive maintenance for power generation equipment, reducing downtime and improving the overall reliability of energy systems. Furthermore, AI is being leveraged to enhance the performance of renewable energy systems, such as improving the tracking of solar panels or optimizing wind turbine performance based on real-time weather data.
Energy-efficient building technologies are also playing a key role in the reduction of energy consumption. The integration of smart building technologies such as automated lighting, climate control systems, and energy-efficient appliances has led to significant improvements in energy efficiency in residential, commercial, and industrial buildings. Innovations in building materials, such as aerogels and phase-change materials, are enabling buildings to maintain optimal temperatures with minimal energy use. Green buildings, which are designed to minimize their environmental impact, often incorporate energy-efficient systems, renewable energy technologies, and waste reduction strategies. These buildings not only reduce energy consumption but also promote healthier living and working environments for occupants.
Energy management systems (EMS) are becoming more sophisticated, allowing consumers and businesses to better monitor and control their energy usage. EMS technologies can integrate data from various sources, such as smart meters, weather forecasts, and energy consumption patterns, to optimize energy use and reduce costs. These systems can also automate energy-saving actions, such as adjusting heating or cooling systems based on occupancy levels or time-of-day pricing. By providing real-time insights and control over energy usage, EMS helps businesses and individuals make smarter decisions about energy consumption and contribute to overall energy efficiency goals.
The growing focus on electrification is also driving innovation in energy technologies. In particular, electric heating and electric cooking technologies are gaining traction as cleaner alternatives to traditional fossil-fuel-based systems. The adoption of electric heat pumps for space heating and cooling, as well as induction stoves for cooking, can significantly reduce carbon emissions, particularly when powered by renewable energy sources. Electrification is also playing a key role in the decarbonization of transportation, as the shift from internal combustion engine vehicles to electric vehicles (EVs) continues to accelerate. EVs, powered by renewable energy, offer a clean alternative to fossil-fuel-powered transportation, contributing to the reduction of greenhouse gas emissions.
The continued development of geothermal energy technologies is also an exciting frontier in the renewable energy space. Geothermal energy, which harnesses heat from beneath the Earth’s surface, is a reliable and sustainable source of energy. Innovations in geothermal drilling and enhanced geothermal systems (EGS) are making it possible to access geothermal resources in regions that were previously thought to be unsuitable. Geothermal power plants can provide baseload power, complementing intermittent renewable sources like solar and wind, and are particularly well-suited for regions with significant geothermal potential.
Finally, fusion energy represents one of the most ambitious and long-term technological innovations in the energy sector. While nuclear fusion has long been seen as a potential “holy grail” of clean energy, significant advancements in magnetic confinement and laser fusion technologies are bringing us closer to making fusion energy a reality. Fusion energy promises to provide virtually unlimited, clean, and safe energy by replicating the process that powers the Sun. Though commercial fusion power plants are still years, if not decades, away, recent breakthroughs in fusion research are pushing the boundaries of what is possible and generating excitement within the energy community.
In conclusion, technological advancements and innovation are driving the transformation of the energy sector, offering new solutions for generating, storing, and managing energy. From the development of renewable energy technologies to breakthroughs in energy storage, smart grids, and electrification, these innovations are enabling the transition to a more sustainable, resilient, and efficient energy system. As new technologies continue to emerge, they will not only improve energy production and consumption but also create opportunities for greater energy equity, environmental stewardship, and economic growth. With continued investment in research and development, the future of energy holds tremendous promise in addressing the challenges of climate change and creating a cleaner, more sustainable world.
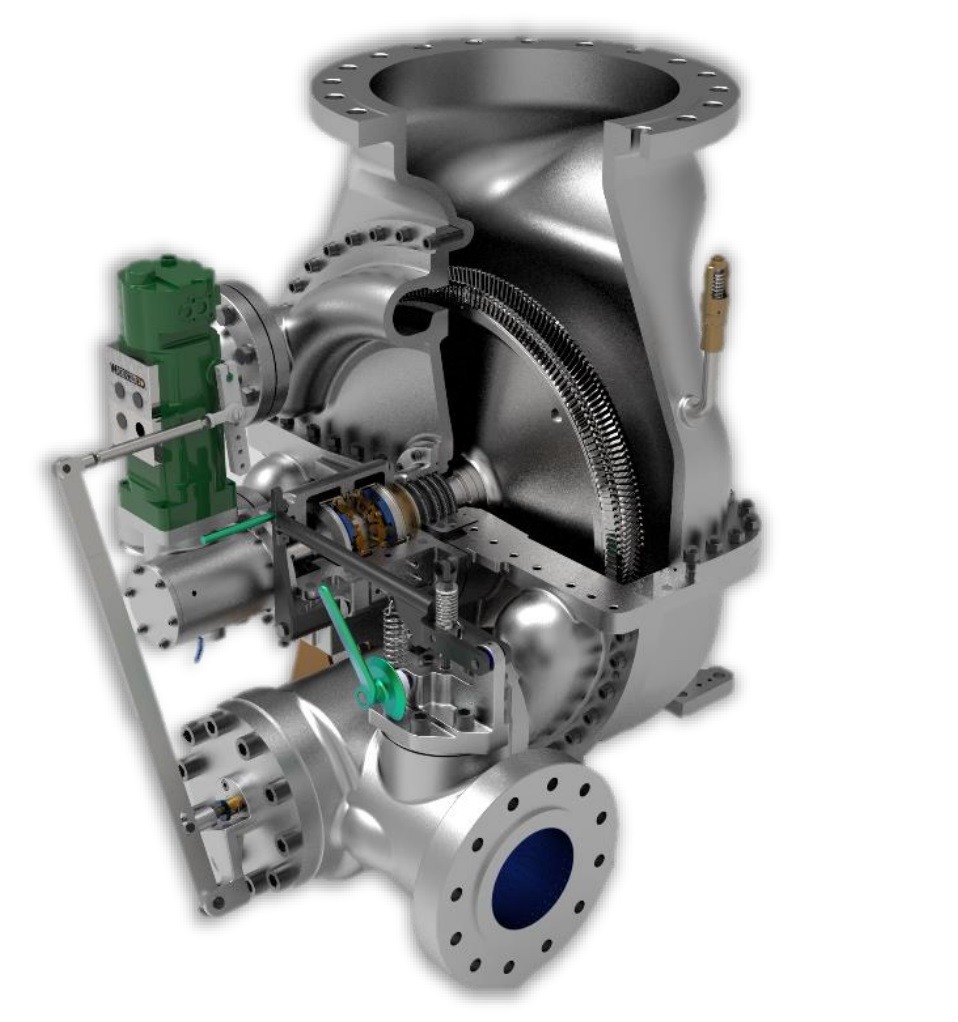
The ongoing evolution of energy technologies will further accelerate the transition to a cleaner, more efficient, and sustainable energy future. The interplay between new innovations, regulatory policies, and market dynamics will continue to shape the path forward, making energy systems more flexible, resilient, and accessible for everyone.
One of the key trends that will emerge from these technological advancements is the decarbonization of traditionally hard-to-abate sectors. Industries like heavy manufacturing, cement production, shipping, and aviation are increasingly turning to alternative fuels, electrification, and carbon capture technologies to reduce their environmental impact. As global pressure to meet net-zero emissions goals increases, innovations in sustainable aviation fuels (SAFs), electric and hybrid aircraft, and alternative propulsion technologies will help reduce carbon emissions from the transportation sector. The development of carbon-neutral shipping vessels, powered by renewable energy sources and new propulsion systems, will also play a critical role in decarbonizing global trade and shipping.
Technological advancements in bioenergy are also poised to provide solutions for decarbonization. The development of second-generation biofuels made from non-food feedstocks, such as agricultural waste, algae, and forestry residues, is becoming increasingly viable as these technologies scale up. Advanced biofuels, combined with emerging techniques such as biogas production from organic waste and biomass gasification, could be used in various sectors, including transportation, power generation, and industrial processes. As these bioenergy solutions evolve, they will offer carbon-neutral alternatives to fossil fuels while promoting waste reduction and circular economies.
Another transformative development is the growing integration of digital twins in energy systems. A digital twin is a virtual replica of physical assets, processes, or systems, used to simulate and optimize performance in real-time. In the energy sector, digital twins can be applied to power plants, grids, and energy storage systems, helping operators predict maintenance needs, optimize energy generation, and improve efficiency. By using real-time data and advanced simulations, digital twins can help identify potential issues before they cause downtime, reduce operational costs, and improve the overall efficiency of energy infrastructure.
The smart home revolution is another area where technological advancements are gaining momentum. Smart home systems, powered by connected devices, sensors, and artificial intelligence, enable homeowners to monitor and control energy consumption in real-time. Through the use of smart thermostats, automated lighting, and energy-efficient appliances, homes can optimize energy use based on occupants’ behavior, weather conditions, and electricity pricing. In combination with demand response programs, smart homes can help reduce peak demand on the grid, lower energy bills, and promote overall energy efficiency.
The growing adoption of artificial intelligence (AI) and machine learning (ML) technologies in energy management is also creating opportunities for more sophisticated energy systems. These technologies can optimize everything from grid operations to power generation, load balancing, and energy distribution. In particular, AI-driven optimization algorithms are being used to forecast energy demand, predict renewable energy generation, and automate energy storage and dispatching. The ability to incorporate machine learning into grid management systems enables utilities to respond to fluctuations in energy supply and demand more efficiently, improving grid stability and reliability.
Circular economy principles are also influencing technological innovation in the energy sector. Innovations in energy-efficient recycling technologies, such as those focused on recovering valuable materials from used batteries, wind turbine blades, and solar panels, are gaining traction. As the global demand for renewable energy technologies increases, the need for efficient recycling and resource recovery will become more important. The development of closed-loop systems where materials are continually reused and repurposed can help reduce the environmental impact of energy technology production, making renewable energy even more sustainable.
The integration of renewable energy sources into the grid will continue to rely on advancements in grid flexibility. As more intermittent renewable energy sources, such as wind and solar, are added to the energy mix, the ability to balance supply and demand becomes increasingly important. Technologies such as grid-scale energy storage, demand response, and advanced grid management software will enable grids to absorb fluctuations in renewable energy production, maintain system stability, and ensure reliable power delivery. Innovations in hydropower storage, compressed air energy storage, and pumped storage hydropower will further enhance grid flexibility, providing large-scale storage solutions to support a higher share of renewables in the grid.
The transition to smart cities will also be influenced by technological advancements in energy. Smart grids, microgrids, and renewable energy systems will be at the core of city-wide efforts to reduce carbon emissions, optimize energy use, and enhance resilience to climate change and natural disasters. Integrated energy management platforms that monitor and control the flow of energy throughout a city will help utilities and residents manage their energy consumption more efficiently. Furthermore, the widespread deployment of electric vehicle (EV) charging stations, coupled with vehicle-to-grid (V2G) technologies, will enable cities to harness the potential of EVs as both consumers and suppliers of energy.
Off-grid solutions are also poised to play an important role in expanding access to electricity in remote areas. The development of solar microgrids, wind-powered systems, and mini-grids powered by renewable energy sources can provide electricity to underserved communities, improving quality of life and supporting economic development. The ability to deploy small-scale energy systems that can operate independently from the main grid is especially important in regions with limited or no access to centralized energy infrastructure. Energy-as-a-service models are also emerging, enabling individuals and businesses to access affordable and reliable energy without the upfront costs of installing their own systems.
As the energy sector evolves, a growing focus on system integration and interoperability will facilitate the seamless interaction of various energy technologies. The development of open-source platforms and standardized protocols will allow different energy systems, such as solar, wind, energy storage, and electric vehicles, to work together harmoniously. This integration is key to maximizing the potential of renewable energy sources and creating flexible, decentralized energy systems that can meet the demands of a rapidly changing world.
Ultimately, the success of these technological advancements depends on continued investment in research, development, and innovation, as well as supportive policy frameworks and market incentives. Governments, industries, and research institutions will need to collaborate to overcome technical challenges, scale up promising solutions, and bring new technologies to market. Public-private partnerships will be crucial in advancing breakthroughs, sharing knowledge, and accelerating the deployment of innovative energy solutions.
In conclusion, technological advancements will remain the cornerstone of the global transition to sustainable energy. From renewable energy technologies to energy storage, digitalization, and electrification, these innovations will continue to drive the energy sector toward greater efficiency, resilience, and sustainability. As the world moves toward a low-carbon future, these advancements will not only help reduce environmental impacts but also create new opportunities for economic growth, job creation, and social equity. The future of energy is bright, powered by a diverse array of innovative technologies that are transforming the way we produce, consume, and manage energy across the globe.
Environmental and Economic Benefits
Environmental and economic benefits are two of the most compelling reasons driving the global transition to cleaner and more sustainable energy systems. As the world faces unprecedented environmental challenges, including climate change, air pollution, and resource depletion, the adoption of renewable energy technologies and energy efficiency measures offers a pathway to mitigate these impacts while promoting economic growth and resilience. These benefits extend beyond environmental protection and are intricately linked to creating new job opportunities, fostering innovation, and improving energy security. By reducing reliance on fossil fuels and embracing cleaner alternatives, societies can address critical environmental concerns while stimulating economic activity and creating a more sustainable future.
One of the most significant environmental benefits of the transition to clean energy is the reduction of greenhouse gas emissions. Fossil fuel-based power generation, which has been the dominant source of electricity for over a century, is responsible for a substantial share of global carbon dioxide (CO2) emissions. These emissions contribute to global warming, rising sea levels, and extreme weather events. By shifting to renewable energy sources such as solar, wind, and hydropower, we can drastically reduce emissions, helping to slow the pace of climate change. Solar and wind power, in particular, produce electricity without emitting CO2 or other pollutants, making them crucial components of the global effort to meet climate goals like those outlined in the Paris Agreement. The widespread adoption of these technologies will be essential for limiting global temperature rise and preventing catastrophic climate impacts.
Furthermore, renewable energy systems generate minimal air and water pollution, which are major contributors to health problems and ecosystem degradation. Fossil fuel power plants emit pollutants like sulfur dioxide (SO2), nitrogen oxides (NOx), particulate matter, and mercury, all of which have harmful effects on human health and the environment. These pollutants are linked to respiratory and cardiovascular diseases, premature deaths, and environmental damage such as acid rain and soil degradation. In contrast, clean energy technologies produce no direct emissions or air pollution during operation, leading to cleaner air and healthier communities. Additionally, many renewable energy sources, such as solar and wind, require significantly less water than traditional power plants, which consume large amounts of water for cooling. This reduces stress on local water resources and minimizes the environmental impact on aquatic ecosystems.
The economic benefits of transitioning to clean energy are equally significant. The growing demand for renewable energy technologies has spurred innovation, creating new industries and job opportunities. The renewable energy sector has become a major driver of economic growth, providing employment in areas such as solar panel manufacturing, wind turbine production, energy storage, and grid modernization. According to various reports, the renewable energy industry already employs millions of people worldwide, and this number is expected to grow as renewable energy technologies continue to scale up. Furthermore, the widespread deployment of energy-efficient technologies, including smart grids, high-efficiency appliances, and electric vehicles, creates additional job opportunities in manufacturing, installation, and maintenance.
In addition to job creation, the economic benefits of clean energy extend to the local level, where investments in renewable energy projects can stimulate regional development. For example, many wind and solar farms are built in rural areas, where they create jobs, attract investment, and generate local tax revenue. These projects can revitalize communities that have traditionally relied on industries such as agriculture or mining, providing them with new sources of income and economic diversification. In many cases, renewable energy projects have lower operating costs compared to fossil fuel-based power plants, as the “fuel” for wind and solar energy is free, and the maintenance costs are relatively low. This can result in lower electricity prices for consumers and businesses, improving affordability and reducing energy poverty.
The transition to renewable energy also improves energy security by reducing dependence on imported fossil fuels. Many countries rely heavily on oil, coal, and natural gas imports to meet their energy needs, which can create vulnerabilities related to price volatility, supply disruptions, and geopolitical tensions. By investing in domestic renewable energy resources, countries can reduce their reliance on foreign energy sources and increase their energy independence. This not only provides greater stability in energy prices but also strengthens national security by reducing exposure to international energy market fluctuations.
Another important economic benefit is the potential for long-term cost savings. While the initial investment in renewable energy infrastructure may be high, the ongoing costs are often lower than those associated with fossil fuel-based systems. Renewable energy systems, such as solar panels and wind turbines, have relatively low operational and maintenance costs once installed. In addition, the cost of renewable energy technologies has decreased significantly over the past decade due to technological advancements, economies of scale, and increased competition. The price of solar energy, for example, has dropped by more than 80% since 2010, making it more accessible and economically viable for both consumers and businesses. As the cost of renewable energy continues to fall, the economic case for clean energy becomes stronger, particularly for long-term investments in infrastructure.
The development of energy-efficient technologies and the adoption of green building standards also offer significant cost savings. Energy-efficient buildings reduce the need for heating, cooling, and lighting, lowering energy bills for homeowners and businesses. The adoption of LED lighting, advanced insulation, and high-efficiency HVAC systems can result in substantial savings over time, while also reducing the overall demand for energy. Green buildings, which are designed to be energy-efficient and environmentally friendly, can also command higher rental rates and property values, providing a strong return on investment for property owners.
Another key benefit of clean energy investments is the promotion of innovation and technological leadership. Countries and businesses that prioritize renewable energy technologies and energy efficiency can position themselves as global leaders in the emerging clean energy economy. This leadership can lead to greater influence in international energy markets, as well as the development of new intellectual property, patents, and export opportunities. Companies at the forefront of clean energy innovation can benefit from expanding global markets, particularly as countries and corporations commit to achieving net-zero emissions and sustainable development goals. The growing demand for renewable energy solutions provides opportunities for innovation in areas such as energy storage, smart grids, and sustainable transportation, creating a dynamic ecosystem of research, development, and entrepreneurship.
As the world faces the pressures of climate change, the economic resilience provided by clean energy systems becomes increasingly important. Diversifying energy portfolios with renewable energy sources reduces the economic risks associated with fossil fuel price fluctuations, supply chain disruptions, and environmental regulations. By investing in climate-resilient infrastructure, countries and businesses can safeguard their economies against the impacts of extreme weather events, natural disasters, and other climate-related challenges. Clean energy technologies, such as distributed solar power and microgrids, also offer communities greater energy resilience, allowing them to maintain power in the face of grid disruptions or natural disasters.
In conclusion, the environmental and economic benefits of transitioning to cleaner and more sustainable energy systems are vast and far-reaching. From reducing greenhouse gas emissions and improving air quality to fostering job creation, energy security, and economic growth, the shift to renewable energy and energy efficiency brings significant advantages to societies around the world. As technology advances and the cost of clean energy continues to decline, these benefits will only increase, providing an opportunity to build a more sustainable, prosperous, and resilient future for all. The transition to clean energy is not only a necessary response to climate change but also a powerful driver of economic innovation, local development, and global competitiveness. By embracing these opportunities, we can create a more sustainable, equitable, and economically vibrant world.
As the world continues to prioritize sustainability, the transition to clean energy will not only drive environmental benefits but also catalyze a profound transformation in the global economy. The widespread adoption of renewable energy, energy-efficient technologies, and cleaner industrial practices will help mitigate the impacts of climate change, reduce pollution, and safeguard natural resources for future generations. These changes, however, will also provide new economic opportunities that can foster innovation, job creation, and social development, creating a cycle of prosperity for communities around the globe.
One of the most notable long-term benefits of clean energy adoption is the promotion of sustainable development. Clean energy systems offer a pathway to meet the growing demand for electricity while reducing environmental degradation. Renewable energy sources such as wind, solar, and hydropower are inherently sustainable because they rely on natural processes that are replenished over time. This contrasts with the finite nature of fossil fuels, which are subject to resource depletion and extraction-related environmental damage. By investing in sustainable energy infrastructure, countries can build resilient economies that are less reliant on exhaustible resources and more capable of adapting to future challenges.
Additionally, the reduction in environmental degradation from cleaner energy systems helps protect ecosystems, biodiversity, and natural resources. Fossil fuel extraction, such as coal mining, oil drilling, and natural gas fracking, often leads to habitat destruction, air and water pollution, and loss of biodiversity. Renewable energy technologies, on the other hand, typically have a much lower impact on ecosystems. Solar and wind farms, for example, require relatively minimal land disturbance compared to the environmental degradation associated with conventional energy extraction methods. By preserving natural ecosystems, clean energy technologies help maintain the balance of ecosystems, contributing to better soil quality, water conservation, and overall ecological health.
The decentralization of energy systems is another significant benefit that clean energy brings. With the rise of technologies such as rooftop solar panels, small-scale wind turbines, and community-based microgrids, energy generation can be localized, reducing reliance on centralized power plants and large-scale transmission networks. Decentralized energy systems improve resilience by allowing local communities to continue generating and consuming energy even in the event of major grid disruptions or natural disasters. This increases the energy autonomy of regions, giving them greater control over their energy sources and helping to prevent power outages that could otherwise disrupt economic and social activities. As a result, communities become more adaptable and self-sufficient, which is particularly beneficial for areas with limited access to centralized electricity infrastructure.
The growing emphasis on clean transportation is another area where the economic and environmental benefits of sustainable energy systems intersect. Electric vehicles (EVs), hybrid cars, and alternative fuels such as hydrogen are poised to revolutionize the transportation sector, reducing reliance on fossil fuels and improving air quality in urban areas. EVs, for example, produce zero tailpipe emissions, which can significantly reduce the levels of air pollution caused by conventional internal combustion engine vehicles. This, in turn, leads to better public health outcomes by lowering the incidence of respiratory diseases, cardiovascular problems, and other pollution-related health conditions. The transition to electric mobility also offers economic benefits, including reduced fuel costs for consumers and the creation of jobs in the production and maintenance of EVs, charging infrastructure, and alternative fuel technologies.
Another critical aspect of the economic transformation driven by clean energy is the development of energy storage technologies. The integration of renewable energy into the grid requires solutions that can store excess energy produced during periods of high generation, such as during sunny days or strong winds, and release it when demand is high or generation is low. The advancement of energy storage technologies, such as batteries, pumped hydro storage, and thermal energy storage, is essential for maintaining grid stability and ensuring a continuous and reliable power supply. As the cost of energy storage continues to decrease, these technologies will play an increasingly important role in facilitating the widespread adoption of renewable energy and in helping to smooth out fluctuations in energy production. The development and deployment of energy storage systems also create new industries and job opportunities, from manufacturing to installation and maintenance.
The shift toward clean energy and sustainable practices is also spurring global innovation and technological leadership. Countries and companies that invest heavily in the research and development of clean energy technologies position themselves as leaders in the global energy market. By advancing technologies in areas such as solar energy, wind energy, energy storage, and smart grids, these innovators can capture new markets and export their expertise and products to countries around the world. The clean energy transition is transforming the energy landscape into one that is more dynamic and competitive, providing nations with opportunities to enhance their geopolitical standing by becoming hubs of energy innovation.
Moreover, the widespread implementation of clean energy technologies supports the growth of circular economies. In a circular economy, the focus is on maximizing the lifespan of materials, reducing waste, and promoting the reuse, recycling, and repurposing of resources. The energy sector is increasingly adopting circular economy principles by integrating the recycling of materials used in solar panels, wind turbines, and batteries into its business models. For instance, the recycling of lithium-ion batteries used in electric vehicles and energy storage systems helps reduce the demand for raw materials, minimizes environmental harm, and ensures that valuable materials are kept in circulation. By incorporating these principles into the energy sector, businesses and governments can create a more sustainable and regenerative system of energy production and consumption.
A significant aspect of the clean energy transition is its potential to address energy poverty. Clean and affordable energy solutions can provide communities with reliable electricity, improving access to essential services such as healthcare, education, and clean water. In many developing regions, off-grid renewable energy systems like solar home systems and mini-grids are helping to provide electricity to areas that have traditionally been underserved by central grid systems. These systems offer an affordable, scalable, and sustainable solution to energy poverty, enabling rural communities to access the benefits of modern energy without the environmental and economic costs of fossil fuels. Furthermore, access to clean energy can contribute to the development of small businesses, enhance agricultural productivity, and improve quality of life, leading to enhanced economic opportunities for local populations.
The environmental and economic benefits of clean energy also extend to reducing dependence on fossil fuel imports, which can be particularly important for countries that rely heavily on imported oil, coal, and natural gas. By investing in domestic renewable energy resources, countries can strengthen their energy security, reduce their exposure to fluctuations in global fuel prices, and create local jobs in the renewable energy sector. This is especially important for nations with limited access to fossil fuel resources but abundant renewable energy potential, such as those located in areas with high solar or wind energy capacity. Renewables offer these countries a path toward energy independence and a more resilient economy.
Finally, the transition to a low-carbon energy system has the potential to address the growing global environmental crisis, from rising sea levels and biodiversity loss to extreme weather events caused by climate change. By shifting away from fossil fuels and embracing cleaner alternatives, the global community can reduce the negative impacts of environmental degradation, mitigate future risks, and protect natural ecosystems. The environmental benefits of clean energy are also closely tied to the social benefits—healthier communities, improved access to resources, and a more stable climate. These collective benefits underscore the importance of a coordinated global effort to transition toward sustainable energy systems, with significant contributions to the well-being of both the planet and its inhabitants.
In conclusion, the environmental and economic benefits of the clean energy transition are vast and interconnected. Through the reduction of emissions, improvement in air quality, job creation, and the promotion of sustainable development, the shift to cleaner energy systems offers the opportunity to build a more prosperous, equitable, and resilient world. The collective pursuit of cleaner, more efficient energy systems will shape the future of global energy, driving innovation, enhancing energy security, and reducing environmental impact. By embracing these changes, nations can not only safeguard the health of the planet but also create a foundation for long-term economic stability and growth.
Challenges and Barriers to Adoption
The transition to clean energy and the widespread adoption of renewable energy technologies come with a range of challenges and barriers that need to be addressed in order to fully realize their potential. These challenges are complex and multifaceted, encompassing economic, technological, social, political, and institutional issues. Overcoming these barriers is essential to accelerating the global shift toward more sustainable energy systems, reducing reliance on fossil fuels, and mitigating the impacts of climate change. While progress has been made in many regions, there remain several critical obstacles to the broader deployment of renewable energy technologies, energy efficiency measures, and cleaner industrial practices.
One of the primary barriers to the adoption of clean energy is the high initial capital cost associated with renewable energy infrastructure. Although the cost of technologies such as solar panels, wind turbines, and energy storage systems has decreased significantly in recent years, the upfront investment required for large-scale renewable energy projects remains substantial. This can be particularly challenging for developing countries or regions with limited access to financing. The need for long-term financing options and affordable capital is critical to ensuring that these technologies are accessible to a wide range of stakeholders, including governments, utilities, businesses, and individuals. In many cases, the financial barriers are compounded by the fact that renewable energy projects often require significant upfront investments in infrastructure and technology, with returns that are realized over the long term.
Alongside financial barriers, there are technological challenges that hinder the adoption of renewable energy. Despite advances in renewable energy technologies, some forms of clean energy, such as solar and wind power, face challenges related to intermittency and variability. These technologies rely on natural resources—sunlight and wind—that are not always available, making it difficult to ensure a constant and reliable supply of electricity. The need for advanced energy storage solutions and smart grid technologies is critical to addressing this issue. Energy storage systems, such as batteries, are required to store excess power generated during periods of high production and release it when demand is high or when generation is low. However, the current state of energy storage technology is still evolving, and cost-effective, large-scale energy storage solutions remain a significant challenge.
The integration of renewable energy into existing energy grids is another technological challenge. Grid modernization is needed to accommodate the increasing share of renewable energy sources, many of which are decentralized and often located in remote areas. The current energy grid infrastructure was designed for centralized power generation from fossil fuels, and integrating distributed renewable energy sources requires substantial upgrades. These upgrades may include the installation of smart meters, advanced control systems, and more efficient transmission lines. The development of a flexible, resilient, and interoperable energy grid that can handle renewable energy generation and manage fluctuating supply and demand is essential for the successful integration of clean energy.
Another challenge is the lack of supportive policy frameworks and regulatory barriers. While many countries have adopted policies to promote renewable energy development, others have yet to create the necessary regulatory environment to encourage clean energy investments. In some regions, existing energy policies may favor fossil fuel industries due to historical economic ties, creating market distortions that undermine the competitiveness of renewable energy sources. Furthermore, the regulatory approval process for renewable energy projects can be lengthy and complex, with issues related to land use, environmental impact assessments, and grid access. A lack of clear, consistent, and transparent policies can create uncertainty for investors and developers, which may discourage investment in renewable energy projects.
Subsidies and incentives for fossil fuels in some countries also present a significant barrier to clean energy adoption. Fossil fuel subsidies reduce the cost of energy derived from coal, oil, and natural gas, making these energy sources artificially cheap and reducing the incentives for individuals, businesses, and governments to switch to cleaner alternatives. Phasing out fossil fuel subsidies and redirecting those funds toward renewable energy development, energy efficiency programs, and research into clean technologies could help accelerate the transition to a more sustainable energy future. However, the political will to enact such changes may be lacking in regions where fossil fuel industries are a major economic driver.
In addition to policy and technological barriers, there are also social and behavioral challenges. Public perception of renewable energy technologies can vary significantly, with some individuals and communities expressing resistance to new energy projects, especially when these projects involve land use changes or the construction of large-scale energy infrastructure. NIMBYism (Not In My Backyard) is a common reaction in some regions where people are opposed to the siting of wind farms, solar installations, or transmission lines near their homes, even if they support renewable energy in principle. This opposition can delay or halt the development of renewable energy projects, particularly in densely populated or environmentally sensitive areas. Educating the public about the long-term benefits of clean energy and engaging communities early in the planning and decision-making process is essential to overcoming these social challenges.
Another significant social challenge is the need for workforce development and skills training. The clean energy transition creates new job opportunities, but these require a workforce with specialized skills in renewable energy technologies, energy efficiency, and sustainable practices. In many regions, there is a shortage of skilled workers in fields such as solar panel installation, wind turbine maintenance, and energy storage system design and management. Governments, educational institutions, and businesses must collaborate to create training programs and educational pathways that prepare workers for the new jobs in the clean energy sector. This workforce transition is especially important in regions that have historically relied on fossil fuel industries, where workers may face displacement as coal, oil, and gas jobs decline. Ensuring that workers can transition to clean energy jobs with adequate training and support is a key element of a just and equitable energy transition.
The economic transition in regions dependent on fossil fuel industries can also present challenges. The decline of traditional energy sectors can lead to job losses, economic dislocation, and social unrest, particularly in regions where the fossil fuel industry is a significant part of the local economy. To mitigate these impacts, it is crucial to invest in economic diversification strategies that help affected communities transition to new sources of income and employment. This can include the development of clean energy industries, such as renewable energy manufacturing, energy efficiency services, and sustainable agriculture. Additionally, governments can provide financial support and retraining programs to help workers and communities adapt to the new economic landscape.
Another challenge that complicates the adoption of clean energy technologies is the lack of infrastructure for electric vehicles (EVs) and other clean transportation options. While EVs have become increasingly popular, the widespread adoption of electric mobility requires significant investment in charging infrastructure, including fast-charging stations in urban, suburban, and rural areas. In many regions, the lack of a comprehensive and accessible charging network remains a barrier to the widespread adoption of EVs. In addition, the availability and affordability of EVs themselves can be a limiting factor, particularly in developing countries where consumers may not have access to the necessary financial resources or incentives to purchase electric vehicles.
Finally, the political will to prioritize renewable energy over fossil fuels is a critical barrier in many countries. In some cases, governments may face pressure from powerful fossil fuel industries, which have deep economic and political ties. This can lead to a reluctance to implement policies that favor renewable energy, such as carbon pricing, emissions reductions targets, or investment in clean energy technologies. Additionally, political instability or shifting priorities due to changing administrations can result in a lack of long-term commitment to renewable energy development. To overcome these challenges, it is essential to build broad political support for clean energy transition policies through public advocacy, evidence-based policymaking, and international cooperation.
In conclusion, while the transition to clean energy offers significant benefits for the environment, economy, and society, there are a range of challenges and barriers that must be overcome. These include financial and technological obstacles, regulatory and policy hurdles, social resistance, workforce training needs, and political opposition. Addressing these challenges will require coordinated efforts from governments, businesses, communities, and individuals, as well as sustained investments in innovation, infrastructure, and education. Only by overcoming these barriers can the world achieve a sustainable, equitable, and resilient energy future for all.
Policy, Incentives, and Global Collaboration
The successful transition to clean energy and the widespread adoption of renewable energy technologies require a comprehensive approach that involves effective policies, targeted incentives, and robust global collaboration. Governments play a crucial role in creating an enabling environment that fosters innovation, attracts investment, and ensures the equitable distribution of clean energy solutions. While technological advancements have made renewable energy increasingly cost-competitive with fossil fuels, the policy framework and financial incentives still remain critical for overcoming barriers, accelerating deployment, and ensuring long-term sustainability.
One of the most effective ways to drive clean energy adoption is through the implementation of policy frameworks that provide clear, long-term signals to investors and industry stakeholders. Governments can set ambitious renewable energy targets, such as achieving a certain percentage of energy generation from renewable sources by a specific year, which helps create market certainty. Additionally, carbon pricing mechanisms such as carbon taxes and cap-and-trade systems can be used to internalize the environmental cost of carbon emissions, thus making fossil fuels more expensive and encouraging the transition to cleaner energy sources. These policies can also create an incentive for industries to adopt more sustainable practices and reduce their carbon footprints.
Another important policy instrument is the renewable energy portfolio standard (RPS), also known as a renewable energy standard (RES), which mandates utilities to generate a certain percentage of their electricity from renewable sources. These standards push utilities to invest in renewable energy projects, thereby creating demand for clean energy technologies. Additionally, governments can introduce feed-in tariffs or power purchase agreements (PPAs) that guarantee long-term contracts for renewable energy producers at a fixed price, ensuring financial stability and lowering the risks for investors in renewable energy projects. By stabilizing the economic returns for clean energy investments, these policies help lower the cost of capital and make renewable energy projects more attractive.
A key challenge, however, is the incentivization of private investment in clean energy infrastructure. While policy measures such as tax credits and subsidies can help, they must be designed in a way that addresses the high initial capital costs of renewable energy projects. Financial incentives, such as investment tax credits (ITCs) and production tax credits (PTCs), can help make renewable energy projects more financially viable by providing subsidies for investments in specific technologies or for the production of renewable energy. Similarly, accelerated depreciation schedules for renewable energy assets allow investors to recover their capital investment more quickly, improving the return on investment. These financial incentives lower the barrier to entry for new market participants and help make renewable energy technologies competitive with conventional fossil fuel-based power generation.
In addition to financial incentives, governments can also offer subsidies for energy storage technologies, which play a critical role in addressing the intermittency challenges associated with renewable energy sources like wind and solar. Energy storage solutions are essential for ensuring a reliable, continuous power supply, and by offering targeted incentives for their deployment, governments can encourage the development of more advanced, cost-effective storage technologies. Research and development (R&D) funding and support for pilot projects can also play a vital role in advancing the commercialization of new and emerging clean energy technologies.
Global collaboration is also an essential component of driving the clean energy transition, as climate change is a global challenge that requires coordinated international efforts. The Paris Agreement, adopted in 2015, serves as a key framework for global climate action, setting targets for countries to limit global temperature rise to well below 2°C above pre-industrial levels, with the ambition to limit the temperature increase to 1.5°C. The agreement emphasizes the importance of collective action, with each country submitting its nationally determined contributions (NDCs) outlining its climate goals and efforts to reduce greenhouse gas emissions. While the Paris Agreement has been instrumental in encouraging governments to commit to climate action, the full realization of its goals depends on the continued commitment and collaboration of all nations.
The transition to clean energy also requires the sharing of knowledge, technologies, and best practices between countries. For example, developed countries with advanced clean energy technologies and expertise can collaborate with developing nations to help them leapfrog traditional energy systems and adopt clean energy solutions more quickly. Technology transfer is crucial to ensuring that all countries, regardless of their level of economic development, have access to the tools and knowledge needed to implement renewable energy technologies. This includes the sharing of energy efficiency technologies, grid modernization solutions, and renewable energy systems like solar and wind power, which can be adapted to local conditions and help accelerate the deployment of clean energy solutions worldwide.
In addition to technology transfer, financial support from international organizations, such as the World Bank, International Renewable Energy Agency (IRENA), and Green Climate Fund, is critical for enabling developing countries to make the clean energy transition. These institutions provide funding for renewable energy projects, energy efficiency initiatives, and capacity-building programs in emerging economies. Such funding helps overcome financial barriers, provides technical assistance, and ensures that developing countries can take advantage of clean energy opportunities.
However, trade policies can sometimes pose a challenge to global collaboration and the clean energy transition. Protectionist trade policies, such as tariffs on renewable energy equipment, can hinder the international flow of clean energy technologies and slow down the adoption of renewable energy. For example, tariffs on solar panels or wind turbine components can increase the cost of renewable energy projects, making them less attractive to investors. It is essential for countries to align their trade policies with the goal of promoting clean energy and enabling the free flow of renewable energy technologies across borders. International agreements that promote the use of clean energy technologies, eliminate trade barriers, and encourage investment in green technologies can help foster greater global collaboration.
In addition to international agreements and technology transfer, regional cooperation is also important in achieving clean energy goals. Neighboring countries with complementary energy resources, such as solar power in one region and wind power in another, can collaborate to build regional electricity grids that facilitate the exchange of renewable energy. For instance, a solar-rich country can export electricity to a wind-rich country when solar generation is low, and vice versa. Such regional interconnections improve grid reliability, increase the share of renewable energy in the energy mix, and lower the overall cost of electricity.
At the local level, cities and municipalities play a key role in driving the clean energy transition. Urban areas are major energy consumers and have the potential to implement energy-saving initiatives, promote the use of electric vehicles, and invest in clean energy infrastructure such as rooftop solar panels, district heating systems, and electric charging stations. Cities can also set ambitious renewable energy targets, improve energy efficiency in buildings, and engage citizens in sustainability efforts. By integrating renewable energy into urban planning and policy frameworks, cities can help lead the way in demonstrating how decentralized energy solutions can be effectively deployed at the community level.
Lastly, public engagement and education are essential in ensuring the success of clean energy policies and initiatives. The transition to a sustainable energy future will require the active participation of individuals, communities, businesses, and governments. Governments can play a vital role in educating the public about the importance of clean energy and the benefits of renewable technologies. Public awareness campaigns, educational programs, and outreach efforts can help build support for clean energy policies, encourage sustainable behaviors, and foster a culture of energy efficiency. By involving citizens in decision-making processes and raising awareness of the economic, environmental, and social benefits of renewable energy, governments can generate public support and ensure that policies are successfully implemented.
In conclusion, achieving a clean energy future will require coordinated efforts at every level of society—national, regional, and global. Effective policies, targeted incentives, and international collaboration are essential to overcoming the barriers to clean energy adoption and accelerating the transition to a sustainable energy system. Governments, businesses, and individuals must work together to create an enabling environment that fosters innovation, supports renewable energy development, and ensures that the benefits of clean energy are shared equitably. By building strong policy frameworks, incentivizing investment, and collaborating across borders, the global community can successfully navigate the challenges of the clean energy transition and build a more sustainable, resilient, and prosperous future for all.
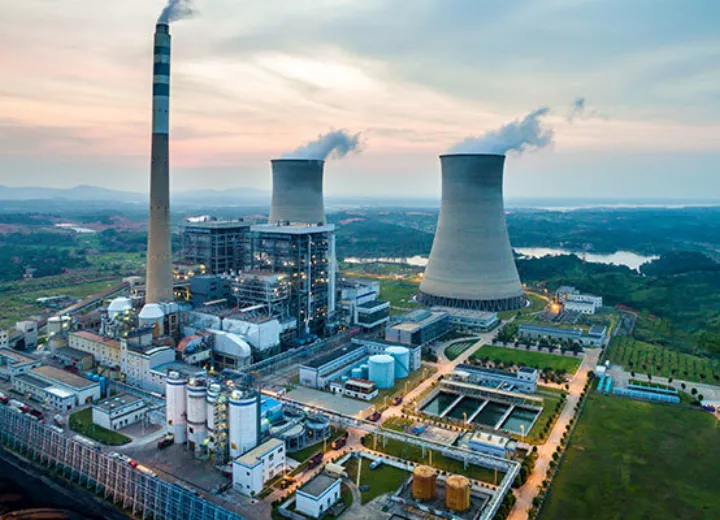
To further strengthen the transition to clean energy and address the global challenges associated with it, it is essential to continue expanding and improving the mechanisms for international collaboration, policy coordination, and technology deployment. This cooperation can extend beyond financial support and technology sharing; it also involves aligning international efforts to mitigate climate change with broader economic and developmental objectives.
One important avenue for international collaboration is through the creation of regional energy partnerships that focus on shared energy goals. These partnerships allow countries with complementary energy resources to combine their strengths in a more integrated and efficient way. For example, regions that are abundant in solar power could work together with those rich in wind or hydropower to build a more reliable and resilient energy network. Such regional cooperation can create economies of scale, lower energy costs, and provide access to cleaner, more affordable energy for all regions involved. Furthermore, energy interconnection projects like cross-border electricity transmission lines enable renewable energy to be shared seamlessly between neighboring countries, overcoming issues related to the intermittency of individual energy sources.
Global collaboration also entails working together to foster global standards and best practices for clean energy technologies. Developing and promoting international standards for equipment, systems, and performance will help reduce costs, improve efficiency, and ensure that technologies are compatible across different markets. This is particularly important as clean energy technologies, such as solar panels, wind turbines, and energy storage systems, continue to scale globally. Aligning standards can improve the global supply chain, make it easier for countries to adopt these technologies, and enhance international trade in clean energy solutions. Global standards also provide a framework for ensuring that renewable energy projects adhere to high environmental and social safeguards, contributing to more sustainable outcomes.
In addition to technical and policy coordination, public-private partnerships (PPPs) are another powerful tool in driving clean energy adoption. These partnerships leverage the strengths of both the public and private sectors, combining the public sector’s ability to create and enforce policies with the private sector’s capacity for innovation, efficiency, and financing. Through PPPs, governments can reduce the risk associated with renewable energy investments and attract private capital to clean energy projects. These partnerships can be particularly effective in developing countries, where the private sector can bring in the necessary capital and technology, while the government can help create a favorable regulatory environment.
At the same time, as the world strives to meet the goals set under the Paris Agreement, it is essential to recognize that climate justice is a critical component of the clean energy transition. Developed countries, which have historically contributed the most to global greenhouse gas emissions, have a responsibility to lead the way in reducing emissions and assisting developing countries in their efforts to mitigate climate change. Financial support, technology transfer, and capacity-building are vital to ensuring that developing countries are not left behind in the transition to clean energy. This includes helping to build the infrastructure and technical expertise needed for renewable energy deployment, as well as providing financing for energy access in regions where it is still limited.
Equitable energy access is a key consideration, particularly in rural and underserved communities, where access to modern energy services remains a major challenge. In many parts of the world, people still rely on traditional biomass and fossil fuels for cooking, heating, and lighting. These sources of energy can be harmful to health, contribute to air pollution, and increase greenhouse gas emissions. Ensuring that clean, affordable, and reliable energy is available to all is essential for achieving the United Nations’ Sustainable Development Goals (SDGs), particularly those related to poverty eradication, education, health, and gender equality. Renewable energy technologies such as solar home systems, mini-grids, and small-scale hydropower projects have proven to be effective in providing off-grid solutions to rural and remote communities, and continued investment in these areas is crucial to achieving universal energy access.
The development of energy storage technologies remains one of the most pressing challenges for ensuring the reliability of renewable energy systems. As renewable energy generation becomes a larger portion of global energy capacity, the need to store electricity produced during peak renewable generation periods (e.g., during the day for solar power) becomes more critical. To address this challenge, continued investment in battery storage, thermal storage, and other energy storage solutions is necessary. These technologies can store excess power generated by renewable sources and release it when demand is high, ensuring a reliable and consistent energy supply. The development of advanced, low-cost storage systems will be a game-changer in the clean energy transition, making it possible to rely more on renewable sources without the risk of power shortages or grid instability.
In addition to energy storage, smart grid technologies will play an essential role in managing the growing share of renewable energy in the grid. A smart grid uses digital communication technology to detect and react to local changes in energy usage. By making the grid more flexible and efficient, smart grids can better accommodate distributed energy sources, integrate storage solutions, and enable more precise management of electricity supply and demand. This will improve the stability of the grid and help prevent power outages, particularly as renewable energy sources are more widely integrated into national grids.
Furthermore, there must be a focus on reducing energy consumption through energy efficiency measures in buildings, transportation, and industry. Energy efficiency is often the most cost-effective way to reduce emissions, and it can also provide significant economic savings. Programs that promote the adoption of energy-efficient appliances, high-performance building materials, and green construction practices can reduce energy consumption across sectors. Governments can implement building codes, standards, and incentive programs to encourage the adoption of energy-efficient technologies. Similarly, energy efficiency in the transportation sector, such as through the promotion of electric vehicles (EVs), public transportation, and transportation infrastructure, can significantly reduce the overall demand for fossil fuels.
As the world transitions to a clean energy future, it is crucial that the energy transition be just and inclusive, ensuring that no one is left behind. Addressing issues of energy equity and ensuring that all communities benefit from the clean energy transition will be key to gaining broad public support and ensuring a fair distribution of the benefits of clean energy. Just transition policies are essential in supporting workers and communities affected by the decline of fossil fuel industries. These policies can provide workers with training and support to transition to new jobs in the clean energy sector, while also ensuring that communities affected by the closure of coal plants or oil refineries receive adequate support for economic diversification and infrastructure development.
In conclusion, the transition to a sustainable, low-carbon energy future requires concerted efforts at the national, regional, and global levels. Policy frameworks, financial incentives, and global collaboration will be key drivers of this transition, enabling the widespread adoption of renewable energy technologies, improving energy access, and supporting economic development. By working together—governments, businesses, and individuals can accelerate the clean energy revolution, create new job opportunities, reduce greenhouse gas emissions, and build a more resilient and equitable energy future for all. The collaborative, coordinated efforts of countries, industries, and communities will be pivotal in shaping the success of the clean energy transition in the coming decades.
Future Directions and Emerging Applications
The future of clean energy and the widespread deployment of renewable technologies is marked by ongoing innovation and the emergence of new applications that promise to revolutionize the way energy is produced, stored, and consumed. As the global community continues to address climate change, the need for transformative solutions that not only reduce carbon emissions but also enhance energy security and resilience is becoming more critical than ever. While significant progress has already been made in renewable energy deployment, the path forward will see the convergence of new technologies, business models, and policies that will unlock even greater potential in the coming decades.
One of the most promising areas for the future of clean energy lies in the development and integration of advanced energy storage systems. While renewable energy sources such as solar and wind offer vast potential, their inherent intermittency creates challenges for grid reliability. The ability to store excess energy when renewable generation is high and release it during periods of low generation is critical to achieving a stable and sustainable energy system. As such, the advancements in battery technologies, including solid-state batteries, lithium-sulfur batteries, and flow batteries, hold the potential to significantly increase the efficiency, capacity, and affordability of energy storage solutions. These innovations will allow for the large-scale deployment of renewable energy while ensuring grid stability, reducing reliance on fossil fuels, and ultimately decarbonizing the power sector.
In addition to battery storage, hydrogen is emerging as a key component in the future of clean energy. Green hydrogen, produced using renewable electricity to split water into hydrogen and oxygen, holds enormous promise as a clean fuel for various sectors. Hydrogen can be used to decarbonize hard-to-abate industries such as steel manufacturing, chemicals production, and shipping, where direct electrification may not be feasible. Furthermore, hydrogen can be used in fuel cells to provide energy for transportation (e.g., fuel cell vehicles), heating, and electricity generation. As hydrogen production becomes more cost-effective through economies of scale and technological improvements, it could play a central role in decarbonizing multiple sectors and achieving global climate goals.
Moreover, the integration of artificial intelligence (AI) and machine learning into the energy sector is poised to transform how energy systems are optimized. AI can be used to improve the efficiency of renewable energy forecasting, enabling better predictions of energy generation from sources such as wind and solar, thereby helping grid operators manage supply and demand. Additionally, AI-powered algorithms can optimize the operation of smart grids, improve energy storage management, and enable demand-side energy management. By using predictive analytics, AI can identify patterns in energy consumption, forecast peak demand, and optimize energy dispatch, which helps integrate renewable energy sources more effectively into the grid while reducing energy costs.
The rise of distributed energy resources (DERs) is another transformative development on the horizon. As renewable energy generation becomes more widespread, individual homes, businesses, and even entire communities are increasingly becoming active participants in the energy system. This shift is facilitated by technologies such as rooftop solar panels, small-scale wind turbines, home energy storage systems, and electric vehicles (EVs), which can not only reduce individual energy bills but also enable users to sell excess energy back to the grid. The growing popularity of microgrids—localized energy systems that can operate independently of the main grid in case of emergencies—further enhances energy resilience and security, particularly in remote or disaster-prone areas. The expansion of these distributed energy systems will shift the energy landscape from a centralized model to a more decentralized, flexible, and resilient one, where consumers become prosumers, actively participating in energy production and management.
In the transportation sector, the future of clean energy is increasingly linked to the widespread adoption of electric vehicles (EVs). As EV technology continues to improve, including the development of longer-lasting batteries and faster charging capabilities, the cost of EVs is expected to continue declining, making them more accessible to consumers. The growth of the EV market will also create synergies with renewable energy generation, as electric vehicles can serve as mobile energy storage units, helping balance electricity demand on the grid. As more vehicles transition to electric power, the transportation sector will contribute significantly to global emissions reductions, further accelerating the shift away from fossil fuels.
Another emerging application is the use of carbon capture, utilization, and storage (CCUS) technologies, which are designed to capture carbon dioxide emissions from industrial processes and power generation and either store them underground or utilize them for the production of valuable products. As the world continues to decarbonize, CCUS will play an essential role in offsetting emissions that are difficult or impossible to eliminate. In addition to capturing emissions from conventional power plants, CCUS can also be integrated into bioenergy systems (such as bioenergy with carbon capture and storage, or BECCS), creating a negative emissions solution that could be critical for meeting global climate targets.
In parallel, building-integrated renewable energy systems are gaining traction. These systems incorporate renewable energy generation directly into the structure of buildings, reducing the need for additional infrastructure and enabling more efficient use of space. Building-integrated photovoltaics (BIPV), for example, integrate solar panels into windows, facades, and roofs, turning the building itself into an energy generator. Similarly, solar thermal systems can be incorporated into building designs to provide hot water or even contribute to space heating. These systems, combined with smart building technologies and energy-efficient designs, will help reduce energy consumption and improve the sustainability of the built environment.
As digital technologies continue to evolve, blockchain is also emerging as a tool for enhancing transparency and efficiency in energy transactions. Blockchain can be used to create decentralized energy markets where energy transactions are recorded securely, transparently, and without the need for intermediaries. This can streamline the process of buying and selling energy between individuals, communities, and businesses, promoting greater efficiency and reducing transaction costs. Blockchain technology can also enhance the traceability of renewable energy, ensuring that energy from renewable sources is verified and tracked throughout the supply chain, providing consumers with confidence in the sustainability of their energy choices.
The role of climate engineering or geoengineering technologies in the future energy landscape is also an area of ongoing research. These technologies aim to directly manipulate the Earth’s climate to counteract the effects of climate change, such as solar radiation management (e.g., by reflecting sunlight back into space) or carbon removal technologies. While these approaches are controversial and still in the experimental phase, they could potentially play a role in managing global temperatures if other mitigation efforts fall short. However, these technologies raise complex ethical, environmental, and geopolitical questions that must be carefully considered as research progresses.
As we look toward the future, collaborative innovation will be a key factor in accelerating the clean energy transition. The interplay between public policy, private sector innovation, and international collaboration will create the enabling conditions necessary for the widespread deployment of emerging technologies. Governments will need to continue providing the right policy signals and incentives to stimulate investment in research and development, while businesses will need to scale up innovative solutions that make clean energy technologies more accessible, affordable, and efficient. International cooperation and knowledge-sharing will ensure that the benefits of these emerging technologies can be realized globally, especially in developing countries where clean energy access is most needed.
In conclusion, the future of clean energy is not only about transitioning to renewable energy sources but also about integrating innovative technologies and emerging applications that can transform every sector of the economy. From advanced energy storage and hydrogen production to artificial intelligence and blockchain, the potential for clean energy solutions is vast. The coming decades will witness a revolution in how energy is produced, consumed, and managed, driving the world closer to a low-carbon, sustainable, and resilient energy future. However, the realization of this future will require continued investment, collaboration, and innovation from all stakeholders, from governments and businesses to individuals and communities. The path ahead is challenging but filled with opportunity, and the benefits of a clean energy future will be felt by all.
As the world moves forward in its clean energy transition, it is important to emphasize the necessity of scalable solutions that can be deployed quickly and effectively across a wide range of regions and sectors. These scalable solutions will be key in addressing the global demand for affordable, reliable, and clean energy. One such solution lies in the rapid deployment of decentralized renewable energy systems. These systems, such as small-scale solar installations and microgrids, can be particularly impactful in regions where central electricity grids are unreliable or non-existent. They provide a sustainable and resilient means of energy access in both rural and urban areas, especially in developing countries, where a large portion of the population still lacks reliable electricity.
In tandem with decentralized energy solutions, the digitalization of the energy sector will play a pivotal role in shaping the future of energy systems. Smart meters, advanced grid management technologies, and energy management systems will enable consumers to monitor and optimize their energy consumption in real time. These systems can provide real-time data on energy use, helping consumers make informed decisions about their energy consumption, reduce waste, and lower costs. For utilities and grid operators, the digitalization of the energy sector allows for better demand forecasting, enhanced grid reliability, and improved integration of variable renewable energy sources. This seamless exchange of information between producers, consumers, and the grid will be a cornerstone of future energy systems, ensuring that energy is distributed more efficiently and sustainably.
The rise of sustainable urban planning and green building technologies will also be central to the future of energy efficiency. As the global population continues to urbanize, cities are becoming increasingly important in the fight against climate change. Future cities will need to be designed with energy efficiency, renewable energy integration, and resilience in mind. Urban areas can be transformed into smart cities, which integrate renewable energy systems, green infrastructure, and cutting-edge technologies to minimize energy consumption and reduce carbon footprints. Urban buildings and transportation networks will be redesigned to optimize energy use, incorporate renewable energy sources, and create a more sustainable environment for residents. The implementation of green roofs, vertical gardens, and solar panel integration into buildings will contribute to reducing energy demands while also improving air quality and urban biodiversity.
Additionally, future energy trading platforms and peer-to-peer energy sharing models are expected to emerge as new ways to democratize energy production and distribution. These platforms, enabled by blockchain and other technologies, will allow individuals and communities to trade excess energy with one another. This will empower consumers to take control of their energy choices, create local energy markets, and foster a more equitable energy system. By decentralizing energy markets, these platforms can reduce dependence on centralized utilities and lower energy costs, especially in areas where renewable energy production is abundant but access to traditional power grids is limited.
Furthermore, the application of bioenergy and waste-to-energy technologies is set to grow as a means of closing the loop on waste and creating a circular economy. By utilizing organic waste (such as agricultural residues, food waste, or municipal solid waste) to generate energy, bioenergy systems can provide an additional source of renewable energy while reducing the environmental impact of waste disposal. Technologies such as anaerobic digestion, biogas production, and pyrolysis can convert waste materials into biofuels, biogas, and biochar, which can then be used for heating, electricity generation, or even transportation. This not only helps address waste management challenges but also contributes to reducing emissions and generating clean energy.
The marine and tidal energy sectors represent another exciting frontier for renewable energy development. With oceans covering more than 70% of the Earth’s surface, the potential for harnessing tidal, wave, and ocean thermal energy is vast. As technology advances, tidal turbines, wave energy converters, and ocean thermal energy conversion systems are expected to become more efficient and commercially viable. These technologies harness the predictable and renewable power of the oceans to generate electricity, providing a consistent source of clean energy that can be integrated into national grids. Ocean energy has the advantage of being highly predictable, unlike solar and wind power, which are subject to weather conditions. This makes it an attractive option for providing reliable, baseload power, especially for island nations and coastal regions.
The agriculture sector will also see growing integration of clean energy technologies, particularly through agrovoltaics, which involves the combination of solar energy production with agricultural land use. Agrovoltaic systems can optimize land use by allowing solar panels to be installed over crops or pastures, generating renewable energy while still allowing agricultural production to continue underneath. This dual-use approach has the potential to improve food security while also contributing to renewable energy generation, making it a promising solution for sustainable farming in regions facing land and resource constraints. Additionally, precision agriculture technologies that use AI, IoT (Internet of Things), and drones can help optimize irrigation, reduce the use of chemical fertilizers and pesticides, and improve energy efficiency on farms.
As the energy landscape evolves, climate finance and private sector investment will play a central role in scaling clean energy technologies. Financial mechanisms such as green bonds, impact investing, and climate funds are increasingly being used to direct capital toward sustainable projects. These financial tools are helping bridge the funding gap for clean energy technologies and providing a means for investors to support environmentally and socially responsible projects. The growth of green finance is crucial for accelerating the deployment of emerging technologies and ensuring that the clean energy transition is both economically viable and environmentally sound. Private sector innovation and competition will also drive down costs, making clean energy technologies more accessible to businesses, governments, and individuals.
Another critical element in the future of energy is the evolution of policy frameworks that can address the challenges and opportunities presented by new technologies. Governments will need to adapt existing regulatory frameworks to account for the rapid development of emerging technologies and ensure that incentives are aligned with the goal of achieving a low-carbon economy. This will involve creating flexible, forward-looking regulations that can accommodate technological innovation while also providing the necessary protections for consumers and the environment. It will also require international cooperation to harmonize regulations, standards, and trade policies, ensuring that clean energy technologies are deployed efficiently and effectively across borders.
In conclusion, the future of clean energy is both exciting and challenging. The emerging applications and technologies, such as advanced energy storage, hydrogen, AI, decentralized energy systems, and marine energy, offer transformative potential to decarbonize the global energy sector and build a more sustainable future. However, achieving this vision will require continued innovation, investment, and collaboration across sectors and borders. As technological advances reshape the energy landscape, it will be essential to ensure that these solutions are inclusive, equitable, and accessible to all. With the right policies, investments, and partnerships, the world can unlock the full potential of clean energy, creating a more sustainable, resilient, and prosperous future for generations to come.
Metallurgical Waste Heat Recovery Steam System
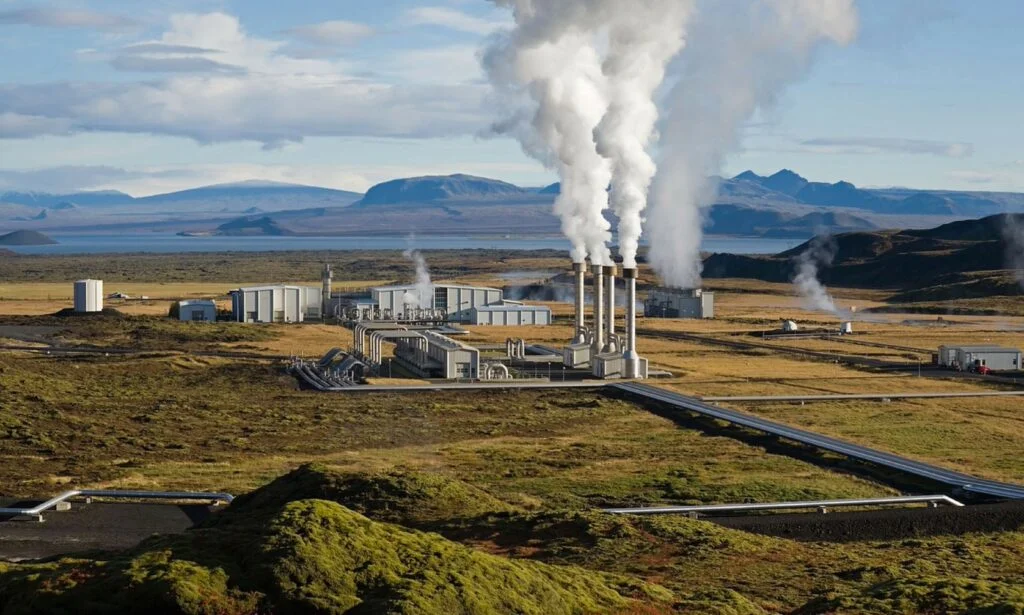
Metallurgical industries, including steel, aluminum, and other metal production, are among the most energy-intensive sectors worldwide. The processes involved in extracting, refining, and shaping metals require large amounts of heat energy, often derived from the combustion of fossil fuels. However, a significant portion of this heat is typically lost to the environment as waste heat, which represents a substantial opportunity for improving energy efficiency and reducing emissions in these industries. Metallurgical waste heat recovery (WHR) systems, specifically steam-based systems, have emerged as effective solutions for capturing and utilizing this wasted heat, thereby enhancing the overall energy efficiency of metallurgical operations while contributing to environmental sustainability.
The concept of waste heat recovery (WHR) in the metallurgical industry revolves around the process of capturing heat that would otherwise be lost from hot exhaust gases, cooling systems, or other high-temperature processes. This recovered heat can then be utilized in various ways, including generating steam for power production, district heating, or even direct process heat reuse. Steam-based WHR systems are particularly useful in metallurgical industries due to their ability to capture high-temperature heat and convert it into a usable form of energy. The process typically involves the installation of heat exchangers, steam boilers, or organic Rankine cycle (ORC) systems, which are designed to recover waste heat and convert it into steam for power generation or other applications.
One of the key advantages of steam-based WHR systems in metallurgical industries is their versatility. The recovered steam can be used in several applications within the plant. For instance, it can power steam turbines to generate electricity, which can be used to meet the plant’s own energy needs, reducing the reliance on external power sources and cutting operational costs. Alternatively, the steam can be used for preheating raw materials, process heating, or cooling within the facility, improving the efficiency of metallurgical processes. Moreover, the steam produced can be used for district heating, where excess energy is supplied to nearby communities or industrial zones, further reducing waste and maximizing the utility of recovered heat.
One of the most significant metallurgical processes that can benefit from waste heat recovery is blast furnace operations, where iron is produced from ore. During the process, a large amount of heat is generated and typically wasted through exhaust gases. By installing waste heat recovery steam systems in these operations, the energy lost in the exhaust gases can be captured and used to generate steam. This steam can be directed to power turbines, generate electricity, or provide heat to other parts of the plant. For example, a system may capture heat from the blast furnace exhaust gases and use it to drive a steam turbine, which, in turn, generates electricity to offset the plant’s energy consumption. This helps reduce fuel consumption, lower carbon emissions, and improve the overall energy balance of the facility.
Another critical metallurgical process where WHR is applicable is steelmaking, especially in electric arc furnaces (EAFs), which are commonly used for producing steel from scrap metal. The high temperatures generated by these furnaces lead to significant waste heat that can be recovered. By installing heat recovery steam generators (HRSGs) and utilizing the recovered heat to produce steam, steelmaking plants can reduce their energy consumption and carbon emissions. The steam generated in this process can be used for various purposes, such as preheating the furnace, supporting other heat treatment processes, or generating electricity through steam turbines.
The recovery of waste heat can also improve energy efficiency in rolling mills, which are used to shape hot metal into desired forms, such as sheets, bars, and coils. The temperature of the rolling mill process is extremely high, and much of the heat generated during the rolling operation is lost through radiation, convection, or cooling water. Installing steam-based WHR systems can help recover this waste heat and use it to generate steam. This steam can either be used for process heating or converted into electricity to support other energy-intensive operations within the mill. In doing so, metallurgical facilities can reduce their reliance on external energy sources and make their operations more energy-efficient.
Flue gas heat recovery is another common method of capturing waste heat in metallurgical plants. Flue gases, which are the exhaust gases released during the combustion of fuel, typically contain significant amounts of thermal energy. By installing heat exchangers in the flue gas stack, it is possible to capture a portion of this waste heat and convert it into steam using water or another heat transfer medium. This steam can then be used to drive turbines for power generation or to provide heat for other parts of the plant. In some cases, the recovered steam can even be used to supplement the plant’s heating needs, reducing the need for additional fossil fuels and minimizing environmental impact.
In addition to energy savings, steam-based WHR systems in the metallurgical industry also contribute to significant environmental benefits. The reduction in fossil fuel consumption through the recovery and reuse of waste heat directly lowers greenhouse gas emissions, helping metallurgical plants reduce their carbon footprint. Since energy-intensive industries like steel and aluminum production are among the largest contributors to industrial carbon emissions, the implementation of waste heat recovery systems can play a vital role in meeting climate goals and adhering to increasingly stringent environmental regulations. Furthermore, by decreasing the amount of energy drawn from external sources, waste heat recovery systems also reduce the overall demand for fossil fuels, contributing to the broader goal of energy transition and decarbonization.
Economic benefits also play a major role in the adoption of WHR systems. The initial capital investment required for the installation of waste heat recovery systems can be significant, but the long-term cost savings typically outweigh the upfront costs. By reducing energy consumption, WHR systems lower the overall energy bills for metallurgical plants, which can account for a large portion of operational expenses. Additionally, the recovery of heat can reduce the need for expensive fuel purchases and lower maintenance costs, particularly when it comes to maintaining separate heating and power systems. Over time, the payback period for such systems becomes shorter, making them a financially viable option for improving the efficiency and sustainability of metallurgical operations.
Moreover, the integration of advanced technologies such as superheated steam cycles, high-efficiency heat exchangers, and advanced turbine systems can further improve the performance of waste heat recovery systems in metallurgical plants. For example, superheated steam has a higher energy content than saturated steam, allowing for greater efficiency in driving turbines and generating electricity. By utilizing these advanced technologies, metallurgical facilities can maximize the amount of recoverable heat and achieve higher levels of overall energy efficiency.
The role of industrial symbiosis in waste heat recovery is also gaining traction. In certain industrial areas, multiple companies or sectors are located in proximity to one another and share resources, including waste heat. In these scenarios, metallurgical plants can capture their waste heat and supply it to neighboring facilities, creating a circular economy of shared energy. This approach reduces overall energy consumption, minimizes waste, and enhances the environmental sustainability of industrial regions.
While there are numerous benefits to implementing waste heat recovery steam systems in metallurgical industries, there are also several challenges that need to be addressed. One of the main challenges is the high upfront cost of installing and retrofitting waste heat recovery systems, especially in older plants that were not initially designed for such systems. However, financial incentives, government support, and long-term savings make these systems more feasible over time. Another challenge is the technical complexity involved in integrating waste heat recovery systems with existing plant infrastructure. Metallurgical plants often have highly specialized and complex processes, and retrofitting heat recovery systems requires careful engineering and planning to ensure compatibility and minimal disruption to operations.
In conclusion, metallurgical waste heat recovery steam systems represent a crucial opportunity for improving energy efficiency, reducing carbon emissions, and promoting sustainable industrial practices in energy-intensive sectors. By capturing and utilizing waste heat from processes such as blast furnaces, steelmaking, and rolling mills, metallurgical facilities can enhance their operational efficiency, cut energy costs, and reduce their environmental impact. As technology continues to improve, the adoption of waste heat recovery systems is expected to grow, contributing to a more sustainable and low-carbon future for the global metallurgical industry. Through investment in advanced technologies, better integration with other industries, and overcoming technical challenges, metallurgical waste heat recovery systems will play an essential role in transforming the way energy is produced and consumed in these vital industrial sectors.
As the demand for metals and industrial products continues to rise globally, the need for more energy-efficient and sustainable practices in the metallurgical industry will become increasingly urgent. In light of this, the development of next-generation waste heat recovery systems will play a pivotal role in ensuring that metallurgical operations can meet both economic and environmental goals. These systems will likely integrate advanced materials, innovative heat transfer methods, and automation technologies to further improve efficiency and reduce energy waste.
One emerging area of interest is the integration of heat storage technologies into metallurgical waste heat recovery systems. By coupling thermal storage with waste heat recovery, metallurgical plants can store excess heat generated during off-peak times and use it during periods of higher demand, thereby improving the stability and flexibility of energy supply. Thermal energy storage systems, such as molten salt, phase-change materials (PCMs), and thermal batteries, can be integrated with steam-based WHR systems to create more reliable and flexible energy solutions. This integration will allow plants to operate more efficiently, as they can access stored energy when needed, reducing reliance on external energy sources and mitigating the impact of fluctuating energy prices.
Furthermore, the application of artificial intelligence (AI) and machine learning (ML) can help optimize waste heat recovery systems in real time. By using AI algorithms to analyze plant data, energy consumption patterns, and system performance, plants can more accurately predict when and where waste heat recovery should be maximized. These systems can adjust operational parameters, such as flow rates and temperature setpoints, in real-time to ensure that the maximum amount of waste heat is captured and converted into usable energy. Over time, these AI-driven systems could become fully automated, continuously optimizing energy efficiency, identifying maintenance needs, and enhancing the overall performance of waste heat recovery units.
In addition to AI and ML, advanced sensor technologies are also expected to play an important role in the future of waste heat recovery. Sensors capable of detecting minute temperature variations and pressure changes can provide real-time insights into the condition of heat exchangers, boilers, and turbines, helping operators identify inefficiencies or equipment malfunctions early. The integration of these sensors with IoT (Internet of Things) networks will allow for continuous monitoring and data collection, further optimizing the recovery of waste heat and minimizing downtime or energy losses due to equipment failure.
The role of process integration in maximizing energy efficiency cannot be overstated. By optimizing the way different systems within the plant work together, metallurgical facilities can significantly reduce energy consumption. For example, by integrating waste heat recovery with combustion processes or electrical systems, plants can ensure that heat recovery efforts complement existing processes and contribute to overall energy savings. Using a systems approach, where waste heat recovery is considered alongside other energy efficiency measures such as heat integration, energy optimization, and process intensification, metallurgical plants can achieve higher levels of sustainability and cost-effectiveness.
Another area where innovation is driving improvements is in the development of advanced heat exchanger technologies. Heat exchangers play a central role in waste heat recovery by transferring thermal energy from hot exhaust gases to water or other fluids, which can then be used to generate steam or provide heating. Next-generation heat exchangers are being designed to be more compact, more efficient, and more resistant to corrosion, which can improve the durability and lifespan of waste heat recovery systems. The development of heat exchanger networks will also allow plants to capture and recover heat from multiple sources within the facility, further improving overall energy efficiency and reducing reliance on fossil fuels.
Carbon capture, utilization, and storage (CCUS) technologies are also becoming an integral part of the energy transition in energy-intensive industries, including metallurgy. The integration of waste heat recovery systems with CCUS could help significantly reduce the carbon footprint of the metallurgical industry by capturing CO2 emissions and utilizing the captured carbon for various purposes, such as producing synthetic fuels or chemicals. By pairing waste heat recovery with carbon capture, metallurgical plants could operate in a more sustainable and climate-neutral manner, further aligning their operations with international climate targets and regulations.
The global shift towards circular economy principles is another trend that will impact the future of metallurgical waste heat recovery. In a circular economy, waste is minimized, resources are reused, and energy is recovered and recycled. This concept aligns closely with the goals of waste heat recovery systems in metallurgy, as they facilitate the reuse of thermal energy that would otherwise be lost. The adoption of circular economy principles within metallurgical industries will not only reduce the environmental impact of metal production but also create new business opportunities by transforming waste into valuable resources. This approach can be particularly effective in industries such as aluminum production, where waste heat recovery can be used to support the recycling of aluminum scrap, reducing energy demand and minimizing the need for primary aluminum extraction.
The policy landscape surrounding waste heat recovery systems is also evolving, with governments and regulatory bodies increasingly recognizing the importance of energy efficiency and carbon reduction in industrial sectors. Various subsidies, tax credits, and incentive programs are being introduced worldwide to encourage the adoption of energy-efficient technologies, including waste heat recovery systems. In addition, stricter environmental regulations, such as carbon pricing or emissions caps, are motivating metallurgical plants to implement waste heat recovery as part of their overall strategy for reducing greenhouse gas emissions. As policies continue to evolve, the financial and regulatory incentives for adopting waste heat recovery technologies are expected to grow, making them more attractive for companies in the metallurgical sector.
On the global stage, international collaboration and knowledge-sharing are crucial for accelerating the adoption of waste heat recovery technologies in metallurgical industries. As countries and regions work together to meet their climate goals and transition to a low-carbon economy, there will be a growing need for knowledge transfer, joint research, and development initiatives. Collaborative efforts between governments, academic institutions, research organizations, and the private sector will help unlock new technological advancements, optimize waste heat recovery systems, and drive cost reductions, making these systems more accessible to metallurgical plants worldwide.
In conclusion, the future of metallurgical waste heat recovery systems is poised to play a critical role in the industry’s transition to more sustainable and energy-efficient practices. By recovering waste heat from processes such as blast furnaces, steelmaking, and rolling mills, metallurgical plants can significantly reduce their energy consumption, lower emissions, and cut operational costs. The integration of advanced technologies such as AI, machine learning, heat storage, and carbon capture will further enhance the performance of waste heat recovery systems, driving the industry toward greater efficiency and sustainability. As policies evolve, and the global push for decarbonization intensifies, metallurgical companies will be well-positioned to leverage waste heat recovery systems as a key component of their strategy to reduce energy waste, minimize carbon emissions, and contribute to a more sustainable future.
Here are 10 main sections for a detailed analysis of Metallurgical Waste Heat Recovery Steam Systems:
- Introduction to Metallurgical Waste Heat Recovery
- Overview of the metallurgical industry’s energy consumption and the need for waste heat recovery (WHR).
- Significance of improving energy efficiency in high-temperature processes.
- Types of Waste Heat in Metallurgical Processes
- Breakdown of the various sources of waste heat within metallurgical plants (e.g., blast furnaces, electric arc furnaces, rolling mills).
- Characteristics of high-temperature exhaust gases and other waste heat streams.
- Steam-Based Waste Heat Recovery Systems
- Explanation of steam generation using waste heat.
- Overview of the components of steam-based WHR systems: heat exchangers, HRSGs (Heat Recovery Steam Generators), and steam turbines.
- Applications of steam: electricity generation, process heating, district heating.
- Key Metallurgical Processes Benefiting from WHR
- Detailed description of metallurgical processes that benefit from waste heat recovery:
- Blast furnace operations
- Steelmaking (Electric Arc Furnace)
- Rolling mills
- The role of WHR in reducing energy consumption and improving efficiency in each process.
- Detailed description of metallurgical processes that benefit from waste heat recovery:
- Technological Advancements in WHR Systems
- Emerging technologies such as advanced heat exchangers, superheated steam cycles, and high-efficiency turbines.
- Role of automation, sensors, and AI in optimizing WHR systems.
- Integration with Other Industrial Processes
- How waste heat recovery can be integrated with other systems in the metallurgical plant (e.g., combustion processes, electrical systems).
- Benefits of process integration and energy optimization across the facility.
- Economic Benefits of Metallurgical WHR Systems
- Analysis of the economic advantages of installing waste heat recovery systems, including reduced energy costs, lower fuel consumption, and improved plant efficiency.
- Payback periods and financial incentives for WHR adoption.
- Environmental Benefits and Carbon Footprint Reduction
- How WHR systems help reduce greenhouse gas emissions by minimizing the need for external energy sources.
- The contribution of WHR to meeting global climate goals and environmental regulations in metallurgy.
- Challenges to WHR Implementation in Metallurgy
- Technical and financial challenges: high initial costs, integration with existing infrastructure, and retrofitting in older plants.
- Overcoming issues related to the complexity of metallurgical processes and system compatibility.
- Future Trends and Global Collaboration
- The future outlook for metallurgical waste heat recovery, including advancements in heat storage, carbon capture integration, and circular economy principles.
- The role of international collaboration in driving innovation and ensuring the widespread adoption of WHR technologies in the metallurgical industry.
These sections can provide a comprehensive understanding of how waste heat recovery steam systems are being utilized in the metallurgical industry and the evolving technological, economic, and environmental aspects of these systems.
Introduction to Metallurgical Waste Heat Recovery
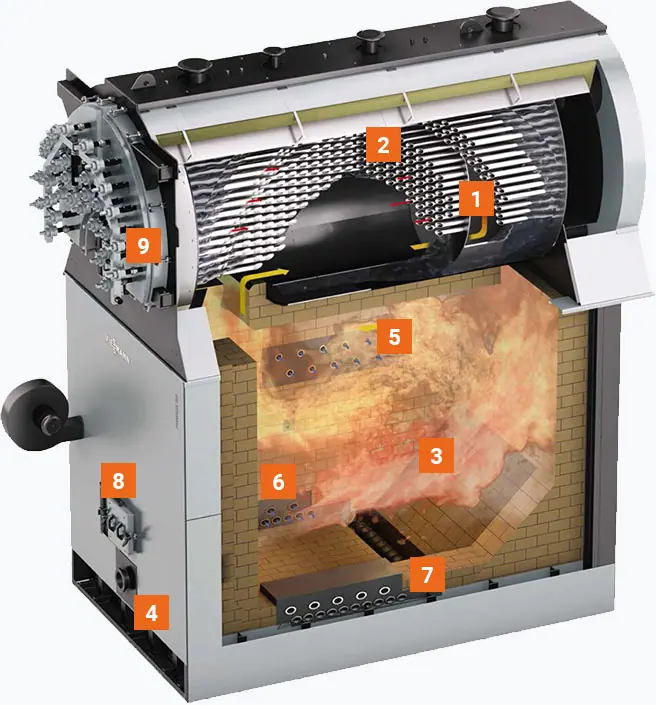
Metallurgical industries are among the largest consumers of energy in the world, driven by the high temperatures required in the extraction and processing of metals. The processes involved in smelting, refining, and shaping metals—such as in steel and aluminum production—consume vast amounts of thermal energy. However, a significant portion of this energy is typically lost as waste heat through exhaust gases, cooling systems, and other byproducts. This waste heat, often at high temperatures, represents a substantial opportunity for improving energy efficiency, reducing operational costs, and mitigating the environmental impact of these industries. Metallurgical waste heat recovery (WHR) systems offer an effective solution to capture and utilize this otherwise wasted thermal energy, turning it into a useful form of energy such as steam, which can be used for power generation, process heating, or district heating.
The potential for waste heat recovery in the metallurgical industry is vast, as these plants are responsible for generating large amounts of waste heat throughout their operations. From blast furnaces, where iron is produced from raw ore, to electric arc furnaces used in steelmaking, to rolling mills where metal is shaped, each process involves high-temperature reactions and produces significant waste heat. Much of this heat is released into the atmosphere, where it is lost and underutilized. Waste heat recovery seeks to capture a portion of this heat and convert it into usable energy, such as generating steam for electricity or reusing it directly within the plant to improve process efficiency.
At the core of metallurgical waste heat recovery are systems that use heat exchangers to transfer thermal energy from the hot waste gases or other waste heat sources to a fluid, usually water. This heated fluid can then be used to produce steam, which in turn can drive steam turbines to generate electricity or provide heat to other processes within the plant. Steam-based systems are particularly effective in metallurgical applications, as they can operate at high temperatures and offer a flexible range of applications, from electricity generation to direct use in heating processes.
The introduction of waste heat recovery systems in metallurgy not only improves energy efficiency but also provides economic benefits. Reducing the amount of external energy required for operations can lower fuel costs, which are a significant portion of the expenses for metal producers. Furthermore, the installation of such systems helps mitigate the financial risks associated with fluctuating energy prices. In addition, some governments offer financial incentives, such as tax credits or subsidies, to encourage industries to adopt energy-saving technologies like waste heat recovery, making the investment more financially attractive.
Another driving factor behind the adoption of waste heat recovery systems in metallurgy is the increasing emphasis on environmental sustainability. The metallurgical sector is a major contributor to global carbon emissions due to its reliance on fossil fuels for heating and power generation. By recovering waste heat and using it to reduce reliance on fossil fuels, metallurgical plants can lower their carbon footprint and comply with stricter environmental regulations. In some cases, the integration of waste heat recovery systems can help companies meet their emissions reduction targets and contribute to the achievement of international climate goals, such as those set by the Paris Agreement.
The development of advanced technologies is accelerating the effectiveness of waste heat recovery in the metallurgical industry. Innovations such as superheated steam cycles, high-efficiency heat exchangers, and organic Rankine cycles have improved the efficiency and performance of WHR systems, making them more viable for large-scale industrial applications. Additionally, automation and digitalization through the use of AI (artificial intelligence) and machine learning (ML) can optimize system performance in real-time, allowing plants to adapt their energy recovery strategies based on varying operational conditions.
Despite the clear advantages, the adoption of waste heat recovery systems in metallurgical operations is not without challenges. The high upfront capital cost of installing such systems can be a significant barrier, especially for smaller or older plants that may not have been designed with waste heat recovery in mind. Additionally, the integration of WHR systems into existing infrastructure requires careful planning and may necessitate significant modifications to equipment or processes. Overcoming these challenges often requires a combination of technical expertise, financial incentives, and long-term planning to ensure that the benefits of waste heat recovery outweigh the initial investment.
Moreover, the success of waste heat recovery systems depends heavily on the type of metallurgical process, the temperature and nature of the waste heat being recovered, and the specific energy needs of the plant. While blast furnaces, electric arc furnaces, and rolling mills are all prime candidates for waste heat recovery, each has its unique characteristics that affect the efficiency and design of recovery systems. Therefore, an in-depth understanding of the specific process and heat recovery potential is necessary to develop tailored solutions that will maximize the benefits of these systems.
In conclusion, metallurgical waste heat recovery is a critical step toward improving energy efficiency, reducing carbon emissions, and enhancing the sustainability of metal production. By recovering waste heat from high-temperature processes such as blast furnaces, steelmaking, and rolling mills, metallurgical plants can improve their operational efficiency, reduce their dependence on external energy sources, and cut costs. With continued advancements in technology and growing support from both the public and private sectors, waste heat recovery systems will play a crucial role in transforming the metallurgical industry into a more sustainable and energy-efficient sector. As the industry continues to innovate and overcome barriers to adoption, the potential for waste heat recovery to contribute to the global transition to a low-carbon economy remains immense.
As metallurgical industries continue to evolve, the integration of waste heat recovery (WHR) systems becomes increasingly critical in meeting both economic and environmental objectives. In addition to addressing the rising energy costs and the need for reducing environmental impact, WHR systems help extend the lifecycle of valuable resources and reduce the overall demand for fossil fuels. These systems can enhance the sustainability of operations by promoting resource efficiency and reducing the amount of waste generated by processes that rely heavily on thermal energy.
One key factor in advancing the adoption of waste heat recovery systems in metallurgy is the ongoing development of innovative heat recovery technologies. For example, the integration of heat pumps into WHR systems offers the potential to improve the efficiency of heat recovery, particularly in processes that involve lower-temperature waste heat. These heat pumps can transfer thermal energy from lower temperature sources and upgrade it to a higher temperature level, making it more suitable for industrial processes that require significant heat input.
Another noteworthy advancement is the use of advanced materials in heat recovery systems, such as high-temperature alloys and ceramics, which are capable of withstanding the extreme conditions found in metallurgical plants. These materials improve the durability and performance of heat exchangers and other components, making waste heat recovery systems more reliable and cost-effective in the long term. The use of corrosion-resistant materials also addresses one of the common challenges in implementing WHR systems, particularly in environments where high temperatures and reactive gases are present.
Additionally, new thermal storage technologies are beginning to play a role in the metallurgical industry’s approach to waste heat recovery. By storing excess heat during periods of low demand, thermal storage systems ensure that energy can be utilized during times of peak demand or when operations require additional heat input. This ability to store heat and use it when needed enhances operational flexibility, improves overall energy efficiency, and reduces reliance on external energy sources. Thermal energy storage technologies, such as molten salt storage or phase-change materials (PCMs), are emerging as promising solutions for metallurgical plants seeking to maximize the use of recovered heat.
In the realm of digitalization and smart manufacturing, the use of IoT (Internet of Things) sensors, big data analytics, and machine learning algorithms has the potential to greatly improve the operation and optimization of WHR systems. By embedding sensors throughout the plant, real-time data on temperatures, pressure, and flow rates can be collected and analyzed. This data can then be used to optimize heat recovery processes, predict maintenance needs, and improve system reliability. Predictive analytics, powered by machine learning, can enable operators to anticipate potential issues and proactively adjust operations to ensure optimal performance and energy recovery.
Moreover, the ability to simulate and model metallurgical processes and WHR systems using advanced software tools is improving the design and integration of these technologies. By using sophisticated computational models, engineers can predict how waste heat recovery systems will perform under various conditions, optimizing their layout, size, and configuration before installation. This can reduce trial-and-error during implementation, ensuring that systems are properly designed to meet the specific needs of the plant and its processes.
As demand for energy-efficient and low-carbon solutions in the metallurgical sector grows, the role of government incentives and industry collaborations becomes increasingly important. Governments are offering financial incentives, such as tax credits, grants, and subsidies, to encourage the adoption of technologies that reduce energy consumption and lower carbon emissions. In some regions, regulatory frameworks, such as carbon taxes and emissions reduction targets, provide additional motivation for industries to invest in waste heat recovery systems.
At the same time, global collaboration between governments, private industries, and research institutions is essential to accelerate the development of next-generation waste heat recovery systems. Knowledge sharing, joint research projects, and partnerships across borders can help unlock new technologies and business models that drive further innovation in this field. Such collaborations can also provide valuable insights into the challenges and opportunities facing different metallurgical sub-sectors, enabling tailored solutions to meet specific needs.
Another avenue for advancing waste heat recovery in metallurgy is through the integration of carbon capture, utilization, and storage (CCUS) technologies. CCUS can be coupled with waste heat recovery to help reduce CO2 emissions while simultaneously improving the energy efficiency of metallurgical plants. By capturing and storing the carbon dioxide generated during the process, plants can significantly reduce their environmental impact. Additionally, the captured CO2 can be repurposed for use in other industrial applications, such as enhanced oil recovery or the production of synthetic fuels.
Looking to the future, the next frontier for waste heat recovery in metallurgy lies in the advancement of circular economy principles. In a circular economy, waste is minimized, and energy is recovered and reused, closing the loop on energy and material flows. The concept of industrial symbiosis, in which the waste heat from one plant is used by another facility, offers an innovative way to further reduce waste and optimize energy use. For example, the waste heat from a steel plant could be used to generate power or heat for nearby industries, creating a regional energy network that maximizes the efficiency of waste heat recovery on a larger scale.
In conclusion, metallurgical waste heat recovery is not only an essential component of improving the energy efficiency and sustainability of the industry but also a pathway to long-term economic and environmental resilience. By harnessing the potential of waste heat, metallurgical plants can reduce their dependency on fossil fuels, lower emissions, and create significant cost savings. The ongoing development of advanced technologies, coupled with supportive policies and global cooperation, will continue to enhance the effectiveness of waste heat recovery systems, enabling the metallurgical sector to play a key role in the global transition to a low-carbon, energy-efficient economy.
The continued evolution of metallurgical waste heat recovery (WHR) systems holds great promise for addressing some of the most pressing challenges faced by the industry. As global demand for metals continues to increase, so does the urgency to adopt more energy-efficient, environmentally friendly, and cost-effective technologies. Waste heat recovery represents a critical pathway toward achieving these goals, offering the potential to not only improve operational efficiency but also contribute to the global push for sustainability and decarbonization.
One of the next steps in this technological evolution is the integration of renewable energy sources with waste heat recovery systems. For instance, combining solar thermal energy with WHR could enable metallurgical plants to tap into renewable energy, further reducing their reliance on fossil fuels and lowering carbon emissions. Solar concentrators or parabolic trough systems can be used to generate additional heat, which can be added to the waste heat recovery loop, increasing the overall thermal energy available for power generation or industrial processes. This hybridization of renewable and waste energy can help create more robust and resilient energy systems for metallurgical operations, particularly in regions with high solar potential.
Moreover, the integration of advanced combustion technologies into waste heat recovery systems is also emerging as an important development. New approaches to low-emission combustion in metallurgical furnaces, combined with waste heat recovery, could drastically reduce the environmental footprint of the industry. Oxy-fuel combustion, where oxygen is used instead of air to burn fuels, has gained attention for its potential to capture more waste heat while reducing NOx and CO2 emissions. This approach, in conjunction with waste heat recovery, could enable plants to meet stringent environmental regulations while increasing their operational efficiency.
Another promising direction is the exploration of next-generation heat exchangers. These devices are crucial for transferring thermal energy from waste gases to fluids, and improvements in their design could significantly enhance the performance of waste heat recovery systems. The development of compact and modular heat exchangers that can be tailored to the specific needs of different metallurgical processes is key to making WHR systems more cost-effective and adaptable to various industrial applications. These advanced heat exchangers could provide higher thermal efficiency and better performance in harsh operating conditions, ensuring that the full potential of waste heat recovery is realized.
As digitalization continues to transform industries globally, the metallurgical sector is expected to benefit from smart manufacturing techniques in the operation of waste heat recovery systems. Predictive maintenance and performance monitoring through real-time data analytics are already making it easier to optimize the operation of WHR systems. Sensors and data acquisition systems can track the condition of key components, such as heat exchangers and steam turbines, and alert operators to potential issues before they result in costly downtime. This not only ensures optimal performance but also prolongs the lifespan of WHR equipment, enhancing the return on investment for metallurgical plants.
The growth of industrial symbiosis could also lead to the development of more complex networks of waste heat exchange between industries. In regions where multiple heavy industries coexist, the establishment of waste heat sharing systems could be a highly effective strategy. For example, a steel plant could supply excess waste heat to a nearby chemical plant or a district heating system, creating a mutually beneficial ecosystem where energy flows are optimized. This concept could significantly increase the efficiency of regional industrial clusters, reducing the collective carbon footprint and contributing to the sustainability of entire sectors.
In the context of global regulatory frameworks, the pressure on the metallurgical industry to reduce carbon emissions will only intensify. Countries around the world are introducing more stringent environmental regulations and carbon pricing mechanisms, which are encouraging industries to innovate in their approaches to energy consumption. Governments may continue to incentivize the adoption of waste heat recovery systems by offering financial support, carbon credits, and tax benefits for companies that reduce their energy use and emissions. These measures, combined with stricter emissions standards, will make waste heat recovery an even more attractive option for metallurgical companies seeking to meet compliance requirements and enhance their environmental performance.
The drive toward a circular economy is another factor that will accelerate the adoption of waste heat recovery technologies in metallurgy. The circular economy model advocates for the continuous reuse and recycling of materials and energy, and waste heat recovery aligns perfectly with this philosophy. By capturing and reusing waste heat, metallurgical plants contribute to the overall goal of reducing waste and maximizing the use of available resources. The closed-loop energy systems enabled by waste heat recovery could minimize the environmental impact of metal production, reduce the demand for raw materials, and reduce reliance on non-renewable energy sources.
Looking ahead, as more metallurgical plants adopt advanced waste heat recovery technologies, the scalability and modularity of these systems will become increasingly important. Modular systems that can be customized to the size and needs of a particular plant offer the flexibility to scale operations up or down without significant additional investments. The ability to tailor WHR systems to specific industrial environments will also make them more attractive to a broader range of industries, helping to drive adoption in smaller-scale facilities and ensuring that even those with limited energy needs can benefit from waste heat recovery.
In conclusion, metallurgical waste heat recovery is poised to play a vital role in the future of the industry, enabling plants to enhance their energy efficiency, reduce emissions, and achieve significant cost savings. The ongoing technological advancements, coupled with global environmental pressures, will continue to drive the development of more efficient, flexible, and scalable waste heat recovery systems. With the continued integration of renewable energy, digital technologies, and innovative materials, the metallurgical sector can realize its full potential in waste heat recovery, ultimately contributing to a more sustainable and economically resilient global manufacturing landscape.
Types of Waste Heat in Metallurgical Processes
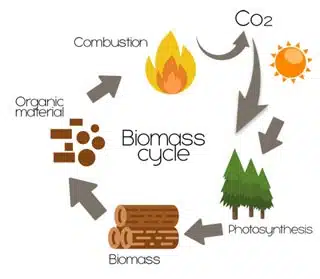
In metallurgical processes, waste heat is a common byproduct generated throughout various stages of production. The nature and amount of waste heat depend on the specific metallurgical process being employed, such as smelting, refining, or forming. This waste heat is often released through exhaust gases, cooling systems, and other industrial operations, and represents a significant opportunity for improving energy efficiency and reducing environmental impact through recovery technologies. Understanding the types of waste heat in metallurgical processes is crucial for identifying effective methods of heat recovery and optimizing overall energy usage within the industry.
One of the most significant sources of waste heat in metallurgical operations is the exhaust gases produced during the high-temperature reactions involved in metal production. In processes such as blast furnace and electric arc furnace operations, large quantities of hot gases are emitted as a byproduct of combustion and reduction reactions. These exhaust gases typically have high temperatures, ranging from 300 to 1,200°C, depending on the specific process and fuel used. The gases may contain a variety of components, including CO2, CO, nitrogen, and other combustion products, as well as trace metals and particulates. Despite their high temperature, these exhaust gases are often released directly into the atmosphere, contributing to both energy inefficiency and environmental pollution. However, they present a significant opportunity for waste heat recovery, as their thermal energy can be captured and reused for various purposes, such as generating steam for power production, heating other areas of the plant, or preheating incoming raw materials.
Another key source of waste heat is the molten metal and slag produced during smelting and refining operations. During processes such as steelmaking or aluminum production, metals are melted at extremely high temperatures, often exceeding 1,500°C, in order to facilitate the separation of impurities. The molten metal and slag can retain a substantial amount of thermal energy, which is typically lost during cooling. In some operations, the cooling of molten metal and slag is accelerated through water-cooling systems or air cooling, further releasing heat to the environment. Capturing and utilizing the heat from molten metal and slag, such as by employing slag heat recovery technologies, can provide an additional source of energy recovery, potentially increasing the overall efficiency of the plant. This captured heat can be used for process heating, electricity generation, or even for preheating the feedstock used in subsequent production cycles.
In addition to exhaust gases and molten metal, high-temperature fluids used for cooling purposes are another significant source of waste heat in metallurgical plants. Many high-temperature processes, including metal casting, rolling, and forging, generate substantial amounts of heat that must be dissipated to prevent equipment overheating and ensure safe operations. To achieve this, cooling systems, such as water-cooled jackets, air cooling, and cooling towers, are employed to absorb and release the heat. These systems often involve circulating water or air that absorbs thermal energy from the hot equipment, which is then transferred to the environment or cooled further in heat exchangers. However, the heat in these cooling fluids is frequently discarded without being put to productive use. By recovering the heat from these cooling fluids, metallurgical plants can improve energy efficiency and reduce the need for additional heating or cooling systems, which can significantly lower operational costs.
Furnace waste heat is another prominent category of waste heat in metallurgical plants. High-temperature furnaces are integral to various metallurgical operations, including iron ore reduction in blast furnaces and melting processes in electric arc furnaces. These furnaces are designed to operate at temperatures upwards of 1,200°C, and a large portion of the heat generated is lost through exhaust gases, furnace walls, and flue gases. The heat recovery systems integrated into furnaces, such as regenerators or preheating chambers, can help capture and reuse some of this lost energy. However, much of the heat remains unutilized and is expelled into the atmosphere, representing a missed opportunity for energy recovery. Innovations in furnace design, including improved insulation, advanced burners, and heat exchangers, are helping to reduce the amount of waste heat lost to the environment, thereby increasing the efficiency of the overall process.
The rolling mills used to shape metals after they have been melted or cast are another source of waste heat. These mills operate at high temperatures, typically between 800 and 1,200°C, depending on the type of metal being processed. In rolling operations, metal is heated to a malleable state and passed through a series of rollers to achieve the desired shape. The process generates heat, which is usually dissipated through the cooling of the metal and through heat emitted by the rolls and other equipment. In some cases, the cooling water used for quenching the metal also contributes to waste heat production. By capturing this heat through heat recovery systems, such as direct-contact heat exchangers or air-to-water heat recovery units, plants can improve their overall thermal efficiency, lower energy consumption, and reduce their reliance on external energy sources.
Finally, waste heat from material handling systems in metallurgical plants can also be an important source of energy recovery. While not as significant as heat generated from the primary production processes, material handling systems, including conveyors, crushers, and grinders, often require large amounts of energy to operate. These systems are also subject to friction and heat generation, especially when handling high-temperature materials. This incidental heat is often neglected but can be captured and used to preheat raw materials or to assist in heating other areas of the plant. The integration of waste heat recovery technologies within these secondary systems can further enhance the efficiency of the entire plant.
In conclusion, the types of waste heat in metallurgical processes are varied and stem from multiple stages of production, including exhaust gases, molten metal and slag, cooling fluids, furnace waste, rolling mills, and material handling systems. While waste heat has traditionally been seen as an unavoidable byproduct of high-temperature operations, advances in waste heat recovery technologies have made it possible to capture and repurpose this thermal energy for productive use. By harnessing waste heat, metallurgical plants can improve their energy efficiency, reduce operational costs, and contribute to a more sustainable industrial sector. The ability to recover waste heat from multiple sources within a plant offers an immense opportunity to improve energy performance, lower carbon emissions, and support the transition to a more energy-efficient and environmentally responsible metallurgical industry.
As the metallurgical industry continues to grow and evolve, the opportunities for waste heat recovery (WHR) are becoming increasingly significant. Beyond the types of waste heat discussed earlier, advancements in energy management strategies are playing an essential role in how metallurgical plants capture and utilize their waste heat. The development of integrated energy systems within these plants, where multiple heat recovery sources are combined and optimized, is one of the most promising areas for increasing energy efficiency. For instance, cogeneration systems that combine waste heat recovery with power generation can allow metallurgical plants to generate electricity from the recovered heat, further improving overall plant efficiency. These systems, often referred to as combined heat and power (CHP) systems, use waste heat from exhaust gases or other high-temperature sources to produce both thermal energy and electricity, thus enhancing energy autonomy and reducing dependency on external energy supplies.
Further optimization of waste heat recovery is being driven by advances in thermal storage technologies. Storing recovered heat for use during periods of peak demand or low production is a key strategy in improving energy efficiency. Thermal energy storage (TES) systems, such as molten salt or phase-change materials (PCMs), are gaining traction as methods to store excess heat for later use. By storing heat that would otherwise be lost, metallurgical plants can reduce the need for additional fuel input, as well as minimize fluctuations in energy demand. This type of thermal storage can be particularly effective in balancing the cyclical nature of many metallurgical processes, where heating requirements fluctuate throughout the day or production cycle.
In addition to energy storage, process integration techniques are becoming a valuable tool for maximizing the use of waste heat in metallurgical operations. Pinch analysis is a widely used method to assess and optimize the thermal integration of industrial processes. It helps identify areas where heat recovery opportunities exist by mapping the temperature differences between streams and the available heat sources and sinks. By applying pinch analysis, metallurgical plants can improve the efficiency of their heat recovery systems, optimize energy consumption, and reduce unnecessary heat losses. The result is a more effective and energy-efficient operation, where heat is recovered and redistributed throughout the plant in the most efficient manner possible.
Another approach gaining ground is the use of advanced heat exchangers. The design of heat exchangers has improved significantly over the years, with more compact and efficient versions now available. Plate heat exchangers and shell-and-tube heat exchangers are two common types, but there are also newer innovations such as compact heat exchangers that use micro-channel designs to maximize heat transfer while minimizing the required space and materials. These advanced heat exchangers are particularly effective in capturing low-temperature waste heat from exhaust gases, cooling fluids, and slag, making them a versatile solution for various metallurgical applications. Their use can significantly enhance the performance of WHR systems, helping plants capture and transfer heat from a range of different waste heat sources more efficiently.
Moreover, as the global push for decarbonization intensifies, metallurgical plants are increasingly turning to renewable energy sources in combination with waste heat recovery. The integration of solar thermal systems, wind power, and even biomass into waste heat recovery operations allows for greater sustainability and reduces reliance on fossil fuels. For example, solar thermal systems can be used in conjunction with existing WHR systems to supplement heat recovery during periods of high solar radiation, reducing the amount of external energy required for industrial processes. Likewise, wind power and biomass systems can be employed to generate electricity for plant operations, further reducing energy costs and improving the environmental performance of the plant.
Additionally, metallurgical plants are embracing digitalization and smart manufacturing technologies that enable them to monitor, analyze, and optimize their waste heat recovery efforts in real-time. Industrial Internet of Things (IIoT) devices, such as temperature sensors and flow meters, provide critical data that can be used to adjust operational parameters dynamically. Data analytics platforms can process this data to identify trends and inefficiencies, while artificial intelligence (AI) and machine learning algorithms can predict potential issues and recommend adjustments to optimize energy recovery. By integrating these advanced technologies into their operations, metallurgical plants can maximize the efficiency of their waste heat recovery systems, predict maintenance needs, and reduce downtime.
Environmental considerations continue to be a driving force in the development of waste heat recovery technologies. In response to growing pressure to reduce carbon emissions, governments and regulatory bodies are increasingly requiring industries, including metallurgy, to adopt energy-efficient practices and reduce their carbon footprints. Carbon pricing mechanisms, such as carbon taxes or emission trading schemes, incentivize metallurgical plants to recover waste heat, as the reduction in energy use and emissions can lead to significant cost savings. In some cases, plants that implement waste heat recovery systems may also be eligible for carbon credits or other forms of financial support, further encouraging the adoption of these technologies.
At the same time, public awareness of the environmental impacts of industrial activities is growing, and many consumers and investors are demanding more sustainable practices from industries. Metallurgical plants that invest in energy-efficient and environmentally friendly waste heat recovery technologies are likely to enhance their corporate reputation and attract both environmentally conscious customers and investors. This growing emphasis on sustainability is helping to shape the future of the metallurgical industry, with companies increasingly focusing on reducing their energy consumption, lowering their emissions, and adopting circular economy principles.
In conclusion, waste heat recovery in metallurgy presents a significant opportunity to enhance the energy efficiency, environmental sustainability, and economic viability of metallurgical operations. The types of waste heat generated, including exhaust gases, molten metal, slag, cooling fluids, and furnace heat, offer substantial potential for recovery through a variety of technologies, including heat exchangers, thermal storage, cogeneration systems, and process integration techniques. As the industry continues to embrace innovation and digitalization, it is poised to realize even greater gains in efficiency and sustainability. The integration of renewable energy sources, along with advanced materials and smart manufacturing, will further strengthen the role of waste heat recovery in achieving a low-carbon, energy-efficient metallurgical industry. Ultimately, the widespread adoption of waste heat recovery technologies will play a key role in the global transition to a more sustainable and circular industrial economy.
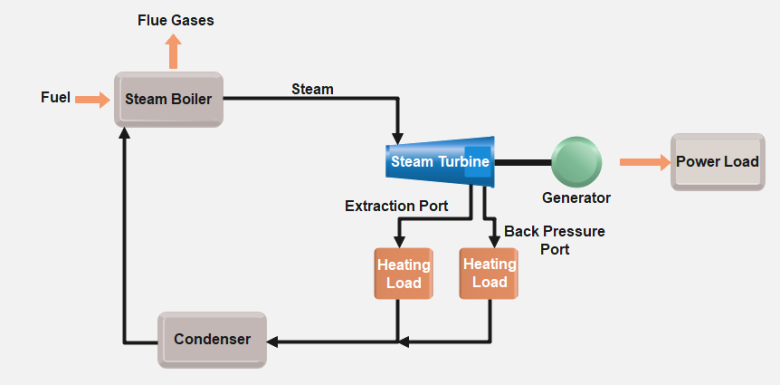
The ongoing advancements in metallurgical waste heat recovery technologies are setting the stage for significant transformations in industrial energy management. One of the key areas where these developments are particularly promising is in the optimization of energy flows within integrated metallurgical systems. By employing multi-source waste heat recovery, it is possible to tap into a variety of heat sources from different stages of production and even from auxiliary systems such as material handling or scrap processing. This enables a more comprehensive approach to energy management, where heat recovery efforts are not limited to a single process but instead encompass a network of interconnected energy flows throughout the plant.
In parallel, the integration of advanced control systems plays a critical role in refining waste heat recovery systems’ performance. Automated control mechanisms, combined with real-time monitoring and predictive analytics, can dynamically adjust the operation of recovery systems to respond to changes in production demand or fluctuating energy availability. For example, adaptive control algorithms can modulate the flow of recovered heat based on factors such as furnace temperature, exhaust gas composition, or energy demand, ensuring that the heat recovery system operates at peak efficiency without overloading or underutilizing resources. These smart control systems help to optimize energy use, reduce wear and tear on equipment, and minimize downtime, ultimately leading to a more sustainable and cost-efficient operation.
Furthermore, the use of artificial intelligence (AI) and machine learning (ML) algorithms is gaining traction in the realm of waste heat recovery. By analyzing historical data and continuously monitoring system performance, AI can predict fluctuations in heat availability and demand, recommend the most efficient recovery strategies, and even identify maintenance needs before they lead to system failures. ML models can be trained to detect patterns in the heat recovery system’s operation, allowing for more accurate forecasting of heat flows, system performance, and potential issues. This predictive capability helps plants avoid energy inefficiencies, improve system reliability, and extend the lifespan of critical components, thereby maximizing the long-term economic benefits of waste heat recovery technologies.
In terms of policy and regulatory frameworks, the growing recognition of the need for climate action and energy efficiency improvements is encouraging governments to provide stronger incentives for industries to adopt waste heat recovery. Many countries are rolling out more stringent emissions standards, offering subsidies, grants, and tax credits for energy-efficient technologies. In addition, the implementation of carbon pricing mechanisms is directly incentivizing industries like metallurgy to reduce their carbon footprint by recovering waste heat and reducing their dependency on fossil fuels. Governments are also providing technical support for the integration of waste heat recovery systems, which can be particularly valuable for smaller plants or companies that may lack the expertise to design and install these technologies.
The global supply chain dynamics are also contributing to the push for more sustainable metallurgical practices. As industries across the world face increasing pressure from consumers and international organizations to minimize their environmental impact, sustainability is becoming a key factor in supply chain decisions. Companies that can demonstrate a commitment to reducing their carbon emissions and improving energy efficiency are more likely to attract partnerships, investments, and customers. As a result, metallurgy plants that adopt waste heat recovery technologies are positioning themselves as leaders in sustainability, offering a competitive edge in an increasingly environmentally conscious market.
One of the long-term trends in the metallurgical industry is the growing emphasis on decarbonization and the transition to cleaner production methods. Waste heat recovery is not only an energy-saving strategy but also an integral part of decarbonization efforts. As steel, aluminum, and other metal industries account for a significant share of global industrial emissions, the integration of waste heat recovery technologies will play a central role in achieving emissions reduction targets. The ability to reduce the need for external energy sources and use heat more efficiently is a step toward reducing reliance on coal, natural gas, and other carbon-intensive fuels. In some cases, waste heat recovery can also be paired with carbon capture technologies, which further enhance the environmental benefits of these systems.
Moreover, as the circular economy model becomes more widely adopted, waste heat recovery aligns with the goal of reducing waste and optimizing resource use. By recovering heat from various industrial processes and reusing it within the same system or even across different sectors, metallurgical plants can minimize waste, lower energy consumption, and increase the efficiency of material flows. This approach not only contributes to sustainability but also enhances the overall resilience of industrial operations, particularly as energy costs fluctuate or become less predictable. Waste heat recovery, therefore, supports both economic and environmental goals by helping plants reduce their operational costs while adhering to sustainability principles.
Looking ahead, the continued development of energy storage technologies, such as thermal energy storage systems and battery energy storage, will further enhance the viability of waste heat recovery in metallurgy. Storing recovered heat for later use—particularly in combination with renewable energy sources like solar and wind—can help smooth out the intermittency issues associated with renewables and create more stable, efficient energy systems within metallurgical plants. This could involve using stored thermal energy to preheat materials, supply energy during peak demand periods, or generate electricity when other energy sources are unavailable. The integration of thermal storage with waste heat recovery is therefore a powerful strategy for achieving both energy efficiency and sustainability.
Additionally, the development of heat recovery technologies for new materials and processes presents opportunities for extending waste heat recovery beyond traditional metallurgy. Innovations in advanced manufacturing techniques, such as additive manufacturing or 3D printing, may create new avenues for waste heat recovery, especially in industries that rely on high-temperature materials or processes. Similarly, the use of new alloys or materials with higher thermal conductivity can improve the effectiveness of waste heat recovery technologies, allowing for more heat to be captured and reused with greater efficiency.
In conclusion, the future of metallurgical waste heat recovery is closely tied to innovations in technology, regulatory frameworks, and energy management strategies. The continual advancement of heat exchangers, digitalization tools, and process integration techniques is enabling plants to recover more waste heat and use it more effectively. Coupled with global environmental pressures and the transition to cleaner, more sustainable production practices, waste heat recovery represents a critical pathway toward reducing energy consumption, cutting emissions, and ensuring the long-term viability of the metallurgical industry. By investing in these technologies, the sector can not only improve its energy efficiency and reduce costs but also contribute to the global effort to address climate change and build a more sustainable industrial economy.
Steam-Based Waste Heat Recovery Systems
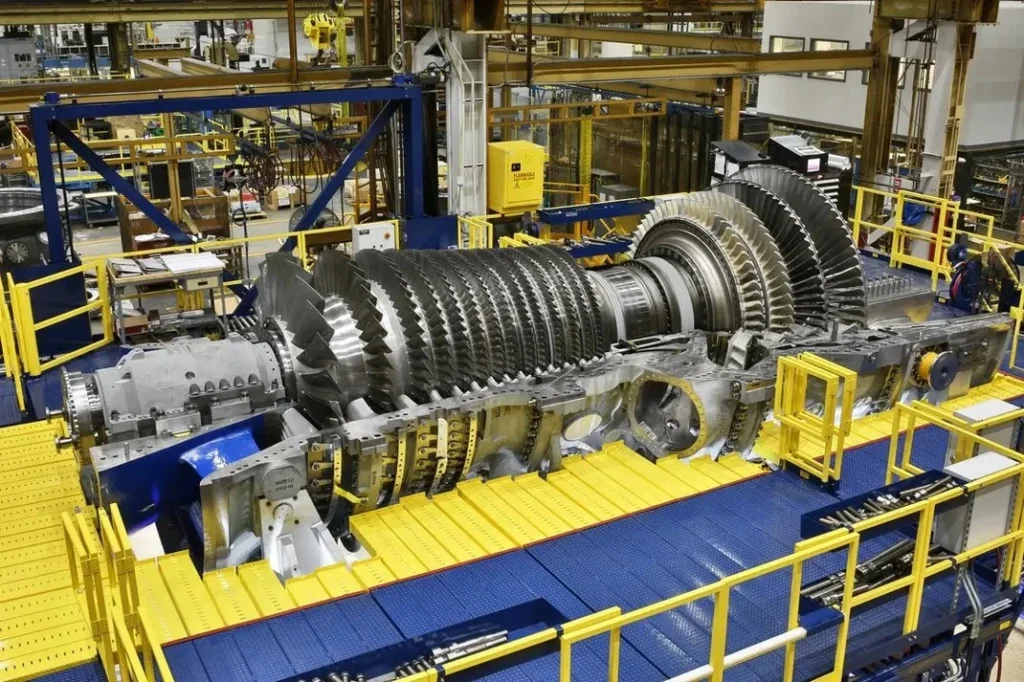
Steam-based waste heat recovery systems are widely used in industrial processes to capture and repurpose waste heat from high-temperature sources, converting it into useful energy for heating, power generation, or process optimization. These systems are particularly valuable in industries like metallurgy, chemical processing, cement manufacturing, and food processing, where large quantities of thermal energy are often wasted through exhaust gases, cooling systems, or other byproducts. By harnessing this waste heat, steam-based recovery systems help improve energy efficiency, reduce fuel consumption, lower operational costs, and minimize environmental impacts.
The basic principle behind a steam-based waste heat recovery system involves using heat exchangers or other types of recovery units to capture waste heat from exhaust gases, hot fluids, or other high-temperature streams. This heat is then used to produce steam, which can be fed into a steam turbine for power generation or used directly in industrial processes for heating, drying, or other thermal applications. The recovered steam can be integrated into the plant’s existing infrastructure or used to offset energy needs, thus reducing the reliance on external fuel sources such as natural gas, coal, or electricity.
One of the most common applications of steam-based waste heat recovery is in cogeneration systems, also known as combined heat and power (CHP) systems. These systems utilize the steam generated from waste heat to simultaneously produce electricity and useful thermal energy. For example, in a metallurgical plant, the high-temperature exhaust gases from furnaces or electric arc furnaces can be used to produce steam, which drives a steam turbine to generate electricity. The recovered steam can then be used to preheat incoming raw materials, heat the plant’s water supply, or provide process heat to various parts of the production line. By using the same energy source for both power generation and heating, cogeneration systems offer a highly efficient solution for industrial plants, significantly reducing the need for external energy sources and improving overall operational efficiency.
In addition to cogeneration, steam-based waste heat recovery systems are commonly employed in industrial processes that require large amounts of heat, such as drying, distillation, and evaporation. In these processes, the recovered steam can be used directly in heat exchangers or heating coils to raise the temperature of materials or fluids. For example, in the chemical industry, the heat recovered from exhaust gases or cooling water can be used to produce steam that drives distillation columns or evaporators, reducing the need for additional fuel or energy to achieve the desired process conditions.
Another important application of steam-based waste heat recovery systems is in district heating networks, where recovered steam or hot water is used to provide heat to nearby buildings or industrial facilities. In these systems, excess steam generated from waste heat recovery can be distributed through a network of insulated pipes to supply heat for space heating, hot water, or industrial applications. This approach helps to reduce the environmental impact of energy consumption by utilizing otherwise wasted heat and reducing the need for separate heating systems, which would otherwise rely on conventional energy sources.
The design and operation of steam-based waste heat recovery systems depend on several factors, including the temperature and flow rate of the waste heat source, the specific thermal requirements of the plant, and the intended use of the recovered steam. Key components of these systems include heat exchangers, economizers, and boilers. Heat exchangers are typically used to transfer thermal energy from hot gases or fluids to water or another heat transfer fluid, which is then converted into steam. Economizers are designed to capture residual heat from exhaust gases and preheat feedwater before it enters the boiler, improving the efficiency of the overall system. In some systems, additional components such as steam turbines, condensers, and de-aerators are included to optimize the conversion of recovered heat into useful steam for power generation or process heating.
The performance of steam-based waste heat recovery systems is largely determined by the temperature gradient between the waste heat source and the heat recovery medium (typically water or steam). The greater the temperature difference, the more efficient the heat transfer process will be, and the higher the potential for steam production. In some cases, organic Rankine cycle (ORC) systems may be used as an alternative to conventional steam-based recovery. ORC systems are similar to steam turbines but use organic fluids with lower boiling points to generate power from lower-temperature heat sources. While steam-based systems are ideal for high-temperature waste heat streams, ORC systems can be used to recover energy from lower-temperature waste heat, further enhancing the overall energy recovery potential in industrial plants.
While steam-based waste heat recovery systems are effective in improving energy efficiency, they are not without challenges. One of the main obstacles to widespread adoption is the high initial capital cost associated with the installation of heat recovery units, steam turbines, boilers, and other equipment. The cost of retrofitting existing plants with steam-based recovery systems can also be significant, especially in industries where infrastructure is already established. However, the long-term energy savings, reduced operational costs, and environmental benefits often outweigh the initial investment, making steam-based systems a compelling choice for many industrial operators.
Another challenge is the maintenance and operation of steam-based systems. These systems are complex and require regular monitoring to ensure optimal performance. Components such as heat exchangers, boilers, and steam turbines can experience wear and tear over time, requiring maintenance and occasional replacement. Additionally, the quality of the steam produced must be carefully controlled to prevent scaling, corrosion, and other issues that can reduce the efficiency of the system. To mitigate these risks, many industrial plants implement predictive maintenance strategies and advanced monitoring systems that allow operators to detect potential issues before they result in system failures or inefficiencies.
In addition, the integration of steam-based waste heat recovery into a plant’s existing infrastructure can be challenging, particularly in older facilities or in plants with multiple energy-consuming processes. Retrofitting these systems requires careful planning to ensure compatibility with existing equipment and operations. Plant operators must also take into account factors such as the availability of space for new components, the need for additional piping or ductwork, and the potential impact on the plant’s overall production efficiency.
Despite these challenges, steam-based waste heat recovery systems offer substantial benefits, particularly in industries with high energy consumption and waste heat generation. By capturing and reusing waste heat, these systems help reduce fuel consumption, lower emissions, and decrease dependence on external energy sources. They also contribute to the overall sustainability of industrial operations by promoting energy efficiency and minimizing environmental impact. With advancements in heat recovery technologies, materials, and system designs, the potential for steam-based waste heat recovery to play a central role in industrial energy management continues to grow.
In conclusion, steam-based waste heat recovery systems represent a critical component of modern energy management in industries with high thermal energy demands. Through the efficient capture and use of waste heat, these systems provide significant economic and environmental benefits by reducing energy consumption, improving process efficiency, and minimizing emissions. While challenges such as high capital costs, maintenance requirements, and system integration must be addressed, the advantages of steam-based systems make them an attractive solution for industries looking to optimize energy usage and enhance their sustainability. With continued innovation and investment in heat recovery technologies, steam-based systems will remain a key part of the industrial sector’s efforts to achieve greater energy efficiency and environmental responsibility.
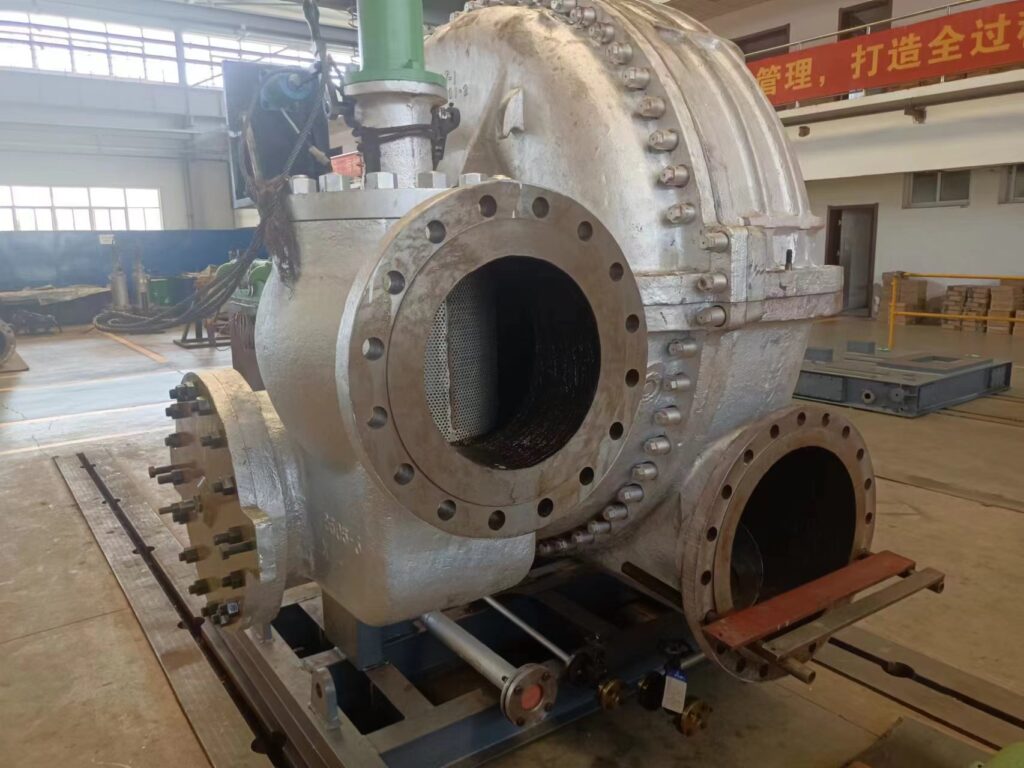
The future of steam-based waste heat recovery systems is promising, with ongoing technological advancements, better integration strategies, and increased awareness of the environmental and economic benefits of waste heat recovery. As industries face growing pressure to reduce their carbon emissions and improve energy efficiency, steam-based systems are likely to play an even more significant role in meeting these goals. One of the key factors driving this future development is the advancement of materials technology, which is improving the durability and efficiency of components such as heat exchangers, turbines, and boilers. New materials with better heat resistance, corrosion resistance, and thermal conductivity are being developed, allowing these systems to operate at higher temperatures and pressures while maintaining or improving performance.
Furthermore, the digitalization of industrial operations is revolutionizing the way steam-based waste heat recovery systems are monitored, controlled, and optimized. Advanced sensors, data analytics, and cloud-based systems allow operators to continuously track system performance, predict maintenance needs, and adjust operations in real-time. With the integration of artificial intelligence (AI) and machine learning (ML), these systems can learn from historical data and provide actionable insights for process optimization. For example, AI could predict the ideal operating conditions for heat recovery systems, recommend maintenance schedules based on real-time performance data, and even automate some of the control processes to improve efficiency.
The integration of renewable energy sources with steam-based waste heat recovery is another promising avenue for the future. Renewable technologies such as solar thermal energy and biomass can be used to supplement steam-based systems, especially during periods when waste heat availability is low. For example, solar collectors can be integrated into steam-based waste heat recovery systems to provide supplementary heat during sunny days, reducing the need for fossil fuels and further improving the sustainability of the operation. Similarly, biomass combustion could be used to generate additional steam or electricity when waste heat alone is insufficient to meet demand. These hybrid systems, combining both waste heat recovery and renewable energy, are poised to provide greater energy independence and a lower carbon footprint for industries across various sectors.
The increasing implementation of circular economy principles will also play a key role in the expansion of steam-based waste heat recovery systems. The idea of reusing waste heat within the same system or across different processes aligns perfectly with the circular economy’s emphasis on reducing waste, maximizing resource use, and minimizing environmental impact. By using recovered heat in multiple stages of production or sharing it with nearby industries or communities (through district heating networks), steam-based systems are helping create more resource-efficient, closed-loop systems. This approach not only reduces energy consumption but also enhances industrial sustainability by promoting a more integrated and circular use of thermal energy.
In addition, energy storage technologies are expected to significantly enhance the performance of steam-based waste heat recovery systems. Thermal storage, such as molten salt or phase change materials (PCMs), can store excess heat generated during low-demand periods and release it when energy demand is higher. By incorporating thermal storage into the system, plants can smooth out the fluctuations in heat recovery and better match energy supply with demand. This can be particularly valuable in industries with intermittent or seasonal energy needs. For instance, during peak production periods, the stored heat can be used to supplement the energy needs of the plant, ensuring continuous operations without the need for additional external energy sources.
The financial viability of steam-based waste heat recovery systems is also improving. With the increasing availability of incentives, tax credits, and subsidies from governments and regulatory bodies, industries are finding it easier to justify the initial capital investment in these technologies. As global policies around carbon pricing and green energy transitions become more stringent, industries that adopt steam-based waste heat recovery systems are better positioned to meet regulatory requirements and avoid penalties. In some regions, companies that invest in energy-efficient technologies may even benefit from financial rewards, such as carbon credits or energy efficiency certificates, which can further improve the return on investment.
The global push for decarbonization and sustainable development goals (SDGs) are also influencing the adoption of steam-based waste heat recovery technologies. As nations and companies set more ambitious targets to reduce greenhouse gas emissions, the need for cleaner and more energy-efficient processes in industries like metallurgy, cement, and chemicals is greater than ever. Steam-based waste heat recovery systems are integral to meeting these targets, offering a practical solution to minimize waste, reduce reliance on fossil fuels, and reduce the overall carbon footprint of industrial operations. This shift toward cleaner production methods will likely lead to increased demand for waste heat recovery technologies as companies seek to comply with environmental regulations and demonstrate their commitment to sustainability.
As the technology matures and adoption increases, there will be more opportunities for collaboration and knowledge-sharing within the industrial community. Industry consortiums, academic research, and public-private partnerships will continue to advance the development of new, more efficient heat recovery technologies, including advanced heat exchangers, improved steam turbine designs, and novel energy management techniques. Through such collaboration, industries can share best practices, conduct joint research, and leverage each other’s experiences to accelerate the adoption of steam-based waste heat recovery systems and realize the full potential of this technology.
In conclusion, steam-based waste heat recovery systems are expected to continue evolving as critical components of industrial energy management. With ongoing innovations in materials, digitalization, renewable energy integration, and energy storage, these systems will become more efficient, cost-effective, and sustainable. Their ability to reduce fuel consumption, minimize environmental impact, and enhance the overall efficiency of industrial operations will make them a cornerstone of efforts to decarbonize industries and transition to a more sustainable energy future. As technological advancements continue, steam-based waste heat recovery systems will play an even more integral role in achieving global sustainability goals, improving industrial performance, and contributing to a more resource-efficient and low-carbon economy.
Key Metallurgical Processes Benefiting from WHR
Metallurgical processes are energy-intensive and often involve the use of high temperatures, resulting in significant amounts of waste heat. The integration of Waste Heat Recovery (WHR) technologies into these processes can substantially improve energy efficiency, reduce environmental impact, and lower operational costs. Several key metallurgical processes stand to benefit from WHR, particularly in sectors such as steelmaking, non-ferrous metal production, and casting. By recovering heat from exhaust gases, cooling systems, and hot metal, WHR systems can convert this otherwise wasted energy into useful steam, electricity, or process heat.
One of the most prominent metallurgical processes benefiting from WHR is steelmaking. Steel production, particularly in blast furnaces and electric arc furnaces, generates large amounts of high-temperature exhaust gases that contain substantial thermal energy. Blast furnaces, used for producing pig iron from iron ore, typically release exhaust gases at temperatures above 1,000°C. These gases are rich in thermal energy and are prime candidates for WHR systems. By using heat exchangers, heat recovery boilers, or steam generators, the heat from these exhaust gases can be recovered and used to produce steam or preheat the blast air for the furnace, improving the efficiency of the process. In electric arc furnaces, which are used for melting scrap steel, WHR systems can capture heat from the furnace exhaust to produce steam or generate electricity. The integration of WHR in steelmaking operations not only lowers energy consumption but also reduces the need for external power sources, contributing to cost savings and emission reductions.
Another metallurgical process benefiting from WHR is aluminum production, particularly in the Hall-Héroult process, which is the primary method for extracting aluminum from its ores. This process involves the electrolysis of alumina, producing molten aluminum and oxygen. The electrolytic cells operate at high temperatures, generating significant amounts of waste heat from the electrical currents and the hot gases emitted from the cells. WHR systems can capture and recover this heat for use in other parts of the process or to generate steam for power production. In addition, heat recovery can be applied to the cooling of aluminum during the casting process, where large volumes of thermal energy are typically dissipated. By recovering this heat, aluminum plants can reduce their energy consumption, improve efficiency, and decrease operational costs.
Copper smelting is another metallurgical process that can benefit from WHR. Copper is typically produced by either the pyrometallurgical or hydrometallurgical method, with pyrometallurgical smelting involving high temperatures to separate copper from its ores. The furnaces and converters used in copper smelting emit large quantities of exhaust gases, which often contain a significant amount of thermal energy. By installing WHR systems, copper smelters can recover heat from these exhaust gases and use it to produce steam for power generation or to preheat incoming feed materials. Additionally, WHR can be applied to the cooling systems used in the casting of copper alloys, allowing the energy to be reused rather than wasted. The use of WHR in copper production can contribute to the reduction of energy consumption, improve the overall sustainability of the process, and reduce greenhouse gas emissions, as it reduces the need for additional fuel or electricity.
In the cement industry, which is another energy-intensive sector, WHR can play a crucial role in reducing energy consumption. Cement production involves the calcination of limestone in rotary kilns, which reach temperatures exceeding 1,400°C. The exhaust gases from these kilns contain large amounts of thermal energy that can be recovered through WHR systems, such as heat exchangers or heat recovery boilers. The recovered heat can be used to preheat raw materials, reduce fuel consumption, or even generate steam to power turbines for electricity generation. By recovering heat from the exhaust gases, cement plants can reduce their reliance on external energy sources, lower operational costs, and decrease their carbon footprint. This is particularly important in light of the global push for the decarbonization of industries, as cement manufacturing is one of the largest sources of industrial CO2 emissions.
Casting operations in the metallurgical industry also benefit from WHR. These operations typically involve the pouring of molten metal into molds to produce cast parts, and during this process, significant amounts of heat are lost through cooling systems and exhaust gases. WHR technologies can capture and repurpose this heat for various applications, such as preheating the metal prior to casting or generating steam for power production. By recovering this thermal energy, casting operations can reduce the need for additional fuel and energy while improving the overall efficiency of the process. The use of WHR in casting can also enhance the quality of the final products by ensuring more consistent temperature control during the casting process.
Iron and steel rolling mills are yet another area where WHR can bring significant benefits. In rolling mills, where steel is heated to high temperatures and then passed through rollers to produce sheets, plates, or bars, large amounts of waste heat are generated. This heat is typically lost to the atmosphere through cooling systems and exhaust gases. By integrating WHR systems, the thermal energy can be recovered and used to preheat the steel or generate steam for use in other parts of the plant. This not only reduces energy consumption but also minimizes the environmental impact of rolling mills by reducing the amount of heat wasted and the need for additional fuel or electricity.
In the electrometallurgical processes, which include processes such as electrowinning and electrorefining, WHR can also improve energy efficiency. These processes, used in the production of metals such as zinc, nickel, and lead, involve the use of electrical currents to extract or refine metals from their ores. High-temperature gases and heat are often produced during these processes, providing a rich source of waste heat. WHR systems can recover this thermal energy and use it to generate steam or electricity, which can either be fed back into the process or used elsewhere in the plant. The adoption of WHR in electrometallurgy not only enhances process efficiency but also helps reduce the overall energy demand of the industry, supporting more sustainable production practices.
The integration of WHR into these metallurgical processes can be achieved through various technologies, including heat exchangers, steam turbines, organic Rankine cycles, and direct energy recovery systems. The choice of technology depends on the specific temperature and characteristics of the waste heat, as well as the intended use of the recovered energy. Heat exchangers are often used to transfer heat from hot exhaust gases to water or another fluid, which can then be converted into steam. Steam turbines can be used to generate electricity from the recovered steam, while organic Rankine cycle (ORC) systems are often employed for lower-temperature waste heat recovery, as they can operate efficiently at temperatures lower than those required for traditional steam turbines.
The benefits of implementing WHR in metallurgical processes go beyond energy savings. The reduction in fuel consumption leads to lower operational costs and a smaller carbon footprint, making these systems an integral part of efforts to meet environmental regulations and achieve sustainability goals. Additionally, by recovering and reusing waste heat, companies can improve their overall production efficiency, enabling them to produce more output with less energy input. This enhances their competitiveness in the market while contributing to global efforts to reduce energy consumption and minimize industrial emissions.
In conclusion, key metallurgical processes, including steelmaking, aluminum production, copper smelting, cement manufacturing, and casting, can greatly benefit from waste heat recovery technologies. These systems help industries capture and repurpose waste heat, improving energy efficiency, reducing operational costs, and lowering environmental impacts. As industries increasingly focus on sustainability and energy efficiency, the role of WHR in metallurgical processes will continue to grow, contributing to both economic and environmental benefits. With the right integration of WHR technologies, metallurgical operations can become more resource-efficient, competitive, and aligned with global sustainability goals.
As the metallurgical industry continues to evolve and respond to increasing environmental pressures, the implementation of waste heat recovery (WHR) systems will become even more essential. These technologies not only enhance operational efficiency and reduce costs but also support the transition to a more sustainable, low-carbon future. Several key trends and innovations are likely to shape the future of WHR in metallurgy, contributing to further gains in energy efficiency and emissions reductions.
One promising development in the realm of WHR is the integration of renewable energy sources with traditional metallurgical processes. In many regions, the energy-intensive nature of metallurgy has led to a heavy reliance on fossil fuels, contributing significantly to carbon emissions. However, by coupling WHR systems with renewable technologies such as solar thermal or biomass energy, the energy footprint of metallurgical processes can be significantly reduced. For example, excess thermal energy recovered from the production process can be stored and used during periods when renewable energy generation is lower, such as on cloudy days or during the winter months. This hybrid approach not only enhances the sustainability of the industry but also ensures a more consistent and reliable energy supply for plants.
Additionally, the development of advanced heat recovery technologies continues to drive improvements in WHR systems. New innovations in heat exchanger design, thermal storage systems, and organic Rankine cycles (ORC) are making it possible to recover and repurpose waste heat from a wider range of temperatures, from high-temperature exhaust gases to lower-temperature flue gases. These advancements enable metallurgical processes to recover even more of the thermal energy generated, which can be used to further improve plant efficiency. For instance, advanced compact heat exchangers can significantly reduce the footprint of WHR systems while improving heat transfer efficiency, making them suitable for a broader range of industrial applications, including those with limited space or strict regulatory requirements.
Another area of growth is the use of digitalization and automation in WHR systems. With the advent of smart sensors, data analytics, and artificial intelligence (AI), metallurgical plants can now monitor and optimize waste heat recovery processes in real-time. Predictive maintenance, powered by machine learning algorithms, can identify potential issues before they lead to system failure, minimizing downtime and ensuring optimal system performance. Additionally, the ability to continuously track and analyze system data allows plant operators to fine-tune energy recovery operations for maximum efficiency. This digital approach not only improves the effectiveness of WHR systems but also provides valuable insights for process improvement and overall plant optimization.
The role of policy and regulation will also continue to shape the adoption of WHR technologies in the metallurgical industry. As governments and international organizations set stricter environmental targets and promote the decarbonization of industries, there is likely to be increased pressure on metallurgical plants to adopt energy-efficient and low-emission technologies. Policies such as carbon pricing, emission trading systems, and green energy incentives could provide financial incentives for companies that invest in WHR systems. These regulatory frameworks could help offset the initial capital costs of implementing WHR technologies, making them more financially viable for companies looking to reduce their carbon footprint and comply with environmental standards.
The circular economy model, which emphasizes the reuse and recycling of materials, is also influencing the adoption of WHR systems in metallurgy. By recovering and reusing waste heat, metallurgical plants are aligning their operations with circular economy principles, contributing to a more sustainable production process. This approach not only reduces waste and energy consumption but also helps reduce the overall demand for virgin raw materials, promoting a more resource-efficient industrial system. In this context, WHR systems play a critical role in closing the loop on energy and material use, making metallurgical operations more sustainable and less dependent on external energy sources.
As the demand for sustainable steel and other metals continues to rise, driven by industries such as construction, automotive, and renewable energy, the metallurgical sector will increasingly focus on improving energy efficiency and reducing emissions. The adoption of WHR systems is expected to grow in parallel with these efforts, helping the industry meet global sustainability goals. Furthermore, as the cost of renewable energy technologies continues to decrease and the availability of low-carbon power increases, the integration of WHR with renewable energy systems will become even more viable, driving further innovation and adoption of these technologies.
The development of energy storage systems will also complement WHR efforts in metallurgy. Energy storage technologies, such as thermal storage or battery storage, can help address the intermittency of waste heat availability and renewable energy generation. By storing excess heat or electricity during times of low demand, these systems can release energy when required, improving the overall reliability and flexibility of the plant’s energy supply. This is particularly valuable in industries with fluctuating energy needs or where process demand is not constant throughout the day.
As the metallurgical sector embraces these technological advancements and innovations, it is likely that global collaboration between industry stakeholders, governments, and research institutions will play a key role in driving the development and adoption of WHR systems. Sharing best practices, conducting joint research, and implementing pilot projects can help accelerate the deployment of energy-efficient technologies across the metallurgical industry. This collaboration will also facilitate the exchange of knowledge and expertise, ensuring that WHR systems are optimized for specific metallurgical processes and can be scaled effectively.
In conclusion, the integration of waste heat recovery (WHR) systems in metallurgical processes is set to become a cornerstone of energy efficiency, sustainability, and cost reduction in the industry. By recovering and repurposing waste heat, companies can significantly reduce their energy consumption, lower emissions, and minimize operational costs. The future of WHR in metallurgy will be shaped by advancements in technology, digitalization, policy, and global collaboration. As the industry continues to prioritize sustainability and decarbonization, the adoption of WHR systems will play a critical role in achieving a more energy-efficient and environmentally responsible metallurgical sector. With the right investments in innovation and the integration of renewable energy, the metallurgical industry can take significant steps toward meeting global sustainability goals while ensuring the continued competitiveness and profitability of the sector.
Technological Advancements in WHR Systems
Technological advancements in Waste Heat Recovery (WHR) systems have revolutionized the way industries capture, store, and reuse thermal energy that would otherwise be wasted. Over the years, continuous improvements in material science, engineering designs, and control technologies have increased the efficiency, versatility, and applicability of WHR systems. These advancements have expanded the scope of WHR applications, providing industries with innovative solutions to enhance energy efficiency, reduce costs, and minimize their environmental impact.
One of the major advancements in WHR technology has been in the area of heat exchanger design. Heat exchangers are at the heart of WHR systems, facilitating the transfer of thermal energy from hot exhaust gases or liquids to a working fluid, which can then be used for power generation, heating, or preheating processes. Traditional heat exchangers often faced limitations in terms of heat transfer efficiency and material durability, particularly when dealing with high-temperature or corrosive environments. Recent innovations have led to the development of compact heat exchangers, which are more efficient at transferring heat while occupying less space. These heat exchangers use advanced materials like ceramics, superalloys, and composite materials that can withstand extreme temperatures and harsh conditions, allowing WHR systems to recover heat from a broader range of processes.
Furthermore, the development of plate heat exchangers has provided a significant boost to the efficiency of WHR systems. These exchangers consist of multiple thin plates stacked together, with each plate creating a small channel for fluid flow. The plates offer a larger surface area for heat transfer, making them more efficient than traditional tube-and-shell designs. Plate heat exchangers are particularly effective in low-to-medium temperature waste heat recovery applications, such as in industrial processes involving exhaust gases or flue gas cleaning. They also allow for easier maintenance and improved heat transfer performance, contributing to lower operational costs and increased reliability of the WHR system.
Another breakthrough in WHR technology has been the development of organic Rankine cycle (ORC) systems. ORC systems have gained significant attention for their ability to recover heat from lower-temperature sources (such as exhaust gases below 400°C) and convert it into useful work or electricity. Traditional steam Rankine cycles require high temperatures to achieve high efficiency, but ORC systems use organic fluids with low boiling points, which enables them to operate effectively at lower temperatures. This technology has opened up new opportunities for WHR in industries where the available waste heat is not hot enough for traditional steam-based power generation, such as in cement manufacturing, chemical production, and waste-to-energy plants. ORC systems are compact, highly flexible, and scalable, making them an ideal choice for decentralized waste heat recovery applications.
In parallel with advances in heat exchanger and ORC technologies, significant progress has been made in heat storage solutions for WHR systems. Thermal storage allows excess heat to be captured and stored during periods of low demand and released when needed, ensuring a constant supply of energy even during fluctuating heat availability. Innovations in phase change materials (PCMs) and molten salts have greatly enhanced the ability to store thermal energy efficiently. PCMs absorb and release heat as they change phase (e.g., from solid to liquid or vice versa), providing high energy density and relatively low-cost storage options. Molten salts, which are often used in concentrated solar power plants, have also proven to be effective for large-scale heat storage, offering the capability to store high-temperature energy for extended periods. These storage technologies enable WHR systems to become more versatile and adaptable, providing energy savings and reducing reliance on external energy sources, particularly in industries with fluctuating heat demands.
The integration of digital technologies has also had a transformative impact on WHR systems. Advances in sensors, smart controls, and data analytics have improved the monitoring, optimization, and efficiency of waste heat recovery. Real-time data collected from sensors placed throughout the system can be analyzed to identify inefficiencies, predict maintenance needs, and optimize system performance. Machine learning and artificial intelligence (AI) can be applied to continuously analyze operational data and provide insights into the best operating conditions, reducing energy losses and improving the overall performance of WHR systems. This digitalization also allows for predictive maintenance, where potential issues can be detected before they result in costly system failures, thereby minimizing downtime and extending the life of the equipment.
Heat recovery steam generators (HRSGs) have also seen significant improvements in recent years. HRSGs are used to recover heat from exhaust gases to generate steam, which can then be used for power generation or industrial processes. Recent advancements have improved the design of HRSGs to achieve higher efficiency and faster response times. Modern HRSGs incorporate advanced materials that can withstand higher temperatures and pressures, improving the overall efficiency of the steam generation process. The use of multi-pressure systems and advanced control strategies allows HRSGs to recover more energy from the exhaust gases, reducing fuel consumption and minimizing emissions. This makes HRSGs particularly valuable in industries such as gas turbine power generation and refining, where optimizing energy recovery from exhaust gases is critical to improving efficiency.
In the area of gas turbines, technological innovations have enabled more efficient waste heat recovery. The integration of WHR systems with combined cycle power plants has been enhanced by developments in high-efficiency gas turbines that can operate at higher temperatures, increasing their ability to recover more energy from exhaust gases. These advances allow for the recovery of both low- and high-temperature waste heat, improving overall system efficiency and reducing the need for additional fuel. Advanced combustion techniques, such as lean combustion and part-load optimization, further improve the energy efficiency of gas turbines, enabling them to work in conjunction with WHR systems to maximize energy recovery.
Another important development in WHR technology is the use of membrane technology for heat recovery. Membrane-based systems are capable of selectively recovering heat from gas streams without requiring direct contact with the gases themselves. These systems use membranes to separate and recover waste heat from the gas, making them highly efficient for capturing low-grade heat from processes such as distillation or chemical reactors. The adoption of membrane technology is still in the early stages, but it holds great promise for expanding the applicability of WHR systems to more diverse industrial processes.
The integration of waste heat recovery with renewable energy systems has also seen advancements. For example, coupling WHR systems with solar thermal energy can provide a more sustainable and reliable energy source for industries that require high levels of thermal energy. In this setup, WHR systems capture excess heat from industrial processes, which can then be supplemented by solar thermal energy when waste heat levels are low. This combination reduces reliance on conventional fossil fuels and improves the sustainability of the production process, contributing to a cleaner energy mix and a lower carbon footprint.
Finally, there has been a growing trend toward the modularization and standardization of WHR systems, allowing for faster deployment and easier scalability. Modular systems can be quickly integrated into existing industrial operations, making it more feasible for companies to adopt WHR technology without significant downtime or disruption. Standardized systems also reduce the complexity and cost of installation, making WHR solutions more accessible to a broader range of industries, from small-scale operations to large, energy-intensive manufacturing plants.
In conclusion, technological advancements in waste heat recovery systems have significantly enhanced the ability of industries to capture, store, and reuse thermal energy. Innovations in heat exchanger design, organic Rankine cycles, thermal storage, digitalization, and modularization have expanded the potential applications of WHR technologies, improving their efficiency, cost-effectiveness, and adaptability. As industries continue to seek solutions for energy optimization and sustainability, WHR technologies will play an increasingly vital role in reducing energy consumption, lowering emissions, and supporting the transition to a more sustainable, low-carbon industrial future.
As the focus on energy efficiency and sustainability grows across industries, the integration of waste heat recovery (WHR) technologies is becoming increasingly important. Future developments in WHR systems are expected to further enhance their ability to recover more heat, increase their efficiency, and integrate with other energy technologies. Several trends and innovations are likely to shape the next generation of WHR systems, improving their scalability, flexibility, and performance.
One promising area of development is the advancement of thermoelectric generators (TEGs). These devices convert heat directly into electrical energy by exploiting the Seebeck effect, where a temperature difference across a material generates a voltage. TEGs are being explored as a way to capture low-grade heat from industrial processes that would otherwise be wasted. Recent advancements in materials science have improved the efficiency of TEGs, particularly by developing nanostructured and advanced semiconductor materials that can better capture heat and convert it into electricity. Although TEGs are still in the research and development stage for many industrial applications, their potential for recovering waste heat, especially at lower temperatures, is significant. In the future, we may see widespread adoption of TEGs in industries such as automotive, electronics, and chemical manufacturing, where low-grade heat is abundant but difficult to harness with traditional WHR technologies.
Another exciting avenue for future WHR systems is the integration of advanced artificial intelligence (AI) and machine learning (ML). AI and ML algorithms are already making a significant impact in various industries, and their application to WHR systems promises to enhance system performance and efficiency even further. By continuously analyzing data from sensors throughout a WHR system, AI can optimize the heat recovery process in real time, adjusting operational parameters to ensure the maximum recovery of thermal energy. Moreover, machine learning can improve predictive maintenance, reducing downtime and preventing costly breakdowns by identifying issues before they escalate. These technologies will make WHR systems smarter, more adaptable, and capable of operating at peak performance over long periods.
The evolution of modular, scalable, and flexible WHR systems is another key trend that will impact the future of waste heat recovery. The modular approach to WHR systems allows for the easy addition of new components or systems, providing greater flexibility to industrial plants as their energy recovery needs change over time. This scalability also ensures that WHR systems can be tailored to the specific needs of each plant, from smaller operations to large, energy-intensive facilities. Moreover, these systems are often designed to be easily integrated with existing infrastructure, minimizing the need for extensive retrofitting or downtime. The growing trend toward modularity is particularly valuable in industries such as cement, steel, and chemical manufacturing, where energy recovery needs may vary depending on production levels and process variations.
In parallel with advancements in system design, next-generation materials are playing a crucial role in improving the efficiency and lifespan of WHR technologies. For instance, advanced coatings and nanomaterials are being developed to enhance heat transfer, reduce corrosion, and increase the durability of components exposed to high temperatures and aggressive environments. Graphene, a material with exceptional thermal conductivity and strength, is one such example. The use of these cutting-edge materials can significantly improve the performance and reliability of heat exchangers, steam generators, and other components of WHR systems. As materials science continues to advance, new innovations will further extend the range of temperatures and environments in which WHR systems can operate, making them viable for a wider array of industrial applications.
The combination of waste heat recovery with carbon capture technologies is another area of emerging potential. The need to reduce carbon emissions from industrial processes is driving the development of carbon capture, utilization, and storage (CCUS) technologies. By integrating WHR systems with carbon capture technologies, industries can not only reduce their energy consumption but also capture and store carbon dioxide (CO2) emissions. For example, heat recovered from the flue gas of a power plant can be used to regenerate the absorbent material in a CO2 capture unit, improving the overall efficiency of both systems. This combined approach could help industries achieve ambitious decarbonization goals while simultaneously improving energy recovery and reducing operating costs.
The future of WHR systems will also see an increased emphasis on circular economy principles. By designing systems that enable the recycling of energy, materials, and waste products, industries can move toward a more sustainable and resource-efficient model. Waste heat recovery fits naturally into the circular economy by capturing heat that would otherwise be lost and repurposing it for other processes. As more industries adopt circular economy practices, the demand for efficient and scalable WHR systems will grow, further driving innovation in the field.
In industries such as metallurgy, cement, glass, and chemicals, where high-temperature processes are common, the ability to capture and reuse waste heat is crucial for improving overall efficiency and reducing operational costs. Advanced WHR technologies will allow these industries to recover and repurpose more heat from their processes, reducing their reliance on external energy sources and lowering their carbon footprints. In addition, these industries will benefit from more flexible, efficient, and durable systems that can adapt to the changing demands of production and energy usage.
As global energy demands continue to rise, there will be an increasing need for industries to reduce their energy consumption and environmental impact. WHR technologies, in combination with renewable energy sources, will become essential for industries to meet sustainability goals while remaining competitive in a rapidly changing market. Future WHR systems will be more integrated, flexible, and energy-efficient, offering industries a path toward net-zero emissions and energy independence.
The integration of renewable energy into WHR systems will also play a significant role in the future of industrial energy recovery. By combining WHR with renewable sources such as solar power, wind energy, or geothermal energy, industrial plants can further reduce their reliance on fossil fuels, contributing to the global transition to a low-carbon economy. Hybrid systems that combine waste heat with renewable energy offer a more stable and reliable energy supply, especially for industries that require constant or high energy input. For example, in a cement plant, waste heat could be used to generate power during periods of low sunlight or wind, ensuring that operations continue smoothly regardless of renewable energy fluctuations.
Finally, international collaboration will be key in accelerating the development and adoption of advanced WHR technologies. As industries across the globe face similar energy and sustainability challenges, sharing knowledge, research, and best practices will help accelerate the adoption of efficient waste heat recovery systems. Government incentives, research partnerships, and cross-border collaborations will help lower the cost of implementing these technologies, making them accessible to a broader range of industries and regions.
In conclusion, the future of waste heat recovery (WHR) systems will be shaped by innovations in system design, materials science, digital technologies, and the integration of renewable energy and carbon capture. These advancements will drive the continued evolution of WHR systems, improving their efficiency, scalability, and adaptability across industries. As industries seek to reduce energy consumption, minimize emissions, and enhance sustainability, WHR systems will play a crucial role in achieving these goals. With continued innovation, collaboration, and investment, WHR systems will remain a cornerstone of industrial energy recovery, offering a path toward a more sustainable, efficient, and low-carbon future.
Integration with Other Industrial Processes
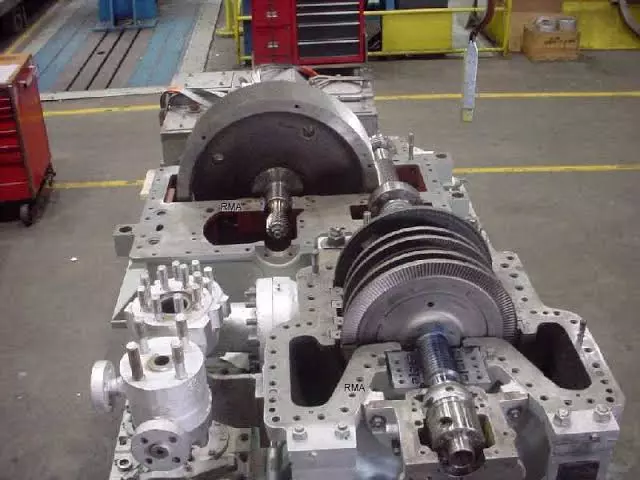
Integration of waste heat recovery (WHR) with other industrial processes is an essential strategy for improving energy efficiency, reducing operational costs, and minimizing environmental impact across various sectors. By capturing and repurposing waste heat that is typically lost to the environment, industries can make better use of their energy resources, improving their overall sustainability. WHR integration can take multiple forms, ranging from incorporating energy recovery systems into existing infrastructure to designing new systems that synergistically combine various energy processes. The increasing emphasis on energy efficiency, carbon reduction, and circular economy principles is driving industries to seek solutions that optimize energy flows, integrate different processes, and enhance the performance of their operations.
In the cement industry, for example, WHR systems are commonly integrated with the production process to recover heat from the kiln and other high-temperature equipment. Cement manufacturing is energy-intensive, with the rotary kiln accounting for a significant portion of the energy consumed in the process. By installing heat recovery systems in this sector, waste heat from the kiln exhaust gases can be used to preheat the raw materials or generate electricity to power other parts of the plant. Integration of WHR with the kiln’s combustion system can also help reduce fuel consumption, lowering the overall carbon emissions of the plant. Additionally, integrating WHR systems with other parts of the cement plant, such as grinding mills, can further enhance energy efficiency by utilizing heat for drying processes, reducing the need for additional external heat sources.
In the steel industry, where high temperatures are a constant feature of production processes, integrating waste heat recovery into various stages of steelmaking can have significant energy-saving potential. Steel production is highly energy-intensive, with the blast furnace and electric arc furnace being key sources of waste heat. By incorporating WHR systems into these stages, energy can be recovered from the exhaust gases and used to generate steam, which can be employed to power turbines or preheat materials. This integration helps reduce the reliance on external energy sources and lowers operational costs, while also decreasing greenhouse gas emissions. Furthermore, integrating waste heat recovery with processes like steel reheating furnaces or rolling mills can recover additional heat, further improving energy efficiency and overall system performance. By fully integrating WHR into the steelmaking process, plants can reduce their energy consumption, lower operating costs, and reduce their carbon footprint, contributing to a more sustainable and competitive industry.
Chemical processing industries, such as the production of petrochemicals, fertilizers, and plastics, also benefit greatly from waste heat recovery integration. In these industries, energy-intensive processes like distillation, cracking, and refining generate significant amounts of waste heat. Integrating WHR into these processes can recover heat from hot exhaust gases, cooling fluids, or even chemical reactions to improve overall energy efficiency. The recovered heat can be used for preheating feedstock, heating reactors, or driving thermodynamic cycles like organic Rankine cycles (ORC), which generate electricity from low-grade waste heat. Additionally, heat exchangers and heat pumps can be integrated into various stages of the production line to capture excess heat and reuse it for heating, cooling, or drying applications. This integration not only reduces fuel consumption but also enhances the overall sustainability of the chemical plant by lowering emissions and reducing the environmental impact.
In refining industries, where energy is required for processes such as distillation, cracking, and catalytic reforming, waste heat recovery can be integrated at multiple points to improve efficiency. For example, integrating WHR into the distillation columns of a refinery can help recover heat from the overhead vapors, which can then be used to preheat the incoming feedstock or generate steam for other purposes. Similarly, the exhaust gases from furnaces and process heaters can be captured and used for energy recovery, either for heating or for generating electricity through steam turbines. Such integration can reduce the need for external fuels, lower production costs, and minimize the carbon emissions associated with refining operations. Furthermore, heat pumps or absorption chillers can be used to convert low-grade waste heat into useful cooling, which can be employed in various stages of the refining process, such as in the cooling of fluids or the condensation of distillation products.
The glass industry, which requires significant amounts of heat to melt raw materials and shape glass products, can also benefit from WHR integration. High-temperature furnaces and kilns used in glass production are major sources of waste heat, and capturing this heat for reuse can improve energy efficiency. Integrating WHR systems can involve recovering heat from the exhaust gases and using it for preheating the incoming raw materials or generating steam to power turbines for electricity production. In some cases, recovered heat can also be used to power equipment such as dryers or melting tanks, reducing the overall energy demand. Additionally, integration of WHR with cooling systems can help recover heat from the glass forming process, which can then be used in other areas of the plant. By optimizing the energy flow through these processes, the glass industry can reduce fuel consumption, lower emissions, and achieve a more sustainable and cost-effective operation.
The food and beverage industry, known for its energy-intensive processes, can also integrate waste heat recovery systems to improve energy efficiency. Processes such as drying, pasteurization, sterilization, and cooking generate large amounts of waste heat that can be recovered and reused. By integrating WHR systems into these operations, excess heat can be used to preheat ingredients or water, reducing the need for additional heating. This integration can help companies reduce their reliance on external energy sources, lower operational costs, and improve their sustainability profile. Additionally, integrating WHR with combined heat and power (CHP) systems can provide both heat and electricity, further improving the energy efficiency of food production facilities.
In the textile industry, where energy is required for processes like dyeing, finishing, and drying fabrics, waste heat recovery can be integrated at multiple points to improve energy utilization. Recovered heat from exhaust gases or cooling processes can be used to preheat water, steam, or air, reducing the need for additional energy inputs. The integration of WHR systems can also improve the energy efficiency of dryers, boilers, and finishing equipment, contributing to overall cost savings and enhanced sustainability. Furthermore, the use of heat pumps can allow for the recovery of low-grade waste heat, which can be converted into useful heat or cooling, depending on the specific requirements of the textile plant.
The integration of WHR systems with renewable energy sources is also a growing trend in industries where sustainability is a priority. By coupling WHR with renewable energy technologies like solar thermal, wind, or geothermal energy, industrial plants can further optimize their energy use and reduce their dependence on fossil fuels. For instance, integrating waste heat recovery with solar thermal collectors can help capture excess heat during the day and store it for use during off-peak hours, providing a more reliable and sustainable energy supply. Similarly, WHR systems can be integrated with geothermal heat pumps to recover waste heat from ground sources and use it to power industrial processes or provide space heating.
The integration of WHR with district heating systems is another promising application. In regions where industrial plants are located near residential or commercial areas, the recovered heat can be used for district heating, supplying hot water or space heating to nearby buildings. This integration helps reduce the overall demand for conventional energy sources and provides a more sustainable way to utilize excess waste heat. In some cases, WHR systems can also be used to provide cooling through absorption chillers or other cooling technologies, making them more versatile and capable of meeting diverse energy demands across various sectors.
In conclusion, the integration of waste heat recovery systems with other industrial processes provides an opportunity to optimize energy use, reduce operational costs, and contribute to environmental sustainability. Through the careful capture and repurposing of waste heat from key processes, industries can improve their energy efficiency, reduce emissions, and make better use of their existing energy resources. Whether in cement, steel, chemical, refining, glass, or food processing industries, the integration of WHR systems can lead to significant cost savings and enhanced operational performance. As industries continue to embrace energy efficiency and sustainability, the integration of WHR with other industrial processes will become increasingly important in achieving these goals.
Building on the integration of waste heat recovery (WHR) systems, industries can achieve substantial reductions in energy consumption, environmental impact, and operational costs. However, it’s important to note that successful integration requires careful planning, optimization, and often a shift in how energy is managed within industrial operations. This process involves not just adding WHR systems, but also rethinking the entire energy flow across the facility to ensure seamless integration with various processes.
To begin with, a critical component of integration is the design and configuration of heat exchangers, which are used to transfer heat from one part of the process to another. The design of heat exchangers must be tailored to the specific needs of the industrial process, taking into account factors like temperature, pressure, flow rates, and the chemical properties of the materials involved. Proper selection and design can significantly improve the efficiency of WHR systems. Moreover, advanced materials for heat exchangers, such as corrosion-resistant alloys, are essential in ensuring the durability and longevity of the systems, especially when dealing with aggressive or corrosive gases, liquids, and particles common in industrial settings.
Moreover, in industries like petrochemical refining, the integration of WHR is not just about capturing heat from exhaust gases but also about coupling the recovered heat with energy storage systems. For instance, thermal storage technologies can help store heat during periods of low demand and release it during peak demand, smoothing out energy consumption profiles and increasing the overall efficiency of operations. Phase-change materials (PCMs) are often used in this context because of their ability to store heat at a nearly constant temperature as they change phases from solid to liquid or vice versa. This allows for more stable and reliable heat supply, particularly in processes where energy demand fluctuates throughout the day.
Additionally, the integration of combined heat and power (CHP) or cogeneration systems with waste heat recovery systems can maximize energy efficiency by producing both electricity and useful heat from the same energy source. By combining power generation and heat recovery, industries can significantly reduce their need for external electricity and fossil fuels. The integration of CHP with WHR systems is particularly beneficial in industries like paper and pulp manufacturing, chemicals, and cement production, where both high heat and electricity are required in large quantities. Such a system allows industrial plants to operate more autonomously, lowering energy procurement costs while reducing greenhouse gas emissions and reliance on the grid.
In industries with fluctuating heat loads or where specific temperature conditions are needed for various stages of production, dynamic energy management systems are essential to optimize the integration of WHR. These systems use real-time data from sensors and advanced control algorithms to adjust the operation of heat recovery units based on the current energy demand and supply conditions. Such smart systems can dynamically balance the use of recovered heat, grid power, and stored thermal energy to ensure that the plant operates at peak energy efficiency without overloading systems or wasting energy.
In the food and beverage sector, for instance, heat recovery can be integrated with drying and evaporation systems to provide significant energy savings. Drying processes in food processing require large amounts of heat, and waste heat from other operations can be used to reduce the demand for additional heating. Similarly, integrating waste heat with sterilization or pasteurization processes can minimize the need for external energy sources while maintaining product safety and quality standards. By optimizing the energy flow between these processes, the food industry can reduce both energy consumption and environmental impact, leading to lower production costs and improved sustainability profiles.
In metallurgical operations, where high-temperature processes are common, the integration of WHR systems can capture waste heat not just from the furnaces but also from other sources, such as molten metal cooling or slag handling systems. By installing heat exchangers and steam generators at various stages in the production process, recovered heat can be converted into electrical power or used for preheating materials, further reducing the need for external energy sources. Integrating waste heat recovery with other energy-intensive operations like electric arc furnaces or blast furnaces can help create a more efficient and closed-loop energy system within the plant.
The integration of WHR with renewable energy sources is also gaining momentum. For example, coupling solar thermal systems with waste heat recovery can provide continuous energy supply, especially in industries operating in sunny regions. The ability to integrate solar collectors with WHR systems to provide energy for preheating feedstock or for auxiliary power generation can significantly reduce a facility’s reliance on conventional grid power. This combination of renewable energy and waste heat recovery also enhances the sustainability of the entire operation, contributing to the transition to a more circular and low-carbon economy.
Hybrid systems, which combine multiple technologies such as WHR, solar, wind, and biomass, are becoming increasingly common in industries striving to achieve energy independence and carbon neutrality. By diversifying energy sources and optimizing energy recovery, these hybrid systems ensure that operations can maintain steady energy supply even during periods of low renewable energy availability. For example, biomass can provide a constant heat source during the winter months, when solar or wind energy may be insufficient, while waste heat can be used to complement these renewable sources during times of high heat generation.
The digitalization of industrial plants is also playing a major role in enabling effective integration of WHR systems. Through the implementation of Industrial Internet of Things (IIoT) sensors and big data analytics, companies can continuously monitor the performance of their energy systems and identify opportunities for further optimization. Predictive maintenance, energy usage forecasting, and process optimization can all be improved using real-time data, enabling companies to achieve greater efficiency in their WHR systems. Furthermore, integrating WHR with digital platforms allows for the remote monitoring and control of systems, enabling operators to adjust settings in real-time to respond to changing conditions, improving both energy efficiency and operational flexibility.
In industries such as pharmaceuticals, automotive, and textiles, where specific temperature control is required for precise production processes, the ability to integrate waste heat recovery with the temperature management system is critical. Heat recovery systems can be used to maintain the required process temperatures by using waste heat to offset cooling or heating needs in these operations, ensuring consistent product quality and reducing reliance on traditional energy sources.
In summary, the integration of waste heat recovery with other industrial processes plays a critical role in achieving energy efficiency, cost reduction, and environmental sustainability across a wide range of industries. Through careful design, advanced materials, and the adoption of innovative technologies, industries can capture waste heat at various stages of production and repurpose it for multiple uses. Whether through combining WHR with CHP systems, renewable energy sources, or dynamic energy management, the potential for improving industrial energy systems is immense. As industries continue to push for greater sustainability, the integration of WHR will be key in transforming operations, reducing emissions, and contributing to a more circular and energy-efficient industrial landscape.
Economic Benefits of Metallurgical WHR Systems
The economic benefits of metallurgical waste heat recovery (WHR) systems are substantial, impacting both the operational efficiency of metallurgical plants and the broader economic landscape in which they operate. As industries worldwide face increasing pressure to reduce their environmental footprints and operational costs, the adoption of WHR technologies in metallurgical processes offers an attractive solution to these challenges. By recovering and reusing waste heat, which would otherwise be lost, these systems not only contribute to energy savings but also enable companies to realize significant cost reductions in various areas of their operations.
One of the primary economic benefits of metallurgical WHR systems is the reduction in energy consumption. Metallurgical industries, particularly those involved in steel, cement, and aluminum production, consume vast amounts of energy for high-temperature processes like furnace operations, casting, rolling, and smelting. These processes generate large quantities of waste heat, which is typically released into the environment. By installing WHR systems, plants can recover this wasted energy and reuse it in other areas of the operation, such as preheating incoming materials, generating steam, or driving electrical generators. This leads to a reduction in the overall demand for external energy sources, such as coal, natural gas, or electricity from the grid, directly lowering energy costs for the plant.
In the case of steelmaking, for example, the integration of WHR systems allows for the recovery of heat from blast furnaces or electric arc furnaces. The recovered heat can be utilized to preheat the combustion air used in the furnaces, reducing the amount of fuel required to maintain the necessary temperatures for steel production. This directly lowers fuel consumption and reduces operating costs. Additionally, WHR can be used to generate electricity through steam turbines or organic Rankine cycles (ORC), creating a secondary source of revenue or offsetting power costs by reducing reliance on external energy suppliers. These savings can be reinvested into the plant or contribute to increased profitability.
Another significant economic advantage of metallurgical WHR systems is the potential for capital savings through improved energy efficiency. By recovering waste heat, plants can avoid the need to invest in additional energy infrastructure, such as new boilers, furnaces, or power plants. Instead, they can optimize their existing facilities by installing heat recovery units that maximize the use of available energy. This makes WHR systems a relatively low-cost, high-return investment in terms of capital expenditure, especially in comparison to the costs associated with constructing new energy supply infrastructure. Moreover, the improved energy efficiency resulting from WHR can extend the life of existing equipment by reducing the thermal load on furnaces, boilers, and other energy-consuming systems, lowering maintenance and replacement costs.
The reduction of greenhouse gas emissions resulting from the use of WHR systems is another indirect economic benefit. As governments and regulatory bodies around the world introduce increasingly stringent environmental regulations, industries are facing higher costs associated with carbon taxes, emissions permits, and compliance with environmental standards. By implementing WHR systems, metallurgical plants can significantly reduce their carbon emissions, which helps them meet regulatory requirements and avoid penalties. Additionally, by reducing reliance on fossil fuels, WHR contributes to a decrease in the plant’s overall environmental impact, aligning with global sustainability goals and enhancing the plant’s reputation in terms of corporate social responsibility (CSR). This can have long-term economic benefits by improving the plant’s brand image and attracting environmentally-conscious investors, customers, and business partners.
Cost savings are also realized through the recovery of waste heat for use in other operational processes within the plant. In many metallurgical facilities, heat is required for a variety of processes beyond just furnace operations. For instance, in the rolling mill stage, heat recovery can be used to preheat billets or other raw materials, reducing the need for additional heating energy. Similarly, heat recovery can be used in drying or annealing processes, providing the necessary thermal energy without the need for supplementary fuels. By providing heat for multiple processes, WHR can reduce the need for external energy sources and create a more self-sufficient and cost-effective plant.
The long-term economic viability of metallurgical WHR systems is also supported by the trend toward increased energy prices. As global energy demand rises and fossil fuel resources become scarcer, energy prices are expected to continue increasing. Metallurgical plants that have integrated WHR systems will be better insulated from these rising energy costs, as they will rely more on recovered energy and less on purchased fuel or electricity. This energy independence can enhance the financial stability of the plant, allowing it to weather fluctuations in energy prices and maintain profitability even during periods of high fuel costs.
The adoption of WHR systems also helps to improve the competitiveness of metallurgical plants. By reducing operational costs, improving energy efficiency, and lowering the carbon footprint, companies can gain a competitive edge in the market. This can translate into better pricing for their products, increased demand from environmentally-conscious customers, and a stronger position in international markets where carbon emissions and energy consumption are closely scrutinized. Furthermore, the operational savings generated by WHR systems can be reinvested into innovation, research and development, and process optimization, further enhancing the company’s market position and long-term profitability.
Another financial benefit of metallurgical WHR systems is their potential to enhance operational resilience. By improving energy efficiency and reducing reliance on external energy suppliers, plants that implement WHR are less vulnerable to disruptions in energy supply, such as price volatility or shortages. This resilience can be especially valuable in regions with unstable energy markets or where energy supply is unreliable. WHR systems allow companies to maintain steady production even during periods of energy disruption, safeguarding against the potential financial losses associated with production downtime or energy price spikes.
Finally, the implementation of waste heat recovery systems in metallurgical industries can attract government incentives and funding opportunities. Many governments offer financial support for energy efficiency projects, including tax credits, grants, and low-interest loans for companies that invest in technologies that reduce energy consumption and environmental impact. These incentives can significantly offset the initial capital cost of installing WHR systems, further improving the return on investment and making these systems even more attractive from an economic standpoint.
In conclusion, the economic benefits of metallurgical waste heat recovery systems are multifaceted and impactful. These systems not only lead to direct cost savings through reduced energy consumption but also provide capital savings, lower greenhouse gas emissions, and enhanced operational resilience. By optimizing energy usage, improving competitiveness, and enabling compliance with environmental regulations, WHR systems contribute to the financial health and long-term viability of metallurgical plants. The continued rise in energy prices and the increasing pressure on industries to reduce their environmental impact only amplify the economic advantages of implementing WHR technologies, making them a wise investment for companies seeking to remain competitive and sustainable in a rapidly changing global market.
Environmental Benefits and Carbon Footprint Reduction
The environmental benefits of metallurgical waste heat recovery (WHR) systems are profound and multifaceted, playing a key role in reducing the industry’s overall environmental impact. The implementation of these systems not only aids in the reduction of energy consumption but also contributes significantly to reducing greenhouse gas emissions and mitigating climate change. Waste heat recovery systems offer a practical and effective solution to addressing some of the most pressing environmental challenges faced by metallurgical industries, particularly in the context of reducing their carbon footprint.
One of the most significant environmental advantages of WHR systems is their contribution to the reduction of greenhouse gas emissions. Metallurgical industries, particularly those involved in the production of steel, cement, aluminum, and other metals, are some of the most energy-intensive industries worldwide. A large portion of their carbon emissions comes from the combustion of fossil fuels used to generate the high temperatures required for smelting, forging, and other key processes. By capturing and reusing the waste heat generated in these processes, WHR systems reduce the need for additional fossil fuel consumption, thereby decreasing the volume of CO2 emissions released into the atmosphere. This reduction in emissions can be particularly impactful in industries like steelmaking, where the recovery and reuse of waste heat can lead to a substantial decrease in the carbon intensity of production.
Furthermore, WHR systems help to reduce air pollution by minimizing the need for additional fuel combustion. When waste heat is recovered and used efficiently, it decreases the demand for burning additional fuels, such as coal, natural gas, or oil, to meet energy needs. This reduction in fuel consumption directly lowers the emissions of not only carbon dioxide but also other harmful pollutants, such as sulfur dioxide (SO2), nitrogen oxides (NOx), and particulate matter. These pollutants contribute to air quality issues, acid rain, and respiratory problems for both the local population and the global environment. By cutting down on the reliance on external energy sources, WHR systems help mitigate these harmful emissions, contributing to cleaner air and better public health outcomes, particularly in regions near industrial zones.
In addition to reducing direct emissions, WHR systems also have a positive impact on reducing the environmental footprint of industrial processes by promoting more efficient use of resources. The efficient use of waste heat helps to reduce the overall energy demand, which, in turn, reduces the extraction and processing of natural resources such as coal, oil, and natural gas. By reducing the need for raw materials and minimizing energy losses, WHR systems foster a more sustainable, circular economy that conserves resources and reduces environmental degradation. This is particularly relevant in industries like mining and metallurgy, where the extraction and processing of raw materials can have significant ecological consequences, such as habitat destruction, water contamination, and soil erosion.
The energy efficiency gains facilitated by WHR systems also contribute to reducing the overall energy demand on the grid. In many regions, electricity generation still relies heavily on fossil fuels, including coal and natural gas, which contribute to both local and global environmental pollution. By recovering waste heat and using it to generate electricity or preheat materials, metallurgical plants can reduce their dependence on the grid and the fossil fuels used to generate electricity. This not only reduces the carbon footprint of the individual plant but also helps ease the environmental pressure on local and national energy infrastructures, which may otherwise rely on non-renewable resources. Additionally, plants that implement WHR systems may be able to feed excess energy back into the grid, further supporting the transition to renewable energy sources and reducing reliance on fossil fuels.
Another environmental benefit of WHR systems is their contribution to water conservation. In many metallurgical processes, water is used for cooling purposes, and large quantities of water are often required to absorb and dissipate excess heat. By implementing WHR systems, plants can reduce the amount of water needed for cooling, as the recovered heat can be used to preheat water or other fluids, reducing the need for fresh water inputs. This not only conserves precious water resources but also reduces the environmental impact associated with water usage, such as the depletion of local water supplies and the thermal pollution of nearby rivers or lakes.
The integration of WHR systems can also lead to reduced thermal pollution in ecosystems surrounding industrial plants. In many cases, the waste heat generated by metallurgical processes is released into the environment, often via cooling towers or direct discharge into nearby water bodies. This can result in an increase in local temperatures, which can have harmful effects on aquatic life, biodiversity, and overall ecosystem health. By capturing and reusing this heat, metallurgical plants can significantly reduce the amount of excess thermal energy released into the environment, mitigating the risk of thermal pollution and supporting the health of local ecosystems.
Moreover, the use of WHR systems aligns with global sustainability goals and initiatives aimed at reducing carbon emissions and promoting climate action. As countries and corporations alike commit to meeting the targets set by the Paris Agreement and other international climate protocols, the adoption of energy-efficient technologies like WHR becomes crucial in achieving these goals. By reducing the carbon intensity of industrial production and cutting down on fossil fuel consumption, WHR systems play a key role in helping industries and governments meet their emission reduction targets. This, in turn, contributes to the global effort to limit global warming and mitigate the worst impacts of climate change.
In the context of industrial sustainability, WHR systems also promote the reuse and recycling of energy within a closed-loop system. Instead of allowing waste heat to escape into the environment, these systems enable industries to capture and repurpose energy that would otherwise be wasted. This creates a more sustainable model for industrial operations, reducing the need for virgin resources and lowering the environmental impact of production. The circular nature of this energy recovery process helps foster long-term sustainability within industries by maximizing the use of existing resources and minimizing environmental harm.
Overall, the environmental benefits of metallurgical waste heat recovery systems extend far beyond energy savings. By reducing carbon emissions, lowering air pollution, conserving water, and minimizing thermal pollution, WHR systems contribute significantly to the global effort to combat climate change and protect the environment. The integration of these systems into metallurgical processes not only benefits the industries themselves in terms of cost savings and improved operational efficiency but also plays a vital role in creating a more sustainable and environmentally responsible industrial sector. As industries continue to face increasing pressure to reduce their environmental impact, the widespread adoption of WHR technologies will be critical in driving the transition toward a cleaner, more sustainable future.
The environmental benefits of metallurgical waste heat recovery (WHR) systems extend to promoting a more resilient and sustainable industrial ecosystem. By reducing the need for external energy sources, metallurgical plants can become less vulnerable to the fluctuating prices and supply issues associated with traditional fuels like coal, oil, and natural gas. As the global energy market continues to experience price volatility and increasing uncertainty, the adoption of WHR systems helps plants mitigate risks associated with energy price hikes or disruptions in supply chains. The energy independence facilitated by waste heat recovery contributes to the stability and long-term sustainability of metallurgical operations, while also reducing the environmental burden of sourcing and transporting raw energy materials.
Another significant aspect of the environmental benefits of WHR systems is the role they play in shaping the circular economy within the metallurgical sector. Traditional industrial processes often operate in a linear fashion, extracting raw materials, producing goods, and discarding waste. WHR systems, on the other hand, embody the principles of a circular economy by capturing and reusing energy, thus minimizing waste and improving overall efficiency. In the context of the metallurgical industry, this circular approach not only reduces energy consumption but also helps reduce the environmental impact of mining, refining, and other resource-intensive processes. By rethinking how energy is used and ensuring that as much as possible is recovered and reused, WHR systems contribute to the broader goal of resource conservation and waste minimization across the industrial landscape.
The widespread implementation of WHR systems can also act as a catalyst for innovation and new technologies that further reduce the environmental footprint of metallurgical processes. As industries invest in waste heat recovery and integrate it with other energy-saving technologies, such as combined heat and power (CHP) systems, organic Rankine cycles (ORC), and solar energy systems, there is potential for continuous innovation and improvements in energy efficiency. The development of new materials, more efficient heat exchangers, and smarter control systems can further enhance the performance of WHR systems, creating a virtuous cycle of sustainability that drives continuous improvements in both energy efficiency and environmental protection.
Moreover, life cycle assessments (LCAs) of metallurgical WHR systems demonstrate that their benefits extend beyond the operational phase of the system. When considering the entire life cycle of a metallurgical plant—from raw material extraction to the end-of-life disposal of equipment—WHR systems offer significant environmental savings by reducing the energy demands and emissions associated with plant operations. This comprehensive assessment ensures that WHR systems not only provide short-term environmental gains but also support long-term sustainability by reducing the need for energy-intensive infrastructure, minimizing waste, and lowering the carbon footprint of the industry over its entire lifespan.
In addition to their direct environmental benefits, WHR systems also have societal advantages. By contributing to cleaner air, water, and reduced greenhouse gas emissions, these systems improve the quality of life for communities living near metallurgical plants. In many cases, industrial facilities are located in regions where air and water quality may already be impacted by other industrial activities, and the implementation of WHR technologies can significantly reduce the harmful environmental impacts associated with traditional energy consumption. This can lead to a reduction in respiratory diseases, cardiovascular conditions, and other health problems linked to air pollution. Furthermore, the economic development resulting from the energy savings and cost reductions achieved through WHR can help create jobs, stimulate local economies, and support a more sustainable industrial workforce.
As industries continue to adopt and refine WHR technologies, there is also growing potential for global collaboration and knowledge sharing. As environmental challenges like climate change and resource depletion become more urgent, the need for international cooperation and the sharing of best practices is becoming increasingly clear. The implementation of WHR in the metallurgical sector can serve as a model for other industries, encouraging the spread of innovative, environmentally responsible practices worldwide. Countries, industry groups, and multilateral organizations can work together to promote the adoption of WHR systems, facilitate research and development in this field, and provide financial incentives or subsidies to make these technologies more accessible to companies around the world.
Finally, the environmental benefits of metallurgical WHR systems are strongly aligned with the global agenda for sustainable development. As countries strive to meet the targets outlined in the United Nations’ Sustainable Development Goals (SDGs), particularly those related to affordable and clean energy (SDG 7), industry innovation (SDG 9), and climate action (SDG 13), the implementation of WHR systems will play an important role in achieving these objectives. The ability to reduce energy consumption, minimize waste, and lower carbon emissions directly supports efforts to combat climate change, promote sustainable industrialization, and build resilient infrastructure, all of which are core components of the SDGs.
In conclusion, the environmental benefits of metallurgical waste heat recovery systems are wide-ranging, from reducing greenhouse gas emissions and air pollution to fostering resource conservation and contributing to a more circular economy. By improving energy efficiency, reducing reliance on fossil fuels, and promoting cleaner production processes, WHR systems offer a practical, cost-effective, and sustainable solution for the metallurgical industry. As global pressure to reduce environmental impact continues to grow, the widespread adoption of waste heat recovery will be crucial in advancing both industry and society toward a more sustainable and low-carbon future. The environmental gains achieved through WHR not only improve the sustainability of individual plants but also contribute to the broader global effort to combat climate change, protect ecosystems, and build a more sustainable industrial economy for generations to come.
Challenges to WHR Implementation in Metallurgy
The implementation of waste heat recovery (WHR) systems in the metallurgical industry, while offering substantial benefits in terms of energy efficiency and environmental sustainability, presents a variety of challenges that need to be addressed for successful adoption and operation. Despite the clear advantages of WHR, the process of integrating these systems into metallurgical plants is not without difficulties. These challenges range from technical and economic hurdles to organizational and regulatory factors, each of which must be considered to ensure that WHR systems can be effectively deployed in a way that maximizes their potential.
One of the most significant challenges to the implementation of WHR systems in metallurgy is the high initial capital cost of installation. While the long-term savings and environmental benefits of WHR systems are substantial, the upfront investment required to install these systems can be prohibitive, particularly for smaller or less financially robust companies. The cost of purchasing and installing the necessary equipment, such as heat exchangers, steam turbines, or organic Rankine cycle (ORC) units, can be a significant barrier. Additionally, there may be costs associated with retrofitting existing plants to accommodate WHR systems, particularly in older facilities where infrastructure may not be designed for energy recovery. Although these costs can often be offset by energy savings over time, the initial investment remains a key challenge that many companies must overcome.
Another challenge is the complexity of integrating WHR systems into existing metallurgical processes. Metallurgical plants are typically large, complex, and involve multiple interconnected processes, each with its own unique energy needs. Integrating WHR systems into these processes requires careful planning and technical expertise to ensure that the recovered heat is efficiently captured and reused in a way that aligns with the plant’s operations. For instance, the temperature and quality of the waste heat generated can vary significantly depending on the specific metallurgical process, making it difficult to design a one-size-fits-all WHR solution. This variability requires customized solutions that may increase the complexity and cost of implementation. Moreover, the integration of WHR systems may require modifications to the plant’s existing infrastructure and process flows, which can disrupt normal operations and lead to additional costs in terms of downtime and engineering design.
The efficiency and performance of WHR systems also present challenges. Not all waste heat can be effectively recovered and reused, particularly if the waste heat is at a low temperature or if it is not generated consistently throughout the process. The efficiency of WHR systems depends on factors such as the temperature differential between the waste heat and the system’s heat recovery mechanism, the heat transfer capabilities of the system components, and the operational conditions within the plant. In some cases, the efficiency gains from waste heat recovery may not justify the investment, especially if the quantity of waste heat available is limited or if the recovered heat cannot be effectively utilized in other processes. The design of the WHR system must, therefore, take into account the specific energy demands of the metallurgical process and the characteristics of the waste heat to ensure that the system operates optimally.
Operational disruptions and downtime associated with the installation and maintenance of WHR systems can also pose challenges. The integration of WHR systems into existing plant operations often requires shutdowns or reduced production capacity, which can lead to lost productivity and revenue. For many metallurgical plants, particularly those operating in highly competitive markets, these disruptions may be difficult to justify, especially when the benefits of WHR may not be immediately realized. Furthermore, once the WHR system is in operation, regular maintenance and monitoring are essential to ensure its efficiency and longevity. The complexity of these systems means that highly specialized knowledge is often required for maintenance, and any failure or inefficiency in the WHR system can lead to operational disruptions that affect the overall plant performance.
Technological limitations also play a role in hindering the widespread adoption of WHR systems in the metallurgical industry. While there have been significant advancements in heat recovery technologies, such as improvements in heat exchangers, steam turbines, and ORC systems, many of these technologies remain in the developmental or pilot stages, especially for high-temperature processes common in metallurgy. As a result, not all technologies are mature enough to be deployed at scale in industrial environments, particularly in highly demanding and complex processes. In some cases, available heat recovery technologies may not be sufficiently cost-effective or reliable to justify their widespread implementation in metallurgical plants.
The lack of standardized solutions for waste heat recovery in metallurgy is another challenge. Each metallurgical plant is unique in terms of the processes it employs, the type of materials it handles, and the amount and quality of waste heat it generates. As a result, WHR systems must often be tailored to meet the specific needs of each facility, requiring custom engineering and design solutions. This lack of standardization can increase the cost and complexity of WHR implementation, as plant managers may need to engage with multiple vendors and service providers to design and install a system that works for their specific operational needs. The absence of a standardized approach also makes it more difficult for the industry to scale up the adoption of WHR technologies.
Economic and market conditions also play a critical role in determining whether metallurgical plants invest in WHR systems. In many cases, metallurgical industries operate under tight profit margins and are highly sensitive to changes in the market. Fluctuations in the prices of raw materials, energy, and labor can have a significant impact on a plant’s ability to invest in energy-efficient technologies such as WHR systems. In regions where energy prices are low or where fossil fuel subsidies are in place, the economic incentive to adopt WHR technologies may be reduced, making it more difficult to justify the initial investment. Additionally, in times of economic uncertainty or financial stress, metallurgical companies may prioritize short-term cost-cutting measures over long-term sustainability investments like waste heat recovery.
Regulatory and policy barriers can also impede the adoption of WHR systems. While some governments and organizations offer incentives, subsidies, or tax credits for energy-efficient technologies, the regulatory landscape can vary significantly from one country or region to another. In some cases, the regulatory framework may not adequately support or encourage the implementation of WHR systems, making it more difficult for companies to justify the investment. Furthermore, the complexity of navigating regulatory approvals for new energy systems, as well as the potential for changes in energy policies, can create uncertainty and delay the adoption of WHR technologies. This lack of regulatory clarity can make it harder for companies to assess the long-term financial viability of WHR investments.
Finally, the lack of awareness and technical expertise within the metallurgical industry can also hinder the adoption of waste heat recovery systems. Many companies may not fully understand the potential benefits of WHR or may lack the internal expertise required to design, implement, and operate these systems. Additionally, the absence of trained personnel or dedicated energy managers to oversee WHR projects can lead to a lack of technical capacity, further complicating implementation. Educational initiatives, training programs, and the sharing of best practices within the industry can help mitigate this challenge, but it remains a significant barrier to widespread adoption.
In conclusion, while metallurgical waste heat recovery systems offer clear environmental and economic benefits, their implementation is accompanied by numerous challenges. These challenges include high capital costs, technological limitations, integration complexities, and potential operational disruptions. Additionally, economic factors, regulatory barriers, and the need for specialized expertise contribute to the difficulties in adopting WHR technologies. Overcoming these challenges requires a combination of technical innovation, regulatory support, financial incentives, and industry collaboration to create an environment in which WHR systems can be effectively implemented and scaled across the metallurgical sector. By addressing these obstacles, the industry can unlock the full potential of waste heat recovery and make significant strides toward improving energy efficiency and reducing its environmental footprint.
To further address the challenges surrounding the implementation of waste heat recovery (WHR) systems in metallurgy, it’s crucial to focus on collaboration and knowledge-sharing across the industry. One of the key factors limiting the widespread adoption of WHR systems is the lack of access to real-world data and success stories. Many metallurgical plants may be hesitant to invest in WHR due to concerns about performance or cost-effectiveness, especially when they lack access to concrete examples of successful deployments. Collaborative platforms, industry alliances, and partnerships between plant operators, technology providers, and research institutions can help facilitate the sharing of best practices, lessons learned, and case studies that demonstrate the long-term advantages of WHR systems.
For instance, large corporations or multinational companies with experience in WHR could partner with smaller plants or emerging markets to provide the necessary expertise and guidance. This could involve establishing pilot projects or demonstration sites where WHR systems are installed and monitored, allowing others to evaluate their impact before committing to a full-scale implementation. Additionally, regional or global industry conferences and technical forums focused on energy efficiency and waste heat recovery can provide valuable opportunities for networking and knowledge exchange, ultimately leading to the development of more effective and affordable WHR solutions.
Another aspect to consider is the advancement of digitalization and smart technologies. The integration of digital tools such as Internet of Things (IoT) devices, sensors, and real-time data analytics into WHR systems can help improve the overall efficiency and operational performance of these systems. By monitoring key parameters such as temperature, pressure, and flow rates, plants can identify inefficiencies, optimize the heat recovery process, and predict maintenance needs. The application of machine learning algorithms and artificial intelligence (AI) can further enhance system performance by allowing for predictive analytics and automated optimization of heat recovery operations. For example, AI could be used to determine the best time to recover waste heat based on changes in production schedules or fluctuating energy demands. The use of digital twins (virtual representations of physical systems) could also help in simulating WHR system performance before installation, allowing for better planning and design choices, reducing the risk of costly mistakes.
The development of modular and scalable WHR systems is another potential solution to the challenges of implementation. Many metallurgical plants, particularly smaller or older facilities, may find the complexity and expense of large-scale WHR systems daunting. Modular systems, which allow for gradual expansion or modification based on evolving needs, could provide a more flexible solution. These systems can be tailored to different types of plants and processes, enabling companies to start with smaller investments and scale up as the benefits become more evident. Furthermore, the ability to add or modify components in a modular system allows plants to adapt to changes in production processes, energy prices, or regulatory requirements without undergoing major overhauls.
Government policies and regulatory frameworks play a pivotal role in overcoming barriers to WHR implementation. Policymakers can encourage the adoption of WHR technologies by offering financial incentives such as tax credits, subsidies, or grants. These incentives can help offset the high initial investment costs and make WHR systems more attractive to metallurgical companies, particularly in regions where energy prices are low or fossil fuel subsidies are prevalent. Additionally, regulatory frameworks that set clear guidelines and performance standards for waste heat recovery can create a more predictable environment for investors, ensuring that WHR systems meet safety and environmental criteria. Governments can also facilitate the adoption of WHR systems by introducing stricter emission standards or carbon pricing mechanisms that create a financial incentive for companies to reduce their carbon footprint through energy efficiency measures like WHR.
However, while financial incentives and supportive policies can provide the necessary push for adoption, the challenge of market readiness remains. Many metallurgical companies operate in regions where energy costs are low, and fossil fuel subsidies reduce the perceived value of energy efficiency technologies. Without a clear economic incentive, these companies may be less motivated to invest in WHR systems. To overcome this barrier, governments and industry stakeholders can create market conditions that drive long-term value creation by incentivizing energy efficiency, reducing subsidies for fossil fuels, and promoting low-carbon technologies as part of a broader industrial policy.
Furthermore, the long-term financial viability of WHR projects must be evaluated in the context of fluctuating energy prices and the ongoing costs of maintenance and operation. While WHR systems can provide substantial energy savings over time, these savings are often influenced by external factors such as global energy markets and government policies. For example, in regions where energy prices are volatile or fossil fuel subsidies are rolled back, the financial benefits of WHR may vary significantly over time. To address this uncertainty, metallurgical plants can conduct comprehensive life-cycle assessments (LCAs) to better understand the long-term financial impact of WHR investments and identify ways to mitigate risks associated with energy price fluctuations.
The need for a skilled workforce to manage, operate, and maintain WHR systems is another challenge. As the technology continues to evolve, there will be an increasing demand for professionals with expertise in waste heat recovery, energy systems engineering, and digitalization. To address this gap, industry stakeholders can collaborate with academic institutions to develop training programs, certifications, and degree programs focused on WHR technologies and energy management. Additionally, plant operators may need to invest in continuous training for their existing staff to ensure that they are equipped with the knowledge and skills to operate and maintain these systems effectively. This investment in human capital is essential for maximizing the performance and longevity of WHR systems.
Finally, the time horizon for return on investment (ROI) can be a major consideration when deciding to implement WHR systems in metallurgical plants. While the energy savings and environmental benefits are significant, the financial returns on WHR investments may take several years to materialize, especially when factoring in installation, maintenance, and operational costs. This long payback period can be a deterrent for companies that are under pressure to deliver short-term financial results. To address this, stakeholders can explore financing options such as green bonds, energy performance contracts, or leasing arrangements that allow companies to spread the costs of WHR systems over time while still reaping the long-term benefits. Additionally, alternative financing mechanisms, such as public-private partnerships or international climate funds, can help support the transition to energy-efficient technologies by providing capital or low-interest loans for WHR projects.
In summary, while waste heat recovery systems offer numerous advantages for the metallurgical industry, their adoption is hindered by a range of challenges, including high capital costs, integration complexity, technological limitations, market conditions, and the need for specialized knowledge. Overcoming these challenges requires a multifaceted approach that includes technological innovation, collaboration, financial support, and regulatory frameworks. By addressing these obstacles, the metallurgical industry can unlock the full potential of WHR systems, reducing energy consumption, lowering carbon emissions, and contributing to a more sustainable and competitive industrial sector. With the right combination of policy, investment, and technological development, the barriers to WHR implementation can be mitigated, paving the way for a more energy-efficient and environmentally responsible metallurgical industry.
Future Trends and Global Collaboration
The future of waste heat recovery (WHR) in the metallurgical industry looks promising, with technological advancements, changing global policies, and growing environmental awareness driving significant shifts in how industries approach energy efficiency. As the world continues to grapple with the need to reduce carbon emissions and move towards a more sustainable energy landscape, WHR systems are becoming increasingly vital. Several trends are emerging that will shape the future of waste heat recovery and its role in the global effort to combat climate change.
One of the most notable trends is the advancement of heat recovery technologies. As research and development in this field continue to accelerate, we can expect more efficient, cost-effective, and versatile waste heat recovery systems. Innovations in materials science, such as the development of higher-efficiency heat exchangers, and improvements in thermodynamic cycles like the organic Rankine cycle (ORC), are expected to enhance the overall performance of WHR systems. For example, advancements in nano-technologies could lead to the creation of heat exchangers that are smaller, lighter, and more efficient, making waste heat recovery feasible even in smaller or older plants that have historically been unable to adopt such systems.
Furthermore, the integration of digital technologies such as the Internet of Things (IoT), artificial intelligence (AI), and machine learning is poised to revolutionize the performance and optimization of WHR systems. Sensors embedded within the WHR system can continuously monitor key performance metrics such as temperature, pressure, and flow rates. This real-time data can then be analyzed using AI algorithms to detect inefficiencies, predict potential failures, and optimize the performance of heat recovery systems. Additionally, predictive maintenance powered by machine learning can help reduce downtime and extend the lifespan of WHR equipment, leading to lower operational costs and greater energy savings. As these technologies become more integrated into industrial systems, the effectiveness and affordability of WHR will continue to improve.
Another future trend is the growing interest in circular economy models that prioritize resource recovery and minimize waste. As industries transition from traditional linear models—where raw materials are used and discarded—to more sustainable, circular practices, WHR technologies will play a central role in helping metallurgical plants reduce their environmental impact. Waste heat recovery aligns perfectly with the principles of a circular economy, as it transforms what would otherwise be a byproduct (waste heat) into a valuable resource. As more industries adopt these models, the demand for WHR systems is expected to rise, contributing to a broader shift towards sustainability and closed-loop production systems.
The rise of renewable energy integration is another trend that will impact the future of waste heat recovery. As the world shifts towards renewable energy sources like solar, wind, and geothermal, there is an increasing opportunity to combine WHR systems with these technologies to create more resilient, low-carbon energy solutions. For instance, WHR can be paired with solar thermal systems or geothermal heat pumps to enhance the overall efficiency of energy recovery. By utilizing waste heat alongside renewable energy, industries can reduce their reliance on fossil fuels, further decreasing their carbon footprint and contributing to the global goal of achieving net-zero emissions. This integration could also pave the way for hybrid systems that combine multiple renewable and waste heat sources, optimizing energy use across industrial processes.
The decentralization of energy generation is also emerging as a key trend, particularly in regions where centralized power grids are unreliable or insufficient to meet growing industrial demands. In these areas, metallurgical plants can take advantage of decentralized energy solutions, such as on-site waste heat recovery systems, to generate power locally and reduce their reliance on external energy sources. This decentralization can lead to greater energy independence, reduced transmission losses, and enhanced resilience against energy supply disruptions. Decentralized energy solutions also open the door for smaller, more flexible plants to benefit from WHR, as they can scale up or down based on their specific energy needs.
As more companies adopt waste heat recovery technologies, there is a growing trend towards collaborative efforts between industries, governments, and research institutions. Global collaboration is becoming increasingly important in tackling the challenges associated with climate change, and the industrial sector is no exception. Governments are beginning to recognize the importance of energy efficiency and the role that WHR can play in achieving their environmental and economic goals. Through international climate agreements and national policy frameworks, governments are encouraging industries to adopt cleaner technologies by offering incentives such as tax credits, grants, and subsidies for energy-efficient practices like waste heat recovery.
In parallel, industries are forming partnerships with universities, research centers, and technology developers to innovate and improve WHR systems. This collaborative approach facilitates the exchange of knowledge and resources, helping to accelerate the development of more efficient, scalable, and cost-effective WHR technologies. For instance, multinational corporations in the metallurgical sector can collaborate with smaller firms or startups that are pioneering innovative heat recovery solutions. By sharing resources and expertise, industries can overcome some of the common barriers to WHR adoption, such as high upfront costs or technological limitations, and collectively work toward the widespread implementation of energy-efficient solutions.
International collaboration is also crucial for sharing best practices and success stories. Companies around the world can learn from one another’s experiences in implementing WHR systems and adapt these lessons to their own operations. For example, a metallurgical plant in one country that has successfully integrated a particular type of waste heat recovery system could serve as a model for other plants in similar industries or regions. This exchange of knowledge helps to drive the adoption of WHR technologies, spreading the benefits of energy efficiency and reducing environmental impacts globally.
Governments, NGOs, and international organizations are also focusing on the role of policy frameworks in facilitating the adoption of WHR technologies. By introducing clear regulations, standards, and long-term energy goals, policymakers can create the conditions for widespread industry uptake of waste heat recovery systems. Globally, there is a growing consensus that energy efficiency will be critical to achieving the targets set under the Paris Agreement and other international climate accords. WHR is seen as an important tool in achieving these targets, especially in energy-intensive industries like metallurgy. As a result, governments are increasingly offering financial incentives, tax rebates, and low-interest loans to encourage the adoption of WHR technologies.
The emerging role of financing mechanisms will also play a critical role in the future of WHR systems. In addition to government incentives, private investors and banks are beginning to recognize the financial potential of energy-efficient technologies like WHR. Green financing, green bonds, and other forms of low-cost capital will likely become more accessible to companies seeking to implement WHR solutions. These financial products provide the necessary funding for plant upgrades and new technology adoption, making it easier for companies to offset the high initial costs of WHR systems.
Looking ahead, the future workforce will also play a key role in the evolution of waste heat recovery in metallurgy. As WHR technology becomes more complex and integrated with other energy systems, there will be an increasing demand for skilled labor in areas such as energy management, data analytics, and system integration. Training programs, university degrees, and technical certifications focused on energy efficiency and waste heat recovery will be essential for developing the expertise needed to manage and maintain these systems effectively. The growing need for a skilled workforce will also drive innovation in education and professional development, ensuring that workers are prepared to meet the challenges of a rapidly changing energy landscape.
In conclusion, the future of waste heat recovery in the metallurgical industry is marked by a convergence of technological innovation, collaborative efforts, and policy support that will make WHR systems more accessible, cost-effective, and impactful. As industries strive to reduce their environmental footprints and improve energy efficiency, the role of waste heat recovery will become increasingly central. The future will see enhanced integration of WHR technologies with renewable energy sources, the rise of decentralized energy systems, and a greater emphasis on global collaboration. Through these efforts, the metallurgical industry will be better positioned to contribute to the global sustainability agenda, helping to meet climate targets while maintaining economic viability and resilience.
Power Plant Turbine Components
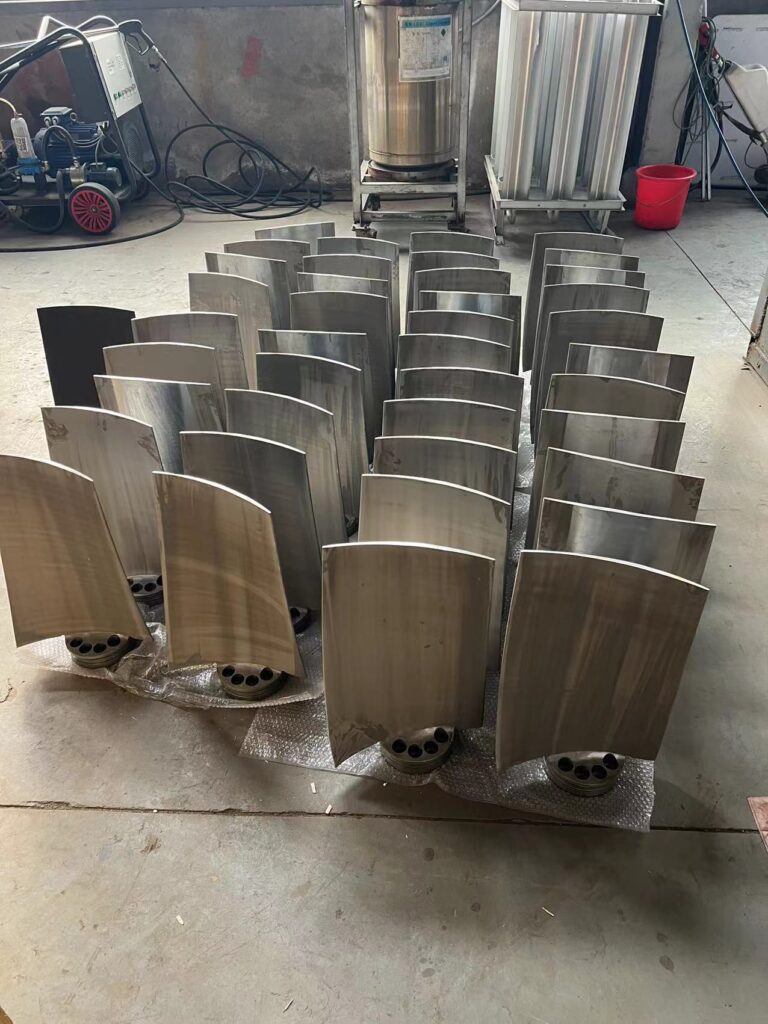
Power plant turbines are critical components in the generation of electricity, playing an essential role in converting thermal energy into mechanical energy and subsequently into electrical power. As the global energy landscape continues to evolve, turbines remain central to the efficiency, reliability, and performance of power generation systems. These components are integral to various types of power plants, including those that use fossil fuels, nuclear energy, and renewable resources such as geothermal energy or biomass. The operational characteristics of turbines—such as efficiency, power output, and lifespan—are influenced by several technological innovations, design features, and materials developments. This ongoing evolution reflects the broader push towards more sustainable, efficient, and reliable energy systems.
The design and functioning of turbines in power plants involve a variety of components, including rotors, blades, stators, bearings, seals, and governors. These elements work together to harness the energy produced from steam, gas, or water and convert it into mechanical energy that drives a generator to produce electricity. Turbines can be broadly classified into steam turbines, gas turbines, and hydraulic turbines, each of which is optimized for a specific type of energy source. Each turbine type has its own set of components designed to maximize performance and efficiency based on the operational demands and energy source being used.
Steam turbines are commonly used in thermal power plants, which burn fossil fuels or use nuclear energy to heat water and produce steam. The steam drives the turbine, which is connected to a generator that converts the mechanical energy into electrical energy. The turbine’s key components include rotor blades, nozzles, stator rings, and bearings, all of which must be carefully designed and constructed to withstand high temperatures and pressures. Steam turbines are often further classified into condensing turbines and back-pressure turbines, each offering different benefits in terms of efficiency, energy recovery, and application flexibility. In a condensing turbine, steam is condensed after it passes through the turbine, maximizing the conversion of thermal energy. Back-pressure turbines, on the other hand, allow for the partial extraction of steam for use in district heating or industrial processes, which is beneficial in combined heat and power (CHP) plants.
Gas turbines, primarily used in combined-cycle power plants, operate on the principle of converting the chemical energy in natural gas into mechanical energy through combustion. The hot gases produced in the combustion chamber pass through the turbine blades, causing the rotor to spin and generate power. Gas turbines are designed for high efficiency, rapid start-up, and operational flexibility, making them ideal for peaking power plants and backup power generation. They consist of components such as compressors, combustion chambers, rotors, turbine blades, and exhaust systems. Gas turbines can be integrated with steam turbines in combined-cycle configurations, where the exhaust heat from the gas turbine is used to generate steam that drives a steam turbine, increasing the overall efficiency of the system.
The hydraulic turbine or water turbine is used in hydroelectric power plants, where the energy of moving water is converted into mechanical energy. This type of turbine is typically used in dams, rivers, or ocean tidal flows to generate power through the movement of water. The key components of hydraulic turbines include runner blades, guide vanes, shaft, and bearings. The design of these components must be optimized for the specific characteristics of the water source, such as flow rate, pressure, and turbulence, to maximize energy capture and minimize mechanical wear.
Across all turbine types, one of the most important considerations is the material selection. Turbines are exposed to extreme conditions, including high temperatures, high pressures, and corrosive environments. To ensure longevity and high performance, components such as blades and rotors are made from advanced materials that can withstand these harsh operating conditions. Materials such as superalloys, titanium, ceramics, and composite materials are commonly used for high-stress turbine components, offering improved strength, fatigue resistance, and thermal stability. For instance, nickel-based superalloys are frequently used for turbine blades in gas turbines due to their ability to maintain strength at high temperatures. The development of heat-resistant coatings and thermal barrier coatings is another key area of research to improve the durability and efficiency of turbine components.
Efficiency remains a driving force in turbine development. As energy demands increase and environmental regulations become stricter, there is a growing emphasis on optimizing turbine performance to reduce fuel consumption, minimize waste heat, and lower carbon emissions. Engineers are continually working to enhance the aerodynamic design of turbine blades and optimize their geometries for better fluid flow and energy extraction. Additionally, advanced cooling technologies are being developed to maintain the integrity of turbine components in high-temperature environments. Hybrid cooling systems, which combine air and liquid cooling methods, are being explored to achieve more efficient temperature management.
Another significant focus in turbine design is operational flexibility. Power plants need turbines that can handle a wide range of operating conditions, from full-load operation to partial-load operation, and be able to start up and shut down quickly in response to changing energy demands. This flexibility is especially important in the context of integrating renewable energy sources, such as wind and solar, which are intermittent in nature. Gas turbines, in particular, are well-suited for this role due to their ability to start up quickly and adjust output rapidly. However, advancements in steam turbine and combined-cycle turbine technologies are also making these systems more flexible, allowing them to respond more effectively to fluctuations in energy supply and demand.
Digitalization and the adoption of smart grid technologies are transforming the way power plants operate and manage turbines. The integration of sensors, predictive analytics, and digital twins allows operators to monitor the health and performance of turbine components in real-time. Predictive maintenance, powered by machine learning and artificial intelligence, enables early detection of potential issues, reducing downtime and minimizing maintenance costs. Moreover, condition-based monitoring systems can optimize turbine performance by adjusting operational parameters based on the data collected from sensors embedded in turbine components.
Hybrid systems and advanced turbine configurations are also gaining attention as power plants seek to maximize their efficiency. For instance, supercritical steam cycles and ultra-supercritical cycles are pushing the boundaries of steam turbine performance by operating at higher temperatures and pressures, which increases their efficiency and reduces fuel consumption. Combined with technologies like carbon capture and storage (CCS) and energy storage systems, these hybrid configurations are helping to decarbonize power generation while maintaining high output and reliability.
In addition to technological advancements, global collaboration is becoming increasingly important in driving the development and implementation of cutting-edge turbine technologies. International standards and best practices are being developed to ensure that turbines operate efficiently and safely across different regions and power plants. Collaboration between governments, industries, and research institutions plays a critical role in fostering innovation and ensuring that new turbine technologies are deployed in a cost-effective manner. This collaboration is essential for addressing challenges such as climate change, energy security, and sustainable development while meeting the growing global demand for electricity.
Looking ahead, the future of turbine components in power generation will be shaped by the convergence of various trends. There will be a continued focus on energy efficiency, reliability, and environmental sustainability. Innovations in materials, cooling technologies, and digitalization will enhance the performance and lifespan of turbine components, while hybrid systems and advanced turbine configurations will offer greater flexibility and efficiency. As global energy markets evolve, turbine technologies will play a central role in transitioning towards cleaner, more resilient energy systems.
Ultimately, the role of turbines in power plants is not just limited to providing electricity but extends to shaping the future of energy production. With the right technological advancements and global collaboration, turbines will continue to be key components in meeting the world’s energy needs while addressing the environmental challenges of the 21st century.
Here are the 10 main sections for the topic of Power Plant Turbine Components:
- Introduction to Power Plant Turbines
Power plant turbines are essential components in the generation of electricity, converting thermal energy (from steam, gas, or water) into mechanical energy that powers generators. This section provides an overview of the different types of turbines used in power plants and their critical role in energy production. - Types of Power Plant Turbines
There are three primary types of turbines used in power generation: steam turbines, gas turbines, and hydraulic turbines. Each type operates on different principles and is suited for specific energy sources, such as thermal, gas, or hydroelectric power. - Steam Turbine Components
Steam turbines are the cornerstone of many thermal and nuclear power plants. This section focuses on the individual components of steam turbines, including rotors, blades, nozzles, and stators, and how they work together to convert steam energy into mechanical power. - Gas Turbine Components
Gas turbines are widely used in combined-cycle power plants and are critical for efficiency and flexibility. This section details the components of gas turbines, including compressors, combustion chambers, turbines, and exhaust systems, and discusses how they convert natural gas into mechanical energy. - Hydraulic Turbine Components
Used in hydroelectric power plants, hydraulic turbines convert the energy of flowing water into mechanical power. This section explores the components of hydraulic turbines, such as runner blades, guide vanes, and shafts, and examines the impact of water flow characteristics on turbine design. - Material Science and Durability in Turbine Components
Turbines operate under extreme conditions, requiring advanced materials for their construction. This section delves into the importance of material selection in turbine components, such as the use of superalloys, ceramics, and composite materials to ensure the durability and efficiency of turbines in high-temperature and high-pressure environments. - Efficiency Enhancements in Turbine Technology
Increasing the efficiency of turbines is a primary objective in power generation. This section discusses the technological advancements aimed at improving turbine performance, including aerodynamic blade design, enhanced cooling technologies, and hybrid cooling systems to optimize energy recovery. - Advanced Turbine Configurations and Hybrid Systems
Advanced turbine configurations, such as ultra-supercritical steam cycles and combined-cycle systems, are key to achieving higher efficiency. This section explores how these systems work and the role of hybrid power generation systems that integrate turbines with renewable energy sources like solar and wind. - Digitalization and Smart Technologies in Turbine Operations
The digitalization of turbine operations has revolutionized how power plants monitor and maintain their turbines. This section covers the role of sensors, predictive analytics, and AI-driven maintenance strategies, as well as the benefits of condition-based monitoring and real-time performance optimization. - Global Trends and Future Directions for Turbine Technologies
The future of turbine technologies in power plants is shaped by global trends, including the increasing demand for energy efficiency, the rise of renewable energy integration, and the push towards carbon reduction. This section looks at the emerging technologies, such as next-generation materials, hybrid systems, and the global collaboration needed to meet future energy needs.
These 10 sections comprehensively cover the role, components, advancements, and future trends associated with power plant turbines.
Introduction to Power Plant Turbines
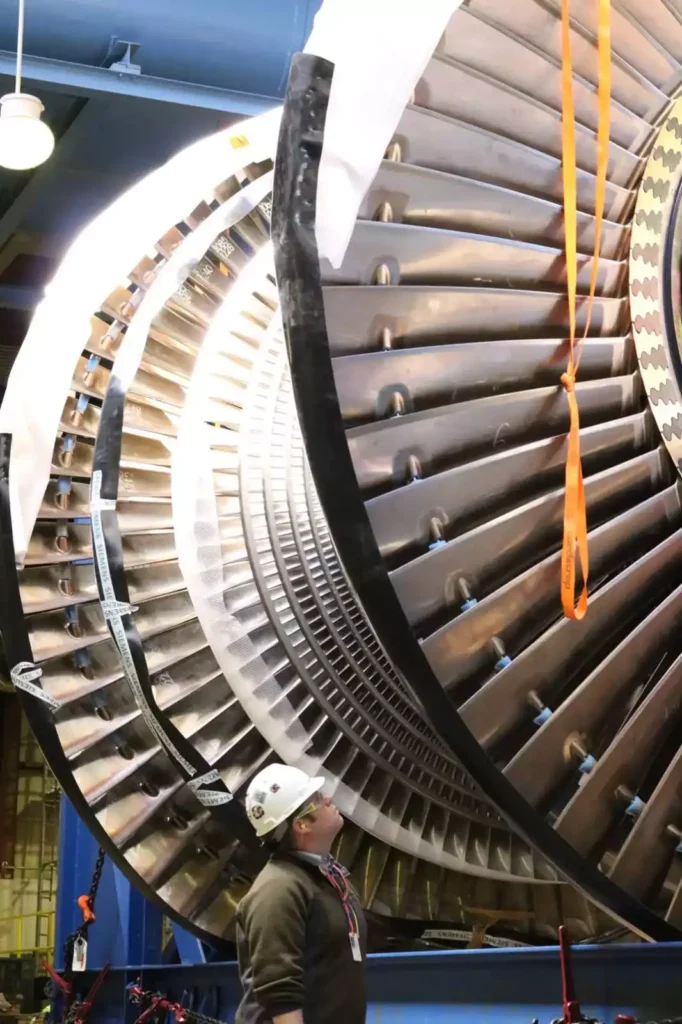
Power plant turbines are the heart of modern electricity generation, transforming thermal, gas, or hydro energy into mechanical energy, which is then used to produce electricity. These turbines are designed to harness energy from various sources—whether it’s the heat produced by burning fossil fuels, the steam created in nuclear reactors, or the kinetic energy of water flowing through hydroelectric dams. The turbine converts thermal or fluid energy into mechanical power by rotating a shaft, which is connected to a generator. The movement of this shaft spins the generator’s rotor, thus generating electrical power.
The importance of turbines in power generation cannot be overstated. They are the primary drivers of efficiency in thermal, nuclear, and hydroelectric plants, and are central to the operation of combined-cycle power systems, which enhance the overall efficiency of electricity generation. The design and functionality of these turbines have evolved over time, driven by technological advancements and increasing demands for efficiency, cost-effectiveness, and environmental sustainability.
In power plants, turbines operate under a wide range of conditions, often subject to high temperatures, pressures, and mechanical stresses. The material selection for turbine components, including the rotor blades, nozzles, and stators, is crucial for maintaining performance, reducing wear, and prolonging operational life. Additionally, advancements in cooling technologies, aerodynamics, and digital monitoring systems have significantly improved turbine efficiency and reliability.
There are three primary types of turbines used in power generation: steam turbines, gas turbines, and hydraulic turbines. Steam turbines are used in most thermal and nuclear power plants, where they convert steam generated by heating water (from burning fuel or nuclear reactions) into mechanical power. These turbines are typically large, multi-stage machines designed to maximize energy conversion and operate at high temperatures and pressures. Gas turbines are typically used in combined-cycle power plants, where they convert energy from the combustion of natural gas into mechanical power. Gas turbines are prized for their efficiency, flexibility, and rapid start-up capabilities, making them ideal for peaking power generation and integration with renewable sources of energy. Hydraulic turbines, found in hydroelectric plants, convert the potential energy of flowing water into mechanical energy, and these turbines are specifically designed to operate in environments with high fluid flow rates, such as rivers or waterfalls.
The key to maximizing the performance of power plant turbines is continuous innovation. Engineers and researchers focus on improving turbine efficiency, reducing operational costs, and extending service life. This includes innovations in materials science, where advanced alloys and composite materials are increasingly used to withstand the high temperatures and mechanical stresses in gas and steam turbines. Furthermore, the use of digital monitoring systems is expanding, allowing real-time analysis of turbine performance. These digital systems can detect inefficiencies and predict maintenance needs, helping power plants operate at peak performance.
In addition to technological advancements, power plant turbines are also at the forefront of efforts to reduce the environmental impact of energy generation. Modern turbines are more energy-efficient, which leads to lower fuel consumption and reduced carbon emissions. This is especially crucial as the global community moves towards a low-carbon future, striving to reduce greenhouse gas emissions and mitigate climate change. Turbines are increasingly integrated into combined-cycle systems that improve efficiency by capturing waste heat and converting it into additional energy, thus reducing the overall environmental footprint of power plants.
Despite the advancements, there are several challenges that come with the operation and maintenance of power plant turbines. These include the wear and tear of turbine components due to the extreme conditions under which they operate, the need for regular maintenance to avoid downtime, and the high capital investment required for turbine technology. However, with the continued evolution of turbine design and materials, coupled with innovative maintenance techniques like predictive maintenance and the use of digital twins (virtual models of physical turbines for performance optimization), these challenges are becoming more manageable.
In conclusion, power plant turbines are fundamental to the operation of modern electricity generation systems. Whether used in thermal, gas, or hydroelectric plants, these turbines are central to the transformation of energy into electricity. With advancements in materials, design, and digital technology, turbines are becoming more efficient, more reliable, and more environmentally friendly. They continue to evolve, playing a key role in meeting the world’s growing energy demands while minimizing environmental impacts. The future of power plant turbines is closely tied to the ongoing efforts to improve energy efficiency, reduce emissions, and integrate renewable energy sources, ensuring that turbines will remain at the heart of global energy systems for decades to come.
As the global energy sector continues to transition towards sustainability, power plant turbines will increasingly face the challenge of integrating with renewable energy sources, such as solar, wind, and biomass. The intermittent nature of renewable energy production—where energy generation varies based on environmental conditions—requires that turbines be more flexible and responsive than ever before. This is where combined-cycle systems and hybrid power plants come into play. These systems combine different types of turbines (such as gas and steam turbines) to maximize efficiency and ensure reliable power output, even when renewable energy production is low. For example, in a combined-cycle gas turbine system, the exhaust heat from the gas turbine is used to generate steam, which drives a steam turbine, allowing for greater overall efficiency.
One of the emerging trends in power plant turbines is the use of advanced turbine materials that can withstand extreme operating conditions and improve performance. Superalloys, ceramic composites, and thermal barrier coatings are being increasingly employed in gas and steam turbine components, enabling them to operate at higher temperatures and pressures. This not only enhances efficiency but also extends the lifespan of turbine components, thereby reducing maintenance costs and downtime.
In addition to material innovation, aerodynamic advancements in turbine blade design are also crucial. Optimizing the shape and geometry of turbine blades can significantly increase their efficiency by reducing drag and improving the conversion of thermal energy into mechanical power. Modern computational tools and simulations allow engineers to design blades with optimal aerodynamics, taking into account factors such as airflow dynamics, temperature gradients, and mechanical stresses. These improvements help turbines operate more efficiently, even in challenging conditions.
The implementation of digital technologies is also revolutionizing the way turbines are operated and maintained. The integration of sensor networks, data analytics, and artificial intelligence enables real-time monitoring of turbine performance. This “smart” monitoring allows operators to track the health of turbines, predict potential failures, and optimize their performance. Predictive maintenance systems can identify wear patterns and potential issues before they lead to costly downtime, reducing operational costs and improving the reliability of the entire power plant. The use of digital twins, which are virtual models of turbines, allows operators to simulate different operating conditions and assess the impact of changes in performance or maintenance schedules.
Despite these technological advancements, the challenge of balancing the demand for energy with the need to minimize environmental impact remains. In this context, carbon capture and storage (CCS) technologies are being explored to reduce the carbon footprint of fossil-fuel-based power plants. By capturing carbon dioxide emissions before they are released into the atmosphere, CCS technology helps to mitigate the environmental impact of power generation. Turbines are central to the integration of CCS in power plants, as they must be able to handle the additional energy requirements of the capture process without compromising overall efficiency.
The future of power plant turbines will also be influenced by global regulatory frameworks and the increasing demand for clean energy solutions. As governments implement stricter emissions standards and push for carbon neutrality, turbine manufacturers and power plant operators will need to adapt to new regulations while continuing to improve turbine performance. This will require ongoing research and development in areas such as turbine efficiency, emission control technologies, and the integration of renewable energy sources. Moreover, turbine manufacturers will need to collaborate with governments, research institutions, and energy companies to ensure that turbines are not only technologically advanced but also aligned with global energy goals.
The transition to a more sustainable energy future will also lead to greater global collaboration in turbine development. As countries across the world seek to decarbonize their energy sectors and reduce reliance on fossil fuels, the demand for innovative turbine solutions will increase. This will spur greater investment in research and development, as well as partnerships between manufacturers, governments, and energy providers. Collaborative efforts will drive the creation of new turbine technologies that are more efficient, flexible, and environmentally friendly.
Furthermore, the future of power plant turbines will likely see an increased role for renewable energy sources, particularly wind and solar. Wind turbines, which are a form of gas-powered turbine technology, already play a key role in global power generation, and as wind energy technologies continue to evolve, turbines will become more efficient and adaptable to different environmental conditions. Similarly, the integration of solar power with storage systems may necessitate the development of turbines that can work in tandem with these technologies, ensuring a continuous and reliable energy supply.
In summary, power plant turbines are integral to the production of electricity across various sectors. With ongoing advancements in materials, design, digital technologies, and system integration, turbines will continue to evolve to meet the growing demands for efficiency, flexibility, and sustainability. As the energy landscape shifts towards cleaner, renewable sources, turbines will play a pivotal role in ensuring a reliable, low-carbon energy future. The innovation and collaboration occurring today will shape the next generation of turbines, ensuring they remain central to the global energy transition while driving improvements in both performance and environmental impact.
Types of Power Plant Turbines
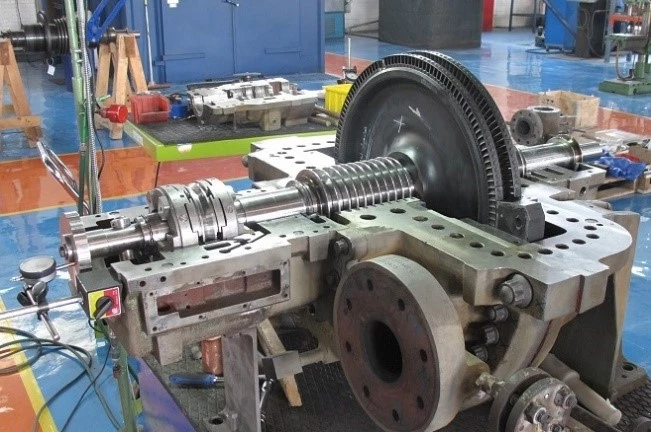
Power plant turbines are essential machines that convert energy from various sources into mechanical power, which is subsequently used to generate electricity. The most common types of power plant turbines are steam turbines, gas turbines, and hydraulic turbines. Each of these turbines is designed to operate based on different principles, suited to the specific type of energy they are harnessing. While all turbines function to drive generators, they differ in their operation, applications, and efficiency based on the energy input they receive.
Steam turbines are the most widely used turbines in power generation, particularly in thermal power plants and nuclear power plants. These turbines operate on the principle of steam expansion, where high-pressure steam produced by heating water (usually via burning coal, natural gas, or nuclear reactions) passes through the turbine blades. As the steam expands and cools, it loses energy, which is captured by the turbine blades and used to rotate the turbine’s rotor. This mechanical energy is transferred to a generator, which produces electricity. Steam turbines are commonly used in both fossil fuel-based and nuclear power plants, where the heat generated from burning fuel or nuclear reactions is harnessed to create steam. The steam turbine’s design often consists of multiple stages, with each stage progressively extracting energy from the steam to maximize efficiency. The efficiency of steam turbines is greatly influenced by factors such as steam temperature, pressure, and the design of the turbine blades, as well as the quality of the steam used.
Gas turbines, on the other hand, are typically used in combined-cycle power plants, where they are paired with steam turbines to improve overall efficiency. These turbines operate on the principle of thermodynamics, where air is compressed, mixed with fuel, and ignited in a combustion chamber. The resulting high-temperature and high-pressure gases then pass through the turbine blades, causing the rotor to spin. As the gases expand through the turbine, they lose energy, which is converted into mechanical energy. Gas turbines are known for their rapid start-up times and their ability to operate efficiently at partial load, which makes them ideal for handling peak demand and serving as backup power sources in systems with intermittent renewable energy. Gas turbines are typically more compact and versatile than steam turbines, and they can run on a variety of fuels, including natural gas and diesel. Their design often includes components like compressors, combustion chambers, and expansion turbines, all of which work in tandem to extract energy from the combustion process.
In hydroelectric power plants, hydraulic turbines are employed to harness the energy from flowing water. These turbines convert the potential energy of water stored at a height into mechanical energy. The force of the falling water, typically from a dam or river, drives the turbine blades, causing them to rotate and generate electricity. Hydraulic turbines are commonly used in large-scale hydroelectric plants, where large amounts of water flow are available. The design of these turbines is highly dependent on the specific characteristics of the water source, such as flow rate and pressure. Hydraulic turbines can be further classified into different types, such as Francis turbines, Pelton turbines, and Kaplan turbines, each of which is optimized for different flow conditions and operational requirements. For instance, Francis turbines are best suited for medium to high-head applications and are often used in plants with relatively consistent water flow. Pelton turbines are typically used in high-head, low-flow scenarios, where water falls from great heights. Kaplan turbines, on the other hand, are designed for low-head, high-flow conditions and are ideal for large rivers or tidal power applications.
Combined-cycle turbines represent a hybrid system that combines both gas and steam turbines to maximize efficiency. In a combined-cycle power plant, a gas turbine generates electricity through the combustion of natural gas, and the exhaust gases produced by the turbine are then used to generate steam, which drives a steam turbine. The steam turbine is connected to the same generator as the gas turbine, allowing the plant to produce more electricity with the same amount of fuel. This combined process improves the overall efficiency of the plant, making it one of the most efficient types of power plants for electricity generation. Combined-cycle systems are increasingly used in modern power plants because they offer high efficiency and lower greenhouse gas emissions compared to traditional single-cycle plants.
In addition to these traditional turbine types, geothermal turbines are used to convert the energy from the Earth’s heat into electricity. These turbines operate by utilizing steam or hot water extracted from underground reservoirs. Geothermal plants are typically located in regions with high levels of geothermal activity, such as near tectonic plate boundaries. The geothermal steam or hot water is used to drive a turbine, which is connected to a generator to produce electricity. While geothermal power plants are limited to specific geographic locations, they offer a renewable and stable energy source.
Turbine technology is continuously evolving, and advancements are made to improve the efficiency, flexibility, and performance of turbines in various applications. One notable advancement is the development of supercritical steam turbines, which are designed to operate at higher pressures and temperatures than traditional steam turbines. These turbines achieve higher thermal efficiency by operating at extreme conditions, making them ideal for reducing fuel consumption and minimizing emissions in power plants. Additionally, turbines are increasingly integrated into hybrid systems that combine renewable energy sources like solar and wind with traditional fossil fuel-based generation, providing cleaner, more reliable energy.
Another area of focus is the development of smaller-scale turbines, which can be used in decentralized or off-grid power systems. These turbines are particularly useful for providing power to remote areas or industrial facilities that require a constant and reliable energy supply. Small-scale turbines can be used in a variety of applications, such as industrial cogeneration, where waste heat is recovered to produce electricity, or in residential microgrids, where local energy generation is critical for energy independence.
In summary, the types of turbines used in power generation vary significantly depending on the energy source and the specific requirements of the power plant. Steam turbines, gas turbines, and hydraulic turbines each have their own unique designs and applications, with each being optimized for specific operating conditions. Combined-cycle systems, geothermal turbines, and smaller-scale turbines represent further innovations in turbine technology that continue to improve the efficiency and environmental impact of power generation. As the world transitions to cleaner and more sustainable energy sources, turbine technology will play a pivotal role in ensuring that power plants remain efficient, reliable, and adaptable to the changing needs of the global energy market.
As the global energy landscape continues to shift towards more sustainable and cleaner energy solutions, the role of power plant turbines is expected to evolve. One of the key challenges will be integrating renewable energy sources into the power grid. While wind, solar, and other renewable sources have gained prominence, their intermittent nature makes them challenging to rely on as consistent sources of energy. Turbines, particularly gas turbines and combined-cycle systems, are playing an increasingly important role in balancing the energy grid. These turbines provide the flexibility required to respond quickly to fluctuations in renewable energy production, ensuring grid stability by acting as backup or peak-load power sources. Gas turbines, in particular, are well-suited for this role due to their ability to start up rapidly and operate efficiently at various loads.
One significant innovation is the development of flexible gas turbines. These turbines are designed to quickly adapt to changing conditions and load requirements, making them ideal for systems that integrate renewable energy. Flexible gas turbines can modulate their output efficiently, ramping up or down based on the availability of solar or wind power. This flexibility ensures that there is always a reliable supply of electricity, even when renewable energy generation is low or intermittent.
In the realm of steam turbines, the drive towards higher efficiency and lower emissions is pushing the development of ultra-supercritical steam turbines. These turbines operate at even higher temperatures and pressures than conventional steam turbines, which allows for increased efficiency in power generation. Ultra-supercritical technology allows power plants to extract more energy from the same amount of fuel, thereby reducing fuel consumption and lowering carbon emissions. As a result, these turbines are becoming more common in modern coal and natural gas power plants, and they are also seen as key players in the future of cleaner fossil-fuel power generation.
Furthermore, there is increasing interest in offshore wind turbines, which represent an emerging and rapidly growing sector of renewable energy. Offshore wind turbines are capable of harnessing stronger and more consistent winds found at sea, offering a more reliable source of power than their onshore counterparts. These turbines, often larger and more powerful than land-based wind turbines, are integral to future wind energy projects, especially in coastal regions with high wind potential. As turbine technology advances, offshore wind turbines are becoming more efficient, cost-effective, and environmentally friendly. The development of floating wind turbine platforms is one such innovation that promises to unlock new offshore wind resources, particularly in deep-water areas where traditional fixed turbines cannot be deployed.
The importance of hydropower turbines is also expected to continue as countries look for renewable energy solutions. Hydroelectric power generation remains one of the most reliable and efficient forms of renewable energy. The expansion of hydropower plants, especially in developing countries, will drive demand for advanced hydraulic turbines designed to optimize energy capture from flowing water. New developments in turbine design are focused on improving efficiency in low-flow conditions, reducing environmental impact on ecosystems, and enhancing the overall performance of hydroelectric plants.
In addition to these advancements, integrated turbine systems will likely become more prevalent in the future. These systems combine multiple turbine technologies—such as gas, steam, and renewable energy turbines—into a single unified power generation unit. This integration improves overall system efficiency and reduces the reliance on any single source of energy. For example, in a combined gas-steam cycle, waste heat from the gas turbine can be used to generate steam, which drives a steam turbine, thus improving overall efficiency. These integrated systems also help reduce emissions by utilizing cleaner energy sources and optimizing energy recovery.
Another critical aspect of the future of power plant turbines is the growing emphasis on digitalization and smart grids. The integration of Internet of Things (IoT) technologies, advanced sensors, and artificial intelligence (AI) into turbine operations is transforming how power plants monitor and control their turbines. Condition-based monitoring, predictive maintenance, and performance optimization are becoming standard practices, allowing plant operators to detect early signs of wear or inefficiencies and take corrective actions before they lead to costly failures. Digital tools also enable real-time performance analysis, helping optimize turbine output based on changing demand and energy conditions. This digital approach is especially important as power plants move towards more complex and dynamic grid systems that incorporate renewable energy sources.
In light of the ongoing push for decarbonization, carbon capture and storage (CCS) technologies are becoming increasingly important in the context of power plant turbines. CCS involves capturing carbon dioxide emissions from power plants and storing them underground or using them for industrial purposes, thereby reducing the plant’s carbon footprint. For steam turbines, which are commonly used in fossil fuel plants, integrating CCS systems is a key challenge that requires modifications to the turbine and its associated equipment. However, advancements in CCS technologies, including more efficient capture methods and lower operational costs, are making it more feasible to apply these systems to a wider range of power plants, including those that rely on steam turbines.
As energy demands continue to rise globally, there is also growing interest in microturbines and small-scale turbine systems for decentralized energy generation. Microturbines are small, highly efficient turbines that can operate on natural gas, diesel, or even biogas. These systems are increasingly being deployed for industrial and residential applications where large-scale power plants are not feasible. Microturbines offer significant advantages in terms of reliability, cost-effectiveness, and environmental sustainability, as they provide on-site energy generation with low emissions and high efficiency.
In the future, fuel flexibility will be a critical feature of power plant turbines. The development of turbines that can operate on a variety of fuels, including hydrogen, biofuels, and synthetic fuels, is becoming increasingly important as the world seeks to diversify its energy sources. Hydrogen turbines, for example, represent a promising area of innovation, as hydrogen can be used as a clean fuel source that produces only water vapor as a byproduct when burned. The integration of hydrogen into power plants—particularly gas turbines—could significantly reduce carbon emissions and provide a pathway to a more sustainable energy future.
In conclusion, the future of power plant turbines lies in increasing efficiency, reducing emissions, and integrating renewable energy sources. Advances in turbine technology, from steam and gas turbines to hydro and wind turbines, are helping meet the global demand for cleaner, more reliable energy. The shift towards flexible, digital, and integrated turbine systems will allow power plants to adapt to changing energy demands, reduce environmental impact, and support the global transition to a sustainable energy future. As technology continues to evolve, power plant turbines will remain at the core of efforts to provide efficient, cost-effective, and environmentally friendly electricity generation.
Steam Turbine Components
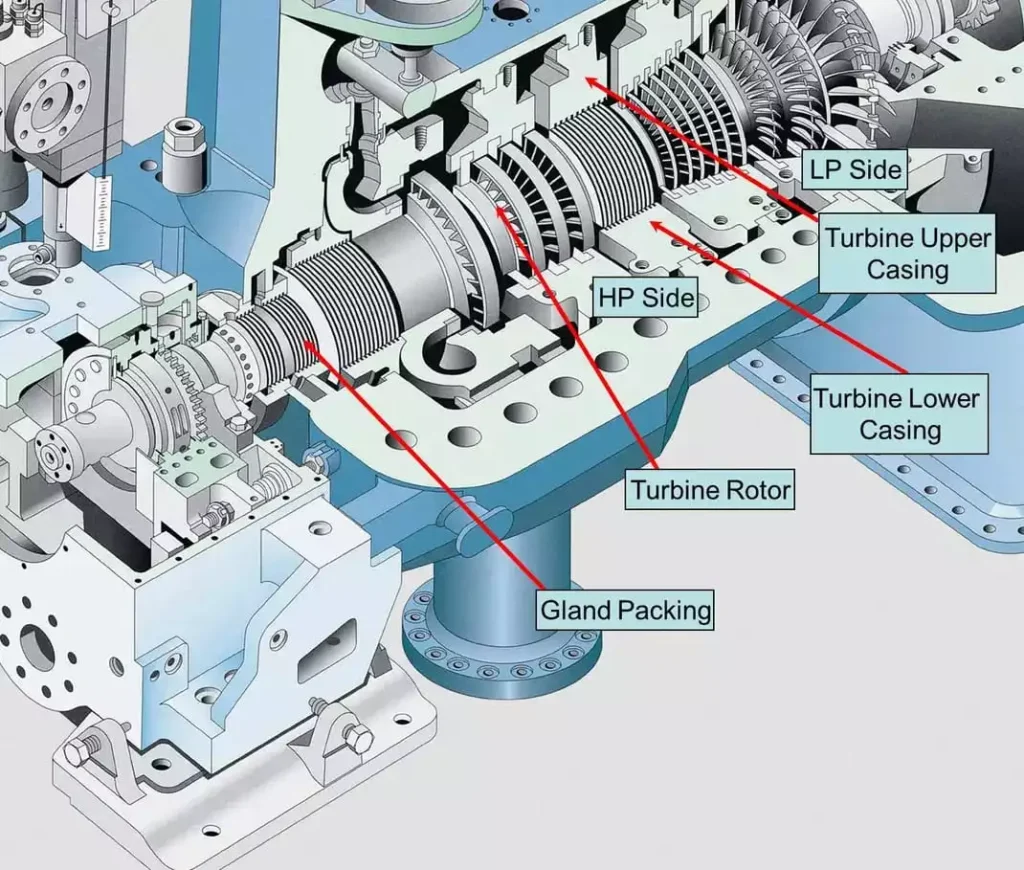
Steam turbines are complex machines composed of multiple components, each designed to work together to convert thermal energy from steam into mechanical energy. These components must operate in harsh conditions, enduring high temperatures, pressures, and rotational forces. The main components of a steam turbine include the rotor, stator, blades, nozzles, bearings, and shaft, each playing a critical role in the overall functioning and efficiency of the turbine.
At the heart of any steam turbine is the rotor, the rotating part of the turbine that is driven by the steam’s pressure. The rotor consists of a series of discs mounted on a central shaft, and it is attached to the turbine blades. As the steam flows over the blades, it transfers its energy, causing the rotor to spin. The rotor is subject to high mechanical stresses and must be made of strong, heat-resistant materials such as superalloys or stainless steel. The shaft, which is the central axis of the rotor, transmits the mechanical power generated by the turbine to the generator or other equipment. The shaft must be robust enough to handle the high torque generated by the steam’s expansion, ensuring smooth operation and minimal vibration.
The blades of the turbine are mounted on the rotor and are responsible for extracting energy from the steam. The blades are designed with highly precise aerodynamics to optimize the steam’s conversion into mechanical energy. They are usually divided into two stages: moving blades and stationary blades. Moving blades, located on the rotor, interact directly with the steam, causing the rotor to turn. Stationary blades are fixed in place and are designed to redirect the steam flow as it passes through the turbine stages. The blades’ material composition is critical to their ability to withstand the intense thermal and mechanical stresses they experience. Alloyed steels, often with advanced coatings to resist corrosion and erosion, are commonly used for the turbine blades. Over time, advancements in blade design have led to the development of blades with improved efficiency, optimized shapes, and resistance to wear.
Nozzles play an essential role in directing the steam onto the turbine blades. The nozzle is a precisely shaped opening that accelerates the steam and converts its thermal energy into kinetic energy. By narrowing the steam’s flow, the nozzle increases its velocity as it enters the blades. This high-velocity steam imparts its energy to the blades, causing them to rotate. The design of the nozzle is crucial for maximizing the energy transfer to the blades, ensuring that the turbine operates at peak efficiency. The nozzle’s construction is usually designed to endure high temperatures and pressures, often incorporating high-performance materials that can resist erosion and corrosion.
The stator refers to the stationary part of the turbine that houses the nozzles and stationary blades. It is a critical part of the steam path, as it helps manage the steam flow and directs it onto the blades. The stator is designed to withstand extreme conditions, and its design often includes cooling systems to ensure it does not overheat under high-pressure steam conditions. The stator serves as a housing for various components, including the bearings, and helps maintain the overall integrity of the turbine’s mechanical structure. Additionally, the stator is crucial for maintaining the alignment of the rotating and stationary parts of the turbine, ensuring smooth and efficient energy conversion.
Bearings are essential components that support the turbine’s rotor and reduce friction between moving parts. Bearings allow the rotor to spin freely, providing the necessary support to handle the mechanical stresses of turbine operation. They are typically made from high-strength, low-friction materials, such as bronze or ceramic composites. Bearings are often cooled using oil or other lubrication systems to prevent overheating and ensure long-term operational reliability. The design of the bearing system is critical for maintaining the stability and precision of the rotor’s movement, preventing wear and reducing vibration.
The casing or housing of the steam turbine is another key component. The casing encloses the rotor, blades, and stator, providing structural support and protection. The casing is designed to withstand the internal pressures of the turbine and direct the steam flow in the most efficient way possible. In some cases, the casing is divided into several sections that are bolted together, allowing for easier maintenance and repair. The casing is typically constructed from materials such as carbon steel, stainless steel, or other high-strength alloys to withstand the forces generated during operation.
Another important component of steam turbines is the governor, which is used to control the turbine’s speed and ensure that it operates within safe and efficient parameters. The governor adjusts the steam flow to the turbine, regulating its output based on demand. This component ensures that the turbine maintains the correct speed regardless of variations in load, protecting the turbine from over-speeding or under-speeding, which could lead to mechanical failure. Modern steam turbines often use digital governors that employ sophisticated algorithms to precisely control steam input and optimize performance.
Condensers are critical components in steam turbine systems, particularly in rankine cycle power plants. After the steam has passed through the turbine, it needs to be condensed back into water so it can be reused. The condenser is responsible for cooling the steam, turning it back into a liquid by removing the heat from the exhaust steam. The condenser operates by transferring heat from the steam to cooling water, which typically circulates through the condenser’s tubes, absorbing the heat before being released into a cooling tower or another cooling system. The condenser is essential for maintaining the efficiency of the system, ensuring that the steam can be reused in the cycle, and reducing the need for additional water consumption.
In addition to these core components, steam turbines also incorporate a variety of auxiliary systems to ensure reliable operation and longevity. These include lubrication systems for the bearings and rotor, cooling systems for the stator and casing, and control systems to manage turbine operation. The maintenance of these components is critical to turbine performance, and regular monitoring is necessary to detect any issues before they lead to system failure. Vibration monitoring systems and temperature sensors are often used to ensure that the turbine is running within safe limits, providing early warning signs for potential malfunctions.
Over the years, advancements in materials science and manufacturing techniques have enabled the development of turbine components with higher strength, improved corrosion resistance, and greater overall efficiency. Superalloys and ceramic materials are increasingly being used for turbine blades and other critical components, allowing steam turbines to operate at higher temperatures and pressures, which translates into increased thermal efficiency. Additionally, additive manufacturing (3D printing) is being explored as a method to produce complex turbine components with improved precision and reduced manufacturing costs.
In conclusion, steam turbines are highly sophisticated machines with many critical components that work together to convert thermal energy into mechanical energy. From the rotor and blades to the bearings, nozzles, and stator, each part must be designed to withstand extreme conditions and ensure efficient energy conversion. As the demand for cleaner, more efficient power generation increases, the continued development of advanced materials and designs for steam turbine components will be essential to improving the performance and sustainability of power plants around the world.
Steam turbines are essential for the operation of a wide range of power plants, from traditional fossil-fuel plants to modern renewable energy systems like geothermal and biomass facilities. Their efficiency and ability to generate large amounts of power make them integral to meeting the world’s growing energy demands. The performance of steam turbines is closely tied to the design and function of their components. Over the years, innovations in steam turbine technology have enabled significant improvements in efficiency, reliability, and cost-effectiveness.
One of the key areas of development in steam turbine technology is high-temperature materials. As steam temperature and pressure increase, the materials used in turbine components must withstand even more extreme conditions. Advanced nickel-based alloys and tungsten-carbide coatings are commonly used for turbine blades and nozzles to improve their resistance to high-temperature oxidation and erosion. These materials help extend the life of turbine components, reduce maintenance costs, and improve the overall efficiency of the turbine. Additionally, the use of ceramic coatings on turbine blades has gained traction due to their superior heat resistance and ability to withstand thermal cycling, which can lead to cracks and material degradation over time.
Another critical aspect of turbine design is aerodynamic efficiency. The blade profile and the way steam flows over the blades significantly affect turbine performance. Modern steam turbines are designed with highly optimized blade shapes to ensure that steam flows smoothly over them, minimizing energy losses and maximizing power output. Advanced computational fluid dynamics (CFD) simulations are used to model steam flow and improve blade designs for better efficiency. These simulations help engineers test and refine turbine designs before physical prototypes are built, reducing development time and improving the likelihood of successful performance.
The efficiency of steam turbines can also be greatly enhanced by integrating them with combined-cycle systems. In a combined-cycle power plant, a gas turbine is used in conjunction with a steam turbine. The waste heat from the gas turbine is used to produce steam, which then drives the steam turbine. This setup significantly improves the overall efficiency of the power plant, as it allows for the recovery of heat that would otherwise be wasted in a simple cycle. Combined-cycle systems are widely used in natural gas plants and are increasingly being considered for carbon capture and storage (CCS) applications, where the captured CO2 can be sequestered underground or used in industrial processes.
Advanced control systems are another area of focus in steam turbine development. The role of digital technologies and automation in power generation is rapidly increasing. Modern steam turbines are equipped with sophisticated control systems that monitor and adjust parameters such as steam flow, turbine speed, and exhaust pressure in real time. These systems ensure that the turbine operates at optimal conditions, maximizing output while minimizing fuel consumption and emissions. Additionally, predictive maintenance systems use sensors and data analytics to predict when parts may fail, enabling proactive maintenance and reducing downtime.
Vibration monitoring is another crucial element in turbine operation. Excessive vibration can lead to premature wear and even catastrophic failure of turbine components. Steam turbines are equipped with advanced sensors that constantly monitor vibration levels throughout the system. These sensors detect any irregularities, allowing plant operators to take corrective action before serious damage occurs. Vibration monitoring systems are often linked to the turbine’s digital control system, providing operators with real-time data on the condition of critical components like the rotor and bearings.
As steam turbines are increasingly integrated with renewable energy systems, such as geothermal and biomass power plants, there is growing interest in making turbines more adaptable to different fuels and operating conditions. Biomass-fired plants, for instance, require turbines that can handle variable fuel quality and moisture content, which can affect combustion efficiency. Steam turbines designed for these applications must be flexible enough to handle a wide range of fuel types, including wood chips, agricultural waste, and other organic materials. Similarly, geothermal power plants require turbines capable of handling high-pressure steam from the earth’s core. These specialized turbines are designed to operate efficiently in extreme conditions and can be optimized for specific geothermal sites.
Environmental sustainability continues to be a driving factor in the evolution of steam turbine technology. Efforts to reduce greenhouse gas emissions and improve the carbon footprint of power plants have led to the development of turbines that are more energy-efficient and capable of operating on cleaner fuels. For instance, the use of hydrogen as a fuel source for steam turbines is a promising solution for decarbonizing power generation. Hydrogen can be used in place of fossil fuels to generate steam, with the byproduct being water vapor, making it a zero-emission option. Steam turbines designed to run on hydrogen require special materials and combustion technologies to safely burn hydrogen at high pressures and temperatures.
The operation of steam turbines in high-efficiency power plants is crucial for meeting the world’s energy needs while reducing environmental impact. Advances in supercritical and ultra-supercritical steam cycles have enabled power plants to operate at higher temperatures and pressures, significantly improving their thermal efficiency. Supercritical steam plants operate above the critical point of water (374°C and 22.1 MPa), allowing for more efficient conversion of heat into work. Ultra-supercritical plants go even further, achieving even higher efficiencies by operating at temperatures exceeding 600°C and pressures above 30 MPa. These advancements contribute to reducing the overall fuel consumption and emissions of power plants, making them more sustainable.
Looking ahead, steam turbines are expected to play a key role in carbon capture and storage (CCS) technologies. As the global community strives to reduce CO2 emissions, power plants equipped with steam turbines will be increasingly integrated with CCS systems to capture and store carbon emissions underground. CCS technology requires the adaptation of turbines to handle additional processes, such as compressing and transporting CO2. However, with continued research and development, steam turbines will continue to evolve to accommodate the growing demands of a low-carbon energy future.
In conclusion, the development of steam turbine components continues to be driven by the need for higher efficiency, lower emissions, and increased operational flexibility. From improvements in material science to advancements in control systems and predictive maintenance, steam turbines are evolving to meet the challenges of modern power generation. As the energy landscape continues to shift towards more sustainable and efficient systems, the ongoing innovation in steam turbine design will be crucial for ensuring that power plants can deliver reliable and environmentally friendly electricity for years to come.
Gas Turbine Components
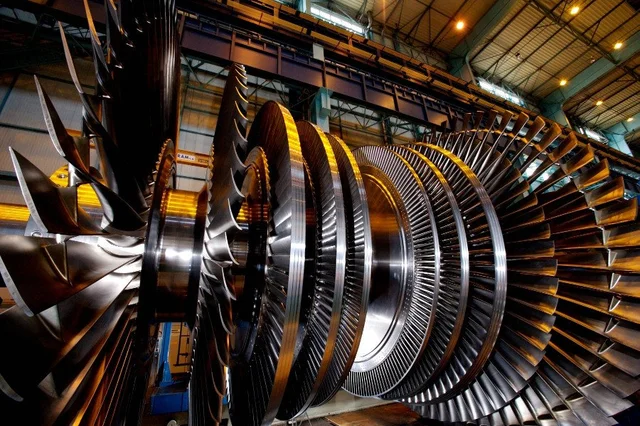
Gas turbines are complex machines used in various power generation, aviation, and industrial applications. These turbines operate by converting energy from hot gases, produced through the combustion of fuel, into mechanical energy. The gas turbine consists of several critical components, each designed to perform specific functions that allow for the efficient conversion of energy and optimal operation under extreme conditions. The main components of a gas turbine include the compressor, combustion chamber, turbine, rotor, shaft, bearings, and exhaust system, all working together to produce power. Each component must be meticulously designed to handle high temperatures, pressures, and rotational forces inherent in turbine operations.
The compressor is one of the most essential components of a gas turbine. It is responsible for compressing the incoming air before it enters the combustion chamber. This compression process increases the air’s pressure and temperature, enabling the gas turbine to achieve greater efficiency. The compressor is made up of a series of rotating blades (rotor blades) and stationary blades (stator blades) that help to sequentially compress the air in multiple stages. The design of the compressor blades is crucial, as they must maintain a delicate balance between high aerodynamic efficiency and the structural strength needed to withstand extreme stresses and temperatures. The rotor blades are typically made from high-strength alloys or composite materials that can withstand thermal fatigue and corrosion, while the stator blades are made from materials with high resistance to heat and wear.
Next in the process is the combustion chamber, where the compressed air is mixed with fuel and ignited to produce high-temperature, high-pressure exhaust gases. This is where the majority of energy conversion occurs in a gas turbine. The combustion chamber is equipped with injectors that spray fuel into the compressed air, and the ignition system ensures that the fuel-air mixture ignites at the right moment. The design of the combustion chamber is key to ensuring complete combustion, efficiency, and minimal emissions. Combustion chambers are typically lined with advanced ceramic materials and heat-resistant alloys that can withstand extremely high temperatures. The heat generated in the combustion process causes the exhaust gases to expand rapidly, creating the high-pressure flow necessary to drive the turbine.
The turbine is the part of the gas turbine responsible for extracting energy from the exhaust gases. It consists of a series of stages, each containing rotating blades that are driven by the high-energy gases exiting the combustion chamber. The rotating blades of the turbine convert the thermal energy from the exhaust gases into mechanical energy, causing the turbine to spin. The turbine is connected to the rotor, which is the central rotating element of the turbine. The rotor is typically mounted on a shaft that connects to a generator, where the mechanical energy is further converted into electrical energy. The turbine blades are typically made from advanced alloys, such as nickel-based superalloys, which offer excellent resistance to high temperatures, oxidation, and mechanical stresses.
The rotor is one of the most crucial parts of the gas turbine. It is a rotating component that is driven by the expanding gases from the turbine. The rotor is usually made up of several discs mounted on a central shaft. The rotor blades are attached to the discs and rotate with them, transferring the mechanical energy generated by the exhaust gases. As the rotor spins, it drives the shaft, which is connected to a generator or another machine that utilizes the mechanical power produced by the turbine. The rotor must be made from materials with high strength and fatigue resistance, as it undergoes significant centrifugal forces and thermal stresses during operation. In modern gas turbines, rotor components are often cooled using internal air channels to ensure they do not overheat and maintain optimal performance.
The shaft connects the rotor to the rest of the power generation system. The shaft transmits the mechanical energy generated by the turbine to the generator or other machinery, such as compressors or pumps. The design of the shaft is critical, as it must withstand the high rotational forces and ensure minimal deformation during operation. The shaft is often made from high-strength alloys to prevent failure under high mechanical stresses. It is also subjected to regular maintenance and monitoring to ensure that it is properly aligned and functioning efficiently.
Bearings are essential for supporting the rotating components of the gas turbine, including the rotor and shaft. Bearings reduce friction between the moving parts, allowing the rotor to spin freely and efficiently. Bearings in gas turbines are typically made from high-strength, low-friction materials such as ceramic composites or bronze and are often lubricated with oil or other specialized fluids. These bearings must be designed to withstand extremely high temperatures and mechanical stresses, and their performance is critical for maintaining the overall efficiency and longevity of the turbine. Gas turbines may have several different types of bearings, such as journal bearings (which support the shaft’s weight) and thrust bearings (which absorb axial loads and prevent the rotor from moving too far along the shaft).
The exhaust system of a gas turbine is responsible for directing the hot exhaust gases away from the turbine after they have passed through the turbine blades. The exhaust system is designed to handle high temperatures and pressures, ensuring that the gases are safely channeled out of the turbine and into the atmosphere or to a heat recovery system. In some power plants, the exhaust gases from the turbine are used to produce additional energy in a combined-cycle system, where the heat is used to produce steam that drives a steam turbine. This helps to improve the overall efficiency of the system by recovering heat that would otherwise be wasted. The design of the exhaust system also includes nozzles that help direct the exhaust gases with high velocity, maximizing the energy extracted from the exhaust gases.
Gas turbines also incorporate various control systems to manage their operation. Modern turbines are equipped with digital control systems that monitor performance in real time, adjusting parameters such as fuel flow, air intake, and exhaust conditions to ensure that the turbine operates at peak efficiency. These control systems can make adjustments based on changes in operating conditions, such as load demand, temperature variations, and fuel quality. The integration of sensors and predictive maintenance technologies into gas turbines allows for more efficient operation and proactive identification of potential problems before they lead to failures.
Another important component is the cooling system. Gas turbines operate at very high temperatures, and excessive heat can damage critical components. As a result, many turbines incorporate advanced cooling systems, such as air cooling or water-cooling channels built into key components like the turbine blades and rotor. Air cooling is typically achieved by directing compressed air from the compressor over turbine blades to absorb excess heat, while water cooling is used in larger turbines where higher thermal loads are present.
Lastly, the fuel system is an integral part of the gas turbine, as it is responsible for delivering the appropriate amount of fuel to the combustion chamber. Fuel systems in gas turbines are highly engineered to ensure precise fuel injection and efficient combustion. These systems must accommodate different fuel types, such as natural gas, diesel, or biofuels, while maintaining the turbine’s optimal performance and emissions control. Advanced fuel nozzles and injectors help ensure the efficient atomization of fuel for complete combustion, which improves turbine efficiency and reduces pollutant emissions.
In conclusion, the components of a gas turbine work together in a highly coordinated manner to convert fuel into mechanical energy. Each part, from the compressor and combustion chamber to the turbine, rotor, and exhaust system, plays a critical role in ensuring efficient and reliable operation. As gas turbine technology continues to advance, there are ongoing developments in materials science, cooling technologies, control systems, and fuel adaptability to improve efficiency, reduce emissions, and enable turbines to meet the growing demand for power generation in both industrial and commercial sectors.
As gas turbine technology evolves, ongoing advancements continue to enhance their performance, efficiency, and environmental sustainability. One key area of progress is the development of advanced materials that can withstand the increasingly demanding operating conditions. For instance, ceramic matrix composites (CMCs) are being explored as a potential replacement for metal components in turbine blades and other hot section parts. These materials offer significant advantages in terms of high-temperature resistance, lighter weight, and improved fuel efficiency. CMCs are particularly suited for use in the combustion chamber and turbine blades, where they can handle higher temperatures than traditional superalloys, contributing to improved turbine efficiency and reduced fuel consumption.
The integration of additive manufacturing (3D printing) technology is also gaining traction in gas turbine design and manufacturing. 3D printing allows for the creation of more complex and optimized geometries, particularly in turbine blades and other critical components, which can lead to improved airflow and reduced weight. By using this technology, manufacturers can produce parts with intricate cooling channels that would be difficult or impossible to create with traditional manufacturing methods. Additive manufacturing also offers potential for quicker prototyping and reduced lead times, which is particularly advantageous in industries where quick turnaround times are important.
Hybrid gas turbines, which combine the functionality of gas turbines and other power generation technologies, are another area of innovation. These turbines often incorporate hydrogen combustion or carbon capture capabilities to reduce carbon emissions. Hydrogen, as a clean fuel source, has gained significant attention in gas turbine development. Turbines designed to burn hydrogen can operate with zero carbon emissions, producing only water vapor as a byproduct. Additionally, gas turbines that can integrate with carbon capture and storage (CCS) technologies allow for the extraction of CO2 from exhaust gases, helping power plants achieve near-zero emissions. These hybrid systems, though still in the developmental stages, are expected to play a crucial role in meeting global decarbonization targets.
In terms of operational efficiency, combined cycle systems continue to be a focus of research. In a combined cycle power plant, a gas turbine is paired with a steam turbine, using the waste heat from the gas turbine’s exhaust gases to generate steam and produce additional electricity. This results in a much higher overall efficiency compared to standalone gas or steam turbines. By improving the performance and integration of gas and steam turbines in combined-cycle systems, the efficiency of power plants can reach up to 60% or higher, which is significantly better than older single-cycle plants. The growing trend of coupling gas turbines with renewable energy sources, such as wind or solar power, is another innovative development that helps create more stable and reliable power generation systems.
As environmental regulations continue to tighten, there is a growing emphasis on emissions reduction technologies for gas turbines. Turbine manufacturers are working to develop systems that can reduce nitrogen oxide (NOx) emissions, which are a major contributor to air pollution and smog. Advanced lean-premixed combustion techniques help reduce NOx emissions by ensuring more complete combustion at lower temperatures. In addition, the use of selective catalytic reduction (SCR) systems, which use a catalyst to convert NOx into harmless nitrogen and water, is becoming more widespread in gas turbine plants. These systems are being integrated into both new turbines and retrofitted to existing plants to meet stricter environmental standards.
The role of digitalization and predictive maintenance in optimizing turbine performance is also becoming increasingly important. Gas turbines are equipped with sensors that monitor key operational parameters such as temperature, pressure, vibration, and fuel flow. This real-time data is sent to digital control systems, which analyze it to ensure the turbine operates at optimal performance. Predictive maintenance involves the use of data analytics and machine learning algorithms to predict when a component is likely to fail, allowing for timely repairs and minimizing unplanned downtime. This approach not only improves the reliability of turbines but also extends their lifespan and reduces maintenance costs.
The internet of things (IoT) has further enhanced the monitoring capabilities of gas turbines. IoT-enabled sensors allow for constant remote monitoring of turbine conditions, enabling operators to make adjustments or perform maintenance from anywhere in the world. This interconnectedness enhances the operational efficiency and performance of turbines while providing valuable insights for continuous improvement. Additionally, gas turbines are becoming more integrated with other industrial systems, enabling improved energy management across entire facilities or even regional grids.
Another area where gas turbines are seeing significant improvements is in fuel flexibility. Traditional gas turbines have been designed to operate primarily on natural gas, but recent advancements are enabling turbines to run efficiently on a wider range of fuels. This includes biomass, synthetic fuels, and liquid fuels, which can help reduce dependency on fossil fuels and enhance energy security. The ability to switch between different fuel sources also provides operational flexibility, enabling gas turbines to respond to changes in fuel availability or price fluctuations.
In addition to fuel flexibility, the concept of distributed energy generation is gaining popularity, with gas turbines being deployed in smaller, modular systems that can be installed closer to the point of use. These systems can be used for combined heat and power (CHP) applications, where both electricity and useful heat are generated simultaneously. This type of localized generation reduces transmission losses and can be particularly beneficial for industrial facilities, commercial buildings, or even communities that require a reliable and self-sustaining power source. Small-scale, distributed gas turbines are also being used to complement renewable energy sources, providing backup power when solar or wind energy is unavailable.
Gas turbines are also playing a role in offshore and remote power generation. In places like offshore oil and gas platforms or remote mining sites, where the infrastructure for conventional power plants may be unavailable, gas turbines provide a compact and reliable power source. These turbines are specifically designed to operate in harsh environmental conditions, with enhanced corrosion resistance and the ability to withstand high winds, saltwater, and temperature extremes. The growing demand for energy in remote locations and offshore facilities will likely drive further innovations in turbine design and performance.
Looking toward the future, gas turbines will continue to be integral to the global energy landscape, especially as countries strive for a balance between reducing carbon emissions and ensuring a reliable power supply. The future of gas turbines lies in optimizing their efficiency, enhancing their environmental sustainability, and expanding their ability to operate with cleaner, renewable fuels. The ongoing integration of digital technologies, advanced materials, and hybrid systems will drive the next wave of innovation in gas turbine technology, ultimately contributing to a more sustainable and resilient energy system.
Hydraulic Turbine Components
Hydraulic turbines are vital components in the generation of hydroelectric power, which harnesses the energy of flowing or falling water to produce electricity. These turbines are designed to convert the mechanical energy of water into rotational mechanical energy, which can then be used to generate electrical power through a connected generator. Hydraulic turbines operate on the principle of fluid dynamics, where water flows over or through turbine blades, imparting energy to them and causing them to rotate. The key components of a hydraulic turbine are designed to work together efficiently to maximize energy extraction from the water flow and to ensure long-term durability and reliable operation.
One of the most critical components of a hydraulic turbine is the runner. The runner is the rotating part of the turbine that directly interacts with the water flow. It is typically designed with curved blades, or buckets, that are shaped to capture the energy of the moving water. As the water enters the turbine, it strikes the blades of the runner, causing the blades to move and rotate. The shape and size of the runner blades are carefully engineered to optimize energy conversion and minimize losses. The material used for the runner must be highly durable, often consisting of stainless steel or other corrosion-resistant alloys, as the turbine operates in an environment where it is constantly exposed to water and potential contaminants.
Connected to the runner is the shaft, a key component that transmits the rotational energy generated by the runner to other parts of the system, such as a generator. The shaft is usually made of high-strength steel to withstand the forces generated during operation. It must also be designed to handle high levels of torque and rotational speed without deforming. The shaft is connected to the runner via a hub, a central component that allows the runner blades to be mounted securely. The shaft is typically supported by bearings that reduce friction and ensure smooth rotation, preventing excessive wear and tear.
The bearings in hydraulic turbines are critical for ensuring the smooth rotation of the shaft and the runner. Bearings support the rotating components, allowing them to turn freely while minimizing friction and heat generation. These bearings are typically designed to operate in high-pressure environments where water and debris may pose a risk to their longevity. Journal bearings and thrust bearings are the most common types found in hydraulic turbines. Journal bearings are used to support the shaft, while thrust bearings absorb axial loads, preventing the shaft from moving excessively in the axial direction. Both types of bearings are designed for high durability and are often made from bronze, carbon composite materials, or other materials resistant to wear and corrosion.
The draft tube is another important component in a hydraulic turbine, serving to guide the water from the runner to the outlet, allowing the water to exit the turbine. The draft tube is typically located beneath the runner and is designed to convert the remaining kinetic energy of the water into pressure, which enhances the overall efficiency of the turbine. The draft tube also helps in controlling the flow of water and ensures that it exits the system in a controlled manner, minimizing turbulence and maximizing energy extraction. The shape and design of the draft tube are important for optimizing the efficiency of the turbine, and it is typically built with concrete or steel materials that can withstand the forces generated by the water flow.
The governor is a key component that regulates the speed of the turbine by controlling the flow of water into the system. The governor adjusts the position of the guide vanes or nozzles that control the amount of water entering the turbine. By regulating the water flow, the governor ensures that the turbine operates at a constant speed, regardless of variations in water flow rate. This helps maintain the desired electrical output from the connected generator and ensures that the turbine operates within safe parameters. Governors can be either mechanical, electronic, or hydraulic, depending on the design of the turbine and the specific requirements of the hydroelectric plant.
Guide vanes are stationary blades that direct the water flow toward the runner blades at the correct angle. These vanes are positioned around the runner and are designed to optimize the flow of water into the turbine, ensuring that the energy is transferred efficiently. The angle and position of the guide vanes can be adjusted by the governor to control the flow rate, providing better control over the turbine’s speed and performance. Guide vanes can be designed to open or close depending on the turbine’s operational conditions, allowing for fine adjustments to the system’s efficiency.
The stator is a stationary part of the generator that surrounds the rotating rotor. The stator houses the electromagnetic windings that interact with the rotor to generate electricity. In a hydraulic power generation system, the mechanical energy produced by the rotating runner is transferred via the shaft to the rotor of the generator. As the rotor turns, the magnetic field generated by the rotor induces a flow of current in the stator windings, generating electrical power. The design of the stator is crucial to ensuring maximum efficiency and preventing energy losses. The stator must be carefully aligned and insulated to ensure proper functioning and prevent short circuits or overheating.
The seal system is another important component in a hydraulic turbine. Seals are used to prevent water from leaking out of the turbine and to ensure that water is directed efficiently toward the runner. The seal system must withstand high pressures and the abrasive action of water, as well as the effects of temperature changes. Seals are typically made from materials such as rubber, carbon, or ceramic, and they are designed to provide a tight seal while reducing friction and wear.
The control system of a hydraulic turbine is responsible for monitoring and adjusting the turbine’s operation. This system includes sensors that track parameters such as rotational speed, pressure, and flow rate, and it uses this data to optimize performance and prevent damage to components. Modern turbines are often equipped with digital control systems that allow operators to monitor and adjust the turbine’s operation remotely. These systems can detect anomalies, such as changes in water flow or mechanical stress, and can automatically adjust the turbine’s settings to maintain optimal performance.
The electrical generator is another vital component connected to the hydraulic turbine. The generator converts the mechanical energy produced by the turbine into electrical energy. It is typically coupled to the turbine via a shaft and operates on the principles of electromagnetic induction. In many systems, the generator consists of a rotating rotor surrounded by a stationary stator. As the rotor turns, it generates a rotating magnetic field that induces an electric current in the stator windings. The electricity produced is then sent to the grid or to specific industrial users. The design and maintenance of the generator are critical for ensuring efficient energy conversion and reliable operation.
In conclusion, hydraulic turbine components are designed to work together in a highly efficient and synchronized manner to convert the energy from flowing or falling water into electrical energy. Each component, from the runner and shaft to the generator and governor, plays a crucial role in optimizing the turbine’s performance and ensuring the system operates reliably and efficiently. The materials used in the turbine’s construction must be carefully selected to withstand the harsh conditions of constant exposure to water, pressure, and mechanical stress. Technological advancements continue to improve the design, efficiency, and longevity of hydraulic turbines, enabling them to meet the growing demand for renewable energy while reducing environmental impacts.
As hydraulic turbines continue to evolve, several trends and innovations are shaping their development to meet modern energy demands and address environmental concerns. One notable area of advancement is the improvement of turbine efficiency through design modifications, materials enhancements, and more advanced control systems. In particular, advancements in blade aerodynamics and the hydrodynamic design of the turbine components contribute significantly to increasing the energy extracted from the water. Enhanced blade shapes that reduce turbulence and optimize the interaction between water flow and the turbine can boost the overall efficiency of the system. Additionally, the use of computational fluid dynamics (CFD) in the design process allows for more precise predictions of flow patterns and turbine behavior, leading to more optimized designs.
Another important area of innovation is the development of variable-speed turbines, which allow for more flexible operation under different water flow conditions. Traditional hydraulic turbines often operate at a constant speed, but variable-speed turbines can adjust their rotational speed to match variations in water flow, optimizing efficiency over a wider range of operating conditions. This feature is particularly beneficial in regions with fluctuating water availability or seasonal variations in water flow, such as river-based hydroelectric plants. Variable-speed turbines are also better suited to integrate with grid stabilization systems, as they can adjust their output in response to fluctuations in electricity demand or supply, especially when combined with renewable energy sources like wind and solar power.
The adoption of digital twin technology is also becoming increasingly common in the monitoring and maintenance of hydraulic turbines. A digital twin is a virtual model of a physical system, in this case, the turbine, which is continuously updated with real-time data from sensors embedded in the turbine. This allows operators to monitor the turbine’s performance remotely, simulate different operating conditions, and predict potential failures before they occur. By leveraging machine learning algorithms and predictive analytics, digital twins help optimize turbine performance, reduce downtime, and extend the lifespan of critical components. Additionally, digital twin technology enables better decision-making when it comes to scheduling maintenance or making upgrades to the turbine system.
The sustainability of hydraulic turbines is another area of focus as the world transitions toward greener energy solutions. Hydraulic turbines have long been considered a sustainable form of energy generation due to their low carbon emissions, but there is increasing pressure to further reduce the environmental impact of turbine construction and operation. Life cycle assessments (LCAs) are being used to evaluate the environmental impact of turbine components, from materials extraction and manufacturing to installation, operation, and decommissioning. This comprehensive assessment allows for improvements in material selection, recycling practices, and energy usage during the manufacturing process. Additionally, efforts are being made to minimize the impact of hydropower installations on surrounding ecosystems. Modern turbine designs aim to reduce the environmental disruption caused by large dams, with technologies such as fish-friendly turbines and fish passage systems helping mitigate harm to aquatic life.
One specific advancement in turbine technology is the development of low-head turbines, which are designed to generate power from sites with relatively low water heads (height differences). Traditionally, hydroelectric plants required significant water heads to produce enough pressure for turbine operation. However, low-head turbines are designed to operate effectively at sites with small elevation changes, expanding the potential locations where hydropower can be harnessed. These turbines are particularly beneficial for run-of-river applications, where water is diverted through a channel without the need for large reservoirs or dams. By utilizing existing water infrastructure, low-head turbines provide an opportunity for decentralized and more sustainable power generation in regions where conventional hydropower would not be feasible.
The integration of hydropower with energy storage systems is another promising development for the future of hydraulic turbines. Pumped storage systems, which are often paired with large hydroelectric plants, allow excess electricity generated during periods of low demand to be used to pump water back up to a higher elevation for storage. When demand increases, the stored water is released through turbines to generate electricity. This energy storage method acts as a form of grid stabilization, enabling utilities to manage supply and demand more effectively. There is growing interest in developing small-scale pumped storage and off-river storage solutions that can be integrated with smaller turbine systems to provide local or regional energy storage and balancing capabilities.
Remote monitoring and automation are also transforming the way hydraulic turbines are operated and maintained. The use of Internet of Things (IoT) devices and cloud computing allows for continuous remote access to turbine data, enabling operators to track turbine performance, diagnose issues, and adjust settings from anywhere in the world. These systems can be coupled with artificial intelligence (AI) to analyze large volumes of data and detect anomalies or inefficiencies. AI algorithms can predict when a turbine component is likely to fail, allowing for proactive maintenance and minimizing the risk of unexpected breakdowns. The integration of AI with machine learning algorithms can also help optimize the operation of multiple turbines in a hydropower plant, improving overall system efficiency.
As the demand for renewable energy grows, the potential for hydraulic turbines to be used in offshore applications is increasing. Offshore hydropower, particularly in tidal and wave energy generation, involves using turbines to capture the energy of moving water in marine environments. These systems are more challenging to design and implement due to the harsher conditions at sea, such as high winds, saltwater corrosion, and extreme weather. However, innovations in materials science, engineering, and offshore infrastructure are making these projects increasingly feasible. In tidal energy applications, turbines are placed on the seabed or attached to floating structures to capture the kinetic energy of the ocean’s tides. These projects, although still in the early stages, hold significant promise for diversifying the sources of clean, renewable energy.
The advancements in turbine controls also continue to play a crucial role in improving turbine performance. The use of adaptive control systems allows turbines to automatically adjust to changes in water flow or load demands, ensuring optimal operation and minimizing wear on components. These systems continuously assess the performance of the turbine and adjust parameters such as the positioning of guide vanes, speed of rotation, and load settings to maintain the most efficient operation. Advances in smart grid technology also enable better integration of hydropower systems with other renewable sources, creating more resilient and reliable energy networks.
The future of hydraulic turbines looks promising as new technologies and design improvements continue to increase their efficiency, environmental sustainability, and ability to meet the world’s growing energy needs. With ongoing innovation in turbine design, materials, and control systems, hydraulic turbines will continue to play a pivotal role in renewable energy generation, contributing to global efforts to transition to a cleaner and more sustainable energy future.
Material Science and Durability in Turbine Components
Material science plays a critical role in the design, performance, and longevity of turbine components, as turbines operate in extreme conditions where materials are subjected to high levels of mechanical stress, temperature fluctuations, corrosion, and erosion. The durability and efficiency of turbines depend significantly on the selection and development of advanced materials that can withstand these challenging environments. Whether in steam, gas, hydraulic, or wind turbines, the materials used must not only support the structural integrity of the components but also enable optimal performance over extended operational lifespans.
In steam turbines, which operate under high-pressure steam and temperatures, materials need to endure extreme thermal stresses while maintaining strength and resistance to fatigue. Steel alloys, particularly stainless steel and nickel-based alloys, are commonly used in steam turbines because of their ability to retain strength and resist oxidation at high temperatures. Heat-resistant steels, such as martensitic and austenitic stainless steels, are frequently used in components like rotors, blades, and nozzles. These materials are designed to resist creep, which is the slow deformation of material under constant stress at high temperatures, as well as thermal fatigue from repeated heating and cooling cycles. Additionally, to mitigate corrosion, these materials are often alloyed with elements like chromium and molybdenum, which enhance resistance to oxidation and other forms of corrosive wear.
Gas turbines face similar challenges, with components exposed to even higher temperatures and rapid cycles of heating and cooling. Superalloys, typically made of nickel, cobalt, or iron, are commonly used for parts that endure the highest levels of thermal and mechanical stress. These materials can withstand temperatures exceeding 1,000°C and offer excellent resistance to creep and oxidation. The turbine blades, for example, often feature advanced thermal barrier coatings (TBCs) made from ceramic materials, such as yttria-stabilized zirconia (YSZ), which insulate the metal from the extreme heat produced during combustion. These coatings are applied in thin layers on turbine components to reduce heat transfer, allowing the underlying metal to operate at higher temperatures without degrading. The ceramic coatings not only enhance performance by enabling more efficient combustion but also extend the service life of critical turbine components.
In hydraulic turbines, the primary challenge is corrosion, as these turbines are often submerged in water, which can contain various minerals, salt, and sediments that promote rusting and erosion. The materials used in these turbines need to be resistant to both erosion from the water flow and corrosion caused by the chemical composition of the water. Stainless steel and bronze alloys are commonly employed in the construction of the runner, shafts, and other critical parts of hydraulic turbines. In particular, high-chromium stainless steels offer superior resistance to rust and corrosion, making them ideal for use in high-flow environments. In areas exposed to seawater, marine-grade alloys, such as duplex stainless steels, are favored for their enhanced resistance to chloride-induced corrosion. Additionally, titanium alloys are used in some high-performance applications due to their excellent corrosion resistance and strength-to-weight ratio. To protect against erosion, hydraulic turbines are often designed with smooth, polished surfaces to reduce the impact of debris and sediment in the water, while coatings and cladding materials are also applied to further enhance durability.
Material selection in wind turbines is also critical, particularly in the blades, which must be lightweight, strong, and able to withstand the cyclical stress caused by wind forces. Fiberglass composites are the most commonly used materials for wind turbine blades due to their high strength-to-weight ratio and durability. These composite materials are typically made by combining fibers (usually glass, carbon, or aramid) with a resin matrix, creating a material that is both light and strong. Carbon fiber composites are sometimes used for high-performance blades, offering even greater strength and stiffness than fiberglass while reducing the overall weight. However, carbon fiber is more expensive, so it is generally used in larger, more advanced turbines. The outer surfaces of wind turbine blades are often coated with polyurethane or epoxy to protect them from environmental wear, UV radiation, and the accumulation of ice or debris.
In addition to the primary materials used in turbine construction, various surface treatments and coatings are employed to enhance the durability of components. For example, turbine blades are often coated with chromium carbide or tungsten carbide coatings to improve wear resistance, particularly in regions where erosion and corrosion are most prevalent. These coatings provide a hard, wear-resistant surface that extends the lifespan of the turbine while maintaining its efficiency. Similarly, plasma spraying and electroplating techniques are used to apply thin, protective layers of materials like nickel, cobalt, and titanium to components exposed to extreme conditions. These coatings not only protect the underlying metal from environmental factors but also help maintain the turbine’s aerodynamic properties by providing a smooth, uniform surface.
Another consideration in material science for turbine components is fatigue resistance. Many turbines operate under cyclical loading conditions, where components are subjected to repeated stress and strain as the turbine starts, stops, and continues to operate at various speeds. This repeated loading can cause material fatigue, leading to cracks and eventual failure if not properly managed. Titanium alloys and nickel-based superalloys are often selected for their excellent fatigue resistance, particularly in the high-stress regions of the turbine. Additionally, advanced welding techniques are used to join turbine components, and materials with similar fatigue properties are carefully selected to ensure that welded joints maintain the same strength and durability as the base materials.
Additive manufacturing, or 3D printing, is beginning to have an impact on turbine component design, especially for complex, small-scale parts that are difficult or expensive to manufacture using traditional methods. This technique allows for the creation of intricate shapes with precise material properties, reducing waste and improving efficiency. In the future, additive manufacturing could enable the production of turbine components with optimized geometries that reduce material usage and improve performance while maintaining or even enhancing the strength of critical parts. However, there are still challenges in ensuring the durability and reliability of 3D-printed turbine components, particularly under the extreme operating conditions encountered in industrial and power generation environments.
Finally, as the demand for renewable energy continues to grow, there is an increasing emphasis on sustainable materials for turbine construction. The environmental impact of turbine manufacturing, operation, and decommissioning is a significant consideration in the overall lifecycle of these systems. Efforts are underway to find alternatives to some of the more resource-intensive materials, such as rare earth elements used in magnets for wind turbines or certain alloys used in turbine blades. Recycling and material reuse are also critical aspects of turbine component longevity and sustainability. As turbines reach the end of their operational life, materials such as steel, copper, and even composite blades are being explored for their potential to be recycled or repurposed in other applications.
In summary, material science is central to the development of turbine components, as the materials must not only withstand harsh operating environments but also ensure the longevity and efficiency of the turbine. From the selection of alloys and coatings to the use of advanced materials like composites and superalloys, every component must be carefully engineered to meet the demands of power generation. Ongoing research in material science is focused on improving turbine durability, reducing environmental impact, and enhancing the performance of turbines across various energy sectors, all of which will contribute to more efficient, sustainable energy generation in the future.
As turbine technology continues to evolve, ongoing research and development in material science will lead to even greater innovations in turbine component durability and performance. One of the emerging areas of focus is the use of nanomaterials, which have shown promising potential for improving the properties of turbine components. Nanomaterials, such as carbon nanotubes, graphene, and other nanocomposites, possess remarkable mechanical strength, thermal stability, and resistance to wear and corrosion. These properties make them ideal candidates for applications in turbine components that experience extreme conditions. The ability to modify the structure of materials at the nanoscale allows for enhanced performance while maintaining lightweight and energy-efficient designs. Although the widespread application of nanomaterials in turbines is still in the research phase, their integration into critical components, such as turbine blades and nozzles, could revolutionize the industry by significantly improving the lifespan and efficiency of turbines.
Another area of material science innovation is the development of smart materials and self-healing materials. Smart materials are materials that can change their properties in response to environmental stimuli, such as temperature, pressure, or electromagnetic fields. These materials could potentially be used in turbine components to adapt to fluctuating operating conditions, improving performance and preventing damage. For example, materials with shape-memory properties could automatically adjust their shape or stiffness in response to thermal changes, reducing the risk of deformation and extending component life. Additionally, self-healing materials, which can automatically repair damage such as cracks or erosion, offer the potential to significantly reduce maintenance requirements and downtime. While these materials are still in the experimental stage, they hold considerable promise for enhancing the durability of turbine components and minimizing the need for costly repairs or replacements.
In terms of material coatings, further advancements are being made in the development of high-temperature coatings that can enhance turbine performance and longevity. These coatings are designed to protect turbine components from the damaging effects of extreme heat and oxidation, particularly in gas and steam turbines. Recent innovations have focused on thermal cycling resistance and the development of coatings that can withstand sulfur-induced corrosion—a major issue for turbines that burn fossil fuels or operate in sulfur-rich environments. Researchers are investigating novel materials, including ceramic-metallic composites and multilayer coatings, that can withstand the high temperatures of modern gas turbines while also offering superior resistance to corrosion and erosion.
One of the major drivers of material innovation in turbine technology is the increasing push for efficiency improvements in energy generation systems. As energy production becomes more competitive, optimizing turbine performance has become a critical focus. Advanced materials with higher thermal conductivity, lower thermal expansion, and greater fatigue resistance will enable turbines to operate at higher temperatures and pressures, resulting in more efficient energy conversion. This, in turn, can help reduce fuel consumption and emissions, contributing to a more sustainable energy future. For example, the use of high-performance ceramic materials in turbine components can facilitate higher operational temperatures, which can increase thermodynamic efficiency and allow turbines to produce more energy from the same amount of fuel.
The development of advanced manufacturing techniques is also playing a significant role in improving the performance of turbine components. The use of additive manufacturing (3D printing) has the potential to reduce the material waste traditionally associated with manufacturing large turbine components. Additive manufacturing allows for precise control over the material composition and geometry of turbine parts, enabling the creation of lightweight, high-strength components that are optimized for performance. The ability to produce complex, custom-shaped components with fewer material defects also reduces the likelihood of component failure and enhances the overall reliability of the turbine system. As 3D printing technologies continue to improve, they will likely be used more extensively in the production of turbine components, particularly those with intricate designs or requiring specialized materials.
Furthermore, the integration of advanced diagnostics and monitoring systems into turbine design is enhancing the ability to detect material degradation before it leads to failure. Sensors embedded in turbine components can monitor various parameters, such as temperature, pressure, vibration, and wear, and provide real-time data on the condition of the material. By leveraging machine learning algorithms, operators can predict when a turbine component is likely to fail due to material degradation, such as cracks or corrosion, allowing for proactive maintenance and replacement. This predictive maintenance approach not only reduces downtime and maintenance costs but also improves turbine performance by ensuring that components are always operating within optimal parameters.
Recycling and material reuse are also becoming key considerations in the development of turbine components, particularly as sustainability becomes an increasing priority in the energy sector. Many turbine materials, such as metals and alloys, can be recycled at the end of their life cycle, reducing the environmental impact of manufacturing and disposal. Additionally, researchers are exploring ways to reuse materials from decommissioned turbines in the production of new components. This approach not only helps to conserve raw materials but also reduces the carbon footprint associated with the production of new turbine components. As a result, the circular economy model is gaining traction in the turbine industry, encouraging manufacturers to design turbines with end-of-life recycling and reuse in mind.
In conclusion, the field of material science continues to drive innovation in turbine technology, with advancements in material properties, manufacturing techniques, coatings, and monitoring systems all contributing to the development of more efficient, durable, and sustainable turbines. As the demand for clean energy grows, turbines will play an increasingly important role in meeting global energy needs. By improving the materials used in turbine construction and enhancing their ability to withstand extreme operating conditions, the turbine industry can continue to evolve, providing more reliable and cost-effective energy solutions. The future of turbine technology will be shaped by ongoing research and development in material science, ensuring that turbines remain at the forefront of renewable energy generation for years to come.
Efficiency Enhancements in Turbine Technology
Efficiency enhancement in turbine technology is a critical aspect of modern energy generation, aiming to optimize the conversion of thermal or mechanical energy into useful work while minimizing losses. As global energy demand continues to rise and environmental concerns intensify, improving the efficiency of turbines, whether in steam, gas, hydraulic, or wind power plants, has become a top priority. The focus on enhancing turbine efficiency is not only driven by the need for better fuel economy and reduced emissions but also by the demand for greater performance in more challenging operating conditions. Advances in turbine technology, driven by material science, design innovations, and system integration, have significantly increased the efficiency of turbines over the past decades, resulting in improved power output, reduced operational costs, and minimized environmental impact.
One of the primary approaches to enhancing turbine efficiency is through increasing operating temperatures and pressures. In steam turbines, for instance, raising the temperature and pressure of the steam entering the turbine allows for greater thermodynamic efficiency. The Rankine cycle, the thermodynamic cycle used in steam turbines, operates more efficiently at higher temperatures because it results in a greater temperature differential between the heat source (e.g., a boiler) and the heat sink (e.g., a condenser), increasing the potential energy extraction. However, high temperatures also introduce challenges for material durability, as the turbine components must be capable of withstanding the stresses and corrosion caused by the elevated heat. Advances in superalloys and ceramic coatings have been crucial in enabling these higher operating conditions by providing better resistance to thermal stresses, oxidation, and erosion.
In gas turbines, improving efficiency is often a matter of pushing the limits of combustion temperature and pressure. Modern gas turbines achieve high efficiency by utilizing combined cycle systems, which integrate both gas and steam turbines. In these systems, the waste heat from the gas turbine is used to generate steam, which is then used to drive a steam turbine, thus increasing the overall efficiency of the power plant. The thermal efficiency of a combined cycle plant can exceed 60%, far higher than that of a simple cycle gas turbine, which typically operates at efficiencies around 35-40%. To achieve this, gas turbines are designed to operate at higher pressures, temperatures, and fuel efficiencies, and advances in heat recovery steam generators (HRSGs) and turbine blade materials have played a significant role in improving performance.
Another key approach to improving turbine efficiency is the optimization of the aerodynamics of turbine blades and rotors. Turbine blades are exposed to high forces and temperatures, so their design must minimize drag and maximize the energy extraction from the fluid (steam, gas, or water) flowing over them. In steam and gas turbines, the blade profile is continuously refined to optimize flow conditions and minimize energy losses due to turbulence, friction, and shock waves. Advances in computational fluid dynamics (CFD) allow engineers to simulate and optimize the airflow around blades with greater precision, leading to more efficient designs. These optimized blade designs, combined with advanced cooling technologies, such as internal cooling channels or film cooling, ensure that the blades remain effective at the elevated temperatures and pressures they face.
The development of advanced materials has also been pivotal in enhancing turbine efficiency. In both steam and gas turbines, components such as blades, nozzles, and rotors must withstand high temperatures while maintaining strength and resistance to wear. Materials like nickel-based superalloys, ceramics, and composite materials have enabled turbines to operate at higher temperatures and pressures without compromising structural integrity. For instance, thermal barrier coatings (TBCs) applied to turbine blades help to insulate the blades from the extreme heat of the combustion gases, allowing them to operate at higher temperatures while reducing the risk of overheating and degradation. Furthermore, low-friction coatings and wear-resistant alloys help minimize friction and wear, improving the lifespan and efficiency of turbine components.
Another technological advancement contributing to turbine efficiency is variable turbine geometry (VTG), particularly in gas turbines. VTG systems allow for the adjustment of the blade angles in response to changing operating conditions. By optimizing the blade angles for various stages of operation, VTG systems enable turbines to maintain high efficiency across a wider range of load conditions. This flexibility allows for more efficient operation during startup, shutdown, and variable load conditions, ensuring that the turbine operates at peak efficiency throughout its entire operating range.
Hybrid systems are also gaining traction in the pursuit of higher turbine efficiency. In some cases, turbines are combined with other energy generation technologies to enhance overall system performance. For example, solar thermal systems can be coupled with gas turbines to provide supplemental heating for the combustion process, thereby reducing the need for fuel and increasing overall efficiency. Similarly, battery storage systems can be integrated with turbines to help balance load fluctuations and improve efficiency during periods of high demand or variable energy input. By using multiple technologies in tandem, hybrid systems can optimize the efficiency of the entire power generation process.
The integration of advanced monitoring systems and predictive maintenance also plays a crucial role in improving turbine efficiency. Real-time data from sensor networks embedded in turbine components allows operators to monitor the performance of the turbine and detect potential issues before they lead to failures or inefficiencies. For example, sensors can detect vibration, temperature, and pressure changes, which may indicate wear or degradation in turbine components. Advanced analytics and machine learning algorithms can analyze these data points to predict when components need maintenance or replacement, preventing unplanned downtimes and ensuring that turbines operate at peak efficiency.
In the case of wind turbines, enhancing efficiency is focused on improving blade design, increasing the aerodynamic performance, and making use of advanced control systems that optimize the turbine’s response to changing wind conditions. Modern wind turbines utilize active pitch control systems to adjust the angle of the blades in real-time, ensuring that the blades are always operating at an optimal angle for maximum energy capture, regardless of wind speed. Additionally, advancements in control algorithms and power electronics allow for more precise and efficient operation, ensuring that wind turbines can extract the maximum possible energy from the wind.
In hydroelectric turbines, efficiency improvements come from refining turbine design, improving flow conditions, and optimizing the integration of turbines with hydropower plants. Modern Francis, Pelton, and Kaplan turbines have been designed to offer higher efficiency by reducing mechanical losses, improving cavitation resistance, and optimizing the flow distribution across the blades. The use of flow optimization technologies, such as variable speed operation and advanced flow control mechanisms, also contributes to higher efficiency in hydroelectric turbines by allowing the turbines to adjust to changing water flow conditions.
Finally, cogeneration (or combined heat and power, CHP) is an approach that improves turbine efficiency by capturing and utilizing waste heat for additional energy production. This method, used primarily in industrial applications and large-scale power plants, recycles the exhaust heat from turbines to generate additional power or provide heating for industrial processes, increasing the overall energy efficiency of the system. By integrating heat recovery systems, such as heat recovery steam generators (HRSGs), cogeneration systems can operate at efficiencies exceeding 80%, compared to the typical efficiency of 35-45% in standalone thermal power plants.
In conclusion, efficiency enhancements in turbine technology are driven by innovations across multiple domains, from advanced materials and optimized designs to hybrid systems and real-time monitoring. By improving turbine components, optimizing energy conversion processes, and integrating complementary technologies, the industry continues to make significant strides in maximizing the efficiency of turbines. As the demand for cleaner, more efficient energy grows, these advancements will be critical in meeting global energy needs while minimizing environmental impacts.
As the pursuit of higher turbine efficiency continues, there are several emerging trends and innovations that will further propel the development of turbine technology in the coming years. These trends will involve advances in material science, power conversion processes, and integration with renewable energy sources, ultimately making turbines more efficient, cost-effective, and environmentally friendly.
One of the key areas of ongoing research is advanced cooling technologies. As turbines operate at increasingly higher temperatures to improve thermodynamic efficiency, cooling becomes a critical factor in maintaining the integrity of turbine components, especially turbine blades and rotors. Advanced cooling techniques, such as internal cooling channels, film cooling, and heat exchangers, are being developed to manage the extreme heat generated during turbine operation. The introduction of new heat-resistant materials and innovative nanofluid cooling systems, which use nanoparticles suspended in liquids for enhanced heat transfer, could further improve cooling efficiency and allow turbines to operate at even higher temperatures, thus increasing overall efficiency.
Another exciting development in turbine technology is the concept of electrification in gas turbines, particularly for use in power plants. Electrification involves replacing some of the mechanical energy typically used for driving auxiliary systems with electrical energy, which could increase efficiency by minimizing energy losses associated with mechanical drives. The adoption of high-efficiency electrical generators and power electronics could enable the turbine to better integrate with the grid, reducing losses associated with transmission and distribution. Moreover, hybrid power systems, where turbines are combined with renewable energy sources like solar or wind, would allow for more stable and efficient operation while helping to reduce dependence on fossil fuels.
The trend towards decarbonization and net-zero emissions is also influencing the development of more efficient turbine technology. The burning of fossil fuels in conventional steam and gas turbines is a major source of greenhouse gas emissions. However, emerging technologies like hydrogen-powered turbines and carbon capture and storage (CCS) technologies are being explored to help mitigate the environmental impact of turbine operations. Hydrogen has the potential to be a clean fuel for turbines, producing zero emissions when burned. As hydrogen infrastructure and production technologies continue to mature, it is expected that gas turbines designed to run on hydrogen or hydrogen-blended fuels will become a key part of decarbonized power generation systems.
In addition to hydrogen, biomass and biofuels are becoming increasingly important for enhancing turbine efficiency in sustainable energy generation. Biomass, derived from organic materials like wood, agricultural residues, and even algae, can be used as a carbon-neutral fuel in turbines. Biofuels, such as synthetic diesel and ethanol, offer the advantage of being compatible with existing turbine designs, providing an easier pathway for transitioning to cleaner fuels. Biomass and biofuel-based turbine systems are expected to play a significant role in replacing fossil fuels in the energy mix, thus improving the overall sustainability of turbine-powered power plants.
Further developments in smart grid integration will also have an impact on turbine efficiency. Smart grids enable better coordination between electricity generation, distribution, and consumption. With turbines integrated into a smart grid, real-time data on power demand and supply can help optimize turbine operation, reduce energy waste, and balance power generation more effectively. This integration will allow turbines to operate in a more dynamic, responsive manner, adjusting their output based on the fluctuating needs of the grid, which is especially important with the increasing share of intermittent renewable energy sources like wind and solar.
Another innovation expected to play a significant role in enhancing turbine efficiency is additive manufacturing, or 3D printing. The ability to manufacture complex and lightweight components with intricate geometries allows for the creation of turbine parts that are more aerodynamically efficient, have better cooling capabilities, and are optimized for performance. Additive manufacturing also reduces material waste and production costs, allowing for rapid prototyping and customization. With the continued advancement of 3D printing technologies, turbine manufacturers will have more flexibility in designing and producing high-performance turbine components that are tailored to specific operational conditions, thus improving efficiency and longevity.
In the case of wind turbines, next-generation large-scale turbines are being designed to further push the limits of efficiency. These turbines are incorporating longer, more flexible blades that can capture more energy from lower wind speeds, thus increasing the energy output. Additionally, floating wind turbines are being developed for offshore applications, enabling turbines to be installed in deeper waters where wind speeds are typically higher, further enhancing their efficiency. These innovations, along with advancements in turbine design and control systems, will continue to make wind power an increasingly important and efficient part of the global energy mix.
The future of turbine efficiency will also involve integrated multi-phase systems, such as those that combine multiple types of turbines for enhanced energy recovery. For example, combined steam-gas turbine systems and combined cycle systems allow for the capture of waste heat from one turbine to feed into another, resulting in higher overall efficiency. Additionally, innovations in multi-stage turbines that incorporate multiple working fluids or processes (e.g., organic Rankine cycle (ORC) turbines for waste heat recovery) are helping to improve the efficiency of energy conversion systems by expanding the range of temperatures and pressures over which the turbine can operate effectively.
As digital technologies continue to develop, digital twin technology and artificial intelligence (AI) are emerging as powerful tools for improving turbine efficiency. A digital twin is a virtual replica of a turbine that simulates its performance under various operating conditions. This digital model allows engineers to test different scenarios, predict maintenance needs, and optimize turbine settings before they are implemented in real life. Additionally, AI can be used to analyze operational data from turbines, detect inefficiencies, and suggest improvements, leading to higher efficiency and reduced operational costs over time.
Finally, as turbines continue to evolve, there will be an increasing focus on modular and decentralized turbine systems. These smaller, more flexible turbine systems can be deployed in a variety of settings, from remote areas to industrial facilities, where they can operate independently or in conjunction with local power grids. By providing localized energy generation, these modular turbine systems can enhance energy security, reduce transmission losses, and provide a more efficient and sustainable energy solution for various applications.
In conclusion, the future of turbine technology is marked by continuous innovation aimed at improving efficiency across a wide range of energy generation systems. From advanced materials and cooling techniques to hybrid systems and integration with renewable energy sources, the ongoing advancements in turbine technology will play a critical role in meeting the growing global demand for clean, reliable, and cost-effective energy. As the industry moves forward, these innovations will enable turbines to operate more efficiently, reduce their environmental impact, and contribute to the transition to a more sustainable energy future.
Advanced Turbine Configurations and Hybrid Systems
Advanced turbine configurations and hybrid systems are playing a critical role in the evolution of power generation technologies, as the demand for more efficient, sustainable, and flexible energy solutions continues to rise. These innovations aim to optimize energy production, reduce emissions, and enhance the overall performance of turbine-based systems by integrating different types of turbines and energy generation technologies. The use of hybrid systems and advanced turbine configurations offers significant improvements in efficiency, operational flexibility, and fuel diversity, making them increasingly important in modern power plants, industrial applications, and renewable energy integration.
Advanced turbine configurations involve the integration of multiple turbine types, operating conditions, and fuel sources to maximize energy output while minimizing waste. One of the most prominent examples of this is the combined cycle power plant. This configuration involves the coupling of both gas and steam turbines, where the waste heat from the gas turbine is used to generate steam for the steam turbine. This process significantly enhances overall efficiency, as it allows the energy from the exhaust gases of the gas turbine to be recovered and utilized for additional power generation. The combined cycle approach can reach efficiencies of over 60%, which is much higher than the typical 35-40% efficiency achieved by single-cycle gas turbines. The integration of a heat recovery steam generator (HRSG) is crucial to the process, allowing the recovery of the waste heat to convert water into steam, which in turn powers the steam turbine.
Beyond the combined cycle, other advanced turbine configurations include integrated gasification combined cycle (IGCC) systems, where coal or biomass is gasified to produce synthetic gas (syngas) that fuels a gas turbine. The syngas is then used in the gas turbine, and the exhaust heat is routed to a steam turbine. This configuration is particularly promising for utilizing non-fossil fuels, such as biomass and waste materials, and reducing the environmental impact of traditional coal-fired power plants. IGCC systems offer the potential for higher efficiency and cleaner emissions when compared to conventional coal-based plants.
Another advanced configuration is the co-generation or combined heat and power (CHP) system, which is particularly beneficial for industrial applications. In a CHP system, a turbine generates both electricity and useful heat for industrial processes, space heating, or district heating. By simultaneously producing power and heat, CHP systems can achieve efficiencies of up to 80%, much higher than conventional power plants that only generate electricity. This configuration is commonly used in industries such as paper, chemical manufacturing, and food processing, where both electricity and heat are essential for operations. Additionally, CHP systems can significantly reduce the carbon footprint by utilizing waste heat and improving the overall energy utilization of the facility.
Hybrid systems represent another innovation that blends different energy generation technologies to enhance overall efficiency and flexibility. A prime example of a hybrid system is the solar-gas turbine hybrid system. In this configuration, concentrated solar power (CSP) systems, such as parabolic troughs or solar power towers, are used to provide thermal energy to a gas turbine. The solar energy augments the turbine’s fuel, reducing the reliance on fossil fuels and improving the environmental performance of the system. This hybrid approach allows for higher efficiency than either technology alone, as the gas turbine operates more efficiently at higher temperatures, which are enhanced by solar energy. The integration of solar power also reduces fuel consumption, making the system more cost-effective in the long term and decreasing greenhouse gas emissions.
Wind-gas turbine hybrid systems are also gaining traction, particularly in regions with abundant wind resources. In these systems, the variable power output from wind turbines is combined with the flexibility of gas turbines to create a reliable, low-emission power generation solution. Wind power is intermittent, meaning that it does not always align with peak energy demand. However, by integrating wind turbines with gas turbines, the gas turbines can fill in the gaps during periods of low wind, ensuring that the grid remains stable. This type of hybrid system can optimize the use of renewable energy while maintaining grid reliability, reducing the overall carbon footprint of the energy generation system.
Another promising hybrid system is the hydrogen-gas turbine hybrid, where hydrogen, either produced from renewable energy sources (green hydrogen) or from natural gas reforming, is used as a fuel in gas turbines. Hydrogen combustion produces only water vapor as a byproduct, making it a highly sustainable fuel option for turbines. The integration of hydrogen with gas turbines enables the use of renewable hydrogen as a clean fuel source, helping to decarbonize power generation. Moreover, hydrogen turbines can complement renewable energy generation by providing a flexible, dispatchable power source when wind or solar energy is unavailable.
Advanced turbine configurations also include hybrid offshore wind systems that combine gas turbines with floating wind turbines. This integration allows for the exploitation of high-wind potential in deep-sea locations where traditional offshore wind turbines cannot be deployed. Floating wind turbines, which are mounted on floating platforms anchored to the seabed, can generate electricity in areas with stronger and more consistent winds. By pairing these turbines with gas turbines, hybrid offshore systems can provide more stable and continuous power generation, even in the absence of wind.
In the industrial sector, hybrid systems are used to improve energy efficiency in manufacturing plants. A common example is the integration of waste heat recovery systems (WHR) with turbines. In such configurations, excess heat from industrial processes, such as metal smelting, cement production, or glass manufacturing, is recovered and used to drive a steam turbine. The turbine generates electricity, which can either be used on-site or sold back to the grid. This approach reduces the need for external energy sources, cuts down on operating costs, and reduces the carbon footprint of industrial operations. By using a hybrid combination of waste heat recovery and turbine power generation, these systems optimize energy use and increase overall efficiency.
Geothermal-gas hybrid systems represent another innovative approach in hybrid turbine technology. Geothermal energy provides a constant and reliable heat source, which can be used in conjunction with gas turbines to generate electricity. The geothermal heat is utilized to create steam or hot fluids, which are then used to drive turbines. By combining geothermal energy with gas turbine technology, this hybrid system offers a flexible, low-emission power generation solution, especially in areas with geothermal resources. It helps provide consistent, base-load power while reducing reliance on fossil fuels.
The integration of energy storage into turbine systems is becoming increasingly important as part of hybrid solutions. Battery storage systems can be integrated with both gas and renewable energy turbines to store excess energy generated during peak production periods. This stored energy can then be used when demand is high or when renewable energy generation is low. By enabling turbines to operate more flexibly and efficiently in conjunction with energy storage, hybrid systems can better balance the grid and enhance the resilience of power generation systems.
In conclusion, advanced turbine configurations and hybrid systems are key to the future of energy generation. These innovative systems enable the integration of various fuel sources, renewable energy, and storage technologies to enhance the efficiency, flexibility, and sustainability of power generation. By combining different turbine technologies with complementary energy sources, hybrid systems provide a reliable, low-emission, and cost-effective solution to meet the growing global energy demand while minimizing environmental impact. As technology continues to advance, these systems will play an increasingly important role in shaping the future of the energy landscape.
As the energy sector continues to evolve, the development of advanced turbine configurations and hybrid systems will become increasingly critical in addressing the challenges associated with climate change, energy security, and the transition to sustainable energy sources. Several emerging trends indicate that these systems will not only improve the efficiency and sustainability of power generation but will also foster a more resilient and flexible energy infrastructure.
One significant advancement is the continued exploration of multi-fuel turbines, which are capable of operating on a wide variety of fuels. These turbines are designed to switch seamlessly between different fuel sources, such as natural gas, hydrogen, biogas, and even waste materials. Multi-fuel turbines provide a higher level of operational flexibility, making it easier for power plants to adapt to changing fuel availability, cost fluctuations, and environmental regulations. This flexibility is particularly important in regions where access to a single fuel source may be limited or where fuel prices are volatile. As the world transitions to cleaner energy sources, the ability to operate on renewable fuels like hydrogen and biogas will allow turbines to remain relevant and effective in a decarbonized energy landscape.
Another important development in advanced turbine technology is the growing focus on high-temperature materials. Turbines are increasingly being pushed to operate at higher temperatures to improve their efficiency, as the efficiency of thermodynamic cycles increases with temperature. Materials capable of withstanding the extreme conditions inside turbines are being developed, including superalloys, ceramic coatings, and composite materials. These advanced materials improve turbine durability and performance while reducing maintenance needs and extending the lifespan of components. As turbines are subjected to higher pressures and temperatures, these materials play a crucial role in preventing failure and ensuring the turbine operates efficiently over extended periods.
In the realm of digitalization and control systems, advancements in artificial intelligence (AI), machine learning (ML), and predictive maintenance are driving improvements in turbine performance and operational efficiency. AI algorithms can analyze vast amounts of operational data to optimize turbine performance in real-time, adjusting parameters like speed, temperature, and fuel flow to maximize efficiency and minimize wear and tear. Predictive maintenance techniques, powered by AI, help identify potential issues before they become critical, reducing downtime and extending the life of turbine components. These technologies are also being integrated into turbine design, allowing engineers to simulate different operational scenarios and test turbine performance before physical deployment, thereby improving the overall design process.
The integration of smart grid technology into turbine systems is another key innovation. Smart grids are designed to optimize the flow of electricity across power networks, balancing supply and demand more efficiently. By linking turbines with smart grid systems, power plants can better manage fluctuations in energy demand, incorporating renewable energy sources more effectively. Turbines can be used to provide flexible backup power when intermittent renewable generation, such as wind or solar, is unavailable. The integration of turbines into smart grids enables the creation of demand response systems, where turbines can be ramped up or down in response to real-time changes in energy demand, helping stabilize the grid and improve efficiency.
Energy storage systems are also playing an increasingly vital role in hybrid turbine configurations. Battery storage, pumped hydro storage, and compressed air energy storage (CAES) can store excess energy generated during periods of low demand or when renewable energy generation is high, such as during the daytime when solar power is abundant. This stored energy can then be used during periods of high demand or when renewable energy generation is low, providing a steady and reliable power supply. By combining turbines with energy storage systems, the energy sector can overcome the intermittency challenges associated with renewable energy sources and reduce reliance on fossil fuels. Energy storage also allows for better grid integration, ensuring that power plants can operate more efficiently and respond to changing demand.
Floating wind turbines represent a promising frontier in turbine innovation, particularly for offshore wind farms. These turbines are designed to be installed on floating platforms, allowing them to be deployed in deeper waters where wind speeds are higher and more consistent. Floating wind turbines are equipped with advanced control systems that optimize their position and angle to capture the maximum amount of wind energy. When combined with other turbine technologies, such as gas or hydrogen turbines, floating wind turbines can contribute to hybrid systems that offer a stable and continuous power supply, even when wind conditions vary. This innovation is opening up new possibilities for harnessing offshore wind resources and expanding the geographic areas where wind energy can be generated.
In the context of district energy systems, which are used to supply heating and cooling to multiple buildings or even entire cities, advanced turbine configurations are being utilized to enhance energy efficiency and sustainability. Microturbines and small-scale combined heat and power (CHP) systems are increasingly being used in district energy applications. These turbines provide a reliable and localized source of power and heat, reducing the need for centralized power generation and improving the overall efficiency of energy distribution. By integrating small-scale turbines into district energy networks, urban areas can better manage energy consumption, reduce transmission losses, and lower carbon emissions, contributing to the overall goal of creating more sustainable cities.
Moreover, as the energy industry moves toward decarbonization, carbon capture and storage (CCS) technologies are being integrated with turbine systems to further reduce greenhouse gas emissions. CCS technologies capture carbon dioxide (CO2) produced by turbines and other industrial processes, preventing it from being released into the atmosphere. This captured CO2 is then stored underground in geological formations or repurposed for use in other industries. The combination of CCS with advanced turbine configurations can help mitigate the environmental impact of fossil fuel-based power generation while still utilizing existing turbine infrastructure.
In the long-term future, fusion power may also emerge as a potential source of energy that could significantly impact turbine technology. While nuclear fusion is still in the early stages of development, it has the potential to provide an almost unlimited source of clean energy. If successful, fusion reactors could be used to generate heat that drives advanced turbines, providing a new and highly efficient method of generating electricity with minimal environmental impact. Fusion power is not expected to be commercially viable for several decades, but ongoing research into fusion energy could lay the groundwork for future innovations in turbine technology.
Finally, the global collaboration between research institutions, energy companies, and governments is essential in driving the continued development of advanced turbine configurations and hybrid systems. As the demand for cleaner, more efficient energy solutions increases, international cooperation will be key to accelerating the adoption of these technologies and ensuring their widespread deployment. By sharing knowledge, resources, and best practices, stakeholders across the energy sector can work together to overcome technical challenges, reduce costs, and create scalable solutions that can be applied globally.
In conclusion, advanced turbine configurations and hybrid systems are at the forefront of the transition to a more efficient, flexible, and sustainable energy future. By integrating different turbine technologies, energy storage solutions, and renewable energy sources, these systems offer significant potential to improve energy efficiency, reduce emissions, and enhance the reliability of power generation. As technology continues to advance and new innovations emerge, turbines will remain a cornerstone of the global energy infrastructure, helping to meet the world’s growing demand for clean and reliable energy.
On Site Power Generator
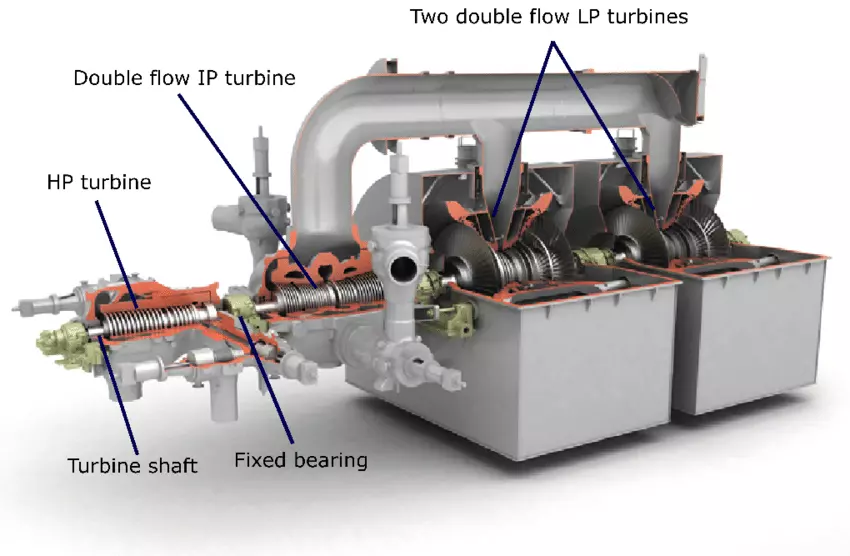
On-site power generation refers to the production of electricity or thermal energy at or near the point of use, as opposed to relying on centralized utility grids for supply. This approach is particularly valuable for industries, commercial enterprises, and residential buildings that require a reliable and cost-effective energy solution, or for locations where grid access is limited or unreliable. On-site power generation systems are designed to provide a continuous and localized energy source, offering numerous benefits, including enhanced reliability, reduced energy costs, and increased energy independence. These systems are diverse, ranging from small-scale generators to large, complex energy systems that integrate renewable and non-renewable energy sources.
One of the main advantages of on-site power generation is the ability to provide a consistent, independent energy supply. For businesses or industries, the integration of power generation systems can reduce downtime due to power outages and ensure that operations continue smoothly without interruptions. This is especially critical in sectors where energy disruptions can result in significant financial losses, such as manufacturing, data centers, healthcare facilities, and communications infrastructure. On-site generation can significantly improve operational efficiency, as it allows businesses to meet their energy needs in real-time without relying on external utility providers.
On-site power generation also plays a pivotal role in reducing energy costs. By generating electricity on-site, businesses and residential users can offset or eliminate their reliance on external energy providers, which often involves high transmission and distribution fees. Depending on the configuration of the system, businesses can produce electricity at a lower cost per kilowatt-hour (kWh) than what would be available from the grid. This can result in substantial savings, particularly for energy-intensive operations or locations with high electricity tariffs. Additionally, the integration of energy-efficient systems and technologies, such as combined heat and power (CHP) or cogeneration systems, can further reduce operating costs by utilizing waste heat for heating or other industrial processes.
On-site power generation is also instrumental in enhancing energy security and reliability. For remote locations, particularly those in off-grid or underdeveloped regions, on-site generators offer an effective solution to energy access challenges. In many parts of the world, grid infrastructure is limited or unreliable, making it difficult for communities or industries to access a stable power supply. On-site generation systems such as solar panels, small wind turbines, or diesel generators can provide consistent power, improving living standards and supporting economic growth in these areas. In regions prone to natural disasters or where grid infrastructure is vulnerable to disruptions, on-site generators offer a resilient backup power solution to ensure continuous operations during emergencies.
The adoption of renewable energy sources for on-site power generation is increasing rapidly. Technologies such as solar power, wind power, biomass, and geothermal energy are being integrated into on-site systems to reduce reliance on fossil fuels and decrease greenhouse gas emissions. Solar photovoltaic (PV) panels are among the most widely used renewable on-site power generation technologies, as they can be easily installed on rooftops or in open areas. Solar power provides a clean, abundant, and renewable energy source that can be harnessed anywhere sunlight is available. Wind power is another renewable option, particularly in areas with consistent wind resources. Small-scale wind turbines can be deployed on-site to generate electricity, either in standalone systems or as part of a hybrid system that combines multiple renewable sources.
Combined heat and power (CHP) systems are also gaining traction in on-site power generation. These systems simultaneously produce electricity and useful heat from a single energy source, such as natural gas, biomass, or even waste materials. By capturing the waste heat generated during power production, CHP systems achieve efficiencies of up to 80% or more, making them a highly efficient energy solution. They are particularly well-suited for industrial applications, where both electricity and thermal energy are required for manufacturing processes, space heating, or hot water production. CHP systems are also a viable option for large residential buildings, hospitals, and universities, where heating and cooling demands are significant.
For industrial users, on-site power generation can be implemented in a variety of configurations to meet specific energy needs. These systems range from small, standalone diesel generators to more sophisticated, integrated solutions such as gas turbines, reciprocating engines, or waste heat recovery systems. Diesel generators are one of the most common types of on-site power generation, especially for backup power applications. They offer reliable performance, quick start-up times, and scalability, making them ideal for both emergency and continuous power needs. However, their use is typically associated with higher operating costs and environmental concerns due to their reliance on fossil fuels.
Gas turbines are another popular technology for on-site generation, particularly in larger applications where higher power output is required. Gas turbines operate by combusting natural gas to produce high-speed exhaust gases that drive a turbine to generate electricity. They are highly efficient and capable of delivering large amounts of power, often used in industrial processes, power plants, or combined cycle systems. Gas turbines also offer the flexibility to switch between fuels, including natural gas and hydrogen, allowing for more sustainable operations.
On-site generation can also involve microgrids, which are localized energy networks that integrate multiple distributed energy resources (DERs), including renewable energy, batteries, and backup generators, into a single cohesive system. Microgrids are designed to operate independently of the main grid, providing energy resilience and stability during grid disruptions. These systems are particularly valuable in remote locations or for critical infrastructure that cannot afford downtime. Microgrids also enable demand response capabilities, where energy consumption is adjusted in real-time to match the availability of local generation, further enhancing the efficiency and sustainability of the system.
An important aspect of on-site power generation is its ability to reduce carbon emissions. By utilizing renewable energy sources like solar and wind, or more efficient technologies like CHP, businesses and homeowners can significantly reduce their carbon footprint compared to conventional grid-based electricity. On-site generation also provides the opportunity to decarbonize industrial processes by incorporating low-carbon technologies into daily operations, such as replacing fossil fuel-based heating systems with electric or renewable-powered heating alternatives. As regulatory pressures to reduce emissions continue to rise, on-site power generation becomes an essential tool for meeting sustainability goals.
Energy storage systems are an integral component of many on-site power generation setups, allowing excess energy produced during periods of low demand or high generation to be stored for later use. Battery storage, thermal storage, or pumped hydro storage can be used in conjunction with renewable energy technologies, such as solar and wind, to smooth out fluctuations in energy production and consumption. Storage systems ensure that the energy generated on-site is available when needed, reducing reliance on external energy sources and improving the overall efficiency of the system.
The cost-effectiveness of on-site power generation has improved significantly in recent years, making it an increasingly attractive option for businesses and homeowners alike. The cost of renewable energy technologies, particularly solar PV, has decreased substantially, while the efficiency of storage systems has also improved. Financial incentives and subsidies for renewable energy adoption, as well as the rising cost of grid electricity, have further accelerated the adoption of on-site generation. Businesses and residential users can expect to see a return on investment through energy savings, reduced grid dependency, and increased resilience against energy price fluctuations.
Regulatory and policy support is another important factor driving the growth of on-site power generation. Many governments around the world are implementing policies and regulations that incentivize the use of renewable energy, such as tax credits, rebates, and net metering programs. These policies not only make on-site power generation more affordable but also help businesses and consumers align with sustainability goals and meet local emissions reduction targets. Furthermore, as governments and international organizations continue to focus on reducing carbon emissions and achieving net-zero targets, on-site generation systems will be a key component of the global transition to clean energy.
In summary, on-site power generation offers a wide range of benefits, including improved energy reliability, reduced costs, and enhanced sustainability. With advancements in renewable energy, energy storage, and combined heat and power systems, these technologies are becoming increasingly efficient, affordable, and widely applicable. On-site generation provides energy security for industries, residential users, and remote locations, while helping to reduce carbon emissions and support global decarbonization efforts. As the demand for cleaner, more resilient energy systems grows, on-site power generation will play an essential role in shaping the future of the energy landscape.
Looking ahead, on-site power generation systems will continue to evolve and adapt to the changing needs of industries, businesses, and residential users. As renewable energy technologies improve, energy efficiency increases, and storage systems become more cost-effective and scalable, on-site generation is poised to become a cornerstone of energy strategy worldwide. Several key trends are expected to shape the future of on-site power generation.
One of the most promising developments is the integration of advanced energy management systems (EMS). These systems leverage real-time data, AI, and machine learning algorithms to optimize energy usage, manage energy storage, and coordinate power generation sources. EMS will be increasingly used to intelligently control the flow of electricity, balance supply and demand, and ensure that the right mix of energy sources is used at the right time. For example, during peak energy demand periods, an EMS can draw from energy storage or seamlessly integrate with the grid to meet the required demand. This enables on-site generators to operate more efficiently and helps businesses and residential users optimize their energy consumption.
Another major trend is the hybridization of energy systems, where multiple forms of power generation are combined into one cohesive, flexible solution. For example, a business may combine solar PV panels with a backup diesel or natural gas generator, energy storage, and a microgrid to create a resilient energy system that can operate independently of the grid during outages or periods of high demand. Additionally, hybrid systems can combine renewable energy sources with traditional generators or CHP systems, maximizing the benefits of each technology. This flexibility allows businesses to choose the most cost-effective and environmentally friendly energy mix while ensuring a reliable power supply.
As the focus on decarbonization intensifies, electrification will become an increasingly important part of on-site power generation. The shift from fossil fuel-based heating and transportation systems to electricity-based systems will require greater emphasis on generating clean, renewable electricity. For example, electric heating systems, electric vehicles, and green hydrogen production may all require on-site power generation. Green hydrogen, produced using renewable electricity, can be stored and used in fuel cells or combustion processes to generate electricity or heat. This shift to electrification, combined with on-site generation, will help reduce reliance on fossil fuels and facilitate the transition to a low-carbon energy system.
Smart grid integration is also expected to play a crucial role in the future of on-site power generation. As more decentralized energy resources come online, power grids will need to become smarter to manage the increased complexity of energy distribution. Smart grid technology enables bidirectional energy flow, where excess energy produced from on-site generation can be fed back into the grid, providing additional supply during periods of high demand. This capability is particularly important for renewable energy sources, which can be intermittent in nature. By integrating on-site generation with smart grids, consumers can benefit from lower energy costs, greater energy resilience, and a more flexible, reliable power supply.
Blockchain technology is another emerging trend that could play a role in optimizing on-site power generation. Blockchain can be used to create decentralized, transparent energy markets where consumers and businesses can buy and sell excess energy generated from on-site systems. This would enable peer-to-peer energy trading, reducing reliance on centralized utility providers and improving the economic efficiency of energy systems. By using blockchain for energy transactions, on-site power generation systems could become more integrated into local energy networks, creating a more decentralized, efficient, and equitable energy distribution model.
As the demand for sustainable and resilient energy solutions increases, battery storage technologies will become an even more integral part of on-site power generation systems. The development of higher-capacity, faster-charging, and longer-lasting batteries will enable on-site systems to store greater amounts of energy for later use, allowing businesses and residential users to better manage fluctuations in energy supply and demand. The continued innovation in battery technology, including advancements in solid-state batteries and flow batteries, could drastically improve the efficiency and scalability of energy storage systems, making on-site generation more reliable and cost-effective.
In parallel, geothermal energy is gaining attention as a reliable and sustainable energy source for on-site power generation. While geothermal energy is most commonly associated with large-scale power plants, there is increasing interest in small-scale, residential, and commercial geothermal systems. These systems utilize the constant temperature of the earth’s subsurface to provide heating, cooling, and electricity generation. Geothermal heat pumps, for example, are becoming popular for residential and commercial heating and cooling, while geothermal power generation systems are being deployed in regions with high geothermal potential. As geothermal technology advances, it could become an increasingly viable option for on-site energy production, especially in areas with abundant geothermal resources.
The expansion of distributed energy resources (DERs) will continue to transform on-site power generation systems. In addition to solar and wind, technologies such as micro-hydro, biogas, and fuel cells are becoming more prevalent in distributed energy systems. As DERs proliferate, the overall energy landscape will become more decentralized, with a greater emphasis on local energy production. By integrating multiple DERs into a cohesive system, businesses and homeowners can ensure that they meet their energy needs sustainably and efficiently. This decentralized energy approach will also foster energy resilience by reducing the vulnerability of large-scale, centralized power systems to natural disasters, cyber threats, or other disruptions.
In summary, on-site power generation is an increasingly important part of the global energy transition, offering numerous benefits, including enhanced reliability, energy savings, and sustainability. As technologies continue to improve and evolve, on-site systems will become more flexible, efficient, and cost-effective. With the integration of renewable energy, energy storage, hybrid systems, smart grids, and advanced energy management tools, on-site power generation will play a pivotal role in shaping the future of energy production and consumption. By providing localized, resilient energy solutions, on-site generation will help reduce dependence on fossil fuels, decrease carbon emissions, and contribute to the overall goals of energy security and sustainability.
Looking further into the future, on-site power generation will likely see even greater advancements in terms of technology integration, scalability, and customization. As energy demand continues to rise and environmental concerns increase, businesses and residential users will continue seeking more personalized, efficient, and flexible energy solutions. The ongoing development of digital tools, sensors, and artificial intelligence (AI) will further revolutionize the way energy is produced, managed, and consumed on-site.
Digitalization of energy systems will be a key enabler for optimizing on-site generation. As sensors, smart meters, and digital controllers become more advanced, energy systems will become increasingly capable of real-time monitoring and automated control. These innovations will allow energy managers to better predict and respond to fluctuations in energy demand, manage energy storage, and balance renewable energy sources with backup generators. By integrating predictive analytics, AI algorithms, and machine learning, energy consumption patterns can be accurately forecasted, allowing systems to adjust automatically, making on-site generation more efficient and cost-effective.
The growing availability of smart appliances and internet of things (IoT) devices will also contribute to the optimization of on-site power generation. These devices will be able to communicate with energy management systems, enabling the more efficient use of power throughout a home or facility. For example, energy usage from appliances can be scheduled during off-peak hours when electricity is cheaper or when renewable energy production is at its peak. The integration of IoT into power systems will allow for more fine-grained control over how energy is consumed, ensuring maximum efficiency and reducing waste.
Moreover, advanced materials and engineering innovations will continue to drive the performance of on-site power generation technologies. The development of more efficient, durable, and lightweight materials for use in renewable energy systems, such as solar panels, wind turbines, and batteries, will reduce costs and improve the overall efficiency of these systems. Perovskite solar cells, for instance, are showing great promise as a next-generation solar technology that is both more cost-effective and efficient than traditional silicon-based panels. Similarly, advancements in high-temperature superconductors could lead to significant efficiency gains in energy storage and power transmission.
A critical trend is the decentralization of power production. The global shift toward decentralized energy generation is transforming the energy grid, moving away from traditional large-scale, centralized power plants toward smaller, distributed sources. This shift is being facilitated by the rise of energy technologies that enable consumers and businesses to produce, store, and manage their own energy. As on-site generation becomes more common, the need for centralized grid infrastructure may decrease, leading to the creation of more local and resilient microgrids. These microgrids can operate autonomously or in coordination with the larger grid, providing a more reliable and flexible power supply, particularly in areas vulnerable to power outages, natural disasters, or grid instability.
Hybrid energy systems will continue to be a strong feature of future on-site power generation. As energy technologies mature, combining different sources—such as wind, solar, energy storage, and CHP systems—into hybrid configurations will maximize the efficiency, flexibility, and reliability of energy systems. These hybrid systems can adjust to the variability of renewable energy production, providing a stable energy supply under varying conditions. For example, during cloudy days or low-wind periods, energy storage systems can provide backup power, ensuring a constant energy supply. By reducing dependence on any single energy source, hybrid systems provide a more reliable, sustainable, and cost-effective solution for both residential and industrial applications.
Another emerging opportunity lies in green hydrogen production as part of on-site power generation. Green hydrogen, produced through the electrolysis of water using renewable electricity, offers a promising way to store energy and decarbonize industries that are difficult to electrify. Hydrogen can be used for power generation, transportation, and industrial processes, and as such, could become an important part of decentralized energy solutions. On-site hydrogen production systems could be integrated with renewable energy sources such as solar or wind to provide both electricity and hydrogen, creating a dual benefit for businesses seeking to decarbonize their operations.
The integration of renewable heating systems will also play a pivotal role in shaping the future of on-site power generation. Technologies such as heat pumps, solar thermal systems, and biomass heating systems are increasingly being used to provide efficient heating solutions alongside electricity generation. These technologies can be integrated into existing on-site power systems to provide comprehensive energy solutions that meet both heating and cooling needs. By combining renewable electricity generation with renewable heating, businesses and homes can reduce their reliance on fossil fuels and achieve a more energy-efficient, sustainable energy mix.
Collaboration between private companies, governments, and international organizations will also be key to accelerating the adoption of on-site power generation technologies. Policies that encourage investment in renewable energy, provide financial incentives, and support the development of energy infrastructure will be crucial for making on-site generation more accessible and affordable. At the same time, global collaboration will help standardize technologies, share best practices, and create frameworks for scaling up on-site generation across different regions and sectors.
Looking ahead, energy independence will become increasingly important as geopolitical and economic factors continue to impact global energy markets. On-site power generation offers a way for individuals, businesses, and communities to reduce their dependence on imported energy, providing greater control over their energy sources and costs. For industries in particular, this energy autonomy can help protect against volatile energy prices, supply chain disruptions, and regulatory changes. On-site generation also contributes to the resilience of local communities by enabling them to remain self-sufficient in the face of energy crises or natural disasters.
Finally, the economic potential of on-site power generation cannot be overstated. As the technologies become more efficient and affordable, the overall market for decentralized energy solutions will expand. On-site generation systems will provide significant job creation opportunities in sectors such as renewable energy technology, installation, maintenance, and energy management. This could also lead to new business models, such as energy-as-a-service, where consumers and businesses lease or pay for energy systems rather than own them outright, further democratizing access to renewable energy.
In conclusion, the future of on-site power generation will be shaped by technological innovation, increased efficiency, and the global push toward sustainability. With advancements in renewable energy technologies, energy storage, hybrid systems, and smart grids, on-site generation will continue to provide affordable, reliable, and resilient energy solutions. As more businesses, industries, and communities adopt on-site power systems, the world will move closer to a decentralized, clean, and sustainable energy future.
As on-site power generation continues to evolve, several emerging trends and innovations will shape its future trajectory. These trends will not only focus on technological advancements but also on enhancing the user experience, improving energy accessibility, and addressing the broader challenges of the global energy transition.
One area of growing importance is the integration of advanced data analytics and AI for predictive maintenance and optimization. As on-site power systems become more sophisticated, they will generate large volumes of data that can be leveraged for real-time monitoring, predictive maintenance, and optimization of energy flows. By using AI and machine learning algorithms, energy systems can anticipate potential failures before they occur, reducing downtime, extending the lifespan of components, and ensuring that energy production is as efficient as possible. These intelligent systems will be able to self-adjust based on energy demand and supply fluctuations, further enhancing the resilience and reliability of on-site power solutions.
The adoption of energy-as-a-service (EaaS) business models will likely increase as on-site generation systems become more ubiquitous. EaaS allows businesses and homeowners to access energy solutions without having to own and manage the infrastructure themselves. This model provides flexibility and scalability, as users can lease or subscribe to energy systems rather than making large upfront investments. By offering energy services rather than just selling energy, companies can provide comprehensive, customized solutions that include energy generation, storage, management, and optimization. This could be particularly attractive for businesses seeking to reduce capital expenditure and maintenance costs while still reaping the benefits of renewable energy.
Another important development will be the expansion of community-based on-site generation. As energy systems become more modular and affordable, it is likely that smaller communities or neighborhoods will start to develop localized energy systems that incorporate renewable energy, energy storage, and smart grid technologies. These systems, often referred to as community microgrids, can provide reliable, low-cost energy to a group of homes or businesses while offering greater resilience against grid failures or natural disasters. In addition, by pooling resources, these communities can achieve economies of scale and further reduce the cost of energy generation, benefiting from shared ownership, operation, and maintenance of energy systems.
In parallel, the growing role of electric vehicles (EVs) in on-site power generation will be increasingly significant. As EVs become more common, they will serve as both consumers and potential storage systems for energy. Through vehicle-to-grid (V2G) technology, EVs could store excess electricity generated by on-site power systems and feed it back into the grid or power the home or business when needed. This creates a more dynamic and flexible energy network, where vehicles serve not only as transportation but also as mobile energy assets. This trend could further reduce reliance on traditional grid infrastructure and improve the efficiency of renewable energy integration.
As the focus on sustainability and environmental stewardship grows, more businesses and residential users will seek to offset their carbon footprint through on-site generation systems. The development of carbon capture and storage (CCS) technologies may also find a role in this space, especially for facilities that rely on fossil fuels for backup generation. By capturing and storing carbon emissions from power generation processes, these systems can further reduce the environmental impact of on-site energy production. The use of green certificates or carbon credits associated with renewable energy systems will also become more widespread, offering consumers and businesses the opportunity to enhance their sustainability profile and meet environmental targets.
The integration of waste-to-energy technologies will also expand in the context of on-site generation. As more companies and homes adopt on-site power generation, the potential to incorporate waste-to-energy solutions such as biogas production or incineration with energy recovery becomes more viable. These systems can convert organic waste materials, such as food waste or agricultural byproducts, into electricity or heat, providing a renewable energy source while reducing waste disposal costs. These solutions can be particularly beneficial for industries with large amounts of organic waste, such as food processing or agriculture, creating a circular economy where waste is utilized to generate power.
To further boost energy security, energy resilience will become a key consideration for industries and businesses adopting on-site generation. As natural disasters, geopolitical instability, and other external factors continue to threaten the reliability of the global energy grid, on-site generation systems will provide a critical safety net. For example, in areas prone to hurricanes, floods, or wildfires, businesses may rely on on-site power generation as a means of ensuring business continuity during extended grid outages. By coupling on-site generation with microgrid systems, which can operate independently from the main grid, organizations can create self-sustaining energy ecosystems capable of maintaining operations even in the face of external disruptions.
The increasing adoption of smart home technologies will also play a major role in shaping the future of on-site power generation for residential users. Homes equipped with smart thermostats, smart appliances, and home automation systems will be able to optimize energy use based on real-time data, adjusting settings to ensure that power is consumed efficiently. By integrating on-site power generation systems such as solar panels and energy storage with these smart home devices, homeowners can achieve a greater degree of control over their energy consumption, lower utility bills, and reduce their environmental impact.
Furthermore, public-private partnerships will likely play a crucial role in scaling up on-site power generation technologies, particularly in underserved regions or for small and medium-sized enterprises (SMEs). Governments and private companies can work together to fund research and development, deploy pilot projects, and provide financial incentives that make these systems more affordable and accessible. By promoting policies and incentives that support innovation in energy technology, governments can accelerate the transition to decentralized, renewable energy solutions, benefiting both businesses and local communities.
The global move toward a circular economy will also impact the design and implementation of on-site power generation systems. As the world shifts to systems that prioritize resource efficiency and minimize waste, on-site generation technologies will be increasingly designed with end-of-life considerations in mind. This could include the use of recyclable materials in the construction of renewable energy technologies, as well as the development of systems that allow for easy repurposing or refurbishment of components once they are no longer operational. As part of this circular approach, manufacturers will also focus on improving the lifecycle performance of energy systems, ensuring that their environmental impact is minimized at every stage—from production to disposal.
As these trends unfold, on-site power generation will continue to be a pivotal component of the global energy landscape. It will allow for more distributed, sustainable, and resilient energy systems that empower consumers, businesses, and communities to take control of their energy future. By combining advanced technologies, innovative business models, and a commitment to sustainability, the future of on-site power generation is set to transform the way we produce, consume, and think about energy. With these advancements, the world will move closer to achieving its broader energy goals—ensuring a cleaner, more secure, and more efficient energy future for generations to come.
EMS Power Machines
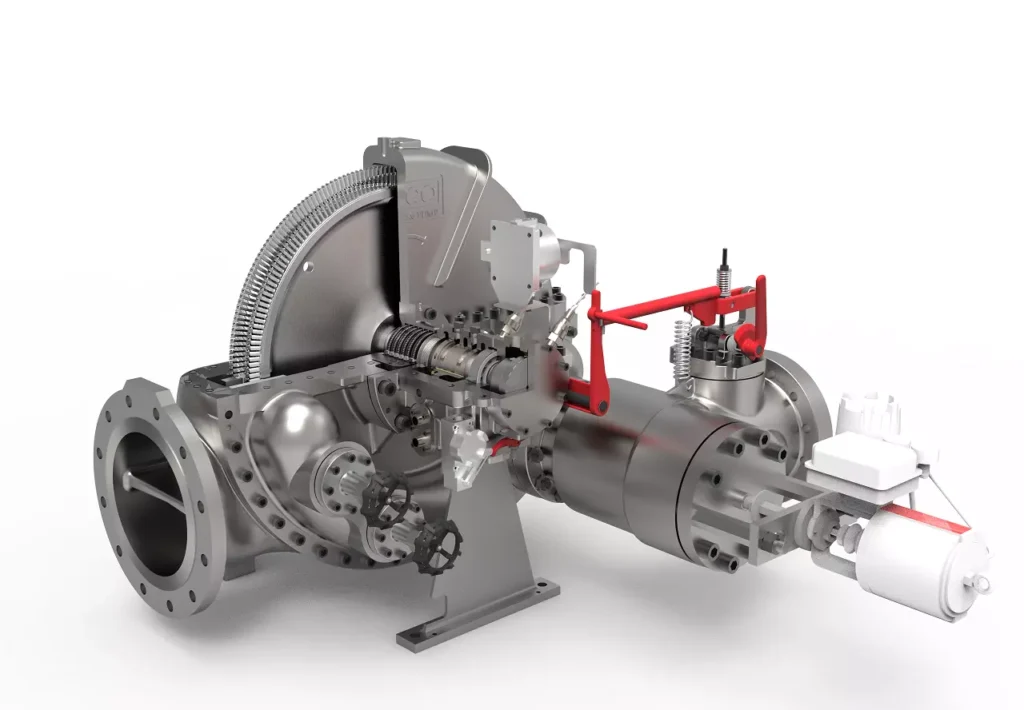
We design, manufacture and assembly Power Machines such as – diesel generators, electric motors, vibration motors, pumps, steam engines and steam turbines
EMS Power Machines is a global power engineering company, one of the five world leaders in the industry in terms of installed equipment. The companies included in the company have been operating in the energy market for more than 60 years.
EMS Power Machines manufactures steam turbines, gas turbines, hydroelectric turbines, generators, and other power equipment for thermal, nuclear, and hydroelectric power plants, as well as for various industries, transport, and marine energy.
EMS Power Machines is a major player in the global power industry, and its equipment is used in power plants all over the world. The company has a strong track record of innovation, and it is constantly developing new and improved technologies.
Here are some examples of Power Machines’ products and services:
- Steam turbines for thermal and nuclear power plants
- Gas turbines for combined cycle power plants and industrial applications
- Hydroelectric turbines for hydroelectric power plants
- Generators for all types of power plants
- Boilers for thermal power plants
- Condensers for thermal power plants
- Reheaters for thermal power plants
- Air preheaters for thermal power plants
- Feedwater pumps for thermal power plants
- Control systems for power plants
- Maintenance and repair services for power plants
EMS Power Machines is committed to providing its customers with high-quality products and services. The company has a strong reputation for reliability and innovation. Power Machines is a leading provider of power equipment and services, and it plays a vital role in the global power industry.
EMS Power Machines, which began in 1961 as a small factory of electric motors, has become a leading global supplier of electronic products for different segments. The search for excellence has resulted in the diversification of the business, adding to the electric motors products which provide from power generation to more efficient means of use.