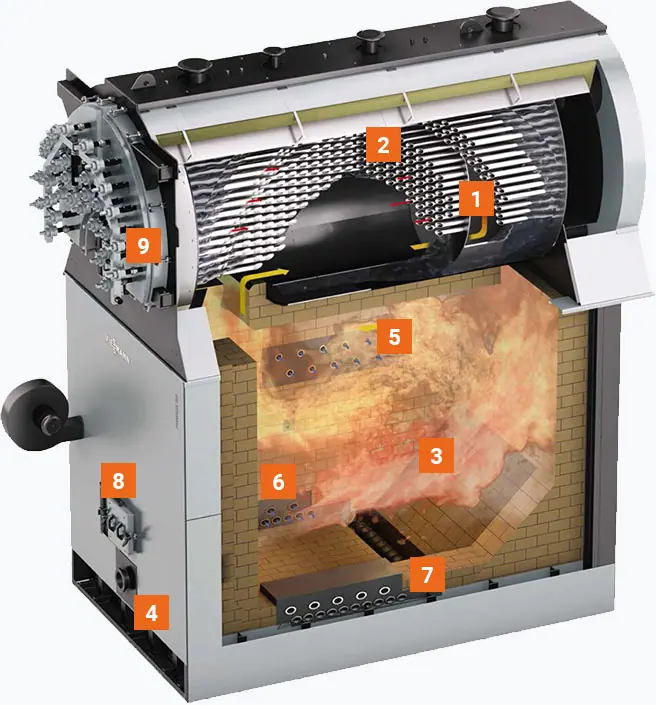
Wood Burning Power Generator: The turbine bearing cooling system is a critical component in large-scale industrial machinery such as steam, gas, and hydro turbines. These cooling systems play an essential role in maintaining operational efficiency, preventing equipment damage, and ensuring safety during prolonged operation. Bearings in turbines support the rotating shaft and handle the weight of rotating elements; thus, they are subject to extreme friction and heat generation. If left unchecked, overheating can lead to bearing failure, turbine shutdowns, and costly repairs.
This section will explore the intricacies of turbine bearing cooling systems, including their types, functions, working principles, materials, and recent technological advancements.
1. The Role of Bearings in Turbine Systems
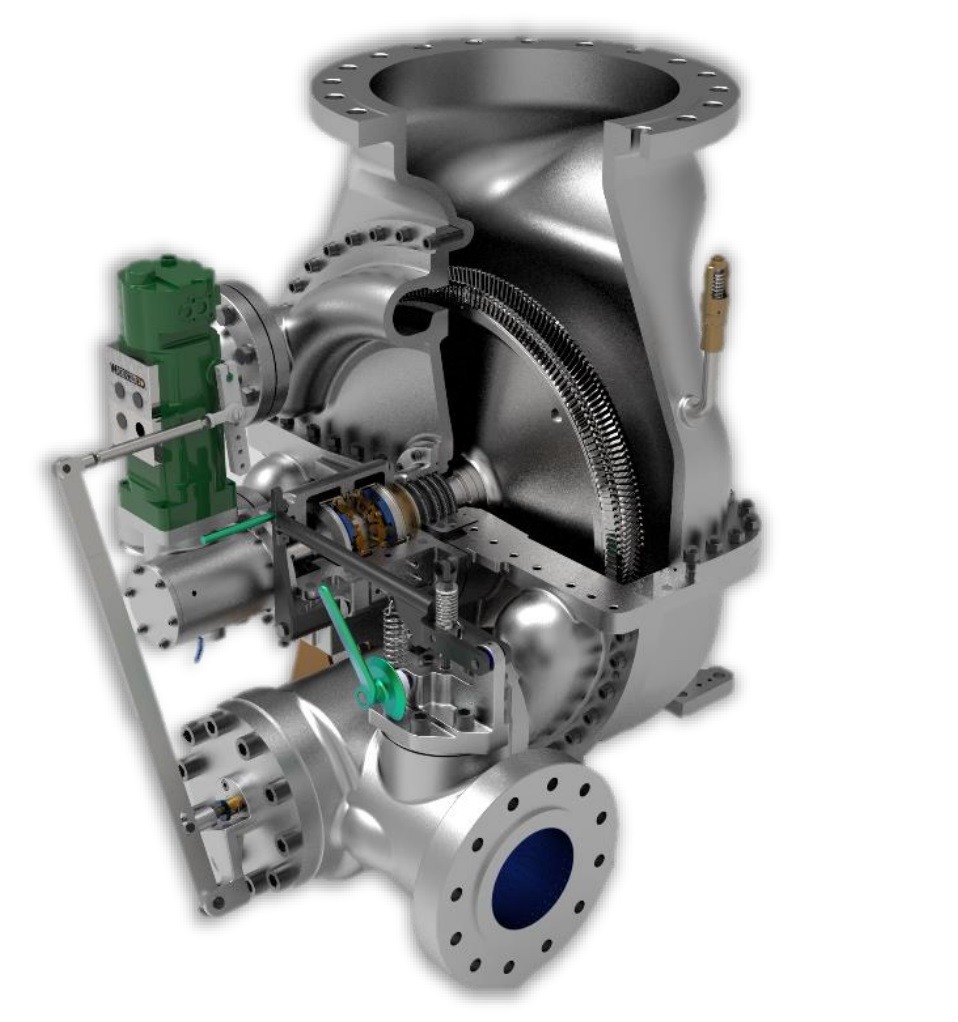
Turbine bearings are mechanical components that allow for the smooth rotation of the turbine’s shaft, reducing friction between the moving and stationary parts. Their primary roles include:
- Support and Stability: Bearings support the load of the rotating shaft, allowing for smooth and stable operation.
- Reducing Friction: By minimizing friction between the rotating shaft and stationary elements, bearings reduce energy loss and prevent wear.
- Heat Management: The bearings themselves can generate significant amounts of heat, particularly in high-speed turbines, necessitating an effective cooling system.
2. Why Cooling is Essential
High operational temperatures in turbine systems can severely affect the bearings’ performance, potentially leading to premature wear, thermal degradation, and even bearing seizure. To avoid such issues, maintaining an optimal temperature is essential. Some specific reasons cooling is necessary include:
- Preventing Lubricant Breakdown: The lubricant used in bearings can degrade at high temperatures, reducing its viscosity and leading to metal-on-metal contact.
- Ensuring Dimensional Stability: Metal components expand when heated, potentially causing misalignment in the turbine shaft. Adequate cooling helps maintain dimensional stability.
- Prolonging Component Life: High temperatures accelerate wear and tear. Cooling extends the lifespan of bearings and related components.
3. Types of Bearing Cooling Systems
There are several types of bearing cooling systems used in turbine applications, depending on the size and type of turbine, operating conditions, and design considerations. These include:
- Air Cooling: One of the simplest methods, air cooling involves blowing cool air over the bearing surfaces. It’s typically used in smaller turbines or in systems with lower heat output. However, it may not be effective for high-temperature environments.
- Water Cooling: Water cooling systems are more effective than air cooling, especially in larger turbines where substantial amounts of heat are generated. Water circulates around the bearing housing, absorbing heat and carrying it away. Water-cooled systems are more complex and require monitoring to avoid leaks or contamination.
- Oil Circulation Systems: In this system, a specialized oil (which may also act as a lubricant) is circulated around the bearing to absorb heat. The oil is then cooled via heat exchangers before being recirculated. Oil-based systems are common in larger gas and steam turbines, where they offer both cooling and lubrication functions.
- Hybrid Systems: Some turbines employ a combination of cooling methods, such as oil cooling combined with air or water cooling, to enhance efficiency. These systems provide a more adaptable solution for different operating conditions.
4. Components of a Turbine Bearing Cooling System
A typical turbine bearing cooling system comprises several key components, including:
- Cooling Medium (Air, Water, or Oil): The fluid responsible for absorbing and dissipating heat.
- Heat Exchangers: These devices transfer heat from the cooling medium to the surrounding environment, ensuring the cooling medium remains at an optimal temperature.
- Circulation Pumps: Pumps are necessary to circulate the cooling medium around the bearings, ensuring continuous heat removal.
- Sensors and Control Systems: Temperature sensors and control systems monitor the bearing temperature and regulate the flow of the cooling medium accordingly.
- Filters: Filters remove contaminants from the cooling medium, which could otherwise damage the bearings or reduce cooling efficiency.
5. Working Principle of a Turbine Bearing Cooling System
The working principle of a turbine bearing cooling system is relatively straightforward. As the turbine operates, heat is generated in the bearings due to friction and the immense forces exerted on them. The cooling system works to dissipate this heat and maintain an optimal temperature range.
In the case of an oil cooling system, oil is circulated through the bearing housing via a pump. As the oil absorbs heat from the bearings, it is transported to a heat exchanger where it releases the heat into a secondary cooling medium, such as air or water. The cooled oil is then recirculated back to the bearings to continue the cooling process.
Water-cooled systems function similarly, with water flowing around the bearings, absorbing heat, and then passing through heat exchangers to release the heat into the environment. In air-cooled systems, fans direct cool air across the bearings to remove heat.
6. Challenges and Maintenance
Despite the effectiveness of turbine bearing cooling systems, several challenges need to be addressed to ensure reliable operation:
- Contamination: The cooling medium (especially oil or water) can become contaminated with debris, leading to bearing damage or reduced cooling efficiency. Regular maintenance and filtration are essential to prevent this.
- Leakage: Water- and oil-based systems can suffer from leaks, which reduce cooling performance and may cause environmental or safety concerns. Regular inspection and prompt repairs are vital.
- Corrosion: Prolonged exposure to moisture can cause corrosion of metal components in water-cooled systems. Using corrosion-resistant materials and additives in the cooling medium helps mitigate this issue.
- System Monitoring: Sensors and control systems play a critical role in ensuring the system operates correctly. Faulty sensors or outdated control mechanisms can result in temperature fluctuations, reduced efficiency, or even system failure. Regular calibration of sensors and controllers is necessary.
7. Advances in Turbine Bearing Cooling Technology
In recent years, advancements in turbine bearing cooling systems have improved efficiency and reliability. Key innovations include:
- Nanofluids: Research is ongoing into using nanofluids (fluids containing nanoparticles) in cooling systems. These fluids have superior heat transfer properties compared to traditional cooling media, potentially allowing for more efficient cooling.
- Smart Cooling Systems: Modern cooling systems integrate advanced sensors, AI, and machine learning to predict when cooling is needed, automatically adjusting the system’s operation to optimize efficiency and reduce energy consumption.
- Improved Materials: Advances in materials science have led to the development of new alloys and coatings that are more resistant to heat, wear, and corrosion. These materials extend the life of bearings and reduce the need for intensive cooling.
8. Applications in Different Types of Turbines
Turbine bearing cooling systems are employed in a variety of turbine types, including:
- Steam Turbines: Large steam turbines, used in power generation, require robust cooling systems due to the extreme heat produced by the steam cycle.
- Gas Turbines: Gas turbines, often used in aviation and power generation, operate at very high speeds and temperatures, making effective cooling essential.
- Hydroelectric Turbines: In hydroelectric plants, water-cooled bearings are common due to the availability of water. However, care must be taken to prevent contamination of the cooling water.
- Wind Turbines: In wind turbines, bearings are subject to lower heat loads than in steam or gas turbines. However, they still require efficient cooling systems, particularly in large-scale offshore installations where environmental factors may increase wear.
Conclusion
Turbine bearing cooling systems are essential to the long-term reliability and efficiency of turbine machinery across industries. Whether through air, water, oil, or advanced hybrid systems, maintaining optimal bearing temperatures ensures smooth operation, reduces the risk of catastrophic failure, and prolongs the life of expensive turbine components. As technology advances, cooling systems will continue to evolve, improving energy efficiency and reducing maintenance costs. For industries relying on turbines, staying up to date with the latest cooling technologies is crucial to maintaining a competitive edge.
How to Go Off Grid UK
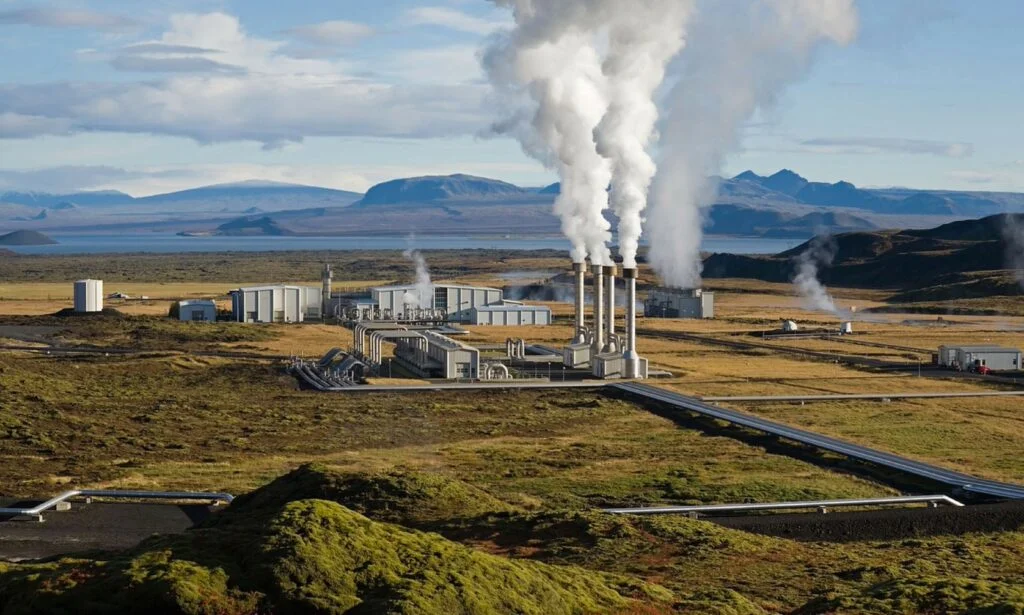
Going off-grid is becoming an increasingly popular choice for those looking to reduce their dependence on public utilities, minimize their environmental impact, and embrace a more self-sufficient lifestyle. In the UK, this movement has gained traction in recent years, driven by concerns about energy costs, sustainability, and the desire for a simpler, more independent way of living. However, going off-grid requires careful planning, a good understanding of legal requirements, and knowledge of how to create a sustainable infrastructure for energy, water, and waste management.
This section will explore the ins and outs of going off-grid in the UK, from generating your own power and sourcing water to handling waste and meeting legal obligations.
1. What Does “Going Off Grid” Mean?
Going off-grid means severing your reliance on public utilities such as electricity, water, and gas, and instead generating or sourcing all of your resources independently. It typically involves:
- Generating your own electricity: Using renewable energy sources like solar, wind, or hydropower.
- Water sourcing: Harvesting rainwater or utilizing a well to meet your water needs.
- Waste management: Handling your own sewage and waste, often through systems like composting toilets and greywater recycling.
- Food production: While not strictly necessary, many people who go off-grid also grow their own food, further increasing self-sufficiency.
In the UK, going off-grid is entirely legal, but it involves careful planning to meet legal requirements and ensure sustainability.
2. Legal Considerations for Going Off-Grid in the UK
While going off-grid is legal in the UK, there are several regulations and legal considerations that individuals must take into account:
- Planning Permission: If you plan to build a new home off-grid, you’ll need to apply for planning permission from your local council. This process ensures that your property complies with UK building regulations and environmental laws. While planning permission for off-grid homes can sometimes be more challenging to obtain, especially in protected areas (e.g., National Parks), it is possible if you can demonstrate that your build will have minimal environmental impact.
- Building Regulations: Even off-grid homes must adhere to UK building regulations. These regulations cover everything from structural integrity and insulation to ventilation and energy efficiency. Ensuring that your home meets these standards is crucial to avoiding legal issues down the line.
- Council Tax: Even if you live off-grid, you are still required to pay council tax. However, there may be some discounts available if you’re living in a very small, self-built property, or if your off-grid home is classified differently by the council.
- Water Abstraction and Waste Disposal: Sourcing water from a well or river requires compliance with UK water abstraction laws. If you plan to extract more than 20 cubic meters of water per day, you will need to apply for a license from the Environment Agency. Additionally, if you plan to install a septic tank or any form of off-grid waste disposal system, this must meet Environment Agency guidelines.
3. Energy Solutions for Off-Grid Living
One of the most significant aspects of going off-grid is generating your own electricity. In the UK, there are several viable renewable energy options that can help you achieve energy independence. Each option has its pros and cons, and the best solution will depend on your location, budget, and energy needs.
- Solar Power: Solar energy is one of the most popular choices for off-grid living. The UK’s solar potential might not match sunnier regions, but modern solar panels are efficient enough to generate a significant amount of electricity, even in cloudy conditions. A typical off-grid solar system will require:
- Photovoltaic (PV) panels to generate electricity from sunlight.
- Batteries to store excess energy generated during the day for use at night or during cloudy periods.
- Inverters to convert the direct current (DC) from the panels into alternating current (AC) used by most household appliances.
- Wind Power: If you live in a windy area, wind turbines can be an excellent addition or alternative to solar. Wind turbines harness kinetic energy from the wind and convert it into electricity. They work especially well in rural or coastal areas of the UK where wind is more consistent. A typical small wind turbine can generate between 5 to 10 kW of power.However, there are some challenges associated with wind power, including:
- Planning permission: Large wind turbines often require planning permission due to their height and visual impact.
- Inconsistent energy generation: Wind turbines only generate electricity when the wind is blowing, so a battery storage system is essential to maintain a consistent power supply.
- Hydroelectric Power: For properties located near running water, small-scale hydroelectric systems can provide reliable, constant power. Micro-hydro systems are highly efficient, capable of generating energy 24/7. The key components of a hydroelectric system include:
- A water turbine.
- A generator.
- A battery storage system for times when water flow might be reduced.
- Backup Generators: While renewable energy sources like solar and wind are the backbone of an off-grid energy system, many off-grid households keep a backup generator, typically powered by diesel, gas, or even biomass. These generators can provide power during extended periods of low renewable energy output.
4. Water Supply and Waste Management
For off-grid living, securing a clean and reliable water source is a priority. In the UK, you can achieve this through several methods:
- Rainwater Harvesting: This is one of the most common methods of sourcing water off-grid. Rainwater harvesting systems collect rainwater from roofs and store it in tanks. The water can then be filtered and treated for drinking, or used directly for gardening, flushing toilets, and washing clothes. In the UK, a typical rainwater harvesting system can collect thousands of liters annually, depending on your location and roof size.
- Wells and Boreholes: If your property has access to underground water, you can install a well or borehole. These systems draw water from underground aquifers, providing a reliable and independent water source. Boreholes require a significant upfront investment and may need regular maintenance and filtration to ensure water quality.
- Greywater Recycling: This involves reusing wastewater from sinks, showers, and washing machines for purposes like flushing toilets or irrigating gardens. Greywater systems reduce your overall water consumption and are particularly useful in off-grid homes that rely on limited water supplies.
- Wastewater Management: Handling wastewater responsibly is essential when living off-grid. Some popular methods include:
- Septic tanks: A septic tank is an underground chamber that processes and decomposes sewage. It’s important to ensure that septic systems meet UK environmental standards to avoid contamination of local water sources.
- Composting toilets: Composting toilets break down human waste into compost, eliminating the need for water-based sewage systems. These toilets are eco-friendly and particularly useful in areas where installing a septic tank might be challenging.
5. Heating and Cooking
- Wood Burning Stoves: Many off-grid homes use wood-burning stoves for heating and cooking. Wood is a renewable resource, and stoves provide both heat and the ability to cook without relying on gas or electricity. In rural areas, gathering or purchasing firewood is a practical way to stay warm during the colder months.
- Biomass Boilers: Biomass heating systems use organic materials like wood chips or pellets to heat your home. Biomass boilers are efficient and can heat water as well as air, making them a good all-round solution for off-grid heating.
- Solar Thermal Systems: Solar thermal panels can be used to heat water, reducing the need for electricity or gas for heating. While they’re most effective during the summer months, solar thermal systems can reduce reliance on traditional heating methods year-round.
6. Communication and Internet
Going off-grid doesn’t mean you have to disconnect entirely from the modern world. Staying connected is important for work, communication, and emergencies. Options for off-grid communication in the UK include:
- Satellite Internet: Satellite internet provides coverage in remote areas where traditional broadband may not be available. It can be slightly more expensive than standard broadband, but it ensures a reliable internet connection even in isolated locations.
- Mobile Hotspots: With mobile networks expanding across the UK, a mobile hotspot or 4G router is another option for staying connected. This solution works well in areas with good mobile coverage.
7. Cost of Going Off Grid in the UK
While going off-grid can save you money in the long term, especially on utility bills, the initial investment can be significant. Some of the key costs include:
- Solar panels: £5,000 to £10,000 depending on the size of the system.
- Wind turbines: £20,000 to £40,000 for a residential-scale turbine.
- Water systems: £1,000 to £5,000 for rainwater harvesting or a well installation.
- Septic systems: £3,000 to £5,000.
- Backup generators: £500 to £2,500.
Despite the upfront costs, off-grid living can provide substantial savings over time, especially as energy prices continue to rise.
Conclusion
Going off-grid in the UK is not just a lifestyle choice; it’s a journey toward self-sufficiency, sustainability, and environmental consciousness. While it requires careful planning and a significant initial investment, it offers the potential for financial savings, independence, and a reduced ecological footprint. By considering energy generation, water supply, waste management, and legal requirements, individuals and families can successfully transition to an off-grid life, gaining both freedom and a closer connection to nature.
Biomass Generators
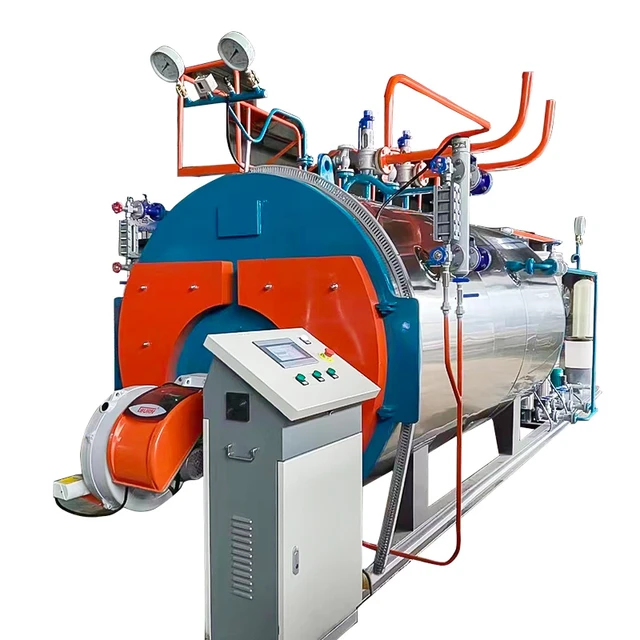
Biomass generators are an increasingly popular option for producing renewable energy from organic materials. As the world grapples with the need to reduce carbon emissions and find alternatives to fossil fuels, biomass energy has emerged as a reliable and sustainable solution. Biomass generators convert biological materials—such as wood, agricultural residues, or waste products—into usable energy, typically in the form of electricity or heat.
This section explores how biomass generators work, the types of biomass materials used, their advantages and disadvantages, and how they fit into both off-grid applications and larger energy infrastructure.
1. What is Biomass Energy?
Biomass energy is derived from organic matter. This can include plant materials, animal waste, and agricultural by-products. When these materials are processed, burned, or broken down in specific ways, they release energy, typically in the form of heat, which can then be converted into electricity or used directly for heating purposes.
Some common sources of biomass include:
- Wood and wood residues: Timber, sawdust, and wood chips.
- Agricultural residues: Crop stalks, straw, and husks.
- Energy crops: Fast-growing plants like switchgrass or miscanthus specifically grown for energy production.
- Animal waste: Manure and other organic waste from livestock farming.
- Organic waste: Biodegradable municipal waste and food waste.
The key advantage of biomass as an energy source is that, unlike fossil fuels, it is renewable. While burning biomass does release carbon dioxide, the plants from which it is derived capture carbon during their growth, making the overall process carbon-neutral, or close to it, when managed sustainably.
2. How Do Biomass Generators Work?
Biomass generators produce electricity through the combustion or gasification of organic materials. There are several different methods by which this can be achieved, and the exact process can vary depending on the type of biomass and the generator design.
- Direct Combustion: This is the most straightforward way of using biomass for energy. In direct combustion systems, biomass is burned in a boiler to generate heat, which is then used to produce steam. The steam drives a turbine connected to a generator, which produces electricity. These systems are similar to traditional fossil fuel power plants but use biomass as the fuel source.
- Gasification: Biomass gasification involves heating biomass in an oxygen-limited environment to produce a synthetic gas (syngas) made up of carbon monoxide, hydrogen, and methane. This syngas can be used to drive internal combustion engines or turbines to generate electricity. Gasification is more efficient than direct combustion and produces fewer emissions.
- Anaerobic Digestion: Anaerobic digestion is a biological process in which microorganisms break down organic matter in the absence of oxygen, producing biogas (mainly methane and carbon dioxide). The biogas can be used to fuel generators that produce electricity or heat. This method is particularly suited for using wet organic materials like animal manure or food waste.
3. Types of Biomass Generators
There are various types of biomass generators, each tailored to specific scales of operation and types of biomass. These include:
- Small-Scale Biomass Generators: Designed for individual households or small communities, these generators can run on wood pellets, chips, or small agricultural residues. They are ideal for off-grid settings where other forms of renewable energy, such as solar or wind, might not be sufficient. Small biomass generators often use direct combustion or gasification to produce energy.
- Medium to Large Biomass Power Plants: Larger biomass generators are often part of industrial-scale power plants that supply electricity to the grid. These systems can process large quantities of biomass, including agricultural waste, forest residues, and industrial organic waste. Many of these plants use combined heat and power (CHP) systems, which produce both electricity and useful heat for industrial or residential purposes.
- Anaerobic Digesters: Anaerobic digesters can be scaled to serve anything from a small farm to a large municipal waste processing facility. These systems are particularly effective in agricultural settings where livestock waste and crop residues are plentiful.
4. Biomass Feedstocks
One of the most important aspects of biomass energy production is the type of feedstock used. Different biomass materials have varying energy contents, combustion properties, and sustainability implications. Some common types of feedstocks include:
- Wood and Wood Pellets: Wood is one of the most widely used biomass materials, as it is abundant, renewable, and easy to process. Wood pellets, made from compressed sawdust, are often used in biomass boilers due to their high energy density and efficient combustion.
- Agricultural Waste: Crop residues, such as straw, husks, and stalks, can be used in biomass generators. These materials are often by-products of farming activities and are readily available in rural areas.
- Energy Crops: Some plants are grown specifically for energy production. For example, switchgrass and willow are fast-growing and can be harvested regularly. These crops can help avoid the environmental degradation associated with deforestation or over-extraction of natural resources.
- Biodegradable Waste: Organic waste, such as food scraps, yard waste, and animal manure, is often processed in anaerobic digesters to produce biogas. This waste would otherwise end up in landfills, where it contributes to methane emissions.
5. Environmental and Economic Benefits of Biomass Generators
Biomass generators offer several environmental and economic benefits, particularly when compared to traditional fossil fuel-based energy sources:
- Carbon Neutrality: One of the main advantages of biomass energy is its potential for carbon neutrality. The carbon dioxide released during the combustion of biomass is offset by the carbon absorbed by plants during their growth. However, the actual carbon balance depends on factors like transportation, feedstock type, and land-use changes.
- Reduction of Waste: Biomass energy systems can make use of waste products that would otherwise be discarded, such as agricultural residues, municipal organic waste, and wood industry by-products. This helps reduce the amount of waste sent to landfills and lowers methane emissions, which are much more potent as greenhouse gases than carbon dioxide.
- Energy Security: Biomass energy contributes to energy security by diversifying the energy mix and reducing dependence on imported fossil fuels. In rural areas, where access to the national grid might be unreliable or expensive, biomass generators offer a viable alternative energy source.
- Job Creation: The biomass industry creates jobs in rural areas, particularly in agriculture, forestry, and waste management. Collecting, processing, and transporting biomass feedstocks requires labor, which helps stimulate local economies.
6. Challenges of Biomass Generators
Despite the numerous benefits, biomass generators also face several challenges that must be addressed to make them a truly sustainable energy solution:
- Feedstock Supply: A consistent and sustainable supply of biomass feedstock is essential for the successful operation of biomass generators. In some cases, the demand for biomass can lead to deforestation or the overuse of agricultural land, which can negatively impact biodiversity and food production.
- Efficiency: Biomass generators are generally less efficient than fossil fuel plants in terms of energy conversion. However, advancements in technology, such as gasification and combined heat and power systems, are helping to improve efficiency.
- Land Use: The production of energy crops can compete with food production, leading to higher food prices or land-use conflicts. Careful management is required to balance energy production with agricultural needs.
- Emissions: While biomass energy is considered carbon-neutral, the combustion of biomass can still produce pollutants, including particulate matter, nitrogen oxides, and volatile organic compounds. Advanced filtration systems and cleaner combustion technologies are necessary to minimize these emissions.
- Transport Costs: The transportation of biomass feedstock to the generator can increase the overall carbon footprint of the system, particularly if the distances are large. Sourcing biomass locally or creating decentralized energy systems can help mitigate this issue.
7. Applications of Biomass Generators
Biomass generators are versatile and can be used in a variety of settings, from rural households to large industrial plants:
- Off-Grid Homes: For individuals and communities looking to go off-grid, small-scale biomass generators provide a reliable source of electricity and heat. By using locally sourced wood or agricultural waste, off-grid homes can reduce their reliance on external energy sources while maintaining a low environmental impact.
- Rural and Agricultural Communities: Biomass generators are particularly suited to rural and agricultural areas, where there is often an abundance of organic waste. Farmers can use crop residues, animal manure, and other by-products to generate energy, reducing waste and lowering their energy costs.
- Urban Waste Management: In urban areas, anaerobic digestion can be used to process food waste and organic matter from households and businesses. This reduces landfill use and produces both electricity and heat that can be fed back into the grid or used locally.
- Industrial Applications: Larger biomass power plants can provide energy to industrial facilities that require consistent, large-scale energy production. Many industries, such as the paper and pulp industry, generate their own biomass waste, which can be used to power the plant.
8. The Future of Biomass Generators
As the demand for renewable energy continues to grow, biomass generators are likely to play an increasingly important role in the global energy mix. Several technological advancements are making biomass energy more efficient and environmentally friendly:
- Improved Gasification Technology: Advances in gasification technology are increasing the efficiency of biomass generators while reducing emissions. By converting biomass into cleaner syngas, these systems can produce more electricity with fewer pollutants.
- Bioenergy with Carbon Capture and Storage (BECCS): BECCS technology aims to capture and store the carbon dioxide released during biomass combustion, effectively creating a system that removes carbon from the atmosphere. This could make biomass energy not only carbon-neutral but carbon-negative.
- Integration with Other Renewable Energy Sources: Biomass generators can be combined with other renewable energy sources, such as solar and wind, to create hybrid energy systems that ensure a reliable and consistent power supply.
Conclusion
Biomass generators provide a viable and sustainable solution for producing renewable energy from organic materials. Whether used in small-scale off-grid applications or as part of large industrial power plants, biomass energy offers numerous environmental and economic benefits. As technology continues to evolve, the efficiency and sustainability of biomass generators are likely to improve, solidifying their role in the global transition to cleaner energy sources.
Small Steam Engine
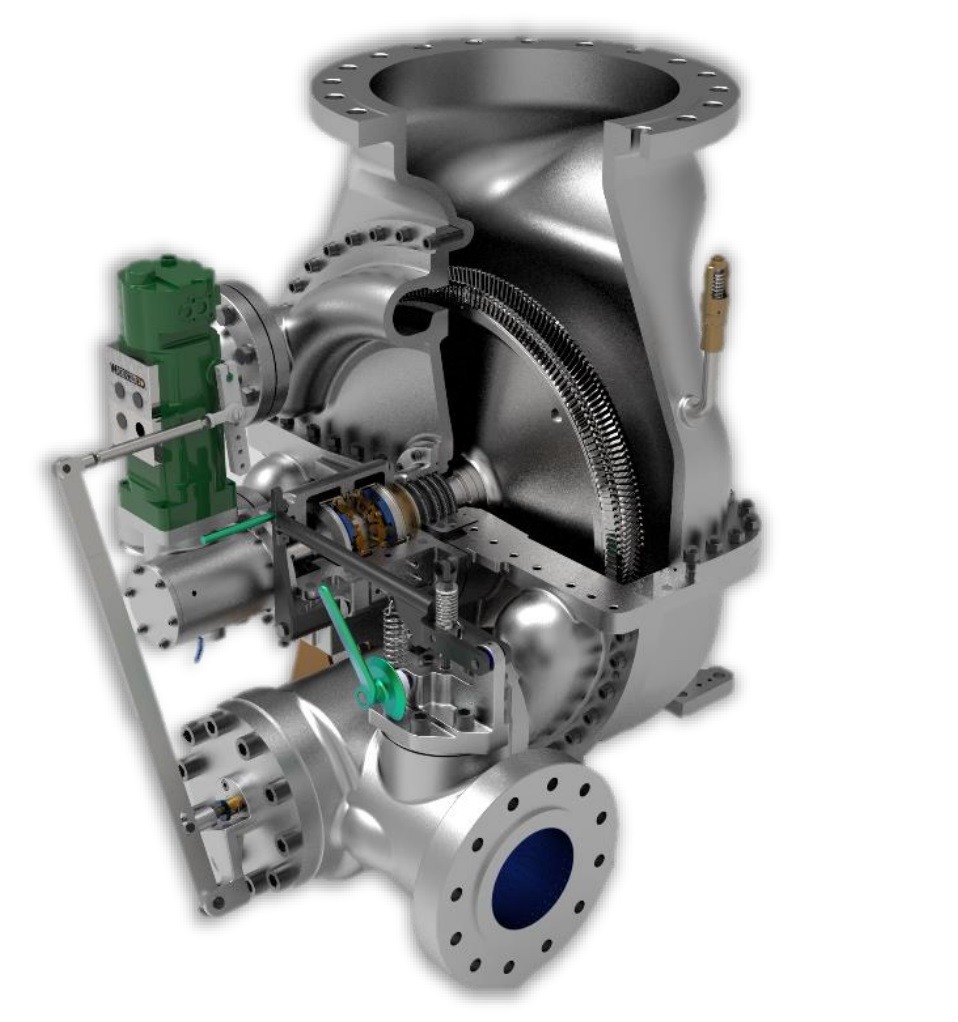
A small steam engine is a device that converts steam pressure into mechanical energy. While steam engines are often associated with the industrial revolution and large-scale power plants, smaller versions of these engines have been used for a variety of purposes throughout history, from powering early machinery to driving small boats and vehicles. Today, small steam engines are still in use, particularly in educational demonstrations, hobbyist projects, and niche applications where other power sources may not be as effective.
This section will explore the history, design, working principles, and modern uses of small steam engines, as well as their continued relevance in a world increasingly dominated by electrical and internal combustion technologies.
1. A Brief History of Steam Engines
Steam engines have a rich history dating back over 300 years. Their invention was a turning point in human development, revolutionizing industries such as mining, manufacturing, and transportation. The origins of steam power can be traced to ancient times, but it wasn’t until the 17th century that functional steam engines began to emerge.
- Early Innovations: In the early 1600s, a simple steam-powered device known as the “aeolipile” was described by Hero of Alexandria, but it wasn’t practical for performing work. The first practical steam engines were developed in the late 17th century. Thomas Savery’s engine, patented in 1698, was one of the earliest devices used for pumping water out of mines. However, it was inefficient and prone to explosions.
- James Watt’s Improvements: In the mid-18th century, James Watt introduced key improvements that made steam engines much more efficient. His design, which included a separate condenser, greatly reduced the amount of energy lost in the heating and cooling process, allowing steam engines to become more widely adopted in industries.
- The Rise of Smaller Steam Engines: As steam engine technology progressed, smaller versions were developed for more specialized uses. By the 19th century, small steam engines were powering everything from early automobiles to small factories and workshops. They were also used in trains, steamboats, and agriculture.
While steam engines have largely been replaced by internal combustion engines and electric motors in most modern applications, small steam engines are still used in specific areas and have a dedicated following among hobbyists and educational institutions.
2. How Small Steam Engines Work
At their core, all steam engines operate on the same basic principle: steam is generated by heating water, and the pressure from the steam is used to drive a piston or turbine, which in turn performs mechanical work. In a small steam engine, this process is scaled down, but the underlying principles remain the same.
The key components of a small steam engine include:
- Boiler: The boiler is where water is heated to produce steam. In small steam engines, the boiler is usually a compact vessel that can be heated using a variety of fuel sources, such as wood, coal, propane, or even solar power.
- Piston or Turbine: In most small steam engines, a piston is used to convert the pressure of the steam into mechanical energy. The steam enters the cylinder and pushes the piston, which then moves a crankshaft or flywheel. Some small steam engines use turbines instead of pistons, especially in applications where continuous rotational motion is required.
- Condenser: In larger steam engines, condensers are used to convert spent steam back into water, which can then be reused. However, in many small steam engines, especially those used in hobbyist projects, the steam is simply vented into the air after it has done its work.
- Flywheel: The flywheel is a large rotating mass that stores the mechanical energy produced by the engine. In small steam engines, the flywheel helps smooth out the piston’s reciprocating motion and provides a consistent source of mechanical energy.
- Governor: Some small steam engines, particularly those used for industrial or educational purposes, include a governor. The governor controls the engine’s speed by regulating the amount of steam that enters the cylinder. This ensures the engine runs at a consistent speed, which is important for precision tasks.
3. Applications of Small Steam Engines
Although steam engines are no longer the primary source of power for most industries, small steam engines still have a variety of applications today. These applications range from educational demonstrations and hobby projects to niche industrial uses.
- Hobbyist and Model Engineering: Small steam engines are a popular choice among model engineers and hobbyists who enjoy building and operating miniature engines. These enthusiasts often replicate historical steam engines in miniature form, showcasing the intricate workings of steam power on a smaller scale. Model steam engines are also used to power small locomotives, boats, and vehicles in hobbyist settings.
- Educational Use: Small steam engines are widely used in education to teach the principles of thermodynamics, mechanical engineering, and energy conversion. In schools and universities, these engines offer a hands-on way for students to see how steam power works and to understand concepts such as pressure, heat transfer, and mechanical efficiency.
- Power Generation in Remote Areas: In some remote or off-grid locations, small steam engines can still be used to generate electricity. By burning locally available biomass or wood, steam engines can drive small generators to produce power. This method is particularly useful in areas where solar or wind power is not feasible, or as a backup to other renewable energy sources.
- Historical Reenactments and Museums: Small steam engines are often featured in museums, steam fairs, and historical reenactments, where they demonstrate how early machinery operated. Steam traction engines, miniature trains, and other steam-powered devices are popular attractions at these events, providing visitors with a glimpse of how steam technology powered the industrial revolution.
- Industrial and Agricultural Uses: Although rare today, small steam engines are still used in niche industrial applications where other power sources might not be suitable. In some agricultural settings, steam engines are used to drive machinery such as pumps or threshers, particularly in areas with abundant biomass for fuel.
4. Types of Small Steam Engines
Small steam engines come in various designs, each tailored to specific applications and performance requirements. Some common types of small steam engines include:
- Single-Cylinder Engines: The simplest type of steam engine, the single-cylinder engine has one piston and one cylinder. It is commonly used in hobbyist projects and educational settings due to its straightforward design. Single-cylinder engines can power small machines or vehicles, and their simplicity makes them easy to maintain.
- Double-Acting Engines: In a double-acting steam engine, steam is supplied alternately to both sides of the piston, allowing for more efficient operation. This design produces more power than single-acting engines and is often used in small steam locomotives or boats.
- Oscillating Steam Engines: An oscillating steam engine, also known as a wobbler, is a compact type of engine where the entire cylinder oscillates to allow steam to enter and exit. These engines are often used in model steam engines because of their simplicity and small size.
- Vertical Steam Engines: Vertical steam engines have a vertical cylinder and are commonly used in small boats and vehicles. Their vertical design allows them to be more compact, making them suitable for applications where space is limited.
- Horizontal Steam Engines: In contrast to vertical engines, horizontal steam engines have their cylinders arranged horizontally. This design is more stable and can handle higher loads, making it ideal for industrial applications where more power is needed.
5. Advantages of Small Steam Engines
Small steam engines offer several advantages, particularly for niche applications and hobbyist uses:
- Simplicity and Reliability: Steam engines, particularly small ones, have relatively few moving parts compared to internal combustion engines. This makes them easier to maintain and repair, especially in settings where high-tech tools and expertise may not be readily available.
- Fuel Flexibility: One of the key advantages of steam engines is their ability to run on a wide variety of fuels. While modern engines are designed to run on specific fuels (such as gasoline or diesel), steam engines can operate on wood, coal, propane, or biomass. This makes them particularly useful in off-grid or rural areas where fuel supplies may be limited.
- Low Cost for Small-Scale Power Generation: For individuals or communities looking for small-scale power generation in remote areas, steam engines can be a cost-effective solution, especially if fuel (such as wood or biomass) is locally available.
- Educational Value: Small steam engines provide a hands-on way to learn about the principles of mechanical engineering and thermodynamics. Their relatively simple design allows students and hobbyists to easily understand how they work, making them an excellent educational tool.
- Durability: Steam engines are incredibly durable and can last for decades if properly maintained. This longevity, combined with their simple mechanics, makes them a viable option for applications where other engines may wear out quickly.
6. Challenges and Limitations
Despite their advantages, small steam engines also have several limitations that have led to their decline in mainstream use:
- Efficiency: Steam engines are generally less efficient than internal combustion engines or electric motors. The process of generating steam, transferring heat, and converting steam pressure into mechanical energy results in significant energy losses. This makes them less suitable for applications where energy efficiency is a priority.
- Complexity of Operation: While steam engines are mechanically simple, operating them requires careful management of steam pressure, fuel, and water levels. This can be a challenge for those unfamiliar with their workings, particularly in off-grid settings where reliability is critical.
- Fuel Requirements: Small steam engines require a steady supply of fuel and water, which can be a challenge in some settings. While they can run on a wide range of fuels, managing fuel storage and ensuring a constant supply of water can be labor-intensive.
- Environmental Concerns: While steam engines can run on renewable fuels such as wood or biomass, they can still produce emissions, particularly when coal or other fossil fuels are used. In today’s push for cleaner, zero-emission energy, steam engines may not align with environmental goals unless they are operated using carbon-neutral fuels.
7. The Modern Revival of Small Steam Engines
In recent years, there has been a resurgence of interest in small steam engines, driven by the hobbyist community, educational institutions, and niche industries. Several factors are contributing to this revival:
- Sustainability and Off-Grid Living: As more people seek sustainable and off-grid living solutions, small steam engines offer an attractive option for generating power using locally available renewable resources. For example, in areas with abundant wood or biomass, a small steam engine can provide a reliable source of power without relying on the electrical grid.
- Hobbyist Appeal: Steam engine enthusiasts continue to design, build, and operate small steam engines for fun, education, and historical preservation. Many hobbyists enjoy the challenge of constructing their own steam engines and powering miniature trains, boats, or stationary engines.
- STEM Education: Steam engines remain a popular tool for teaching STEM (Science, Technology, Engineering, and Mathematics) concepts. Their visible mechanisms and clear demonstration of thermodynamic principles make them an effective educational tool.
Conclusion
Small steam engines may no longer dominate industries as they once did, but they continue to hold a unique place in the world of engineering, education, and sustainable energy. From hobbyist projects to off-grid power generation, these engines provide a practical and durable solution for a variety of applications. As the world seeks new ways to generate energy sustainably, small steam engines, particularly those running on renewable fuels, may find new relevance in niche sectors and educational environments.
Used Steam Turbine Generators
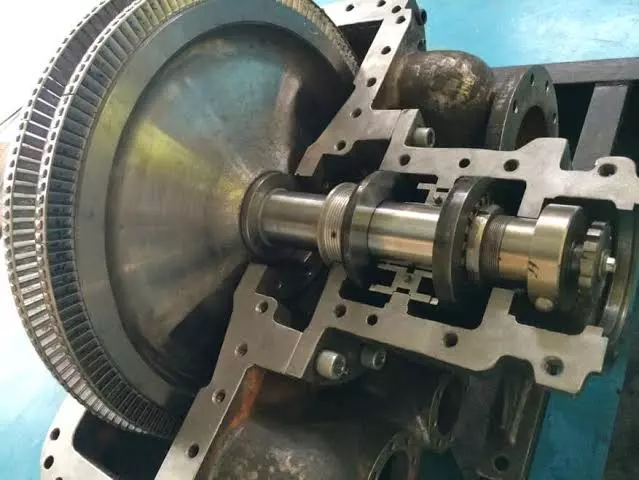
Steam turbine generators are essential components in power generation, converting thermal energy from steam into mechanical energy and, ultimately, electrical power. These generators are widely used in various industries, from power plants to manufacturing facilities, and play a critical role in ensuring reliable energy output. While purchasing a brand-new steam turbine generator can be a significant investment, many companies opt for used or refurbished steam turbines as a cost-effective alternative.
Used steam turbine generators offer a viable solution for businesses looking to expand their power generation capacity without the high costs associated with new equipment. However, buying a used steam turbine requires careful consideration of several factors, including the condition of the equipment, the specific needs of the facility, and long-term maintenance strategies.
This section will cover how steam turbine generators work, the benefits and challenges of buying used equipment, key considerations for selecting a used turbine, and the industries that rely on these systems.
1. How Steam Turbine Generators Work
A steam turbine generator converts steam energy into mechanical and then electrical energy. This process involves the interaction of several critical components:
- Boiler: The process begins in the boiler, where water is heated to produce steam. This steam is often generated using various fuel sources, including fossil fuels (coal, natural gas), nuclear power, or renewable sources (biomass).
- Steam Turbine: The steam produced in the boiler is then directed towards the turbine. As the high-pressure steam passes through the turbine blades, it causes the rotor to spin. The spinning rotor converts the thermal energy of the steam into mechanical energy through rotational motion.
- Generator: Attached to the turbine rotor is an electrical generator. As the rotor spins, the generator’s internal magnetic field creates electricity. This electricity is then transferred to the power grid or used directly by the facility.
- Condenser: After passing through the turbine, the steam is cooled and condensed back into water by a condenser, allowing it to be reused in the boiler, making the process more efficient.
Steam turbines can be classified based on how steam enters and exits the turbine. Impulse turbines use the velocity of the steam to drive the blades, while reaction turbines rely on steam pressure. Depending on the application, steam turbines may also be designed to operate at different pressure levels, including high-pressure, intermediate-pressure, and low-pressure stages.
2. Why Consider Buying a Used Steam Turbine Generator?
The decision to buy a used steam turbine generator is often driven by economic and logistical factors. Used turbines offer several advantages over new units, particularly for companies looking to balance cost with performance.
- Cost Savings: One of the most significant advantages of buying used steam turbines is the cost savings. Brand-new steam turbine generators can be incredibly expensive, especially for large-scale industrial applications. By purchasing used equipment, companies can save a significant portion of their budget, sometimes as much as 50-70% compared to the cost of new units.
- Faster Deployment: New steam turbines often come with long lead times, sometimes taking months or even years to manufacture and deliver. Used turbines, on the other hand, are typically available for immediate purchase and installation. This is especially important for businesses that need to expand power generation capacity quickly or replace malfunctioning equipment on short notice.
- Proven Reliability: Many used steam turbines come from decommissioned power plants or facilities that have upgraded their equipment. In many cases, these turbines have already proven their reliability and durability in real-world conditions. Purchasing a refurbished unit from a reputable supplier often comes with guarantees or warranties that ensure continued performance.
- Environmental Benefits: By purchasing used equipment, companies contribute to the circular economy, reducing waste and the need for new manufacturing. Extending the life of used turbines also helps conserve resources and minimizes the environmental impact of producing new units.
- Customization and Retrofitting: Used steam turbines can often be retrofitted or customized to meet the specific needs of a new facility. Whether the original turbine was designed for a different application or fuel source, experienced suppliers can modify the system to meet new operational requirements.
3. Challenges of Buying Used Steam Turbines
Despite the advantages, there are also challenges associated with buying used steam turbine generators. Understanding these challenges is essential to ensure a successful purchase and long-term operation.
- Potential for Wear and Tear: Steam turbines are subject to high temperatures, pressure, and mechanical stresses, which can cause wear and tear over time. When buying used equipment, it is essential to assess the condition of the turbine carefully. Some parts, such as the turbine blades, bearings, and seals, may need replacement or refurbishment to ensure optimal performance.
- Technological Obsolescence: While steam turbines are built to last for decades, older models may lack the efficiency and technological advancements found in newer designs. This can result in higher operational costs or reduced performance. Buyers should consider whether the used turbine’s technology is still relevant and if it can be upgraded to improve efficiency.
- Uncertainty About Maintenance History: A turbine’s past maintenance record is crucial to understanding its condition and future reliability. Without a detailed history of repairs and servicing, buyers may face unexpected breakdowns or performance issues. It’s important to obtain as much information as possible about the turbine’s maintenance history before purchase.
- Limited Availability of Spare Parts: For older turbine models, sourcing replacement parts can be challenging, particularly if the original manufacturer no longer supports the design. Buyers should confirm that spare parts are available and consider partnering with a supplier who can provide ongoing maintenance and support.
- Energy Efficiency: Newer turbine models are typically more energy-efficient than older versions. While a used steam turbine may be less expensive upfront, it could result in higher operational costs due to lower efficiency. Buyers must weigh the long-term energy costs against the initial savings of purchasing a used unit.
4. Key Considerations When Selecting a Used Steam Turbine
Selecting the right used steam turbine generator requires careful evaluation of several factors to ensure the equipment meets the operational needs of the facility.
- Size and Capacity: The first consideration is the size and capacity of the turbine. Steam turbines come in a wide range of sizes, from small units designed for individual factories to massive generators capable of producing hundreds of megawatts of electricity. The turbine’s capacity must align with the energy needs of the facility to avoid underperformance or overproduction.
- Steam Conditions: Steam turbines are designed to operate under specific steam pressure and temperature conditions. Buyers should ensure that the used turbine is compatible with the steam conditions available in their facility. High-pressure and high-temperature turbines are more efficient but require more robust materials and maintenance.
- Condition Assessment: Before purchasing a used steam turbine, a thorough condition assessment should be conducted by an experienced engineer. This assessment should include:
- Visual inspection of the turbine’s mechanical components.
- Vibration analysis to detect misalignment or wear in the bearings.
- Steam path inspection to check for erosion or damage to the blades.
- Examination of the lubrication system and seals for potential leaks.
- Maintenance and Warranty: It’s important to work with a supplier that offers a warranty or maintenance agreement. Even used turbines can come with warranties, providing peace of mind that the equipment will perform as expected. Additionally, buyers should consider setting up a long-term maintenance plan to ensure ongoing reliability.
- Fuel Compatibility: While steam turbines themselves can work with various steam sources, it’s essential to ensure that the boiler and other components are compatible with the fuel source available. Whether using natural gas, coal, or biomass, the turbine must be part of a system designed for the specific fuel type.
- Availability of Parts and Support: Ensuring that spare parts are available for the turbine is crucial for long-term operation. Buyers should confirm that the manufacturer or a third-party supplier can provide parts and ongoing support, especially if the turbine model is older or no longer in production.
5. Industries Using Steam Turbine Generators
Steam turbine generators are used in a variety of industries where reliable and efficient power generation is critical. Some of the most common industries include:
- Power Generation: Steam turbines are a staple in power plants worldwide, particularly in coal, nuclear, and biomass power plants. Used steam turbines are often sourced from decommissioned power plants and repurposed for smaller facilities or industries with lower power demands.
- Manufacturing: Many manufacturing plants use steam turbines as part of their power generation systems. In industries such as chemicals, paper, and steel production, steam turbines provide both electricity and process heat through combined heat and power (CHP) systems. These systems help improve energy efficiency and reduce costs.
- Petrochemical and Oil Refining: Steam turbines are used in the petrochemical and oil refining industries to drive compressors and pumps. In these sectors, reliability and continuous operation are essential, making used steam turbines a cost-effective solution for expanding production capacity.
- Sugar Mills and Agriculture: In agricultural industries, particularly sugar mills, steam turbines are used to convert steam from bagasse (the fibrous material left over after sugar extraction) into electricity. This renewable biomass source helps sugar mills operate sustainably by producing their own power.
- District Heating: Steam turbines are also used in district heating systems, where they provide both electricity and heat for residential and commercial buildings. These systems are common in Europe and are designed to maximize energy efficiency by using the waste heat from electricity generation.
6. The Process of Refurbishing Used Steam Turbines
When purchasing a used steam turbine, it is common for the equipment to go through a refurbishment process to restore its performance and extend its lifespan. Refurbishment typically involves the following steps:
- Disassembly: The turbine is disassembled, and each component is inspected for wear, damage, or corrosion. This includes the turbine blades, bearings, seals, and casings.
- Replacement of Damaged Components: Any worn or damaged components are replaced, including bearings, seals, and blades. In some cases, the rotor may be rebalanced to ensure smooth operation.
- Reconditioning: Critical parts of the turbine, such as the blades and steam path, may be reconditioned to restore their original performance. This can involve polishing or machining components to remove erosion or pitting.
- Reassembly and Testing: After refurbishment, the turbine is reassembled and tested to ensure it meets the required specifications. Performance tests, including vibration analysis and steam path diagnostics, are conducted to verify that the turbine operates efficiently.
- Documentation and Certification: Refurbished turbines should come with detailed documentation, including maintenance records, inspection reports, and certifications. This documentation is essential for ensuring the equipment complies with regulatory standards and for future maintenance planning.
7. Maintenance and Long-Term Care of Used Steam Turbines
Proper maintenance is critical for ensuring the longevity and reliability of used steam turbines. Regular maintenance tasks include:
- Lubrication System Checks: The turbine’s lubrication system should be checked regularly to ensure that bearings and other moving parts are properly lubricated. Oil filters should be replaced as needed to maintain clean, efficient operation.
- Steam Quality Control: Poor steam quality can cause erosion and damage to turbine blades. It’s important to maintain clean, dry steam by ensuring the boiler system is properly maintained and steam traps are functioning correctly.
- Vibration Monitoring: Regular vibration monitoring can help detect early signs of misalignment, bearing wear, or other mechanical issues. Addressing these problems early can prevent more significant damage and costly repairs.
- Thermal Expansion Management: Steam turbines experience significant thermal expansion and contraction due to high temperatures. Regular inspection of casing joints and seals is essential to prevent steam leaks and maintain efficient operation.
- Performance Testing: Periodic performance testing should be conducted to ensure the turbine is operating at peak efficiency. Testing may include checking steam pressures, temperatures, and output to identify any areas where performance can be improved.
Conclusion
Used steam turbine generators offer a cost-effective and reliable solution for industries seeking to expand power generation capacity without the high investment required for new equipment. By carefully assessing the condition, capacity, and maintenance history of used turbines, businesses can benefit from proven technology while reducing costs and lead times. With proper refurbishment and maintenance, used steam turbines can continue to deliver efficient and sustainable power for many years, making them a valuable asset in both small and large-scale industrial operations.
Types of Impulse Turbine
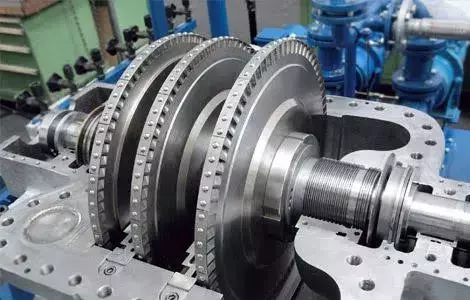
Impulse turbines are a class of turbines where high-velocity jets of steam or water strike the blades to generate mechanical power. Unlike reaction turbines, which use both pressure and velocity changes within the turbine itself, impulse turbines rely purely on the kinetic energy of the fluid to generate power. This makes impulse turbines particularly effective in applications where high-pressure fluid streams are available, and the design of these turbines allows for relatively simple, robust, and efficient operation under specific conditions.
Impulse turbines are most commonly used in hydroelectric and steam power plants, and there are several different types designed for different applications. Each type of impulse turbine has its unique characteristics that make it suitable for specific conditions related to fluid velocity, pressure, and energy requirements.
This section will explore the working principles of impulse turbines, the different types of impulse turbines, and their applications in modern energy systems.
1. Working Principle of Impulse Turbines
Impulse turbines operate based on Newton’s third law of motion: for every action, there is an equal and opposite reaction. In an impulse turbine, high-pressure steam or water is directed through nozzles to create high-speed jets. These jets are directed at the turbine’s blades, which convert the kinetic energy of the fluid into mechanical energy.
Here’s a step-by-step breakdown of how an impulse turbine works:
- Nozzle Action: The fluid (either steam or water) is passed through a nozzle, where its pressure is converted into kinetic energy. The result is a high-velocity jet that exits the nozzle and strikes the turbine blades.
- Blade Impact: The high-speed jet impacts the turbine’s blades. The blades are designed to change the direction of the fluid’s flow, which generates a force that rotates the turbine. The velocity of the fluid decreases as it transfers energy to the blades.
- Energy Conversion: The rotational movement of the turbine shaft, driven by the kinetic energy of the fluid, is converted into mechanical energy. This shaft is connected to a generator, which then converts the mechanical energy into electrical power.
- Exhaust: After striking the blades, the fluid leaves the turbine at a lower velocity and is either discharged or passed to a condenser (in the case of steam) to be reused.
Unlike reaction turbines, where the pressure continuously decreases as the fluid moves through the turbine, in an impulse turbine, the pressure drop occurs entirely in the nozzle. The turbine itself experiences only kinetic energy transfer, which simplifies its design and makes it well-suited for high-head (high-pressure) applications.
2. Types of Impulse Turbines
There are several types of impulse turbines, each designed to operate efficiently under specific conditions. The key types include:
- Pelton Turbine
- Turgo Turbine
- Crossflow Turbine
Pelton Turbine
The Pelton turbine is one of the most common and widely used types of impulse turbines. It was invented by Lester Pelton in the late 19th century and is primarily used in hydroelectric power plants that operate under high head conditions, where water is available at very high pressure but relatively low flow rates.
- Design: A Pelton turbine consists of a series of spoon-shaped blades (or buckets) mounted around the edge of a wheel. The high-velocity water jet is directed at these blades, which are designed to split the water jet into two streams. This minimizes the energy loss and maximizes the rotational force exerted on the turbine wheel.
- How It Works: In a Pelton turbine, water from a high head source (such as a dam) is directed through a nozzle, which converts the pressure into a high-velocity jet. The jet strikes the Pelton wheel’s blades, causing the wheel to rotate. As the water is directed away from the turbine after hitting the blades, most of its kinetic energy is transferred to the turbine, leaving the water with very little velocity.
- Applications: Pelton turbines are ideal for high-head, low-flow scenarios, typically found in mountainous regions where water can fall from great heights. They are commonly used in hydroelectric power stations, where they convert the potential energy of water into electrical power.
- Advantages:
- Highly efficient for high-head applications.
- Simple and robust design.
- Low maintenance costs due to fewer moving parts.
- Disadvantages:
- Less efficient in low-head, high-flow conditions.
- Large installation footprint due to the need for high-head structures.
Turgo Turbine
The Turgo turbine is another type of impulse turbine that is similar to the Pelton turbine but with a few key differences in design. The Turgo turbine was developed to operate more efficiently at medium heads and higher flow rates compared to the Pelton turbine.
- Design: Unlike the Pelton turbine, which has buckets mounted along the rim, the Turgo turbine has a single runner with blades angled in such a way that the water jet strikes the blades at an angle. This design allows the water to pass through the turbine, rather than bouncing off the buckets as in a Pelton turbine.
- How It Works: In a Turgo turbine, the water jet is directed at the runner blades at an angle (typically 20°), allowing the water to pass through the turbine. The angular impact allows for higher rotational speeds and greater power generation efficiency compared to Pelton turbines in medium-head applications.
- Applications: Turgo turbines are used in hydropower plants where medium heads (around 30 to 300 meters) and relatively higher flow rates are available. They are also used in smaller-scale hydroelectric plants where the simplicity and efficiency of an impulse turbine are desired.
- Advantages:
- Can handle higher flow rates than Pelton turbines.
- More compact than a Pelton turbine for the same power output.
- Efficient at medium head and flow conditions.
- Disadvantages:
- Slightly lower efficiency than the Pelton turbine in very high-head applications.
- Requires more maintenance due to the complex flow dynamics.
Crossflow Turbine
The crossflow turbine, also known as the Banki turbine or Michell-Banki turbine, is a unique type of impulse turbine that is designed to operate efficiently across a wide range of flow rates and heads. It is commonly used in smaller hydroelectric projects due to its versatility and simplicity.
- Design: The crossflow turbine features a cylindrical runner with multiple blades arranged radially around it. The water flows through the turbine in a horizontal direction, crossing the blades twice—once as it enters and again as it exits—hence the name “crossflow.”
- How It Works: Water enters the turbine through a rectangular nozzle and strikes the blades of the runner. As the water passes through the blades, it loses part of its kinetic energy, which is transferred to the turbine shaft. After passing through the first set of blades, the water crosses the runner and strikes a second set of blades, extracting additional energy.
- Applications: Crossflow turbines are ideal for low to medium head hydroelectric projects, especially in small-scale or micro-hydro installations. They are highly versatile and can operate efficiently across a broad range of flow conditions.
- Advantages:
- Simple and low-cost design.
- Efficient over a wide range of flow rates and head conditions.
- Can handle debris-laden water better than other types of impulse turbines.
- Disadvantages:
- Less efficient than Pelton and Turgo turbines in high-head applications.
- Not ideal for large-scale power generation.
3. Advantages of Impulse Turbines
Impulse turbines offer several benefits that make them suitable for a variety of power generation applications, particularly in hydroelectric and steam power plants.
- High Efficiency at High Head: Impulse turbines, especially Pelton turbines, are highly efficient at converting the potential energy of high-head water into mechanical power. This makes them ideal for hydroelectric power stations located in mountainous regions or areas with significant water pressure.
- Simplicity and Durability: The design of impulse turbines is relatively simple compared to other turbine types, such as reaction turbines. This simplicity makes impulse turbines easier to maintain and more durable, even in harsh operating conditions.
- Flexibility: Impulse turbines can be designed to operate under a wide range of conditions, from very high-head, low-flow situations to medium-head, higher-flow scenarios. This flexibility makes them suitable for a variety of hydroelectric projects, from large dams to small run-of-the-river installations.
- Low Cavitation Risk: Cavitation, which occurs when vapor bubbles form in a liquid and cause damage to turbine blades, is less of a concern in impulse turbines because the pressure in the turbine remains relatively constant. This reduces the risk of damage and prolongs the life of the turbine.
- Modularity: Impulse turbines can often be scaled or adapted to different sizes, making them suitable for a wide range of applications. This modularity is particularly beneficial for small-scale and off-grid hydroelectric installations.
4. Applications of Impulse Turbines
Impulse turbines are used in various settings where high-pressure water or steam is available. Their versatility allows them to be employed in a range of industries, including:
Hydroelectric Power Plants: Impulse turbines are the most common choice for high-head hydroelectric plants. Pelton turbines, in particular, are used in large-scale hydroelectric stations in mountainous regions, where the potential energy of falling water can be converted efficiently into electricity.
EMS Power Machines
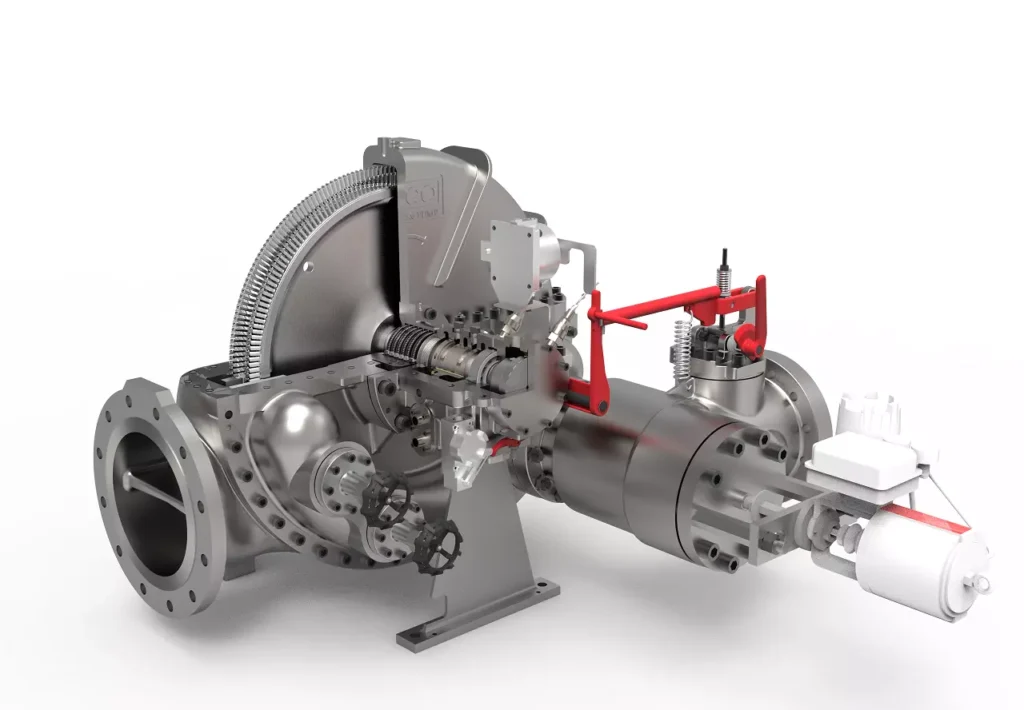
We design, manufacture and assembly Power Machines such as – diesel generators, electric motors, vibration motors, pumps, steam engines and steam turbines
EMS Power Machines is a global power engineering company, one of the five world leaders in the industry in terms of installed equipment. The companies included in the company have been operating in the energy market for more than 60 years.
EMS Power Machines manufactures steam turbines, gas turbines, hydroelectric turbines, generators, and other power equipment for thermal, nuclear, and hydroelectric power plants, as well as for various industries, transport, and marine energy.
EMS Power Machines is a major player in the global power industry, and its equipment is used in power plants all over the world. The company has a strong track record of innovation, and it is constantly developing new and improved technologies.
Here are some examples of Power Machines’ products and services:
- Steam turbines for thermal and nuclear power plants
- Gas turbines for combined cycle power plants and industrial applications
- Hydroelectric turbines for hydroelectric power plants
- Generators for all types of power plants
- Boilers for thermal power plants
- Condensers for thermal power plants
- Reheaters for thermal power plants
- Air preheaters for thermal power plants
- Feedwater pumps for thermal power plants
- Control systems for power plants
- Maintenance and repair services for power plants
EMS Power Machines is committed to providing its customers with high-quality products and services. The company has a strong reputation for reliability and innovation. Power Machines is a leading provider of power equipment and services, and it plays a vital role in the global power industry.
EMS Power Machines, which began in 1961 as a small factory of electric motors, has become a leading global supplier of electronic products for different segments. The search for excellence has resulted in the diversification of the business, adding to the electric motors products which provide from power generation to more efficient means of use.