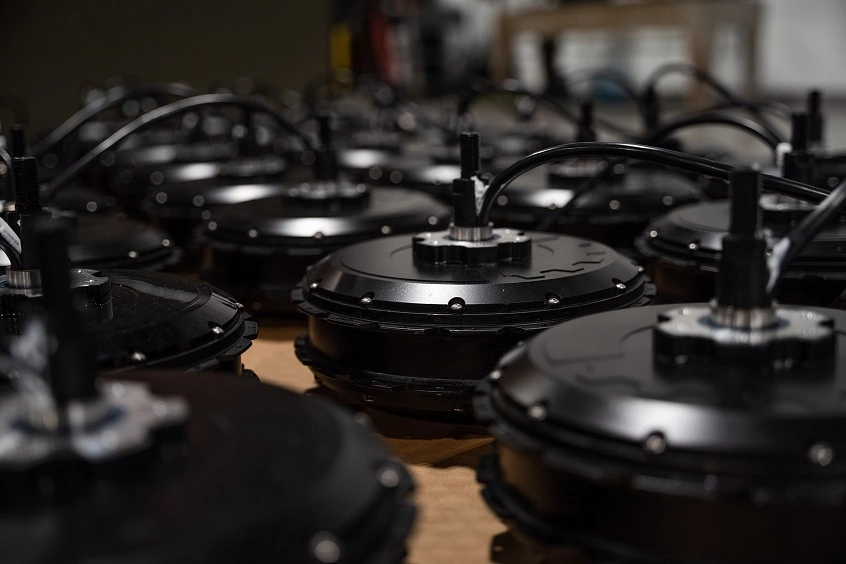
As one of the main Electric Motor Manufacturers, we produce electric motors in various sizes. Free consultation with good prices & high quality
An electric motor manufacturer is a company that designs, develops, and produces electric motors for various industrial and commercial applications. These manufacturers produce different types of electric motors such as AC motors, DC motors, servo motors, stepper motors, and others. They also offer customized solutions based on the specific requirements of their clients. Electric motor manufacturers play a crucial role in the electrical industry by providing reliable and efficient electric motors for use in a wide range of applications, including manufacturing, automotive, aerospace, robotics, and more.
Parts of the Electric Motor
An electric motor consists of several parts that work together to convert electrical energy into mechanical energy:
- Stator: The stator is the stationary part of the electric motor that contains the coils of wire that create a magnetic field.
- Rotor: The rotor is the rotating part of the electric motor that is connected to the shaft and rotates within the stator. It is made up of a series of conductive bars, usually made of copper, that are connected by end rings.
- Shaft: The shaft is the rotating component that connects the rotor to the outside world, allowing the motor to transmit mechanical energy to a load.
- Bearings: Bearings are used to support the shaft and reduce friction between the shaft and the housing. There are two types of bearings: sleeve bearings and ball bearings.
- End bells: End bells are mounted on either end of the motor and serve to protect the interior components and provide a mounting surface for the motor.
- Windings: The windings are made up of insulated wire and are wound around the stator poles. When a current is passed through the windings, it creates a magnetic field that interacts with the rotor to produce torque.
- Commutator: The commutator is a segmented metal ring that connects the rotor to the power supply through brushes. It provides a way to reverse the direction of the current in the rotor, which allows the motor to rotate in a specific direction.
- Brushes: The brushes are typically made of carbon or graphite and conduct electricity between the stationary part of the motor and the rotating part of the motor through the commutator.
Electric Motor Manufacturers
The electric motor manufacturing process is a complex one, involving many different steps and processes. The basic steps are as follows:
- Design: The first step is to design the electric motor. This involves determining the desired performance characteristics of the motor, such as its speed, torque, and efficiency. The designer also needs to choose the appropriate materials and components for the motor.
- Sourcing materials: Once the motor has been designed, the necessary materials and components need to be sourced. These materials can include copper wire, steel, magnets, and electrical insulation.
- Manufacturing the components: The next step is to manufacture the individual components of the motor. This may involve machining, stamping, and winding the copper wire.
- Assembling the motor: Once the components have been manufactured, they need to be assembled into the complete motor. This process can be very complex, as there are many different parts that need to be fitted together precisely.
- Testing: Once the motor has been assembled, it needs to be tested to ensure that it meets the desired performance specifications. This testing may involve measuring the motor’s speed, torque, and efficiency.
Once the motor has passed testing, it is ready to be shipped to the customer.
Here is a more detailed look at some of the key steps in the electric motor manufacturing process:
- Stator core manufacturing: The stator core is the stationary part of the motor. It is made up of a stack of laminated steel sheets. The laminations are insulated from each other to prevent eddy currents.
- Copper wire winding: The copper wire is wound around the stator core to create the stator coils. The coils are connected electrically in such a way that they create a magnetic field when an electric current is passed through them.
- Rotor manufacturing: The rotor is the rotating part of the motor. It is made up of a steel shaft with magnets attached to it. The magnets are arranged in such a way that they create a rotating magnetic field.
- Assembly: The stator and rotor are assembled together to create the complete motor. The motor is then tested to ensure that it meets the desired performance specifications.
Electric motors are manufactured in a variety of sizes and types. The manufacturing process for each type of motor may vary slightly, but the basic steps outlined above are the same for all electric motors.
Electric motors are used in a wide variety of applications, including appliances, industrial equipment, and transportation. They are an essential part of our modern world, and the manufacturing process for electric motors is a complex and important one.
Electric Motor Manufacturers
Electric motors are devices that convert electrical energy into mechanical energy. They play a crucial role in various applications and are widely used in industries, transportation, household appliances, and more. Here are some key points about electric motors:
- Basic Principle: Electric motors operate on the principle of electromagnetic induction, discovered by Michael Faraday. When an electric current flows through a coil placed in a magnetic field, a force is exerted on the coil, causing it to rotate. This rotation is then used to perform mechanical work.
- Components:
- Stator: The stationary part of the motor that produces a magnetic field.
- Rotor (Armature): The rotating part of the motor, usually a coil or a set of coils, which experiences the magnetic field and rotates.
- Types of Electric Motors:
- DC Motors: Direct current motors operate on a constant voltage and are commonly used in applications where precise speed control is required.
- AC Motors: Alternating current motors are more common and come in various types, including:
- Induction Motors: Widely used in household appliances and industrial applications.
- Synchronous Motors: Maintain synchrony with the frequency of the applied AC voltage.
- Brushless DC Motors: Similar to traditional DC motors but use electronic controllers instead of brushes for commutation.
- Applications:
- Industrial Applications: Electric motors power machinery, pumps, fans, compressors, and various manufacturing processes.
- Transportation: Electric motors are used in electric vehicles (EVs), trains, and other forms of electric transportation.
- Household Appliances: They power everything from kitchen appliances like blenders and mixers to HVAC systems and vacuum cleaners.
- Renewable Energy: Electric motors are used in wind turbines and hydropower generators to convert rotational energy into electricity.
- Efficiency and Sustainability: Electric motors are generally more energy-efficient than traditional internal combustion engines, making them a key component in the transition to more sustainable and environmentally friendly technologies.
- Control Systems: Advanced control systems, such as variable frequency drives (VFDs) and programmable logic controllers (PLCs), are often used with electric motors to regulate speed, torque, and direction.
- Maintenance: Electric motors require maintenance to ensure optimal performance. This includes lubrication, checking for worn-out parts, and monitoring electrical components.
The choice of the type of electric motor depends on the specific application’s requirements, such as power output, speed, and efficiency. Advances in motor technology continue to contribute to increased efficiency, reduced environmental impact, and broader applications for electric motors.
Basic Principle
The basic principle behind the operation of electric motors is electromagnetic induction, a phenomenon discovered by Michael Faraday in the early 19th century. Faraday’s law of electromagnetic induction states that a change in magnetic field within a closed loop of wire induces an electromotive force (EMF) or voltage in the wire. This principle is fundamental to the operation of electric motors.
Here’s a simplified explanation of the basic principle:
- Magnetic Field: An electric motor consists of a stationary part called the stator, which produces a magnetic field. This magnetic field can be created by a permanent magnet or by passing an electric current through coils of wire.
- Moving Coil (Armature or Rotor): Inside the magnetic field, there is a moving part called the rotor or armature. The rotor typically consists of a coil of wire or a set of coils.
- Electrical Current: When an electric current is passed through the coil in the rotor, it generates its own magnetic field. This magnetic field interacts with the magnetic field produced by the stator.
- Force and Rotation: According to the laws of electromagnetism, when a current-carrying conductor (the coil in the rotor) is placed in a magnetic field, a force is exerted on it. This force causes the rotor to rotate.
- Continuous Rotation: The rotation of the rotor continues as long as there is a flow of electric current through the coil and the magnetic field is present. The direction of rotation can be reversed by reversing the direction of the current.
In summary, the basic principle of electric motors involves the interaction of magnetic fields and electric currents, resulting in the generation of mechanical motion. This principle is fundamental to various types of electric motors, including DC motors and AC motors, and it forms the basis for the conversion of electrical energy into mechanical work.
Components of an Electric Motor – Electric Motor Manufacturers
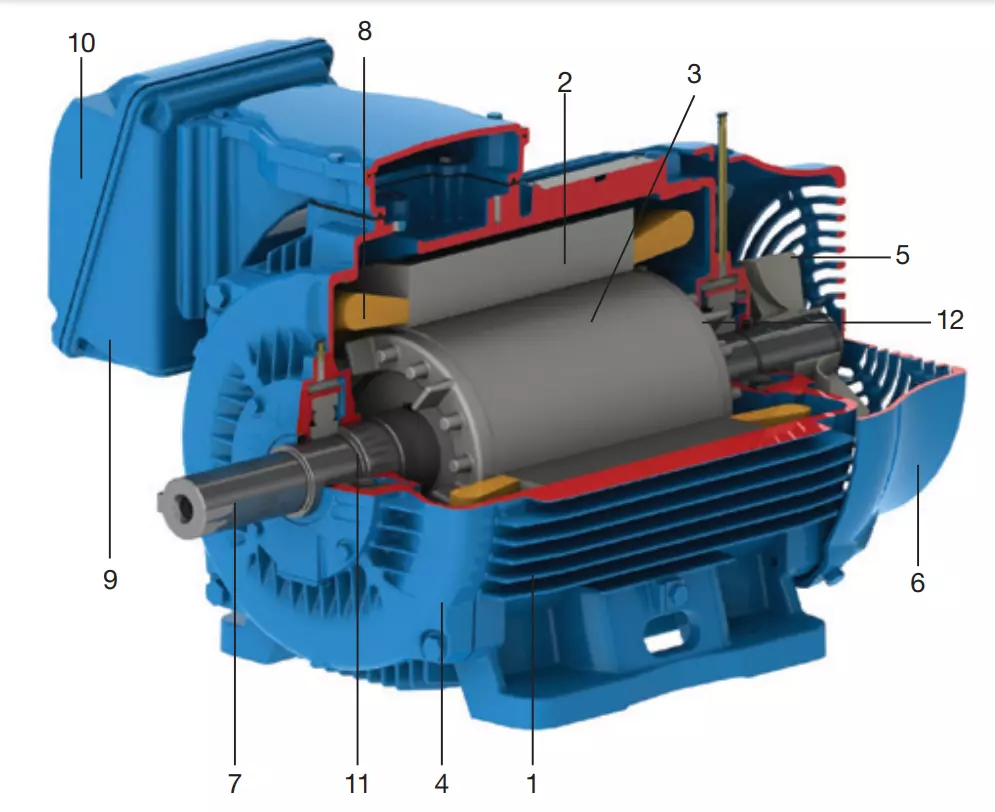
Electric motors consist of several key components that work together to convert electrical energy into mechanical motion. The specific components may vary depending on the type of motor, but the fundamental parts are common to many motor designs. Here are the main components of an electric motor:
- Stator:
- The stator is the stationary part of the motor.
- It typically consists of a core made of laminated iron or steel sheets to minimize eddy current losses.
- Coils or windings are wound around the stator to produce a magnetic field when an electric current flows through them.
- In AC motors, the stator windings are connected to the power supply, creating a rotating magnetic field.
- Rotor (Armature):
- The rotor is the rotating part of the motor.
- It is usually located inside the stator.
- In DC motors, the rotor typically consists of a coil or coils of wire mounted on a shaft.
- In AC motors, the rotor can take different forms, such as a squirrel-cage rotor in induction motors or a wound rotor in some types of synchronous motors.
- Coil or Windings:
- Coils or windings are conductive wires wound around the stator and/or rotor.
- When an electric current flows through these coils, they generate a magnetic field.
- The interaction between the magnetic fields of the stator and rotor is what produces the mechanical motion.
- Communator (in DC Motors) or Slip Rings (in Some AC Motors):
- In DC motors, the commutator is a rotary switch that reverses the direction of the current in the rotor windings, ensuring a continuous rotation.
- In some AC motors, slip rings are used instead of a commutator to transfer electrical power to the rotor.
- Bearings:
- Bearings support the rotor and allow it to rotate smoothly within the stator.
- They reduce friction and wear between moving parts.
- Brushes (in Some DC Motors):
- In DC motors with a commutator, brushes are used to maintain electrical contact with the rotating commutator.
- The brushes carry current to the rotor windings, allowing the motor to continue rotating.
- Housing or Frame:
- The housing or frame encloses and protects the internal components of the motor.
- It provides structural support and helps dissipate heat generated during operation.
- Cooling Mechanism:
- Many motors include a cooling mechanism, such as a fan, to dissipate heat generated during operation.
- Efficient cooling is crucial for maintaining optimal motor performance and preventing overheating.
These components work together to enable the motor to convert electrical energy into mechanical motion, serving various industrial, commercial, and residential applications. The specific design and arrangement of these components can vary depending on the type and purpose of the motor.
Types of Electric Motors – Electric Motor Manufacturers
There are various types of electric motors, each designed for specific applications and operating on different principles. Here are some common types of electric motors:
- DC Motors:
- Brushed DC Motors: These motors use brushes and a commutator to switch the direction of the current in the rotor windings, causing the rotor to rotate.
- Brushless DC Motors (BLDC): Instead of brushes and a commutator, BLDC motors use electronic controllers to switch the direction of current in the stator windings. They are more efficient and have a longer lifespan compared to brushed DC motors.
- AC Motors:
- Induction Motors:
- Single-Phase Induction Motors: Commonly used in household appliances.
- Three-Phase Induction Motors: Widely used in industrial applications due to their efficiency and reliability.
- Synchronous Motors:
- Permanent Magnet Synchronous Motors (PMSM): Use permanent magnets in the rotor, providing better efficiency and power factor.
- Wound Rotor Synchronous Motors: Have windings on the rotor connected to external resistors, allowing for controlled torque.
- Induction Motors:
- Linear Motors:
- Instead of rotational motion, linear motors produce linear motion along a straight path.
- Linear induction motors and linear synchronous motors are examples of linear motor types.
- Servo Motors:
- Servo motors are designed for precise control of position, velocity, and acceleration.
- They are often used in robotics, CNC machines, and other applications requiring high precision.
- Stepper Motors:
- Stepper motors move in discrete steps, making them suitable for applications where precise positioning is essential.
- They are commonly used in 3D printers, CNC machines, and various automation systems.
- Hollow Shaft Motors:
- These motors have a central opening in the rotor, allowing for the passage of cables, fluids, or other mechanical components through the center of the motor.
- Hermetic Motors:
- Sealed and designed to operate in environments where they are exposed to liquids or gases. Commonly used in refrigeration and air conditioning.
- Universal Motors:
- These motors can run on both AC and DC power.
- Commonly used in small household appliances like vacuum cleaners and power tools.
- Fractional Horsepower Motors:
- Motors with a power rating less than one horsepower.
- Widely used in applications where a small and economical motor is sufficient, such as fans and pumps.
- Gear Motors:
- Combines an electric motor with a gearbox to provide increased torque and lower speed.
- Used in applications where high torque is required, such as in automotive windshield wipers.
The choice of electric motor depends on factors such as the application requirements, power efficiency, size, speed, and cost considerations. Each type of motor has its advantages and disadvantages, making them suitable for specific tasks and industries.
DC Motors – Electric Motor Manufacturers
DC motors, short for direct current motors, are devices that convert electrical energy into mechanical energy through the interaction of magnetic fields. They operate on the principle of electromagnetism and find applications in various industries due to their simplicity and controllability. Here are some key aspects of DC motors:
Basic Structure:
- Stator: The stationary part of a DC motor, usually consisting of permanent magnets or electromagnets that create a magnetic field.
- Rotor: The rotating part of the motor, typically made up of a coil of wire or multiple coils (armature) wound around a core. The rotor is placed within the stator’s magnetic field.
- Commutator: Found in brushed DC motors, the commutator is a segmented metal ring that ensures the direction of current in the rotor windings changes as the rotor turns, allowing for continuous rotation.
- Brushes: In brushed DC motors, brushes are conductive components that maintain contact with the commutator, supplying electric current to the rotor windings.
Types of DC Motors:
- Brushed DC Motors: These motors use brushes and a commutator for current reversal in the rotor windings. They are relatively simple but may require more maintenance due to the brushes.
- Brushless DC Motors (BLDC): BLDC motors use electronic controllers instead of brushes and a commutator. They are more efficient, produce less noise, and require less maintenance compared to brushed DC motors.
Working Principle:
- When a direct current flows through the coils of the rotor, an electromagnetic field is generated around the rotor.
- The interaction between the magnetic fields of the stator and rotor causes a torque, resulting in the rotation of the rotor.
- In brushed DC motors, the commutator and brushes ensure that the direction of the current in the rotor windings changes as the rotor turns, maintaining the rotation.
Applications:
- Automotive: DC motors power various components in vehicles, such as power windows, windshield wipers, and seat adjustment mechanisms.
- Industrial Machinery: They’re used in conveyors, pumps, compressors, and other equipment requiring variable speed control.
- Household Appliances: Found in appliances like electric razors, mixers, and some types of fans.
Advantages:
- Controllability: DC motors offer precise speed control and torque adjustments.
- Simple Design: Particularly brushed DC motors have a relatively straightforward design, making them easy to understand and maintain.
Limitations:
- Brush Wear: In brushed DC motors, the brushes can wear out over time, requiring periodic replacement and maintenance.
- Electromagnetic Interference: In some cases, DC motors can produce electromagnetic interference that might affect nearby electronic devices.
DC motors remain a vital part of various industries despite the rise of other motor types, thanks to their simplicity, controllability, and suitability for specific applications.
Applications
Electric motors find applications in a wide range of industries and everyday devices due to their ability to convert electrical energy into mechanical motion efficiently. Here are some common applications of electric motors:
- Industrial Machinery:
- Electric motors power various industrial machines, including conveyor systems, pumps, compressors, fans, and manufacturing equipment.
- Transportation:
- Electric Vehicles (EVs): Electric motors drive the wheels in electric cars, buses, and bikes, contributing to the shift towards more sustainable transportation.
- Trains and Light Rail: Electric motors are used in electric trains and light rail systems for propulsion.
- Household Appliances:
- Electric motors are integral to many household appliances, such as washing machines, refrigerators, air conditioners, vacuum cleaners, blenders, and electric fans.
- HVAC Systems:
- Heating, ventilation, and air conditioning (HVAC) systems use electric motors in fans, compressors, and pumps to circulate air and control temperature.
- Pumps and Water Systems:
- Electric motors power water pumps for domestic water supply, irrigation, and industrial processes.
- Power Tools:
- Many power tools, including drills, saws, and grinders, are powered by electric motors for various applications.
- Renewable Energy:
- Electric motors are used in renewable energy systems, such as wind turbines and hydropower generators, to convert rotational energy into electricity.
- Robotics:
- Servo motors and stepper motors play a crucial role in robotics, providing precise control of movement in robotic arms, drones, and other automated systems.
- Aerospace:
- Electric motors are used in various aircraft systems, including landing gear, pumps, and auxiliary power units.
- Medical Devices:
- Electric motors are used in medical equipment such as ventilators, infusion pumps, and diagnostic devices.
- Consumer Electronics:
- Electric motors are present in devices like electric toothbrushes, cameras, and computer hard drives.
- Elevators and Escalators:
- Electric motors power the movement of elevators and escalators in buildings.
- Gaming and Entertainment:
- Electric motors are used in gaming consoles, virtual reality devices, and amusement park rides.
- Automotive Systems:
- Besides electric vehicles, electric motors are used in various automotive applications, including power windows, windshield wipers, and cooling fans.
- Oil and Gas Industry:
- Electric motors are employed in pumps, compressors, and other equipment used in the extraction and processing of oil and gas.
- Mining:
- Electric motors power equipment such as crushers, conveyors, and drills in the mining industry.
These examples highlight the versatility and widespread use of electric motors in modern society, contributing to increased efficiency, automation, and the transition to more sustainable energy sources.
AC Motors – Electric Motor Manufacturers
AC motors, or alternating current motors, are devices that convert electrical energy from an alternating current power source into mechanical energy. These motors are widely used in various applications due to their reliability, efficiency, and adaptability to different power systems. Here are key aspects of AC motors:
Types of AC Motors:
- Induction Motors:
- Single-Phase Induction Motors: Commonly used in residential applications and small industrial equipment.
- Three-Phase Induction Motors: Widely used in industrial applications due to their efficiency, reliability, and ability to handle higher power loads.
- Synchronous Motors:
- Permanent Magnet Synchronous Motors (PMSM): Use permanent magnets in the rotor, providing efficiency benefits.
- Wound Rotor Synchronous Motors: Feature windings on the rotor connected to external resistors, allowing for controlled torque.
Basic Structure:
- Stator:
- The stator contains coils or windings that are connected to the AC power supply.
- When AC voltage is applied, it induces a rotating magnetic field in the stator.
- Rotor:
- The rotor is placed inside the stator and can take different forms depending on the motor type.
- In induction motors, the rotor is typically a squirrel-cage rotor consisting of conductive bars.
- Working Principle:
- In induction motors, the rotating magnetic field in the stator induces a current in the rotor, creating a secondary magnetic field.
- The interaction between the stator’s rotating magnetic field and the rotor’s magnetic field generates torque, causing the rotor to turn.
Applications:
- Industrial Machinery:
- AC induction motors are used in a wide range of industrial equipment, including pumps, fans, compressors, conveyors, and manufacturing machinery.
- HVAC Systems:
- AC motors power the fans and compressors in heating, ventilation, and air conditioning (HVAC) systems.
- Electric Appliances:
- Many household appliances, such as washing machines, refrigerators, and air conditioners, use AC motors.
- Power Tools:
- AC motors are employed in various power tools, such as drills, saws, and grinders.
- Transportation:
- AC motors are used in electric trains, trolleys, and some types of electric vehicles.
- Renewable Energy:
- AC motors are integral components in wind turbines, converting wind energy into electrical power.
Advantages:
- Efficiency: AC motors are known for their high efficiency, especially in larger industrial applications.
- Low Maintenance: Induction motors, in particular, have fewer moving parts, resulting in lower maintenance requirements.
Limitations:
- Control Complexity: Compared to DC motors, AC motors can be more complex to control, especially in terms of speed regulation.
- Starting Torque: Induction motors may have lower starting torque compared to some DC motors, although this can be addressed with additional components.
AC motors are a cornerstone of modern industrial and commercial applications, providing reliable and efficient means of converting electrical energy into mechanical motion. The specific type of AC motor chosen depends on the requirements of the application.
Electric Motors from the Electric Motor Manufacturers
Electric motors are devices that convert electrical energy into mechanical energy. They are commonly used in a wide range of applications, from household appliances to industrial machinery, and are essential components in many modern technologies.
The basic principle behind an electric motor is simple. It consists of a magnetic field and a conductor. When a current is passed through the conductor, it experiences a force due to the interaction between the magnetic field and the electric charge. The direction of the force depends on the direction of the current and the orientation of the magnetic field.
There are two main types of electric motors: AC (alternating current) motors and DC (direct current) motors. AC motors are typically used in applications where constant speed is required, while DC motors are used in applications where variable speed is required.
AC motors operate by changing the direction of the current flowing through the windings of the motor, causing the magnetic field to rotate. This rotation creates a torque on the rotor, which causes it to turn. AC motors are typically used in household appliances, such as fans and refrigerators, as well as in industrial applications, such as pumps and compressors.
DC motors operate by applying a voltage to the motor, causing the current to flow through the windings of the motor. This creates a magnetic field, which interacts with the permanent magnets on the rotor, causing it to turn. DC motors are typically used in applications where variable speed is required, such as in electric vehicles and power tools.
Electric motors come in a wide range of sizes and power ratings, from small motors used in household appliances to large motors used in industrial machinery. They are also used in a variety of applications, including robotics, automation, and renewable energy systems.
In recent years, electric motors have become increasingly important due to their role in the transition to clean energy. Electric motors are used in electric vehicles, wind turbines, and solar panels, making them key components in the transition to a low-carbon economy. As technology continues to improve, electric motors are expected to become even more efficient and versatile, driving innovation and growth in a wide range of industries.
Electric Motors – Electric Motor Manufacturers
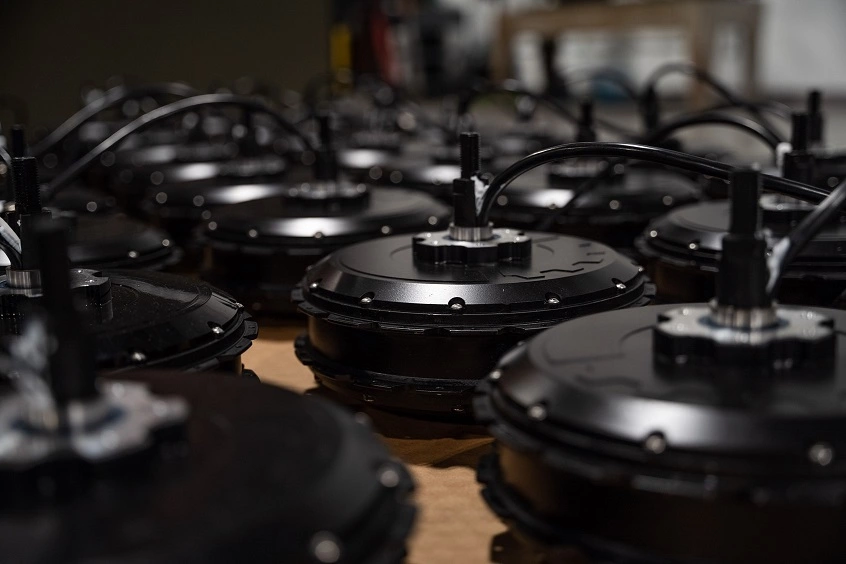
An electric motor is a machine capable of converting electrical energy into mechanical energy. The induction motor is the most widely used type of motor because it combines all the advantages offered by electrical energy such as low cost, ease of supply and distribution, clean handling, and simple controls – together with those of simple construction and its great versatility to be adapted to wide ranges of loads and improved efficiencies. The most common types of electric motors are:
- Direct current motors: These motors are quite expensive requiring a direct current source or a converting device to convert normal alternating current into direct current. They are capable of operating with adjustable speeds over a wide range and are perfectly suited for accurate and flexible speed control. Therefore, their use is restricted to special applications where these requirements compensate for the much higher installation and maintenance costs.
- Alternating current motors: These are the most frequently used motors because electrical power is normally supplied as alternating current. The most common types are:
- Synchronous motors: synchronous motors are three-phase AC motors that run at a fixed speed, without slip, and are generally applied for large outputs (due to their relatively high costs in smaller frame sizes).
- Induction motor: these motors generally run at a constant speed which changes slightly when mechanical loads are applied to the motor shaft. Due to its simplicity, robustness, and low cost, this type of motor is the most widely used and, in practical terms, is quite suitable for almost all types of machines. Currently, it is possible to control the speed of induction motors with frequency inverters.
Electric motors are so much a part of everyday life that we seldom give them a second thought. When we switch on an electric drill, for example, we confidently expect it to run rapidly up to the correct speed and we do not question how it knows what pace to run, or how it is that once enough energy has been drawn from the supply to bring it up to speed, the power drawn falls to a very low level.
When we put the drill to work it draws more power, and when we finish the power drawn from the mains reduces automatically, without intervention on our part.
The humble motor, consisting of nothing more than an arrangement
of copper coils and steel laminations, is rather a clever energy converter, which warrants serious consideration. By gaining a basic understanding of how the motor works, we will be able to appreciate its potential and its limitations, and (in later chapters) see how the addition of external electronic controls can further enhance its already remarkable performance.
Mechanism of Electric Motors
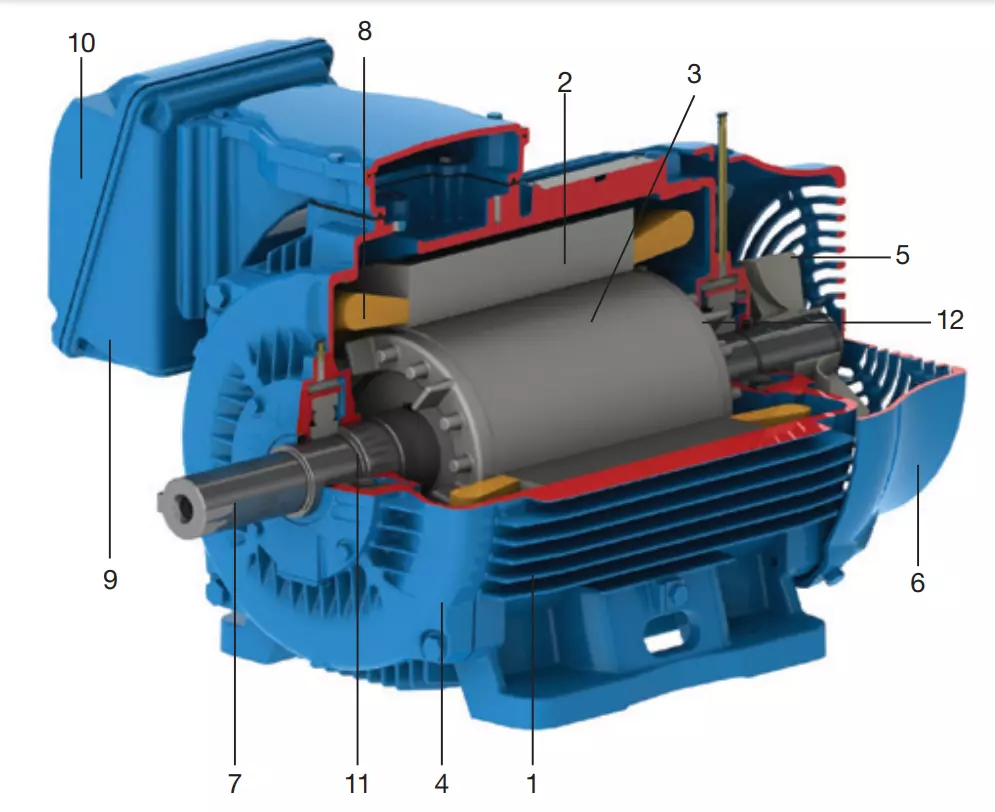
This chapter deals with the basic mechanisms of motor operation, so
readers familiar with magnetic Xux, magnetic and electric circuits, torque, and motional e.m.f can probably afford to skim over much of it. In the course of the discussion, however, several very important general principles and guidelines emerge.
Nearly all motors exploit the force which is exerted on a current-carrying conductor placed in a magnetic Weld. The force can be demonstrated by placing a bar magnet near a wire carrying current, but anyone trying the experiment will probably be disappointed to discover how feeble the force is, and will doubtless be left wondering how such an unpromising effect can be used to make effective motors.
We will see that in order to make the most of the mechanism, we need
to arrange a very strong magnetic Weld, and make it interact with many
conductors, each carrying as much current as possible. We will also see
later that although the magnetic Weld (or ‘excitation’) is essential to the
working of the motor, it acts only as a catalyst and all of the mechanical
output power comes from the electrical supply to the conductors on
which the force is developed.
Energy in Electric Motor Works
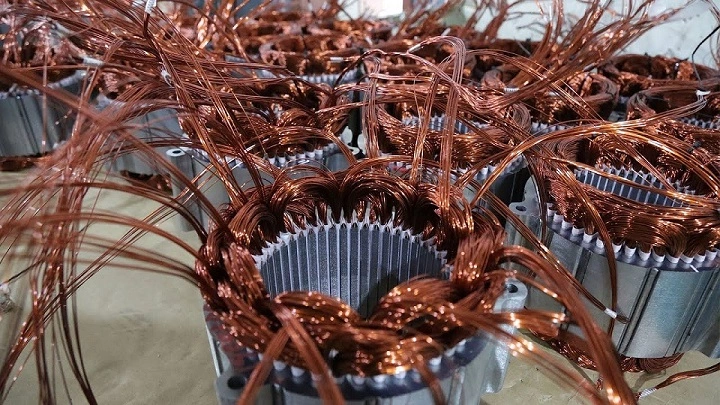
It will emerge later that in some motors the parts of the machine responsible for the excitation and the energy-converting functions are distinct and self-evident. In the d.c. motor, for example, the excitation is provided either by permanent magnets or by Weld coils wrapped around clearly defined projecting Weld poles on the stationary part, while the conductors on which force is developed are on the rotor and supplied with current via sliding brushes.
In many motors, however, there is no such clear-cut physical distinction between the ‘excitation’ and the ‘energy-converting’ parts of the machine, and a single stationary winding serves both purposes. Nevertheless, we will find that identifying and separating the excitation and energy-converting functions are always helpful in understanding how motors of all types operate.
Operation Principle of Electric Motors
A large percentage of AC motors are induction motors. This implies that there is no current supplied to the rotating coils (rotor windings). These coils are closed loops that have large currents induced in them. Three-phase currents flowing in the stator windings lead to establishing a rotating magnetic field in the air gap. This magnetic field continuously pulsates across the air gap and into the rotor. This is a single-phase representation of windings and current flow.
As magnetic flux cuts across the rotor bars, a voltage is induced in them, much as a voltage is induced in the secondary winding of a transformer. Because the rotor bars are part of a closed circuit (including the end rings), a current circulates in them. The rotor current in turn produces a
magnetic field that interacts with the magnetic field of the stator. Since this field is rotating and magnetically interlocked with the rotor, the rotor is dragged around with the stator field.
Wound Rotor Electric Motor Types
Wound-rotor motors — Although the squirrel-cage induction motor is relatively inflexible about speed and torque characteristics, a special wound-rotor version has controllable speed and torque. The application of wound-rotor motors is markedly different from squirrel-cage motors because of the accessibility of the rotor circuit. Various performance characteristics can be obtained by inserting different values of resistance in the rotor circuit.
Wound rotor motors are generally started with secondary resistance in the rotor circuit. This resistance is sequentially reduced to permit the motor to come up to speed. Thus the motor can develop substantial torque while limiting the locked rotor current.
The secondary resistance can be designed for continuous service to dissipate heat produced by continuous operation at reduced speed, frequent acceleration, or acceleration with a large inertia load. External resistance gives the motor a characteristic that results in a large drop in rpm for a fairly small change in load. Reduced speed is provided down to about 50%, rated speed, but efficiency is low.
Electrical motors are the workhorses of modern technology, powering everything from household appliances to industrial machinery. Their significance in contemporary society cannot be overstated, as they convert electrical energy into mechanical energy, enabling countless applications across various fields. As the backbone of automation and industrial processes, understanding electrical motors is essential for engineers, designers, and professionals engaged in technology-driven industries.
The role of electrical motors in modern industry is critical. They are integral to manufacturing processes, transportation systems, and consumer electronics, among other areas. This article aims to provide a comprehensive overview of electrical motors, exploring their history, types, components, performance characteristics, applications, and the latest advancements. By understanding these aspects, professionals can better appreciate the complexities and capabilities of electrical motors and their impact on technological progress.
2. History of Electrical Motors
Early Developments
The history of electrical motors dates back to the early 19th century when the principles of electromagnetism were first discovered. Michael Faraday, an English scientist, made significant contributions to the understanding of electromagnetic induction, which laid the groundwork for the development of electrical motors. In 1821, Faraday demonstrated the first simple electric motor, known as the homopolar motor, which used a magnetic field to produce continuous rotation.
Key Innovators and Milestones
The development of electrical motors accelerated in the following decades, with several key innovators contributing to the field. In 1834, Moritz Jacobi, a German engineer, built the first real rotating electric motor, which was capable of performing mechanical work. This achievement marked a significant milestone in the evolution of motor technology.
Thomas Davenport, an American blacksmith, is credited with developing the first commercially viable electric motor in 1837. His invention, patented in 1837, was used to power a small printing press, showcasing the potential of electric motors in practical applications.
Evolution of Motor Technology
The late 19th and early 20th centuries witnessed significant advancements in motor technology. Nikola Tesla, a Serbian-American inventor, developed the alternating current (AC) motor in the 1880s, revolutionizing the electrical power industry. Tesla’s AC motor was more efficient and reliable than its direct current (DC) counterparts, leading to widespread adoption in various industries.
With the advent of semiconductors and microelectronics in the 20th century, electrical motors became more sophisticated and efficient. Innovations in motor design, materials, and control systems have continued to enhance their performance and broaden their applications.
3. Basic Principles of Electrical Motors
Electromagnetism
At the core of electrical motor operation is the principle of electromagnetism. An electrical motor operates by converting electrical energy into mechanical energy through the interaction of magnetic fields. When an electric current flows through a conductor within a magnetic field, a force is exerted on the conductor, causing it to move. This phenomenon is known as the Lorentz force and is the basis for all types of electrical motors.
Motor Components
An electrical motor typically consists of several key components, including a stator, rotor, bearings, windings, and, in some cases, commutators and brushes. The stator is the stationary part of the motor that generates a magnetic field, while the rotor is the rotating part that interacts with the magnetic field to produce motion. Bearings support the rotor and reduce friction during rotation. Windings are coils of wire through which current flows, generating the magnetic field. In DC motors, commutators and brushes are used to maintain the direction of current flow.
Operating Principles
Electrical motors operate on the principle of electromagnetic induction, which involves the conversion of electrical energy into mechanical energy. When an electric current passes through the windings, a magnetic field is created, which interacts with the magnetic field of the stator. This interaction generates a force that causes the rotor to rotate, producing mechanical energy.
Different types of motors use various methods to achieve this conversion. For example, in AC motors, the stator’s magnetic field rotates, inducing a current in the rotor and causing it to follow the rotating field. In DC motors, the current direction is switched using a commutator, allowing for continuous rotation.
4. Types of Electrical Motors
AC Motors
- Induction Motors
Induction motors, also known as asynchronous motors, are the most common type of AC motor. They operate on the principle of electromagnetic induction, where the stator’s rotating magnetic field induces a current in the rotor. This induced current generates a magnetic field in the rotor, causing it to follow the stator’s field and produce torque. Induction motors are widely used in industrial applications due to their simplicity, reliability, and low maintenance requirements.
- Synchronous Motors
Synchronous motors differ from induction motors in that the rotor’s magnetic field is synchronized with the stator’s rotating field. This synchronization is achieved using either permanent magnets or electromagnets on the rotor. Synchronous motors are known for their high efficiency and precise speed control, making them suitable for applications requiring constant speed, such as in compressors and conveyors.
DC Motors
- Brushed DC Motors
Brushed DC motors are among the oldest types of electrical motors. They consist of a rotor with windings and a commutator that switches the direction of current flow, allowing continuous rotation. Brushed DC motors are simple and cost-effective but require regular maintenance due to brush wear and commutator erosion.
- Brushless DC Motors
Brushless DC motors eliminate the need for brushes and commutators by using electronic commutation. They have a rotor with permanent magnets and a stator with windings. The rotor’s magnetic field interacts with the stator’s magnetic field, causing rotation. Brushless DC motors are known for their high efficiency, low maintenance, and long lifespan, making them ideal for applications requiring precision and reliability, such as in robotics and aerospace.
Specialty Motors
- Stepper Motors
Stepper motors are a type of brushless DC motor that rotates in discrete steps, allowing precise control of position and speed. They are commonly used in applications requiring accurate positioning, such as in 3D printers and CNC machines. Stepper motors are known for their high torque at low speeds and ability to hold position without feedback.
- Servo Motors
Servo motors are designed for applications requiring precise control of position, speed, and torque. They consist of a motor coupled with a feedback mechanism, typically an encoder or potentiometer, which provides information about the motor’s position and speed. Servo motors are widely used in robotics, automation, and motion control systems.
5. Components of Electrical Motors
Stator and Rotor
The stator and rotor are the two primary components of an electrical motor. The stator is the stationary part that generates a magnetic field, while the rotor is the rotating part that interacts with the magnetic field to produce motion. The stator is typically made of laminated iron cores with copper windings, while the rotor can be a squirrel cage or wound type.
Bearings
Bearings are critical components that support the rotor and reduce friction during rotation. They ensure smooth and efficient operation of the motor by minimizing mechanical losses. Bearings are designed to withstand radial and axial loads and are available in various types, including ball bearings and roller bearings.
Windings
Windings are coils of wire through which electric current flows, generating a magnetic field. The windings are typically made of copper due to its high electrical conductivity. In AC motors, the windings are distributed around the stator to create a rotating magnetic field. In DC motors, the windings are located on the rotor and connected to the commutator.
Commutators and Brushes (for DC Motors)
Commutators and brushes are essential components of brushed DC motors. The commutator is a cylindrical device connected to the rotor windings, while brushes are stationary conductive elements that make contact with the commutator. As the rotor rotates, the commutator switches the direction of current flow, allowing for continuous rotation. However, commutators and brushes require regular maintenance due to wear and tear.
6. Motor Performance Characteristics
Torque and Speed
Torque and speed are fundamental performance characteristics of electrical motors. Torque is the rotational force produced by the motor, while speed refers to the rotational velocity of the motor’s output shaft. The relationship between torque and speed is crucial for determining the motor’s suitability for specific applications. Motors can be designed for high torque at low speeds or high speeds with lower torque, depending on the requirements.
Efficiency
Efficiency is a measure of how effectively an electrical motor converts electrical energy into mechanical energy. High-efficiency motors consume less energy, produce less heat, and have lower operating costs. Efficiency is influenced by factors such as design, materials, and operating conditions. Advances in motor technology have led to the development of energy-efficient motors that meet stringent regulatory standards.
Power Factor
Power factor is a measure of how effectively a motor uses the electrical power supplied to it. It is the ratio of real power (measured in watts) to apparent power (measured in volt-amperes) and is expressed as a percentage. A high power factor indicates efficient use of electrical power, while a low power factor suggests that the motor is drawing more current than necessary. Power factor correction techniques, such as using capacitors, can improve the motor’s efficiency.
Thermal Management
Thermal management is essential for maintaining the performance and longevity of electrical motors. Excessive heat can lead to insulation breakdown, reduced efficiency, and motor failure. Effective thermal management involves dissipating heat generated during operation through methods such as air cooling, liquid cooling, or using heat sinks. Proper thermal management ensures reliable motor operation and extends its lifespan.
7. Applications of Electrical Motors
Industrial Uses
Electrical motors are indispensable in industrial applications, driving machinery and equipment in manufacturing, processing, and automation. They power conveyors, pumps, compressors, and machine tools, among other equipment. Motors are also used in HVAC systems, providing efficient heating, ventilation, and air conditioning in industrial facilities.
Consumer Electronics
In the consumer electronics sector, electrical motors are used in a wide range of devices, from household appliances to personal gadgets. They power fans, refrigerators, washing machines, vacuum cleaners, and more. In the entertainment industry, motors are used in devices such as DVD players, projectors, and gaming consoles, enhancing the user experience through precise motion control.
Transportation
The transportation sector relies heavily on electrical motors, particularly in the automotive industry. Electric vehicles (EVs) use motors for propulsion, offering a sustainable and energy-efficient alternative to internal combustion engines. Motors are also used in hybrid vehicles, trains, and aircraft, contributing to advancements in transportation technology.
Renewable Energy
Electrical motors play a vital role in the renewable energy sector, enabling the conversion of natural resources into usable energy. Wind turbines use motors to generate electricity from wind, while solar power systems use motors in tracking systems to optimize the capture of sunlight. Motors are also used in hydroelectric power plants, converting the kinetic energy of flowing water into electrical energy.
8. Advancements in Motor Technology
Smart Motors
The integration of digital technology and smart systems has led to the development of smart motors. These motors are equipped with sensors and communication capabilities, allowing for real-time monitoring and control. Smart motors offer improved performance, efficiency, and reliability through features such as predictive maintenance, fault detection, and remote diagnostics. They are ideal for applications requiring advanced automation and control.
Energy Efficiency Improvements
Advancements in motor technology have focused on improving energy efficiency to reduce environmental impact and operating costs. High-efficiency motors are designed with optimized materials, geometries, and control systems to minimize energy losses. Variable frequency drives (VFDs) are used to control motor speed and torque, enhancing efficiency and reducing energy consumption in variable-load applications.
Integration with IoT
The Internet of Things (IoT) has transformed the way electrical motors are used and managed. IoT-enabled motors can communicate with other devices and systems, providing valuable data on performance, condition, and energy usage. This data can be used to optimize motor operation, predict maintenance needs, and improve overall system efficiency. IoT integration enhances the capabilities of electrical motors in various applications, from industrial automation to smart home systems.
9. Challenges and Solutions in Motor Design
Noise Reduction
Noise is a common challenge in motor design, particularly in applications requiring quiet operation. Motor noise can be caused by mechanical vibrations, electromagnetic forces, and airflow. To address this issue, engineers use advanced materials, precision manufacturing techniques, and noise-dampening technologies. Proper alignment, balancing, and insulation also contribute to noise reduction in electrical motors.
Vibration Management
Vibrations in electrical motors can lead to mechanical wear, reduced performance, and premature failure. Effective vibration management involves designing motors with balanced components, minimizing mechanical clearances, and using vibration-dampening materials. Advanced diagnostic tools and monitoring systems can detect and address vibration issues before they impact motor operation.
Durability and Maintenance
Durability and maintenance are critical considerations in motor design, as they impact reliability and lifespan. Motors must be designed to withstand harsh operating conditions, including high temperatures, moisture, and corrosive environments. Maintenance practices such as regular inspections, lubrication, and cleaning help extend motor life and ensure optimal performance. Advances in materials and manufacturing techniques have led to the development of motors with enhanced durability and reduced maintenance requirements.
10. Future Trends in Electrical Motors
Green Technologies
The future of electrical motors is closely tied to the development of green technologies that reduce environmental impact and promote sustainability. Electric vehicles, renewable energy systems, and energy-efficient appliances are driving the demand for advanced motor solutions. Researchers are exploring new materials, designs, and control systems to enhance motor efficiency and reduce carbon emissions.
Advanced Materials
The use of advanced materials is revolutionizing motor design, offering improved performance and durability. Lightweight materials such as composites and high-strength alloys reduce motor weight and enhance efficiency. Nanomaterials and superconductors are being explored for their potential to improve electrical conductivity and reduce energy losses. These advancements are paving the way for the next generation of high-performance electrical motors.
Emerging Applications
As technology continues to evolve, new applications for electrical motors are emerging in various fields. In the healthcare sector, motors are used in medical devices, robotic surgery systems, and diagnostic equipment. In the aerospace industry, motors are powering advanced aircraft propulsion systems and drones. The increasing demand for automation, robotics, and smart technologies is driving the development of innovative motor solutions for a wide range of applications.
11. Conclusion
In conclusion, electrical motors are essential components of modern technology, driving progress across various industries. From their early development to the latest advancements, motors have evolved to meet the changing needs of society. The diverse types of motors, each with its unique characteristics and applications, highlight the versatility and importance of these devices.
As the demand for energy-efficient, sustainable, and smart technologies continues to grow, electrical motors will play a crucial role in shaping the future. The ongoing research and development in motor technology will lead to new solutions that enhance performance, efficiency, and reliability, paving the way for a more sustainable and technologically advanced world. Understanding the complexities and capabilities of electrical motors is essential for professionals in the field, as they contribute to the advancement of modern industry and society.
- Introduction
- Overview of Electrical Motors
- Importance in Modern Industry
- History of Electrical Motors
- Early Developments
- Key Innovators and Milestones
- Evolution of Motor Technology
- Basic Principles of Electrical Motors
- Electromagnetism
- Motor Components
- Operating Principles
- Types of Electrical Motors
- AC Motors
- Induction Motors
- Synchronous Motors
- DC Motors
- Brushed DC Motors
- Brushless DC Motors
- Specialty Motors
- Stepper Motors
- Servo Motors
- AC Motors
- Motor Comparisons
- AC vs. DC Motors
- Brushed vs. Brushless DC Motors
- Induction vs. Synchronous Motors
- Stepper vs. Servo Motors
- Components of Electrical Motors
- Stator and Rotor
- Bearings
- Windings
- Commutators and Brushes (for DC Motors)
- Motor Performance Characteristics
- Torque and Speed
- Efficiency
- Power Factor
- Thermal Management
- Applications of Electrical Motors
- Industrial Uses
- Consumer Electronics
- Transportation
- Renewable Energy
- Advancements in Motor Technology
- Smart Motors
- Energy Efficiency Improvements
- Integration with IoT
- Challenges and Solutions in Motor Design
- Noise Reduction
- Vibration Management
- Durability and Maintenance
- Future Trends in Electrical Motors
- Green Technologies
- Advanced Materials
- Emerging Applications
- Conclusion
- Summary of Key Points
- The Future of Electrical Motors in Industry
5. Motor Comparisons
Understanding the differences between various types of electrical motors is crucial for selecting the right motor for specific applications. Each type of motor has unique characteristics that make it suitable for certain tasks while presenting limitations in others. This section provides a detailed comparison of the most common types of electrical motors.
AC vs. DC Motors
- Efficiency and Control:
- AC Motors: Generally more efficient for applications requiring high power output. They are less complex in design compared to DC motors and often provide better performance in heavy-duty applications.
- DC Motors: Offer precise speed control and high starting torque, making them ideal for applications requiring variable speed and position control.
- Maintenance:
- AC Motors: Require less maintenance than DC motors due to their simpler construction and absence of brushes.
- DC Motors: Require regular maintenance, particularly brushed DC motors, due to wear and tear on brushes and commutators.
- Applications:
- AC Motors: Widely used in industrial applications, HVAC systems, and large machinery.
- DC Motors: Common in automotive applications, robotics, and portable devices where precise control is necessary.
Brushed vs. Brushless DC Motors
- Efficiency and Lifespan:
- Brushed DC Motors: Less efficient and have a shorter lifespan due to brush and commutator wear.
- Brushless DC Motors: More efficient with a longer lifespan, as they do not have brushes that wear out.
- Control and Complexity:
- Brushed DC Motors: Simpler design and control but require regular maintenance.
- Brushless DC Motors: More complex control systems due to electronic commutation but offer better performance and reliability.
- Applications:
- Brushed DC Motors: Used in cost-sensitive applications where high precision is not critical.
- Brushless DC Motors: Preferred in high-performance applications such as drones, electric vehicles, and computer peripherals.
Induction vs. Synchronous Motors
- Starting Mechanism:
- Induction Motors: Simple starting mechanism and do not require additional starting equipment.
- Synchronous Motors: Require starting auxiliaries or variable frequency drives (VFDs) for starting and synchronization.
- Speed Control:
- Induction Motors: Speed varies with load and is generally not suitable for applications requiring constant speed without additional control systems.
- Synchronous Motors: Maintain a constant speed regardless of load, ideal for applications needing precise speed control.
- Efficiency:
- Induction Motors: Less efficient at low loads but provide excellent performance at full load.
- Synchronous Motors: Highly efficient and provide power factor correction capabilities.
- Applications:
- Induction Motors: Widely used in industrial and commercial applications for their robustness and simplicity.
- Synchronous Motors: Used in applications requiring constant speed and power factor correction, such as in power plants and high-precision manufacturing.
Stepper vs. Servo Motors
- Positioning Accuracy:
- Stepper Motors: Provide accurate and repeatable positioning without the need for feedback systems, ideal for open-loop control systems.
- Servo Motors: Offer high precision and closed-loop control with feedback, suitable for dynamic applications requiring precise control.
- Speed and Torque:
- Stepper Motors: High torque at low speeds but can lose steps at high speeds, making them less suitable for high-speed applications.
- Servo Motors: Provide consistent torque across a wide speed range, ideal for high-speed applications.
- Applications:
- Stepper Motors: Used in applications such as 3D printers, CNC machines, and other systems where precise positioning is required.
- Servo Motors: Common in robotics, automation, and applications requiring high-speed and high-precision control.
Including diagrams and visual aids will significantly enhance the comprehension of the technical aspects of electrical motors, especially in a professional article. Diagrams can help illustrate motor components, different types of motors, and specific principles of operation, making the content more engaging and accessible.
Since we can’t directly create diagrams here, I’ll guide you on how to incorporate them into the article. I’ll describe the diagrams that should be included and how they relate to the content. You can then use these descriptions to create or source appropriate diagrams.
Revised Outline with Diagrams
- Introduction
- Overview of Electrical Motors
- Importance in Modern Industry
- History of Electrical Motors
- Early Developments
- Key Innovators and Milestones
- Evolution of Motor Technology
- Basic Principles of Electrical Motors
- Electromagnetism
- Motor Components
- Operating Principles
- Types of Electrical Motors
- AC Motors
- Induction Motors
- Synchronous Motors
- DC Motors
- Brushed DC Motors
- Brushless DC Motors
- Specialty Motors
- Stepper Motors
- Servo Motors
- AC Motors
- Motor Comparisons
- AC vs. DC Motors
- Brushed vs. Brushless DC Motors
- Induction vs. Synchronous Motors
- Stepper vs. Servo Motors
- Components of Electrical Motors
- Stator and Rotor
- Bearings
- Windings
- Commutators and Brushes (for DC Motors)
- Motor Performance Characteristics
- Torque and Speed
- Efficiency
- Power Factor
- Thermal Management
- Applications of Electrical Motors
- Industrial Uses
- Consumer Electronics
- Transportation
- Renewable Energy
- Advancements in Motor Technology
- Smart Motors
- Energy Efficiency Improvements
- Integration with IoT
- Challenges and Solutions in Motor Design
- Noise Reduction
- Vibration Management
- Durability and Maintenance
- Future Trends in Electrical Motors
- Green Technologies
- Advanced Materials
- Emerging Applications
- Conclusion
- Summary of Key Points
- The Future of Electrical Motors in Industry
Suggested Diagrams
Below are the descriptions of diagrams to include in each relevant section of the article:
3. Basic Principles of Electrical Motors
Diagram 1: Electromagnetic Force in Motors
- Description: Illustrate the basic principle of electromagnetic force. Show a simple setup with a coil of wire (conductor) placed within a magnetic field, highlighting the direction of current flow and the resulting force.
- Purpose: To visually explain how the interaction between magnetic fields and electric currents creates motion.
Diagram 2: Basic Motor Components
- Description: Show a cross-sectional view of a generic electric motor, labeling key components like the stator, rotor, bearings, windings, commutator, and brushes.
- Purpose: To help readers understand the fundamental parts of an electric motor and their functions.
4. Types of Electrical Motors
Diagram 3: AC Induction Motor
- Description: Display the internal structure of an AC induction motor, including the stator windings and rotor. Include arrows indicating the rotating magnetic field.
- Purpose: To illustrate how induction motors work and highlight the differences from other motor types.
Diagram 4: Brushed DC Motor
- Description: Depict the internal workings of a brushed DC motor, highlighting the rotor, commutator, and brushes. Show the flow of current and rotation of the rotor.
- Purpose: To clarify the operation of brushed DC motors and show how commutators and brushes interact.
Diagram 5: Brushless DC Motor
- Description: Provide an illustration of a brushless DC motor, showing the rotor with permanent magnets and the stator with windings. Include an electronic control circuit for commutation.
- Purpose: To explain how brushless DC motors function without brushes and commutators.
5. Motor Comparisons
Diagram 6: AC vs. DC Motor Characteristics
- Description: Create a side-by-side comparison table or infographic that highlights key characteristics of AC and DC motors, such as efficiency, speed control, and maintenance requirements.
- Purpose: To provide a quick reference for comparing the two motor types.
Diagram 7: Induction vs. Synchronous Motors
- Description: Use a comparative diagram to show the key differences in operation between induction and synchronous motors, focusing on how each achieves rotation and synchronization.
- Purpose: To visualize the distinct features of these AC motor types and their applications.
6. Components of Electrical Motors
Diagram 8: Stator and Rotor Interactions
- Description: Illustrate the interaction between the stator and rotor, showing how the magnetic fields interact to produce motion. Highlight different rotor designs, such as squirrel cage and wound rotors.
- Purpose: To explain the mechanics behind motor operation and the role of these key components.
Understanding Electrical Motors
1. Introduction
Electrical motors are the workhorses of modern technology, powering everything from household appliances to industrial machinery. Their significance in contemporary society cannot be overstated, as they convert electrical energy into mechanical energy, enabling countless applications across various fields. As the backbone of automation and industrial processes, understanding electrical motors is essential for engineers, designers, and professionals engaged in technology-driven industries.
The role of electrical motors in modern industry is critical. They are integral to manufacturing processes, transportation systems, and consumer electronics, among other areas. This article aims to provide a comprehensive overview of electrical motors, exploring their history, types, components, performance characteristics, applications, and the latest advancements. By understanding these aspects, professionals can better appreciate the complexities and capabilities of electrical motors and their impact on technological progress.
2. History of Electrical Motors
Early Developments
The history of electrical motors dates back to the early 19th century when the principles of electromagnetism were first discovered. Michael Faraday, an English scientist, made significant contributions to the understanding of electromagnetic induction, which laid the groundwork for the development of electrical motors. In 1821, Faraday demonstrated the first simple electric motor, known as the homopolar motor, which used a magnetic field to produce continuous rotation.
Key Innovators and Milestones
The development of electrical motors accelerated in the following decades, with several key innovators contributing to the field. In 1834, Moritz Jacobi, a German engineer, built the first real rotating electric motor, which was capable of performing mechanical work. This achievement marked a significant milestone in the evolution of motor technology.
Thomas Davenport, an American blacksmith, is credited with developing the first commercially viable electric motor in 1837. His invention, patented in 1837, was used to power a small printing press, showcasing the potential of electric motors in practical applications.
Evolution of Motor Technology
The late 19th and early 20th centuries witnessed significant advancements in motor technology. Nikola Tesla, a Serbian-American inventor, developed the alternating current (AC) motor in the 1880s, revolutionizing the electrical power industry. Tesla’s AC motor was more efficient and reliable than its direct current (DC) counterparts, leading to widespread adoption in various industries.
With the advent of semiconductors and microelectronics in the 20th century, electrical motors became more sophisticated and efficient. Innovations in motor design, materials, and control systems have continued to enhance their performance and broaden their applications.
3. Basic Principles of Electrical Motors
Electromagnetism
At the core of electrical motor operation is the principle of electromagnetism. An electrical motor operates by converting electrical energy into mechanical energy through the interaction of magnetic fields. When an electric current flows through a conductor within a magnetic field, a force is exerted on the conductor, causing it to move. This phenomenon is known as the Lorentz force and is the basis for all types of electrical motors.
- Diagram 1: Electromagnetic Force in Motors
- Description: This diagram illustrates a simple setup with a coil of wire (conductor) placed within a magnetic field, highlighting the direction of current flow and the resulting force.
- Purpose: The diagram visually explains how the interaction between magnetic fields and electric currents creates motion.
Motor Components
An electrical motor typically consists of several key components, including a stator, rotor, bearings, windings, and, in some cases, commutators and brushes. The stator is the stationary part of the motor that generates a magnetic field, while the rotor is the rotating part that interacts with the magnetic field to produce motion. Bearings support the rotor and reduce friction during rotation. Windings are coils of wire through which current flows, generating the magnetic field. In DC motors, commutators and brushes are used to maintain the direction of current flow.
- Diagram 2: Basic Motor Components
- Description: This diagram shows a cross-sectional view of a generic electric motor, labeling key components like the stator, rotor, bearings, windings, commutator, and brushes.
- Purpose: It helps readers understand the fundamental parts of an electric motor and their functions.
Operating Principles
Electrical motors operate on the principle of electromagnetic induction, which involves the conversion of electrical energy into mechanical energy. When an electric current passes through the windings, a magnetic field is created, which interacts with the magnetic field of the stator. This interaction generates a force that causes the rotor to rotate, producing mechanical energy.
Different types of motors use various methods to achieve this conversion. For example, in AC motors, the stator’s magnetic field rotates, inducing a current in the rotor and causing it to follow the rotating field. In DC motors, the current direction is switched using a commutator, allowing for continuous rotation.
4. Types of Electrical Motors
AC Motors
- Induction Motors
Induction motors, also known as asynchronous motors, are the most common type of AC motor. They operate on the principle of electromagnetic induction, where the stator’s rotating magnetic field induces a current in the rotor. This induced current generates a magnetic field in the rotor, causing it to follow the stator’s field and produce torque. Induction motors are widely used in industrial applications due to their simplicity, reliability, and low maintenance requirements.
- Diagram 3: AC Induction Motor
- Description: This diagram displays the internal structure of an AC induction motor, including the stator windings and rotor. Include arrows indicating the rotating magnetic field.
- Purpose: The diagram illustrates how induction motors work and highlight the differences from other motor types.
- Synchronous Motors
Synchronous motors differ from induction motors in that the rotor’s magnetic field is synchronized with the stator’s rotating field. This synchronization is achieved using either permanent magnets or electromagnets on the rotor. Synchronous motors are known for their high efficiency and precise speed control, making them suitable for applications requiring constant speed, such as in compressors and conveyors.
DC Motors
- Brushed DC Motors
Brushed DC motors are among the oldest types of electrical motors. They consist of a rotor with windings and a commutator that switches the direction of current flow, allowing continuous rotation. Brushed DC motors are simple and cost-effective but require regular maintenance due to brush wear and commutator erosion.
- Diagram 4: Brushed DC Motor
- Description: This diagram depicts the internal workings of a brushed DC motor, highlighting the rotor, commutator, and brushes. Show the flow of current and rotation of the rotor.
- Purpose: To clarify the operation of brushed DC motors and show how commutators and brushes interact.
- Brushless DC Motors
Brushless DC motors eliminate the need for brushes and commutators by using electronic commutation. They have a rotor with permanent magnets and a stator with windings. The rotor’s magnetic field interacts with the stator’s magnetic field, causing rotation. Brushless DC motors are known for their high efficiency, low maintenance, and long lifespan, making them ideal for applications requiring precision and reliability, such as in robotics and aerospace.
- Diagram 5: Brushless DC Motor
- Description: This diagram provides an illustration of a brushless DC motor, showing the rotor with permanent magnets and the stator with windings. Include an electronic control circuit for commutation.
- Purpose: To explain how brushless DC motors function without brushes and commutators.
Specialty Motors
- Stepper Motors
Stepper motors are a type of brushless DC motor that rotates in discrete steps, allowing precise control of position and speed. They are commonly used in applications requiring accurate positioning, such as in 3D printers and CNC machines. Stepper motors are known for their high torque at low speeds and ability to hold position without feedback.
- Servo Motors
Servo motors are designed for applications requiring precise control of position, speed, and torque. They consist of a motor coupled with a feedback mechanism, typically an encoder or potentiometer, which provides information about the motor’s position and speed. Servo motors are widely used in robotics, automation, and motion control systems.
5. Motor Comparisons
Understanding the differences between various types of electrical motors is crucial for selecting the right motor for specific applications. Each type of motor has unique characteristics that make it suitable for certain tasks while presenting limitations in others. This section provides a detailed comparison of the most common types of electrical motors.
AC vs. DC Motors
- Efficiency and Control:
- AC Motors: Generally more efficient for applications requiring high power output. They are less complex in design compared to DC motors and often provide better performance in heavy-duty applications.
- DC Motors: Offer precise speed control and high starting torque, making them ideal for applications requiring variable speed and position control.
- Maintenance:
- AC Motors: Require less maintenance than DC motors due to their simpler construction and absence of brushes.
- DC Motors: Require regular maintenance, particularly brushed DC motors, due to wear and tear on brushes and commutators.
- Applications:
- AC Motors: Widely used in industrial applications, HVAC systems, and large machinery.
- DC Motors: Common in automotive applications, robotics, and portable devices where precise control is necessary.
- Diagram 6: AC vs. DC Motor Characteristics
- Description: Create a side-by-side comparison table or infographic that highlights key characteristics of AC and DC motors, such as efficiency, speed control, and maintenance requirements.
- Purpose: To provide a quick reference for comparing the two motor types.
Brushed vs. Brushless DC Motors
- Efficiency and Lifespan:
- Brushed DC Motors: Less efficient and have a shorter lifespan due to brush and commutator wear.
- Brushless DC Motors: More efficient with a longer lifespan, as they do not have brushes that wear out.
- Control and Complexity:
- Brushed DC Motors: Simpler design and control but require regular maintenance.
- Brushless DC Motors: More complex control systems due to electronic commutation but offer better performance and reliability.
- Applications:
- Brushed DC Motors: Used in cost-sensitive applications where high precision is not critical.
- Brushless DC Motors: Preferred in high-performance applications such as drones, electric vehicles, and computer peripherals.
Induction vs. Synchronous Motors
- Starting Mechanism:
- Induction Motors: Simple starting mechanism and do not require additional starting equipment.
- Synchronous Motors: Require starting auxiliaries or variable frequency drives (VFDs) for starting and synchronization.
- Speed Control:
- Induction Motors: Speed varies with load and is generally not suitable for applications requiring constant speed without additional control systems.
- Synchronous Motors: Maintain a constant speed regardless of load, ideal for applications needing precise speed control.
- Efficiency:
- Induction Motors: Less efficient at low loads but provide excellent performance at full load.
- Synchronous Motors: Highly efficient and provide power factor correction capabilities.
- Applications:
- Induction Motors: Widely used in industrial and commercial applications for their robustness and simplicity.
- Synchronous Motors: Used in applications requiring constant speed and power factor correction, such as in power plants and high-precision manufacturing.
- Diagram 7: Induction vs. Synchronous Motors
- Description: Use a comparative diagram to show the key differences in operation between induction and synchronous motors, focusing on how each achieves rotation and synchronization.
- Purpose: To visualize the distinct features of these AC motor types and their applications.
Stepper vs. Servo Motors
- Positioning Accuracy:
- Stepper Motors: Provide accurate and repeatable positioning without the need for feedback systems, ideal for open-loop control systems.
- Servo Motors: Offer high precision and closed-loop control with feedback, suitable for dynamic applications requiring precise control.
- Speed and Torque:
- Stepper Motors: High torque at low speeds but can lose steps at high speeds, making them less suitable for high-speed applications.
- Servo Motors: Provide consistent torque across a wide speed range, ideal for high-speed applications.
- Applications:
- Stepper Motors: Used in applications such as 3D printers, CNC machines, and other systems where precise positioning is required.
- Servo Motors: Common in robotics, automation, and applications requiring high-speed and high-precision control.
6. Components of Electrical Motors
Stator and Rotor
The stator and rotor are the two primary components of an electrical motor. The stator is the stationary part that generates a magnetic field, while the rotor is the rotating part that interacts with the magnetic field to produce motion. The stator is typically made of laminated iron cores with copper windings, while the rotor can be a squirrel cage or wound type.
- Diagram 8: Stator and Rotor Interactions
- Description: Illustrate the interaction between the stator and rotor, showing how the magnetic fields interact to produce motion. Highlight different rotor designs, such as squirrel cage and wound rotors.
- Purpose: To explain the mechanics behind motor operation and the role of these key components.
Bearings
Bearings are critical components that support the rotor and reduce friction during rotation. They ensure smooth and efficient operation of the motor by minimizing mechanical losses. Bearings are designed to withstand radial and axial loads and are available in various types, including ball bearings and roller bearings.
Windings
Windings are coils of wire through which electric current flows, generating a magnetic field. The windings are typically made of copper due to its high electrical conductivity. In AC motors, the windings are distributed around the stator to create a rotating magnetic field. In DC motors, the windings are located on the rotor and connected to the commutator.
Commutators and Brushes (for DC Motors)
Commutators and brushes are essential components of brushed DC motors. The commutator is a cylindrical device connected to the rotor windings, while brushes are stationary conductive elements that make contact with the commutator. As the rotor rotates, the commutator switches the direction of current flow, allowing for continuous rotation. However, commutators and brushes require regular maintenance due to wear and tear.
7. Motor Performance Characteristics
Torque and Speed
Torque and speed are fundamental performance characteristics of electrical motors. Torque is the rotational force produced by the motor, while speed refers to the rotational velocity of the motor’s output shaft. The relationship between torque and speed is crucial for determining the motor’s suitability for specific applications. Motors can be designed for high torque at low speeds or high speeds with lower torque, depending on the requirements.
Efficiency
Efficiency is a measure of how effectively an electrical motor converts electrical energy into mechanical energy. High-efficiency motors consume less energy, produce less heat, and have lower operating costs. Efficiency is influenced by factors such as design, materials, and operating conditions. Advances in motor technology have led to the development of energy-efficient motors that meet stringent regulatory standards.
Power Factor
Power factor is a measure of how effectively a motor uses the electrical power supplied to it. It is the ratio of real power (measured in watts) to apparent power (measured in volt-amperes) and is expressed as a percentage. A high power factor indicates efficient use of electrical power, while a low power factor suggests that the motor is drawing more current than necessary. Power factor correction techniques, such as using capacitors, can improve the motor’s efficiency.
Thermal Management
Thermal management is essential for maintaining the performance and longevity of electrical motors. Excessive heat can lead to insulation breakdown, reduced efficiency, and motor failure. Effective thermal management involves dissipating heat generated during operation through methods such as air cooling, liquid cooling, or using heat sinks. Proper thermal management ensures reliable motor operation and extends its lifespan.
8. Applications of Electrical Motors
Industrial Uses
Electrical motors are indispensable in industrial applications, driving machinery and equipment in manufacturing, processing, and automation. They power conveyors, pumps, compressors, and machine tools, among other equipment. Motors are also used in HVAC systems, providing efficient heating, ventilation, and air conditioning in industrial facilities.
Consumer Electronics
In the consumer electronics sector, electrical motors are used in a wide range of devices, from household appliances to personal gadgets. They power fans, refrigerators, washing machines, vacuum cleaners, and more. In the entertainment industry, motors are used in devices such as DVD players, projectors, and gaming consoles, enhancing the user experience through precise motion control.
Transportation
The transportation sector relies heavily on electrical motors, particularly in the automotive industry. Electric vehicles (EVs) use motors for propulsion, offering a sustainable and energy-efficient alternative to internal combustion engines. Motors are also used in hybrid vehicles, trains, and aircraft, contributing to advancements in transportation technology.
Renewable Energy
Electrical motors play a vital role in the renewable energy sector, enabling the conversion of natural resources into usable energy. Wind turbines use motors to generate electricity from wind, while solar power systems use motors in tracking systems to optimize the capture of sunlight. Motors are also used in hydroelectric power plants, converting the kinetic energy of flowing water into electrical energy.
9. Advancements in Motor Technology
Smart Motors
The integration of digital technology and smart systems has led to the development of smart motors. These motors are equipped with sensors and communication capabilities, allowing for real-time monitoring and control. Smart motors offer improved performance, efficiency, and reliability through features such as predictive maintenance, fault detection, and remote diagnostics. They are ideal for applications requiring advanced automation and control.
Energy Efficiency Improvements
Advancements in motor technology have focused on improving energy efficiency to reduce environmental impact and operating costs. High-efficiency motors are designed with optimized materials, geometries, and control systems to minimize energy losses. Variable frequency drives (VFDs) are used to control motor speed and torque, enhancing efficiency and reducing energy consumption in variable-load applications.
Integration with IoT
The Internet of Things (IoT) has transformed the way electrical motors are used and managed. IoT-enabled motors can communicate with other devices and systems, providing valuable data on performance, condition, and energy usage. This data can be used to optimize motor operation, predict maintenance needs, and improve overall system efficiency. IoT integration enhances the capabilities of electrical motors in various applications, from industrial automation to smart home systems.
10. Challenges and Solutions in Motor Design
Noise Reduction
Noise is a common challenge in motor design, particularly in applications requiring quiet operation. Motor noise can be caused by mechanical vibrations, electromagnetic forces, and airflow. To address this issue, engineers use advanced materials, precision manufacturing techniques, and noise-dampening technologies. Proper alignment, balancing, and insulation also contribute to noise reduction in electrical motors.
Vibration Management
Vibrations in electrical motors can lead to mechanical wear, reduced performance, and premature failure. Effective vibration management involves designing motors with balanced components, minimizing mechanical clearances, and using vibration-dampening materials. Advanced diagnostic tools and monitoring systems can detect and address vibration issues before they impact motor operation.
Durability and Maintenance
Durability and maintenance are critical considerations in motor design, as they impact reliability and lifespan. Motors must be designed to withstand harsh operating conditions, including high temperatures, moisture, and corrosive environments. Maintenance practices such as regular inspections, lubrication, and cleaning help extend motor life and ensure optimal performance. Advances in materials and manufacturing techniques have led to the development of motors with enhanced durability and reduced maintenance requirements.
11. Future Trends in Electrical Motors
Green Technologies
The future of electrical motors is closely tied to the development of green technologies that reduce environmental impact and promote sustainability. Electric vehicles, renewable energy systems, and energy-efficient appliances are driving the demand for advanced motor solutions. Researchers are exploring new materials, designs, and control systems to enhance motor efficiency and reduce carbon emissions.
Advanced Materials
The use of advanced materials is revolutionizing motor design, offering improved performance and durability. Lightweight materials such as composites and high-strength alloys reduce motor weight and enhance efficiency. Nanomaterials and superconductors are being explored for their potential to improve electrical conductivity and reduce energy losses. These advancements are paving the way for the next generation of high-performance electrical motors.
Emerging Applications
As technology continues to evolve, new applications for electrical motors are emerging in various fields. In the healthcare sector, motors are used in medical devices, robotic surgery systems, and diagnostic equipment. In the aerospace industry, motors are powering advanced aircraft propulsion systems and drones. The increasing demand for automation, robotics, and smart technologies is driving the development of innovative motor solutions for a wide range of applications.
12. Conclusion
In conclusion, electrical motors are essential components of modern technology, driving progress across various industries. From their early development to the latest advancements, motors have evolved to meet the changing needs of society. The diverse types of motors, each with its unique characteristics and applications, highlight the versatility and importance of these devices.
As the demand for energy-efficient, sustainable, and smart technologies continues to grow, electrical motors will play a crucial role in shaping the future. The ongoing research and development in motor technology will lead to new solutions that enhance performance, efficiency, and reliability, paving the way for a more sustainable and technologically advanced world. Understanding the complexities and capabilities of electrical motors is essential for professionals in the field, as they contribute to the advancement of modern industry and society.
Final Steps
You can create or source the diagrams based on the descriptions provided, ensuring they align with the content and help illustrate the key points. Once the diagrams are ready, you can integrate them into the article, either as inline images or downloadable resources, depending on the format of your professional website.
8. Applications of Electrical Motors
Electrical motors have become an indispensable part of modern technology, powering a wide array of applications across different industries. Their ability to convert electrical energy into mechanical motion efficiently and reliably makes them essential in numerous sectors. This section explores the diverse applications of electrical motors, emphasizing their significance in industry, consumer electronics, transportation, and renewable energy.
Industrial Uses
Electrical motors are the backbone of industrial processes, driving machinery and equipment that are vital to manufacturing and production. They are used in:
- Conveyors and Material Handling Systems:
- Description: Motors drive conveyor belts and systems, facilitating the movement of materials and products throughout manufacturing plants and warehouses.
- Benefits: They offer efficient and continuous operation, enhancing productivity and reducing manual labor.
- Pumps and Compressors:
- Description: Motors power pumps and compressors used in fluid and gas handling applications, such as water supply systems, chemical processing, and HVAC systems.
- Benefits: They provide reliable and efficient performance, essential for maintaining consistent pressure and flow rates.
- Machine Tools:
- Description: Motors are integral to machine tools, including lathes, milling machines, and grinders, providing the necessary torque and speed for metalworking and fabrication.
- Benefits: They enable precise control and high accuracy, crucial for producing high-quality parts and components.
- Robotics and Automation:
- Description: Motors drive robotic arms and automated systems used in assembly lines, packaging, and quality control.
- Benefits: They enhance efficiency, reduce human error, and increase safety in manufacturing environments.
- HVAC Systems:
- Description: Motors are used in heating, ventilation, and air conditioning systems to drive fans, blowers, and compressors.
- Benefits: They ensure efficient climate control and energy conservation in industrial and commercial buildings.
Consumer Electronics
In the consumer electronics sector, electrical motors are found in a variety of devices and appliances, providing functionality and convenience to everyday life:
- Household Appliances:
- Washing Machines and Dryers:
- Description: Motors drive the drums in washing machines and dryers, enabling the cleaning and drying of clothes.
- Benefits: They provide variable speed and torque control, optimizing wash cycles and energy use.
- Refrigerators and Freezers:
- Description: Motors power compressors in refrigeration systems, maintaining low temperatures for food preservation.
- Benefits: They offer efficient and quiet operation, crucial for domestic and commercial refrigeration.
- Vacuum Cleaners:
- Description: Motors drive suction mechanisms in vacuum cleaners, removing dust and debris from floors and surfaces.
- Benefits: They provide powerful and adjustable suction, enhancing cleaning effectiveness.
- Washing Machines and Dryers:
- Personal Gadgets:
- Electric Shavers and Toothbrushes:
- Description: Motors power the oscillating or rotating actions in personal grooming devices.
- Benefits: They offer precise and gentle operation, improving user comfort and hygiene.
- Hair Dryers:
- Description: Motors drive fans in hair dryers, providing airflow for quick and efficient drying.
- Benefits: They enable variable speed and heat settings, enhancing user control and styling options.
- Electric Shavers and Toothbrushes:
- Entertainment Devices:
- DVD Players and Gaming Consoles:
- Description: Motors drive disc-spinning mechanisms in media players, enabling playback and data access.
- Benefits: They provide smooth and reliable operation, essential for uninterrupted entertainment.
- Projectors:
- Description: Motors adjust lens and focus mechanisms in projectors, optimizing image quality.
- Benefits: They enhance user experience through precise control and adjustment.
- DVD Players and Gaming Consoles:
Transportation
Electrical motors are at the forefront of innovations in transportation, playing a critical role in the development of sustainable and efficient mobility solutions:
- Electric Vehicles (EVs):
- Description: Motors power the wheels of electric cars, providing propulsion without the need for internal combustion engines.
- Benefits: They offer zero-emission operation, high efficiency, and smooth acceleration, contributing to environmental sustainability.
- Example Applications: Tesla Model S, Nissan Leaf, and Chevrolet Bolt.
- Hybrid Vehicles:
- Description: Motors work alongside internal combustion engines in hybrid vehicles, optimizing fuel efficiency and performance.
- Benefits: They reduce emissions and fuel consumption, offering a balance between power and efficiency.
- Example Applications: Toyota Prius, Ford Fusion Hybrid, and Honda Accord Hybrid.
- Public Transport:
- Description: Motors are used in electric buses, trams, and trains, providing efficient and reliable mass transit solutions.
- Benefits: They enhance public transportation systems by reducing noise and emissions, improving urban air quality.
- Example Applications: Electric trains in metropolitan areas like the London Underground and New York City Subway.
- Aerospace:
- Description: Motors power various systems in aircraft, including actuators and control surfaces, improving efficiency and reliability.
- Benefits: They offer precise control and lightweight solutions, essential for modern aviation and emerging drone technologies.
- Example Applications: Electric actuators in Boeing 787 Dreamliner and various drone models like DJI Phantom.
Renewable Energy
Electrical motors play a pivotal role in the renewable energy sector, facilitating the conversion of natural resources into sustainable energy:
- Wind Energy:
- Description: Motors are used in wind turbines to convert wind energy into electricity, providing a clean and renewable power source.
- Benefits: They enable efficient energy generation, reducing reliance on fossil fuels and lowering carbon emissions.
- Example Applications: Large-scale wind farms like the Hornsea Project in the UK and the Alta Wind Energy Center in California.
- Solar Energy:
- Description: Motors are used in solar tracking systems, optimizing the angle of solar panels to capture maximum sunlight.
- Benefits: They increase the efficiency and output of solar power systems, enhancing the viability of solar energy.
- Example Applications: Solar tracking systems used in photovoltaic installations worldwide, such as in the Topaz Solar Farm in California.
- Hydroelectric Power:
- Description: Motors convert the kinetic energy of flowing water into electricity in hydroelectric power plants.
- Benefits: They provide a reliable and large-scale energy source, contributing to the stability of energy grids.
- Example Applications: Hydroelectric dams like the Hoover Dam in the US and the Three Gorges Dam in China.
- Geothermal Energy:
- Description: Motors are used in geothermal power plants to convert heat from the earth’s core into electricity.
- Benefits: They offer a constant and sustainable energy source, complementing other renewable technologies.
- Example Applications: Geothermal plants like the Geysers in California and the Hellisheiði Power Station in Iceland.
Visual Aids
To enhance this section, consider including the following diagrams and images:
- Diagram 1: Conveyor System with Motor
- Description: An illustration of a motor-driven conveyor system, showing the motor’s integration with the conveyor belt and material flow.
- Purpose: To highlight the motor’s role in material handling and industrial automation.
- Diagram 2: Electric Vehicle Powertrain
- Description: A schematic of an electric vehicle powertrain, showing the motor, battery, and drivetrain components.
- Purpose: To explain how motors provide propulsion in electric vehicles and their impact on sustainable transportation.
- Diagram 3: Wind Turbine System
- Description: An illustration of a wind turbine, showing the motor’s role in converting wind energy into electricity.
- Purpose: To demonstrate the motor’s contribution to renewable energy generation and environmental sustainability.
7. Motor Performance Characteristics
Motor performance characteristics are essential for evaluating how effectively an electrical motor converts electrical energy into mechanical energy. Among these characteristics, efficiency metrics play a crucial role in determining a motor’s performance, operating cost, and environmental impact. This section delves into the key metrics and factors influencing motor efficiency, as well as strategies to enhance efficiency.
Motor Efficiency Metrics
Motor efficiency metrics help quantify how well a motor converts electrical input power into useful mechanical output power. These metrics are crucial for assessing a motor’s performance and identifying opportunities for energy savings. Key efficiency metrics include:
Efficiency (%):
- Definition: Efficiency is the ratio of mechanical output power to electrical input power, expressed as a percentage. It indicates how effectively a motor converts electrical energy into mechanical work.Efficiency(%)=(Output PowerInput Power)×100\text{Efficiency} (\%) = \left( \frac{\text{Output Power}}{\text{Input Power}} \right) \times 100Efficiency(%)=(Input PowerOutput Power)×100
- Significance: Higher efficiency indicates less energy loss in the form of heat, resulting in lower operating costs and reduced environmental impact.
- Typical Values: Efficiency varies depending on the motor type and application, but most modern motors achieve efficiencies between 85% and 95%.
Power Factor (PF):
- Definition: Power factor is the ratio of real power (measured in watts) to apparent power (measured in volt-amperes). It indicates how effectively a motor uses the electrical power supplied to it.Power Factor=Real PowerApparent Power\text{Power Factor} = \frac{\text{Real Power}}{\text{Apparent Power}}Power Factor=Apparent PowerReal Power
- Significance: A higher power factor indicates more efficient use of electrical power, resulting in reduced power losses and lower energy costs.
- Typical Values: Power factor values for motors typically range from 0.7 to 0.95. Motors with a power factor close to 1 are considered more efficient.
Torque per Amp (Nm/A):
- Definition: Torque per amp is a measure of the torque produced by the motor for each ampere of current supplied. It indicates how effectively the motor converts electrical current into mechanical torque.Torque per Amp=Torque (Nm)Current (A)\text{Torque per Amp} = \frac{\text{Torque (Nm)}}{\text{Current (A)}}Torque per Amp=Current (A)Torque (Nm)
- Significance: Higher torque per amp values indicate more efficient conversion of electrical energy into mechanical motion, which is especially important in applications requiring high torque.
Load Factor:
- Definition: Load factor is the ratio of the motor’s actual load to its rated load. It indicates how efficiently a motor operates under different load conditions.Load Factor=Actual LoadRated Load\text{Load Factor} = \frac{\text{Actual Load}}{\text{Rated Load}}Load Factor=Rated LoadActual Load
- Significance: Motors operating near their rated load tend to be more efficient. Underloading or overloading a motor can result in reduced efficiency and increased energy losses.
- Typical Values: Ideal load factor values are close to 1, indicating that the motor is operating at or near its rated capacity.
Slip (%):
- Definition: Slip is the difference between the synchronous speed and the actual speed of an induction motor, expressed as a percentage of synchronous speed. It indicates the amount of relative motion between the stator and rotor magnetic fields.Slip(%)=(Synchronous Speed−Actual SpeedSynchronous Speed)×100\text{Slip} (\%) = \left( \frac{\text{Synchronous Speed} – \text{Actual Speed}}{\text{Synchronous Speed}} \right) \times 100Slip(%)=(Synchronous SpeedSynchronous Speed−Actual Speed)×100
- Significance: Lower slip values indicate better efficiency and performance. High slip can result in energy losses and reduced torque output.
- Typical Values: Slip values for induction motors typically range from 2% to 5%.
Losses:
- Definition: Losses refer to the energy that is not converted into useful mechanical work and is dissipated as heat. Common types of losses include copper losses, iron losses, and mechanical losses.Losses=Input Power−Output Power\text{Losses} = \text{Input Power} – \text{Output Power}Losses=Input Power−Output Power
- Significance: Minimizing losses is essential for improving motor efficiency and reducing energy consumption.
Factors Influencing Motor Efficiency
Several factors can influence the efficiency of an electrical motor, including:
- Design and Construction:
- Stator and Rotor Design: The design of the stator and rotor, including the use of high-quality materials and precision engineering, can significantly impact motor efficiency. Properly designed cores and windings reduce losses and enhance performance.
- Bearing Quality: High-quality bearings reduce friction and mechanical losses, improving overall efficiency. Proper lubrication and maintenance also contribute to efficient operation.
- Operating Conditions:
- Load: Motors operating near their rated load are generally more efficient. Underloading or overloading can lead to increased losses and reduced performance.
- Temperature: Excessive heat can reduce efficiency by increasing resistance and causing insulation breakdown. Effective thermal management is crucial for maintaining optimal efficiency.
- Control Systems:
- Variable Frequency Drives (VFDs): VFDs enable precise control of motor speed and torque, optimizing efficiency under varying load conditions. They reduce energy consumption by matching motor output to the required load.
- Power Factor Correction: Implementing power factor correction techniques, such as using capacitors, can improve efficiency by reducing reactive power and minimizing losses.
- Maintenance Practices:
- Regular Inspections: Routine inspections and maintenance help identify and address issues affecting efficiency, such as worn bearings, misalignment, and electrical faults.
- Lubrication: Proper lubrication of moving parts reduces friction and mechanical losses, enhancing efficiency and extending motor lifespan.
Methods to Improve Motor Efficiency
Improving motor efficiency involves optimizing design, operation, and maintenance practices. Key methods include:
- Upgrading to High-Efficiency Motors:
- Premium Efficiency Motors: Replacing standard motors with premium efficiency models can result in significant energy savings and reduced operating costs. These motors are designed with advanced materials and technologies to minimize losses.
- IE3 and IE4 Motors: International Efficiency (IE) standards classify motors based on efficiency levels. IE3 and IE4 motors offer higher efficiency than standard IE1 and IE2 models, making them ideal for energy-conscious applications.
- Implementing Advanced Control Systems:
- Variable Frequency Drives (VFDs): VFDs provide precise control of motor speed and torque, optimizing efficiency across a range of operating conditions. They reduce energy consumption and improve performance in variable-load applications.
- Soft Starters: Soft starters reduce the initial inrush current during motor startup, minimizing energy losses and mechanical stress. They enhance efficiency by ensuring smooth acceleration and deceleration.
- Optimizing Motor Sizing and Selection:
- Proper Sizing: Selecting the right motor size for the application is crucial for maximizing efficiency. Oversized motors can lead to underloading and energy waste, while undersized motors may be inefficient and prone to overheating.
- Application-Specific Motors: Using motors specifically designed for the intended application can improve efficiency by matching motor characteristics to operational requirements.
- Enhancing Thermal Management:
- Cooling Systems: Implementing effective cooling systems, such as air or liquid cooling, helps dissipate heat and maintain optimal operating temperatures. Proper cooling enhances efficiency and prevents overheating.
- Heat Sinks and Insulation: Using heat sinks and high-quality insulation materials reduces thermal losses and improves motor performance.
- Maintaining Power Quality:
- Power Factor Correction: Correcting power factor with capacitors or other devices reduces reactive power, improving efficiency and reducing energy costs.
- Voltage Optimization: Ensuring the motor receives the correct voltage levels minimizes energy losses and enhances performance.
Visual Aids
To enhance understanding of motor efficiency metrics, consider including the following diagrams and graphs:
- Diagram 1: Motor Efficiency vs. Load Graph
- Description: A graph illustrating how motor efficiency varies with load, showing peak efficiency at rated load.
- Purpose: To demonstrate the importance of operating motors near their rated load for optimal efficiency.
- Diagram 2: Power Factor Improvement Techniques
- Description: A schematic showing power factor correction methods, such as using capacitors, and their impact on efficiency.
- Purpose: To explain how power factor correction enhances motor efficiency and reduces energy consumption.
- Diagram 3: Variable Frequency Drive (VFD) System
- Description: An illustration of a VFD system, showing how it controls motor speed and torque to optimize efficiency.
- Purpose: To highlight the role of VFDs in improving motor performance and energy savings.
Efficiency Improvement Tips for Electrical Motors
Improving the efficiency of electrical motors is crucial for reducing energy consumption, lowering operating costs, and minimizing environmental impact. By implementing best practices and advanced technologies, businesses can optimize motor performance and achieve significant energy savings. This section provides practical tips and strategies for enhancing motor efficiency.
1. Select the Right Motor for the Application
Proper Sizing:
- Tip: Choose a motor that matches the load requirements of the application. Oversized motors operate inefficiently under low-load conditions, while undersized motors can become overloaded and prone to failure.
- Benefits: Ensures optimal efficiency by matching motor output to demand, reducing energy waste and extending motor life.
- Action: Conduct a thorough analysis of the application’s load profile and select a motor with the appropriate power rating.
Application-Specific Motors:
- Tip: Use motors specifically designed for the intended application. Specialized motors, such as high-torque or high-speed models, offer tailored performance characteristics.
- Benefits: Maximizes efficiency by aligning motor features with application needs, improving performance and reliability.
- Action: Evaluate the application’s requirements and select motors designed for specific tasks, such as variable speed drives for dynamic loads.
2. Upgrade to High-Efficiency Motors
Premium Efficiency Motors:
- Tip: Replace standard motors with premium efficiency models, such as IE3 or IE4 motors, which offer improved energy performance and lower losses.
- Benefits: Reduces energy consumption and operating costs, contributing to sustainability goals and regulatory compliance.
- Action: Identify motors with high operating hours and significant energy use for upgrades to premium efficiency models.
Permanent Magnet Motors:
- Tip: Consider using permanent magnet motors, which offer higher efficiency and performance compared to traditional induction motors.
- Benefits: Provides high torque density, reduced losses, and improved control capabilities, especially in variable-speed applications.
- Action: Evaluate the feasibility of replacing induction motors with permanent magnet alternatives in critical applications.
3. Implement Advanced Control Systems
Variable Frequency Drives (VFDs):
- Tip: Install VFDs to control motor speed and torque, optimizing efficiency across varying load conditions.
- Benefits: Reduces energy consumption by matching motor output to load demand, improving performance in dynamic applications.
- Action: Integrate VFDs into systems with variable loads, such as fans, pumps, and compressors, to enhance efficiency.
Soft Starters:
- Tip: Use soft starters to reduce inrush current and mechanical stress during motor startup, enhancing efficiency and extending motor life.
- Benefits: Minimizes energy losses and improves power quality by ensuring smooth acceleration and deceleration.
- Action: Implement soft starters in applications with frequent startups, such as conveyor systems and material handling equipment.
Power Factor Correction:
- Tip: Implement power factor correction techniques, such as capacitors, to improve power factor and reduce reactive power.
- Benefits: Enhances efficiency by minimizing energy losses and lowering demand charges from utilities.
- Action: Assess the power factor of existing motor systems and install correction devices to optimize efficiency.
4. Optimize Maintenance Practices
Regular Inspections and Monitoring:
- Tip: Conduct routine inspections and monitoring of motor systems to identify and address issues affecting efficiency.
- Benefits: Prevents energy losses and downtime by detecting faults, misalignments, and wear before they impact performance.
- Action: Implement a preventive maintenance program with scheduled inspections, monitoring, and diagnostics.
Proper Lubrication:
- Tip: Ensure motors are properly lubricated to reduce friction and mechanical losses, enhancing efficiency and extending component life.
- Benefits: Minimizes wear and tear, reducing the likelihood of failures and inefficiencies.
- Action: Establish a lubrication schedule based on manufacturer recommendations and operating conditions.
Alignment and Balancing:
- Tip: Maintain proper alignment and balancing of motor components to minimize vibrations and energy losses.
- Benefits: Enhances efficiency by reducing mechanical stress and improving performance.
- Action: Use alignment tools and techniques to ensure proper installation and maintenance of motor systems.
5. Enhance Thermal Management
Cooling Systems:
- Tip: Implement effective cooling systems, such as air or liquid cooling, to dissipate heat and maintain optimal operating temperatures.
- Benefits: Improves efficiency by preventing overheating and maintaining consistent performance.
- Action: Evaluate cooling requirements and install appropriate systems to manage motor temperatures.
Heat Sinks and Insulation:
- Tip: Use heat sinks and high-quality insulation materials to reduce thermal losses and improve motor performance.
- Benefits: Enhances efficiency by minimizing heat dissipation and protecting motor components from thermal damage.
- Action: Incorporate heat sinks and insulation into motor designs and retrofits to improve thermal management.
6. Maintain Power Quality
Voltage Optimization:
- Tip: Ensure motors receive the correct voltage levels to minimize energy losses and enhance performance.
- Benefits: Improves efficiency by preventing overvoltage and undervoltage conditions that can lead to energy waste.
- Action: Monitor voltage levels and implement voltage optimization strategies to maintain power quality.
Harmonic Mitigation:
- Tip: Implement harmonic mitigation techniques to reduce harmonic distortion and improve power quality.
- Benefits: Enhances efficiency by minimizing energy losses and reducing stress on motor components.
- Action: Use filters, reactors, or active harmonic mitigation devices to address harmonic issues in motor systems.
Visual Aids
To further illustrate these efficiency improvement tips, consider including the following diagrams and graphs:
- Diagram 1: Motor Efficiency Improvement Strategies
- Description: A flowchart or infographic summarizing the key strategies for enhancing motor efficiency, including sizing, control systems, maintenance, and thermal management.
- Purpose: To provide a visual overview of the various approaches to improving motor efficiency.
- Diagram 2: VFD System Benefits
- Description: An illustration of a VFD system, highlighting its impact on motor efficiency and energy savings.
- Purpose: To explain how VFDs optimize performance and reduce energy consumption in variable-load applications.
- Diagram 3: Power Factor Correction Impact
- Description: A schematic showing the effects of power factor correction on motor efficiency and energy costs.
- Purpose: To demonstrate the benefits of improving power factor through correction devices.
Word Count Allocation for Efficiency Improvement Tips
Here’s a breakdown of the word count allocation for the efficiency improvement tips section:
- Select the Right Motor for the Application (150 words)
- Upgrade to High-Efficiency Motors (150 words)
- Implement Advanced Control Systems (200 words)
- Optimize Maintenance Practices (200 words)
- Enhance Thermal Management (150 words)
- Maintain Power Quality (150 words)
This distribution ensures comprehensive coverage of efficiency improvement tips, offering practical insights for enhancing motor performance and reducing energy consumption.
Case Study 1: Efficiency Improvements in a Manufacturing Plant
Here are some detailed case studies that demonstrate how specific organizations have successfully implemented efficiency improvement strategies for electrical motors. These case studies will provide practical examples of the benefits and outcomes achieved through targeted efficiency improvements.
Background:
A large manufacturing plant specializing in automotive components faced rising energy costs and increasing pressure to reduce its carbon footprint. The plant operated over 500 electrical motors, ranging from small pumps to large conveyors, many of which were outdated and inefficient.
Objective:
To reduce energy consumption and operating costs by improving the efficiency of electrical motors across the facility while maintaining or enhancing production capacity.
Actions Taken:
- Motor Audit and Assessment:
- Conducted a comprehensive audit of all motors within the facility to assess their efficiency, age, and condition.
- Identified motors with high energy consumption and low efficiency as candidates for replacement or retrofit.
- Upgrading to High-Efficiency Motors:
- Replaced over 150 outdated motors with new high-efficiency IE3 and IE4 motors, targeting applications with the highest energy use, such as air compressors and large conveyors.
- Selected motors with improved power factor and torque characteristics to match the specific load requirements of each application.
- Implementation of Variable Frequency Drives (VFDs):
- Installed VFDs on pumps, fans, and other variable-load applications to optimize motor speed and torque based on real-time demand.
- Configured VFDs with automated control systems to adjust motor performance dynamically, reducing energy consumption during low-demand periods.
- Enhanced Maintenance Practices:
- Established a preventive maintenance program, including regular inspections, lubrication, and alignment checks.
- Implemented condition monitoring tools, such as vibration analysis and thermal imaging, to identify and address issues proactively.
- Power Factor Correction:
- Installed power factor correction capacitors to reduce reactive power and improve overall power quality across the facility.
- Monitored power factor levels continuously and adjusted correction measures as needed to maintain optimal efficiency.
Results:
- Energy Savings: Achieved a 25% reduction in energy consumption for motor systems, translating to annual savings of approximately $250,000.
- Return on Investment (ROI): Realized a payback period of less than two years for the motor upgrades and efficiency improvements.
- Environmental Impact: Reduced the plant’s carbon emissions by 1,200 metric tons per year, supporting sustainability goals and regulatory compliance.
- Operational Efficiency: Improved overall reliability and performance of motor-driven systems, resulting in reduced downtime and maintenance costs.
Case Study 2: Energy Efficiency in a Commercial HVAC System
Background:
A commercial office building in a metropolitan area sought to reduce its energy usage and operational costs associated with its heating, ventilation, and air conditioning (HVAC) systems. The building’s HVAC system relied heavily on electric motors to drive fans, pumps, and compressors.
Objective:
To enhance the energy efficiency of the HVAC system by optimizing the performance of its electric motors and associated control systems.
Actions Taken:
- System Assessment and Optimization:
- Conducted a detailed analysis of the HVAC system’s energy usage patterns and motor performance.
- Identified inefficiencies in motor sizing and control that contributed to excess energy consumption.
- Installation of VFDs:
- Installed VFDs on all HVAC fans and pumps to allow precise control of motor speed and airflow based on real-time building occupancy and environmental conditions.
- Implemented a building management system (BMS) to integrate VFDs with automated controls, enabling dynamic adjustments to motor operation.
- Retrofitting with High-Efficiency Motors:
- Replaced old, inefficient motors with high-efficiency models specifically designed for HVAC applications, including ECM (Electronically Commutated Motors) for fan systems.
- Selected motors with improved efficiency ratings and reduced noise levels to enhance occupant comfort and reduce energy costs.
- Improved Thermal Management:
- Upgraded insulation and cooling systems for motor components to reduce thermal losses and improve efficiency.
- Implemented regular cleaning and maintenance schedules to ensure optimal heat dissipation and performance.
- Power Quality Improvements:
- Addressed power quality issues by installing harmonic filters and voltage regulators to reduce harmonic distortion and improve motor efficiency.
- Conducted ongoing monitoring of power quality metrics to ensure consistent performance and efficiency.
Results:
- Energy Savings: Reduced HVAC system energy consumption by 30%, resulting in annual savings of $150,000 in electricity costs.
- Occupant Comfort: Improved indoor air quality and climate control, enhancing occupant satisfaction and productivity.
- Sustainability: Decreased carbon footprint by 800 metric tons per year, aligning with the building’s sustainability objectives.
- Long-Term Efficiency: Extended the lifespan of HVAC motors and components through improved maintenance and performance optimization.
Case Study 3: Efficiency Improvements in a Wastewater Treatment Facility
Background:
A municipal wastewater treatment facility faced high energy costs due to the operation of numerous pumps and aeration systems powered by electric motors. The facility aimed to improve efficiency and reduce its environmental impact while maintaining water treatment quality.
Objective:
To enhance the energy efficiency of motor-driven systems in the wastewater treatment process, reducing operational costs and environmental impact.
Actions Taken:
- Motor Audit and Energy Analysis:
- Conducted a detailed audit of all motor-driven systems, focusing on energy consumption, load profiles, and efficiency.
- Identified motors with high energy usage and potential for efficiency improvements.
- Replacement with High-Efficiency Motors:
- Replaced inefficient motors in critical areas, such as aeration and pumping systems, with high-efficiency IE4 motors.
- Selected motors with superior corrosion resistance and durability to withstand harsh operating conditions.
- VFD Implementation:
- Installed VFDs on pumps and blowers to control motor speed and optimize energy use based on real-time demand and process requirements.
- Configured VFDs with automated controls to adjust motor operation dynamically, improving process efficiency and reducing energy consumption.
- Power Factor and Harmonic Correction:
- Implemented power factor correction measures, including capacitors and harmonic filters, to improve power quality and reduce losses.
- Monitored power factor levels continuously and adjusted correction measures as needed to maintain optimal efficiency.
- Process Optimization and Monitoring:
- Optimized treatment processes to align with motor efficiency improvements, ensuring consistent water quality and operational performance.
- Implemented real-time monitoring and analytics tools to track energy usage and motor performance, identifying opportunities for further improvements.
Results:
- Energy Savings: Achieved a 35% reduction in energy consumption for motor-driven systems, resulting in annual savings of $300,000.
- Environmental Impact: Reduced greenhouse gas emissions by 1,500 metric tons per year, contributing to sustainability goals and regulatory compliance.
- Operational Efficiency: Enhanced the reliability and performance of wastewater treatment processes, improving water quality and reducing downtime.
- Scalability: Developed a framework for continuous improvement and scalability, enabling future efficiency initiatives and cost savings.
Visual Aids for Case Studies
To enhance the understanding of these case studies, consider including the following visual aids:
- Diagram 1: Motor Audit and Efficiency Analysis Process
- Description: A flowchart illustrating the steps involved in conducting a motor audit and energy analysis, highlighting key metrics and assessment criteria.
- Purpose: To provide a visual overview of the process for identifying efficiency improvement opportunities.
- Diagram 2: VFD Installation and Control Integration
- Description: A schematic showing the integration of VFDs with motor systems and automated controls, highlighting their impact on efficiency and performance.
- Purpose: To explain the role of VFDs in optimizing motor operation and reducing energy consumption.
- Diagram 3: Power Factor Correction and Harmonic Mitigation
- Description: An illustration of power factor correction and harmonic mitigation techniques, showing their effects on motor efficiency and power quality.
- Purpose: To demonstrate the benefits of improving power factor and reducing harmonic distortion.
EMS Power Machines
We design, manufacture and assembly Power Machines such as – diesel generators, electric motors, vibration motors, pumps, steam engines and steam turbines
EMS Power Machines is a global power engineering company, one of the five world leaders in the industry in terms of installed equipment. The companies included in the company have been operating in the energy market for more than 60 years.
EMS Power Machines manufactures steam turbines, gas turbines, hydroelectric turbines, generators, and other power equipment for thermal, nuclear, and hydroelectric power plants, as well as for various industries, transport, and marine energy.
EMS Power Machines is a major player in the global power industry, and its equipment is used in power plants all over the world. The company has a strong track record of innovation, and it is constantly developing new and improved technologies.
Here are some examples of Power Machines’ products and services:
- Steam turbines for thermal and nuclear power plants
- Gas turbines for combined cycle power plants and industrial applications
- Hydroelectric turbines for hydroelectric power plants
- Generators for all types of power plants
- Boilers for thermal power plants
- Condensers for thermal power plants
- Reheaters for thermal power plants
- Air preheaters for thermal power plants
- Feedwater pumps for thermal power plants
- Control systems for power plants
- Maintenance and repair services for power plants
EMS Power Machines is committed to providing its customers with high-quality products and services. The company has a strong reputation for reliability and innovation. Power Machines is a leading provider of power equipment and services, and it plays a vital role in the global power industry.
EMS Power Machines, which began in 1961 as a small factory of electric motors, has become a leading global supplier of electronic products for different segments. The search for excellence has resulted in the diversification of the business, adding to the electric motors products which provide from power generation to more efficient means of use.